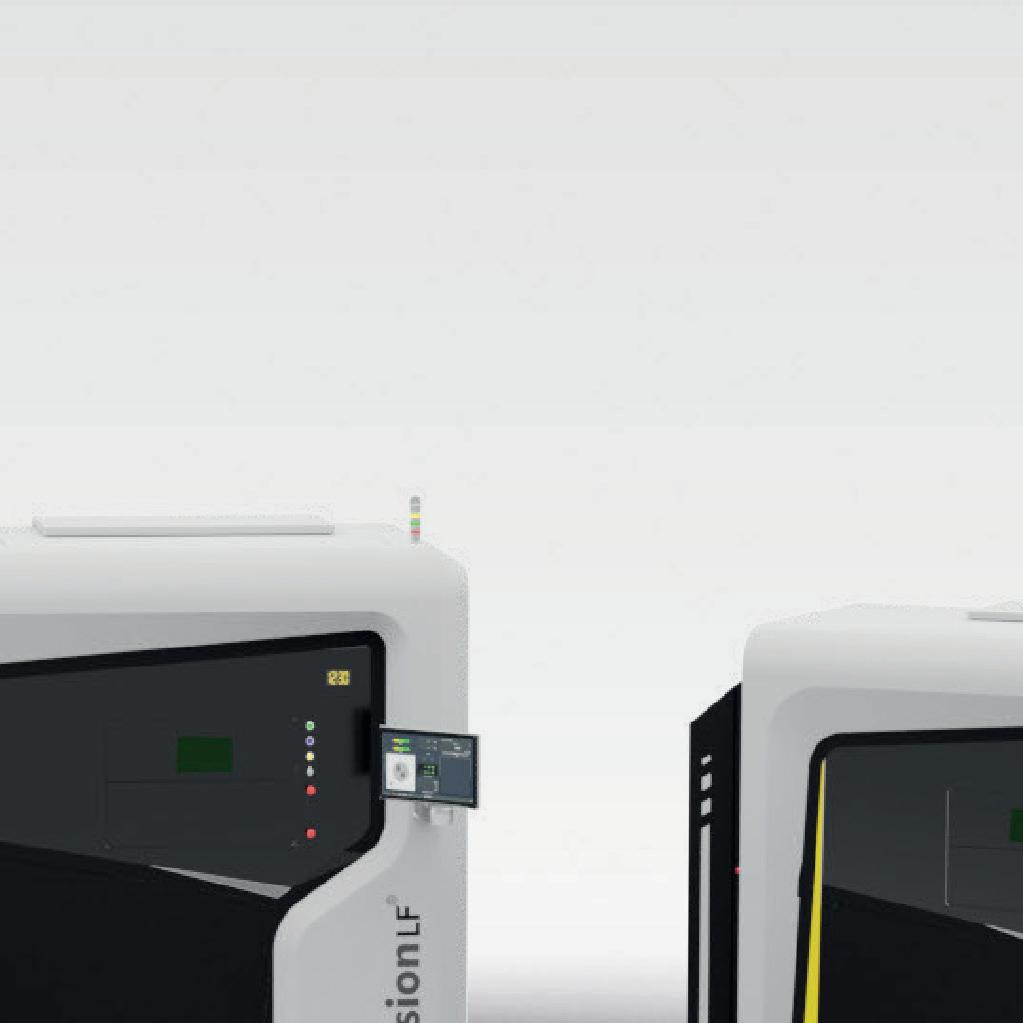
7 minute read
A NEW ENERGY
WORDS: laura griffiths
The UK government has ambitions set on delivering 24 gigawatts of nuclear capacity by 2050 as part of its new energy security strategy. The Nuclear Advanced Manufacturing Research Centre (Nuclear AMRC), with its base in South Yorkshire and specialist manufacturing centers around the UK, is exploring how advanced manufacturing processes may help us to get there. Additive manufacturing (AM) is one such process and Udi Woy [UW], Nuclear AMRC Additive Manufacturing Technology Lead, who is responsible for developing the center’s strategy for AM and AMfocused projects, recently spoke to TCT about the center’s work with DED, where AM is uniquely equipped to meet the demands of the nuclear market, and future application opportunities.
TCT: Hi Udi. Tell us about the types of AM technologies you’re working with at the Nuclear AMRC.
UW: Predominantly we use Directed Energy Deposition (DED). PBF (Powder Bed Fusion) is also of signifi cant interest but our emphasis is on DED because of the fl exibility and ability to scale. When you're looking at large-scale or ultra large-scale products and parts, one of the main considerations from an R&D perspective is to investigate the scaling factors because it has a signifi cant bearing on the industrial relevance of our outputs. With AM, you don't have a linear relationship between inputs and outputs. If you're going to make a small part, you concentrate a lot of heat in a small area. But when you're building a much larger part, you're concentrating heat locally but over the scale of the build. If you're using DED, even if you're using powder bed, you're cooling at diff erent rates, you're heating at diff erent rates. That has implications even beyond the localized heat input so if you're looking at your design requirements, you have to scale that appropriately.
One of the things we were quite clear about at the start were bulk additive manufacturing applications. The emphasis on bulk meaning we’re appropriately scaling the research, the requirements, the parameters, we’re appropriately controlling all of the factors that are of interest in industry so when they come to adopt the process and take the parameters, it's immediately relevant to the work that they want to do.
TCT: Can you share any examples of where AM is being used in the sector currently?
UW: The trajectory is similar in some respects to those of other industries where you usually start with prototyping and tooling applications but there are also opportunities to fabricate high entropy materials, which are generally challenging to process but off er the desired combination of characteristics that are required for critical parts and components. We're quite interested in developing qualifi cation procedures around not just the application but also the alloy. For instance, on one of the projects we've been investigating 316L and we've produced debris fi lters, which are usually used in fuel assemblies. It's got a network of holes and features that make it challenging to fabricate using traditional approaches without the right sort of tooling, which is expensive to do and so there is interest in using AM to manufacture stuff like that.
On the other end, we are looking at obsolescence issues and legacy parts. For legacy parts, it's a bit more challenging because it's already been in service so you want to preserve the properties and the performance, you're essentially restoring it or maintaining it to continue being used in service. It's not like starting on a blank canvas where if you make any errors, you can maybe scale it back and start again, these are legacy parts and the industry requires solutions to ensure that plants are operating at optimum capacity and doing so effi ciently.
In terms of where AM could be used is in addressing the requirements for obsolescence
LPBF
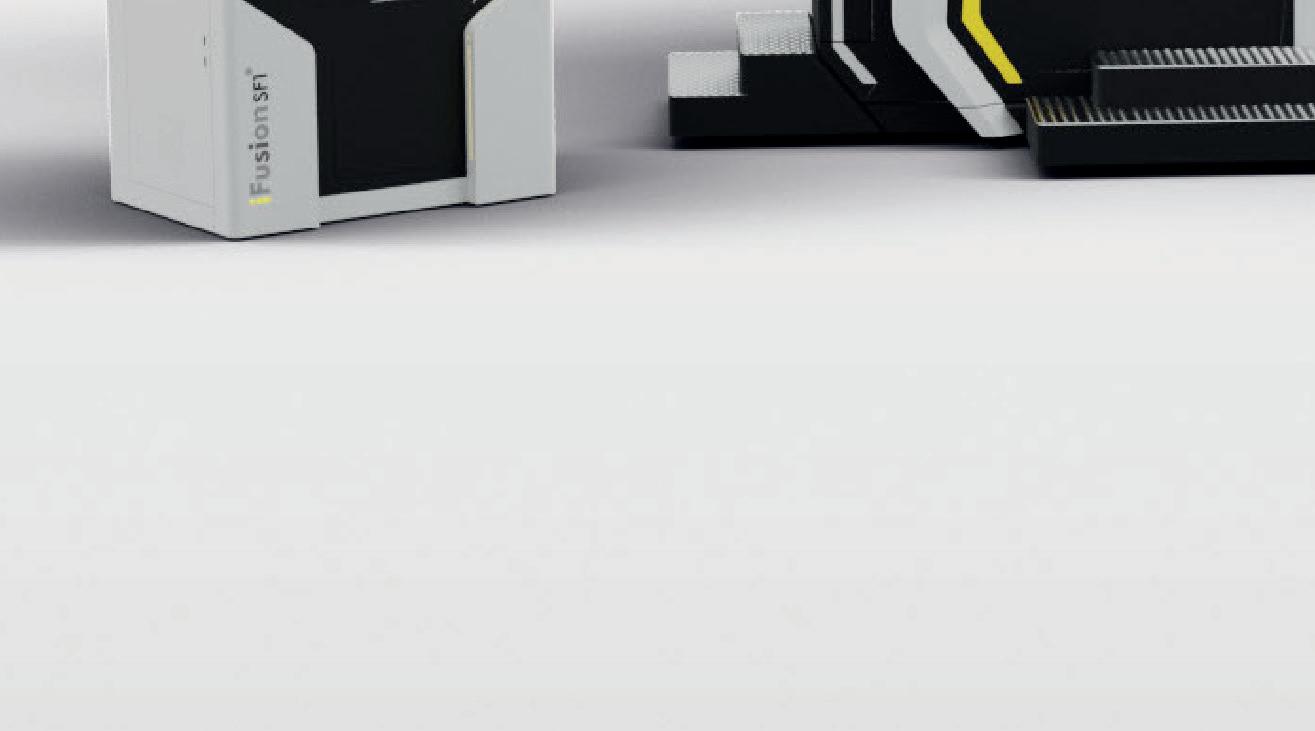
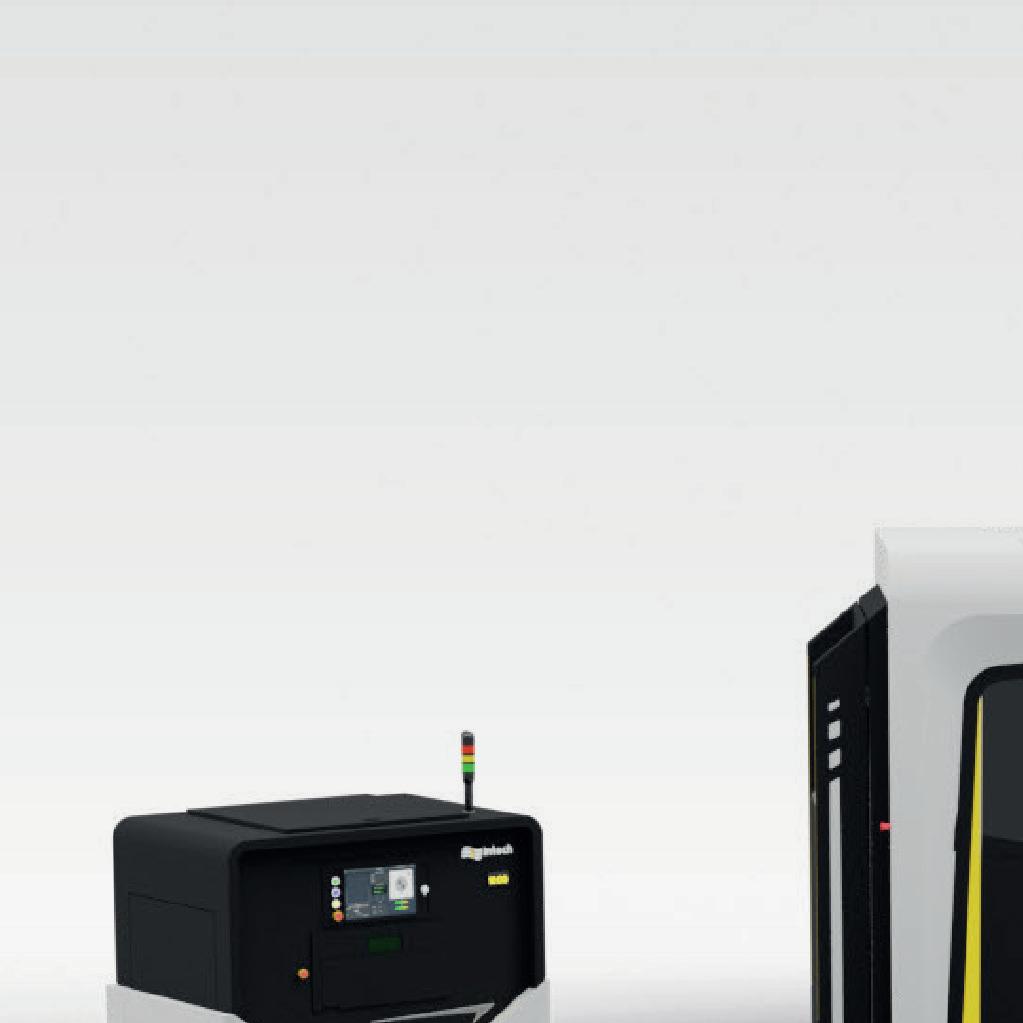
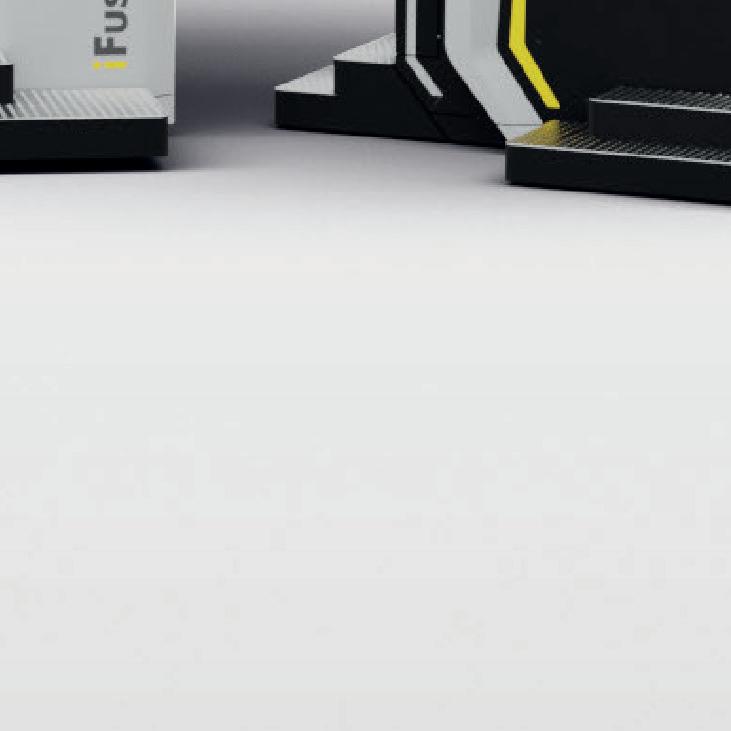
and management of legacy parts. I said could because we're not there yet because current applications are in prototyping, tooling. The older the component, the more stringent the regulations to ensure that it satisfi es the requirements for safety and performance.
TCT: On a panel at TCT 3Sixty, you spoke about opportunities around designing AM parts for maintainability. How signifi cant is redesigning for AM? Or do certifi cation requirements make those redesign opportunities a challenge?
UW: With AM, it's not like a traditional part where you have homogenized materials from which you're maybe machining. With AM, you're creating the material and even though it looks similar, it doesn't mean it's comparable. In nuclear, the whole point is to ensure that critical requirements have been met and in terms of qualifi cation, that your material and your product complies or is equivalent to existing codes and standards for similar products. But the approach for demonstrating compliance or equivalence is where you have a lot of work in the creation of standards and implementing nuclear design codes and standards for additive because some may be transferable, in terms of maybe the base material or if you're using wire for DED, but there are other elements that are specifi c without any basis for comparison.
I think durability and maintenance go hand in hand because when you want a part to last for 60 or more years, then you need to be able to maintain it for that length of time. In order to understand how it behaves, then you're looking at fatigue because over time, things wear and tear. In addition to your normal wear and tear, you're also looking at your operating environment so that adds an interesting dynamic to an already interesting situation where you have to think about your long-term implications for design for manufacturing and for maintenance.
TCT: You also talked about the sustainability opportunities, particularly around large structures. Can you elaborate?
UW: You need heavy engineering and plans to forge the reactor pressure vessels and you need special tooling and methods. AM is currently used for prototyping and tooling in the industry so that's another way to look at sustainability, rather than the traditional methods of making tooling, we can explore new methods. Some of the research I've been doing with another partner is on how we stack diff erent types of materials and use AM to layer it or get the fi nished dimensions to be more creative in the way we apply the technology. I think the most important question is, how can we further exploit the potential of advanced manufacturing technologies to deliver the manufacturing effi ciencies that are so desperately needed to address present and future challenges? I think, for instance, deploying AM for advanced on-site fabrication of large structures. There are so many things we could do but the question is, how can we further exploit it? I don't think we're where we would like to be but I think we're heading in the right direction.
TCT: Where might AM capabilities need to improve in order to meet the demands of the nuclear sector?
UW: I think that work is ongoing, developing standards and submitting code cases but we have to substantiate the outputs on which these code cases and standards are formulated. In terms of the factors that would really help is a combination of skills training and experience. This is essentially looking at the challenges facing the sector and how AM can help. When I did my apprenticeship, I was handed a toolbox and I had to make the tools that went into it but our CEO talked about how he had to make his own toolbox and the tools. Now the next generation has the potential to print the toolbox and print the tools that go into the toolbox. So, I think it's just attracting the next generation of potential nuclear professionals and AM is such an attractive technology because the ability to really create what you're thinking, you can eventually review those designs, but the ability to start there, it creates that freedom for the next generation. I think that's the most important going forward because nuclear is not a short-term thing. It's a long-term approach and strategy. Part of that strategy is not just for the now, it's for the next generation, and the generations that have come before. How do we bring it all together? I think AM has the ability to unify all of these perspectives around a single technology and approach for working. It opens up the world of possibilities, but you have to start somewhere and AM is an accessible way of starting that journey and introducing the next generation to the whole world of nuclear manufacturing because the goal is to deliver clean energy for future needs.
[Editor: Answers have been edited for brevity and clarity.]