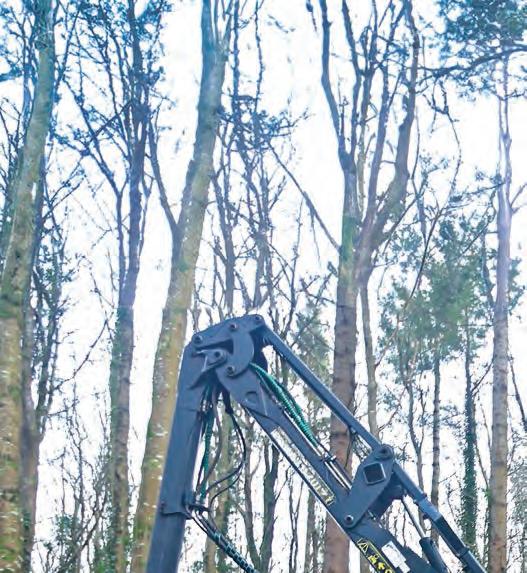
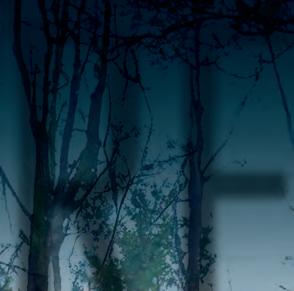
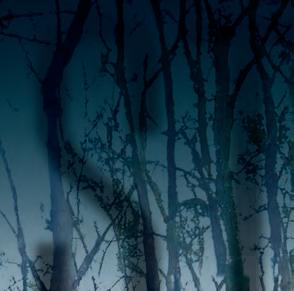

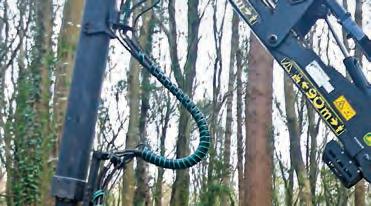
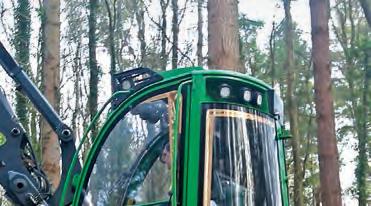

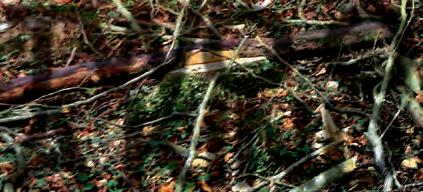
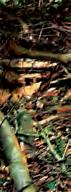
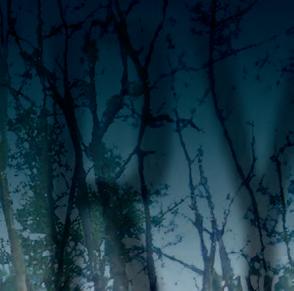

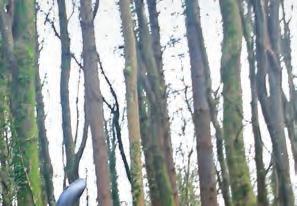
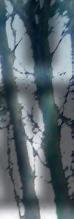



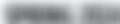

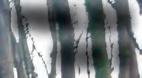
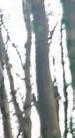

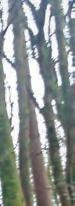
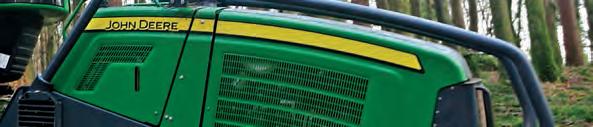
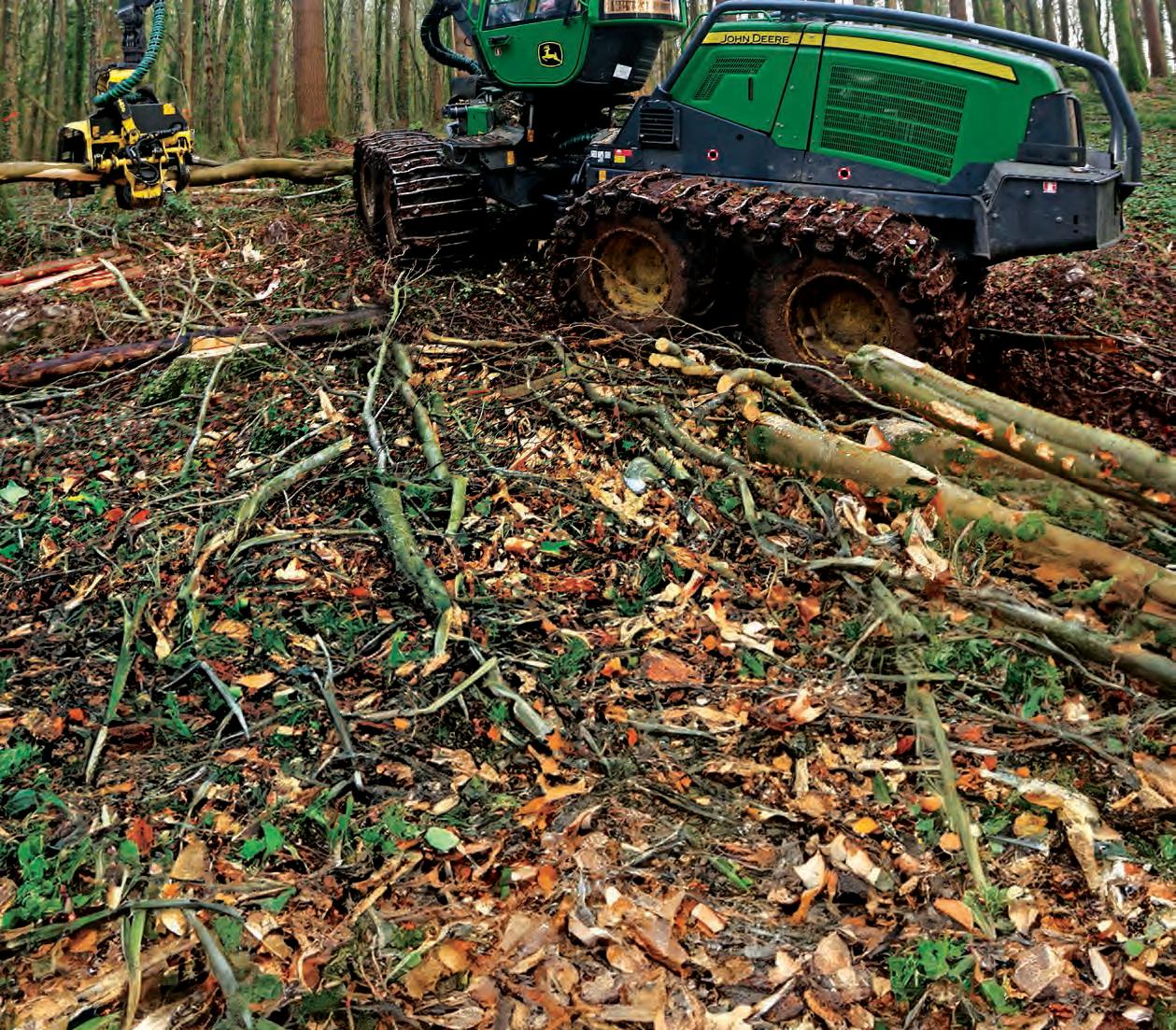
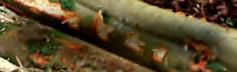





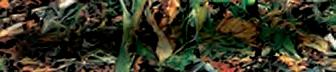
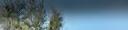
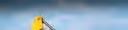

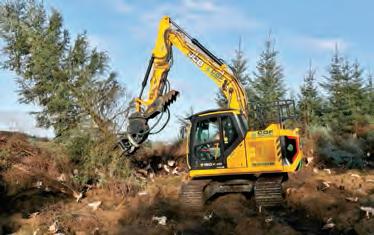
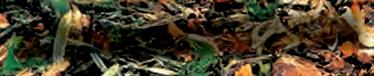


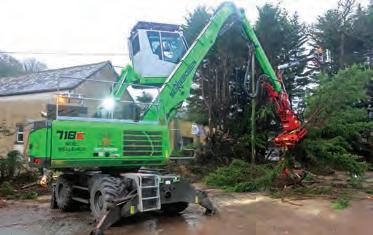
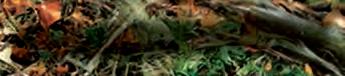

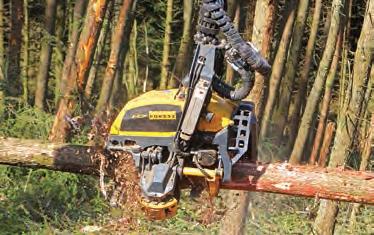
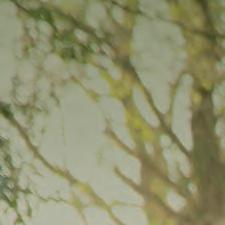

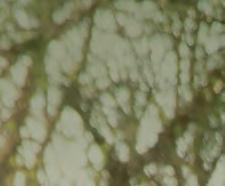
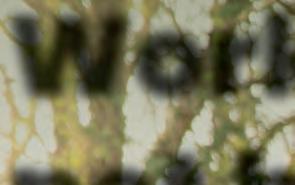
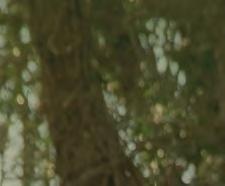
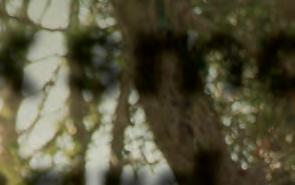
Learn more at avant.co.uk Avant 530
Discover unparalleled versatility and strength with Avant Loaders. From lifting heavy loads to maneuvering with precision, our machines excel in forestry tasks. Explore our diverse range of over 200 attachments and unleash the full potential of Avant on your business.
Optidrive™ drive circuit gives more power for the drive and hydraulic attachments.
Greater reach with Avant’s signature telescopic boom
EDITOR Jim Gerrard editor@forestrymachinerymagazine.co.uk
ART DIRECTOR David ‘Spike’ McCormack
DESIGNERS Sarah Mortimer, Claire Trent
ADVERTISEMENT SALES
Aaron Wilson 020 8639 4406
ADMINISTRATOR Martin Attis 020 8639 4409
PUBLISHING DIRECTOR Paul Cosgrove 020 8639 4401
CONTRIBUTING WRITERS AND PHOTOGRAPHERS
Eoghan Daly, David Wylie, Ken Topham and Gary Connelly
Forestry Machinery is published by Sundial Magazines Ltd, Sundial House, 17 Wickham Road, Beckenham, Kent, BR3 5JS
TEL 020 8639 4400 FAX 020 8639 4411
EMAIL info@forestrymachinerymagazine.co.uk
WEB www.forestrymachinerymagazine.co.uk
SUBSCRIPTIONS
Earthmovers subscriptions, Trinity House, Sculpins Lane, Wethersfield, Essex, CM7 4AY
TEL +44 (0)1371 853632
EMAIL earthmovers@escosubs.co.uk
Farm Machinery Journal subscriptions, Trinity House, Sculpins Lane, Wethersfield, Essex, CM7 4AY
TEL +44 (0)1371 853634
EMAIL farmmachineryjournal@escosubs.co.uk
NEWSTRADE
Seymour Distribution, 2 East Poultry Avenue London, EC1A 9PT TEL 020 7429 4000
REPRO
Design & Printing Solutions Ltd, The Coach House 101 Northwood Road, Whitstable, Kent CT5 2HE TEL 01227 770034
PRINTING
William Gibbons & Sons Ltd, 26 Planetary Road, Willenhall, West Midlands, WV13 3XB
COPYRIGHT
Sundial Magazines Ltd 2024. All rights reserved. Reproduction in whole or in part is forbidden without the express permission of the publishers.
Sundial Magazines Ltd. Registered in England no. 4134490.
CONDITIONS FOR ADVERTISING
All advertisements are accepted subject to the publisher’s standard conditions of insertion. For a copy of advertising terms & conditions, please write to Paul Cosgrove at Sundial Magazines Ltd, Sundial House, 17 Wickham Road, Beckenham, Kent, BR3 5JS
Whilst it seemed that the value of the forestry industry was beginning to become more appreciated by UK policymakers, two recent developments in Scotland have thrown this into question. Firstly, from April, ‘direct emission heating systems’, which includes wood burners, cannot now be installed in new homes or newly converted buildings, with the exception as an emergency heating system. Secondly, a report published in February by the Royal Society of Edinburgh encourages Scottish ministers to heavily reduce the public funding and tax breaks for commercial conifer plantations.
In the same way that agriculture is being treated, there seems to be a heavyhanded trend of ignoring the utter importance of UK tree, and food, production and what could be considered an exaggerated emphasise on environmental schemes and policies. No doubt this will lead to an even larger increase in imported timber, and food, whilst not considering the detrimental effect that this will have on the environment and take away much needed business from the UK. This is at a time when forestry machinery is being increasingly designed to minimise its impact on the woodland, and the wider environment, and huge efforts are being made to operate this machinery via clean energy and with the smallest possible environmental ‘footprint’.
In my new role as editor of Forestry Machinery I hope you nd an interesting selection of articles celebrating the good work of the forestry industry here in the UK and Ireland, showcasing forestry businesses at both the smaller and larger ends of the scale.
Jim Gerrard, Editor
Canadian machinery rm Tigercat have added a new harvesting head to their attachment range. The fth model in the harvesting head line-up, the Tigercat 573 has an 800mm (31 inch) maximum cut and is claimed to perform at its best in 400-600mm (16-24 inch) diameter timber. The feed rollers close down to 60mm (2.4 inches) so it can delimb and process smaller diameter trees.
The triangulated feed wheel arm con guration operates in a locked three-
wheel drive. This, combined with timed knife arms, provides a fast harvesting process. The top knife and lower/back knife, pivot on the same side of the chassis frame, thus aligning the position and ow of each stem centrally through the head. This set-up endorses contact with all three feed rollers and the measuring wheel at all times. The 573 can continuously rotate with help of effective hose routing and protection. Wi-Fi connectivity between the cab and attachment modules reduces wire routing
along the boom and should result in a quick and effective command response.
The new head did appear at a live demonstration in Washington State processing logs whilst attached to a Tigercat 875E Logger. It is shaping up to be a good candidate to aid roadside processing and harvesting of timber. The head ts to the H250D, 850 and 875E processors for roadside processing jobs and the H822E and H855E harvesters for harvesting standing timber.
A new model of harvester has been launched by Swedish forestry firm Vimek - the 470. Many of its technical features are similar to that of the Vimek 870 forwarder, but Vimek claim it is a new larger, stronger and more e cient model. Built for first thinning operations, the harvester is fitted with a Mowi P50 crane and a Keto 42 harvesting head with a maximum diameter cut of 420mm.
Vimek said, “Used in conjunction with the Vimek 870 forwarder, you get the benefit of minimum strip road area and a machine that allows operators the best opportunity to make active decisions about which trees should be harvested and which should be retained to grow further to enhance the timber quality and increase future yield.
“The 470 and 870 are bigger and stronger than their predecessors but gentler on the environment, and designed to work with thinning trees and cause minimal damage to the ground and remaining trees.”
As things continue to gear up for APF 2024, over the 19-21 September, the show announced its 200th exhibitor just before Forestry Machinery went to press. Serra Sawmills will be making their first appearance at the event who are based near Rimsting in south-east Germany and manufacture sawmill machinery and other forestry related equipment.
Exhibition secretary Ian Millward said, “We are delighted to welcome Serra Sawmills to the APF show for the first time. The 3800m of demonstration frontage is now 85% booked and more bookings are coming in every day. The show’s reputation for being the place to demonstrate your products and equipment and sell them into the forestry, woodland and arboriculture sectors is a major attraction to exhibitors given they will have a targeted audience of 23,000 visitors. We are well on course to match the 300 exhibitors we had at APF 2022.”
The show is taking place this year again at the Ragley Estate in Warwickshire, for information please visit www.apfexhibition.co.uk.
Edinburgh-based Field & Forest have been appointed as Yanmar Compact Equipment EMEA’s (Yanmar CE) agent for central Scotland. Field & Forest cover from the southern border area with England, up to Edinburgh, Glasgow and as far north as the Isle of Mull in the Inner Hebrides. This will allow Scottish customers access to Yanmar’s range of excavators, wheeled loaders, track carriers, etc, as well as their service support through the new partnership. In fact, four Yanmar excavators were sold in the first month following the agreement.
Nine Yanmar machines, including the new SV86 and SV100-7 compact machines, will be displayed on Field & Forest’s stand at the ScotPlant trade show over 26-27 April at the Royal Highland Centre, Edinburgh.
+44 (0) 2380 236 313 info.uk@nmtshipping.com www.nmtshipping.com
NMT Shipping UK Ltd 1st Floor, 5 Town Quay, Southampton, SO14 2AQ, United Kingdom
The NMT Group is proud to continue to serve the farming industry. Moving all wheeled and tracked cargo around the world in addition to static cargo. We can also arrange your shipment on a port to port basis, to getting the import clearance, to total door to door service.
Here at NMT Shipping, we help you to navigate the often rough waters of importing and exporting around the world. Contact us today for a quote:
This John Deere duo are the perfect harvester and forwarder combination for this Irish timber harvesting contractor, as Eoghan Daly found out during a visit to see the machines tackling some Beech and Douglas Fir
IMAGES EOGHAN DALY
Having clocked up 8000 hours, this six-year-old John Deere 1170G continues to work flawlessly.
The manner in which thinning operations are conducted has long-term impacts on the quality and viability of any forest, and so it is important to engage a contractor who has the right equipment and, most importantly, the expertise to carry out the job. One County Laois-based timber harvesting company has built up a successful business around this ethos and is regarded as one of the most pro cient contractors when it comes to forest thinning operations.
From his base at Abbeyleix, Seamus Bergin handles timber harvesting and extraction operations on both private and state-owned forests, and since establishing his own business he has concentrated almost exclusively on thinning. This decision was motivated by the immense potential for a dedicated thinning contractor to work with a high volume of privately owned plantations that were approaching the thinning stage.
Consequently, Seamus formed Seamus Bergin Timber Harvesting Ltd back in 2007 and has maintained a regular machine replacement policy to maintain consistent performance and reliability. The current eet consists of three units, a John Deere 1170G purpose-built harvester with extraction catered for by a John Deere 910G as well as an older generation John Deere 810E model.
Saeamus initially worked as a forwarder driver for 11 years for a number of leading Irish timber harvesting contractors, where he amassed a lot of practical experience before deciding to establish his own business. Seamus recalls, “Going out on my own was a big step because of the much higher level of responsibility and commitment needed, but looking back it is something I have never regretted. Between working for private forest owners, thinning for Robin Tottenham of Tottenham Timber and Coillte there has always been a steady stream of work. Keeping things at a manageable level without expanding too much has also been important. Running a tight operation carrying out quality work and maintaining the machines properly is key to what we do. I am lucky to have the same harvester operator, Pakie Cuddy, with me since I started out on my own with his loyalty and experience being a major help.”
When starting out, Seamus bought
a new John Deere 810D forwarder and a JD 1070D harvester. Although this was initially a substantial outlay, it was viewed as the only way to achieve consistent work rates and avoid the costly breakdowns of used equipment. A new six-wheeled JD 1170E replaced the older harvester in 2010, and a new 810E forwarder arrived in 2015. From there, Seamus upgraded to his current machinery line-up. The eight-wheeled JD 1170G harvester had a H414 harvesting head added in 2020. Extraction continued to be carried out by the JD 810D and 810E forwarders with the former making way for the latest John Deere 910G in 2023.
The various generations of the John Deere 810 have served Seamus well and have helped him create what the business is today. He says, “I always considered the 810 to be a brilliant machine. I’m still running the 810E and the 810D that I traded-in against the new 910G last year which had operated over 16,000 hours and was still capable of working perfectly. With the positive past record I have had with the 810, it sets a high long term standard for the latest 910G to live up to but I have every con dence in it as the machine has a very high standard of build quality.”
Forming the ideal thinning duo, the 910G forwarder, with its short load bunk, and its 1170G harvester counterpart have proven effective across a wide range of harvesting situations and varying ground conditions. With the eight-wheeled 1170G model in mind, Seamus considers it the most effective machine in its size category for many reasons as he explains, “There may be a number of choices of eight-wheeled harvesters from other manufacturers in the same size class as the 1170G, but I don’t think they could compare to it. The rst 1170G I ran was a six-wheeled machine and the current eight-wheeler is just a totally different machine. It would be dif cult to improve on this machine as it has everything going for it with good oatation, stability, oil ow, crane power and it is de nitely able to get the most from the H414 harvesting head. During drier weather it is possible to run the harvester without tracks and it is still good to climb.”
Having clocked up over 8000 hours, the current 1170G has been very reliable and still performs very well. The manoeuvrability of the 1170G is second to none based on its tight turning radius, whilst the mounting of the crane and slewing cabin on independent bases is viewed by Seamus as very effective design traits. He says, “The manoeuvrability of the 1170G is unbelievable and it has a really tight steering
lock which is excellent for thinning jobs. There are no blind spots when reversing out of a thinned rack since you just slew the cab to the side and have an equal view to the front and rear which would not be as easy if the cab and crane were on a common base like other manufacturers do.”
The 1170G has proved itself to be a capable performer at all stages of thinning work and continuous cover forestry harvesting. Whilst recently working on a thinning operation in a continuous cover stand at Castletown, near Nenagh, Co.
“WHEN STARTING OUT, SEAMUS BOUGHT A NEW JOHN DEERE 810D FORWARDER AND A JD 1070D HARVESTER”
A large volume of Douglas Fir was being harvested by the JD 1170G upon FM’s visit.
Tipperary, the 1170G demonstrated the capacity of its crane and harvesting head to handle larger stems. Containing a mixed stand of Douglas Fir and beech, the maturity of the stand meant that large stems needed to be harvested as part of this continuous cover thinning exercise. The H414 harvesting head has also proved its might and showed how it can be a capable all-round unit even when faced with working at the upper extremes of its working range. This is partly down to the stability of the base machine and its ability to utilise the full reach of the crane which extends to ten metres. Even when faced with harvesting the beech material in this plantation, the head coped particularly well. Despite when processing some of the larger trees with forked crowns proved somewhat time consuming, their sheer volume compensated for the extra effort, as operator Pakie Cuddy explained “Handling the larger Douglas Fir and beech in this continuous cover thinning might be at the upper end of the 1170G’s working range but it showed to be well up to the challenge. It is a harvester that can work equally well in rst
thinning or this kind of larger timber with the base machine able to get the maximum from the H414 head which has a good balance of power and speed.”
Looking at the JD 910G forwarder, which was going to be used for continual thinning work as its main duty, was speci ed with a short bunk and an 8.5 metre reach CF5 double extension crane. The machine features a xed cabin which is favoured in the interests of greater simplicity. However, the xed cab also meant a substantial amount of weight was saved when contrasted with a 910G that has a revolving and levelling cabin option. “Personally, I would nd a slewing cabin hard to justify. It has advantages in a harvester but when it comes to the forwarder, I prefer a xed cabin. There is far less to go wrong and the view to the crane and all around the machine is still good so I’m not losing out by going down
profile
in the head during processing.
the xed cab route. Another bene t is that it helps keep the machine’s weight low as the optional slewing and levelling cabin results in an increase of about 1.5 tonnes in weight. This all adds up when you’re trying to keep the machine as light and ground friendly as possible,” says Seamus.
One of the machine’s greatest attributes is how it evenly spreads its weight, thus minimising its ground impact, which is also down to the correct tyres being tted. Running on 710mm wide tyres, the machine’s overall width is still kept to a minimum which ensures positive stand penetrating ability without causing damage to remaining trees. Of even greater importance is the manoeuvrability of the machine through its short overall length and tight turning circle. Additional options have also made the machine well suited to this terrain.
“I PREFER A FIXED CABIN. THERE IS FAR LESS TO GO WRONG AND THE VIEW TO THE CRANE AND ALL AROUND THE MACHINE IS STILL GOOD”
Among these options are the selection of higher pro le 24.5 tyres over the 22.5 option. This has helped increase the machine’s ground clearance while the higher pro le tyre option results in much higher tractive force. This is quoted at 150kN when running on 24.5 pro le tyres over the 110kN of the lower pro le 22.5 variants. Also, the higher pro le tyres when encased in band tracks mean there is an increase in the level of ground contact.
“POWERED BY A JOHN DEERE 4045 FOURCYLINDER ENGINE, THE 910G IS RATED AT 118KW WHILST THE ENGINE YIELDS 650NM AT A MERE 1400-1600 RPM”
Powered by a John Deere 4045 four-cylinder engine, the 910G is rated at 118kW whilst the engine yields 650Nm at a mere 1400-1600 rpm, which is a key contributor to its operating ef ciency. Comparing this higher powered and larger machine to the previous 810E model looking at fuel consumption, Seamus has observed the latest machine as consuming a similar amount of fuel despite it being a more powerful forwarder in relation to its size.
After being in service just over a year, the 910G has clocked up 1600 hours while working on a single shift with Seamus operating the machine on a full-time basis. It is an upgrade which he believes as being particularly successful and has contributed greatly to bringing the extraction interests of his operation into the modern age. This has been helped by the machine’s userfriendly systems such as IBC (Independent Boom Control) while the sophistication of the machine is furthered by the incorporation of the Timber Maps system. Seamus sees the IBC system as being particularly bene cial, “Even though the harvester has been using the John Deere IBC system with proven results, the 910G is the rst forwarder I have used with the IBC system. Anything that makes the job of operating the machine more user friendly is always welcome which can make a difference at the end of the working day. IBC works very well, and the crane is still fast, smooth and precise.”
The John Deere forwarder control system works well for setting up forestry jobs and John Deere’s TimberMatic Maps software is an important feature for the harvester operator as it clearly shows the boundaries of the block being thinned. At the same time, a record of the volume and locations of each log classi cation is subsequently presented to the forwarder operator which helps greatly in planning the approach to the extraction process and sourcing speci c log grades, should they be required as a priority.
Classic are lumber trailers made to give you as a user the best overall economy, and to create a sustainable overall solution – year after year.
T6 / T7 / T8 / T9F / T10F
FARMA G2 are robust trailers in forwarder style. As a user you are met by an innovative design and technical development that goes one step further.
T10 G2 / T12 G2 / T14 G2
David Wylie travelled to Forth, central Scotland, to revisit Colin Forster, owner of CGF Services, to catch up on his growing fleet of forestry machines and attachments and to see his new fleet of JCB 150X HD Pro excavators
In the last couple of years,
from
Interior
The 150X HD model undercarriage is 210mm wider and 350mm longer compared to the LC derivative. The HD machine also has a 45mm higher ground clearance and increased tractive e ort, which is suited to rough and steep terrain applications. Colin’s machine is fitted with the wide 600mm track pads.
At the heart of the 150X HD is JCB’s ultra-low emissions, 4.4-litre, four-cylinder DieselMax engine, which has a common rail direct injection, turbocharger and intercooling technology to produce 109hp at 2200rpm. The engine drives two variable displacement axial piston type pumps, each of which produce 130 lit/min maximum flow at 345bar with the use of power boost.
An extra auxiliary hydraulic line has been added for their rotating Powerhand saw grapple attachment, and these JCB Pro models allow Colin and his operators to set hydraulic flow and save those settings using the large LCD screen in the cab. The JCB hydraulic pump software had just been updated, resulting in flow being even more precisely set for di erent attachments. The travel motors can propel the machine at 4.3 km/h (high) or 2.5 km/h (low) speed, with a tractive e ort of 194.3kNm, which can be sustained on a grade of 70% (35 degrees) of continuous e ort.
“WITHIN SIX MONTHS OF BUYING THE FIRST 150X HD WE KNEW WE HAD MADE THE RIGHT DECISION AND PLACED AN ORDER WITH SCOT JCB FOR A SECOND MACHINE”
Colin Forster has been involved in the agricultural and forestry sector since the 1990s. He trained at Barony College in Dumfries and then held various positions in the machinery supply services sector, as well as main dealers, as his career progressed. In 2017, Colin decided he wanted to go self-employed again and started CGF Services, a division of Agri Accessories Ltd, which is a custom tractor parts and accessories business based in Canonbie, near Langholm, which he runs with his wife Kerry.
Colin and his skilled team of operators cover the whole of Scotland and are willing to travel anywhere in the UK. He started out with a pre-owned Volvo EC160 excavator and then traded that in for a new 2017 Doosan DX140 excavator and various attachments for forestry work. This included thumb attachments which were made by RGL Plant Engineering
based in Moffat. Early in 2020, Colin bought a used Iseki TA100 crawler tractor and operated it for six months for mounding work. Looking to run the most modern kit with the best service back-up, in 2021 Colin invested in a new Deutz-Fahr 5115K crawler tractor which offered a long track frame for extreme low-ground-pressure applications.
Since then, this one-man operation, plus subcontractors, has grown steadily and now employs six people, including Colin’s son who has recently joined the business after leaving school. Wishing to meet his growing customer demand, Colin has recently invested in two new 17-ton JCB 150X HD Pro models from Michael Robinson at Scot JCB’s Carlisle depot. Their Powerhand saw grapples are designed and supplied by Clark Engineering and Colin is also working with Clark’s team to trial the very latest Mense RP hedge cutter attachment.
Whilst visiting Colin and one of his operators, Kieran McDairmant, on a wind farm project near Forth, Colin explained that he has a much bigger customer base now and has added a lot of different machines and attachments to his growing eet. For example, his Deutz-Fahr 5115K crawler tractor has been changed from standard 450mm to 700mm super wide track pads from Astrak UK Ltd based in Kirkcaldy. This is to cope with wetter conditions, jobs on peat terrain and to provide low ground disturbance as well as to meet tender speci cations for ground pressure. Colin said, “The service from Greg at Astrak has been outstanding and the new wider track pads and track chains have really transformed this crawler into a very good low-ground-pressure machine to tackle a wider range of applications.”
When not using the crawler for mounding work, and for improved machine utilization both in the summer and winter, Colin has added a sprayer unit with a 12-metre-wide boom to the crawler to cover large areas and has used it recently to spray-off some heather. He also has a large rear mounted mower attached for tackling long grass during site preparation work. Colin is pleased to report that the reliability
At the heart of the 150X HD is JCB’s 4.4 litre DieselMax engine
access roads as well as hardstanding areas. He also hires in subcontractors to help with this workload.
As his business had steadily grown over the last three years, Colin wanted a UK-built excavator with good service support as his business activities now extended further a eld into Wales and England. Colin
“COLIN HAS WORKED ALONGSIDE RGL FORESTRY LTD FOR MANY YEARS DESIGNING AND SUPPLYING FORESTRY RELATED ATTACHMENTS AND HAS TWO OF THEIR HYDRAULIC ACTUATED THUMBS FITTED TO BOTH JCB EXCAVATORS”
of the Deutz-Fahr 5115K crawler tractor has been very good overall, as is the service backup from his local dealer DW Toppin Ltd, based in Cumbria.
Also in Colin’s eet, for less demanding terrain, is a Valtra tractor which can be tted with double wheels for extra traction/ otation on soft ground when mounding. It also works with a tipping trailer as Colin and his team build all sorts of forestry and farm
explained that when the JCB 150X HD (heavy duty) was launched a few years ago, he and Kieran McDairmant took the opportunity to visit Scot JCB and look over the machine. They were both immediately impressed with the cab design, build quality and the overall appearance.
Colin said, “Some say initial impressions are lasting impressions, and that was the case with the JCB 150X HD. As soon as we
sat in the extremely comfortable cab, red up the fuel-ef cient engine, and felt the smooth hydraulics, we were both immediately struck by the overall package. These new JCB X series machines are some of the best on the market.
“Once we considered all the possible options, we had a good conversation with Michael Robinson at Scot JCB’s Carlisle depot for a new JCB 150X HD Pro model. With its powerful twin hydraulic pumps to feed different power-hungry attachments, it tted the bill. Also, working with the JCB team to support us with a service agreement and nance package was a good experience. They take time to understand your business needs and you can tell they are keen to help you succeed and grow the relationship for additional machines in the future.
Colin continued, “Within six months of buying the rst 150X HD we knew we had made the right decision and placed an order with Scot JCB for a second machine. This was because the 150X HD has performed brilliantly, service support from Scot JCB has been excellent and we are enjoying lower operating costs. We also
Colin is delighted with the investment he has made in two Powerhand saw grapples for his new JCB 150X machines. He said, “The Powerhand saw grapple is a very good piece of kit as we have carried out a lot of work where damaged trees are hung-up, so it would be dangerous to put a hand cutter in there to deal with it. We have also found it ideal for tackling hardwood/broadleaf trees. It has got a tremendous amount of cutting power for de-limbering the tree and the powerful and robust Hardox steel grapple is able to cope with large branches once they have been sawn o .
“We currently run with a 40cm long bar in the Powerhand saw grapple, but this EX28-B model can cope quite easily with the bigger 60cm long cutting bar to section, fell and cut through the trunks of some bigger trees. It Is also a very well designed, strong grapple, and a well-balanced attachment for our JCB 150X HD machines.”
enjoy a very good warranty package built into the service agreement so that we have xed costs for the next four years.”
Colin has worked alongside RGL Forestry Ltd for many years designing and supplying forestry related attachments and has two of their hydraulic actuated thumbs tted to both JCB excavators. RGL Forestry also designed and tted a bespoke set of cab guards as the roof is curved to match the OEM pro le and the front screen guard is shaped to protect the large wiper mechanism and screen. As they use a powerful ail attachment, the front screen glass has been armored with Margard polycarbonate glazing, as part of the machine spec through Scot JCB. Also, an RGL hoist cylinder guard and underbelly plate of the carbody has been added to protect the hydraulic hoses in these areas. Other modi cations include the rewiring of the joystick controls by Scot JCB to suit the Powerhand harvesting head.
Colin explained they have also invested in a GPS datalogger from Risutec. It has proven to be invaluable, and he has placed an order for a second unit. This is for either mounding work, where at the press of a button on the joystick it records the number
This picture and inset below left: For tree clearance at this wind farm, Colin has hired in a JAK 300 excavator tree shear grapple with a twin ram system and features a fixed Hardox blade capable of cutting 30cm diameter trees.
The JAK 300 excavator tree shear grapple has a twin ram system with a fixed Hardox blade capable of cutting 30cm (12inch) diameter trees. As a result, a JAK 300 tree shear grapple is a fast, e cient and
and location of each mound which in turn calculates the mounding density, or for the job at the wind farm the number of trees felled and the area cleared. This data is then sent back to the of ce or the client via GPS in real-time to keep check of progress with the project.
Colin also explained that Jas P. Wilson of Dalbeattie have been the UK dealer for JAK shear grapples and other attachments for many years, mainly on a new sales and
cost-e ective tool for first thinnings, site management, embankment clearing and similar jobs. The grapple design makes it possible to cut a tree from its base very close to the ground. The replaceable blade can be quickly unbolted if needed for sharpening or replacement. It weighs in at between 550-590kg (depending on the exact specification) with an operating pressure of 250-300 bar. To speed up the job further, it can be fitted with an optional extra collector to act like a feller-buncher, grabbing and cutting multiple trees before the final swing to the stockpile area.
Left: The JAK 300 grapple has a replaceable blade which can be unbolted quickly for sharpening or replacement.
service basis. However, with good timing, Colin just wanted to hire a JAK 300 excavator tree shear grapple for three to four weeks, and at the same time Kris Wilson, of Jas P Wilson, was looking to move into the attachment hire market, and also offer a try before you buy deal.
At the time of the visit, the two JCB 150X HD machines were deployed on a large wind farm project, as some site exploration work was being undertaken to test the
Colin is currently working on another project with Clark Engineering and is trialling a new Mense RP hedge cutter attachment which he feels will significantly reduce the amount of flying debris compared to using a conventional mulching head/flail tool on the JCB 150X.
Colin said, “This new Mense RP hedge cutter is quite impressive, particularly in eliminating flying debris when compared to the traditional hi-speed/rotating flail unit, as this will significantly reduce the exclusion zone for ground workers as we are currently working with 50 metre zones, and we could possibly reduce this safely to somewhere around 10-15 metres with this new cutter. It will also be an ideal cutting tool when working with utility companies near high-voltage powerlines.
“It is also going to be great for trimming hedges, and for some species that have razor sharp foliage. It will reduce or eliminate the potential for car tyres to be punctured on access roads due to flying debris as it will be able to leave whatever we are cutting with this tool in a nice, neat heap. With that in mind, for customers looking for increased biodiversity, the Mense RP hedge cutter will also cut and leave a nice pile of brash for wildlife habitat, rather than flail it into a million pieces,” he explained.
“Whilst we have only been trialling it for a few days (at the time of writing), I am already impressed with its double-sided cutting performance from the tough Hardox blade. We were tackling plants up to 160mm in diameter with relative ease, and when tackling stu that Is around 110mm in diameter, it goes through that like a hot knife through butter.”
site’s ground conditions and viability to install a further 12 turbines. Thus, a safe access path and work area for the tracked drilling rigs to enter and drill was required. The vast majority of the trees that were being felled were around 25 to 30cm in diameter, the ideal size for the JAK 300 excavator tree shear grapple to handle. Colin explained that if they encounter larger diameter trees, then they will simply disconnect the two supply hoses and unlatch it from their automatic coupler, then t their own powerful Powerhand chainsaw grapple attachment.
trees and can be a bit more surgical when de-limbering as required.”
With nearly 1000 hours racked up on one of the 150X machines, Kieran McDairmant said, “Sitting in the cab of this 150X HD, compared to other diggers, is night and day,
work, and with the twin hydraulic pumps it has got plenty of ow to power this big rotating shear attachment or our rotating Powerhand grapple saw unit.
“THE JAK 300 EXCAVATOR TREE SHEAR GRAPPLE IS PROVING TO BE THE IDEAL ATTACHMENT TO REMOVE THESE SMALLER CROP TREES”
Colin and Kieran were making good progress, as the JAK 300 tree shear grapple was cutting the tree at the base of the trunk, and thus the twin-cylinders closed the heavy-duty Hardox steel grapple ngers which pressed the tree against the sharp blade bolted to the lower part of the attachment. Once cut through, and with the tree safely and securely gripped in the grapple, the powerful slew motor of the 150X and the screw-drive rotor of the rotating attachment would quickly swing the tree to the stockpile area in a smooth arc of operation.
Colin said, “The JAK 300 excavator tree shear grapple is proving to be the ideal attachment to remove these smaller crop trees, as the shear action is really quick and offers greater productivity for this particular application. That said, our own Powerhand saw grapple can tackle bigger
as it offers superior comfort as it is just like sitting in your armchair at home and this machine has been absolutely faultless over the last eight months. Digging wise, it has plenty of get up and go about it, as we do a lot of mounding and restock mounding
“The JCB 150X HD also offers a higher stance for straddling over tree stumps and a longer track frame for good low ground pressure performance sitting on these 600mm wide track pads. The long heavy-duty undercarriage also offers much greater stability, particularly when slewing over the side when you have a hefty tree gripped in the saw or sheer grapple.” Kieran also commented on the merits of the reach and stability of this machine with its three-metre-long standard stick and swinging and rotating the huge sheer grapple attachment that weighs nearly 600kg!
With a growing order book, and diverse range of customers, Colin is delighted with the heavy-duty performance and exibility of these 17-ton class JCB 150X HD Pro models, as well as the sales and service, nance support and backup provided by the Scot JCB team. He is equally as impressed with his Deutz-Fahr 5115K crawler tractor, that is becoming more versatile for each new customer and the machine’s performance and dealer backup from D.W. Toppin Ltd has been good. His ongoing working relationship with attachment suppliers and manufacturers such as Jas P Wilson and Clark Engineering has allowed Colin to provide the best possible service to his customers by using the very latest kit.
Above: An elevating cab can be specified with 30 degrees of tilt.
Below: The 718E with the Groeneveldt Grijpers grapple saw has opened up considerable work opportunities for Noel Kelleher.
Right: The choice of the Groeneveldt Grijpers 711T-1550 grapple saw and its dedicated hitch mechanism was seen as key to achieving the most from the Sennebogen 718E.
Eoghan Daly recently went to see Noel Kelleher’s Sennebogen 718E tree handler in action, matched with a Groeneveldt Grijpers 711T-1550 grapple saw. Eoghan reports on how it has transformed Noel’s business
With 30 years of site clearance and tree care work under his belt, Noel Kelleher of Noel Kelleher Plant Hire has become one of the leading providers of these services over the south, south-west and up into the south midlands of Ireland.
IMAGES EOGHAN DALY
Recently, two new machines have joined the eet; a Sennebogen 718E tree handler, with matching attachments, and a Volvo EC140E L excavator.
Noel began his involvement in site clearance and tree care work, due to a growing demand for such work, back in
1994 and originally offered hedge cutting services as a supplementary activity to his livestock farming interests. Working close to his base at Kilnamartyra, near Macroom, County Cork, he was eager to pursue other avenues of work, and with this increasing demand he saw huge potential.
Initially working on a modest scale with minimal equipment, Noel needed to advance and expand due to his increasing workload while also endeavouring to offer a more comprehensive service. This included building up a team of experienced staff with Noel’s son Evan also joining the operation, who today maintains a key role in the company’s on-site activities.
As Noel focused speci cally on clearance and tree care work, he purchased a Jenz HEM 360 terrain chipper back in 2009 which was matched with a Valtra T191 forestry spec tractor, which featured a roof mounted Botex crane for chipper feeding operations. Incredibly, this chipper still remains at the centre of the business 15 years later and is now propelled by a more recent Valtra T193, purchased new in 2015 from local dealership Paudy Buckley Tractor Sales. Based on the success story of his initial Valtra tractors, the decision was taken in
2022 to add a second dedicated forestry spec tractor from the Finnish manufacturer which led to the purchase of a T255 with Versu transmission.
Noel said, “The T255 was chosen based on the equipment I had planned to add to the operation which has included a high-capacity stump grinder and an FAE
PAIRED WITH THE 718E IS THE GROENEVELDT GRIJPERS 711T-1550 GRAPPLE SAW, WHICH FEATURES A MAXIMUM OPENING OF 1.55 METRES”
The Sennebogen 718E o ers excellent control and precision when removing tree crowns and limbs near structures as well as power and telecommunication lines.
forestry tiller which has been successfully used to reinstate Christmas Tree farms, nurseries and other areas back to agricultural land.”
More new kit arrived in 2023, as Noel bought a Sennebogen 718E tree handler. The machine has incredible working capabilities with its level of reach, accessibility, working exibility and its compatibility with different attachments. Whilst others in similar sectors are increasingly pursuing the route of utilising machine-based solutions for tree removal over the use of tree climbers, Noel saw a number of important bene ts of using the Sennebogen 718E which are absent from other machines. He said, “There are a range of different options when it comes to choosing a dedicated machine for taking down trees. These include mounting a grapple saw on a large rotary telescopic loader, a crane or an off-road truck, but
having looked at all these different choices, a dedicated tree handler like the Sennebogen 718E was a far more versatile solution. It is purpose built for the task which means it has clear advantages and, in the end, it was the only machine worth considering.”
With the Sennebogen 718E identi ed as the most desirable machine, ultimately the choice of attachments which can be worked with it had a great in uence. Even though there is an almost in nite array of shears, grapple saws and mulchers available for such machines, a lot of research was conducted in advance of making the purchase, as Noel revealed, “As there was never a machine like this working in Ireland previously, I had nothing to base working experiences upon and was very much dependant on outside help to nd the right
718E has an impressive working range which is enhanced by its single telescopic extension.
attachments that would offer the greatest working exibility. I approached the UFKES Greentec dealer who recommended a manufacturer based in the Netherlands and on looking at the package they were offering, it seemed like the best possible option to get the most from the machine.”
Based on this advice, the 718E was kitted out with a dedicated headstock from Groeneveldt Grijpers BV. Linked to its boom end, this permanently xed unit comprises of a tilt ram assembly
and quick hitch which allows the mounting of either the dedicated grapple saw or mulcher head from this Dutch based manufacturer. They produce a wide range of grapples for various uses as well as a comprehensive line of other specialist handling equipment.
Paired with the 718E is the Groeneveldt Grijpers 711T-1550 grapple saw, which features a maximum opening of 1.55 metres by the four grapple jaws which are composed of Hardox steel. As an added safety feature, the grapple’s hydraulic cylinders are equipped with check valves which ensure accidental discharge of tree limbs in the event of a hose rupture.
While the tilt hydraulic cylinder on the mounting headstock can be adjusted for gripping the tree, its working versatility is furthered by its rotational capability, delivered by four Parker rotary motors. Another important feature is the incorporation of a hydraulic tilt function on the saw box which allows it to be moved in or out from the tree trunk to ensure it aligns perfectly with the limb it is about to sever. The saw motor is rated at 30cc while the maximum cutting diameter is quoted at 700mm. Large tree limbs are well within the machine’s working capabilities, with its four gripping jaws being a major advantage and makes the attachment safer when handling larger limbs.
Even though the Sennebogen 718E has an impressive working range and adequate lifting capabilities working with the Groeneveldt Grijpers 711T-1550 grapple saw, it is still relatively compact and makes only a small footprint in its operation. Nevertheless, it is clearly not a machine that suits every situation, but when it does, it works very well. Noel said, “We wouldn’t have work for the Sennebogen tree handler every day as it is a specialist machine that suits certain applications. However, once the right kind of work arises, it gets through it very quickly and safely, and brings a new level of progress to the work we do.”
The working range of the machine helps it get through jobs very quickly, as it is tted with a two-piece tree handler boom with outer single telescopic extensions. The maximum upward reach is quoted at 13m and can extend to a great length at ground level.
Stability at these working extremes is safeguarded by the combination of the machine’s balanced formation and adequate counterweight as well as the
use of outriggers and a blade once lowered. With the machine purpose-built as a tree handler, no third-party intervention has been necessary for this set-up.
It is also reassuring to discover how user friendly the 718E is to operate with a dedicated elevating operator’s cabin being central to providing the ultimate view of the tree cutting operation. Mounted on a dedicated elevating arm, which allows a raising and tilting action of thirty degrees, the maximum elevated height is six metres. Even though this is still well below the maximum height, the boom can raise the grapple saw as well. Noel said, “Using a machine like this would be almost impossible without the elevating cabin. It takes you much closer to the action and gives a clear view to select the next limb and watch the sawing action before lowering the limb safely to the ground. The hydraulics on the machine are fast and precise which is also a major help, and the level of reach it has brings a large area within range from a single setup point.”
Looking more closely at the machine’s speci cation, it is tted with a Cummins B4.5 four-cylinder Stage V compliant engine at its heart with a power rating of 123 kW, with optimal performance obtained from the machine’s hydraulic system. Looking at its LDUV load sensing system, it uses a swash plate type variable displacement piston pump with the main pump delivering a maximum ow rating of 320 litres per minute. This is complimented by the supplementary pump which delivers ow of up to 182 litres per minute. Consequently, the machine delivers consistent performance even when multiple attachments are in operation.
The working capabilities of the machine were clearly proven during a recent project. The job involved the removal of mature conifer and deciduous trees located around the perimeter of a commercial business premises on the edge of Cork, at Sallybrook
Bottom
The
Bottom right: The Volvo EC140E L is another recent addition to Noel
near Glanmire. The premises was the Cork depot of construction equipment dealership Pat O’ Donnell & Co Ltd, with the work carried out over a weekend to minimise disruption.
Some initial work was required to remove tree limbs surrounding an insulated powerline via manual trimming by subcontractor Martin Hough and his team from Munster Tree Services. They used a Hinowa LightLift 20.10 tracked hoist offering a 20.15 maximum working height. The Sennebogen 718E tree handler then got involved as it moved in to take down the dense line of trees forming the boundary. It reached both over and under the insulated powerline and strategically removed each crown and major limb with military precision in a totally safe and controlled manner.
USING A MACHINE LIKE THIS WOULD BE ALMOST IMPOSSIBLE WITHOUT THE ELEVATING CABIN”
With each limb placed on the ground, they were downsized by a TMK 400 tree shear mounted on the new Volvo EC140E L excavator which successfully led to the segregation of larger material for rewood and the remaining ‘lop and top’ stockpiled beside the adjacent Jenz HEM 360 chipper. It ravaged through the material in a true demonstration of its immense appetite.
Noel concludes, “Where possible I like to purchase equipment that not just meets our current needs, but also the demands we are likely to face in the future. Because of this, taking a long-term view when selecting machines and deciding on their speci cation is important. This has paid dividends based on the long-term service delivered by the Valtra tractor with its Botex crane and Jenz chipper combination.”
Main image: The showroom displays Powerhand’s range of attachments and forestry tanks, it also features a retail area selling chainsaws, signage, protective clothing and more.
PRight inset: A recent 50,000 square foot extension has more than doubled the size of the factory.
owerhand is a division of Wm Clark and Son that was founded in 1924 by the late William Clark and thus is celebrating its centenary in 2024. William was a skilled blacksmith and farrier on the same site that the new factory is situated today at Parkgate in Dumfries. Their association with the forestry industry started out with the repair of forest cultivation spades and hand tools, and the shoeing of horses used for forestry work.
In the 1940s, William Clark’s son, Murray, began to design and manufacture a wide range of forest cultivation ploughs, working closely with the UK Forestry Commission. Over 2000 ploughs were sold worldwide, cultivating ground for tree planting on plantations in Iceland to Africa and Canada to Scandinavia. Additionally, a large number of UK forests were initially cultivated using Clark ploughs. The company also developed deep working ploughs for various specialist applications such as salt ridging in Iraq, oil exploration in Australia, irrigation in Africa and subsea cable trenching around the UK coastline.
By the early 1980s, the decline in bare ground tree planting in the UK, along with changes in cultivation techniques, resulted in the reduction of plough manufacture. For many years Wm Clark and Son had been involved with the harvesting of timber, manufacturing of winch hooks, ttings and hand tools, along with the repair of forest harvesting machinery. This was therefore a natural diversi cation for the third generation of the Clark family, and the business moved into the sale and manufacture of specialised timber harvesting equipment. This included the manufacture of Clarks Tracks that provided extra grip, low soil compaction and long tyre life for wheeled harvesters and forwarder machines.
“ALL THE HYDRAULIC COMPONENTS USED IN POWERHAND PRODUCTS ARE DESIGNED AND MANUFACTURED INHOUSE”
Over the following years Wm Clark and Son have continually grown and invested in their business and in addition to their own new Powerhand products, they have secured the dealerships of many of the world’s leading forestry equipment manufacturers that compliment and integrate into their attachments.
Fourth generation Managing Director Murray Clark provided an interesting tour of the new and expanded factory where Clark’s design, build and test a large range of Powerhand attachments. They take the mentality that the only way to guarantee the best quality is to control 100% of the design and manufacture process from their factory. The family business has strived to work with their customers to engineer and manufacture the attachments and portable tanks that are popular on the market today.
Their aim is to create the ultimate ‘end of arm’ attachment experience, which begins with the customers’ input. They have invested in modern manufacturing technology and have an experienced team of in-house engineers to ensure their products are built to last in the most demanding of applications. Also, all the hydraulic components used in Powerhand products are designed and manufactured in house.
Powerhand offer a range of robust timber grapples for log handling and a range of tined biomass grapples to handle brash and biomass, feed chippers, clear up sites and move oversized logs. Their EX series of grapples - EX25 to the EX40 – feature timber grapple geometry for improved bundling performance and Clarks say they are extremely popular with operators wishing to better utilize their 6-30 tonne excavator as a multipurpose tool.
Wm Clark and Son have been the UK and Irish distributor for Indexator for nearly 40 years, producing rotators for forestry work such as the
Following a jobsite visit to see Powerhand’s grapple, rotator and sawbox combination in action, David Wylie was invited to see their Dumfries factory, where their extensive range of products are designed, manufactured and tested for demanding forestry and timber handling applications
XR400 HT X2C unit, which produces 7000Nm of torque and has two extra internal oil channels to allow continuous rotation when a grapple saw is installed. They also supply hydraulic saws from Hultdin System AB.
One of Powerhand’s customers is Agriforest Ltd, who specialise in the timber harvesting and forest management sectors. They were one of the rst to help test Powerhand’s hydraulic rotating EX36 grapple with a Hultdin 555-S sawbox and the Indexator rotator which made for a powerful package. During a jobsite visit, Agriforest Ltd owner Douglas Mathison commented, “We have been working closely with Murray Clark for a number of years, and we had been talking about developing a saw attachment to t on their robustly engineered EX series of grapples and Indexator hydraulic rotators to make a very robust rotating grapple saw package to meet our needs on the demanding large-scale windblow clean-up projects.
“Whilst each of the three components were not new to the market, what was new and exciting was
Above: Clarks have a full hydraulic testing and service facility for rams, pumps and rotators.
making the three components work well together to produce a very powerful grapple saw attachment to dramatically improve safety, increase machine productivity and be more cost effective for our clients. Since the Powerhand package was tted, we have seen a signi cant increase in productivity, and we can reduce our headcount on site - as expert hand cutters are dif cult to come by. Machine operator Dom can now work safely on his own, and with the powerful saw now on the grapple, the machine utilisation has also signi cantly improved, as it can now process, as well as stack the wood, quickly and ef ciently.”
Murray Clark comments, “Agriforest has been a really good forward-thinking customer over the years, and it has been a pleasure working with Douglas and Dom to bring our Powerhand EX36 Grapple, rotator and sawbox into a nely tuned integrated package to meet their needs on demanding projects where safety is paramount. The attachments can yield greater productivity and machine utilisation than just a grapple working on its own.”
The tour of the factory started in the showroom. On display were the Powerhand EX series of grapples, EX25 to the EX40 for 6-30 tonne excavators. Mounted on top of these grapples were the Indexator range of vane-type hydraulic rotators. As you might expect, their new 50,000 square foot state-ofthe-art manufacturing plant is light and spacious and equipped with an array of the very latest computer-controlled lathes and milling machines. Powerhand manufacture their own hydraulic cylinders which are designed exactly to match the requirements of their EX series grapples and other large timber handling equipment.
Clark’s father, Doug Clark is chairman and technical director of the family business, and he says, “Design and innovation is our DNA”. Under the Clark Engineering brand, they also design and manufacture a large range of modular, patented and UN ADR approved road legal ‘grab tanks’ for forestry applications. These products are sold in the UK and across Europe by direct sales or through authorised dealerships. Not only do they meet UN ADR standards for transporting fuel on the public highway, but they are also designed to meet strict European environmental standards that help ensure there is no product spillage/forestry contamination during refuelling.
“POWERHAND OFFER A RANGE OF ROBUST TIMBER GRAPPLES FOR LOG HANDLING AND A RANGE OF TINED BIOMASS GRAPPLES”
explained they only sell the best forestry related products on the market, such as the comfortable and high-tech hard hats from ProTos.
It is also worth noting that the showroom also has a retail section for the likes of sawbar and chain consumables ranging from Oregon Chainsaws to Rock Oil. Safety apparel is also sold, and Murray
Moving along to the factory, which has a workforce of some 45 people, Murray says how Swedish steel and Hardox plate comes in at one end and is plasma cut, welded, machined, assembled, painted, and nally tested and quality checked before the nal product is dispatched direct to the customer or international dealerships. They also have a large workshop for full hydraulic services and the testing of cylinders, pumps and rotators. This area was ultra clean and had a ltration system to ensure there was no contamination of the OEM’s hydraulic systems when new Powerhand attachments are commissioned.
With 100 years of design and technical innovation to serve the forestry and timber handling markets, this third and fourth generation family business continues to develop and manufacture new products to very high standards and continues to invest in their production capacity within the new factory.
Not that long ago, the work of E.J. Agriculture was largely agricultural, but since then Ed Jones has transitioned to forestry work and has found a niche that has completely changed his business, as Ken Topham found out
IMAGES
KEN TOPHAM
E.J. Agriculture’s forest machinery fleet. A complete change from broad-acre agricultural contracting took place only two years ago.
In 2021, sister magazine Farm Machinery Journal visited E.J. Agriculture, to look at a Case Puma tractor at which point Ed Jones was shredding tree root stock, thus only dipping his toe into forestry work. His agricultural work ran alongside a wholesale log supply business which operated out of a yard near Oswestry, Shropshire.
Since then, the whole business model has been ipped on its head, the Case tractor was sold and replaced with a harvester and forwarder. Additionally, a PTO-powered log processing plant has been switched to a vertical splitter to handle unwieldly lumps of timber and a continuous splitter to deal with more uniform pieces.
“After the Covid-19 pandemic, prices of everything went up,
except the rates for work, so I decided to get out of the eld-based agricultural sector and expand some of the forestry work we were getting into,” says Ed. He had been carrying out some low impact thinning and management which involved a chainsaw team and a small excavator for moving the timber from the woods.
In the space of two years Ed has switched over completely to forestry work, but not commercial harvesting. Instead, Ed looks for thinning and management work, generally at the more challenging end of forestry work, mixing chainsaws with machines and all the way up to the business’ latest addition, a Logset 8H harvester.
The site visited by FM was an estate near Shrewsbury which has 175 acres of woodland, Ed’s team had already carried out thinning in one wood and had moved onto the next block. The woodland is on the banks of a small steep sided valley which is about a kilometre in length and work had already begun to gain access to the wood.
The wood had not been tightly managed and needed about 30% of the woodland thinning and
“IN THE SPACE OF TWO YEARS ED HAS SWITCHED OVER COMPLETELY TO FORESTRY WORK, BUT NOT COMMERCIAL HARVESTING”
removing a mix of species. Work was in the early stages and a chainsaw was doing the lion-share of the felling, starting out with the trees at the edge of the eld, which was to create a brash mat. The prolonged wet weather had made the neighboring eld, to where the timber would be extracted, impassible to anything but foot travel.
Opening up the woods for vehicle access had so far been a delicate process; Ed works with some chainsaw contractors who had come in and starting the felling to allow access for the larger kit. They also picked out the awkward multi-stem trees which are not easy to handle with the harvester.
A good deal of the work involved preparing the hard standing. Several loads of hardcore were delivered throughout the visit, and the Bobcat E27 was employed in levelling the hardcore out. The wet ground made the job more dif cult than it should have been.
The steep parts of the site were to be thinned with chainsaws and the plan was to then extract this timber to the eld employing a new piece of kit which Ed commissioned from Welsh forestry fabrication specialist, Hywel Evans Fabrications (HEF). Ed already owned a hydraulic winch, he just needed to graft it to his Bobcat E27, which had already been through Hywel’s workshop when it was new, to have a forestry guard tted to the cab.
In theory the Bobcat excavator could access the woodland and pull the trees up where they could be lifted and processed with the harvester, and then forwarded to the hard standing for transport. The wood extracted will be sold to wholesale timber processors and with Ed’s contacts and previous experience in the forestry sector, customers have been easy to nd.
The Bobcat was bought new and as mentioned HEF tted the cab guarding and also moved the extra service pipes on the dipper stick for convenience. There is a 50mm ball hitch on the blade so a small log trailer can be towed, and with an Intermercato grapple tted on a rotator, it makes for the perfect low-impact timber extractor.
E.J. Agriculture’s latest addition; a 2006 Logset 8H harvester.
CURRENT FLEET
• 2006 Logset 8H harvester
• 2006 Logset 8F Forwarder
• Bobcat E27
Formerly, E.J. Agriculture had supplied the wholesale market for logs. Ed says, “We were busy with that, but drying capacity was a problem. We have a small kiln, but the tonnage we were dealing with meant we had to ship logs out to dry them, and that eroded away the margin.” Currently the business is supplying the domestic market directly.
“THE HARVESTER CAME FROM SCOTLAND AND THE CRANE RECEIVED A REFURBISHMENT AND IS EQUIPPED WITH AN 8X HEAD” Owner and operator of E.J. Agriculture, Ed Jones.
Naturally, with the change from broad-acre agricultural contracting there was very little equipment that crossed over and so within the last two years the rm has switched to using forestry equipment. Ed has been fairly cautious about his machinery purchasing policy. The forwarder was the rst big piece of forestry kit that Ed bought; it was a 2006 Logset 8F with 20,000 hours on the clock but was still in good order.
There are a full set of tracks for the forwarder, but the eld boundary on this job was incredibly soft so it seemed more prudent not to use all of the tools in the traction cabinet, because if anything was to get stuck, it would lead to a very large extraction operation. Until earlier this year, Ed had a Doosan 140 excavator which had been forestry hardened with cab guarding and undercarriage reinforcement for working in woodland. Unfortunately, that
machine was lost to a re which led to the purchase of the 2006 Logset 8H with 18,000 hours on the clock.
The harvester came from Scotland and the crane received a refurbishment and is equipped with an 8X head which is amongst the larger harvester attachments. The machine is now very capable and as well as felling, Ed will utilise it to process timber that has been winched to the eld on this current job. Ed says, “We will mix it up, there is quite a lot of hardwood at the edge of the wood that is easier to address with the chainsaws, but as we get further in to the softwoods it will be easy to de-limb with the harvester.” Usually, the logs are cut to 2.7m which works for the processing systems that most log businesses use.
With enough work to keep one person busy at the yard, Ed dispatches some of the less uniform timber back to base, which is processed either with a Fuelwood Splitta 400, which handles cut rings, or a vertical Rock Machinery Venom hydraulic splitter for the dif cult pieces. Ed adds, “Supplying directly means the logs make a better margin, and at a lower volume we are not under pressure for drying capacity.”
Where contractors who operate in commercial woodland will use fresh kit, Ed does not need the same output compared to contractors who work for mills, so running the older kit makes more sense. “We do have to build in a bit of redundancy, but we are not working to the same pressures as the commercial harvesting out ts,” says Ed. Switching sectors has been a big stretch for Ed. He has changed pretty much all of his equipment, and also traded some of the hours. Less than two years ago, he was out working with potato farmers on eld preparation jobs working sixteen-hour days. Whilst now, he puts the work into the woodland, forestry is less impacted by the weather so the job can carry on most days.
As Eoghan Daly reports, when looking for a high-capacity mulcher, Irish-based firm Delamere Tree Services chose the route of an excavator-based mulcher combination
IMAGES EOGHAN DALY
Based at Mullingar in County Westmeath, Delamere Tree Services has been providing a range of tree surgery and other arborist services for over two decades. However, over the past few years, the rm has diversi ed into site clearance work, which is now a key aspect of the business. It ranges from simply felling trees and clearing the vegetation, to leaving a site development
ready for more intensive works, where the tree stumps and vegetation roots are also removed.
Delamere has come to be recognised as a leading site clearance contractor, and much repeat work comes from a group of regular clients. Part of its success is down to investing in a eet of dedicated equipment to conduct such work in a fast and ef cient manner. Their agship site clearance
machine is a Komatsu PC228US excavator that had been previously converted by the American specialist manufacturer Shinn Systems. A second engine on the modi ed Komatsu is used to drive an extreme duty FAE hydraulic mulcher attachment.
Company owner Sean Delamere said, “Mulchers on standard excavators are satisfactory for lighter work. But when faced with larger material on bigger sites, the only way to make progress is a larger mulcher and a base machine capable of driving it to full capability. Once we were getting more site clearance work, the only way to reach the kind of progress on a project called for by the client was by using a machine with the highest output.
“There are many options out there, including mulchers on purpose-built
“NOW THAT THE KOMATSU PC228US WAS FITTED WITH AN FAE MULCHER, IT MADE IT EVEN MORE ATTRACTIVE”
carriers. But for us, the only realistic option was an excavator-based machine, as a boom-mounted mulcher that gives a much greater working range over anything else.”
Such a high-capacity mulching combination clearly represents a signi cant investment for the rm, to say nothing of the dif culty of nding such a rig for sale on the international market, at a price that made commercial sense.
It was therefore a pleasant surprise when Sean discovered that a potential candidate had been sitting idle for a few years in County Cavan. It had apparently been converted in America to a very high standard by Shinn Systems, before spending the rst chapter of its working life in
Scotland. The excavator/mulcher had been shipped over to Ireland, worked for a few years, and was then left untouched.
As the price re ected its sorry state, Sean came away from the initial inspection asking if this was all too good to be true. He therefore contacted Shinn Systems in the United States (see panel), who were able to provide a valuable insight into the machine’s con guration and performance envelope, which seemed perfect for Delamere’s needs.
Sean recalls, “Everything about the machine looked positive and I just needed some extra information to ensure there wasn’t something I had overlooked. Having spoken to Shinn Systems, I was con dent the machine was genuine and was well worth the risk, especially since it did seem to
offer very good value for money, even though it needed a good deal of work to bring it back to full working condition.”
Purchased on an ‘as seen’ basis, the mulcher’s separate engine and hydraulic system were not working due to a fault in its control module, which is presumably why it was parked up. Sean continued, “It might have needed a high level of commitment to bring it back to full working condition, but based on the earning potential of such a machine and the amount of work it can get through in a short time, these efforts were certainly justi ed.
“We started by replacing hoses, seals and O-rings and had a unit made to control the engine and hydraulics driving the
mulcher. We were quoted $7000 to have an original unit sent over from the USA, which seemed very expensive.
“An electrical engineer, who worked in the Bord na Mona power station, came to look at what was needed and went away and made a custom control unit, all within a few days, which only cost €500. He has reconditioned and repaired ECUs for many excavators, so I knew he would be able to build the unit I needed for the machine.”
Having the hydraulics and control unit issue resolved, a full overhaul of the machine was conducted and all areas deserving attention treated to an upgrade or replacement. This included a complete replacement of the undercarriage and a full rebuild of the FAE mulcher. Due to the quality of the base machine and the conversion work, little needed to be added to bring the combination up to common site standards: just a rear-view camera, a set of ashing LED warning lights and amber rotating beacons.
During this commissioning process, two things became apparent. Firstly, the base Komatsu and auxiliary power system were all in decent condition, even the big Cat engine mounted at the back of the machine just required a routine service.
As the team worked on the machine, they also grew to appreciate the quality of the conversion work undertaken by Shinn, on a machine that now weighed close to 30 tonnes. Starting with a short-tailswing excavator, the rear counterweight was removed and replaced by an extended auxiliary engine bay. The result is a far more compact machine than an engine piggybacked on to a conventional counterbalance excavator.
The original conversion also included the provision of side and rear impact frames, a branch de ector on the offside front corner and a frame surrounding the cab, all of which had withstood the test of time well.
This was all done while maintaining decent service access to the base machine and to the auxiliary power pack.
Left, right and below inset: A new control system for the auxiliary powerpack was built locally. Apart from the undercarriage, the rest of the combination was in good condition.
A small access ladder drops down at the rear of the machine to provide service access to the large auxiliary engine compartment. From its door locking mechanism to its robust construction, it resembles a mini shipping container. The door swings well clear, and one of the radiators is attached to its inner surface, providing good access to the six-cylinder Cat engine rated at 450hp. It is fed by a separate fuel tank located on the upper rear of the auxiliary housing.
Now that the Komatsu PC228US was tted with an FAE mulcher, it made it even more attractive, as Sean commented, “FAE mulchers are the best we have used so far, are a very well built and capable of standing up to intensive long-term work.
“When we started using mulchers, we tried a number of other brands that may have been a lot cheaper to buy, but just didn’t have the build quality for continuous work and were constantly giving mechanical and structural problems. For this kind of work, there are no shortcuts when it comes to buying equipment and if it is not up to the job, it doesn’t take long for the design weaknesses to show.”
With a 450hp Cat engine driving a separate hydraulic system solely to power the heavy-duty, 6ft-wide mulcher, this combination can chew its way through whatever is in its way. Sean added, “The range of material the mulcher can handle considerably broadens the type of work we can take on. It is not just restricted to clearing sites, as it can also be used successfully to mulch tree roots.
“During earthworks, tree roots are separated and are a disposal problem for contractors and developers. We regularly use the machine to mulch these root stockpiles on site and can get through very large volumes quickly. On our very rst root mulching project, 25 ADT loads of roots had been stockpiled and, despite the volume involved, the machine got through all the material in just over one and a half days, which is real progress.”
The Shinn mulcher combo is operated by Sean himself, who said, “Like using any machine, you need to plan the work properly and continually read the ground
around you. The working range the machine gives allows a large area to be cleared, but in wetter ground it’s a case of working closer to the base machine and over the front of the tracks more, as working over the side can cause the tracks to dig in. For very wet sites, we have purchased a set of 30ft bog mats, which open up even greater working possibilities for the machine.”
We encountered the mulching combo on a large project to rehabilitate an agricultural holding near Ballynacarrigy in County Westmeath. The farmer who had just bought the land wanted to bring the unit back into full production. Hedgerows had become extremely overgrown, pockets of scrub had established themselves and there were many decaying trees, including those suffering from Ash Dieback disease.
In addition to the Komatsu, the Delamere eet deployed to this project included a pair of Hitachi 130 excavators, the younger Zaxis 130LCN-6 model being equipped with a 4ft-wide FAE mulcher. The excavator has been tted with a non-return pressure valve, maximising its auxiliary hydraulic output.
The older Zaxis 130LCN-3 was con gured with a log grab to sort and stack the timber. This included laying the tree crowns and branches in windrows for subsequent mulching by the Shinn Komatsu. The
“FOR THIS KIND OF WORK THERE ARE NO SHORTCUTS. IF IT’S NOT UP TO THE JOB, IT DOESN’T TAKE LONG FOR THE WEAKNESSES TO SHOW”
former scrubland was left devoid of any trace of vegetation and the ground looked cultivated and level on completion of the nal pass.
Sean still rates the older Dash 3 Hitachi, saying, “When it comes to standard excavators, I nd it hard to look beyond Hitachi. They are reliable machines and hold their value very well even after long service. Even though the newer 130LCN-6 works very well with the mulcher, for certain tasks the older Dash 3 model is still excellent, despite having worked over 10,000 hours now, and having had only 2000 on it when it was purchased second-hand.
“We would typically put 800 to 1000 hours on each excavator during a working season, since there have been no real problems over this long service, even an older excavator like this can still get through a lot of work.”
It is the speed and ef ciency of Delamere’s specialist eet in site clearance work that is attracting repeat business from property
Above, right and below: Two mulchers and a log handler quickly cleared this overgrown agricultural land, ready to be returned into production.
developers. It also helps to maximise the work the team can get through in the hedge-cutting season. The Shinn converted Komatsu excavator may not yet be kept fully occupied all year round, but with a ban on burning such green waste on the near horizon, the demand for a high-capacity mulcher will rise.
Sean concluded, “As a result of the work rates the machine can get through, which sees it clearing very large areas in just a few days, there can be idle periods between the projects it serves. Based on the lower level of investment needed in buying the machine, and the costs involved in getting it back
working at peak performance, this allows us some working exibility, as it is not a liability at quieter times of the year.
“However, there is a steady ow of work for a high-performance mulcher like this and, based on changing regulations on burning cleared material, the applications for the machine are set to increase. Its work rates allow the maximum amount of work to be carried out during the short hedgecutting season. On site clearance for road construction, the machine can completely clear one kilometre in a single day, if it is a good straight run without obstacles to slow down progress.”
Shinn Systems was founded in Charlotte, North Carolina, USA, in 1995 by Rickey Shinn, a former pilot with American Airlines. The initial focus of the firm was the design and manufacture of site-clearing machines, but the range soon expanded to include auxiliary powered stump grinders. The firm also developed military kit, including land mine clearance machines for the US Army, and has a factory capable of manufacturing a wide range of specialist machines. However, conversions of standard machines to work in conjunction with heavy-duty mulcher attachments remains at the core of the business. Known for their robust physical designs and not shy of providing plenty of grunt, Shinn Systems’ motto is ‘The intelligent application of power’.
In the woods, the forestry hardened JCB 140X plucks trees from the track, cutting them to length after felling.
John Cooper Recycling Ltd was established in 2008 and runs as a small and efficient operation. The business has evolved from handling green waste and now includes forestry and land clearance work, as Ken Topham found out
IMAGES KEN TOPHAM
Based near Preston in Lancashire, John Cooper Recycling Ltd was originally set up as a green waste handling business with a 25,000-tonne license to handle green/brown bin waste. John Cooper’s roots are embedded in the transport and poultry sectors, and he was running a number of trucks before transitioning to waste handling. He still runs the trucks today, but in the form of hook loaders, a 7.5t unit used for transporting kit to clearance sites, and an eight-wheeler for removing waste. The business has now evolved in to an arboreal and forestry out t. The waste removal side of the
business becomes busy in the summer when people are working in their gardens and lling their bins on a weekly basis. Whereas the forestry/clearance side tends to be busier in the winter months when hedges and brush can be cleared without the worry of disturbing nesting birds.
The ability to deal with green waste led to some land clearance jobs working with home building companies and this impacted the business’ machinery eet to an extent. Adding a tractor powered chipper was a big step as John explained, “We bought an UFKES Greentec chipper which at the time was an expensive piece of kit for a young business. It cost £128,000, but there were no secondhand machines in the UK then, so we had to buy new.”
An onboard bunker was the driving factor in buying the Greentec chipper, not normally a feature found on chippers of this size, but John’s entrepreneurial mind saw the value. John says, “We had used and seen chippers working on sites, and the limiting factor was getting trucks or trailers to them, or then double handling timber. I wanted a bunker to enable us to bring the chip to a better loading place.” So, the Greentech chipper won out, and the business hasn’t looked back. “When we are working on any jobs we use hook loader skips, whether we haul chip to them or base the chipper where the skips are placed and blow straight in, it keeps everything ef cient.”
It was whilst working with woodland consultants on land clearance work that raised the next question, which was ‘can you do some thinning?’ Naturally, John’s answer
Where traditional forestry contractors would leave the brash, John’s team extract it, in their eyes everything has some value.
was yes and this work has expanded into regular woodland jobs. When we caught up with John’s team, they were thinning a woodland in Cheshire as part of a stewardship scheme.
The two operators Tom Beaumont, the chipper driver, and Dougie Burns, the excavator driver, were enjoying the dry weather of 2023. They were removing all of the felled material, extracting it with a Kubota M6040 and Botex forwarder trailer. John has found this lightweight and low impact set up is particularly well suited for working in sensitive areas. In the woods, a JCB JS140 with a GMT050 harvester head was thinning the woodland. The logs were being cut to t in a standard 40-yard skip, these were then hauled back to base and either shredded for biomass or processed into logs.
The grapple saw has given the business the ability to carry out selective thinning while utilising an excavator that can be used for other work. The cab has more protection and extra services can be brought to the boom to run the grapple saw. Brash is extracted and chipped into skips, this is also processed back at base with a good deal of the material being screened and sent for biomass. Any ne material is processed for use as planting and landscaping media, such as the ne material from the bin waste.
John now supplies logs as a small diversi cation to the business which is why the large bows and trunks are cut to length in the woods and returned to the yard. A Uniforest 40 rewood processor is used, and logs are sold in half-tonne dumpy bags once they are seasoned. As a commodity, logs are more valuable than chip as the domestic market is turning to wood for heating. John says that in their rst winter of the operation, 2023-24, 300 bags were sold, and his projection is for 1000 bags to be sold over the winter of 2024-25.
Clearance work usually keeps the team busy during the winter months, and this was the nature of the work that the team were carrying out during another visit - working on sites that have returned to nature, and either managing the brush or clearing it completely. John says the team and kit he uses are ideal, both are small in numbers, and most of the machines are small in size. John says, “We use smaller kit, in part because it is easy to move, it works well on restrictive sites, and because we can deal with the waste, which means there is one less link in the chain.”
The latest machine to the eet at the time of writing was only three weeks old; a Bobcat T86. Having been speci ed for forestry use, it featured a hardened cab with guarding, a heavy-duty front screen/door, which is about 25mm thick and all but bullet proof and high output oil pumps. John also speci ed a Bobcat mulcher which communicates with the skid steer to optimise power usage. John says, “We really like the Bobcat as it suits our work perfectly and the mulcher is brilliant. We are getting more work done whilst using less fuel compared to using a larger mulcher mounted on a tractor.” Another recent addition is the Dipperfox SC600 stump grinder which has been mounted on a plate for use with the Bobcat, and another adaptor for use with the eight-tonne excavator.
The bene ts of this new machine on sites where the public are nearby are very clear, as John explains, “It is not quite as
BUSINESS
John Cooper
Recycling Ltd
LOCATION
Preston, Lancashire
WORK TYPE
Waste handling, forestry, and arb
Right: John removes material that can be recycled, whilst brambles and rotten material is mulched with the Bobcat T86.
Far right: The JCB wheeled loader fitted with its scrap grab serves well as a log and clearance grapple.
effective as a high-speed grinder, but it doesn’t ing debris around, so it is safer and there is less mess to clean up. Where the machine was working on this site is a prime example as it is right next to a fence. If we were using a high-speed machine, we would have to put somebody out on the path to keep pedestrians away and then clean up everything up.”
Working in tandem with the Bobcat, John himself runs the JCB 403 wheeled loader with a JCB scrap grapple for clean-up jobs, the combination works very well. “It punches above its weight; I can move large logs and roots and load them into the skips comfortably. We try to clear the sites of any recyclable material.” Again, the size of the JCB 403 means it is easy to transport and can be loaded onto a trailer and pulled with a 7.5-tonne truck. The site clearance kit is all compact and can be transported without any specialist vehicles.
Currently an ARJES RZ850 medium-speed shredder is based in the yard near Farrinton Moss, this handles everything from logs to brash. Naturally the business operates rotary trommels for screening, as people often add soil and stones to their garden bin waste. The medium-speed shredder is favoured due to its fuel economy and exibility, using 50% less fuel than a high-speed machine, but it also offers the business the exibility to shred material like tree roots that contain
soil and are not of a uniform shape. John explains, “The ARJES doesn’t produce a uniform sample as some shredders, but it does handle a wide range of material, particularly odd shaped pieces which is important when dealing with land clearance jobs.”
Small material is separated out of the ‘ nes’ and is repurposed for landscapers and gardeners as a peat-free planting medium. The larger material is shredded, composted and made t for land deployment. Some logs are processed into chip for energy production, usually the roots and knotty pieces.
John rotates his kit according to the hours recorded, if a machine is clocking 1500 hours per year or more it will be swapped after three years. If it is clocking 1000 hours per year, it stays for ve years, 500 hours or
Most material is returned to base, but some is beyond use and so it is shredded into the soil on site.
WE REALLY LIKE THE BOBCAT AS IT SUITS OUR WORK PERFECTLY AND THE MULCHER IS BRILLIANT”
less and it is on the books until something changes in the business and becomes obsolete.
The Valtra T254 is an ex. demonstration machine from John Bownes and is the rm’s sixth or seventh Valtra. John did a stint of spreading compost where he ran two tractors but found it more cost effective to deliver it to the farm rather than applying the compost himself. Thus, the eet was scaled back to just one tractor. John says, “We stayed with Valtra, we like them and have had excellent service from John Bownes, their backup is brilliant.”
With the business continuing to develop, John is keen to keep things tight in terms of headcount, preferring to keep his team smaller and maintain the high quality of work and high ef ciency that they currently deliver. That is not to say that he isn’t looking to the future, as there are plans for alternative energy production from wood on the horizon, to further utilise the main medium the business works with. Doing ‘more with less’ is the company ethos.
Eoghan Daly focuses on the large selection of harvesting heads available in the 650-700mm size range and looks at the many options which are now available. All the big names are covered to let you decide what is most suitable for your forestry set-up
Whether kitting out a new machine or injecting new harvesting vigour into an existing piece of machinery, the choice of harvesting heads is huge with a wide range of manufacturers in the market. This is true across all sizes, not least the upper end of the scale in the 650-700mm felling diameter classi cation. Traditionally associated with base machines for harvesting of clear fell stands, the need for added versatility by contractors means that heads with a larger diameter felling capability are now often used in both thinning and clear fell operations.
There are a great number of options to consider when purchasing a harvesting head. Firstly, the feed roller motors - which can either be of a high-feed force with a slower feed speed, or a low-feed force which delivers a higher feed speed. Another increasingly popular option is the variable torque feed roller motors which deliver extra speed when appropriate and add feed force when harvesting
more challenging material with coarse limbs. Thought must be given to the saw box pro le, especially in the larger harvesting head category, as its design can have a major in uence on stump heights if a low placement on ared butts is not possible. A high performance saw motor is also vital on a larger head for fast cross cutting and to avoid splintering in valuable sawlog material, especially when longer lengths are being harvested. The head’s knife con guration must also be given some thought.
The accuracy of harvesting heads has improved dramatically over the years, as have the capabilities of the head’s control and measuring systems, the former can now be tailored for individual contractor’s exact requirements. It is now also possible to mount a different manufacturer’s head on a base machine without restricting the capabilities of the new head’s system. Some older base machines tted with new control joysticks and keypad consoles, together with the latest measurement and control systems, are working well. This also breathes new life into existing machines, bringing them into the modern era and lengthening their working lifespan.
AFM are a long-standing manufacturer of harvesting heads and have recently diversi ed into the production of felling heads. Two models of interest in the 650-700mm range are the 60 and 65 units. As one of the earliest manufacturers to adopt the three-feed roller concept, the 60 and 65 heads continue this trend. The adjustment of the feed roller and knife pressure, according to the stem diameter, is very useful.
The AFM 65 features four movable delimbing knives which have a distinctive pro le with an outer straight probe section. This is particularly bene cial when picking up stems from a stockpile during roadside processing or when working in windblown pockets of standing timber. AFM offer a number of measuring and control systems for use with their heads and they are compatible with a range of other systems.
The current options of 650-700mm harvesting heads from John Deere comprises of the H425 and H219 units. Despite the H219 being the original harvesting head made by JD, the majority of UK and Irish users are now leaning towards the H425. Based around the original H219 head, the H425 has been re ned, featuring a short frame design along with a variable feeding ring. This ring operates through the use of angled outer rollers and a xed roller embedded in the rear frame.
While the H425 offers many improvements and design advances, its use of the SuperCut 100S saw unit is amongst the most bene cial, as the chain can be reliably tensioned, and the saw can be easily replaced. Standard and heavy-duty variants of the JD H425 are available which have been strengthened in their design such as in the tilt arm. Other improvements in the H425’s design include’s improved hose routing and access.
Despite their more recent entry into the harvesting head market, Kesla has quickly gained a respected position. Their contribution to the 650-700mm category is the 26RH-III model which utilises
progressive feed roller geometry. This enables a rm grip of the tree whilst the roller (no drive), embedded in the rear of the head, reduces friction that can be transferred to the head structure during feeding.
Offering a good combination of speed and feed force, the 26RH-III can be speci ed with a wide range of feed rollers and measuring wheels, and there are also a broad range of measuring and control systems. Among the options are the Kesla ProLog or Technion systems.
As probably the only manufacturer to use a track feed system on their harvesting heads, the Keto head provides a reassuringly
“THE CURRENT OPTIONS OF 650-700MM HARVESTING HEADS FROM JOHN DEERE COMPRISES OF THE H425 AND H219 UNITS.”
rm yet gentle grip on the tree due to the large contact area of the tracks. The heads can work using signi cantly lower knife pressures, thereby reducing the pressures on the host machine.
Also unique to the Keto head concept is how the length is measured by the feed tracks, instead of the use of an independent measuring wheel. Another interesting feature is the integration of the rotator in the tilt arm, and they have also begun to offer their continuous rotator with 360 degree rotating capability. A wide range of variants of their 500 and 600 models are available and can be speci ed with a broad range of options to ensure the individual requirements of the customer are met. Keto offer heads for speci c markets, with units such as the K-660C2, which has the option of a top saw, aimed at North America.
The Komatsu harvesting head range has expanded and now includes a wide range of additional models due partly to the
branding of Logmax heads as Komatsu’s current S-series units. Komatsu took over the Swedish manufacturer in 2012. Despite the availability of the Logmax heads, the original Komatsu head range still remains a popular choice.
Two very distinct head designs coexist in the range and give customers a real choice when it comes to specifying their most desirable harvesting head. Heads of Logmax origin include the S132 which is complimented by the original Komatsu C144 in the 650-700mm range. Among the attributes of the C144 head are its use of the Constant Cut system for improved sawing performance and its centralised lubrication points.
Key improvements have been made to the S132 including the Constant Cut system which is now a standard feature as well as the use of a new measuring wheel system featuring an independent hydraulic valve for the measuring wheel cylinder. The head can also incorporate the ‘ nd end’ laser which detects when the saw reaches the butt end of the trunk when reverse feeding. This eliminates the need to saw off a small block to register a start point for feeding. Other improvements include structural enhancements throughout the head’s construction.
“KEY IMPROVEMENTS HAVE BEEN MADE TO THE S132 INCLUDING THE CONSTANT CUT SYSTEM WHICH IS NOW A STANDARD FEATURE”
Even though Logmax are now part of the Komatsu Forest Group they continue to offer their extensive range under their own identity whilst also offering the heads with Komatsu branding. With a good reputation and a very comprehensive range of harvesting heads, they have been highly regarded for their performance and ease of access for maintenance, troubleshooting and repair.
The range continues to evolve with the latest in the 650-700mm class being their 6000V model. Using the TruCut 318 saw motor and chain tensioning system, the latest 6000V model also gives an increased tilt angle of 133 degrees making it more adaptable to work in steeper areas. The head also has a reinforced frame with alterations made to the area around the measuring wheel and stronger delimbing knife rams. Continuing Logmax’s tradition of the two-feed roller design, the head features the AFC system (Active Friction Control) which reduces stress on the head structure during processing. It maintains great accessibility for service, inspection and repair to the valve block assembly which can be reached through a large opening cover which reveals a very open layout beneath.
Later thinning and clear-felling operations are catered for by the Logset TH75 harvesting head which is a popular choice from the company’s harvester models. The TH75 has shown to have a durable frame construction, as many long-term customers claim. Delimbing work is catered for by the two xed and four movable knives whilst the head’s three feed rollers are driven by four feed motors. Feed motor options include 315cc or 400cc units for the chassis roller with 680cc or 820cc motor options available for the outer rollers. Lower feed force motor combinations deliver a feed speed of 5.6 metres per second with the higher torque variants slowing the speed to 4.4 metres per second. The head employs the Supercut 100 saw unit featuring automatic chain tensioning.
“THE PONSSE H7 HARVESTING HEAD IS REGARDED AS ONE OF THE MOST CAPABLE ALLROUND HEADS ON THE MARKET”
Finnish manufacturer Nisula have risen to great prominence in the industry in recent years and now offer one of the most comprehensive ranges of harvesting heads. These are complimented by energy heads and grapple saws as well as their harvester range. Among their largest harvesting heads is the 755X which boasts three feed rollers driven by four feed motors, four wraparound knives and a xed top knife for delimbing. Nisula have incorporated a range of improvements on the latest model including a high-strength steel frame, a new length-
and a high performance NSU saw motor. The head is offered with a range of different Nisula measuring and control systems with varying levels of complexity and these can also be used successfully with other systems.
The Ponsse H7 harvesting head is regarded as one of the most capable all-round heads on the market. It has a proven reputation with harvesting contractors in both thinning and clear fell work on a range of tracked and wheeled base machines. The head is offered in standard and heavy-duty speci cations and is known for delivering a good combination of speed and feed force as well as being suitable for delimbing. Not only is the head popular on Ponsse’s own base machines, but it is also frequently
chosen as a replacement head on other harvesters and excavator conversions.
Utilising the HH360 rotator, with 360-degree rotating capability, this makes the head even more attractive. As well as mounting on Ponsse’s own bases, there has been a trend of using the head on other manufacturer’s base machines as replacements. These conversions include full computer, joystick and control pad replacement bringing older machines into the modern era in the process.
Swedish manufacturer SP has been producing harvesting heads for longer than most other manufacturers. The company claims to have produced the rst ever single grip timber harvesting head in the world
which was the SP21 launched in 1980. Currently, there are two models at the larger end of the scale, with the 661 LF rmly embedded in the 650-700mm range.
The angle of the feed roller can be adjusted with the greatest angle applied when handling large stems, which ensures a rm hold and eases the pressure on the delimbing knives. The head can be speci ed with a oating or xed top knife and since it can work with most measuring and control systems, it is compatible with many different base machines.
Waratah has one of the most diverse ranges of harvesting heads which consist of three individual series, the 200, 400 and 600 ranges. The 600 models are at the upper end of the scale and are most popular in the North American and Canadian markets. The 200 and 400 series are aimed at European customers. Similar to the John Deere, with the exception of the distinctive Waratah red and black livery, the H270 and H425 are the manufacturer’s 650-700mm options. Even though the H425 is a very popular choice and
is available in standard, HD and X variants, the H270 Series-II and larger H219 are also appealing and are based on a different design. The H270 Series-II can be speci ed with range of options including a oating version of the xed top knife, whilst the head can have a wide roller opening and feed roller motors up to 934cc, which can deliver the highest feed force of 33.9kN. The H219 is a larger head of a similar design to the H270 Series II and is intended for larger trees. A wide range of options are also available for the H219 head.
Notes:Someweightsexcluderotator.Knives–f=fixed,fl=floating,m=moving
During the 1970s, James Jones & Sons were best known for their specialist forestry conversions. Gary Connolly went to look at one their rare James Jones Highlander 60 forestry tractors in north-west Ireland
IMAGES GARY CONNOLLY
With its bolt-on Highland halftracks, extensive forestry guarding and bright red paintwork, you could never call Declan Harkin’s James Jones & Sons Highlander 60 forestry tractor a ‘standard’ Ford forestry conversion. There are no prizes for guessing that the Highlander 60 is based on a standard Ford 4000, though by the time the tractor left the Jones factory it was far removed from the agricultural tractor’s original speci cation.
The most striking feature of the tractor is its half-tracks - the very attachment that prompted Declan’s uncle, Dan, to purchase the tractor back in 1985. At the time, Dan and his brother Frank, who is Declan’s father, were both working for the Forestry Service – Ireland’s equivalent to the UK’s Forestry Commission – close to their home near Carndonagh, Co. Donegal, on the northern tip of Ireland. Just as Declan was just about to leave school, the Forestry Service was looking for contractors to carry out thinning and timber extraction. Dan
decided to take on the work on a contract basis and asked Declan to join him. They needed a tractor, something local, but unfortunately the choice, in terms of anything in decent condition, was very limited.
After a fruitless search, Dan contacted Cowan Brothers in Eglinton, who had previously sold him a new Fiat tractor, to see if they could source anything suitable. Dan and Declan thought that Cowans would come up with a robust old four-wheel-drive tractor, so they were surprised when the dealership suggested the Jones Highlander 60. Having said that, both men were quick to realise the potential of the half-tracks, while the twin Igland winches tted to the rear were an unexpected bonus. A deal was struck, and the unusual tractor was delivered to Co. Donegal.
The Highlander 60 was produced by James Jones & Sons Limited, a major player in the timber extraction and processing industry in the UK and overseas. Established at Larbert in Stirlingshire, Scotland, in the late 1800s, James Jones & Sons developed into an extensive forestry and sawmill
business, and ultimately became one of the UK’s largest suppliers of timber. The company is still going strong today.
During the 1960s, James Jones & Sons began to address what they considered to be a lack of suitable harvesting equipment for tackling the mountainous conditions and soft grounds often found in many Scottish forests. The company’s service division set-up its own manufacturing operation to build specialist forestry machines.
Under the direction of Airlie Bruce Jones, great grandson of the founder James Jones, the company instigated a policy of sourcing specialist components, such as Igland winches, from OEMs then assembling them into dedicated forestry machines.
Airlie Jones had been impressed by the timber harvesting processes used in Scandinavia but realised that the techniques employed there would need to be adapted to suit British conditions. He produced a number of specialist forestry machines, as well as more straightforward modi cations to existing farm tractors.
This James Jones Highlander 60 is believed to have started work with the Northern Ireland Forest Service in the early 1970s.
The Jones Highlander 60, for example, was based on a two-wheel drive Ford Force 4000 tractor. It was tted with a set of Scandinavian-designed half-tracks that consisted of a frame bolted to the tractor’s rear axle, with a bogey or jockey wheel in front of the rear wheels, and tracks that wrapped around the tyres.
As well as adapting and converting British-built tractors and skid units into forestry machines, the company also modi ed German-built Mercedes-Benz Unimogs for forestry work. Airlie attributes the success of the conversions to the fact that the company was an end user of the equipment as well as the manufacturer.
The policy was successful and the company subsequently exported forestry equipment to most of the English speaking countries across the world. A link-up with County tractors proved to be particularly successful and many James Jones forestry tractors were sold overseas through the well-established County distributor network.
As time progressed, the larger-scale timber extraction companies moved from tractor-based forwarders to higher-capacity, purpose-built machines.
The increasingly specialist nature of the timber industry led James Jones & Sons’
“THE JONES HIGHLANDER 60 WAS BASED ON A TWO-WHEEL DRIVE FORD FORCE 4000 TRACTOR”
divesting their engineering operation many years ago. How, then, did Declan Harkin’s James Jones Highlander 60 nd its way from Larbert in Scotland to one of the most northerly points in Ireland?
Declan can’t be certain, but he believes the tractor was one of the ve Jones Highlander 60 tractors purchased in the early 1970s by the Northern Ireland Forest Service, the government organisation responsible for managing the vast majority of NI’s forests.
The Forest Service’s association with James Jones & Sons began in 1968 with the purchase of a modi ed Mercedes-Benz Unimog tted with Igland 3000 winches. Impressed by their initial machine and the support provided by James Jones, the Forest Service acquired several more Unimogs. It was these machines that laid the foundations for the arrival of a batch of Highlander 60 tractors, also tted with
Igland 3000 winches. In addition to the modi cations carried out by James Jones & Sons, the Forest Service also did some tweaking of its own, most notably tting a front stacking blade.
Joe Bradley, a senior forestry of cer with Forest Service, recalls the tractors being used in forests throughout the region. Thinning was a very important part of forestry management at the time and James Jones Highlander tractors performed well in this environment.
“The tractors travelled well on poor ground and the Igland winches were very effective at extracting the timber,” recalls Joe. “Only two faults spring to mind; rstly, the lack of power steering meant that steering the tractors was hard work. In addition to that, you had to be careful not to hit stumps with the front wheel as the sharp movement of the steering wheel could easily injure the driver’s thumb!”
When the NI Forest Service nished with the Highlander 60 tractors they were sold at auctions and it seems likely that Cowan Brothers acquired this tractor either at an auction or from another dealer.
Once the tractor had been delivered by Cowans to Donegal, the rst task was to t the half-tracks. This initially caused much head scratching as no matter what Dan and Declan did, they couldn’t get the tracks to meet up so they could be re-joined. Declan was almost at the point of contacting the dealer to complain about the ‘missing’ sections of track when a nal investigation under the tractor revealed a mystery hydraulic ram.
Further examination revealed that the ram allowed the idler wheel to move backwards and forwards, thereby tensioning the tracks - problem solved! In fact, once understood, the convenience of the system meant that the tracks could be removed and re tted very quickly, which made moving the tractor between sites very straightforward.
Once the tracks had been re tted, Declan put the tractor to work immediately. It was, he says, a baptism of re. “The rst day in the forest, I broke a stub axle.” He quickly realised that the tractor had so much grip that in the event of the front wheel becoming lodged against a stump, the tractor would simply drive on and something had to give. Most normal tractors would simply spin their rear wheels in a similar situation, but not the Highlander. “I soon learned the capabilities of the tractor and only ever broke one stub axle after that,” he adds.
Over a period of time, Declan says he became adept at using the Highlander’s innovative weight transfer system to extract himself from some potentially sticky
“THE 60 WAS AN INCREDIBLY POWERFUL LITTLE MACHINE FOR ITS SIZE AND WAS CAPABLE OF TAKING OUT UP TO THREE TONNES OF TIMBER IN ONE PULL USING THE TWIN WINCHES”
situations. The ability to raise the front wheels and transfer weight to the rear axle using the jockey wheels provided tremendous grip, he notes, but if the driver tried to turn with too much weight on the rear end, the tractor would throw a track. Working in forestry was always a challenge, recalls Declan, adding that not many days went by when the Highlander didn’t get stuck at least once in the soft peat soils. “There were many times I was bogged down so badly that the back wheels weren’t visible.”
The 60 was an incredibly powerful little machine for its size and was capable of taking out up to three tonnes of timber in one pull using the twin winches. Because it spent most of its time on tree thinning work, this meant it could pull out up to 30 trees in one go. If the tractor got stuck, Declan was normally able to release the winches, drive the tractor on to better ground and then winch the logs back into the rear plate.
To increase traction, he often loaded the modi ed front blade with shorter logs. This allowed the tracks to transfer even more weight to the rear driving wheels, improving the grip, albeit sometimes at a cost. “In 10 years, I broke three half-shafts due to the incredible torque,” he recalls.
The Ford 4000-based Highlander 60 was of robust construction and 20 plus years of forestry work has had surprisingly few ill e ects on this example.
The tractor worked commercially until 1996, as Dan decided to retire and Declan went into the construction industry, thus the tractor was parked up. At the end of the 2000s, Declan decided to put the old Highlander back into serviceable condition, mainly as a tribute to his late uncle.
The subsequent overhaul involved three generations of the family – Frank (Declan’s father), Declan himself and his son Ryan. The strip-down wasn’t exactly easy, although thanks to the protection added by James Jones & Sons, the tractor had stood up well to life in the forest.
Mechanically the engine, gearbox, back end and brakes were in surprisingly good condition, so were left untouched. With very little mechanical work required, most of the
time went into the bodywork and ancillary components. All the rams were removed and overhauled. A new manifold and exhaust were tted, together with new front wheels and a number of smaller parts.
Declan decided to paint the tractor himself and since there were one or two very small areas of paint that hadn’t been exposed to the sun, Declan was able to scratch off a sample and take it to his local motor factory. Declan is keen to point out that it wasn’t his intention to refurbish the tractor to as-new condition, let alone concours, but there is no doubt that he has made a good job of preserving this relatively rare Ford conversion.
Our thanks to Airlie Bruce Jones and Joe Bradley for their contributions to this article.
Thanks to a previous modification to the front-mounted logging blade by the NI Forest Service,the front blade can lift and carry logs.
The powerful grapple saw for versatile use! For tree fellings due to safety reasons.
max. 75 cm
max. 160cm
20 - 28 t
TECHNICAL FEATURES:
•Two strong, independently controllable grippers
•Automatic chain tensioner
•Power-Tiltator
APPLICATION:
•Maintenance work along traffic roads and routes.
•In rough terrain, hill areas and swamplands.
•Quick processing of the already logged tree lying on the ground.