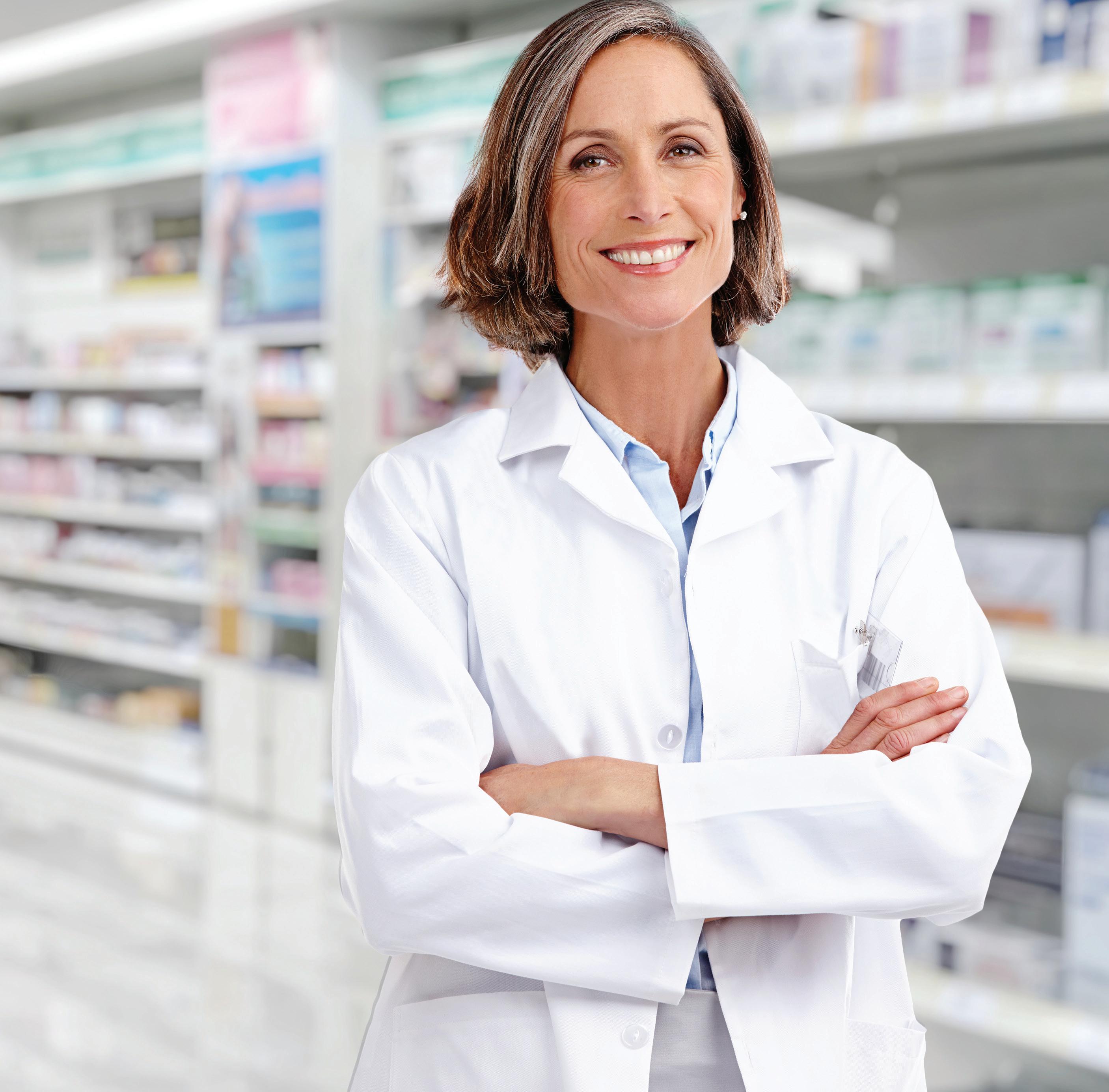
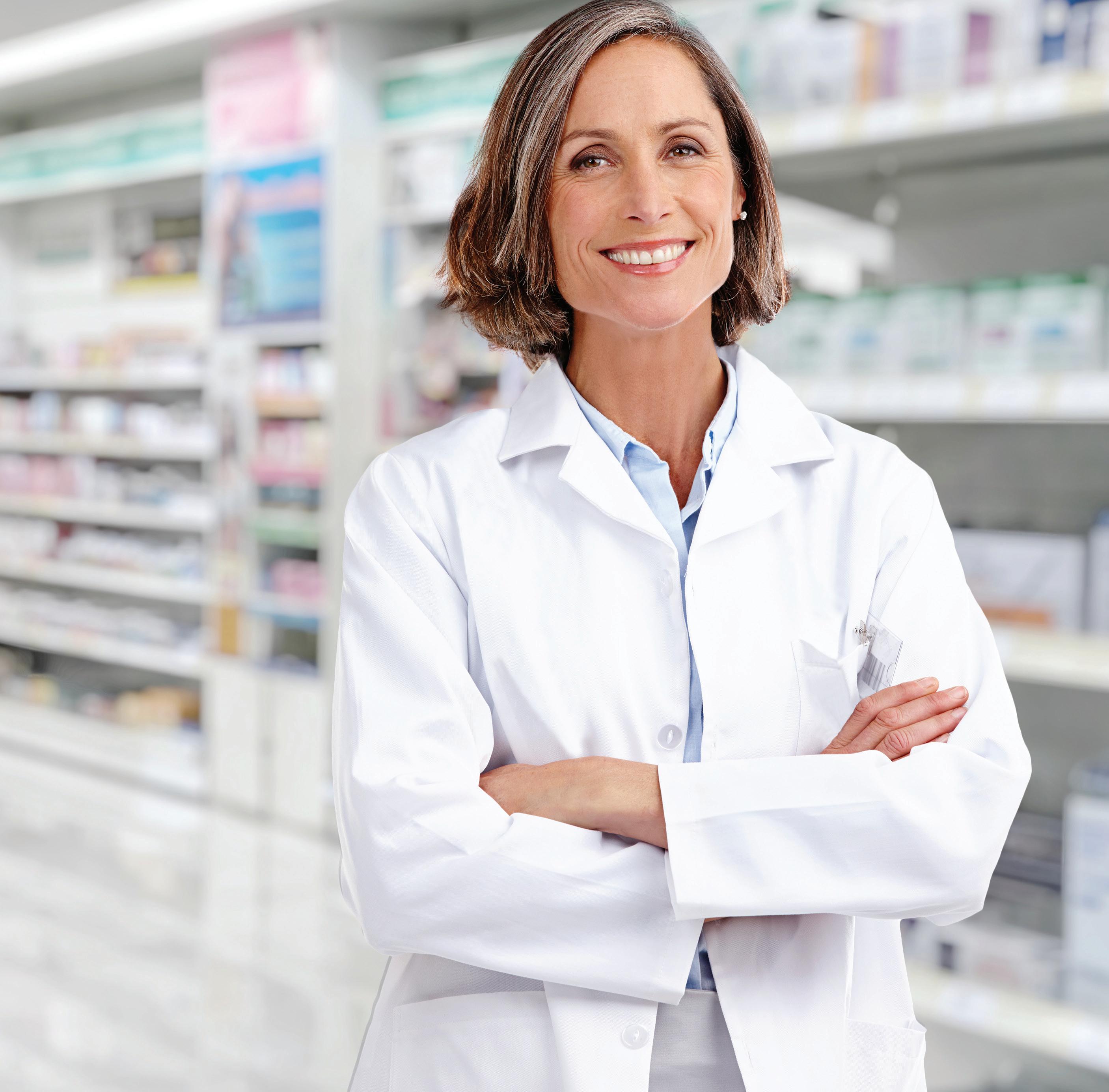
Safet y needles designed to protect
Because more than 40% of needlestick injuries happen af ter use,1 we designed Cardinal Health™ Monoject™ Magellan™ Hypodermic Safety Needles to keep patients and clinicians safe at ever y step. Magellan™ Safety Needles are engineered to comply with OSHA regulations and help you standardize solutions across ever y job with one safety technology
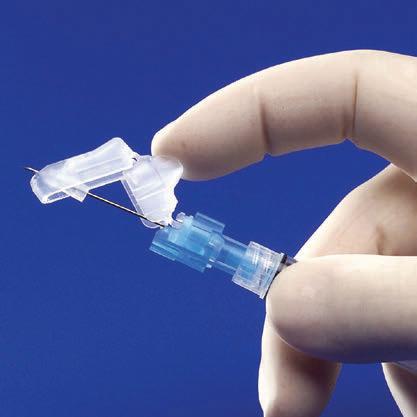
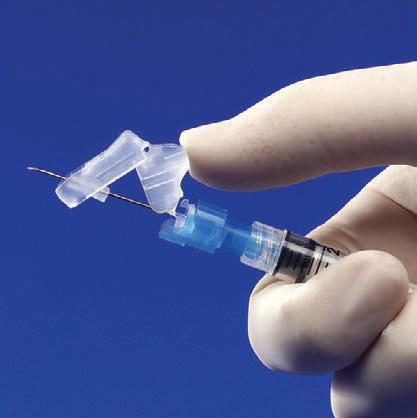
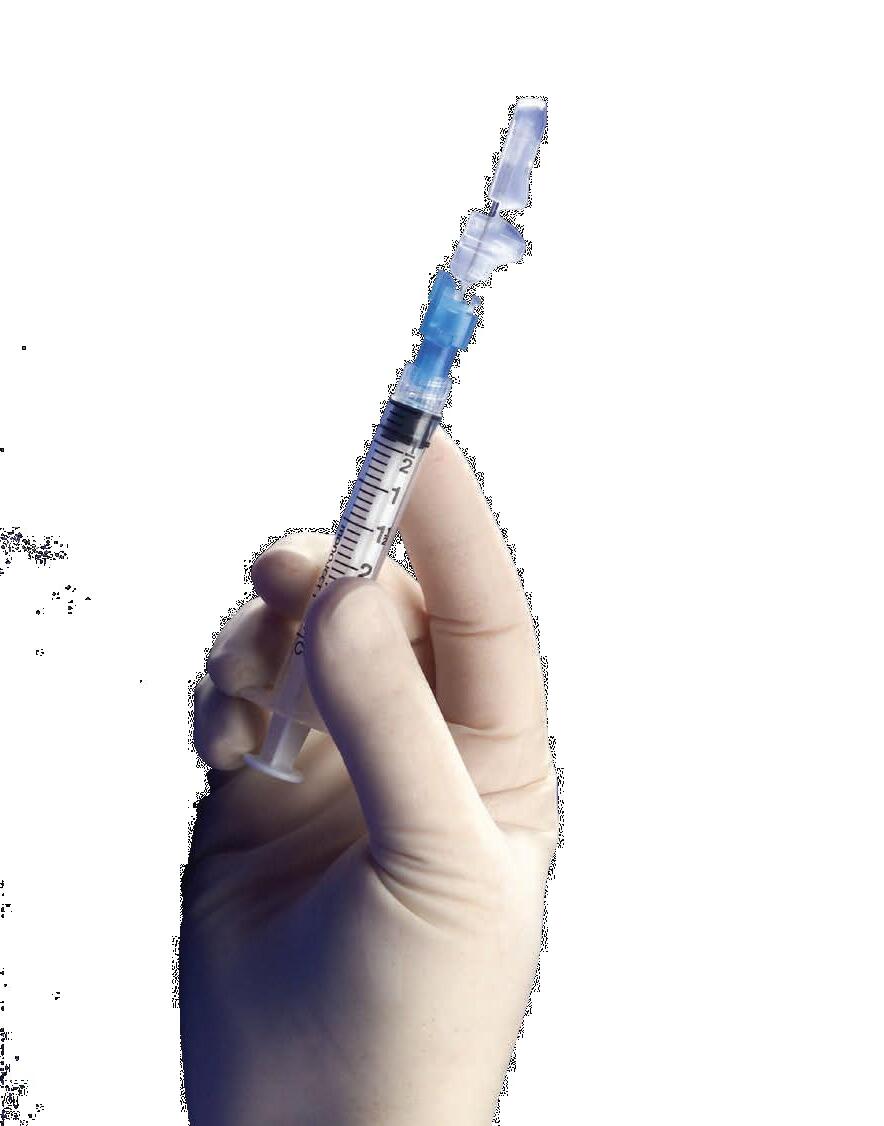
Robust safet y shield provides coverage of entire cannula and is not easily removed One -handed ac tivation, three ways Keeps hand behind needle Audible ac tivation cue
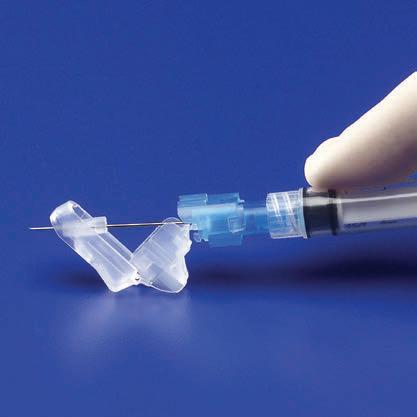
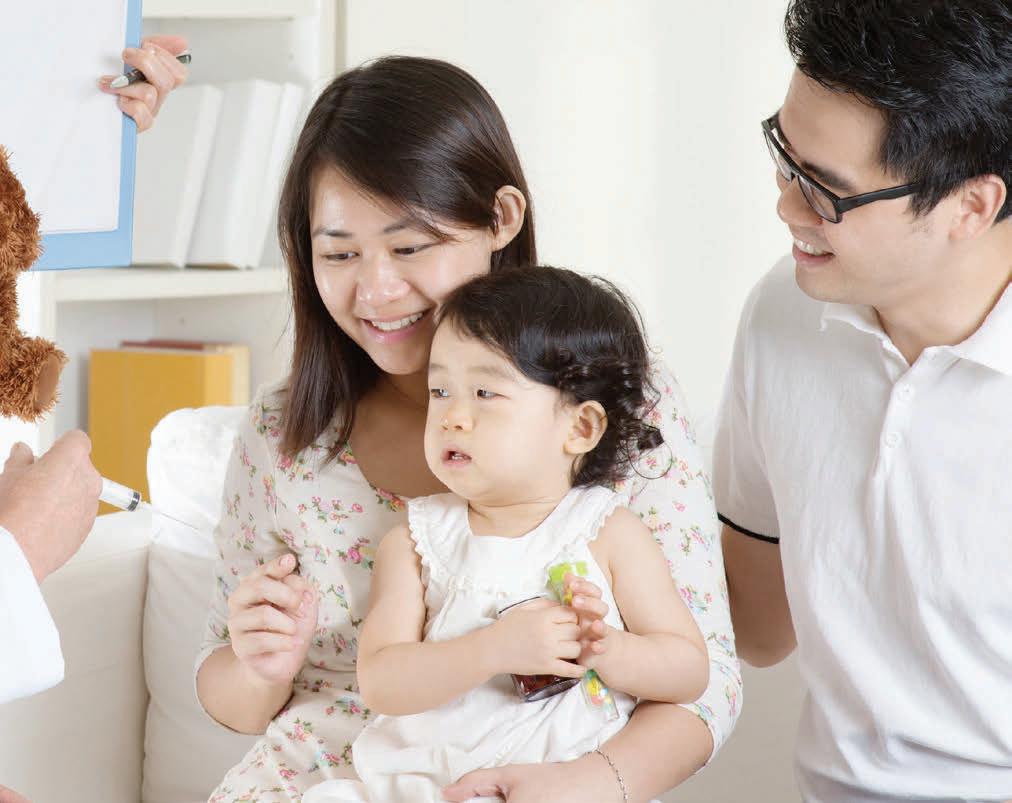
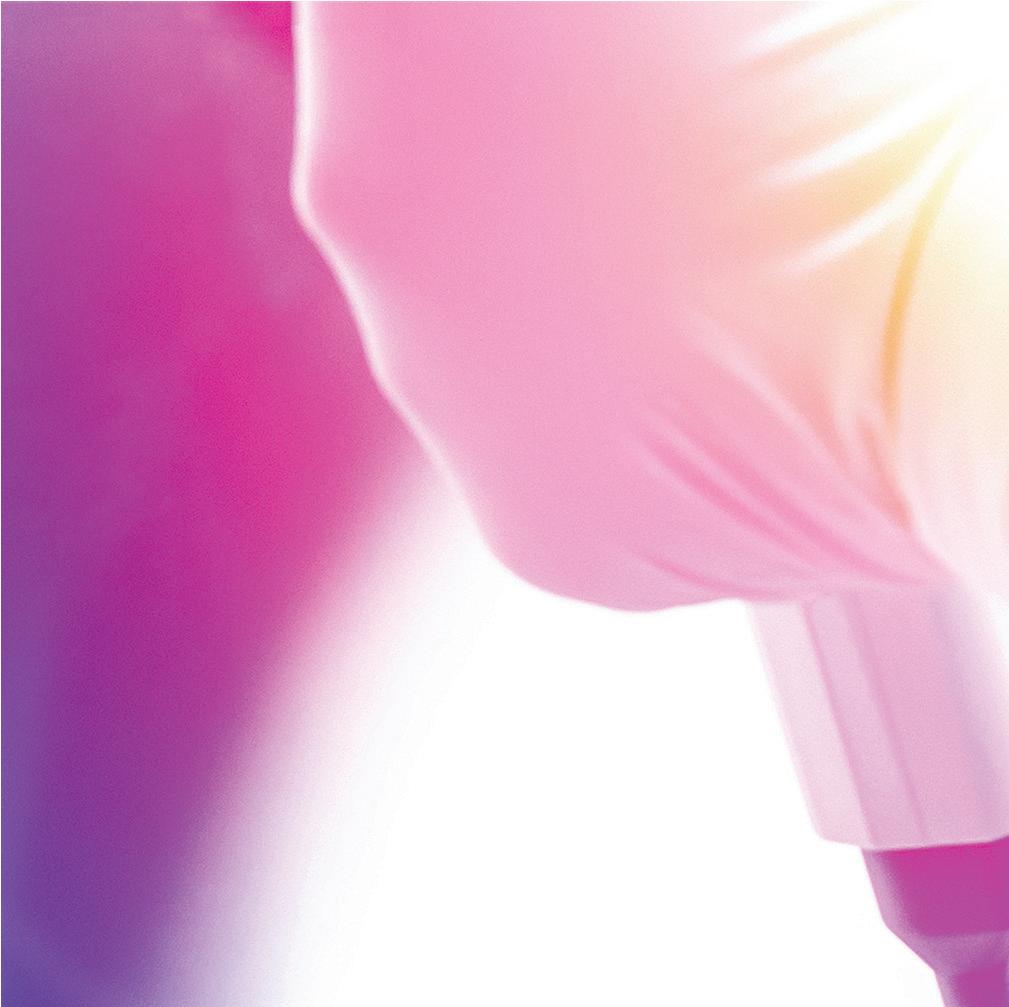
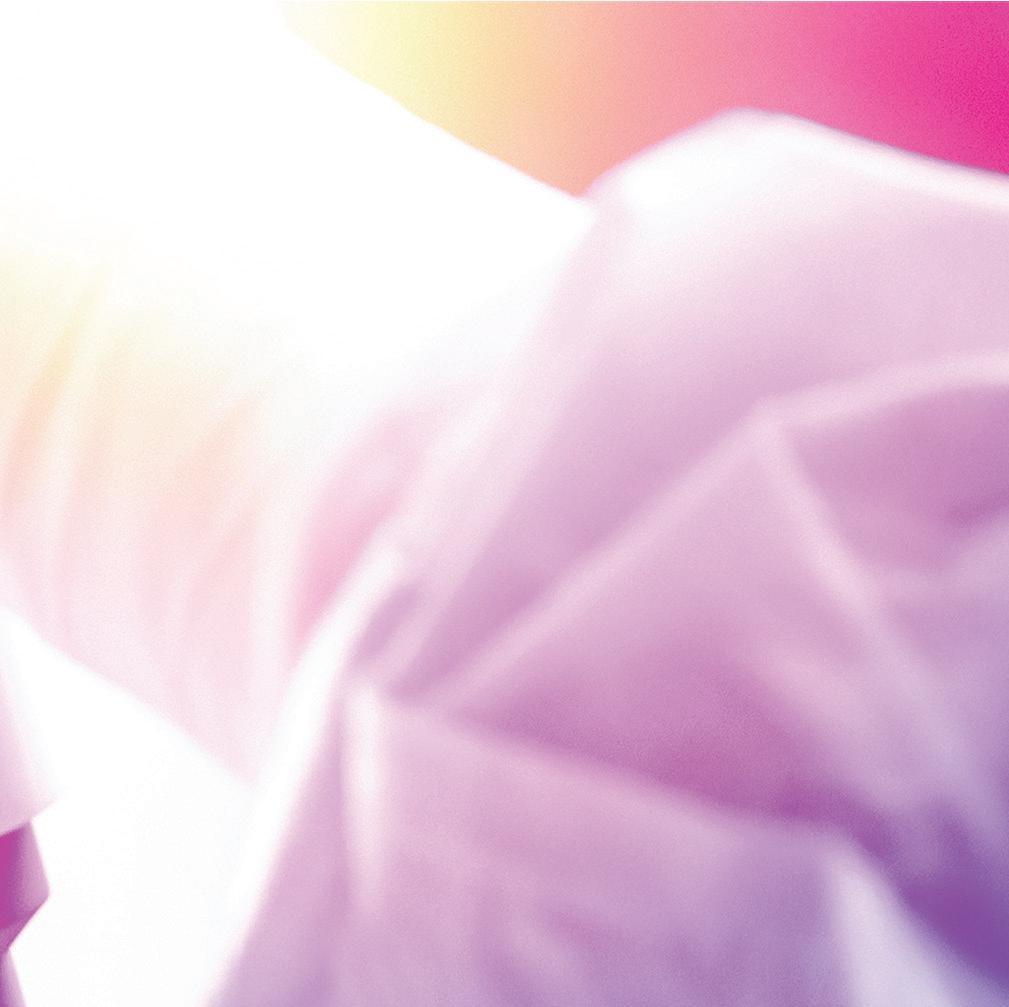
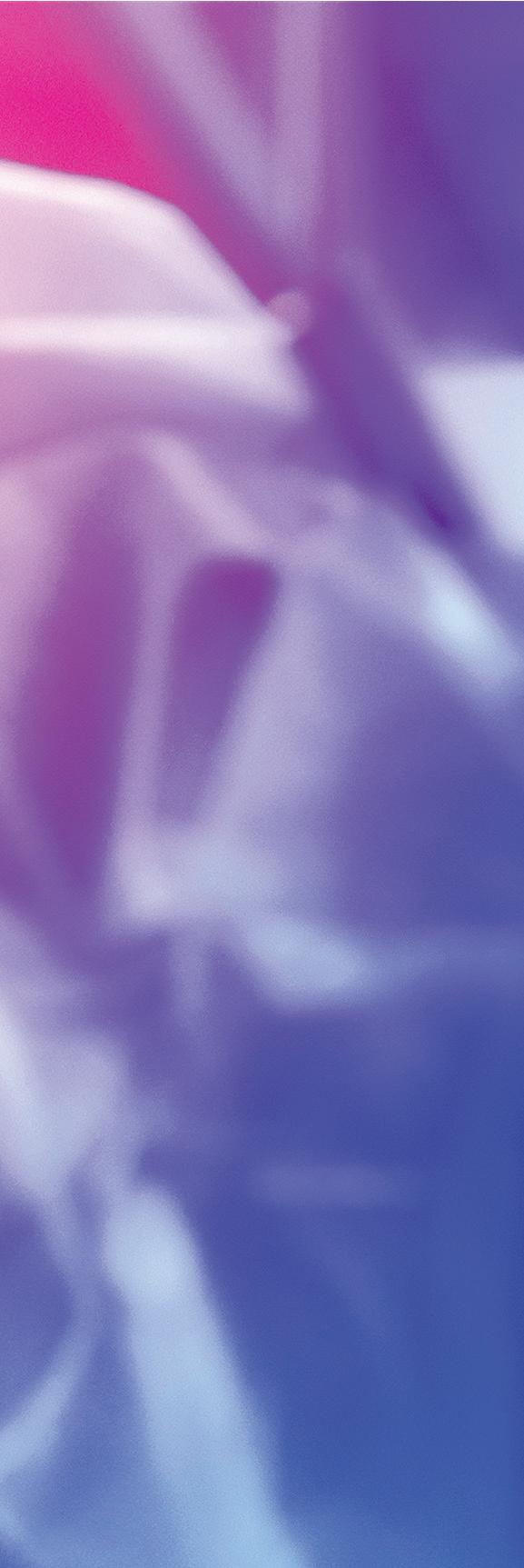
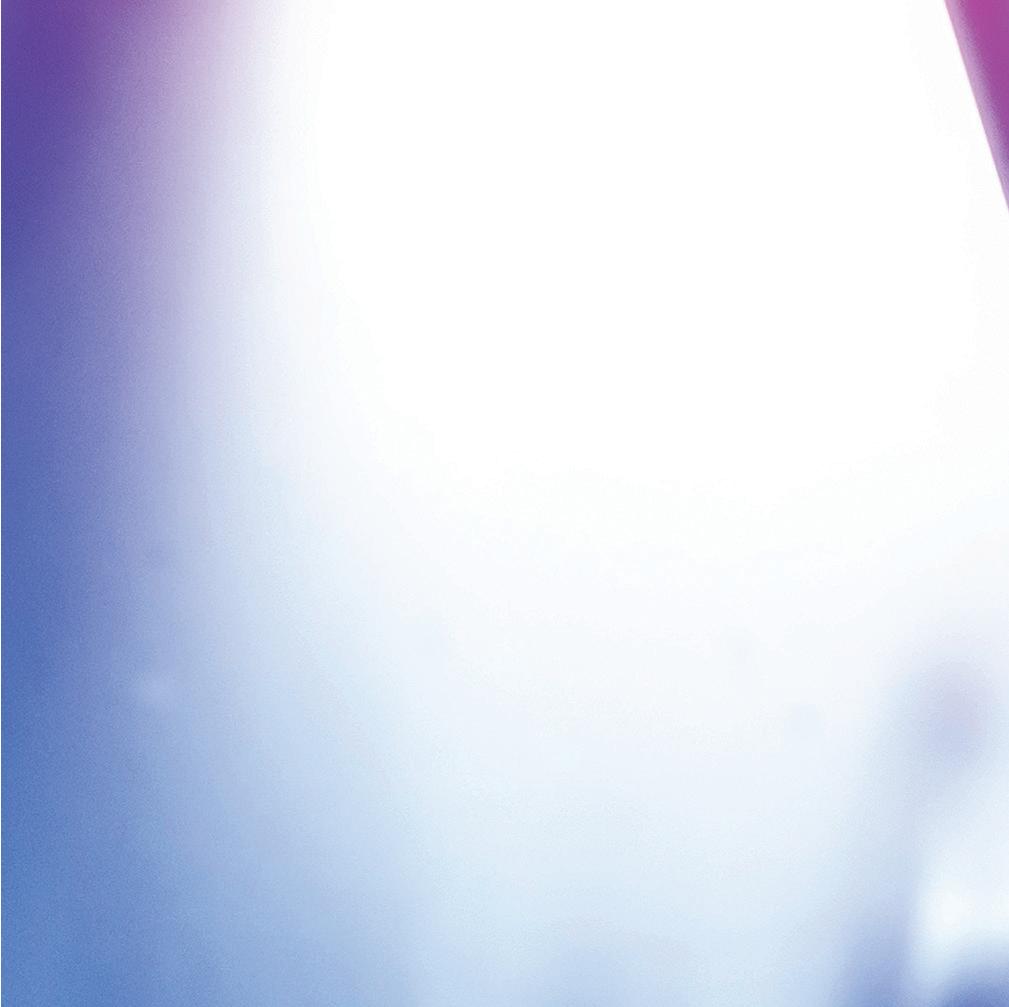

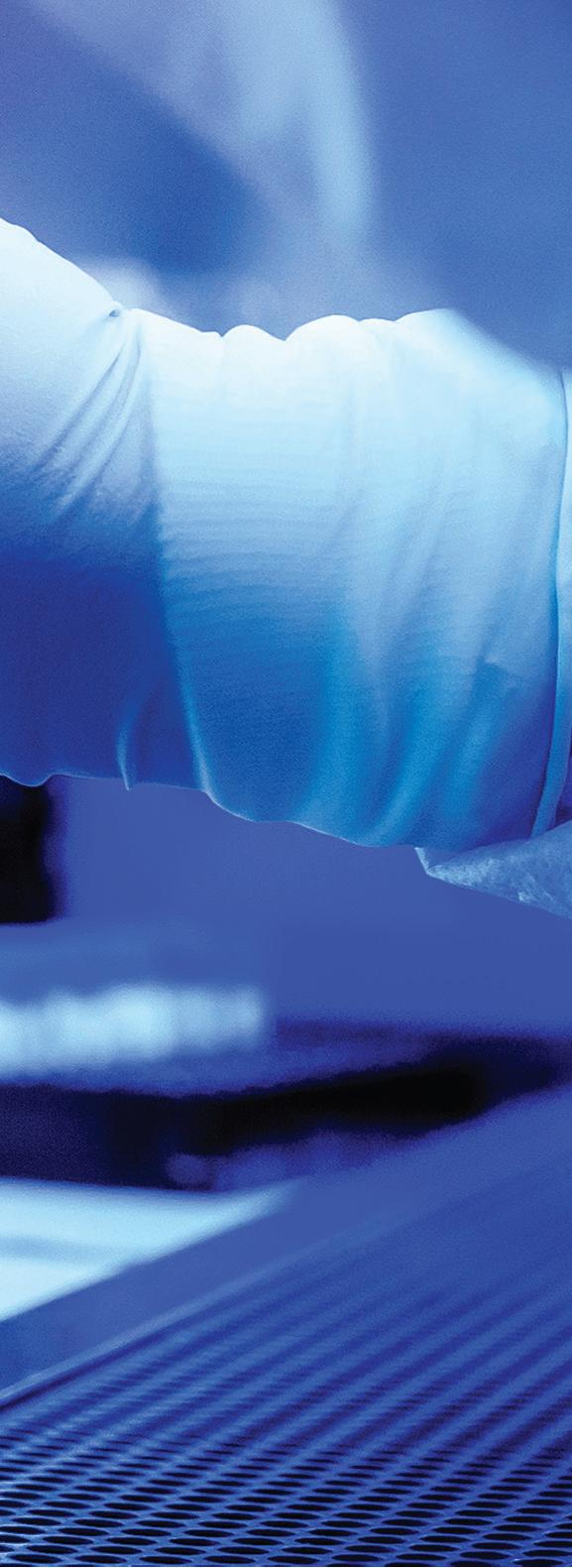
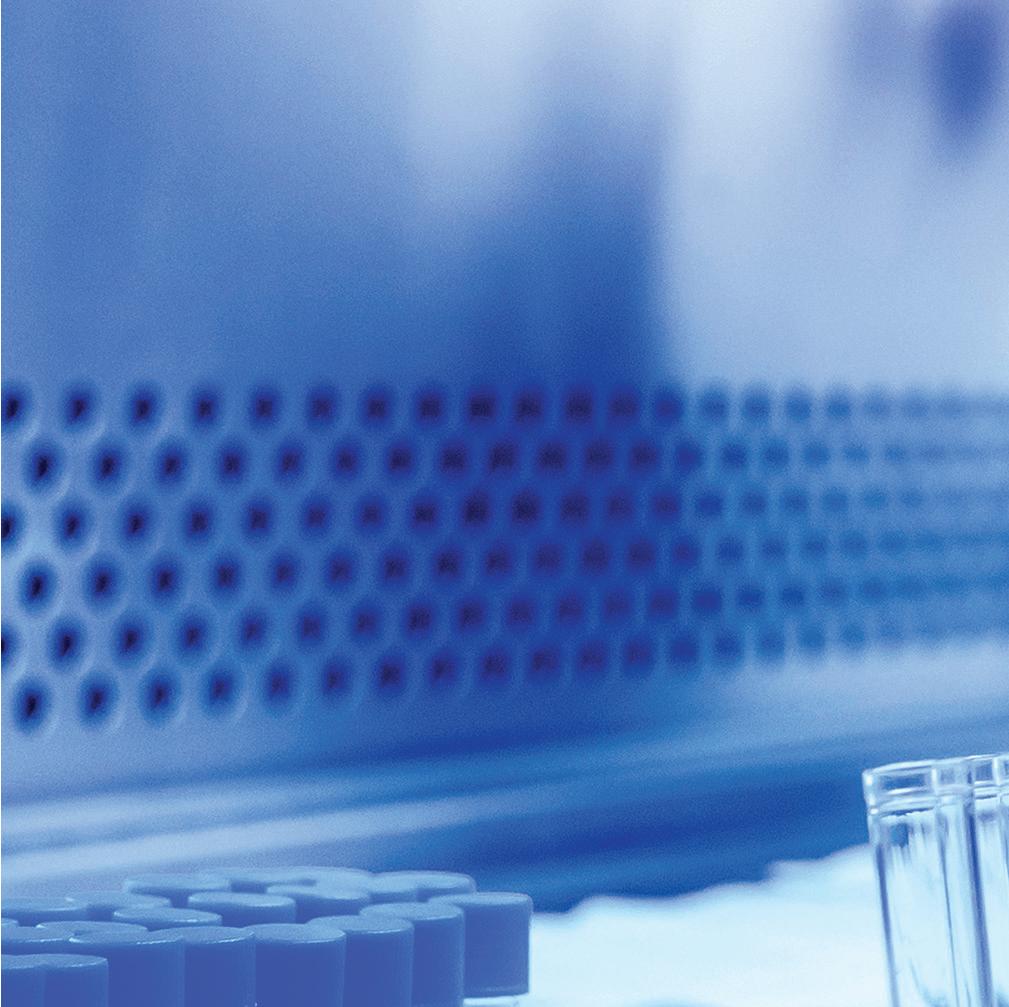
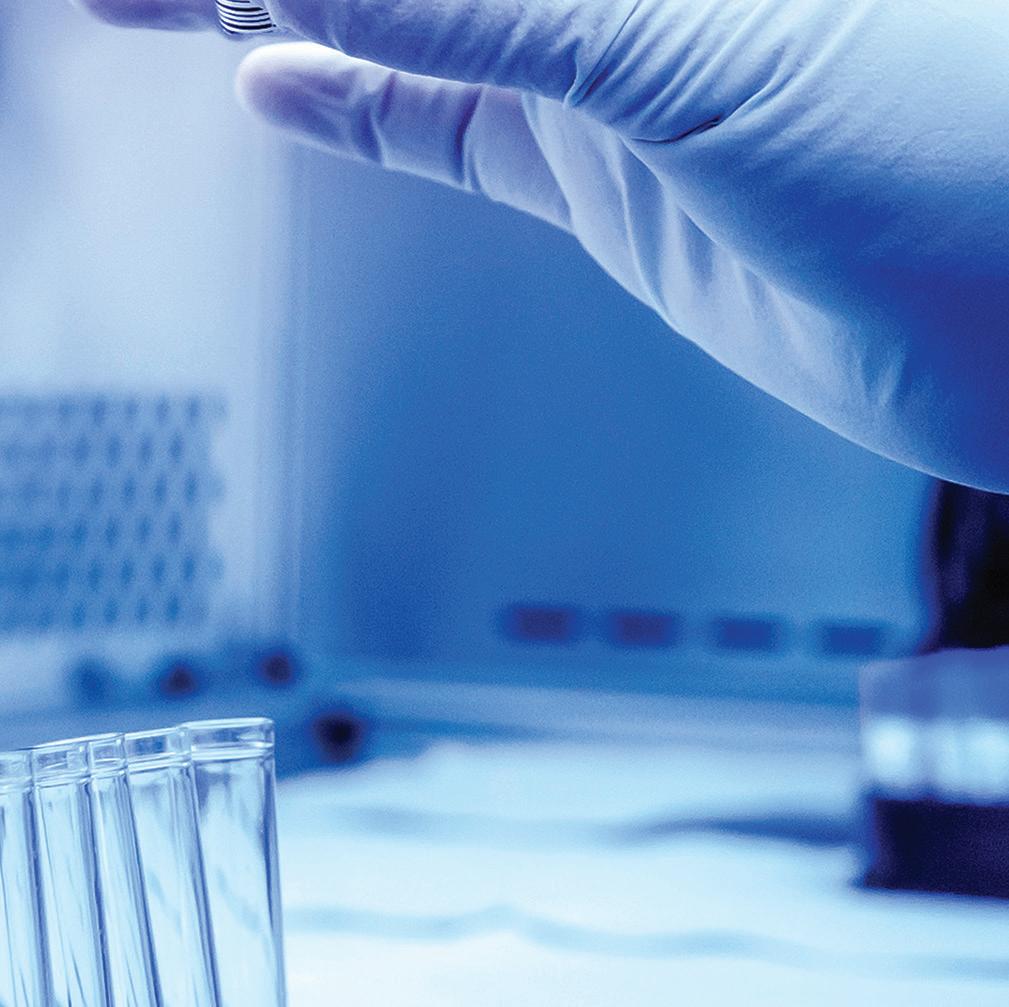

Hairstyles have changed over the years. Shouldn’t your air sampler?

Modernize your air sampling with TRIO.BAS™ today
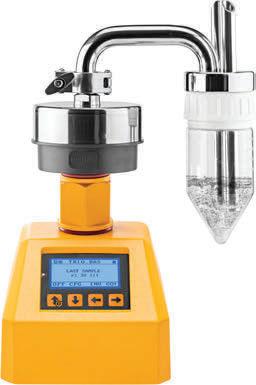
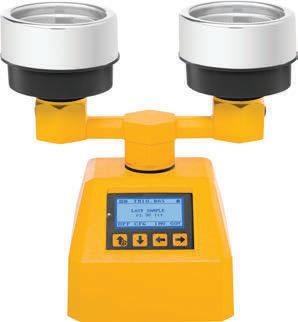
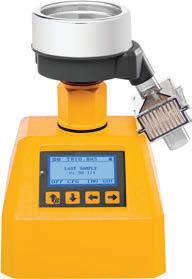
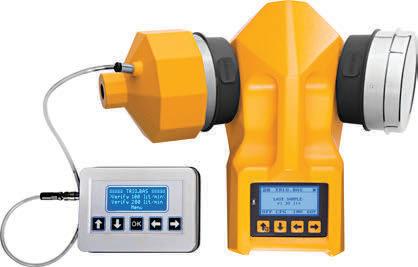
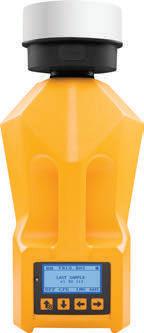
Hardy Diagnostics’ line of TRIO.BAS™ microbial impact air samplers has been designed specifically to bring air sampling up to date by addressing the drawbacks of older air sampling instruments. These lightweight and ergonomic instruments were designed with portability in mind. Three heads are better than one! The TRIO.BAS™ lineup features instruments with one, two, or even three heads so you have your entire process covered, start to finish. Multiple airflow rates are available to fit your specific need. Sample using standard or contact Petri plates. No proprietary media necessary. IQ/OQ/PQ documents available with purchase. Trade in that old air sampler and receive a discount upon purchase!
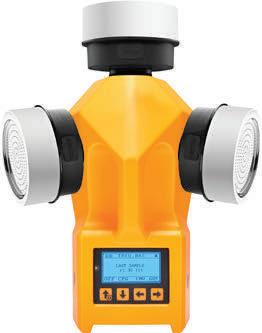
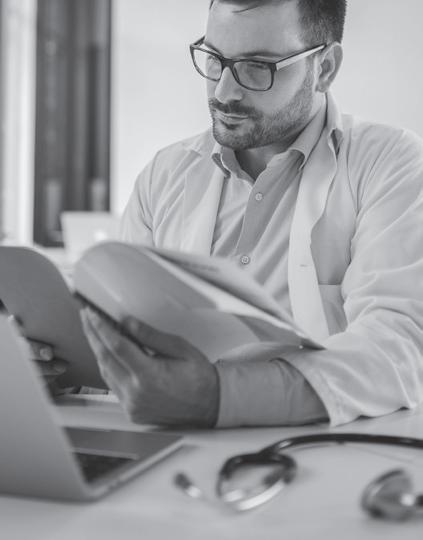
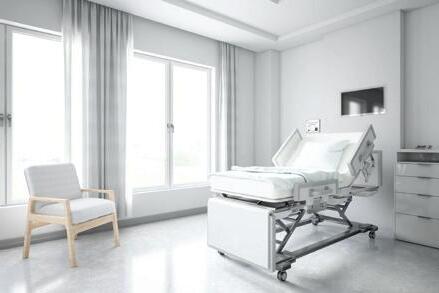
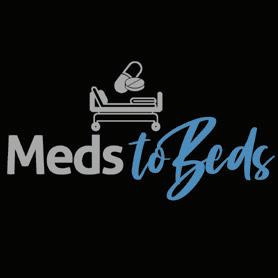



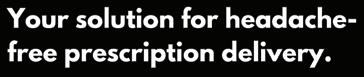

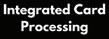

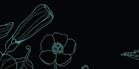
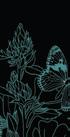
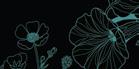
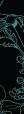








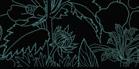
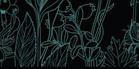


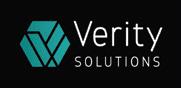
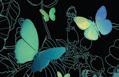

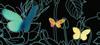
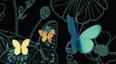


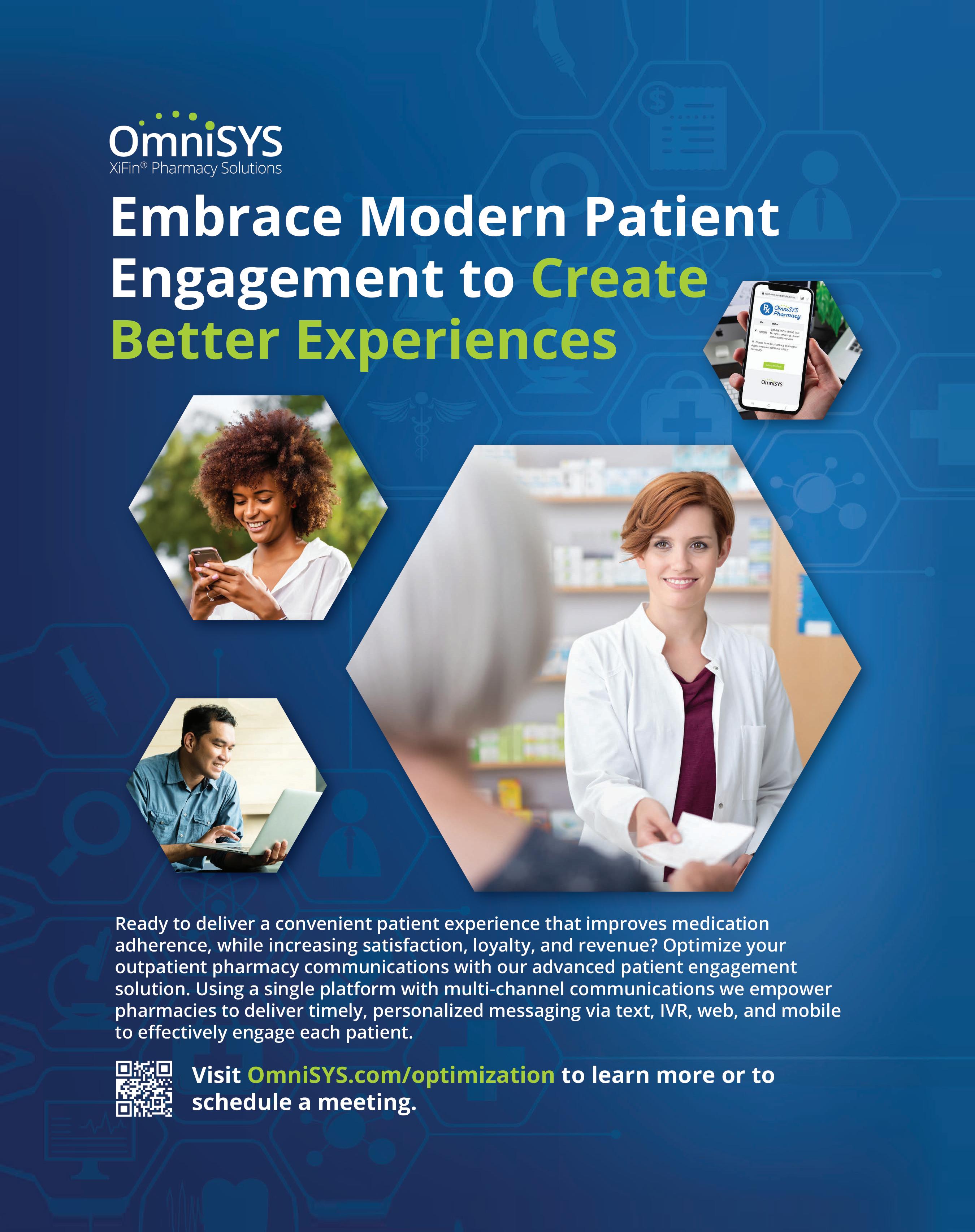
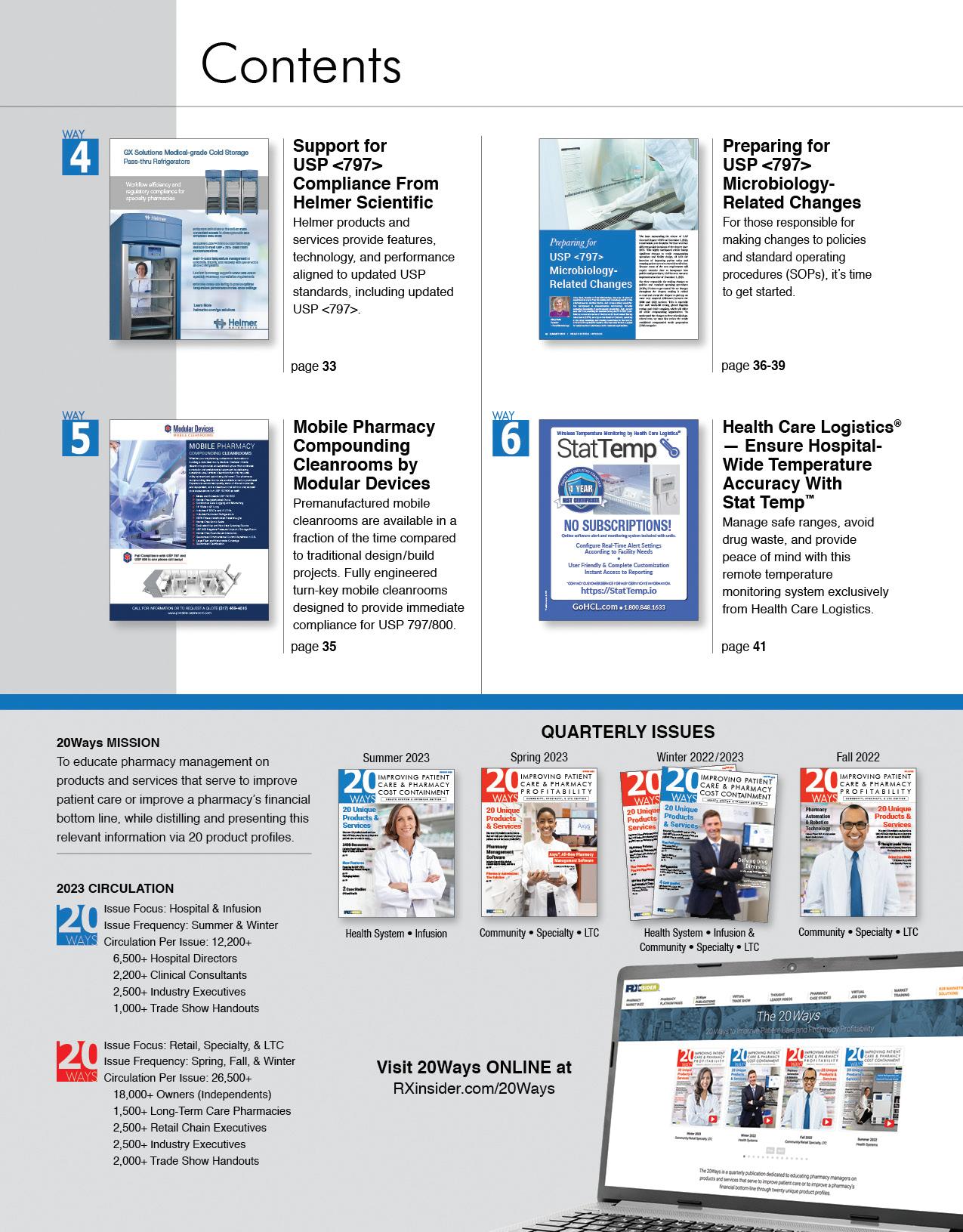
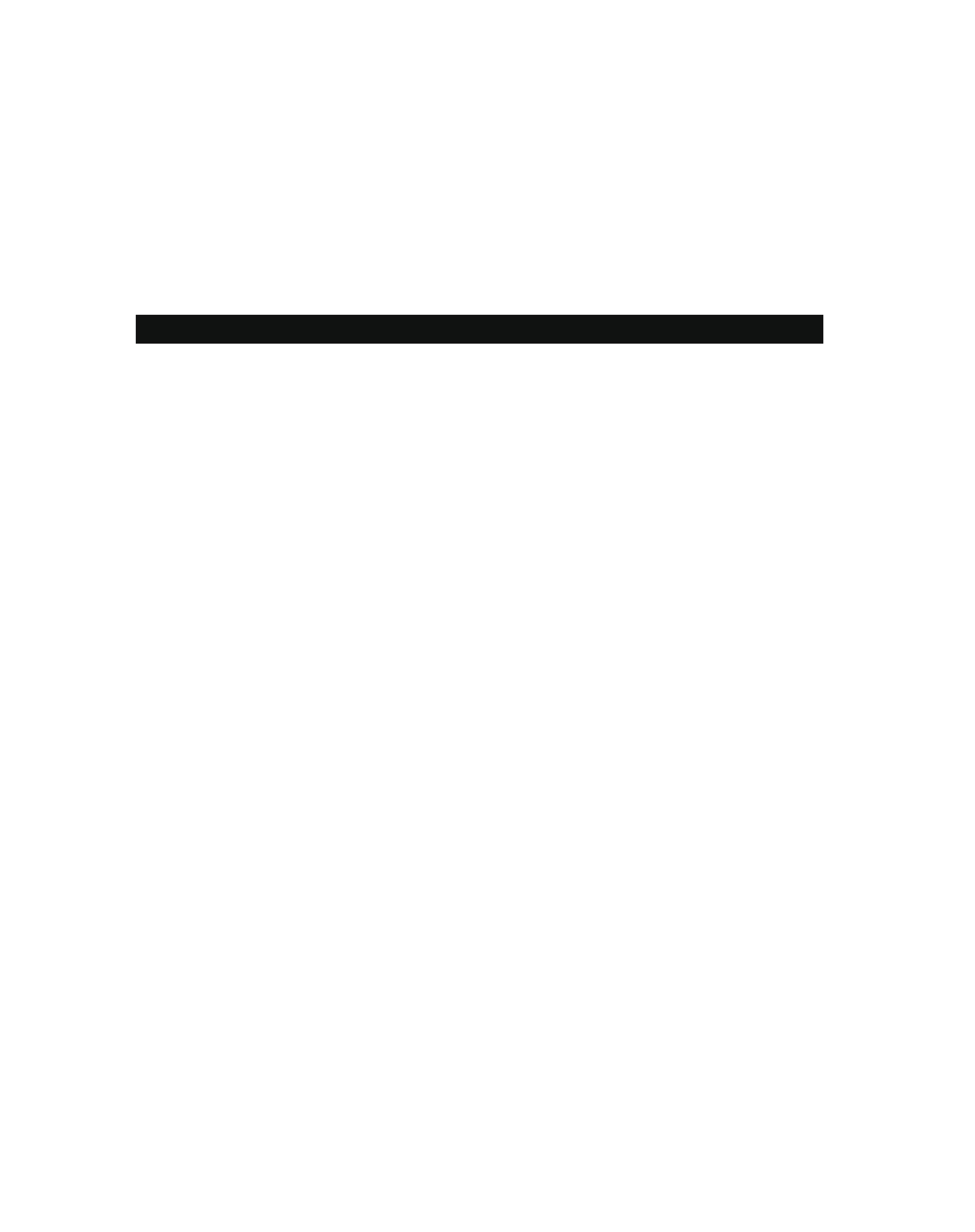
NEW! 5G WiFi Solutions with the ability to operate on 2.4 and 5 GHz
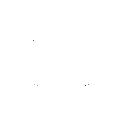
Monitor temperature of any cold storage (refrigerators, freezers, ultra-low freezers)
Continuous, real time monitoring
Monitoring rate exceeds requirements of CDC
Receive alarm noti cation via interactive phone, texts and e-mail
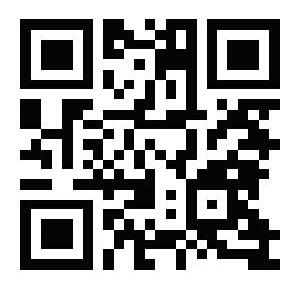
Meet compliance for FDA, WHO, USP<797>, USP <800>, VFC, GxP & more
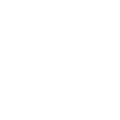
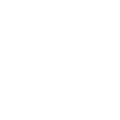
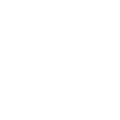
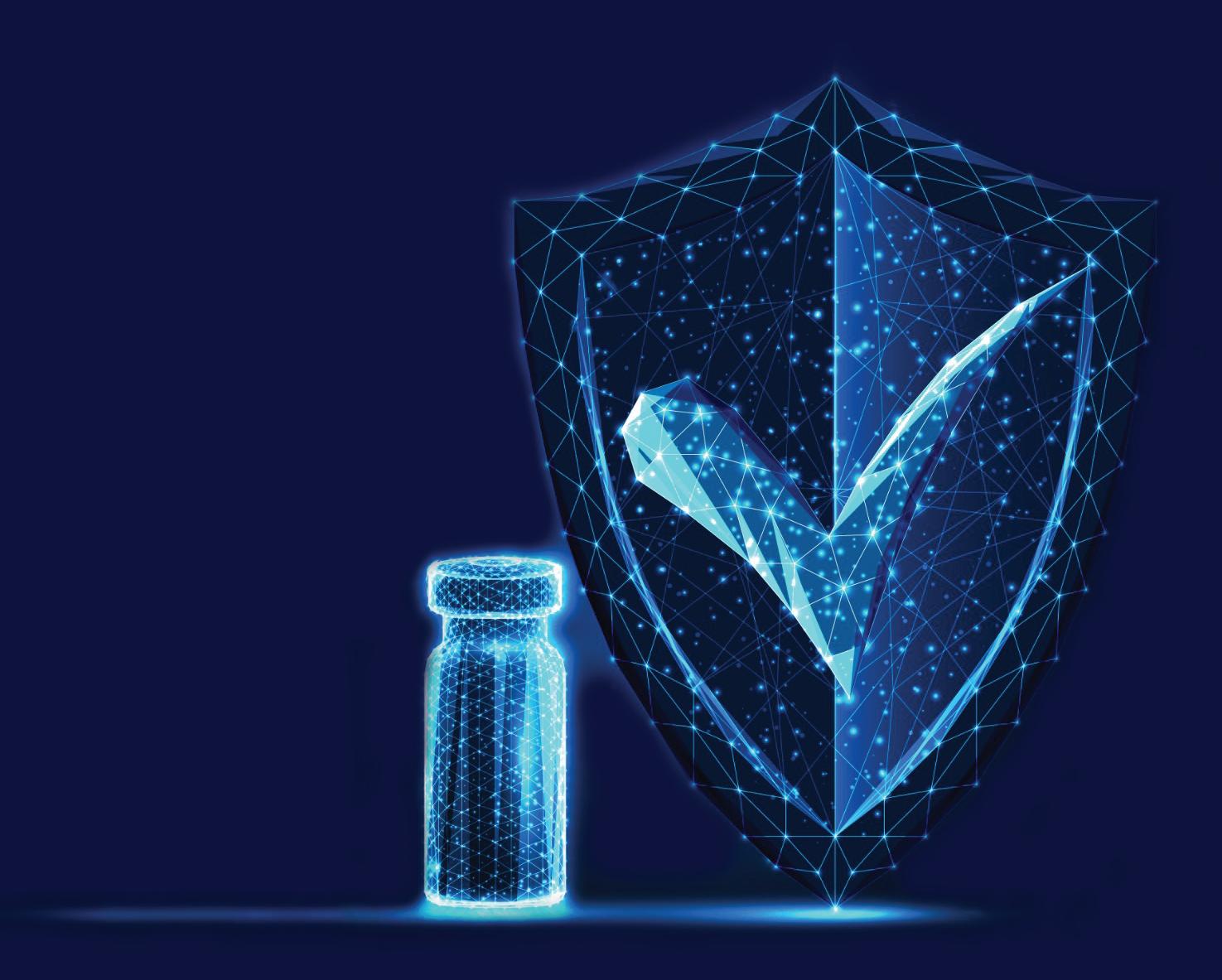
Exceeds data logger capabilities
Local audio and visual (LED) alarm available
View sensors min/max conditions with the LCD Module
609.530.1055
www.reesscienti c.com
Damaged Barcodes Be Damned
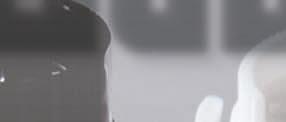
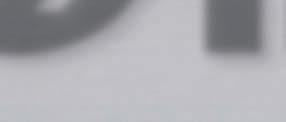
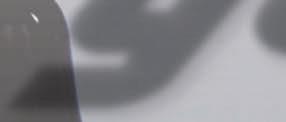
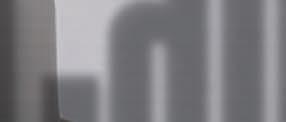
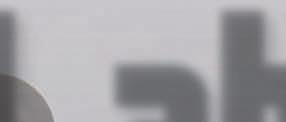
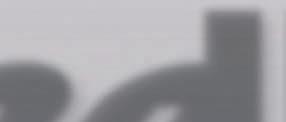
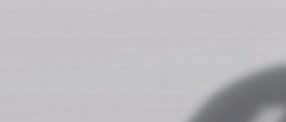
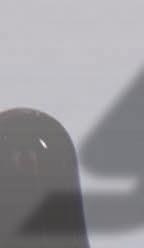
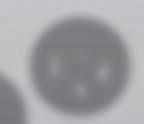

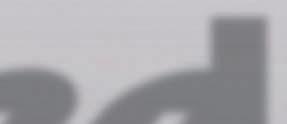
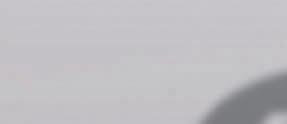
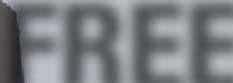


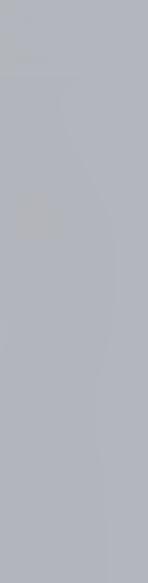
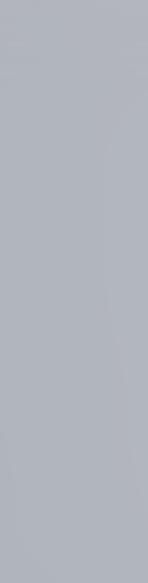
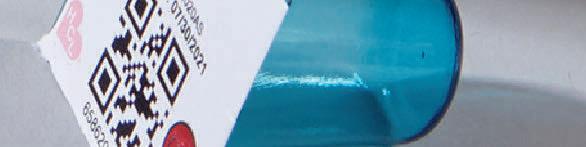
One scan of a medication package can reveal practically everything you need to know about the drug, its contents, warnings, expiration and more. As long as the barcode isn’t damaged, that is.
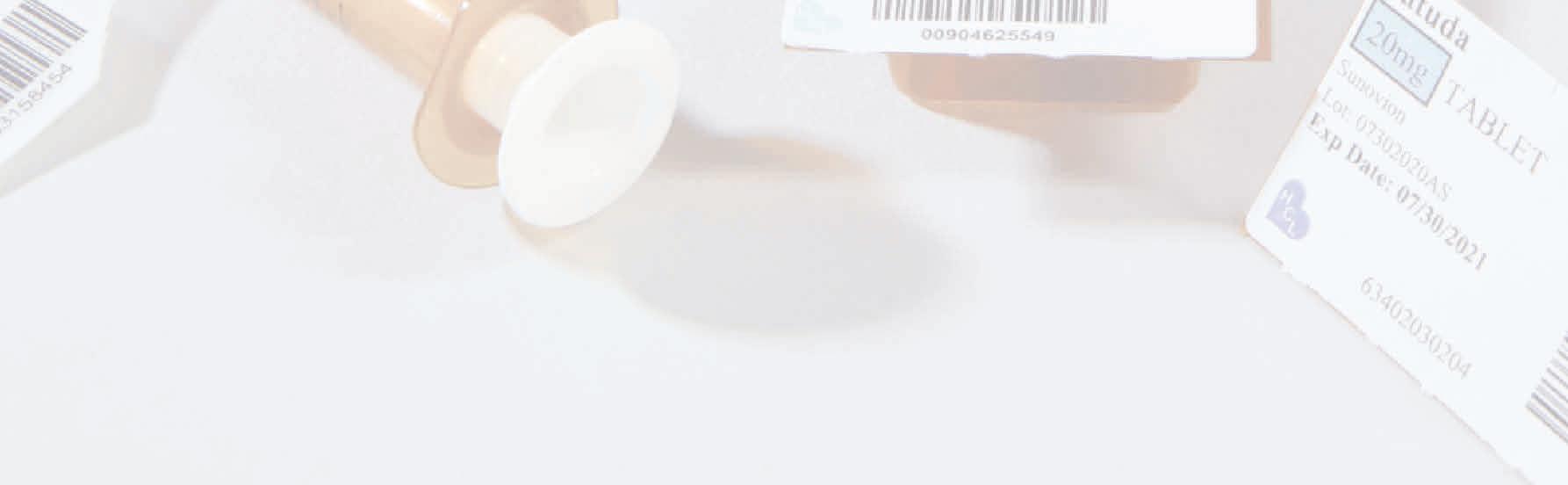
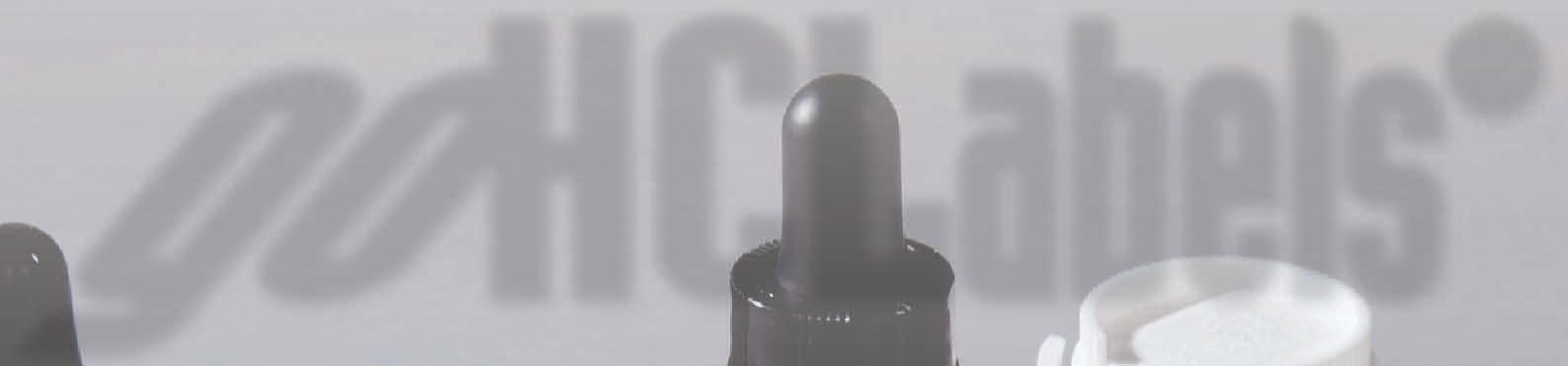
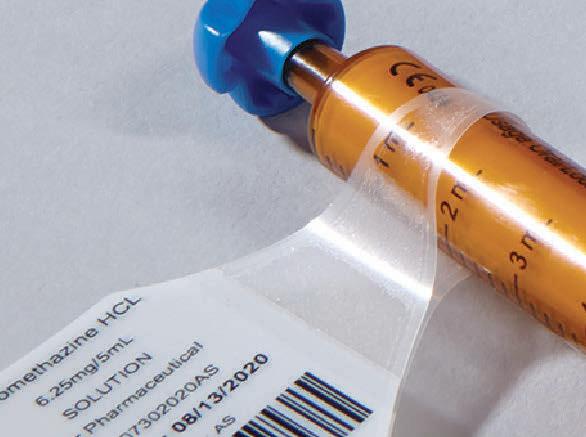
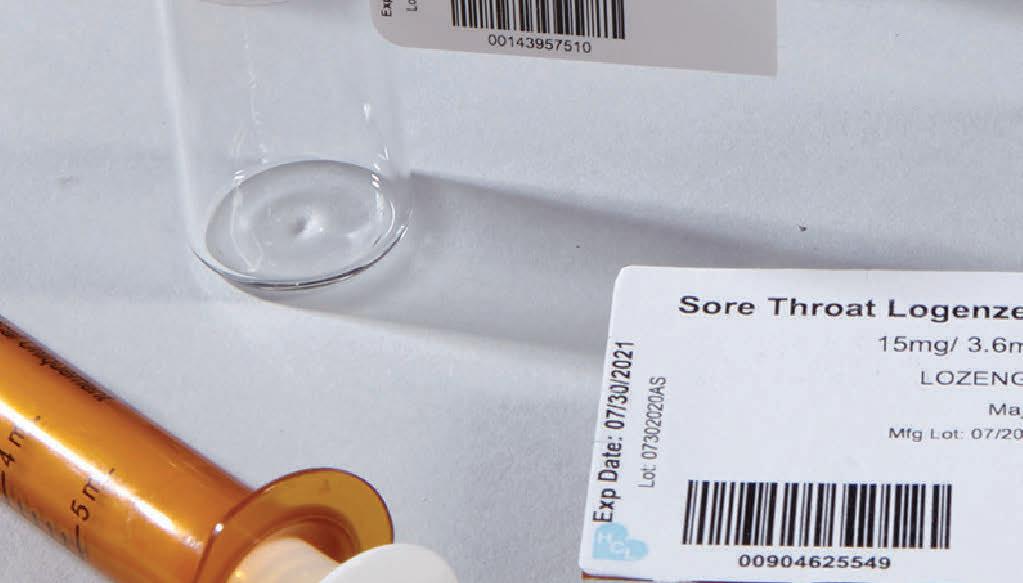
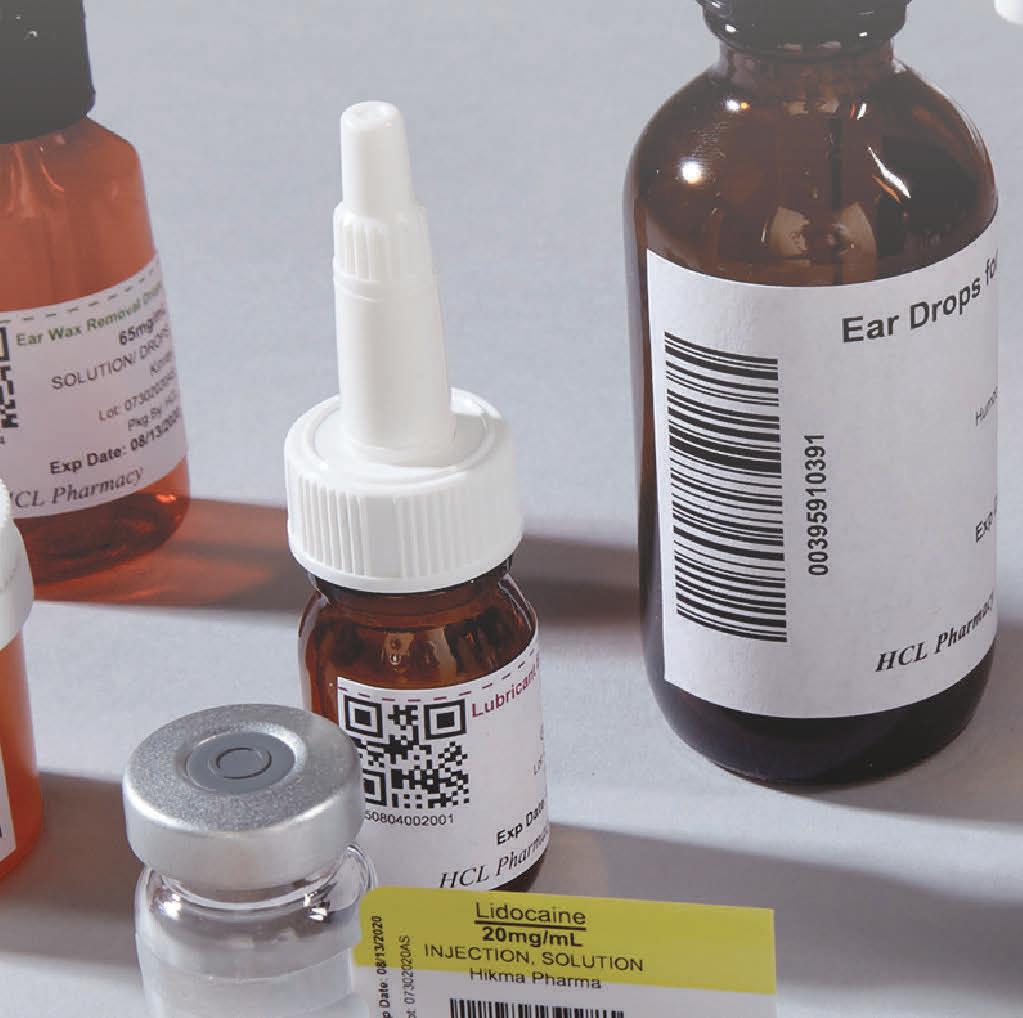
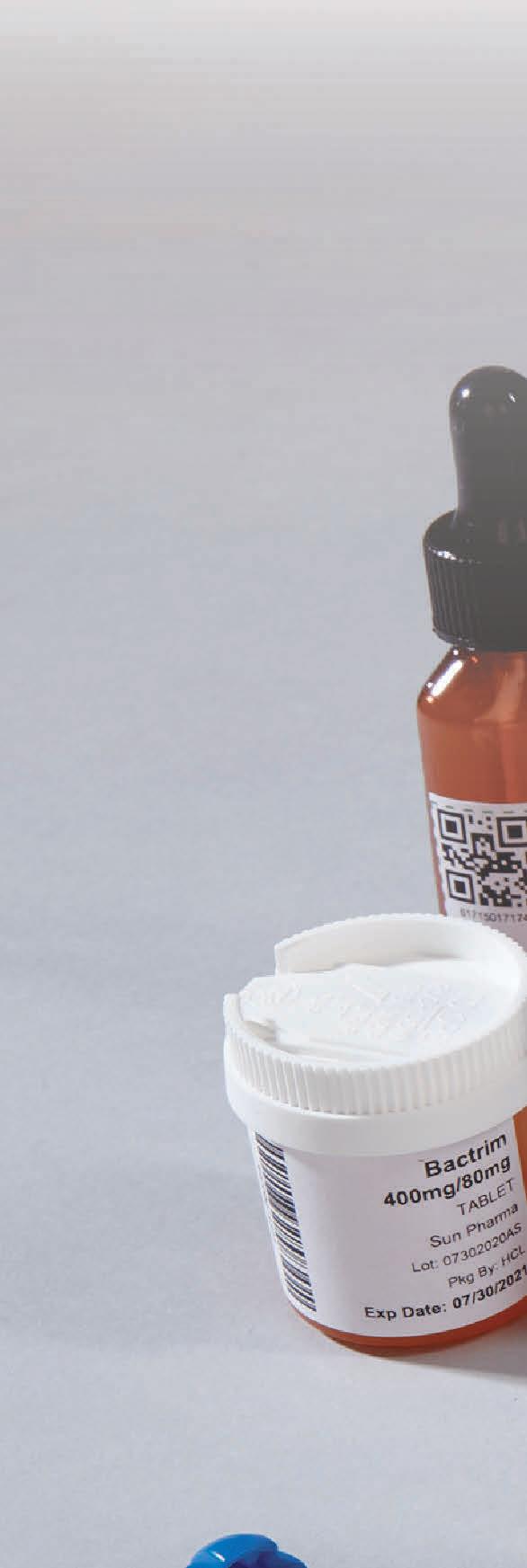
Avoid delays in data retrieval with blank Laser Labels designed to t over damaged or otherwise unscannable manufacturer barcodes.
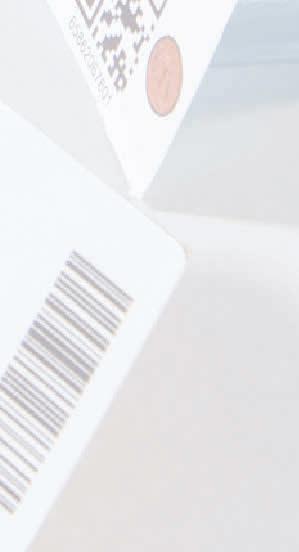
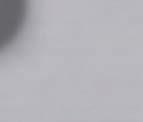
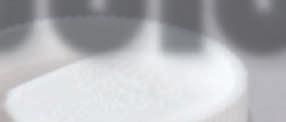
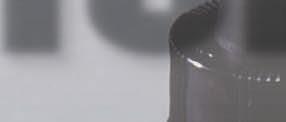
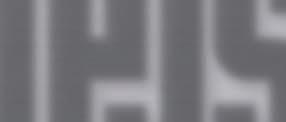
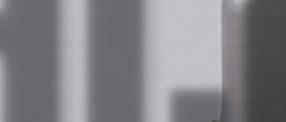
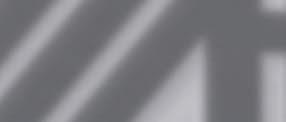
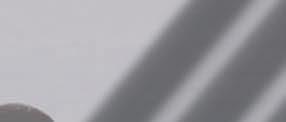
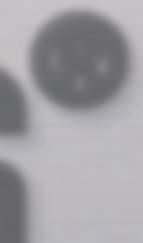
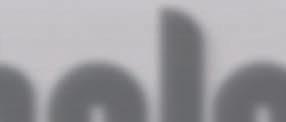
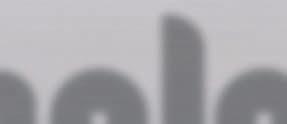
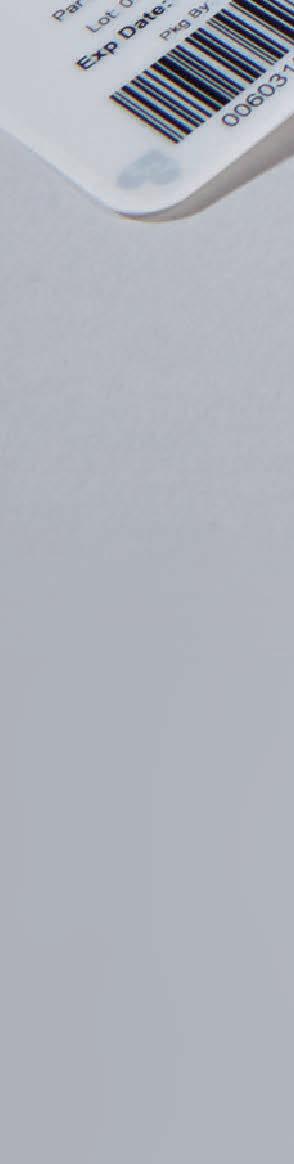
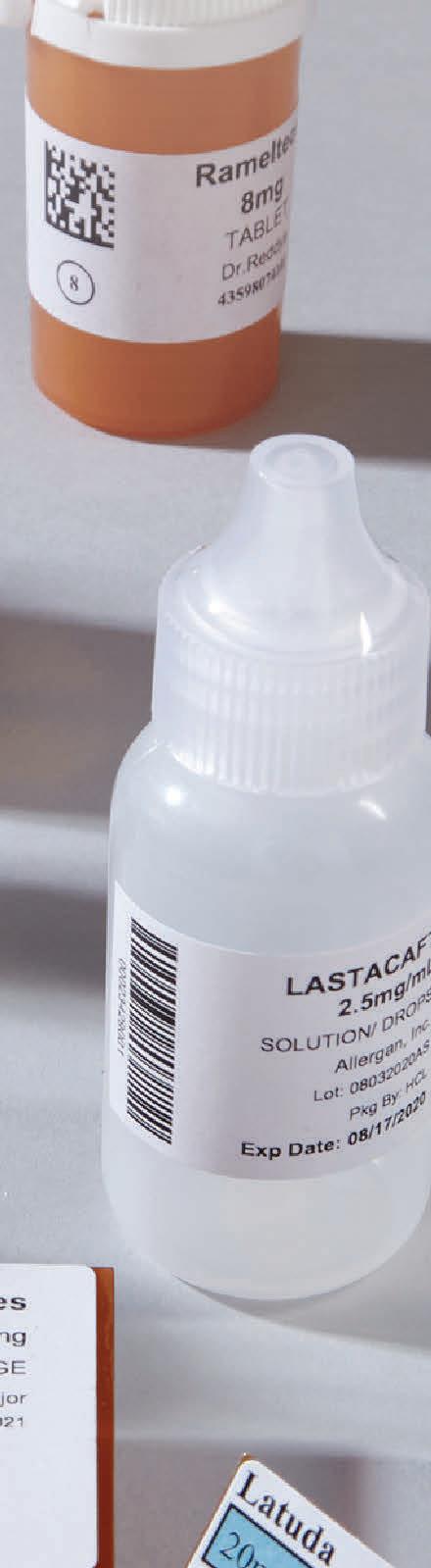
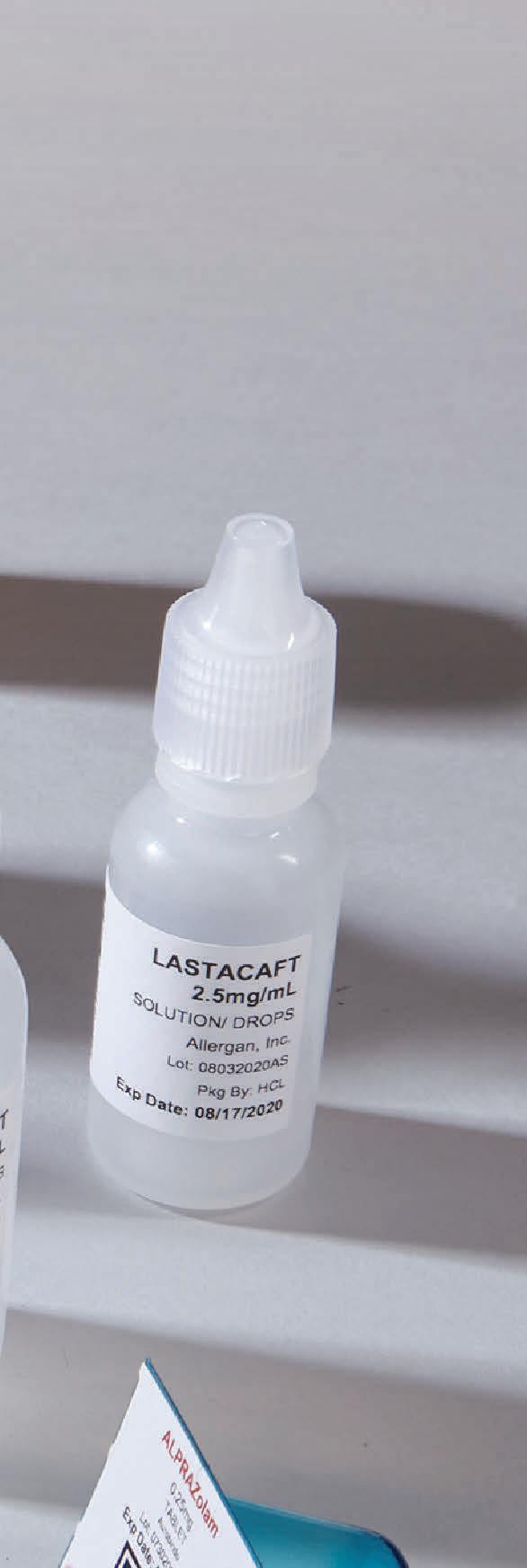

Easily create and print them yourself using our free online site, goHCLabels.com, and tailor the information to meet your needs. Don’t let a snag in technology steal your productivity. Save time, save the cost of package replacement and save your sanity with this seamless solution instead!
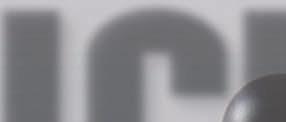
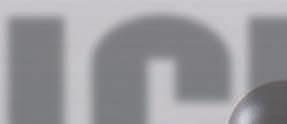
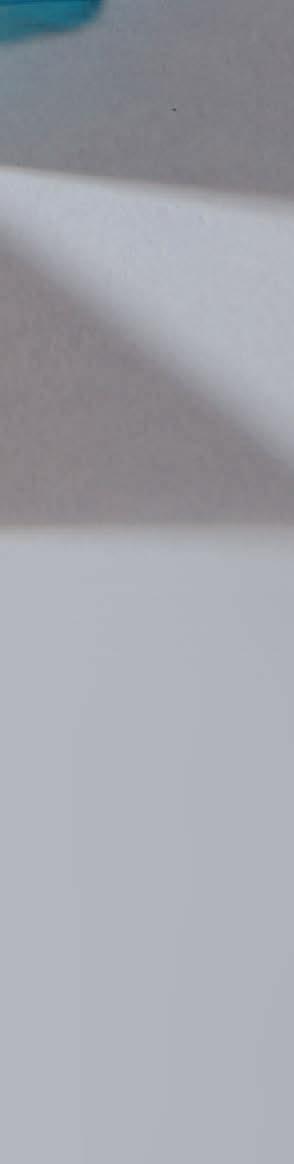
Acute Care Pharmaceuticals, Your Premier Supplier of USP <797> and <800> Cleanroom Disposables
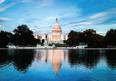
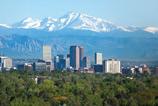
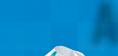
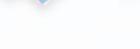
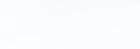
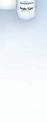









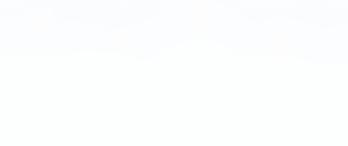


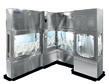

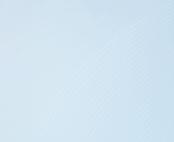

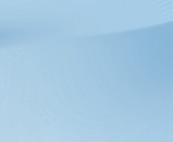
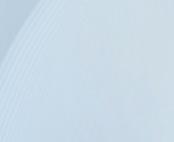
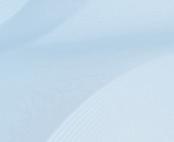
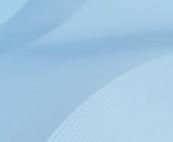
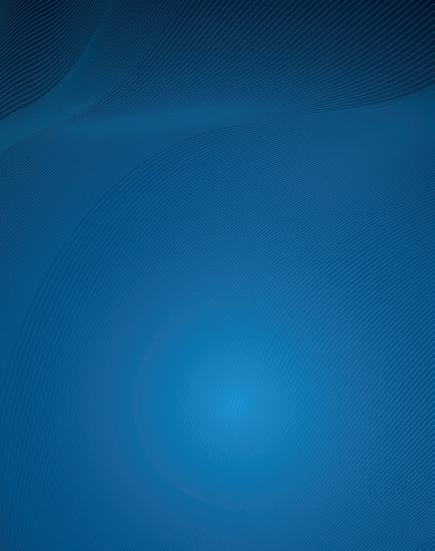
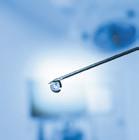
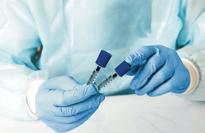
We at Acute Care Pharmaceuticals aim to make your buying experience easier. We offer our products at your wholesaler and provide education, and your pharmacy will have its own dedicated account manager.
page 63
page 71
Trade Show & Meeting Calendar
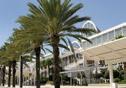
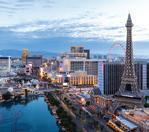
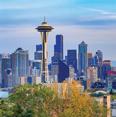
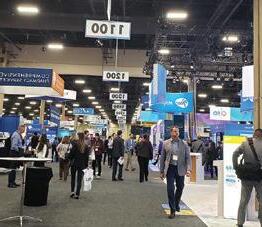
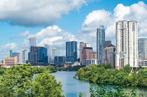
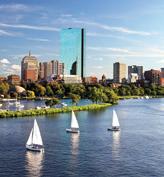
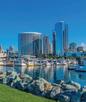
page 74-79
Esco® — Safer Workstation for USP 797, USP 800, and 503B Pharma Compounding



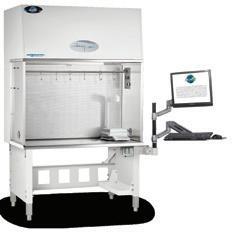
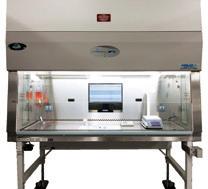
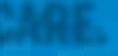
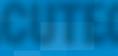

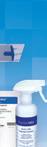


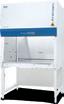
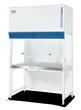

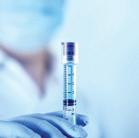
Improve product sterility and patient safety with our standard ULPA Filter that creates an ISO Class 3 compounding area that is 100 times cleaner than ISO Class 5 found on other biosafety cabinets, laminar flow cabinets, and isolators with regular HEPA filter.
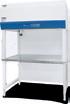
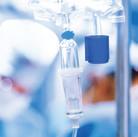
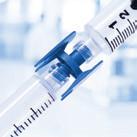
page 73 page 81
D2
page 83
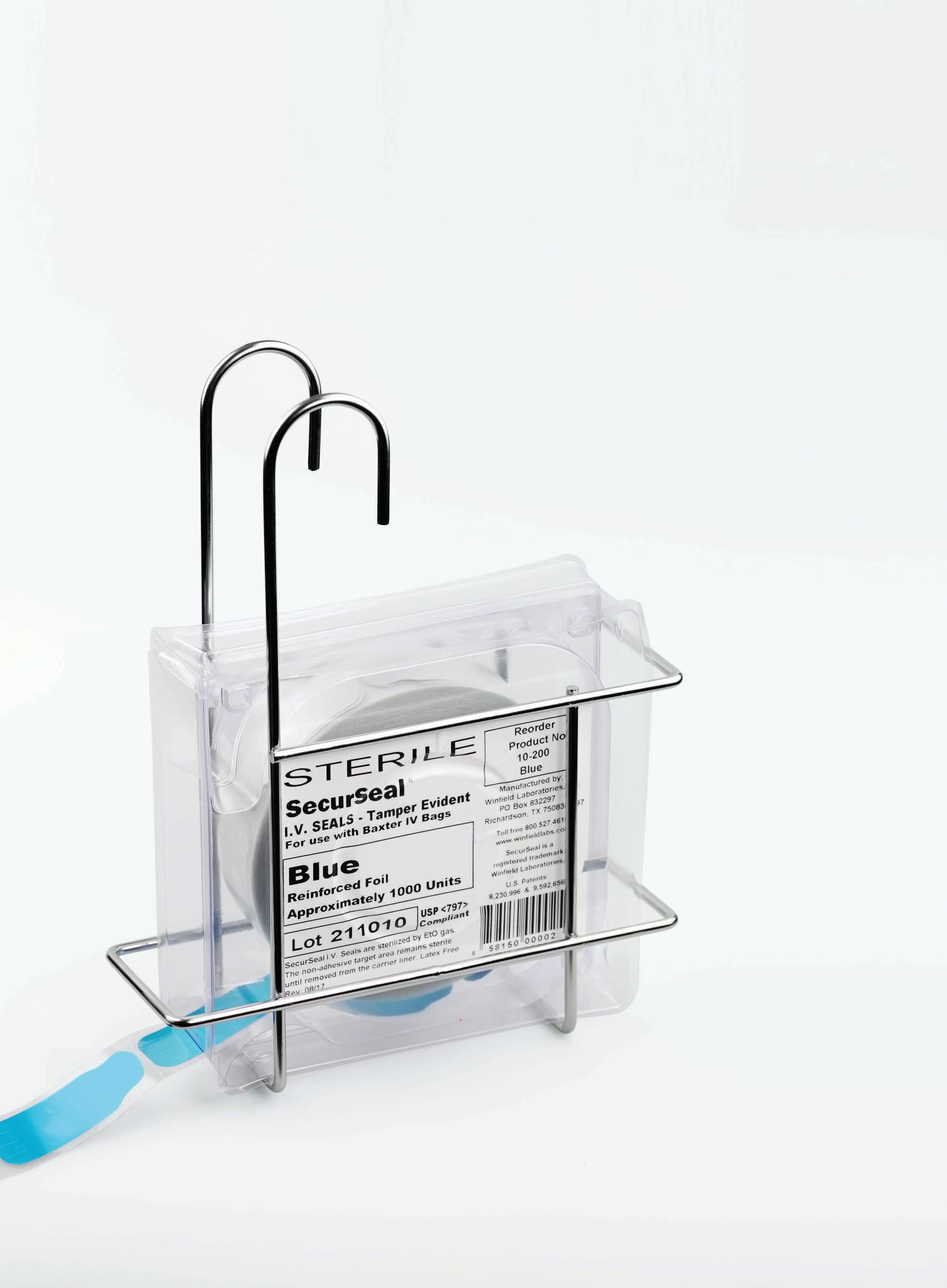
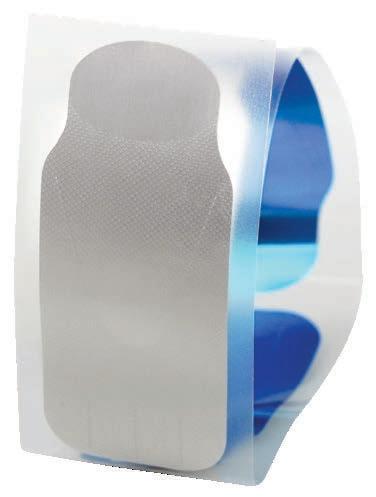
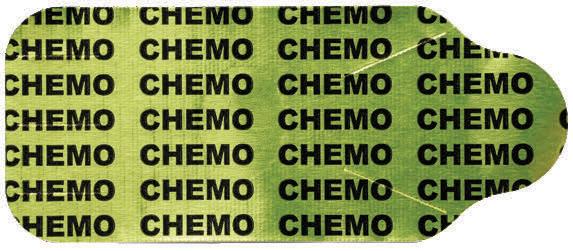
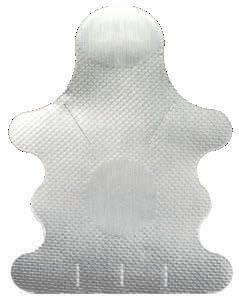
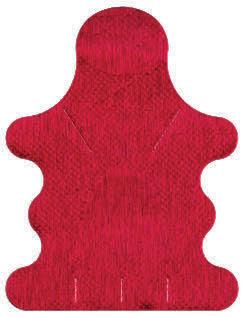
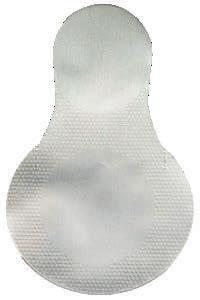
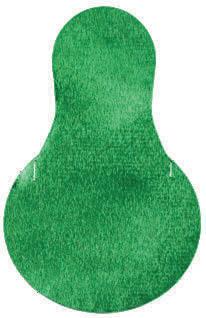
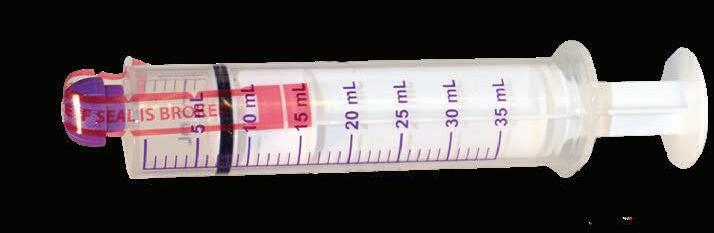
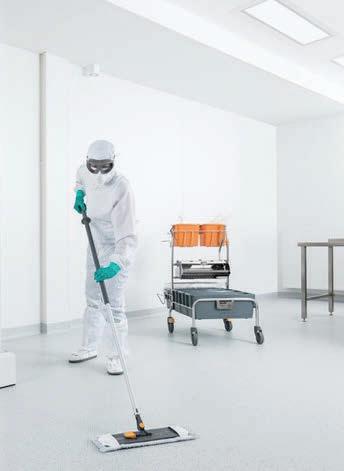
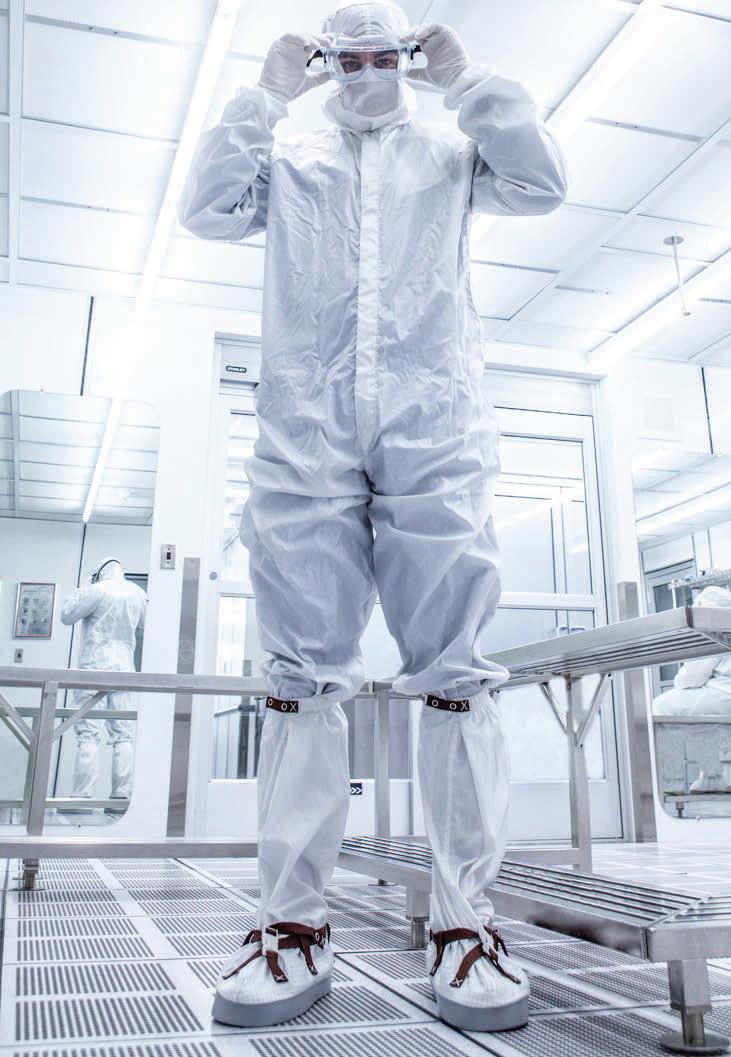
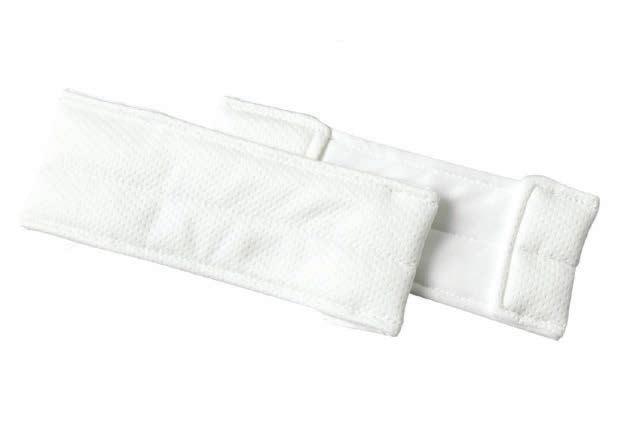
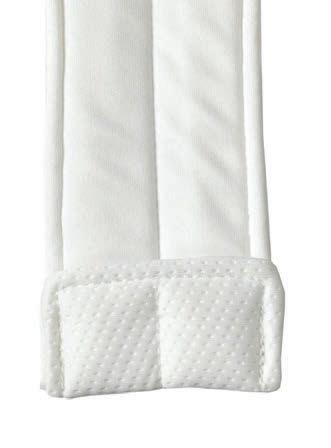
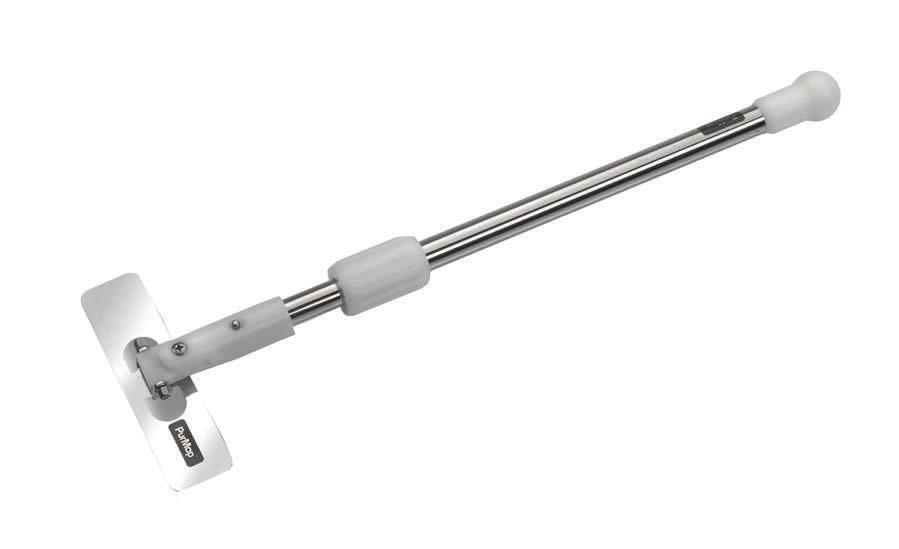
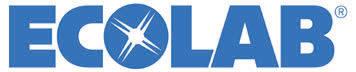
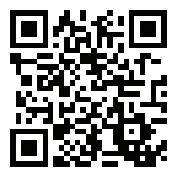

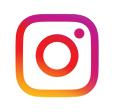
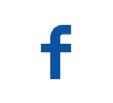
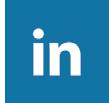
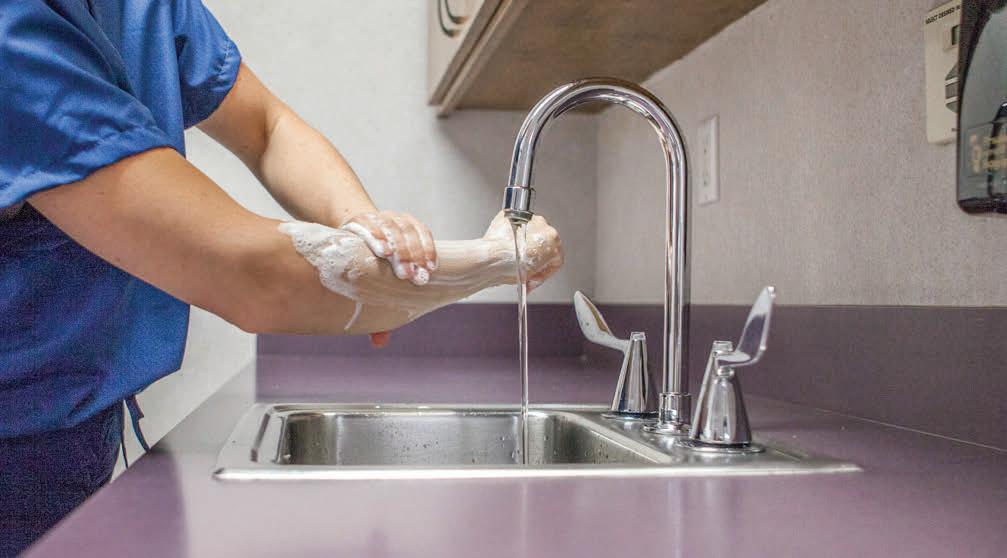
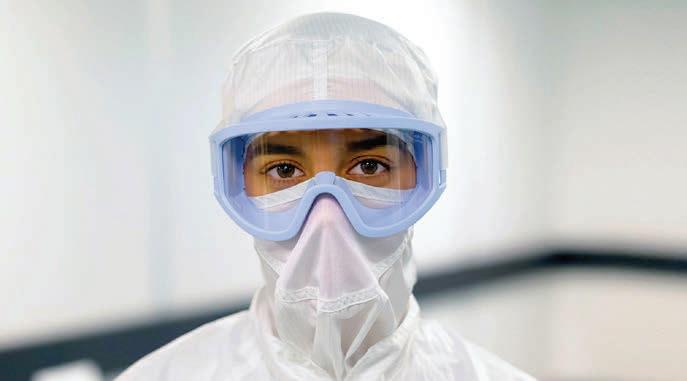
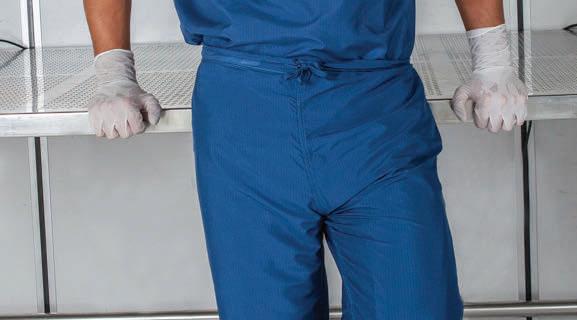
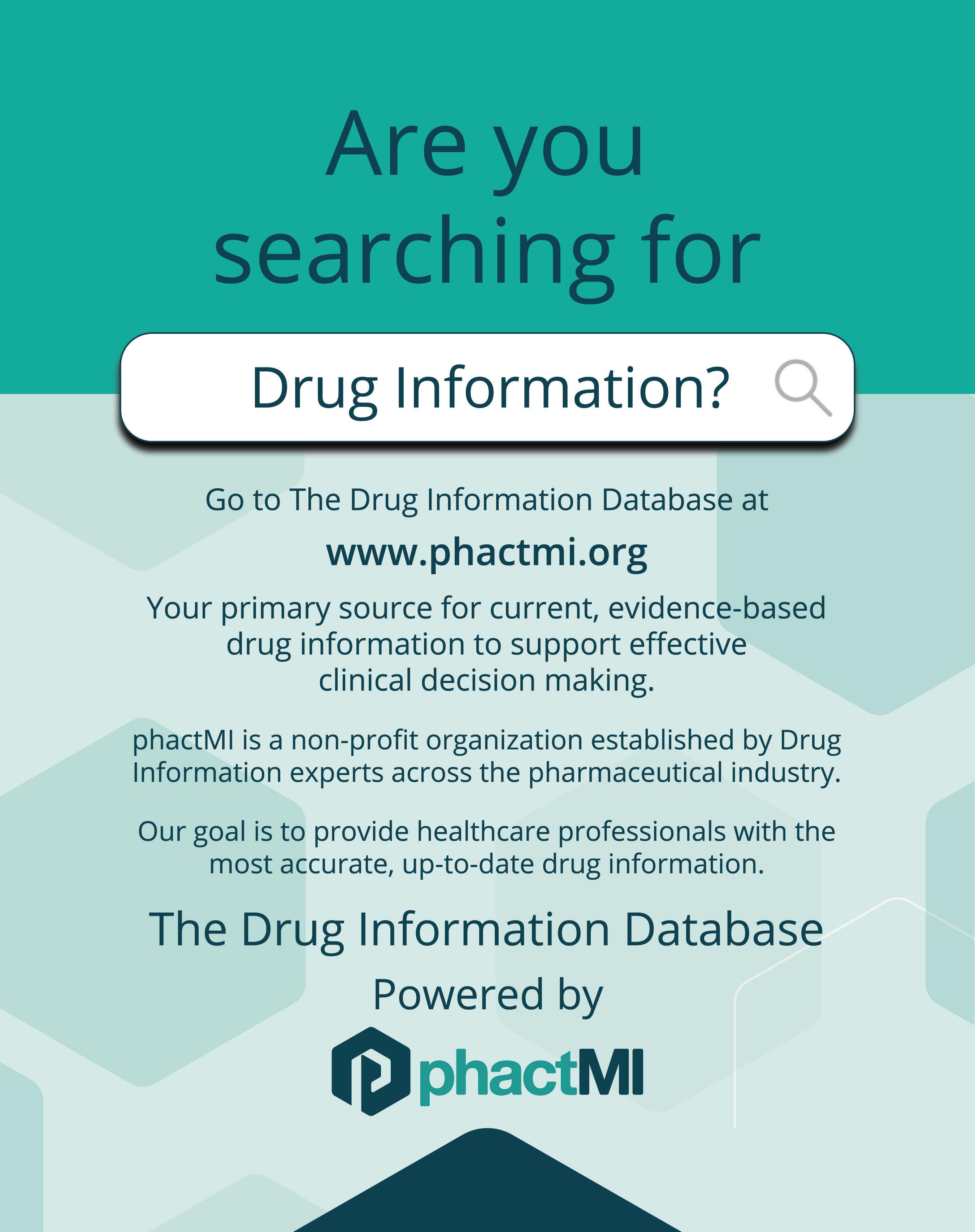
Don’t worry. Be happy.
For compliance, transparency and easy, user friendly reverse distribution services, GRx has your back...and forth.
• Comprehensive return reporting that provides compliance, accountability, and a wealth of business intelligence
• Complete detailed inventory of all products returned for processing
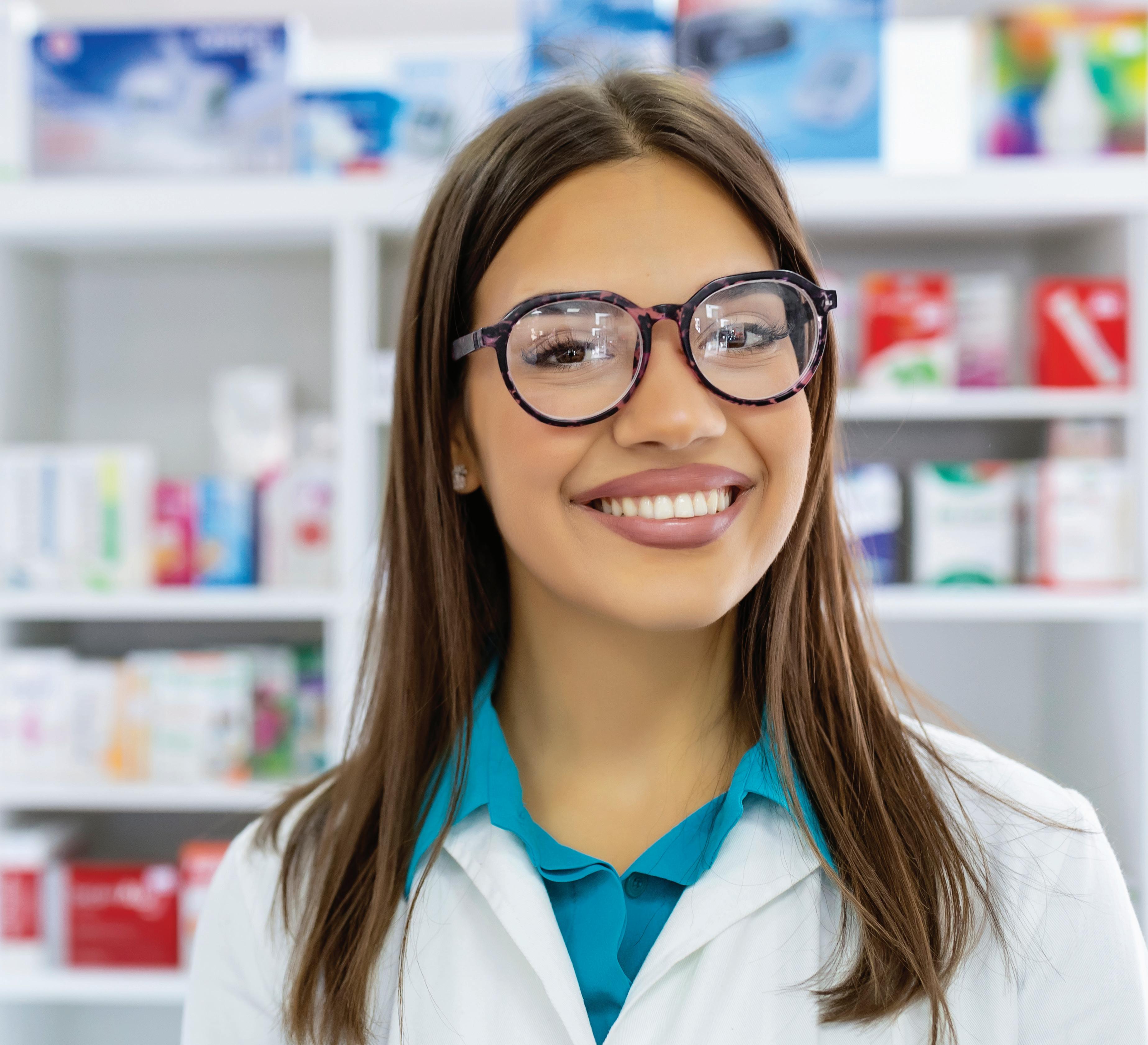
• Clear and concise reconciliation of your credit recovery for each return cycle, including a breakdown of all fees charged
• Competitive rates for the processing and disposal of expired or unsaleable products Built
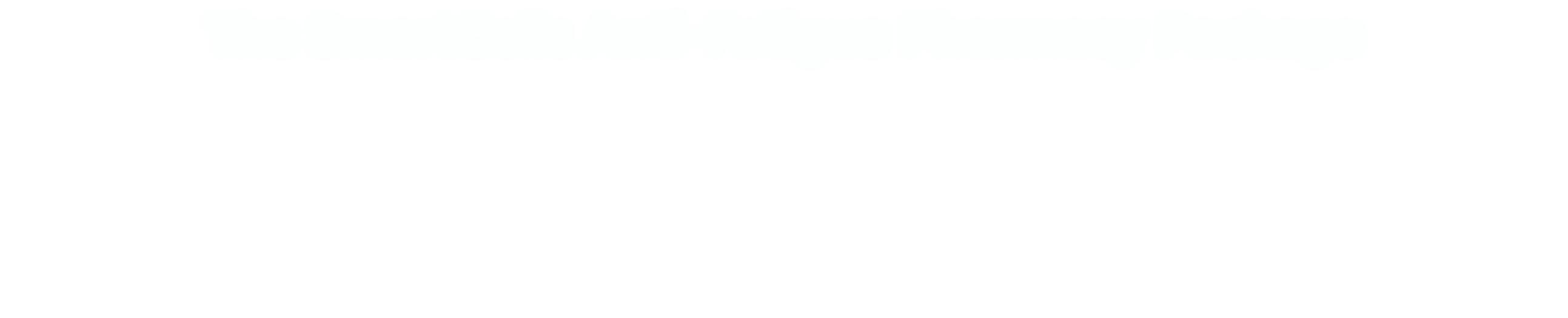

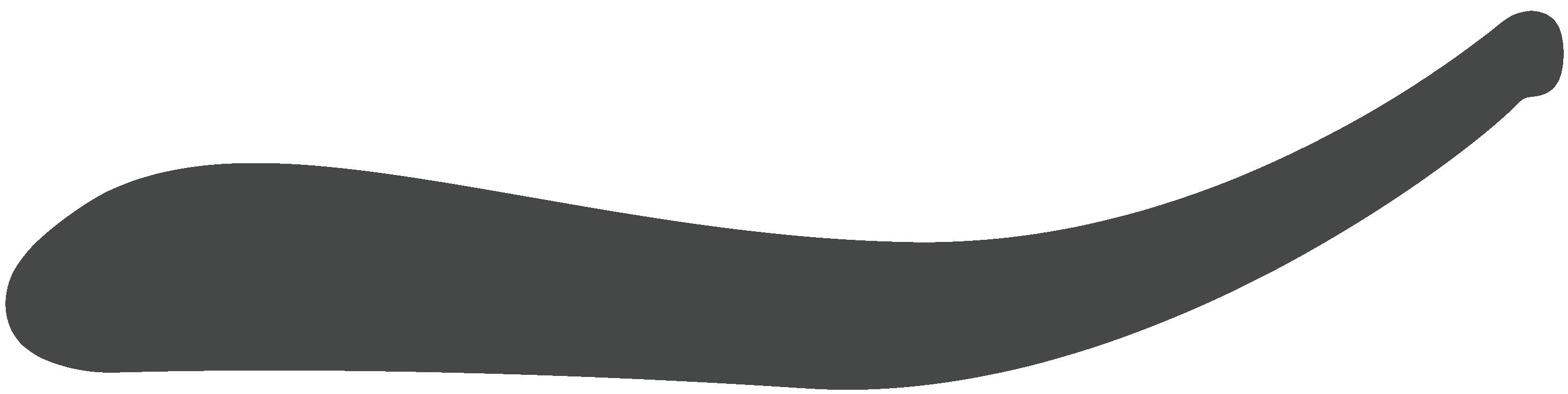
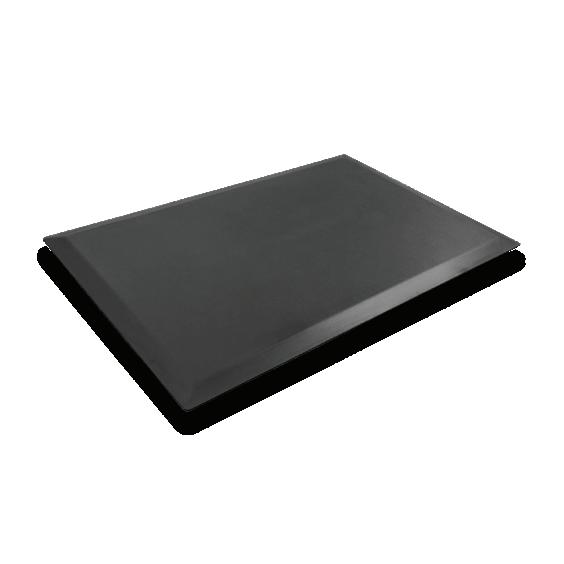
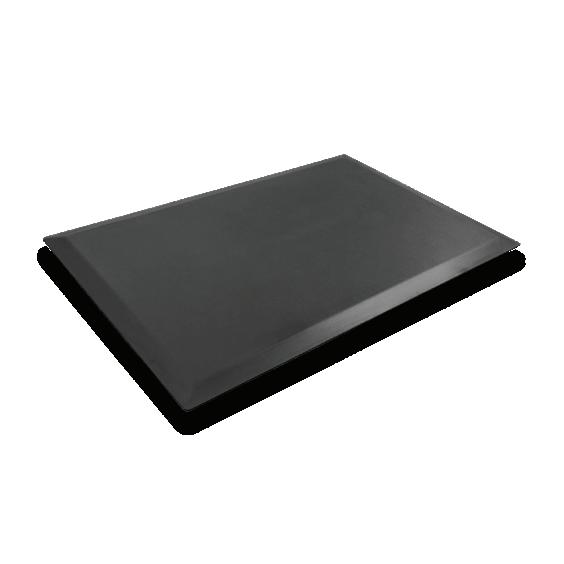
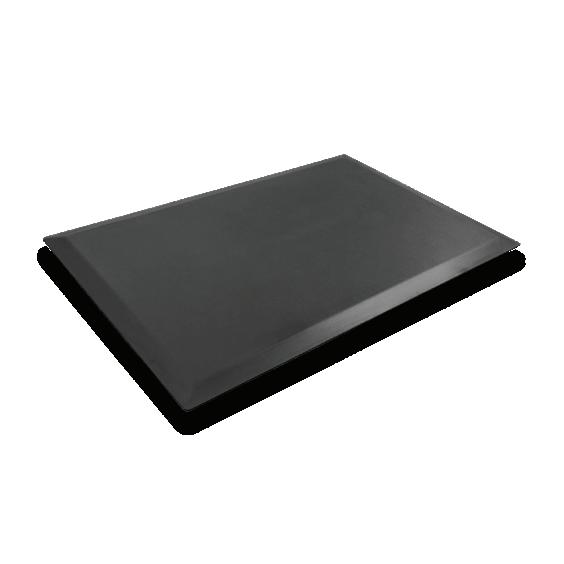
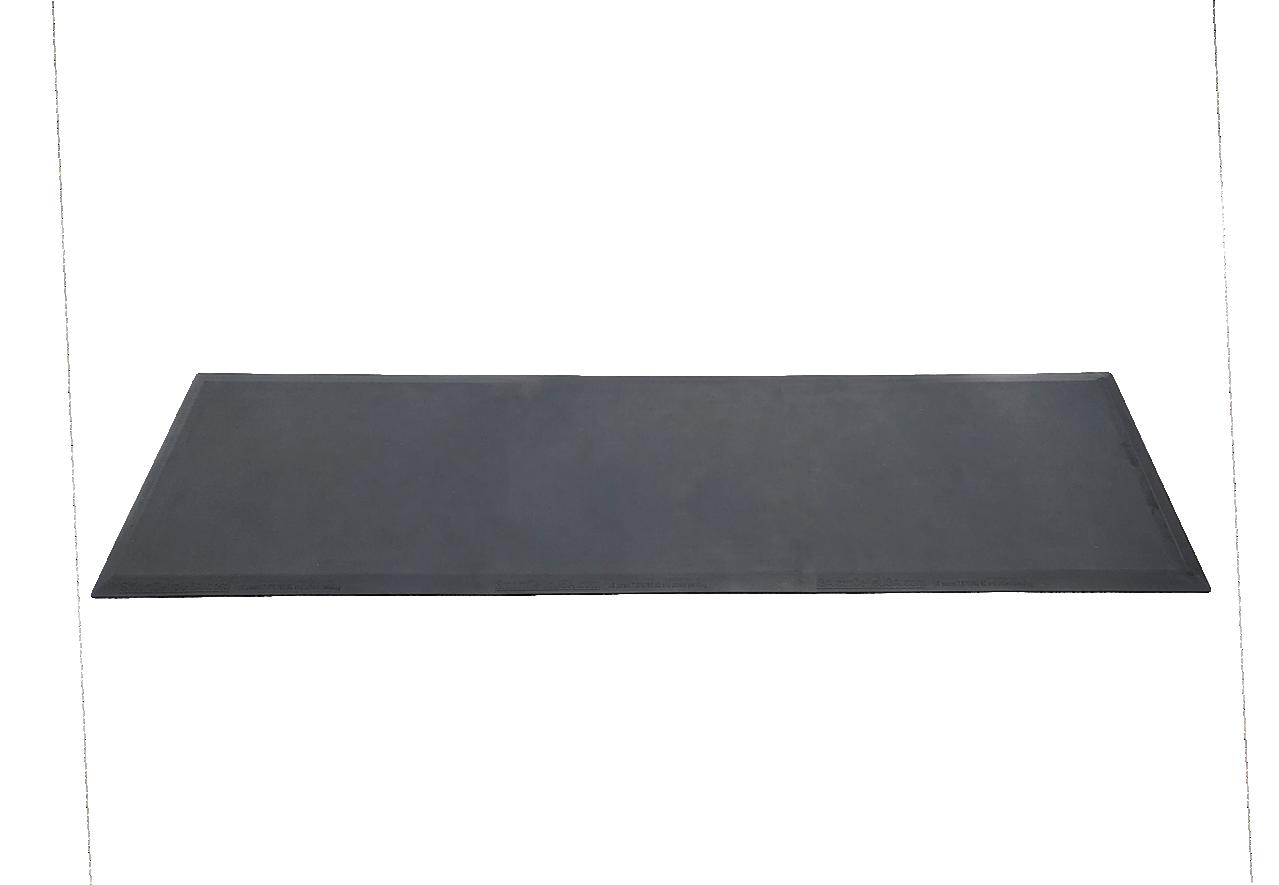
longer
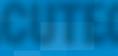
Transforming the Business of Healthcare To learn more visit thecranewaregroup.com Helps pharmacy leaders ectively transition Compare Formulary 340B Contract Pharmacy Management Streamlines the claims adjudication process, assisting with complex payor requirements Claim Financial Management Solutions simplify the complexities of pharmacy procurement, utilization, and compliance 340B Pharmacy Management & Compliance Leveraging the power of the Trisus platform, pharmacy leaders can take control of their operations and with Trisus Medication Analytics and 340B Suite, turn their disparate data into useful information to achieve better results related to revenue, pricing, cost, and compliance. Our Trisus® Medication Analytics and 340B Suite is Connected Technology in Action! Trisus® Medication Analytics Suite Powered by The Craneware Group
Acute Care Pharmaceuticals, Your Premier Supplier of USP 797 and 800 Cleanroom Disposables
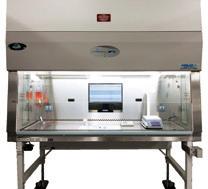
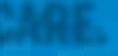
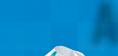
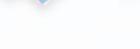
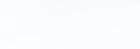
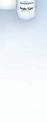






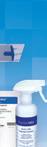



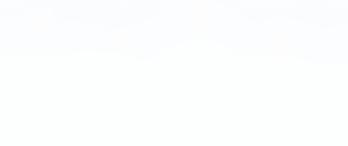


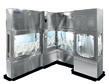
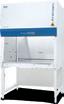
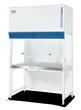
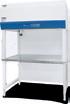

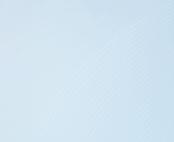

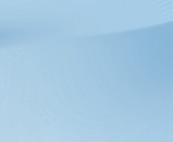
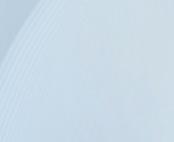
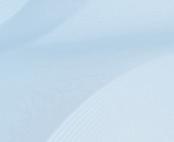
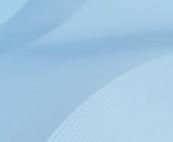
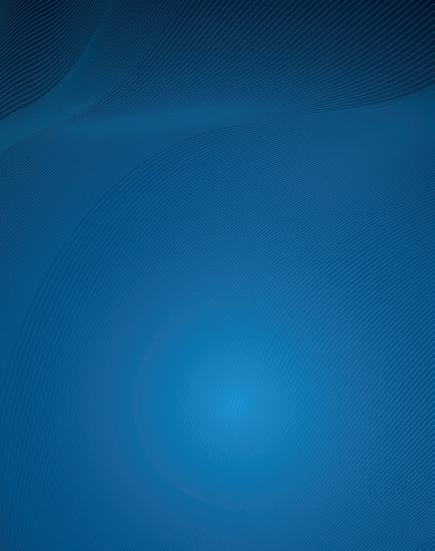
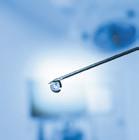
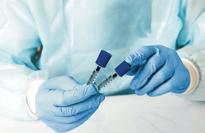
Q A&
Choose
Medication Workflow NuAire, Inc. Plymouth, MN 55447 Model: NU-543 Series IV Bar with Height Locations and 6 Hooks for IV Preparation Back-Wall Cutout for Viewing Computer Monitor Interior Duplex GFCI Outlets and Cord Pass-Through Ports Motorized Auto-Rising Base Stand for Optimal Comfort Up to 12 inch (305 mm) Access Opening Model: NU-240 Series Optimized for Sterile Non-Hazardous Compounding Sidewall Cord Pass-Through Ports Sterile Hazardous Workflow Containment Primary Engineering Control (C-PEC) Sterile Non-Hazardous Workflow Primary Engineering Control (PEC) Class II, Type A2 Biosafety Cabinet Horizontal Laminar Airflow Workstation www.nuaire.com *Product Configurable Engineering Controls From NuAire to Optimize Medication Workflows
page 74-79
Engineering Control Solutions for USP 797/800 and Fed 503B cGMP Compliance L 215-441-9661 Horsham, PA, USA ETI.Admin@escolifesciences.com www.escolifesciences.com ALSO AVAILABLE FROM ESCO ULPA filter, creating ISO workzone, cleaner than ULPA filter, creating ISO workzone, cleaner than ECM blower, creating stable airflow at energy-efficient 200 Watts Lowest height in the Two HEPA filter in series, allowing exhaust to room instead of ducting Multi-step stations combining several isolators Fully customizable according to your needs Horizontal Laminar Flow Cabinet Class II Type A2 Biosafety Cabinet Class Ventilated Enclosure Filling Line A. USP 797 Sterile Non-Hazardous Drugs C. USP 800 Sterile Hazardous Drugs B. USP 800 Non-Sterile Hazardous Drugs D. Full cGMP Filling Line for Fed 503B Facilities
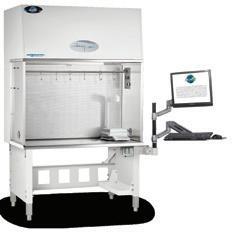



66-69
—
page 71
Solutions is focused on profitability maximizing patient access to specialty drug.



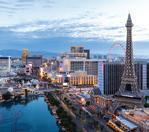
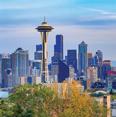
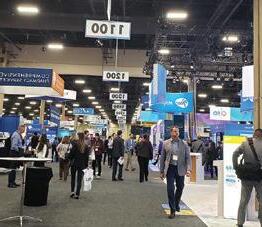
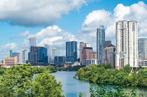
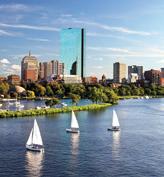
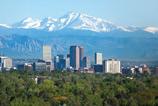
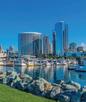

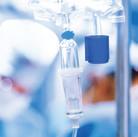
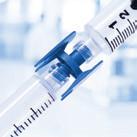
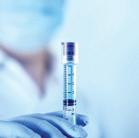
SUMMER 2023 I HEALTH SYSTEM • INFUSION 15
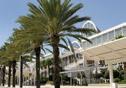
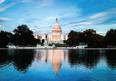
SMART THINKING.
Propofol Injectable Emulsion, USP supplied by Samson Medical Technologies, under the Avet label, is the smart choice for your pharmacy service, offering you the same formulation as Diprivan® , free of benzyl alcohol, sulfites, and latex, with the easy ordering and excellent service that you have come to expect from the providers of SmartPak® .

SmartPak® provides a revolutionary delivery system for these essential drugs, offering faster, easier preparation more economically. It’s also safer. The SmartPak bag system is a convenient alternative to using multiple glass vials. No glass means no breakage during handling. SmartPak saves time and labor with less waste. SmartPak — the smart choice for your pharmacy service.
This important product now in the exclusive delivery system.
important product now in the exclusive delivery system.
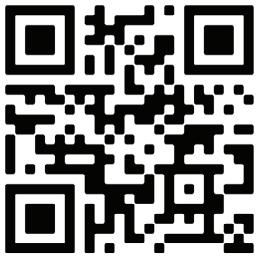
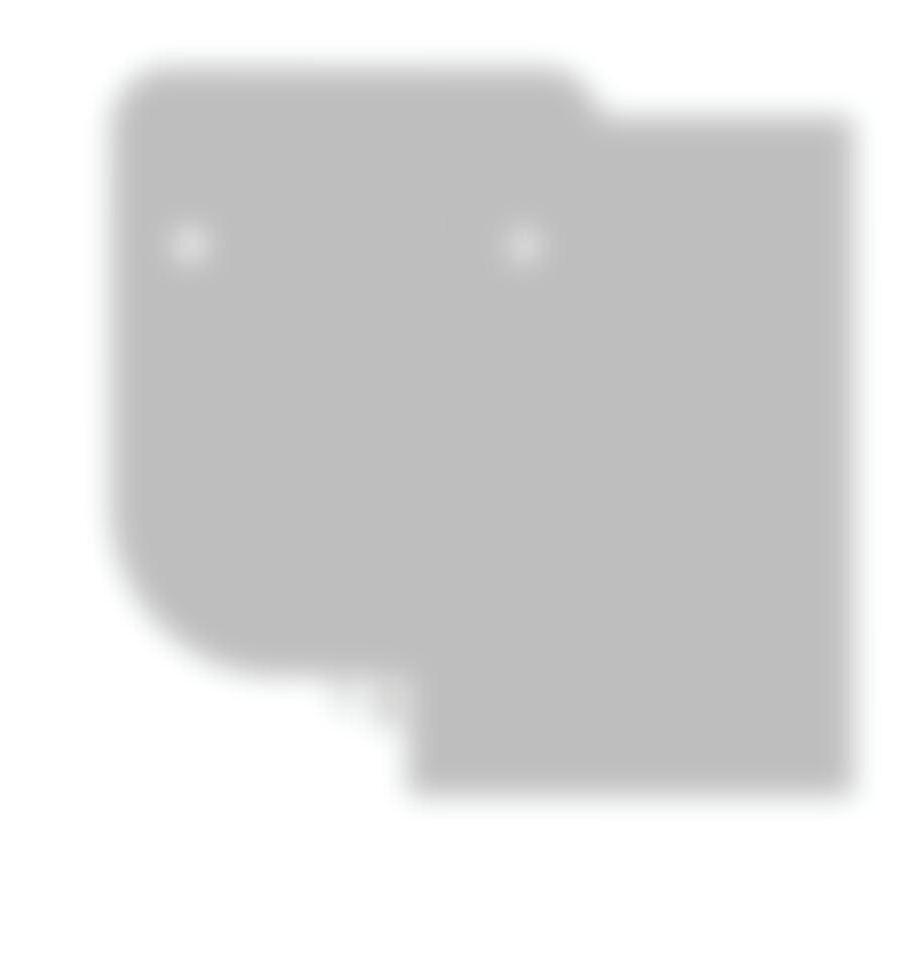
This important product now in the exclusive delivery system.

SmartPak® provides a revolutionary delivery system for these essential drugs, offering faster, easier preparation more economically. It’s also safer. The SmartPak bag system is a convenient alternative to using multiple glass vials. No glass means no breakage during handling. SmartPak saves time and labor with less waste. SmartPak — the smart choice for your pharmacy service.
provides a revolutionary delivery system for this essential drug, offering faster, easier more economically. It’s also safer. The SmartPak bag system is a convenient using multiple glass vials. No glass means no breakage during handling. SmartPak labor with less waste. SmartPak — the smart choice for your pharmacy service
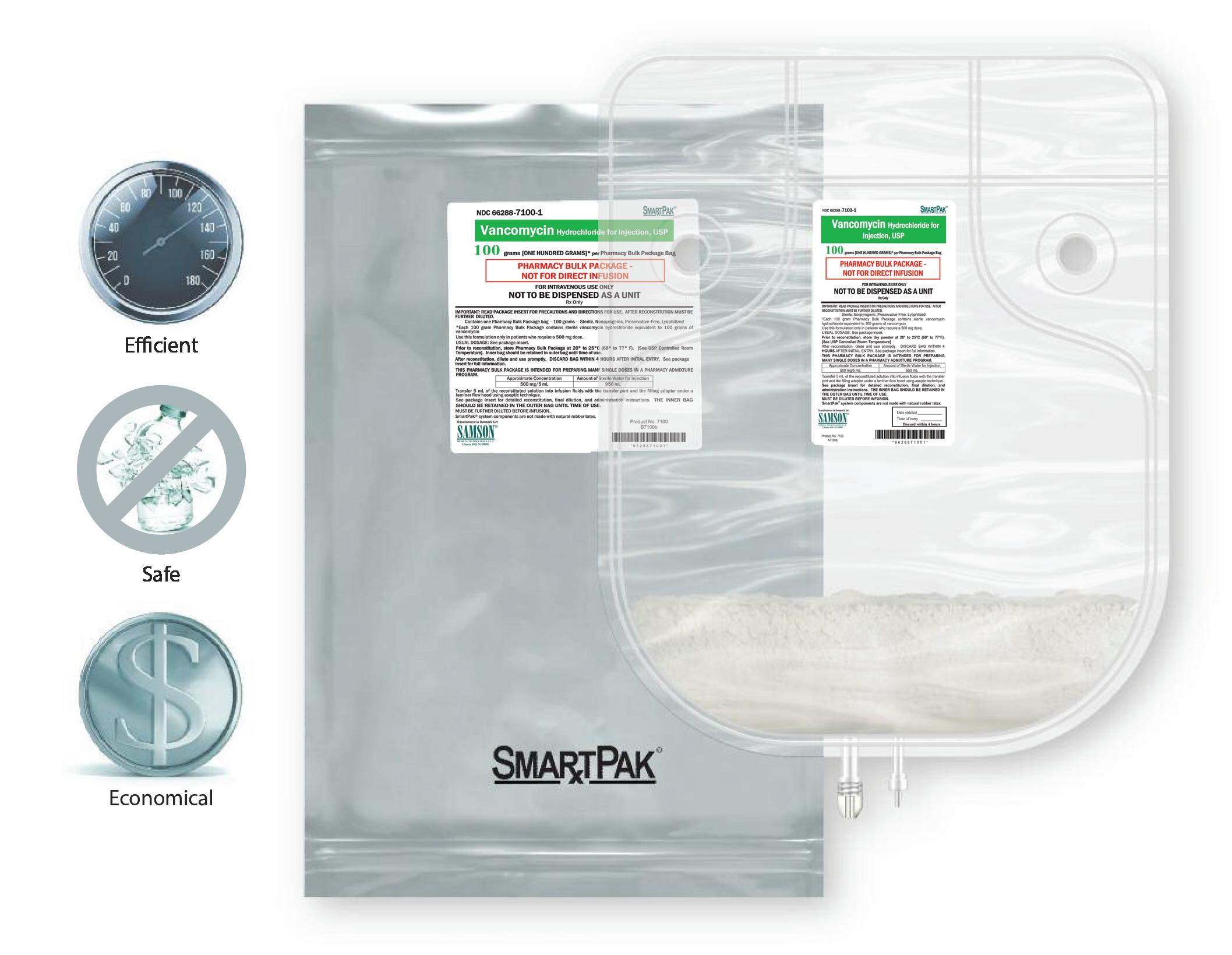
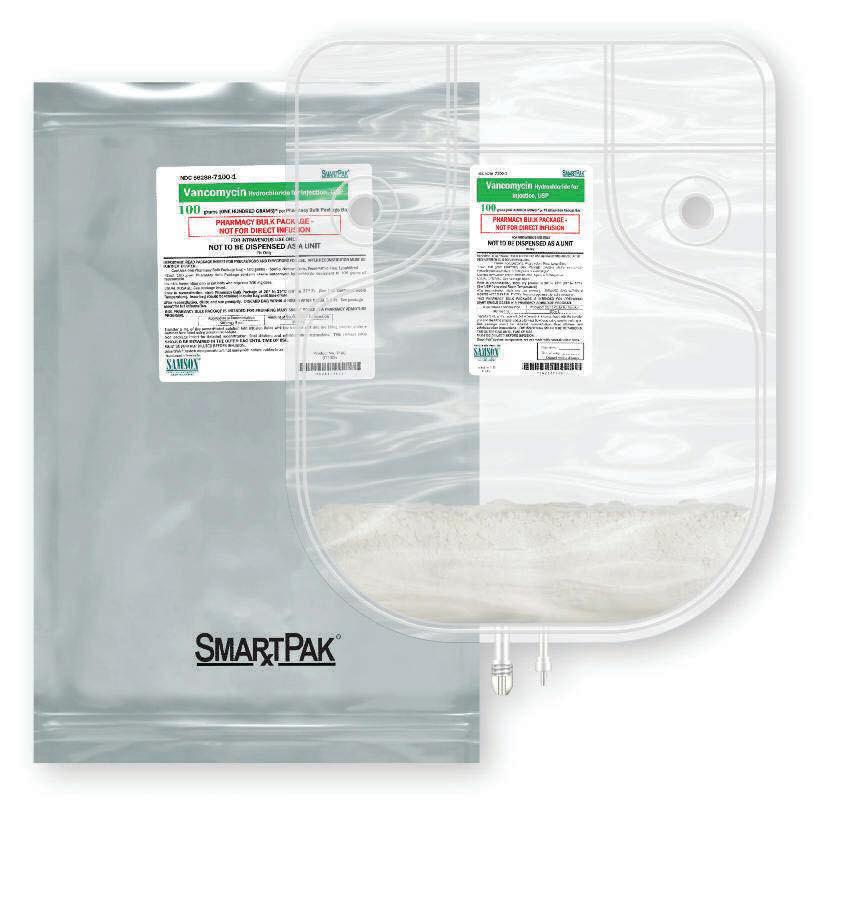
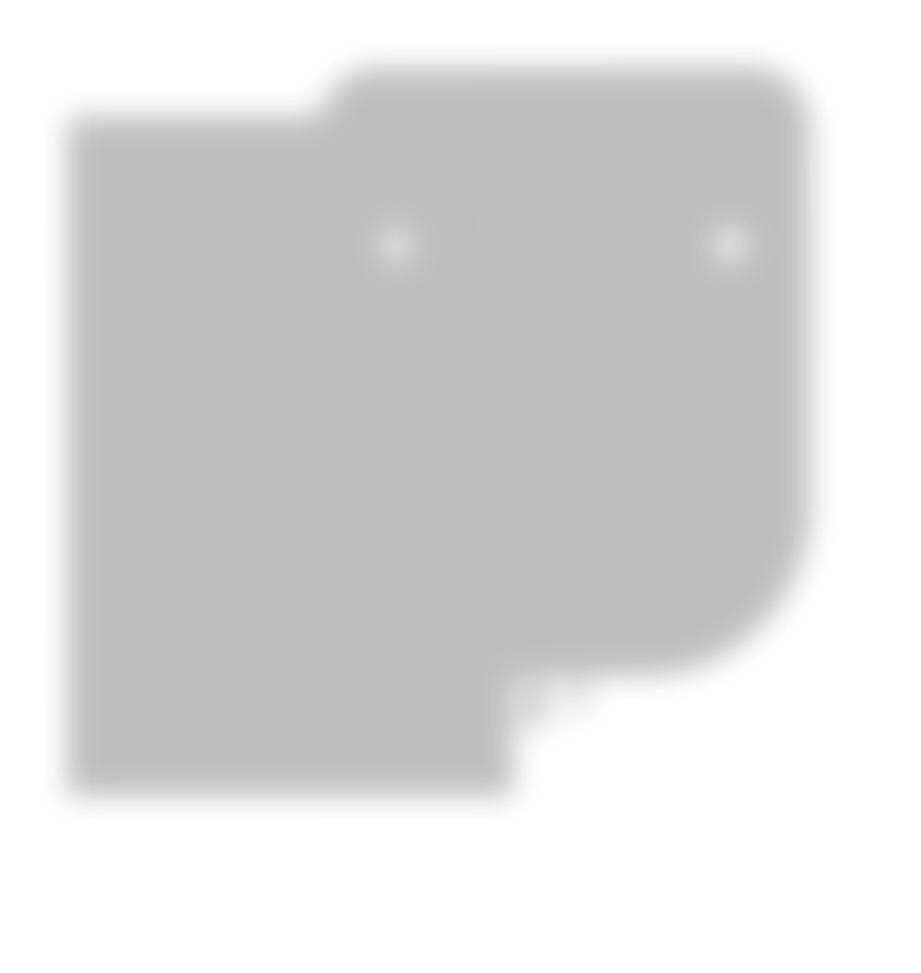
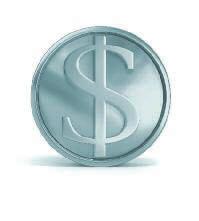
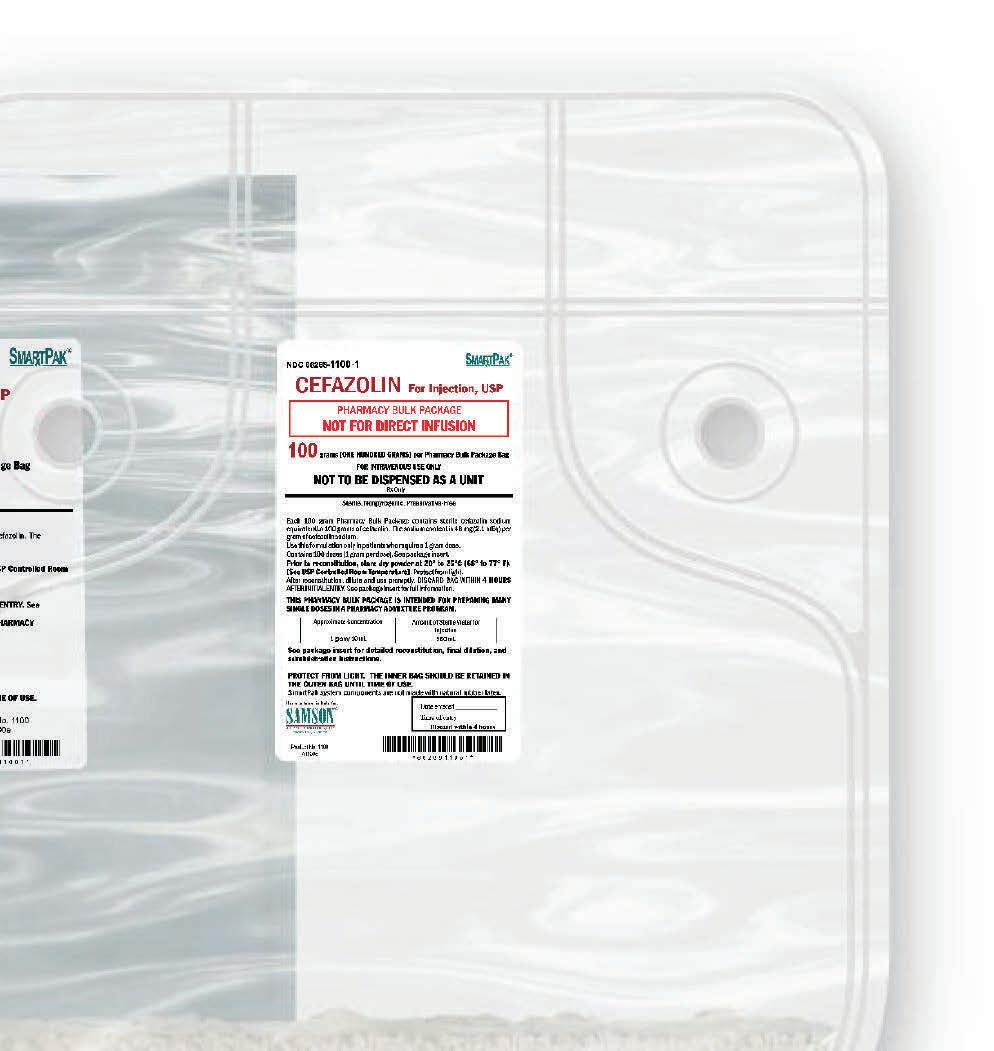
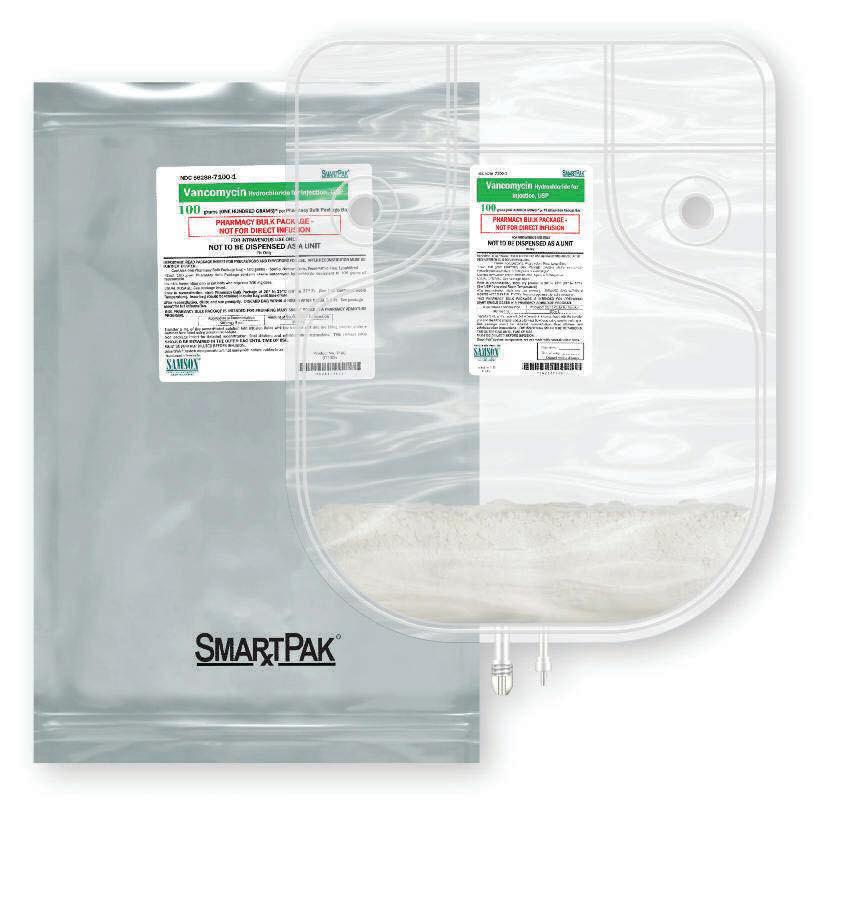
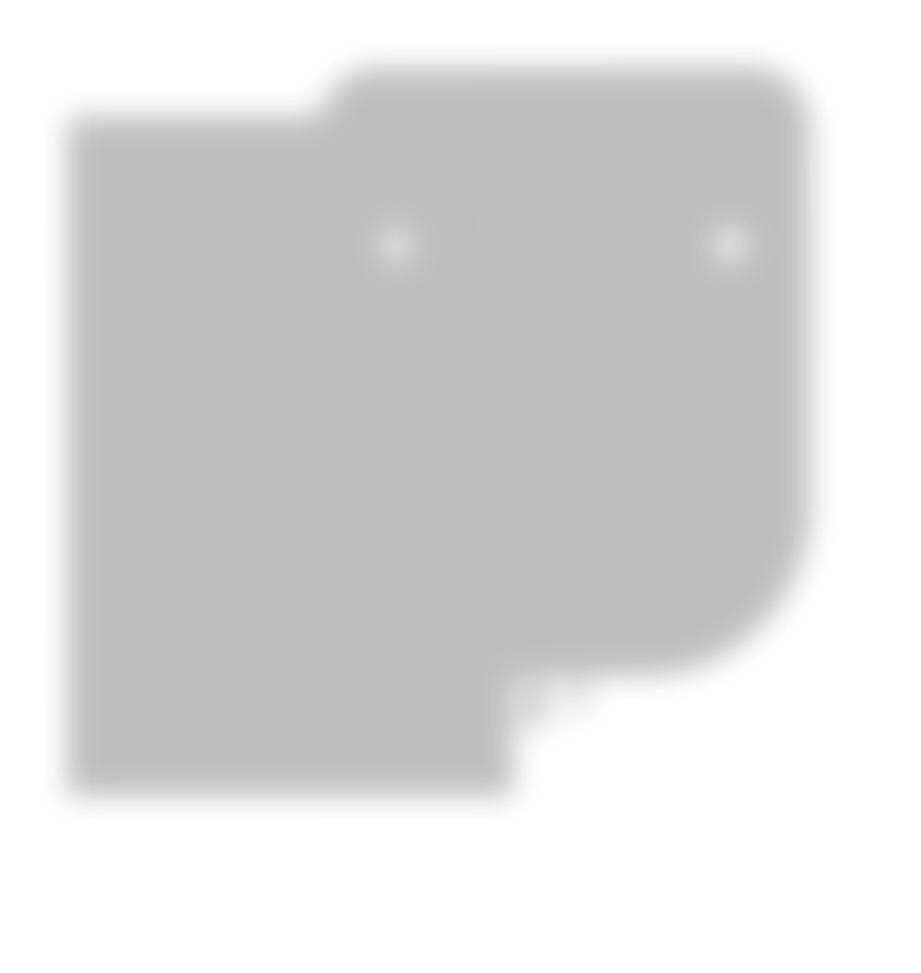
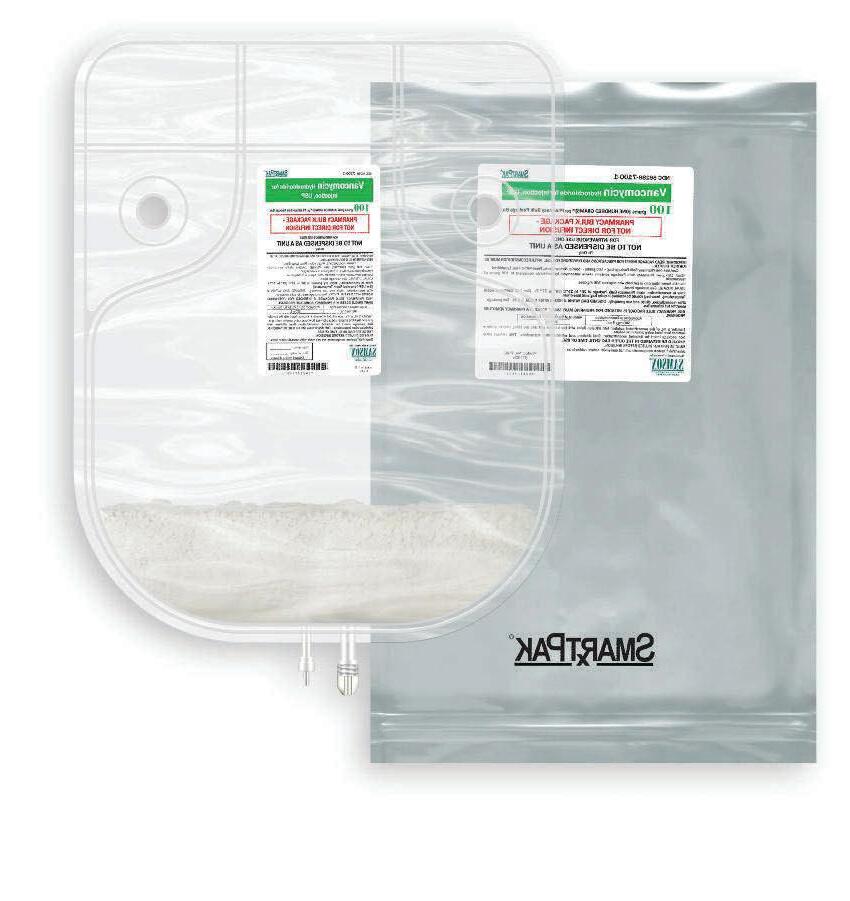
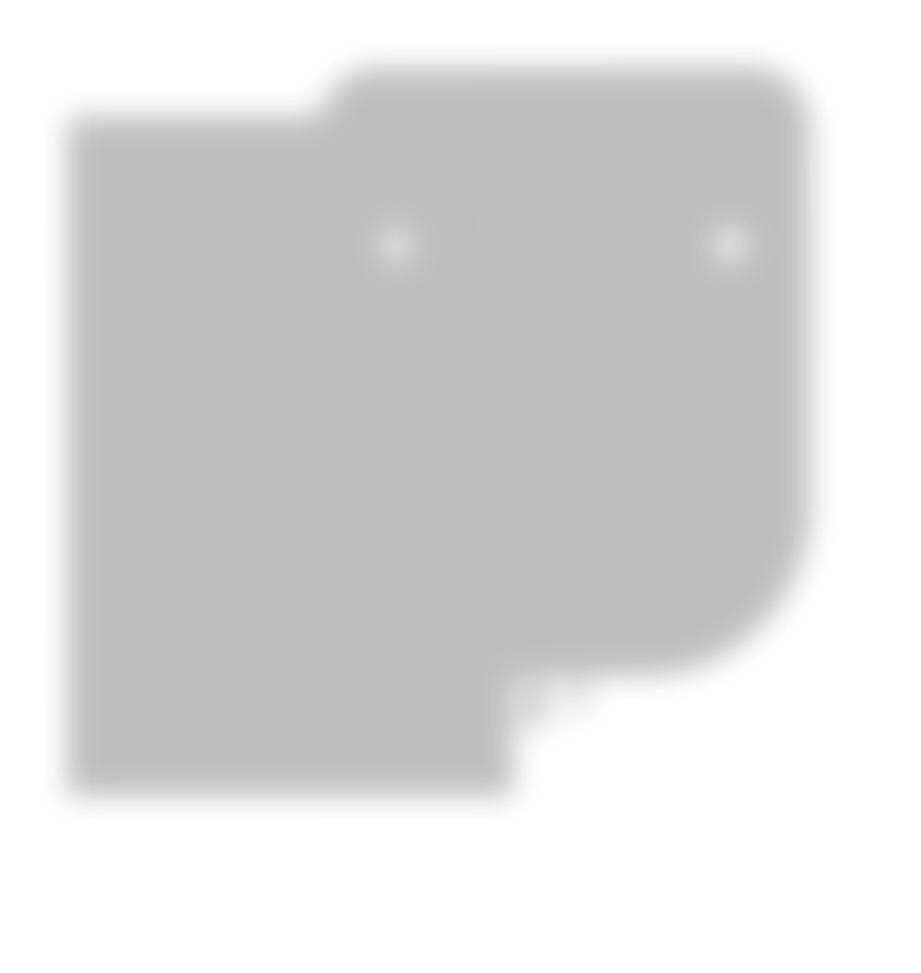
SmartPak® provides a revolutionary delivery system for this essential drug, offering faster, easier preparation more economically. It’s also safer. The SmartPak bag system is a convenient alternative to using multiple glass vials. No glass means no breakage during handling. SmartPak saves time and labor with less waste. SmartPak — the smart choice for your pharmacy service
SmartPak® provides a revolutionary delivery system for this essential drug, offering faster, easier preparation more economically. It’s also safer. The SmartPak bag system is a convenient alternative to using multiple glass vials. No glass means no breakage during handling. SmartPak saves time and labor with less waste. SmartPak — the smart choice for your pharmacy service
SmartPak® provides a revolutionary delivery system for these essential drugs, offering faster, easier preparation more economically. It’s also safer. The SmartPak bag system is a convenient alternative to using multiple glass vials. No glass means no breakage during handling. SmartPak saves time and labor with less waste. SmartPak — the smart choice for your pharmacy service.
page 84-87
page 89
PUBLISHER
RXinsider, LTD



































RXinsider Chairman: Gregory Cianfarani, RPh




DESIGN AND PRODUCTION
Design & Layout

Lora Bourque
Multimedia Eric Simmons
Marketing and Operations
SALES AND BUSINESS DEVELOPMENT
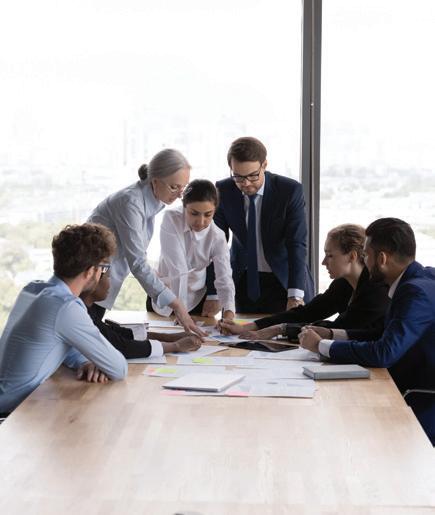
Samantha Roy Alexa DiLuca
Kristin Fennessey
Chris Kolkhorst, EVP chris.kolkhorst@rxinsider.com
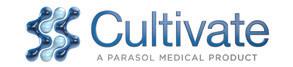
Mike Rahme mike.rahme@rxinsider.com
Shaun Russell shaun.russell@rxinsider.com
Jillian Ricci jillian.ricci@rxinsider.com
Email sales@rxinsider.com
Toll-Free Phone 800.972.2083
Fax 646.329.9766
Website www.RXinsider.com
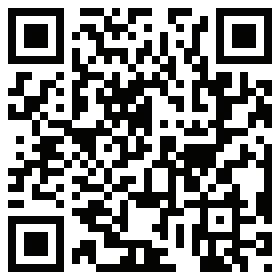
NOTICE OF POLICY 20Ways is published quarterly by RXinsider LTD, 1300 Division Road, Suite 103, West Warwick, RI 02893. Postmaster: Send address changes to 20Ways/RXinsider, 1300 Division Road, Suite 103, West Warwick, RI 02893. Notification of address change must be made six weeks in advance, including old and new address with zip code.


Editorial – views expressed in articles or profiles in the 20Ways are those of the author(s) and do not necessarily reflect the policies and opinions of RXinsider, our editorial board(s), our advisory board(s), or staff. Advertising – products, services, and educational institutions advertised in 20Ways do not imply endorsement by RXinsider.
Copyright © 2023 RXinsider LTD. All rights reserved. Reproduction without permission is prohibited.
Make the transition to the new USP <797> testing and documentation seamless with carefully crafted testing supplies.
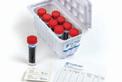
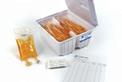
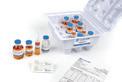




page 91
Download the 20Ways App RXinsider.com/20ways
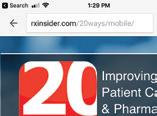
20Ways is an official publication of RXinsider
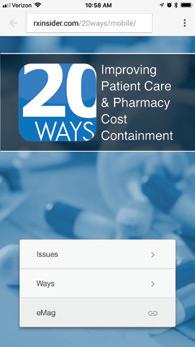
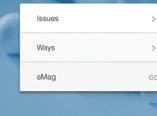
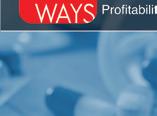
GENERAL SUBSCRIPTION INQUIRIES
RXinsider LTD c/o 20Ways 1300 Division Road, Suite 103 West Warwick, RI 02893

20Ways Online: www.RXinsider.com/20Ways
General Information: 20Ways@RXinsider.com
Circulation: See page 5

Drug Disposal Made Simple for Pharmacists
Rx Destroyer is a fast acting ready-to-use chemical digestion formula that begins neutralizing medications on contact, complying with the DEA Non-Retrievable Standard 21 CFR and the EPA’s 40 CFR. Pharmacists are key educators to their patients on medication safety and disposal. Your advocacy for drug disposal both behind and in front of the counter protects people, communities and the environment by eliminating the risk of wrongful misuse or incorrect disposal.
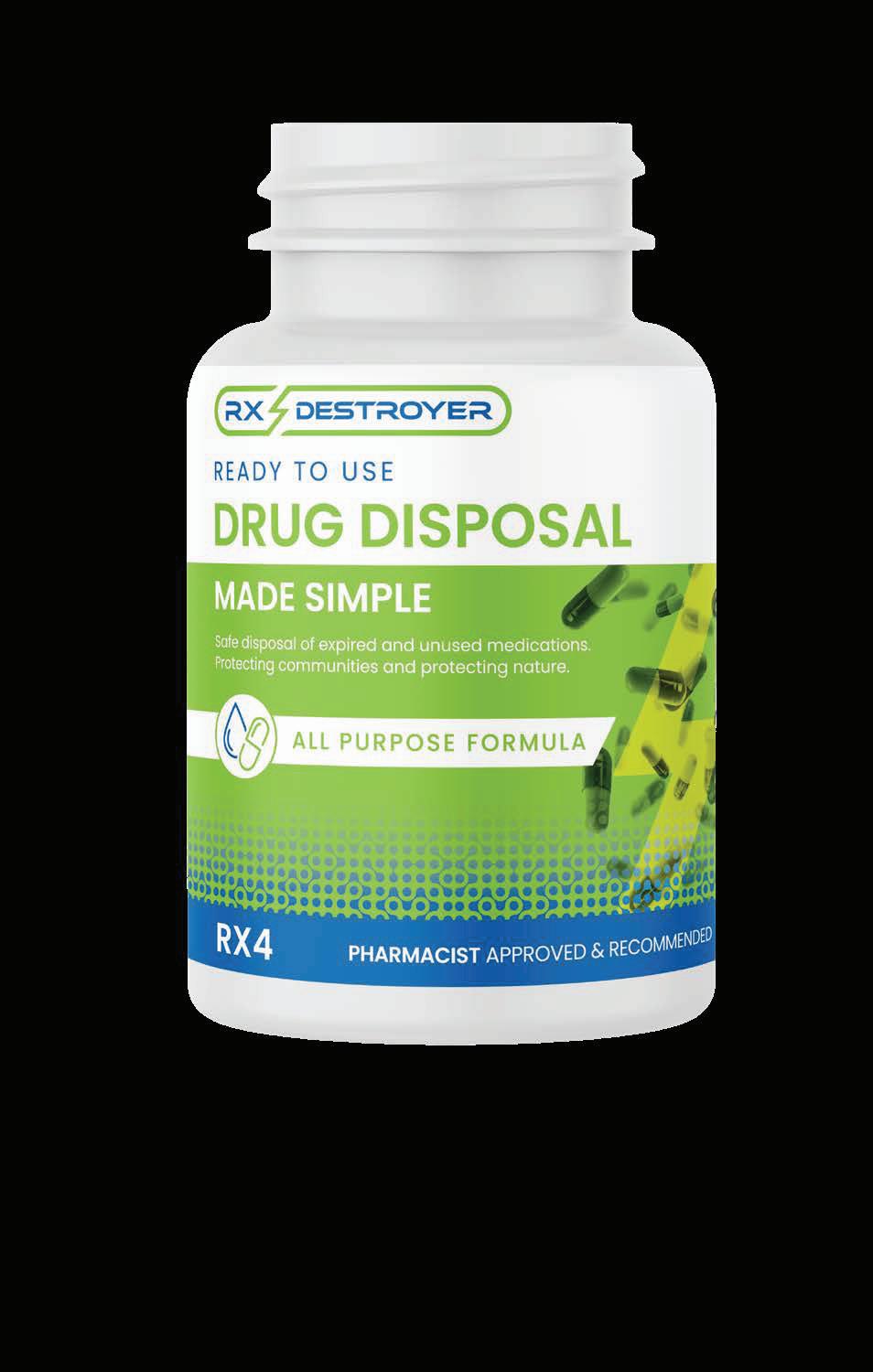
Behind the pharmacy for pharmacists
Integrating Rx Destroyer drug disposal systems into your existing pharmaceutical program is easy, cost effective, and simply the most comprehensive solution in preventing drug abuse, drug diversion, and stockpiling.
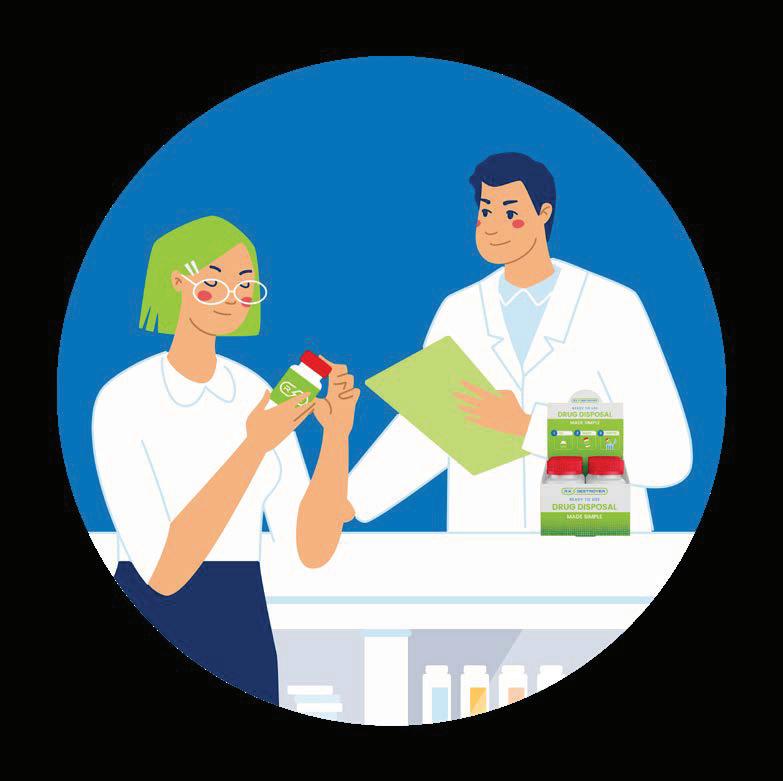
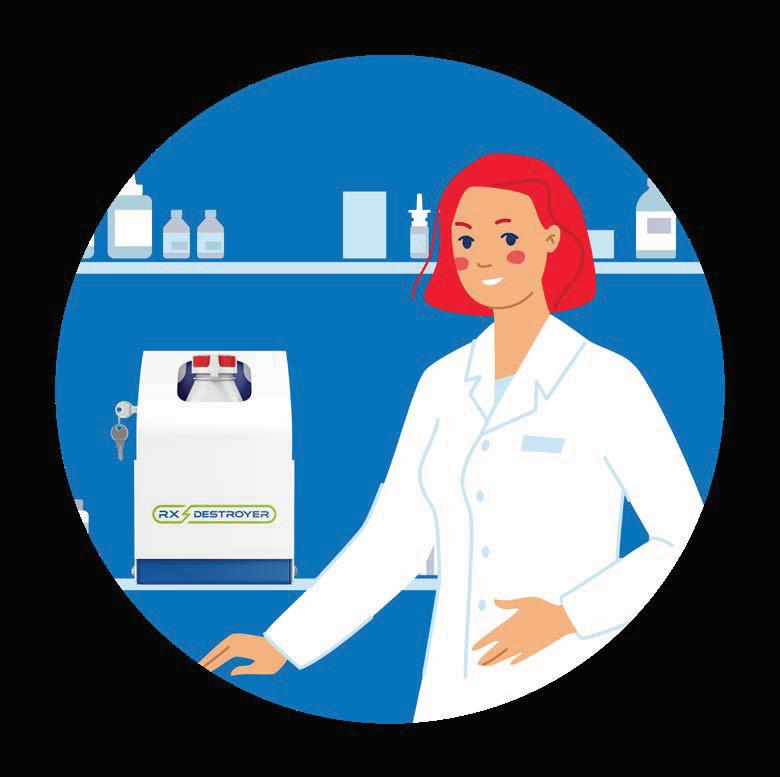
On the counter for your patients
Non-retrievable drug deactivation actively protects your patients by eliminating risk of wrongful misuse or incorrect disposal of medications.
ACCEPTS ALL FORMS OF MEDICATION INCLUDING: pills & tablets, narcotics, lonzenges, powders, capsules, suppositories, liquids, injectables, patches, creams, lollipops, fentanyl, marijuana, and more.
Meet
The solution you need to ensure proper controlled substance disposal and prevent drug diversion in healthcare settings.
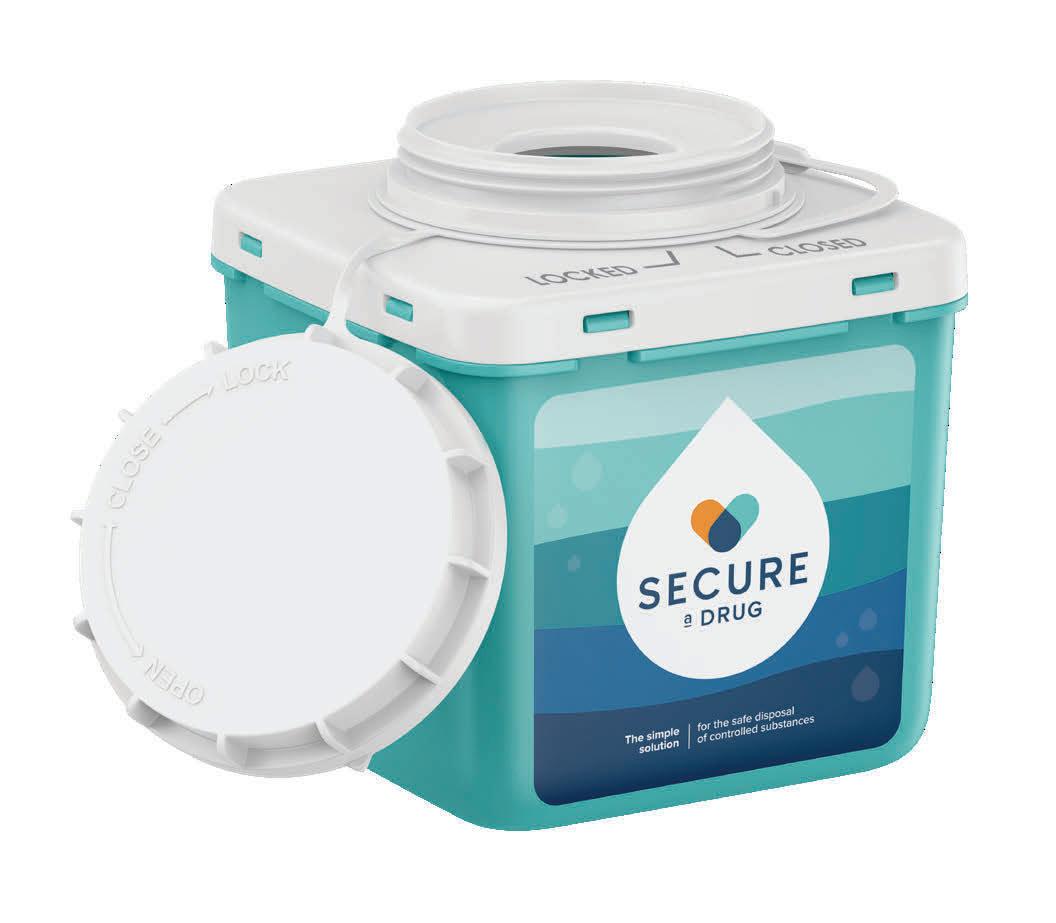
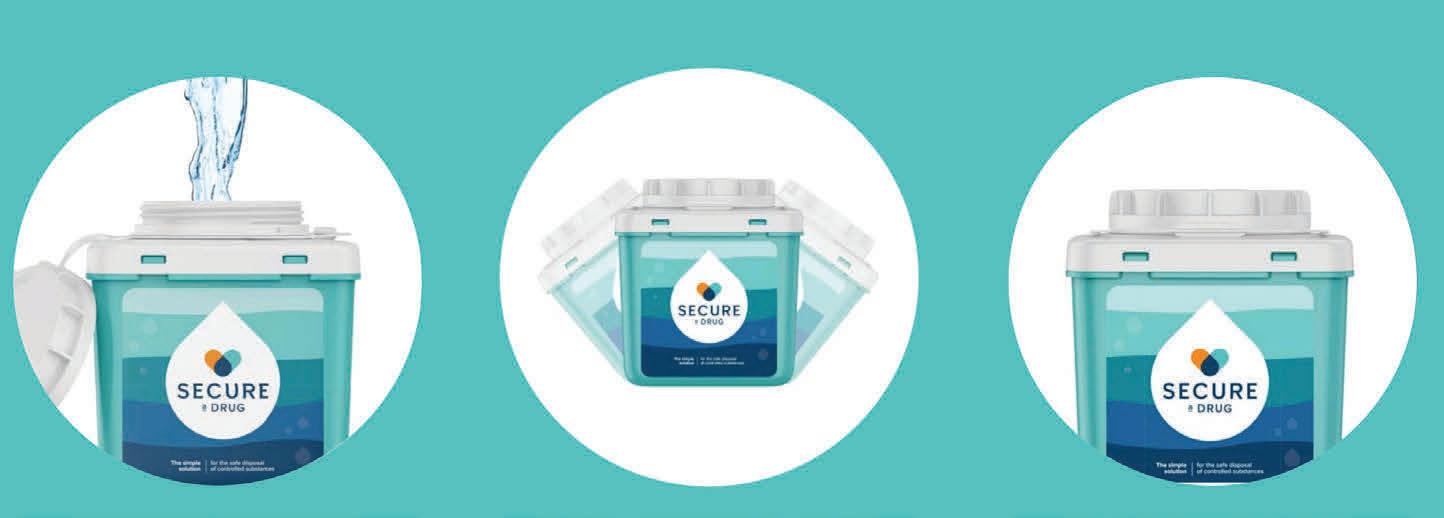
When to Use Secure a Drug?
Secure a Drug should be used to meet non-retrievable drug standards for any expired or unwanted pharmaceuticals. When used in pharmaceutical settings, Secure a Drug offers a simple solution for drug denaturing that ensures both compliance with all federal regulations and the safety of your patients and staff.
Empowering Clinicians
While regulatory compliance is a critical benefit of Secure a Drug, at its core it is designed to promote human wellbeing by eliminating risk of drug diversion and opioid abuse. Give healthcare professionals simple tools, and they will make a lasting impact. Secure a Drug empowers clinicians to combat, and ultimately end the opioid epidemic at its source through efficient and safe disposal of controlled pharmaceutical substances.
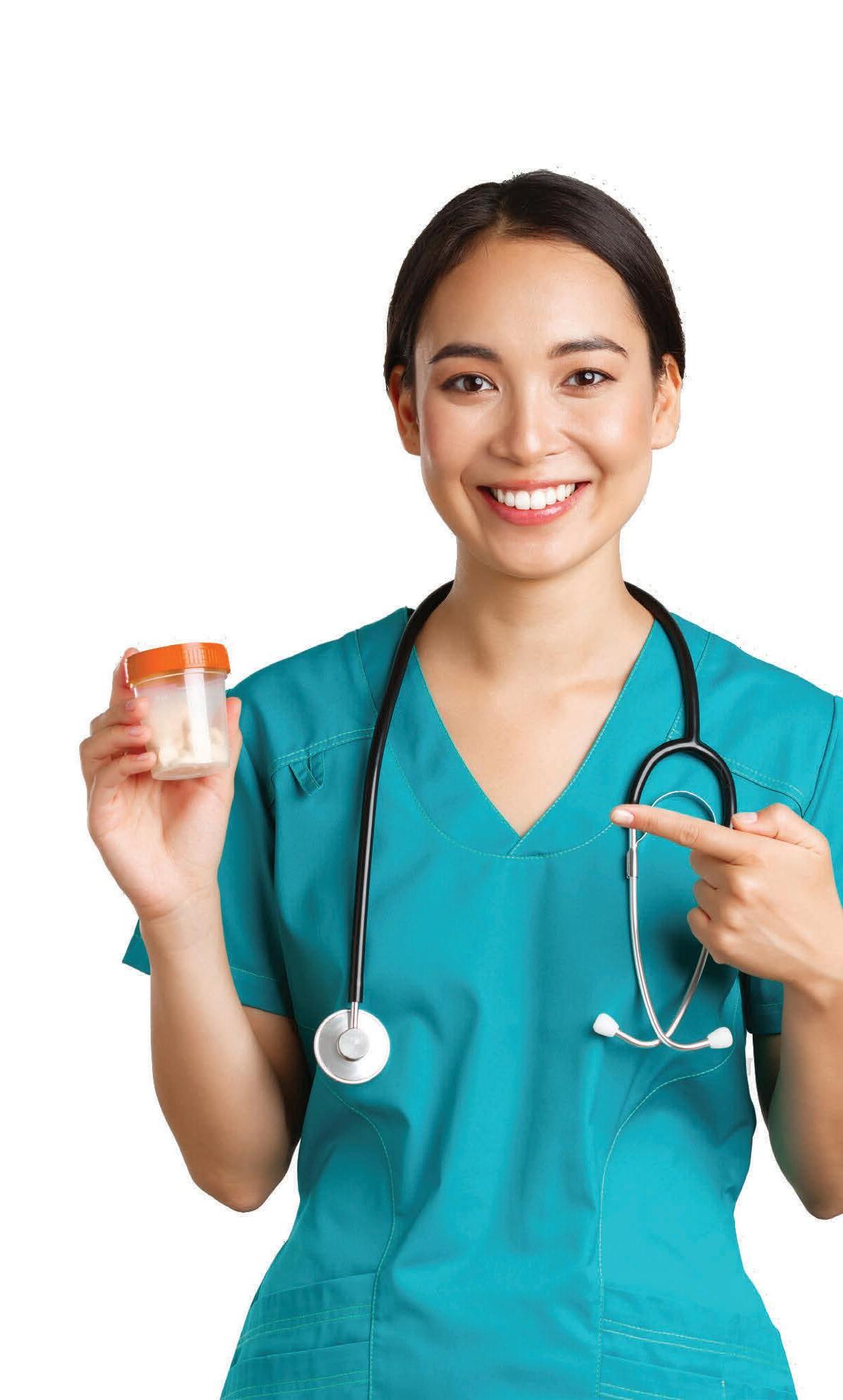
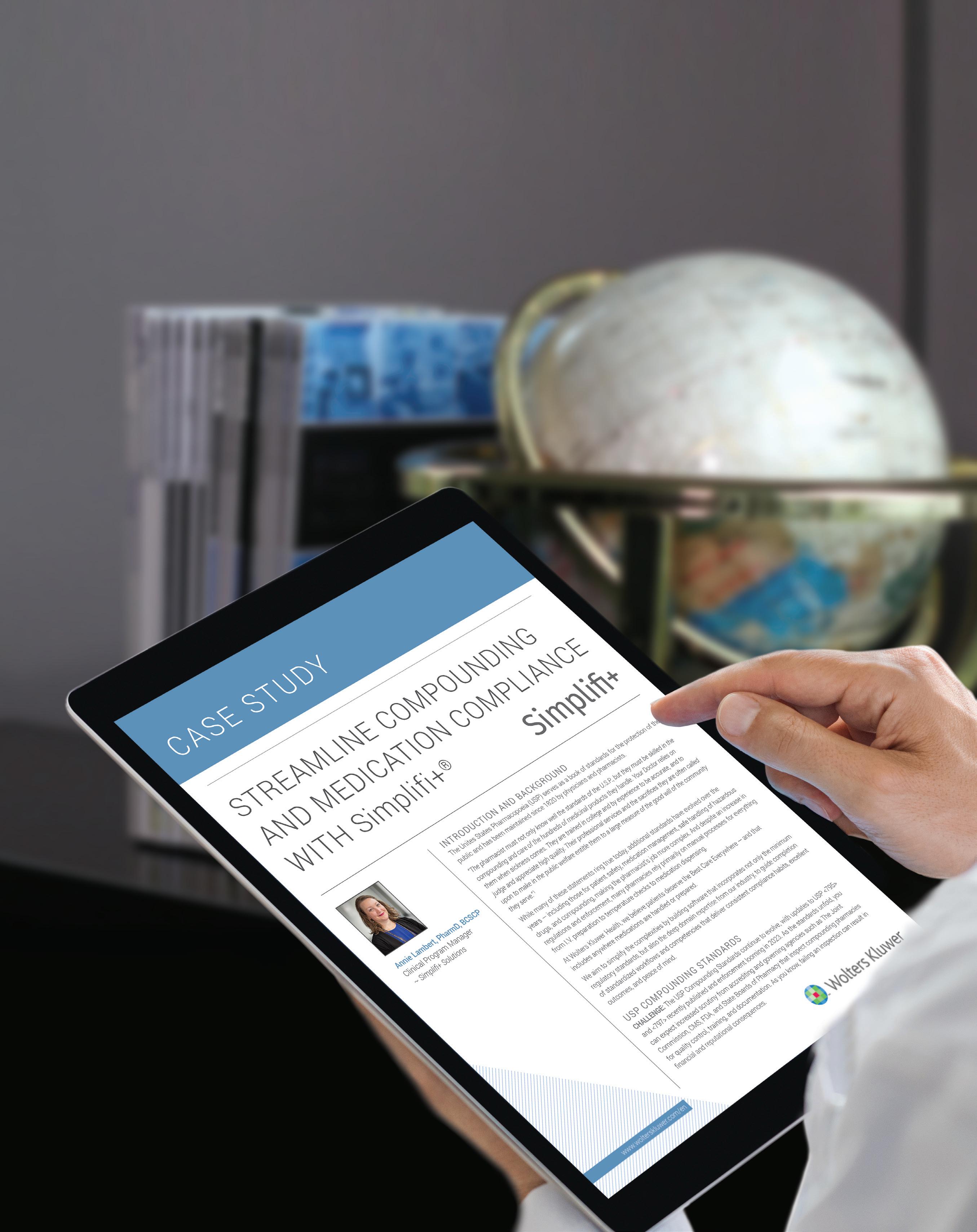
The Most Innovative Tamper-Evident Seals In Hospital Pharmacy Today
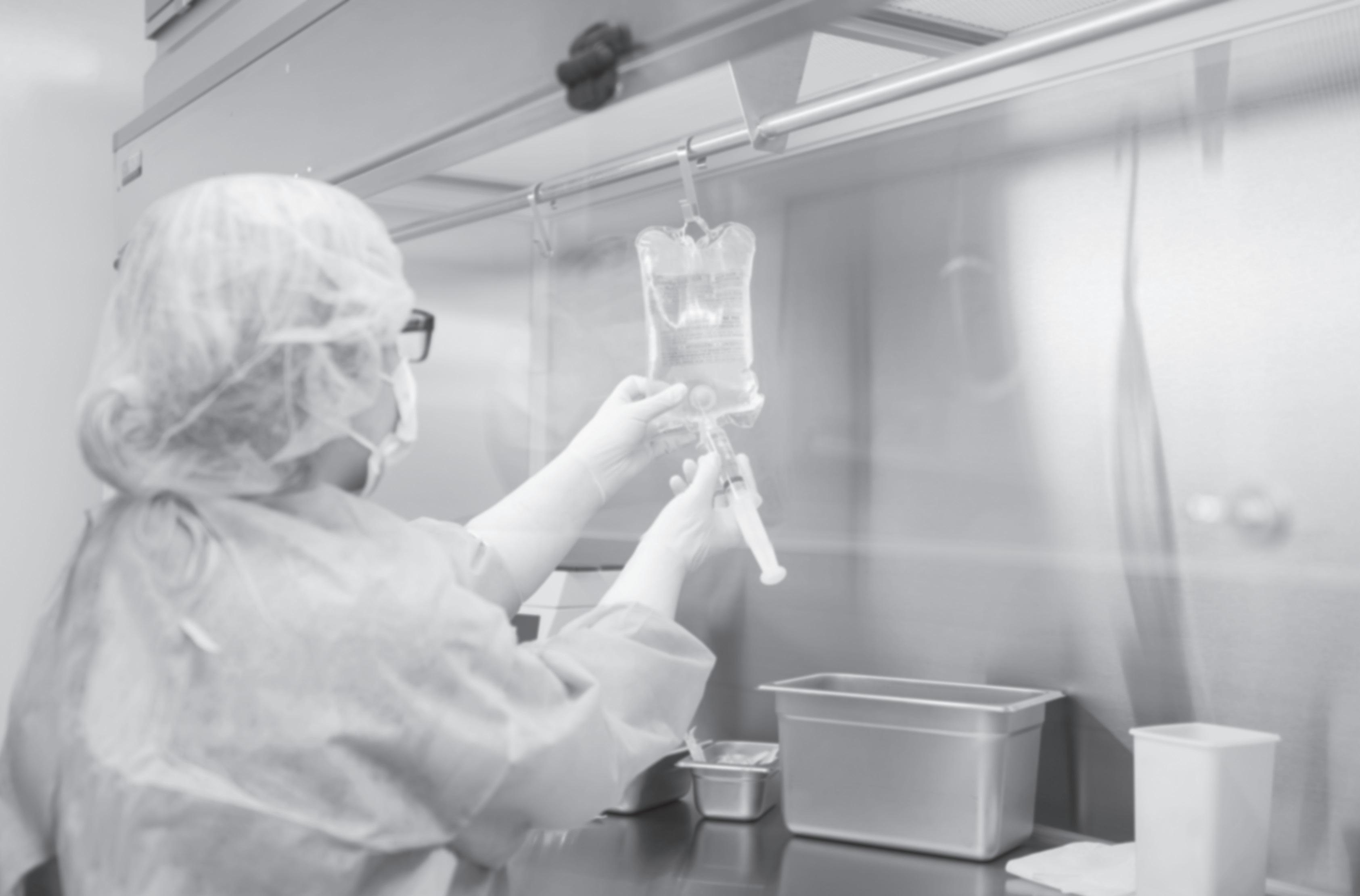
• Sterile & Paper Free (USP 797 Compliant).
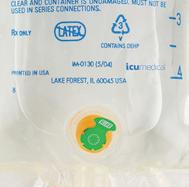
• Maintains a 100% sterile barrier* with 3X greater adhesion.
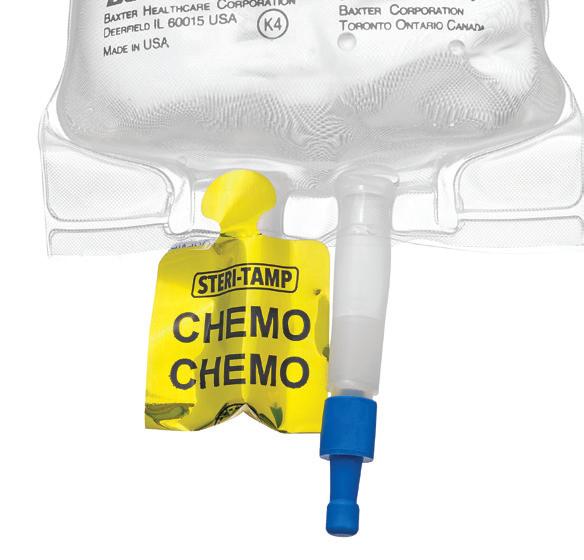
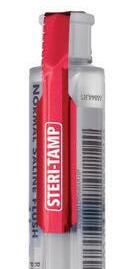
*Tested in Nelson Labs, Salt Lake City, UT
• Helps prevent contamination of drugs and provides added protection to pharmacists.
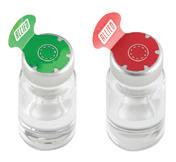
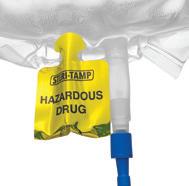
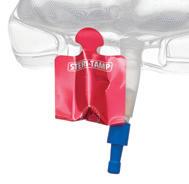
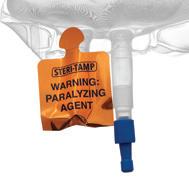
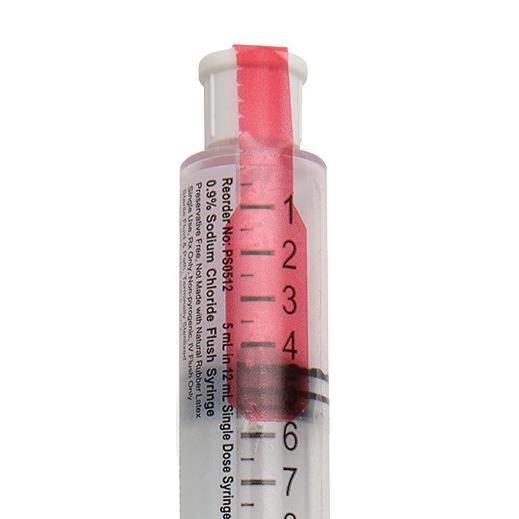
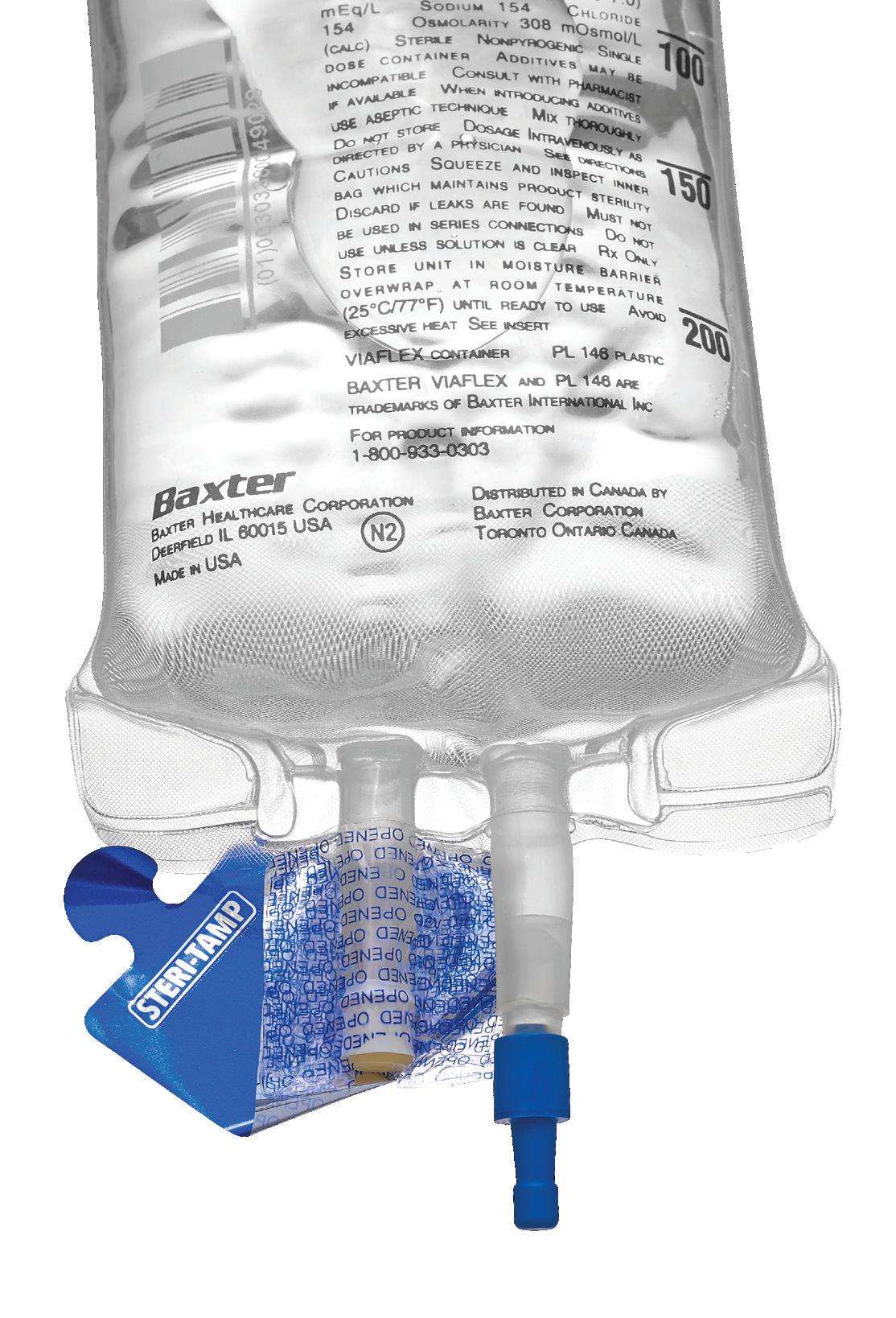
• Will not fall off, even in cold storage conditions (down to -20 degrees centigrade).
• Patented dual-layer indicates true tamper-evidence with “OPENED” marking.
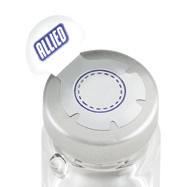
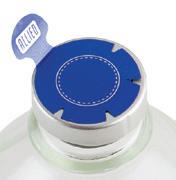
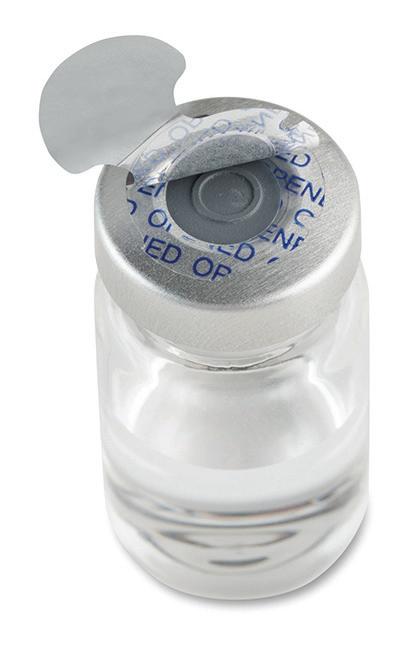
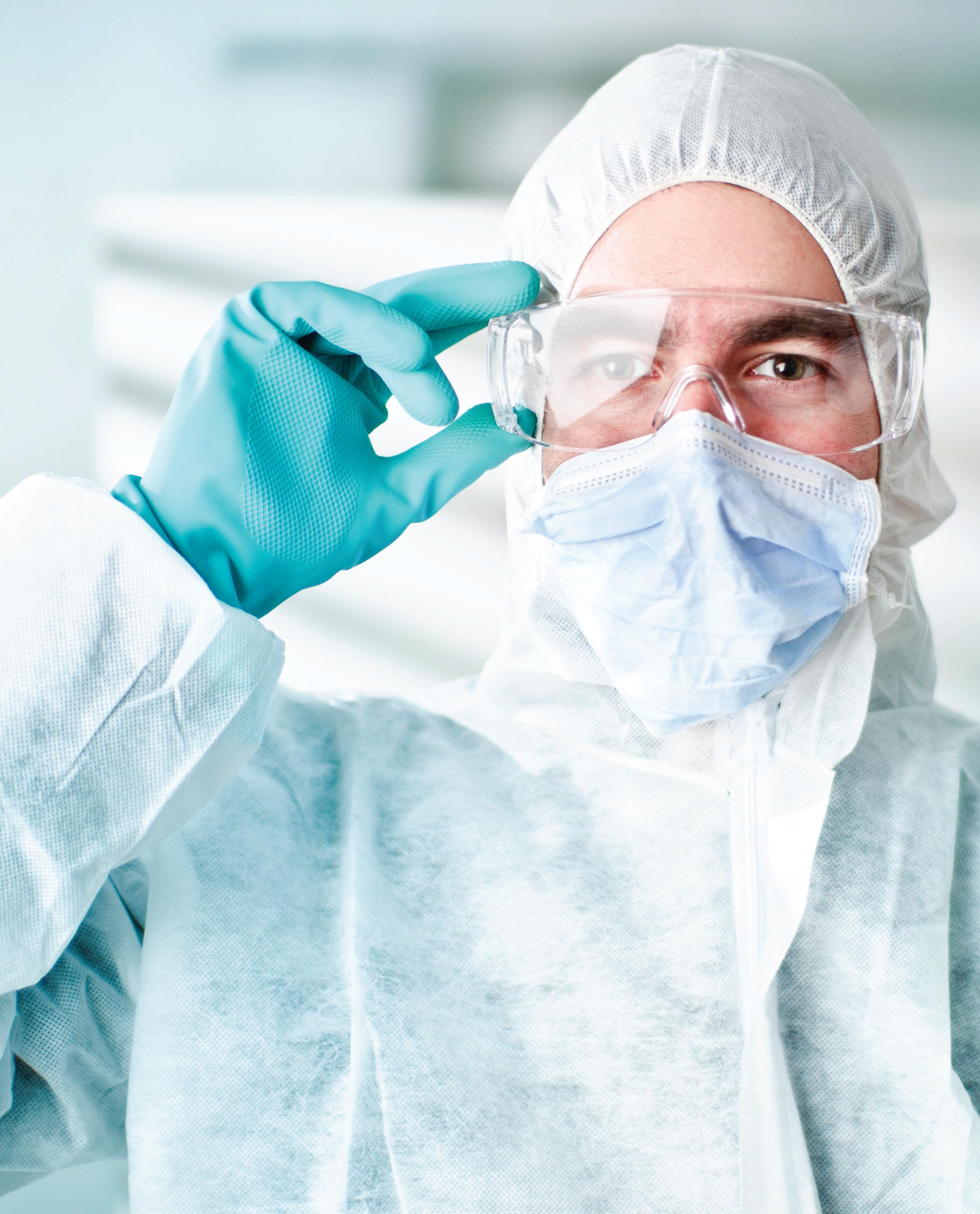
Rees Scientific
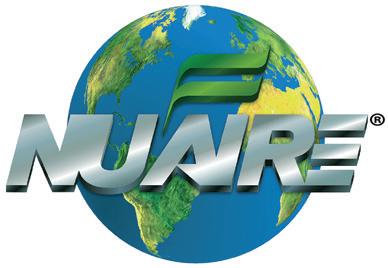
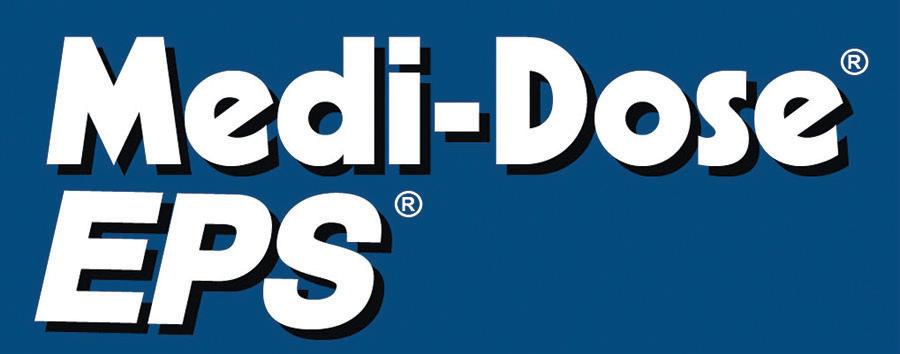

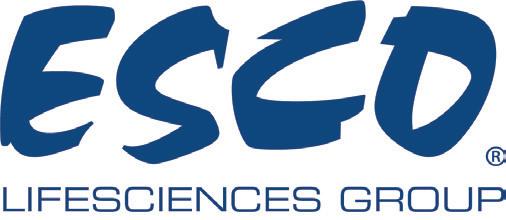

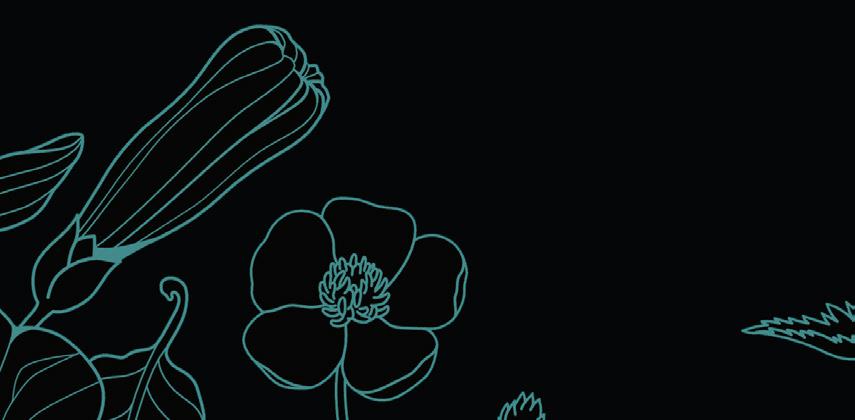
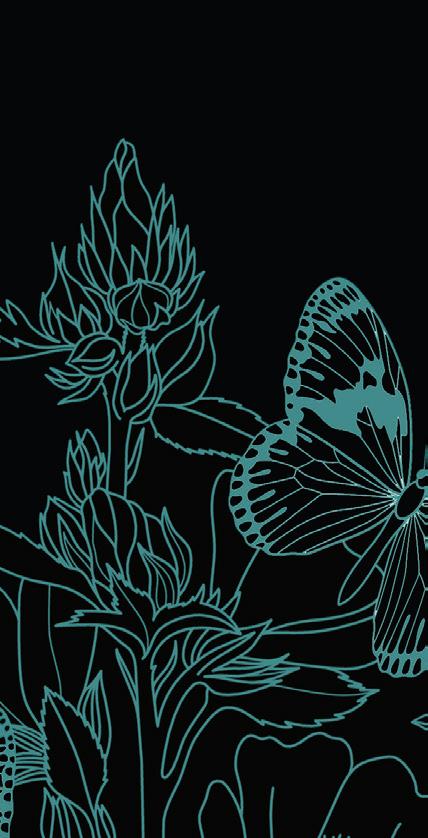
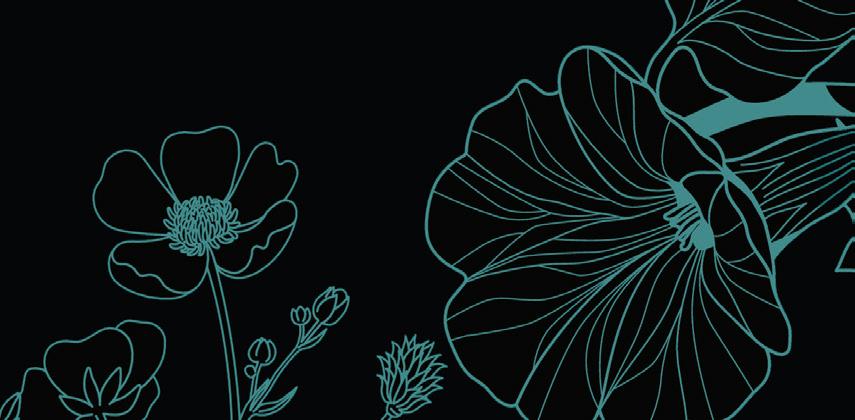
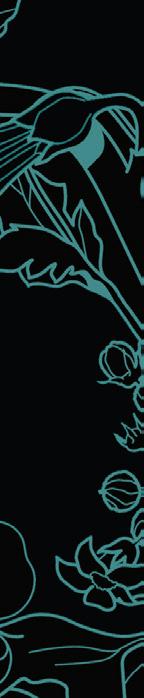
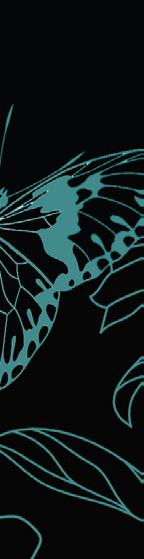

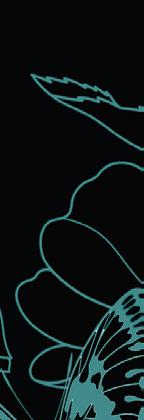
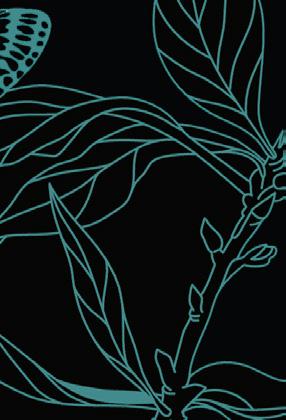
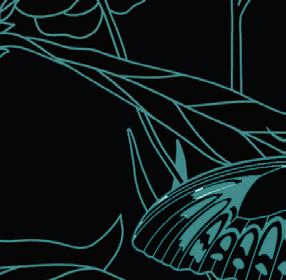
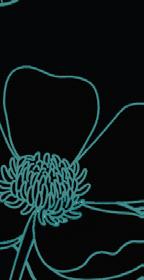

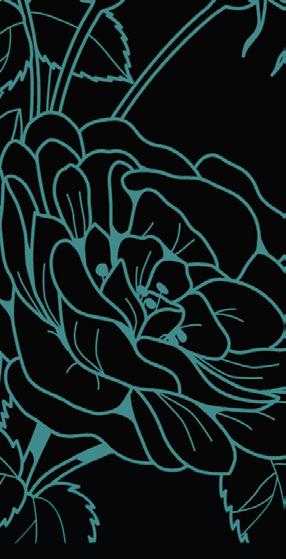
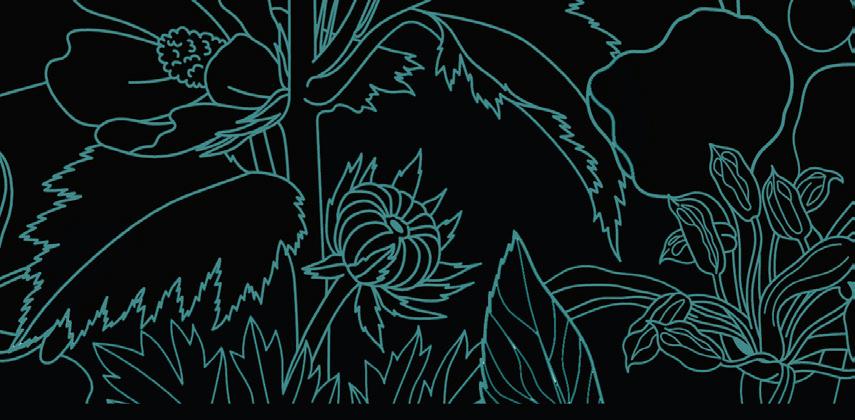
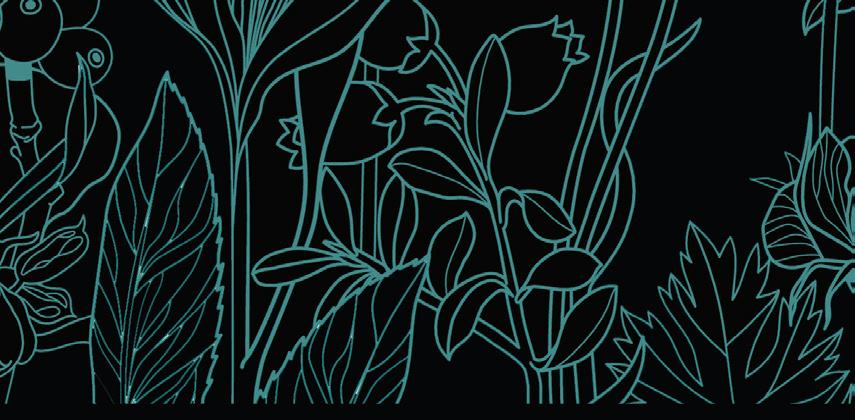
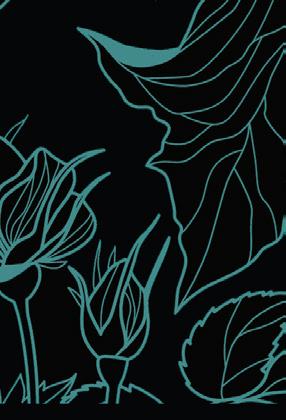


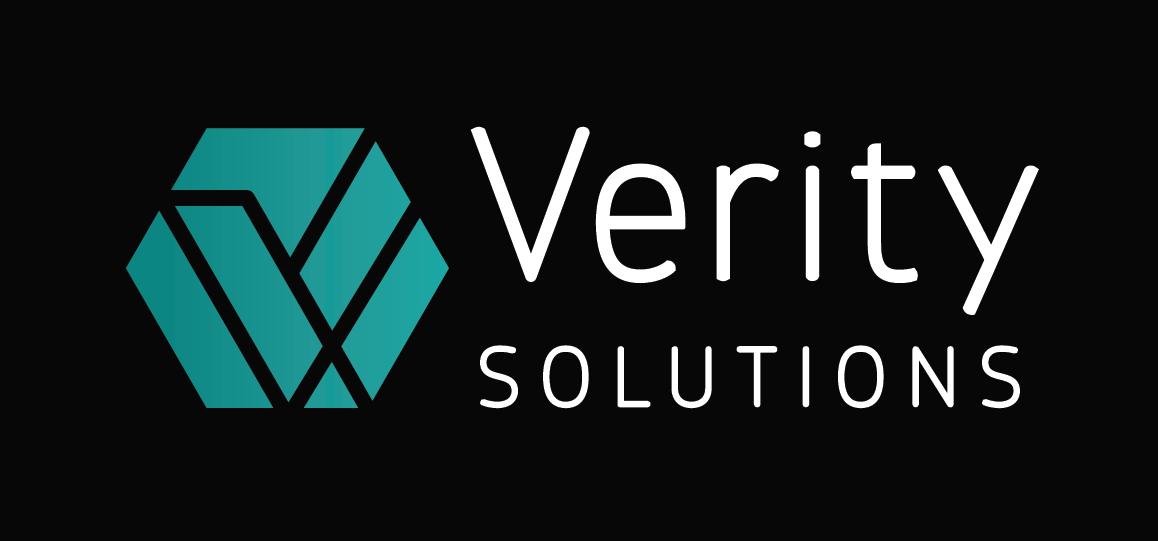
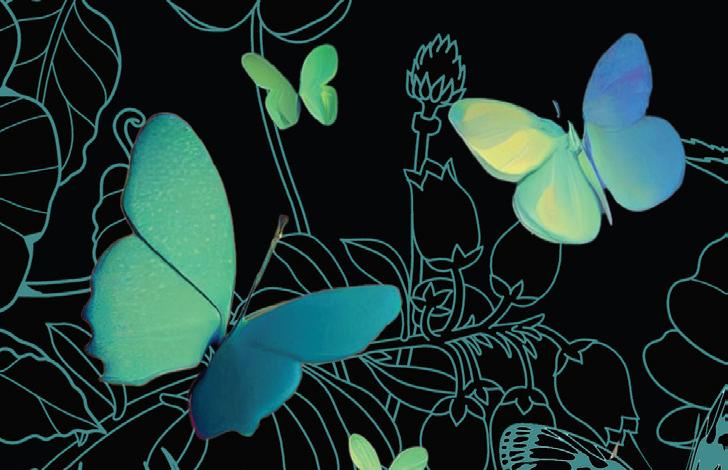
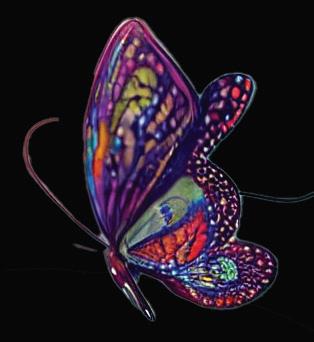
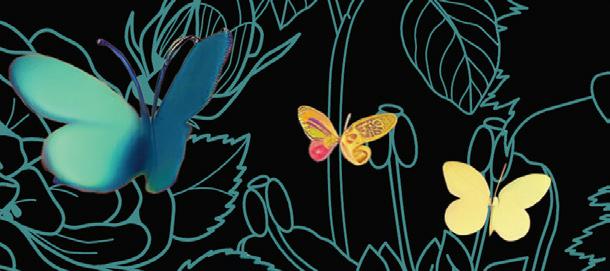
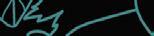
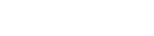
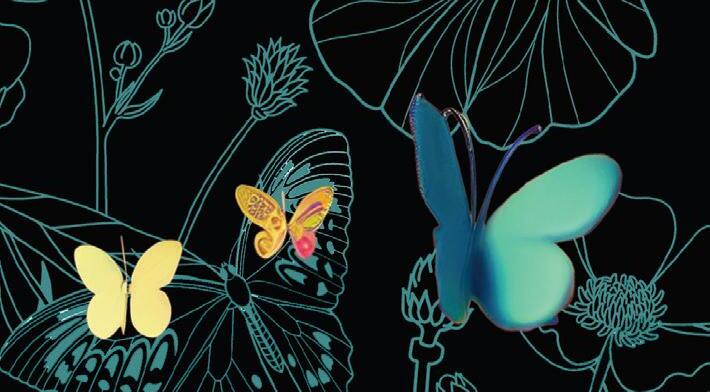


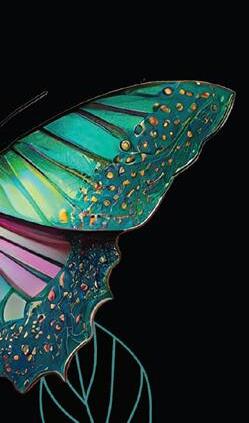
Verity Solutions — Your Invested Partner for 340B
What Sets Verity Solutions Apart?
CEO: George Puckett
Founded: 2015
Employees: 100
Toll-Free Phone: (800) 581-1378
Phone: (425) 947-1922
Address: 12131 113th Avenue NE, #200 Kirkland, WA 98034
Website: www.verity340b.com
Company Background
Verity Solutions is a leader in 340B program administration. Recognized as Best in KLAS: 340B Management Systems for five years, our mission is to make every aspect of 340B program management clear and easy to understand. We believe in optimizing program benefits through predictable automation and outstanding support so that every customer can maximize their savings. We partner with integrated healthcare systems, acute-care hospitals, community health centers, federally qualified health centers, pharmacies, and other 340B-eligible covered entities throughout the U.S. who rely on Verity 340B® software and services to successfully manage their 340B program.
Product Overview
Our powerful V340B® cloud-based software platform provides comprehensive solutions for split billing, contract pharmacy, specialty contract pharmacy, compliance management, purchase analytics, and pharmacy network management (VHUB®). Our innovative new product, VERISAVE™, automatically selects the best blended priced products available for your complete order before it is submitted, reducing tedious manual processes and dramatically decreasing your drug spend.
Our depth of in-house technical and software development resources and our highly skilled account management team are closely aligned to swiftly adapt as changes arise in the 340B program. We offer:
• Agile Software Platform: Built and deployed with security, performance, scalability, and agility as primary goals. The Verity 340B platform is HITRUST certified, demonstrating robust HIPAA compliance.
• Intuitive Application: Designed with our users in mind, we maintain ongoing feedback and collaboration with our clients. This collaboration steers our continual software and services development.
• Responsive Support: Designated account managers provide focused support, training, audit readiness, and regular business reviews to maximize your 340B program success and help you maintain compliance.
We continually invest in our technology and people to ensure 340B program success for our clients. With increasing 340B regulatory complexity and demand for audit preparedness, it’s more important than ever to have the right solution for your 340B program management — and the right partner.
n Highlights
• Industry leading core functionality of our V340B platform with optional, patent-pending add-on modules to enhance all aspects of 340B operations in challenging and unique environments.
• Rapid 120-day average implementation time frame for both split billing and contract pharmacy solutions upon receipt of compliant dataset.
• Access to your own unique 340B program test environment — before and after implementation. Test environment runs continually in parallel to your live system.
• Easy and exportable reporting functionality including detailed data for manufacturer audits, HRSA audits, and UDS reporting.
• New — Advanced Reporting Insights gives users rich data visualization, interactive reports, and performance trends to help drive strategic change.
• Transition from one electronic medical record (EMR) to another without downtime (contingent upon receipt of dispense file from the covered entity).
• Multiple vendor support with controlled substances ordering system (CSOS) — efficiently place orders with both EDI (electronic data interchange) and non-EDI vendors.
• Two-week sprint release cycles ensure timely software updates driven by customer feedback, regulatory changes, and user needs.
• Flexible and “winners only” contract pharmacy pricing models. No true-ups.
• Verity Care Card Program — directly pass 340B savings to uninsured and underinsured patients.
• Referral capture opt-in functionality to compliantly add meaningful savings lift to your 340B program.
• Responsive customer service provided by our in-house staff and the ability to submit and track issues in our online customer portal.
• 80% of our customer support cases resolve within two hours, and 95% within 24 hours.
Partner with us to simplify 340B administration, confidently optimize federal pricing benefits, and benefit from the dedication and knowledge of our expert team.
Leiters. We Are Compounding Health™
Leiters is a trusted FDA-registered 503B outsourcing provider of compounded sterile preparations committed to providing healthcare professionals and their patients with the highest-quality medications.
Additional Information
President & CEO: Joseph Cosgrove
Founded: 1926
Employees: 350
Toll-Free Phone: (800) 292-6772
Phone: (720) 697-5140
Fax: (408) 288-8252
Address: 13796 Compark Boulevard, Englewood, CO 80112
Website: www.leiters.com
Company Background
Leiters, founded in 1926, is an FDA-registered 503B outsourcing provider of high-quality compounded sterile preparations and pharmacy services. Leiters has a long history of evolving and innovating to meet the latest regulatory requirements and market needs.
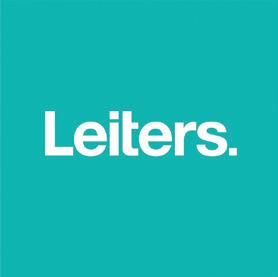
All sterile preparations are produced under Section 503B of the FD&C Act (503B Guidance), follow current good manufacturing practices (cGMP), and USP <797>. The Leiters facility consistently upholds all standards based on the audits conducted by the FDA, the states of California and Florida Boards of Pharmacy, multiple health systems, group purchasing organizations, and other independent accreditation organizations.
The Leiters team of experts in sterile pharmaceutical manufacturing, repackaging, and compounding provide a sophisticated understanding of what it takes to elevate the quality and consistency of supply in pharmaceutical outsourcing. Leiters combines a highly experienced team, with robust processes, in a state-of-the-art outsourcing facility to ensure delivery of the highest-quality products and services.
Product Overview
Leiters provides ready-to-use compounded sterile preparations and pharmacy services across the continuum of healthcare, including hospitals, surgery centers, physician offices, and clinics.
n Hospital Products
• Prefilled syringes, I.V. bags, and vials.
• PCA (patient-controlled analgesia) prefilled syringes.
• Surgical Pain Services portfolio including opioid free medications.
n Ophthalmology Products
• Prefilled syringes, vials, and dropper bottles including: injections, antibiotics, dilating agents, and topical anesthetics.
• FDA-Compliant† Repackaged Avastin® Service.
n ON-Q* Pump Fill Service
• Pharmacy fill service for the Avanos Medical opioid sparing ON-Q* Pain Relief System.
• Prefill pump services offered for both Bupivacaine HCl and Ropivacaine HCl.
We combine our team, robust processes, and state-of-the-art outsourcing facility to ensure the highest-quality medications for healthcare professionals and their patients. Through three key pillars: people, place, and product, we are elevating the standards in pharmaceutical outsourcing.
Key Business Partners
Leiters is partnered with many market leading innovative healthcare companies that compliment what we do. The products and services offered by these companies may provide additional value to your organization. Our business partners include: Avanos Medical, Besse Medical, Bluesight, Cardinal Health, End Drug Shortages Alliance, Eye Connect International, Prodigy Health, and The Academy.
Trade Shows/Meetings Attended
Leiters supports and attends various regional and national industry trade shows and conferences. Please visit www.leiters.com to view a list of 2023 events we will attend.
GPO Affiliations
Leiters provides its products and services to many leading health systems, community hospitals, clinics, and physician offices. In addition, we currently have national contracts with: AmerisourceBergen, Captis, Cardinal Health, Healthtrust, Premier, US Retina, and Vizient. Please contact us for additional information regarding our contracts.
Ordering Information
Leiters offers four convenient ways to place your order.
1. Toll-Free Phone: (800) 292-6772
2. Fax: (408) 288-8252
3. Email: orders@leiters.com
4. Visit the Leiters Online Ordering Portal: orders.leiters.com
Site Visits
We don’t want to simply tell you about what we do, we want to show you! We invite you to visit our facility to better understand the cGMP regulations, sterile manufacturing processes, and automation we use to elevate the quality of our products and services. Come join the growing list of organizations who have visited our facilities. To schedule a site visit or learn more about how Leiters is Compounding Health™, please visit www.leiters.com.
COMPOUNDING HEALTH™ is a registered trademark of Leiters. Avastin® is a registered trademark of Genentech, Inc. ON-Q* is a registered trademark of Avanos Medical, Inc., or its affiliates. 1BUD is from date compounded. † Mixing, Diluting, or Repackaging Biological Products Outside the Scope of an Approved Biologics License Application Guidance for Industry https://www.fda.gov/downloads/drugs/guidances/ucm434176.pdf
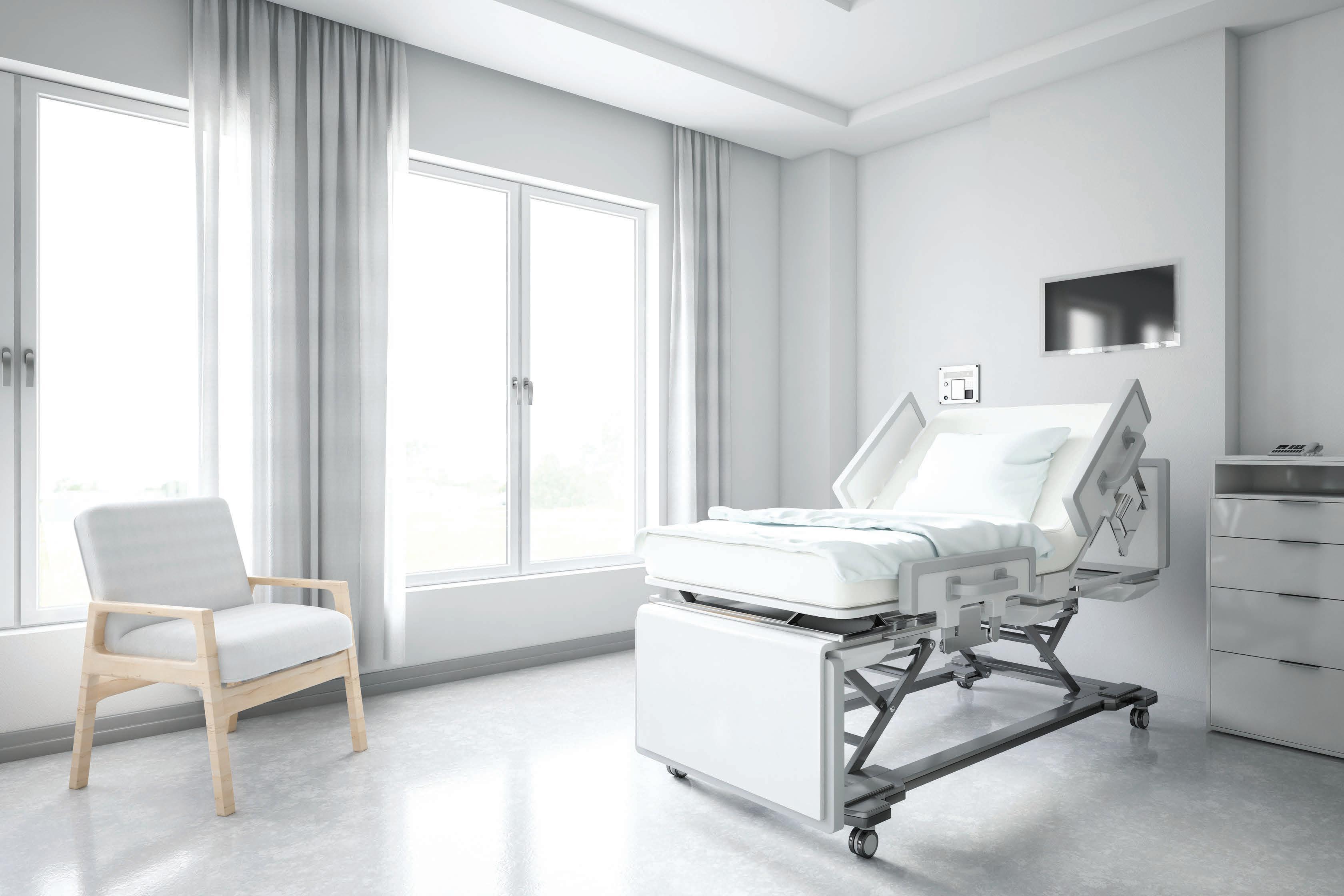
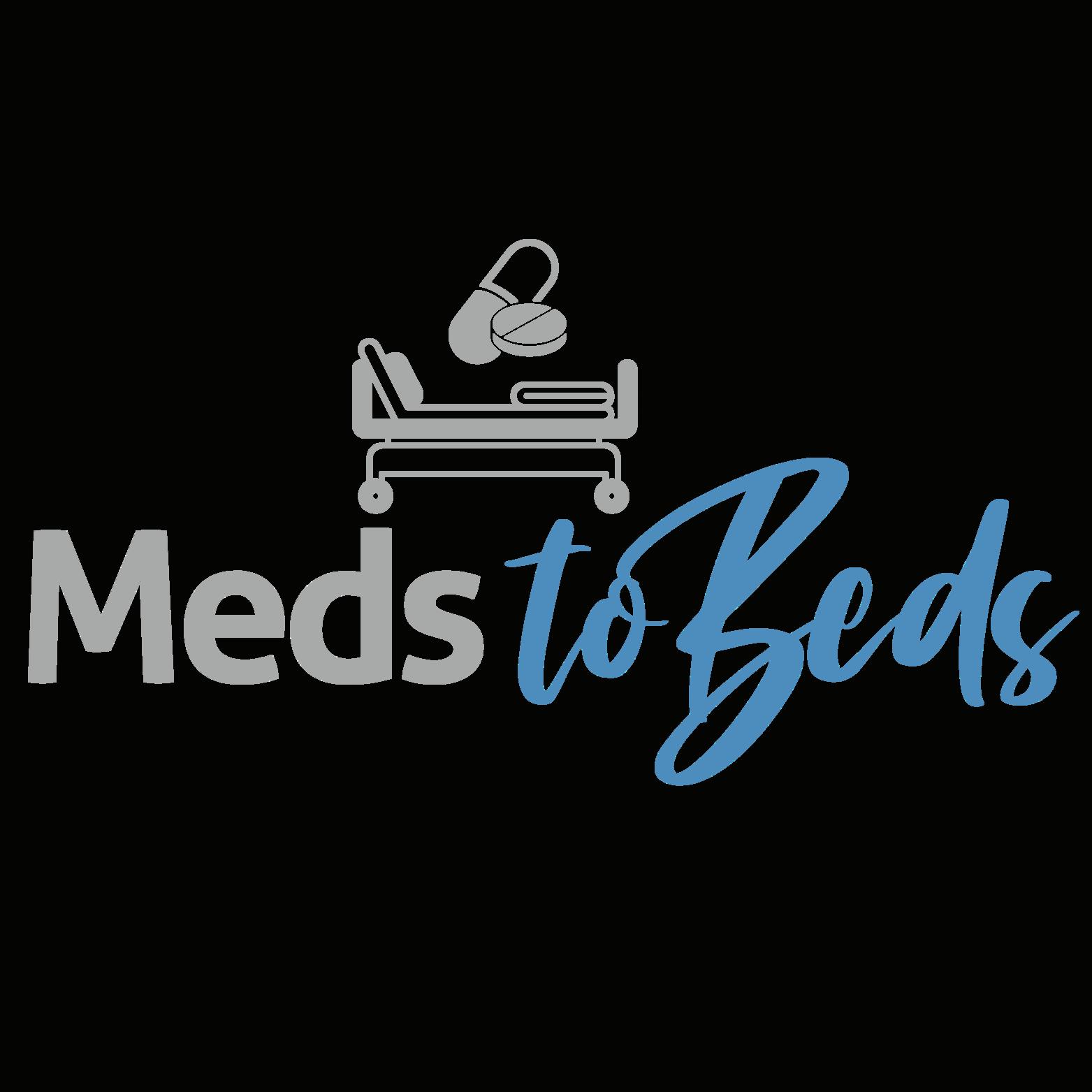



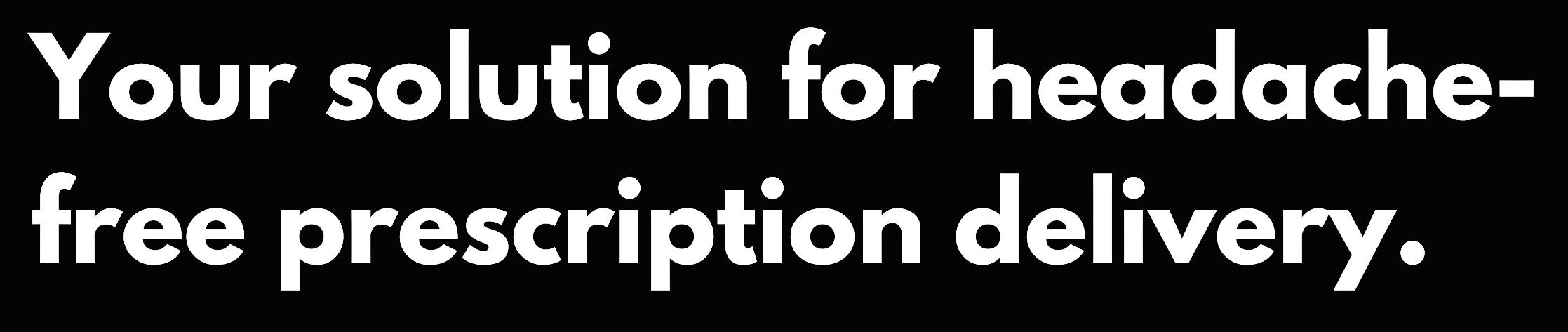
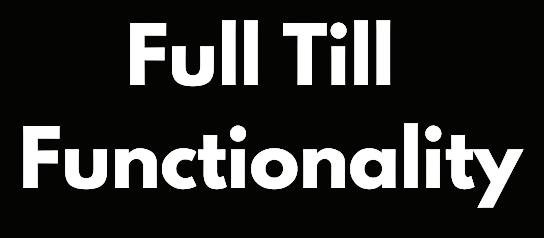
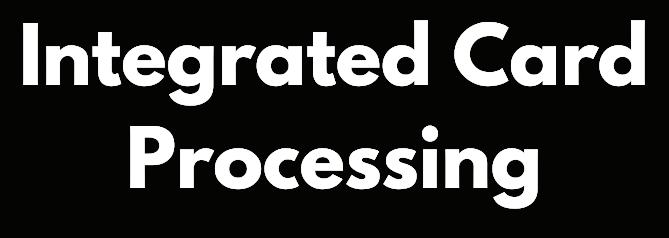
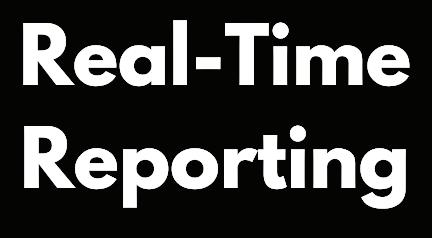
A Meds-to-Beds Program That Really Works From Retail Management Solutions
President & CEO: Brad Jones
Founded: 1998
Toll-Free Phone: (877) 767-1060
Phone: (360) 438-8276
Fax: (360) 438-8284
Address: 4315 6th Avenue SE, Lacey, WA 98503
Website: www.rm-solutions.com
Company Background
Retail Management Solutions was founded in 1998 with a mission to help pharmacies understand and use technology-based tools to run more profitable and customer-centric businesses. Today, RMS continues to prioritize technology innovation and strives to offer the most comprehensive point-of-sale solutions in the retail and outpatient pharmacy markets. RMS pioneered the first pharmacy management system integrations and proudly supports integrations with 30+ systems at no additional cost. RMS also created the very first meds-to-beds solution and continues to lead the industry in meds-to-beds technology.
Product Overview
RMS’ holistic approach is comprised of four major components: software, hardware, training, and support. Each component plays an important role.
n Software: RMS’ software solutions are comprehensive, scalable, flexible, and easy to use. RMS’ software programs and their 30+ pharmacy system integrations go beyond the basics of what you might expect from a POS system. RMS empowers their users to work with the partners of their choosing and build a system that is tailored to their needs. There are a number of software capabilities built to help pharmacies grow profits and improve customer-centricity.
• Meds-to-Beds by RMS: Leverage full transaction processing capabilities at the patients’ bedside. Scan prescriptions and OTC’s, capture electronic signatures, and process payments in real time.
• RMS + UPS WorldShip: A fully integrated feature that allows streamlined preparation and processing of mail-order transactions.
• WillCall by RMS: Saves time and your wallet by using built-in functionality to batch multiple prescriptions into a single bag. Scan a single barcode at checkout for faster transactions and no forgotten prescriptions.
• RMS Delivery: Simplify management of the home delivery process. This essential service is streamlined with easy transaction prep and offline electronic signature capture.
• NutriButler by RMS: Integrates supplement recommendations based on drug-induced nutrient depletions right into the transaction, making it easy to help improve patient outcomes and increase supplement sales.
• Centralized Management & Multi-Store: Enterprise-level, multilocation software can link any number of locations together for centralized management of products, customers, employees, and more.
• Payment Solutions: Flexible payment processing solutions include FSA, NFC, and standard end-to-end encryption as well as tokenization for compliant card-not-present transactions. Validated point-to-point encrypted solutions are also available.
• Customer Loyalty: A fully integrated module that aids in strengthening customer relationships, including advanced promotion and rewards options that you can customize to suit your needs. Easily support charitable giving through any RMS’ system, strengthening your ties with the community you serve.
• Inventory Management: For pharmacies managing retail departments, these solutions open the door for advanced management of front-end products. Wholesaler interfaces allow automated price updates and a streamlined purchasing and receiving process. Integrated shelf labels keep your shelf prices and system prices in sync. Advanced product reporting can help you reduce overhead costs by identifying products that aren’t selling, enabling you to take a more agile approach to the products you carry and make the most of your retail space.
A host of additional reports, both canned and customizable, are also available; from cash management to employee performance, A/R balances, and more. RMS systems give you the data you need to drive important decisions and run a more profitable and efficient pharmacy.
n Hardware: RMS’ flexible hardware options mean that there’s a solution for every scenario. Transactions can be processed in many different ways to meet the unique needs of your pharmacy. Whether you need standard retail lanes, an option for drive-thru payments and signatures, meds-tobeds hardware, curbside pickup solutions, or an easy way to track home deliveries, you can mix and match to create the perfect modern technology scheme. RMS works with your IT team to ensure the right infrastructure is in place to support your pharmacy and organization.
n Training: RMS’ Training Programs are tailored to the needs of your pharmacy. In addition to product training and expert implementation, customers can choose one of our outcome-focused approaches. RMS Boost focuses on ways to make your pharmacy more profitable, and the RMS Care training program puts an emphasis on customer-centricity. If you’re not sure where you’re at, the RMS CLIMB Checkup will help you evaluate and create a roadmap to reach your goals.
n Support
Every RMS customer has access to their 24-seven support line staffed by a team of U.S.-based technical specialists.
Ordering Information
To learn more about RMS and to schedule a free demo today, please visit www.rm-solutions.com or call (877) 767-1060.
Take the industry’s most powerful point-of-sale system directly to your patients with full till functionality that can be used in the pharmacy, bedside, curbside, and more.
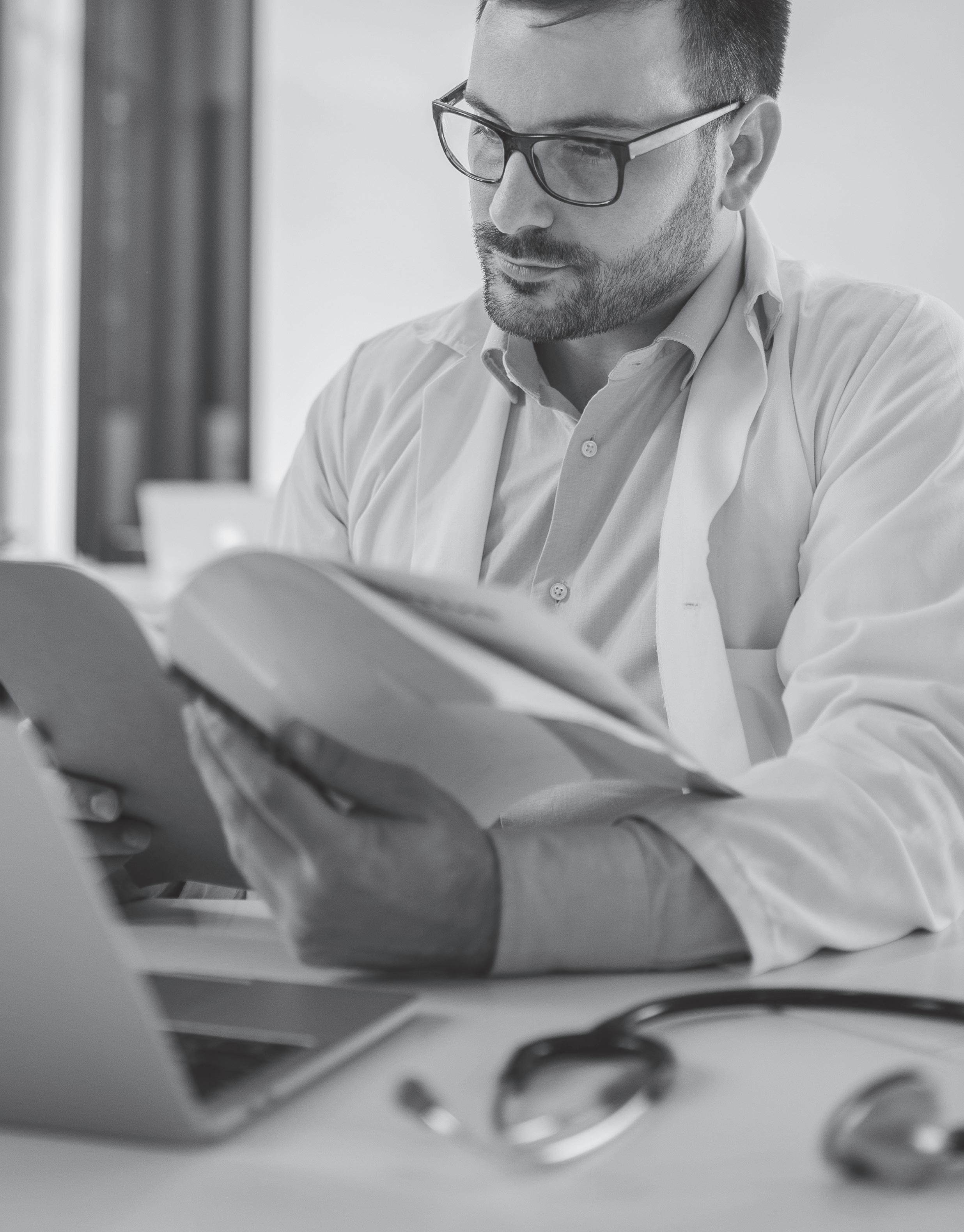
Simplifi+
Streamline Compounding and Medication
Compliance with Simplifi+
AUTHOR: Wolters Kluwer
SUBJECT: Compounding & Medication
Compliance
SUMMARY: Simplifying the complexities by building software that incorporates not only the minimum regulatory standards, but also the deep domain expertise from our industry, to guide completion of standardized workflows and competencies that deliver consistent compliance habits, excellent outcomes, and peace of mind.
Infirmary Health
Mobile Infirmary Pilots Innovative Concentrated Norepinephrine Vials
AUTHOR: Leiters
SUBJECT: FDA-registered 503B Outsourcing Provider | Concentrated Vials
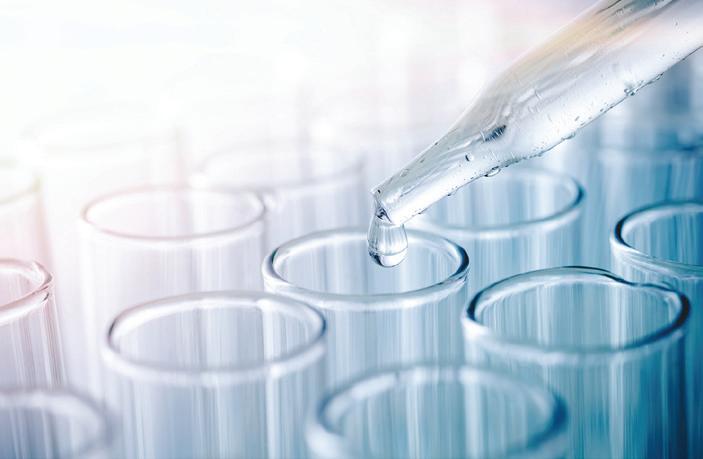
SUMMARY: Mobile Infirmary - Infirmary Health’s flagship hospital’s participation in a workflow study for new concentrated vials.
Holzer Health System
Strategic Partnerships Drive Inpatient and Outpatient Pharmacy Performance
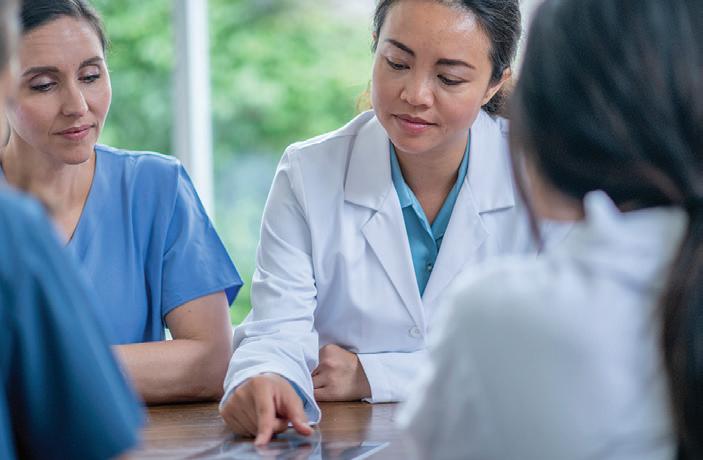
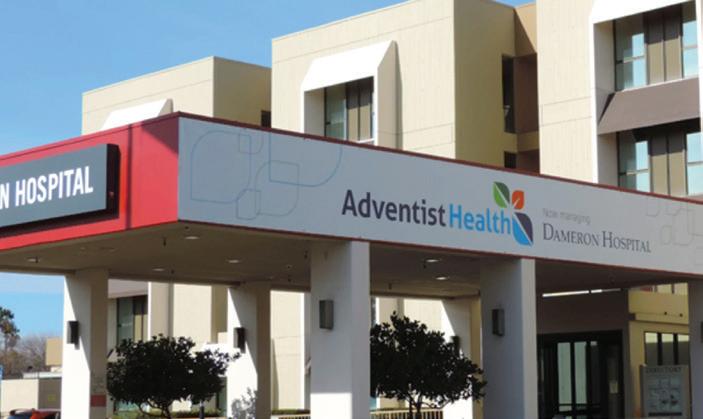
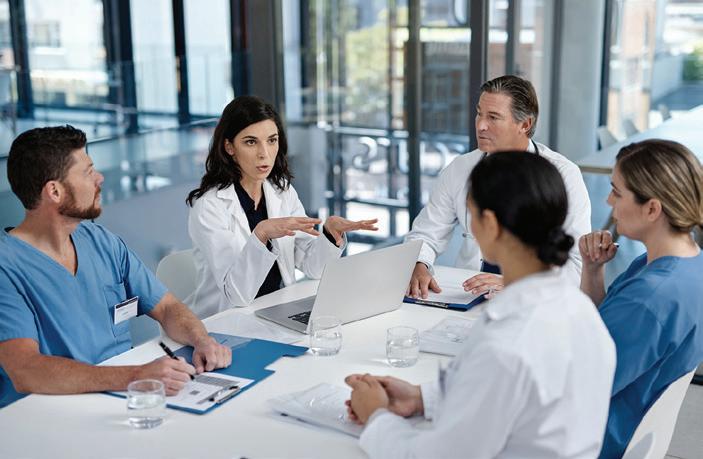
AUTHOR: CPS
SUBJECT: Inpatient and Specialty Pharmacy Management
SUMMARY: Over a 20+ year relationship, CPS has consistently driven value for Holzer through initiatives supporting clinical performance, cost savings, and operational expertise.
Dameron Hospital
Dameron Hospital’s Data-Driven Temperature Monitoring Strategy
AUTHOR: Rees Scientific
SUBJECT: Environmental Temperature Monitoring
SUMMARY: Various regulatory bodies and accreditation agencies — such as the FDA, CDC, WHO, USP, and more — have requirements and guidelines for monitoring the temperatures of medication and vaccines. Dameron decided to automate its temperature monitoring protocols to streamline processes.
Medacist Defying Drug Diversion
AUTHOR: Medacist
SUBJECT: Drug Diversion
SUMMARY: The Pharmacy Executive, Nurse Executive, and Drug Diversion Analyst tell how: through insights, challenges within nursing departments, and analytics when managing a drug diversion program.
HealthPoint
HealthPoint Chooses Liberty Software to Empower the Pharmacy Team
AUTHOR: Liberty Software
SUBJECT: High-profile Upgrade — Pharmacy Management Software
SUMMARY: Robust dispensing software is about accuracy, efficiency, productivity, compliance, safety, and adaptability to meet ever-changing business and compliance needs. Healthpoint wanted a low-touch system to support the delivery of high-touch pharmacy-based services for patients.
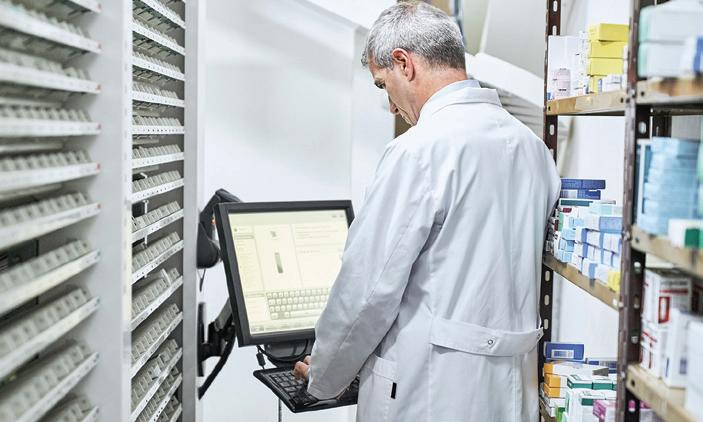
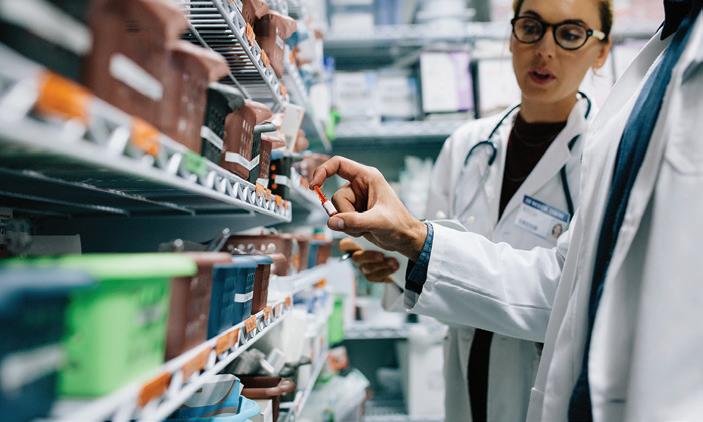
GX Solutions Medical-grade Cold Storage
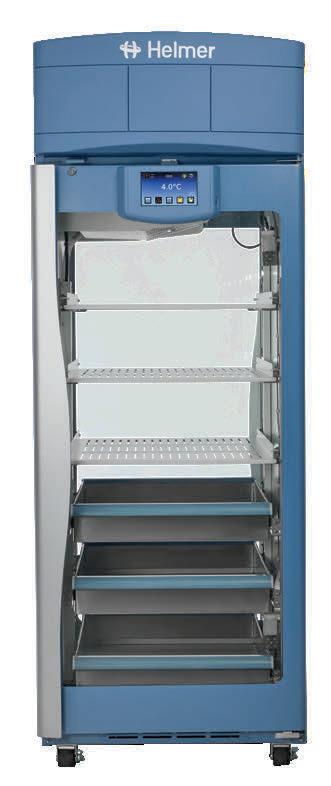
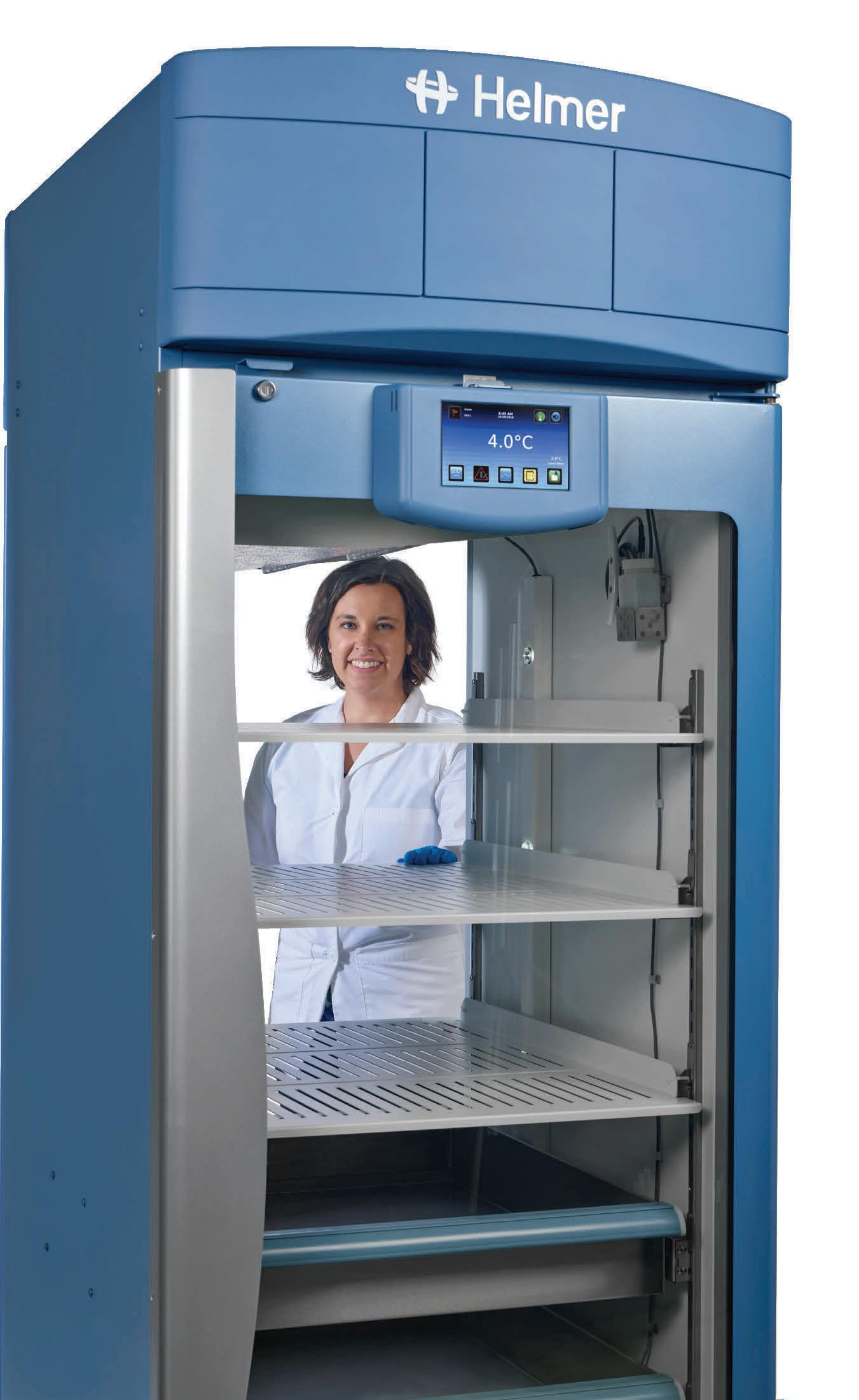
Pass-thru Refrigerators
Workflow efficiency and regulatory compliance for specialty pharmacies

Entry from both sides of the unit for more convenient access to stored products and enhanced work flows
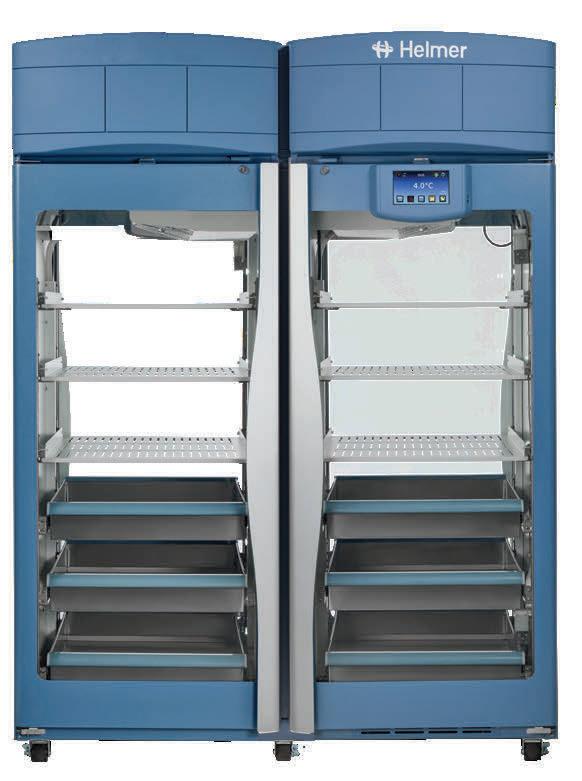
Exclusive i.Lock™ interlock door technology available to meet USP <797> clean room recommendations
Best-in-class temperature management of uniformity, stability, and recovery with use of VCCs and HC refrigerants
i.Series® technology supports URAC and ACHC Specialty Pharmacy Accreditation requirements

Extensive heavy-use testing to provide optimal temperature performance in real-world settings
Learn More helmerinc.com/gx-solutions
Support for USP <797> Compliance From Helmer Scientific
Helmer products and services provide features, technology, and performance aligned to updated USP standards, including updated USP <797>.
President: Bruce King
VP Sales & Marketing: Lori Gabrek
Founded: 1977
Employees: 500
Toll-Free Phone: (800) 743-5637
Address: 14400 Bergen Boulevard Noblesville, IN 46060
Website: www.helmerinc.com
Company Background
Helmer Scientific is a U.S.-based manufacturer and worldwide distributor of medical-grade cold storage and laboratory processing equipment. We have over 45 years of experience in providing high-quality temperature-controlled environments, with our products used in more than 125 countries. Precise temperature performance and control are essential to the successful storage of pharmaceuticals, and Helmer cold storage products are designed and developed with these considerations.
Product Overview
Updates to USP <797> become fully enforceable on November 1, 2023. USP <797> provides updated guidance related to sterile compounding practices. Products and services from Helmer Scientific can help support USP <797> compliance.
n Gx Solutions Pass-Thru Refrigerators
Pass-thru equipment is commonly used in USP <797> validated clean rooms. Pass-thru chambers and refrigerators provide efficient workflows that allow cleanrooms to be stocked without direct access. Limiting cleanroom access reduces the risk of contamination. It also reduces the time and materials required for garbing.
The updated USP <797> chapter requires that if a pass-thru chamber is in use the cleanroom and anteroom doors never be opened simultaneously. USP recommends the use of interlock technology to support this requirement. The GX Solutions PassThru Refrigerator from Helmer Scientific is available with i.Lock™ interlock technology which prevents cabinet doors from being opened simultaneously, supporting USP <797> standards.
Along with interlocking doors, GX Solutions Pass-Thru Refrigerators are equipped with the i.C3® Advanced Information Center which provides comprehensive temperature performance data and intelligent diagnostic information directly from the unit. Additionally, detailed event logs related to system alarms and the i.Act™ Event Acknowledgment function capture corrective actions, including signatures and completion dates.
As with all GX Solutions products from Helmer, the GX Solution Pass-Thru Refrigerator utilizes OptiCool™ cooling technology which delivers world class temperature performance as well as reduced noise output and reduced energy consumption compared to traditional medical-grade cold storage equipment.
OptiCool™ technology pairs a variable capacity compressor (VCC) and natural hydrocarbon (HC) refrigerants to deliver temperature uniformity, stability, and recovery while also reducing greenhouse gas emissions. GX Solutions Cold Storage Equipment can reduce global warming potential up to 99% per unit, compared to traditional medical-grade cold storage.
n Controlled Room Temperature Cabinets
Helmer Controlled Room Temperature (CRT) Cabinets can be used in USP <797> environments to store medications that required controlled storage between 20°C and 25°C.
CRTs may also support updated testing and sampling requirements outlined in USP <797>. Glove testing, media-fill testing, active air sampling, and surface sampling all require incubation at CRT temperatures for between five and seven days.
Ordering Information
Contact a Helmer Scientific sales representative at sales@helmerinc.com.
MOBILE PHARMACY COMPOUNDING CLEANROOMS
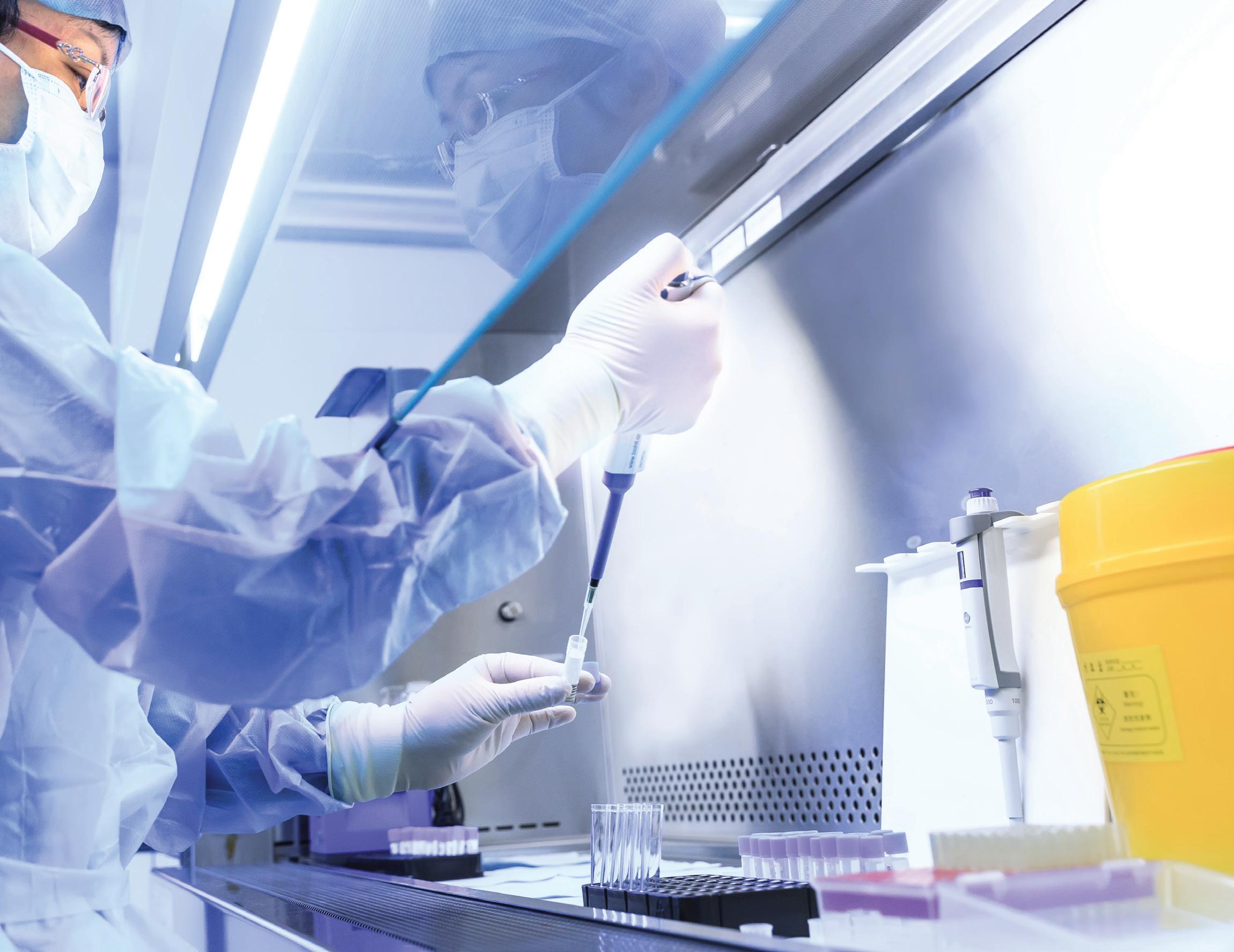
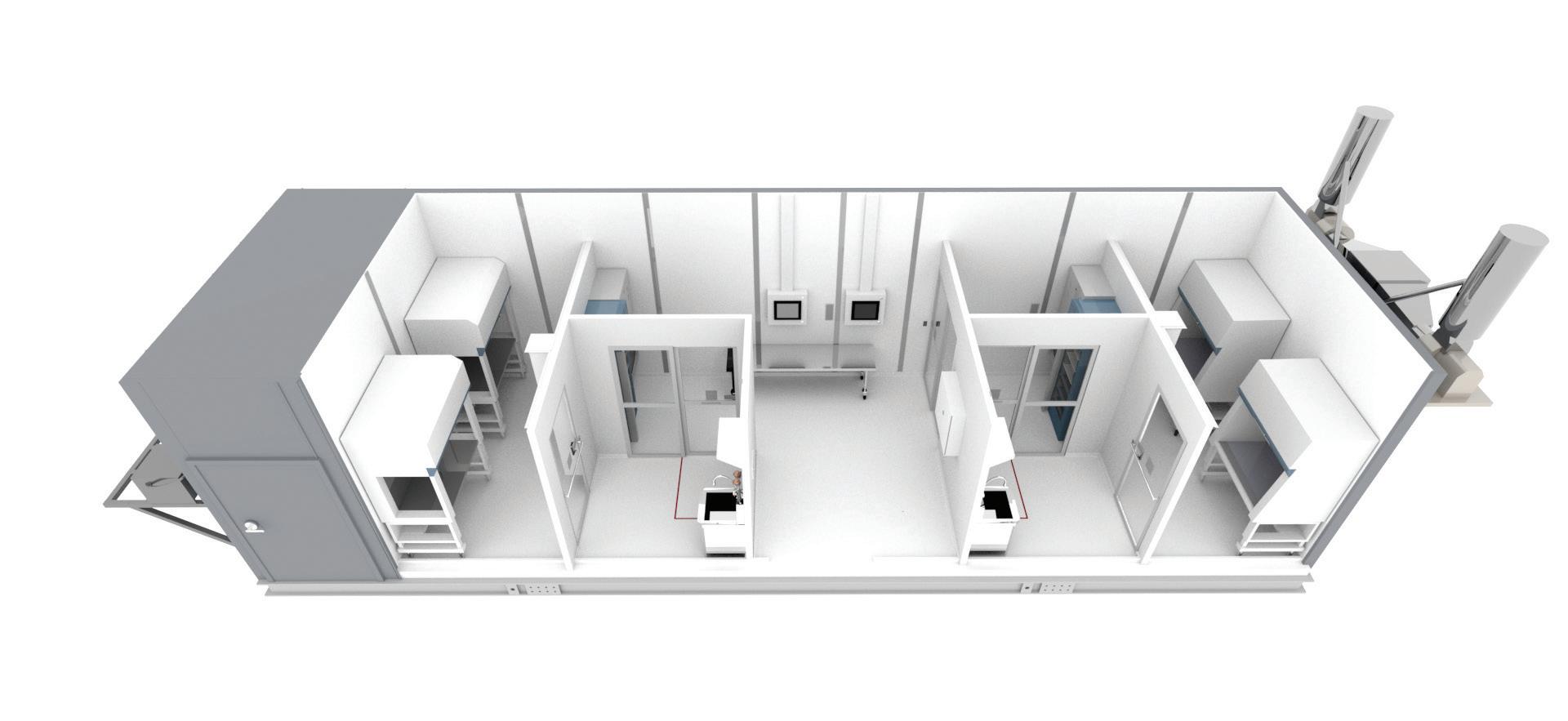
Whether you are planning a cleanroom renovation or building a new cleanroom, Modular Devices’ mobile cleanrooms provides an expedited option that combines a modular and prefabricated approach by delivering a ready-to-use, turnkey cleanroom that only requires utility connections upon being delivered. Our pharmacy compounding cleanrooms are available to rent or purchase! Experience unmatched quality, state-of-the-art materials and equipment, and a cleanroom that will not only exceed your expectations but USP 797/800 as well!
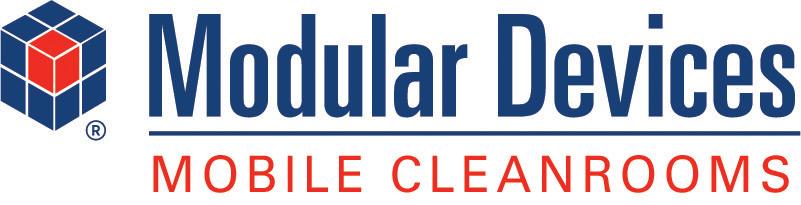
» Meets and Exceeds USP 797/800
» Hands-Free Interlocked Doors
» Continuous Data Logging and Monitoring
» 14' Wide x 48' Long
» Includes 4' BSC’s and 4' LFH’s
» Includes Dedicated Refrigerators
» HEPA Filtered Interlocked Passthroughs
» Hands-Free Scrub Sinks
» Dedicated Haz and Non-Haz Gowning Rooms
» USP 800 Negative Pressure Unpack / Storage Room
» Hands-Free Flush Mount Intercoms
» Guaranteed Environmental Control Anywhere in U.S.
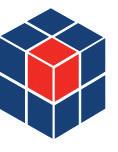
» Large Fleet and Nationwide Coverage
» Guaranteed Certification
Mobile Pharmacy Compounding Cleanrooms by Modular Devices
Premanufactured mobile cleanrooms are available in a fraction of the time compared to traditional design/build projects. Fully engineered turn-key mobile cleanrooms designed to provide immediate compliance for USP 797/800. Rent one today as an interim solution, or purchase one as your new permanent, state-of-the-art cleanroom. We make compliance as simple as a phone call.
Product Specifications
President & CEO: Greg Mink
Founded: 1987
Toll-Free Phone: (800) 456-3369
Phone: (317) 489-4616
Address: 1515 Brookville Crossing Way Indianapolis, IN 46239
Website: www.portable-cleanroom.com
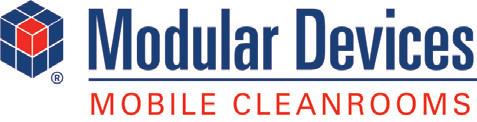
Company Background
Modular Devices is based in Indianapolis, Indiana and offers short and long-term mobile cleanroom solutions for any industry or application that requires controlled environments throughout the U.S. and North America. Every cleanroom that we offer meets our high-quality standard commitment, has the most state-of-the-art materials and equipment, and includes unmatched customer service. We have all the required expertise under one roof. This includes architects, engineers, construction disciplines, and cleanroom experts that can guide you through the entire project.
As the race continues to become compliant with USP 797 and USP 800, our primary focus as a company is to provide solutions for our clients by solving problems. We are a company that puts your needs first, and that takes care of the many complexities of building a compliant cleanroom so that you can focus on what is most important to you, your patients and staff!
Product Overview
We offer high-quality, cost-effective mobile cleanroom solutions which are pre-engineered and pre-built, then delivered as turnkey compounding cleanrooms ready for use immediately upon delivery. Compared to traditional design/build, our mobile cleanrooms can be built in a fraction of the time as we control the entire production at our facility — eliminating delays and wasted capital, and providing immediate compliance and peace of mind.
What sets MDI/CRD Mobile Pharmacy Cleanrooms apart?
• Pre-certified prior to delivery and guaranteed to pass third-party inspection.
• 14' wide mobile cleanrooms, up to 40% larger than 8' wide trailers.
• Short or long-term rentals, or as permanent additions.
• Cloud-based control and monitoring system with real-time data-logging and alarms.
n Safety
• All rooms have hands-free interlocking doors with red and green light indicators to ensure the integrity of differential pressures.
• USP compliant hazardous unpack/storage room, dedicated gowning rooms, HEPA filtered pass-throughs, and gowning room sinks deep enough for fingertip to elbow scrubbing.
n Productivity
• Our mobile cleanrooms are 14' wide, 6' wider with over 40% more space than other mobile cleanroom trailers (on wheels). This provides a much more functional environment for personnel and workflow.
• Each compounding room comes equipped with two 4' wide biosafety cabinets and/or two 4' wide laminar flow hoods.
n Flexibility
• Two standard size mobile pharmacy cleanroom products.
• Single purpose: Either USP 797 or USP 800.
• Dual-purpose: Larger size engineered for USP 797 and USP 800.
• Turnkey building and HVAC systems designed and engineered to be placed in locations anywhere in the U.S.
• Custom HEPA-filtered pass-through designs include single- and double-door, through-the-wall pass-throughs, cart pass-throughs, and pharmacists’ checking pass-throughs.
n Security
• Real-time data-logging and alarming for out-of-range temperatures, humidity, and pressures.
• Video recording systems and fire protection systems included.
Testimonial
“Thank you for the excellent service Modular Devices has provided to us for the temporary pharmacy compounding cleanrooms for the Staten Island University Hospital Campus. Upon delivery the NYS Board of Pharmacy conducted an inspection and approved the unit for operation in the capacity of compounding both hazardous and traditional I.V. solutions for patients. The unit surpassed our expectations and was able to maintain the high-volume production necessary during the recent COVID-19 outbreak.”
— Otto VonEilbergh, Director — Capital Projects, Corporate Facilities Services, Northwell Health
Ordering Information
To learn how our mobile cleanrooms can assist with your pharmacy upgrade or expansion, or to help meet new USP 797 or USP 800 standards, contact us by phone at (317) 489-4616 or visit our website for a free quote, www.portable-cleanroom.com.
Preparing for USP <797> MicrobiologyRelated Changes
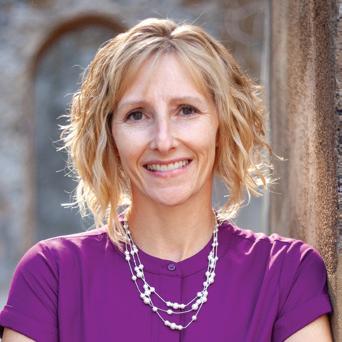
The buzz surrounding the release of USP General Chapter <797> on November 1, 2022, is undeniable, as it should be. We have seen four different possible iterations of the chapter since 2015. This highly anticipated release brings significant changes to sterile compounding operations and facility design, all with the intention of improving patient safety and ensuring patient access to essential medication. Because many of the new requirements will require extensive time to incorporate into policies and procedures, USP has set a one-year implementation date of November 1, 2023.
For those responsible for making changes to policies and standard operating procedures (SOPs), it’s time to get started. We see changes throughout the chapter, making it critical to read and reread the chapter to pick up on some very nuanced differences between the 2008 and 2022 versions. This is especially true with mediafill testing, gloved fingertip testing, and viable sampling, which will affect all sterile compounding organizations. To understand the changes to these microbiology-related tests, we must first review the newly established compounded sterile preparation (CSP) categories.
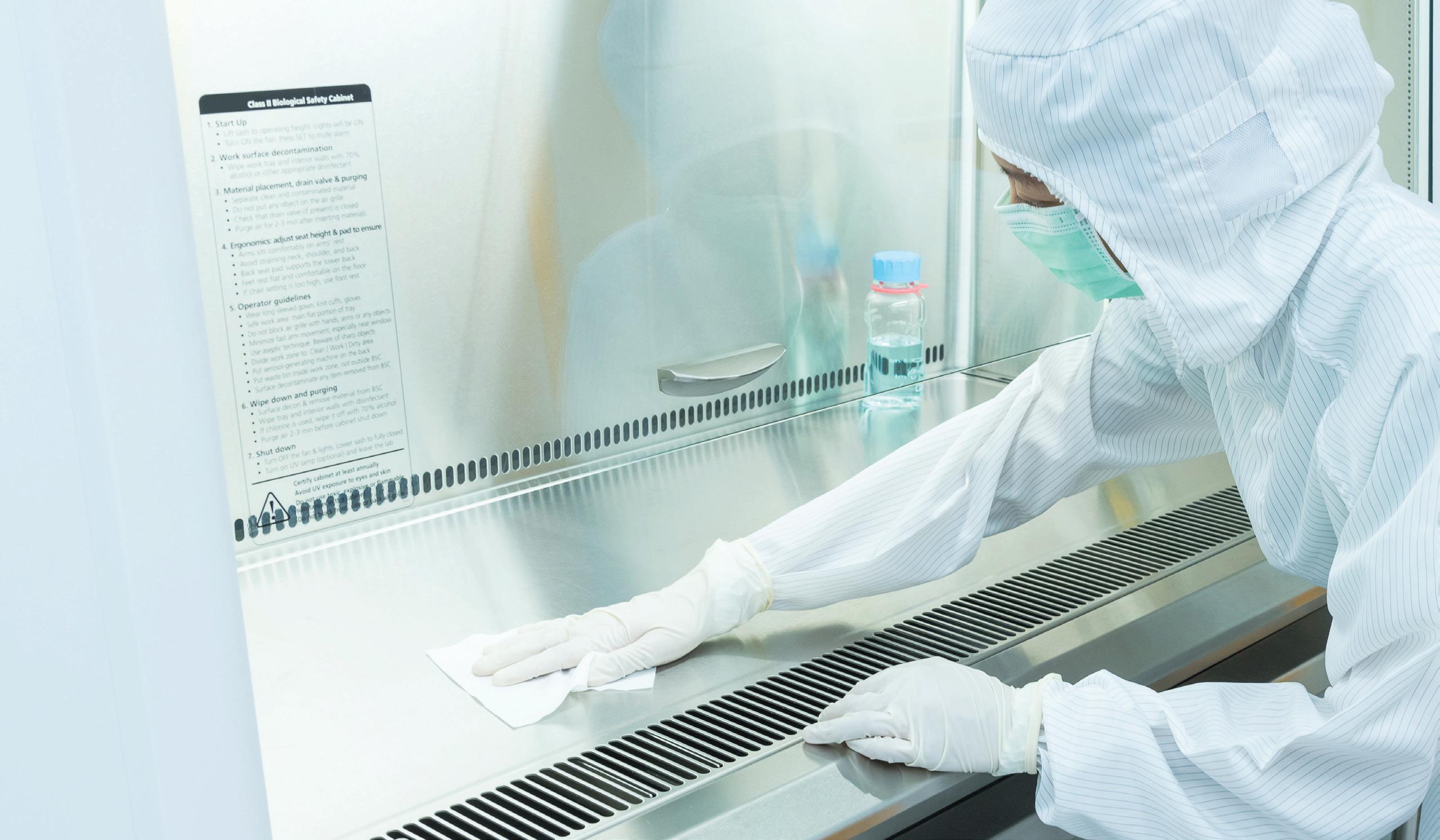
CSP Categories & BUDs
The traditional compounding risk levels of low, medium, and high have become ingrained in daily practice. But with the new chapter, they are replaced with CSP Categories 1, 2, and 3. It is important to note that low, medium, and high risk do not directly correlate with Categories 1, 2, and 3. The new categories are based on where the primary engineering control (PEC) in which a CSP is prepared, is located, and other quality-related elements, not the number or type of components used in the preparation of the sterile medication. Table 1 provides a summary of Category 1, 2, and 3 requirements. Be sure you review Section 14 of USP <797> for the full dating that can be assigned to CSPs. If you have a compounding aseptic isolator (CAI) or compounding aseptic containment isolator (CACI) in a segregated compounding area (SCA), you face a major BUD change. You are no longer afforded full dating and the CSPs you prepared are limited to the Category 1 BUDs. Because of this, many are moving away from the use of CAIs and CACIs in their SCAs and replacing them with laminar airflow workbenches (LAFWs) and biological safety cabinets (BSCs).
• Personnel qualification
• Garb
• Cleaning and disinfection
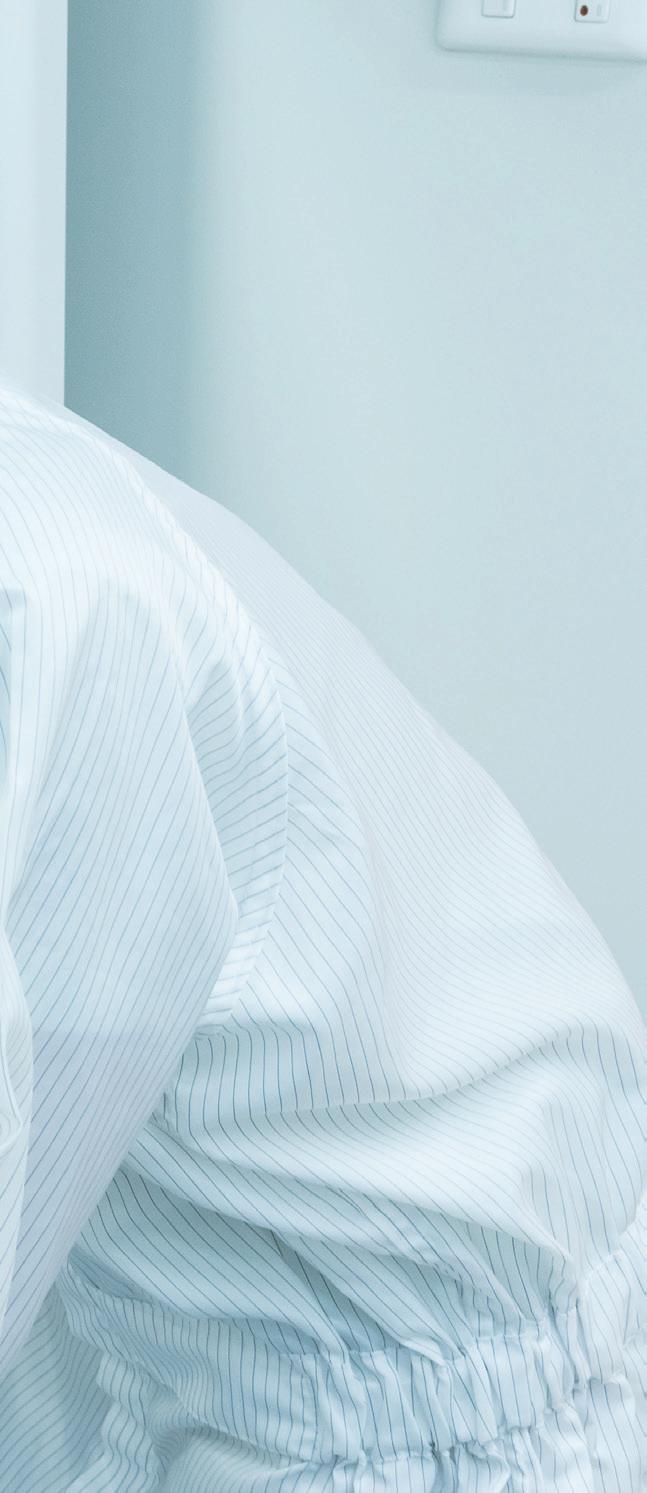
• Viable sampling
• Stability determination
One other requirement, in addition to those listed, is that sterility testing must be performed on all Category 3 CSPs, supplemented with appropriate endotoxin testing. It is also important to note that Category 3 BUDs are limited to those indicated in the chapter and cannot be extended further, even with stability data.
Media-Fill & Gloved Fingertip Testing
There are numerous changes related to media-fill and gloved fingertip testing (GFT) and the related competencies. The garbing and hand hygiene competency includes visual observation and GFT. Perform GFT after garbing to confirm staff can don sterile gloves without contaminating them. We also see changes to the aseptic manipulation competency where a surface sample must be collected from the work surface of the direct compounding area (DCA) after the completion of the media-fill test but before the area is cleaned and disinfected. In the event the surface sample exceeds the action level, the growth must be identified to the genus level. Identification is not required for microorganisms recovered on GFT or the media-fill test.
For the initial garbing and hand hygiene competency, it must be performed three times initially, and the staff member tested must pass consecutively. For example, if the individual passed the first two gloved fingertip tests and failed the last one, they would have to do three more tests and pass all three. For the aseptic manipulation competency, the number of replicates or total number media-fill units prepared is not defined by the chapter and the sterile compounding facility is left to decide. Figure 1 defines the required aspects of each competency.
Table1. CSP Category General Requirements and BUDs1
Upon review of the chapter, the longer Category 3 BUDs may seem appealing, but they come with additional requirements for:
Let’s look at the numbers. For every new staff member that must complete the garbing and hand hygiene and aseptic manipulation competencies, you will minimally need 9 tryptic soy agar (TSA) with lecithin and polysorbate 80 media devices and the designated media-fill components.
Garbing & Hand Hygiene
• 6 TSA With Lecithin and Polysorbate 80 Media Devices for GFT
2
• Media-Fill Test
• 2 TSA With Lecithin and Polysorbate 80 Media Devices for GFT
• 1 TSA With Lecithin and Polysorbate 80 Media Devices for Surface Sampling
For every existing staff member that must complete the garbing and hand hygiene and aseptic manipulation competencies, you will minimally need 5 TSA with lecithin and polysorbate 80 media devices and the designated media-fill components.
• 2 TSA With Lecithin and Polysorbate 80 Media Devices for GFT
• Media-Fill Test
• 2 TSA With Lecithin and Polysorbate 80 Media Devices for GFT
• 1 TSA With Lecithin and Polysorbate 80 Media Devices for Surface Sampling
One of the most impactful changes to sterile compounding operations is the increased frequency of these competencies. Annual training and competency assessments remain; however, the garbing and hand hygiene and aseptic manipulation competencies are required to be completed more frequently than what was required in the 2008 version of the chapter.3 We also see the introduction of a defined competency frequency for those who oversee compounding but do not actually compound. Table 2 defines these frequencies based on the CSP Category an individual compounds or if the individual oversees compounding.
samples at least monthly and surface samples at least weekly. Table 3 defines viable sampling frequencies for all compounding categories. These increased frequencies will likely result in many sterile compounding organizations taking at least surface sampling in-house. If your organization decides to take on the collection of air or surface samples, ensure staff are trained and deemed competent in sampling technique and how to properly execute a sampling session.
•
One other major change is the incubation requirements for GFT and media-fill testing. All samples must be incubated in an incubator. GFT now has a two-stage incubation. The samples are incubated at 30 to 35 °C for at least 48 hours and then transferred to 20 to 25 °C and incubated for at least five days. Media-fill testing incubation is flexible, with the chapter providing two options as seen in Figure 2 (top of next column).
Viable Sampling
There are significant changes to viable air and surface sampling frequencies. Those compounding Category 1 and 2 CSPs are required to perform viable air sampling at least every six months and surface sampling at least monthly. Those that perform Category 3 compounding are required to collect viable air
•
Many organizations have relied on their certification providers to choose sampling locations for them. It is critical that you evaluate your sampling plan and take responsibility for where samples will be collected. You must ensure viable air and surface samples are collected in each ISO classified space. Additionally, surface samples must be collected in the DCA of the PEC and in the pass-throughs. The chapter recommends that surface samples also be collected on equipment located in the PECs, on work areas adjacent to the PECs, and on frequently touched surfaces. Use a risk-based approach to identify viable air and surface sample
Table 2. USP <797> Defined Competency Frequencies Table 3. Viable Sampling Frequencieslocations that will provide valuable data regarding the state of control of the compounding area.
The 2008 version of the chapter required a viable air sample to be collected in the SCA in close proximity to the PEC.3 This is no longer a requirement. However, it is a recommended best practice to collect both a viable air sample and a surface sample within the perimeter of the SCA as a baseline in the event there are exceeded action levels on the samples collected in the PEC. There are no action levels for these samples and they are for information only.
The only media required to be used for sample collection is TSA. If an organization chooses, it can also use fungal media. Surface sample collection devices must contain neutralizers, such as lecithin and polysorbate 80. After collecting a surface sample, it will no longer be acceptable to wipe the surface with sterile 70% IPA. The 2022 version of the chapter will require that the surface be cleaned and disinfected after the sample is collected. The facility’s designated EPA-registered one-step disinfectant cleaner is the best option and if the sample is collected in the PEC, sterile 70% IPA would follow the application of the EPAregistered one-step disinfectant cleaner.
Viable air and surface samples must be incubated in an incubator. Incubation depends on whether one or two samples are collected at each location. Figure 3 defines the specifications for single and dual plate incubation.
Summary
These are just some of the many changes made to media-fill testing, gloved fingertip testing, and viable sampling. It is critical to read and reread the chapter to pick up on all the changes that will affect your operation. In doing so, you will likely find that there are gaps in the chapter, leaving you with more questions than answers. Utilize other industry standards and guidance documents or reach out to industry experts for help. It is also important to have multiple media suppliers, as the sterile compounding industry’s media use is about to skyrocket. Change is here. Be ready.
The 2008 version of the chapter did not define how to count colony forming units (CFU) recovered on dual plate samples.3 The chapter now specifies that the TSA sample and TSA/fungal sample are to be treated as separate samples, all recovered growth counted, and compared to the action level. If one of the samples exceeds the action level, both should be resampled as part of the investigation and confirmation of a return to a state of microbial control.
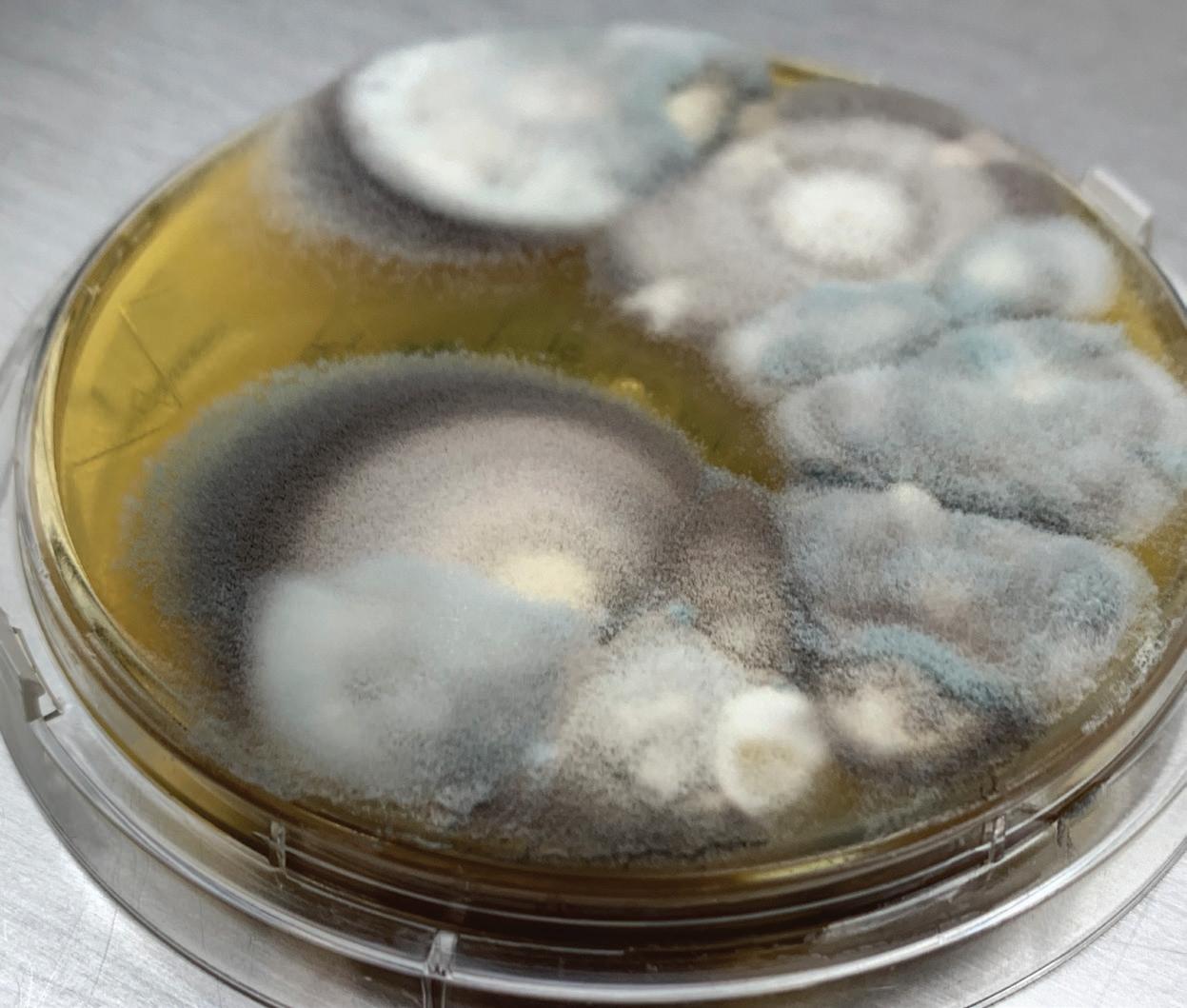
The chapter will no longer require the identification of every CFU recovered. Instead, only samples that exceed the action levels will be required to have each colony type identified to the genus level. Additionally, the term “highly pathogenic organisms” was removed from the chapter, eliminating the need to “immediately remedy” the recovery of coagulase positive staphylococcus, gram negative rods, yeast, and mold.
Resources
USP <1116> Microbiological Control and Monitoring of Aseptic Processing Environments
USP <1117> Microbiological Best Laboratory Practices
CETA CAG-009 Viable Environmental Monitoring for Sterile Compounding Facilities
CETA CAG-011 Gloved Fingertip Testing for Sterile Compounding Personnel
CETA CAG-013 Media Fill Testing for Sterile Compounding Personnel
References
1. United States Pharmacopeial Convention, Inc. <797> Pharmaceutical Compounding — Sterile Preparations. 2022.
2. United States Pharmacopeial Convention, Inc. <797> Pharmaceutical Compounding — Sterile Preparations FAQs. November 1, 2022.
3. United States Pharmacopeial Convention, Inc. <797> Pharmaceutical Compounding — Sterile Preparations. 2008.
4. Roth, A. National Home Infusion Association. Talk Infusion Webinar. Change is Here: Complying with the 2022 Version of USP General Chapter 797. November 9, 2022.
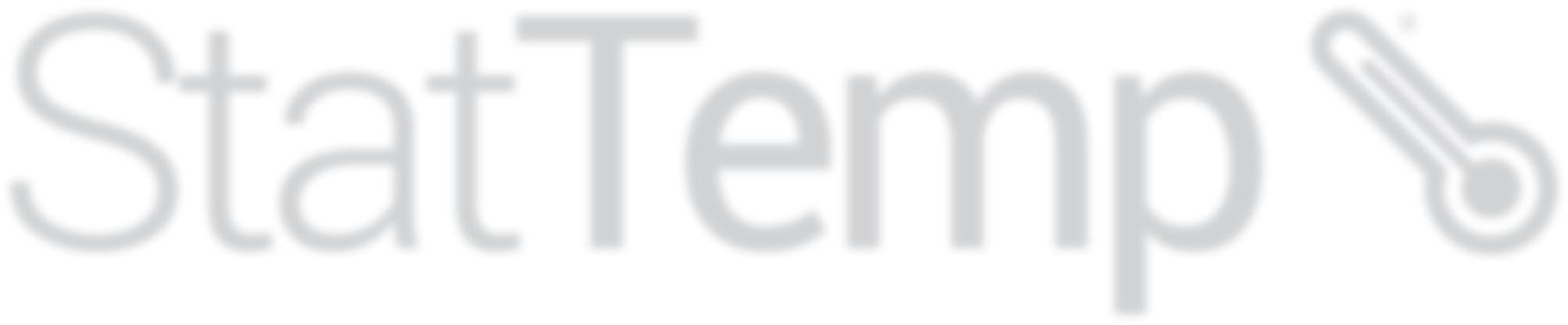
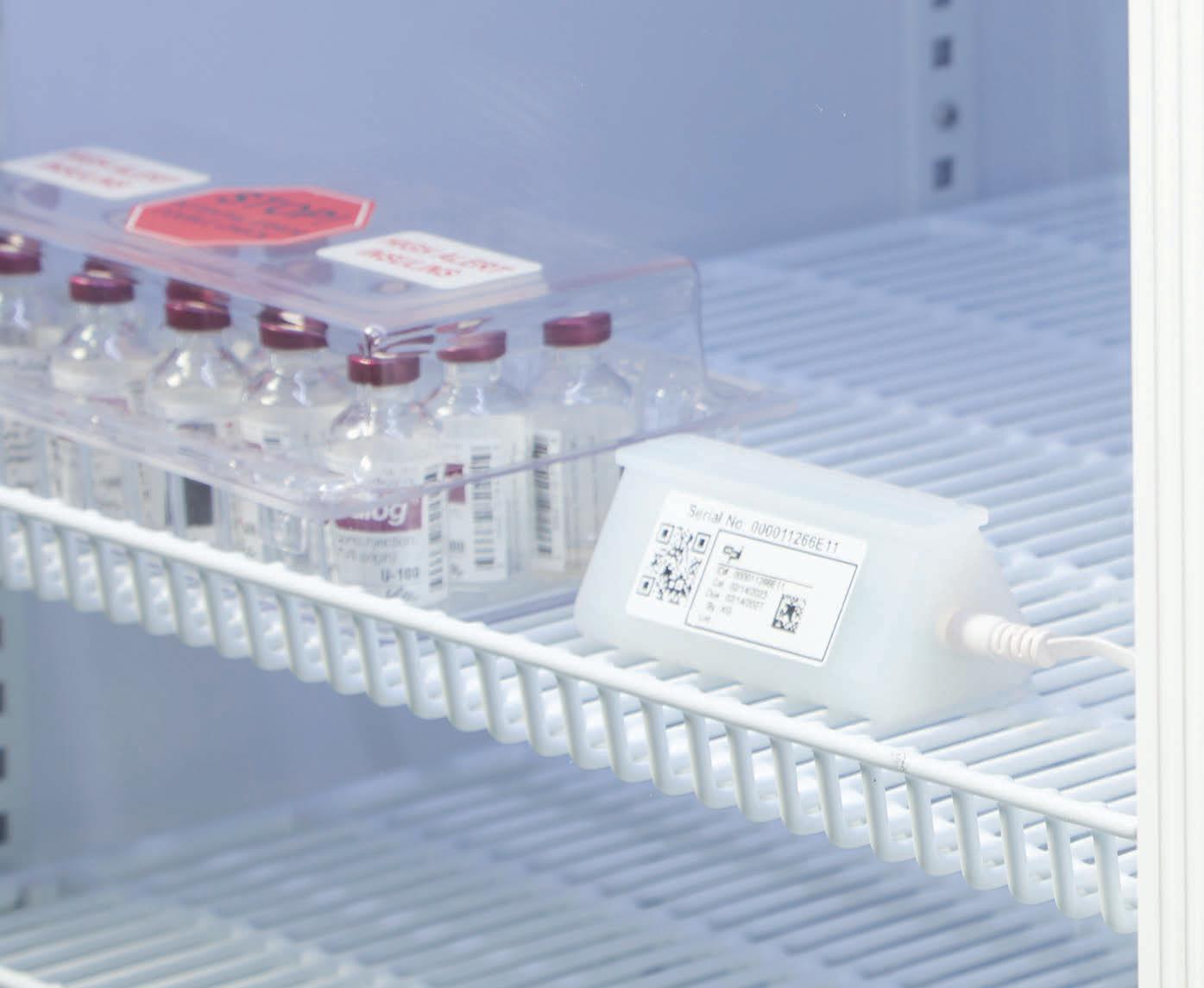
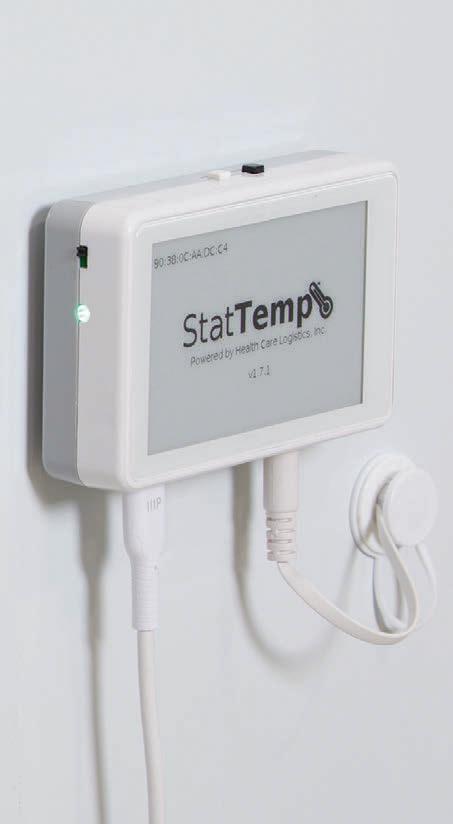
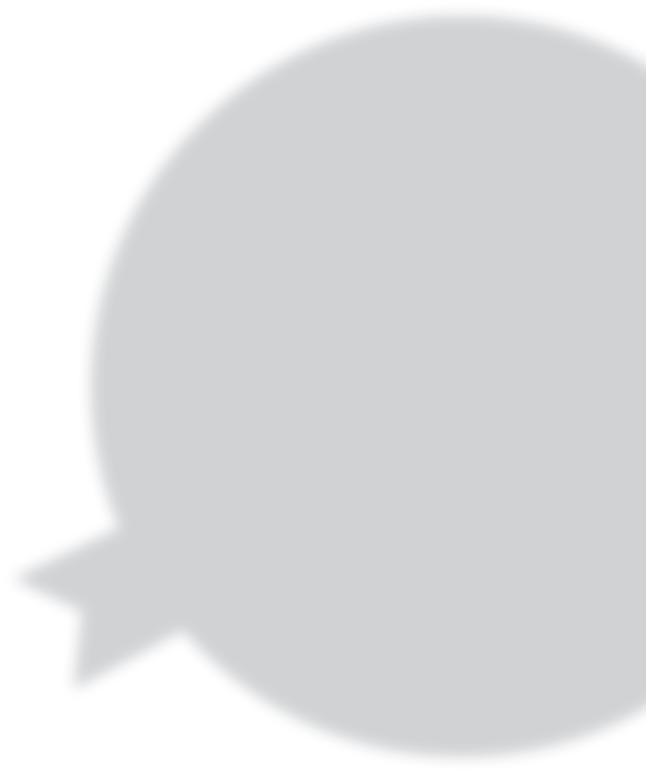
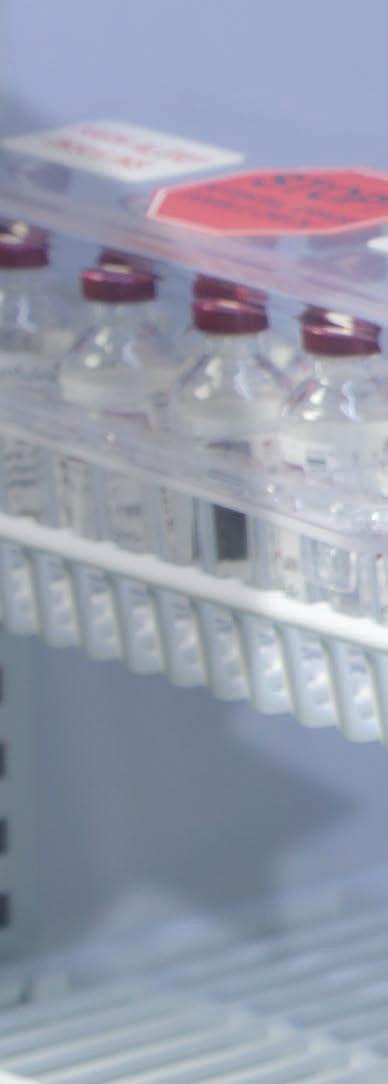
Health Care Logistics® — Ensure Hospital-Wide
Temperature Accuracy With Stat Temp™
Manage safe ranges, avoid drug waste, and provide peace of mind with this remote temperature monitoring system exclusively from Health Care Logistics.
n Metals by Design and Plastics by Design
President & CEO: Gary Sharpe
Founded: 1978
Toll-Free Phone: (800) 848-1633
Phone: (740) 477-3755
Address: P.O. Box 25 Circleville, OH 43113
Website: GoHCL.com
Company Background
Unique and hard-to-find products are the lifeblood of our business. That includes manufactured solutions made by skilled technicians in our central Ohio facilities. By Design is where our manufacturing talent converts customer ideas into highquality cabinet, metal, plastic, or print products made to their exact specifications. Best of all, we deliver those made-to-order solutions in five working days or less.
Product Overview
Our goal is firm — create functional products to improve everyday workflow — there are no limits to our design capabilities. We can turn virtually any idea into reality without outrageous upcharges or extended shipping schedules. Start with a no-obligation, no-cost digital proof for a cabinet, metal, plastic, or print project today!
Product Specifications
n Cabinets by Design
Cabinets, shelving, and storage units for those who want to renovate existing spaces or outfit newly constructed areas with high-quality pieces made to their exact specifications.
The process starts with our free 3D Design Service, which provides a virtual layout of the targeted space paired with unique solutions that showcase specific design goals. We can create performancerich products in multiple sizes, styles, and colors that make it easier than ever to achieve a customized brand.
Cabinets by Design offers the quickest, easiest, and most affordable way to maximize organization and efficiency. All units ship in five working days or less so customers can get the look they want without the wait.
One-of-a-kind items manufactured to match individual customer requests. Modifications to stock products are also available. These allow customers to work more efficiently and produce better results. From stainless steel storage containers, lock boxes, and utility trays to specially sized plastic lock boxes and dividers, we have the engineering and manufacturing capabilities to design and modify products or create affordable replacements that meet the everyday needs of our customers.
We can create and modify functional products using stainless steel, aluminum, acrylic, PETG, polycarbonate, polystyrene, HDPE, and PVC. There are no limits to our design capabilities. Whether customers want to simplify USP compliance or better manage changing trends, we can design a solution and deliver it quickly.
n Printing and Graphics by Design
From labels, magnets, and clings to banners, signs, and stamps, our print specialists can create solutions for any situation. Prevent the confusion that results from the unknown by communicating a consistent message for all products across all departments. Choose the size, color, and style of your message and our print team will create it.
Kicking off a marketing campaign? We can help with an assortment of fun promotional materials. Our print experts can hot stamp a customer logo, message, or facility information on a variety of products. Our process ensures a professional finish with lasting results. We can print as few as 50 or as many as 1,000+ — and quick!
Ordering Information
It’s easy for customers to begin their design journey. Complete a cabinets, metal, or plastics options request form, view our Print By Design options, or call our product specialists at (800) 848-1633 to discuss options.
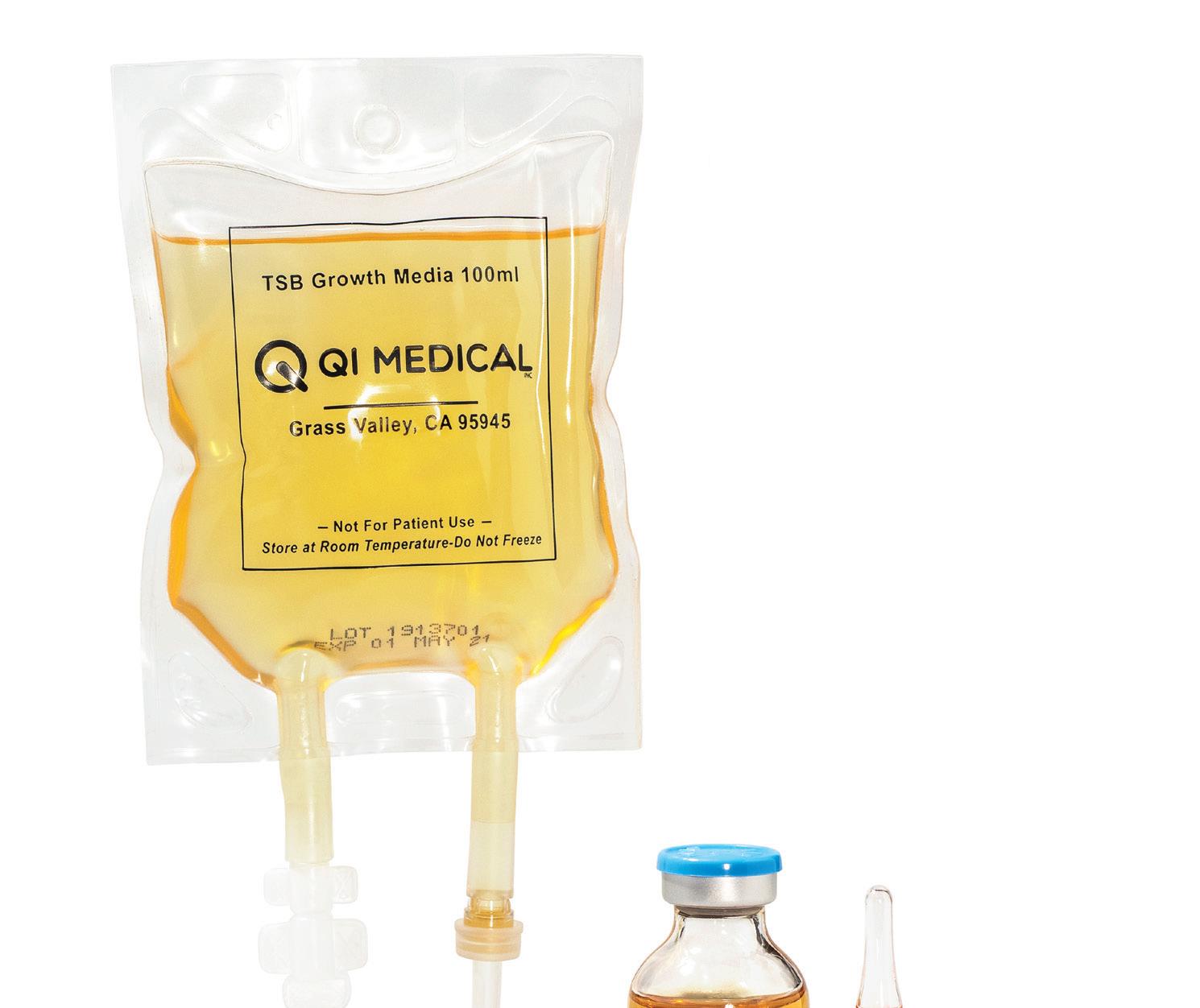

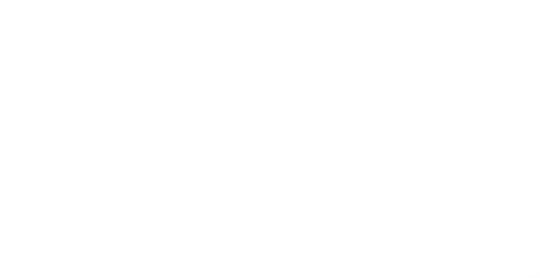
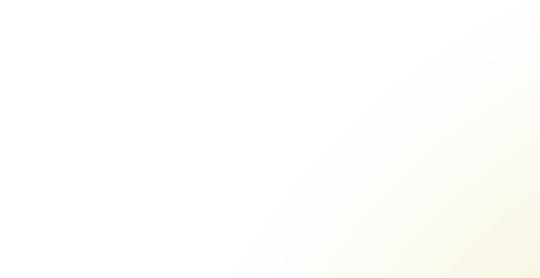
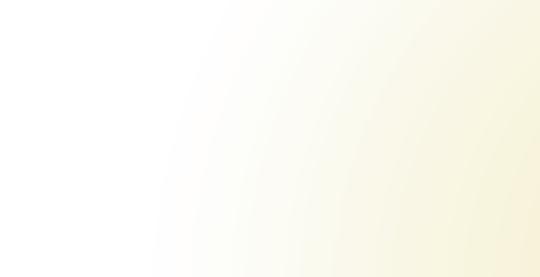
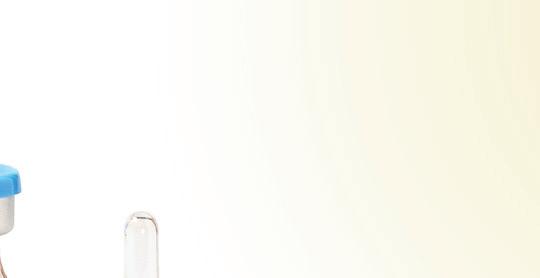
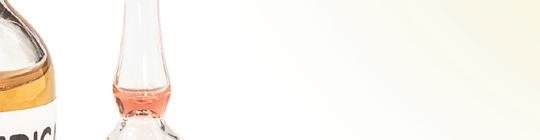
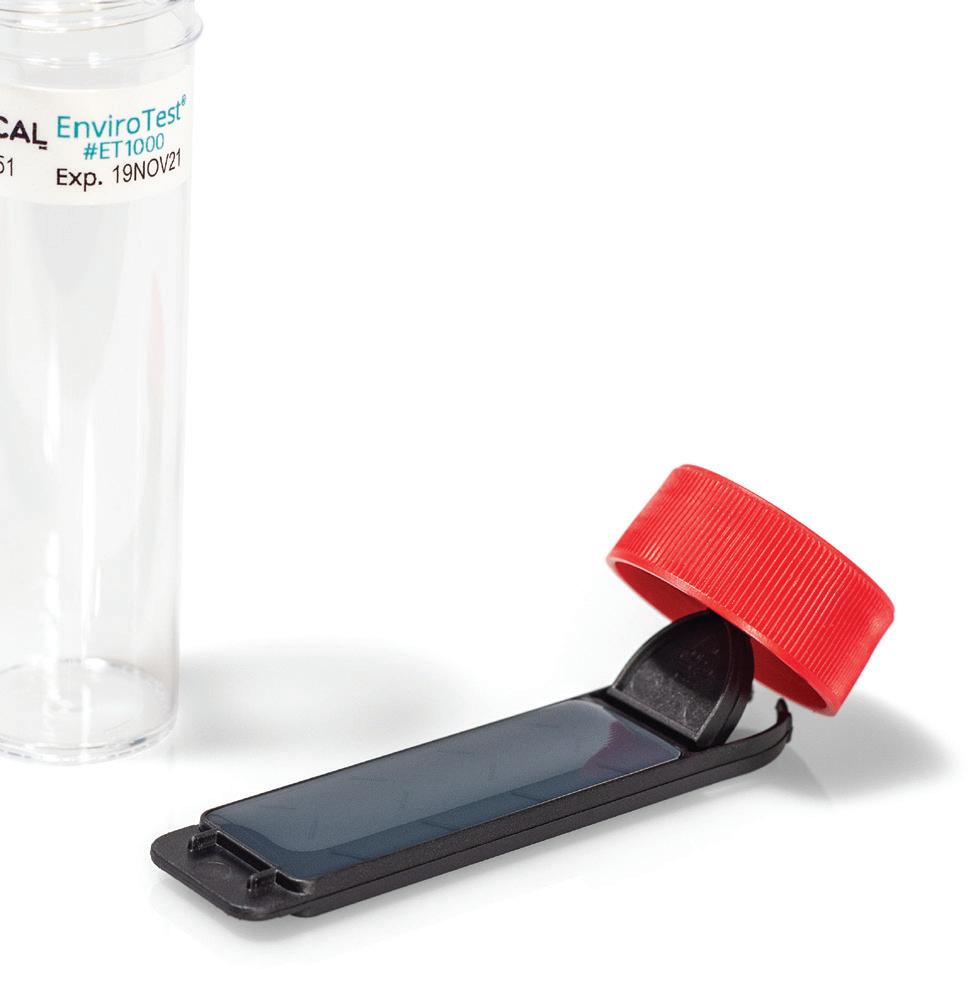
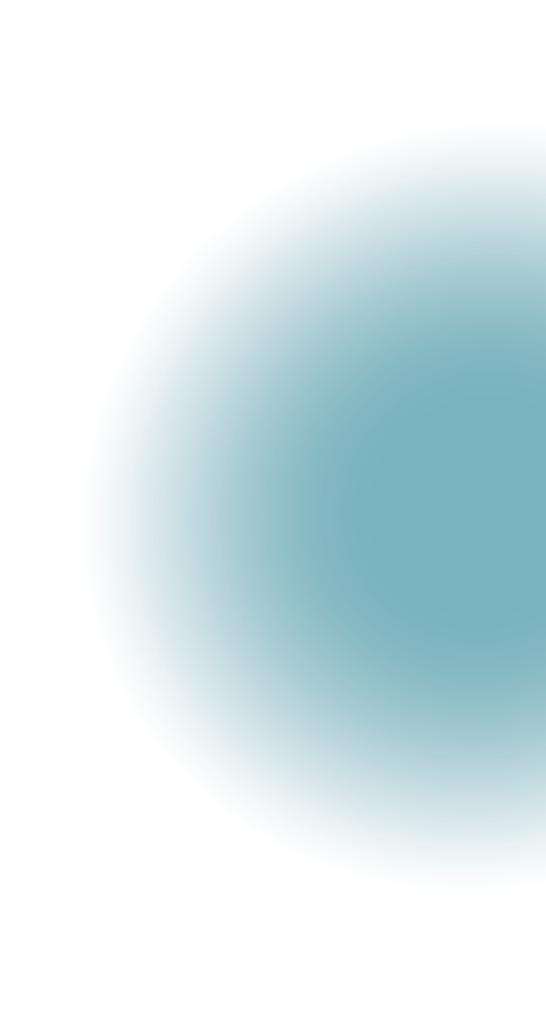
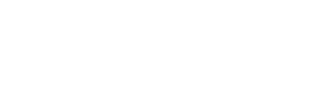
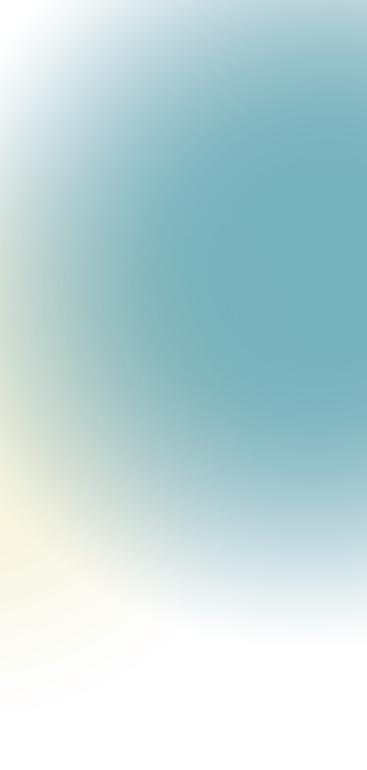
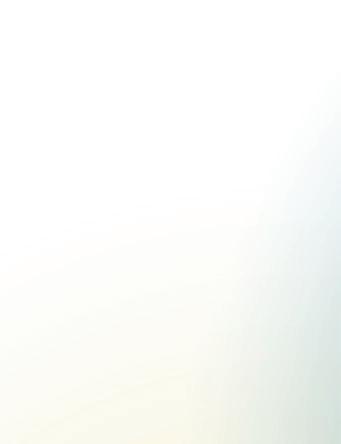
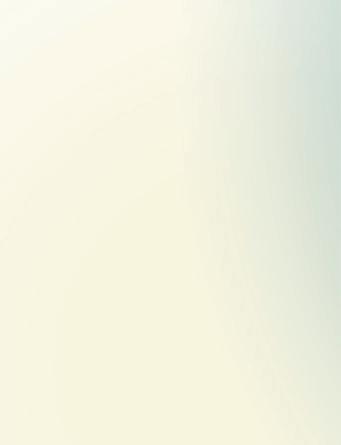
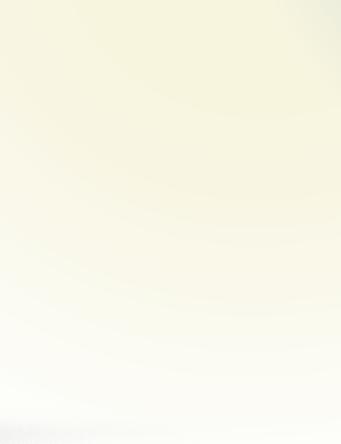
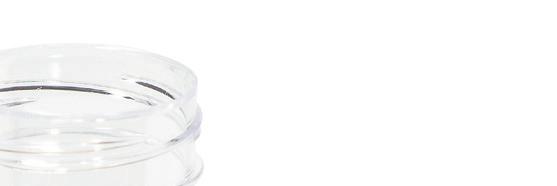
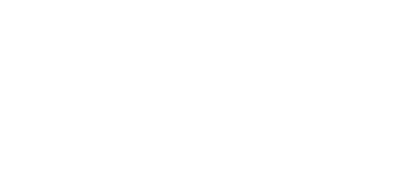
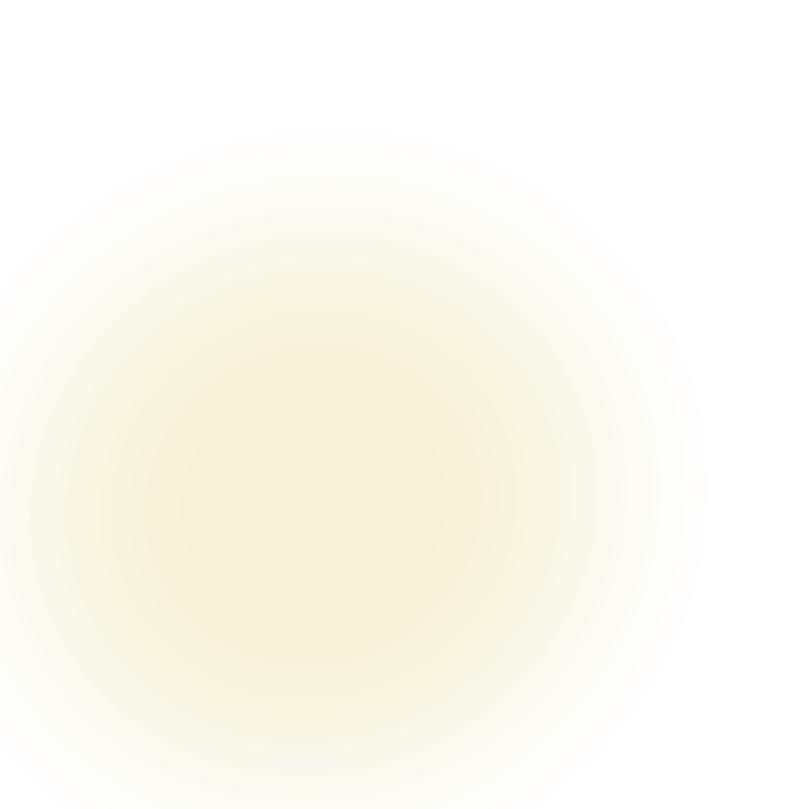
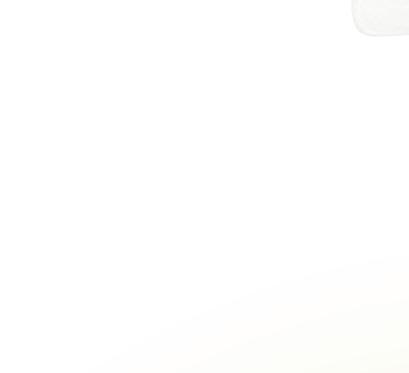
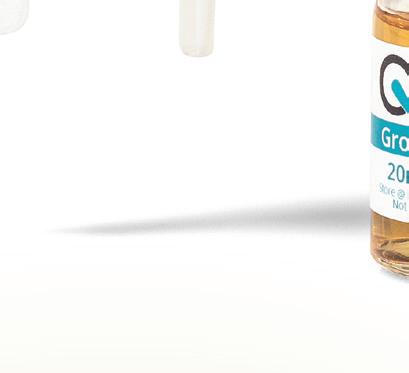
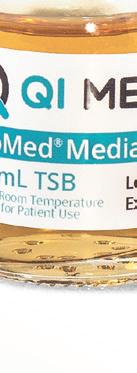
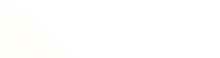
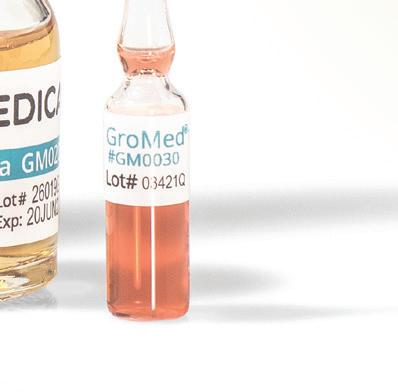
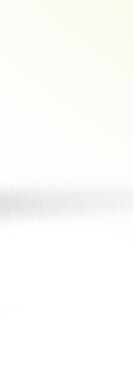
Q.I. Medical, Inc.™ Your Partner in USP <797> Pharmacy Compliance

Providing quality assurance products to hospitals and pharmacies practicing sterile compounding, with a singular focus on pharmacy compliance. Our long-standing regional distribution partners are able to provide exceptional in-person service and training.
Additional Product Lines
President & CEO: Brady K. Schwarz
Founded: 1992
Toll-Free Phone: (800) 837-8361
Phone: (530) 272-8700
Fax: (530) 272-8702
Address: 1415 Whispering Pines Lane, Suite 150 Grass Valley, CA 95945
Website: www.qimedical.com
Company Background
Q.I. Medical, Inc. was founded in 1992 with a focus on providing the sterile compounding industry with testing kits and products to assure proper technique and quality is maintained in their facility. We have a broad network of distribution partners throughout North America, Canada, and other international markets. These distribution partners provide in-person servicing and education to accounts to comply with USP guidelines.
Product Overview
Our cost-effective, disposable products are available for various needs in the compounding pharmacy. Aseptic technique validation kits are available for low, medium, and high-risk settings. We also sell multiple à la carte sizes of vials, bags, tubes, and syringes of growth media for facilities looking to create a custom media fill test that mimics their day-to-day practice. In regard to environmental monitoring/gloved fingertip sampling, our EnviroTest™ paddle is ideal for both. The rectangle shape and built in hinge allow for testing critical areas such as edges and corners of a hood and behind latch handles. Sterility testing products are available in both USP 71 approved methods of testing. For the full filtration method, the QT Micro™ and QT Junior™ systems work for both small and large volume solutions. For the direct inoculation methods, our TuffTest 2™ product is ideal.
All Q.I. Medical growth media is challenged with a battery of USP specified organisms and lot specific Certificate of Analysis (CofA) are available for download.
All products are sold through regional stocking distributors in order to provide fast local service and support.
Additional products are available for validation of hazardous drug handling, automated compounder manipulation validation, filter integrity testing, and vial adaptors.
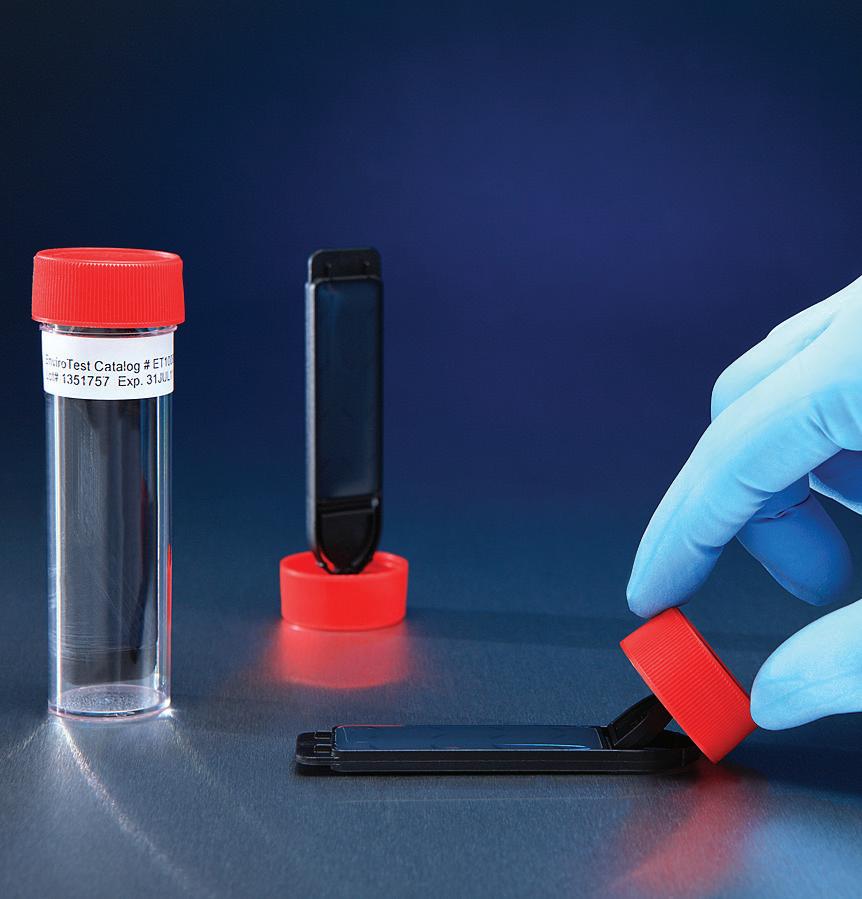
n Support Equipment Includes:
• Incubators
• Sterile Filters
• Vial Blocks
• UV Lights
Ordering Information
To learn more about how Q.I. Medical, Inc. can help your facility, please contact us at (800) 837-8361 or email info@qimedical.com.
PACKAGING
In today’s fast-paced world of new pharmaceutical products and evolving patient care needs, supply chain challenges, and medication shortages, the ability to balance the above components is often a key to survival for any pharmacy dispensing business or production environment. Inpatient, outpatient settings, and long-term care — all depend on safe and fiscally responsible medication management processes. Assurance of lean medication dispensing practices and waste reduction through targeted inventory turnover and avoidance of expired medications due to low use or over-order is equally important.
Utilization of medication repackaging techniques in both inpatient and outpatient settings provides one of the reasonable solutions to the above challenges. Not only does medication repacking allow for a cost-effective way to obtain and dispense medication, it also allows for additional dosage customization for oral solids, liquids, and injectables through the use of unitdose and multi-dose containers. As noted in American Society of Health System Pharmacists (ASHP) Technical Assistance Bulletin, a single-unit package contains one discrete pharmaceutical dosage form (such as one tablet, one volume of liquid). A unitdose package contains the particular dosage of the medication, ordered for a patient.1 Introduction of a multi-dose package to the market provides a solution to combine tablets or capsules in an organized blister pack or a pouch and, in addition to medication dose and strength, provides information with the day and time when this medication needs to be taken. Overall, such an approach to medication packaging presents an opportunity for enhanced patient safety, helps with adherence to the regimen as well as easy tracking of NDC (national drug code) in the event of medication recalls, to ensure compliance. Medication repackaging, as a process, has the potential for significant cost savings, as many manufacturer-made unit dose packages are more expensive per single unit-dosed unit, as compared to the same dose dispensed from a bulk bottle. In addition, multi-dose packaging may provide cost savings on labor hours and consumables. Matching production volume and needs with a correct packing system is important. Selecting the correct package type, in alignment with the guidelines, is a part of decision-making process as well.
Contributor:
Julia West, PharmD, BCPS, MBA Director of Inpatient Pharmacy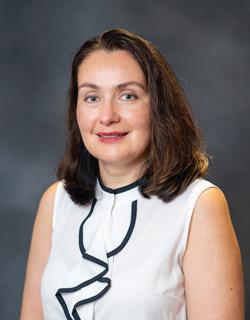
When selecting a unit-dose or multi-dose packaging system, one needs to be aware of packaging materials, shape, size, and form of available packaging, as well as federal labeling requirements. Packaging materials need to meet the requirements to protect the content. Packaging needs to meet physical characteristics that allow protection of the content from light, moisture, possibly temperature changes, air, and handling. Ideally, packaging should not be bulky; it needs to be inert towards the product. It should not absorb or adsorb any of the content or affect in any way the medication. If packaging is recyclable and bio-degradable, after use — this is a plus.1
MATTERS
Medication packaging systems provide a variety of packaging options and sizes within those options. When selecting a singledose or a multi-dose packaging, having an idea of production volume, most frequently used medications, and their sizes or volumes is, once again, important. Selecting an improper size (i.e., packaging a small, 3 mm tablet in a single unit, designed to comfortably hold several 12 mm capsules) may create unnecessary storage space needs for the packaged inventory. The same is true with respect to multi-dose packaging, including packaging designed for direct shipping of packaged products to patients (for example, a pharmacy working with a long-term care facility setting). Incorrectly selected packaging sizes may result in the need for additional delivery charges or additional delivery truck space. Developing a close working relationship with the packaging vendor of choice is always a good step toward a lean production process, customization, and reduced waste. Durability — packaging should be able to withstand normal handling, should be easy to open, requiring no special training to use.1
Special considerations are worthy of note — blister packaging should have non-reflective backing, be easy to print on and to peel. A blister or a bubble needs to be of transparent material and ideally provide UV light protection, comparable to the original container. If used to package controlled substances, sequentially numbered packaging will help accountability. If utilizing pouches — one side of the packaging needs to be opaque and non-reflective. Proper sizing — large tablets in large pouches, small tablets in small pouches — to ensure the best fit for storage and delivery. Packaging needs to be easy to tear. When packaging liquids, the containers must be able to accommodate volume to deliver the labeled content. If utilizing a syringe-type container, it should be properly labeled “For Oral Use Only.”1
Medications repackaging must follow stringent guidelines. FDA provides guidance on mixing, diluting, and repackaging of biological products. Policies provided by the FDA are designed to ensure safety and reduce health risks to patients, due to
medication repackaging. Within their guidelines, FDA includes definitions, such as what defines repackaging as “the act of taking a finished drug product from the container in which it was distributed by the original manufacturer and placing it into a different container without further manipulation of the drug.”4 Among other things, the FDA evaluates container closures, packaging systems, and the conditions under which the medication will be repackaged. As previously discussed, container or package design and quality can affect the stability of the drug.2,4 When selecting a unit-dose container, United States Pharmacopeia (USP) is a resource that contains minimum standards to be used as a guideline for drug repackaging. Not only does it provide the listings of requirements, it also specifies container class types. Beyond use dating as well as clear delineating of most current compounding practice also cannot be overlooked; staying on top of most current USP Chapters <795>, <797>, and <800> is important.3
In conclusion, unit-dose and multi-dose packaging provide great flexibility options for cost-effective, customized medication dispensing. When selecting unit-dose and multi-dose package options, the availability of different package sizes as well as a realistic assessment of production needs, are important. A close working relationship with a reputable vendor that follows FDA and USP-defined specifications and guidelines for their product cannot be underscored, as well as the facility’s knowledge of the most current guidelines — both align to provide the best care to patients.
1. ASHP Technical Assistance Bulletin on Repackaging Oral Solids and Liquids in Single Unit and Unit Dose Packages. American Society of Health System Pharmacists. Accessed April 25th, 2023. https:// www.ashp.org/-/media/assets/policy-guidelines/docs/technical-assistance-bulletins/technicalassistance-bulletins-repackaging-oral-solids-liquids.pdf
2. United States Pharmacopeia Chapter <1146> Packaging Practice-Repackaging a Single Solid Oral Drug Product into a Unit-dose Container
3. 2023 USP on Compounding: A Guide for Compounding Practitioners; current with USPNF 2023 Issue 1 (includes USP Chapters <795> and <797>)
4. FDA issues final guidance on repackaging and revised draft guidance on mixing, diluting, and repackaging biological products. U.S. Food and Drug Administration. Accessed April 24, 2023. https://www.fda.gov/drugs/drug-safety-and-availability/fda-issues-final-guidance-repackagingand-revised-draft-guidance-mixing-diluting-and-repackaging
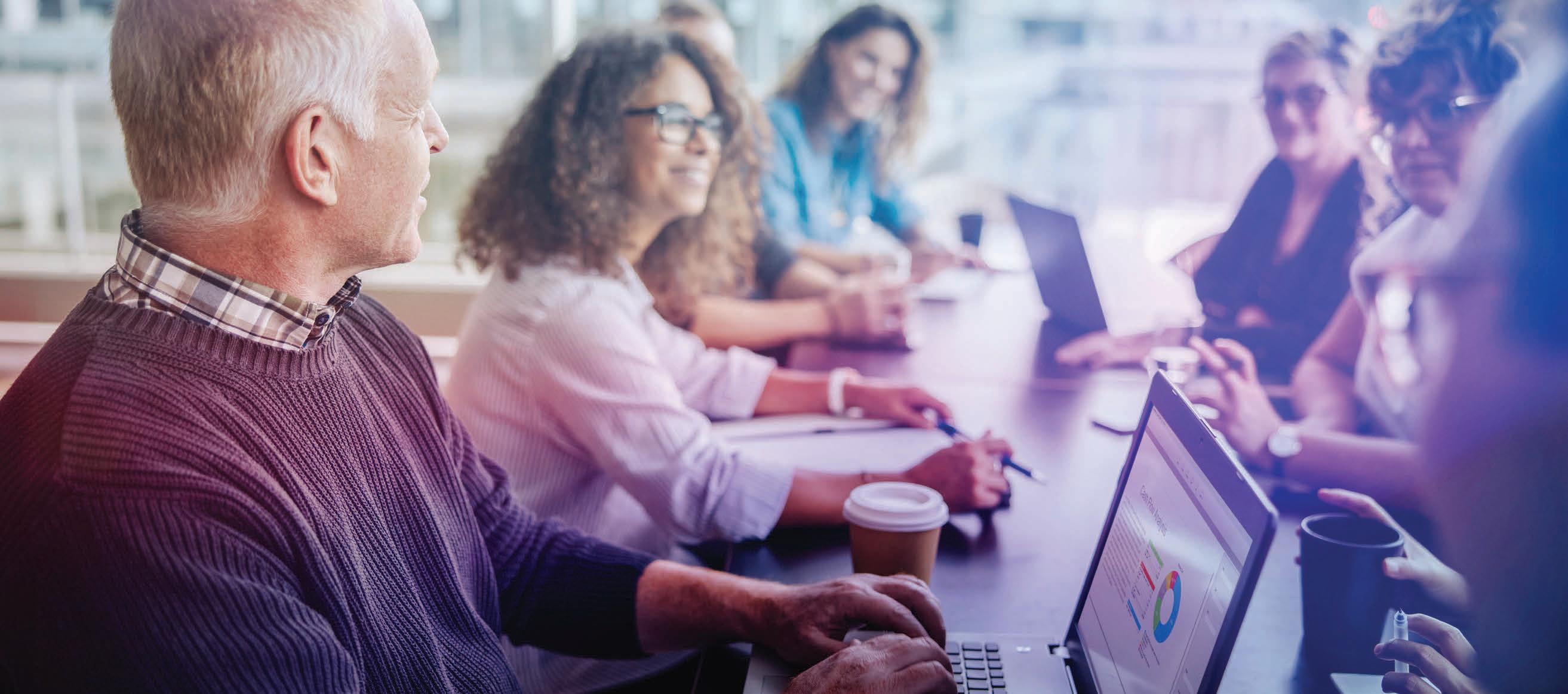
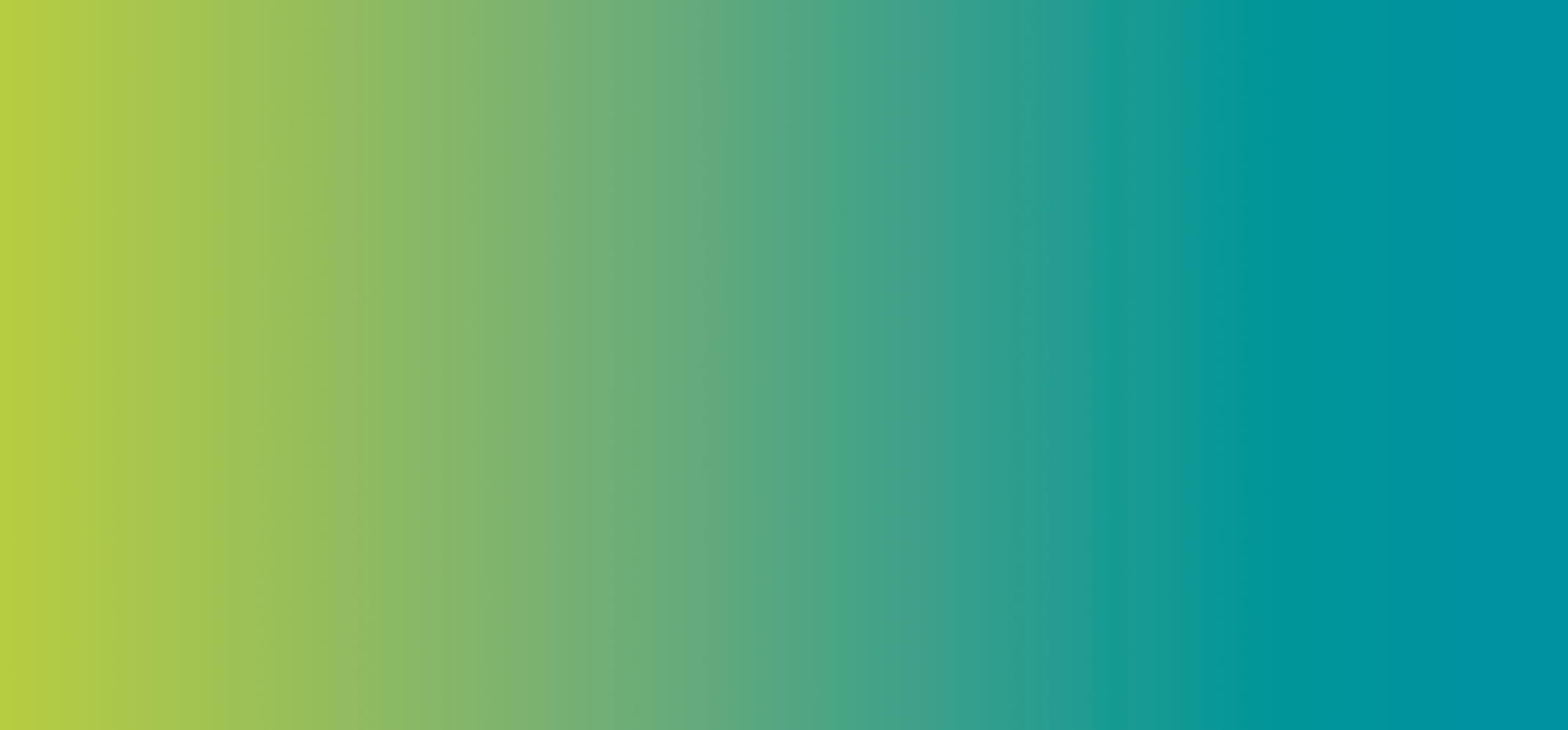

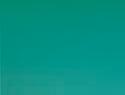

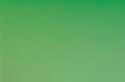






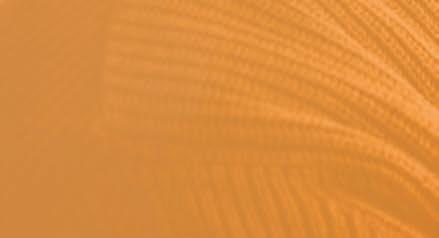


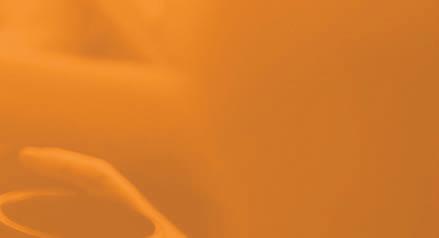
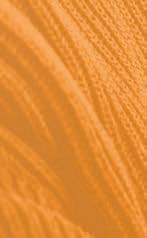
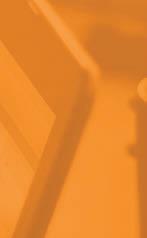
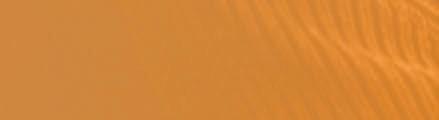

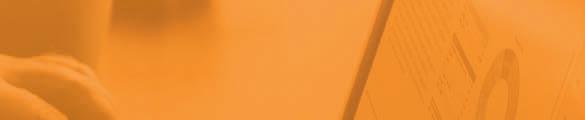
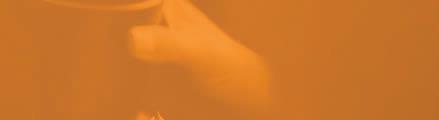
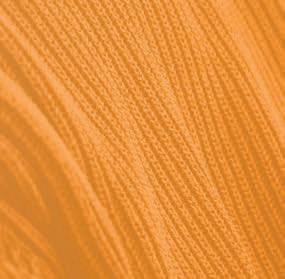
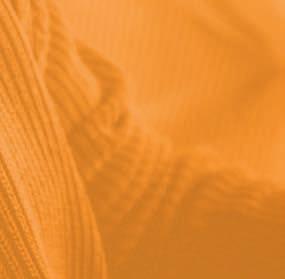
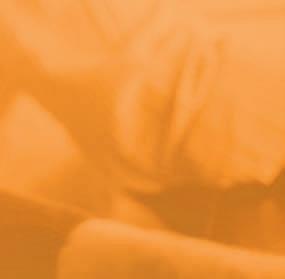
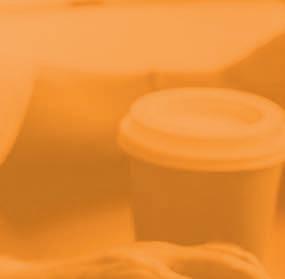
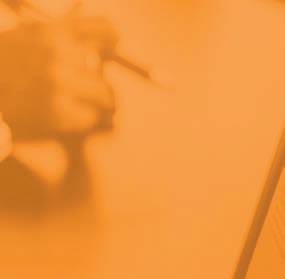
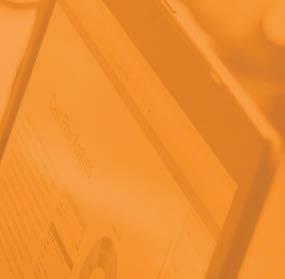
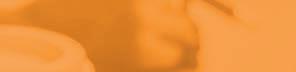
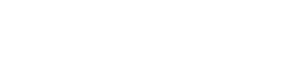


Visante — High-Performing Pharmacy is Who We Are
n Infusion Solutions
President & CEO: James Jorgenson
Founded: 1999
Toll-Free Phone: (866) 388-7583
Address: 101 East 5th Street, #2220 St. Paul, MN 55101
Website: www.visanteinc.com
Company Background
Visante is a specialized consulting firm focused exclusively on helping health systems accelerate strong financial and operational performance through pharmacy. Our team of professionals brings deep, contemporary expertise and innovation to optimizing all aspects of a fully integrated health system pharmacy program, driving significant value quickly. By providing customized solutions to fit the needs of our clients, we deliver sustained financial results through revenue growth, cost savings, and optimal business performance.
Featured Services
n Specialty Pharmacy Services
A clearly defined specialty pharmacy strategy can help improve patient care and greatly improve your bottom line. Developing a specialty pharmacy strategy or expanding your existing services can be a complex process, but our team of experts guides you through each phase and delivers lasting ROI. Our specialty pharmacy consulting capabilities include: operational assessment and pro forma models; multi-year business and strategic plans; facility design including workflow and automation options; implementation and project management; accreditation support (URAC/ACHC/CPPA); contract pharmacy strategy, if applicable; wraparound strategy to include consideration for site of care challenges (infusion); and home infusion, DME strategies, and business planning.
n 340B Solutions
Visante’s independent, external audit support provides transparency to your 340B processes, allowing you to recognize compliance gaps while focusing on new opportunities within the program. Our 340B team offers unique expertise in supporting 340B ESP™ data submission and price restoration analysis. Our services include: internal and external audit support, on-site HRSA audit support, and corrective action plan guidance in the event of HRSA audit findings; gap analysis and targeted recommendations, focusing on long-term strategy in the mixed-use and contract pharmacy space to ensure program optimization; program implementation and development of internal oversight structure and maintenance; and split billing RFP guidance, implementation, and program re-designs.
A comprehensive home infusion pharmacy business plan can help lower total cost of care, maximize patient outcomes and access to quality care, and optimize organizational financial performance. Visante infusion consulting helps with business planning, design, and implementation of comprehensive infusion care strategies using our deep and specialized expertise in all areas, including home infusion therapy, supply chain strategies, and innovative solutions to drug delivery and therapy administration.
n Pharmacy Revenue Cycle
Sustained financial growth is one of the top challenges for even the most successful organizations in the healthcare industry. Effective pharmacy programs can increase revenue by maximizing existing opportunities, creating new programs and services, and reducing costs. Our team of experts is here to help maximize financial performance within your organization through our mastery of both pharmacy and revenue cycle operations. Our consultants bring a wide range of experience to the table to assist each of our clients in a way that best fits them and their financial goals.
n Pharmacy Supply Chain Optimization
Supply chain and utilization management are complex and ever-changing functions of a pharmacy enterprise. To find success in these areas, disciplined focus and alignment must be prioritized. Visante’s supply chain experts help hospitals and health systems achieve reliable, safe, and efficient drug supply chain performance while also realizing significant financial returns.
n Drug Diversion
Our program takes a comprehensive multidisciplinary approach to identify drug diversion risk points in your medication use processes. Minimize risk through assessment of pharmacy operations, informatics, automation, nursing, and perioperative processes to identify and strengthen points of vulnerability. Our drug diversion experts have real-life experience in hospitals and health systems and understand the challenges hospitals face today and in the future.
n Sterile and Non-Sterile Compounding Compliance
Safely compounded medications are essential to quality patient care. Hospitals face the challenge of optimizing care while also meeting safety requirements and managing cost. We will prepare you for compliance with USP Chapters <795>, <797>, <800>, and <825>. We’ll also assist you in preparing for compounding related inspections by the CMS, FDA, DEA, and Joint Commission/DNV. Our consulting services include: USP <795>, <797>, <800>, and <825> as well as gap assessment and facility design; 503A, 503B assessment, facility design, and implementation support; and home infusion compounding services.
We’re in the business of advancing pharmacy. Our consultants work with hospitals and health systems combining a wealth of expertise with personalized and comprehensive support to optimize your pharmacy operations and deliver better patient care.
An Innovative Non-Aerosol Unit Dose Topical Anesthetic Spray
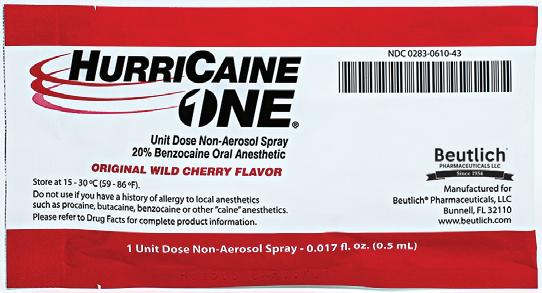
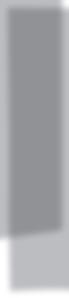
• Meets Joint Commission Standard for the most ready-to-administer form available.*
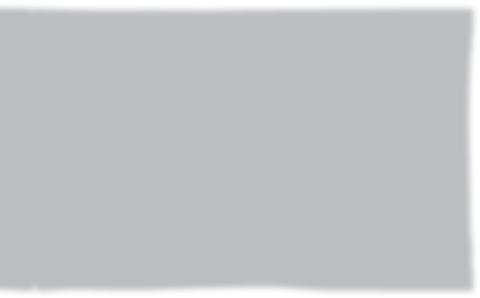
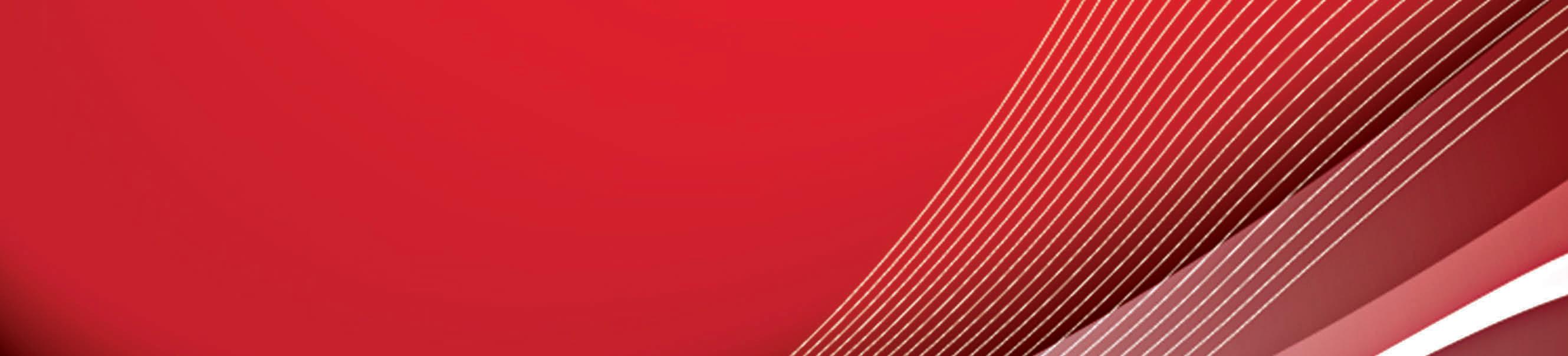
• Fast onset. Short duration. Virtually no systemic absorption.

• Utilizes bar code medication administration (BCMA) to accommodate point-of-care scanning.
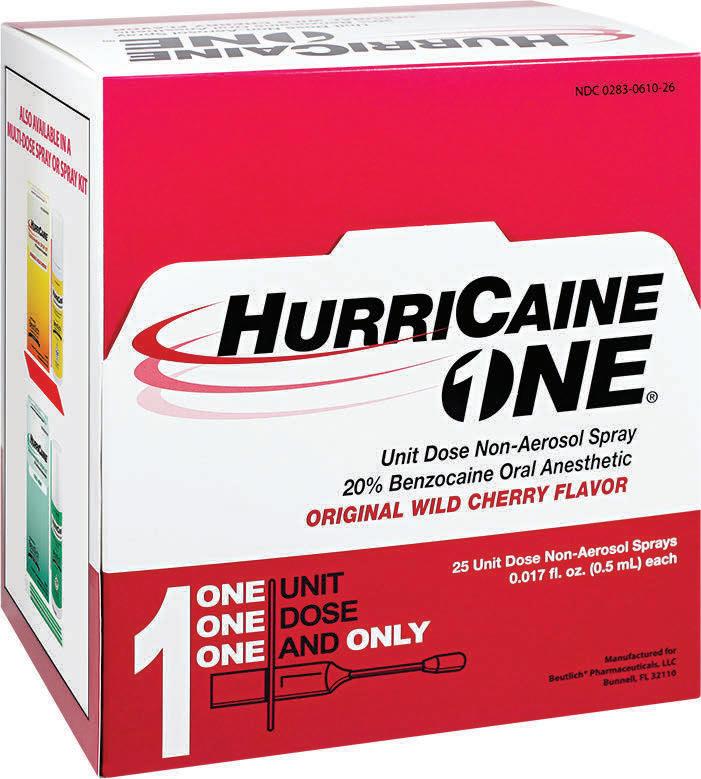
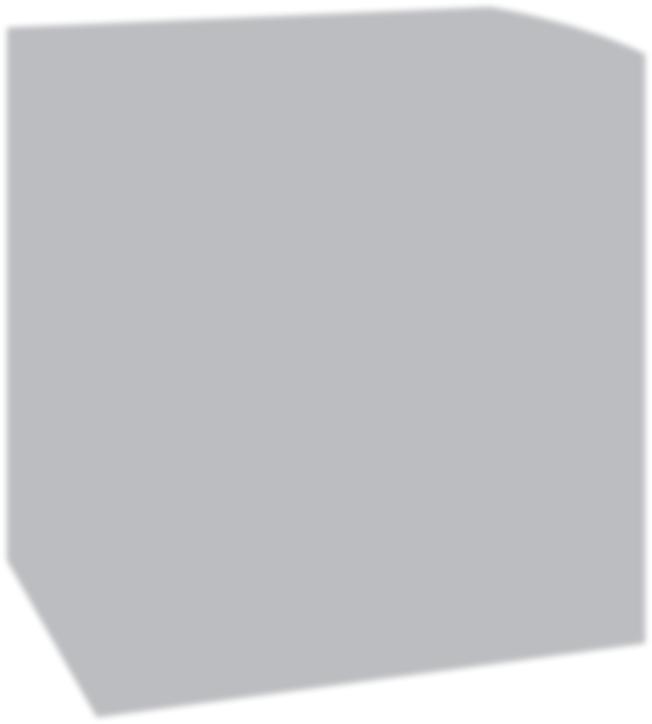
• Virtually eliminates adverse events resulting from preventable medication errors, ensuring the “5 Rights” are met: √ Right Drug
√ Right Patient √ Right Dose
√ Right Route √ Right Time
• Single unit-of-use packaging eliminates the potential for cross-contamination.
• Increases billing accuracy and improves supply chain costs.
*Joint Commission Standard: MM.05.01.11, EP4
No needle means no
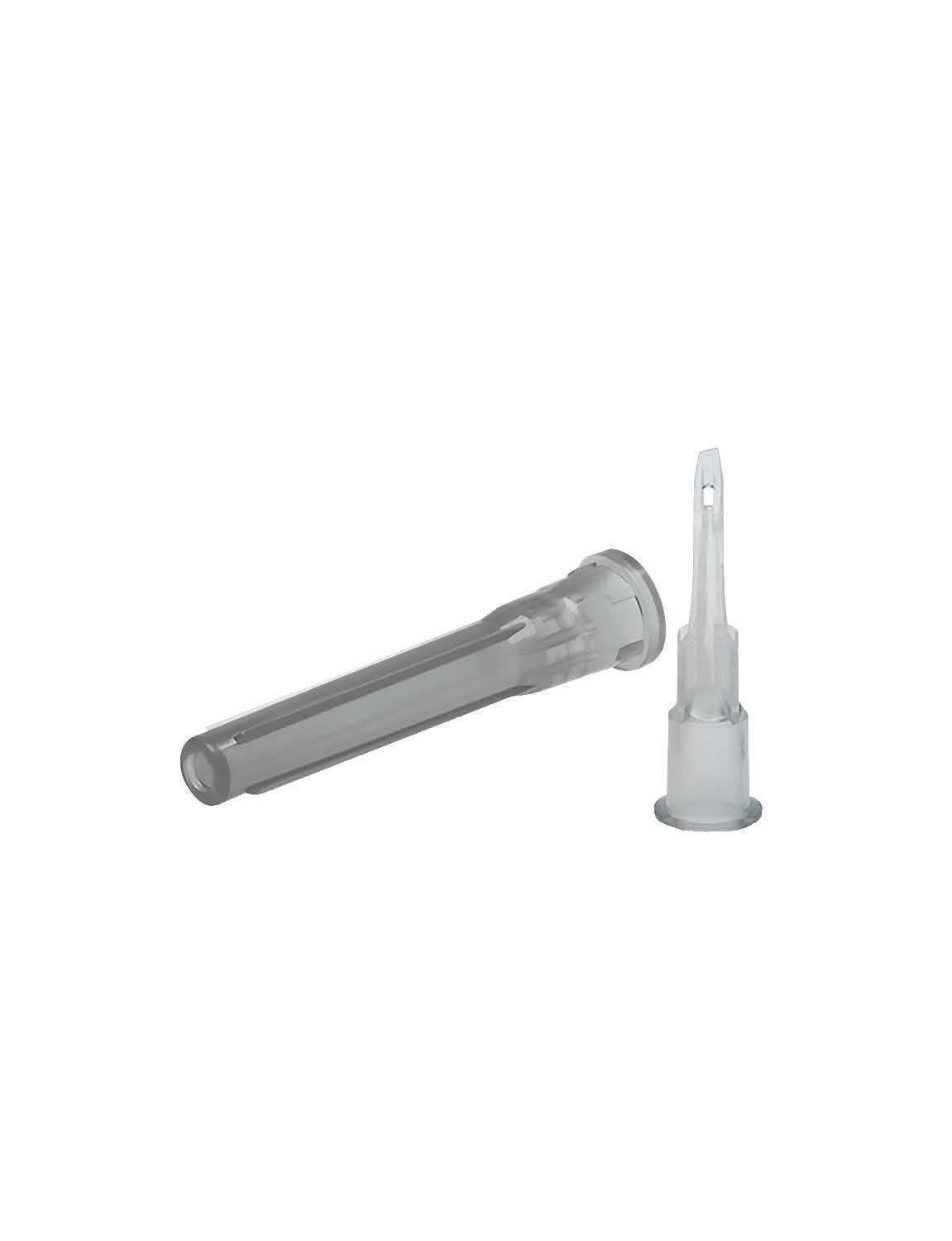
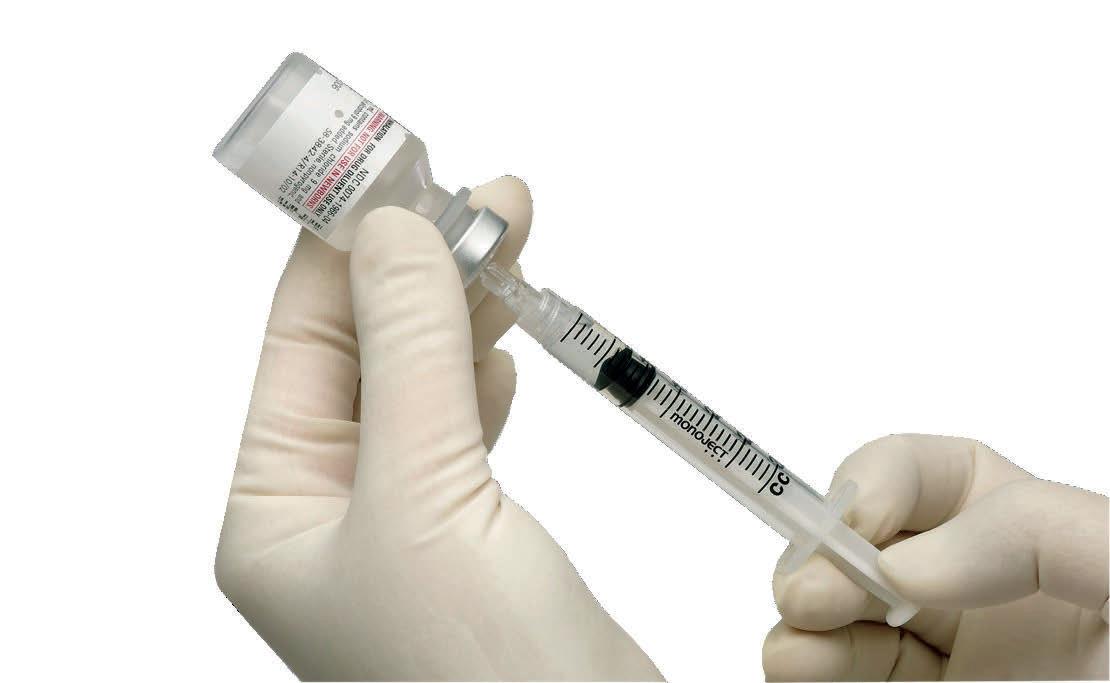
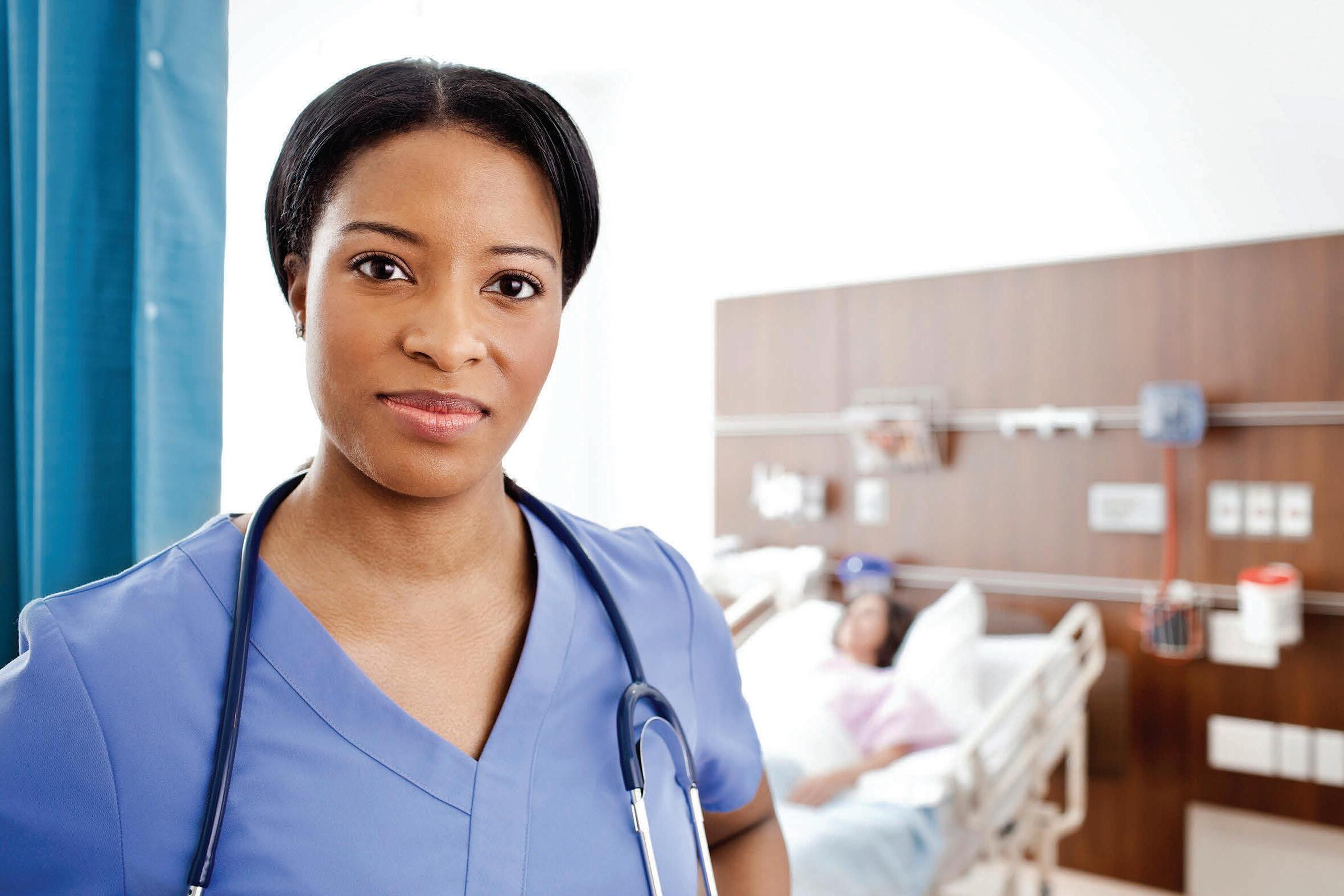
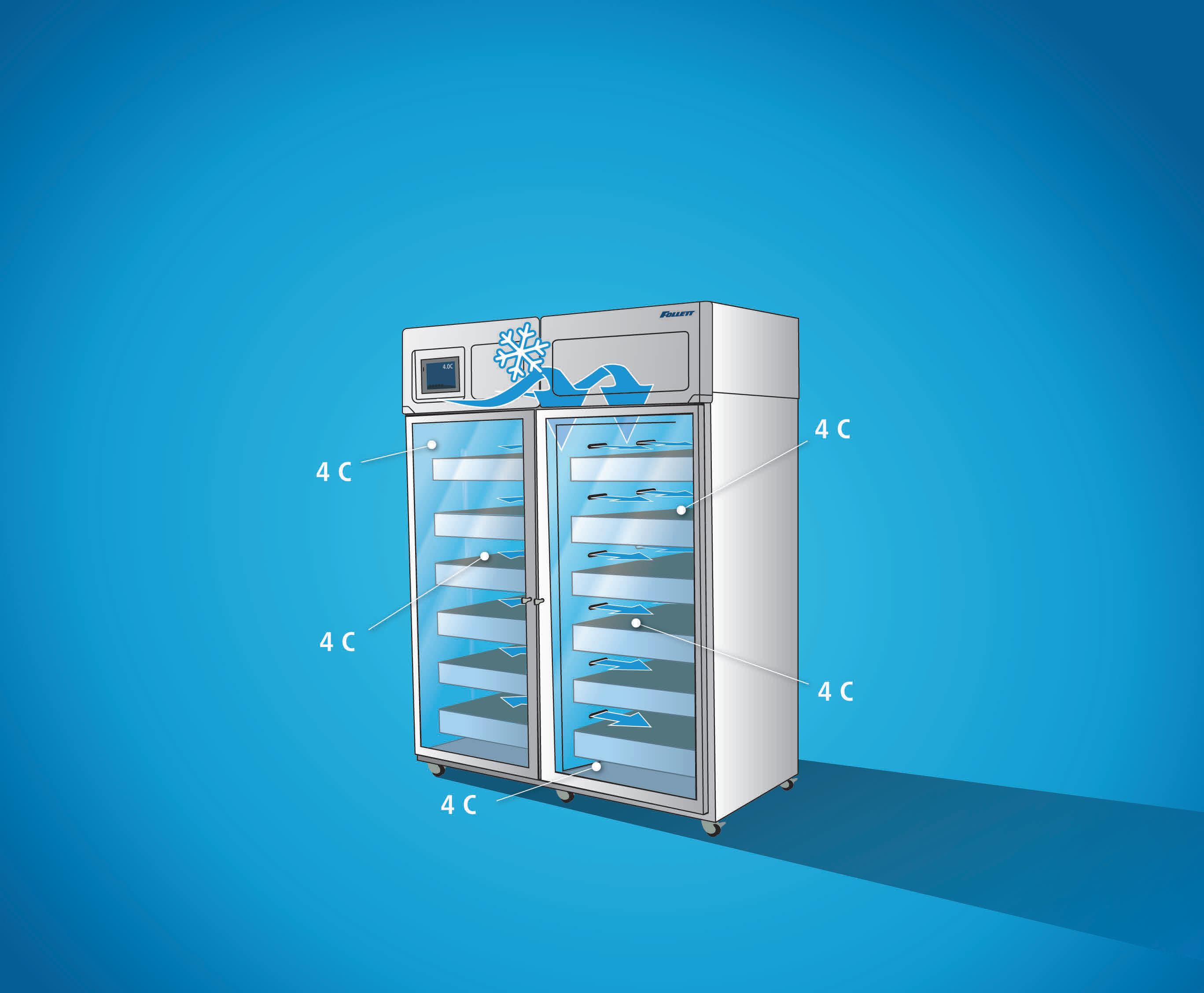
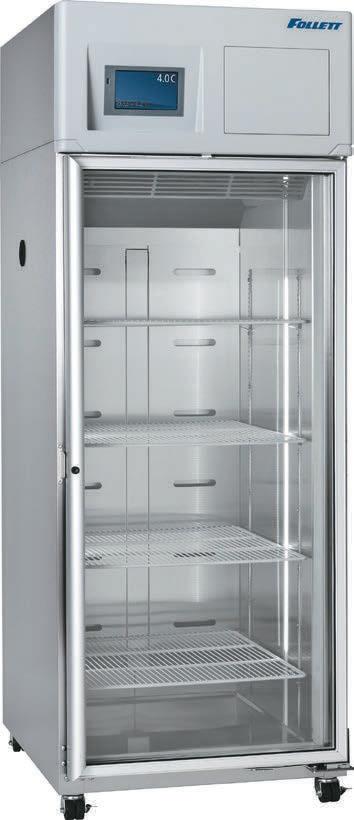
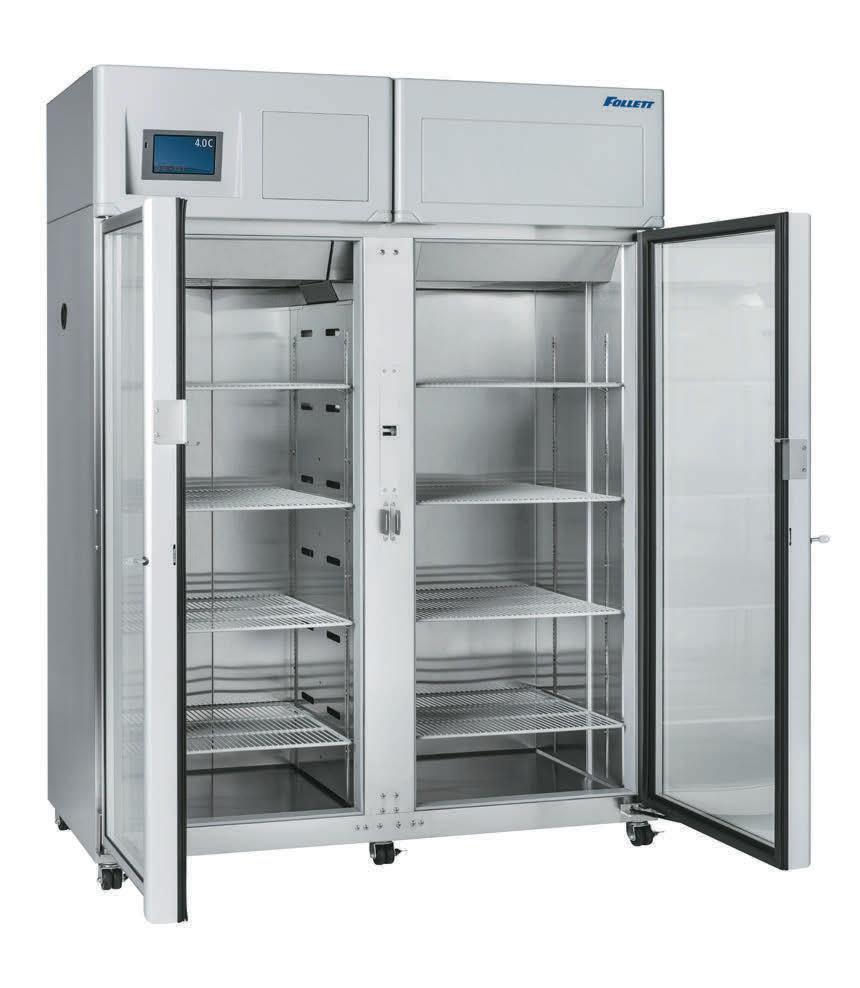
With Vaccine Storage, There is No Room for Error
Follett high-performance NSF 456-certified refrigerators provide precise temperature control for safely storing vaccines and medications.
n Choice of superior storage options.
General Manager: Mike Raycher
Founded: 1948

Employees: 500+
Toll-Free Phone: (800) 523-9361
Phone: (610) 252-7301
Fax: (610) 250-0169
Address: 801 Church Lane Easton, PA 18040
Website: www.follettpharmacy.com
Company Background
Follett Products, LLC is a leading manufacturer of innovative equipment for the healthcare market, including medical-grade refrigerators and freezers, ice and water dispensing equipment, and ice machines. Our focus on 100% customer satisfaction results in equipment that provides outstanding innovation and design excellence to meet the specific needs of each healthcare facility.
Product Line Overview
Follett medical-grade pharmacy refrigerators and freezers maintain precise and consistent temperatures for your valuable medications and vaccines. Powerful forced air refrigeration enables quick recovery after door openings, ensuring your critical products are stored at specified temperatures and reducing the risk of lost product.
n Follett upright refrigerators and freezers feature a powerful top-mounted refrigeration module and innovative plenum air distribution system for superior temperature consistency.
• Industry-exclusive ducted air distribution delivers cold air at multiple levels for top-to-bottom temperature uniformity, allowing full utilization of the storage space.
• Proprietary microprocessor controller provides a ±1⁰C temperature consistency throughout the storage cabinet, ensuring all product is stored within the proper range.
• Intuitive full-color touchscreen user interface features enhanced data management with data downloading capability, providing the ultimate in user convenience.
n Full stainless-steel cabinet and high-quality components designed with the user in mind.
• Heavy-duty, self-closing doors provide important energy savings and lock open at 90 degrees to allow easy product loading.
• Industry-exclusive “floating” basket system on pharmacy models.
• Six full extension, epoxy-coated “floating” baskets move with a gentle push or pull.
• Baskets and slide assemblies lift out without tools for full cleaning access.
• Four heavy-duty epoxy-coated shelves, adjustable in ½" (1 cm) increments are standard on laboratory models.
n Follett’s innovative modular refrigeration system provides outstanding serviceability.
• Top-mounted modular design allows the entire refrigeration system to be removed as one unit without cutting refrigerant lines. If needed, a spare system can slide into place, virtually eliminating downtime or the need to relocate product.
n High-performance countertop refrigerators and freezers offer superior temperature performance in space-saving configurations.
• 1 and 2 cu ft models fit on standard 24" deep counters.
• Forced-air cooling provides cabinet-wide temperature consistency and quick recovery after door openings.
• External digital temperature display in user-selectable F or C with integral high/low alarming and display sleep mode.
• Keyless entry via keypad and electronic lock option.
n Powerful undercounter refrigerators and freezers are designed for use below standard and lower ADA-compatible counters.
• Heavy-duty forced air cooling for quick recovery after door openings.
• External digital temperature display in user-selectable F or C with integral high/low alarming and display sleep mode.
• Keyless entry via keypad and electronic lock option.
Contact information
For more information, contact Follett at (800) 523-9361 or visit www.follettpharmacy.com.
Every successful story starts with an easy read
Minimize complexity. Maximize safety.
You want barcodes that scan easily and reliably the first time. Our broad range of unit dose medications can help. They feature large barcodes for easy readability.
Plus, they:
• Use the Barcode Medication Administration (BCMA) system to verify the ‘5 rights’ of medication administration
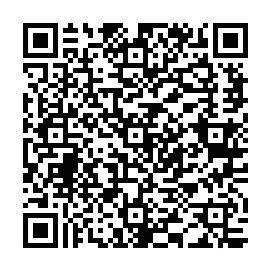
• Come ready to dispense
• Reduce medication errors
• Support positive patient outcomes
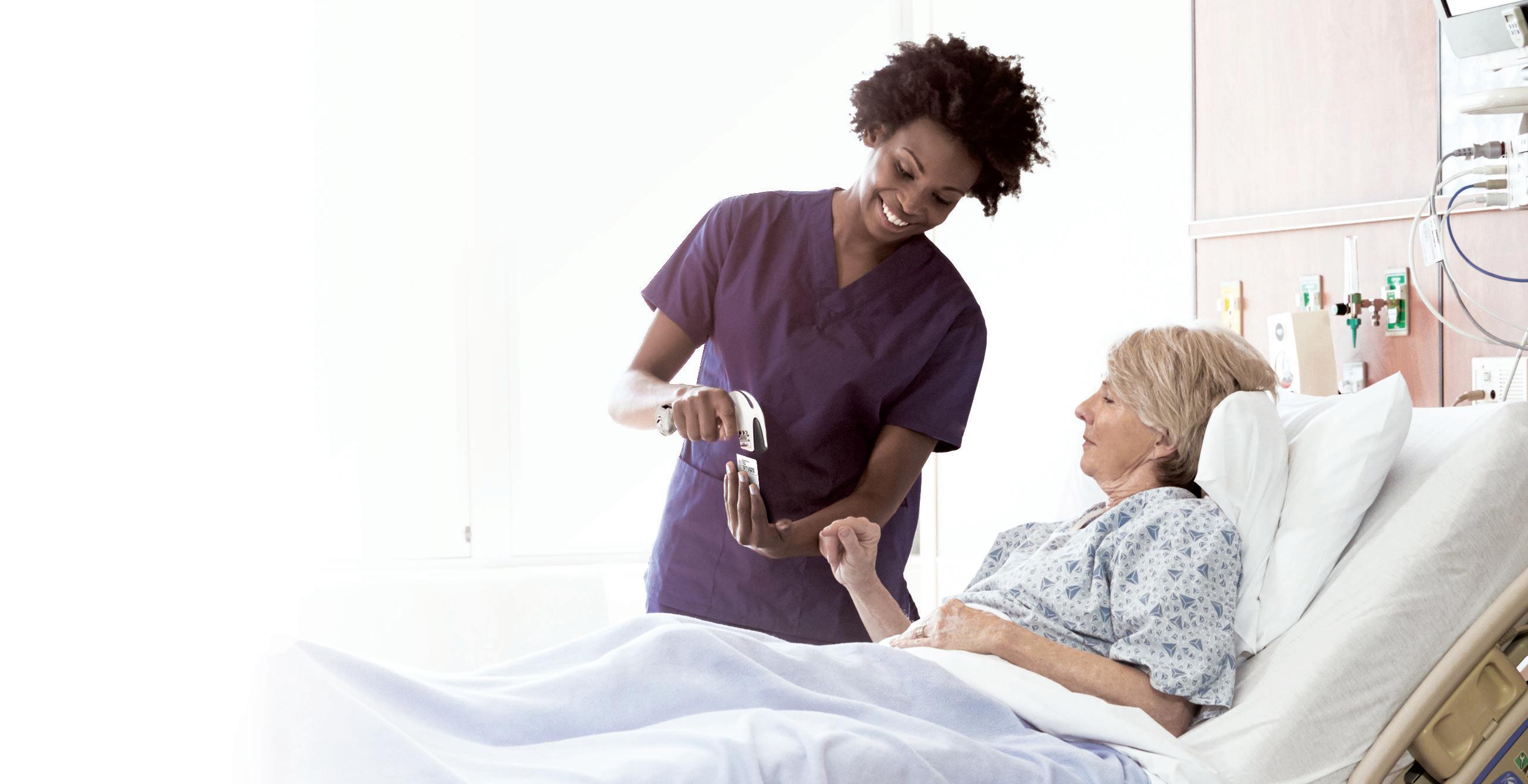
Curious how the AHP portfolio can support safe and efficient delivery of BCMA?
Visit americanhealthpackaging.com to learn more.
American Health Packaging is a Leading Manufacturer of Serialized Barcoded Unit-Dose Products
With a responsive line of barcoded unit-dose oral solutions, a growing liquid unitdose offering, as well as individually wrapped inhalants, American Health Packaging continues to deliver on their commitment to supporting pharmacy efficiency.
Additional Product Modules
Senior VP & General Manager: Sasha Kellerman
Toll-Free Phone: (800) 707-4621
Address: Columbus, OH 43217
Website: www.americanhealthpackaging.com
Company Background
Located in Columbus, Ohio, American Health Packaging (AHP) is an industry leader in manufacturing serialized, barcoded unit-dose (UD) medications provided for the healthcare marketplace. As a UD manufacturer, AHP’s commercially-available UD products are available to hospital, institutional, and long-term care pharmacies nationwide through partner GPOs and wholesalers.
AHP’s reputation for quality is supported by a 30+ year history of broad manufacturing expertise — operating a facility that is registered with the FDA, fully adherent to cGMP guidelines, and licensed by the DEA to package Schedule II-V controlled substances. Synonymous with unit dose, following years of success and leadership in the production of oral solids, AHP expanded their offering in 2017 to include liquid unit-dose cups and inhalants in 2019.
Product Overview
AHP is committed to supporting pharmacy efficiency through a diverse range of both high-utilization and niche treatments. Producing nearly 600 UD oral solid SKUs for the healthcare marketplace, AHP’s broad selection of products are produced with quality components and printed with legible barcodes that facilitate effective execution of BCMA initiatives. Their wide selection of products reduces the gap between what pharmacies are forced to repackage themselves, and what is commercially available on the market — supporting health systems nationwide in their efforts to create efficiencies throughout the chain of care.
AHP’s tailored offering of UD oral liquids provide similar efficiency, safety, and cost-savings benefits as their oral-solids products. Product features include right-sized packaging, thoughtful tray design, differentiated labelling, and accurate barcodes. AHP’s unit-dose inhalants provide efficiency and feature individually-wrapped vials and pouches barcoded to the dose level. AHP oral solids, liquids, and inhalants include major therapeutic classes and product groups to meet unique pharmacy needs. They are continuously evolving to meet the changing demands of caregivers and staff to support more effective medication procurement strategies.
As facilities nationwide compete to demonstrate they provide the highest quality of care, AHP UD supports caregivers as they strive to promote positive outcomes for patients. Pharmacies simultaneously strive to be cost-effective as they provide necessary resources for caregivers.
AHP UD supports these objectives while providing cost-savings opportunities. Sourcing pre-packaged UD allows pharmacies to obtain adequate supply while mitigating capital expenses, such as those related to repackaging equipment, bulk supply, and labor.
Benefits for Health Systems
n Patient Safety: Ensuring the right medication is given to the right patient at the right time — and in the right strength — is imperative. Pharmacies can facilitate effective execution of these “rights” by providing caregivers with as many products in a pre-packaged UD format as possible. Removing repackaging tasks from the pharmacy eliminates a potential point of failure during the UD process as medications arrive to pharmacies ready to dispense.
n Pharmacy Efficiency: Pharmacies strive to process orders and supply the proper medications to caregivers for their patients as quickly as possible. Adding potentially-complex repackaging steps to the procurement process not only harms the ability of pharmacy to supply caregivers effectively, but also removes clinicians from their core patient care competencies. In addition, pre-packaged UD often allows for products to be sourced more quickly than third-party repackaging can support.
n Cost-Savings Opportunity: Health systems that choose to package on-site must consider all direct costs, such as purchasing capital equipment for packaging areas and paying highly trained clinical professionals to perform, manage, and support non-core work. AHP UD products allow for pharmacies to avoid these costs while also shifting the potential costs associated with packaging errors. The pre-packaged format also prevents additional fees that may result from utilizing thirdparty repackaging services.
n Liability Management: Pharmacy repackaging operations can be subject to distractions from a variety of sources. An active pharmacy environment can encourage lapses in concentration and present opportunities for staff error. Since these errors may vary in gravity and place liability on the facility and caregivers, mitigation of risk is key. Unit dose from American Health Packaging can help shift liability burden away from staff.
Hitting the Mark for BCMA, USP <800> Support
Effective execution of BCMA initiatives require medications that scan correctly at the bedside. With a robust, and growing, unit-dose portfolio AHP provides reliable access to UD treatments. AHP products promote safety towards BCMA and efficiency in pharmacy while freeing up internal resources. AHP UD supports pharmacies as they strive for compliance with USP General Chapter <800> guidelines. As pharmacies craft effective procurement strategies to meet the needs of their facilities, protecting patients and caregivers alike from potential harm while handling hazardous drugs is a priority. AHP’s UD portfolio has a number of NIOSH/USP <800> products already packaged for bedside dispensing which supports compliance to USP <800> handling procedures.
UHS Expands Specialty Pharmacy Services to Improve Patient Care
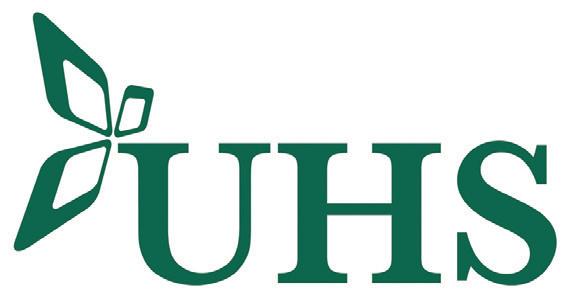
A COMMITMENT TO COMMUNITY
United Health Services (UHS), a large health system located in upstate New York with over 60 locations, including three hospitals, is committed to giving patients easy access to quality healthcare across the region. That’s why in 2019, the health system launched its outpatient specialty pharmacy for UHS Binghamton General Hospital, which includes the Wilson Medical Center.
Leigh Briscoe-Dwyer, PharmD, BCPS, FASHP System Director of Pharmacy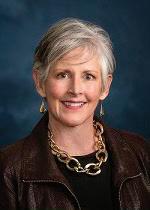
According to William Waldron, RPh, MHA — Director of Outpatient Services at UHS, their journey to establish a specialty pharmacy began in 2018. “After our previous director of pharmacy attended a focused session on specialty pharmacy services at a national industry conference, we decided to take a closer look at our infrastructure to see if it made sense for our organization and our community,” he explains. Working with an external consultant on this analysis, UHS found that nearly 50% of their clinics served specialty patients. Additionally, patients in many surrounding counties continued to lose access to medications as local pharmacies closed their doors.
“This led us to the conclusion that adding a specialty pharmacy division would be an important, clinically effective service for the communities we serve.”
William Waldron, RPh, MHA Director of Outpatient Services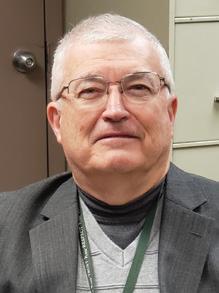
~
United Health Services (UHS)Given the complexity of launching and managing a specialty pharmacy, UHS chose to work with a company to establish and operate its service just before the COVID-19 pandemic in 2020. While the service grew steadily, Waldron believed opportunity existed to maximize growth and results.
“We transitioned our partnership to Trellis Rx in October of 2022, and their unique model began to make a difference — to our patients and physicians — right away.”
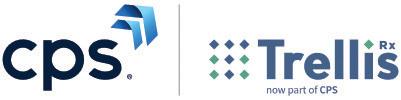
A PATIENT-CENTRIC BUSINESS MODEL
Trellis Rx, a division of CPS and one of the country’s largest pharmacy and hospital service providers, works with health systems to offer integrated specialty pharmacy care to patients. For UHS, this partnership meant helping them realize their patient-focused goals by embedding onsite pharmacists and liaisons into clinics and expanding medication access, specifically in chronic disease management.
Local Pharmacists and Liaisons
“One of the things that makes our approach different,” says Fredrick Campogni, PharmD, BCMAS, 340B ACE, AAHIVP, CSP, DPLA — VP, Onsite Operations at Trellis Rx and GM of UHS Specialty
CASE STUDY
Pharmacy Services, “is our commitment to embed local people directly into the health system.” That includes pharmacists and pharmacy liaisons who assist providers, nurses, and patients as integrated, accessible members of the care process. “By working in clinics side-by-side with the providers and meeting with our patients in person,” says Alexis Gately, PharmD — Clinical Operations Manager at UHS Specialty Pharmacy, “the pharmacy becomes a familiar face — not someone in the distance or at some other pharmacy miles away.”
With this local approach, Trellis Rx first set out to hire seven pharmacists and 21 pharmacy liaisons from the surrounding community to support existing UHS clinic staff. Campogni says, “This onsite model allows our team members to establish strong personal relationships with clinic staff and patients, some of whom they might already know, which is critical to managing patient health.”
As direct resources for those patients and providers, the new pharmacy team implemented Trellis Rx’s comprehensive care model. Liaisons introduce patients to the UHS Specialty Pharmacy, process prior authorizations on the clinic’s behalf, and secure financial assistance to ensure affordable access to care. “As specialty pharmacists,” Gately says, “being that resource for the providers is huge.” Pharmacists can advise providers about which prescription may be more suitable given a patient’s financial situation or medical history, and they can do so before the medication even gets dispensed. “Being able to use my pharmacy knowledge and directly benefiting patient care in this way is just so rewarding.”
Expanded Access to Medications
When they first launched the specialty pharmacy, UHS started with a select list of medications. “One of the most difficult things for us in the beginning — especially during the pandemic shutdowns — was payor access,” Waldron says. Given Trellis Rx’s expertise and relationships with health plans across the country, they immediately helped increase access to insurance markets so more patients could access UHS services and facilities. The first step, explains Campogni, was to conduct an in-depth data analysis to identify patients who might already be eligible for specialty pharmacy services and those payors who could bring more patients into the health system. Trellis Rx then focused on pursuing the best networks for UHS to reach the most patients. “The best care for a UHS patient is a UHS provider and a UHS pharmacy,” says Campogni. “That’s why we really focus on bringing patients here in the community back into the health system.”
THE SUCCESS: INCREASED PATIENT ACCESS TO MEDICATION AND CARE
When Trellis Rx began managing UHS’ specialty pharmacy program in late 2022, the results were immediate and significant. It started with Trellis Rx securing two new payor contracts — and in just five short months, UHS increased its specialty pharmacy prescriptions by 50%. This included a wide range of newly covered medications for chronic disease management, such as insulin for patients with diabetes and blood thinners for cardiology patients.
“The increase in prescriptions helped us grow revenue by about 40%,” explains Waldron.
“This growth has also allowed us to provide better care for our patients, including more than $4.3 million in financial assistance to patients over those five months.” This, he adds, is a big deal since specialty medications are typically very expensive. Plus, Leigh Briscoe-Dwyer, PharmD, BCPS, FASHP — System Director of Pharmacy at UHS, points out that many of their patients come from a lower socioeconomic background. “That financial assistance is important.”
With Trellis Rx as a partner, Briscoe-Dwyer says the assistance goes far beyond the financial. “One of the things I like best about our current partnership is the embedded pharmacists and liaisons
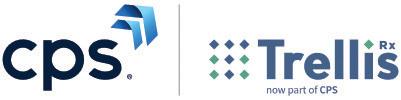
The increase in prescriptions helped us grow revenue by about 40%. This growth has allowed us to provide more than $4.3 million in financial assistance to patients.”
The more patients we can bring on board, the more services UHS can offer to the community for better overall access to care and treatment.”
William Waldron, RPh, MHA Director of Outpatient Services
~ United Health Services (UHS)
Fredrick Campogni, PharmD, BCMAS, 340B ACE, AAHIVP, CSP, DPLA
Vice President of Onsite Operations
~ Trellis Rx, a division of CPS General Manager
~ UHS Specialty Pharmacy Services
CASE STUDY
in the clinics.” They work hand-in-hand with physicians, patients, the nursing staff, and providers to ensure patients get the best possible care. An essential part of that includes obtaining prior authorizations so patients don’t have to wait for the medications they need. “Getting therapies to patients quickly is critical,” says Briscoe-Dwyer. “When dealing with diseases like hepatitis and HIV, days matter. When dealing with diseases like rheumatoid arthritis, where patients are in pain, days matter.”
Once medications are approved, Trellis Rx liaisons then work on the financials for patients, always striving to bring out-of-pocket costs as close to $0 as possible. Medications are shipped free of charge, and the pharmacists and liaisons guide patients from the start of therapy through monthly follow-up calls to coordinate refills, ensure medications are taken as prescribed, monitor their side effects, and intervene when necessary. “Trellis Rx’s role has just had such a significant impact on our patients. That’s one of the things I’m proudest of,” says Briscoe-Dwyer.
The bottom line, says Campogni, is that managing patient care and prescriptions within the health system is a win-win. “The more patients we can bring on board, the more services UHS can offer to the community for better overall access to care and treatment.”
LOOKING AHEAD TO THE FUTURE
“Our vision for the specialty pharmacy has really grown since its inception,” says Briscoe-Dwyer. “At first, it was a way to provide specialty medications to specialty patients. Now we’re providing specialty care for those patients — reaching them throughout all their visits.” With this growth, UHS is increasing the space dedicated to the specialty pharmacy. “We were able to find a new 10,000 square foot space very close to our medical center,” explains Briscoe-Dwyer. This move will allow the program to continue expanding well into the future. The health system is also planning to enhance their specialty pharmacy service offerings in 2023 to help link the patient journey from an inpatient to outpatient environment. In line with UHS’ philosophy, the goal of the Transitions of Care program is to minimize the risk of hospital readmission by providing a seamless patient experience. To help make that happen, Trellis Rx liaisons coordinate between inpatient and outpatient departments to ensure a patient has everything they need to continue their care in the specialty program and outpatient services when they leave the hospital.
“The partnership with Trellis Rx has gone beyond our expectations,” says Briscoe-Dwyer. “What started as a business agreement very quickly became much more like a family.” Now, she adds, the Trellis Rx employees who have joined us are just part of the health team community. “They fit so well into our culture — we’ve formed a bond and a collaboration I can’t ever imagine doing without.”
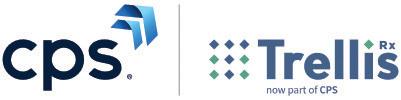
“What started as a business agreement very quickly became much more like a family ... they fit so well into our culture — we’ve formed a bond and a collaboration I can’t ever imagine doing without.”
Leigh Briscoe-Dwyer, PharmD, BCPS, FASHP System Director of Pharmacy ~ United Health Services (UHS)
Engage patients at every step of their journey by elevating pharmacy into the care team.
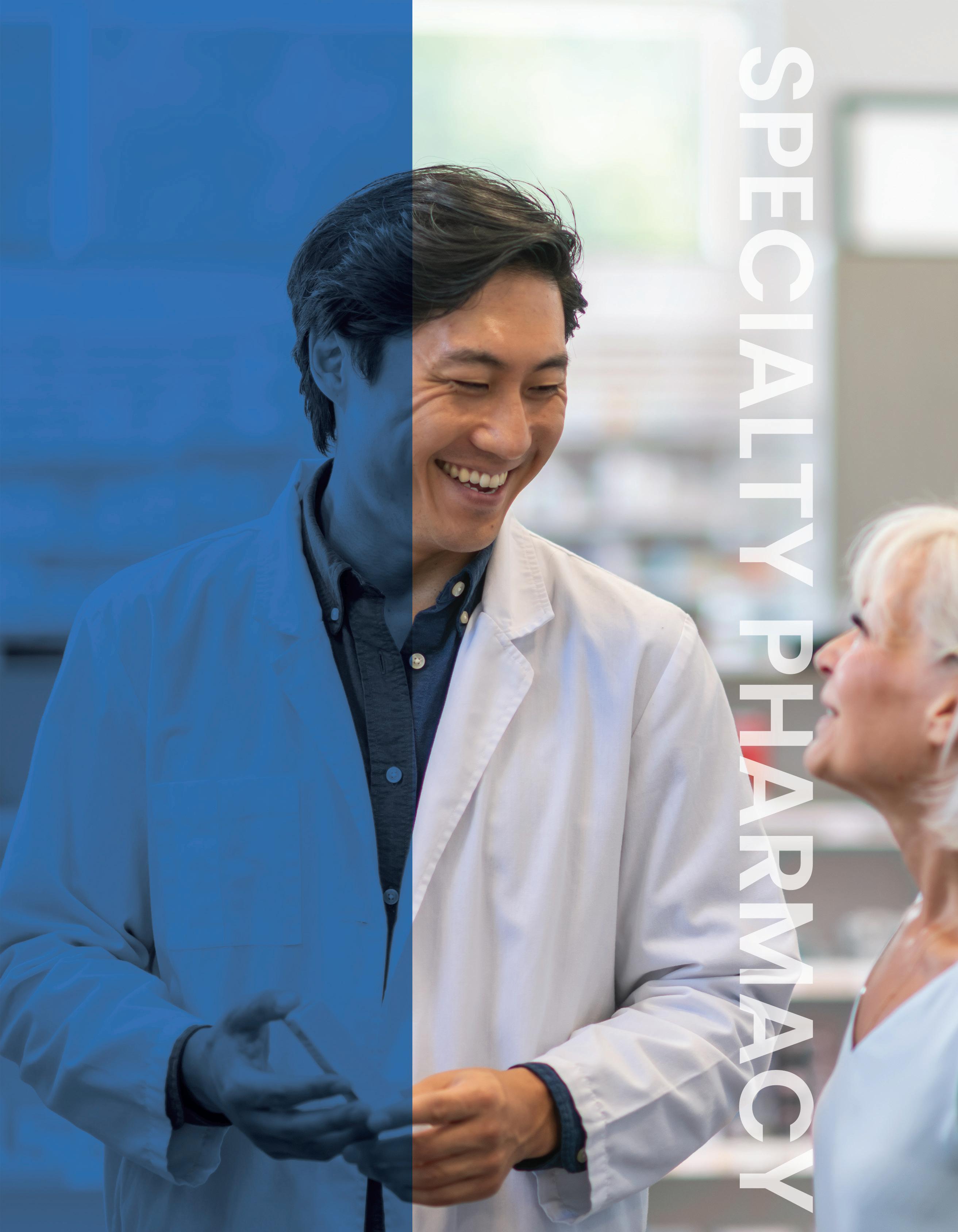
Build, grow, and optimize patient-centered specialty pharmacy services under your brand for your patients.
cps.com
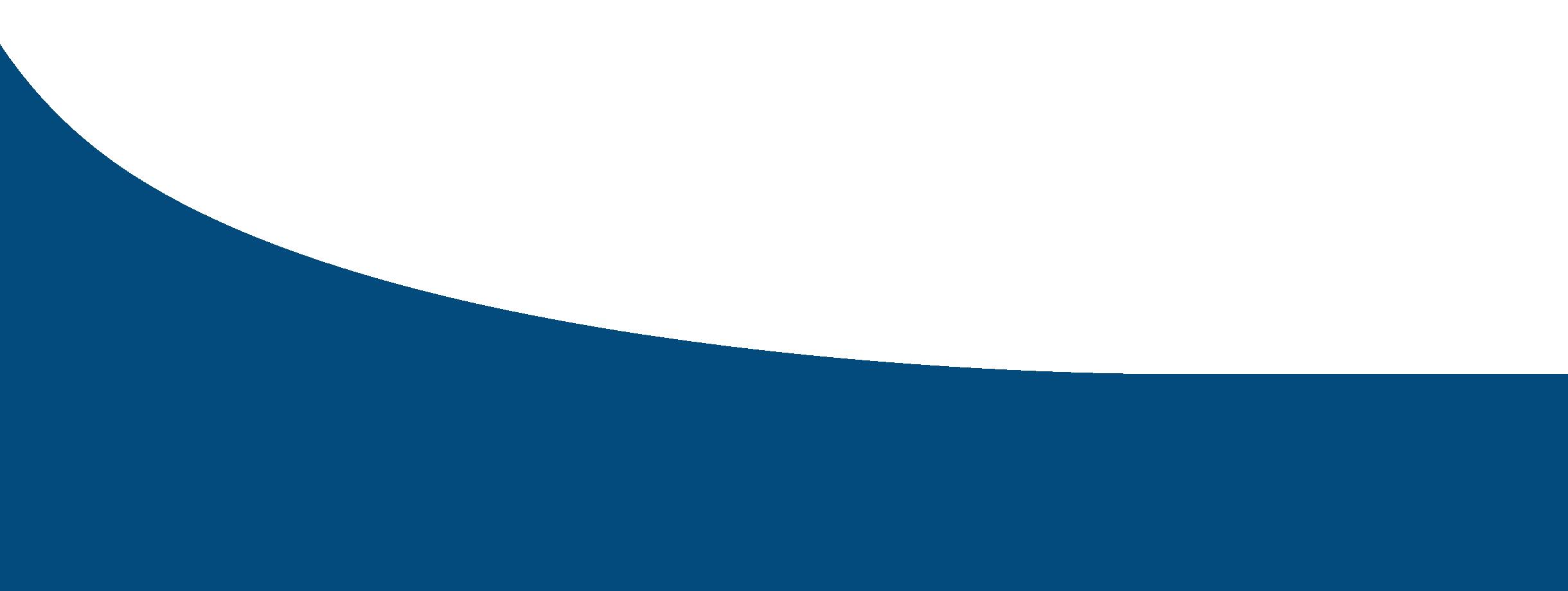
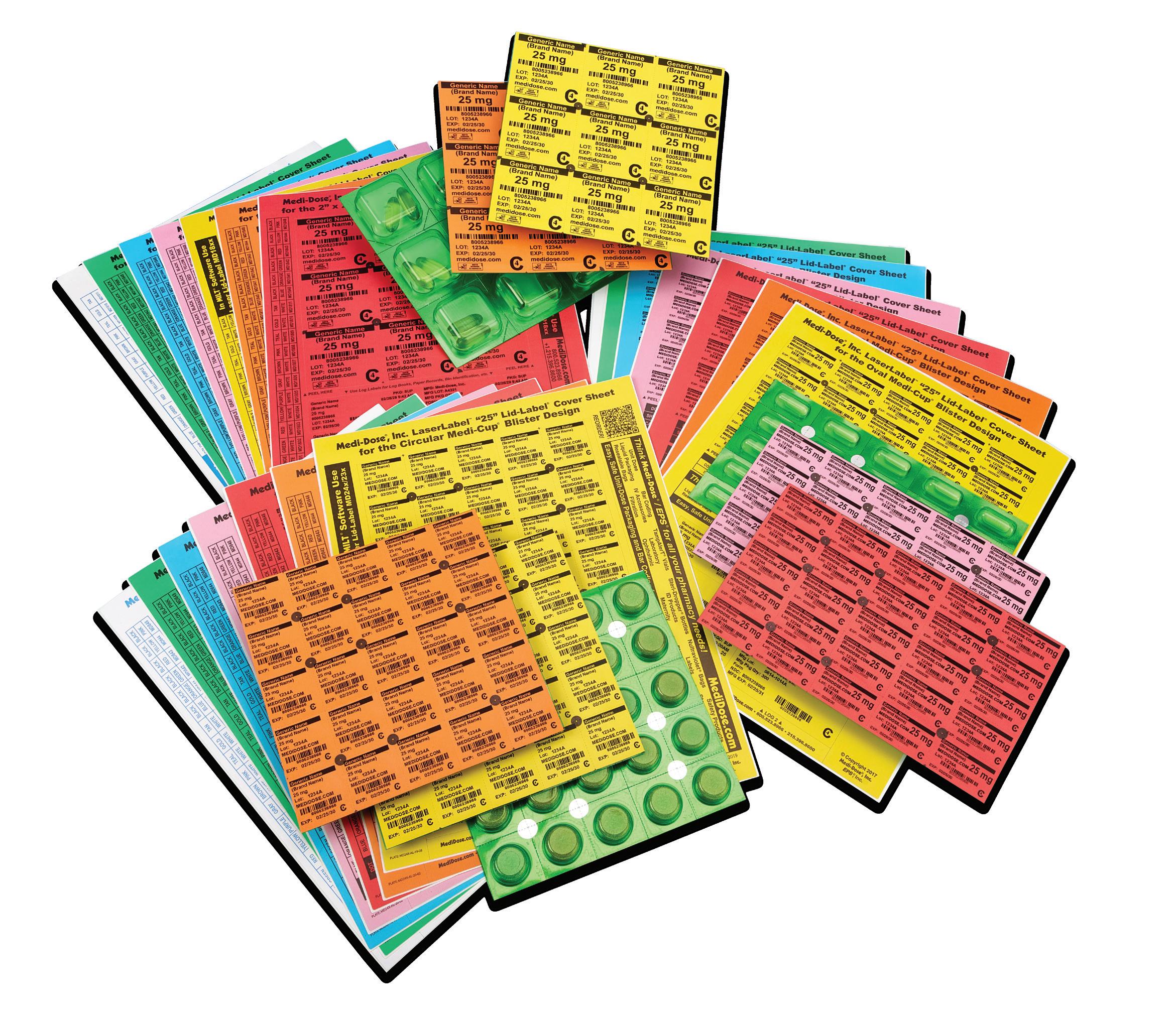
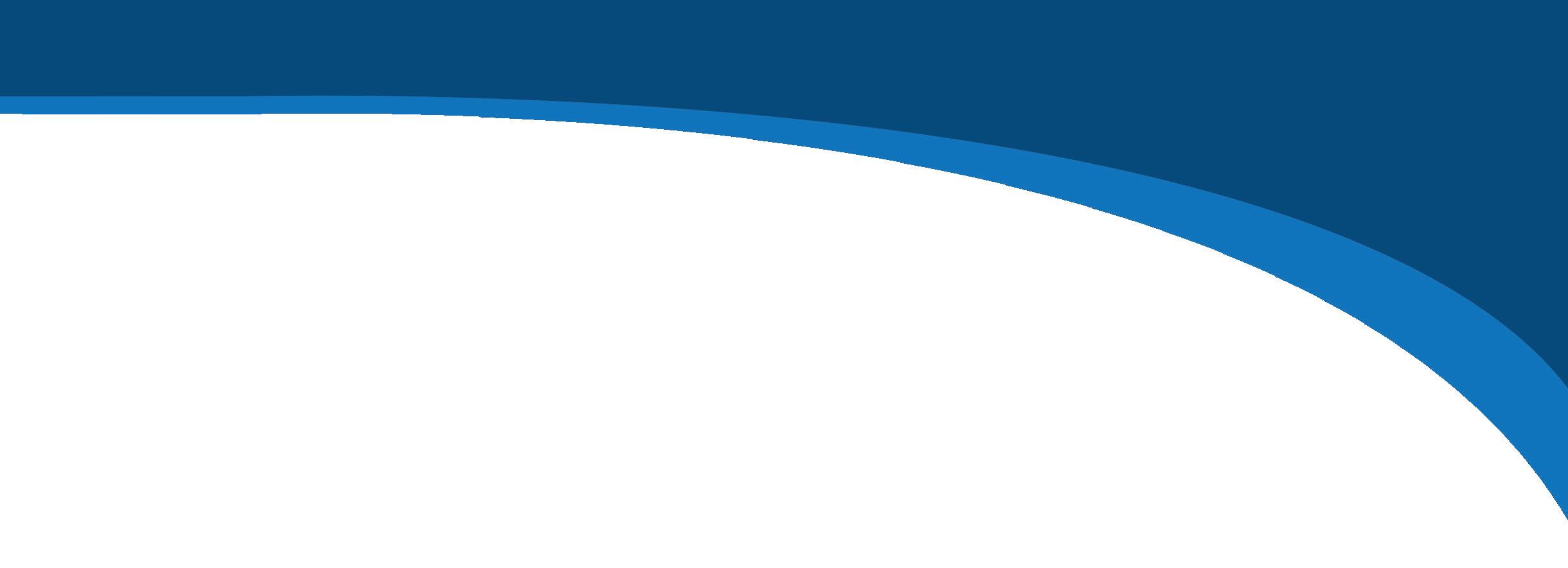
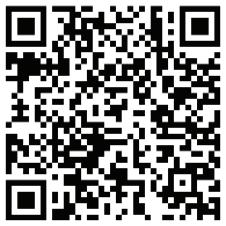
Medi-Dose, Inc./EPS, Inc. Delivers Bar Coding, Packaging, and Labeling Pharmacy Solutions
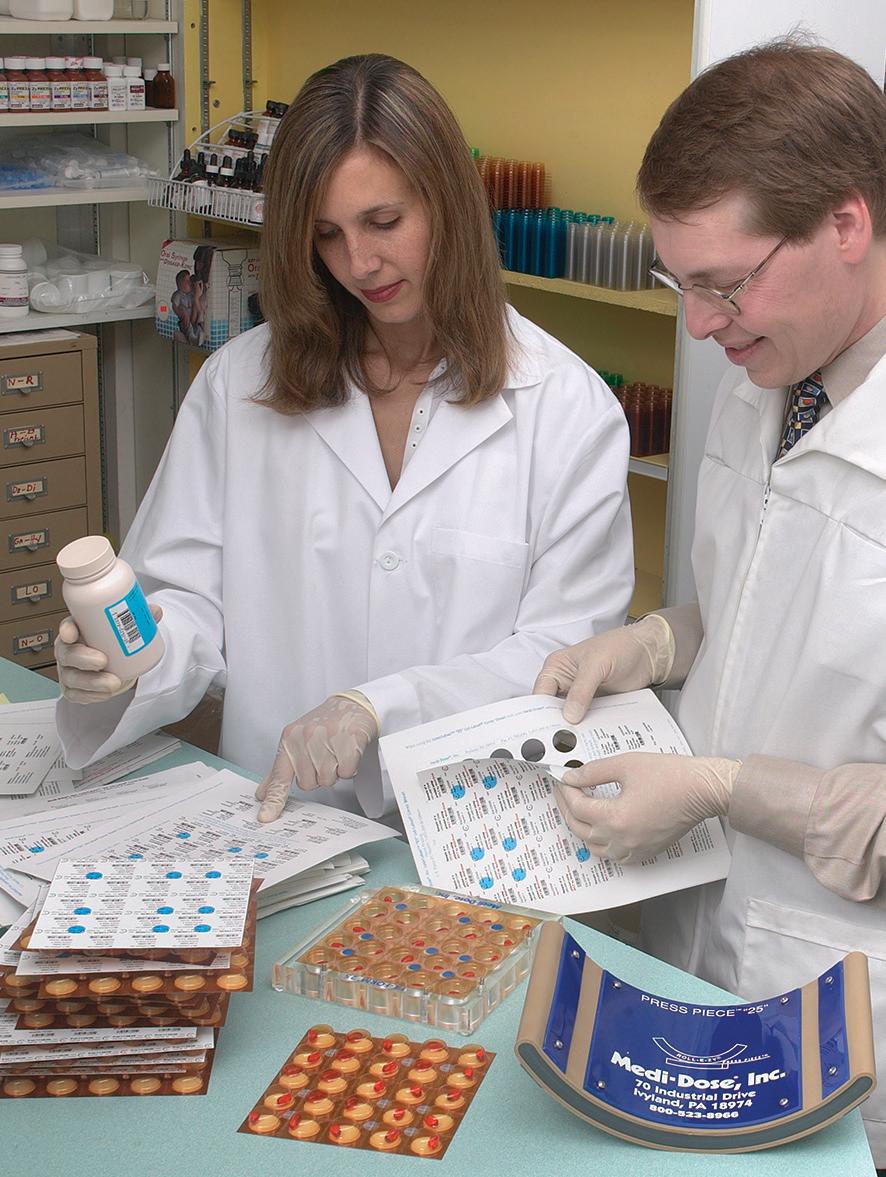
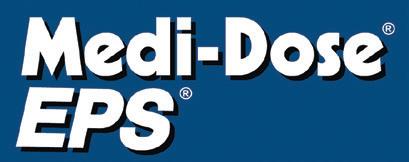
Improve your Solid Oral Unit Dose needs with our comprehensive Bar Coding, Packaging, and Labeling Solutions — designed by healthcare professionals, for healthcare professionals.
President: Robert Braverman
Founded: 1971
Employees: Private
Toll-Free Phone: (800) 523-8966
Phone: (215) 396-8600
Toll-Free Fax: (800) 323-8966
Address: 70 Industrial Drive Ivyland, PA 18974
Website: www.medidose.com
Company Background
Medi-Dose/EPS was founded in 1971 when Milton Braverman, a former pharmaceutical company territory manager, saw the need for inexpensive, manual unit dose packaging allowing a hospital to convert from traditional dispensing. He developed the Medi-Dose System to package, handle, and dispense predetermined amounts of medication so they would be accessible for one regular dose. Comprehensive bar coding and labeling identification is accomplished using our innovative MILT 4 software. Because of the continued success of the MediDose System, Medi-Dose/EPS expanded its product line to include the TampAlerT System, offering tamper-evident liquid packaging without the need for heat tunnels and accessory sealing equipment, as well as a full line of supplies and disposable products designed specifically for the pharmacy and health care professional.
Product Overview
Medi-Dose provides Tamper-Evidence as well as UV and Moisture Resistance for one-year beyond-use dating. Our MILT® 4 software maintains packaging logs and lets you design and print your Lid-Label® Covers with color, bar codes, tall man lettering, and graphics. You can format the labels any way you want, directly from your own computer and printer!
Medi-Dose works well in any pharmacy operation and can be used with all classifications of drugs (chemo meds, meds covered by USP 800, compounded drugs, controlled substances, etc.). It’s affordably priced for all pharmacy budgets. For the best in manual unit dose packaging, check out Medi-Dose!
Features & Options
n Packaging and Labeling Solutions
• Simple to use — no extensive training needed.
• 1-D and 2-D bar coding — including NDC, lot numbers, and expiration dating.
• Ideal for hazardous medications and USP 800 drugs.
• Tall Man Lettering and dynamic formatting options.
• Built-in NDC lookup database and extensive image library.
• Packaging logs and error reporting.
• Six-month and one-year beyond-use dating.
• UV and moisture resistance.
• Tamper-Evidence.
• 15 styles of blisters to accommodate virtually all meds.
• No machinery or space requirements.
• Inexpensive — no capital outlay required.
Product Specifications
n Accompanying Labeling Software
• MILT 4
• MILT 3.0
• MILT 2.6
• Medi-Dose 2000
Trade Shows/Meetings Attended
ASHP Midyear, ASHP Summer, Joint Forces Pharmacy Seminar, National Pharmacy Purchasing Association, EAHP, IACP, and various state, regional, and pharmacy compounding conferences.
Ordering Information
For additional information, please contact us at (800) 523-8966, visit our website at www.medidose.com, or email us at info@medidose.com.
We make it easy to get what you need.
Count on ISO-MED to stock all the USP <797> and <800> compliance products you need to help ensure patient safety. Plus, we make it easy to get those products quickly and economically onto your pharmacy shelves, with exceptional ease of ordering and fast online payment.
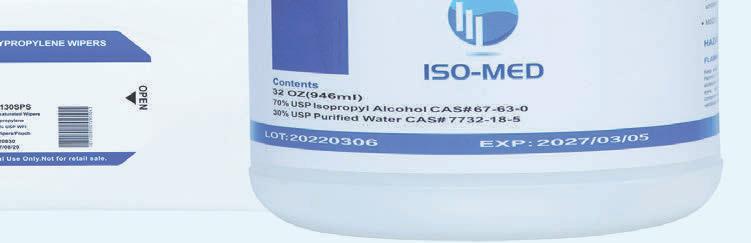

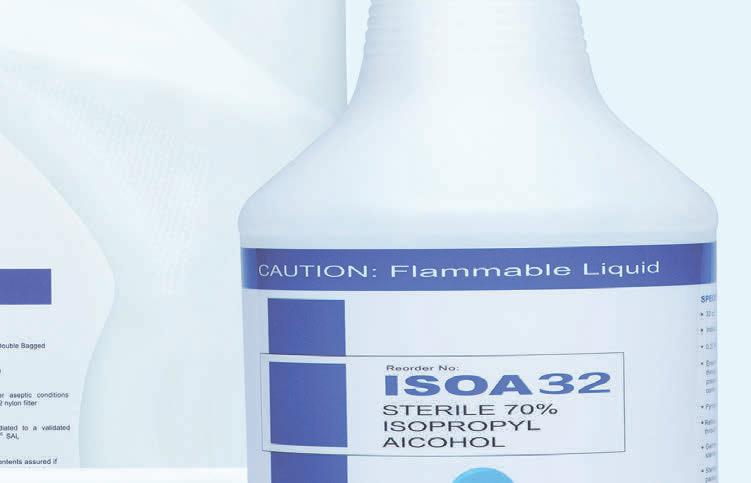
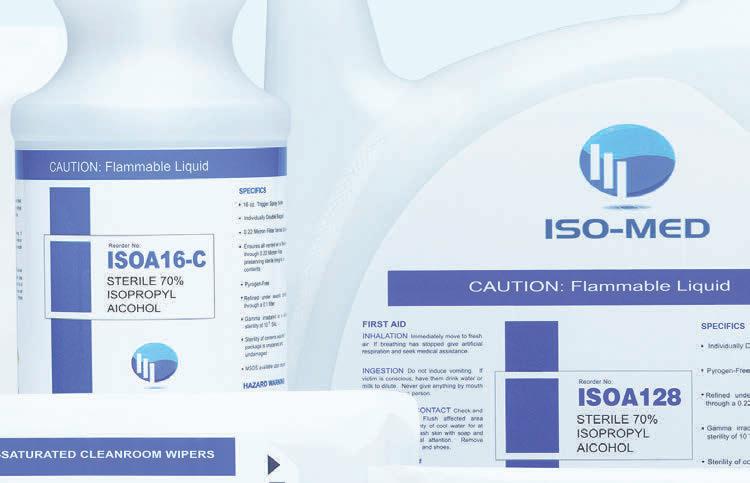

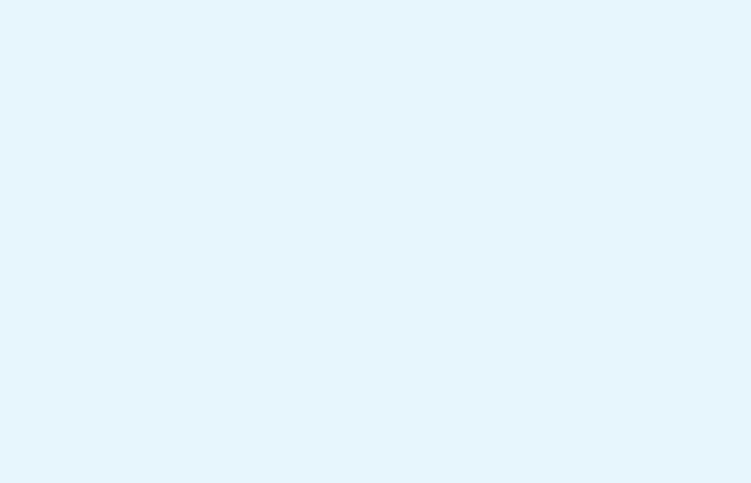
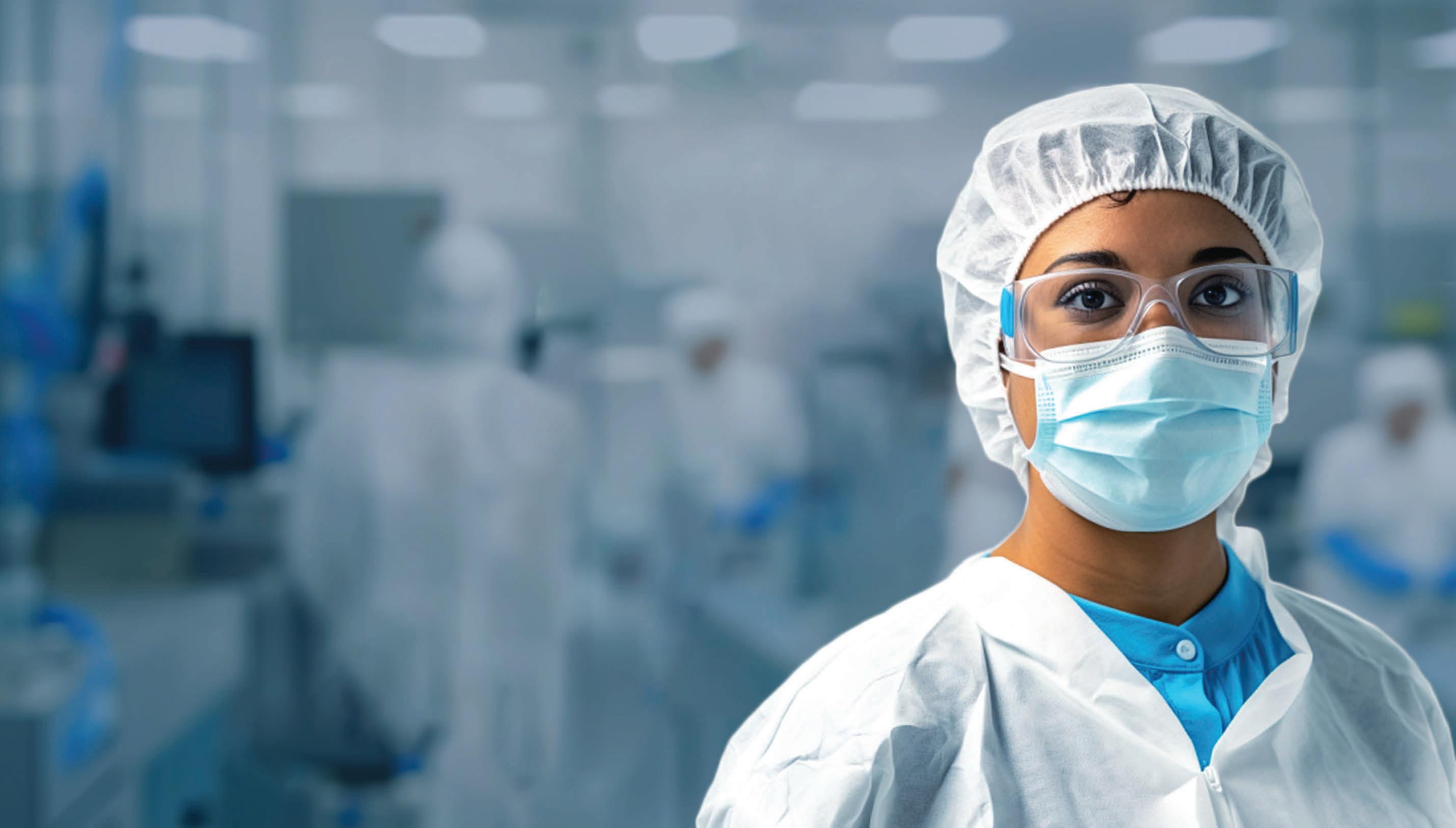
Pharmacy safety made easy
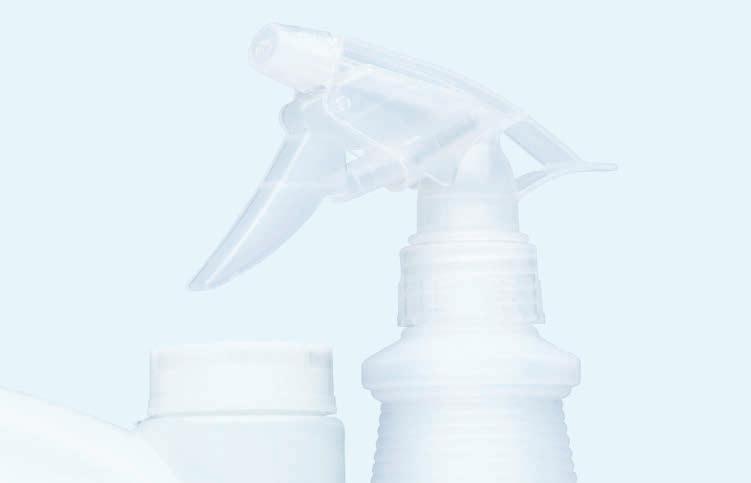
Order online or call today.
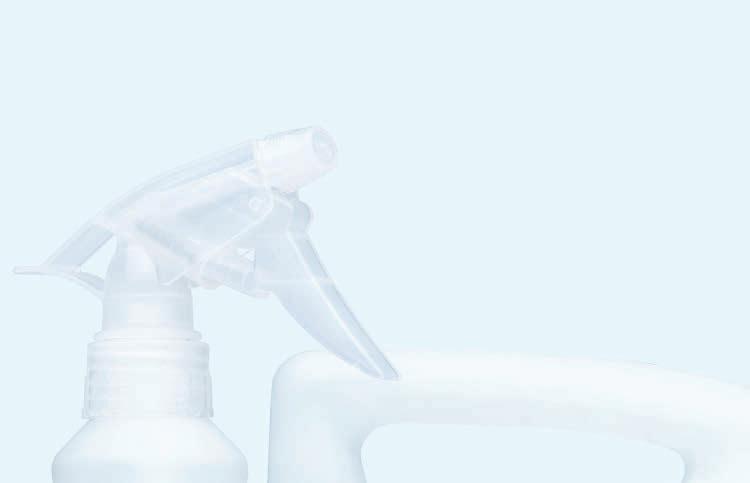
ISO-MED Makes it Easy to Stay Compliant
President: David Lowrie
Founded: 2010
Toll-Free Phone: (800) 797-1405
Fax: (951) 547-1681
Address: 1220 Graphite Drive Corona, CA 92881
Website: www.iso-med.com
Company Background
Since 2011, ISO-MED, Inc., a medical supply distributor, has been a trusted hospital supplier with a solid combination of quality, selection, service, and convenience. We supply quality products for pharmacy cleanrooms and other medical industries in the United States.
Providing high-grade supplies for cleanrooms, laboratories, homecare, and more. We strive to achieve and maintain compliant sterile compounding environments.
Product Overview
ISO-MED maintains the largest and broadest portfolio of on-theshelf warehouse supplies.
We offer customized supply plans, a seamless e-commerce customer experience, easy ordering with matching manufacturer, and dependable purchasing/supplier aggregation services. With one-on-one scheduled training services, we increase the efficiency of your purchasing processes, consolidate your portfolio, and link your on-site supply demand to your inventory management processes.
Offering value-added services, we provide consistent customer service and on-time delivery with a streamlined transaction process. We are driven to help healthcare-oriented organizations save money.
Features & Options
ISO-MED not only has products that help a hospital conform to cleanroom standards, but we also offer the following products for testing cleanliness.
n ICR Plus TSA LT Contact Plates
Environmental monitoring for isolators and cleanrooms (surface and air monitoring).
n Tryptic Soy Agar
Added measure to assure sterility in your environmental monitoring program! Hardy Diagnostics contact plates are recommended for use in the cultivation of microorganisms from environmental surfaces.
Additional Product Modules
n Premier Product Offerings
• PPE Product Selection
• HD Spill Kit
• Chemotherapy Gowns and Supplies
• Cleaning and Disinfection Solutions
For every cleanroom or critical environment cleaning and disinfection program, ISO-MED offers several brands and ISO-MED, Inc. formularies.
Markets Served
• Hospital
• Compounding
• Infusion
• Retail
Ordering Information
Contact us by phone at (800) 797-1405 or email sales@iso-med.com to gain access to our exclusive online ordering platform.
As one of the top leading suppliers for pharmacy cleanroom supplies, we provide an unparalleled selection of specialized medical products, globally trusted quality and service, and delivery convenience for meeting USP <797> and USP <800> standards.
Trisus® Medication Analytics Suite Powered by The Craneware Group
President & CEO: Keith Neilson
Founded: 1999
Employees: 750
Stock Symbol: AIM:CRW.L
Toll-Free Phone: (800) 411-4566
Website: www.thecranewaregroup.com
Company Background
n Transforming the Business of Healthcare
As The Craneware Group since March 2022, Craneware and Sentry Data Systems, in their unified vision to transform the business of healthcare, collaborate with U.S. healthcare providers to plan, execute, and monitor operational and financial performance so they can continue to deliver quality care and services to their communities. Customers choose The Craneware Group’s Trisus data and applications platform as their key to navigating the journey to financially sustainable value-based care. Trisus combines revenue integrity, cost management, 340B performance, and decision enablement into a single, SaaS-based platform, connecting actionable insights to deliver sustainable margin and operational efficiency — something no other single partner can provide.
Product Overview
n 340B Pharmacy Management
The Craneware Group can help you maximize your 340B benefit with powerful solutions that deliver the precision, compliance, insight, and savings you need to run a successful 340B program and transform your pharmacy business.
• 340B Pharmacy Management & Compliance Solutions
simplify the complexities of pharmacy procurement, utilization, and compliance, while providing advanced NDC mapping functionality with flexible configuration options offering a complete audit trail and visibility into more efficient pharmacy operations. The Sentinel module uses proven methodologies and a robust feature set to take control of hospital pharmacy mixed-use costs, contracts and compliance.
• 340B Contract Pharmacy Management Solutions simplify an array of complex compliance challenges. Sentrex helps you manage your 340B contract pharmacy relationships and expand medication access to more patients. Sentrex330 helps community health centers expand 340B benefits to as many eligible patients as possible and remain compliant while freeing up resources for other important matters.
Trisus Medication Analytic Solutions
Pharmacy leaders can optimize pharmacy performance and profitability using data analytics from the Trisus Medication Analytic Solutions portfolio that provides value cycle insights to deliver revenue integrity and 340B compliance, visibility into at-risk revenue, and opportunities for revenue optimization. The Craneware Group is committed to delivering applications that help pharmacy leaders navigate and prioritize data as needed, with a focus on enhancing financial and operational outcomes.
• Trisus Medication Claim streamlines the claims adjudication process, assisting with complex payor requirements and providing you with insight into all pharmacy charges. This solution integrates with any EMR or split-billing software. It provides you with a real-time dashboard to monitor claims and identify missed revenue, making the compliance of the claim application an important addition for CE’s where modifiers and Actual Acquisition Costs are required.
• Trisus Medication Compare helps pharmacy leaders effectively transition to value-based care by comparing medications, processes, and costs to achieve the best possible outcomes. This application empowers clinical staff and P&T committees to yield data-driven improvements in quality metrics such as average length of stay and 30-day readmissions.
• Trisus Medication Financial Management assesses purchase, billing, and remittance data sets to provide visibility into margins, at the medication level, giving pharmacy leaders the insights needed to make informed business decisions on a multitude of pharmacyrelated areas.
• Trisus Medication Formulary analyzes the formulary and improves charge capture, ensures coding compliance, and verifies cost accuracy to drive optimal pharmacy financial performance.
Testimonial
“The product’s web interface is user friendly ... the reporting functionality is significant. We can really drill down into just about anything that we can think of within the product.”
— AnalystContact Information
Find out how Trisus Medication Analytic Solutions can help streamline your claims processing, manage complex reporting requirements, and transform your business of pharmacy by visiting thecranewaregroup.com and requesting a free demo today!
No longer limited by poor visibility into drug reimbursement, pharmacy business leaders can tackle difficult budgets and profit and loss with transparent intelligence to enhance financial and operational performance in pharmacy.
Medication
Class II, Type A2 Biosafety Cabinet
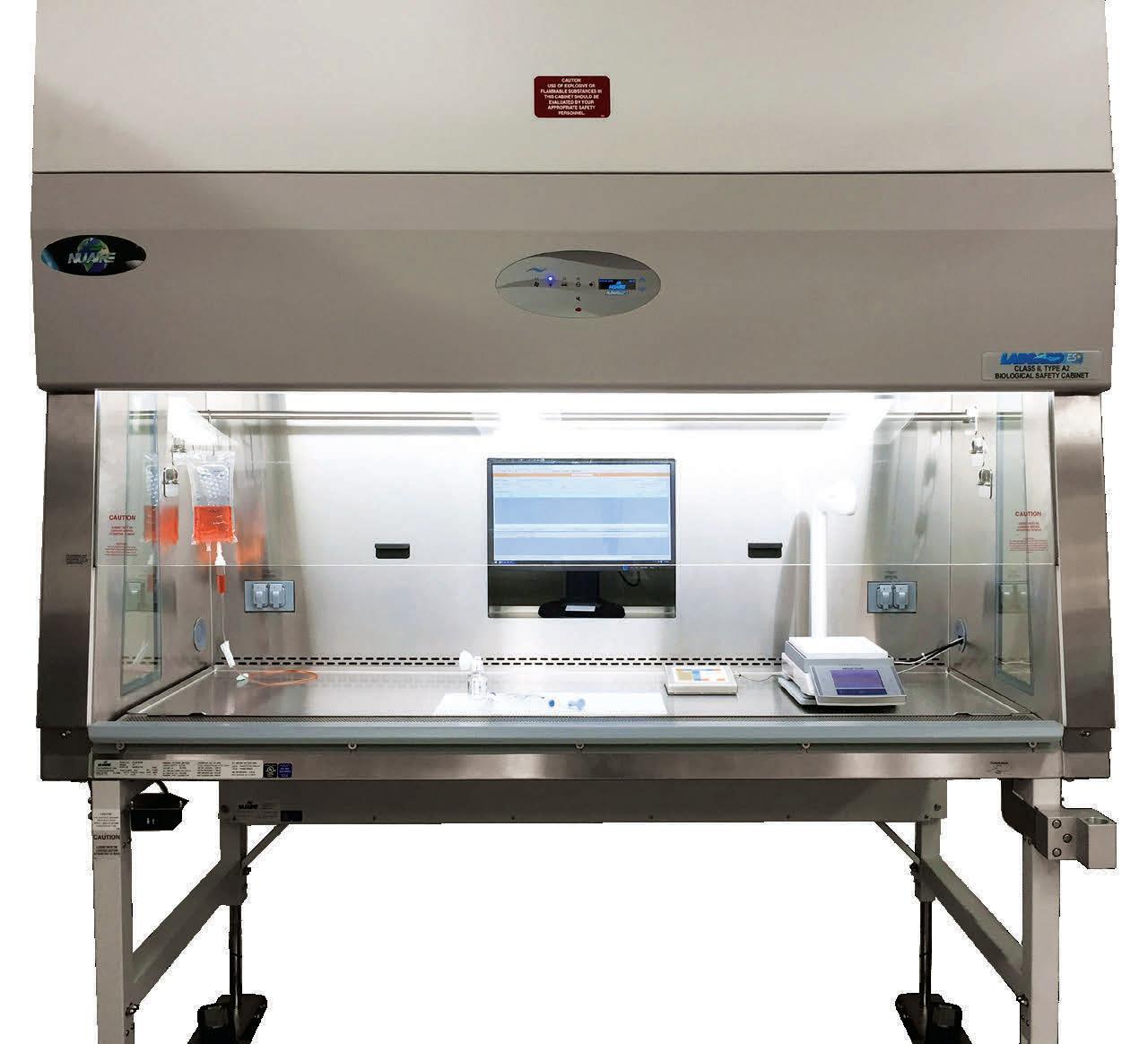
Protection: Product, Personnel, & Environmental
Sterile Hazardous Workflow
Containment Primary Engineering Control (C-PEC)
Model: NU-543 Series
Optimized for Sterile Hazardous Drug Compounding Systems
IV Bar with 3 Height Locations and 6 Hooks for IV Preparation
Back-Wall Cutout for Viewing Computer Monitor
Interior Duplex GFCI Outlets and Cord Pass-Through Ports
Motorized Auto-Rising Base Stand for Optimal Comfort
Up to 12 inch (305 mm) Access Opening
*Product shown with optional features
Sterile Non-Hazardous Workflow
Primary Engineering Control (PEC)
Model: NU-240 Series
Optimized for Sterile Non-Hazardous Compounding
ErgotronTM Mount for Monitor, Keyboard, and Mouse
Easy-to-Clean Stainless Steel Work Surface
IV Bar with 3 Height Locations and 6 Hooks
Telescoping Base Stand with Shelf Attachment
Exterior Mounted Duplex GFCI Outlet
Sidewall Cord Pass-Through Ports
Learn more or request a quote online at: www.nuaire.com
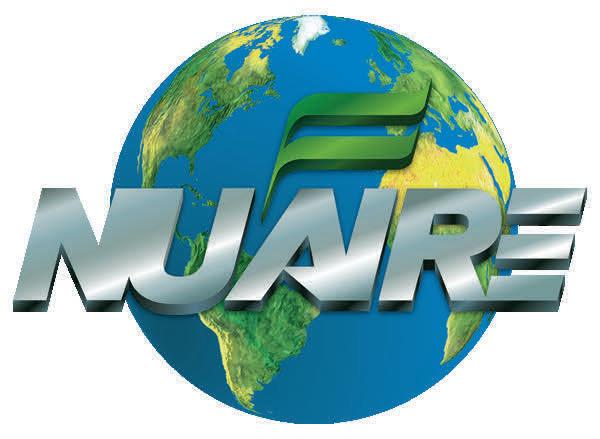
Horizontal Laminar Airflow Workstation
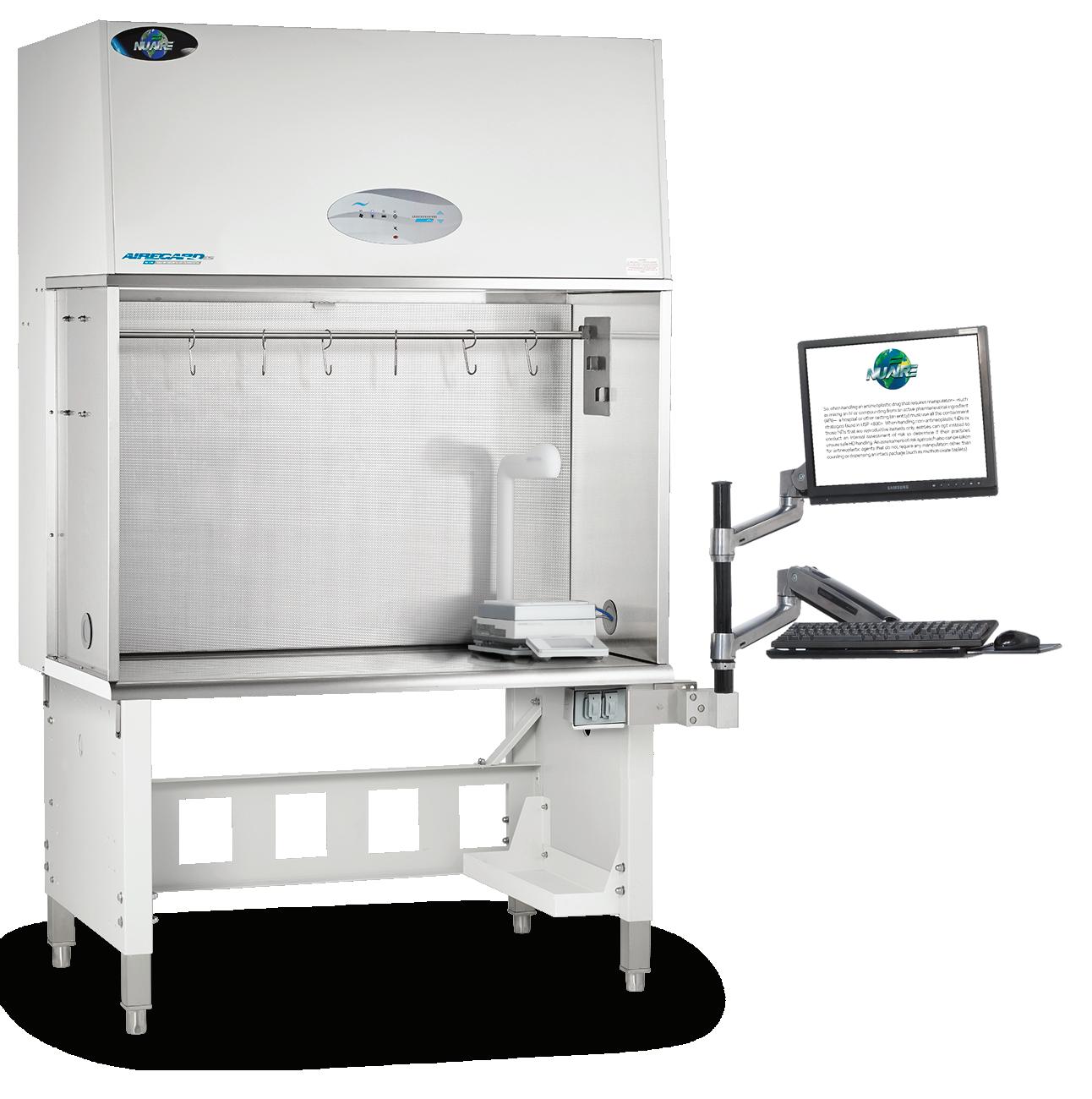
Protection: Product
*Product shown with optional features
Configurable Engineering Controls From NuAire to Optimize Medication Workflows
Choose Containment Primary Engineering Controls (C-PECs) built around your pharmacy’s workflow to enable you to perform safe, ergonomic, and efficient drug compounding.
President & CEO: Bill Peters
Founded: 1971
Employees: 265
Toll-Free Phone: (888) 468-2473
Phone: (763) 553-1270
Toll-Free Fax: (800) 328-3352
Address: 2100 Fernbrook Lane
Plymouth, MN 55447
Website: www.nuaire.com
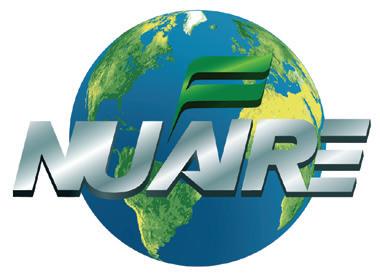
Company Background
To help you with the compounding process, NuAire has created a range of pharmacy equipment that meets the U.S. Pharmacopeia’s <797> standard for compounding sterile preparations and U.S. Pharmacopeia’s <800> standard Hazardous Drugs — Handling in Healthcare Settings. You can use NuAire’s primary engineering controls such as a compounding aseptic isolator (CAI), which provides a clean, positive pressure work environment for compounding non-hazardous drugs, or a compounding aseptic containment isolator (CACI), which provides a clean, negative pressure work environment that minimizes exposure to airborne toxins and other hazardous materials. NuAire also has biosafety cabinets (BSC), laminar airflow workstations (LAFW), containment ventilated enclosures (CVE), and fully customizable enclosures for use in a compounding pharmacy.
Choose NuAire as the Safer Choice for Your Pharmacy.
Product Overview
n NU-543 Class II Type A2 Biosafety Cabinet
The LabGard® ES NU-543 provides the pharmacy with a Containment Primary Engineering Control (C-PEC) to optimize sterile, hazardous drug compounding workflows. This model features a dual thermistor airflow sensor and alphanumeric display with two outlets and a cord pass-through port for electrical devices. The NU-543 can be built with an optional smooth interior and includes a prop up work tray to ease regular cleaning under the work surface. Optional base stands are available with motorized height adjustability and support arms for PC keyboards and monitors. A separately available exhaust canopy with configurable side air gaps provides the installer with flexibility when connecting the cabinet to an external exhaust system.
n
NU-240 Laminar Airflow Workstation
The AireGard™ ES NU-240 creates HEPA-filtered horizontal laminar airflow to provide product protection for sterile but non-hazardous drug compounding in pharmacies. The DC ECM blower creates ISO Class 5 air cleanliness inside a work zone surrounded by stainless steel or
optional polycarbonate sidewalls and stainless steel with a PVC core work surface. You can easily monitor airflow performance via the Aeromax™ control system that visualizes pressure in real time. The work zone comes standard with cord-pass throughs and LED lighting. An optional I.V. bar, electrical outlets, and service valves/couplings can also be added to fit your specific needs. Optional base stands are available with motorized or telescoping height adjustability with support arms for PC keyboard and monitor to further support an ergonomic workflow.
n Custom Containment Solutions
NuAire can meet you at the drawing board to create a one-of-a-kind, tailor-made solution just for you. NuAire is proud to be able to offer product customization for those with specific needs outside the scope of the standard product lines. We offer large welded or assembled containment solutions to meet your every specific need.
Additional Product Lines
• Class II Type B1 Biosafety Cabinets
• Class II Type B2 Biosafety Cabinets
• Horizontal Laminar Airflow Workbench (Console Style)
• Vertical Laminar Airflow Workbench
• Restricted Access Barrier Systems (RABS)
• CO2 Incubators
• Ultralow Freezers
• Animal Transfer Stations
Trade Shows/Meetings Attended
• CALAS/ACSAL, May 6-9, Montreal, QC
• AACC, July 23-27, Anaheim, CA
• CABS/ACSB, September 18-20, Montreal, QC
• Tradeline, October 5-6, Austin, TX
• ABSA, October 13-18, Omaha, NE
• AALAS, October 22-26, Salt Lake City, UT
• ASHP, December 3-7, Anaheim, CA
GPO Affiliations
Vizient, HealthTrust, Premier, Ascension
Ordering Information
To learn more or request a free quote online, scan the QR code below or visit www2.nuaire.com/20ways-2023/med-workflow.

Q A&
Wyley McCoy, BS Pharm, PharmD, MBA
SVP Medication & Supply Portfolio
Q. With the growing amount of data, do hospital pharmacies have the labor resources to turn the data into information to drive decision-making?
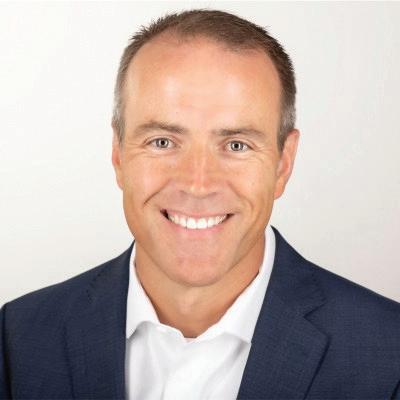
Current technology provides access to large amounts of data which can be overwhelming. Hospital pharmacies, specifically, may need significant resources to ingest, synthesize, and act on the data. Within pharmacies, it is easy to retrieve information from multiple sources such as automated dispensing cabinets, robotic compounding devices, environmental documentation, and radio frequency identification tags. For example, advanced pharmacy information systems (PIS) can automate data collection and provide real-time analytics on medication orders, inventory levels, and other critical data points. This can help pharmacists identify trends, make informed decisions, and optimize workflows. With more systems having pharmacy integrated into the larger electronic health record, these trends can be even more impactful to patient outcomes and system performance. Additionally, hospitals may employ data analysts or data scientists who specialize in healthcare analytics to help turn the data into actionable insights. These professionals can use advanced data mining and visualization techniques to identify patterns, correlations, and outliers that may not be immediately apparent.
While there is no doubt that managing and analyzing the growing amount of data in hospital pharmacies can be a challenge, hospitals have a range of resources available to help them turn that data into meaningful information that can drive decision-making. Tapping into resources not traditionally used by pharmacy leadership has the potential to improve efficiency and maximize the benefits of interdepartmental data sharing.
Q. Do hospital pharmacy leaders have the skill set to manage revenue cycle activities?
Hospital pharmacy leaders may have a range of skills and expertise, but their ability to manage revenue cycle activities will depend on their specific training and experience in that area. Revenue cycle management is a complex and specialized field that requires a deep understanding of healthcare reimbursement and billing processes, as well as knowledge of healthcare regulations and compliance requirements. This landscape is dynamic, so continuous learning to stay up to date with changing laws and regulations is essential to
maximize both the value and efficiency of reimbursement. There are many opportunities for pharmacy professionals to learn in this area that are either self-directed, administrative residencies, nontraditional rotations and fellowships, certificate programs and training through professional organizations, or coterminous business-focused degrees offered by colleges of pharmacy.
While some health systems may have pharmacy leaders experienced in revenue cycle management, it is more likely that hospitals will have dedicated revenue cycle teams or consultants who specialize in this area. These teams or consultants will experience the greatest success when they work closely with pharmacy leaders to ensure that revenue cycle activities are aligned with overall pharmacy goals and strategies.
A novel approach is to own the pharmacy revenue cycle process within the pharmacy department, with a strategic focus on high-cost specialty therapeutics to maximize reimbursement. In some cases, maximizing reimbursement for the health system requires spending on more expensive medications or growing a service that requires higher cost medication.
It’s important for hospital pharmacy leaders to have a basic understanding of revenue cycle management, particularly as it relates to pharmacy operations. This may include knowledge of medication billing codes, reimbursement rates, and insurance requirements. By working closely with revenue cycle teams or consultants, pharmacy leaders can ensure that revenue cycle activities are optimized to support high-quality patient care and efficient pharmacy operations.
Q. What data gaps exist working with cross-functional healthcare teams?
Working with cross-functional healthcare teams can create a range of data gaps that can hinder effective collaboration and decisionmaking. Some common data gaps that may exist include:
1. Data Silos: Different healthcare teams may be working with their own sets of data, and this data may be stored in different systems or formats. This can make it difficult to share data across teams and create a comprehensive view of patient health.
2. Lack of Standardization: Healthcare teams may use different terminologies, coding systems, or data formats, which can create confusion and inconsistencies in data interpretation.
3. Data Quality Issues: Data may be incomplete, inaccurate, or outdated, which can compromise its usefulness for decision-making.
4. Privacy and Security Concerns: Sharing patient data across different teams can raise concerns around patient privacy and security, particularly when sensitive health information is involved.
5. Limited Access to Data: Some healthcare teams may have limited access to certain types of data, which can limit their ability to make informed decisions.
6. Timeliness: Even if teams can manually collate data, by the time the work is done, it is too late for decision making at the time of care, leading to expensive claim re-work.
To address these data gaps, cross-functional healthcare teams need to work together to establish data-sharing agreements, develop common data standards and protocols, invest in data quality and privacy controls, and ensure all team members have access to the data they need to make informed decisions. Collaborative efforts to address these data gaps can help to optimize patient outcomes and improve the efficiency and effectiveness of healthcare delivery. Overall, technology can help bridge data gaps in healthcare by improving data collection, analysis, and sharing. By making health data more accessible and actionable, technology can help providers deliver more effective and personalized care.
Q. Pharmaceutical manufacturers are increasing restrictions, forcing submission of data to maintain access to 340B pricing. What should a health system consider when evaluating data submission?
Are there alternatives? What are health systems needs around data access and analysis to make these decisions?
When evaluating whether to submit data requested by manufacturers to maintain access to 340B pricing, health systems should consider the following factors:
1. Cost-Benefit Analysis: Health systems should weigh the potential benefits of maintaining access to 340B pricing against the value of the data.
2. Compliance With Regulations: Health systems must ensure that any data sharing is compliant with applicable laws and regulations, such as HIPAA and the 340B program requirements.
3. Data Quality and Timeliness: Health systems should verify that the data they are sharing is timely, complete, and relevant. Once the decision is made to submit data, submit daily.
4. Closely monitor wholesaler pricing to verify 340B price is restored and maintained.
5. Carefully review each manufacturers programs for limitations, including distance and dates.
In summary, health systems need to carefully consider the implications of data sharing when evaluating manufacturer demands for data related to 340B pricing. Health systems should also have the necessary data analytics capabilities to make informed decisions about data access and use.
Q. As hospitals are preparing for the future related to government changes to how healthcare is reimbursed, what are key areas where software applications may play a role?
We know that drug pricing is a target area that will see change as it is top of mind for patients experiencing the direct impact of rising drug costs, and therefore it has become top of mind for elected officials. With the passage of the inflation reduction act, attention will be turning to the implementation to negotiate drug prices in Medicare, reduce patient out of pocket costs, and provide access to new biosimilar drugs in the market and the trickle effect to commercial payers. Leaders will need to be sure that they are monitoring their operations for changes to reimbursement, 340B price changes, and coding and billing requirements. Software solutions can assist leaders recognize opportunities to impact contract reimbursement terms, purchasing patterns, and clinical decision support to make impactful clinical, operational, and financial changes.
Wyley McCoy, BS Pharm, PharmD, MBA, is the senior vice president medication and supply portfolio, and oversees Craneware’s Medication and Supply Portfolio,
which includes 340B and pharmacy financial and analytic solutions that enable the highest-quality patient care through access to real-time, relevant, and rich data.
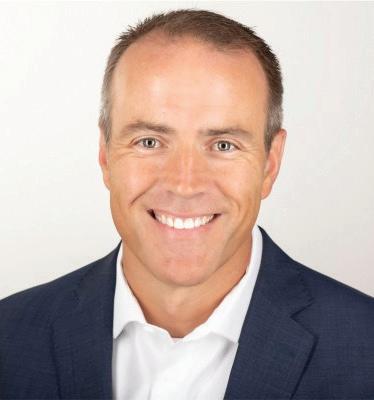
340B RESOURCES Buyer’s Guide
340B Health
1101 15th Street NW Suite 910
Washington, DC 20005
(202) 552-5864
340bhealth.org
340Basics
161 Gaither Drive Suite 201
Mount Laurel, NJ 08054
(609) 541-1300
340basics.com
Apexus/Acentrus Specialty
290 E. John Carpenter Freeway Suite 4
Irving, TX 75062
(469) 299-7300
apexus.com
Aventi Health
1433 North Water Street 4th Floor
Milwaukee, WI 53202
(414) 792-9673
aventihealth.com
Cervey
410 Kay Lane
Shreveport, LA 71115
(800) 710-9348
cervey.com
Clearway Health
1 Boston Medical Center Place
Boston, MA 02118
(833) 966-0506
clearwayhealth.com
Cloudmed, an R1 company
1100 Peachtree Street Suite 1900
Atlanta, GA 30309
(857) 574-5213
cloudmed.com
Codonics
17991 Englewood Drive
Middleburg Heights, OH 44130
(440) 243-1198
codonics.com
CPS Solutions, LLC
655 Metro Place S Suite 450 Dublin, OH 43017
(800) 968-6962
cps.com
Hudson Headwaters 340B 333 Glen Street Floor 7 (Pharmacy Services)
Glen Falls, NY 12801
(855) 835-3402
hudson340b.com
iA
8888 Keystone Crossing Suite 1550
Indianapolis, IN 46240
(317) 664-7592
iarx.com
Liberty Software 3205 E Southlake Boulevard
Southlake, TX 76092
(800) 480-9603
libertysoftware.com
McKesson Corporation
6555 North State Highway 161
Irving, TX 75039
(972) 446-4800
mckesson.com
Micro Merchant Systems
6800 Jericho Turnpike Suite 203E
Syosset, NY 11791
(866) 495-3999
micromerchantsystems.com
Omnicell, Inc.
2625 Augustine Drive Suite 301 Santa Clara, CA 95054 (800) 850-6664 www.omnicell.com
Optimal340B 3359 S Milan Place Meridian, ID 83642 (866) OPT340B (866-678-3402) optimal340b.com
ProxsysRx, Inc.
1500 Urban Center Drive Suite 530 Birmingham, AL 35242 (205) 533-9119
proxsysrx.com
R&S Northeast
8407 Austin Tracy Road Fountain Run, KY 42133 (800) 262-7770
rsnortheast.com
Ravin Consultants
6322 Glen Abbey Lane Bradenton, FL 34202 (941) 441-6212
ravinconsultants.com
RS Software
2600 Technology Place Norman, OK 73071 (877) 290-7774
rssoftware.net
ScriptPro 5828 Reeds Road Mission, KS 66202 (800) 606-7628
www.scriptpro.com
Shields Health Solutions
100 Technology Center Drive Suite 600 Stoughton, MA 02072
shieldshealthsolutions.com
SpendMend Pharmacy (f.k.a. Turnkey Pharmacy Solutions)
2680 Horizon Drive SE Grand Rapids, MI 49546 (616) 257-6300
spendmend.com/solutions/ pharmacy-solutions
SUNRx
10181 Scripps Gateway Court San Diego, CA 92131 (800) 786-1791
www.sunrx.com/contact
The Craneware Group 800 Fairway Drive Suite 400 Deerfield Beach, FL 33441 (800) 411-4566
thecranewaregroup.com
Trellis Rx
1175 Peachtree Street NE 10th Floor, Suite 1000 Atlanta, GA 30361 (800) 503-5420
trellisrx.com
Verity Solutions 12131 113th Avenue Suite 200
Kirkland, WA 98034 (425) 947-1937
verity340b.com
Visante 101 East Fifth Street Suite 2220
Saint Paul, MN 55101 (866) 388-7583
visanteinc.com
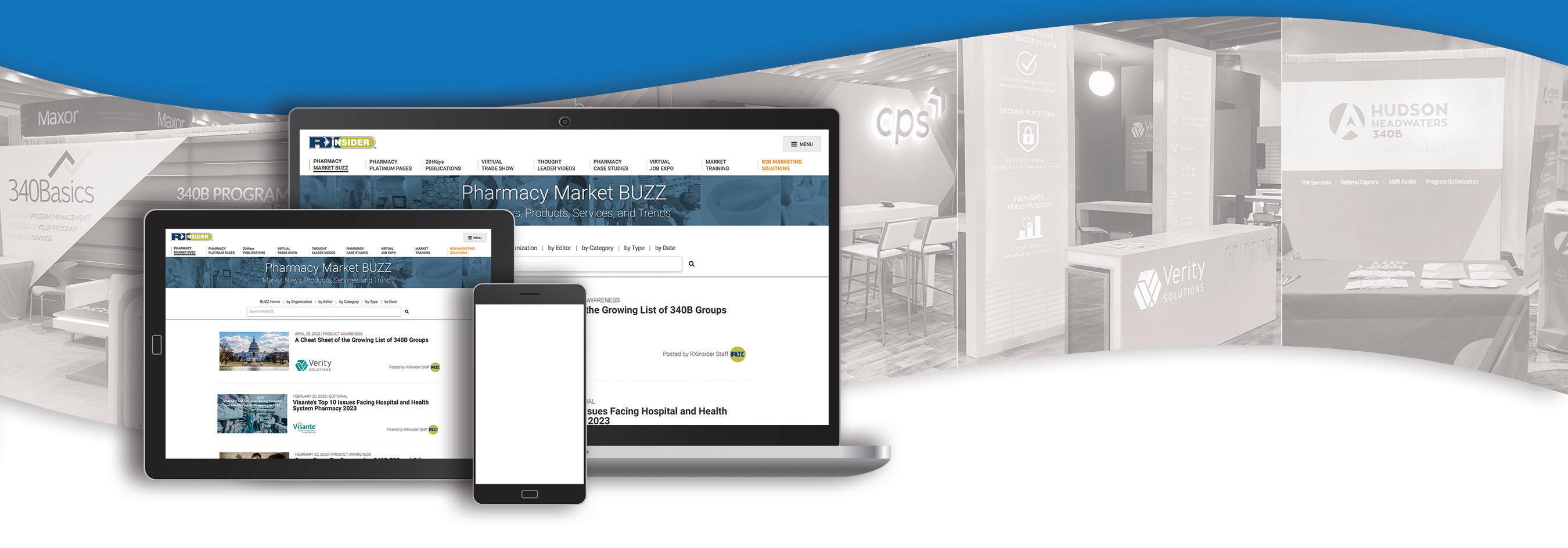

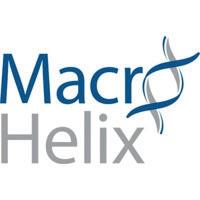
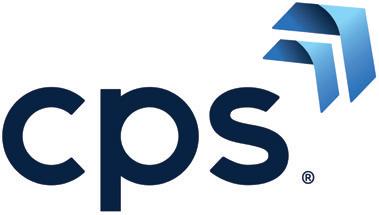
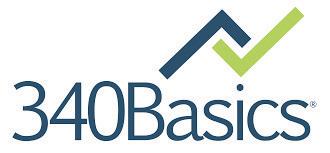
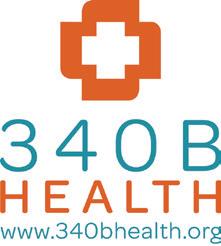
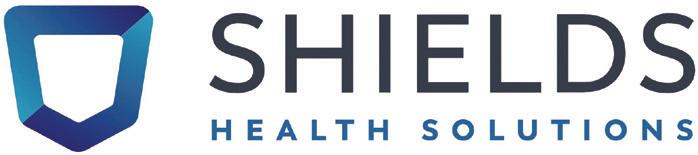

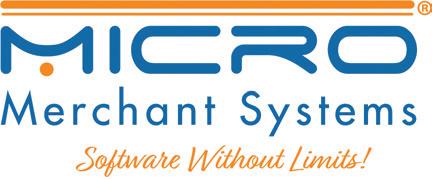
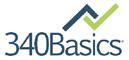
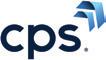
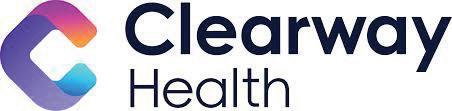
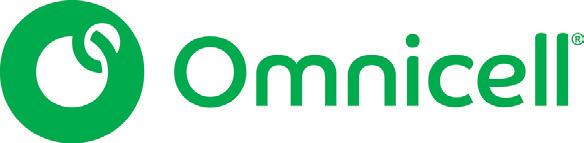
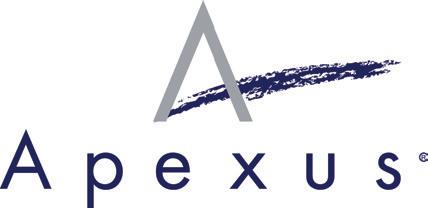
IMI designs innovative medical devices that enhance the security of medication from pharmacy to patient. Fifty years of product design exclusively focused on the needs of the compounding pharmacist means exceptional quality, reliability and customer-driven innovation. From Tamper Evident Caps to essential sterile compounding supplies, ensure the integrity and security of your medications with solutions from the leader in secure drug delivery.
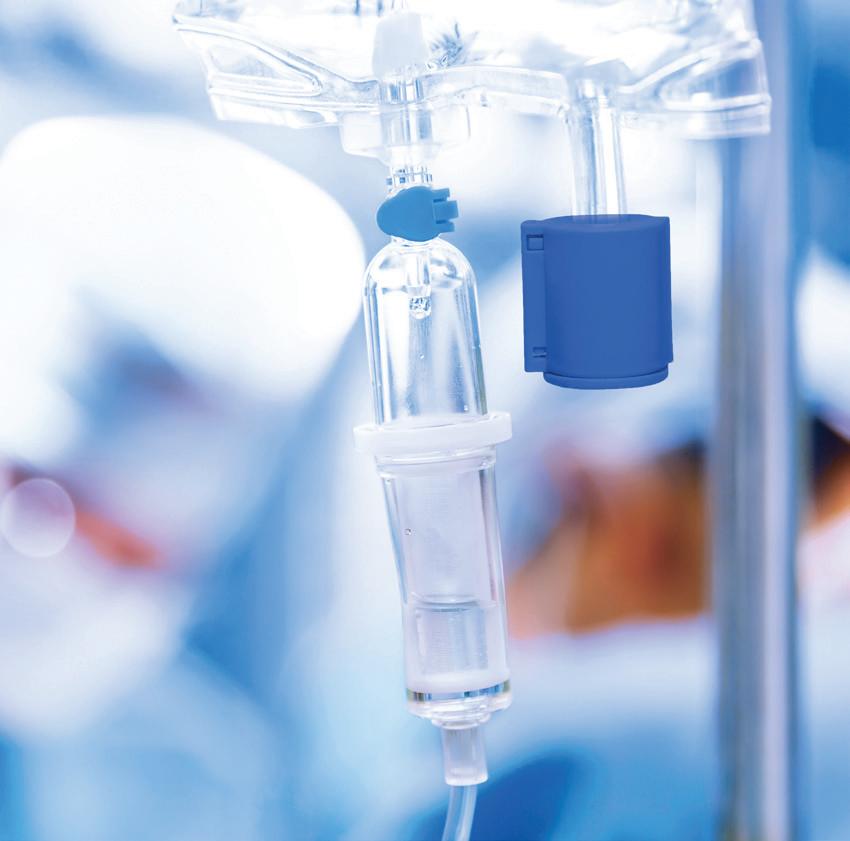
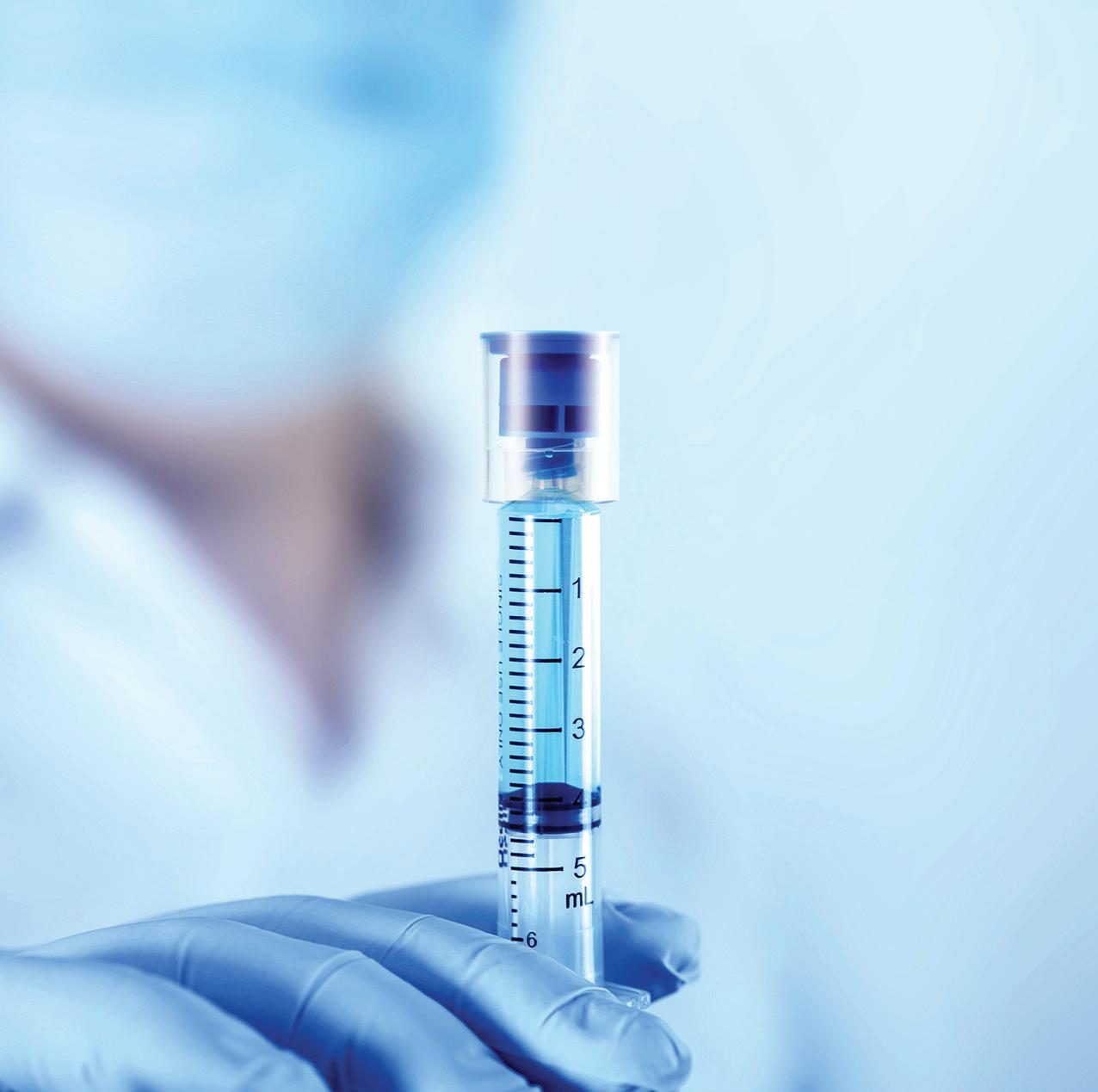
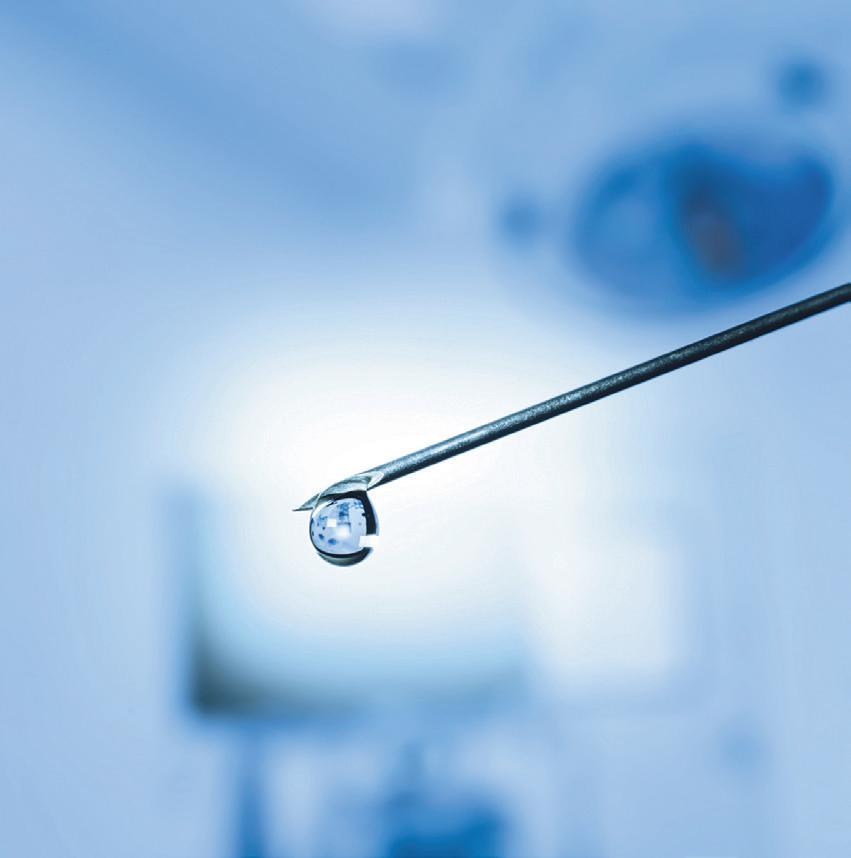
Over 50 Years Serving The Industry
Exceptional Quality & Reliability
Enhance Your Drug Security Program
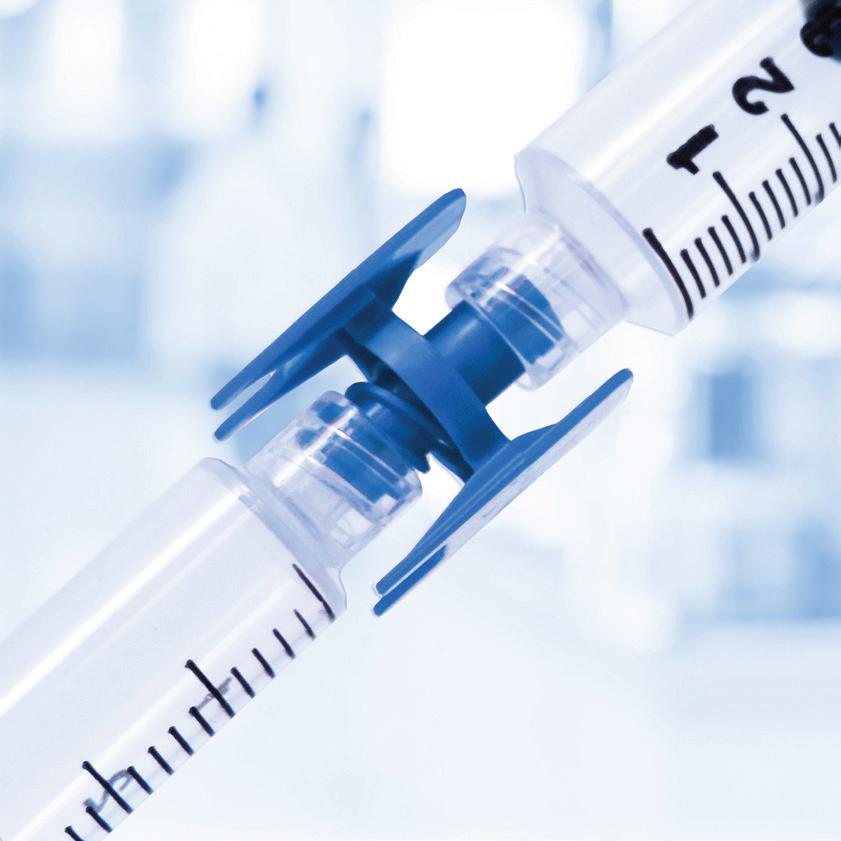
Strengthen USP <797> Practices
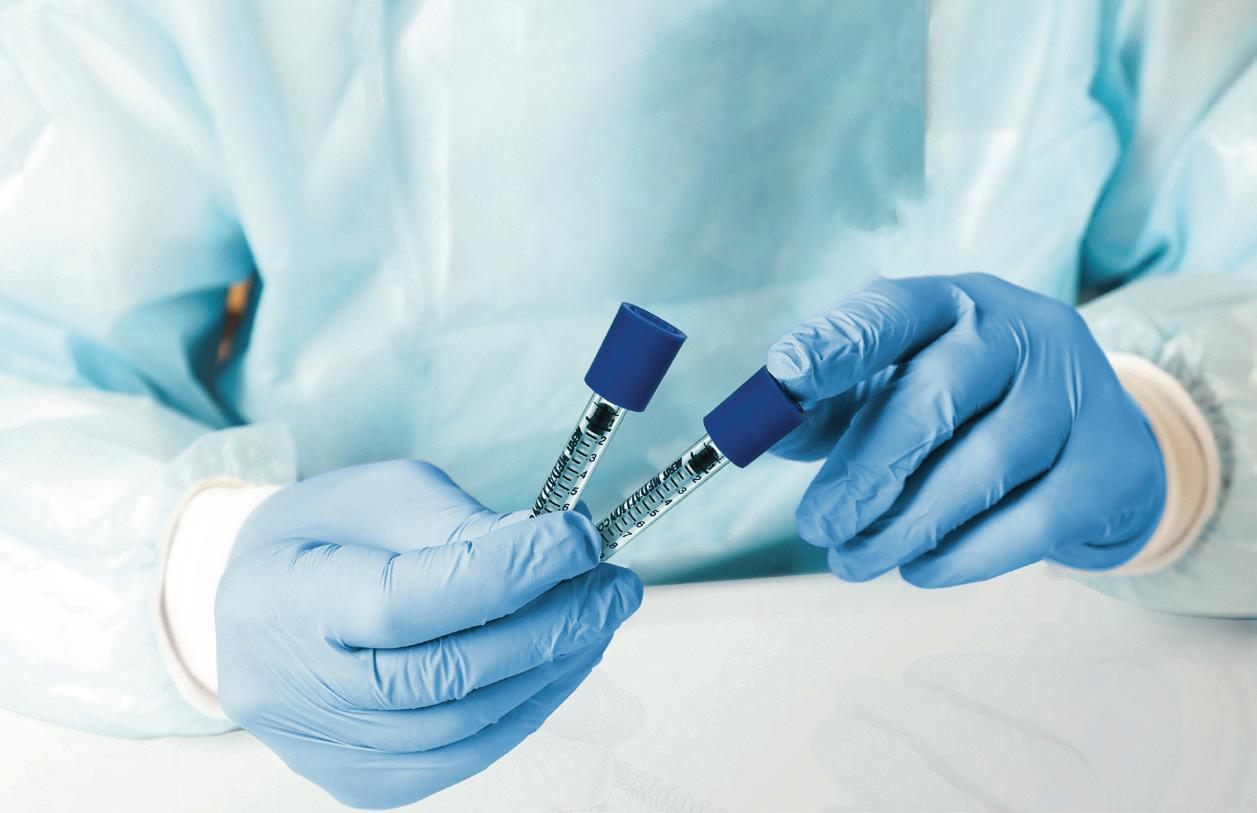
International Medical Industries — Innovation in Secure Drug Delivery
President: Jonathan Vitello
Founded: 1969
Employees: 100+
Toll-Free Phone: (800) 344-2554
Phone: (954) 917-9570
Fax: (954) 917-9244
Address: 2981 Gateway Drive, Pompano Beach, FL 33069
Website: www.imiweb.com
Company Background
Founded in 1967 and exclusively devoted to the needs of the compounding pharmacist, at IMI creating products for the compounding pharmacist is our sole focus. As a result, our customers experience the quality, service, and value that only a specialized partner can offer. Through our partnerships with compounding professionals, we continue to advance our devices to serve the healthcare community. From new product developments to customized packaging configurations IMI’s customer-focused ethos and superior engineering capabilities allow us to be responsive to the needs of our partners and customers. Our capabilities and highly trained teams are the reasons we have remained the industry standard for tamperevident cap technology and how we continue to deliver customer-focused products to enhance pharmacy productivity, safety, and security. All IMI products are manufactured in the United States at our FDA-registered, ISO 13485-certified facility under the strictest quality standards.
Product Overview
n Prep-Lock™ Tamper Evident Caps
Compounded preparations are at their greatest risk when they leave the custody of your pharmacy. The benefits of tamper-evident products to address this risk have been recognized within the standards and guidelines of multiple influential organizations including the American Society of Health-System Pharmacists and the FDA. Tamper-evident products increase overall accountability in the chain of custody of mediation, maintain sterility, prevent leakage, ensure patients receive the full intended dose, and reduce the risk of contamination. Experts agree that the use of tamper-evident products increases the confidence of pharmacies, health care workers, and patients. IMI’s Prep-Lock™ line of products provide high-value, high-quality, tamper-evident closures devices for a variety of drug delivery containers, including I.V., enteral and oral syringes, medication cassettes, and I.V. bags.
n Prep-Lock Tamper Evident Caps Featuring RFID
RFID Technology continues to garner adherents in hospital pharmacy systems. The technology enables real-time scanning that optimizes inventory management, efficiency, and medication safety while creating quantifiable pharmaceutical supply chain benefits by providing item level inventory
visibility down to NDC and lot. Recognizing the advantages that RFID technology presents, IMI joined the industry consortium UnitVisID to help increase the interoperability, quality, and performance of RFIDtagged products. Tamper-evident caps with incorporated UnitVisID RFID provide a labor-reducing solution to adding RFID to your drug doses. With a simple twist of a syringe, your CSPs are equipped with renowned tamperevident protection and robust analytic capabilities provided by compatible RFID systems. These two powerful technologies, in combination, enhance workflow efficiencies, eliminate time-consuming manual inventory control processes, provide assistance with growing regulatory demand, and supply a comprehensive strategy to prevent, detect, and resolve drug diversion events. In addition, by incorporating RFID technology into IMI’s Industryleading Tamper Evident Caps, facilities can significantly reduce their cost of RFID implementation with little time-to-live and minimal staff investment, procedural changes, or capital investments.
n Prep-Lock Tamper Evident Additive Port Caps
The tamper-evident additive port cap provides remarkable protection, and protocol assurance to the medication ports of a variety of I.V. bags, including Baxter, B. Braun, Fresenius Kabi, and more. The simple one-handed installation and considerable contributions to the integrity of I.V. compounds have gained acclaim with pharmacists and healthcare professionals. “I find their products to be the best on the market in terms of the device itself, the functionality, and the securement,” says Neil Colby, RPh, director of infusion pharmacy services CDRX infusion. These products extend the intention of USP <797> from pharmacy to patient by providing last mile security that strengthens pharmacist and HCP confidence and reduces risk of contamination and diversion.
Testimonial
“I find their [tamper-evident] products to be the best on the market in terms of the device itself, the functionality, and the securement.”
— Neil Colby, RPh, Director of Infusion Pharmacy Services, CDRX InfusionAdditional Product Lines
IMI manufactures a variety of high-quality devices for the compounding pharmacist including: Prep-Lock™ Tamper Evident Caps, Prep-Seal™ Caps and Plugs, Prep-Fill™ Sterile Connectors, Rx-Vent™ Filtered Venting Needles, Rx-Tract™ Aspirating Needles.
Trade Shows/Meetings Attended
IMI regularly participates at a variety of industry trade shows and conferences including:
• American Society of Health‑System Pharmacists (ASHP)
• European Association of Hospital Pharmacists (EAHP)
• National Pharmacy Purchasing Association (NPPA)
• International Health Facility Diversion Association (IHFDA)
• Hospital Pharmacy Conference (Health Connect Partners)
• Visit the event website or contact IMI for dates and booth numbers.
Increase pharmacy productivity and safety with economical, American-made devices designed to advance the safety and security of your drug products and ultimately your patients.

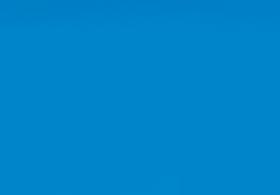
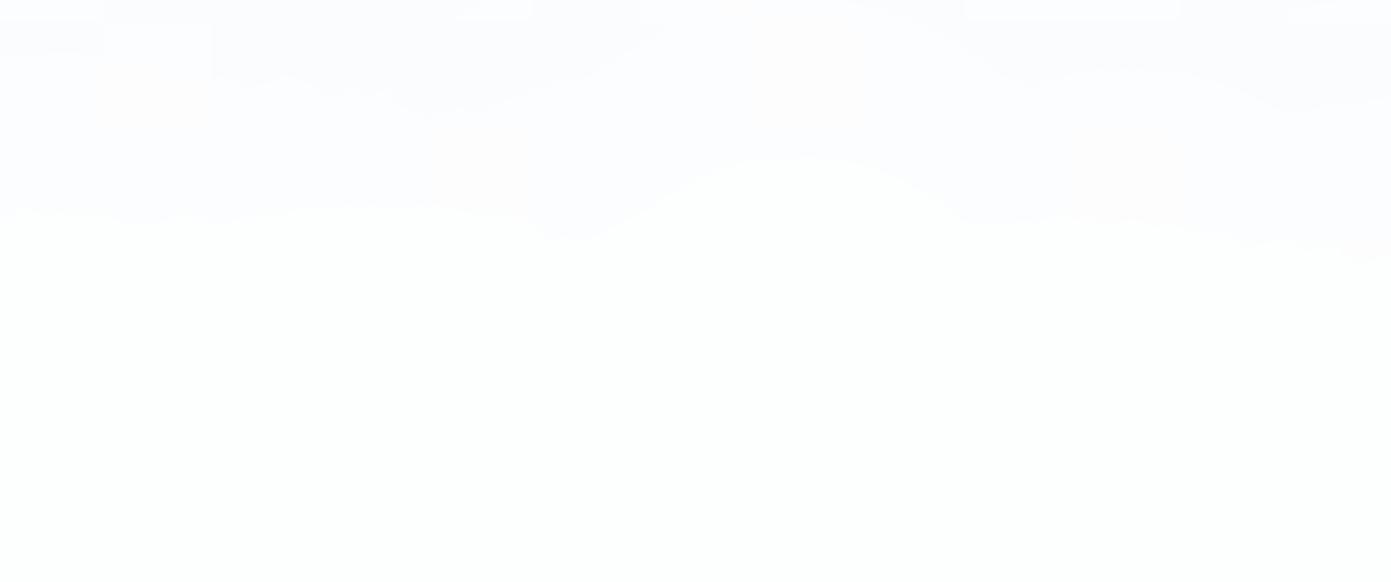
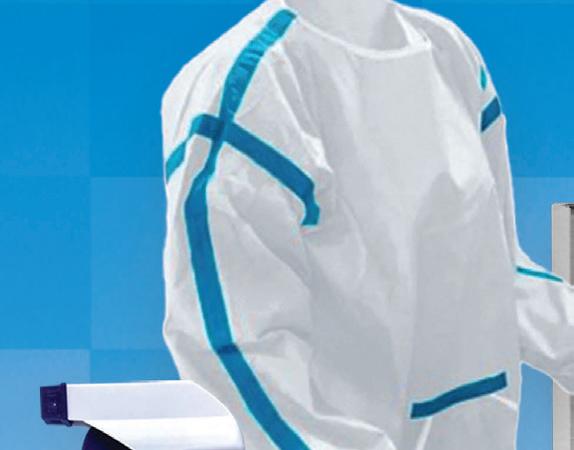
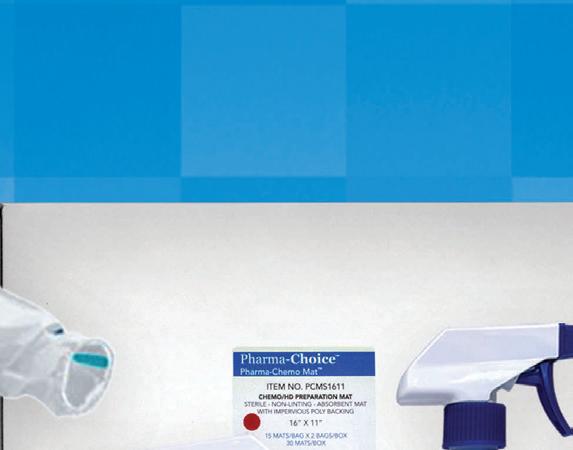
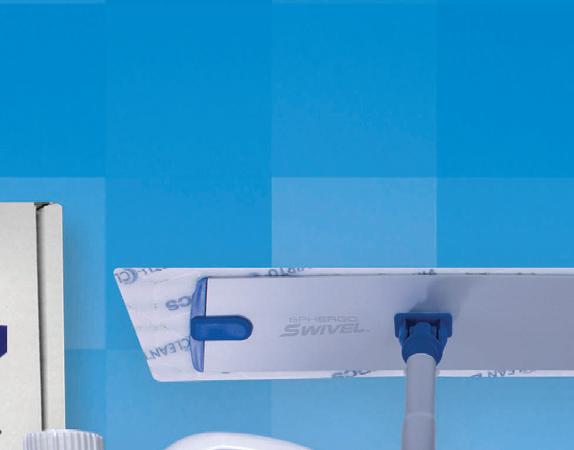
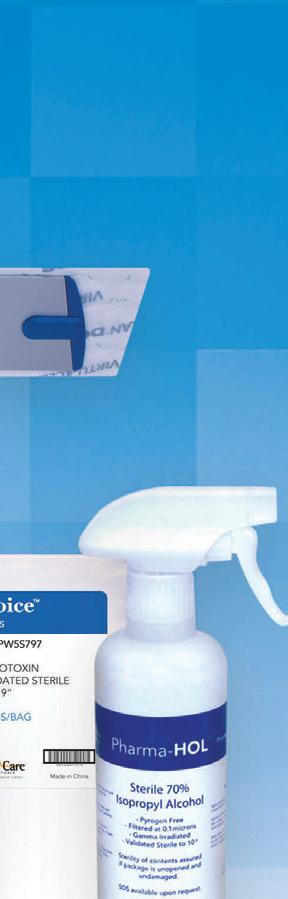
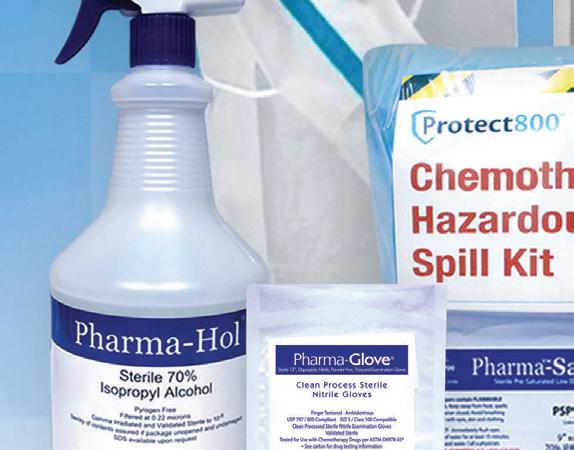
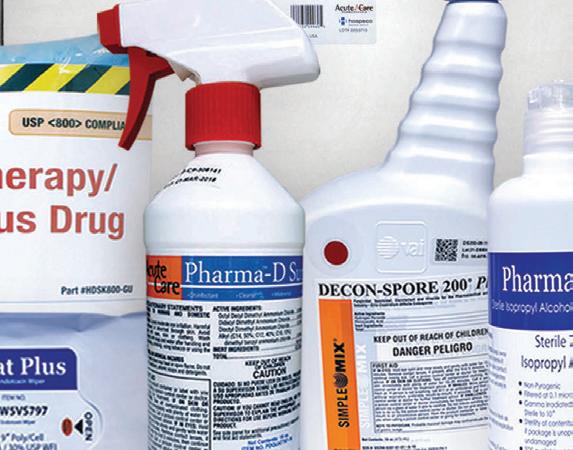
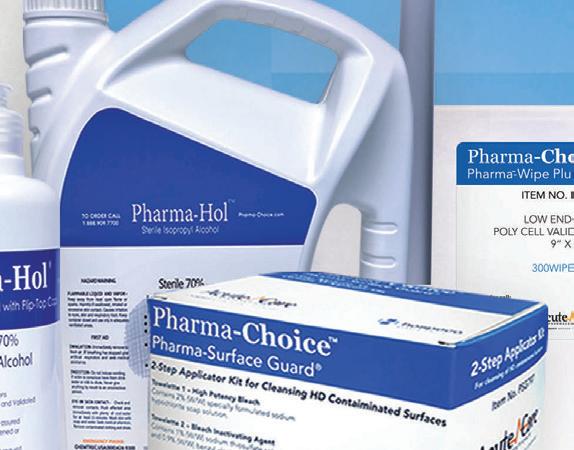
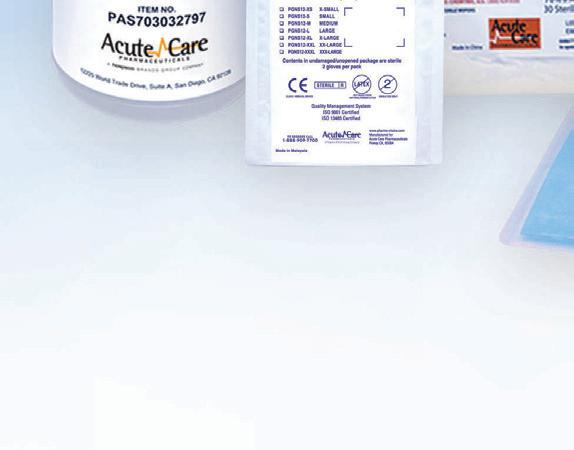
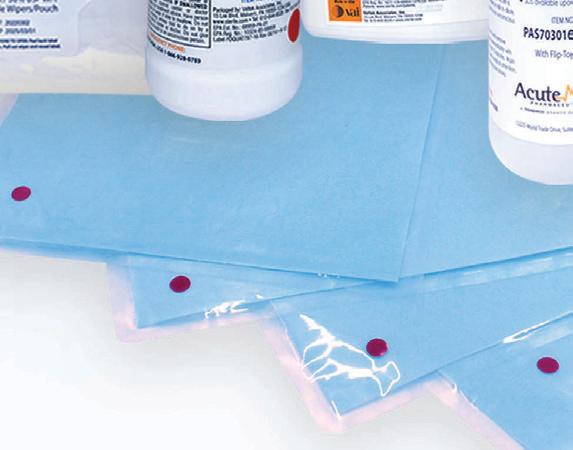
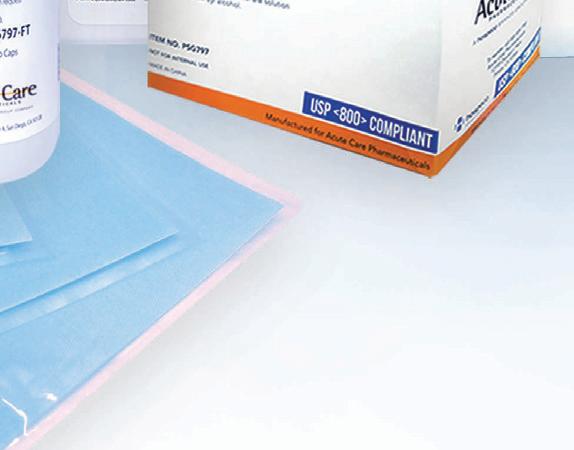
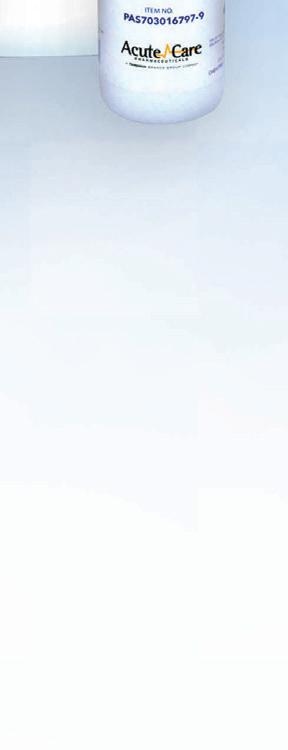
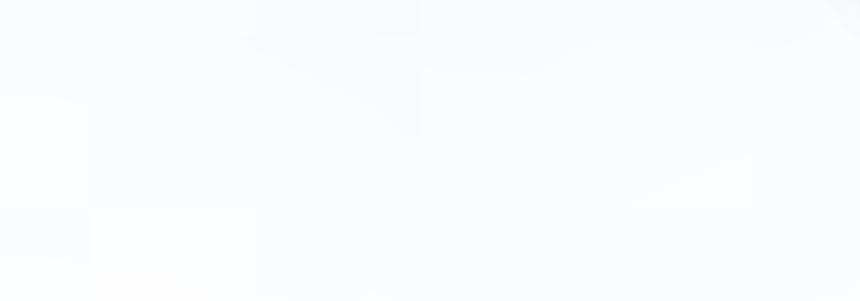
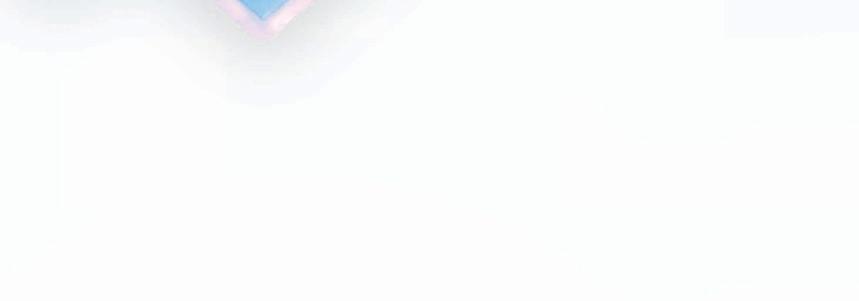



















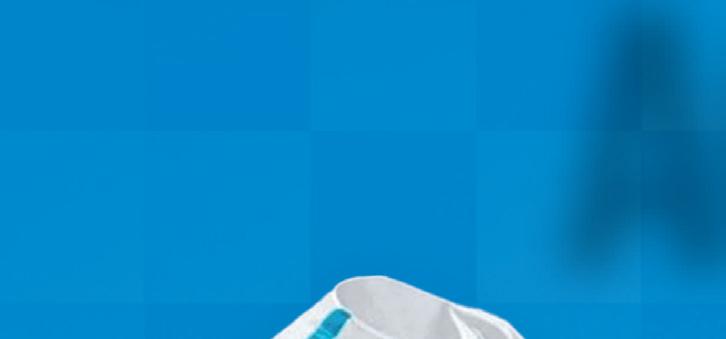
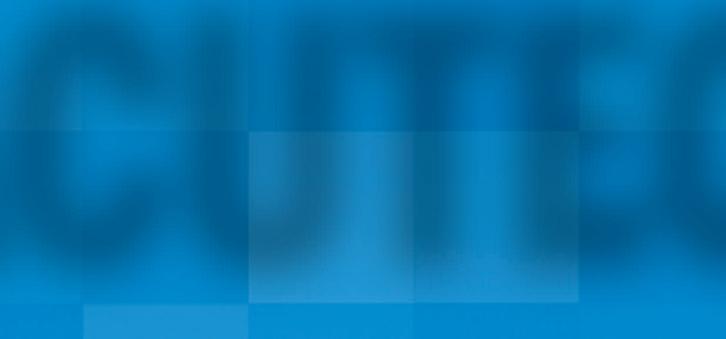
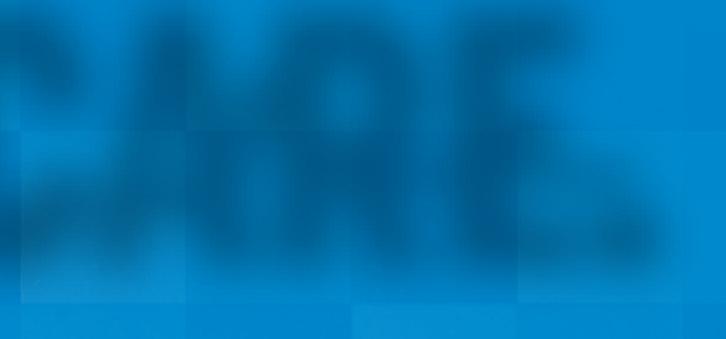
Acute Care Pharmaceuticals, Your Premier Supplier of USP <797> and <800> Cleanroom Disposables
We at Acute Care Pharmaceuticals aim to make your buying experience easier. We offer our products at your wholesaler and provide education, and your pharmacy will have its own dedicated account manager.
Our Products Include
President & CEO: Tom Friedl
Founded: 1997
Employees: 17
Toll-Free Phone: (888) 909-7700
Fax: (858) 675-9380
Address: 12195 Dearborn Place Poway, CA 92064
Website: www.pharma-choice.com
Company Background
Acute Care Pharmaceuticals was founded in 1998 and was acquired by Tranzonic® in 2019. Acute Care, with its PharmaChoice™ and Protect 800™ brands, is a leading supplier of compliant, disposable medical products used in compounding pharmacies and other critical environments. All products are compliant with strict regulatory guidelines as required by USP <797> and USP <800>. Our products undergo testing and audits to ensure compliance. This unique dedication to compliance, coupled with its decades-long commitment to partner with hospital pharmacies, makes Acute Care a market leader. The company’s various sterile disposable products are mandated for use in cleanroom environments. As such, Acute Care enjoys strong market penetration at hospital compounding pharmacies, standalone pharmacies, infusion, and cancer centers. Popular products include wipers, sterile alcohol, gloves, mop covers, and CAT kits. As part of Tranzonic® companies, Acute Care Pharmaceuticals, and the PharmaChoice™ brand are available to a range of customers with or without their GPO contract.
Product Overview
Acute Care manufactures and distributes products for healthcare affiliated critical environments. As per USP <797> and <800>, we produce products to meet or exceed the required guidelines. We offer a full suite of cleanroom disposables for your pharmacy practice. Many of our products can be found with free and next day shipping from AmerisourceBergen, Cardinal Health, McKesson, and Medline. In cooperation with our friendly account managers, we can assist you in sourcing the products you need to be a successful USP <797> and <800> compliant pharmacy.
• Sterile Cleaners
• Sterile Non-Shedding Wipers
• Sterile Alcohol Wipes
• Sterile Disinfectants
• Sterile Gloves
• Sterile Gowns
• Hazardous Drug Control Products
• Environmental Testing Plates and Kits
• PPE
Key Business Partners
• AmerisourceBergen
• AvMedical
• Cardinal Health
• McKesson
• Medline
• Owens & Minor
• Spectrum Chemical
• Fisher Scientific
GPO/IDN Affiliations
• Vizient
• Premier
• HPG
• MHA
• APCI
• Asembia
• Gerimed
• Ascension
• Northside Hospital System
Ordering Information
For direct orders, call (888) 909-7700, visit pharma-choice.com, or email info@acutecareonline.com. Account setup is free and easy, and we’ll even set up the account for you.
For ordering through your wholesaler, your account manager can provide you with your wholesaler’s itemized list of products available within their network. Give us a call and we’d be happy to assist you.
Trade Shows, Meetings, & Expositions
RXinsider’s Virtual Pharmacy Trade Show
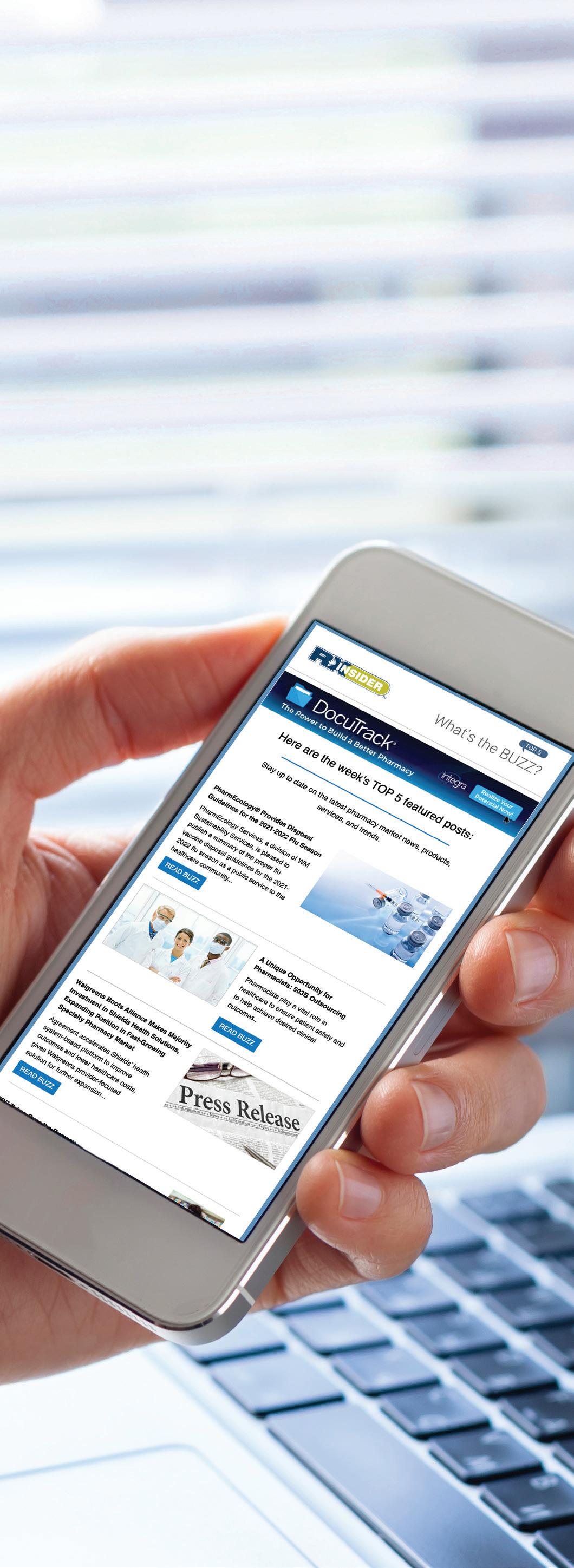
24 / 7 / 365
450+ Booths, 89 Aisles www.rxinsider.com
ASHP Summer Meetings and Exhibition
June 10-14, 2023
Baltimore, MD www.ashp.org/Meetingsand-Events
McKesson ideaShare
June 22-25, 2023
Mandalay Bay Resort & Casino
Las Vegas, NV Mckessonideashare.com
340B Coalition Summer Conference
July 10-12, 2023
Gaylord National Resort & Convention Center National Harbor, MD 340bsummerconference.org
Cardinal Health RBC
July 19-22, 2023
Boston Convention and Exhibition Center
Boston, MA Rbc.cardinalhealth.com
AACP Annual Meeting 2023
July 22-25, 2023
Aurora, CO www.aacp.org/events
NACDS Total Store Expo
August 12-14, 2023
San Diego Convention Center
San Diego, CA Tse.nacds.org
Compounding Pharmacy Compliance
August 17-18, 2023
The Westin Copley Place Boston, MA informaconnect.com/ compounding-pharmacycompliance
NASP 2023 Annual Meeting & Expo
September 18-21, 2023
Gaylord Texan Resort and Convention Center Grapevine, TX naspnet.org/annual-meeting
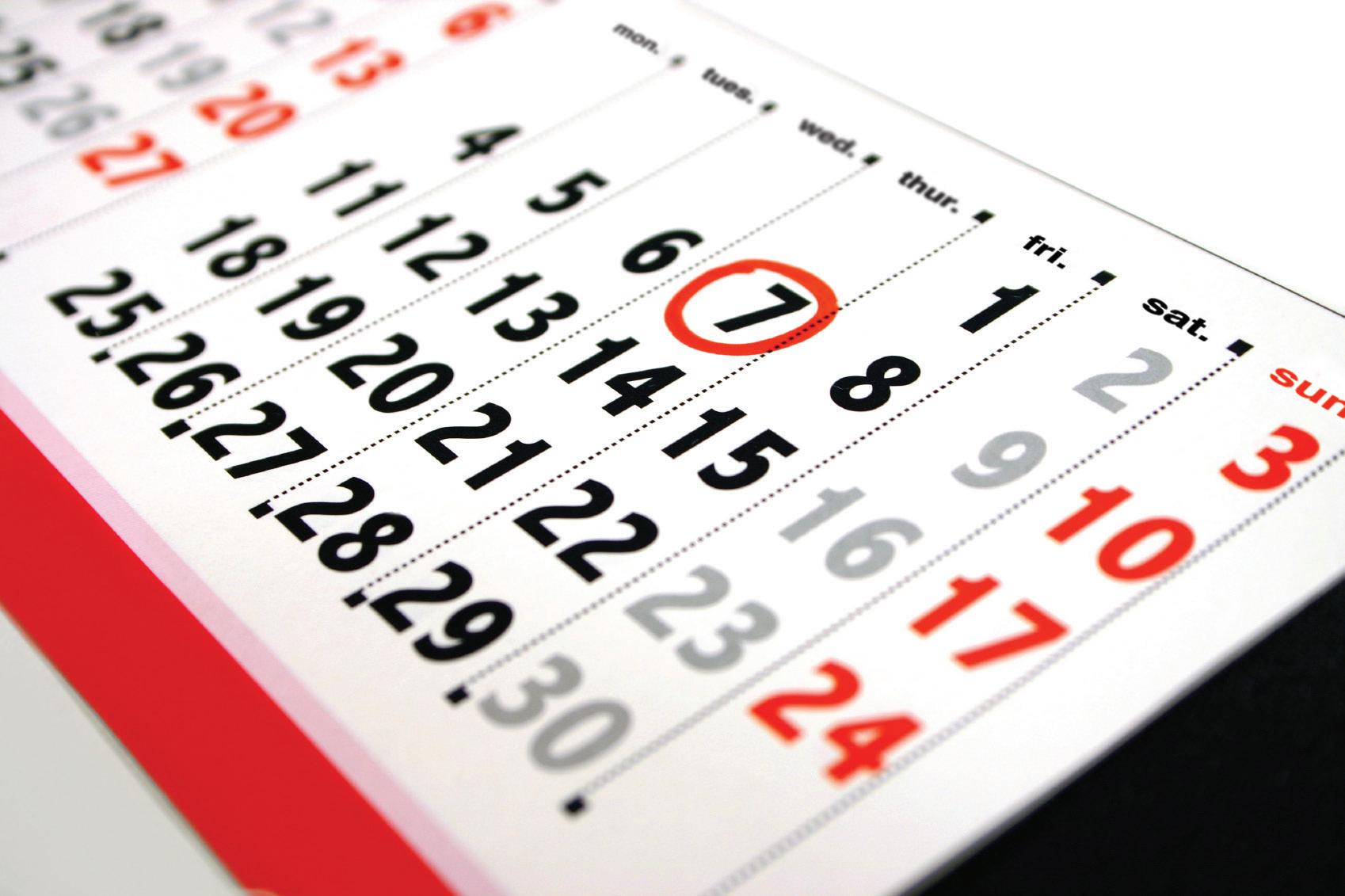
We cordially invite you to the nation’s capital for the 340B Coalition Summer Conference, occurring July 10–12, 2023, at the Gaylord National Resor t & Convention Center in National Harbor, Maryland, just minutes from downtown Washington, D.C. This event is the largest gathering of the 340B community—covered entities, pharmacies, service providers, drugmakers, government officials, and others—and it focuses on the 340B issues of greatest impor tance to those caring for patients in need.

Register to join your colleagues in the 340B community to ensure your continued success in using 340B to serve your patients in need. Conference sessions will enable you to learn best practices for operating compliant, effective 340B programs. Briefings and breakout groups will keep you apprised of impor tant 340B and drug pricing developments in Congress, statehouses, the cour ts, and the administration. Exhibit hall events and receptions will give you forums in which to connect with your peers and explore areas for new par tnerships.
Join us at the 340B Coalition Summer Conference to take advantage of all these oppor tunities to engage on the 340B issues that matter the most to you. We look forward to seeing you in National Harbor in July!
3 Days of curriculum
47+ Information-packed sessions
Learn
3 Pre-conference workshops
9 Networking breaks
www.340bsummerconference.org/rxinsider
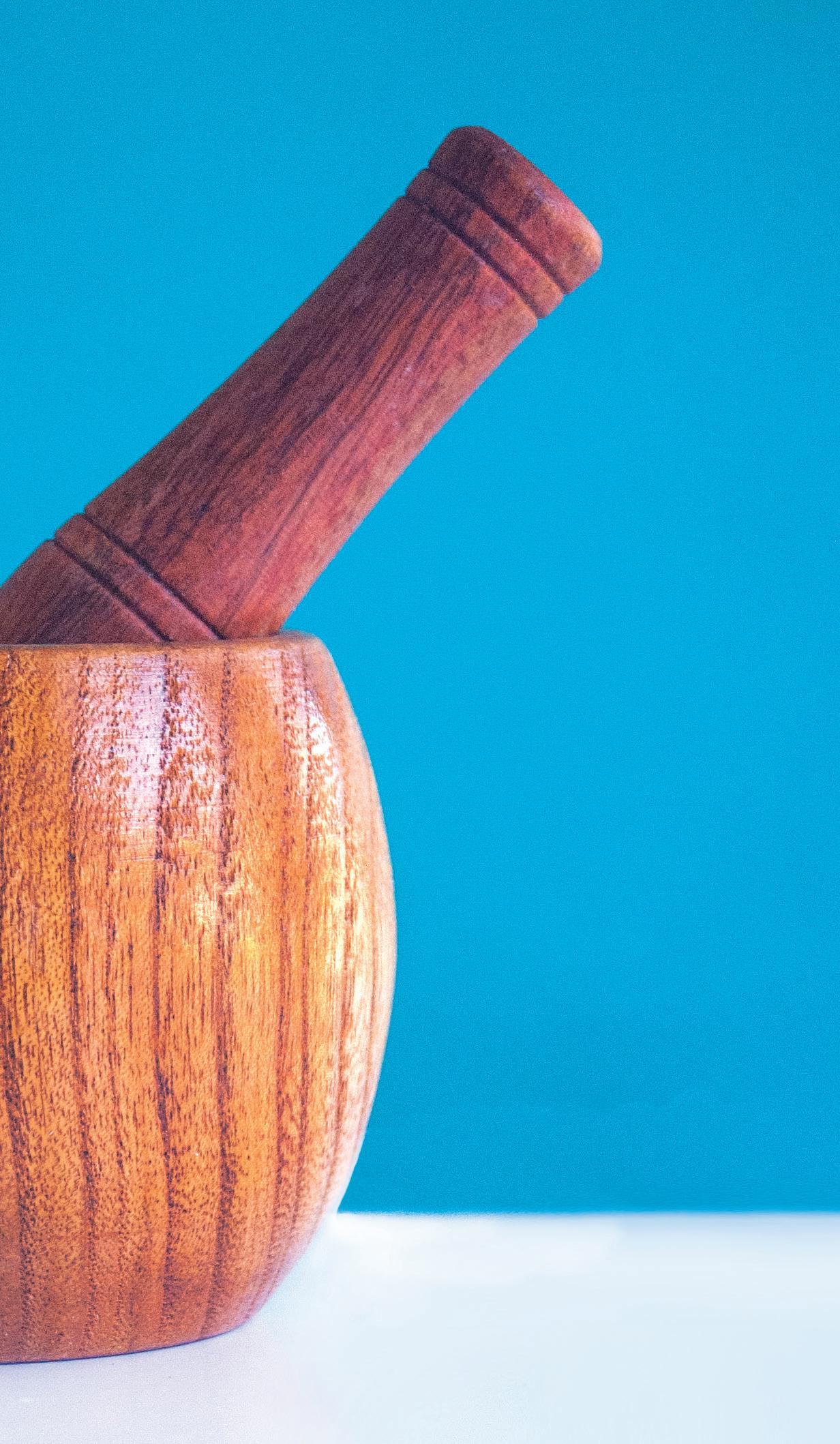
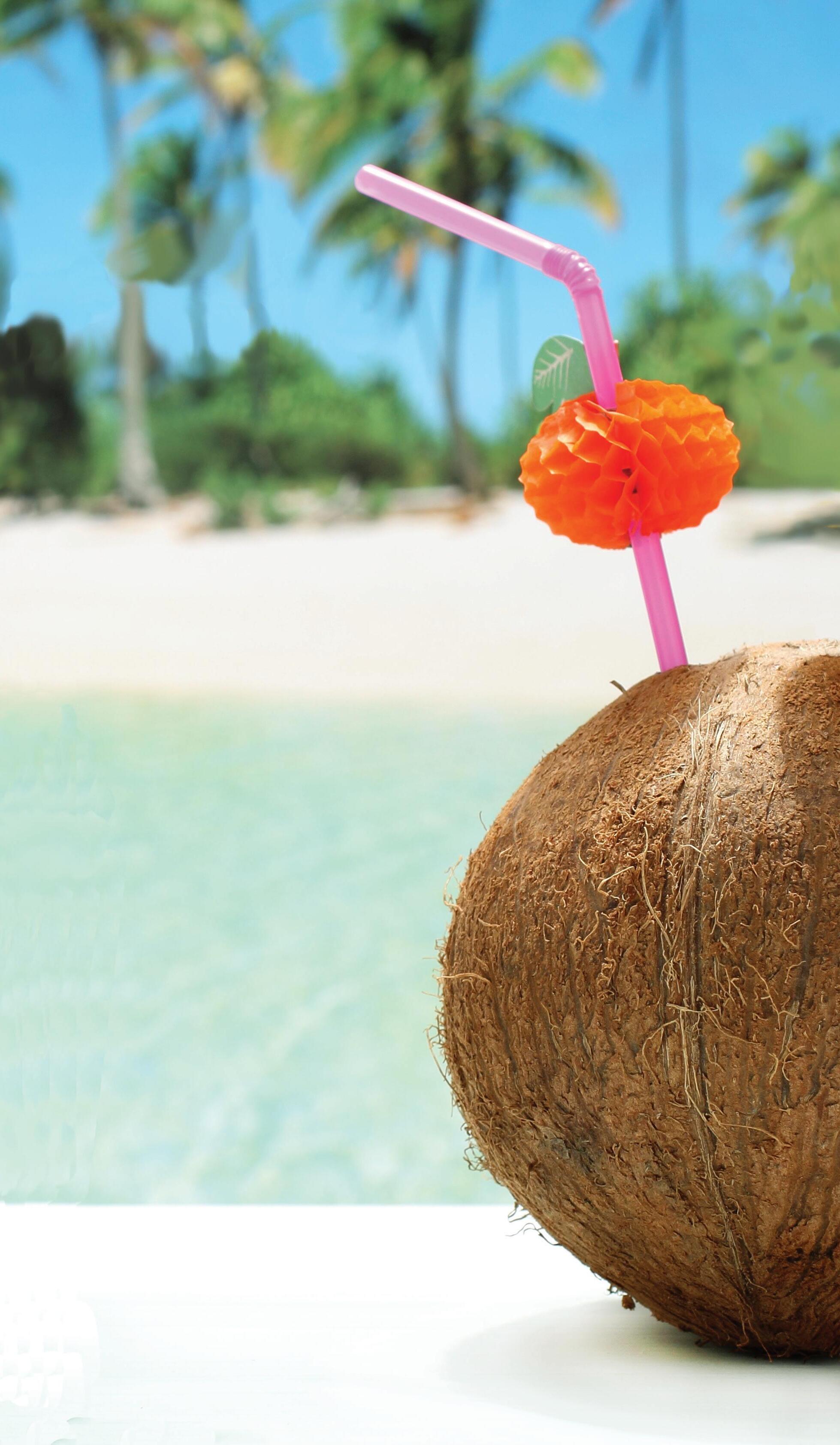

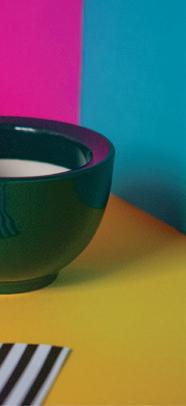
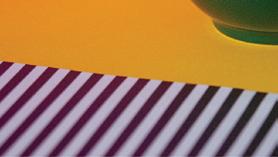
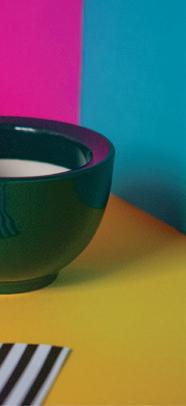
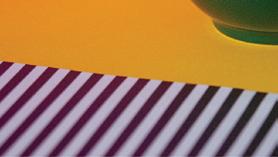

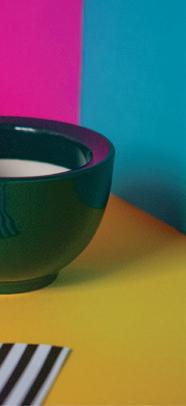
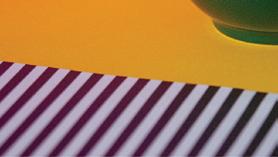

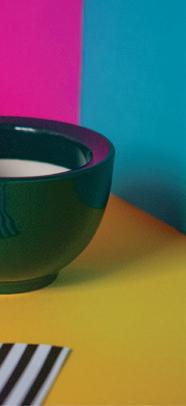
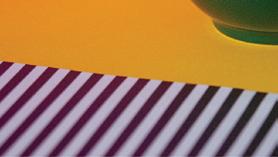

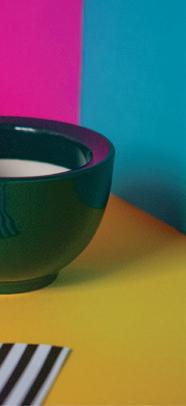
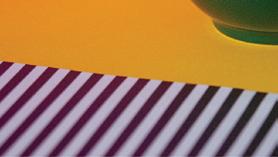

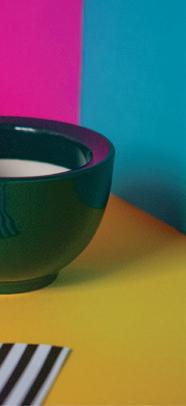
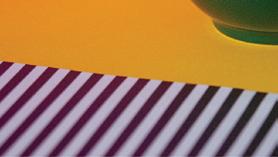
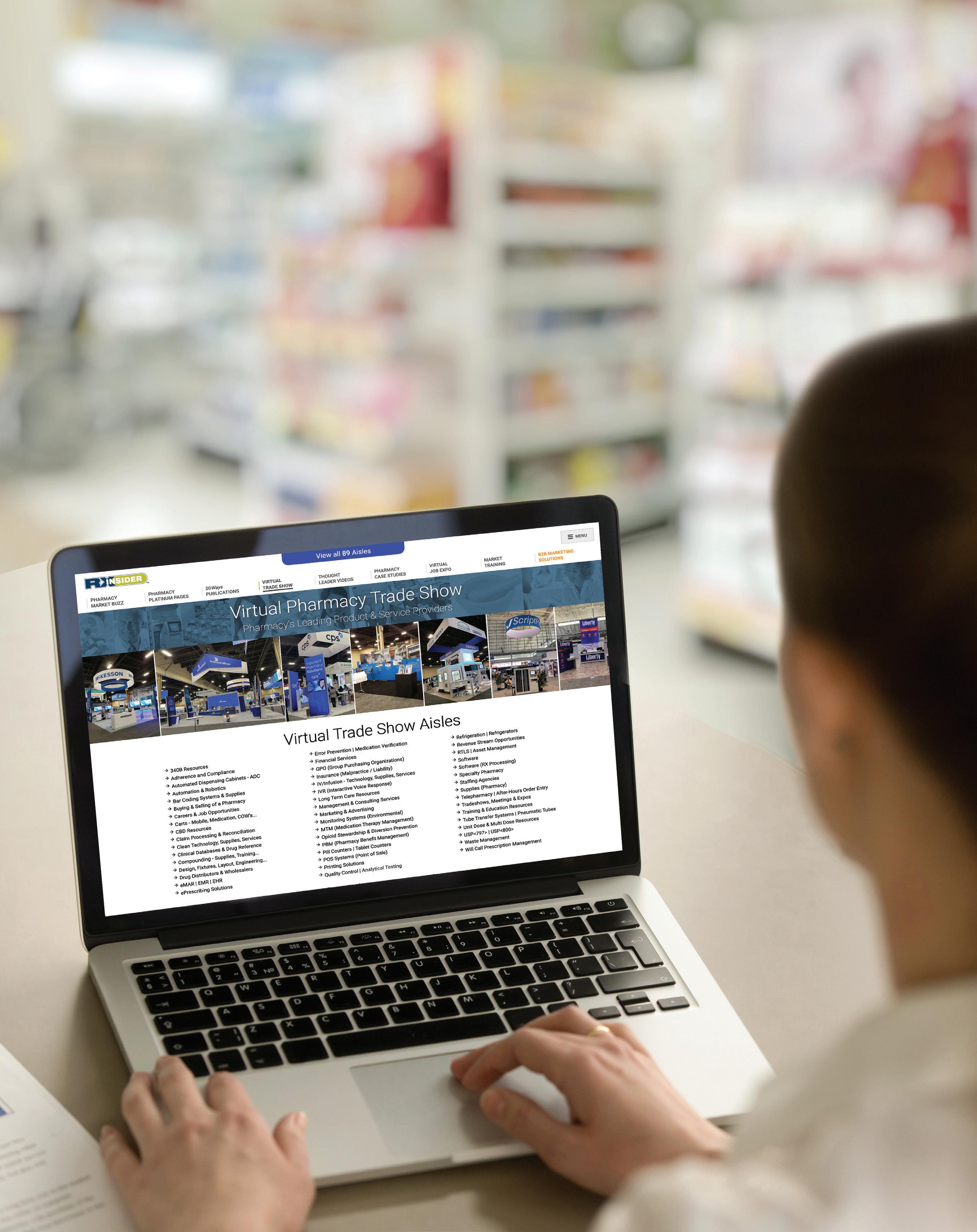
TIP THE SCALE IN YOUR FAVOR
CONNECT YOUR BRAND WITH THE RIGHT BUYERS
Promote your health, nutrition, and wellness products directly to buyers and retailers in one-on-one meetings.
VIRTUAL THE HEALTH CARE SESSION
July 31, 2023 - August 03, 2023
IN-PERSON
THE VITAMIN, WEIGHT MANAGEMENT & SPORTS NUTRITION SESSION
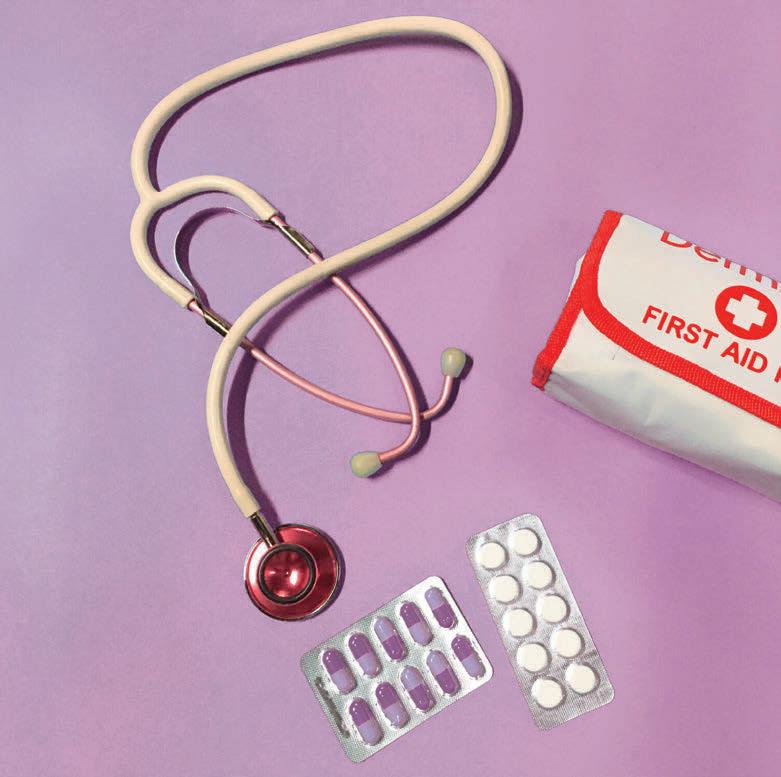
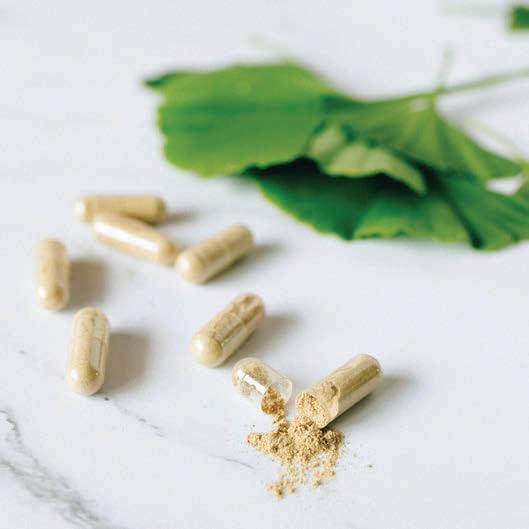
Sep 10 - 13, 2023
Bonita Springs, FL at the Hyatt Regency Coconut Point Resort & Spa
For more information contact: Lisa Carrillo Senior Vice President of Beauty Care at lisac@ECRM.MarketGate.com or call 440-528-0427.
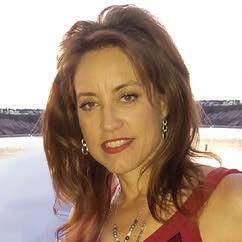
Event Calendar
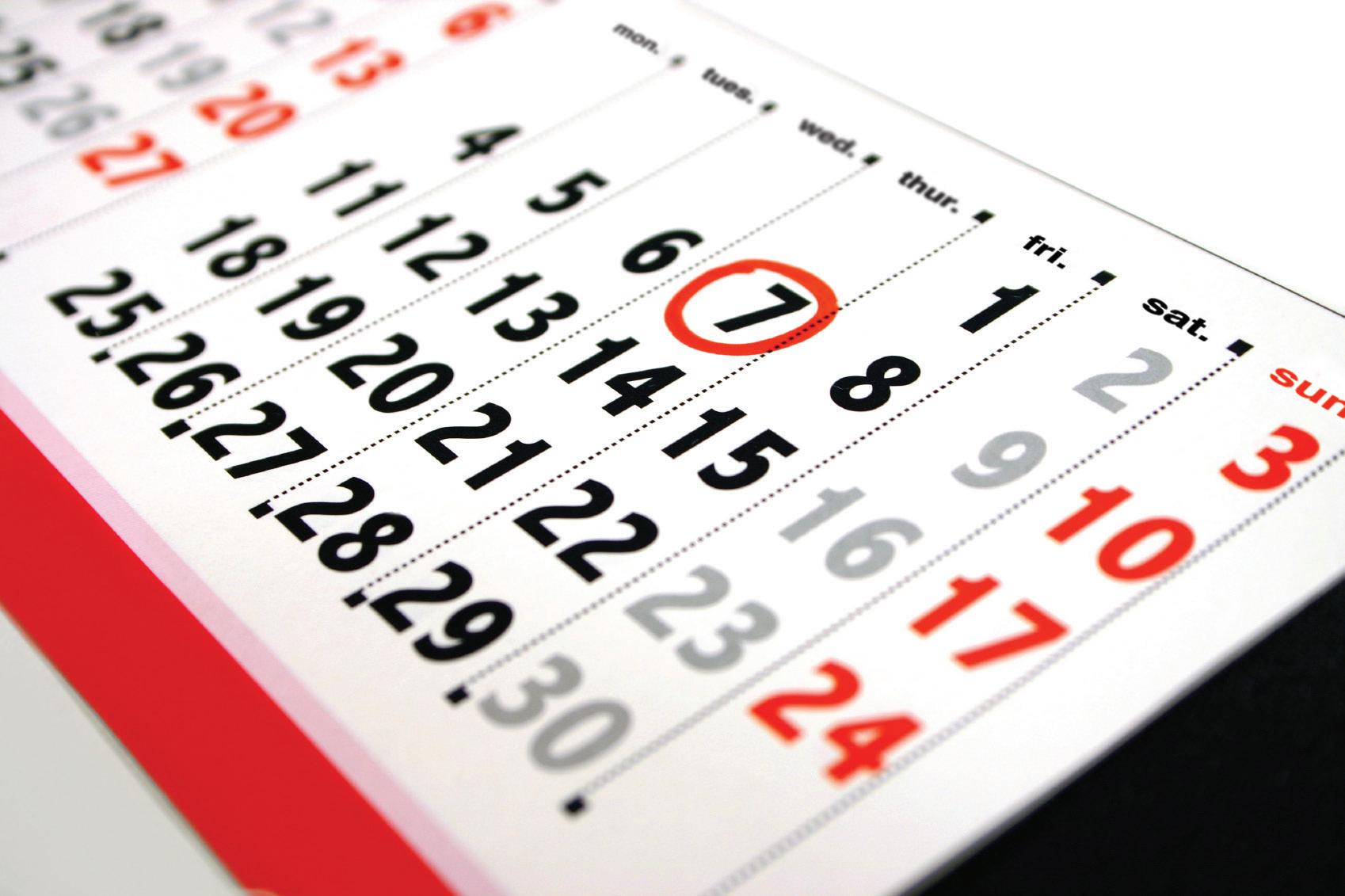
Continued from page 74
Compounders on Capitol Hill
September 19-20, 2023
Hilton National Mall
Washington, DC a4pc.org/cch
NCPA Annual Convention
October 14-17, 2023
Orange County Convention Center
Orlando, FL ncpa.org/annual-convention
ASCP Annual Meeting & Exhibition
October 26-29, 2023
Gaylord Palms Resort & Convention Center
Kissimmee, FL ascp.com/page/events
ECRM - Specialty Pharmacy/Distribution Session
November 5-7, 2023
New Orleans, LA ecrm.marketgate.com/ Sessions
ECRM - Pharmacy Technology, Services, Supplies, and Automation Session
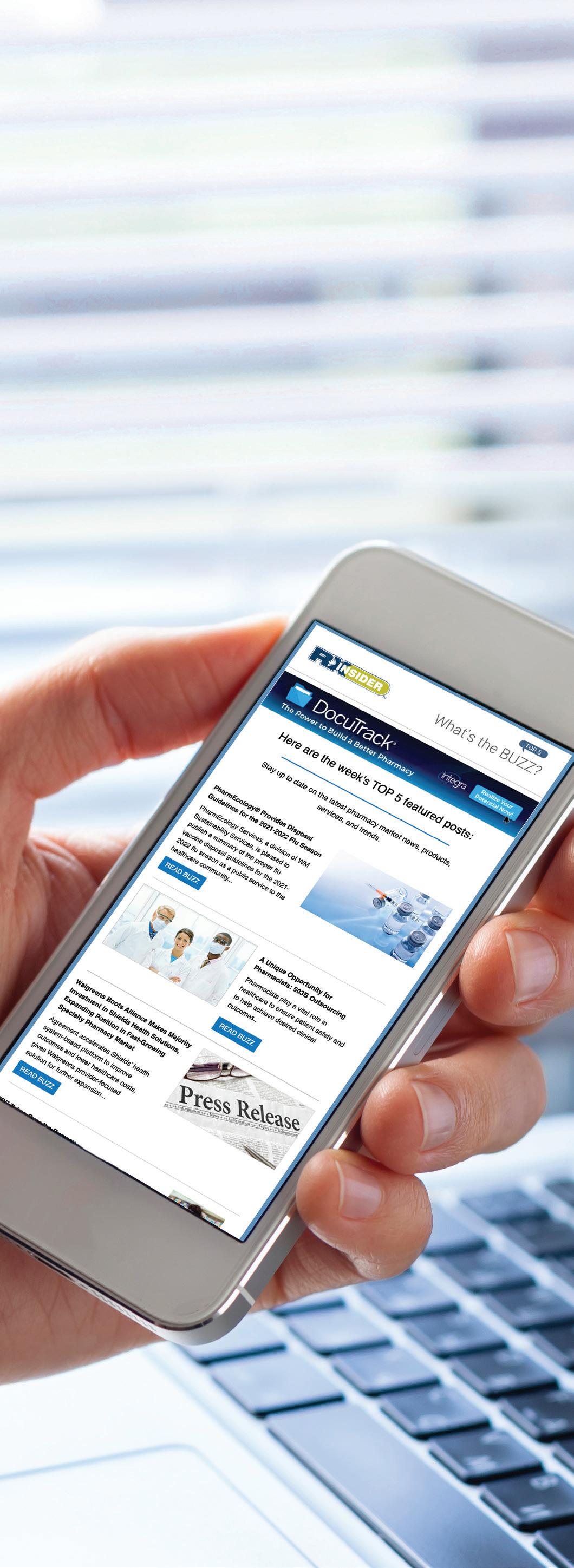
November 6-8, 2023
New Orleans, LA ecrm.marketgate.com/ Sessions
ASHP Midyear
Clinical Meeting and Exhibition 2023
December 3-7, 2023
Anaheim, CA ashp.org/Meetings-andConferences/MidyearClinical-Meeting-andExhibition
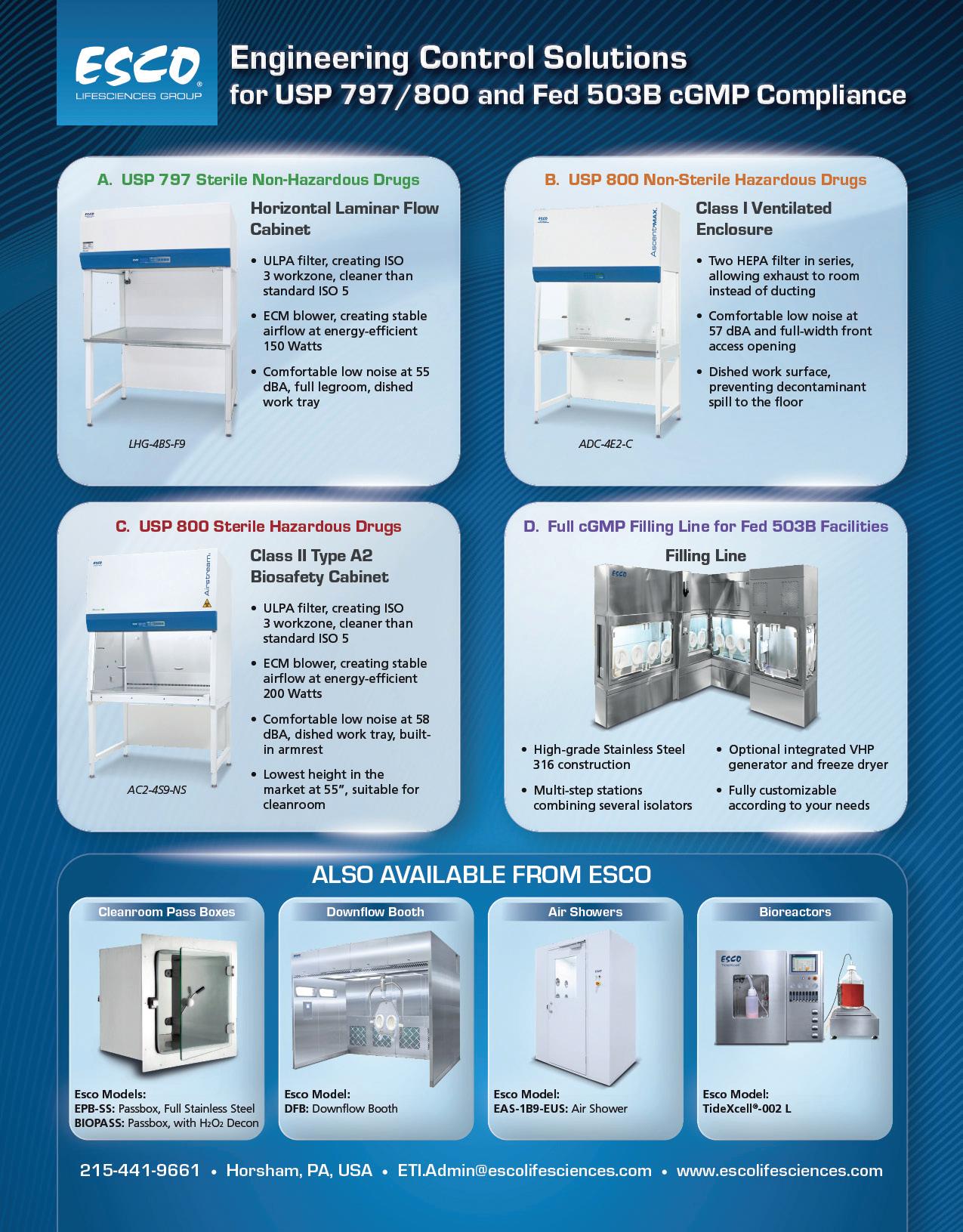
Esco® — Safer Workstation for USP 797, USP 800, and 503B Pharma Compounding
Improve product sterility and patient safety with our standard ULPA Filter that creates an ISO Class 3 compounding area, that is 100 times cleaner than ISO Class 5 found on other biosafety cabinets, laminar flow cabinets, and isolators with regular HEPA filter.
President & CEO: XQ Lin
Founded: 1978
Employees: 1,400+
Toll-Free Phone: (877) 479-3726
Phone: (215) 441-9661
Address: 903 Sheehy Drive, Suite F, Horsham, PA 19044
Website: www.escolifesciences.com
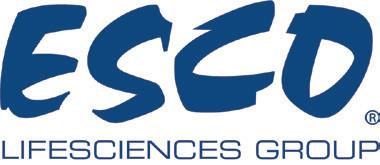
Email: ETI.Admin@escolifesciences.com
Company Background
Esco Group is a renowned life science company with a diversified portfolio and sales in over 100 countries. As a world leading manufacturer of laboratory and biopharma equipment, and IVF medical devices, Esco offers tailored solutions that fit the needs of laboratories.
With three divisions, namely, life sciences, medical, and healthcare, Esco contributes to meet the challenges of the 21st century by continuously innovating our products to support cutting-edge research, helping biopharmaceutical companies make their drugs safer and more costeffective, enabling lower cost manufacturing of vaccines, and directly through innovative medical devices and diagnostics.
Product Overview
We design and manufacture cutting edge primary and secondary engineering control for small to large scale pharmaceutical facilities, such as:
• USP 797 Workstation: Laminar Flow Cabinets
• USP 800 Workstation: Biosafety Cabinets
• FDA 503B Workstation: cGMP Isolators
• Customized Workstation: Contact Us for Your Needs
• Clean Room Components: Pass Boxes, Air Showers
• Bulk Containment Room: Downflow Booths, Large BSCs
• Cell Growing: Bioreactors (Small to Large), Cell Harvesters
Biosafety Cabinets for USP 800 Compounding
Esco is the world’s largest manufacturer of biosafety cabinets with advanced key features:
1. The most energy efficient BSC in the market. Consumes only 200 Watts (four-foot unit) using latest generation, U.S.-made, single DC-ECM Blower. Helps LEED certification.
2. Best filtration. Using ULPA filter that’s 10 times more efficient than HEPA, giving ISO Class 3 work zone and 10 times safer exhaust, at the same 10-year filter life and same cost.
3. Large performance envelope. Provides wide margin of operator and product protection in the event of imbalanced loading of exhaust and downflow filters.
4. Anti-microbial coating. Silver ions kill the contaminants that last through the lifetime of the cabinet. Reduces bio-burden, product, and lab contamination.
5. Durable metal plenum. Resist puncture and leak, unlike BSCs with plastic bag plenum. Coupled with anti-microbial coating to reduce bioburden inside BSC.
6. Double layer side wall with negative pressure. Prevents hazardous pathogens from escaping into lab, by pulling them into plenum and be captured by filters.
7. Raised Arm Rest. Provides comfortable place to put arms, and prevent hazardous grille blocking by operator arms. Made from durable stainless steel to resist wear.
8. Easy to clean. Single piece interior wall with large corner radius, and angled drain pan, for easy cleaning. Polished seams and accessible drain corners for easy wiping.
9. Centered, angled down controller. Enables the user to easily see and operate the controller from stationary sitting position, including from wheelchairs.
10. Lowest height. At only 55" tall, our compact Airstream AC2 BSC has the lowest height in the market, enabling the user to work while sitting or standing even inside clean rooms with low height.
Laminar Flow Cabinets for USP 797 Compounding
Esco is also one of the world’s largest manufacturers for laminar flow cabinets, with advanced key features:
1. The most energy efficient LFC in the market. Consumes only 155 Watts (four-foot unit) that comes standard with latest generation, DC-ECM blower.
2. Best filtration. Using ULPA filter that’s 10 times more efficient than HEPA, giving ISO Class 3 work zone required for electronics industry at the same eight-year filter life and cost.
3. Stable airflow. The combination of DC-ECM blower and digital speed control maintains stable airflow and protection, despite input voltage fluctuation.
4. Anti-microbial coating. With silver ions to kill the contaminants that last through the lifetime of the cabinet. Reduces product and lab contamination.
5. Low noise. Designed to create the quietest laminar flow clean bench in the market with 55 dBA noise (four-foot unit) at industry standard 90 fpm filter velocity.
6. Automatic airflow compensation. The blower control system automatically compensates >3 times filter loading without manual speed control adjustment.
7. Centered, angled down controller. Enables the user to easily see and operate the controller from stationary sitting position, including from wheelchairs.
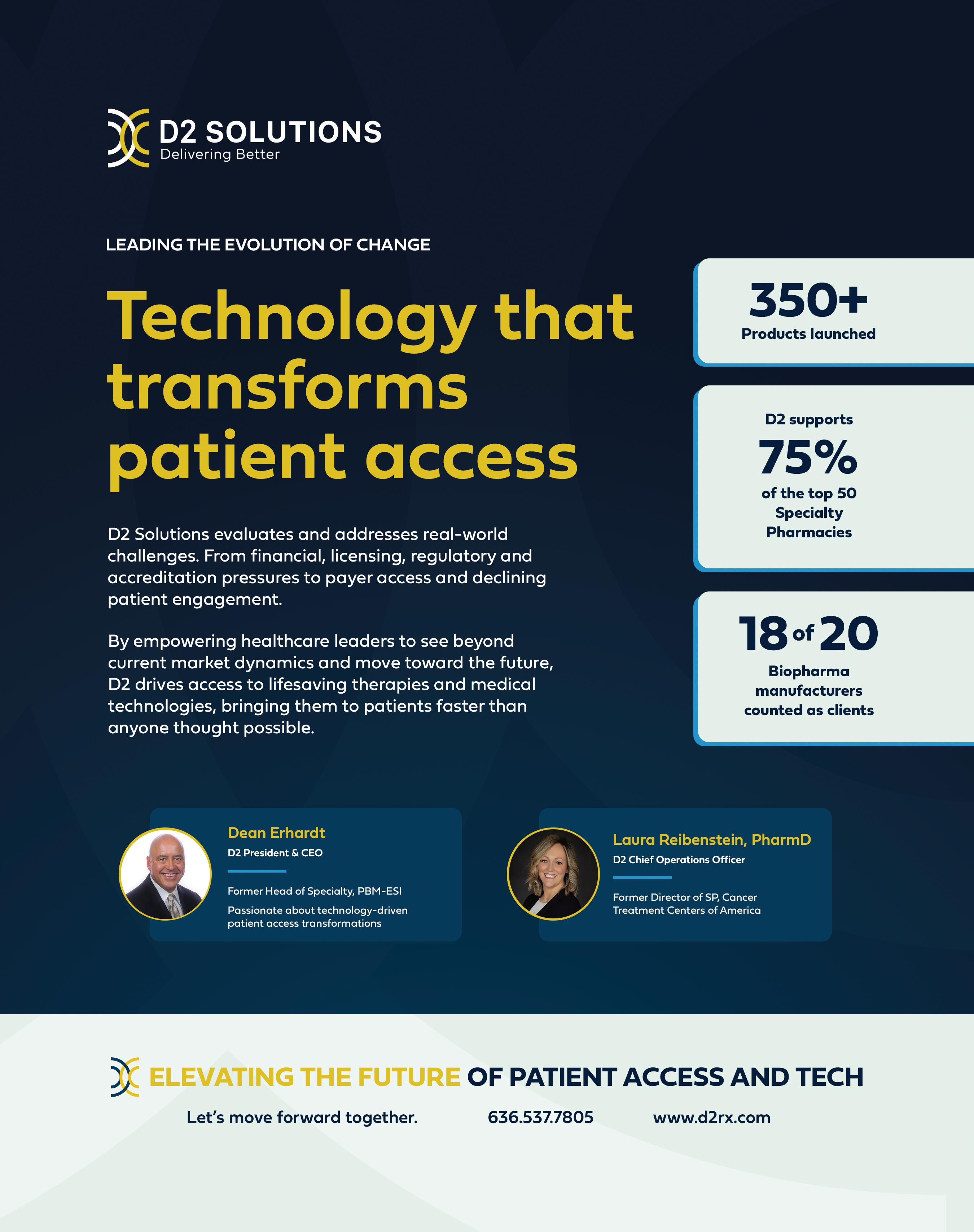
D2 Solutions — Consulting and Technology
D2 Solutions is focused on profitability maximizing patient access to specialty drug. We are former biopharmaceutical and specialty pharmacy leadership with a unique understanding of how to maximize access with a combination of consulting, technology, and decision making experience at D2 Solutions.
n RegComply™
President & CEO: Dean Erhardt
Founded: 2008
Employees: 60
Phone: (636) 537-7805
Website: www.d2rx.com
Company Background
D2 Solutions advances patient access via a unique combination of strategic consulting, tactical execution, and SaaS based technologies. D2 works with our client-partners to drive revenue, enhance operating margin, and decrease exposure to regulatory risk.
Our client base includes established pharma and biopharma companies, emerging and venture backed startups, leading specialty pharmacies, hospitals, HUBs, and others. This diversity of customers provides D2 a unique advantage as we develop leading edge solutions that drive patient access, accelerating therapy start and ensure medication persistence.
D2 Two Divisions — Consulting and Technology
n Consulting
• Pharmaceutical Manufacturer Consulting
• Specialty Pharmacy Consulting
n Technology
• ComplySuite™ Solutions
• UltraTouch™ Solutions
Product Overview
ComplySuite™ is an automated licensure and accreditation system built by D2. Over the last 11 years, D2 has been collaborating with the major accreditation bodies and regulatory agencies to uncover ways to streamline the process. With keen insight from our clients and our pharmacist consultants, we have developed an automated, web-based compliance solution. Within ComplySuite™ there are four platforms:
n AccredComply™
• Centralized Database
• Task Optimization
• Meet Payer and Manufacturer Requirement
• Stay Informed on Regulation
• New Legislation and Bills
• Reduce Labor Costs
n LicenseComply™
• Maintain, Track, and Manage
• Never Miss a Renewal
• Streamline Communication
n ContractComply™
• Store Contracts in One Place
• Manage Tasks
• Organize Approval
UltraTouch™ engagement, prior authorization, and therapy management solutions enhance the patient experience by increasing speed to therapy, medication adherence, and patient/ caregiver communication.
n UltraTouch™ Verify
Smart, ePA platform that speeds approvals, reduces internal staffing requirements, and improves workflow by storing PAs within a single environment and automating PA renewals.
n UltraTouch™ Engage
An immersive, bi-directional, proactive patient engagement technology that enables healthcare providers and stakeholders to more effectively engage with patients/caregivers
n UltraTouch™ Patient Management
Innovative technology that supports disease and drug specific therapy management programs. Patient management supports accreditation standards management and performance measure reporting.
THE ROLE OF PROBIOTICS IN HEALTHCARE: PAST, PRESENT, AND FUTURE
Rosemary Pauley, APRN, MS, FNP Pediatric Gastroenterology Nurse Practitioner
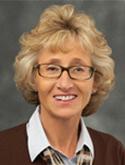
~ Boys Town National Research Hospital

John Damianos, M.D. Internal Medicine, Resident, Yale New Haven Hospital incoming Gastroenterology and Hepatology
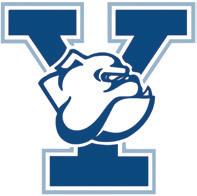
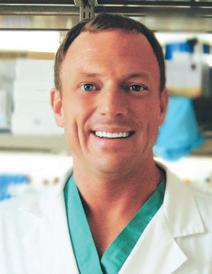
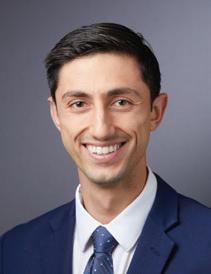
~ Fellow, Mayo Clinic
Paul Wischmeyer, M.D., E.D.I.C., FASPEN, FCCM Professor of Anesthesiology and Surgery, Associate Vice Chair for Clinical Research, Dept. of Anesthesiology, Physician Director, TPN/Nutrition Support Service, DUH
~ Duke University, School of Medicine
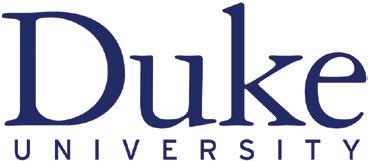
PROBIOTICS AND GUT HEALTH
Gut health and how it impacts our overall health has been a growing topic of interest and investigation for several years. What seems to be emerging from the research is that an imbalance in the gut microbiome — not having enough healthy microbes to fight off less healthy ones — can make us more susceptible to a wide range of illnesses.
Several factors can damage gut health. According to Rosemary Pauley, APRN, MS, FNP, pediatric gastroenterology at Boys Town National Research Hospital, she sees the impact on children who might not have had good microbiome colonization at birth, which can happen with cesarean delivery. She says children who take a lot of antibiotics in their first year of life can also have gut issues 10, 20, or 30 years down the road. Anesthesiologist and Critical Care Specialist, Dr. Paul Wischmeyer, M.D., at Duke University Hospital, agrees, saying that evolutions in medicine and even a Western diet have led to major disruptions of what the normal bacteria living in our gut should look like. “That has set us up to be prime victims of gastrointestinal disorders, autoimmune diseases, pandemics like COVID, allergies, obesity and more,” he says.
WHERE THE RESEARCH BEGAN
Pauley has been working in pediatric gastroenterology for nearly 40 years. In that time, she's seen the research and attitudes toward the value of probiotics evolve. “When I started in the field, we didn't know much about probiotics,” she explains. “So we just didn't use them.”
It wasn't until the early to mid-2000s that the research into various strains of probiotics started to take off. That's when Pauley, and the doctor she still works with today, were asked to lead some studies. “We were particularly interested in the effect of probiotics on Clostridioides difficile — or C. diff – and antibiotic associate diarrhea,” she says.
Around this time, Wischmeyer began researching the effects of probiotics in critical care explicitly related to pneumonia and peritonitis in animals. “We found that the animals we gave probiotics to, before the illness had a chance to damage the gut, did not get nearly as sick as those that had no probiotics.” What was really exciting, he says, is that they found no bacteria got into the bloodstream at all. “Normally, when you have severe pneumonia or a leaky gut causing peritonitis, bacteria will get into the bloodstream and lead to infection everywhere.” As his career progressed, Wischmeyer was also involved in the first longitudinal study of microbiome changes in critically ill patients. The multicenter trial found that ICU patients experienced dramatic losses of healthy
CASE STUDY
bacterial families within a day of being admitted. “We saw incredible growth of pathogenic bacteria that would just take over the gut and cause severe infection.”
PROBIOTICS IN ACTION TODAY
In his practice, Dr. John Damianos, M.D., Internal Medicine at Yale New Haven Hospital, works in inpatient and outpatient environments. He recommends probiotics for people taking a course of antibiotics, as many physicians do today, and for other GI-related issues such as irritable bowel syndrome, functional dyspepsia, pouchitis, and more. He says there's also developing evidence that probiotics can increase the likelihood of Helicobacter pylori eradication when combined with the current standard of care of either triple or quadruple therapy. “So there are really multiple specific indications that I'm recommending probiotics for — but I'm not recommending taking any probiotic off the shelf. I'm recommending specific strains or mixes of strains that specify doses based on clinical trial data for people.”
Pauley regularly uses probiotics for babies with allergic colitis due to an allergy to cow's milk or sometimes even breast milk. “I've also found probiotics useful in treating post-COVID and other post-viral diarrhea that seems to linger,” she says. Beyond that, she notes there is growing research that indicates probiotics can affect the immune system in a way that makes people less prone to viral infections. “This seems to be especially true for people — like some of the children, teenagers, and young adults I see — who don't have great diets or access to whole foods, so the daily use of a probiotic is interesting to me in those cases.”
In addition to his role as a critical care physician, Wischmeyer is also the director of the nutrition team at Duke University Hospital and associate vice chair for clinical research for the department of anesthesiology. As a result, he spends about half his time researching nutrition, exercise, probiotics, and microbiomes to help people prepare for surgery and bone marrow transplants to lower the risk of pneumonia and hospital-acquired infections. “We know, for instance, probiotics can reduce C. diff by as much as 70%.” This is important, he explains, because C. diff is one of the fastest-growing iatrogenic diseases he sees today.
~ Duke University HospitalA large meta-analysis has also indicated that using a probiotic can reduce the risk of upper respiratory infection by as much as 50%. This led Wischmeyer and his team to study the effect of probiotics to help minimize the spread of COVID-19. Funded through the FDA's Investigational New Drug (IND) program, the study used Culturelle® probiotics, delivering the probiotic strain Lactobacillus rhamnosus GG. “Although the study was small, we had some encouraging signals,” he says. “Our initial data showed that we could significantly reduce the symptoms from COVID-19 and the actual time to diagnosis.”
CHOOSING THE RIGHT PROBIOTIC
“The thing to understand is that not all probiotics are the same,” says Pauley. “You need to know you're using the right one for the right condition.” And that, she says, comes down to the data. Damianos, who serves on the Scientific Advisory Committee for the Alliance for Education on Probiotics (AEProbio), an international organization focused on advancing the science of probiotics, agrees. “One of the challenges in the field is that probiotics are considered supplements, so they aren't regulated in the same way as medications.” Although there's a lot of research and funding going into the field, there's a lot of misinformation out there as well. He says this leads many people to write probiotics off as a class.
That's one of the reasons as part of his work with AEProbio, Damianos writes a quarterly research review about the latest science as it pertains to probiotics. “I encourage people to consider probiotics like any other medication.” He uses antibiotics as an example. “Doctors don't
“ “
I encourage people to consider probiotics like any other medication.”
We know, for instance, that probiotics can reduce C. diff by as much as 70%.”
John Damianos, M.D. Internal Medicine
~ Yale New Haven Hospital
Paul Wischmeyer, M.D. Anesthesiologist, Critical Care Specialist
CASE STUDY
just prescribe antibiotics — they diagnose an infectious disease syndrome first, identifying a particular bug. Then they treat the patient empirically, picking an antibiotic with a unique action mechanism that targets the specific pathogen.” The same goes for probiotics, he says. How do we know what works best for a particular indication? By taking the same steps as with any other pharmacological intervention. “We analyze the data from well-designed clinical trials that ideally have been replicated,” he explains. “Then, at some point, you have meta-analyses for a particular strain.”
Another challenge Damianos points out is that because of the current regulatory environment, there's no accountability for companies. “There have been numerous studies looking at this,” he says. “One took 16 commercially available probiotics off the shelf that claimed to contain some sort of Bifidobacterium.” The result? Only a single probiotic out of the 16 contained what it claimed. That's one of the reasons he, Pauley, and Wischmeyer all recommend Culturelle® probiotics. “L. rhamnosus GG is the best studied probiotic strain,” he says. “And Culturelle as a company adheres to rigorous FDA-level standards so people — and doctors — can be confident in the stability and purity.”
LOOKING AHEAD — WHAT MORE CAN WE LEARN
All three would like to see more robust and broader-ranging clinical trials. “There's a much greater appreciation today for the gut-brain axis and a recognition of the microbiome's impact outside of uniquely gastrointestinal disorders,” says Damianos. “So now we're seeing people in dermatology, rheumatology, and neurology studying the importance of gut health.”
“Forty years ago, we really didn't understand the interaction between gut health and all these conditions,” says Pauley. “But today, we know how important a healthy gut is to our overall health.” She feels there could be something to learn about the role of probiotics in treating oral thrush.
“It isn't only babies who get oral thrush. It happens to adults — especially those undergoing cancer treatments, and I'd love to see a placebo-controlled trial studying that,” she says.
Wischmeyer agrees, saying he thinks there's an opportunity to look at preventing pandemic viruses in particular. “COVID is still a big issue, and there are a lot of probiotic studies in animals that indicate a normal microbiome can make vaccines for viruses more effective. I think we need to look at how combining probiotics with vaccines in the winter can help prevent these pandemic infections.”
FIND OUT MORE
Visit the refreshed Culturelle® probiotics healthcare professional website for more information and resources relating to the portfolio.
PubMed is a good resource for keeping up-to-date on research in the field. In addition, AEProbio publishes The Clinical Guide to Probiotic Products each year, which details probiotic strains and related applications.
Culturelle® probiotics: https://culturellehcp.com/
PubMed: pubmed.ncbi.nlm.nih.gov
The Clinical Guide to Probiotic Products: usprobioticguide.com
“The thing to understand is that not all probiotics are the same ... You need to know you’re using the right one for the right condition.”
Rosemary Pauley, APRN Pediatric Gastroenterology
~ Boys Town National Research Hospital
Evidence-based ingredients
Clinically proven probiotic strains

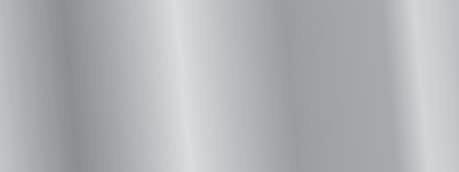
Safe & effective products for all ages
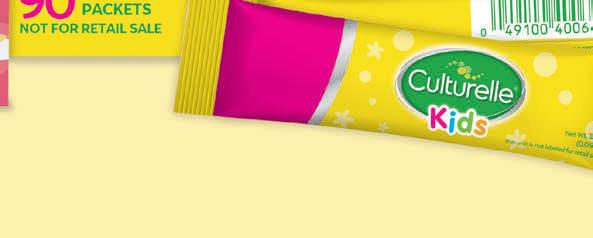

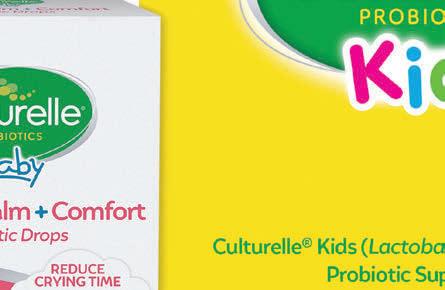
Adherence to FDA cGMP guidelines
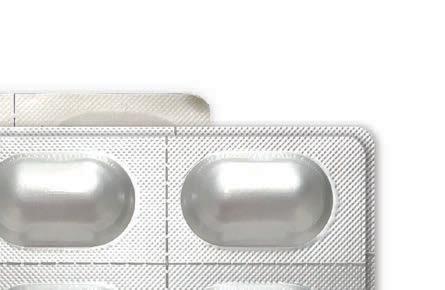
Generally Recognized As Safe (GRAS) ingredients
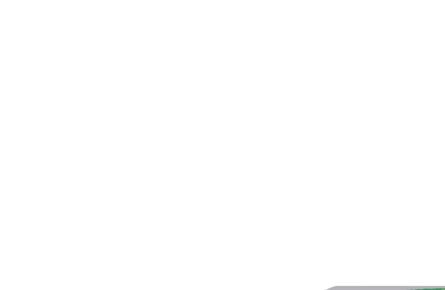
Packaged to ensure probiotic viability until end of shelf life
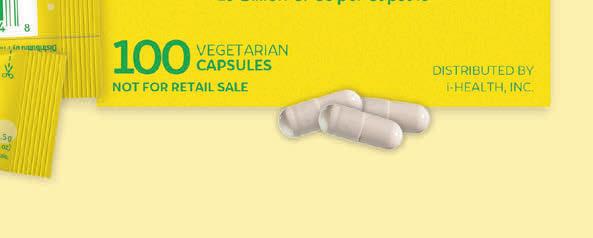
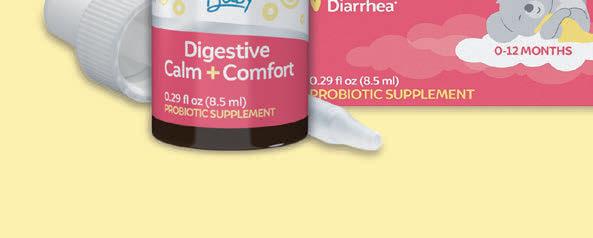
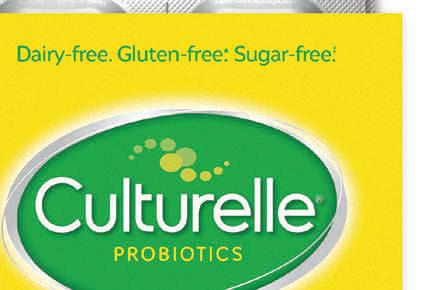
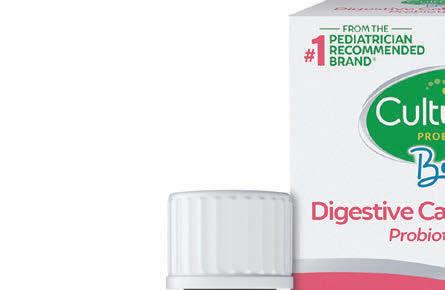
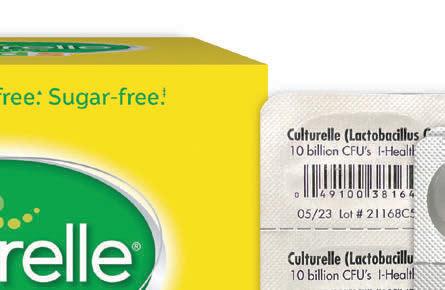
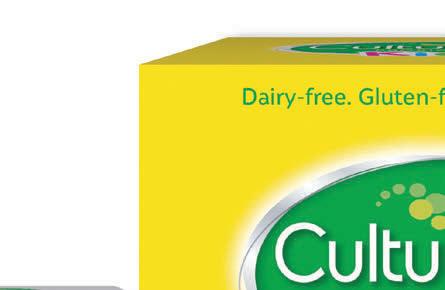
EMR-compliant barcoded products available
Each product lot inspected for conformance
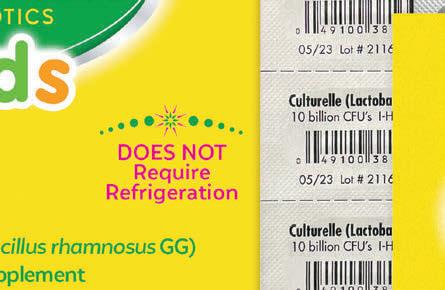
The All-in-One Answer
Resolving ineligible 340B discounts can be a time-consuming challenge. That’s why Apexus has standardized the manufacturer refund process with an all-in-one solution.
Your Refund Challenges
Historical drug pricing information is difficult to find.
Manufacturer refund contacts are often not publicly available.
Refunds are not governed by a statutorily defined process.
Your Streamlined Solution
Be prepared when an ineligible 340B discount occurs. Apexus CRS streamlines the refund resolution process to save time, increase efficiency, and ensure accuracy. Our solution provides a best-practice approach built on three assets:

Manufacturer Contacts
Historical Pricing
Standardized Documentation Communications templates and project documentation tools to standardize the refund offer and approval process.
Save Time, Increase Efficiency, and Simplify 340B Discount Refunds With Apexus CRS
The Apexus Covered Entity Refund Service (CRS) streamlines the process of returning ineligible 340B discounts to manufacturers. Take advantage of Apexus’ expertise in 340B compliance, analysis, project management, and reporting to standardize refunds.
Tested & Validated Pilot Program
President & CEO: Chris Hatwig
Founded: 2007
Employees: 50-100
Toll-Free Phone: (888) 340-2787
Address: 290 E. John Carpenter Freeway, 4th Floor Irving, TX 75062
Website: Apexus.com
Company Background
Apexus solves for medication access and affordability for America’s safety net by delivering access, education, and sourcing solutions for 340B stakeholders. In addition to serving as the HRSA-designated Prime Vendor for the 340B Drug Pricing Program, Apexus offers professional training and validation through its Advanced 340B Operations Certificate Program and facilitates a streamlined solution for returning ineligible 340B discounts with the Covered Entity Refund Service.
Product Overview
n What is the Apexus Covered Entity Refund Service?
The Apexus Covered Entity Refund Service (CRS) facilitates the return of ineligible 340B discounts to individual manufacturers. Apexus works directly with covered entities or contracted consultants to efficiently process refunds to manufacturers through a proprietary process, reducing the time and effort spent resolving errors. 340B covered entities must manage the difficult task of returning ineligible 340B discounts to manufacturers accurately and efficiently.
Both covered entities and manufacturers struggle to resolve these errors for a number of reasons:
• Historical drug pricing information is difficult to access for covered entities.
• Manufacturer contacts for refunds are not publicly available.
• No statutorily defined process governs refunds of ineligible 340B discounts.
• There is no industry standard for 340B refunds.
n What are the benefits of the Apexus CRS?
The Apexus CRS brings the expertise of Apexus to 340B compliance, analysis, project management, and reporting. Covered entities benefit by using the Apexus CRS to manage their 340B refunds to streamline the process of refund calculation, documentation, and resolution. A database of manufacturer contacts along with a database of historical WAC prices and NDC codes are maintained by Apexus CRS to improve response time and accuracy. The Apexus CRS provides a best practice process for facilitating covered entity refunds.
As a thought leader and go-to resource in pharmacy solutions for the nation’s safety net providers, Apexus developed a solution to streamline the process of returning ineligible discounts to manufacturers. The pilot program launched over a two-year period and successfully refunded over $5 million to more than 200 manufacturers with minimal impact on day-to-day processes at eight separate covered entities and several manufacturers. The CRS solution streamlined the process to quickly resolve 340B refund issues, significantly reduced the impact on day-to-day processes for both the covered entity and the manufacturer, and resulted in an eight times faster response rate from manufacturers when Apexus CRS extended the refund offer.
How does the CRS process work?
1. Findings are identified during HRSA audit, independent outside audit, or self-audit.
2. Covered entity contracts with Apexus CRS to facilitate refund to manufacturers.
3. Apexus has a kickoff call with the covered entity and/or consultants to launch the refund process.
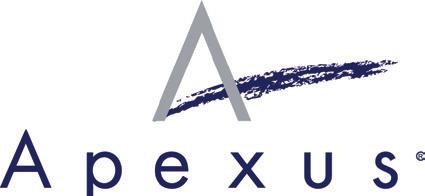
4. Covered entity completes standardized documents to validate refund offer.
5. Covered entity transfers funds to Apexus.
6. Apexus sends refund offer to manufacturer for approval or denial.
7. Apexus forwards approved funds to manufacturer or works to resolve denials.
8. Covered entity receives fully auditable final report from Apexus.
Testimonials
“Managing a 340B repayment is time-consuming and difficult because historical price information is not available, manufacturer contacts are not publicly available, and the response rate is very low.”
— 340B Program Manager, Hospital in Northeast
“Manufacturer repayments are an important part of 340B compliance work. Apexus engagement with repayment makes the process more efficient for both the covered entities and manufacturers.”
— Pharmacy Specialist, 340B Program, Health Care System in Southeast
Ordering Information
Are you ready to save time, increase efficiency, and simplify 340B discount refunds? Learn how our refund solution can streamline your success. Contact Apexus today to learn more about Apexus CRS.
Email: coveredentityrefunds@apexus.com
Phone: (888) 340-2787
Website: Apexus.com/CRS
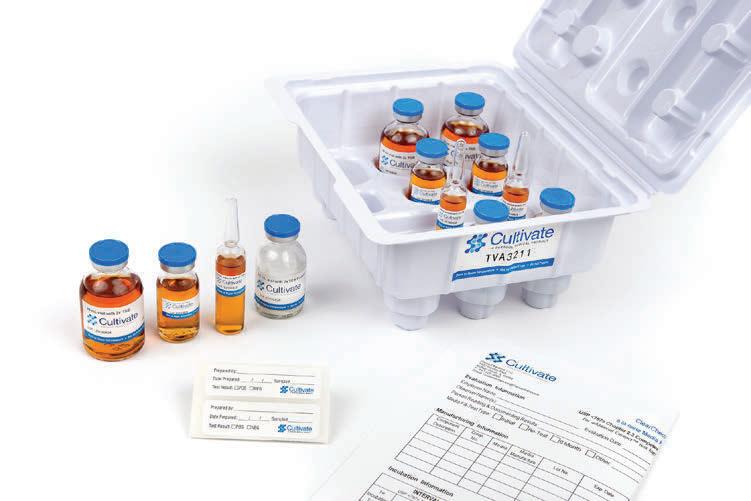
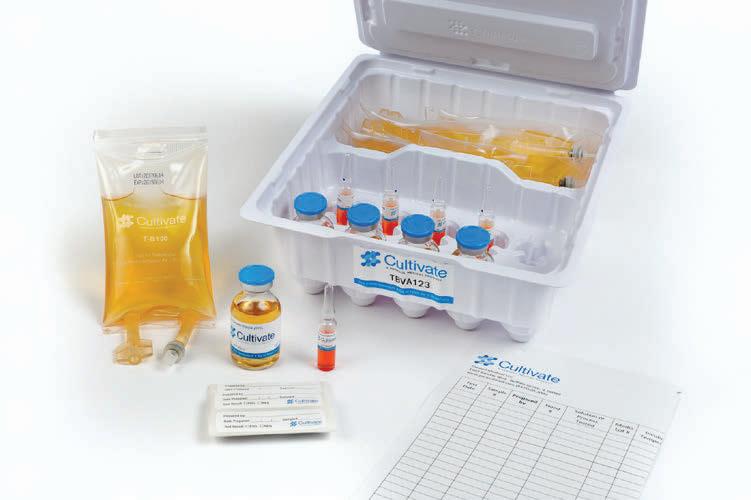
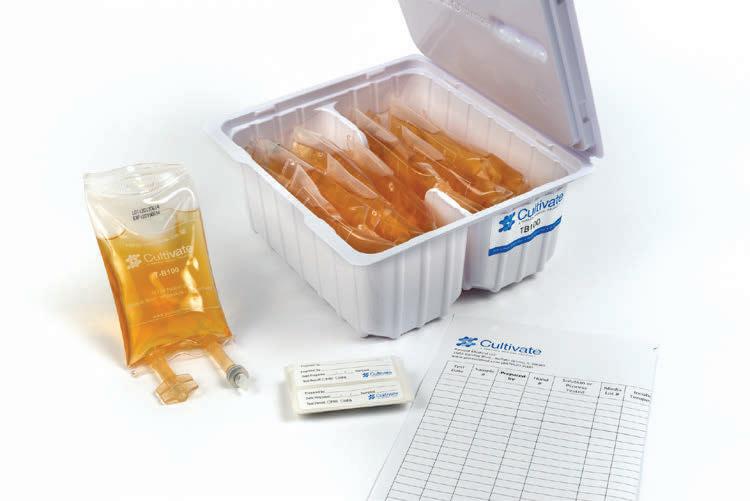
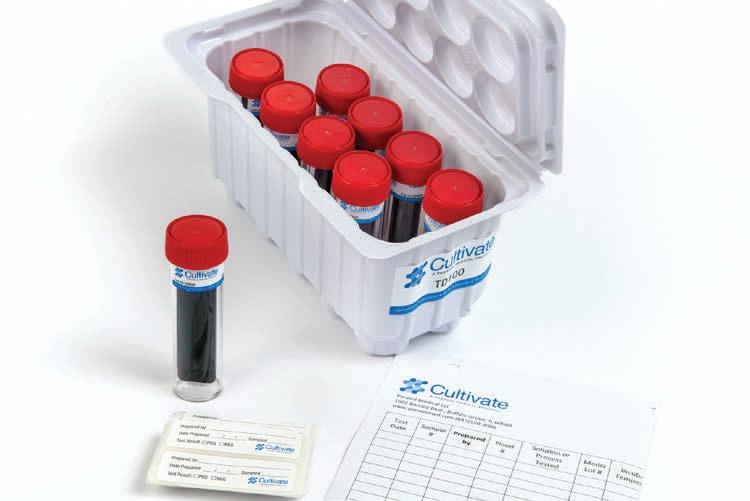
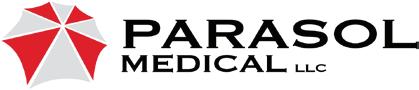
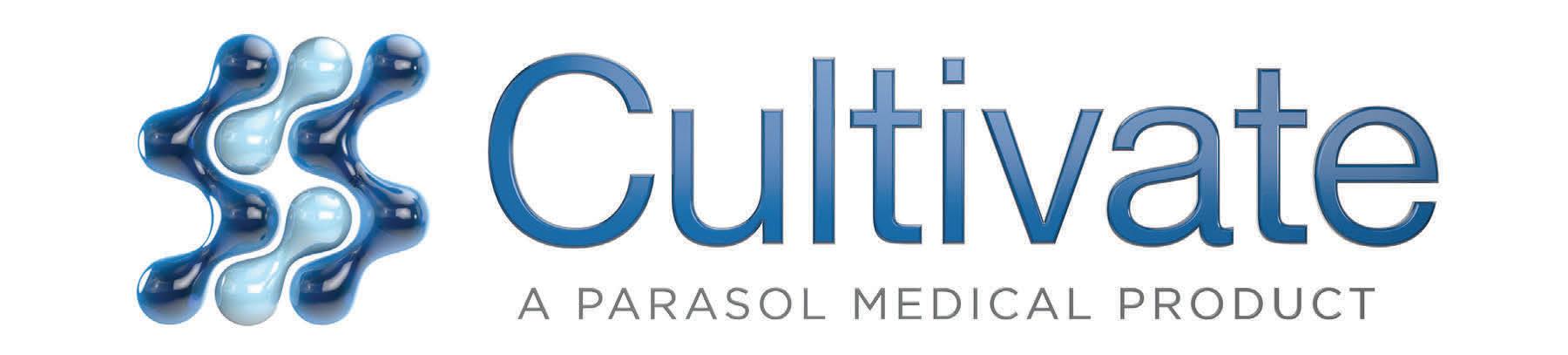
Cultivate™ From Parasol Medical™ is Here to Help Your Facility Comply With the New USP <797> Standard
Make
President & CEO: Michael Kilcran
Founded: 2013
Toll-Free Phone: (800) 444-6451
Phone: (847) 520-3000
Fax: (847) 520-4268
Address: 1000 Asbury Drive, Suite 1 Buffalo Grove, IL 60089
Website: www.parasolmed.com
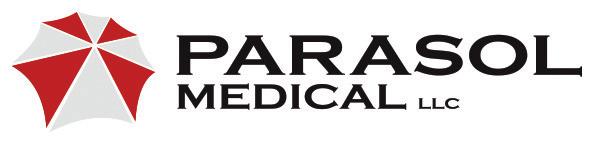
Company Background
Parasol Medical is proud to celebrate a decade of being at the forefront of healthcare innovation, delivering innovative medical devices and pharmacy products that improve patient outcomes and streamline clinical workflows. Our commitment to improving patient outcomes, customer satisfaction, and market agility remains stronger than ever. We understand that transitioning to the new USP <797> standard and complying with increased testing and documentation requirements can be challenging. At Parasol, we provide our customers with the necessary resources and guidance to ensure compliance every step of the way. With our extensive industry experience and unwavering commitment to customer success, you can trust Parasol Medical to help you navigate the changing landscape of healthcare and pharmacy regulations and deliver exceptional quality.
Product Overview
n Updated directions for use, log sheets, and support documents to help your facility comply with the increased documentation requirements:
We understand that keeping up with regulatory standards can be a challenge. In response, we have developed new user-friendly directions for use and log sheets to help customers comply with the updated USP <797> standard. By providing clear, concise guidance and covering all essential information required by the standard, our new log sheets and directions for use make compliance easier and more accessible for customers. Each document is tailored to the specific section of the USP <797> standard that applies and has been carefully crafted to cover all the essential information required by the standard. We believe that the new documents will be a valuable asset in streamlining compliance and empowering customers to test with confidence.
n Variety of Convenient Preassembled Test Kits
We offer a variety of preassembled test kit options that are ready to use, making the testing process easier and more efficient for busy pharmacy teams. Our à la carte test kits are designed to supplement our preassembled kits and provide a more tailored testing solution that closely mirrors daily compounding practices in your facility. Need a custom test kit, contact our team to design a test using the à la carte kits or to discuss a unique preassembled test kit for your facility.
n Dedicated Team to Help With Your Questions
Our experienced team is available to provide guidance on the new regulations and help pharmacies navigate the changes. We are committed to providing the support our customers need to maintain compliance and work through challenges during the transition.
Key Product Features
• Best in market log sheets, directions for use, and support materials.
• Variety of preassembled kit options.
• Comparable product configurations to most competitor’s kits.
• Competitive pricing.
• Superior, non-lint producing packaging.
Key Product Lines
n Contact™ — Media Flex-Paddles
• 12-month self-life, can use for gloved fingertip and thumb, and surface sampling.
Applicable USP <797> Uses:
• Section 2.2 Demonstrating Competency in Garbing and Hand Hygiene Section
• Section 6.3 Monitoring Surfaces for Viable Particles
• Section 2.3 Competency Testing in Aseptic Manipulations — a Gloved fingertip and Thumb Test Must Immediately Follow the Media Fill Test
n PASS™— Preassembled Aseptic Media Fill Test Kits
• Several kit configurations to mimic daily compounding practices.
Applicable USP <797> Uses:
• Section 2.3 Competency Testing in Aseptic Manipulation
n ClearCheck™ — À La Carte Kits
• A variety of component type and sizes.
Applicable USP <797> Uses:
• Section 2.3 Competency Testing in Aseptic Manipulation
the transition to the new USP <797> testing and documentation seamless with carefully crafted testing supplies.
Precision cooling for optimal care: The power of medical grade cold storage
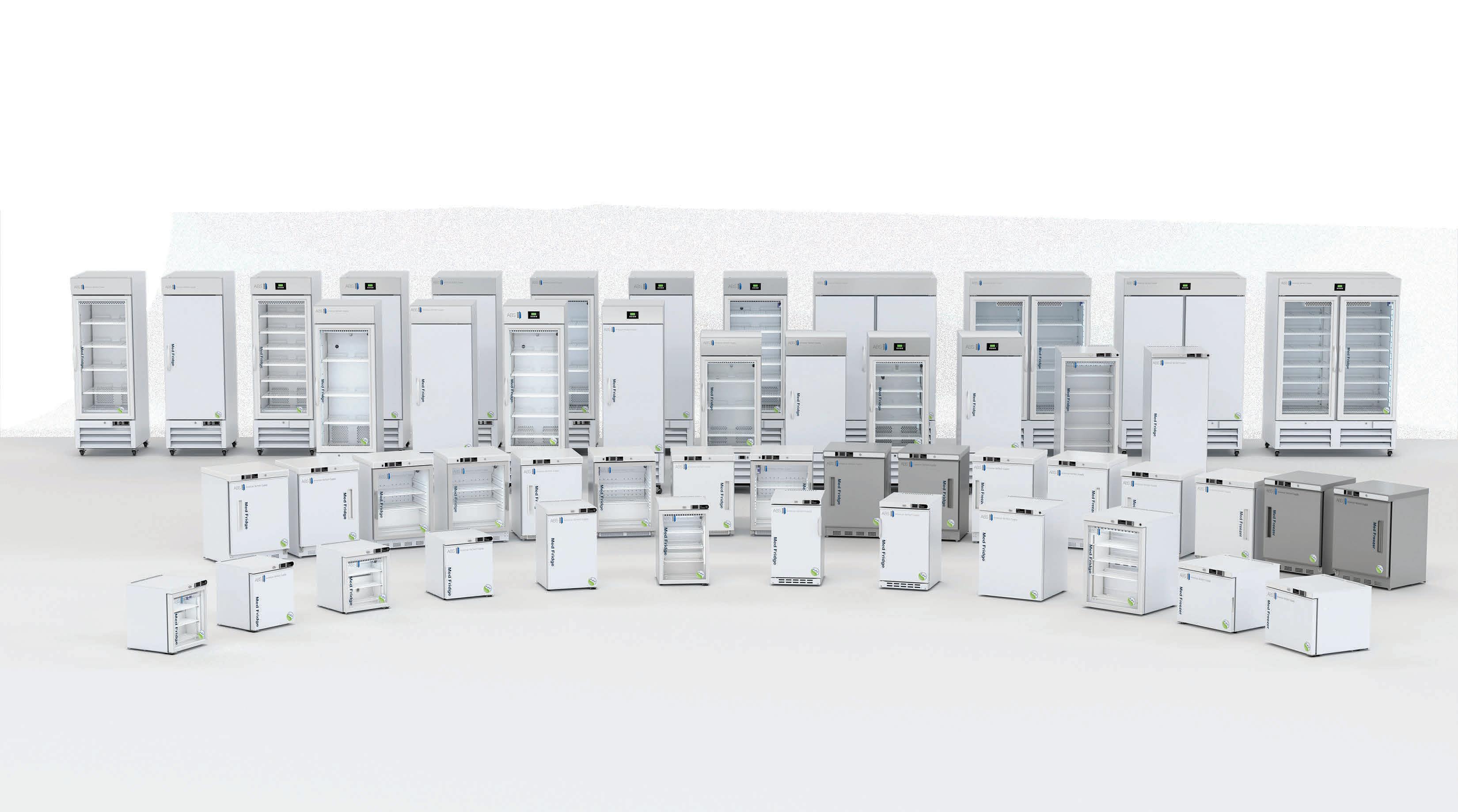
Elevate your cold storage with our premium selection of vaccine refrigerators and freezers designed in accordance with the NSF/ANSI 456 Standard for Vaccine Storage. These state-of-the-art units protect pharmaceuticals at optimal temperatures, preventing waste and allowing for peak delivery of vaccines.
At American BioTech Supply, we prioritize excellence in design and engineering to ensure that our units maintain the precise temperatures necessary to preserve the integrity of your medical supplies. Our product line is certified to the NSF/ANSI 456 standard for vaccine storage, and every vaccine dose benefits from optimal cold storage performance while prioritizing patient safety.
EPA/SNAP compliant, hydrocarbon, natural refrigerants Large selection of models ranging from 1 to 49 ft3 Microprocessor temperature controller - superior temperature control and recovery Array of temperature alarms with audible and visual indicators Temperature monitoring device with 3-year certificate of calibration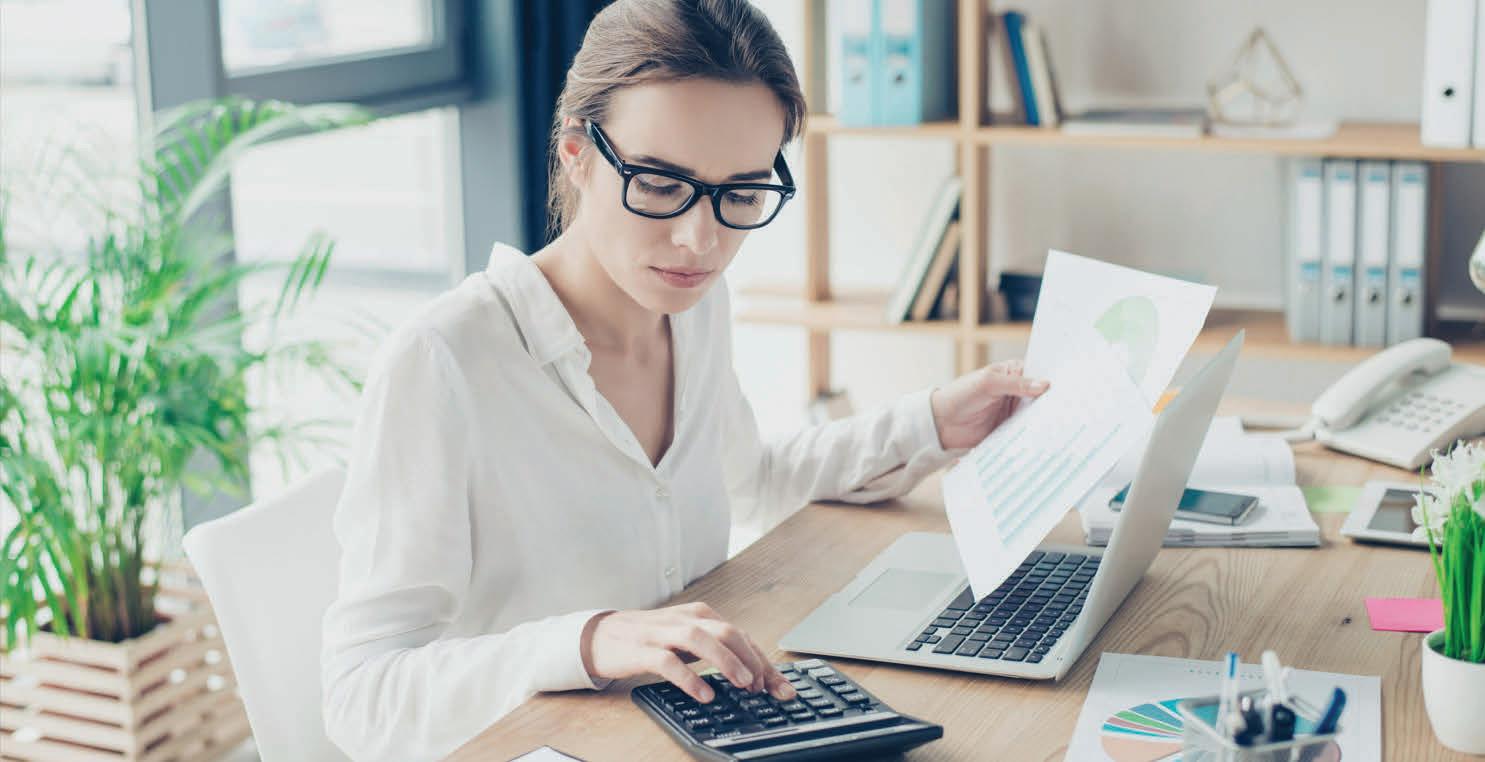
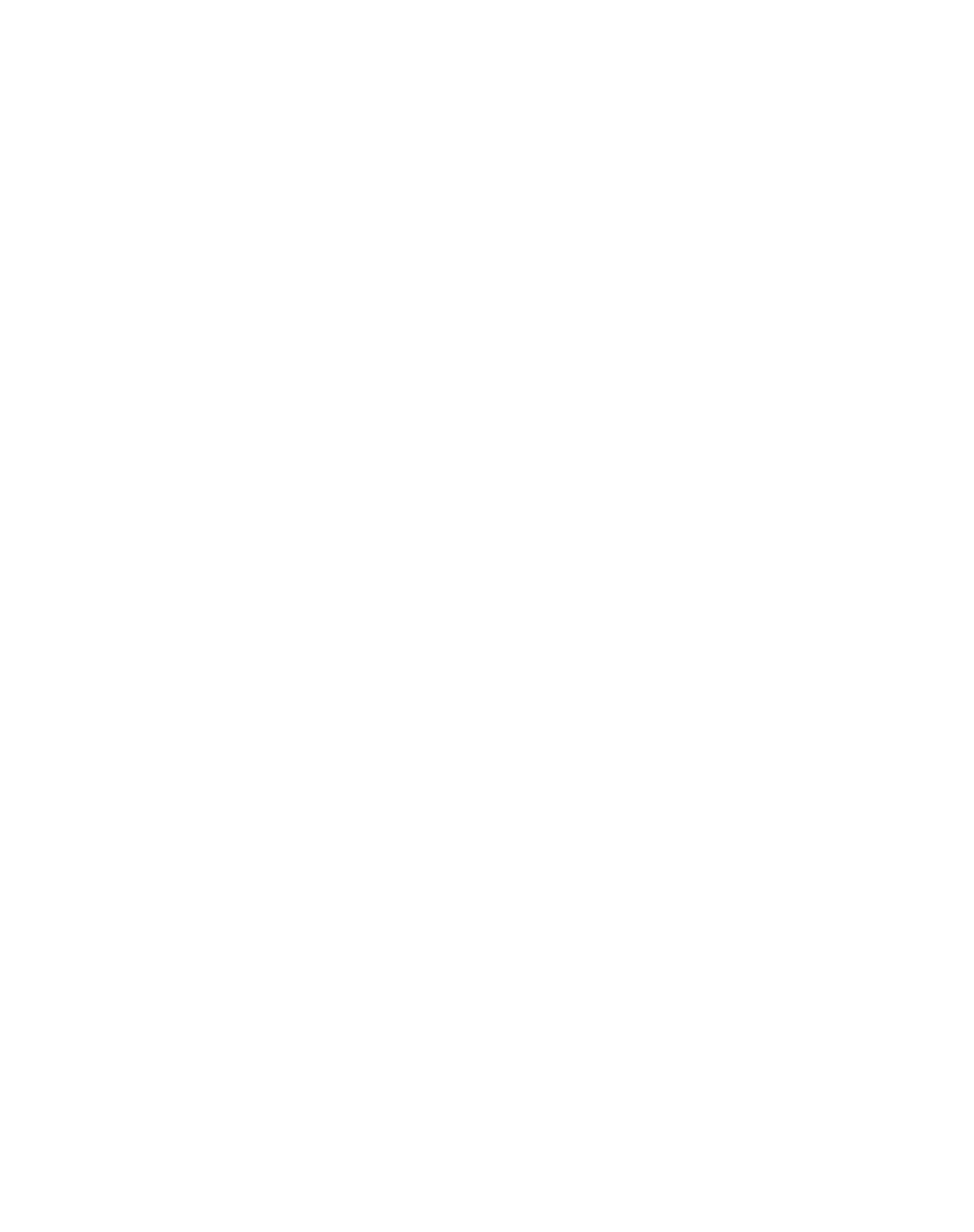
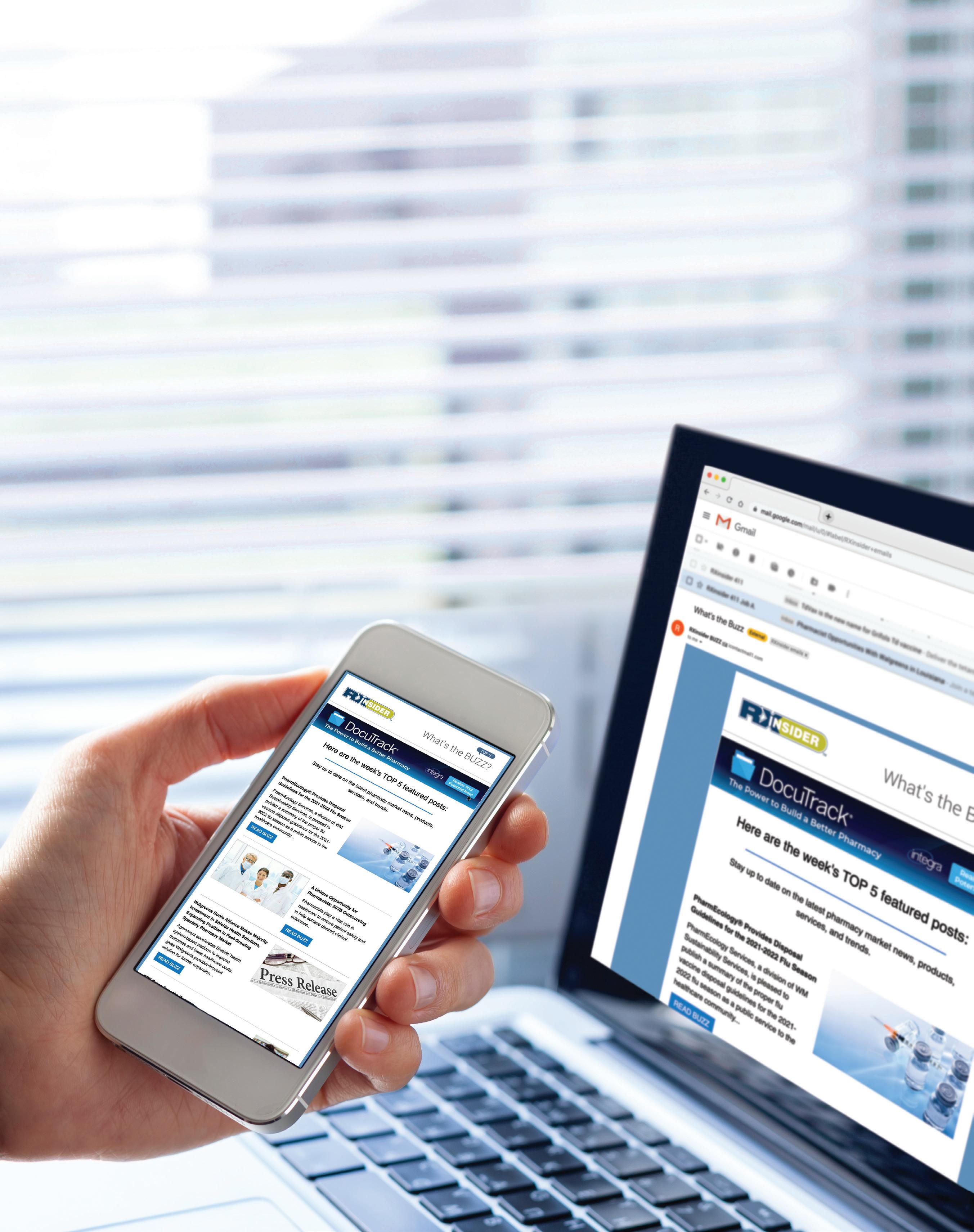
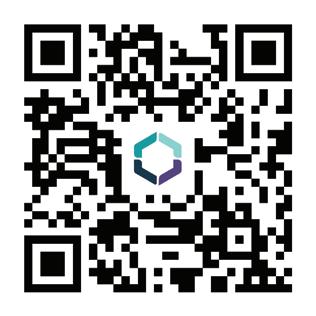
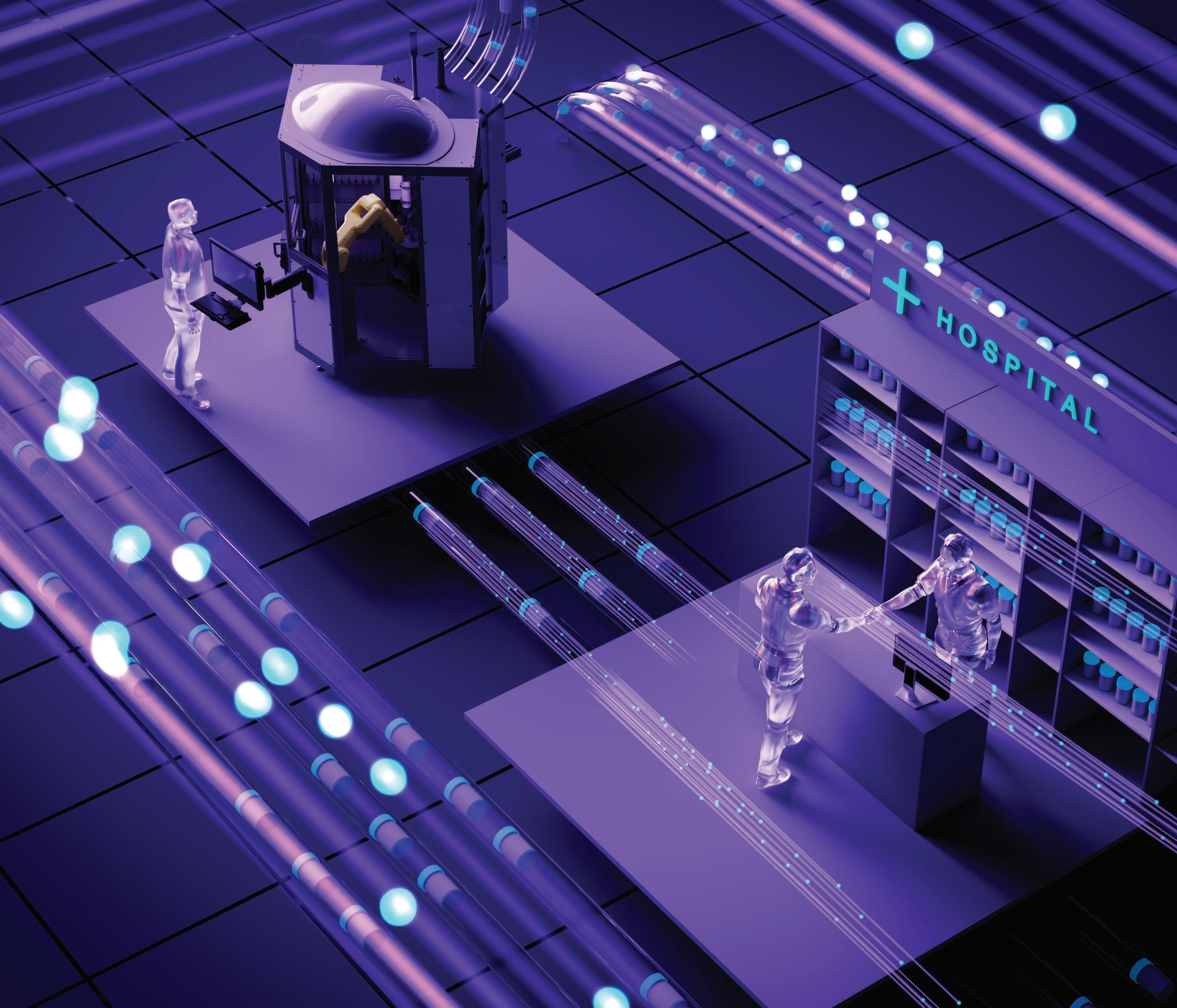
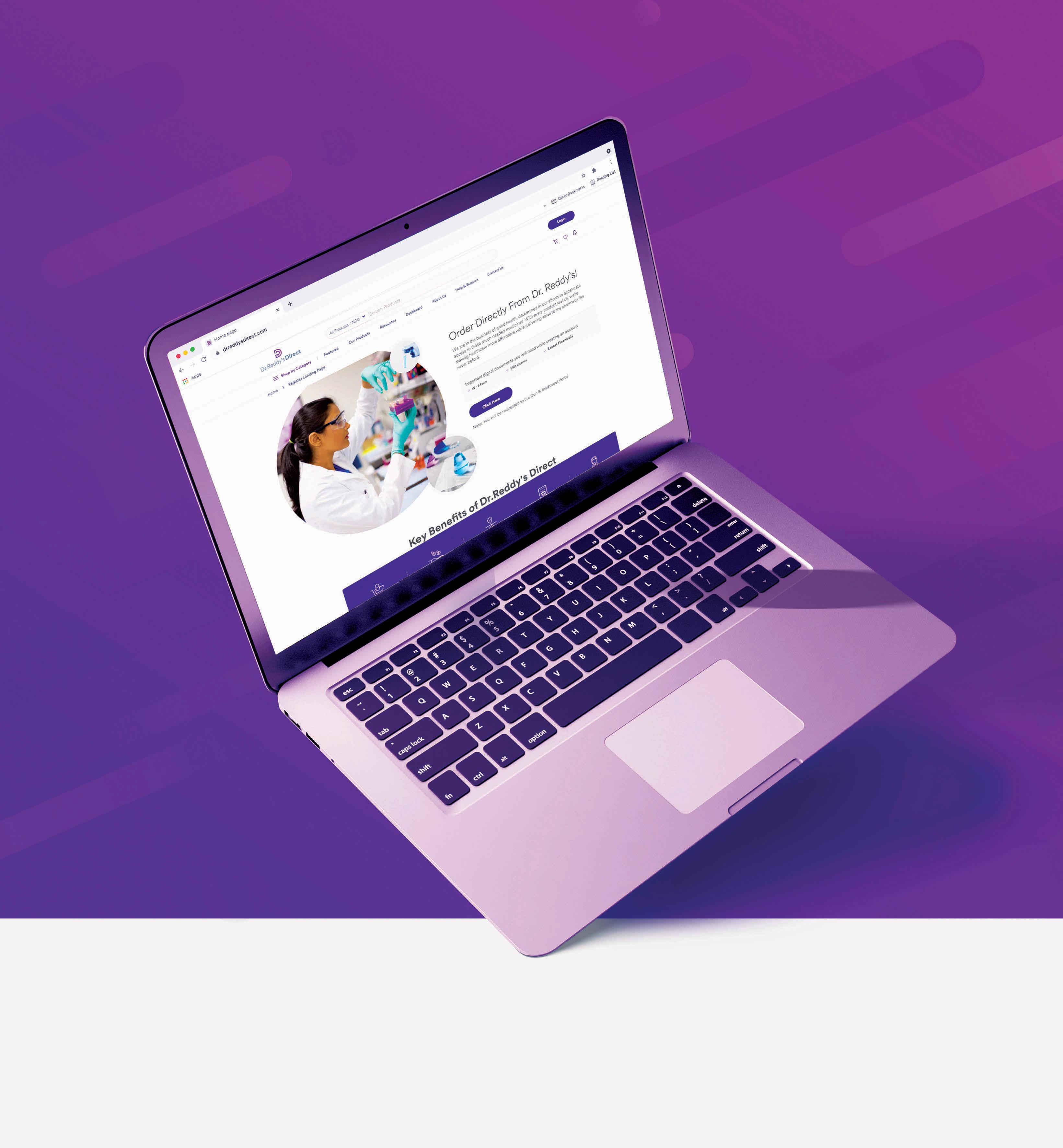