
11 minute read
Sección especial
Avances en el análisis de la dispersión de cargas de refuerzo en compuestos de caucho - Segunda parte
COLUMNISTA
Ing. Carlos Leszman (ARG) Ingeniero químico - Industria del neumático.
cleszman@yahoo.com.ar
Tal como comentamos en la primera parte de este trabajo, existen técnicas que analizan la dispersión en el nivel del agregado sin la necesidad de una observación directa. Es decir, son técnicas muy simples pero que están fuertemente influenciadas por la experiencia y el criterio del operador.
TÉCNICAS DE MEDICIÓN DE DISPERSIÓN Método óptico: baja magnificación
Estos tipos de mediciones de dispersión se basan en una comparación entre las imágenes observadas en el microscopio estereoscópico con un aumento de 30 X con las fotografías estándar presentadas en la figura 1. A veces, esta técnica se conoce como dispersión de Phillips.
El bajo aumento utilizado en estas mediciones ópticas limita la resolución a objetos relativamente grandes con las dimensiones en un rango entre 10 µm y milímetros. Además, en este trabajo, se
desarrollaron numerosos métodos automatizados basados en imágenes ópticas de bajo aumento de
la superficie del caucho. Todos ellos, sin embargo, también midieron la dispersión en el nivel de fragmentos de pellets sin dispersar en lugar del de agregado / aglomerado.
Microscopía óptica por transmisión
La microscopía óptica generalmente se realiza con un aumento de entre 500 X y 750 X. No obstante, este grado de magnificación no proporciona información a nivel de agregado, sino sobre fragmentos de pellets no dispersados y/o cualquier otro tipo de materiales no dispersos.
Pese a ello, se trata de una técnica muy interesante que describiremos con más detalle a continuación. Al respecto, cabe decir que la
preparación de la muestra de caucho requiere cortes delgados de aproximadamente 1 µm de
grosor utilizando un microtomo criogénico. Por lo general, se preparan aproximadamente 10 muestras para cada compuesto.
En este proceso, una cámara digital suele grabar imágenes que luego son procesadas por un software de análisis de imágenes. El número de fragmentos de pellets no dispersados, su área
10 9 8 7 6
5 4 3 2 1
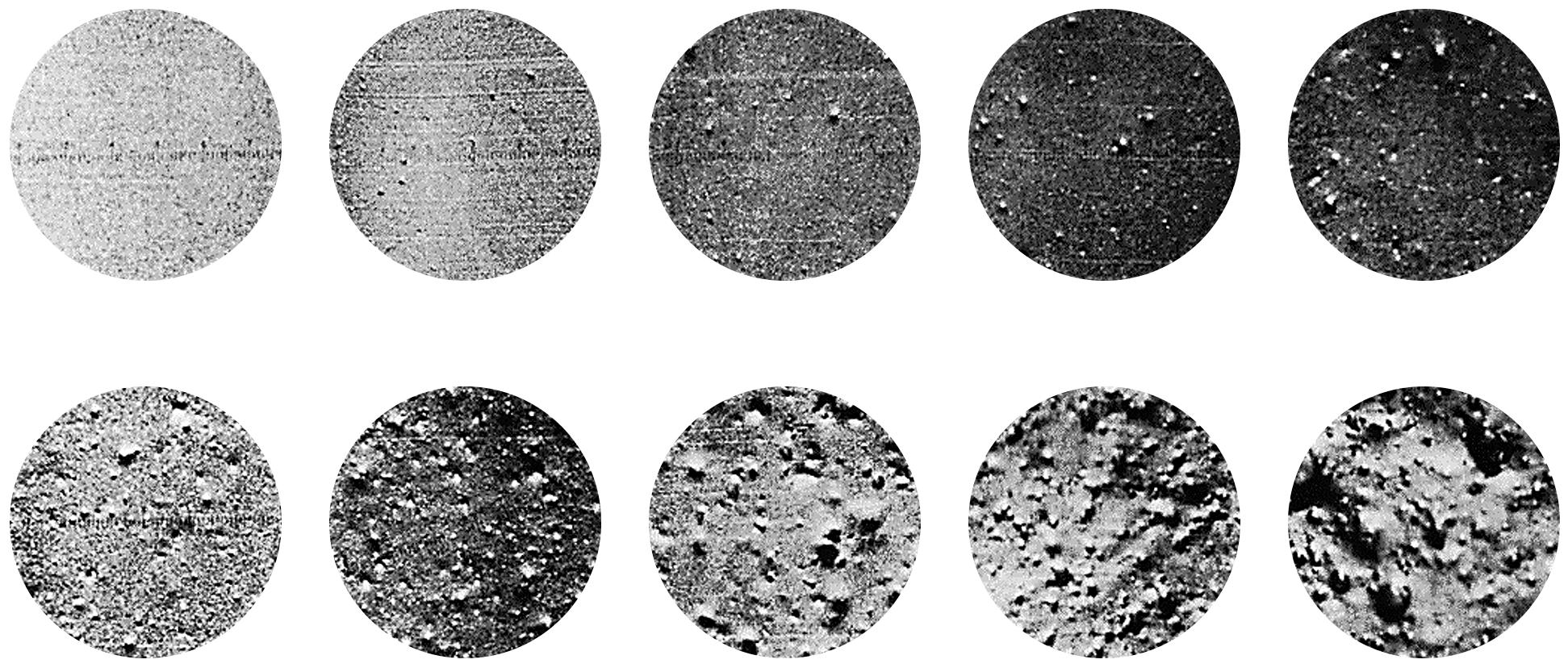
Figura 1. Fotografías de referencia con análisis de dispersión Phillips. Como se puede ver, las fuerzas de cizallamiento mecánico desgarran los fragmentos de los pellets.
Figura 2. Imágenes típicas obtenidas por la técnica de microscopía óptica con un aumento de 750 X, que representan tiempos de mezclados cortos. En A, después de 60 segundos de tiempo de mezclado y en B después de 120 segundos.
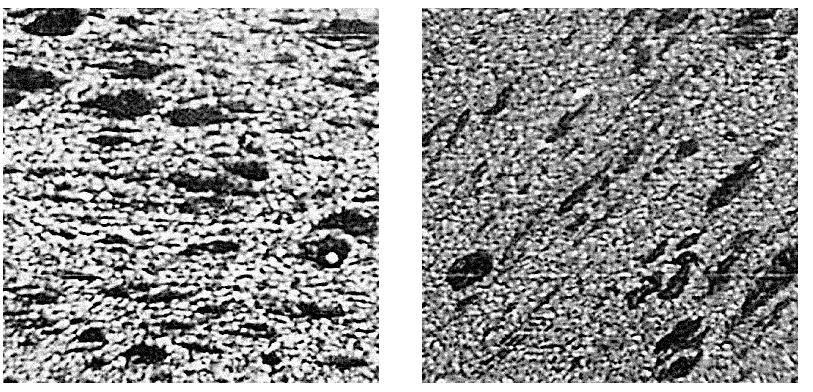
superficial y su perímetro se calculan después de la binarización de la imagen digital y luego se comparan con otras características del compuesto, como el tiempo de mezclado o la energía total aportada durante el proceso de mezclado (esto último es mucho más preciso). Las imágenes típicas de microscopía óptica se presentan en la figura 2, en la cual se observan áreas oscuras alargadas que indican que los fragmentos de pellets están experimentando un proceso de incorporación / dispersión.
Imágenes similares muestran que el proceso de dispersión se puede observar a una escala mucho más pequeña usando las técnicas de microscopía electrónica de barrido (SEM) descriptas más
A. B.
adelante. Los datos típicos obtenidos por el método de microscopía óptica usando el software de análisis de imágenes se representan en el gráfico 1 como un número de fragmentos de pellets sin dispersar. Otros datos interesantes se presentan en la misma figura, donde el
experimento se realizó en función de la carga de
negro de humo y del tiempo de mezclado.
Es interesante observar que el área total de
fragmentos de pellets no dispersos disminuye con
el aumento del tiempo de mezclado. Sin embargo, la efectividad de la fuerza de corte responsable de la dispersión del negro de humo depende del nivel de carga empleada en la formulación. En este ejemplo particular, durante un tiempo de mezclado, el área de fragmentos de pellets no dispersos aumenta hasta aproximadamente 20-30 phr.
Después de este punto, incluso cuando la carga del negro de humo aumenta, el área de fragmentos de pellets no dispersos, disminuye. Además, las fuerzas de corte son más efectivas cuando los agregados de negro de humo tienen contacto entre sí. Este fenómeno está asociado con el umbral de percolación (se denomina así a la región que representa la transición entre la fase aislante y la conductora).
A. B.
Gráfico 1. En A, área de fragmentos de pellets no dispersos calculados en función del tiempo de mezclado obtenido, por la técnica de microscopía óptica. En B, área de fragmentos de pellets no dispersos en función de la carga de negro de humo obtenida para diferentes tiempos de mezclado utilizando el método de microscopía óptica.
Medidas eléctricas: resistividad de volumen
La resistividad eléctrica de los compuestos de caucho cargados con negro de humo ha sido un tema de considerable interés. La idea detrás de estas mediciones se basa en el hecho de que, desde un punto de vista simplificado, los compuestos de caucho son una mezcla de dos materiales: el polímero resistivo (con una
resistividad de aproximadamente 1014 Ωcm) con el negro de humo conductor (con una resistividad
de aproximadamente 10-2 Ωcm). Vale decir, en este sentido, que todos los negros de humo de horno poseen una resistividad de volumen intrínseca similar.
Múltiples experimentos muestran que, bajo compresión, la resistividad de la banda de rodadura, la carcasa y los llamados grados conductivos, se acercan a la misma meseta a cerca de 10-2 Ωcm. La resistividad del compuesto de caucho se rige por la forma en que el negro de humo se distribuye / dispersa en las matrices poliméricas.
Por debajo del punto de percolación, cuando los agregados / aglomerados o fragmentos de pellets se separan entre sí, la resistividad del compuesto es muy alta y la técnica de resistividad de volumen no siempre proporcionará información de dispersión significativa. Al aumentar la carga de negro de humo, se logra el punto de percolación y se crean los caminos continuos de los agregados / aglomerados o fragmentos de pellets conectados.
En este punto, el compuesto de caucho se vuelve
muy sensible a las mediciones de resistividad
de volumen. Por ello, pequeños cambios en la dispersión conducen a cambios significativos en la lectura de la resistividad. La dispersión mejorada conduce a una mayor separación de los agregados de carbono, eliminando algunas conexiones directas entre ellos y colocando a las cadenas del polímero entre los agregados previamente conectados.
Ω-1.m-1
Gráfico 3.
Gráfico 2. Cinética de dispersión medida por la técnica de resistividad de volumen obtenida para Sn-SSBR y SSBR OS cargados con 30 phr de N330 (HAF) (cerca del punto de percolación).
Debe mencionarse en este punto que el contacto directo entre los agregados de negro de humo no es absolutamente necesario para lograr el camino conductor. Cuando los agregados están muy cerca entre sí (medidos en Angstroms), se produce el efecto túnel. Sin entrar en detalles, el efecto túnel dependerá del potencial eléctrico aplicado a la
muestra y, por supuesto, de las distancias entre los
agregados del negro de humo.
Cuando la carga de negro de humo aumenta aún más y alcanza el nivel que normalmente se encuentra en compuestos de neumáticos u otros productos de caucho terminados, la técnica
de resistividad se vuelve menos sensible a la
dispersión. Las mediciones de dispersión basadas en resistividad de volumen deben aplicarse sólo cuando se comparan muestras de exactamente la misma composición, incluido el mismo tipo o grado de negro de humo. Cuando se aplica correctamente, la resistividad de volumen es una técnica muy poderosa que puede proporcionar información no sólo sobre la dispersión sino también sobre la cinética de la dispersión, como se demuestra en los gráficos 3 y 4.
Gráfico 4.
Una de las grandes ventajas de las mediciones de dispersión basadas en resistividad de volumen es que pueden sondear la dispersión en el nivel
del agregado y, dependiendo de la aplicación específica, podrían ser extremadamente sensibles. Una de las mayores desventajas es que estas mediciones son aplicables sólo a compuestos cargados con negro de humo analizándose solamente la dispersión de esta carga. La
dispersión de ingredientes no conductores se analiza de forma exclusiva e indirecta por esta técnica. En consecuencia, interpretar los resultados de sistemas compuestos tan complicados puede ser problemático.
Resistividad volumétrica: este ensayo consiste en colocar una lámina delgada del elastómero entre dos electrodos especificados aplicando una diferencia de potencial directa de 100 V o de 500 V durante un minuto. En casos especiales se utilizan tiempos más largos y diferencias de potencial más altos. La unidad de la resistividad volumétrica es Ohm-cm.
Resistividad superficial: el aparato para medir la resistividad superficial es parecido al de la resistividad volumétrica pero las conexiones de los electrodos son diferentes. Como en la volumétrica, se aplica una diferencia de potencial de 100 V o de 500 V durante un minuto, al cabo del cual se toma la lectura de la resistividad superficial. La unidad de la resistividad superficial es Ohm/sq. ■
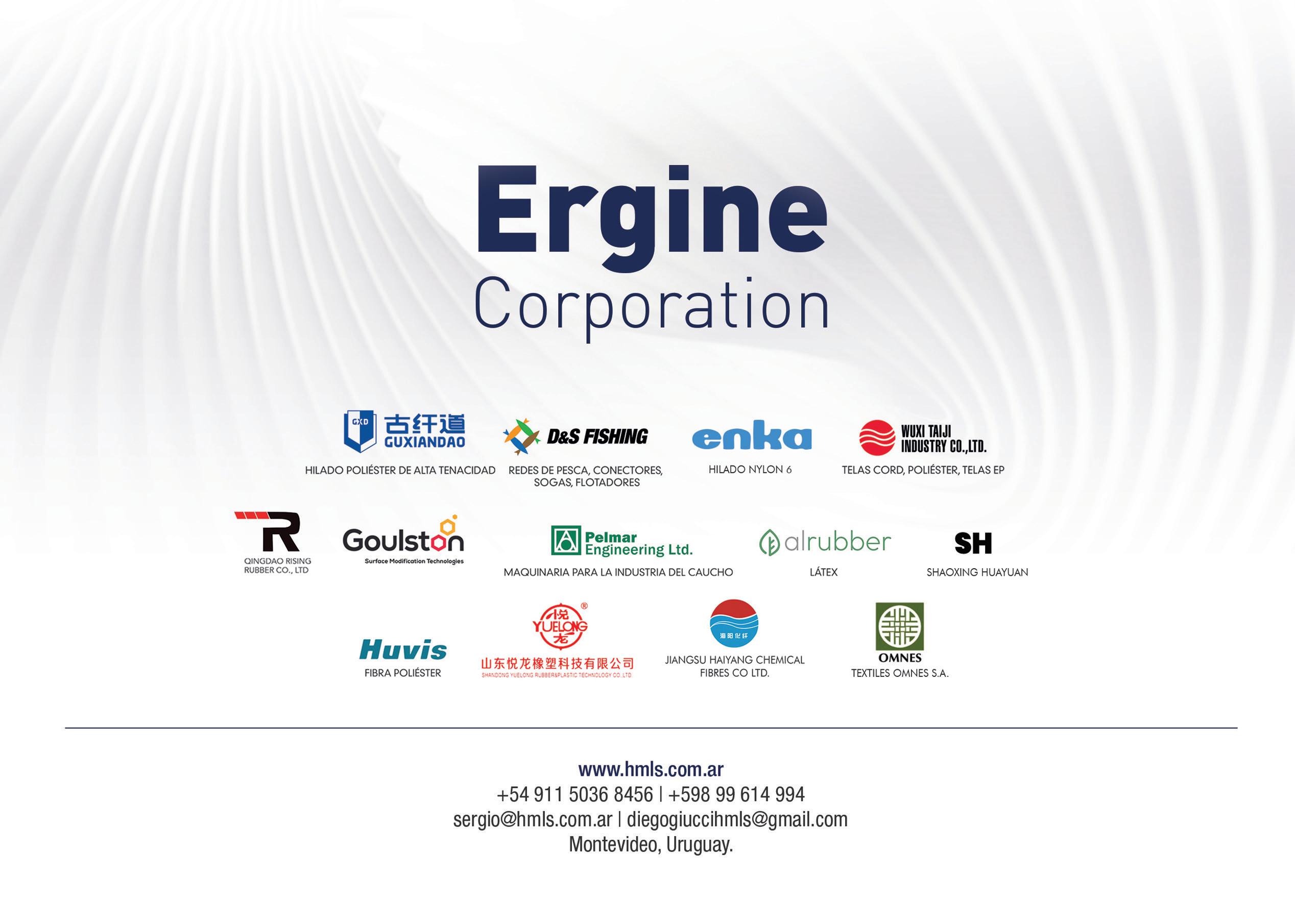
Acuerdo con Revista Caucho del Consorcio Nacional de Industriales del Caucho (España) para el intercambio de artículos de interés entre ambas publicaciones | www.consorciocaucho.es
Calcular el moldeo por compresión por primera vez: simulación del proceso más antiguo con un software de última generación
En la feria Fakuma 2021, SIGMA Engineering presentó la última versión de SIGMASOFT® Virtual Molding, la cual, además de una predicción mejorada del alabeo, incluyendo numerosas innovaciones para el cálculo de piezas formadas por varios componentes, constituye la posibilidad de analizar los procesos de moldeo por compresión.

CALCULAR EL MOLDEO POR COMPRESIÓN POR PRIMERA VEZ
En la Fakuma, celebrado entre el 12 y 16 de octubre de 2021, en Friedrichshafen (Alemania), SIGMA Engineering GmbH presentó los nuevos desarrollos de SIGMASOFT® que, en la nueva versión 5.3.1, permite por primera vez simular el moldeo por compresión tradicional del caucho.
Hasta ahora, el diseño de moldes y el proceso de simulación se limitaba esencialmente a la tecnología moderna del moldeo por inyección. Dado que SIGMASOFT® ya es utilizado con mucho éxito por los principales procesadores de elastómeros, el mercado desea también analizar los procesos más antiguos, ya que son y seguirán siendo necesarios técnica y/o económicamente para la producción de piezas de precisión y juntas tóricas, a veces en lotes pequeños.
De este modo, la simulación permite determinar de forma fiable el grado de reticulación y los datos del ciclo. Asimismo, se pueden investigar, por ejemplo, las cuestiones relativas al número, la forma, el peso y la posición de las piezas utilizadas en bruto. Por lo tanto, se puede optimizar la
calidad de las piezas moldeadas y reducir el uso de materiales sin necesidad de realizar largas y
costosas series de pruebas.
"Parece sencillo, pero la puesta en práctica fue bastante compleja", explicó Timo Gebauer, CTO de SIGMA. "El reto consiste en que el molde, es decir, el espacio en el que se moldea, cambia continuamente cuando se cierran las placas y en el proceso las piezas en bruto insertadas ya se calientan, se plastifican y se deforman. Sin el asesoramiento y la validación de nuestros clientes, este nuevo desarrollo no habría sido posible", añadió.
Sin embargo, a diferencia de los termoplásticos, existen pocos materiales estandarizados en la industria de los elastómeros. Por lo tanto,
SIGMASOFT® permite la creación de sus propios

materiales basados en mediciones internas o
externas y apoya a sus clientes en el proceso de creación.
"Interesante es que con este enfoque apenas haya diferencias entre el moldeo por transferencia y el moldeo por compresión en términos de
simulación. Técnicamente, el bebedero pasa a formar parte de la cavidad a través de la placa intermedia. Por lo tanto, las herramientas de moldeo por transferencia también se calcularon con éxito en la validación", comentó Gebauer.
Cabe decir que SIGMASOFT® v5.3.1 no sólo incluye la capacidad de simular el moldeo por compresión para elastómeros por primera vez, sino que también ofrece numerosas innovaciones y mejoras
en el área de los termoplásticos, en particular para
la predicción precisa de la contracción y el alabeo. La optimización autonómica que puede llevar a cabo el software también puede procesar piezas de dos componentes y se ha ampliado la base de datos de materiales.
SOBRE SIGMA
Desde hace 23 años, SIGMA Engineering GmbH impulsa el avance de los procesos de moldeo por inyección con su producto de simulación SIGMASOFT® Virtual Molding. Esta máquina virtual
de moldeo por inyección, permite la optimización y el desarrollo de piezas plásticas y moldes, así
como la ilustración de toda la gestión del proceso. La tecnología SIGMASOFT® Virtual Molding combina la geometría 3D de las piezas, el molde y el sistema de atemperamiento, integrando además parámetros y condiciones de producción reales. Con esta solución integral no solo se logra eficacia
en costos y manejo de recursos en la producción, sino también calidad del producto desde la primera inyección.
SIGMASOFT® Virtual Molding integra gran variedad de modelos específicos de proceso en
la tecnología de simulación 3D, la cual durante décadas se ha desarrollado y validado, siguiendo hasta hoy, un proceso continuo de investigación y optimización. La solución de SIGMA y el equipo de desarrollo apoyan los objetivos técnicos del cliente con soluciones personalizadas. La firma de software SIGMA brinda de manera directa el soporte comercial y técnico, formación, instalación y un servicio de solución a través de la ingeniería a nivel mundial.
SIGMA Engineering GmbH, fundada en 1998 en Aachen (Alemania) está representada en toda Europa bajo el liderazgo de su CEO Thomas Klein. Con sucursales de empresas hermanas en Chicago, Brasil, Singapur, China, India, Corea y Turquía, SIGMA tiene la capacidad de atender usuarios del Virtual Molding de gran variedad de empresas internacionales e institutos de investigación de todo el mundo. ■
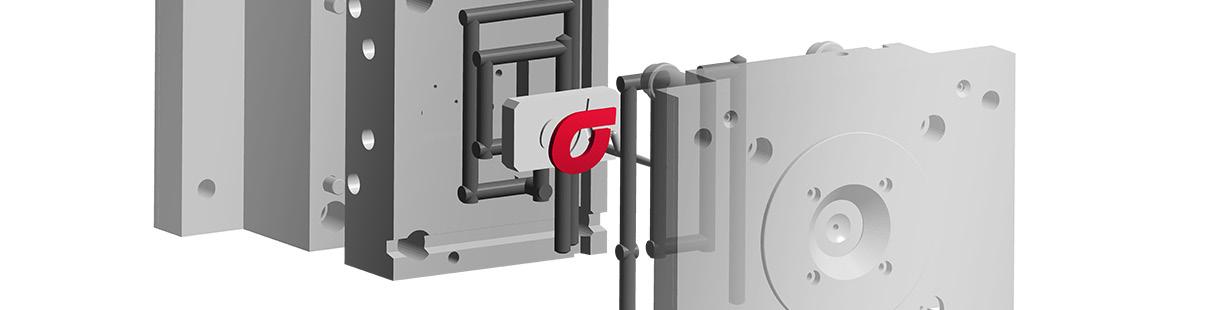
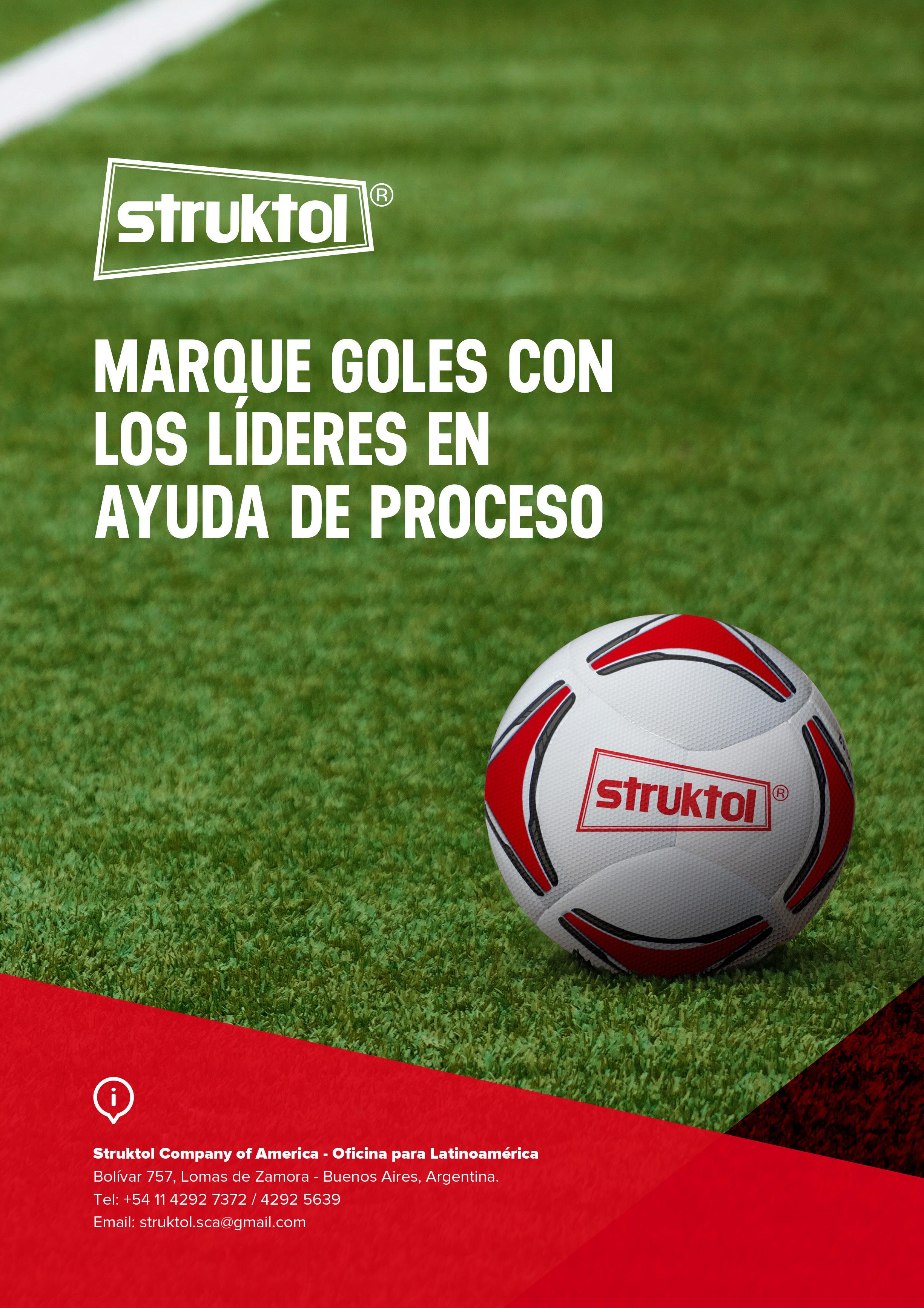