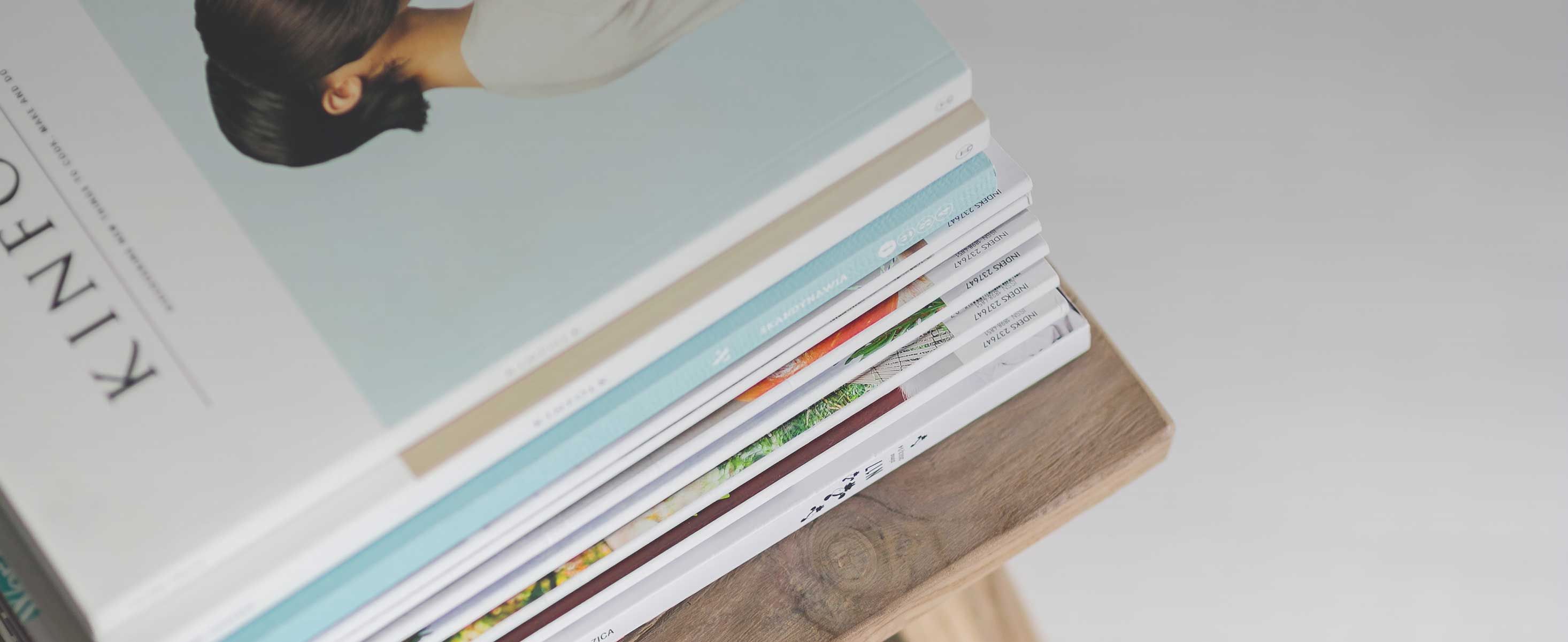
6 minute read
THE FACTS OF LIFE
WORDS: SAM DAVIES THE FACTS OF LIFE
The subject of climate change is now a mainstay of our news cycles. Whether it’s protests by activists, pleas from campaigners or the policies (or lack thereof) set by governments, rarely a day goes by without the theme debated or the latest developments reported.
In additive manufacturing (AM), it is not quite a daily occurrence, but the soundbites in interviews and declarations in marketing messages aren’t exactly rare. Through TCT’s editorial and conferencing channels, we have covered the topic extensively, platforming those who believe AM can be used to boost the sustainability of products, and those who warn of potential greenwashing.
As recent extreme weather events would suggest, it is important that AM, like any other manufacturing sector, gets it right.
In 2019, Sintavia led the charge and set up the Additive Manufacturer Green Trade Association (AMGTA) - read our Q&A with the AMGTA's Sherri Monroe on page 35 to learn more. In establishing the AMGTA, Sintavia CEO Brian Neff suggested that while the AM industry focuses on its cost and time benefi ts of the technology, less emphasis is placed on the ‘very real environmental benefi ts of AM over traditional manufacturing.’ That point may be up for debate, but from the outset, the AMGTA aimed to raise awareness of said benefi ts… in good faith.
To do that, the organization was to commission its own research eff orts, and as of this year, award those members of its organizations that did the same. In May, the AMGTA handed out 27 awards to 20 of its member companies – including 6K Additive, EOS and Materialise, all of whom have recently carried out lifecycle assessments (LCA) on 3D printed products.
“We want data-driven decisions,” 6K Additive President Frank Roberts told TCT. “Our goal is, ultimately, we want carbon neutrality. The only way to understand how to get there is to generate the data and benchmark, so that was the fi rst step. But other companies are starting the process – some are doing more ESG (Environmental, Social & Governance), some are doing LCA – but the fact that people are talking about it, I think it’s awesome. I spent a lifetime in wrought products, and no one really talks about it, so it’s exciting that that’s now happening. But getting the data is key.”
Getting the data is what 6K Additive has sought to do via Foresight Management, which recently carried out two LCAs on behalf of 6K. While a titanium material processed with UniMelt was found to use up to 76.7% less energy and produce up to 78.4% fewer carbon emissions compared to plasma and gas atomization processes, its nickel material faired even better. Measuring UniMelt against induction furnace gas atomization for the nickel LCA, Foresight Management reported that UniMelt used 125kg of material for 100kg product compared to 400kg with the gas atomisation process, while also only using 6,265 megajoules (MJ) of primary energy and 5,135 MJ of non-renewable energy compared with 69,780 MJ and 58,759 MJ. This is said to amount to a 91.5% reduction in global carbon emissions.
When carrying out LCAs, vendors like 6K Additive typically seek to outsource the testing of processes to third-party organizations that have no dog in the fi ght. Then, the organisation will make a holistic assessment of a process, considering, for example, the extraction and raw processing of raw material, the inbound shipping, the printable powder production, and the distribution of the fi nal product to the customer. The information gathered here can then be used to either promote the sustainability benefi ts of a product and its manufacturing process or to guide the relevant parties in fi nding ways to mitigate whatever issues have been highlighted – often bringing things into scope that hadn’t previously been considered.
As LCAs become more prevalent, the process is becoming slicker and companies like EOS are learning to re-use fi ndings where applicable.
“What we see is we’re getting faster because [for] some parts,
you can use them again for other [LCAs],” Björn Hannappel, EOS’ Head of Sustainability, said. “If we’re doing an LCA on PA 1101 and then we have the next one which is based on a PA 1101 but [with] more ingredients added to it, then we already have half of it. We don’t need to do this again.”
“It’s similar to where we were years ago when it came to calculating business cases and cost per part,” added Florian Alefeld, Senior Manager, Academy & Consulting, EOS. “It used to be we have a time study, now we need to measure the energy input into the system – it was
pretty manual, we had to do a lot of calculations to get a very accurate cost per part that was more than +/- 20%. Now, we’re at a point where we need a few input data, we have a database in the back end that spits out a cost per part and even a return-on-investment calculation. It’s the same for carbon footprint. Today, we do a lot of manual labor and data collection, but we will get to a point where, just like a fi ve-dollar cost per part, we will have a fi ve-kilogram carbon equal emissions per unit and additional data, such as how much agricultural lands have to be used.” Last year, both EOS and Materialise carried out
LCAs on 3D printed eyewear products, with both returning positive assessments compared with conventional means of manufacture. In the EOS study, which was carried out by Fraunhofer EMI, the 3D printed YOU MAWO eyewear product was said to yield a carbon footprint that was 58% lower than the conventional product and create 80% less waste. It also posited a reduction in powder refresh rate, the development of bio-based materials and the use of less expensive packaging as areas for improvement.
Though all the LCAs highlighted in this feature point to positive environmental benefi ts of AM, it would be remiss to suggest as a blanket statement that AM is a sustainable technology. As industry consultant Phil Reeves noted during a panel session at TCT 3Sixty, “it’s application based.”
He continued: “I did some studies years ago with Virgin Atlantic on metal additive parts and what we realized was if we were making airframe components that would last for the duration of the aircraft, which is 30 years, it would be sustainable. But cabin interiors are refi tted every fi ve to seven years, so a fi ve-to-sevenyear lifecycle on a metal additive lightweight part doesn’t off set the fuel gain. So, even in aerospace, you could say, well, lightweight, aerospace, [it] must be good in terms of reduction of fuel. But it’s not always the case.”
Not every LCA carried out for an AM process, then, can expect to yield a positive outcome. But as the world looks to turn greener in the face of a climate emergency, it will provide valuable intel for technology suppliers as to what application opportunities they can target today, and the improvements that need to be made to widen that scope tomorrow.
In its role as the foremost sustainability organization in the AM space, the AMGTA will continue to recognize eff orts made by the industry players, but the true incentive will come from manufacturers who are working toward ever more demanding CO2 emission targets.
“We need to do more work around the lifecycle analysis,” Stephen Fitzpatrick of the National Manufacturing Institute Scotland added on the same TCT 3Sixty panel. “Until we’re able to measure that, we can’t prove something as sustainable or not. We all talk about the design opportunity for additive manufacturing and when you look at manufacturing in general, 80% of the top three emissions are locked in at the design phase. So, additive, with that design opportunity, does present that opportunity for us to be more sustainable. But we do need to measure that and until we do, we can’t prove that.”