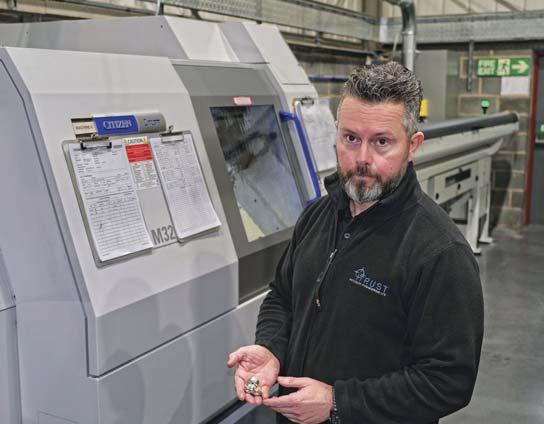
8 minute read
Medical
When the pandemic hit demand in the aerospace sector Trust Precision was able to quickly move to take on new work in the medical sector.
Over the past decade, Managing Director Nick Street has driven the growth of Trust Precision in Eastwood, near Nottingham, which has become one of the leading providers in the Midlands of sliding-head turn-milled components. He said, "With a cando attitude and living up to our slogan 'where reputation is everything', we have established ourselves as a benchmark for quality and reliability."
Last year the company installed a 20 mm bar capacity Citizen L20-XII with a programmable B-axis and low frequency vibration (LFV) chip breaking software, and this soon came into its own.
Until the pandemic took hold in early 2020, up to 60% of turnover at Trust was derived from aerospace contracts, but the proportion is more like one-third of that now. The current shortfall in commercial aerospace work, due to Covid-19, has been largely offset by winning new business, primarily from the medical industry.
The fall-off in work from the aerospace sector has presented the opportunity to focus more on training, which had been identified as the crucial element for the future development of the business.
Fortuitously, the presence on the shop floor of the L20-XIILFV meant that its superior chip breaking ability could be harnessed for more efficient
Moving to medical
turning of medical parts from stainless steel bar. The material normally forms stringy swarf that wraps itself around the component and tooling, risking damaging both, but programmable LFV avoids the problem by breaking the swarf into a short, manageable length.
In the case of an early medical job whose dimensional tolerances needed to be within ± 25 μm, LFV was switched on for about 25% of the cycle. After 1,000 components had been produced, there was no swarf damage to components or tool breakage, even though a 0.8 mm diameter hole was being drilled and reamed in the reverse end of the part.
Mr Street continued, "LFV is a must if you are buying a Citizen lathe that offers the option. It is a major technological advance, the more so because it can be activated by the part program. So the slightly lower metal removal rate during LFV can be restricted to those elements of the cutting cycle that benefit most from the chip control. "Although the volume of our aerospace work diminished at the start of last year, just after we acquired the L20, the machine is proving useful for fulfilling medical contracts. The benefits will be felt even more in the future as the aviation sector recovers, as the stainless steels, titanium alloys and plastics we turn-mill for those customers all benefit from the chip breaking technology." 8 trustprecisionengineering.co.uk
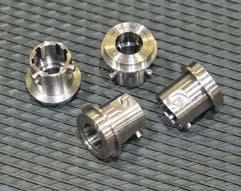
Crossen Engineering has installed a new spark erosion machine that is being used to produce mould and press tools for a range of medical projects.
The Sodick AD35L spark-erosion machine from Sodi-Tech EDM arrived in December last year.
Belfast-based Crossen Engineering is a full service provider, offering everything from component design and prototyping to complete injection moulding and presswork production. An upturn in medical work over the past 12 months created to need to install a new die-sink EDM.
“Medical work has high demands in terms of accuracy, complexity and turnaround time, which we know from experience is ideally suited to the attributes of Sodick machines,” explains Managing Director Paul Crossen.
The medical sector is proving resilient for Crossen Engineering. Among current projects is the manufacture of aluminium prototype mould tools for colostomy draining solutions, walking aids to improve mobility among arthritis sufferers, and bespoke wheelchair parts for children with disabilities.
“Also, during the pandemic, the demand for PPE has been strong,” says Mr Crossen. “For instance, we’ve already made three injection mould tools for face shields, producing the finished parts on site. We received an order near the beginning of the pandemic to supply 70,000 face shields a week to our local NHS facilities as part of the HeroShield project, which is still running, but on a reduced level. In addition, we have machined a prototype mould for another face covering solution, as well as mouldings for sanitising stations.
“Since installation, the machine has been busy producing mainly medical moulds, both prototype and production [aluminium and tool steel],” says Mr Crossen. “P20 tool steel was used for the mould that makes the mobility product, for instance. The level of surface finish we require, along with mould complexity, means the AD35L is a great solution.”
Crossen Engineering offers injection-moulding capacity from 30t to 550t, for parts ranging in weight from 1g to 2.5kg. The new machine can create tools for the largest moulding machine on site, which was an important factor in its selection. The machine also finds use producing press-tool parts. Crossen can provide capacity up to 500t for metal stamping, which it says is the highest in Northern Ireland. 8 crossenengineering.co.uk
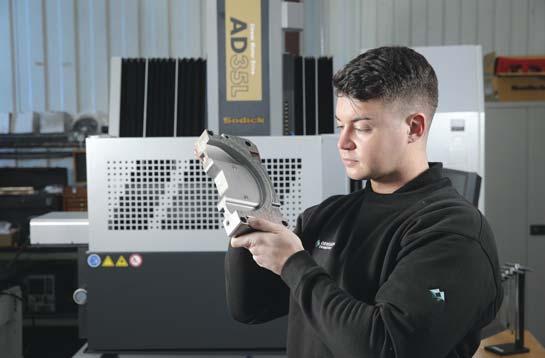
EDM for increased medical demand
DNow Accredited to
FM10101
Manufacturers of High Quality Mill-Turned Parts
From robotic surgery and therapy applications to laboratory robots sorting blood samples and undertaking testing procedures, robotic utilisation within the MedTech sectors is on the increase across a broad range of applications, some of which, when undertaken manually, can be time consuming, monotonous even and also present opportunities for errors to occur.
Workflows in hospitals and laboratories can be simplified by automation, reducing the workload of personnel and ensuring their safety, as well as the safety of the materials being handled in scenarios such as clinical analysis, surgery or even rehabilitative therapy, a process that requires the physical interaction of personnel with patients; lifting, bending, moving etc. Though distinctions should be made between the different field s of applications: • Robots used to carry large loads, such as linear accelerators or X-ray devices. • Robotic processes that require great precision, such as the exact positioning of an instrument. • Robots that undertake perennial sequences, requiring consistently high precision. • Robotics performing repetitive processes over long periods.
The use of robotics and automation within the medical and pharmaceutical sectors is broad, as detailed above, and in order to provide as comprehensive an overview as to what exactly can be achieved and delivered through
Robotics and Automation in the MedTech Sectors:
Technological Progress is Presenting an Array of Possibilities.
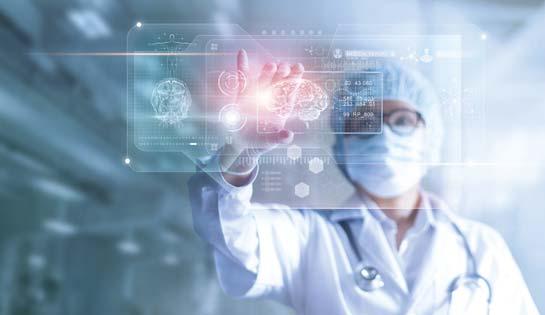
the implementation of robotic process automation, we should examine all areas in which benefits can be afforded.
When we talk about robots and robotics, many envisage an industrial machine, employed to undertake tasks within an industrial environment; palletising in a warehouse, press tending in a factory, automated welding in a fabrication facility – ‘traditional’ applications that utilise mechanized programmable tools, such as robots. The medical and pharmaceutical/life science sectors conjure a completely different setting in one’s mind, of cleanliness, hygiene, sterility and sanitation, the exact converse of those environments in which we would naturally assume that a robot would operate. But there are models of robots and applications that exist solely for use within the MedTech sectors and this wide range of high-tech products and solutions have been used extensively, for as long as the last 30 years, from robot-based assistance systems to assistive components. The evolution of MedTech technology means that today, aside from those preexisting applications that are still used to this day, robots and components are now supplementing a wide range of
medical technology applications, such as: minimal invasive surgery, bone surgery, non-contact bone cutting and orthopaedic surgery, aesthetic surgery such as hair transplant procedures, monitoring and sorting blood samples and undertaking tests and experiments that could take human researchers months to complete – essentially making a complex process, or sequence of processes autonomous.
The age of medical robotics has only just begun. Sensitive and collaborative robots, in particular, will play a defining role in the future of robotics in medicine, and have already proved themselves in several ground-breaking applications. Consider the autonomous ‘robot scientist’. The Royal Society of Chemistry, based out of Liverpool University, developed a robot scientist, consisting of a KMR (KUKA mobile robot) a flexible and autonomous navigation platform equipped with an LBR iiwa sensitive robot arm. The robot scientist was instrumental in maintaining vital research and development processes during a time when social distancing measures prevented developers from working on premise. The development of the robot has been hailed as ‘a new digital age for science’ by the organisation, as the robot continued to operate throughout lockdown, undertaking a series of tests on the behaviour of solar cells.
Dr. Benjamin Burger, one of the developers at the University said the robot had transformed the speed at which he could carry out research. "It can easily go through thousands of samples, so it frees up my time to focus on innovation and new solutions."
The university hospital in Aalborg, Denmark uses a system of lab robots and intelligent transport boxes to automatically monitor and sort blood samples. Up to 3,000 blood samples arrive in the lab there every day. They must be tested and sorted – a time-consuming and monotonous process which was undertaken manually until now. The pick-andplace application reduces the workload for hospital personnel and gives them time to attend valuable tasks.
“We wanted to automate this process to ease the burden on our employees,” explains Annebirthe Bo Hansen, Department Head at Aalborg University Hospital.
Robotics in MedTech had never been about dehumanizing processes, but about improving quality, safety, and access. The ever-evolving global demographic shift dictates that existing services are going to continue to struggle under the strain.
Current advances are great, but the use of a robot system remains entirely dependent on its acceptance by physicians and patients alike. It is the doctor who, ultimately, decides what the robot does and who has control over the entire medical application. Young doctors, in particular, demonstrate a great willingness to work with such systems. With regard to patients, however, more educational work is required. The challenge today, therefore, requires a delicate transition and combination of tradition and modernity to ease the minds of those new to these exciting applications. 8 kuka.com
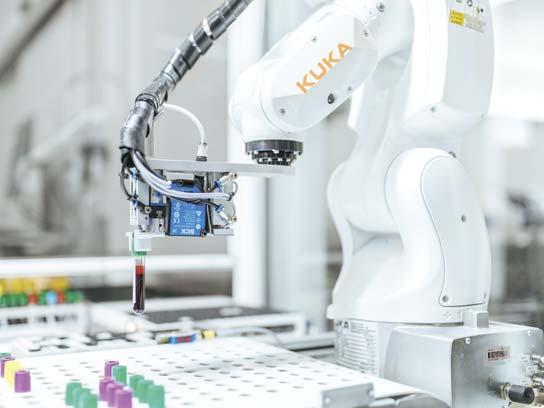
8 Blood sample handling Aalborg University Hospital