
9 minute read
Tecnología del latex
COLUMNISTA
Ing. Diego Hernández Mejía (COL) Asesor en Investigación y Desarrollo en la fabricación de artículos en látex y espuma de látex. dhernandez_mejia@hotmail.com
En la presente columna analizaremos posibles fórmulas, procesos de preparación y maquinaria necesaria para la producción de globos, bodies y fajas adelgazantes de látex.
FÓRMULA PARA LA OBTENCIÓN DE GLOBOS. a) 100.0 phr. látex 60 % b) 0.5-0.75 phr. estabilizante solución acuosa 20 %. c) 0.8 phr. dispersión de azufre. 0.25 phr. dispersión óxido de zinc. 0.6 phr. dispersión acelerante. 1.5 phr. colorante o pigmento.
Vulcanización 20-25 minutos en aire caliente a 100ºC. Para globos blancos, en lugar de 1.5 phr. de colorante, se emplea 4.0 phr. de TiO2 y los componentes indicados bajo la letra c).
Preparación de la mezcla. Para lograr la distribución fina de los agentes de vulcanización, necesaria para la obtención de globos, es recomendable elaborar muy bien la dispersión de los ingredientes bajo c).
Proceso. Básicamente, el proceso de moldeo por inmersión es la transferencia de una película de caucho a un molde.
EQUIPOS Horno. Los hornos deben ser fabricados en su interior con un material que conserve eficientemente la temperatura en forma homogénea. Esto se logra con controles para la temperatura, termocuplas tipo J, pirómetros para regular la llama de los quemadores, sopladores o blowers, para la circulación de aire (con el fin de mantenerla homogénea). El rango de temperatura puede estar entre 0 y 220ºC, aunque se trabaja habitualmente con rangos que oscilan entre 100º y 150ºC. Estos hornos son llamados también de convección o aire forzado.
Tanques de inmersión. Estos pueden estar fabricados en porcelana, hierro esmaltado o acero inoxidable. Por lo general, los tanques poseen dispositivos de control de temperatura y mezcladores, que garantizan una temperatura homogénea constante. Moldes. Pueden estar elaborados en aluminio,
acero inoxidable, porcelana, yeso cerámico o fibra de vidrio.
Maquinaria. Operadas manualmente o automáticas de acuerdo al volumen de producción.
COAGULANTES • Solución de nitrato cálcico al 20 % en metanol. • Solución de acético o fórmico al 20 % en metanol.
Cuando sea necesario, puede ser adicionada agua al metanol, especialmente cuando se utiliza ácido acético. Para el ácido fórmico, son mezclados volúmenes iguales de metanol y agua, con el fin de hacer la película de látex más gruesa, aunque esto genera mayor tiempo de coagulación, de modo que es necesario esperar un tiempo mayor entre la inmersión en el coagulante y la inmersión en el látex.
TÉCNICA 1. Los moldes, limpios y precalentados, son sumergidos lentamente en el látex, para prevenir que queden atrapadas burbujas de aire. Luego son retirados lentamente a una velocidad uniforme. Idealmente, los moldes deben ser retirados a una velocidad ligeramente más lenta que aquella a la cual escurre el látex.
2. Inversión de los moldes (esto se realiza después de cada inmersión, para minimizar la formación de gotas de látex en la parte inferior del molde) antes del secado. Esto conlleva tres minutos aproximadamente.
3. Los moldes calientes recubiertos de látex son entonces sumergidos en el coagulante y retirados lentamente.
4. Antes de la segunda inmersión se deja evaporar el solvente del coagulante, manteniéndolo por unos 60 segundos en el látex. Luego, los moldes son retirados lentamente, invertidos y secados por 20 minutos a 60-70ºC.
5. Se repite la inmersión en el coagulante tal como en 3. 6. Se repite la inmersión tal como en 4.
7. Si al producto se le realiza un enrollado en el extremo superior, se debe hacer sobre el látex parcialmente seco, entonces se completa el secado (10 minutos a 60-70ºC).
8. Se sumergen en agua, preferentemente caliente, los artículos en los moldes. Esto facilitará la posterior operación de desmoldeo.
9. Los artículos deben ser lixiviados aproximadamente 20 horas en agua fría, conteniendo 0.2% de tenso-activos, para remover algunas trazas de coagulante, productos químicos auxiliares o enzimas de la superficie. La transparencia y la resistencia al agua son mejoradas mediante este proceso.
10. Luego del paso anterior, los artículos son secados entre 60-70ºC hasta volverse transparentes. Esto puede llevar 24 horas. Es esencial que la temperatura de secado no sobrepase los 80ºC, el intentar acelerar el secado puede originar quemaduras o decoloración.
11. Finalmente, se realiza una inmersión en un baño clorado, de concentración de 168 ppm de cloro de 3 a 4 minutos, se lava con agua y se lleva al horno de secado por 10 minutos. Esto evita que los artículos se peguen entre sí (esto también puede lograrse mediante un baño de emulsión diluida de silicona).
Parámetros del proceso. El espesor de la película de látex formada sobre el molde durante la inmersión puede variar de acuerdo a la temperatura y el tiempo de inmersión.
Inmersión con moldes porosos. Ha tenido también una amplia acogida el empleo de moldes porosos de porcelana sin esmaltar o yeso, cuyo tamaño de poro debe ser menor que el de las partículas de caucho más pequeñas. Estos moldes porosos filtran las partículas de caucho sobre su superficie donde el látex, en virtud de su elevada concentración y bajo la acción simultánea de los iones de calcio Ca++ del yeso,
coagula formando una película. La posibilidad de empleo del material de moldeo es limitada, debido a que, con el suero de látex, los componentes de albúmina penetran los poros y los cierran poco a poco. Después de haberse empleado 20 ó 30 veces, los moldes no se pueden volver a usar. El espesor de la película que se logra en un solo proceso de inmersión depende de la porosidad del material de moldeo, del tiempo de inmersión, de la diferencia de presión, que existe entre el látex y el interior del molde, de la temperatura y del pH de la mezcla.
FÓRMULA PARA GLOBOS CON BASE EN UNA MEZCLA TERMOSENSIBLE a) 23.0 phr. látex 73 % 10.0 phr. aceite mineral. 1.0 phr. antioxidante. b) 143.0 phr. látex 60 %. c) 84.0 phr. agua. 3.0 phr. solución acuosa de caseína 10 %. d) 0.8 phr. dispersión de azufre. 0.25 phr. dispersión de óxido de zinc. 0.8 phr. dispersión acelerante. 1.5 phr. colorante o pigmento. e) 0.4 phr. acelerante soluble, disuelto en 3.5 phr en agua. f) 10- 15 phr. poliéter-politioéter solución acuosa (coagulante o gelificante). 20.0 phr. éter-polivinil-éter solución acuosa (coagulante o gelificante). 7.0 phr. formaldehído.
Las dispersiones del numeral d) se pueden elaborar en una sola dispersión, llamada dispersión vulcanizante (DV).
PROCEDIMIENTO DE TERMOSENSIBILIZACIÓN. Adicionando ciertas sustancias puede lograrse que las mezclas de látex se hagan termosensibles, es decir, que coagulen espontáneamente a determinada temperatura. En el procedimiento Kaysam se agregan al látex electrolitos, de acción coagulante débil, como soluciones de sales de amonio y fluosilicato de sodio o amonio, en combinación con grandes cantidades de óxido o carbonato de zinc. Estas mezclas son estables por varias horas sin fenómenos de coagulación, pero lo hacen espontáneamente cuando se calientan a 50 o 60ºC. Siguiendo un nuevo proceso, se agrega a la mezcla poliéter-politioéter o éter-polivinil-metílico, como agente termosensibilizante. Ambos productos se disuelven en agua fría, aunque al alcanzar el punto de enturbiamiento se vuelven insolubles arrastrando las partículas de látex como coagulado irreversible.
El coagulante poliéter-politioéter se emplea de preferencia en países tropicales o bien durante la estación calurosa del año y también cuando se desee obtener, artículos de inmersión con películas finas. Se deja secar la película durante 40 minutos con aire caliente y se vulcaniza unos 30 minutos a 100ºC.
Las mezclas termosensibilizadas con poliéterpolitioéter si se almacenan a 30-35ºC son sumamente estables y se conservan durante mucho tiempo. El punto de coagulación prácticamente no varía durante su almacenamiento. En la mezcla de látex termo sensibilizada se inmergen los moldes precalentados a 70-80ºC. El espesor de las películas que se obtienen depende sobre todo del tiempo de inmersión. Las propiedades que posee el látex, lo tornan extremadamente versátil para el proceso de moldeo por inmersión. La habilidad de las partículas de caucho de coagular y formar una película coherente de polímero, que es impermeable al agua y al aire, hace que el látex sea adecuado para fabricar una gran gama de productos.
Los artículos de látex presentan una mayor resistencia al envejecimiento, resistencia y tolerancias a los solventes, que aquellos fabricados directamente con caucho seco. Hay dos maneras de producir películas de látex,
una es curando el látex en estado líquido (llamada pre-vulcanizado) y la otra, adicionando los ingredientes a la mezcla de látex, para su posterior vulcanización.
FÓRMULA PARA LÁMINAS DE PARA LA ELABORACIÓN DE BODIES Y FAJAS ADELGAZANTES CON BASE EN UNA MEZCLA TERMOSENSIBLE
a) 100 phr. látex 60%. b) 3.0 phr. estabilizante. c) 2.5 phr. dispersión vulcanizante (DV). d) 50 phr. carga. e) 3.0 phr. coagulante. f) 0.4 phr. preservante.
Preparación de la mezcla. Según el orden indicado, se agregan al látex los componentes bajo las letras b), c), d), e) y f), se mezclan a baja velocidad, por un tiempo aproximado de 4 a 6 horas (dependiendo de la cantidad elaborada del compuesto) y se deja en reposo para su maduración, por un tiempo mínimo de 24 horas. Luego, hay que dejar que las burbujas de aire introducidas en el proceso de preparación vayan a la superficie y eliminar así la mayor cantidad, de tal forma que no se presenten irregularidades en la obtención de las láminas.
Asimismo, para evitar que se vuelva cremosa o que se formen pieles, la mezcla puede ser agitada suavemente durante el tiempo de maduración. El compuesto es tamizado a través de una malla de nylon (media de nylon) y el resultante es vaciado, evitando la presencia de aire dentro del o de los tanques de inmersión. Los moldes se precalientan a una temperatura entre 75 y 77°C, mientras que el tiempo de inmersión determina el espesor de la capa. OBTENCIÓN DE ESPUMA DE LÁTEX. El caucho esponjoso y el celular se obtienen a partir de caucho sólido. Mientras que el caucho esponjoso posee grandes poros abiertos, el caucho celular posee poros pequeños y cerrados.
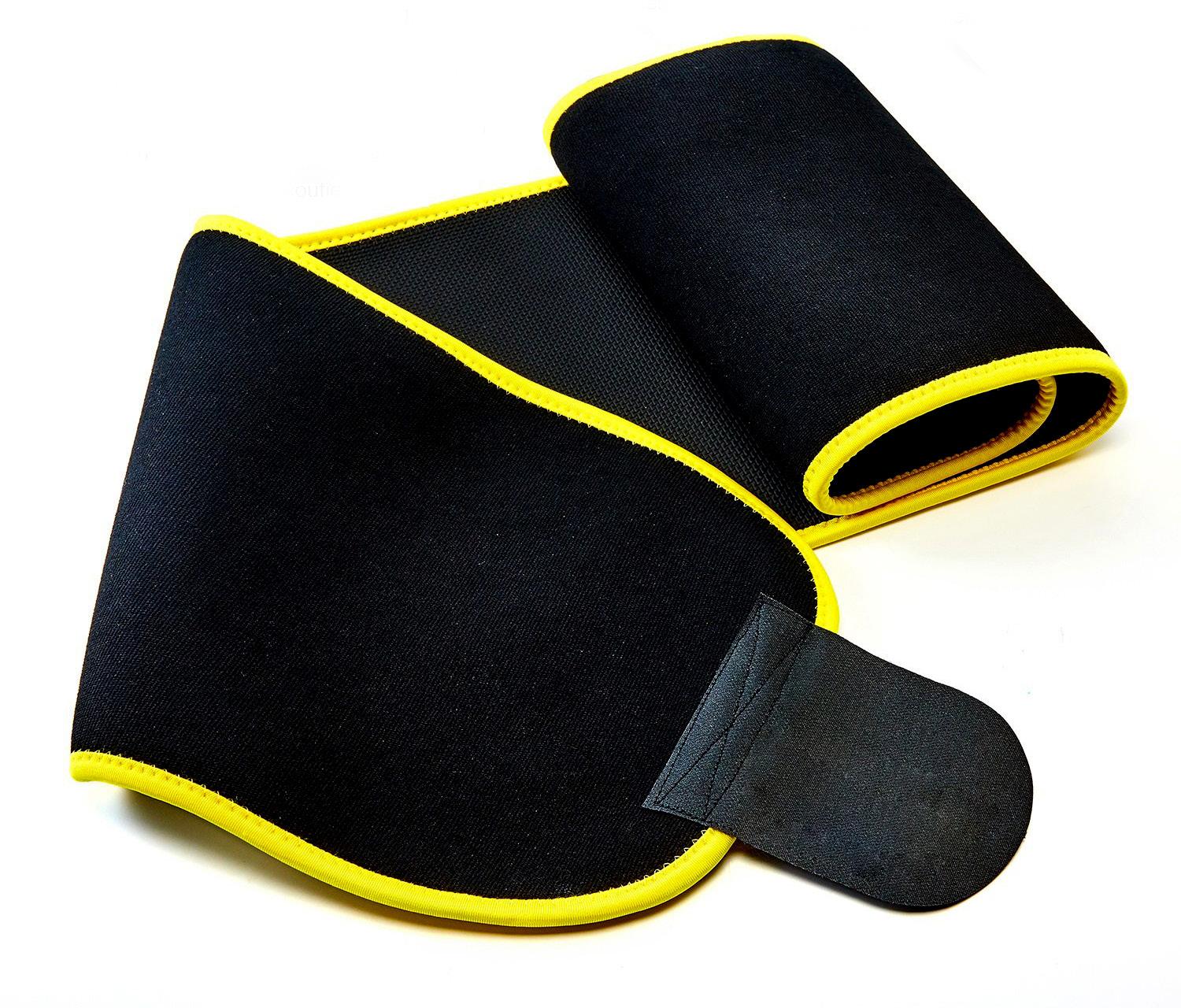
El caucho espumoso se obtiene del látex y posee poros abiertos. La mayor parte del látex empleado en el mundo sirve para obtener espuma de látex. El procedimiento más extendido hoy en día es el llamado de batido de espuma, en el cual una mezcla de látex conteniendo jabones y agentes vulcanizantes se bate hasta obtener una espuma estable, de un volumen 7 a 14 veces mayor al volumen inicial. En la gelificación con fluosilicato de sodio (proceso Dunlop), la espuma permanece durante largo tiempo, capaz de ser colada, para gelificar y coagular luego muy rápidamente. Trabajando con cloruro de amonio como sensibilizante, la gelificación es más rápida. Además del procedimiento con fluosilicato de sodio y cloruro de amonio, se va imponiendo también el llamado proceso Talalay. En este, la espuma de látex ya dentro del molde especial, que posee cierre hermético a fin de permitir que con la ayuda de una bomba de vacío sea sacado el aire, es de anotar, que dadas las características especiales del molde y del proceso, posee en su interior cámaras para el paso de gases (anhídrido carbónico) y de líquidos, tales como una mezcla de agua con etilenglicol, lo que permite obtener temperaturas bajas (-15 a -25ºC), sin que el agua se congele o altas ( 100 – 150ºC), sin que se evapore, en la vulcanización, con el proceso Talalay, se obtienen espumas que poseen, una estructura de poros finos y uniformes. ■