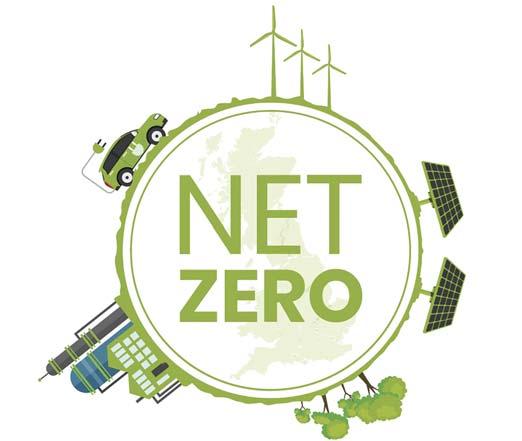
14 minute read
Sustainability
Control Energy Costs (CEC) is helping SMEs become more sustainable by launching a new e-book and short film.
They are designed to be a simple guide to help businesses understand more about renewable energy, how they can start reducing their carbon footprint and why it is important to engage with your employees. There are also sections covering the differences between Net Zero and carbon neutral.
It comes after CEC made its own commitment to become Net Zero within 12 months, with management working with its 25-strong workforce to review its current carbon footprint, before putting in place a blueprint to reduce energy consumption, purchase energy from renewable sources and rebalance any carbon emissions.“Sustainability is firmly in the news and our Government has an ambitious target for when the entire country will be Net Zero,” commented Phil Ager, Managing Director of CEC.
“Our experts have so much knowledge and experience, we decided to package this expertise into an e-book and short animation.
“All sectors need to do more and there is legislation on the way that will make reporting and reducing carbon mandatory. We want to make sure our clients are in a position to comply with the new rules.”
The guide covers five main sections, ranging from the different types of renewable energy you can choose and the risk of falling for ‘greenwashing by companies’ to engaging employees, Government legislation/schemes and how you can carbon offset.
It also tackles the importance of having an ESG (Environmental, Social and Governance) framework in place, which could deliver companies a commercial and competitive advantage when tendering for new work.
“For manufacturers that lead the way in transitioning to a low carbon economy, there can be significant opportunities,” added Phil.
Control Energy Costs offers an initial ‘no cost, no obligation’ audit review of both current and historic energy arrangements, looking for opportunities to secure retrospective refunds and rebates, reduce non-commodity/third party charges and, where appropriate, advise on future energy contracts. 8 cec.uk.com/greenenergy
Get help to achieve Net Zero
Visit our website or contact us for a quote or advice
Scottish fabricators have completed a new wave energy machine that will take to the seas at Scapa Flow in Orkney for trials.
Wave power specialists Mocean Energy has unveiled its Blue X wave energy prototype, a 20-metre long, 38-tonne machine that will be first deployed at the European Marine Energy Centre’s (EMEC) test site for initial trials and then moved to the EMEC’s large scale Billia Croo test site this summer.
Next year, the wave pioneers plan to connect the device to a subsea battery which will be used to power a remotely operated autonomous underwater vehicle (AUV).
The manufacture and testing programme is supported by £3.3 million from Wave Energy Scotland (WES) through its Novel Wave Energy Converter programme.
The Blue X wave machine has been fabricated in Scotland by Fife fabricator AJS Production and painted by Montrose-based Rybay Corrosion services. Numerous hardware and services were supplied by companies who have developed capabilities though the WES programme, including Supply Design, based in Rosyth, and Blackfish Engineering Design.
The machine was unveiled at a ceremony at Forth Port’s Rosyth Docks by WES Managing Director Tim Hurst who said:
“This is a significant milestone for Mocean Energy and for WES. The product of five years of the WES programme and three phases of development for the Mocean technology that has seen the Blue X progress from concept, through wave tank testing and now to a scaled, real sea demonstrator.
“Against the backdrop of Covid-19 restrictions Mocean Energy and their subcontractors have completed build of the prototype. The focus is now on commissioning and the learning to be gained from the open water test campaign.
“This demonstration of credible wave technology comes at a time when there is a real prospect of a market support mechanism for marine energy, that taken together, will enable wave energy to make a significant contribution to the future Scottish and UK low carbon energy mix needed to meet our net zero obligations.”
The Blue X will now undergo ballasting and wet testing at Rosyth before being transported to Orkney.
Mocean Energy Managing Director Cameron McNatt said: “As we drive toward net zero, we will need many forms of renewable energy and wave energy can make a significant contribution.
“Our test programme in Orkney will allow us to prove our concept at sea, particularly that its novel hull shapes will produce more power than traditional raft designs. This enables the development of commercial scale technologies suited to the oil and gas and other industries.”
Last month Mocean Energy announced a £1.6 million project with OGTC, oil major Chrysaor (now newly formed Harbour Energy) and subsea specialists EC-OG and Modus to demonstrate the potential of the Blue X prototype to power a subsea battery and a remote underwater vehicle – using onshore testing at EC-OG’s Aberdeen facility. 8 mocean.energy
Riding the green energy wave

Heat treatment specialist Bodycote is targeting the marine renewables sector after securing work with wave energy pioneer CorPower Ocean.
The UK-headquartered firm, which has previously focused on automotive, aerospace, energy and broader industrial sectors, is now breaking into ocean energy after helping Swedish developer CorPower optimise key components in its Wave Energy Converters (WECs) by applying its Corr-I-Dur treatment.
CorPower’s high-efficiency WECs, inspired by the pumping principles of the human heart, offer five times more energy per ton of device compared to previously known technologies. Incorporating a series of unique features to boost storm survivability and power capture, the WECs also benefit from thermochemical treatment to protect against the harshest marine conditions.
CorPower Ocean Senior Procurement and Quality Engineer Thomas Lindahl said: “After our initial collaboration we have now worked with Bodycote at a number of plant locations across Sweden to develop mechanical components for our WECs using Corr-I-Dur.
This thermochemical treatment simultaneously improves corrosion resistance and wear properties by generating an iron nitride-oxide compound layer. Durability and robustness are of paramount importance in the wave energy sector, and effective protection of devices in the hostile ocean environment has always presented a major challenge to our industry.
“Corr-I-Dur has proved a particularly favourable solution being specifically designed for components subjected to a corrosive environment in combination with wear. From a commercial perspective, solid proof of the long-term resilience of our WECs makes them infinitely more valuable. We believe this collaboration will play a crucial role protecting our WECs during our next phase of testing in the Atlantic Ocean, and for the years to come.” 8 bodycote.com
Charting a maritime course
engineering, composites
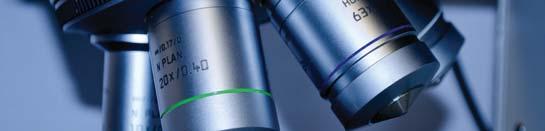
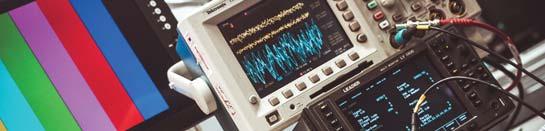
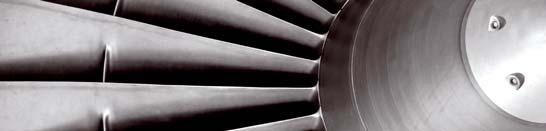
PR | Marketing | | Copywriting | Events Awards | Design | | Web & SEO
01752 894786 www.aroprandmarketing.co.uk
Caunton Engineering has fabricated a 3m cubed ‘blast box’ for testing high explosives using a novel UK-developed modular construction system.
The patented Steel Bricks system developed by Modular Walling Systems Ltd, based in Renfrewshire, Scotland, has been used to construct an Environmental Blast Chamber for the University of Illinois at Urbana-Champaign. Known as a ‘blast box’, the revolutionary ultrastrong three-metre cubed chamber is now being used for explosives testing as part of a research programme on advanced warhead technologies for the US Department of Defense.
The University of Illinois blast box uses the patented Steel Bricks modular construction system which comprises two steel face plates internally connected to create a ‘sandwich’ panel. The steel structure is then manufactured off-site as a single piece, before being filled with 72 tons of self-consolidating concrete in a continuous pour once installed.
According to Dr. Stewart Gallocher, founding director of Modular Walling Systems, it is this proprietary process which gives the blast box its unique strength as well as vastly reducing on-site time and labour costs - making it ideal for nuclear Small Modular Reactor construction, a market estimated to be worth US $1.2 trillion globally.
He explains: “The Steel Bricks system, with trademark diaphragm holes running through the webs, has been assembled in such a way that the concrete is poured through holes in the roof, flowing down the walls and filling the base mat before coming back up the walls and lining the ceiling – all in one continuous pour. This is a ‘first of a kind’ concept in the fast-emerging world of steel composite construction and proves that the Steel Bricks system can provide not only the walls and suspended floors or roofs in steel composite but most importantly a base mat.”
The Environmental Blast Chamber was fabricated in the UK by Caunton Engineering in Nottingham before being shipped to the University of Illinois at Urbana-Champaign. Now installed, the blast box is expected to deliver some impressive results, as testified by Professor Nick Glumac who leads the explosive testing and weapons research faculty at the University. He says: “The test facility allows for large scale high explosive testing with advanced imaging, spectroscopic and flash x-ray diagnostics. The system can be operated as a fully enclosed or partially vented structure enabling a wide variety of tests of high explosives, propellant systems and pyrotechnics.
“The chamber has optical access on three sides for multiple views of testing, while internal walls are amenable to instrumentation and fragmentation shields, allowing the testing of heavily fragmenting warheads. The main advantage of the blast box is that it can be ‘dropped-in’ on site, arriving fully assembled and ready for the concrete pour. This means less site preparation, fewer personnel needed for installation and rapid times from delivery to first operation.” 8 steelbricks.co.uk
caunton.co.uk
Thinking inside the box
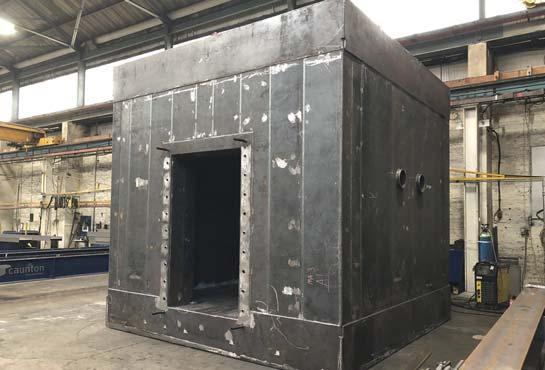
Fabrication milestone in the can
ECS Engineering Services has fabricated its 300th machine frame for an industry-leading can making machine –CarnaudMetalbox (CMB) Engineering's industry 5000 Series Bodymaker machine.
The machine frame was produced entirely in-house by ECS' fabrication department.
CMB Engineering is a designer and manufacturer of highperformance metal forming and finishing machinery for the production of beverage, food and aerosol cans. The 5000 Series Bodymaker is one of its most successful machines. The 5000 Bodymaker is a horizontal, double-action press for the manufacture of steel or aluminium cans. It is designed to function at high-speed, offering up to 400 strokes per minute (spm). It can produce cans with a capacity of up to 1000ml and up to 84mm in diameter.
ECS has a steel fabrication capability accredited to CE Mark Execution Class 4 (EXC4) and is experienced in providing fabrications to support civil infrastructure, water control and construction projects. The company operates its design studios and fabrications department in close proximity to each other, ensuring seamless transition of information and quality assurance. It says this combination of close collaboration and extensive capacity ensures reduced lead times.
Clark Williamson, Contracts Director at ECS, commented: "We are pleased to have been involved in reaching this milestone for this incredibly successful machine. The food and beverage industry demands the highest quality levels at all stages of the production process, and thanks to our facilities, this is something we can provide from a fabrications perspective. The fact that CMB Engineering entrusts us to produce frames for their flagship 5000 Series Bodymaker illustrates this." 8 ecsengineeringservices.com
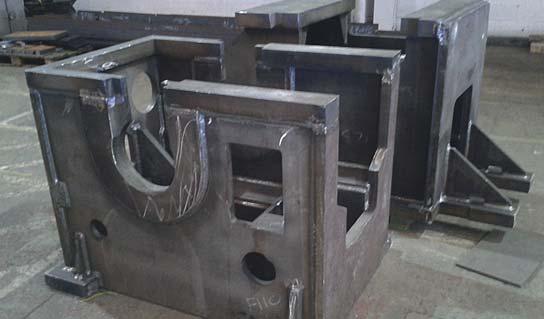
KMF Precision Sheet Metal has expanded its robotic, automatic bending capabilities with the addition of a new bending cell.
The latest addition is a Trubend Cell 7000 complete with Wireless ACB (Automatically Controlled Bend technology).
Terry Stanway, KMF Purchasing and Facilities Director said: “The combined offerings from the current technology will
Robot bending expansion
ensure that we can now investigate lights out production opportunities for larger volume demand, particularly for smaller components, where additional capacity is required.
“The installation of the Autobend Cell represents the first phase of investment in 2021, during which time we also expect to commit to further technology advancements with an upgrade to our existing automated twin system Laser Cell.
“From initial investigations it is expected that this project is likely to result in production cycle reductions of up to 60% across a range of material types and gauges.” 8 kmf.co.uk/
£100,000 press investment
Source Engineering, a specialist in precision pressed parts and machined components has invested more than £100,000 in a new high-speed press line to boost capacity.
The line can do the work or four conventional mechanical presses.
The BSTA 200M 20 tonne stamping press was identified as the ideal solution and is now up and running at the company’s Langage Business Park facility, achieving 300 strokes per minute which represents a 200% increase in production output across a range of products destined for the automotive, electrical wholesale and oil and gas markets.
Engineers at the firm have freed up an additional 500 sq ft of production space to use for the introduction of new projects and to help them cope with an increase in demand for its range of automation solutions.
Andy Dunkerley, Chairman at Source Engineering, commented: “Buying a Bruderer is like buying the Swiss watch of machines¬… you get unrivalled precision, speed and repeatable quality, all wrapped up in a relatively small footprint.
“We already had one in another part of the factory and were fully aware of its capabilities, so when it came to looking at how we optimised the factory floor space by replacing four machines with one high-speed line we called in its technical experts to review the options.”
He continued: “They really understood what we were looking to achieve in space utilisation without giving up the versatility and the volumes, which basically meant we needed one machine to do the work of four.”
The Bruderer BSTA 200M high precision, high performance stamping press was identified as the preferred option and was fitted with a high-speed Servo Feeder and Pallet Decoiler to help achieve ultimate precision control of material de-coiling and pinpoint pitch control through the progression press tool.
Specified with a tool area of 510 x 400mm, the machine can deliver up to 1800 strokes per minute and is capable of handling a maximum material thickness of up to 2mm and material width of 100mm
It has also been equipped with Press Force Monitor, which ensures protection of the press from overload and limit damages to the tool if any stray material is pulled back up into the process stopping the machine within 1 stroke, even at high speed.
Pablo Gutierrez, Technical Director at Source Engineering, went on to add: “Sales are now back to pre-pandemic levels and we are looking to grow, with our ability to provide design, tooling and manufacturing all in one place driving the need for more production space.
“There are lots of new opportunities domestically and overseas and we are hoping to turn some of the potential into contracts that will see turnover rise by 20% over the next twelve months.” 8 s-eng.co.uk
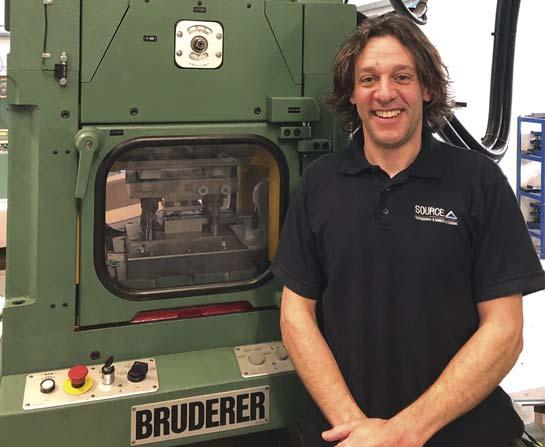
Precision sheet metal specialist Fife Fabrications has added a fifth SafanDarley electric press brake to create capacity for growth and increase its capabilities on larger panels.
The new SafanDarley E-Brake 130-3100 ULTRA represents a significant six figure investment for the company.
The first four E-Brake machines installed at Fife Fabrications in 2013 have been a great success story for the business, and this new technology will ensure that the folding capacity of its operations can further support its increasing customer base in 2021.
Based in Glenrothes, Fife Fabrications manufactures precision sheet metalwork, electromechanical assemblies and precision machined components and offers a complete service from design for manufacture support to manufacturing and full customer delivery. The company says the investment in this new technology will ensure it can maintain a clear focus on continuous improvement, flexible customer support and offering the lowest possible acquisition cost, whilst creating further streamlining for its manufacturing operations.
The original 100Ton E-Brake will be replaced by a 130Ton machine, with tooling supplied by Wilson Tool Ltd as Fife Fabrication’s preferred tooling partner. In addition to the higher tonnage, which will allow the machine to perform heavier work more efficiently, this latest machine has a number of new features such as the E-Mate Plus Bending Aid which will make bending of larger components simpler, easier and even more accurate.
Installed in March 2021, the model features lifting aids as a safety feature for managing larger panels and a larger opening height to form higher height flanges or parts. Like all E-Brakes, the ULTRA will be fully integrated into the company’s ERP system utilising the dual screen of the ULTRA and the fully 3D CNC Back gauge enables the most complicated of components to be programmed and processed with ease. 8 fifab.com
Fifth E-Brake for FiFab


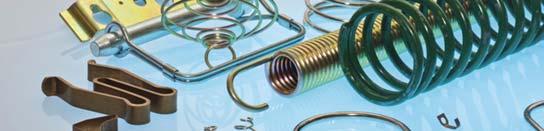