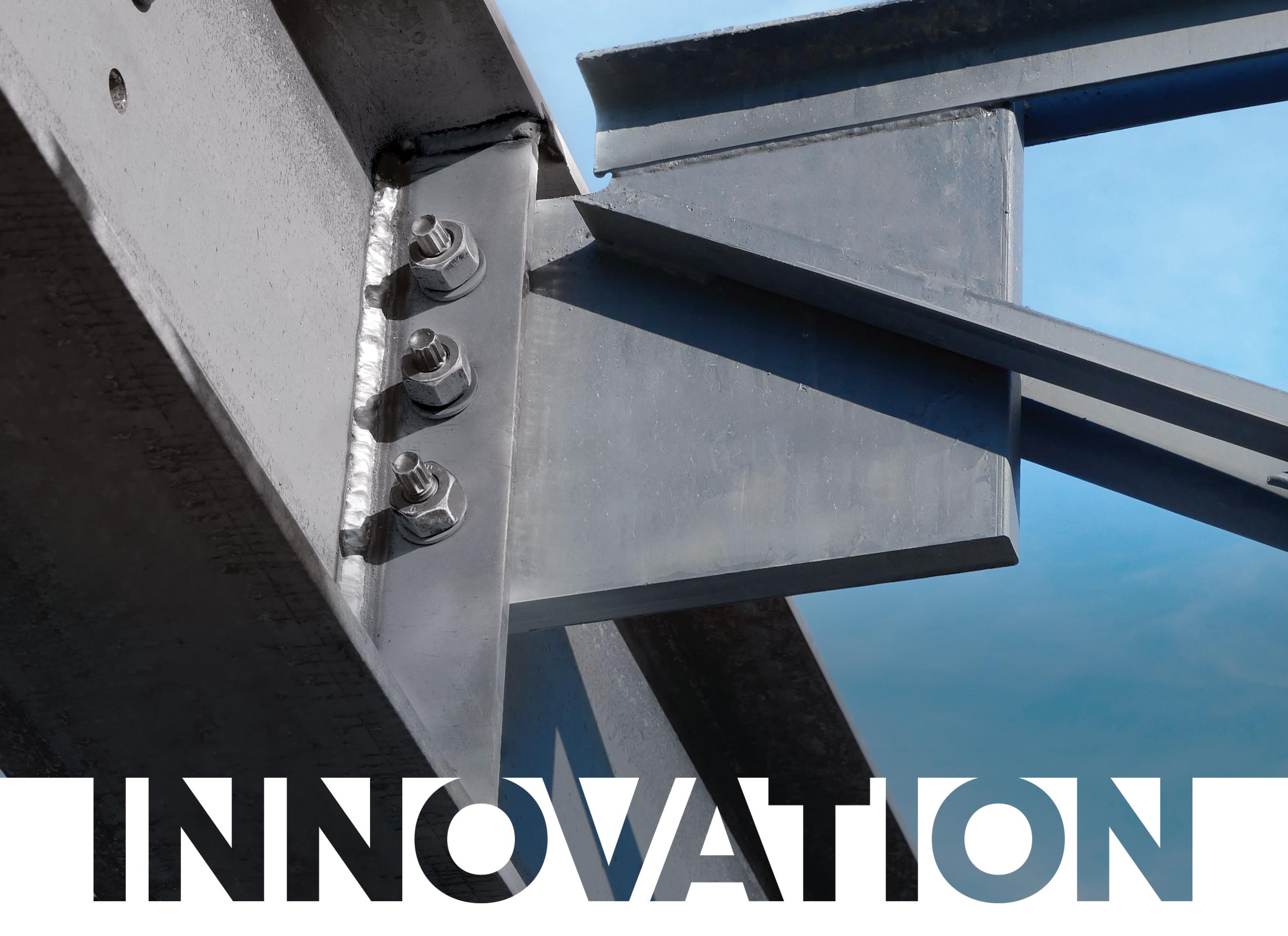
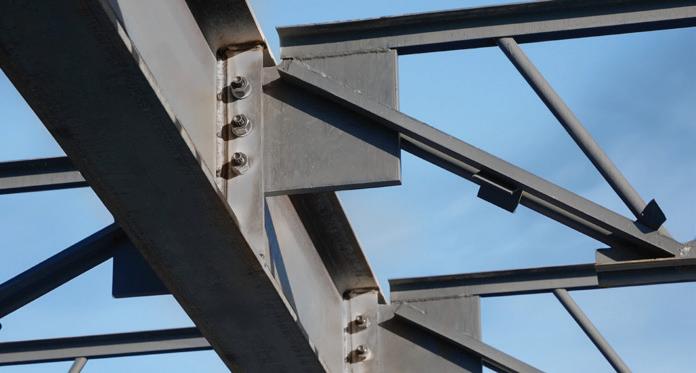
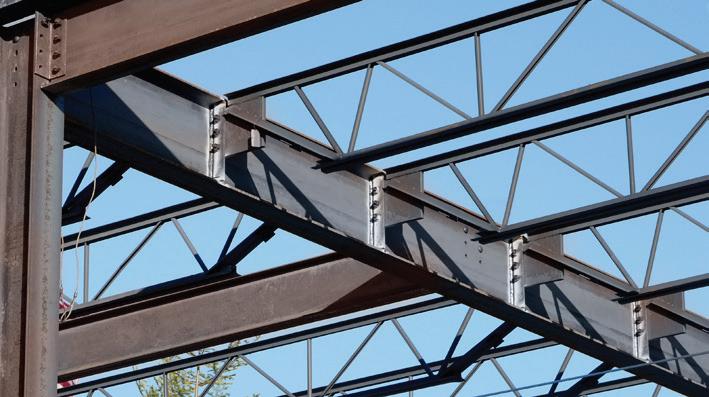
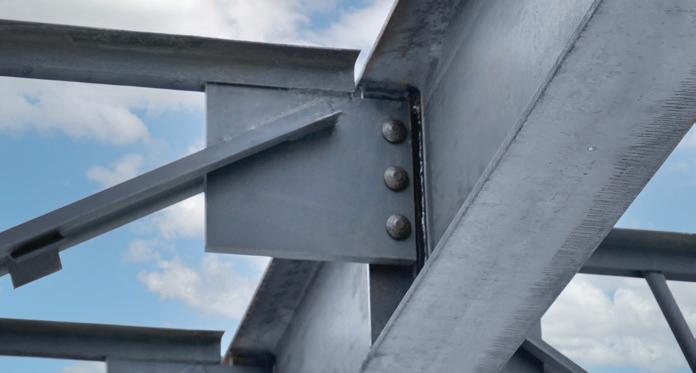
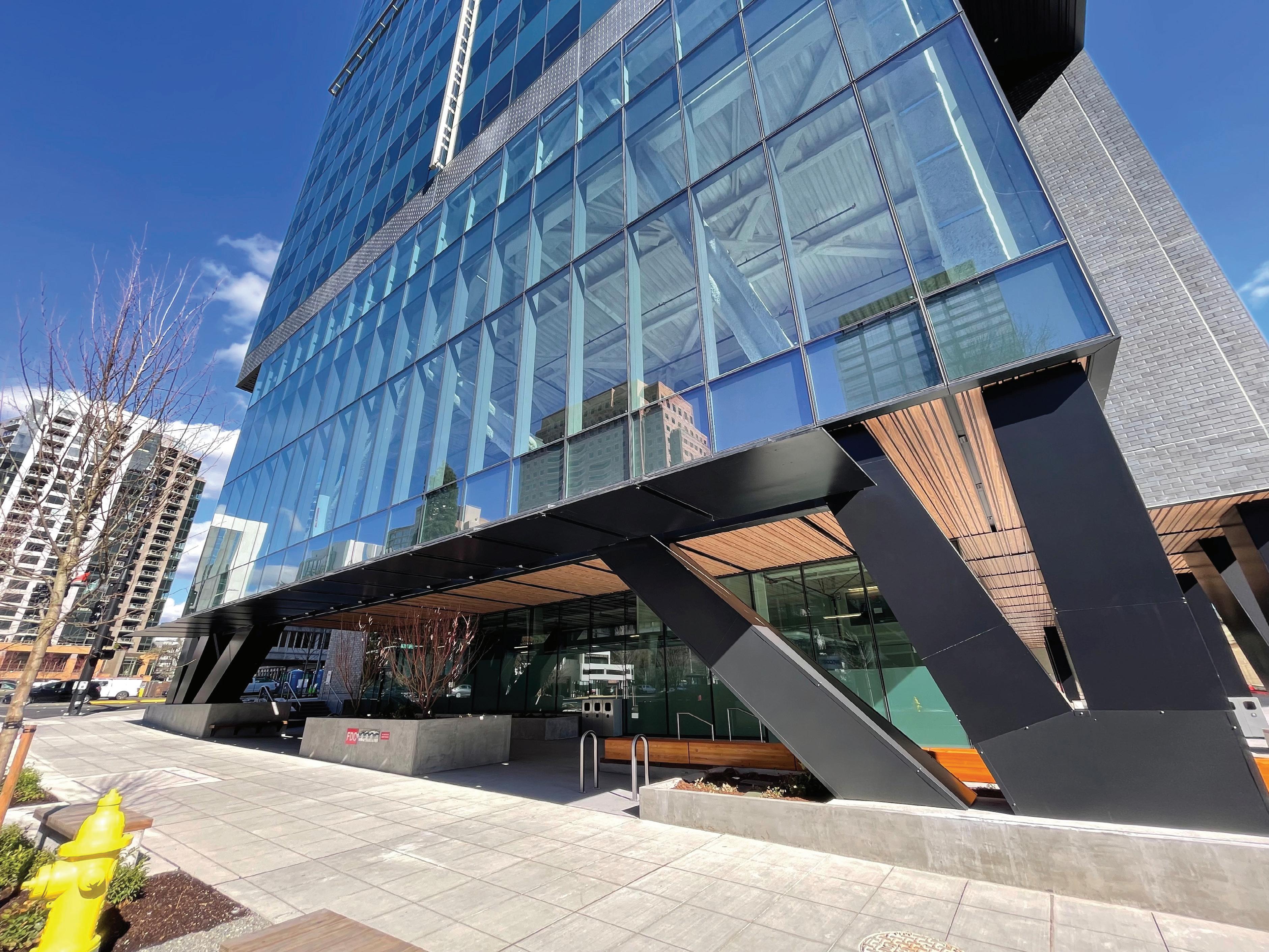
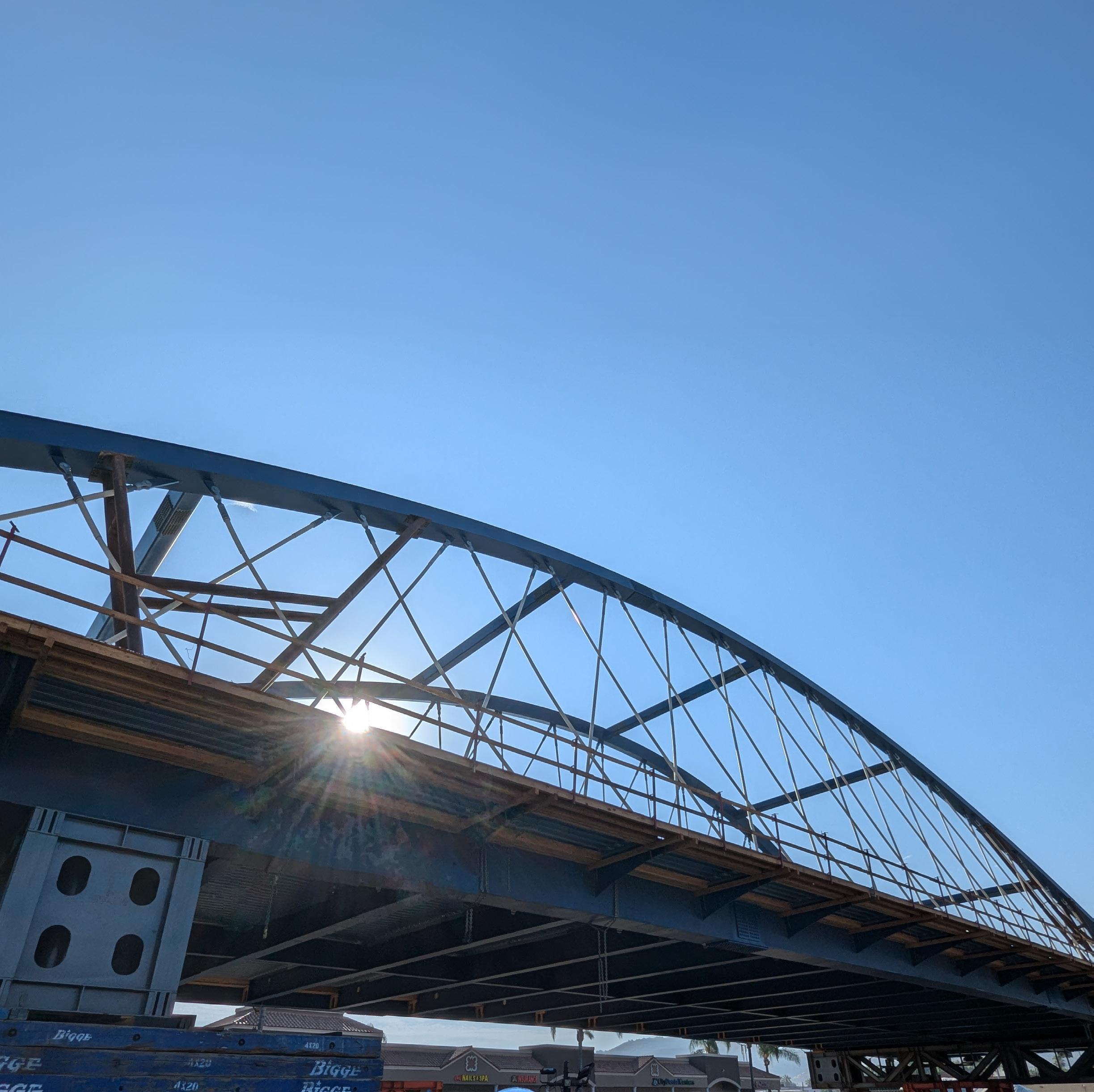
The railroad passing through Corona, California, has bolstered the local citrus industry for an entire century, earning Corona the nickname “Lemon Capital of the World.” However, that same rail infrastructure that connected Corona to the rest of the world also divided it from itself as it snaked through the very center of the city. For drivers on McKinley Street, long waits for freight and passenger trains to clear the gradelevel crossing became customary. In 2018, the City of Corona began the environmental and final design phases to build a new bridge over the railway and the open-channel drainage canal that runs beside it.
The project engineer, Biggs Cardosa, decided to go big with American steel. By spanning the entire 291-foot gap over the railway, canal, and access roads, any conflicts with the drainage
canal were eliminated. Utilizing a lightweight steel span meant that the bridge could be constructed adjacent to its final location and then lifted into place, minimizing railway disruption. In this case, an arch design was the perfect solution. Using interlaced “network” suspenders to support the deck reduced moments imposed on the arch ribs when compared to vertical suspenders, allowing the arch ribs to be lighter, more slender, and more aesthetically pleasing.
Initial designs included wide-flange X-bracing between the arch ribs, but those members were switched to parallel 22x22x7/8” Jumbo HSS members from Atlas Tube due to their ease of constructability and cleaner aesthetics. Atlas Tube’s 100% domestic Jumbo HSS helped engineers avoid the obstacles presented by wideflange beams, and its near-immediate availability provided the benefits of closed sections without fabricating additional built-up boxes for the structure.
Thompson Metal Fab (TMF), with 85 years of history in oil and gas, marine structures, and transportation, fabricated the geometrically complex structure. Walsh Construction, the largest bridge builder in the country, would self-perform the steel erection. TMF’s expertise was critical as the project included several heavy weldments with complex geometry, especially at the joint where the arch rib connects to the tie girder. According to TMF, Atlas Tube’s Jumbo HSS made a difficult job simpler.
Atlas’ domestic Jumbo HSS was not the only innovation that made the bridge a reality. While the tie girders were large enough to allow ironworkers to reach the interior of the bolted splices, the arch ribs, tie beams, and support diaphragms were not. A new technology, Shuriken® by Atlas Tube, was a logical answer to this challenge.
Shuriken allows the installation of A325 and A490 bolts from one side and was the perfect solution to the connection conundrum confronting the team. By mounting the nuts on the interior of the HSS and box members, splices could be bolted up from the exterior. The built-in lateral flexibility of Shuriken preserved erection tolerance, while DuraSquirt® DTI washers from Applied Bolting Technologies made accurate tensioning and inspection easy for the slip-critical A490 bolts.
All these innovations came together to give Corona a beautiful, efficient new bridge as well as a safer and betterconnected community.
atlastube.com
Chair John A. Dal Pino, SE Claremont Engineers Inc., Oakland, CA chair@STRUCTUREmag.org
Marshall Carman, PE, SE Schaefer, Cincinnati, Ohio
Erin Conaway, PE AISC, Littleton, CO
Sarah Evans, PE Walter P Moore, Houston, TX
Linda M. Kaplan, PE Pennoni, Pittsburgh, PA
Nicholas Lang, PE Vice President Engineering & Advocacy, Masonry Concrete Masonry and Hardscapes Association (CMHA)
Jessica Mandrick, PE, SE, LEED AP Gilsanz Murray Steficek, LLP, New York, NY
Brian W. Miller
Cast Connex Corporation, Davis, CA
Evans Mountzouris, PE Retired, Milford, CT
Kenneth Ogorzalek, PE, SE KPFF Consulting Engineers, San Francisco, CA (WI)
John “Buddy” Showalter, PE International Code Council, Washington, DC
Eytan Solomon, PE, LEED AP Silman, New York, NY
Jeannette M. Torrents, PE, SE, LEED AP JVA, Inc., Boulder, CO
EDITORIAL
Executive Editor Alfred Spada aspada@ncsea.com
Managing Editor Shannon Wetzel swetzel@structuremag.org
Production production@structuremag.org
Director for Sales, Marketing & Business Development
Monica Shripka Tel: 773-974-6561 monica.shripka@STRUCTUREmag.org
CAST CONNEX ® custom steel castings allow for projects previously unachievable by conventional fabrication methods.
Innovative steel castings reduce construction time and costs, and provide enhanced connection strength, ductility, and fatigue resistance.
Freeform castings allow for flexible building and bridge geometry, enabling architects and engineers to realize their design ambitions.
Custom Cast Solutions simplify complex and repetitive connections and are ideal for architecturally exposed applications.
Scan this QR-Code to learn more about this project.
Architect: Passero Associates
Structural Engineer: Passero Associates
General Contractor: Christa Construction
Steel Fabricator: Raulli & Sons, Inc.
Photography by Don Cochran
By Scott Erickson
How challenges for The Artise turned into a willingness to create something new.
By Dylan Richard, PE, and Katherine Chan, MSFE
Peeling away conventional design, USF’s Judy Genshaft Honors College is a modern attraction of the Tampa, Florida, campus.
By
Alexander Stephani, PE; Xiaoxiao Wu, PE; Andrew Angelilli, PE; Kevin Poulin; Guy Nordenson; and Filippo Masetti
One of the most striking elements in the new Studio Museum Harlem is the four-story monumental stair, crafted from structural steel members and adorned with terrazzo panels.
By Dan Bergsagel, Fernando Sima, Christoph Paech, and Knut Stockhusen
One of the eight new stadia built for the 2022 World Cup in Quatar was engineered with circular construction in mind, and the 40,000 capacity, multi-tiered venue is the first fully de-mountable stadium of its kind.
By Alec Thompson, EIT; Owjan Hashtroodi, PE; Nicholas Christie, PE; Jason Krolicki, SE, PE
The Sonic Sphere at The Shed in New York City represents a cutting-edge collaboration between engineering, architecture, and art, creating a deeply engaging experience for the audience.
By Peter Somers, PE, SE, and Jeremy Hasselbauer, PE, SE
The seismic retrofit of an 1960s-era office building involved 272 viscous dampers across 23 stories.
Simpson Strong-Tie equips you for success at every stage of tilt-wall construction. From panel formwork, erection and bracing to structural and roof framing, decking and interior finishing, our code-approved connectors, mechanical anchors, adhesives and fastening systems keep you moving ahead. Builders also rely on our onsite training, service and technical support, plus web apps and calculators that simplify and streamline project management. Our nationwide distribution network ensures that products are readily available for jobsite delivery when and where you need them. Altogether, it’s a total solution designed to elevate performance. So you can take your operation to new heights.
To learn more, visit go.strongtie.com/tiltwall or call (800 ) 999-5099.
Kevin H. Chamberlain,
Scott Neuman PE,
M. Hochwalt PE,
D’Aloisio,
By Don Dotson, Ph.D.,
Bruce, C.Eng.
Jack Armstrong
By Kevin H. Chamberlain, PE
I’ve been in one of those reflective moods lately. My youngest just started college over 700 miles from home, and my wife and I miss her like crazy. My time on the Executive Committee of CASE ended this year. And 2024 was my 30th year at DeStefano & Chamberlain (yes, I started as an intern). It’s been a bittersweet year of wanting to slow down the clock.
We take on about 150 projects a year with our firm of seven. I guess that’s about 4,500 projects in three decades. I enjoy scrolling our job list from time to time to remember the good clients, the not so good clients, and the learning experiences along the way. Clients are sort of like characters in a Seinfeld episode. Here are few characters that stand out to me—maybe some sound familiar:
• The One and Done—Some clients will only hire a structural engineer one time in their lives. A homeowner building their dream home will probably not build another dream home in the foreseeable future. Not much prospect for a long-term relationship if there will be no other projects.
• The Quick Payer—From time to time, you find a gem of a client who pays invoices within a few days of receipt. The best payers get the best service, so we give priority to these clients and do everything we can to keep them happy.
• The Slow Payer—Any client that takes more than 30 days to pay an invoice. My electrician friend follows every invoice with a call asking when he can pick up his check. Try getting the brakes fixed on your car without paying when you pick it up. As a profession we need to politely demand promptness like the rest of the civilized world.
• The Bad Payer—Any client that is consistently over 90 days to pay an invoice. At that point, whether you like it or not, you are helping to finance their project for them.
• The Non-Payer—Once in a blue moon, a “one and done” client doesn’t pay ... at all ... ever. Sometimes with an excuse complaining about your work, but sometimes they just ghost you.
• The I’ll Pay You When I Get Paid—This is most architects; they wait to be paid by
their client in order to turn around and pay us. Some take this sport to an extreme, and won’t send us a retainer until they’ve gotten that money from their client too.
• The Start Up—Some relationships start off great. The client has lots of enthusiasm and are quick to sign a proposal. But then the relationship sort of peters out. The other work promised fails to materialize. They turn into a slow payer (or bad payer).
• The Shopper—We have certain architects or developers who appear every few years when the groundhog sees its shadow asking for a proposal for a new project. They never hire us, but just like to shop around and keep whomever they normally work with honest. One has been asking for proposals every five years or so, for about 20 years now.
• The Ones You Fire—Nothing feels as good as getting rid of a really bad client.
Clients are sort of like characters in a Seinfeld episode. Here are few characters that stand out to me—maybe some sound familiar.
• The Honest Abe—I had an association request a proposal to evaluate a bridge. Not only did they divulge they were seeking multiple proposals, they also reminded me they didn’t hire us for the same study previously because they were shopping around back then too.
• The Risk Taker—Sometimes a client’s appetite for taking chances doesn’t match yours. An Architect who won’t listen when you explain why their vision has structural problems. Or the design doesn’t match the budget. Better yet, you’re being told “not to worry” about aspects of the design that clearly don’t work because the code official allegedly said it was “ok.” Those are the clients who will inevitably get you in trouble and should be shed like a bad habit.
• The Hangers On—Some clients you just can’t seem to get rid of. They keep coming back with lousy projects or impossible deadlines or budget fee requests. There are many reasons you want them to go away but can’t quite bring yourself to tell them off for good. Maybe because you will cross paths with them again and want to stay on good terms.
It’s like a breath of fresh air when they are gone. There are different ways to handle this group. Often, it’s a soft landing with a “sorry we’re just too busy.” In rare instances though, we are just honest and tell them to find another structural engineer because we’re done.
• The Lifers—I had to save the best for last. Clients who, after working with you, ONLY want to work with you, and never want to work with another structural engineer again. You’re their go to. And you love working on their projects, they aren’t tortured or stressful. They know how to herd cats. They listen to your advice, and you appreciate what they bring to the table. Those are the client relationships to spend your time on. Those are the clients who make you glad you became a structural engineer. Yes—they do exist! ■
Janiece Williams is the Co-Founder and Executive Director of LeaderFlow, a non-profit organization created to provide a leadership development program that empowers diverse mid-career professionals. The goal of LeaderFlow is to address a critical gap in the AEC career pipeline, which continues to face significant underrepresentation of diverse leadership, with ongoing challenges in retaining diverse talent. Trained as an architectural designer, and one of the original cohort participants from the pilot program, Williams is deeply committed to supporting emerging professionals as they navigate and advance within the AEC industry.
STRUCTURE: What inspired you to go into architecture?
Williams: Choosing to study architecture was unexpected. I had just graduated from a specialized high school for health professions because, at one point, I thought I might go into medicine—mainly driven by my desire to help people. But honestly, I had no clear idea of what I wanted to study in college or what career path to pursue. I remember feeling so much pressure, as if whatever I chose would lock me into a single career for life, making the decision feel so heavy. My interest in architecture was sparked by one of my older sisters, who has an extensive career in the construction industry. Although I knew little about the architecture profession at the time, I saw it as a chance to explore my interest in helping people through community building.
STRUCTURE: How has your architectural background contributed to where you are today?
Williams: Leaps of faith have been a recurring theme in my life, often filled with uncertainty and struggle. Throughout my journey, I wrestled with my identity in architecture, grappling with imposter syndrome even before I knew what it was. I never saw myself as the most creative designer or technically skilled, but I knew that I excelled in working with people, building effective teams, and solving problems. After graduating from Howard University in 2010, despite the industry still recovering from the recession, I committed to working in architecture for a few years to find my path. I moved to Los Angeles, and what was supposed to be a short stint turned into 10 years.
Although I was advancing in my role and more engaged with the architecture community, I felt disconnected and unfulfilled. By 2021, after struggling to align my career with my passions and dealing with mental health challenges, I knew it was time to take a step back and explore a new direction. During this time, I joined a pilot leadership development program, which came at a crucial moment. It aided me with the support and clarity I needed to navigate these transitions. This leadership program was an initiative by Southern California Chapter of the National Organization of Minority Architects (SoCal NOMA) and KPFF Consulting Engineers in response to the social unrest following George Floyd’s murder. KPFF’s CEO, John Gavan, proposed adapting their internal leadership development program framework to support mid-career professionals of color in the AEC industry. I was invited to apply. The result was life-changing. The program helped me embrace my identity, both personally and professionally, and boosted my confidence in the value I bring to this industry. I completed the pilot leadership program in September 2021. But
after a decade in Los Angeles, I decided to return to my hometown of Houston to be closer to family and figure out my next chapter.
STRUCTURE: You were actively involved with NOMA for many years prior to co-founding LeaderFlow. How did that experience shape LeaderFlow ?
Williams: When I was struggling to find my place in architecture, I found a sense of community through SoCal NOMA. I became a dedicated volunteer with the Project Pipeline Summer Camp planning committee and served on the Executive Board for two terms from 2018-2021.
As a repeat volunteer, I was content flying under the radar, standing in the back of the room without needing recognition. However, it wasn’t until my SoCal NOMA colleagues encouraged me to run for a board position that I began to break out of my shell and embrace a leadership platform.
Through my involvement, I realized the value of having a strong community in this industry—especially as the only woman or person of color in many of the professional spaces I found myself in. The supportive, empowering community I found at NOMA inspired me to create a similar space for diverse professionals in AEC through LeaderFlow, fostering that same sense of belonging and growth among our cohorts and facilitators.
STRUCTURE: What is LeaderFlow and how is it unique to the AEC industry?
Williams: My move coincided with the creation of LeaderFlow, which I envisioned as my way to help others by sharing my newfound sense of purpose. John Gavan and I questioned why leadership in the AEC industry does not reflect the diverse available talent. We recognized the need to support a part of the talent pipeline that had been overlooked: mid-career professionals. Those who’ve been working in the industry but would benefit from mentorship and coaching outside of project management to achieve leadership positions. This realization led us to expand this initiative and launch LeaderFlow as a nonprofit in January 2022, with a mission to support and empower diverse professionals in the AEC industry.
What makes our program unique is that we focus our recruiting
efforts primarily on professionals of color that will make up a cohort of 12-15 participants from within the same city, but ideally not from the same company. We found that this blend of architects, engineers and construction professionals helped to create more authentic and vulnerable conversations as the emerging leaders can openly discuss their experiences and perspectives in a safe space without openly challenging their co-workers or firm leaders.
While many mentorship programs target recent graduates or earlycareer professionals, LeaderFlow is unique in focusing on mid-career individuals who may feel stuck or uncertain about how to advance into leadership roles. We’re proud to offer this program at no cost to participants, thanks to our sponsors, ensuring that financial barriers don’t prevent access to critical leadership training.
In the few years we’ve been running LeaderFlow, we’ve seen significant growth in participants' confidence, self-awareness, commitment to personal development, and overall performance.
LeaderFlow currently operates in Houston, Los Angeles, Seattle, New York, and Chicago, with plans to expand nationally.
STRUCTURE: What do you believe defines a leader in today’s workplace?
Williams: I believe that an impactful leader in today’s workplace is someone who continuously commits to their personal growth and shares their learned lessons with others to create a culture of understanding and belonging. A strong leader prioritizes emotional intelligence, adapts to growth and change, builds trust through accountability and places a strong emphasis on mentorship and the development of others.
STRUCTURE: What is your “why” (or purpose), and how does that define you as a leader?
Williams: I believe that my purpose is to help others realize their potential by exercising their voice, starting with learning who they are as individuals so they can be their biggest advocates. Through my work, I often recognize in others the same obstacles that inhibited my growth, such as imposter syndrome, fear, and limiting beliefs.
I believe this defines me as a leader because my core mission is to share the tools and lessons I’ve learned to help others remove these barriers. I feel most fulfilled when I get to witness those "lightbulb moments" in others—whether they are personal or professional breakthroughs. Each moment of clarity or achievement, no matter how small, signifies progress, one person at a time.
STRUCTURE: What advice would you give to companies for developing and retaining future leaders?
Williams: My advice to company leaders starts with prioritizing mentorship by providing opportunities to build leadership skills and
confidence. People want to know they are being invested in just as much as the company wants people to invest in it.
I believe that this can be accomplished by providing growth opportunities, creating clear career paths by intentionally making leadership progression more transparent, and promoting work-life balance.
STRUCTURE: How have you stayed authentic to yourself in your leadership journey?
Williams: I have stayed authentic to myself by intentionally engaging in self-reflection as I grow, and staying grounded in my core values to build confidence in my ability to tackle challenges. I recognize that I don’t have all the answers, and I don’t strive for perfection, but I believe it’s essential to be open and vulnerable about my journey. This honesty drives my commitment to lead with empathy and create meaningful connections with others along the way.
STRUCTURE: What is the best advice you’ve been given in your career, or otherwise?
Williams: One of the best pieces of advice I’ve ever received came from another one of my older sisters. She told me that my passion doesn’t have to be defined by my work. This was a big revelation for me. For so long, I thought that I had to find my passion through my job. But her advice shifted my perspective; she helped me realize that I should focus on what truly fulfills me, like being of service to others and connecting with people. Once I embraced that, my path started to reveal itself, which eventually led me to the work I’m doing now with LeaderFlow.
STRUCTURE: What is your advice on figuring out their “why” and being more intentional in forging a path to leadership?
Williams: My advice to anyone trying to figure out their “why” is to start by assessing your level of curiosity. Discovering your purpose requires a deep curiosity about yourself and a commitment to exploring it through self-reflection and learning. Be patient and give yourself time—this is a journey that unfolds gradually, not something to figure out overnight.
Once you gain clarity on your "why," use that understanding to be intentional in forging your path to leadership. Align your actions with your values, seek opportunities that resonate with your purpose, and stay open to growth. Leadership is built on authenticity, and knowing your "why" will help guide your decisions and interactions as you grow into a leadership role.
STRUCTURE: What is the biggest challenge for DEI within the AEC industry?
Williams: The biggest challenge for DEI in the AEC industry has been the historical lack of diverse representation, which has made progress slow and difficult. One of the major issues is attracting and retaining underrepresented groups, many of whom leave the industry due to feelings of isolation, lack of mentorship, or limited opportunities for career advancement.
I also believe that DEI has contributed to burnout in the industry, due to the lack of consensus and buy-in from firm leadership, lack of engagement, and the tendency to lean on people of color to lead DEI efforts without broader support. Additionally, we're now facing even bigger challenges with the political and legal attacks on DEI initiatives, which threaten the progress we've made thus far.
STRUCTURE: If you could wave a magic wand, what does the AEC industry look like in 10 years?
Williams: If I could wave a magic wand, in 10 years the AEC industry would undergo a complete transformation in its educational and organizational culture. We would foster people-centric habits that prioritize mental health, diversity, equity, inclusion, belonging, and work-life balance. I believe these changes would make the industry far more attractive and sustainable for generations to come. ■
HIGH-STRENGTH STRUCTURAL STEEL
Design with Aeos™ high-strength ASTM A913 structural steel. A high strength-to-weight ratio means fewer tons and a lower carbon footprint for your project. Aeos is also the lowest embodied carbon steel of its kind, made with more than 95% recycled content using a circular steelmaking process with electric arc furnace (EAF) technology.
DISCOVER THE AEOS™ ADVANTAGE
Understanding the requirements for seismic separations and associated building components is necessary for code-compliant design.
By Scott Neuman PE, SE and John M. Hochwalt PE, SE
Everyone knows how to design a seismic joint. Or at least it seems so due to the small amount of published information on the topic. In practice, there is frequently a gap not just between structures but also between the code and its application. The goal of this article is to narrow that gap and improve the uniformity of these designs across our profession.
ASCE 7-22 has three separate criteria for the design of structural separations (also known as seismic joints) and elements that cross separations. The applicability of each criterion is not always clear, and their requirements may seem contradictory. The three criteria discussed in ASCE 7 are for structural separations (Section 12.12.2, Figure 2), structural members spanning between structures (12.12.3, Figure 3), and nonstructural elements spanning between structures (Section 13.3.2, Figure 4). Mindfully considering each section, including interactions between the sections, will produce a wholistic and
unified design for both the structures and elements that cross the gap between the structures.
Minimum structural separation distances need to be provided when two independent structures are located close to one another and there is a possibility of the structures colliding during an earthquake, resulting in what the code refers to as “damaging contact,” more commonly referred to as “pounding.” The minimum widths of structural separations including seismic joints are prescribed in ASCE 7, Section 12.12.2 –Structural Separation. Commentary Section C12.12.2 introduces the term “seismic joint” as an alternative to “structural separation.”
At locations where one structure is close to another independent structure on the same property, or where a structural separation occurs within a building, the maximum inelastic response displacement δDE is calculated for each structure at the location of the separation per Equation (12.8-16).
I C DE e de di d d d =+ (12.8-16)
The required minimum separation between the structures (δSS) is calculated using the Square Root of the Sum of the Squares (SRSS) of the Design Earthquake (DE) Displacements in accordance with Equation (12.12-2).
() () ss DE DE 1 2 2 2 dd d =+ (12.12-2)
Use of the SRSS method to calculate the structural separation between seismically independent structures has remained unchanged in ASCE 7 through several code cycles and is based on the underlying assumption that it is unlikely that the independent building structures will displace completely out-of-phase. This check is performed at the DE hazard level; damaging contact will be possible, if not likely, at the MCER hazard level. A smaller separation is permitted where an inelastic analysis is performed justifying the smaller value. Where floors in adjacent buildings do not align, the edges of floor
plates may laterally impact columns along their height, which is a more hazardous condition than when the floors in the buildings are aligned. When this condition occurs, the engineer should consider the architectural detailing in the area of potential impact to decide if damage will remain largely nonstructural or if it is possible that structural damage to the columns will occur, in which case a seismic separation larger than the code minimum may be warranted. Section 12.12.2 states that a new building should be designed so that it does not displace across a privately owned property line, however, where an existing building already exists on the property line, designing a new building so that it does not displace across the property line will not be sufficient to avoid damaging contact. This is because the existing building located on the property line will sway across the line during an earthquake. This condition should be discussed with the building owner, and an engineer should consider providing a minimum structural separation based on Equation (12.12-2), as if the buildings were located on the same property, so that the buildings do not impact during smaller earthquakes than would be otherwise intended by the building code.
When displacements of an existing building on a neighboring property have not been directly calculated, it is usually acceptable to assume that the drift of the existing building is 3% per the recommendations of ASCE 41-23, Section 7.2.15.1, unless the adjacent structure can be characterized as a rigid shear wall structure with rigid diaphragms, in which case ASCE 7 Section C12.2.2 suggests that a drift of 0.42% can be assumed. The ASCE 41 recommendation is a conservative estimate if the existing building is not badly deficient—it is likely that the displacements for the existing building could be reduced if they are quantified using a more detailed method. Where ASCE 41-23 is the design standard, ASCE 41-23 Section 7.2.15.2 contains additional criteria for the evaluation of the separation.
Lastly, it may be desirable to slightly oversize the gap to avoid construction tolerances or thermal movements compromising the displacement capacity of the joint. An additional 1-inch separation is adequate to account for slab placement tolerance because one slab will be placed first, and the slab that is placed second will have a nearby hard edge from which to measure. This additional inch also allows for small amounts of other movement that is typically unquantified, such as thermal movement and shrinkage. Where thermal and shrinkage
movements at the separation are expected to be significant, as may be the case in open parking structures, these movements should be quantified and included in the separation width calculations directly as required by ASCE 7 Section 2.4.4.
Where a structural element such as a pedestrian bridge spans between independent structures, the element must be supported such that there is a load path for both gravity and lateral loads while the relative movement of the structures is accommodated. One method to achieve this is to provide a fixed support at one end of the element, and a vertical-only support at the other end of the element. The vertical support is detailed to allow the element to translate and rotate freely in the horizontal plane. Another method of support is to use a pin connection at one end and a roller support at the other end, which allows the element to pivot to accommodate movements perpendicular to the span, and slide to accommodate movements in the direction of the span.
The amount of horizontal movement required to be accommodated by the supports is called the maximum anticipated relative displacement and is defined in ASCE 7 Section 12.12.3 – Members Spanning Between Structures. This Section has more conservative requirements than the requirements for structural separations because of the risk of local collapse if an element becomes unseated from its support.
To calculate the displacement requirements of the support, the maximum anticipated relative displacement is calculated using the Maximum Considered Earthquake Displacement (δMCE) per ASCE 7 Section 12.8.6. Then the total movement is calculated by summing the absolute value of the displacements at both support locations.
As described by this process, the maximum anticipated relative displacement is as defined below. Use of the factor R applied to the displacement value instead of Cd is intended to correct for an underprediction of displacements that has been shown to occur when the Cd factor is used. maximum anticipated relative displacement= δMCE1+δMCE2
The term δ e is defined as the elastic displacement that is computed under design earthquake forces and is not limited to horizontal movement. Where vertical movements and rotations occur due to the earthquake response, these movements should be considered in the design as well.
The movements prescribed for nonstructural elements crossing structural separations are greater than the movements used for determining the seismic separation itself and are less than the movements used for structural elements crossing seismic joints, suggesting that their importance to building performance also lies somewhere in the middle. However, the acceptance criteria used with these movements leaves much more room for the judgment of the responsible design professional. For nonstructural systems in general, ASCE 7 Section 13.3.2 simply states that these movements “shall be considered.” The commentary helpfully clarifies that this vague language is intentional, and that damage as a result of these movements may be acceptable.
ASCE 7 Section 13.5.2 states that architectural components are required to accommodate seismic relative displacement requirements if failure of the element represents a life safety hazard. Typically, the only architectural component crossing a seismic joint is the seismic joint cover, which is discussed in detail in the following section.
ASCE 7 Section 13.6.2 emphasizes that mechanical equipment in a building is required to be designed to accommodate seismic relative displacements if the component importance factor Ip is greater than 1.0. The component importance factor is defined in Section 13.1.3 and is 1.5 for components that are required to function for life safety purposes after an earthquake. So, while allowing damage might be one way to accommodate the movements, the mechanical designer is responsible for determining whether such damage represents an impermissible life safety hazard.
The seismic displacements required for design of nonstructural components that cross structural separations are governed by ASCE 7 Sections 13.3.2 and 13.3.2.2. These displacements are calculated as the absolute sum of the building displacements on either side of the separation, similar to Section 12.12.4. Movement can occur either perpendicular or parallel to a separation, which is important to make clear on the construction documents for the designers of the nonstructural systems. Displacements are amplified by the seismic importance factor from ASCE 7 Table 1.5-2 to provide enhanced seismic performance of nonstructural components within important facilities. Seismic Relative Displacements (D pI) at a structural separation are required to be calculated as shown below. Note that the subscript in Equation (13.3-8) is the capital letter “I,” which is intended to show that the importance factor is included within the parameter.
While some nonstructural systems may be exempt from
accommodating seismic displacements, any nonstructural system crossing a seismic separation should be designed to accommodate service level movements without distress or loss of function. Possible sources of service level movements include: the 10 or 50-year wind or seismic loads, thermal changes (especially in unconditioned structures), and concrete shrinkage. One approach to determining serviceability movements would be to remove the C d factor from Equation (12.8-16). The resulting displacement corresponds to the sum of the elastic drifts in both structures on either side of the joint, and represents the expected movement of the buildings at their design strength.
As referenced before, architectural components typically stop on either side of the seismic separation and a joint cover bridges the gap. Of most interest to the structural engineer are the seismic joint covers and associated fire-resistive joint systems at the floors and roof as these may affect the size of the gap between structures. In the extreme, the structural separation required to accommodate these joint systems can impact not just the edge of concrete, but also column locations, and even building layout grids. Thus, it is important to discuss this issue with the architect early in the project so that the appropriate design criteria can be applied and changes to the structural layout are not required late in the project.
The design or selection of the joint cover starts with establishing its intended functionality for both seismic and in-service conditions. ASCE 7 Section C13.5 provides insight into the performance needed to maintain life safety conditions, such as avoiding falling hazards or blocking egress paths. Joints that are part of a fire-resistant assembly must also comply with Section 715 of the International Building Code (IBC) which requires that such joints be capable of accommodating “expected building movements.” The IBC does not define what expected movements are, but we believe this is commonly understood to include nonstructural movement criteria from ASCE 7.
Where failure of a seismic joint cover creates a life safety hazard, or the building is required to remain operational following an earthquake, the joint cover should be sized for the criteria discussed in the nonstructural section, which will likely govern the width of the structural separation where the joint cover is placed. Where failure of a seismic joint cover is not a life safety hazard, it is not required to accommodate the ASCE 7 Chapter 13 nonstructural movements and the joint cover can be sized to maintain the minimum separation as determined by ASCE 7 Equation (12.12-2). When this criterion is used, the cover may be damaged following an earthquake. As a result, these joint covers should also have movement criteria established for serviceability that meets the owner’s expectations.
With the criteria established, a joint cover can be designed or a commercial product selected. Many different types of joint covers exist, ranging from simple cover plates to complex assemblies that create a seamless appearance. Not all joint covers can close to zero width during seismic movement, and there may be other material such as fireproofing or hardware that occupy space within the structural gap and that would prevent the separation from closing fully. As a result, determination of the structural gap width requires working with the architect to understand the type of joint cover that is wanted and what the displacement capabilities of the cover are. If the type of joint cover cannot be known early in the design, the final width of the structural separation may need to be modified once the joint cover is selected, and the location of walls and columns near the joint should accommodate some increase in the width of separation.
If failure of a seismic joint cover is a life safety hazard only due to disruption of the fire rating, it may be preferable to provide a separate architectural detail that can maintain a fire rating while accommodating the nonstructural displacement requirements, instead of increasing the width of the structural separation. In this condition, it would be reasonable for the fire-rated detail to accommodate the maximum displacements that can occur, which is limited by the as-built separation when the gap is closing, but per Equation (13.3-8) when the separation is opening or displacing along its length. This will, however, be subject to the Authority Having Jurisdiction’s interpretation of expected building movements as applied to IBC Section 715.
Minding the gap in seismic separations requires paying attention to much more than just the physical space—it requires minding the gaps between the various code requirements, owner expectations, and practical constraints. In addition, it requires bridging the gap between the structural code provisions and the design professionals responsible for the nonstructural elements crossing these joints. ■
Scott Neuman, PE, SE is a Senior Structural Engineer at Amazon in Seattle, WA and is the Chair of the Structural Engineers Association of Washington Earthquake Engineering Committee. This article was written while Neuman was the Director of Earthquake Engineering at KPFF. (scotneu@gmail.com)
John M. Hochwalt, PE, SE is the Director of Engineering for the structural engineering group of KPFF Consulting Engineers’ Seattle office and is involved in code development for seismic design through his work with The Masonry Society and the Building Seismic Safety Council’s Publications Update Committee. (john.hochwalt@kpff.com)
Attention to structural details can minimize thermal energy losses and avoid problematic condensation in buildings.
By Jim D’Aloisio, PE, and Ivan Lee, P.Eng.
Over the past several years, the need for structural engineers to pay attention to and mitigate structural thermal bridging, especially the most severe conditions, has grown in importance. This is primarily because architects, pushed by more stringent energy codes, have improved the thermal performance of the building envelope in areas such as walls, roofs, and floors. However, many architects and engineers have not accounted for thermal bridging in these insulated building envelope designs, which reduces the overall thermal performance of the building envelope by increasing energy loss. Without considering thermal bridging, many architects and engineers have falsely believed the building envelope has better thermal performance than it actually does. This can lead to underperformance of actual versus modeled building energy consumption, which leads to failure to meet energy targets such as net-zero operational energy or higher costs due to higher-than-expected energy consumption. Structural thermal bridging through exterior walls, roofs, and foundations can impact not only the energy performance of the building, but also occupant comfort and durability of materials. Excessive heating or cooling energy loss from structural thermal bridging can create cold spots which increases the risk of condensation and moisture-related damage to finishes and structural elements. Details that seemed to work fine 10 years ago may cause severe condensation problems today.
from buildings. Recent attention has been paid by structural engineers to understand and reduce the embodied carbon of the structural materials used on their projects, and rightly so. But operational carbon—the carbon emissions from the energy needed to heat and cool the building—is equally significant. Here as well, when caused by thermal bridging energy losses, the carbon emissions can only be effectively mitigated by the structural engineer. Severe structural thermal bridging conditions across a building envelope that is otherwise well-insulated and airsealed can cause in excess of 20% of the building’s thermal losses. This will occur during every year of the service life of the building for both heating and cooling energy, resulting in a significant increase in operational carbon emissions—which the project’s structural engineer could prevent.
Tightening of energy codes alone is reason enough for structural engineers to pay attention to thermal bridging conditions. Some building energy codes now explicitly require thermal bridging conditions, such as balconies and parapets, be addressed by the design team. To the extent that these details are structural, they cannot be addressed without the structural engineer’s collaboration and input—even if they had not considered thermal losses to be part of their responsibility.
Litigation cases involving deterioration of building elements due to thermal bridging-related condensation are on the rise. Remedying an existing building condition to minimize problematic thermal bridging can be challenging and expensive—much more so than incorporating details that mitigate thermal bridging in the original design. If the cause of such problems is identified as thermal bridging through structural elements, they might still be considered legally and financially culpable, if the problem-causing details are on the structural drawings.
Another big factor that is growing in importance is limiting structural thermal bridging energy losses for the reduction of operational carbon
The Structural Engineering Institute (SEI ) Sustainability Committee’s Thermal Bridging Working Group has been working to increase awareness of, and communicate solutions to, the problem of structural thermal bridging to practitioners. In this three-part series on thermal bridging, we’ll identify the various types of problematic thermal bridging conditions that occur on building design projects. For each we’ll illustrate some examples of effective mitigation strategies to reduce, if not eliminate, thermal bridging energy losses. We’ll also provide resources for more information to assist designers who don’t necessarily want to become experts in thermal flow analysis but want to prevent excessive thermal losses and avoid problems on their projects.
Cantilever concrete balconies and other appurtenances that project out across a building’s thermal envelope are problematic thermal bridging details because the penetration through the building envelope is continuous; that is, the thermal bridge is linear, creating a greater magnitude of thermal loss. For a typical high-rise concrete residential building with balconies equal to 20% of the intermediate floor area, thermal bridging from cantilevered balconies can account for 13% of the building envelope heat loss.
An effective remedy is to reframe the balcony with exterior supports so that the bridging elements are discrete, i.e., creating discrete point thermal bridging, rather than a continuous cantilever.
If this is not feasible, the cantilever support condition can be modified
to reduce thermal flow by the use of a proprietary manufactured structural thermal break assembly, inserted in the plane of the thermal envelope. These have been used in Europe and other countries for decades. They can be considered design-delegated components, that is, the loading requirements can be specified as well as thermal properties, which should be determined in conjunction with the project architect, and the manufacturer’s engineer can verify that the manufactured connection element can resist the design loads. Other methods include wrapping the balconies with insulation; however, this may be difficult to implement due to durability concerns of the insulation.
The thermal performance of these balcony details is described by the Psi-value which is the incremental heat loss due to thermal bridging from continuous details such as balconies, parapets, and shelf angles. The Psi-values listed in Table 1 were determined using 2D and 3D thermal simulations.
Steel-framed and wood-framed balconies usually can avoid continuous thermal bridging, with a discrete number of cantilever beams providing support. However, the high thermal conductance of steel can result in significant thermal losses unless mitigated. Wood has less conductance; however, it is still more conductive than any continuous insulation used in the building wall, so it is still vulnerable to the development of cold spots, leading to condensation.
Calculating the thermal losses and determining the areas of potential condensation through linear thermal bridging can be determined using thermal simulation software following thermal simulation standards such as the ISO 10211 and procedures in ASHRAE 1365 RP. 2D thermal simulation software, such as THERM, which is a free program available through Berkeley Lab can simulate heat loss for continuous
thermal bridging details. However, for details with discrete components, such as the intermittently supported balconies, 3D thermal simulation software will provide accurate results, since 2D simulation results may be too optimistic. Pre-calculated thermal bridging catalogs such as the BC Hydro Building Envelope Thermal Bridging (BETB) Guide (thermalenvelope.ca) and the ISO 14683 Default values are great sources of thermal bridging values for architects and structural engineers in lieu of thermal simulation data.
Discrete thermal bridging elements, such as steel beams or columns penetrating through the thermal envelope, usually do not cause large amounts of thermal losses. However, if the elements have large crosssectional areas, or if a series or cluster of discrete thermal bridging elements occurs, the thermal losses can add up. In addition, the local areas of these thermal bridges are just as likely to create condensation problems as linear thermal bridges.
A variant of this type of thermal bridging is the connection of sunshades or other projecting architectural elements to the building structure. Such metallic elements can act as thermal collectors or radiators, especially when they are made of aluminum, which conducts heat about five times as well as carbon steel. One of the authors has seen condensation dripping onto and staining ceilings and causing rust on structural members, at locations adjacent to the attachment points of aluminum solar shades (Fig. 2).
To remedy these conditions, some type of thermal intervention is required, ideally at the plane of the building’s insulation. An effective option is, again,
a manufactured structural thermal break assembly; there are versions to connect to steel on both sides, as well as steel on one side and concrete on the other.
Also possible is the use of a thickness of low-conducting highstrength structural shim material. When using this approach, keep in mind the following:
1. Thickness matters. Using too-thin thermal break material will have minimal effect on reducing the thermal loss, and in some cases will actually increase the thermal flow if the surface area of heat transfer is increased. Ideally the material is used at a location where there is already a steel end plate, since such conditions increase thermal flow due to the increase in cross-sectional area. If the beam needs to be interrupted with end plates and a thermal shim or thermal break, the shim or thermal break should be at least 2 inches thick or as thick as the wall insulation. A shim or thermal break that is not aligned with the insulation can still be a major source of heat loss and condensation due to flanking heat loss.
2. The use of stainless-steel bolts connecting across the thermal shim or thermal break significantly improves the thermal resistance of the assembly due to the relatively low conductance of stainless steel.
3. If using fiberglass reinforced plastic, keep the compressive stress levels below about 10% of the material’s ultimate compressive strength to avoid the potential for long-term creep deformation under sustained load.
4. If specifying the connection to be design-delegated by the Contractor’s Engineer, include the specific requirements of the thermal performance of the assembly, to avoid getting a minimally effective solution. Examples of thermal bridging at beam and column penetration details are shown in Tables 2 and 3. The heat loss at these penetration details is quantified by the Chi-value, which is the incremental heat loss from point thermal bridges. These values were determined using 3D thermal simulations from the BETB Guide.
Similar to balconies, a concrete or other type of continuous cantilever canopy can create significant thermal losses and condensation potential. The mitigation strategies are similar to that which we described for balconies.
Canopies supported by diagonal ties above and connected back to the buildings generally have point-type thermal bridges at the connection points—both at the main beam supports and at the ties. If stainless-steel connection elements are used, the thermal losses become much smaller, since stainless steel has a heat transfer coefficient about one-third that of carbon steel. To further mitigate the losses, a properly detailed connection incorporating low-conductance pads, or shims, can be used, such as fiberglass reinforced plastic.
Often overlooked, parapets can cause a large amount of thermal loss, depending on their construction. One common detail that is particularly problematic is when the cold-formed steel studs that comprise the wall structure below the roof plane are extended up past the spandrel beam to form the parapet. With the parapet exposed to exterior temperatures
Partially Insulated Parapet Fully Insulated Parapet Thermally Broken Parapet
Psi: 0.260 Btu/h.ft.F Psi: 0.186 Btu/h.ft.F 28% decrease in heat flow
Psi: 0.058 Btu/h.ft.F 78% decrease in heat flow
on three sides, both faces and the top surface of the parapet must be insulated—and air sealed—to prevent heat flow out of the building (Fig. 3).
An alternative to enclosing all surfaces of the parapet with a welldetailed thermal blanket is to provide a manufactured thermal break assembly at the base of the parapet—in line with the roof insulation. This relegates the parapet structure to being outside of the building’s thermal envelope, avoiding thermal bridging.
Another option for parapets is to design their structure with discrete vertical cantilever beams, rigidly connected to the spandrel beam with a base plate of low-conductance material such as fiberglass reinforced plastic. Here again, it is important to use a thick enough shim—at least 1 inch—or the reduction of the thermal flow may not be significant. Table 4 illustrates some thermal bridging details showing the relative performance of some thermal bridging mitigation strategies for parapets. Like balconies, thermal bridging at parapets is also recognized as linear thermal bridges and quantified using Psi-values. These values were also found in the BETB Guide.
The best way to address and mitigate problematic structural thermal bridging is to work with the project architect and envelope consultant, if there is one, early in the design process. Early and active collaboration on building envelope designs can result in details that are less in need of remedial thermal bridging mitigation once the limitations caused by thermal bridging are understood by the team. It’s always easier to steer clear of conditions that would cause severe thermal bridging than to try to mitigate them after the architect has established their details. Also, early engagement with the project’s energy modeler, if there is one, might allow them to provide quantitative feedback on what works regarding thermal energy flow mitigation. This is especially useful, because most structural engineers are not equipped to perform these types of analyses themselves. Working with the team to practice integrative design—possibly thinking of your role as a structural consultant rather than the structural engineer—can lead to better coordinated, and better designed, projects. ■
Jim D’Aloisio, P.E., LEED AP is a Principal with Klepper, Hahn & Hyatt of East Syracuse, NY, focusing on structural engineering and building envelope consulting services.
Ivan Lee, P.Eng., M.A.Sc., LEED APBD+C, WbLCA AP, is a Building Science Engineer and Team Lead in the Building Performance Analysis department with a focus on thermal analysis, hygrothermal analysis, and Life Cycle Assessment. Lee has worked at Morrison Hershfield now Stantec for over 14 years and has been involved with various projects including 3D thermal modelling to assess thermal bridging details for the Building Envelope Thermal Bridging Guide (BETB Guide).
Basic knowledge of industry practices and adherence to guidelines by PTI are critical to specifying anchors.
By Don Dotson, Ph.D., PE, and Donald Bruce, Ph.D., C.Eng.
Ground anchors have been around for a long time as a mechanism to transfer tensile loads into the ground for dams, tunnel roofs, and slope stabilization (Littlejohn and Bruce, 1977). As early as 1872, rock bolts were used at a slate quarry in North Wales (Schach et al., 1979). The French engineer, André Coyne used ground anchors to reinforce La Jument Lighthouse in Brittany in 1930 (Juran and Elias, 1991, Filipot et al., 2019), before stabilizing Cheurfas Dam in North Africa in 1934.
Some of the earliest guidance for ground anchor design and construction was provided by the Prestressed Concrete Institute (PCI, 1974), followed closely by Littlejohn and Bruce (1975a, 1975b, 1976, 1977).
The U.S. Army Corps of Engineers published an Engineering Manual with the purpose of outlining “techniques and procedures for rock reinforcement for underground and surface structures in civil engineering works” (USACE, 1980), including both rock bolts and high capacity rock anchors. The Federal Highway Administration published a study outlining the anchor design and construction methods employed by Nicholson Construction Company (Nicholson et al., 1982) followed by a FHWA- sponsored state-of-the-practice design and construction manual for “cement-grouted ground anchors and anchored systems for highway application” (Sabatini et al., 1999).
Starting in 1980, the Post-Tensioning Institute began publishing Recommendations for Prestressed Rock and Soil Anchors. The current edition is the fifth edition (PTI, 2014). It is this publication which is often referenced in construction specifications (e.g., Unified Facilities Guide Specifications 31 68 13, “Soil and Rock Anchors”, available at wbdg. org) as PTI DC-35.1-14 (hereafter, PTI) and is the de facto guide for permanent and temporary prestressed rock and soil anchors for use in the U.S., given the absence of recommendations in the International Building Code (IBC, 2021) and ACI 318-19 (ACI, 2019). In Canada, engineers
also refer to the Canadian Foundation Engineering Manual (CGS, 2023). For commercial applications, ground anchors are often used to transfer tensile loads from wind or seismic forces to shear walls and other structural elements or structures subject to hydrostatic uplift to the underlying ground. (A discussion of the use of ground anchors in high seismic areas has been published by the New Zealand Geotechnical Society at https:// fl-nzgs-media.s3.amazonaws.com/uploads/2023/05/NZGS-GroundAnchor-Guideline-Mar-2023-DRAFT-FOR-COMMENT.pdf.) They are also used for temporary structures such as crane pads, especially when founded on rock; crane pads founded on soil often incorporate piles to carry both tensile, compressive, and lateral loads. Contract Documents typically show the location where ground anchors are to be installed along with the tension loading under delegated design, though sometimes the complete design has been performed by the project structural engineer, generally with bond zone strength recommendations from the geotechnical engineer.
Ground anchors are installed using specialized drilling equipment (Fig.1). Many engineers are familiar with drilling with augers and diamond core drilling to obtain geotechnical information in soil and rock, respectively. Diamond core drilling uses water or drilling mud to lubricate and cool the core barrels and to return cuttings to the surface. Engineers are also familiar with air track drills used by grading contractors to drill blast holes. Most ground anchors are installed using rotary percussive drilling where the drill bit oscillates up and down from the percussive action of the hammer as well as rotates. A detailed discussion of drilling methods can be found in Bruce (2003). This rotation improves the efficiency of the percussive drilling mechanics. Rotary percussive drilling uses either a top hammer or down-the-hole (DTH) hammer. A benefit of the DTH hammers is that several manufactures make retractable underreamer systems that allow the hole to be cased as the drill hole is advanced (Fig. 2). Casing the hole is important in soils that "cave" when the drilling tools are extracted. Caving contaminates the bond zone and can also prevent insertion of the tendon and grout.
The first author provides delegated designs to contractors for ground anchors and has reviewed many plans and specifications where ground anchors are required. The quality and consistency of the plans and specifications varies considerably, and many appear to have been developed without knowledge of the requirements of PTI. For example, one provision of PTI is that the center-to-center spacing of anchors should be at least four times the diameter of the bond zone with a minimum spacing of four feet. This is to prevent load transfer interaction between anchors as well as interference during installation as drilling tools tend to drift laterally during drilling depending on ground conditions and driller experience, amongst numerous other factors. Anchors are often placed on either side of the intersection of two shear walls and the spacing between anchors can be too close.
Another requirement in PTI is that the design of anchors must consider the resistance to pullout of the "failure wedge." Too often, the length of
the bond zone is based solely on the grout-toground surface area within the drillhole and the bond strength without consideration of the global resistance to pullout of the rock engaged by the anchor system. PTI establishes minimum bond lengths of 15 feet for strand anchors and 10 feet for bars smaller than 1¾ inch and 15 feet for bars larger than 1¾ inch. Most geotechnical reports will not consider the need for anchors and will not provide recommendations on anchor global stability unless alerted to their inclusion. Guidance for the analysis of global anchor system resistance can be found in USACE (1994) and Sabatini et al. (1999). Failure to consider this failure mode can lead to in-service anchor failure, even though the anchor tests are acceptable. The minimum free stressing length for strand anchors is 15 feet and 10 feet for bar anchors. The amount of rock included in the failure wedge can be enlarged by increasing the free length which essentially lowers the depth of the bond zone and increases the amount of overburden which provides additional resistance.
Fig. 2. Retractable underreamer systems like this one allow the drilled hole to be cased, which is important in soils that “cave” when the tool is extracted. (Photo courtesy numahammers.com)
Another issue involves pressure grouting of the bond zone of soil anchors to increase the bond strength and reduce the number of anchors. If the overburden pressure of the ground is not sufficient when pressure grouting, the ground can fracture and reduce the bond strength that you are trying to achieve. As a simple example, a grouting pressure of 50 psi in granular, moist soil with a unit weight of 115 pcf would require about 63 feet of overburden to equal the grouting pressure (h=144 p/γ). The bond zone should be deep enough to compensate for grouting pressures. When considering ground anchors in commercial buildings, the designer needs to consider whether the anchors should be post-tensioned or not. The purpose of post-tensioning ground anchors is to minimize the movement of the anchored structure under service loading conditions. Depending on the situation, this may or may not be important. Post-tensioned anchors are usually limited to foundations on competent bedrock because post-tensioning loading greatly increases the compressive force on a foundation, often beyond the bearing capacity.
For post-tensioned ground anchor tendons, PTI requires the use of either low-relaxation strand or bar. For commercial use, bar is most often used, generally because the design loads do not warrant highcapacity strand anchors, bar is readily available, and it is relatively easy to install and increase the length of the anchors in the field by adding a coupler. PTI requires that bar used in post-tensioned anchors be ASTM A722, subjected to cold stressing to not less than 80% of the Minimum Ultimate Tensile Strength (MUTS, sometimes referred to as GUTS: Guaranteed Ultimate Tensile Strength) and then stress relieved. One advantage of this requirement is that the cold stressing requirement serves as an early-warning system that the bar is free of imperfections that could lead to a catastrophic failure in service (McCray, 2023).
ASTM A722 bars are either Type I or Type II. Type I bars are plain bars with nominal diameters ranging from 3/4 inch to 13/8 inch. Type II bars are deformed bars with nominal diameters ranging from 5/8 to 3 inches. MUTS of A722 bars is 150 ksi and the minimum yield strengths are 85% and 80% of MUTS for Type I and Type II, respectively. Threads are cold-rolled onto Type I bars and hot-rolled onto Type II bar (McCray, 2023). DYWIDAG product literature states Type II bars have a relaxation tension loss after 1,000 hours of 1.5-2.0% whereas Type I losses are significantly higher. Another advantage of post-tensioned anchors is that each installed
anchor is stressed and tested. Stressing and testing is performed (1) to demonstrate that the anchor meets acceptance criteria and (2) to stress and lock off the anchor at a specified load. Two types of testing are used for commercial applications: Performance tests and Proof tests. Performance tests are conducted on production anchors and the number of tests depends on the size of the project, the likelihood of anchor creep, and the variability of the subsurface conditions. For most projects, the number of Performance tests is between 2-5% of the total number of anchors. According to PTI, the purpose of Performance testing is to determine (a) whether the anchor has sufficient load-carrying capacity; (b) that the apparent free tendon length has been satisfactorily established; (c) the magnitude of residual movement; and (d) that the rate of creep stabilizes within the specified limits. Performance tests are conducted by cyclically loading and unloading the anchor in six cycles up to 133% the design load (PTI). Once 133% of design load (DL) is achieved the anchor load is held for ten minutes to determine anchor creep. If the amount of creep exceeds 1 mm (0.040 in), the anchor load is held for an additional 50 minutes while keeping the testing pressure within 50 psi of 133%DL. The initial 10 minute hold is called the creep test; the additional 50 minute hold is called the extended creep test.
Proof testing is performed on all post-tensioned anchors that are not performance tested. The purpose of Proof testing is similar to performance testing except that the testing is not cyclical. The anchors are loaded in six increments to 1.33 DL, creep tested for 10 minutes, brought back down the alignment load which is a nominal load applied to an anchor sufficient to keep the testing equipment positioned correctly, and then brought back up to the lock-off load.
Another type of testing is Verification testing which is performed on a sacrificial anchor to verify the bond strength between the ground and the grout. These tests are performed on shortened bond zones and are taken to failure to establish the ultimate ground-to-grout bond strength which can be used to optimize the anchoring system.
Where post-tensioning is not feasible (i.e., to hold down shear wall foundations on soil), passive anchors can be used. Although passive anchors do not strictly fall within the purview of PTI, since they are not post-tensioned, many of the guidelines in PTI should be followed. While ASTM A722 bar can also be used for passive anchors, ASTM A615, grade 75 threaded bar is a viable option that is available from the suppliers of ASTM A722 threaded bar. Like ASTM A722 Type I bars, threads are also cold rolled onto A615 bar. Both ASTM A722 and A615 bars are commonly used in micropile construction (FHWA, 2005). The design of anchors using either A722 or A615 bars is identical; the design load on bars should not exceed 60% of MUTS and test loads should not exceed 80% MUTS. Lock-off loads for bar should not exceed 70% of MUTS.
Where post-tensioned anchors are used, the anchors terminate in a concrete mat or footing with a bearing plate locked off with a nut on top. Often, the bar is extended, and a tension plate located higher in the mat or footing is used to transfer the load from the ground anchor to the mat or footing. The tension plate is sized and located to resist punching shear and often has a full nut above the plate and a half nut below to position the plate during concrete placement. Reinforcement is then cast into the concrete to attach the superstructure to the mat
or footing. This same arrangement should be used for passive anchors, but there is a recent trend to forego the tension plate and extend the anchor bar up into the superstructure, sometimes several stories, using couplers. The authors do not recommend this practice. Installing a single bar in a drill hole, sometimes 50 or more feet into the ground and expecting that the alignment will be perfect enough that the bar can be extended up several stories inside an 8-inch wall is problematic. Bending the bars to keep them inside walls is not a good idea, although ASTM A722 requires that the bars pass a 135° bend test.
Another important component of ground anchors is the grout used to bond the tendon to the ground. Ground anchors are typically grouted with neat cement grout consisting of cement and water without aggregates. Grouts are best mixed on-site by the anchor contractor using high-shear colloidal mixers (Fig. 3).
PTI specifies Type I, II, III, or V Portland cement conforming to ASTM C150 with a minimum compressive strength of 3,000 psi (FHWA requirements are the same). More recently Type 1L has become popular. A recent trend among some structural engineers is to specify grout strengths as high as 8,000–10,000 psi for anchors. This is unnecessary and often unachievable. The PTI commentary states that blended
cements are “typically neither necessary nor used for anchors.” A recent trend in some projects is to specify ‘non-shrink grout’ in the bond zone. Non-shrink grouts are covered under ASTM C1107 and are for use under applied load to support structures or machines. While the use of non-shrink grout sounds like a good idea, they are not intended to be tremied into a drillhole to bond steel to the ground, often below the groundwater table, and should not be used. Additionally, non-shrink grouts have not been subjected to decades of use and testing as have neat cement grouts. Expansive admixtures may be added to neat cement grout only for filling trumpets and anchor covers, but PTI prohibits their use in the bond zone. Finally, corrosion protection should be considered for permanent anchors, defined by PTI as those having at least a 5-year service life. PTI recognizes two types of corrosion protection: Class I and Class II. Class I has a higher level of corrosion protection than Class II. All permanent anchor installations should use Class I corrosion protection. Class I was often called double corrosion protection and consists of encapsulating the tendon inside a plastic sheath filled with either grout or corrosion-inhibiting compound (Fig. 4). Class I protection can also be provided by epoxy-coating of the tendon and installing the tendon in a grouted drill hole that has been successfully water pressure tested. This
is performed in the bond zone in competent rock and consists of filling the hole with water and applying a constant pressure of 5 psi above hydrostatic for 10 minutes. If leakage exceeds 2.75 gallons of water, then the hole should be grouted, re-drilled, and tested until it passes the test. The purpose of the test is to limit the intrusion of water that can displace the grout or corrode the tendon. This procedure can become very expensive and is primarily used for applications where differential head is present and seepage occurs. PTI states that water pressure testing is not required where there is no seepage or differential head, and the method of grout placement fills the drill hole without loss of grout in the bond zone. On commercial projects, this criterion is often met. In the free length portion of the anchor, the bar manufacturer can provide anchors that are sheathed and filled with a corrosion inhibiting
grease, gel, or wax.
In conclusion, properly specifying ground anchors requires basic knowledge of industry practices and adherence to guidelines that have been established by PTI. Specifying materials and methods contrary to PTI guidelines opens structural engineers up to contractor claims as well as unnecessary liability for poor anchor performance. The authors encourage structural engineers to obtain a copy of PTI and to incorporate its provisions into the plans and specifications that they prepare. ■
Note: Both authors have previously worked for Nicholson Construction Company.
Full references are included in the online version of the article at STRUCTUREmag.org
Don Dotson, PhD, PE, BC.GE. is a partner in the structural engineering firm of Geo/Structural Services Group, LLC in Nashville, Tennessee, specializing in the structural design of deep foundations, substructures, earth retention, and underground works. (Don.Dotson@GeoSSG.com).
Donald Bruce, PhD, BC.GE, CEng, PG, LG, LEG is the president of Geosystems, LP, an independent consultancy located in Venetia, PA offering technical, advisory, and managerial services in the specialty geotechnical aspects of civil, mining, and tunneling engineering. (dabruce@geosystemsbruce.com).
Peeling away conventional design, USF’s Judy Genshaft Honors College is a modern attraction of the Tampa, Florida, campus.
By Dylan Richard, PE, and Katherine Chan, MSFE
The Judy Genshaft Honors College on the University of South Florida’s (USF) Tampa campus is a new architectural landmark for USF students, faculty, and staff. Opened in 2023, the $56 million, 85,000-square-foot, five-story building aggregates honor students from every undergraduate college previously distributed across three separate campuses into a modern facility for their experience-based educational studies.
Once the idea to design and construct the Honors College in a central location was hatched, several donations were made to ensure the structure was built, including a $20 million donation from former USF President Judy Genshaft and her husband, Steve Greenbaum. Genshaft served as the USF president from 2000-2019.
The Judy Genshaft Honors College features a glazed ground floor level that anchors more opaque floors above. The asymmetrical facade is made up of 127 prefabricated aluminum panels. The cladding’s iridescent dichroic coating—which changes color from maroon to yellow to green in different light conditions and from different view perspectives—has a shimmering metallic finish. The architect specified this type of panel because it helps reflect sunlight to minimize solar heat gain, in addition to the green hue nearly matching the University’s “USF Green” core color. Hovering above the inviting outdoor stair the same facade panel is perforated and suspended from the building’s steel and concrete structure and appears to “peel away” from the structure to accentuate its dynamic form and create shaded outdoor terraces. The “peel away” is a specific design-oriented area with perforated metal panel above a monumental
circulation stair. It is not part of the facade or building envelope in its role to keep water out or controlling thermal conductivity but instead provides solar shading and iconic architectural intent.
The LEED Silver certified building also features an expansive five-story atrium at the main level as well as open and closed classrooms, collaboration spaces, 39 distinctly designed learning lofts, student terrace, a professional kitchen, and dedicated studio spaces for students.
Designed by Morphosis Architects with architect of record FleischmanGarciaMaslowski, the sophisticated and unique design, with geometries that shift along the building’s facade, required precise planning and coordination to ensure the varied design elements and materials meshed effectively and efficiently. Working in concert with the architectural teams, Walter P Moore served as the structural engineer, enclosure consultant as well as the steel and concrete rebar detailer for the project.
To achieve the vision set forth by the architectural team and USF, engineers from Walter P Moore developed a fully coordinated 3D structural model in Tekla using the firm’s proprietary collaborative digital process known as Connected Transformative Integrated Delivery (ConnecTID). The model was used to solicit and onboard the subcontractors and helped reduce risk on the project by being openly shared with the construction manager, The Beck Group, who engaged key design assist partners
including the concrete contractor, Ceco Concrete Construction, the steel contractor, Morrow Steel, and the facade systems contractor, MG McGrath.
The connected model allowed shop drawings to be developed in 3D as the permit documents were being completed, which included advanced detailing of all the structural steel connections and the rebar. The process included a three-month’s accelerated shop drawing timeline, which ultimately helped to reduce the number of requests for information as the Level of Development (LOD400) fabrication level model served to build and coordinate the complex integrated structural framing virtually prior to construction in real life.
The connected model workflow allowed the entire building team to understand the expectations asked of them before construction started. For example, it allowed the concrete contractor to get a near exact count on the amount of rebar so they could define an accurate bid. The modeling also allowed for the architect to visualize how the coordination between trades could impact their design vision and they could respond with necessary modifications as required to address unique conditions.
The initial facade assembly to achieve the complex geometry for the Judy Genshaft Honors College building was to use stud framed “mega panels.”
However, this design evolved to utilizing a large-format off-the-shelf aluminum curtain wall panelized system. This move increased the required coordination needed to accommodate the massing’s curves in a cohesive and appealing manner. The original geometric discretion of the curves into panels worked with faceting of the geometry just like the curtain walls. The
Opposite Page: The Zimmerman Family Foundation Atrium is an expansive five-story atrium at the center of the Judy Genshaft Honors College and includes a network of timber lattices as well as 39 learning lofts that hang over the atrium. Photo Credit: © Seamus Payne
Left: Most of the facade panels are unitized, large format curtain wall panels measuring 10 x 10 feet—twice as wide as the panels commonly used in the industry—which resulted in a decreased installation time compared to a similar sized project using standard-sized unitized panels. Photo Credit: © Seamus Payne
change resulted in revisiting the panelization for capability and joinery. Revisiting with curtain wall capabilities required rethinking some of the more bespoke areas, and ultimately, design architect Morphosis Architects modeled the curtain wall geometry.
The complexity for the facade lies in achieving the aspirational curved geometry with a unitized curtain wall system. Faceting a curved geometry with large format rectilinear flat panels makes achieving the complex geometry challenging. If not done with a detail-oriented perspective, the smooth curve would result in a slatted or angular surface. Typical large format panels on rectilinear areas of the project were completely fabricated in the shop and arrived on site ready to be installed on the building. Areas with particularly challenging geometries required the team to be flexible and create deviations from the previously defined assemblies to enable the installation. Face panels and insulation were left uninstalled on these panels, which were installed with penetrations to adjust for consistent joints and alignment of the facade surfaces. After the panels were adjusted properly on site, the insulation and face panel were installed.
The curtain wall panels and associated cladding system were engineered detailed, fabricated, and installed by MG McGrath, while the geometry of the cladding system was defined by Morphosis Architects. The Enclosure Engineering Group from Walter P Moore provided consultation to properly design and uphold best practices for technical performance given the ambitious geometry. The close collaboration on facade, structure, and connection design enabled quick turnaround for structural changes and modifications as the design of the facade progressed during MG McGrath’s design assist process.
Most of the facade panels are unitized, large format, curtain wall panels measuring 10 x 10 feet, twice as wide as units commonly used in the
industry, which required enhanced precision but also resulted in decreased installation time when compared to a comparable sized project with standard-sized unitized panels. While attaching the panels to a floor slab to allow the loads to transfer through the embedded floor plates is standard, the slabs on the project were relatively ambitiously cantilevered floor plates. Limiting the differential movement allowed for the curtain wall system to accommodate the vertical movement within the slotted attachment along the top and bottom edges of the panels. Panels followed standard unitized curtain wall approach, which is to hang the units along the upper part of the panel. Maximum differential movement up and down that can be accommodated is ¾-inch.
As the design team reviewed the shop drawings and engineering for the prefabricated rainscreen system panels from MG McGrath, Walter P Moore’s Structures Group concurrently reviewed specifications and drawings for the rebar, embed plates, and structural steel to ensure there were no conflicts.
To facilitate the installation process, the connected model was color-coded to allow the contractor to install the numerous unique embed plates in their correct locations. Because there were more than 600 total embeds that penetrated the facade to connect the secondary structure of the “peel away” facade to the primary structure, each penetration was carefully sealed to prevent water ingress. Of the total embed count, less than one percent were out of the established tolerance of +/- 1 inch. This was managed through extensive coordination with the design team and a multi-tier quality control program including laser scanning and drone photography. While most of the building has an opaque exterior envelope, the glazing panels were positioned in a manner so those inside the building would feel a connection to the outside. Most of the glazing is located on the north side of the building to balance daylighting while minimizing heat from solar exposure. Maximizing the glazing on the ground floor of the north elevation allows for more connectivity of the inhabitants to the exterior in an otherwise opaque building. Glazing oriented on the south, west, and east exposures has more solar heat gain which is controlled by perforated cladding panels integrated into the curtain wall.
With the project being procured, engineered, and constructed during a pandemic, material availability was a substantial challenge for the implementation of the complex design. For example, there was a shortage of mineral wool as well as the procurement and logistical challenges with fabricating the metal panels, including the coating process. In response, flexibility and ingenuity were required to review material substitutions and deviations from previously defined assemblies to minimize cost and schedule increases, while still maintaining the complex design and aesthetic goals for the project.
Beck worked closely with the design team and MG McGrath to monitor design production and material procurement and fabrication to ensure material availability challenges were mitigated.
The Zimmerman Family Foundation Atrium, which is the expansive five-story atrium at the center of the structure is defined by a network of timber lattices and the 39 uniquely crafted learning lofts with a white oak exterior that hang over the spacious atrium. The learning lofts can accommodate between two and eight students and are suspended around the atrium between levels two through five.
The atrium connects all users into a single spatial experience to encourage
Above the outdoor stairs, the facade panel is perforated and suspended from the building’s steel and concrete structure. This design feature allows the facade to “peel away” from the structure to accentuate its dynamic form and create shaded outdoor terraces.
interaction and collaboration among students, faculty, and visitors. Defined by a network of timber lattices and suspended study pods, the atrium becomes a communal “beehive” of activity at the heart of the Honors College. Modeled by the architect, it filters natural daylighting providing an ethereal, warm, and welcoming backdrop for interdisciplinary collaboration.
To facilitate attachment of the atrium cladding, individual slotted anchors are installed in cast in channels which line the edges of the floor slabs. This design choice prioritized versatility, cost effectiveness, and constructability, allowing for adjustable fixings to accommodate the timber lattices, which are supported by cantilevered cast-in-place concrete slabs around the atrium. The atrium’s construction posed significant challenges due to the need for precise coordination between vastly different trades and materials, including poured in place concrete and finished wood millworks. The A/E team had to meticulously consider construction tolerance to seamlessly integrate these elements.
Moreover, managing the acoustics within such a large atrium space presented another challenge. To address this, each learning loft was equipped with acoustic design features tailored to control sound within the pod, ensuring optimal learning and collaborating environments. Additionally, acoustic wood paneling envelops the entire atrium, effectively mitigating unwanted reverberations and enhancing overall sound quality.
Flexible spaces adjacent to the atrium on the ground floor can be opened and combined to accommodate large-scale events. The second floor features an exterior, shaded terrace accessible from the inside and outside of the building and serves as an outdoor study and meeting space.
As with many projects of this scale and scope, the Judy Genshaft Honors College project managed substantial risk during the construction when several different contactors and materials intersected. To ensure the project was successful, it was critical to have accurate and detailed coordinated models, especially given the building’s complex facade where the steel, concrete, glass, and aluminum panels interfaced with one another.
By detailing each unique structural and facade connection in advance, the ConnecTID model flagged any conflicts between the facade panel anchors and the proposed superstructure that would have caused costly schedule and budget issues had those conflicts had been discovered later
Page
in the field. The Beck Group utilized Walter P Moore’s superstructure model in a holistic and comprehensive coordination process, ensuring a fully coordinated workflow and compiled model. This building model allowed for detailed coordination of systems provided by multiple trades and ensured accurate sequencing and phasing to prevent costly rework.
The connected model enabled the development of a custom structural steel solution to support the panels’ peel-away feature and provided the facade contractor with a “single point of truth” from which they can rely on to develop the support strategies for the building’s skin.
The integrated workflow and detailed modeling process provided Beck with the details needed for construction while concurrently preserving the owners’ and architects’ design vision for the Judy Genshaft Honors College. The connected model ensured this complex project would be achievable, but that it also would stay within budget and on schedule
because of the digital model’s clarity and precision.
Judy Genshaft Honors College on the University of South Florida’s Tampa campus provided the opportunity for Walter P Moore to collaborate closely with both the design and contractor teams to leverage our technical expertise in the face of ambitious geometry and architecture to uphold technical facade performance, structural design and design, while tracking and minimizing risk.
One of the most striking elements in the new Studio Museum Harlem is the four-story monumental stair, crafted from structural steel members and adorned with terrazzo panels.
By Alexander Stephani, PE; Xiaoxiao Wu, PE; Andrew Angelilli, PE; Kevin Poulin; Guy Nordenson; and Filippo Masetti
Studio Museum in Harlem, New York, which was completed this year and will open in 2025, has more than doubled its space for exhibitions and programming with a new iconic building that will soon become a cultural anchor for the community. The building was designed by architects Adjaye Associates and Cooper Robertson. Simpson Gumpertz & Heger Associates, Inc. P.C. (SGH) was the Engineer of Record, and they collaborated with consulting engineer Guy Nordenson and Associates (GNA). GNA started the structural design for the building during the initial phases of the project, and they completed the construction documents for the monumental stair. Rowan Williams Davies & Irwin Inc. (RWDI) served as the vibration consultant for the stair, and Plan B Engineering (Plan B) was the specialty structural construction engineer for the contractor, Sciame Construction. The six-story building has a steel superstructure and is supported by a concrete mat foundation. The facade is clad with precast panels that evoke the masonry architecture of Harlem (Fig. 1).
The new building features a four-story monumental steelframed stair clad with terrazzo panels. As an architectural focal point of the museum, the stair allows visitors to view artwork along an 85 foot-tall vertical art gallery. (Paintings and sculptures are supported on the walls enclosing the stair). At the center of the stair, balustrade trusses, concealed within the architectural finishes, form a helical column (a central spine) that extends from the top of the stair to the mat foundation (Fig. 2). Large platforms with additional balustrade trusses cantilever off the central spine of the stair to create gathering spaces for visitors as they view works of art or watch events in the lecture hall below (Fig. 3). However, these visitors would both cause and feel vibrations from the stair. To mitigate the vibrations, a series of Tuned Mass Dampers (TMDs) are incorporated inside the balustrades between truss members.
Cladding the stair with terrazzo panels provides a contextual material and color that harmonizes with the distinctive exterior precast panels of the building (Fig. 4). To support the terrazzo, the architects designed light-gauge framing members that span from the treads or landings to the top of the balustrades. This back-up wall is sheathed with plywood, to which the terrazzo panels are adhered. The architects showed narrow, grouted joints between precast
panels. As the joint sizes between terrazzo cladding panels are greatly affected by truss deflections and vibration characteristics, in-situ load testing of the steel stair was required to validate the expected results from structural modeling and to determine final joint sizes and jointing materials.
To determine the behavior of the complex stair, GNA modeled the entire stair, including the central spine, mat foundation, truss balustrades, in-plane bracing, and concrete-on-metal deck slabs at the landings using finite element analysis (FEA) software, SAP2000. SGH performed an independent review. The model represents steel members as frame elements and concrete landings as thin shell elements. Because of the large, cantilevered platforms and the proposed terrazzo architectural finish, it was critical to understand and manage vertical deflections under dead and live loads (Fig. 5).
The model incorporated adjacent base-building slab bays at the stair support points to accurately capture the floor stiffness and mass that can be activated by pedestrian footfall. The engineers assumed viscous modal damping at one percent of critical damping (typical for steel monumental stairs), applied walking forces as a percentage of body weight at corresponding modal frequencies, and determined acceleration responses. These procedures were iterated several times with different member sizes until an optimal design was found that met recommended peak acceleration limits, as further described here.
The central spine and balustrade trusses have significant strength and stiffness compared to typical long-span trusses. However, the four-story height and the long-cantilevered landings create vibration characteristics similar to a slender monumental stair. Because the American Institute of Steel Construction (AISC) Design Guideline 11: Vibrations of Steel-Framed Structural System Due to Human Activity does not provide tolerance criteria for stairs, SGH and GNA used the analysis procedure described by
Davis and Murray (2009). In their paper, they performed a literature review, an experimental study, and a finite element analysis of a slender stair structure, considering ascent and descent harmonic forces that are often much larger than those on a flat surface. Their method consists of calculating the response acceleration that would be generated by a single individual or a group of individuals walking on the stair. The calculated accelerations are then compared to tolerance limits for human comfort of people standing on the stair.
Walking footfall rates that produce vibrations of floor structures typically vary between 1.0 Hz and 2.5 Hz (or footfalls per second). However, people commonly ascend and descend stairs at frequencies that are higher than the frequencies of walking on a flat surface. The forcing frequencies can be as high as 4.0 Hz to 4.5 Hz, as in the case of a person “trotting” down a stair. In their procedure, Davis and Murray considered the maximum frequency for one person at 4.0 Hz. Therefore, the second, third, and fourth harmonics of the walking frequencies are 8.0 Hz, 12.0 Hz and 16.0 Hz. The stair can be excited by the forces in all these harmonics, though to lesser degrees as their contributing mass decreases.
The walker’s location (excitation) and the affected occupant’s location (response) must be identified using engineering judgement. Typically, the worst accelerations are obtained when both the excitation point and the response point are taken at the maximum mode shape. The number of steps required to develop resonant response is highly variable, and AISC Design Guideline 11 recommends considering 7 to 8 consecutive steps (or jumps). Taking this into account, the walker’s position should be as close as possible to the maximum mode shape. The affected occupant must be stationary, so the guide recommends that the affected occupant location should be at an intermediate landing or at mid-span as close as possible to the maximum mode shape (i.e. maximum likely amplitude).
The analysis indicated that the maximum mode shapes typically corresponded to the far corners of each landing. The affected occupant location was chosen at those points for further study. Five landings were initially identified as sensitive locations based on the modal shapes from the model, and for every landing, four walker locations were analyzed:
• At the same point as the affected occupant (maximum mode shape value).
• At the center of the top tread of the of the stair flight furthest from the adjacent exterior wall.
• At the top of the stringer furthest from the adjacent exterior wall.
• At the middle of the stringer furthest from the adjacent exterior wall.
The initial results showed that individuals walking up and down the steps would not pose vibration concerns for the stringers. Nevertheless, the long-cantilevered landings are susceptible to peak accelerations that could cause discomfort for people standing on them, when others rapidly descend stairs, especially because of the low inherent damping in the steel structure.
To minimize vibrations, a series of custom tuned mass dampers (TMD) with viscous dampening devices were designed to be integrated into the stair at five locations
with risk of high accelerations. RWDI, the vibration consultant, performed an assessment of the dynamic response due to pedestrian traffic and detailed the custom-shaped dampers so that they could be seamlessly incorporated into the design and concealed in the balustrade. The effective dynamic mass of each tuned mass damper is around 450 pounds, and the total mass (including bearing, springs and viscous damping devices, etc.) is about 600 pounds. RWDI designed a total of five tuned mass dampers with frequencies tuned to target stair natural vibration modes 2, 3, 4, 7, and 12 (between 5-8Hz), which are most susceptible to human-induced vibrations.
Plan B assisted the design team in specifying the terrazzo panel joint size, with particular attention to the calibration of joint widths with the local deflections of the complex stair structure under design dead and live loads.
The initial review involved a geometric study of the relationship between the steel truss nodes and the terrazzo joint spacing (5 feet on center truss nodes versus 14 inches on center joint spacing +/-). The stair framing included several cantilevered conditions that were identified as critical regions for local deflection analysis. Vertical and lateral nodal deflections of these trusses were tabulated from FEA models provided by SGH. The relative nodal deflections between adjacent nodes were calculated and further processed to determine the relative movement of one terrazzo panel to the next. This enabled an understanding of the maximum local movement that panel joints could accommodate without closing the gap and risking damage to the panels. The output from the modeling also included pattern loading to ensure that no isolated live-load conditions governed the joint movement.
The theoretical deflection shown in the FEA model from one cantilevered end of the stair framing to the opposite end was predominantly vertical. A review of the relative horizontal movement between truss node points of the same chord indicated a value that was a nominal displacement relative to the vertical—indicating a low amount of chord lateral movement. A further comparison between top and bottom chords indicated little differential in lateral movement, suggesting a low amount of relative geometric rotation. This relative movement between truss panel nodes should be divided by the number of terrazzo panels between nodes (60 versus 14 inches) to determine the relative respective terrazzo panel movement.
While there was a concern that axial strain in the truss chords could magnify relative movements between nodes, the FEA analysis proved that this was a non-factor. In fact, all of the vertical movement was a product of the truss flexural stiffness and the rotational stiffness (fixity) of the end supports.
Theoretical FEA results pointed to the suitability of a 1/16-inch gap; however, Plan B recommended a scaled load test on the already erected stairs. Survey points were established to measure vertical deflections of the steel truss framing. Digital strain gauges were also placed across mockup “terrazzo” (plywood) panels. This allowed for both
calibration of the FEA model based on the global stiffness and a direct measurement of movement between panels, insitu. The load test was set to a scaled load of 60% of the full live and superimposed dead loads to optimize the size and scope of the surcharge (understanding that the results of the loading were linearly related to the actual loads). The contractor filled water barrels on site to alleviate the logistics of mobilizing solid weights and located the barrels on the stair framing to simulate the loading associated with the largest computed vertical deflection, based on the FEA analysis. The load test results showed that the system was stiffer than modeled with tested deflections at 75% of the scaled theoretical movement (likely because of local rigidity at truss nodes). Most panel joints closed only a fraction of the joint design width. The load-test instrumentation used was sensitive enough to capture changes in size due to thermal expansion, correlating with temperature changes, as well as loading/unloading of water barrels. The data also showed daily variations in displacement that matched the frequency of temperature changes throughout the day. Plan B recommended sizes of terrazzo and plywood joints that accounted for the omission of finished grouting.
The Studio Museum in Harlem's newly unveiled architectural marvel not only marks a significant expansion in space for exhibitions and community engagement but also stands as a testament to visionary design and collaborative engineering prowess. At its core, the building features a robust steel superstructure supported by a concrete mat foundation, providing a stable base for the building. One of the most striking elements is the four-story monumental stair, crafted from structural steel members and adorned with terrazzo panels. With careful attention to detail and innovative solutions, the Studio Museum's new building will not only serve its community as a cultural hub but will also showcase exemplary architectural and engineering design. Its impact is expected to resonate beyond Harlem, enriching lives, and inspiring future generations. ■
Full references are included in the online version of the article at STRUCTURE mag.org
Alexander Stephani, PE, is a Structural Engineer with Simpson Gumpertz & Heger (SGH), specializing in new design, repair and rehabilitation, and flood resiliency design.
Andrew Angelilli is a licensed Professional Engineer at Plan B Engineering, a structural engineering firm specializing in construction means & methods.
Xiaoxiao Wu is a licensed Professional Engineer and Associate Partner at Guy Nordenson and Associates, a New York-based structural engineering practice.
How challenges for The Artise turned into a willingness to create something new.
By Scott Erickson
The Artise, in Bellevue, Washington, is a 25-story, 1 million-square-foot, steel office building with six levels of below-grade parking for 900 parking stalls. Topped out in February 2023, The Artise utilized a one-of-a-kind structural system aimed to solve several design challenges at once and, consequently, resulted in at least 25% material savings compared to what’s traditionally required for an office building of comparable size and materials. By using buckling restrained braces and fluid viscous dampers that skip floors, and a moment frame sub system in between brace points, the lateral resisting footprint was spread out and the pieces minimized. This reduced demands on the superstructure and the foundations. Further, by eliminating all lateral framing below grade, the design saved even more on cost.
The design and construction teams faced several challenges, including:
• Contaminated seepage from the soil to the north side from across the street was not allowed to be diverted into the aquifer below the entire site. This meant that traditional shoring piles could not be used on half of the site and the base excavation was limited in depth. Traditionally, 900 parking stalls would have required seven levels. The site restraints on this project required the project team to fit that many stalls in six levels.
• During the design team discussions on arranging the brace points, the owner expressed a desire to clear span the entire west side retail experience at the ground floor, and transfer three lateral frame columns, to create a substantially more open entrance that would attract pedestrian traffic
• Due to the configuration of the building on the site, caused by setback requirements to the south and
one-story deep street easements for the city on the north and west, a conventional 42-foot office span configuration in the tower, which would accommodate an 18-feet parking stall area and a 24-feet drive aisle, did not align well with an efficient parking layout below grade.
• Once the design was about 85% complete, just before structural steel was ordered, the building was changed to a category III building (from category II) to satisfy tenant needs. The performance based seismic design not only had to be redone in short order, but new ways of stabilizing the building were required due to the more stringent drift requirements.
Many times, engineers revert to what they know, what has been done before, and what they are comfortable with. But for those who are willing to venture off the beaten path, and take risks with possible distractions and setbacks, the creation of something entirely new and rewarding is possible.
For The Artise, the engineering team threw out traditions and focused on the core goals of ownership, one of which was obtaining 900 parking stalls in six levels below grade. The project team decided to optimize the entire below-grade footprint for parking without any concern whatsoever for superstructure to test fit the idea of not using a lateral system below grade. The traditional concrete core was taken out of consideration, as was every lateral system horizontal brace or wall element from the space, to make room for the required available parking and maintain the structure above the aquifer.
What about the other 25 floors sitting on top of the below grade parking? The design team now needed to find a way to transfer the entire lateral system out at grade to maintain the parking count.
Owner: Schnitzer West, LLC
Structural Engineer of Record: DCI Engineers
Architect: NBBJ
General Contractor: Sellen
The baseline solution started with a short span steel parking configuration with a column grid of 30 feet or less below grade to minimize structure depth to W16 beams and W18 girders, which reduced excavation as a result. To support the steel-framed office tower above, the project team configured the extent of the office tower such that the perimeter columns extended straight down to the foundation without interrupting the parking drive aisles and without encroaching into the easements and setbacks. The interior columns from above landed in drive aisles and still needed a solution. But the perimeter column layout provided something to work with.
The decision was made to use a perimeter buckling restrained brace frame system. In the spirit of trying something new, the design team made it a super brace system—where braces extend over multiple floors and pass-through other floors on the way to their connection points. This more efficient system uses less braces and less connection material than a brace system that connects at each floor. Additionally, the longer length of the braces provides for more displacement, which also drives structural efficiency of each brace. At the floors where the
braces passed through, small sections of moment frames were used only between the braced floors to transfer the diaphragm forces either up or down to the floors that were connected at brace points. Brace points on each side do not always align at a given floor. Some sides of the building have braces that skip one floor while others skip two.
The superstructure interior gravity columns were sloped over five floors to match up with the column configuration below grade. The added kick from the sloped columns was fairly well balanced by sloping both sides, but even so, unbalanced loading was considered, which added a lateral gravity force to the super brace system.
To achieve the owner’s goal of opening up the ground floor retail on the west side, three of the five west building face lateral frame columns near the base were transferred out to the corners. A star-shaped pattern of braces and columns was used to achieve this. The braces had to be elastic (not yield) for the transfer, which required a fine-tuned balancing act to navigate the non-linear analysis.
When the building was changed to a category III building (from a category II) with stricter drift requirements, a significant challenge was posed as braced frames are typically limited by drift. At this point in the design, the layout of the braces, their arrangement patterns, and
their attachment points were configured to be aesthetically aligned with architectural goals of the tower. In addition, boxed out W14x873 columns were already used at the base (so columns could not be easily upsized), and the design had already doubled up on some of the larger producible BRBs with 40 inch-square cores and 24 inch-square casings. There were not many options left.
As a result, the project team decided to explore fluid viscous dampers. After trial and error, some of the BRBs were swapped out with dampers. Some dampers were placed within each frame, 24 in total. This solution controlled not only the drift, but the residual drift as well, and was especially important in helping balance the stiff star shaped brace on the west side with the east side frame.
At the end of the day, not only did 900 stalls fit into six levels (instead of seven) with a short span steel gravity system, but this unique structural lateral system configuration saved at least 25% of the cost of material than a traditional building would have required by eliminating a concrete core, reducing foundation reinforcing, eliminating a lateral system below grade, using a spread-out super brace lateral system, and reducing drift demand by using fluid viscous dampers.
Typically, lateral systems are carried directly down to the foundation. Since The Artise only had perimeter columns extend to the foundation, the basement walls became the primary lateral system below grade. Wanting to save as much as possible on cost, a spread footing system and donut configured mat foundation below the lateral frame columns was used. As this didn’t directly tie into the basement walls on all sides, soil structure interaction modeling, both vertically and horizontally, was required to determine the interaction of forces below grade. This alone would require many pages to elaborate on.
The super brace lateral system skips floors, requiring unique localized
points. The interaction of these partial frames and how to model them properly in Perform 3D, along with the diaphragm design itself for the proper forces, became quite complicated.
Structural seismic lateral analysis requires that 90% of the mass participation be captured to ensure proper force distribution. Because the below grade structure was equal in mass to the superstructure and the basement wall lateral system was extremely stiff, scaling to 90% of the effective mass participation meant capturing a very large number of modes. This presented a unique challenge for properly scaling the conditional mean spectra.
The super brace lateral system is drift sensitive to both long period and short period ground motions, so optimization of the fluid viscous damper locations was key to controlling localized mean and residual drifts. This was especially true due to the elastic behavior of the transferred out west side frame, which created a stiffer frame than the east side.
It would be easy to look at this process and see it as a never-ending cycle of compounded challenges and hours of problem solving. But, the best solutions do not usually come from the path of least resistance. The project team set out to determine the best way to optimize the structure, and in the end, the uniquely framed building not only met the project goals but saved considerable construction costs in the process. The ultimate goal in engineering is for solutions to transcend their immediate challenges and become universal in practice. For that alone, this project was a success, as the use of fluid viscous dampers in particular provides insight into how future projects can benefit from their use as well. ■
One of the eight new stadia built for the 2022 World Cup in Quatar was engineered with circular construction in mind, and the 40,000 capacity, multi-tiered venue is the first fully de-mountable stadium of its kind.
By Dan Bergsagel, Knut Stockhusen, Christoph Paech, and Fernando Sima
Large, short-term international events like the soccer World Cup or the Olympic Games require suitable large stadia to host them. Where the existing infrastructure is insufficient, host countries or cities construct new stadia specifically for the event. Following the event, these new stadia are often underutilized due to a mismatch between a stadium’s characteristics and long-term demand, such as new stadiums having: a larger capacity than needed, being sited in inaccessible locations, or being surplus to the typical event use requirements of the host. An underutilized stadium—a White Elephant—can have both negative impacts on the surrounding community and be expensive to maintain. It is also a waste of economic and material resources, making it hard to justify the emission of greenhouse gases associated with its construction. Stadia are built to be enjoyed. Yet, unlike residential or office buildings that are regularly occupied, stadia are used only sporadically. Typical metrics for comparing the environmental performance, such as kgCO2e/m2 or kgCO2e/seat are less informative than metrics that evaluate the embodied carbon emissions per stadium use, such as kgCO2e/seat/event. This can be illustrated by comparing two similar stadia over the first 20 years of their life: one that is regularly used by a club soccer team, and another that is built to host a short-term event. Both stadia could have associated embodied carbon emissions of 1,000kgCO2e/seat, however due to the number of events each stadium hosts there could be an order of magnitude difference in the embodied carbon emissions per stadium event: a club stadium hosting 25 matches a year would have 2kgCO2e/seat/event, while a short-term event stadium hosting 10 events in the first month followed by two events each year would have 20kgCO2e/seat/event. Structural engineers are implored by the SE2050 challenge to “understand, reduce and ultimately eliminate embodied carbon in their projects by 2050.” The first and most impactful step a structural engineer can take in reducing the embodied carbon of our project work is through reviewing the brief and interrogating project needs to avoid the construction of underutilized structures. This is where the application of circular economy principles such as design for disassembly (DfD) and structural element reuse can have the largest impact. This case study presents some of the key DfD decisions that were taken for Stadium 974, focusing on: simplicity, generality, modularity, transportability, reversibility, rationalization, and tracking. The goal is to demonstrate how DfD principles can be implemented on large-scale commercial projects.
Three successful strategies to avoid constructing underutilized stadia have been demonstrated by past hosts of large short-term international events. The first strategy avoids new construction altogether by using available existing facilities, such as at the Paris 2024 Olympics—constructing only one new permanent venue—or the UEFA 2024 European Championship hosted across Germany in eight existing club soccer stadia. The second strategy involves careful planning of the stadium legacy to ensure that any constructed stadia are utilized after the event, such as at the London 2012 Olympics where temporary stands were removed to reduce capacity, and longterm use deals were made with community stakeholders. However, these strategies are only suitable for economically developed hosts who have large permanent local populations that have either justified previous infrastructure investment or can benefit from long-term future infrastructure use.
A third successful strategy is to design temporary structures that
can be removed following the event, such as the aquatics and handball venues at the Rio 2016 Olympics or the International Cricket Council T20 World Cup stadium in Nassau, NY. For host cities and nations with relatively small permanent local populations, removable temporary structures can avoid the burden of constructing and maintaining white elephants. However, these temporary venues are typically small capacity, built using generic modular systems that require large areas to assemble, and do not allow for dense use of the space below the stands.
To host the FIFA World Cup Qatar 2022, Qatar built eight stadia with a combined capacity of 380,000. This is a long-term oversupply of stadium capacity, sufficient to simultaneously seat 1 in 7 of the population. To reduce the number of underutilized stadia following the event, one of the venues—Stadium 974—was designed as a unique temporary facility: Designed to meet the demanding requirements of a FIFA World Cup stadium, with a 40,000 capacity multi-tiered venue and roof covering all seats, it is also the first fully demountable stadium of its kind. The inventive design allows the stadium to host 13 events then be disassembled, transported, and reassembled elsewhere.
The suitability of DfD as a strategy for reducing the environmental impact of structures is primarily weighted on three factors: how many times will the structure be reused, how far will it be transported between its uses, and the additional embodied carbon associated with building a structure specifically for disassembly. A DfD structure can have a higher upfront embodied carbon investment compared to a conventional one-installation structure, due to element rationalization and connections which facilitate easy disassembly and reassembly. A study prepared for FIFA, Greenhouse Gas Emission Analysis of a Demountable FIFA World Cup Stadium, compared a combined average of the embodied carbon of four other 40,000 capacity permanent stadia constructed for the event against Stadium 974, estimating that Stadium 974—including the structure, services, and finishes—had over 60% more initial embodied carbon emissions. For DfD to be a sustainable strategy, this initial investment in embodied carbon must be counterbalanced by reusing the structure to avoid new
construction; a DfD structure must be disassembled and reused to justify the investment of the initial upfront embodied carbon. Finally, the carbon dioxide emissions released from transporting the structure must be monitored: if a DfD structure is transported too far then the avoidance of new construction emissions may be outweighed by the emissions released due to transport. The same FIFA study concluded that, if reusing Stadium 974 once, it could be transported over 4,350 miles and still have a lower total embodied carbon than building a second new stadium from scratch (Fig. 1)—equivalent to the distance from New York to Peru by water.
Stadium 974 is a DfD structure first assembled on the east shore of the Doha Bay in the municipality of Ras Abu Aboud, Qatar. The stadium occupies an area of 695 feet x 656 feet on plan and at its highest point is 154 feet above ground level with no basement. The design concept is based around a highly repetitive grid of identical structural frames, supporting standardized modular components: bleachers, concourse slabs and custom shipping containers pre-equipped with services. Stadium 974 was designed to be demounted after the event and relocated, either to be reassembled as a complete stadium or repurposed into alternate configurations at different locations (Fig. 2). Structural joints are located between the curved and straight sections of the stadium, resulting in eight different sectors on plan which are split into two tiers of stand modules and one level of roof modules. The specific legacy designs focused on five alternative configurations of the modules: a 20,000-capacity soccer stadium, a 7,500-capacity swimming pool complex, a 7,500-capacity multipurpose pavilion, and two 5,000-capacity athletics stadia.
Stadium 974 was conceived as a simple structure. The stadium structure consists of a series of steel braced frames resembling the appearance of a high-bay warehouse on a larger scale; while a highbay warehouse is designed to support goods on standard 40 inch x 48 inch packing pallets, Stadium 974 is designed to support programs in standard 8 feet x 40 feet shipping containers. Basing the design around a standardized volumetric unit enables the structure to follow
a regular grid with repetition of structural element lengths within the frame (Fig. 3).
The frame features efficient direct vertical load-paths and regularly spaced bays of stiff bracing struts. Horizontal diaphragms are created on each level through tension rod cross-bracing, avoiding the need for the floor system to act as part of the horizontal lateral system. The column elements are pinned at their base, and bending stiff from bottom to top with pinned connections between the columns and the radial and tangential girders. The frame follows an approximate 30-foot grid.
The structure of the bowl and roof is divided in eight sectors: four straight sectors and four corner sectors, each separated by expansion joints. The expansion joints feature a sliding connection between the last bay of tangential beams and purlins of the straight sectors and first radial frame of the corner sectors. If the structure is reassembled in an alternate configuration, then additional elements may be required at the expansion joint to complete an independent self-stable sector module. The external circulation cores are designed as completely independent laterally stiff structures uncoupled from the primary bowl.
The roof structure follows the bowl grid and consists of a series of radial main trusses supported on the outer perimeter columns by means of V-shaped supports, cantilevering 89 feet over the short sectors and 177 feet over the long sectors. The cantilever is counterbalanced with back stays connecting the back of the roof main trusses to the foundation level. The roofing consists of uninsulated trapezoidal sheet spanning 15 feet in the radial direction over tangential purlins.
The main structure was analyzed and verified according to the Eurocodes. Along with the International Code Council, this is one of the two dominant design code methodologies used globally, allowing for good cross-compatibility with other jurisdictions when the structure is relocated, and easy understanding of the analysis and verification process when the structure is reviewed by local engineers.
The lightweight slab panels, bleachers, containers, and modular staircases were all verified for compliance to strict stadium serviceability limit states for vibrations, limiting the lower vertical frequency to six Hz to allow for the maximum flexibility of future use scenarios. All concourse slabs are designed for a 105 psf live load to allow for future interchangeability. All the cross sections were designed to ensure no plastic strains occurs in the ultimate limit state to avoid permanent deformation which could restrict disassembly and reassembly. Wind, temperature, and seismic loading were incorporated based on the specific environmental conditions of the stadium in Doha. If the stadium is reassembled in its entirety in its next location, then loading conditions will need to be verified against the initial design assumptions; if the stadium sectors are reassembled in an alternate configuration, then the overall stability design will need to be reanalyzed. The MEP services have also been designed in a modular arrangement with reuse and flexibility in mind. However, depending on the new location and configuration, the services strategy may require some power, heating, and cooling adjustments.
The stadium’s name and its common moniker—Container Stadium—both highlight the modular concept behind the stadium; a total of 974 specially modified shipping containers were used to allocate all the required functional spaces of the stadium—ranging from hospitality suites to restrooms, and concession stands to mechanical plant rooms. In some cases, clusters of up to three containers were connected to achieve the required functional area. Many variations in container customization were considered, such as the complete removal of load-bearing walls of the container, or differing load requirements. In all situations, the base of the container acts as the permanent structural slab, with no additional slab below. All other walking and seating surfaces in the stadium are lightweight modular steel systems that can easily be removed, stacked, and reinstalled interchangeably throughout the structure. The focus on
lightweight structures is to easily facilitate installation and demounting, to reduce the structural demand on the primary frame and foundations, and to reduce the total weight of material that must be transported to a new location. These lightweight systems contrast with typical concourse and bleacher solutions made from heavy precast concrete components. The concourse slabs are thin gauge orthotropic steel plates that weigh less than 20 psf and span 30 feet between tangential beams. The bleacher elements are single folded steel plates, bolted to the adjacent elements and raker beams resulting in a very efficient, stiff, and flatpack solution.
For a DfD project to be successful, as many of the barriers to future reuse must be removed as possible. A key design focus of Stadium 974 was to plan for future transportability of the structural elements by ensuring they could be fit within a standard 40-foot shipping container. Nearly all of the structural elements were designed to be less than 40 feet long through the selection of the overall 30-foot structural grid and the arrangement of the column and raker beam splice locations. This structural grid also ensured that all insert modules—such as the bleachers and concourse slabs—were capable of fitting within the containers.
However, within the design two structural elements would typically require elements that exceed the 40-foot limit—fabricated portions of the longer cantilevering roof trusses, and the backstays tying the roof down to the ground. The backstays were subdivided into four segments that are spliced together on site, while the long
roof trusses were left as a small number of special items that instead of being transported within a container would require space on a ship deck. If transportation of the trusses on the deck of a ship is not feasible, these elements could still be subdivided and spliced into individual lengths less than 40 feet.
To facilitate future disassembly all the connections between elements, and splices along elements, are designed as reversible. Splices in continuous elements such as columns, raker beams, and backstays are achieved through bolted headplates that can transfer moments. All connections between elements—beams to columns, bracing to nodes—are resolved with single pin connections. Much of this reversibility is achieved by condensing the complexity of the connection into an isolated fabricated central node. The design approach using single pins simplifies the assembly and disassembly process and has the potential to reduce the size of the connection zone when compared to a more conventional multi-bolt solution.
In addition to incorporating reversibility in the structural design of the connections, it was also important to embed the process of assembly and disassembly into the design. Each connection was modelled in a 3D CAD environment including the presence of MEP and architectural finishes to simulate the restricted access to the connections and confirm the installation and de-installation sequence. The concourse slabs and containers are fixed to the tangential beams using a standard flange-clamping system.
Successful rationalization of structural cross-sections in a design is about finding a balance between minimizing the use of material by designing each element close to 100% structural utilization while also taking advantage of the fabrication and installation efficiencies of grouping elements. In addition, for a DfD structure rationalizing the element sizes allows for increased interchangeability between elements in the design. This was achieved in Stadium 974 by rationalizing both the overall cross-section dimension and cross-section thicknesses. All columns in the stadium were selected from one of eight square hollow section sizes with three outer dimensions and three plate thicknesses.
Rationalizing beam and column crosssections still leaves an extensive range of potential column-to-beam connection configurations. A standardized connection detail was developed that could be flexibly applied to different combinations of cross-section sizes. The concept was based around a set of four channels welded to the outside dimensions of the columns, a standardized pin length, and doubler plates to make up the dimensional tolerance. Depending on the column dimension, the connecting beams either slot over the channel or within it.
Fig. 6. A typical column-beam connection capable of supporting different beam widths, depths, and thicknesses
A key difference between conventional one-installation structural design and DfD is in the requirement to maintain knowledge about which structural elements are which through disassembly, storage, and reassembly. Stadium 974 used an alternative to the impermanent element tagging systems—paint sticks, paper or plastic tags—that are typically obscured by paintwork. Instead, each steel beam and column in Stadium 974 has a visible QR code attached, allowing the contractor to scan and read element information. The ability to scan and digitally organize elements is helpful for initial assembly, but crucial for disassembly, storage, and tracking through the container transport process.
The presence of individual QR codes on elements also allows for the development of material passports—digital identity documents cross-referenced to each element which store additional further information, such as material grade, design capacity, and element embodied carbon.
The only elements of the structure of Stadium 974 not designed for disassembly and reuse are the foundations. Foundations are specific to a location’s geotechnical conditions, and their design can often vary from one end of a structure to the other. Additionally, foundations are typically made of concrete, making them substantially heavier than the elements in the structural steel frame. Transporting heavier construction materials releases more carbon dioxide emissions per mile travelled, thus reducing the benefits of DfD. For Stadium 974, new foundations would need to be installed at any future locations as part of the reassembly process.
For Stadium 974’s first installation in Doha, a combination of favorable site conditions (a thick layer of Simsima limestone) and a lightweight stadium without concrete bleacher or concourse slabs allowed for relatively small shallow isolated concrete pad foundation at each column location with limited excavation required.
The inclusion of these DfD features on a large-scale commercial project led to some unexpected challenges. The transportability of the system allowed for complete off-site fabrication in a workshop, which led to a comparatively fast on-site assembly sequence. However, the use of reversible single pin connections on site imposed tight
Credit: sbp
construction tolerances of 1/8 inch, which required a trial assembly of large portions of the bowl frame and roof in the workshop to confirm the tolerances had been met. The only adjustability for tolerance available on site was in the bolted head plate splices in the columns, backstays, and raker beams. The use of steel for all superstructure elements means the embodied carbon emissions total of the stadium is particularly sensitive to the extraction, transport, and manufacturing of the steel. The steelwork for Stadium 974 was fabricated in Vietnam and then transported to Doha for installation. Fabricating DfD structures using steel from lower-emission steel-producing regions, such as the U.S., could reduce the total embodied carbon associated with the project. A second strategy to reduce the initial embodied carbon of a DfD structure would be ensuring that the fabrication facility is closer to the initial target installation site. The distance from the Port of Saigon to Doha is over 5,000 miles, while the maximum distance that the stadium should be transported for one reuse was estimated at 4,350 miles. If this initial material transport distance was reduced, the final sensible relocation distance could be increased.
It is expected that both the rationalization of the structural elements into fewer size groups and the fabrication of standardized and reversible connections may have led to an increase in material usage in Stadium 974 compared to an equivalent conventional one-installation design. sbp plans to complete a detailed analysis comparing Stadium 974 to an equivalent stadium design for one-installation. This direct structural comparison will allow us to understand the embodied carbon implications of each of the individual structural DfD decision categories, such as rationalization and reversibility.
Stadium 974 is the first completed stadium project at such a large scale to be successfully Designed for Disassembly. It can act as a prototype for other ambitious projects to apply circular economy principles and presents a series of interconnected design topics which should be considered in DfD projects. The discussion of demountable stadia also hopes to demonstrate the potential clarity in assessing the environmental performance of stadia projects based on their embodied carbon per event instead of their embodied carbon total. ■
Dan Bergsagel is the International Sustainability Lead for schlaich bergermann partner (sbp) based in their NYC office, and is a visiting scholar at Cornell AAP’s Circular Construction Lab. He chairs the Circular Economy Working Group for the ASCE Structural Engineering Institute Sustainability Committee. (d.bergsagel@sbp.de)
Knut Stockhusen is a Board Member and Managing Director at schlaich bergermann partner. He developed the innovative concept for the modular container stadium and realized it with the team for the first time as Stadium 974.
Christoph Paech is a Managing Director at schlaich bergermann partner’s Stuttgart office and leads sbp’s special structures team. Stadium 974 is one of many international sports arena, stadia, and other large-scale projects that he has successfully managed.
Fernando Sima is a Director at schlaich bergermann partner’s Berlin office. He was part of the team that planned and executed Stadium 974 and acted as sbp’s design representative in Qatar during the design and construction phases.
The Sonic Sphere at The Shed in New York City represents a cutting-edge collaboration between engineering, architecture, and art, creating a deeply engaging experience for the audience.
By Alec Thompson EIT, Owjan Hashtroodi PE, Nicholas Christie PE, Jason Krolicki SE PE
The Sonic Sphere is envisioned as a laboratory of the senses, an interactive architecture of sound, light, and movement that charts the edges of experience and consciousness. The Sonic Sphere is an ongoing project to bring all-encompassing audio-visual experiences to as many people as possible. The project has evolved over the past three years using a strategy of rapid iteration to develop the audio-visual systems, content, and structural form. The 11th iteration was placed at The Shed in Hudson Yards, Manhattan, New York City (The Shed). For this installation, the Sonic Sphere was suspended from the ceiling of The Shed’s McCourt arena.
The installation at The Shed was characterized by a breadth of tight constraints: three-month schedule (concept to opening day); material
availability; coordination between many fabricators; installation with minimal heavy equipment in just two weeks; and compliance with the applicable codes.
To meet these constraints, Resurget Engineering worked with the Sonic Sphere team to develop a structure and a delivery process that was lean, adaptive, and strategically leveraged advanced analysis.
The Sonic Sphere is comprised of three major independent structural components: the geodesic steel sphere, the amphitheater structure, and the stairs/elevator platforms along with gangways.
The first is the 65-feet diameter geodesic steel sphere suspended from The Shed roof framing. The sphere supports a surrounding array of synchronized LED lights and light cloths at each intersecting node in addition to 124 speakers and 12 subwoofers that create an occupiable multisensory audio and lighting experience. The faceted sphere was constructed out of steel pipes that were bolted together at each node. The amphitheater structure is the second independent component. The amphitheater platform was framed with trusses built from HSS members, radially attached to a cylindrical core truss. The radial trusses supported secondary wide flange members concentric to the core with custom preconstructed trapezoidal floor plates that span between wide flange beams. To achieve a structure with light and sound permeability, the floor plates were constructed with mitered channels and perforated steel grating as the finish surface for occupants to walk on. The trusses also supported custom prebuilt stairs along with seating platforms and aisles with capacity for an audience of up to 250. The amphitheater was independently suspended from hang
points located at the outer ends of each radial truss that connected to cables hung from The Shed roof framing.
To get participants in and out of the shows, two independent stairs and platforms were erected from standard scaffolding framing on either side of the sphere and provided support to gangways that bridged across to the amphitheater structure. ADA access was provided by a temporary elevator.
The unique geometric and performance demands of the installation required a return to the fundamental principles of material science and dynamics to design a safe yet functional structure, while considering all project-specific constraints. To develop the design for a one-of-akind structure like the Sonic Sphere, with all its constraints, it was imperative to first establish the design process.
From the first meeting, Resurget Engineering worked with the Sonic Sphere team to define the limit states and loading criteria for the design to meet the intent of the applicable codes, while not overly constraining the design. Depending on the complexity of the elements considered, the type of analysis and design approach varied to efficiently engineer each component and allow for iteration.
In addition to engineering, the two main design constraints were limited material availability and the necessity for rapid assembly of the structure in an enclosed space. The coordination with suppliers was essential to utilize member sizes that were in stock and ready to be shipped to site with minimal fabrication modifications. The other constraint was to ensure members were spliced for transport, and that they could be assembled and disassembled on site utilizing light lifting equipment options and with bolted connections.
Lastly, a full 3D model of all components, geometry, and fit up, was created in Rhinoceros 3D (Rhino) and maintained by the Sonic Sphere team. This model proved to be required as a single source of truth to establish both fabrication and erection documentation.
To design the sphere struts, Oasys GSA (GSA) was utilized to conduct stress analysis and determine the load transfer between elements. GSA also allowed for non-rectilinear wind loads to be applied normal to the surface of the structure.
The sphere material supplier, Pacific Domes, had an abundance of 2-inch diameter nominal steel pipe of varying gauges in stock, which was incorporated into the design to maintain the critical schedule. The typical pipe thickness of 15 gauge was determined based on the peak tensile and compressive forces resulting from the 12 suspension points vertically supporting the sphere. These hang points induced peak tensile forces into the members radially connected to the suspension node, and peak compressive forces into the hexagon of members surrounding the node. The regular repeating geometry of the sphere was disrupted by the gangway openings, resulting in force concentrations that required the pipe thickness be increased to 12-gauge steel.
Each node of the sphere was wrapped in a tensioned fabric cover that was beneficial for the lighting experience of the show. These fabric covers significantly increased the surface area of the sphere, resulting in a much greater lateral incidental wind force being applied to the system. The lateral forces were resisted at eight nodes on the sphere, with two inclined cables at each node. This configuration insured that
during any movement, at least four cables and nodes would be in ten sion at any given time, preventing the entire lateral load being trans ferred into a single node.
The sphere required coordination throughout design to accommo date limitations of the existing Shed structure regarding the allow able weights and locations of hang points. Collaboration with The Shed’s design team was essential to locate appropriate rigging loca tions and capacities to support the amphitheater and sphere. The gravity support cables for both the amphitheater and sphere required rigging attachments to the panel points of the existing roof framing. Based on this coordination, at each hang point, three gravity cables from the sphere were connected to a single turnbuckle per location that tied back to the roof framing. The lateral cables for the sphere tied into corner columns of The Shed.
in a matter of days. To achieve this end, Rhino was utilized to model every component of the structure and ensure sufficient clearance was provided for bolting connections on site. This specialty modeling was done primarily by the architectural team after specific member sizes and connection detailing was provided to them by the consultants and fabricators.
All elements of the amphitheater platform were designed utilizing a combination of GSA, RISA-3D, and custom spreadsheets. To account for the rapid construction timeline, coordination with steel supplier County Fabricators and the detailer Rosewich Engineering was essential to determine what member sizes were readily available in stock and could be fabricated in a few weeks. This inversion of the typical workflow, where we started with sizes and had to design the spacing or length around them, led to a unique iterative design process. The transportation of these elements also resulted in dimensional restrictions where each truss had to be less than 8 feet deep and 24 feet long to fit on a standard flatbed.
Due to the timeline constraints, the platform steel framing had to be finalized and released for fabrication, prior to design and programming completion of the aisles, stairs, and seats for the amphitheater. As the project developed, it became evident that the demand at the cantilevering tips of the radial trusses exceeded the capacity of the top chord truss, due to heavier than originally anticipated super-imposed dead loads.
Rather than field-modifying the radial trusses, the engineering team developed an alternate design where the sphere and amphitheater platform were suspended as separate structures. With this new supporting approach, the differential movements of the systems had to be accounted for to prevent collisions. A finite element analysis was performed to investigate and mitigate the differential deflections based on the rigging cable layouts.
To facilitate the rapid design and construction of this unique structure, it was essential to employ innovative engineering strategies and work in synergy with fabricators, erectors, and architects to design a structure that could be both assembled and disassembled by hand
The accuracy of this Rhino modeling also aided the steel suppliers with fabrication as each element was modeled precisely and could be isolated to simplify shop drawings. Having a master model where all disciplines lived also provided instant feedback to the architectural team regarding clashes and expedited the design cycle when adjustments had to be made. This precise level of coordination was paramount to maintaining the three-month design and fabrication schedule, and assuring the on-site assembly and installation could proceed without costly infield modifications.
The Sonic Sphere at The Shed represents a cutting-edge collaboration between engineering, architecture, and art, creating an immersive experience for the audience. Through careful planning and innovative design, the project overcame challenges related to time, materials, fabrication, and space. This installation showcases the potential of rapid iteration and adaptive design, redefining the limits of structural and experiential art.
As the Sonic Sphere continues to evolve, it sets a new standard for projects that blend technology and creativity, transforming our interaction with space and sound. ■
Alec Thompson joined Resurget in 2022 and since then has gained project experience in multiple construction sectors across the United States. His working experiences includes a wide variety of materials as well as a specialty on structures with complex geometries.
Owjan Hashtroodi, an Associate at Resurget Engineering, brings over a decade of experience leading projects across various market sectors. His expertise covers a wide range of structures, including high-rise buildings, specialty structures, commercial and educational facilities, as well as vehicular and pedestrian bridges.
Nicholas Christie is Chief Engineering Officer at Sonic Sphere, responsible for the design and delivery of the spheres. He has 16 years experience in structuralmechanical engineering, specializing in structural dynamics, kinetic structures and large-scale art installations.
Jason Krolicki is a founding Principal at Resurget Engineering with more than 20 years of experience leading multiple award-winning projects across the world. His broad range of experience and passion for design, inspires a focus on performance and innovation.
The seismic retrofit of an early 1960s-era office building involved 272 viscous dampers across 23 stories.
By Peter Somers, PE, SE, and Jeremy Hasselbauer, PE, SE
At 28 stories and 1.06 million square feet, 300 Lakeside is the largest office building in Oakland, California. At the time of its completion in 1960, the project, previously known as the Kaiser Center, also claimed the title of tallest building in the city. Following a significant renovation completed in 2023, 300 Lakeside has added a new accolade as it is one of the largest office buildings ever seismically retrofitted. With 272 viscous dampers weighing half a ton each across 23 stories, 300 Lakeside is reborn and ready to withstand another 60-plus years in a region with heightened earthquake risks.
Prominently located on the northwest arm of Lake Merritt, the historic office is instantly recognizable by its long, curved shape (Figs.
1-2). TMG Partners purchased 300 Lakeside in 2020 and subsequently entered a long-term lease with a purchase option with Pacific Gas and Electric Company (PG&E), a California-based, investor-owned utility. TMG began a major tenant improvement renovation that same year to deliver the spaces to PG&E's workplace standards, including seismic risk reduction goals. Although the planned renovations did not trigger a seismic retrofit under Oakland’s building code, PG&E requested TMG increase the building's seismic performance, as 300 Lakeside was to serve as PG&E’s headquarters following the company’s move from San Francisco. Magnusson Klemencic Associates (MKA) was selected as the structural engineer for the massive voluntary seismic upgrade in 2020. Coordination began immediately to find the right
solution with the constricts of the preexisting renovation schedule. While 300 Lakeside escaped relatively unscathed in the 1989 Loma Prieta earthquake, which caused significant damage in downtown Oakland, how the building might fare in the future was unknown. Working with TMG Partners, PG&E, lead architect Gensler, and Plant Construction, MKA vetted multiple options before settling on viscous dampers as the suggested upgrade solution—as they most effectively balanced the need to maintain interior and exterior appearance, cost-efficiency, and minimization of additional strengthening to protect 300 Lakeside’s historic stature while achieving the safety and performance necessary without significantly affecting the timeline for occupancy.
Before selecting viscous dampers, MKA evaluated the existing structure to determine performance targets based on PG&E’s goals as an owner/operator, the complexity of the existing moment frame system, budget constraints, and the proximity of the Hayward Fault Zone running through Oakland. Notably, the upgrade needed to address several critical considerations:
• Renovation efforts could not affect the existing foundation and basement levels to avoid disrupting building operations or significantly impacting cost and schedule.
• The retrofit construction had to be tightly coordinated with the move-out and move-in schedules of various tenants throughout the building.
• It was desired to avoid work on the top five floors to prevent displacing the existing tenants.
While a complete set of original construction documents was available for this building, the details for the critical connections (beam-column and column splices) were sometimes ambiguous and allowed for more than one connector (e.g., bolts versus rivets). They did not list all the specific material properties and were not dimensionally complete.
Given this uncertainty, MKA developed a detailed on-site investigation and material testing program, which was later implemented by Plant Construction. The investigation involved removing the existing concrete encasement around several beam-column connections and column splices and studying the materials and geometry used to make them. Each component was thoroughly documented, allowing the project team to model the components to evaluate their behavior more accurately. The steel moment frame at 300 Lakeside is unique in that unlike most “Pre-Northridge” moment frames, 300 Lakeside’s frame features bolted and riveted connections that utilize “double split tees” (Figs. 3-4).
During the testing program, MKA found the bolts would not experience brittle bolt shear failure and snap off as was anticipated. Instead, the split tee stem allows the frame to yield, indicating more ductility available in the frame than expected.
Since simplified linear analyses were insufficient to accurately inform building performance, MKA subjected a nonlinear model of the existing building to ground motions representative of the regional seismicity. With earthquake time histories conditioned to the natural periods of the structure, analyses of the building subject to a ground motion level consistent with a 225-year earthquake—a Mean Recurrence Interval (MRI) of 225 years/BSE-1E per ASCE 41— combined with the results of the investigation and testing program showed moment frame beam rotations exceeding those permitted by ASCE 41 for Life Safety acceptance criteria. This demonstrated that the building is susceptible to significant damage and potential life loss even under moderate ground motions.
MKA explored various retrofit options using the nonlinear dynamic procedure per ASCE 41-17. After several iterations of seismic evaluation and the development of retrofit strategies, the seismic performance objective for the voluntary retrofit was selected as Collapse Prevention for a 475-year seismic hazard (10 percent chance of exceedance in 50 years). Given the somewhat unique seismicity in the Oakland area— more frequent earthquakes are not much smaller than rarer, larger earthquakes due to the city’s proximity to the Hayward fault—this seismic hazard is fairly consistent with 75 percent of the seismic forces for new building design under ASCE 7-16, the conditions that would be required were this a code-triggered retrofit.
The various options MKA considered to achieve Collapse Prevention using ASCE 41 included:
• Adding braced-frame or shear wall cores. While structurally efficient solutions, these cores were quickly eliminated from consideration because any placement of new cores would have significant impacts on either interior space or exterior appearance depending on if either new interior or exterior cores were added—an issue for the historical building wanting to preserve as much original integrity as possible. Furthermore, and most importantly, additional foundations or foundation strengthening would be required.
• Adding distributed Buckling Restrained Braces (BRBs). This approach would maintain the historical appearance, and BRBs are well-known as a cost-effective seismic bracing approach. However, the increased stiffness and corresponding shorter
period would increase global demands, requiring considerable column and foundation strengthening.
• Using distributed supplemental damping to reduce drift and deformation. This approach features a minimal increase in stiffness, keeping global forces approximately the same, with energy dissipation in these added elements reducing drifts and plastic rotations in the moment frame members. MKA identified it as the ideal solution early on.
Once the retrofit approach was determined, MKA evaluated two types of dampers: friction and viscous.
• Friction dampers provide significant energy dissipation due to the nearly rectangular hysteretic loops with negligible stiffness increase once slip occurs in the dampers. However, the force in friction dampers is in-phase with the force in the moment frames, meaning that the damper forces are additive to the column forces resulting from overturning in the frames. This increases specific column and foundation loads despite the global reduction in seismic demands, leading to increased column and column splice strengthening and potential foundation impacts.
• Viscous dampers provide similar benefits as friction dampers in that the global stiffness increase is negligible after small movements occur, and significant energy dissipation reduces building movements. The key difference is that viscous damper forces are out-of-phase with the moment frame forces, so despite slightly less efficient hysteretic behavior, increases in column and foundation loads are minimal.
Ultimately, adding viscous dampers, the selected retrofit approach, was the best balance between interior and historical appearance impacts, cost-efficiency, and minimization of additional strengthening (Fig. 5). Most importantly, this approach allowed the retrofit to move forward without needing to access the basement levels. Also, damper sizing and layout could be designed without requiring work on the top five floors.
The dampers were laid out to permit better control of force concentration in columns, minimizing column and column splice strengthening and preventing significant increases in local foundation loads (Fig. 6). MKA worked with Gensler, the tenant improvement architect, to locate and place the dampers strategically, maximizing space usage
weighing approximately half a ton each, in addition to the HSS extension pieces, cranes had to lift each damper into place versus using the manlift—a significant effort that required careful coordination with Plant Construction and their subs.
Another complication of construction was that the occupied floors were not vacated from the bottom of the building upward as the structural upgrades naturally should occur. Given this, damper installation was taking place above some floors that had yet to be retrofitted. To prevent portions of the frame without retrofit being subjected to increased loads from dampers installed above, it was determined that only a limited number of dampers above columns pending retrofit could be engaged. To address this, MKA designed damper-end connections with temporary slotted holes, allowing the contractor to install the dampers and complete most of the work while keeping the dampers from engaging before access was available to floors below. The contractor then returned and “locked off” the dampers by installing the permanent bolts once the necessary column strengthening below was complete. This significantly compressed the construction schedule compared to requiring the damper installation to progress bottom-to-top, allowing the retrofit work to be performed within the TI schedule.
In the end, the strengthening of the existing moment frame was very limited. Less than three percent of the building’s columns required strengthening, which consisted of adding side plates across the flanges of the columns. These plates were added only to the accessible sides of the perimeter columns to avoid having to remove additional cladding for access, as the columns were too close to the façade to access otherwise. Less than 20 percent of the building’s column splices required strengthening, and the approach varied based on the failure mechanism. In many cases,
simply welding the existing splice plates was sufficient because the bolts were the controlling element. In other locations, the bolts were removed, and the splice plate was replaced and welded to the column flanges. For one-sided access, different designs were provided at each flange so that the plates could be placed from the same side (one on the outside of the flange and a pair of plates on either side of the web on the inside of the flange, Fig. 7). Lastly, kickers were added at fewer than 2.5 percent of the building’s beams to brace the bottom flange to prevent buckling before the development of plastic hinging at the beam ends.
The immense effort at 300 Lakeside was successfully completed in September 2022, with PG&E completing its move into the space in March 2023. Despite being a retrofit of immense scale, navigating an occupied building, and working within the schedule constraints for separate tenant improvement modifications, MKA’s addition of viscous dampers to the moment frame system achieved each performance goal within the established retrofit budget and without extending the TI schedule. This solution controls drifts and framing deformations without significantly increasing column and foundation loads. The project team’s thorough preconstruction investigation and planning, as well as its collaboration with TMG, Gensler, and Plant Construction, ensured that the damper installation and structural upgrade construction went smoothly and were seamlessly integrated into the overall tenant buildout project without impacting the building’s exterior, the overall project timeline, or building operations (Fig. 8). PG&E already occupies all but three floors at 300 Lakeside and exercised its option to purchase the building with planned transaction close mid-2025, enjoying residence in a renovated and seismically improved building that maintains its historic integrity while providing the safety and performance needed in California’s earthquake-prone territory.
SIPs have been specified for use in seismic and hurricane zones.
By Jack Armstrong
In the last couple of decades, the need for durable and sustainable building technologies has come to the forefront in the global dialogue on the future of the built environment. These innovations are especially crucial in areas prone to extreme weather. According to the United Nations Office for Disaster Risk Reduction (UNDRR), between 2000 and 2019, 7,348 major recorded disaster events affected 4.2 billion people and resulting in approximately US$2.97 trillion in global economic losses. These staggering figures underscore the importance of reliable and safe buildings.
Just like a skeleton supports the body, the structural system makes a building’s core, providing strength and endurance. Naturally, paying close attention to the selection of advanced building technologies for these systems can help structural engineers create code-compliant and enduring structures that can stand strong.
One proven way that structural engineers can deliver dependable buildings in seismic zones and regions prone to heavy wind velocities is by specifying forward-thinking building envelope solutions such as structural insulated panels (SIPs). SIPs can be specified in walls, roofs or floors of residential and light commercial projects to improve durability while also elevating performance by creating a nearly air-impermeable envelope.
SIPs are load-bearing panels most commonly composed of expanded polystyrene (EPS) rigid foam insulation sandwiched between two sheets of oriented strand board (OSB). SIP design mimics the structural principles of a steel I-beam, where the OSB serves as the flange to resist bending and the foam core acts as a continuous bracing to absorb shear forces.
Manufactured under factory-controlled conditions, SIPs are precisely assembled using techniques similar to traditional wood construction but with a consistent bonding between the insulation and the board. All these factors give SIPs their structural strength to shoulder in-plane loads, offering an equivalent load-bearing area that is possible when building with 2 x 10 studs. For example, a 6 1/2-inch-thick SIP offers an equivalent load-bearing capacity to a 2x10 at 2 feet on center of equal height.
SIPs can be manufactured in large sizes up to 8 feet X 24 feet and in thicknesses ranging from 4-1/2 inches to 15 inches. Just as wide flange profiles have higher strength with increased depth, thicker SIPs have higher compression and bending capacities. Consequently, they are typically used for walls and roofs to resist both out-of-plane and in-plane forces induced by gravity, wind or seismic loads. The
variation allows structural engineers to meet project specifications and performance requirements even in areas prone to natural calamities.
In application, SIPs provide significant advantages in terms of loadcarrying capacity and support member spacing. For example, in residential and light commercial projects, a 12-1/4-inch-thick SIP spanning 8 feet can carry up to 106 pounds per square foot (psf), which is greater than many traditional systems of similar dimensions. Structurally self-sufficient SIPs require less support from framing members and allow structural engineers to have wider member spacing compared to stick framing.
Consequently, fewer members can result in lighter structures, helping reduce seismic inertia. For example, a floor constructed with a relatively thick 1-3/32-inch wood structural panel (WSP) sheathing using stick framing would require support members placed every 4 feet to be able to carry a 55 psf load. In contrast, a 6-1/2-inch SIP floor panel with support spacing at 8 feet can carry the same load. This equates to SIPs’ framing factor of about five percent, compared to nearly 25 percent in traditional framing. Similar comparisons can be made for roofs, demonstrating that the use of SIPs compared to stick framing requires far fewer support members to carry equivalent loads. SIPs are ductile, which means they can bend and deform under stress without breaking. In application, SIPs are fastened similar to traditional wood construction, which offers additional flexibility because nails provide less resistance to external forces compared to adhesives or screws. These factors set up SIP structures to allow small amounts of flex and movement, absorbing even multi-directional vibrations and reducing their impact.
To develop performance test data on the response of SIP shear walls with high-aspect-ratio segments, the United States Department of Agriculture’s (USDA) Forest Products Laboratory (FPL) and Structural Insulated Panel Association (SIPA) commissioned a study. They tested fully anchored shear segments with aspect ratios of 1:1, 2:1, 3:1 and 4:1 using the perforated shear wall (PSW) method. The findings revealed that the unit shear capacity of these segments ranged from 1,400 pounds per foot (lb/ft) to over 2,100 lb/ft, depending on the aspect ratio. Similarly, the measured unit shear stiffness varied up to a factor of two. Additionally, it was observed that both unit shear wall capacity and stiffness decreased as the number of panels joined with a spline connection increased. For instance, a 20-foot wall with four spline joints exhibited a 25 percent decrease in unit shear compared to an 8-foot wall with a single spline joint. Moreover, the unit shear wall capacity decreased with higher aspect ratios, showing a 16 percent reduction for a 2-foot segment compared to a 4-foot segment. In the same vein, unit shear wall stiffness saw a maximum decrease of 33 percent for a 2-foot segment compared to either 8-foot or 4-foot segments. The results indicated that perforated SIP shear walls align closely with the PSW method trends in terms of both strength and stiffness.
Additionally, engineers also often look closely at a material’s ability to resist creep to ensure long-term structural integrity. In engineering, creep is the increased strain or deformation of a structural element under constant load, which can cause significant displacements in a structure. This, in turn, can result in serviceability problems, stress redistribution, prestress loss and even failure of structural elements. When a study at the FPL tested SIPs’ behavior under long-duration gravity loading, the building system stood strong . Not only was there
no significant deflection but they also showed no loss in their load capacity. Owing to its strength and resilience, a 6-1/2-inch-thick SIP can carry up to 80 psf in roofs at a deflection limit of L/180, which is adequate for most roof snow load situations in the U.S. Furthermore, SIPs demonstrate seismic equivalency to light-frame wood shear wall construction, meeting ASTM D7989 Standard Practice for Demonstrating Equivalent In-Plane Lateral Seismic Performance to Wood-Frame Shear Walls Sheathed with Wood Structural Panels for in-plane lateral seismic performance. SIP walls are code-approved by the International Residential Code (IRC) to be used in seismic design categories A, B and C for aspect ratios as high as 4:1 as well as D, E, and F for common wall aspect rations 1:1, 2:1 and 3:5:1. SIPs’ strength and durability allow engineers to minimize the risk of structural failure and provide a very comfortable safety factor to buildings. In fact, after carefully evaluating its proven performance benefits, many residential and light commercial projects in Nevada, Montana and Alaska, where seismic considerations are especially important, have utilized SIPs in their structural design.
High-velocity winds pose a challenge to the structural stability of a building. Due to SIP’s strength, the IRC provision R610.2 permits exterior SIP walls in sites where the ultimate design wind speed is not greater than 155 miles per hour in Exposure B or 140 miles per hour in Exposure C. This allows SIPs to create dependable structures even in regions that experience high-velocity winds and hurricanes. In some cases, SIPs can resist wind loads exceeding 180 mph, making them suitable for coastal and hurricane-prone regions. Many manufacturers offer SIPs that meet the stringent standards set by the Florida building code for all High-Velocity Hurricane Zones (HVHZ), which includes hurricane-prone Miami-Dade County. To further bolster its performance, SIP screw connections can be strengthened to resist the additional concentrated loads.
Even when exposed to wind-driven rain, SIPs can maintain their structural integrity. In rigorous testing by APA- The Engineered Wood Association to illustrate their performance upon exposure to moisture, SIPs were subjected to transverse, lateral and axial load testing after they dried and regained their original weight. The results found that SIPs easily recovered from the condition, demonstrating excellent structural stability and the ability to regain their load capacity after moisture exposure.
Leveraging SIPs' proven performance in areas prone to wind and rain, the Joann A. Alexie Memorial K-12 School in Atmautluak, Alaska utilized them as exterior walls (Figures 1 & 2). Because the school was situated in an area devoid of natural windbreaks like trees or mountains, the design team created an elevated aerodynamic building to
face gusts straight from the Bering Strait. In addition to using 8-inch SIPs as standard walls, the project team specified 12-inch-thick SIPs as angled walls. These large, angled walls face the spring wind direction, standing strong against the uninterrupted force and breaking its speed. Besides bearing the brunt of the winds, SIPs also helped create an airtight envelope that supported the project’s energy-efficiency goals— a priority among many owners and design professionals alike.
While sidelined as a concern for energy-efficient envelopes, air and moisture infiltration can have negative consequences for a building’s structural system. If not addressed, uncontrolled air penetration can lead to condensation on the interior surfaces. This moisture build-up can promote mold growth, which can damage building materials and compromise the structural integrity of the building.
Among various reasons causing condensation is temperature fluctuation due to thermal bridging. Metal components within a traditional wall assembly such as fasteners enable heat transfer and can cause condensation risk. But factory-made SIPs have a consolidated makeup with insulation and facing in one unit. As a result, the structure is not vulnerable to thermal bridging. In fact, this property allows SIP structures to be nearly air impermeable.
When the Department of Energy's Oak Ridge National Laboratory (ORNL) tested a SIP building compared to a stick-framed building, it found the SIP structure was 15 times more airtight. This illustrates SIPs efficiency in limiting air intrusion, which can play an important role in the long-term durability of the building. Additionally, this ability is instrumental in a SIP structure’s performance in events of fire. Typically, SIP walls and roof/ceiling assemblies with the appropriate amount of gypsum board can achieve a 1-hour fire-resistance rating. But the air-sealing capabilities prevent the circulation of air and smoke within the structure, minimizing the risk of fire spreading through the building. After all, as basic fire science tells us, without oxygen, fire will not burn.
The nearly airtight nature of the SIP structures, while beneficial for long-term durability and fire resilience, necessitates mechanical make-up air to prevent mold and dampness, which can compromise structural integrity if left unaddressed. Proper HVAC sizing as per the ASHRAE Manual J guidelines is critical in SIP structures because an oversized system will not reach its intended operating rate, leading to "short cycling," where the system runs briefly but fails to dehumidify the air effectively. Conversely, a properly sized HVAC unit within the conditioned SIP envelope may require half the British thermal
units (BTUs) compared to traditional framing to efficiently take in and redistribute air, enhancing a structure’s durability.
SIPs have been specified for use in seismic and hurricane zones, and they have historically performed very well. After knowing its properties, structural engineers can rely on this construction technology and create buildings that can stand the test of time.
To help structural engineers create technically sound structures, the Structural Insulated Panel Association (SIPA) offers an in-depth analysis of SIP design principles through several resources, including “SIP Design Best Practice BP-3: SIP Structural Capabilities.” Some key considerations elaborated in this document include:
1. Engineers can increase SIP structural performance by adjusting gage and spacing patterns of fasteners, modifying the SIP connection splines (i.e. surface splines, block splines, dimensional lumber or I-joists) or adding additional straps and hold-downs.
Essentially, SIPs provide a combination of roof diaphragm and shear walls that are already double-sheathed. Adding and/or increasing the size of embedded lumber and fasteners creates the opportunity for significantly increased chord force capacities to resist significant storms and other events. It is important to note that hold-downs and straps are used on SIPs in the same manner as with traditional wood frame construction.
2. SIPs can act as their own door and window headers.
The section of a SIP wall above an opening always has embedded lumber at the top of the opening and at the top of the wall. With the SIP facers, this creates a strong box beam that can act as a structural header with no additional lumber needed in many cases.
3. Point loads may dictate the need for additional structural components to be embedded internally and should be avoided over openings. SIP walls transfer the axial loads of a structure by fully bearing on the supporting element or structure. If the compressive resistance of the OSB facer is exceeded, additional compression elements (typically dimensional-sawn lumber, engineered wood products or steel) must be used to adequately transfer the design loads. In particular, if a structural designer can minimize point loading conditions over openings, a SIP wall may be able to act as the header without the addition of other structural elements in the SIP wall above the opening.
4. Wall SIPs may require a cap plate to meet high-point load conditions.
Structural engineers should meticulously assess the load path of structural elements transferring loads to the SIP wall. If the localized loading exceeds a SIP wall's pounds-per-lineal-foot capacity, engineers should consider adding an additional cap plate (Figure 4). This addition enhances the localized capacity at the load transfer point, ensuring the structural integrity of the system.
For more SIP design considerations, structural engineers can refer to SIPA’s free content, available for download at www.sips.org/resources/design.
Tom Moore, a SIPA Board Member and the Principal Structural Engineer at Pinnacle Engineering shared his expert input for this article.
Jack Armstrong is the Executive Director/COO for the Structural Insulated Panel Association (SIPA). He’s been on the SIPA board since the mid-2000s and transitioned to leadership in 2014. Armstrong worked for the BASF chemical company for 24 years, focusing on energy efficiency and durability for sustainable construction in the built environment. He can be reached at jack@sips.org.
Innovative engineering that enabled the new Olympia DUMBO residential tower in Brooklyn, New York, to billow towards the sky with an eye-catching, sail-shaped silhouette has earned DeSimone Consulting Engineering official recognition.
Olympia DUMBO combines luxury living with a cuttingedge design and delivery approach, offering 175,000 square feet of upscale residences atop a 70,000-square-foot podium and best-in-class amenities that include New York City’s highest private outdoor tennis court, indoor and outdoor pools, a shipwreck-themed playground, and waterpark for kids.
highly functional. It enabled the facade engineers to devise a customized facade that met the design parameters while making construction more efficient, reducing labor costs, and shortening the project timeline all while contributing to the overall sustainability of the property.
Completed this spring, the tower was designed by Hill West Architects, with interiors crafted by Workstead. DeSimone’s structural engineers and facade and building envelope experts brought the architects’ vision to life and earned the company two early accolades; The Concrete Industry Board of New York will recognize the project with the 2024 Roger H. Corbetta Mid-Rise Award of Merit with Special Recognition in November, and the UK’s Society of Facade Engineering (SFE) has shortlisted DeSimone for its 2024 New Build International award.
Situated next to Brooklyn Bridge and rising to a height of 450 feet over the waterfront, the 26-story tower has a sail-like architectural form inspired by the building’s waterfront location. Managing the building’s complex loads was highly challenging and DeSimone’s structural engineers addressed the dilemma by supplementing the traditional vertical column arrangement with sloping columns positioned along the building’s height. This approach effectively balanced the divergent load distribution resulting from the tower’s unique shape—and ensured the structure's stability as it achieved Hill West’s architectural vision.
The sloping columns themselves added another layer of complexity to the structural design, because the horizontal forces they generate impact the building’s structural slabs. DeSimone’s engineers worked with the architects to calculate the necessary thickness of the slabs and position of the sheer walls in order to create load paths that would ensure stability. The team employed high-strength, pre-cast concrete as well as lightweight, sustainable, voided concrete slabs to provide longer spans for open spaces in select locations.
With the structural design challenges of Olympia’s unconventional design resolved, DeSimone’s facade engineers addressed Olympia DUMBO’s building envelope as two distinct zones. The design called for a textured surface for the lower podium zone, with deep reveals around windows and balconies in the upper tower zone, which twists and steps as it rises.
Closely collaborating with the project architects and contractors proved key to ensuring Olympia DUMBO was both visually stunning and
For the podium, DeSimone introduced a novel technical design which incorporated a bespoke ship lapped precast concrete panel system, windows, and storefront glazing.
The tower facades consist of a custom, unitized window wall system. The north and south elevations involve predominantly flat surfaces, while the east and west elevations twist and step as the tower tapers upward. The west facade balconies wrap around the north elevation in a twisting way, maximizing views of the Brooklyn Bridge and Manhattan skyline.
A project-specific coating devised to mimic the texture and appearance of masonry was used on the envelope’s prefabricated panels, each adjusted to accommodate the divergent surface geometry, and enclosed by a single contractor, without any secondary fix of elements after the panels were hung—eliminating the need for different trades.
A demanding schedule, high field-labor costs, and restricted logistics space at a dense urban site made it essential for the project team to develop efficient, shop-fabricated, and custom-panelized solutions for some 196,000 square feet of facade surface area.
The use of those prefabricated panels, fitted with thermal insulation and weather barriers, also greatly enhances the building’s energy efficiency and weather resistance. Assembled off-site and then installed on site, the custom, panelized system expedited construction. It also reduced the building’s carbon footprint by minimizing the amount of cement used in construction, and in turn, the fuel to transport it.
Additional sustainable design approaches included the tower’s geometry and aluminum cladding, which provide natural shading, reducing the need for air conditioning, and lowering the building’s energy consumption over time. DeSimone’s facade specialists, in collaboration with the architect, selected high-performance glass for the windows, which helps regulate the indoor temperature while allowing natural light to flood the interior spaces. The glass is specially designed to reduce glare and filter out low-frequency sounds, creating a more comfortable living environment.
Olympia Dumbo was developed by Fortis Property Group.
The Council on Tall Buildings and Urban Habitat (CTBUH) named Singapore’s Pan Pacific Orchard "2024 Best Tall Building Worldwide" at its recent annual international conference, in London and Paris. The award recognizes the project’s groundbreaking approach to high-density urbanism, combining nature, community and sustainability within the city’s bustling Orchard district.
Amidst Orchard's renowned shopping malls, tree-lined boulevards and mixed-use towers, Pan Pacific Orchard stands out as a beacon of Singapore’s environmental vision. The project’s “hotel in nature” concept transforms the traditional high-rise into a vertical green space, with multiple terraced gardens and water features integrated into the building, achieving a green plot ratio of more than 300 percent. By holistically incorporating greenery into its design, Pan Pacific Orchard honors Singapore's heritage while pushing the envelope of sustainable urban development in a dense, urban setting.
Both structurally and conceptually, Pan Pacific Orchard breaks from tradition: instead of a tower-on-podium design, it delineates a series of four terraced sky gardens with individualized motifs—forest, beach, garden and cloud—which provide guests distinctive amenities and biomimetic landscapes at each level. The “forest” terrace at ground level features lush foliage and a cascading water plaza, while the “beach” terrace includes a tranquil lagoon surrounded by palms. The “garden” terrace offers serene walking paths, and the “cloud” terrace, capped with a photovoltaic canopy, hosts events with views of the surrounding city. These spaces create a unique connection between guests and nature while mitigating Singapore’s tropical heat through passive design strategies that reduce energy consumption and improve ventilation.
The project departs from conventional tower designs by carving out large open-air atria that not only reduce the building’s environmental footprint but also foster interaction between nature, the city and its many
diverse communities. Its semi-outdoor tropical climate reduces reliance on mechanical cooling systems, while its 45 percent external to 55 percent internal surface area ratio optimizes energy efficiency. These features align with Singapore’s broader sustainability goals and reflect a global push to lower the environmental impact of dense urban environments.
The project’s focus on sustainability extends to its Green Mark Platinum rating, which recognizes its commitment to minimizing energy consumption, water usage and waste. Solar panels power the common areas, rainwater is harvested for irrigation and food waste is processed via an on-site biodigester. These measures contribute to Pan Pacific Orchard’s nature-positive ethos, where the building not only connects with the environment but actively enhances the local ecosystem and biodiversity. The design’s innovative approach to energy efficiency also helps reduce the urban heat island effect, contributing to a more livable cityscape.
Pan Pacific Orchard also received CTBUH’s Space Within category award, which recognizes tall building projects that have integrated extraordinary interior spaces and demonstrate exceptional functional success in terms of the user experience, elevating the solutions and possibilities for interior space design to the next level. In addition to evaluating the interior design of the space, the judging process also considers the design and integration of movement between spaces (vertically and horizontally), the performance of building systems, vertical transportation and smart technologies, among others.
As the CTBUH 2024 Best Tall Building Worldwide, Pan Pacific Orchard joins an illustrious group of past winners, including Quay Quarter Tower, in Sydney (2023), The David Rubenstein Forum, in Chicago (2022), and One Vanderbilt Avenue, in New York City (2021). These projects represent the pinnacle of innovation in sustainable tall building design and serve as benchmarks for future urban developments.
The University of Texas at Dallas (UT Dallas) held a ribbon-cutting ceremony for Phase I of the O’Donnell Athenaeum in celebration of the opening of a second location for the Crow Museum of Asian Art. The Phase I building serves as the anchor museum for what will be known as the UT Dallas Art Museums.
Leaders also broke ground on a performance hall and music building that will become part of the UT Dallas Harry W. Bass Jr. School of Arts, Humanities, and Technology. It is projected to open in fall 2026. The cultural complex is being constructed in three phases:
• Phase I (UT Dallas Art Museums)—A two-story, 57,000-square-foot building with exhibition space that more than doubles the Crow Museum’s current gallery space in its downtown Dallas Arts District location.
• Phase II—A two-story performance hall and music building with a 680-seat performance hall, an outdoor performance space, rehearsal rooms, practice rooms, teaching studios, percussion studio, recording studio, administrative offices, classrooms, multifunctional lobby space, study spaces and student lounge.
• Phase III—A future museum building as well as a parking structure that will include two levels above grade and one basement level walkout that will serve the O’Donnell Athenaeum and the campus.
Led by design partner Arne Emerson, principal architect Morphosis developed the master plan for the O’Donnell Athenaeum, as well as designing the buildings within. Partnering with Morphosis is GFF, the local architect.
The 266-foot Ralph Wilson Park bridge was successfully installed over the I-190 in Buffalo, New York, marking another important milestone in the complex construction project underway at the park. Designed with community input to increase access to the waterfront, the bridge will create a new pedestrian and bicyclist entrance to Ralph Wilson Park when it opens to the public in early 2026. Ralph Wilson Park (former LaSalle Park) is a 100+ acre waterfront park in the City of Buffalo that is currently undergoing a transformation to create a world-class public space that is safe, accessible and fun for all to enjoy.
The bridge installation started late on Saturday, October 5, and wrapped up in the morning of Sunday, October 6. Dozens of emer gency services agencies, along with state and local partners, worked in coordination to remove the old pedestrian bridge by crane and place the new 220-ton bridge superstructure over the I-190 and railroad tracks. Two gantry cranes and one 100-ton rough terrain assist crane were used and placed on either side of the highway, with one in the roadbed.
The bridge design was chosen through a community-based design competition led by the University at Buffalo Regional Institute in early 2020. The community chose schlaich bergermann partner (sbp), known for its creative, elegant, sustainable design of long-span bridges and other structures throughout the world. The design illustrates an appreciation for Buffalo’s rich architectural and industrial heritage, coupled with a desire to create an innovative and optimized structure. The structure is an enclosed steel arch that protects pedestrians from
the noise and traffic below, while also creating a safe and welcoming crossing into the park.
The Ralph Wilson Park bridge was manufactured by Cimolai in Italy and traveled across the ocean in four pieces earlier this year. After passing through the New York harbor, the four pieces were loaded onto two barges for trip to Buffalo on the Erie Canal. Additional construction work will now take place on the bridge structure including pouring a concrete deck, adding guard and hand railings, and installing LED-lighting.
DeSimone Consulting Engineering (New York) has acquired Ohio-based MER Engineers, Inc., a recognized leader in precast and tilt-up design and detailing. The move is the latest in DeSimone’s strategy to expand while increasing the depth and breadth of the services the company offers its clients across global markets.
The latest in a series of strategic growth transactions completed by DeSimone over the past four years, the acquisition of MER strengthens DeSimone’s global capabilities and resources with local experience and presence. Since 2020, the company has grown its workforce to almost 700, adding nine new offices in the US, Canada, the United Kingdom, and more.
The Charles Pankow Foundation (CPF) along with several partners announces the award of a new research grant to understand the recent and impending market penetration of electric vehicles which has created a situation in which current design live loads for parking may not adequately
reflect true, real world, loadings. Principal investigators are Dr. Ross Corotis, University of Colorado Boulder, and Dr. Sanjay R. Arwade, University of Massachusetts. The ASCE 7-28 Dead & Live Load Subcommittee of ASCE/SEI, the Structural Engineers Association of New York (SEAoNY), the New York City Department of Buildings, and others have already committed to be involved in this important and timely research.
Wright Structural Engineers announced the appointment of Scott Jones, SE, as its new President. With over 24 years of experience as a structural engineer, he has demonstrated his expertise in project management, strategic planning, and team development. Jones holds BS and MS degrees in civil engineering and a minor in business management from Brigham Young University. He is a licensed SE and/or PE in 41 states, Washington DC, and the U.S. Virgin Islands. He is a member of the Structural Engineers Association of Southern California, an allied member of the American Institute of Architects, a member of the International
Statement of Ownership, Management, and Circulation (All Periodicals Publications Except Requester Publications)
Publication Title: STRUCTURE; 2) Publication Number: 1536-4283; 3) Filing Date: 9/23/21; 4) Issue Frequency: Monthly; 5) Number of issues Published Annually: 12; 6) Annual Subscription Price: $75-Domestic; $90-Canada; $135-International; 7) Complete Mailing Address of Known Office of Publication: 20 N. Wacker Drive, Suite 750, Chicago, IL 60606; Contact Person: Alfred Spada; Telephone: +1 (312) 649-4600; 8) Complete Mailing Address of Headquarters or General Business Office of Publisher (Not printer): 20 N. Wacker Drive, Suite 750, Chicago, IL 60606; 9) Full Names and Complete Mailing Addresses of: Publisher – Alfred Spada, 20 N. Wacker Drive, Suite 750, Chicago, IL 60606, Editor – Alfred Spada, 20 N. Wacker Drive, Suite 750, Chicago, IL 60606, and Managing Editor – Alfred Spada, 20 N. Wacker Drive, Suite 750, Chicago, IL 60606; 10) Owner: NCSEA Media, Inc., 20 N. Wacker Drive, Suite 750, Chicago, IL 60606; No individual owners; 11) Known Bondholders, Mortgagees, and Other Security Holders Owning or Holding I Percent or More of Total Amount of Bonds, Mortgages, or Other Securities: None; 12) Tax Status, N/A; 13)
Publication Title: STRUCTURE magazine; 14) Issue Date for Circulation Data Below: September 2024; 15)Extent and Nature of Circulation. (Average No. Copies Each Issue During Preceding 12 Months, No. Copies of Single Issue
Council of Shopping Centers, an associated member of the Building Industry Association of Orange County, and is active with HomeAid Orange County.
Jeff Ellis Selected to Join the Structural Engineers Association of California (SEAOC) College of Fellows
The Structural Engineers Association of California (SEAOC) has selected Jeff Ellis, SE, Director of Strengthening at Simpson Strong-Tie, to join its prestigious College of Fellows. Ellis, the nominee this year from the Structural Engineers Association of Southern California (SEAOSC), was inducted on September 5 during the annual SEAOC Convention in Portland, Oregon.
The SEAOC College of Fellows represents the organization’s highest honor, recognizing members for their distinguished service and outstanding contributions to structural engineering. Nominees are evaluated based on their professional achievements, contributions to the industry through publications and presentations, and active involvement in SEAOC and other professional engineering organizations.
Published Nearest to Filing Date); 15a) Total Number of Copies (Net press run): 28008, 28064; 15b) Paid Circulation (By mail and outside the mail) 1. Mailed Outside County Paid Subscriptions Stated on PS Form 3541: 27153, 27590; 2) Mailed In-County Paid Subscriptions Stated on PS Form 3541: 0, 0; 3. Paid Distribution Outside the Mails Including Sales Through Dealers and Carriers, Street Vendors, Counter Sales, and Other Paid or Requested Distribution Outside USPS: 0, 0; 4. Paid Distribution by Other Classes of Mail Through the USPS: 0, 0; 15c) Total Paid Distribution (Sum of 15b (I), (2), (3), and (4)): 27419, 27948; 15d) Free of Nominal Rate Distribution (By mail and outside the mail); 1. Free or Nominal Rate Outside-County Copies Included on PS Form 3541: 0, 0; 2. Free or Nominal Rate In-County Copies Included on PS Form 3541: 0, 0; 3. Free or Nominal Rate Copies Mailed at Other Classes Through the USPS: 0, 0; 4. Free or Nominal Rate Distribution Outside the Mail: 9, 0; 15e) Total Free or Nominal Rate Distribution [Sum of 15d (I), (2), (3) and (4)]: 9; 0; 15f) Total Distribution (Sum of 15c and 15e): 27162, 27590; 15g) Copies not Distributed: 846; 474; 15h) Total (Sum of 15f and 15g,) 28008, 28064; 15i) Percent Paid(15c divided by 15f times 100): 99.97%, 100%; 16) Electronic Copy Circulation: None; 17) Publication of Statement of Ownership: Will be printed in the October 2023 Issue of this publication; 18) I certify that the statements made by me are correct and complete: Alfred Spada, Executive Editor.
The National Council of Structural Engineers Associations (NCSEA) is proud to announce the recipients of its 2024 Special Awards, recognizing individuals who have demonstrated exceptional service and leadership within the structural engineering profession. These prestigious awards celebrate the significant contributions that the recipients have made to advance the profession and support the mission of NCSEA. The 2024 NCSEA Special Awards recipients are:.
NCSEA Service Award
Ed Quesenberry, S.E., Founding Principal, Equilibrium Engineers
With over 35 years of experience, Ed Quesenberry has committed his career to making communities safer and more resilient through structural engineering. A graduate of Cal Poly, San Luis Obispo, Ed founded Equilibrium Engineers in 2003, where he continues to lead projects in various sectors, contributing to both new construction and structural renovations. He has served as Past President of both NCSEA and the Structural Engineers Association of Oregon (SEAO) and is currently the Chair of NCSEA’s We SEE Task Group and a member of the AISC Committee on Parking Garages. Ed also played a pivotal role in the establishment of the NCSEA Foundation, contributing his expertise and vision to ensure success. His dedication to the profession and volunteer efforts make him a standout leader.
Erik Madsen, P.E., Principal, DCI + Madsen Engineers
Erik Madsen’s exemplary service to the Structural Engineers Association of New York (SEAoNY) has spanned more than two decades, during which he devoted his time and expertise to enhancing both the organization and the broader structural engineering community. From his early work in Chicago to his leadership in New York, where he has specialized in high-rise concrete structures and historic renovations, Erik has made a significant impact on the profession. As the founder of Madsen Engineering and now Principal at DCI + Madsen Engineers, he has been a tireless advocate for code development, serving on the NCSEA Code Advisory Committee for over a decade. His deep involvement with SEAoNY, where he has held multiple positions, including state delegate and President, reflects his passion for advancing the field and supporting his peers.
Lauren Posey, P.E., Structural Engineer, Martin/Martin, Inc.
Lauren Posey has quickly established herself as a leader within the structural engineering community, particularly through her involvement with NCSEA and her dedication to the Young Member Support Committee. As the Young Member Secretary of the NCSEA Code Advisory Committee, Lauren plays an active role in shaping the future of industry standards. Her contributions to SEAONC and SEAOC, as well as her leadership within the Young Members Forum, underscore her commitment to fostering the next generation of structural engineers.
Sam Rubenzer, P.E., S.E., Founder, FORSE Consulting
Sam Rubenzer has devoted his career to educating and mentoring structural engineers, particularly through his work at RAM/Bentley and as the founder of FORSE Consulting. With over 25 years of experience, Sam has become a trusted resource for structural engineers seeking guidance on complex projects and design tools. His passion for teaching and empowering others through education has made a lasting impact on the profession, making him a deserving recipient of the Susan M. Frey NCSEA Educator Award.
Gary Chock, S.E., D.CE, F.SEI, Dist. M. ASCE, President, Martin, Chock & Carden, Inc
Gary Chock is a distinguished leader in structural engineering and hazard mitigation. As President of Martin, Chock & Carden, Inc., he has overseen numerous high-profile projects in Hawaii and beyond, focusing on hazard resilience in areas prone to natural disasters such as tsunamis, hurricanes, and earthquakes. His expertise has contributed to the development of the first national standard for tsunami-resistant design, making a profound impact on building safety. His dedication to risk analysis, code development, and hazard research is a testament to his commitment to advancing the profession.
American Institute of Steel
Construction (AISC)
American Society of Civil Engineers (ASCE)
Applied Software, Graitec Group
ArcelorMittal
Armatherm Thermal Bridging
Solutions
ASC Steel Deck
Atlas Tube
Bekaert
Bentley Systems
Blind Bolt
Bull Moose Tube Company
Cast Connex
CBS2, LLC
Chicago Clamp
CMC
Concrete Reinforcing Steel Institute (CRSI)
CoreBrace
Crystal Instruments
CTS Cement
DACS, Inc.
Dayton Superior
DEWALT
Dlubal Software
DrJ Engineering, LLC
DuraFuse Frames
Earthbound Corporation
ENERCALC, LLC
Engineers Alliance for the Arts
EPIC Metals
Euclid Chemical
EVER Seismic LLC
Exploration Instruments, LLC
Fabreeka International
FARO Technologies Inc.
FORSE Consulting
Foundation Technologies
FSD Active Ltd / CALMFLOOR
Fyfe FRP
GDK Insurance Brokerage, LLC
Giza Steel
Gsource Technologies LLC
Headed Reinforcement Corporation (HRC)
Hilti
IDEA StatiCa
International Code CouncilEvaluation Service (ICC-ES)
International Masonry Institute (IMI)
Intsel Steel
Kinemetrics
LeJeune Bolt Co.
Lindapter
LNA Solutions
Magnum Piering, Inc.
MAX USA CORP
Menard USA
MiTek
National Ready Mixed Concrete Association (NRMCA)
New Millennium
Nucor
Paragon
Peikko
Pirros
PS=0
PYTHON Fasteners
Qnect
QuickFrames USA
QuickTie Products
Ram Jack
RedBuilt
RISA
SAFE-T-PROOF
SAFI Structural Technologies
Seismic Bracing Company
SEU by SE Solutions, LLC
Simpson Strong-Tie
SkyCiv
SmartLam North America
Splice Sleeve North America, Inc.
STABIL-LOC ARKANSAS LLC
Steel Deck Institute (SDI) &
Steel Joist Institute (SJI)
Steel Tech USA
Steel Tube Institute (STI)
Sterling Structural
struct.digital
Trimble/Tekla
Truss Plate Institute (TPI)
VoidForm
W&W | AFCO Steel
NCSEA launched its brand-new Compensation & Benefits Study, the only national survey dedicated exclusively to the U.S. structural engineering profession. The survey, which takes 30-45 minutes to complete, covers essential topics like salary, benefits, PTO, retirement policies, and job satisfaction. This resource will help inform compensation negotiations and benefit selection. Participants receive a discount on the final report, which includes interactive tools to analyze data by geography, firm size, and more. Plus, the report will offer real-time updates as more engineers share their input. To participate, visit www.ncsea.com/business-practices/compensation-benefits-study.
Remember that moment you first fell in love with structural engineering? That spark when you realized the impact you could have on the world? That spark becomes a powerful flame when amplified by a community of peers who share your passion for leveraging technical skills to make a difference in the built environment. That’s exactly what SEI is all about, and I’m thrilled to help fan those flames as your new President.
I’m Stephanie Slocum, and I am honored to be the first woman to serve you in this role. I believe that structural engineers are uniquely positioned to lead the multi-disciplinary efforts to solve the massive challenges in our world today. These are things like climate change, equity in the built environment, building the workforce leaders of our future, and leveraging emerging technologies like AI for good. We need individuals at all stages of their careers and with all backgrounds to bring their unique perspectives to address these issues. Will you join me in committing to leveraging your skills to serve the greater mission?
My vision for SEI is that it is the premier hub for structures and built environment collaboration, innovation, and learning. We are uniquely able to unite diverse perspectives to address the critical challenges of our built environment to create a more sustainable, resilient, equitable, and, above all, safe future.
This isn’t just a lofty vision—it’s something we’re already doing. Today’s big challenges are solved at the intersection of perspectives and disciplines. It takes bringing our industry together and spearheading research and development efforts—something that SEI, as an Institute of ASCE, is uniquely positioned to do.
A snapshot of these efforts includes our four focus initiatives: Education and Leadership, Young Professionals, Performance Based Design, and SE 2050. Are you interested in getting involved directly? Your brainpower and perspective can make a difference, whether you’re a seasoned expert or new to the field. Your perspective brings valuable insights to our work, and you can contribute to these and other SEI activities regardless of where you are in your career journey.
Want to learn and connect with peers in person? Structures Congress 2025 (www.structurescongress.org) and ETS Conference 2025 (www. etsconference.org) registration is open now. I hope to see you there!
We are standing on the shoulders of the giants of our profession. I want to express my heartfelt thanks to Jerry Hajjar, our outgoing President, whose leadership in sustainability, resilence, and equity has set the stage for future growth.
Get ready to enhance your expertise with our in-depth ASCE/SEI 41 series, designed to keep you at the forefront of seismic evaluation and retrofit standards. Each session will dive into the most recent updates and specialized topics shaping the future of performance-based seismic design. Whether you’re a seasoned structural engineer or just starting your career, this series offers valuable insights to sharpen your skills and apply the latest ASCE 41 standards with confidence.
I also want to acknowledge the extraordinary efforts of our Technical Community (TC) and Professional Community (PC) Excoms over the past year, as we began implementing the SEI Reorganization. Thank you especially to the Nicole Baer, the outgoing PC Excom Chair, and Greg Soules, the TC Excom chair, for your leadership in this time of transition. I also want to welcome Trevor Walker, the incoming PC Excom Chair, and highlight all of our community Excom members efforts for their tireless efforts, including Anil Agrawal, Maria Garlock, Emily Guglielmo, Sreenivas Alampalli, Cherylyn Henry, Douglas Rammer, Ken Sharpless,Elaina Sutley Mark Webster, Andrea Reynolds, Julian Lineham, Arman Tatar, David Aucoin, and John Cleary. Thank you all for your dedication and the difference you are making to the profession through your work with SEI. We are also welcoming new members to the board as a result of our historic 2025 SEI Board elections, which included the first-ever open call competitive election for an SEI At-large Board member and the President-Elect position. Thank you to all who made their voices heard through your vote! Welcome to incoming board member Robin Kemper as the new SEI At-large Governor and President-Elect Ed Huston. I am excited to work together with you for the betterment of SEI and our profession.
As my Presidential term kicks off, know that I am here to serve you. I’m here to listen, guide, and amplify your impact so that together, we can make a bigger difference in the world than any of us could make alone. If you have ideas, concerns, or simply want to talk with your FY 24-25 President, my virtual door is open to connect with you.
Together, we’re going to build a future that’s structurally sound, sustainable, inclusive, and inspired. It’s time to spark a broader recognition of our vital role in solving global challenges.
To sparking progress, one structure at a time, Stephanie Slocum, PE, M.ASCE
SEI President FYP’25
November 21 ASCE/SEI 41-23 Tier 1 and Tier 2 Updates Sesson 2
December 17 ASCE 41 Concrete Walls Session 3
January 22 ASCE 41 Reinforced and Unreinforced Masonry Session 4
February 25 ASCE 41 Foundations Session 5
The SEI Futures Fund is dedicated to advancing the structural engineering profession by investing in future leaders and supporting initiatives that foster growth. Make an impact—donate today and help shape the future of the profession. Hear from a past SEI Futures Fund scholarship recipient about the incredible impact of attending a major industry conference. Their experience highlights the value of the opportunity your donation can provide. Learn more about the fund and donate: go.asce.org/seifuturesfund. For information on ETS Student Scholarship: www.etsconference. org/student-scholarship.
CROSS US is seeking passionate professionals to collaborate on our mission by serving as Members or Corresponding Members on one of our three subcommittees. Apply here: go.asce.org/applycrossus
SEI Performance-Based Design Committee is seeking new members. The committee is charged to pursue and advance performance-based principles along with engaging, educating and encouraging stakeholders to adopt these principles.
SEI Standard 76 committee is seeking new members to begin work on the next edition of the standard. If you are interested in applying for the main committee, or any of the subcommittees or task committees, please apply by November 30, 2024. Apply here to these committees: go.asce.org/sei-committees.
SEI is currently accepting proposals to modify the 2022 edition of ASCE/SEI 7 Minimum Design Loads and Associated Criteria for Buildings and Other Structures, as the committee prepares for the 2028 revision cycle.
The committee will accept public proposals until December 1, 2024. Public proposals are available from SEI Staff sei@asce.org.
Now released! State of the
The “State of the Art and Research Needs in Design for Tornadoes to Improve Community Resilience” report is an exciting outcome of the Tornado Design Workshop held back in March. This document outlines a roadmap for advancing tornado-resistant building design, paving the way for safer, more resilient communities. It presents essential recommendations on critical topics such as windspeed estimation, tornado-borne debris, and strategic community resilience objectives. By focusing on enhancing tornado resilience across U.S. communities, this report serves as an invaluable resource for researchers, practitioners, and educators in the fields of wind engineering and resilient design, empowering them to make informed decisions that protect lives and properties.
Access here: https://bit.ly/TornadoReport.
February 25-26, 2025
Phoenix, AZ
The 2025 Winter Coalition Meeting will take place on February 25-26 in Phoenix, Arizona, and is open to all who are interested. This event brings together ACEC’s coalition members to discuss strategic initiatives and industry challenges for the year ahead. The CASE Executive Committee (ExCom) and its subcommittees will also meet to advance structural engineering initiatives in practice, advocacy, and education. This gathering provides a valuable opportunity for coalition leaders and attendees to collaborate on solutions impacting the engineering profession. Look for registration to open in mid-November on the ACEC website.
Online Education COMING SOON—Visit ACEC EDUCATION AND EVENTS for more information
An education session on BIM hosted by the ACEC COPS Coalition and USIBD focusing on standardizing and optimizing building documentation practices across project stages, from design to completion. The session will address developing best practices, ensuring highquality documentation, maintaining ethical standards, and supporting the collaboration between professionals like architects, engineers, and surveyors.
The session is a must for professionals seeking to enhance documentation quality, efficiency, and cross-team coordination. For more on USIBD’s mission, visit USIBD About Us.
Alyson McGuire attends George Mason University and was granted $6,500 CASE Scholarship to further her career in Structural Engineering.
Support the Future of Structural Engineering: Donate to the CASE Scholarship Fund
The CASE Scholarship Fund is more than just financial support; it’s an investment in the next generation of structural engineers who will shape the built environment and drive innovation forward. Each year, CASE provides scholarships to dedicated students working toward a career in engineering, empowering them to pursue their education and make meaningful contributions to the industry.
Your donation—no matter the amount—can have a lasting impact. It helps cover tuition, supports students’ access to critical resources, and ultimately brings talented, enthusiastic new professionals into the field. Let’s ensure that financial barriers don’t stand in the way of their potential.
Join us in building a stronger, more resilient future by contributing to the CASE Scholarship Fund today. Together, we can make a difference! Below is a QR code for you to make your donation today. Please remember to select the CASE Scholarship Fund when contributing. Thank you for your support!
Now more than ever we need to support the upcoming generation of the workforce.
Give to the CASE Scholarship today!
Be sure to explore the latest CASE publications. If you’re not a CASE member, don’t forget to use your discount code, NCSEASEI2022, to save on your purchase.
Clear and descriptive subject lines are essential for effective email communication. Conciseness and directness enhance readability, making short paragraphs and bullet points valuable tools. Personalization and specific calls to action can significantly improve engagement, while proofreading ensures professionalism.
Flexible work schedules and remote work options have become a top priority for employees today. Many companies are adapting to this shift and seeking long-term solutions, particularly in structural engineering, where finding qualified candidates is becoming more difficult. By expanding candidate pools beyond local offices, companies can attract quality hires. However, this shift also presents challenges related to business operations, insurance, IT and security, productivity, training, and company culture. Tool 2-8 provides guidance on navigating these challenges effectively
Succession planning is a key aspect of talent management. It includes training, career planning, and replacement strategies. Effective succession planning helps organizations manage talent scarcity, identify skill gaps, promote knowledge transfer, boost employee morale, and build a robust skill set.
This tool provides guidelines for verifying analysis and design software results, focusing on linear elastic structures and small deformation/ small strain analysis, which are prevalent in design work.
Teaming agreements are essential for joint projects between contractors, design professionals, and structural engineers. These agreements outline the roles of parties before contract award and are often used in design-build projects. This commentary reviews standard teaming agreements from various organizations, including:
• AIA: Contract C102-2015
• EJCDC: Contracts D-580 and E-580
• DBIA: Contract No. 580
• Consensus Docs: Contracts 296 and 498
You can purchase these and other CASE Publications at CASE Resources.
If you have suggestions for tools that could benefit your business, CASE welcomes your input. Contact coalitions@acec.org.
Engineers and their clients are well-served by having a conversation up front about "what is good enough."
By John Dal Pino
My mother passed away in late April. Since then, my sister Jean and I have spent the last few months preparing mom’s 1960s wood framed ranch house for sale. We grew up there, and “going to Fremont” was part of our family routine around the holidays. But the shortage of housing in Silicon Valley has created a hot market for home sales, despite the higher interest rates than many would like, so it is time to move on. If you have ever undertaken such an endeavor, you will know that painting is a major part of the work. And if you have ever painted beyond simply changing the color in a bedroom, you will know that preparation for painting is 90% or more of the work. The painting part is just the reward for the prep work. Kind of like eating the cake after making it.
During the preparation work, you will ask yourself often, as I did, “is this good enough?” Since painting prep gives you plenty of time to think, I started making correlations to my engineering work. When designing a new structure or evaluating an existing one, when is the effort I am employing “good enough?” An almost endless list of issues could be addressed in different ways, if you really think about it. Do I address each one, or focus on just a subset? How many options should I consider? How many assumptions can I safely make? Every engineer has his or her
own standard and individual answer to the “good enough” question.
Before I get to the quality question, I want to make a pitch for the importance of a fair and comprehensive signed contract. If you haven’t gotten to the point in your career when you write and negotiate contracts, trust me on this. It is really important. If you have, you already know. Contracts are basically the vehicle where the parties resolve as many potential misunderstandings and disputes as possible before they actually occur. You can read articles on contracts elsewhere, like those prepared by CASE, but a good contract includes:
• Description of the project (size in square feet, general characteristics of the structural engineering design and estimated construction cost)
• Project goals and design criteria
• Scope of work by phase (list of what you are going to do)
• Statement regarding knowns and unknowns
• Proposed team members
• Fee
• Deliverables and schedule
• Payment timing
• Terms and Conditions, including a Limitation of Liability clause. But what is missing? A statement on quality!
This brings me back to my painting story. What is “good enough?” How much quality should I provide? Quality, in painting, can be roughly defined as appearance and longevity. It is difficult to specify both exactly. If you have ever painted anything, you will remember asking yourself about quality many times, with increasing frequency, the longer the project takes. Making a statement on quality in structural engineering is equally hard.
Issues that will come up in painting (and corollaries in structural engineering for say evaluating and renovating an existing concrete structure) are:
• How much sanding and scraping do I need to do? If the surface condition isn’t too bad, do I need to sand to bare wood or is leaving the “stuck on” paint okay? SE Corollary: How much selective demolition is required to really understand the existing conditions? How accurately do the drawings need to depict the existing conditions?
• If I leave the “stuck on” paint, should I take the additional step of applying Bondo or plastic wood to transition the rough edges and then sand to create a more uniformly smooth surface, or just hope no one looks too closely? SE Corollary: How do I define the acceptable appearance of the final structure, particularly where new and existing concrete meet and the structure is exposed?
• If I find deteriorated wood, which is likely or perhaps almost certain, do I remove it and replace the entire piece or just the worst part, and then fill with Bondo? Or can I save some time by hiding it with caulk and paint? SE Corollary: How much concrete requires removal when the compressive strengths vary? Can I leave some under-strength concrete or should large portions be removed and re-cast?
• If the work is in a difficult location to access (like a high or low corner, or eave), should I employ the same standards as elsewhere or hope the paint will cover it up? SE Corollary: In areas where the existing conditions don’t impact the overall structural performance or will be hidden from view, can I just leave it as-is?
• What brand of paint should I purchase? Even within a particular brand, which quality of paint should I pick? SE Corollary: Should I do my work like I have always done, or be smarter and tailor my work to the anticipated abilities of the likely subcontractors?
• Should I tape off the trim to shield it or can I get away with using my steady hand and eye? Careful taping can take a lot of time. Do I religiously move the drop cloth in every room, or do I “try to be careful” and then wipe up spills and splatters? SE Corollary: Do I design and detail for variabilities in the existing construction, or can I assume that the contractor will take care of it by making it work?
• How many coats of paint do I need to apply? One coat is rarely enough despite the manufacturer’s statements but is two enough? Do I really need to spend the extra time to apply three coats for high traffic areas, like doors, cabinets, etc.? SE Corollary: Should I design, detail, and draft every condition, or rely heavily on typical details, and liberally use the term “similar”? Have I anticipated all of the potential bar conflicts and layering issues?
• When I am “finished” should I go back and repaint areas that look like they needed more paint in the first place? SE Corollary: How much personal back-checking and independent review is necessary?
Back to structural engineering. Unfortunately, most contracts just state that the standard is compliance with the building code. But what does that say about “quality”? Actually nothing, to be frank. Or at best very little, unless you assume that special inspections and structural observations do more than just confirm that the construction matches the design intent of the drawings.
During the design process, quality is infused into the work by the engineer when making design decisions regarding system selection, material selection, connection style, etc. Five engineers could design the same building and come up with five entirely different designs. An expert could rank them based on quality and find that some would perform better than others, despite all of them satisfying the requirements of the building code and the local standard of care.
Most clients will be hard pressed to know the differences amongst the five or likely know what approach the engineer should take when faced with all of the choices to be made amongst alternatives during the design process. But later if a dispute arose, don't be surprised if the client states firmly that the engineer’s effort fell well short of what was expected and clearly established by “industry standard,” whatever that actually is.
My point is that in engineering work, like painting, you will face the same question: What quality should I provide?
I started off my painting project intending to do a “good job”, the kind of effort I would employ on my own house. Not a slap dash cover-up that I suspect many home sellers do to freshen up a property for sale “as-is.” But I soon realized that my personal “good job” standard was really the way that I have always painted. A painting expert would have to opine on whether I painted like others would under similar circumstances (the standard of care), or whether there was room for improvement with more time and effort, or different techniques. Engineers do this naturally too, performing the work like they have always done. Every engineer will have his or her own standard and employ different amounts of effort. That standard will be influenced by who they worked with in their developmental years. It should come as no surprise that every engineering firm has a different philosophy on exactness and thoroughness. But ultimately engineering approach translates to fee. And fee implies a certain engineering effort that eventually translates to construction cost, and the number of RFIs and change orders. And at the end to either a happy or an unhappy client.
I am advocating for a conversation with the client about the engineering quality to be employed. Many engineers will find this an uncomfortable conversation, but I will state that any avoidance of communication plays directly into the hands of the client and to the detriment of the engineer. The engineer can be silent on the issue and just do what he or she has always done (personal standard) but the engineer might find oneself losing out on the project because their personal standard is too high. Or being awarded the project and then finding oneself on the losing end of the bargain when a dispute arises, or when the effort normally employed doesn’t measure up to what the client was expecting.
Better to have to this discussion up front, than being silent. Otherwise, you won’t be happy with your painting job. ■
John A. Dal Pino is a Principal with Claremont Engineers, Inc. in Oakland, California. He serves as the Chair of the STRUCTURE Editorial Board (jdalpino@claremontengineers.com).
Engineers are equipped to apply their skills and influence to improve the global economy in terms of being socially equitable and environmentally sustainable. By
Ashvin A. Shah, P.E.
Professor Jerome Hajjar writes in his informative editorial in March 2024 STRUCTURE magazine, Leading the Way in Sustainability and Resilience in Structural Engineering: “It is my hope that sustainability and resilience become premier design objectives within our profession” and that it "will require an evolving mindset within the profession and the public.” He calls on each structural engineer to "take steps to accelerate this transformation through continuing to learn about and adopt structural systems and practices that are more sustainable and resilient and advocating for these designs within the profession and to the public.”
Prof. Hajjar’s commendable call to structural engineers to lead the way in sustainability and resilience in structural engineering, I believe, should extend to all engineers to lead the way in social equity and environmental sustainability in the global economy.
Our current design objectives Prof. Hajjar mentions are “safety, serviceability, constructability, aesthetics, and economy.” These objectives, with the exception of perhaps aesthetics, are in various codes and standards developed by engineers working with owners, architects, academia, industry, and regulatory officials. In the U.S., the codes and standards are arrived at by a consensus process that has evolved over a century of American experience of regulating buildings and other structures.
As I wrote in an April 2015 article in STRUCTURE magazine, "The engineering (and architecture) profession has a compelling story to tell about how we have successfully avoided going to the federal government to regulate safety in buildings. There is no giant Department of Buildings in Washington, DC, or even in most state capitals. Buildings, even big buildings, are generally regulated at the local level, by small departments in each town or city who enforce a uniform building code developed within an open and democratic consensus process. This system evolved strictly in the American domestic politics arena, untouched by the events that tended to centralize power at the national level. This is a success story worth touting for the benefit of other professions.”
The Hajjar editorial is an excellent starting point for not merely structural engineers in the U.S., but all engineers in our global engineering profession, to work together in a similar global consensus process to define and implement in the global economy the twin premier design objectives of social equity and environmental sustainability.
The 2015 Paris Climate Agreement (PCA) was signed with much fanfare on Earth Day in 2016 by over 200 nations. The PCA was brokered by global scientists working in a consensus process at the UN’s Intergovernmental Panel on Climate Change (IPCC). The UN IPCC consensus process for approval of IPCC’s documents is very rigorous—it’s almost a line-by-line consensus approval by all national representatives at the UN.
However, during the past eight years the calls from IPCC for global action on adaptation and mitigation has not resulted in a plan of action for reaching the PCA goal of net-zero greenhouse gas (GHG) emission by 2050. A deep-seated pessimism is evident in the concluding remarks of IPCC chair during the opening of the March 2024 Copenhagen climate ministerial meeting:
"To sum up, the scale and pace of climate change poses unprecedented challenges for humanity. But IPCC’s recent work has shown that we have the means and the tools to address these challenges, if we choose
to use them. And just to say, the newly elected scientific leadership of IPCC stands ready to play its part in supporting a move from problems to solutions, from analysis to action."
It is likely we missed the date of 2050 for net-zero GHG emission; it is now time for the next step from analysis to action—developing and implementing a plan of action—that’s the role of engineers.
The success of the IPCC consensus process to deal with highly scientific and technological issues in a global political setting has made the IPCC process a model to follow in other such issues at the UN. Similarly, to implement the PCA it is necessary for global engineers to create a global consensus process to develop and implement a plan of action for the global economy to become socially equitable and environmentally sustainable by a certain date. This global consensus process for engineers may be modeled along the lines of the consensus process engineers use to develop and implement the American building codes and standards for safety, serviceability, constructability, and economy.
The first step the engineering profession needs to take for the net-zero transformation of the global economy is to seek consensus of the civil society on the proper purpose of engineering within this long-established consensus process. In his editorial in January 2013 STRUCTURE magazine [The Proper Purpose of Engineering], Jon Schmidt explained "engineers ought to work toward the material well-being of all people, not just a privileged group.” The global economy today is not only in need of becoming net-zero carbon, but it also needs to become socially equitable to assure material well-being of all 8 billion people in the global economy. Social equity in the global economy is measured by equitable access for all humans to the following eight material benefits of the global economy: clean air, clean water, nutritious food, shelter, clean energy, health, education, and transportation. It is the role of engineers in the global economy to define and deliver the infrastructure for each material benefit.
In addition to climate change, scientists point out that for longterm habitability eight other critical biospheric boundaries should be accounted for: ocean acidification, depletion of stratospheric ozone, atmospheric aerosols, interference in nitrogen and phosphorous cycles, freshwater use, land use changes, biodiversity loss, and various forms of chemical pollution.
To achieve these additional premier design objectives, a new engineering framework is required. Further, these objectives should not only be led by scientists. To quote Henry Petroski “science is about knowing; engineering is about doing.” The lack of participation of engineers in leadership in the ongoing global initiatives on climate and economic development is a primary reason for lack of action. Engineers need to get involved to take steps in a global consensus process to accelerate the transformation of global economy to become socially equitable and environmentally sustainable. ■
Full references are included in the online version of the article at STRUCTUREmag.org
Ashvin A. Shah, PE, F.ASCE is a retired professional engineer in Scarsdale, New York. Prior to retirement he was on the technical staff of ASCE from 1990 to 1996 managing ASCE’s Codes and Standards program and then as a consultant from 1996 to 2000.
INTRODUCING THE MEP GUSSET PLATE. Available overnight through Clip Express.SM Now you’ve got the upper hand. When the trade’s field cuts and modifications compromise the integrity of your studs, the MEP Gusset Plate’s two-piece design quickly and easily restores it. Don’t waste another round patching up untested fixes from leftover scraps. For the full rundown, hit clarkdietrich.com.