
18 minute read
Ciencia y tecnología
Excelente agente de pegajosidad para EPDM y nuevo método de medición del “Tack”
COLUMNISTA INVITADO
Mayu Si (CHI / EUA) Gte. internacional de ventas - STRUKTOL msi@struktol.com
Víctor Dvoskin (ARG) TRADUCCIÓN
Mayu Si recibió un doctorado en Ciencia e Ingeniería de Materiales de la Universidad Estatal de Nueva York en Stony Brook. En 2007, se unió al Centro de Investigación de Productos de Ingeniería de Goodyear como compositor senior, trabajando en el desarrollo de compuestos de caucho y soporte técnico para la producción de plantas. De 2013 a 2017 fue químico jefe global de cintas transportadoras en Veyance Technologies / ContiTech. Desde 2017, ha sido gerente internacional de ventas de caucho en Struktol Company of America.
INTRODUCCIÓN
En nuestra industria, cuando se fabrican artículos de caucho multicapa a partir de materiales crudos, la pegajosidad (“tacking”) se transforma en un parámetro crítico de los compuestos de caucho.
Los compuestos utilizados en la fabricación de neumáticos, llantas reencauchadas, bandas transportadoras, correas trapezoidales, mangueras industriales, recubrimientos para rodillos y revestimiento de tanques deben tener cierto nivel de adherencia para mantener unidos los componentes y mantener la forma hasta el curado.
Además, si los artículos de caucho ensamblados en crudo han atrapado aire debido a la falta de pegajosidad, los productos terminados presentarán defectos, que resultarán en problemas de rendimiento de las piezas finales.
Para una definición simple y clara, la pegajosidad es la capacidad de dos materiales para resistir la separación después de poner sus superficies en contacto por un corto tiempo bajo una ligera presión 1 .
La preparación de una probeta para su medición se puede describir en tres etapas: primero, las superficies de goma deben entrar en contacto entre sí para obtener un contacto molecular íntimo; segundo, a continuación, las cadenas de caucho deben difundirse rápidamente a través
de la interfaz para obtener un alto grado de entrecruzamiento entre las cadenas que formen un enlace robusto, para que el caucho fluya bien en poco tiempo son convenientes los compuestos de baja viscosidad; finalmente, el enlace formado en la interfaz debe ser lo suficientemente fuerte como para resistir la separación por fuerzas externas 1 .
En la literatura se encuentran diversos métodos para evaluar la pegajosidad, tales como Tel-Tak Tackmeter y The BFGoodrich Portable Universal Tester 2,3 . Sin embargo, hoy en día, se sigue utilizando la prueba manual en fábrica por su simpleza.
No existen métodos de prueba estándar ASTM o ISO disponibles para medir cuantitativamente la pegajosidad de los compuestos de caucho sin curar. Por consiguiente, es necesario desarrollar un

método de prueba confiable que pueda predecir el procesamiento de caucho en fábrica. En términos de medición de la pegajosidad, hay tres parámetros que son muy críticos: presión de contacto, tiempo de contacto y velocidad de separación 3 .
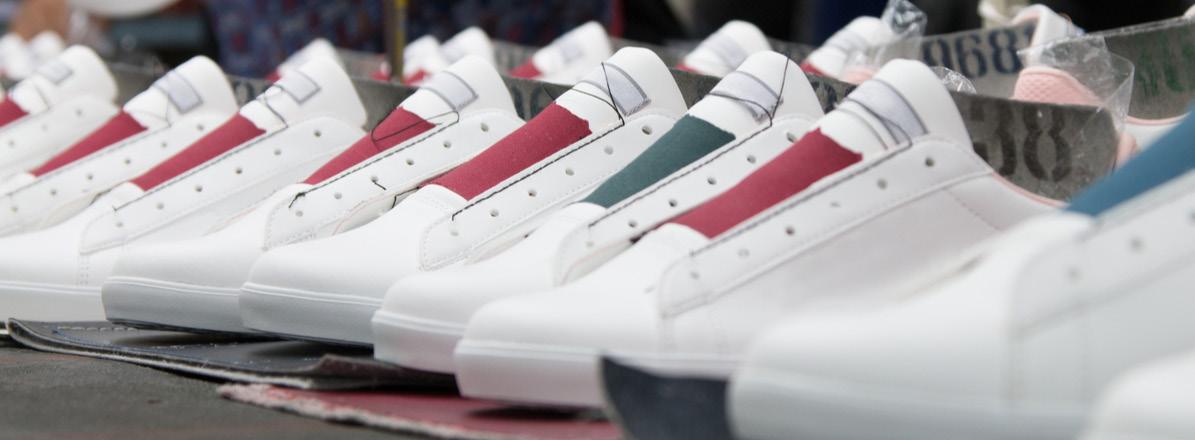
Para el procesamiento del caucho, la presión de contacto y el tiempo son los más importantes en lo que respecta a generación de la pegajosidad.
Generalmente, la pegajosidad llega a una meseta después de suficiente tiempo y presión. No obstante, esta tendencia podría variar dependiendo del tipo de caucho, la viscosidad del compuesto, la resistencia del compuesto en crudo y las características de la superficie.
Un buen método de prueba de “tacking” debería considerar detenidamente cómo medir con precisión el efecto del tiempo de contacto y la presión, que debe estar controlado por el instrumento y la computadora. Además,la preparación de la muestra debe ser consistente para minimizar el ruido experimental de la misma muestra.
Así, desarrollamos un nuevo método de prueba considerando los factores anteriormente descriptos.
La presión y el tiempo de contacto son controlados con precisión a través de una máquina de ensayo que contiene una celda de carga de baja capacidad.
La muestra se preparó en un molino abierto y consiste en láminas lisas para mitigar el efecto de rugosidad de la superficie.
A diferencia de los métodos de prueba, el nuevo método desarrollado adoptó áreas de contacto relativamente pequeñas para la medición, con el fin de mantenerlo más concentrado y evitar grandes irregularidades en la superficie.
Además de medir con precisión la pegajosidad, aumentarla efectivamente en los compuestos de producción se convierte en un desafío aún mayor.
Excepto NR o CR, la mayoría de los cauchos sintéticos tienen una pegajosidad baja o pobre y normalmente se agregan agentes de pegajosidad a los compuestos para mejorar el “tacking”.
En general, las resinas de pegajosidad son oligómeros de bajo peso molecular con un promedio de 3.000.
Hay dos tipos principales de pegajosantes: naturales y sintéticos.
El primero incluye colofonias, derivados de colofonia y terpenos.
Sin embargo, los más eficaces son los de tipo sintético, que son resinas de cumarona-indeno procedentes del carbón, resinas de hidrocarburos C5 y C9 y de tipo fenólico productos de la síntesis química 1 .
El tipo fenólico se vuelve más dominante debido a su eficiencia y rendimiento, especialmente el super agente de pegajosidad “Koresin”, que no sólo puede aumentar significativamente la pegajosidad inicial, sino también prevenir la degradación de la pegajosidad bajo humedad y calor.
Por otro lado, el EPDM es un elastómero muy importante en la industria del caucho, ampliamente utilizado en mangueras, cables, membranas para techos y correas. Debido a su cristalinidad parcial (contribución del segmento de etileno), la movilidad de la cadena de las moléculas de EPDM es muy limitada, lo que puede reducir significativamente el enredo de la cadena a través de la interfaz de unión ¹.
Consecuentemente, el EPDM en sí mismo tiene muy poca adherencia.
Estudios y análisis previos indicaron que la resina de cumarona-indeno y la resina de fenolformaldehído son efectivas para aumentar la pegajosidad del compuesto EDPM 4. Sin embargo, la pegajosidad obtenida con estos aditivos en fábrica no es suficiente para responder a los desafíos del procesamiento.
A continuación, se presenta el uso de un nuevo tipo de agente de pegajosidad para aumentar el "tacking" de compuestos de EPDM de manera eficiente y se ha demostrado en la práctica, utilizándolo con éxito en algunos productos de caucho.
EXPERIMENTO
Mezclado - Los compuestos se mezclaron en un Ferro lab Banbury (1,5 litros). - Los compuestos de SBR / BR se mezclaron con un factor de llenado del 67 %. - Los compuestos de EDPM se mezclaron "al revés" (Up side down) con un factor de llenado del 72 %. - Todos los ingredientes son productos comerciales, disponibles en el mercado. - Se utilizaron dos resinas adhesivas, Koresin de BASF y TS 50 Flakes de Struktol.
Ensayos - La prueba de viscosidad Mooney, ML (1 + 4) a 100 ºC, se realizó siguiendo la norma ASTM D1646 utilizando un viscosímetro Alpha Technologies 2000 Mooney. - El comportamiento de curado se caracterizó mediante el uso de Alpha Technologies MDR siguiendo ASTM D5289, probado a 150 ºC / 160 ºC durante 30 min. - Las propiedades físicas se midieron siguiendo ASTM D412, las muestras se curaron a 150 ºC / 160 ºC durante 30 minutos. - La prueba de adhesión de la tela se realizó midiendo la fuerza de despegado de una tira de sándwich curada de 25 mm por 150 mm formada por tela / compuesto / capas de tela.
Ensayo de pegajosidad - Preparación de la muestra: todos los compuestos se laminaron en fajas lisas de 4 mm de calibre.
- La temperatura de los rodillos del molino se fijó en 55 ºC.
- El molino se limpió a fondo para librarlo de cualquier contaminación.
- El lado de prueba de la faja de muestra es el área directamente contactada con el rodillo.
- Las láminas se cortaron en tiras de 100 mm por 30 mm y se almacenaron en un área limpia para evitar el polvo y la contaminación (Imagen 1).
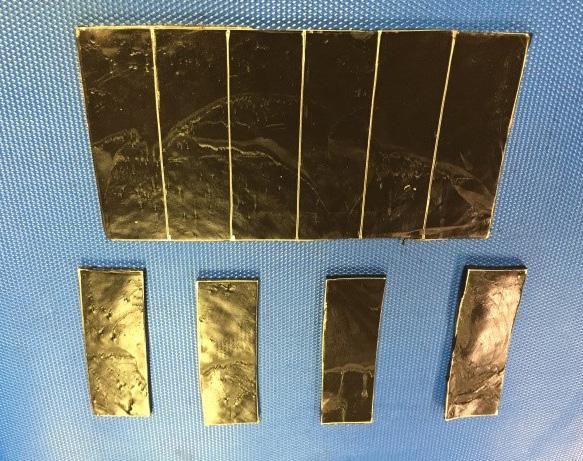
Imagen 1
- Procedimiento de prueba: se envolvieron dos tiras cortadas alrededor de barras redondas con un diámetro de 10 mm y una longitud de 40 mm, los bordes de estas tiras se cubrieron con películas de revestimiento para evitar que el compuesto de goma se adhiera a la abrazadera bajo presión de aire (Imagen 2).
Imagen 2
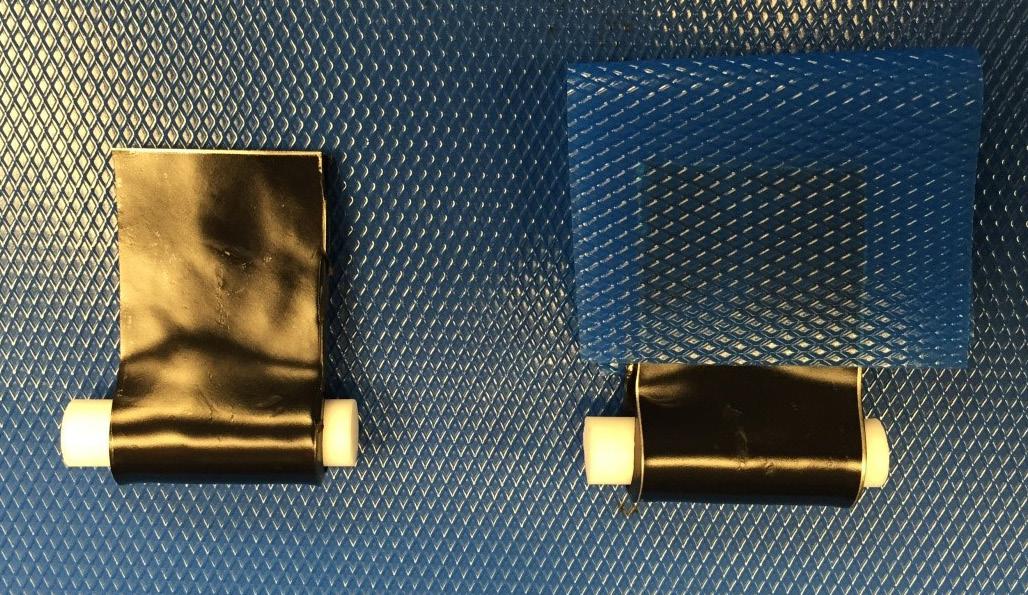
- La medición de la pegajosidad se llevó a cabo presionando, manteniendo y separando las muestras de prueba con el dinamómetro Instron.
- Las mordazas de tensión se instalaron con una rotación de 90º entre sí.
- La celda de carga se calibró automáticamente antes de cada ejecución (Imagen 3).

Imagen 3
- La prueba comenzó preferiblemente con una velocidad de cruceta de 10 mm / min hasta una fuerza de compresión de 10 N, luego siguió un tiempo de retención de 5 segundos.
- Después de eso, las muestras se separaron con una velocidad de 50 mm / min.
- El ciclo completo se registró en un diagrama fuerza-desplazamiento.
- Dependiendo del nivel de pegajosidad de los compuestos, el ajuste de la fuerza de compresión y el tiempo de retención pueden variar.
- Los resultados fueron los valores medios de las fuerzas de ruptura máximas calculadas a partir de 5 pruebas para cada uno.
Resultados y discusión Para garantizar que el nuevo método de prueba de pegajosidad sea sensible, se seleccionó una formulación modelo con baja adherencia, que es un compuesto a base de SBR / BR cargado con negro de humo N220 y una pequeña cantidad de aceite.
Debido a la base de caucho SBR / BR y la alta viscosidad, cabe esperar que este compuesto tenga una pegajosidad deficiente.
Para mostrar que el nuevo aditivo de pegajosidad desarrollado puede diferenciar los compuestos con varios niveles de pegajosidad, se agregó Koresin (súper “tackifier”) al compuesto modelo.
Ambas formulaciones de compuestos se muestran en la Tabla 1.
La Tabla 2 enumera los valores máximos de fuerza de rotura, la tensión de rotura y su desviación estándar.
Compuesto 1 Compuesto 2
SBR 1507 70.00 100
Buna CB24 30.00 30
N220 50.00 50
6PPD 1.60 5
Óxido de zinc 3.00 1
Ácido esteárico 0.50 2.5
Sundex 790TN
5.00
0
Koresin 1.5
TBBS
1.20
1.20
Azufre 1.80 1.80
Tabla 1: Modelo SBR / BR Compuesto de formulación.
La Figura 1 muestra un gráfico de prueba de pegajosidad de la fuerza de compresión (valor negativo) y la fuerza de separación (valor positivo) frente a la extensión del compuesto 1 bajo 10 N durante 5 segundos.
Figura 1: Medición del compuesto 1.
La Figura 2 muestra los resultados de las pruebas de pegajosidad del Compuesto 2 con 10 partes de Koresin en las mismas condiciones de prueba que el compuesto 1. El valor de la pegajosidad del compuesto mejoró 4 veces con la adición de Koresin.
Figura 2: Medición del compuesto 2.
Los valores de pegajosidad de ambos compuestos tuvieron una pequeña desviación estándar, 0.32 y 0.22, lo que indica que los números de prueba individuales están muy cerca del valor medio y los resultados de la prueba son consistentes.
El transductor A100 N con 0.25 % de repetibilidad de lectura se utilizó en la Instron para el control de precisión.
Este nuevo método de prueba de pegajosidad puede medir tanto valores bajos como altos, manteniendo una buena reproducibilidad y precisión.
Es común suponer que una gran superficie de contacto puede representar mejor las características reales del compuesto y los
1 2 3 4 5 media Desviación estándar
Compuesto 1 2.30 2.72 2.68 3.19 2.80 2.74 0.32
Compuesto 2 9.16 9.35 9.50 8.98 9.49 9.30 0.22
resultados de las pruebas sean más consistentes. Sin embargo, la medición de la pegajosidad es para caracterizar la superficie del compuesto crudo, que es blando y viscoelástico.
Incluso con un aspecto liso y fresado, a nivel microscópico, la superficie de la muestra no es homogénea.
Asimismo, es difícil lograr un buen contacto uniforme mediante poca fuerza de compresión aplicada durante un corto tiempo, lo que puede ser un factor importante que contribuye a la variabilidad de las pruebas de pegajosidad. En particular, algunos compuestos con mucho nervio (bajo nivel de carga) presentan una superficie rugosa y la consistencia de la medición de la adherencia es muy pobre.
El nuevo método de medición de pegajosidad se centra en áreas pequeñas, definidas por el posicionamiento a 90º de las dos muestras: un círculo pequeño con un diámetro de alrededor de 0.5 mm.
Después de cinco repeticiones, que pueden ser más, consigue representar las características de toda la superficie y las propiedades de masa del compuesto. Debido a la viscosidad Mooney y rigidez de cada compuesto, incluso bajo la misma condición de carga, el área de contacto de las muestras cambiará.
El método se basa en el principio de que dos superficies de goma se presionan juntas, después de la compresión, al cambiar a la dirección opuesta el movimiento de Instron, se rompe la unión de la interfaz y la fuerza de separación se registra como valor de pegajosidad. En consecuencia, la presión de contacto y el tiempo son dos factores importantes que contribuyen a los valores de pegajosidad. Los primeros estudios y la literatura indican que, en la pegajosidad, la etapa de formación de puentes está más controlado por el contacto que por la inter-difusión 1 . El proceso de difusión interna es rápido (se completa en segundos). En general, el aumento de la presión y el tiempo de contacto facilita el acercamiento molecular entre las dos superficies ayudando a la formación de enlaces hasta que se completa, llegando a una meseta.
Figura 3. Efecto del tiempo de contacto sobre la pegajosidad del compuesto SBR / BR por debajo de 10 N
La Figura 3 muestra la comparación de la pegajosidad del compuesto 1 y 2 en función del tiempo de contacto para una fuerza de carga de 10 N. La pegajosidad del compuesto de control aumentó ligeramente con el tiempo antes de 15 segundos y, transcurrido ese lapso, tiende a estabilizarse. El compuesto 2 con 10 partes de Koresin alcanzó un alto valor de pegajosidad después de sólo 5 segundos y continuó aumentando gradualmente.
Los datos sugieren que el compuesto con resina adhesiva tarda menos tiempo en obtener un buen contacto con la superficie que el compuesto de control.
La resina adhesiva puede acelerar el contacto molecular debido al flujo rápido y la fuerte influencia de las fuerzas de Van Der Walls.
La Figura 4 muestra el efecto de la presión de contacto sobre la pegajosidad del compuesto por menos de 5 segundos de tiempo de retención.
La tendencia general es similar a la informada antes de1, con alta presión, se logra un buen contacto con la superficie y se mejora la resistencia de la adherencia.
El gráfico también indica que hay una diferencia entre los compuestos que responden al aumento de presión. El compuesto de control alcanzó rápidamente una meseta con una fuerza de carga superior a 10 N, pero el valor de la pegajosidad del compuesto con Koresin continuó aumentando, incluso después de 20 N, solo la velocidad de aumento disminuyó.
En general, la adición de resina adhesiva aumenta significativamente el pegamento compuesto. Mientras tanto, la modificación de la superficie del compuesto con resina adhesiva también cambia la respuesta de la resistencia adhesiva a señales externas, como la presión de contacto y el tiempo.
Figura 4. Efecto de la presión de contacto sobre la pegajosidad del compuesto SBR / BR en menos de 5 segundos.
La condición de procesamiento en fábrica puede optimizarse para alcanzar el nivel de pegajosidad requerido. El EPDM, debido a su alto nivel de saturación, tiene una excelente resistencia al calor y al ozono, lo que resulta en una amplia gama de aplicaciones.

No obstante, algunos compuestos industriales de caucho EPDM con alto nivel de carga tienden a tener una pegajosidad en crudo muy baja, lo que puede causar la separación de los componentes.
Los resultados obtenidos por la incorporación de resinas adhesivas estándar en EPDM no son tan efectivos como con los cauchos basados en dieno.
TS 50 Flakes, una resina sintética suave y aromática, se estudió por primera vez en un compuesto de membrana de techo EPDM típico.
La Tabla 3 muestra las formulaciones compuestas, las originales y las que tienen 5 y 10 partes de TS 50 Flakes. Todos los compuestos se mezclaron con una sola etapa y luego se molieron para obtener hojas lisas para la prueba de adherencia.
La Figura 5 muestra los valores de pegajosidad de los compuestos en función del tiempo por debajo de 10 N. Con la adición de TS 50 Flakes, la pegajosidad del compuesto de membrana de techo EDPM mejoró significativamente, cuando TS 50 Flakes se incrementó a 10 partes, el valor de la pegajosidad se incrementó en un factor de 4.
El efecto de la presión de contacto sobre la pegajosidad del compuesto se muestra en la Figura 6, que indica claramente la efectividad de TS 50 Flakes.
La pegajosidad del compuesto de control aumenta
Vistalon 9301 90.0 90.0 90.0
Vistalon 2502 10.0 10.0 10.0
N650 80.0 80.0 80.0
N326 15.0 15.0 15.0
Suprex arcilla 75.0 75.0 75.0
Supar 150 60.0 60.0 60.0
ZnO
5.0
5.0
5.0
Ácido esteárico 2.0 2.0 2.0
TS 50 Copos 5.0
10.0
Azufre 1.0 1.0 1.0
TBBS 2.9 2.9 2.9
ZDBC 0.2 0.2 0.2
Tabla 3. Formulación modelo de membrana de techo de EPDM
ligeramente con la presión de contacto, mientras que los compuestos con adhesivo tienen un aumento continuo de la pegajosidad con esta presión (más efectivo que el tiempo de contacto). Debido a su baja insaturación, el EPDM tiene una resistencia al envejecimiento por calor mucho mejor que la mayoría de los cauchos con alto contenido de dieno.

Figura 5. Efecto del tiempo de contacto sobre la pegajosidad del compuesto de EPDM por debajo de 10 N.
Para algunas condiciones severas de alta temperatura, se selecciona EPDM de bajo grado ENB junto con el curado con peróxido para mejorar aún más el rendimiento del envejecimiento por calor del compuesto. Por lo tanto, TS 50 Flakes también se investigó en el compuesto EPDM curado con peróxido.
La Tabla 4 muestra la formulación de los compuestos estudiados.
Como la insaturación del TS 50 Flakes puede consumir peróxido, los curativos se ajustaron en el compuesto 3 para compensar la pérdida de densidad de reticulación y mantener las propiedades del compuesto original.
La Figura 7 muestra el aumento del valor de pegajosidad de los compuestos 2 y 3 con la adición de 5 partes de TS 50 Flakes.
Dado que este compuesto es la capa delgada para proporcionar adhesión a la tela, es necesario mantener una buena pegajosidad del compuesto, lo cual es muy crítico para el procesamiento.
Los datos en la Figura 8 muestran que hubo un tremendo aumento de la pegajosidad entre el compuesto y la tela con la adición de 5 partes de TS 50 Flakes, que puede aumentar drásticamente
Figura 6. Efecto de la presión de contacto sobre el pegamento del compuesto EPDM en menos de 5 segundos.
la humectación del compuesto en la tela, más penetración en la superficie. Los siguientes datos de adhesión del compuesto curado que se muestran en la Figura 9 refuerzan aún más la importancia de una buena pegajosidad del compuesto, incluso el aumento de la adhesión del compuesto curado al tejido podría ser contribuido por la modificación de las características de curado del compuesto y el cambio de propiedades.
CONCLUSIONES
A partir de todo lo expuesto, se introduce un método innovador de prueba de pegajosidad. Debido al nuevo diseño de preparación de muestras, ajuste del área de superficie de contacto y equipo de control computarizado, los resultados de la pegajosidad muestran una alta consistencia y precisión.
Figura 7. Datos de pegajosidad de los compuestos de EPDM curado con peróxido.
Compuesto 1 Compuesto 2 Compuesto 3
Vistalon 2502 100.00 100.00 100.00
N550 20.00 20.00 20.00
Ultrasi GR7000 25.00 25.00 25.00
Carbonato de calcio R06 325 mesh 25.00 25.00 25.00
Stan lubricante 80 25.00 25.00 25.00 Ácido esteárico 1.00 1.00 1.00
Óxido de zinc 5.00 5.00 5.00
Resina de penacolita B-19S 4.50 4.50 4.50 Struktol TS 50 Copos 5.00 5.00
VulCup 40KE 7.50 7.50 9.50
Cyrez 964 3.00 3.00 3.00 Sarcómero SR 350 2.50 2.50 3.50
Tabla 4: Formulaciones de EPDM curadas con peróxidos.
Figura 8. Datos de pegajosidad a la tela de los compuestos de EPDM curados con peróxido.
Estos datos son reproducibles. Además, se investigó el efecto de la presión de contacto y el tiempo sobre la pegajosidad y los resultados siguen tendencia similar a la expuesta en la literatura.
Un adhesivo especialmente diseñado, Struktol TS 50 Flakes, se estudió en dos tipos de compuestos de EPDM: uno curado con azufre con alto nivel
Figura 9. Datos de adhesión a la tela de los compuestos de EPDM.
de carga y el otro para capa delgada curado con peróxido. La adición de TS 50 Flakes aumenta significativamente la pegajosidad del compuesto crudo. En el caso del compuesto curado con peróxido, hay aumentos dramáticos de la pegajosidad del compuesto en crudo a la tela y la adhesión de la tela curada con la introducción de TS 50 Flakes. ■
AGRADECIMIENTOS
Los autores desean agradecer a Struktol Company of America por su apoyo y permiso para publicar este documento.
Además, enviamos un agradecimiento especial a la Sra. Bárbara Eikelberry y al Sr. Kevin Tracy por su apoyo en el experimento.
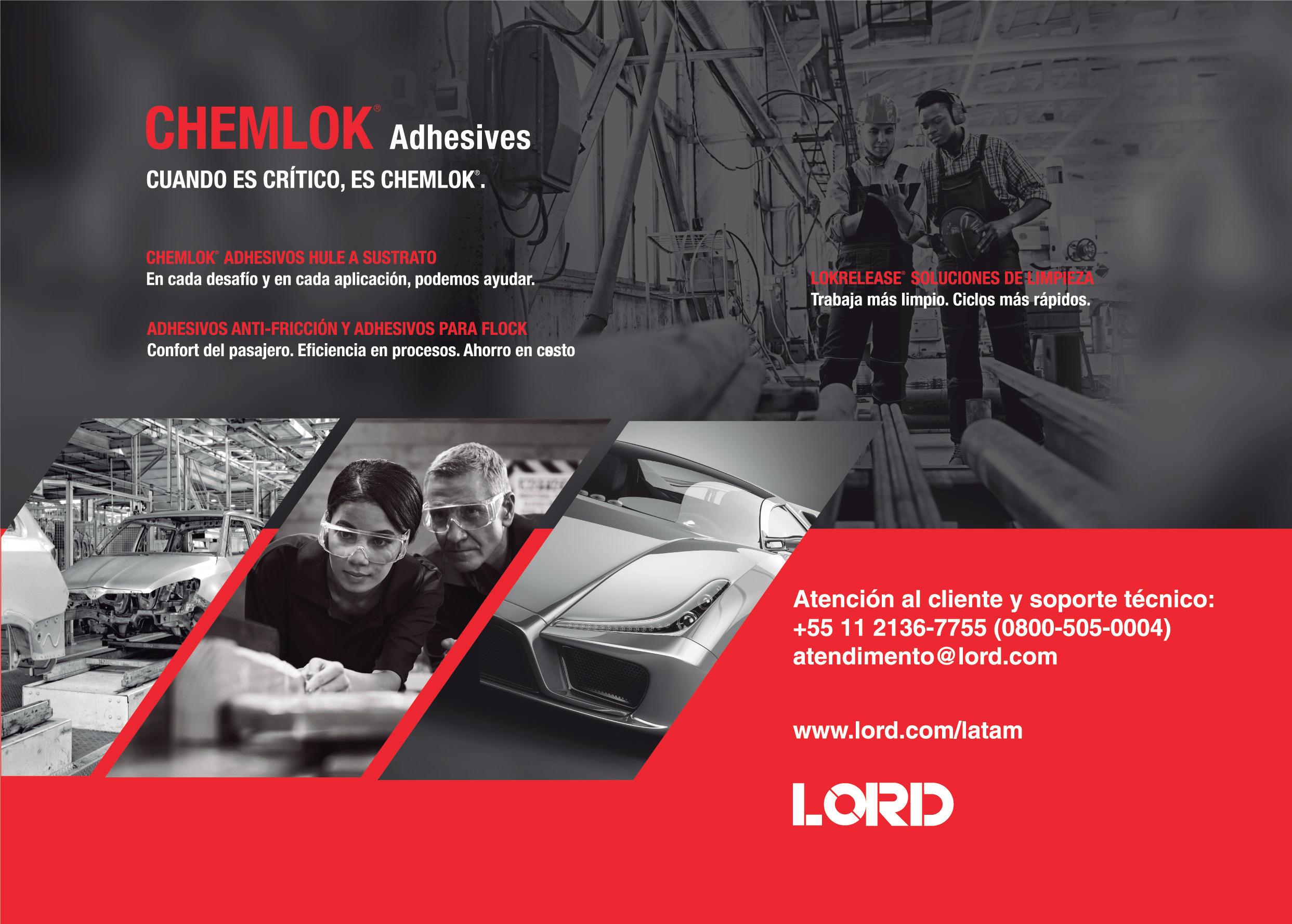
REFERENCIAS
1. GR Hamed, Rubber Chemistry and Technology, 54, 576, (1981). 2. JR Beatty, Rubber Chemistry and Technology, 42, 1040 (1981). 3. TE Banach, Rubber World, 1, 30 (2016). 4. GC Basak, A. Bandyopadhyay y AK Bhowmick, Journal of Materials Science, 47, 3166, (2012). 5. OKF Bussemaker y WVCV Beek, Rubber Chemistry and Technology, 37, 28, (1964).