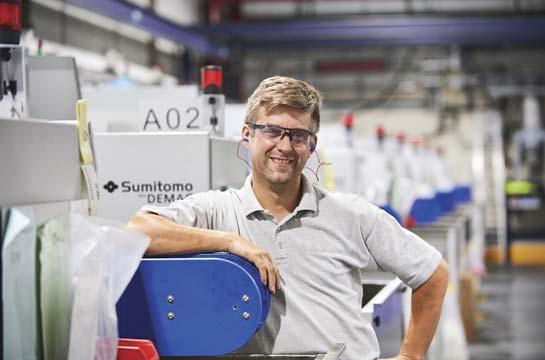
4 minute read
Moulding
All-electric moulding upgrade
Essentra Components has embarked on a multi-million pound, long-term investment programme to upgrade its hydraulic injection moulding machine portfolio to become electric by the end of 2031.
The company is working with a small number of key equipment suppliers with global support networks to replace 180 machines that have been operating for 15years or more (and currently heading towards the end of their working lives). The replacement machines will be both all-electric and hybrid electric, the latter using Vireo servo drive technologies.
The transition will result in an estimated 33% reduction of energy consumed, cycle to cycle, and a 25% uplift in cycle time gain, tool-to-tool.
The predicted process and productivity improvements will effectively enable three electric machines to do the work of four hydraulic models, reducing the overall footprint. The increased capacity is complemented by the guaranteed repeatability that electric machines can deliver, ensuring even greater product quality.
Chris Butler, Global Process Development Manager, says there are clear customer advantages: “Although electric machines demand a substantial initial capital outlay, these costs are more than balanced by the increased capacity and reduced energy costs which makes for exciting news for both our business and customers alike.
“Electric machines are more reliable and last longer than their hydraulic counterparts, with a cost of ownership calculated over a 20+ year life cycle as opposed to 15. They also deliver significantly greater productive hours per annum. With this performance, and greater automation, we can support even greater efficiencies for our customers.”
Chris says that standardising equipment brings additional advantages: “Standardisation simplifies our training requirement and also leads to better spare parts availability, which in turn converts to even more uptime for the machines installed,” he adds. “As well as the machines, we are also reviewing our tooling and retooling processes and increasing cavitation for higher yields, enabling us to take on unusual projects that might previously have been considered out of scope.”
Essentra trialled its first electric machine more than a decade ago, but recent advances in technology and a drive towards a more sustainable future have coincided to make a renewed focus on an electric vision a priority. The new technology will allow for accelerated turnaround times for new lines and faster cycling times, whereas zero standard deviation on electric machines leads to greater accuracy and fewer rejected parts, all of which are essential to attracting and retaining key customers.
Chris says the programme is part of Essentra’s journey towards a more sustainable future: “All major manufacturers will be allelectric within the next decade,” he adds. “Our customers are always looking to do more with less, and electric machines not only give our customers a better-quality product, but they also help them meet their own sustainability agendas.” 8 essentracomponents.com
Ricoh 3D has introduced carbon fibre composites to its line-up of high-performance materials through a partnership with composite-based manufacturer Impossible Objects.
Ricoh 3D is one of the first AM service bureaus to make 3D printed Carbon Fibre PEEK and Carbon Fibre PA12 materials commercially available in Europe for functional prototypes and small batch production. The unique printing process leverages highspeed 2D graphics technology to create a high performance, reinforced composite part.
The end result is said to be extremely cost-effective parts with impressive strength-to-weight ratios and a performance similar to that of metals. Compared to traditional composite manufacturing, Impossible Objects’ Composite Based Additive Manufacturing (CBAM) process creates much stronger parts with very few geometric restrictions, at significantly lower prices than have been possible before. This is especially good news for aerospace and drone manufacturers, as fine features and flat parts were previously impossible with FDM and FFF technologies due to the short, chopped fibre formation and lamination between layers, causing parts to fall apart under force.
With powder-based 3D composite, continuous carbon fibre is contained in long fibre printing sheets which allows full homogenous coverage of the fibres – making point features and feathered edges possible. As the excess fibres support the unprinted areas, issues with shrinkage, curling or deformation of parts are eliminated.
Mark Dickin, Additive Manufacturing & Moulding Engineering Manager at Ricoh 3D, said: “Composites are set to be an area of huge growth in additive manufacturing in the coming years, so we are proud to be working with Impossible Objects to be at the forefront of the European movement. Carbon Fibre composites are industry-leading when producing lightweight yet strong parts.
“These properties make the materials ideal for tooling and end-use applications in a range of industries, including medical, aerospace, automotive, sport and industrial; creating anything from propellers to gear components, golf clubs to prosthetics.
“It was very important to us that this was a sustainable offering. All powder is recycled by extracting the waste material off the sheet, ensuring nothing is wasted and making the process even more efficient than SLS.
“We are working closely with the team at Impossible Objects on future material developments and our engineers look forward to demonstrating how these new materials can change the game across a range of industries.”
Composite materials are a combination of two or more dissimilar materials – typically a core polymer and a reinforcing material - that are used together in order to combine their best properties.
The end product is usually extremely strong as a result - but traditional composite manufacturing is very labour, resource and capital intensive. 3D printing has allowed production to be automated with minimal manual input, streamlining the process and making it far more cost effective. Ricoh 3D have shared a series of sample parts on its website which demonstrate the cost savings possible with powder-based 3D composite. 8 rapidfab.ricoh-europe.com
3D composite printing
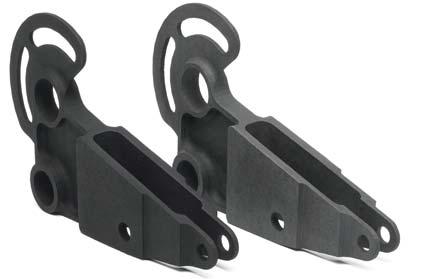