
4 minute read
DRIVING SUSTAINABILITY
Jaime Garcia, Solutions Manager, Truck, Bus & Rail at 3D Systems on sustainability opportunities in commercial and public transportation.
With the advent of the pandemic, we’ve been forced to quickly learn how easily economic sustainability can be disturbed. Its negative impact on supply chains and the global economy has been so signifi cant that Governments are implementing initiatives in an eff ort to reverse the trend (e.g., President Biden’s Additive Manufacturing Forward (AM Forward), India’s National Strategy on Additive Manufacturing (AM)).
Globally, commercial and passenger transportation such as truck, bus, and rail has also fallen victim to this trend. These industries are in the midst of a deep slump due to reduced demand, labor shortages, and supply chain delays. Many of these manufacturers have begun to implement customized product confi gurations to maintain competitive advantage, however, their ability to deliver these products has been deeply aff ected. When I worked as a program manager at John Deere Mexico, Antonio Garcia, then-President for John Deere Argentina said, “There is no more expensive part than the part that is not available.” He, like many others currently are, acknowledged the need to implement more agile product innovation and fl exible manufacturing processes to maintain sustainability strategies and assure business growth in this new postpandemic reality.
The consequences of the deep reduction in cargo movement and passengers’ transit forced commercial freight companies and public transportation operators to park large portions of their assets. They are now in a position to return them in revenue service, and now fi nd themselves in need of qualifi ed maintenance labor and looking for hard-to-fi nd spare parts. In light of this, transportation manufacturers and direct suppliers are re-evaluating their fi nancial strategies to achieve resilient supply chains – placing increasing value on speed and component availability for critical parts, integrating vertical processes and establishing partnerships with regional suppliers located closer to their assembly sites. Additive manufacturing (AM) has demonstrated its value in bolstering economic sustainability by enhancing productivity. It also demonstrates environmental sustainability advantages by enabling the production of parts, manufacturing aids, and tooling that requires less material yielding lower waste compared with subtractive manufacturing. Being able to produce parts and production tooling on-demand versus stocking them on shelves also saves warehouse space while eliminating the need to store costly inventory to support discontinued products. Finally, because AM provides design freedom to create parts not possible to produce with traditional manufacturing technologies, it off ers engineers a path to design for the application versus designing for the manufacturing capability, thus enabling them to develop more energyeffi cient products.
Production parts without tooling: AM is a process that inherently eliminates a major artifact in the production process – the tooling. The ability to directly produce a component from its digital representation not only makes the process more effi cient but allows for the decentralization of the business model, quick adaption, and delivery for the customer experience, as well as achieving this with less manufacturing overhead and waste.
Digital inventory management: Thanks to the fast growth of digital encryption and IP protection technologies like Digital Right Management (DRM) or Blockchain systems, protecting 3D models and 3D printing parameters is a reality that perfectly marries with AM. Design owners can now distribute digital information globally and control how many physical parts will be produced and guarantee quality while remote users or manufacturers can print them on demand without needing to ship, insure, store or maintain inventory. Rapid production tooling: Compared to the auto industry, commercial and public transportation requires much larger parts and while AM technology is growing in productivity and build sizes, some critical parts still cannot be produced using current printers. Many parts (e.g., large metal castings, external body parts, large interior panels) also cannot be produced as effi ciently as desired for end-use consumption and thus need to be manufactured conventionally. In these cases, AM is the perfect solution to create rapid low-mid volume molds and casting patterns, either sacrifi cial or re-usable, with the advantage of maintaining them as digital inventory tools and eliminating the need for environmentally controlled storage spaces for years.
Companies with a solid long-term vision for sustainability endeavor to operate in a way that fosters economic growth, solves social challenges, and helps the planet by using renewable resources and eliminating waste. Leading transportation manufacturers and direct suppliers are re-evaluating their fi nancial strategies to achieve resilient supply chains – placing increasing value on speed and component availability for critical parts, and many are realizing success by incorporating AM into their production workfl ows.

Digital inventory management: Thanks to the fast growth of digital encryption technologies like Digital Right Management (DRM) or Blockchain printing parameters owners can now distribute digital information globally and control how many physical parts will be produced and guarantee quality
SHOWN:
CUT SECTION OF AN OPTIMIZED LIQUIDCOOLED HEAT EXCHANGER PRINTED WITHOUT SUPPORTS ON 3D SYSTEMS’ DMP FLEX 350 DUAL USING LASERFORM ALSI7MG0.6 (A) MATERIAL SAVING 83% SPACE AND ELIMINATING 97 PARTS COMPARED WITH A CONVENTIONAL AIR-COOLED HEAT SINK.
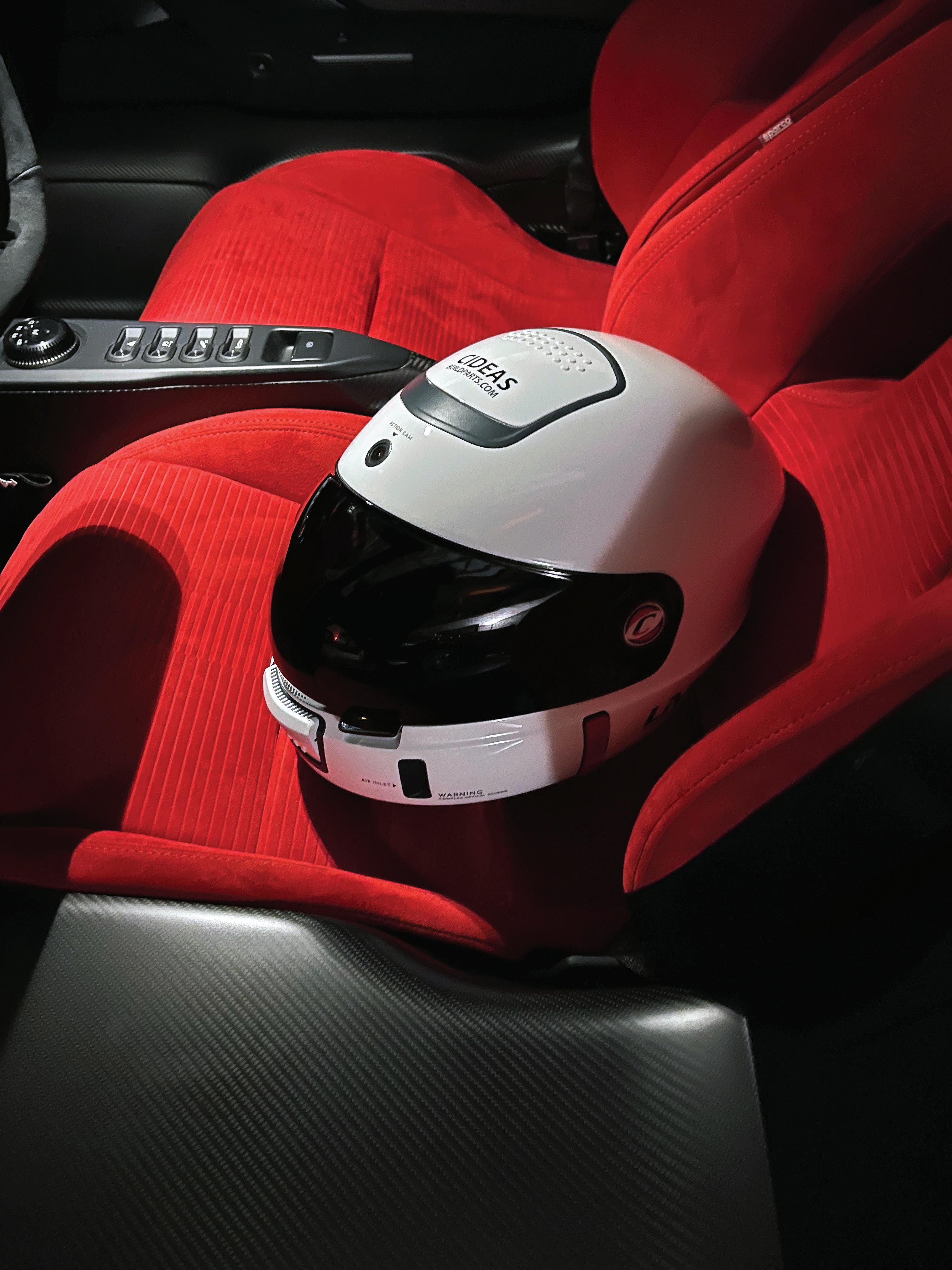