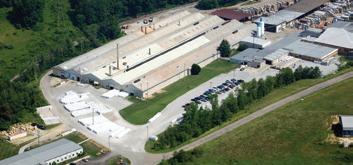
4 minute read
Remote controlled robots clean tanks safely and efficiently
Feature remote controlled robots clean tanks safely and efficiently
For decades, traditional industrial tank cleaning methods often included 100% confined space entry that was unsafe, very inefficient, and often had unpredictable results. Even within the past five years, tank cleaning in the Gulf Coast region would have involved personnel in orange jump suits and helmets with lights and bulky PPE waiting for the atmosphere of the tank to be tested and approved prior to entry. However, with new robotic technology, that approach has changed allowing the oil and gas industry to reduce, or, in most cases, completely eliminate human entry while providing superior cleaning in less time at lower cost.
Driven to improve safety, quality, and efficiency, Ecorobotics developed a Robotic Cleaning System (RCS). The system was designed, engineered, and built in-house after 10 years of research and development. Ecorobotics RCS systems can safely and remotely remove hazardous and non-hazardous materials from industrial containment such as above ground storage tanks, piping, sumps, ponds, and culvert/ditches. The RCS requires fewer people on site and virtually eliminates the need for confined space entry or additional equipment for the bulk removal process.
The Ecorobotics RCS maneuvers by using a hydraulically driven track system and can be equipped with either a vacuum attachment or an articulating robotic arm that can spray high pressure water or other cleaning fluids as dictated by the project. The crawler employs an all-hydraulic system for operation, allowing for the cleaning process to proceed in an elevated LEL environment.
Recently, Ecorobotics performed a project for a fertilizer producer located in the Southeast United States. The project scope was to remove phosphoric acid sludge safely and efficiently. Initially, a manway cannon robot, also known as the Viper Cannon, was affixed to the tank manway flange on the roof so that the walls of the tank could be washed without confined space entry. This technology utilized a remotely-operated high-pressure directed flow for cleaning. This portion of the project took approximately 3 days. Next, an H Series robotic crawler with an articulating arm attachment was inserted through the ground level manway to clean and remove the majority of the extremely hard phosphoric acid solids and liquids from the tank. A 20,000 psi pump and nozzle were used to break up the material. The bulk removal process took approximately 41 days. At the request of the client, on the last shift of the project, confined space entry was made to perform a final rinse. The entire project was concluded in only 44 days with a total of 3,813 bbl (26 bbl/ hr) of material removed.
For more information, contact Will Putman at wputman@ecorobotics.com, Tim Kelly at tkelly@ecorobotics.com, or visit www.ecorobotics.com. q

Robot crawlers fitted with vacuum or articulating arm sub for conventional labor inside closed spaces.
Now Manufacturing and Stocking Acid Resistant Brick Over 50,000 Acid Resistant Bricks IN STOCK!
At Koch Knight LLC, our goal is to provide engineered solutions by focusing on specific customer needs. By applying our extensive experience in the industry and on-going product development, Koch Knight has developed brick lining materials capable of providing reliable service in the most demanding corrosive applications. Whatever your corrosive application, Koch Knight has the acid-proof solution.
East Canton, Ohio (USA) - Baytown, Texas (USA) Santiago, Chile - Parramatta, Australia - Seoul, Korea - Istanbul, Turkey Visit us on the web: kochknight.com | Phone: +1 (330) 488-1651
Manually pushing material to vacuum (above) takes longer than vacuuming material directly.
OPTIMIZED SOLUTIONS FOR SULFURIC ACID PRODUCTION
DRAMATICALLY REDUCE PLUGGING
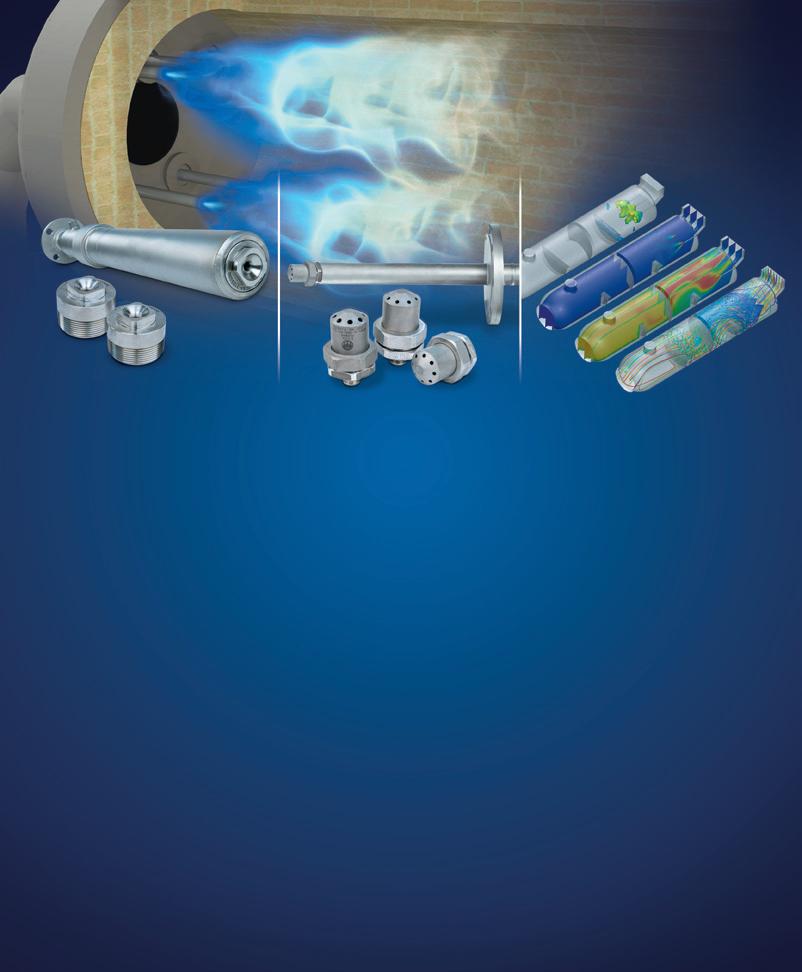
Maximize uptime in combustion furnaces by minimizing downtime caused by clogged sulfur guns. Our new CBA WhirlJet® sulfur gun is recessed into the steam jacket to ensure temperature uniformity even when sulfur flow is decreased or turned off and greatly reduces the risk of pluggage. Upgrade without disruption – the performance of the CBA guns is the same as our BA WhirlJet sulfur guns. Optimize performance based on the operating conditions in your furnace prior to purchase. Using Computational Fluid Dynamics, we can determine the ideal drop size and gun placement to eliminate post-installation problems like wall wetting, carryover and damage to downstream equipment.
MAXIMIZE EFFICIENCY, MINIMIZE CARRYOVER VALIDATE PERFORMANCE WITH MODELING
Spent acid producers are changing to high-efficiency air atomizing sulfur guns for better decomposition without carryover. Using less air than other guns, our FloMax® sulfur guns produce small, uniformly-sized droplets that evaporate quickly and maximize process efficiency.
For unmatched service and support, visit spray.com or call 1.800.95.SPRAY
