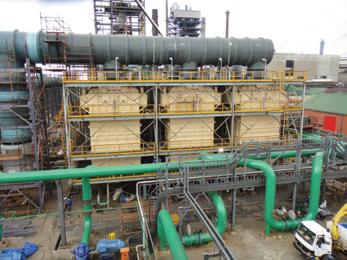
3 minute read
Wet electrostatic precipitators for superior sulfuric acid gas and mist cleaning
Feature Wet electrostatic precipitators for superior sulfuric acid gas and mist cleaning
By: Gary Siegel, Marketing Director, Beltran Technologies Inc.
A sulfuric acid plant that is downstream from any one of a number of operations, such as metallurigical smelters and refineries, petrochemical operations, natural gas processing facilities, spent acid regenerating plants, electric generating units, municipal waste incinerators, and ore mining is not only practicable but also highly profitable.
This versatile mineral acid is both the world’s most widely used chemical, and the one with the highest production volume. Its use as both a primary and intermediate raw material spans hundreds of industrial processes, especially agricultural fertilizer manufacturing, which consumes 70 percent of H2SO4 production. This application alone may continue to fuel a vigorous global trade in this chemical. Sulfur provides both a direct nutritive value for plants, as well as an indirect value as a soil amendment. It also facilitates a plant’s use of the three other major nutrients: nitrogen, phosphorus, and potassium. Growth in the fertilizer industry, and consequently in the global sulfuric acid trade, is expected to be driven due to the need for more farm land for developing countries as their populations expand.
As global trade in sulfuric acid accelerates, acid plant operators will be under increasingly intense competition to supply the purest, highest quality product. At the same time, operators must remain price competitive by achieving maximum cost efficiency as they maintain these high levels of purity.
To remain competitive in price and quality, an efficient sulfuric acid manufacturing process requires the maximum possible removal from input gas streams of fine particulates, acid mists, condensable organic compounds, and other contaminants. This is necessary for protecting downstream components such as catalyst beds from corrosion, fouling, and plugging, as well as for preventing the formation of a “black” or contaminated acid endproduct. Proper gas cleaning also results in lower costs for maintenance, operations, and equipment replacement.
Wet electrostatic precipitators (WESPs) can vary greatly in design, materials, gas flow rates, durability, and collection efficiency. It is thus important for engineers to recognize the key differences among these various systems. Beltran Technologies’ advanced WESPs are designed around a multistage system of ionizing rods with star-shaped discharge points, enclosed within square or hexagonal tubes which are lined with grounded collection surfaces. The unique electrode geometry generates a corona field 4-5 times stronger than that of ordinary wet or dry ESPs. The multistage charging configuration also avoids corona quenching due to high particle densities, and assures maximum corona field strength with a minimum of energy load.
As flue gas travels through the tubular array, these intense corona fields induce a negative charge, propelling even submicron-size particulates and acid mists toward the collection surfaces, where they adhere as cleaned gas is passed through. The surfaces are cleansed of residues by recirculating water sprays. A heated purgeair stream should be used to keep the high-voltage insulators dry, reducing maintenance costs. Since fine particles have little significant mass, they generally pass through scrubbers and other devices, but are captured with remarkable efficiency by advanced Beltran WESP equipment.
The cool, saturated environment in the WESP is highly effective on condensable or oily compounds, which can elude conventional equipment. The continuous aqueous flushing process prevents re-entrainment of particles, sticky residue buildups, and particle resistivity. By eliminating the need for mechanical or acoustical rappers, the cleansing system also minimizes energy costs.
With very little pressure drop through the WESP, gas velocities can be extremely high, boosting efficiency. Plant engineers can use smaller-scale, less costly equipment and still achieve superior collection efficiencies. Other critical features to look for in WESP equipment are sophisticated electronic controls linked to a close-coupled gas flow management system. These components can squeeze even more efficiency out of the system by optimizing such operating parameters as gas velocity, saturation, temperature, corona intensity, etc.
Forward-thinking industrial plant operators around the world constantly seek out and deploy more advanced gas cleaning technologies throughout their enterprises, not only to stay ahead of the regulatory compliance curve, but also to achieve superior operating performance and to control maintenance and other costs in a competitive marketplace. In this context, the role of wet electrostatic precipitators should continue to grow as an essential primary or adjunct gas treatment option.
For more information, contact Beltran Technologies, Inc., at (718) 338-3311 or info@ beltrantechnologies.com;or visit the company website at www.beltrantechnologies.com. q
In Zambia, Mopani Copper Mines’ WeSp unit from Beltran Technologies. Doe Run’s peru operation equipped with Beltran’s WeSp.
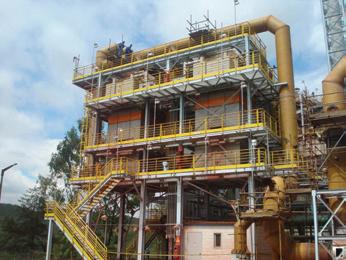