scaffmag
RISING FROM THE ASHES
The monumental scafolding project that’s reconstructing Notre Dame
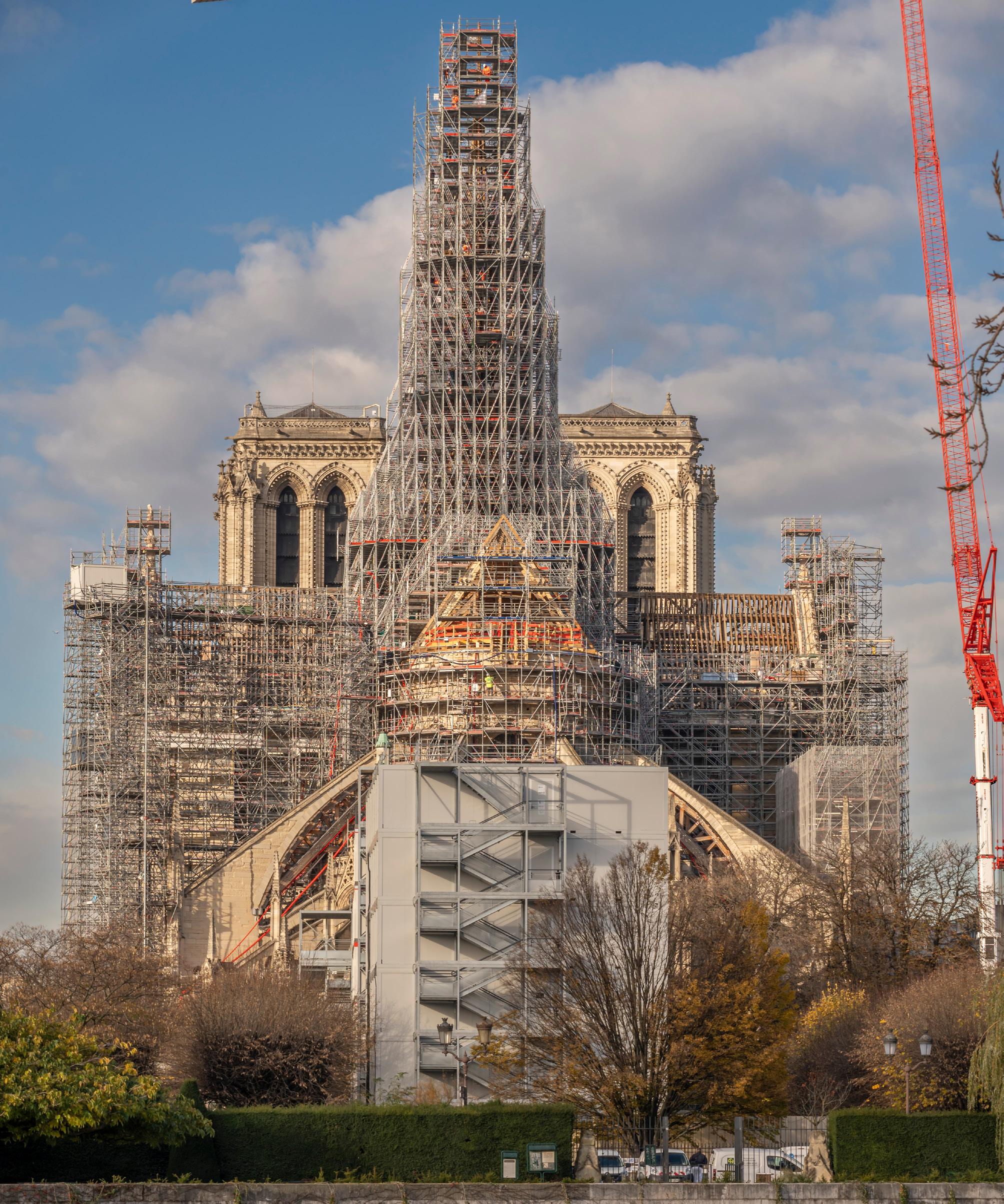
Scafolding success: Celebrating 15 years of ScafMag magazine
Elevating excellence: Layher UK’s strategic shifts for growth
BUILDING A LEGACY: GKR SCAFFOLDING AT 30 - INSIGHTS FROM LEE AND NEIL ROWSWELL
ScafEx24: Pioneering the future of scafolding and access
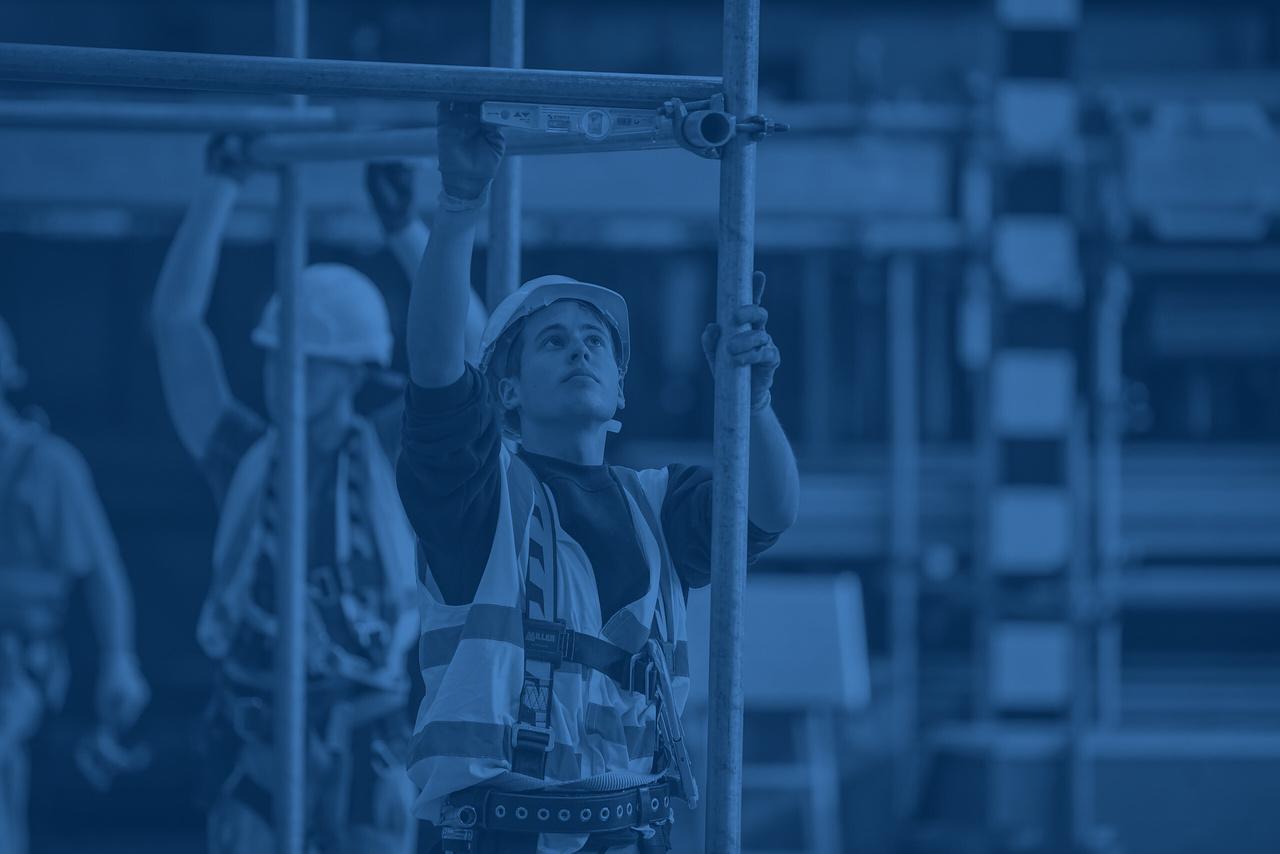
T H E R E ’ S S T A N D A R D S . .
A N D T H E N T H E R E ’ S
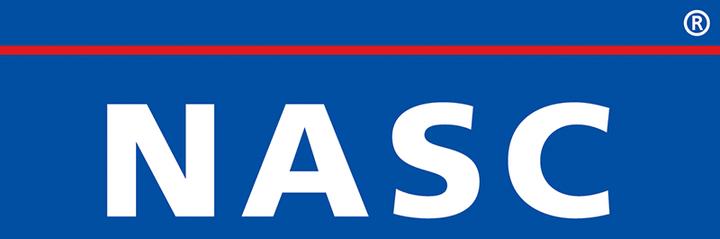
A R E Y O U R E A D Y T O T A K E
Y O U R B U S I N E S S T O N E W H E I G H T S ?
N A S C r e d u c e s y o u r r i s k a n d i m p r o v e s y o u r e f f i c i e n c y .
O p e n d o o r s t o n e w b u s i n e s s o p p o r t u n i t i e s a n d p r o v i d e y o u r c u s t o m e r s w i t h a n a s s u r a n c e t h e y c a n t r u s t .
A t r u s t t h a t h a s b e e n e a r n e d .
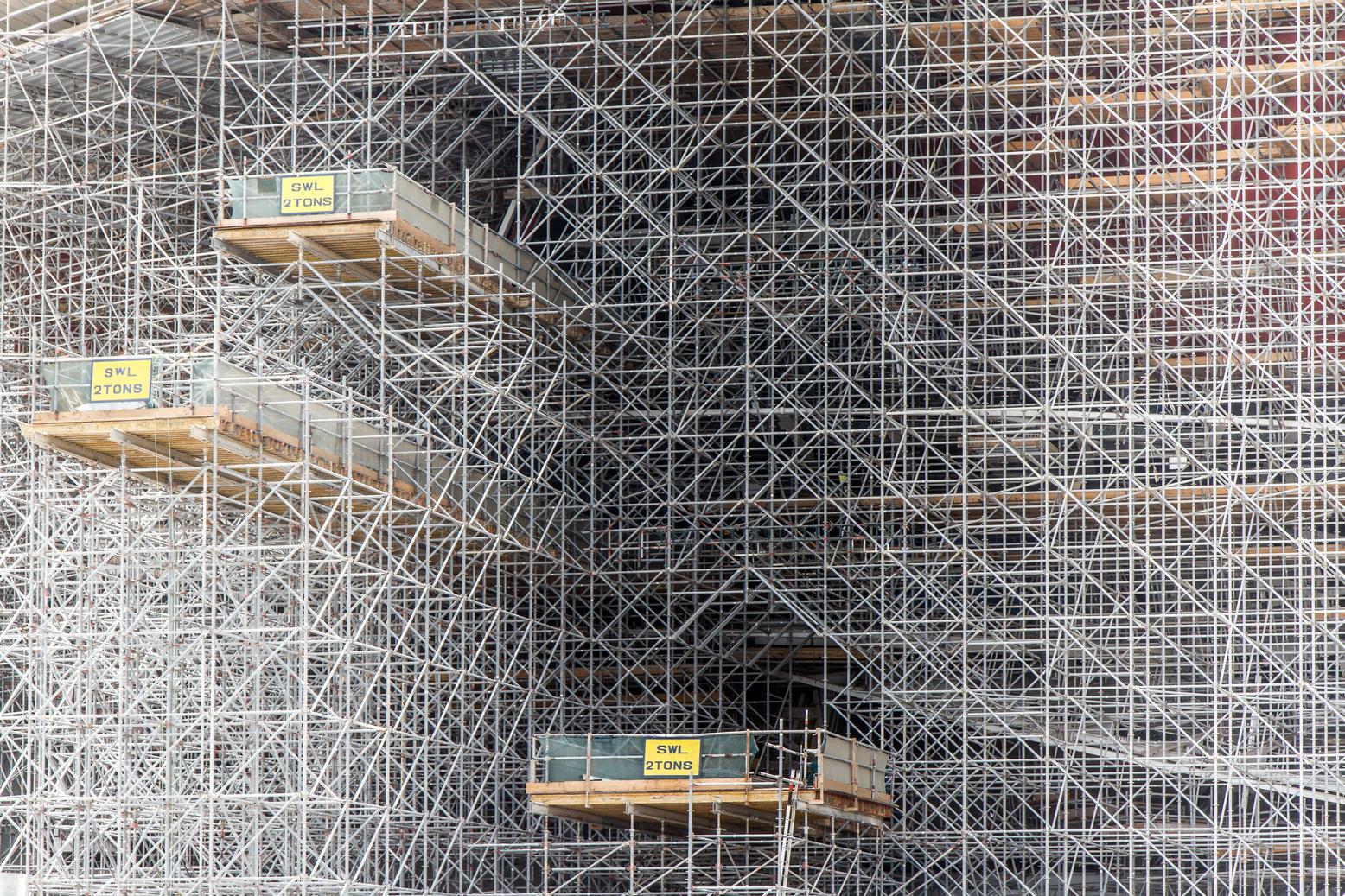
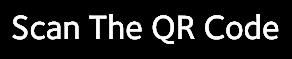
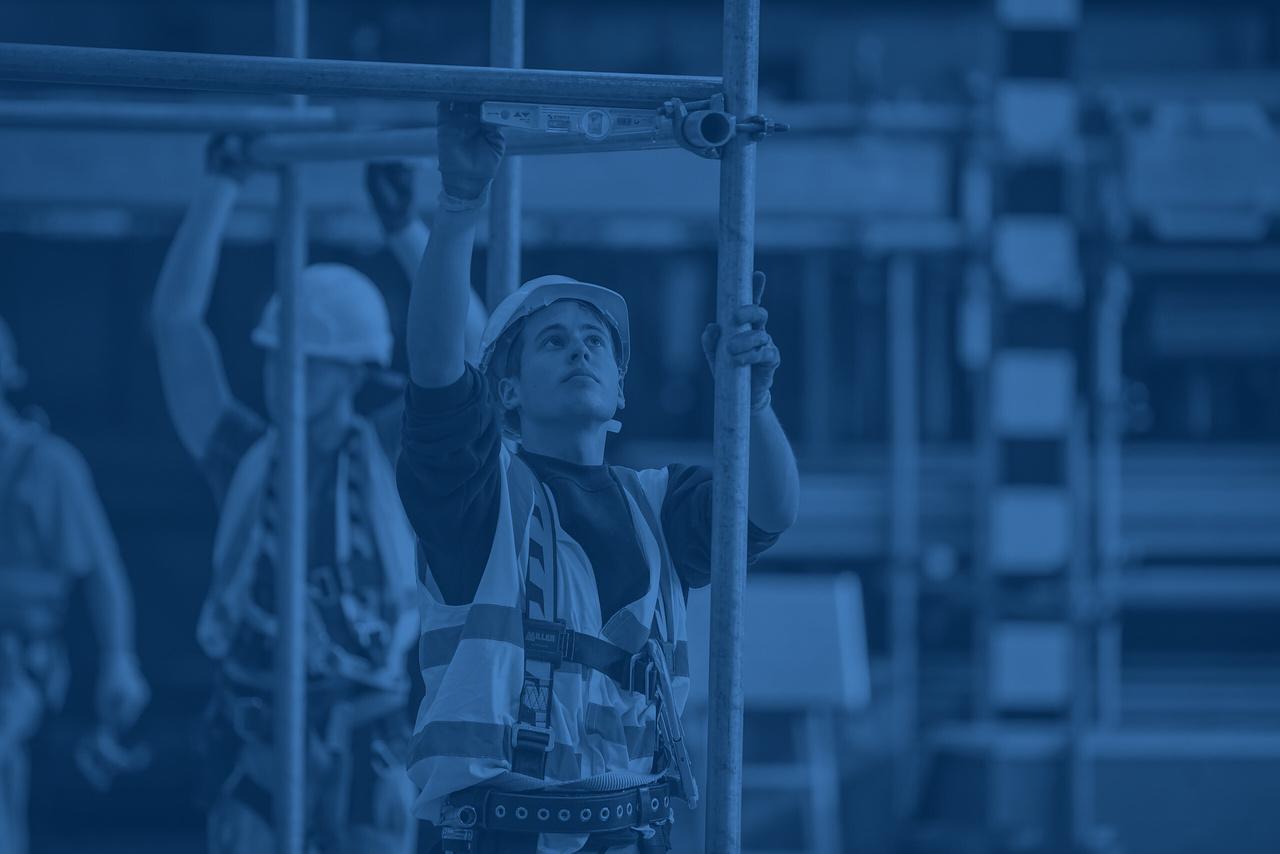
Contents
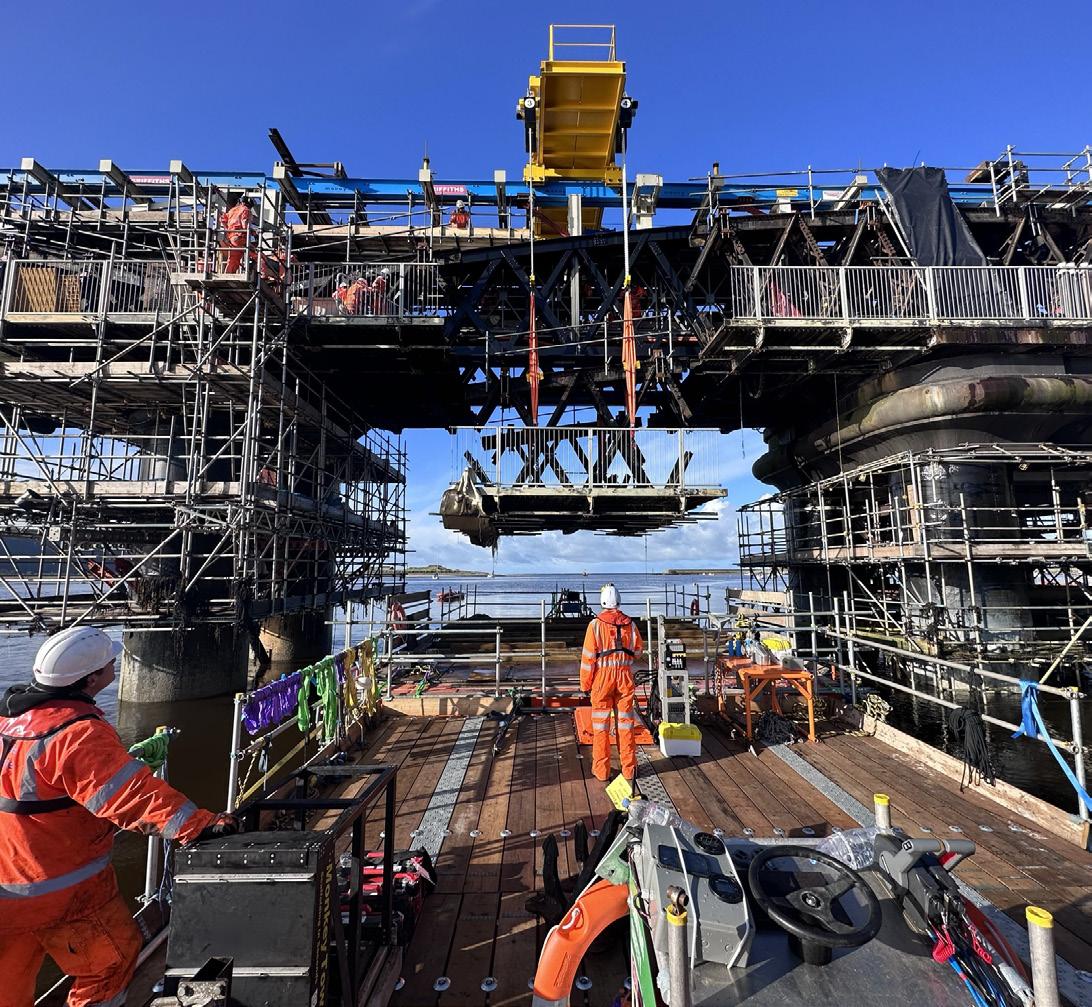
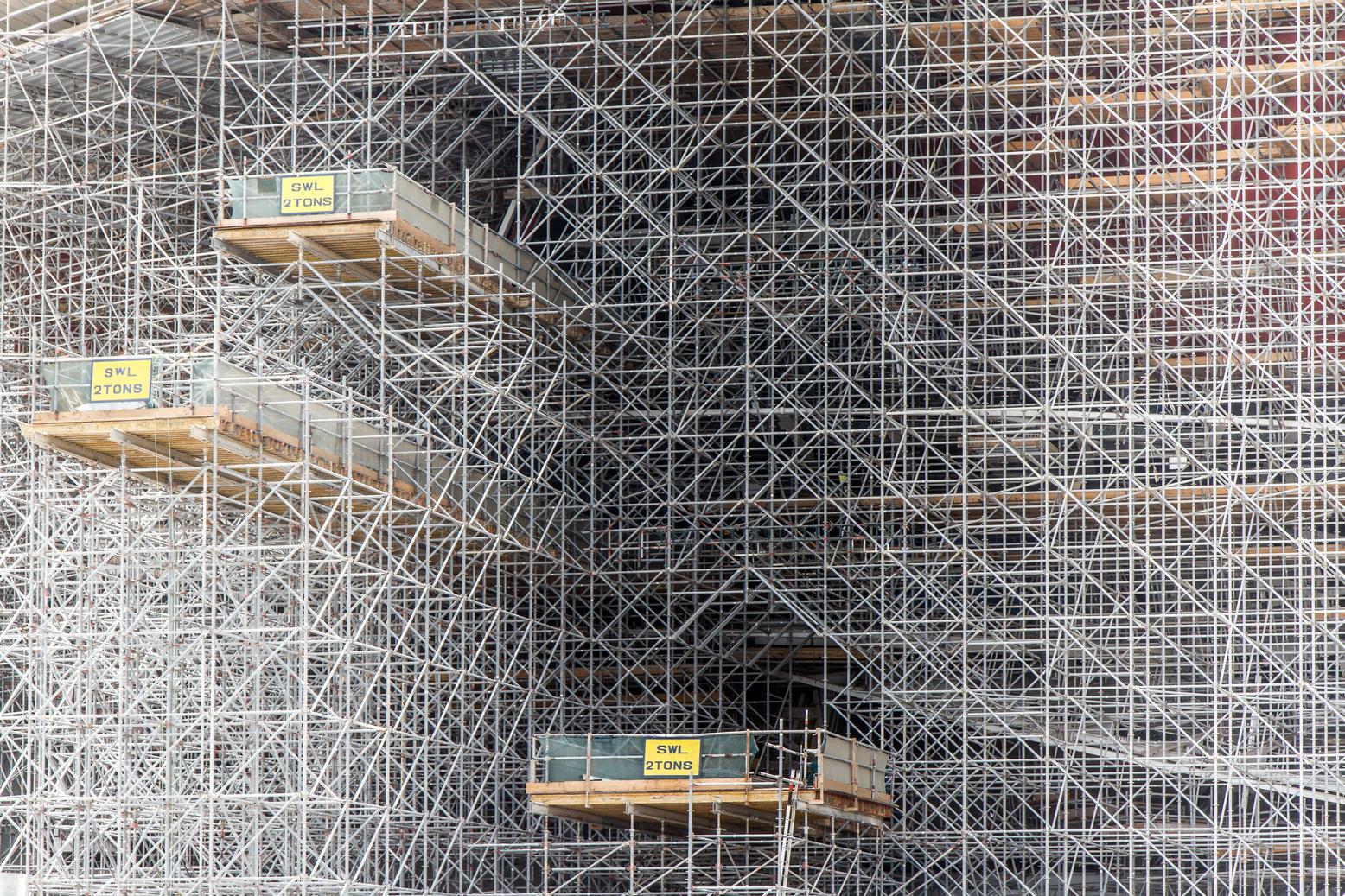
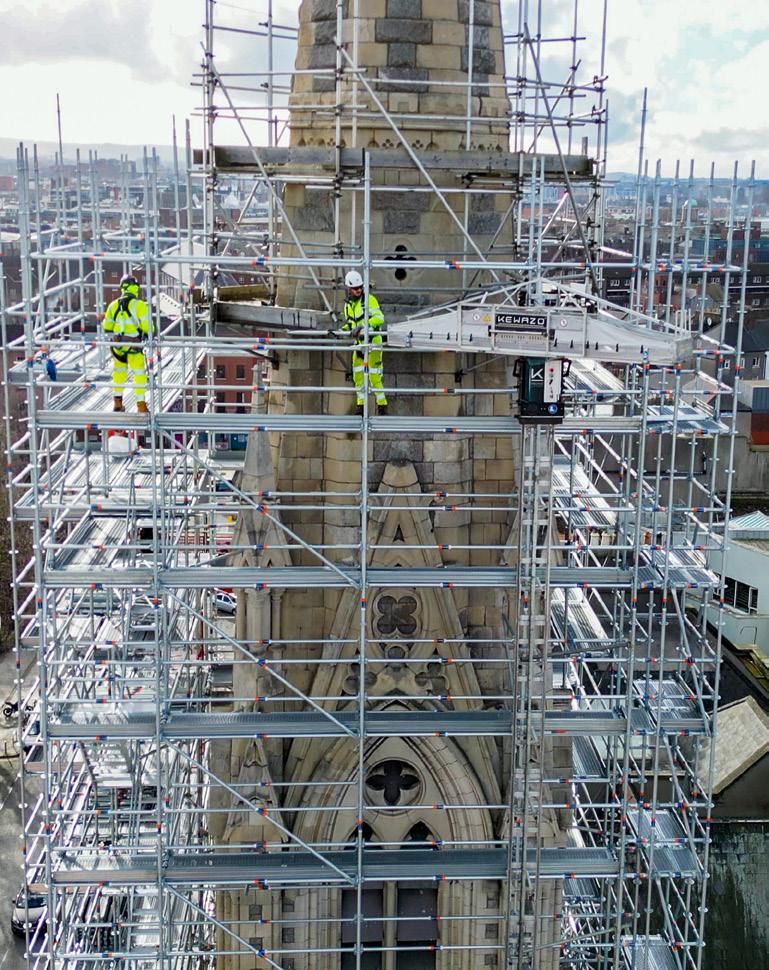
64
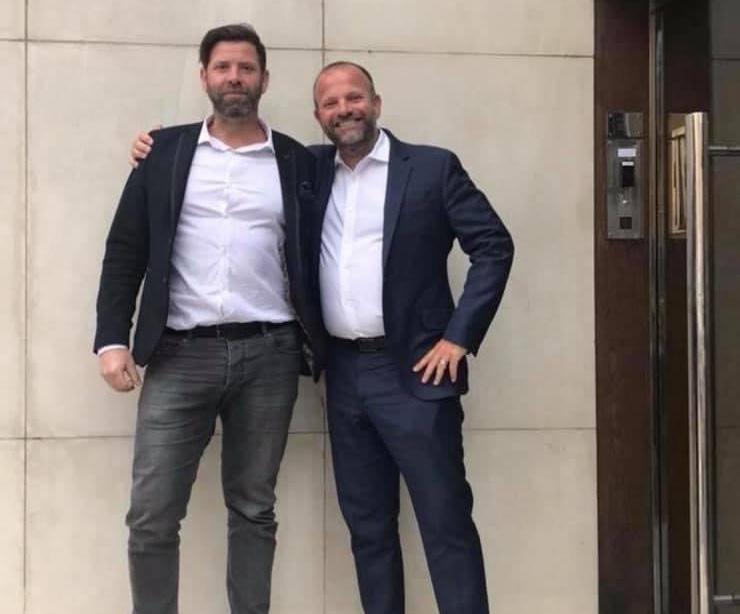
28 Interview
Sean Pike, MD of Layher UK, explains the company’s strategy for the year ahead – and beyond, following some signifcant management shifts.
32 Spotlight
Following the shocking blaze that badly damaged the famous Notre-Dame Cathedral in Paris, nearly 500 craftspeople have been painstakingly working on its restoration.
36 People
Mark Parkin is a respected and recognised leader in the scafolding industry – his story is a testament to the power of resilience and his profound impact on the profession.
40 Business Spotlight
GKR Scafolding is a beacon of excellence in the industry. ScafMag hears from the Rowswell brothers on their 30-year journey.
43 Business
Des Moore explores how to manage your business after becoming part of a bigger group.
50 Opinion
Millcroft’s MD, Billy Jones, addresses the pressing issue of the shortage of new workers in the industry.
55 Products
Devine Scafolding used a new ring-lock system during their restoration of Dublin’s Abbey Church.
57 System
2024 looks set to be a challenging year for the industry, but a long-term business strategy might prove helpful.
62 Projects ScafFloat’s groundbreaking work in Barmouth, North Wales; Alltask’s Silvertown Tunnel project; and Liddiard refurbishment of Broad Oak facility.
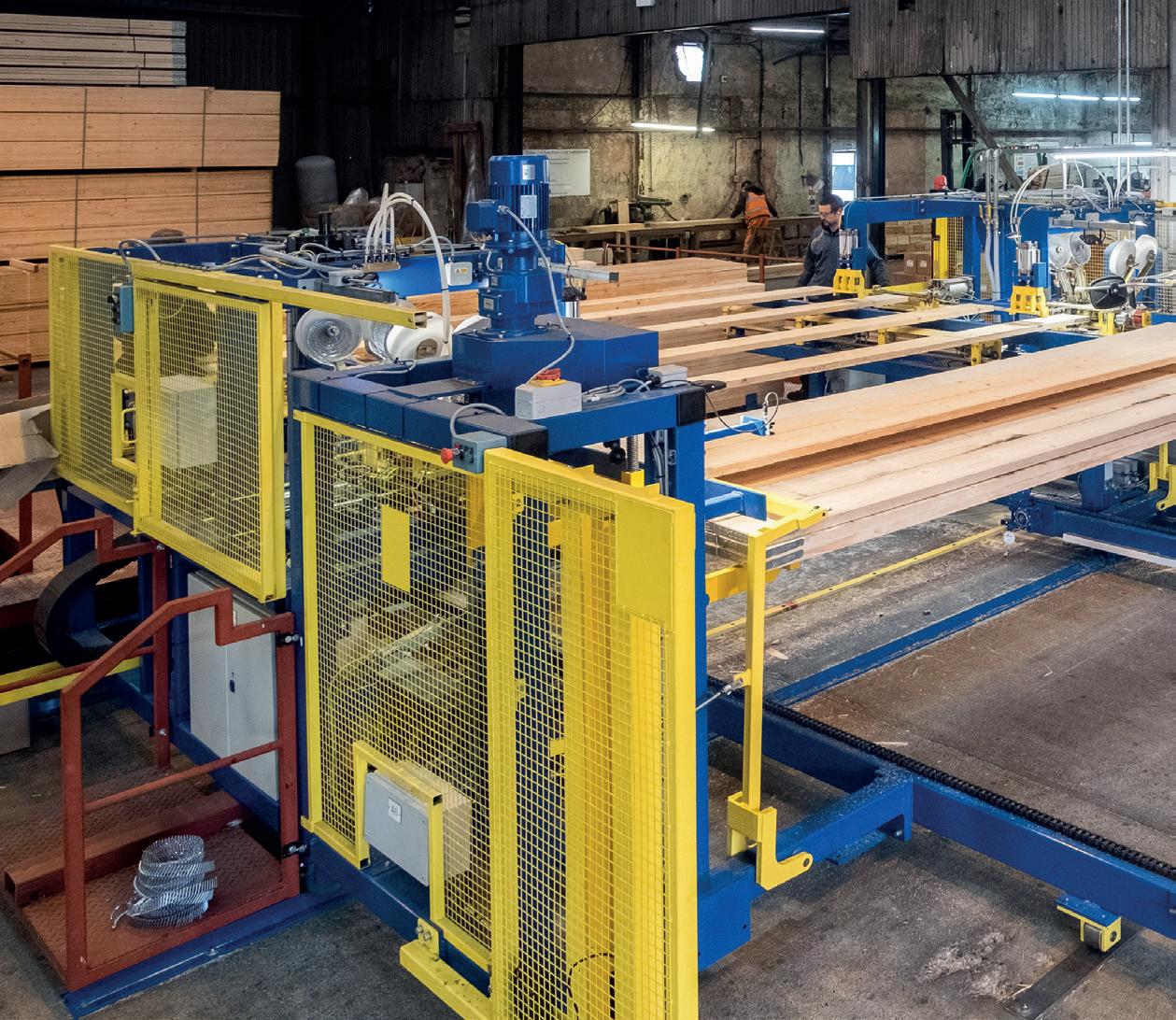
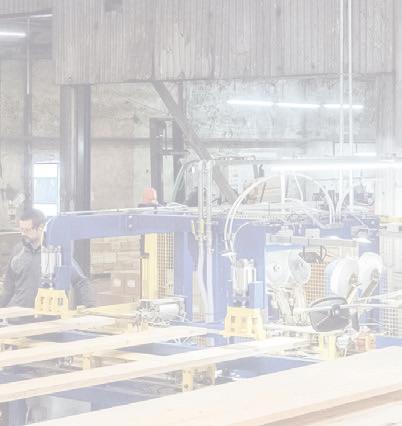

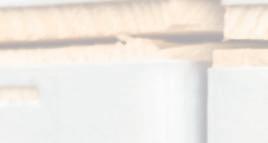
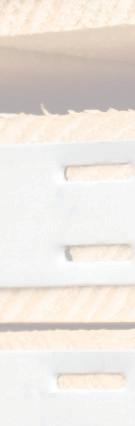
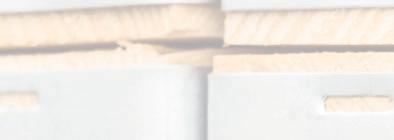
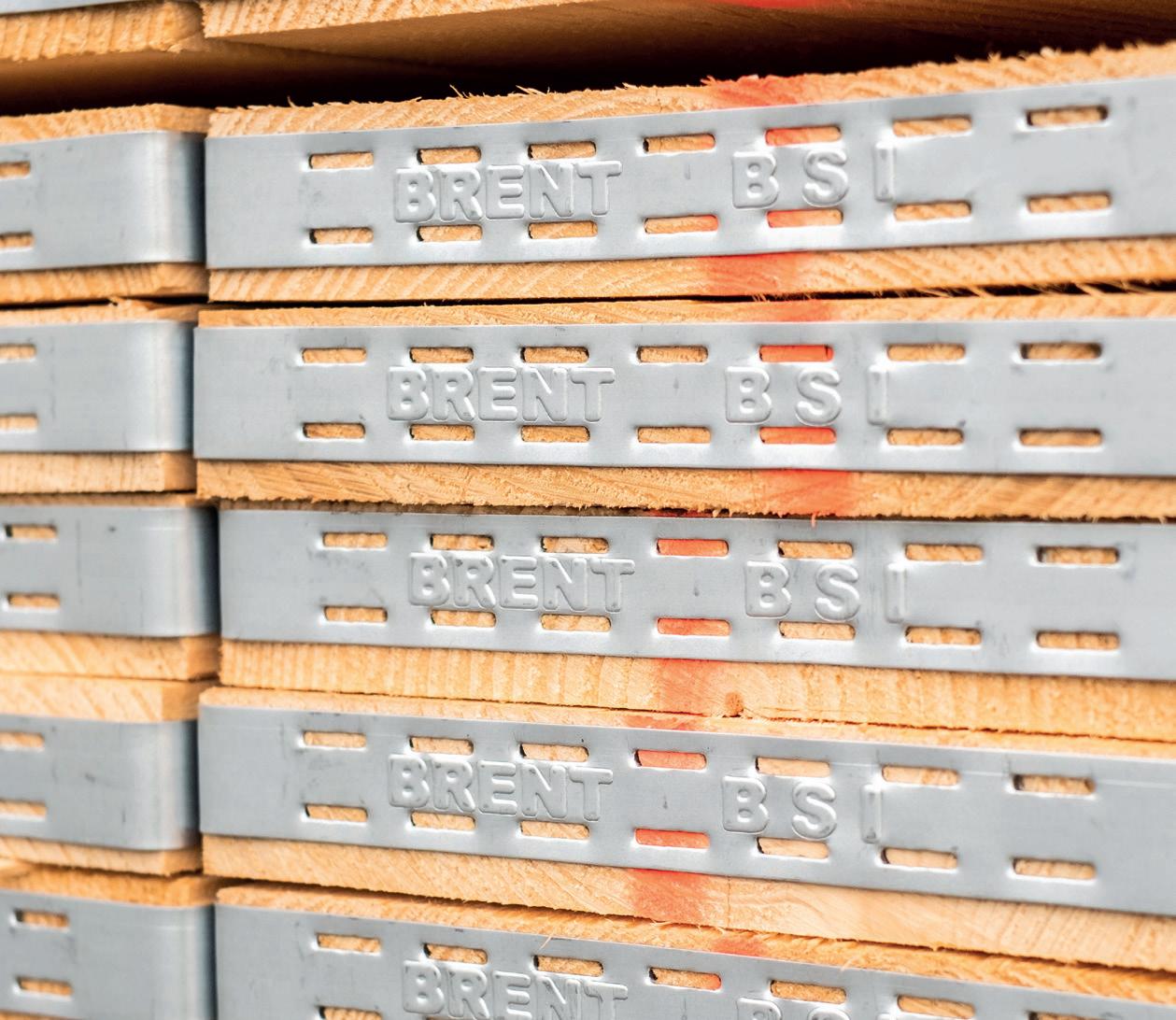
Welcome
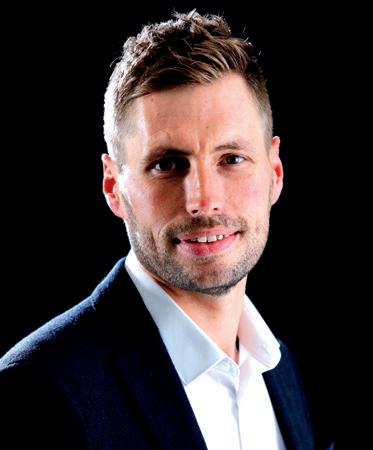
As we proudly present issue 21 of ScafMag, we fnd ourselves at a momentous juncture, celebrating 15 remarkable years of dedication to the scafolding industry. Since our inception in 2009, we have been committed to elevating industry standards, sharing knowledge and fostering a community of professionals as passionate about scafolding as we are. I take a moment (on page 20) to refect on our journey, highlighting the milestones and achievements that have shaped our publication and the industry at large.
Tis issue is particularly special as it embodies our commitment to honouring our past and anticipating the future. In an exclusive interview (on page 28), Sean Pike, Managing Director of Layher UK, unveils the company’s strategic vision for growth and innovation, ofering a glimpse into the exciting developments ahead.
In this issue, the spotlight shines brightly on an iconic scafolding project, the incredible scafolding works at Notre Dame Cathedral in Paris. Following the devastating fre in 2019, this detailed spotlight report (on page 32) exemplifes the pinnacle of skill, innovation and dedication that defnes our industry.
We also celebrate a signifcant milestone with the multi-award winning GKR Scafolding Ltd, marking 30 years of leadership and excellence in our feld. Our in-depth conversation (on page 40) with the Rowswell brothers provides invaluable insights into their journey and colossal success.
Regular contributor Des Moore explores the nuanced challenges of integrating into a larger group, ofering strategies and wisdom for businesses navigating this transition (on page 46). Meanwhile (on page 50), Billy Jones of Millcrof voices his concerns about attracting young talent to the scafolding sector, igniting a conversation on how we can collectively reshape perceptions and engage the next generation.
Tis issue is rounded of with comprehensive project reports showcasing the diverse and dynamic nature of our industry’s work across the globe. As we commemorate 15 years of ScafMag, we extend our deepest gratitude to you, our readers, for your continuous support and engagement. Your enthusiasm and feedback inspire us to push boundaries and continue delivering content that not only informs but also inspires.
Happy reading and stay safe!
Daniel Norton – Editor dan@scafmag.comEDITORIAL
Editor Daniel Norton
T 01472 476024
M 07776 218831
E dan@scafmag.com
@ScafMagDan
Features writers
Grahame Anderson
Richard Trenchard
Design
Demot Rushe
Dermotrushe.co.uk
CONTRIBUTORS
Billy Jones - Millcroft Scafolding
Des Moore - MOR1X
Garry Grifths - UKSSH
ADVERTISING
Manager Jessica Norton
T 01472 476024
M 07776 218831
E jess@scafmag.com
PUBLISHED BY ScafMag Ltd
Ofce G8
The Enterprise Village
Prince Albert Gardens
Grimsby
DN31 3AT
facebook.com/scafmag
twitter.com/ScafoldingNews
News
The scafolding sector is bracing itself for a year of challenges and opportunities in 2024
❖ As we embark on a new year, the industry fnds itself at a crossroads, navigating economic uncertainty, cost volatility and a persistent shortage of skilled labour. However, amidst these hurdles, there are signs of growth driven by sustainability initiatives and technological advancements.
WORKFORCE CHALLENGES PERSIST
One of the foremost challenges facing the scafolding sector is the ongoing shortage of skilled labour. Tis shortage has plagued the industry for several years and shows no signs of abating in 2024.
Te need for more qualifed workers continues to pressure construction projects, potentially delaying timelines and increasing labour costs. As a result, companies are intensifying eforts to attract and retain skilled labour, ofering competitive wages and training programmes to bridge the skills gap.
ECONOMIC UNCERTAINTY AND RISING MATERIAL COSTS
Economic uncertainty remains a cloud over the industry in 2024, with high interest rates and tighter lending standards impacting construction activity. Te cost of construction materials, according to the Construction Products Association, is projected to rise by 5.9% this year, exceeding the expected infation rate. Tis surge in material prices could further strain construction budgets, making project viability a concern for stakeholders.
BRIGHT SPOTS ON THE HORIZON
Despite these challenges, there is a silver
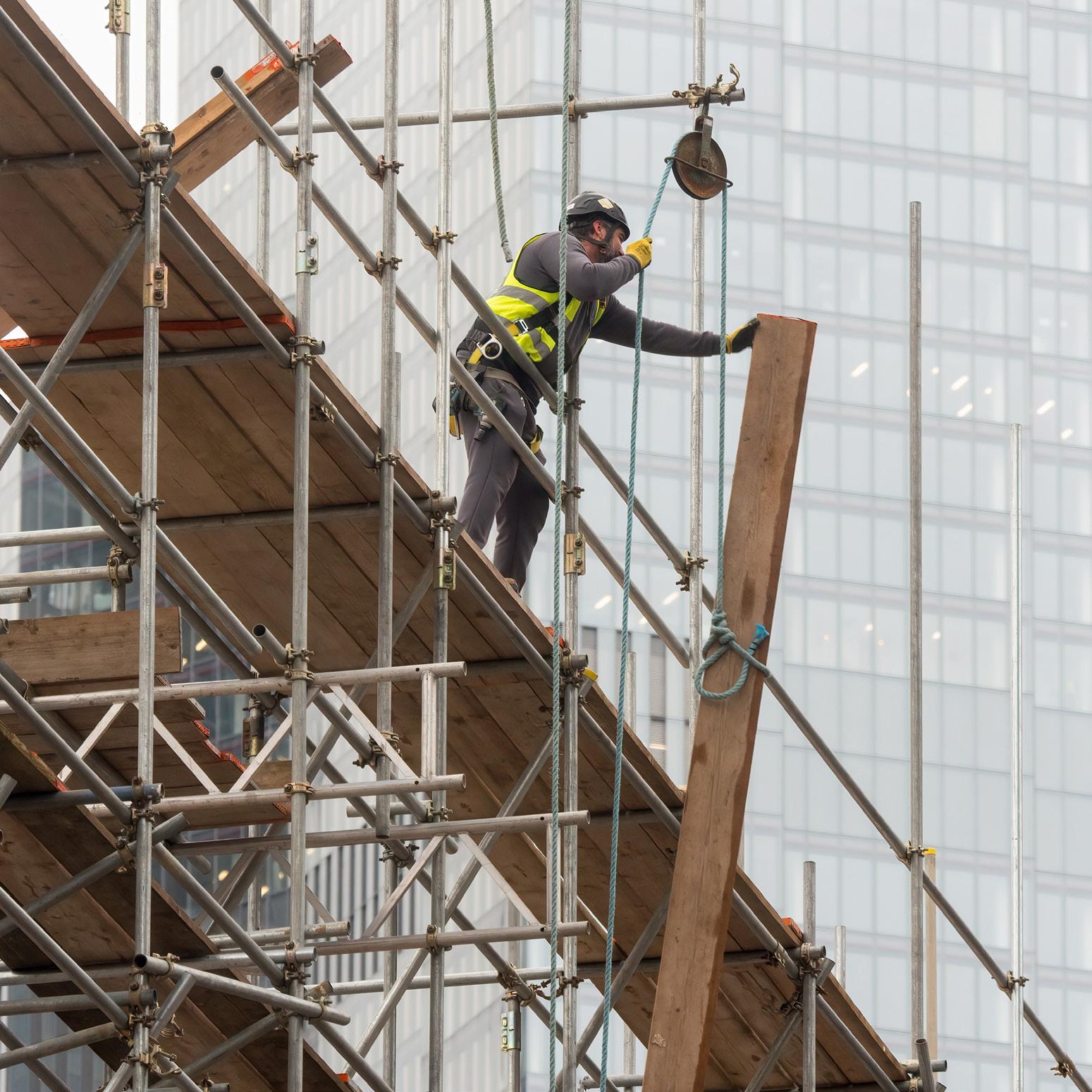
SCAFFOLDING SECTOR 2024: A year of challenges and growth
lining for the scafolding sector. Deloitte Insights predicts growth in 2024, primarily fuelled by sustainable practices and technological advancements.
Te industry is aligning with the International Energy Agency’s Net Zero Emissions by 2050 Scenario, which demands that all new buildings and 20% of existing structures be zero-carbonready by 2030. Tis commitment to sustainability is expected to drive demand for green buildings and construction activity.
Furthermore, the industry may receive a much-needed boost from funds allocated through key pieces of legislation passed in 2021 and 2022. Investments in manufacturing, transportation infrastructure and clean energy infrastructure could welcome capital into the sector. Tis fnancial support could spur growth and ofset some of the challenges posed by the shortage of labour and rising material costs.
TECHNOLOGICAL ADVANCEMENTS TO THE RESCUE
In addition to sustainability eforts, the adoption of technological advancements is set to revolutionise the scafolding industry in 2024. Innovations in construction technology are expected to improve the efciency of scafolding processes, reducing costs and increasing productivity. Companies are increasingly exploring the use of drones, artifcial intelligence and advanced materials to enhance safety and streamline operations.
A YEAR OF ADAPTATION
In conclusion, 2024 presents both hurdles and opportunities for the scafolding sector. Economic uncertainty, labour shortages and rising material costs will require adaptability and resilience from industry players. However, the commitment to sustainability and the adoption of cutting-edge technology ofer pathways to growth and improved efciency. As the year unfolds, the scafolding sector will need to navigate these challenges while embracing innovation to secure a prosperous future.
GEORGE ROBERTS CHARTS NEW COURSE WITH EMPLOYEE OWNERSHIP
❖ In a strategic move aimed at securing the future of its workforce and maintaining its exceptional service standards, George Roberts (North West) has announced the formation of an Employee Ownership Trust (EOT).
Efective now (from February 26, 2024), this groundbreaking decision underscores the company’s commitment to its employees and customers, ensuring business strategy continuity and rewarding its dedicated workforce.
Establishing the EOT promotes employee engagement and commitment while providing long-term benefts from its ongoing success.
According to George Roberts, the move comes after carefully considering various succession plan options, including a third-party sale. Ultimately, the leadership concluded that the EOT would best serve the interests of both employees and customers.
Chairman George Roberts, who founded the business in 1992, expressed his pride in the company’s achievements over the last 32 years. He emphasised the EOT’s uniqueness within the industry and its potential to foster continued growth while allowing the loyal team to share in the company’s success for years to come.
“Since the business was founded in 1992, we have followed the strategy of keeping comprehensive stocks of high-quality products, sold and hired to clients both domestically and internationally via enduring personal relationships,” stated Mr. Roberts.
“I am extremely proud of the company’s achievements and feel strongly that the EOT will allow continued growth and the opportunity for the loyal team within the business to share in its success in the years to come.”
George Roberts will remain Chairman, providing continuity and drawing upon his over 50 years of industry experience. The company boasts a solid and established management team with extensive industry knowledge, supported by a network of technically minded salespeople covering the entirety of the UK.
With a turnover exceeding £50m, George Roberts (North
West) Limited supplies a diverse range of industries, including housebuilding, nuclear, oil & gas, formwork, defence and general construction sectors.
Operating from a purpose-built 16-acre site in Liverpool, the company serves both domestic and international markets with its scafolding equipment and systems.
The company’s product range includes tube, fttings, boards and accessories, along with being a leading distributor of Genuine Layher, K/Lok, K/Stage Systems, Uniscaf Stair Towers and System Temporary Roofs. Its success is built on a strong brand, unrivalled stock availability, and a reputation for high-quality, fully certifed products maintained through an in-house HSEQ regime to ensure consistent conformity to all relevant standards.
Implementing the Employee Ownership Trust marks a signifcant milestone in the company’s journey, solidifying its commitment to its employees and customers, and continued success in the industry.

Millcroft wins Blashford Tower safety works contract
Millcroft has started work on the contract to provide an essential logistics gantry for the major works project at Blashford Tower on the Chalcots Estate in Camden
❖ Situated on Adelaide Road in north-west London, Blashford Tower comprises 72 fats over 19 storeys and is one of fve high rise towers that form the Chalcots Estate. Te £22m design and build recladding and fre safety works contract is part of Camden Council’s commitment to deliver a new standard of safety for residents. GRAHAM, awarded the Blashford Tower contract in September 2021, is delivering the project in two stages. Te frst stage involved extensive design work and tests to determine how the safety improvements would be implemented. Te ongoing second phase includes setting up the site and installing an A1rated cladding system, a curtain wall, new windows and the replacement of brickwork to the underground level.
Millcrof’s integral role in the project is to provide scafolding, which will form a logistics gantry and distribution route and provide safe access to the site accommodation for workers. Tis entails the erection of a heavy-duty gantry extending from the face of Blashford Tower towards the site welfare facility, with scafolding spreading to the Adelaide Medical Centre adjacent to Blashford Tower. Te tower’s location and tight site constraints, including limited storage, have presented several challenges for Millcrof’s team. Tis is a live site with residents remaining in the tower until work on their respective foor level starts, when they will be moved to temporary accommodation. Further complications arise from the need to always keep the pedestrian ramps along the tower’s east and west sides clear, as it serves as vital access to the medical centre.
Te tower’s location has also required careful consideration. Te site runs adjacent to Network Rail tracks at the bottom of a densely vegetated slope. A ground investigation was conducted to
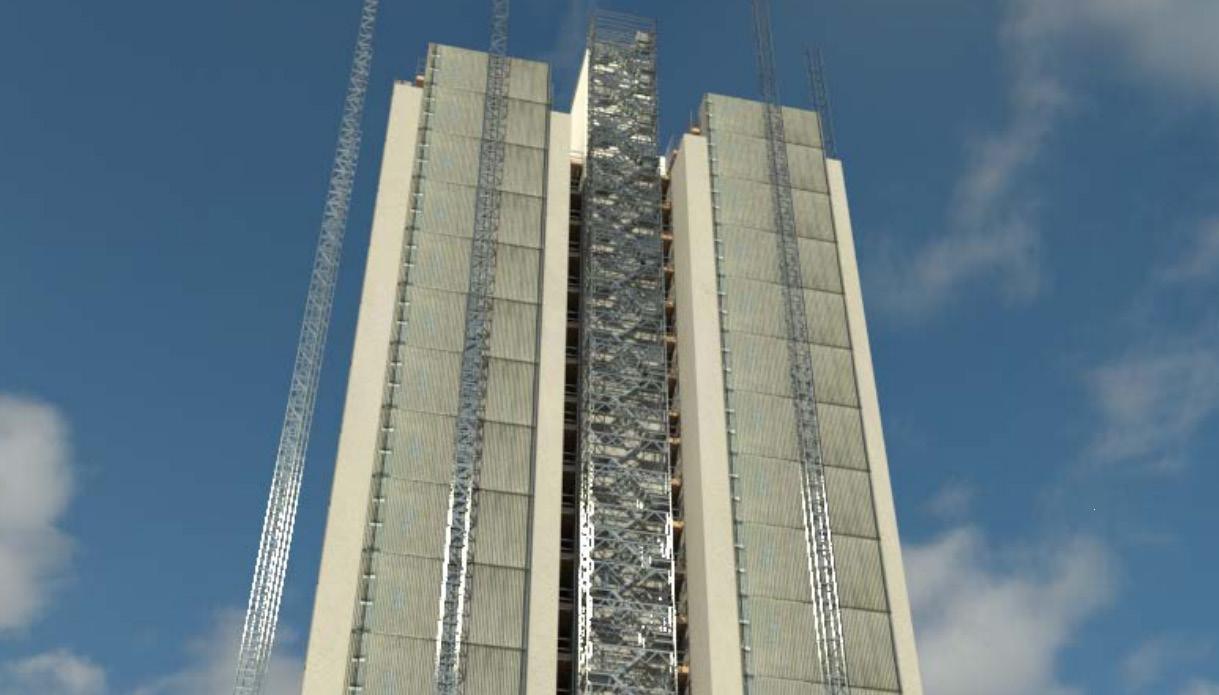
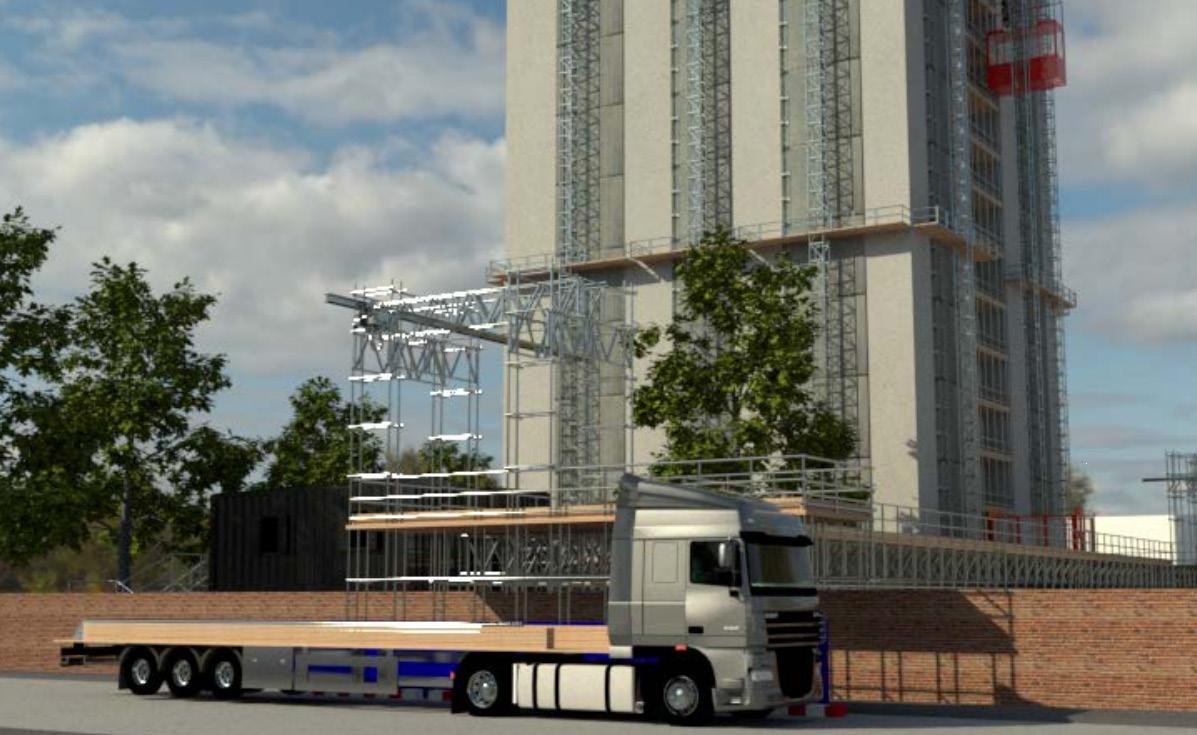
assess the slope’s stability and confrm its capacity to withstand the additional force and loads imposed by the gantry and scafolding. Additionally, as the scafolding is being erected on Network Rail land, the design of the scafold had to be submitted to Network Rail for approval.
Billy Jones, Managing Director at Millcrof, said, “GRAHAM is a long-term strategic partner and valued client of ours, and our PreCommencement team has been working with them on this project for around three years to ensure all aspects of our scafolding meet the required standards and design for this complex site. We started on site at the beginning of November and expect to complete our part of the contract installation works by February 2024.”
Blashford Tower comprises 72 fats over 19 storeys and is one of fve high rise towers that form the Chalcots Estate.
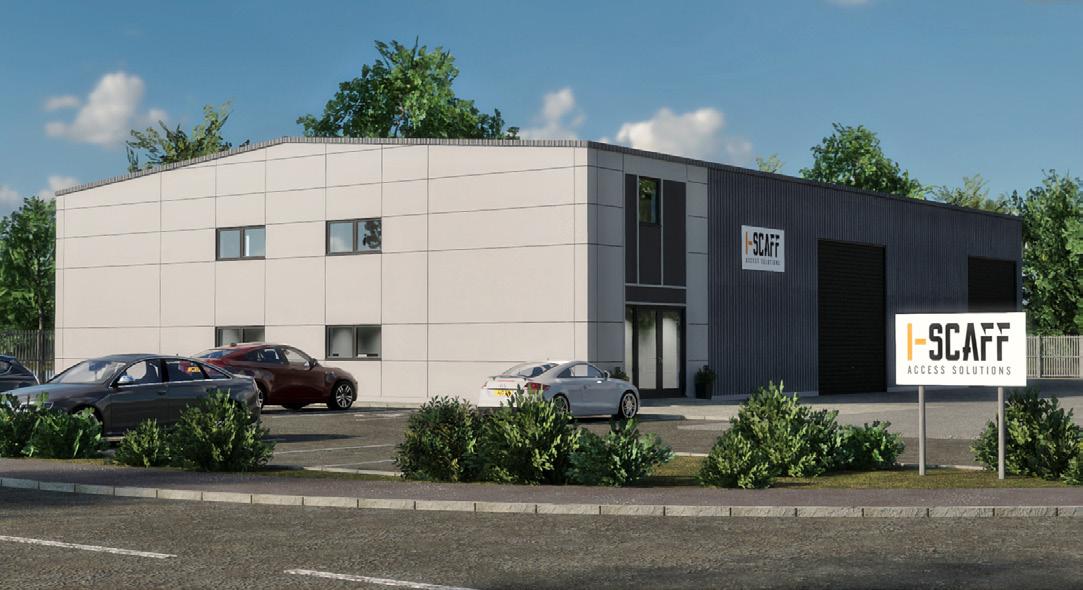
I-SCAFF UNVEILS PLANS FOR STATE-OF-THE-ART WEST COAST EXPANSION
I-Scaf Access Solutions has announced the commencement of construction on a new £1.2 million headquarters in Glenrothes, Fife.
❖ This strategic development comes as part of the company’s broader plan to enhance its operational capabilities and service reach across Scotland, particularly the West Coast.
Ross Brown, Managing Director of I-Scaf, shared insights into the journey towards this momentous milestone. “After an eight-month wait due to planning approvals delayed by Fife Council staf shortages, we’re thrilled to break ground on our new headquarters,” Brown stated. The development, sprawling across 1.5 acres, is a testament to I-Scaf’s commitment to innovation, sustainability and local collaboration.
Designed by D. Stewart Contracts/ARV Design, the headquarters will be constructed by REALM Construction with a focus on utilising the local supply chain.
“REALM has indicated project completion and entry by the end of October 2024,” Brown added, highlighting the anticipated swift progress towards the new facility’s operational status.
The Glenrothes project will feature a 660m2 bespoke building encompassing new ofce space, internal storage, a heavy goods vehicle (HGV) service bay, and meeting/training facilities.
Additionally, a 5,640m2 concrete yard area is set to streamline the servicing of equipment and vehicle-loading operations.
I-Scaf is also exploring opportunities to establish a satellite yard in the Lanarkshire area. This strategic addition aims to service contracts across the West Coast more efciently and reduce travel requirements for staf commuting to Fife. “Collectively, these eforts are poised to signifcantly reduce our carbon footprint,” explained Brown.
The decision to anchor the new headquarters in Glenrothes underscores I-Scaf’s dedication to its roots and the local community.
“Staying in Glenrothes was crucial for us. We’ve built our business around our staf and local clients.
For those reporting to the HQ daily, it was important to maintain their commute,” Brown highlighted.
As I-Scaf Access Solutions embarks on this ambitious project, the company reafrms its commitment to growth and sustainability and strengthens its position as a leading player in the system scafolding industry.
With these developments, I-Scaf is poised to signifcantly enhance its service delivery and operational efciency, marking a new chapter in its illustrious history.
NEWS IN BRIEF
LONDON AND BRISTOL SCAFFOLDING FIRMS ENTER ADMINISTRATION
❖ London-based BCM Scafolding Services Ltd and Bristol’s Scafteq West Ltd, employing over 100 staf, have plunged into administration. These frms, integral to the Saferise Scafolding Group’s network, have been hit hard by the sudden withdrawal of fnancial support, as revealed in an internal memo seen by ScafMag from BCM’s Managing Director, Adele McLay, to staf. The memo outlined the immediate cessation of operations and the uncertainty surrounding employee salaries and ongoing projects. McLay’s message conveyed deep regret over the developments, highlighting recent eforts to expand and the positive strides made by the company. The situation leaves employees facing uncertainty, with the industry losing two of its established players.
PALMERS SCAFFOLDING SECURES £500K FROM WALES’ £130M INVESTMENT FUND
❖ Deeside-based Palmers Scafolding, the oldest scafolding contractor in the UK, has received a £500,000 investment from the British Business Bank’s £130m Investment Fund for Wales. Managed by FW Capital, this frst debt deal aims to support Palmers’ growth, including their involvement in the Hinkley Point C Nuclear Power Station project. The fund ofers fnancial support ranging from £100,000 to £2m for Welsh businesses, promoting regional economic growth and innovation.

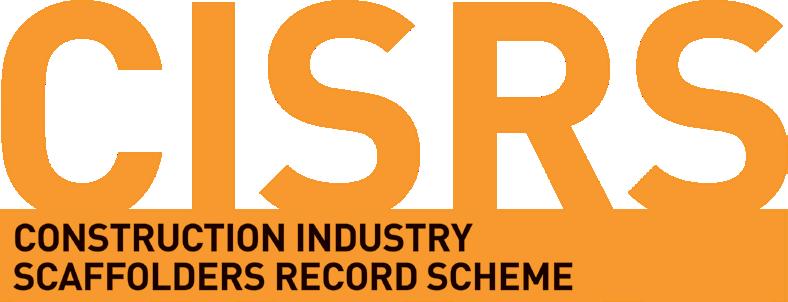
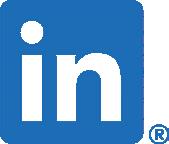
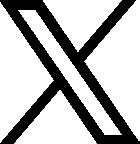

ScafPlan strengthens leadership with industry pioneer Ben Beaumont
In a signifcant development that underscores its commitment to innovation and excellence in the scafolding technology sector, ScafPlan has exclusively revealed to ScafMag the appointment of Ben Beaumont as the company’s director
❖ Te move signals a new era for ScafPlan, an Australian company renowned for its pioneering scafolding sofware. ScafPlan seeks to cement its position as a construction technology (contech) leader.
With an illustrious career spanning two decades in scafolding and temporary works, Ben Beaumont is wellregarded within the UK scafolding and access sector for his technical acumen and entrepreneurial spirit. He has spent many years in scafold and temporary works in the UK, successfully founding and leading his own consulting business, 48.3, for over 13 years and being a Director of the Temporary Works Forum since 2014
His expertise and vision are expected to synergise with ScafPlan’s ambitions, ofering fresh perspectives on how scafolding and temporary works can be designed, managed and executed more efciently.
Te partnership between Beaumont and ScafPlan founder Simon Boyes materialised naturally, following Ben’s deep interest in ScafPlan’s sofware solutions afer witnessing the transformative potential of ScafPlan’s technology frst-hand.
Both leaders are committed to pushing the boundaries of what’s possible in the construction sector, driven by shared values and a mutual goal of enhancing industry standards.
“Joining ScafPlan is a great opportunity and privilege,” said Beaumont. “We’ve been working towards this for some time, discussing our values, strategy and vision for the future. We now have a unique
opportunity to change the way scafolding and temporary works are conceived, designed, collaborated on and executed. Te potential for positive change is huge, and that’s really exciting!”
Refecting on the new collaboration, Simon Boyes expressed his enthusiasm: “Uniting with Ben is a strategic move that brings together unmatched practical experience and technical prowess. We are poised to drive substantial advancements in the temporary works sector, delivering solutions that are groundbreaking in
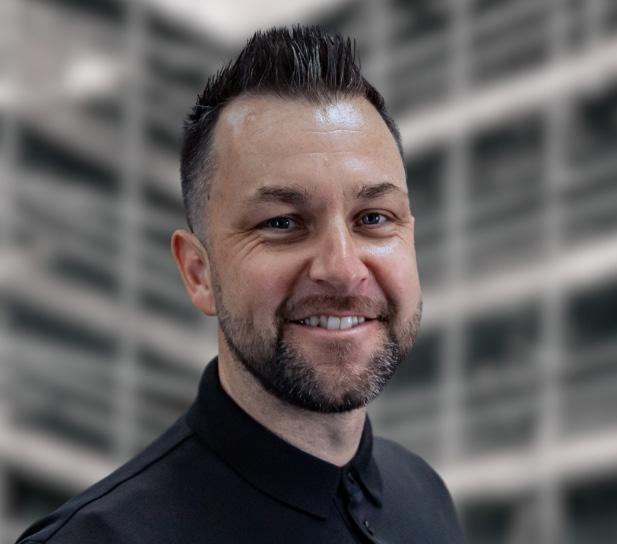
their potential to transform industry practices.”
As ScafPlan welcomes Ben Beaumont into its leadership fold, the company is more determined than ever to develop solutions that make construction safer, more efcient and cost efective. Tis partnership is not just a testament to ScafPlan’s growth trajectory but also a clear indication of its resolve to remain at the forefront of technological innovation in construction.
WE HAVE A UNIQUE OPPORTUNITY TO CHANGE THE WAY SCAFFOLDING IS CONCEIVED, DESIGNED, COLLABORATED ON AND EXECUTED. THE POTENTIAL FOR POSITIVE CHANGE IS HUGE, AND THAT’S REALLY EXCITING
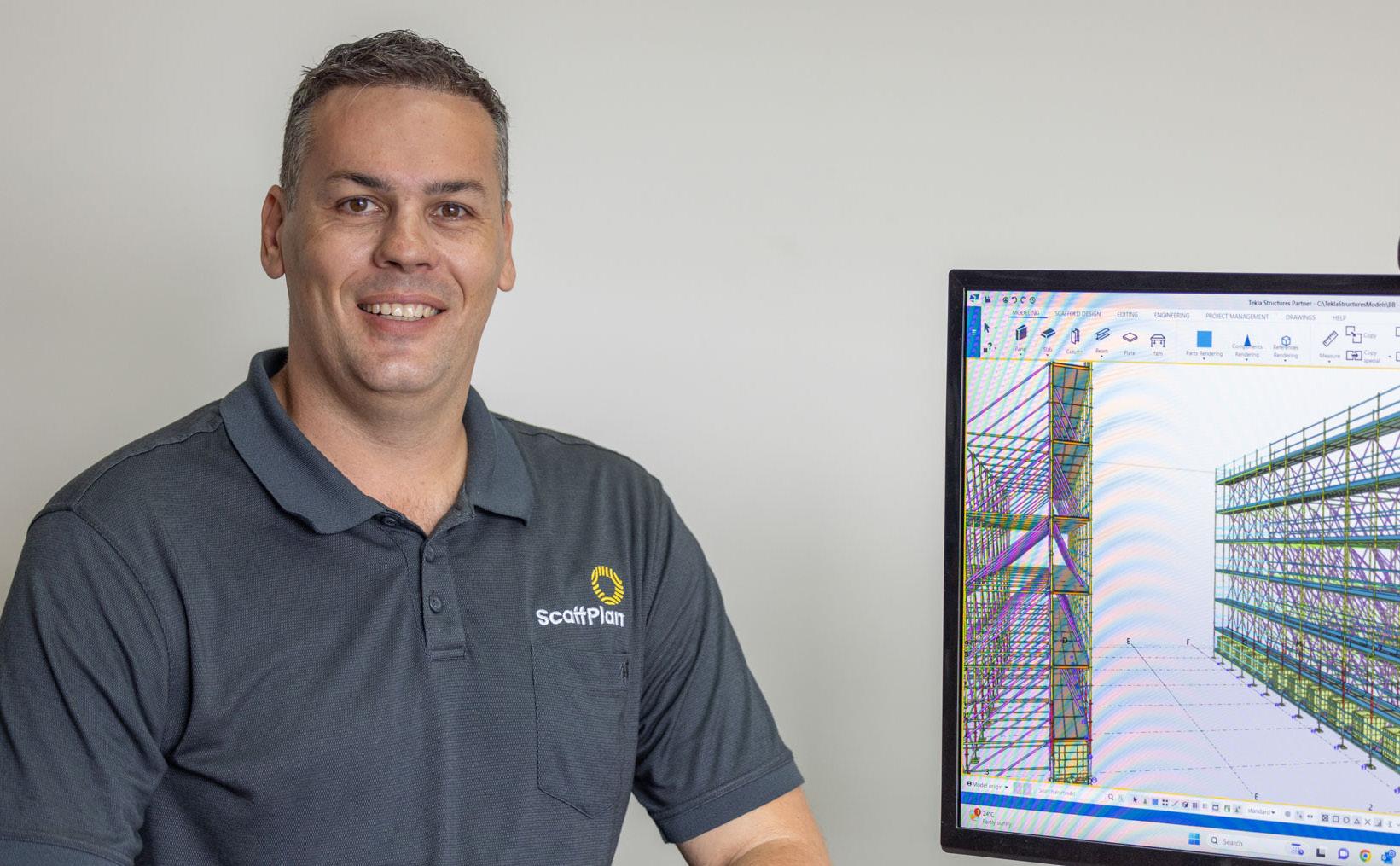
ALL ACCESS ACADEMY SET TO SHAPE TOMORROW’S SCAFFOLDING PROFESSIONALS
In a bold move to meet the surging demand for skilled workers in the construction sector, Redcar and Cleveland College, in collaboration with NETA Training, has unveiled plans for the groundbreaking £4.7m All Access Academy
❖ Tis ambitious initiative, made possible through government funding, represents a signifcant step towards addressing the region’s critical shortage of trained scafolders. Located on the college’s Corporation Road site in Redcar, the All Access Academy is poised to become a beacon of excellence in scafolding training.
With a comprehensive curriculum designed to equip individuals with the practical skills and theoretical knowledge essential for success in the feld, the academy aims to bridge the gap between industry demand and workforce capabilities.
Jason Faulkner, Executive Principal of Redcar and Cleveland College, expressed enthusiasm for the project, highlighting its potential to transform the scafolding landscape in the region. “Tis facility will deliver the training of skills that are in huge demand, not just here in the Tees Valley but across the UK,” Faulkner remarked. “Building on the specialist clean and low-carbon energy training available through the college’s Clean Energy Education Hub, these are skills that will further support the major projects the likes of SeAH Wind, bp and many others are bringing to the area and, in doing so,

support economic growth.”
Te All Access Academy will ofer specialised training in areas such as scafolding, rope access, riging, lifing and welding, catering to the diverse needs of the construction industry. With its state-of-the-art facilities, including purpose-built scafolding training areas and an industrial welding facility, the academy is poised to set new standards in scafolding education.
Sean Johnston, Director of NETA Training, highlighted the academy’s role in nurturing a skilled workforce capable of driving economic growth. “Te All Access Academy in Redcar will now build on our commitment to meet the skill demands that will drive our economy,” Johnston stated. With over 45 years of experience in meeting the region’s training needs, NETA Training is well-positioned to lead this transformative endeavour.
Industry leaders have also welcomed the establishment of the All Access Academy, recognising its potential to address critical skills shortages and propel the construction sector forward.
Dave Mosley, Managing Director of the Construction Industry Scafolders Record Scheme (CISRS), praised the
initiative for its focus on qualifying future scafolding apprentices and trainees, stating, “I am confdent this initiative will contribute signifcantly to the growth and enhancement of skills within our industry, providing invaluable opportunities for training and professional development.”
Local ofcials and policymakers have hailed the All Access Academy as a catalyst for economic development and social mobility in the region. Cllr Alec Brown, Leader of Redcar and Cleveland Borough Council, underscored the council’s commitment to investing in the future of its residents. “Our plans are designed to improve and enhance the lives of our communities by not only investing in major infrastructure projects but also investing in the people of the borough and their future,” Brown said.
Te establishment of the All Access Academy marks a signifcant milestone in Redcar’s journey towards becoming a hub for scafolding excellence. With its cuttingedge facilities, industry-aligned curriculum and unwavering commitment to fostering talent, the academy is poised to empower individuals to scale new heights in their scafolding careers while driving economic growth and prosperity in the region.
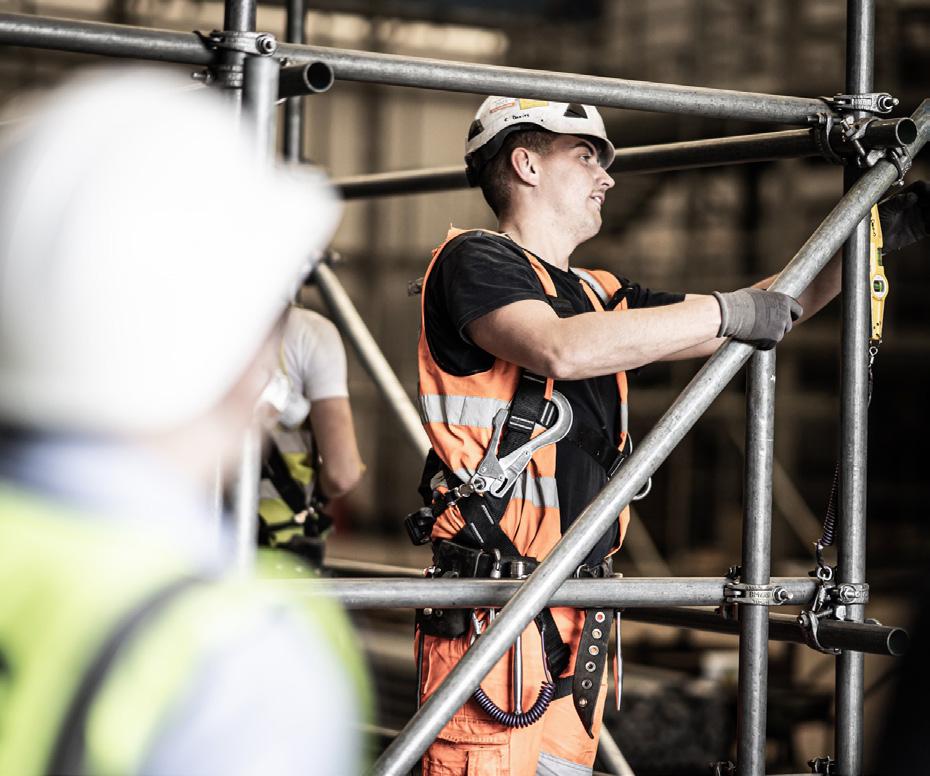
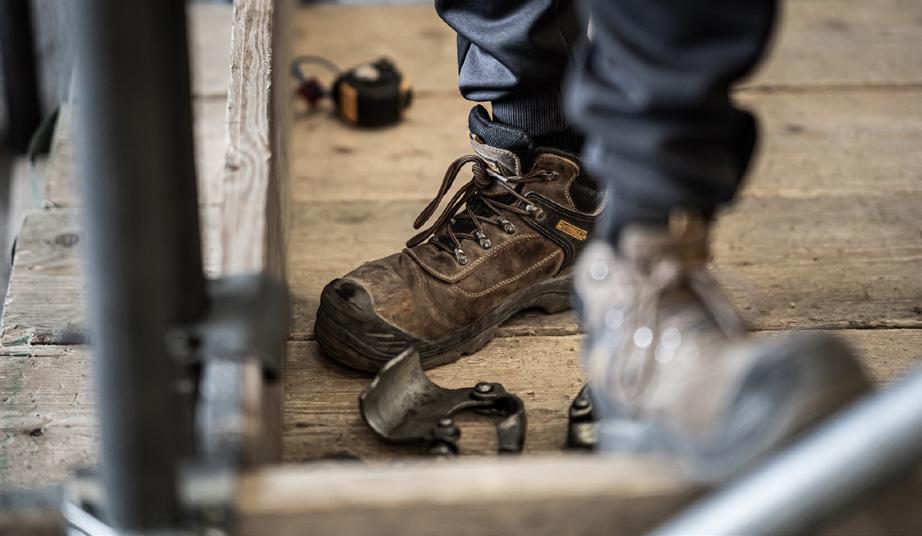
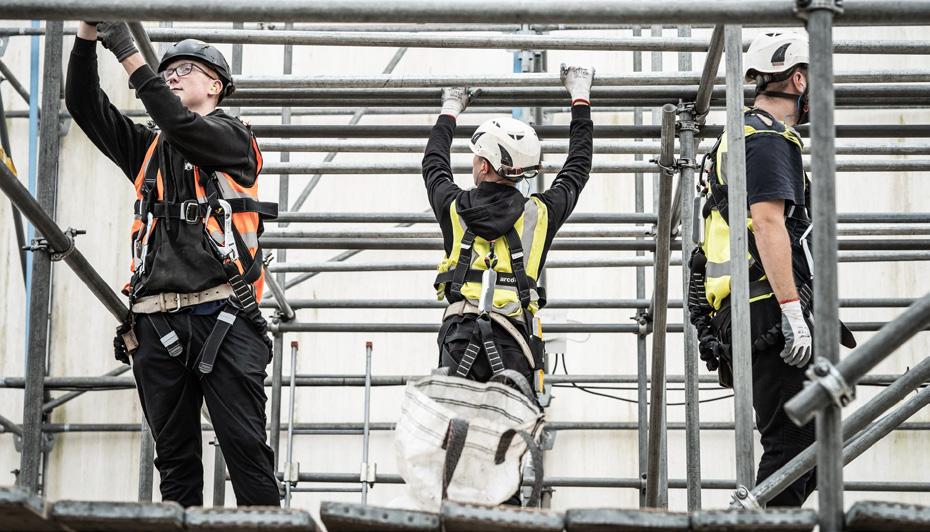

CISRS unveils scafold training overhaul for 2024
❖ In a bid to enhance safety standards and streamline the training process for scafolding operatives, the Construction Industry Scafolders Record Scheme (CISRS) has announced signifcant changes to its certifcation rules, set to take efect from March 1, 2024.
Under the revamped guidelines, delegates enrolling in the CISRS Operative Training Scheme (COTS) course will now only be eligible for a CISRS Labourer card upon completion, marking a departure from the previous option to apply for a Trainee Scafolder card.
This shift ensures that individuals have a solid foundation before advancing to higher-level qualifcations.
Moreover, the initial issuance of an
18-month CISRS Trainee Scafolders card will be contingent upon the successful completion of the CISRS Part 1 course. This requirement ensures that operatives possess essential skills in erecting and dismantling scafold structures, along with knowledge of industry guidelines and best practices.
The revised rules allow operatives three years to accrue on-site experience, complete the Part 2 course, attain S/NVQ2 certifcation and undergo a skills assessment. This extended timeline provides ample opportunity for comprehensive training and development.
Noteworthy among the changes is the reduced prerequisite time for holding a
Labourer card before attending the part 1 course, now shortened from six to three months. While some express concerns regarding accelerated training, CISRS clarifes that this adjustment accommodates individuals with prior informal experience without compromising standards.
Dave Mosley, CISRS Managing Director, highlights the scheme’s commitment to monitoring industry feedback to ensure the relevance and achievability of training content. The overarching goal remains to optimise safety and competence within the scafolding sector through comprehensive training and adaptable certifcation pathways.
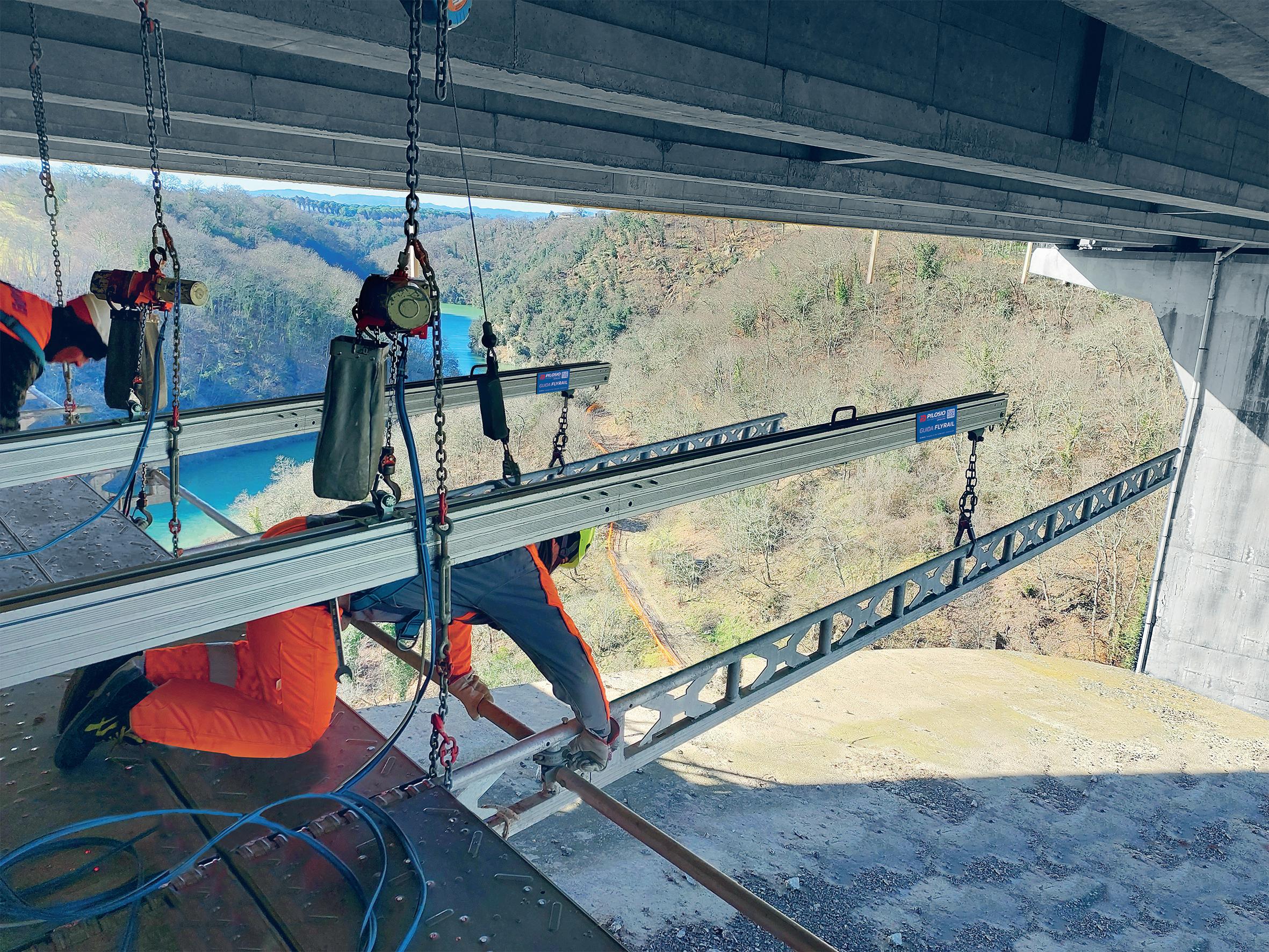
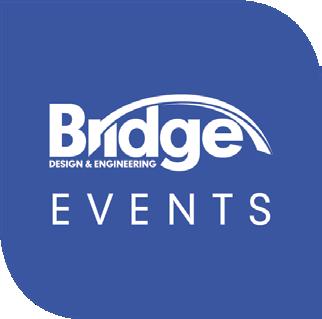
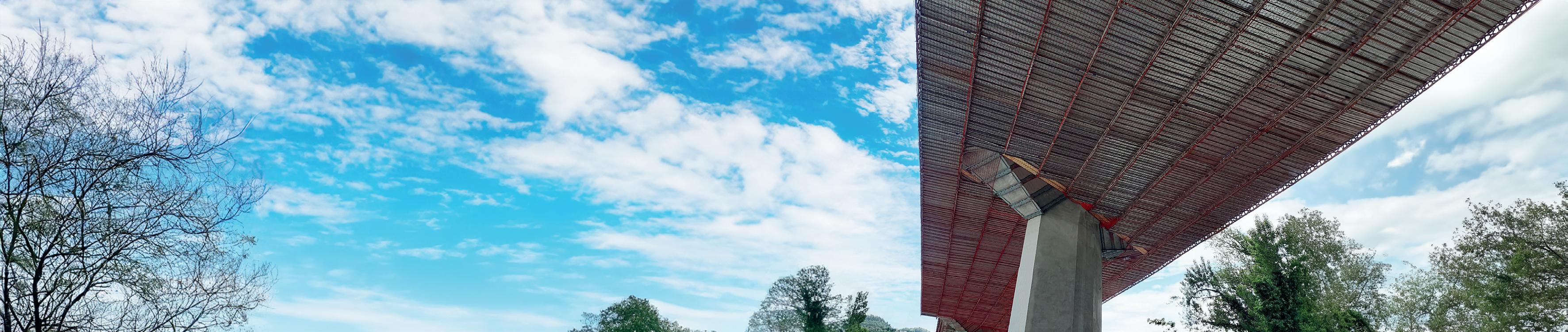
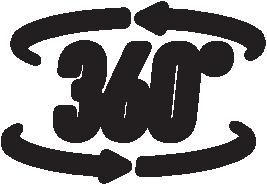
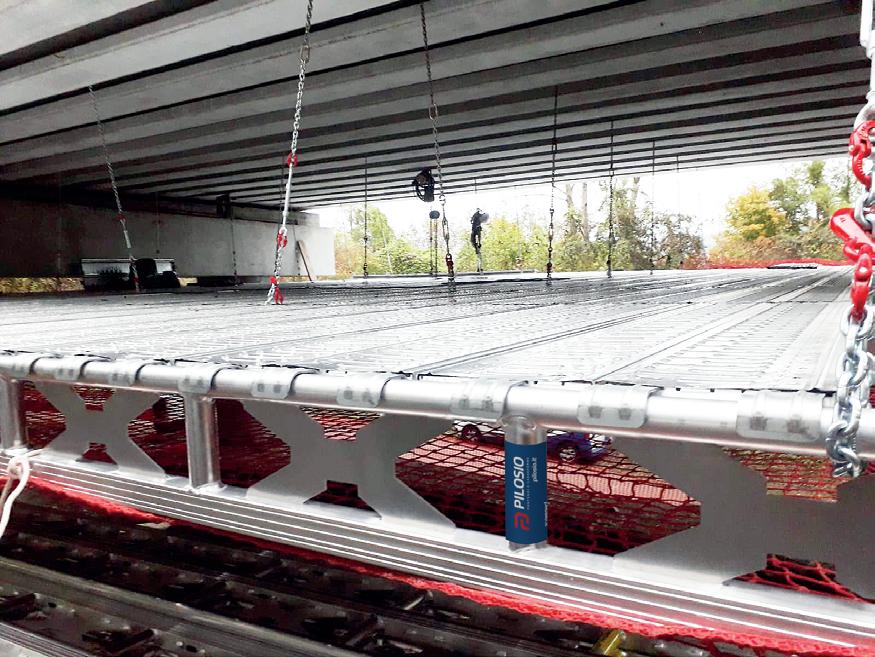
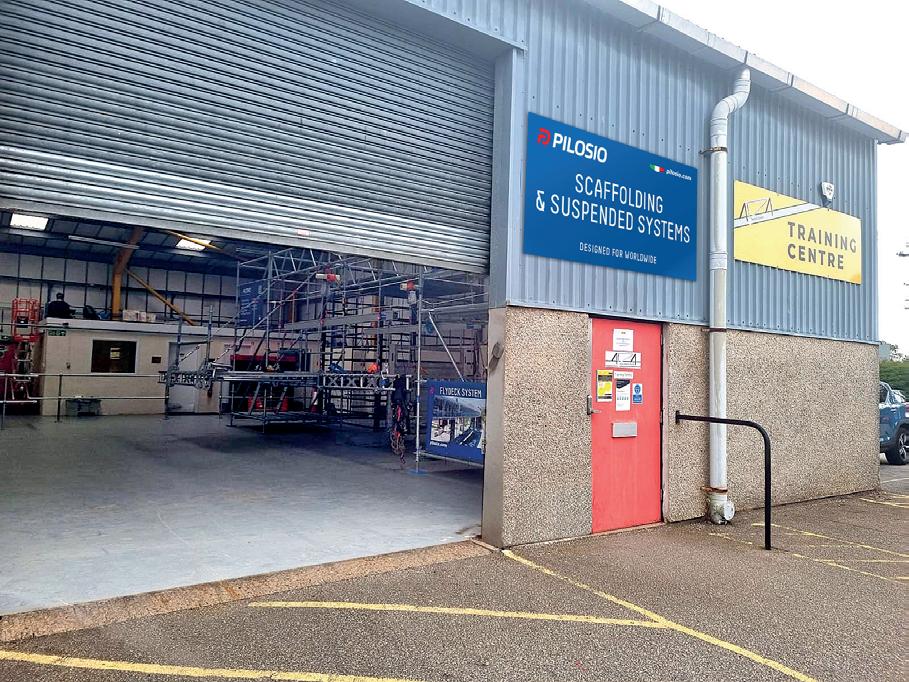
STATOM GROUP EXPANDS WITH £5.4M PERI INVESTMENT
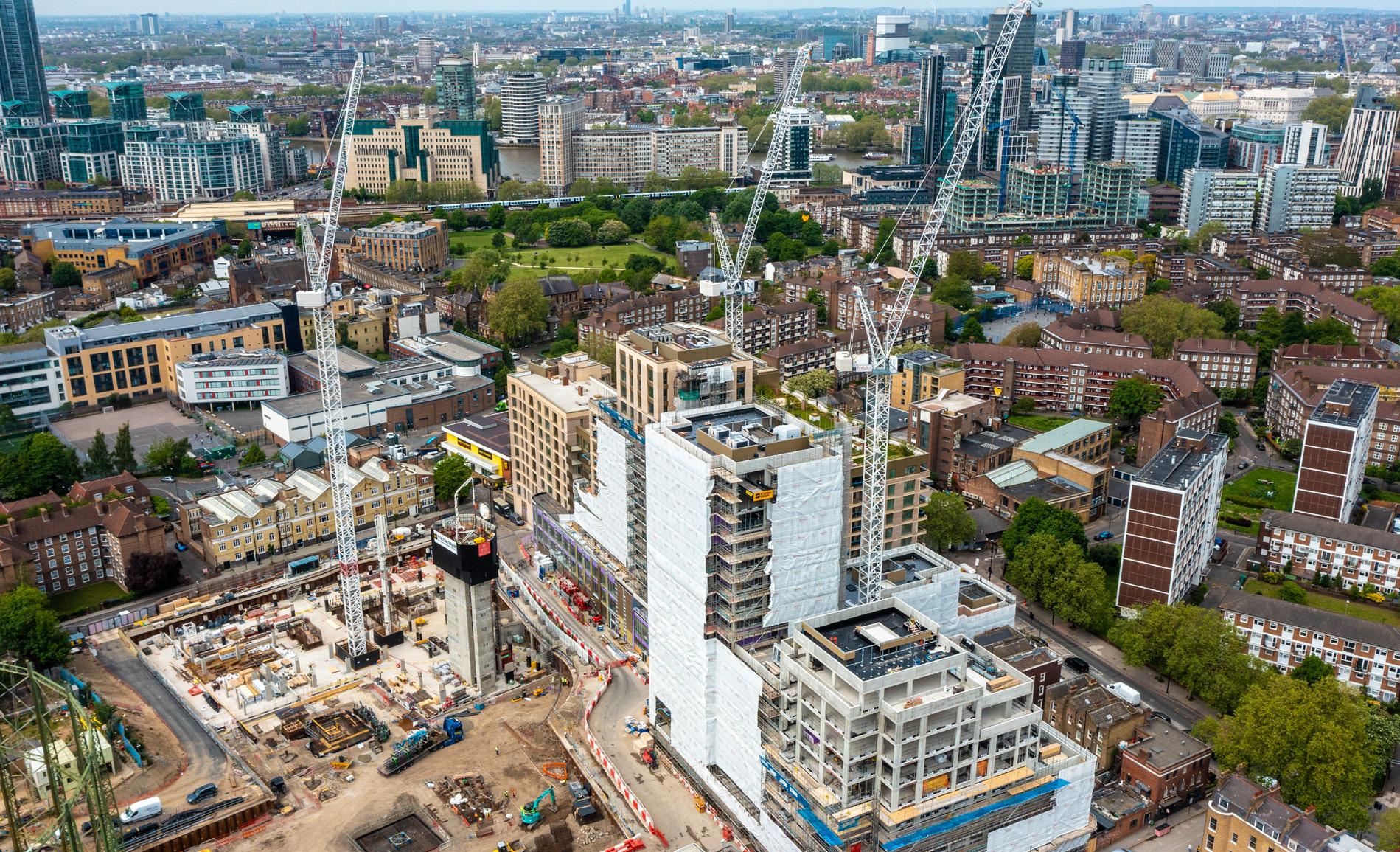
❖ Statom Group, a prominent construction contractor, has invested £5.4m in cutting-edge equipment from PERI, a leading formwork and system scafolding specialist. Te move underscores Statom Group’s commitment to growth and expanding its presence across the UK.
Te investment includes state-of-theart equipment like SKYDECK, TRIO, PERI’s climbing formwork and PERI UP
scafolding, totalling £400,000.
Stan Nikudinski, Managing Director of Statom Group, emphasised the decision, citing PERI’s high quality and efcient design as crucial factors in their investment strategy. Te partnership with PERI is integral to Statom Group’s success as they navigate complex projects and evolving market demands.
Nick Mills, Sales Manager – London at PERI UK, expressed gratitude for Statom
Group’s continued trust and highlighted the collaborative eforts between the two companies. Te investment reafrms PERI’s commitment to providing tailored solutions and fostering long-term partnerships with its customers.
Statom Group’s investment in PERI systems not only strengthens their construction capabilities but also positions them for sustained growth and success in the industry.
Des Moore joins Layher UK
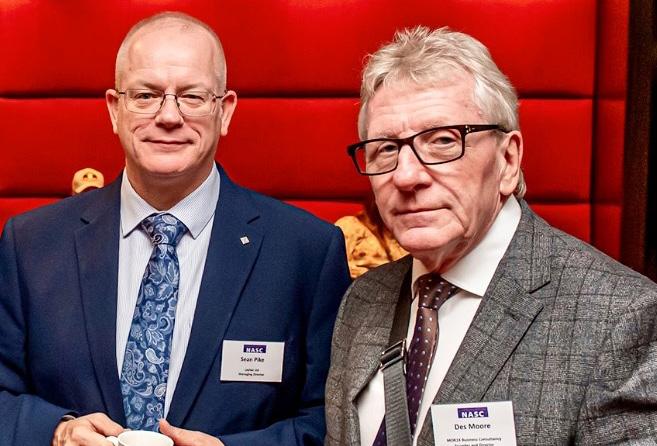
❖ Layher UK Ltd has appointed Des Moore as its Brand Ambassador in a move set to bolster its market presence and drive growth. Moore, a seasoned veteran with over fve decades of experience in the scafolding industry, brings invaluable expertise to Layher’s team.
Moore’s journey with Layher dates back to the early 1990s when he played a pivotal role in expanding TRAD Scafolding’s operations using Layher’s innovative Allround Scafolding System. In his new role, Moore will collaborate closely with Layher to enhance their market position further and facilitate strategic initiatives.
His appointment underscores Layher’s commitment to delivering cutting-edge solutions and customer-focused strategies.
ALARM RAISED OVER DODGY PPE
❖ Te British Safety Industry Federation (BSIF) has revealed shocking fndings regarding the quality of personal protective equipment (PPE), prompting urgent action within the scafolding industry.
In a recent investigation spanning December 2022 to December 2023, BSIF examined 123 non-member products, with only 21% meeting safety standards. Examples of failure include a fameretardant parka that catastrophically failed fame spread testing, and safety boots lacking proper documentation and structural integrity.
Alan Murray, CEO of BSIF, urged scafolding professionals to exercise
vigilance in procurement, emphasising the importance of sourcing from reputable suppliers endorsed by BSIF.
In contrast, products from BSIF Registered Safety Suppliers demonstrated signifcantly higher compliance rates, with 91% passing rigorous testing. Murray highlighted the necessity of aligning with trusted suppliers to ensure access to certifed and reliable protective gear.
Te BSIF’s fndings underscore the critical need for stringent adherence to safety standards in PPE procurement within the scafolding industry. With the safety of scafolders at stake, swif action is imperative to mitigate risks and prioritise worker wellbeing.
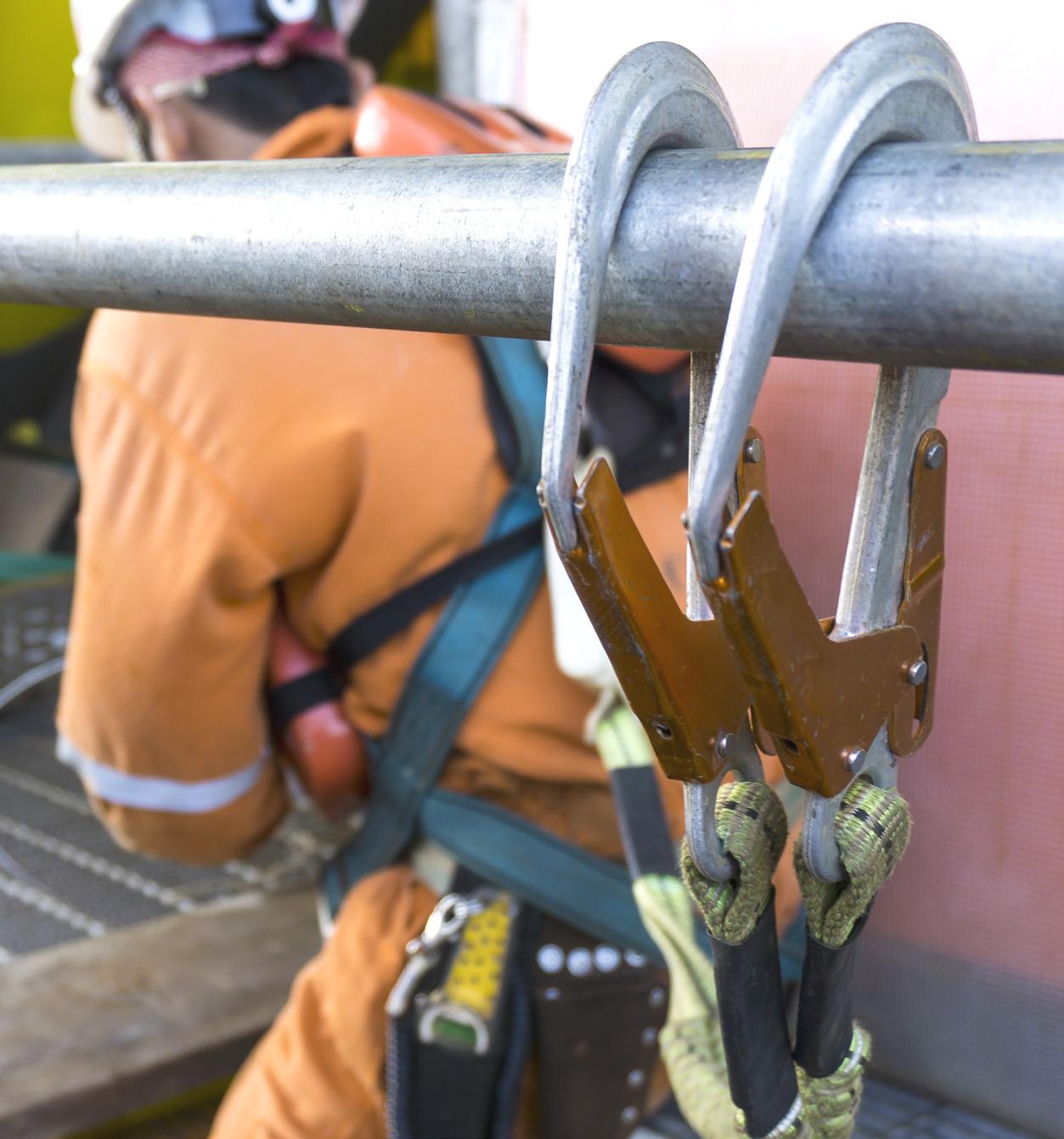
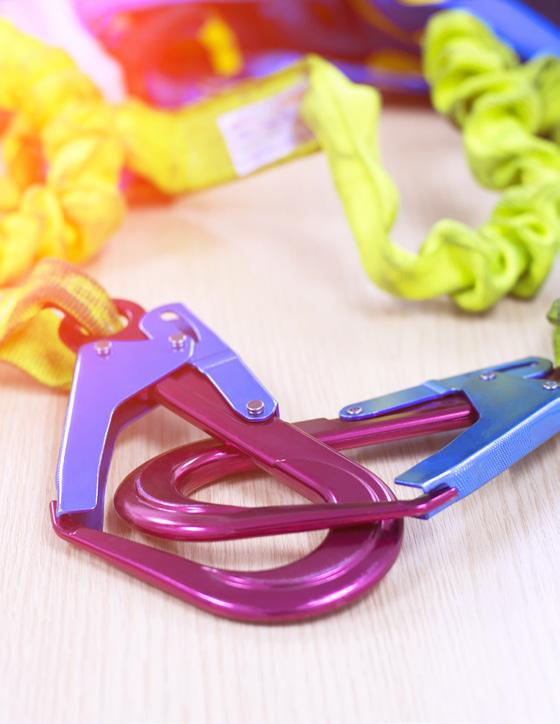
Scafolder injured in fall on Royal Navy ship
Devonport Royal Dockyard and Kaefer Limited face charges under Health and Safety Act
❖ A scafolder’s serious injury on board the Royal Navy ship HMS Bulwark has resulted in charges against Devonport Royal Dockyard and Kaefer Limited. The incident, which occurred on April 11, 2023, has led to legal proceedings under the Health and Safety at Work Act 1974, as announced by the Ofce for Nuclear Regulation (ONR).
The incident happened in Plymouth, where HMS Bulwark was undergoing maintenance. A scafolder working on the warship sufered severe injuries after falling approximately 15 feet (4.5m) into a tank during his duties.
The Devonport Royal Dockyard, which is a part of Babcock, and Kaefer Limited, the scafolding frm involved in the work, have both been charged in connection with the incident.
The legal proceedings are set to commence with the frst hearing scheduled at Plymouth Magistrates’ Court on March 27, 2024.
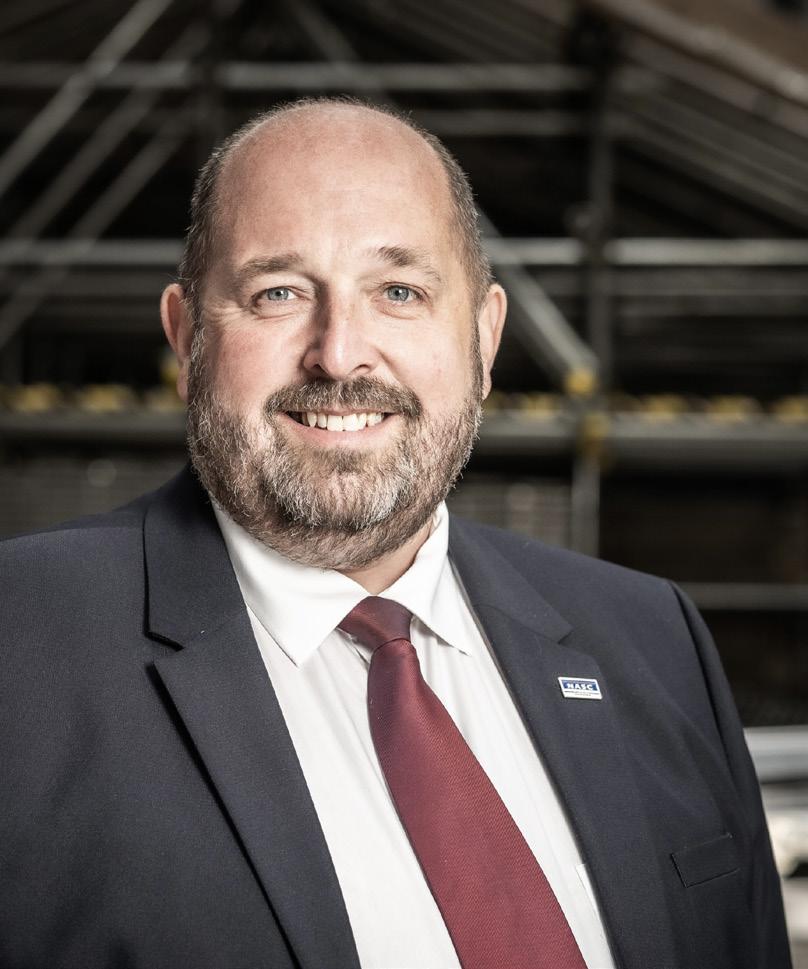
❖ In a signifcant move aimed at enhancing safety and quality standards within the construction industry, the National Federation of Builders (NFB) has formally endorsed the membership standards of the National Access and Scafolding Confederation (NASC), marking a milestone collaboration between two leading industry bodies.
Te endorsement comes afer an extensive review by the NFB of NASC’s Membership Charter and Audit process, which rigorously evaluates the operational, yard and site standards of contracting scafolding or access businesses.
NASC’s commitment to maintaining the highest levels of industry standards through regular audits and its publication of respected guidance and
NFB BACKS NASC STANDARDS FOR SAFER CONSTRUCTION SITES
annual safety reports has been a cornerstone of its operations for nearly eight decades.
Clive Dickin, CEO of NASC, expressed his enthusiasm about the endorsement, stating, “It is truly exciting that the NFB has formally recognised the value and reliability of our standards, encouraging its members to adhere to the most recognised and tested standards for scafolding and access. Tis endorsement underlines our commitment to safety and excellence in the construction industry.”
Te NFB, known for its dedication to improving standards across the construction sector, views this endorsement as a step forward in its eforts to ensure the safety and wellbeing of builders, contractors and housebuilders. Richard Beresford, Chief
Executive of the NFB, remarked on the importance of supporting trade bodies that maintain a transparent and rigorous approach to membership standards.
“Following our review of NASC’s processes, procedures, and gold-standard technical and safety guidance, we are confdent that utilising an NASC member will signifcantly reduce the risks for all working on construction sites,” Beresford said.
Te collaboration between NFB and NASC is set to include joint initiatives aimed at promoting best practices for scafolding and access procurement and usage. Tese eforts are geared towards informing clients, principal contractors and their supply chains about the risks associated with working at height and how to mitigate these risks by selecting quality suppliers.
WAHSA Updates Guidance on Energy-Absorbing Lanyards
The Working at Height Safety Association (WAHSA) has unveiled new guidelines.
❖ The guidelines comprehensively cover the proper selection, use, maintenance and periodic inspection of single and twin energy-absorbing lanyards, which are critical for preventing accidents and fatalities in work-at-height scenarios.
The updated guidance emphasises the importance of understanding both single and twin energy-absorbing lanyards’ specifc safety features and application
scenarios. It provides detailed advice on ensuring compatibility between lanyards and other personal protective equipment (PPE), facilitating safer work environments for individuals operating at height.
Key highlights include recommendations for regular inspections, criteria for decommissioning and replacing lanyards, and insights into the technological advancements in energy-absorption materials and designs. The guidance aims to empower
employers and safety professionals with the knowledge to select the right lanyard types based on the nature of work, thereby minimising risks and enhancing overall safety.
WAHSA’s new guidelines serve as an essential resource for individuals and organisations seeking to adhere to the highest safety standards. Download the ofcial document at https://lnkd.in/ ecFpM79g to access the complete guidance and implement these critical safety measures in your workplace.
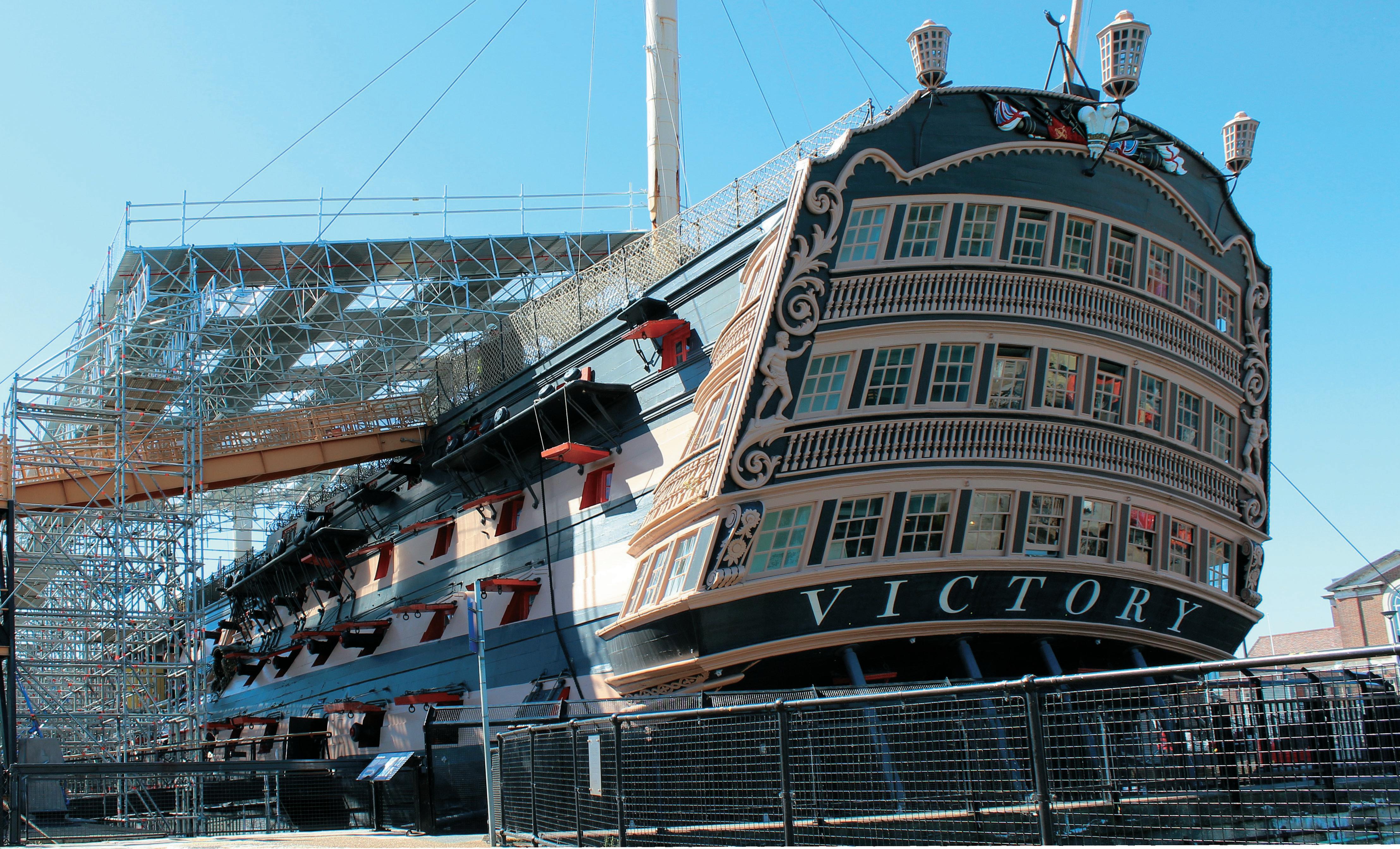
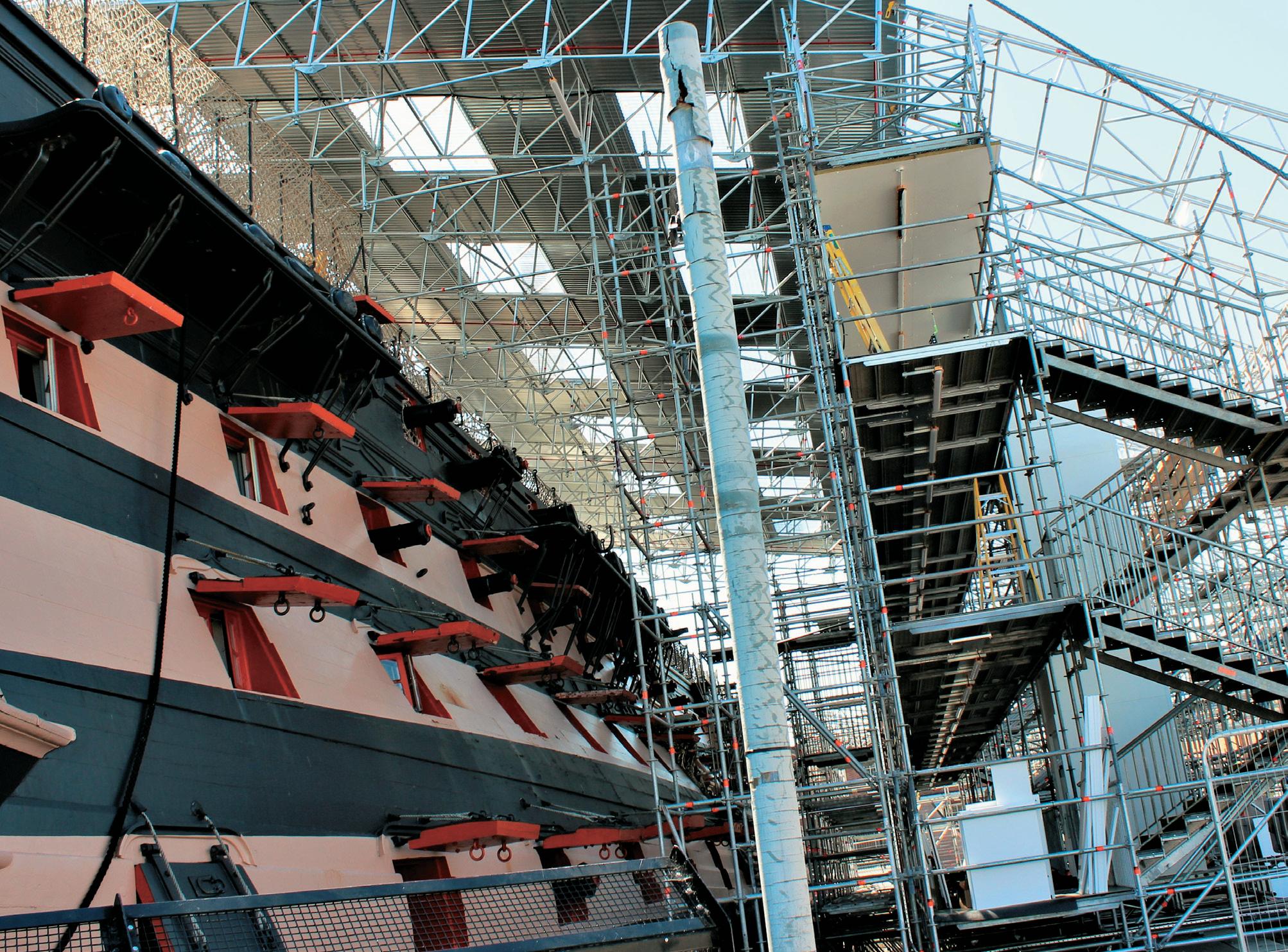
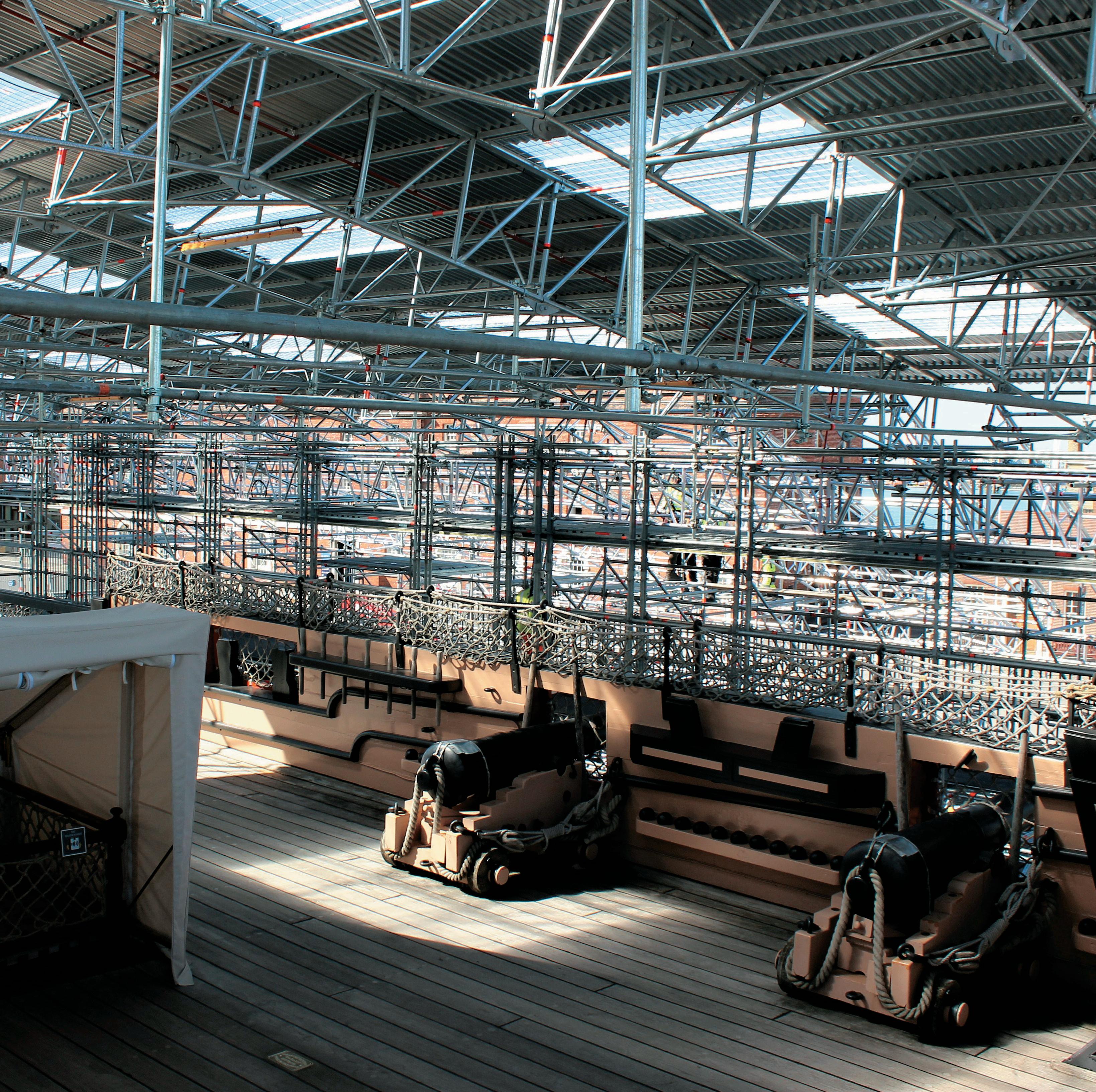
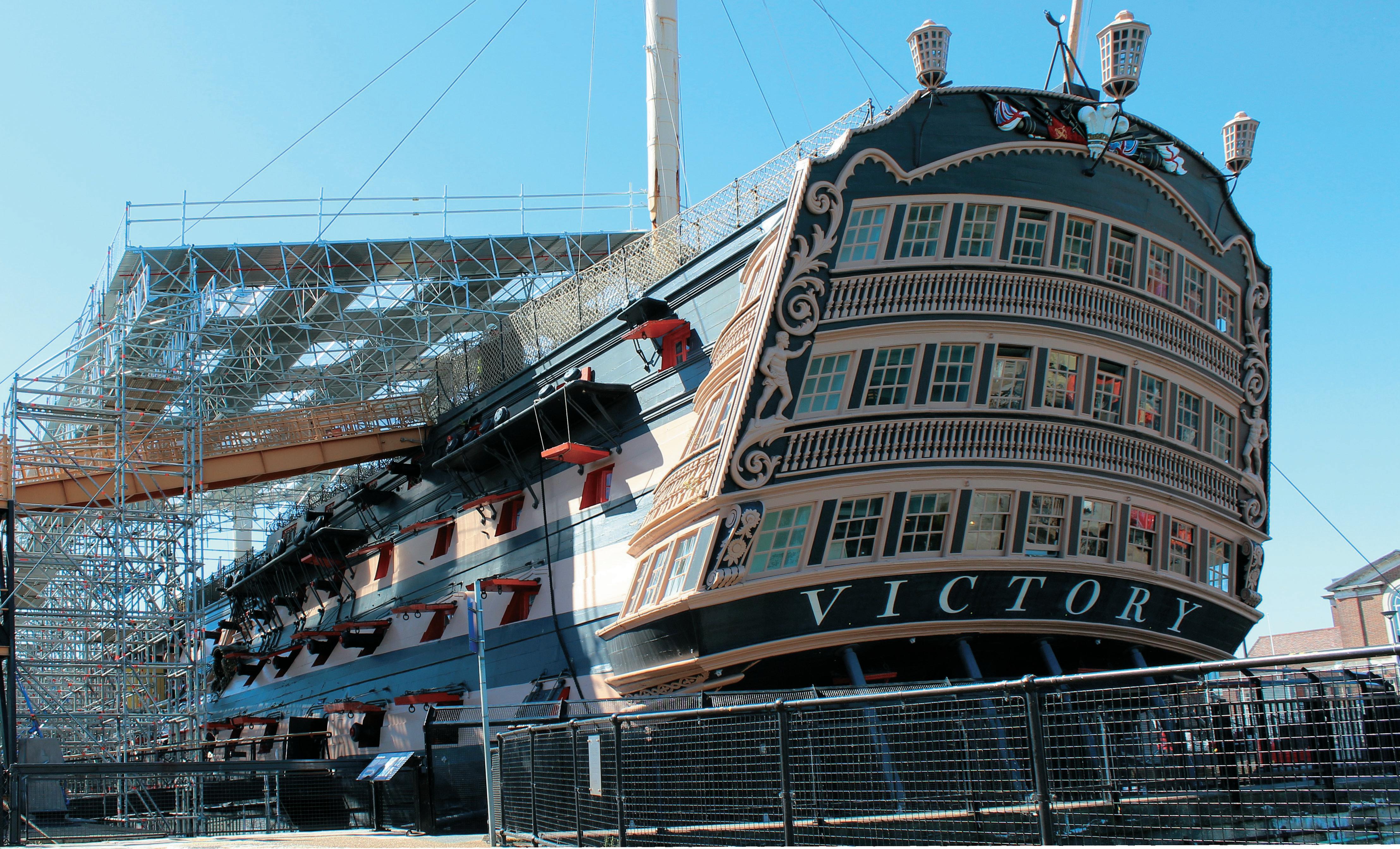
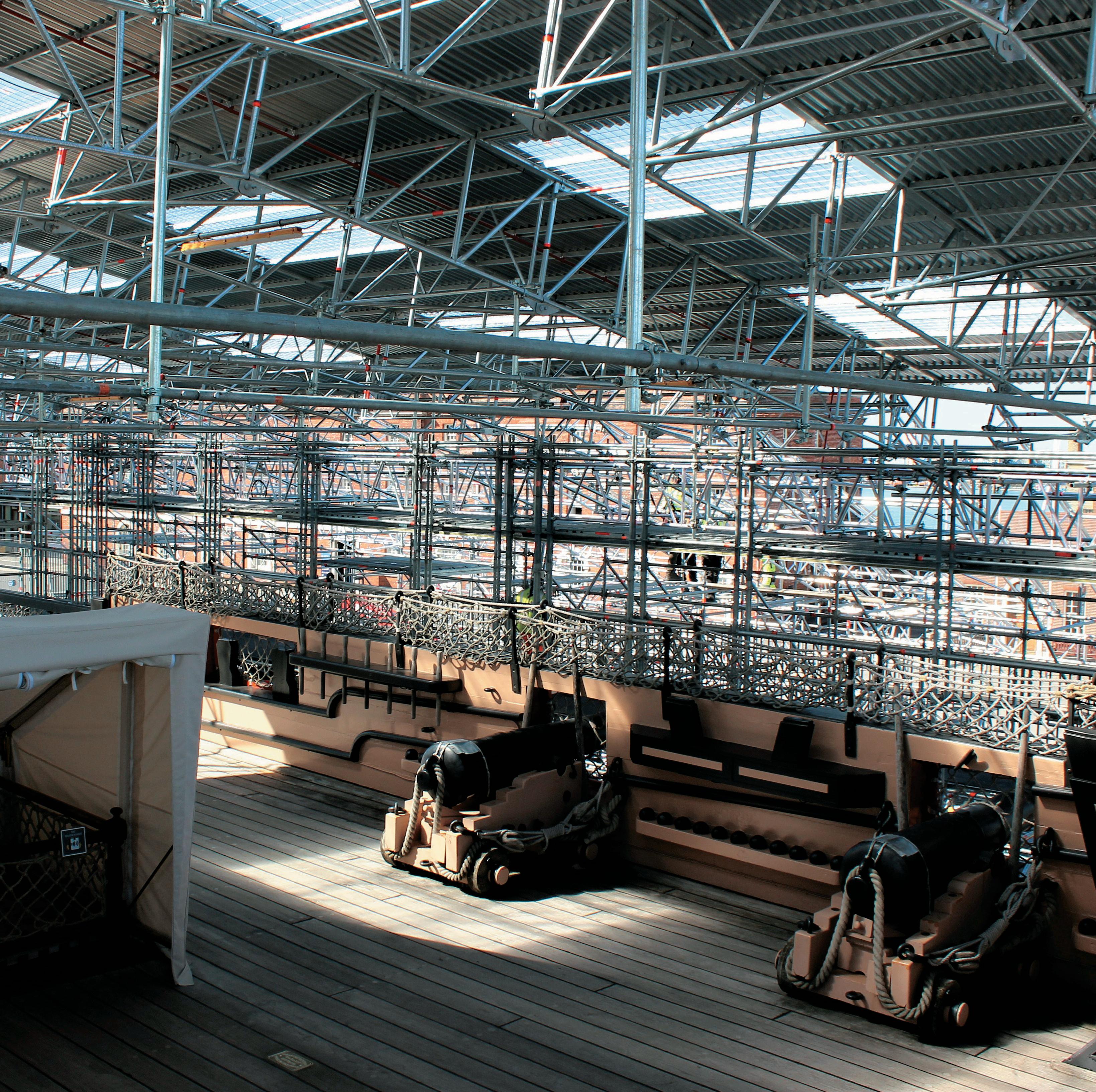
PROTECTING our HERITAGE
INNOVATIVE SOLUTIONS FROM LAYHER
THE WORLD’S LEADING MANUFACTURER OF MODULAR SCAFFOLDING SYSTEMS
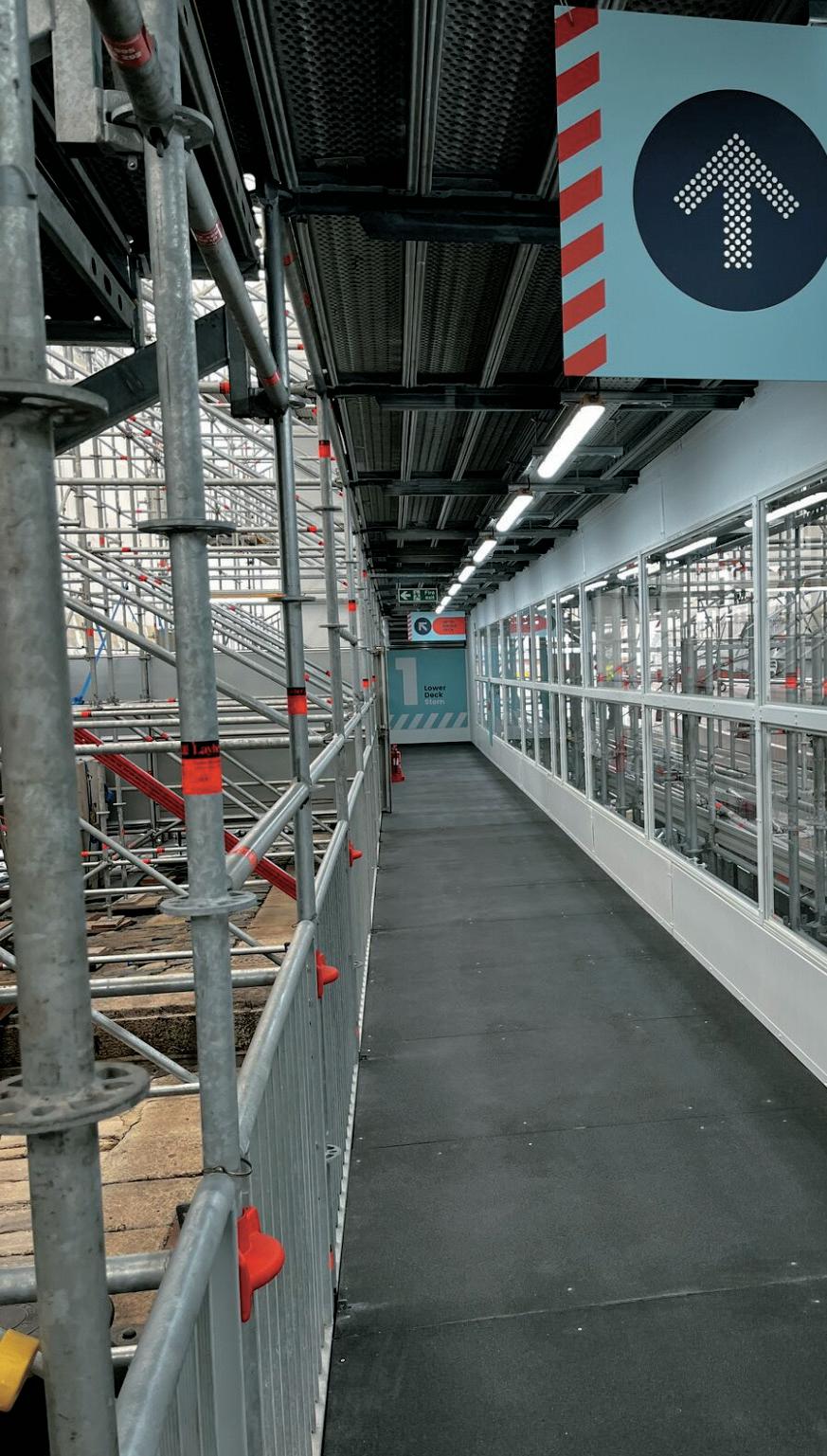

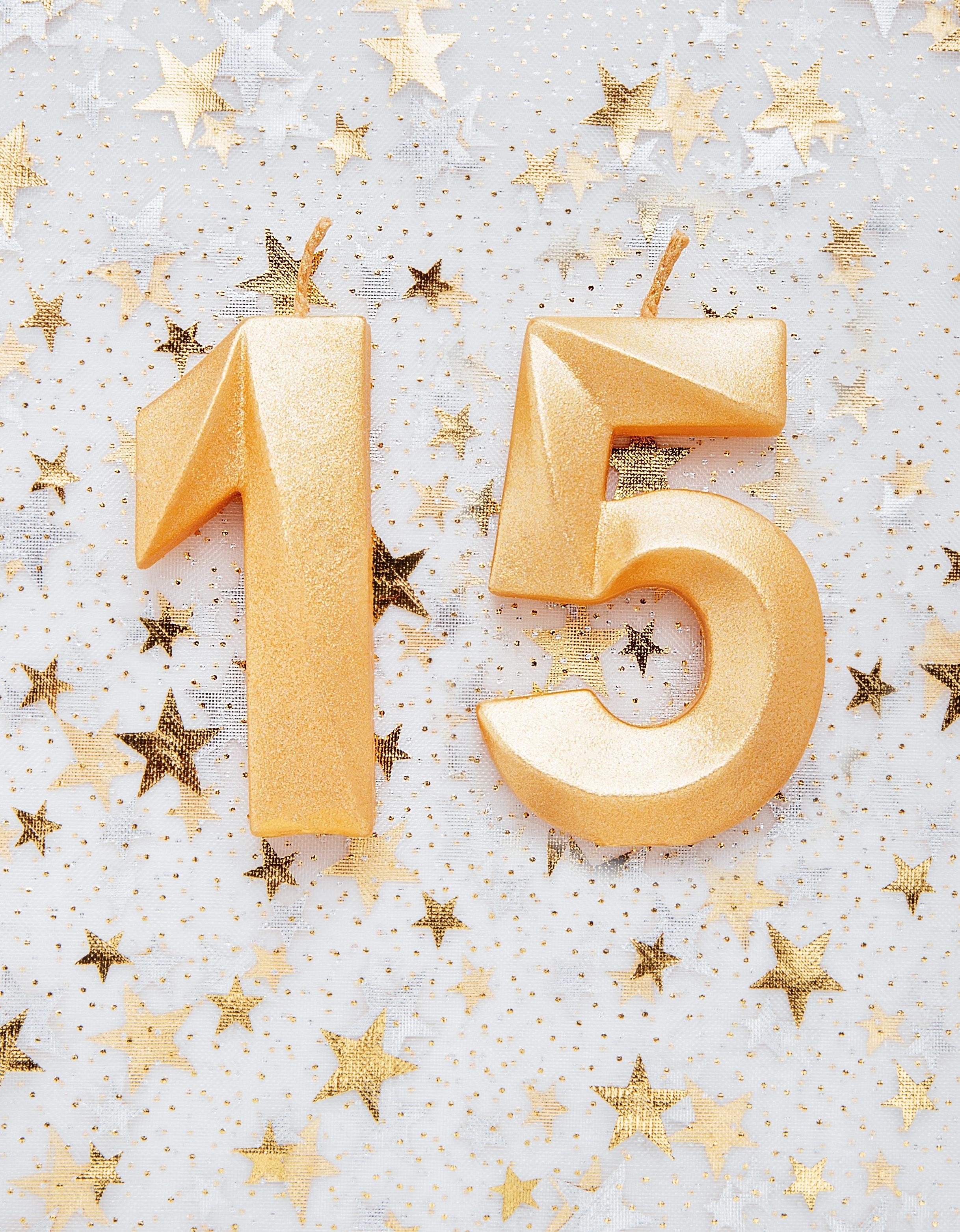
Celebrating Celebrating years of ScafMag years of ScafMag

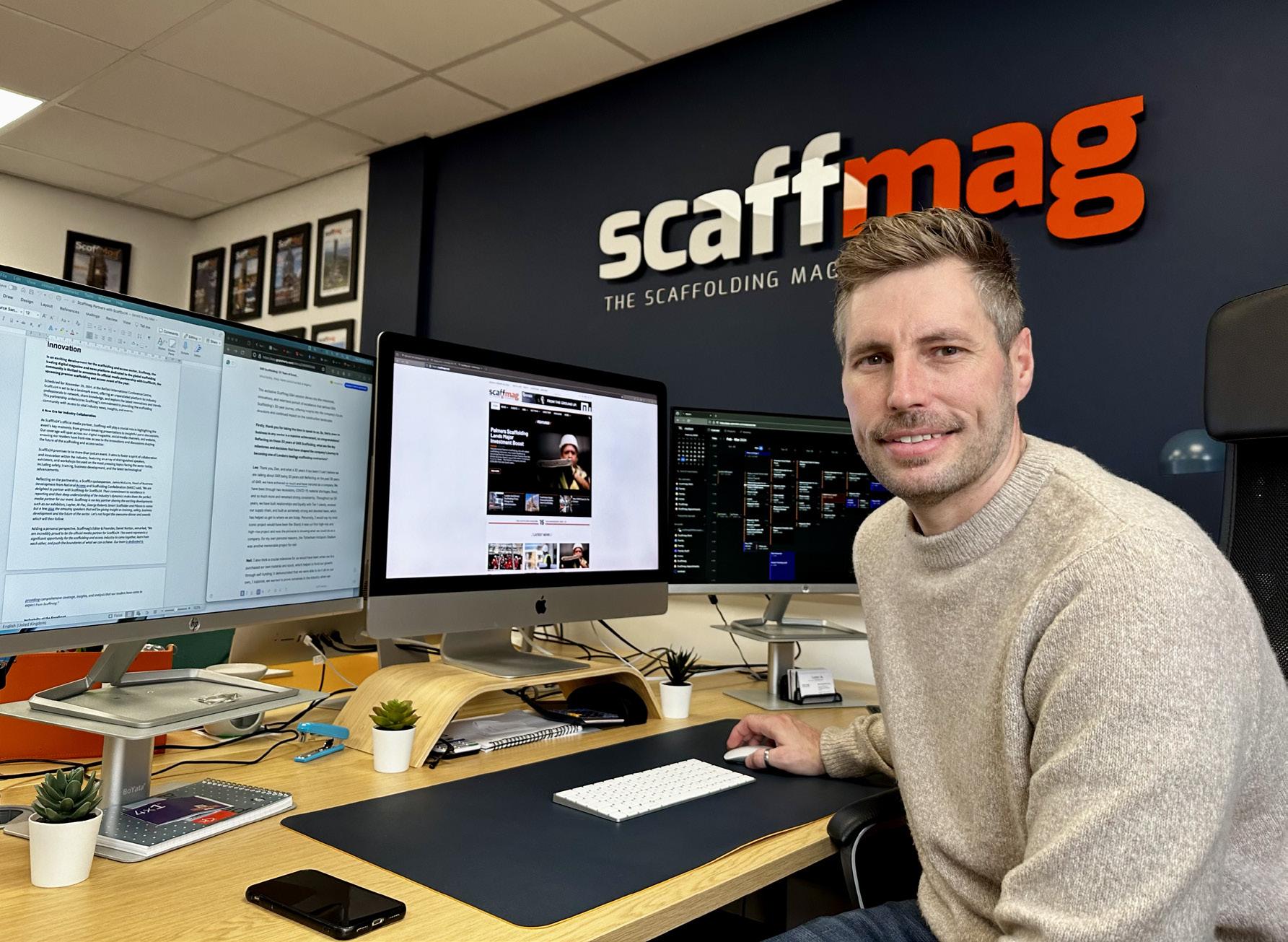
This year marks a signifcant milestone for us at ScafMag –our 15th anniversary
Founded in 2009 by Dan Norton, a visionary with deep roots in the scafolding and access industry, ScafMag was born out of a passion for the trade and a desire to create an independent platform dedicated to sharing the most compelling stories and insights from across the UK and around the globe.
Our journey from a fedgling newsletter and blog to the industry’s leading source for cutting-edge news, in-depth feature articles and informed industry commentary is a testament to our commitment to journalistic excellence. Over the years, we’ve become a must-read for professionals within the scafolding sector, earning a place at the very heart of the industry we serve.
Refecting on the origins of ScafMag, our founder, Dan Norton, shares, “Like many others in our industry, starting my career in scafolding was a family afair for me, working alongside my older brother erecting scafolding on various construction and industrial projects in our local area. My passion for the industry grew, as did my frustration with the lack of positive and informative community platforms, I am looking at you ‘Scafolders Forum’,” Dan said with humour.
“I had a background in web development while studying at college in my teenage years and a fairly good
understanding of scafolding, I saw an opportunity to create something unique – thus, ScafMag was born.”
“In my free time, when not scafolding for hours during evenings and weekends, I built the website from the ground up and registered Scafmag.com in November 2009. Since then, I have dedicated myself to providing industry news coverage for the masses, and luckily enough, it’s just grown naturally to where it is today.
“ScafMag grew at such a rate I was fortunate enough to hang my spanners up several years ago and concentrate on the website and magazine full-time. I feel so lucky to do this daily; it’s a passion!”
A DECADE AND A HALF OF MILESTONES
Looking back on the past 15 years, ScafMag has achieved numerous milestones that we take immense pride in. One of the most memorable moments came in 2016 when ScafMag was featured in the ‘Missing Word’ round on the BBC’s Have I Got News For You. It was a surreal experience that underscored our status not just within our industry but as a part of broader cultural conversations.
Another signifcant highlight in our journey occurred in 2018, when we had the extraordinary opportunity to cover the scafolding works by PHD on one of the UK’s most iconic landmarks: Big Ben in London. Tis project was not only a testament to the innovation and skill within our industry but also a privilege that allowed us to experience the magnifcence of system scafolding at an unprecedented scale.
“Being able to climb to the top of Big Ben and touch
I HAD A BACKGROUND IN WEB DEVELOPMENT AND A FAIRLY GOOD UNDERSTANDING OF SCAFFOLDING, I SAW AN OPPORTUNITY TO CREATE SOMETHING UNIQUE – THUS, SCAFFMAG WAS BORN
the famous clock face frst-hand was a moment of profound pride and excitement,” Dan recollected.
Tis assignment showcased the incredible capabilities of scafolding professionals and highlighted the importance of our work in preserving and maintaining national treasures. It was a milestone that not only celebrated our industry’s contribution to signifcant historical and cultural preservation but also solidifed ScafMag’s role in documenting and sharing these monumental achievements with the world.
Tese moments, among others, illustrate the remarkable journey ScafMag has been on. From providing in-depth coverage of industry-leading projects to being recognised on national TV, our commitment to elevating the scafolding community and sharing its stories has remained unwavering.

Travelling has been integral to our journey, bringing global perspectives to our content. A standout assignment took us to the Middle East with the late, great industry legend Terry Sennett in 2014, highlighting the efectiveness of UK scafolding training schemes in the Gulf Cooperation Council (GCC) region. Tese experiences have reinforced our belief in the universal bond within the scafolding community, transcending borders and cultures.
“Simian Risk and the great Terry Sennett invited me to spend a week in the Middle East to write a story about the efectiveness and progress of the UK scafolding training schemes in the Gulf Cooperation Council (GCC) region.
“Terry was a true industry leader and very inspirational and was always a great supporter of ScafMag in the early days. I accompanied Terry on his travels to Dubai, Qatar and Saudi Arabia, where I met many trainee scafolders from all diferent cultures and backgrounds. I realised at that very moment it doesn’t matter where you’re from or what culture or creed you are; we are all the same and part of one global scafolding community.
“Unfortunately, a few months afer my trip with Terry, his life was tragically cut short by Sepsis, and he is still missed to this day.”
EVOLVING WITH THE INDUSTRY
Te scafolding industry has seen considerable changes over the past ffeen years, and Scafmag has been at the forefront of documenting this evolution. One such change was the
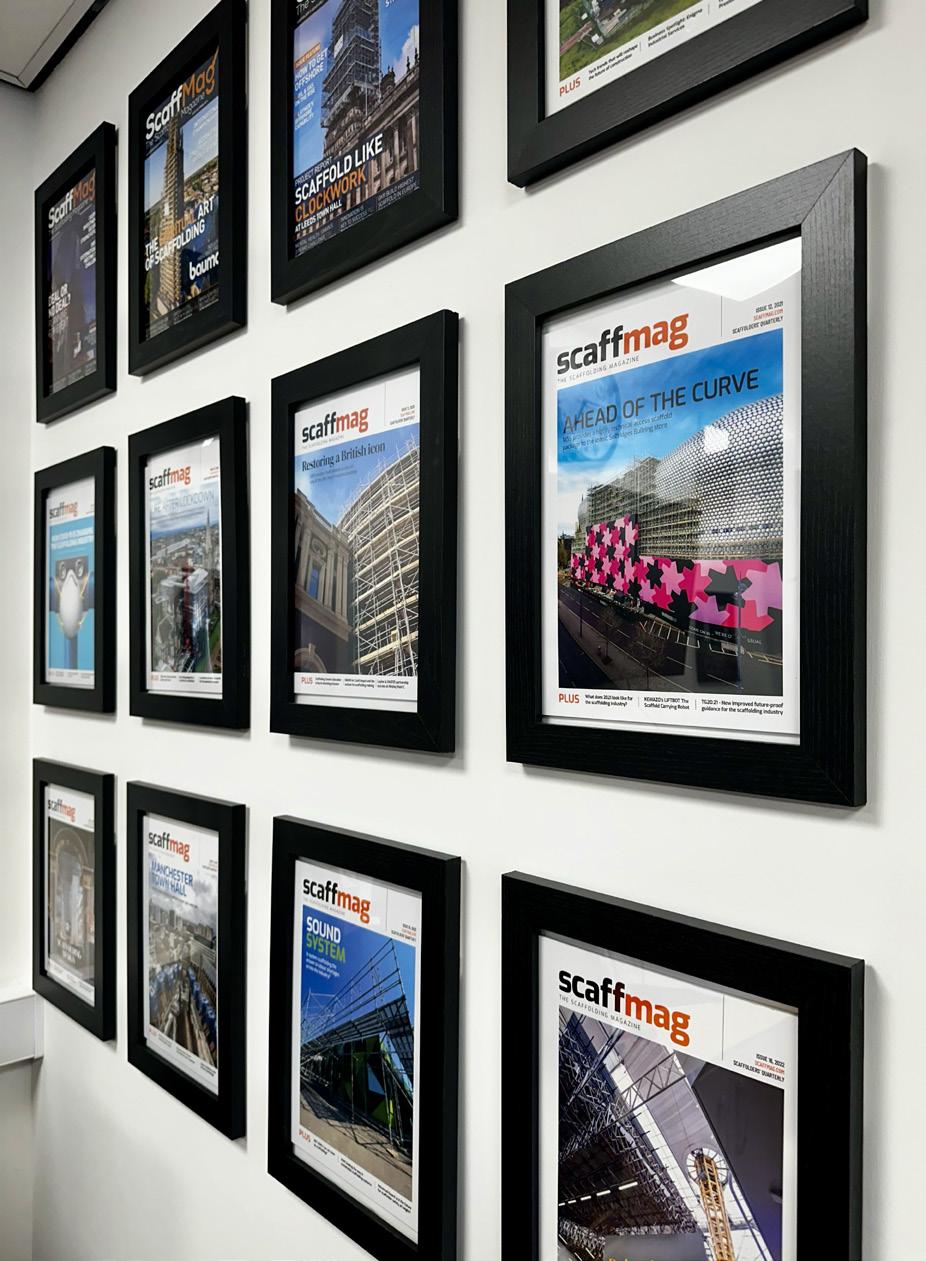
publication of TG20:13 guidance and Eguide by the NASC. It was a revolutionary moment for the industry, and we were proud to play a part in spreading the word about this signifcant guidance.
“Te launch of TG20:13 was an enormous deal at the time. I was fortunate to be at the TG20:13 media launch in London and was able to play my part in spreading the news about the guidance.” Dan remarked.
THE FUTURE OF SCAFFMAG
As we celebrate this milestone, our focus remains on elevating the voices of scafolders, contractors and system manufacturers, and highlighting the amazing work of scafold design engineers. Te industry is evolving rapidly, and ScafMag is committed to highlighting innovations, sharing best practices and fostering dialogue among professionals. Our dedication to creating a connected and informed community is stronger than ever.
Looking ahead, we are excited about the opportunities to further enrich our content, embrace new technologies and expand our global reach. Our mission to serve as a beacon of journalistic excellence and industry insight continues, driven by the same passion and dedication that marked our founding.
In closing, we extend our deepest gratitude to our readers, contributors, our fantastic sponsors and the global scafolding community for your unwavering support. Here’s to the next 15 years and beyond as we continue to build on our legacy of excellence and community within the scafolding industry.
From all of us at ScafMag, thank you for being a part of our journey.
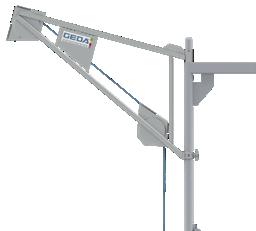
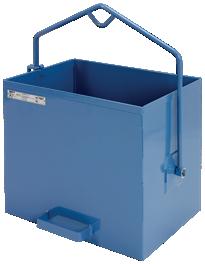
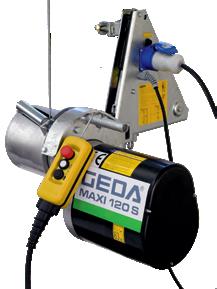
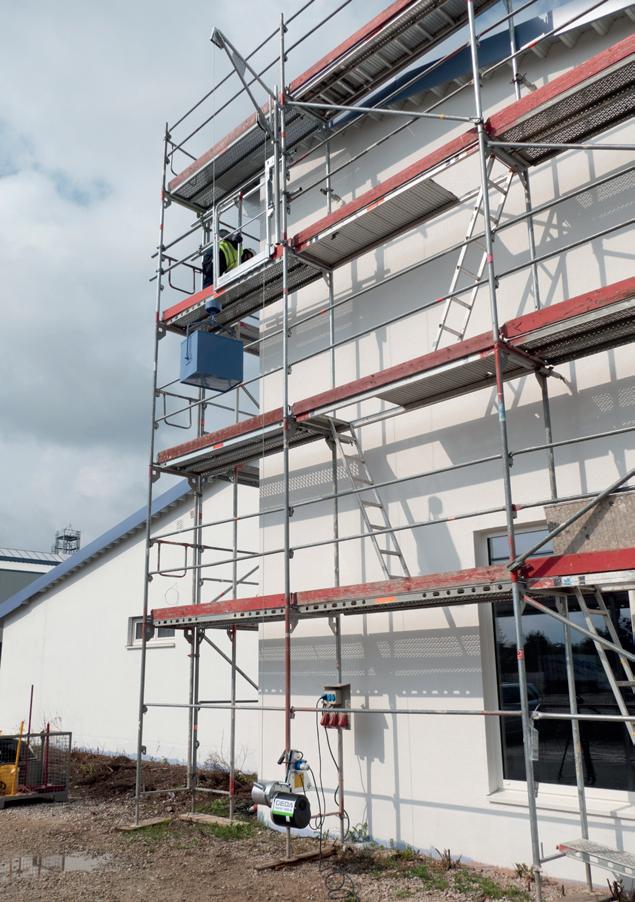
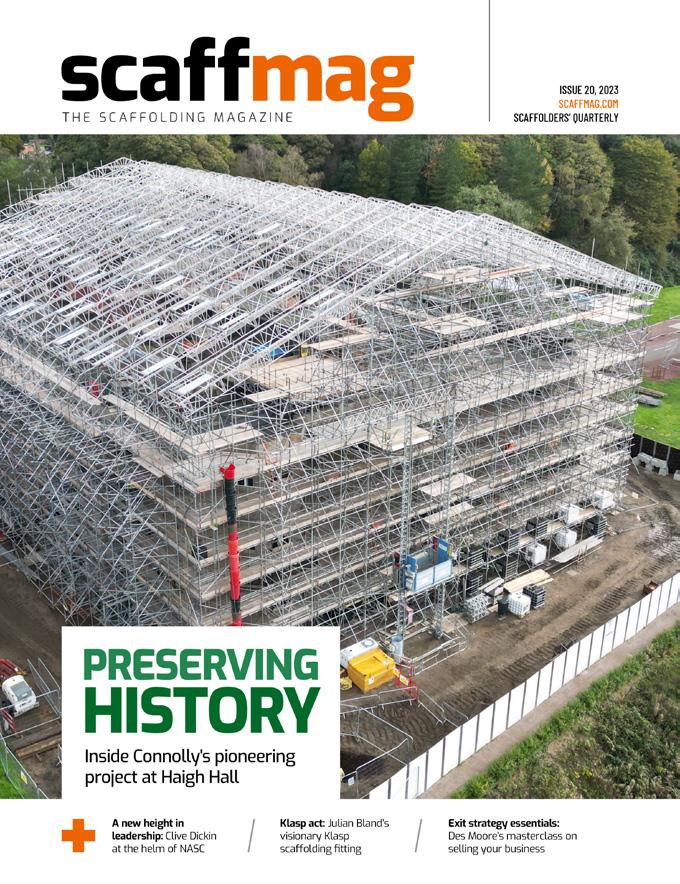
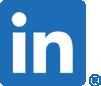


ScafEx24: Pioneering the future of scafolding and access
In a bold move that signifes a new era for the scafolding and access industry, the National Access and Scafolding Confederation (NASC) has launched ScafEx24, a groundbreaking conference and expo anticipated to transform the sector’s landscape
Set against the backdrop of the Belfast International Conference Centre on November 29, 2024, ScafEx24 emerges as the quintessential gathering for professionals seeking to explore the latest trends, innovations and safety protocols within the scafolding and access market.
A NEW DAWN FOR INDUSTRY NETWORKING AND INNOVATION
ScafEx24 is not just another industry event; it is a meticulously designed platform that aims to bridge the gap between scafolding clients and providers, fostering an environment of collaboration and learning. Tis free-toattend conference and exhibition is tailored to cater to the evolving needs of the UK scafolding and access market, addressing crucial aspects such as training, design principles, products, safety and meet-the-buyer opportunities.
Te exposition will see over 40 industry suppliers and service providers converge to showcase the latest products and services shaping the industry’s future. In parallel, the conference segment promises engaging sessions with keynote speakers, thought-provoking panel discussions and inspiring presentations from esteemed experts.
Tese sessions are designed to ofer invaluable perspectives on the industry’s trajectory, ensuring attendees leave with a wealth of knowledge and insights.
CELEBRATING EXCELLENCE: GALA DINNER AND AWARDS
A highlight of ScafEx24 is the NASC gala dinner and awards ceremony. Tis celebrated tradition ofers an evening of glamour, recognition and celebration, honouring excellence within the scafolding sector. It’s an opportunity for professionals to network in a more relaxed setting, building relationships that could pave the way for future collaborations.
INCLUSIVITY AND ACCESSIBILITY AT ITS CORE
In a signifcant move, the NASC has made ScafEx24 entirely free to attend, underscoring the event’s commitment to inclusivity and accessibility. Tis decision opens the doors wide to professionals from all corners of the industry, ensuring that a wealth of knowledge and networking opportunities are available to everyone. It’s a testament to the NASC’s dedication to fostering growth and innovation within the scafolding and access sector.
A VISIONARY OUTLOOK AND FUTURE PLANS
Under the leadership of Clive Dickin, the new CEO of NASC, ScafEx24 is poised to be just the beginning of an
ambitious journey. Te future of ScafEx looks bright, with plans already in motion to expand the scope of the event to encompass the entire working environment of the scafolding sector. Venues such as G-Mex, the NEC and Excel in London are being explored to host future editions of ScafEx, promising to elevate the event to new heights.
SHAPING THE FUTURE TOGETHER
ScafEx24 represents a pivotal moment for the scafolding and access industry. It’s a platform where professionals can come together to network, learn and contribute to shaping the sector’s future. With its inclusivity, diverse content and vision for expansion, ScafEx is undoubtedly set to become a staple event in the scafolding industry’s calendar.
As the industry looks toward ScafEx24 and beyond, it’s clear that this event is not just about showcasing the latest innovations and best practices; it’s about coming together to build a safer, more efcient and more collaborative future.
SCAFFMAG & SCAFFEX24
In a signifcant development, ScafMag has proudly announced its partnership with ScafEx24, becoming the event’s ofcial media partner.
Tis collaboration signifes a strong alignment in vision and commitment to the advancement of the scafolding and access industry. As the ofcial media partner, ScafMag will play a crucial role in amplifying the reach and impact of ScafEx24, providing comprehensive coverage, insights and highlights from the event.
Tis partnership not only enhances the visibility of ScafEx24 but also reinforces ScafMag’s position as a leading voice in the industry, dedicated to delivering cutting-edge content and fostering a sense of community among professionals. Together, ScafMag and ScafEx24 are setting the stage for an unprecedented gathering that promises to be both informative and transformative for the scafolding and access sector.
IN A SIGNIFICANT DEVELOPMENT, SCAFFMAG HAS PROUDLY ANNOUNCED ITS PARTNERSHIP WITH SCAFFEX24, BECOMING THE EVENT’S OFFICIAL MEDIA PARTNER


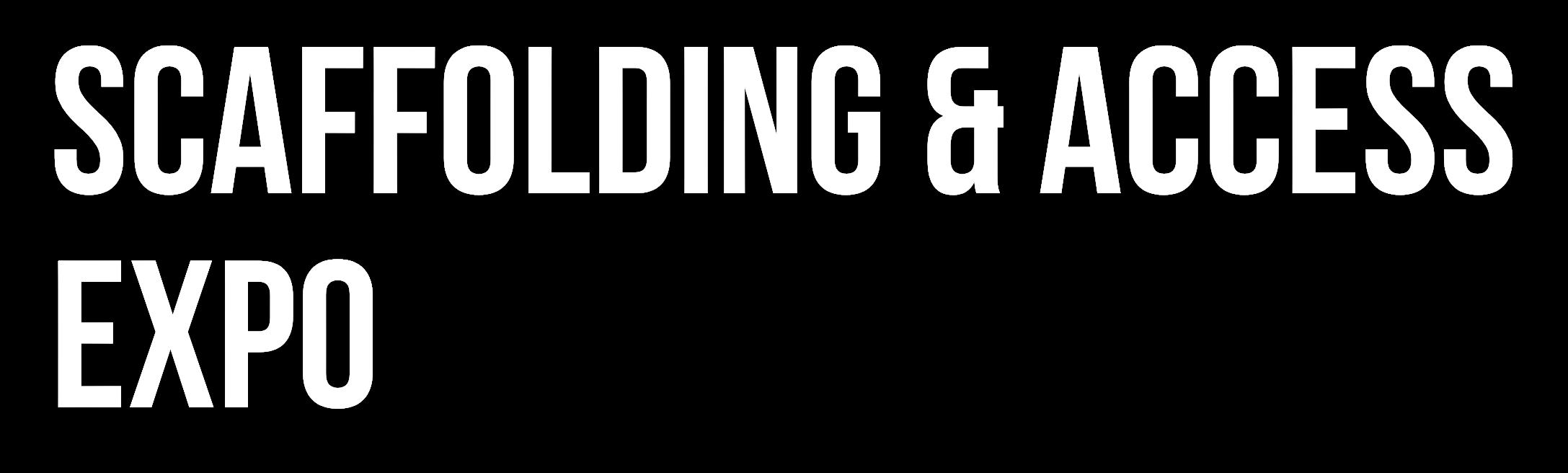

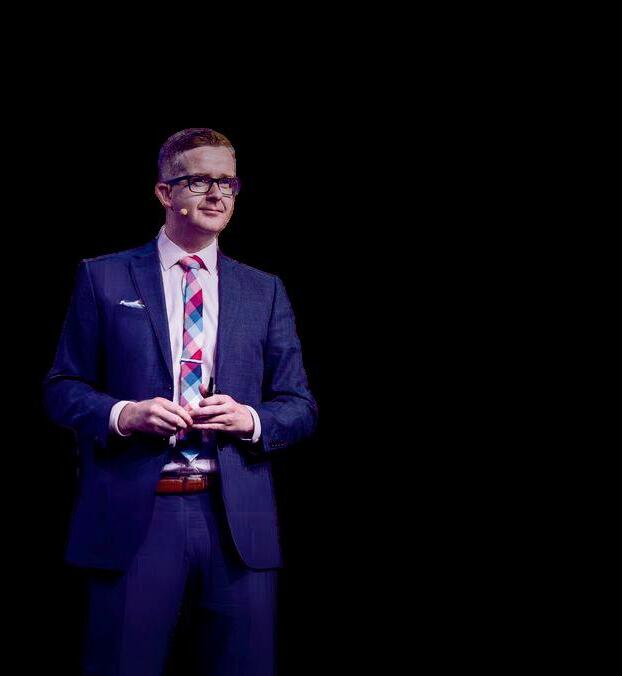


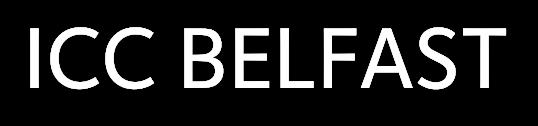
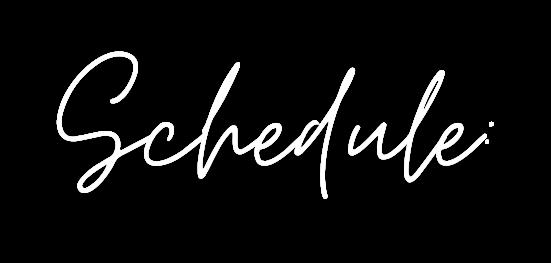
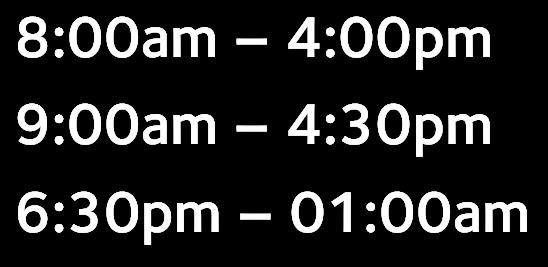
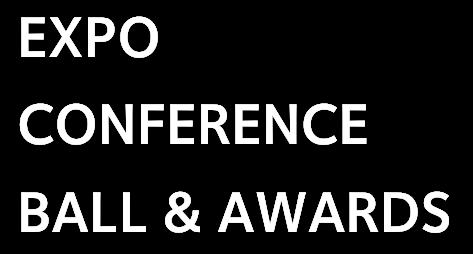

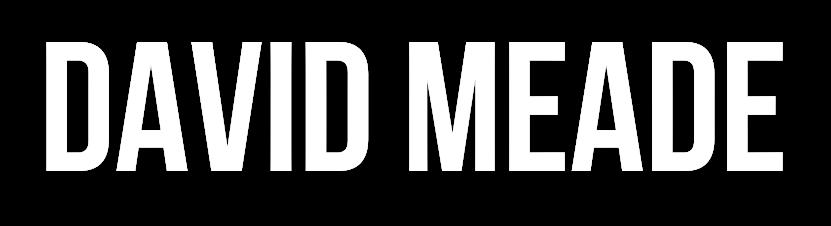

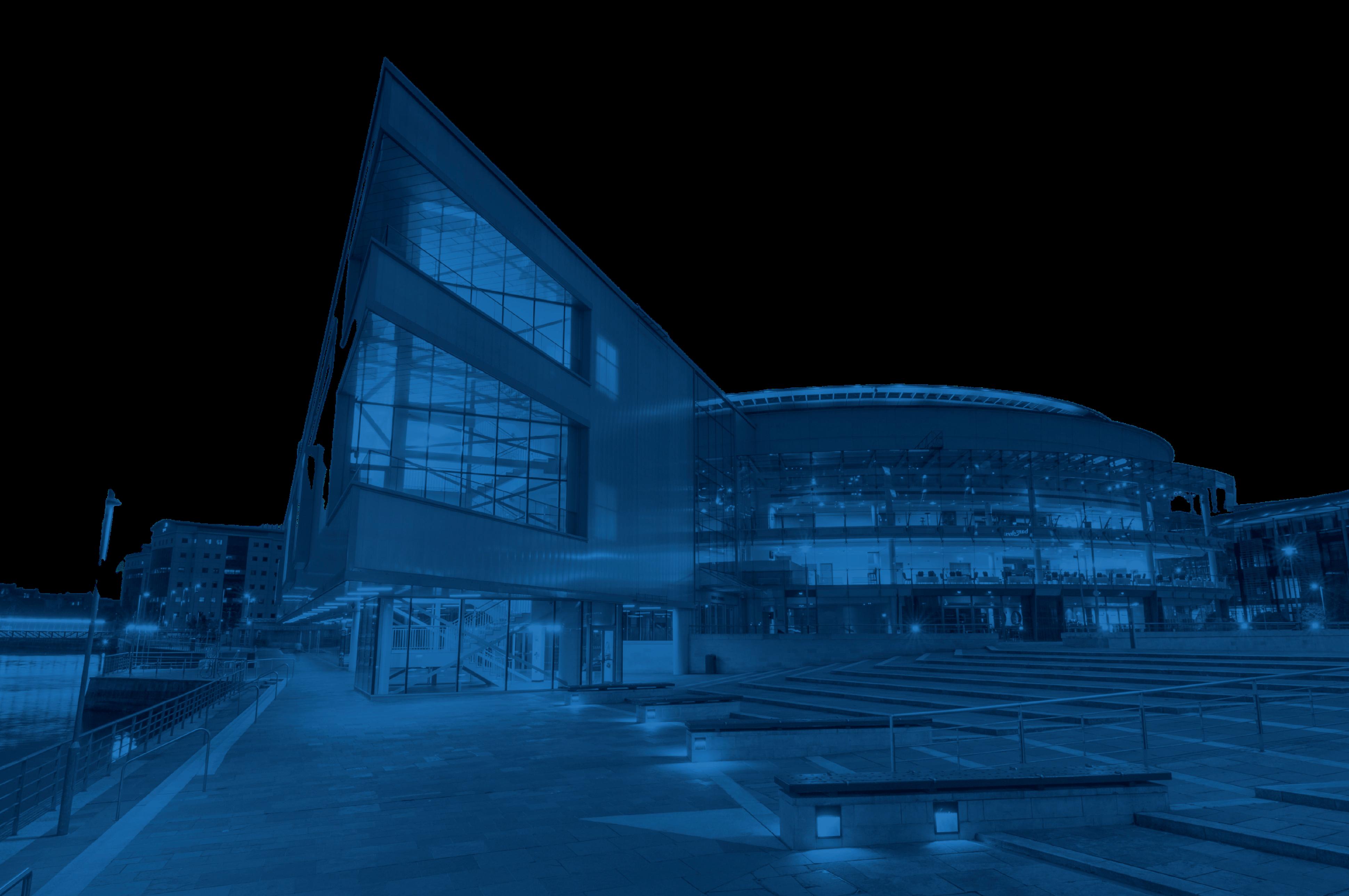
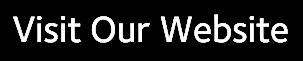
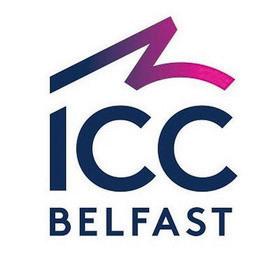
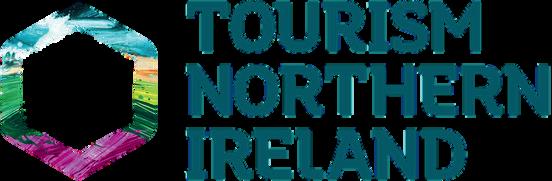
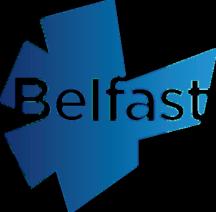
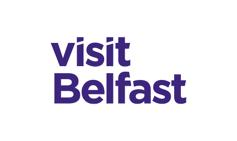

The line-up for ScafChamp 2024 continues to take shape as three prominent UK teams specialising in system scafolding have ofcially signed up to compete in the prestigious international championship
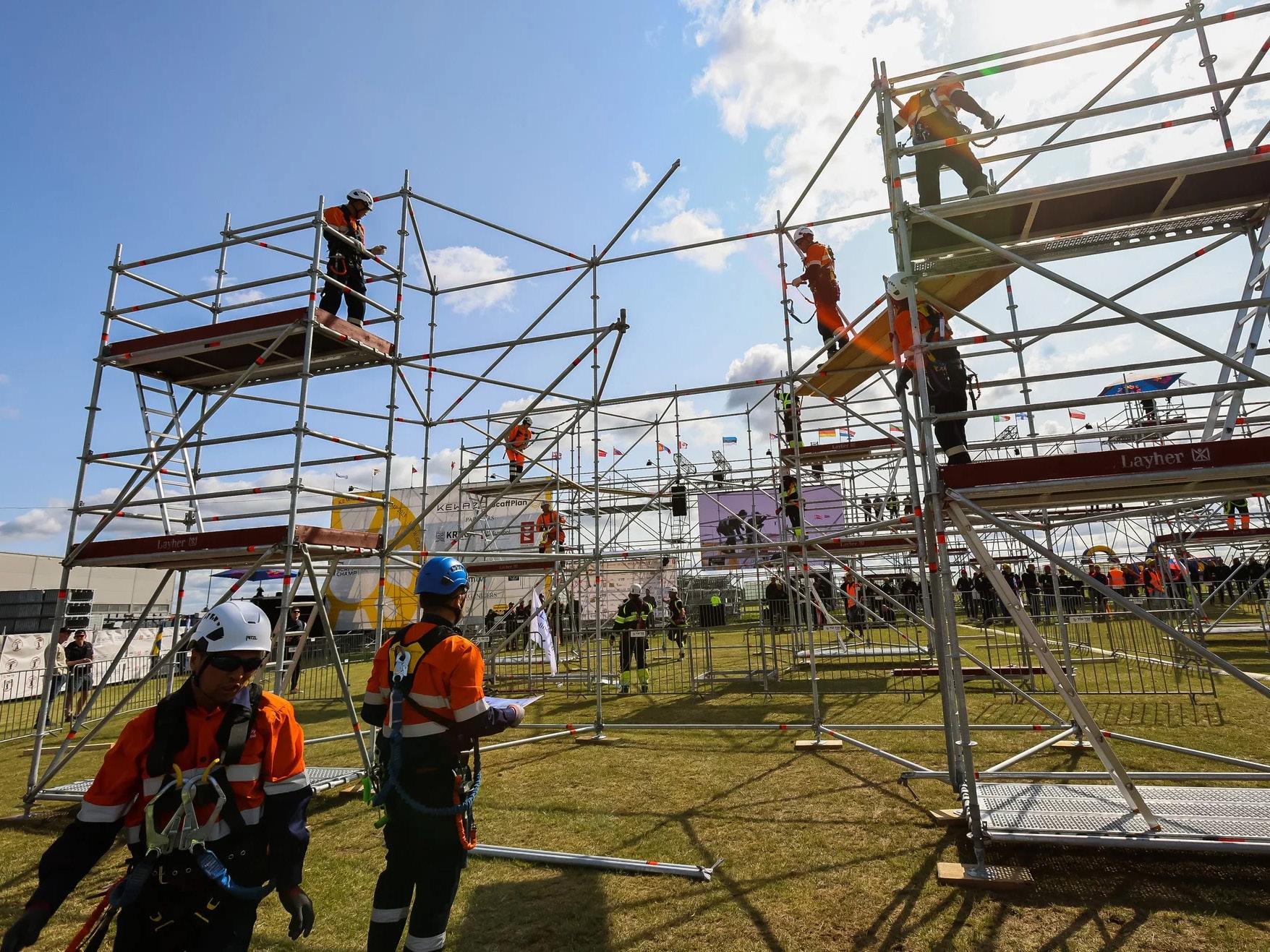
UK TEAMS READY TO SHINE AT SCAFFCHAMP 2024
Representing expertise and innovation within the UK scafolding industry, these teams are poised to make their mark on the global stage at the upcoming event in Vilnius, Lithuania.
Among the teams set to represent and fy the fag for the UK is Connect Scafolding Ltd, based in Hertfordshire, another specialist contractor with a strong emphasis on system scafolding.
Speaking to ScafMag, Katie Boswell from Connect Scafolding expressed the team's excitement about participating in ScafChamp 2024. She highlighted the sense of community and teamwork that the competition fosters, highlighting the opportunity to showcase the team's talent and learn from the best in the industry.
"We are thrilled to be part of ScafChamp 2024," said Boswell. "Connect were inspired by the sense of community and teamwork that ScafChamp brings. It's been great to see how the competition has developed and
grown over the past few years. Tis is a great opportunity to show the level of skill our team have gained through years of hard work and determination, and what better way to showcase our talent than to represent our country!"
Also set to compete is Rose System Scafolding Ltd, headquartered in Oldham. With a culture rooted in teamwork and shared vision, Rose System Scafolding embodies the spirit of collaboration and innovation. James Brierley of Rose System Scafolding noted the alignment between ScafChamp's ethos and Rose's culture and highlighted the opportunity to engage with like-minded individuals, share stories and learn from the international Layher community.
"From my perspective, the ScafChamp event seems to align with Rose's culture," said Brierley. "ScafChamp 2024 is an opportunity for us to engage with a community of likeminded people and share stories and ideas. For us, it wasn't necessarily the
competitive side of the event that attracted us, although we'll try our best to represent the UK alongside our esteemed colleagues at Connect, to the best of our abilities. We want to spend time with the international Layher community, share stories and ideas and be open to learn."
Also joining the competition is Star Scafolding Ltd, headquartered in West Bromwich. With a focus on system scafolding, Star Scafolding is renowned for its precision and efciency in delivering complex projects. Teir participation underscores their commitment to excellence and their readiness to showcase their skills on an international platform.
Te participation of these UK teams adds another dimension to ScafChamp 2024, showcasing the depth of talent and expertise within the country's scafolding sector. As the competition draws nearer, anticipation mounts for what promises to be an unforgettable showcase of scafolding skill and camaraderie.
“Great leaders surround themselves with great people, and we are committed to building a team that can deliver our growth strategy”
In an exclusive interview, Sean Pike, Managing Director at Layher UK, ofers an insightful glimpse into the company’s visionary strategies for the year ahead and beyond following some signifcant management shifts
Layher UK, the system scafolding powerhouse, remains a beacon of quality, innovation and growth in the ever-evolving scafolding and access solutions sector. With its headquarters based in Letchworth, Hertfordshire, backed up by a network of regional depots, the company has recently undergone notable management transitions and welcomed fresh talent into its fold. Tese developments signal an exciting path forward for Layher UK as it charts its course through 2024 and beyond.
ScafMag’s Editor sat down with Sean Pike, Managing Director at Layher UK, to delve deeper into the company’s strategies for growth and adaptation in the coming year.
Daniel Norton: Layher UK has recently undergone some fundamental management changes and new appointments and hinted that 2024 will be a year of growth for the company. Can you provide some insights into the rationale behind these changes and how they ft into the company’s overall growth strategy?
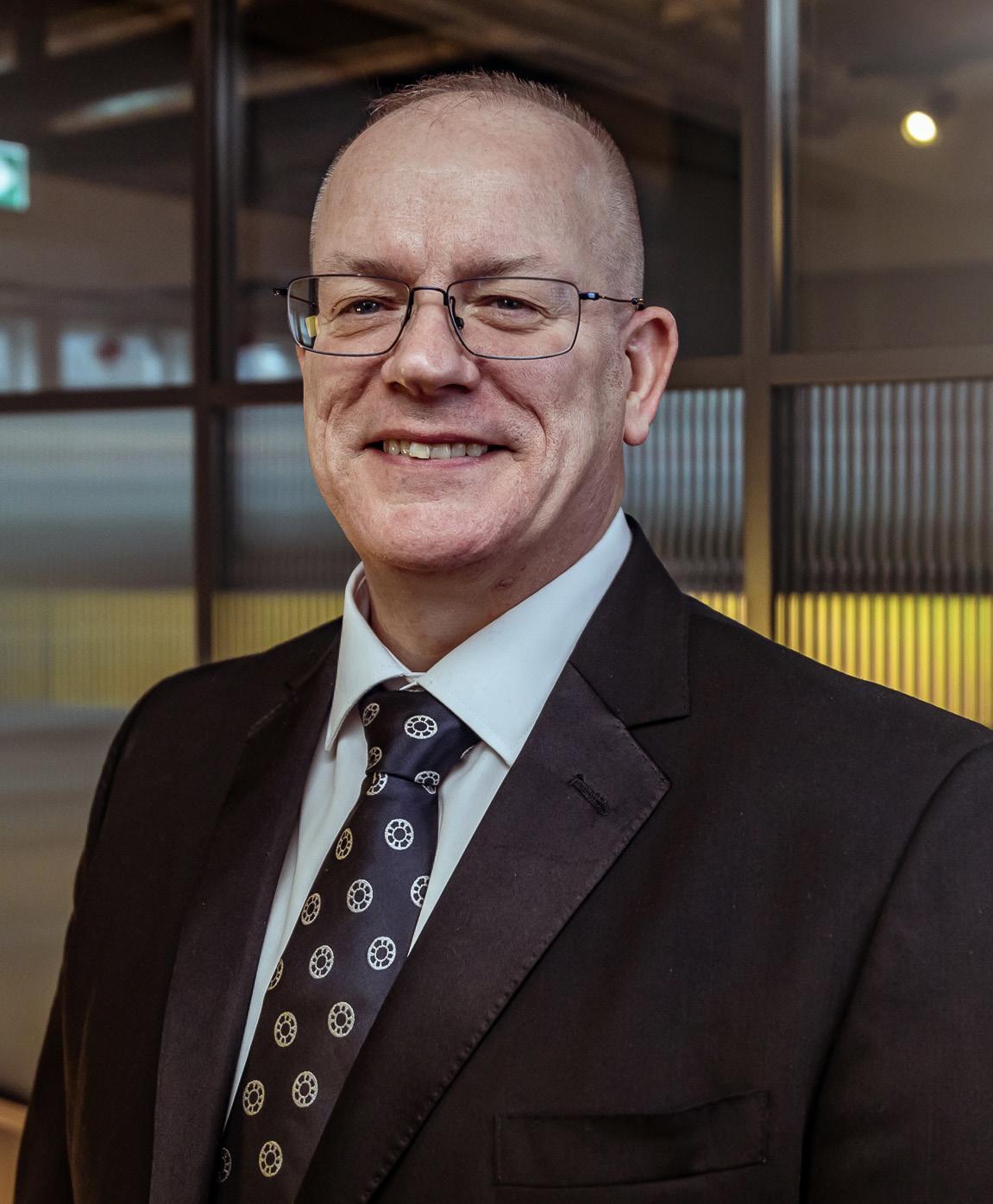
Sean Pike: Great leaders surround themselves with great people, and we are committed to building a team that can deliver our growth strategy. We have ambitious plans to double the current turnover within the next fve years and realise that we cannot continue to do the same thing and expect a diferent result.
When you ask for growth, you must remember not to be surprised when it challenges you, and as a leadership team, ‘WE’ will very much be focused on being agile in our turbulent and ever-changing industry. Being at the forefront of innovation whilst providing trusted services is a balance we pride ourselves on delivering. Our primary focus will always be on providing the turnkey service our customers greatly rely on.
DN: Katherine Fox joined Layher UK as Operations Director in 2022. Could you share the impact she has had on the company’s operations and what her role will be in driving growth in 2024?
SP: As an experienced change leader, Katherine has been perfectly positioned to drive our growth strategy’s key elements.
Over the past 18 months, she has focused on aligning our depots to operate as one Layher UK, removing aspects of silo working and identifying opportunities to improve service and meet our customer’s needs.
For instance, the development of our rental hub in West Bromwich has been a concept that Katherine has worked with the team to implement. Katherine is passionate about making sure Layher is
accessible to all, and our Allround Rent To Try option is growing and evolving. She is currently leading the transition into a new Microsof business operating system, improving every aspect of our sales processes, fnance, warehouse functionality and CRM operation.
Her relentless pace and motivation to achieve business goals have positively impacted the speed at which decisions are now made and new processes are implemented. Her passion for people means she naturally leads with compassion and has built trust throughout the team by championing collaboration and empowerment.
You will only sometimes see Katherine customer-facing, as she will be focusing on supporting all our teams to deliver the best possible service for our customers.
DN: Following her promotion last year, Anita Singh now holds the position of Technical Director. Under her leadership, what specifc initiatives or innovations can we expect, and how do they relate to Layher UK’s growth plans?
SP: By nature of her expertise, Anita is a detailfocused leader who always seeks to do things right. Having gained valuable insights working closely with our customers over many years at Layher, she is now ideally placed to develop and grow a team of talented engineers. She has listened to what needs to be improved within our service and is leading the most extensive change programme Layher’s technical team has seen in 25 years.
Anita is passionate about CPD and supporting
our experienced team through continuous improvement and chartership. Her team is the only technical team that designs Layher, and only Layher, projects 24/7. She is also setting up initiatives to ensure Layher UK is at the forefront of new design innovations, such as introducing 3D scanning as standard.
She will work closely with our design and innovation team at our global head ofce in Germany to deliver this continuous improvement. Anita is leading the implementation of the new commercial process for technical design, working through sprints of critical process development before launching in September 2024.
DN: Des Moore was announced as Layher UK’s new Brand Ambassador in January. Could you tell us more about his role and how it aligns with Layher’s brand recognition and expansion goals?
SP: Des Moore has a long history with Layher Allround and was one of our bigest customers at Trad for many years. We are delighted to be working with Des, who, with his years as an industry leader, will give insight into specifc areas. Tese include the scafolding contractor’s unique requirements, the system’s benefts versus tube-and-ftting, and his familiar history with the contracting hire business to support the development of our rental hub.
Des will be completing regular workshops with our key sales team to share his commercial experience and meeting customers to share his signifcant frst-hand knowledge and benefts of using the Layher system. His values align with our own and support our leadership strategy to increase market share, raise brand awareness and make Layher accessible to all scafolding companies. I think we all know the value Des can add to any business in our industry and we are lucky to work with him as our brand ambassador.
DN:ScafMag understands that Ben Beaumont, Director of the Temporary Works Forum and MD of Elevation 81, is working with Layher UK in an advisory role for the Technical Design Department. How might his expertise contribute to Layher’s growth?
SP: As a 10-strong team of design engineers, we pride ourselves on the knowledge and service we deliver to our customers. As our customers grow and take on more challenges, we have listened to them and realised that we need to change the way
our technical department functions in order to meet the needs of our customers.
We have been discussing for many months how to implement a new commercial process to meet those required demands. Ben is ideally placed to support Layher through this growth period, working with the leadership team to develop our strategy and break down the key elements of a new commercial process and how it would be implemented successfully. Working alongside Ben helps provide clarity of goal, identify challenges we will have to work through and how to support our valued team to fourish during this process.
His industry expertise and years of business leadership have helped springboard our strategy implementation.
DN: Are there any specifc market trends or opportunities that Layher UK plans to leverage to drive growth and remain competitive in the coming year?
SP: Te markets we operate in have had a turbulent 2023, but we, of course, now begin to see, since December, a re-emergence aided by falling infation and a steadier interest rate, plus it’s an election year, and we will seek to capitalise on the efects to specifc markets that the politicians will inevitably promise.
We are ready to support and deliver to the market our strategic and humble promise of the best possible customer service and support, as well as total reliability of supply, geared towards helping our customers to grow.
DN: How does Layher UK plan to maintain a competitive edge in the scafolding industry, and what strategies are in place to diferentiate the company from competitors?
SP: We are aware of how other system manufacturers operate in the market, and there are many look-alike versions of Layher Allround available.
However, at Layher we concentrate our eforts on ensuring we deliver the consistency of quality, service, solutions, support and depth of supply.
We will remain focused on what we do best: ensuring our vision, values and purpose are part of everything we do.
Our main objective will always be to help our customers grow their businesses through our strategic partnership. Teir success is our success.
OUR MAIN OBJECTIVE WILL ALWAYS BE TO HELP OUR CUSTOMERS GROW THEIR BUSINESSES THROUGH OUR STRATEGIC PARTNERSHIP. THEIR SUCCESS IS OUR SUCCESS
DN: Could you provide some insight into any new product developments or expansions that Layher UK has in the pipeline for the year ahead?
SP: Our product development and innovation team at our head ofce in Germany are continuously working on new solutions parts. We have recently worked with one of our Scottish customers to develop a specifc solution and given our fndings to Germany to include in the development… Watch this space!
PIONEERING PROGRESS
As Layher UK looks ahead to 2024 and beyond, it’s evident that the company is not just embracing change but actively driving it. With a
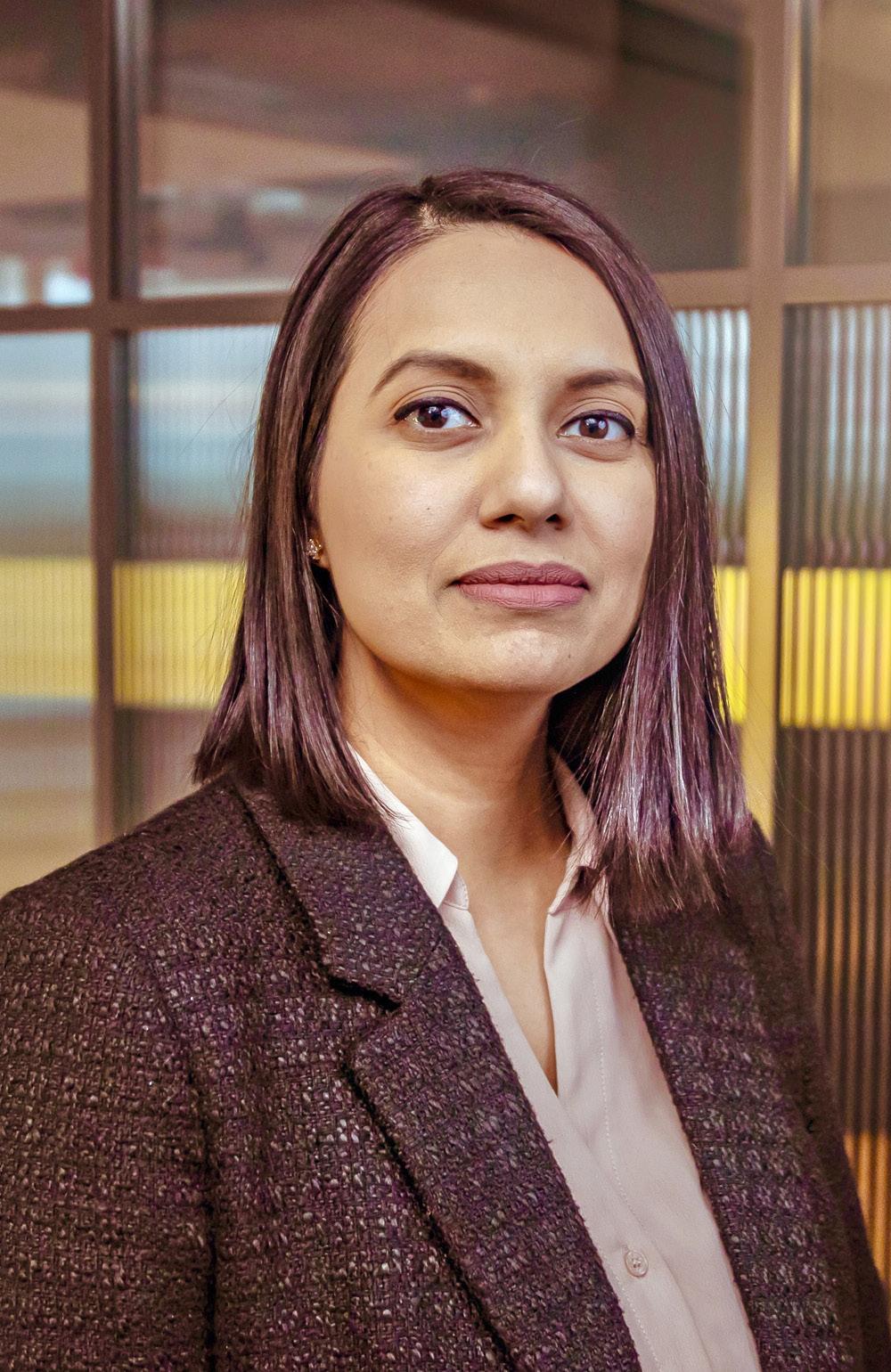
leadership team committed to fostering innovation, collaboration and customercentricity, Layher UK is poised to navigate the complexities of a dynamic industry landscape. From strategic management transitions to investments in talent and technology, every move underscores the company’s unwavering dedication to excellence.
As they embark on this growth journey, Layher UK remains steadfast in its mission to provide unparalleled service, reliability and customer support, cementing its position as a true leader in the system scafolding and access solutions sector. Te future holds boundless opportunities, and Layher UK stands ready to seize them with determination and vision.
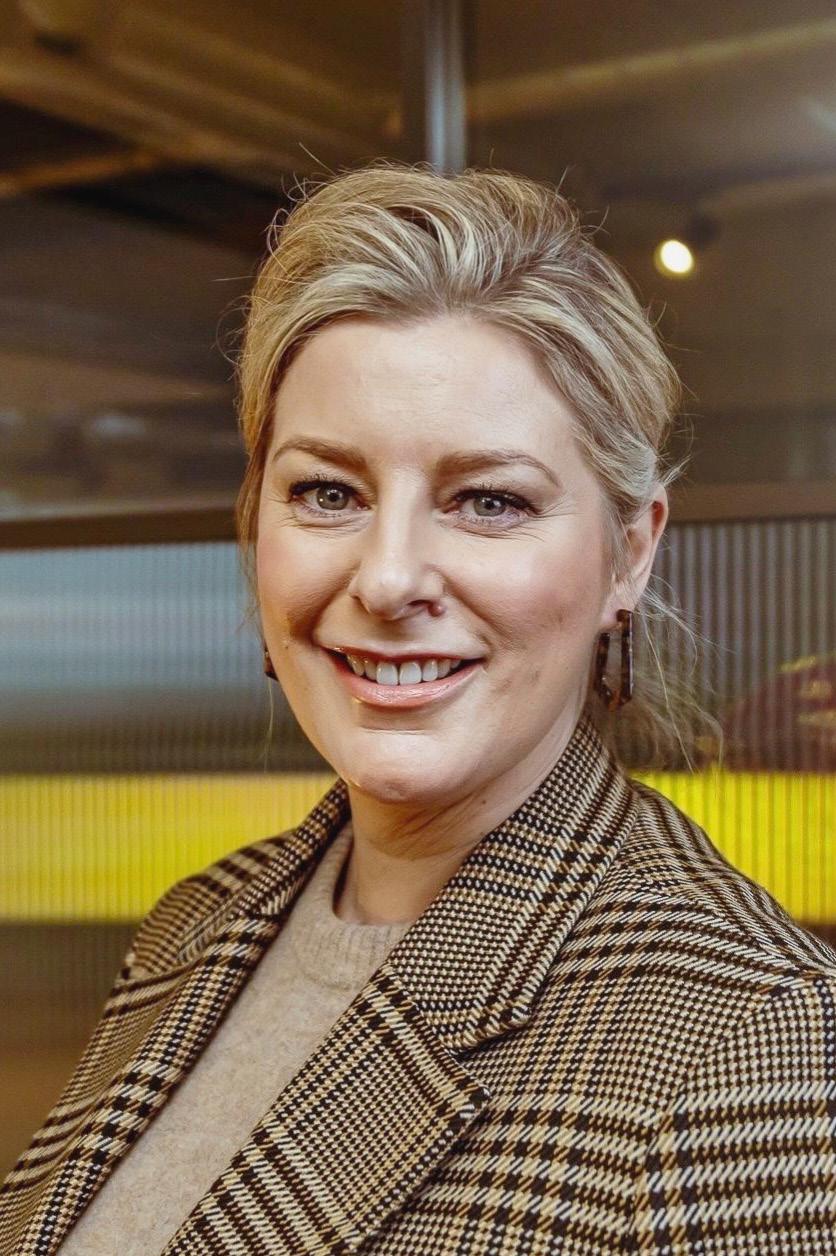
AFTER THE FLAMES
In the heart of Paris, where history whispers through the cobblestone streets and the Seine fows as the city’s lifeline, stands the wounded but ever-resilient Notre-Dame Cathedral. Following the harrowing blaze of April 15, 2019, that left the world in collective shock, a beacon of restoration emerged against the skyline of the French capital
Nearly 500 crafspeople, a battalion of skilled artisans, are immersed in the painstaking work of rebuilding. Tis army of talent spans 250 companies and art workshops from every corner of France, each contributing their expertise to the cathedral's renaissance. Carpenters, stonemasons, scafolders, sculptors, gilders, glassmakers and organ builders collaborate in a symphony of restoration eforts that promise to breathe life back into the 860-year-old structure.
Central to this monumental efort is the colossal scafolding works erected by Europe Échafaudage, a testament to engineering prowess and a symbol of hope and resilience in the face of adversity.
A SCAFFOLD RISES FROM THE ASHES
Europe Échafaudage, known for its expertise in complex scafolding projects, was tasked with one of the most signifcant challenges in cultural heritage restoration: stabilising and supporting the fragile bones of Notre-Dame. Tis wasn’t just any scafolding project; it was a mission laden with the weight of history and the eyes of the world watching intently.
Te scafolding erected by Europe Échafaudage served multiple critical roles in the cathedral’s restoration process. Firstly, it provided the framework to stabilise the structure, ensuring the weakened walls and vaults did not succumb
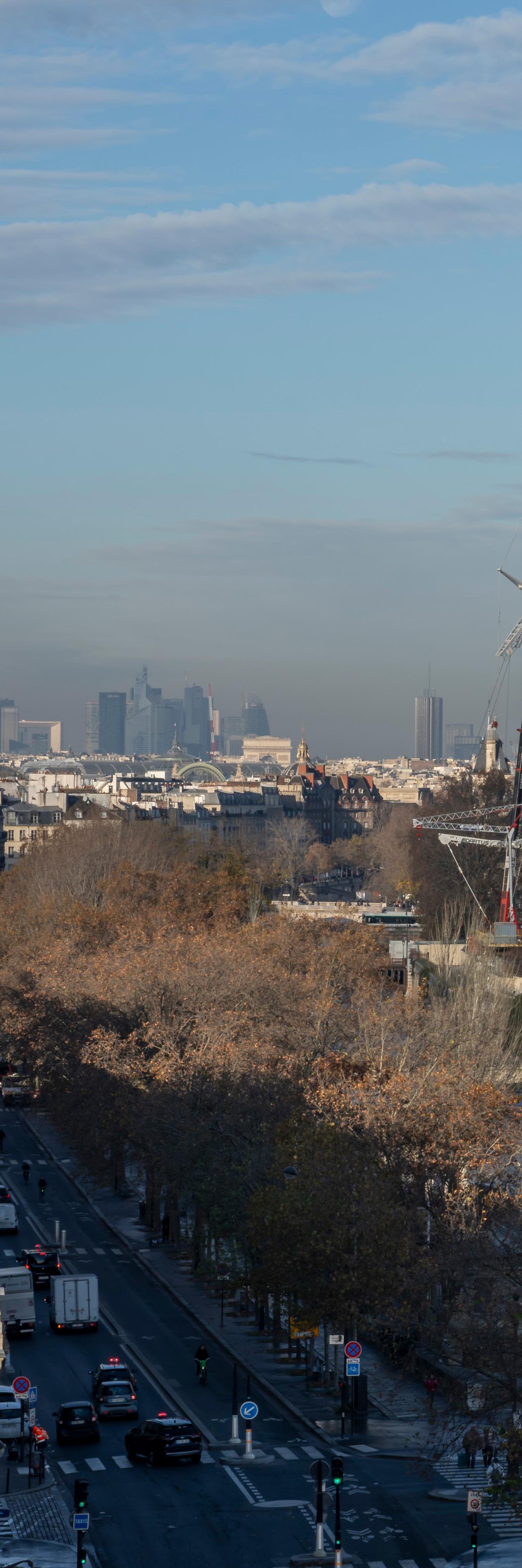
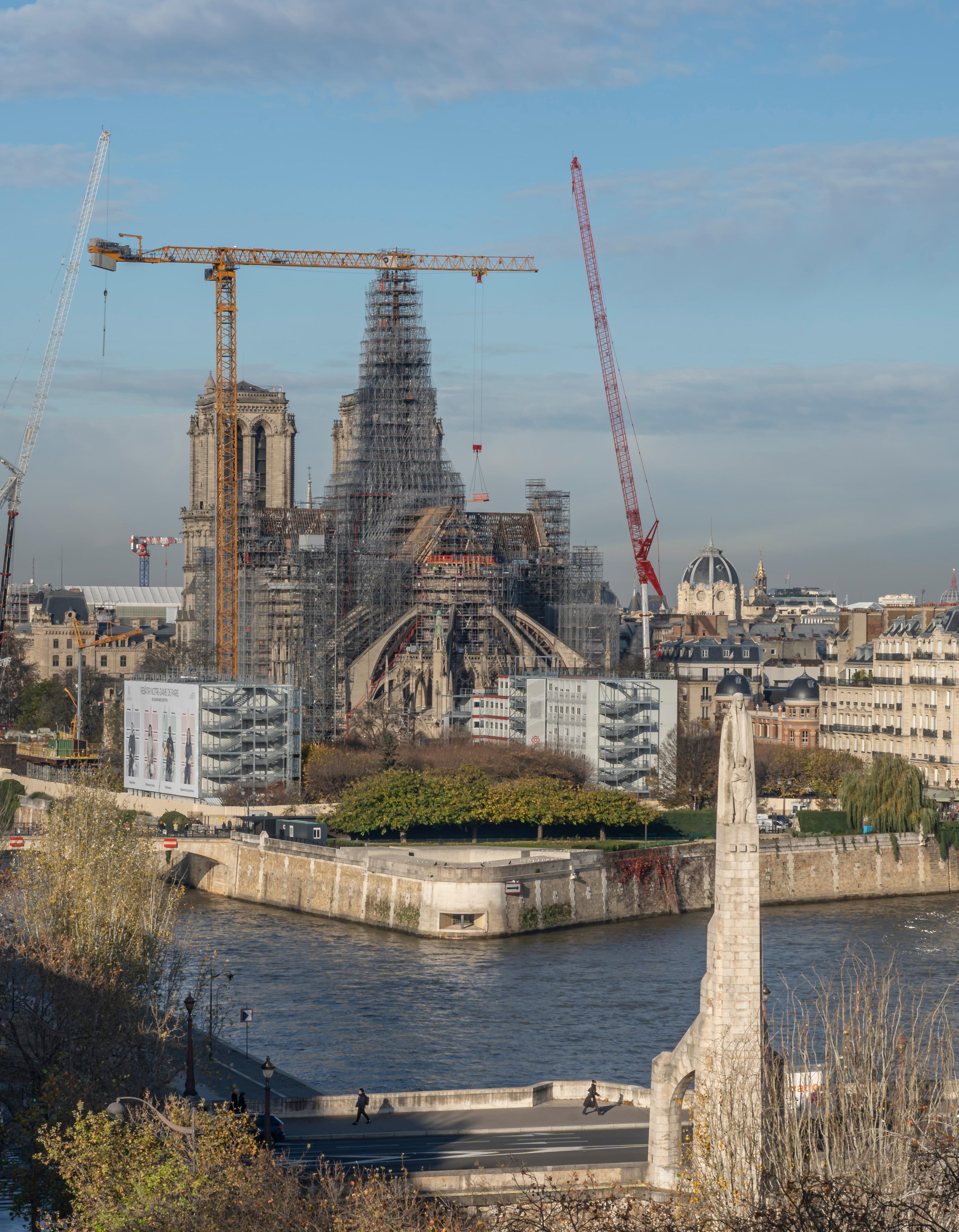
to further damage. Tis intricate network of tubes and steel also ofered a platform for experts to meticulously assess the full extent of the damage, a crucial step in charting the path forward.
NAVIGATING HISTORICAL COMPLEXITIES
Te task was fraught with complexities because of the pre-existing scafolding that had melted into a twisted mass during the fre. Europe Échafaudage’s expertise was paramount in delicately removing this hazardous tangle without causing additional harm to the cathedral’s fragile structure. Tis operation blended surgical precision and engineering acumen, showcasing the company’s capacity to navigate the delicate balance between modern restoration techniques and preserving historical integrity.
THE BACKBONE OF RESTORATION
Beyond stabilising and providing access, the scafolding erected by Europe Échafaudage became the cathedral’s temporary backbone. It allowed artisans, crafsmen and restoration experts to repair and restore stone, wood and stained glass. Tis scafold was not just a structure of steel; it was a bridge to the past and a conduit for the future, enabling the hands of today to mend the work of yesteryears.
2019’s terrible fre shocked the world, but its restoration will be a testament to collaboration.
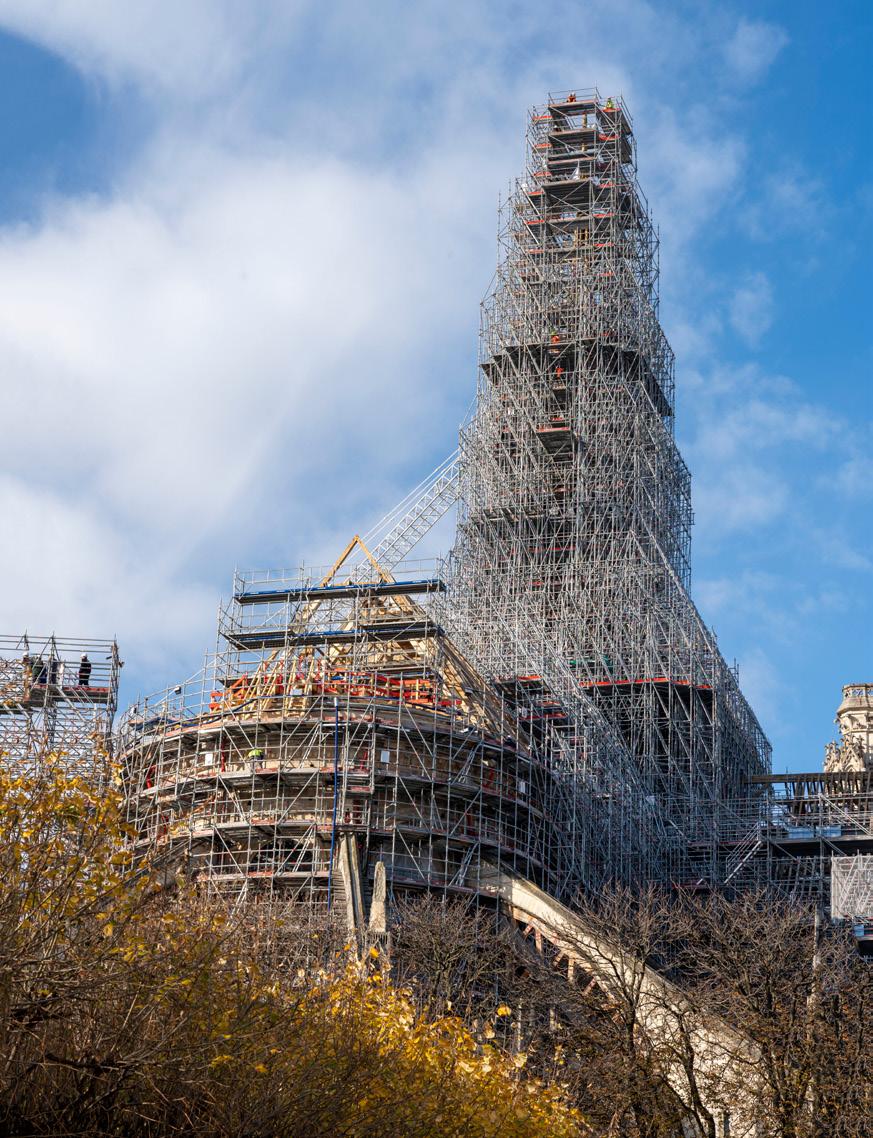
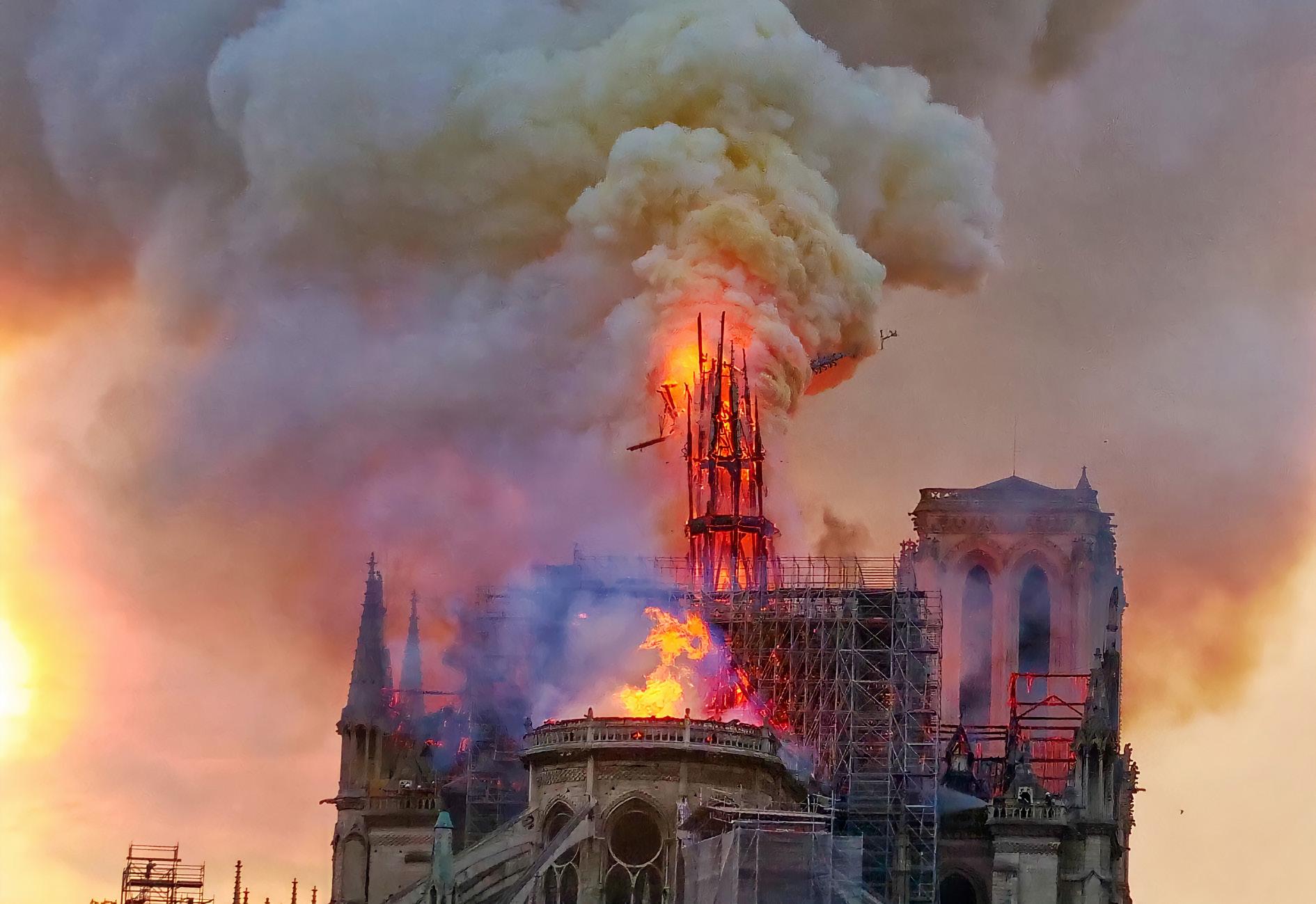

A SYMBOL OF UNITY AND HOPE
Te scafolding around Notre-Dame, while primarily functional, symbolises much more. It represents the unity and collective efort of people from across the globe who have contributed to the restoration, be it through donations, expertise or moral support. Europe Échafaudage, in undertaking this monumental task, has woven itself into the fabric of Notre-Dame’s ongoing story of resilience and renewal.
LOOKING TO THE FUTURE
As the scafolding stands tall against the Parisian skyline, it serves as a poignant reminder of the tragedy that occurred at Notre-Dame. Yet, more powerfully, it signifes the unwavering spirit of humanity to restore, preserve and protect our cultural heritage. Te work of Europe Échafaudage is a critical chapter in the story of Notre-Dame’s restoration, a narrative of overcoming adversity that will be told for generations to come.
In a recent visit that underscored the national signifcance of the project, President Emmanuel Macron toured the construction site, afrming the progress and reiterating his promise that Notre-Dame will reopen its doors to the public on December 8, 2024. Tis date is symbolically charged, marking fve years and seven months afer the tragedy that seemed to pause the heartbeat of France.
“Te work is on schedule,” declared President Macron, a sentiment that resonates with the dedication and passion of those working behind the scenes. Tis assertion brings
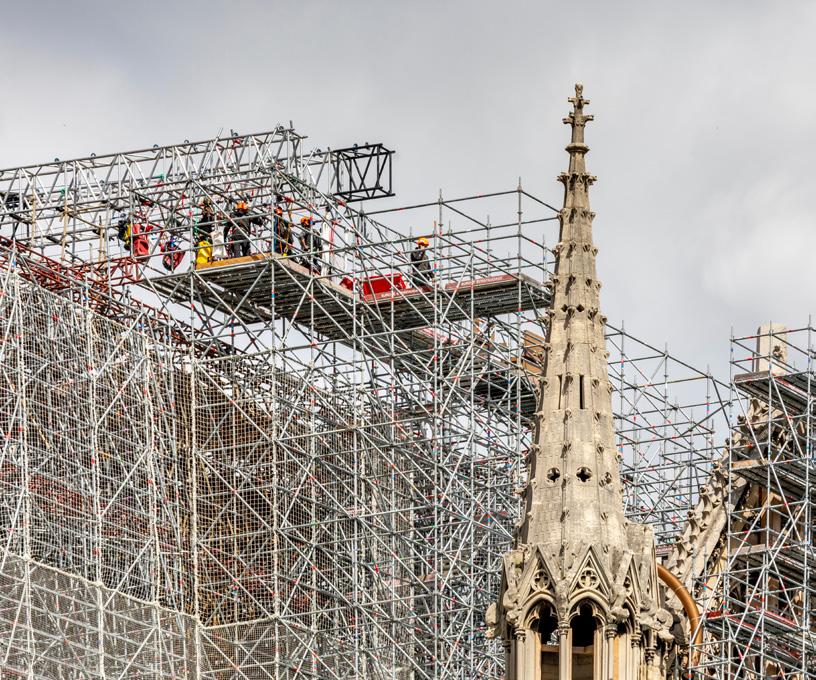
PRESIDENT EMMANUEL MACRON TOURED THE CONSTRUCTION SITE, AFFIRMING THE PROGRESS AND REITERATING HIS PROMISE THAT NOTRE-DAME WILL REOPEN ITS DOORS TO THE PUBLIC ON DECEMBER 8, 2024
hope to millions who are eagerly awaiting the moment Notre-Dame will reclaim its place as a beacon of cultural and spiritual magnifcence.
As Europe Échafaudage continues to scafold the dreams of a restored Notre-Dame, their work is a testament to the power of collaboration in the face of challenges. Once restored, the cathedral will stand as a beacon of resilience, a monument not just to its history but to the collective will to preserve and protect our shared heritage for the future.
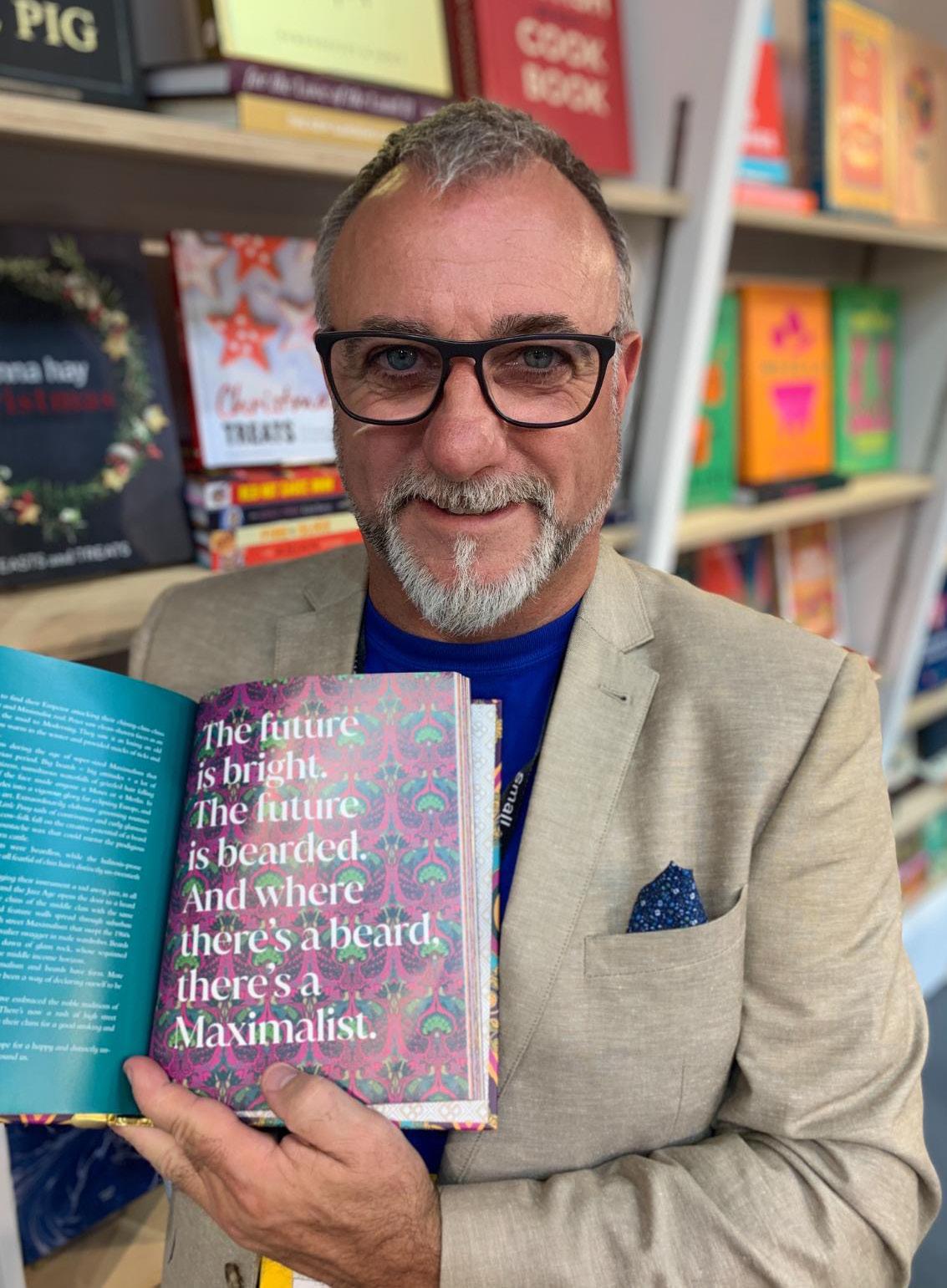
In the competitive and ever-evolving scafolding industry, Mark Parkin stands out, not just for his remarkable career achievements, but for his profound impact on the profession and those within
it
True leader, innovator & inspirator
At 52 years old, Mark has navigated a path that many would fnd daunting, transforming each obstacle into a stepping stone towards greater success. His story is more than a tale of personal triumph; it’s a blueprint for resilience, innovation and mentorship that has the power to inspire generations.
FROM WHITBY TO INDUSTRY INNOVATOR
Born and raised in the scenic town of Whitby, North Yorkshire, Mark’s early life was dramatically shaped by adversity. A severe hit-and-run accident at just fve years old lef him in a coma, challenging his physical capabilities from the onset.
“Te accident and its afermath were my frst teachers,” Mark shared. “Tey instilled in me a sense of resilience that has been my guiding principle. It’s about not just facing adversity but embracing it as a part of your growth.” Tis philosophy of embracing challenges head-on has been a constant in Mark’s life and career, driving him to achieve remarkable success in an industry as demanding as scafolding.
His entry into the scafolding world was somewhat fortunate, guided by his father’s insistence on the importance of hard work and responsibility. What began as a reluctant journey into an unknown feld soon blossomed into a passionate career.
Mark’s rapid ascent from a novice to an advanced, highly skilled scafolder and eventually to a successful business owner is a testament to his work ethic, determination and innate ability to see potential where others might see obstacles.
FACING AND OVERCOMING CHALLENGES
Mark’s journey was not without its trials. From navigating the complexities of business management to facing personal bankruptcy and the demise of Tiger Scafolding, he encountered numerous setbacks. Yet, Mark has viewed each challenge as an opportunity for growth.
“Each setback has been a lesson in disguise,” he explained. “Facing bankruptcy was one of my life’s most challenging phases, but it taught me the value of resilience, the importance of surrounding yourself with positive infuences, and the power of starting anew.”
His approach to overcoming adversity – focusing on positive infuences, learning from mistakes and always moving forward – has not only shaped his career trajectory but also serves as a powerful model of resilience for others in the industry to follow.
Mark’s experiences have taught him invaluable
lessons about the signifcance of surrounding oneself with the right people. From mentors and family to friends and professional acquaintances, Mark credits his network of support for providing the strength and inspiration needed to navigate life’s challenges.
INNOVATION AND LEGACY
Mark’s contributions to the scafolding industry go beyond his personal achievements. His development of Klawz, a scafolding ftting that represents a leap forward in efciency and safety, showcases his commitment to innovation. Klawz is more than just a product; it’s a refection of Mark’s vision for an industry that prioritises not only productivity but also environmental sustainability and worker safety.
His dedication to pushing the boundaries of what’s possible in scafolding extends beyond product innovation. Mark’s involvement with ScafChamp, an international scafolding competition, underscores his commitment to promoting excellence and innovation within the industry.
“Being asked to serve as the Ambassador for ScafChamp 24 in Lithuania was an honour and a profound responsibility. It’s not just about the competition; it’s about bringing the scafolding community together, celebrating our achievements and setting new standards of excellence,” Mark explains. Tis role allows him to engage directly with the scafolding community, showcasing the importance of skill, safety and innovation, further solidifying his impact on the industry.
As he looks to the future, Mark’s goals extend well beyond the confnes of the scafolding industry. His dedication to environmental conservation, evidenced by the restoration of a 16th-century farmhouse and the planting of 2,700 trees, underscores his commitment to leaving a positive mark on the world.
MENTORSHIP AND FUTURE OUTLOOK
Perhaps the most signifcant aspect of Mark Parkin’s legacy is his new role as a mentor and consultant. Trough his work, he aims to share the lessons learned from his own experiences, guiding companies and individuals towards success.
“Mentorship is about lighting the way for others. It’s incredibly rewarding to see individuals and companies grow and succeed with a little guidance,” he refects. Mark’s approach to mentorship, which emphasises the importance of stability, optimisation and maximisation, refects his belief in the fundamental principles of business and personal success.
As he looks forward, Mark is excited about the potential for continued innovation within the scafolding industry. He remains committed to inspiring the next generation of industry professionals, fostering a culture of continuous learning, and exploring new opportunities for growth and development.
A VISIONARY LEADER
Mark’s journey from a small town in Yorkshire to becoming a recognised leader in the scafolding industry is a narrative of overcoming adversity, embracing innovation and committing to mentorship. Mark shares, “My journey has been about more than just building structures; it’s about building resilience, fostering innovation and creating a community. As we look to the future, I’m committed to continuing this work, inspiring others, and leaving a positive legacy in the scafolding industry and beyond.”
Mark Parkin’s story is a compelling testament to the power of resilience, the importance of community and the endless possibilities that arise from pursuing one’s passions. As he continues to help shape the future of scafolding and beyond, his legacy serves as an enduring source of inspiration for all who seek to make a meaningful impact in their professional and personal lives.
BEING ASKED TO SERVE AS THE AMBASSADOR FOR THE SCAFFCHAMP 24 EVENT IN LITHUANIA WAS AN HONOUR AND A PROFOUND RESPONSIBILITY
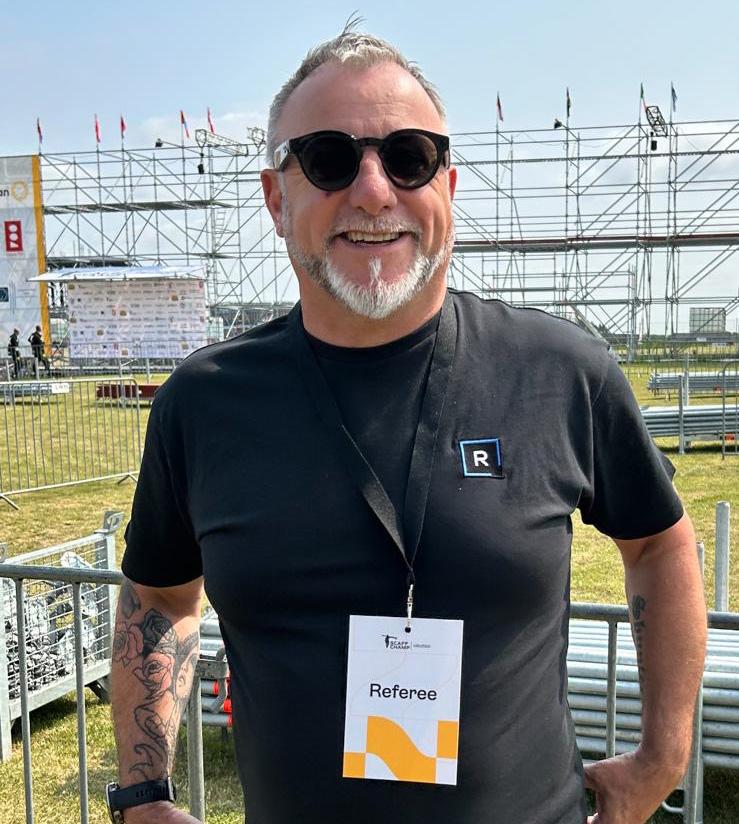
EASIER. SAFER. SMARTER.
EASIER. SAFER. SMARTER.
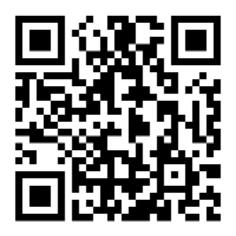
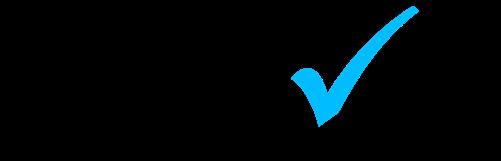
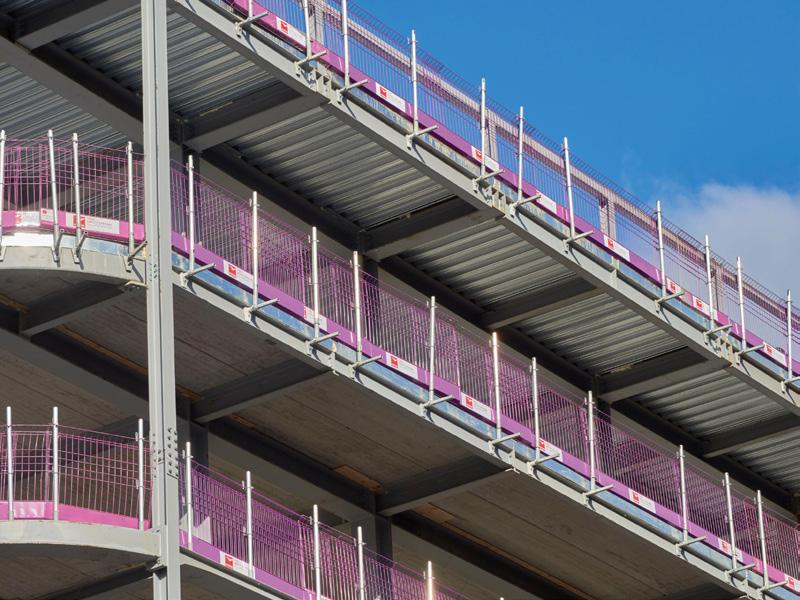
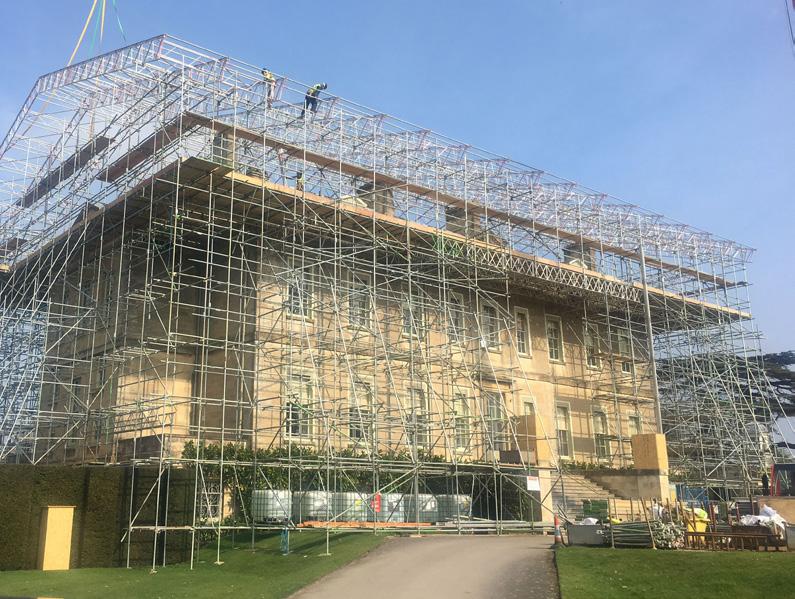
EXPERTS IN FALL FROM HEIGHT SAFETY SOLUTIONS AND SCAFFOLDING SUPPLY.
An industry-leading provider of solutions. We specialise in crafting bespoke roof access, safety, and fall prevention equipment, as well as cutting-edge roof and leadingedge protection products.
Finance options available through our business partner:
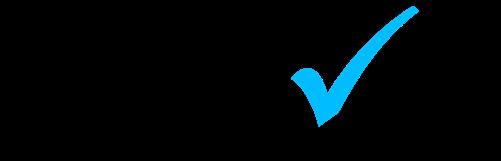
construction safety solutions. We specialise in crafting bespoke roof access, safety, and fall prevention equipment, as well as cutting-edge roof and leading-edge protection products.
0345 899 0845
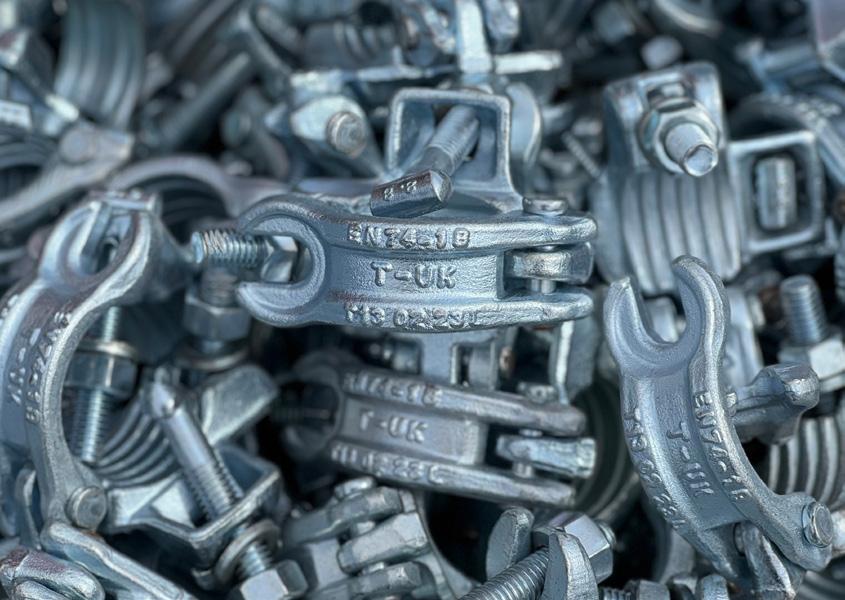
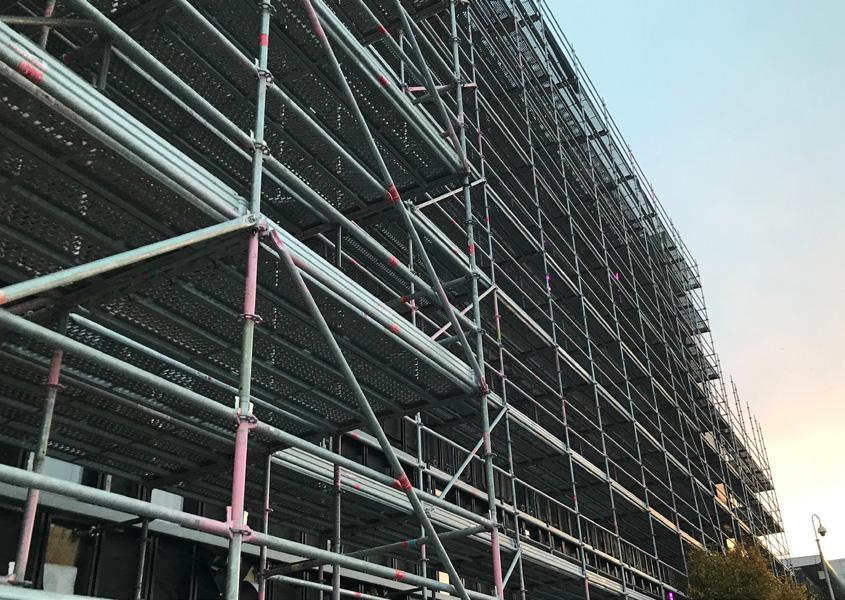
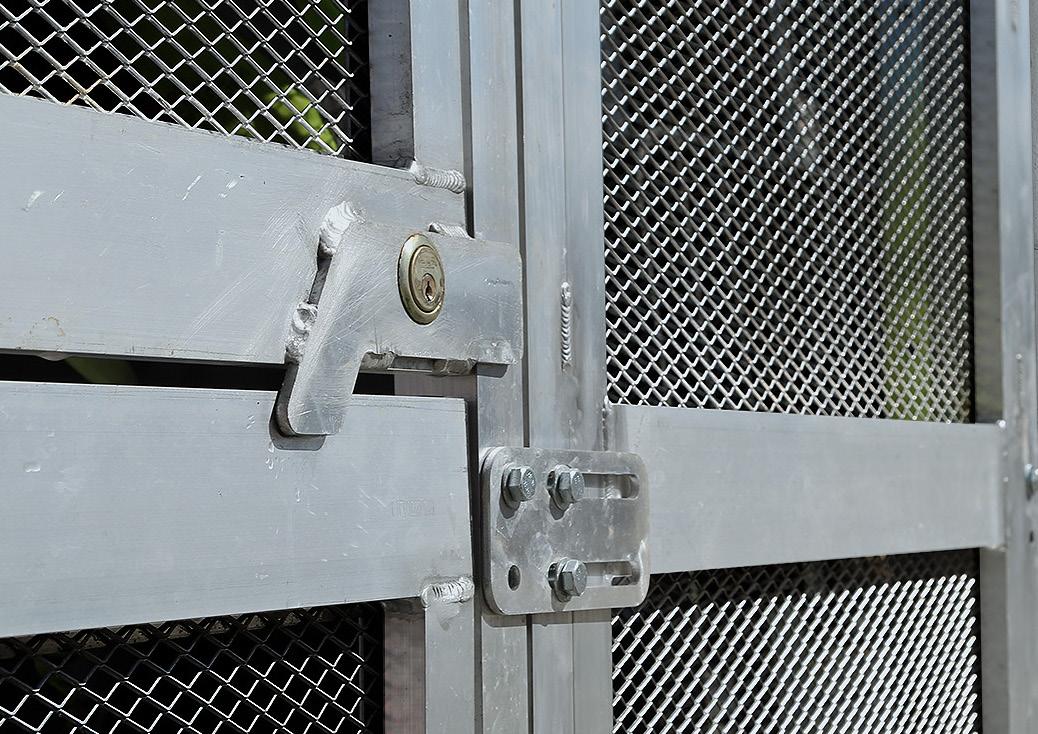
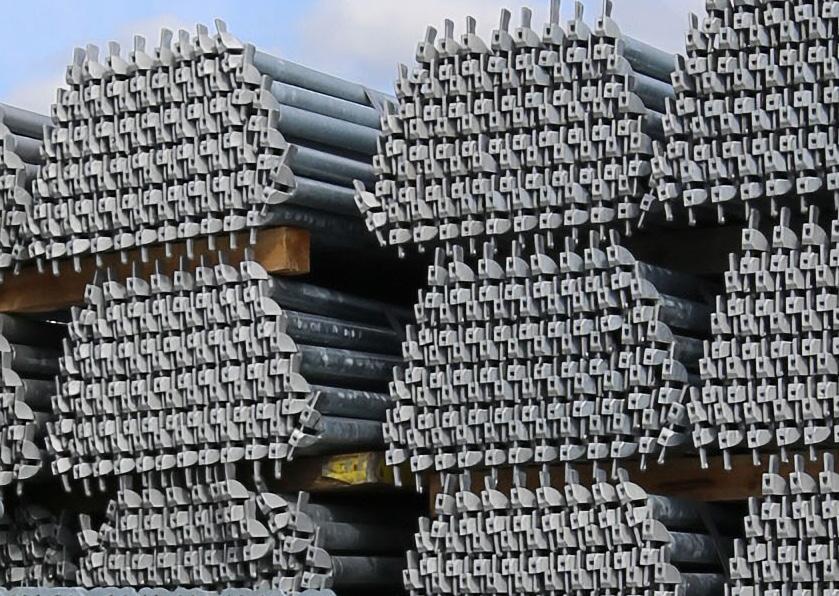


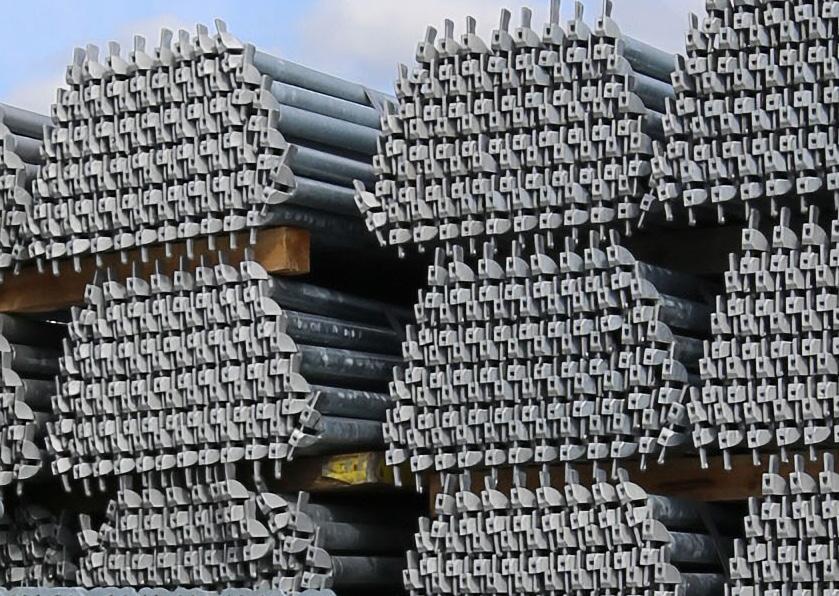


TRAD UK HIRE & SALE SCAFFOLDING & SAFETY SYSTEMS
our innovative range and our dedication to highest levels of service, delivered by our experienced team and nationwide support network of depots, we make it easier than ever to
TRAD Safety Deck
ALTRIX Roof System
Catch Fan
PLETTAC METRIX
Lift Shaft Gate
Fabrication
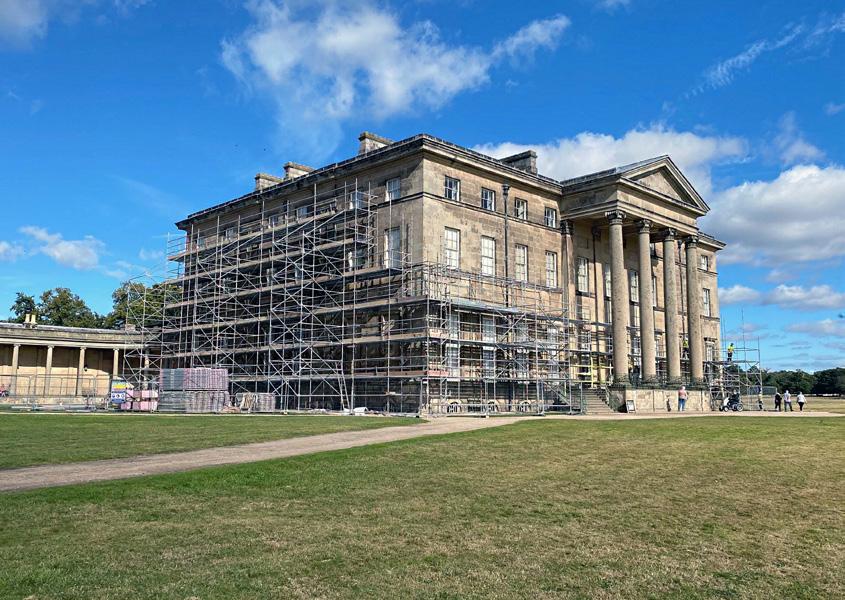
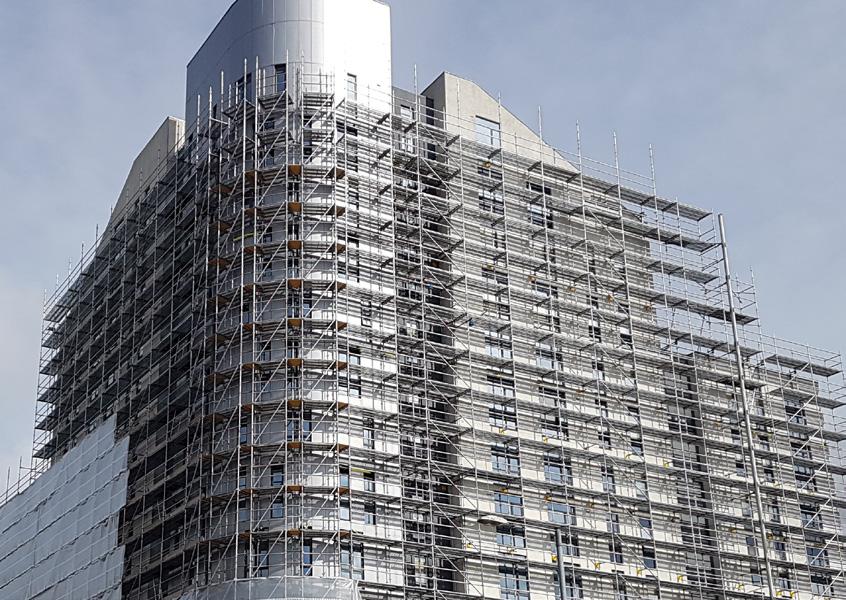
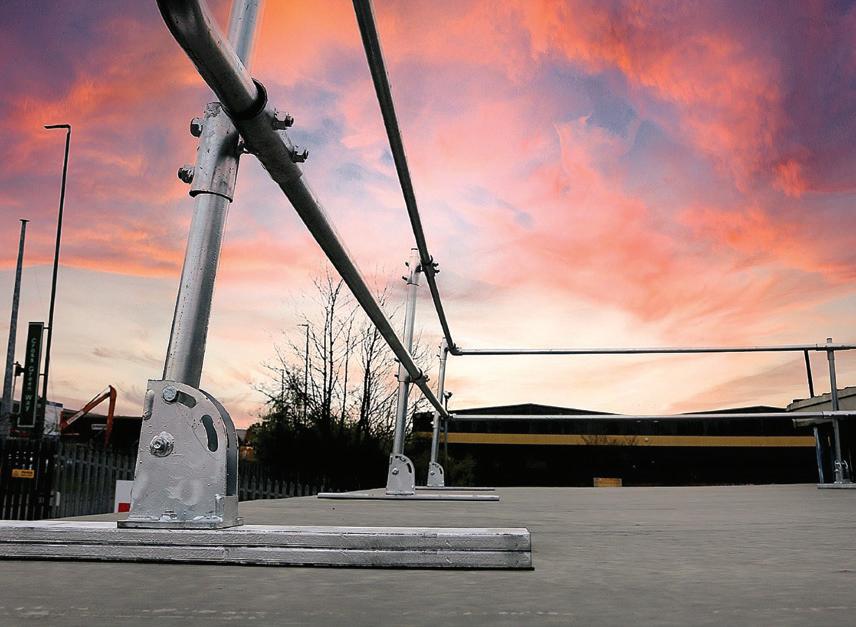
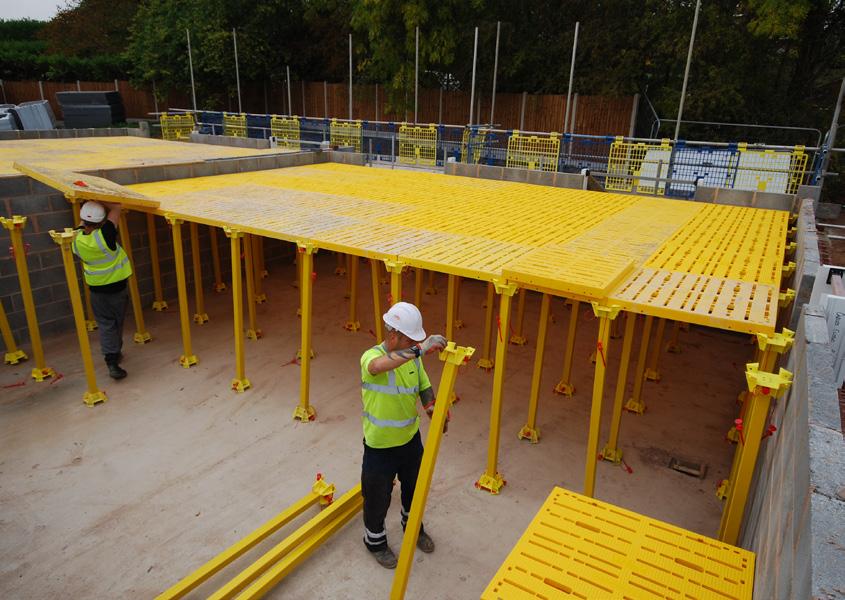
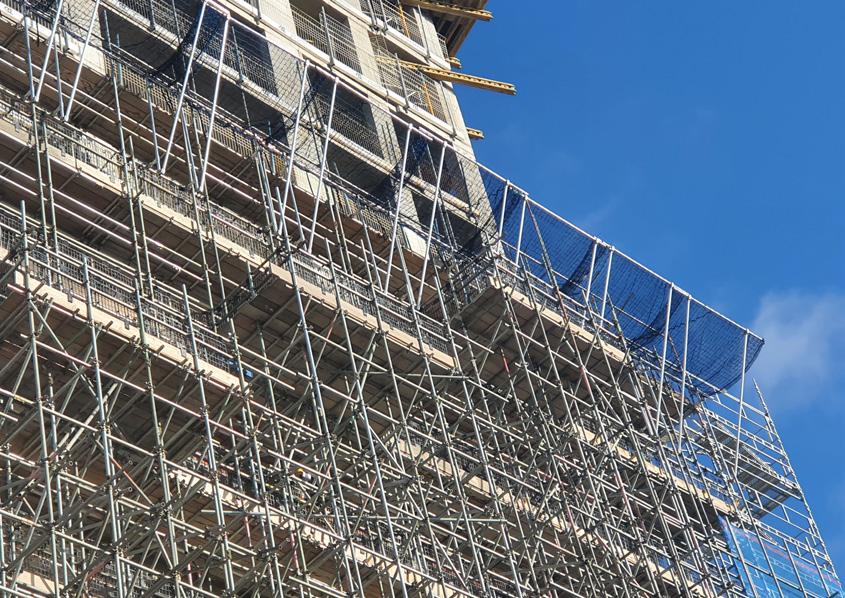

Mini Catch Fan
TRADLOK
TRADGUARD


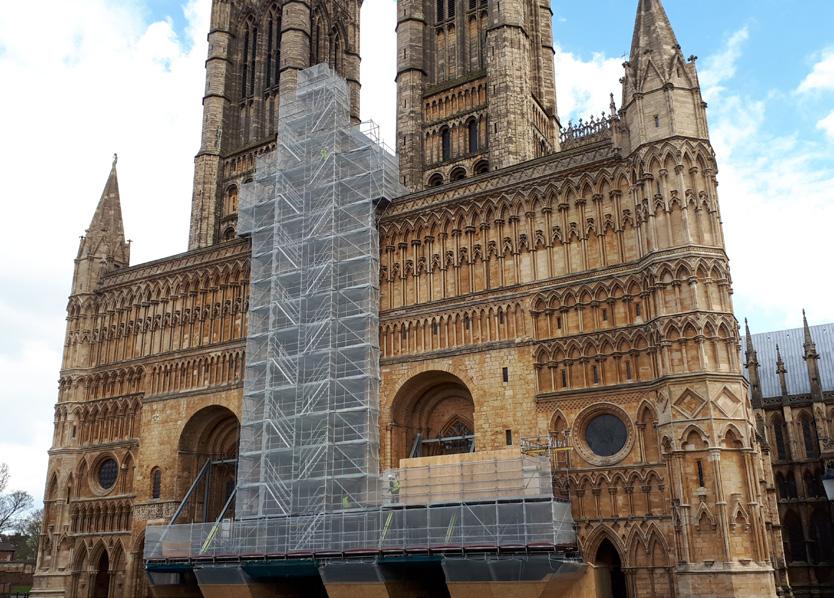
BROTHERS IN ARMS
Celebrating three decades of architectural mastery and steadfast growth, GKR Scafolding stands as a beacon of excellence in the construction industry. Founded on the principles of safety, innovation and unwavering dedication, this London-based frm has etched its name on some of the most iconic skylines in the UK
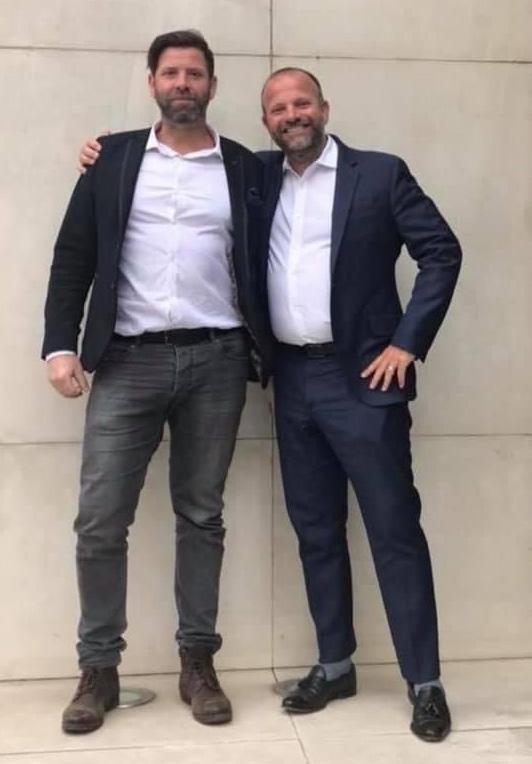
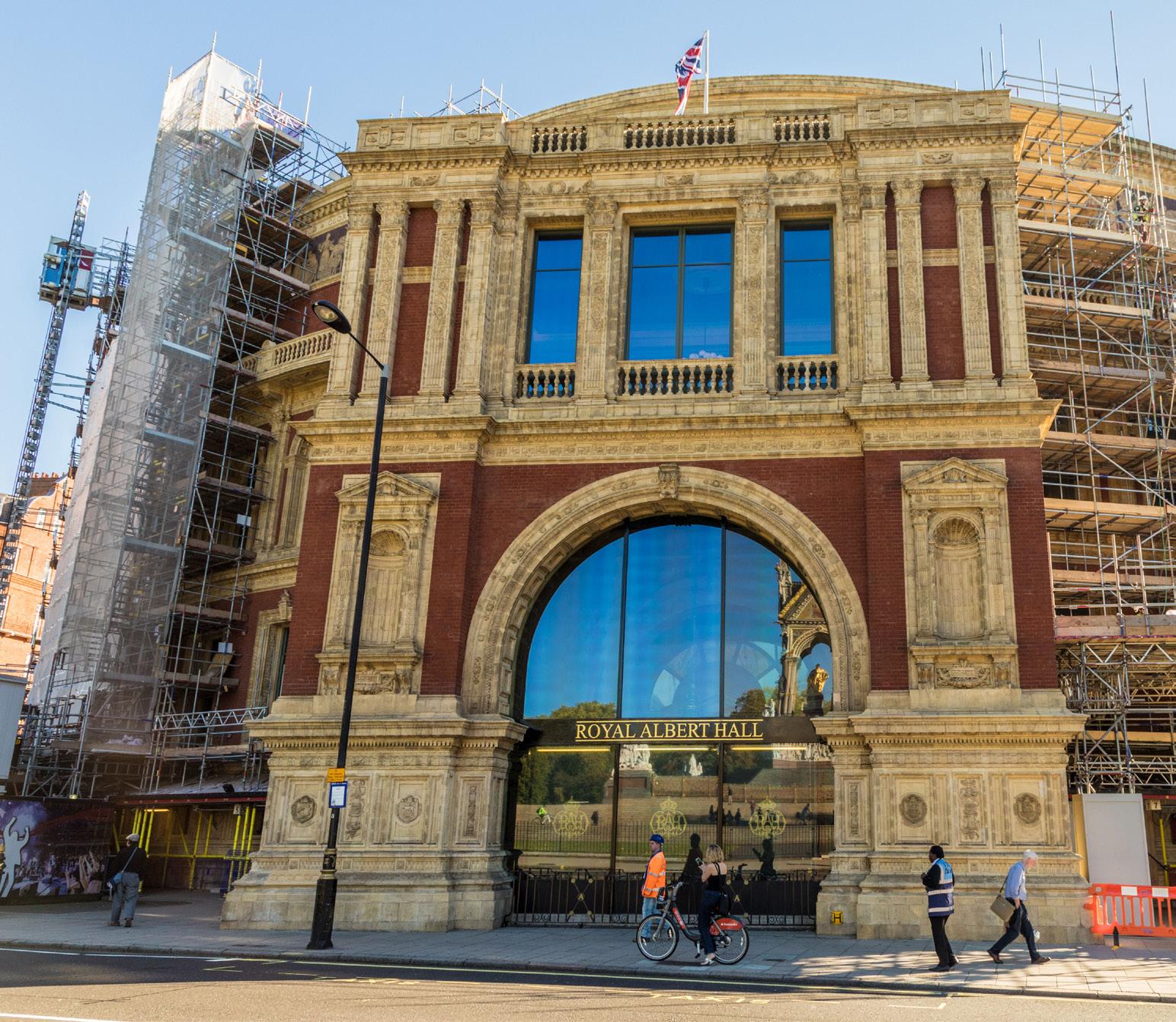
From the soaring heights of Te Shard to the historic contours of the Royal Albert Hall, GKR’s contributions have not only reshaped London’s skyline but have also set new benchmarks in scafolding and structural engineering.
As GKR Scafolding marks its 30th anniversary, we sit down with the visionary minds behind this monumental success, Lee and Neil Rowswell, to refect on the journey that has positioned GKR as a leader in one of the most challenging and dynamic sectors. In an industry where the only constant is change, GKR Scafolding has navigated through economic recessions, material shortages and the unprecedented challenges of Covid-19, emerging stronger with each hurdle. With a portfolio that boasts participation in landmark projects and a trophy cabinet adorned with multiple

business awards, the Rowswell brothers have not just built structures, they have constructed a legacy.
Tis exclusive ScafMag Q&A session delves into the milestones, innovations and relentless pursuit of excellence that defned GKR Scafolding’s 30-year journey, ofering insights into the company’s future directions and continued impact on the construction landscape.
Firstly, thank you for taking the time to speak to us. So, 30 years in business in any sector is a massive achievement, so congratulations! Refecting on those 30 years of GKR Scafolding, what are the key milestones and decisions that have shaped the company’s journey to becoming one of London’s leading scafolding contractors?
Lee: Tank you, Dan, and what a 30 years it has been! I can’t believe we are talking about GKR being 30 years old! Refecting on the past 30 years of GKR, we have achieved so much and have matured as a company. We have been through two recessions, Covid-19, material shortages, Brexit and so much more, and remained strong consistently. Troughout our 30 years, we have built relationships and loyalty with Tier 1 clients, evolved our supply chain, and built an extremely strong and devoted team, which has helped us get to where we are today. Personally, I would say my most iconic project would have been the Shard; it was our frst high-rise project and was the pinnacle in showing what we could do as a company. For my own personal reasons, the Tottenham Hotspur Stadium was another memorable project for me!
Neil: I also think a crucial milestone for
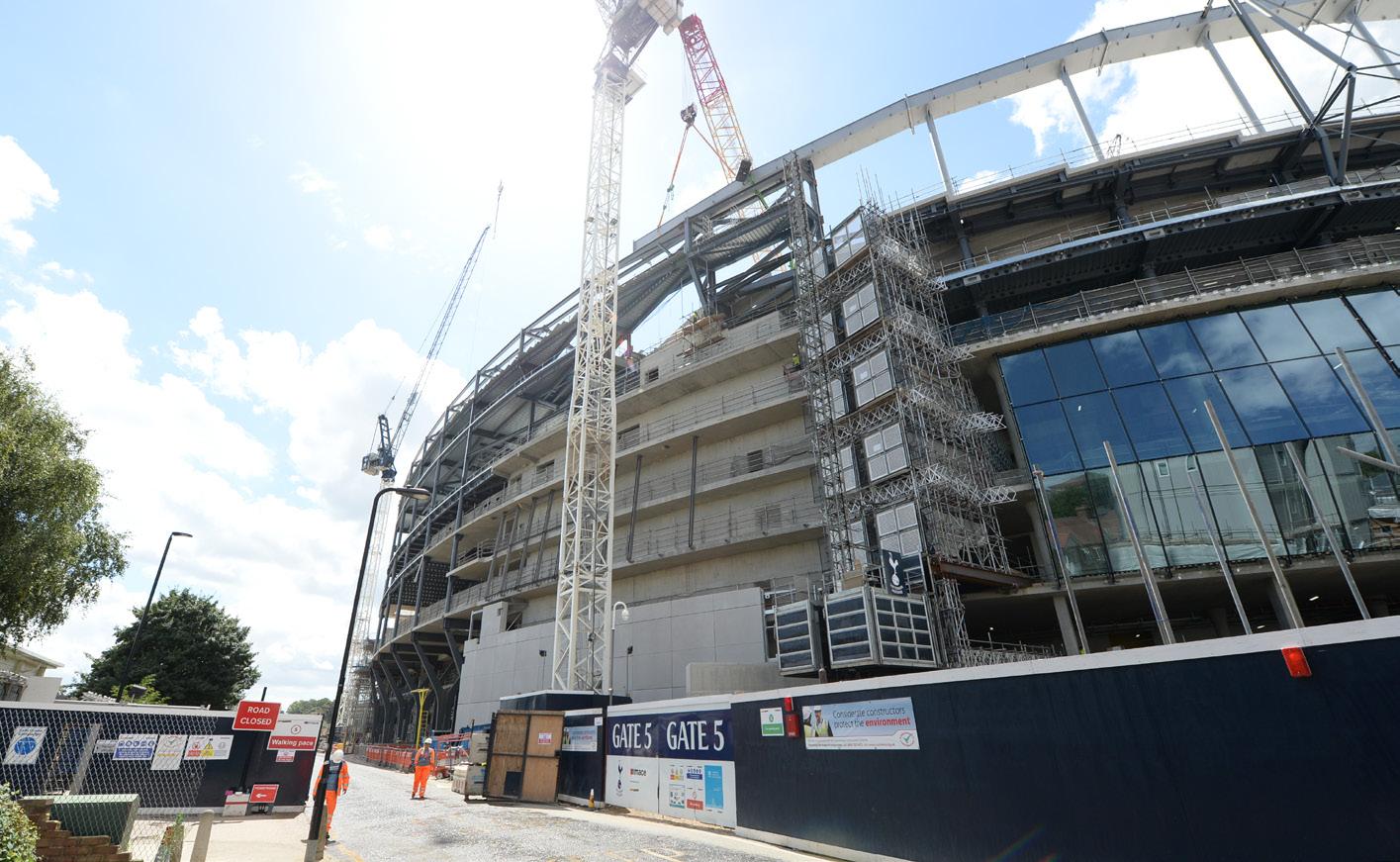
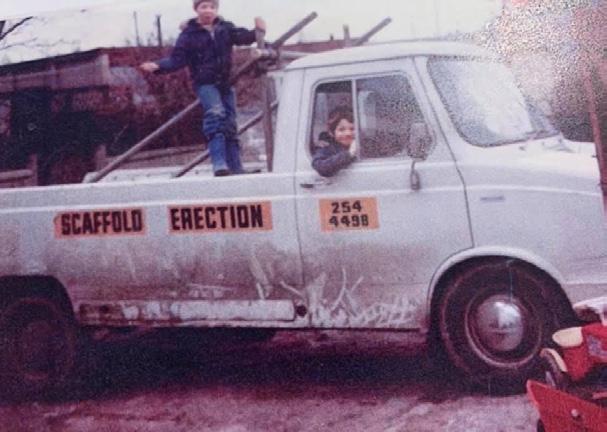
us would have been when we frst purchased our own material, because like most companies starting out, we hired in most of the materials needed for the early projects, which helped to fund our growth through self-funding; it demonstrated that we were able to do it all on our own. I suppose we wanted to prove ourselves in the industry when we were a young business. It was important for us to purchase our own assets and premises to help give the company the security it needed.
Another key milestone for us was when we frst landed a main contractor as a client when we were a young business; they saw the potential in us from the early days, which helped us land biger projects and start showcasing what we were capable of. Our frst million-pound project, Shaw Park Plaza, was a great achievement, being our frst large-scale project working over 15
foors and demonstrating the scale of work that we could undertake.
GKR has been involved in some of London’s most iconic construction projects. Could you share insights into how these opportunities came about and what they meant for the company’s growth and reputation?
Lee: Tese opportunities come from our reputation, relationships and experience. Our operational skill set is second to none, and we can undertake high-profle projects to the highest of standards, which helps to set us apart from our competition. Fundamentally, the relationships we have developed with our clients and the trust we have created have helped us form loyalty and repeat business as we have proven that we can provide them with experience and highperforming teams.
Neil: We thrive on high-risk projects; it’s what helps to motivate us and our teams as we like a challenge. Since working on the Shard, a lot of the team wanted to work on high-risk projects and the challenge that comes with it, motivating us to keep reaching for more. We know that we have the ability and the team behind us to undertake highprofle and high-risk projects from our previous experience and successes. We have developed our own control measures, which have allowed us to take these projects on safely and efciently, such as our Elimin8 tethering system and VR training to ensure that our staf are safe in these high-risk environments. We provide excellent service, and we are still family-run; Lee and I are still contactable with our clients to aid in the smooth running of the business.
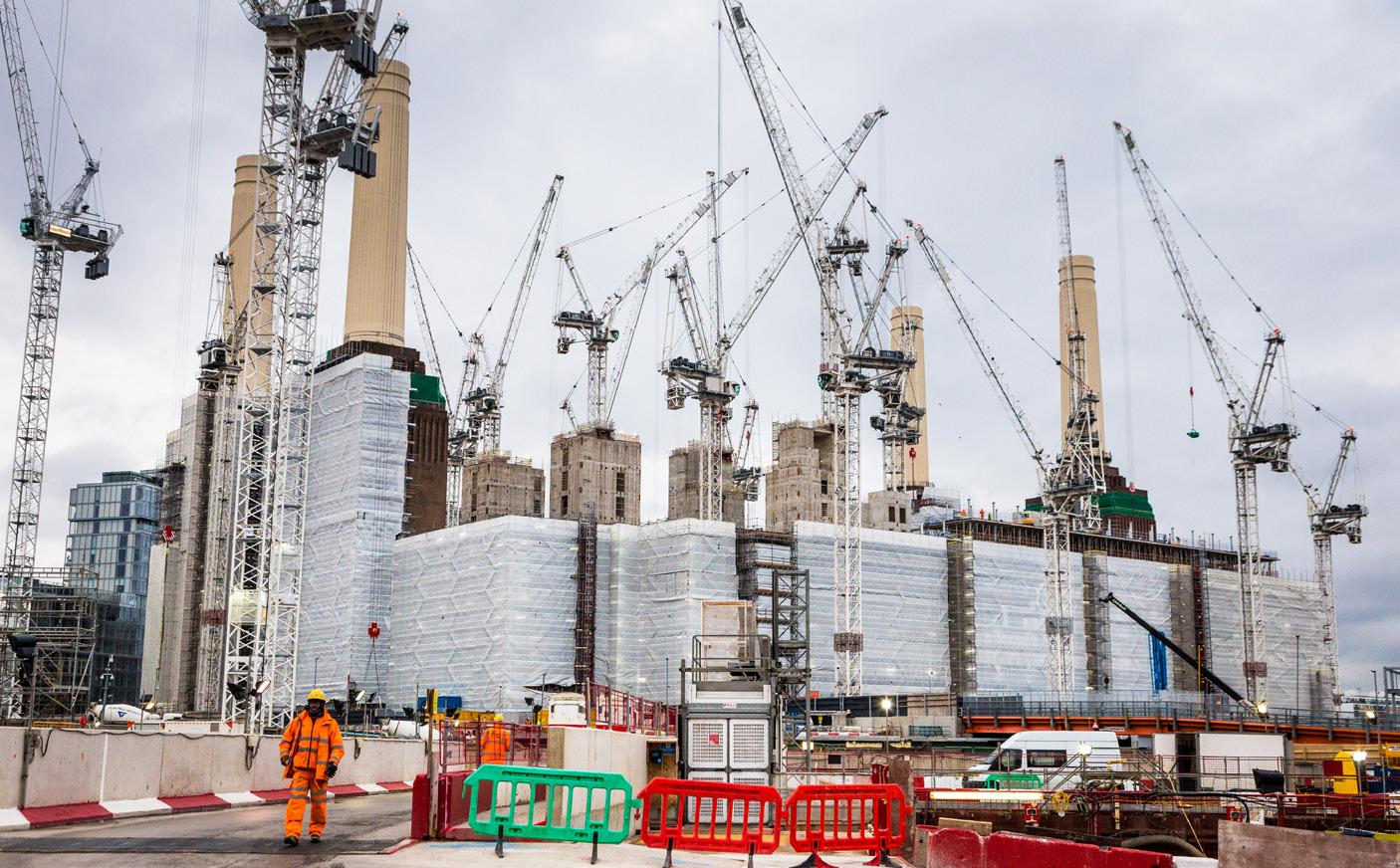
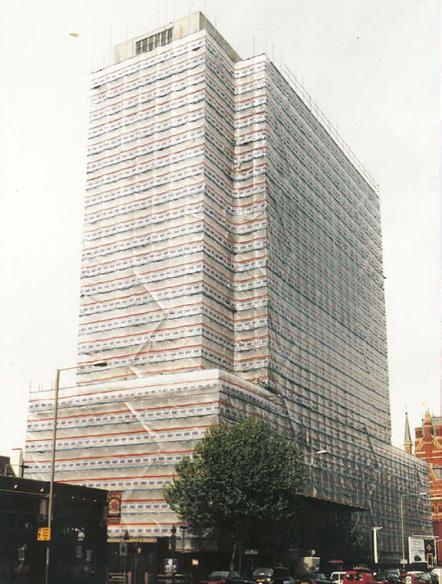
OUR OPERATIONAL SKILL SET IS SECOND TO NONE AND WE CAN UNDERTAKE HIGH-PROFILE PROJECTS TO THE HIGHEST OF STANDARDS
The construction industry is known for its challenges, particularly around safety and innovation. How has GKR maintained its commitment to safety and continued to innovate in such a competitive and high-risk environment?
Lee: At GKR, we maintain our commitment to safety whilst encouraging a culture of innovation. Delivering value through our supply chain in what is increasingly becoming a knowledge-based economy is one of our main aims as a leading scafolding contractor. We have continued to innovate and maintain our commitment to safety whilst posed with some clear challenges.
We hold internal pre-start project meetings, ensuring we select the right personnel to deliver our projects and that they have the correct resources and knowledge prior to commencing with works from commercial design to key health and safety risks. Tis is coupled with our internal health and safety project audits, where supervisors are measured against a number of health and safety compliance areas, ensuring that a level of competition is brought amongst our projects through a scoring league table to maintain project ownership and commitment to maintaining high performance.
Research also shows that highperforming teams are more likely to feel more psychologically safe. We run an internal audit system for all our projects, continually measuring our performance for consistency across projects and aspiring to achieve high-performing teams on all projects through our scoring matrix against diferent areas of health and safety. Tis is also recognised annually through internal company health and safety awards. We have recently implemented task video analysis, comparing the methodology of works and safety in diferent environments, gathering whether there is a change in risk perception and what additional protocols we can put in place where necessary. We are mission-focused on being ahead of the curve where innovation and safety are concerned, which is essential to
maintaining our position at the forefront of the scafolding industry.
Ultimately, we at GKR encourage our industry partners to invest themselves in innovative solutions to combat the challenges we all face. Te labour shortage has been exacerbated by the 46,000 workers that Te Centre for European Reform estimates we’ve lost through the end of the free movement of labour. We need policies that prioritise a long-term strategy with investment in apprenticeships and training. Adopting a performance mindset to safety whilst continuing to innovate our processes has enabled GKR to meet head-on some of the challenges we are all facing as a collective.
Leadership and training are evidently core to your company’s success. Can you discuss your approach to developing high-performing teams and the impact of your award-winning VR training programmes?
Neil: We start by recruiting and employing the right people; those who demonstrate our high standards and value consistently. Te GKR Leadership Team has analysed what drives highperformance teams, and we have outlined two main themes: continuous improvement and psychological safety.
Our people are our bigest asset, and it is important that we invest in them to create a strong team. We have multiple ways in which we help to develop highperforming teams. We relaunched our internal GKR Academy, which adopts neuro-inclusive training. Our academy helps to provide our project managers and supervisors with the relevant leadership and management tools that they cannot access with the current standard industryrecognised training. We also equip our teams with any other additional and essential training and tools that are transferable to deliver our projects.
Te National Federation of Builders has discovered that neurodiversity is not only common amongst construction workers, but being neurodiverse is actually encouraging people to pursue a career in construction. We at GKR Scafolding believe that a diverse team
that includes neurodiverse individuals can ofer unique perspectives, problemsolving abilities and attention to detail, which can lead to improved safety practices and reduced accidents on the job site. With one in four construction workers identifying as neurodiverse, we ensure that we adapt to these diferent learning styles where possible to increase performance amongst our workforce.
At GKR, training is conducted via simulated learning experiences related to management theory and practice. In addition, we have an industry-leading apprenticeship programme, actively supporting trainee scafolders with personal development plans that develop skills outside technical training. Tis is supplemented with our bespoke training plans that we also deliver to our project supervisors.
We’ve become leaner by becoming more digital, helping to optimise our operations and minimising wastage of time and resources. Virtual reality has been a fantastic risk aversion tool for recreating real-life scenarios without causing potential harm. We put our people in an environment where they can positively intervene to prevent a person from being harmed, but they do get to experience what would have happened if they had not intervened. Tey then get the option to decide if they should report the near miss or incident. Our discussions with our team afer the VR experience are extremely powerful as we focus on the importance of not walking by an unsafe act, reporting incidents and understanding why high-performing teams record more incidents than lowperforming teams. Te impact of VR is that we are now recording more near-miss incidents than ever because our highperforming teams understand the importance of incident reporting. We can then learn, and share those learnings and implement corrective measures to prevent a reoccurrence.
Tis contributes to our aim to be a learning organisation where we actively measure and encourage feedback to improve what we do. Continuous improvement is embedded in our
culture, and its process is applied to everything we do, from planning and implementation to measuring the impact and using the results to learn and improve.
GKR has achieved carbon-neutral status and has a strategic roadmap to reach net zero carbon. What inspired this ambitious sustainability goal, and what challenges and opportunities have you encountered along the way?
Neil: Te inspiration to achieve a carbonneutral status came naturally from recent data and the efects climate change has had on our planet, such as extreme weather and rising sea levels. We are in a strong position as a leading subcontractor to set an example to others that good progress can be made in a short time with the proper assistance, encouragement, education and motivation. We have also measured all three scopes and have published our net zero targets on the SBTI website; as well as pledging to net zero, we continue to measure all three scopes manually. With very little ofset under Scopes 1&2 to become carbon neutral, we are still strugling to fnd a zerosubmission solution with our feet. As technology evolves, we hope that there will be more opportunities for this within the next fve years. Until these advancements arise, we will continue to keep our feet fuelled with HVO biofuel. Te challenge for 2024 will be carbon onboarding our supply chain to think with the same carbon mindset that we at GKR have adopted. We are still setting out a plan to tackle this with support from our partners at Equans; without the supply chain onboard, net zero is impossible, which creates a challenge for us.
In a rapidly evolving industry, technology plays a crucial role. How has GKR integrated new technologies into its operations, and what benefts have you observed, both on-site and in management processes?
Neil: We have recently digitalised every element of our health and safety operation through the SafetyCulture application, which Premier League and Formula 1 teams also use. Our supervisors are now
profcient with conducting audits, inspections and checklists online, allowing immediate data capture and communication for the Health and Safety Team. Te predictive capabilities of new technology coupled with the large amount of data now available through the ‘Internet of Tings’ has helped transform our business from a safety point of view.
The company prides itself on a unique approach to service quality. Can you elaborate on the pillars of this approach and how they contribute to the exceptional service GKR is known for?
Neil: Lee and I obviously both started on the tools. From a young age, we were both motivated to create the best possible standard of service and quality for our clients and for the industry. I believe we have maintained this throughout the past 30 years, and we have been able to engrain this mindset into all our staf at present. It can be a hard industry to be involved in, but I like to think we do it diferently and provide our staf with the best people, training, safety and culture. We set a standard that is measured against our KPIs in terms of health and safety, productivity and more to ensure that we are continuing the standard that Lee and I started with, and maintaining this with our current members or staf and supply chain.
Lee: All scafolding frms use the same products, tube-and-ftting or system; what sets you apart is your team, your delivery and your relationships, which I believe we have built to an exceptional standard, and it helps to set us apart from our competition. Our quality of service is not down to specifc individuals; it’s because of the teams we have built. One of my favourite quotes is, “You are only as good as your weakest link”; therefore, we ensure that we nurture and grow our teams to a high standard.
GKR Scafolding has been honoured with multiple business awards throughout its history, showcasing its excellence in the scafolding and construction industry. Can you share what these awards mean to the company?
Neil: Winning awards is always a proud moment for us; it helps us get recognised for our service and shows that we are doing it right. We are up against great competition, so it is nice to know we stand out against others in our industry. We push boundaries within our sector and want to show that the industry is a professional and skilled environment to be in, which these awards help to illustrate. Along with our competition, we can showcase that scafolding is a skilled and important trade within the industry that should be recognised for the hard work that goes into it.
How do you foresee the scafolding and construction industry changing in the next decade, and what steps is GKR taking to stay at the forefront of these changes?
Neil: I do see AI becoming a huge advancement within our industry in terms of design, estimating and document writing. I think in the not-so-distant future, we could see AI having the ability to scan a building from Google Earth and produce the dimensions to assist with creating designs; this could then generate load sheets for our yard to calculate required materials and then further help to generate calculations and health and safety documentation. I still believe that this will require some form of human intervention to input parameters and check for accuracy. I think, as an industry, we have somewhat stood still in terms of innovations when it comes to the mechanical side of things in comparison to the demolition works and what they have created.
I do believe that, as an industry, we need to create a more seamless way of accessing materials and can transport scafolding up and down a building safely and easily. I think, as a sector, we have the ability to create some form of lifing kit to help with the transportation of scafolding through a project, which I believe is something that our industry needs. We have lots of new and young scafolders who help give us new and exciting ideas on what we could do diferently in our operations, which we
always acknowledge and see if we can take these ideas on board.
GKR Scafolding remains owneroperated after three decades. How has this infuenced the company’s values, culture and decision-making processes?
Neil: I think this is a massive part of our success. Lee and I are still massively involved in GKR and still undertake critical roles within the business. Our clients know that they can come to us, and we will react positively and get any problems solved. We can respond to situations quickly as there are only a few layers of management to go through; therefore, communication externally and internally is a lot more seamless and efcient in comparison to more giant corporations. We are still investing in GKR constantly, and we are still looking at what we can do for the future of the business, like looking at new premises to keep up with expansion and our apprenticeship schemes. I think keeping the “family run” morals and culture has been benefcial for our employees as it helps to create a physically and mentally safe environment for everyone; they are comfortable talking to us and feel more like a member of the team rather than just an employee. We have seen the third generation start to make their way into the business, which is exciting, and we hope to see the longevity of the “familyrun” business continue.
Lee: As much as we are a family-run business, our success comes from the teams we have built; everyone we have ever employed has played an important role and contributed to our growth. Our clients like the business model of owner-operated businesses as I believe it helps to form stronger and more loyal relationships.
Lastly, looking forward, what are the long-term goals for GKR Scafolding, and how do you plan to continue contributing to the London skyline and the broader construction industry?
Neil: Well, Lee and I are not planning on going anywhere anytime soon. We are still
committed to GKR and the scafolding industry; we want to see us excel in the industry for many more years to come. We have a great team behind us who can achieve anything they get tasked with to a high standard. We are committed to our operatives; we want to continue to give them the best support, the best training and the best team to help them become the best that they can be. We want to nurture the next generation to help form a strong team for the future of the scafolding industry, which is why we have focused on apprenticeships in recent years. I would like to invest in more stock and innovations to see what we can achieve as a scafolding contractor. As an industry, we have a very tarnished ‘look’ about us, and it’s very stereotypical, which I would like to see change. I worked on the tools for 18 years, and I know from experience that it is a very highly skilled profession.
I would like to see this showcased and have these stereotypes of scafolding change to show what a great industry it is to work in.
WE WANT TO NURTURE THE NEXT GENERATION TO HELP FORM A STRONG TEAM FOR THE FUTURE OF THE SCAFFOLDING INDUSTRY
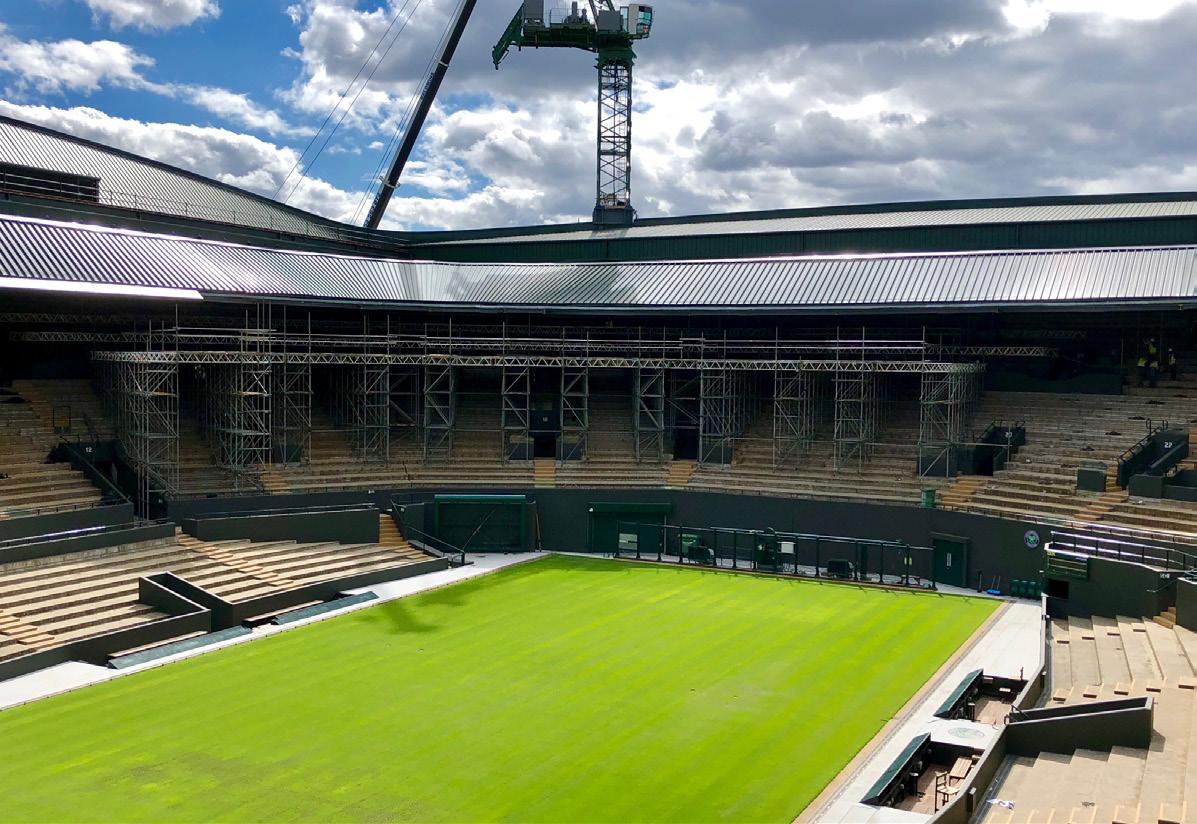
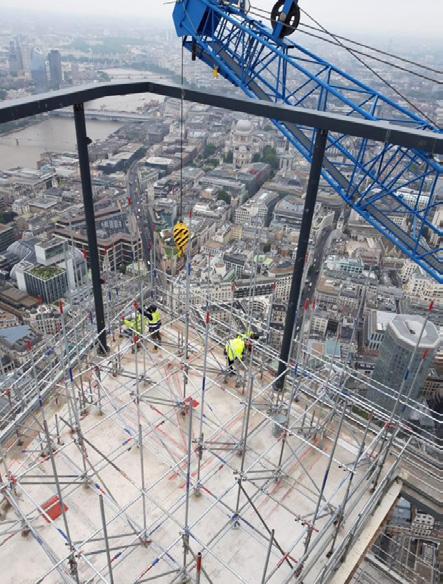
Managing your business postacquisition
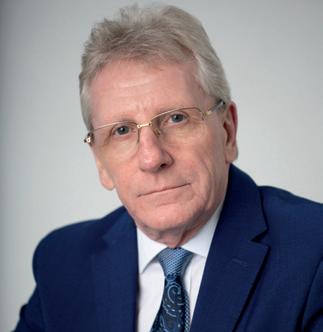
ADes Moore looks at how to manage the challenges of becoming part of a bigger group – and how to make sure your acquisition is a success
few months ago, I wrote an article for ScafMag about preparing your business for sale. But the challenges don’t stop once you’ve sold your business – in fact, they’ve only just begun.
Tere are a number of new things to consider as you become part of a big group of companies or just start working for a new owner.
So how do you manage, both commercially and culturally, to adapt to your new ownership and make the deal a success?
Read any article about acquisitions; you’ll see that around 50–90% of mergers and acquisitions fail. Tere are three common reasons for failure:
1. Poor strategic focus
2. Poor cultural integration
3. Poor delivery of synergies
Let’s remind ourselves of your starting point. Most acquired businesses are either independent or family-owned. Te sale of the business is either to allow the owners to exit, or to open up new opportunities for growth.
Afer sale, the business simply becomes another business in the group – and that position requires a completely diferent mindset and approach from what you might be used to. Essentially, all large commercial groups are the same – they have the same goals and outcomes. Tink of them like a mannequin – all the same underneath, but just clothed in a diferent way.
As you get to this point, it’s worth reminding yourself why
you sold the business. I think there are seven clear commercial reasons to take this step – and the top three of these are usually the most important:
• Access to exit capital for new ventures or retirement
• Access to capital for business growth
• Access to new clients
• Access to new horizontal or vertical markets
• Access to broader product range or innovation expertise
• Access to experienced leadership team with wider commercial knowledge and experience
• Access to other group companies for knowledge sharing
Any type of sale or acquisition exercise will create change. How you manage that change for yourself, your leadership team and your employees is critical to long-term success.
PREPARING FOR THE CHALLENGE
Although I have run several businesses, I have never been a majority shareholder. However, before the sale of TRAD to Altrad, I had complete autonomy to run the companies as I thought ft. Tis was, and still is, highly unusual in our industry. Hayden Smith operated on an arm’s length basis, so I ran the business the way I wanted to – making decisions on everything from stafng and salaries to equipment and markets without any restrictions or approval processes. Although clearly, as a majority shareholder, Hayden wouldn’t hesitate to tell me if I overstepped the mark!
Change doesn’t always suit the senior team. And this was certainly a challenge I faced, knowing that one of my management abilities was to be able to instantly implement new ideas, opportunities or ways of working. It’s easy to feel, in those circumstances, that your essential value and potential productivity is being eroded. In fact, in my own personal journey through acquisition, I certainly felt this way. But it is important to remember that you are now working from a group perspective and not on your own.
So, the frst thing to be ready for afer acquisition is that you are no longer in complete charge. In fact, you move from being an owner or MD to being an employee of the new group. You may be in the same named role as before – but this is an important change to manage, nevertheless.
Also be prepared to lose your visibility over the ‘biger picture’. As a business owner or MD, you are used to having complete visibility and control over your business. As part of a larger group, you ofen have limited access to the decisions being made or the reasons for those decisions. You will have to come to terms with this, and be honest with your teams about it.
You and your senior leadership team will now have to work within strict fnancial rules and restrictions that you have not been used to, and you will have to adapt to these quickly and with a positive attitude.
UNDERSTANDING THE PROCESS
Your new group is likely to put a transition period in place to help everyone adjust to their new position. When I was involved in the acquisition of TRAD by Altrad, I found the new owners operated with honesty and acted with integrity, and this is reliant on mutual respect and trust, which is important. Tere were certainly times when messages may have been confusing, because I didn’t have the same visibility of the workings of the larger group as I was used to, but again, you have to adapt, and take a positive approach.
Don’t underestimate the challenge of replacing the spontaneous way you may have made decisions in the past with working under a new corporate framework – you will now be reporting to someone, and your decisions will require justifcation and approval before you can go ahead. Tis can, at times, be a long, laborious and frustrating process, which may lead to missed opportunities, so make sure you understand these processes and how best to use them to run your business smoothly and meet your targets.
Tere will also be changes to the way you handle fnancial planning and commitments, and you should be ready for these. Being part of a group comes with strict regulations and overviews – which are there for a reason. It may seem onerous, but they are essential for a larger group to run smoothly. Tey have to be commercially practical and clinical – and so do you. You’re likely to see an immediate focus on EBITDA and free cash fow (FCF). Groups are all about maximising the value of their investment, satisfying shareholders and continuing growth. Everything is commercial frst – and I know that if I were running a large group of companies, this is exactly the focus I would have to apply.
OPEN, HONEST COMMUNICATIONS
You and your employees are facing a journey into a new corporate culture, and your people will look to you to lead them through that journey.
Although new owners ofen try to retain your existing culture for a while, your identity will, over time, naturally change so that you are aligned with the group culture. Tis must be carefully handled so that everyone has as much information and reasoning as possible – this helps you to retain key people and manage a smooth transition to new ways of working.
Be honest with your employees from the start of the acquisition process. Don’t say ‘nothing will change’ because you can’t go through a sale without things changing – many things do. So be open, communicate the potential for change and, as soon as you know what those changes are, make sure you support your people through them.
It is likely that employees will be managed or transferred into the group hierarchy and salary bandings. It’s important to be aware of these changes so that you can communicate them to your staf. You should also feel confdent to challenge those decisions at times – particularly in regard to remuneration –with the new owner where appropriate.
You will probably have to accept that there is almost certainly going to be a focus on overhead reduction. Tis could be people, facilities or suppliers – or across the board. Tink about Twitter, for example. As soon as Elon Musk took over, he dramatically reduced the workforce and refocused the business.
Your sale is unlikely to be so dramatic, but new owners see the potential for proftability, and ofen want to make visible changes and savings that demonstrate they can make the acquisition work. Be realistic about why the sale happened, and how your business can thrive with new ownership.
MEETING EARN-OUT REQUIREMENTS
Part of the sale will rely on an earn-out phase, where the business has to meet agreed targets during the period afer acquisition.
In this phase, the group needs the buy-in of the senior leadership team to help the business reach earnings goals and deliver the promised value to shareholders. You need to keep this end of the deal, and so, as a leader, you need to make sure your senior team and all your staf have this focus in mind.
It’s usually better if as much of your original approach and culture is retained during the earn-out phase of the deal, to help your business to meet the agreed targets.
HOW CAN YOU MANAGE THE INITIAL TRANSITION PERIOD?
Afer the sale has completed, you are committed to being a successful part of your new group. Tere are likely to be lots of initial communications, and it’s critical that you are able to be a reliable conduit between the new owner and your employees.
I found that the best way to do this was to absorb everything that our new owners told me, and then re-message it to our employees in the way I usually communicated with them.
Communicate the values of the new group to your team by relating them to the way you already work. Most values are similar – they are just called diferent things, or looked at from a diferent perspective, so refer to and reference your own values to show your team that you share these with the new group already.
In this way, you’re shielding them from what can be corporate ‘coldness’ and instructions coming from head ofce, or your own line manager, while maintaining the relationships and communications that have made your company a good acquisition target in the frst place.
So, when given instructions by the group – always look to say yes, until such time as the answer has to be ‘no’. And where you have said yes, deliver on those instructions. It may be tempting to push back – because you are used to being in sole control, or because the new group does things diferently – but the best thing to do is work with the group and deliver what it wants. Ten, when there are issues or mandates where you really have to say no, the group is more likely to listen to you.
THREE CRITICAL STEPS TO ACQUISITION SUCCESS
At the top of this article, I listed the three reasons why acquisitions ofen fail. Understanding this can help you prepare yourself, your leadership team and your employees for success. My advice is to:
1. Remember why you have sold the business in the frst place, and take the time to understand the strategic focus of your new owners.
2. Take time to adapt to the culture of your new owners, by being open and honest with your employees, and making sure your messages refect the way you have always communicated with them.
3. Support your team to adapt quickly to new processes and requirements, so you can take advantage of the opportunities available to your business.
Taking the time to get this right will put you in a positive and proactive position to make the most of this new chapter in your business life.
Is it worth selling your business to a new owner? You should certainly give due consideration to the alternatives – an employee ownership trust, for example, or a management buyout. If you decide to sell, you need to do so with a clear understanding of what such a sale entails, and with a positive attitude towards making it a success.
Put simply, as long as you enter into the transaction and the new relationship with your eyes open, and you fully understand and accept that your business will change, a sale can transform your business prospects.
If you are thinking about selling your business and you’d like some advice on any of these sale or buyout options, you can contact me on des@mor1x.co.uk
Business consultancy, but not as you know it.
Straight-talking, valuable business advice you can trust, backed up by 30 years’ senior leadership experience in the Scaffolding and Access Industry
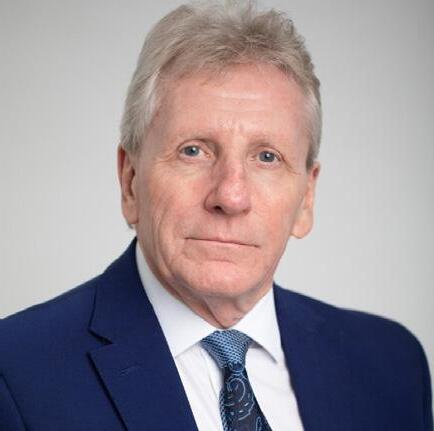
“I

Des Moore Founder
would have absolutely no hesitationrecommending Des,hedeliveredgood value on what we spent.”
“Deshasprovedinvaluable insavingustimeand helpingusnavigatethenext stagesofourgrowthplan.”
COMMERCIAL STRATEGY
GROWTH STRATEGY
CORPORATE STRUCTURE AND OPERATIONS
FINANCE
PRODUCTS AND EQUIPMENT
ADDITIONAL SERVICES
YOUNG BLOOD
Billy Jones, Millcroft’s Managing Director, discusses his concerns and what he believes the industry can do to challenge how the younger generation perceives and approaches working in this sector
It is no secret that the construction sector, particularly scafolding, is dealing with a pressing issue – a shortage of new workers. While scafolding can ofer a rewarding career, it’s clear that there are challenges in recruiting and retaining young people.
Te quality of candidates, particularly young people coming into our sector, has been playing a lot on my mind recently. At Millcrof, we’re proud of our low staf turnover and the opportunities we ofer our employees, however, we’re fnding it increasingly difcult to attract and recruit the right talent, and I’m sure we’re not the only company facing this problem.
A recent YouGov survey for the Deconstruction campaign found that 77% of 18–24-year-old students would not consider a career in construction. Why is this? What is putting the younger generation of, and how do we, as an industry, change perceptions?
THE POST-PANDEMIC GENERATION
Following the Covid-19 pandemic, there has been a sharply increased demand for
hybrid and fexible working in some sectors. I appreciate that times have changed post-pandemic, and we need to be considerate to employees’ needs, but while these working practices might work well in some ofce environments, they do not easily lend themselves to scafolding. Tis could put some recruits of a career in our industry, so rather than present it as a rigid work environment, we need to promote the clear benefts: a rewarding and potentially lucrative career path, good pay and support, interesting work, fresh air and ftness from the job, and camaraderie, to name but a few. We can still provide the positive workplace experience many people are looking for, but this does need to be face-to-face, either in the ofce or out on site. Starting a new job is daunting, and the workplace can be an unfamiliar environment for many of the younger generation. Suddenly, they must learn diferent policies, working practices and how to interact with people other than their friends or family. Working in person, whether in an ofce or on site,
helps them to develop their interpersonal skills, create collaborative relationships with colleagues and managers, socialise and generally feel like an integral part of the company. It builds confdence and enables a person to learn ‘on the job’ and through mentoring by other experienced team members. If working remotely, young people can feel disconnected, less committed and are more likely to miss out on career development opportunities.
THE ETHICAL DILEMMA
I’m sure this will be incendiary, but from our experience, there does appear to be a decline in the commitment of young candidates coming through today. Many of the candidates we have seen recently have failed to grasp the ethics required for the scafolding sector. Fundamental principles such as respect for supervisors and foremen can ofen be lacking, and many seem to become disenchanted with routine tasks.
Scafolding is an excellent career choice, but those entering the sector today must be under no illusion. On the labouring side, it is manual work and


can be tough; you need to put in a solid day’s efort, which can mean early starts and working in unpleasant weather. But the rewards are great: stability, variety and pride in what you do are just a few.
Our senior contracts manager, Darren Hayward, likens the qualities needed for a role in scafolding to those he learned during his time in the Royal Marines. “Te Marines is a highintensity environment, but scafolding can be too. Resilience is a key skill to have. Scafolding is a tough job and is easily underestimated, but it is also extremely rewarding and can provide a very good living. A strong work ethic, good moral values and a humbleness to learn from others will always give you a positive return.”
UNREALISTIC EXPECTATIONS
Linked to this ethical dilemma is the unrealistic expectations some young starters can have around salaries and progression. In our experience, there is sometimes a sense of entitlement, with many expecting pay raises and promotions without necessarily earning them.
At Millcrof, we try to overcome this by being very clear on what our business is about and what we expect. It’s a two-way thing. We ofer competitive salaries, an excellent working environment, training and career progression, and in return, we ask for commitment and loyalty.
Many of our team members have spent years developing their skills, and starting at the bottom and working up is ofen an integral part of scafolding. Mark Stimpson is a perfect example. Mark joined Millcrof in 1985 as a labourer and is now our operations director, responsible for helping to deliver our commercial strategy and ensuring our clients’ requirements are met on site.
Likewise, Richard Ramkissoon, our Health & Safety Advisor, started his career as a ganger man. Learning on the job has given Richard a great
understanding of construction sites and safe practices, which have helped him to develop his career in health & safety.
LACK OF DIVERSITY
Tere can be an outdated perception that scafolding lacks diversity. Tese views are based on stereotypes and need to be quashed to attract the right talent.
Millcrof’s workforce comprises people with diverse backgrounds, including several females. For example, Corita Ware originally joined us as credit controller/ofce administrator, a role that included managing our numerous accreditations and audits. Corita has a great work ethic and an excellent ‘can-do’ attitude and is now our project coordinator, spending part of her week at our HS2 site in Acton, where she is instrumental in helping to ensure the project runs smoothly.
Something Corita has noticed while working on site, which I hope potential young employees will take on board, is there’s an increased presence of women in what were traditionally seen as male roles. “It’s nice to see the diferent ages, young women and older ladies on site. One hundred per cent, I’ve noticed a change. It’s lovely to see the diferent age groups and backgrounds,” says Corita.
EDUCATION IS KEY
If we want to tackle the recruitment and skills gap issues, we must present scafolding as an attractive career with many opportunities.
As an industry, we need to engage with local education providers and the community to educate the workforce of the future and demonstrate the variety of roles within the scafolding sector. Tis is something we have done through our work with the Construction Youth Trust and also as part of our social vale commitment to HS2 where our senior contracts manager has led presentations to young people at careers fairs. It’s not just about working ‘on the tools’. Tere are roles for anyone, from a site foreman or contracts manager to an accountant or within human resources.
Furthermore, contrary to popular belief, our industry is innovative and has embraced technological advancements, so there are opportunities for people to work with AI, 3D imaging, and 4D video. Indeed, one of our original young ‘Kickstart’ recruits is now a key member of our design team.
We can bring in new talent and invest in the next generation by showcasing varied opportunities, supporting apprenticeship and trainee schemes, and encouraging career development through training and support.
COLLABORATING TO RESHAPE PERCEPTIONS
Sometimes, you need to tell it how it is and be slightly controversial to start a discussion. So, hopefully, by being open about the recruitment issues we’re facing at Millcrof and discussing how we’re trying to change perceptions, we can encourage the industry to work together to dispel the misconceptions many have.
Te challenges of recruiting and retaining young talent in our sector are real, but with a concerted efort, we can change this. We need to communicate what the job involves and emphasise the opportunities it provides for those willing to work hard and develop their skills over time. Realistic messaging is important so that new starters understand both the demands and the rewards a career in scafolding ofers them.

SCAFFOLDING IS A TOUGH JOB AND IS EASILY UNDERESTIMATED, BUT IT IS ALSO EXTREMELY REWARDING AND CAN PROVIDE A VERY GOOD LIVING. A STRONG WORK ETHIC, GOOD MORAL VALUES AND A HUMBLENESS TO LEARN FROM OTHERS WILL ALWAYS GIVE YOU A POSITIVE RETURN
The
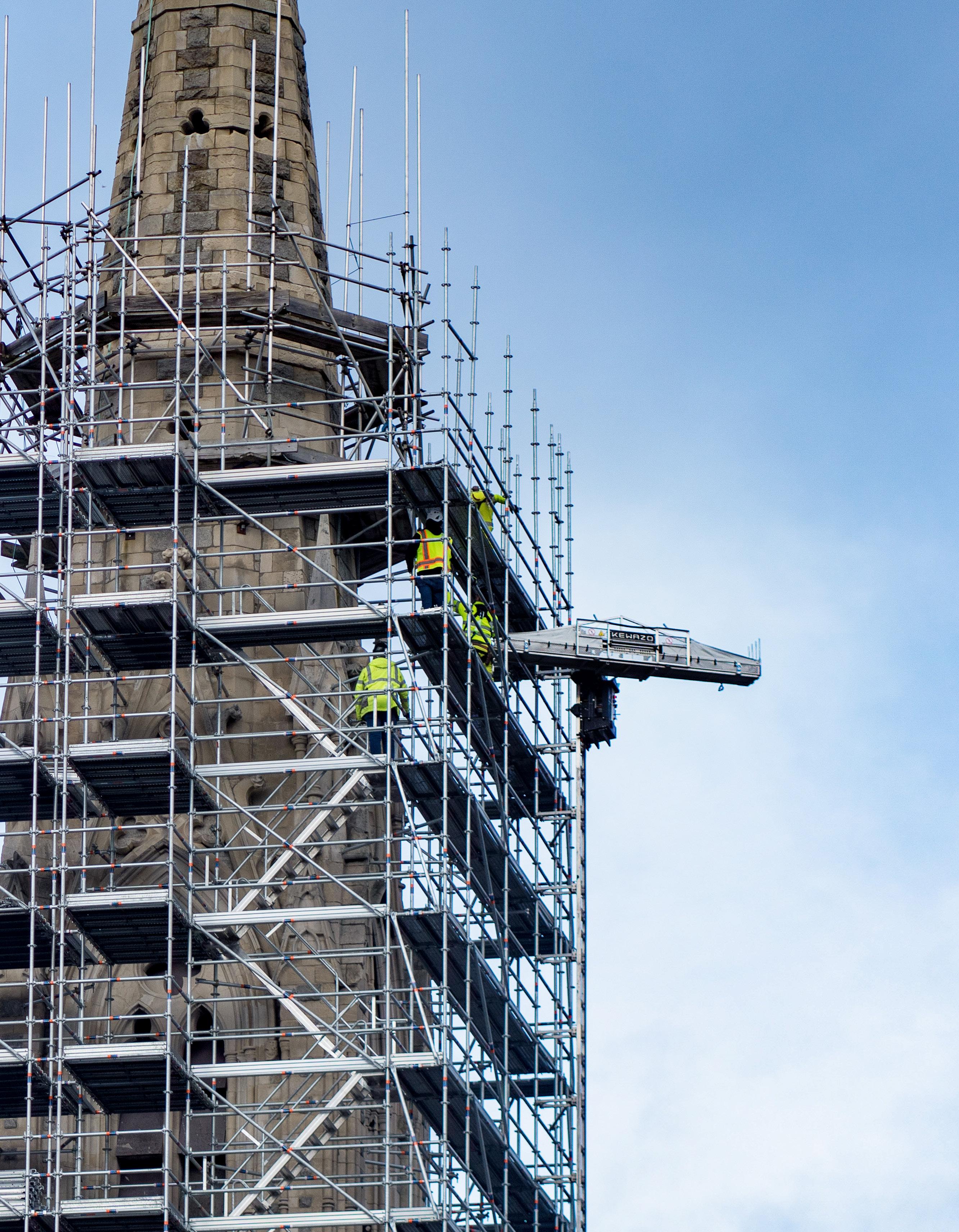
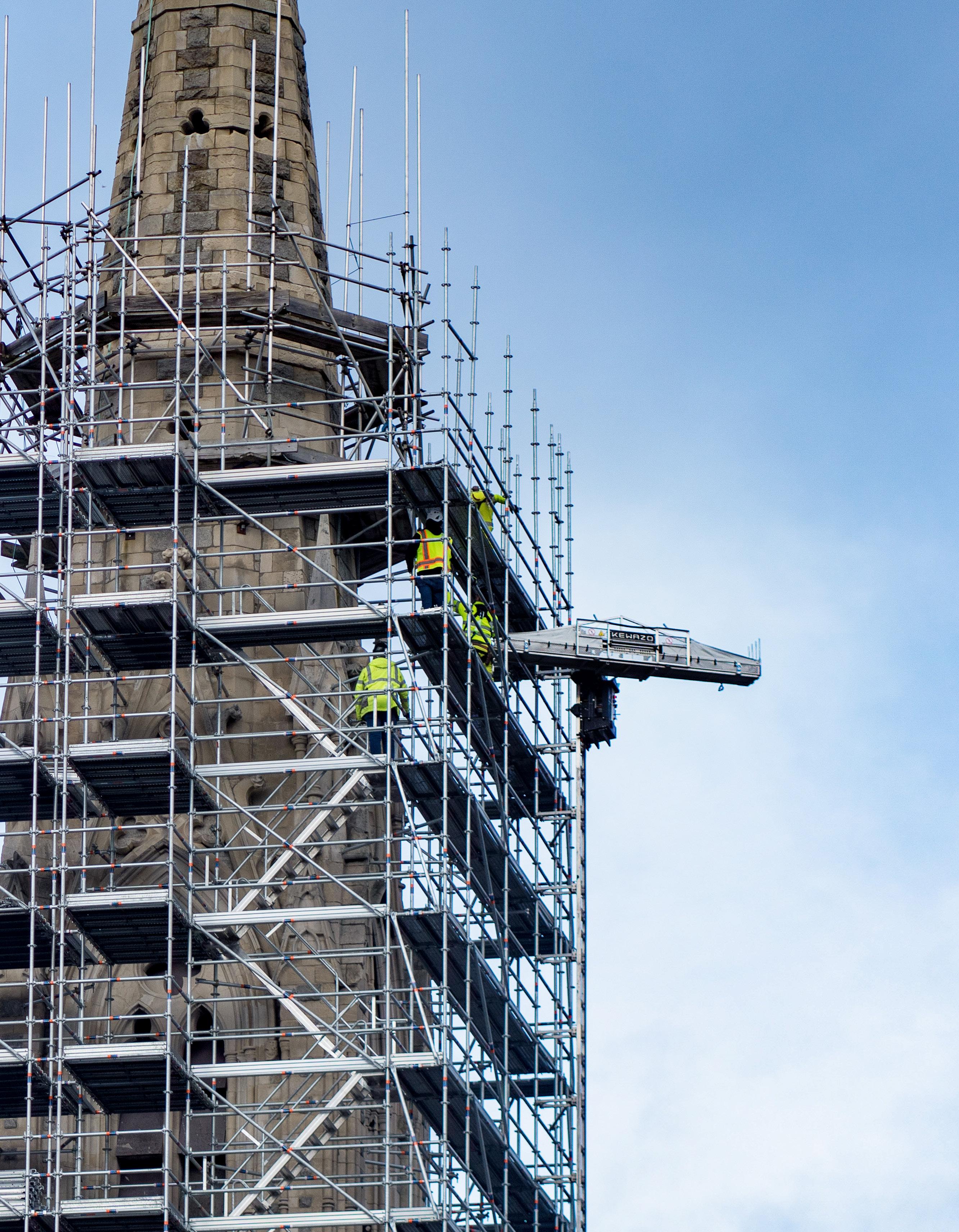
Devine Scafolding undertook a new ring-lock system scafolding project in Dublin, removing the remnants of the old platforms and breathing new life into the 19thcentury Presbyterian church
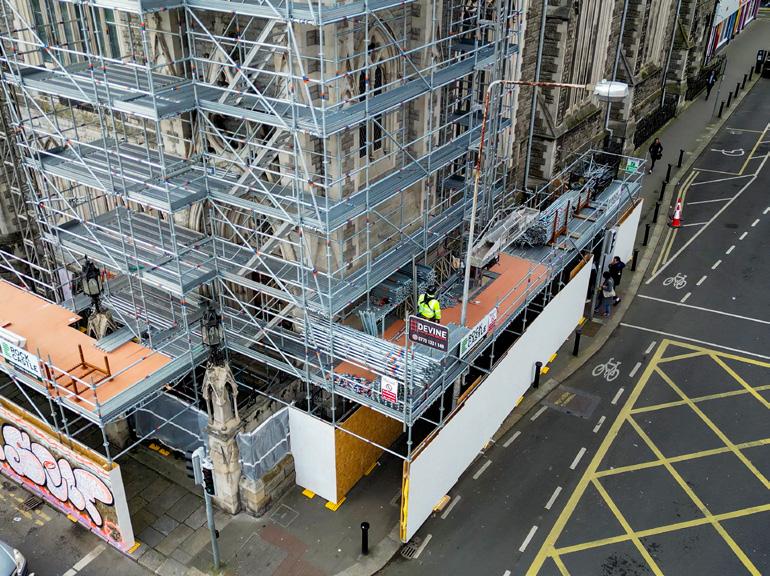
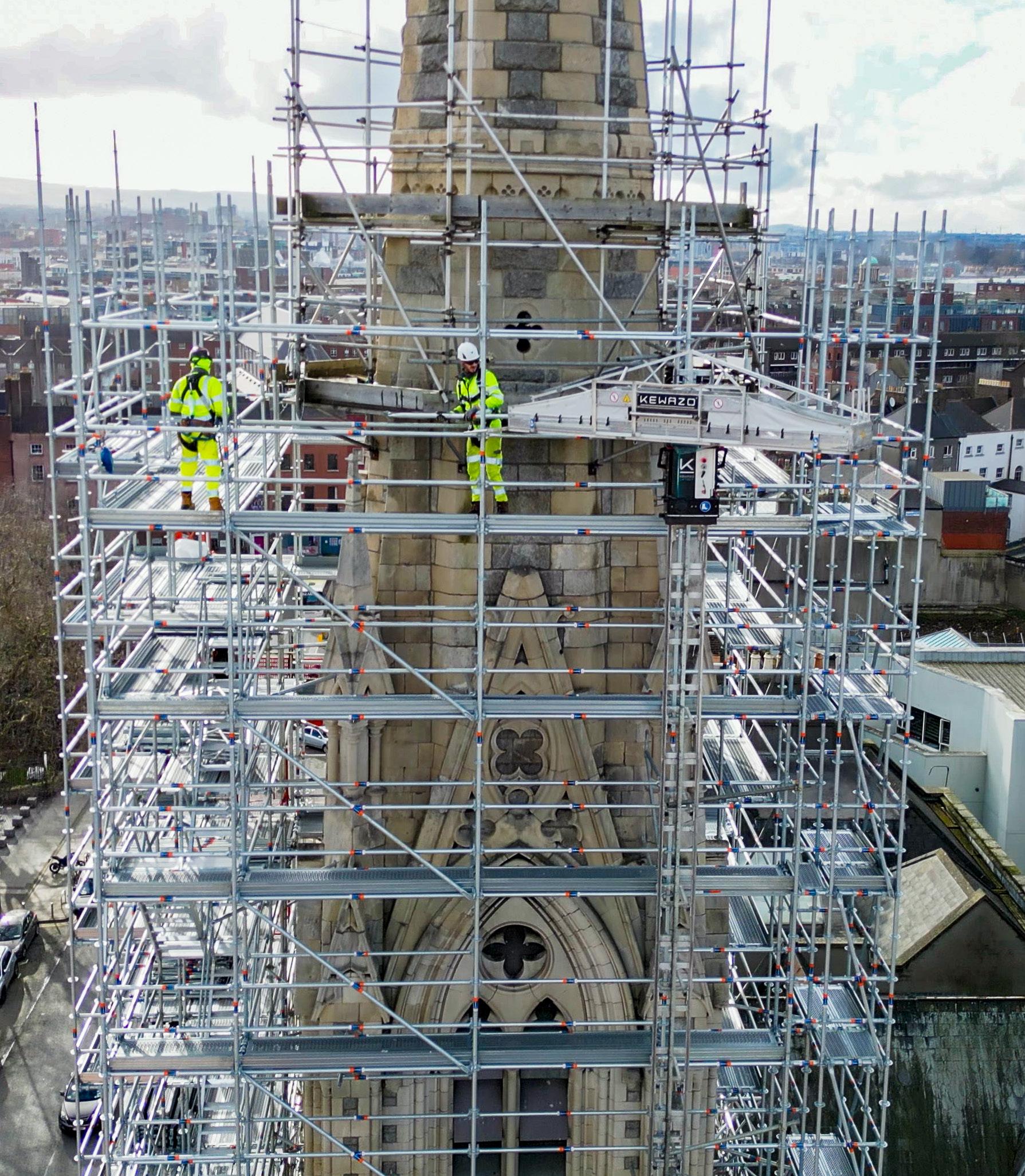
City heights
Abbey Church, a picturesque landmark in the heart of Dublin, Ireland, was frst erected in 1864. Known colloquially as ‘Findlater’s church’, the stunning 19th-century Presbyterian church inspired the works of author James Joyce, who mentioned it by name in two of his famous novels. Troughout its history, the church has undergone numerous restorations. In its most recent project, over 20 years ago, plans were made to renovate the steeple.
Unfortunately, afer erecting scafolding, the renovation project was put on hold due to funding limitations. For the last two decades, segments of the ageing tube-and-ftting scafolding platform remained in place, obstructing the view of the iconic building.
Tis year, Devine Scafolding undertook a project to erect new ringlock system scafolding, removing the remnants of the old platforms and preparing the site for new restorations to the facade.
Because of the church’s central location in the bustling heart of Dublin, Devine had to complete the project without disrupting the fow of trafc or obstructing the footpaths around the church. Due to these constants, the company considered chain-lining the scafolding material as their only traditional option. However, afer getting in contact with KEWAZO, the company was able to deploy the material lifing robot LIFTBOT for quick vertical transportation of equipment while keeping the pavements
free for pedestrian trafc.
To accomplish their objectives, Devine built a gantry over the pavement, and deposited scafold equipment onto the platform at night to minimise the disruption to trafc. During the day, the team used the lightweight, batterypowered LIFTBOT to transport the parts up the tower as pedestrian trafc fowed undisturbed below the gantry. Using LIFTBOT, Devine was able to complete the project with only four men instead of the initially estimated 7-10 required for chain-lining while also reducing the physical strain on the scafolders.
Tanks to the innovative thinking of Devine Scafolding, Abbey Church is now back on track for its longawaited restorations!
Hire

Public Access Staircases
Public Access Bridges
Temporary Buildings
Weather Protection
Temporary Roofs
Site Staircases
Haki System
Suspended
Tripods
UKSSH are there to support you every step of the way.
With over 150 years of collective knowhow and experience, substantial stocks and a commitment to excellence, you can trust UKSSH to get it right every time.

To find out more visit www.UKSSH.co.uk

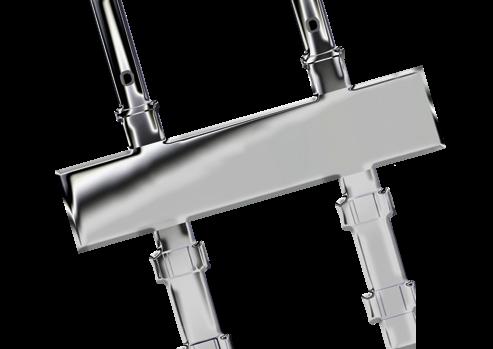
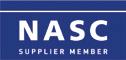
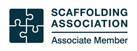
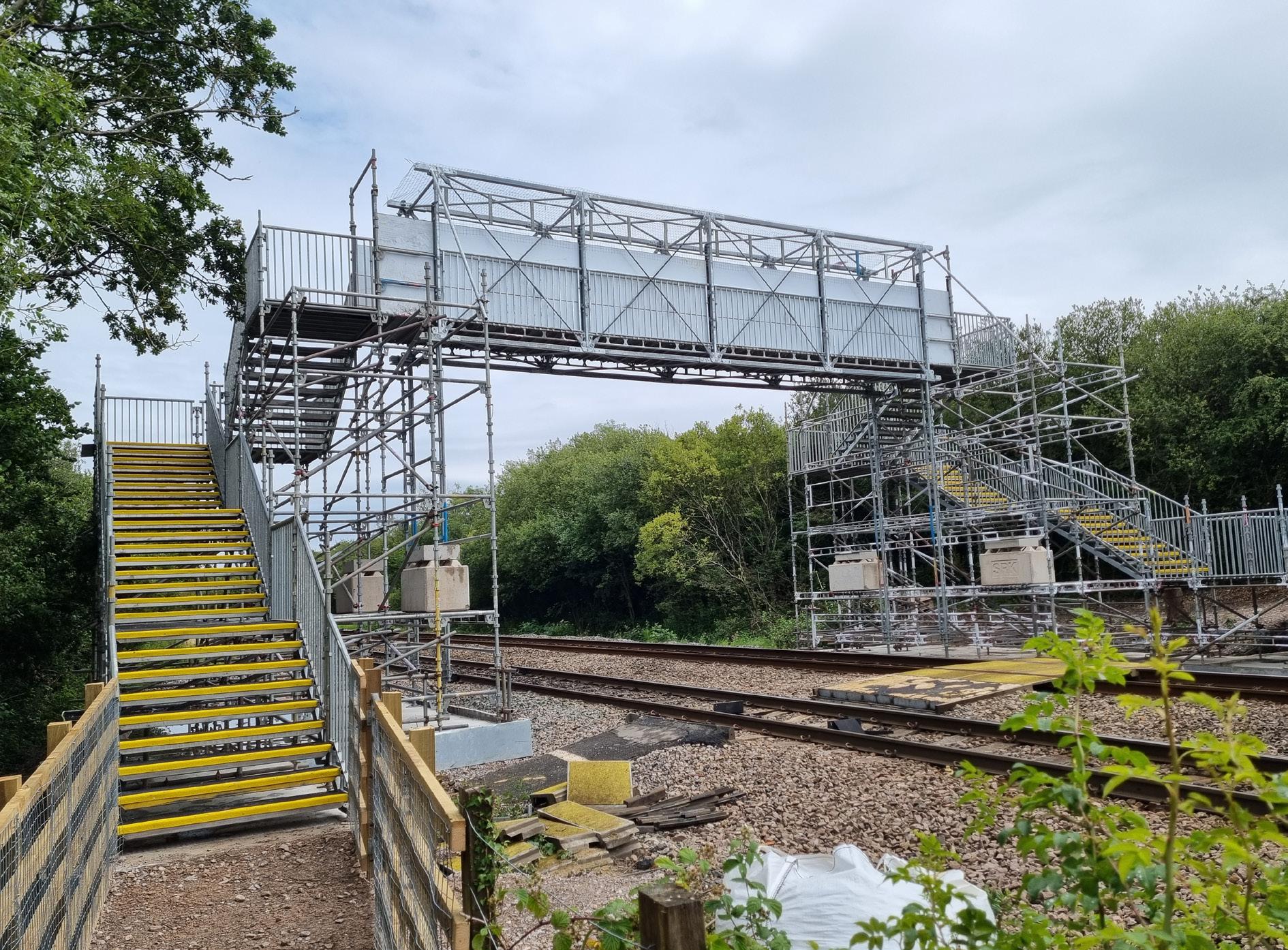
BUILDING BRIDGES
There are no short cuts to make 2024 less challenging – but a long-term business strategy can deliver benefts sooner than you may think
Economic uncertainty combined with a chronic skills shortage creates a perfect storm for the scafolding industry –fnding the solution to one of the problems can be hindered by constraints created by the other. Te solution is to be pragmatic and develop long-term strategic partnerships that allow change to be introduced as painlessly as possible and in a way that is mutually benefcial.
In theory, system scafold is the ideal answer to the current skills shortage: Compared to tube-and-fttings it is quicker and easier to erect and has fewer components – it can actually reduce man
hours on some projects by 80%.
So, what is stopping everyone from making the transition from tubeand-fttings?
Te reason is that nothing in the world of business is ever that simple. Tere are frequently very valid arguments which persuade companies that ‘now’ is never quite the right time to make the move to system scafold – and that is because other considerations are always in play.
SYSTEM SCAFFOLD IS ONLY PART OF THE ANSWER
Look at individual projects – particularly larger or technically challenging ones
– and system scafold really does sell itself, cutting costs and opening doors to more lucrative contracts. However, on a corporate level, the transition to system scafold is ofen a balancing act – not just in terms of fnancing the transition but also in terms of optimising the assets that you already have, not just in terms of equipment, but also manpower.
A COLLABORATIVE APPROACH MAKES
THE TRANSITION SO MUCH EASIER
Te transition to system scafold can’t be done at a stroke – on projects that are already in the pipeline, companies will have built in their existing skilled labour force into project costs, so reducing their time on site in the short to medium term wouldn’t reduce costs, although it would increase capacity. Furthermore, having bemoaned the shortage of skilled scafolders, the frst priority of any company is to look afer the ones they have!
ECONOMIC UNCERTAINTY
Ten there’s the economic uncertainty created by high interest rates and tighter lending standards meaning that companies are more inclined to optimise the use of what they already have rather than to make the transition away from tube-and-fttings.
UKSSH’S PROACTIVE APPROACH TIPS
THE BALANCE IN FAVOUR OF INVESTMENT
Te solution is to be pragmatic and develop long-term strategies to introduce change as painlessly as possible and in a way that is mutually benefcial.
Tat long-term view ofen means UKSSH will invest many hours helping prospective clients prepare proposals well before the contract has been awarded: Te ‘secret’ is not to view that time as a short-term gamble, but as a long-term investment in the future.
UKSSH’s involvement at the pretender stage ofen provides an entirely new perspective to many of the excellent scafold designers who are charged with the task of proposing the most efective
solutions. Frequently it’s a combination of UKSSH’s practical experience combined with the designers’ technical abilities that helps to arrive at the optimum solution.
It’s a matter of having the opportunity to get involved from the outset that allows the ‘UKSSH knowhow’ to come into play and – once all parties are satisfed with the concept –UKSSH ofen prepares a trial erection of the scheme at its Tamworth HQ to ensure that everything is deliverable in terms of safe systems of work, buildability and time scales.
UKSSH believes that investing time ‘up front’ results in long-term and mutually benefcial relationships –clients know that once they make the decision to hire or buy HAKI system scafold, they are investing as much in UKSSH’s expertise and support as in the products themselves.
Te pragmatism extends to fnancial arrangements too – ofering an option to hire or buy (or a combination of the two) – and ofen converting hire to sales as projects evolve.
ACCESS TO THE BRIDGE REQUIRED CLEVERLY DESIGNED PUBLIC ACCESS STAIRCASES ON EACH SIDE OF THE TRACK, BOTH TO ACCOMMODATE DIFFERENT ACCESS LEVELS AND A CHALLENGING FOOTPRINT FOR THE STAIRS

SRK CHOSE TO PURCHASE FROM UKSSH
SRK Scafolding, which has its head ofce in Somerset, knew that, working with UK System Scafold Hire, they could deliver the perfect solution to provide public access across a mainline railway in South Wales: a HAKI Public Access Bridge accessed by a HAKI Public Access Staircase on either side of the track.
Ray Luscott, Regional Manager at SRK Scafolding’s Newport ofce, explained that because of the length of time the bridge would remain in position SRK decided to buy the equipment from UKSSH rather than hire it, but UKSSH’s speed of response and expertise with HAKI’s public access products made them the obvious partner for the project:
“Access to the bridge required cleverly designed public access staircases on each side of the track, both to accommodate diferent access levels and a challenging footprint for the stairs.
“We knew that UKSSH would work hand in hand with us, both to devise the best solution and to quickly and efciently meet any challenges that would require last-minute ‘tweaks’ to the design”.
OVERCOMING LOGISTICAL CHALLENGES
Not every company has the yard capacity to manage stocks of system scafold in addition to their stocks of tube-and-fttings.
A vital part of UKSSH’s collaborative approach is to provide a logistical service that integrates seamlessly with a client’s operational needs. UKSSH understand the importance of scheduling component deliveries in accordance with the build programme rather than by the lorry load, they understand the importance of adhering to delivery schedules – and ensuring that when the components do arrive on site they are in good working order.
Working with UKSSH also delivers peace of mind on those occasions when urgent supplementary deliveries are

required – UKSSH’s huge stock levels means that they can ofer fexibility and rapid response times to save the day –helping clients to hit deadlines and control costs.
PUTTING PRINCIPLES INTO ACTION WITH HIGH STANDARDS SCAFFOLDING
Tat pragmatic approach also means being happy to mix and match –combining a client’s own stock of tubeand-fttings with HAKI components.
Faced with providing two temporary roofs over a steeply pitched roof, High Standards Scafolding of Hemel Hempstead found the perfect solution: Teir in-house design team integrated the company’s own stock of tube-andfttings to support two HAKI temporary roofs supplied by UK System Scafold Hire.
High Standards Scafolding’s design featured one HAKI temporary roof with 23 2.5-metre bays to create a roof that was 60.3m long with a span of 15.6m and a 22° pitch, while the second roof was 75.6m long with a span of 15.6m and a 22° pitch.
Karl Yarham, High Standards Scafolding’s MD commented that the HAKI temporary roof delivered on all
OPPOSITE: High Standards Scafolding integrated the company’s own stock of tube and fttings to support two Haki temporary roofs supplied by UKSSH.
ABOVE: Ardgillan Castle in Ireland is the latest in a number of prestige projects in which McCrory Access has collaborated with UKSSH.
its promises: “Up to fve times faster to install than traditional structures, HAKI has fewer components compared to other systems and its lightweight design delivered real advantages throughout the project.”
IN CHALLENGING TIMES, WORKING WITH LIKE-MINDED INDIVIDUALS MAKES ALL THE DIFFERENCE
When you are looking for creative solutions to help drive your business forward, don’t dismiss options even before you have explored them. If you fnd like-minded companies who are prepared to invest time and efort into making relationships work, you may be surprised how much easier life becomes!
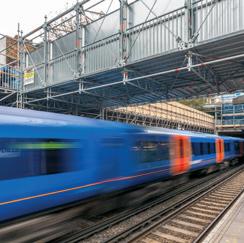
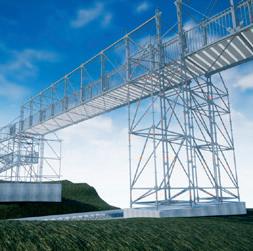
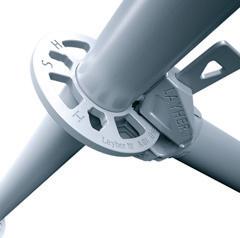
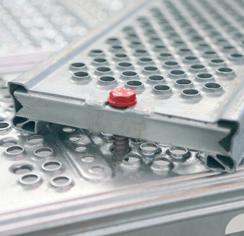
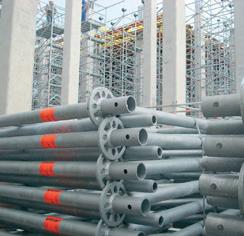
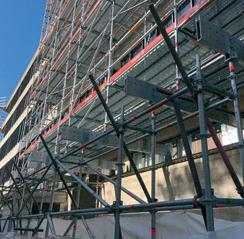

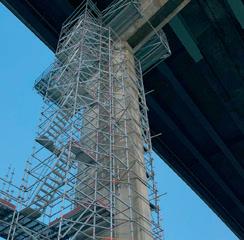
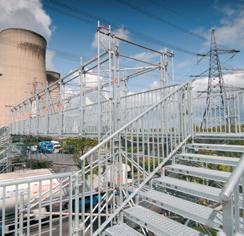
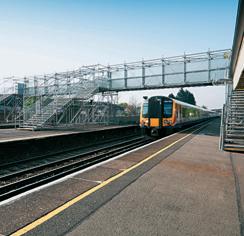
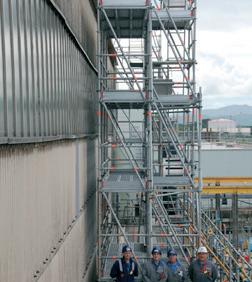

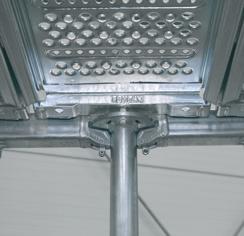
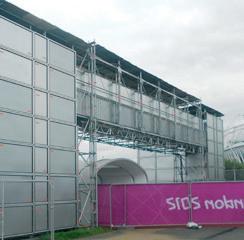
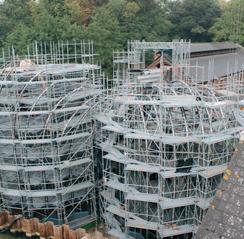
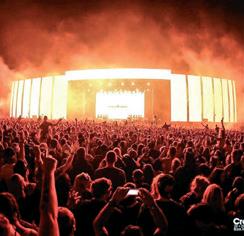
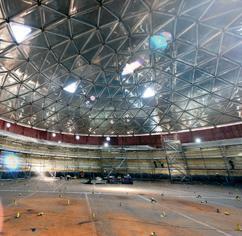
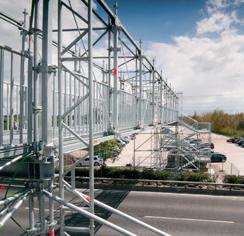
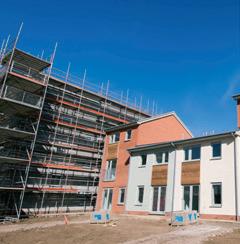
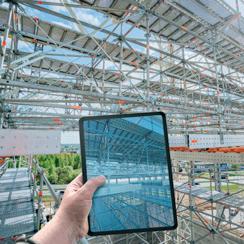
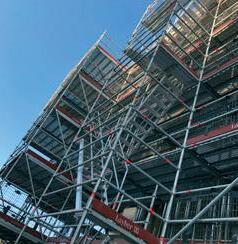
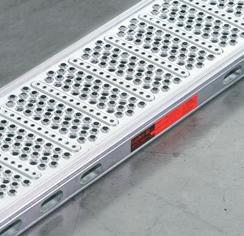
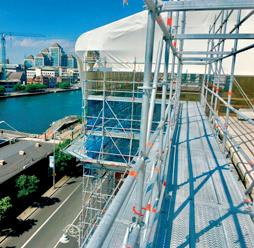
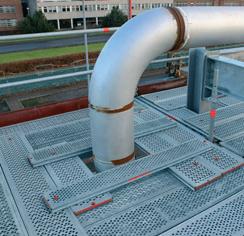
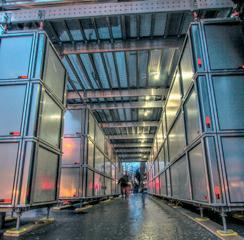
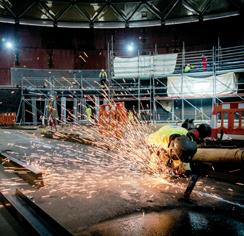
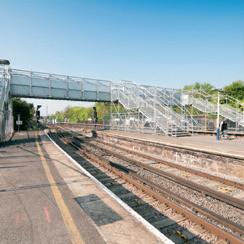
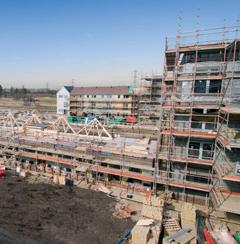
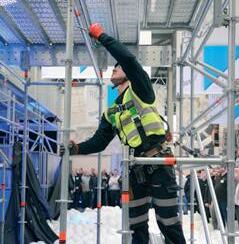
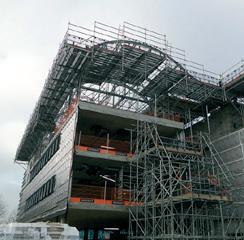

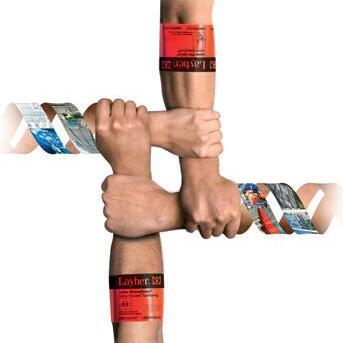
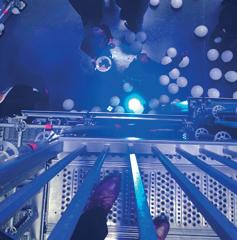
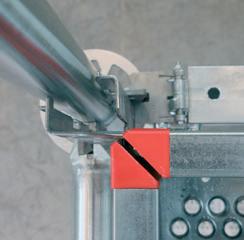
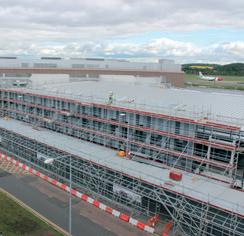
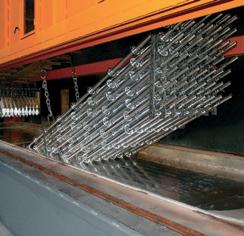
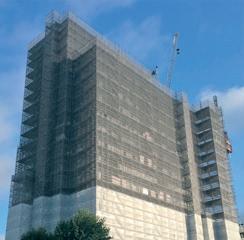

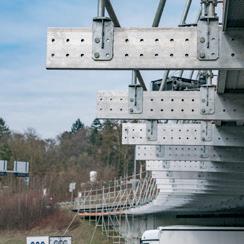
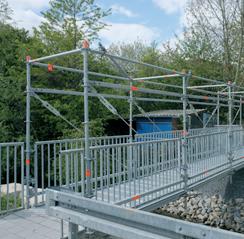
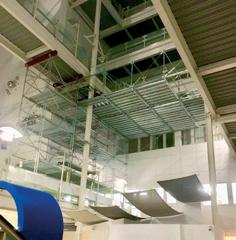
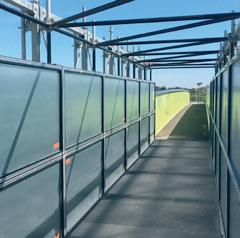

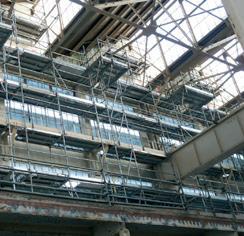
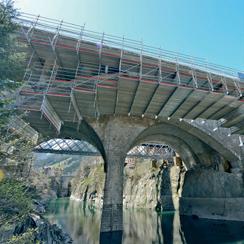

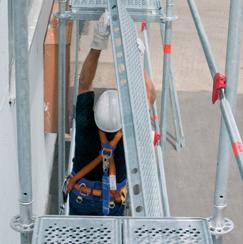
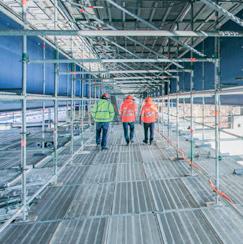
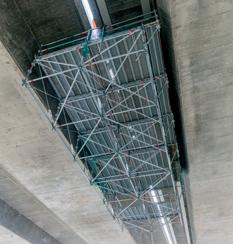
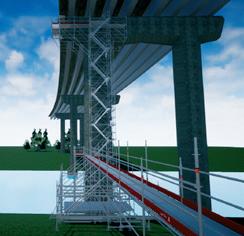
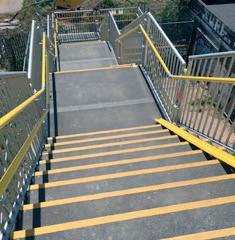
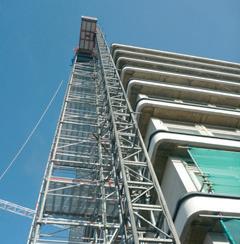
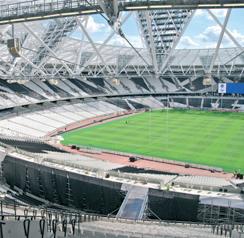
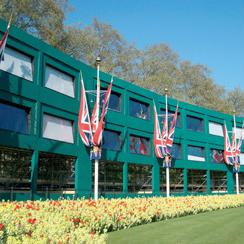
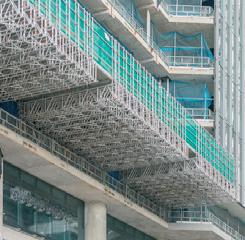
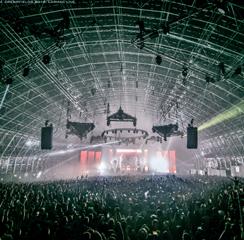
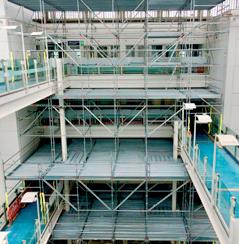
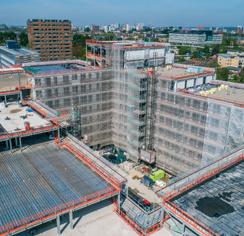
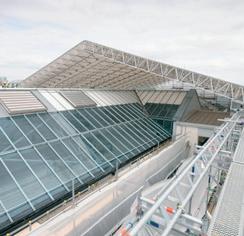
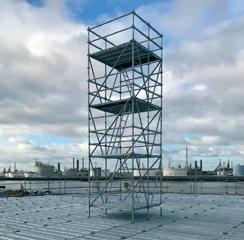

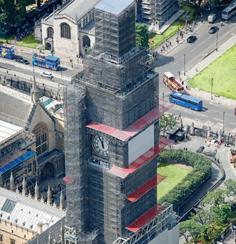
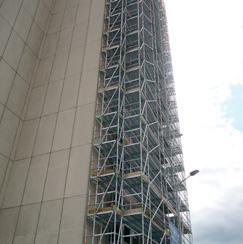
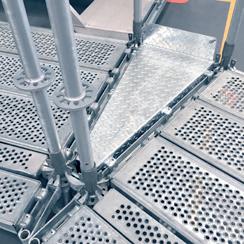
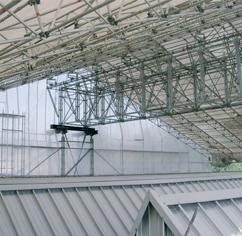
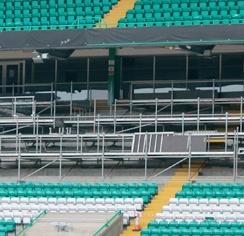
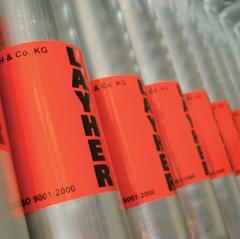
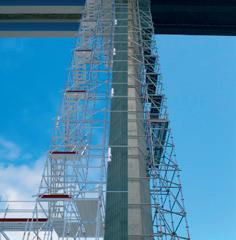
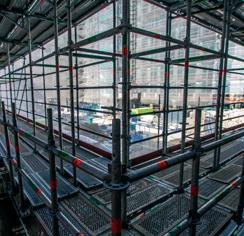
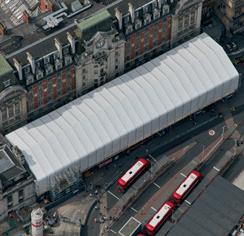
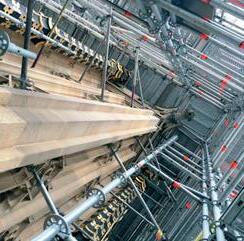
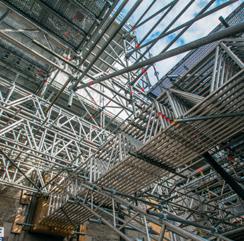
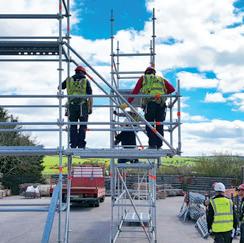
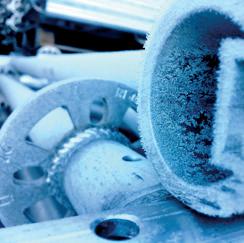
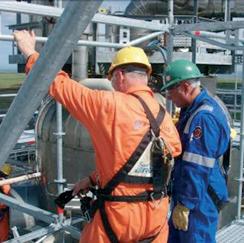
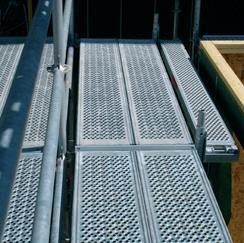


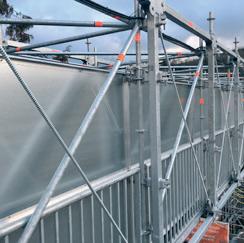


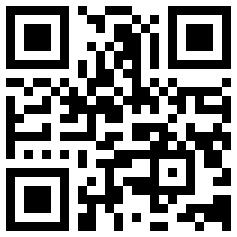
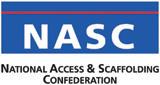
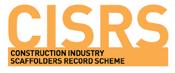

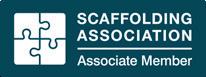
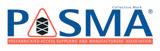



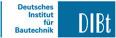



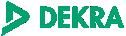




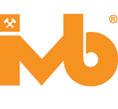
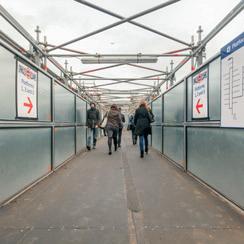
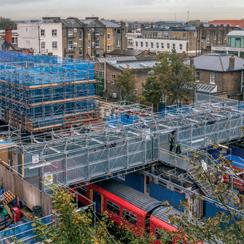
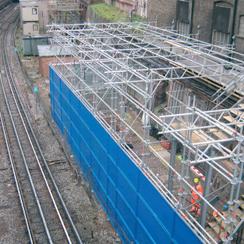

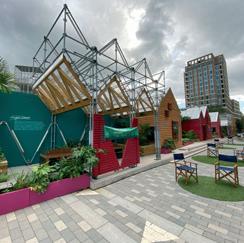
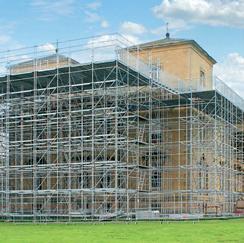


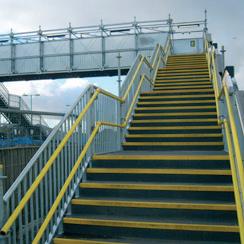
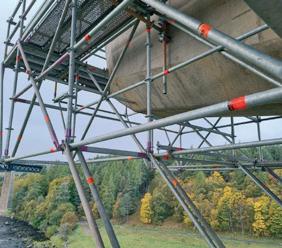
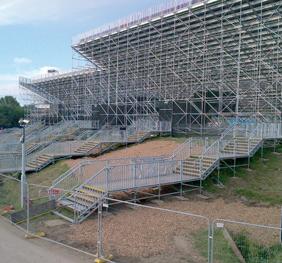
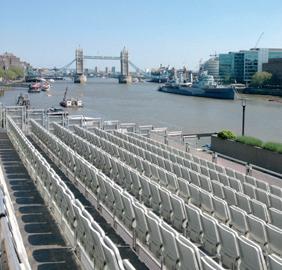
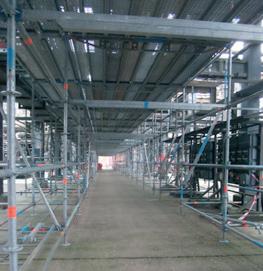
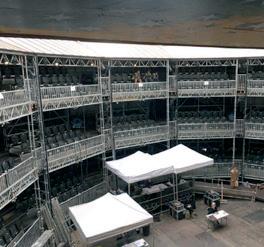
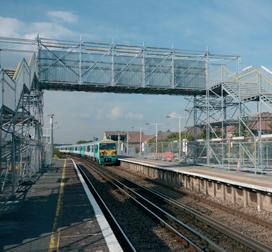
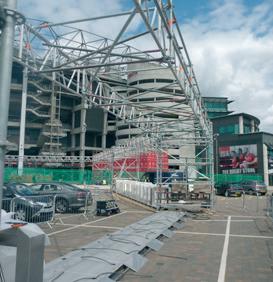
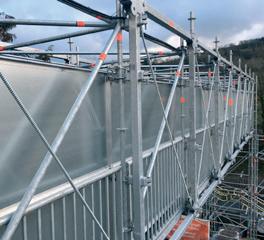
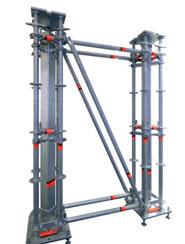
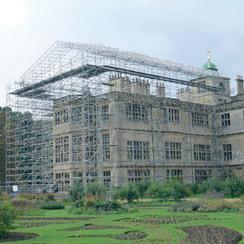

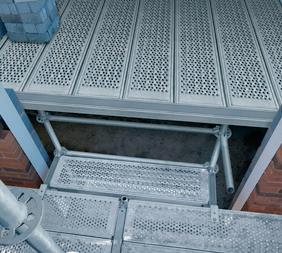

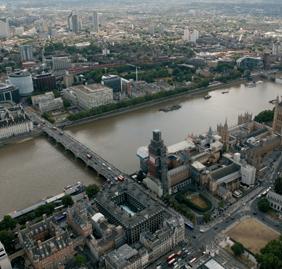
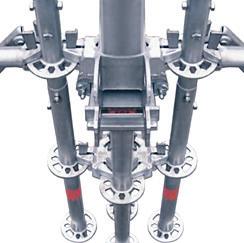
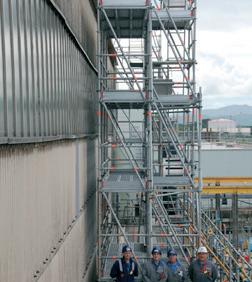


For more than 75 years, Layher has focused on innovation not imitation.
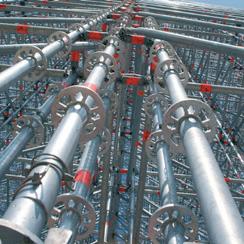
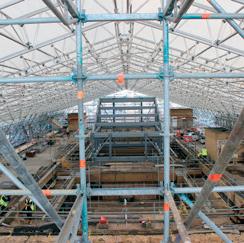


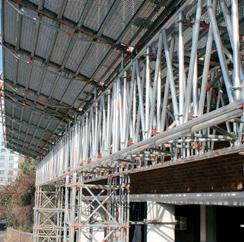
It’s why we remain the past, present and future of system scaffolding.


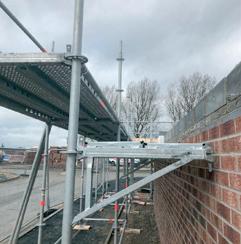

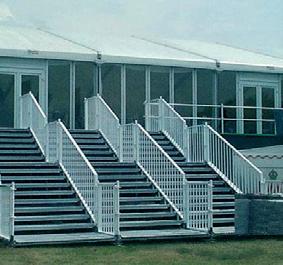
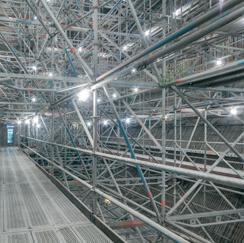

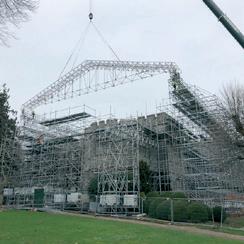
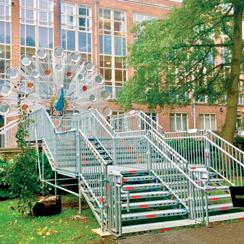
WINNER NASCInnovation oftheYearAward2021 LayherAllroundAGSFaçadeSystem
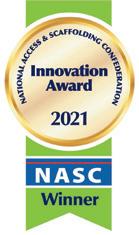
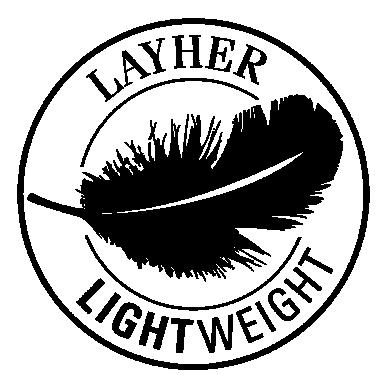
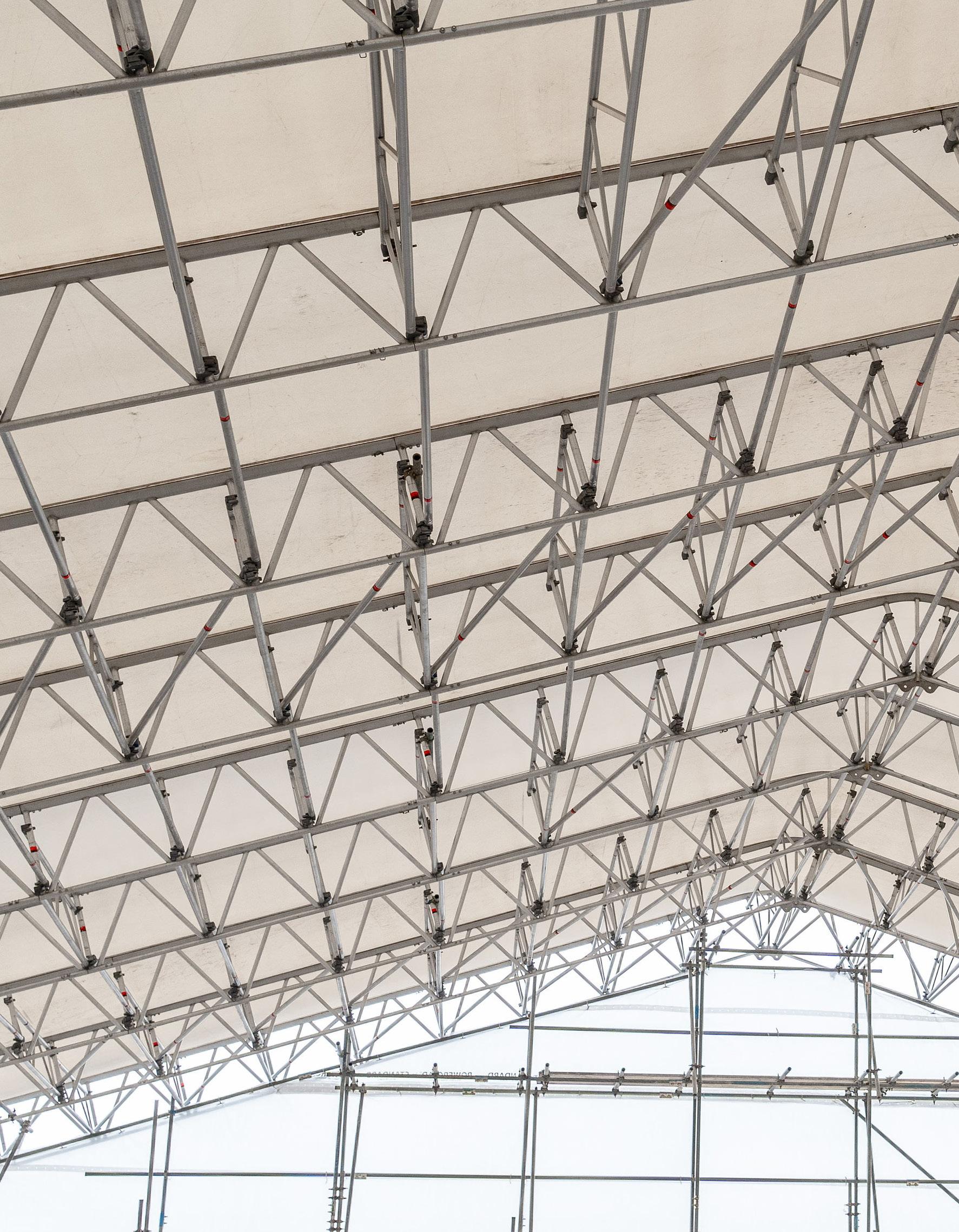
PROJECTS
● Barmouth, North Wales
● The Silvertown Tunnel, London
● Broad Oak Facility, Portsmouth
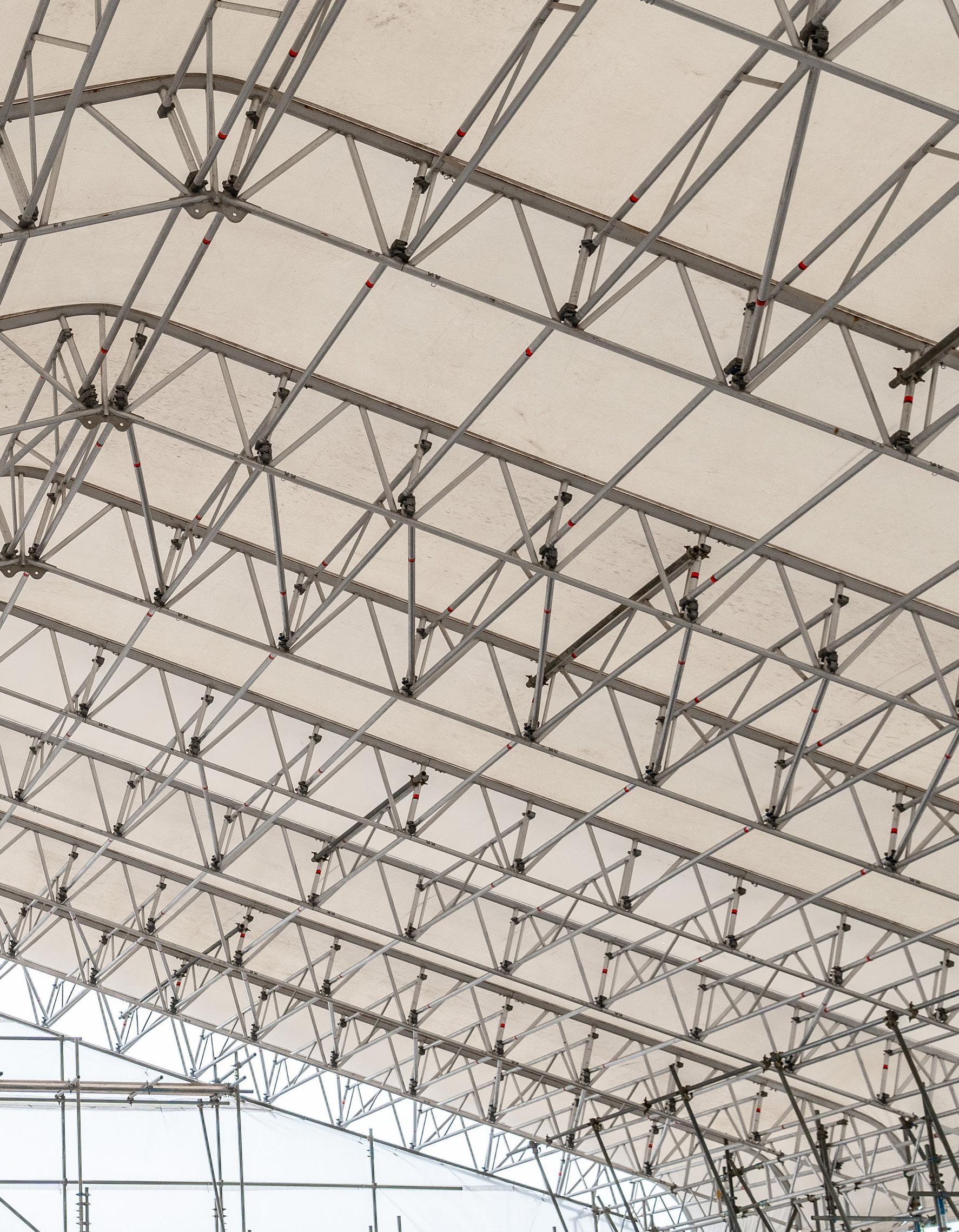
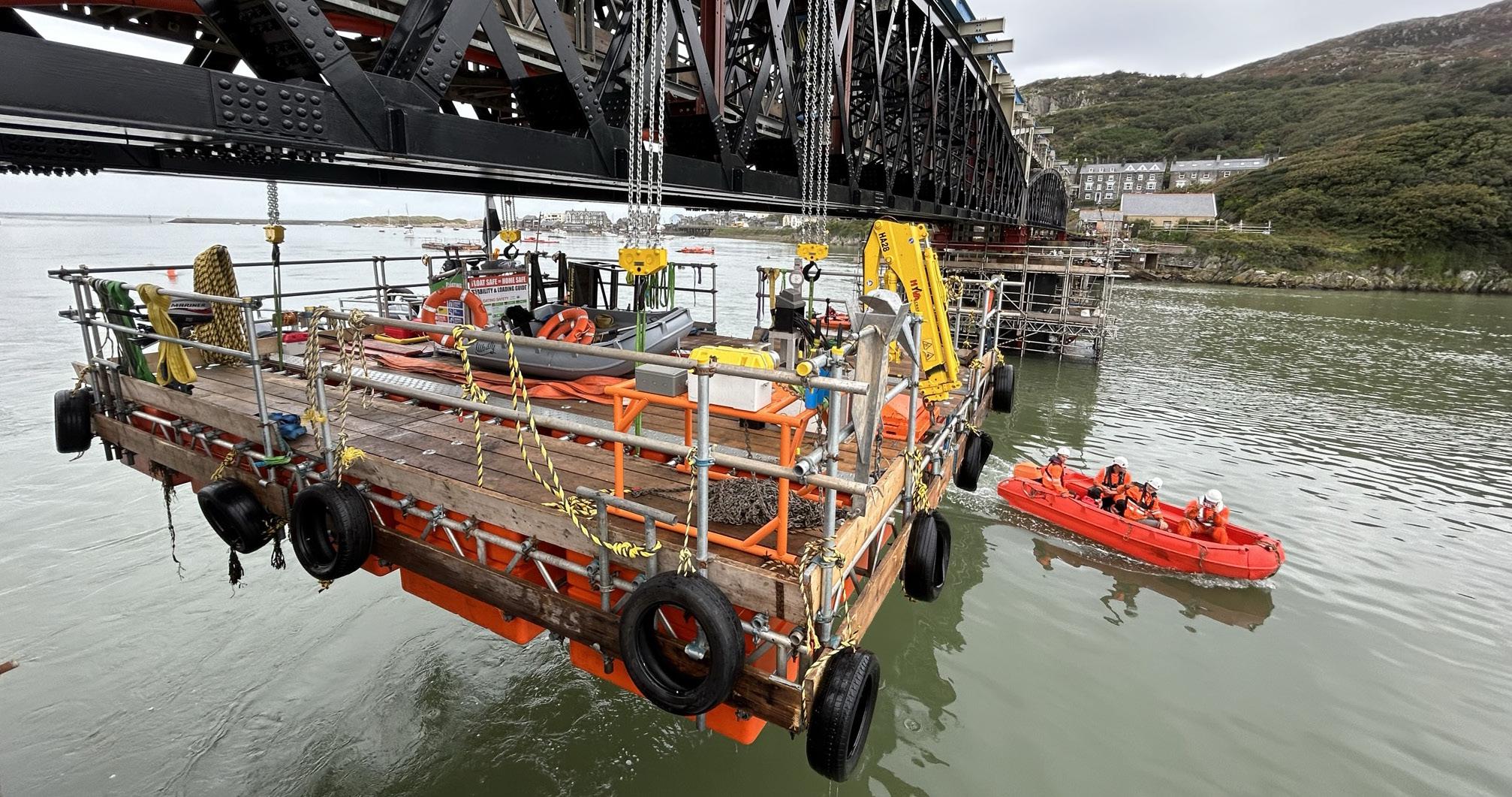
BRIDGING THE GAP
In an impressive demonstration of engineering innovation, the Cornwall-based start-up ScafFloat has recently accomplished a groundbreaking project in Barmouth, North Wales
In collaboration with Pennys Demolition and Alun Grifths, this efort focused on replacing an old railway bridge for Network Rail across a tidal estuary, demonstrating signifcant progress in construction methodologies. Te operation, marked by its complexity and the hefy weight of 300 tons for the bridge sections, required innovative solutions, and ScafFloat rose to the occasion.
Central to this project was ScafFloat’s innovative foating scafold system, which merges 100% recyclable plastic foats with standard scafold components to craf pontoons, rafs and workboats. Tis inventive solution facilitated the movement of 25-ton bridge sections from the old structure to shore and the installation of new deck sections for the bridge.
For the undertaking, ScafFloat supplied a complete marine package, including four heavy lif pontoons, two workboats with diverse capabilities, and a fast workboat, all outftted with features to ensure operational safety and efciency.
Toby Budd, the Managing Director of ScafFloat, provided insight into the project’s innovation and the collaborative efort required for its success. He noted the integration of their foating scafold system into the construction process, which allowed for the efcient and safe relocation of bridge sections across the estuary.
ScafFloat’s expertise in navigating logistical and environmental challenges was evident throughout the demolition and installation phases. Te team’s precision and fexibility were vital in managing the complexities presented by
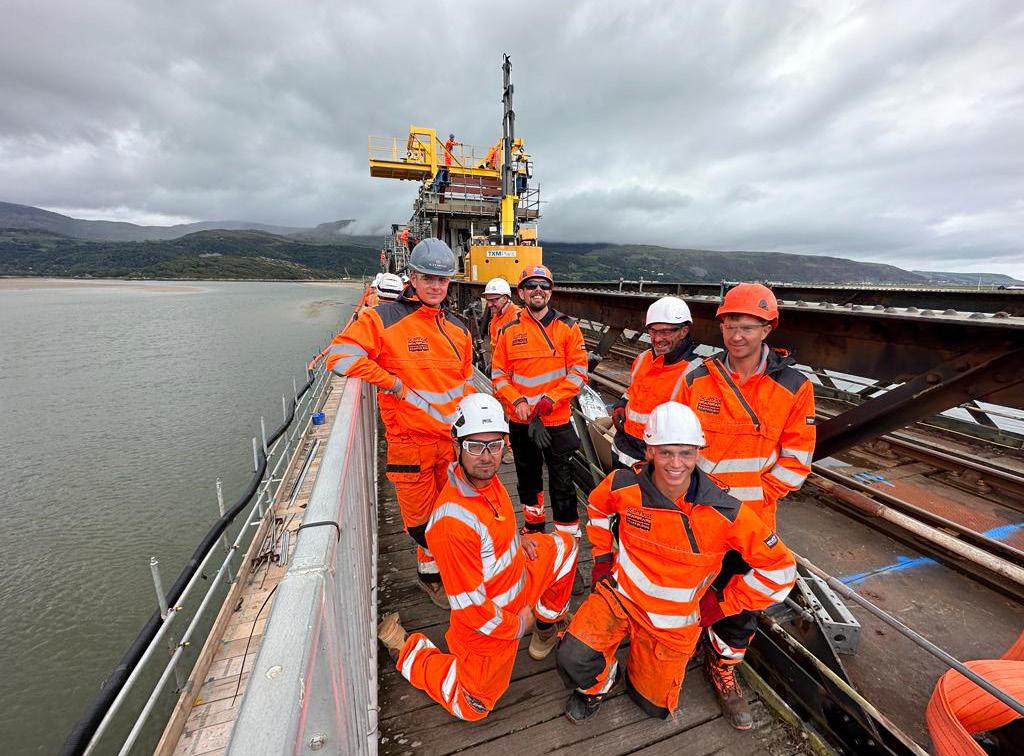
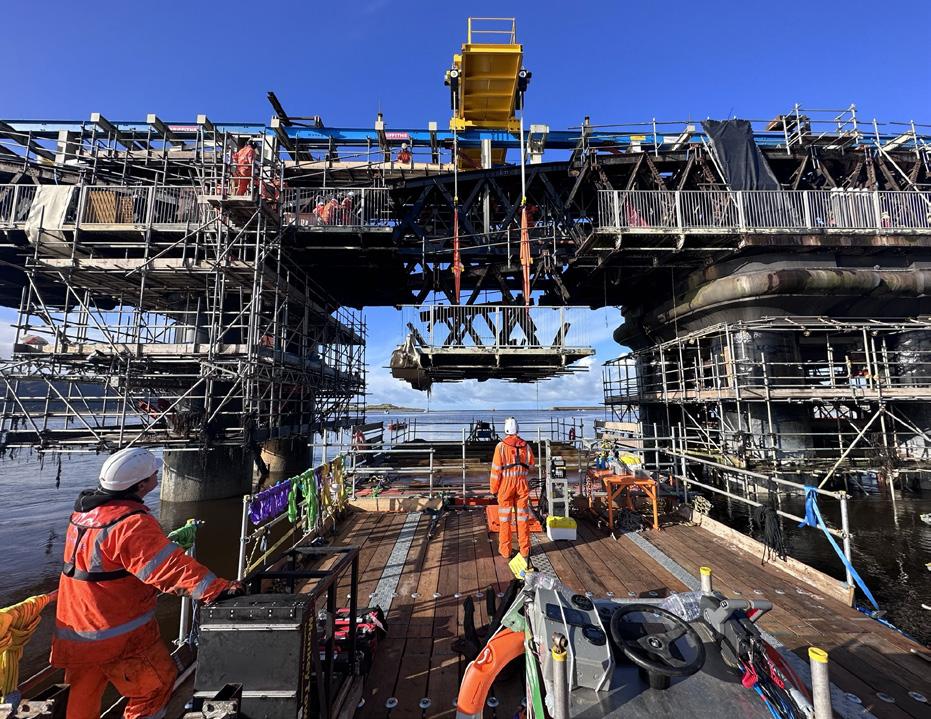
the tidal estuary. “Te team’s ability to adapt and accurately execute the project plans under varying conditions was critical to overcoming the challenges faced,” Budd mentioned in his refections on the project.
Budd also addressed the difculties encountered, particularly the unpredictable weather and the constraints imposed by the tide.
“One of the most signifcant challenges was aligning our operations with the tide and weather, demanding accurate timing and adaptability from our team,” he elaborated.
Moreover, Budd highlighted the project’s commitment to safety and risk management. He underscored that while there was a solid drive to complete the project, ensuring safety was never compromised. Tis balance between
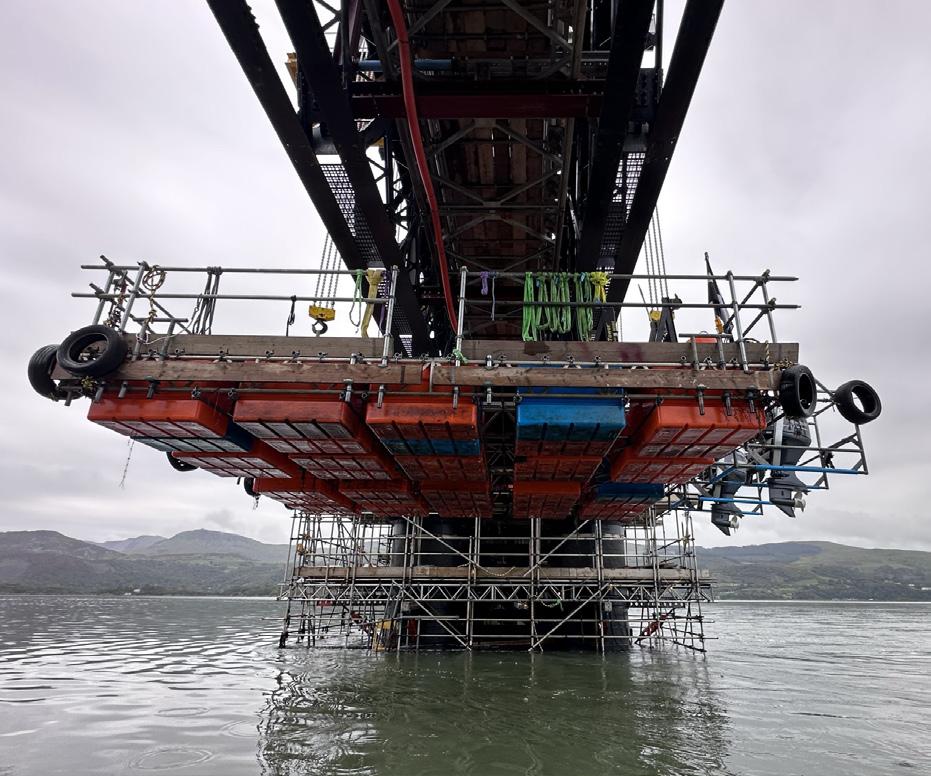
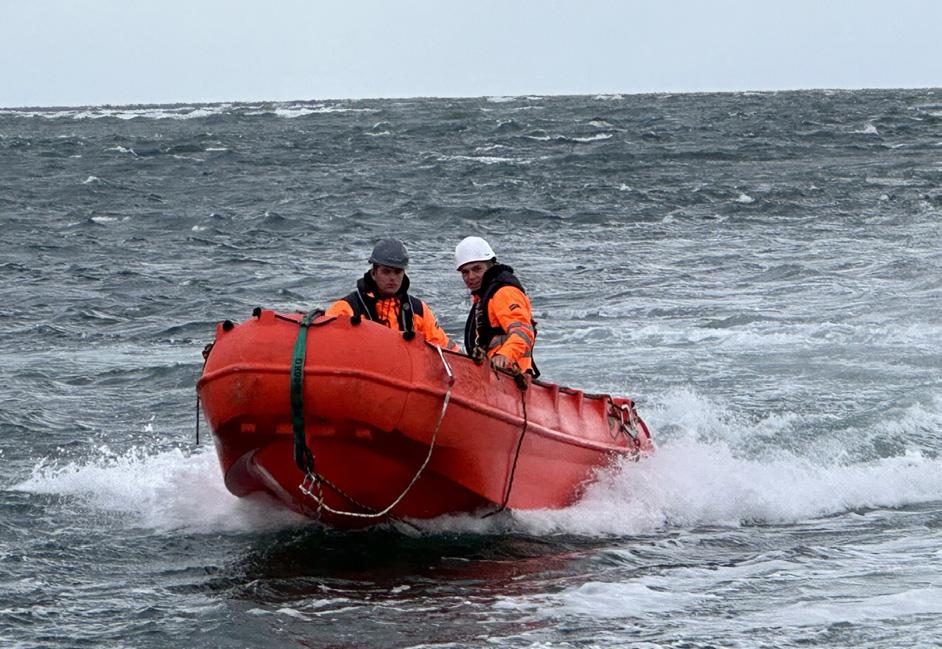
innovation, teamwork and safety protocols was instrumental in the project’s completion.
Te reopening of the railway line and the subsequent operation of a train on December 8 stand as proud achievements for Budd and his team. “Te successful conclusion of the project and its contribution to North Wales’ infrastructure are sources of immense satisfaction,” Budd shared.
Te completion of the Barmouth bridge replacement project by ScafFloat showcases the company’s innovative approach to construction. It establishes a new benchmark for addressing engineering challenges in marine environments, highlighting the transformative potential of foating scafold technology in modern construction practices.
THE TEAM’S ABILITY TO ADAPT AND ACCURATELY EXECUTE THE PROJECT PLANS UNDER VARYING CONDITIONS WAS CRITICAL TO OVERCOMING THE CHALLENGES FACED
Tunnel vision
In the heart of London, a transformative transportation project is taking shape beneath the River Thames, promising to revolutionise connectivity between the Greenwich Peninsula and Newham
Spearheaded by Riverlinx CJV on behalf of Transport for London, the construction of the new Silvertown Tunnel is a testament to vision, expertise and teamwork. In this project report, we delve into the crucial role played by Alltask in providing access scafolding for the Control Building of this ambitious project.
Te Silvertown Tunnel, a 1.4km twinbore road tunnel with two lanes in each direction, is more than just a road tunnel; it symbolises progress and innovation –creating a new link across the river which will support improved public transport by allowing more buses to cross at this location. To support this monumental endeavour, Alltask was responsible for creating a robust scafolding system for the Control Building, where equipment, ofces and staf facilities would be housed. Tis scafolding would be pivotal in safely installing all cladding and glazing, ensuring the project’s precision and safety.
One of the remarkable challenges faced by Alltask was the client’s demand for the scafold to be bridged with the fewest possible supports, eliminating the need for roof-based back propping to
avoid interfering with internal work. Additionally, the project called for the simultaneous installation of a green roof while completing the cladding elements. Tese requirements demanded a high degree of precision and creativity in scafold design.
DESIGN CHALLENGES AND CREATIVE SOLUTIONS
Te Control Building itself added to the complexity of the project. Its distinctive circular funnel shape necessitated a scafold that could adapt to this unique structure. Alltask’s solution involved multiple levels of intersecting beams, strategically positioned puncheons, and accommodating multiple boarded levels for various trades. Tis bespoke design showcased the team’s dedication to fnding innovative solutions to complex challenges.
While the design phase was intricate and demanding, the true test of Alltask’s capabilities came during construction.
Te team, led by the skilled hands of Henry Challis, worked tirelessly to turn the vision into reality. Sean Hunt and his team played a pivotal role in executing this challenging scafold design, which required careful planning and precise execution.
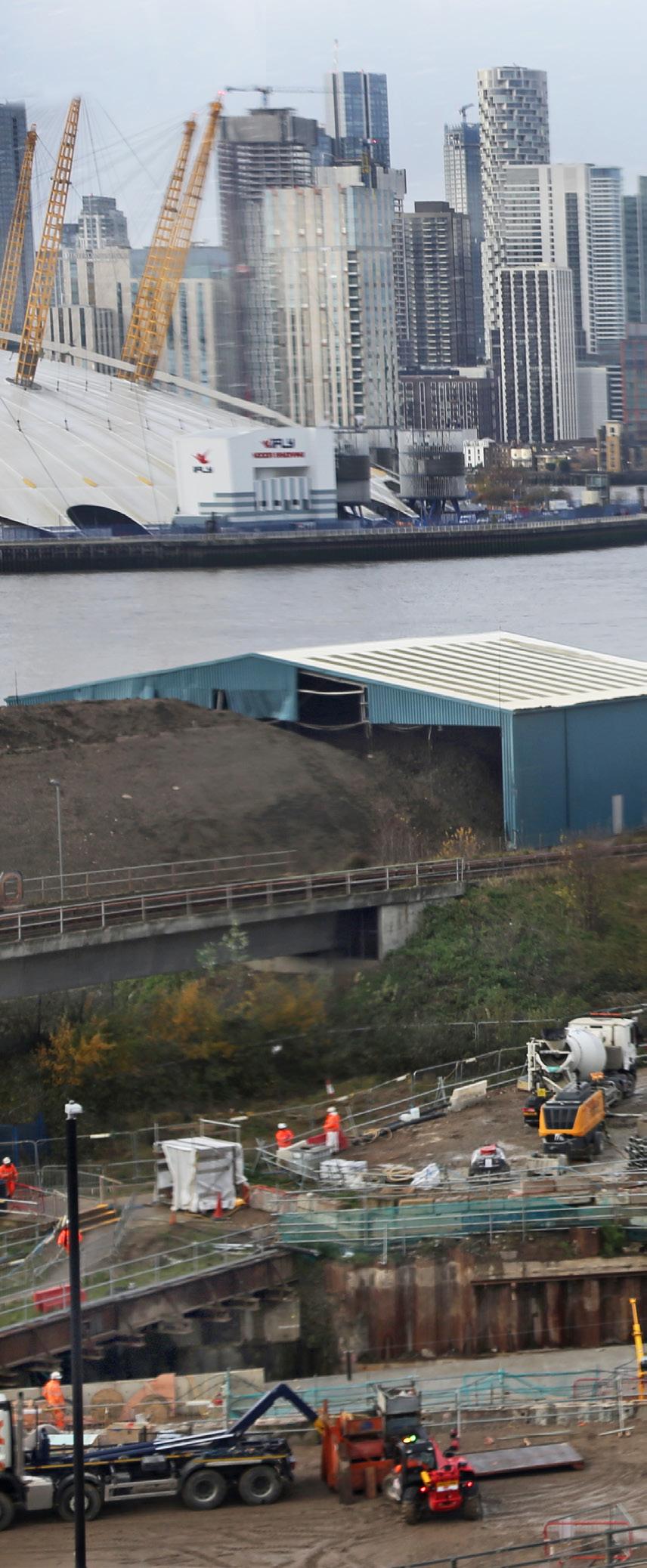
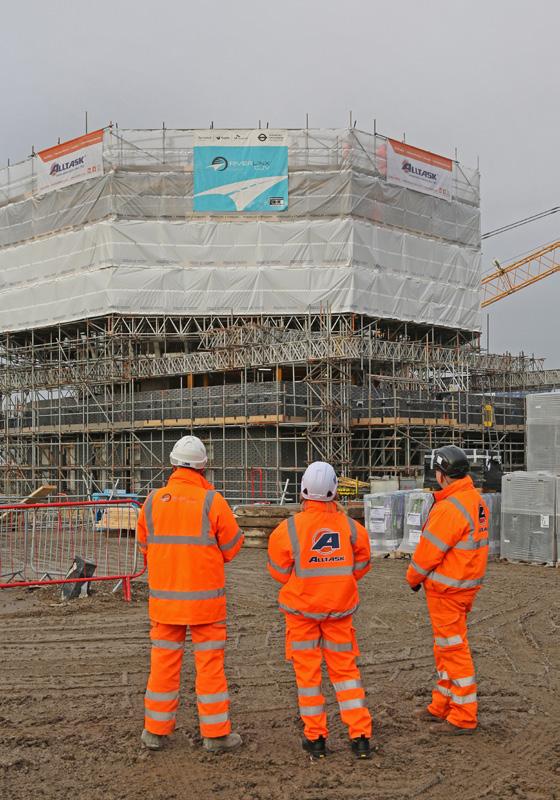
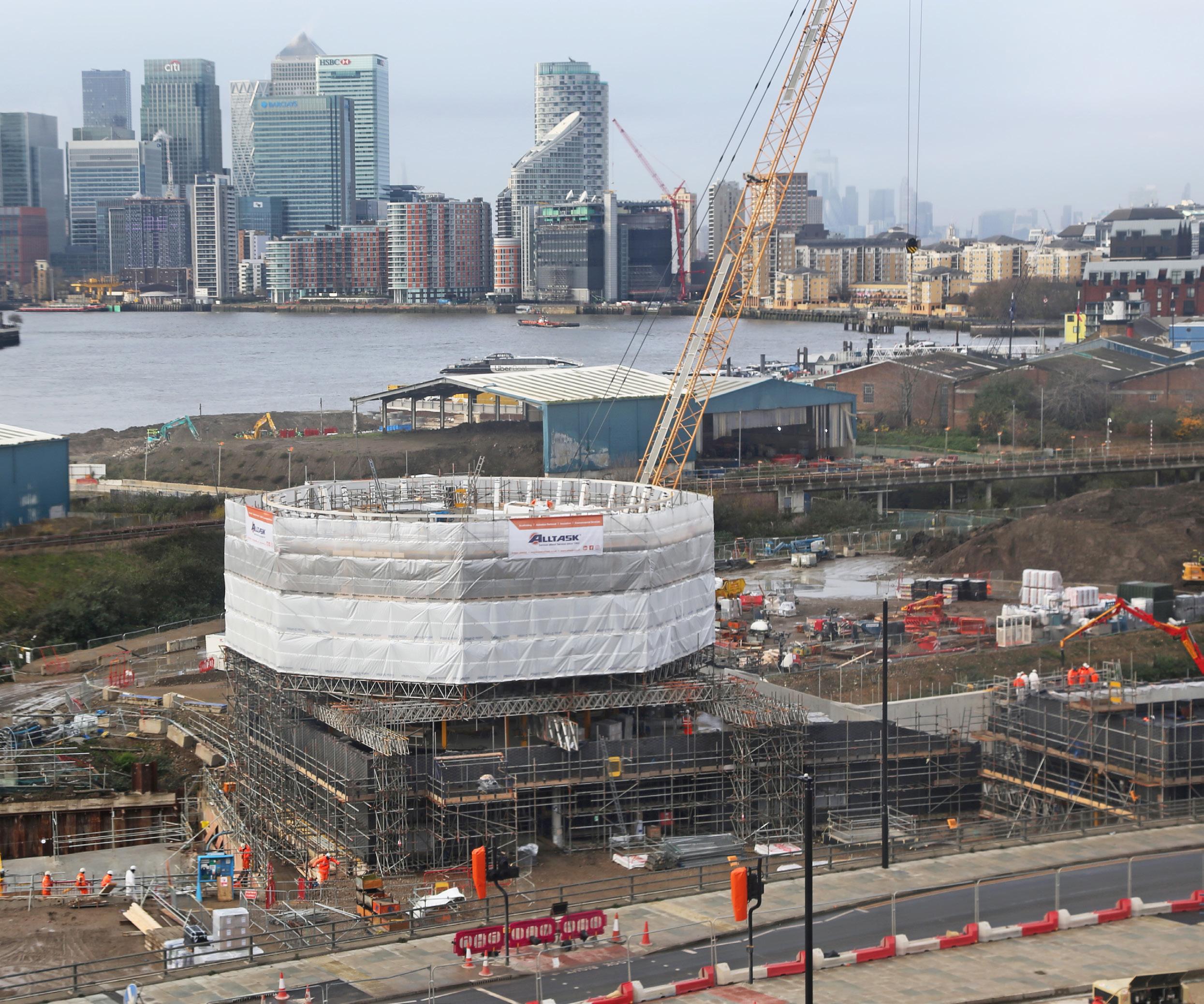
COMMITMENT TO SAFETY AND PROFESSIONALISM
Te Control Building scafolding was not just an architectural feat; it was a testament to the collective efort and professionalism of every team member. Alltask’s unwavering commitment to health and safety was evident in the fact that no lost time occurred due to safety issues throughout the project. Tis achievement underscored the team’s dedication and focus on maintaining the highest standards of safety and quality.
As the Silvertown Tunnel project nears completion, it is a shining example of what can be achieved when vision, expertise and teamwork converge.
Alltask’s access scafolding for the Control Building played a crucial role in making this vision a reality.
In conclusion, the Silvertown Tunnel Control Building stands as a testament to the power of collaboration and dedication in the construction industry. Alltask’s remarkable scafolding design and execution have not only contributed to the project’s success but also served as a reminder of what can be achieved when challenges are met with innovation and determination.
Te Silvertown Tunnel project will undoubtedly shape the London landscape for years to come, leaving a lasting legacy of excellence.
AS THE SILVERTOWN TUNNEL PROJECT NEARS COMPLETION, IT IS A SHINING EXAMPLE OF WHAT CAN BE ACHIEVED WHEN VISION, EXPERTISE AND TEAMWORK CONVERGE
RELIABLE
SCAFFOLDING EXPERTS
Providing c t, reliable scaffold and access solutions globally.
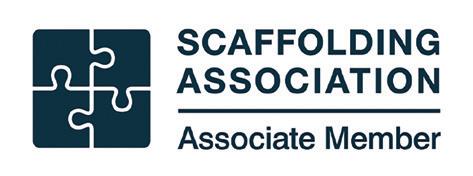

Providing total scaffolding management for projects of all sizes all over the world, giving the client everything they need f rom inception to completion.
OUR SERVICES
• Suppliers of all scaffolding and access products
• Scaffold design and drawings
• Scaffold calculations • Scaffold support
• Access consultancy • Scaffold training
• Quality assurance services
• Provision of scaffolding personnel
WWSA is a proud supporter of the
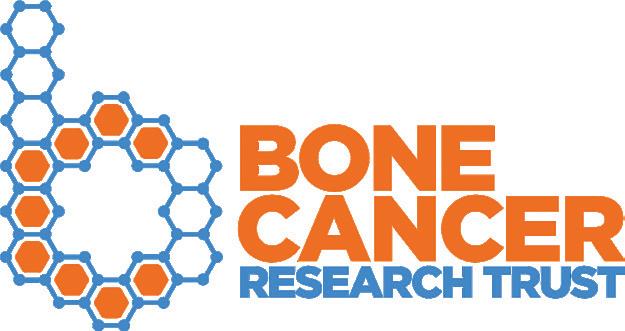
+44
+44
Proud to have worked in Trinidad & Tobago, United Kingdom, Sweden, Poland, Dubai, USA , Germany, South Af rica, Jamaica, Holland, Nigeria and Kazhakstan.
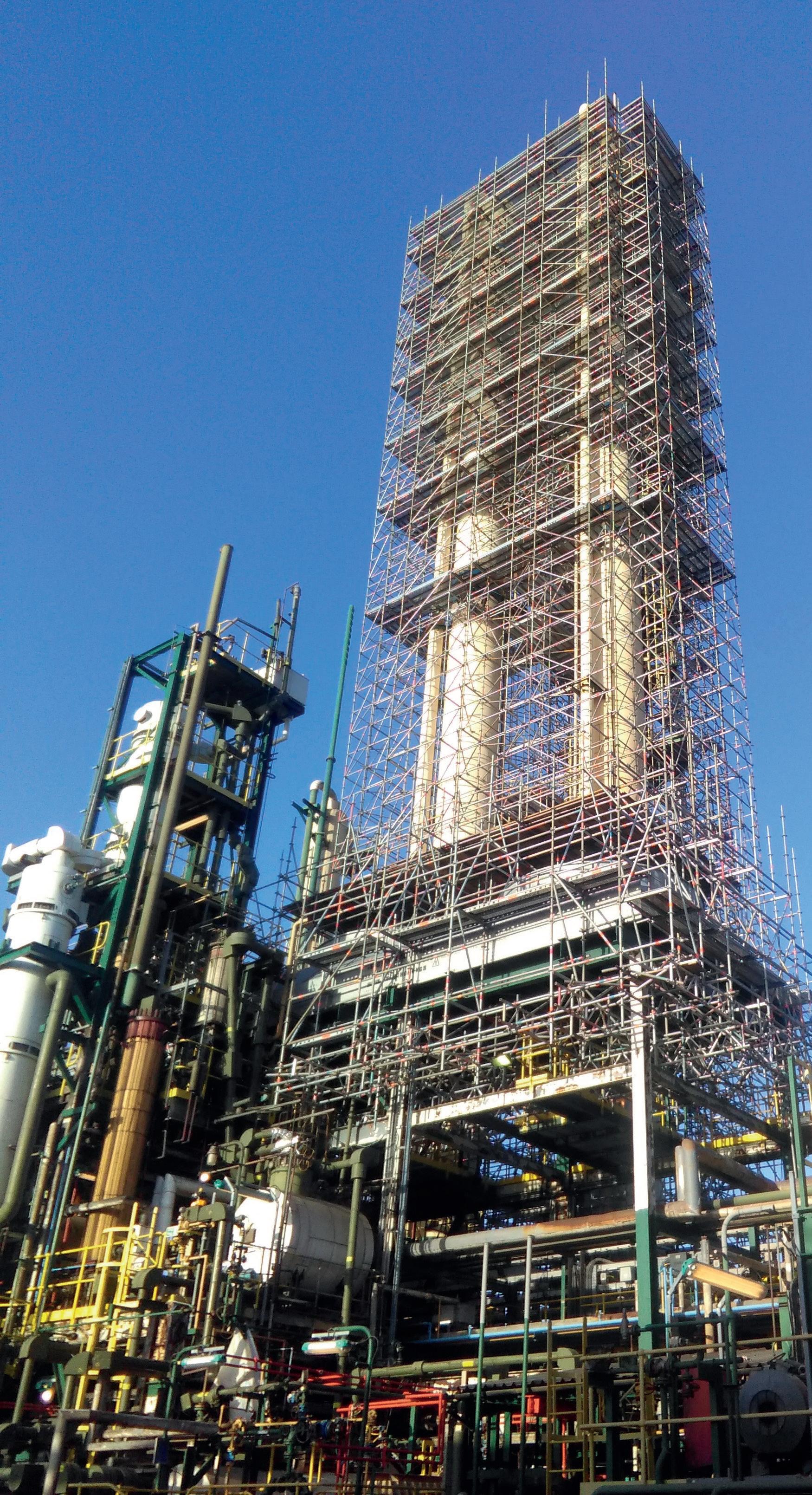
www.wwsa.co.uk
In the heart of BAE Systems’ Broad Oak facility in Portsmouth, a remarkable refurbishment project is under way, ensuring the modernisation and functionality of a highsecurity ofce building
SECURITY CHECK
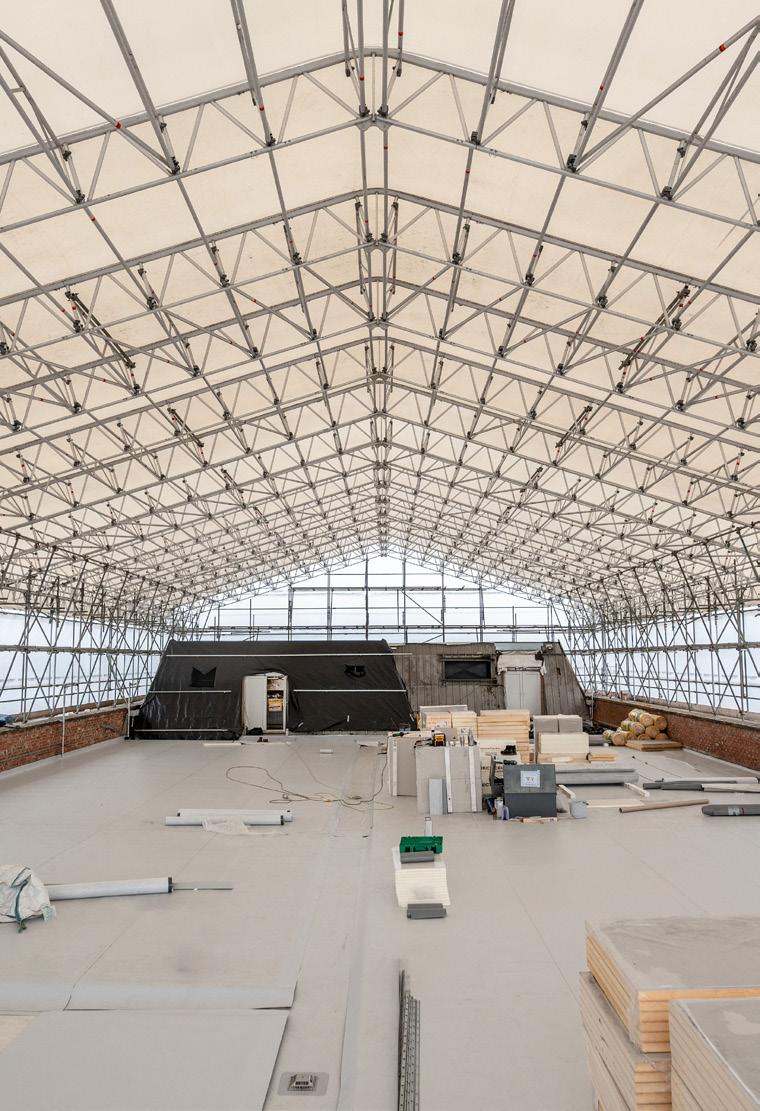
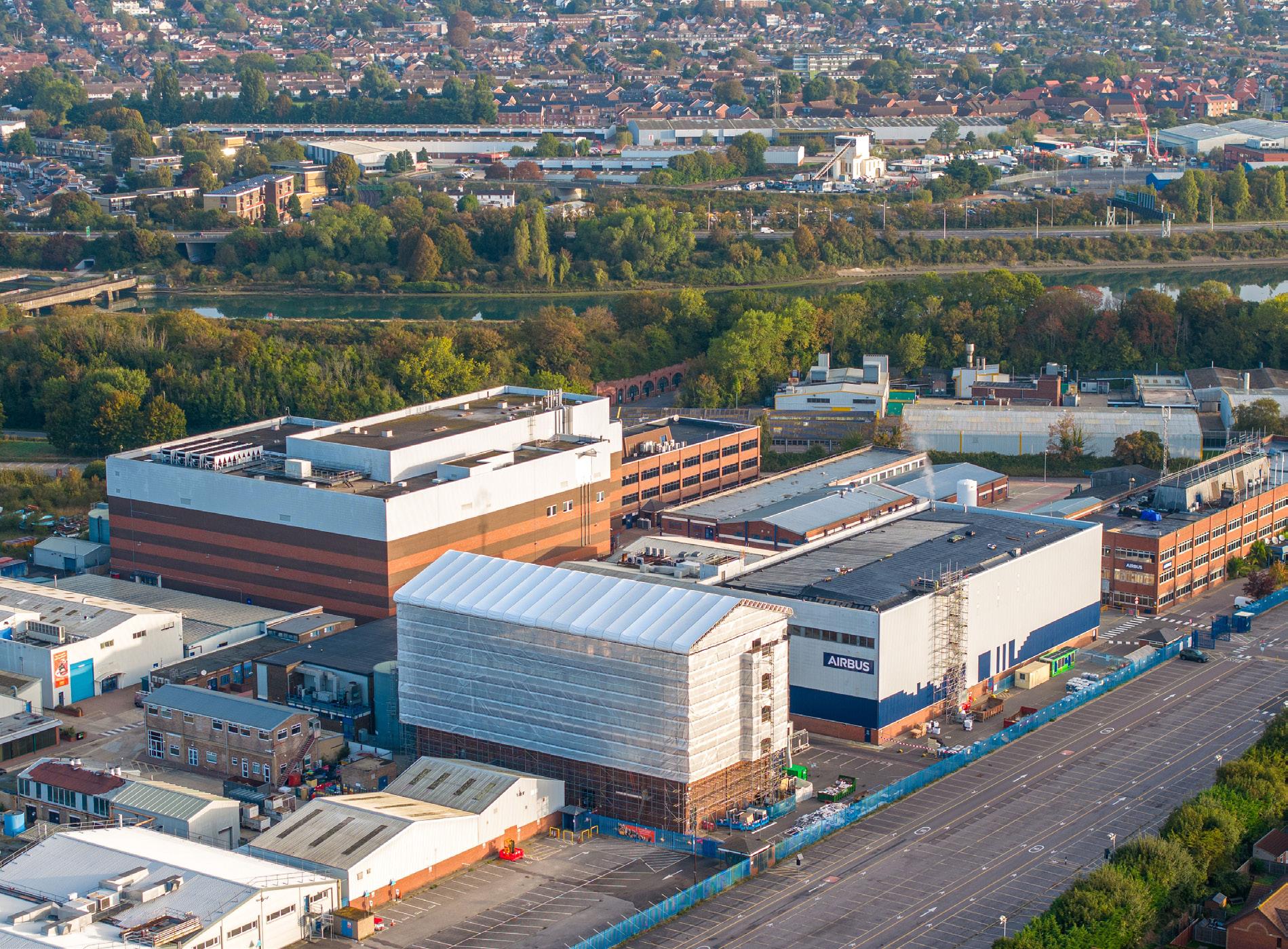
Liddiard Scafolding Ltd, based in Petersfeld, has taken centre stage in erecting the scafolding necessary for this intricate endeavour, utilising the versatile Layher Allround and Keder Roof scafolding system.
Dubbed the ‘Bldg 49 Refurbishment’, the project, managed by Fifh Elevation, entails a meticulous renovation of an ofce complex accommodating various entities involved in government and defense-controlled operations.
Te stringent security measures and complex operational requirements make this undertaking both challenging and crucial.
Steve Chipps, Senior Estimator at Liddiard Scafolding, sheds light on the intricacies of the project, “Our objective was clear – to facilitate safe access for window replacements, internal refurbishments and the installation of a temporary roof for weather protection during roof surface replacement.”
Te scale of the project is substantial, with a building perimeter stretching 138m and 10 lifs installed. Notably, sections of the scafold towered up to 35m, penetrating the warehouse roof, necessitating meticulous planning to ensure structural integrity and safety.
One of the unique challenges encountered was the stringent security protocols within the BAE facility. Chipps emphasises, “Planning was paramount, requiring advanced security clearances for operatives and meticulous
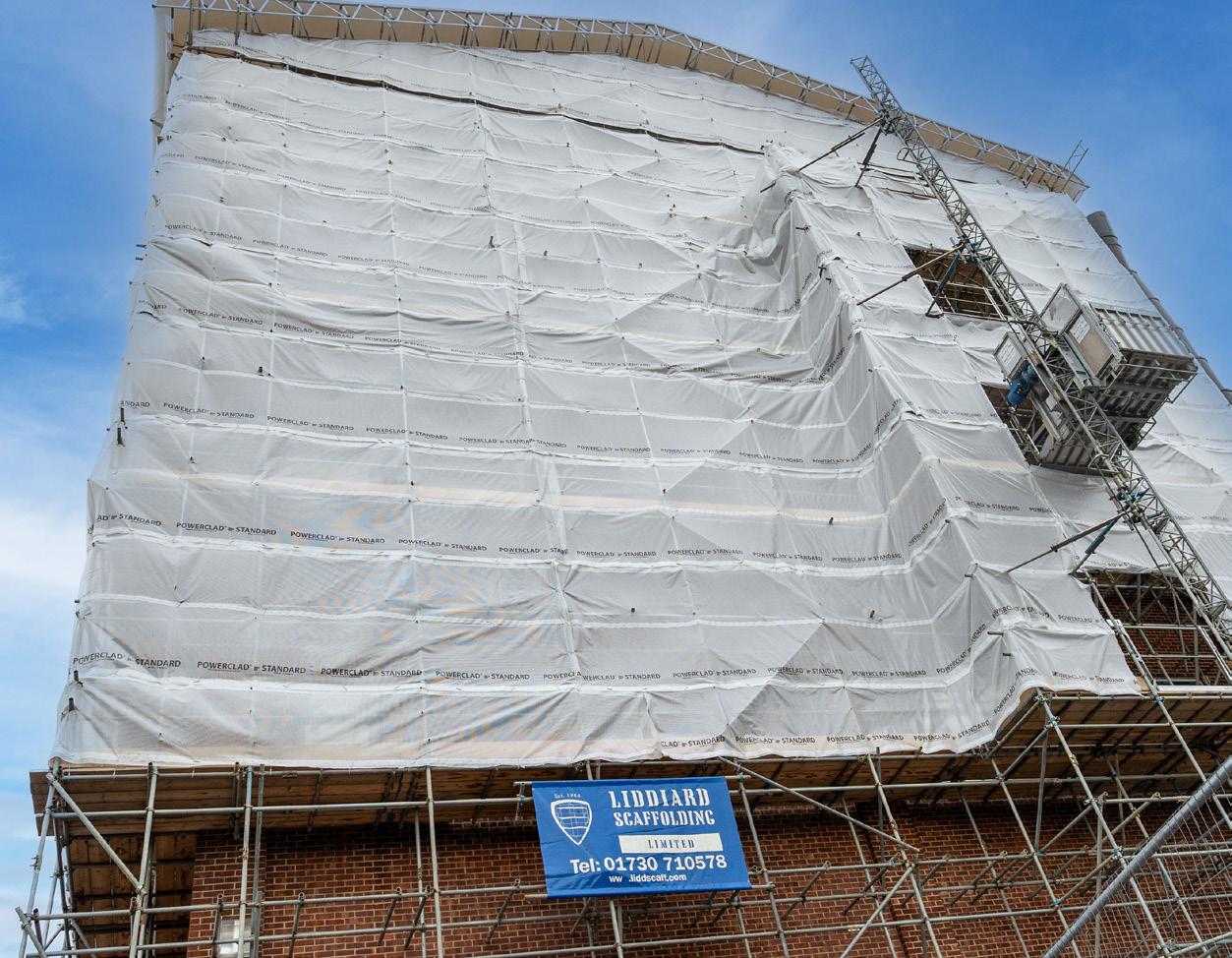
coordination for material deliveries and storage.” Additionally, measures were taken to shield certain areas, with windows covered in silver flm to maintain confdentiality.
INNOVATIVE SOLUTIONS WITH LAYHER
Te Layher Keder Roof System proved instrumental in meeting the project’s demands, particularly in providing crucial weather protection. Its innovative design facilitated the construction of a temporary roof, ensuring the safety and integrity of the refurbishment process amidst varying weather conditions.
Te modular nature of the Layher system allowed for fexible confgurations, showcasing its adaptability to the unique requirements of the project.
Despite the complexities, a collaboration between Layher UK, Liddiard Scafolding, Fifh Elevation and BAE Systems was seamless. Chipps notes, “We fostered a partnership
approach, ensuring alignment on objectives and addressing challenges proactively.” Tis close collaboration contributed to the project’s success, with safety being a top priority throughout the execution.
Refecting on the project’s outcome, Chipps expresses satisfaction with the results achieved. Despite minor delays, the project was completed on time, showcasing the efectiveness of the collaborative eforts. Notably, Liddiard Scafolding received accolades for its exemplary safety standards, garnering praise from Fifh Elevation and BAE’s Safety Inspector.
“To date, this project has gone very well, and it’s been a pleasure working with Liddiard,” remarked the Health & Safety and Quality Manager from Fifh Elevation.
COLLABORATIVE TRIUMPH
In conclusion, the Bldg 49 Refurbishment stands as a testament to the capabilities of Liddiard Scafolding and the efcacy of the Layher Allround system in meeting the most demanding construction challenges.
PLANNING WAS PARAMOUNT, REQUIRING ADVANCED SECURITY CLEARANCES FOR OPERATIVES AND METICULOUS COORDINATION FOR MATERIAL DELIVERIES AND STORAGE
As the project nears its completion, it serves as a beacon of excellence in highsecurity refurbishments, showcasing the seamless integration of Layher’s four core pillars: Service, Support, Solutions and Supply. Tis collaborative approach not only ensured the project’s success but also exemplifed the commitment to delivering unparalleled service and innovation in the scafolding industry.
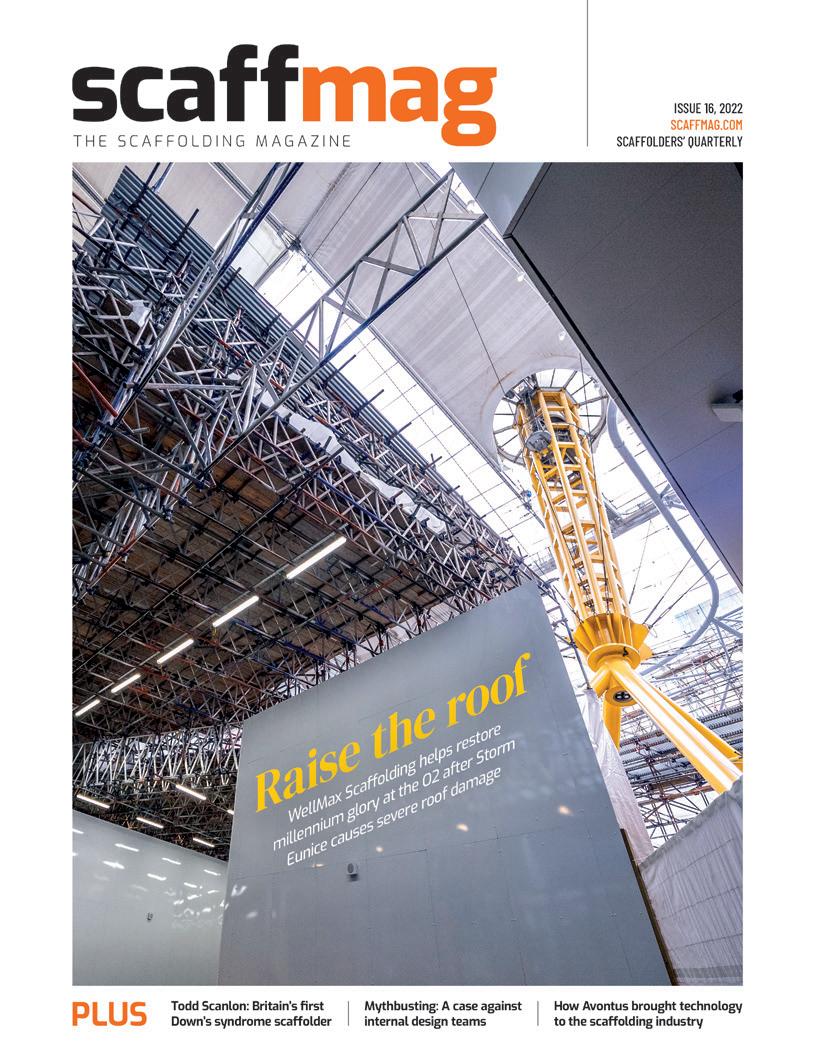
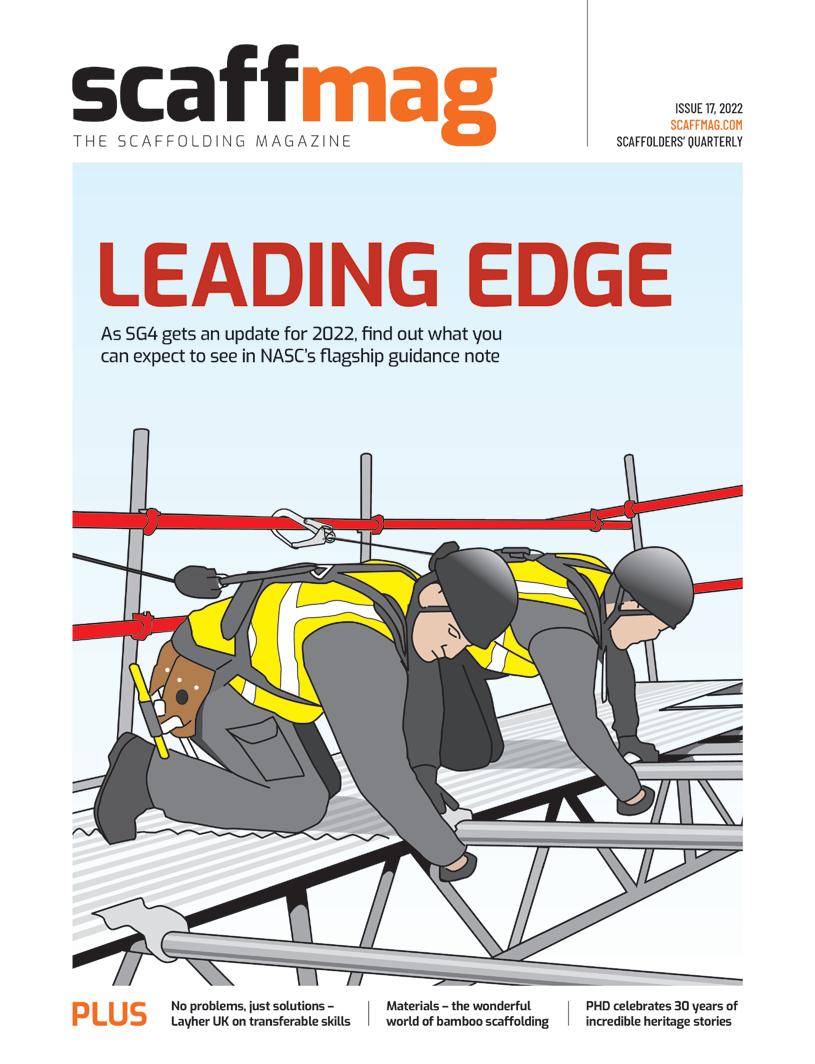
The best-read quarterly magazine in scafolding
At the very heart of the scafolding and access industry, ScafMag has been serving the industry since 2009 by championing best practice, raising awareness of safety issues on-site and promoting business excellence.
ScafMag delivers its mixture of news, views, trends and product updates through digital channels and in print.
ScafMag gives businesses and brands an unrivalled opportunity to advertise their products or services 24 hours a day, seven days a week to a highly targeted audience.
To fnd out more about advertising, contact Jessica Norton on 01472 476024 or email jess@scafmag.com