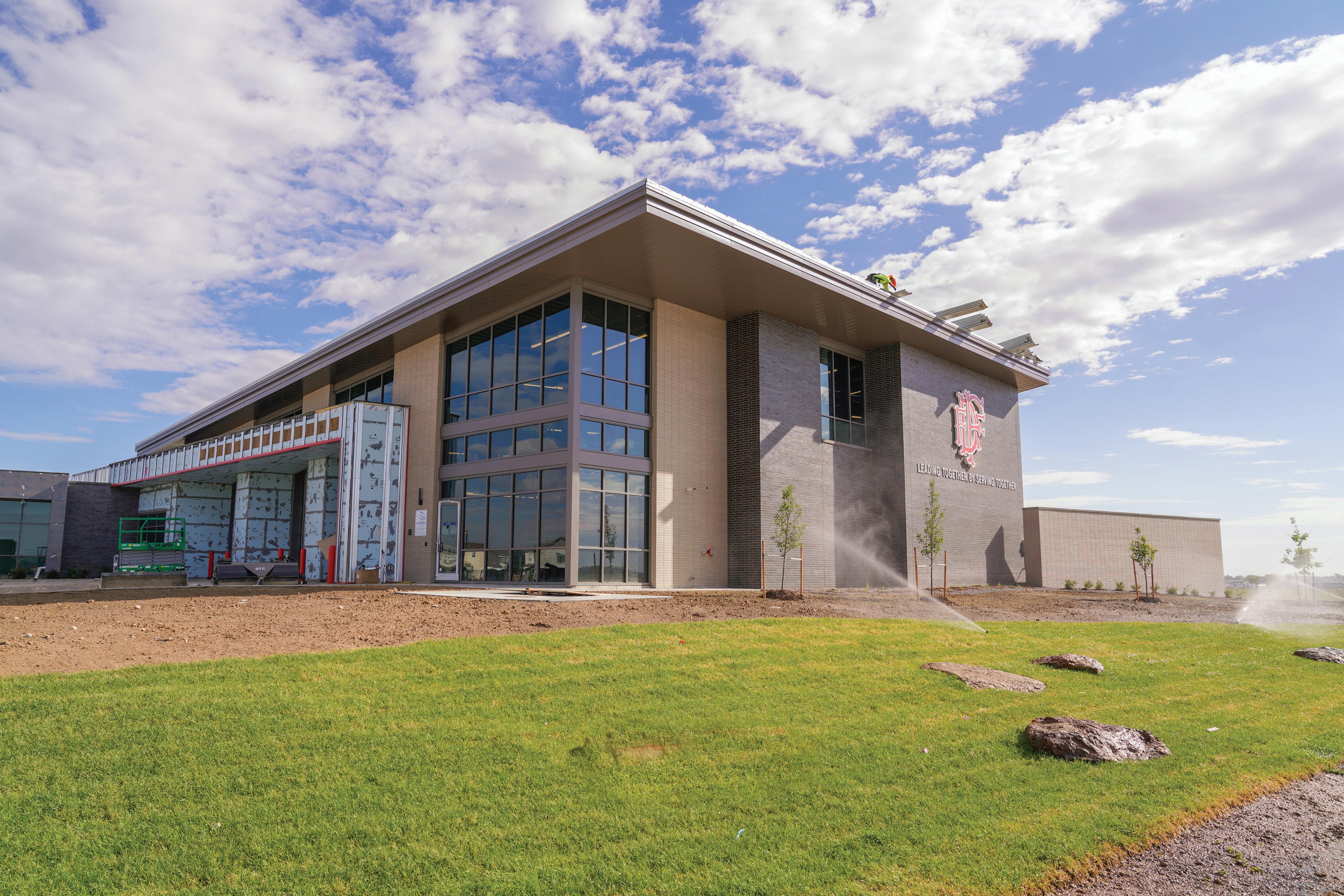
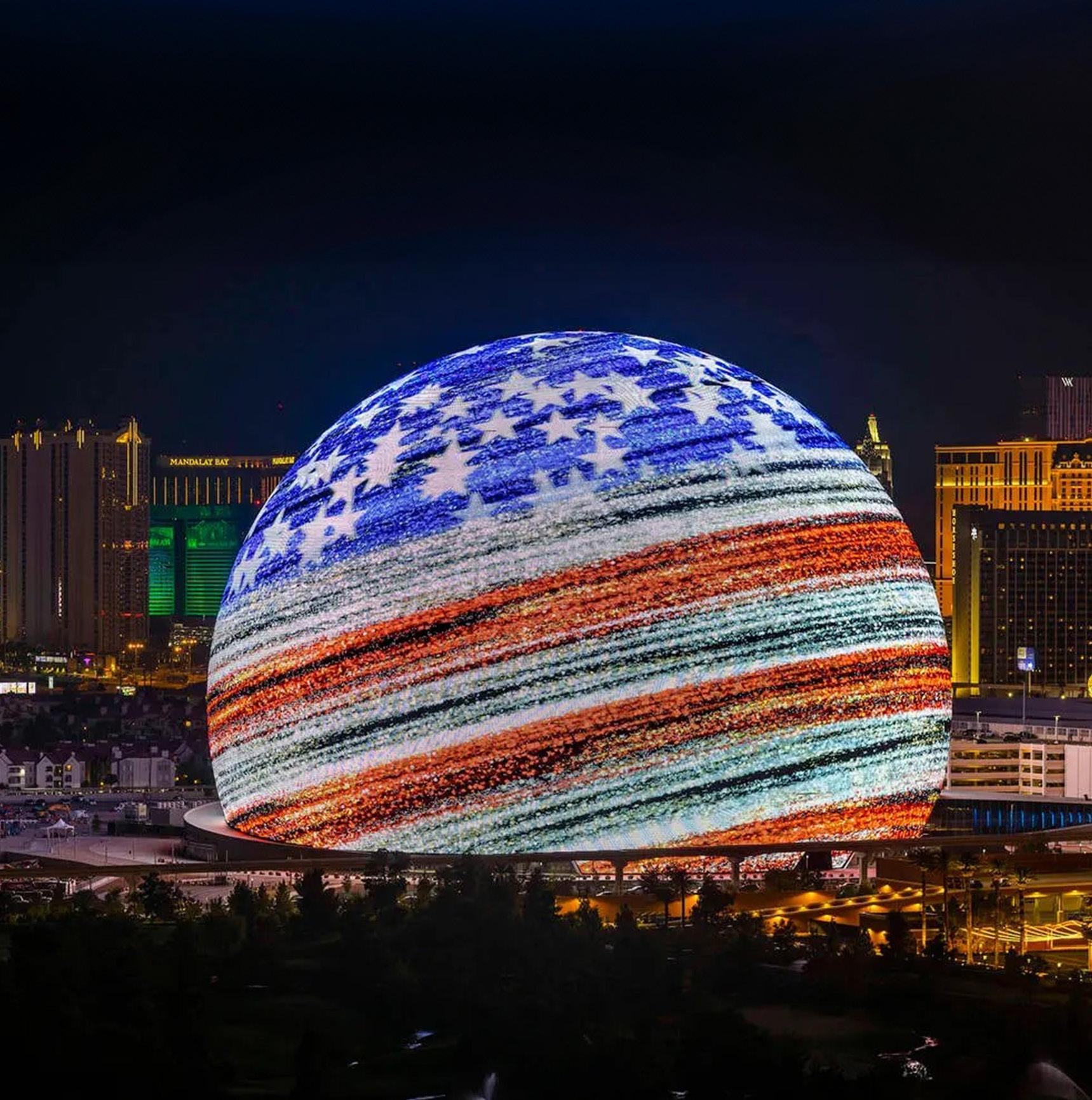
The venue’s massive, semispherical frame sits just south of Sands Avenue and east of Las Vegas Boulevard. The Sphere’s revolutionary design takes up 750,000 square feet and comfortably seats 18,500 concert goers. It boasts an eye-catching steel frame that has quickly become a landmark representative of the world-class entertainment and recre ation that Las Vegas has to offer.
To meet the Sphere’s aesthetic require ments, the engineering design called for unique sizes of round hollow structural sections (HSS). Atlas Tube was chosen as a partner due to its ability to quickly tool up, produce, and deliver those unique sizes within North America.
Atlas’ Engineering Support team had worked with fabricator W&W | AFCO on challenging projects before, and the ex isting partnership paved the way for col laboration that made the project a success. Achieving the intended vision of the Sphere required HSS sizes that are listed in the AISC Steel Manual but have never been rolled by Atlas Tube. Atlas invested in the necessary tooling to create the full range of required sizes for W&W, ultimately producing 2,460 tons of HSS ect. The strict quality standards of Atlas’ 100% domestically made steel combined with its wealth of experience and expertise with custom tooling and logistics helped W&W | AFCO deliver the project on time.
Though simple from the outside, the Sphere is composed of several interacting structural systems:
• A pile-supported foundation
• A structure supporting interior seating and vertical transportation
• The parametrically designed exterior skeleton, known as the geosphere
• A domed roof below the geosphere that supports an allencompassing screen over the concert venue
The round HSS members of the geosphere are connected to custom nodes produced by Cast Connex, which reduced fabrication cost and provided precise, repeatable geometry at each of the many connection points.
These parts work in perfect balance to create a unique, jaw-dropping superstructure that greatly benefits from the HSS compact profile and its unique ability to accomplish the engineering and architectural goals of the project.
In addition to the Sphere itself, the venue features a 1,200-foot-long off-site pedestrian bridge with a unique serpentine pattern that connects the Sphere to the larger Las Vegas Strip. The bridge features a metal walking deck and a metal deck roof, founded on pipe piles just like the Sphere.
Ultimately, Atlas Tube’s ability to quickly set up custom tooling for uncommon sizes of HSS, close relationships with fabricators, and its speed of delivery helped to make the MSG Sphere one of the world’s premier concert venues and a contemporary American icon.
Owner: Sphere Entertainment Company
General Contractor: MSG LV Construction LLC
Architect: Populous
Structural Engineer: Severud Associates
Erection Engineer: Stanley D. Lindsey and Associates Ltd.
Steel Team
Fabricator and Erector: W&W | AFCO Steel
Detailer: Prodraft Inc.
Bender-Rollers: Max Weiss Co.; Chicago Metal Rolled Products
Casting Manufacturer: Cast Connex
750,000 SQUARE FEET
18,500 SEATS
2,460 TONS OF HSS
Scan for a downloadable copy of the project highlight. More on the design and engineering of Las Vegas’ Sphere is covered in Modern Steel Construction and Informed Infrastructure. To learn more about Atlas or to discuss your design ambitions, call 800.733.5683 or visit atlastube.com
On the Cover: Building Frederick Firestone Fire Station No. 5 above an abandoned coal mine required a solution that lowered the subsidence risk.
Image courtesy of Salas O’Brien and Elevate Snaps Photography.
subscriptions@structuremag.org
Chair John A. Dal Pino, S.E. Claremont Engineers Inc., Oakland, CA chair@STRUCTUREmag.org
Kevin Adamson, PE Structural Focus, Gardena, CA
Marshall Carman, PE, SE Schaefer, Cincinnati, Ohio
Erin Conaway, PE AISC, Littleton, CO
Sarah Evans, PE Walter P Moore, Houston, TX
Linda M. Kaplan, PE Pennoni, Pittsburgh, PA
Nicholas Lang, PE Vice President Engineering & Advocacy, Masonry Concrete Masonry and Hardscapes Association (CMHA)
Jessica Mandrick, PE, SE, LEED AP Gilsanz Murray Steficek, LLP, New York, NY
Brian W. Miller Cast Connex Corporation, Davis, CA
Evans Mountzouris, PE Retired, Milford, CT
Kenneth Ogorzalek, PE, SE KPFF Consulting Engineers, San Francisco, CA (WI)
John “Buddy” Showalter, PE International Code Council, Washington, DC
Eytan Solomon, PE, LEED AP Silman, New York, NY
Executive Editor Alfred Spada aspada@ncsea.com
Managing Editor Shannon Wetzel swetzel@structuremag.org
Production production@structuremag.org
Director for Sales, Marketing & Business Development
Monica Shripka Tel: 773-974-6561 monica.shripka@STRUCTUREmag.org
CAST CONNEX ® custom steel castings allow for projects previously unachievable by conventional fabrication methods.
Innovative steel castings reduce construction time and costs, and provide enhanced connection strength, ductility, and fatigue resistance.
Freeform castings allow for flexible building and bridge geometry, enabling architects and engineers to realize their design ambitions.
Custom Cast Solutions simplify complex and repetitive connections and are ideal for architecturally exposed applications.
FEBRUARY 2025
By Russ Leffler, PE, SE, P.Eng, MLSE and Bryan Peters, PE, PMP
Frederick-Firestone Fire Station
No. 5 in Colorado met the challenges brought on by its unique site location.
By
Rebecca Lubrano, PE, and Paul Kassabian, PE, P.Eng., and C.Eng.
The structural design approach to sculptures is more complex than the classic load-bearing capacity of a structure; it expands into complex issues, including load application, structural response, and performance expectations.
By Peter Bourke, Adam van Duijneveldt, and Roy Denoon
The adaptive reuse and extension of a Sydney icon relied on wind engineering.
John Dal Pino
Linwood
Marcus
Nabeel Abdulazeez Al-Ayish
John Dal Pino
By John Dal Pino
Afew years ago, I read an excellent book on the Great Depression of the 1930s authored by Amity Shlaes titled The Forgotten Man: A New History of the Great Depression . It was a study of the depression and the economic policies enacted under the administrations of Presidents Herbert Hoover and Franklin Roosevelt that, in the author’s opinion, proved to be counterproductive and served to prolong the Great Depression.
However, what really stuck with me at the time and even today was what I expected to read about and who it was actually about. I was expecting, based on the book’s title, to read about people who had lost their jobs, traveled from town to town on railroad boxcars, lived on the edge of society, and stood in long lines at soup kitchens hoping to get something to eat. Think Woody Guthrie and his famous song Hobo’s Lullaby.
Bringing this back to my own career, I want to recognize a group of people who weren’t famous and never got their names published but without them, we structural engineers, and I, would not have been successful.
My career started at Degenkolb in 1982. Frankly, looking back, my knowledge of the company itself and how an engineering company operated was embarrassingly limited. Basically, I figured if I kept my head down and didn’t speak, my ignorance would be hidden. I was happy to have a job. And then I prayed.
more than anything in the world, and when his cat was sick or dying, production came to a halt. When the cat died, we designed a reinforced concrete burial tomb.
Jessie Wallace
But the key to success for a young engineer was to work with the drafters in producing engineering drawings.
What I read instead was a book about the people that through the tough times got up each day, went to work, earned enough money, however they could, to support their families and quietly, stoicly kept the country plugging along. They are The Forgotten Man. In any business, in any society, a mass of forgotten men and women make everything function. Today we think of the firefighters in Los Angeles, who, as we speak, are working thanklessly to save the homes of people they don’t know or will likely never meet. Their lives had to take a backseat to their job of protecting others. There was no other option for them. And then there are the countless individuals who serve others in some capacity or another—drive the bus, deliver the mail, serve our meals, make us fancy coffees, grow and pick our food, make sure the grocery store is stocked, build our buildings, etc.
After a few introductions, I learned there were the principals, a handful of engineers with varying amounts of tenure, the drafters, and the office administrative staff. Slowly it sunk in that the principals were quite well regarded, Henry Degenkolb being the most famous of them all. I learned not to mess with Henry’s secretary Doris Helterhoff. Doris answered all incoming phone calls, and you learned quickly if the number of your social calls exceeded her patience. She was our pit bull at the front door. If I wanted my letters and reports typed, I also better be on good terms with our shared secretary Diane Quirley.
But the key to success for a young engineer was to work with the drafters in producing engineering drawings. I learned a great deal from the drafters, how to depict the design intent and how contractors liked to build things. They left work at 5 p.m. and hated it when we engineers made corrections to “their drawings” in the afterhours.
After all of these years, I still remember their names and faces as if it were yesterday:
Don Smith—Head drafter. Don grew up in Oakland, helped his dad make moonshine during prohibition and was map maker in World War II. His drawings were works of art. He preplanned the sections and details in his mind before he started to draw. No erasing. No moving details around in CAD/ Revit like we do today.
Stuart Bowles—Stu was a Captain in the Army Air Corp and flew bombers over Germany in World War II. He loved his cat
old “prune picker” from the Central Valley. Before I knew there was a difference between an engineer and a drafter, I asked him a question about design ing a retaining wall. His response was “you better ask an engineer.”
Lionel Robinson “they pay me the same amount to draw it as to erase it.” His wife was a security guard. She occasionally visited the office, and it was clear to all that she was a person that you didn’t want to mess with.
Manuel Micaller—Manuel was trained as an engineer in the Philippines but because of the education rules for licensure, he had to settle for being a drafter. He was a bit of a card shark, but he didn’t cheat any more than everyone else. He was famously adept at taking unannounced vacations. When he wasn’t in the office on a Monday morning, we would run to the vacation calendar and discovered, lo and behold, that he was going to be gone for a week. But what about the deadline?
Ramon Padre —Ramon was also from the Philippines. I loved working with Ramon because his speed of drafting matched perfectly with my speed of designing. Ramon was the youngest of the Degenkolb drafters and the only one who, through self-education, made the transition to CAD. How many people have extended their career this way? So to sum up, I think it behooves us to appreciate all of the forgotten men and women who make our lives, professionally or otherwise, possible. They are critical to your business functioning or your community thriving. Let’s not forget. ■
Fungibility—or adaptability—can be achieved through intentional over-design of structures to fit a wider range of uses.
By Eka Linwood
Despite being one of the oldest engineering professions, structural engineering continues to evolve rapidly, much like the technology it supports. Just as Non-Fungible Tokens (NFTs) surged in popularity in 2020 alongside cryptocurrencies, today’s engineers face the challenge of designing adaptable structures in a world where speed and flexibility are paramount. Four years later, the NFT craze has waned, reminding us how quickly trends can shift in the tech industry.
This rapid pace highlights the pressing need for structural solutions that not only support swift deployment but also ensure mission-critical operations through adequate redundancy. To meet these demands, tech companies require robust hardware and infrastructure. Speed-to-market is essential; however, supply chain issues often hinder progress, with lead times for various equipment enclosures stretching to a year or more.
As structural engineers, we tend to view each project as unique, each requiring a bespoke design. Building authorities mandate that a licensed structural engineer design each structure. Tools like the ASCE Hazard Tool calculate environmental loads (wind, seismic, ice, etc.) based on precise latitude and longitude, which complicates the idea of fungible design—where structures are treated as productized solutions.
Fungible design is most commonly seen in generator enclosures, where generator suppliers create standardized containers around their products, allowing for reuse across multiple geographies. However, compliance with local authority requirements is still necessary. Structural design adjustments must be coordinated with various pipes, cables, and vents running through the enclosure. In this scenario, conservatively sizing structural members can streamline the design process and minimize coordination challenges with other engineering disciplines.
The most critical design decision that needs to be made early in the design process, is determination of “Risk Category” for the data center facility. The 2024 International Building Code (IBC) defines this in Table 1604.5, generically represented in Table 1.
The term “hazard to human life” helps us understand that the intent of the building code is first and foremost, life-safety. Although this concept works well in most cases, some facilities have significant consequential losses. Data center facilities are prime examples of this, where consequential losses are much more relevant than life-safety.
AISC’s Engineering Journal recently issued a journal entry titled “Construction Cost Premiums for Risk Category IV SMF Buildings”. The study examined an example building located in Los Angeles and found that a Risk Category IV building is between 6 to 16% more expensive compared to a Risk Category II building. The case studies in this journal focused on the building’s stiffness.
ASCE 7-22 Minimum Design Loads and Associated Criteria for Buildings
Enhancing fungibility of modular equipment and enclosures enables project owners to easily reallocate procured assets to different projects as priorities shift, expediting procurement lead-times.
and Other Structures has added a new Chapter 32 requiring Risk Category III and IV buildings located in tornado-prone regions to be designed to resist tornado loads. Tornado loads may sometimes necessitate weights to be added to the roof structure to act as ballasts against the uplift from tornado loads. The fact that Risk Category III buildings will now be required to be designed for tornado loads may prompt some owners to reconsider the building’s Risk Category selection.
ASCE 7-22 Section 13.1.3 and Table 13.1-1 consider Risk Category when determining requirements for anchorage of non-structural components. The cost premium referenced in the previous paragraph does not account for the additional reinforcements associated with non-structural components. Since selection of Risk Category affects several other design elements, some Engineers of Record would show two columns: “AHJ Minimum Requirements” and “Owner’s Requirements,” in either the specifications, or General Note section of the drawing set. Vendors on delegated-design items are then instructed to use Owner’s Requirements while permit evaluation will be based on both Authority Having Jurisdiction (AHJ) and Owner’s Requirements being surpassed. The only risk with this approach is that some AHJs may take issue with this approach, thereby delaying the permit approval process.
The discussion on Risk Category naturally progresses to selection of the Importance Factor for the project. Table 1.5.2 on Importance Factor in ASCE 7-16 has been simplified in ASCE 7-22, now only showing Seismic Importance Factor (Ie). This is the life-safety portion: if an owner contemplates the use of Risk Category IV, the building frame’s Ie should be defined as such at a minimum.
Table 1.5.2 references Section 13.1.3 on the Component’s Importance Factor (Ip), where the code requires Ip=1.5 for any life-safety components. The assignment of Ip is where an engineer’s judgement can heavily influence a project’s costs. Ip = 1.5 is required for “Risk Category IV” projects “for the continued operation of a structure.”
In ASCE’s context of Risk Category (life-safety), this requirement makes sense. When the Risk Category selection is Owner-driven, the definition of I p becomes more of a risk/cost-efficiency evaluation. Some components could be considered “mission-critical” and should be designed
with sufficient redundancy. Consider an ice-cream factory: an owner may require continuous operation of ice-cream storage, but not production. Components required to maintain functionality of the cold storage (such as generators, UPS, etc.) would then be assigned Ip = 1.5 for continuous operation, while components only associated with production would be assigned Ip = 1.0 to maintain cost efficiency.
Table 13.1-1 is where the impact of Ip selection becomes clear. The requirements in Chapter 13 would typically apply to mechanical/electronical components in SDC D, E and F but exemptions may still apply if the component weighs less than 400 pounds (discrete) or 5 pounds/ foot (distribution).
The most recent iteration of ASCE 7-22 has moved toward the use of a “multi-period” spectrum, moving away from “two-period” (0.2s and 1s) spectrum definitions. Meanwhile, ASCE 7-22 continues to evaluate SDC based on the two-period spectrum concept through a two-step process:
1. Determine Site Classification, based on the measured Shear Wave Velocity (Table 20.2-1 in ASCE 7-22). The geotechnical engineer would perform the required test (e.g., MASW: Multichannel Analysis of Surface Waves) and provide a recommendation on Site Class.
2. The Engineer would then go to https://ascehazardtool.org/ and input the project’s location, Risk Category and Site Class (referred to as “Soil Class” in the ASCE Hazard Tool). Based on this information, the ASCE Hazard Tool would provide the SDC and both the two-period and multi-period design spectrums.
ASCE 7-22 has significantly revamped Site Class Table 20.2-1 to provide a more granular breakdown of each Site Class. In prior ASCE iterations, SDC and Site Class had similar categories (A through F) which can create misunderstandings among project stakeholders who are less familiar with these concepts. Along a similar note, Section C11.4.3 has also indicated that the Fa & Fv values previously used to convert Ss & S1 into SMS & SM1 are no longer needed and thus eliminated.
Table 11.6-1 and 11.6-2 in ASCE 7-22 is summarized into a single table below. SDC selection depends heavily on the seismicity of the project site and to a lesser extent, the project’s Risk Category. Use of Risk Category IV essentially bumps the SDC up by one bracket, unless the project is located in an area with virtually no seismicity.
The addition of Table 13.1-1 in ASCE 7-22 helps communicate the impact of SDC selection on non-structural components requirements:
• Buildings categorized into SDC A & B are generally exempted by the requirements in Chapter 13.
• Buildings categorized into SDC C are generally exempt from the requirements in Chapter 13, provided:
o The mechanical and electrical components have an Importance factor (Ip)>1, and is “positively attached” to the structure, or
o The components weigh less than 20 pounds.
• Buildings categorized into SDC D and above are likely required to comply with the requirements in Chapter 13, with a few exceptions for light equipment/distribution systems.
The term “positive attachment” is not specifically defined under Chapter 13, but Section 12.1.4 requires a “positive connection” to have “a minimum design strength of 5% of the dead plus live load reaction.”
So, what exactly does this mean when we consider fungibility of modular equipment? One way to analyze this is by analyzing the
geography of the project portfolio. In the case of data centers, Table 2 indicates the total Megawatt (MW) for the largest data center regions in the U.S.
A few insights to be gained from this table:
1. Based on the Table 11.6-1 & 11.6-2 from ASCE7-22, a structure designed with SDS=0.16 and SD1=0.066 aligns well with SDC=A, irrespective of Risk Category designation. IAD (Northern Virginia) represents about 37% of the data center market, and likely falls within this threshold.
2. Designing a structure based on seismic design criteria of SDS=0.2 and SD1=0.13, would cover about 82% of the data center market. Risk Category selection starts affecting cost at this point, due to its impact on SDC and thus seismic bracing requirements. Bumping up SDS to 0.33 and SD1 to 0.133 may cover more geographies, without a significant impact on costs.
3. Consistent with the Pareto principle, the “vital few” geographies will be unique to each site and the concept of a fungible design starts to become very expensive. At this point, site-specific design parameters will likely be required: designing a project with PDX’s seismicity will be very different compared to a project with LAX’s seismicity.
For Engineers of Record and Owners Reps, the concept of fungibility is essential for ensuring flexibility of equipment purchased. Enhancing fungibility of modular equipment and enclosures enables project owners to easily reallocate procured assets to different projects as
priorities shift, expediting procurement lead-times. Design checks are likely still required by the AHJs but should be simpler since the design criteria is likely conservative enough to satisfy the localized loads imposed on the structure.
Use of energy dissipation devices can be used to achieve a more efficient design while maintaining fungibility. Displacements should be identified ahead of time where base isolation is used, to make sure any mechanical/electrical distribution routes are properly supported. Dampers can also be a good way to limit displacements while maintaining fungibility.
From a product vendor’s perspective, adopting fungible design is advantageous to minimize non-productive hours. Fungible products can be standardized across various clients and geographies and total inventory can be reduced since parts of fungible products will be more interchangeable.
Fungibility can be enhanced by analyzing critical project design criteria. Structures designed for Risk Category IV can be used for other Risk Categories and may be desirable in small structures. Analysis of project portfolio for seismicity and weather conditions (such as snow, rain, wind/tornado) design criteria can be optimized for enhanced fungibility. ■
Underestimated foundation settlements can lead to structural performance issues and potential overstress in members and connections.
By Gary R. Marcus, PE
One aspect of the effective design and long-term stability of any structure is considering the need to construct the foundation on suitable subsurface conditions. During the design phase, structural engineers evaluate various combinations of dead and live loads for the design of beams, girders, and columns and their connections and joints within a structure . They analyze how these forces and moments are transmitted through the structure and into the foundation elements. Often, structural engineers collaborate with geotechnical engineers who characterize subsurface soil and bedrock conditions and provide recommendations on allowable bearing pressures for appropriately sizing the foundation elements. The design process considers the allowable bearing pressure and potential settlement under design loads. Estimating settlements involves understanding soil behavior under load and using data from soil borings to predict vertical displacement of foundations. This article focuses on quantifying the potential settlement of shallow foundation elements, such as spread footings and isolated footings, which bear on granular soils (primarily sandy or gravelly).
Before structural analyses begin, the geotechnical engineer coordinates a subsurface exploration at the construction site. This exploration may involve various methods to determine the soil and bedrock present, including soil borings with Standard Penetration Testing (SPT) per ASTM Standard D1586, undisturbed soil sampling of soft and loose soils per ASTM Standard D1587, and rock coring to retrieve physical samples of the underlying bedrock per ASTM Standard D2113. Other methods might include test pits to evaluate subsurface conditions along adjacent property lines (especially for excavation support or underpinning) or cone penetrometer testing (CPT) for deep foundations or specific subsurface soil properties needed for seismic evaluation. However, most reports received by structural engineers for straightforward sites include soil borings and their associated logs. These boring logs provide essential information for estimating settlement. While log formats may vary, they should include basic information such as:
Soil Descriptions: These can range from the concise Group Name in the Unified Soil Classification System (e.g., Silty Sand, SM) to the detailed description system developed by Donald Burmister of Columbia University in the 1940s (e.g., Brown coarse to fine SAND, some (+) Silt, little (-) medium to fine (+) Gravel). Note the difference in these descriptions, even though they refer to the same soil sample.
Depth to Groundwater: This may be based on fluid level observations in the completed borehole, descriptions of encountered soil materials (dry, moist, or wet/saturated), or a temporary observation well or wellpoint installed upon boring completion. This information is used to evaluate neutral stresses from water in the soil mass and for subsequent computations requiring effective or buoyant unit weights for geotechnical analyses.
The SPT N-Value (N): This value may be noted separately but often needs
Fig. 1. Influence factors for use in the Schmertmann (1978) Method is charted.
to be computed from field boring logs. Most logs indicate the number of hammer blows on the split spoon soil sampler in 6-inch intervals. A 2-footlong soil sampling interval typically will have four consecutive numbers listed, sometimes separated by slashes or dashes. According to ASTM Standard D1586, N is the sum of the second and third blow count numbers (i.e., the number of blows needed to drive the soil sampler from a depth of 6 inches to 18 inches below the testing depth). N correlates with the relative density of a soil; for sands, this can indicate loose sands (N < 10 blows per foot), medium dense sands (N between 10 and 30 blows per foot), dense sands (N between 30 and 50 blows per foot), or very dense sands (N > 50 blows per foot). Subsequent corrections to N can be made based on sampling method (depth of sample below ground surface, borehole size, use of a liner within the sampler, and sampling hammer efficiency) and overburden soil pressure (including consideration for effective stresses from groundwater).
For the following discussion on estimating foundation settlement, N is a key component, requiring some correction based on sampling methods and overburden pressure.
Numerous methods are given in published texts, scholarly articles, and professional journals to estimate the magnitude of settlement of shallow foundations. Many of these methods consider the same fundamental information. These include:
Footing Dimensions. While it is basic information, some earlier formulas only considered the width of the foundation or estimated the footing to be circular (for allowing stress calculations that developed radially from
shape of a footing, whether it is square, circular, rectangular, long (usually the ratio of length to width is greater than 10), or strip footings.
Existing Overburden Pressure. Before any new construction begins, the ground is in its own “happy place,” at equilibrium with the forces and pressures acting on it. The addition of a new footing will increase the stress to the underlying soil. To identify the increase in the new stress, information about the existing stresses at the subgrade level of the footing need to be evaluated. For example, in New York City, footing depths for buildings are governed by Section 1809.5 of the NYC Building Code, requiring a minimum depth of 4 feet below finished exterior grade. If the ground surface remains the same, the effective overburden pressure at the frost depth may be between 400 and 500 pounds per square foot (based on a unit weight that ranges between 100 and 125 pounds per cubic foot). If a new footing designed by the structural engineer is intended to impart a contact pressure of 2,000 pounds per square foot at the same depth, the net increase in pressure that the soil would experience would be the difference of the contact pressure and the effective overburden pressure (in this case, 1,500 or 1,600 pounds per square foot). This net increase in pressure would be considered for estimating the magnitude of settlement.
“Stiffness” of the Soil. The stiffness of the soil can be correlated to the N-Value. Some formulas use the N-value—either corrected for overburden or the uncorrected field value—in the direct calculation of settlement. More recent methods consider the Modulus of Elasticity of the soil (E), which is based on the theory of elasticity and considers the soil to be an elastic material that shortens or compresses under loading like a spring. The Modulus of Elasticity can be obtained by testing of soils in the laboratory setting, by use of correlations with SPT N-Values, or by use of correlations with CPT data.
To perform a settlement analysis, guidance using the many formulae available is not simple, or using a “one formula fits all” may not be suitable.
Designers may consider one method to use for certain soil types (for which mine whether the overall magnitude of settlement is in the same range. If the results of one method are greatly different than other approaches used, it may be a sign that the parameters may be incorrect, the wrong units of measurement were considered, or an assumption used for a correlation for strength or stiffness parameters may need to be reevaluated. As an example, consider three different methods currently in use and compare their results. These three methods are as follows:
Terzaghi and Peck (1948), with adjustments from Teng (1962). While the study of modern geotechnical engineering dates to the early 1900s, most significant advancements in analysis occurred between the late 1920s and the 1940s. Terzaghi and Peck’s first edition of Soil Mechanics in Engineering Practice in 1948 introduced an empirical method for computing settlement by comparing it to a reference settlement of 1 inch. Their original formula and procedure included graphs based on their observations and empirical data for footings of various sizes, with footing width plotted along the x-axis. In 1962, Teng revised these graphs and the original formula to include a component for footing width, as well as corrections for groundwater depth and embedment depth.
Bazaraa (1967, 1969). This method resulted from the doctorate dissertation of Bazaraa while studying at the University of Illinois under Dr. Peck—the same Peck mentioned in the previous method. The formula for this method considers values of N corrected for overburden only and considers the lowest weighted average of the corrected values of N for this formula to a depth of B below the foundation (where B is the width of the footing). Additional corrections for the depth of groundwater and embedment depth are also included, which are intended to incorporate effective overburden pressures and changes to the unit weights being evaluated based on the presence of groundwater below the subgrade level of the footing.
Schmertmann (1978). Building on the research and developments of academics and scholars in geotechnical engineering, Schmertmann devised a method for estimating foundation settlement on sand and gravel. This method is based on field observations, laboratory models, finite element
analyses, and the theory of elasticity. Schmertmann’s equation, initially developed in 1970 and refined by 1978, includes several enhancements: a semi-empirical strain influence factor that varies with depth and footing dimensions, a correction factor for the effective overburden pressure at the foundation depth, a correction factor for soil creep over time (e.g., the design life of the structure), and the Elastic Modulus (or Young’s Modulus) for estimating soil stiffness beneath the foundation.
Assume a 10-foot-wide square footing is built 5 feet below the existing ground surface, supporting a load of 200 tons (including the self-weight of the column and footing). The groundwater table is approximately 8 feet below the ground surface. The soil consists of a medium to fine sand deposit, consistent with depth, with an overburden-corrected SPT N-Value of 28 blows per foot (indicating medium dense soils). This soil was sampled using drilling equipment with a safety hammer (60% efficiency). The soil has a moist unit weight of 120 pounds per cubic foot above the groundwater table and a saturated unit weight of 125 pounds per cubic foot below the groundwater table. Estimate the footing settlement after one year.
Considering the three methods presented, the settlement range varied between 0.37 inches and 0.87 inches, giving a range of about 0.5 inches between the highest and lowest estimated values. While these settlements may fall within acceptable limits, the results are highly dependent on the values used in the analyses. The first two methods rely on a weighted average of an overburden-corrected SPT N-value, whereas the third method (Schmertmann) can vary based on the correlation used for the Modulus of Elasticity, the number of discrete soil layers considered, variations in N values, and the timeframe considered for evaluating long-term settlement. For this example, variations of the Modulus of Elasticity selected for the soil could result in the magnitude of settlement ranging between 0.74 inches and 1.05 inches, a difference of 0.31 inches. Due to this variability, designers may need to consider variations in the correlation between the Modulus of Elasticity and the SPT N-Value (or CPT data, if used) to evaluate the sensitivity of the analysis and potential variations in stresses and moments in connections, joints, and structural members. Although all three methods yielded different settlement estimates, the overall settlement can be assessed by using multiple methods to ensure the estimates are within an acceptable range.
Like financial investing, diversifying methods is better than relying on a single method
for settlement estimation. This approach will add to developing a range of settlement estimates that a designer may need to consider to best identify movements that the structure may experience during its design life. If additional guidance is needed, the project’s geotechnical engineer may also be able to suggest methods which are suitable for the type of foundation and in-situ site soils. ■
Gary Marcus, PE, F.ASCE, BC.GE, is a geotechnical engineer with 27 years of experience, which includes the evaluation of soil and bedrock properties for the design of structures and infrastructure. He is currently a VP and Director of Geotechnical Engineering in NV5’s New York City Office and is also an adjunct assistant professor at Cooper Union in New York City and SUNY Farmingdale State College on Long Island. (gary.marcus@nv5.com)
The world‘s largest database of 400,000+ pre-designed 2D/3D connections, base plates, HSS connections, steel-to-timber, and other connection types
Model and design any bolted or welded connection
Comply with AISC checks, including advanced analyses
Fully customizable reports with equations and graphics
BIM integrations with SAP2000, STAAD.PRO, SDS/2, RISA, TEKLA, REVIT, export to IFC, and many more
Enabling parametric design with IDEA Open Model
Increasing the building heights of three steel-framed warehouses in Iraq for added food storage capacity brought unique challenges to overcome.
By Nabeel Abdulazeez Al-Ayish
The owner of a warehouse, Al-Maha Co. for Food Stuff, wanted to know whether it was possible to increase the height of three sheds each by 4 meters (13.1 feet) to increase capacity. The project under consideration was constructed in the mid-1990s . It consists of three typical structural steel warehouse sheds that are 9-meters high (29.5 feet), 30-meters (98.4 feet) wide, 150 meters (492 feet) long and with 6 meters (19.7 feet) typical bay size. The project is located about 20 kilometers (12.4 miles) southeast of Baghdad, Iraq. All sheds are fabricated with structural steel from European shape sections, some of which were non-standard (commercial). The shed roofs consist of trusses made up of double angle sections for the upper and lower chords, as well as the vertical and diagonal members. The sheds' steel column bases were designed as fixed-based connections, as reflected in custom detailing.
This challenge was extensively studied. Due to the lack of original construction design drawings, a comprehensive site survey also was conducted for all warehouse sheds. This included exposing structural components to determine their dimensions and non-destructive/destructive material testing. For instance, existing concrete core samples were extracted from
the foundation for compressive strength values. In addition, scanning for steel reinforcement location and bar size within the foundation were conducted.
Based on the site survey, as-built drawings were prepared for the sheds. Gravity loads (dead and live) and wind load were calculated in accordance with the specifications of the American Society of Civil Engineers ASCE 7-22. Then, shed steel frames were modeled using the STAAD-Pro structural analysis software. AISC Load Resistance Factor Design method (LRFD) was adopted as the design code/method, and a static loading structural analysis was conducted. Before increasing the building height, analysis results and design checks showed that all members were sufficient for strength. The shed span deflection and drift (lateral displacement) were also checked against the limits recommended in standard practice and international specifications. Lateral drift was limited to H/65 to H/100 for such type of structures (warehouses), where “H” is defined as building full height.
The next step was to increase the height of the main columns from 9 to 13 meters (29.5 to 42.6 feet). This was accomplished by inserting steel extensions at the top of the columns, as shown in the AutoCAD BIM
model used for construction (Figure 1). The structure was re-analyzed and as expected, the main columns and parts of the truss failed in strength since the increased structural height also increases the lateral wind projection area. As such, the main columns required shear, flexure, and torsion strengthening.
In addition, and as one of the biggest challenges of the project, the increased building height significantly increased the force demands to the foundation and the fixed-based column connections. Per owner direction, it was not possible nor practical to enlarge the existing foundation footprints, especially in plan dimension. The design solution was then directed toward changing column base connection from a fixed-base to a pinned-based (hinge) connection. The latter is particularly advantageous to use since a pinned-base connection theoretically does not transfer flexural moment into the foundation, which is the governing foundation design.
The design solution for the column base connection had to satisfy increased force demands to both reinforced concrete and steel elements and at the same time combine ease of application, economy, and aesthetic issues. In addition, construction and equipment could not occupy the interior space of the warehouses since material goods were still actively being stored there. As a result, structural details were developed to change the existing column fixed-base connection to a new hinged connection. This was accomplished through the following construction sequence and graphically shown in Figure 2.
1. Provide temporary shoring and lateral support to the main steel columns.
2. Disconnect the roof trusses from the steel columns and store the still-in-tact trusses on the ground. This releases a majority of the gravity loading to the columns.
3. Partially cut the steel plate stiffeners and flange/web components at the column base (Fig. 2a).
The design solution for the column base connection had to satisfy increased force demands to both reinforced concrete and steel elements and at the same time combine ease of application, economy, and aesthetic issues.
E7018 All-Around Fillet Field Weld (Typ.)
PL160x16mm Outer & Inner Flange Cover Plate Existing H360x180x10x7mm
4. Cut the column end connection to the existing base plate in order to make a gap.
5. Prepare and chamfer 4 – M30 mm (1.18 in.) threaded studs that are approximately 140 mm (5.5 in.) long, and weld them to old existed base plate with pre-defined spacing.
6. Prepare a 2L150X5mm angles with cut end and drill 4-Ø35mm (1.38 in.) holes in to their horizontal leg with same spacing of studs. Insert them through prepared welded studs of step (5), and weld their vertical leg to column web as shown (Fig. 2b).
7. Fill the gap between the existing and new base plates with nonshrink epoxy grout.
8. Cut the outer remaining parts of the existing steel stiffener plate. Aside from the column bases, the main column steel section required strengthening. This was accomplished by adding flange cover plates along the full height of the columns and with circular cut holes at vertical increments. These holes were introduced to weld plates to the column flanges to obtain greater cross-sectional properties (Fig. 3).
In conclusion, the column height extensions, column base connection modifications, and column strengthening are almost finished to date. However, additional project work continues for installation of other services per the owner request. ■
Nabeel Abdulazeez Al-Ayish, consulting engineer at National Center of Engineering Consultancy (NCEC)/Ministry of Construction of Iraq, and specializes in design & solutions of steel structures. (nabeelaibraheem@ yahoo.com).
Design strategies and materials can aid in avoiding energy loss through the roof and foundation structure.
By Russ Miller-Johnson, PE, SE
Integrated design measures at the top and bottom of a building are required as structural engineers meet the industry’s increasing need to reduce operational energy losses and monetary costs, mitigate harmful environmental effects, and safeguard the public’s health. Designs that incorporate insulative or even less conductive material in the load path provide measurable improvements in building energy and air quality performance. Breaking a highly conductive energy loss path through the roof and foundation structure with simple insulative materials, designed for load using common mechanics, can have a significant effect on operational energy savings that offsets the embodied energy of the insulation used.
This third part of a series on thermal bridging in basic building design outlines example strategies for mitigating damages to the rated thermal assembly at foundation or base levels, and roofs. The previous two articles on thermal breaks published in the November 2024 and December 2024 issues of STRUCTURE serve as a reference with respect to various material conductance properties, thermal break layout effectiveness; and design process and protocols implementations.
Insulating foundations and base level floors is critical in achieving high performance buildings. Available locations for insulation layers are limited.
Frost-Protected Shallow Foundations (FPSF) can have the added benefit of limiting the excavation and fill work and reducing reinforced concrete volumes. Comparative LCA studies have indicated FPSFs can reduce embodied carbon impacts as well as initial monetary costs. Following the code design requirements of SEI/ASCE-32 and emphasizing overall
appropriate drainage have resulted in time-tested well-functioning structural designs in commercial and industrial facilities.
While a necessary part of foundation and slab design involves analysis using the mechanical properties of underlying insulation, the use of Environmental Product Declaration (EPD) or similar product data would also be part and parcel of comparing the effects of various options. Just like soils are essentially a spring, so too are insulations, with pressure and deformation characteristics. (Though common spread footings waste concrete by being of uniform thickness, it does allow them to behave as effectively rigid in distributing loads uniformly to the subgrade.)
Plastic-based foam insulations have been commonly used in recent times. Although these petroleum products offer improved thermal performance over earlier use of cork and cinders below slabs and treated hardwood column bearing blocks for example in refrigerated structures, they are also subject to long-term performance degradation from moisture infiltration. Mineral wool and stone-based products such as FoamGlas and RockWool offer durable performance with R-value of approximately 4.0 per inch and moderate compressive resistance. These products can be energy-intensive to produce, and product EPDs are established to evaluate GWP impacts.
However, the increasing availability of mineral-based glass insulation offers materials with lower embodied carbon from heightened use of recycled materials and lowered waste, in addition to enhanced durability due to its effective impermeability. Also, as energy codes and certification programs may now require the entire slab area to be insulated, simplified insulation placement is availed by recycled glass insulation aggregates that also have enhanced durability due to their
effective impermeability. The foamed glass products are available as lightweight aggregate or in board form with a range of R-values of 0.9 – 1.7 per inch. Their use shows significant reductions in embodied carbon impacts over foam board insulation.
Column bearing blocks, from treated hardwood and to high-strength foams, have been long used in cold-storage buildings to address thermal bridges that waste energy and could lead to frost heave. Two conditions of note are where:
1. The foundation wall is insulated on the inside and columns pierce the sub-slab insulation.
2. The envelope is above grade such as in podium structures and the columns break the through the soffit.
Column bearing blocks are acutely effective in enhancing the building’s modelled thermal performance with compressive strengths of 300 to over 2000 psi at 2% deformations; and R-values of 1.5 to 2.5 per inch. Column bearing blocks also serve well as thermal breaks for roof penetration for fall protection and dunnage framing.
The base insulation required by energy codes will be in at least one of three locations, the “inside,” the “outside,” or “the middle” around a building’s perimeter. The insulation on the exterior continues up to the facade wall and is usually an uninterrupted envelope that does not require primary structural measures. (The durability and protection of exterior insulation at a building base is a related, but different study however.) Where the insulation is on the inside of a basement or foundation wall and requires a transition under the exterior wall to connect with the envelope or insulate the wall’s base, a structural design incorporating insulative material is often required.
Block and Mineral Wool
“Inside” Insulation
Use of materials at wall base that are less conductive than concrete,
but durable, is an effective design method to follow. Moisture protected Autoclaved Aerated Concrete (AAC) or hemp-based block, compression-rated insulations including graphite polystyrene (GPS) that greatly reduces water absorption, treated wood, or proprietary insulated “sill” products are examples of materials in-service.
Insulation in the middle of a foundation is a similar construction to concrete sandwich wall panels. Proprietary systems in the market use low conductance form ties to maintain foam insulation panels to not float about on a vertical pour and allow for the foundation wall insulation to align with the exterior wall envelope above and obviate transitional insulated sill elements required for “inside” conditions and additional insulation protective measures for “outside” arrangements.
The thermal bridges encountered in roof penetrations are similar to those for beams or facades as they present intermittent violations of the envelope. In addition to energy efficiency reductions, the penetration points can generate condensation, especially above closed ceilings or in high-performance enclosure buildings, if adequate thermal break measures in the structural load path are not provided. Thermal break connections can use available product assembly specifications with the less conductive layer in alignment with the roof insulation to achieve greater efficiency. Even without this alignment, an improvement of 10% at the penetration point has been determined possible.
The obvious steel post framing for equipment dunnage, screen walls, fall protection anchors, and solar energy racks are common thermal breaks to be attenuated. Note that carbon steel screws for mechanically
fastened roofs protruding into the building are also an operational energy waste factor. Recent studies indicate that such roofing fasteners can result in effective R-value losses in the range of 4-16%; projects looking to address that loss have considered ballasted roof systems and using Structural Insulated Panels (SIPs) above the above a conventional metal roof deck and connected to the primary framing only to reduce the aggregate area of fasteners through the envelope.
While this three-part series has shown that thermal break designs engender integrated, interdisciplinary work, the articles have also provided the basis and background for structural engineers to invoke the lead in meeting energy codes; attaining enhanced, durable building performance; and actualizing sustainable measures. In addition to evaluating operational energy improvements, thermal break options
can be differentiated with regard to embodied energy as part of the structure’s Life Cycle Analysis. These assessments can be verified by specifying EPDs, equivalent industry, or product information to be submitted. The structural engineer’s roles and responsibilities can be preserved and surely enhanced by reducing the wasted energy pollution. ■
The structural design approach to sculptures is more complex than the classic load-bearing capacity of a structure; it expands into complex issues, including load application, structural response, and performance expectations.
By Rebecca Lubrano, PE, and Paul Kassabian, PE, P.Eng., and C.Eng.
Unique structural sculptures in public spaces fulfill a demand for art, city beautification, memorials, etc., as well as to meet the desire for more geometric forms and materials.
Bringing creativity to life, however, requires a design approach that is more complex than the classic load-bearing capacity of a structure. It expands into issues including load application, structural response, and performance expectations. However, specific guidance for the structural design of sculptures is lacking.
Examples include new materials or systems with little to no prior data in structural use, methods of applying loads to non-standard geometries, how humans might interact with the sculpture (whether intentional to the art or not) with defining limit state design approaches that are applicable, and approaches of communicating expectations with Clients for the behavior of unique non-standard structural sculptures.
Most importantly, if the structural engineer is to contribute to the success of the artwork, they must understand the artist’s creative intentions to create a material object in space that has not existed before (and may never again). This is the antithesis of classic engineering education and examination based on complete provided information and a singular correct answer. You are in the land of the unknown, assigned to make it real!
As every artwork is unique, there cannot be a singular checklist that will suffice, but sculpture projects in general face some or all the issues discussed here. These guidelines are a starting place for future engineers in this creative realm—providing the flexibility required to truly encapsulate the very artistic spirit you are working to protect.
A common question for structural engineers about sculpture design is, “You’re designing the plinth for the sculpture, right?” While the authors have certainly done this for both the standard monolithic concrete base and for “smarter” plinths such as an isolation table for slender sculptures in high seismic zones (Fig. 1), the focus of this article is the design of the sculpture itself, the heart of the artist’s expression. Another common question: “Is there a minimum size when you need a structural engineer for a sculpture?” The answer is “no.” A large sculpture may be “typical” whereas a small sculpture may be unique and of higher risk to the public. In general, a structural engineer is required when:
1. Someone has explicitly required a structural engineer such as: the owner asks based on where it’s being installed; a code requirement triggers the need due to the scale of the installation or local loads; or a building official says the installation needs an engineer.
2. Life safety: When the location and/or premise of the particular installation could present a risk to human life such as in a large and/or very public place. For example, the “Heart of Hearts” sculpture, which was
located in Times Square NYC over Valentine’s Day in 2015, a busy location where a lot of people interacted with the installation (Fig. 2).
3. Something is unique about the installation. This category can cover a large variety of situations, and some examples include: 1) The geometry is unique so understanding the structural behavior and necessary sizes and connections is not intuitive; 2) the material(s) intended for the sculpture may either be new to the artist, new to the application, or generally have limited industry guidance for the intended application. These limitations often lead to the need for laboratory testing and more careful performance considerations; and 3) The artist might be looking for (or looking to avoid) a particular type of behavior that requires some analysis or structural consideration.
The Ashby plot in Figure 3 shows the range of material types plotted as Youngs Modulus vs. Strength. It is a reminder of the broad world of material options when based only on their material properties. Given the size and specificity of unique sculpture projects, the full range of material options is available and, when considered with combinations of complementary materials and fabrication processes, opens a world of possibilities.
The authors have worked on projects using robotically milled stone with and without GRP rod reinforcement, 3D-printed glass, 3D-printed titanium, 3D-printed concrete
(post-stressed with steel tendons), bamboo with steel rods, double-curved corian surfaces, glass and UV-cured adhesive, rigid foam, inflatable membranes etc.
As engineering design is based on data, new materials (or new combinations of materials) require physical testing. Establishing the extent of testing, acceptable standard deviation in the results, and an appropriate safety factor requires significant engineering judgment given the specific use case of the sculpture while managing budget constraints given the data is required only for a single project.
The authors have established the following approach, with the help of an in-house materials testing lab and materials specialists on staff:
• Given the specifics of the sculpture, define the highest risks associated with the least known material information.
• Determine the appropriate tests to address the above and with what test sample size(s).
• Consult appropriate ASTM standards but also allow for flexibility in the approach to testing from the standards as needed by the specific installation.
• Determine a number of tests to perform either based on the referenced ASTM standards or based on past experience with the material type and test.
• Determine what constitutes “passing” and “failing” the test. This is often dictated by the referenced ASTM standards but, when none are applicable, we reference the International Building Code (IBC) section on Preconstruction Load Tests, which recommends a Factor of Safety of 2.5 (Section 1709 in IBC 2021). The resulting
magnitude of the load for this testing can vary greatly, from a couple hundred pounds for a unique but small wood connection to multiple tons for a compression test.
• Observe the testing in person, specifically the failure mechanism, as this can produce a reassessment of the defined process.
Inviting the artist and/or client to witness the physical tests or sharing video of the results afterwards becomes a critical moment to manage expectations as, while any material can be tested to failure, many of the people involved have never seen actual material failure. They can become concerned (or better educated) watching the moment of failure in the technical process that is providing the data required for a safe design. Two concerns related to material testing data for projects are:
• The testing and data are specific to a singular use and hence there is no mechanism for sharing this with the wider design community who may be using the same or similar materials in a future design.
• Engineers may lack access to material specialists and/or the range of appropriate physical testing equipment such that critical tests are not identified or not completed to the extent sufficient for a safe design.
Typically, the primary environmental loading conditions for an outdoor sculpture are snow and wind loads. While the geometry can make load application and determining wind/snow forces in accordance with ASCE difficult, ASCE continues to evolve with additional guidance and research around some of these more unique non-building forms.
A frequent consideration introduced with sculptures is the potential for the installation to be “temporary” with seasonal exhibits, often over the summer months. While this often allows for ignoring snow load or reducing the wind load in accordance with the ASCE guidance, it is common for artwork to be available for purchase, so a temporary summer-only sculpture can become a permanent year-round installation in a different location. Not only is the reduced snow and/or wind load no longer applicable for the permanent installation, but the load requirements of the new site can be far greater than the original location, such as higher wind loads for a sculpture moving to the Florida coast or higher snow loads for a sculpture moving to the White Mountains of New Hampshire. Hence, discussion on design loads and expectations for future use becomes critical to prevent code-required changes the to the structure of the sculpture in the future that might adversely affect the artistic intent.
The loading conditions for an interior sculpture are typically less clear. Situations where the sculpture may have human interaction loads is
discussed below, but when sculptures will not be occupied, there is limited code guidance. The authors generally utilize the code suggested partition load of 5psf. While IBC directs this for use in partitions of 6 feet in height, it is a reasonable way to confirm lateral stability of the installation. This also gives some sense of the magnitude of the sculpture’s movement under lateral loads from doors opening and mechanical equipment for discussion with the owner.
Unique among structural design with sculptures is the range of human interaction which can be fundamental to the performance of the piece or extend to acts of vandalism.
While ASCE addresses considerations for some non-building structures, the bulk of the code provides guidance on objects of the scale of buildings, where forces from a few human occupants are minor and not usually an explicit consideration beyond the consideration of vibrations and the wellknown guardrail loads. When considering human interaction with artwork, the artist’s intent and even the fundamental idea of art exemplifies how this interaction element cannot always be defined.
When artwork is accessible at grade, analyze two lateral loads:
1. A 30-pound lateral load at 42 inches above grade to know the movement achieved by someone standing adjacent to the sculpture and “giving it a shove.” If there’s enough movement, the person might continue to interact more, which can be discussed with the artist whether this is desirable.
2. The equivalent of the single guardrail type point load of 200 pounds to confirm the structure is stable should someone (or a group) run into it. Although the job of a guardrail is to contain people from a fall which may not be applicable to the sculpture at grade, we do this both to meet some aspect of code safety and, as noted, because no other guidance exists.
In one example, a client wanted a vertical cantilever (30-feet tall tower of glass bricks connected
with UV-cured adhesive) positioned in a public city park “for two guys coming from the bars on a Saturday night who try to shake it” only for the client to add “wait they might have friends, so you should design it for four guys shaking it.” While ASCE 7 is obviously silent on this particular load case, the concern behind the request is clear: make sure this sculpture is safe from a circumstance we can all imagine happening. This is the essence of the recommended design approach and discussion: given the particular artwork and what the artist wants, what we can all imagine is likely to happen, and what is the Client/Owner willing to accept in terms of performance that should be designed for?
The most common theme related to the above is that of human interaction with the sculpture and expected movement. The “Untitled Sounding Sculpture” by Harry Bertoia in Chicago 1975 is an ethereal piece of vertical steel rods sufficiently slender and closely spaced that a strong breeze causes them to sway and hit each other creating a beautiful sound. This level of slenderness and intended movement has related consequences. Over time, many are no longer perfectly vertical, some seem to be permanently curved and out of plane (therefore not just visually misaligned but less effective at sounding), and any or all of this piece can be easily vandalized and bent.
Seaport by Skylar Tibbits (2020) is similar to Bertoia’s piece but with the intent of sounding only when people move the vertical rods as opposed to a breeze. Initial design and prototyping of the preferred size for movement by children resulted in the ability of an adult being able to permanently damage the rod by leaning back and progressively moving their hands further up the bent rod (a creative P-delta effect). The end result shown in Figure 6 allowed for successful movement and sounding by energetic children with vigorous shaking although it did not protect one of the rods from later being damaged and bent from an accidental impact of a snowplow.
Putting a “Do Not Climb” or equivalent warning sign adjacent to certain sculptures is often discussed.
This addresses the legal “attractive nuisance” issue where someone may climb an interesting
sculpture, fall, and file a claim. However, the authors are also conscious of the reality of both installing and maintaining the sculptures and the human desire for a photo regardless of warning signs. Hence in addition to the 200-pound guardrail load, the authors typically design sculptures for a minimum of one person point load of 250 pounds (representative of OSHA’s ladder loads) located anywhere on the sculpture. For larger sculptures, the number of point loads may be increased accordingly, especially when it will take multiple workers to erect and/or maintain the structure. These load considerations are not meant to capture all instances of possible use but build a defined level of safety and stability into the sculpture that might not otherwise be captured.
As a result of form, material, and exposure to elements or people, sculptures can noticeably move; however, there are no guidelines on what is or is not acceptable or, more relevantly, what the right approach is to discuss what is acceptable with various parties.
Sculptures do not have to meet typical deflection limits for buildings if their form, performance, and materials are different. AISC Design Guide 3 implies that if a structure is only occupied for maintenance, the allowable drift can be h/240 with a maximum of 2 inches under those maintenance lateral forces or the ten-year wind should be considered for the maintenance person to feel “safe.”
However, some sculptures are meant to move in the wind or easily with
human interaction. The important discussion here is if others will consider it dangerous when they observe movement.
Proactive approaches during the design phase include:
• Relate wind speed discussions to the Beaufort Scale. The empirical and descriptive nature of the scale keeps the discussion focused on human experience rather than technical aspects. The reference provided at https://www.weather.gov/mfl/beaufort is helpful.
• Use videos taken of items such as suspended lights or window blinds moving inside tall buildings on windy days showing movement is perceptible (and to counteract assumptions that something must “not move”).
• Use videos of everyday outdoor objects vibrating e.g. long cantilever traffic lights.
• Use videos of recorded high wind speeds. Showing a client a video of 120mph winds (various exist on YouTube) reminds them that people are not outside looking at a moving sculpture in such conditions. These approaches were used in discussions with various parties for the carbon-fiber MIT Kendall Pavilion placed on slender cantilever columns and above an active metro station.
Note, in some cases, an alternate path can reduce the concern about movement under large loads, especially predictable loads like snow and wind. Some Owners are willing to modify the artwork by either removing large portions of the structure or by adding stabilizing systems when a large snow or windstorm is expected. However, if the artwork is permanent, it is not guaranteed this requirement will always be adhered to, so consider this method only for temporary installations.
While the idea of multiple structural engineers on the same installation is not unique (many documents address delegated design responsibilities), the unique nature of design and procurement of various sculptures can also leave communication and responsibility gaps. If the sculpture is interacting with another structure, whether it be a foundation designed by someone else or the sculpture being hung from an existing building, it is important to define early on where the sculpture engineer’s responsibility ends and the supporting structure’s engineer’s responsibility begins, making sure there is a continuous load and responsibility path all the way through. The authors typically physically draw out what this means, color coding who is responsible for what and providing “red dashed lines” where the line shows demarcation of responsibility and the “dashed” nature noting information needs to be exchanged between the associated parties for coordination purposes.
For example, Figure 10 represents a suspended artwork designed by Engineer 1, who gives load information to Engineer 2 to design the supporting hangers, and who gives load information to Engineer 3, the
designer of the base building. Also, as per IBC, a registered design professional must be responsible for both the overall structural system behavior and coordination of the parties involved. Some of the roles shown in the diagram may be the same engineer (e.g. suspended hangers and the artwork) or multiple parties. The more parties involved, the higher the need for a diagram to prevent confusion during design. Also, if there is the possibility of interaction between the structural elements then that also must be communicated and addressed.
While this approach is standard on building projects with multiple engineers, if some parties are not experienced with sculptures or non-standard materials, they may push back on engaging as required. Guidelines for the structural design of sculptures would provide a reference document for this process as well.
Helping to realize the artistic vision from a structural and material engineering design approach for sculptures, installations, pavilions, canopies etc., is a joy. These projects hold many unique aspects that extend beyond the typical experience of a structural engineer to ensure both the built sculpture and all parties involved are successful. The majority address human understanding and emotions while providing a technical service. Given how unique sculptures can be and the importance of the structural engineer’s role in their success, this article is a starting point for engineers considering appropriate guidelines for the successful creation of more beautiful art in the public realm. ■
Rebecca H. Lubrano, PE, is a Senior Project Manager with Simpson Gumpertz & Heger in Waltham, MA (rhlubrano@sgh.com).
Paul E. Kassabian, PE, P.Eng., C.Eng., is a Principal with Simpson Gumpertz & Heger in Waltham, MA (pekassabian@sgh.com).
Frederick-Firestone Fire Station No. 5 in Colorado met the challenges brought on by its unique site location.
By Russ Leffler, PE, SE, P.Eng, MLSE and Bryan Peters, PE, PMP
The design of Frederick-Firestone Fire Station No. 5 in Frederick, CO, exemplifies cutting-edge structural design. Built atop an abandoned coal mine, the design team faced extraordinary challenges, including mitigating subsidence risk by crafting an innovative foundation and superstructure. More than just a building, the new fire station No. 5 is a testament to advanced engineering solutions and seamless teamwork. From its design as three separate buildings to its unique foundation that floats on the soil to the combination of cold-formed steel (CFS) infill wall framing with CMU veneer for durability and easy repairability, every aspect of this structure has been meticulously crafted to withstand the unpredictable forces of nature.
Beginning in the 1850s, Northern Colorado developed coal mining alongside precious metal mining. In addition to providing the fuel needed to transport gold and silver ore out of Colorado, coal warmed the growing number of homes in Denver and other burgeoning towns across the Front Range, making coal mining a key economic driver of the area.
Frederick, 39 miles north of Denver, was the home of the secondlargest coal mine that Colorado Fuel & Iron, a company foundational to the industrialization of the American West, ever operated. Opened in 1907, it employed around 500 workers and produced an estimated 1,500-2,000 tons of bituminous coal per day at its peak in 1927. The mine closed in 1960.
Coal mines were constructed using the “room and pillar” mining technique, which involves creating a network of tunnels and rooms supported by coal pillars and allows for controlled collapse. Miners tunneled into a coal seam and dug rooms off the side between pillars of coal. Beginning at the tunnel's far end, they shaved coal off the pillars until the room was deemed unsafe. Then it was left abandoned to cave in. Some rooms caved immediately, and some are just now doing so decades after a mine's closure.
Geologists refer to the event of room collapse as a “subsidence,” which can take the shape of a bell-shaped pit, hole, trough, or sag at the earth’s surface. Tension cracks can also form around the perimeter of the subsided ground. The closer these rooms and shafts are to the surface, the more impact the subsidence has on structures built above them.
The Frederick-Firestone Fire District (FFFD), which currently serves
the Towns of Frederick and Firestone and areas of unincorporated Weld County, considered several sites for the new station No. 5. The fire district chose the final site location due to the clear need for additional fire protection services in the area which was identified in FFFD’s 2021-2026 Strategic Plan. Population growth within the district was driving this need, as it was projected to continue up to a staggering 7% per year. To accommodate this growth, the Towns of Frederick and Firestone needed to continue to annex unincorporated areas and increase commercial and residential development, leading to a rapid increase in calls for service and expansion of their service area, which now includes 36,000 residents across 36 square miles.
In situations where response times are measured in seconds, new fire
station locations are carefully chosen according to how quickly apparatus can arrive at the scene after a call for service is received. According to its website, FFFD’s stated goal is to get lifesaving equipment and rescuers to an emergency scene within 5.5 minutes of receiving notification from the dispatch center. FFFD chose the final site for the new fire station No. 5 according to its ability to best meet this goal upon completion of a capital infrastructure needs assessment.
The location came with significant subsidence risk, estimated at 0.45 feet over the building’s length. To minimize the potential risk, the Colorado Geological Survey report recommended the station design consist of several smaller buildings, each no longer than 78 feet in length, instead of one large facility, which would reduce subsidence to 0.23 feet, nearly half the original estimate. With these guidelines, the building structure would not be subject to subsidence-induced surface strains capable of producing greater than slight damage in a worst-case event.
In accordance with the geological report recommendation, the station design consisted of three separate buildings with complete isolation joints through the foundation and superstructure. The design team considered three foundation options:
1. Deep Foundation System: Deep foundation systems comprised of straight-shaft drilled piers founded in claystone bedrock are a common foundation type along Colorado’s Front Range. Large foundation loads and/or the foundation’s ability to resist the effects of expansive soils necessitate the use of piers. Shale bedrock typically has high bearing capacities and
limits foundation movement over time. However, the geological report recommended a flexible structure with foundation seg ments less than 78 feet in length to allow the subsidence to occur. With the inherent rigidity of this foundation system, the design team was concerned that focused areas of severe damage would occur within the structure, and this approach was eliminated as a viable solution.
2. Shallow Foundation System: A shallow foundation system using concrete spread footings is also common for buildings in the area and was also considered for the project. Although inde pendent footings supporting the building columns would allow for differential settlements across the site, the induced stresses and strains within the superstructure could be considerable, as
well as unpredictable, depending on the subsidence profile. These factors eliminated this foundation type.
3. Shallow Raft Foundation System: The selected foundation system uses shallow raft foundations broken up into three monolithic pieces that could float on the soil below while providing the necessary shear and bending capacity to resist the additional forces induced by a subsidence event. By limiting the differential deflections within each raft, the induced stresses and strains in the superstructure resulting from the soil subsidence are more manageable and predictable.
A finite element foundation analysis was performed and included nodal displacements in a parabolic profile to emulate a variety of subsidence events, resulting in additional concrete thickness and reinforcing steel in the final design while maintaining safe subgrade bearing pressures. In addition, the displaced foundation profiles were analyzed to resist the applied gravity, wind, and seismic loading to ensure the long-term performance of the structure should subsidence occur during the structure’s life.
The resulting raft foundations are 18 inches thick and reinforced with #6 reinforcing steel top and bottom, spaced at 12 inches on center with 8-foot square, 30-inch-thick integral foundations at the column locations. A reinforced turned-down edge detail at the perimeter of each
grade to protect against frost heave.
Like the foundations, the primary superstructure system needed careful consideration to evaluate performance and flexibility requirements. Fire stations are typically designed with highly durable surfaces, including intermediate or special-reinforced concrete masonry (CMU) walls, due to CMU’s ability to be thoroughly washed down to disperse contaminants from apparatus and firefighter gear. Unfortunately, structural CMU walls lack the necessary flexibility to survive building settlement without requiring substantial repairs, which would not be an acceptable solution for an emergency response facility.
To create the necessary flexibility above the foundations, the primary superstructure consisted of fixed-base ductile steel moment frames encompassing each of the three buildings. Although the project site was found to be Seismic Design Category A, the design incorporated a response modification factor, R of 3.0. The design team incorporated the increased moments and displacements due to the settlement that would occur during subsidence and then analyzed and designed the steel superstructure to resist the applied gravity, wind, and seismic forces. In several locations, over 50% of the bending moment reaction at the foundation was caused by this assumed coal mine subsidence, going from 55 kip-ft due to soil settlement to 106 kip-ft after adding
the vertical and horizontal loads. A 2-inch isolation joint through the foundations and a 3-inch isolation joint between the walls and roof structures were maintained to allow for the predicted tilt of the structure during a subsidence event, plus horizontal drift under lateral loading and P-delta effects.
The moment frame column locations along the interface between individual buildings were offset to one another to allow for the constructability of the beam-to-column moment connection joints. Without this, the steel erector would not be able to complete the required bolting and welding for the connections, as the adjacent framing would block the far side of the joints.
All the design disciplines were carefully coordinated to ensure the structure could be efficiently constructed and provide long-term performance for the Owner. The station design specified flexible utility connections across the expansion joints for electrical, mechanical, data, and plumbing lines to allow for differential settlement across the three buildings over time. The expansion joints were located at physical transitions between the different building surfaces wherever possible at both the interior and exterior of the buildings, for example, along the interface between roofs and exterior walls, at wall corners, along separating parapets, etc.
The station’s design also addressed the challenge of maintaining structural integrity after a subsidence event for both the secondary structural elements and the architectural finishes. As mentioned previously, fire station design typically employs concrete masonry CMU walls. However, CMU walls were deemed not ductile enough for this project due to the settlement concerns. Therefore, in lieu of traditional CMU walls, the interior containment perimeter and the exterior envelope design specified CFS infill wall framing with CMU veneer. This pairing combines a lighter, ductile, and more sustainable material choice in CFS with the necessary durability of CMU. Although masonry veneer with CFS wall framing backup is a common system for building exterior walls, this was employed throughout the apparatus bays and containment areas within the fire station as well. By designing and detailing the CFS wall framing to allow for the
predicted deflection and movement of the building structure, including careful coordination of the veneer control joint locations, the intent of this approach is to limit potential damage after a subsidence event to drywall and non-structural veneer repairs, preserving the superstructure's performance and operation. After careful evaluation, the design team felt this system and approach was the best selection to balance functionality for the Fire District, while also achieving the geological report goal of incurring only slight damage levels and maintaining the structural integrity of the superstructure and CFS wall framing after a subsidence event.
The subsidence and estimated movement impacted all design disciplines. The team worked together and creatively, embracing the challenge of designing a structure required to provide emergency response 24 hours a day, 365 days a year despite the site's significant constraints. The station design included material choices that address the hazardous contaminants inherent in the operation of a fire station while providing a modern design that respects the community context and includes all the necessary amenities for firefighters’ health, wellness, and workplace efficiency. ■
Full references are included in the online version of the article at STRUCTUREmag.org .
Russ Leffler, PE, SE, P.Eng, MLSE , is a Principal at Salas O'Brien, with technical expertise in many areas, including industrial structures, public works projects, CFS engineering design, and blast-resistant design.
Bryan Peters, PE, PMP, graduated with a civil engineering degree from the University of Nebraska-Lincoln and is a Senior Project Engineer
The adaptive reuse and extension of a Sydney icon relied on wind engineering.
By Peter Bourke, Adam van Duijneveldt, and Roy Denoon
Wind engineering, including wind tunnel studies, is conducted most commonly during the design phase of a project. As repurposing, adaptation, and extension of existing buildings are adopted more to meet sustainability goals, wind engineering can play a larger role during construction by demonstrating performance targets are being achieved, while safety and reliability requirements are met. Quay Quarter Tower (QQT) in Sydney, Australia, is a notable example of this and serves as a model of suc cessful integration of structural engineering, wind engineering, and construction practices.
The QQT project has received multiple awards for taking an exist ing iconic building on the Sydney Harbour waterfront, reconfigur ing it, and extending it into a much larger tower of greater height, with contemporary architecture to meet modern needs. The original AMP Centre Tower was opened in 1976
and was a centerpiece of the Sydney skyline, serving as the headquarters of one of Australia’s largest financial service companies. By the early 2010s, the owners realized that the tower configuration was no longer meeting its needs. The tower owners made a farsighted decision to try and preserve the invested construction energy and embodied carbon within the existing tower structure through adaptive reuse of
as much of the existing structure as possible. The previous square plan tower footprint was to be extended toward the north incorporating facade articulation to better capture spectacular harbour views, and the structure was to be reclad and internally fitted with modern, energy efficient materials and building systems. While this approach meets a lot of sustainability goals, it also adds complexity to design and
construction processes. The team set a goal of re-using two-thirds of the existing structure, and in the end, the project met this goal. CPP Wind Engineering Consultants was engaged from the start of design through commissioning to provide a range of wind engineering and field monitoring services. Quay Quarter Tower is owned by Dexus Wholesale Property Fund, Mirvac Wholesale Office Fund and Rest. QQT is managed by Dexus.
As is normal practice in the City of Sydney, wind engineers are engaged during the planning approval process to ensure any new construction will not result in excessively windy conditions for pedestrians at ground level. Environmental wind tunnel tests were conducted on a scale wind tunnel model of QQT and the surrounding cityscape in several stages. This included comparative tests with the existing AMP Centre at the time and the adjacent city precincts. Initial testing to investigate pedestrian level wind effects continued for four years by the Sydney CPP team*. From the outset, the
The integration of wind tunnel testing, structural engineering, and field verification assisted in a slew of awards, including the 2023 Council on Tall Buildings and Urban Habitat award for Best Tall Building Worldwide.
impact of various basic building massing concepts was investigated to understand the impact upon the public domain wind environment. CPP then tested the architectural excellence competition winning scheme to develop the design, particularly with regard to refinement of canopy designs and windbreaks on outdoor terrace areas.
Once development approval was received, CPP began its first wind tunnel test to determine wind-induced structural load and accelerations. This initial highfrequency balance wind tunnel test was conducted in 2014. Initial structural wind tunnel test results on QQT were used to develop some modest stiffness refinements to the tower core framework and to assess the impacts of future building surrounds upon structural wind loads. Revisions of the predicted tower responses continued up until 2019, taking into account changes in design and advancement of the structural modelling and dynamic properties. Given the reuse of the existing structure, including 95% of the existing core, this was a structurally challenging project (with several structural engineering companies involved through the course of the design) but one that offered multiple design approach opportunities that can’t always be taken advantage of during more typical design projects.
One key area where CPP was able to support BG&E, the structural engineers who completed the project, and Multiplex, the
contractor, was in a series of field measurements of as-built structural properties of both the existing tower and the new additions through construction.
The first early set of short duration site measurements of the structural properties of the existing AMP Centre tower were made in 2011 and 2012 led by CPP Director Dr. Graeme Wood. Accelerometers were used to measure the natural frequencies of vibration and to gain some estimates of inherent structural damping at low amplitudes of vibration. A primary use of these measurements was in calibrating the structural models of the existing tower that would be used as the basis of modeling the performance of the new tower and its impact on the existing structure.
CPP was re-mobilized from 2019 through 2021 to instrument the new tower for long duration site measurements to allow comparison of actual and expected tower behavior during construction. Instrumentation, including accelerometers and tilt meters, was installed on multiple levels throughout the tower and monitored remotely to assess natural frequencies, mode shapes, and structural damping under the guidance of CPP Director Dr. Matt Glanville with reference to measurement and analysis techniques developed in earlier research. The tilt measurements in particular ensured the tower did not lean beyond tolerances prescribed by BG&E. Data was logged continuously and periodically downloaded remotely from the CPP Sydney office.
The system was custom designed by CPP’s David Bourke and assembled specifically for this
application. The presence of accelerometers throughout the construction phase enabled continuous acquisition of acceleration data which was advantageous compared to more typical spot check methodologies, ensuring capture of significant wind events, even those occurring overnight. The continuous data was also important in monitoring
the evolution of the structural dynamics of the tower through construction phases and providing feedback to the structural engineering team. This data allowed the structural team to update their structural models of the tower and served as a metric for building structural integrity. Due to the novel nature of reusing an existing structure, the
condition of the aged structure was somewhat uncertain. The trend of measured natural frequency (analogous to stiffness to mass ratio) over time was used as a metric for assessing structural integrity relative to expectations, where a sudden deviation could be indicative of a failure in the existing structure, triggering a halt in construction until such
an event could be adequately investigated to maintain safety for the site.
The quantity of data available also allowed statistical techniques such as Random Decrement analysis to be implemented for assessment of damping without requiring a specific exercise for the measurement of this parameter.
The wind tunnel tests, supplemented by the field measurements, indicated that tower accelerations during strong wind events were likely to exceed perceptible motion design goals in specific prestigious areas of the tower and supplementary damping would be needed to
meet occupant comfort performance targets. A range of auxiliary damper concepts was considered, including tuned sloshing dampers (TSDs) and tuned mass dampers (TMDs). Performance of the TSD option was investigated through multi-phase computational fluid dynamics studies, but a tuned mass damper (TMD) was selected as the preferred option based on a combination of price and space requirements.
Structural damping is one of the least predictable parameters in building response to wind excitation; direct measurements from the existing building provided valuable input for the auxiliary damper design. By knowing the existing tower’s inherent structural damping, it was much easier to predict the additional damping needed and to design the auxiliary damper accordingly. In order to measure structural damping accurately, the structure must be excited to serviceability amplitudes of oscillation. In some cases, this excitation can be achieved by controlled crane drops providing an impulse load or by forced vibration tests as described in earlier co-authored publications by CPP Glanville and Wood, who each played management and technical rolls over the duration of the project. For the team designing QQT, forced vibration tests utilized three scissor lifts that were already on site at the top of the tower and these were moved back and forth in time with a metronome to provide a
sustained excitation at the natural frequency of vibration of the tower. Once the tower was oscillating, the excitation ceased, and the tower was allowed to vibrate freely to rest allowing a more accurate estimate of damping to be achieved.
To reduce the accelerations identified from the wind tunnel testing phase, a 175-ton TMD, designed and built by GERB, was installed in the tower. The TMD is a dualaxis sliding design, to meet space constraints and allow damping of both the first sway and torsional modes. CPP took part in the commissioning and performance validation of the damper system. Along with the accelerometers present on-site, an additional accelerometer was installed on the TMD itself to measure the motion of the damper mass. Measurements of tower motion were then analysed to confirm the additional damping introduced by the TMD.
In addition to the standard wind tunnel test for components and cladding pressures, CPP conducted a range of other tests and analyses to improve the performance of the building, including a natural ventilation assessment of the car park and atrium, with particular attention on the impact of smoke exhaust from a fire safety perspective. The CPP team also worked with the designers of the rooftop sunshades to
minimize the sunshades’ potential to generate tonal noise. Quay Quarter Tower has set a new global benchmark for the adaptive reuse of tall buildings, demonstrating how innovative structural engineering can contribute to ambitious sustainability goals. Wind engineering played a key role in the success of this project, ensuring maximum structural efficiency while meeting reliability and wind comfort performance targets. The integration of wind tunnel testing, structural engineering, and field verification undoubtedly assisted in the slew of awards garnered by the project, including the 2023 Council on Tall Buildings and Urban Habitat award for Best Tall Building Worldwide. ■
*Wind Engineering consulting for the project was conducted out of the CPP Sydney office including staff members Peter Bourke, Adam van Duijneveldt, Matt Glanville, Graeme Wood, David Bourke, Joe Paetzold, Christian Rohr, Thomas Evans, Kenneth Fung, Joe Sun and Andrew Nguyen.
Full references are included in the online version of the article at STRUCTUREmag.org .
Adam van Duijneveldt is Associate Principal for CPP Wind Engineering Consultants, St Peters, NSW, Australia.
Post-elastic performance-based design concepts are explored as a better way to develop ordinances and retrofit existing structures than force-based design criteria.
By John Dal Pino
Two summers ago, I had the opportunity and pleasure to present on “Post-Elastic Design” at the 12th Annual Structural Engineers Association of Alabama (SEAoAL) Code Conference & XPO in Homewood, Alabama. To narrow the subject, I chose to discuss many of the seismic ordinances (cantilevering brick parapets, concrete tilt-ups, soft-story buildings, etc.) enacted in California over several decades to improve the expected performance of building structures in future earthquakes based on performance observed in past earthquakes.
The intent of my presentation was to demonstrate that the prescriptive force-based design criteria provided in these ordinances and similarly in various editions of the Uniform Building Code improve performance, but in my opinion, not to the degree that the ordinance authors may have intended. My conclusion for the attendees was that following postelastic performance-based design concepts is a far better way to develop ordinances, retrofit existing structures, and design new buildings. By that I mean, first, defining a performance goal or objective for the structure and then secondly, back-figuring appropriate design criteria.
I came to this conclusion about performance-based design after reviewing the ordinances and thinking (or you might say “discovering”) that the design criteria would work well for some structures in some locations and not so well for other structures in other locations, mainly because all structures are different (to some degree all structures are prototypes) and respond to earthquakes differently.
To be crystal clear, I am not being critical of the ordinance authors as I am certain they were doing the best they could with the information and analytical tools available at the time. Today, it is difficult to remember what it was like before cell phones with cameras, or before the internet, let alone when hand calculators were the new thing, displacing slide rules. I wasn’t “in the room” (not many alive today were) so it is difficult or impossible to ascertain today what the authors’ specific motivations were and what conflicting political pressures they were under. They were probably thinking about post-elastic concepts based on observed earthquake damage, but they also lived during the allowable stress/ force-based design era. It is definitely worth one’s time to read any or all of the excellent Oral History Series books published by the Earthquake Engineering Research Institute (EERI) focusing on the legends in the field to get a glimpse into their thinking.
The most important thing I learned, and still employ today, is to first configure and design a structure using the best materials and configurations available according to the required loads/design criteria, and then check to make sure I have complied with the building code.
What I am advocating for is another approach going forward. This applies to the building code itself, future seismic retrofit ordinances and the evaluation of structures previously retrofitted following the provisions of past ordinances.
I was in my first year (around 1980) of graduate school at the University of California before I took a class that required that I buy a copy of the Uniform Building Code. Prior to that, the structural engineering classes had focused on the theoretical basics of mechanics of materials, statics, structural analysis with a few material-specific design classes for concrete, prestressed concrete, steel and wood. There was no class on masonry.
After graduation, I was lucky enough to land a job at a prestigious firm in San Francisco, starting in early 1982. That is when I learned that the Uniform Building Code—that book I hardly knew anything about—would become one of the most important books to possess, in addition to the AISC Steel Construction Manual, ACI 318 and the NDS for wood. Our firm’s mix of work was diverse and involved design of new buildings, seismic retrofits usually as part of major renovations, structural studies of existing buildings, and construction engineering (for which I learned there is NO building code, not even today). We were proudly not a “design shop.”
We had happy hour on most Friday afternoons starting around 5 pm. We usually put a few beers, sometimes a bottle of rye whiskey (left over from the previous year’s Christmas party), a tin of mixed nuts, and a deck of playing cards on the lunchroom table and chatted. We discussed current events or weekend plans, and sometimes a project. But, if we did talk shop, the conversation eventually turned to the question posed by the older engineers in the room, namely “what would have happened if there was no building code?” The very thought scared the younger engineers. I suspect the older engineers knew the effect that the question would have, like pulling a cat’s tail.
The younger engineers would ask:
by learning from earthquakes and other natural hazards.
1. Are you suggesting a society with no engineering rules?
2. Who would protect public safety?
3. Wouldn’t some buildings collapse?
The responses from the more experienced crowd included:
1. The engineers who have enough knowledge and experience to convince a client that they can be trusted with a design commission will get more work. Others won’t.
2. Maybe some buildings might have structural problems, but the designers of those buildings wouldn’t get future clients. The system will naturally correct itself.
3. Doctors, lawyers, and airline pilots don’t have codes.
4. Wouldn’t we all be better off, eventually?
We were reminded that California did not have a building code before 1927 and that if we walked along Market Street or around the Financial District in San Francisco, we would see many dozens of buildings that were designed and built without a “code,” several of which even survived the 1906 San Francisco earthquake. We were also reminded that there never has been a “building code” for construction engineering, since it is considered the “contractor’s means and methods.” That scared me a bit more since I was involved in that line of our firm’s practice. I came away with the conclusion that I just had to do it right and not make mistakes, since there was no code to defend me, nor to limit me as well. The larger takeaway for us (maybe intended, maybe not) was that it was important to understand how buildings responded under earthquake excitation, and what aspects of various designs worked better and what should be avoided. I was really thankful to my mentors for making me a critical thinker and teaching me that I really needed to be a “professional,” which meant that I had to continuously learn about buildings whether by walking around and observing, reading journals, staying abreast of recent developments, engaging in engineering laboratory research, discussing engineering with more experienced engineers, or
The most important thing I learned, and still employ today, is to first establish the required loads/design criteria, then configure and design a structure with appropriate load paths (avoiding irregularities to the extent possible) and the best materials and configurations available, and then check to make sure I have complied with the building code. It is never the other way around. As we all know, building codes only establish the minimum requirements for a design and are by their nature backward looking in that they are written based on past experiences. They are imperfect at best and subject to varying interpretations even by those working within the same city jurisdiction or entity.
I recognize that we are never going to go back to the pre-1927 era, since the building code is necessary to reassure the general public. The reality is too many well-intentioned people are involved in research, writing codes and standards, selling codes and standards (every three years for example), reviewing design documents, checking structural calculations (sometimes), and issuing permits for it to be anything else.
The evolving field of performance-based design may be the best we can hope for. In the past, and currently, this is called the “alternative means of compliance” provision. I have worked on a few performance-based design projects and find it quite exciting to look at the building as a whole (rather than a bunch of parts) to determine how it will perform in an earthquake. Sometimes it is discovered that the building can be economized and made less expensive. Sometimes certain aspects may need to be strengthened or stiffened, but the end result is that the engineer needs to be a real engineer and think hard about how the building is going to perform. I do not think prescriptive building code provisions can ever achieve this result or allow us to sleep comfortably at night. ■
This article is Part 1 of a four-part series. Part 2 will appear in the March issue of STRUCTURE.
19th Century Mississippi River Bridges
By Dr. Frank Griggs, Dist. M. ASCE
James Hill was one of the first railroad tycoons. He emigrated from Canada in 1855 to St. Paul, Minnesota, and quickly rose through management positions in steamboat and coal companies. He and his partners entered the railroad business purchasing the bankrupt St. Paul & Pacific Railroad in 1862. This was the successor to the Minnesota & Pacific Railroad that was chartered in 1857. This was followed by the formation of the St. Paul, Minneapolis, and Manitoba Railroad in 1879. This line ran northerly from Minneapolis to Grand Forks, North Dakota, where it turned west towards the Pacific. Hill then had a line from St. Paul to St. Anthony across the river from Minneapolis and from Minneapolis to North Dakota. What he needed was a connecting bridge across the Mississippi. He and associates from Minneapolis also wanted a new, and major, station in downtown Minneapolis. At the time the station was in St. Anthony, which merged with Minneapolis in 1872, and passengers had to cross the river on the Fr. Hennepin Bridge (STRUCTURE September 2022) just upstream.
Hill and his associates met to consider a bridge in late November 1881 and on December 1, 1881, formed the Minneapolis Union Railway Company to build a bridge and new train station in downtown Minneapolis. Hill owned most of the stock in the Company. He hired Col. Charles C. Smith as his Chief Engineer. Smith had been his Chief Engineer on the St. Paul, Minneapolis, and Manitoba Railroad. Originally Hill planned to build an iron bridge across Nicollet Island north of the Hennepin Bridge as that was where the river was narrowest
and a good rock foundation was present—both of which cut down the cost of the proposed bridge. Smith, however, convinced Hill that the masonry piers would block the river causing ice jams in the winter and log jams in the summer. In addition, Smith thought it possible that breaking up the sandstone river bottom could accelerate the movement of the falls upstream. Smith’s plan was to place his bridge below the falls about 500 feet south of the Fr. Hennepin Bridge and cross the river at a large skew with a portion of a masonry bridge on a curve, thus building a bridge on an S curve to accommodate the tracks of the St. Paul line that ran northerly along the east bank of the river and the St. Paul, Minneapolis and Manitoba that ran northerly along the west bank of the river. This alignment permitted the new station to be placed between Nicollet and Hennepin Avenue.
After purchasing the land needed for the project he retained Darragh & Haviland as his contractors. What Smith had proposed was a series of stone arches varying in span from 40 feet to 100 feet. The Thomas Viaduct had been built by the B & O Railroad as early as 1835 and was also on a curve. The famous Starrucca Viaduct by Julius Adams on the New York & Erie Railroad was built in 1848. Both of these bridges still carry railroad traffic today. While having a higher first cost than iron, their maintenance was low and the useful life much longer. The method of building the arches had not changed much from the time of the Romans.
Ground was broken in January 1882 in the middle of a cold
During construction many started to call the bridge “Hill’s Folly.” When completed, however, they were writing it was, “firmer than the earth” and “more solid than the ground itself.”
Minnesota winter. Cofferdams were built around each foundation down to rock and pumped out to permit the setting of the foundation masonry that was set in mortar. The piers extended above the highwater mark. Working throughout the winter, the bridgemakers placed all of the 23 foundations by the spring of 1882. The foundations were connected by a tramway on wooden supports. Wooden formwork was placed, and the cut arch stones placed and anchored into place with a keystone. Stone spandrel walls were built up to retain the fill, which supported the twin track ties and rails.
The best description of the bridge was given by F. B. Maltby in an article entitled "The Mississippi River; Historical and Description of the Bridges over the Mississippi River in 1902." He wrote,
The first bridge below the falls is a magnificent stone arch viaduct, built and owned by the Minneapolis Union Railway. It is located immediately below the falls, the west end in fact passing above them. The river at this point is about 1,000 feet wide, with steep banks, rocky bottom and is not navigable at any stage. The bridge crosses the river diagonally and has a total length of 2,490 feet; the eastern 1,033 feet is on a straight line and the remainder is on a 6-degree curve to the right. Commencing at the east abutment the structure consists of first nine stone arches with a span of 80 feet each…then four arches with a span of 100 feet each… then six arches with the same dimensions as the first mentioned, then one arch with 71.36 feet span…then a 40-foot arch…then an arch with a span of 43.86 feet.. to the stone dam at the falls. Thence across this dam to the structure across the water power canal above the dam, forming a continuation of the viaduct. The latter structure consists of two skew iron girder spans aggregating 85 feet in length, two through pin connected iron spans each 130 feet in length, resting on tubular piers made of boiler iron filled with concrete, then a 40-foot iron girder reaching to the west abutment…
The piers are Minnesota granite up to the spring line, and all above that is magnesian limestone. The foundations below the dam are on soft sandstone which underlies the limestone at the falls. The deepest foundation is at Pier No. 13 and is 17 feet below low water. The bridge is a double track structure and is 28 feet wide over the parapet walls; the grade line is 65 feet above low water... It was built by Darragh & Haviland, and contains 30,554 yards of masonry, and about 10,000 yards of stone filling. It cost approximately $650,000.
This magnificent structure is the only stone bridge on the river below the falls.
During construction many started to call the bridge “Hill’s Folly.” When completed, however, they were writing it was, “firmer than the earth” and “more solid than the ground itself.” On August 30, 1884, newspapers were reporting the bridge and new depot, later called the Great Northern Depot, “will be brought into use for the movement of passenger business between St. Paul and Minneapolis and points beyond” on Monday September 1, 1884. The Depot was finished in April 1885.
The bridge was a huge success and Hill’s investment paid off for many years. Hill later merged all of his lines into the Great Northern Railroad that reached Puget Sound in 1892. The last train over the bridge was in 1978; the tracks were removed shortly after. In 1994 it was reopened as a pedestrian and bicycling bridge. It has been named a National Historic Civil Engineering Landmark and is on the National Register of Historic Places. ■
Dr. Frank Griggs, Dist.M. ASCE, specializes in the restoration of historic bridges, having restored many 19th Century cast and wrought iron bridges. He is now an Independent Consulting Engineer (fgriggsjr@verizon.net).
TThe $75 million contract with the joint venture was approved on Jan. 8 by the Maryland Board of Public Works.
en months after the collapse of the Francis Scott Key Bridge, Maryland Transportation Authority (MDTA), owner, selected Bridging Maryland Partnership—a joint venture that includes WSP, a engineering and design services firm—to provide general engineering consultant services for the reconstruction of the bridge.
The $75 million contract with the WSP-led joint venture, including engineering firms Rummel, Klepper & Kahl (RK&K); and Johnson, Mirmiran & Thompson (JMT); was approved on Jan. 8 by the Maryland Board of Public Works. Pre-construction activities for the Key Bridge Rebuild project are underway.
Bridging Maryland Partnership will perform planning,
engineering, construction management and program support services to rebuild the bridge along Interstate 695 that crosses the Patapsco River near the Port of Baltimore for MDTA.
The team will assist MDTA in managing Kiewit Infrastructure Co. as it completes the bridge’s design and construction as part of a progressive design-build contract. The WSP team will act as auditor of Kiewit's processes, review engineering and construction submittals, and confirm that design and construction meet the standards and specifications.
As MDTA’s engineering representative for the Key Bridge Rebuild, Bridging Maryland Partnership will manage the accelerated design and construction process. The team’s support services include risk
management/analyses; establishing, reviewing, tracking and monitoring cost and schedules; managing project documentation; and consulting with environmental regulators.
WSP has been assisting MDTA as salvage contract manager for the Key Bridge since March 26, 2024, the day of the collapse.
“We were wrapping up work with MDTA on another bridge project when the Key Bridge collapsed,” said Srinivas Gunna, PE, senior vice president and construction manager for the Key Bridge Rebuild project. “That same morning, I was asked if we could assist with the salvage operation, so WSP has been working for MDTA on the project since day one.”
Bridge design is still being finalized.
■
The SOM Foundation is pleased to announce the opening of the 2025 Structural Engineering Fellowship.
Applications to this year’s Structural Engineering Fellowship should conduct original research that contributes to the topic, “Advancing Toward a Water-Secure Future.” The deadline to apply is Friday, March 14.
The $20,000 Structural Engineering Fellowship is awarded annually to a student currently enrolled in a master’s or PhD program or in the final year of their bachelor’s program based in the United States who specializes in structural engineering to conduct independent travel and research that contributes to the SOM Foundation’s current topic.
The Structural Engineering Fellowship was created in 1998 to support research that has the potential to influence the practice and teaching of how structures can positively impact our built environment.
As shared during the United Nations 2023 Water Conference, two billion people lack access to safe drinking water; 40% of the world’s population is affected by water scarcity; agriculture demands alone account for 70% of water usage; more than 90% of disasters are water-related; and pressure on freshwater is projected to increase by more than 40% by 2050.
From macro multinational ecosystems to microclimates, there is an urgent need for bold and collaborative solutions to a myriad of existing and future water-related challenges. This year, the SOM Foundation will direct its support toward proposals that address the complex relationship between water, people, and the built environment. Creating a sustainable, equitable, and water-secure future will require innovative and multidisciplinary ideas that shape long-term policies, define comprehensive plans, and identify immediate actions.
The 2025 Structural Engineering Fellowship jury will be led by Yunlu Shen, Associate Principal at SOM, New York, and will include:
• Christopher Cerino (Vice President and National Technical Director of Structural Engineering, Urbanism, and Planning, STV, New York).
• Negar Elhami-Khorasani (Associate Professor in the Department of Civil, Structural and Environmental Engineering, University at Buffalo, NY).
• Alexis Taylor (Vice President of Climate Resilience, NYC Economic Development Corporation, New York).
More information about the fellowship and how to apply can be found
In response to the devastating wildfires still ongoing in Los Angeles, Simpson Strong-Tie is donating $100,000 to the American Red Cross to support disaster relief efforts in affected areas.
Since the week of January 6, the Los Angeles area has experienced six major wildfires, resulting in
at least 24 deaths, thousands of structures destroyed and countless residents evacuated and unable to return to their homes.
The American Red Cross has deployed workers and volunteers to help provide food, shelter, emotional support and other services to those who have been displaced or otherwise impacted.
“The utter destruction we’re witnessing across swaths of Los Angeles is heartbreaking and terrifying; our thoughts go out to everyone affected and to the city at large,” said Simpson StrongTie President and CEO Mike Olosky. “We’re grateful to the Red Cross and all the organizations that are on the ground
supporting those impacted by this tragedy.”
This contribution reflects the company’s ongoing commitment to aid in disaster relief and recovery efforts around the world. To join Simpson Strong-Tie in donating, visit the company’s Red Cross site at www.redcross.org/donate/ cm/simpsonstrongtie-emp.html/.
The calculation and control of embodied carbon (emissions due to the production and use of construction materials) for all buildings and infrastructure projects must become a key part of every design process, according to the latest edition "How to calculate embodied carbon" guidance from the Institution of Structural Engineers (IStructE).
Aligned with the guide, IStructE has also updated its Structural Carbon Tool, developed in collaboration with Elliott Wood. This excel-based interactive resource helps engineers, building designers, and architects estimate the embodied carbon in their structures.
IStructE highlights that achieving net zero carbon by 2050, with a halving of emissions by 2030, demands a significant, but achievable, change across the design, construction, use, and reuse of buildings and infrastructure.
"As we argue in the guide, significant change across the design, construction, use and reuse of buildings and infrastructure are needed if we are to have any chance of providing a sustainable environment for the whole of humanity, and this can only happen if we first understand the emissions of our designs. These updates to our guide and tool help engineers and other professionals to calculate these emissions quickly and consistently." —Will Arnold, Head of Climate Action at IStructE.
Cemex announced the U.S. Department of Energy's (DOE) Office of Fossil Energy and Carbon Management (FECM) has selected a project for funding to develop a pioneering carbon capture, removal, and conversion test center at its cement plant in Knoxville, Tennessee. It will serve as a proving ground for innovative carbon capture technologies needed to accelerate deep decarbonization of the cement industry at scale. This project is one of five selected to share $101 million to begin and continue developing test centers for cement plants and power facilities.
In collaboration with the University of Illinois
Urbana-Champaign (UIUC), Cemex and a coalition of U.S. cement producers will develop the conceptual design, business, technical and managerial structures for the test center. This Phase 1 project includes the nec-
selection for Phase 2 will involve building and operating the carbon capture, removal and conversion test center, providing a platform to research and evaluate advanced systems for decarbonizing the cement industry. This research will facilitate cost-effective and
Paired with existing levers to reduce the carbon footprint of cement production, carbon capture, utilization, and storage (CCUS) technologies are the key to achieving Net Zero CO2 in cement production. This initiative is part of a more extensive portfolio of Cemex CCUS solutions, including permanent storage or use of CO2 from biogenic sources and contributes to Cemex’s 2050 net-zero carbon emissions target. CCUS is part of the roadmap for Future in Action, Cemex’s sustainability and decarbonization program through which it has achieved record-breaking progress in reducing its carbon footprint since its launch in 2020.
Adraft of the next edition of the AISC Standard for Certification Programs (AISC 207) is now available for public review and comment.
The next edition of AISC 207 will supersede the 2023 version and is anticipated to be finalized and released later this year.
The updated standard will notably exclude safety program requirements in recognition of the evolution of safety standardization and practices in the industry over the past several decades. The updated standard also harmonizes terminology with the AISC Code of Standard Practice, among other improvements.
The draft will be available as a free download at aisc.org/publicreview between January 14 and February 28. If you’d prefer to review a hard copy, please contact Martin Downs at downs@aisc.org; there is a $35 nominal charge for printed copies.
Please submit comments using the form provided online or by email to Jeanne Homer (homer@aisc.org) by February 28 for consideration.
NCEES is seeking licensed structural engineers to participate in a professional activities and knowledge study, or PAKS, for the PE Structural exam. The results of this online survey will be used to update the content of the exam, a process that occurs every six to eight years.
NCEES requires a cross section of licensed professional engineers practicing structural engineering—including those working in industry, consulting, the public sector, and academia—to complete the survey. Licensed professional engineers are invited to provide their input. The survey can be completed in about 50–60 minutes.
To access the online survey, go to ncees.org/STRPAKS.
The survey will be open until March 10.
For more information, contact NCEES Exam Development Engineer
The Parisian agency HEMAA (Charles Hesters and Pierre Martin-Saint-Etienne) completed the Les Violettes school complex in November 2024 in Mareil-Marly (France), commissioned by the city. This project includes 16 classrooms, comprising a new kindergarten, an extension of six classrooms for the elementary school, and a recreation center. The building, has a material palette of wood and glass with a spatial layout that emphasizes transparency between building volumes and openness to the sky. Lightweight, prefabricated French wooden structure reduced the noise and duration of the construction work, minimizing the impact on the site, which remained in use by the school community. The ground floor forms a base that is widely open the courtyards. It is clad in factory-treated vertical wooden slats. This cladding, made of French Douglas fir, is pre-aged with a gray finish to ensure its appearance remastable over time. The upper level is wrapped in a reflective skin of mirrored aluminu panels interspersed with glass windows. Inside, the wooden framework is exposed throughout, and the prefabricated concrete walls of the halls, which stabilize the structure, are left untreated. Acoustics are managed with compacted natural wood fiber placed between the structural beams.
Mainstay Engineering Group, Inc., a civil and structural engineering firm, has acquired Professional Engineering Associates (PEA), a Greenville, South Carolina-based, civil and structural engineering firm. PEA has significant design experience in the industrial, manufacturing, healthcare, and commercial sectors with a presence in South Carolina, North Carolina, Georgia, and Texas. This strategic acquisition expands the company’s geographic footprint and deepens its service capabilities, benefiting its clients, partners, and employees.
McAdams, a multidisciplinary design and engineering firm headquartered in Raleigh, North Carolina, specializing in civil/site design, planning and design, transportation, water resources, geomatics, and construction administration, has announced the acquisition of two offices from TPD, formerly known as Traffic Planning and Design, Inc. These offices, located in Asheville, North Carolina, and Greenville, South Carolina allow McAdams to strengthen its connection to its roots in North Carolina and expand into South Carolina. With this acquisition, McAdams will further develop
its transportation solutions division and continue to nurture existing relationships with cities, towns, and public officials. Adding additional local employees is critical to generating growth within the company and the communities it serves.
Richard Szecsy, Ph.D, PE, CEO of Big Town Concrete, has started his three-year term on the ASTM International board of directors.
ASTM International’s board is made of 25 leaders from a variety of companies, associations, universities, government bodies, and other organizations around the world.
A 30-year veteran of the concrete industry, he has also been active in the American Concrete Institute (ACI), the American Society of Civil Engineers (ASCE), and the National Ready Mixed Concrete Association (NRMCA), and is the current Chair of the Texas Aggregate and Concrete Association.
TYLin, a global full-service engineering and advisory firm announced that TYLin Silman Structural Solutions is now operating as TYLin, fully embracing the breadth, depth, and reach of TYLin’s Buildings Market.
TYLin's buildings expertise is rooted in the legacies of four firms that have united to form a team of structural engineers, who are now affiliated with a wide range of engineering
expertise, code experts, and architects around the globe.
“Our long history of collaboration with passionate designers, thoughtful owners, and incredible builders in all manner of building structures will contribute significantly to the communities we work in, whether supporting the growing need for transformative adaptive reuse and iconic new construction, throughout North America,” said Nat Oppenheimer, Senior Vice President and Buildings Market Leader for the Americas for TYLin.
William “Bill” Brown is the new CEO at Bennett & Pless Structural Engineers (Atlanta) as of January 1. He is the company’s fourth CEO in 60 years, following Moe Bennett, Rex Pless, and Ed Gazzola. The transition highlights Bennett & Pless Structural Engineering’s commitment to leadership development and remaining an independent midsize firm. Chief Operating Officer since 2020, Brown was chosen for his strong leadership and alignment with the firm’s vision.
Blackwell 3D Construction Corp., a 3D house printing technology company, has entered into an agreement with Narshimulu Madugula, a landowner near Hyderabad, India, to develop a 25-villa residential project using 3D construction techniques. This collaboration aims to bring sustainable, cost-effective, and innovative housing solutions to the region. As a crucial first step, Blackwell
3D has commenced field studies, feasibility assessments, and soil testing to evaluate the compatibility of 3D-printed construction with the local terrain. These studies will determine the viability of deploying largescale 3D printing technology in the region’s topography and ensure the project meets the highest standards of structural integrity and durability. Upon successful completion of these assessments, the project will move into subsequent phases of planning, design, and construction.
In parallel, Blackwell 3D is in the midst of acquiring a 3D construction printer under a lease-to-own model for this project and future projects in India. This approach will allow the company to adopt the most advanced technology while optimizing costs, efficiency, and scalability for future projects in India.
STRUCTURE Magazine has added a new member to its Editorial Board. Kevin Adamson, senior design engineer at Structural Focus, joins John Dal Pino, chair (Claremont Engineers); Marshall Carman (Schaefer); Erin Conaway, (American Institute of Steel Construction); Sarah Evans (Walter P Moore); Nicholas Lang (NCMA); Linda Kaplan (Pennoni); Jessica Mandrick (Gilsanz Murray Steficek LLP); Brian W. Miller (Cast Connex Corporation); Evans Mountzouris (retired); Kenneth Ogorzalek (KPFF Consulting Engineers); John "Buddy" Showalter (International Code Council); and Eytan Solomon (Silman).
NCSEA has released two new videos aimed at educating the public, government officials, and state licensing boards about the essential contributions of structural engineers. These resources are designed to raise awareness of the profession’s importance and can be shared on social media platforms to expand their reach.
In today’s fast-paced world, structural engineers play a vital role in designing, evaluating, and maintaining the built environment to ensure its safety, functionality, and durability. However, their work often goes unnoticed by the general public. These videos aim to bridge that gap by showcasing the importance of structural engineers and their specialized expertise, helping to raise awareness of this crucial profession.
One video, “Responding to Disasters: The Role of the Structural Engineer,” highlights the critical work of structural engineers as second responders, assessing the safety of structures following natural disasters and other catastrophic events. This message is particularly timely given the recent fires in southern California.
The second video, “The Importance of Structural Engineering Licensure,” underscores the role of licensed structural engineers in ensuring the safety and integrity of the built environment, emphasizing the specialized expertise required in this field.
Sharing these videos helps spotlight the vital work of structural engineers and fosters greater understanding of their role in creating safer, more resilient communities. Both videos, along with additional resources, can be found on NCSEA’s YouTube channel at www. youtube.com/@NCSEA-Videos.
Terry Malone, CEO and Co-Founder of the STEM Exploration Center, will deliver the keynote address at the 2025 Structural Engineering Executive Retreat. The event, taking place March 5–7, 2025, in Napa Valley, California, is the premier gathering for structural engineering firm leaders.
Malone’s keynote will center on leadership development, offering invaluable insights for professionals navigating today’s rapidly evolving business landscape. As an accomplished leader and advocate for workforce development in STEM fields, Malone brings a wealth of expertise and a compelling vision for fostering leadership.
“Terry Malone’s leadership and his work in building the STEM talent pipeline make him an extraordinary keynote speaker for the retreat,” said Al Spada, NCSEA Executive Director. “His insights will inspire the audience to not only grow as leaders but also play an active role in shaping the next generation of talent in our profession.”
The 2025 Structural Engineering Executive Retreat is a must-attend event for those shaping the future of structural engineering. In addition to Malone’s keynote, the event will feature informative sessions, roundtable discussions, and exclusive networking opportunities.
To learn more about the 2025 Structural Engineering Executive Retreat and to register, visit www.ncsea. com/exec-retreat.
The NCSEA Foundation is proud to announce that it has surpassed its ambitious $30,000 fundraising goal for the month of December 2024, thanks to the incredible generosity of its supporters. This milestone achievement highlights the dedication of the structural engineering community to fostering innovation, leadership, and resilience in the profession.
The 30 Days, $30K, 30 Years of Impact fundraiser celebrated NCSEA’s 30th anniversary in 2024. The funds raised will directly support the NCSEA Foundation’s vital programs, including scholarships for aspiring engineers, mentorship opportunities, and grants for local Structural Engineering Associations (SEAs). These initiatives are designed to empower current and future leaders, advance cutting-edge practices, and underscore the critical role structural engineers play in building safe, resilient communities.
“We are deeply grateful for the overwhelming support we received,” said Al Spada, NCSEA Executive Director. “This milestone reinforces the importance of our mission to strengthen the structural engineering profession and inspire the next generation of leaders.”
For those who may have missed the December campaign, it’s not too late to contribute. Donations are accepted yearround and continue to fuel the Foundation’s impactful work. Contributions can be made on the NCSEA website at www. ncsea.com/foundation/donate.
Leadership Week demonstrates NCSEA’s commitment to empowering leaders and fostering innovation in the structural engineering profession. Stay tuned for more details on this impactful event.
NCSEA is excited to announce the release of a new resource created by the Communication Committee’s Public Awareness & Outreach Task Force. Designed to make structural engineering presentations at career days engaging and effective, the resource is now available for download.
The customizable slide deck, titled “Introduction to Structural Engineering,” offers a fun and informative overview of the profession and provides guidance on how students can pursue a career in this vital field. Ideal for high school audiences, the slideshow simplifies complex concepts and highlights the exciting opportunities within structural engineering.
This new resource is part of a broader collection of tools available under “The World of Structural Engineering” on the STEM & Outreach page of the NCSEA website at www. ncsea.com/stem. Additional resources include activities, videos, ready-to-print graphics, and other tools aimed at making structural engineering education both enjoyable and impactful. These materials are designed to inspire curiosity, encourage educators and students, and pave the way for future structural engineers.
Visit www.ncsea.com/stem to download the “Introduction to Structural Engineering” presentation and explore the full range of educational resources available.
Visit www.ncsea.com/education for the latest news on upcoming webinars and other virtual events.
March 6
webinars (25+) and a recorded library of past webinars (170+) – all developed by leading experts; available whenever, wherever you need them!
Taking place February 5, 2025, this free, virtual, halfday event convenes structural engineers and related industries to discuss practical steps that can be taken immediately to meaningfully reduce the climate impact of the industry. The conversation will go beyond sustainability 101, feature lessons learned, best practices, and case studies. Discussions will include talking through Life Cycle Assessment results with key stakeholders, procuring better materials, circular construction successes, and more. Use the QR code to register.
An article is now available from the ASCE 7-28 committee, authored by J. G. (Greg) Soules, Ph.D, SE, PE, P.Eng., F.SEI, F.ASCE, Chair of the ASCE 7-28 Main Committee, and Emily M. Guglielmo, SE, PE, F.SEI, Chair of the ASCE 7-28 Seismic Subcommittee. If your projects are in the Central and Eastern United States, the updated seismic ground motion values in ASCE 7-28 might surprise you. This article provides essential guidance to help structural engineers avoid overly conservative designs. It also ensures compliance with the latest standards. Read here: go.asce.org/ASCE 7-22groundmotions.
Get ready for an unforgettable experience at
Join us April 9–11, 2025, in vibrant Phoenix, Arizona, for three days of learning, networking, and inspiration. Earn 11.5 PDHs while diving into a dynamic technical program packed with cuttingedge sessions on sessions on bridges, buildings, education, leadership, climate change, Life Cycle Assessment, forensic engineering, natural disasters, research and much more.
Explore the technical program and register today: www.structurescongress.org/program.
ASCE has recently released two new publications, available for purchase at asce.library.org:
Cold-Formed Steel Connections to Other Materials: A Design Guide: This comprehensive guide examines the use of cold-formed steel in connection with materials such as steel, concrete, concrete masonry units, brick masonry, and wood in the design and construction of buildings and structures. By providing practical examples and expert insights, it equips engineers, material industry professionals, and students with the tools needed to address connection design challenges across material boundaries. Covering key topics like clip angle strength checks, material sizing, and collaboration with industry organizations, this resource is invaluable for navigating modern construction practices.
Life-Cycle Design, Assessment, and Maintenance of Structures and Infrastructure Systems: This cutting-edge report provides a comprehensive overview of the current state and research priorities in the life cycle of civil structures and infrastructure systems. It highlights key aspects such as the degradation mechanisms of concrete and steel in harsh environments, strategies for life-cycle design and assessment under uncertainty, and innovative management concepts for structures and infrastructure networks. The report also delves into maintenance scheduling and policy applications for aging systems. Ideal for engineers, managers, and government agencies, it offers valuable insights for optimizing the design, assessment, and upkeep of critical infrastructure.
ASCE 24-24 Flood Resistant Design and Construction: This revised standard provides minimum requirements for flood resistant design and construction of structures that are subject to building code requirements or floodplain management regulations in flood hazard areas. This standard applies to new construction and to substantial improvements of non-historic existing structures and aligns with the provisions in ASCE 7-22 Supplement 2.
Another publication is also set for upcoming release. Look out for the SE2050 Commitment program: 2023 Data Analysis and Findings Report, which will be published this winter.
Improving the transmission and distribution network is critical to enhance the capacity, reliability and resiliency of the grid, and the demand for civil engineers has never been greater, with rewarding opportunities. The once-every-three-year Electrical Transmission and Substation Structures Conference will be held September 14-18 in Dallas, TX.
Students: Apply for the Student Scholarship | SEI ETS Conference
and encourage student colleagues in this unique opportunity.
Invest in your future and apply for an SEI Futures Fund registration/travel scholarship to participate with an informal mentor at the conference, learn about important trending topics, and forge valuable connections with professionals and industry leaders. Apply at: www.etsconference.org/student-scholarship.
Join us for the first of a three part ASCE eLearning webinar series by the SEI Business Practice Committee: Client value for structural/civil engineers | ASCE on Tuesday, February 4, designed to equip students, young and mid-level structural/civil engineering professionals with essential skills for success.
The Client Value session delves into the art of building strong, lasting client relationships and consistently delivering exceptional results. Learn how to drive sustainable business growth by mastering often-overlooked skills that can propel your career to new heights.
Don’t miss this opportunity to enhance your career with valuable knowledge and practical strategies. Register now and prepare for upcoming sessions on Productivity and Entrepreneurship.
ASCE eLearning webinars are free for members. Encourage nonmember colleagues to join at www.asce.org/SEIMembership, then sign up for the webinar. Membership for students and the first year after graduation are free.
Register: go.asce.org/client-value-for-structural-engineers
The 2025 Coalitions Winter Meeting, held February 25-26 at Hyatt Regency Phoenix in Phoenix, Arizona, brings together ACEC’s coalition members to discuss strategic initiatives and industry challenges for the year ahead. This year’s Winter Meeting will highlight sustainability efforts in the industry and is a chance for the CASE Executive Committee (ExCom) and its subcommittees to work on this year’s publication and education initiatives for CASE members. This gathering provides a valuable opportunity for coalition leaders and attendees to collaborate on solutions impacting the engineering profession.
If you are interested in attending this year’s meeting or want to find out more visit www.acec.org/education-events/ events/coalitions-winter-meeting/.
With the engineering industry in the recruitment trenches fighting for talent in a scarce market, any organization that can turn its high-potential employees into future leaders—and its good managers into great ones—will enjoy a tremendous competitive advantage in the workforce wars.
The Small Firm Workshop 2025, “Blueprint for Success: Developing the Next Generation of Firm Leaders, will address those challenges February 23-24 in Phoenix, Arizona.
prepare to pick up the mantle of leadership?
In every business, you’ll find them: those superstar employees whose drive, dedication, and sheer talent make every project better for their being part of it. They are an invaluable asset, so what can managers do to create a path forward—and upward—for these high potential employees? Conversely, how can these high performing employees
ACEC’s Small Firm Workshop will help firms answer some of those questions. Conceived for firm leaders and high-potential employees alike—and with unique content tailored for both—this comprehensive, hands-on workshop will focus on cultivating the next generation of leadership. This dayand-a-half long session will offer principals actionable strategies to help top performers grow into confident leaders. At the same time, those top performers will take part in concurrent sessions focused on skills—both hard and soft—that one must bring to leadership roles. Join us in Phoenix, where you and your top performers will gain valuable insight into how managers become mentors—and how exceptional employees can evolve into visionary leaders. Attendees will earn eight PDHs. Visit www.acec.org/education-events/ events/small-firm-workshop/ for more information.
The CASE Scholarship Fund is more than just financial support; it’s an investment in the next generation of structural engineers who will shape the built environment and drive innovation forward. Each year, CASE provides scholarships to dedicated students working toward a career in engineering, empowering them to pursue their education and make meaningful contributions to the industry. Your donation, no matter what the amount, can have a lasting impact. It helps cover tuition, supports students’ access to critical resources, and ultimately brings talented, enthusiastic new professionals into the field. Let’s ensure that financial barriers don’t stand in the way of their potential.
Join us in building a stronger, more resilient future by contributing to the CASE Scholarship Fund today. Together, we can make a difference! Below is a QR code for you to make your donation today. Please remember to select the CASE Scholarship Fund when contributing. Thank you for your support!
Explore CASE’s top publications that inspire and inform professionals like you. From cutting-edge research to actionable insights, this year’s bestsellers are not to be missed. Plus, if you’re not a CASE member, don’t forget to use your discount code NCSEASEI2022 at checkout for exclusive savings.
Growth and job satisfaction of employees is an important objective of any professional organization. Robust two-way communication between the employee and the employer foster both. Open and frank communications are essential to providing the space for assessing growth and setting realistic goals for progress. Effective coaching, mentoring, and enabling resources guide professional growth which benefits the employee, the employer, and the profession at large. Self-reflection and employer evaluation are essential ingredients for establishing the goals and objectives of a professional. Maintaining alignment between the two can eliminate wasted efforts that diverge from the mission and vision of the organization, as well as prevent unmet employee expectations.
Any goal-setting exercise must balance individual preferences with nonnegotiable requirements such as project needs, professional responsibilities and ethics, and business constraints.
Users of this tool should understand that it is not sufficient to rely solely on feedback and goal-setting processes regardless of the cadence of meetings between employees and supervisors. These do not eliminate the need for proper day-to-day coaching and mentoring in the course of activities in a professional office.
This project Status Report is intended to be sent to the Client, the owner, and any other stakeholder or project participant who should be kept informed about the project status. Be aware that adding stakeholders or participants might require altering the tone or content of the information presented.
The Template is designed in Word format, so it can be edited according to the requirements of each individual company. If more room is required, additional lines can be added by clicking on Table/Insert/ Rows Below.
The status report should be sent out at any regular interval of time (weekly, monthly, etc.), depending on how active the project is. If completed on a regular basis, this status report will greatly improve the communications with the Client, the owner and other stakeholders. It will also provide a written record of what has been happening on the project and can protect from the “you never told me,” or the “I never knew you didn’t get that piece of information.”
Time and time again, poor communication is listed among the top reasons for lawsuits and claims. Sending out a project status report on a regular basis is an easy way to significantly increase the communication level on a project.
This tool can be used together with: Tool #4-6 Project Team Coordination and Prioritization Log.
The construction administration phase of a project is often not met with the same excitement as the initial design phases of a project. At this time, the design project has potentially gone on for some time and the initial project enthusiasm may have waned among the design team. New players are introduced such as the contractor team and the fury of RFI’s, submittals and change requests begin. This time can especially be challenging for newer engineers who may not be as experienced dealing with the time constraints and pressures with having to review these items quickly as well as working through adjustments for unforeseen or varying existing conditions, not to mention the occasional repair of contractor errors and omissions. This issue can have increased challenges when firms assign construction administration duties to less experienced staff, staff that may not have had direct involvement during the design phase or construction administrative/ field inspection staff.
Nonetheless, the quality of our services during the construction administration phase could be considered the most important phase from a risk management perspective. With good teamwork, communication and a collaborative approach, many of these issues can either be avoided or successfully managed. Often times, it is in the trenches of a project during construction that strong relationships are formed between the structural engineer and other team members including the owner and contractor. In addition, this end phase of the project is often how we are remembered for the level of service provided and can have a significant impact on the firm’s success with future pursuits with clients and the design team.
Streamline your joint projects with clear, comprehensive teaming agreements! Essential for successful collaborations among contractors, design professionals, and structural engineers, these agreements define roles and responsibilities upfront—especially valuable in design-build projects.
This commentary offers insights into standard teaming agreements from top organizations, including:
• AIA: Contract C102-2015
• EJCDC: Contracts D-580 and E-580
• DBIA: Contract No. 580
• ConsensusDocs: Contracts 296 and 498
Explore these agreements and other indispensable CASE publications at CASE Resources.
Got ideas for tools that could enhance your business? We’d love to hear them! Reach out to us at coalitions@acec.org and help shape the future of structural engineering resources.
Many engineering firms offer flexible work options, but it is a balance of meeting both employee and business needs.
By Rachel Mosier, PE, Ph.D and Erin Conaway, PE
For more on this topic, read “Engineering a Better Work-Life Fit: A Business Case for Flexibility in the Workplace” (STRUCTURE January 2024) available at www.structuremag.org. This article focuses on the changing landscape and perspective for flexible workstyles during the pandemic and after.
ork-Life Fit is a concept that seeks to address the AEC industry’s continuing struggle to increase its workforce, a company’s greatest asset, while simultaneously balancing employee and firm expectations in the post-pandemic hybrid work environment. Sometimes referred to as Work/Life Integration (WLI), Work-Life Fit fosters synergy and compromise between personal and professional life rather than keeping them separate at the risk of creating conflict between them. Work-Life Fit is an evolution of the more traditional Work-Life Balance, which was idealized as a 50/50 lifestyle but has proven unrealistic in the modern workplace with women in professional engineering roles and men in caregiver roles. Work-Life Fit is focused on multiple areas, including flexible work models, leave policies, and a healthy work environment; it is NOT a one-size fits all solution and will not always be easy to implement, with some
employers expected to have valid concerns about secondary impacts on their business practices. The recent “return to office” mandates within the AEC and other industries have rekindled the conversation about flexible and remote work models, in particular. Most of the current and future workforce have now experienced flexible work styles in some form (hours worked per day, minimum days in the office, work location, remote learning, etc.). As such, the demand for flexible work continues, which creates an opportunity for companies to recruit and retain engineers by offering various options. However, for this to work for both a company and an individual, flexible work options must be transparent and part of an ongoing, documented discussion of work styles that provide the maximum value for individuals and companies. Work-Life Fit is not about working less but working differently and more efficiently for mutual gain.
Data in this article was collected via Menti during a presentation at the Structural Engineers Association of Arizona conference in June 2024. Some of this information, along with other industry insights, are presented in this article to support both individuals and companies in designing flexible work styles. This article highlights and addresses specific concerns of employers about flexible work styles. While the Arizona presentation topic was based on Work-Life Fit, which incorporates different employee benefits packages like family leave and healthy work environments, many of the challenges identified by the participants were remote work-related.
Remote work inhibits collaboration, which is a foundation of company culture.
The use of required “core hours” is one solution. One firm principal stated that to maintain their company culture, they have a required collaboration timeframe within the typical workday. Everyone is expected to be in the office during these times. This work schedule allows drop-off and pick-up for child caregivers and recognizes that rush hour traffic can impede a more restrictive 8-5 schedule. A shift in the scheduled arrival and departure times can allow employees to avoid the increased commute times and support employees' personal lives and obligations. To further address the company culture concern, a well-crafted employee engagement plan can help to support employee relationships and foster a collaborative workplace. Employee engagement plans can include any of the following: compensation, coaching, mentoring and goal setting, personal and professional support, social events, transparent communication, and training and professional development.
Today, there are multiple examples of fully remote structural engineering firms and project teams successfully collaborating 100% remotely.
Mentoring is difficult in a remote work environment. Remote Engineer-in-Training interns cannot learn “organically” by overhearing office dialogue on the project, similar challenges, or code applications.
Remote structural engineering firms may only hire licensed engineers to avoid this mentoring challenge as part of their remote work paradigm. A solution may be adopting a “core hours” schedule where interns, and perhaps all staff, must be in the office on certain days and/or hours. This allows interns their desired flexibility while facilitating their participation in the company culture and “knowledge by osmosis.”
Leaves of absence and part-time employees cause disruptions to project continuity.
The Family Medical Leave Act (FMLA) is protected by law, and there are a variety of reasons— beyond maternity/paternity leave—that an employee may require a leave of absence or reduced hours, including elder care, mental health concerns, or addiction. Regardless of the type of leave, there is no easy management solution to long-term leave, and employees may be concerned with taking extended leave or working part-time for fear of reduced potential promotion and raises. This concern particularly impacts anyone who is a primary caregiver for children or adults. Typically, when extended leaves occur, a new project engineer/ project manager must be assigned to the project. From a company perspective, transferring the project responsibilities incurs a cost. However, offering part-time or reduced hours, and even a transitional period back to full-time employment for these employees, can help to reduce attrition and gain long-term loyal employees.
An additional option is to provide task-based work, like reviewing submittals, for flexible work employees. Job-sharing, where more than one person is responsible for the overall project or set of tasks, can reduce knowledge loss at a company. Redundancy is an important factor for all forms, albeit harder to do in smaller firms.
Flexible work styles are not conducive to providing client support. Employees in the office have many benefits, as mentioned here, such as mentoring, company culture, and learning by osmosis. These topics are all focused internally. However, when employees are not in a physical office, value-added client interaction and support
may also be a concern. The shift to remote work was challenging during the pandemic because many companies were not set up technology-wise to support this work model. Fortunately, as a testament to the resilience of the engineering profession, many firms have since implemented an infrastructure that supports digital collaboration and seamless, integrated, remote client communication and support. Client expectations of interactions with engineering firms have permanently changed post-pandemic, relying increasingly on digital platforms.
Expectations for site visits and inspections are aligned with cost, vicinity, and need. Firms may employ personnel who focus on construction administration, site visits, and inspection, which provides options for clients. Fortunately, in the post-pandemic environment, numerous tools are available for collaboration, and business does not need to wait for in-person visits.
If provided with flexible work options, employees may request to live and work for periods of time in a different state.
Employees working from another state may cause employer concerns with employment law and income tax liabilities (the location where the revenue is being earned). This can be particularly burdensome for a smaller company.
For employees working in one state but living in another, the employer may withhold both state taxes. It is also possible that the employee takes care of this challenge through their own personal income taxes.
For some states, working from another state may require the employer to file state taxes in the employee's physical state, with some states requiring this in as little time as 14 days (ADP). However, many states will match their requirement for residency,
which is typically closer to 30 days, or the same requirement as the need for a driver’s license and license plate. Employees must communicate their residence as it changes if remote work is allowed.
Errors & Omissions claims may increase when employees work full-time outside the office, resulting in legal expenses and increased E&O insurance premiums. Employers can reduce risks by creating more detailed operating procedures and checklists for reviewing and evaluating work performed remotely. A continuous and managed improvement plan can be beneficial for demonstrating the company’s efforts to control errors to insurance companies. Little data is published currently on actual increases in cost for E&O insurance, and it is an area of ongoing discussion.
Companies and individuals have many recognized challenges regarding Work-Life Fit and flexible work models beyond basic work-life balance; however, the realized benefits of flexible work options are well documented and lead to increased productivity and bottom lines. Significant data exists across many industries to make the business case for implementing flexible work models, most notably the positive impact on retention and recruitment. The key is understanding the types of Work-Life Fit policies that address both the individual and company needs. ■
Rachel Mosier, PE, Ph.D, is an Associate Professor in Construction Engineering Technology at Oklahoma State University in Stillwater, OK (rachel.mosier@okstate.edu).
Erin Conaway, PE, LEED AP, is the Senior Director of Market Development with the American Institute of Steel Construction, based in Denver, CO (conaway@aisc.org).
Mentorship can be a mutually beneficial relationship that helps raise the bar of the structural engineering profession.
By Ciro Cuono, PE
Milo Ketchum, a renowned 20th century structural engineer, wrote in 1983 in an editorial called “Training Recent Graduates” that “We all seem to agree that the recent graduates we hire for structural offices, are not well trained for our work, and that we do not get our money’s worth for a considerable length of time.” (Structural Engineer Practice-Volume 2, Number 2, 1983). Ketchum then went on to illustrate examples of where he thought recent graduates lacked training and suggested a training program for structural consulting offices that would run for two or
three weeks. He suggested that this program would start with a test to identify strengths and weaknesses and include training in drafting and a series of design problems of increasing complexity, including training in computer modeling. Ketchum then went on to conclude that this investment of approximately 4% of a year’s time would result in at least a 4% increase in efficiency and therefore would not be a loss to the employer.
This proposition, now over 40 years old, is quite interesting and raises lots of questions for the education and training of structural
engineers today. First, is t only so much can be accomplished in a four-year engineering program (including perhaps a master’s program as well), hence the common complaint that recent graduates lack some skills to be immediately productive. The world is much more complicated than it was in 1983 and certainly significantly more so than it was in the 1930s when Ketchum was educated. On the other hand, our access to instant information and incredible computing power is tremendous compared to Ketchum’s days. However, there is a limit to what can be taught in
a four-year program, particularly when one considers there are few or no “Structural Engineering” degrees at the undergraduate level. What we have are Civil Engineering” degrees where the core courses of structural analysis and design can get easily drowned out in the broader context of the Civil Engineering program. So, for those who empathize with Ketchum’s sentiment, we have to ask ourselves, “What can we expect?” We would not want a medical student, just finishing his or her studies to perform heart surgery without even doing a residency. So, as Ketchum suggested, whether formalized (as he outlined) or not, we, as an industry, have our own form of “residency” in the form of on-the-job training and mentorship. Now, some firms have a more organized way of doing this (e.g. Ketchum type onboarding) while others simply do it in an ad hoc way. In either case, a mid-level or senior structural engineer today practices his or her profession based on their education in first principles (hopefully) and years of on-thejob training and mentorship. Like a medieval carpenter or stone mason, most entry level engineers today work almost in an apprenticeship (albeit generally well paid) under the tutelage of their senior supervisors and mentors. Ketchum’s suggested onboarding program is quite attractive when one considers the time and cost of entry level engineers, particularly in their first year. We are charged with designing the infrastructure of the world, so this responsibility should include organized internal training and apprenticeship so we can continue to perpetuate our craft.
A formalized training program for young structural engineers, however, is not the end goal but just the beginning. Engineering as a profession is hard. We are expected to basically deliver on time, error-free designs day-in and day-out in a world of tight fees, tight schedules, increasingly complex codes, and ever-changing technology. All with having taken
say, maybe one or two formalized classes in steel or concrete design. The reality is that the profession of engineering means a lifelong of learning. Many states require continuing education to maintain licensure. This should be the bare minimum as there is always something new to learn in such a complicated profession. Continuing education should be part of any training program (formalized or otherwise). But along with training and continuing education, mentorship is just as critical.
But what exactly is “mentorship”? According to the Merriam Webster Dictionary, the word mentor has its roots in a character of the same name in Homer’s Odyssey. Mentor was entrusted with the education of Odysseus’ son. Fast forward to today and mentorship is a hot word in the business world with many large companies and institutions having formalized programs where more experienced employees provide some form of guidance or mentorship to less experienced employees. A March 2023 article in Forbes entitled “The Power of Mentorship: How Mentors Can Help Employees Grow and Succeed” (March 27, 2023, by Kara Dennison, Forbes) provides seven examples of mentorship:
traditional mentorship relationship except it is done online, perhaps opening up possibilities of pairing people who would otherwise be geographically limited.
• Peer-to-Peer Mentorship: Employees at the same or similar level help each other and build a sense of community.
• Sponsorship: A sponsor is an influential person within the organization who supports the career development of a less experienced employee.
The reality is that the profession of engineering means a lifelong of learning.
• Traditional Mentorship: a one-on-one relationship where more experienced employees partner with those who need support.
• Reverse Mentorship: When the less experienced employee becomes a mentor to someone more experienced.
• Group Mentorship: Like the name sounds, it involves a group of employees mentored by one or more experienced employees, perhaps leading to cost efficiencies.
• Virtual Mentorship: This is essentially a version of the
• Onboarding Mentorship: provides new employees with a mentor who can help them navigate the organization and learn the ropes during onboarding. Most engineers will find some or most of these examples familiar in some fashion, whether formalized or not. Engineering is not just codes and equations but art and judgment as well—not to mention the great amount of personal interaction in the form of communication: texts, emails, calls, memorandums and reports, office meetings, or meetings on an onsite trailer. Learning the craft of our structural engineering profession takes years of training and on the job mentorship. Formalizing a training program underlain by a formalized mentorship program would surely go a long way to responding to Ketchum’s concern on recent graduates and help run more efficient organizations by passing along valuable knowledge and craft.
But the journey does not end there. A young engineer lucky enough to work for an organization that has a formalized training program and takes the time to create a mentorship program must recognize that as they move along their careers, they must give back and reinvest. They must reinvest in the form of giving back to their school or
schools, their professional organizations, their companies, and perhaps their local community boards and organizations by becoming mentors to the next generation. This is the best way to continue our profession and have a knowledge-and-experience capture system. The give-back can start small and early on. A first step could be giving a small amount to their college or participating in a STEM (Science, Technology, Engineering and Mathematics) or engineering program at a local high school. Then perhaps they can continue by peer mentoring their colleagues and/ or by joining a local architectural review board or planning board. As one moves along the career path, the give-back can be even more impactful and include setting up a company scholarship or internship program and of course, direct mentoring of the next green engineer who walks in the office and reminds you of yourself the day you started.
I have been lucky to have many mentors in my career so far, some. from 25 years ago and some within the last year. Mentorship can happen in many forms and is a give-and-take process. The more we work at it the greater our professionalism as engineers stands out which will help raise the bar of our profession.
Let us make Milo Ketchum proud and train, mentor, and give back to our profession. ■
the founding Principal of Cuono Engineering PLLC, a structural engineering firm located in White Plains and Manhattan, NY, and is an Adjunct Instructor at Manhattan College. He has over 24 years of experience in structural design of new buildings and renovations and restorations of existing historic structures. (ccuono@ cuonoengineering.com)
By Dain Drake, PE
As the U.S. races to rebuild its semiconductor manufacturing industry, New York-based DeSimone Consulting Engineering was able speed up delivery of a new chip fabrication plant in Texas based on a new integrated delivery model. Chip fabrication plants are hugely complex and expensive ventures that involve thousands of construction workers and usually long construction timelines, so DeSimone’s ability to shave five weeks off the project timeline resulted in cost savings and a faster time-to-market.
Following an acquisition of Canadian detailing firm DOWCO (now DOWCO—A DeSimone Company), DeSimone launched a fabricated steel procurement service that, integrated with engineering and detailing, provides clients more options and presents a new delivery model for steel-structured building projects. This integrated service model offers an increased level of control over an often-unpredictable aspect of construction, saving both time and money for clients.
On the chip fabrication plant, the project team worked collaboratively in a connected digital construction environment, enabling structural engineers and detailers to bring added value to the project by developing accurate digital structural models early in the design process. Procuring steel in-house and employing integrated structural steel design and detailing services enabled the detailing team to apply AISC and CISC specifications rapidly and accurately with increased productivity, improving quality and lowering costs for all project stakeholders.
The steel construction industry has recently experienced significant challenges related to steel procurement. Price fluctuations and material availability have made it increasingly difficult to manage project budgets, especially for large-scale developments that require extensive design, permitting, and planning time. Historically, steel prices have remained relatively stable, with typical changes occurring annually or quarterly. However, due to unprecedented market dynamics in recent years, prices have increased unexpectedly—and at a more rapid pace—making long-term forecasting a risky endeavor.
By integrating steel procurement with design and detailing, more price transparency is provided from the outset of a project which can mitigate risks associated with price volatility. The complete shop fabrication steel details can be used for the bidding and procurement process, which eliminates the time usually needed for detailing, RFIs, and design revisions that may postpone a project and create the need for change orders in the fabrication process.
For clients, this enhanced offering reduces project risk and change orders, expedites the project schedule, minimizes the cost, and produces better outcomes all around.
An integrated service model sets a new paradigm for how project teams can collaborate. Traditionally, communication between structural engineers, detailers, fabricators, and general contractors has been complex, time-consuming, and labor-intensive. Requests For Information (RFIs) often pass through multiple channels before reaching the appropriate party, causing delays and increasing the potential for miscommunication. The integration of steel design, detailing, and procurement forges a direct line of communication between the architect, structural engineer, and fabricator much earlier in the process. The result is a faster, more cohesive process that empowers the project team to deliver higher-quality results in less time—and shorter timelines translate into significant cost savings. This streamlined process eliminates friction, enhances accuracy, and reduces the likelihood of errors while ensuring that key decisions are made quickly and efficiently.
This new approach, integrating steel procurement with engineering and detailing, transforms the way project teams can operate and better meet clients’ needs. In initiating a close collaboration between procurement, structural design, detailing, and the steel fabricator from the earliest stages of a project, engineers can influence design and material costs, leading to more informed decision-making and better outcomes for their clients. ■
Break from the norm with Vulcraft steel specialty joists. Our team of experts can help you find unique, custom-engineered joist solutions for even your most complex designs. Our products are manufactured for durability and versatility, transforming your vision into a building that makes a statement.
Contact an expert today.
Contact our experts to find the specialty joist solution for your next project.