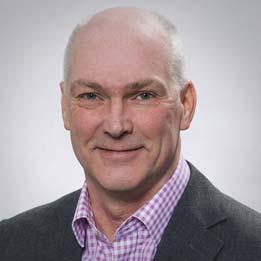
13 minute read
Investment
Tim Paddison, managing director of Hoffmann Group UK, asks what the Government’s ‘Super Deduction’ incentive means for manufacturing businesses.
After a turbulent year for the manufacturing sector, the government’s 2021 Budget contained several positive developments and promises to businesses. In addition to the announced extension of the furlough scheme until September, and the bonus for hiring apprentices that is now doubled to £3,000, the centrepiece of the Chancellor’s speech is the “Super Deduction” a move that will significantly benefit the sector.
Under the super deduction arrangement, for every pound that a company invests, their taxes will be cut by up to 25p. From the start of April this year, until the end of March 2023, companies can claim 130% capital allowances on qualifying plant and machinery investments. Such investments include assets used in the course of a business and, for manufacturing businesses, this could include anything from drills, cranes and machinery to new computer equipment or a company van for delivering tools to customers.
So, with the growing opportunity and incentive for manufacturing businesses to spend and invest, what benefits could this bring to the sector?
An opportunity to prioritise business growth
After a year of disrupted service caused by the complications of the pandemic and the ongoing issues posed by Brexit, the super deduction announcement is a real opportunity for manufacturers to look ahead and prioritise their business growth.
Encouragingly, along with the promise of this announcement, the sector is already starting to
Supercharged investment opportunity
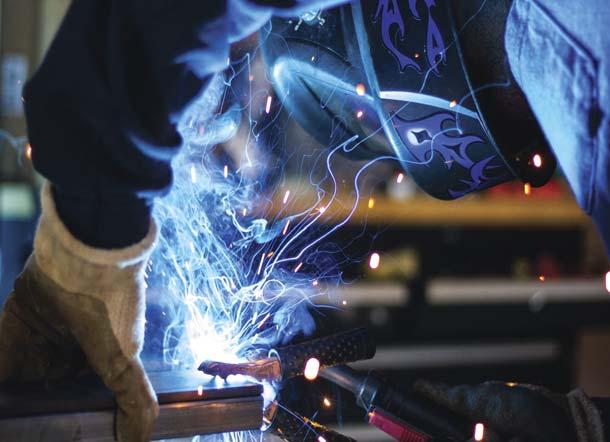
witness growth with the IHS Markit Manufacturing PMI reading for April 2021 reporting that in March of this year, the sector has seen the fastest output growth since late 2020. This reading attributes this growth to recent inflows of new business from both domestic and overseas markets across the sector as developments such as the vaccine rollout, ease buyers’ concern.
To further boost this upward trajectory of the sector, the super deduction also offers manufacturers the much-needed wriggle room to invest in areas they wanted to grow, prior to the pandemic. For example, if the business had wanted to invest in automation to expand its service
offering, this option is now increasingly attractive with the new support that the deduction offers.
The ability to improve efficiency on the factory floor
With the incentive to spend, the super deduction also enables manufacturers to improve their operational efficiency. Having the extra budget to purchase bigger and better machinery, can not only improve the business’s service offering, but it can also free up time for employees that can be placed in other areas of the company – in potentially, more fulfilling roles.
For example, purchasing an automated packaging system under the super deduction allowance could not only maximise labour productivity, but it could also allow workers to be placed on more challenging or stimulating tasks. Whilst the perception is often that automation does not lead to employees completing more stimulating tasks, research by the World Economic Forum in its Future of Jobs 2020 Report indicated that the shift to automation would create 97 million new jobs by 2025. It was also noted that these additional jobs would have an emphasis on skills in analytical thinking and creativity that would be another benefit to the sector.
Equally, alongside the potential increase in jobs and varied tasks for manufacturing workers, these businesses can also place these employees in other areas that the business is wanting to focus on.
A chance to prioritise pre-pandemic ambitions
Understandably, after the huge disturbance posed by the pandemic, very few manufacturers were able to implement their original plans for 2020. Instead, the industry had to deal with immediate issues such as navigating working from home requirements and budgetary concerns in continuing operations.
Similarly, as if the consequences of the pandemic were not enough, the changing regulations posed by Britain’s official exit from the EU at the end of 2020, have left many manufacturing businesses having to act quickly to change their processes. Many have had to align their products to new technical and safety regulations posed by the EU, with importing and exporting requirements changing almost overnight.
However, it is hoped that now, almost five months into Brexit, and with the vaccine rollout success easing concerns for many across the sector, the industry can reanalyse prioritises and focus on moving forward.
The super deduction allows this opportunity for manufacturers to revisit business ambitions and decide whether these can be implemented again in 2021.
One of the largest priorities for the sector prior to the pandemic (and arguably reinforced throughout), is the worldwide attention paid to the climate crisis. The opportunities in the green/low carbon energy were, and still are, likely to see big growth across the sector. Particularly with the new US administration’s policy moves to re-engage with the climate fight.That Britain needs its trading friend across the ocean more than ever before, points to a renewed focus on investment in less carbon-intensive activities.
Using the super deduction scheme, manufacturers can reprioritise their environmental commitment by adopting renewable energy resources and using the tax relief over the next two years as a real opportunity to take the step. Businesses that can take advantage of the super deduction and use it to boost their environmental credentials will be at the forefront, not least because consumers (and employees) are now demanding it.
The governments’ announcement for the super deduction holds extensive opportunities for the manufacturing industry. Pre-pandemic ambitions, such as boosting green credentials and investing in machinery that can boost efficiency, are just some of the benefits the industry could witness if it takes advantage of the super deduction offering.
According to a survey conducted by Make UK earlier this year, over 48% of manufacturers expect conditions within the industry to either improve or significantly improve throughout 2021. The super deduction could support this progression and those businesses that act now, could be the ones to reap the biggest reward. 8 hoffmann-group.com
JFL Broaches and Broaching
JFL are broach and broaching specialists with many years personal experience. We offer a comprehensive broaching service covering keyways, squares, hexagons and special forms. Unit 2, Deethe Farm Industrial Est, Cranfield Rd, Woburn Sands, Milton Keynes, Bucks MK17 8UR Tel: 01908 585103 www.jflbroaches.co.uk
Qualiturn Products Limited
Qualiturn are a very modern subcontract machining service. We offer CNC precision Turned and Milled components to your specifications and quantities. We work with all sizes of customers, offering the same service to all. Supplying various market sectors across the world. 7 Fountain Drive, Hertford, Herts, UK, SG13 7UB Tel. +44 (0) 1992 584499 www.qualiturn.co.uk
LATHES.CO.UK
Lathes.co.uk
store.lathes.co.uk - where Manuals, Catalogues Drive Belts Books Accessories & Spares are listed The world’s largest machine tool reference archive. Manuals, Catalogues, Books, Pictures Specifications, Technical Guides
Wardlow, Tideswell, Buxton, Derbyshire, SK17 8RP Tel. 01298-871633 (from overseas: +44-1298-871633) from 09:00 to 23:00 UK time www.lathes.co.uk
8
MACHINING (5 AXIS)
8 PRECISION ENGINEERING
8
PRECISION ENGINEERING Mini Gears (Stockport) Ltd
Mini Gears is a subcontract manufacturer of machined components, gears and racks. Winner of 17 Industry Awards, it has a global customer base, 35,000 sq. ft. facility and over 100 machines.
Top Gear House, Bletchley Road Heaton Mersey Industrial Estate Stockport SK4 3ED Tel: 0161 432 0222 www.minigears.co.uk
8
PRECISION ENGINEERING
DAWSON PRECISION COMPONENTS Manufacturing precision machined components since 1965 Services include: CNC milling, CNC turning, turn/mill machining, sub contracted services, finishing and project management.
Greenfield Lane, Shaw, Oldham, Lancashire, OL2 8QP Tel: 01706 842311 dpc.co.uk
8
PRECISION ENGINEERING
5 High quality precision machined components 5 Trusted technical support service 5 Complete and bespoke service from conception to completion 5 AS9100D & ISO 9001:2015 approved
Oldfield Street, Crosland Moor Huddersfield HD4 5AJ T: 01484 548903 www.thomas-brown-engineering.co.uk
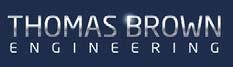
Wealdpark Ltd
CNC mill-turn facility using Star sliding head lathes with bar capacity up to 32mm diameter. Miyano and Doosan fixed head lathes with bar capacity up to 65mm. Hurco vertical machining centre. Sutton Road, St. Helens Merseyside WA9 3DJ Tel: 01744 22567 www.wealdpark.co.uk
8
REPETITION TURNED PARTS Kirkham Engineering Co Ltd

13 - CNC Sliding Heads up to 1”; 14 CNC Twin Turret Fixed Heads up to 65mm; 5 - Twin Turret Twin Spindle; 5 - Twin Turret with Sub-Spindle and 4 - Twin Turret; 4 - CNC Single Turret Fixed Heads up to 6” Billet. Centreless Grinding & T/rolling. All materials - Stainless Steel; Nickel Alloys and other exotics a speciality. Prestwood Place, East Pimbo, Skelmersdale, Lancashire WN8 9QE Tel: 01695 727401 www.kirkhamengineering.co.uk

Grenville Engineering (Stoke-on-Trent) Ltd
With more than three decades of experience and dedication in producing the highest quality products, Grenville maintains its position as the leading precision sheet metal fabrication company.
Unit 3 Newfield Industrial Estate, High Street,Tunstall, Stoke-on-Trent ST6 5PD Tel: 01782 577 929 www.grenville-engineering.co.uk
8
SUBCONTRACT CNC TURNING
Engineering Capacity|INDUSTRY NEWS SEPTEMBER 2017 Growth support helps 1000 SMEs More than 1000 small tomedium-sized manufacturers(SMEs) have been given a business boost over the last tenmonths thanks to a new £9.7mbusiness support initiative. The Manufacturing GrowthProgramme (MGP), funded by theEuropean Regional DevelopmentFund (ERDF) and delivered byEconomic Growth Solutions (EGS),has helped companies across the UK to grow, develop newproducts and overcomeproduction issues that werepreviously holding them back.This has already led to 400 newjobs, with an additional 359 positions expected to be created once ongoing projects arecompleted. By the end of July,£1.6m of grant contributions havebeen made, with money in placeto support another 2200 firmsbetween now and March 2019.Lorraine Holmes, ChiefExecutive Officer of EGS, explained: “We are way above thetargets we have set for ourselves,proving that there is a real appetitefrom SMEs for targeted businesssupport that can help them grow.“The difference with ourprogramme is that it is deliveredby manufacturing experts whounderstand the challengescompanies are facing. Theyunderstand the language MDs are talking and can guidethem on making the right decisions, before bringing inspecialists on specific issues theyare facing or opportunities they’re looking to explore.”She continued: “1000 beneficiaries is just the start. We’ve still got a lot of grants todeliver and we wantmanufacturers to come forwardand see how they can take advantage of the assistance on offer. It’s never been easier, as theprocess is quick and the scope of support can be tailored to the exact needs of the business.” The Manufacturing GrowthProgramme was set up to fill the void left by the ManufacturingAdvice Service (MAS) by providing access to specialistassistance to help manufacturersto grow and improve.This is being achieved throughan 18-strong network ofexperienced manufacturinggrowth managers (MGM), accessto industry specialists and theopportunity to apply for an average grant of £1400, rising to amaximum £3,500. Support can be used for leadership and management,R&D, lean manufacturing, productivity and capacity, qualitysystems and supply chaindevelopment.Martin Coats, OperationsDirector at EGS, continued: “Whenfirms come to us they receive astrategic review from one of ourMGMs that determines what barriers are in the way and whatsupport is needed to help them reach their potential. “Since October 2016, thehighest barrier with 15% of clientswas ‘Continuous Improvement’,followed by ‘Environmental’ and‘Marketing and MarketKnowledge’ (12% each). Once theinitial stage has been completed,we then bring in an expert whoworks with the management teamto address these issues.”8 manufacturinggrowthprogramme.co.uk MACHINED COMPONENTS|Engineering Capacity 14 www.engineeringcapacity.com SEPTEMBER 2017 Mill-turning supports lean approachIn the first half of this year Roscomatic has committed to £750,000 of investment, including the installation of the latest Miyano BNE-51MSY multi-axis turn-mill centre. The Worthing-based subcontract machinist company dispatches some 1.5 million parts a year – ranging from completed assemblies and sub-assemblies to large machined castings and small turned parts – and is currently achieving a record on-time delivery rate of 98%. Managing director Joe Martello explains that the company is driven by a philosophy of constant development of lean manufacturing techniques, supported by investment often exceeding £1 million a year and an ‘open-liaison’ people strategy which keeps the workforce up to date on the company and any issues arising. He says: “We invest in automation and the latest production technology which helps to overcome the shortage of skills we would require. However, it is so important that we still need to grow our own engineers through constant support and by training, in order to maximise our return-on-investment and so improve how we support and what we deliver to customers.”In addition to the new Miyano the company has already ordered two Citizen CNC sliding head turn-mill centre machines. The two machines, a Citizen L20-VIII LFV (LFV featuring low frequency vibration cutting technology) and a top-of-the-range M16-V will bring the total Citizen installations to 14. Cell Leader Sean Keet says: “The levels of operational flexibility in the Miyano BNE has enabled us to significantly reduce machining times and most important, improve overall productivity.” He says the new machine has replaced existing 3-axis machines so that a family of 10 aluminium parts that previously required four turning operations and a separate milling operation can now be produced in one turn-milling cycle. A massive bonus is that average total cycle times per part has been cut from 13 mins to just 2.5 mins. A further complex stainless steel component which had three operations taking 11 minutes is now reduced to a single, four-minute cycle.Further return-on-investment comes from freeing-up setters to perform other tasks and from the reduction of lost time for each first-off inspection, reducing the risk of setting and relocation errors and cutting work in progress. The flexibility of the BNE-51MSY is key to its success as it is capable of single cycle cutting with three tools simultaneously overlapped at both ends of a workpiece at the same time, and using bar up to 51 mm bar diameter. The fixed-head 15 kW main spindle and two-axis 7.5 kW secondary spindle, both with maximum speeds of 5,000 revs/min, have the advantage of synchronised / superimposed control for both 12-station, all-driven turrets. Ideal for
www.engineeringcapacity.com 5
Get your company noticed with an Engineering Capacity classified profile advert
FOR MANUFACTURERS ABOUT SUBCONTRACTORS September 2017
INDUSTRY NEWS | MACHINING | AUTOMOTIVE | SHOW PREVIEWS 8
SPRING MAKING
MACHINED COMPONENTS: Prismatic parts from bar
www.engineeringcapacity.com
Call 01737 270648
Subcontract mill turned Subcontract mill turned parts up to 65mm in parts up to 65mm in diameter from bar diameter from bar and 300mm and 300mm billet billet work. work.
– – – r – – s yol l A repuS ssaB leetSssel ni a t S scitnimuAl salPmui
Simpson Springs & Pressings Ltd
Precision manufacturers of a wide range of compression tension and torsion springs. Also circlips, wireforms, contacts, antennas and light pressings. Quality approved to BS EN ISO 9001:2000.
Unit 1, Latimer Road Industrial Est, Latimer Road, Wokingham, Berkshire RG41 2YD Tel: 0118 978 6573 www.simpsonsprings.co.uk
8
TURNING (CNC)
8 TURNED PARTS
8
WATERJET CUTTING Batchflow Engineering Ltd
CNC turning capacity from 2mm200mm using high precision Fixed and Sliding Head CNC Lathes. Experience in machining a range of materials, from Low to Medium volumes, to customers specifications. Budbrooke Road, Warwick, Warwickshire CV34 5XH Tel: 01926 492889 www.batchflow.co.uk
Precision Products (Brighton) Ltd
A one-stop-shop for high-quality turned parts
Accredited to AS9100 Rev D
Unit 2 Brookside Avenue, Rustington, West Sussex BN16 3LF Telephone: +44 (0) 1903 776 171 www.precisonproducts.co.uk
ICEE
Comprehensive fabrication facilities offering complete turnkey solution. Design, Precision Engineering, Sheet Metal Fabrication and Welding. Prototypes, one off or batch work. Waterjet Capacity: 4m x 2.25m & dash; materials up to 230mm depth. Aluminium Alloy Specialists. 20 Arnside Road, Waterlooville, Hampshire PO7 7UP Tel: 023 9223 0604 www.icee.co.uk
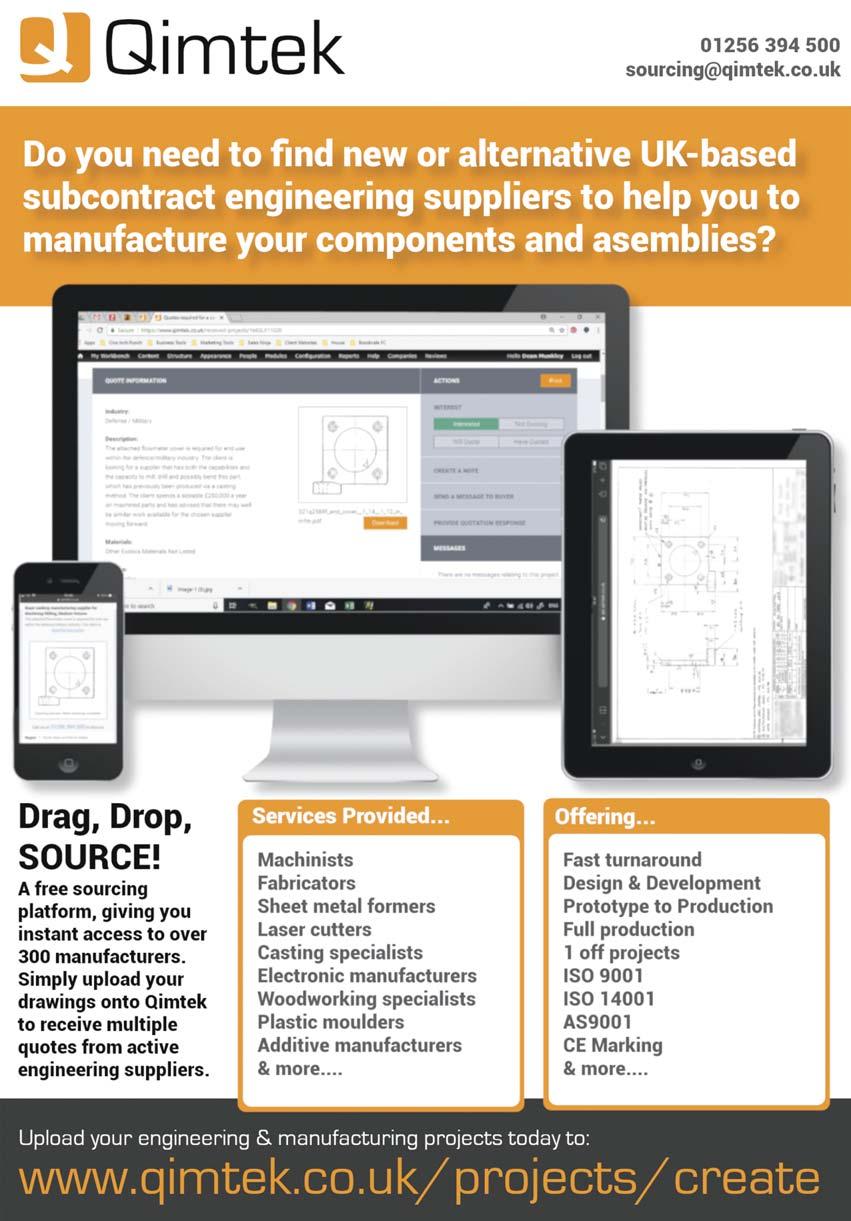