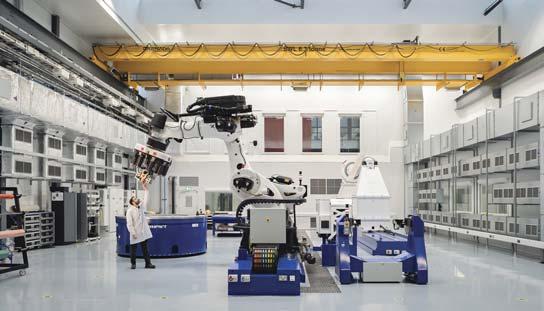
14 minute read
New markets for
New markets for composites
A new state-of-the art automated fibre placement and tape layup cell (AFP-ATL) could pave the way to expanding the use of composites in renewable energy, construction and transport.
The innovations provided by AFP and ATL have transformed the aerospace industry allowing fuselage sections and wing spars to be manufactured at an industrial scale, not previously possible using traditional composite manufacturing methods. Currently though, these breakthroughs have almost exclusively benefitted the traditional composites manufacturing industries mentioned. Through collaboration, the NCC believe that AFP-ATL has the ability to reduce the barrier to entry to these game changing technologies and expand the composite market into other areas such as renewable energy, oil & gas, construction and rail.
The cell, created in partnership with Electroimpact (Flintshire, UK) is a uniquely designed capability that combines both AFP and ATL in a single system. The dual system can be used individually or together to collaborate and create large, complex structures with minimal downtime. The robot is intended for medium to large scale manufacturing with high performance and accuracy robotic motion platform.
The new cell is the exciting final piece in an impressive £36.7m jigsaw of ten new fully digital automated composite manufacturing capabilities that have been installed in the past 18 months.
The Automated Fibre Placement (AFP) process head utilises x 8 tows, each measuring 12.7mm wide, with either an infrared heater to manufacture thermoset composites, or the novel humm3® flash technology which has been developed by Heraeus Noblelight Ltd and tested at the NCC for to manufacture thermosets of low temperatures (30-60 degrees) and high temperature thermoplastics or bindered dry fibre (100-300 degrees).
The Automated Tape Layup (ATL) head can deposit tapes of 75, 200 or 300mm widths using the same heating systems and material processing capability as AFP.
Vertical and horizontal rotators allow for complex tools to be used to create geometries such as convex and concave panels, large scale diameter pipes, spars or barrel/tower structures. The rotators enable components of up to 4.6m diameter, and 7m in length to be manufactured. The cell's flat tables also allow for smaller scale analyses such as material testing or prototype trials to de-risk programs and build knowledge prior to larger scale projects.
Eva Sastres Collardo from the NCC said “The NCC's AFP-ATL capability is a perfect test bed for automated composite manufacturing at a medium to large scale level. The system will enable new and existing markets to build up their innovation platforms from the ground up, from small scale prototyping and material testing through to full scale demonstrators and data analytics. The output for customers will be the enabling of high-performance products, created at high volume with reduced cost and waste to achieve step change technology in their field.” 8 nccuk.com
A suite of on-line training courses in diecasting technology is now available from the Cast Metals Federation, CMF, and supported by the Diecasting Society and the Institute of Cast Metals Engineers.
The new programme, which has been complied by industry experts and offered on a blended learning basis, will provide participants with a range of courses covering the fundamentals of the process as well as more in depth and detailed topics such as die and process design, die casting defects and how to avoid them, setting process parameters for optimum quality and die layout.
“The flexibility of this programme will be attractive to companies and individuals since the subjects can be accessed at any time,” explained Pam Murrell, CMF CEO. “This is not a new programme, as the compilers of the teaching and learning materials, the Die Cast Training Network, set up the programme some time ago. But what we are now able to offer to the sector is the support of the Federation, with group workshops to bring the programme to life, as well as direct access to a tutor who has relevant experience from the industry.
Learning in isolation is not easy, so we recognise that these additional support mechanisms will be very important to ensure that learners are able to stay engaged.”
The programme includes courses that will be suitable for production engineers, technicians and designers as well as machine operators and whilst the focus is around high pressure diecasting, there are courses that will be equally relevant to gravity and low pressure companies.
CMF Chairman, Stuart Gregory, agreed saying, “I am sure that this programme will prove popular. We have all got much more used to working ‘on-line’ in the recent months so the timing is good. We are only too aware of the shortage of diecasting specific training opportunities for those joining the industry as well as those seeking to upskill and progress their careers. To remain competitive, we need to be able to teach the future generations to problem solve and for this they need underpinning knowledge of the process in addition to instruction about how to use their particular machines. We look forward to supporting the Federation and the wider diecasting sector with this new programme.”
For more information about the programme, please contact the Cast Metals Federation on tel: +44 (0)121 809 3500, email: admin@cmfed.co.uk
Developed by industry experts, the programme includes access to on-line teaching and as well as tutor support, mentoring and workshops all aimed at supporting the learner and enhancing the learning experience.
formae inFor mor ol tionabouthowtoennr and pricing options please contact: act:options please cont
: 0121 809 3500 email: ad .ukmin@cmfed.co
Future-proofed with automation
In the past two years the Bowmill Group has invested in three 5-axis machining centres and moved to automated lights-out operation.
Supplying predominantly to the aerospace industry, the Bowmill Group encompasses both volume and complex manufacturing disciplines; assembly and test, grinding and material surface processing. It employs 180 staff in four UK facilities.
In 2019, after securing a prime contract that required a high accuracy machine that also offered flexibility Bowmill decided to invest in a Matsuura a MX-330 PC10 for its main site in Poole, Dorset. This offered full 5-axis capability and probing, which was critical for the required positional tolerances (3 – 4 microns). The machine also had the benefit of 10 pallets so Bowmill could run several component variations through the same machine utilising unmanned/lights out operations, which provided a measurable competitive advantage from conventional methods and standard single table machines.
After six months of running the machine and improving cycletimes and implementing flexible manufacturing sequencing on not only the new components but also existing components, Bowmill decided to purchase a second Matsuura MX-330 PC10 for its site in Tewkesbury, Gloucestershire in March 2020.
The MX-330 PC10 is configured with 10 pallets and 90 tools, offering Bowmill assured and reliably unmanned 5 axis production, a route to growth and returning real value to customers with efficiencies and productivity gained from this investment.
Some months later, the company needed a larger 5-axis machine (500mm cube) for its Tewkesbury Facility and again looked to Matsuura to invest. Following the success of the first two MX-330 PC10, it decided to purchase a Matsuura MX-520. 8 matsuura.co.uk
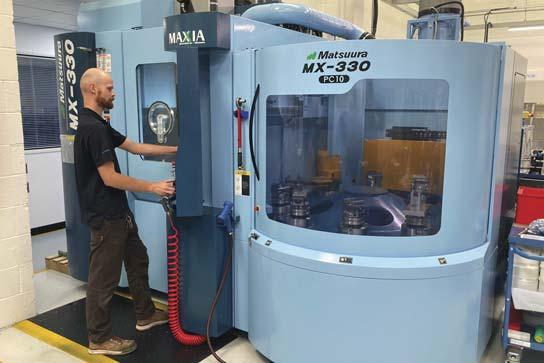
– – – s – – sarB leetSssel ni a t S alPmuinimuAl s yol l A repuS scits n Subcontract mill turned parts up to 65mm in diameter from bar and 300mm billet work. billet bar and 300mm and 30 billet work meter diameted300mm mill turnedto65mm inu up to 65 eterfrom mill turned parts to65 m bcontSubcodparts k.
Euro cylinder locks are some of the most commonly used on the market today and remain in huge demand across the residential security sector. In recent years, APT Leicester has worked to refine and improve a new process to manufacture Euro locks with outstanding efficiency and precision.
Until now, the usual way to make Euro locks has always started from an extruded lock shape in brass. It’s an ideal material for making intricate turned parts due to its versatility and ease of machining.
However, the process is very labour intensive since extrusions need to be pre-cut to the length of a lock before machining on a 5-axis CNC centre. These unmachined brass lock bodies are placed in a jig by hand but there’s some room for error since they might not be positioned correctly, resulting in small inconsistencies in the finished parts.
All in all, manufacturing antisnap Euro locks on a machining centre is a complicated process and one that APT Leicester felt could be drastically improved. They began to draw on their decades of knowledge and experience to come up with a new and innovative solution.
Since investing in two new lathes, APT has come up with a novel way of machining locks, developing a new technique on a Doosan fixed head lathe.
The lathe works like a CNC machining centre but it has the added ability of rotation and more importantly, can feed an extruded
Transforming lock manufacture

bar automatically rather than needing labour-intensive lock body blanks to be cut first.
The 7-axis state-of-the-art lathe is also able to work on many lock variants, such as key shapes or body lengths, at the touch of a button. With this capability to run different macroprograms, there’s no time lost in setting the machine up to run all the variations needed.
For APT, the result has been a manufacturing process that’s incredibly accurate, flexible and efficient; a fully automated system with the capacity to turn out extremely complex, intricate parts with ultimate precision, faster than ever before.
APT has since applied this knowledge not only to machine Euro lock bodies but other parts including different pins, outer shells, plugs and housings.
From design to precision machining, assembly and delivery, APT says it can take care of the entire process, looking after their customers and providing the kind of quality and reliable turned parts that is making it into a leader in lock manufacture. 8 aptleicester.co.uk
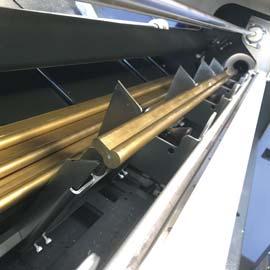
Something to shout about
Setting itself up to be in prime position for the expected manufacturing upturn, Skelmersdale subcontractor Kirkham Engineering has invested in three new multi-axis turning/milling machines in the past 12 months.
The new machines include two Citizen sliding head turning centres – an L32-X 8-axis machine and an L20-VIII machine upgraded to 25mm. Both are fitted with Citizen’s LFV (Low Frequency Vibration) system to improve cutting performance and swarf control on difficult materials.
The third machine is a fixed head Nakamura AS200L MYSF twin-spindle single turret turning centre. This joins a similar AS200 that was purchased new in 2017.
Founded in 1955, Kirkham Engineering established its reputation as a specialist in the production of repetition turned parts on CNC fixed head and sliding head machines. With a focus on the oil and gas industries and petrochemical sectors it produces everything from simple to complex parts in material types from ferrous and non-ferrous metals through to exotic nickel alloys such as Duplex, Monel, Inconel, Hastelloy, Titanium and Stellite.
As well as investing in new machines, Kirkham has built up a fleet of high-quality, high technology used machines including 5 Nakamura WT250 twin-turret, twin-spindle machines, 7 Citizen sliding head machines, 6 Miyano turning centres, including twin-turret, subspindle machines, and two Traub TNC 42 DGY machines that came direct from Rolex in Switzerland.
Director Barry Lynam says that the company has invested over £1.8m in its turning capacity since 2012.
The two Citizen machines had been due to be demonstrators at MACH 2020, but when that didn’t go ahead Kirkham was able to purchase them at a very attractive price.
“The L20 hadn’t even been taken out of the wooden crate it was delivered in, so we jumped at the opportunity,” says Barry.
He adds that the LFV technology really does do everything that is claimed for it in terms of swarf control and machining quality. “You only have to look in the swarf bin to see the difference,” he says.
At the same time as these two sliding head machines, Kirkham also bought a used Miyano BNJ 42SY twin-spindle, twin-turret fixed head machine from Citizen. All three were delivered and installed within a week.
“We’ve built up quite a Miyano village over the past few years. We didn’t have any and now we have six,” says Barry.
The new Nakamura AS 200 will give Kirkham Engineering more flexibility and fast response times on low-volume, quickturnaround parts.
Supplied as a complete package from Wellesbourne based ETG, the AS-200-LMYSF arrived complete with tooling, a Hydrafeed MSV-65 plus a BSU bar support unit to give 1.5m barfeed and swarf conveyor. The machine also had full fire suppression and an oil mist extraction system. It was also upgraded with a bigger sub-spindle chuck, giving 65mm capacity on both spindles.
Having got the new machine, Kirkham then set the first machine up with a similar configuration.
Barry Lynam says that apart from its compact footprint the AS 200 machine has a lot of similarities with the Nakamura
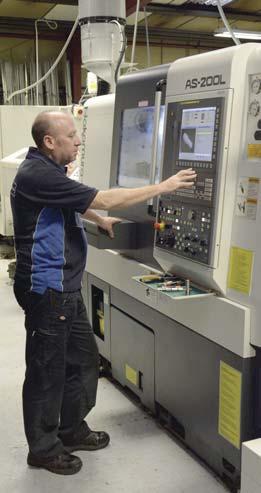
WT 250 twin spindle, twin turret machines.
“It is very much like a WT 250 with one turret, and that is where it is really versatile. Sometimes using a twin-spindle, twin turret machine can be like using a sledgehammer to crack a nut. When we bought the first AS 200 our WT 250 machines were backing up with work and so we hived off some of the less complex components onto the single turret machine and that has proven to be very beneficial.
“The turret on the AS 200 is identical to the ones on the WT 250 so we can use the same tooling.”
Barry adds that thanks to the programming and simulation capabilities of the latest generation Nakamura software and Fanuc CNC the AS 200 machines are quicker to set up than the WT 250s.
“This allows us to be even more responsive to customer demands on low-volume, fast turnaround hobs,” says Barry.
He concludes: “We have invested a lot of money in our mill-turning capabilities for machining complex components in difficult materials, and now we want to shout about it. Oil and gas is a tough market and you have to be equipped with the right tools to survive and stay competitive.” 8 kirkhamengineering.co.uk
Wealdpark Limited
Stand number 5126
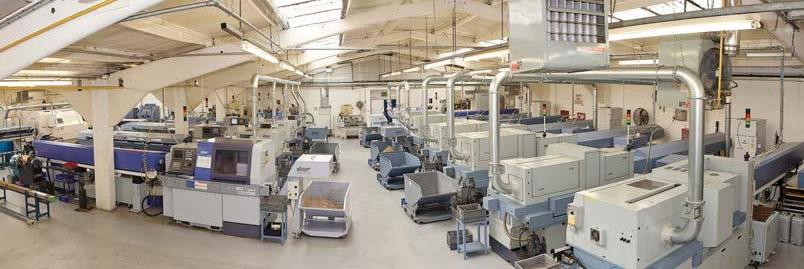
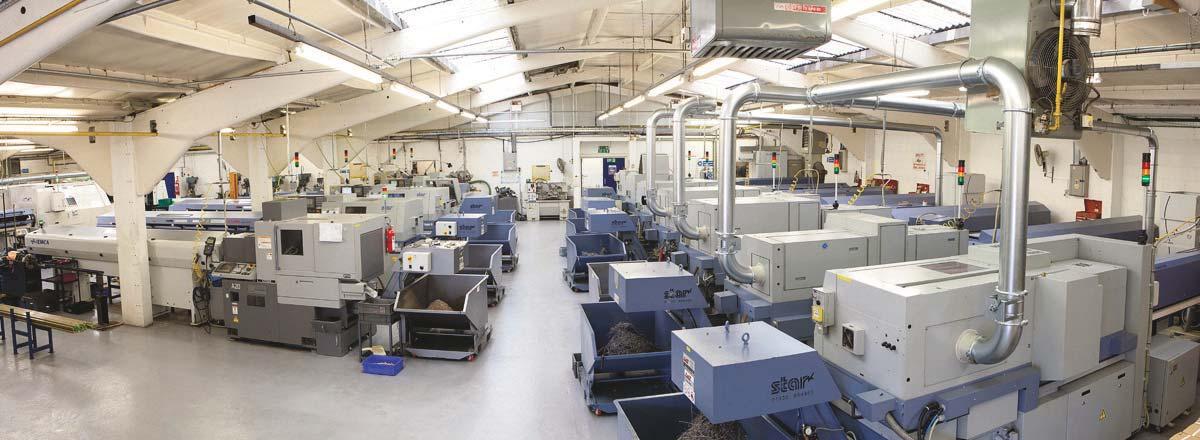
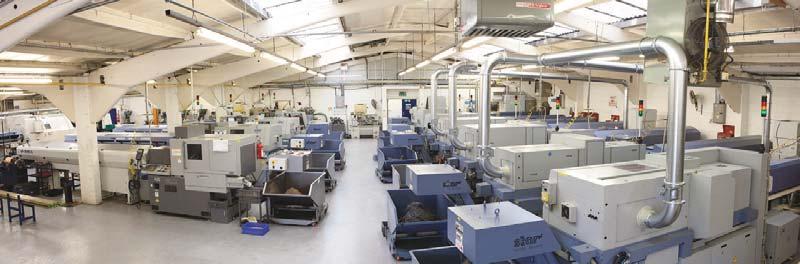
Subcontract Capacity
BS EN ISO 9001:2008. Approved by BSI since 1991.
Company Contact Details
Phil Smith, Director, Wealdpark Limited Sutton Road, St. Helens, Merseyside, WA9 3DJ Tel. 01744 22567 / 732083 Fax. 01744 451339 E: sales@wealdpark.co.uk www.wealdpark.co.uk
Cobot boosts 5-axis output
Scottish subcontractor NPI Solutions is using a collaborative robot to maximise machine uptime time and improve output on a 5-axis machining centre.
The Doosan M1013 cobot, which has a 1.3 metre reach radius and 10kg payload, is integrated with a Doosan DNM 350 5AX 5-axis machine that was installed in 2016. Both pieces of equipment were supplied by Mill CNC.
Since being installed the cobot has proved its worth by helping NPI optimise spindle up time, minimising operator interventions and dramatically improving the machine’s output.
NPI’s managing director, Kevin Priestley said: “We invested in a Doosan 5-axis machine tool in 2016 to help make us more productive, efficient and competitive. The ability to machine precision parts in one set-up, via 3 + 2 and 4 + 1 machining was the appeal, and the goal.”
However, analysis of the machine’s performance over a period of time revealed that it was failing to deliver the expected results.
“It wasn’t the machine’s fault”, explains Kevin Priestley. “It was directly related to the type of production work we do which is
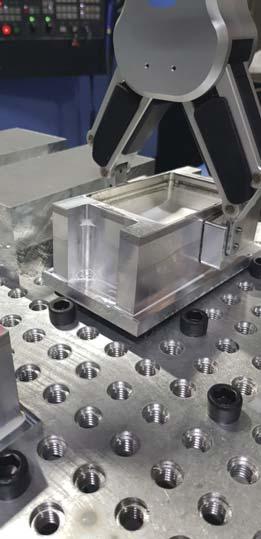
characterised by low volumes and small batches, and by short part cycle times.”
As a consequence the company began to explore automation as a route to improving the machine’s utilisation and output.
Mr Priestley says: “We looked at automatic workpiece pallet change systems and industrial robots but their cost, floorspace requirements and complexity ruled them out.
“The versatility of cobots in addition to their safety, their relatively lower investment cost and their ease of deployment were attractive propositions.”
Situated adjacent to the DNM 350 5AX which, as part of the installation was fitted with an automatic door opening/closing facility, the cobot is programmed to pick up blanks positioned on a peg table and load them, in turn, into the machine where they are machined to completion.
Once machining operations have been completed the cobot takes the finished (machined) component from the machine and places it back on the peg board in its predetermined position. This cycle is then repeated, with no operator intervention, until all the parts have been machined.
Cycle times can be as short as 2 minutes or up to 60 minutes depending on part size, complexity and features.
Says Kevin Priestley: “The ambition to create a flexible automated manufacturing cell has been realised through the cobot investment.
“During the day the cell is programmed to machine components with relatively short cycle times unattended allowing operators to work on other machines or perform other tasks.
“For parts with longer cycle times the cell is programmed to run attended overnight.”
NPI’s new cobot cell has helped dramatically improve its productivity, efficiency and competitiveness. The DNM 350 5AX is now running at 85% efficiency as opposed to just 50% efficiency prior to the cobot investment. 8 npi-solutions.com