STATE OF TRANSPORTATION: IN THE DRIVER’S SEAT AND BRACING FOR IMPACT
Sometimes even the most cutting-edge technology can’t predict what’s going to happen next.
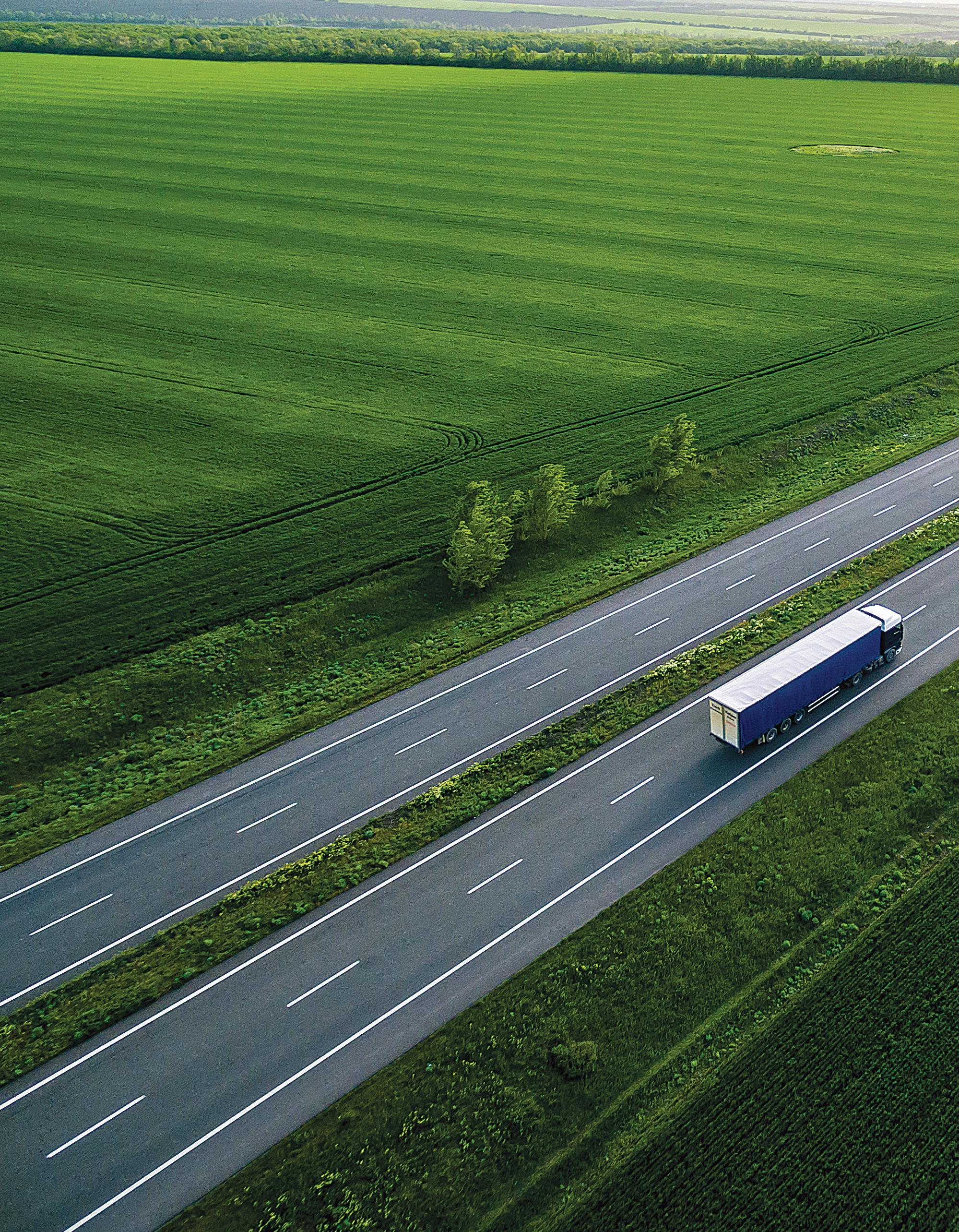
Sometimes even the most cutting-edge technology can’t predict what’s going to happen next.
Propane is the safe, reliable energy for material handling.
Propane-powered forklifts produce fewer emissions than those using an equivalent amount of electricity. That can improve air quality inside your facilities—for a healthier, more productive workforce. And because they only require a quick and easy cylinder change to get back to work, your propanepowered equipment does more than move inventory—it gives your bottom line a big lift, too.
To learn more, visit propane.com/for-my-business/material-handling/
Editor-in-chief Marina Mayer details why the supply chain space needs to brace for impact.
In my column in Food Logistics’ Nov/Dec 2020 issue, I dubbed the year 2020 as the Year of Upended Supply Chains. Then, a year later, I dubbed 2021 as the Year of Mended Supply Chains.
But, while supply chains started to heal, the damage was done, marking 2022 as the State of Grim Supply Chains.
While it may be too early to name 2023, for now, let’s call it the Year of Bottlenecks.
That’s because, as of press time, there are several disruptions and bottlenecks impacting the supply chain space, and it’s only July.
• Truckers in Florida set to boycott.
• UPS set to strike.
• Labor slowdown at West Coast ports.
• Droughts, fires and flooding damaging crops and creating shipping delays.
• El Niño. Enough said.
• Cargo fraud still not under control.
• Russia/Ukraine war still ongoing.
• Poor infrastructure challenging shippers.
Not to mention inflation, rising fuel costs, labor shortage, product shortage and a slew of others that should be included.
And this is just for the first seven months of the year. This doesn’t begin to scrape the surface of what’s still to come.
Lately, the disruptions have become more… disruptive and less predictive. They’re becoming annoying and cumbersome. They’re impacting companies and consumers alike. They’re creating ripple effects from farm to fork, and the repercussions are endless.
And, while software and technology only improves the visibility of these situations; it doesn’t solve the human aspect of what the supply chain industry is facing..
Not sure the resolution, not sure how supply chains recover or even when, but what is certain is that all of logistics should continue to brace for impact because the year isn’t over yet, and disruptions continue to disrupt.
EDITORIAL
Editor-in-Chief Marina Mayer mmayer@ACBusinessMedia.com
Managing Editor Alexis Mizell-Pleasant amizell@ACBusinessMedia.com
AUDIENCE
Audience Development Manager Angela Franks
PRODUCTION
Senior Production Manger Cindy Rusch crusch@ACBusinessMedia.com
Art Director Willard Kill ADVERTISING/SALES
Brand Director Jason DeSarle jdesarle@ACBusinessMedia.com
Account Executive Brian Hines bhines@ACBusinessMedia.com
Account Executive Jay Gagan jgagan@ACBusinessMedia.com
AC BUSINESS MEDIA
Chief Executive Officer Ron Spink
Chief Financial Officer ........................................ JoAnn Breuchel
Chief Revenue Officer .......................................... Amy Schwandt
VP, Audience Development ................................. Ronda Hughes
VP, Operations & IT Nick Raether
Content Director Marina Mayer
Director, Online & Marketing Services Bethany Chambers
Content Director, Marketing Services Jess Lombardo
Director, Demand Generation & Education Jim Bagan CIRCULATION & SUBSCRIPTIONS
P.O. Box 3605, Northbrook, IL 60065-3605 (877) 201-3915 | Fax: (847)-291-4816
circ.FoodLogistics@omeda.com
LIST RENTAL
Sr. Account Manager Bart Piccirillo | Data Axle (518) 339 4511 | bart.piccirillo@infogroup.com
REPRINT SERVICES
Account Executive Brian Hines (647) 296-5014 | bhines@ACBusinessMedia.com
Published and copyrighted 2023 by AC Business Media. All rights reserved. No part of this publication may be reproduced or transmitted in any form or by any means, electronic or mechanical, including photocopy, recording or any information storage or retrieval system, without written permission from the publisher.
Food Logistics (USPS 015-667; ISSN 1094-7450 print; ISSN 19307527 online) is published 6 times per year in January/February, March/ April, May/June, July/August, September/October, and November/ December by AC Business Media, 201 N. Main Street, Fort Atkinson, WI 53538. Periodicals postage paid at Fort Atkinson, WI 53538 and additional mailing offices.
POSTMASTER: Send address changes to Food Logistics, P.O. Box 3605, Northbrook, IL 60065-3605. Subscriptions: U.S., one year, $45; two years, $85; Canada & Mexico, one year, $65; two years, $120; international, one year, $95; two years, $180. All subscriptions must be paid in U.S. funds, drawn from a U.S. bank. Printed in the USA.
Competition is everywhere. From choosing between electric, hybrid and traditional gas cars to determining if a sugar cone, cake cone or waffle cone should hold that next scoop of ice cream. Dennis Raffa, senior program manager of Zero Waste World for CHEP, gives reasons for how collaboration within supply chains can lessen their impact on the environment.
Scan the QR Code to learn more.
https://foodl.me/steawk
Webfleet introduced Webfleet Cold Chain, a single-platform solution designed to help temperature-controlled fleets maintain cargo quality and safety. Webfleet Cold Chain helps fleet managers easily monitor, control and record temperature conditions across their refrigerated assets in real time. This cold chain solution can support any refrigerated fleet, making it suitable for any semi-trailer, rigid-body truck or delivery van as long as the vehicles are equipped with refrigeration devices and utilized to keep cargo at correct temperatures.
Scan the QR Code to learn more. https://foodl.me/s78xgp
Enterprise food CPG has been one of the last manufacturing verticals to broadly shift to outsourcing. But the shift is accelerating, and nearly every modern brand acknowledges that nimble and flexible production is necessary in the age of the Gen-Z consumer. In this article, Vince Tseng, CEO of PartnerSlate, says there are many up and coming brands that will thrive if they can obtain the capital to do so. Contract manufacturers that can adapt their businesses to help address the pain points of growth customers will be well positioned to reap the benefits from this for years to come.
Scan the QR code to learn more. https://foodl.me/z3ia5l
The supply chain industry is always doing new and interesting things to help educate and improve communities. Here’s how Toyota, Federal Motor Carrier Safety Administration and British International Freight Association are improving workforce development by providing education and training to those who are less fortunate or need assistance.
Scan the QR code to learn more.
https://foodl.me/z56mpn
Nucor Warehouse Systems announced its new corporate responsibility and sustainability initiative called Closed Loop Sustainability, which allows customers to find new ways to meet sustainability goals by reducing the need to source out new steel. When a warehouse rack needs to be replaced, Nucor can dismantle and recycle the existing rack, create and install a new one and then use the material to re-engineer and install a new rack system.
Scan the QR code to learn more.
https://foodl.me/pmb6co
The food and agriculture industry has witnessed steep rises in core commodity prices and shortages in 2022 and this is carrying on into 2023 due to high inflation rates and the cost of energy, with big supermarkets recently limiting product sales, according to Efficio’s latest report. Meanwhile, air freight—in particular, global jet fuel prices—has reached an 8-year high since 2014. Over the last 12 months, the prices for milk and chicken have increased by over 40%.
Scan the QR code to learn more.
https://foodl.me/9ukyx6
More than 30% of companies lack the technology to adequately engage frontline employees and 54% of companies recognize that failing to help frontline employees stay connected and engaged is costing them productivity, according to a survey from Simpplr. The study also finds that a technology gap is making it more difficult to retain (37% of respondents) and recruit (38%) talent. Over half (54%) of respondents reported the lack of engagement amongst their frontline employees impacts their productivity.
Scan the QR Code to learn more.
https://foodl.me/d78o6b
Matt Murdock, technical content writer for LogiNext Solutions, says to plan your last-mile delivery, use the right technology, create a digital footprint of operations, be customer-centric and make use of 3PL or your own fleet to get the items delivered. Understanding the last-mile delivery logistics is only the beginning for such businesses. Gen-Z is more into setting up cloud kitchens to start their food business. Even if you hire the best chef or do the cooking yourself, delivering the items hot and fresh will be the key to a successful business. Evaluating the right strategies that align with customers and meet business use cases will be the key to cracking last-mile delivery.
Scan the QR Code to learn more.
https://foodl.me/hu4baj
Stöcklin Logistics launched Stöcklin CasePicker to address the specific product logistics challenges and opportunities now facing produce shippers. The Stöcklin CasePicker offers a completely automated solution for distribution centers serving hundreds of retail outlets, with freshness zones from 4-14°C and up to 135,000 cases a day for fruit and vegetables, to ensure that only the intended goods are picked directly from the produce pallet for the retail-outlet pallet. In addition, the system speed depends on the order volume. This process optimization and variable utilization reduces the energy required in comparison to conventional solutions.
Scan the QR code to learn more.
https://foodl.me/u98eki
Heather Hampton-Knodle, president of American Agri-Women, explains how farmers take responsibility as stewards of the land seriously and work every day to leave farm’s soil in better condition than the day before. In fact, farming is truly an exercise in responsibility, each and every day. However, pesticides are one of the most regulated industries in the world. And the United States has one of the most thorough and science-based review processes globally. This means that the process a pesticide product must go through to make it from the lab to the field involves hundreds of tests and will likely take more than 11 years.
Scan the QR code to learn more.
https://foodl.me/v6a62f
Like so many other industries, the food distribution space has grappled with supply chain disruptions, logistics hurdles, price volatility and decreased predictability over the last few years. But food distributors grapple with the added complexities that come with balancing new and recurring orders and frequent last-minute changes, all while managing operational costs and prioritizing customers. Navigating this complex landscape requires food distributors to leverage the right technology and tools to optimize their delivery operations. Shailu Satish, co-founder and COO at DispatchTrack, lists 4 top challenges facing the food distribution industry and how distributors can tackle them.
Scan the QR code to learn more.
https://foodl.me/x2uiv9
Dr. Jim White, CEO of Post Harvest Technologies, says right now, an estimated 1.3 billion metric tons of food is wasted annually, translating to a financial loss of $1 trillion per year. Without significant changes, this problem is expected to grow to 2.1 billion metric tons and $1.5 trillion by 2030. Employing pre-cooling, cold storage and refrigerated transportation systems nationwide is the solution to prevent food wastage. Extending the shelf life of produce provides Americans with fresher, higher quality products, prevents waste and ultimately helps feed the hungry.
Scan the QR code to learn more.
https://foodl.me/hrka4s
Uber Freight, WattEV and CHEP
announced a joint effort to deploy electric trucks on select routes in Southern California. As part of this collaboration, WattEV will provide electric trucking capacity to Uber Freight shippers, starting with CHEP. The pilot serves as a milestone in electric freight transportation and establishes Uber Freight’s first electric vehicle (EV) deployment. Via the Uber Freight platform, CHEP will be able to book, schedule and complete loads, track status and load KPIs and manage paperwork all in one place.
Scan the QR code to learn more.
https://foodl.me/8wq47x
Technology-oriented companies understand the value of data and are always looking for innovative approaches to apply it in unexpected ways. The most common use for data offers a rear-view look that reports on what happened in the past, like financial results. But if looking to get ahead of what is coming next, especially in a dynamic marketplace, using available forecast systems can help place businesses at the forefront and in-step with demand months in advance to best align their supply chains. Jason Lockard, SVP of managed logistics at BlueGrace Logistics, provides more insights.
Scan the QR code to learn more.
https://foodl.me/a1etxk
Exploring nearshoring and deglobalization strategies in the context of South America presents a wealth of enticing business opportunities. From improved supply chain resilience to accessing untapped markets and capitalizing on abundant resources, the region’s advantages are abundant. Jeff Eckel, director of product marketing at e2open, explains that with South America knocking on the door as a new supplier, businesses have the opportunity to diversify their sourcing and strengthen their supply chains, setting themselves on a path toward longterm success in an ever-changing world.
Scan the QR code to learn more.
https://foodl.me/r0uwlm
Registration is open for this year’s Women in Supply Chain Forum, an in-person event presented by Food Logistics and Supply & Demand Chain Executive, designed to bring together CEOs, Presidents, Partners, VPs and Director-level decision makers at shippers, DCs, warehouses and 3PLs to learn, grow, network and more. This year’s theme, Better Together: How Collaboration Promotes Women in Supply Chain, will bring together leading experts in the industry to discuss company culture, mentorship, women in STEM, DEI efforts and industry trends.
Scan the QR code to learn more.
https://foodl.me/6yly2p
If you walk down any aisle of a grocery store, you will notice that the prices for pretty much everything has gone up, and everyone from the manufacturers to the consumers are suffering as a result. There are factors such as climate issues and crop failures driving up food prices that are outside anyone’s control. Yet there is one issue within the industry’s control, and it impacts everyone from the farmer down to the consumer. Anne Reinke, president and CEO of the Transportation Intermediaries Association, explains unlawful brokering’s impact on food quality and safety.
Scan the QR code to learn more.
https://foodl.me/wiyr7j
There are a lot of differences between a W-2 and 1099 truck driver that should be considered before deciding what’s right for you. The Cliffs Notes version is, W-2 drivers can get paid benefits and have less to worry about come tax season, whereas 1099 drivers can earn a little bit more money because of tax write-offs and have more control over how they run and distribute their money. Alex Dovgal, founder of DVL Express, weighs out the pros and cons of both.
Scan the QR code to learn more.
https://foodl.me/csirru
The United States imports over $22 billion worth of fresh produce annually worldwide, and while it receives fresh produce from over 125 countries, 77% of fresh fruits and vegetables come from Mexico and 11% from Canada. Since fresh fruit and vegetables have limited shelf lives, it is imperative to transport them efficiently. Andrew Welling, director of cross border services for TA Services, highlights what to consider when transporting fresh produce.
Scan the QR code to learn more.
https://foodl.me/3gxzoc
Only 55% of shippers filled their trucks to capacity last year, while the rest were unable to fill 25 out of 53 linear feet of deck space, according to a study by Flock Freight and Drive Research. In fact, one in five truckload shipments moved completely empty in 2022. What’s more is, 45% of shippers in 2022 reported shipping partially empty truckloads with an average of 25 linear feet of unused deck space, while 21% of U.S. truckload freight capacity is going to waste within partially empty trucks.
Scan the QR code to learn more.
https://foodl.me/f1s46t
The U.S. Department of Transportation Maritime Administration opened applications for the Port Infrastructure Development Program, which allows for more than $600 million in grant funding for projects that include environmental and emissions mitigation measures and terminal equipment upgrades. With this funding, ports can begin replacing their diesel and gasoline-powered equipment with clean energy alternatives such as propanepowered port tractors, forklifts and other cargo handling equipment.
Scan the QR code to learn more.
https://foodl.me/vvd691
Aviant launched its home delivery service, Kyte, now capable of delivering groceries, takeaway food and non-prescription medicines to sparsely populated areas and holiday homes in Norway. Aviant’s drones are capable of flying as far as 120 km in a straight line, similar to an airplane. The increased efficiency and speed means Kyte’s delivery range is significantly higher than other airborne door delivery services, being able to deliver within a 30 km radius for return flights, compared to the 2-3 km offered by other providers.
Scan the QR code to learn more.
https://foodl.me/7rrga8
Mike McPeak, director of growth marketing at Hale Trailer, says the industry has been struggling with a driver shortage for years, and the problem only seems to be getting worse. Enter self-driving trucks, or driverless trucks, which have been hailed as a potential solution to this issue. While the technology is still in its early stages, many industry experts are excited about the future of trucking automation and the impact that autonomous trucks could have on the industry. Autonomous trucks have the potential to revolutionize the trucking industry. They could improve safety, efficiency, and productivity, and help to address the growing shortage of truck drivers.
Scan the QR code to learn more.
https://foodl.me/vwu7gp
It’s clear now, in 2023, that visibility is a must. But it’s also being hyper-commoditized and is becoming table stakes, explains Ami Daniel, CEO and co-founder at Windward. Both shippers and logistics service providers (LSPs) need to take a two-pronged approach: On one hand, push to create a more open ecosystem and push for better underlying data quality. On the other hand, organizations should adopt vertical AI solutions to automate and optimize exception management in order to get better and more predictable results.
Scan the QR code to learn more.
https://foodl.me/g2hapj
The California Air Resources Board (CARB) announced a Clean Truck Partnership with the nation’s leading truck manufacturers and the Truck and Engine Manufacturers Association (EMA) to advance the development of zero-emission vehicles (ZEVs) for the commercial trucking industry. The Clean Truck Partnership, which includes Cummins, Inc., Daimler Truck North America, Ford Motor Company, General Motors Company, Hino Motors Limited, Inc., Izuzu Technical Center of America, Inc., Navistar, Inc., Stellantis N.V., Truck and Engine Manufacturers Association and Volvo Group North America marks a commitment from the companies to meet California’s vehicle standards that will require the sale and adoption of zero-emissions technology in the state, regardless of whether any other entity challenges California’s authority to set more stringent emissions standards under the federal Clean Air Act.
Scan the QR code to learn more.
https://foodl.me/ezgvpu
For the past 3 years, the trucking industry has faced numerous challenges stemming from the onset of COVID-19. The overnight shift in home delivery and the impending driver shortage continue to pose a constant pivoting act for the transportation sector.
What’s more, the heat is felt to keep workers happy, carbon footprints down and product moving, from fleet to rail to ports. That’s why companies continue to adopt emerging technologies such as artificial intelligence (AI), automation, wearables and more to help predict—and prevent—supply chain disruptions.
However lately, the disruptions have become more… disruptive and less predictive.
Present day, it’s not just a lack of visibility that’s creating bottlenecks along the way; today’s challenges run deep, are more personal and stem from a variety of causes such as the passage of certain laws, the lack of agreements to better protect contract workers and more.
Sometimes even the most cutting-edge technology can’t predict what’s going to happen next.
Here’s a breakdown on the State of the Transportation Sector, and the impact of worker strikes, bill passages, Mother Nature occurrences and more.
The trucking industry moves more than 72% of the nation’s freight tonnage, and over the next decade, will be tasked with moving 2.4 billion more tons of freight than they do today, according to an
American Trucking Associations (ATA) press release.
What’s more is, the global trucking market is anticipated to surpass $4 trillion by 2031, according to Allied Market Research. This means, now is the time to address the challenges impacting how trucks keep on truckin’.
For starters, Owner-Operator Independent Drivers Association (OOIDA) reports the average age of a truck driver is 55 years old, “and over the next 10 years, as many of these drivers retire, it will answer the age-old question of whether we have a driver shortage or not in the United States. The reality is this will be a steady turnover, but as parallel industries grow, such as home building and construction, it puts a ton of tension on the drivers in trucking,” says Koepke.
In May, Florida truckers announced a possible boycott, where, as of press time, one in five truckers are boycotting or planning to boycott driving in Florida due to the recently passed Immigration Law, Senate Bill 1718.
To put this into perspective, the Florida transportation industry generates more than 99,000 jobs held by heavy and tractor-trailer truck drivers, according to U.S. Bureau of Labor Statistics.
The boycott, which organizers say may include thousands of drivers, calls for a suspension of deliveries to and from Florida, one of the states with the highest share of intrastate shipments by value, according to the U.S. Department of Transportation.
“With one in five truckers currently boycotting or planning to boycott diving into Florida due to the passage of Senate Bill 1718, Florida residents have been experiencing disruptions in the supply
chain. In fact, since the bill was signed into law, nearly one in three Floridians have been unable to find at least one specific food or beverage product at a store and over one in four Floridians have seen empty grocery shelves,” says Eric Weisbrot, digital marketing manager at JW Surety Bonds.
Then, on June 12, a large tanker truck transporting 8,500 gallons of 87 octane gasoline caught fire and forced a bridge collapse near the Cottman Avenue exit in the Tacony section of Philadelphia. This truck fire caused major infrastructure damage, detouring drivers 43 miles out.
“We have become accustomed to disruptions in the supply chain these past few years. The I-95 collapse specifically highlights the vulnerability of critical infrastructure and the need for robust contingency plans,” says Bart De Muynck, chief industry officer at project44. “Investments in preventive measures, such as regular inspections, fire suppression systems and early warning systems can help mitigate the impact of such disasters. Companies should be reviewing their transportation plans regularly. They should be armed with real-time, accurate data to quickly identify alternative routes or modes of transportation that can be utilized to bypass the affected area.”
As of press time, on-time performance for last-mile shipments coming into Philadelphia are already starting to decrease, jumping from 83.6% down to 67.1% in just a few days, according to recent project44 data.
Other things to consider are inflation and the continuous increase in cost of goods, fuel, etc. In fact, total marginal costs climbed to a new high in 2022 for the second year in a row, increasing by 21.3% over 2021 to $2.251 per mile, according to new research from the American Transportation Research Institute (ATRI).
And, though fuel was the largest driver of this spike (53.7% higher than in 2021), many other line items also rose by double digits, such as a jump in equipment costs, worker wages, total costs in trucking and more.
The transportation sector is also sitting at an inverted market for the past 14 months; a cycle that typically should only happen for short periods of time.
& Analytics, explained in a recent webinar with Food Logistics. “It’s going to take a while for that to close. This is why we say we’re in a freight recession.”
However, other data reveals a different story, one that reflects a more favorable outcome for the trucking sector.
Case in point: Earlier this year, FTR’s Shippers Conditions Index (SCI) in March dipped to a reading of 4.5 from the previous 5.1, reflecting slightly less favorable overall conditions. For only the third time since May 2020, all four SCI freight factors—freight demand, capacity utilization, rates and fuel costs—were positive contributors to the index.
“Despite the small decline, the overall story of positive shipper conditions and a stable outlook remains in place this month and are expected to hold firm for the balance of 2023. All four components of the index were positive for the first time since 2020 this month, signaling the lack of pressure in the system at the present time,” says Todd Tranausky, VP of rail and intermodal at FTR.
The real takeaway, Caplice adds, is that “we won’t stay inverted forever because as the price of spot goes down, it’s going to hit the level that makes it unprofitable for a majority of carriers. If you’ve been in this business long enough, cycles happen. They will continue to happen.”
While the trucking industry experiences a freight recession of sorts, the same can be said for ports.
Notably, the ports of Tacoma, Oakland and Seattle have experienced the most significant week-over-week impact, with dwell times increasing by 87%, 43% and 24%, respectively, according to FourKites.
“The work stoppage at the ports will impact manufacturer’s production schedules, distribution and ultimately fulfilling orders to end consumers,” says Tom Gregorchik, VP of industry strategy at FourKites. “As the busy season approaches in the summer, manufacturers need to be more diligent in tracking shipments to ensure a synchronized supply chain and even have contingency plans to hedge bets on different routes and transportation methods to mitigate risk.”
Earlier over the summer, the International Longshore and Warehouse Union reached a tentative agreement on a new 6-year contract covering 22,000 dockworkers at all 29 West Coast ports. Meanwhile, more employees are required at land ports and for road transfers over seaports and intermodal transfers, as outlined in a report by KPMG in association with Association for Supply Chain Management (ASCM).
In fact, inbound ocean freight from Asia dropped 27% in the quarter, while inbound air freight from Asia dropped 50%. And, the Laredo, Texas, land port surpassed the ports of Los Angeles and Long Beach, in October 2022, with $27 billion in trade volume.
“Contract rates move slower than spot rates. We are in what’s known as an inverted market where spot rates are below contract. That is not normal. That usually only happens for short periods of time. We are already 14 months into this inverted market, and as you can see, the gap between contract and spot is only getting bigger right now,” Dr. Chris Caplice, chief scientist at DAT Freight
Yet, what’s coming down the pipeline is another disruption of sorts. As of press time, ILWU Canada is “attempting to aggressively expand their scope and redefine regular maintenance work far beyond what is set out in the industry-wide agreement, which has been legally well established for decades,” according to a press release from the BC Maritime Employers Association (BCMEA),
further stating that “ILWU Canada’s proposals for compensation are unreasonable and well outside the established norm of union settlements in Canada.”
As a result, a union representing port workers in Western Canada officially went on strike, stranding an estimated $12 billion in trade off the ports of Vancouver and Prince Rupert.
El Niño, the weather phenomenon characterized by above-normal warming of sea surface temperatures, is poised to unleash a wave of disruptions to the global food supply chain. According to the National Oceanic and Atmospheric Administration, El Niño conditions were present in May and are expected to gradually strengthen into the winter of 2023 and into 2024.
In fact, by winter, there is an 84% change of greater than a moderate strength El Niño and a 56% change of a strong El Niño developing, according to the National Weather Service.
“Notably, the effects of this weather pattern are not immediate, with production impacts often becoming apparent 9-12 months later. This implies that the effects of the 2023 El Niño could have a prolonged impact,” Nidhi Jain, associate specialist at The Smart Cube penned in an expert column.
At a time when most of the nation is experiencing a drought compounded by effects from the Canadian wildfires, crops are already in a dismal state. Pack on the possible impacts of El Niño, and consumers can expect fluctuations from everything from wheat and canola oil to fresh produce and cocoa.
Many times, it’s the rules and regulations of the road changing the game for fleet managers.
The California Air Resources Board (CARB) announced a Clean Truck Partnership with the nation’s leading truck manufacturers and the Truck and Engine Manufacturers Association to advance the development of zero-emission vehicles (ZEVs) for the commercial trucking industry, which includes flexibility for manufac-
turers to meet emissions requirements while still reaching the state’s climate and emission reduction goals.
“The unprecedented collaboration between California regulators and truck manufacturers marks a new era in our zero-emission future, where we work together to address the needs of both the trucking industry and the Californians who deserve to breathe clean air,” says CARB chair Liane Randolph. “This agreement makes it clear that we have shared goals to tackle pollution and climate change and to ensure the success of the truck owners and operators who provide critical services to California’s economy.”
CARB also voted unanimously to finalize its Advanced Clean Fleets rule, which requires all new medium- and heavy-duty vehicles sold or registered in the state of California to be zero-emission come 2036.
Fleets will continue to modernize and costs will naturally rise as more state-ofthe-art, high-tech trucks are introduced to the market, adds Koepke.
“Electrification of trucks will inch closer to their diesel counterparts, even though they still command a higher upfront investment. Lobbyists, activist groups and industry associations will continue to push back, pointing out that clean emission vehicles still require manufacturing and these manufacturing processes aren’t as clean as the vehicles intend to be. It’s also important to remember that California has often been a bellwether for environmental regulations, and it’s unknown whether other states will follow,” he says.
And, California is not alone.
“Thirteen other states and the District of Columbia have a history of adopting California’s zero-emission regulations. These states will surely be monitoring the ACF in California and evaluating whether it makes sense for them,” says Nate Springer, VP market development at Gladstein Neandross & Associates, and project director of the State of Sustainable Fleets report. “Zero-emission battery electric and hydrogen fuel cell technologies are new to the medium- and heavy-duty fleet industry, so fleets will need as much time as possible to learn the technology and where it does and does not yet fit into their operations, so that they can begin to pilot and adopt.”
Yet, while the ruling is expected to drive more investment and innovation in ze ro-emission drive train options, it may also present new challenges.
“These regulations are designed to reduce greenhouse gas emissions and improve fuel efficiency and require man ufacturers to improve the aerodynamic design of their vehicles. This includes using features such as tractor-trailer gap reducers, aerodynamic bumpers, and side skirts, which can reduce drag and improve fuel efficiency,” says Dan Burrows, CEO and founder, TruckLabs. “However, these regulations also require manufacturers to make significant investments in research and development, which can lead to higher costs for customers. Overall, the Phase 2 regulations will likely drive innovation in the industry, leading to more efficient and sustainable cold food chain logistics. Aerodynamics, tire management, idle controls, etc. become much more critical in zero-emission vehicles as range and weight become bigger factors than in traditional diesel engines.”
Meanwhile, the Federal Motor Carrier Safety Administration (FMCSA) changed its Hours of Service (HOS) regulations to allow expansions to the workday.
“That allowance from the FMCSA is based on operational needs that have been clearly demonstrated at pandemic peaks and even now in a much slower market. Extended hours, especially at certain gateways like LA-Long Beach, will fill a clear market need, and flexible hours of service regulations will allow for more cargo to move overall,” says Lynn Stacy, managing director OEC Group – Liquid Logistics Solutions. “Shippers may have to pay after-hours fees depending on their relationships with a specific port or their provider, but it seems like this change will be [an] overwhelming positive from a freight processing standpoint.”
However, some in the industry express concern that drivers may become over worked, leading to fatigue and higher turnover, Koepke says.
“Historically, 2 hours has been a norm for driver waiting time before detention starts, and leading companies are trying to shrink that to less than one hour or even less than 30 minutes. Automated check-in,
pallet put away and retrieval automation, process layouts and electronic documents are several areas that companies are focused on to keep drivers on the road instead of waiting and idling at their facility,” he adds.
Electrification continues to become more prevalent. In fact, the Infrastructure Investment and Jobs Act (IIJA) allocated $7.5 billion to establish long-distance EV traveling and install charging stations near residences or workplaces.
“Certain heavy-duty applications, such as high utilization material handling equipment and dedicated regional distribution operations are likely to be the earliest heavy-duty segments to transition entirely to battery-electric technologies,” says Springer. “Eventually, we expect to see hydrogen fuel cell vehicles as the zero-emission technology of choice for over-theroad lanes if vehicle and fuel costs become significantly more competitive.”
Yet, there is still a lot of work that needs to be done in infrastructure and technol-
ogy advancement, says Jai Ranganathan, chief product officer, Motive, “but passage of the IIJA and general industry appetite signal this trend will likely only continue to grow.”
And, in the long term, the industry will need to adapt to align to new regulations for sustainability.
“Although many companies are looking into electric vehicles, electrification is currently not the answer to the sustainability requirement in the short term as production of Class 8 EVs and the need for charging infrastructure would not be able to keep up with demand. Cost is also a consideration as many drayage carriers buy third-generation assets with an average cost of $50K. Those carriers would not be able to afford an electric vehicle,” says De Muynck.
Mobility-as-a-Service (MaaS) is also on the rise, making the traceability and transparency of temperature data more important.
“MaaS also supplies a lot of data, and by leveraging the data of what is being hauled and to where, route and load optimization can occur. This in turn would reduce cost by reducing empty miles and reduce overall fuel consumption and carbon emissions,” says Ranganathan.
MaaS, trucking as a service (TaaS), or charging as a service (TaaS) providers of zero-emission equipment will begin to shoulder some of the risk, cost, and complexity of transitioning to ZEVs for fleet operators though.
“Just as in any new service that comes to market, some food and beverage fleets will want to take operations on entirely inhouse and others will outsource significant portions of these activities to providers that can prove reliability and performance,” says Springer.
“For startups in the food manufacturing industry, MaaS does offer an opportunity to scale operations without significant capital investment in fleet and infrastructure by leveraging shared mobility services when needed, but oftentimes, once food products gain traction in the market, they
are acquired by the industry giants and absorbed into their distribution network,” adds Koepke.
Supply chains need to get back in sync in 2023 coming out of the disruptions faced as a result of the pandemic, according to De Muynck.
“We will soon see a shift among logistics executives from strictly transactional perspectives to a more strategic and holistic sense of their function’s role,” he adds.
And, while the market appears to be resettling (even the White House recently expressed claims of supply chain normalization, see page 27), the transportation industry shouldn’t get comfortable.
“Now is not the time to sit back and be idle. Demand has not yet caught up with added capacity, but as carriers continue to make capacity adjustments accordingly, rates will eventually change course. Procuring space may also be much more complicated than it is right now. Shippers, retailers and even suppliers need to be aware that this market will shift. When it
does, it’ll be extremely difficult for anyone that isn’t already prepared,” says Stacy.
Recent current events have posed different kinds of disruptions to the supply chain space, ones that even technology can’t solve.
As of press time, there are several disruptions and bottlenecks impacting the supply chain space, and it’s only July (see page 4 for more).
• Truckers in Florida set to boycott.
• UPS reaches tentative agreement.
• Labor slowdown at West Coast ports.
• Droughts, fires and flooding damaging crops and creating shipping delays.
• El Niño. Enough said.
• Cargo fraud still not under control.
• Russia/Ukraine war still ongoing.
• Poor infrastructure challenging shippers.
Yet, thanks to innovation, optimization and next-level preparedness, trucking and transportation sectors are bracing for impact and in the driver’s seat for what’s ahead.
• The national benchmark contract rate for dry van freight has not increased for 12 consecutive months. At $2.58 per mile, the rate was 70 cents lower than a year ago.
• The DAT Truckload Volume Index (TVI), an indicator of loads moved during a given month, decreased marginally for van and refrigerated (“reefer”) freight and increased slightly for flatbed loads: Van TVI: 230, down 1% from May; Reefer TVI: 167, down 3% from May; Flatbed TVI: 267, up 2% from May.
• On the spot market, the national benchmark rates for van and reefer freight rose while the flatbed rate declined compared to May: Spot van rate: $2.08 per mile, up 3 cents, the first increase in five months; Spot reefer rate: $2.47 a mile, up 3 cents; and Spot flatbed rate: $2.61 a mile, down 4 cents.
Truckload freight volumes and spot rates held firm in June while contract rates fell to their lowest points in almost two years, according to DAT Freight & Analytics.
“The gap between spot and contract rates was the narrowest since April 2022,” says Ken Adamo, DAT chief of analytics. “Rates for van and refrigerated freight increased for the third straight month, and volumes were almost unchanged from May. These are signs that spot truckload prices have reached the bottom of the current freight cycle.”
• The national average van load-to-truck ratio was 2.6, meaning there were 2.6 loads for every van posted to the DAT One marketplace last month. The ratio was 2.5 in May and 3.9 in June 2022.
• The reefer ratio averaged 3.8, up from 3.6 in May and down from 7.0 in June 2022.
• The flatbed ratio fell to 9.7, down from 11.7 in May and 37.6 in June 2022.
In June., U.S. container import volumes decreased slightly compared to May, according to new data from Descartes Systems Group. Although the decline was not as much as in previous years, volumes were higher than pre-pandemic 2019.
• Port transit times decreased to their lowest levels since Descartes began tracking. The U.S. West Coast labor situation appears to be resolved with a tentative agreement between the parties, but the major Canadian West Coast ports are in the throes of a strike.
• The July update of logistics metrics shows slightly stronger import volume performance than previous years and signs that key challenges to global supply chain performance in 2023, such as U.S. West Coast labor relations and port transit time delays, continue to improve.
• June U.S. container import volumes decreased 0.7% from May to 2,081,793 twenty-foot equivalent units (TEUs) vs. June 2022, TEU volume was down 16.1%, but up 6.0% from pre-pandemic June 2019.
• Unlike the first four months of 2023, the growth in import
volume in June accelerated past 2019 volumes by 2.1% for the same period in each year.
fees remain higher as compared to 2020.
• Demurrage and detention (D&D) rates in the shipping industry have reached unprecedented levels, especially with the Federal Maritime Commission (FMC) set to make crucial decisions.
• The pending U.S foreign trade regulator’s decisions on new shipping line regulations “will significantly impact D&D practices.”
• In April, even before the official FMC decision, major carriers contemplated waiving D&D surcharges on weekends and holidays when terminals are closed. The Port of Houston stopped charging import container storage fees during closed terminal gates but raised daily rates in specific positions by 32% beginning May 1.
Average demurrage and detention charges experience a yearon-year decline of 25% in 2023, with a significant 14% decrease compared to the rates in 2020, as found by Container xChange However, there are still 11 ports where demurrage and detention
• Ports in North America stand out as the most expensive when it comes to D&D charges. Leading this list of costly ports are New York, Oakland, and Los Angeles, taking the Top 3 spots.
• The overall average charge has at least decreased by 25% in 2023 and stands at a value of $2,008 per container per day (down from $2,692 in 2022).
Global demand, measured in cargo ton-kilometers (CTKs), fell 5.2% compared to May 2022 (-6.0% for international operations), according to new data released by The International Air Transport Association (IATA).
• Capacity, as measured by available cargo ton-kilometers (ACTKs), rose 14.5% compared to May 2022, primarily driven by belly capacity, which increases as demand in the passenger business recovers. Capacity is now 5.9% above May 2019 (pre-pandemic) levels.
• The global manufacturing Purchasing Managers Index (PMI) indicates an annual contraction of 1.4% in new export orders and a decrease of 5.2% year-on-year in production PMI. This suggests a cooling in global manufacturing demand.
• Global goods trade decreased by 0.8% in April, due to macroeconomic challenges and supply chain constraints. Trading conditions appeared to favor maritime cargo as demand for container shipping contracted by 0.2% while air cargo demand weakened by 6.3% year-on-year.
• The global supplier delivery time PMI increased to 54.5 in May, up from its low of 35 in October 2021, indicating shorter delivery times and some relief for supply chains. However, this is also a sign of weaker global goods trade demand.
• North American carriers saw the weakest performance of all regions for the third consecutive month with an 8.1% decrease in cargo volumes in May compared to the same month in 2022. This was a slight improvement in performance compared to April (-12.4%). Notably, airlines in the region saw the third month of double-digit contractions in volumes on the North America-Europe trade lane (-10.3%). Capacity increased 1.2% compared to May 2022.
• Latin American carriers had the only positive performance in May, posting a 3.6% increase in cargo volumes compared to May 2022. This was an improvement in performance compared to April (-1.6%).
As the world continues to grapple with environmental challenges, the importance of sustainability in foodservice distribution has garnered significant attention—and for good reason.
A recent study by Descartes Systems Group found that, compared to their 2022 study, consumers are being influenced by environmental impacts more when considering food delivery. Roughly 41% of respondents says they regularly make purchasing decisions based on the product or company’s environmental impact and 60% were interested in 100% carbon-neutral options in food delivery specifically. The foodservice industry plays the critical role of ensuring the efficient delivery of food products, so embracing sustainable practices within this distribution process can mitigate environmental impact, reduce waste and minimize energy consumption that lead to greater change.
When it comes to improving the sustainability in the delivery process, it’s important to consider the background. Historically, the delivery stage of food logistics has proven to be one of the biggest challenges in food e-commerce. Juggling sustainability with food safety and cost is a constant balancing act many companies are still ironing out. Options like route optimization, order consolidation, monitoring and tracking and the use of eco-friendly transport are among the improvement tools being harnessed today.
According to a recent report by the Environmental Defense Fund (EDF), electric vehicles (EVs) will provide lifetime cost savings of up to $18,440 and increase as battery prices fall and production improves. In a similar report, EDF found an increase in the future of charging availability. The report lists government agencies, automakers, service stations and major retailers who plan to deploy EV charging stations that will likely result in a nationwide charging network expansion in the United States, for rural and urban areas.
1. Transitioning to EV or hybrid vehicles can significantly reduce greenhouse gas emissions and air pollution associated with foodservice delivery. It also can be cost
effective as the future of vehicle power continues to change.
Dana Krug, VP and general manager at Phononic, explains that EVs are already making strides, including large tractor trailers, to help in the middle mile.
“These giant trucks have massive battery systems where gross vehicle weight and range can co-exist with high energy draw chilling system. With this, you get the sustainability from the electric tractor trailer that offsets the existing chilling system’s adverse effects caused by refrigerants with high global warming potential (GWP),” says Krug.
While these vehicles can offer sustainability in this way, food quantity, safety and labor challenges remain for cost efficiency. Dissecting these issues, a 2020 Hindawi study found that when using EVs in cold chain distribution, “it is necessary to reasonably plan their distribution routes based on the actual conditions (e.g., urban traffic network, client’s time window, power consumption and battery capacity of EVs, and public charging stations) to rationally avoid congestion time periods and reduce the distribution cost.”
The study concludes that with the increase of customers’ requirement for fresh value loss cost reduction, costs can increase but be mitigated through a planned distribution route according to the specific requirements of customers to improve satisfaction.
2. Employing advanced technology, such as GPS and route-planning software, can optimize delivery routes to minimize distance traveled and reduce fuel consumption, leading to lower carbon emissions.
Coupling EV capability with management software for things like route planning and delivery tracking can create the greatest opportunity for sustainable growth in foodservice. Matt Murdock, technical content writer for LogiNext Solutions, describes this software as crucial for the future of the last-mile in food
“The ability to optimize routes for last-mile deliveries offer real-time tracking, payments and more,” says Murdock. “Last-mile delivery software will be the key to resolving challenges faced by the food industry for final-leg of deliveries. Getting the parcels delivered using the best routes will help meet deadlines for 10- to 30-minute deliveries. A last-mile delivery route optimization software will help businesses attain their goals.”
Route planning software also collects and analyzes data, which can provide significant insights into company operations that create room for educated decision making, including sustainable ones.
3. Collaborating with other foodservice providers to consolidate orders can help maximize delivery efficiency, reduce the number of trips and lower carbon emissions.
We’ve learned the valuable lesson of collaboration through years of disruption and unexpected challenges. One great thing to emerge from these trials and tribulations is understanding how working together to consolidate practices can be a gift to all parties involved. In foodservice distribution, consolidation offers sustainable benefits by lowering emissions, planning and relieving space constraints that often lead to alternative modes of transportation and warehousing. Earlier this year, Extensive gave a
growing outlook for collaboration between 4PLs and 3PLs for this very reason. With rising costs and the environment on the mind, this becomes even more pertinent as an option for working together for a greater good.
Further concerns in sustainable food logistics center around food safety and waste. With the strides in software and technology today, the answer is hidden in the ability to monitor. Krug says active monitoring lends the ability to alarm and proactively notify the right person to correct most issues before they result in food waste, or customer dissatisfaction for that matter.
1. Implementing management and monitoring systems can track food products’ freshness, expiration dates and stock levels.
Current regulations, and those of the future, are pushing for more visibility in the way food moves, harnessing technology and data in this way only works to improve further facets of the business. Today, blockchain-backed IoT devices can verify information about the origin of food and automate farming operations that allow distributors to track food in real time. This technology pinpoints the origins and methods of food production, and through smart tracking, can identify waste and operational inefficiencies.
“In the future, I believe with technology advancements and options available to protect food safety that can be provided cost-effectively in a sustainable solution, regulation will push for active cooling that can be monitored with sustainable refrigerants with single-digit GWPs,” says Krug. “As a result, regulators will no longer accept passive cooling solutions with high waste and no control or visibility into food safety temperatures.”
But, this might not be so far in the future. Graham Rihn, CEO and founder at RoadRunner Recycling, explains the basics available now: businesses can collect data on critical factors such as temperature, humidity and location, ensuring products are stored and transported under optimal conditions. Other tech options like waste
metering or dumpster monitoring can be integrated into distribution practices to optimize waste management. Through deploying cameras, sensors and AI-enabled devices in waste receptacles, businesses can collect data on waste generation, fill levels and disposal frequency.
“In the food and beverage industry, this tool allows businesses to measure and track the quantity of food waste across various stages of the supply chain and operations,” says Rihn. “Quantifying the scale of waste allows a clear understanding of the scope of the issue and identifies areas where waste is being generated. These smart metering solutions allow for measurement and analysis of food waste at the point of disposal to make sure that food is actually being diverted from landfills and also to inform how to reduce the production of food waste overall.”
2. Education on energy-saving equipment, practices and partners can foster a culture of sustainability within the organization.
Crafting a knowledgeable consensus for sustainable work, John McCaw, VP, sustainable solutions at Breakthrough, says a growing number of CPG and food industry shippers are turning to the EPA’s SmartWay program for insights on carriers’ fleets. The SmartWay program provides a system for tracking, documenting and sharing information about fuel use and freight emissions across supply chains. It works to support global energy security and offset environmental risks for companies, and countries.
“With this resource, you can effectively identify and choose carriers that not only meet your transportation sustainability objectives, but also meet cost and efficiency requirements,” says McCaw. “Look for partners with a proven track record of documenting and sharing emissions data through the SmartWay program. This will enable you to select carriers based on their sustainability performance across various transportation modes and equipment types, including cold chain. CPG and food shippers have an outsized influence over emissions reduction progress and carrier behaviors. By nurturing carrier partnerships that align with your sustainability goals and leveraging the insights provided by programs like SmartWay, you can pave the way for a more sustainable future.”
The food logistics industry holds so much responsibility. A strategic approach to the everyday work in foodservice distribution can bring about cost effectiveness and build a greener future. By implementing sustainable delivery processes that rid food waste and utilize more operative transportation resources, foodservice distributors can significantly reduce their environmental impact. Anticipated changes in regulations, increased demand for local sourcing and the adoption of green technologies will shape the future of foodservice distribution, requiring businesses to adapt and embrace sustainable practices. By doing so, they can contribute to a more sustainable and resilient food system while meeting the evolving needs of consumers and safeguarding our planet.
Reimagined to deliver a world-class experience for all food distributors, the IFDA Solutions Conference returns Sept. 11-13 in Fort Worth, Texas.
New this year: no higher pricing for non-members! Access industry-leading education and technology at the standard $1,095 rate.
ONE EVENT
SEPTEMBER 11-13, 2023 FORT WORTH, TX
This must-attend event is the home of interactive education designed by and for operations professionals in food distribution.
SIX EDUCATION TRACKS
Your conference badge gets you access to world-class education across six content tracks: transportation, warehouse, talent, technology, retail food distribution, and management. Each workshop session is jam-packed with the info you need to take your team to the next level.
We have 150+ of the industry’s top tech vendors on our expo floor, ready to support your growth strategy.
In today’s world, the traditional image of someone stocking shelves from a neat little box and engaging with customers seems outdated. While the task of stocking shelves remains, the methods of the past are no longer effective. With SKU proliferation, space constraints and labor shortages, running a grocery store has become a challenging endeavor. While there is no magical solution to instantly stock shelves, automation can make a significant difference.
Mixed case fulfillment is a solution designed to help companies operate more efficiently and competitively by creating mixed case pallets that are aisle-ready and compact for transportation. For instance, instead of receiving a pallet of only one variety of cheese, with mixed case fulfillment, the pallet can accommodate multiple varieties like shredded, brick and more. This flexibility addresses the reality of SKU proliferation in today’s market.
Mixed case fulfillment combines multiple automation systems to create a comprehensive solution. It starts with products stored in a high-density case/tote buffer system. The cases or totes are then retrieved and automatically transported to the palletizing station, either manual or automatic, based on their pre-defined sequence on the shipping pallet. The cases
are arranged on pallets by either automatic palletizers or operators at ergonomic palletizing stations. Once the pallets are complete, they are wrapped to ensure stability and then sent for delivery to the store.
While the focus often lies on the mechatronics involved in this system, it wouldn’t be possible without the software behind the scenes. Software enables the system to ensure consistent operations optimized for the specific needs of the store. With the right software in place, changes to pallet building can be implemented quickly, ensuring the right products are available on the shelves when needed.
Mixed case fulfillment is not just a theoretical concept; it is already being implemented in the market. A leading wholesale grocery distributor is in the process of implementing a system that can palletize 165,000 cases per day, with the capacity to reach 200,000 cases per day for future growth.
The pallets themselves will be densely packed and shelf-ready, allowing for quick stocking at stores and creating a safer and more efficient work environment.
This mixed case fulfillment system will feature a high-bay unit load automated storage/retrieval system (AS/RS) for pallets, a multishuttle for case buffering and sequencing, and palletizers to automat-
ically build mixed-case pallets. Additionally, a goods-to-person piece picking module will be integrated to handle smaller order quantities. The entire system is controlled and operated through software to ensure consistency and visibility.
Sustainability is a crucial consideration for businesses across sectors, including grocery. While there is still work to be done, solutions like mixed case fulfillment can contribute to reducing carbon emissions by maximizing space in available trailers. By doing so, the number of trucks needed on the road at any given time can be reduced, resulting in up to an 18% decrease in transportation costs.
It’s challenging to know if mixed case fulfillment is the right choice, as each retailer has unique needs. However, it is an automated solution that can drive operational improvements throughout a facility, addressing the most pressing challenges.
ABOUT THE AUTHOR BY MATT BRAYMAN VP, solution development, Americas, DematicThe White House released claims that today’s supply chains are more fluid and resilient since COVID-19. “Today, we see increased access to transportation and warehousing capacity and equipment, solid throughput at the ports, improved delivery times, greater ocean shipping reliability, and steady declines in transportation costs,” according to a press release from the White House. And, while “the onset of the pandemic in early 2020 caused a large, negative shock to both supply and demand,” as outlined in a separate White House blog, “the high correlation between [Producer Price Index] and supply chain pressures suggests that the easing we are seeing in supply chains may continue to show up in measures of inflation.”
Some key points are:
• The nation’s ports moved record levels of cargo in 2021 (25.8 million units) and 2022 (25.5 million units) through increased collaboration across the logistics industry, which has helped reduce the significant backlog of anchored vessels from a peak of 155 to roughly a dozen in May 2023.
• 92% of goods at grocery and drug stores are in stock—above where they were pre-pandemic.
• There are over 120 new trucking firms with Registered Apprenticeship programs to help attract, train and retain talent in this critical sector.
• The New York Fed’s Global Supply Chain Pressure Index has eased off of its highest level on record. This has happened alongside a historic surge in East-West ocean shipping prices, which have fallen by roughly 90% since their peak in September 2021, as well as a 30% drop in gas prices since their summer 2022 peak. Moreover, annual core goods inflation has fallen more than 65 % since its peak in February 2022.
To get to this point, President Biden signed Executive Orders and took on comprehensive reviews on various aspects of the supply chain in order to get to this point.
For starters, on Feb. 24, 2021, President Biden launched a 100-day review of supply chains critical to national security, public health and public safety. The review targeted four key industries—semiconductors, critical minerals, pharmaceuticals and electric vehicle batteries.
Two years later, more than 70 recommendations across the report have been completed to date—from providing financing across the full battery supply chain to leveraging the Defense Production Act in historic ways to diversifying supply chains by supporting small- and medium-sized businesses. Spurred by President Biden’s Investing in America agenda, the private sector has invested over $470 billion in manufacturing of semiconductors, electric vehicles (EVs) and EV batteries, clean energy technologies and pharmaceutical and medical products.
Last year, the Biden Administration also developed Freight Logistics Optimization Works (FLOW), designed to tap supply chain visibility and information sharing to keep goods moving throughout the supply chain.
As of late last year, the number of participants has doubled, and existing partners having begun securely sharing data with USDOT for the first time, according to the U.S. Department of Transportation.
The largest impact though has been the improvement in port infrastructure. Late last year, the United States Department of Transportation Maritime Administration
announced $703 million in grants to fund 41 projects in 22 states through the Port Infrastructure Development Program, the largest amount than any year in the program’s history.
More than 60% of the awards will benefit ports in historically disadvantaged communities and several of the projects will help reduce emissions at the ports through electrification. Additionally, more than $150 million in awards include a focus on electrification of port equipment to reduce emissions and improve air quality; and nearly $100 million for port projects that will advance offshore wind deployment. The funding, made possible by the Bipartisan Infrastructure Law and additional Congressional appropriations, will benefit coastal seaports, Great Lakes ports, and inland river ports, helping improve supply chain reliability through increased port capacity and resilience, more efficient operations, reduced port emissions, and new workforce opportunities.
Select grants include the JAXPORT Express Project, Cleveland-Cuyahoga County Port Authority, Port of Camden Access and Infrastructure Resiliency Project, Salem Wind Port Project and more.
All this being said, actions are in place to keep supply chains moving, and money is becoming available to help fund many of these initiatives. Regardless of supply chain visibility—or sometimes lack thereof—normalized supply chains are here.
There is no doubt across the freight community in the fallout from COVID-19, there remains a significant demand for improved efficiency and operation control. Heading into 2023, concerns about freight rail service are already setting off alarm bells, including a narrowly avoided strike with a supply chain running on life support. The problem is so severe that CNN recently reported, “Many of the problems tangling up the supply chain, driving up prices and slowing the economy can be traced to the steady decline in freight rail service in recent years.” Operational control and efficiencies remains an obstacle for much of the industry.
It is no secret that U.S. rail systems have been falling behind their global and European counterparts for decades. Even for something as rudimentary as Wi-Fi, the current bandwidth aboard American trains continues to fall well short of customer demand across the country. But thinking beyond customer rail, freight runs on networks and relies on high-speed operations to run smoothly and correctly. Having access to reliable gigabit broadband along the wayside, loading stations and on-board trains would enable these services and allow for freight to potentially leap ahead of rail in Europe.
The reality is that freight rail cannot wait for the long overdue investments necessary to deliver the broadband capacity it needs to meet its latent demand now and in the future.
One proven solution designed specifically for railways is rail-5G, a safe, wayside internet network for trains, stations, staff and communities. A series of poles and antennas are mounted along the track to ensure direct line of sight and 100% coverage for an “always-on” connection, whether the train is in a tunnel, crossing a bridge or in deep countryside. Rail-5G requires no profound structural changes for deployment to the railways and can be deployed on existing infrastructure. The beamforming antennae can be deployed
on self-powering poles to give operational systems, railroad assets and passengers access to an average of 1Gb/s, or more, of continuous connectivity expanding the operational capacity. Rail-5G is currently the world’s first and only solution deployed on operational railways, capable of delivering over a gigabit of bandwidth and being solar-powered as the most cost-effective technology dedicated to the railroad. This technology and fully integrated solution were born out of a desire to finally meet customer demand to drive reasons to use rail. But this innovation can equally be scaled to best meet the needs of freight rail. Having already deployed rail-5G in the UK and Spain, it is no longer an issue of capability but cost and having been developed by rail experts for the railroad, rail-5G has been designed to be a fraction of the cost of mobile data services. Compared to traditional mobile providers, rail-5G offers a new way of looking at gigabit connectivity to power Wi-Fi along train routes. Along with access anywhere for additional safety, operational system, station Wi-Fi and poorly served local communities. This will be a game changer for freight rail, where their operation capacity and automation can rely heavily on access to broadband networks and perform seamlessly at the same time.
Knowing that the technologies used today are often locked in for decades to come, evolving with the times is critical
for all industries, including rail. Part of that evolution is also ensuring that new innovations are not harmful to the future of the planet. Much like American car companies have long started shifting focus from gas to electric-powered vehicles, the time has come for the decarbonization of the railways to make the shift to sustainable and net-zero-compliant infrastructure and technologies. As the United States begins implementing President Biden’s Infrastructure Package and transforming its rail systems, there will be both an opportunity and a need for an innovative, globally collaborative and sustainable connectivity solution for U.S.railways.
Modernizing America’s infrastructure means futureproofing its technologies for generations. Rail-5G comes with proven safe installation methodologies and techniques such that it can be added to routes without causing major service disruptions.
Rail-5G has the potential to revolutionize transportation for both the consumer and freight rail. As the United States modernizes its infrastructure, and with it its telecoms, rail-5G is a formidable solution that ticks all the key boxes of sustainability, deliverability, affordability and meeting customer demand for years to come.
I’m almost certain this won’t be the first article you come across this week talking about ChatGPT. Since its release back in November 2022, the OpenAI bot tool has been taking the news, and the world, by storm. According to Business Insider, chat bots like GPT are powered by large amounts of data and computing techniques to make predictions that string words together in a meaningful way. From creating meal plans to teaching physics, this technology has been dubbed the “smarter Google” by many, and industries are taking notice.
So, what about its use in the supply chain and logistics sector?
We continue to see the rise of artificial intelligence (AI) in the supply chain space due to the process capabilities that save time, money and create in-depth reporting for data use. According to Priyesh Ranjan, CEO of Vorto, AI is well-suited for the environment of logistics, which is often in a state of constant evolution, as new variables are introduced and disruptions continue to arise.
“The dynamic and interconnected supply chain forces constant communication between shippers, carriers and suppliers for ordering products, scheduling ap-
pointment times, communicating with the carrier about delivery, solving for unpredictable but inevitable problems that arise in transit and communicating with the shipper and the receiver about delivery,” says Ranjan. “We believe ChatGPT would be a superior tool for dealing with that dynamic communication and solving for logistics challenges quickly and optimally across the separate but interconnected domains of shippers, suppliers, warehouses and truckers.”
Utilizing ChatGPT as resources to predict and plan for delays, as well as strategy, could prove beneficial specifically for shippers and suppliers, where communication needs timely answers to offer a seamless service. The supply chain depends on complex communication in order to keep each moving part on track—from supply, shipping, storage and last-mile.
Ranjan explains, “These domains are each individually complicated and nuanced, and the frequent crossover causes challenges because communicating effectively and at a high level to solve problems is so difficult; ChatGPT can bridge these divides across domains and raise the level of communication to levels that will allow for better outcomes.”
And although this seems futuristic enough, the possibilities for the future of AI technology like ChatGPT or others that come along is hard to predict.
“Because OpenAI is so powerful, we are unable to predict all the knock-on effects which could substantially reorder and disrupt supply chain,” says Ranjan. “Since supply chain is at the core of the trade and commerce that impacts everyone on the planet, supply chain will be where we experience some of the most far-reaching impacts from OpenAI. Think of how the COVID-19 lockdowns briefly disrupted supply chain and how that led to toilet paper shortages. Likewise, the potential impacts from OpenAI on supply chain will be vast, unpredictable and experienced by everyone.”
Though the use of ChatGPT for one case or another is varied, the options truly aren’t known until you try. As for job security and the fear that ChatGPT could fill the spot of a human worker, the current technology, known as “large language model tools,” doesn’t have the sentience that people do—and that means, at the end of the day, there will always be a human behind the technology, offering the key knowledge and “feelings” in its utility. At least for now.
Lift truck operator assist systems (OAS) are often misunderstood. Just another telemetry tool? A magic wand that makes equipment capable of operating itself? Or a cumbersome tool that gets in the way of productivity? High employee turnover and labor shortages continue to strain food distribution and cold storage operations, exacerbating the risk of safety incidents and making it even more imperative for businesses to understand and consider technology tools engineered to enhance operator awareness and adherence to best practices.
Myth #1: OAS is just another name for the telemetry systems that lift truck manufacturers already have on the market.
Reality: The truth is that OAS is an umbrella term that encompasses a variety of products and technologies designed to do exactly what the name suggests—assist operators. It includes telemetry and aids like pedestrian awareness lights and alarms, automatic slow-down, lift lockout and so much more to help operators adhere to best practices that support safety and efficiency.
To further distinguish, telemetry captures and reports lift truck status and usage, providing the data to inform a more reactive approach to managing operator behavior. Features that enable truck monitoring and operator access control can make telemetry an especially useful tool for food distribution operations that need to take steps to enhance visibility and traceability of food products under the Food Safety Modernization Act. Digitization and enforcement of OSHA pre-shift checklist completion can also help isolate potential problems. Other OAS features, however, can take a more active role, providing operators
with real-time alerts and automatic performance limitations based on the real-world operating environment, equipment status and load. Further capabilities include line of sight support, location-based fork height restriction, speed controls and more.
Myth #2: Having an OAS installed on your truck can risk reduced productivity and decreased throughput.
Reality: OAS is capable of supporting site-specific initiatives AND maintaining productivity, as opposed to prioritizing one at the expense of the other. In fact, fast-paced e-commerce warehouses are well-represented among early adopters of OAS.
In fact, some solutions thrive in warehouses with high throughput expectations. For example, some systems feature in-aisle muting. While lift trucks could be subject to performance reduction if they are in close proximity in main thoroughfares, the narrow nature of tight warehouse aisles means equipment cannot maintain the same distance. In practice, the in-aisle muting capability can allow two trucks to work in the same aisle without slowing each other down.
Myth #3: OAS is typically limited to ultrasonic technology for object and pedestrian detection, so it cannot register all potential hazards in the environment.
Reality: Many companies and OEMs use different technologies to detect objects, pedestrians or both. Technologies such as lidar, ultrawideband (UWB) and ultrasonic are all ideal for these applications. Some OAS solutions can use either single or multiple means of detection, depending on the goals and needs of the specific warehouse application.
Myth #4: Object and pedestrian detection only work in the path of travel and if the object or pedestrian is standing straight up or vertically.
Reality: While vision technologies like lidar and ultrasonic sensing can detect obstacles in the direction of their orientation, trucks equipped with certain OAS can be configured with multiple sensors to enable detection in the appropriate direction. But what about unseen obstacles, such as a truck hidden inside of racking?
Some systems offer line of sight support that uses UWB technology to account for and react to objects
equipped with a powered badge within a certain radius. Lift truck speed can be slowed to a crawl based on locationspecific rules to discourage operators from entering certain areas, such as designated pedestrian zones, aisles, doorways and tunnels.
Myth #5: OAS reduces truck performance only to avoid obstacles.
Reality: Another hazard is operators traveling quickly around corners, risking a tip over. While some OAS offerings may reduce speed when making turns, certain systems offer true lateral stability when cornering, decelerating equipment based on the combined center of gravity of both the truck and load.
Myth #6: OAS provides only audible and visible alerts.
Reality: Most OAS solutions deploy beeping sounds and flashing lights for various situations, but those can get lost in a loud and busy warehouse environment. What if alerts went a step further, enabling operators to “feel” what’s happening?
An advanced OAS adjusts the truck’s performance in real-time, alerting operators through the feeling of performance reduction, such as limited speed or an inability to raise forks. For example, when entering a zone designated as having heavy pedestrian traffic, the system proactively reduces travel speed to help alert the operator and improve situational awareness.
Myth #7: An OAS can expand load capacity, allowing trucks to go beyond their maximum load capacities.
Reality: OAS does not enable extra load capacity. Instead, these systems help lift truck operators avoid lifting loads that exceed the lift truck’s capacity limit.
Some OAS offer a feature that automatically stops lifting if load weight exceeds the truck’s threshold. Rather than simply telling operators they are lifting a load that is too heavy, such a system actually prevents them from doing so.
Myth #8: OAS only applies performance controls based on other trucks,
objects and pedestrians connected to the same technology.
Reality: While an OAS can use a network of ultra-wideband tags to sense equipment, personnel and infrastructure, a technology like lidar can offer an extra layer of detection to sense obstacles in the path of travel even if not connected to the same network of tags.
OAS technology helps warehouses boost efficiency and adherence to lift truck operating best practices. But as with any new technology, figuring out what makes sense for your food distribution operation requires digging into details.
These days, there are several glaring problems that most folks in the supply chain notice but aren’t quite sure how to tackle. The solutions require investment, but not addressing them can require even more in the end such as lawsuits, employee safety and valuable time. Ultimately, safety will keep you in business.
It’s no secret that loading docks are challenged with more safety hazards than nearly any other part of a facility. According to OSHA , 25% of all warehouse accidents occur at the loading dock, and for every injury, there are 600 near-misses. But despite this knowledge and the serious safety issues that loading docks present, many businesses are still struggling to sufficiently address challenges.
Here are some of the most common mistakes and tips for how they can be avoided.
1. Not using restraints or not using them to their full capability.
Restraints grab the back end of a truck and hold it in dock position. When used properly, the driver can’t accidentally drive away, and there’s no chance of a forklift being left on the truck. More accidents happen in this situation than anywhere else, but danger is easily avoided by adding restraints and training employees on full, proper and consistent use.
2. Skipping dock levelers.
The safety mechanisms involved with dock levelers were invented solely for this purpose, but many times are overlooked. It’s important to remember that your dock leveler will not engage with a truck unless the restraint is locked into the truck. Specifically in the cold storage industry, improper dock leveler use creates more opportunities for energy to leak out and pests to potentially get in. Creating a sequence of safety, related to the dock position and ensuring this process is followed consistently can reduce the risk of injury and financial losses from lawsuits.
3. Too many boots on the ground.
In most facilities, when a trailer backs into a dock, someone has to go outside to open the trailer doors. This puts people in harm’s way of truck and forklift traffic, and many drivers aren’t prepared to look out for people walking in the yard. Utilizing a vertical storing leveler mounted inside the building allows the truck to back in completely without someone opening the doors in an unsafe position. The fewer boots on the ground, the less likely you are to experience injuries.
Companies only get so much capital each year, and this often leads facility managers to purchase the cheapest option to get through another 1-2 years, but it isn’t always the safest option. Invest that money in hydraulic levelers, so there’s nothing to work around under the dock leveler. If you have to work around springs, hinges, airbags and other moving parts, you’re increasing the number of pinch points, likelihood of injuries and risk of fatalities to employees. Installing better equipment may have more upfront cost, but it will last longer and reduce the need for replacements.
Most facilities have dock doors positioned everywhere, with older technology that hasn’t been updated. To make these facilities safer, more efficient, last longer and more appealing to customers, consider the best use of your space. Moving to vertically positioned dock levelers will create a safe, efficient, cleaner environment.
Everything has a cost associated with improvement. You might not have the resources to make all of these changes at once, but you also don’t have the capability to handle a costly lawsuit.
Remember, there are always financing options available to help make these investments and improvements possible without having to immediately tap into capital. Consider finding an expert partner or vendor that has deep experience in this sector.
ABOUT THE AUTHOR
WES LEDFORD national account manager, Miner Corp.While it’s important to build each other up for professional accolades daily, International Women’s Day set the stage for celebrating women in various roles, many in the supply chain, trucking and transportation space.
In the supply chain, women have gradually started filling more and more spots traditionally dominated by men. A 2018 Gartner survey showed this progression from 2016-2021, where women in supply chain roles increased from 35-41%.
In 2022, the Women In Trucking index found that 36.7% of leaders in the transportation field are female and about 13% of the driving workforce itself is female.
And, recently, data from Women in Trucking reveal on average, 12.1% of overall professional drivers hold commercial driver’s licenses (CDLs) .
But with initiatives promoting women to join the industry and working to improve their experience in those positions, the numbers are only expected to climb.
Empowering women to take on professions outside of the “norm” comes in many ways.
One of the first and most important is open dialogue and communication that seeks to collaborate and teach the community the importance of diversity in the workforce. Specifically in trucking,
it’s imperative that women teach girls and young professionals that this career option is available—and viable—early on.
Candace Davis, owner-operator of Davis & Davis Transportation LLC, says “recognizing the value of women in trucking rests on the ability of women doing the job as effectively and efficiently as anyone else. It’s imperative that a female presence is known, assisting the global shift of transportation. We must work together to meet common goals, create positive outcomes for everyone and understand all are valuable.”
From the leadership and C-suite level to the seats behind the wheel, both women and men alike, leading and encouraging other women remains the driving factor (pun intended) to moving the dial toward more diversity and equality in transportation.
“If I could tell young girls who may be intimidated by this industry anything, it would be that you are enough and your voice is valued. Although being a woman in the workplace can be difficult, keep moving forward because other girls are watching,” says Erika Iznaola, head of treasury at Super Transport International (STI), whose truck driving force is about 13.7%, a growth of about 3.7% since 2019. In an interview last year, STI truck driver Dora
Santillan explained how women can change the statistics of drivers by being proud of their work and “going for it without letting anything stop you.”
Moreover, creating spaces where the female perspective in the supply chain can be heard is a great way to share testimony that improve experiences.
Although International Women’s Day only happens once a year, these ideals are universal and meant to be implemented in the day-to-day workforce. If we remain dedicated to education and communication about the uniqueness women can bring to a workplace, we can inspire more women to keep on trucking, through all facets of the supply chain.
Last year, Food Logistics launched the Women in Supply Chain Forum to do exactly that. The conversations there reflected on self-advocacy and collaboration, especially with male counterparts that can offer mentorship and sponsorship for women. This year, the Women in Supply Chain Forum hopes to compound upon those themes, celebrate gender diversity and work to improve the future of women in the industry.
Go to www.WomenInSupplyChainForum.com to learn more about the Women in Supply Chain Forum and help inspire women to keep on trucking.
THIS YEAR’S WOMEN IN SUPPLY CHAIN FORUM FOCUSES ON BETTER TOGETHER: HOW COLLABORATION PROMOTES WOMEN IN SUPPLY CHAIN. EXPERTS WILL DISCUSS WAYS TO BUILD A BETTER SUPPLY CHAIN INDUSTRY WITH TOPICS SURROUNDING:
WE LOOK FORWARD TO SEEING YOU IN ATLANTA!
DATE: NOVEMBER 14 & 15, 2023
LOCATION: HOTEL COLEE, ATLANTA BUCKHEAD - ATLANTA, GA
CREATE POWERFUL CONNECTIONS AT THE WOMEN IN SUPPLY CHAIN FORUM