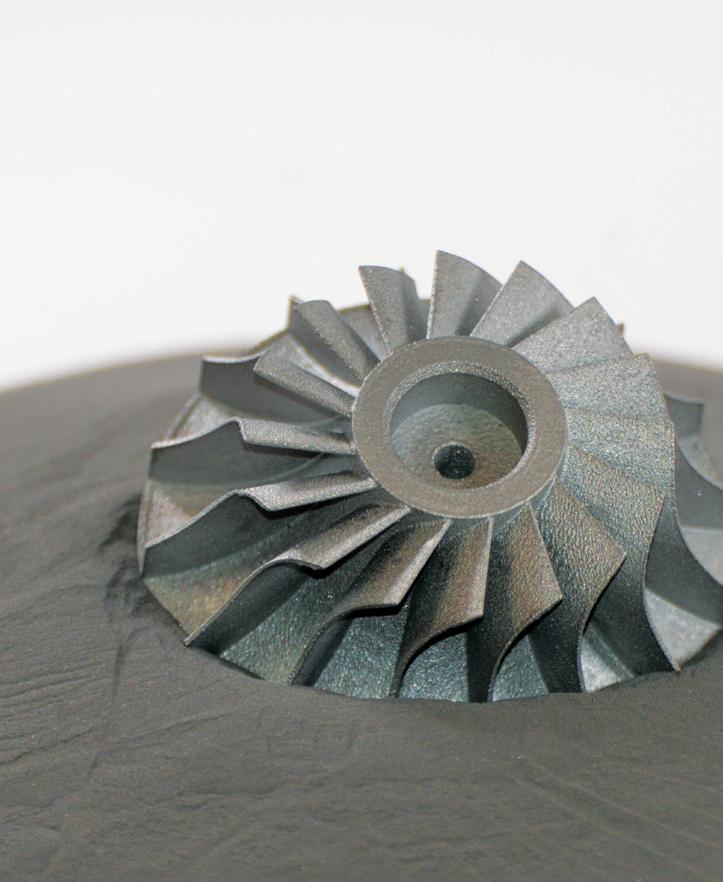
5 minute read
CREATING A CIRCULAR ECONOMY
6K Additive on changing the sustainability game for AM powders.
ABOVE:
INDUSTRIAL IMPELLER PRINTED USING 6K ADDITIVE’S SUSTAINABLE POWDER
Sustainability across the value chain is a trend that is getting increasing coverage internally and externally and is becoming a key part of decision-making for companies that are looking to lower their carbon footprint. Additive manufacturing (AM) has typically been recognized as a much more sustainable way to manufacture in comparison to conventional manufacturing but this does not take into consideration how the metal AM powders are manufactured.
6K Additive has changed not only how metal AM materials are produced but has completely changed the sustainability game for AM powders, helping organizations achieve their goals in a very tangible way.
6K Additive has a storied 25-year history of recycling and upcycling metals such as titanium, where they are made into an additive compact for the aluminum melt industry. Chances are if you drive a Ford F150 your truck bed contains 6K Additive products or if you have had an MRI, your scan was enabled by metal components utilizing 6K Additive products. The company has taken its expertise and extensive knowledge in milling technology and process and combined it with the UniMelt spheroidization technology to develop the most sustainable manufacturing technology for AM powders. As a result, 6K Additive can produce premium AM powders including nickel 718 and 625, titanium 64 grade 5 and 23, copper 18450 and GRCop, stainless steel 316 and 17-4, and refractories like tungsten and tantalum, all made from sustainable sources. THE UNIMELT PROCESS With its proprietary UniMelt technology, the world's only microwave productionscale plasma system, 6K Additive specializes in the sustainable production of metal powders for additive manufacturing. This fast and environmentally friendly process uses virgin, scrap and used powder as feedstock to make high-quality and infi nitely fl exible metal additive manufacturing alloys. 6K Additive uses a proprietary milling and cleaning process that ensures contaminationfree, high-quality powders in under two seconds. UniMelt provides 99% effi ciency (microwave to plasma) and is 99.999% contamination-free.
SUSTAINABLY SOURCED FEEDSTOCK Using feedstock from the manufacturing process, including used AM powders, support structures, failed prints, and certifi ed chemistry scrap, 6K Additive is able to source materials economically and without reliance on overseas sources. UniMelt then achieves nearly 100% yield within the targeted particle size distribution (PSD) producing zero waste.
Customers can also benefi t by selling their scrap material to 6K Additive for credit towards their next metal AM powder purchase, creating a circular economy that is valuable and sustainable for the future of AM. With this realization, organizations now recognize that there is more value in their scrap material both in terms of sustainability and ensuring certifi ed chemistry as the feedstock for the powder-making process. Additionally, having the ability to control supply chain not only for companies but equally important for the Department of Defense and other government agencies, has become vital. Lastly, the availability of new materials that are simply not available for additive in any scalable way, is now being demanded by aerospace and medical companies whose applications surpass the capabilities of today’s available AM powders.
LIFECYCLE ANALYSIS 6K Additive has just completed the fi rst ever Lifecycle Analysis for metal powder manufacturing, carried out by Foresight Management, a third party independent sustainability consulting fi rm. This study looked at the environmental impacts associated with the production of metal powders for additive manufacturing, specifi cally comparing the impacts from traditional production methods (gas atomization and plasma atomization) to 6K Additive’s UniMelt
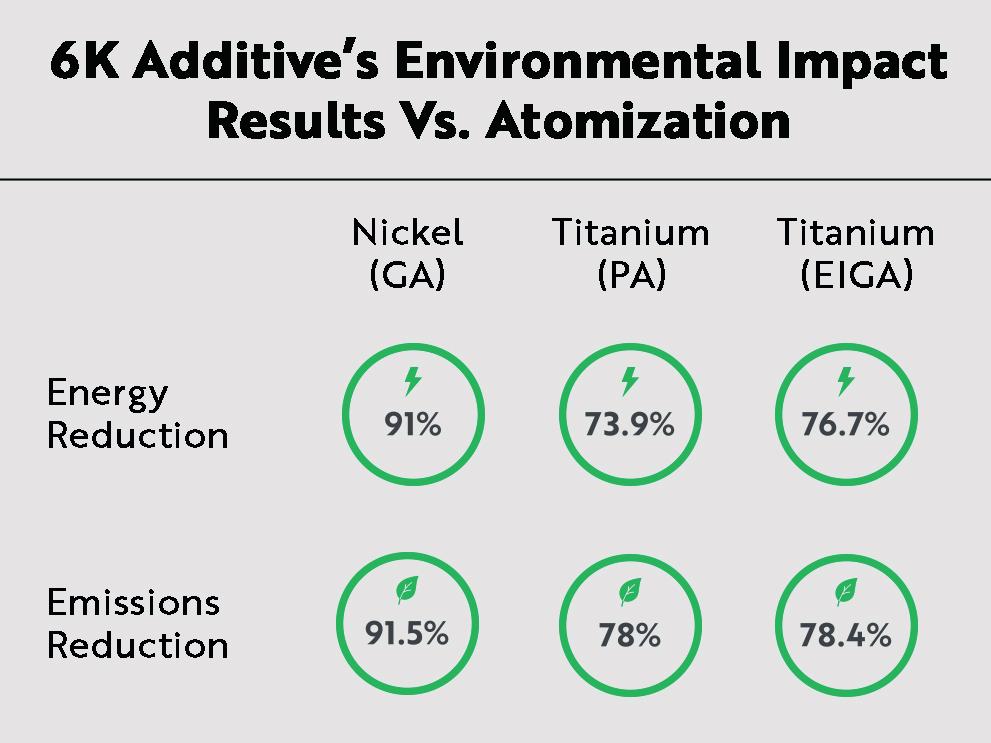
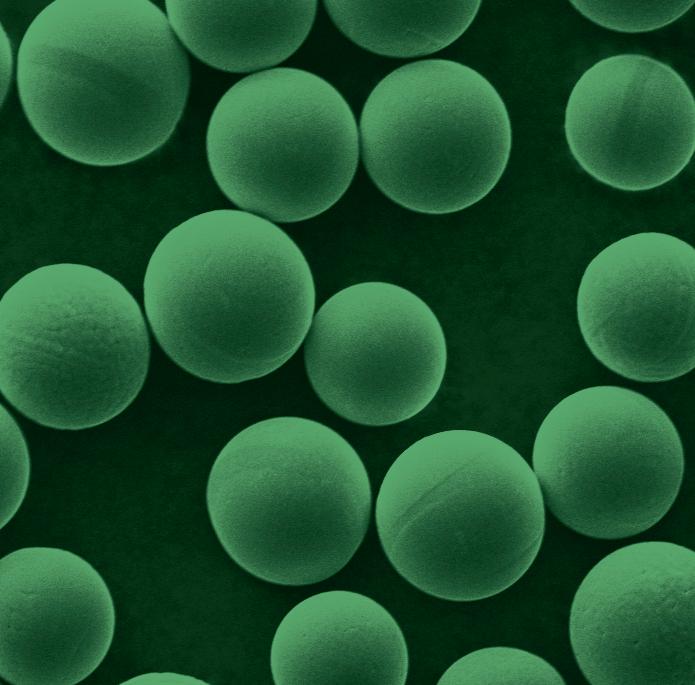

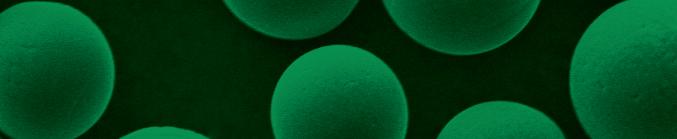
SHOWN:
SEM OF TITANIUM POWDER WITH ZERO SATELLITES, PERFECT SPHERES, AND CONTROLLED PARTICLE SIZE technology for the production of both nickel and titanium AM powders.
While many impact categories were modeled and are included in the full report, the two most relevant categories for reducing the environmental impact were Energy Use and Carbon Emissions. The high-level results are highlighted in the graph (left).
It was found that for nickel, 6K’s UniMelt process used 6,265 MJ of energy and produced 301kg CO2-eq for every 100kg delivered to the customer. This represents a 91% energy reduction and 92% carbon emissions reduction from traditional processes in the Cradle-to-End User Scope.
It was found that for titanium, 6K’s UniMelt process used 56,268 MJ of energy and produced 2,748kg CO2-eq for every 100kg delivered to the customer. This is, at minimum, a 74% energy reduction and 78% carbon emission reduction from traditional processes in the Cradleto-End User Scope.
SUSTAINABLE POWDER THAT SURPASSES
INDUSTRY
STANDARDS 6K Additive powders are not just environmentally friendly - the performance of the UniMelt metal powders surpasses that of other providers’ materials because of the 6000K microwave plasma process that utilizes a much lower gas volume during spheroidization. A uniform plasma beam eliminates gas entrapment within the particles, producing dense powder particles that are highly spherical, without satellites and have no internal porosity, resulting in smooth fl owability and higher tap density than traditional methods.
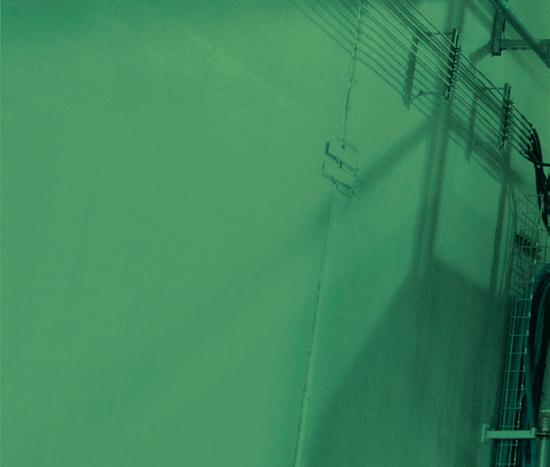


The shape, fl ow, density, and porosity of UniMelt powders are such an improvement that any AM operator will immediately see the diff erence. Gas atomized powders, for example, include many elongated particles that are under-fi nished. With UniMelt, the targeted PSD, consistent spheroidicity, and surface smoothness improves fl owability, feeding of powder into the 3D printer, and helps with the density of the powder in the build chamber, thereby improving part quality and printer productivity.
6K Additive customers have seen an overall improvement in printed part specifi cations including improved part density when using 6K Additive’s powders. The added benefi t of an environmentally friendly process and domestic supply chain adds to the overall benefi t of looking at 6K Additive for your powder needs.
SHOWN:
UNIMELT PRODUCTION BAY AT 6K ADDITIVE’S GLOBAL PRODUCTION FACILITY IN PENNSYLVANIA, USA