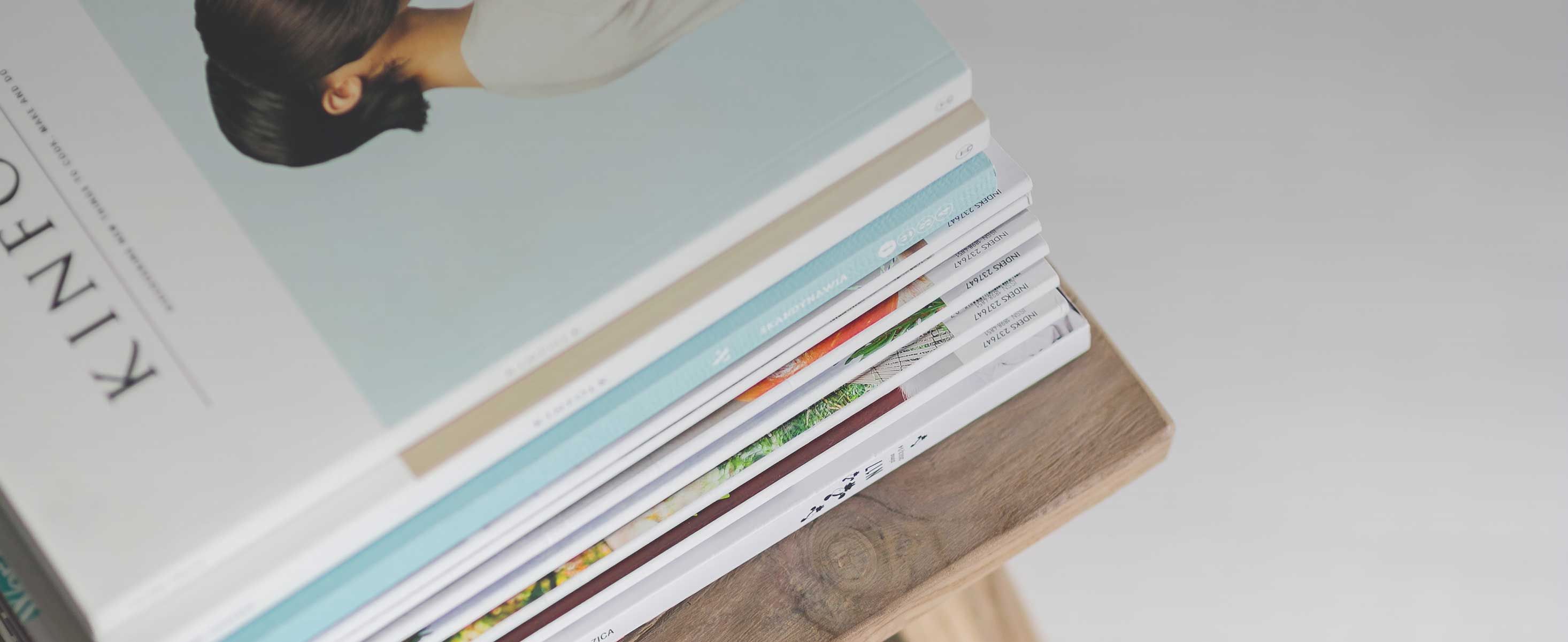
5 minute read
planning for outage ventilation
By: Patrick Ferguson, Technical Project Manager, VIP International Inc.
“Let’s get an air mover on it.” This is a phrase we have all heard time and again during outages. Process-related gases have always presented challenges to operators and maintenance teams alike. They can wreak havoc on outage schedules or worse, put workers and equipment at risk. Many factors contribute to the successful ventilation of a work area, particularly when working in confined spaces. The unique configurations of plant interiors can turn what seems like an easy solution into a complex undertaking. It is important that the proper steps are taken to ensure the safety of workers, keep equipment in operation, and minimize disruption to outage schedules.
When planning for outage ventilation, potential process gasses must be identified and communicated to affected work groups. Sulfur dioxide and sulfur trioxide are the obvious offenders in the process, but gases such as NOx may be present due to operating conditions or byproducts of sulfur, ore, spent sulfuric acid, or weak sulfuric acid. Gases that could be introduced to the space should be analyzed as well. When hot work is performed within a confined space, toxic gases from fluxes or rod coatings can affect the air quality. Hexavalent chromium can also become a hazard depending on the hot work being performed. Recently, industry emphasis has been put on hydrogen gas formation and its risks throughout the shutdown and outage. Knowing the characteristics of these gases will assist in the creation of a ventilation plan and the implementation of respiratory protection for potentially affected workers.
Properly ventilating a work area requires a detailed assessment with calculations. Some confined spaces present challenges due to their size, shape, and internal configuration. Initially, the volume of the space needs to be calculated. Prints or drawings of vessels can provide a basis to get some initial measurements, but they need to be verified. Although the size of the space does not dictate the types of ventilation needed, it is necessary to calculate the air changes per hour (ACH). ACH is how many times per hour the air is completely replaced in the confined space. ACH numbers vary based on national, state, and local requirements. If the ACH is not a requirement, it should still be established based on the severity of toxics present. Once the volume and ACH are determined, they can be multiplied then divided by 60 minutes to calculate the velocity needed to replace the air.
Ventilation plans are not necessarily interchangeable when moving from one vessel to another. Oddly shaped or configured spaces may require additional airflow capacity or duct work to get the proper exchange rate. A standard vertical vessel without internals can be ventilated easily using the decontamination method where air is pushed in through the bottom and out of the top. If a top entry is required to perform work, the tunneling method can be used where a blower is installed on a bottom manway and ambient air is naturally brought in through a top manway. Horizontal vessels such as certain pump tank designs are more likely to require the use of ducting for proper air flow. The internals of towers, exchangers, economizers, and converters will greatly influence the air flow needed for ACH numbers. If additional manways are open to atmosphere, a short circuit can occur and reduce air flow. The angles of ducts must also be considered as multiple bends can lower effective blower capacities. Additional blowers can be used in unison to provide the increased capacity if needed. An important point to remember is that any equipment used at the manway should not impede access to and egress from the confined space in the event a rescue is required.
Tailoring equipment needs for the duration of an outage is essential to preventing delays. Establishing a plot plan of power sources and blowers needed will increase efficiency and ensure that no tasks are overlooked. If an electrical source is unavailable, the use of portable generators may be necessary as long as they are positioned where engine exhaust cannot affect the work area. Pneumatic blowers are also an option when power sources are limited. Electrically powered AC units are an effective way to keep temperatures low in the confined space while still providing the proper air flow. However, if the entry point is elevated or space is limited, portable fans may be more practical. Radial fans are compact and can move more air in a circular motion before pushing it outward. Ducts should match the blower application and should be limited in length so as not to reduce the required air flow.
There are additional considerations that can assist in the proper ventilation of process vessels during outages. Allowing operations enough time to properly blow through the system during cooldown can greatly reduce or eliminate the presence of sulfur dioxide and sulfur trioxide gases. Assessing high points and ensuring that any engineered relief valves are in the open position can prevent hydrogen gas pockets from forming due to weak acid or iron oxide formation. Quickly removing sulfates can reduce the presence of NOx under certain conditions. Isolation and blinding procedures can also contribute if there is a known contamination source that can be separated from the work area.
Even with the preparation and execution of a ventilation plan, confined space air monitoring and proper respiratory protection must be assessed and implemented. Air monitoring is a requirement that confirms the ventilation plan is working. If ventilation equipment or power fails during confined space entry, air monitoring can provide a warning to the affected workers to exit the confined space safely. Potential toxics and their concentrations will dictate respiratory protection requirements. Workers must be trained on the potential effects of gases, certified to don the required respirator, and understand the procedures to follow should levels become elevated. Ultimately, respiratory protection is a redundancy needed to protect workers from the unknowns of gas formation.
Ventilation remains a vital component to the safety of outage work. Developing and implementing ventilation plans will reduce or eliminate risks associated with process gases. Arranging for reliable equipment and power sources ensures that work can continue safely and uninterrupted. Air monitoring confirms that ventilation plans are successful and alerts workers of any changes to the atmospheres within confined spaces. While these steps are not as simple as “getting an air mover on it,” they serve as a fundamental reminder that we must follow through on our responsibility to protect workers.
For more information, please visit www.vipinc.com. q