
22 minute read
Cepezed Kit-of-Parts Methodology
cepezed KoP Methodology Interview with ir. Ronald Schleurholts
by Fredy Fortich
Advertisement
Kit of Parts is an object-oriented construction approach which requires integration and coordination between architects, engineers, manufacturers and builders for the most efficient and cost-effective design. This can also be understood as a pool of different building elements where every element is optimized for production, assembly and disassembly.
© cepezed | Lucas van der Wee
1. How would you define the kit of parts? Does cepezed understand the concept as described in the introduction?
Working with kits of parts is in the DNA of our office, it is our building methodology from the very beginning. The cepezed office was started in the 1970s by three students that decided to take on projects. Their main aim was to professionalize the building industry, making something valuable and of high quality. We believe we should keep the building process away from the building site as much as possible and prepare parts and segments in the factory as much as possible.
Our vision is to avoid on-site fabrication, concrete pouring or welding wherever possible. Instead, building should be limited to the on-site assembly of prefabricated components.
We have various reasons for working with a kit of parts. First and most importantly, it results in better quality due to a more controlled production. Another motive is that building structures put together with a kit of parts have a far more flexible layout and are thus more open to change. Finally, if a building is not used anymore, it can easily be taken apart if it was constructed with a kit of parts.
2. Explain some of your projects which are relevant regarding the kit-of-parts-approach.
In all our buildings, the same methods and concepts are applied. A good example is the Westraven building in Utrecht. The high-rise already existed. We transformed it into a very sustainable building with windows that can be opened and with a lot of daylight. The low-rise section was completely dry-assembled with prefabricated parts. Only the foundations, in this case, are of poured concrete.
All the connections are very clean. You can still take them apart or add an extra wing if necessary. The whole building is set up as a kit of parts. We did that not solely for the sake of circularity, but also because we wanted to have an adaptable building with the best quality for the price.
Figure 1. Kit of Parts along the years © cepezed
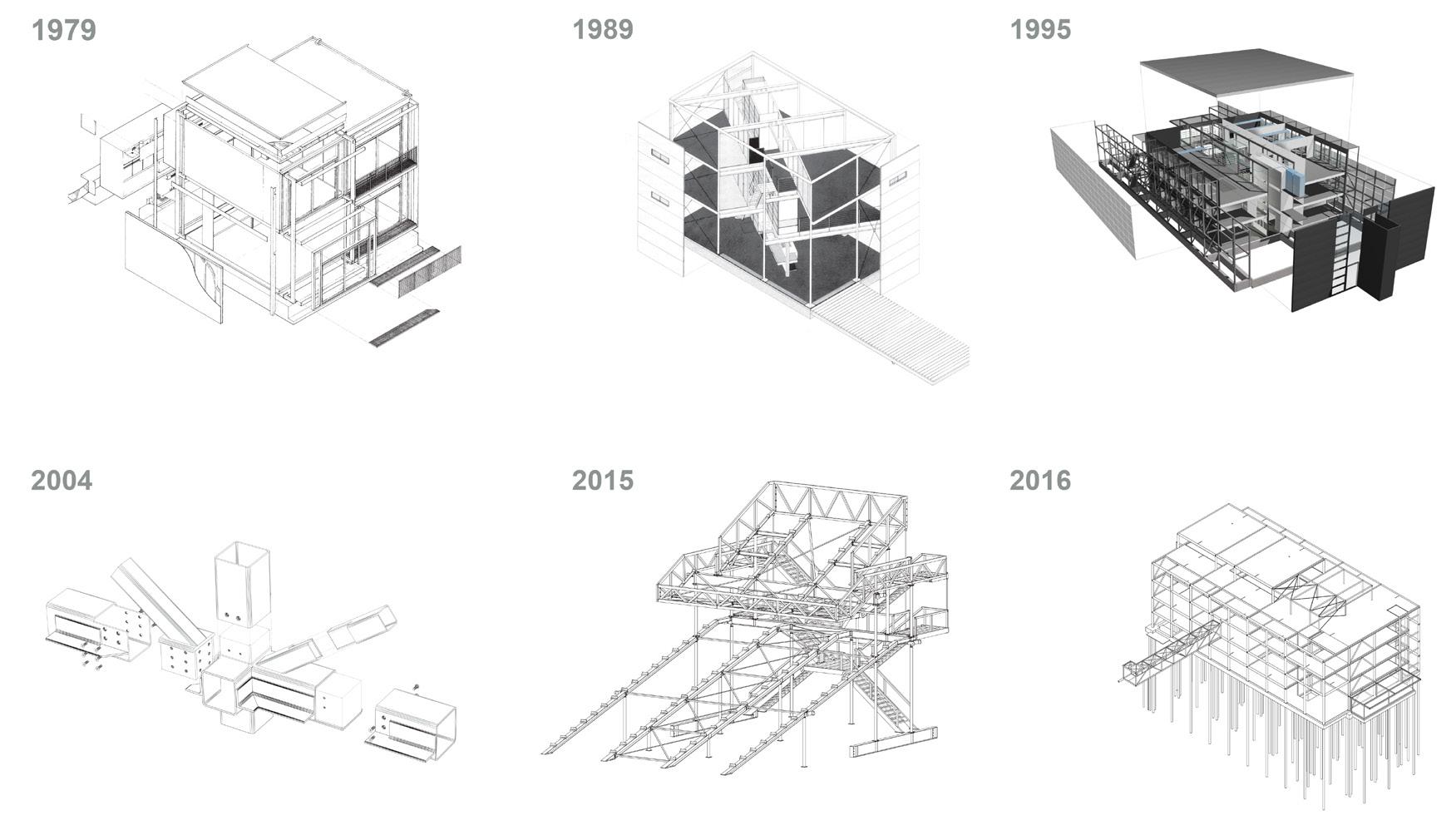
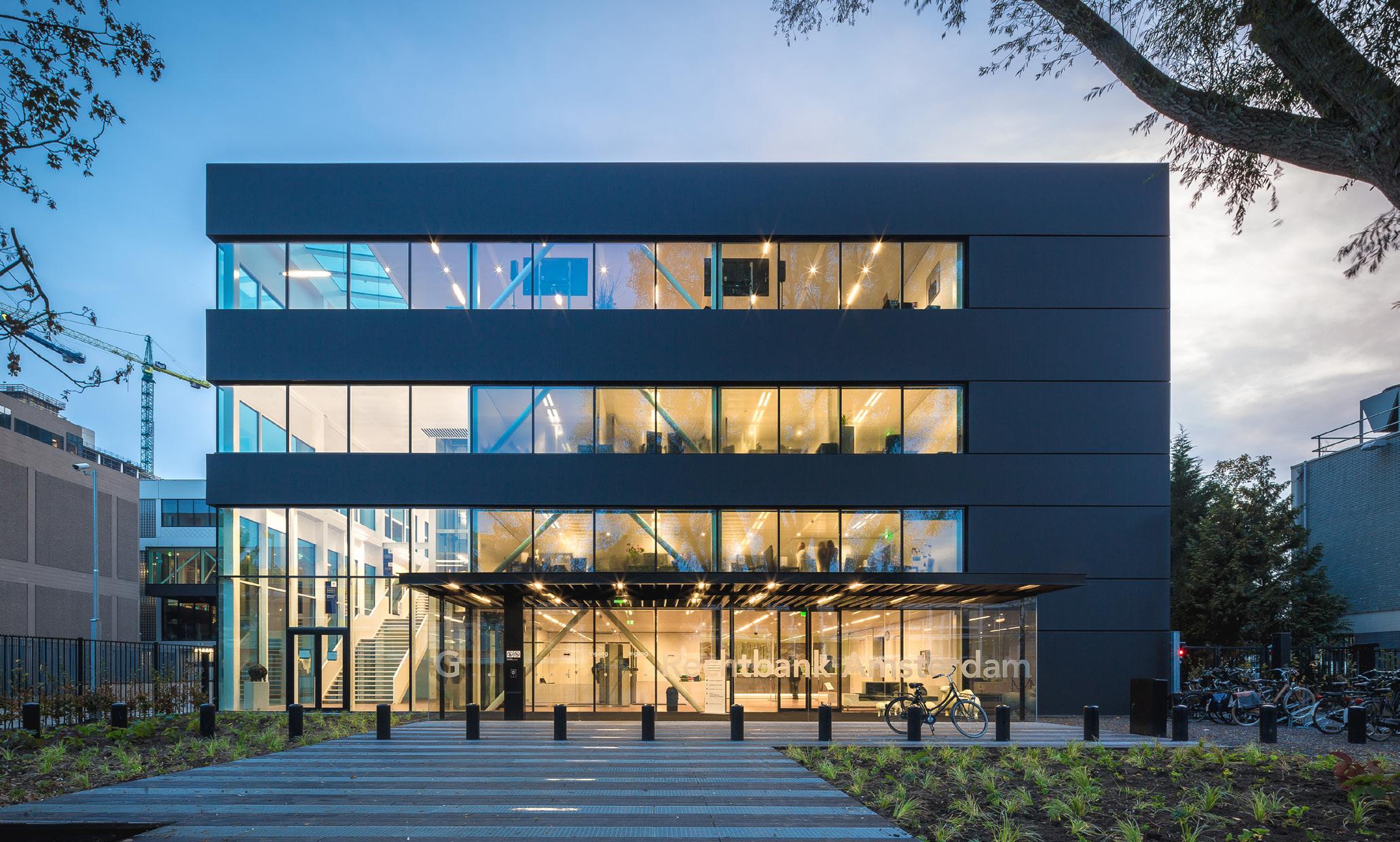
Figure 2. Amsterdam Temporary Courthouse © Léon van Woerkom
Another striking example is the temporary Courthouse in Amsterdam, that was especially designed for deand remounting in the future, won the Amsterdam Architecture Prize and ended up first in a recent survey on demountability. The joints of the columns and beams are all bolted. In contrast with common practice in the Dutch construction industry, the prefabricated concrete floor slabs are not finished with a concrete compression layer and are detachable due to an ingenious method of fixing them to the steel structure. All the ducts and pipes of the utilities are under the raised technical floors. The building’s installations are fully integrated and do not overlap. The kit-of-parts-approach is also very suitable for segmenting a building into bigger components. For the Amsterdam Temporary Courthouse, we needed specific building elements such as an entrance, a flight of stairs, a connecting bridge, etc. Instead of combining everything into a whole, we chose to design these all as separate components. So, when the building is taken apart for rebuild elsewhere, we can change the position of the entrance or stairs. By separating the “specials” like the entrance or the toilets as common denominators we can change their position within a standardized and repetitive grid.
3. Do your current designs contribute to a defined design language for your future projects? Do you believe the kit-of-parts-method results in limitations regarding future designs?
On the one hand, we commonly focus on the joints, not on the dimensions of the large, completely prefabricated components. For example, we do not have a fixed length of modules like there is in e.g. container architecture. For us, span differences are not an issue, it does not matter if the beam is 6 or 8 m long. This way, we are much more flexible. When designing, we can simply cut or elongate the length of a beam if we use the same type of connection at the end. We do not neglect the diversity of building dimensions. But especially if you want to remain flexible during the process, a focus on the connections is very important. On the other hand, we do try to standardize the lengths; partly because it is more efficient, but also because it is cheaper to make all beams and columns of the same lengths.

Figure 3. Detailed Axonometric © cepezed
As for the details of the connections, by the way, these are very minimalistic. Nicolas Grimshaw, for example, makes beautiful buildings that are very expressive. But the architects of cepezed avoid bothering people with their designs; they are there, but not in your face. If you look closely, you can see the connections and their detailing, but the casual observer won’t really notice them.
We are not part of any “High Tech” movement, because expressive detailing is a style in these movements. For us, buildings are about a lot more than solely their aesthetics.
4. Have any of the connections or parts that you invented made their way outside of your office to the industry?
Definitely, the most profound example stems from the 1980’s. At the time, we looked at cooling trucks, that were able to maintain a low temperature of -20°C with a very thin and lightweight construction. The façade of the cooling truck basically consists of insulation in between two sheets of steel. Together with the cooling truck producer, we then introduced the sandwich panel, which is now widely used.
As a first prototype, we even built a new house for producer with these panels. The sandwich panel is a smart construction element: it is very lightweight, you can produce and prefabricate them in different dimensions, and they have insulation capacities that are way better than traditional walls.
When designing components, we frequently ask ourselves if we can integrate multiple functions in one single element. For example, often times the stability structure can also function as a distributor of air or wiring. This results in buildings with a high intelligence per kilogram; when you make something smarter and integrate different functions, you use less materials. This saves resources but also makes for cleaner aesthetics.

Figure 4. Building D(emountable) © cepezed
5. Do you use standard parts available in the industry, or do you design all components in the office?
The concrete slabs of the Temporary Courthouse were an existing product, but we modified them. Often, we work with existing materials and modify them to suit our needs. Traditionally in the Netherlands, all building elements are welded, melted or anchored together during construction; therefore, clean, detachable connections between the different components make for the first step towards circularity. The next step is to look at each component and optimize it, make it smarter. For example, elements can often be produced with less material. Or conceived bio-based. Or even be produced using second-hand materials.
6. Have you had an experience of taking some parts of a building and reusing them in another?
The Centre for Human Drug Research, which we did in the 1990’s, had a perforated screen on both elongated sides. The screens functioned as a second skin façade, to block sun and wind. After 10 years of use, we extended the building using the same construction system. We took down one of the end walls, prolonged the structure and then used the same façade elements to close it back up.
For restaurant and meeting center The Green House in Utrecht, we applied reused materials from scratch. We were assigned to transform an old military building into a contemporary office building with a pavilion almost directly adjoining the office. From the old military block, we used as many materials we could for the pavilion. For example, all the glass in the pavilion’s façade stems from the old military building. The interior separation walls came from the SOM building in Rotterdam. We even used bricks from a quay from a nearby city. So here we used many second-hand materials. Finally, even the concrete foundations are circular: the pavilion is not founded on piles, but on underground Stelcon-slabs with blocks on them. Both slabs and block can easily be removed afterwards.
7. What goes through your mind as you design? Do you Design for a building to be disassembled in the future?
We consider buildings as products. A product is something that has a value, a (high) cost, and a certain functionality. If it ceases to be used, the building should be able to change for another use or even demounted. Our aim is not to create an architectural icon for the ages, but rather a thing that can be used and adapted.
8. Do you think that this methodology has a challenge in terms of aesthetic value? From the experience within cepezed, does this object-oriented construction style limit design possibilities? Are all the products destined to result in regular, predictable forms, to comply with the reusability aspect?
The kit-of-parts-methodology is simply another toolbox. In our case, we still have a lot of freedom in the way we express our buildings. We do not use bricks because of their high weight, but instead make use of lightweight façade panels combined with different
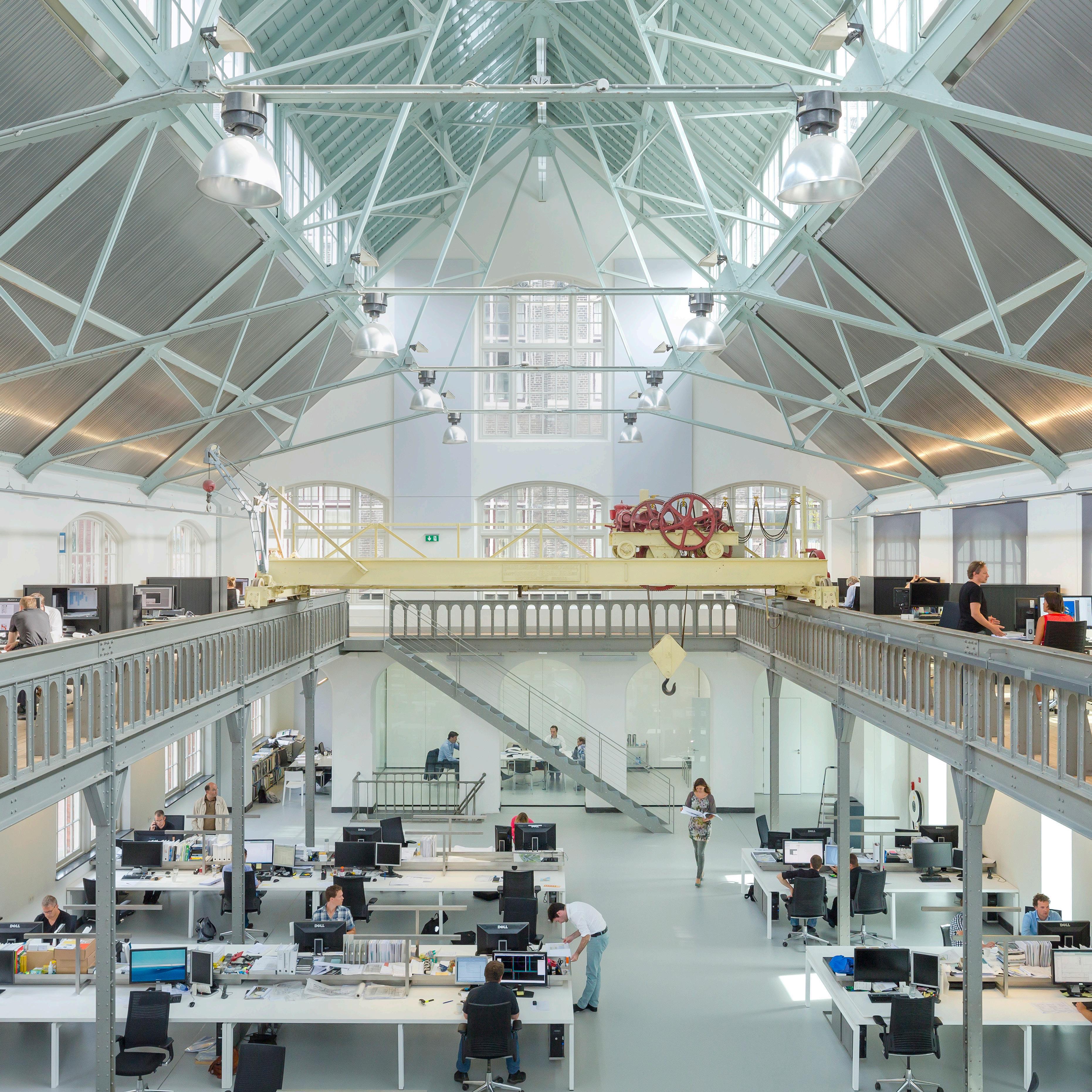

Figure 6. Building D(emountable) © cepezed | Lucas van der Wee
finishing or second skin options such as textiles, Corten steel, lamellas or wood. The joints between materials are more important than the materials themselves. Of course, we could also fake brickwork with tiles but we much prefer buildings with integrity: buildings that show how they are made. refined craftsmanship. Therefore, we already refine the details in our designs. The different components are then prefabricated in the manufacturing plant, with a very high quality and utter accuracy. On-site, they only need dry-assembly. This process strongly reduces the need for on-site labor.
9. Do you consider this construction technique new in the building industry or has it been around before? Has cepezed used the approach in the past?
In the past days, labor was cheap and materials were expensive. Therefore, there was a surplus of time that allowed for beautiful, labor-intensive details. But nowadays, labor is much too expensive for on-site
10. Is BIM a vital tool for this technique? Does cepezed work only with BIM or is there another way of achieving the same degree of coordination ?
One of the reasons we were one of the first offices to work in BIM was that BIM perfectly matched our way of working. It was an obvious choice because, we already used the kit-of-parts-methodology. Revit-families
and BIM-models are based on a similar approach. In it, buildings are an assembly of various construction elements. Also, BIM-modelling requires quite a degree of abstract thinking. That suits our team pretty good: it is almost completely composed of very high-skilled, welleducated architects. We even do not have draftsmen, the designers do all the elaboration themselves. BIM allows us a smarter integration of the utilities, connections and components.
11. Explain the design process within cepezed
Initially, we always try to design nice spatial structure with sequences of different scales. The façade is often one of the last things designed, because it changes the most over the course of the design process. From the very first sketches, we continuously think about how the building can or must be built. This attention for practicalities allows us to develop a more congruent design. We also spend a lot of time on the integration of the different design disciplines. Over the course of time, we developed very nice façade details working hand in hand with the suppliers, who know best what can or cannot be made. Sometimes, we give them the assignment straight away and plan ahead of the contractor. Contractors will often say our design is too difficult, innovative, or expensive, and they cannot provide warranty for its execution.
By working directly with the suppliers, we know if our solutions can or cannot be made. And how much they cost. The contractor then becomes the party that coordinates the tendering of the components and the site. This way of thinking helps the traditional contractor because nowadays they are mostly doing a logistic tendering process, instead of doing the construction themselves.
Furthermore, as we design with clear connections between the façade and the structure, the contractor can more easily tender each component independently.
Figure 7. Building D(emountable) © cepezed | Lucas van der Wee
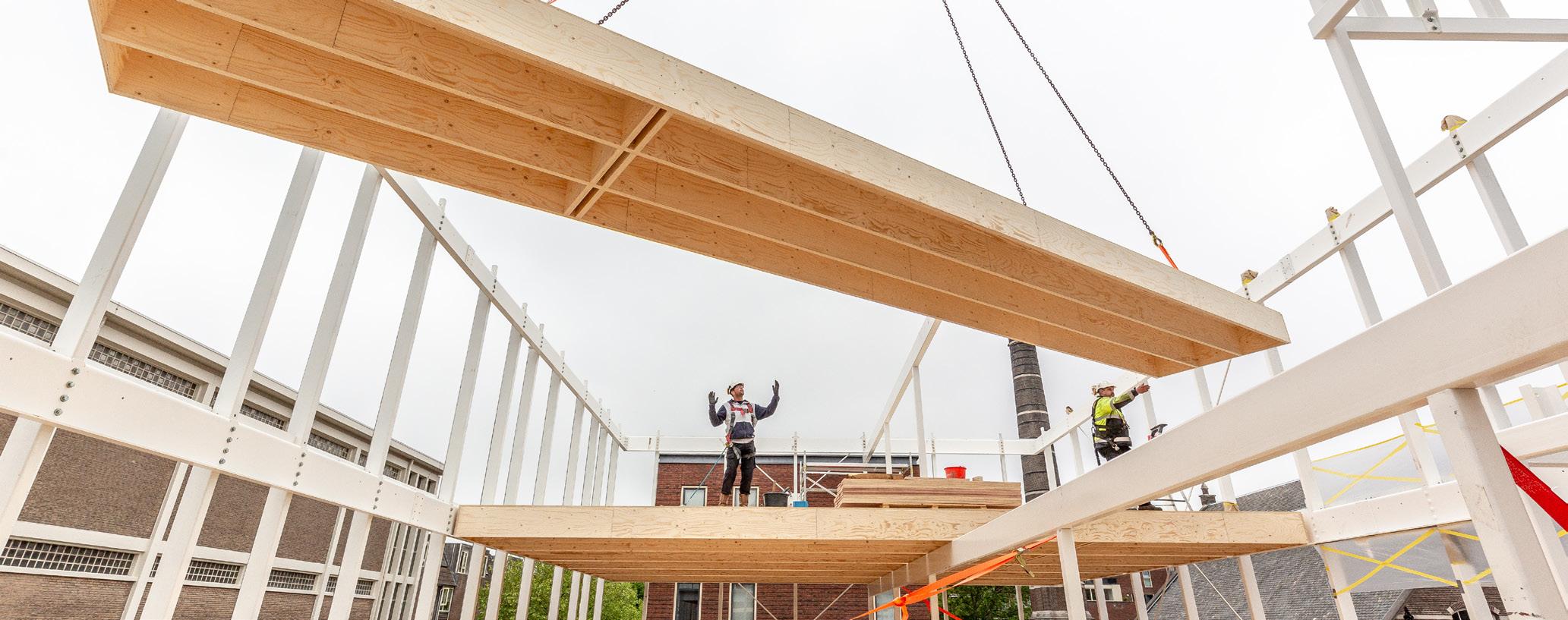
12. Regarding the design phase, when you start a new building, do you start from zero when designing the connections, or do you have a catalog of connections that you improve upon?
The ideas of how to mount or unmount are always similar, although we have variable principles that we apply depending on the building type. If it’s a highrise building, it makes sense to have different kinds of structural joints. If you have a four-story building, you might think of having a prefab frame with a low tolerance. For each project, we think of the best possible way to construct it. Nonetheless, the core ways of reasoning remain the same.
On the product level, there is a continuous evolution. Structural floors of wood are a perfect example. During our initial years, we used wooden floors quite often. Then for about 20 years, we did not use them at all. Now, we have returned to wooden floors in the shape of prefabricated floor elements. When used appropriately, these timber components have great acoustic characteristics and load bearing capabilities for efficient spans. We seek to continue evolving on whatever product is available.
13. Do you also design furniture?
We often do. When we design pieces of furniture, we also think of them as a kit of parts. For example, the benches we did for Schiphol airport. If you look closely, you see that they are composed of multiple detachable elements: the main beam, the kit for seating, the headrest, the stands, the glass tables, the foot rest. The benches have a main beam that can be elongated or cut; they can therefore be compiled in a flexible manner. With the detachable elements, a wide range of configurations can be realized. So our furniture is also a kit of parts. We work from the same ideas, be it in architecture or furniture.
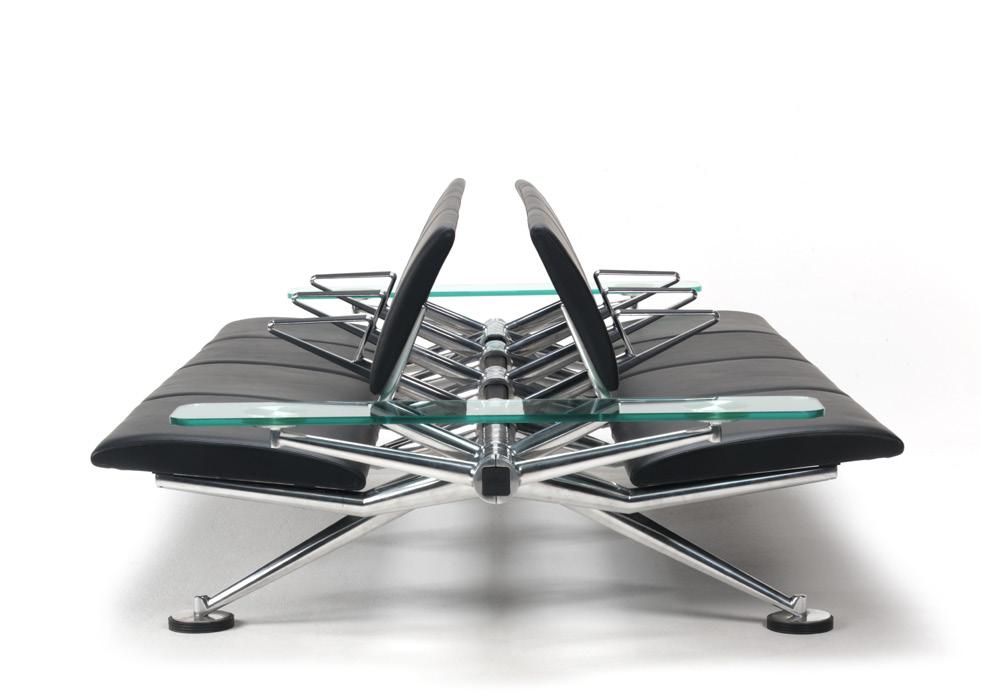
Figure 8. Schipol Airport Furniture © Studio van Assendelft
14. Are you also involved in the subsequent phase of the use of the building? Monitoring the elements? Who is involved in that phase?
Usually we do go back to hear how our buildings are functioning; we do not seek to change them but rather to learn what works well. Additionally, many of our clients have come back to us when they need to expand or build a new building. The Centre of Human Drug Research came back to us repeatedly and now we are working on their fourth building.
An alternative to the traditional process of “finishing a building” is the Amsterdam Temporary Courthouse, for which we got a government assignment together with the contractor. After 5-7 years, we will have to take the whole building back and see after proper re-use. For this reason, we anticipated on detaching and rebuilding the whole structure. That’s a very special feature for that project, and we hope to be able to do more projects based on the same approach.
15. For you, what is the future of the kit-of-partsapproach?
We have been working with this method from the very beginning of our office and now, we see that the rest of the industry is catching up. Recently, a cooperation of different parties in the sustainability field have jointly launched a “detachability index”. The Temporary Court in Amsterdam ranked highest of all test cases, but restaurant The Green House also did very well. Societywide, there is a lot more focus on the kit-of-partsmethodology and designing for disassembly then there was before. This concept is now coming up everywhere. An example is the Erasmus University Rotterdam, that now explicitly requests demountable buildings. It is going in that direction, although there are still very big steps to be taken.
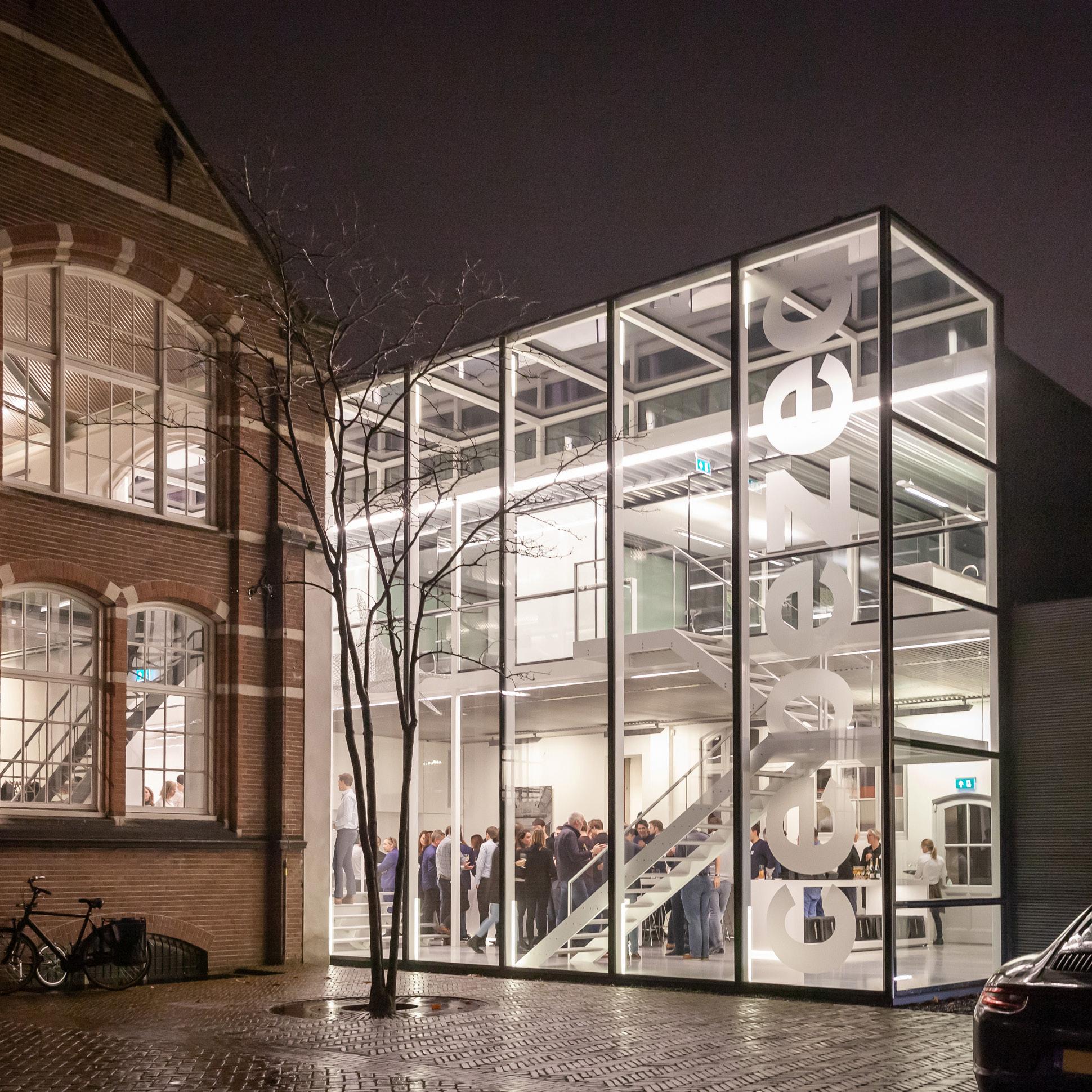
On the other hand, if the industry seeks to refurbish secondhand products within the kit-of-parts-approach, there is a shortage of suppliers. After all, older buildings that were built in the last 50-100 years were never designed for disassembly.
The Dutch government does have serious intentions however. Likewise, all designers have hopeful purpose. Still, we must stop seeing detachability as a nice gimmick, but rather consider it a great opportunity to create a more sustainable world with a truly circular industry. It is up to us as designers and engineers to realize the great potential.

Tamedia Office Building, Zürich
Building study to understand the application of Kit-of-Parts Technology
By Anagha Yoganand and Aditya Soman
The media house envisaged their new building extension to harness their vision of blending the contemporary digital and traditional print media cultures under one roof. The spaces, therefore, are open and flexible to encourage interaction and promote a healthy work environment between the two cultures.
Introduction A striking demonstration of timber construction is realised in a seven-storey tall office building, completed in 2013, in Zurich. The building is designed and visualised by Shigeru Ban Architects in collaboration with BlumerLehmann Corporation. It is a renewed extension to the existing headquarters of Tamedia, a leading Swiss private media group. Tamedia was envisioned as a load-bearing structure designed for dry assembly on-site which largely mimicked the concept of building blocks.
Committee members from Rumoer visited the building as a part of the study trip to Zurich organised by Bout. It was exhilarating to study the building and to understand how the Kit-of-Parts methodology is employed in different phases of the building. The kit-of-parts methodology is closely related to the integration of design, fabrication and assembly. The tamedia building exemplifies this idea of seamless integration of building components. The study was carried out by knowledge gathered during a guided building tour by the communications manager Andres C. Nitsch. The study also referred to the literature available on the building.
Architectural Concept The media house envisaged the new building extension to harness their vision of blending the contemporary digital and traditional print media cultures under one roof. The spaces, therefore, are open and flexible to encourage interaction and promote a healthy work environment between the two cultures. Shigeru Ban, the appointed architect for this project, conceptualised Tamedia entirely in exposed Timber. The load-bearing structural framework consisting of timber columns, beams and joineries are all designed and built without using any screws, nails or metal fasteners. The whole construction kit consists of 1600 prefabricated timber elements, CNC-milled, factory manufactured and transported to site for assembly as a three-dimensional puzzle. The construction of the building took around 22 months until completion.

Figure 2. Initial sketches Source: Andres C. Nitsch
The Kit-of-Parts:
Glulam Structural timber elements
Sourcing the right timber:
The main idea behind material selection concerning the type of timber was emphasised by the architectural desire to keep the material palette local. Spruce, a locally grown timber in the Swiss Alps was hence selected. It is also proved to be cost-effective. However, the main problem encountered with this selection is the warp generated in the timber log due to the internal release of tension while harvesting them from the alpine forests. Additionally, these spruce sections also had many branch holes. Therefore spruce grown in flat planes, sourced from Austria, seemed ideal for the structural timber elements. The complete assembly required 2000 m3 of timber from Austria for the structural members and another 2000 m3 from Switzerland for constructing the flooring panels.
Components:
The building’s length of 31.8m is divided into eight structural timber frames at every 5.45m. Each structural frame consists of four continuous columns that extend till the eave height of 22.5m and a beam couple spanning 11m that connect these columns at every floor height. An oval peripheral girder beam further connects these frames. All these components were manufactured with high precision using CNC milling with a tolerance of 2mm.
Connections:
The elements and their connections were designed accounting for lateral stability as the architectural vision eliminated the use of cross bracings. All connections are friction fit, which implies that every element needed to be precise with least tolerances to ensure ideal load transfer via contact. The connection between two spruce timber elements lacks friction, which resulted in designing unique connections made of beech plywood to reinforce the required friction and allow load transfer. The beam couples are connected by an oval beech plywood dowel which precisely sits into the oval inserts made in the rectangular columns. Figure 3 shows the connection detail of the beech template inside the spruce joint.
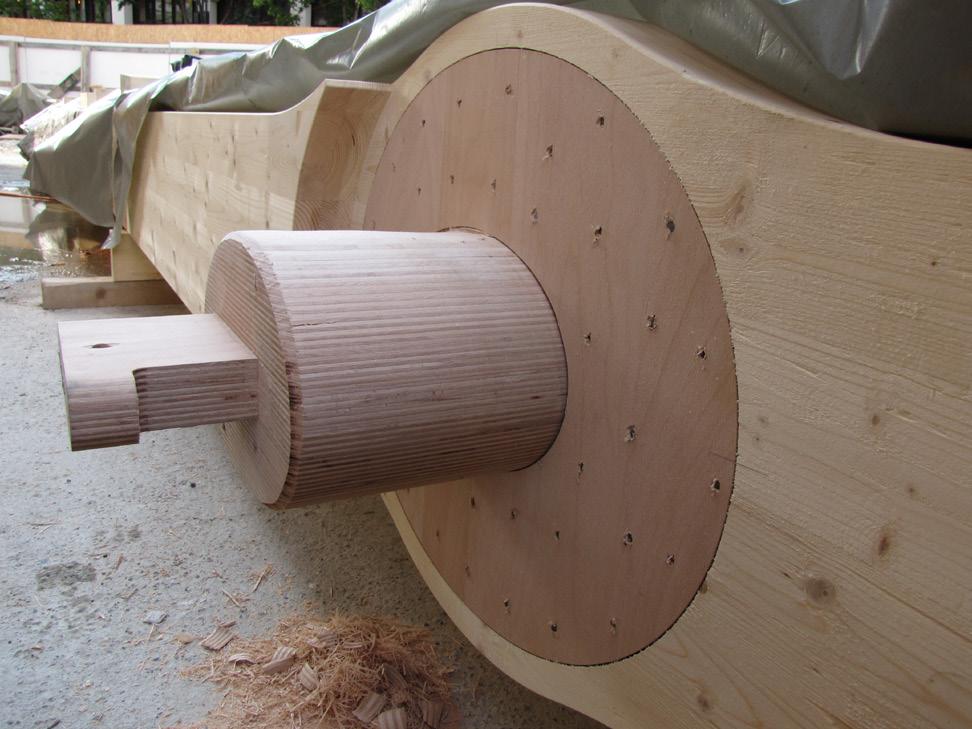
Figure 3. Beech Plywood Dowel Conenction. Source: Andres C. Nitsch

Figure 4. Connection Detail. Source: Andres C. Nitsch
Figure 5. Terrazzo Style Flooring. Source: Andres C. Nitsch
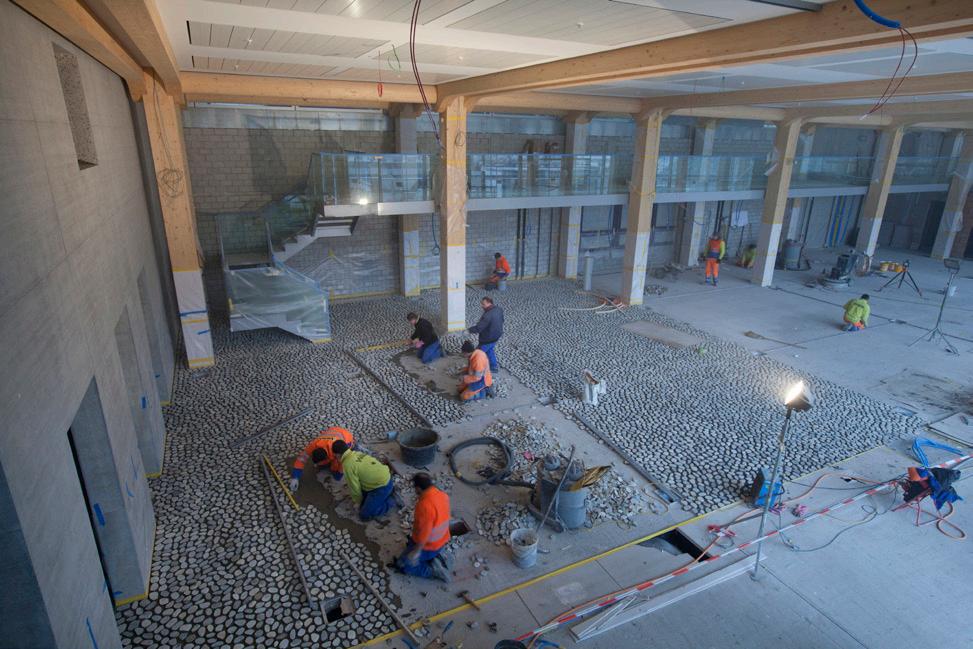
Figure 6. Assembly of Roof Truss. Source: Andres C. Nitsch

Flooring and Ceiling elements
Flooring and ceiling elements were also pre-assembled and erected on site. These consisted of timber floorboards with 8 cm sand filling for increasing the weight of the floor for structural stability and sound insulation. There was a requirement of cut-outs for flooring for including the building services requirements; hence, the flooring was made in double layers with particle board on top of cassettes filled with sand. The flooring in the public space on the ground floor was the only non-prefabricated element in the whole building. The flooring was a highly customised solution where the floor was laid in a terrazzo style which is commonly found in European plazas. One hundred thousand stones were sourced from De chino which is the southern part of Switzerland. They were cut and laid individually to create the flooring pattern. The colours chosen for the flooring pattern by Shigeru Ban were symbolic of the material palette used in the building. Beige for Spruce, green for glass, and Greyish black for the aluminium and metal parts of the building.
Transportation and logistics
Around 80% of the building components were prefabricated in a factory, then transported to a storage house and finally brought to site as per requirement. The logistics were rather challenging to manage, considering the inner-city location of this site. Only one driving lane was available for transportation and unloading of all building components including the large timber sections such as the columns and roof trusses.
Assembly
The assembly started from the south end of the existing building. The eight timber frames were first erected successively on-site, every preceding one being a template for the successive ones. Mobile cranes lifted these pre-assembled timber frames and positioned in place. While these components were elevated, cracking sounds could be heard until all connecting elements were in place. This was a result of friction fit joints that allowed minimal tolerances. The timber frames were held inclined and gradually made vertical as the oval girder beams were being positioned floor by floor, from bottom to top. The flooring and ceiling elements were installed in place following the column grid lines. Lastly, the preassembled roof truss was erected and fixed to each of the eight frames stabilising the whole structural timber frame in place due to its weight.

Figure 7. Vertical Section Details. Source: Andres C. Nitsch
The construction schedule was planned to keep work tasks running simultaneously in the sequence of structural assembly, which lead the project to completion within two years.
Conclusion Tamedia’s novel approach towards design and construction largely complies with the theme Kit-of-parts. The vision of the architect to create a wholly exposed timber structure with in-material connections pushes boundaries in the existing knowledge of contemporary timber construction. However, it raises the question of fire safety. Although, according to Andres, a sacrificial layer of 3 cm is added to the required crosssectional dimensions of all elements as fire protection. In case of a fire, this layer burns and the charcoaling protects the internal cross-section from damage.
A 3cm fireproof gypsum insert was added for fire protecting the junctions. Innovation in pre-engineered timber accompanied by the advancements in digital technology has led to manufacturing the building components with very high precision that led to fast and easy on-site assembly. Tamedia displays qualities of wood that makes the building an excellent reference in the field of building technology.
The kit of parts approach can be one avenue to explore the future of sustainable built environments. Tamedia is a classic example, demonstrating sophistication in using timber, natural and one of the most traditional construction materials.
Literature Reference: Best of Detail: Holz Wood, edited by Cristian Schittich. (2nd edition) (2015)
EXTREME ARCHITECTURE BouT presents the symposium on


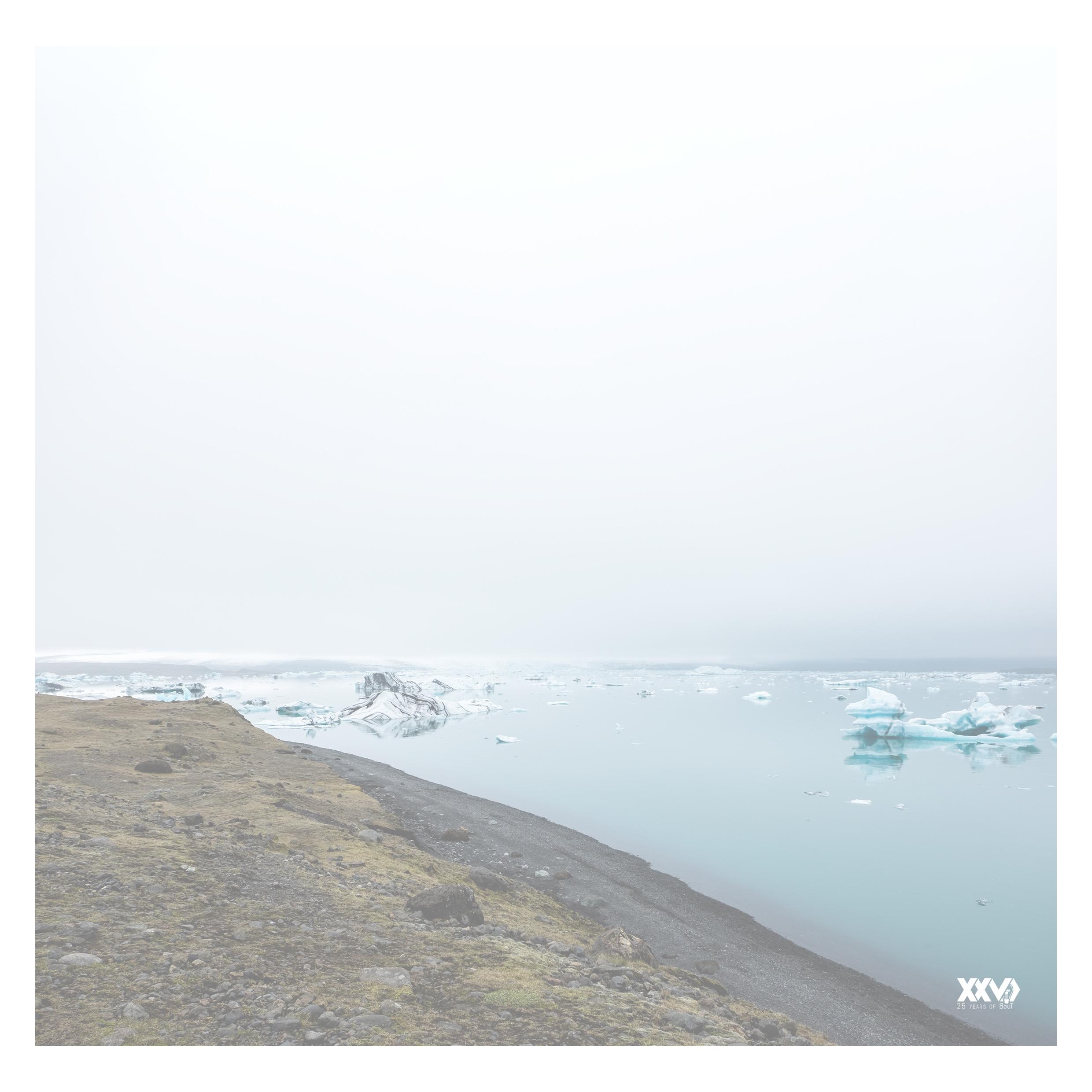
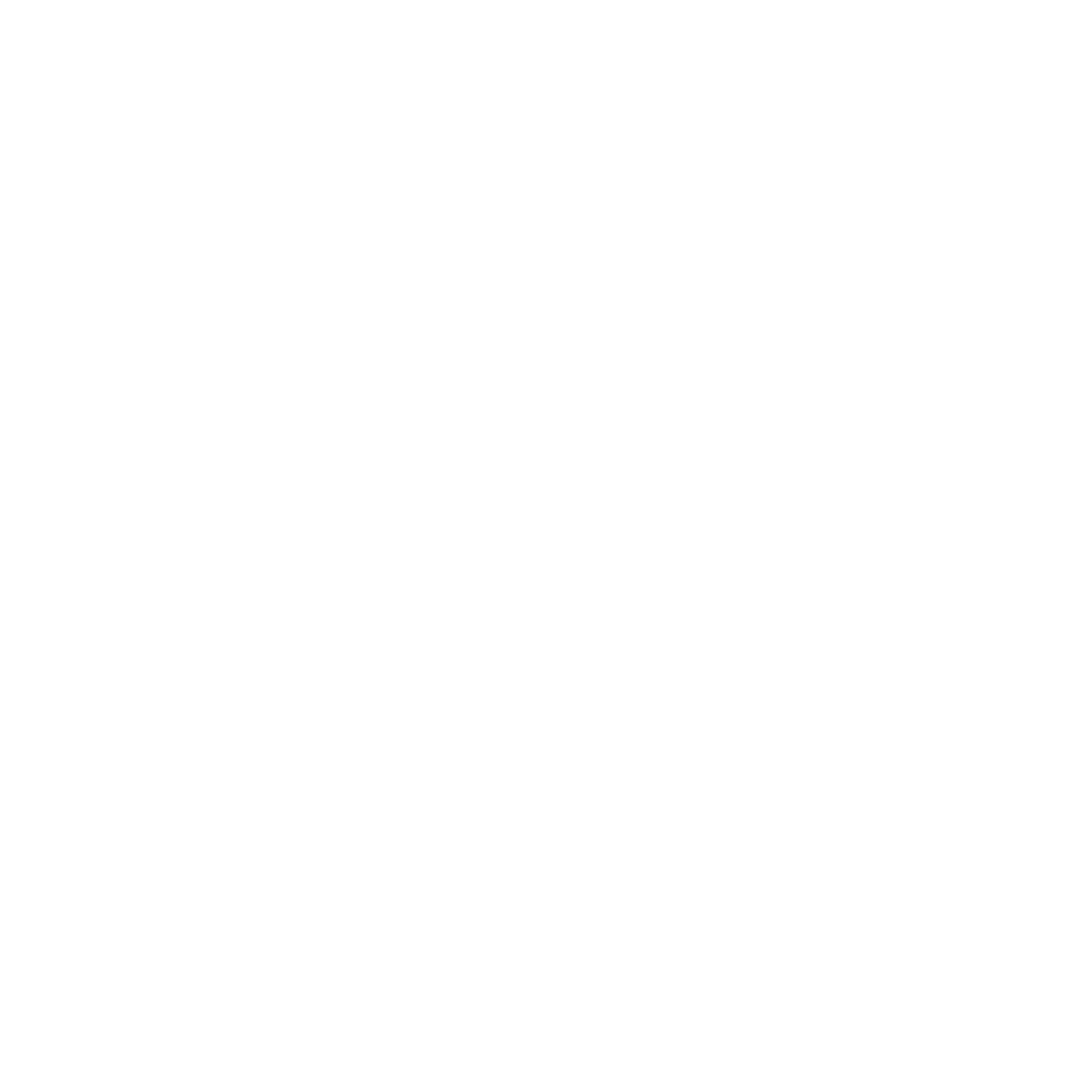

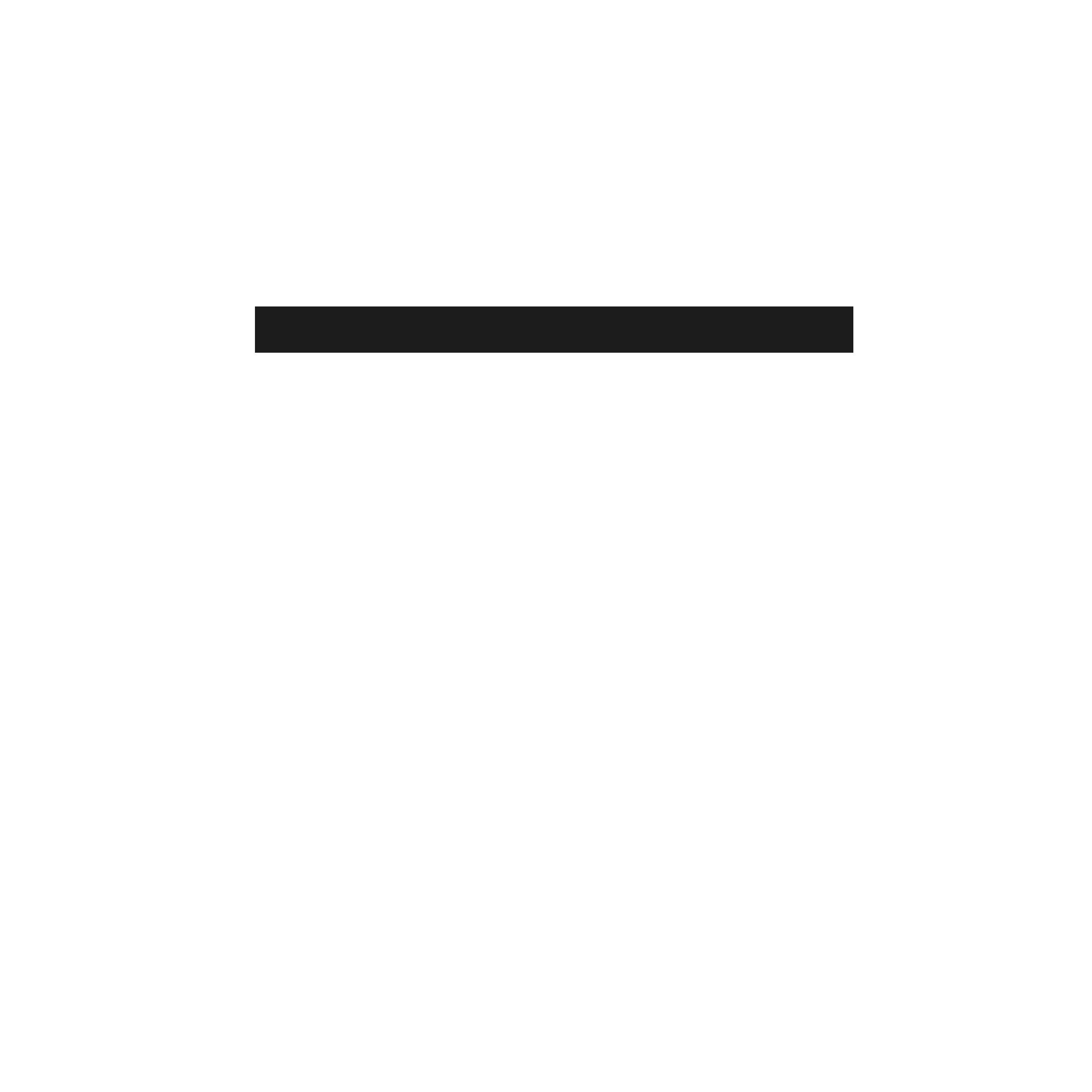
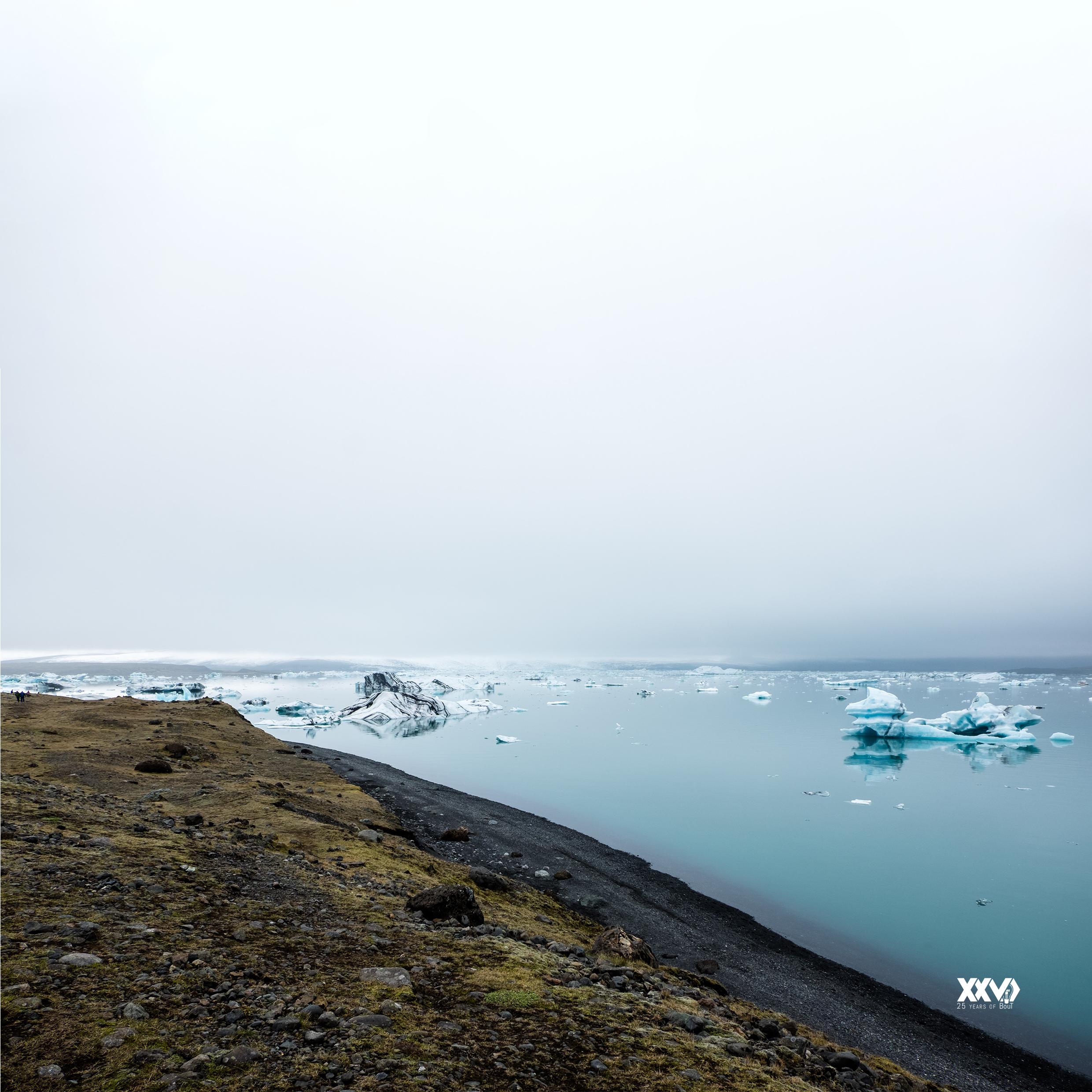
It is well known that society strives and works as a collective in the face of adversity, and history has proven this to us over and over. The extreme challenge within architecture and technology is how we can change our mindset, build over our own paradigms and shape a new future. An engaging debate on projects that utilise cutting-edge technology and engineering, but equally considered aesthetics, sustainability and human need into these ground -b reaking designs and research concepts is needed. How can we learn from reactive architecture? How could we implement preventive architecture in our future designs?