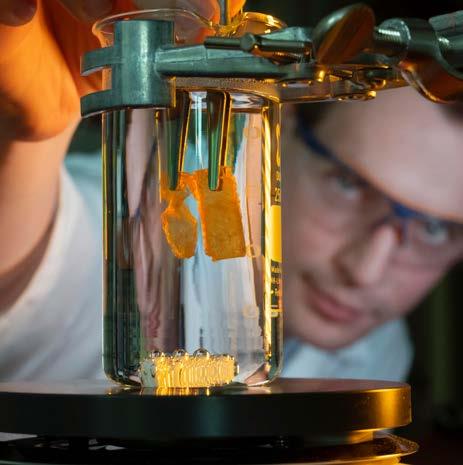
7 minute read
FORSCHUNG/ ENTWICKLUNG
Projekt für wiederverwertbare Kunststoffmaterialien gefördert
Kunststoff kann nachhaltig sein
Advertisement
Nachhaltige Kunststoffe, die sich selbst heilen, intelligente Eigenschaften aufweisen und bei Bedarf recycelt werden können, werden künftig an der Friedrich-Schiller-Universität Jena erforscht. Ein entsprechendes Projekt, koordiniert durch den Chemiker und Materialwissenschaftler Prof. Dr. Ulrich S. Schubert, wird dazu mit zwei Millionen Euro von der Carl-Zeiss-Stiftung gefördert.
«Stellen Sie sich zerkratzte Oberflächen von Wohnungsmöbeln vor, zum Beispiel in der Küche», beschreibt Ulrich Schubert vom Center for Energy and Environmental Chemistry Jena (CEEC Jena) der Friedrich-Schiller-Universität ein mögliches Einsatzgebiet intelligenter Kunststoffe. «Sie erwärmen die entsprechende Oberfläche einfach – etwa mit einem Haartrockner – und sie sieht nicht nur wieder aus wie neu, sondern sie ist neu.» Die sogenannten Vitrimere sollen Gebrauchsgegenstände nicht nur langlebiger machen, sodass sie seltener ersetzt werden müssen – und damit einen Beitrag zum Umweltschutz leisten. Sie können auch leichter wiederverwertet werden. «Besonders Verbundwerkstoffe lassen sich kaum recyceln, denn die hier eingesetzten Materialien lassen sich so gut wie nicht mehr voneinander trennen», erklärt Schubert. Deutlich wird dieses Problem, wenn Windkraftanlagen erneuert werden müssen. «Hier fallen grosse Mengen an Abfall an, allein schon über die Rotorblätter. Bis auf wenige Ausnahmen gibt es hier bisher keine geeignete Strategie, diese Ressourcen weiter zu nutzen.»
Intelligente Materialien
Mit intelligenten Werkstoffen wie den Vitrimeren liesse sich das ändern. «Diese Materialien sind schaltbar», sagt Schubert. «Das heisst, ihre Verarbeitbarkeit kann gesteuert werden.» So lassen sich theoretisch Verbundwerkstoffe herstellen, die bei Bedarf wieder getrennt und weiter genutzt werden können. Genau das will das durch Schubert koordinierte Team in den kommenden fünf Jahren erforschen. «Besonders interessieren uns faserverstärkte Werkstoffe», so Schubert weiter. «Hier wollen wir vor allem Glas- und Kohlenstofffa-
Jens Meyer/Universität Jena
Dr. Stefan Zechel von der Universität Jena untersucht das Formgedächtnisverhalten von Kunststoffen. Dabei wird gezeigt, wie ein Kunststoff in einer deformierten Form (links) in seine ursprüngliche Form (rechts) zurückkehrt. Das Wissenschafter-Team forscht an nachhaltigen Kunststoffen, die sich selbst heilen, intelligente Eigenschaften aufweisen und bei Bedarf recycelt werden können.
sern in die neuen Kunststoffe einbetten, die u. a. für den Leichtbau und die Einsparung von CO²-Emissionen eingesetzt werden können. Uns interessieren aber auch Nanokomposite, in denen Nanofüllstoffe das Material verstärken.»
Noch keine konkreten Anwendungen
Dass diese nachhaltigen Kunststoffe letztlich in unseren Alltag Einzug halten werden und eines Tages in Flugzeugen, auf Oberflächen oder etwa in Tennisschlägern eingesetzt werden, davon ist Schubert überzeugt. «Vitrimere sind noch eine sehr junge Klasse von Kunststoffen. Konkrete Anwendungen sind bisher noch nicht vorhanden. Unser Ziel ist es aber, mit dieser Forschung eine neue Generation von nachhaltigen Materialien zu ermöglichen.» Die Aussichten dafür sind gut. «Bei der Erforschung innovativer Materialien liegt Jena ganz klar im Spitzenfeld der deutschen Universitäten», sagt Schubert. Das zeige sich nicht zuletzt durch die im Neubau befindlichen Gebäude des Center for Energy and Environmental Chemistry Jena II (CEEC Jena II) und dem angeschlossenen Anwendungszentrum CEEC Jena, in die derzeit insgesamt 50 Millionen Euro investiert werden und die den Standort Jena weiter auf diesem Gebiet stärken.
Für fünf Jahre finanziert
Mit seinem Vorhaben hat der Jenaer Wissenschaftler und die Forschungsgruppe auch die Carl-Zeiss-Stiftung überzeugt. Über einen Zeitraum von fünf Jahren wurde nun für das ambitionierte Projekt die hohe Fördersumme von zwei Millionen Euro bewilligt. «So einen Betrag erhält man normalerweise nur für ein grosses koordiniertes Projekt der Deutschen Forschungsgemeinschaft», erklärt Schubert. Etwa acht Doktorandinnen und Doktoranden sollen in den kommenden Jahren diese neue Materialklasse von der Synthese, der Verarbeitung, ihren zugrundeliegenden Mechanismen bis hin zu ihren Umwelteinflüssen untersuchen. Des Weiteren wird eine Nachwuchsgruppe etabliert.
Kontakt Friedrich-Schiller-Universität Jena Philosophenweg 7a D-07743 Jena +49 3641 9-48201 ulrich.schubert@uni-jena.de www.uni-jena.de
Neues 3D-Drucksystem für Hybridmaterialien
3D-Drucker für komplexe Bauteile
Als erste österreichische Hochschule verfügt die Montanuniversität Leoben ab sofort über einen 3D-Drucker für Hybridmaterialien.
Das Gerät CeraFab 7500 der Firma Lithoz GmbH (A) ermöglicht die Fertigung von komplexen, stabilen und hochauflösenden 3D-Objekten aus verschiedenen Werkstoffen. Gedruckt werden können unterschiedliche Keramiken ebenso wie gefüllte und ungefüllte Polymere sowie hochviskose Formulierungen generell, wodurch der Einsatz in anderen Bereichen (z.B. Metall bzw. Werkstoffkombinationen) möglich ist. Die Neuanschaffung entspringt einer Forschungskooperation der beiden Leobener Departments für Werkstoffwissenschaft und Kunststofftechnik im Bereich des Designs, der Herstellung und der Charakterisierung von neuen Materialien mit verbesserten Struktur- und Funktionseigenschaften. Gemeinsam arbeitete man bereits bei verschiedenen Projekten mit der Firma Lithoz zusammen. Das 2011 in Wien gegründete Unternehmen ist eigenen Angaben gemäss Weltmarkt- und Technologieführer für 3DDrucker, Materialien und Lösungen für die industrielle Produktion von Hochleistungs- und bioresorbierbaren Keramiken.
Unterschiedliche WerkstoffKombinationen möglich
«Neue Funktionalitäten erfordern meist die Kombination von verschiedenen Werkstoffen bzw. Materialklassen wie z.B. Metall, Polymer oder Keramik, welche aufgrund ihrer unterschiedlichen thermo-physikalischen Eigenschaften sehr schwierig zusammen verarbeitet werden können. Insbesondere die Realisierung von Bauteilen mit komplexen Geometrien stellt eine grosse Herausforderung dar», erklärt Prof. Dr. Raul Bermejo Moratinos vom Lehrstuhl für Struktur- und Funktionskeramik. «Erst die Entwicklung von additiven Fertigungsverfahren ermöglicht die Verarbeitung von unterschiedlichen Werkstoff-Kombinationen zur Herstellung komplexer Bauteile.»
Bild: Montanuni/Bendl
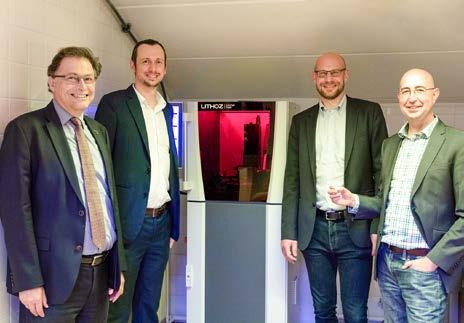
Montanuni-Rektor Wilfried Eichlseder, Assoz. Prof. Dr. Thomas Griesser, Lithoz-CEO Dr. Johannes Homa, Univ.-Prof. Dr. Raul Bermejo Moratinos.
Die Forschung in Leoben soll dazu beitragen, Designrichtlinien in Bezug auf Struktur- und Funktionseigenschaften für künftige 3D-gefertigten Materialien zu entwickeln. «Konkrete Beispiele dafür sind Hochleistungskeramiken für die Biomedizin wie z. B. Zahnimplantate oder Hüftgelenke, 3D-Architekturen mit eingestellten Funktionseigenschaften wie beispielsweise Dielektrika bzw. Piezoelektrika für die Mikroelektronik, Kühlkörper für die Elektronikindustrie oder auch gefüllte Photopolymere für die additive Fertigung von Brillengestellen oder Zahnersatzmaterialien», führt Assoz.Prof. Dr. Thomas Griesser vom Lehrstuhl für Chemie der Kunststoffe an.
Der 3D-Druck-Prozess
Das eingesetzte Verfahren basiert auf der Lithography-based Ceramic Manufacturing (LCM)-Technologie. Ausgehend von einem CAD-Modell ist der erste Schritt des Prozesses die Arbeitsvorbereitung und -optimierung. Die Informationen für das Bauteil werden direkt vom Computer digital auf das CeraFab-System übertragen. Die mit Keramikpartikeln gemischte Flüssigkeit (der sogenannte Schlicker) wird automatisch dosiert und auf eine transparente Wanne aufgetragen. Die bewegliche Bauplattform wird in den Schlicker getaucht, dieser wird dann selektiv sichtbarem Licht von unterhalb der Wanne ausgesetzt und ausgehärtet. Das Schichtbild wird über eine digitale Mikrospiegel-Vorrichtung (DMD) in Verbindung mit einem hochmodernen Projektionssystem erzeugt. Durch die Wiederholung dieses Prozesses kann ein dreidimensionales «Grünteil» Schicht für Schicht erzeugt werden. Beim Ausheizen wird das Bindemittel entfernt und danach werden die Bauteile gesintert, wodurch vollständig dichte Keramikbauteile entstehen. Ziel ist die Realisierung sogenannter «digitaler Materialien» bzw. «digitaler Bauteile», wobei Eigenschaften wie beispielsweise Farbe und mechanische Festigkeit dreidimensional und selektiv innerhalb des Bauteils modifiziert werden können.
Moderne Ausstattung auch für Lehre
«Neben der Forschung wird der neue 3DDrucker an der Montanuniversität Leoben auch im Masterstudium Werkstoffwissenschaft zum Einsatz kommen», kündigt Bermejo an. «Neben Metallen und Polymeren können wir in der Lehre nun alle Materialklassen als Werkstoffe für die additive Fertigung abbilden.» Ergänzende Industrieerfahrung können die Leobener Studierenden durch Praktika im Bereich 3D-Fertigung bei der Firma Lithoz sammeln.
Kontakt Montanuniversität Leoben Franz Josef-Strasse 18 A-8700 Leoben +43 3842 402-7702 office@unileoben.ac.at www.unileoben.ac.at
Startschuss für ressourcenschonende Fertigung von PEEK
Kontinuierliche Fertigung von FKV-Hohlprofilen
Für eine umweltverträgliche und leistungsfähige Luftfahrt fördert das BmWi im zivilen Luftfahrtforschungsprogramm die zukunftsorientierte Technologie der Herone GmbH zur kontinuierlichen Fertigung von Faserverbund-Hohlprofilen. Der Einsatz von Hochleistungs-Polymeren, wie PEEK, kombiniert mit der neuartigen CBM-Technologie, schont Ressourcen und maximiert gleichzeitig die Produktvielfalt.
Im Rahmen des Forschungsvorhabens «InPro» werden erstmalig komplexe Faserkunststoffverbund (FKV)-Hohlprofile auf Basis von Hochleistungs-Thermoplasten, wie z.B. PEEK, PPS oder PPA, kontinuierlich hergestellt. Damit knüpft die Herone GmbH zusammen mit ihren Partnern, der HPF GmbH & Co. KG sowie dem Institut für Leichtbau und Kunststofftechnik (ILK) der TU Dresden, an die bereits durch die Herone GmbH industrialisierte diskontinuierliche Fertigung an. Basis bildet das Intervallheisspressen für Hohlprofile (CBM), ein neuartiger semikontinuierlicher Verfahrensansatz, der von den Gründern der Herone GmbH in ihrer Zeit als wissenschaftliche Mitarbeiter am ILK der TU Dresden erfunden, erprobt und zum Patent angemeldet wurde. Das Verfahren ist eine Kombination aus dem Blasform-Verfahren und dem Continuous Compression Molding (CCM). Es ermöglicht die kontinuierliche, ressourcenschonende und effiziente Fertigung von FTVHohlprofilen. Es zeichnet sich dadurch aus, dass, trotz des semi-kontinuierlichen Fertigungsprinzips, FKV-Hohlprofile mit veränderlichen Lagenaufbauten oder Querschnitten gefertigt werden können. Dies ermöglicht die kontinuierliche Fertigung von Hohlprofilen mit lokal verstärkten Laminaten, die besonders in hochbelasteten Bereichen, z.B. der Krafteinleitung, erforderlich sind. Im Rahmen des Forschungsvorhabens wird die CBM-Technologie zur Verarbeitung des Hochleistungs-Polymers PEEK weiterentwickelt und mit dem SpritzformProzess zur Funktionalisierung der Hohlprofile kombiniert. In dem nachfolgenden Verfahrensschritt des Spritzformens können so lokal formschlüssige bzw. kombiniert stoff-formschlüssige Verbindungen
CBM-Versuchsanlage von Herone

zwischen Funktionselementen (z.B. Zahnräder, Hebelsysteme, Dichtflächen, integrale Faserverbund-Gewinde, etc.) und dem Grundprofil hergestellt werden. Adressierte Bauteile sind z.B. Zug-DruckStreben, Wellen oder auch medienführende sowie speichernde Systeme.

Das Vorhaben InPro – «Integrale Leichtbau-Profilstrukturen aus Faser-Thermoplast-Verbund (FTV) funktionalisiert im Spritzform-Verfahren» – wird im Rahmen des zivilen Luftfahrtforschungsprogramms des Bundesministeriums für Wirtschaft und Energie (BmWi) für drei Jahre bis Ende 2023 gefördert und zur Netzwerkbildung von den internationalen Partnern Victrex und Boeing unterstützt.
Kontakt Herone GmbH Marschnerstrasse 39 D-01307 Dresden +49 351 463-42316 info@herone.de www.herone.de