
3 minute read
gas treatment in sulfur melting plants
Feature gas treatment in sulfur melting plants
By: Jan Hermans, Director, Sulphurnet
The majority of the sulfur present in the market is produced from refinery waste, where hydrogen sulfide (H2S) is converted to sulfur by the Claus process. The sulfur is degassed and then prilled, pelletised, and distributed all over the globe. This solid sulfur contains low concentrations of H2S and during transport water will accumulate (mainly depending on the method of storage).
When remelting solid sulfur, gaseous emissions are constantly being produced. From the evaporated water, H2S will partially release and a lesser known, invisible, and corrosive product called sulfur flour is formed.
Due to environmental regulations, the levels of H2S emission have to be minimized. This can be done by installing a conventional gas scrubbing system like a spray tower. In a spraying tower, H2S is removed from the gas by bringing it into contact with a solution of sodium hydroxide (NaOH) or hydrogen peroxide (H2O2). The H2S reacts with these chemicals and is neutralized.
However, the amount of sulfur flour formed during sulfur melting disturbs the scrubbing process. A conventional scrubber will work only 2-3 days and then an intensive cleaning process has to be performed.
The formation of sulfur flour is a complex process; it depends on various parameters such as the humidity of the vapor, gas volume, and gas-temperature, as well as the temperature of the liquid sulfur.
The vapor exiting the melting tank consists of an aerosol. The sulfur that nucleates on these particles can be either solid or liquid as mentioned in the research literature. The particle size distribution varies widely and can range from sub-micron to micron size particles.
Sulfurnet performed some practical tests in a sulfur plant that melted 20 m ton sulfur per hour. We measured the sulfur flour produced and then compared the experimental data with the results obtained from a semi-empirical model that was developed in house. The results found during testing came within a deviation as close as 10% of the established model.
Based on that outcome a new process was developed that combines the removal of sulfur flour with a H2S neutralization step.
In the initial step, the vapor from the sulfur melter is intensively mixed with a caustic solution. During this step, a large amount of sulfur flour is knocked out of the gas stream with the liquid solution. The second step consists of spraying the gas stream, now almost free of particles, with the NaOH solution to neutralize the H2S. This results in sodium bisulfide (NaHS) and water (H2O). The NaHS reacts further in the presence of the basic environment to form sodium sulphide (Na2S) as seen in reactions 1 and 2.
Reaction 1: H2S + NaOH NaHS + H2O Reaction 2: NaHS + NaOH Na2S + H2O
These reactions happen under basic conditions and may reverse when the pH get neutralized or slightly acidic. The water that contains the product of the reaction is thus brought to a treatment tank where sodium hypochlorite (NaOCl) is added to form sodium chloride (NaCl) and sodium sulfate (Na2SO4), as seen in reaction 3. The treated water is then sent to a water cleaning facility for further processing.
Reaction 3: Na2S + 4 NaOCl 4 NaCl + Na2SO4
The non-reacted sodium hydrogen solution is recycled in the system, preventing losses of the water solution.
Sulfur flour deposit in piping.
Fig. 1: gas treatment sulfur melting tank.
With this new process, Sulphurnet is in the position to analyze the quantity of sulfur flour formed in the process as well as provide a valid end-of-pipe-solution in the sulfur melting section.
For more information, visit www.sulphurnet.com. q
THE ACID PROOF BRICK

NOW AVAILABLE IN US-SIZES
Protection against extremes is what our bricks stand for more than 111 years – worldwide.
No breakage on pallets to be calculated - just order the amount you need for a direct, safe and binding delivery! What other challenges can we solve for you? Please reach out to us and we will find the right lining system for any kind of specification.
Directly from our warehouse in Houston, Texas - Just call us - We deliver!
STEULER-KCH GmbH
Phone: (713) 405-3545 | theacidproofbrick@steuler.com www.theacidproofbrick.com
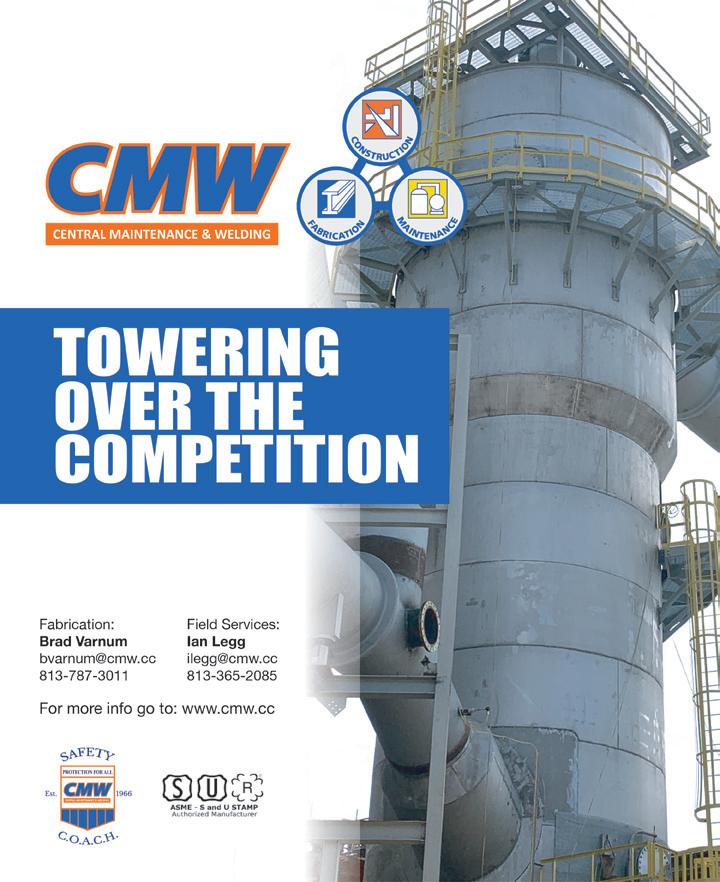