

THE FUTURE OF SCAFFOLDING
ScaffPlan are transforming the industry with gamechanging tech A DIGITAL REVOLUTION: HOW ALTRAD IS TRANSFORMING ITS TEMPORARY WORKS THROUGH INNOVATION
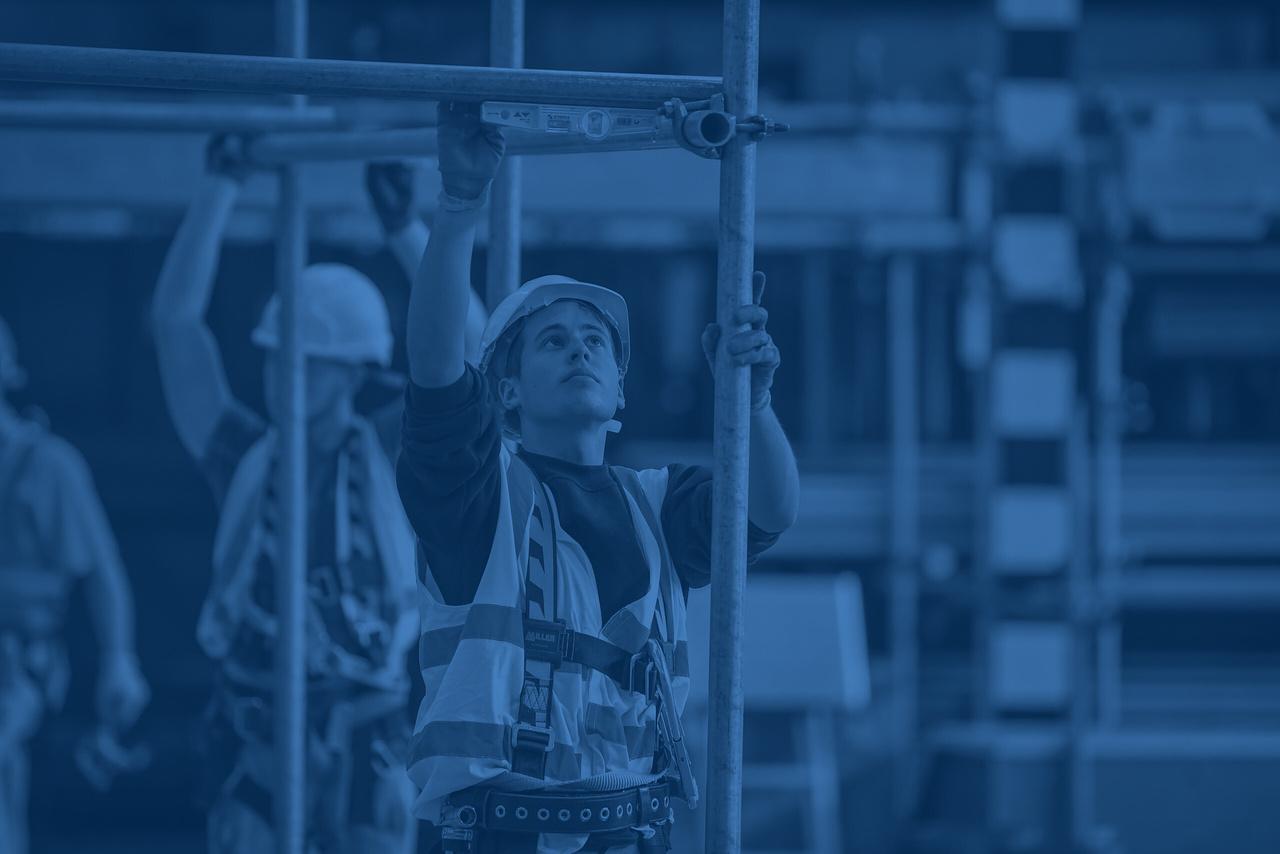
H E R E ’ S S T A N D A R D S . . . A N D T H E N T H E R E ’ S
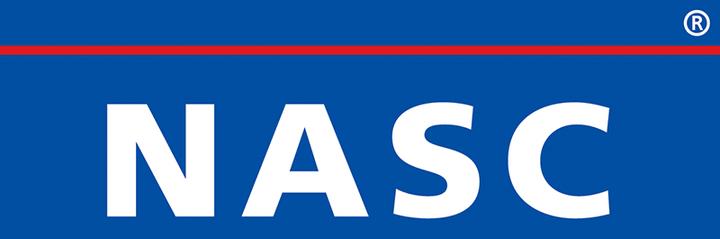
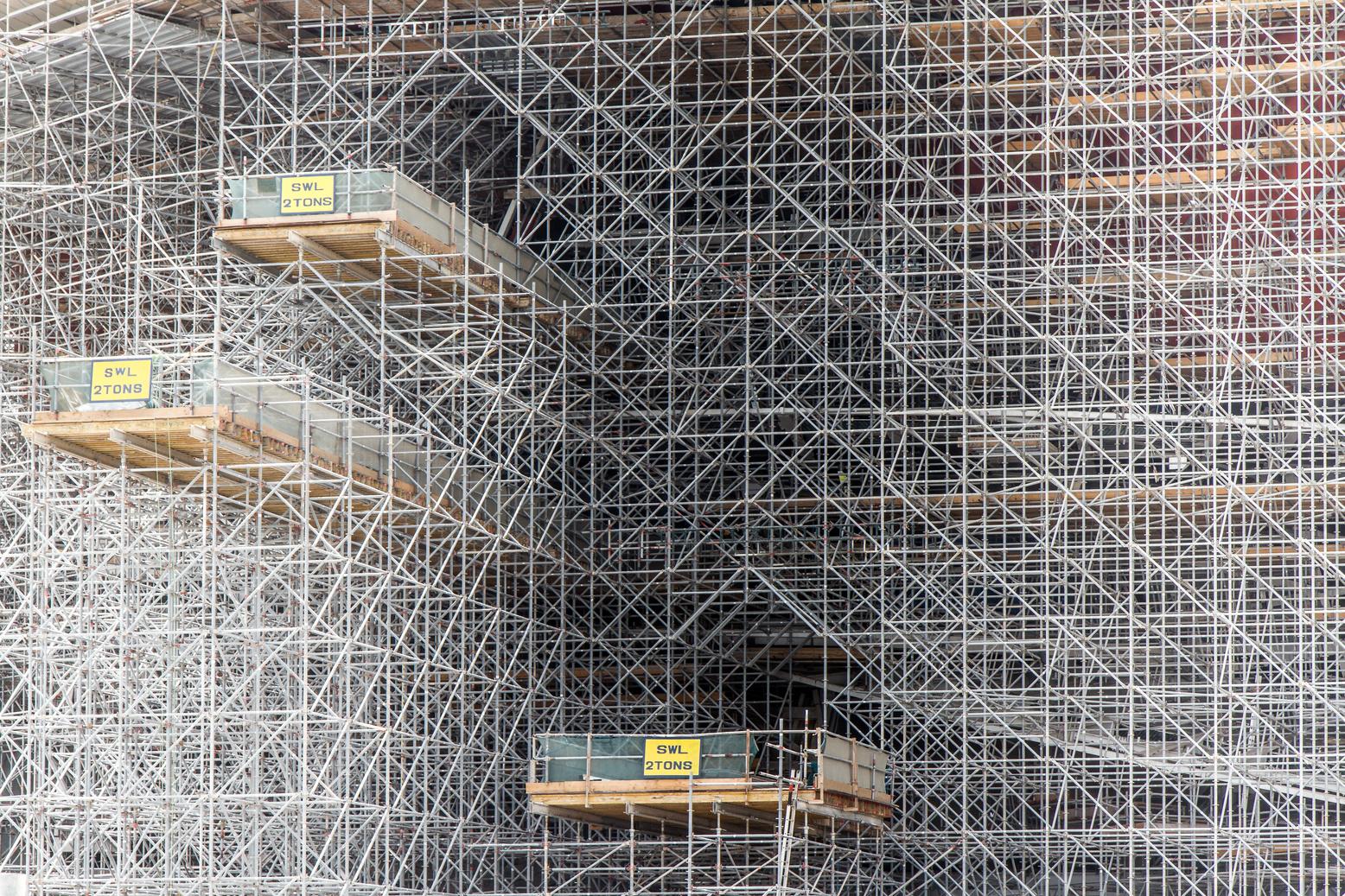
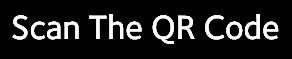
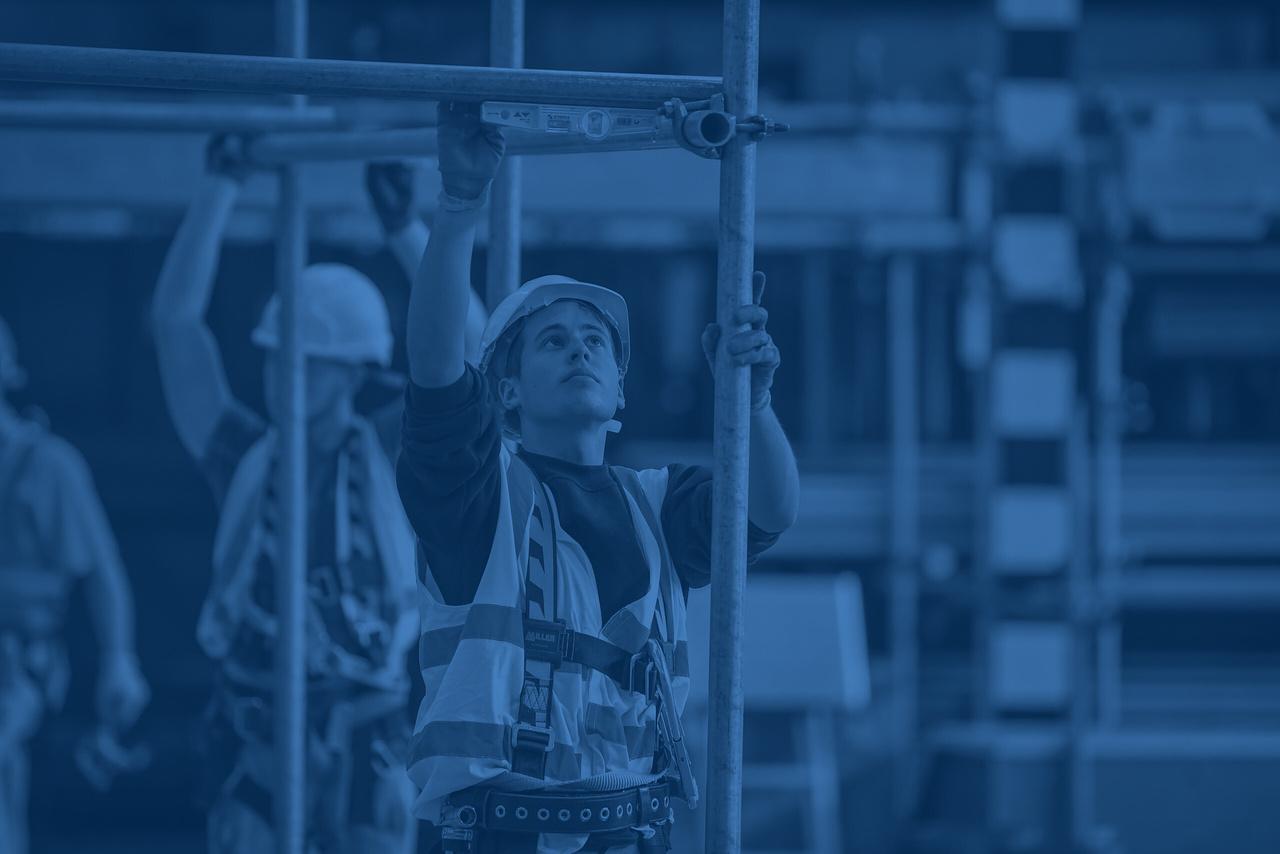
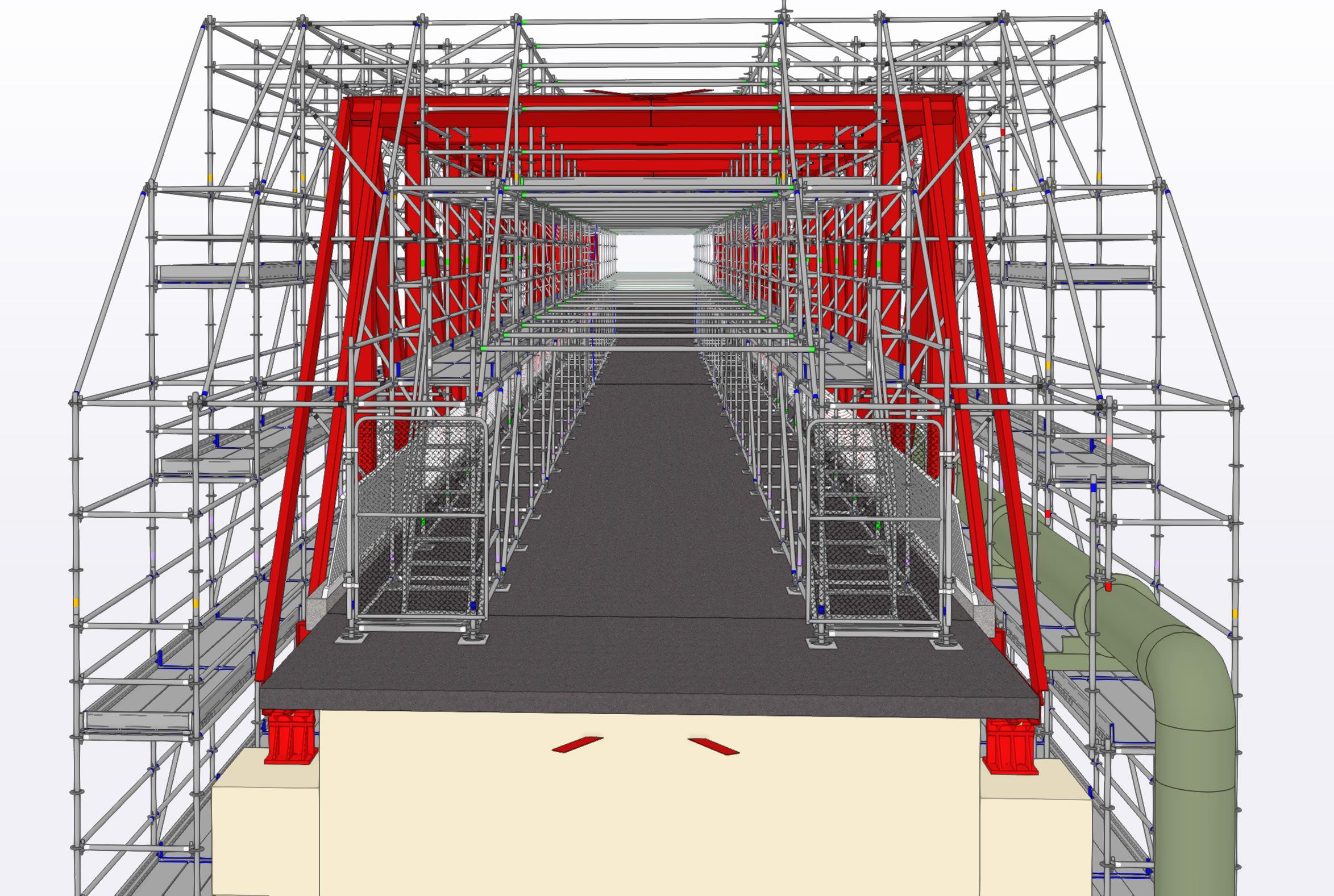
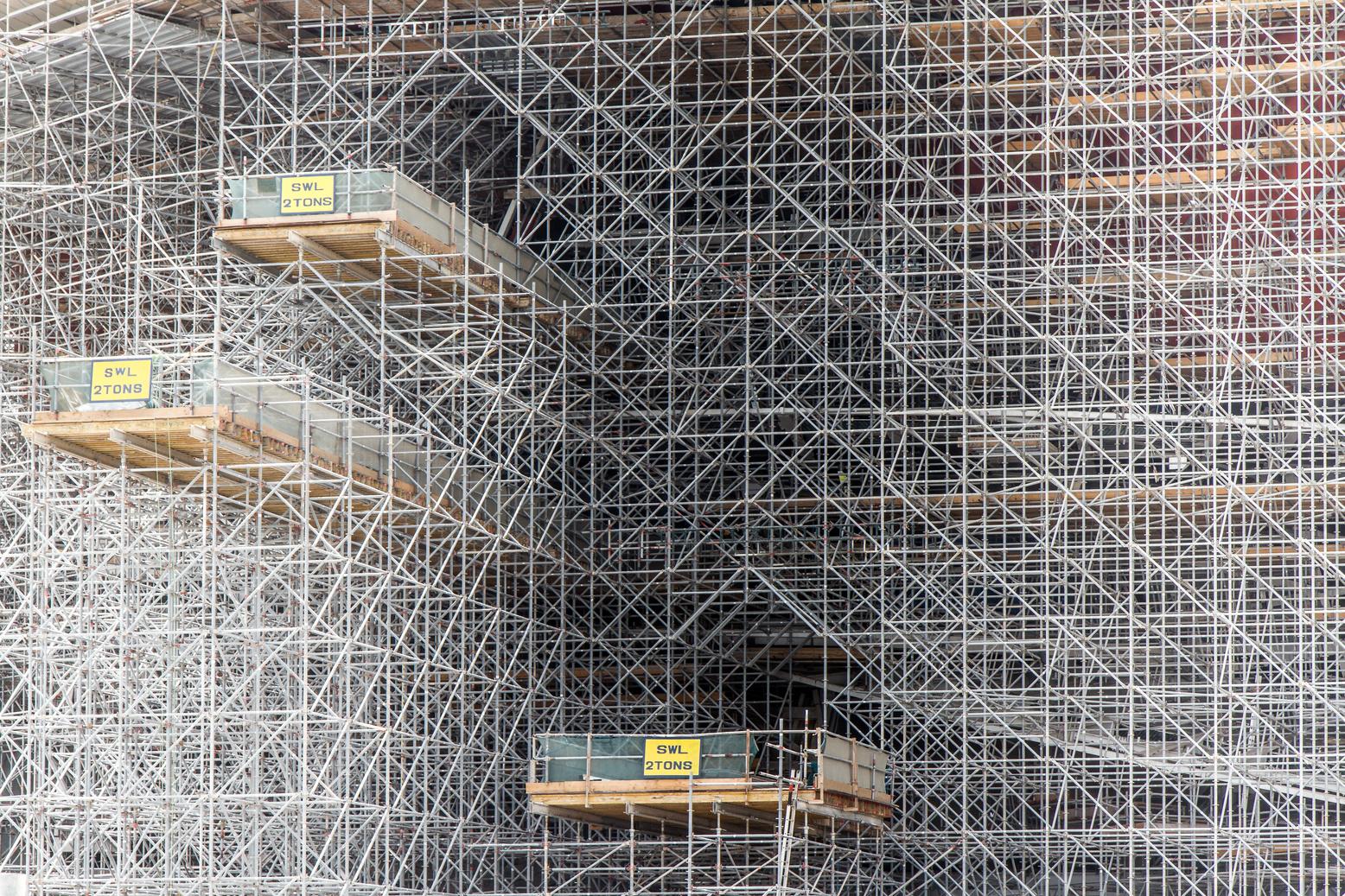
46 Interview
24
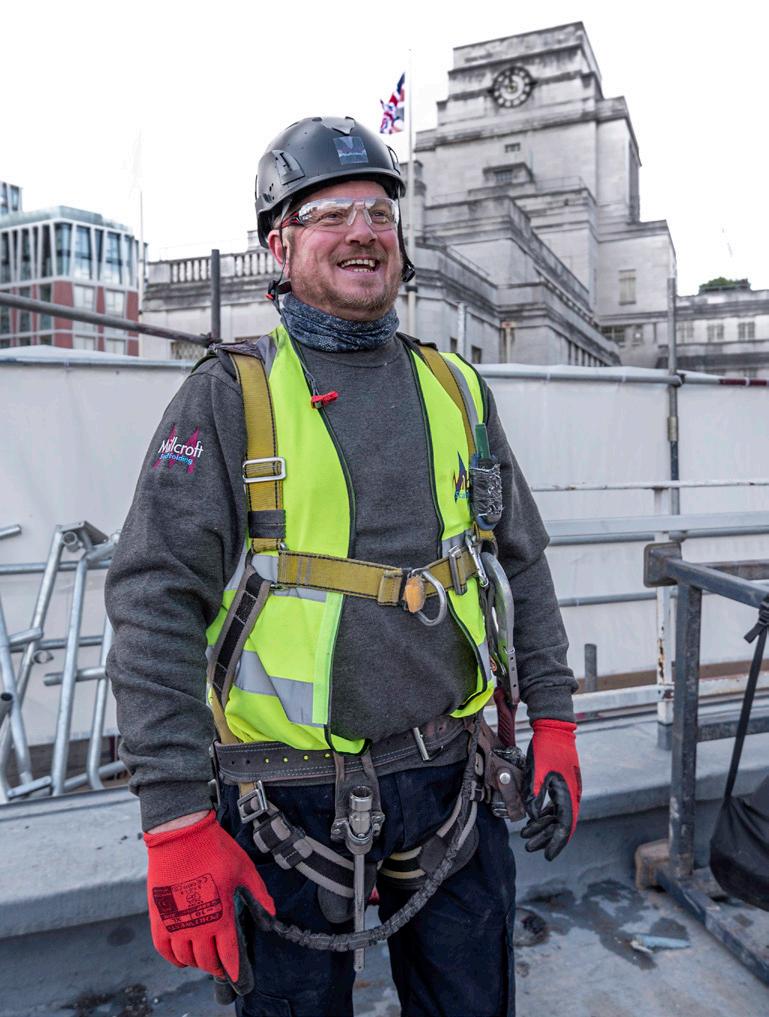
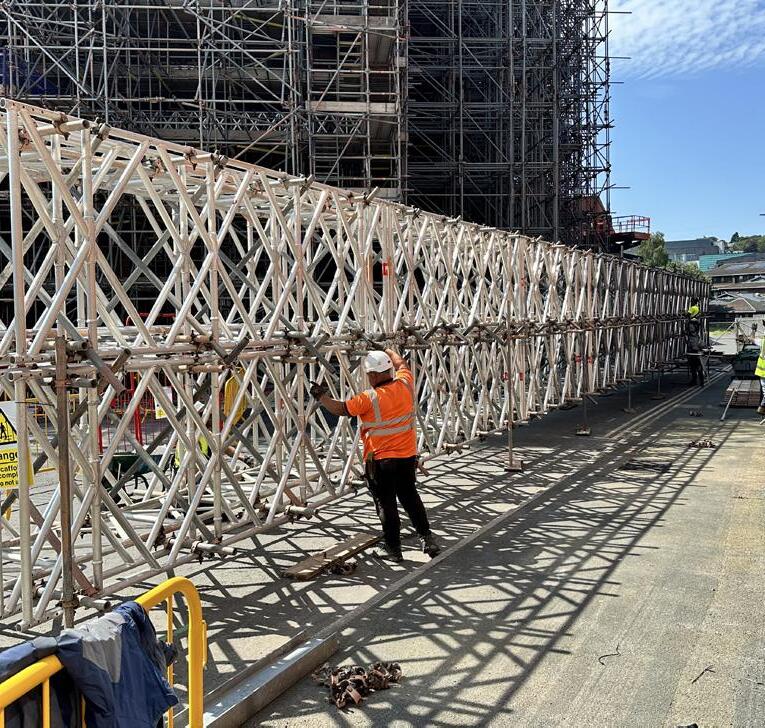
David Brown reflects on the achievements of his two-year presidency what the future holds for the NASC.
50 People
Fulcrum’s David Abraham talks about his time in scaffolding; and Lydia Stanton discusses life in a traditionally male-dominated industry.
56 Business
The gSA aims to unite professionals across the world; Des Moore tells ScaffMag about his new management training course, DM7.
64 Equipment
Australia’s scaffSAFE is set to enter the UK market; a look at Kentledge blocks; and warning from Apollo Cradles about unauthorised X-Beam copies.
70 Opinion
Millcroft’s Billy Jones on the benefits of a career in scaffolding.
76 Events
Winners from Construction News Specialist Awards and nominees for ScaffEx24 awards.


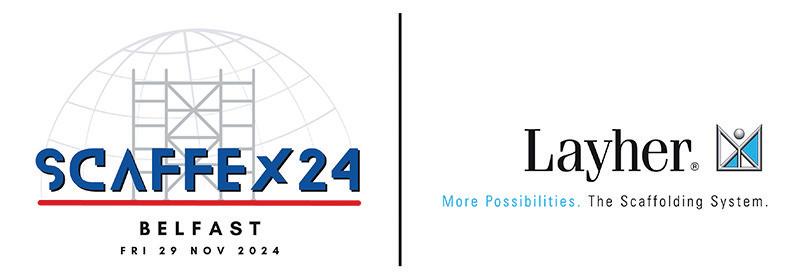

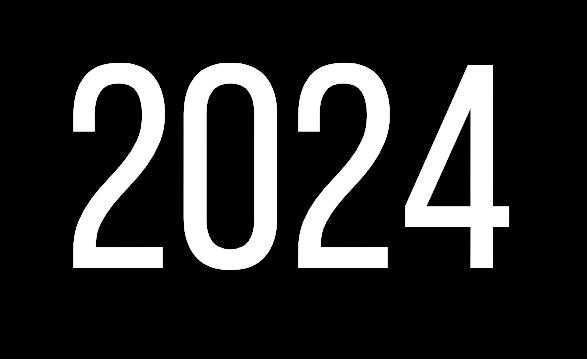



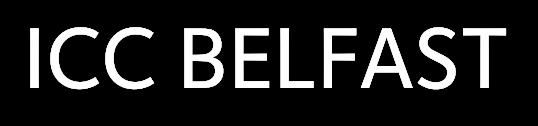
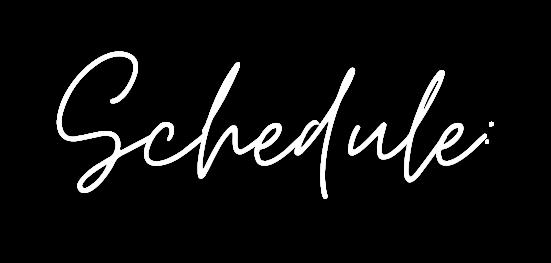
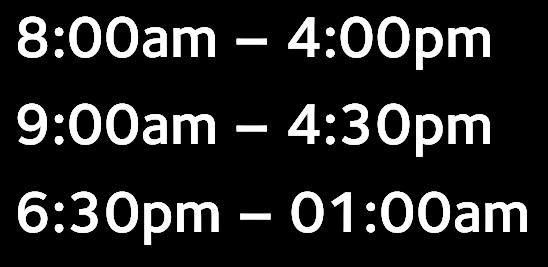
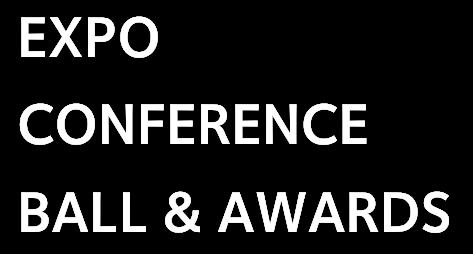


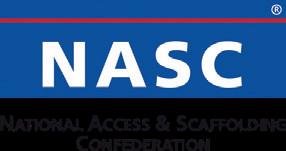

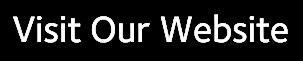
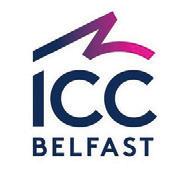

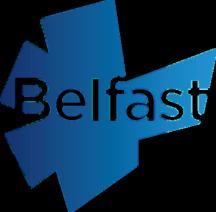


Welcome
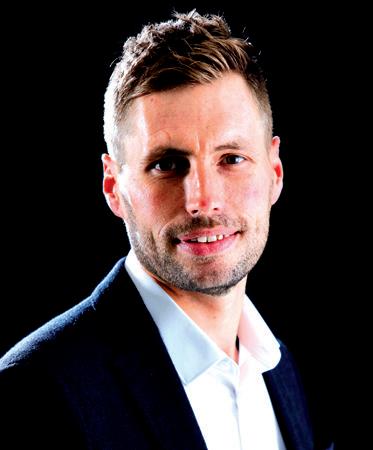
Welcome to the autumn edition of ScaffMag, where we explore the latest innovations and stories shaping the scaffolding industry as we move into the final quarter of the year.
Our main cover feature brings you an in-depth conversation with ScaffPlan directors Simon Boyes and Ben Beaumont. I had the pleasure of sitting down with them to explore their vision for the future of scaffold design, as they unveil major updates and upcoming product releases that are set to transform how scaffolders plan and manage projects. Their insights into ScaffPlan’s growth and direction are sure to inspire.
In our Technology section (page 30), we continue this theme of transformation by examining how cutting-edge tools like automation, artificial intelligence (AI) and 3D modelling are revolutionising scaffold design and temporary works. In an exclusive interview, Colin Murphy from Altrad and Matthew Reeve reveal how these technologies are driving efficiency, collaboration and safety across their projects.
As always, this issue is filled with industry updates and expert contributions. In an exclusive interview with David Brown, we reflect on his term as NASC President, where he discusses the key achievements and ongoing challenges the industry faces, such as addressing the skills gap and enhancing safety measures (page 46).
Meanwhile, on (page 50), we shine a spotlight on the remarkable career of David Abraham. From starting as a trainee in the 1980s to co-founding Fulcrum Scaffold Safety & Training Ltd, David’s journey is both inspiring and transformative. His passion for scaffolding, coupled with his dedication to creating opportunities for ex-offenders through Fulcrum’s HMP training programme, has not only provided valuable skills but also given many a chance to reintegrate into society.
We also feature an insightful article by our long-term contributor Des Moore, who shares invaluable lessons from his 50 years in the scaffolding industry. Des introduces his new management training course, DM7, which is grounded in real-life experience and designed to help scaffolding managers at all levels enhance their leadership skills and drive business growth.
This edition offers a rich blend of technological advancements, personal stories and expert insights to keep you informed and inspired, plus much, much more.
Thank you for being a part of the ScaffMag community. Enjoy reading this issue, and as always, stay safe!
Daniel Norton – Editor dan@scaffmag.com
EDITORIAL
Editor Daniel Norton
T 01472 476024
M 07776 218831
E dan@scaffmag.com @ScaffMagDan
Features writers
Grahame Anderson
Richard Trenchard
Design
Demot Rushe Dermotrushe.co.uk
CONTRIBUTORS
Billy Jones - Millcroft
Scaffolding
Des Moore - MOR1X
ADVERTISING
Manager Jessica Norton
T 01472 476024
M 07776 218831
E jess@scaffmag.com
PUBLISHED BY
ScaffMag Ltd Office G8
The Enterprise Village Prince Albert Gardens
Grimsby DN31 3AT facebook.com/scaffmag twitter.com/ScaffoldingNews
News
The National Access and Scaffolding Confederation (NASC) has officially overtaken its competitors to become the largest trade body in the UK scaffolding sector, announcing record growth with over 800 members
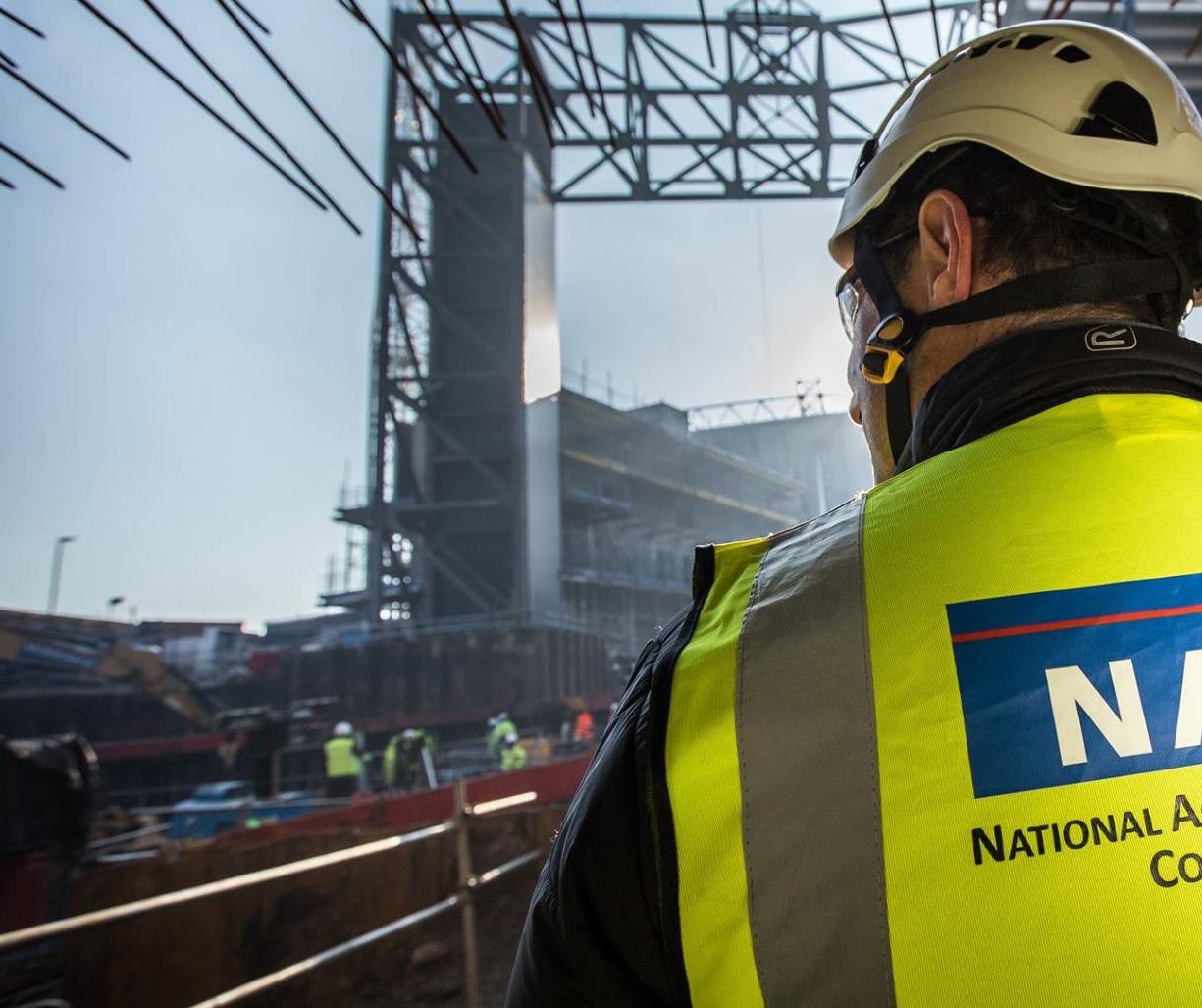
NASC becomes largest trade body in scaffolding industry after membership surge
❖ This surge, which represents a 24% increase in some membership categories over the past year, reinforces NASC’s position as the leading authority on scaffolding standards, safety and quality.
The significant rise in membership follows enhancements to NASC’s entry standards, widely regarded as the most rigorous in the industry. As a result, the confederation’s influence has continued to grow, attracting scaffolding contractors, manufacturers and suppliers who seek the credibility and assurance that NASC’s high standards provide.
PUSH FOR HIGHER PROCUREMENT STANDARDS
The NASC’s recent growth is a testament to its leadership in setting industry standards and reflects its proactive efforts to influence public sector procurement processes. NASC CEO Clive Dickin has written to every local authority, council and unitary authority,
raising concerns about the use of generic accreditations in high-risk scaffolding operations and the unregulated issuing of road permits.
“Recent incidents during the winter storms and less rigorous procurement processes within local government have raised concerns,” Dickin said.
“As the largest scaffolding and access trade body in the UK, we have now raised NASC members’ concerns at the local level and will continue to press for better procurement practices, recognising NASC membership standards and audits as the minimum standard recognised by His Majesty’s Government.”
The NASC’s advocacy for stricter procurement standards, particularly in high-risk operations, highlights the importance of ensuring safety and quality on public sector projects, areas where its membership standards offer a clear advantage.
COMPETITIVE EDGE
NASC’s membership surge comes as a direct challenge to the Scaffolding Association, which has long claimed to be the largest trade body representing the scaffolding industry. This shift in leadership within the trade body landscape signals NASC’s growing influence and its members’ desire for higher standards and recognition within the sector.
The rivalry between NASC and the Scaffolding Association has intensified in the past year, with both organisations competing for contractors, manufacturers and suppliers within the industry.
MEMBER BENEFITS AND INDUSTRY COLLABORATION
NASC’s expanding network of members provides valuable opportunities for collaboration and knowledge sharing within the industry. The organisation’s commitment to promoting best practices,
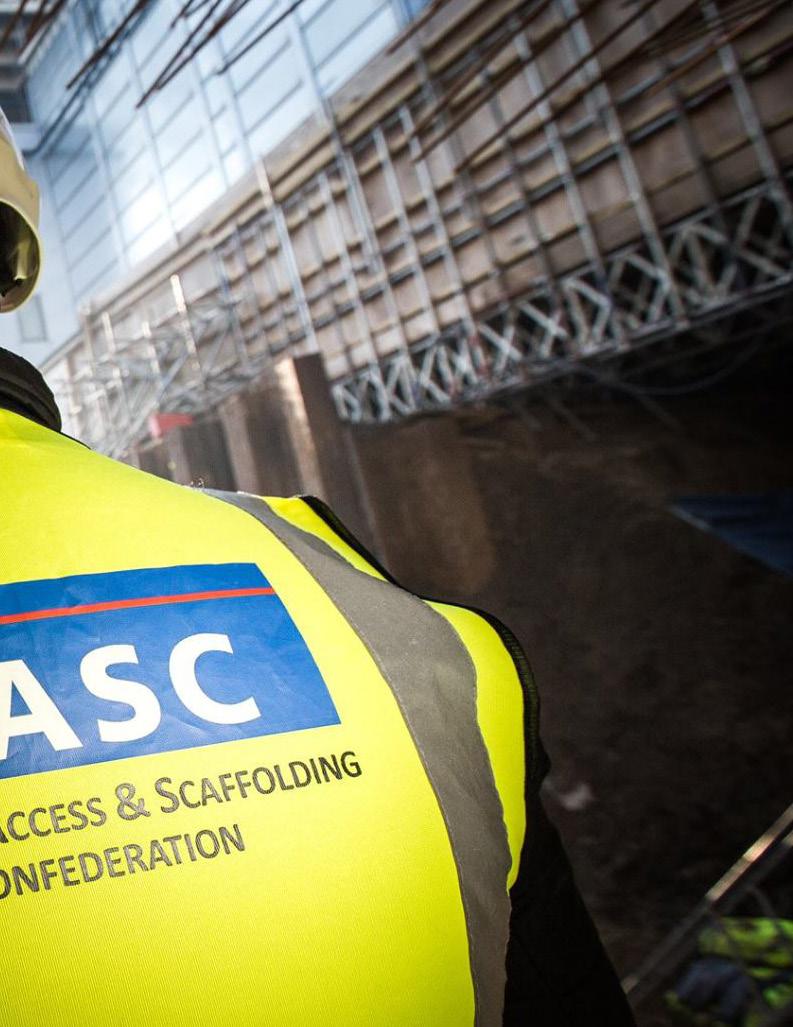
driving innovation and maintaining the highest standards of professionalism has attracted not only contractors but also key manufacturers and suppliers looking to stay ahead of the competition.
As the NASC grows, it continues to serve as a vital resource for scaffolding professionals, offering access to training, industry expertise and opportunities for business growth. This, combined with NASC’s advocacy work and focus on safety, positions its members to be more competitive in securing high-profile contracts and delivering projects to the highest standards.
A FUTURE OF CONTINUED GROWTH
Looking ahead, NASC shows no signs of slowing down. Its continued growth and influence within the scaffolding industry underscore the confederation’s role in shaping the future of the sector. With over 800 members, NASC’s mission to elevate scaffolding safety and quality remains at the forefront of its efforts.
As the scaffolding industry faces new challenges and opportunities, NASC’s position as the leading trade body offers its members a platform for success in an increasingly competitive market. By setting and maintaining the highest standards, NASC continues to ensure that its members are recognised for their excellence, both in the UK and internationally.
SCAFFOLDERS RANKED IN UK’S TOP 3 HIGHEST EARNERS
Scaffolders have been named the third highest-paid trade in the UK, according to new data from Tradefix Direct.
❖ With an average annual salary of £38,365, scaffolders have emerged as one of the most lucrative professions in the construction industry, following closely behind carpenters and gas engineers.
Tradefix Direct’s analysis, based on data from job site Indeed, reveals that carpenters top the list of highest-paid trades, earning £45,482 per year, while gas engineers take second place with an average salary of £39,395. Scaffolders, known for their essential role in supporting large construction projects, are now cashing in on the demand for their skills.
However, regional salary differences within the scaffolding trade are dramatic.
Scaffolders in Chelmsford enjoy the highest earning potential in the UK, pulling in up to £48,199 annually. Meanwhile, those in St Albans are seeing a much lower average wage of £21,744, a striking difference of £26,455. This vast regional disparity highlights the importance of location when it comes to earning power in the trades.
same time, roofers experience the greatest salary fluctuations, with wages varying by as much as £40,967 depending on location.
Though many trade professions show significant regional pay gaps, some, like electricians, have more consistent salaries across the UK. For example, electricians in Westminster earn £40,386 annually, while those in Ripon earn £30,420 – a difference of just £9,966 compared to the large swings seen in other trades.
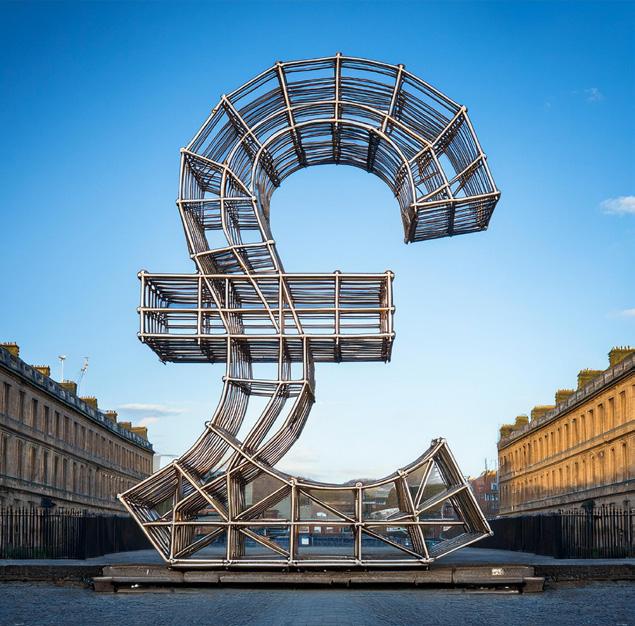
THE DEMAND FOR SKILLED SCAFFOLDERS
DRIVES UP PAY
The rise of scaffolders into the top three highest-paid trades reflects the growing demand for skilled labour in the UK.
As large construction projects and housing developments continue to expand, scaffolders have become indispensable, not only ensuring the safety and efficiency of construction sites but also securing substantial pay cheques for themselves.
The study also explored the broader landscape of UK trade salaries, revealing a patchwork of pay across various professions and cities. Welders in Plymouth take home the highest average salary for any trade, earning an impressive £58,268. At the
As salaries in the trade sector rise, more and more professionals may find themselves considering a career in scaffolding. For those looking to earn top wages in this field, location seems to play a critical role, with key cities offering significantly higher earning potential than others.
IDHG acquires Clarkebond in strategic expansion
❖ Independent Design House Group Ltd (IDHG), a leading engineering design consultancy, has strengthened its position in the industry through the acquisition of Clarkebond (UK) Ltd. This strategic move expands IDHG’s workforce to 140 employees and increases its global reach to seven locations, boosting projected turnover to £10 million.
The acquisition marks a key milestone for IDHG, transforming it into a multidisciplinary consultancy with offices in Bristol, London, Ireland, Poland and Maidstone. By integrating Clarkebond, IDHG enhances its capabilities in permanent works design, complementing
its existing expertise in temporary works.
Tim Burt, CEO of IDHG, will continue to lead the company alongside partner Wojciech Wisnowski.
Ian Fernandes-Johnson will oversee the UK division as managing director, while Michal Rzaski will lead IDHG Poland.
Neil Marks, Clarkebond’s commercial director, and Brian Davis, head of finance, also joined the leadership team.
“We are thrilled to welcome Clarkebond to the IDHG family and look forward to collaborative growth that will benefit our clients and employees,” said Burt.
Founded in 2011, IDHG initially specialised in temporary works design.
With Clarkebond’s addition, the company is now positioned as a fullservice design partner across diverse engineering sectors.
“This acquisition is a game-changer,” added Fernandes-Johnson. “Together, we will provide a comprehensive, end-toend solution for our clients.”
Neil Marks echoed the sentiment: “This deal offers exciting opportunities for both our staff and clients as we continue to deliver outstanding engineering services.”
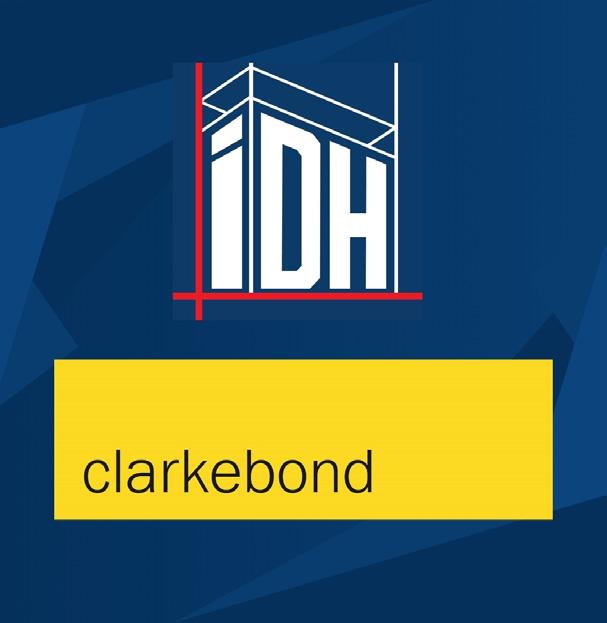
MACE CONSTRUCTION CEO STEPS DOWN
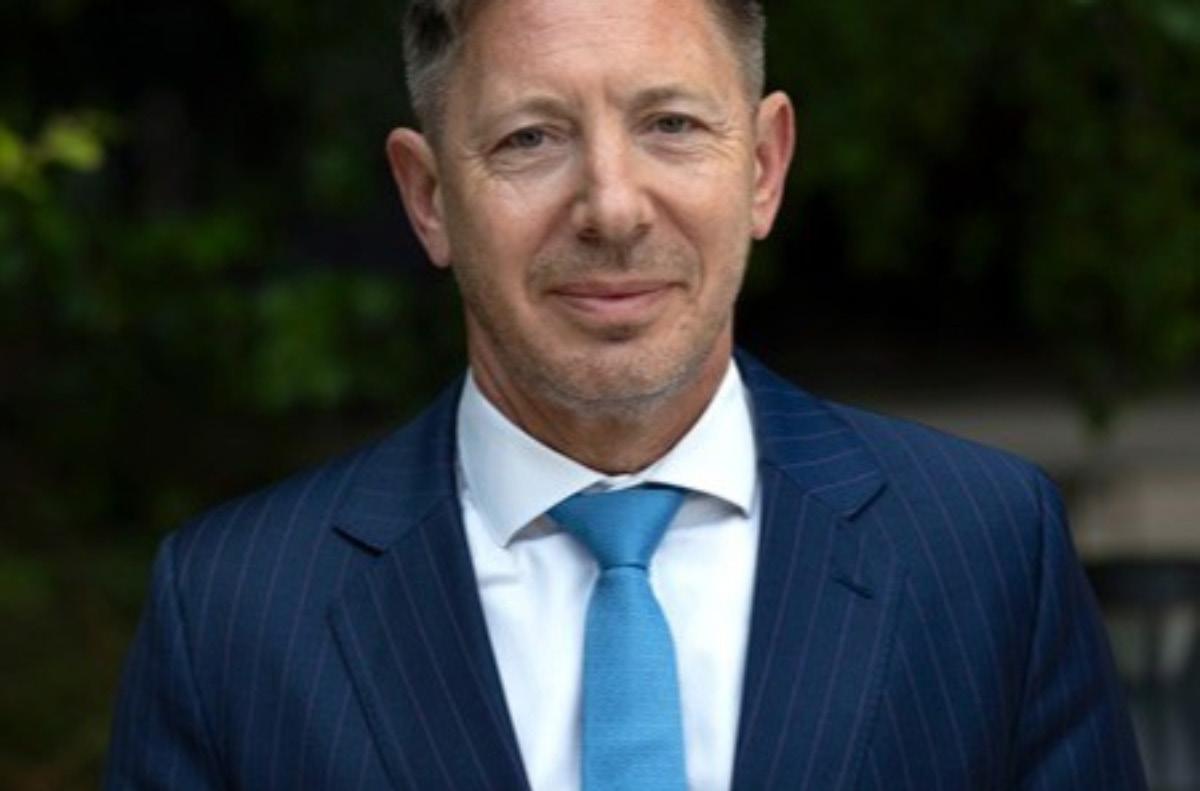
❖ Andrew Jackson, CEO of Construction at Mace, has stepped down for personal reasons just three months after assuming the role. His departure followed his promotion in July when he succeeded long-serving Mace executive Gareth Lewis. Prior to becoming the head of the construction division, Jackson served as Chief Operating Officer, having joined Mace
in 2015 after a 26-year career with Laing O’Rourke.
With Jackson’s exit, Group Deputy CEO Jason Millett will temporarily oversee the construction division while Mace searches for a permanent successor.
In a statement, the company said: “Mace Group has announced that Andrew Jackson, CEO for Construction, has decided to step down for personal reasons. Jason Millett, Group Deputy CEO, will act as interim CEO for the Construct Engine, supported by Chief Operating Officer Stephen Jeffery and business unit managing directors, while the recruitment process for a successor is under way. Jason will continue to fulfil his current duties as Deputy CEO and is set to transition to Group CEO in January.”
Mace’s Group Chairman and CEO, Mark Reynolds, expressed his gratitude to Jackson, saying, “I would like to thank Andrew for his dedication and leadership over the past nine years. He played a pivotal role in our construction division’s growth and has left a lasting impact on our teams. We wish him all the best for the future.”
ISG ADMINISTRATOR WARNS SUBCONTRACTORS OF NO PAYOUT NEWS IN BRIEF
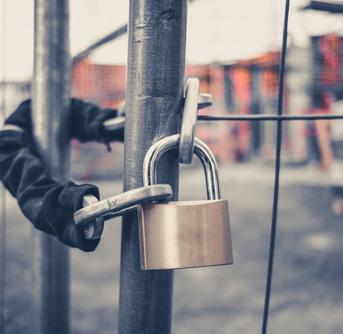
❖ Administrators overseeing the collapsed contractor
ISG have informed subcontractors and suppliers that no funds will likely be available to settle outstanding debts. In letters sent to trade creditors, administrator EY confirmed that no further work would proceed on existing contracts across ISG’s Construction, Fit-Out and Engineering services divisions.
“The companies are being wound down under our supervision as we investigate their financial affairs,” EY stated. “At this time, it is not expected that there will be any funds available for distribution to creditors.” One subcontractor told
the Construction Enquirer:
“We didn’t have high hopes, but hearing this only a few weeks into the administration highlights just how dire the situation at ISG has become. There’s been no word on asset sales or contract novations.
The outlook is bleak.”
EY further explained that, under the Insolvency Act, creditors will be provided with proposals within eight weeks of the administration date (20 September), offering further clarity on any potential changes to dividend prospects.
Despite the grim outlook, creditors are still encouraged to submit claims in the event that the assessment of available funds improves.
PERI UK celebrates 35 years in the industry
❖ PERI UK recently celebrated 35 years of success in the UK construction industry, marking the occasion with a special event at its Rugby head office, including a hog roast for employees across all six offices.
Founded in 1989, PERI UK has grown into a leading provider of temporary works solutions. Its first major project was the Queen Elizabeth II Bridge in 1990, where PERI’s engineering expertise played a key role.
Over the years, the company has achieved significant milestones, including a £15 million redevelopment of its
Brentwood office and the acquisition of Mabey Hire, broadening its service offerings.
Ian Hayes, Managing Director, expressed gratitude for the dedication of employees, customers and partners, and looked forward to continued growth in the years ahead.

NASC TO UNVEIL NEW INITIATIVE AT SCAFFEX24
The National Access and Scaffolding Confederation (NASC) will introduce its highly anticipated Common Assessment Standard (CAS) at ScaffEx24. This initiative aims to simplify the prequalification process for scaffolding contractors, consolidating multiple assessments from bodies like Achilles and CHAS into a single NASC audit. The CAS, backed by the Construction Leadership Council, will replace the PAS91 scheme, making accreditation easier for contractors. With NASC’s ISO9001 and ISO14001 certifications, the organisation is set to become an official Assessment Body by 2025, streamlining compliance and reducing administrative costs for members.
GALLIFORD TRY EXCEEDS PROFIT AND REVENUE EXPECTATIONS
Galliford Try has surpassed its revenue and profit forecasts, reporting a 27.2% increase in revenues, reaching £1.77 billion for the year ending June 30. The construction firm’s building division saw a 17.7% growth, while its infrastructure division posted a 38.8% revenue rise, driven by environmental projects. Pre-tax profits surged nearly 40% to £32.7 million. CEO Bill Hocking highlighted a strong pipeline and strategic contract management as key to their success. Despite broader industry challenges, Galliford Try remains optimistic about future growth.
SPANSET SECURES TWO-YEAR PPE CONTRACT WITH ALTRAD
SpanSet has won a two-year contract to supply personal protective equipment (PPE) to Altrad UK & Ireland. Known for its expertise in height safety and lifting solutions, SpanSet will provide innovative safety equipment to support Altrad’s operations across the region.
SpanSet’s Managing Director, Pete Ward, expressed pride in the longstanding relationship with Altrad, while Altrad’s Head of Technical Authorities, Colin Murphy, praised SpanSet’s class-leading training and innovative approach, which aligns with Altrad’s commitment to safety.
Women Into Construction to cease operations
❖ Women Into Construction, an organisation that has championed gender equality in the industry since 2008, is closing due to what it describes as a “challenging economic climate for both the charitable and construction sectors”.
Kath Moore, Managing Director of the organisation, stated, “After 16 years of changing the face of construction, Women Into Construction has made the difficult decision to cease trading. We recognise that there is still much work to be done to improve diversity in the
industry, but we are immensely proud of what we’ve accomplished.”
Throughout its 16 years, the organisation has supported over 4,700 women, with 3,000 completing industry training and 1,300 securing work placements – ultimately leading to employment for those 1,300 women.
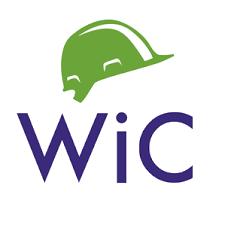
“We’ve collaborated with over 350 companies and built partnerships with training providers, government agencies,
local stakeholders and industry bodies to advance our mission,” Moore added.
“Our efforts have changed the lives of women across the sector, and we trust that these women, alongside their colleagues and supporters, will continue to drive progress in the industry.”
CBW Recovery LLP has been appointed to manage the organisation’s closure.
NASC TO LAUNCH TG30 SYSTEM SCAFFOLDING GUIDANCE
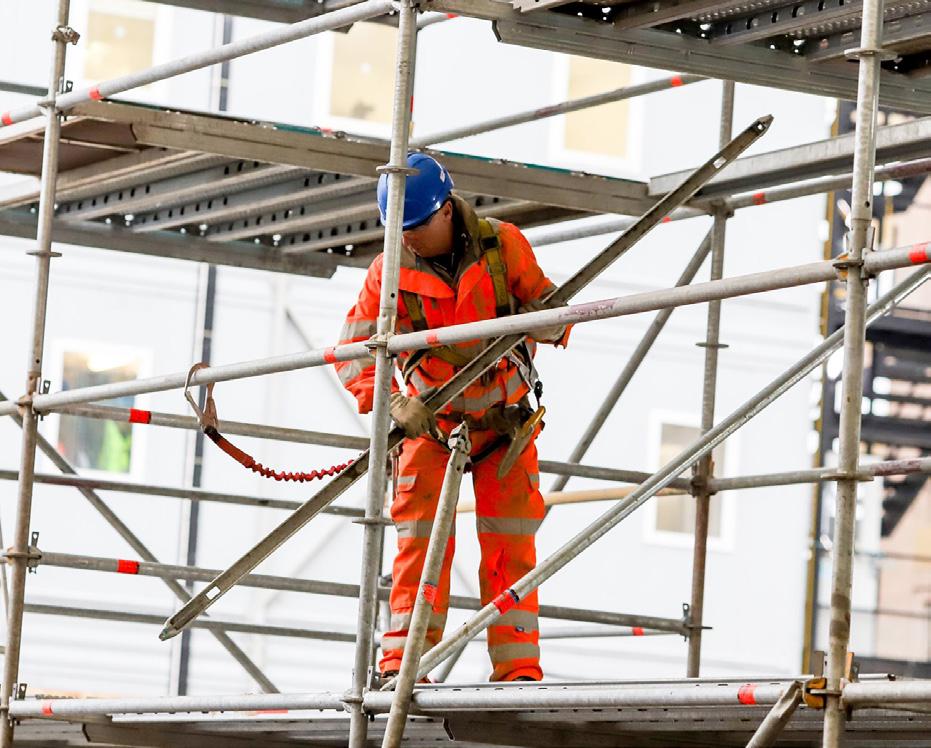
❖ The National Access and Scaffolding Confederation (NASC) will unveil its latest industry innovation, TG30, at ScaffEx24 this November.
TG30 is a groundbreaking guidance suite for system scaffolding, developed in collaboration with scaffolding manufacturers to provide comprehensive, practical standards for the safe design, construction and use of system scaffolds. Much like TG20, which sets the industry benchmark for
tube-and-fitting scaffolding, TG30 aims to offer consistent, reliable guidance that contractors can use to meet safety regulations and demonstrate compliance. Initially focusing on rosette generic systems, the suite will expand to include wedge and cup systems in 2025, with manufacturer-specific products added later.
The TG30 suite includes an e-guide for generating compliance sheets, an operational guide, a design guide, and a pocket-sized user guide, making it a valuable resource for everyone from designers to scaffolders on-site.
TG30’s compliance sheets will follow a format similar to TG20, ensuring consistency and ease of use. These sheets are designed to meet British Standards and the Work at Height Regulations 2005, providing peace of mind for both contractors and clients.
Colin Murphy, Head of Technical Authorities at Altrad UK & Ireland, said, “TG30 compliance sheets will be a game changer, offering a cost-effective, safe approach to system scaffolding while simplifying complex user manuals.”
TG30 also marks a significant step in NASC’s digital transformation strategy, giving its members streamlined access to essential scaffolding guidance. Attendees of ScaffEx24 will get the first look at this innovative guidance system, which promises to set new safety standards for the scaffolding industry.
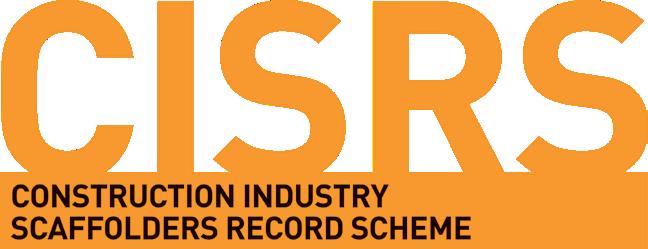
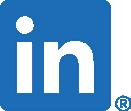

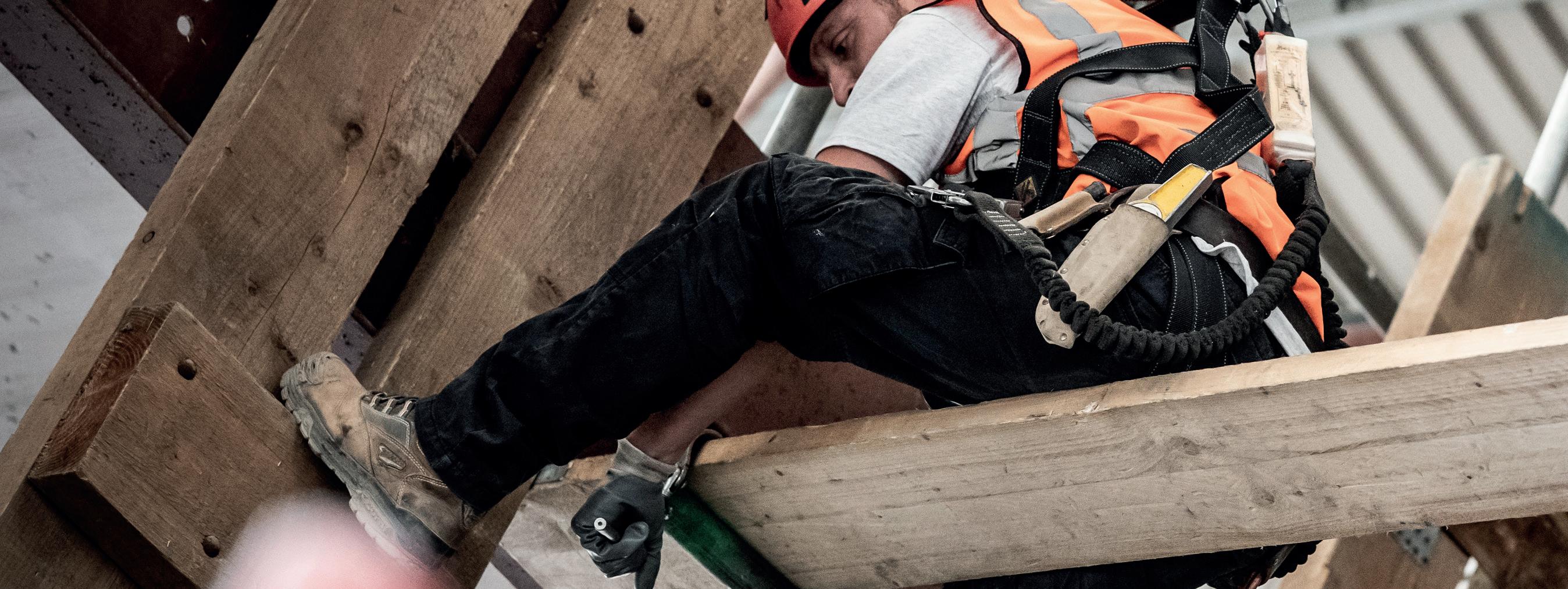
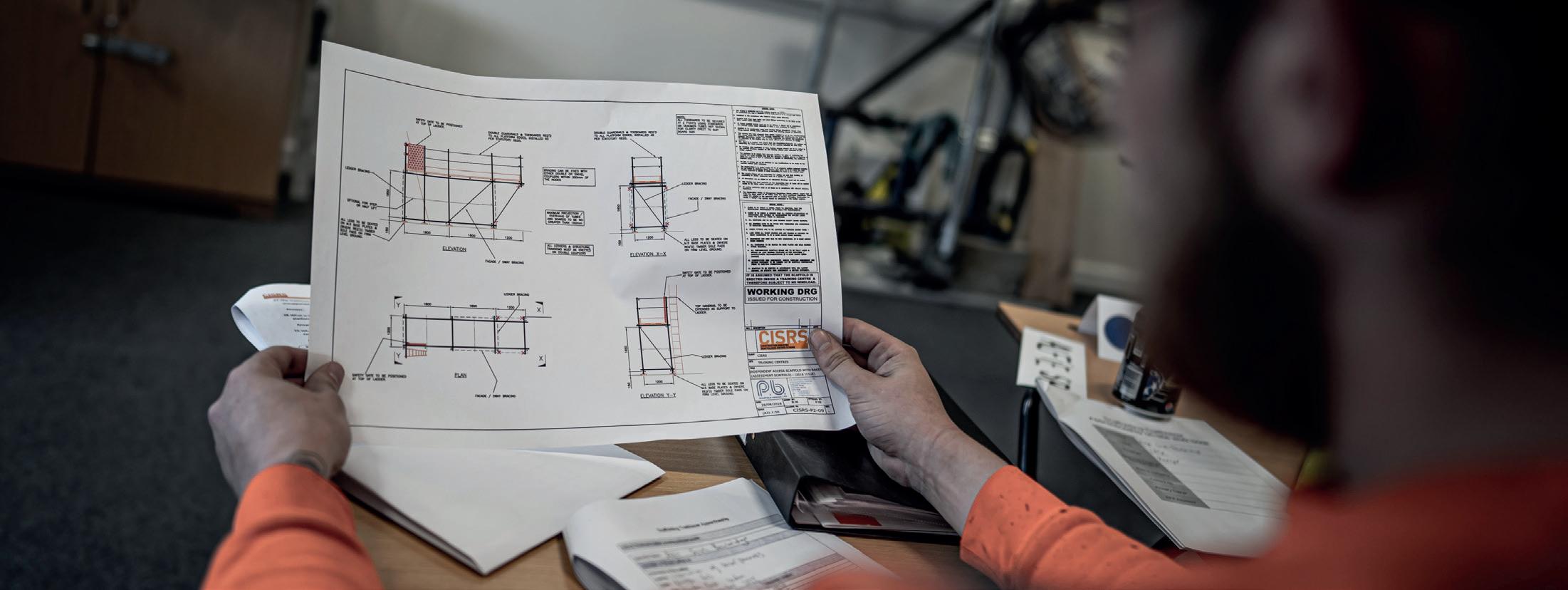

Campaign calls for mental health injuries to be treated equally to physical injuries
Mental health injuries in the workplace have long been overlooked in favour of their physical counterparts. But now, a leading corporate psychologist, Tina Catling, is calling for change. Catling, a Principal Practitioner for the Association for British Psychology and a Fellow of both the Institution of Civil Engineers and the Royal Society of Arts, is leading a campaign that urges mental health injuries to be given the same legal recognition as physical injuries
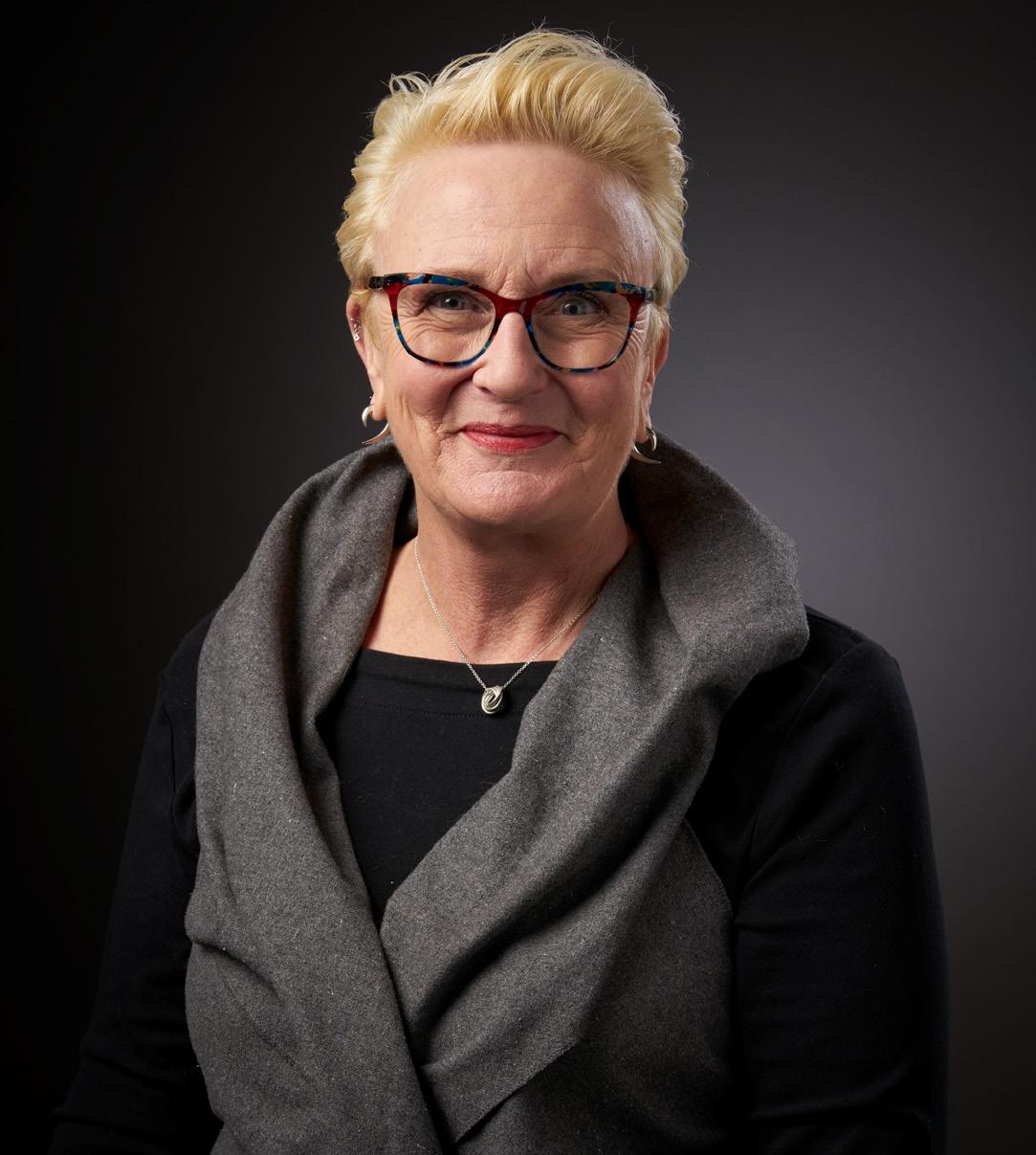
❖ Her mission is simple but powerful: she wants work-related mental health injuries to fall under the scope of the UK’s Reporting of Injuries, Diseases and Dangerous Occurrences Regulations 2013 (RIDDOR). Currently, RIDDOR requires employers to report physical injuries, but there is no such obligation when it comes to mental health injuries.
For Catling, this discrepancy is a glaring omission. “Mental health injuries should be treated on a par with physical ones,” she says. “This would create more psychological safety in the workplace and, in doing so, it would not only save companies significant costs in absences and lost productivity; it would save lives.”
Uditium quam quiscip itintur, secus alician
ihillatur sum ipsusandanis repudi que veliquat que reptassi id ut aut volupta vel ipsae. Ibernatem ut et hilis
A COSTLY PROBLEM
Catling’s campaign comes at a critical time. Mental health in the workplace is becoming an increasingly pressing issue. A recent study by AXA UK found that poor mental health cost the UK economy a staggering £102 billion in 2023. Workplace bullying, stress and harassment remain commonplace in many industries, contributing to low employee engagement and a toxic working environment.
The effects of disengagement aren’t confined to mental wellbeing either. Research from Engage for Success shows that employees who are disengaged at work are 62% more likely to experience a physical injury. This link between poor mental health and increased physical harm demonstrates just how interconnected our mental and physical wellbeing are.
As the founder and director of Leeds-based consultancy ThinkOTB, Catling has seen the consequences of poor workplace culture first-hand. Her firm helps global leaders build psychologically safe teams, fostering environments that support both innovation and employee wellbeing. Having co-authored two best-selling books on workplace culture, she is well-versed in what it takes to build successful, healthy teams.
BRIDGING THE GAP BETWEEN MIND AND BODY
Catling’s campaign raises a fundamental question: why do we continue to separate mental health from physical health in the workplace? “Our heads are connected to our bodies,” she explains. “Yet, if someone suffers a mental health injury as a result of their work, there’s no legal obligation for the employer to investigate or report it.”
For Catling, the solution is simple. If mental health injuries were included under RIDDOR, it would push employers to take psychological safety as seriously as they do physical safety. “We’d see an immediate shift,” she argues. “Employers would be forced to look more closely at issues such as bullying, unconscious bias, microaggressions and the general psychological safety of their staff.”
Currently, there is an existing framework for addressing mental health in the workplace.
ISO 45003, introduced in 2021, is an international standard for managing psychological health and safety at work. However, as Catling points out, there is little incentive for companies to adopt this standard unless there is a legal requirement to do so.
One small but significant step, she suggests, would be to allow mental health injuries to be recorded in the workplace accident book, just as physical injuries are.
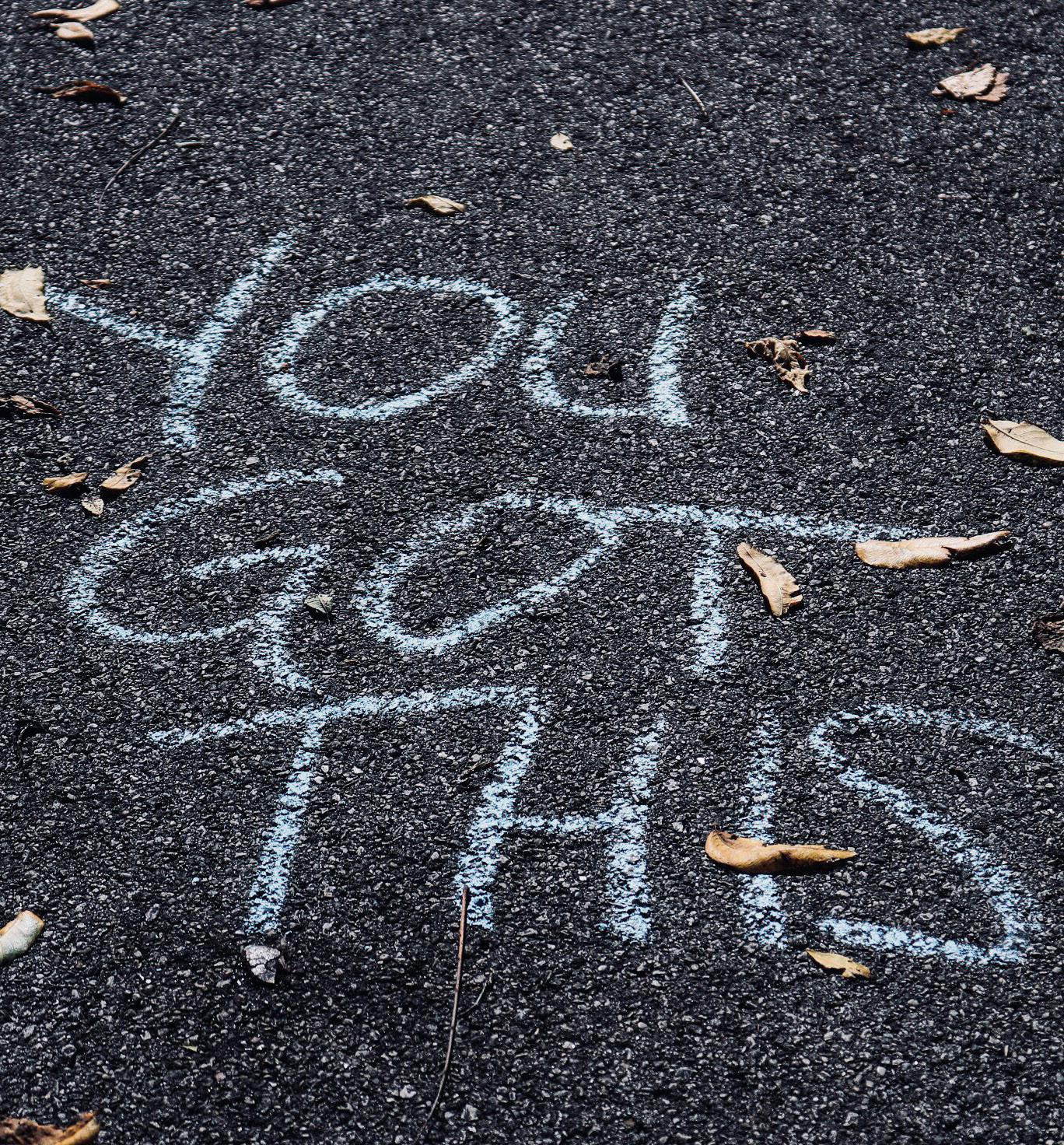
A GROWING MOVEMENT
IF SOMEONE SUFFERS A MENTAL HEALTH INJURY AS A RESULT OF THEIR WORK, THERE’S NO LEGAL OBLIGATION FOR THE EMPLOYER TO INVESTIGATE OR REPORT IT
Catling’s campaign is part of a wider call for change in the workplace. United Minds, part of Unite the Union, is also pushing for similar reforms, highlighting that workplace mental health needs to be taken far more seriously.
For Catling, this campaign is deeply personal. “This cause is very close to my heart,” she says. “I work to create healthy, positive cultures both within my own business and in the organisations we advise. And I coach many senior leaders who are struggling with mental health challenges.”
The fact that psychiatric injuries continue to go unreported and unaddressed is a serious concern for her. “They are not investigated or dealt with in the same way as physical injuries, and that’s simply wrong.”
As businesses continue to grapple with the mental health challenges facing their workforce, campaigns like Catling’s could be the catalyst needed to bring about meaningful change. By recognising mental health injuries on the same level as physical ones, workplaces could take a vital step towards building safer, more supportive environments for all employees.
The message is clear: it’s time to treat mental health with the seriousness it deserves.
3M issues urgent recall for Ultra-Lok lifelines
3M Fall Protection has issued an urgent stop use and remediation notice for select models of their 3M™ DBI-SALA® Ultra-Lok™ Self-Retracting Lifelines due to a potential issue with supplied raw materials
❖ The affected products, produced between November 17, 2023, and June 14, 2024, may fail to lock up properly or may inadvertently switch to retrieval mode during a fall, posing a serious risk of injury or death. Please note: This safety alert does not apply to products sold in Europe under the CE mark.
AFFECTED PRODUCTS:
• 3503882: Stainless Steel Cable, 50ft (specific lots impacted)
• 3503886: Galvanized Cable, 50ft (all lots within date range)
• 3503887: Stainless Steel Cable, 50ft (all lots within date range)
• 3503889: Stainless Steel Cable, 50ft (specific lots impacted)
Additionally, associated tripod systems with model numbers 8301076, 8301077, 8301078, 8301090 and 8301091 are impacted if they include the specified self-retracting lifelines.
IMMEDIATE ACTIONS FOR END USERS:
Identify affected units: Check the model number, manufacture date and lot number on the device label. Compare this information with the detailed list provided in the notice.
Submit repair requests: If your unit is affected, submit a repair request using the provided QR code or visit the specified web link. 3M will cover repair and shipping costs.
Await instructions: Once your request is submitted, you will receive a repair authorisation number and return shipping instructions from 3M’s Block Repair Customer Service department.
ACTIONS FOR DISTRIBUTORS:
Check inventory: Verify if you have any of the impacted products in stock.

Submit repair requests: Use the provided QR code to submit a distributor stock repair request. Forward the notice to customers who may have purchased the affected products and assist them as needed.
3M emphasises the importance of following these instructions to prevent potential accidents. No incidents have been reported so far, but adherence to this notice is crucial for safety.
For further information and to access the necessary forms, visit the provided QR code links or contact your 3M Fall Specialist. 3M remains committed to resolving this issue promptly and ensuring the safety of all users.
View and download the official safety notice here: https://scaffmag.com/wp-content/ uploads/2024/08/3M-DBI-SALA-Ultra-LokImmediate-Stop-Use-Notice.pdf
At et re non etur, quis enihiliquodi corrum aditat aut aciis voluptas eatia non plit, cus ut ut mod utaquist, ium abo. Osam aut autem is voluptaque volut quidelesequi sequidel
NASC OUTLINES NEW FIRE RISK MEASURES IN WAKE OF GRENFELL INQUIRY
❖ Following the final report from the Grenfell Tower Inquiry and a recent fire at a residential block in Dagenham, the National Access and Scaffolding Confederation (NASC) has released an important safety bulletin.
The bulletin provides key guidelines to scaffolding contractors, aiming to ensure compliance with the Building Safety Act 2022 and HSG168, the Health and Safety Executive’s fire safety guidance.
With this release, NASC reaffirms its dedication to improving safety standards within the scaffolding industry and clarifies the role scaffolding plays in fire risk management.
The safety bulletin highlights the need for a comprehensive approach to fire safety on construction sites while noting that scaffolding poses a very low fire risk.
It emphasises that external factors, such as the activities of other contractors often influence fire hazards. To address these risks, NASC encourages collaboration across all aspects of construction projects.
KEY
POINTS FROM THE NASC SAFETY BULLETIN:
• Compliance with Legislation: NASC stresses the importance of scaffolding contractors adhering to the requirements of the Building Safety Act 2022 and HSG168 fire guidance. This ensures that all scaffolding practices align with the latest safety regulations.
• Risk Management: The bulletin emphasises proper management of combustible materials, recommending that contractors ensure all materials meet approved safety standards. It also calls for preventive measures to be put in place, including close cooperation with other trades to address potential fire risks throughout the construction process.
• Enhanced Safety Protocols: To reduce fire hazards, the bulletin advises the integration of robust fire safety protocols into scaffolding practices. This includes ensuring proper material storage, maintaining clear access routes, and conducting regular

inspections to identify and mitigate potential risks.
Training and Education: NASC has updated its CISRS (Construction Industry Scaffolders Record Scheme) courses to include fire safety management. These updates aim to ensure that all scaffolding personnel, including managers and supervisors, are knowledgeable about fire risk management and fully compliant with updated safety regulations.
COMMITMENT TO SAFETY
NASC remains committed to supporting its members with clear and actionable guidance on fire safety, reinforcing its position as a leading authority in scaffolding safety.
By following the updated safety guidelines and incorporating enhanced training, scaffolding contractors will be better equipped to manage fire risks effectively, helping to ensure safer construction environments.
New initiative offers school leavers a path into scaffolding
In an exciting development for young people in the North East, a new initiative is opening doors for school leavers to enter the scaffolding industry, significantly boosting apprenticeships and local employment
❖ W@H Solutions, with support from Procure Plus and the Newcastle United Football Foundation, is leading this effort to offer school leavers the chance to gain hands-on experience and potentially secure apprenticeships through Northern Regeneration at the Construction Skills Village.
The innovative programme offers participants a five-day comprehensive training course, introducing them to the fundamentals of scaffolding. Afterwards, they embark on a five-day workexperience placement with a local scaffolding company. If both parties are satisfied with the fit, participants can enrol onto an apprenticeship programme, providing them with a direct pathway into the trade.
With over 80 young people already signed up, this initiative has gained significant interest. The Newcastle

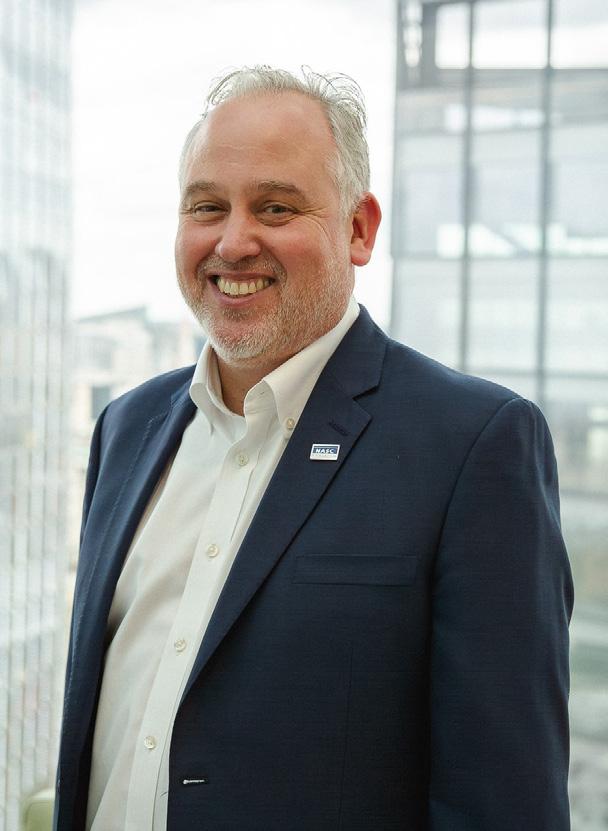
DAVE MOSLEY DEPARTS CISRS
United Football Foundation’s promotion of the programme has led to over 30 individuals, including a 47-year-old, signing up for apprenticeships. The diverse range of applicants underscores the programme’s broad appeal, offering opportunities to both school leavers and older individuals.
Speaking about the initiative, a representative from W@H Solutions said, “We are excited to offer a pathway into scaffolding that is accessible to young people who may not have considered this trade before. By combining training with real-world experience and creating a structured apprenticeship route through Northern Regeneration, we are helping to close the gap between education and employment.”
The programme’s unique structure allows companies to assess potential apprentices while giving participants a real taste of the working environment. Northern Regeneration ensures that those who proceed into apprenticeships receive high-quality, industry-standard training, setting them up for long-term success in the scaffolding industry.
This initiative is seen as a vital step toward securing the future of the scaffolding industry, while also offering young people in the North East a chance to embark on rewarding careers. With strong financial backing from Ofsted, the programme is expected to have a lasting and positive impact on the region’s workforce.
❖ In a surprising move this past July, the Construction Industry Scaffolders Record Scheme (CISRS), the UK’s leading scaffolding and access training provider, announced the immediate departure of its long-standing Managing Director, David Mosley. The announcement, made on 12 July, caught many in the industry off guard.
A CISRS spokesperson stated at the time, “Today we announce the departure of Mr. David Mosley with immediate effect. We thank him for his contributions and wish him all the best in his future endeavours.”
David Mosley’s leadership was pivotal to CISRS’s continued success. During his tenure, the scheme expanded its certification programmes and solidified its reputation as the scaffolding industry’s go-to standard for training and safety. Under Mosley’s guidance, CISRS has played a crucial role in ensuring that scaffolders across the UK receive the highest level of certification and training, upholding stringent safety standards.
Although the reason for Mosley’s departure was not disclosed, and details surrounding the selection process for his successor have yet to emerge, CISRS has assured the industry that the organisation remains committed to its mission of maintaining excellence in scaffolding training.
SCAFFOLDING ASSOCIATION AND CITY & GUILDS UNVEIL FULLY FUNDED SKILLS BOOTCAMPS
❖ To kick-off National Scaffolding Week 2024, the Scaffolding Association has teamed up with City & Guilds to offer fully funded Skills Bootcamps aimed at scaffolding professionals. These bootcamps provide essential training for CISRS Part 1, Part 2 and Advanced Courses, as well as NVQ and skills assessments, all free of charge.
The initiative is open to both CITB and non-CITB registered companies, ensuring wide access to vital qualifications in the scaffolding industry. With the sector contributing £2.86 billion annually to the UK economy and supporting more than 6,000 companies, these bootcamps are an opportunity to enhance workforce skills and meet growing industry demand for qualified professionals.
The Skills Bootcamps offer various CISRS courses, including both Metrix and Layher systems, lasting up to 16 weeks. These courses help workers gain valuable, industry-recognised qualifications that will open doors to career growth in one of the UK’s most in-demand sectors.
Part of the government’s Lifetime Skills Guarantee, the bootcamps are available to adults aged 19 and over, whether currently employed, seeking a career change, or recently unemployed. This targeted training is aligned with the current needs of the job market, offering participants a clear path to advance their careers in scaffolding.
Spaces for these fully funded courses are limited and will be allocated on a first-come, first-served
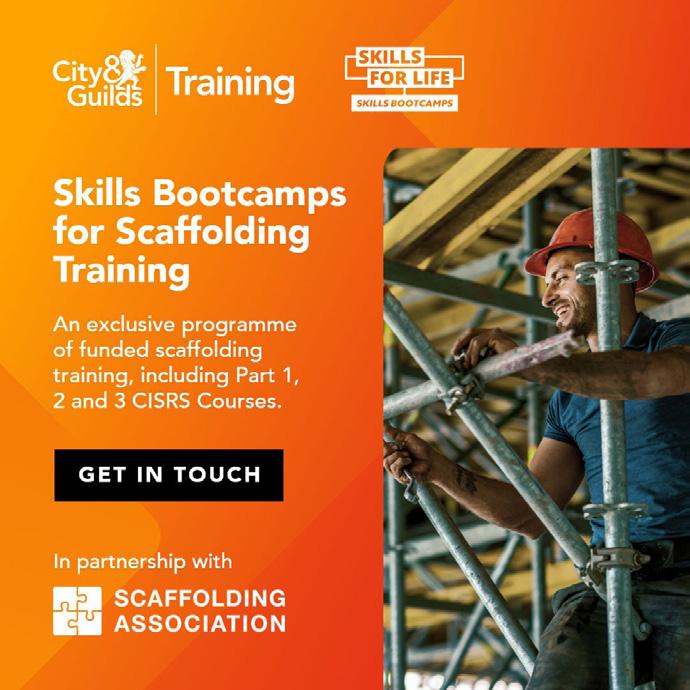
basis. Members of the Scaffolding Association are encouraged to apply quickly by visiting the City & Guilds Training website.
NASC AND CISRS TO OVERHAUL SCAFFOLDING TRAINING FOLLOWING EYE-OPENING
In a bold move that could reshape the scaffolding industry, the National Access & Scaffolding Confederation (NASC) has published its much-anticipated Training in the Scaffolding Industry: Report 2024
❖ The comprehensive report sheds light on the current state of training in the sector, revealing both opportunities and urgent areas for improvement.
NASC, in partnership with the Construction Industry Scaffolders Record Scheme (CISRS), has pledged to take immediate action and use the report’s findings to drive substantial reforms.
The survey, conducted earlier this year, provides an in-depth snapshot of the scaffolding industry as it stood in the first quarter of 2024. With 103 responses from 97 organisations, the report highlights significant challenges facing the sector, including nearly 2,000 job vacancies in
critical scaffold roles, with Part 2 scaffolders being in the highest demand.
The findings underscore the urgent need for strategic interventions to address these workforce shortages and regional disparities in training accessibility.
One of the most striking revelations from the survey is the varying levels of satisfaction with training courses, with larger companies generally expressing higher contentment. However, a consistent theme among respondents was the call for enriched course content, particularly in leadership skills and mental health awareness.
Additionally, the need for more immediate and constructive feedback from training providers was a recurring concern, underscoring the demand for a more responsive and dynamic training environment.
“The membership has spoken,
2024 REPORT
and NASC is listening.”
NASC’s Training and Education Committee is set to take these insights seriously, aiming to close the gaps identified in the training landscape.
The organisation has expressed gratitude to the survey participants and is committed to translating these findings into actionable strategies to future-proof the scaffolding industry.
Clive Dickin, NASC Chief Executive, emphasised the report’s importance:
“The membership has spoken, and NASC is listening. It is without question that improvements are required, and the CISRS board is fully supportive of this.
The feedback from this survey is crucial for enhancing scaffolding training across the UK.”
For those interested in the detailed findings and proposed initiatives, the full report is available for review here.
SKILL SCAFFOLDING’S TRANSPORTABLE PEDESTRIAN BRIDGE WITH LAYHER UK
Skill Scaffolding has partnered with Layher UK to deliver a pedestrian access bridge in Lostwithiel, Cornwall
❖ Together, they’ve supplied a temporary pedestrian bridge using the worldrenowned Layher Allround System, a cutting-edge scaffolding technology known for its versatility, safety and ease of assembly.
The project, known as Skill Bridge, was built in a sensitive environment, designed by Layher UK and completed by Skill Scaffolding. Impressively, the entire project was delivered within an eight-week window, showcasing the efficiency and expertise of the team involved.
The team at Skill Scaffolding has introduced what they’ve dubbed the ‘Skill Bridge, a fully transportable pedestrian bridge built offsite and moved into place at the Lostwithiel rail project. The innovative bridge was quickly installed, and facilitated minimal disruption to both the site and the public.
The installation of a temporary pedestrian bridge can often cause delays or closures, particularly in a busy rail setting. However, Skill Scaffolding’s approach with the Layher Allround Bridging System (ABS) ensured that disruption was kept to a minimum.
By building the Layher Skill Bridge, as Skill Scaffolding refer to it, at their headquarters and transporting it to the site ready for installation, the team was able to reduce the need for prolonged closures and limit inconvenience for pedestrians and rail staff alike.
This method also offers a more timeeffective and cost-efficient solution, something clients in infrastructure projects value highly. In a statement,
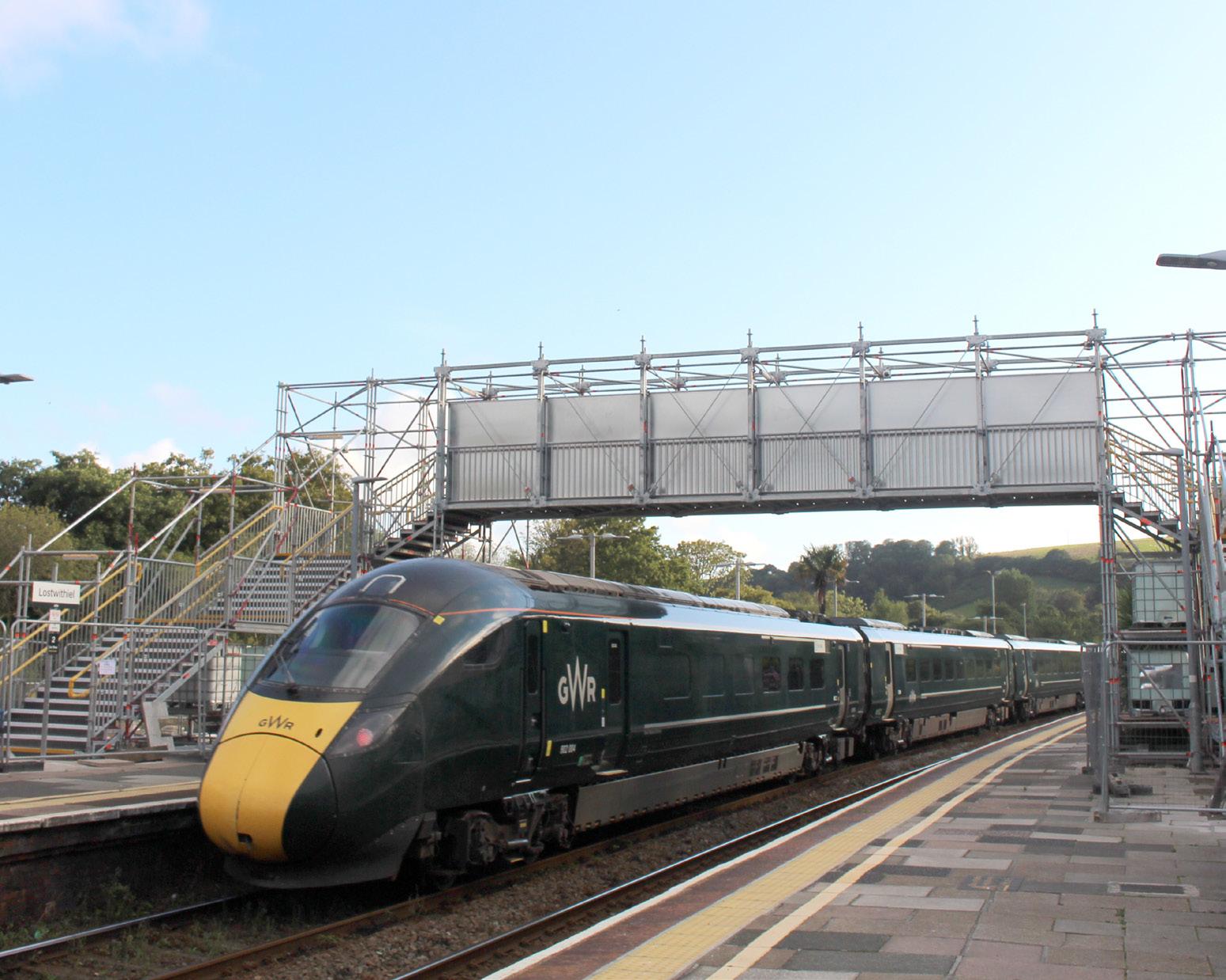
Skill Scaffolding noted: “Our aim is to offer innovative, safe and efficient solutions to our clients. With the Skill Bridge, we can reduce the impact on the public and keep projects running smoothly.”
THE LAYHER ALLROUND SYSTEM: A KEY PLAYER
At the heart of this success is the Layher Allround System. Known for its flexibility and safety, the system allows for complex scaffolding structures to be erected with ease, ensuring that the temporary pedestrian bridge is both strong and reliable.
This modular scaffolding system is ideal for projects like this, where safety and speed are paramount, and disruptions must be kept to an absolute minimum.
Skill Scaffolding has also benefited
from Layher UK’s turnkey after-sales technical and practical site support and expertise with Layher’s strategic partnership promise of Service, Support, Solutions and Supply playing a vital role in making this project successful. Skill Bridge was built to the highest standards, meeting the rail site’s technical and safety requirements.
LOOKING TO THE FUTURE
The success of the Layher Skill Bridge in Lostwithiel signals a new way forward for Skill Scaffolding. With ongoing investment in advanced scaffolding technologies and continuous in-house training, the company is raising the bar for temporary structures in the UK. Whether it’s for rail, construction or public infrastructure, their innovative solutions are proving invaluable.
HAKI Safety expands Geodesy offerings in Norway
HAKI Safety has broadened its geodesy product range in Norway, thanks to its subsidiary, Norgeodesi, securing the sales rights for Trimble’s BuildingPoint instruments and software
❖ This development positions the company to offer advanced total station equipment to a broader range of customers who require precise measurement and surveying solutions.
Norgeodesi, already an authorised distributor of Trimble’s surveying instruments in Norway, is renowned for providing specialised equipment for the construction, civil engineering and surveying sectors. With this new expansion, the company will offer Trimble’s BuildingPoint technology, further enhancing its portfolio for customers in industries such as construction and public infrastructure projects.
Joh Einar Solhaug, Managing
Director of Norgeodesi at HAKI Safety, expressed his excitement about the opportunity to introduce this advanced technology to new markets:
“I am delighted to have the opportunity to market and sell Trimble’s BuildingPoint on the Norwegian market. Norgeodesi has delivered products for surveying and road and tunnel projects for many years. With the expanded Trimble product range, we can target new customers and sectors, broadening our markets. We also see synergies with HAKI Safety’s other product ranges for temporary workplaces, which creates added value for our customers.”
Norgeodesi has a long history of expertise in the geodesy field, having been an authorised distributor of the Swedish Geodimeter since 1983, prior to its acquisition by Trimble in 2000. This established relationship allows the company to provide state-of-the-art equipment and comprehensive services, including technical support, maintenance and training.
The expansion of Norgeodesi’s
Trimble offerings is expected to strengthen its presence in key sectors, particularly municipal and public works and private construction and engineering firms across Norway.
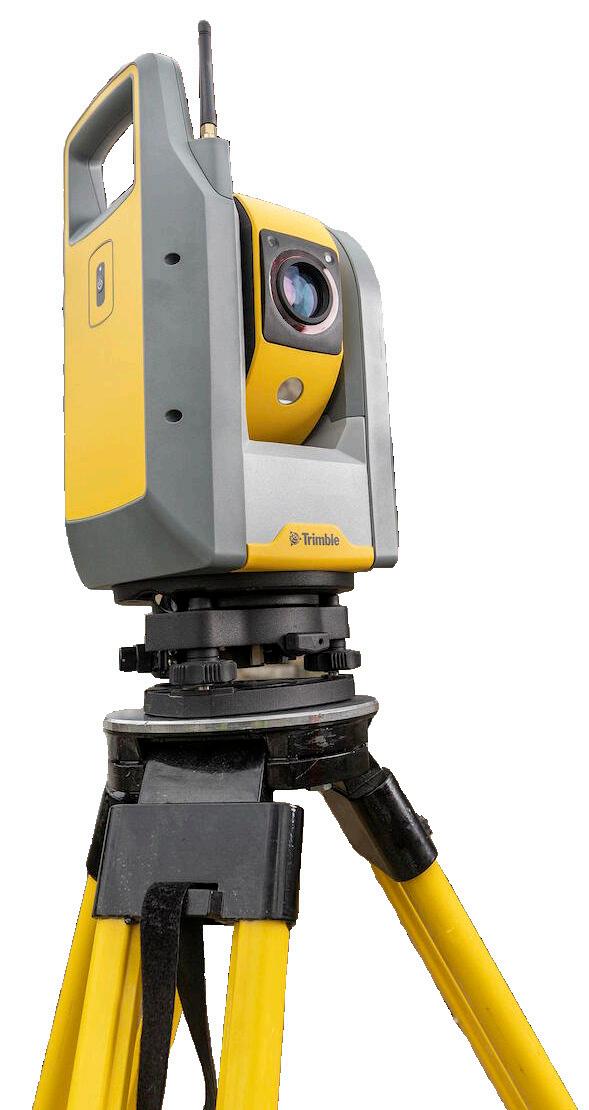
NEW MD FOR AT-PAC CANADA
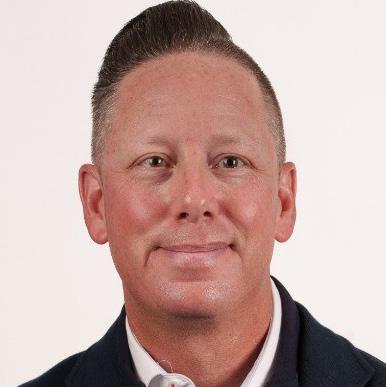
AT-PAC, a global scaffolding solutions provider, has announced the appointment of Allan Hazzard as its new Managing Director for Canada. This strategic move marks a shift towards a more locally focused management structure aimed at bolstering the company’s growth and operations across the country.
AT-PAC has been operating in Canada since 2000, with its branch in Edmonton,
Alberta, previously functioning under a unified North American management. Hazzard’s appointment comes as part of a larger effort to expand the company’s presence in both Eastern and Western Canada.
CEO Josh Dundon praised the decision, saying, “Allan’s appointment is a key step in strengthening our Canadian operations. His leadership will help us build on our 25 years in Canada and position us for future growth in important markets across the country.”
Hazzard brings over two decades of leadership experience to the role, including 10 years in the modular
building industry with WillScot. Based in Calgary, he has a proven track record of growing businesses in both Canada and the US, making him well-suited to lead AT-PAC’s next chapter in the region.
“I’m honoured to take on this role at such a pivotal moment for AT-PAC,” Hazzard said. “I’m excited to work with the talented team here and continue driving growth and innovation in the Canadian market.”
Hazzard will oversee the Canadian team and lead AT-PAC’s expansion into new markets, ensuring strong operational support for its customers.
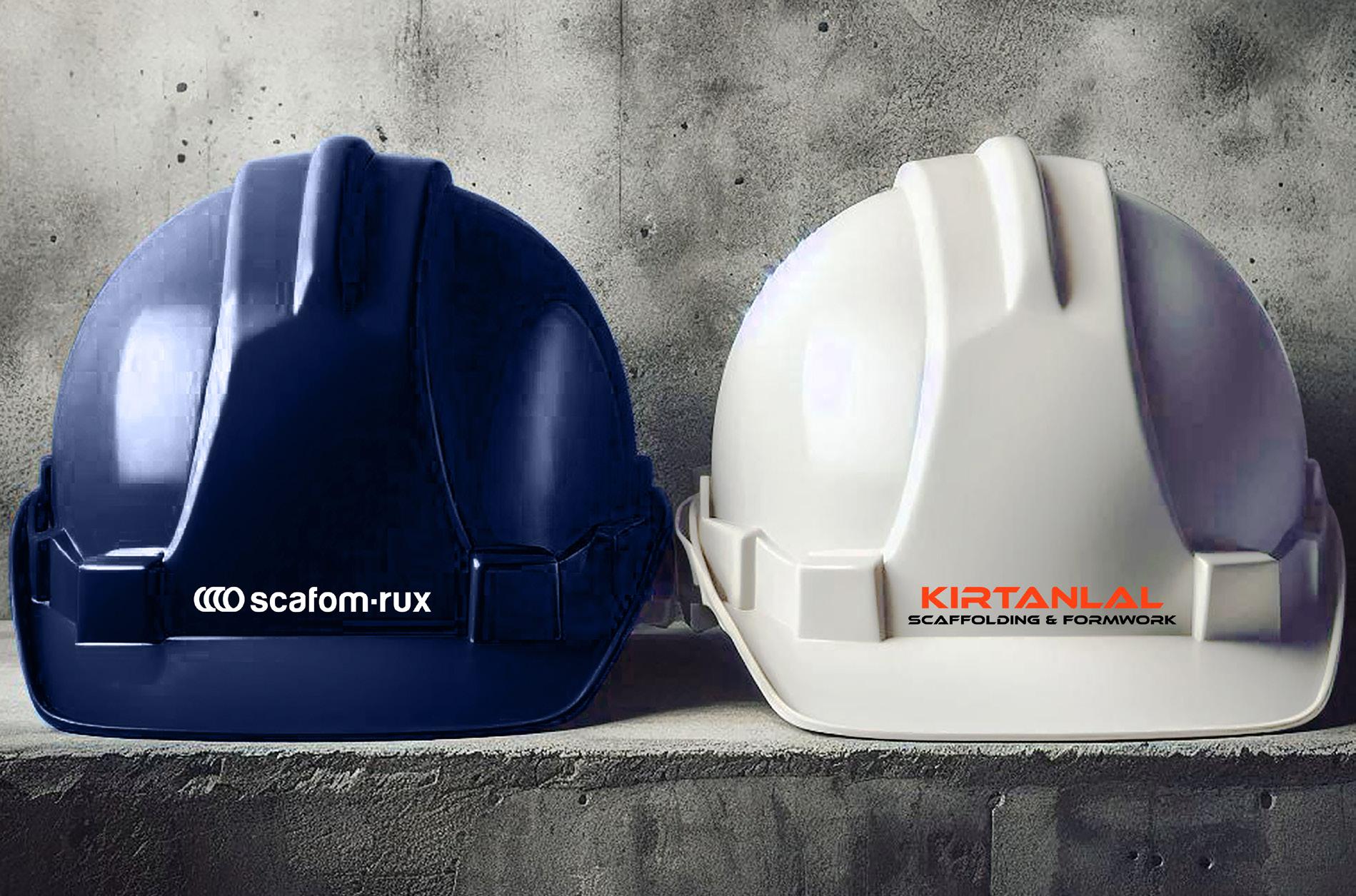
Scafom-rux partners with Kirtanlal for Middle East expansion
Scafom-rux, a global leader in scaffolding and formwork solutions, has entered into a strategic partnership with Kirtanlal Scaffolding & Formwork, a rapidly growing provider in the Middle East.
❖ Headquartered in Dubai, Kirtanlal has expanded swiftly, now operating in 12 locations across the UAE, Saudi Arabia, Qatar, Oman and India.
Known for its high-quality galvanised scaffolding materials and state-of-the-art aluminium formwork systems, Kirtanlal has built a strong reputation for safety, quality and service.
The partnership will enable Kirtanlal to offer Scafom-rux’s full range of innovative scaffolding systems, including Cuplok, Duralok and Ring systems, to its regional clients. Charles Edwards, CEO of Kirtanlal, noted that the collaboration aligns with the company’s zero-compromise approach to safety and product excellence.
Scafom-rux, with over 45 years of
global experience and a presence in 35 locations across 20 countries, views the partnership as a key step in strengthening its market position in the Middle East.
John Brocklehurst, Global Business Development Director at Scafom-rux, emphasised that the two companies share a strong commitment to quality and innovation.
This collaboration not only boosts Scafom-rux’s presence in the region but also supports Kirtanlal’s ambitious plans for global expansion into Europe, the US and Southeast Asia. Both companies are committed to delivering world-class scaffolding and formwork solutions to meet the growing demands of these dynamic markets.
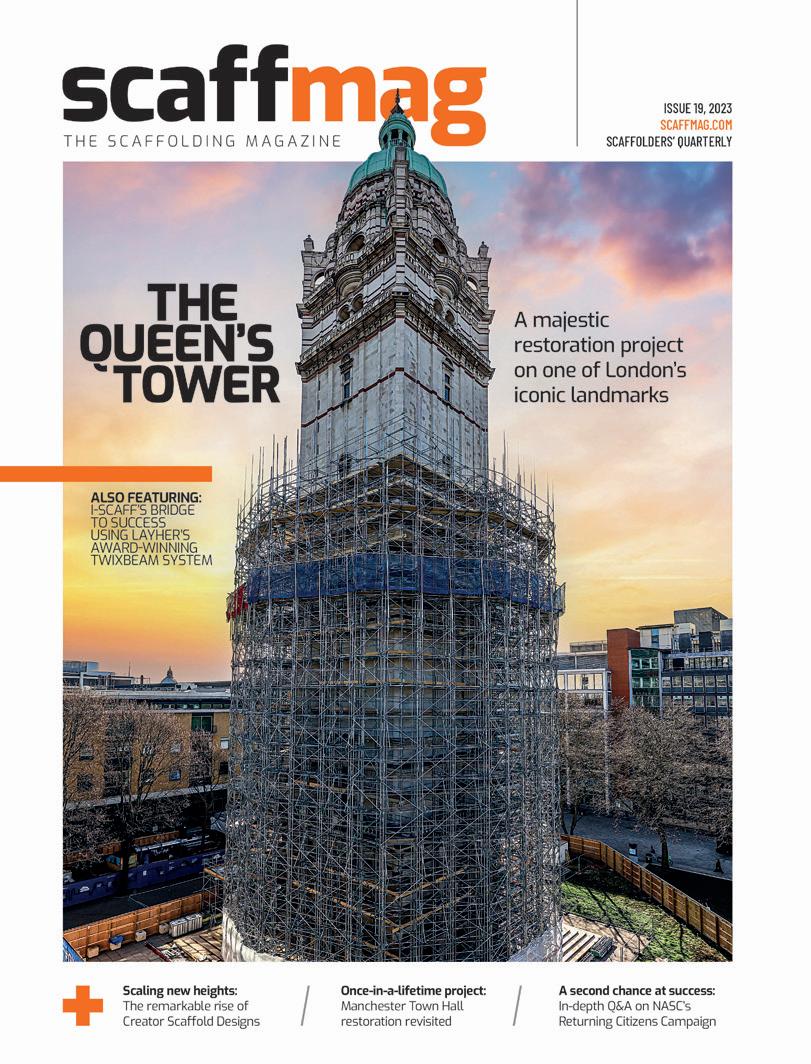
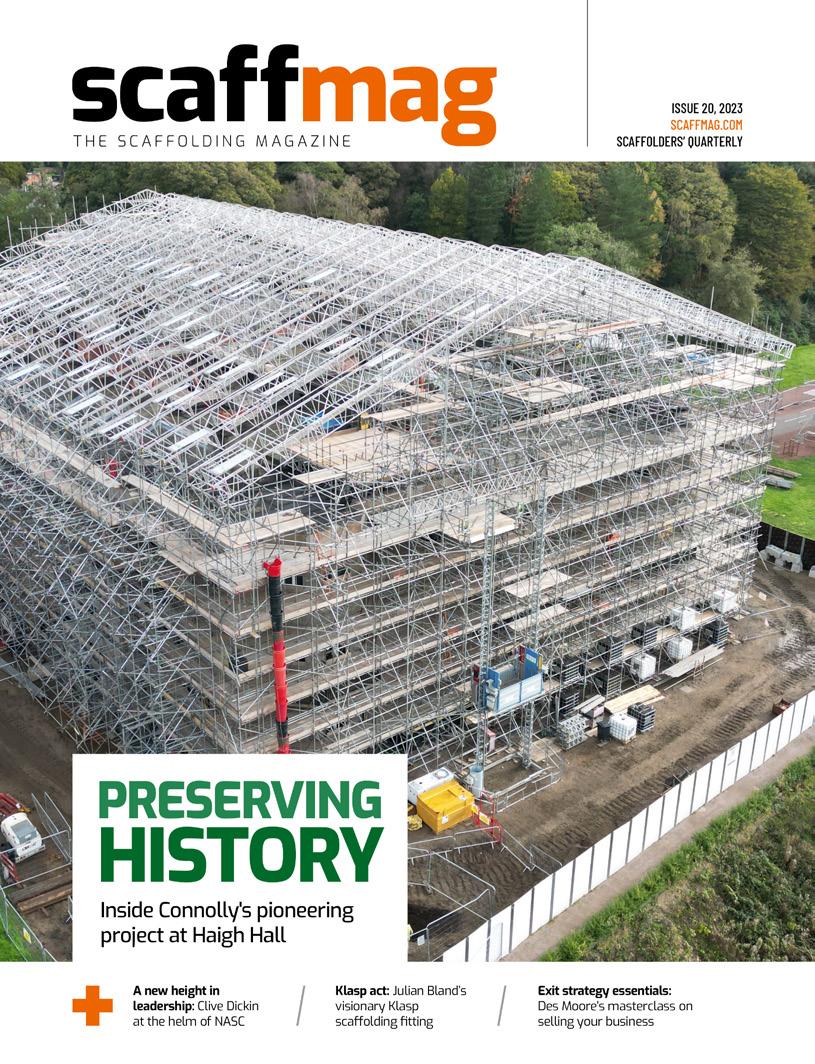
The best-read quarterly magazine in scaffolding
At the very heart of the scaffolding and access industry, ScaffMag has been serving the industry since 2009 by championing best practice, raising awareness of safety issues on-site and promoting business excellence.
ScaffMag delivers its mixture of news, views, trends and product updates through digital channels and in print.
ScaffMag gives businesses and brands an unrivalled opportunity to advertise their products or services 24 hours a day, seven days a week to a highly targeted audience.
To find out more about advertising, contact Jessica Norton on 01472 476024 or email jess@scaffmag.com

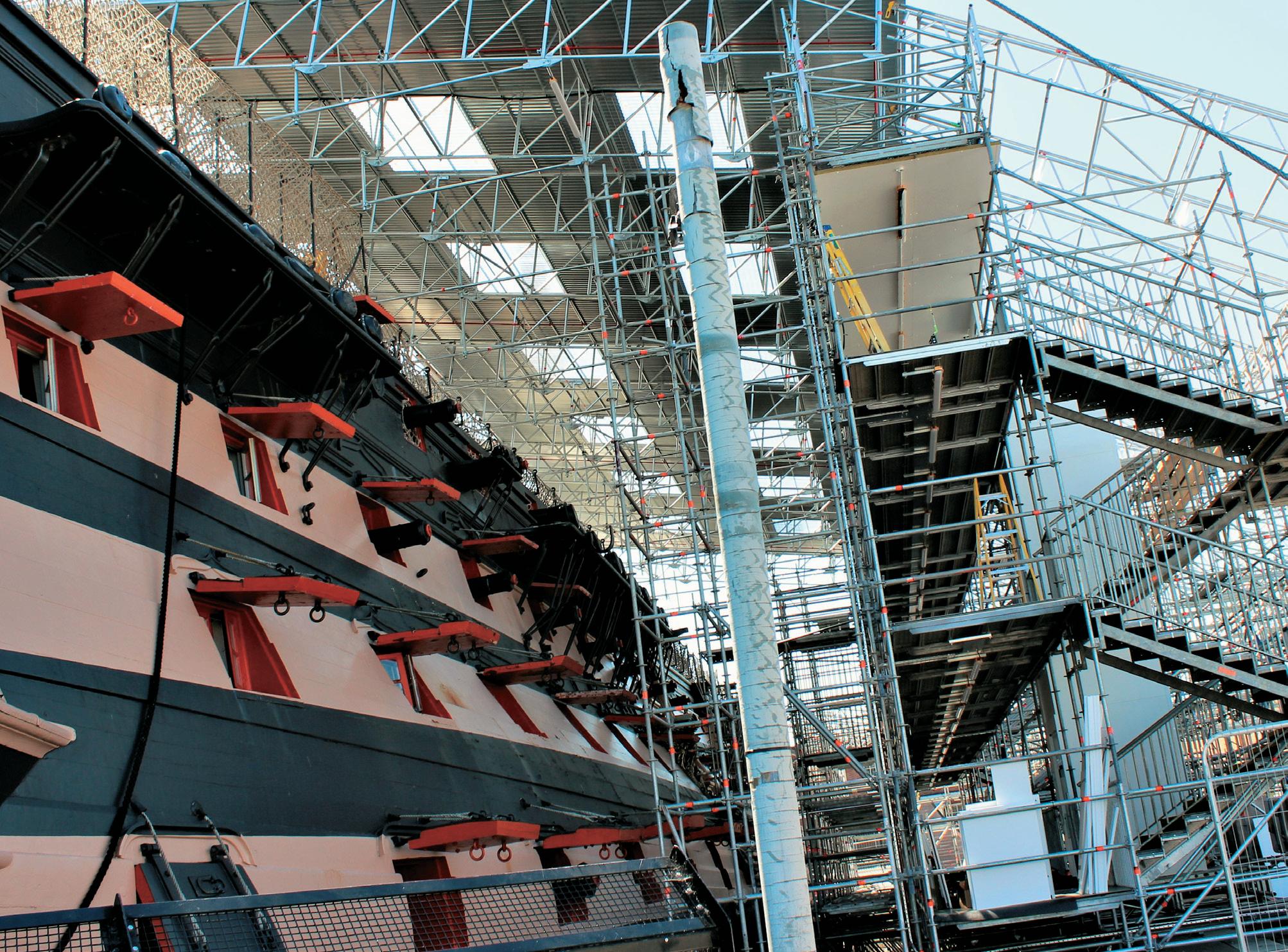
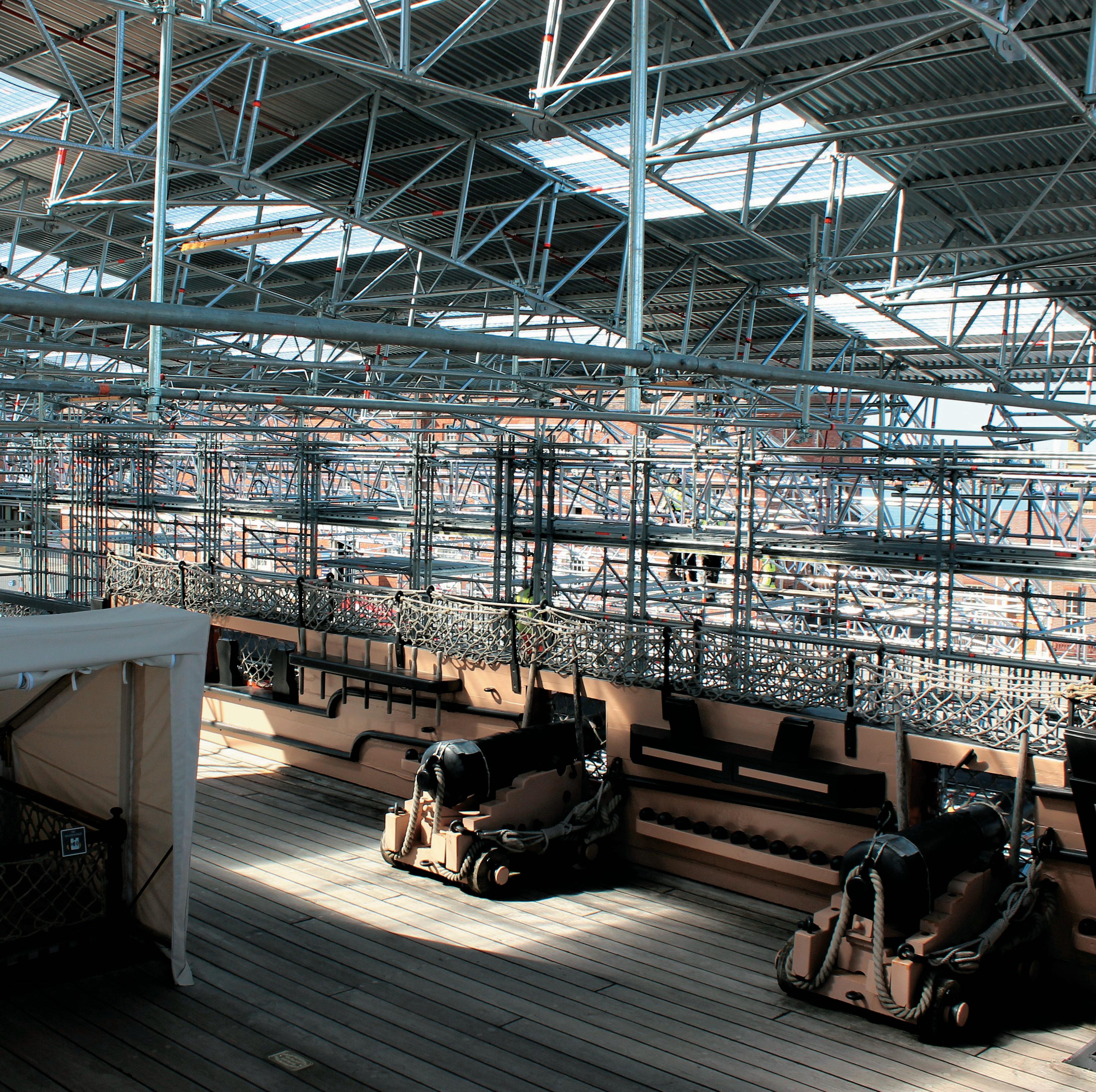

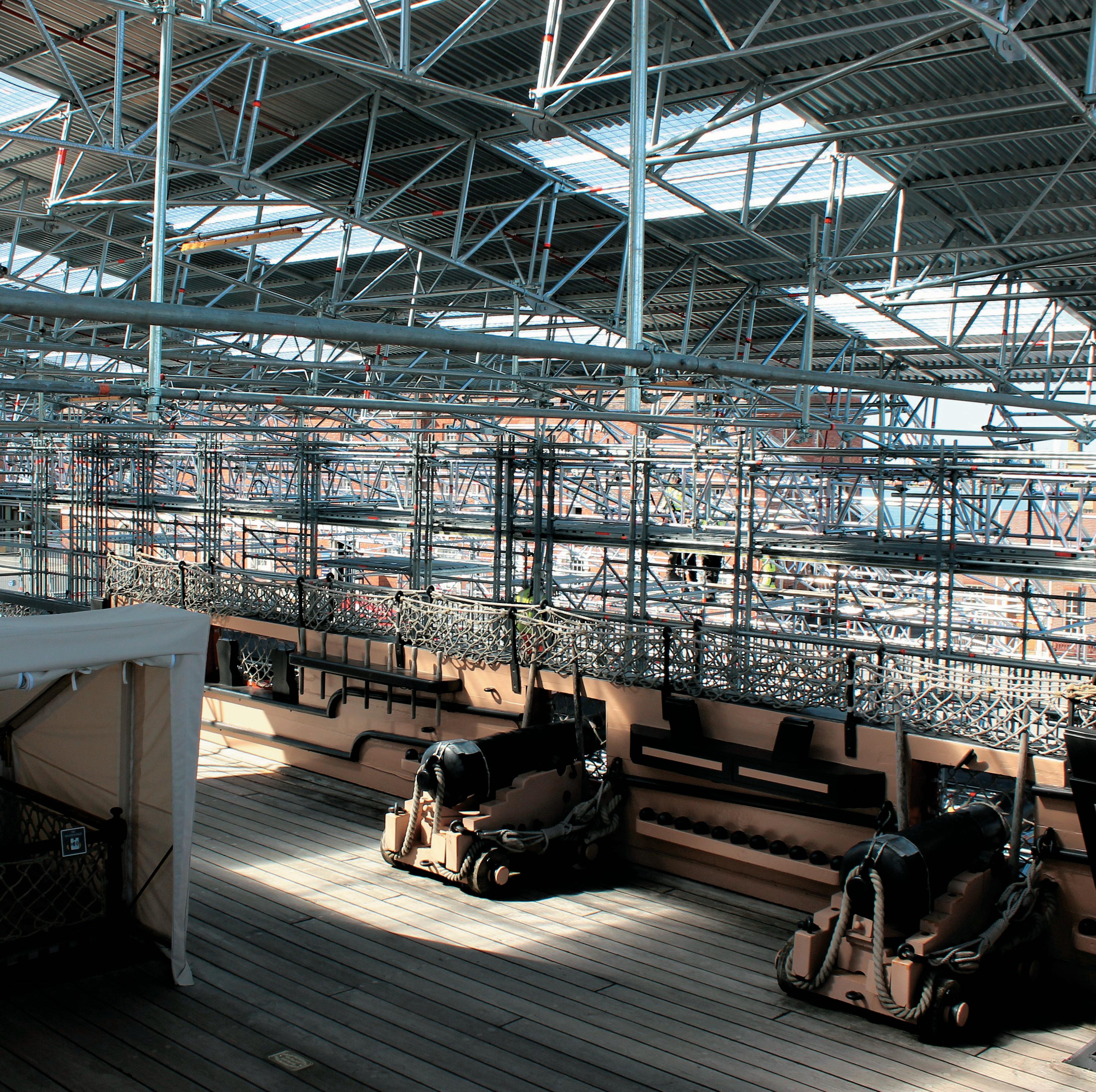
PROTECTING our HERITAGE
INNOVATIVE SOLUTIONS FROM LAYHER
THE WORLD’S
LEADING MANUFACTURER OF MODULAR SCAFFOLDING SYSTEMS
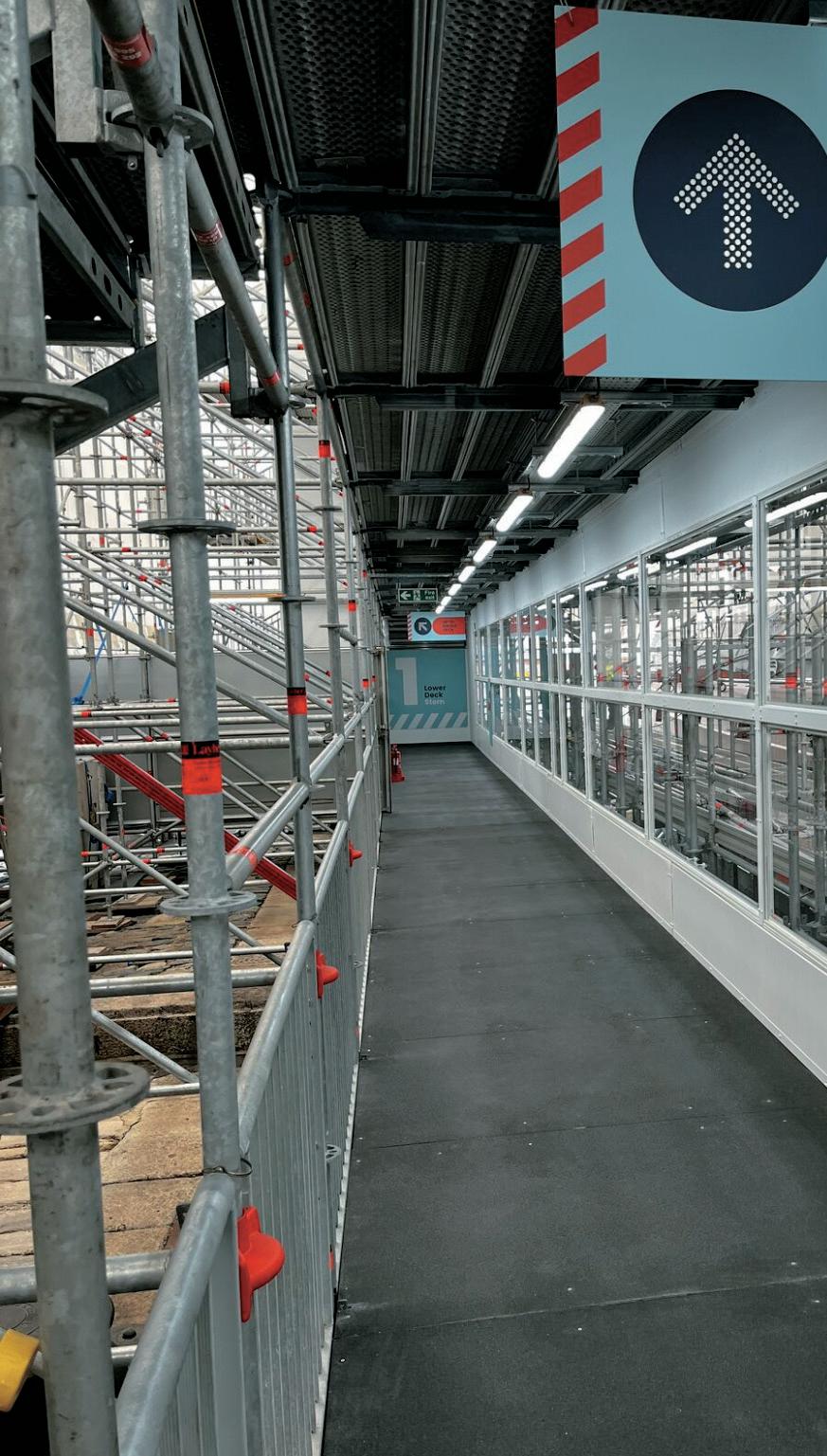
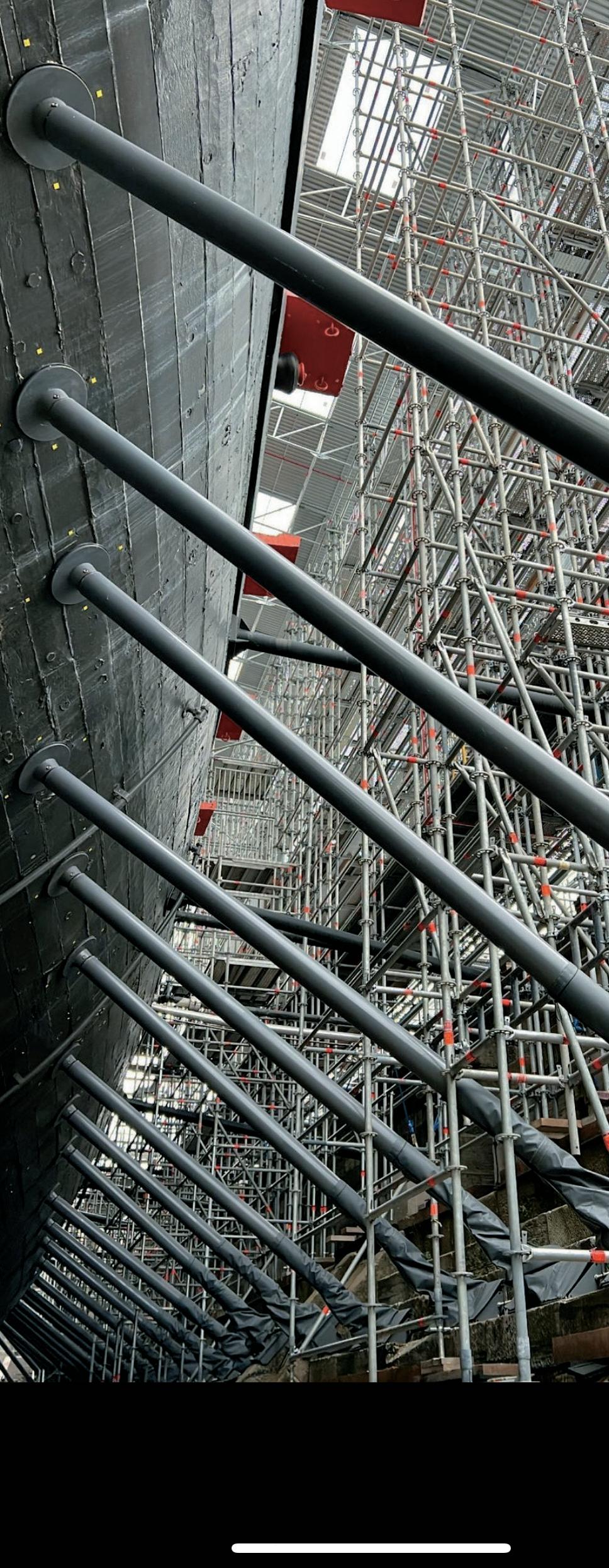
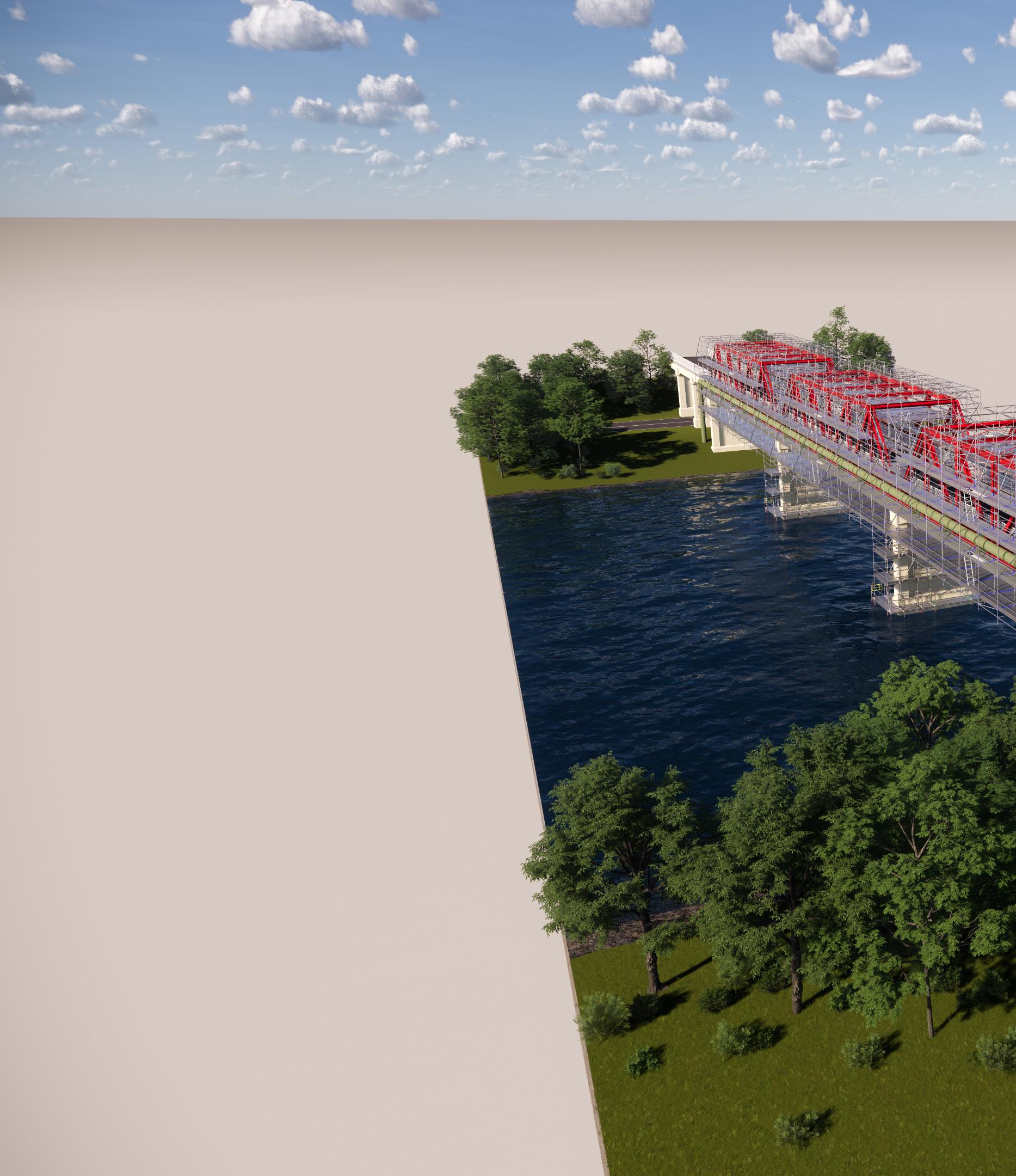
FUTURE
ScaffMag Editor Daniel Norton sat down with ScaffPlan directors Simon Boyes and Ben Beaumont to find out where the company is heading and how it plans to continue transforming the scaffolding industry. With major updates and new product releases on the horizon, Boyes and Beaumont shared insights on ScaffPlan’s growth, upcoming software features, and their vision for the future of scaffold design
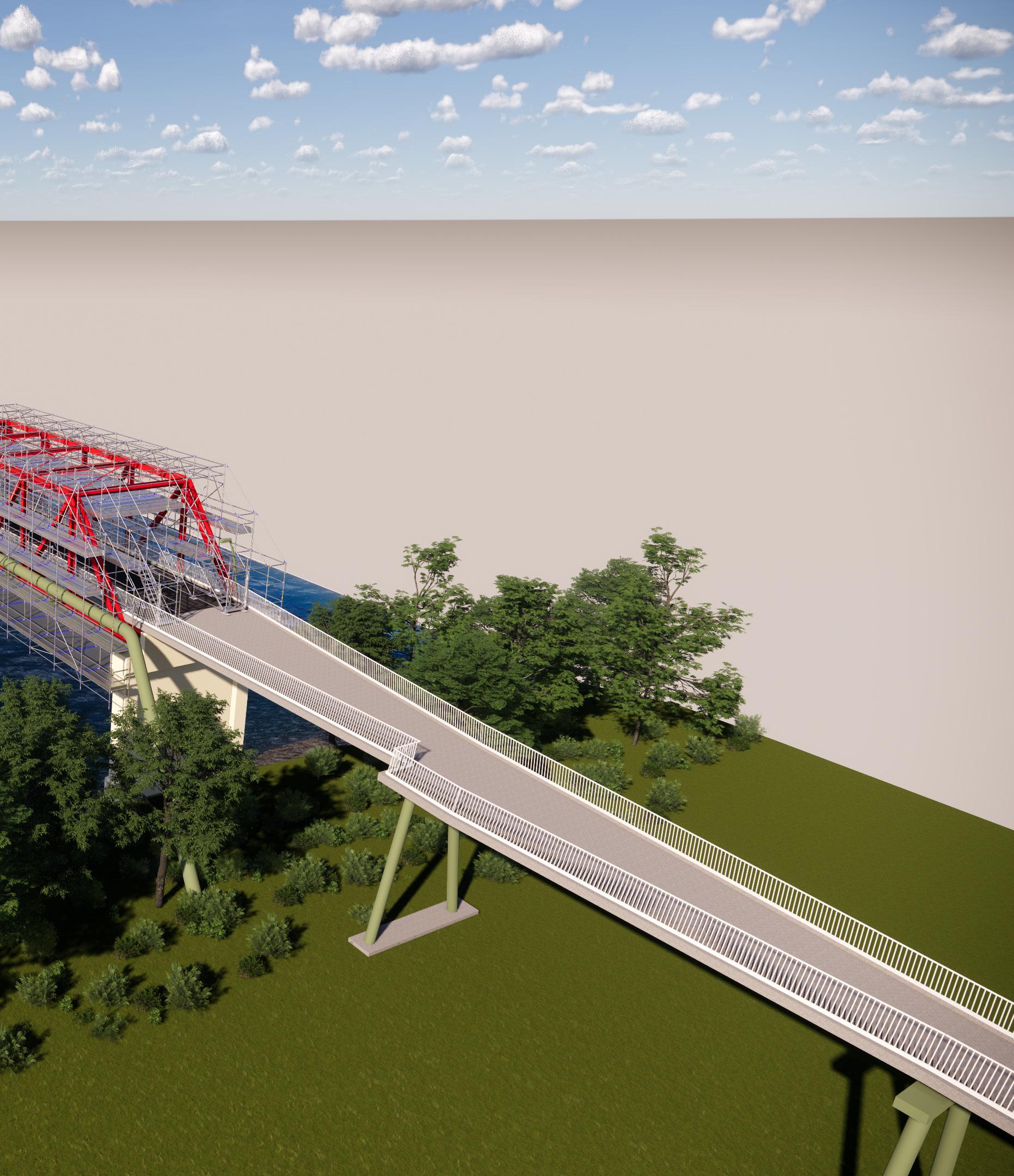
DESIGN
ScaffPlan was born out of necessity in 2020 when Simon Boyes, a scaffolding expert and former owner of Benchmark Scaffolding, saw a need for a more efficient, accurate, and user-friendly solution to scaffold design.
Frustrated by the limitations of existing platforms, Boyes envisioned a solution that could simplify the design process while maintaining millimetrelevel precision. What started as an internal tool for Boyes’ scaffolding business quickly evolved into ScaffPlan, a powerful scaffold design platform integrating advanced 3D modelling and building information modelling (BIM).
In March 2024, Simon Boyes made a pivotal decision by selling Benchmark Scaffolding to focus entirely on the development and growth of ScaffPlan. His commitment to pushing the boundaries of scaffold design technology solidified ScaffPlan’s position as an industry leader, enabling Boyes to dedicate his full energy toward transforming how scaffolders plan, design and manage their projects.
THE BEGINNINGS: ADDRESSING INDUSTRY NEEDS
Simon Boyes’ experience running one of Australia’s largest scaffolding contractors highlighted the inefficiencies inherent in the design process. The scaffold design team and project managers at Benchmark struggled with cumbersome, outdated software that was often too complex or insufficient for the real-world demands of scaffold construction. Recognising the need for a better solution, Boyes and his team set out to build a platform that was intuitive enough for the scaffolding team on site, powerful enough for complex projects, and detailed enough for design engineers.
“We’ve used every design platform on the market, and some of them are really
good at some things, but not so great at others. We wanted to build a platform that was easy to use but super accurate and detailed,” Simon explains.
ScaffPlan delivered on that promise, offering users a 3D modelling solution with parametric modelling tools and with built-in engineering capability that enabled users to design faster, more precisely and with fewer errors.
“At Benchmark we had our scaffold teams using ScaffPlan in the field on their phones, collaborating directly with the design team, who made updates or client-led revisions in real time. Everyone could use it effectively and it made us more efficient.”
EXPANSION AND NEW FEATURES
Earlier this year, ScaffPlan launched version 1.7, which introduced a host of new features aimed at increasing flexibility and usability.
Key among these updates was its expanded system scaffold range, which allows scaffolders to work with systems such as Altrad Futuro, Metrix, ScafomRux, and HAKI Universal – taking the total number of supported systems to 16.
Notable for many UK readers was the update of the tube-and-fitting tools in ScaffPlan, making them faster and much easier to use.
ScaffPlan’s ‘ScaffBlock’ feature is a new tool that simplifies the creation of reusable parametric blocks by the user from any combination of items that can be used time and again in their designs.
“The ScaffBlock tool is one of my favourites, it works really nicely with all scaffolding and is especially powerful for tube and fitting,” explains Boyes. “You can model anything you like, such as a lift of scaffolding, define the properties that you’d like to be able change each time, such as the number of inside boards or transom centres, and then save it and use it over and over again.”
We should also not forget Phase Manager, a feature that enables users to manage different project phases more efficiently and link them to gear lists, sequence drawings and animations.
IF ‘A PICTURE SPEAKS A THOUSAND WORDS’ THEN A SCAFFPLAN MODEL SPEAKS A MILLION!”
BEN BEAUMONT

These additions solidified ScaffPlan’s position as a comprehensive solution for scaffold design, safety checks and project management, making it indispensable for both large-scale and smaller projects.
ScaffPlan’s journey took another pivotal turn at the beginning of this year with the appointment of Ben Beaumont as Director. Beaumont, a respected figure in the UK’s scaffolding and temporary works sectors, brings over two decades of experience and a deep understanding of the industry. His appointment marks a new era for ScaffPlan as it expands its reach globally and enhances its leadership in scaffolding technology.
Beaumont’s expertise in scaffolding and temporary works, combined with an
entrepreneurial background, which came from founding and leading 48.3, a scaffolding design and training consultancy and years of leading the Temporary Works Forum (TWf), align with ScaffPlan’s mission to innovate and revolutionise the scaffolding sector. Together, Boyes and Beaumont are committed to transforming scaffolding design and project management by pushing the boundaries of what’s possible with technology.
“We now have a unique opportunity to change how scaffolding and temporary works are conceived, designed, collaborated on, and executed. The potential for positive change is huge, and that’s really exciting,” Beaumont said.
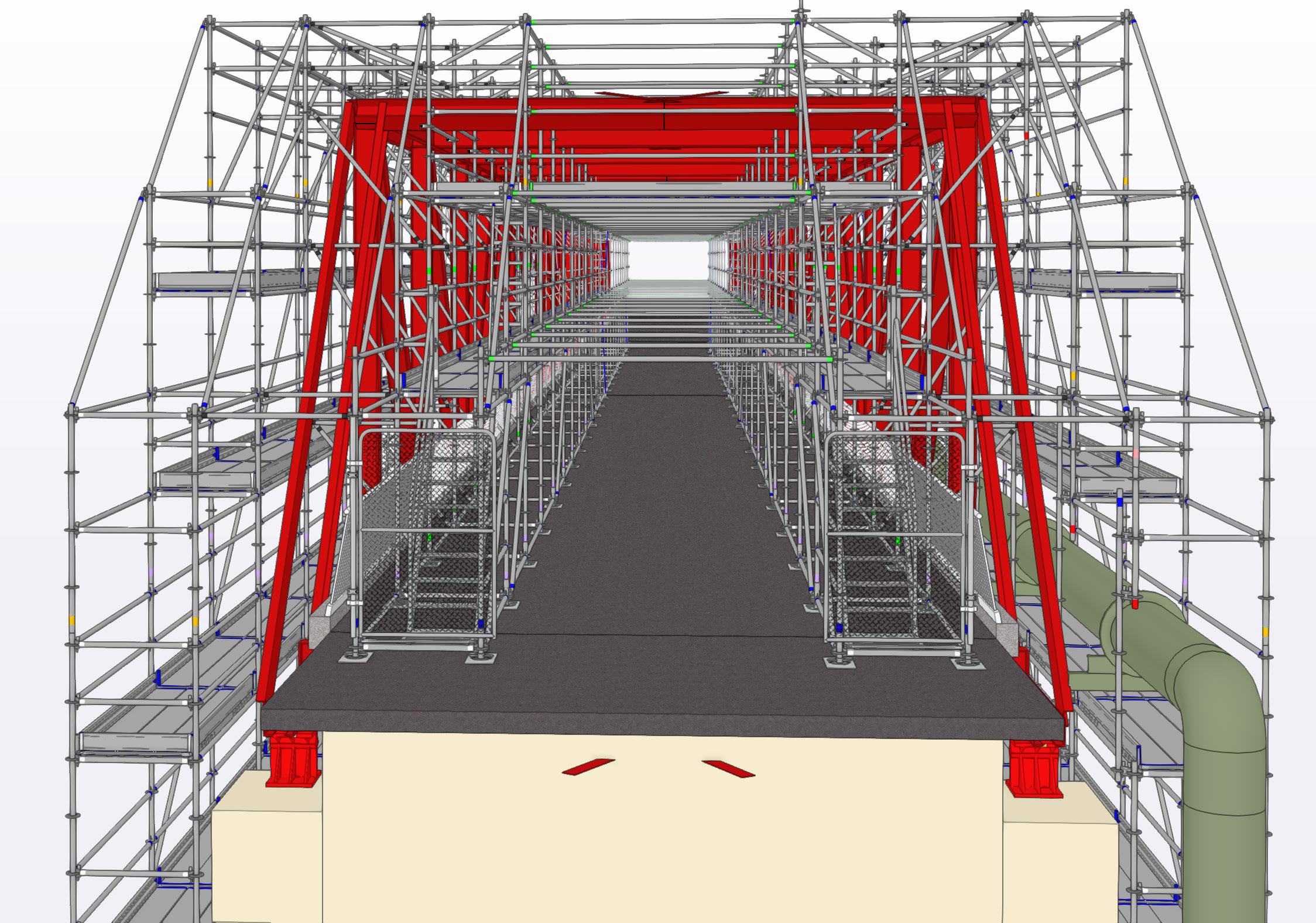
ScaffPlan offers users a 3D modelling solution for faster, more precise scaffolding design.
WHERE SCAFFPLAN IS HEADED
As ScaffPlan continues to evolve, Boyes and Beaumont revealed that the company is working on several exciting new additions to the platform, set to launch in Q1 of 2025. The most notable of these innovations is a new version of the software.
“We’re taking all the power of our existing design platform and putting it into a simpler, easier-to-use, and much cheaper solution,” says Boyes. “This is targeted at a wider audience who will benefit from the ease of use and accessibility.”
The new version will bring accurate and flexible 3D modelling capability to a wider industry audience through the automated tools that ScaffPlan includes. Estimators, contract managers and
supervisors, who would all benefit from the improved communication and planning that this 3D capability offers, will now be able to include it in their tenders and planning documents, improving their professionalism and helping them win more work.
Beaumont said, “It is important that we make our tools accessible for everyone so that collaboration can happen more effectively – scaffold teams, designers and project stakeholders all working together seamlessly. The quality and effectiveness of communication between everyone will improve, and that will drive efficiency and reduce mistakes.”
In addition, ScaffPlan is also developing a bespoke Customer Relationship Management (CRM) system designed specifically for
THE SCAFFBLOCK TOOL IS ONE OF MY FAVOURITES; IT WORKS REALLY NICELY WITH ALL SCAFFOLDING AND IS ESPECIALLY POWERFUL FOR TUBE AND FITTING.” SIMON BOYES

scaffolders and the construction industry. This CRM will allow scaffolding companies to track leads, deals, and quotes, essentially offering a platform that can be used to run their business.
The software is designed to seamlessly integrate with the existing design tools, creating a fully unified system for managing both the technical and business sides of scaffolding operations.
SCAFFPLAN’S VISION FOR THE FUTURE
With its continued commitment to innovation, ScaffPlan is poised to remain at the forefront of the construction technology sector. The upcoming launch of its new version and CRM system highlights the company’s dedication to making scaffold design and management more accessible to businesses of all sizes. By combining 3D modelling, BIM and now business management tools, ScaffPlan is positioned to reshape the way scaffolding companies design, plan and manage their projects.
“For me it’s about how effectively we all work together – key to doing that is communication. If ‘a picture speaks a thousand words’ then a ScaffPlan model speaks a million!” said Beaumont. “Printed 2D drawings will be gradually replaced by fully interactive 3D models; some of our customers are doing this now. They’ve experienced the benefits of transition to 3D on collaboration and communication, and now their customers want it on every project.”
The ScaffPlan team are focused on creating a future where scaffolding businesses, large and small, can leverage cutting-edge technology to improve safety, efficiency and productivity.
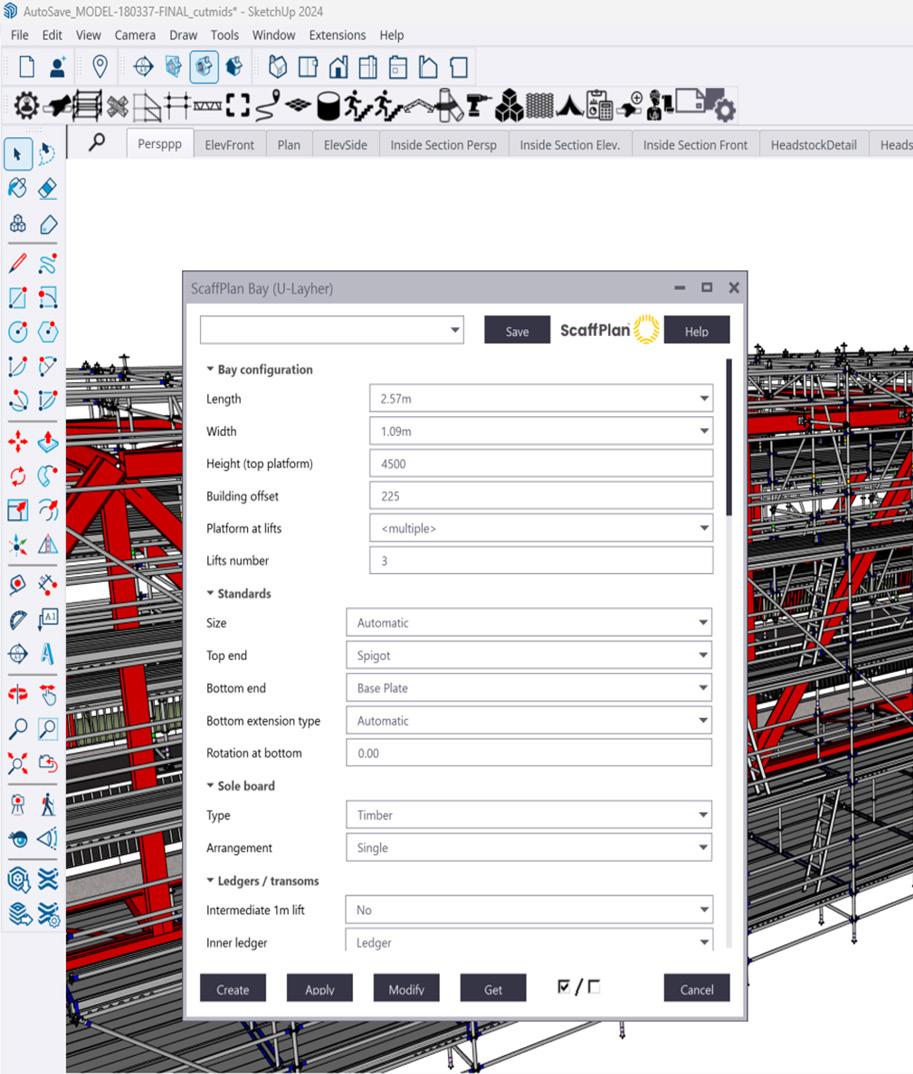
“We want to ensure that every scaffolder has access to the tools they need to be successful, whether they’re a large company working on industrial sites, or a smaller operation focused on residential projects,” Boyes explains.
SHAPING THE FUTURE OF SCAFFOLD DESIGN
Estimators, contract managers and supervisors will all benefit from the improved communication and planning offered by ScaffPlan.
Having seen a first-hand demonstration of ScaffPlan, I was blown away by the level of detail in the 3D models and its effortless simplicity to navigate – even the smallest of details were crystal clear. I’m confident that if any scaffolding contractor were to show this model to a potential client, they would immediately understand what is set to be built. This level of clarity is transformative for the industry, bridging the gap between
design intent and real-world execution.
ScaffPlan’s journey from inception to its current status as an industry leader is a testament to Simon Boyes’ vision and the company’s unwavering commitment to innovation. With the upcoming releases, including the light version and a custom-built CRM system for scaffolders, ScaffPlan is set to transform how the industry operates.
As someone who’s had the privilege of witnessing the platform’s capabilities first-hand, I’m convinced that ScaffPlan is paving the way for a future where scaffold design is more accessible, efficient and collaborative than ever before. The scaffolding industry is evolving, and with tools like ScaffPlan, that evolution is set to be faster, smarter and more impactful for everyone involved.
Talking about a revolution
For centuries, the scaffolding and temporary works industry has relied on traditional, hands-on methods for design. However, a digital revolution is now sweeping through the sector, driven by innovations like automation, artificial intelligence (AI) and 3D modelling. These technologies enable faster, smarter and safer designs, bringing scaffolding and temporary works into a new era.
ScaffMag spoke with industry leaders from the UK, Ireland, Scandinavia and Poland region of Altrad, one of the world’s largest scaffolding and industrial service companies. In this exclusive interview, Colin Murphy, Head of Technical Authorities at Altrad and Matthew Reeve, Design Team Leader, reveal how they’ve introduced and adopted high-tech scaffold design tools to drive remarkable efficiencies, collaboration, and safety across their business. This article explores the scope of how cutting-edge technology is reshaping scaffold design and revolutionising the way projects are executed with benefits to all stakeholders involved
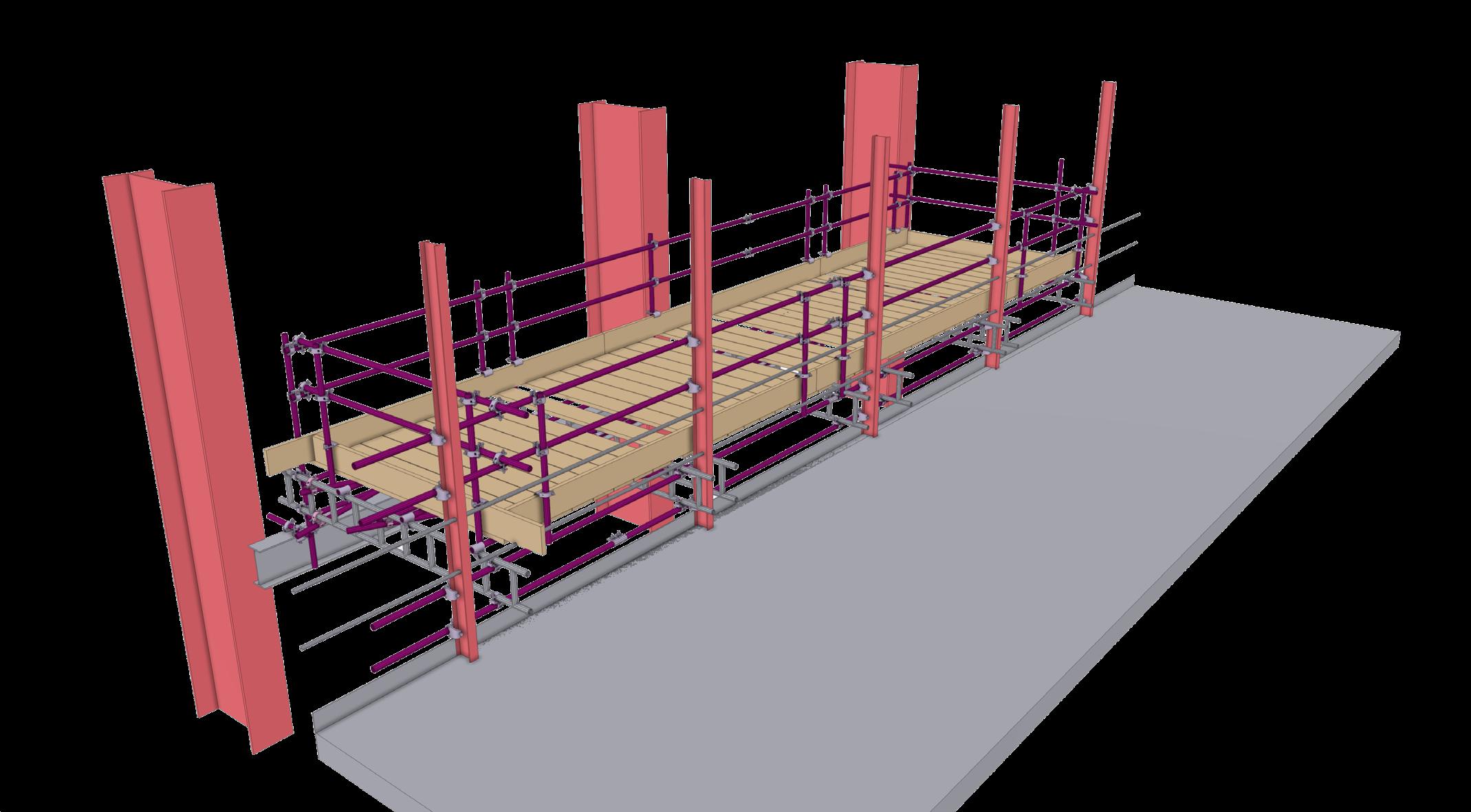
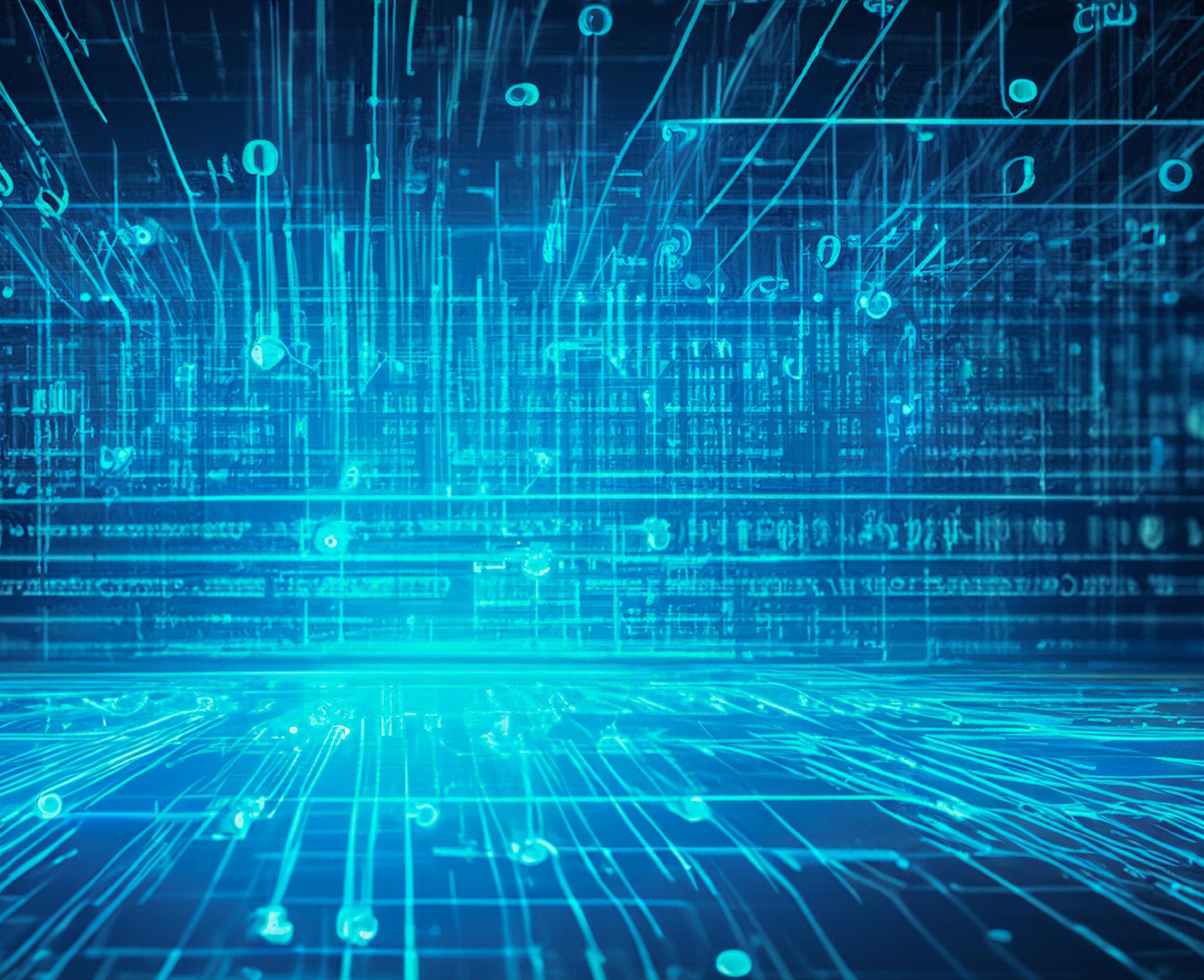


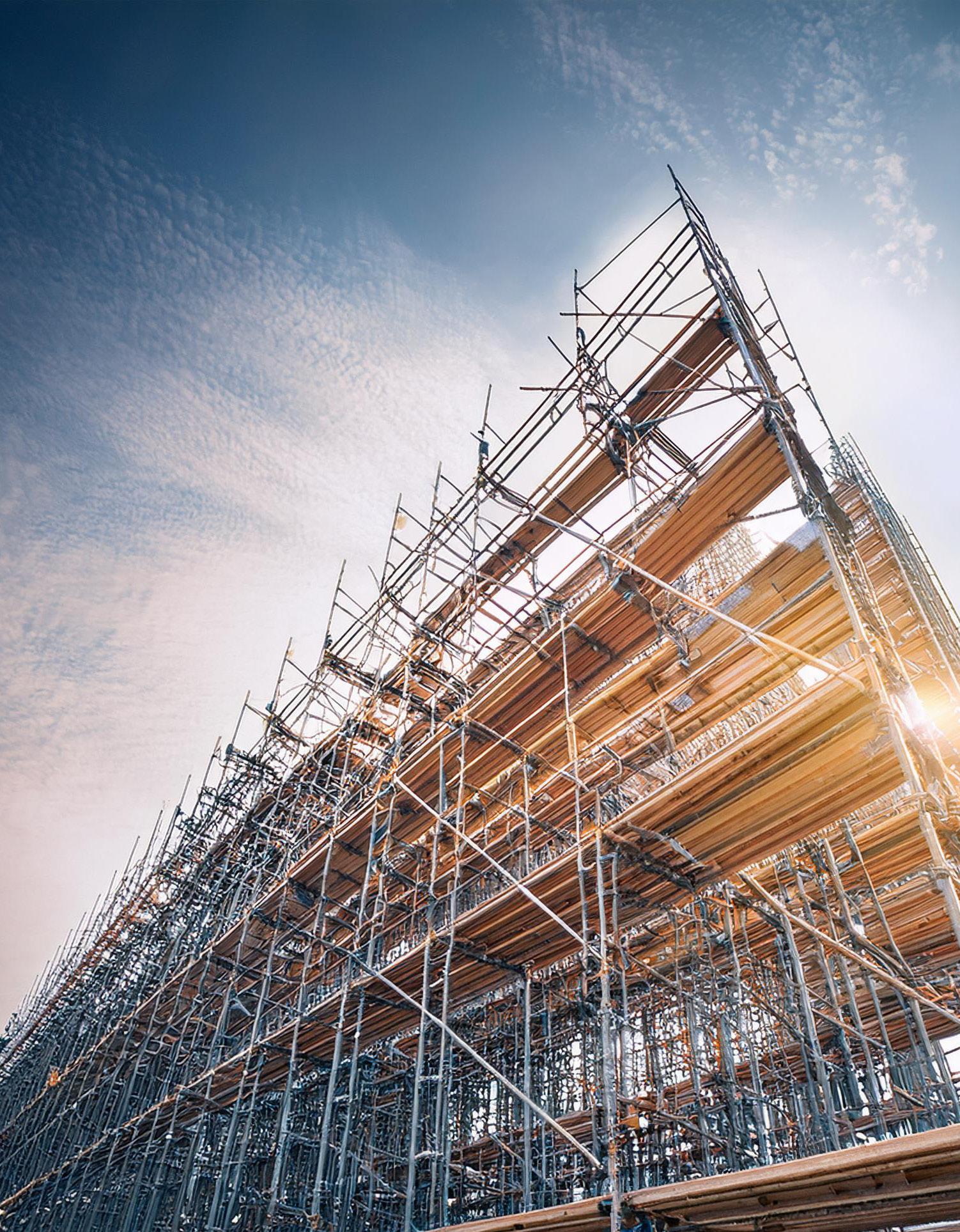
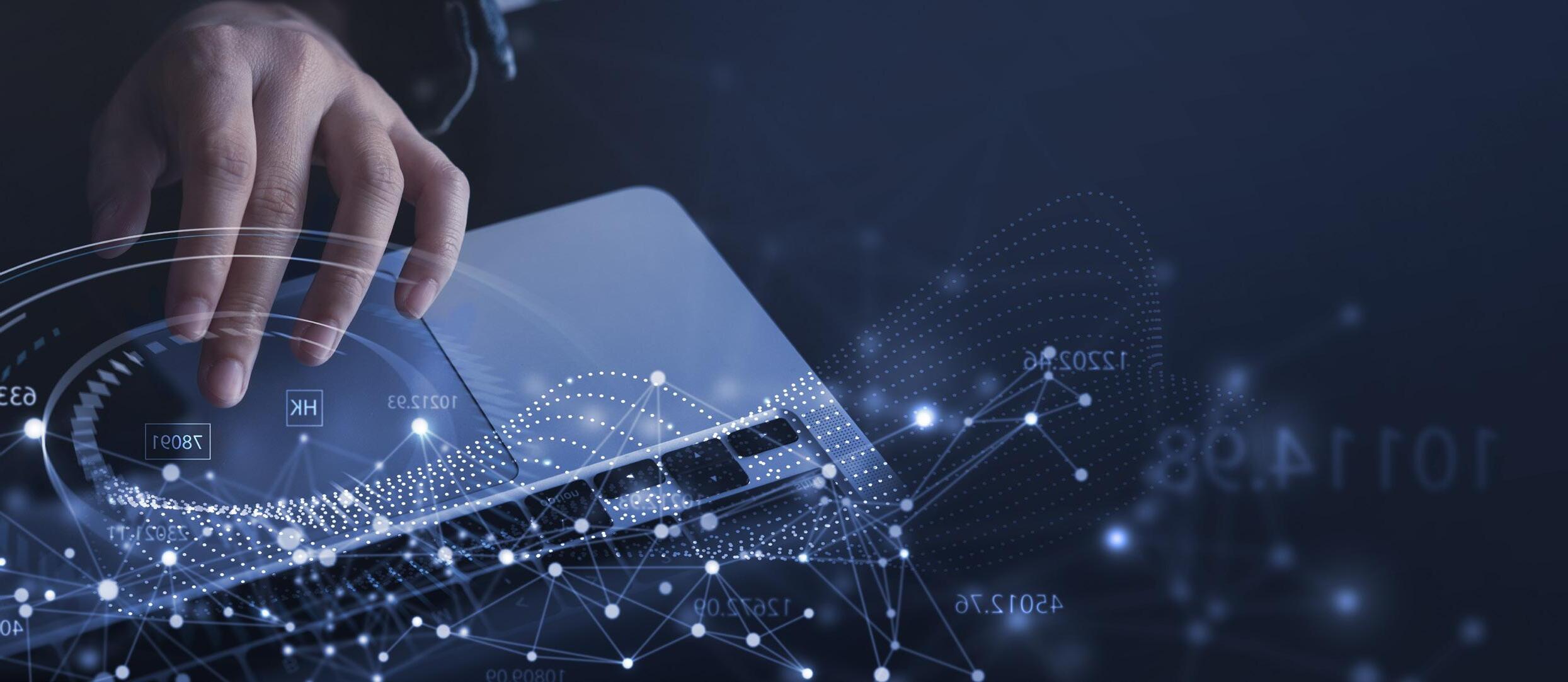
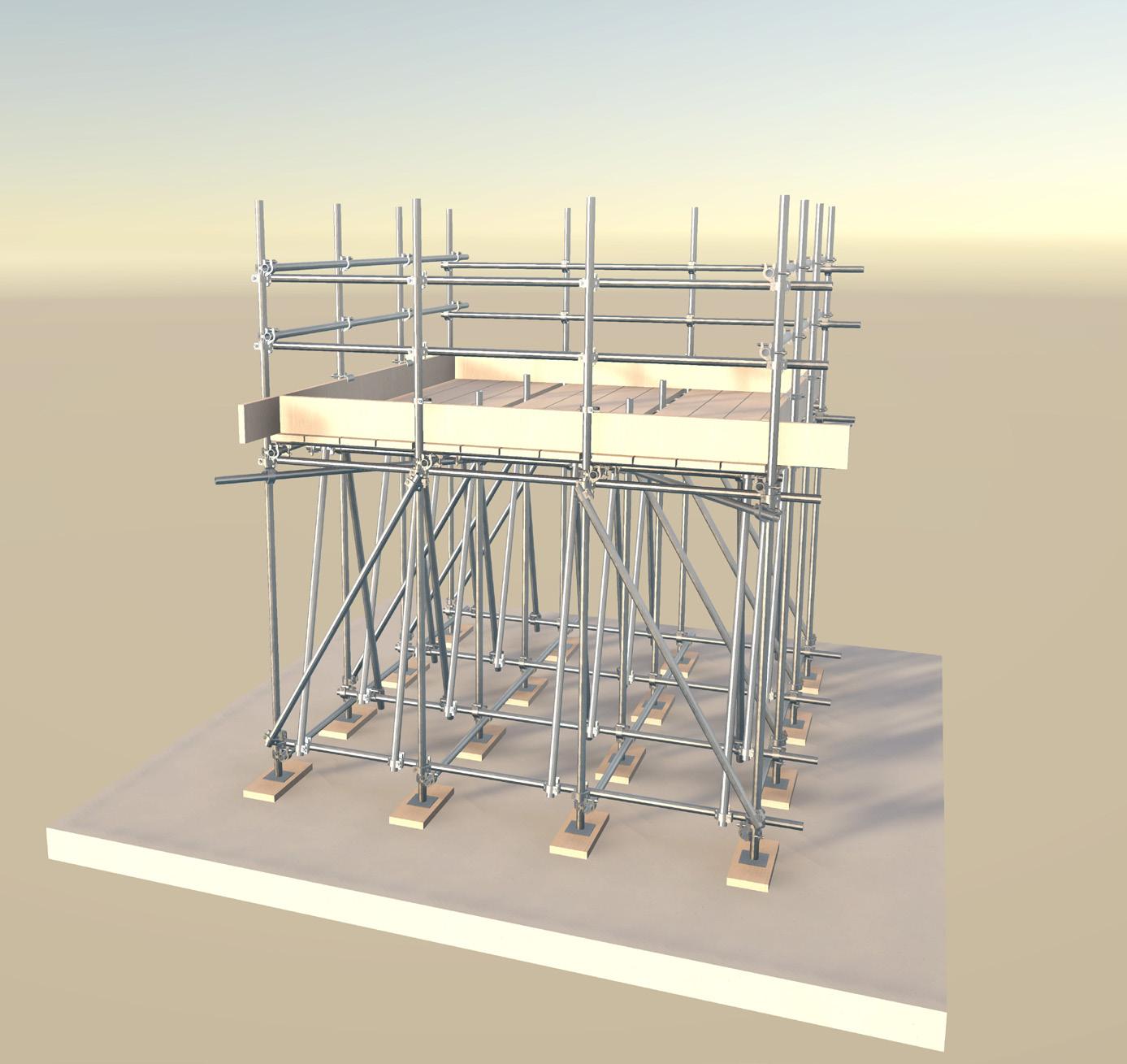
SIMPLIFYING THE TEDIOUS, ENHANCING PRODUCTIVITY WITH AUTOMATION
CLIENTS NOW EXPECT DETAILED DIGITAL MODELS THAT ALLOW THEM TO FULLY VISUALISE WHAT WE’RE PLANNING, THIS LEVEL OF CLARITY HAS REDUCED REVISIONS AND SPED UP PROJECT APPROVALS.”
Altrad provides services across five global regions in over 100 countries. The complex nature of their projects requires intricate planning where teams of highly skilled engineers would typically spend countless hours drafting, liaising with clients and recalculating load capacities. However, Colin Murphy explains that with the adoption of scaffold design software ScaffPlan, they’ve been able to save days in labour, reduce overheads and refocus human resources on more complex design challenges.
“By automating repetitive tasks, we’re able to free up time for more complex design challenges,” Murphy noted during our interview.
Automating calculations ensures precision while significantly cutting down on design time. This is especially crucial for large-scale projects where multiple variables interact, and any error could lead to costly rework or safety risks.
Automation of design and collaboration has transformed scaffolding into a more efficient process by reducing human error and streamlining repetitive tasks, enabling engineers to focus on higher-level decision-making.
3D MODELLING AND LASER SCANNING
As design automation simplifies repetitive tasks, other technologies are revolutionising how scaffolding is visualised and communicated. Digital, fully interactive 3D modelling is now at the forefront of scaffold design, allowing all stakeholders
to instantly visualise complex structures in detail before a single tube is erected. This level of precision is a game-changer.
Matthew Reeve summarised: “Often the client will know what they want to achieve, but they don’t know how to do that, or what they’re going to get.” Murphy added, “The problem with working in 2D is that a client can never really tell what it’s going to be like until it’s been built, and that alone creates the risk of complications and rework.”
3D models offer an unprecedented view of scaffold layouts, improving team communication and collaboration between designers, scaffolders and clients. As Reeve pointed out, “3D models give everyone involved a clear picture of the scaffold layout. It reduces misunderstandings and makes client sign-offs smoother.”
One of the most exciting developments in this space is laser scanning. With laser scanning technology, Altrad can create incredibly detailed digital point clouds of project sites that are accurate down to the millimetre. This is especially valuable in environments where precision is critical, such as offshore platforms or on complex industrial plants. Laser scanning ensures scaffold designs perfectly fit each project’s unique conditions.
Both Reeve and Murphy highlighted how these technologies are reducing on-site revisions and costs. Engineers can modify designs remotely, with updates to drawings happening in real time. This eliminates the need for laborious on-site adjustments, streamlining the entire process. “Clients are often asking for everything in 3D so they can check their own engineering.”
The combination of 3D modelling and laser scanning not only saves time but also ensures that designs are safer and more accurate, setting new industry standards.
CLASH DETECTION: THE NEXT FRONTIER OF SCAFFOLD DESIGN
With the use of laser-scanned sites, Altrad’s designers can overlay scaffold designs and instantly identify any clashes. This tool is particularly powerful when aiding in inspections, especially for sites where there is millimetre tolerance.
It’s these simple, yet groundbreaking tools like intelligent clash detection that allow Altrad to make fast adjustments in real time, reduce unforeseen site issues, complete projects faster and enjoy even greater safety measures.
Imagine a system where potential safety risks are
flagged automatically during the design phase –before any physical work begins. This is now a reality.
TRAINING A NEW WORKFORCE
With skilled labour becoming increasingly scarce, paired with a global shortage of skilled scaffold designers, Murphy has developed a unique and multi-dimensional approach to recruitment and upskilling within his team, noting the best success comes from a workforce that’s not only skilled in traditional scaffolding but also proficient in using digital tools.
Murphy explained that Altrad’s transition to 3D modelling and other advanced technologies has been seamless, thanks to ScaffPlan’s intuitive design and comprehensive training programmes. “We’ve trained everyone from scaffolders to engineers to graduates in using these tools. The transition has been smooth because this software is tailored to scaffolding. It’s not generic design software – it speaks the language of scaffolders,” Murphy explained.
This digital shift is not just confined to the UK. Murphy mentioned that the Altrad Group is adopting ScaffPlan design software globally.
MEETING CLIENT EXPECTATIONS:
COLLABORATION IN THE DIGITAL AGE
Another key driver of digital adoption is client expectations. Today’s clients want more than just paper sketches and verbal assurances – they want to see detailed digital models before construction even begins.
“Clients now expect detailed digital models that allow them to fully visualise what we’re planning,” said Matthew Reeve. “This level of clarity has reduced revisions and sped up project approvals.”
Cloud-based platforms like Trimble Connect are making this new level of collaboration possible. These platforms allow clients, designers and engineers to review and comment on designs in real time, regardless of location. As a result, scaffolding projects are moving forward with fewer delays and misunderstandings.
“We’re using cloud-based storage so we can securely share designs with anyone. This means site supervisors can access 3D models on-site, spin them around, and make live comments. It’s a game-changer for collaboration,” Reeve explained.
For companies like Altrad, digital collaboration isn’t just about speed – it’s about transparency. When everyone is on the same page from the start and has the opportunity to contribute effectively,
projects run more smoothly, saving both time and money.
THE END OF PAPER DESIGNS AND THE RISE OF DIGITAL WORKFLOWS
As automation, AI and 3D modelling continue to evolve, the scaffolding industry is moving toward fully digital workflows. Soon, paper designs will be a relic of the past, replaced entirely by interactive 3D models that offer far greater precision and flexibility.
Colin Murphy and Matthew Reeve both agree that this shift isn’t just about convenience. Real-time design modifications and seamless collaboration between multiple stakeholders reduce costly errors and accelerate project timelines – benefits that every client can appreciate.
“Clients will expect 3D models, and eventually, site teams will ask, ‘Where’s my 3D model?’ It’s far more collaborative, and it’s the future,” Murphy added.
A NEW ERA FOR SCAFFOLD DESIGN
The scaffolding industry is on the cusp of a digital transformation. Automation, AI, 3D modelling and laser scanning are redefining how scaffolds are designed, reviewed and implemented. Companies like Altrad and ScaffPlan are leading the way, proving that these innovations aren’t just trends – they’re the future.
For companies ready to embrace these technologies, the rewards are clear: faster designs, safer projects and happier clients. As Colin Murphy aptly put it, “The future is about working smarter, not harder.” And for the scaffolding and temporary works industry, that future is now.
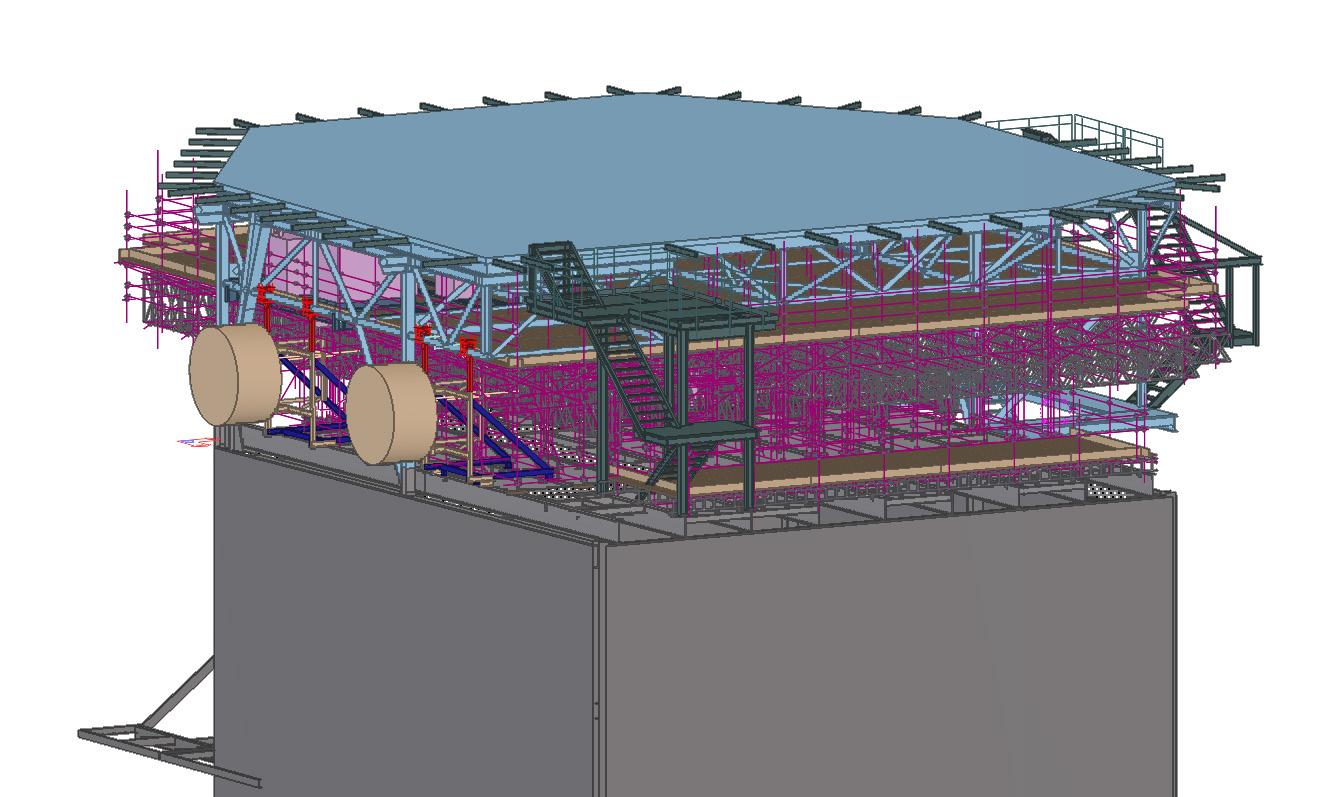
3D modelling and laser scanning produce a clear picture of scaffolding layout and design.

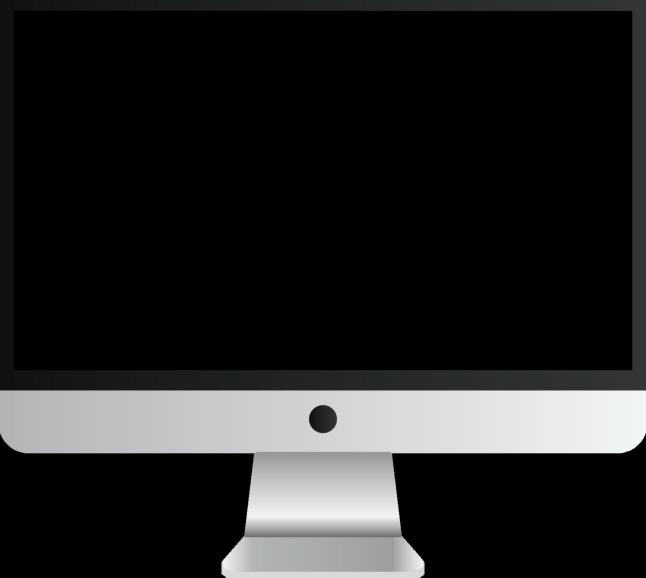
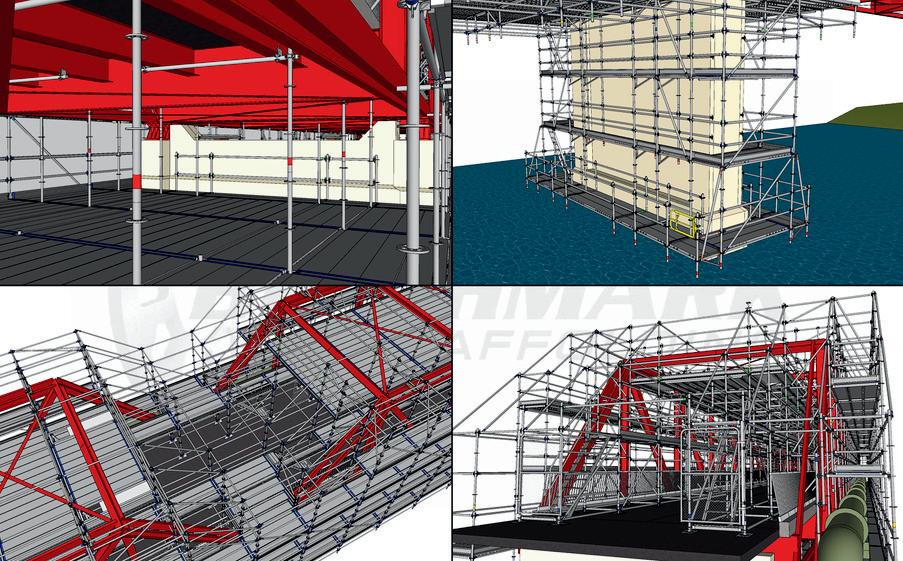
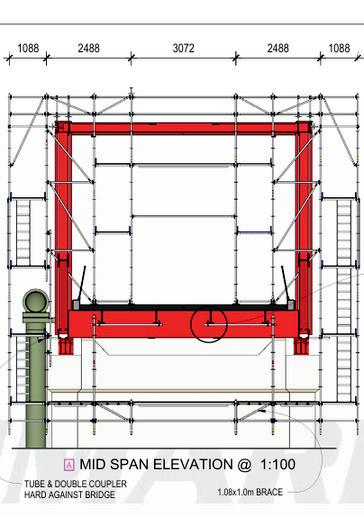
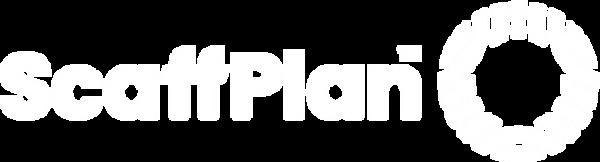
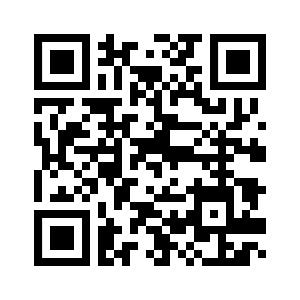

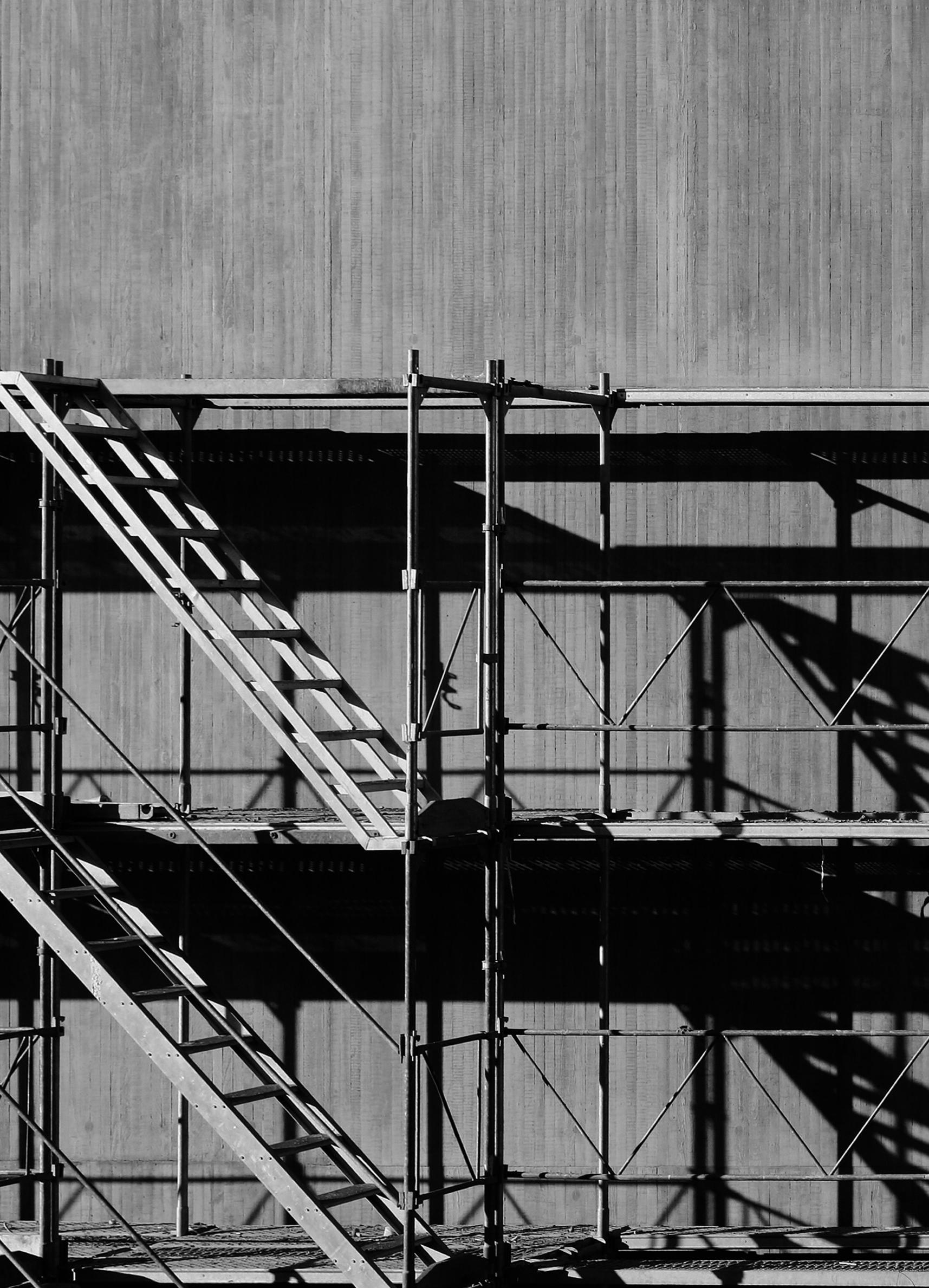
PROJECTS
● Saltburn Viaduct, North Yorkshire
● Victoria Building, Blackburn
● Warner Bros Studios, Watford
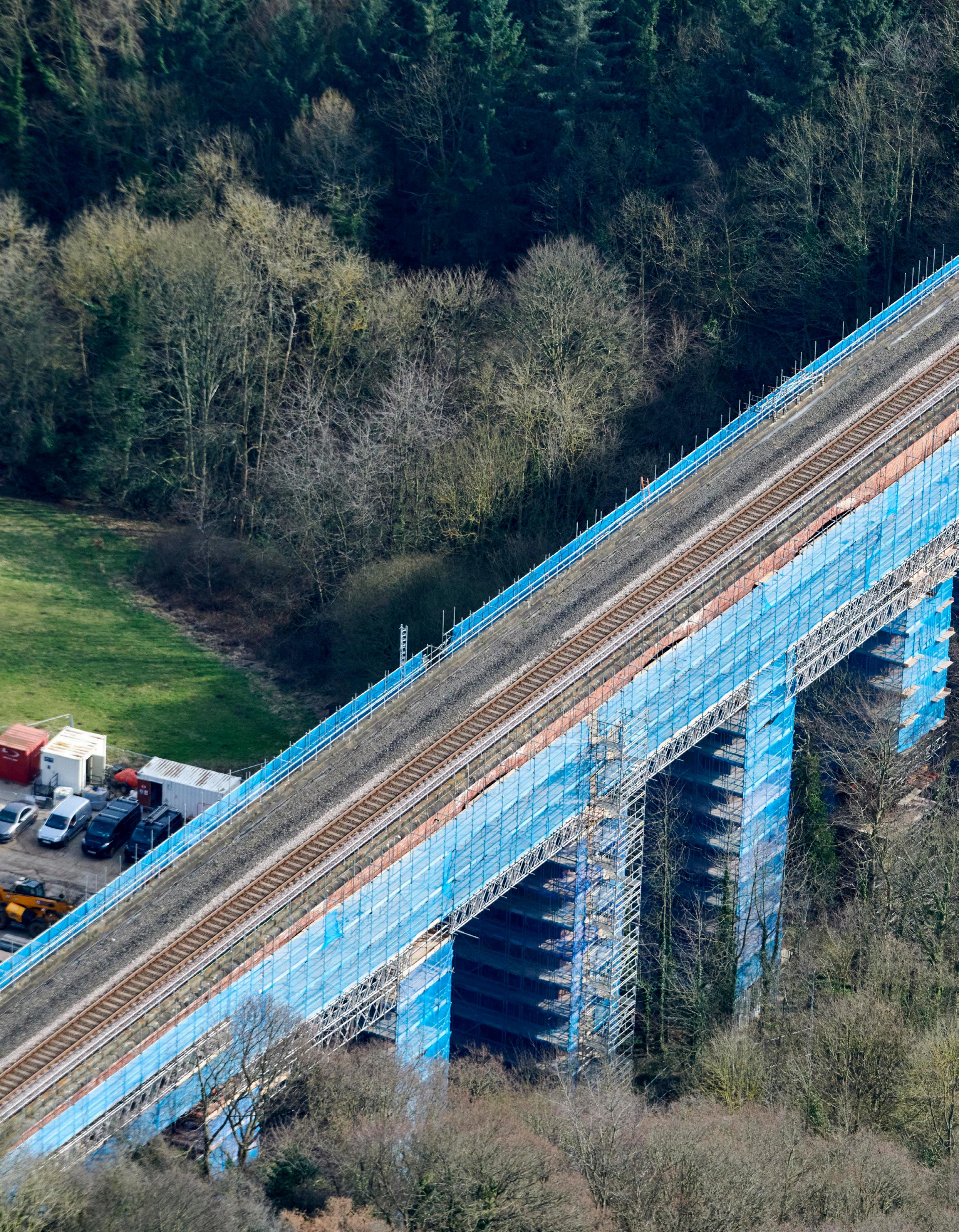
ROUTESUCCESS TO
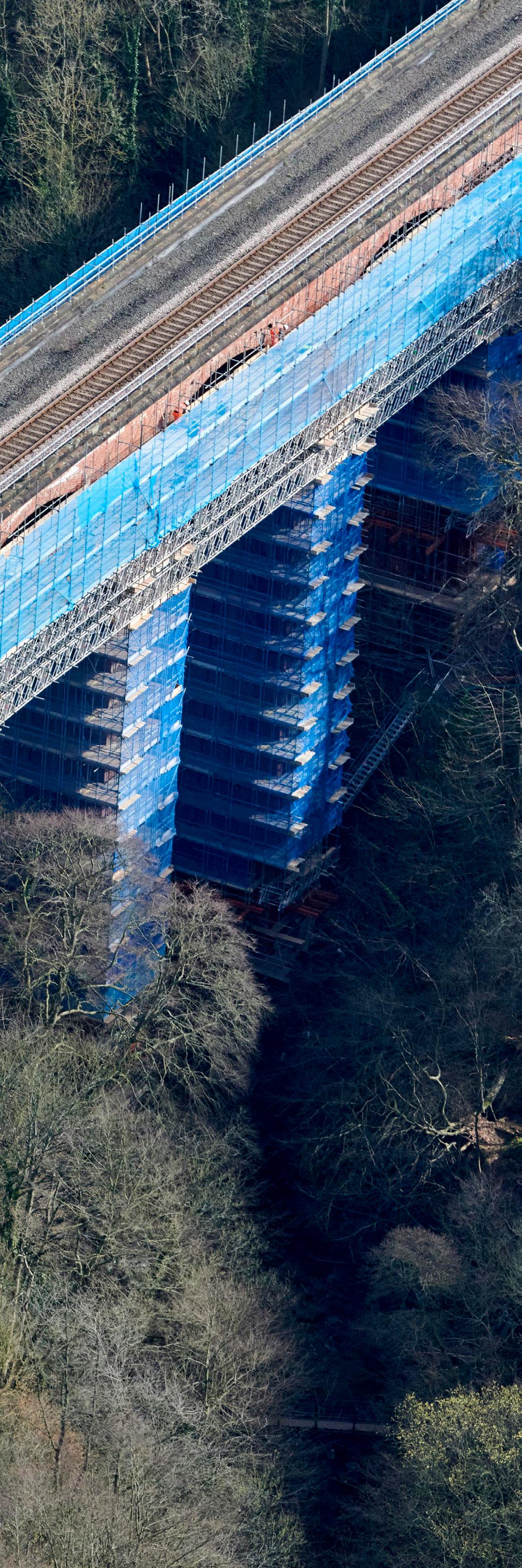
The Saltburn Viaduct stands as a testament to Victorian engineering, towering over Skelton Beck and Mill Fields since its completion in the late 19th century. Originally built between 1865 and 1872 by the NorthEastern Railway Company, the viaduct served as a vital transportation route for the burgeoning industrial activities in the region, notably the Skinningrove Limestone Mine
Now, nearly 150 years later, this towering structure –spanning over 250 metres long and standing 40 metres high – has required meticulous attention and care to preserve its grandeur for future generations.
This recent refurbishment project, headed by AMCO Giffen, required an extensive scaffolding setup to access the viaduct’s 10 red-brick piers and 11 arches. Crossway Scaffolding, a renowned name in the scaffolding industry, was tasked with designing and implementing the access scaffolds that would be critical to the restoration work.
THE SCALE OF THE TASK
The sheer scale of this scaffolding project is awe-inspiring. Crossway’s solution included 720 metres of beams in just one span, with over 5,000 metres of 1.3-metre beams used throughout the entire job. The structure of the viaduct demanded 10 piers to be fully scaffolded, with each tower averaging 11 lifts in height. Additionally, the 11 arches were beamed across to provide 18 elevated platforms, each spanning 11 metres across. This intricate setup supported more than 1,000 tons of scaffolding material at its peak.
One of the standout challenges was access to the highest parts of the viaduct – up to 55 metres above ground – requiring a highly specialised and durable scaffolding system. The Van Theil tube-lock system was chosen for its flexibility and efficiency, enabling work crews to access every nook and cranny of the structure, even the hardest-to-reach areas.
“The Saltburn Viaduct project challenged us in ways we didn’t anticipate, but through teamwork and innovative thinking, we were able to deliver a successful outcome,” says Anthony Lomas, Operations Director, Crossway Scaffolding.
Given its remote location, the Saltburn Viaduct presented numerous logistical hurdles. The ground conditions around Skelton Beck were less than ideal, necessitating innovative approaches to stabilise the scaffolding structure. In several areas, traditional scaffolding foundations were simply not feasible. Crossway utilised specialist RMD equipment to bolt the scaffolding directly to the structure to overcome this, ensuring stability even in these challenging conditions.
Working at such heights also introduced significant safety risks. In response, Crossway implemented a mechanical lifting arm fitted with a stretcher, designed to safely lower any worker in case of an emergency. This extra layer of safety reflected the company’s commitment to prioritising worker wellbeing throughout the project.
The project’s timing added to the complexity – it was carried out during the Covid-19 pandemic. This meant enforcing strict health and safety protocols, such as enhanced personal protective equipment (PPE) and social distancing measures. Crossway arranged for additional vehicles to transport workers to and from the site to minimise the risks, ensuring adherence to social distancing rules.
Scott Grant, SSSTS Supervisor at Crossway Scaffolding, said, “From the ground conditions to working at height, every aspect of this job pushed us to our limits. But seeing the finished project makes it all worthwhile.”
ADAPTING ON THE FLY
Scaffolding projects of this scale often require adjustments as work progresses, and the Saltburn Viaduct project was no exception. Initially, only four piers were set to be scaffolded using RMDs. However, as the team dug deeper into the project, ground conditions necessitated expanding this approach to seven full piers.
One notable adaptation was using a CL 25 general purpose bracket to create platforms lower on the piers. This allowed the team to install RMD gallows brackets more quickly and efficiently. These lightweight brackets were installed from an
alloy tower in the water – a challenging task that highlighted the team’s ingenuity and technical prowess.
COLLABORATION AND COORDINATION
No project of this magnitude can succeed without strong collaboration. Throughout the 12-month project, Crossway worked closely with AMCO Giffen, their design team, and several other key partners. Detailed designs for the scaffolding solutions were provided, while Direct Hoist contributed to the safe and efficient transportation of materials. SIMIAN RISK, an independent safety inspector, conducted frequent inspections to ensure compliance with all safety protocols and best practices.
A TRIUMPH IN SCAFFOLDING
Despite the many challenges, the Saltburn Viaduct scaffolding project was a resounding success. The project was completed within its 12-month timeline, a remarkable feat considering the complexity and scale of the work. Crossway’s innovative solutions, such as the use of RMDs and the mechanical lifting arm, proved critical in overcoming the project’s unique hurdles.
The project has been recognised industry-wide, culminating in Crossway being awarded the prestigious NASC 2021 Project of the Year Award. This accolade is a testament not only to the team’s technical capabilities but also to their commitment to safety, innovation and excellence in scaffolding.
“FROM THE GROUND CONDITIONS TO WORKING AT HEIGHT, EVERY ASPECT OF THIS JOB PUSHED US TO OUR LIMITS. BUT SEEING THE FINISHED PROJECT MAKES IT ALL WORTHWHILE”
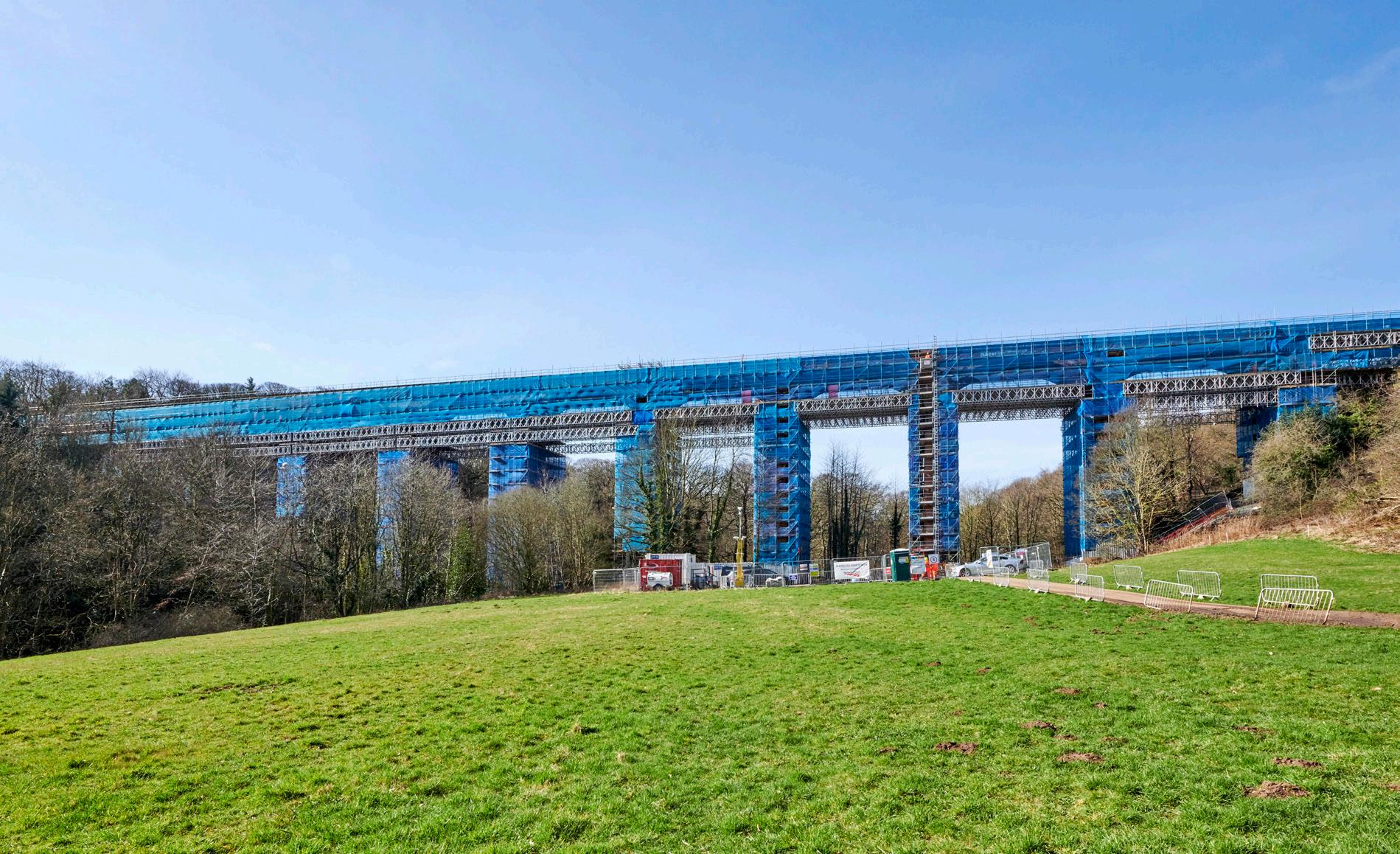
LESSONS LEARNED
The Saltburn Viaduct project offered valuable insights into the importance of adaptability and innovation in scaffolding. The decision to pivot and use RMDs on additional piers was instrumental in maintaining the project’s timeline and safety. Additionally, the use of mechanical lifting equipment highlighted the importance of incorporating advanced safety features when working at height.
For Crossway, the project also underscored the need for solid logistical planning, particularly when working in remote locations or under challenging conditions. The company’s decision to provide local accommodation for its workers during the week improved morale and ensured that work continued without delays caused by long commutes.
LOOKING FORWARD
With the successful completion of the Saltburn Viaduct project, Crossway has once again proven itself as a leader in the scaffolding industry. The company’s innovative approaches and steadfast commitment to safety and quality will undoubtedly serve as a blueprint for future projects of this scale and complexity.
For now, the Saltburn Viaduct continues to stand tall –a lasting symbol of engineering brilliance, preserved for future generations thanks to the skill and dedication of Crossway Scaffolding.
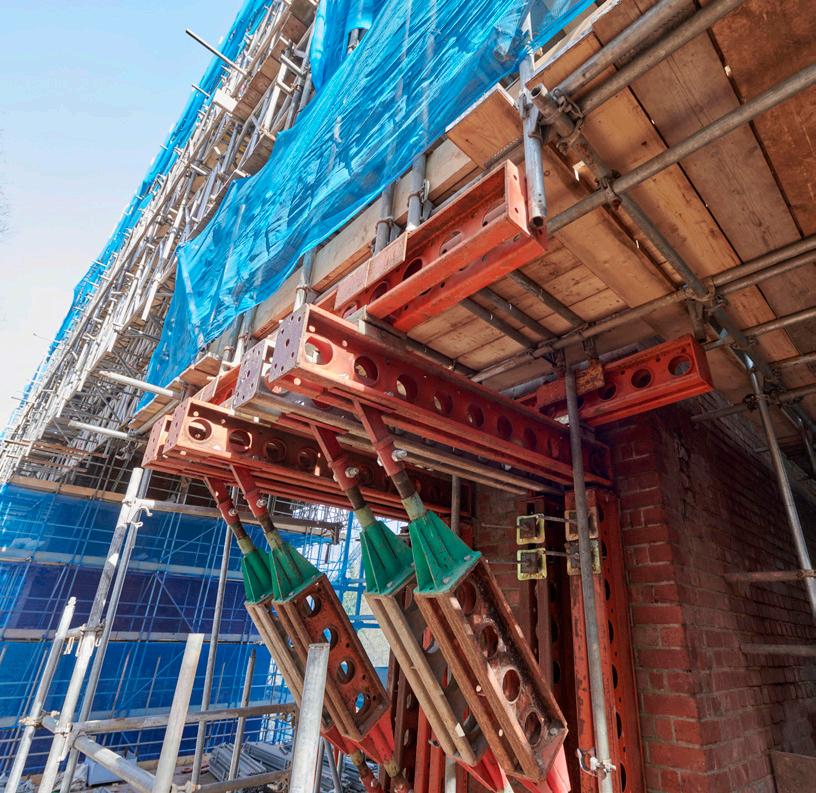
The complex project was completed within its 12-month timeline –remarkable, considering the scale.
Ateam of experts from Allied Access and Buckley Design Solutions (BDS) are spearheading this ambitious, multi-million-pound restoration of Blackburn College’s Victoria Building. Their ingenuity and dedication are breathing new life into this historic landmark.
The Victoria Building’s red-brick facade and ornate details have long been symbols of Blackburn’s architectural heritage. However, time has taken its toll, and the building now requires meticulous internal and external restoration to preserve its structural integrity and aesthetic beauty.
This project, managed by construction giants BAM Construction Ltd., isn’t just about renovation; it’s about respecting and maintaining the historical essence of an irreplaceable piece of Blackburn’s identity.
AN INGENIOUS SCAFFOLDING SOLUTION
Allied Access and BDS took on the Herculean task of designing and erecting a scaffolding system that would support the restoration work while protecting the delicate structure. From the outset, it was clear that this wouldn’t be a typical scaffolding project.
To avoid damaging the building’s facade, BDS designed a freestanding scaffold system for the north, east and south elevations. This approach ensured stability without relying on the fragile walls of the historic structure.
The west elevation, however, required a different strategy. Here, bespoke cantilever brackets were used due to the low load-bearing capacity of the neighbouring roof.
To shield the building and workers from Blackburn’s unpredictable weather, highly skilled scaffolders from Allied installed a comprehensive temporary roof. Spanning 44 metres and supported by a central spine beam through the north light well, this roof protects and enables continuous restoration work.
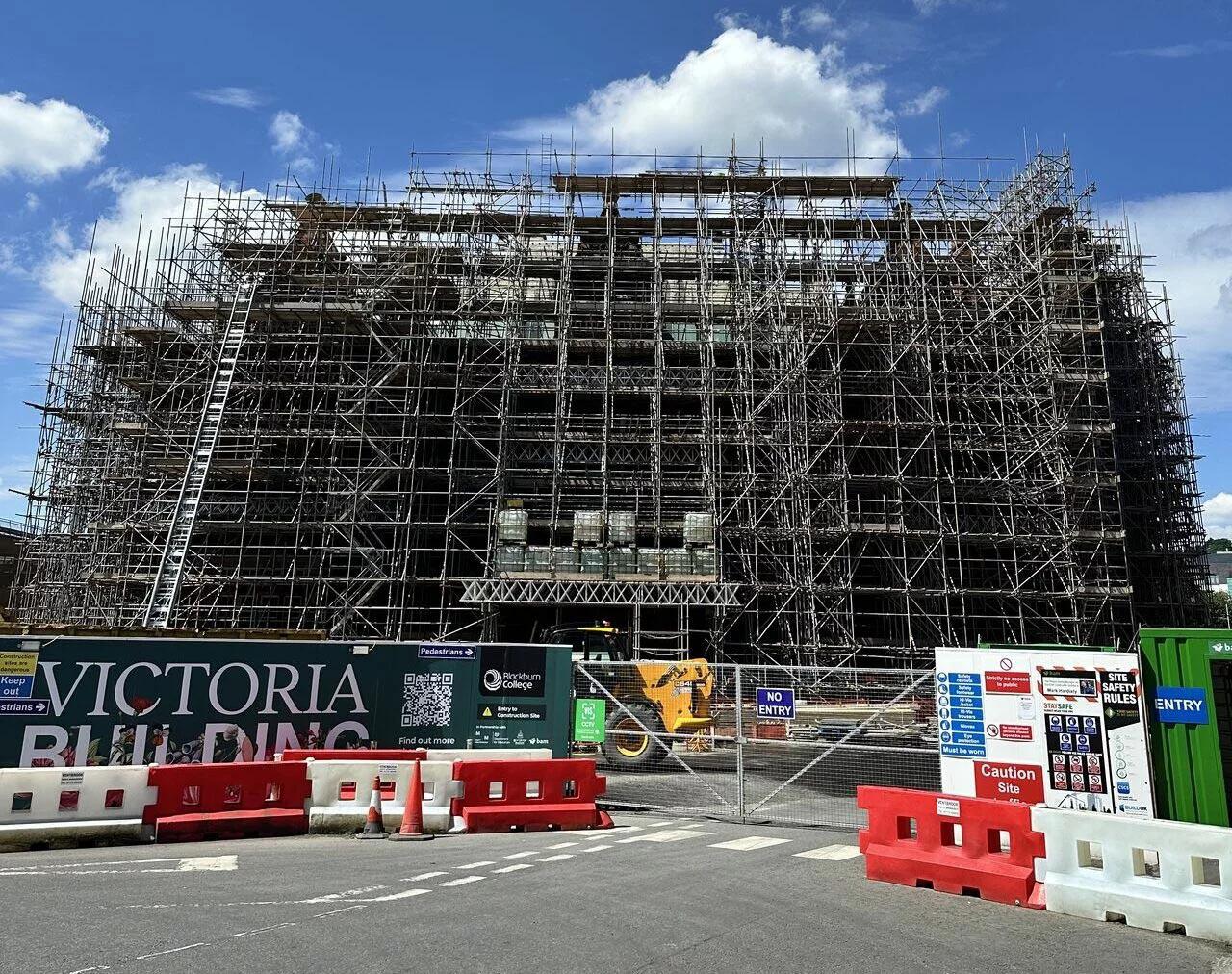
Allied forces
Nestled in the heart of Blackburn, the Victoria Building stands as a grand testament to the town’s rich history. Built in 1888, this Grade-II listed structure has witnessed over a century of change, and now, it faces one of its most significant transformations yet
OVERCOMING DESIGN CHALLENGES
BDS told ScaffMag that the restoration project presented a series of complex challenges that required innovative solutions. Initial design plans were revised to address the building’s structural limitations and ensure the scaffolding’s effectiveness.
Revision A : The first significant design revision removed ties from the north, east and south elevations, replacing them with buttresses. However, due to structural constraints, the west elevation remained fully tied and supported by bespoke cantilever brackets.
Revision B: A critical breakthrough came with introducing a central core tower in the north light well, distributing the load more effectively. This central tower, combined with spine beams running from east to west, significantly reduced external leg loads. A concrete raft foundation further facilitated load distribution, eliminating the need for additional support weights, or ‘kentledge’.
Collaboration with structural engineers from Curtins and Wentworth House Partnerships led to the development of a ring beam system, redistributing localised loads and ensuring stability. The use of 3D design models by BDS allowed the scaffolders to visualise and execute this intricate scaffolding system with precision.
NAVIGATING OPERATIONAL HURDLES
Logistical and operational challenges were ever-present, but the team’s meticulous planning and coordination ensured smooth execution.
Strict Timelines: With a tight schedule to adhere to, detailed project planning and regular progress meetings kept the project on track.
Logistical Coordination: The site’s historical nature demanded careful planning for the transportation and placement of materials. Coordination with Blackburn College and local authorities helped minimise disruptions.


The Victoria Building is a stunning symbol of Blackburn’s architectural heritage.
Resource Management: Securing experienced scaffolding operatives and high-quality materials was crucial. Continuous training ensured the team’s efficiency and adherence to high standards.
THE PATH TO SUCCESS
Key stages of the project highlighted the team’s expertise and adaptability.
Setting the Scaffolding Base: Aligning the scaffolding base correctly was paramount, considering the complex ties into the newly designed concrete raft foundation. The team’s meticulous approach ensured a stable foundation.
Cantilever Brackets Installation: Custom-designed cantilever brackets were carefully installed to support the west elevation without compromising its historical integrity.
Spine Beams Installation: Positioned with precision, the spine beams supported the temporary roof, providing a safe and effective solution for weather protection.
Temporary Roof Installation: The installation of the temporary roof ensured comprehensive coverage, allowing restoration work to proceed uninterrupted, regardless of weather conditions.
ACHIEVING RECOGNITION
As the Victoria Building restoration progresses toward its scheduled completion, the project has already garnered widespread acclaim for its innovative design and seamless execution.
Kevin Walsh, Senior Design Engineer at BAM Construct UK Ltd, remarked, “The design challenges were formidable, but the BDS team rose to the occasion.
Their proactive collaboration with BAM’s site team and the Project Structural Engineer was instrumental in developing a workable design. Without this close cooperation, the temporary roof would have been an impossible feat.”
Lee Buckley, Managing Director of Buckley Design Solutions, reflected
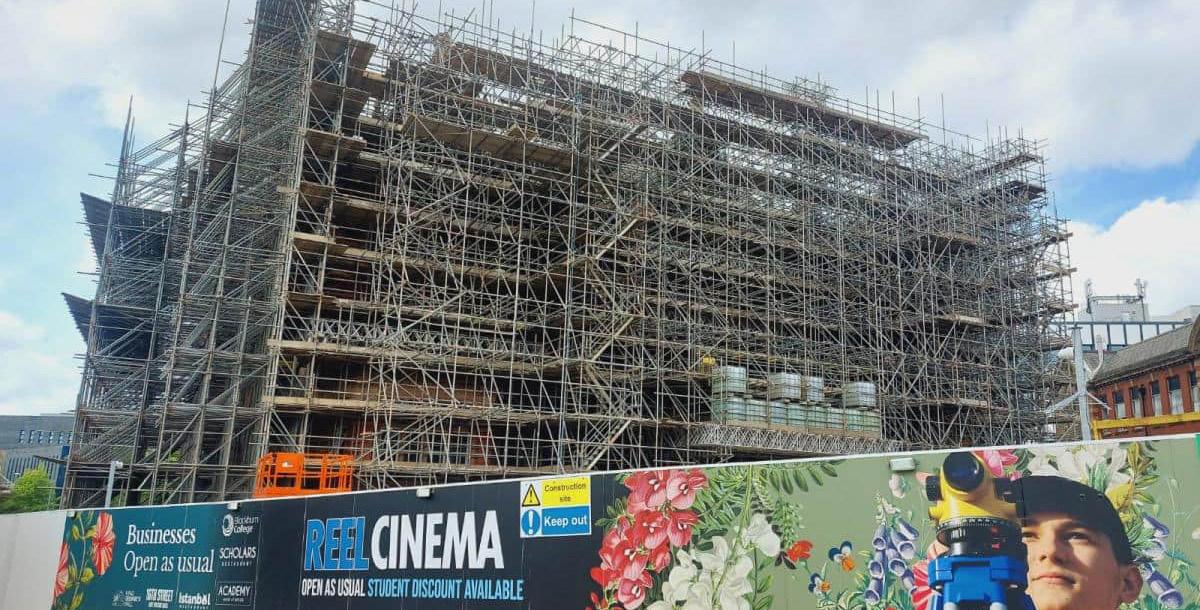
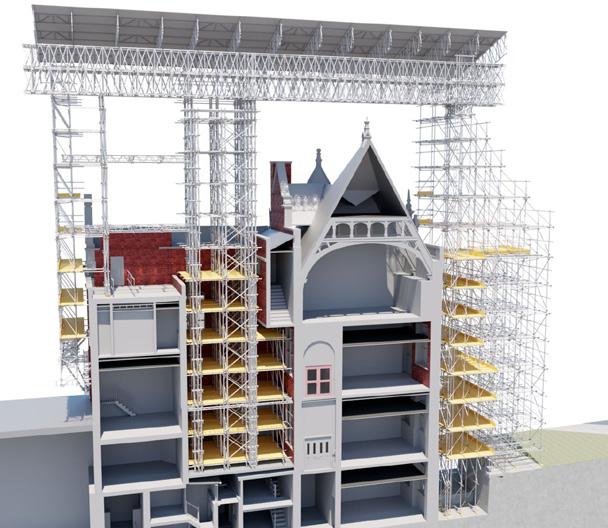
on the project’s complexity, stating, “In nearly 30 years in the scaffolding industry, this design stands out as the most intricate I’ve ever worked on. The ability of the scaffolding team to execute the plan ahead of schedule is truly commendable.”
Steve Bannister, Operations Director at Allied Access, echoed these sentiments, adding, “With over 40 years in the scaffolding industry across various sectors, this project has been a particularly rewarding experience. Early engagement with BAM, the client and BDS was key to bringing this complex plan to life, and the collaborative effort has been nothing short of remarkable.
“The Directors are immensely proud of the Allied team, whose professionalism and swift execution of this exceptional scaffolding structure deserve high praise.”
BAM Construction Director Mick Donoghue and Senior Project Manager Mark Hardisty concluded: “The Victoria Building Project presented a plethora of complex issues to overcome. Being a Grade-II listed structure requiring a
complete reroof, it was imperative that the correct solution to safeguard these finishes whilst the works were being carried out was developed to prevent further damage to the internal fabric.
“With the early engagement of our supply chain partners, Allied Access and BDS, the team has worked hand in hand with BAM’s design and management teams to develop a scheme that achieves this without impacting on the listed facade.
“Our thanks go out to BDS and all involved in working so collaboratively to overcome the many challenges along the way.”
A VISION REALISED
The Victoria Building restoration is more than a project; it’s a labour of love and a testament to the expertise and dedication of Allied Access and Buckley Design Solutions. Their innovative approach and meticulous planning have helped preserve a piece of Blackburn’s heritage and set a new benchmark for future scaffolding and restoration projects.
In reviving the Victoria Building, the team has woven a story of collaboration, innovation and respect for history. Their work ensures that this architectural gem will continue to grace Blackburn’s skyline for generations to come.
The project is a testament to the expertise of Allied Access and Buckley Design Solutions.
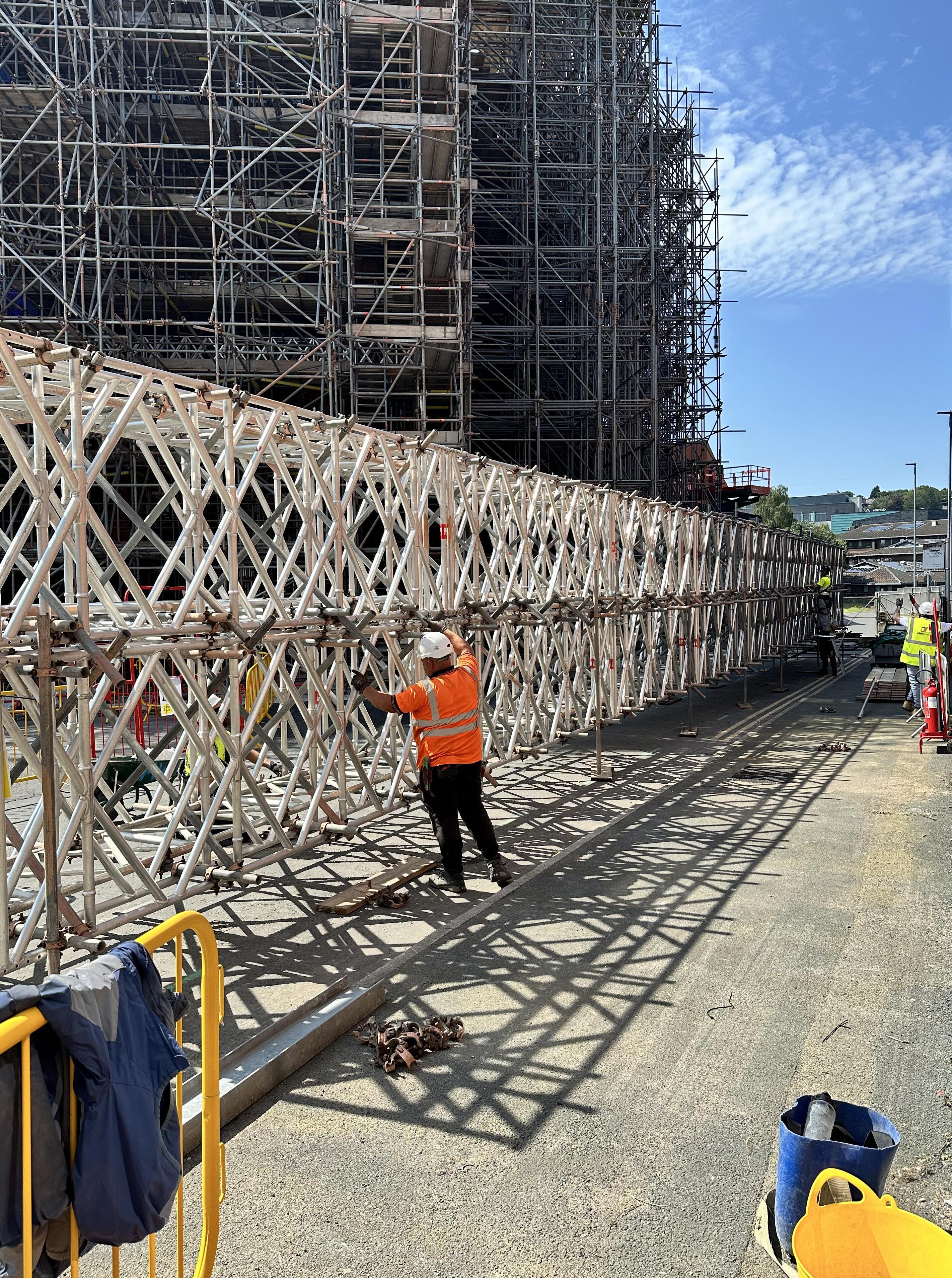
HAVING BEEN INVOLVED IN THE SCAFFOLD INDUSTRY FOR ALMOST 30 YEARS, THIS SCAFFOLD DESIGN IS THE MOST COMPLEX I’VE WORKED ON”
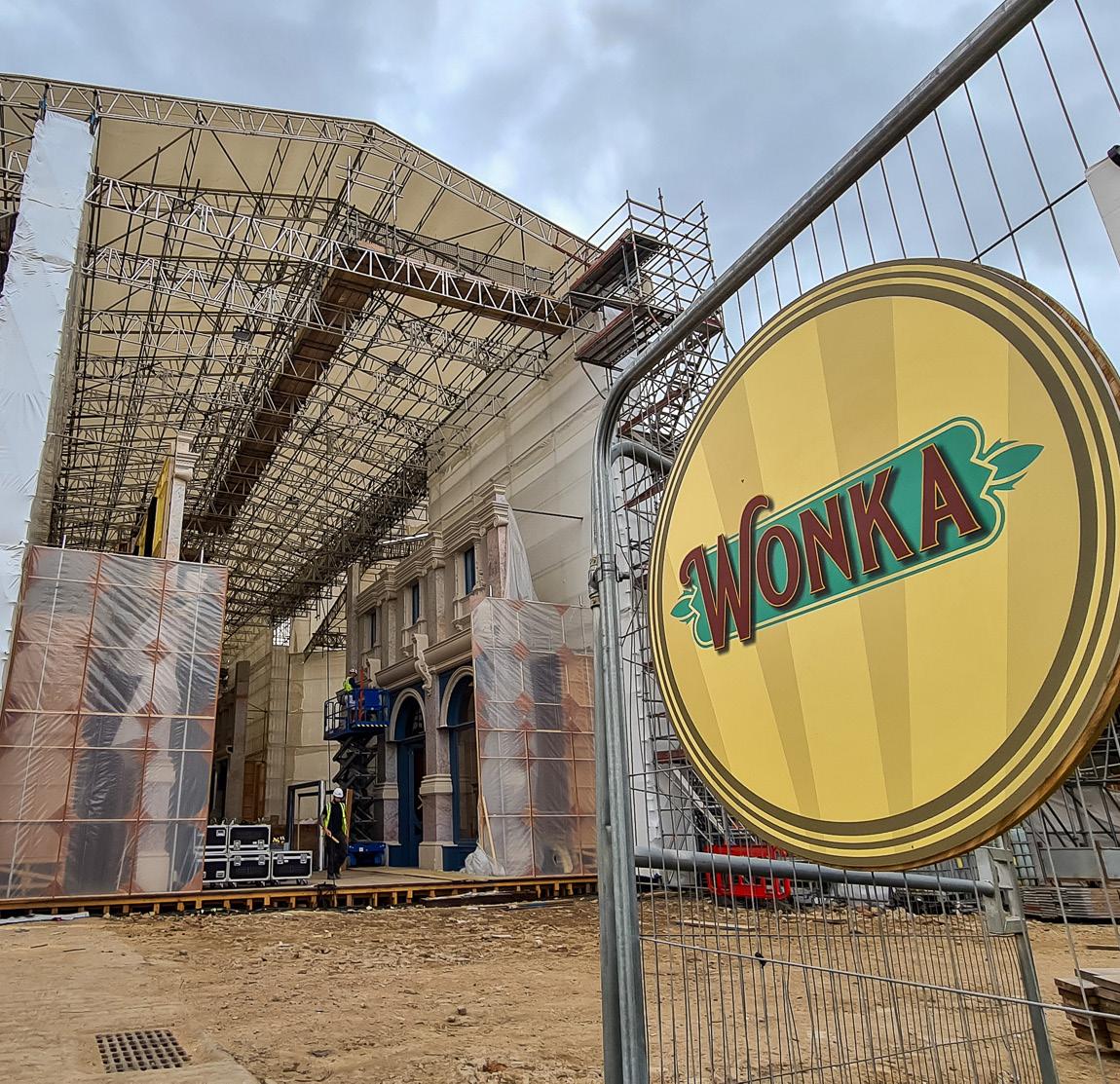
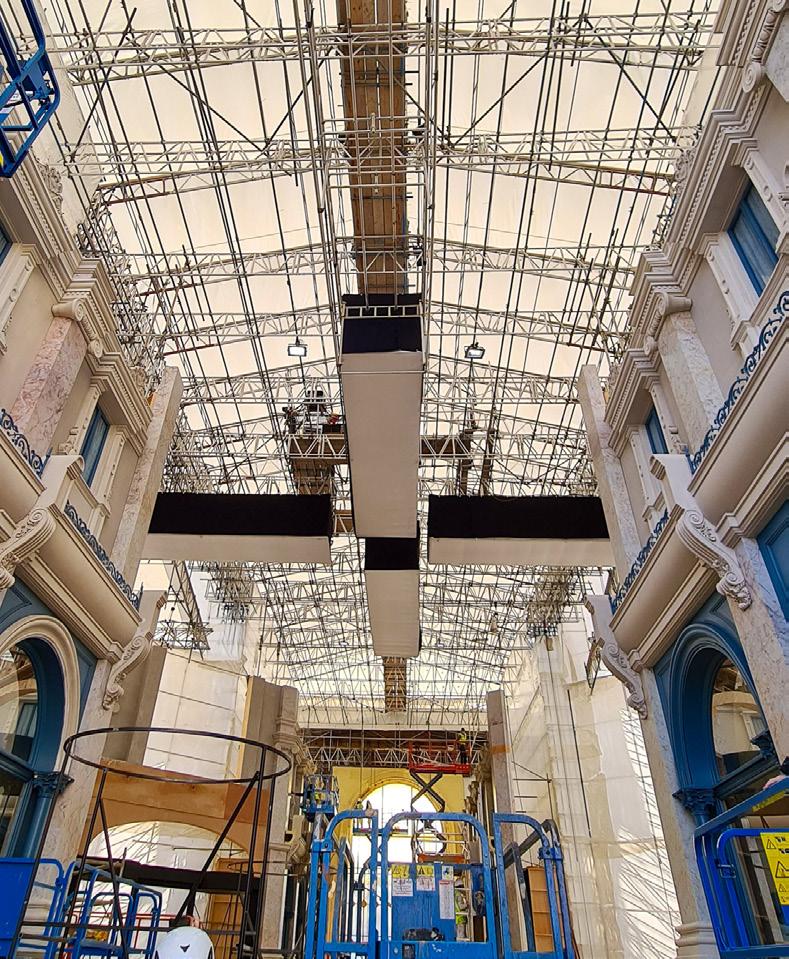
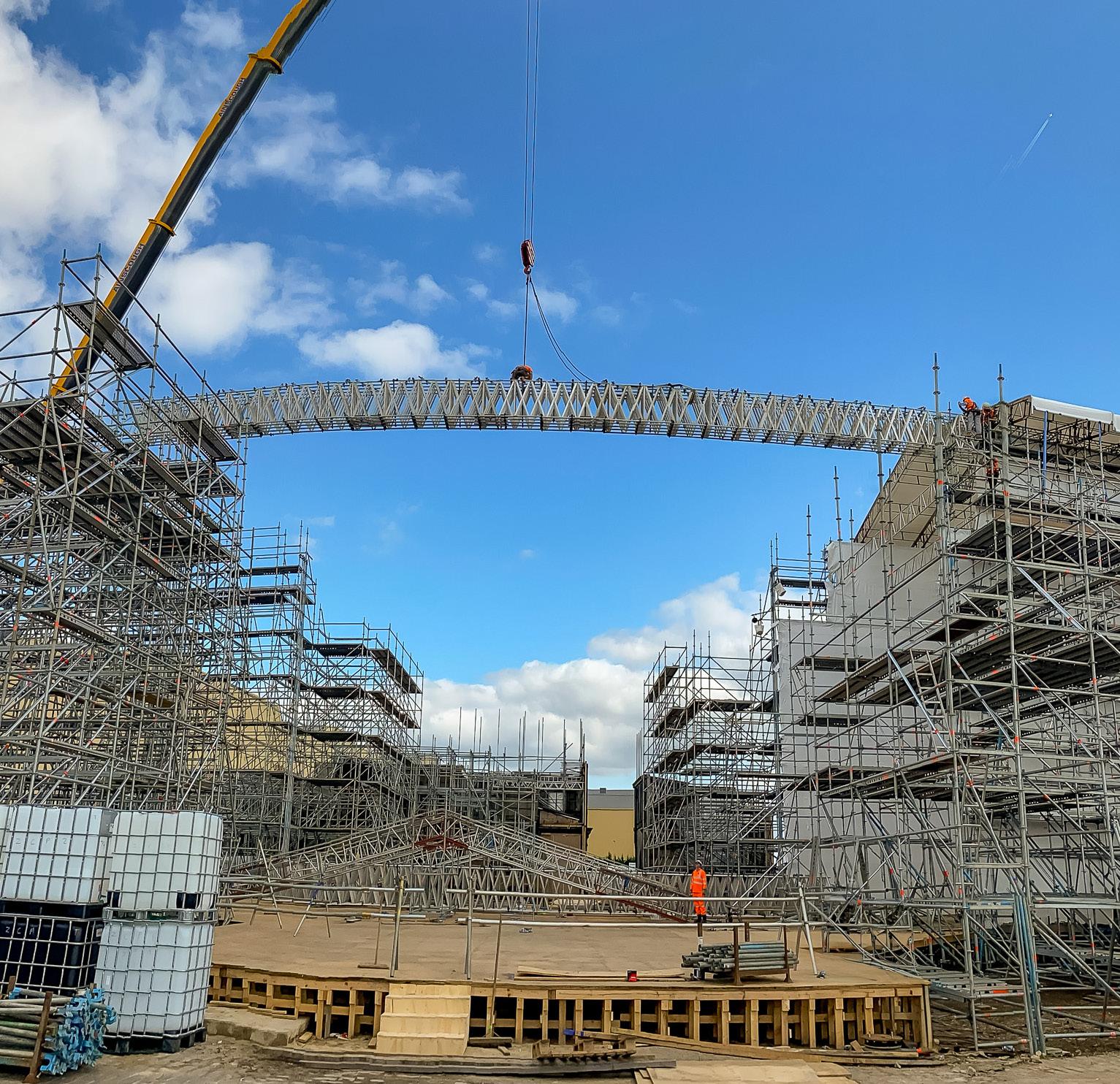
LIGHTS, CAMERA, SCAFFOLD!
In film production, creating the perfect set often requires more than just imagination – it calls for innovative solutions to overcome technical and logistical challenges
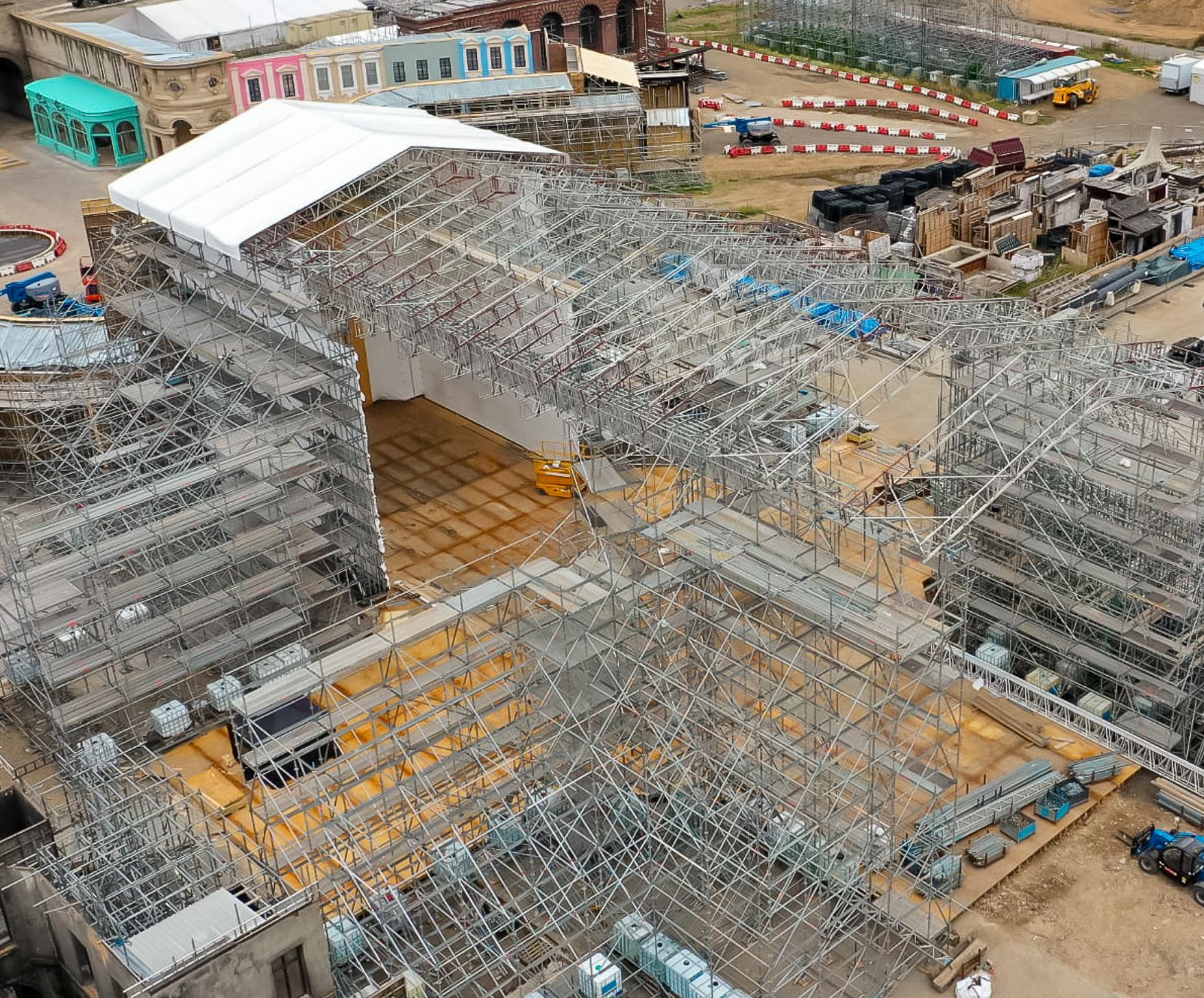
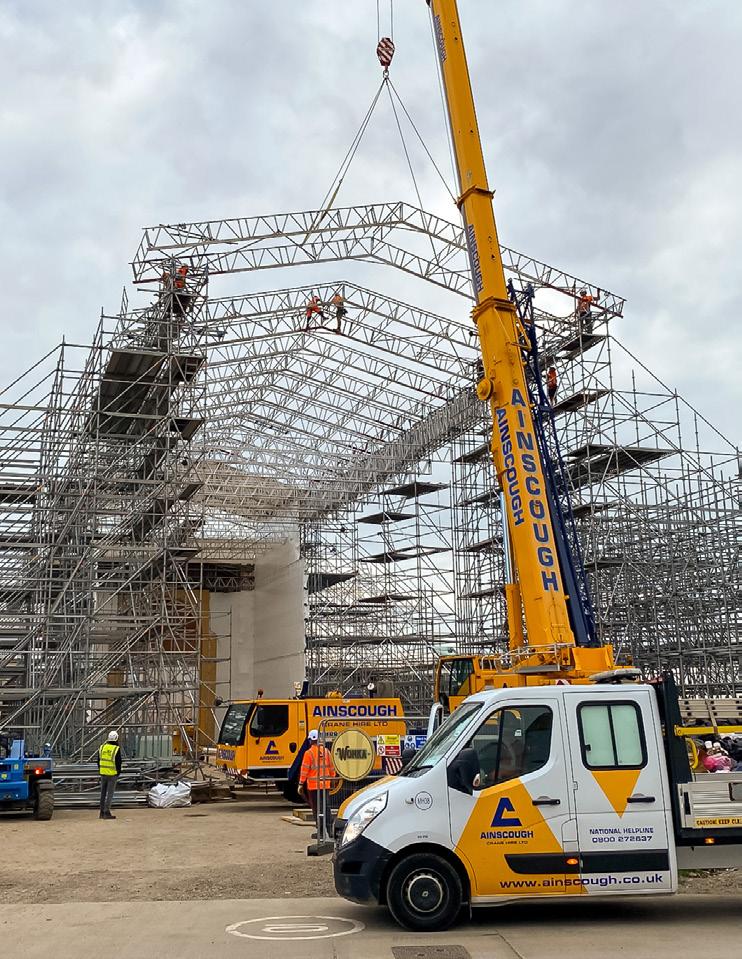
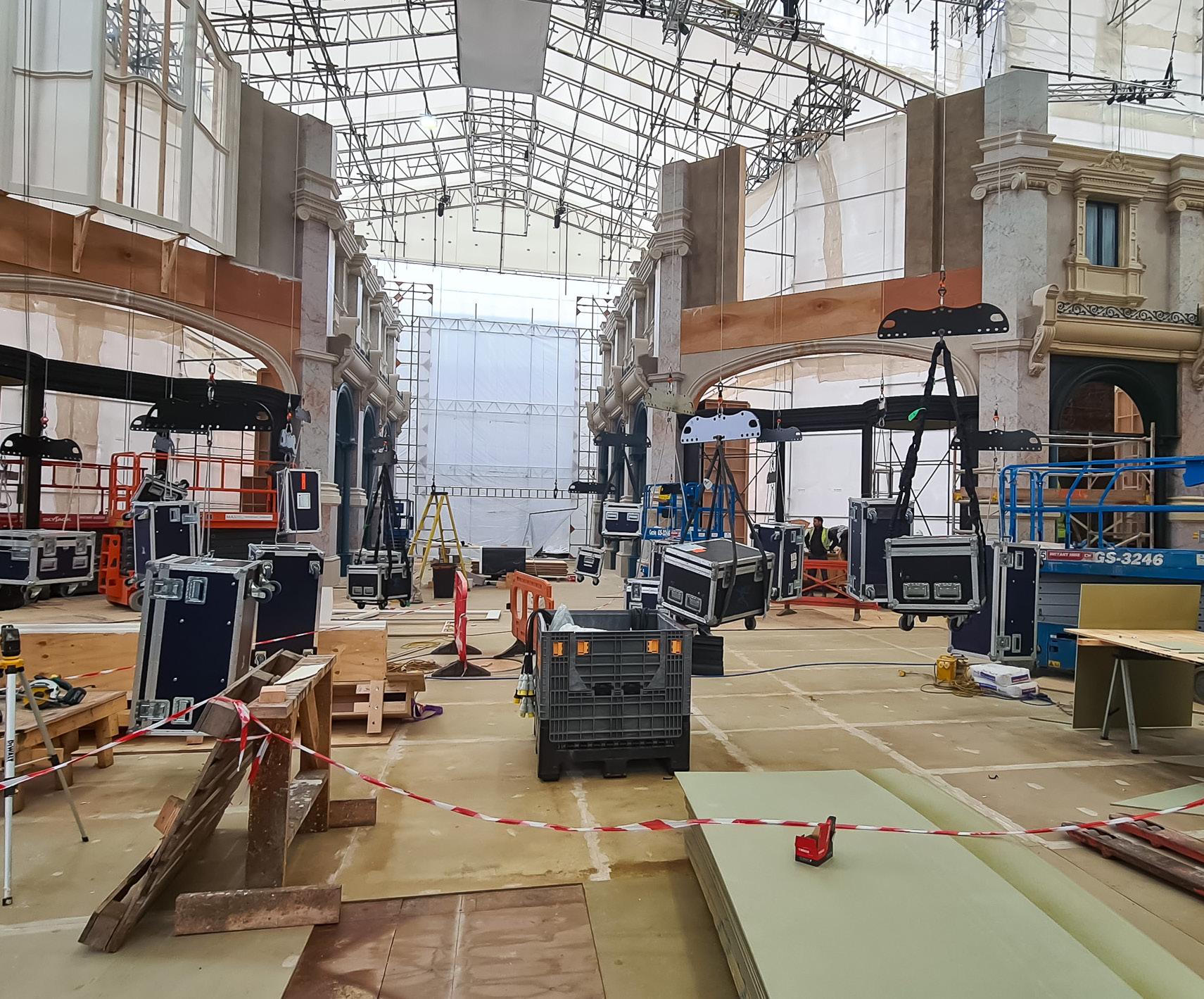
One such instance unfolded during the production of the highly anticipated Wonka movie, where a massive temporary roof scaffold played a pivotal role in bringing the cinematic vision to life.
At the heart of this success was Sky Scaffolding Midlands Ltd, tasked with constructing a highly technical and durable scaffold structure, working in collaboration with Warner Bros Studios Leavesden and SDC Scaffold Design Consultants Ltd.
BUILDING A DREAM: THE CHALLENGE
The project was set at Warner Bros Studios near Watford, where the fictional city and retail complex known as Galeries Gourmet was recreated. Inspired by Milan’s iconic Galleria Vittorio Emanuele II, this vibrant backdrop featured a crossroads that would house storefronts for Wonka and his rival Slugworth. The bustling intersection, set to be a key scene in the movie’s opening sequences, would become the stage for dancers, trapeze artists and more.
To meet the ambitious needs of the production, Warner Bros approached Sky Scaffolding Midlands with a tall order: constructing a 53m x 46m weatherproof structure, capable of supporting lighting, camera gear, a catwalk and an astonishing 20 trapeze artists at a height of 14m. The solution needed to be not only durable and safe but also flexible to accommodate the dynamic demands of filming.
INNOVATIVE DESIGN WITH SDC SCAFFOLD DESIGN CONSULTANTS
Rob Hastings, Managing Director of SDC Scaffold Design Consultants, played a key role in devising a scaffold design that balanced safety with cost-effectiveness. Initially, the team proposed a large square structure with a dual-pitched roof supported by birdcage scaffolding in each corner. However, as the design evolved and the trapeze requirements expanded, the original layout proved to be inefficient
in terms of material usage.
Hastings and his team quickly adapted, introducing a more efficient solution: a cross-like formation of roofs, which reduced the amount of scaffolding material required while still providing full weather protection. This clever reworking of the design cut the amount of roof cover needed by 30%, resulting in significant savings on both materials and labour.
Reflecting on the project, Hastings commented, “When you receive a phone call asking if you want to design a temporary freestanding simulated shopping mall for a major film production, you jump at the chance. And with the complexity of accommodating suspended actors –including Hugh Grant and Matt Lucas – we jumped in with both feet.”
FROM BLUEPRINT TO REALITY
With the design in place, construction began. The first phase involved assembling four scaffolding structures, each standing 17 metres tall and covering an area of 23m x 16m. Built using the Layher Allround system, these structures were braced
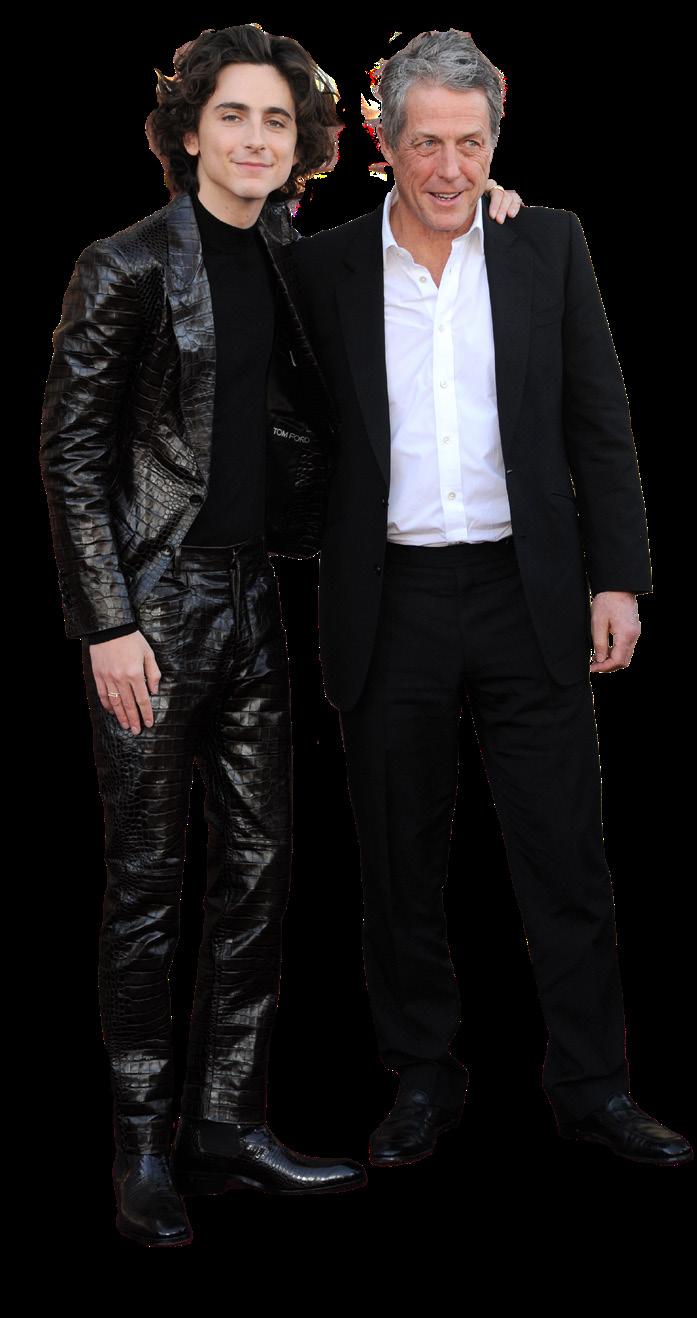
throughout to ensure stability, with water-filled Intermediate Bulk Containers (IBCs) providing additional reinforcement.
Next came the installation of two massive spine beams, each constructed from five parallel Apollo X-Beams. These 23m and 25m long beams, weighing up to three tonnes apiece, were assembled at ground level before being carefully lifted into place by crane.
Finally, the duo-pitched roof beams, measuring 17m in length, were installed using the HAKITEC 750 roofing system. These were also assembled at ground level before being hoisted into position. The final stage involved the installation of 750mm aluminium lattice beams, which provided support for lighting, cameras, catwalks and trapeze equipment.
A TRIUMPH OF COLLABORATION AND EXPERTISE
This ambitious scaffold project was a resounding success, showcasing the best of what teamwork and innovation can achieve. The temporary structure allowed filming to continue safely in all weather conditions, with the roof structure proving robust enough to withstand two major storms without budging.
The partnership between Warner Bros, Sky Scaffolding Midlands Ltd and SDC Scaffold Design Consultants exemplifies the importance of collaboration in largescale productions. UK System Scaffold Hire Ltd provided the materials for the temporary roof, while Shire Shrinkwrap added the final layer of protection with their shrinkwrap services.
As scaffolding continues to play a vital role in ambitious film projects, the Wonka scaffolding team has certainly set the bar high. Their work ensured that the magic of Wonka could be brought to life on screen, leaving audiences none the wiser to the intricate planning and hard work behind the scenes.
For those in the scaffolding industry, this project serves as a reminder that even the most fantastical movie scenes depend on the rock-solid foundation of expert scaffolding solutions.


End of an era
As NASC President David Brown’s two-year term comes to an end at the organisation’s AGM during ScaffEx 24 on 28 November, ScaffMag’s editor Daniel Norton sat down with him to reflect on his presidency, the achievements, and the future of the NASC
Daniel Norton: David, your time as President of the NASC is concluding. How would you summarise your experience leading the organisation over the past two years?
David Brown: It’s been an incredible journey – a period that I would describe as exciting, enjoyable and challenging, but ultimately transformational. The role came with a lot of responsibility, but seeing how much progress we made as a team was immensely rewarding. When I took the presidency, I knew we had to address some longstanding challenges, but I also saw an opportunity to redefine the NASC’s role in the industry and bring it into a new era. It’s been busy and demanding, but our implemented changes have set a strong foundation for the future of scaffolding in the UK.
DN: When you assumed the presidency, what was the state of the NASC, and what were the key areas you aimed to focus on during your term?
DB: When I became President, the NASC was already well-established and respected, but there were areas
where we could improve. The leadership structure needed to be modernised, our business planning processes were not as effective as they could have been, and there was a real issue with how contractors and clients perceived NASC. Too many people didn’t fully understand the value of being an NASC member, and this limited both our growth and the impact we could have on the industry.
At the same time, we were facing a critical talent shortage – an issue affecting not just us, but the entire scaffolding sector. Recruitment and retention were major pain points. From day one, I set three primary objectives: increase the recognition of NASC standards; tackle the industry’s talent gap; and bring about a cultural transformation within the NASC itself. These goals have guided me throughout my tenure.
DN: Let’s start with the first objective. How did you increase recognition of NASC and its standards?
DB: The key initiative here was the #ItHasToBeNASC campaign,
which has been instrumental in raising awareness about the importance of NASC membership. We partnered with influential bodies like the National Federation of Builders and Build UK and engaged with principal contractors, including major players like Vinci, to promote the specification that only NASC members should be employed for scaffolding work. This initiative has been about demonstrating that NASC members uphold the highest standards, not just meeting but exceeding the safety and quality requirements that should be expected in our industry.
Through this campaign, we’ve not only elevated the NASC brand but also helped members secure more work by positioning them as the best in the business. This has also played a crucial role in addressing the ‘race to the bottom’ issue, where companies are tempted to go with the cheapest option without understanding the safety risks involved in scaffolding. The campaign has created a shift in mentality, and we’re seeing real progress in recognising NASC’s authority in the sector.
DN: With PAS91 being phased out, does this create an opportunity to address the issue of multiple accreditations?
DB: Absolutely. The end of PAS91 is a significant moment for us. NASC will soon be introducing the Common Assessment Standard, which will simplify the accreditation process for our members. It’s going to make a huge difference. Currently, many contractors are weighed down by the need to secure numerous accreditations, most of which overlap or don’t address the specific risks in scaffolding and access. Our Common Assessment Standard will streamline this process, reduce bureaucracy and make it easier for NASC members to compete. It’s a significant win for the industry, and I’m excited to see it come into play.
DN: Your second key objective was addressing the talent crisis in the scaffolding sector. What steps has NASC taken under your leadership to tackle this issue?
DB: The talent shortage is one of our industry’s most pressing challenges. We developed a robust support system for members focused on recruitment and training to address it. NASC launched a series of grants designed to incentivise recruiting new talent and upskilling existing staff. For instance, members received grants of £150 for each new recruit, £200 for newly qualified scaffolders, and higher amounts for advanced qualifications like £500 for new supervisor cards. These grants have been vital in encouraging companies to invest in training and development, and in turn, this has helped improve the skill level across the industry.
To date, we’ve awarded over £250,000 in grants, a testament to how seriously we take this issue. But it’s not just about money. It’s about creating an environment where companies feel supported in growing their teams and raising standards across the board. The training grants give them the confidence to bring in new people, knowing that NASC is backing them every step of the way.
DN: That sounds like a significant investment in the future of the industry. What was the final objective you focused on during your presidency?

DB: My third objective was to transform NASC itself. There was a perception that NASC was somewhat of an old boys’ club – which we needed to change. The scaffolding industry is evolving, and we had to ensure that NASC was evolving. That meant diversifying our leadership, bringing in new voices and expanding our membership to reflect the whole industry, not just a specific segment of it. We achieved this through structural changes, including updates to our rules and ensuring a diverse membership representation on council. We also prioritised improving our member engagement through new committees, encouraging participation from a broader range of businesses. As a result, we’ve seen unprecedented growth in our membership. In recent months, we’ve been hitting a 24% monthly growth rate, and NASC is now the largest fully audited scaffolding and access trade body in the UK.
DN: That’s an impressive transformation in such a short period. What would you attribute this success to?
DB: It really comes down to the passion and energy within the NASC team. We’ve got a fantastic group of people deeply committed to making a difference in the industry. The appointment of Clive Dickin as CEO was a pivotal moment –he’s been instrumental in driving this change. Clive brought fresh ideas and a clear vision for the future, which helped create the needed momentum. We’ve seen growth in membership and the resources we can offer our members, which has been incredibly well received.
The enthusiasm of our members has also been vital. The new committees we’ve formed are filled with people who want to contribute and shape the industry’s future. That level of engagement is invaluable.
DN: Looking beyond your presidency, what do you see as the key priorities for the NASC moving forward?
DB: I think the next big challenge will be embracing new technologies and sustainability practices. The industry is changing rapidly, and scaffolding needs to keep pace. The NASC will play an essential role in helping our members adapt to these changes, whether it’s through digital transformation, embracing more sustainable materials, or improving safety with new technologies.
At the same time, I’d like to see us continue focusing on improving workforce diversity. We’ve made some strides, but there’s still more to do.
The industry will benefit from a wider range of perspectives and experiences, and NASC can help foster a more inclusive environment. We’ve laid the groundwork during my presidency, but there’s plenty more to achieve in the years ahead.
The most important priority for NASC, I believe though, is to ensure that it continues to support and represent the membership. It’s through the hard work and dedication of the NASC team and the volunteering members that makes it what it is. We’ve moved so far in the past two years and I’m excited to see this continue.
Construction Hoists
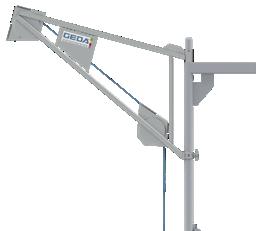

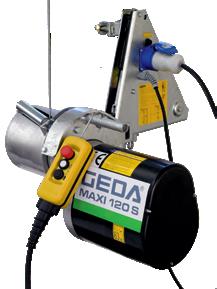
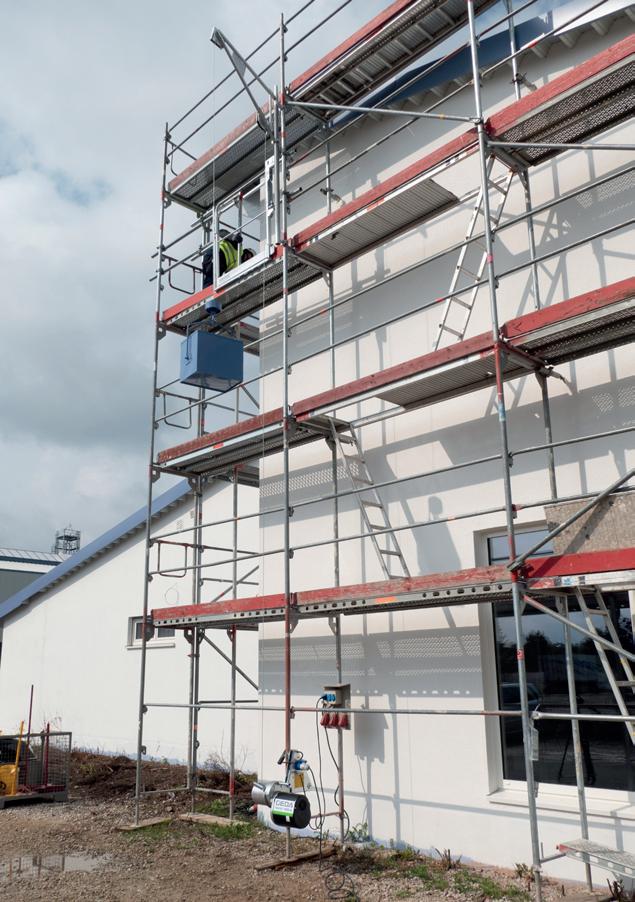

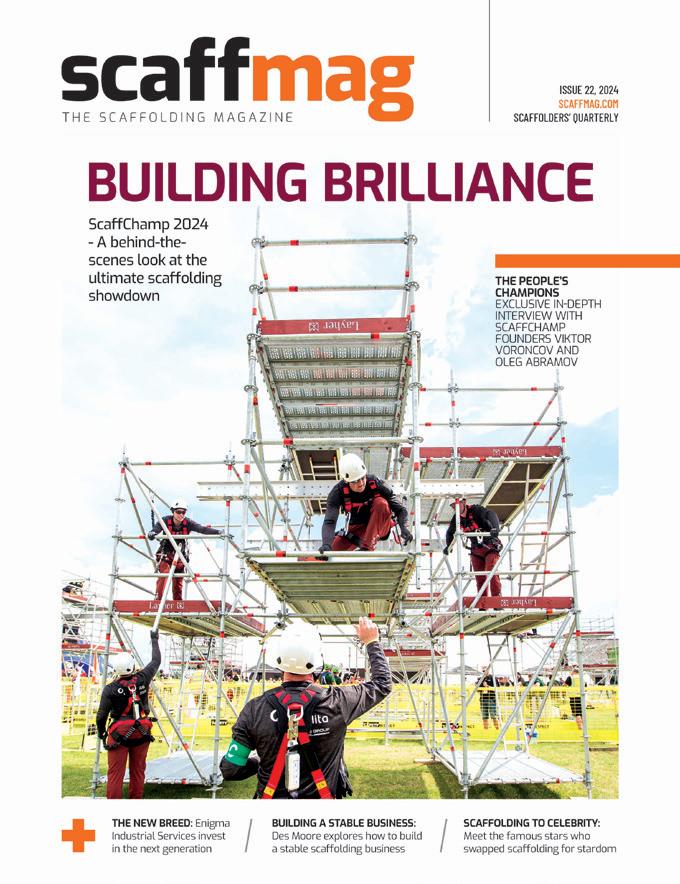
GEDA Mini / GEDA Maxi, Germany
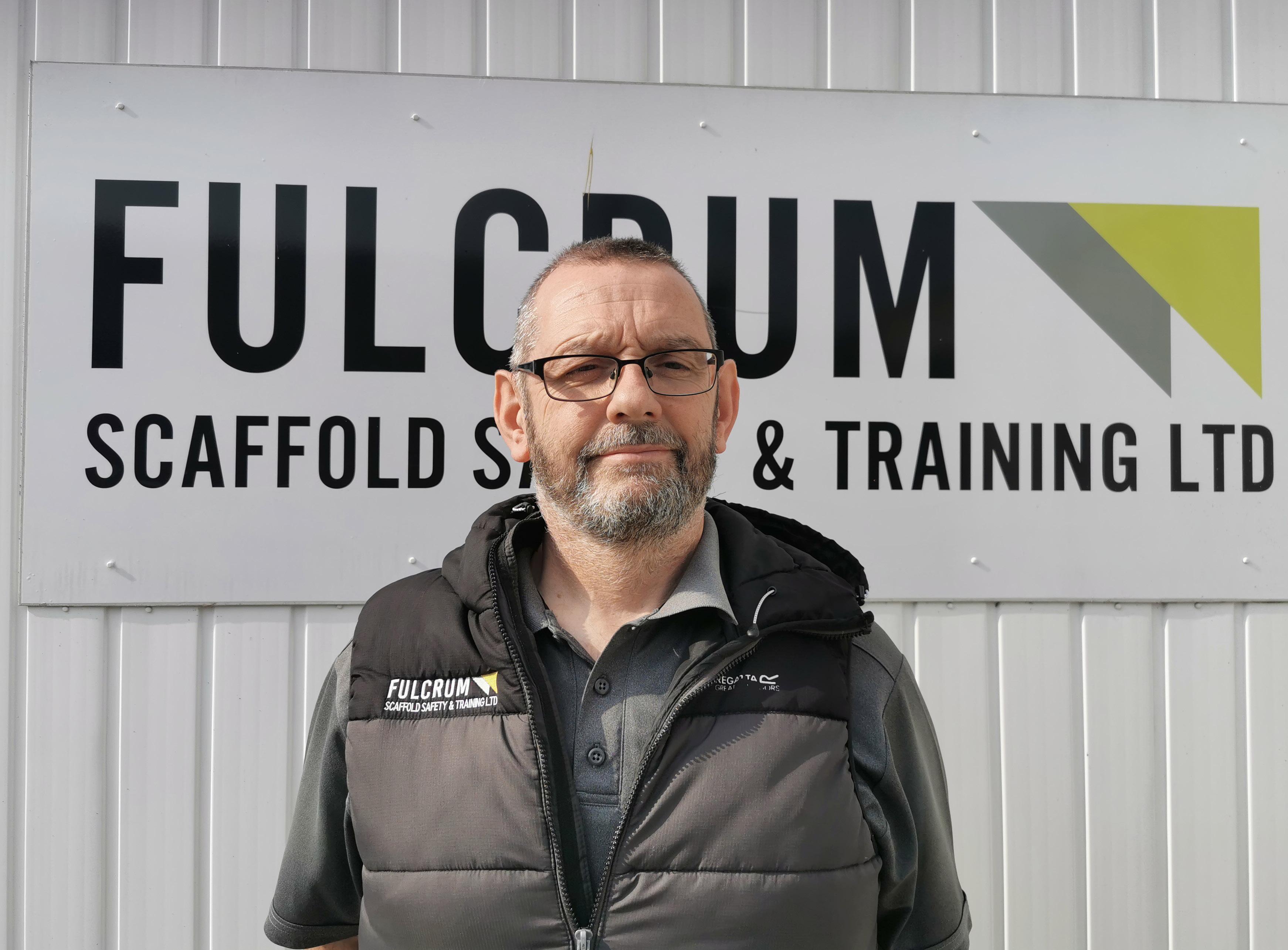
Second chance
David Abraham’s journey in scaffolding is one of grit, determination and a desire to make a difference. Starting in the industry as a young trainee in the 1980s, he has since carved out a successful career, co-founding Fulcrum Scaffold Safety & Training Ltd and becoming a driving force for positive change
While his achievements in scaffolding are impressive, it is his work in creating opportunities for ex-offenders that truly sets him apart, blending social responsibility with his industry expertise.
A CAREER BORN FROM OPPORTUNITY
Dave’s journey into scaffolding began in the early 1980s, and as he reflects on those early days, it’s clear that his start was anything but typical. After being “asked nicely to leave school”, Dave was at a crossroads, unsure of where life would take him.
Fortunately, his uncle, Phil Carr, a scaffolding legend, stepped in and introduced him to Northern Scaffold. After a year in the yard, Dave joined his uncle on site, and it didn’t take long for him to realise that scaffolding was his calling.
“I loved the banter and the physical side of it,” Dave recalls. “Working at height gave me a thrill, and when you’re young and fearless, there’s something incredibly exhilarating about it.”
Dave’s career blossomed from those early days of hard labour and hands-on learning. By 1992, he had earned his Advanced Scaffolder card, a milestone that opened the door to various leadership roles. Yet, his time with Hertel Services, working on major contracts like the ICI Runcorn and Shell Oil Refinery, had the most significant impact on his career.
“I learned so many management skills from John Colligan, a man I’m forever indebted to,” Dave shares. “Those were the moments that shaped my understanding of the industry.”
THE BIRTH OF FULCRUM SCAFFOLD SAFETY & TRAINING LTD
Years of experience eventually led Dave to the logical next step: co-founding his own company. Along with Jen Wood, his business partner, Dave founded Fulcrum Scaffold Safety & Training Ltd with a clear vision. Their goal was to establish a training centre within five years, but demand saw them accelerate their plans. Today, Fulcrum’s growth is
not just measured in business success but in its commitment to solving industrywide problems.
“We offer pre-employment training for the unemployed and school leavers, filling the skills gap in the industry,” Dave explains. “We’re also working inside HMP establishments, delivering scaffolding courses and finding job outcomes for ex-offenders.”
This commitment to addressing labour shortages while giving back to society has set Fulcrum apart. Whether it’s helping scaffolders set up their own businesses or developing bespoke courses for clients, Dave and his team have become synonymous with innovation and integrity.
TRANSFORMING LIVES: THE HMP TRAINING PROGRAMME
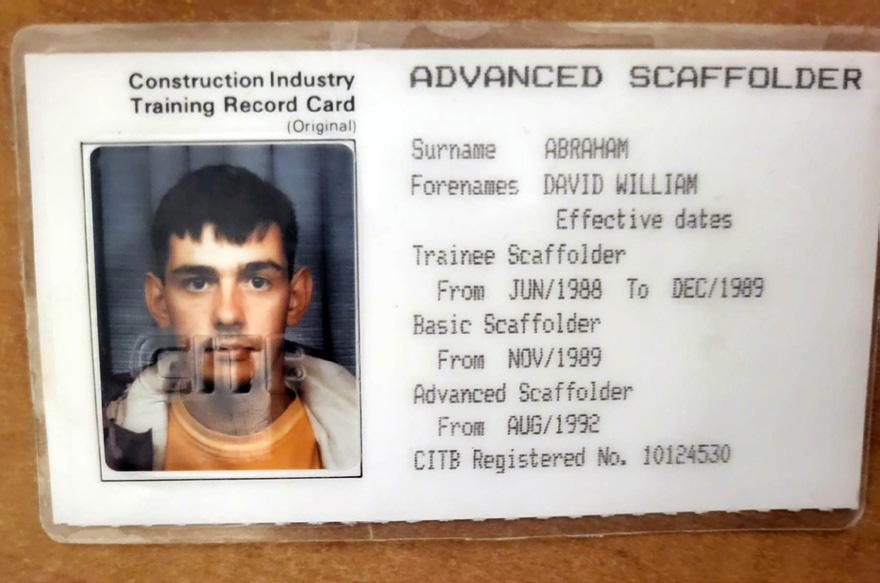
candid about the challenges it faces. From companies reluctant to hire exoffenders to the exorbitant insurance premiums associated with employing them, the road to acceptance has been anything but smooth. Nevertheless, Dave remains hopeful that attitudes will shift, and more companies will embrace the potential of this untapped workforce.
One of Dave’s proudest accomplishments is Fulcrum’s work within His Majesty’s Prison system. Partnering with strategic organisations like Procure Plus, the company has developed training programmes specifically for ex-offenders. The initiative equips prisoners with valuable scaffolding skills and helps them secure employment upon release.
“The idea came from Simon O’Donnell of Procure Plus, and I jumped at the chance,” Dave says. “We wanted to give ex-offenders a real opportunity to reintegrate into society by providing them with skills and a job.”
This programme has yielded remarkable success stories, including those of individuals like Chris Halpin, who is now a CISRS scaffolder running shifts on major sites after going through Fulcrum’s training. Dave believes that creating these opportunities is vital for the individuals involved and society as a whole.
“Without hope of employment, many ex-offenders will return to crime,” Dave says. “But if we can give them the skills and the structure they need to succeed, we’re not just changing their lives, we’re making our communities safer.”
THE CHALLENGES OF CHANGE AND THE FUTURE OF SCAFFOLDING
As for the future, Dave sees both challenges and opportunities ahead for the scaffolding industry. The rise of social media has exposed dangerous practices by untrained workers, which Dave believes is putting the industry at risk. He advocates for stricter regulations and more robust safety protocols to protect workers and maintain the profession’s integrity.
Yet, amid these concerns, Dave is optimistic. Fulcrum continues to work with partners like W@H Solutions and Newcastle Football Foundation to recruit apprentices and provide quality, affordable training. By staying at the forefront of training and safety, Fulcrum is positioned to meet the growing demands of an industry in flux.
“We’ll continue to work closely with CISRS and other organisations to ensure that scaffolding remains a profession people can be proud of,” Dave says.
A LEGACY OF BUILDING AND GIVING BACK
David Abraham’s story is more than just a career profile, it’s a story of transformation, resilience and a deep commitment to giving back. Dave’s passion for scaffolding and people has remained unwavering from his early days as a young scaffolder with everything to prove, to his role as a business leader and social advocate. As Fulcrum continues to grow and innovate, one thing is certain: Dave is not just building scaffolds, he’s building futures.
MAKE THAT CHANGE
In an industry traditionally dominated by men, Lydia Stanton has emerged as a powerful leader, breaking barriers and driving change within the scaffolding sector
As Commercial Director of Star Scaffolding, based in West Bromwich, Lydia has made a significant impact, which led to her being named one of the Top 100 Women in Construction by the National Federation of Builders (NFB). Lydia’s influence goes beyond her business role; her recent appointment as Chair of the NASC Training and Education Committee highlights her deep commitment to the future of scaffolding training and education in the UK.
For Lydia, recognition is a by-product of her passion for making a difference. “Being nominated and winning the NFB Unsung Hero Award West Midlands in 2022 and making the Top 100 Women in Construction was a huge honour,” she shares.
“To be recognised for the work I’ve done for the returning citizens programme was truly wonderful and completely unexpected. I didn’t do it for recognition or to win an award; I did it because I wanted to make a difference.”
Lydia’s work extends to sitting on the Employment Advisory Board for HMP Featherstone, where she contributes her expertise to help prisoners access meaningful training and employment opportunities postrelease. Her advocacy and leadership in this area have made her a true role model, not just for women but for all aspiring professionals in the construction and scaffolding industries.
A VISION FOR TRAINING AND EDUCATION
In her new role as Chair of the NASC Training and Education Committee, Lydia’s main priority is ensuring that the scaffolding industry becomes a more attractive and
sustainable career choice. “At Star Scaffolding, we faced challenges due to a shortage of skilled scaffolders,” she explains.
“We tried numerous approaches – from the DWP Kickstart scheme to the probation office’s returning citizens programme and offering work experience through job centres – but the long-term solution was to revive our in-house apprenticeships.”
Lydia’s hands-on experience with these various initiatives has armed her with invaluable knowledge, which she is now channelling into her role at NASC.
Her goals include promoting the scaffolding industry, ensuring comprehensive workforce training, securing funding for training programmes, and continuing to develop and enhance apprenticeship standards.
CHAMPIONING DIVERSITY IN SCAFFOLDING
Lydia has been at the forefront of encouraging more women to enter scaffolding. “NASC are trailblazers for encouraging and supporting more females in leadership roles,” she says. “There are some powerhouse women in the sector sharing their stories through podcasts, articles and conferences. It would be wonderful if more women came forward to share their own experiences.”
She believes the industry needs to do more to showcase the various roles available, from health and safety to marketing, to shift perceptions. “You don’t have to turn a spanner to be successful in scaffolding,” she emphasises.
INSPIRED BY FAMILY, MOTIVATED BY CHANGE
Lydia’s passion for scaffolding began with her

father, Mark Chard, who founded Star Scaffolding in 2003. “My dad was my inspiration,” she recalls. “I started working at Star during school holidays and eventually joined the business full-time after university. My father has been a great mentor, and I’ve learned so much from him and others in the industry.”
Today, her motivation comes from her daughter and a desire to create a lasting legacy. She draws inspiration from a quote by Michelle Obama: “For me, being a mother made me a better professional... and being a professional made me a better mother.” This balance of professional ambition and personal fulfilment drives Lydia to pursue her vision for the future.
SUPPORTING THE NEXT GENERATION
Lydia is dedicated to mentoring and developing the next generation of scaffolders. Star Scaffolding now employs a Trainee and Skills Manager to support young workers entering the industry. “We often forget that school leavers have never been in a work environment before. It takes patience, commitment and empathy to guide them,” Lydia explains. Star Scaffolding’s
apprenticeship programme is thriving, with a 97% satisfaction rate on project completion.
BALANCING COMMERCIAL AND COMMITTEE ROLES
Balancing her role as Commercial Director and Chair of the NASC Training and Education Committee is no small feat. “It’s something I’m still navigating,” she admits. However, she is supported by a knowledgeable team at NASC and a committee of industry experts, making the challenge more manageable.
A BRIGHT FUTURE FOR SCAFFOLDING
Looking ahead, Lydia has ambitious goals for both Star Scaffolding and the wider industry. “We currently have 20 apprentices at Star, and I don’t see that number decreasing anytime soon. We are also investing in the Layher system, which has proven to be a great asset,” she says.
Star Scaffolding is celebrating its 21st year in business, and under Lydia’s leadership, the company continues to grow. Her dedication to fostering young talent and her commitment to promoting the scaffolding industry ensure that both Star Scaffolding and the sector itself have a bright and sustainable future.
and sustainable career choice.
Lydia Stanton wants scaffolding to become a more attractive
INTRODUCING Plettac Metrix EasyStair
THE LATEST INNOVATION IN STAIRCASE SOLUTIONS
The Plettac Metrix EasyStair is the latest innovation in staircase solutions from TRAD UK. With its robust design, offering load capacities of 2.0kN/m² and 4.0kN/m², and with a compact footprint of 3.0m x 1.5m, the EasyStair is perfect for diverse applications and projects.
Ideal for site access, the Plettac Metrix EasyStair delivers a convenient answer on safety, efficiency, and adaptability. Moreover, the stair tower can be used as part of the Plettac Metrix system but can also be used as a standalone tower and/or with other types of scaffolds. For more details and to see how it can enhance your access solutions, get in touch today.
Key Features:
Versatile heights: Choose from 1.0m, 1.5m, and 2.0m lift heights for complete project flexibility.
Enhanced safety: Unique inner and outer guardrails provide unparalleled security, moving beyond traditional staircase designs.
Lightweight durability: Aluminum stairs with steel connectors offer a strong yet manageable build, without heavy platform units.
Flexible configurations: With front/side exits, anti-uplift protection, and compatibility with standard Plettac Metrix components, the EasyStair adapts to your site requirements.
Efficient flow: Erect in any direction and utilise parallel construction for efficient personnel movement.
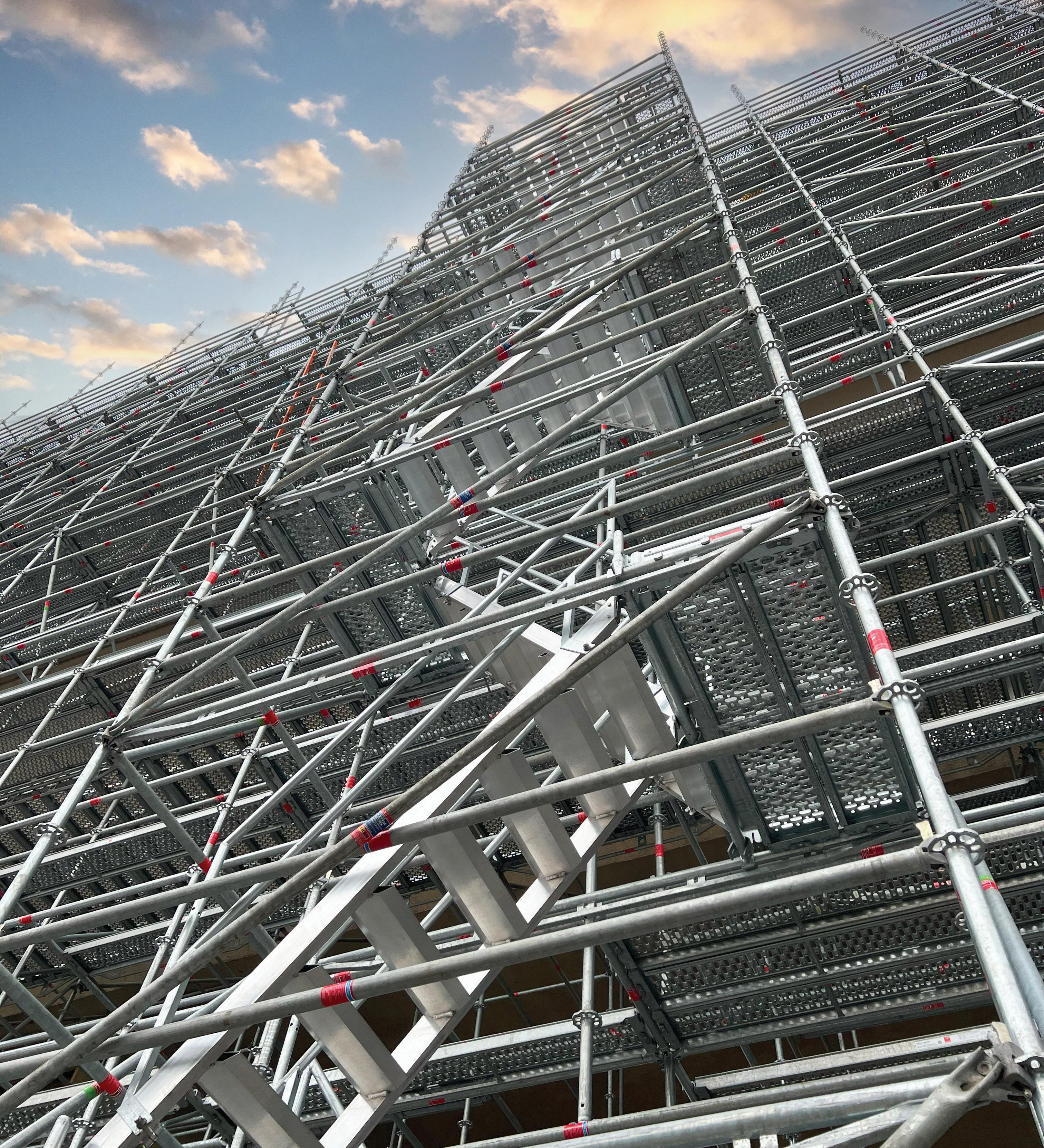
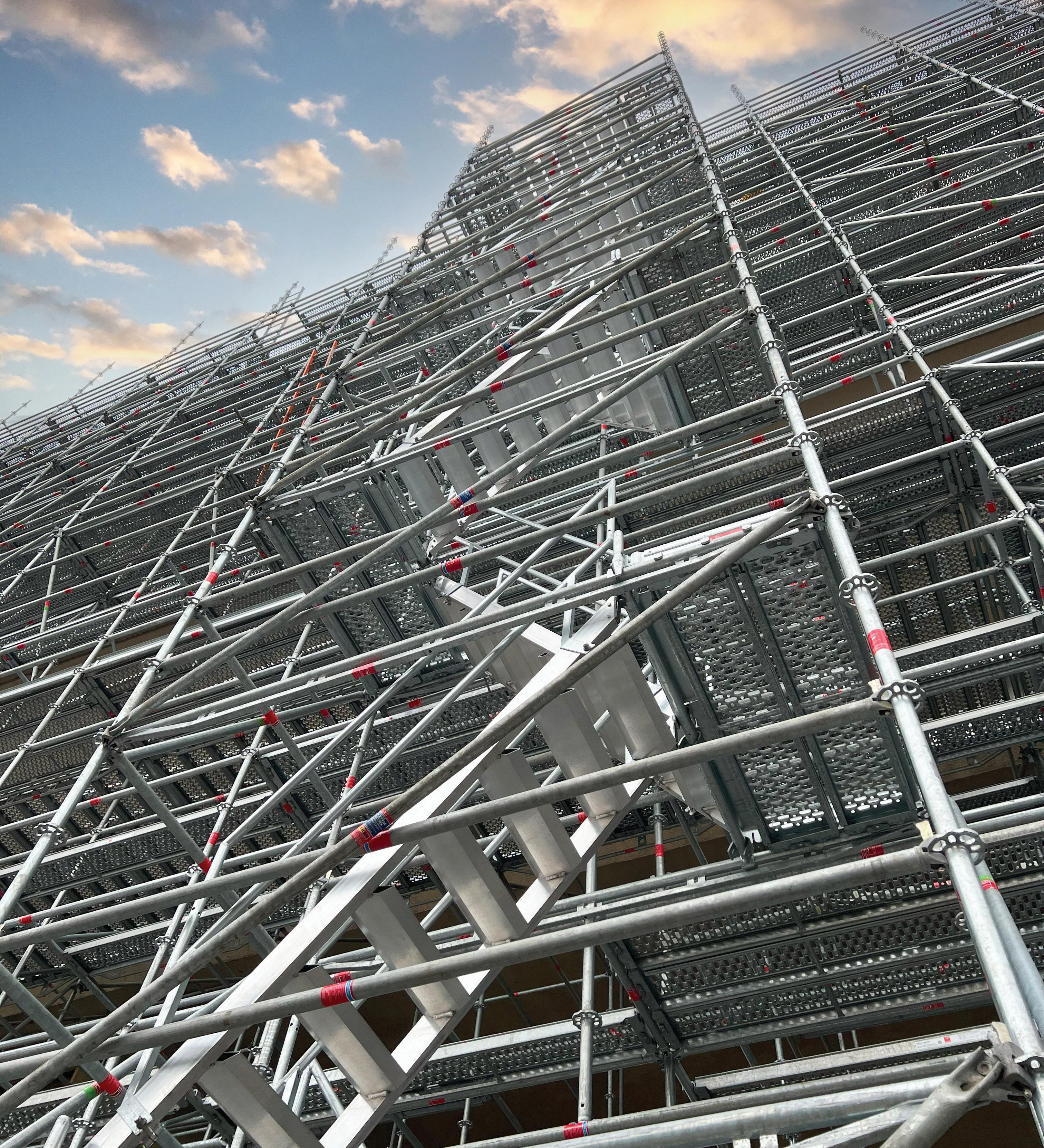
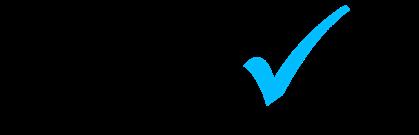
Recently, the scaffolding industry took a giant leap towards global collaboration with the launch of the Global Scaffolding Alliance (gSA). This groundbreaking initiative aims to unite professionals across continents, revolutionising the way scaffolding is built, managed and regulated. But what does this alliance mean for the industry, and how will it impact the thousands of workers, companies and stakeholders that rely on scaffolding every day?
TOGETHER AS ONE
A GLOBAL INDUSTRY, FINALLY CONNECTED Scaffolding is a critical component in construction, maintenance and infrastructure projects around the world.
Yet, despite its importance, the industry has long been fragmented, with different countries following their own safety standards, training protocols and business models.
Recognising this gap, UK-based scaffolding expert Mark Parkin spearheaded the Global Scaffolding Alliance, a platform designed to bridge the divide. Parkin, along with international partners from Australia, Tony Nicolaisen (Norway), and Arka Chorbajian (Canada), formed the gSA with a clear mission:
to create a global community that fosters innovation, safety and collaboration in the scaffolding sector.
“The gSA was born from a vision to transform the scaffolding industry on a global scale,” Parkin explained. “We needed a unified platform where professionals from all over the world can share best practices, ideas and innovations. The gSA is not just an alliance; it’s a global community where every member has a voice in shaping the future of the industry.”
Arka Chorbajian, President of Skyline Scaffold in Canada, shared his perspective on why he joined the initiative: “I have a huge amount of respect for Mark Parkin, not just for his knowledge, but for his integrity. When he called, I didn’t hesitate. The fragmented nature of the industry is something that we need to address, and I believe the gSA is the platform to do it.”
ADDRESSING THE INDUSTRY’S BIGGEST CHALLENGES
The scaffolding industry is facing significant challenges: a shortage of skilled labour, inconsistent safety standards and an increasingly complex business environment. The gSA aims to tackle these issues head-on by offering a platform where professionals can collaborate and address these concerns together.
LABOUR SHORTAGE AND TRAINING STANDARDS
One of the most pressing issues is the shortage of skilled labour. Many countries, including Norway, are hiring workers from abroad to meet demand, but inconsistent training requirements create barriers to entry. Nicolaisen, a key partner in the gSA, highlighted the importance of developing globally recognised qualifications to streamline this process.
“We need a training standard that can be applied across borders. If we can agree on a minimum standard for scaffolders, it will be easier for countries to recognise each other’s certifications, ensuring workers are properly trained wherever they go,” Nicolaisen said. Chorbajian emphasised that in North America, this issue is common: “We often bring in guys from the UK and Europe, but the standards are far different. The gSA can help employers understand what skills are needed locally and what training workers have received. This will save time and reduce the costs of figuring it all out on our own.”
SAFETY AND ERGONOMICS
Another challenge is the need to improve safety and ergonomics. While the risk of falling is well known, the strain on workers’ bodies from years of heavy lifting and repetitive motion is often overlooked. Nicolaisen stressed that technology and improved ergonomics must become a priority.
“We lose several hundred scaffolders each year, not because they fall, but because their bodies give out. It’s crucial to lighten the physical burden through the use of technical aids, so experienced scaffolders can continue working safely for longer.”
BUSINESS MODELS AND INDUSTRY GROWTH
The gSA is also focused on helping new scaffolding companies establish themselves in an increasingly competitive market. Parkin believes that by sharing business models and strategies, the gSA can help newcomers find success without sacrificing safety or quality.
“We want to guide the next generation of scaffolding companies to ensure they grow responsibly. Our goal is to balance profit with safety, training and staff care so that businesses can thrive without cutting corners,” Parkin emphasised.
Chorbajian added that another critical issue is low-quality, untested equipment being used in parts of North America and Europe: “One of the big issues that doesn’t get enough coverage is the widespread adoption of low-quality gear. We need to have a serious conversation in the industry about how to weed out this equipment and prioritise quality.”
A PLATFORM FOR COLLABORATION AND INNOVATION
At its core, the gSA is designed to be an open platform for collaboration. Members will have the opportunity to participate in specialised committees dedicated to areas like safety, product development and innovation. These committees will serve as think tanks, driving forward new solutions that can be applied worldwide.
The alliance is also planning to introduce online training modules and workshops as part of its professional development initiative. These resources will contribute to members’ continuing professional development (CPD), ensuring that scaffolders and companies alike are always up to date with the latest industry advancements.
“The gSA is about creating tangible value for our members,” Parkin said. “We want to ensure that every member, from scaffolders to CEOs, feels connected and engaged. Through events, webinars and discussion groups, there will be endless opportunities to share experiences, learn from others and contribute to the collective wisdom of the industry.”
A GLOBAL VISION FOR THE FUTURE
As the scaffolding industry evolves, the gSA’s vision of ‘Together as One’ stands as a rallying cry for unity and progress. The alliance is not just a solution for today’s

challenges but a blueprint for the future. By fostering collaboration, improving standards and sharing knowledge, the gSA aims to create a safer, stronger and more innovative industry for generations to come.
The success of the gSA will ultimately depend on the willingness of industry professionals to come together and support the initiative. As Nicolaisen pointed out, the potential for impact is enormous if the industry is open to change.
“If people are willing to listen, share and learn from each other, we can make a significant impact. The gSA gives us a platform to do that – it’s about more than just scaffolding; it’s about making the entire industry better for everyone involved.”
Chorbajian is optimistic about the potential of the gSA to bring positive change: “If this initiative helps both employers and employees achieve their goals more easily and efficiently, then why not? It’s time to come together and fix these issues for the future of our industry.”
BUILDING THE FUTURE, ONE SCAFFOLD AT A TIME
The Global Scaffolding Alliance represents a significant step forward for an industry that is often overlooked, yet critical to the success of so many other sectors. By creating a global community, the gSA aims to address the key challenges facing the scaffolding industry, while also fostering innovation and ensuring the safety of workers around the world.
The scaffolding industry is at a pivotal moment. As the gSA moves forward with its plans for global standards, training programmes and collaborative platforms, the question remains: will the industry rise to the challenge and embrace this new era of unity and progress?
For those looking to be part of this revolution, the time to act is now. Joining the gSA means becoming part of a global movement, one that promises to build not just scaffolds, but a brighter, more connected future for everyone in the industry.
For more information, visit the official website: https://www. gsalliance.global

The gSA aims to address the key challenges facing the scaffolding industry worldwide.

The Kentledge Scaffold block is a versatile concrete ballast block. It is primarily used to provide stability and counterweight for scaffolding structures and temporary works, including:
• Scaffolding sites
• Construction sites
• Housing sites
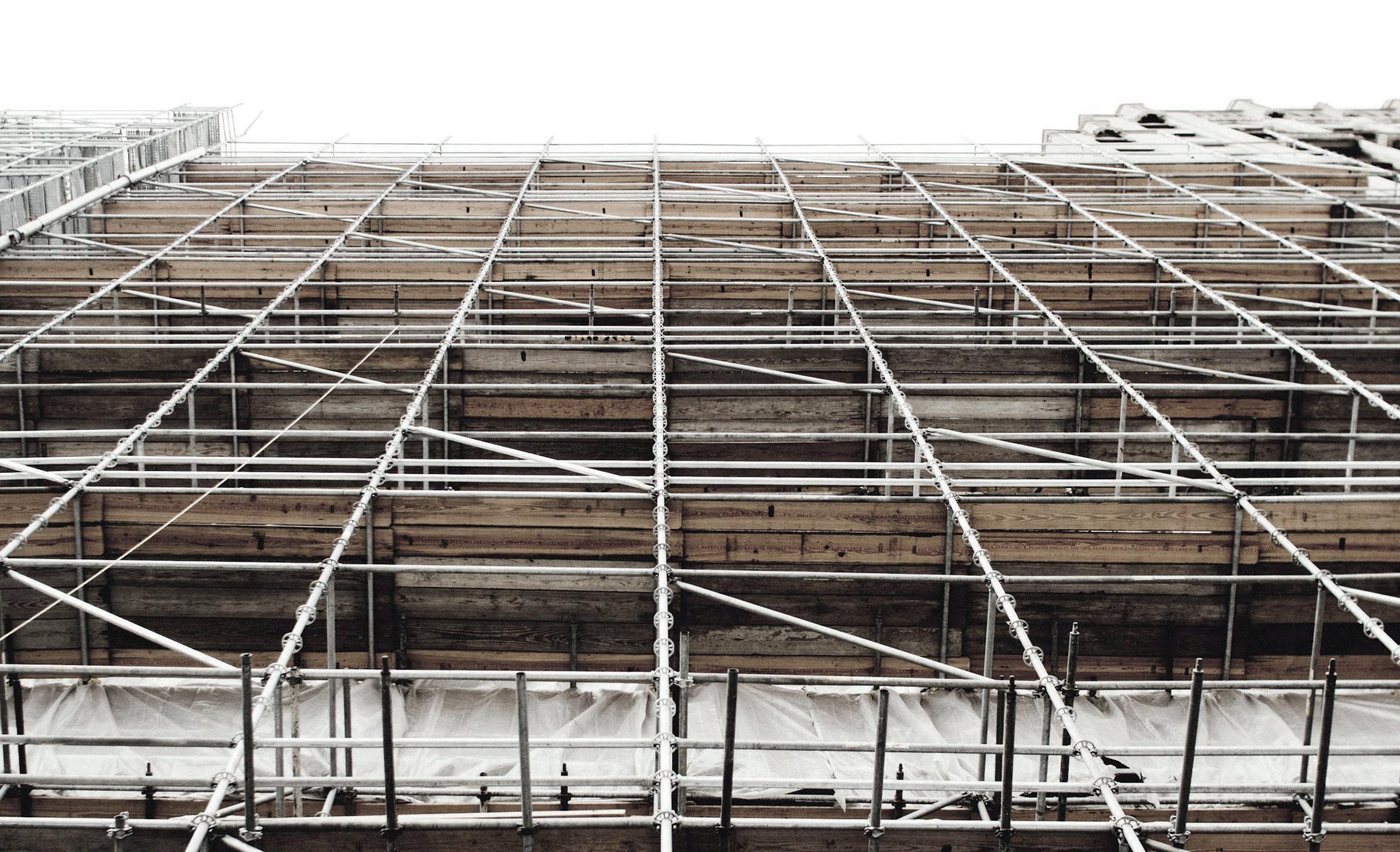
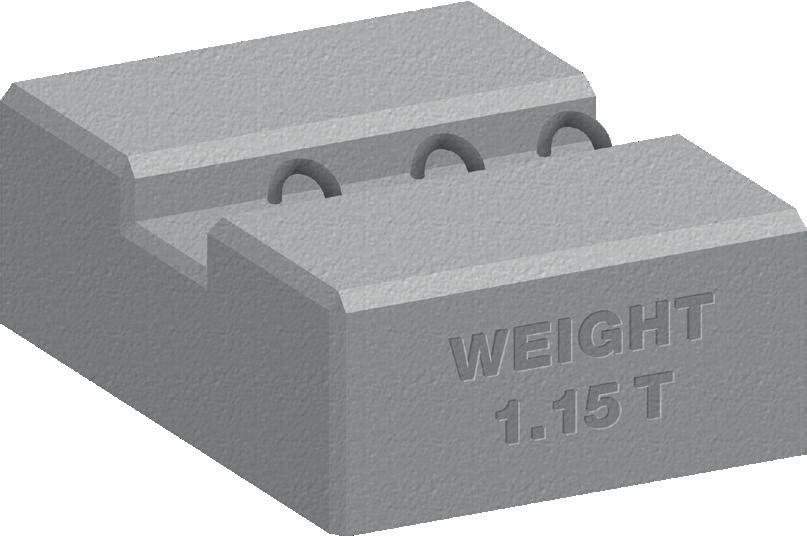
• Building sites
• Civil Engineering projects
• Infrastructure schemes
Elite’s non-invasive concrete ballast blocks come with cast-in lifting pins for easy installation without specialist equipment.

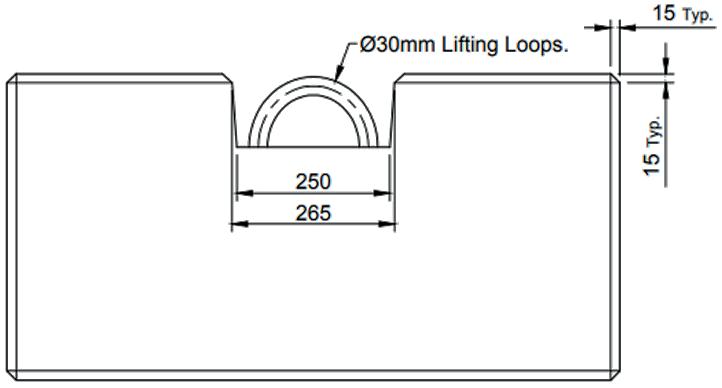
Available within days, speak to our team for delivery options.
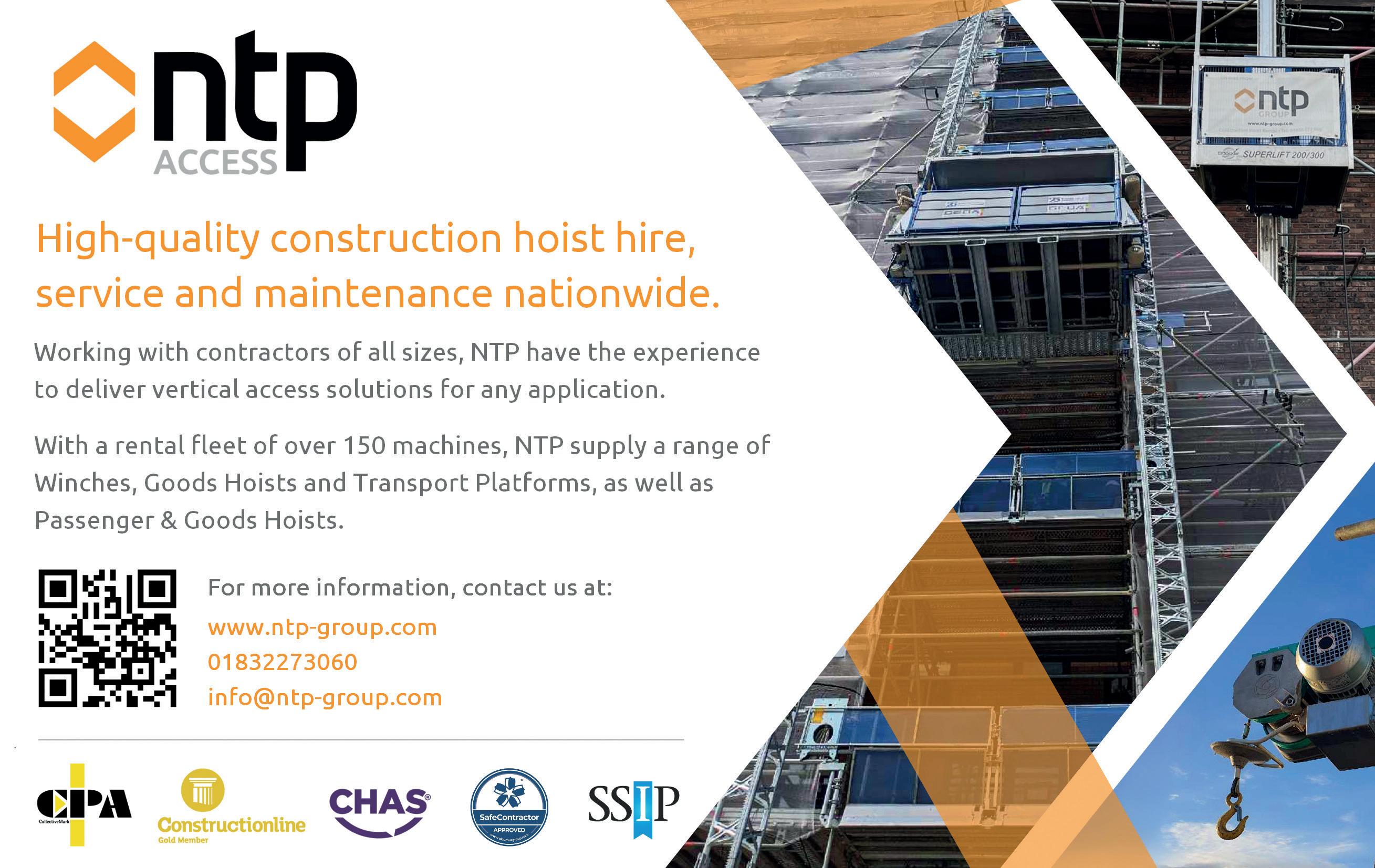
“I learned on the job – and made many, many mistakes”
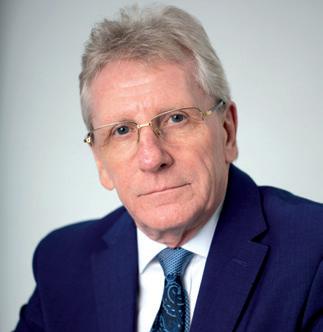
ALong-time scaffolding industry figure Des Moore talks to ScaffMag about learning from mistakes and his new management training course, DM7
lthough some refer to Des Moore as an ‘industry expert’, he won’t refer to himself that way, and is clear that success doesn’t come overnight. “I share that experience regularly through published articles and in consultancy work with my clients, and now I can help others work more effectively in their own businesses, through my new management training course.”
50 YEARS’ EXPERIENCE IN ONE DAY
What will attendees get from this course? It’s based on the seven principles of management that Des has followed during his time in the business. They are about:
• Taking responsibility
• Making yourself available
• Getting things done
• Looking after your people
• The course has been specifically designed for three main groups of managers in the scaffolding industry:
• Those with growth aspirations who need support to take their business to the next level.
• Those in large businesses with a number of junior and senior managers, including black hats.
• Those who’ve been leaders for a while and want to refocus on their management skills.
“People on this course will get real-life, practical and useful information that they can put into practice straight away,” says Des. “It’s grounded in a lifetime’s experience in scaffolding, so it’s completely relevant to today’s working environment and people will be able to see exactly how the principles I work by can benefit them – personally and in their businesses.”
LEARN FROM INDUSTRY EXPERIENCE
Des has never been one to shy away from a challenge. In his early days, he was given the opportunity to build a business – Sevenhurst, a scaffolding company acquired by TRAD’s Hayden Smith, but separate from TRAD’s operations. It had no customers and Des’s office was a portacabin with a desk and a phone. With no other option, he set to work ringing people up to get business.
“I invoiced £850 in my first month,” remembers Des. “But in just five years, turnover was £4.5m, and we’d rebranded the company to TRAD Scaffolding Systems. I learned a lot in those five years – when I often worked seven days a week, 12- to 14-hour days, much to my wife’s annoyance! The business became what I made it through a lot of hard work.”
LEARNING FROM MISTAKES
Like many people in the industry, Des worked his way up to management, and often learned the hard way about the best methods to manage both people and organisations. “Everyone makes mistakes,” he says. “And I probably made more than most. I never had any management training or mentoring, so I just used my instincts and took my cues from people around me. I was lucky to have been so involved with Hayden Smith – he definitely ruled his businesses with a firm hand, but he also cared about the people who worked for him and could be incredibly generous with his time and his advice.”
Des has tried to follow this in his career – as opposed to being remote, single-minded, ruthless and uncompromising, which he admits were the ways of working that came naturally to him. “I had to pretty much teach myself not to be like that,” he says.
Des firmly believes that making mistakes comes with the territory of management, and that as long as you learn from your mistakes and listen to the feedback from people around you, you can actually benefit from them.
“This is a fundamental part of my own experience,” Des says. “No one is perfect, and no manager – or anyone, in fact –should claim to be. That’s why part of my course is about understanding, accepting and moving on from your mistakes so you can do a better job next time – although there is much more to the course than just
“I did some extreme things in my early working life, all legal, of course, but not advisable now.”
this area. In fact, there’s absolutely nothing like it on the training market, to my knowledge.”
THE DM7 TRAINING COURSE
After working with a number of businesses as a consultant, Des found that people were asking him to support their own senior teams with some management training.
“As ScaffMag readers know, I’m always happy to share my experiences,” he says, “but training is a new venture for me, so I have worked with a training delivery professional to put together this course, which is based on the seven principles I work to every day. That makes it completely authentic to my way of doing things. It’s based on what I know works in real life.
“I did some extreme things in my early working life,” he adds. “All legal, of course, but not advisable now. One of these times, as an example, was when I was running a gang of scaffolders who absconded with one of my vans. I needed that van for a job the following day, so despite it being a risky thing to do, I went round to the pub where I knew these guys were and confronted them. Unfortunately, I got beaten up for my trouble, but I got the van keys back!
“Why is that story relevant? It’s because I wasn’t bothered about the potential consequences of confronting them. All that was important to me was that I could service my client the following day, and do what I said I was going to do.
The job – and the client – was always the most important thing. It’s experiences like this that made me who I am, and I will speak about many more examples like that on the course.”
The training course is designed to be delivered either over one day or two half days, making it a flexible option for scaffolding companies whose leaders and managers are often out on site or visiting depots.
“It’s a practical course,” says Des. “So we talk about the challenges that being a manager brings, especially when there’s no real formal training or learning involved. The idea is to show people how being consistent and considered can help them to manage a successful business while also supporting their teams. Looking at management as a 360degree function, rather than as an ad hoc part of the job, really helps you to be more strategic, to get perspective and to be successful.”
By the end of the course, managers should have an action plan that helps them see what they do well, where they can improve and how they can take practical steps to be successful senior leaders. They’ll also get an insight into how Des runs his daily diary – and why that type of organisation really makes a difference!
Des will deliver the course in person, usually internally to scaffolding company senior teams. If you are interested in running the course in your business, contact Des Moore direct on 07555 800700 or des@mor1x.co.uk
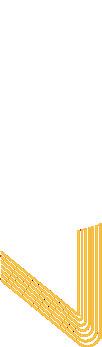
Unique management training from Des Moore
01 02 03 04 05 Based on 50 years of experience in the scaffolding industry
Principles you can put into practice straight
Ways of working that build personal and business success
Ideal for directors, senior, junior and black hat managers in businesses of all sizes
Available as two half-days or one full day, to fit with your business needs
Courses can be delivered internally at your premises, or made available externally across the UK. All courses delivered by Des Moore.
To book a course for the managers in your business, email des@mor1x.co.uk or visit mor1x.co.uk.
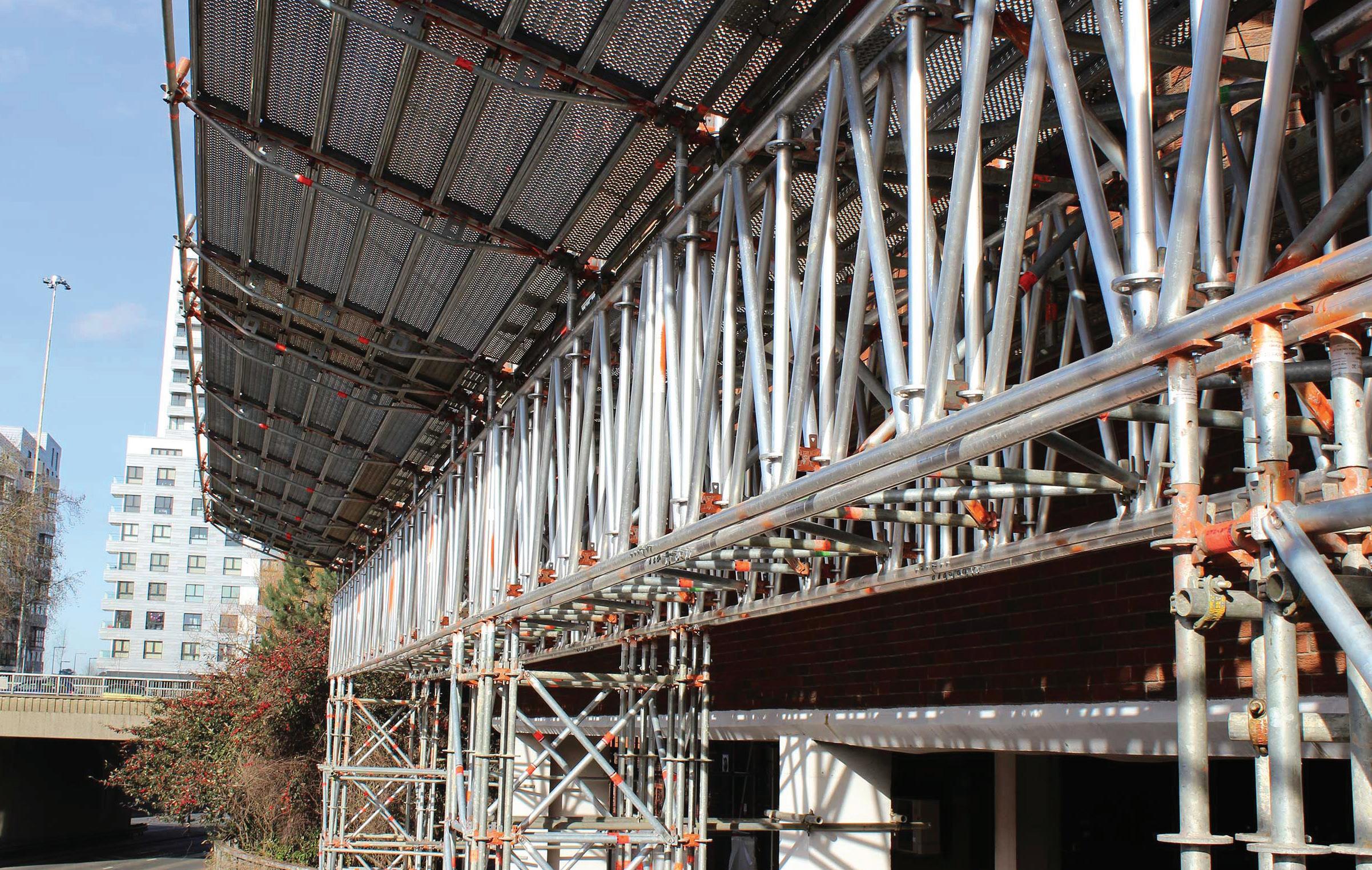
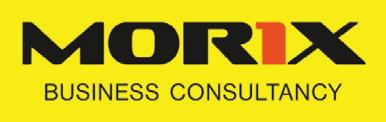

Designed and patented in Australia, this innovative anti-tampering tie system elevates scaffold safety and reduces the risks associated with scaffold installation, maintenance and dismantling.
Incidents involving unauthorised adjustments to scaffolding ties have been a recurring issue on construction sites. Workers from unrelated trades, such as facade installers, have been known to remove or tamper with scaffold ties, often unaware of the dangerous consequences. These actions compromise not only the stability of the scaffold but also the safety of everyone on site.
To address this pressing issue, scaffSAFE was developed. The system is designed to keep the control of scaffolding components solely in the hands of trained scaffolders, ensuring that once scaffolds are in place, they remain secure and tamper-free until properly dismantled by trained scaffolders.
WHAT MAKES SCAFFSAFE DIFFERENT?
The heart of the scaffSAFE system is its proprietary anti-tampering mechanism. This unique tie system includes galvanised couplers and anchor screws that can only be adjusted with a specific, patented tool –preventing unauthorised workers from modifying any part of the scaffold setup.
In an industry where safety is paramount, scaffSAFE is set to make a groundbreaking entrance into the UK market
SAFE AND SOUND
Another notable feature is the bright orange safety cap that covers the coupler nut after installation. This cap makes it visibly clear that the scaffold is secured and tamper-proof.
Not only does this provide peace of mind for the principal contractor and the scaffolding team, but it also minimises the risk of on-site disruptions and serious accidents.
KEY BENEFITS OF SCAFFSAFE
scaffSAFE offers a suite of benefits for both scaffolding professionals and the broader construction site:
• Enhanced Safety: The system drastically reduces the potential for accidents by preventing unauthorised tampering with scaffold ties.
• Minimised Site Risk: By ensuring that scaffolds remain as secure as they were upon installation, the system minimises the risk of scaffold failure and injury.
• Cost Efficiency: The reduction in accidents and unauthorised adjustments leads to fewer disruptions, saving time and money for contractors.
• Traceability: Each tool in the scaffSAFE system is traceable, further ensuring that only authorised personnel are involved in the erection or dismantling of scaffolding structures.
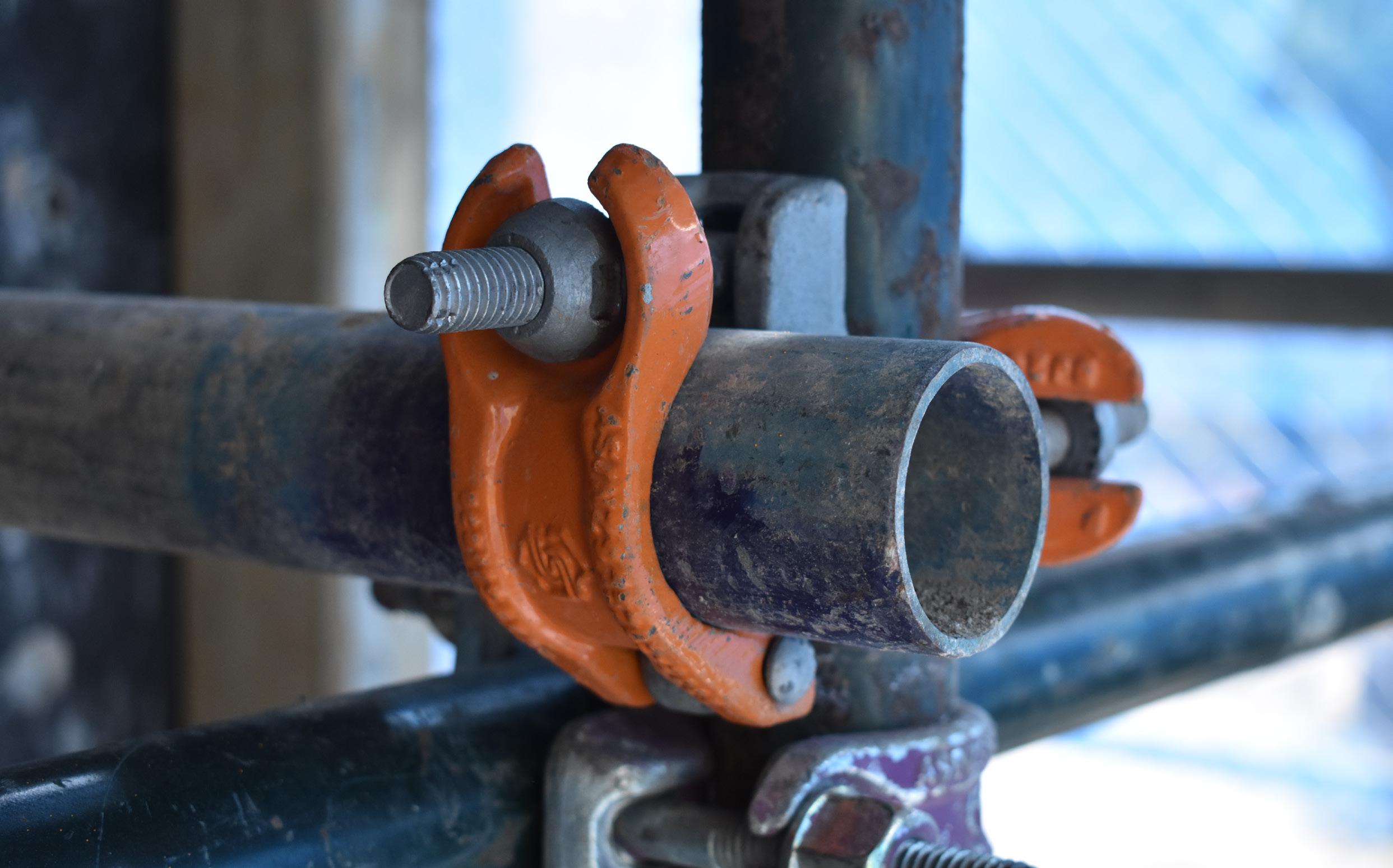
A TOOL DESIGNED FOR EXCELLENCE
The scaffSAFE system includes several key components, all designed to be compatible with standard scaffolding materials:
• scaffSAFE Couplers: Galvanised and durable, these couplers ensure long-lasting stability.
• scaffSAFE Anchor Screws: Available in multiple sizes, these screws feature shallow embedment depths, reducing the time and effort required for installation while maintaining high load capacities.
• Patented scaffSAFE Tools: The specially designed spanner and impact socket tools are essential to the system, preventing anyone without access from altering the scaffold setup.
BRINGING SCAFFSAFE TO THE UK
As scaffSAFE prepares to launch in the UK, its innovative approach to scaffolding safety is hoped to change how the industry thinks about risk management. With construction sites growing more complex and safety regulations becoming more stringent, scaffSAFE offers a forward-thinking solution that not only meets but exceeds current safety standards.
The product is poised to provide scaffolding companies, contractors and site managers with the tools they need to maintain control over scaffolding operations, ensuring the highest levels of safety for all workers on site.
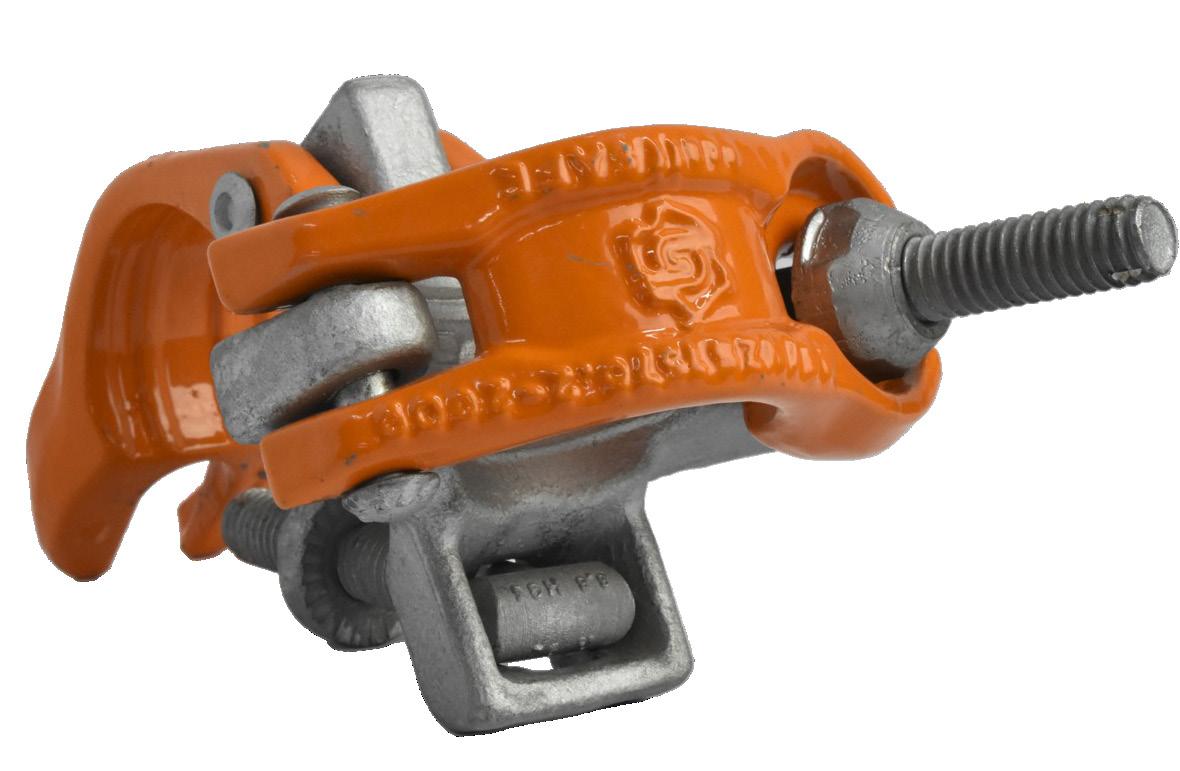
scaffSAFE represents a leap forward in scaffold safety technology, and its arrival in the UK couldn’t come at a more critical time. As the industry continues to prioritise the health and safety of workers, scaffSAFE provides a tangible, effective solution for mitigating the risks associated with scaffolding work.
For those looking to safeguard their sites, reduce liability and streamline operations, scaffSAFE is the tie system that ensures your scaffolding remains secure – every time, all the time.
For more information, visit www.scaffsafeinternational.com
SCAFFSAFE REPRESENTS A LEAP FORWARD IN SCAFFOLD SAFETY TECHNOLOGY, AND ITS ARRIVAL IN THE UK COULDN’T COME AT A MORE CRITICAL TIME
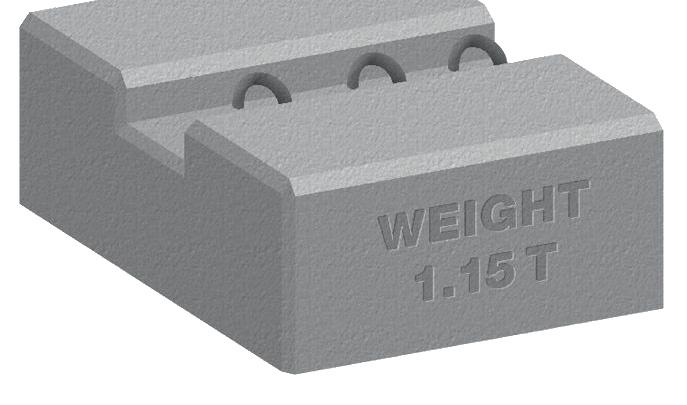
Block party
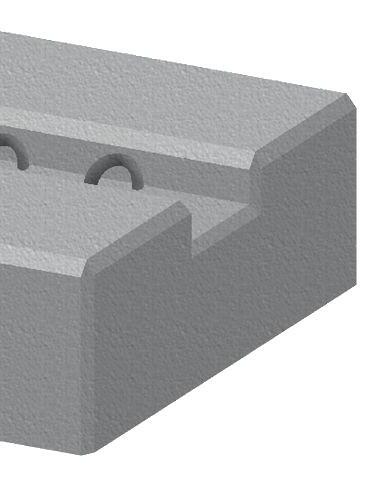
In the ever-evolving world of construction, precast concrete scaffold blocks have emerged as a vital innovation, transforming the way in which scaffolding structures are secured and stabilised. Here, Owen Batham of Elite Precast Concrete, explains how scaffold blocks, also known as Kentledge blocks, are proving indispensable in ensuring the safety of workers and the scaffolding framework itself
THE POWER OF COUNTERWEIGHT
At the heart of their effectiveness lies their substantial mass, which serves as an impressive counterweight. This feature is particularly valuable for cantilevered structures, where balance is paramount. By preventing tipping and instability issues, these blocks significantly enhance the overall safety of scaffolding setups.
not only reduces expense but also aligns with the sustainable practices of clients.
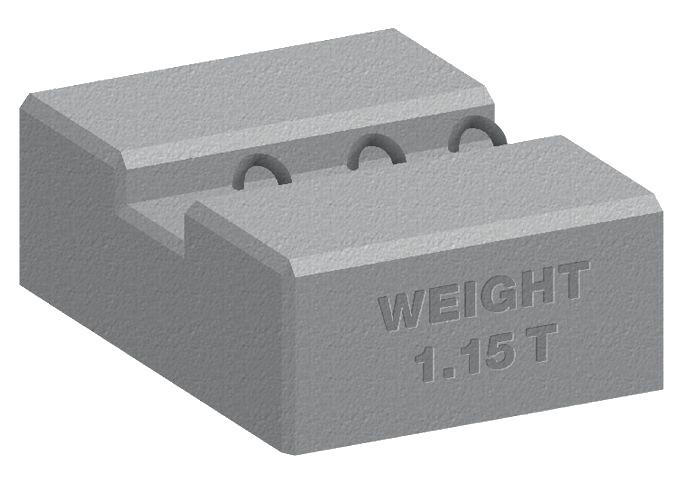
ADAPTING TO CHALLENGES
One of the standout qualities of precast concrete scaffold blocks is their adaptability to challenging conditions. For tall scaffolds, or those exposed to high winds, concrete blocks prove their worth through considered positioning. This flexibility allows for support where it’s most needed, catering to the unique requirements and challenges of each product.
ECONOMIC AND ENVIRONMENTAL BENEFITS
The flexibility of these blocks extends beyond their immediate use. Their reusable nature makes them a cost-effective solution for stakeholders, allowing for repeated use across different projects. This
A
NON-INVASIVE
APPROACH
In contrast to traditional methods that involve digging holes for posts, Kentledge blocks offer a non-invasive installation method. By sitting on the surface, they eliminate the risk of damaging buried services or the client’s land. This approach not only preserves the integrity of the site but also simplifies the installation process.
EFFICIENCY IN TIME AND COST
The use of scaffold blocks offers significant time and cost savings. Their installation is generally faster than traditional posts and doesn’t require surrounding concrete. This efficiency in both materials and labour can have a positive impact on timelines, potentially improving or maintaining sire programme schedules.
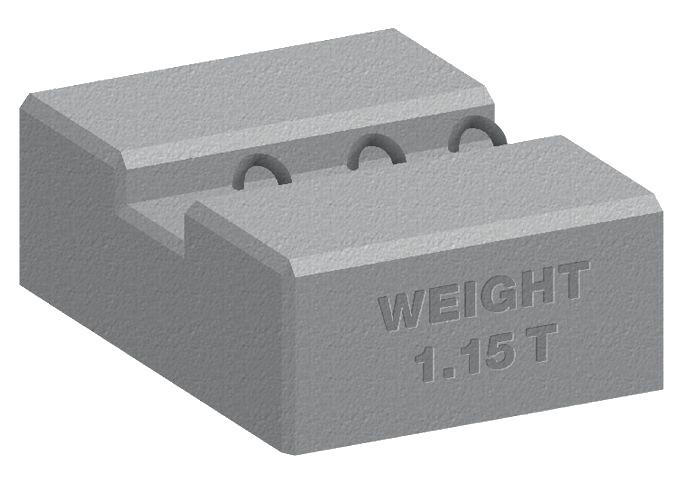
base provided by scaffold blocks allows for easy integration with various scaffolding structures. This versatility makes them a reliable and efficient method for securing scaffolding across a wide range of environments and applications.
INSTANT AVAILABILITY
Adding to their appeal is the quick availability of these blocks. Typically, they can be procured within a couple of days of purchase, ensuring a fast deployment for projects.
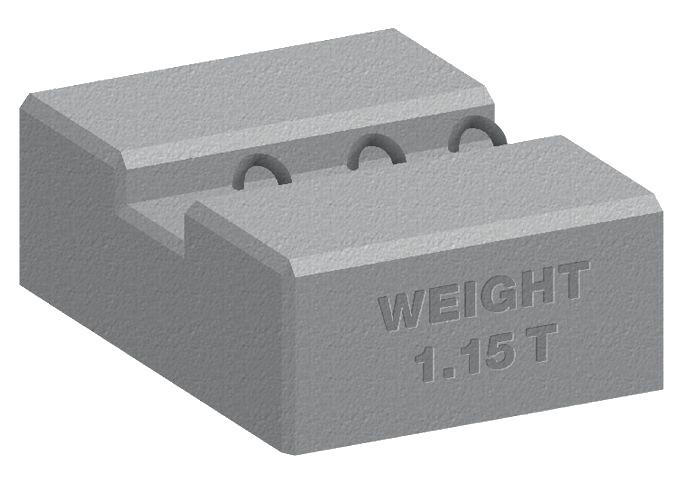
In conclusion, Owen believes that precast concrete scaffold blocks represent positive factors in construction safety and efficiency. Their ability to provide stability, adaptability and cost-effectiveness makes them an invaluable asset in modern construction practices.
As the industry continues to prioritise safety and sustainability, these innovative blocks are set to play an increasingly vital role in scaffolding and temporary works across diverse construction projects.
VERSATILITY IN APPLICATION
The solid, heavy
To find out more about scaffolding blocks, Owen and his team are available on 01952 588885 or visit www.eliteprecast.co.uk

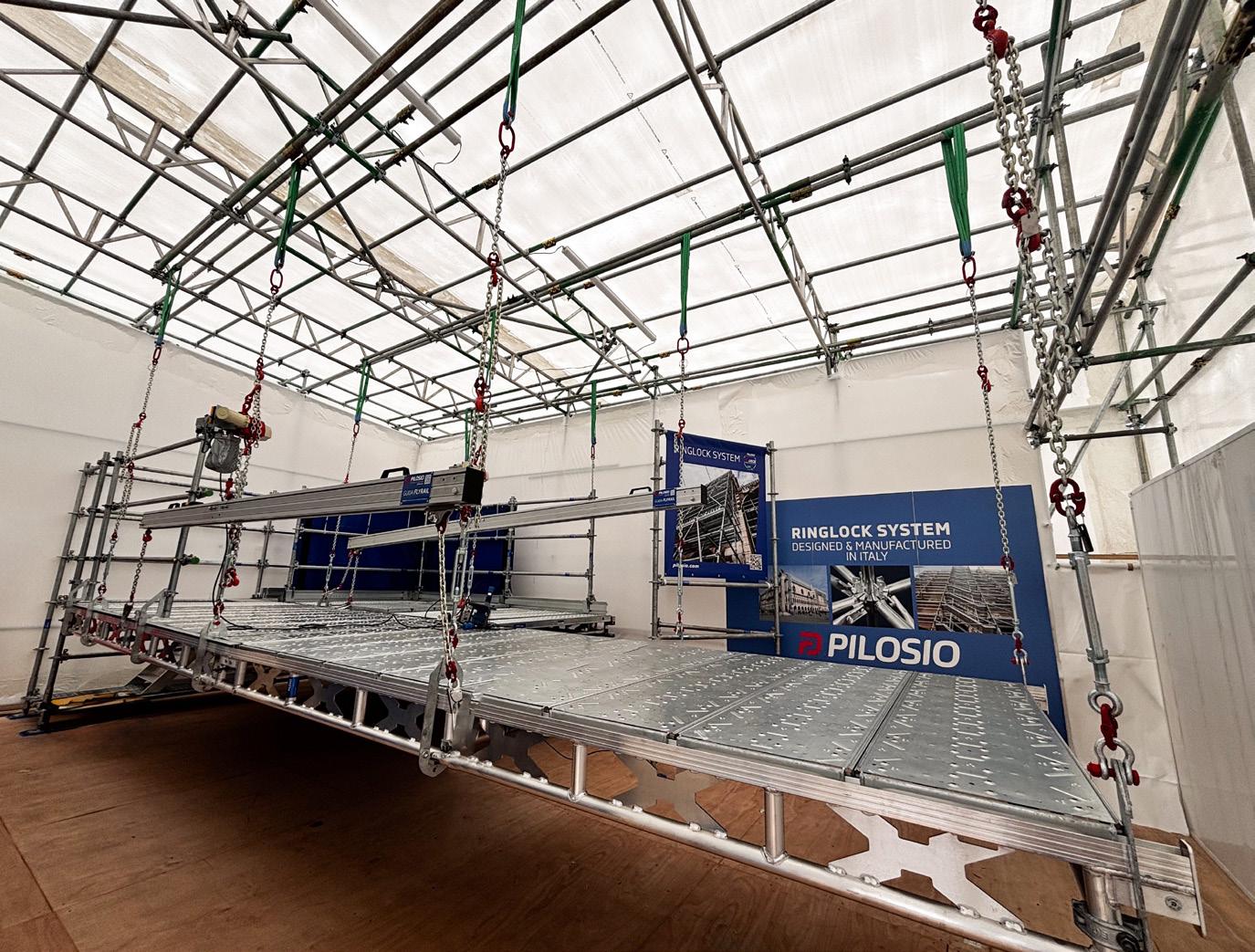
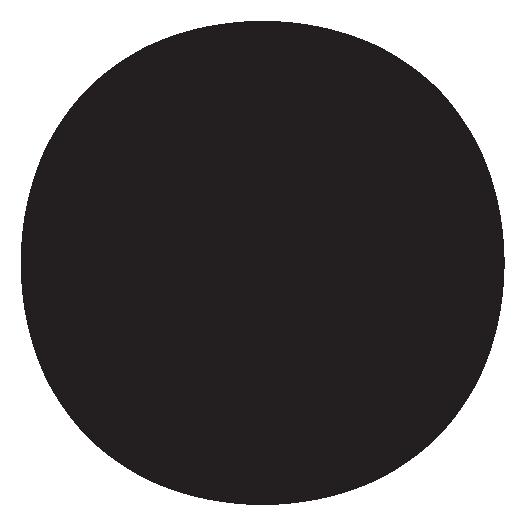
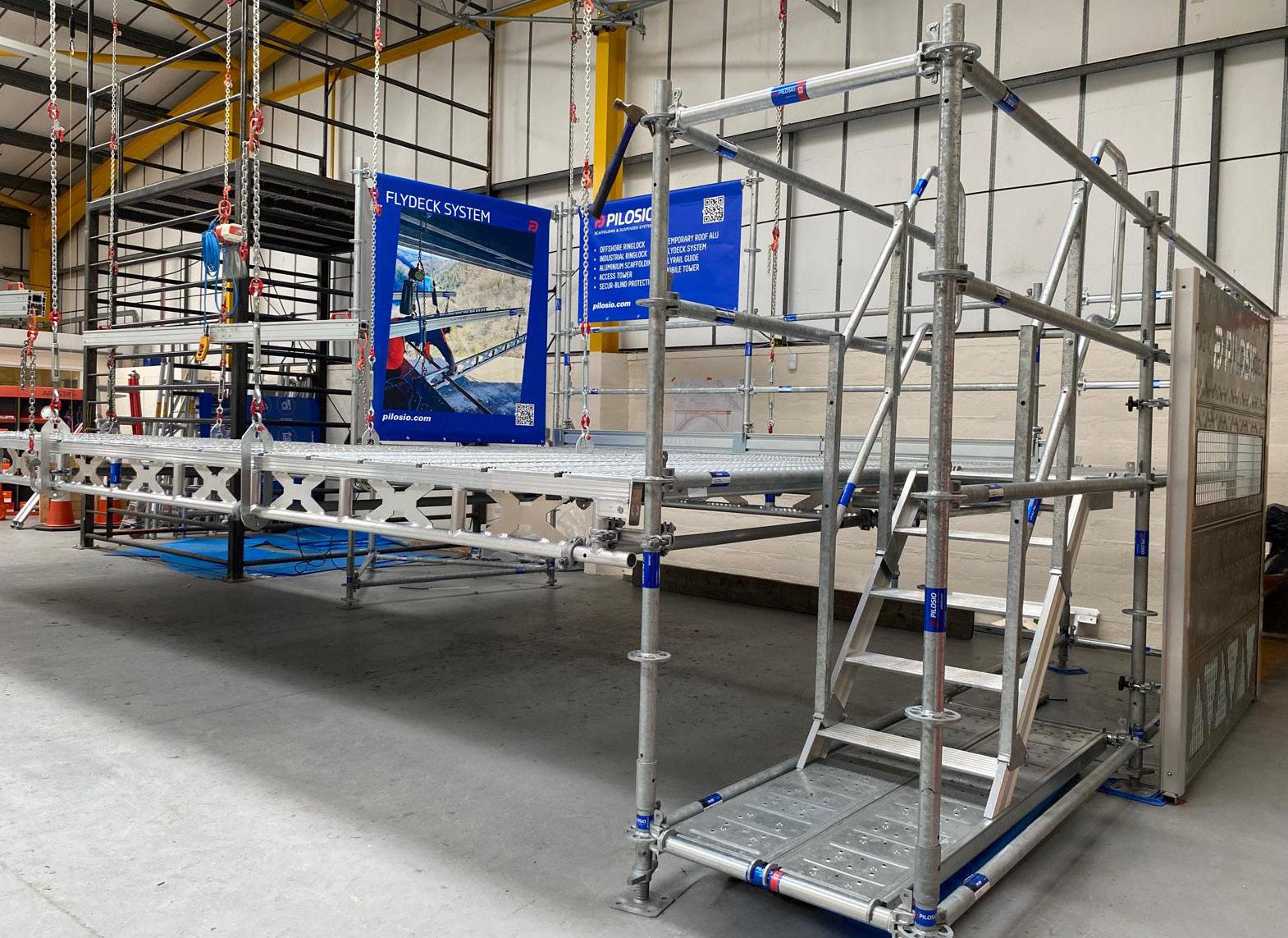
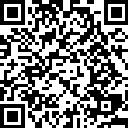

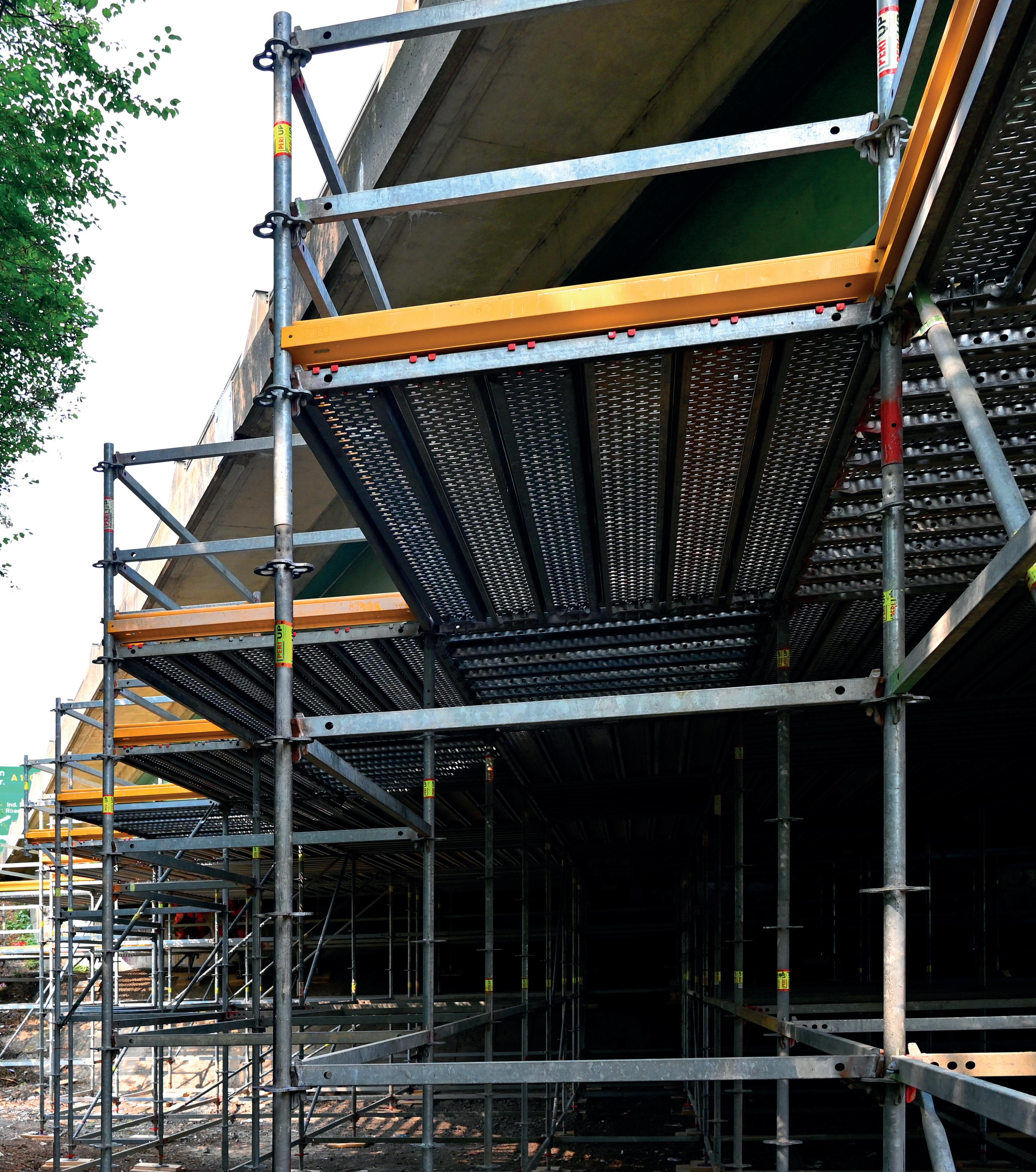
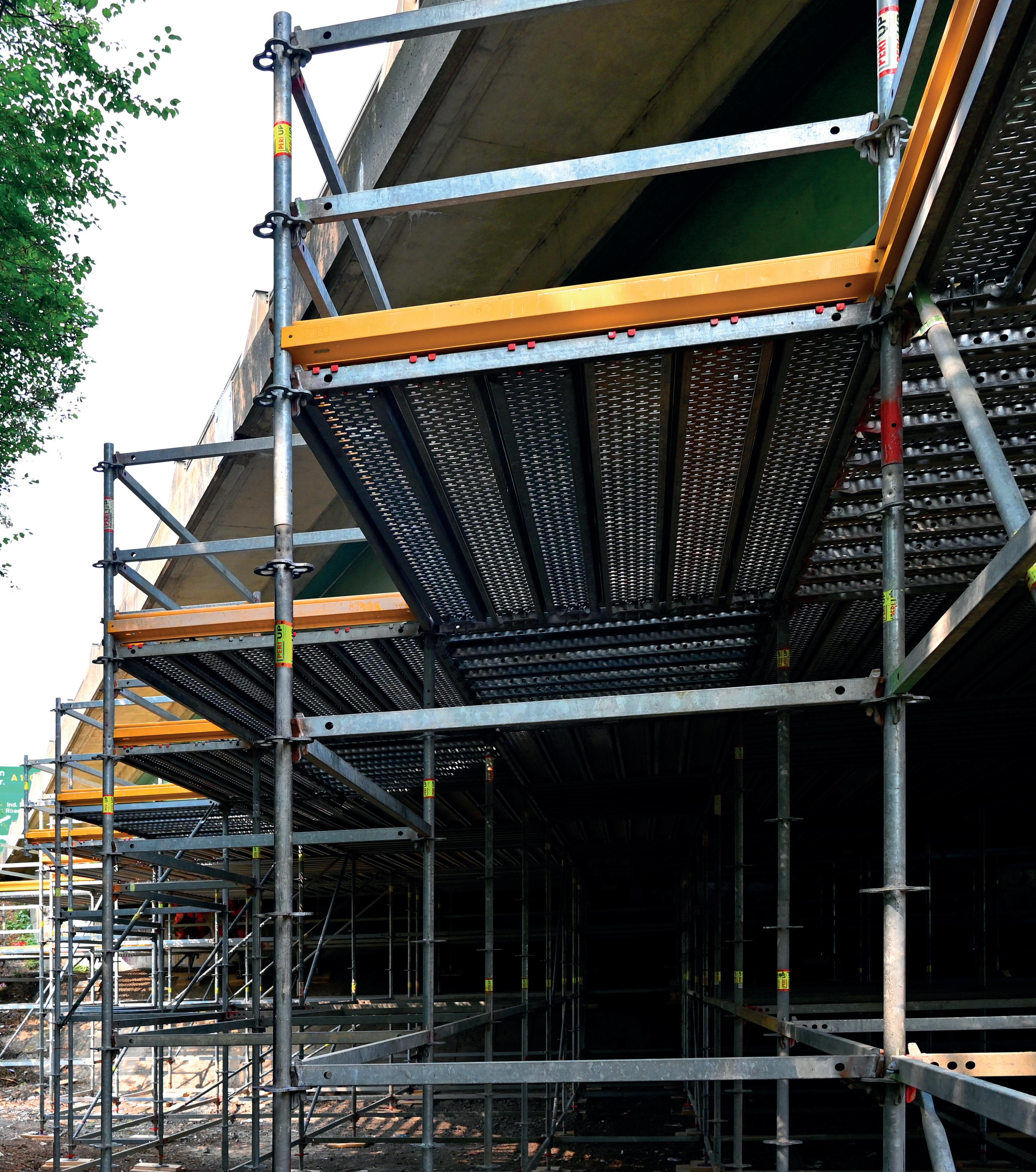

Apollo Cradles has issued a strong warning to the scaffolding industry after discovering that a fellow supplier was manufacturing and selling unauthorised copies of its protected X-Beams
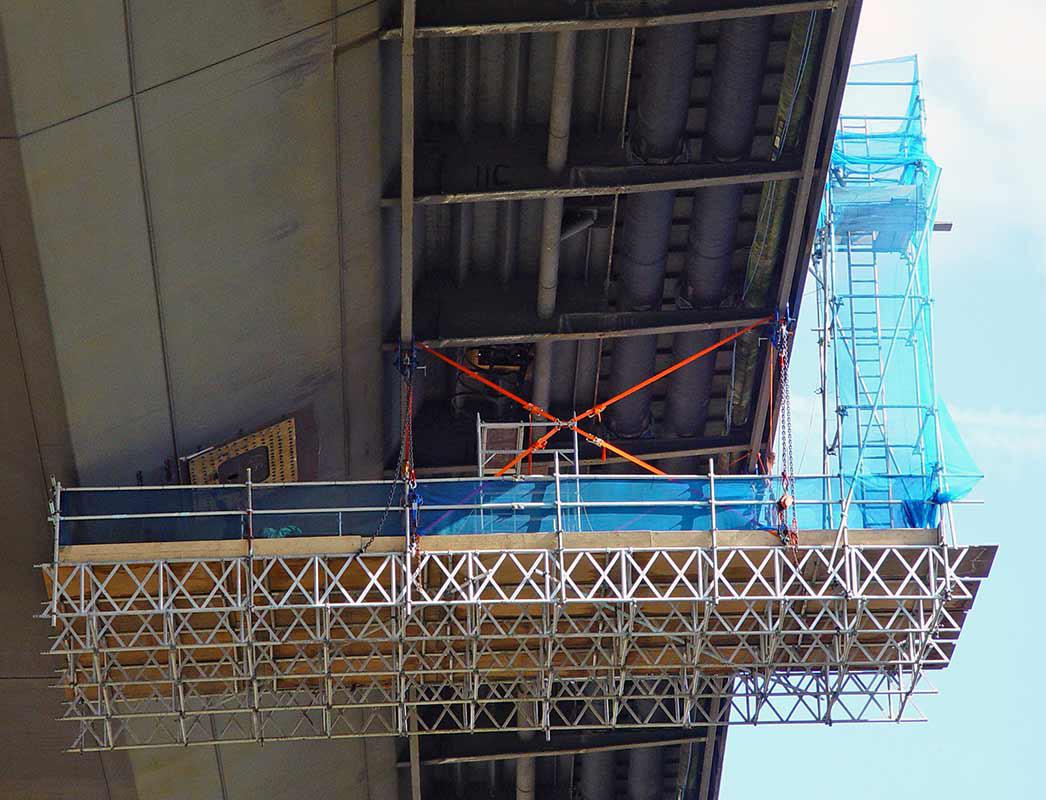
WARNING SIGNS
The company in question, a non-audited member of the National Access and Scaffolding Confederation (NASC), is now facing legal action.
Apollo, which holds the UK design rights for the X-Beams, has sent a ceaseand-desist letter to the offending firm, demanding an immediate halt to the production and sale of the unauthorised beams.
The letter outlines several key demands, including the removal of any unauthorised beams in circulation and compensation for any units already sold. If these demands aren’t met, Apollo says it will pursue legal proceedings.
Mark Holmes, Manager at Apollo Scaffold Services, expressed concern about the safety of the unauthorised products in a LinkedIn post. “We’ve already obtained two of these X-Beams and sent them for independent testing,” he said. “The results were worrying.”
Tests carried out by Solus Testing
IF THE ISSUE ISN’T RESOLVED, AND WE’RE FORCED TO TAKE THIS TO COURT, WE WILL PUBLICLY NAME THE COMPANY INVOLVED SO THAT THE REST OF THE INDUSTRY CAN BE AWARE OF THE RISKS

Limited found that the beams did not meet industry safety standards. The units had several serious welding defects, including gas pores, lack of fusion, and cracks.
These faults mean the beams failed to meet the requirements of BS EN
ISO 5817 Level B: 2023 and BS EN
ISO 23277 2x:2015 – key industry safety benchmarks.
Holmes also noted that all legitimate Apollo X-Beams are easily identifiable by their serial numbers and other specific manufacturing details, which can be traced back to Apollo’s records.
“If the issue isn’t resolved, and we’re forced to take this to court, we will publicly name the company involved so that the rest of the industry can be aware of the risks,” Holmes warned.
Apollo is urging any companies who believe they may have purchased unauthorised beams, or who have been quoted for them, to get in touch immediately.
BUILDING SUCCESS
Millcroft’s Managing Director, Billy Jones, recently voiced his concerns in ScaffMag about attracting and retaining young talent to the scaffolding industry. Here, Billy discusses the many benefits for those willing to embrace the unique challenges and opportunities of the sector
Scaffolding as a career is often overlooked by those entering the workforce. There still appears to be an image problem, with many people seeing it as purely physical work – a job rather than a career. The industry faces challenges in attracting new talent, with many young people unaware of the diverse opportunities and benefits that a career in scaffolding can offer. We within the sector need to challenge and change this, by promoting the many benefits of scaffolding as a career choice.
STRONG SENSE OF COMMUNITY
One of the most significant benefits of a career in scaffolding is the strong sense of community and camaraderie amongst workers. Scaffolding teams often develop firm bonds that are hard to replicate in other industries, as the need to have each other’s backs (literally!) is paramount. At Millcroft, our people work in sensitive and complex locations including confined spaces like tunnels for rail infrastructure projects, and even in water. The sense of unity and support for one another when the environment is challenging can make this line of work incredibly rewarding, with people feeling valued and connected. Teamwork makes the job more enjoyable and also provides a support network
that can be invaluable for someone new to the industry and indeed throughout their career. The bonds formed can lead to lifelong friendships and a warm sense of belonging.
FITNESS AND WELLBEING
For those who dislike being tied to a desk all day, scaffolding offers an active alternative. The work is naturally physical, providing a daily workout that helps maintain fitness and overall health. Yes, the work can be demanding, but many find the physicality of the job satisfying.
The nature of scaffolding work doesn’t just contribute to personal fitness; it also promotes mental wellbeing. The combination of being outdoors and physical exertion can boost mood and reduce stress levels. As does having the structure and discipline of a full day on site or in the office.
Since the Covid-19 pandemic, we at Millcroft have noticed that young people applying to work with us are seeking a job that provides flexibility and hybrid working. In our experience though, particularly early on in a career, this ‘woolly’ approach with undefined boundaries can lead to demotivation and disconnection. We want to recruit people who are fully committed: that are up with the lark and who put in a good, solid shift each time.
Another notable benefit to working in

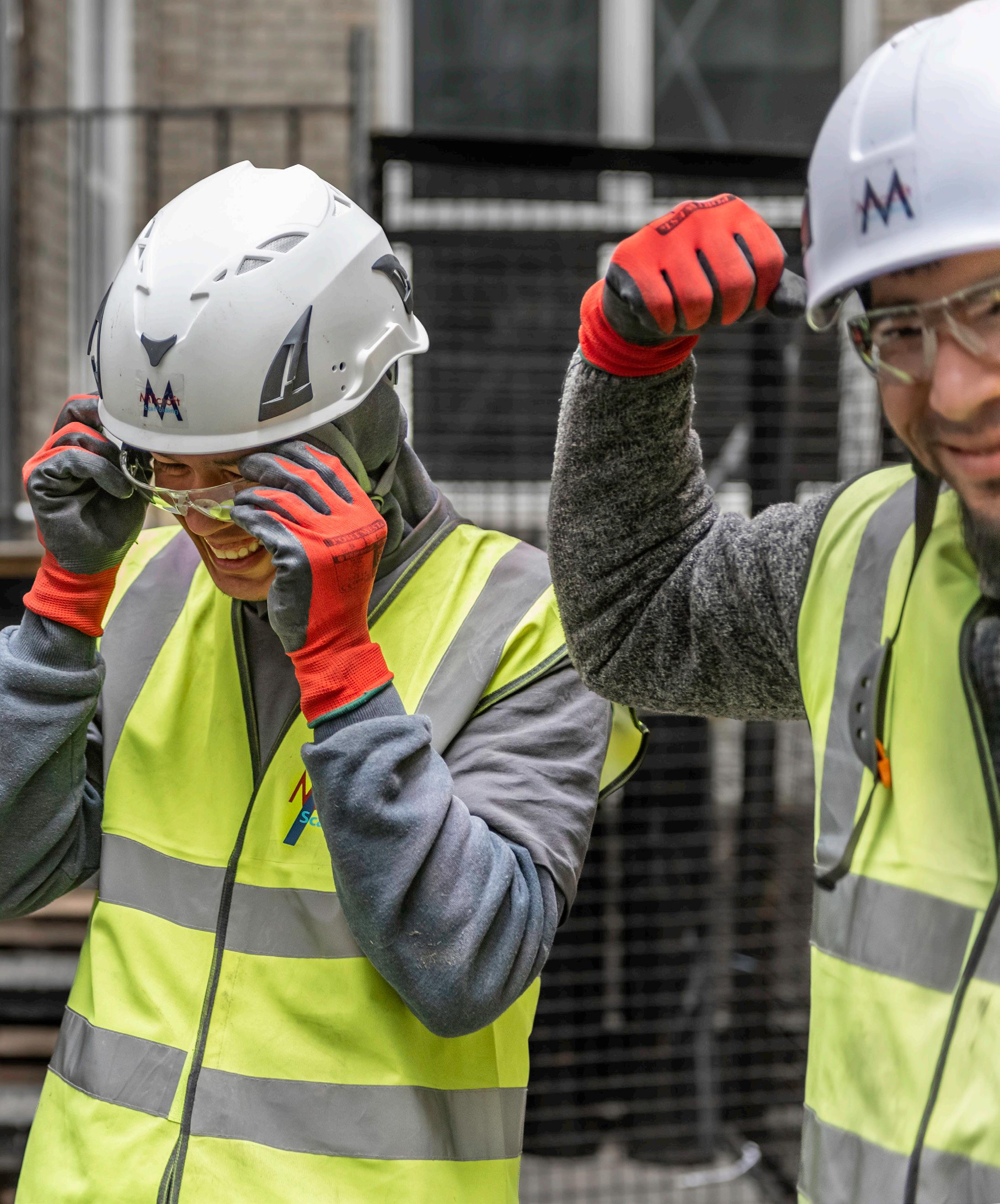
THE EARLY STARTS WERE A BIT OF A SHOCK AT FIRST AS I’VE HAD TO ADAPT AND CHANGE MY LIFESTYLE, BUT THAT IS ALL GOOD
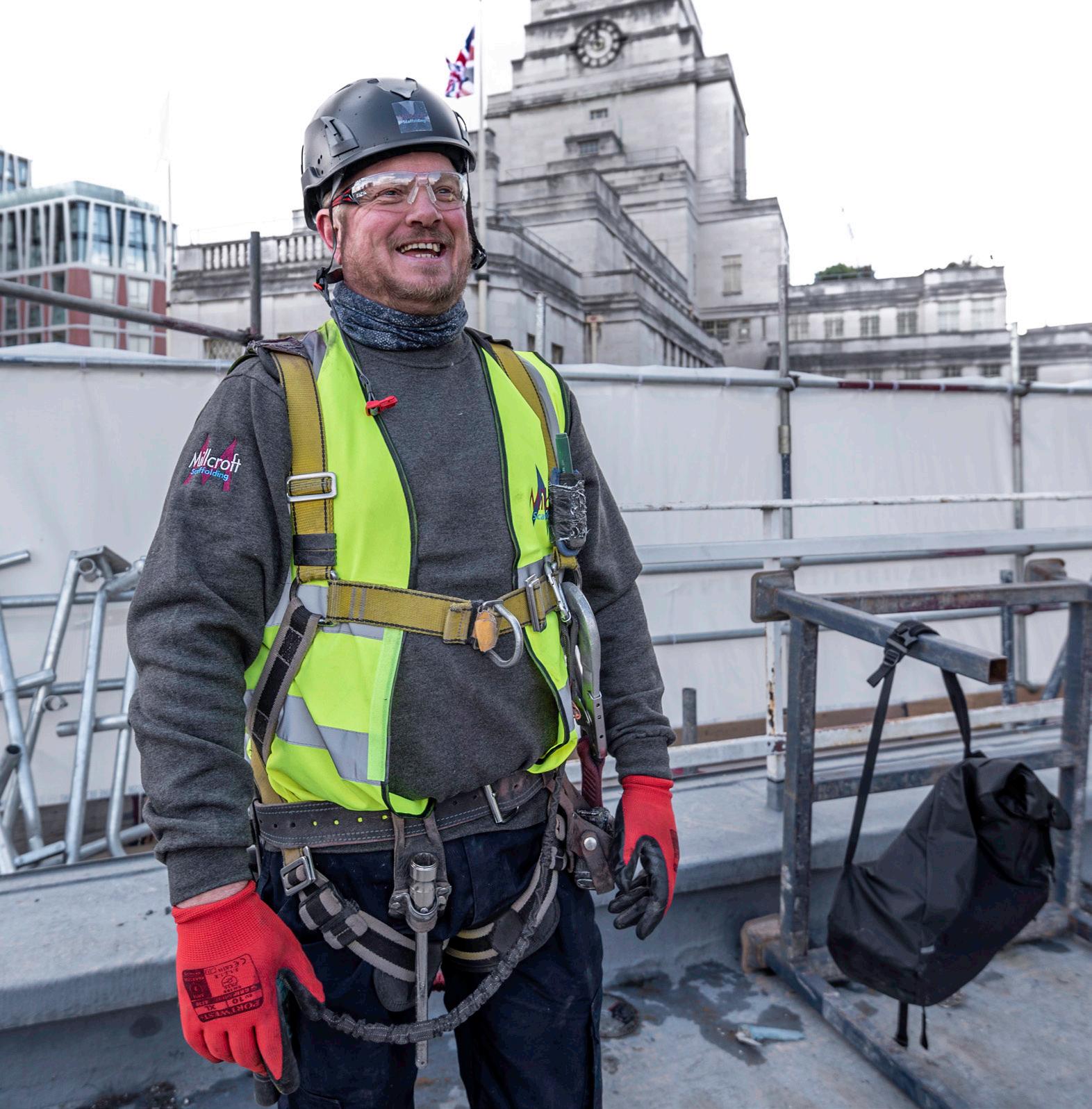
scaffolding is the variety of work environments and projects to keep you mentally stimulated. Unlike many professions that are confined to a single location, scaffolders can work on multiple sites, each with unique challenges and settings. From heritage buildings and towering skyscrapers to major infrastructure projects, the diversity of our work means no two days are the same. This change of scenery can keep the job exciting and prevents the monotony that often comes with other roles.
FINANCIAL REWARDS AND STABILITY
Contrary to some misconceptions, scaffolding can be financially rewarding. Entry-level positions offer competitive wages and plenty of opportunities for advancement. As skills develop and experience grows, so does earning potential. Mark Stimpson’s journey at Millcroft is a testament to this. Starting as a labourer in 1985, Mark has worked his way up through various roles – supervisor, project manager, contracts manager – before being appointed to the Millcroft board as Operations Director in 2018. Mark’s story shows that with dedication and the right attitude, there’s no limit to how far you can climb in this industry.
Although times remain challenging for the
construction industry, scaffolders will always be needed. Whether for construction, industrial works, infrastructure, renovation or refurbishment projects, the demand for skilled scaffolders means job security is higher than in many other sectors.
DIVERSE OPPORTUNITIES BEYOND THE SCAFFOLD
While the image of scaffolding might be someone working at height, the industry is not limited to being ‘on the tools.’ There are various roles available that cater to different skill sets and interests. These include site supervisors, contract managers, accountants, human resource and health and safety professionals. Take Corita Ware, for instance. She joined Millcroft as a credit controller/office administrator, but thanks to her can-do approach and adaptability, she has progressed to become a valued project coordinator for our HS2 projects. Similarly, Richard Ramkissoon, who started his career as a ganger man, shows the potential for growth and diverse job opportunities in this industry. Richard used his on-the-job experience to move into a health and safety advisor role. As well as his day-to-day work, Richard has been instrumental in us winning numerous awards, including 12
consecutive RoSPA Gold Awards and the RoSPA President’s Award.
ADOPTING ADVANCED MODELLING TECHNIQUES
Contrary to outdated perceptions, scaffolding is an innovative industry that has embraced cutting-edge technology. This is opening up exciting new roles and opportunities for people to work with augmented reality, 3D imaging and 4D video. For example, Ahmet Ulusoy, who joined Millcroft in 2021 as an apprentice through the thengovernment’s Kickstart scheme, has progressed to junior estimator and 3D/4D visualiser. Now, Ahmet plays an important role in creating detailed simulations that give our clients a better understanding of the proposed solution and construction sequence. These simulations also help with the estimation process as we can easily work out the required materials and how long the structure will take to construct.
TRAINING, SKILLS DEVELOPMENT AND SUPPORT
Another appealing aspect of a career in scaffolding must be the extensive training and support available. At Millcroft, we’re committed to nurturing new talent and providing opportunities for career development. This can be through formal apprenticeships, on-the-job training or specialised courses; there are always opportunities to expand one’s knowledge and capabilities.
Lewis Mence, another success story from the government’s Kickstart programme, underwent five months of induction, training and mentorship at our scaffolding yard in Greenwich and is now a
trusted team member on sites around the capital. Lewis understands the industry well now and has cultivated a healthy attitude that will help him progress even further, saying: “The early starts were a bit of a shock at first as I’ve had to adapt and change my lifestyle, but that is all good – no more being up late playing PlayStation as I have to start on site at 7.45 am!”
THE IMPORTANCE OF REALISTIC EXPECTATIONS
While scaffolding is rewarding and can be a lucrative career, it requires a strong work ethic and a willingness to start from the bottom and work up. Newcomers need to understand that success in this business doesn’t happen overnight. It comes through experience and practical skills gained over time. By setting realistic expectations and providing clear routes for career progression, we can ensure that recruits understand the demands and rewards of a career in this sector.
EMBRACING THE OPPORTUNITIES
Scaffolding offers a fulfilling and dynamic career path, brimming with opportunities for those who are ready to seize them. From the strong sense of community and camaraderie to the financial rewards and diverse career opportunities, this is an industry where individuals with enthusiasm, openmindedness, team spirit and dedication can thrive.
For those seeking more than a job – those who want to be part of something greater, to see the tangible results of their work, and to have opportunities for growth and advancement –scaffolding is an ideal career choice.
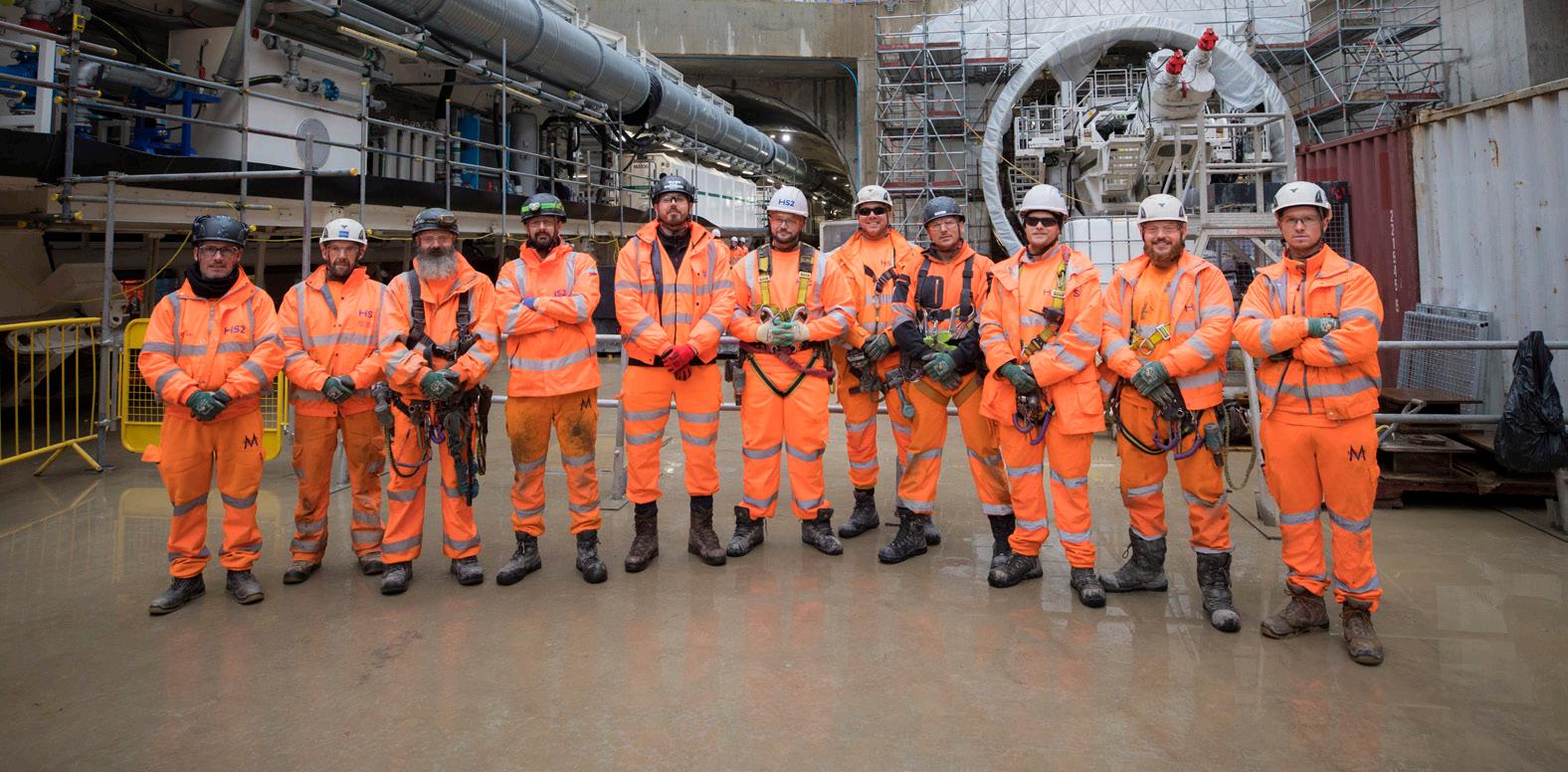
A career in all aspects of scaffolding can provide financial rewards, wellbeing, fitness and a sense of camaraderie.
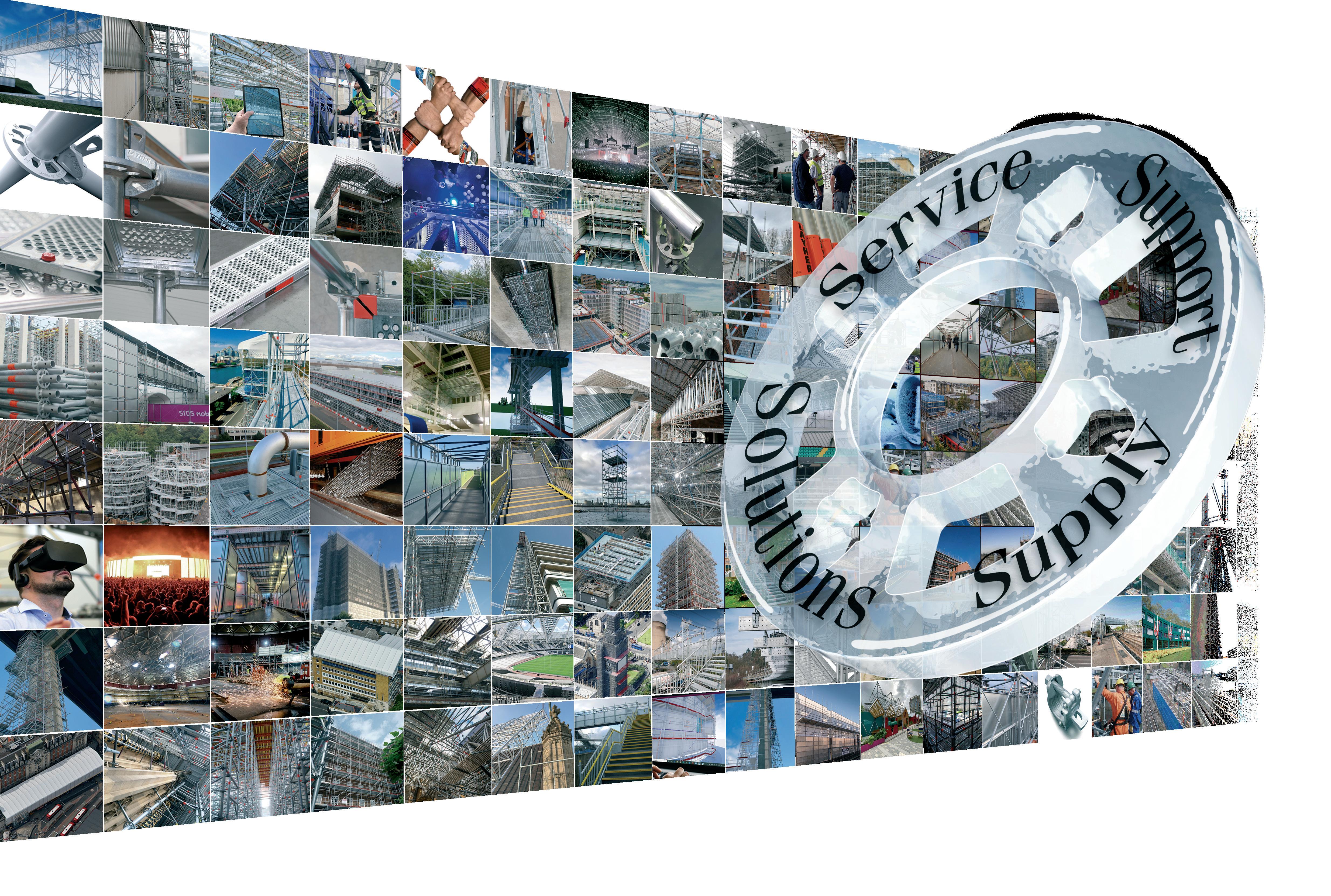

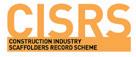


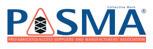
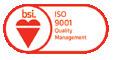


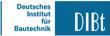



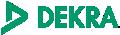



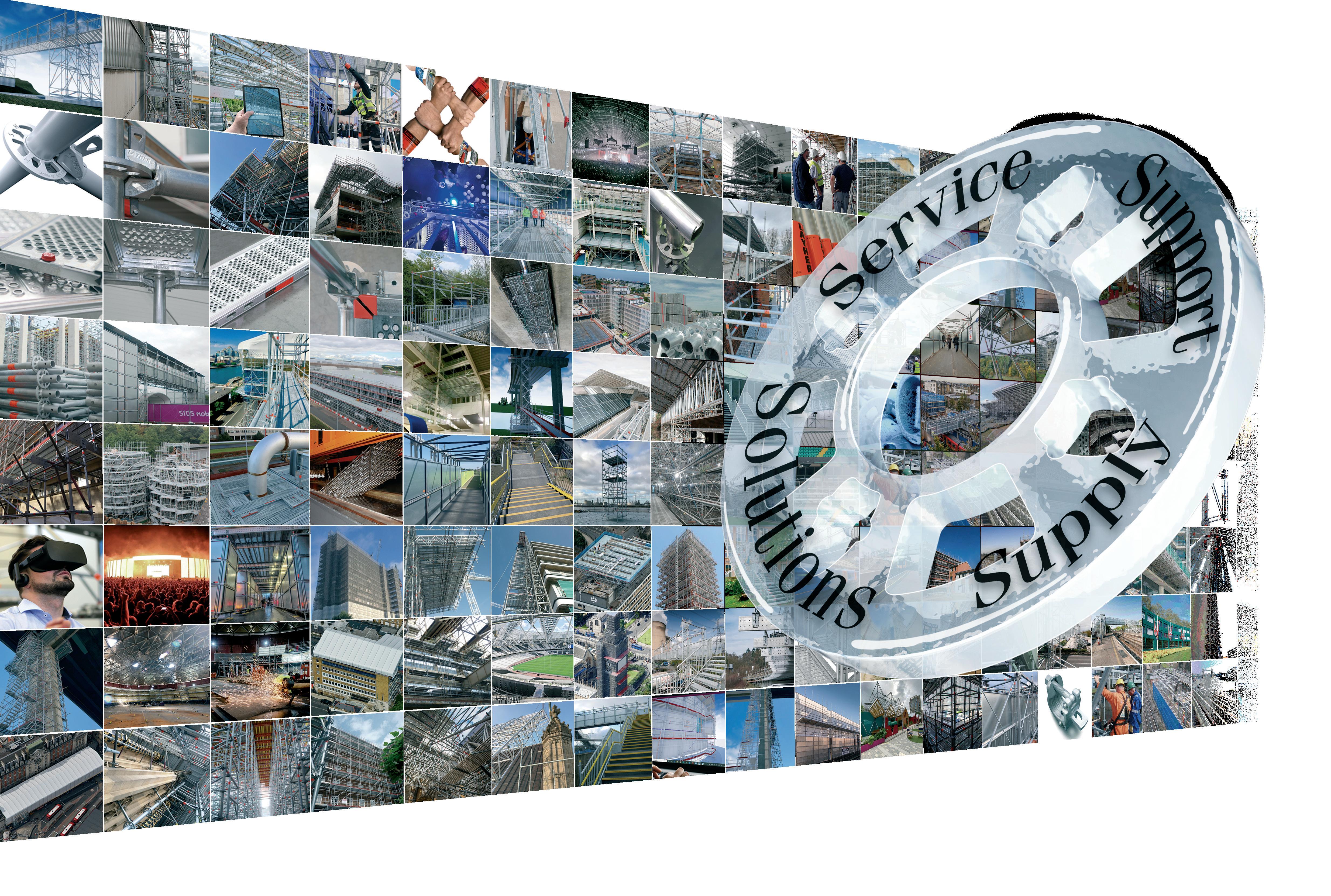
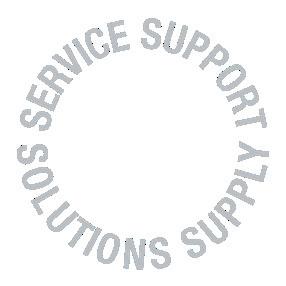
Chris Sedgeman Scaffolding has been crowned Access & Scaffolding Specialist of the Year at the prestigious Construction News(CN) Specialist Awards 2024
The accolade was presented during a gala ceremony held at the Royal Lancaster Hotel, where over 650 industry leaders gathered to celebrate the achievements of the UK’s finest specialist contractors.
This year’s CN Specialist Awards, hosted by comedian Andy Parsons, recognised excellence across 23 categories. With more than 300 submissions reviewed by an independent panel of 83 judges, Chris Sedgeman Scaffolding emerged victorious in the highly competitive Access & Scaffolding Specialist of the Year category, standing out for its impressive work on the Lloyds Bank project in Penzance.
The project involved providing complex scaffolding solutions for the renovation of the historic Lloyds Bank building in the heart of Penzance.
The judges commended Chris Sedgeman Scaffolding for tackling this technically demanding project, which required precision and expertise due to the building’s age and architectural intricacies.

The winner takes it all

The team’s ability to execute the work with minimal disruption to the public, all while maintaining the safety and structural integrity of the iconic site, was a key factor in their success.
In their remarks, the judges highlighted the pride, knowledge and passion evident throughout Chris
Sedgeman Scaffolding’s operations. “The company has built its success on a foundation of developing and investing in its workforce and systems,” they noted, pointing to the establishment of a new training centre and use of innovative interactive training tools. These initiatives and a strong focus on sustainability and community engagement made Chris Sedgeman Scaffolding a deserving winner. Competing against strong finalists such as Allied Access, Connolly Scaffolding and GKR Scaffolding,
Chris Sedgeman Scaffolding stood out not only for its technical capabilities but also for its commitment to leaving a lasting positive impact on both the local community and the scaffolding industry as a whole.
Construction News editor Colin Marrs praised the essential role of specialist contractors in the construction sector, stating: “Without our skilled specialists, there would be no building industry. The tradespeople on sites across the country are the engine of our sector, turning dreams into reality.
“The CN Specialists Awards is a time to celebrate the dedication, craftsmanship and expertise that these individuals bring to the world.”
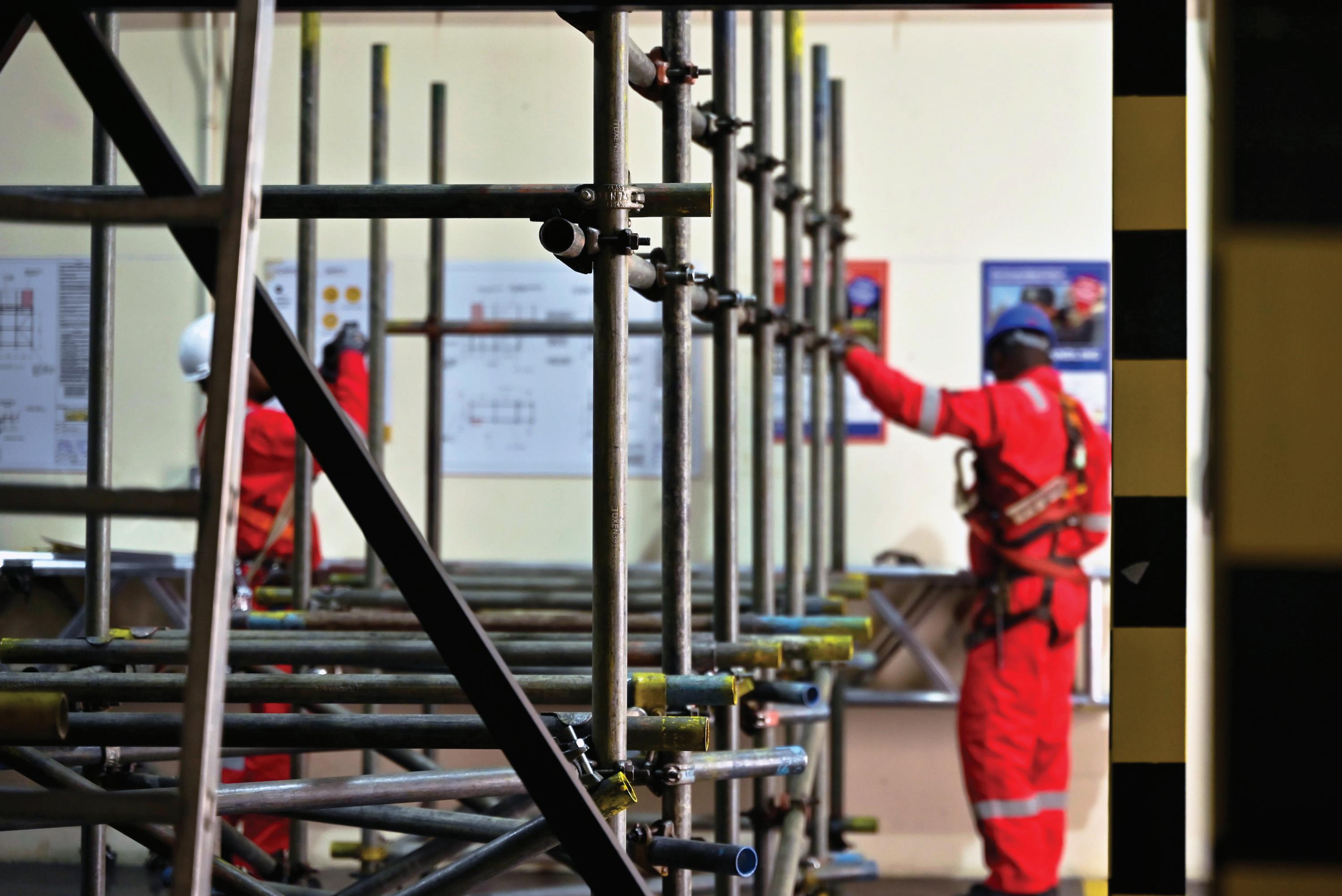
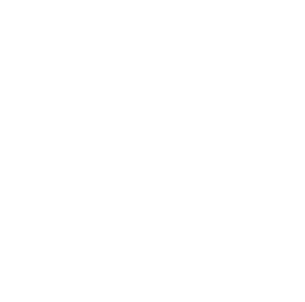
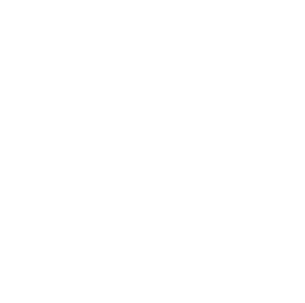
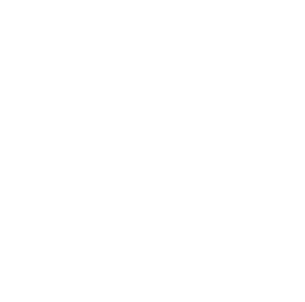
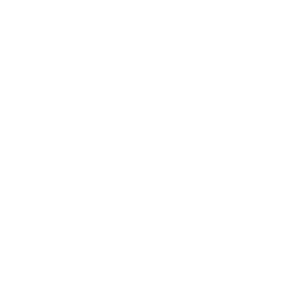
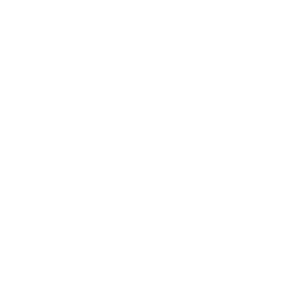

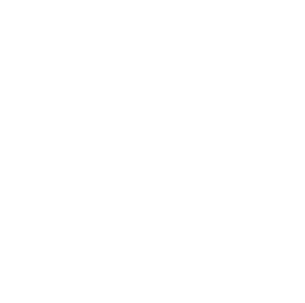
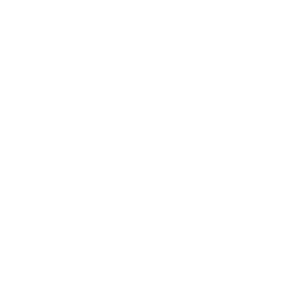
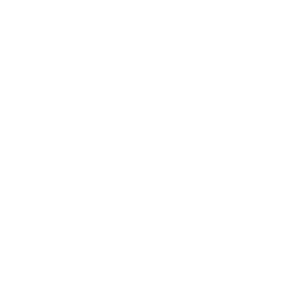

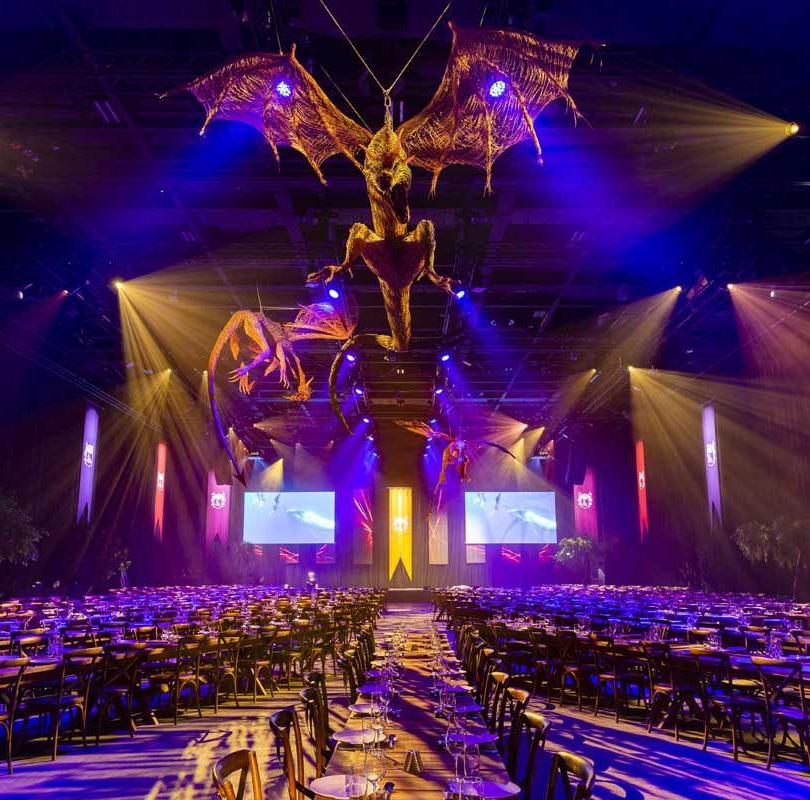
NASC UNVEILS SHORTLIST FOR 2024 SCAFFEX24 SCAFFOLDING EXCELLENCE AWARDS
The NASC (National Access and Scaffolding Confederation) has announced the highly anticipated shortlist for the prestigious ScaffEx24 Scaffolding Excellence
Awards
The awards, which will be presented at the ScaffEx24 Ball and Gala Dinner, which will be held at the Belfast International Conference Centre on Friday, 29 November 2024, aim to celebrate innovation, excellence and outstanding contributions across the scaffolding and access industry.
This year’s nominees include individuals and companies that have made significant strides in areas such as safety, design, service and project execution. The awards span several categories and recognise both seasoned professionals and the next generation of talent in the industry.
APPRENTICE OF THE YEAR
The shortlist for Apprentice of the Year highlights the next generation of skilled scaffolders, with nominees including:
● Albie Cooper, Benchmark Scaffolding Ltd
● Harrison Mapley, Star Scaffolding Ltd
● James Joseph Aicken, K2 Scaffolding (NI) LLP
● Lacey Maclean, Everlast Scaffolding Ltd
SCAFFOLD DESIGN OF THE YEAR
Companies have also been recognised for their excellence in design, including:
● Buckley Design Solutions for their work at Blackburn College
● Lyndon SGB for the New Register House project
● Scaffold Erection Services for HM Prison Birmingham
● SRK Scaffolding for their work on an industrial storage tank
PRODUCT OF THE YEAR
Innovation continues to drive the industry forward, with nominees in the Product of the Year category such as:
● GKR Scaffolding Ltd’s Soterdevice
● Layher Ltd’s FW System
● PERI Ltd’s PERI UP Cladding
SERVICE OF THE YEAR
Services that have transformed project management and training are also recognised, including:
● Footprint WFM Ltd’s Interactive Project Tracking
● Safety & Access Ltd’s Scaffold Training Programme
● Costain/Skanska’s Scaffold Request App, developed for SCS Railways
LIFETIME ACHIEVEMENT
Honouring individuals who have made a lasting impact on the industry, the Lifetime Achievement. Award nominees are:
● Lee Rowswell
● Tom Gent
● Alwyn Richards
● Ray Johnson
PROJECT OF THE YEAR
In recognition of outstanding projects across varying scales, the shortlist for Project of the Year is divided into four categories:
Small:
● Advanced NI Scaffolding Ltd – Royal Victoria Hospital, Belfast
● Ingleford Scaffolding Ltd – St Mary’s Lighthouse, Whitley Bay
● Shield Services Group – Cathedral Park, Bristol
● Malvern Scaffolding – Worcester Cathedral Medium:
● Chris Sedgeman Scaffolding Ltd – Market House, Penzance
● Everlast Scaffolding Ltd – City Exchange, Leeds
● Inner City Scaffolding Ltd – Parkside Court, Chelmsford
● Scaffolding Access Ltd – Former Somerfield Store, Newhaven Large:
● Lyndon SGB – New Register House, Edinburgh
● SCA Group Ltd – Centenary Quays, Southampton
● SRK Scaffolding Ltd – Inovyn Runcorn Power Station
● CASS Supplies Ltd – The Milliners, Bristol
Major:
● Crossway Scaffolding (Elland) Ltd – Lloyds Trinity Road, Halifax
● GKR Scaffolding Ltd – 25 Canada Square, Canary Wharf
● Scaffold Erection Services – HM Prison Birmingham
The winners will be announced at the ScaffEx24 Gala Dinner and Awards Ceremony, marking the culmination of ScaffEx24 in November. This prestigious event will bring together the scaffolding industry’s best and brightest to celebrate their achievements.
An NASC spokesperson said: “These awards not only showcase the incredible talent in our sector but also highlight the ongoing commitment to safety, innovation and quality. We congratulate all of the nominees and look forward to revealing the winners at ScaffEx24.”
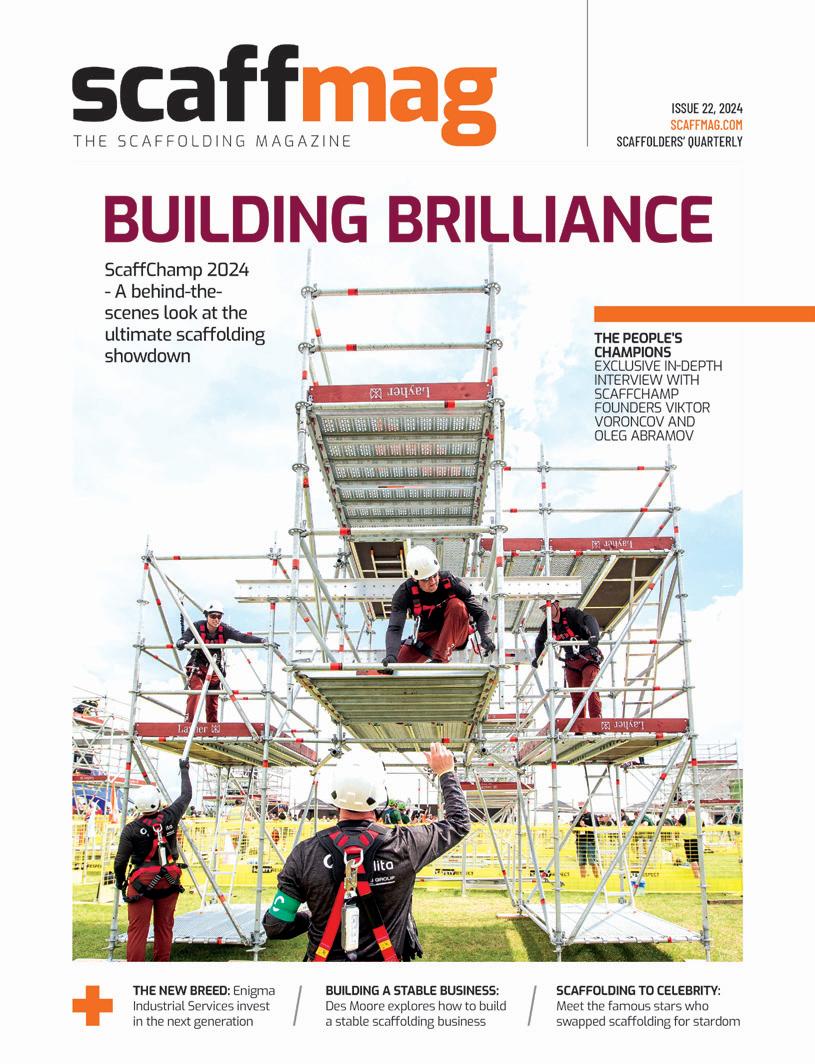

The best-read quarterly magazine in scaffolding
At the very heart of the scaffolding and access industry, ScaffMag has been serving the industry since 2009 by championing best practice, raising awareness of safety issues on-site and promoting business excellence.
ScaffMag delivers its mixture of news, views, trends and product updates through digital channels and in print.
ScaffMag gives businesses and brands an unrivalled opportunity to advertise their products or services 24 hours a day, seven days a week to a highly targeted audience.
To find out more about advertising, contact Jessica Norton on 01472 476024 or email jess@scaffmag.com