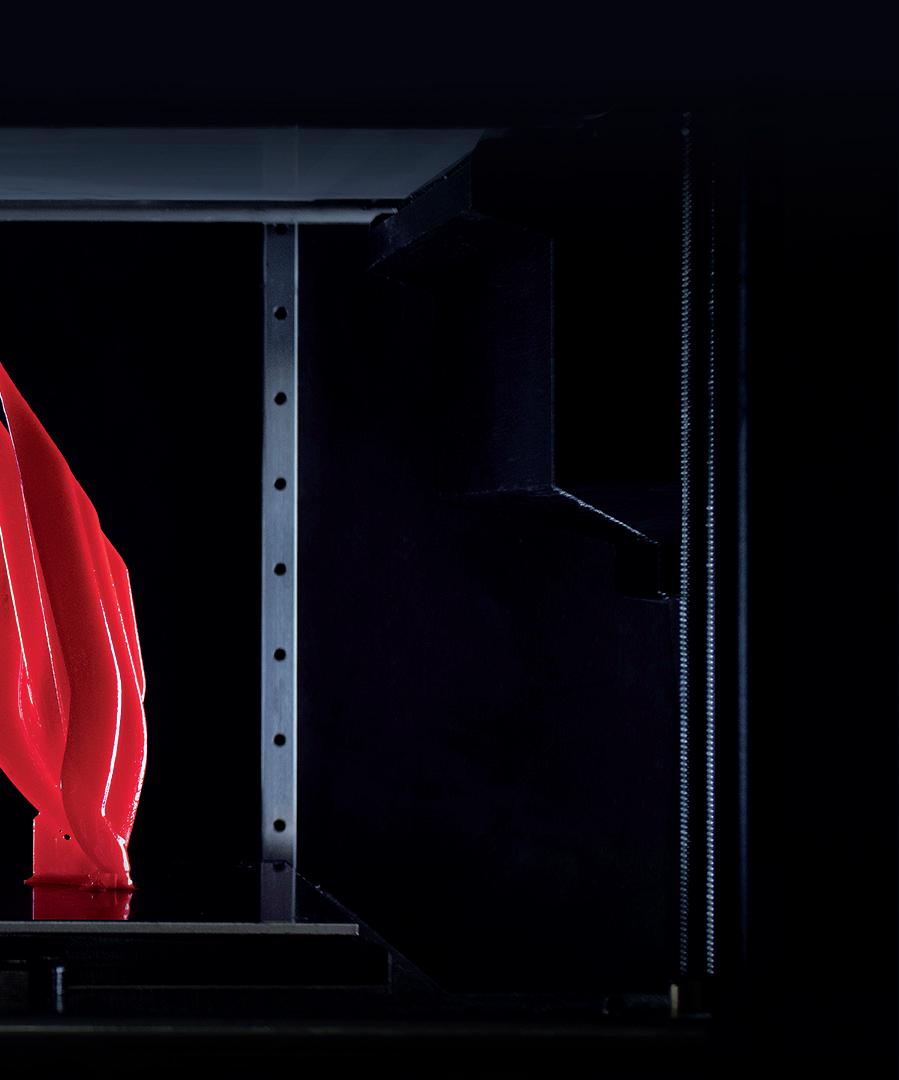
65 minute read
RECIPES FOR SUCCESS?
RECIPES FOR SUCCESS? WORDS: SAM DAVIES
In a university research lab in West Lafayette, IN, a doctoral student is exploring the potential of a novel 3D printing technique to develop solid rocket propellant.
The motivation for trying to 3D print solid rocket propellant is to gain more control over its geometry – since this can aff ect how quickly propellant burns – and by the end of the research, Purdue University Assistant Professor Monique McClain will prove out the ability to 3D print a traditional mixture with all the volume loading content of traditional propellant and with no defects induced by the 3D printing process.
She does this with a 3D printing technology that utilizes a vibrating nozzle which facilitates the fl ow of highly viscous materials. The key material is an ammonium perchlorate, which boasts particle sizes of around 200 microns, while the hydroxyl terminated polybutadiene binder used has a honey-like consistency. The viscosity requirement of the build material and binder is important for this application because, per McClain, there is a minimum number of particles required in rocket propellant for it to burn. Purdue’s novel printing technology – called Vibration Assisted Printing – was developed by Emre Gunduz because there was no such printing technology to be bought off the shelf that could print parts in the viscosities Purdue needed. In 2018, that was not just true of ammonium perchlorate, but polymer materials too. There are markets out there yearning for things to change.
“What we’re doing with solid propellants, doesn’t just have to stay relevant to solid propellants,” McClain told TCT.
Earlier this year, BCN3D joined a select few others in the commercial 3D printing space looking to enable the printing of materials with higher viscosities with its Viscous Lithography Manufacturing (VLM) technology. A material’s viscosity is measured in centipoise (cP) or millipascal-second (mPas) – 1cP equating exactly to 1mPas – and refers to its resistance to fl ow because of its molecular makeup. Such fl ow resistance can make it challenging for some 3D printing technologies to process highly viscous materials.
Though BCN3D has so far specialized in extrusion-based methods, it has not followed in Purdue’s footsteps with a vibrating nozzle technique. Instead, the company landed on a lamination process in its bid to ‘enable manufacturing autonomy.’
“We wanted to bring value to this segment of the market by producing real functional parts, beyond prototyping, using resin,” BCN3D CTO Eric Pallarés Garcia explained. To do that, BCN3D developed a patented photopolymerization technology whereby resin materials are picked up by a roller, laminated to the underside of a transparent fi lm, transferred to the printing area and when the build plate rises to meet the recently laminated resin, a UV light engine cures the resin in specifi c areas to build up parts. The build plate then retreats,
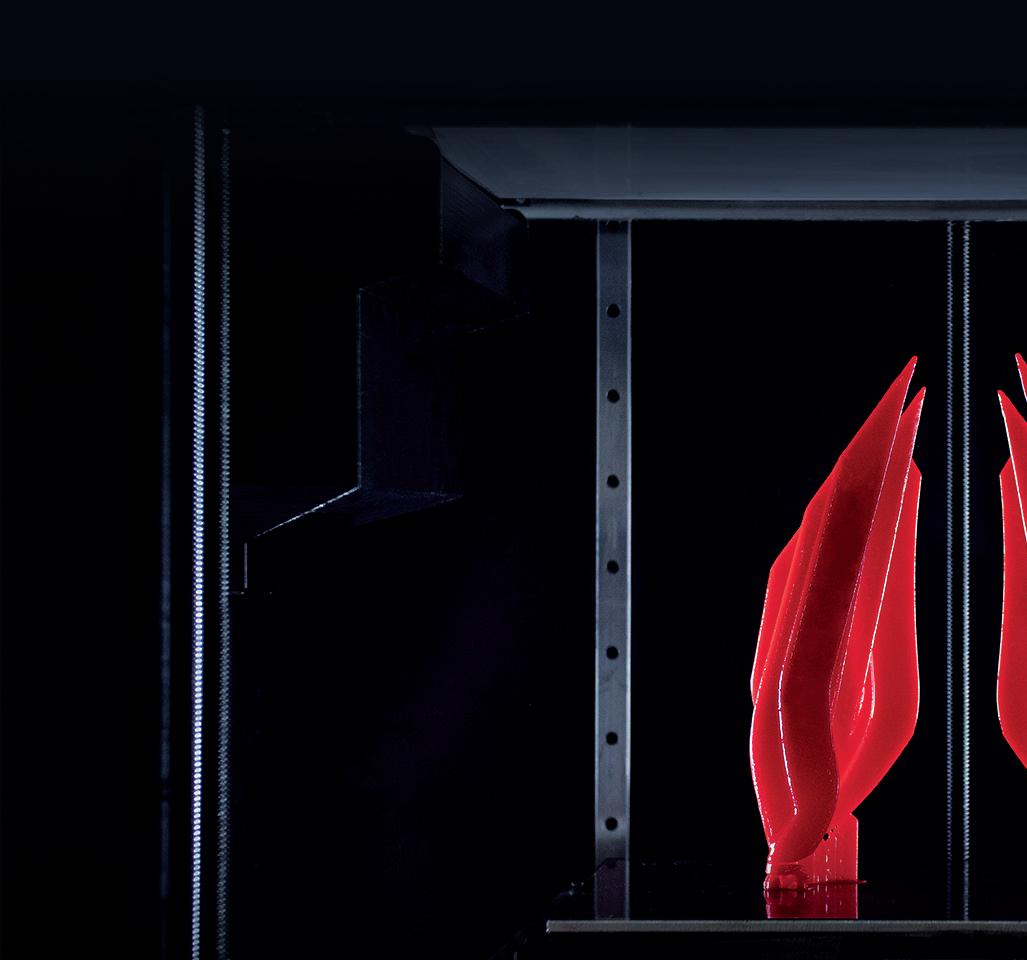
peeling the recently cured layer from the fi lm, with the unused material being recovered for the next print. BCN3D claims VLM can process resins that are ‘50x more viscous than standard market resins’ and says it can also tackle multimaterial applications.
Per Garcia, VLM can process materials of higher viscosities because it is spreading resin like butter, rather than relying on the fl ow of liquid as in vatbased technologies. Other challenges in the 3D printing of highly viscous materials include the durability of the machinery required. Daniel Rothfuss, Global Head of Application Engineering for 3D Printing at Henkel – a BCN3D partner – noted how the high force load of more viscous materials can damage build trays, while there are also concerns with the creation of air bubbles on the resin. Heating resins can make them easier to process but that reduces the viscosity of the material – something the likes of BCN3D are trying to move away from.
In Xaar and ViscoTec there are two more companies who are channeling their expertise into the development of print heads that can facilitate the 3D printing of highly viscous materials. Four years ago, Xaar exhibited its High Laydown inkjet technology for photopolymer materials at TCT 3Sixty, with plenty of additional R&D ongoing since.
High Laydown allows Xaar to output ‘a lot of material very fast’ and increase the viscosities its print heads can handle from 100 centipoise to 130 centipoise, enabling parts with enhanced material properties.
“What high viscosity is enabling is true additive manufacturing,” Xaar Business Development Manager for EMEA + Israel Gareth Neal suggested. “There’s 3D printing, which makes parts in 3D, and then there’s additive manufacturing things which goes beyond making shape. We can put conductives into the ink, we can put dielectric properties into the ink, ceramics for structure or heat defl ection temperature.”
ViscoTec, meanwhile, is developing printheads for fi lament 3D printing systems, with its vipro-HEAD range said to be able to process pastes with viscosities up to 1,000,000 millipascalsecond (mPas). These printheads are said to be able to gently fl ow material when building up parts and are compatible with off the shelf epoxy resins, acrylates, silicones, waxes and more. Xaar has identifi ed several niche applications within 3D printing for High Laydown, including windshield frits (those black dots that protect your eyes from the sun) and digital braille on packaging labels. ViscoTec, on the other hand, sees a lot of scope in automotive, medical and sealing applications, though Business Development Manager Simon Kasböck noted materials supply chain that makes sense for 3D printing volumes are lacking – particularly for silicones.
BCN3D’s solution on materials has been to align with Arkema and Henkel to work on the development and supply of highly viscous 3D printing materials for VLM. With this pair, BCN3D has set its sights on acrylic resins, epoxy resins, silicones and materials fi lled with inorganic fi llers like metals or ceramics. With such an off ering, BCN3D is looking at enabling elastomeric applications with good rebound energy return, while also hoping to facilitate parts with fl ame retardancy, low emissions and good insulation properties.
“If you bake a cake and only have fl our, eggs and sugar, you can do a good cake, but if you have access to more ingredients, you would be able to do something more tasty,” Garcia said. “With high viscosity, you’re getting rid of limitations in terms of the ingredients you can use to make your formulation and to make your product.”
“It’s like giving an artist a full color palette when they’ve had monochrome for their entire career,” Neal off ered.
It would be fair to say that with this year’s launch of VLM, the print head developments for inkjet and extrusion technology by Xaar and ViscoTec, the material development at the likes of Henkel, and even the high viscosity capabilities of machines like the ETEC Xtreme 8K, a trend is emerging. McClain also suggested the vibrating nozzle technique developed at Purdue could, in theory, be used for high viscosity polymers.
And you don’t have to look too far to fi nd the applications. Whether it’s in the implementation of braille on a label, the production of a medical device in a hospital, or the development of rocket propellant in an R&D lab, there is a demand for the durability of traditionally made parts, and the geometric freedom of 3D printed ones.
“The additive manufacturing industry is looking for more durable and functional resins and products to unlock new applications in automotive, railway, medical, everywhere where you have very demanding requirements,” Rothfuss said. “Also, long-term stability is one of the many requirements we are frequently asked [about]. And one possible solution to fulfi l those needs and to develop new resins is to add functional additives into the formulation.
“What you’re enabling with a higher viscosity printhead, or a higher viscosity technology, is not only material capability, there’s [also] a resolution and speed which makes manufacturing viable,” Neal fi nished. “You’re giving materials engineers a wider gamut of materials to play with, you’re giving them a wider range of applications they can fi x, so really what we’re giving is opportunity.”
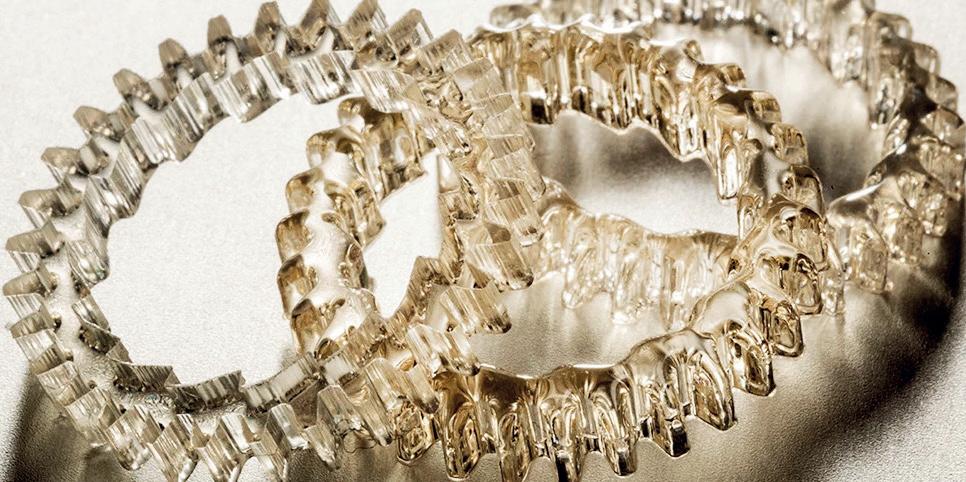
SHOWN:
PARTS PRINTED WITH XAAR'S HIGH VISCOSITY PRINT HEADS
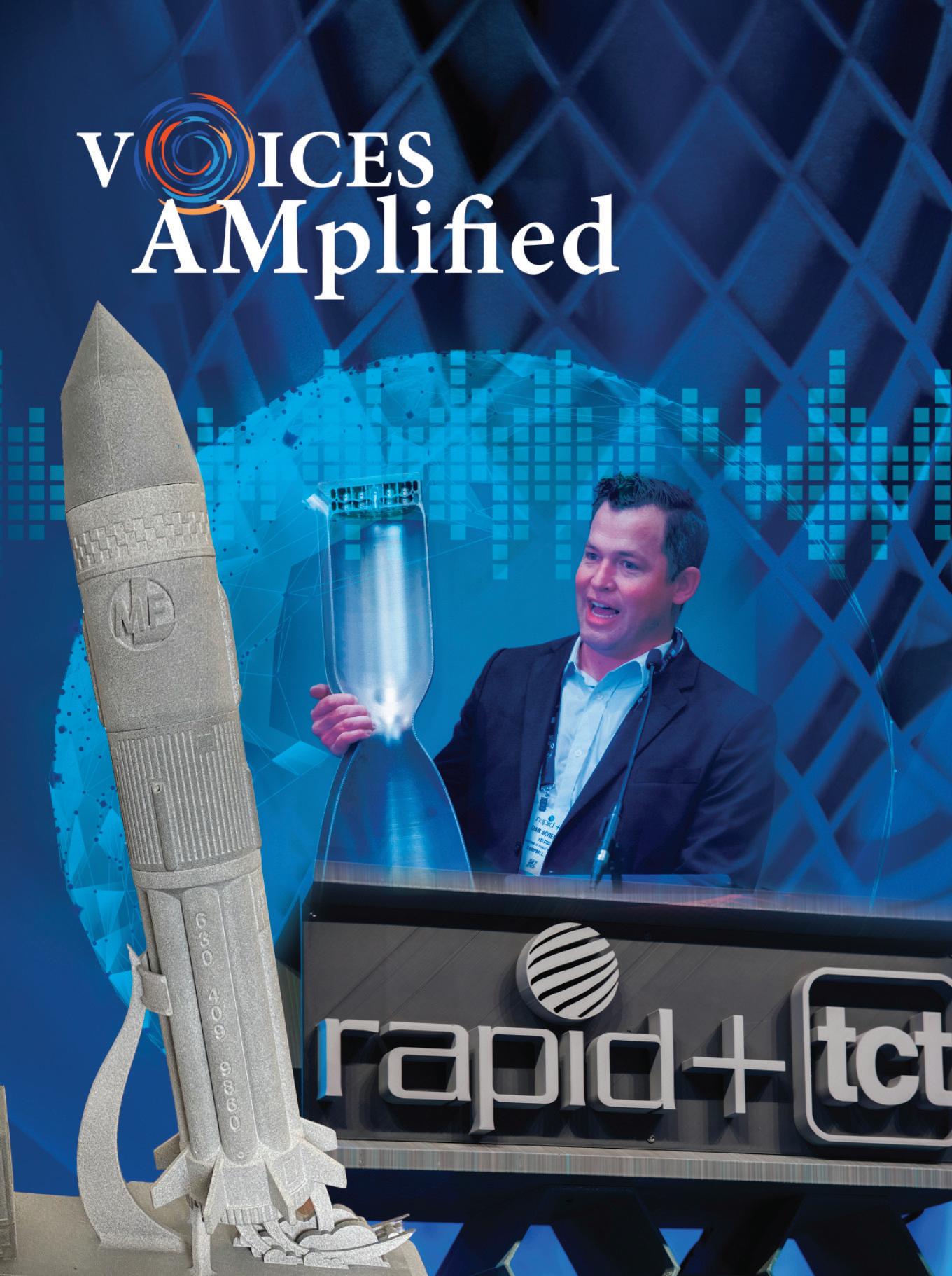

AM Community Shows Off at AM Community Shows Off at RAPID + TCT AM Community Shows Off at RAPID + TCT RAPID + TCT
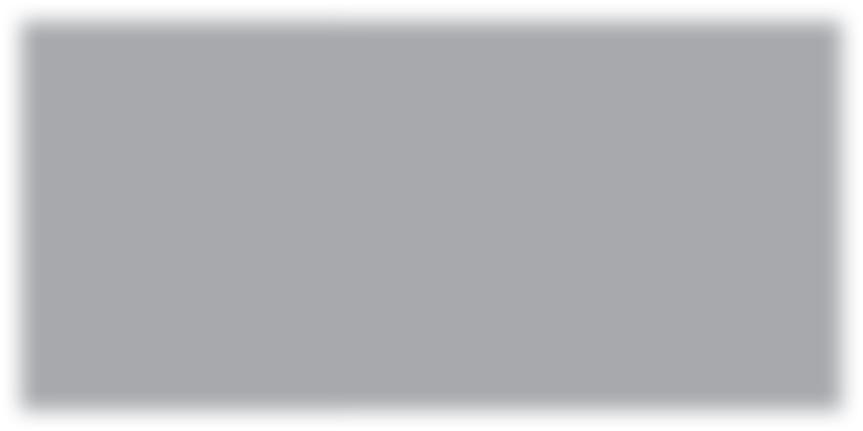
Suzy Marzano
Suzy MarzanoSuzy MarzanoSenior Manager Industry Development and Senior ManagerSenior ManagerTechnical Activities Industry Development and Industry Development and SME Technical ActivitiesTechnical Activities SME SME
It’s official. Additive Manufacturing is thriving and continues to gain momentum with successes across diverse applications. In addition to ongoing technology advances, AM’s growth is fueled by a host of engaged companies, organizations, and dedicated professionals, all of whom are energized and passionate about developing, implementing—and sharing—new ideas and best practices throughout a collaborative community of innovators.
The recent RAPID + TCT conference, which was held May 17–19 in Detroit, is proof positive as to how far AM has come in recent years. The 31st edition of the industry’s marquee event featured more than 400 exhibitors, hundreds of speakers and expert panelists, dozens of technical sessions, networking opportunities, and attendees from 38 countries.
The AM community took center stage throughout the show. This includes the passing of the baton in two key leadership positions. John Barnes assumed the chair of the Additive Manufacturing Technical Community Leadership Committee, succeeding Christopher Williams; and Sarah Rimini now chairs the Medical AM Advisory Committee, succeeding Amy Alexander. I’d like to thank Christopher and Amy, who provided exemplary leadership and vision during their tenures, and welcome their replacements.
John, who heads The Barnes Global Advisors and Metal Powder Works, has been involved in metal additive manufacturing throughout a distinguished career. He’s led teams that qualified the aerospace industry’s first series production metal AM parts, and developed a pilot metal production facility.
It’s official. Additive Manufacturing is thriving and continues to gain momentum with successes across diverse applications. In addition to ongoing technology 3D-printing services. At RAPID + TCT, she moderated a panel discussion on 3D printing for point-of-care medical applications. The panel was one of several during a special town hall advances, AM’s growth is fueled by a host of engaged hosted by the Medical AM Advisory Team. companies, organizations, and dedicated professionals, all Other highlights included the winners of the 2022 SME of whom are energized and passionate about developing, Additive Manufacturing Community Awards: Slade Gardimplementing—and sharing—new ideas and best practicner, founder of Big Metal Additive (Industry Achievement); es throughout a collaborative community of innovators.
The recent RAPID + TCT conference, which was held VELO3D and IMI Critical Engineering (Aubin AM Case Study); May 17–19 in Detroit, is proof positive as to how far AM has and Virginia Tech students Daniel Chirvasuta, Nathanael come in recent years. The 31st edition of the industry’s marHigh, Matthew Martin, Benjamin Nguyen, Omkar Shinde, and quee event featured more than 400 exhibitors, hundreds of Nicolas Tomanelli (Digital Manufacturing Challenge). speakers and expert panelists, dozens of technical sessions, To help foster the next generation of innovators, the SME networking opportunities, and attendees from 38 countries. Education Foundation’s Bright Minds Program welcomed
The AM community took center stage throughout the nearly 1,000 middle and high school students to RAPID + TCT. show. This includes the passing of the baton in two key There also was a special networking lunch for young profesleadership positions. John Barnes assumed the chair of the sionals and a Career Forum Panel. The initiative is led by Ellen Additive Manufacturing Technical Community Leadership Lee and Jennifer Coyne, who are both advisors on the Additive Committee, succeeding Christopher Williams; and Sarah Manufacturing Technical Community Leadership Committee. Rimini now chairs the Medical AM Advisory Committee, SME Media also interviewed dozens of AM leaders during succeeding Amy Alexander. I’d like to thank Christopher and RAPID + TCT as part of its Voices AMplified initiative that Amy, who provided exemplary leadership and vision during showcases the people behind the technology. This month’s their tenures, and welcome their replacements. Voices AMplified report profiles two such visionaries: Olga
John, who heads The Barnes Global Advisors and Metal Ivanova and Carl Dekker. Known as “Dr. O,” Olga has worked Powder Works, has been involved in metal additive manufac- on innovative projects for the medical and defense industries, turing throughout a distinguished career. He’s led teams that and is a tireless crusader for advancing AM. qualified the aerospace industry’s first series production met- Carl puts the emphasis on people. He leads a talented team al AM parts, and developed a pilot metal production facility. at Met-L-Flo, which produces a wide range of 3D-printed prod-
As senior manager of Ricoh’s Healthcare Center of ucts. He also chairs the Direct Digital Manufacturing Advisory Excellence, Sarah is developing a curriculum for the comTeam and moderated a panel at RAPID + TCT. pany’s Learning Institute that focuses on medical managed Carl and Olga represent the spirit behind Voices AMplified. I hope you enjoy their stories.
It’s official. Additive Manufacturing is thriving and continues to gain momentum with successes across diverse applications. In addition to ongoing technology 3D-printing services. At RAPID + TCT, she moderated a panel discussion on 3D printing for point-of-care medical applicaadvances, AM’s growth is fueled by a host of engaged tions. The panel was one of several during a special town hall companies, organizations, and dedicated professionals, all hosted by the Medical AM Advisory Team. of whom are energized and passionate about developing, Other highlights included the winners of the 2022 SME implementing—and sharing—new ideas and best practic- Additive Manufacturing Community Awards: Slade Gardes throughout a collaborative community of innovators. ner, founder of Big Metal Additive (Industry Achievement);
The recent RAPID + TCT conference, which was held VELO3D and IMI Critical Engineering (Aubin AM Case Study); May 17–19 in Detroit, is proof positive as to how far AM has and Virginia Tech students Daniel Chirvasuta, Nathanael come in recent years. The 31st edition of the industry’s marHigh, Matthew Martin, Benjamin Nguyen, Omkar Shinde, and quee event featured more than 400 exhibitors, hundreds of Nicolas Tomanelli (Digital Manufacturing Challenge). To help foster the next generation of innovators, the SME speakers and expert panelists, dozens of technical sessions, Education Foundation’s Bright Minds Program welcomed networking opportunities, and attendees from 38 countries. nearly 1,000 middle and high school students to RAPID + TCT.
The AM community took center stage throughout the There also was a special networking lunch for young professhow. This includes the passing of the baton in two key sionals and a Career Forum Panel. The initiative is led by Ellen leadership positions. John Barnes assumed the chair of the Lee and Jennifer Coyne, who are both advisors on the Additive Additive Manufacturing Technical Community Leadership Manufacturing Technical Community Leadership Committee. Committee, succeeding Christopher Williams; and Sarah SME Media also interviewed dozens of AM leaders during Rimini now chairs the Medical AM Advisory Committee, RAPID + TCT as part of its Voices AMplified initiative that succeeding Amy Alexander. I’d like to thank Christopher and showcases the people behind the technology. This month’s Amy, who provided exemplary leadership and vision during Voices AMplified report profiles two such visionaries: Olga their tenures, and welcome their replacements. Ivanova and Carl Dekker. Known as “Dr. O,” Olga has worked
John, who heads The Barnes Global Advisors and Metal on innovative projects for the medical and defense industries, Powder Works, has been involved in metal additive manufac- and is a tireless crusader for advancing AM. turing throughout a distinguished career. He’s led teams that Carl puts the emphasis on people. He leads a talented team qualified the aerospace industry’s first series production met- at Met-L-Flo, which produces a wide range of 3D-printed prodal AM parts, and developed a pilot metal production facility. ucts. He also chairs the Direct Digital Manufacturing Advisory
As senior manager of Ricoh’s Healthcare Center of Team and moderated a panel at RAPID + TCT. Excellence, Sarah is developing a curriculum for the com- Carl and Olga represent the spirit behind Voices AMplified. pany’s Learning Institute that focuses on medical managed I hope you enjoy their stories.
3D-printing services. At RAPID + TCT, she moderated a panel discussion on 3D printing for point-of-care medical applications. The panel was one of several during a special town hall hosted by the Medical AM Advisory Team.
Other highlights included the winners of the 2022 SME Additive Manufacturing Community Awards: Slade Gardner, founder of Big Metal Additive (Industry Achievement); VELO3D and IMI Critical Engineering (Aubin AM Case Study); and Virginia Tech students Daniel Chirvasuta, Nathanael High, Matthew Martin, Benjamin Nguyen, Omkar Shinde, and Nicolas Tomanelli (Digital Manufacturing Challenge).
To help foster the next generation of innovators, the SME Education Foundation’s Bright Minds Program welcomed nearly 1,000 middle and high school students to RAPID + TCT. There also was a special networking lunch for young professionals and a Career Forum Panel. The initiative is led by Ellen Lee and Jennifer Coyne, who are both advisors on the Additive Manufacturing Technical Community Leadership Committee.
SME Media also interviewed dozens of AM leaders during RAPID + TCT as part of its Voices AMplified initiative that showcases the people behind the technology. This month’s Voices AMplified report profiles two such visionaries: Olga Ivanova and Carl Dekker. Known as “Dr. O,” Olga has worked on innovative projects for the medical and defense industries, and is a tireless crusader for advancing AM.

Although their movie counterparts possess awesome superpowers, the 3D-printed Although their movie counterparts possess awesome superpowers, the 3D-printed Baby Yodas (at left) and Groots (right) that Olga Ivanova gave to visiting high school Baby Yodas (at left) and Groots (right) that Olga Ivanova gave to visiting high school students are unable to do so much as dissipate electrical charge--but they’re still very popular with the kids. students are unable to do so much as dissipate electrical charge--but they’re still very popular with the kids.

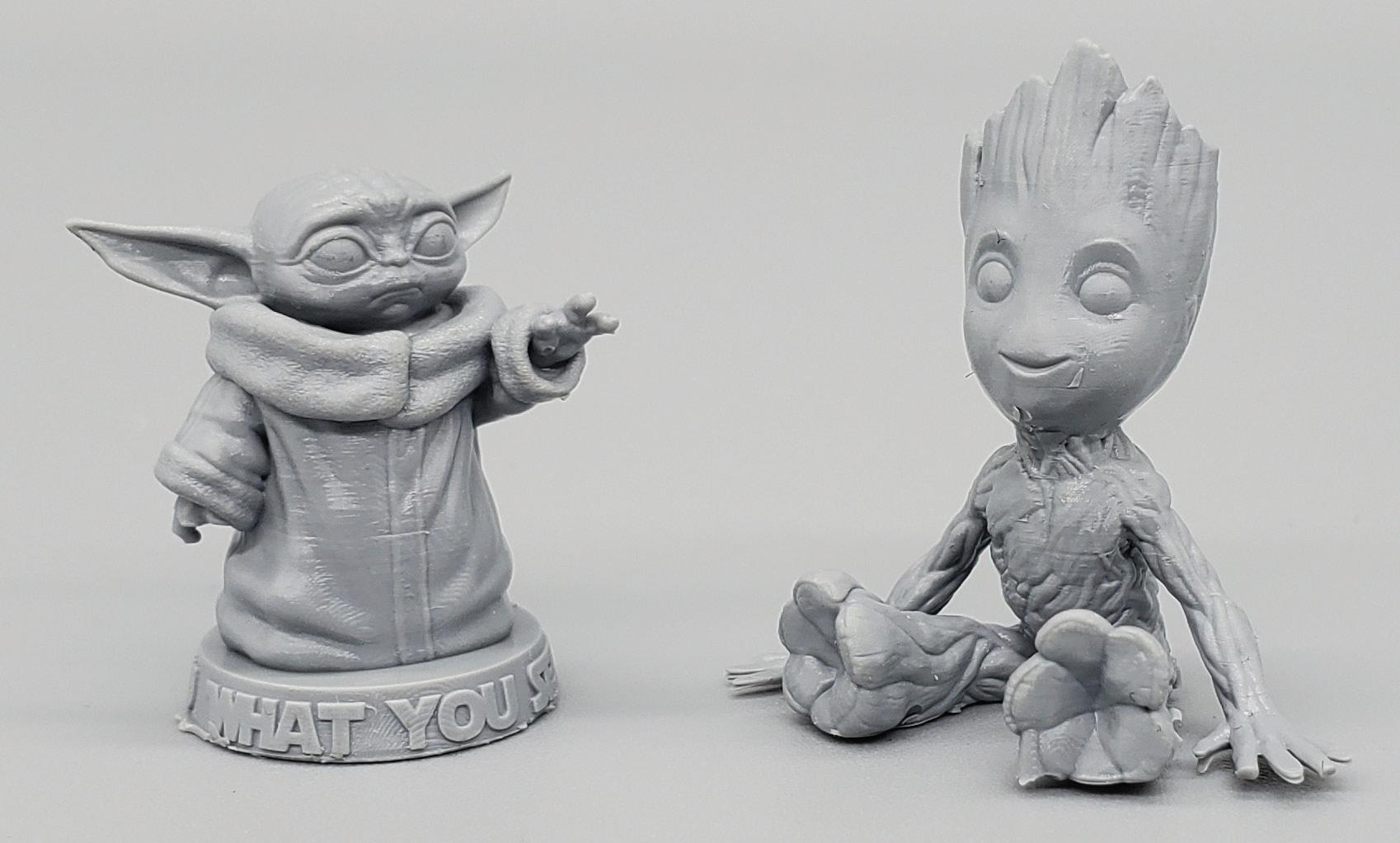
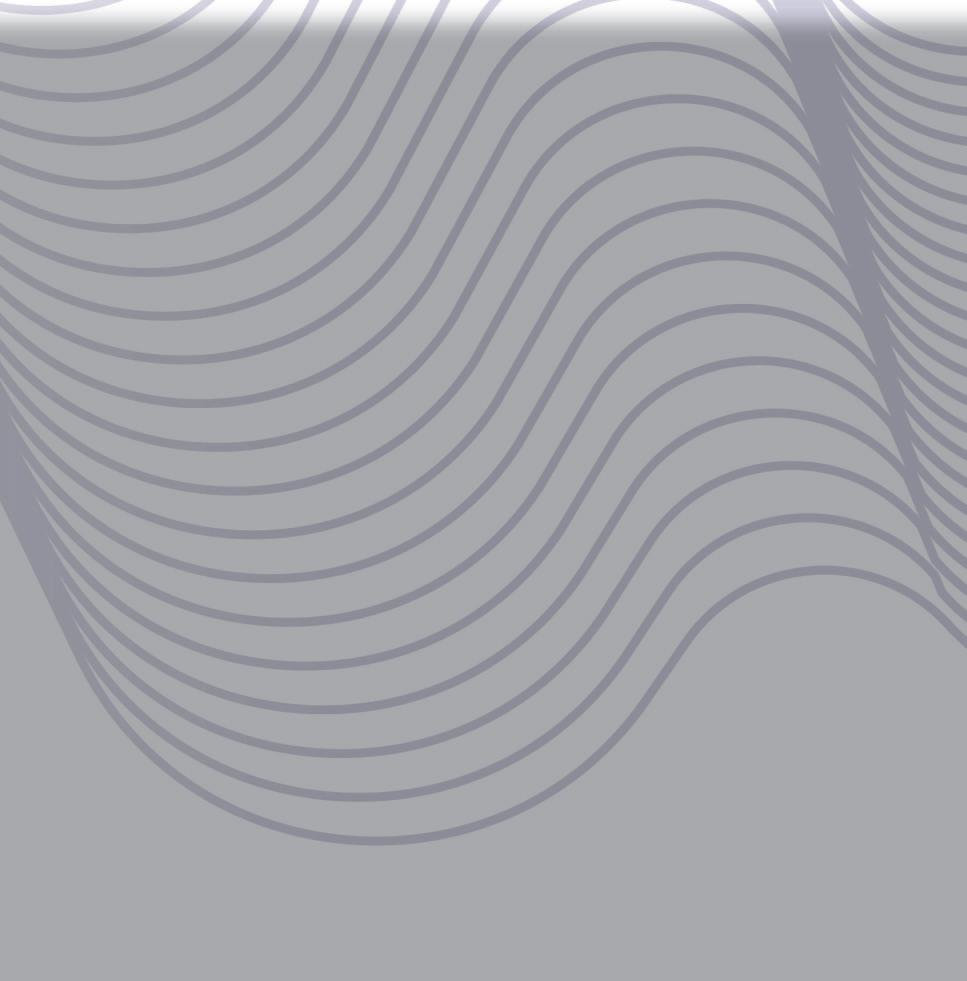
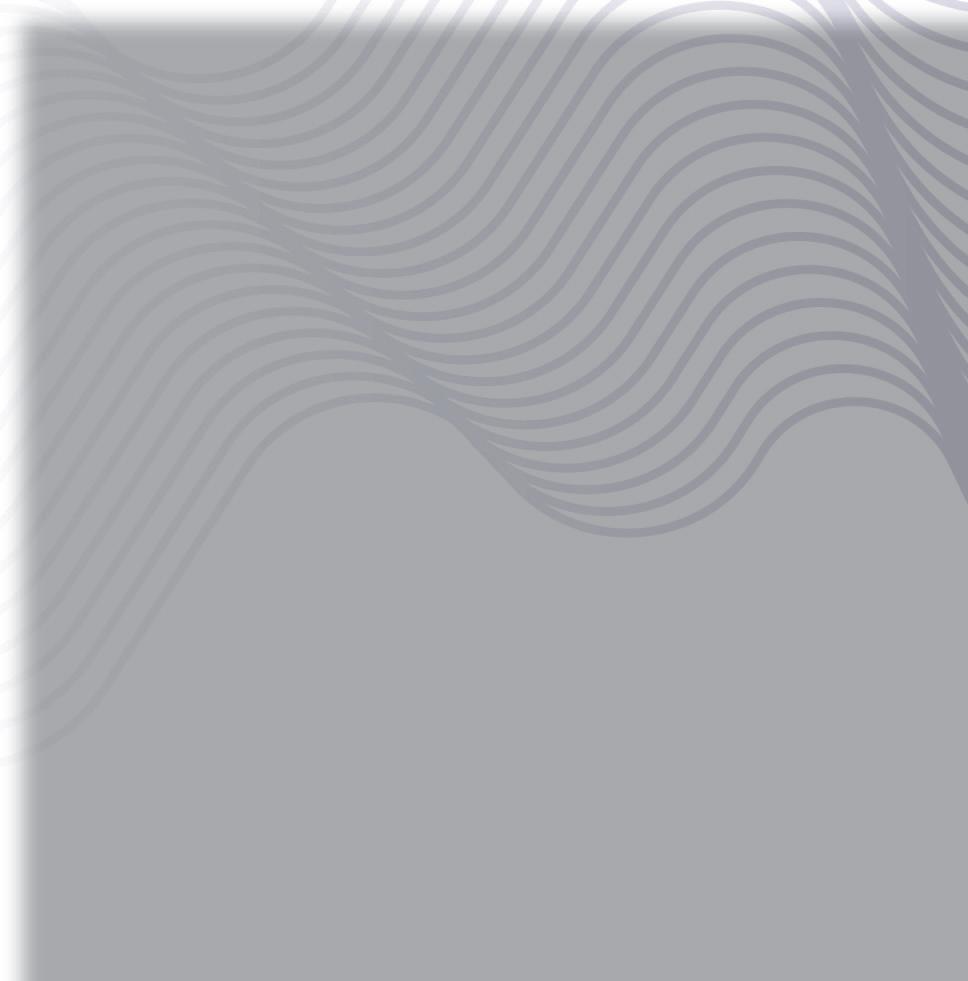
From 3D-printed figurines for students to “quantum dots” and nanocomposites, From 3D-printed figurines for students to “quantum dots” and nanocomposites, Olga Ivanova is a force to be reckoned with in the AM universe Olga Ivanova is a force to be reckoned with in the AM universe
Paging Dr. OPaging Dr. O
Kip Hanson
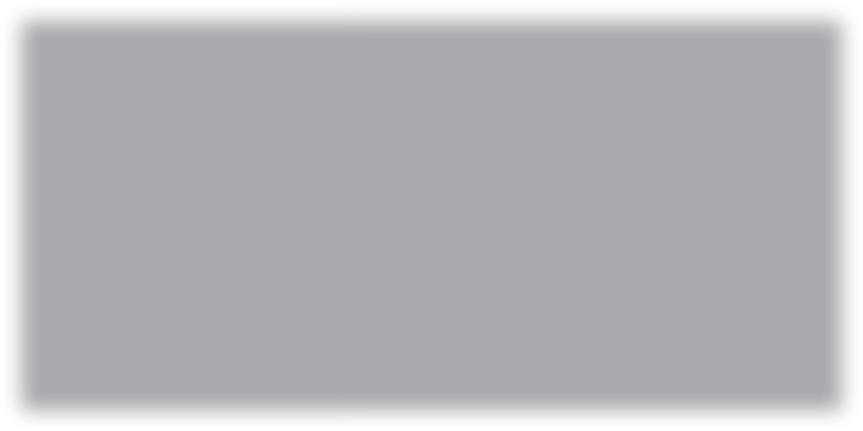
Contributing Editor Kip Hanson
Contributing Editor Olga Ivanova has 3D-printed plenty of interesting parts during her time in manufacturing. Rocket nozzles. Turbine blades and impel- developer near Phoenix. “It’s our way of getting young lers. Neonatal tracheostomy tubes. There are more, people interested in additive manufacturing.” which we’ll get to in a moment, but to Star Wars fans, it’s the Static Dissipative Yoda that’s most intriguing. Padawan Learning “We printed a bunch of Yoda and Groot (Guardians of She’s quick to point out that those educational givethe Galaxy) figurines for high school students who visited aways were made of a gray-colored base resin, not the more our facility recently,” said Ivanova, director of technology expensive static dissipative material (which is black) that she at Mechnano, an additive manufacturing materials spends much of each day working with—and yes, which she occasionally uses to print Yodas that are just as resistant to electrical charge as they are to the Dark Side of the Force.
developer near Phoenix. “It’s our way of getting young people interested in additive manufacturing.”
Padawan Learning
She’s quick to point out that those educational giveaways were made of a gray-colored base resin, not the more expensive static dissipative material (which is black) that she spends much of each day working with—and yes, which she occasionally uses to print Yodas that are just as resistant to electrical charge as they are to the Dark Side of the Force.
Olga Ivanova
Olga Ivanova Master networker Master networker RAPID + TCT Director of Technology RAPID + TCT Mechnano
Director of Technology Mechnano

AM Community Shows Off at RAPID + TCT
It’s official. Additive Manufacturing is thriving and continues to gain momentum with successes across diverse applications. In addition to ongoing technology 3D-printing services. At RAPID + TCT, she moderated a panel discussion on 3D printing for point-of-care medical applications. The panel was one of several during a special town hall advances, AM’s growth is fueled by a host of engaged companies, organizations, and dedicated professionals, all of whom are energized and passionate about developing, implementing—and sharing—new ideas and best practices throughout a collaborative community of innovators.
The recent RAPID + TCT conference, which was held May 17–19 in Detroit, is proof positive as to how far AM has come in recent years. The 31st edition of the industry’s marquee event featured more than 400 exhibitors, hundreds of speakers and expert panelists, dozens of technical sessions, networking opportunities, and attendees from 38 countries.
The AM community took center stage throughout the show. This includes the passing of the baton in two key leadership positions. John Barnes assumed the chair of the Additive Manufacturing Technical Community Leadership Committee, succeeding Christopher Williams; and Sarah Rimini now chairs the Medical AM Advisory Committee, succeeding Amy Alexander. I’d like to thank Christopher and Amy, who provided exemplary leadership and vision during their tenures, and welcome their replacements.
As senior manager of Ricoh’s Healthcare Center of Excellence, Sarah is developing a curriculum for the company’s Learning Institute that focuses on medical managed hosted by the Medical AM Advisory Team. Other highlights included the winners of the 2022 SME Additive Manufacturing Community Awards: Slade Gardner, founder of Big Metal Additive (Industry Achievement); VELO3D and IMI Critical Engineering (Aubin AM Case Study); and Virginia Tech students Daniel Chirvasuta, Nathanael High, Matthew Martin, Benjamin Nguyen, Omkar Shinde, and Nicolas Tomanelli (Digital Manufacturing Challenge). To help foster the next generation of innovators, the SME Education Foundation’s Bright Minds Program welcomed nearly 1,000 middle and high school students to RAPID + TCT. There also was a special networking lunch for young professionals and a Career Forum Panel. The initiative is led by Ellen Lee and Jennifer Coyne, who are both advisors on the Additive Manufacturing Technical Community Leadership Committee. SME Media also interviewed dozens of AM leaders during RAPID + TCT as part of its Voices AMplified initiative that showcases the people behind the technology. This month’s Voices AMplified report profiles two such visionaries: Olga Ivanova and Carl Dekker. Known as “Dr. O,” Olga has worked on innovative projects for the medical and defense industries, and is a tireless crusader for advancing AM. Carl puts the emphasis on people. He leads a talented team at Met-L-Flo, which produces a wide range of 3D-printed products. He also chairs the Direct Digital Manufacturing Advisory Team and moderated a panel at RAPID + TCT. Carl and Olga represent the spirit behind Voices AMplified. I hope you enjoy their stories.

It’s not her first attempt at using technology to reach young people. She’s been known to make soap bubbles in her spare time, and according to her LinkedIn feed, she Suzy Marzanorecently fabricated a family of polar bears for a girl who lost Senior Manager her brother in a car accident. “I made two larger ones to Industry Development and represent mom and dad and Technical Activities SME seven smaller ones that are engaged in various activities to represent kids doing kid things—entirely unaware of the fact that the family had seven children. I was told that the girl was overjoyed.”
That’s how Dr. O rolls. After earning her master’s degree in Physical Chemistry at Perm State University in Russia, she pursued her Ph.D. at Kentucky’s University of Louisville. The school awarded Ivanova a Ph.D. for her thesis, titled “Size and Composition Dependent Electrochemical Oxidation and Deposition of Metal Nanostructures.” She said that working on her Ph.D. forced her to step out of her comfort zone. In her case, it meant setting aside studying bulk parts and “big stuff” to research the mechanics of the ultra-small.
It turned out to be a wise decision. While looking for a postdoctoral position, Ivanova responded to an advertisement from Virginia Tech; the university was looking for someone with expertise in nanocomposites for 3D printing.
“I had plenty of experience with nanocomposites but no clue on 3D printing,” she laughed. “Additive manufacturing wasn’t even a term back then. So I Googled it. I watched some YouTube videos and looked at all the parts people were making, and I thought, ‘This is so cool. I want to be part of it.’ So I applied for the job.”
Fluorescent Frontiers
That was in 2011, and Ivanova has continued to push the boundaries of her chosen field ever since. Working under the tutelage of Tom Campbell, research associate professor AM Community Shows Off at and associate director for outreach of Virginia Tech’s Institute for Critical Technology and Applied Science, and RAPID + TCT co-advisor Chris Williams, It’s official. Additive Manufacturing is thriving and continues to gain momentum with successes across diverse applications. In addition to ongoing technology director of Virginia Tech’s DREAM lab, she spent the next two years or so develadvances, AM’s growth is fueled by a host of engaged oping nanocomposites for companies, organizations, and dedicated professionals, all use in additive manufacturof whom are energized and passionate about developing, ing. She set up a laboratory implementing—and sharing—new ideas and best practicto synthesize semiconductes throughout a collaborative community of innovators. ing nanocrystals made of
The recent RAPID + TCT conference, which was held cadmium selenide, better May 17–19 in Detroit, is proof positive as to how far AM has known as “quantum dots,” then found ways to inkcome in recent years. The 31st edition of the industry’s marjet-print them. quee event featured more than 400 exhibitors, hundreds of The good thing about speakers and expert panelists, dozens of technical sessions, additive manufacturing is networking opportunities, and attendees from 38 countries. that you can print practically
The AM community took center stage throughout the anything, she explained. show. This includes the passing of the baton in two key The bad thing is that it’s leadership positions. John Barnes assumed the chair of the also fairly easy for anyone Additive Manufacturing Technical Community Leadership with a machine to produce Committee, succeeding Christopher Williams; and Sarah illegitimate copies of these Rimini now chairs the Medical AM Advisory Committee, items, then sell them as succeeding Amy Alexander. I’d like to thank Christopher and genuine. This leaves one Amy, who provided exemplary leadership and vision during of the most promising their tenures, and welcome their replacements. technologies of our time rife
John, who heads The Barnes Global Advisors and Metal for fraud. Powder Works, has been involved in metal additive manufac- “Because they fluo-
Olga Ivanova is interested in all aspects of 3D printing,turing throughout a distinguished career. He’s led teams that resce when exposed to UV and is amazed at the technology’s rapid growth. qualified the aerospace industry’s first series production met- (ultraviolet) light, quantum al AM parts, and developed a pilot metal production facility. dots are often used in the
As senior manager of Ricoh’s Healthcare Center of biosciences to tag cancer cells, for example,” Ivanova said. Excellence, Sarah is developing a curriculum for the com- “Our goal at Virginia Tech was to develop the technology to pany’s Learning Institute that focuses on medical managed 3D print them. It was seen as a way to prevent counterfeiting, using quantum dots as a type of barcode that’s invisible to the human eye.” By the end of Ivanova’s term there, she had written six peer-reviewed articles on these and other topics, and contributed to a host of 3D printing conference proceedings.
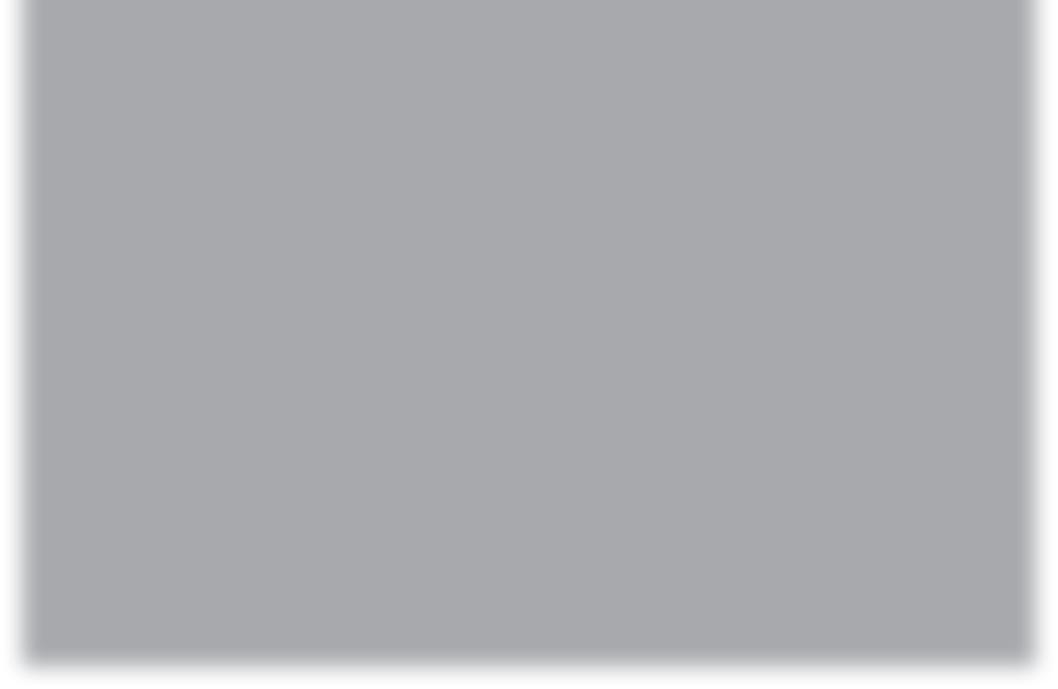
Other highlights included the winners of the 2022 SME Additive Manufacturing Community Awards: Slade Gardner, founder of Big Metal Additive (Industry Achievement); VELO3D and IMI Critical Engineering (Aubin AM Case Study); and Virginia Tech students Daniel Chirvasuta, Nathanael High, Matthew Martin, Benjamin Nguyen, Omkar Shinde, and Nicolas Tomanelli (Digital Manufacturing Challenge).
To help foster the next generation of innovators, the SME Education Foundation’s Bright Minds Program welcomed nearly 1,000 middle and high school students to RAPID + TCT. There also was a special networking lunch for young professionals and a Career Forum Panel. The initiative is led by Ellen Lee and Jennifer Coyne, who are both advisors on the Additive Manufacturing Technical Community Leadership Committee.
SME Media also interviewed dozens of AM leaders during RAPID + TCT as part of its Voices AMplified initiative that showcases the people behind the technology. This month’s Voices AMplified report profiles two such visionaries: Olga Ivanova and Carl Dekker. Known as “Dr. O,” Olga has worked on innovative projects for the medical and defense industries, and is a tireless crusader for advancing AM.
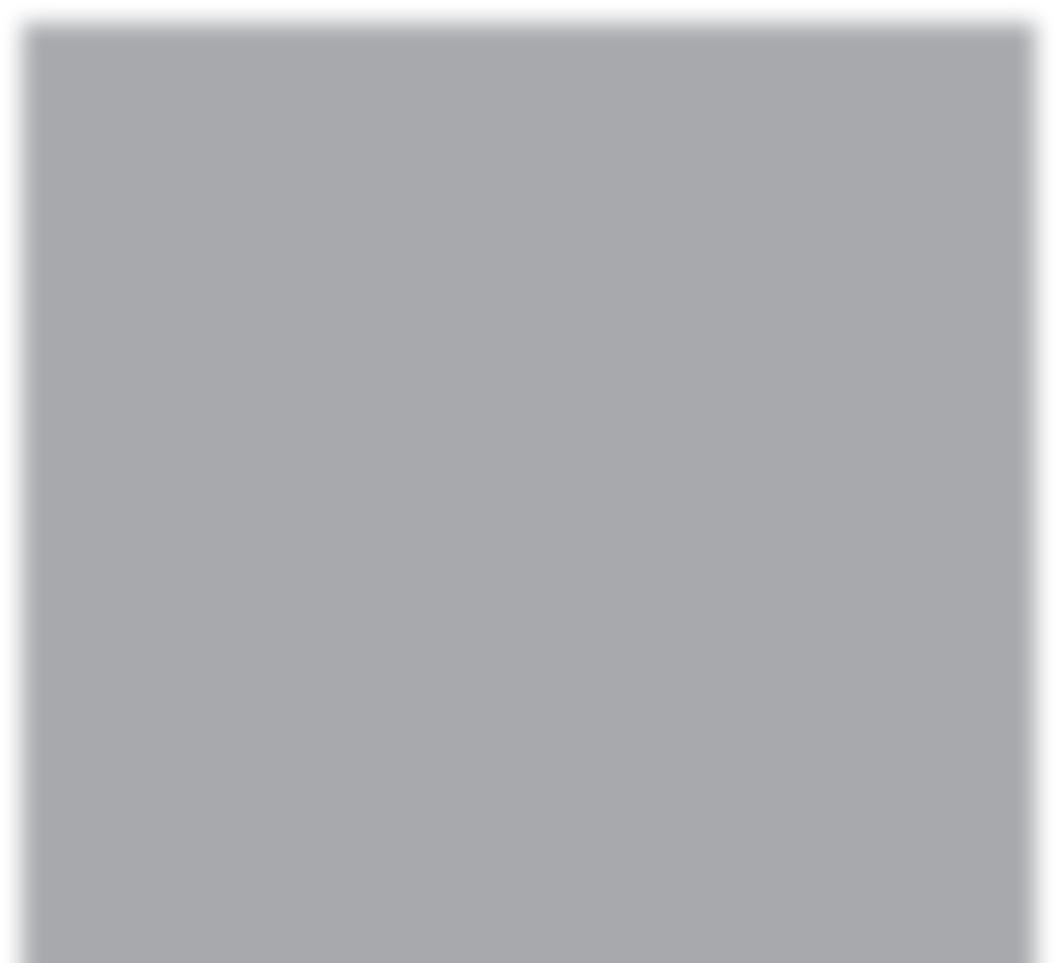

Although their movie counterparts possess awesome superpowers, the 3D-printed Baby Yodas (at left) and Groots (right) that Olga Ivanova gave to visiting high school students are unable to do so much as dissipate electrical charge--but they’re still very popular with the kids.
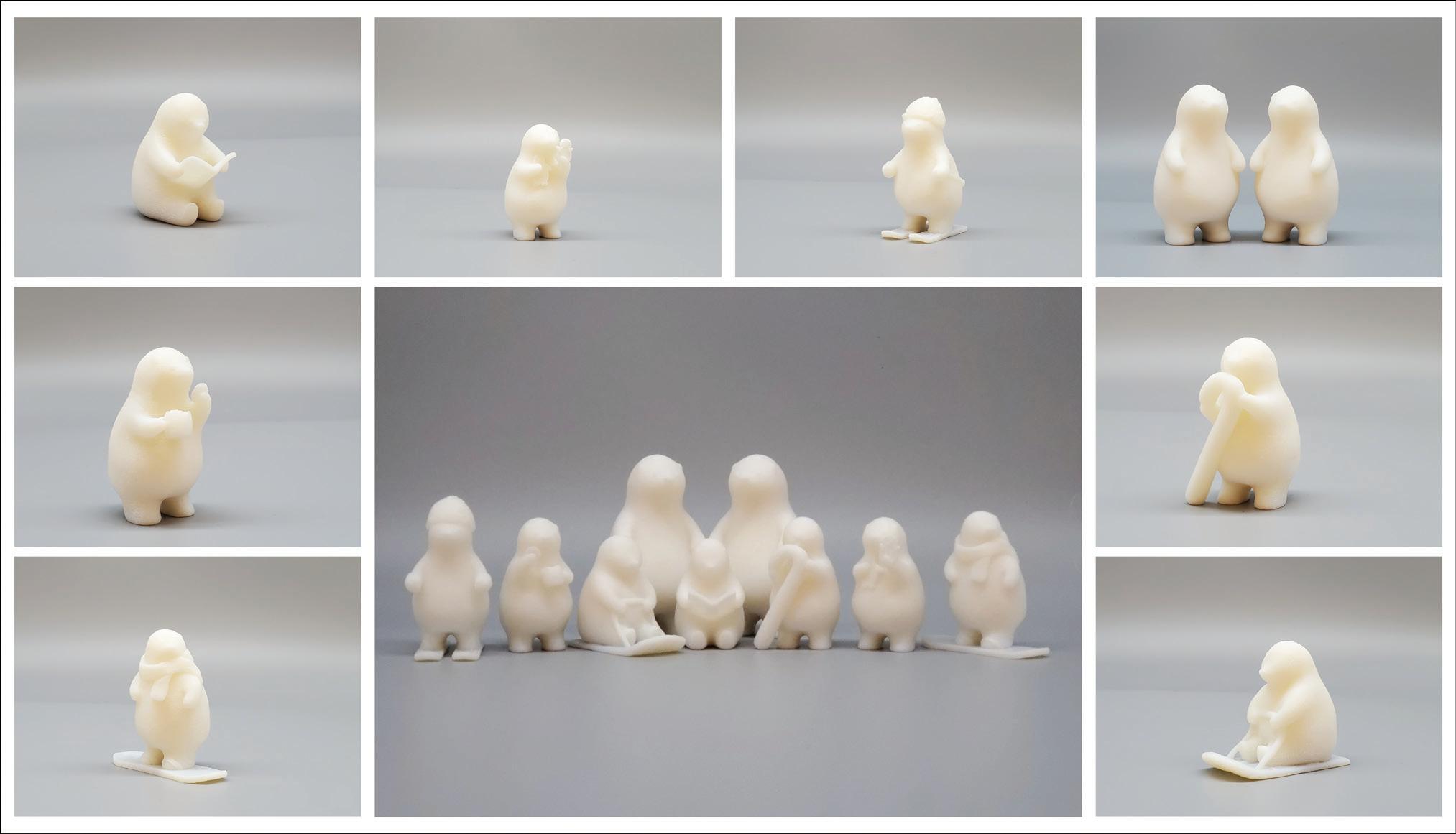

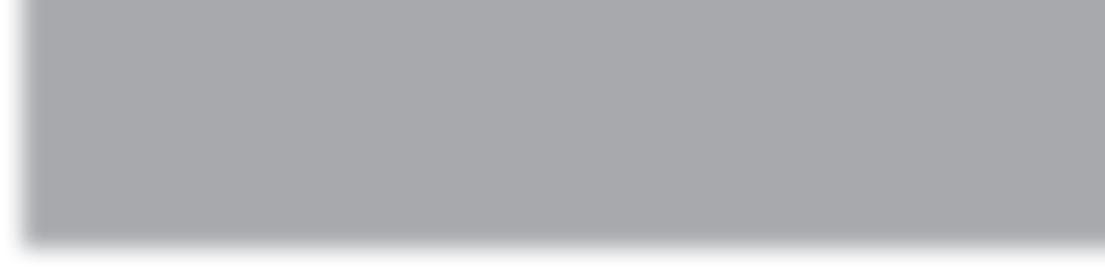
Olga Ivanova 3D-printed this polar bear family as a small gesture to a young girl dealing with the grief of losing her brother in a car accident.
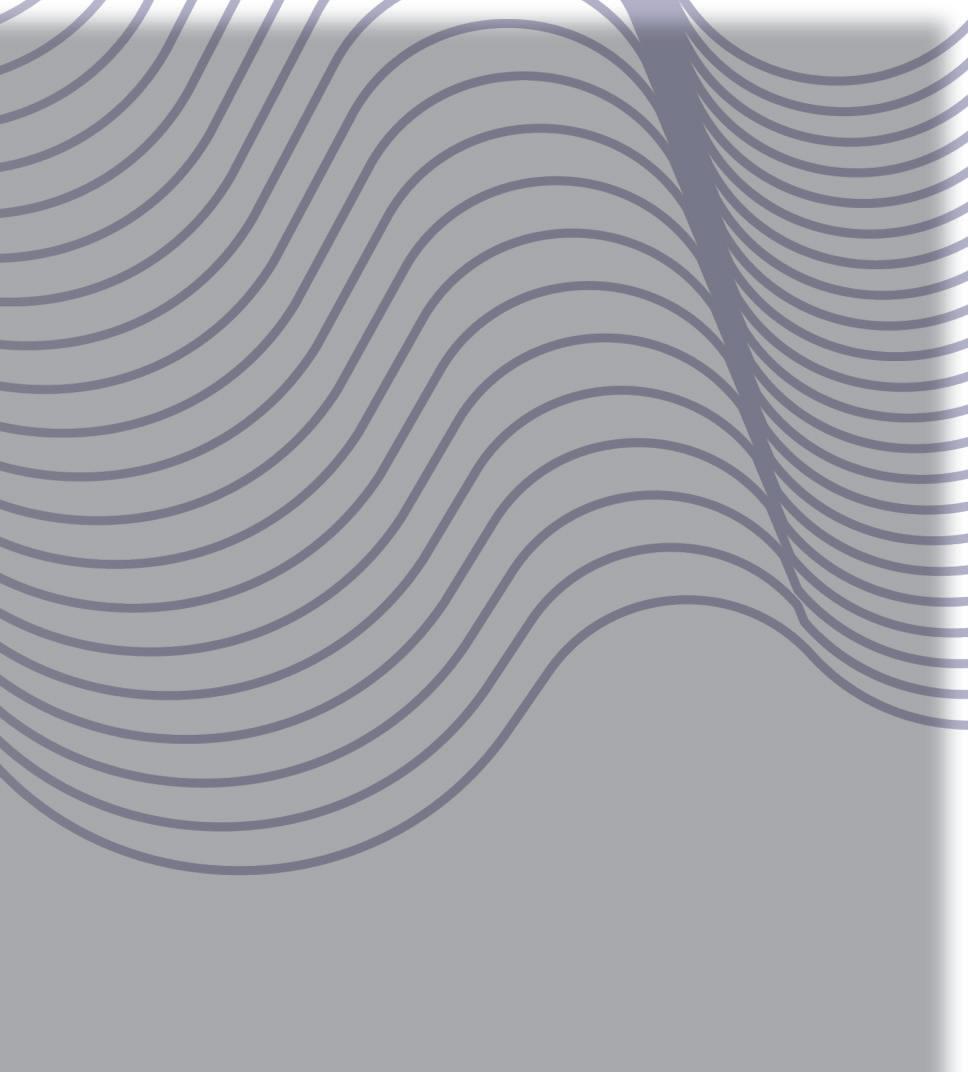
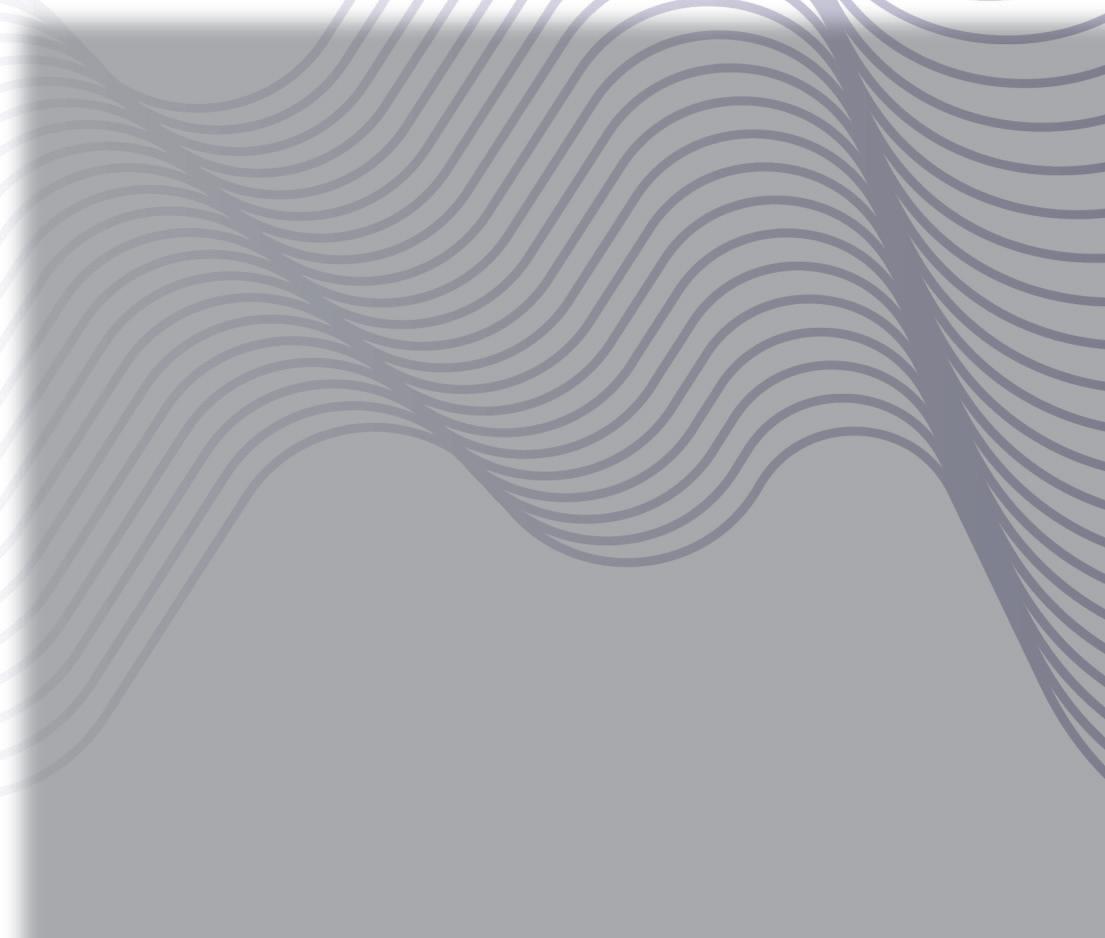

Paging Dr. O
Olga Ivanova is a force to be reckoned with in the AM universeFollowing her stint in academia, Ivanova went into the private sector, and for the next five years focused her energies on the macroworld over the micro. As a scientist for Texas-based government contractor Lynntech, she managed a number of novel research projects, among them Olga Ivanovathe development of UV-curable silicones for use in neonaMaster networker tal medical devices, culminating in the tracheostomy tubes RAPID + TCT mentioned earlier. There was the HAMMER project, in which Director of Technology Kip Hanson Ivanova used a custom-built printer with an “unconventional energy source” to fuse test specimens made of polymers Mechnano Contributing Editorlike polyamide-11 and metals such as iron and copper. And she explored ways to additively manufacture uniforms and undergarments on Navy ships, developing new materials that developer near Phoenix. “It’s our way of getting young replicate textiles and techniques to adjust the strand spacing people interested in additive manufacturing.” for improved breathability in 3D-printed fabrics. One of Ivanova’s favorite (and loudest) projects was also for Padawan Learning the Navy, which focused on developing a more capable pyro- She’s quick to point out that those educational givetechnic flare for military aircraft. The traditional MTV flare they aways were made of a gray-colored base resin, not the more were using contained just one flammable material—magne- expensive static dissipative material (which is black) that she sium—it could only create a single infrared (IR) signature; given spends much of each day working with—and yes, which she occasionally uses to print Yodas that are just as resistant to electrical charge as they are to the Dark Side of the Force. July 2022 | sme.org 53
recent advancements in electronics, the Navy had determined that decoy flares were becoming easier to outsmart. What better way to create one with multiple materials (and therefore multiple IR signatures) than to 3D print it?
“Many of the powders I worked with were flammable and in some cases quite explosive, so we collaborated with Texas A&M University, which has facilities for safely testing such materials,” Ivanova said. “And due to its high melting temperature, there was no commercial way to print the Teflon used in MTV, at least not at that time. We actually had to modify the chemical composition to make it extrudable. It was challenging work, but it was also a lot of fun printing and then setting off these little kabooms in my lab. It was like making fireworks.”
My Friend PANDA
Her next endeavor was with Universal Technology Company, now ARCTOS, in Dayton, Ohio. Here again, she was involved in numerous America Makes and DoD-sponsored research and development projects—Ivanova developed a handful of “recipes” for laser powder bed fusion (LPBF)

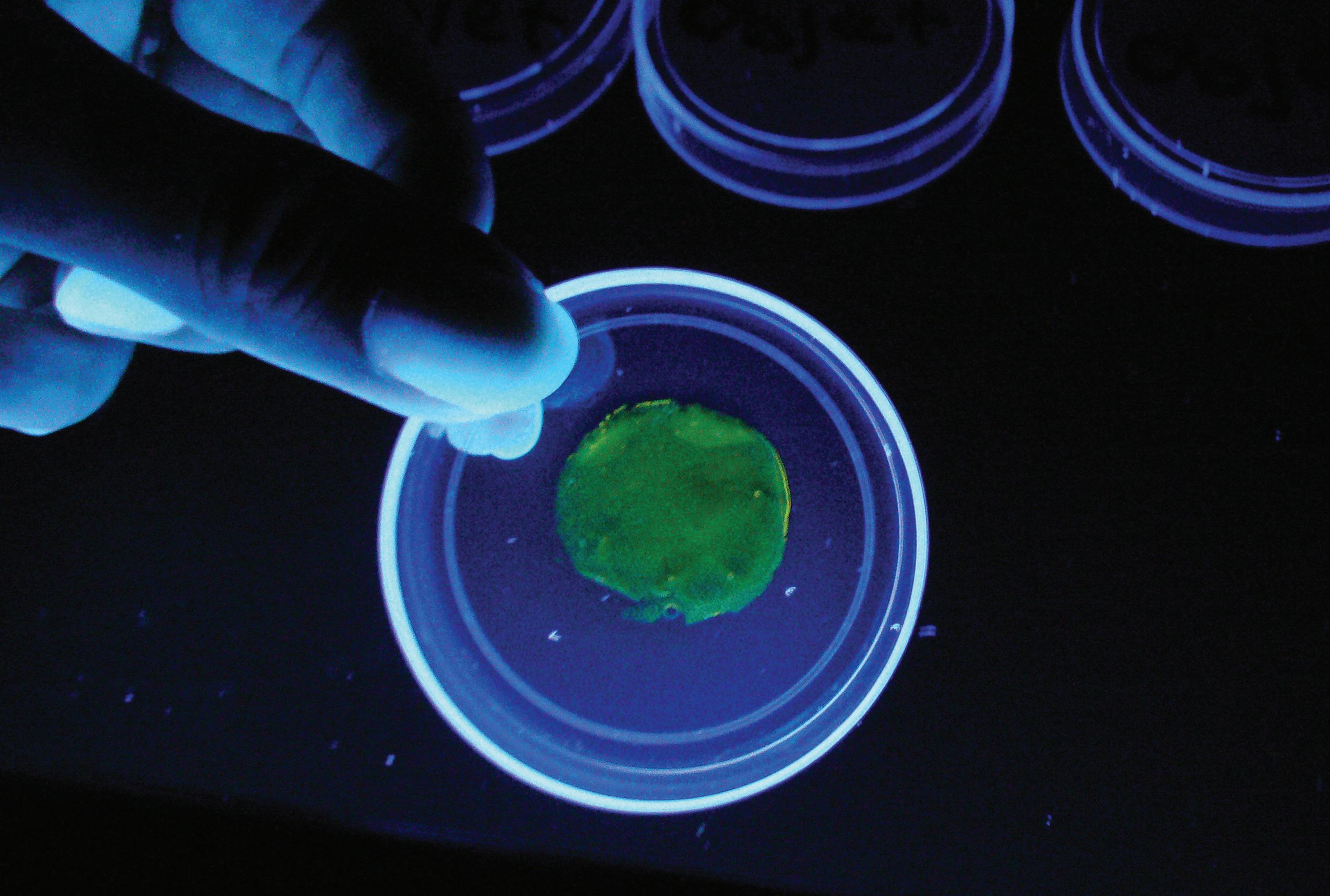
AM Community Shows Off at RAPID + TCT
It’s official. Additive Manufacturing is thriving and continues to gain momentum with successes across diverse applications. In addition to ongoing technology 3D-printing services. At RAPID + TCT, she moderated a panel discussion on 3D printing for point-of-care medical applications. The panel was one of several during a special town hall advances, AM’s growth is fueled by a host of engaged companies, organizations, and dedicated professionals, all of whom are energized and passionate about developing, implementing—and sharing—new ideas and best practices throughout a collaborative community of innovators.
The recent RAPID + TCT conference, which was held May 17–19 in Detroit, is proof positive as to how far AM has come in recent years. The 31st edition of the industry’s marquee event featured more than 400 exhibitors, hundreds of speakers and expert panelists, dozens of technical sessions, networking opportunities, and attendees from 38 countries.
The AM community took center stage throughout the show. This includes the passing of the baton in two key leadership positions. John Barnes assumed the chair of the Additive Manufacturing Technical Community Leadership Committee, succeeding Christopher Williams; and Sarah Rimini now chairs the Medical AM Advisory Committee, succeeding Amy Alexander. I’d like to thank Christopher and Amy, who provided exemplary leadership and vision during their tenures, and welcome their replacements.
As senior manager of Ricoh’s Healthcare Center of Excellence, Sarah is developing a curriculum for the company’s Learning Institute that focuses on medical managed hosted by the Medical AM Advisory Team. Other highlights included the winners of the 2022 SME Additive Manufacturing Community Awards: Slade Gardner, founder of Big Metal Additive (Industry Achievement); VELO3D and IMI Critical Engineering (Aubin AM Case Study); and Virginia Tech students Daniel Chirvasuta, Nathanael High, Matthew Martin, Benjamin Nguyen, Omkar Shinde, and Nicolas Tomanelli (Digital Manufacturing Challenge). To help foster the next generation of innovators, the SME Education Foundation’s Bright Minds Program welcomed nearly 1,000 middle and high school students to RAPID + TCT. There also was a special networking lunch for young professionals and a Career Forum Panel. The initiative is led by Ellen Lee and Jennifer Coyne, who are both advisors on the Additive Manufacturing Technical Community Leadership Committee. SME Media also interviewed dozens of AM leaders during RAPID + TCT as part of its Voices AMplified initiative that showcases the people behind the technology. This month’s Voices AMplified report profiles two such visionaries: Olga Ivanova and Carl Dekker. Known as “Dr. O,” Olga has worked on innovative projects for the medical and defense industries, and is a tireless crusader for advancing AM. Carl puts the emphasis on people. He leads a talented team at Met-L-Flo, which produces a wide range of 3D-printed products. He also chairs the Direct Digital Manufacturing Advisory Team and moderated a panel at RAPID + TCT. Carl and Olga represent the spirit behind Voices AMplified. I hope you enjoy their stories.
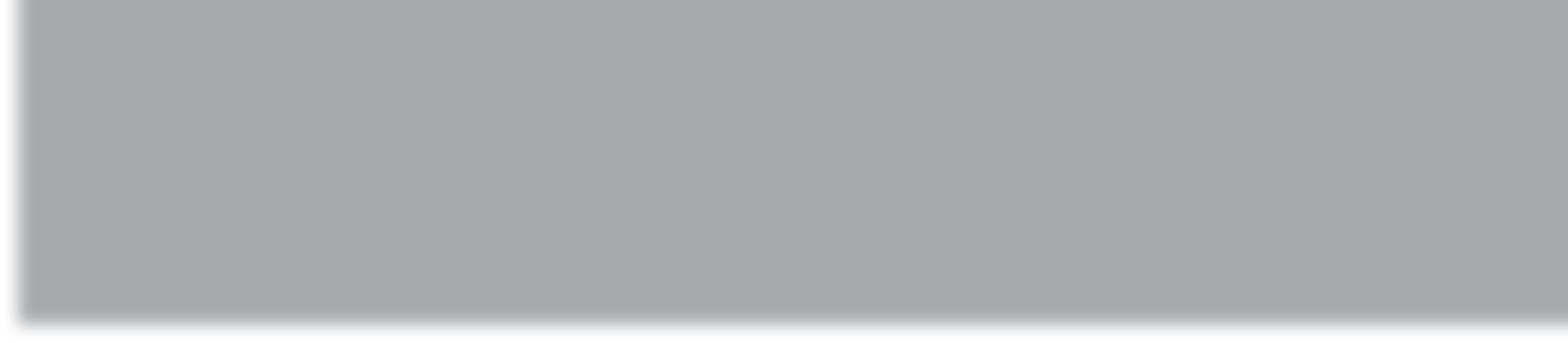
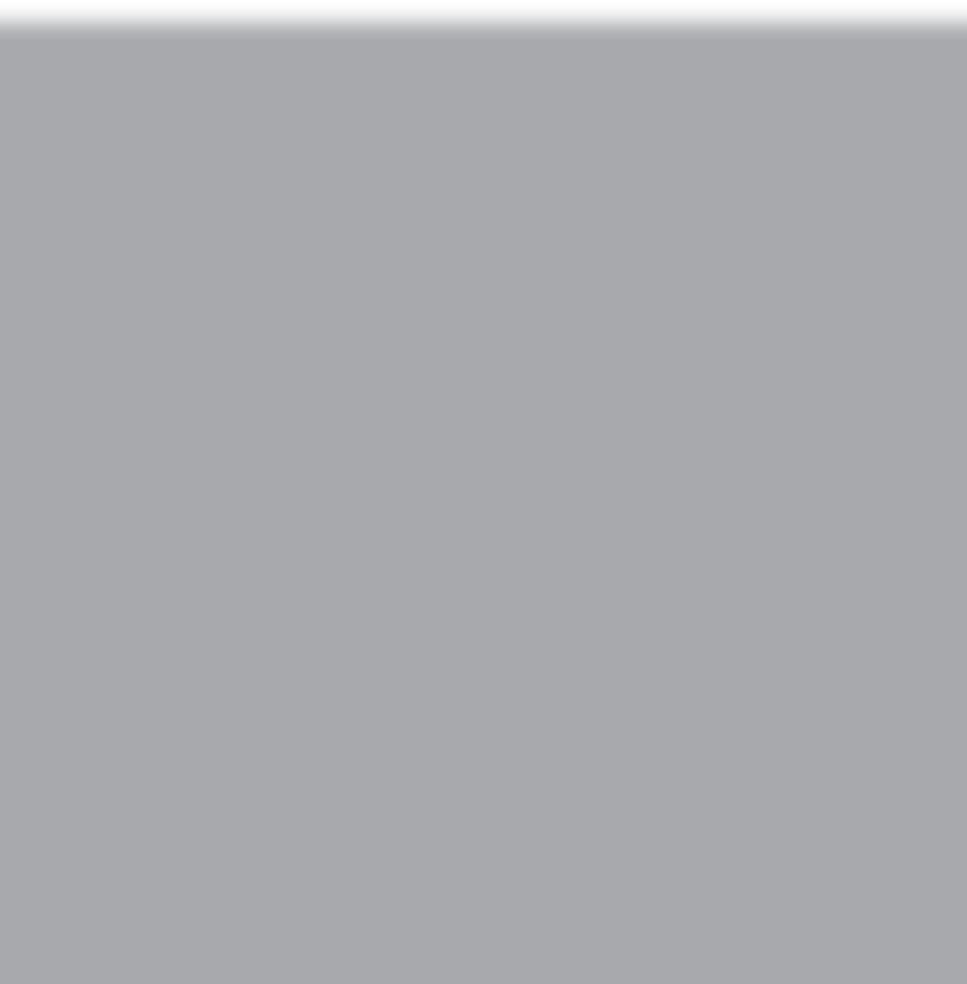
feedstocks, and produced a variety of nozzles, impellers, and turbine blades for aerospace and military use. She also got to be good friends with PANDA, the metal 3D-printing system that she used there and whose manu- Suzy Marzano Senior Managerfacturing has since been spun off into a separate company: Industry Development and Open Additive in Beaver Creek, Ohio. One might argue that Technical Activities her experiences with that machine helped cement her love of SME additive manufacturing. Ivanova referred to one of the parts she made with it as “ginormous, sumptuous, glamorous, and splendiferous”—which is very high praise for a hunk of metal.
As noted earlier, Ivanova currently serves as director of technology at Mechnano. It’s a company where she can apply her love of 3D printing to the furtherance of her first darling: nanotechnology. Even better, Mechnano’s address is in sunny Mesa, Ariz., allowing her to stay warm enough—almost—to fend off her constant case of the chills. “I’m cold all the time,” she laughed. “Walk into our office and I’ll be the only one wearing a hoodie.” Mechnano founder and CEO Steve Lowder agrees on both counts. “Whether it’s printing Groots and Polar Bears for youth, volunteering at area food banks, or painting small homes for families in transition, Olga illustrates the AM Community Shows Off at goodness and care for others that each of us should strive for—these are qualities that our business culture wholeheartedly supports.” RAPID + TCT It’s official. Additive Manufacturing is thriving and continues to gain momentum with successes across diverse applications. In addition to ongoing technology Focused on the Little Things Mechnano is a materials company. It develops and manufactures master-batches and formulations for use in advances, AM’s growth is fueled by a host of engaged 3D printing feedstocks using discrete carbon nanotubes. It’s companies, organizations, and dedicated professionals, all here that Ivanova hands out 3D-printed Yodas—ones that are of whom are energized and passionate about developing, not static dissipative, anyway—to young people interested in manufacturing. And it’s here that she spends her days quite implementing—and sharing—new ideas and best practicliterally unraveling the mysteries of carbon nanotubes. es throughout a collaborative community of innovators. “Ever since their discovery nearly thirty years ago,
The recent RAPID + TCT conference, which was held carbon nanotubes have offered enormous promise,” she May 17–19 in Detroit, is proof positive as to how far AM has come in recent years. The 31st edition of the industry’s marquee event featured more than 400 exhibitors, hundreds of speakers and expert panelists, dozens of technical sessions, networking opportunities, and attendees from 38 countries.
The AM community took center stage throughout the show. This includes the passing of the baton in two key leadership positions. John Barnes assumed the chair of the Additive Manufacturing Technical Community Leadership Committee, succeeding Christopher Williams; and Sarah Rimini now chairs the Medical AM Advisory Committee, succeeding Amy Alexander. I’d like to thank Christopher and Amy, who provided exemplary leadership and vision during their tenures, and welcome their replacements.
As senior manager of Ricoh’s Healthcare Center of Excellence, Sarah is developing a curriculum for the company’s Learning Institute that focuses on medical managed 3D-printing services. At RAPID + TCT, she moderated a panel discussion on 3D printing for point-of-care medical applications. The panel was one of several during a special town hall hosted by the Medical AM Advisory Team. Other highlights included the winners of the 2022 SME Additive Manufacturing Community Awards: Slade Gardner, founder of Big Metal Additive (Industry Achievement); VELO3D and IMI Critical Engineering (Aubin AM Case Study); and Virginia Tech students Daniel Chirvasuta, Nathanael High, Matthew Martin, Benjamin Nguyen, Omkar Shinde, and Nicolas Tomanelli (Digital Manufacturing Challenge). To help foster the next generation of innovators, the SME Education Foundation’s Bright Minds Program welcomed nearly 1,000 middle and high school students to RAPID + TCT. There also was a special networking lunch for young professionals and a Career Forum Panel. The initiative is led by Ellen Lee and Jennifer Coyne, who are both advisors on the Additive Manufacturing Technical Community Leadership Committee. SME Media also interviewed dozens of AM leaders during RAPID + TCT as part of its Voices AMplified initiative that showcases the people behind the technology. This month’s Voices AMplified report profiles two such visionaries: Olga Ivanova and Carl Dekker. Known as “Dr. O,” Olga has worked on innovative projects for the medical and defense industries, and is a tireless crusader for advancing AM. Carl puts the emphasis on people. He leads a talented team at Met-L-Flo, which produces a wide range of 3D-printed products. He also chairs the Direct Digital Manufacturing Advisory Team and moderated a panel at RAPID + TCT. Carl and Olga represent the spirit behind Voices AMplified. I hope you enjoy their stories. Suzy Marzano Senior Manager Industry Development and Technical Activities SME
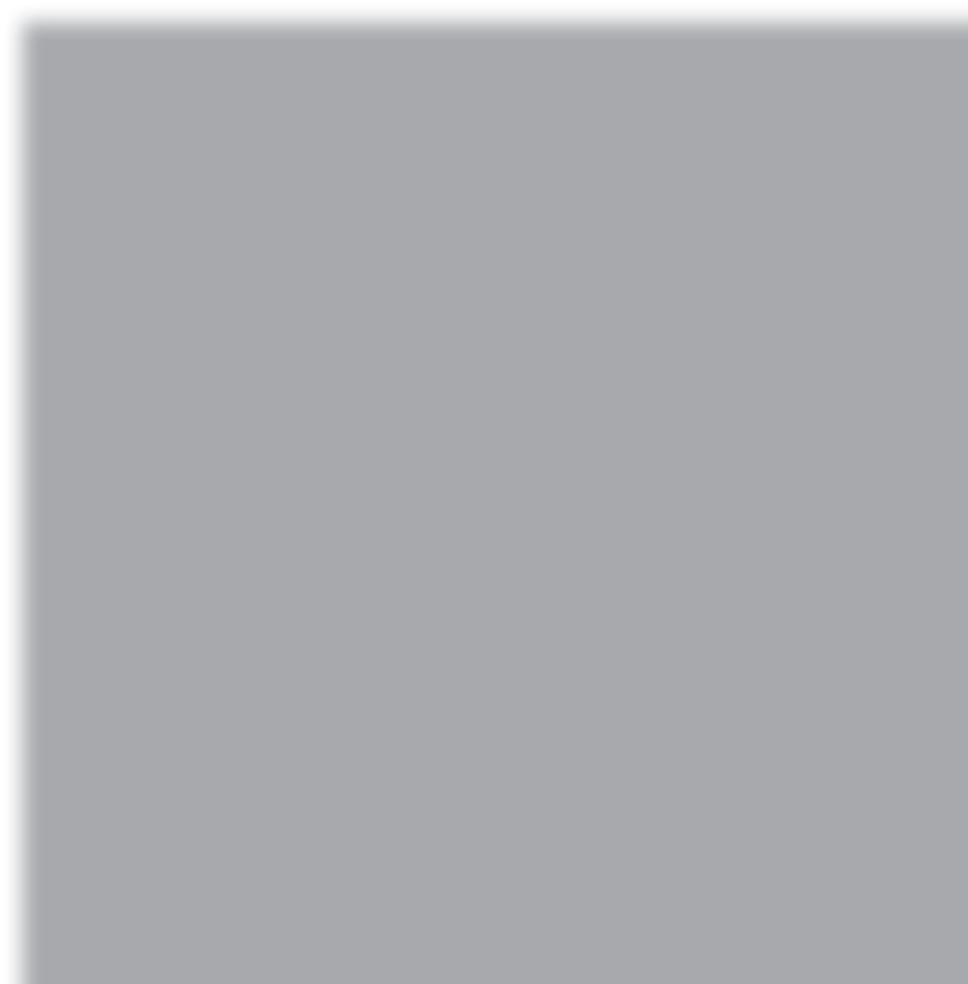
Thanks to their ability to fluoresce under UV light, quantum dots like these might one day be used as a tool to prevent counterfeiting

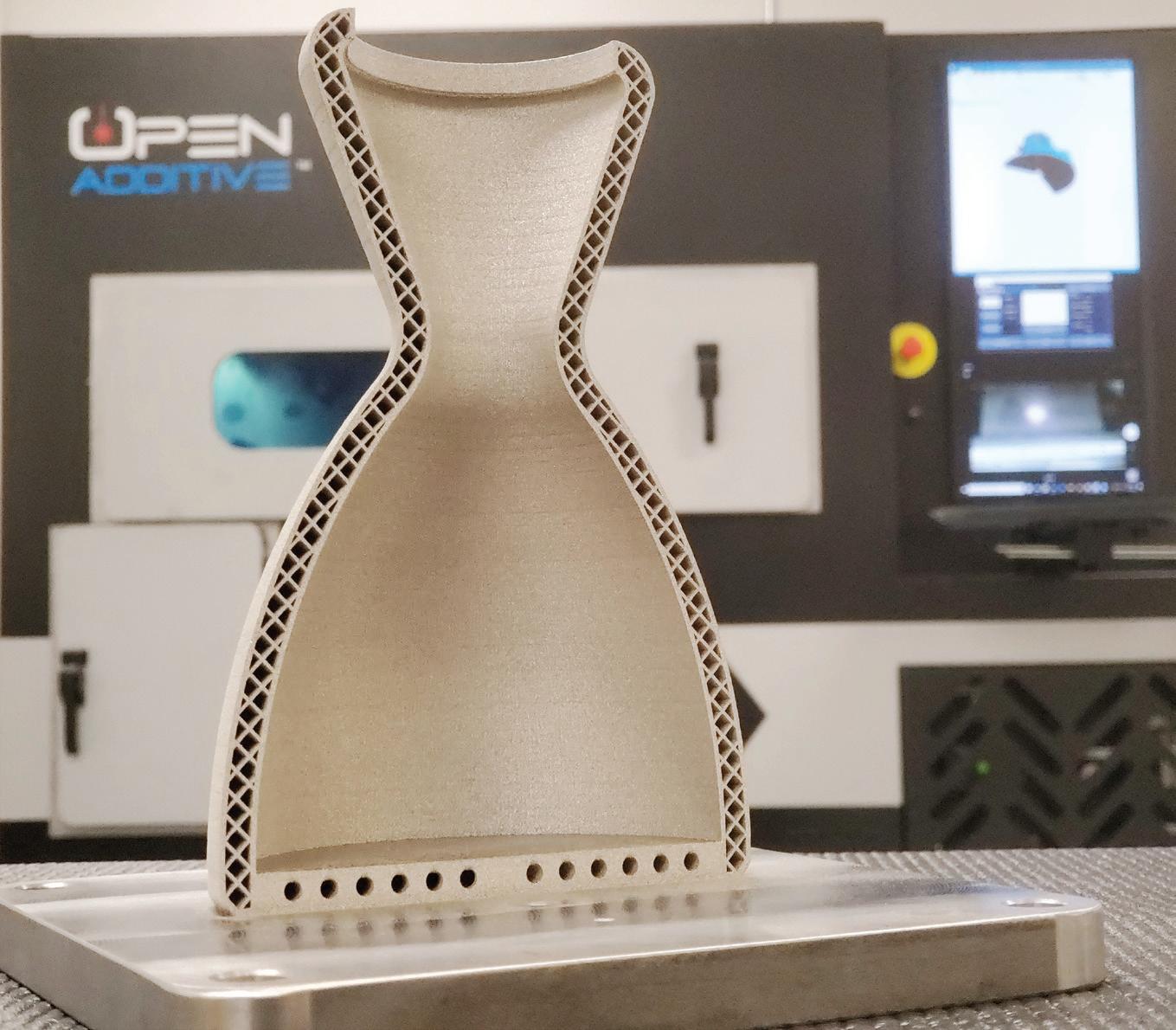
said. “They have extremely high tensile strength, are very light, and their elecAlthough their movie counterparts possess awesome superpowers, the 3D-printed trical conductivity is roughly one-thouBaby Yodas (at left) and Groots (right) that Olga Ivanova gave to visiting high school students are unable to do so much as dissipate electrical charge--but they’re still very sand times that of copper. For these popular with the kids. and other reasons, the government has poured billions of dollars into their development. The challenge, however, is that when you synthesize carbon nanotubes, they take on an agglomerated bundled state, so you can’t harness their unique properties. Our intellectual property centers around untangling those bundles.” Ask Ivanova how she goes about this unlikely task, and she’ll just smile and politely decline. “I can’t tell you much about that, except to say we’re having great success.”
Peering Ahead
Despite her understandable reluctance to discuss proprietary technology, Ivanova is clearly fascinated by all things infinitesimal, with carbon nanotubes and nanocomposites at the top of the list. “It’s groundbreaking work, especially in the context of additive manufacturing,” she said. “Think about it. Many of the current challenges here come down to material selection. Maybe it’s not strong enough, or it’s not conductive, or it can’t resist high temperatures—pick your property. Many companies have looked to ceramics and composites as a means to break that barrier, and some have enjoyed increased material performance as a result. I see discrete carbon nanotubes and other nano-engineered materials as the next frontier, and think we’ve only started to scratch the surface of what’s possible.” When not peeking beneath the covers of the atomic universe, Ivanova keeps a close eye on the additive industry. As many of those who call her Dr. O will attest, she’s keenly interested in all aspects of 3D printing, and is amazed at the technology’s rapid and continuous growth. “You have to keep learning and digging and look at what others are doing if you want to keep up with it all,” she said. “For example, when I visit trade shows like RAPID + TCT and Formnext, I make it a point to stop by every booth whose name I don’t recognize. I look back at the state of the industry as it was when I first graduated and am blown away by the advancements. The cat’s definitely out of the bag.”
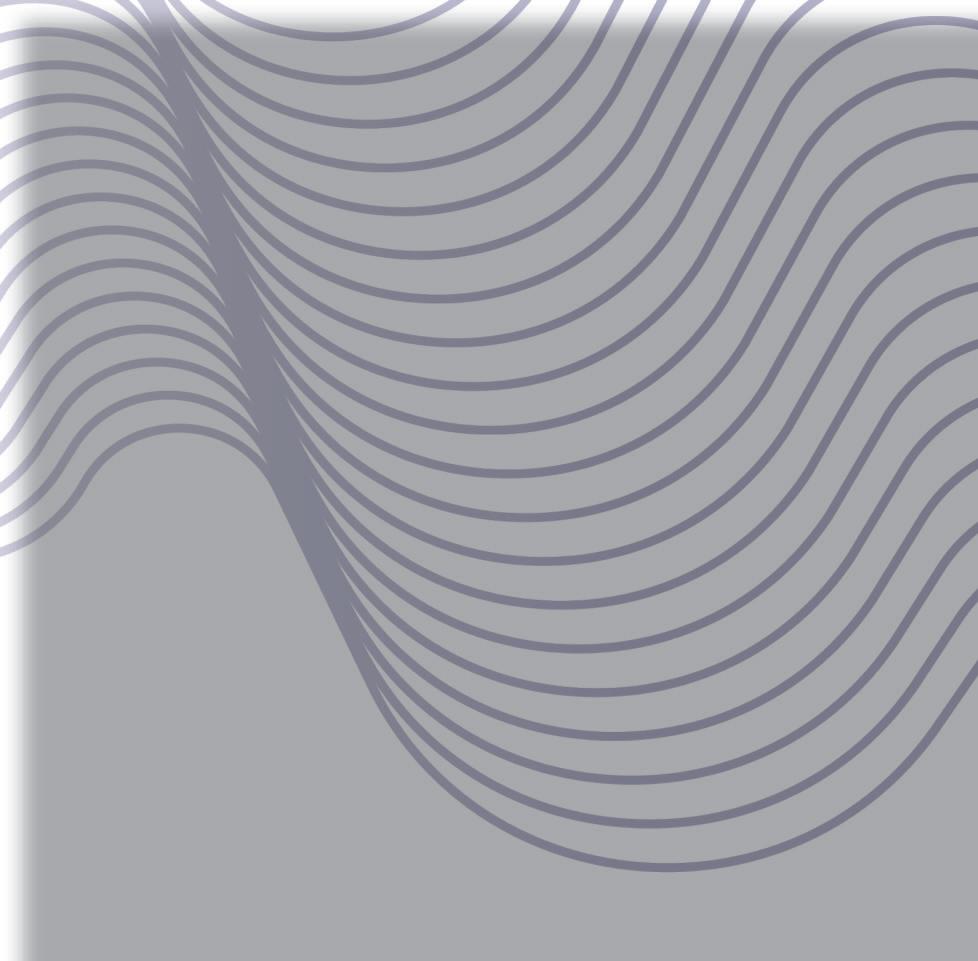
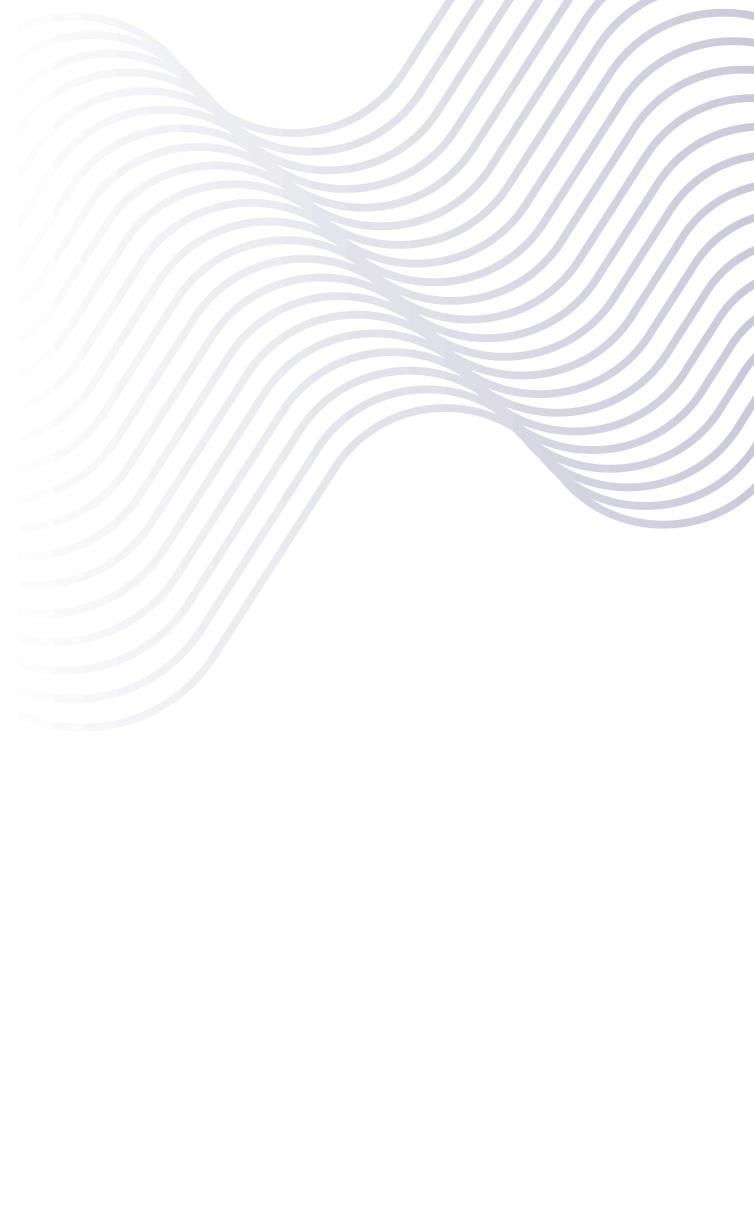
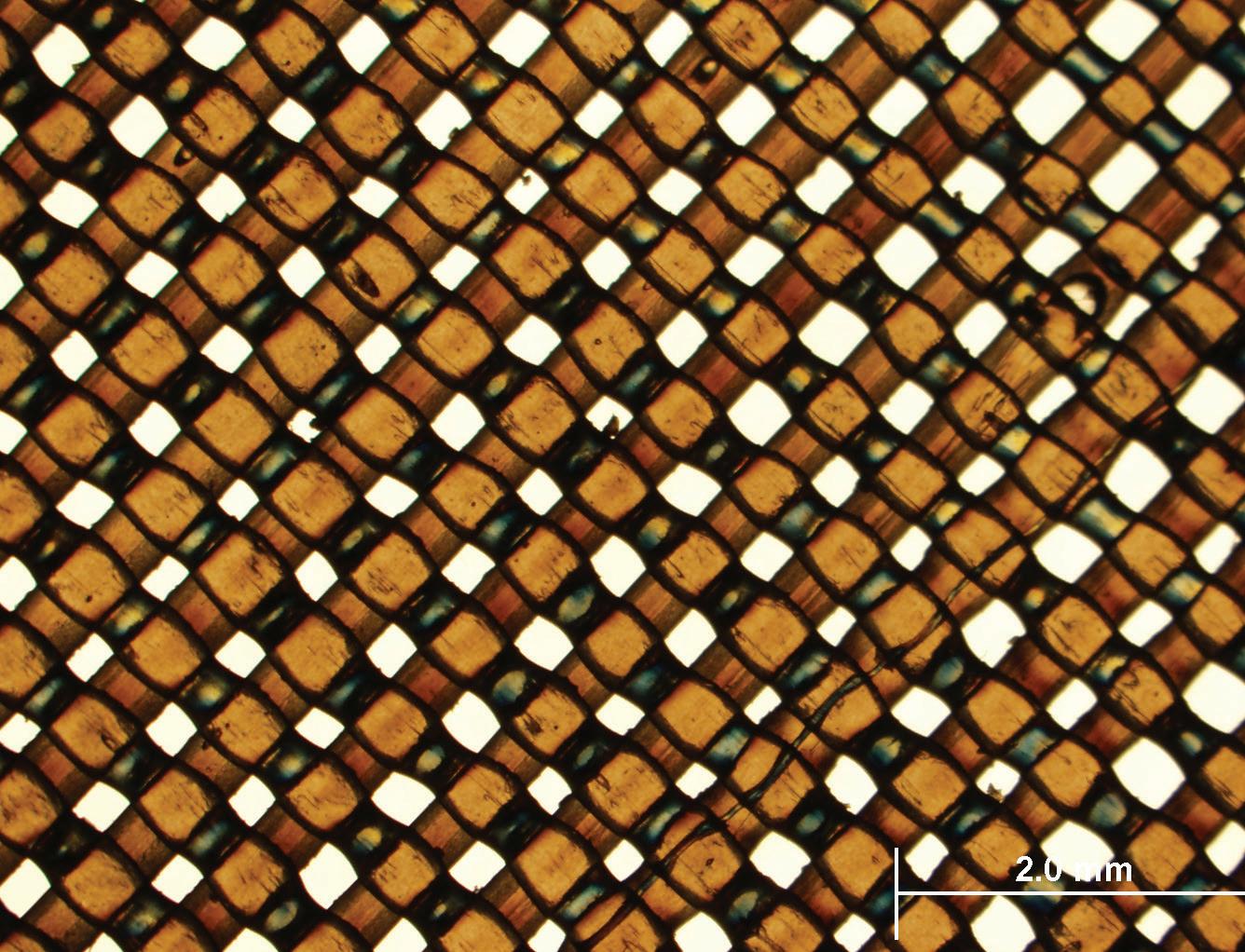
Paging Dr. O
Olga Ivanova has 3D-printed plenty of interesting parts during her time in manufacturing. Rocket nozzles. Turbine blades and impellers. Neonatal tracheostomy tubes. There are more, which we’ll get to in a moment, but to Star Wars fans, it’s the Static Dissipative Yoda that’s most intriguing.
“We printed a bunch of Yoda and Groot (Guardians of the Galaxy) figurines for high school students who visited our facility recently,” said Ivanova, director of technology at Mechnano, an additive manufacturing materials
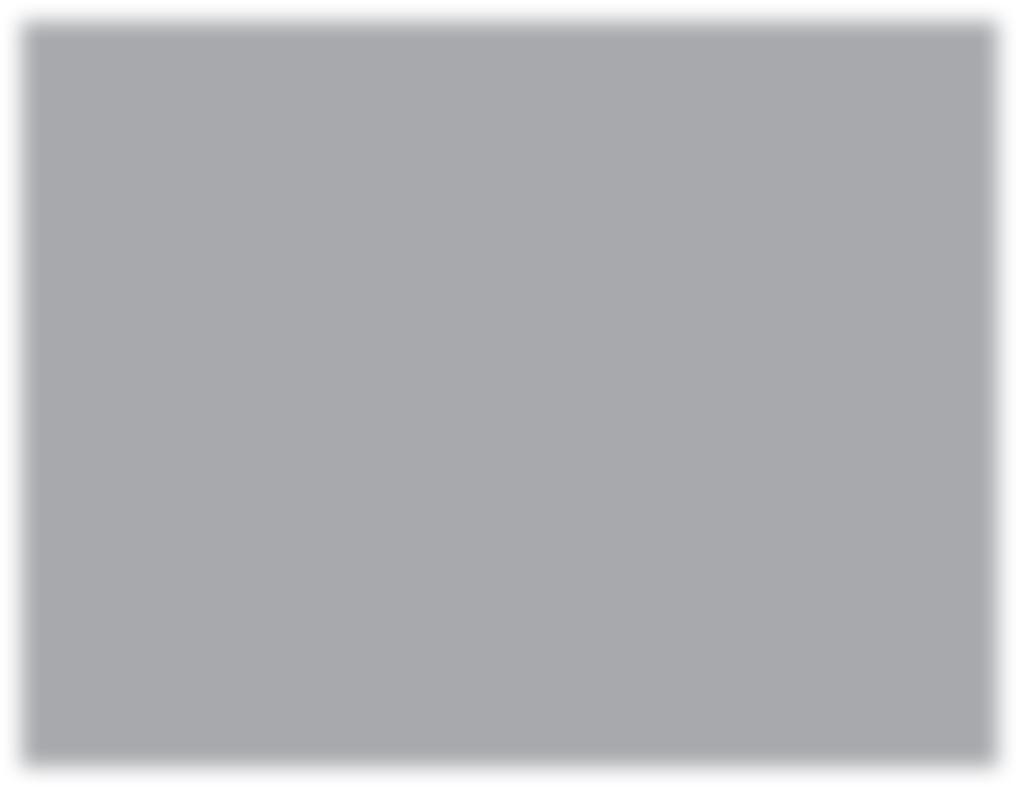
Here’s the aerospace component that additive manufacturing geek Olga Ivanova once referred to as “ginormous, sumptuous, glamorous, and splendiferous.” From 3D-printed figurines for students to “quantum dots” and nanocomposites, Olga Ivanova is a force to be reckoned with in the AM universe Olga Ivanova Master networker RAPID + TCT Director of Technology Kip Hanson Mechnano Contributing Editor developer near Phoenix. “It’s our way of getting young people interested in additive manufacturing.”
Padawan Learning
She’s quick to point out that those educational giveaways were made of a gray-colored base resin, not the more A close-up view of 3D-printed fabric, which the U.S. military expensive static dissipative material (which is black) that she has investigated for use in uniforms and undergarments. spends much of each day working with—and yes, which she occasionally uses to print Yodas that are just as resistant to electrical charge as they are to the Dark Side of the Force. July 2022 | sme.org 55
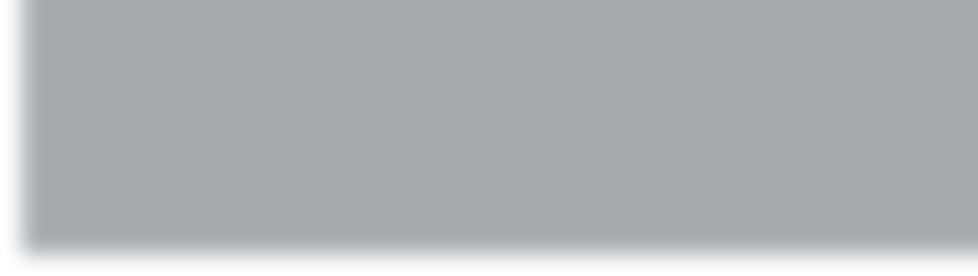

AM Community Shows Off at AM Community Shows Off at RAPID + TCT RAPID + TCT
Suzy Marzano
Suzy Marzano Senior Manager Industry Development and Senior Manager Technical Activities Industry Development and SME Technical Activities SME
It’s official. Additive Manufacturing is thriving and continues to gain momentum with successes across diverse applications. In addition to ongoing technology advances, AM’s growth is fueled by a host of engaged companies, organizations, and dedicated professionals, all of whom are energized and passionate about developing, implementing—and sharing—new ideas and best practices throughout a collaborative community of innovators.
The recent RAPID + TCT conference, which was held May 17–19 in Detroit, is proof positive as to how far AM has come in recent years. The 31st edition of the industry’s marquee event featured more than 400 exhibitors, hundreds of speakers and expert panelists, dozens of technical sessions, networking opportunities, and attendees from 38 countries.
The AM community took center stage throughout the show. This includes the passing of the baton in two key leadership positions. John Barnes assumed the chair of the Additive Manufacturing Technical Community Leadership Committee, succeeding Christopher Williams; and Sarah Rimini now chairs the Medical AM Advisory Committee, succeeding Amy Alexander. I’d like to thank Christopher and Amy, who provided exemplary leadership and vision during their tenures, and welcome their replacements.
3D-printing services. At RAPID + TCT, she moderated a panel discussion on 3D printing for point-of-care medical applications. The panel was one of several during a special town hall hosted by the Medical AM Advisory Team. Other highlights included the winners of the 2022 SME Additive Manufacturing Community Awards: Slade Gardner, founder of Big Metal Additive (Industry Achievement); VELO3D and IMI Critical Engineering (Aubin AM Case Study); and Virginia Tech students Daniel Chirvasuta, Nathanael High, Matthew Martin, Benjamin Nguyen, Omkar Shinde, and Nicolas Tomanelli (Digital Manufacturing Challenge). To help foster the next generation of innovators, the SME Education Foundation’s Bright Minds Program welcomed nearly 1,000 middle and high school students to RAPID + TCT. There also was a special networking lunch for young professionals and a Career Forum Panel. The initiative is led by Ellen What’s in Lee and Jennifer Coyne, who are both advisors on the Additive Manufacturing Technical Community Leadership Committee. SME Media also interviewed dozens of AM leaders during a Name? RAPID + TCT as part of its Voices AMplified initiative that showcases the people behind the technology. This month’s Voices AMplified report profiles two such visionaries: Olga Ivanova and Carl Dekker. Known as “Dr. O,” Olga has worked on innovative projects for the medical and defense industries, “Yes, we also do plastic.” It’s a common refrain at Met-L-Flo Inc. of Sugar Grove, Ill., where President Carl Dekker and his team and is a tireless crusader for advancing AM. Carl puts the emphasis on people. He leads a talented team at Met-L-Flo, which produces a wide range of 3D-printed prodof 20 oversee five of the seven ASTM-recognized addi- ucts. He also chairs the Direct Digital Manufacturing Advisory tive manufacturing (AM) technologies. These include vat Team and moderated a panel at RAPID + TCT. photopolymerization, material extrusion, material jet- Carl and Olga represent the spirit behind Voices AMplified. ting, binder jetting, and powder bed fusion (the latter in I hope you enjoy their stories. both metal and polymer). Within this list are several AM subcategories, such as Carbon’s Digital Light Synthesis (DLS) and 3D Systems’ MultiJet Printing (MJP).
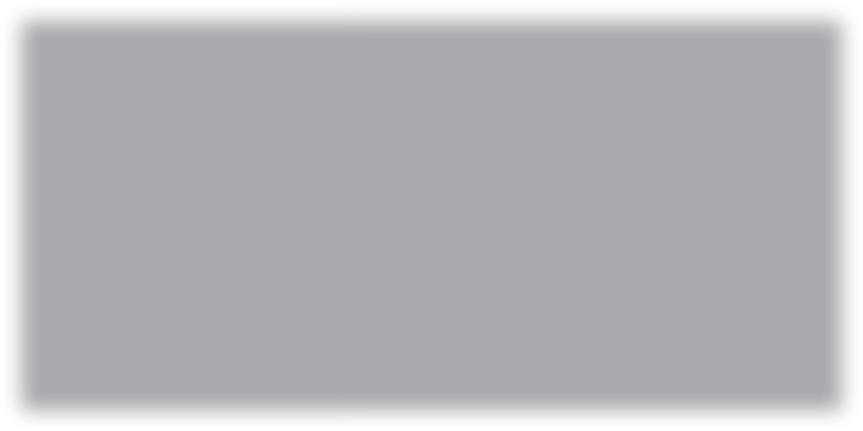
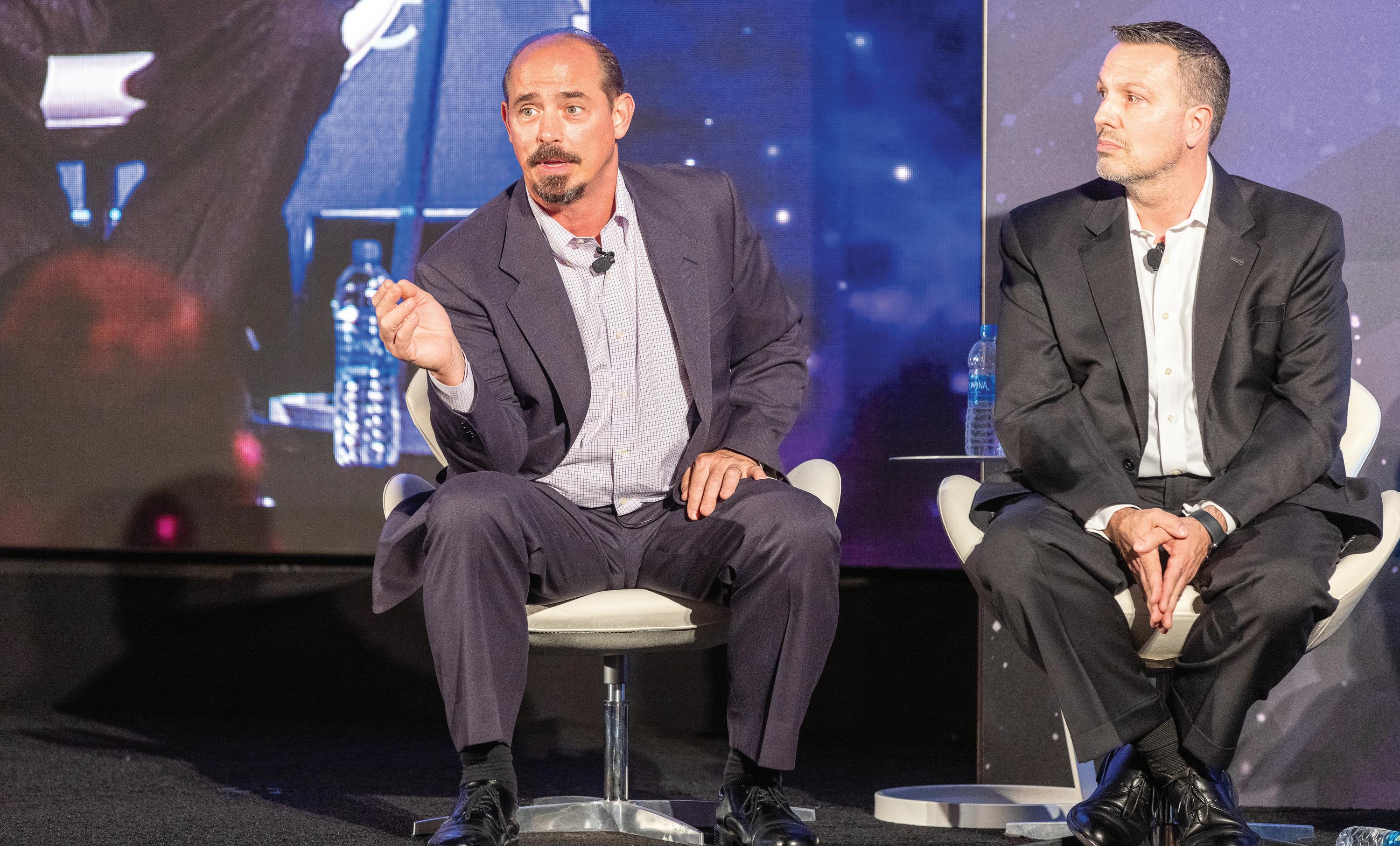
It’s official. Additive Manufacturing is thriving and continues to gain momentum with successes across diverse applications. In addition to ongoing technology advances, AM’s growth is fueled by a host of engaged companies, organizations, and dedicated professionals, all of whom are energized and passionate about developing, implementing—and sharing—new ideas and best practices throughout a collaborative community of innovators.
Carl Dekker (left) presenting come in recent years. The 31st edition of the industry’s marat RAPID + TCT along with quee event featured more than 400 exhibitors, hundreds of
Brennon White of General Motors. speakers and expert panelists, dozens of technical sessions, networking opportunities, and attendees from 38 countries. Met-L-Flo’s eclectic business mix demands innovative AM solutions The AM community took center stage throughout the show. This includes the passing of the baton in two key leadership positions. John Barnes assumed the chair of the Additive Manufacturing Technical Community Leadership Committee, succeeding Christopher Williams; and Sarah Carl Dekker Rimini now chairs the Medical AM Advisory Committee, Seasoned succeeding Amy Alexander. I’d like to thank Christopher and Conference Amy, who provided exemplary leadership and vision during Presenter and Industry Leader Kip Hanson their tenures, and welcome their replacements. John, who heads The Barnes Global Advisors and Metal President Met-L-Flo Inc. Contributing Editor Powder Works, has been involved in metal additive manufacturing throughout a distinguished career. He’s led teams that qualified the aerospace industry’s first series production metAs if that weren’t enough to keep this small company al AM parts, and developed a pilot metal production facility. busy, Met-L-Flo also offers machining, rotational and plastic
As senior manager of Ricoh’s Healthcare Center of injection molding, and more. “We’re primarily a low-volume contract shop, and utilize additive manufacturing and Excellence, Sarah is developing a curriculum for the comAM-enabled technologies to develop parts for end-use pany’s Learning Institute that focuses on medical managed applications,” said Dekker. For example, Met-L-Flo employees are currently producing metal castings for various automotive applications. They’ve made fiberglass layups for trucks, vacuum-formed pieces for aircraft, and built countless tools, jigs, and fixtures

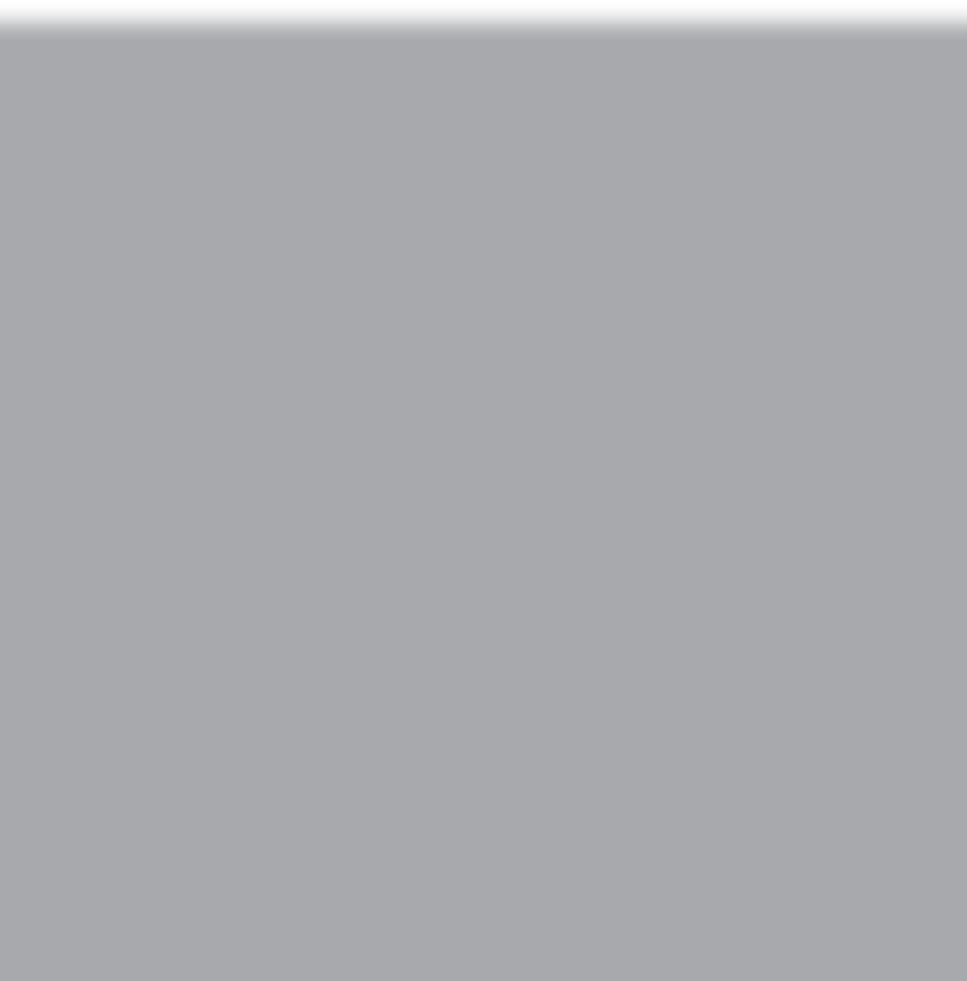
Other highlights included the winners of the 2022 SME Additive Manufacturing Community Awards: Slade Gardner, founder of Big Metal Additive (Industry Achievement); VELO3D and IMI Critical Engineering (Aubin AM Case Study); and Virginia Tech students Daniel Chirvasuta, Nathanael High, Matthew Martin, Benjamin Nguyen, Omkar Shinde, and Nicolas Tomanelli (Digital Manufacturing Challenge).
To help foster the next generation of innovators, the SME Education Foundation’s Bright Minds Program welcomed nearly 1,000 middle and high school students to RAPID + TCT. There also was a special networking lunch for young professionals and a Career Forum Panel. The initiative is led by Ellen Lee and Jennifer Coyne, who are both advisors on the Additive Manufacturing Technical Community Leadership Committee.
SME Media also interviewed dozens of AM leaders during RAPID + TCT as part of its Voices AMplified initiative that showcases the people behind the technology. This month’s Voices AMplified report profiles two such visionaries: Olga Ivanova and Carl Dekker. Known as “Dr. O,” Olga has worked on innovative projects for the medical and defense industries, and is a tireless crusader for advancing AM.
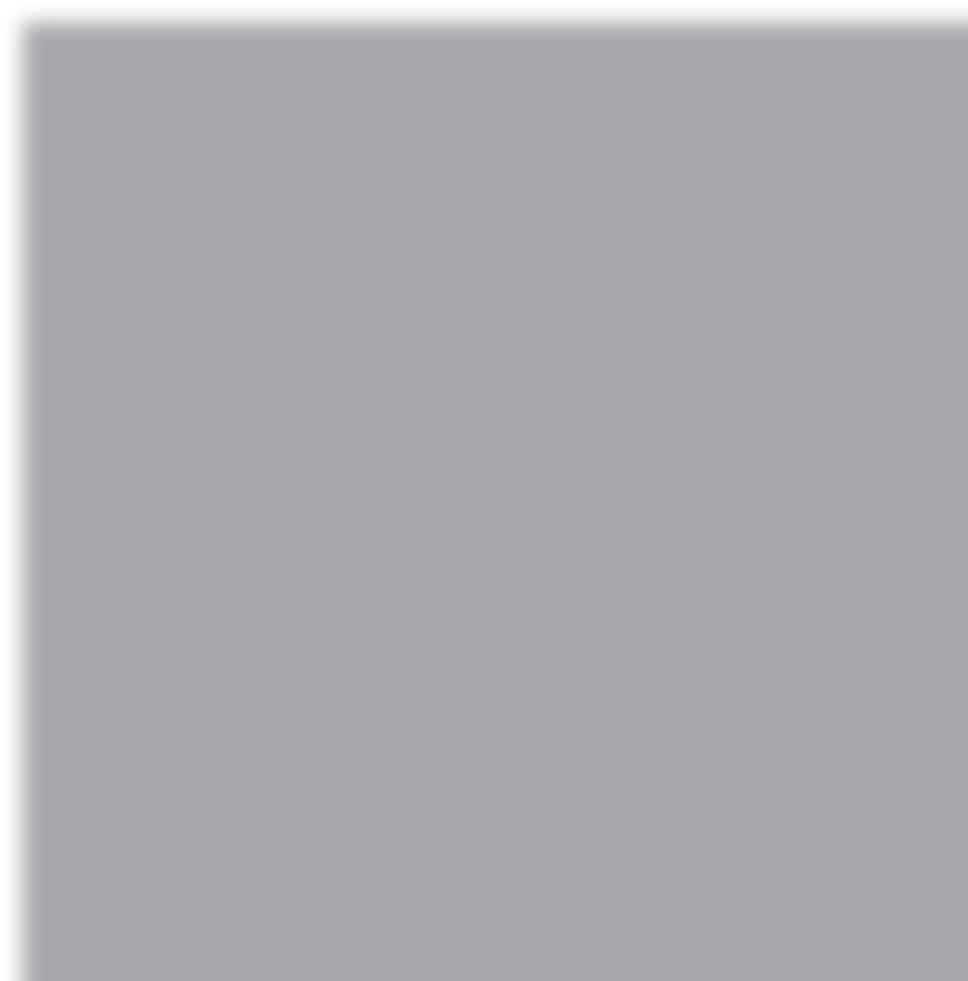

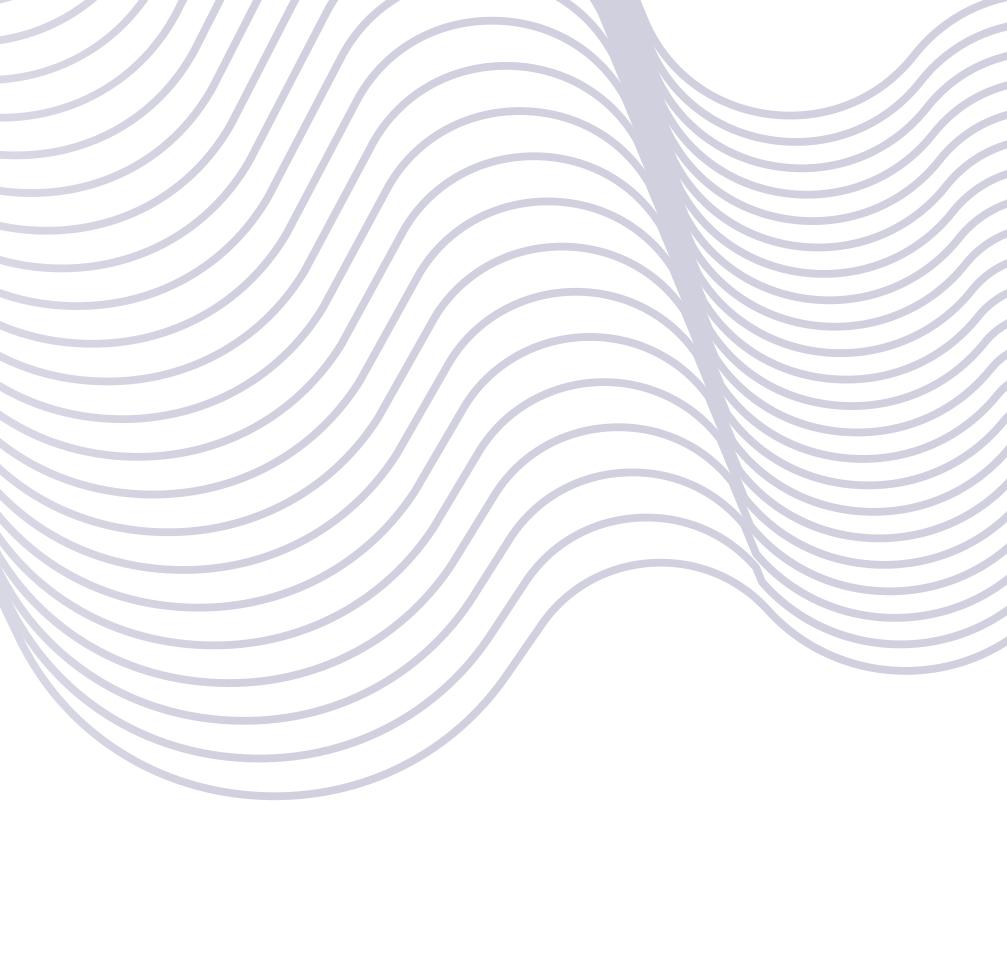
for their customers. They also provide design validation services and guidance on making designs more manufacturable. Although their movie counterparts possess awesome superpowers, the 3D-printed Baby Yodas (at left) and Groots (right) that Olga Ivanova gave to visiting high school In a nutshell, Dekker explained, Met-L-Flo team members students are unable to do so much as dissipate electrical charge--but they’re still very take a customer’s application need, drill down to whatever popular with the kids. manufacturing process will deliver the best possible result, and put together a proposal. If successful, they then manage that program for the client until completion.
It’s an eclectic mix that even many large manufacturing firms can’t lay claim to, yet Dekker is anything but boastful.
When asked how they keep up with it all, his answer was straightforward. “Our focus is on meeting our clients’ demands and helping to make them successful. That’s it.”
He freely admits that not all of his printers are state-ofthe-art. But at the end of the day, he suggested, owning the latest and greatest technology isn’t going to make a better part. That’s where having “really knowledgeable people” comes in. With that is a willingness to let machines sit idle from time to time when demand ebbs, and an understanding that the “latest and greatest” crown grows tarnished within a year or even a few months in the 3D-printing industry.
More than Metal
So why the mismatch between the company name and its service offering? It’s a long story. In 1969, Dekker’s father started Met-L-Flo Engineering as a consultancy to the metal-forging industry. Dekker joined the firm after a two-year stint with a Japanese import/export company attempting to advance silicone molding in the U.S. market. The year was 1991, and his stint was ending, so Dekker began looking for ways to develop what he had learned into the family business. He discovered what at that time was a novel prototyping technology—stereolithography. Within a few years, the consulting side of the company branched off to become Met-L-Flo Inc., one of the first 3D-printing service bureaus. “Back then, we were still very focused on the casting and forging markets, so there weren’t any branding issues at first,” said Dekker. “That began to change with the introduction of direct metal systems in the early 2000s. By then, we’d expanded into other areas, so we started playing with the
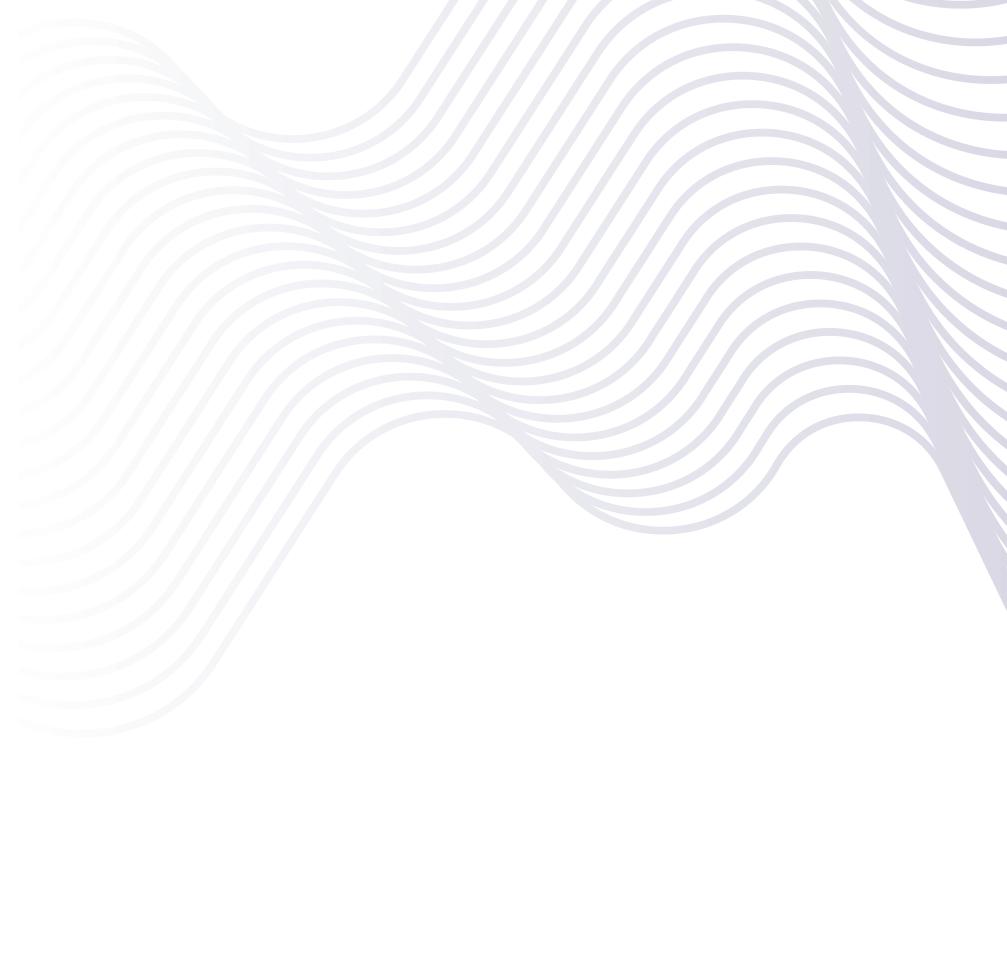
Paging Dr. O
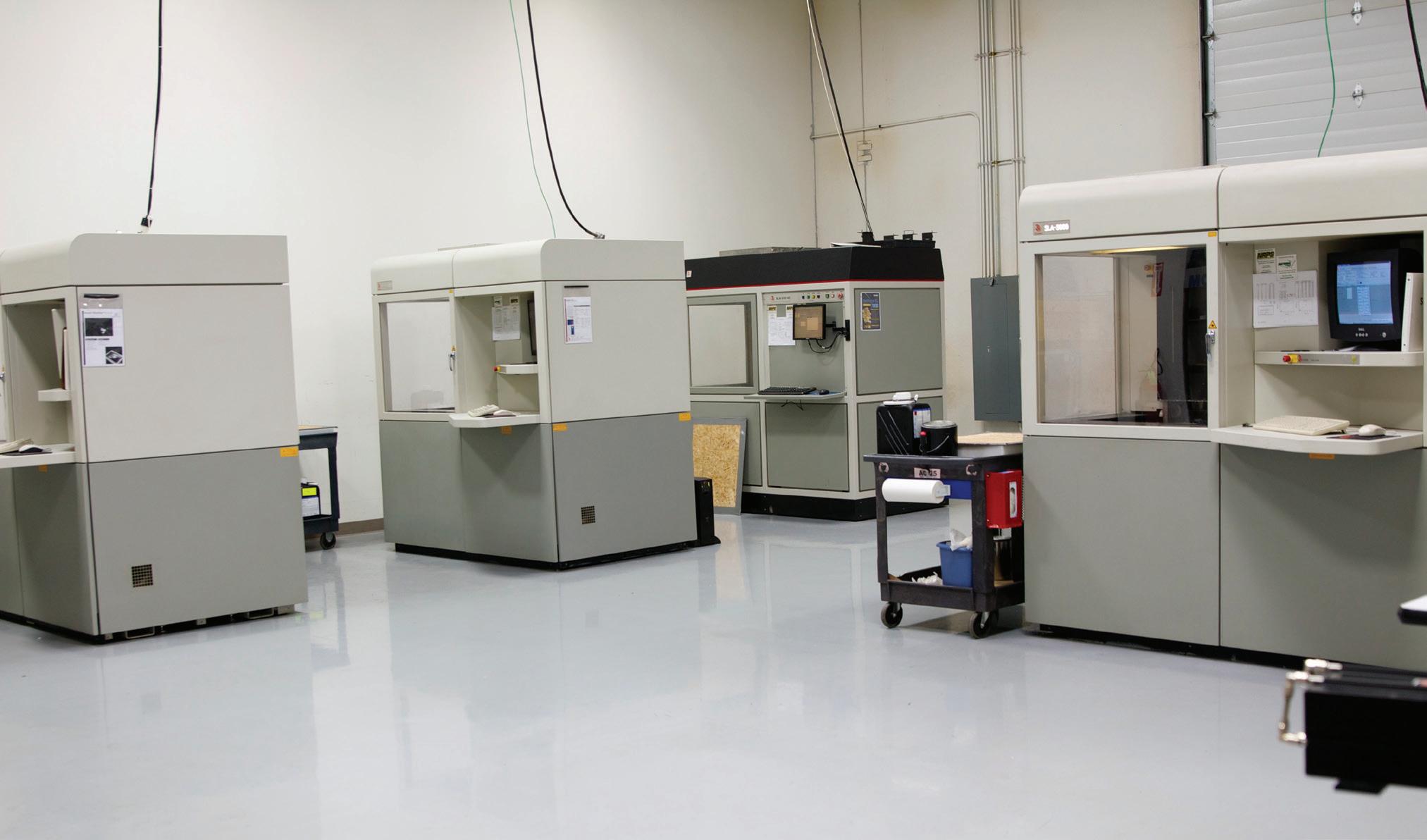
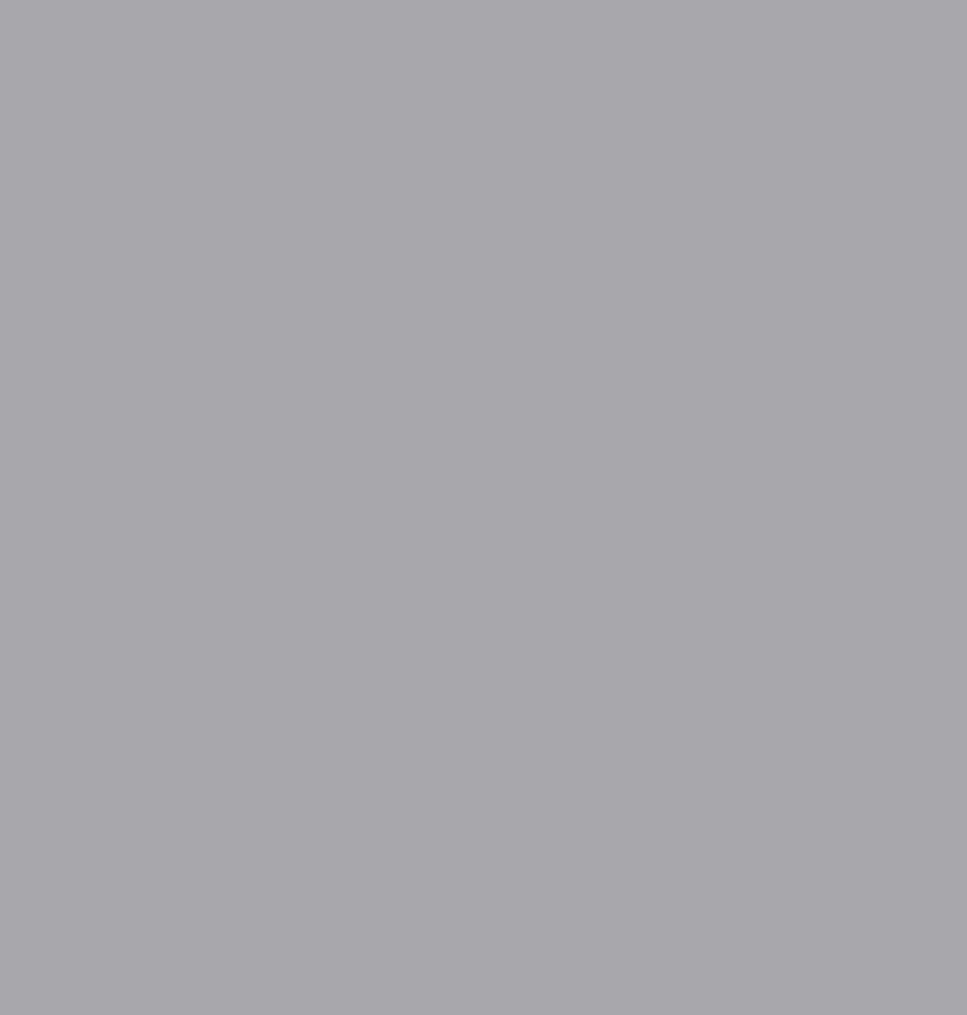
Kip Hanson
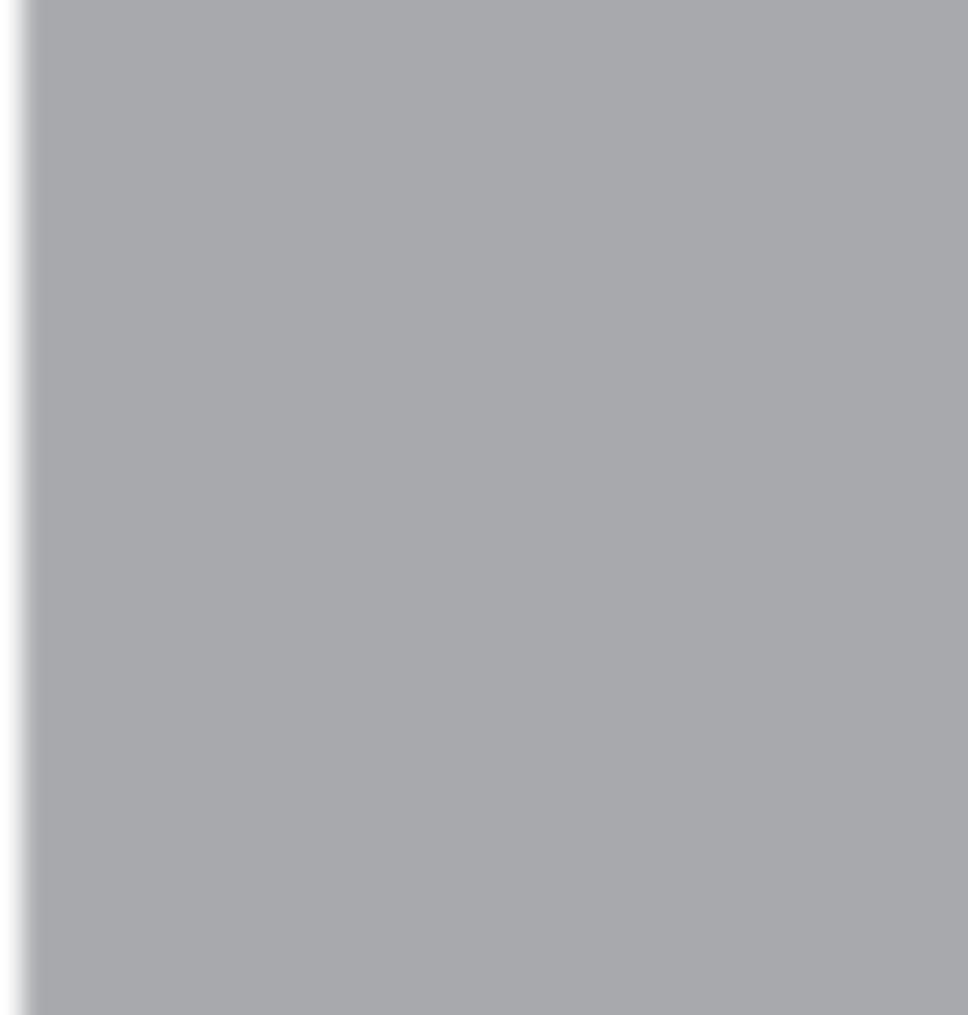
Contributing Editor
Olga Ivanova
Master networker RAPID + TCT
Director of Technology Mechnano
Olga Ivanova has 3D-printed plenty of interesting parts during her time in manufacturing. Rocket nozzles. Turbine blades and impellers. Neonatal tracheostomy tubes. There are more, which we’ll get to in a moment, but to Star Wars fans, it’s the Static Dissipative Yoda that’s most intriguing.
“We printed a bunch of Yoda and Groot (Guardians of the Galaxy) figurines for high school students who visited our facility recently,” said Ivanova, director of technology at Mechnano, an additive manufacturing materials
Padawan Learning
She’s quick to point out that those educational giveaways were made of a gray-colored base resin, not the more expensive static dissipative material (which is black) that she spends much of each day working with—and yes, which she The production floor at Met-L-Flo is home to five of the seven ASTM-recognized additive manufacturing technologies. occasionally uses to print Yodas that are just as resistant to electrical charge as they are to the Dark Side of the Force. July 2022 | sme.org 57

AM Community Shows Off at RAPID + TCT
It’s official. Additive Manufacturing is thriving and continues to gain momentum with successes across diverse applications. In addition to ongoing technology 3D-printing services. At RAPID + TCT, she moderated a panel discussion on 3D printing for point-of-care medical applications. The panel was one of several during a special town hall advances, AM’s growth is fueled by a host of engaged companies, organizations, and dedicated professionals, all of whom are energized and passionate about developing, implementing—and sharing—new ideas and best practices throughout a collaborative community of innovators.
The recent RAPID + TCT conference, which was held May 17–19 in Detroit, is proof positive as to how far AM has come in recent years. The 31st edition of the industry’s marquee event featured more than 400 exhibitors, hundreds of speakers and expert panelists, dozens of technical sessions, networking opportunities, and attendees from 38 countries.
The AM community took center stage throughout the show. This includes the passing of the baton in two key leadership positions. John Barnes assumed the chair of the Additive Manufacturing Technical Community Leadership Committee, succeeding Christopher Williams; and Sarah Rimini now chairs the Medical AM Advisory Committee, succeeding Amy Alexander. I’d like to thank Christopher and Amy, who provided exemplary leadership and vision during their tenures, and welcome their replacements.
As senior manager of Ricoh’s Healthcare Center of Excellence, Sarah is developing a curriculum for the company’s Learning Institute that focuses on medical managed hosted by the Medical AM Advisory Team. Other highlights included the winners of the 2022 SME Additive Manufacturing Community Awards: Slade Gardner, founder of Big Metal Additive (Industry Achievement); VELO3D and IMI Critical Engineering (Aubin AM Case Study); and Virginia Tech students Daniel Chirvasuta, Nathanael High, Matthew Martin, Benjamin Nguyen, Omkar Shinde, and Nicolas Tomanelli (Digital Manufacturing Challenge). To help foster the next generation of innovators, the SME Education Foundation’s Bright Minds Program welcomed nearly 1,000 middle and high school students to RAPID + TCT. There also was a special networking lunch for young professionals and a Career Forum Panel. The initiative is led by Ellen Lee and Jennifer Coyne, who are both advisors on the Additive Manufacturing Technical Community Leadership Committee. SME Media also interviewed dozens of AM leaders during RAPID + TCT as part of its Voices AMplified initiative that showcases the people behind the technology. This month’s Voices AMplified report profiles two such visionaries: Olga Ivanova and Carl Dekker. Known as “Dr. O,” Olga has worked on innovative projects for the medical and defense industries, and is a tireless crusader for advancing AM. Carl puts the emphasis on people. He leads a talented team at Met-L-Flo, which produces a wide range of 3D-printed products. He also chairs the Direct Digital Manufacturing Advisory Team and moderated a panel at RAPID + TCT. Carl and Olga represent the spirit behind Voices AMplified. I hope you enjoy their stories.
AM Community Shows Off at Suzy Marzano Senior Manager RAPID + TCT Industry Development and Technical Activities SME
It’s official. Additive Manufacturing is thriving and continues to gain momentum with successes across diverse applications. In addition to ongoing technology 3D-printing services. At RAPID + TCT, she moderated a panel discussion on 3D printing for point-of-care medical applications. The panel was one of several during a special town hall advances, AM’s growth is fueled by a host of engaged companies, organizations, and dedicated professionals, all of whom are energized and passionate about developing, implementing—and sharing—new ideas and best practices throughout a collaborative community of innovators.
The recent RAPID + TCT conference, which was held May 17–19 in Detroit, is proof positive as to how far AM has come in recent years. The 31st edition of the industry’s marquee event featured more than 400 exhibitors, hundreds of speakers and expert panelists, dozens of technical sessions, networking opportunities, and attendees from 38 countries.
The AM community took center stage throughout the show. This includes the passing of the baton in two key leadership positions. John Barnes assumed the chair of the Additive Manufacturing Technical Community Leadership Committee, succeeding Christopher Williams; and Sarah Rimini now chairs the Medical AM Advisory Committee, succeeding Amy Alexander. I’d like to thank Christopher and Amy, who provided exemplary leadership and vision during their tenures, and welcome their replacements.
As senior manager of Ricoh’s Healthcare Center of Excellence, Sarah is developing a curriculum for the company’s Learning Institute that focuses on medical managed hosted by the Medical AM Advisory Team. Other highlights included the winners of the 2022 SME Additive Manufacturing Community Awards: Slade Gardner, founder of Big Metal Additive (Industry Achievement); VELO3D and IMI Critical Engineering (Aubin AM Case Study); and Virginia Tech students Daniel Chirvasuta, Nathanael High, Matthew Martin, Benjamin Nguyen, Omkar Shinde, and Nicolas Tomanelli (Digital Manufacturing Challenge). To help foster the next generation of innovators, the SME Education Foundation’s Bright Minds Program welcomed nearly 1,000 middle and high school students to RAPID + TCT. There also was a special networking lunch for young professionals and a Career Forum Panel. The initiative is led by Ellen Lee and Jennifer Coyne, who are both advisors on the Additive Manufacturing Technical Community Leadership Committee. SME Media also interviewed dozens of AM leaders during RAPID + TCT as part of its Voices AMplified initiative that showcases the people behind the technology. This month’s Voices AMplified report profiles two such visionaries: Olga Ivanova and Carl Dekker. Known as “Dr. O,” Olga has worked on innovative projects for the medical and defense industries, and is a tireless crusader for advancing AM. Carl puts the emphasis on people. He leads a talented team at Met-L-Flo, which produces a wide range of 3D-printed products. He also chairs the Direct Digital Manufacturing Advisory Team and moderated a panel at RAPID + TCT. Carl and Olga represent the spirit behind Voices AMplified. I hope you enjoy their stories.
idea of a name change, but ultimately decided to leverage our brand recognition and continue with Met-L-Flow.” Suzy Marzano
No matter the company name, Dekker has more AM expeSenior Manager rience than most. Early in his career, he began presenting at Industry Development and seminars for SME in and around Chicago, an opportunity to Technical Activities SME “get the word out and connect with others in 3D printing.” These efforts led him to a group known as the Rapid Prototyping Association, which soon joined forces with SME, and which Dekker chaired at one point.
Today, he’s president of the Additive Manufacturing Users Group (AMUG). It’s a post he’s held for the past two years, preceded by two years as vice president. Dekker is also the current chair of SME’s Direct Digital Manufacturing Tech Group. “When a technology changes as quickly as additive manufacturing, it’s important to stay current,” he said.
Embracing Change
About twenty years ago, Dekker noticed a shift in the way that products are sourced and produced, and the term “direct manufacturing” was becoming more widespread. Met-L-Flo responded by preparing for AS9100 certification, which it achieved in 2010. The company also moved to its current location, a facility with better environmental controls and much more floor space for the growth in contract manufacturing that Dekker saw coming. Finally, with a goal to pursue more defense and aerospace work, Met-L-Flo added ITAR (International Traffic in Arms Regulations) certification to its expanding accreditation list.
While all this was going on, Dekker began working on another more fundamental problem: a lack of standards within the AM community. “Back then, most of my customers had developed their own sets of procedures, technical processes, material specifications, and so on,” said Dekker. “Following each of them, many of which were inconsistent, was becoming a serious complication for Met-L-Flo and others like us. That’s when we as a group started pushing for a standards body to take on the activity of developing what was initially a set of established guidelines for rapid prototyping, but that would soon become a much broader series of industry-wide additive manufacturing standards.” That standards body turned out to be ASTM International (formerly the American Society for Testing and Materials), which formed the ASTM Committee F42 on Additive Manufacturing Technologies in 2009. Dekker has served on the committee ever since—first as vice-chair, then chairperson, and now past chairperson. Knowing that wide-scale adoption of such standards is critical to the future of manufacturing overall, he and his colleagues have continued to grow the organization, while looking for ways to increase AM adoption and further develop the F42 standard. In an attempt to bring F42 to other countries, the ASTM committee joined forces with the International Organization for Standardization (ISO) and developed a presence in Europe. Together, they help direct any company wishing to establish its own standards back to the collaborative activities of the F42 committee, ISO, and the ANSI Additive Manufacturing Standardization Collaborative (AMSC). This move has brought a high degree of AM conformity in Europe, said Dekker. Unfortunately, the U.S. has been slower to climb aboard the standards bandwagon. “We don’t have a mechanism that designates F42 or any other document as the official standard,” he said. “In fact, there are more than a dozen SDOs [standards development organizations] at work here in the U.S., any of which is free to publish its own AM guidelines.”
Facing Challenges
Until everyone is singing from the same AM hymnal, Met-L-Flo and other additive manufacturers will struggle with ambiguity and inefficiency. “How do we get to the point where our customers can say, ‘I want my parts made via this standard’? Once you have that, we’ll be able to re“When a technology changes as spond with certainty, ‘Okay, quickly as additive manufacturing, we understand how to print it’s important to stay current.” the part. We understand how to inspect and post-process it and what materials we can use in its construction.’ Without that, universal conformance and part qualification will remain a question mark in certain applications.” As the industry continues to gain steam, such scenarios will become increasingly common, especially as 3D-printer ownership expands to the consumer market. Dekker described a futuristic scenario in which a parent prints a bicycle

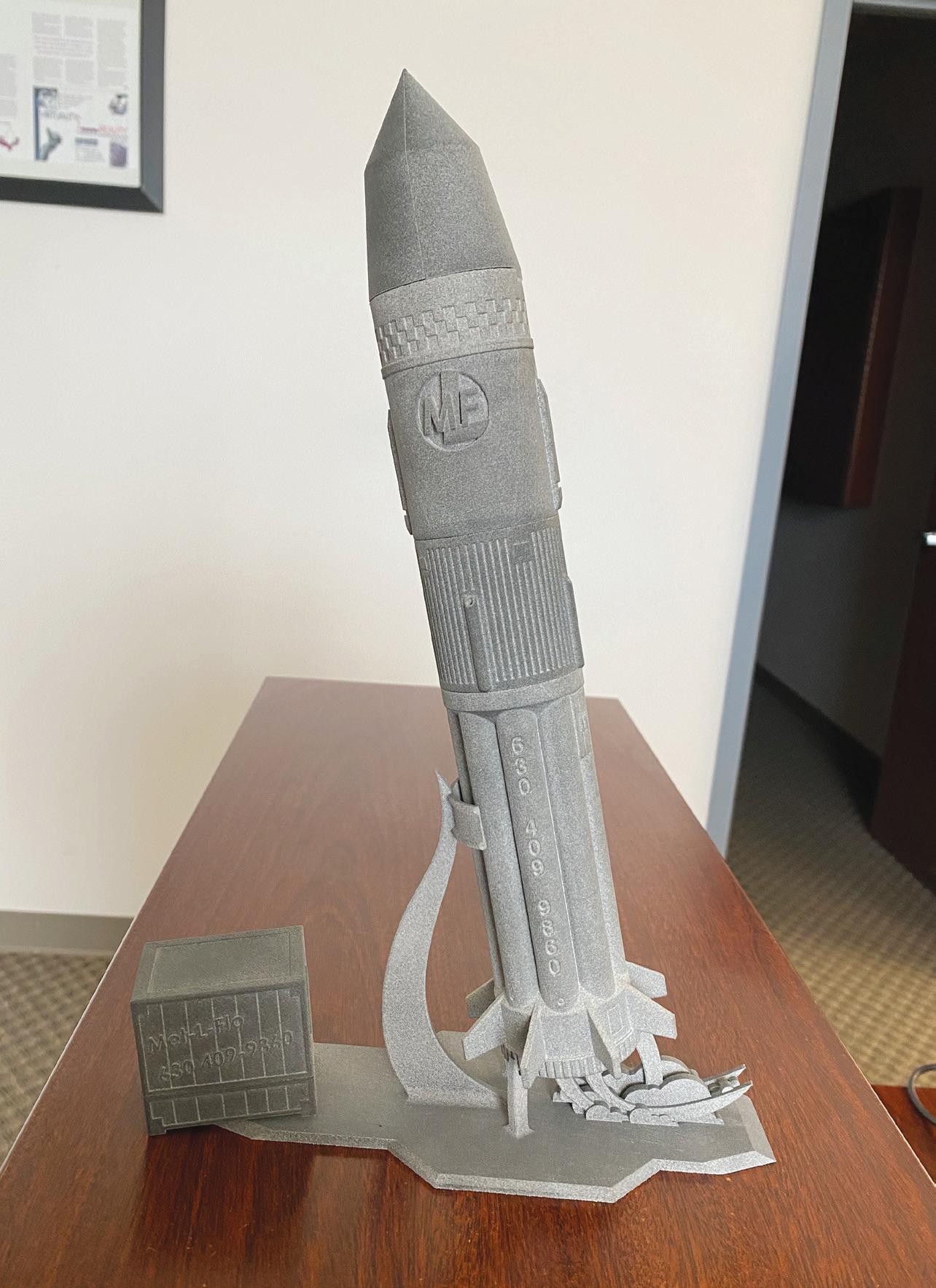
Although their movie counterparts possess awesome superpowers, the 3D-printed Baby Yodas (at left) and Groots (right) that Olga Ivanova gave to visiting high school students are unable to do so much as dissipate electrical charge--but they’re still very popular with the kids. safety-critical items like these on a home safety-critical items like these on a home printer, but that part of the discussion printer, but that part of the discussion really resonated with me. It provided some really resonated with me. It provided some insight into the industry’s maturation level insight into the industry’s maturation level and how far we have yet to go.” and how far we have yet to go.” Manufacturers grapple with similar liability questions, he added. Without robust liability questions, he added. Without robust process controls, reliable equipment and process controls, reliable equipment and materials, and a well-established set of stan materials, and a well-established set of standards to follow, the legal waters can quickly dards to follow, the legal waters can quickly become murky. “As a contract manufacturer, become murky. “As a contract manufacturer, it’s my responsibility to prove that any parts it’s my responsibility to prove that any parts we produced were made according to the we produced were made according to the customer’s data set and requirements, and customer’s data set and requirements, and that we followed agreed upon and docu-that we followed agreed upon and docu mented procedures,” he said. mented procedures,” he said.
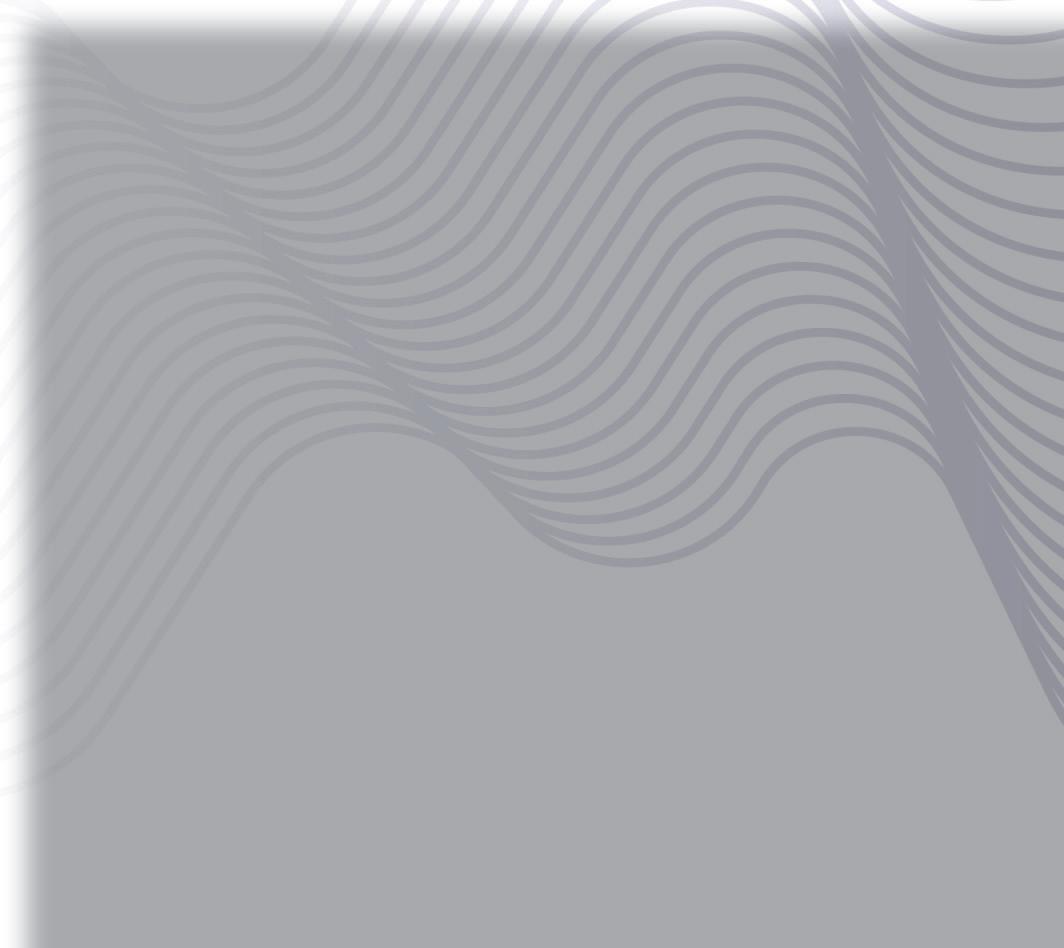
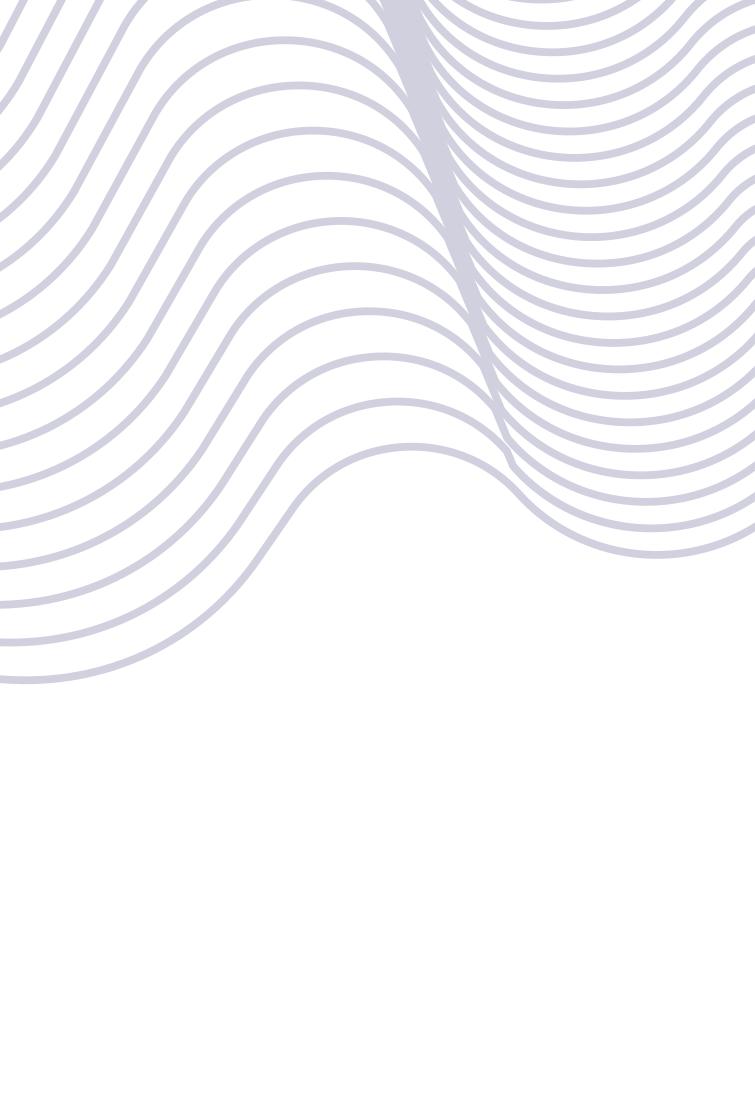
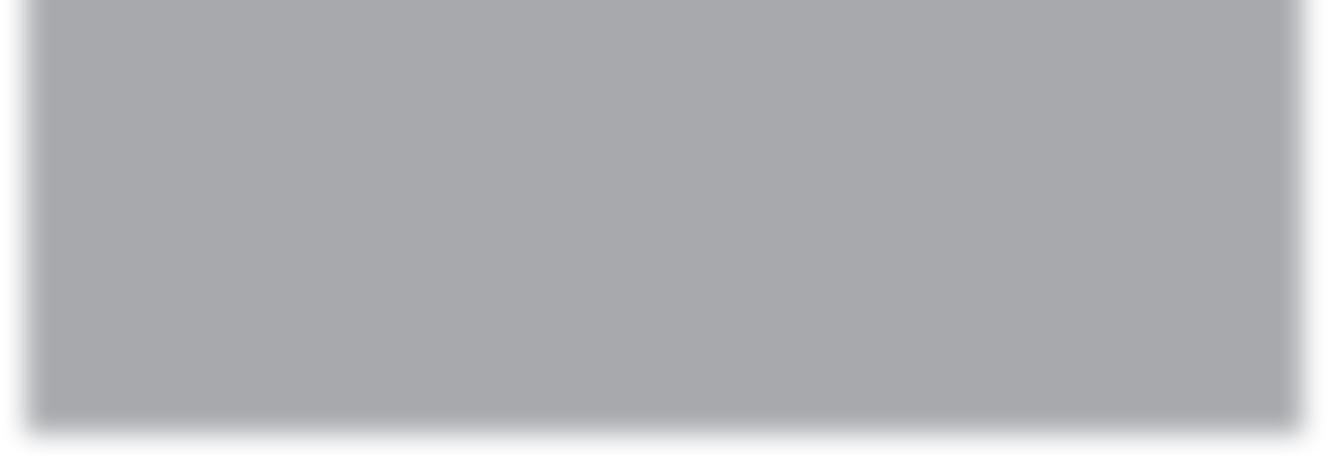
Paging Dr. O
Olga Ivanova has 3D-printed plenty of interesting parts during her time in manufacturing. Rocket nozzles. Turbine blades and impellers. Neonatal tracheostomy tubes. There are more, which we’ll get to in a moment, but to Star Wars fans, it’s the Static Dissipative Yoda that’s most intriguing.
“We printed a bunch of Yoda and Groot (Guardians of the Galaxy) figurines for high school students who visited our facility recently,” said Ivanova, director of technology at Mechnano, an additive manufacturing materials
From 3D-printed figurines for students to “quantum dots” and nanocomposites, Olga Ivanova is a force to be reckoned with in the AM universe Olga Ivanova Master networker RAPID + TCT Director of Technology Kip Hanson Mechnano Contributing Editor helmet. The child gives said helmet to a friend for his birthday, the friend falls off his bike, the helmet breaks, and the friend’s family sues for damages. Who is liable? The 3D-printdeveloper near Phoenix. “It’s our way of getting young er manufacturer? The raw material provider? The internet people interested in additive manufacturing.” site that provided the design model and printing files? Or the well-intentioned consumer? Padawan Learning Said Dekker, “I served on a GAO panel that was putting She’s quick to point out that those educational givetogether a report on 3D printing for congress, and one aways were made of a gray-colored base resin, not the more of the members raised some of these same questions. expensive static dissipative material (which is black) that she We’re not yet at the point where people will be making spends much of each day working with—and yes, which she occasionally uses to print Yodas that are just as resistant to electrical charge as they are to the Dark Side of the Force. July 2022 | sme.org 59
The Right Hammer The Right Hammer
Other questions abound. Dekker mentioned growing concerns over industrial tioned growing concerns over industrial cybersecurity, and the need to comply with cybersecurity, and the need to comply with NIST 800-171 requirements and the DoD’s NIST 800-171 requirements and the DoD’s Cybersecurity Maturity Model Certification Cybersecurity Maturity Model Certification as additional burdens in this brave new man-as additional burdens in this brave new man ufacturing world. Add to that the ongoing ufacturing world. Add to that the ongoing struggle to find and retain qualified employ-struggle to find and retain qualified employ ees, people who not only have the right skill ees, people who not only have the right skill set but also the right attitude, and a desire to set but also the right attitude, and a desire to grow with the company. grow with the company.
Training and workforce development is a huge issue, he noted. So is the need to a huge issue, he noted. So is the need to continually reinvent yourself. “When all you continually reinvent yourself. “When all you
Met-L-Flo customers are eligible to receive the components needed to build this Saturn IB rocket replica, designed and built by Carl Dekker’s have is a hammer, everything’s a nail. That’s engineering team. why manufacturers need diverse capabilities. I can’t tell you how many times a customer has called us to say, ‘Hey, sorry to tell you this, but we just bought a 3D printer and no longer need your services.’ My response is always, ‘Congratulations, but your machine is only good for certain parts and materials. Can we help you with any of the other six additive technologies?’ “Throughout our history, we’ve always invested in whatever’s needed for the application, learned everything we could about it, got it producing successfully, and then added it to our capabilities list. That’s how you grow as a manufacturing company.”
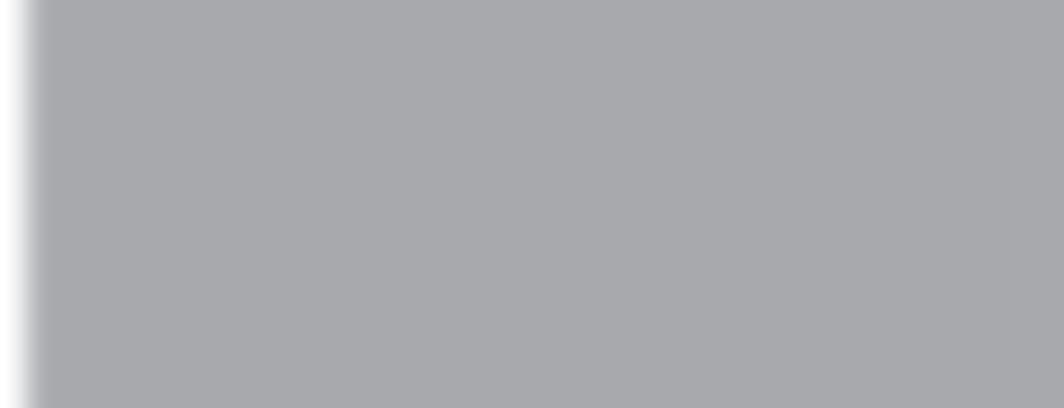
3D PRINTING & AM SERVICE PROVIDER MAP
If the last few years have taught us anything, at least in manufacturing, it’s that our supply chains need to be more agile. Additive manufacturing (AM) has come through as a viable pathway to achieve this responsiveness with the potential to design and produce products ondemand in a matter of days versus months. But that doesn’t necessarily mean installing a 3D printer on your own shop fl oor. For that, 3D printing and AM service providers provide an agile solution to leverage AM processes and expertise for prototyping to production. The 2022 edition of TCT’s annual 3D Printing & AM Service Provider map, which you can fi nd enclosed inside this issue, provides details on location, lead times and in-house equipment of some of the leading providers in North America.
Stick this map on your offi ce wall (or access the digital version via Issuu) and use it for your next project.
8
7
10
10 1
5 6
8 2 3
4
9 11
Access the digital map here: mytct.co/22MapNA