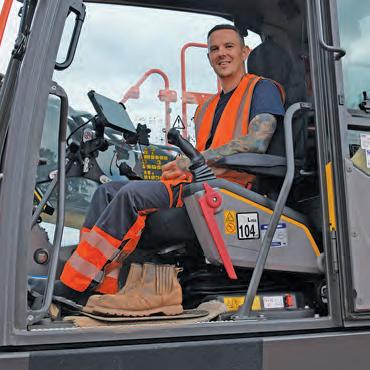
9 minute read
SITE VISIT
QUALITY COUNTS
Nick Drew visits an old-school fi rm that works with the latest high-tech kit, run by some of the south-west’s top operators
Advertisement
stablished in 1960, BT Jenkins is
Eone of the premier earthmoving contractors in the south west. At the beginning of 2017 the fi rm was acquired by Bristol-based CJL Construction. Run in the same professional manner as a wholly separate company, the business continues to go from strength to strength. In addition to its earthmoving contracts, Jenkins also runs inert landfi ll operations, as well as recycling and screening operations at three local waste stations.
BT Jenkins is run by operations manager Russell Lowton, who has been with the fi rm for 25 years, assisted by experienced contracts manager Simon Bray. The business has a long-standing and enviable reputation for directly employing some of the best plant operators in the south west.
The formula is simple enough: treat the operators well, including a good wage, a new van and the latest machines, and they will look after the fi rm. Jenkins is not a massive concern, running around 22
Right and inset: BT Jenkins’s latest excavator, a high-tech Stage 5 Volvo EC250E, has been entrusted to experienced operator Phil Nicholson
machines, but big enough to cope with a wide variety of projects, delivered by an extremely experienced team with a level of professionalism that is highly sought after.
Simon Bray said, “Because the company is not stupidly big, we fi nd it easier to keep control of the operator situation. Some big fi rms have a need to fi ll the seats and end up pulling in people who might not be up to the required standard, which as we all know can cause problems. In that respect, we are lucky. We source the very best operators, look after them well and they stay with us.”

25-TONNERS
Volvo is Jenkins’ long-term excavator supplier, and the fi rm – like countless others – traditionally runs 21/22-tonne excavators. Having tried out the larger EC250E model, Jenkins took the view that it was a relatively small price difference between the two, considering the improvement in lifting and digging performance the EC250E could offer, which would weigh at least 26 tonnes.
Associated with this change, instead of being matched to 25t capacity ADTs, they now run larger Volvo A30G haulers. Running higher capacity load and haul machines will bring the business productivity benefi ts. The same can be said for Jenkins’ latest Cat D6s, which are far more of a dozer than their processors. Regarding preference for Volvo machinery over the years, Simon continued, “In the fi rst instance we have a great relationship with our regional sales manager Richard Shelbourne. In addition to that the back-up we get from Volvo after the sale is fantastic. Dan Thirtle the head engineer for the south west is a great guy, nothing is too much bother.
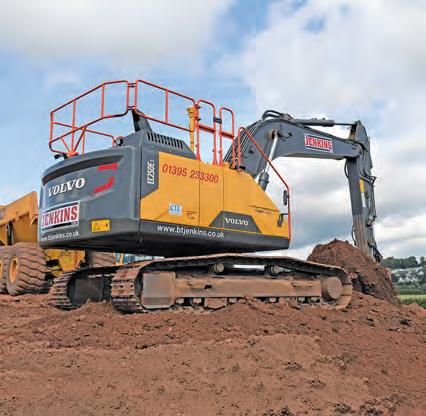
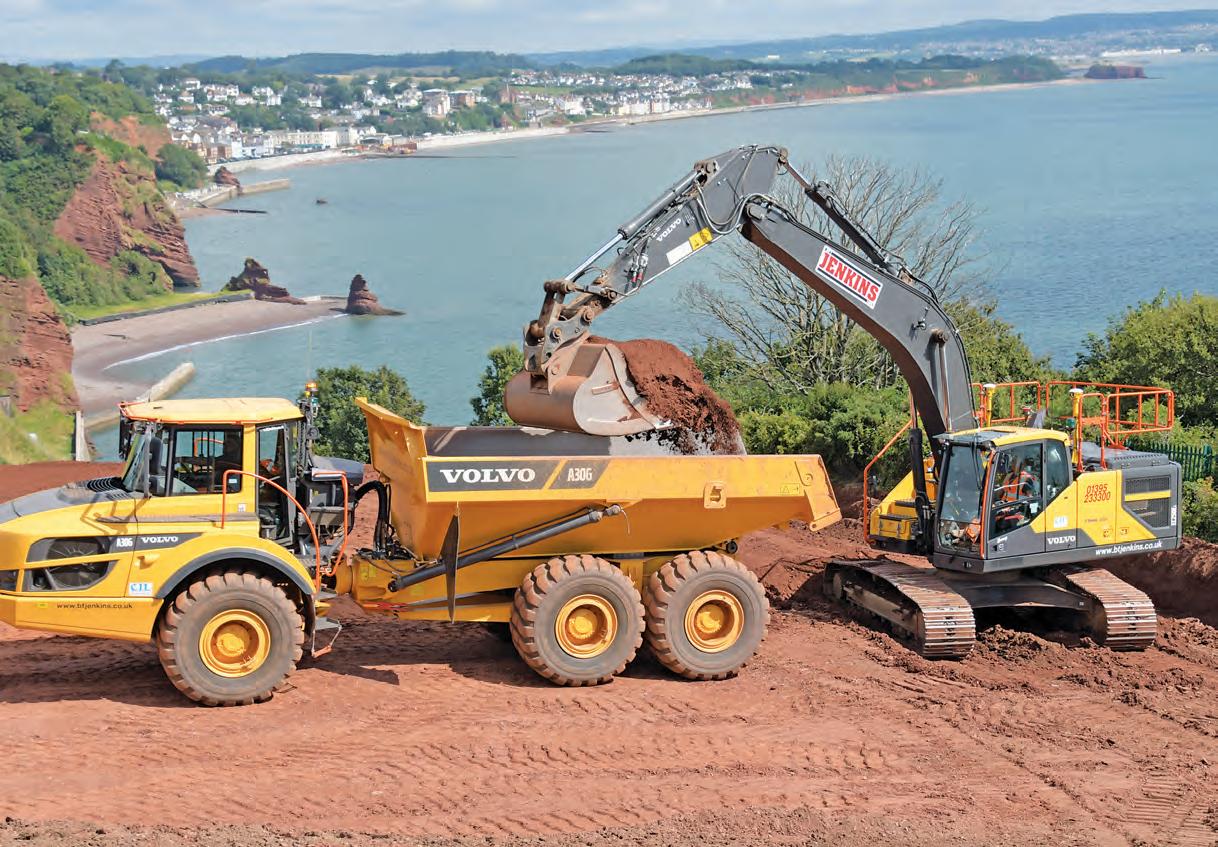
“That is the key really. Good back-up is crucial in our game and that’s another reason we stick with Volvo and dealer SMT GB, which has really come on leaps and bounds in this region over the past 10 years or so. It’s not hard to see why, as it’s just a very good product. The new EC250s are brilliant machines and the drivers love them. They look the part and the cab comfort is second to none by anyone’s standards. As we see it, a happy operator is a productive operator. These lads spend half their lives in the cab, so it pays to have the best.”
We encountered the latest ultra-low emissions Stage 5 version of the EC250E in a stunning location, on a hillside overlooking the Devon seaside town of Dawlish. Not a massive job by Jenkins standards, the team were brought in to construct an access road across agricultural land, then create two large compound areas to serve a £28m project to be undertaken by Morgan Sindall for Network Rail.
The earthmoving involved an initial topsoil strip, followed by a 5500 cube cut-and-fi ll operation. When this was complete, the team were to spread 6500 tonnes of 40mm stone, which would then be cement stabilised to form a strong concrete haul road and compound area. In a year’s time, following the rail works – a 200m-long extension to the rockfall shelter to the north of the Parsons Tunnel – the team will return to site to dig out the compounds and roads, then restore the land for agricultural use.
FEEDBACK
The new EC250E has been entrusted to experienced operator Phil Nicholson, who has been with the fi rm for around eight years. Earlier this year Phil, while operating an older version of the EC250E on the Jenkins’ fl eet, had a little bit too much of an experience. He made TV headlines after unearthing a seriously large WW2 bomb on a site in Exeter. It was destroyed by a so-called controlled explosion, which caused substantial damage to surrounding properties. A scary experience for any excavator operator for sure!
Jenkins adopts the old-school approach of allocating one operator to one machine, with an expectation that they will stay with that machine for the rest of its time on the fl eet. All the front-line kit, which is regularly upgraded, is maintained by main dealers under a service contract.
Modern Volvo excavator cabs have long been the stuff of legend, packed full of creature comforts while being ergonomic and spacious with low interior noise levels. This latest model continues that theme. It certainly looks a nice place to spend your days.

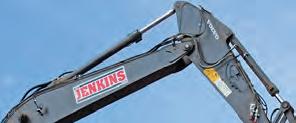
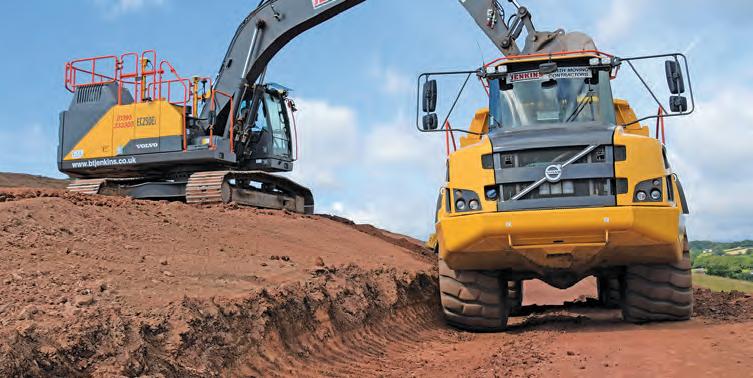
Weighing over 26 tonnes and matched to 30t capacity articulated dump trucks, the EC250E was getting through this task with barely a purr from its ultra-low emissions engine.

EC250E BASIC SPECS
Depending on its configuration, the latest version of the Volvo EC250E will tip the scales at between 26t and an impressive 31 tonnes. It is powered by a Stage 5 ultra-low emissions Volvo six-cylinder engine rated at 225hp (168kW). While providing 5% more power than its predecessor, more importantly this engine is mapped to provide incredibly high torque at a surprisingly low 1600rpm. The engine is physically and digitally linked to Volvo’s cutting-edge electro-hydraulic system. This includes a new auto work mode setting, which matches engine power to the demand on the hydraulic system. According to Volvo, this state-of-the-art excavator driveline offers a fuel economy improvement of up to 10% over its Stage 4 older sibling. When the two EC250Es are working together, the dynamic new design of the latest counterweight is noticeable. The new machine has also been supplied with the hi-viz access handrails and upper-structure fall from height protection. It was supplied Trimble Earthworks ready from the factory and sits on standard UK spec 700mm-wide track pads. At the business end, this example is fitted with a Miller Powerlatch fully automatic hydraulic quick coupler, and came with three Miller buckets that feature the Volvo tooth system.
However, Phil’s new Stage 5 EC250E is brimming with the latest technology, which includes the optional joystick steering system. The thumb rollers on the SVAB joysticks also used for proportional rotation and tilt control, make this excavator tilt-rotator ready – something that Phil is keen embrace. This example is also fi tted with Volvo’s optional multi-camera system, providing a bird’s-eye view around the excavator.
Volvo describes this working environment as the world’s fi rst all-electric excavator cab. In addition to fl y-by-wire joysticks, even the travel pedals are now electric. Phil can even digitally adjust the boom swing and travel functions of the working equipment to suit his operating style, or to match jobsite requirements.
He said, “This is my fi rst brand new machine in eight years and it’s quite simply a dream to drive. I love the fact that it is so stable and remains planted at all times, nothing seems to unsettle it. The electric levers are a dream, very responsive, but you do still get that all-important feel and feedback. Having tracking on the joysticks is a real bonus, I rarely use the tracking levers anymore.”
After a quick chat, Phil was back at work, excavating for the access road by cutting into the side of the fi eld, which would be fi nal trimmed by one of the dozers. The EC250E just purred away as Phil loaded A30G dump trucks in six passes at a slew speed of 11.7rpm. It’s a lively machine, with the power to match. The job looked so effortless, a credit to both the operator and the machine.
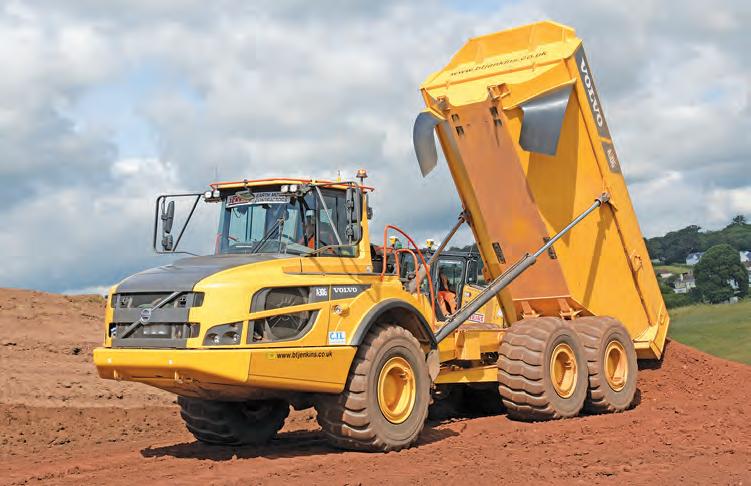
Left and far left: Only two ADTs were required on this part of the job, so the third driver operated the compaction roller.
CONCLUSION
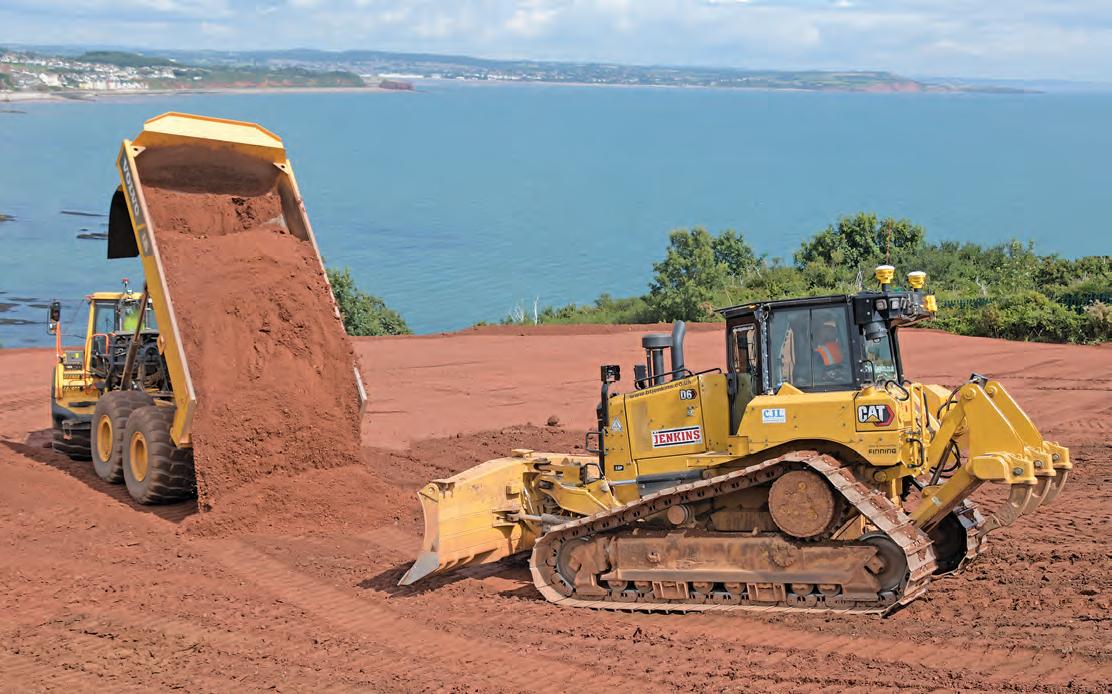
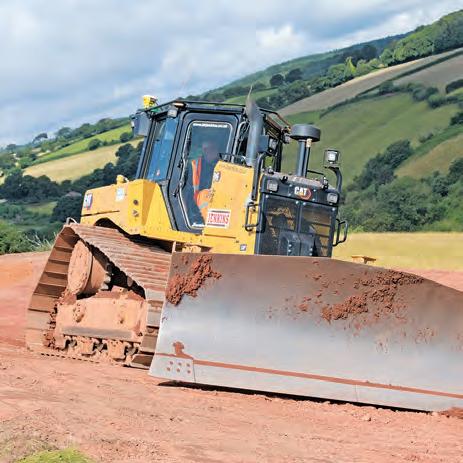
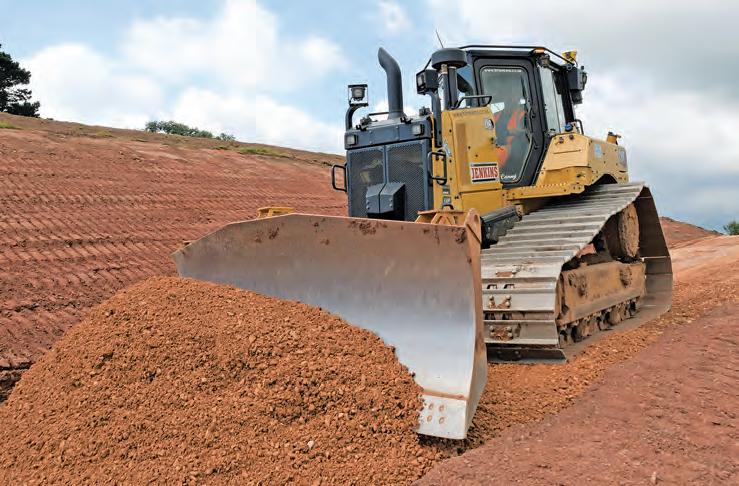
Elsewhere on site, an 18-month-old EC250E was being operated by Danny Austin. On the pair of nearly new Cat D6s were two south-west dozer legends, Mike Cann and Justin ‘Go Back’ Gliddon, who we last featured in the November 2020 edition of Earthmovers. Justin’s son Jamie is one of the A30G operators, alongside Scott Lowton and Dan Warren, who was temporarily operating the Volvo SD135B single-drum vibratory roller.
The main production machines on the fl eet, including the latest Volvo excavators and Cat dozers, are fully kitted-out to work with Trimble machine guidance systems. Boss Russell Lowton concluded, “Although we only run Cat and Volvo these days, we have always historically run a very mixed fl eet and never had an allegiance to one particular brand. With the dozers, a switch to Cat 10 years ago was mainly due to the System One undercarriage and strong residual values, which made future deals easier.
“With our excavators and ADTs, the drivers have more impact than anything. We feel if they fi nd the cab a comfortable place to be, then they are happy. And a happy operator is a profi t-making operator.
Above, below and inset: A pair of nearly new Cat D6s on site were being operated by two south-west dozer legends, Mike Cann and Justin Gliddon.
Both Cat and Volvo offer tracking systems and we use them both to the maximum. On top of this, the integrated Trimble 3D GPS systems and SIM card connection to the machines work very well for us, saving both time and money.
“In conclusion I would have to say a company is only as good as the team and that’s the ethos I work to always, as we are a team here at BT Jenkins.”
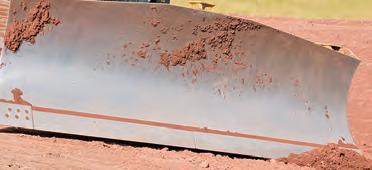