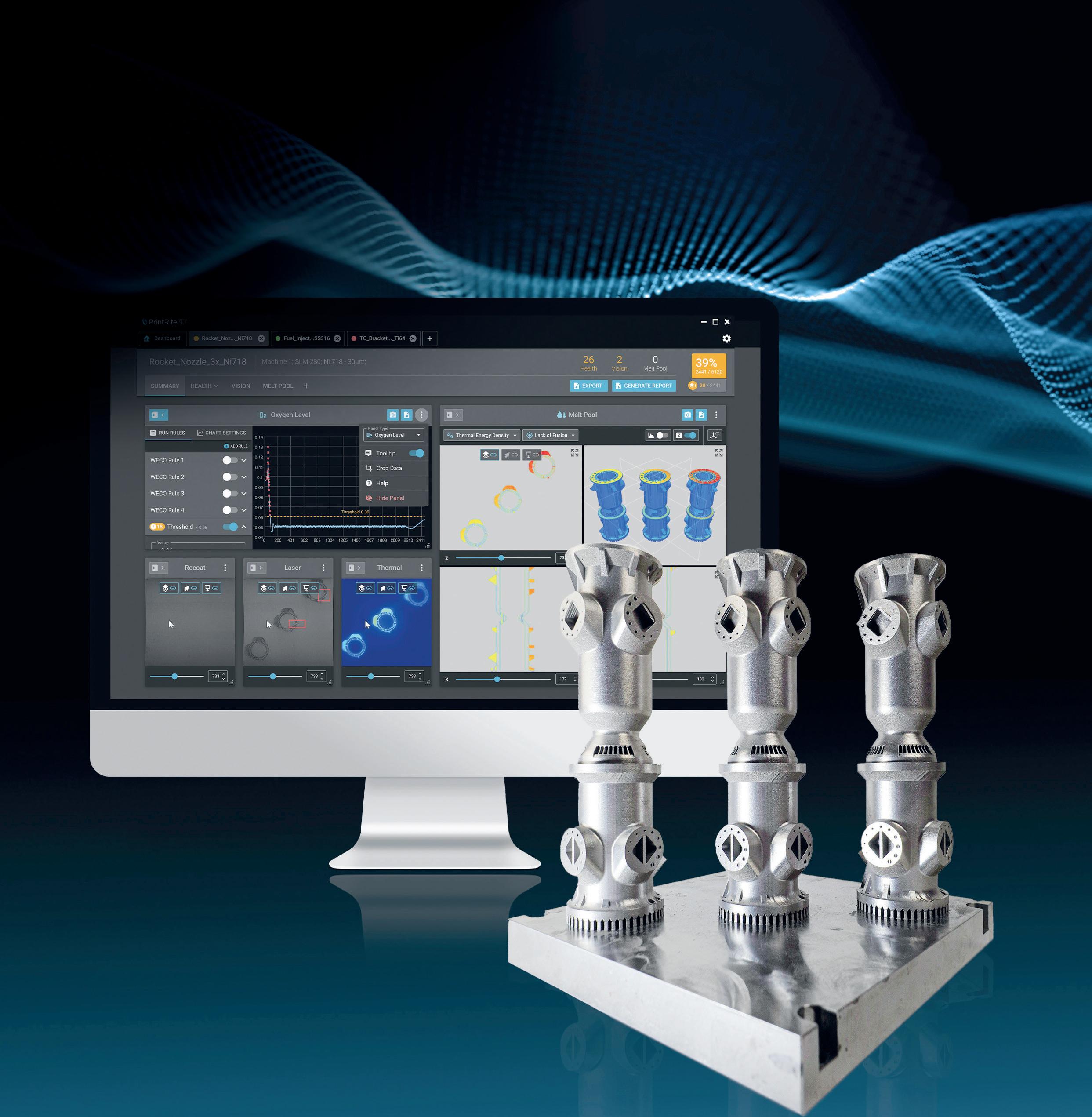
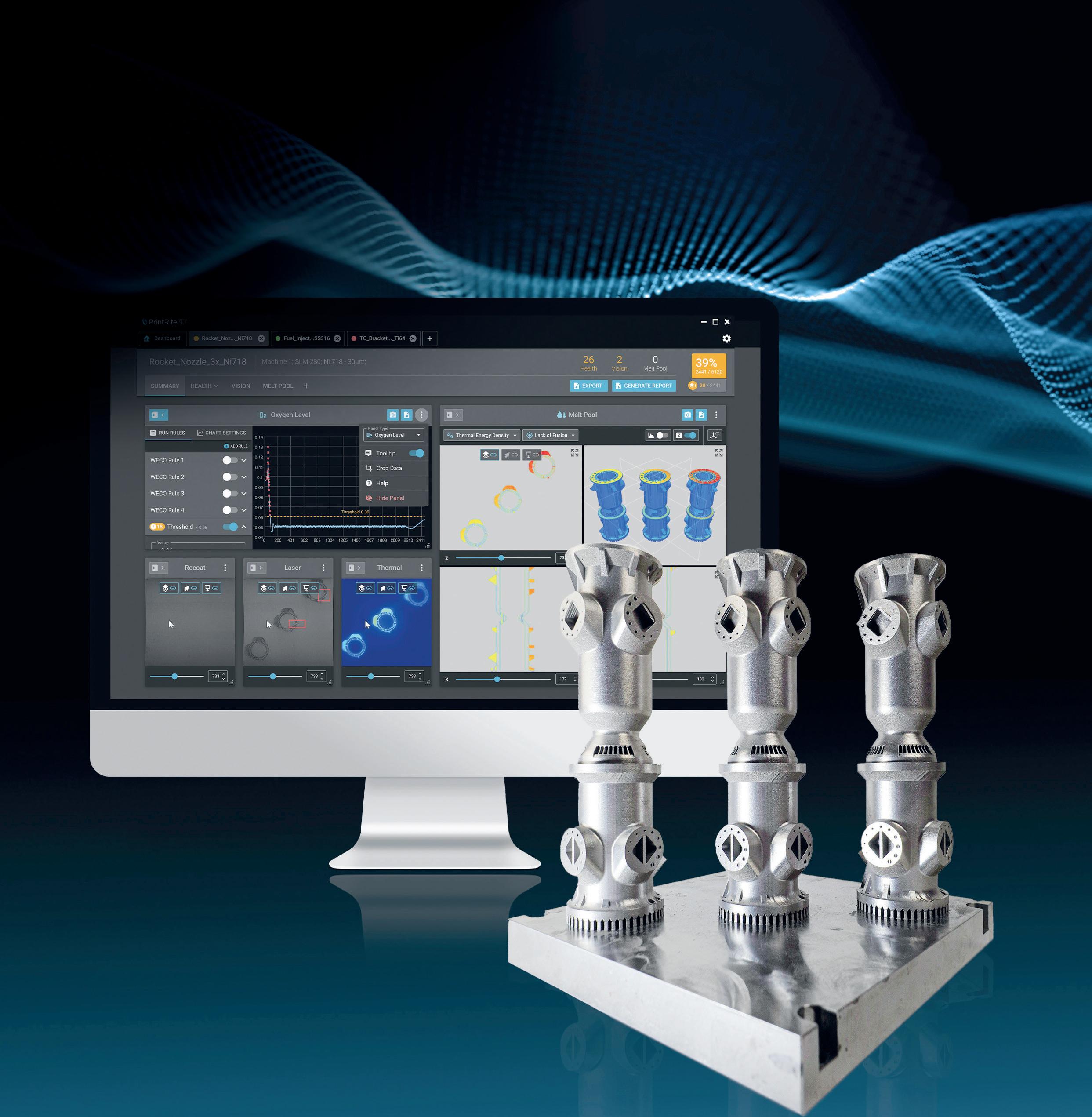
Highly productive serial 3D printing
Imagine: You print larger parts from the titanium alloy Ti6Al4V (Ti64) or the tool steel H11 (1.2343) / H13 (1.2344) and immediately get perfect results.
No cracks, less thermally induced stress in the part and no problems due to detached support structures. You think that doesn't exist?
It does with the TruPrint 5000 and the 500 °C preheating option.
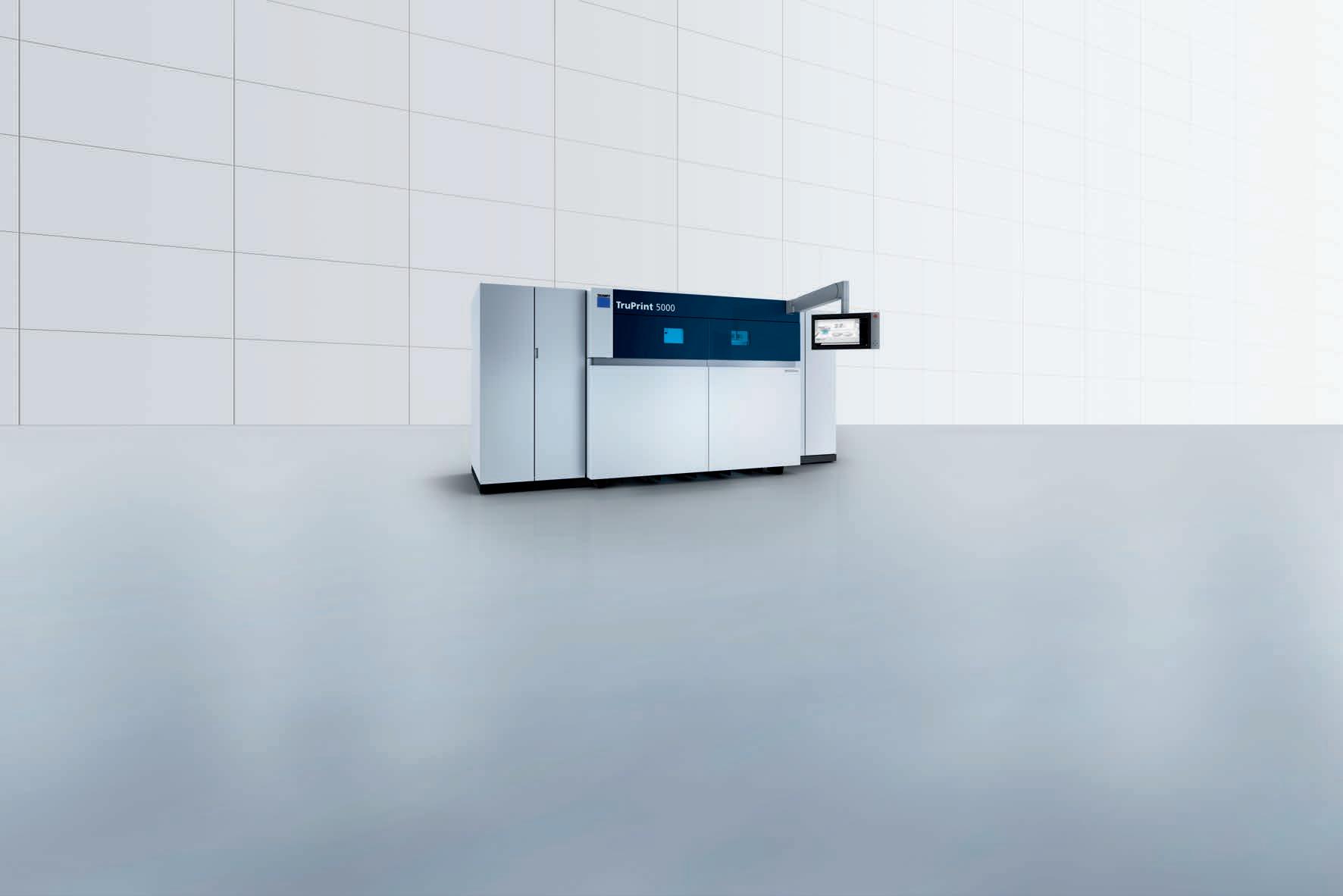
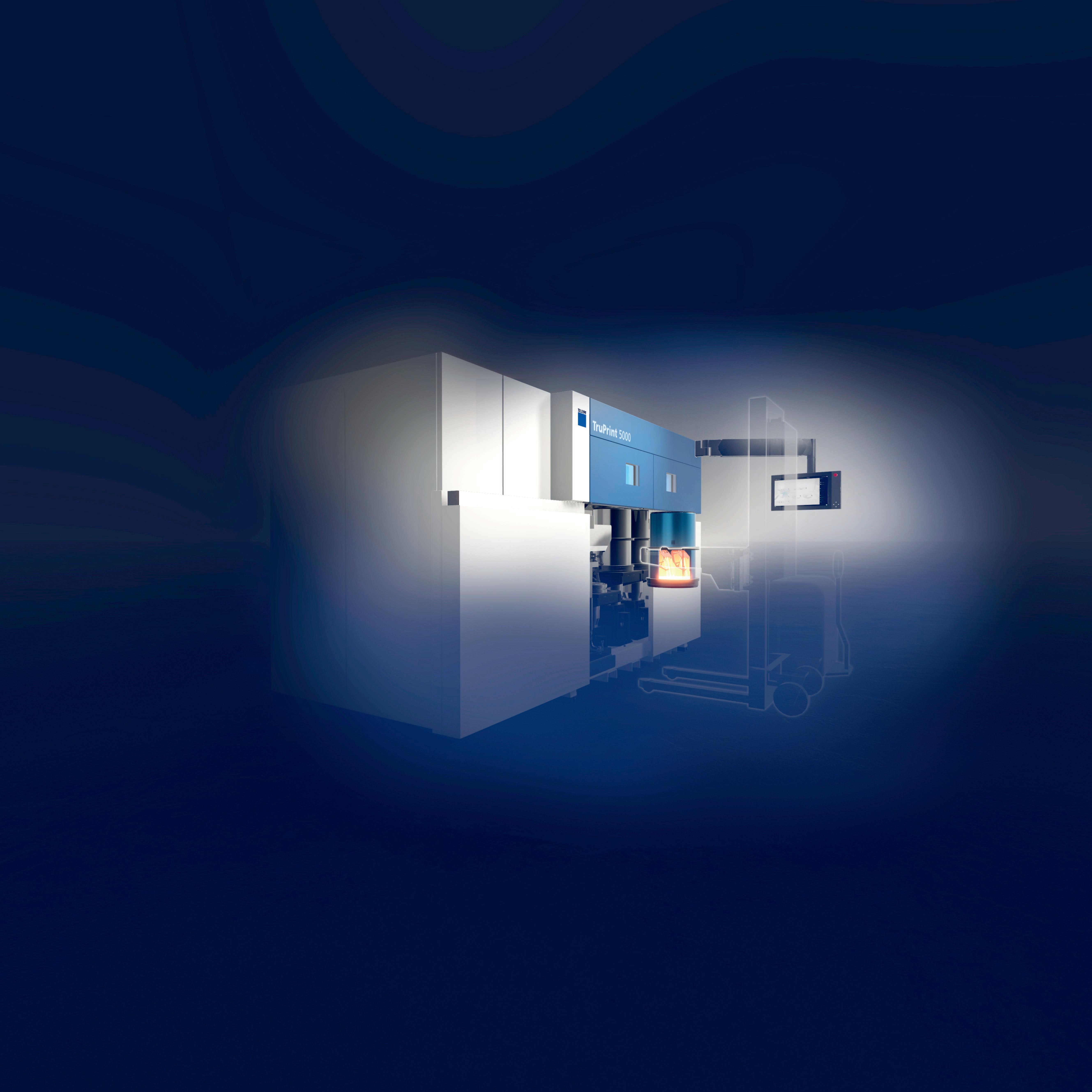
More information at www.trumpf.com/s/500-degree
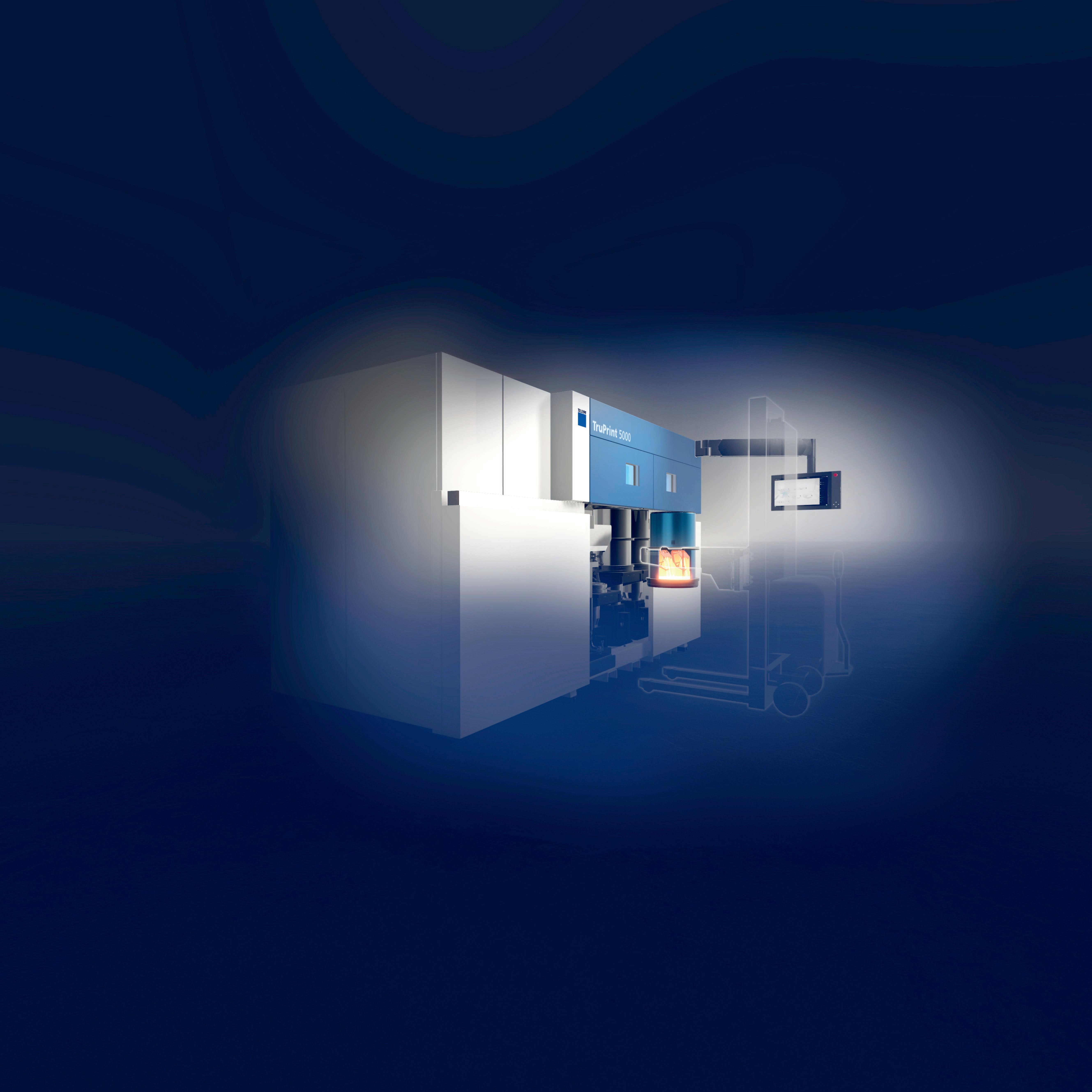
EDITORIAL
HEAD OF CONTENT

Laura Griffiths e: laura.griffiths@rapidnews.com t: 011 + 44 1244 952 389
SENIOR CONTENT PRODUCER
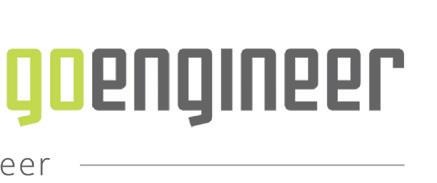
Samuel Davies e: samuel.davies@rapidnews.com t: 011 + 44 1244 952 390
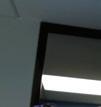
JUNIOR CONTENT PRODUCER
Oliver Johnson oliver.johnson@rapidnews.com
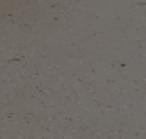
ADVERTISING
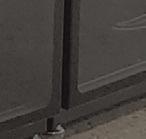
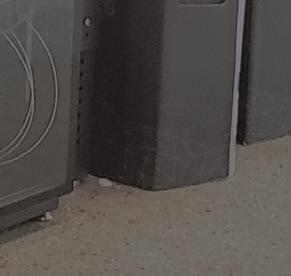
HEAD OF SALES TCT PORTFOLIO
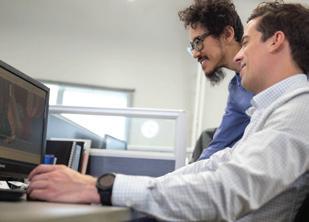

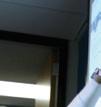
Carol Cooper e: carol@rapidnews.com t: 011 + 44 1244 952 386
SALES MANAGER TCT PORTFOLIO
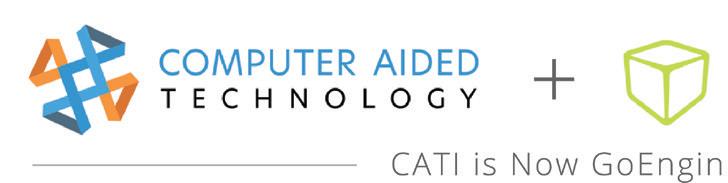

Nicky Martin e: nicky.martin@rapidnews.com t: 011 + 44 1244 952 365
SALES EXECUTIVE TCT PORTFOLIO
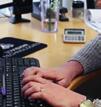
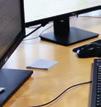
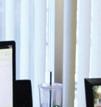
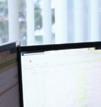

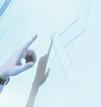
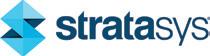
Kristine Baty e: kristine.baty@rapidnews.com t: 011 + 44 (0) 1244 952 341
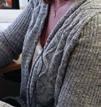
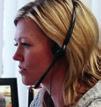
PRODUCTION
SUBSCRIPTIONS
PUBLISHED PRICES
TCT North America Print Subscription - Qualifying Criteria
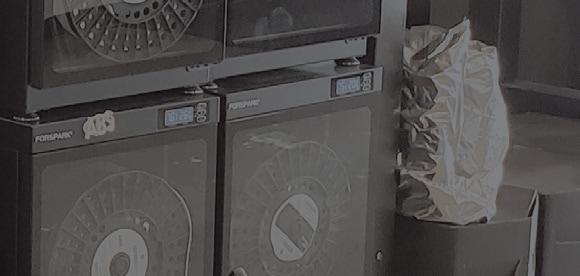
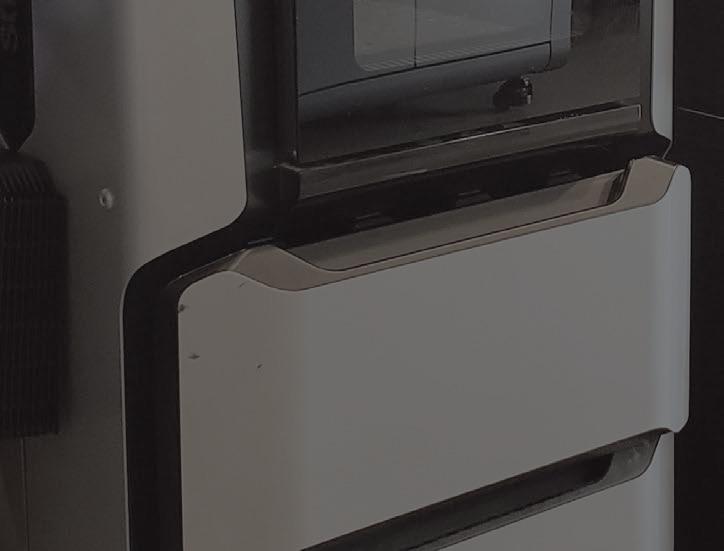
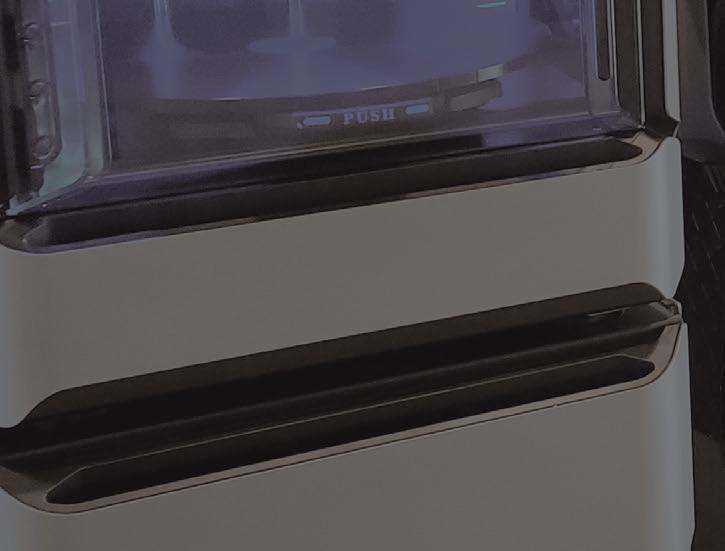
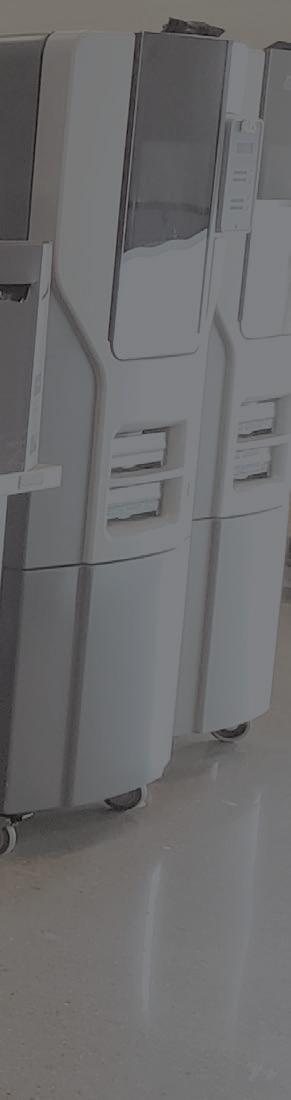
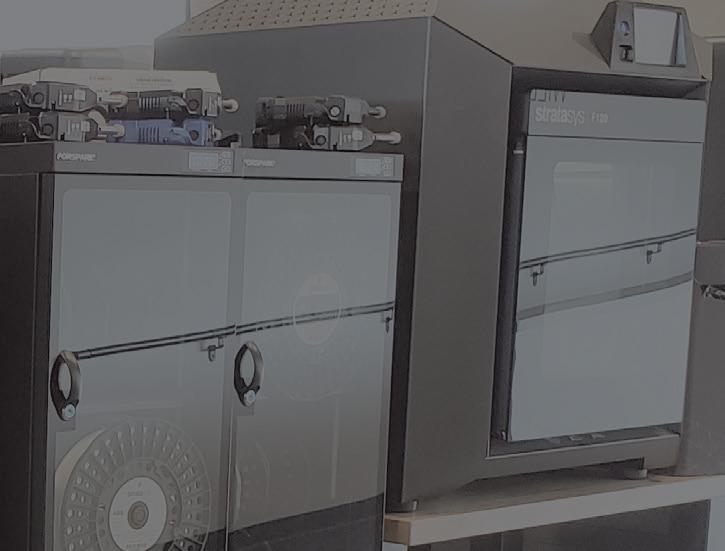
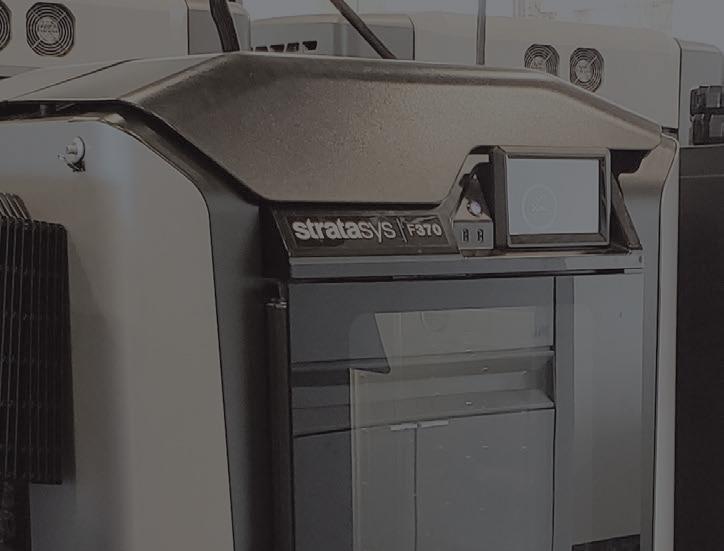
US/Canada - FREE
UK & Europe - $249 ROW - $249
TCT Europe Print Subscription - Qualifying Criteria
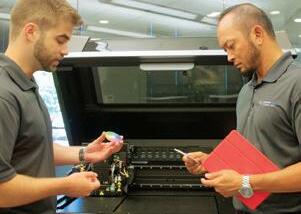
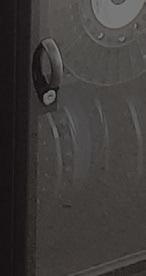
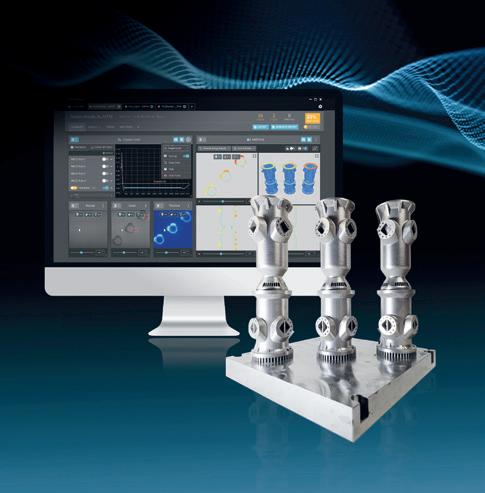
UK & Europe - FREE US/Canada - £249 ROW - £249
TCT German Language Print Subscription - Qualifying Criteria
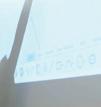
UK & Europe - FREE US/Canada - €249 ROW - €249
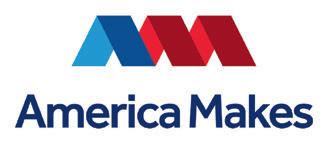
Subscription enquiries to subscriptions@rapidnews.com
Read this and back issues for FREE on Issuuwww.issuu.com/tctmagazine
The TCT Magazine is published bi-monthly by Rapid News Publications Ltd Carlton House, Sandpiper Way, Chester Business Park, Chester CH4 9QE, UK. t: 011 + 44 1244 680222 f: 011 + 44 1244 671074
© 2022 Rapid News Publications Ltd
While every attempt has been made to ensure that the information contained within this publication is accurate, the publisher accepts no liability for information published in error, or for views expressed. All rights for The TCT Magazine are reserved. Reproduction in whole or in part without prior written permission from the publisher is strictly prohibited.

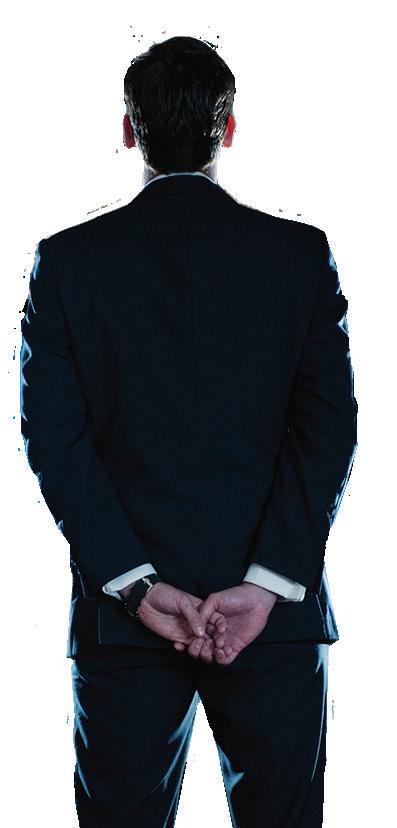
A HARD LESSON
WITH
TOY STORY
Oli speaks to Hasbro and Formlabs about the Selfie Series action figure program.
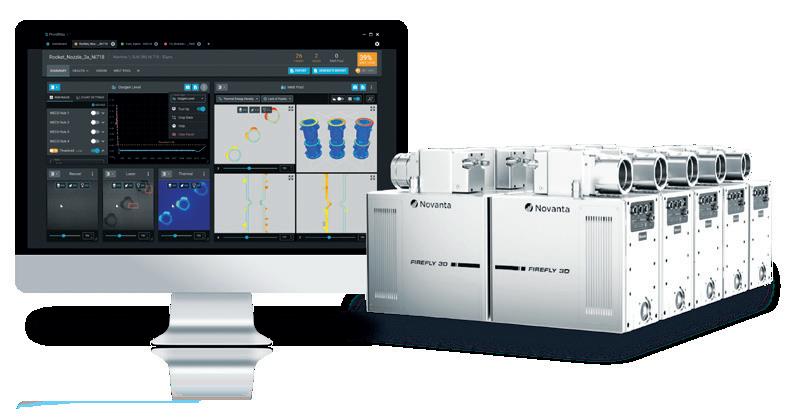
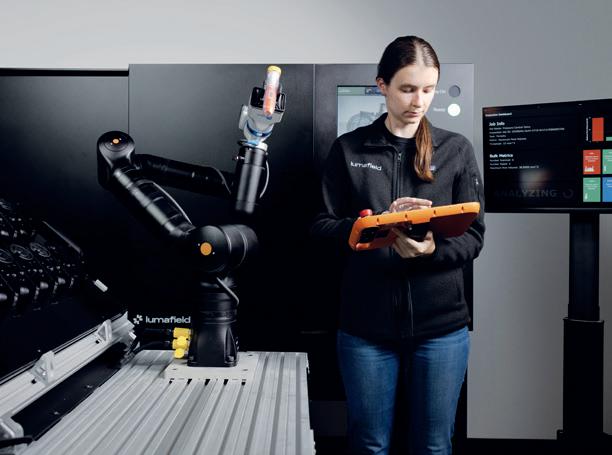
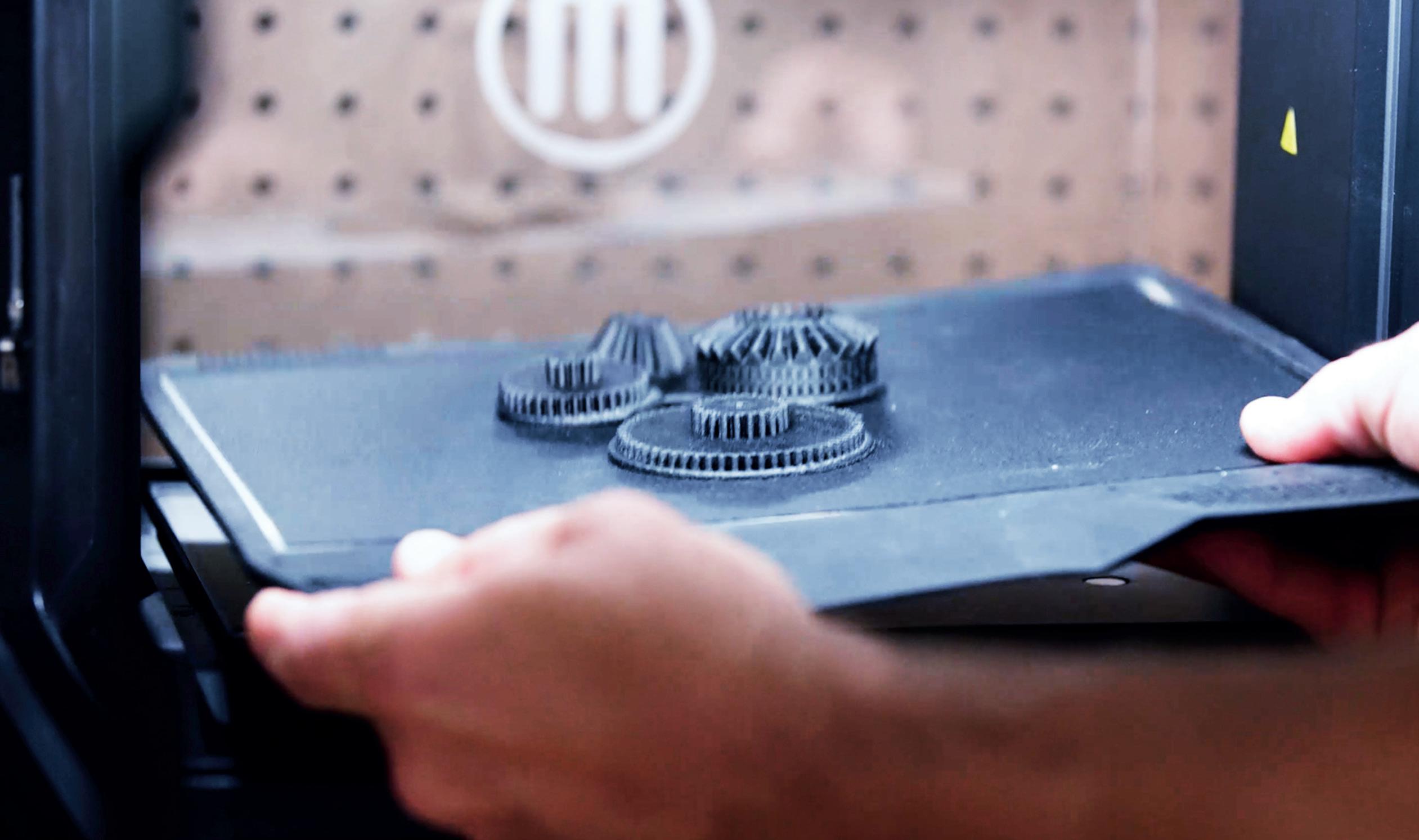
Additive Manufacturing Services to Help You Scale
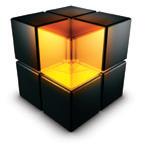
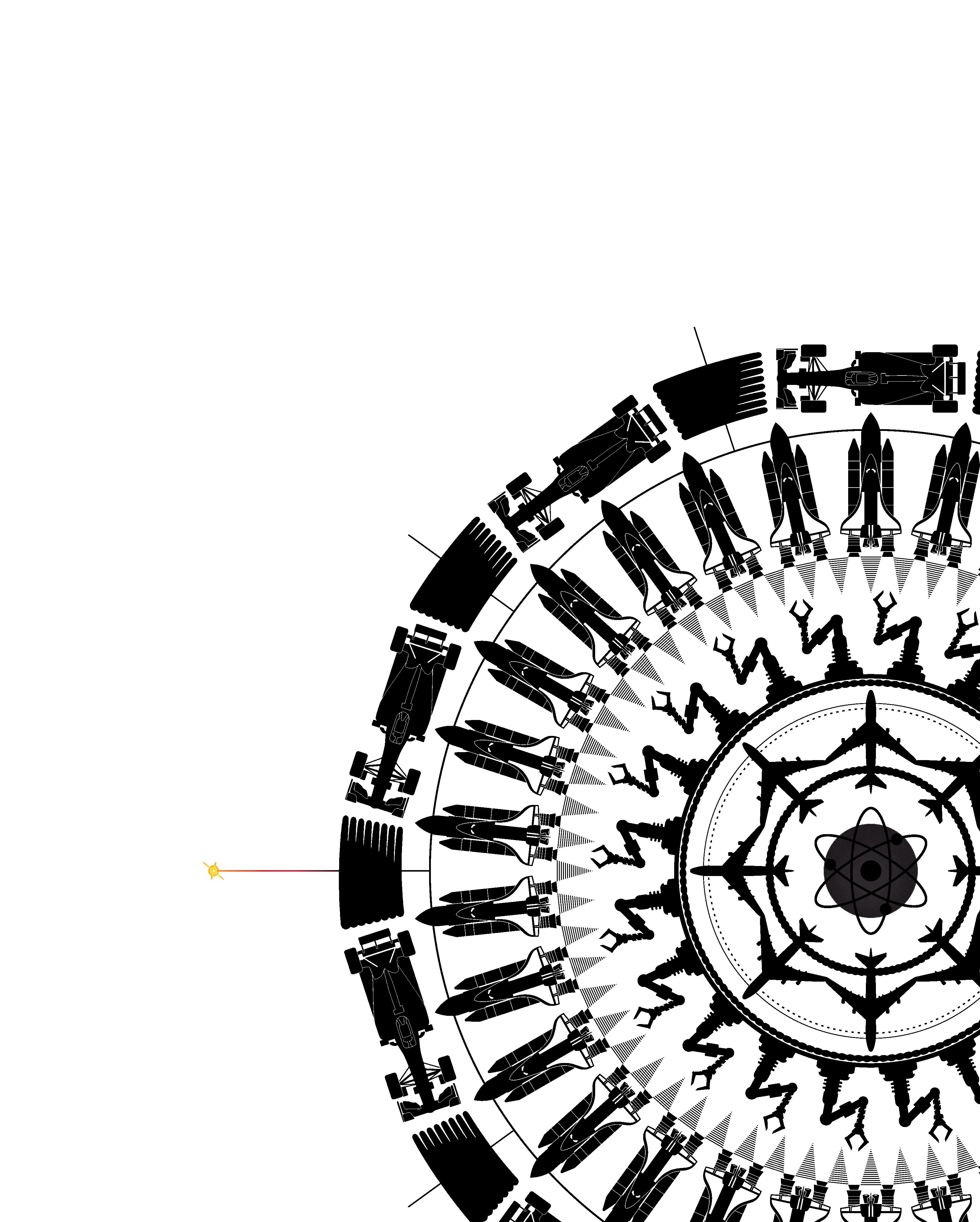
While the world is busy imagining the future of additive manufacturing, Burloak is busy living it.
We have the facilities, the network and the logistics to scale your production and help you realize the efficiencies and advantages of additive manufacturing.
Learn what sets us apart at burloaktech.com
FROM THE EDITOR SAM DAVIES
“Apparently you’ve been with TCT for six years today!?” is the first correspondence I receive on the morning my to-do list dictates that I sit down and write this editor’s letter.
Time for some reflection, then.
“Hofstadter’s Law: It always takes longer than you expect, even when you take into account Hofstadter’s Law” is an epigraph in a book I read that evening; the last words absorbed before the book is closed and laptop flung back open.
In between, the emails come rolling in. One asks for an update on the cover story, another suggests a meeting to gauge progress on the rest of the copy. It would be the third such gathering in the last seven days. This is production week for the last magazine of 2022.
It is always the case that the last issue of the year is, with Formnext and the holiday season back to back, the most arduous to put together. Some things never change. And some do, though per Hofstadter, not always as quickly as first forecast.
This issue - and my six years in AMis testament to that. Our main focus across this edition of the magazine is supply chain. Over the last six years, there has been much talk of additive manufacturing’s (AM) potential to derisk supply networks, but how much of that potential has been realized?
On page 9, we lean on expert insights and real-world case studies to explore the reality of AM’s impact on manufacturing supply chains.
Another market of ‘killer AM applications’ is consumer products, an area said to be primed for AM’s
lightweighting, customization and time-to-market benefits. From page 34, we get a feel for the impression 3D printing is having in consumer goods, featuring Hasbro, Jack Wolfskin and Mattel. Spoiler: there are increasing numbers of production applications but at mass volumes? Not quite yet.
The subjects of our cover story (P6), meanwhile, are not so much applications as they are potential enablers. In a Q&A, Sigma Additive CEO Jacob Brunsberg details a series of company developments pertaining to quality assurance: one of the biggest barriers to AM adoption.
For as long as I have worked in AM, and for many years before, there have been calls for more education and for more thought being applied to it. We’ve needed to teach the engineers, the future engineers, and the teachers themselves. That's still the case. We have it covered on page 19.
Along the same lines, America Makes Director of Education and Workforce Development Josh Cramer has a few ideas on what more the AM industry can do to address the talent gap (P46).
From there, it's off to Frankfurt where we're rounding up some of the biggest news stories across hardware, software and materials from Formnext (P48), which, six years ago, was big. But not this big.
It’s in the aisles of events like Formnext where you often encounter minor grievances with regards to the pace of change in the AM field. Yet, progress is being made, even if incrementally.
After all, it always takes longer than you expect.
POWER OF CONNECTED QUALITY
Brunsberg, CEO of Quality assurance software specialistSigma Additive, on building a new qualification framework for AM.
Q: You were appointed as CEO of Sigma Additive in April – can you outline your vision for the company moving forward?
A: The additive industry has historically lacked a standard approach to qualification and certification of parts. This leads to higher, often hidden costs of quality. If additive is to flourish, it must be cost effective. This means shortening qualification from about two years and two million dollars for flight critical hardware, to a few weeks and much fewer dollars. I came to Sigma because our company has a large role to play in driving this mission. We aim to create the framework for digital quality; connecting everything from CAD/CAM to end inspection, while filling in the missing piece of in-process quality assurance. The time is ripe to drive consolidation of solutions; simplifying from 8-12 software programs and 5-6 excel spreadsheets, into one connected home for digital quality as well as the launch of our new software products, integrated hardware partners, and expanding OEM and software relationships.
Q: The Sigma branding is also pretty new – is this re-brand connected to the new vision of the company?
A: Quality has always been at the heart of what Sigma has done. The team has spent the last decade understanding the most complex parts of the process with its melt pool analytics. The name change to Sigma Additive Solutions from
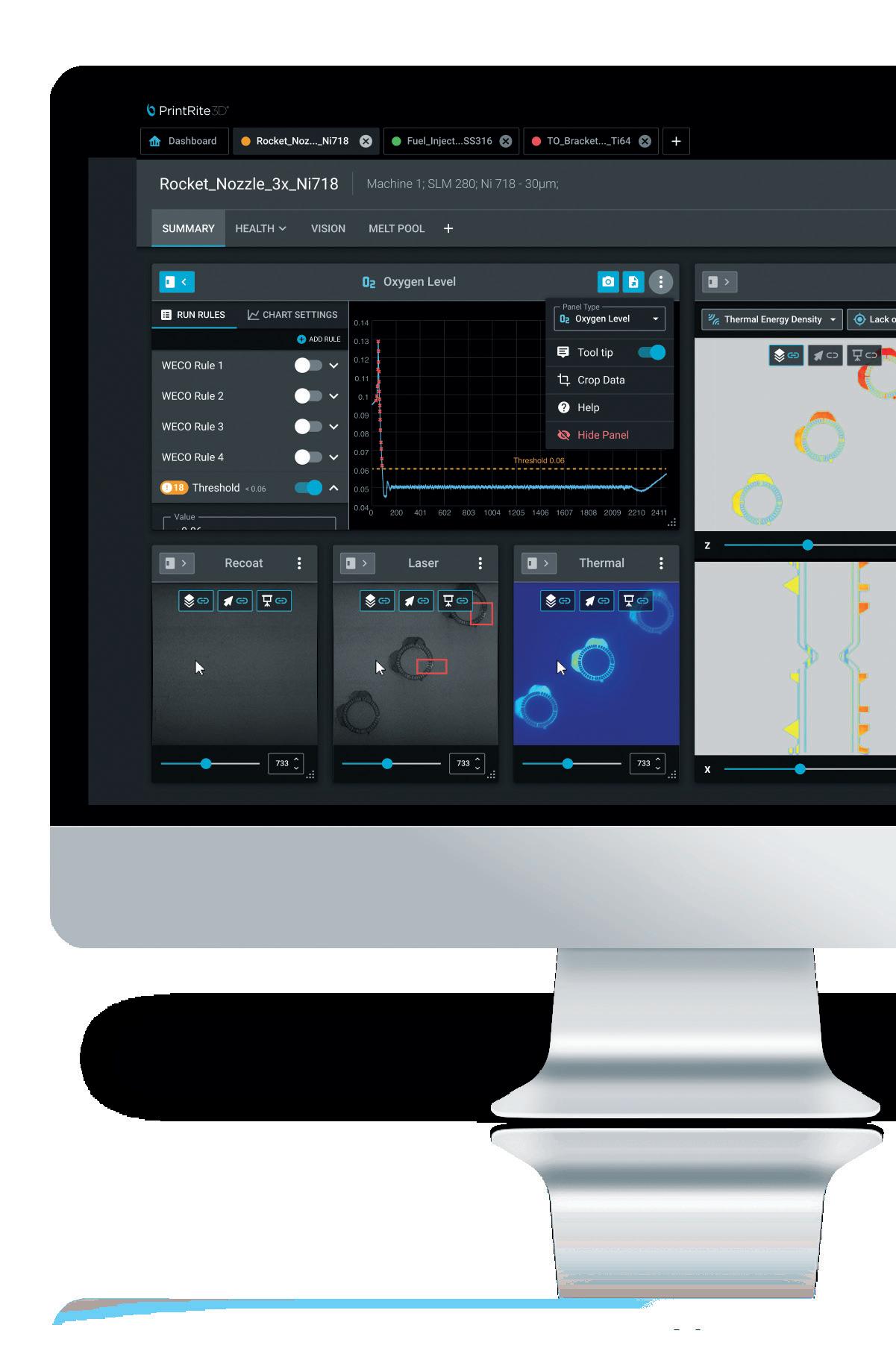
Sigma Labs marked the transition of the company from a laboratorybased company to a solutionsbased, production-oriented company. We’re transforming from melt pool monitoring to a holistic in-process quality company supporting total part qualification and production.
Q: You’ve talked about how your company is moving to a “software-only” model. Can you elaborate?
A: Historically, Sigma was a hardware and software retrofit solution sold as a perpetual license. While we still provide retrofit solutions, we are focused on providing an integrated software-only path to the future. Our new solutions are delivered direct to end-users and OEM/software partnerships via an economical and scalable SaaS model. These software-only solutions leverage newly opened machine APIs, our integrations with other hardware providers like Novanta and Materialise MCP, and future integrations into next generation OEM printers. This opens the door for broad market penetration across the entire industry, supporting OEMs, and delivering an agnostic offering to the market regardless of machine, material, or process.
Q: I understand you just had a major product release. How does this fit into that future?
A: As part of our PrintRite3D Suite, we recently launched the Machine Health module for standardizing
disparate machine health data logs. This is part of our digital quality framework for AM qualification and standardization. In heterogenous environments, the proprietary quality control approaches that additive machine manufacturers have developed often lead to inconsistency in quality assurance across manufacturing operations. Our solution creates a smooth user experience and allows users to connect machines via APIs or upload all machine sensor csv log files new and old. Additionally, it creates a common standards-based file format for analytics, visualization, and reporting agnostic of machine type. This provides users the ability to compare all builds across individual machines or fleets of varying OEM
equipment without manually toggling through excel files and multiple software programs.
Built upon our PrintRite3D monitoring and analytics technology, this seamlessly becomes part of a cohesive environment for ALL inprocess quality data, customizable to users’ unique production requirements. It provides a path to scale to future integrated Process, and Part Health modules containing sensor fusion of camera, thermal camera, melt pool data, and more.
Q: At the start of 2022, Sigma Additive announced a ‘breakthrough technology’ that combines PrintRite3D with Materialise’s Control Platform. How will users benefit from this development and how does this fit in to your broader OEM/hardware strategy?
A: We believe this huge step forward for quality proved two core elements: process monitoring is accurate enough to drive closed loop control and; data speeds are fast enough to react mid-layer in real-time. It’s no surprise closed loop control improves the quality outcome of parts. We’ve

proved closed loop isn’t some far-off theory; it has been demonstrated as a capable technology for today. At a minimum, this provides the industry an integrated in-process quality solution to the physical control structure of the machine. Materialise MCP controller comes Sigma PrintRite 3D-ready.
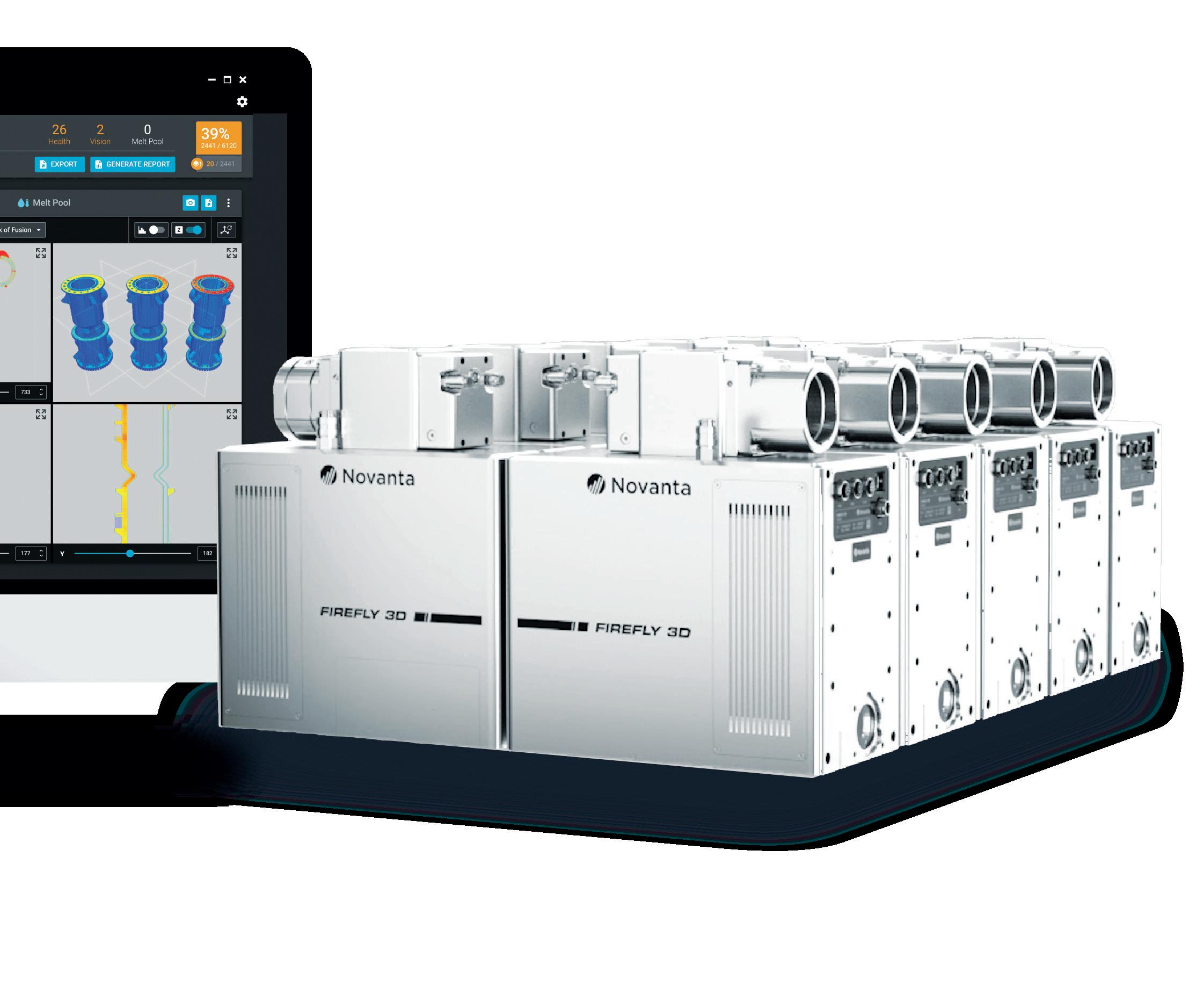
Q: Sigma just made an announcement with Novanta. What does this mean for the individual manufacturers and the additive industry?
A: Quality, and corresponding costs, are perhaps the greatest barriers to industrialized AM at scale. We partnered with Novanta to pioneer the first fully integrated scan head with quality assurance. Novanta’s Firefly 3D scan head brings monitoring into the optical train as a standard, seamlessly linking to Sigma’s Machine, Process, and Part modules. We are focused on improving quality and decreasing the costs by shortening development and qualification time, and reducing the need for post process inspection. Our partnership with Novanta lowers the cost of quality assurance by providing access to an agnostic monitoring and analytics solution, integrated with
scan head technology. As a group passionate about standardization and quality, we have raised the bar for the industry and made in-process quality a standard, not an expensive option.
Q: Are there any other recent announcements that tie in the connected digital quality vision for Sigma?
A: Our OEM and Software Partner group are certainly growing. A list of current partners can be found at sigmaadditive.com/partners. We have been adding new OEM agreements as we build out our agnostic quality tool via their APIs, and support OEMs in their software development. Our recent announcement with Dyndrite is interesting for additive manufacturers since it introduces the ability to connect the CAD/CAM and tool path front end with our quality data. This gives users the experience of connecting CAD design and process parameters to production outcomes. This creates strong synergies with our Novanta, OEM, and software workflow partners. We look forward to connecting more pieces of the digital quality chain... from simulation to post-process inspection!
For more information, visit SigmaAdditive.com

SUPPLY ON-DEMAND
Laura Griffiths and Sam Davies explore the impact of AM on supply chain.
Since 2020, the theme of supply chain has dominated additive manufacturing (AM). In turn, we’ve dedicated many column inches and conference sessions to the technology’s deployment as a solution to pandemic-related challenges, and the longer-term implications of its apparent heightened adoption. Two years later, it’s still top of mind, and with emerging use cases, data, and government involvement, it’s not showing any signs of disappearing.
At this year’s TCT 3Sixty conference, a panel of experts including the University of Bristol’s Jennifer Johns, Boston Consulting Group’s Wilderich Heising, and Equinor’s Pantea Khanshaghaghi, discussed the “transformation” that’s happening around AM in supply chain. While it was suggested that AM applications during the pandemic showed “the beginnings of a utopian ideal” where AM steps in to solve our supply chain woes, the common narrative across industry, academia, and end-users, was the cruciality of knowing when and how to implement the technology, and extending that knowledge to the right people.
“Trying to do this top down and saying, here's my catalogue of 150,000 SKUs, let's go out and start making things using 3D printing – that will break people,” Len Pannett, Supply Chain and Operations Transformation expert and author of ‘Supercharg3d:
AZOTH 3D USE CASE: TAKE ONE MAKE ONE
Manufacturing service provider Azoth is utilizing 3D printing technologies to support its Take One Make One (TOMO) digital inventory strategy. Through TOMO, Azoth empowers its users to convert physical inventory to digital inventory and produce parts as needed without a minimum order quantity to justify up-front tooling or setup costs.
How 3D Printing Will Drive Your Supply Chain’, told TCT. “The other part, of course, is that if you try to do it that way, the rest of the value chain won't be ready. To use an additive approach needs a different way of doing procurement, it needs a different way of doing contracting. In some cases, it needs qualification of those suppliers, as much as you would any other supplier. You also need to convince the engineering teams that the quality of what they're going to get is at least as good as going the traditional route.
“The tough nut to crack is not the engineering, it's the data side, it's how do you identify which of your 150,000 SKUs makes sense to go down this route? And that requires much more than just doing physical assessments and the assessment of physical characteristics. It means also looking at the supply chain characteristics.”
Pannett offers Deutsche Bahn up as an example of a company that has successfully demonstrated “the art of what’s possible” for AM in supply chain. Perhaps one of the most well-known adopters of AM for spare parts production, the company relies on a mix of in-house 3D printing capabilities and service providers, primarily, to produce polymer and
When X number of parts are taken out of inventory, the same amount are made to replace them. Azoth considers this to be the leanest supply chain possible.
The company has proved out this concept by deploying Desktop Metal’s binder jet Shop System to additively manufacture bolt placement grippers that are installed onto a robot arm to pick and place bolts on an assembly line. Using the Shop System, Azoth is
metal components for the railway sector, from rail stops to hand-rail signs featuring braille. Cosmetics giant L’Oreal is another, and is currently using HP’s Multi Jet Fusion (MJF) to create adjustable components for its packaging production line with plans to further leverage the technology via HP’s Global Production Network to “build a truly global supply chain” that will enable more localised manufacture.
“The use of additive manufacturing, notably in a hybrid configuration with other technologies, allows us to react extremely quickly to supply chain fluctuations,” Matthew Forrester, Head of Transformation & Recycling Science at L’Oreal, told TCT. “Empowered teams, deploying their intimate knowledge of manufacturing processes, integrating the specificity of our goods, and even iterating during production, is the perfect combination to create best-inclass, agile tooling.”
FITTING IN
While examples like this from major brands and manufacturers show promise, just how much is AM really being talked about with regards to
able to produce 1,400 of these end-use parts per day in 17-4PH. 3D printing is deployed because of the components’ intricate teeth design.
“These grippers are the perfect TOMO example,” commented Cody Cochran, co-founder and General Manager of Azoth. “They are more cost effective with binder jetting and can be delivered with a ten-day turnaround vs an eightweek lead time.”
supply chain outside of the AM bubble?
According to Mark Cotteleer, Managing Director - Supply Chain and Operations Consulting Deloitte, “a lot.”
“We are seeing across our client base both in the public sector and in the private sector, I would say, an upsurge in discussion,” Cotteleer told TCT. “And that has a lot to do with the fact that additive manufacturing is, in my opinion, the quintessential example of digitally distributed manufacturing. What that means is that it brings together all the interesting attributes of digital distributed manufacturing; the ability to engage in the model-based enterprise, the ability to work across the supply base and distribute production to the point of demand at the time of demand, to bring in ideas around things like digital thread and digital twin, which are very hot topics. Additive is not the only solution. There are lots of solutions and we recommend that our clients take a portfolio approach to it.”
It's true, additive is not the only solution, and sometimes, it’s not the right one either. It’s about finding that sweet spot, developing a business case, and as our TCT 3Sixty panellists agreed, choosing when to apply it, whether that’s on a permanent basis or as an emergency stop gap in times of crisis. The latter, a more temporary outlook, might sound like a negative for an industry that appears to be confidently going after supply chain, but for Cotteleer, that’s actually its USP.
“To me, that's a feature not a bug,” Cotteleer explained. “In the sense that one of the core value propositions of additive is surging production at the point of demand, geographically and in time. Can we deliver production where we need it, when we need it?”
STRATASYS USE CASE: CIRCUIT BOARD BRACKET
When Stratasys was first manufacturing its H350 Selective Absorption Fusion (SAF) 3D printers, the company ran into the same problem many other manufacturers did. A PCB Stepper Controller Board had originally been ordered from a supply chain vendor, but as COVID-19 hit, the product was discontinued.
The H350 Production Team then decided to utilize a new electronics board, which could be sourced easily, but required a mounting bracket to implement a necessary cooling
He notes the work Deloitte carried out with America Makes during the pandemic on the Advanced Manufacturing Crisis Production Response (AM CPR) initiative which acted as a digital stockpile of designs that could be surged into production when and where the point of need materialized. It wasn’t just about COVID-related challenges either and the collaborators ran multiple scenarios – what happens if a supplier goes down or an earthquake hits, for example? – taking into account the many players across that supply chain, from designers to regulators and so on.
In September, Deloitte issued a report in partnership with the Manufacturers Alliance looking at how traditional manufacturing supply chains are evolving to balance costs, efficiency, and resilience. While the term ‘additive manufacturing’ is referenced just once in the 26-page document, in a chart showing the biggest impact on manufacturer’s supply chains, the top three responses - shipping delays (59%), part shortages (56%) and transportation delays (56%) - are key areas where the benefits of AM truly shine. Yet while additive’s value proposition as
an enabler of distributed, on-demand manufacturing is evident, challenges remain.
“All of the old concerns still exist: quality, materials, cost, repeatability,” Cotteleer said. “I think what is changing is that, while the concern exists, many of the technical solutions are increasingly available so people need to be constantly revisiting the state of the art because things are changing quite rapidly. There are instances where we are seeing people quite effectively being able to distribute production, particularly at the lower end. At the higher end, with exotic materials and very expensive machines and very high-end uses, we still see, and in fact recommend, more centralized production models, but even there, you could still solve the time problem, you're just not solving the location problem.”
Interestingly, that singular nod to AM in Deloitte’s report ties into another industry trend: mergers and acquisitions. The report notes the strong M&A activity in manufacturing with 52% year-on-year growth in such deals in 2021,
function. For the solution, the team looked inward and bet on the technology they were working to bring to market. With the H350 machine, they designed and printed a circuit board bracket which could secure the fan to the electronics board and then safely mount the board within the printer.
The bracket, which doesn’t require any screws or tools, is said to occupy a minimal amount of space. Stratasys can nest 132 brackets within the same build with a cost per part of 4.15 USD. The company has implemented the circuit board bracket in every H350 3D printer and has continued to apply SAF technology to its SAF systems.
“This was one of those examples that ‘ticked many of the boxes of additive manufacturing,’” Neil Hopkinson, VP of AM Technology at Stratasys, told TCT.
“The challenge arose from supply chain issues, which are becoming more frequent in manufacturing these days and the solution came from AM technology that actually allowed the team to develop an improved product with easier assembly. In this instance, it was very gratifying that SAF technology itself was the solution for a SAF product development issue. The team has since built on this and each H350 printer has 30 parts produced by SAF technology.”
“The tough nut to crack is not the engineering, it's the data side.”
and suggests some instances of vertical integration can be seen as a tool for achieving supply chain resilience. For instance, earlier this year, aerospace and defence manufacturer Safran, which recently opened a new dedicated 3D printing campus, completed its acquisition of metal AM powder supplier Aubert & Duval, bringing its supply of metal powders inhouse. It’s an extreme example, and bringing AM into your supply chain doesn’t necessarily mean investing in an entire company or bringing in expensive hardware. Manufacturing service providers offer an alternative route to sourcing parts on-demand, and Pannett suggests finding a supplier to produce products with the right QA processes already in place as a “very easy, quick win.”
Joshua Parker, US 3D Printing Supply Chain Manager for Hubs, provides further insight into the benefits of additive. As an online manufacturing platform, Hubs provides engineers access to a network of 3D printing suppliers. The Amsterdam-based company was acquired by Protolabs in 2021, signaling further market consolidation in distributed manufacturing. The platform allows users to upload designs, instantly receive quotes and send their files for production via a network of AM, CNC machining, injection molding, and sheet metal fabrication partners. To date, the service has manufactured over 7 million parts. As part of its annual
3D Printing Trend Report, Hubs spotlighted more robust supply chains and localized on-demand manufacture as the most important AM trends for 2022.
“As additive becomes more of a low volume production solution, there has been increased interest with customers using technologies like SLS and HP’s MJF to either provide a short-term production solution or to switch to 3D printing altogether,” Parker told TCT. “We have seen a lot of success in the EV sector, especially with companies that are highly iterative and innovative and want to stay nimble with their design. With the increased lead times of going overseas for molds, 3D printing provides a quick alternative while tooling is being created.”
PRACTICE WHAT YOU PRINT
If 3D printing is the silver bullet in supply chain resilience, are 3D printer manufacturers taking note?
AM FORWARD & SUPPLY CHAIN
“We believe the initiative is a bold step forward for additive manufacturing, particularly if it revitalizes the US supply chain by enabling more companies to take advantage of the intrinsic benefits of AM. Our hope is the program helps the many small and medium-sized businesses working to unlock new business opportunities and scale sustainable production with AM.”
LAUREN TUBESING | DIRECTOR OF OPERATIONS, MILITARY PROGRAMS | GE ADDITIVE
“Public-private initiatives like the recently announced ‘AM Forward’ initiative will help to address DoD’s sustainment and readiness challenges head on. Strengthening US supply chains by encouraging small and medium sized manufacturers across the United States to adopt metal additive technology will create a nationwide network of qualified additive manufacturing suppliers.”
ELLEN KULLMAN | CHAIR OF THE BOARD OF DIRECTORS | CARBON
“We're at an undeniable inflection point — bringing digital manufacturing to U.S. businesses will be a critical component to the success of the American economy both now and into the future. The administration's acknowledgment of 3D printing to boost the economy is a solid step forward and a proof point that digital manufacturing is critical in addressing our ongoing supply chain challenges and beyond.”
JOSH MARTIN | CO-FOUNDER | FORTIFY
“I think it's still early and I think a lot of people I work with are still wondering what that means. But I think, if anything, it could chart a path towards additive manufacturing playing a more significant role in supply chain resilience. And if there's anything that the last 36 months has taught us, it's that there's vulnerability there and additive can play a role.”
“The more we can get AM in front of supply chain decision makers, the better.”
Signi cant Cost Savings
Signi cant Cost Savings on Additive Tool
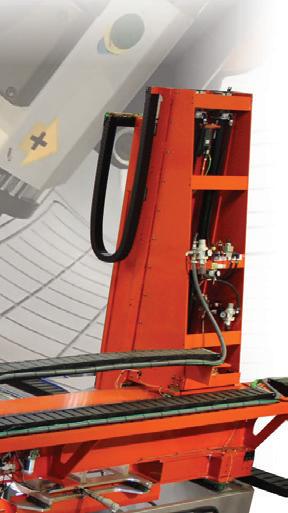
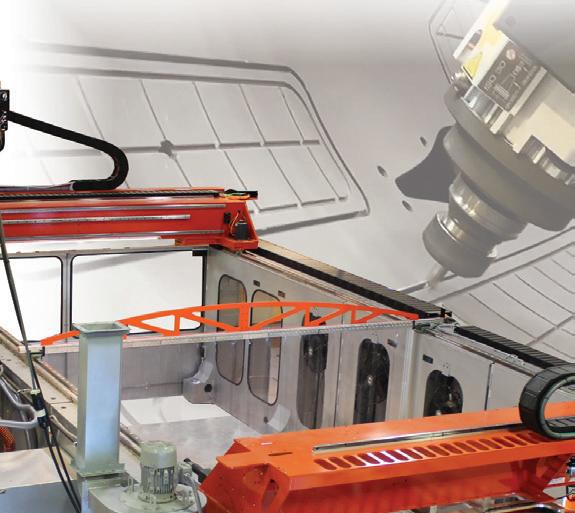
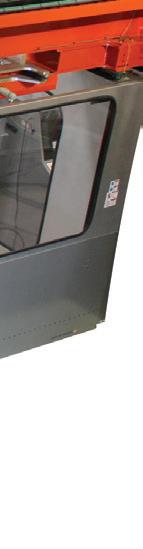
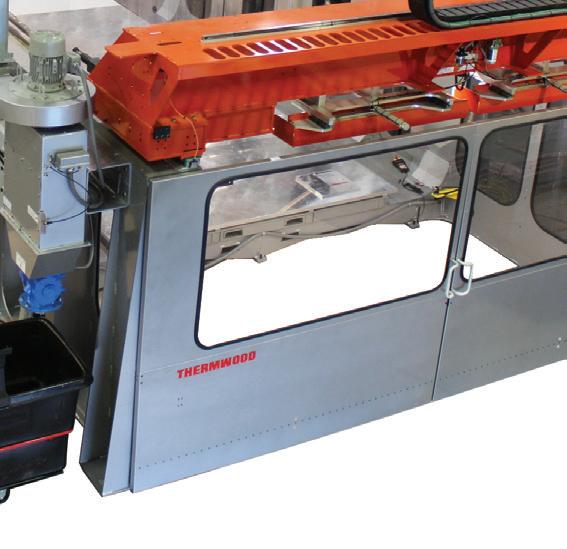
Partnership between ermwood and General Atomics

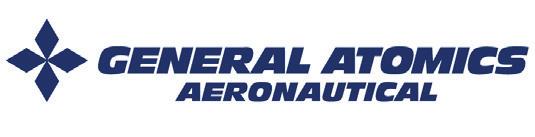
e Details
e Details
Using a ermwood LSAM 1020, the tool was printed from ABS (20% Carbon Fiber Filled) in 16 hours. e nal part weighing 1,190 lbs was machined in 32 hours.
Using a ermwood LSAM 1020, the tool was printed from ABS (20% Carbon Fiber Filled) in 16 hours. e nal part weighing 1,190 lbs was machined in 32 hours.
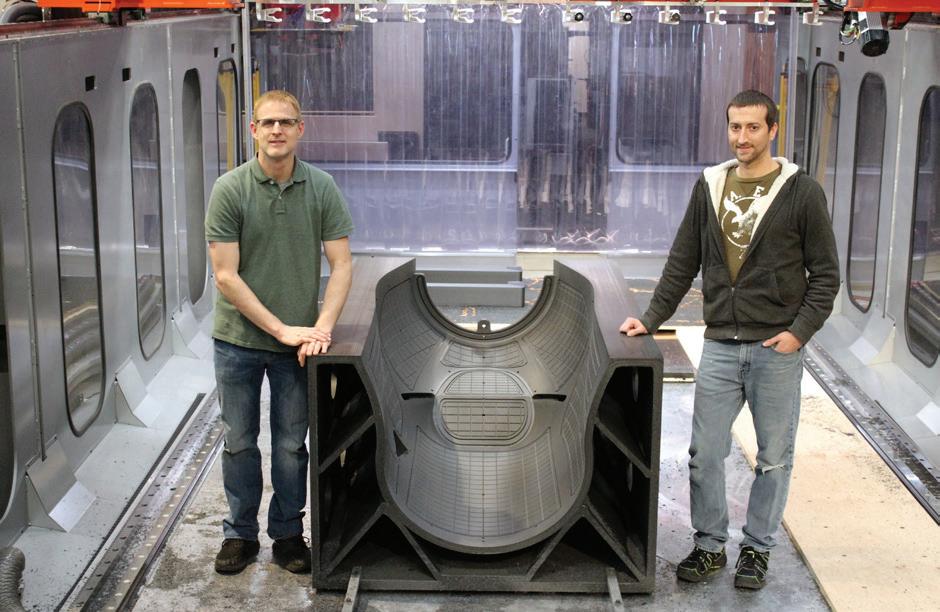
Cost
Savings of around $50,000 vs traditional methods
Cost
Savings of around $50,000 vs traditional methods
Total lead time for the part decreased from 6-8 weeks to less than 2 weeks by utilizing the powerful LSAM system.
Total lead time for the part decreased from 6-8 weeks to less than 2 weeks by utilizing the powerful LSAM system.
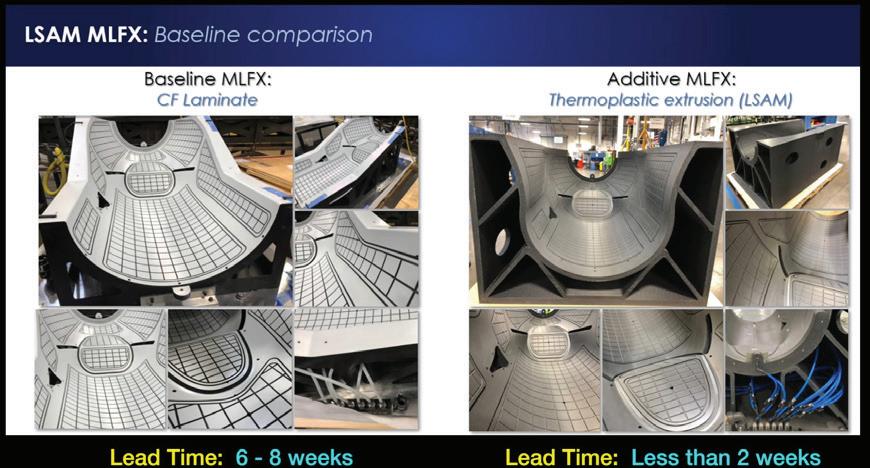
e Results
e Results

• Cost Reduction: 2-3 times
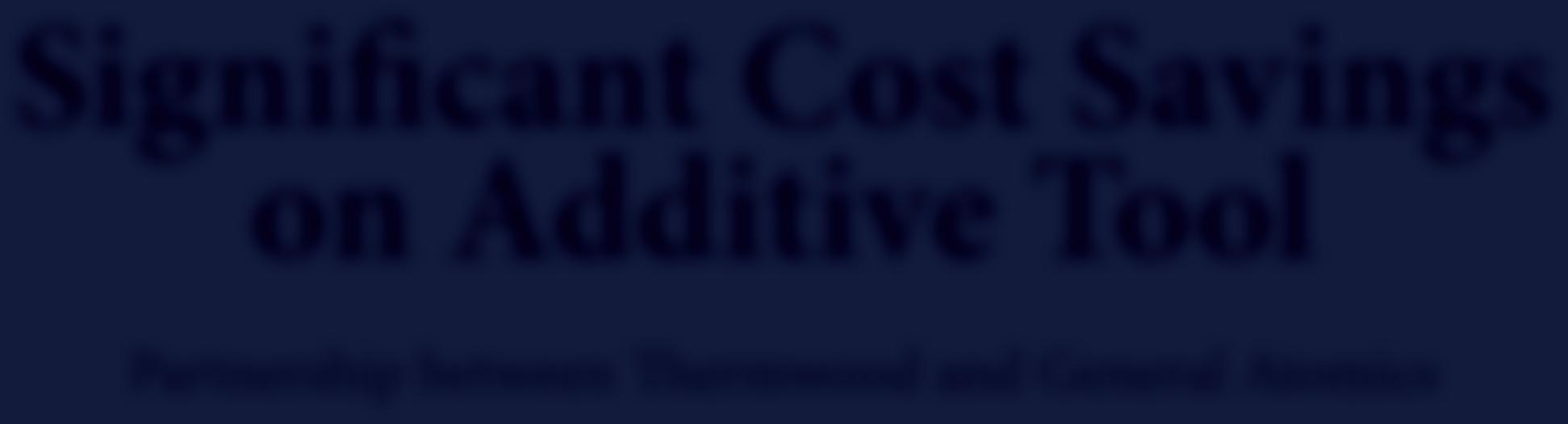
•
•Faster Development: 3-4 times
•Production Capable Tool •Vacuum Integrity

•Suitable for Large, Deep 3D Geometries, Backup Structures & Vacuum Piping
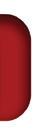
Scan QR code to view a video of the LSAM and General Atomics process.
Scan QR code to view a video of the LSAM and General Atomics process.
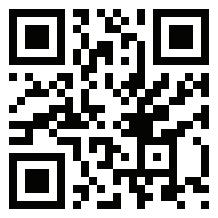
Cost Reduction: 2-3 times • Faster Development: 3-4 times • Production Capable Tool • Vacuum Integrity • Suitable for Large, Deep 3D Geometries, Backup Structures & Vacuum Piping www.thermwood.com 800-533-6901
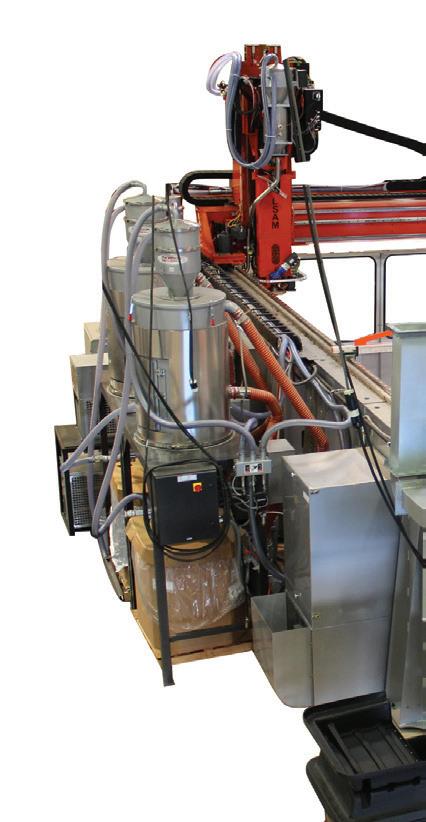

Megan Liu, Supply Chain Engineer at Formlabs, works within the global sourcing team, looking after supply chain for Formlabs products. In fact, several Formlabs machines feature a range of components manufactured with its own printers.
“We, I think, definitely understand that there is a good application for 3D printing in supply chains,” Liu said. “At the same time, most of our printer is not made out of a 3D printed material so there are definitely limitations on 3D printing parts for production. I think the best use cases are really small parts, in terms of geometry, things that nest well in our printers.
“I joined Formlabs because I am super interested in how we can use 3D printing in all different types of industries. It's super exciting for me to see Formlabs practising what we preach.”
The sourcing team’s job is essentially to find suppliers to make and deliver
parts to its contract manufacturer on time. When Formlabs launched its Form Wash L and Form Cure L systems during the pandemic, for example, the team was able to mitigate supply chain issues and material delays by ramping up print production from its materials production facility in Ohio and Somerville HQ.
“Something that has been super exciting to see is, and I know this is kind of a buzzword, but we are able to decentralize our supply chain a little bit by using 3D printing,” Liu said. “If we are ever short on components or things like that, we can use a 3D printer right at the spot to print components to keep production going.”
In addition to a shift in customer applications, which now go beyond prototyping to tooling or production parts on the Fuse and Form 3L, and extend to even more industries, Liu says the last
few years have also produced more awareness and interest in the technology.
“I think a lot of things probably have contributed to that extra interest,” Liu said. “I think the technology has improved and grown a lot over the last couple of years, but then also COVID with all the supply chain issues that brought was also definitely a wake-up call for a lot of people who are relying on traditional manufacturing methods.”
If the wake-up call was missed the first time around, the announcement this past Spring around the Biden Administration’s AM Forward initiative should ring a little louder. The initiative was setup to support the adoption of AM amongst SMEs, with large manufacturers like Siemens Energy, Honeywell, Lockheed Martin, GE Aviation and Raytheon, all longtime users of the technology, committing to purchasing additively
FAST RADIUS USE CASE: STREAMLINING SPARE PARTS
As 3D printing continues to mature, and applying the technology for productiongrade parts becomes more of a reality, Husqvarna has aligned with Fast Radius to implement an advanced manufacturing approach.
The outdoor product manufacturer has worked with Fast Radius to identify parts that could be produced at scale with Carbon Digital Light Synthesis and HP Multi Jet Fusion technology, before establishing a Production Part
Approval Process (PPAP) that included UV resistance, chemical resistance, and dayslong cycle tests, as well as an evaluation of real-world performance. Once parts pass the PPAP, designs and production specifications are stored digitally in the Fast Radius Virtual Warehouse, eliminating a lot of the supply chain costs associated with warehousing, minimum order quantities, material waste and part obsolescence.
From this virtual warehouse, parts can be downloaded, produced and shipped in a matter of days, while also affording Husqvarna and its customers the peace
of mind that products will never be out of stock again. The reduction or elimination of material waste and part obsolescence is also supporting Husqvarna’s ‘Sustainovate’ sustainability programme, in which the company has outlined CO2 reduction targets for the year 2035.
“For Husqvarna, storing parts in the Virtual Warehouse has allowed them to avoid inventory holding cost, scrap at end of life, and has enabled better customer support by eliminating the need to discontinue production of certain spare part SKUs,” Matt Schroeder, Product Manager at Fast Radius, told TCT.
“An additive approach needs a different way of doing procurement.”
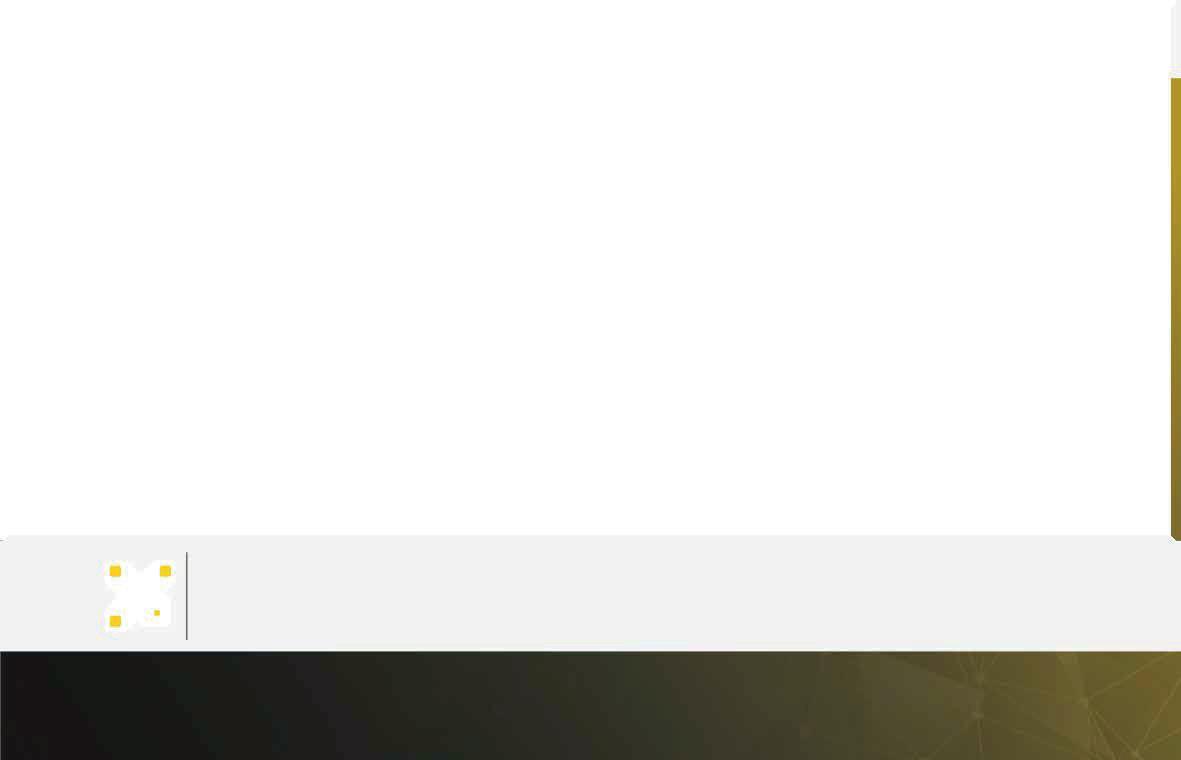
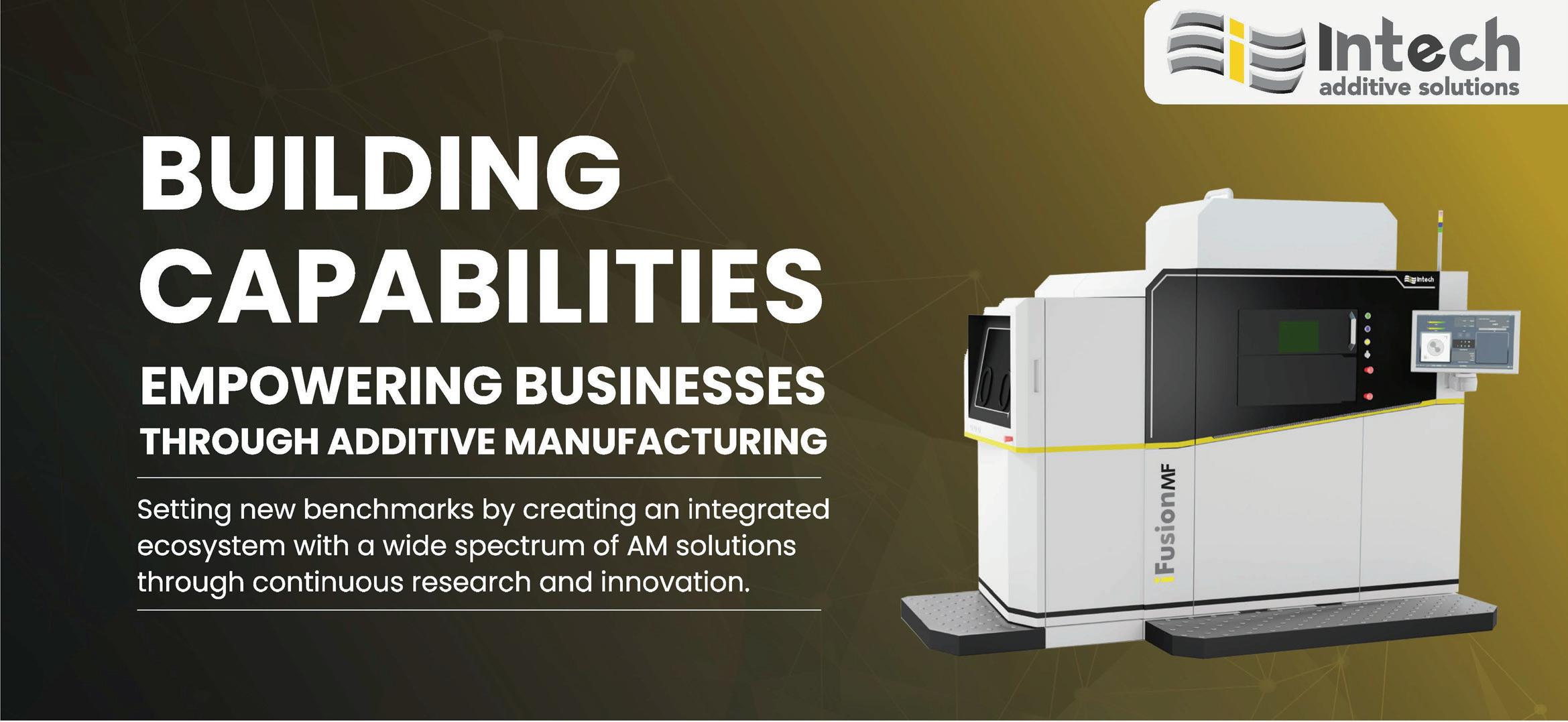
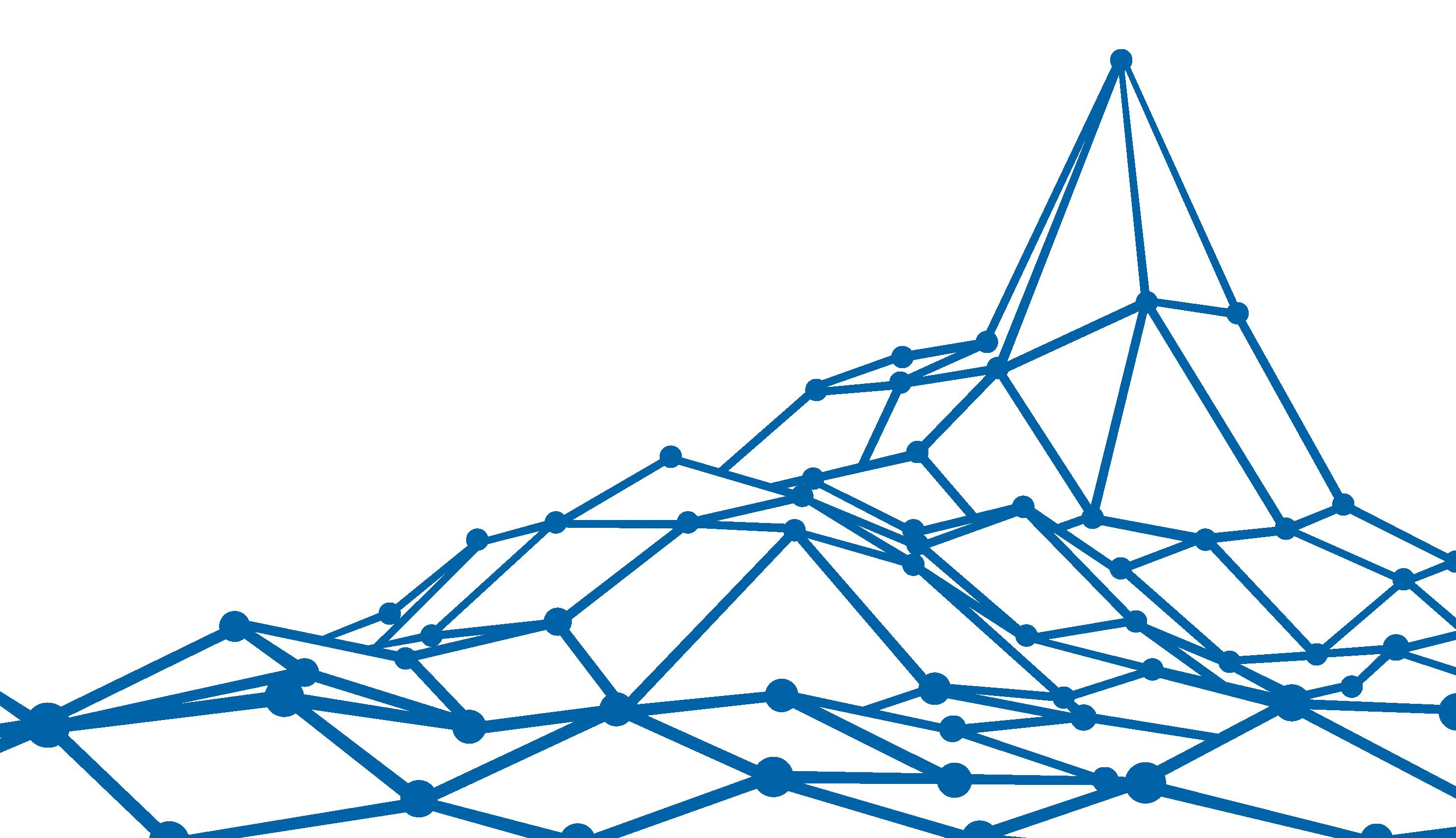
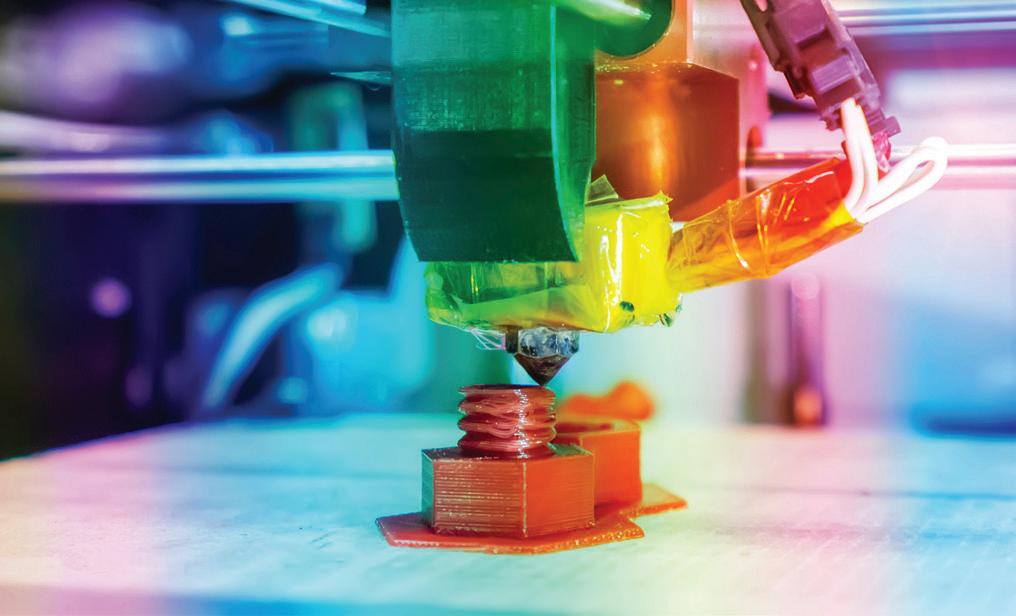
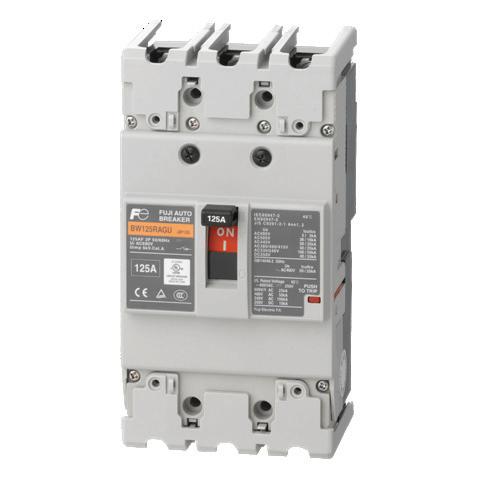
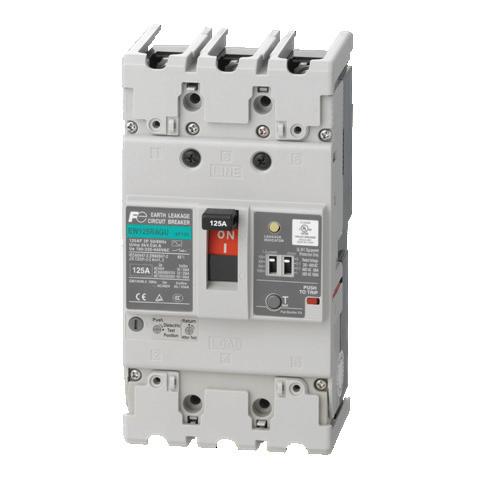
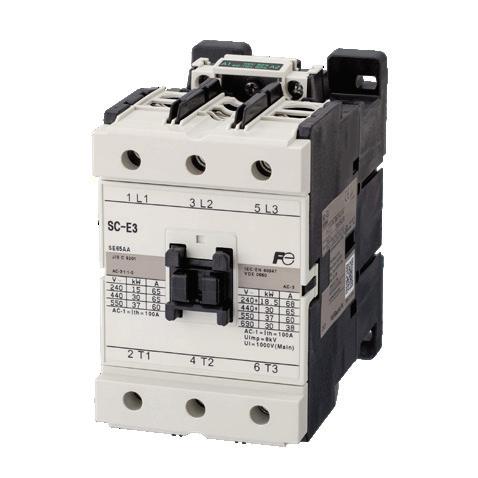
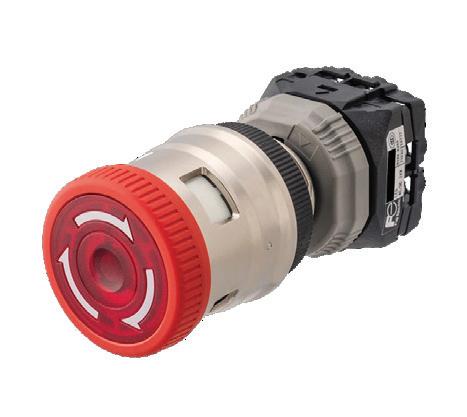
produced parts from smaller USbased suppliers, providing training, and engaging in common standards development and certification for additive products. It’s a bold move, and emphasizes the recognition of additive and distributed, localized manufacturing as tools to achieve supply chain resilience, something which Deloitte shares a confidence in.
is the way the world is going.”
Cotteleer said: “We are very bullish on the concept of distributed digital manufacturing and I think that it will continue to be important for supply chain and operations leaders to stay on top of, and develop strategies for how to deploy these technologies in support of cost, quality, resilience, flexibility, agility – fill in the buzzword – because this, to me, is the way the world is going, and if you're not incorporating these into your strategies, you're very likely falling behind.”
SPEAKING SUPPLY CHAIN
From each of these conversations, it's increasingly clear that AM’s success in supply chain also relies on sharing these wins and having conversations with the people that can make change
happen. Those already working in or using AM will be aware of the benefits of on-demand and decentralization, and Pannett argues AM companies should be putting themselves in front of supply chain professionals in order to see progress.
“I think the more that we can do to get the AM community in front of supply chain decision makers, the better,” Pannett said. “Those events where the supply chain guys are going to be exposed to new ideas, those are the ones that, I think, if we're going to really peak in our sales, have to be included in the roster.”
Having those conversations means being able speak the right language, to understand the needs of those operating along supply chains, and communicating where the benefits of AM, which may be lesser known outside of the industry, come into play.
“Words matter and I think this is a general challenge in the additive and advanced manufacturing space,” Cotteleer said. “And I'll point no further than the use of terms like digital thread and digital twin, which are crucial for the support of additive manufacturing. We often find ourselves at the beginning of a project or discussion, literally saying, ‘when we use these words,’ fill in the blank, ‘here's what we mean,’ because different people can ascribe different meanings to those words.”
Parker adds that it’s important to put that message across early in the procurement process: “A general lack of education and familiarity are the main reasons we see slow adoption. Our Sales and Engineering teams do a great job working with the customer to understand their needs and help companies steer their design towards the final manufacturing method. If you don’t consider 3D printing as a production method during design, it can be more difficult to change the manufacturing method later in the product design cycle.”
That also means educating the right people, not just the engineers who will ultimately be using the technology but personnel along that value chain who need to understand the benefits in order to recognize where and why additive fits, or if it simply doesn’t.
“It's definitely a lot of engineering [people] right now, they're probably the most aware of this technology. [...] When we talk to people in supply chain, they're talking to us about printing spare parts and components and I think that definitely makes a lot of sense," Liu concluded, adding that there is an element of curbing expectations and a learning curve around what 3D printing can currently do in terms of spare parts. "That's, I think, where the knowledge gap starts to show a little bit because I think they're really hoping that 3D printing can solve all their problems in terms of aftermarket parts, spare parts, and things like that. I think maybe there needs to be a little bit more education in terms of the interim. Even though you potentially can't use 3D printing for this grand solution, there are definitely ways in which 3D printing can help aid in that transition, keeping all this excess stock to printing when you need.”
“This
CT-UBIQUITY
Tomaz van der Merwe, Editorial Content Producerat Manufacturing Quality, speaks to industrial CTscanning specialist Lumafield.
Having recently garnered success with its latest round of Series B funding, Lumafield is still a new player. Yet, it’s already breaking through in its mission to make industrial CT scanning affordable and accessible, as Lumafield Co-founder and Head of Product Andreas Bastian, and Head of Marketing Jon Bruner recently told TCT.
Bastian is quick to provide a useful analogy familiar with the additive manufacturing (AM) world: “It’s similar to how industrial metal printing has behaved over the past couple of decades: the technology has been around for a while, but it’s very expensive, difficult to use; kind of a fragmented tool chain. So, what we’re trying to do is take the technology and make it dramatically more accessible so that any engineer, anywhere in the world, can use it to solve problems.”
And that’s exactly what Lumafield is doing, validated by users such as L'Oreal, Trek, and Saucony. Its flagship Neptune industrial scanner is much smaller than conventional CT scanners for medical or industrial applications. Powered by AI, the scanner takes up to thousands of two-dimensional pictures and assembles these into a 3D model that can be easily manipulated. For instance, the nature of CT technology means that it’s a simple affair to only show parts of a certain density range. A recent update has also increased the speed of the scanner by over 300 times. A big point for its accessibility lies with the software. It’s no longer necessary to build a ‘supercomputer’ specifically to analyze your parts, because Lumafield’s software runs in web browsers, meaning any ordinary computer can effectively use it.

ACHIEVING CT-UBIQUITY
“Aerospace,” Bruner said, “is the one field where CT scanning is broadly used as a major product development and production tool.” Until now. Most industries have not conventionally relied on analyzing parts with CT scans, largely because it’s an expensive, time-consuming process. However, with the aim of providing more accessible and affordable CT scanning, Lumafield opens the door to a wide range of industries, some of which are unexpected.
“Folks in the performance footwear space have gotten interested in CT because it gives them deep insight and an ability to measure product performance in a way that they couldn't before. Before adopting CT, the state-of-the-art was using a bandsaw to cut a shoe in half, which is fundamentally destructive and it made it difficult to understand wear over time,” Bastian explained, adding that an unexpected perk of working for a CT scanning company that runs such easy-to-use analyses is
want. “We actually have an engineer in the office who's training for a marathon, and he's been studying the degradation of his shoes. He puts about 90 miles on them per week, and scans them repeatedly over time to look at compression of the sole. This kind of time-series analysis simply isn't possible when you're cutting shoes apart to measure them.”
Bastian noted some of his personal favourite scans are anything organic: “A pomegranate is really fascinating, seeing the actual internal structure of the pomegranate is really interesting. There’s a lot of structure and symmetry that you don’t get to see when you take it apart.”
THE ADDITIVE ADVANTAGE
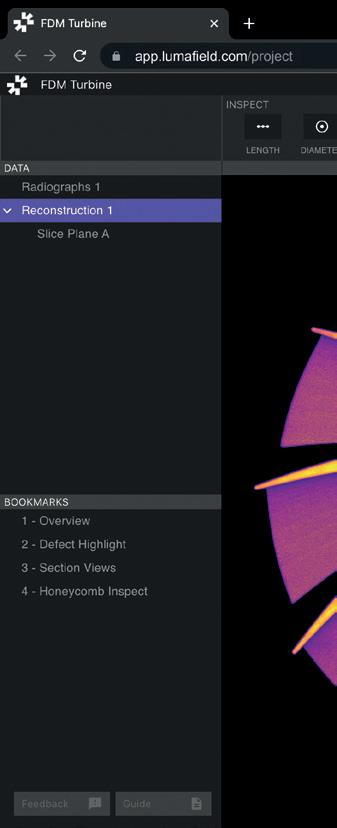
According to Bruner, additive manufacturing and the use of scanning as a process development tool was “one of the founding theses” for the company:
“As manufacturers introduce new manufacturing processes, they need ways to verify and validate them, and to understand those processes and to understand the outcomes of those processes in their products,” Bruner elaborated. “Whether that’s additive manufacturing, which is really still in the early stages of adoption at large
manufacturers, or the processes that go into electric cars involving handling very delicate batteries and assembling them and wiring them together and that kind of thing.”
CT scanning has many advantages for the AM industry, offering unique insights into new parts or manufacturing processes. Lumafield has developed powerful quantitative analysis tools for defects such as porosity voids in parts. Pore volume, sphericity and distance to the surface are among the details that can be assessed with CT. Other areas include analysis of dimensional distortion, warp distortion, support material and part interactions.
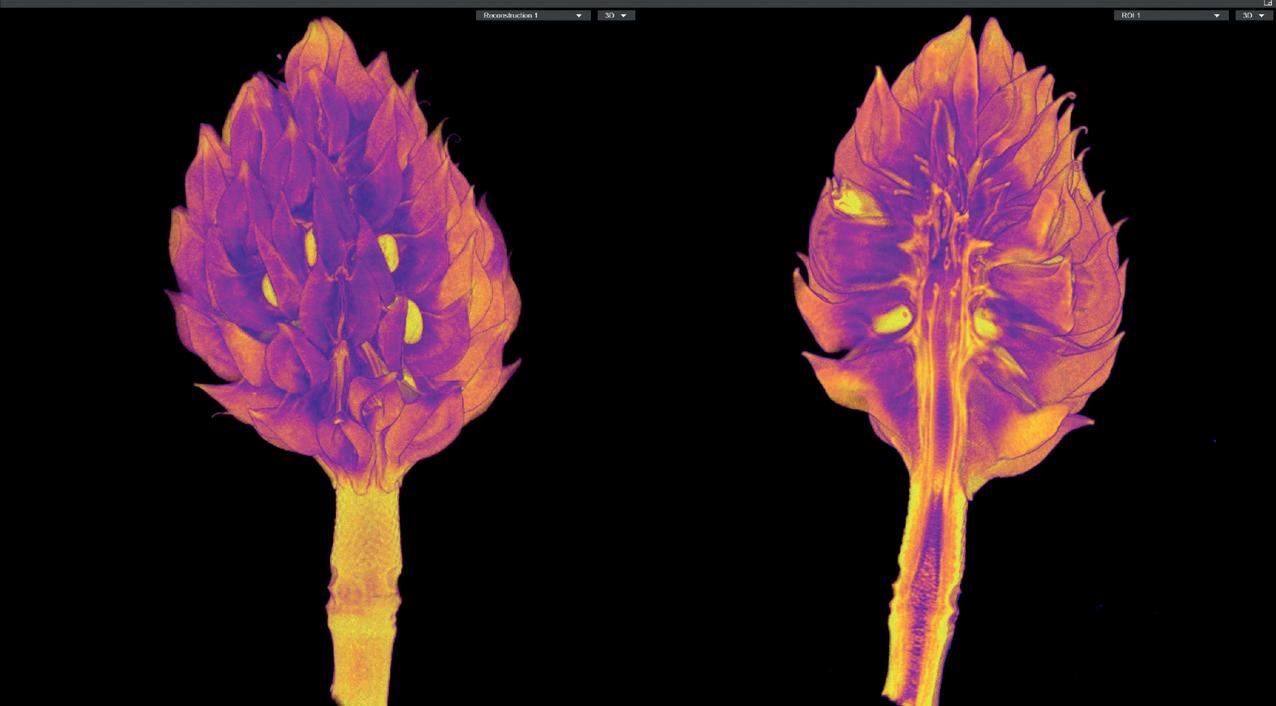
Bastian added that Lumafield’s qualitative analysis tools enable users to identify areas of trapped powder, and better understand support structure and part interactions for AM parts. “We’ve seen a of wide range of problems solved by folks using our technology to study their additively manufactured parts, spanning
both process development all the way through to part characterization,” Bastian said.
LOOKING AHEAD
The scans show a brightly illuminated future for Lumafield, making strides in the fields of AIpowered software, cloud-based user interface and the hardware that powers it all. It comes down to the company’s core:
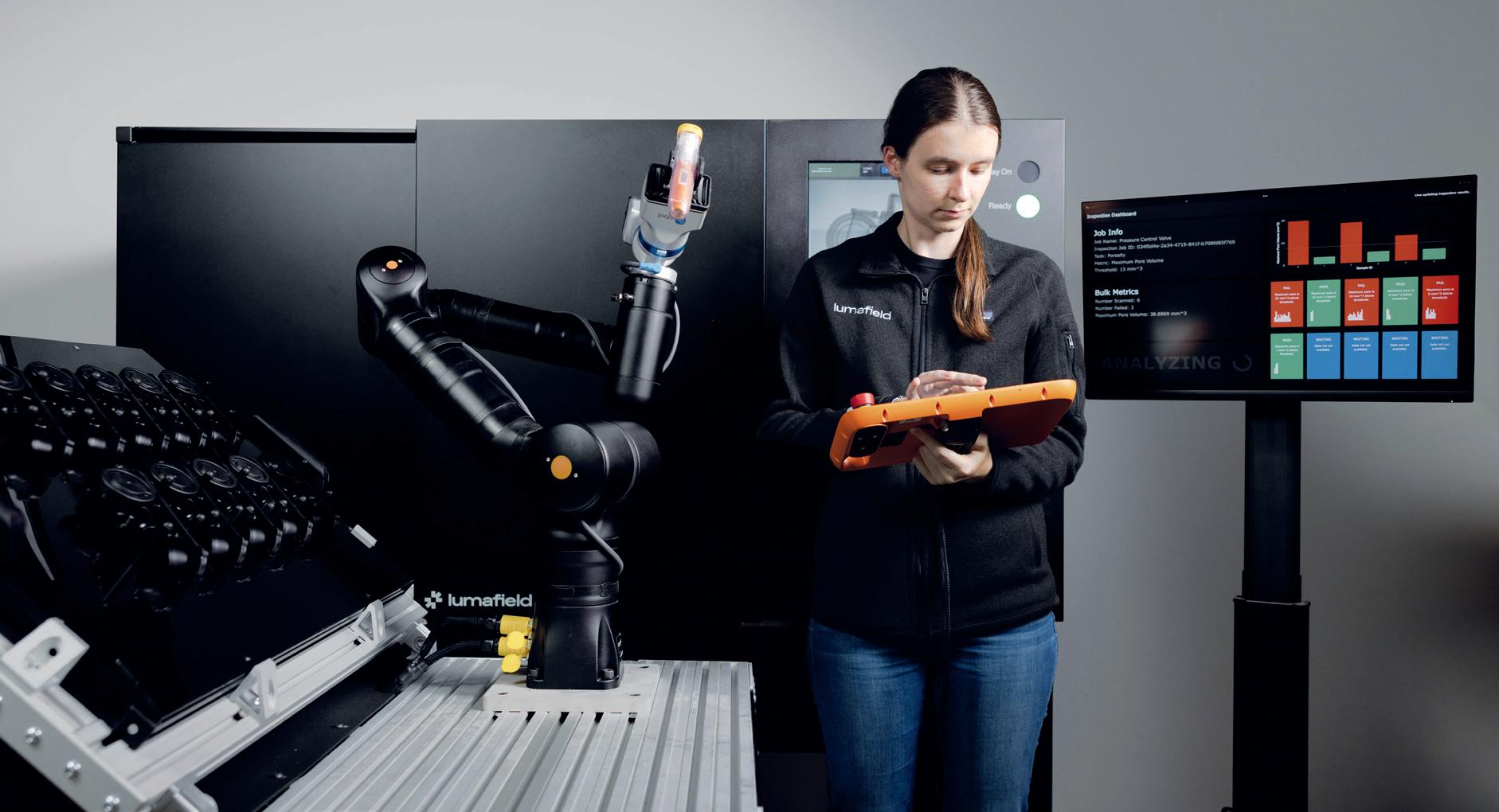
“We are fundamentally systems engineers that build these capabilities from a first principles engineering philosophy, so it’s a really deeply integrated system that we’re constantly evolving, constantly advancing,” Bastian said. “There’s some really exciting technology that lets us make the hardware more and more accessible from both the usability and the cost perspective. There’s a lot of very exciting algorithm developments on the back end to make all of this automatable and scalable. And then there’s really
exciting graphics works that goes on to actually let users interact with CT data in the browser, which is really not something that’s been available before. Moving all of this onto the cloud is really exciting because this allows anybody in the world to immediately, instantly interact with this data.”
It’s a modern approach to a modern niche: world-wide access to in-depth analysis of the most thorough kind. When Wilhelm Roentgen accidentally discovered X-rays in 1895, the potential must have already seemed endless, yet access to such an advanced version of that technology, even for small businesses and manufacturers, must have seemed fantastical. Yet, here is Lumafield, breaking open the market and peering deep through its composition and substance.
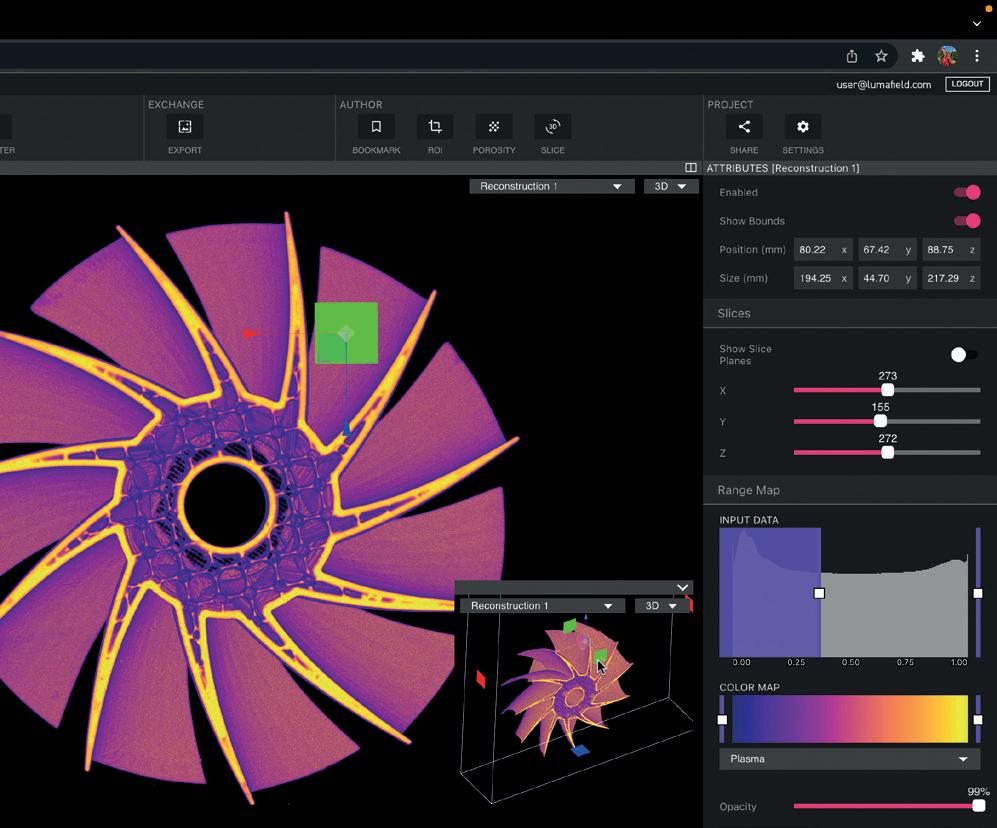
“A CT scanner is a great way to see how spectacularly engineered the world really is.”SHOWN: CT SCAN OF 3D PRINTED TURBINE IN VOYAGER SHOWN: LUMAFIELD NEPTUNE SCANNER SHOWN: SCANS OF MAGNOLIA SEEDS

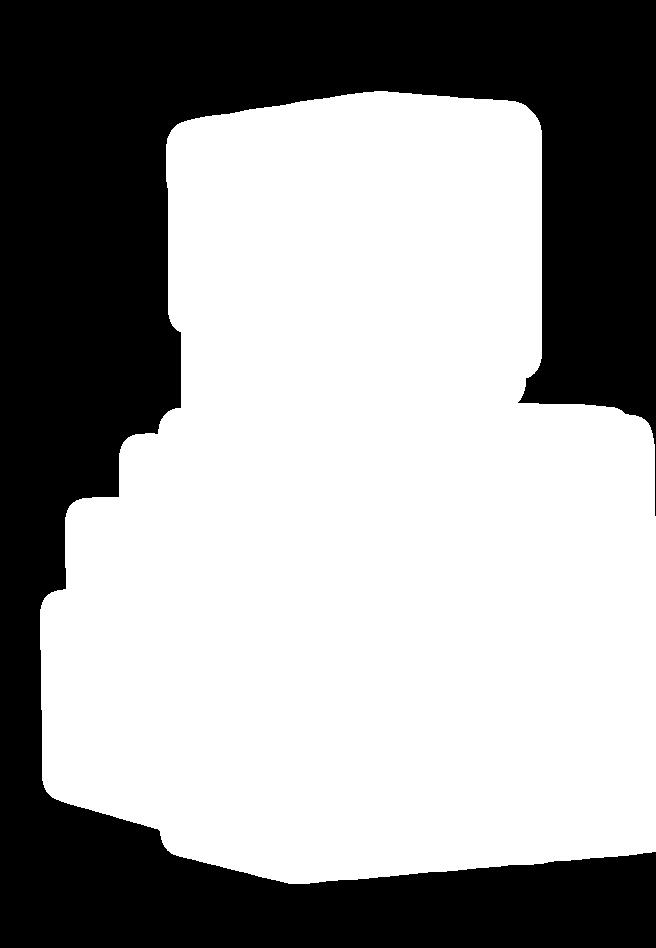
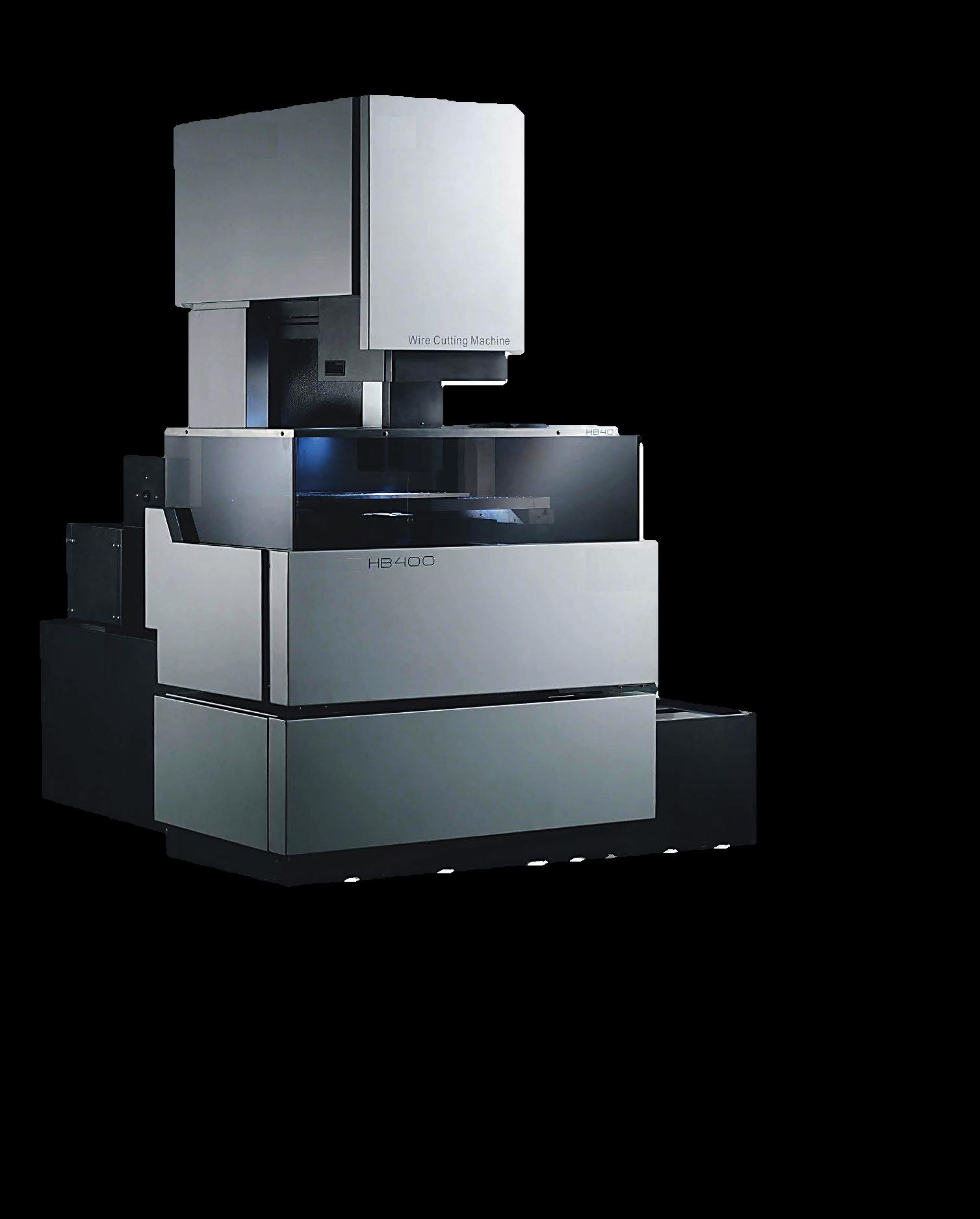
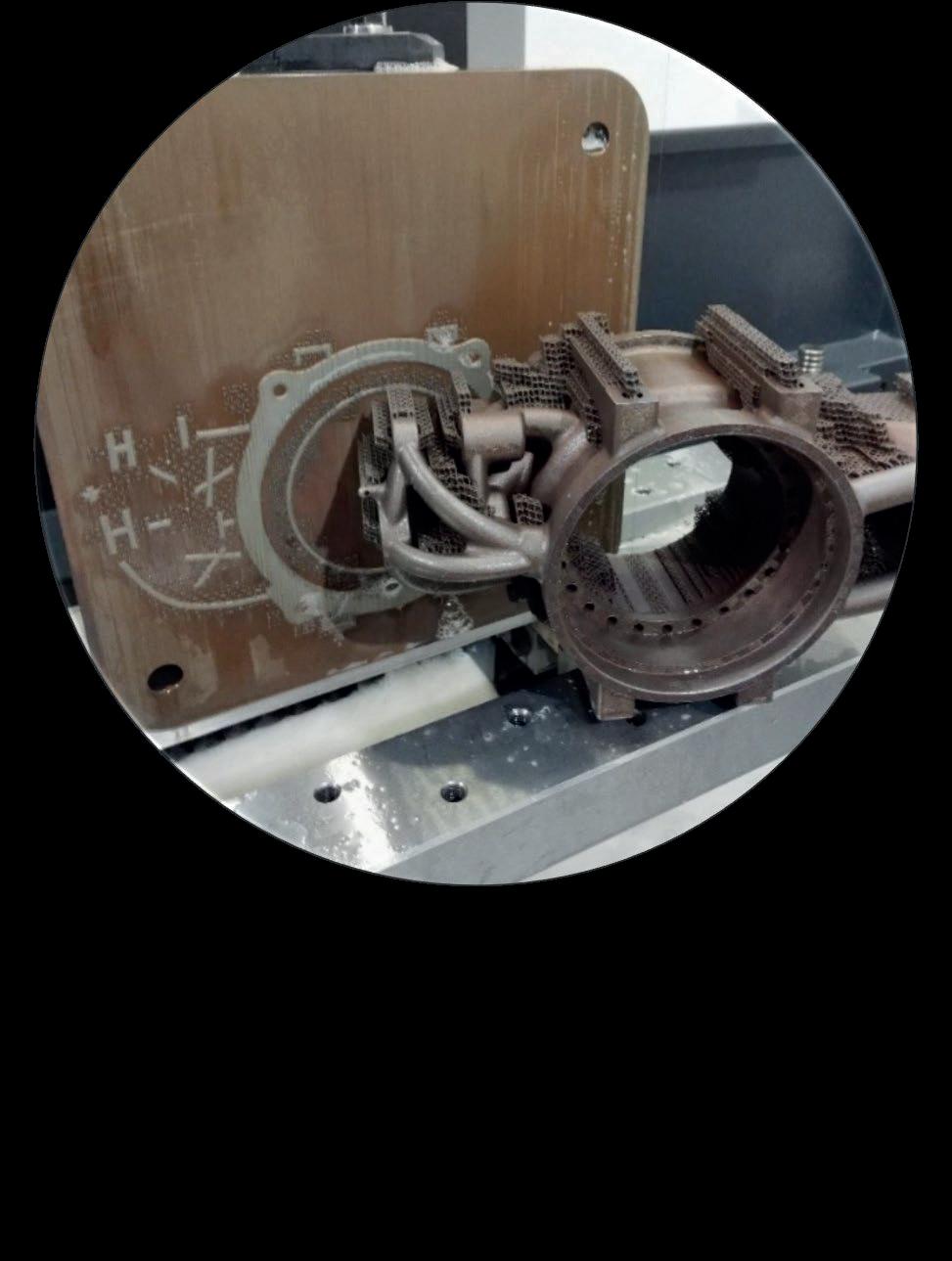
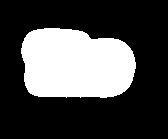
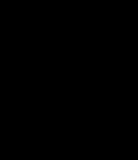
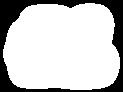

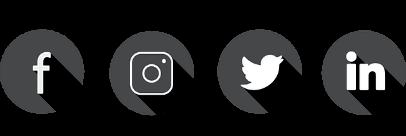



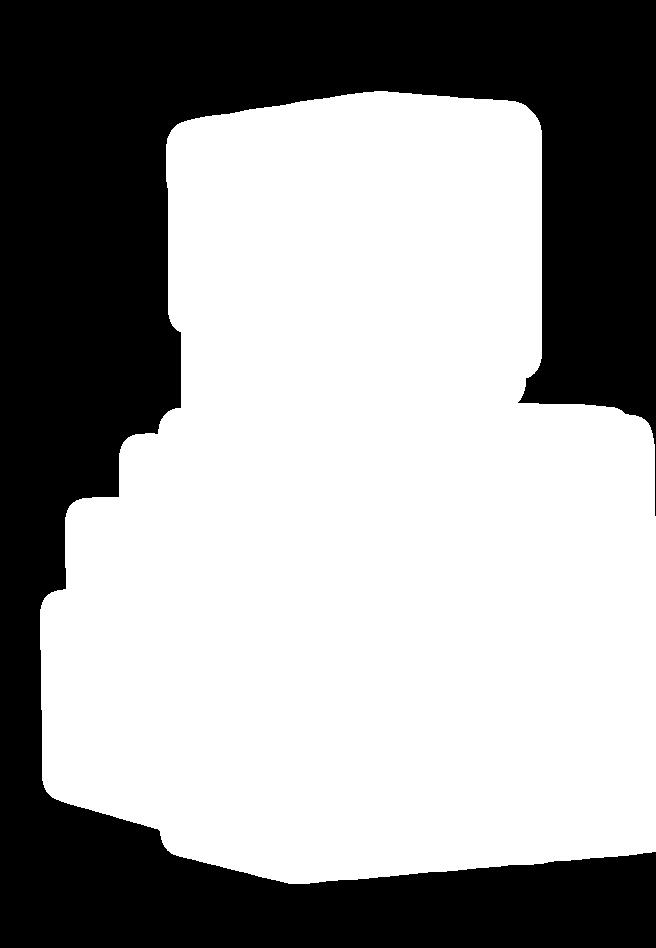
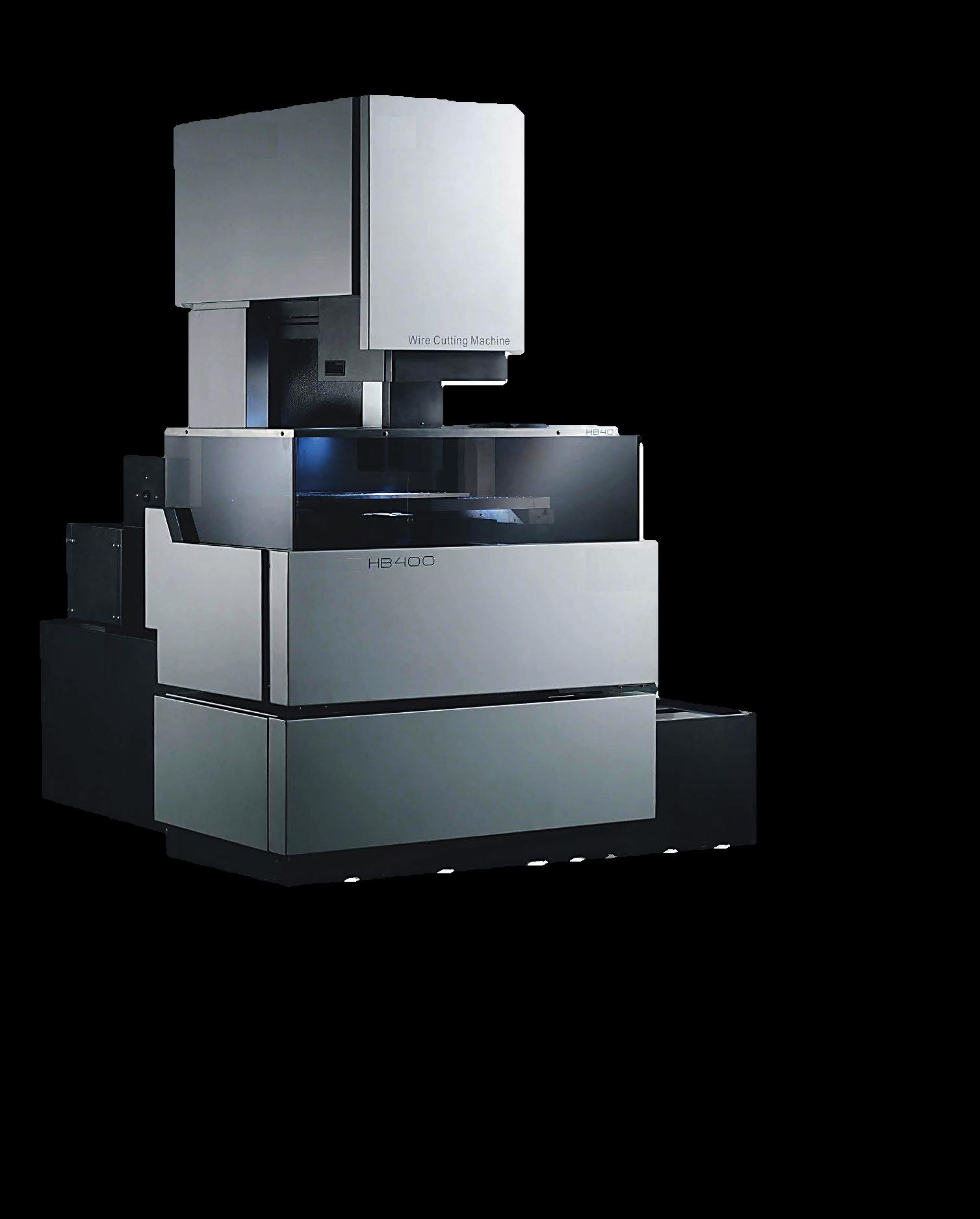
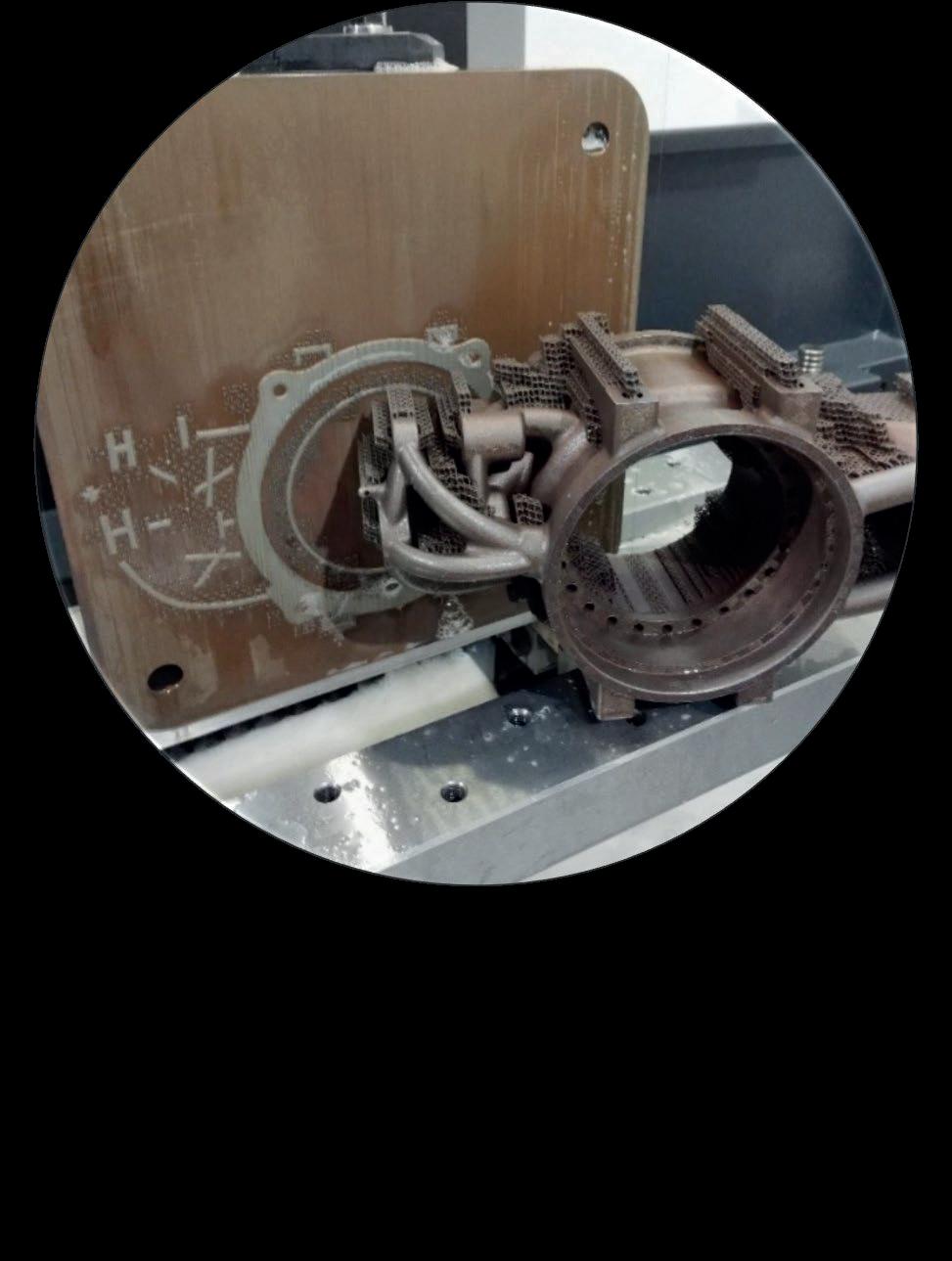
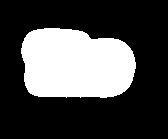
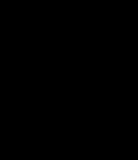
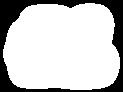
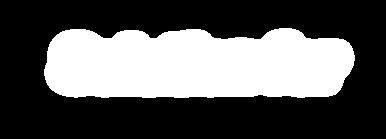

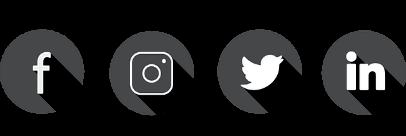

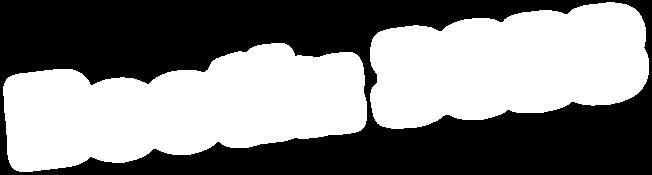


That, or words to that effect, describe a recent conversation I had with a friend who also happens to be a primary school teacher. Living amid the additive manufacturing (AM) bubble, where the drum for 3D printing in education is constantly being banged, the exchange sent me straight back to my own school days where ‘Information Technology’ class meant one PC shared between a class of 30 and each student taking turns to type up a hand-written book report with a basic word processor. I couldn’t have imagined that one day I’d be using one daily to write articles about a technology that was once considered science fiction, saving them to something called ‘the cloud’, and subsequently uploading via the internet for the world to see.
While 3D printing may not have reached that same level of ubiquity in our everyday lives, its growing presence in the working
world, and the skills required to use it, are becoming increasingly difficult to ignore.
TEACHING THE TEACHERS
The skills gap, however, is still very much a reality and the charge to close it requires support, not just for pupils that will one day be entering industry but for the teachers expected to lead those lessons. Unfortunately, it’s not as easy as installing a 3D printer in a classroom.
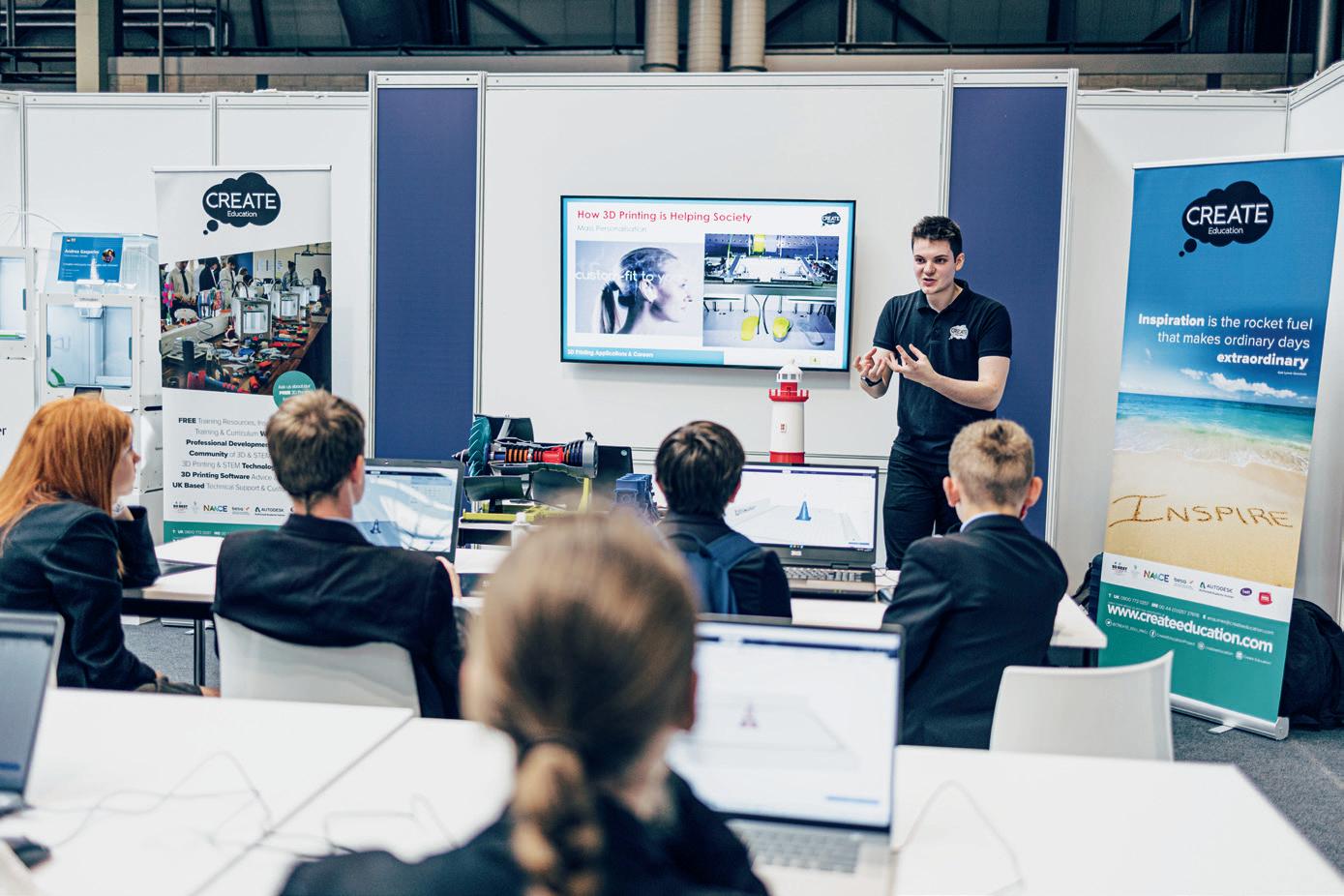
The first challenge, as Sonya Horton, Education Product Manager at CREATE Education Project, a UK-based organization that enables schools, colleges and universities to access 3D technologies and training, told TCT, is that there simply isn’t a requirement to teach it as part of the school curriculum.
“There’s one reference in the entire curriculum that says students should have an awareness of new and emerging technologies, such as 3D printing, but there’s no requirement to be able to use it, to do 3D modelling or to learn any of those skills,” Horton explained. “The reality is that many schools don't do it at all. The ones that want to do it, that see we should be preparing our kids for jobs and for industry,
“3D printing is not going away.”
the ones that get it, then often have very, very little support from the senior leadership teams.”
The UK’s national curriculum does list ‘design and technology’ and ‘computing’ amongst its compulsory subjects from as early as key stage 1 (children aged 5 to 6) but Sonya argues, given there’s no prerequisite for schools to prioritize 3D printing, “students can go through their entire school life never encountering 3D printing technology.” It’s even less encouraging in later stages of education, where ‘design and technology’ is demoted from the core subjects list, along with arts, humanities, and modern foreign languages, of which schools are only required to provide one. For ‘design and technology’, there are multiple factors working against its adoption in the curriculum: expensive equipment, a lack of funding support for qualified technicians, external pressures of league tables, and exam results that often mean D&T becomes ‘just another thing’ to worry about.
“It's understanding that this just isn't another piece of technology that's going to come and go because [teachers] have been bombarded with technologies over the years,” Horton said. “They always seem to have to learn something new and then it disappears but this technology, as we know, is being used throughout industry and it's growing, it's here to stay. Actually, if we're not skilling up our kids to be able to use this technology, we're
Laura Griffiths speaks to CREATE Education about the reality of implementing 3D printing in classrooms.
putting them at a serious disadvantage in future careers and that's even from a very young age. Why should kids do it? Because this is going to be part of their world. It's going to be everywhere. It already is. I was at TCT [3Sixty] just before the pandemic and I saw the launch of the [adidas] trainers with 3D printed midsoles. I was shopping on Friday and guess what I saw a pair of? It's crazy. So, it's about the fact that it's not going away. It's vitally important.”
LESSON PLAN
Setting up a printer is one thing, learning to design for one is another, and that’s before figuring out how to apply that to a classroom of 30 children. CREATE Education offers training packages to educators, ranging from one-hour remote courses for every machine sold, designed to walk teachers through the setup, to hands-on half and full-day courses.
“It's finding schools to actually have the budget to pay for the training but also to get those teachers out of the classroom for a day,” Horton said. “If they do that, we found that they have the most success because they've been there, they've done it, they've had hands-on for a day, gone through the process, learned the software, made something, sliced it, 3D printed it, set up the printer, they know how to do it, so they can walk away and do a project with the kids because they can replicate what they've done in their journey. But they’ve also got lots and lots of ideas for other projects that they can do with the kids, linked to the curriculum that will tick all those boxes that they need to tick.”
Often, interested schools will approach CREATE Education directly but Horton shares that the organization does a lot of outreach work to engage schools, and is currently working with associations like the Design and Technology Association to run programmes and encourage adoption within primary schools. It’s everything teachers need to hold their hands through a six-week loan, enough to run an entire project end-to-end. The persisting challenge, Horton noted, is time.
“I am a former teacher so I think that helps to build trust amongst the teachers because you're not just the technology person,” Horton said. “The feedback from the training is almost overwhelmingly positive because it's hands on, it gives
them the tools to just have a go. But the teachers do recognize that they’re still going to have to invest a little bit of time, but it gives them that starting point and they see why and how, and because they know where to start and take something away that they can do immediately with their classes, it gives them that sort of that motivation, and that impetus to actually do it.”
Change is happening but without the backing of government, that shift is usually spurred by the enthusiasm of individual champions and teachers who see the value in bringing this technology into their classrooms. To guide them, CREATE Education offers a range of resources on how to implement 3D printing throughout the curriculum, including guides and project ideas on how to apply it across various subjects and help tick the required boxes.
Andrew Allshorn, founder of AT 3D-SQUARED, is one such champion and a CREATE Education ambassador. That includes going into schools and supporting the Inspired Minds classroom at TCT 3Sixty, which gives hundreds of children the opportunity to learn about 3D technologies every year. Allshorn shared how his approach means inviting not just design and technology departments, but teachers across the board, from history to cooking, so they can see for themselves how 3D printing spans much further than technology labs.
“When I first did it, I put one in a local school and I said, 'I want the science teachers, I want the geography teacher, I want the cooking teacher, I want everybody in here to see what this thing can be,'” Allshorn explained. “The important thing is we need to find how to get that into curriculum and how to get the teacher engaged.”
Horton added: “There are innovative schools, there are schools that are pushing the boundaries, that are doing some really good stuff, because they get it and the senior leadership get it. They are supporting those design and technology departments to do some amazing stuff.
“What we need is not just 2 or 3% of secondary schools doing that, we want 100% of secondary schools doing that. It's about investment and understanding how important this technology is for future careers.”
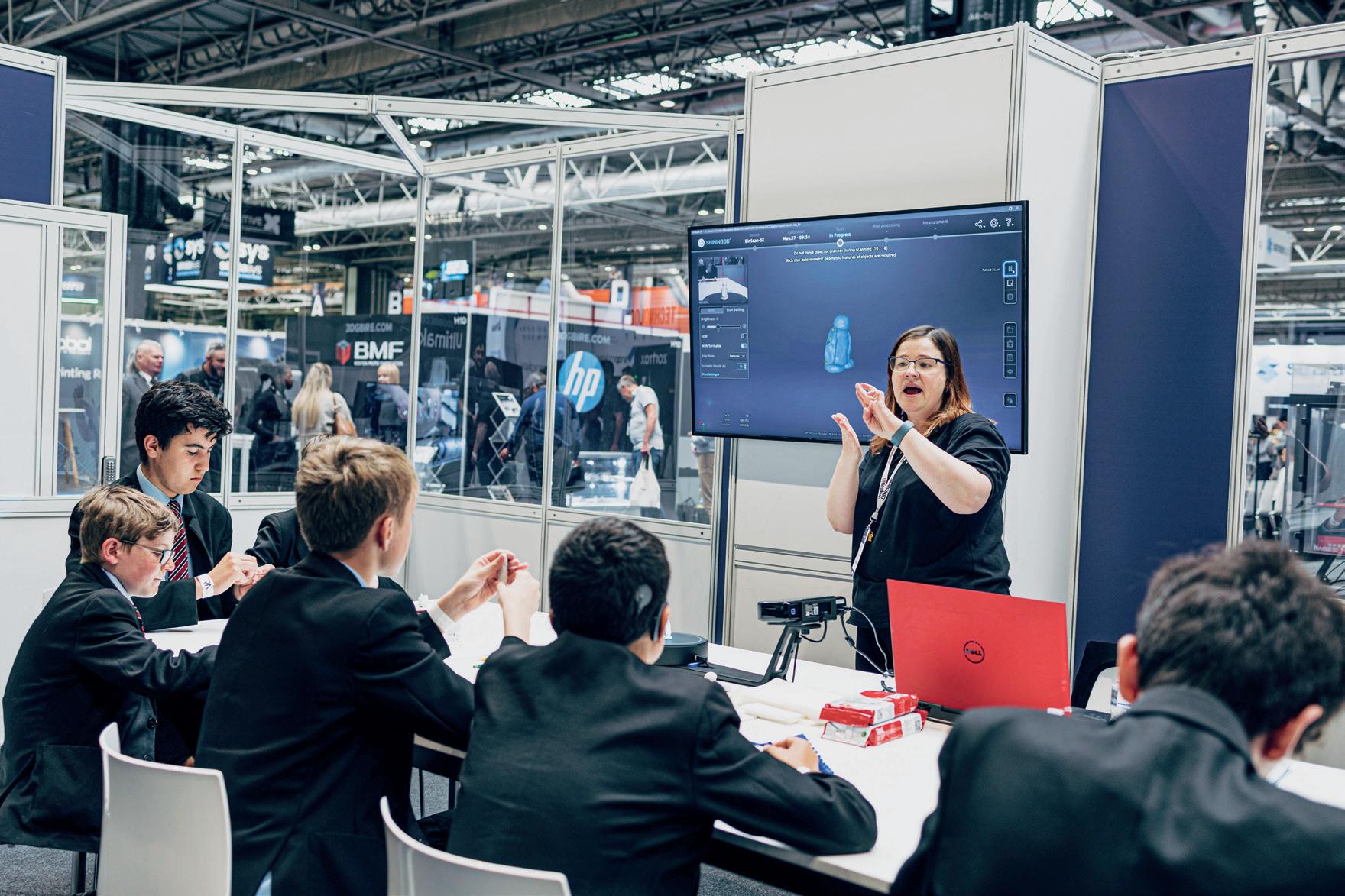
“There are innovative schools pushing the boundaries.”
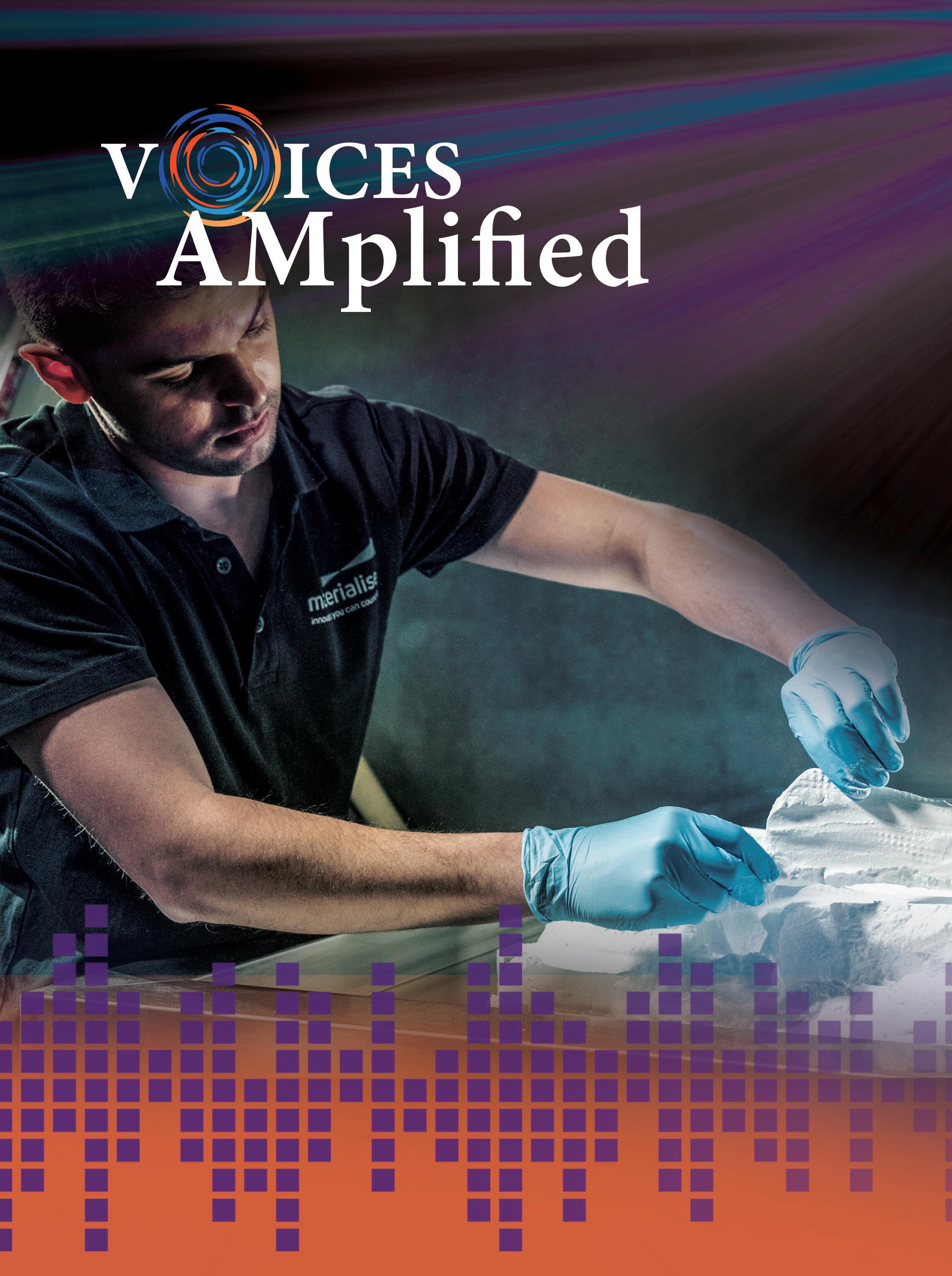
AM Community Shows Off at RAPID + TCT
AM Community Shows Off at RAPID + TCT
Solving Problems and Giving Back
It’s official. Additive Manufacturing is thriving and con tinues to gain momentum with successes across di verse applications. In addition to ongoing technology advances, AM’s growth is fueled by a host of engaged companies, organizations, and dedicated professionals, all of whom are energized and passionate about developing, implementing—and sharing—new ideas and best practic es throughout a collaborative community of innovators.
TIt’s official. Additive Manufacturing is thriving and con tinues to gain momentum with successes across di verse applications. In addition to ongoing technology advances, AM’s growth is fueled by a host of engaged companies, organizations, and dedicated professionals, all of whom are energized and passionate about developing, implementing—and sharing—new ideas and best practic es throughout a collaborative community of innovators.
his edition of Voices AMplified features two lead ers who leverage their experience, insights, and talents to improve the way we, as a communi ty, get the best out of additive manufacturing (AM).
The recent RAPID + TCT conference, which was held May 17 19 in Detroit, is proof positive as to how far AM has come in recent years. The 31st edition of the industry’s mar quee event featured more than 400 exhibitors, hundreds of speakers and expert panelists, dozens of technical sessions, networking opportunities, and attendees from 38 countries.
The recent RAPID + TCT conference, which was held May 17 19 in Detroit, is proof positive as to how far AM has come in recent years. The 31st edition of the industry’s mar quee event featured more than 400 exhibitors, hundreds of speakers and expert panelists, dozens of technical sessions, networking opportunities, and attendees from 38 countries.
The first article explores how a harmonized workflow can link software and equipment needed to 3D print compo nents. Bryan Crutchfield, vice president and general manager of Materialise North America, shares how he and his team worked during the pandemic to solve a problem faced by many software developers-limited interoperability due to the proliferation of numerous, standalone products. And it’s clear that his mission is to move the industry forward. As part of the feature, Crutchfield, who served as a volunteer advisor on SME’s AMTC for six years, shares that the Materialise team is not out to dominate the 3D-printing realm. It’s the opposite. Because closed systems are a path to stagnation, manufac turing workflows must “be digital in nature, and also automat ed as much as possible.” And that requires giving customers the choice to use world-class technology through an open software platform.
The AM community took center stage throughout the show. This includes the passing of the baton in two key leadership positions. John Barnes assumed the chair of the Additive Manufacturing Technical Community Leadership Committee, succeeding Christopher Williams; and Sarah Rimini now chairs the Medical AM Advisory Committee, succeeding Amy Alexander. I’d like to thank Christopher and Amy, who provided exemplary leadership and vision during their tenures, and welcome their replacements.
The second feature profiles the esteemed career of Sheku Kamara, Dean of Applied Research at the Milwaukee School of Engineering (MSOE), who was recently re-appointed as a volunteer advisor to SME’s AMTC. Kamara came to the U.S.
The AM community took center stage throughout the show. This includes the passing of the baton in two key leadership positions. John Barnes assumed the chair of the Additive Manufacturing Technical Community Leadership Committee, succeeding Christopher Williams; and Sarah Rimini now chairs the Medical AM Advisory Committee, succeeding Amy Alexander. I’d like to thank Christopher and Amy, who provided exemplary leadership and vision during their tenures, and welcome their replacements.
John, who heads The Barnes Global Advisors and Metal Powder Works, has been involved in metal additive manufac turing throughout a distinguished career. He’s led teams that qualified the aerospace industry’s first series production met al AM parts, and developed a pilot metal production facility.
John, who heads The Barnes Global Advisors and Metal Powder Works, has been involved in metal additive manufac turing throughout a distinguished career. He’s led teams that qualified the aerospace industry’s first series production met al AM parts, and developed a pilot metal production facility.
As senior manager of Ricoh’s Healthcare Center of Excellence, Sarah is developing a curriculum for the com pany’s Learning Institute that focuses on medical managed
As senior manager of Ricoh’s Healthcare Center of Excellence, Sarah is developing a curriculum for the com pany’s Learning Institute that focuses on medical managed
Suzy Marzano Senior Manager Industry Development and Technical Activities SME E. Barnes Suzy Marzano Senior Manager Industry Development and Technical Activities SME3D-printing services. At RAPID + TCT, she moderated a panel discussion on 3D printing for point-of-care medical applica tions. The panel was one of several during a special town hall hosted by the Medical AM Advisory Team.
in 1996 from Sierra Leone. As we look back on his journey of learning, he shares that his greatest joy has been in teaching others about what is possible through AM. To that end, Ka mara and his MSOE colleagues worked with industry leaders to create the Additive Manufacturing Body of Knowledge (AMBOK), as well as a wealth of training materials to serve as a technology road map for manufacturers. In the article, Kamara also shares his view on the limitless problem-solving powers of technology, and how important it is to help others. A few years ago, he and his friends organized a dialysis clinic in his homeland, which helped community members get the critical care they needed without having to travel or relocate to other countries. Kamara not only talks the talk, but he walks the walk.
3D-printing services. At RAPID + TCT, she moderated a panel discussion on 3D printing for point-of-care medical applica tions. The panel was one of several during a special town hall hosted by the Medical AM Advisory Team.
Other highlights included the winners of the 2022 SME Additive Manufacturing Community Awards: Slade Gard ner, founder of Big Metal Additive (Industry Achievement); VELO3D and IMI Critical Engineering (Aubin AM Case Study); and Virginia Tech students Daniel Chirvasuta, Nathanael High, Matthew Martin, Benjamin Nguyen, Omkar Shinde, and Nicolas Tomanelli (Digital Manufacturing Challenge).
Other highlights included the winners of the 2022 SME Additive Manufacturing Community Awards: Slade Gard ner, founder of Big Metal Additive (Industry Achievement); VELO3D and IMI Critical Engineering (Aubin AM Case Study); and Virginia Tech students Daniel Chirvasuta, Nathanael High, Matthew Martin, Benjamin Nguyen, Omkar Shinde, and Nicolas Tomanelli (Digital Manufacturing Challenge).
To help foster the next generation of innovators, the SME Education Foundation’s Bright Minds Program welcomed nearly 1,000 middle and high school students to RAPID + TCT. There also was a special networking lunch for young profes sionals and a Career Forum Panel. The initiative is led by Ellen Lee and Jennifer Coyne, who are both advisors on the Additive Manufacturing Technical Community Leadership Committee.
To help foster the next generation of innovators, the SME Education Foundation’s Bright Minds Program welcomed nearly 1,000 middle and high school students to RAPID + TCT. There also was a special networking lunch for young profes sionals and a Career Forum Panel. The initiative is led by Ellen Lee and Jennifer Coyne, who are both advisors on the Additive Manufacturing Technical Community Leadership Committee.
As Chair of SME’s AMTC, I recently met in person at IMTS with our committee to plan the next 12 month, and it is going to be exciting. We brought on five fantastic people who are all experts in their area making the AMTC a well-rounded, diverse team. Our promise to the AM community is to do what we can to lift up and promote the industry through the Industry Achievement Award, our Career Forum series, the Dick Aubin Case Study Award, and assisting SME with its forward momentum in AM. We have several new ideas in the works. It’s going to be a great year at the AMTC!
SME Media also interviewed dozens of AM leaders during RAPID + TCT as part of its Voices AMplified initiative that showcases the people behind the technology. This month’s Voices AMplified report profiles two such visionaries: Olga Ivanova and Carl Dekker. Known as “Dr. O,” Olga has worked on innovative projects for the medical and defense industries, and is a tireless crusader for advancing AM.
SME Media also interviewed dozens of AM leaders during RAPID + TCT as part of its Voices AMplified initiative that showcases the people behind the technology. This month’s Voices AMplified report profiles two such visionaries: Olga Ivanova and Carl Dekker. Known as “Dr. O,” Olga has worked on innovative projects for the medical and defense industries, and is a tireless crusader for advancing AM.
Carl puts the emphasis on people. He leads a talented team at Met-L-Flo, which produces a wide range of 3D-printed prod ucts. He also chairs the Direct Digital Manufacturing Advisory Team and moderated a panel at RAPID + TCT.
Carl puts the emphasis on people. He leads a talented team at Met-L-Flo, which produces a wide range of 3D-printed prod ucts. He also chairs the Direct Digital Manufacturing Advisory Team and moderated a panel at RAPID + TCT.
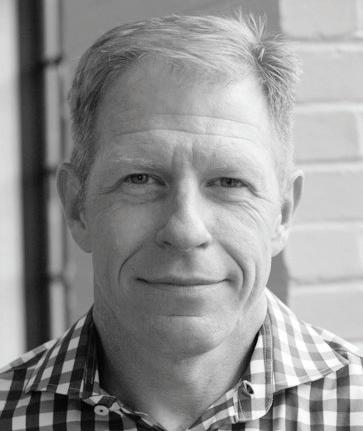
Carl and Olga represent the spirit behind Voices AMplified. I hope you enjoy their stories.
Carl and Olga represent the spirit behind Voices AMplified. I hope you enjoy their stories.

According to Materialise, its RapidFit smart cubing system empowers automakers to speed up their engineering and development processes, as in the Aston Martin prototype shown here.
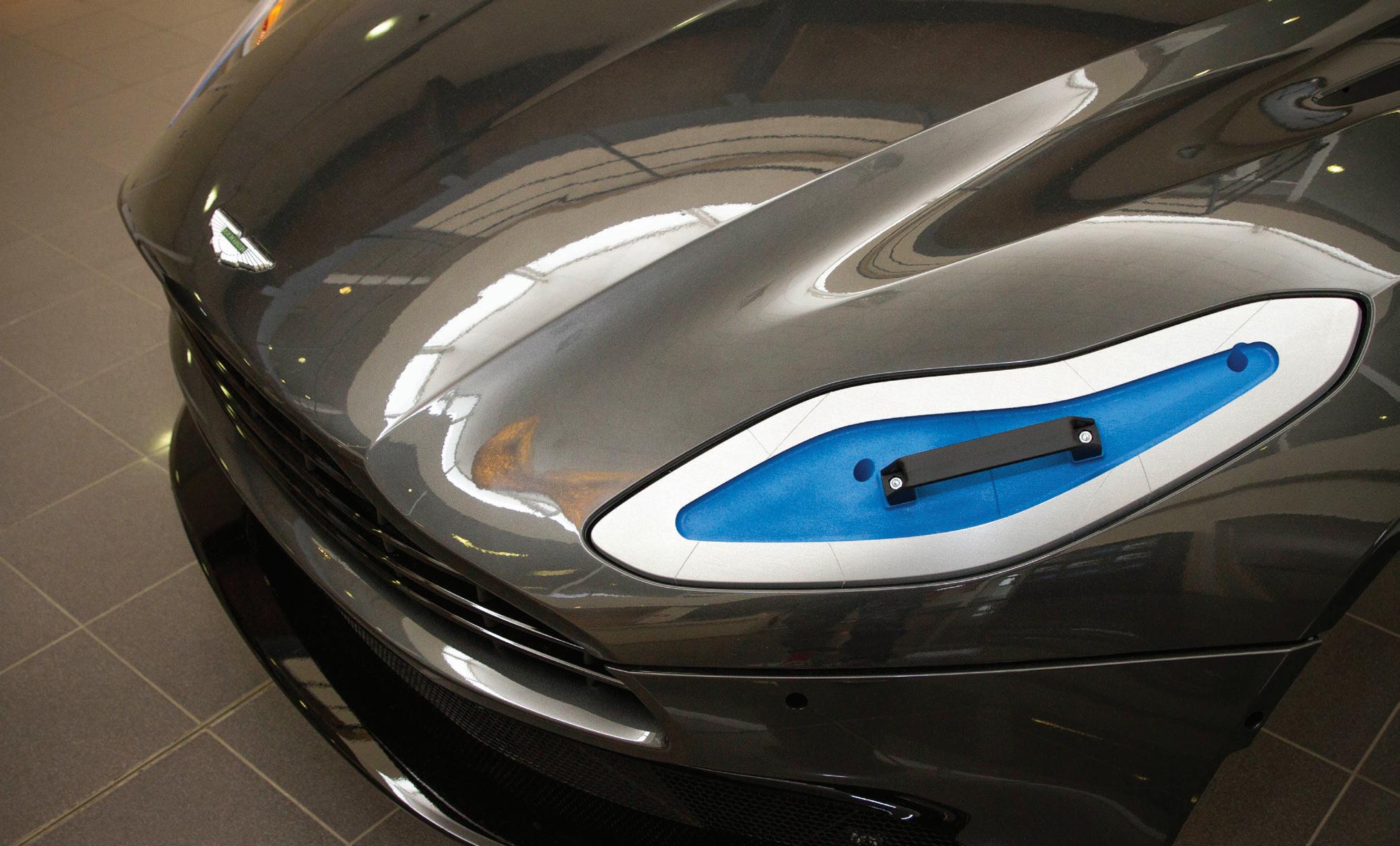
From
From 3D-printed figurines for students to “quantum dots” and nanocomposites, Olga Ivanova is a force to be reckoned with in the AM universe
Striving for Harmony
Paging Dr. O
Kip Hanson Contributing Editorlga Ivanova has 3D-printed plenty of interest ing parts during her time in manufacturing. Rocket nozzles. Turbine blades and impel lers. Neonatal tracheostomy tubes. There are more, which we’ll get to in a moment, but to Star Wars fans, it’s the Static Dissipative Yoda that’s most intriguing.
AOfter the economy tanked during the Great Re cession, Bryan Crutchfield was more than ready for a change. “I’ve been in the Detroit area for my entire career and spent roughly 20 years of that with a Tier 1 automotive supplier,” he said. “So even though I love the industry, I’d ridden it right to the bottom by then and wanted to do something else. That’s when a recruiter approached me looking for someone with oper ational and sales experience to fill a position in the addi tive manufacturing industry. It sounded good to me.”
“We printed a bunch of Yoda and Groot (Guardians of the Galaxy) figurines for high school students who visited our facility recently,” said Ivanova, director of technology at Mechnano, an additive manufacturing materials
developer near Phoenix. “It’s our way of getting young people interested in additive manufacturing.”
Padawan Learning
That opportunity landed him at 3D-printing product and service provider Materialise NV, where Crutchfield now serves as the vice president and general manager for the company’s North American headquarters in Plymouth, Mich. He also sits on the board of Leuven, Belgium-based RapidFit NV, a Mate rialise company specializing in automotive tooling design and manufacturing, and Link3D Inc. of Lafayette, Colo., develop ers of Materialise’s SaaS-based CO-AM software.
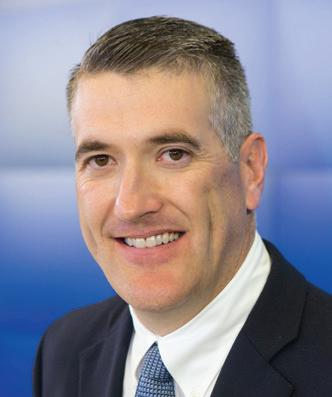
“With the acquisition of Link3D, Materialise brings to market a neutral AM platform that not only supports our
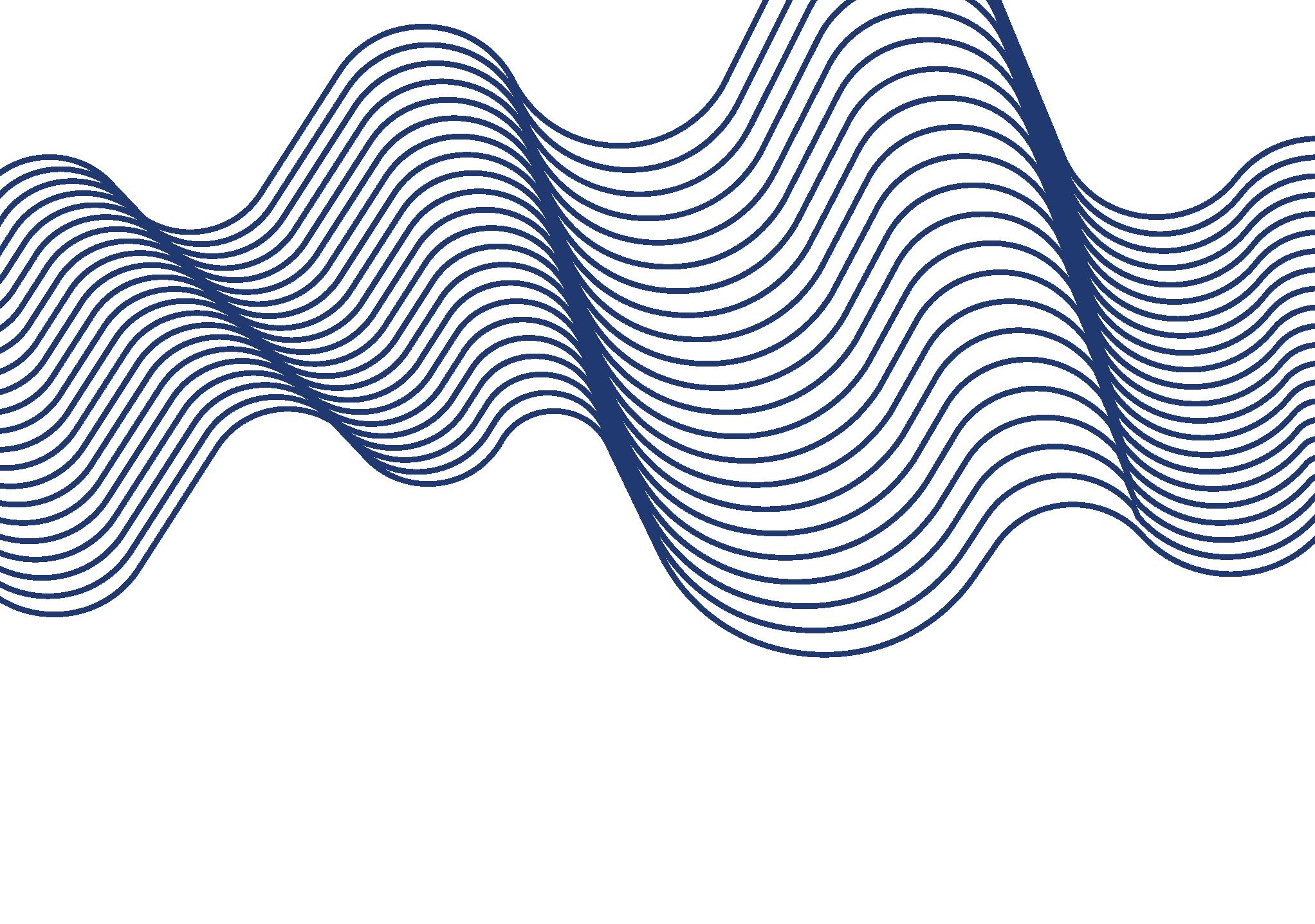

She’s quick to point out that those educational give aways were made of a gray-colored base resin, not the more expensive static dissipative material (which is black) that she spends much of each day working with—and yes, which she occasionally uses to print Yodas that are just as resistant to electrical charge as they are to the Dark Side of the Force.
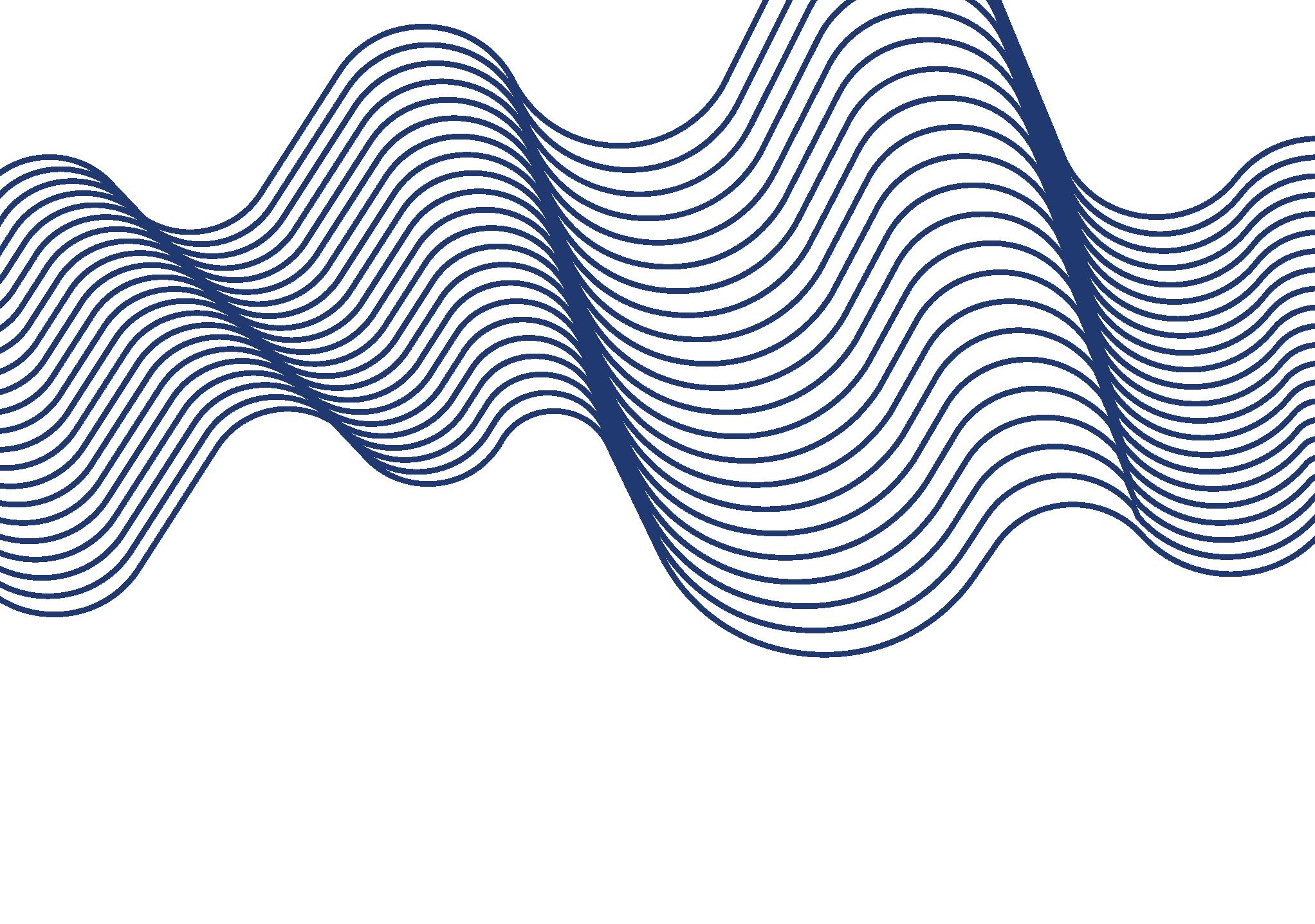
automotive to medical, Bryan Crutchfield suggests additive manufacturing will get more done using streamlined, harmonized workflowsBryan Crutchfield Advisor, SME AM Technical Community Leadership Committee Vice President & General Manager Materialise North America
Voices AMplified

technology, but also that of third-party developers and, at some time perhaps, even our competitors’ software solu tions,” Crutchfield said.
that links all of the software and equipment required to 3D print a component. “Our CO-AM platform accomplishes all this and more,” Crutchfield noted.
AM Community Shows Off at RAPID + TCT
AM Community Shows Off at RAPID + TCT
Suzy Marzano Senior Manager Industry Development and Technical ActivitiesBuilding Interoperability
It’s official. Additive Manufacturing is thriving and con tinues to gain momentum with successes across di verse applications. In addition to ongoing technology advances, AM’s growth is fueled by a host of engaged companies, organizations, and dedicated professionals, all of whom are energized and passionate about developing, implementing—and sharing—new ideas and best practic es throughout a collaborative community of innovators.
It’s official. Additive Manufacturing is thriving and con tinues to gain momentum with successes across di verse applications. In addition to ongoing technology advances, AM’s growth is fueled by a host of engaged companies, organizations, and dedicated professionals, all of whom are energized and passionate about developing, implementing—and sharing—new ideas and best practic es throughout a collaborative community of innovators.
He suggested the AM industry has long needed a harmonized workflow that encompasses all aspects of the 3D-printing process. This begins with what Crutchfield refers to as content creation—the importation and potential cleanup of a CAD file, for example, or using point-cloud data from a 3D scanner to construct a viable model of a part or part feature. Supports, meshes, and lattice structures might then be added, the part nested with others that use the same material, and the build file sent to the 3D printer for processing. After leaving the build chamber, parts enter what many call the “dirty little secret” phase of additive manufacturing—postprocessing—which depending on the technology, includes CNC machining, vapor polishing, heat treatment, and other operations.
COVID has helped create the platform. During the pan demic (and even before), Materialise worked on a problem that eventually plagues any company that develops software: the proliferation of multiple, standalone products suffering from limited interoperability. Materialise “refactored” its software, connecting each module with a series of applica tion programming interfaces (APIs) to create comprehensive workflows that it now offers to the industry.
Suzy Marzano Senior Manager Industry Development and Technical Activities SME“Additive once belonged only to service bureaus and prototyping-only applications,” Crutchfield explained. “Those barriers have slowly melted away as AM has moved into traditional manufacturing, where it assumes its well-deserved role as just one more tool, albeit an important one.
SME3D-printing services. At RAPID + TCT, she moderated a panel discussion on 3D printing for point-of-care medical applica tions. The panel was one of several during a special town hall hosted by the Medical AM Advisory Team.
3D-printing services. At RAPID + TCT, she moderated a panel discussion on 3D printing for point-of-care medical applica tions. The panel was one of several during a special town hall hosted by the Medical AM Advisory Team.
Other highlights included the winners of the 2022 SME Additive Manufacturing Community Awards: Slade Gard ner, founder of Big Metal Additive (Industry Achievement); VELO3D and IMI Critical Engineering (Aubin AM Case Study); and Virginia Tech students Daniel Chirvasuta, Nathanael High, Matthew Martin, Benjamin Nguyen, Omkar Shinde, and Nicolas Tomanelli (Digital Manufacturing Challenge).
Whatever the process and however many steps are need ed, though, each should be part of a harmonized workflow
The recent RAPID + TCT conference, which was held May 17 19 in Detroit, is proof positive as to how far AM has come in recent years. The 31st edition of the industry’s mar quee event featured more than 400 exhibitors, hundreds of
The recent RAPID + TCT conference, which was held May 17 19 in Detroit, is proof positive as to how far AM has come in recent years. The 31st edition of the industry’s mar quee event featured more than 400 exhibitors, hundreds of speakers and expert panelists, dozens of technical sessions, networking opportunities, and attendees from 38 countries.
The AM community took center stage throughout the show. This includes the passing of the baton in two key leadership positions. John Barnes assumed the chair of the Additive Manufacturing Technical Community Leadership Committee, succeeding Christopher Williams; and Sarah Rimini now chairs the Medical AM Advisory Committee, succeeding Amy Alexander. I’d like to thank Christopher and Amy, who provided exemplary leadership and vision during their tenures, and welcome their replacements.
John, who heads The Barnes Global Advisors and Metal Powder Works, has been involved in metal additive manufac turing throughout a distinguished career. He’s led teams that qualified the aerospace industry’s first series production met al AM parts, and developed a pilot metal production facility.
As senior manager of Ricoh’s Healthcare Center of Excellence, Sarah is developing a curriculum for the com pany’s Learning Institute that focuses on medical managed
“But this movement is going to require an even high er level of interoperability,” he continued. “We and other providers will need to provide seamless connectivity to ERP systems, for example, as well as the MES platforms used in CNC machine shops and plastic injection molding houses.
Other highlights included the winners of the 2022 SME Additive Manufacturing Community Awards: Slade Gard ner, founder of Big Metal Additive (Industry Achievement); VELO3D and IMI Critical Engineering (Aubin AM Case Study); and Virginia Tech students Daniel Chirvasuta, Nathanael High, Matthew Martin, Benjamin Nguyen, Omkar Shinde, and Nicolas Tomanelli (Digital Manufacturing Challenge).
To help foster the next generation of innovators, the SME Education Foundation’s Bright Minds Program welcomed nearly 1,000 middle and high school students to RAPID + TCT. There also was a special networking lunch for young profes sionals and a Career Forum Panel. The initiative is led by Ellen Lee and Jennifer Coyne, who are both advisors on the Additive Manufacturing Technical Community Leadership Committee.
To help foster the next generation of innovators, the SME Education Foundation’s Bright Minds Program welcomed nearly 1,000 middle and high school students to RAPID + TCT. There also was a special networking lunch for young profes sionals and a Career Forum Panel. The initiative is led by Ellen Lee and Jennifer Coyne, who are both advisors on the Additive Manufacturing Technical Community Leadership Committee.
SME Media also interviewed dozens of AM leaders during RAPID + TCT as part of its Voices AMplified initiative that showcases the people behind the technology. This month’s Voices AMplified report profiles two such visionaries: Olga Ivanova and Carl Dekker. Known as “Dr. O,” Olga has worked on innovative projects for the medical and defense industries,
SME Media also interviewed dozens of AM leaders during RAPID + TCT as part of its Voices AMplified initiative that showcases the people behind the technology. This month’s Voices AMplified report profiles two such visionaries: Olga Ivanova and Carl Dekker. Known as “Dr. O,” Olga has worked on innovative projects for the medical and defense industries, and is a tireless crusader for advancing AM.
Carl puts the emphasis on people. He leads a talented team at Met-L-Flo, which produces a wide range of 3D-printed prod ucts. He also chairs the Direct Digital Manufacturing Advisory Team and moderated a panel at RAPID + TCT.
Carl puts the emphasis on people. He leads a talented team at Met-L-Flo, which produces a wide range of 3D-printed prod ucts. He also chairs the Direct Digital Manufacturing Advisory
Carl and Olga represent the spirit behind Voices AMplified. I hope you enjoy their stories.
Carl and Olga represent the spirit behind Voices AMplified.
Automotive assembly fixtures like the one shown here make heavy use of carbon fiber and 3D-printed components.
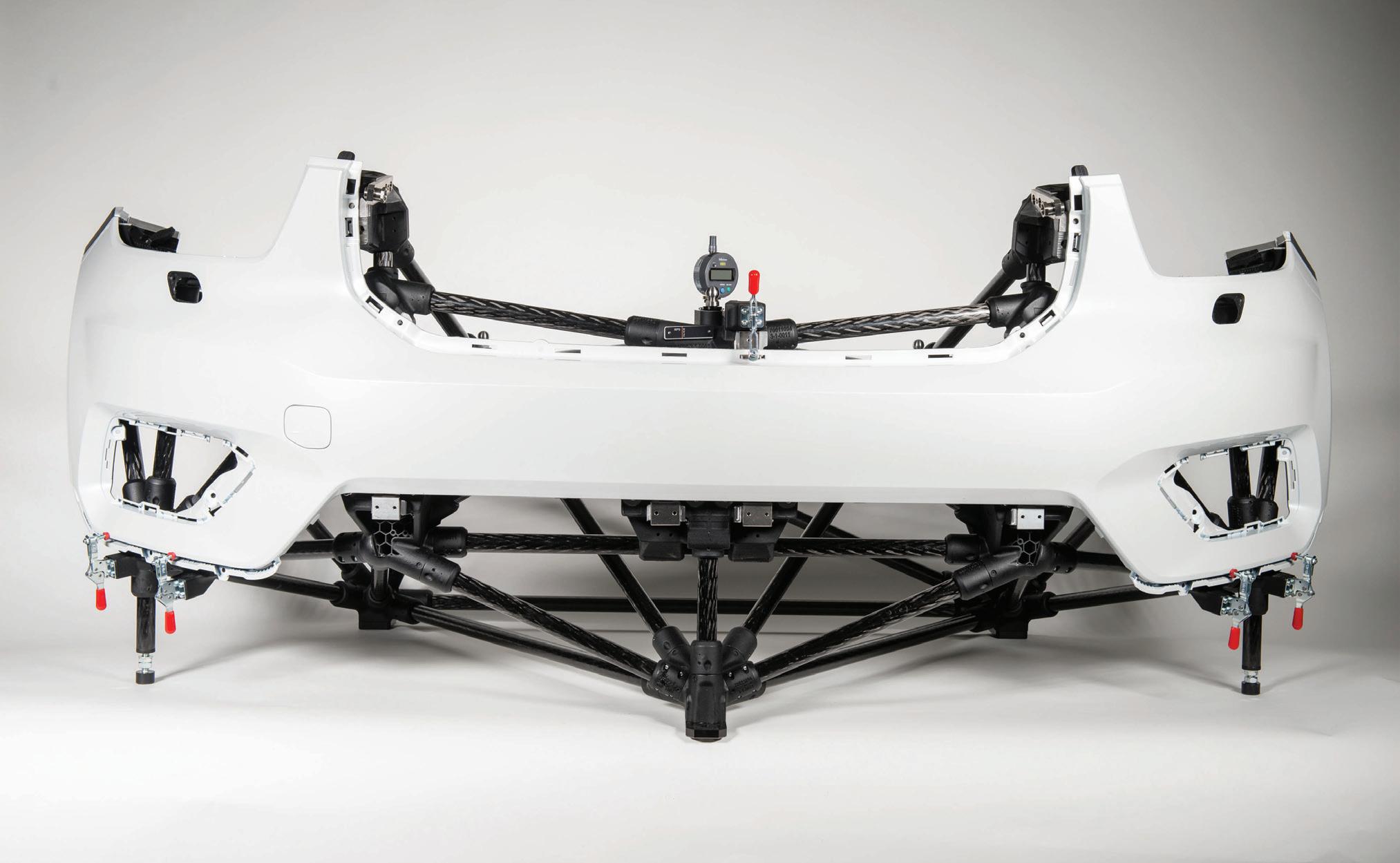
Each of these systems should talk to one another in a smart, digital way.”
on the production floor, he’s resigned to the fact that this will take time. “Anyplace it offers a unique solution, that’s where it will continue to provide its greatest value.”
From 3D-printed figurines for students to “quantum dots” and nanocomposites, Olga Ivanova is a force to be reckoned with in the AM universe

The Best Mousetrap
Paging Dr. O
Kip Hanson Contributing EditorAs Crutchfield is quick to point out, this is not some attempt to rule the 3D-printing software universe. Just the op posite. He and the Materialise team, all the way up to founder Fried Vancraen, believe that closed systems are a path to stag nation. “The world’s going digital, and because of that, manu facturing workflows—additive or otherwise—must be digital in nature, and also automated as much as possible,” Crutchfield said. “But you need to have an open architecture and an open mindset to do that. What’s more, you must be humble enough to realize that you don’t always have the best mousetrap.”
lga Ivanova has 3D-printed plenty of interest ing parts during her time in manufacturing. Rocket nozzles. Turbine blades and impel lers. Neonatal tracheostomy tubes. There are more, which we’ll get to in a moment, but to Star Wars fans, it’s the Static Dissipative Yoda that’s most intriguing.
OEnabling customers to use best-in-class technology through a brand agnostic and open software platform only drives the industry forward, Crutchfield added. Unfortunately, getting to this point has taken longer than he and others at Materialise expected. Vancraen calls it “the slow revolution,” and as someone who’s been in AM since its earliest days, he should know.
“We printed a bunch of Yoda and Groot (Guardians of the Galaxy) figurines for high school students who visited our facility recently,” said Ivanova, director of technology at Mechnano, an additive manufacturing materials
Crutchfield agrees. Though he’s equally eager to see 3D printing assume its rightful position as “just one more tool”
Holding the Line
Speaking of production floors, Crutchfield’s years with Materialise have brought him full circle. Where his initial role with the company was the support of a factory they’d opened to 3D print components for the medical industry, automakers are now among Materialise’s largest customers. Ford Motor Co., for instance, has deployed “fairly large teams” to under stand where and how AM will bring the value Crutchfield just mentioned. In fact, he recently sat alongside Ellen Lee, the leader of one such Ford team, on SME’s Additive Manufac turing Advisory Council.
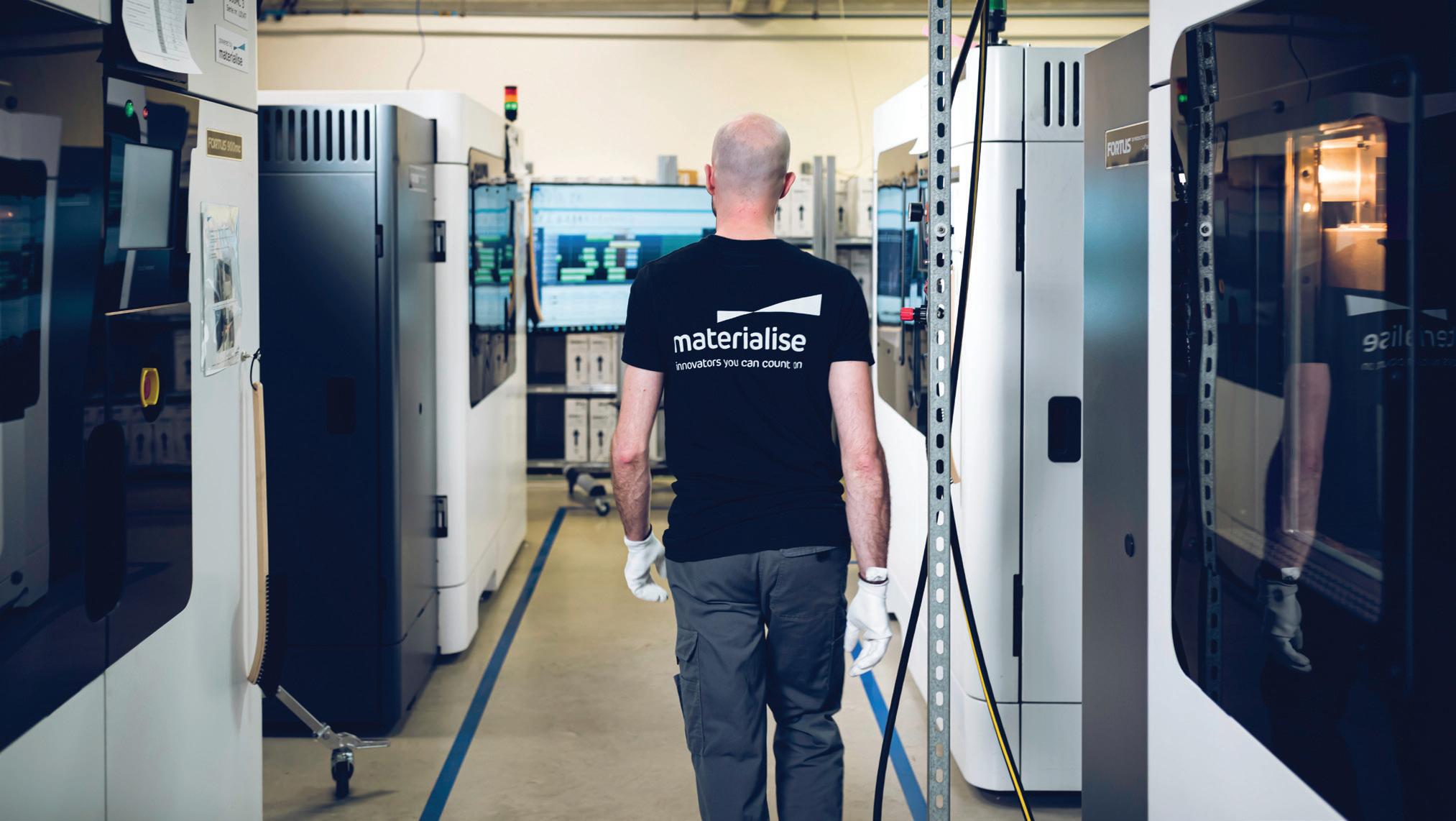
developer near Phoenix. “It’s our way of getting young people interested in additive manufacturing.”
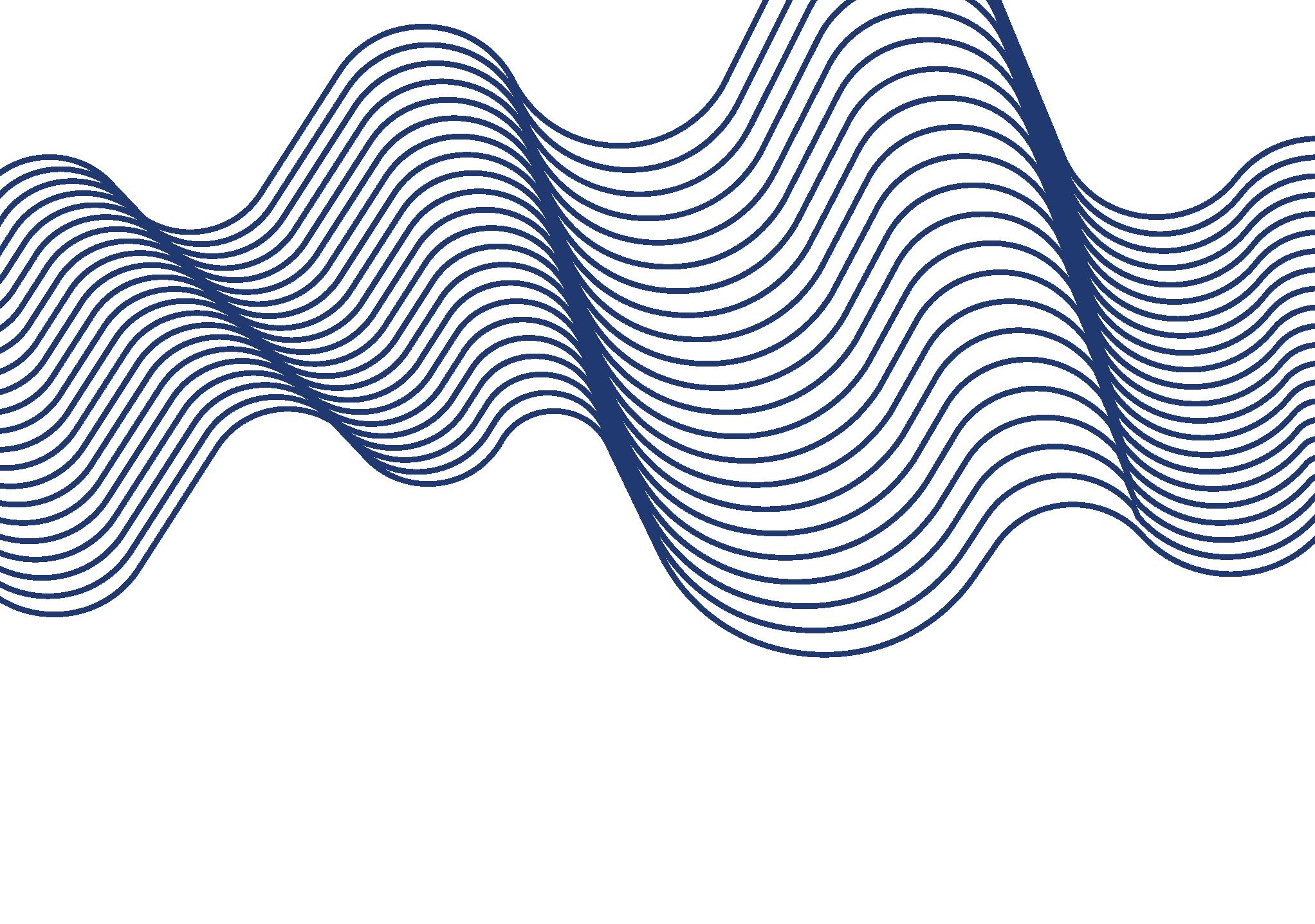
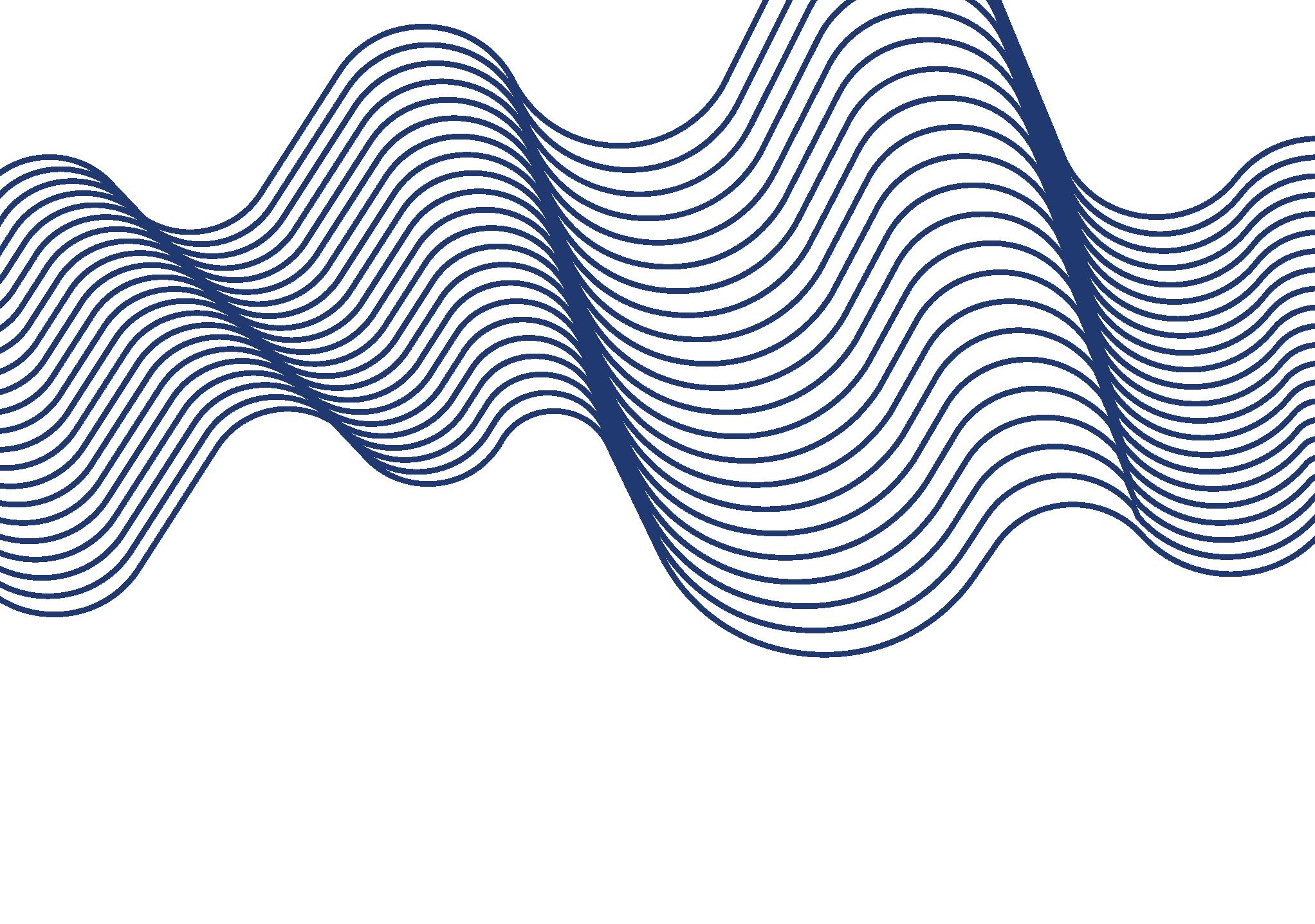
Padawan Learning
“I think a lot of folks look at automotive companies as these stodgy, set-in-their-ways manufacturers, but I can tell you from personal experience that some of them—Ford included—have extensive experience within AM,” he said. “They’re pouring resources into proofs of concept. They’re building out workflows, determining the rules of engagement, and laying the foundations for future growth. And along the way, they’re finding all kinds of small wins.”
She’s quick to point out that those educational give aways were made of a gray-colored base resin, not the more expensive static dissipative material (which is black) that she spends much of each day working with—and yes, which she occasionally uses to print Yodas that are just as resistant to electrical charge as they are to the Dark Side of the Force.
Voices AMplified
approach eliminates the inventory and tooling concerns men tioned earlier while making it possible to “print on demand,” quite possibly on a localized, point-of-need basis.
AM Community Shows Off at RAPID + TCT
AM Community Shows Off at RAPID + TCT
One area of particular interest to automakers is service parts. Crutchfield explained that, as with the aircraft and defense industries, manufacturers are required by law to assure spares availability for a set number of years. The challenge here is they either A) need to maintain minimum inventory for parts they might never sell or B) assure that the tooling necessary to make these legacy parts is available when requested.
“If automakers or any other manufacturing sector can produce spares in an additive manner and still meet form, fit, and function requirements,” Crutchfield said, “it’s definitely a win-win for all concerned.”
Suzy Marzano Senior Manager Industry Development and Technical Activities SME Suzy Marzano Senior Manager Industry Development and Technical Activities SMEThe Virtuous Circle
It’s official. Additive Manufacturing is thriving and con tinues to gain momentum with successes across di verse applications. In addition to ongoing technology advances, AM’s growth is fueled by a host of engaged companies, organizations, and dedicated professionals, all of whom are energized and passionate about developing, implementing—and sharing—new ideas and best practic es throughout a collaborative community of innovators.
Most in the AM community will immediately recognize that 3D printing is a perfect way out of this quandary, a fact that automakers have also come to realize. The question then be comes how to leverage this capability most effectively. Said Crutchfield, “No manufacturer wants to break into a produc tion line to make a handful of spares, so what better solution than to 3D print them?”
It’s official. Additive Manufacturing is thriving and con tinues to gain momentum with successes across di verse applications. In addition to ongoing technology advances, AM’s growth is fueled by a host of engaged companies, organizations, and dedicated professionals, all of whom are energized and passionate about developing, implementing—and sharing—new ideas and best practic es throughout a collaborative community of innovators.
But because the approval process for any vehicle compo nent is quite lengthy, some automakers are now evaluating dual qualification—one for the high-volume, conventionally produced parts and another for 3D-printed spares. This
3D-printing services. At RAPID + TCT, she moderated a panel discussion on 3D printing for point-of-care medical applica tions. The panel was one of several during a special town hall hosted by the Medical AM Advisory Team.
Some might wonder, “What’s taking so long? Service bureaus began 3D-printing parts before many of today’s mechanical engineers and product designers were born. Why hasn’t 3D printing become as mainstream as conventional manufacturing technologies?” But that’s not a fair criticism, Crutchfield cautioned, noting that CNC machine tools have been in use for more than 60 years and yet are still seeing significant, ongoing improvements.
3D-printing services. At RAPID + TCT, she moderated a panel discussion on 3D printing for point-of-care medical applica tions. The panel was one of several during a special town hall hosted by the Medical AM Advisory Team.
The recent RAPID + TCT conference, which was held May 17 19 in Detroit, is proof positive as to how far AM has come in recent years. The 31st edition of the industry’s mar quee event featured more than 400 exhibitors, hundreds of speakers and expert panelists, dozens of technical sessions, networking opportunities, and attendees from 38 countries.
The recent RAPID + TCT conference, which was held May 17 19 in Detroit, is proof positive as to how far AM has
The AM community took center stage throughout the show. This includes the passing of the baton in two key leadership positions. John Barnes assumed the chair of the Additive Manufacturing Technical Community Leadership Committee, succeeding Christopher Williams; and Sarah Rimini now chairs the Medical AM Advisory Committee, succeeding Amy Alexander. I’d like to thank Christopher and Amy, who provided exemplary leadership and vision during their tenures, and welcome their replacements.
John, who heads The Barnes Global Advisors and Metal Powder Works, has been involved in metal additive manufac turing throughout a distinguished career. He’s led teams that qualified the aerospace industry’s first series production met al AM parts, and developed a pilot metal production facility.
As senior manager of Ricoh’s Healthcare Center of Excellence, Sarah is developing a curriculum for the com pany’s Learning Institute that focuses on medical managed
Similar analogies exist for plastic-injection molding machines, stamping, and forming presses, as well as metal

Other highlights included the winners of the 2022 SME Additive Manufacturing Community Awards: Slade Gard ner, founder of Big Metal Additive (Industry Achievement); VELO3D and IMI Critical Engineering (Aubin AM Case Study); and Virginia Tech students Daniel Chirvasuta, Nathanael High, Matthew Martin, Benjamin Nguyen, Omkar Shinde, and
Other highlights included the winners of the 2022 SME Additive Manufacturing Community Awards: Slade Gard ner, founder of Big Metal Additive (Industry Achievement); VELO3D and IMI Critical Engineering (Aubin AM Case Study); and Virginia Tech students Daniel Chirvasuta, Nathanael High, Matthew Martin, Benjamin Nguyen, Omkar Shinde, and Nicolas Tomanelli (Digital Manufacturing Challenge).
To help foster the next generation of innovators, the SME Education Foundation’s Bright Minds Program welcomed nearly 1,000 middle and high school students to RAPID + TCT. There also was a special networking lunch for young profes sionals and a Career Forum Panel. The initiative is led by Ellen Lee and Jennifer Coyne, who are both advisors on the Additive Manufacturing Technical Community Leadership Committee.
To help foster the next generation of innovators, the SME Education Foundation’s Bright Minds Program welcomed nearly 1,000 middle and high school students to RAPID + TCT. There also was a special networking lunch for young profes sionals and a Career Forum Panel. The initiative is led by Ellen Lee and Jennifer Coyne, who are both advisors on the Additive Manufacturing Technical Community Leadership Committee.
SME Media also interviewed dozens of AM leaders during RAPID + TCT as part of its Voices AMplified initiative that showcases the people behind the technology. This month’s Voices AMplified report profiles two such visionaries: Olga Ivanova and Carl Dekker. Known as “Dr. O,” Olga has worked on innovative projects for the medical and defense industries,
SME Media also interviewed dozens of AM leaders during RAPID + TCT as part of its Voices AMplified initiative that showcases the people behind the technology. This month’s Voices AMplified report profiles two such visionaries: Olga Ivanova and Carl Dekker. Known as “Dr. O,” Olga has worked on innovative projects for the medical and defense industries, and is a tireless crusader for advancing AM.
Carl puts the emphasis on people. He leads a talented team at Met-L-Flo, which produces a wide range of 3D-printed prod ucts. He also chairs the Direct Digital Manufacturing Advisory Team and moderated a panel at RAPID + TCT.
Carl puts the emphasis on people. He leads a talented team at Met-L-Flo, which produces a wide range of 3D-printed prod ucts. He also chairs the Direct Digital Manufacturing Advisory

Carl and Olga represent the spirit behind Voices AMplified. I hope you enjoy their stories.
Carl and Olga represent the spirit behind Voices AMplified.
casting equipment. The latter has enjoyed far greater pro ductivity thanks to AM—remember, one of the first commer cial uses for stereolithography in the early ’90s was making 3D-printed patterns used in investment casting. In addition, many sand-casting shops are now using a form of binder
jetting to produce molds and cores from digital models. “Compared to traditional manufacturing technologies, AM is barely out of its toddler years,” Crutchfield said.
Whatever the relative maturity, efficient additive manufacturing requires a robust workflow, he reiterated, adding that the lack of which has made 3D printing more cumbersome and therefore slowed its adoption to some extent. Achieving this, howev er, means that everyone must work together, from the material providers to the equipment manufacturers.
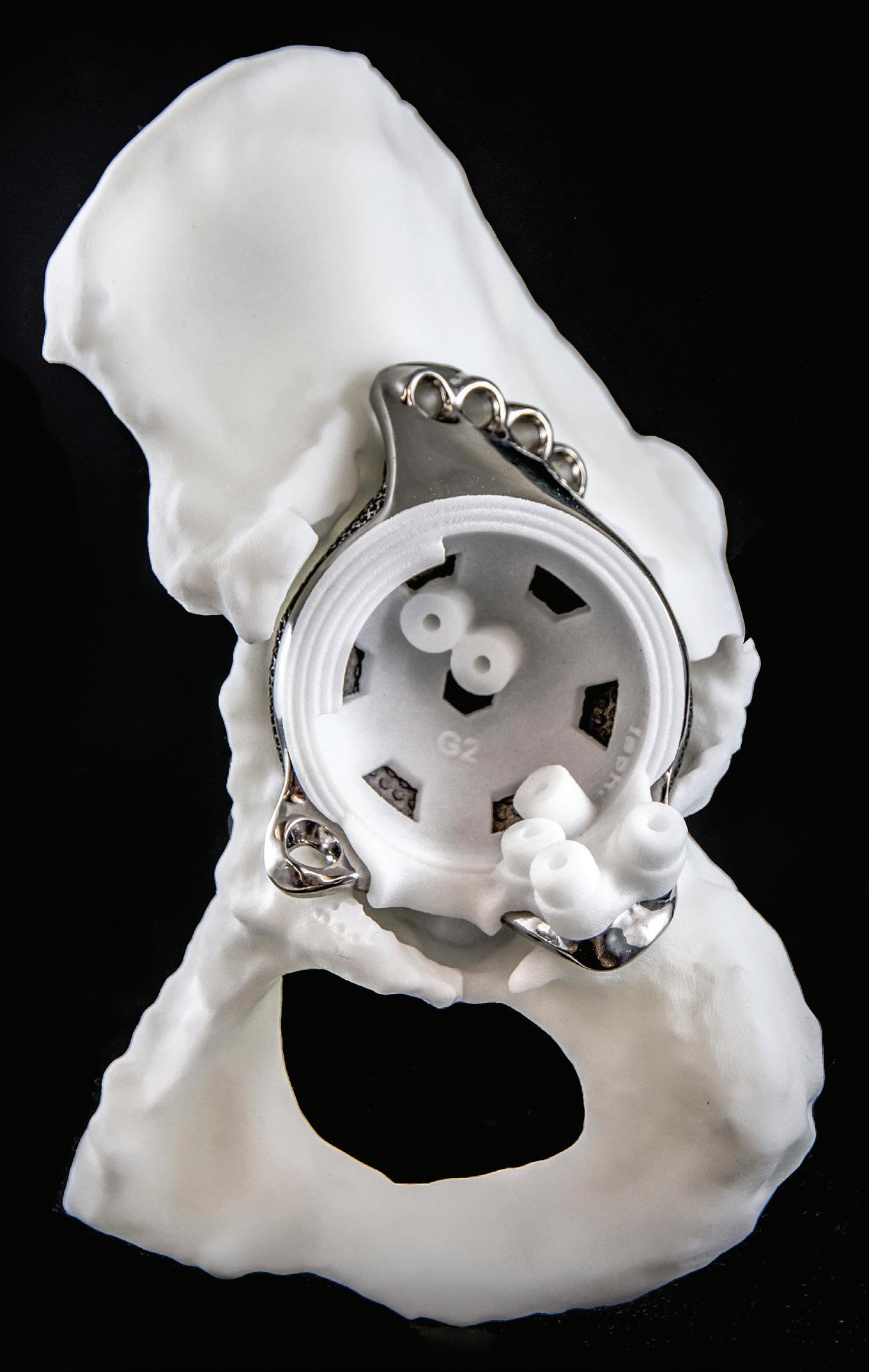
“There aren’t any interoperability standards yet, and all of the 3D printers pretty much march to the beat of their own drum in terms of data formats and communication protocols,” he said. “As such, people must often rely on brute force to get hardware and software to work together.”
A similar statement applies to feed stocks—even though they might have the same chemical characteristics and powder morphology, titanium from one supplier is different from titanium from another supplier, a factor that directly influences 3D-printing processes.

Paging
Kip Hanson Contributing EditorOlers. Neonatal tracheostomy tubes. There are more, which we’ll get to in a moment, but to Star Wars fans, it’s the Static Dissipative Yoda that’s most intriguing.
“We printed a bunch of Yoda and Groot (Guardians of the Galaxy) figurines for high school students who visited our facility recently,” said Ivanova, director of technology at Mechnano, an additive manufacturing materials
“This is what I mean by AM still being in its infancy, in that there are so many challenges yet to conquer,” Crutchfield concluded. “But with every high-value application or unique engineering challenge solved by additive, it gains new ground.
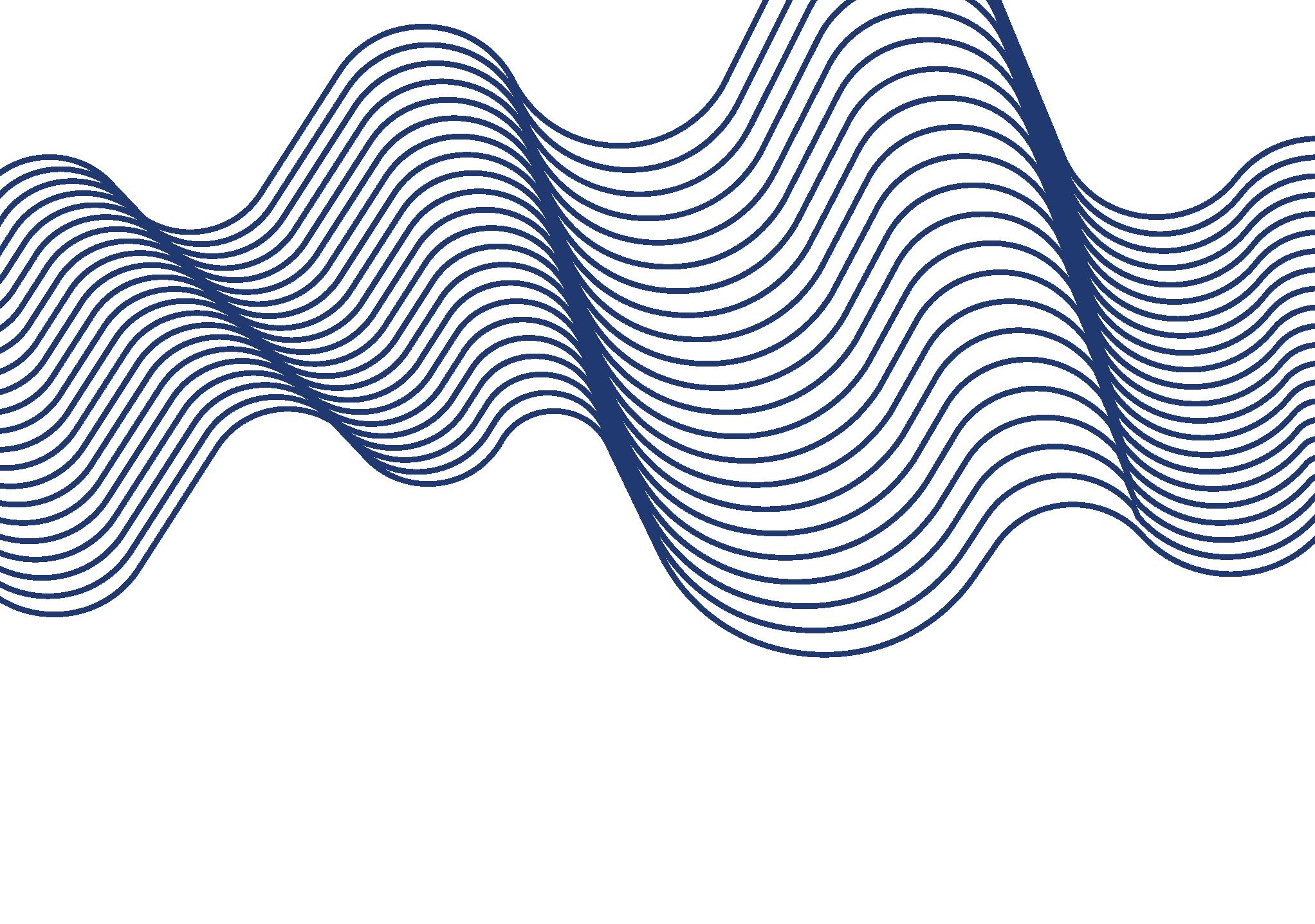
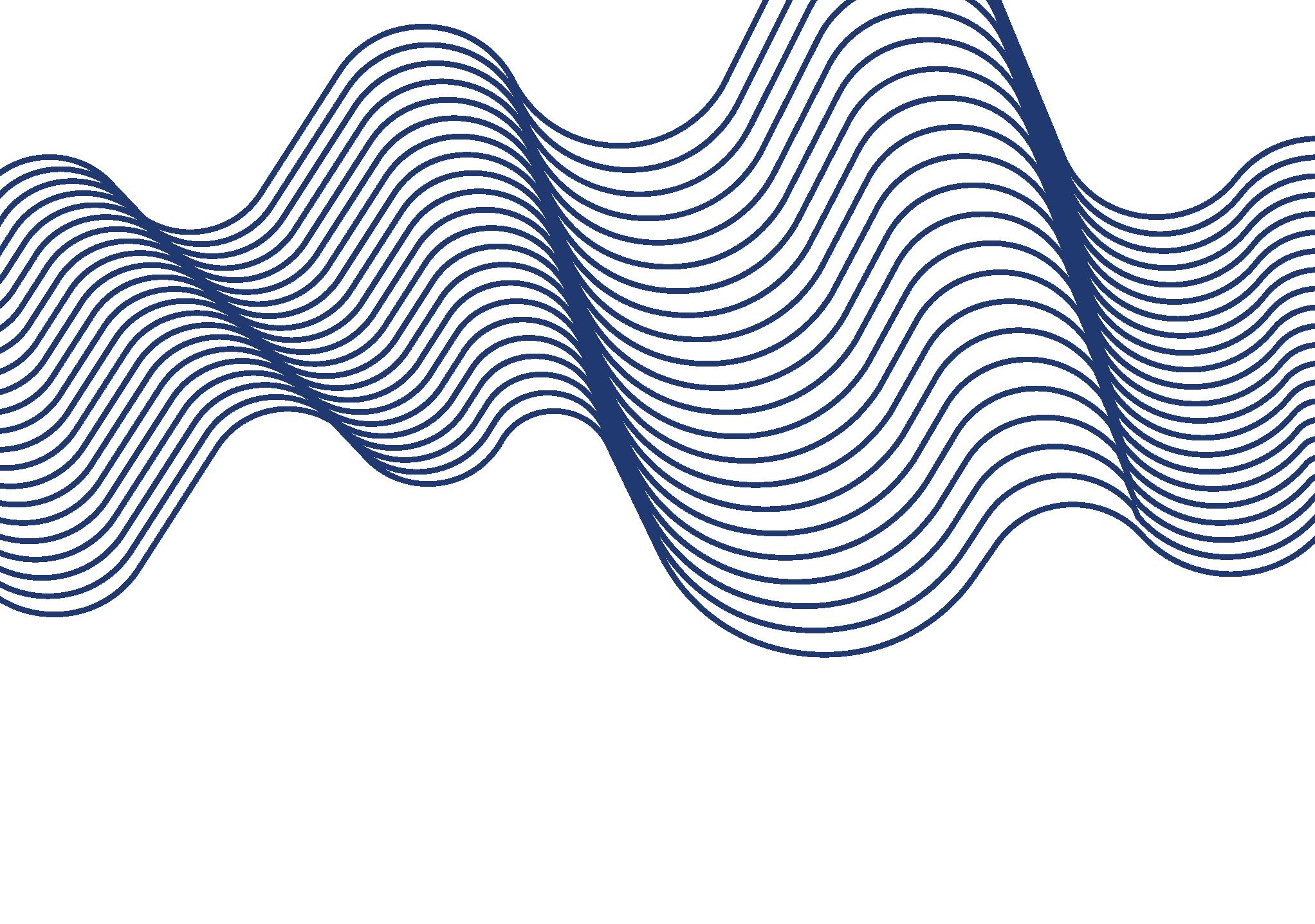
developer near Phoenix. “It’s our way of getting young people interested in additive manufacturing.”
OEMs invest more into research and development, the industry makes additional efforts at standardization, and there’s greater market pressure to reduce operating costs.
“We’ve seen this trend over the past five years or so, and I expect it will only intensify going forward. I like to think of it as a virtuous cycle that will contin uously strengthen AM’s place in the manufacturing industry.”
She’s quick to point out that those educational give aways were made of a gray-colored base resin, not the more expensive static dissipative material (which is black) that she spends much of each day working with—and yes, which she occasionally uses to print Yodas that are just as resistant to electrical charge as they are to the Dark Side of the Force.
October 2022 | sme.org 39
AM Community Shows Off at RAPID + TCT
IIt’s official. Additive Manufacturing is thriving and con tinues to gain momentum with successes across di verse applications. In addition to ongoing technology advances, AM’s growth is fueled by a host of engaged companies, organizations, and dedicated professionals, all of whom are energized and passionate about developing, implementing—and sharing—new ideas and best practic es throughout a collaborative community of innovators.
Suzy Marzano Senior Manager Industry Development and Technical ActivitiesSheku Kamara stands at an open house before the 3D printers named Bart, Dave, and Marie, speaking with a visiting student about additive manufacturing.
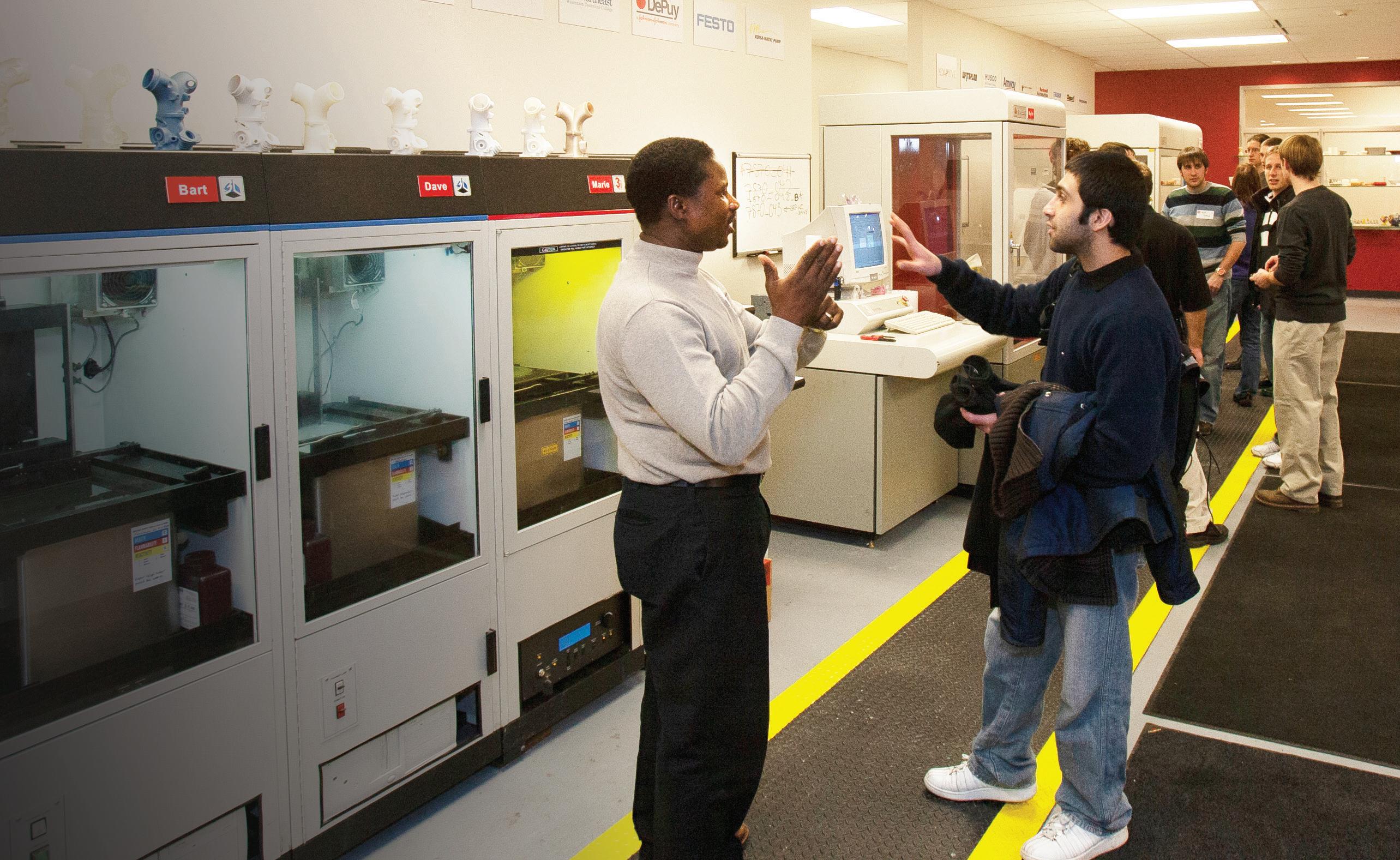
The recent RAPID + TCT conference, which was held May 17 19 in Detroit, is proof positive as to how far AM has come in recent years. The 31st edition of the industry’s mar quee event featured more than 400 exhibitors, hundreds of speakers and expert panelists, dozens of technical sessions, networking opportunities, and attendees from 38 countries.
speakers and expert panelists, dozens of technical sessions, networking opportunities, and attendees from 38 countries.
The AM community took center stage throughout the show. This includes the passing of the baton in two key leadership positions. John Barnes assumed the chair of the Additive Manufacturing Technical Community Leadership Committee, succeeding Christopher Williams; and Sarah Rimini now chairs the Medical AM Advisory Committee, succeeding Amy Alexander. I’d like to thank Christopher and Amy, who provided exemplary leadership and vision during their tenures, and welcome their replacements.
The AM community took center stage throughout the show. This includes the passing of the baton in two key leadership positions. John Barnes assumed the chair of the Additive Manufacturing Technical Community Leadership Committee, succeeding Christopher Williams; and Sarah Rimini now chairs the Medical AM Advisory Committee, succeeding Amy Alexander. I’d like to thank Christopher and Amy, who provided exemplary leadership and vision during their tenures, and welcome their replacements.
Talking to the Dean
Kip Hanson Contributing EditorJohn, who heads The Barnes Global Advisors and Metal Powder Works, has been involved in metal additive manufac turing throughout a distinguished career. He’s led teams that qualified the aerospace industry’s first series production met al AM parts, and developed a pilot metal production facility.
John, who heads The Barnes Global Advisors and Metal Powder Works, has been involved in metal additive manufac turing throughout a distinguished career. He’s led teams that qualified the aerospace industry’s first series production met al AM parts, and developed a pilot metal production facility.
As senior manager of Ricoh’s Healthcare Center of Excellence, Sarah is developing a curriculum for the com pany’s Learning Institute that focuses on medical managed
As senior manager of Ricoh’s Healthcare Center of Excellence, Sarah is developing a curriculum for the com pany’s Learning Institute that focuses on medical managed
Sheku Kamara came to the United States in 1996. Having studied mechanical engineering at Fourah Bay College, a constituent of the University of Sierra Leone, he’d left his troubled homeland several years earlier and moved to Germany with a scholarship through the German Academic Exchange Service, or Deutscher Akademischer Austauschdienst (DAAD). And when the chance came to attend the Milwaukee School of Engineering (MSOE) in Wisconsin as a graduate stu dent, Kamara jumped at it. He’s been there ever since.
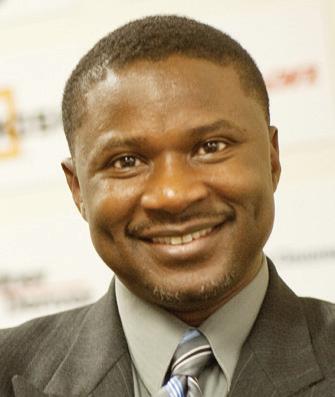
Other highlights included the winners of the 2022 SME ner, founder of Big Metal Additive (Industry Achievement); VELO3D and IMI Critical Engineering (Aubin AM Case Study); and Virginia Tech students Daniel Chirvasuta, Nathanael High, Matthew Martin, Benjamin Nguyen, Omkar Shinde, and
Other highlights included the winners of the 2022 SME Additive Manufacturing Community Awards: Slade Gard ner, founder of Big Metal Additive (Industry Achievement); VELO3D and IMI Critical Engineering (Aubin AM Case Study); and Virginia Tech students Daniel Chirvasuta, Nathanael High, Matthew Martin, Benjamin Nguyen, Omkar Shinde, and Nicolas Tomanelli (Digital Manufacturing Challenge).
To help foster the next generation of innovators, the SME Education Foundation’s Bright Minds Program welcomed nearly 1,000 middle and high school students to RAPID + TCT. There also was a special networking lunch for young profes sionals and a Career Forum Panel. The initiative is led by Ellen Lee and Jennifer Coyne, who are both advisors on the Additive Manufacturing Technical Community Leadership Committee.
To help foster the next generation of innovators, the SME Education Foundation’s Bright Minds Program welcomed nearly 1,000 middle and high school students to RAPID + TCT. There also was a special networking lunch for young profes sionals and a Career Forum Panel. The initiative is led by Ellen Lee and Jennifer Coyne, who are both advisors on the Additive Manufacturing Technical Community Leadership Committee.
SME Media also interviewed dozens of AM leaders during RAPID + TCT as part of its Voices AMplified initiative that showcases the people behind the technology. This month’s Voices AMplified report profiles two such visionaries: Olga Ivanova and Carl Dekker. Known as “Dr. O,” Olga has worked on innovative projects for the medical and defense industries, and is a tireless crusader for advancing AM.
SME Media also interviewed dozens of AM leaders during RAPID + TCT as part of its Voices AMplified initiative that showcases the people behind the technology. This month’s Voices AMplified report profiles two such visionaries: Olga Ivanova and Carl Dekker. Known as “Dr. O,” Olga has worked on innovative projects for the medical and defense industries, and is a tireless crusader for advancing AM.
SME TechnicalCarl puts the emphasis on people. He leads a talented team at Met-L-Flo, which produces a wide range of 3D-printed prod ucts. He also chairs the Direct Digital Manufacturing Advisory Team and moderated a panel at RAPID + TCT.
Carl puts the emphasis on people. He leads a talented team at Met-L-Flo, which produces a wide range of 3D-printed prod ucts. He also chairs the Direct Digital Manufacturing Advisory Team and moderated a panel at RAPID + TCT.
funding from the NSF (National Science Foundation) and had a true rapid prototyping center,” Kamara said. “At that time, folks might have had experience with SLA (sereolithography) or FDM (fused depositon modeling), but they rarely knew multiple technologies. MSOE allowed students to work with all of the leading types of 3D-printing equipment and it still does. It was a great opportunity.”
Carl and Olga represent the spirit behind Voices AMplified. I hope you enjoy their stories.
Carl and Olga represent the spirit behind Voices AMplified. I hope you enjoy their stories.
It was so great that Kamara stayed on after earning his master’s degree. Within two years, he was responsible for

“They were one of the first schools to adopt additive manufacturing with
Looking back on a long career of learning, sharing, and always trying to do your best.Sheku Kamara Advisor Dean of Applied Research at the Milwaukee School of Engineering
the additive manufacturing lab, and today is MSOE’s Dean of Applied Research.
Kamara explained that MSOE is a private university whose focus is experiential learning. As a result, the school has more labs than classrooms, giving students ample time to work with their hands. MSOE also stays quite close to the AM industry and regional businesses, an attribute that is “pretty unique.” From the very beginning, Kamara said, “we were looking for ways to work with manufacturers and help them figure out how they can leverage additive in their operations. Many of the companies went on to buy their own systems.”
No Experience Necessary
Aside from a drive to learn and a newly discovered love of 3D printing, Kamara had another important thing going for him in those early days. Ironically, it was a quality that few of us would brag about: no manufacturing experience. “I encountered people who knew all about machining or plastic injection molding who would tell me, ‘No, you can’t do that, or that will never work.’ But I had no preconceived notions, so it was only natural for me to put forth solutions they might never consider.”
Manufacturing Body of Knowledge (AMBOK), as well as the training materials needed to bring others up to speed more quickly, thereby expediting AM’s further development. The effort was (and remains) a collaboration between MSOE, America Makes, SME’s Tooling U-SME, the National Coalition of Advanced Technology Centers (NCATC), and Technician Education in Additive Manufacturing & Materials (TEAMM), which together form the Additive Manufacturing Leadership Initiative (AMLI).
The group released its first version of AMBOK in 2006 and, as noted, continues to build on its work. “AM is con stantly evolving,” he said. “For example, there was no auto mated post-processing back then. 3D-printed parts were all finished by hand. Nor were there hybrid CNC machine tools, which combine additive and subtractive processes on a sin gle platform.” He laughed: “Where does that fit into a book on 3D printing? That’s why we have to go back and revise it every few years, because, from a standards perspective, the constant state of flux can be quite challenging to keep up with.”
Before his promotion to Dean, Kamara spent nearly two decades proposing such solutions, some unorthodox, others not. He supported dozens of companies and several hundred students during their additive manufacturing journeys, first as MSOE’s manager of operations and then as the director of its Rapid Prototyping Consortium.
Paging Dr. O
Through it all, his greatest professional joy has been teaching others about AM, in many cases helping them to unlearn what they already knew about conventional manu facturing so they can more effectively leverage 3D printing’s unconventional capabilities.
Kip Hanson Contributing EditorOKamara noted that the aerospace and medical industries were early adopters of 3D printing because it makes cus tomization easier and provides greater design flexibility than traditional manufacturing methods. But what manufacturers haven’t yet wrapped their collective heads around is all the untapped potential that AM brings to the table, if only users had the necessary tools and sufficient knowledge.
lga Ivanova has 3D-printed plenty of interest ing parts during her time in manufacturing. Rocket nozzles. Turbine blades and impel lers. Neonatal tracheostomy tubes. There are more, which we’ll get to in a moment, but to Star Wars fans, it’s the Static Dissipative Yoda that’s most intriguing.
The Body of Knowledge
“We printed a bunch of Yoda and Groot (Guardians of the Galaxy) figurines for high school students who visited our facility recently,” said Ivanova, director of technology at Mechnano, an additive manufacturing materials
To meet this last need, Kamara and MSOE have worked with other industry leaders to develop the Additive
Despite these challenges, AMBOK is a vital tool. It has provided manufacturers with a technology roadmap and, just as importantly, given students a benchmark by which to measure themselves: Tooling U’s Fundamentals of Additive Manufacturing Certificate. “I taught the initial classes for that certificate and still teach the review course. It’s something I greatly enjoy doing,” Kamara said.
From 3D-printed figurines for students to “quantum dots” and nanocomposites, Olga Ivanova is a force to be reckoned with in the AM universe
He apparently enjoys writing, also. Together with con sultant and former MSOE professor Kathy S. Faggiani., Kamara recently published the Fundamentals of Additive Manufacturing for the Practitioner, part of the Additive Manufacturing Skills in Practice series, “Additive manufac turing is my passion.”
Olga Ivanova Master networker RAPID + TCT Director of Technology MechnanoImpossible Possibilities
developer near Phoenix. “It’s our way of getting young people interested in additive manufacturing.”
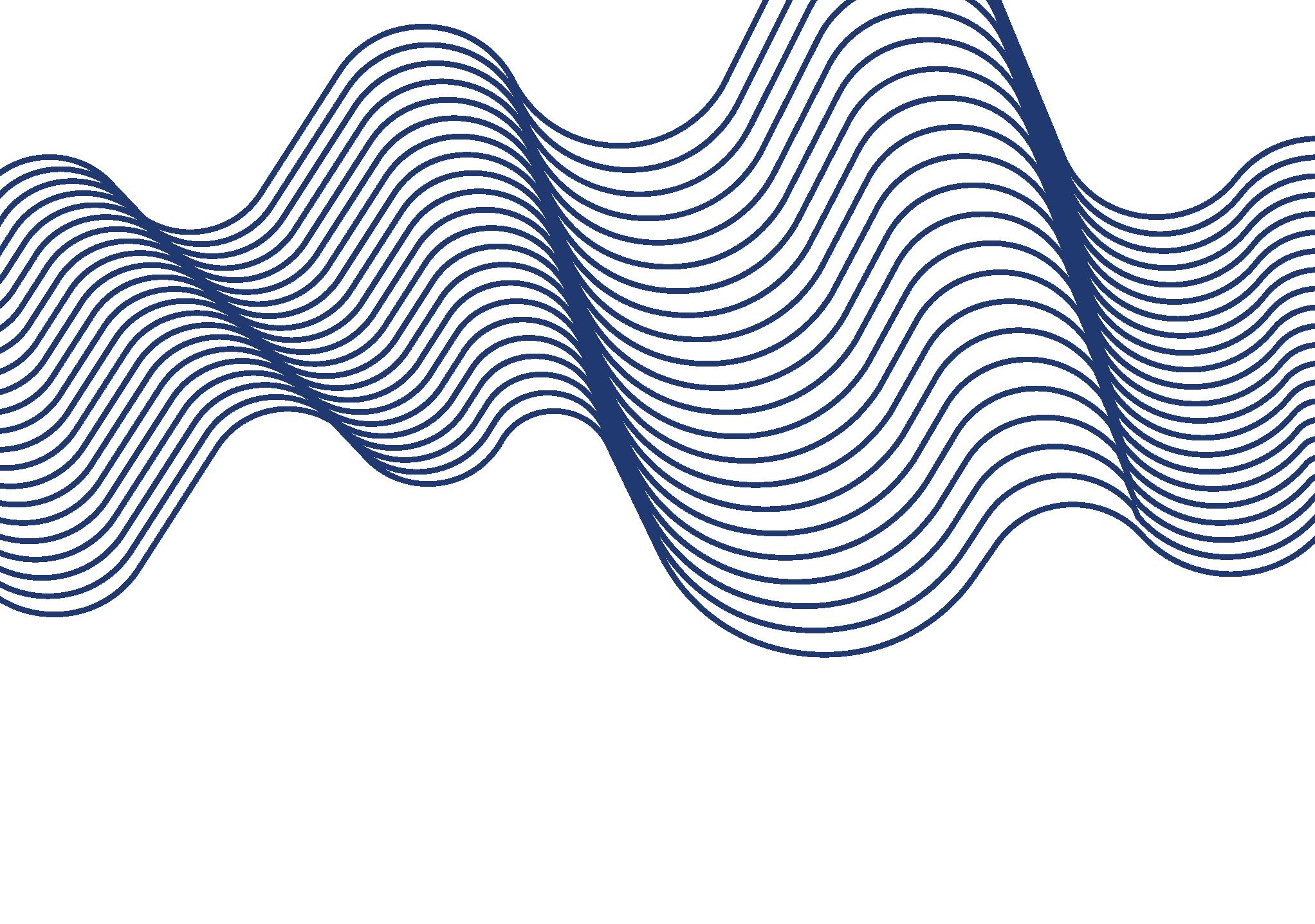
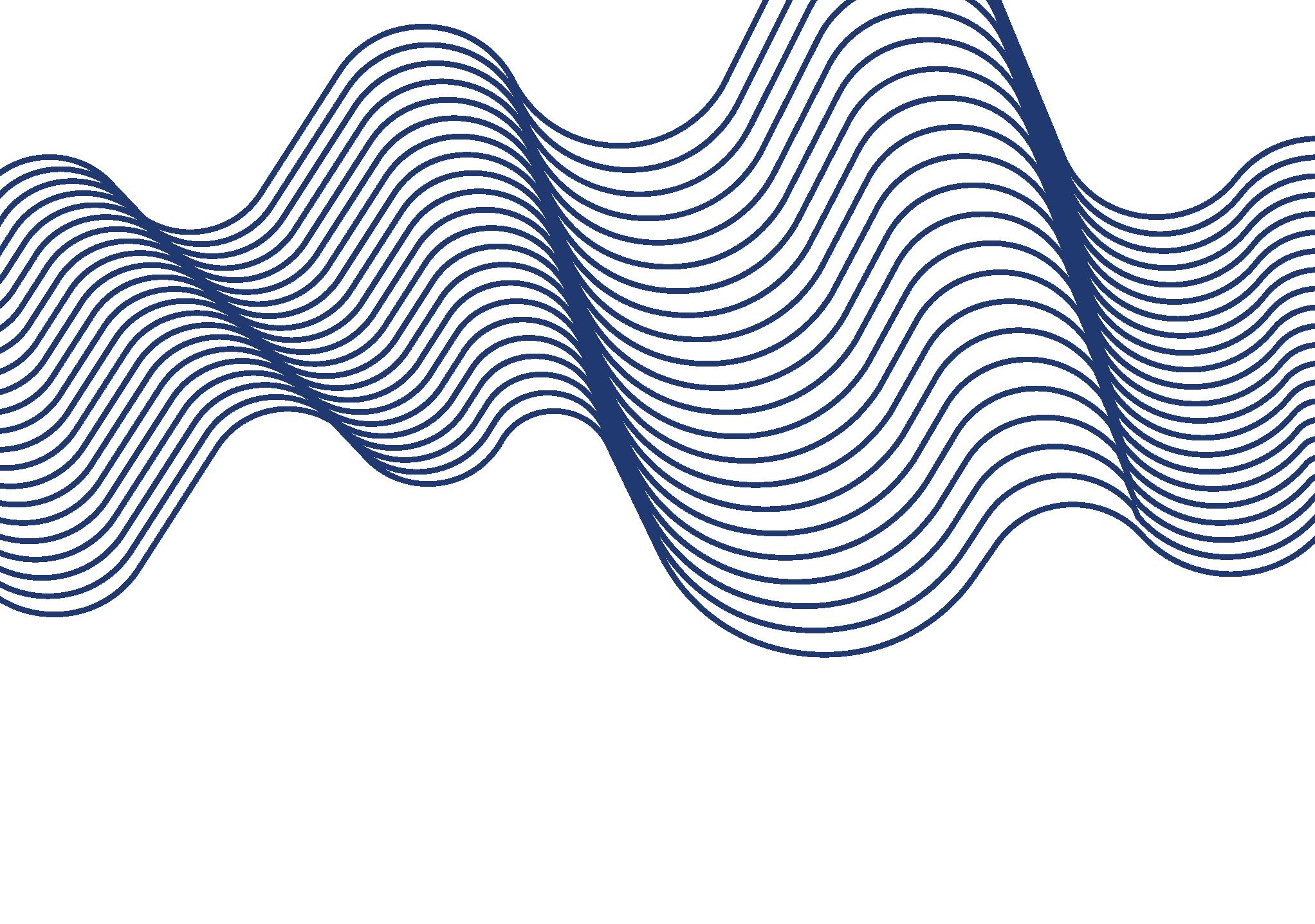
Padawan Learning
Passionate or not, Kamara suggested that we’re just getting started with 3D printing. “People often ask me, ‘What are the limitations of this technology?’ My response is that we simply don’t know. Not only are the materials and equipment constantly evolving, but we can’t yet design for its many possibilities.”
He held up his cell phone to illustrate this last point. “If I were to print this or any other object, it would have fairly con sistent material properties throughout. That’s a good thing. But what would happen if I changed the properties in this
She’s quick to point out that those educational give aways were made of a gray-colored base resin, not the more expensive static dissipative material (which is black) that she spends much of each day working with—and yes, which she occasionally uses to print Yodas that are just as resistant to electrical charge as they are to the Dark Side of the Force.

Voices
plified

section here by adjusting the laser speed or power? I don’t know, because there’s currently no software that allows me to design for this, even though the machine could physically do it.”
AM Community Shows Off at RAPID + TCT
But why would someone want to do such a thing? After all, one of the central tenets of product design is consistency and predictability—won’t capabilities like these lead to a Wild West-like world in which nothing is certain?
“Take the Nylon feedstock used in powder bed fusion printers. If I lower the laser energy during the build process, I can make a part that’s porous, almost like a sieve. But by putting a lot of energy into the Nylon, I can seal it up tight. Combining these two sintering techniques with the right polymer might produce a composite-like material that is both exceedingly strong yet porous and lightweight.”
AM Community Shows Off at RAPID + TCT
Suzy Marzano Senior Manager Industry Development and Technical Activities SME Suzy Marzano Senior Manager Industry Development and Technical Activities SMEIt’s official. Additive Manufacturing is thriving and con tinues to gain momentum with successes across di verse applications. In addition to ongoing technology advances, AM’s growth is fueled by a host of engaged companies, organizations, and dedicated professionals, all of whom are energized and passionate about developing, implementing—and sharing—new ideas and best practic es throughout a collaborative community of innovators.
It’s official. Additive Manufacturing is thriving and con tinues to gain momentum with successes across di verse applications. In addition to ongoing technology advances, AM’s growth is fueled by a host of engaged companies, organizations, and dedicated professionals, all of whom are energized and passionate about developing, implementing—and sharing—new ideas and best practic es throughout a collaborative community of innovators.
Not so fast. As a counter example, Kamara cited a Boe ing 787, an aircraft he flies in frequently. Its wings are com posed of an aluminum structure covered with carbon fiber and epoxy resin. None of these materials is terribly strong on its own, but when laid down in alternating, precisely oriented sheets and fastened in a strategic manner, they’re able to carry an aircraft weighing more than half a million pounds. By mastering 3D printing’s innate ability to alter material properties on the fly, he predicts, manufacturers will one day be able to “program” their wares with specific desirable characteristics.
It also creates other opportunities. For instance, Kamara continued, “automotive engineers struggle to devise failure points in their vehicle designs—in other words, if my car crashes, I want it to crumble in a certain way. If you can pre cisely control and adjust your material properties throughout different regions of a 3D-printed part, functionality like this might become very easy to deliver.”
3D-printing services. At RAPID + TCT, she moderated a panel discussion on 3D printing for point-of-care medical applica tions. The panel was one of several during a special town hall hosted by the Medical AM Advisory Team.
3D-printing services. At RAPID + TCT, she moderated a panel discussion on 3D printing for point-of-care medical applica tions. The panel was one of several during a special town hall hosted by the Medical AM Advisory Team.
A Helping Hand
The recent RAPID + TCT conference, which was held May 17 19 in Detroit, is proof positive as to how far AM has come in recent years. The 31st edition of the industry’s mar
The recent RAPID + TCT conference, which was held May 17 19 in Detroit, is proof positive as to how far AM has
When not writing books or dreaming up lofty goals for additive manufacturing, Kamara donates his time to other manufacturing-related causes. Most recently, he served on
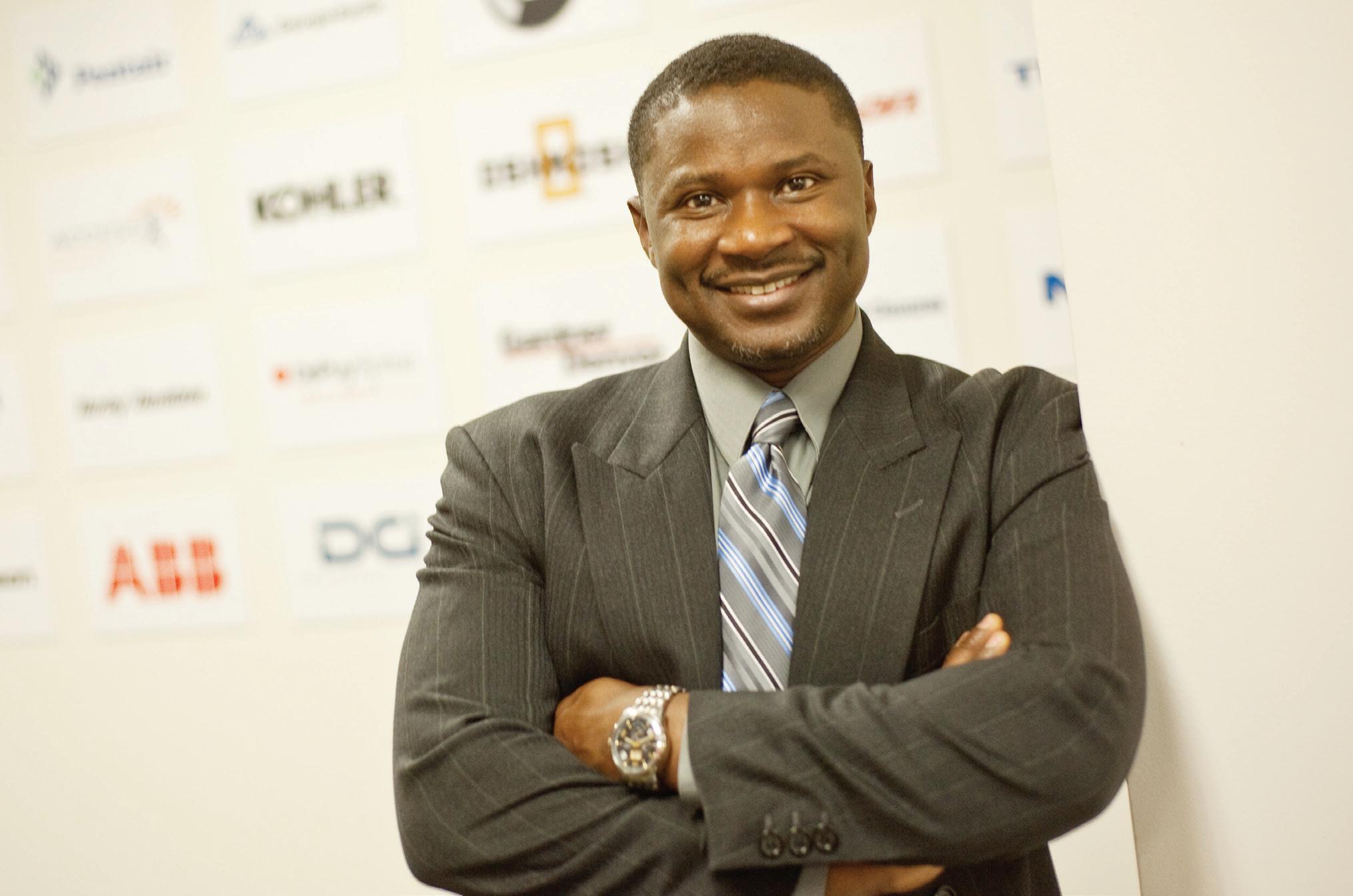
Other highlights included the winners of the 2022 SME Additive Manufacturing Community Awards: Slade Gard ner, founder of Big Metal Additive (Industry Achievement); VELO3D and IMI Critical Engineering (Aubin AM Case Study); and Virginia Tech students Daniel Chirvasuta, Nathanael High, Matthew Martin, Benjamin Nguyen, Omkar Shinde, and
Other highlights included the winners of the 2022 SME Additive Manufacturing Community Awards: Slade Gard ner, founder of Big Metal Additive (Industry Achievement); VELO3D and IMI Critical Engineering (Aubin AM Case Study); and Virginia Tech students Daniel Chirvasuta, Nathanael High, Matthew Martin, Benjamin Nguyen, Omkar Shinde, and Nicolas Tomanelli (Digital Manufacturing Challenge).
To help foster the next generation of innovators, the SME Education Foundation’s Bright Minds Program welcomed nearly 1,000 middle and high school students to RAPID + TCT. There also was a special networking lunch for young profes sionals and a Career Forum Panel. The initiative is led by Ellen Lee and Jennifer Coyne, who are both advisors on the Additive Manufacturing Technical Community Leadership Committee.
To help foster the next generation of innovators, the SME Education Foundation’s Bright Minds Program welcomed nearly 1,000 middle and high school students to RAPID + TCT. There also was a special networking lunch for young profes sionals and a Career Forum Panel. The initiative is led by Ellen Lee and Jennifer Coyne, who are both advisors on the Additive Manufacturing Technical Community Leadership Committee.
SME Media also interviewed dozens of AM leaders during RAPID + TCT as part of its Voices AMplified initiative that showcases the people behind the technology. This month’s Voices AMplified report profiles two such visionaries: Olga Ivanova and Carl Dekker. Known as “Dr. O,” Olga has worked on innovative projects for the medical and defense industries,
SME Media also interviewed dozens of AM leaders during RAPID + TCT as part of its Voices AMplified initiative that showcases the people behind the technology. This month’s Voices AMplified report profiles two such visionaries: Olga Ivanova and Carl Dekker. Known as “Dr. O,” Olga has worked on innovative projects for the medical and defense industries,
Carl puts the emphasis on people. He leads a talented team at Met-L-Flo, which produces a wide range of 3D-printed prod ucts. He also chairs the Direct Digital Manufacturing Advisory
Carl puts the emphasis on people. He leads a talented team at Met-L-Flo, which produces a wide range of 3D-printed prod ucts. He also chairs the Direct Digital Manufacturing Advisory
Carl and Olga represent the spirit behind Voices AMplified.
Carl and Olga represent the spirit behind Voices AMplified.
This manifold is just one of many parts that Sheku Kamara has 3D printed during his decades at MSOE, first as a student and now as dean.
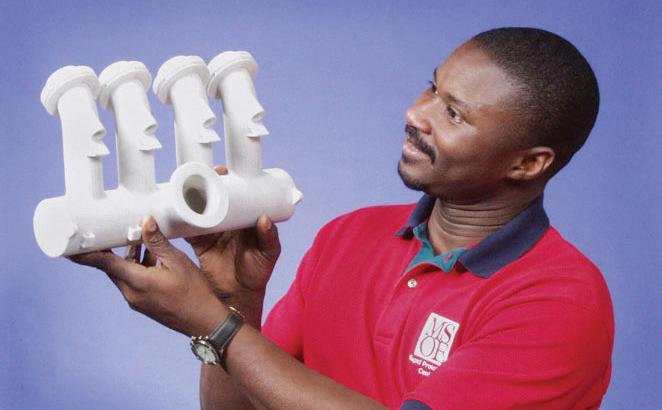
From 3D-printed figurines for students to “quantum dots” and nanocomposites, Olga Ivanova is a force to be reckoned with in the AM universe
the boards of the Wisconsin Center for Manufacturing and Productivity (WCMP), a manufacturing extension partnership (MEP) center sponsored by the National Institute of Stan dards and Technology (NIST), and the Wisconsin Manufactur ing Extension Partnership (WMEP) for a total of nine years.
Paging Dr. O
Kip Hanson Contributing EditorAgain, the goal was to promote AM’s successful adoption, this time with small to medium enterprises. In one notable case, Kamara helped a medical device company develop a pre-surgical planning process to aid surgeons in hip re placement surgery. For more than 18 years, the process has helped thousands of patients with custom implants recuper ate faster. “This is a great example of what companies can do with a little guidance and the time to investigate alternative technologies,” he said. “There are just so many opportunities like this out there.”
Olga Ivanova has 3D-printed plenty of interest ing parts during her time in manufacturing. Rocket nozzles. Turbine blades and impel lers. Neonatal tracheostomy tubes. There are more, which we’ll get to in a moment, but to Star Wars fans, it’s the Static Dissipative Yoda that’s most intriguing.
“We printed a bunch of Yoda and Groot (Guardians of the Galaxy) figurines for high school students who visited our facility recently,” said Ivanova, director of technology at Mechnano, an additive manufacturing materials
Kamara has also has served as a RAPID + TCT Event Advisor since 2004 and was selected to join SME’s Additive Manufacturing Technical Community Leadership Committee last year. And with funding from the NSF, he and MSOE col league Subha Kumpaty provided an opportunity for several
U.S. students to conduct research focused on rapid proto typing for biomedical applications and the linking of materials science with cutting-edge bioengineering for practical appli cations at the Non-Ferrous Materials Technology Develop ment Center (NFTDC) in Hyderabad, India.

He also keeps an eye on his homeland. He’s donated sev eral 3D printers to the Directorate of Science, Technology and Innovation and the Milton Margai College of Education and Technology (MMCET) for them “to wrap their heads around” and was involved in starting an additive manufacturing group in Nigeria.
developer near Phoenix. “It’s our way of getting young people interested in additive manufacturing.”
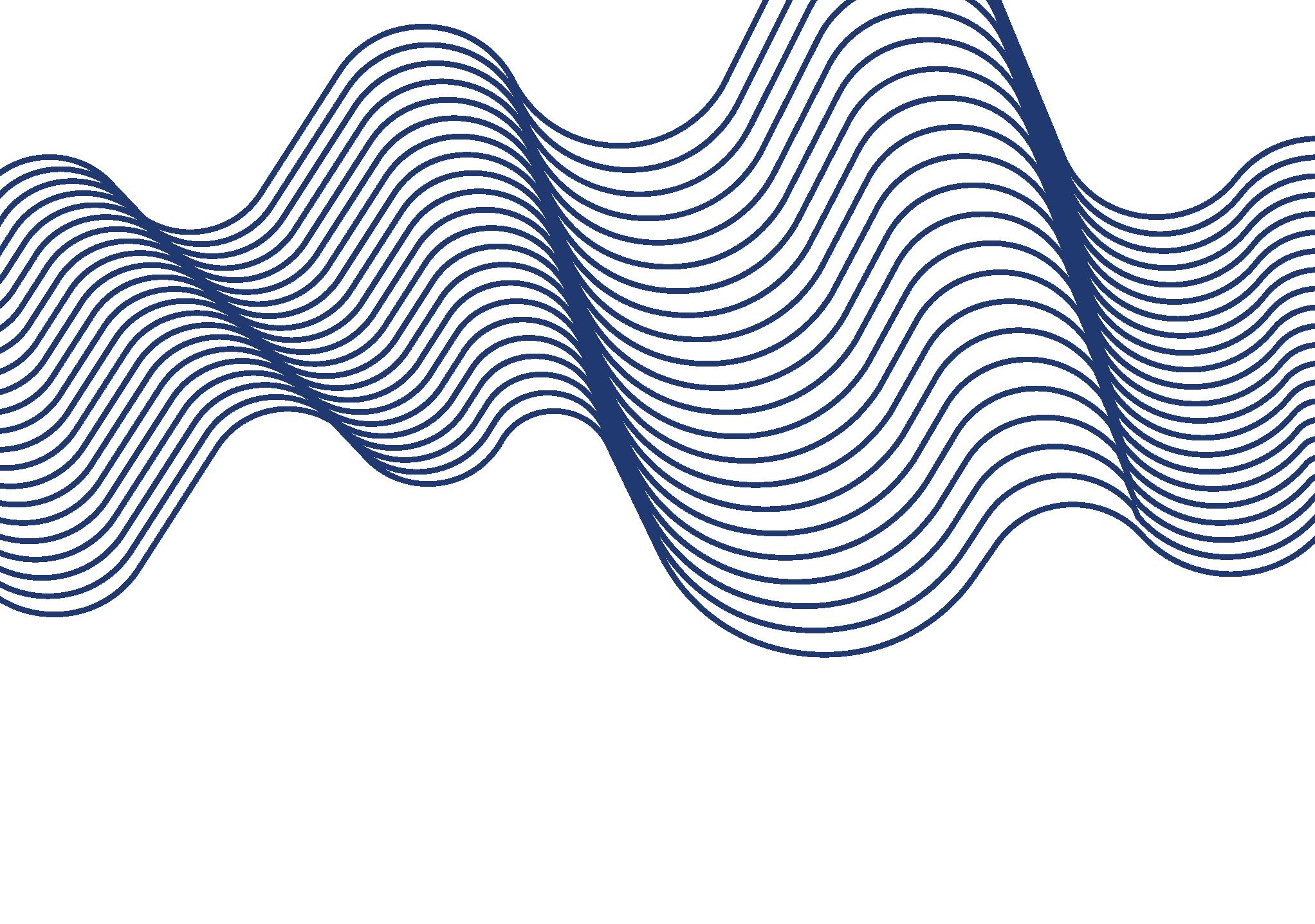
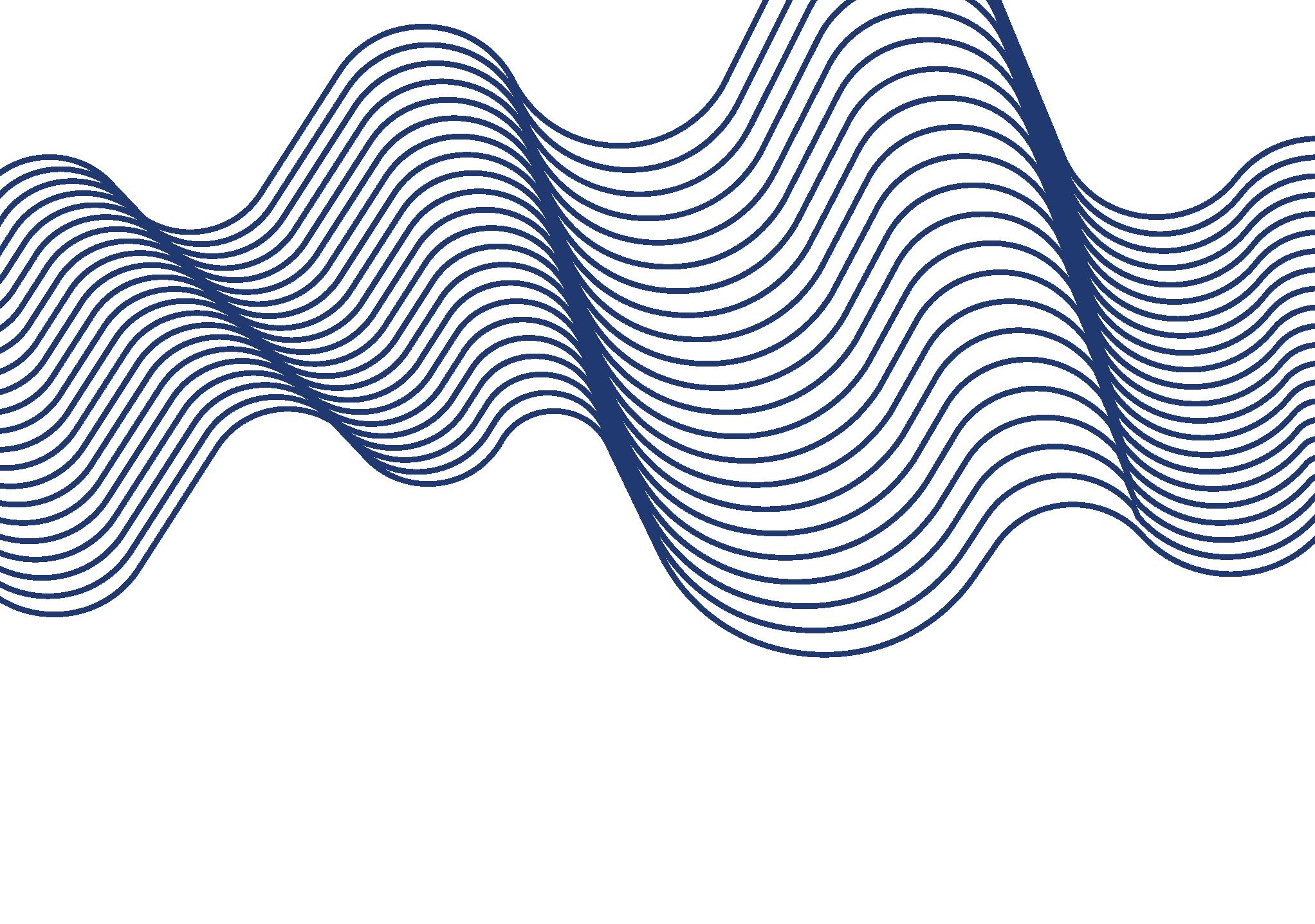
Padawan Learning
“Life in Sierra Leone has gotten better since I left but it remains a very difficult place,” Kamara said. “A few years ago, some friends and I helped put together a dialysis clinic there. The country did not have one, and people would have to travel to other countries for treatment, which at that time meant moving away. Now, some of them have a chance to stay home. So it’s a struggle, but I’m old enough to know that what’s most important in life is to do your best, always tell the truth, and try to help others. That’s all you can do.”
She’s quick to point out that those educational give aways were made of a gray-colored base resin, not the more expensive static dissipative material (which is black) that she spends much of each day working with—and yes, which she occasionally uses to print Yodas that are just as resistant to electrical charge as they are to the Dark Side of the Force.
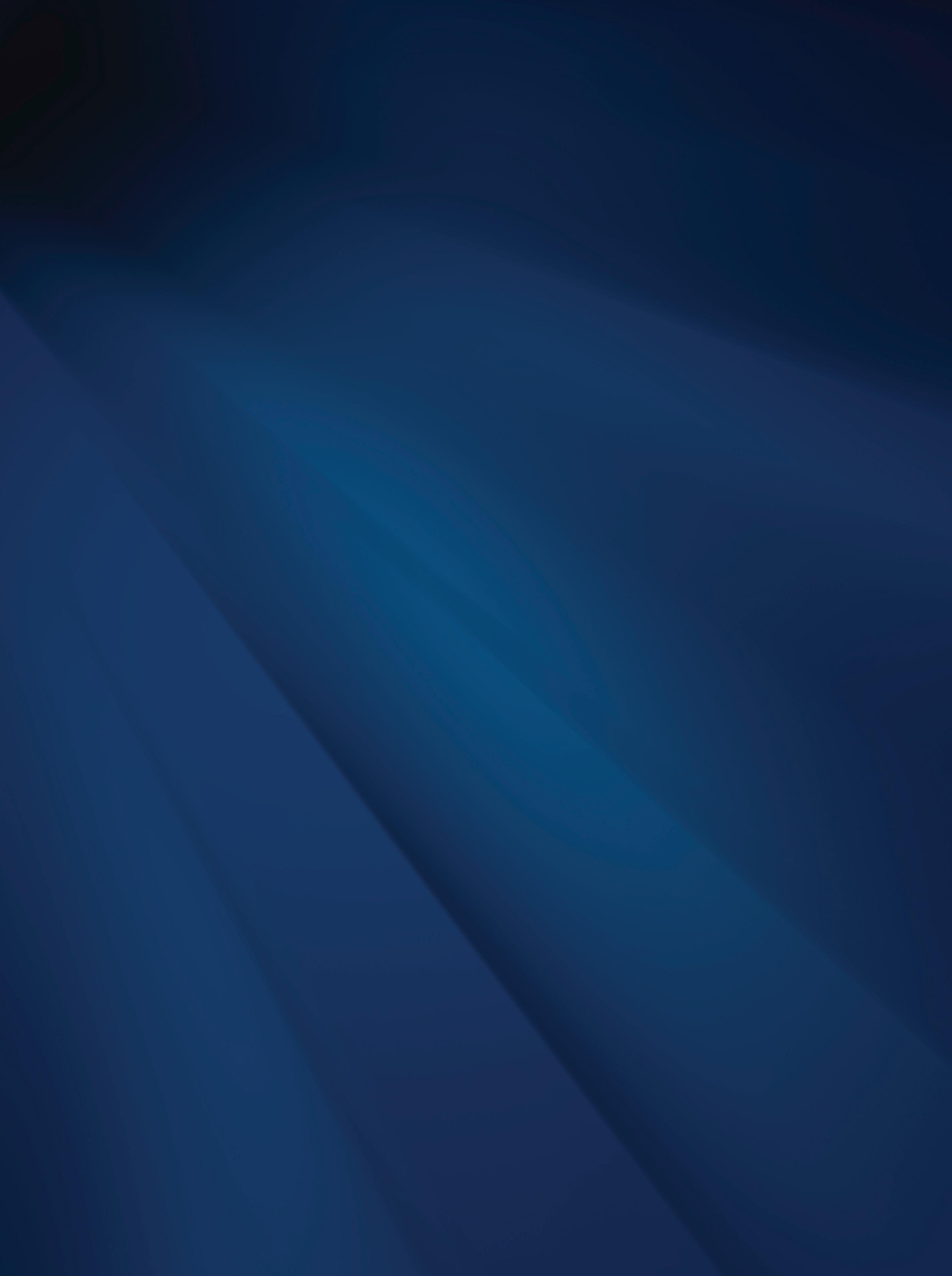
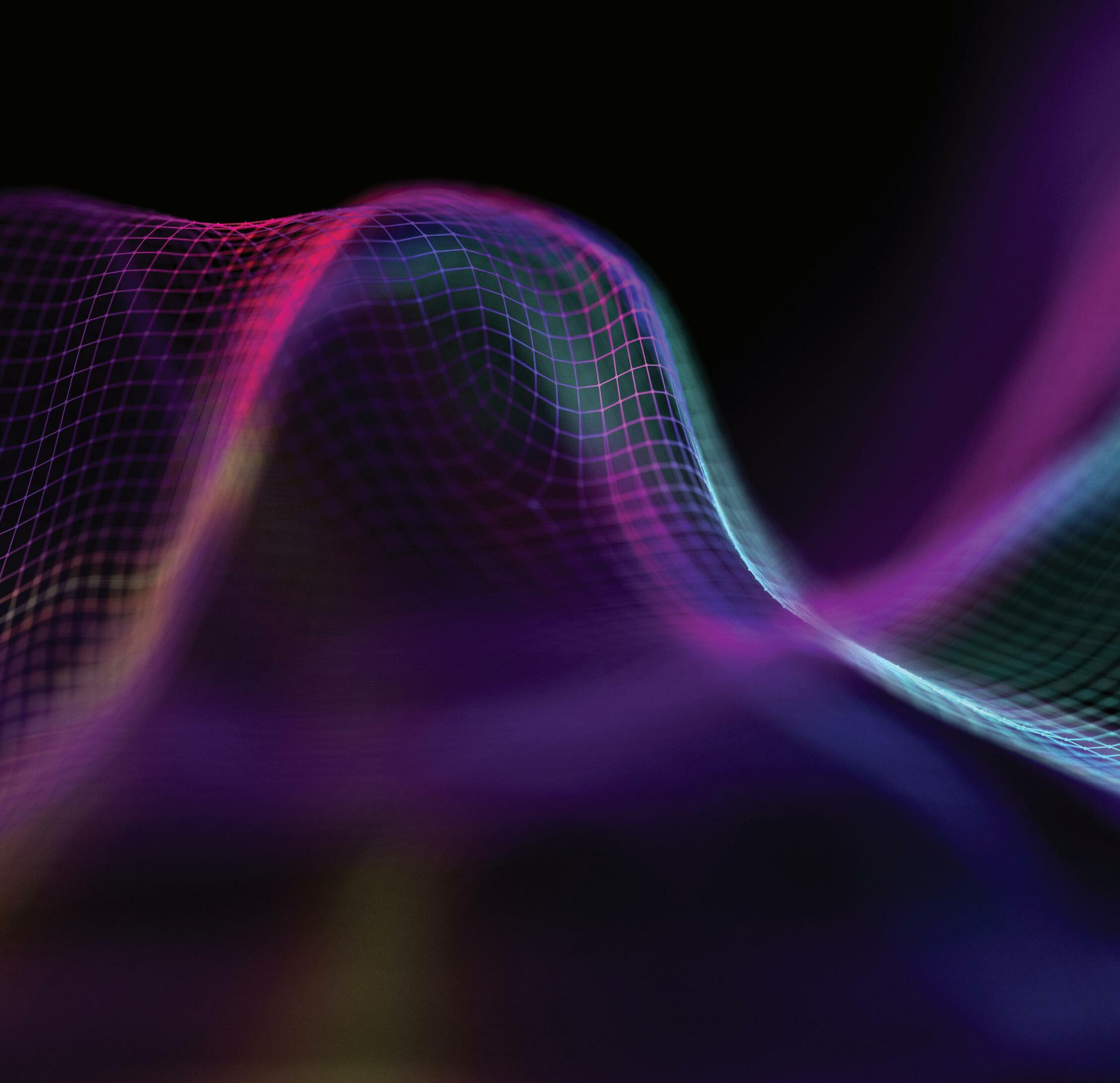
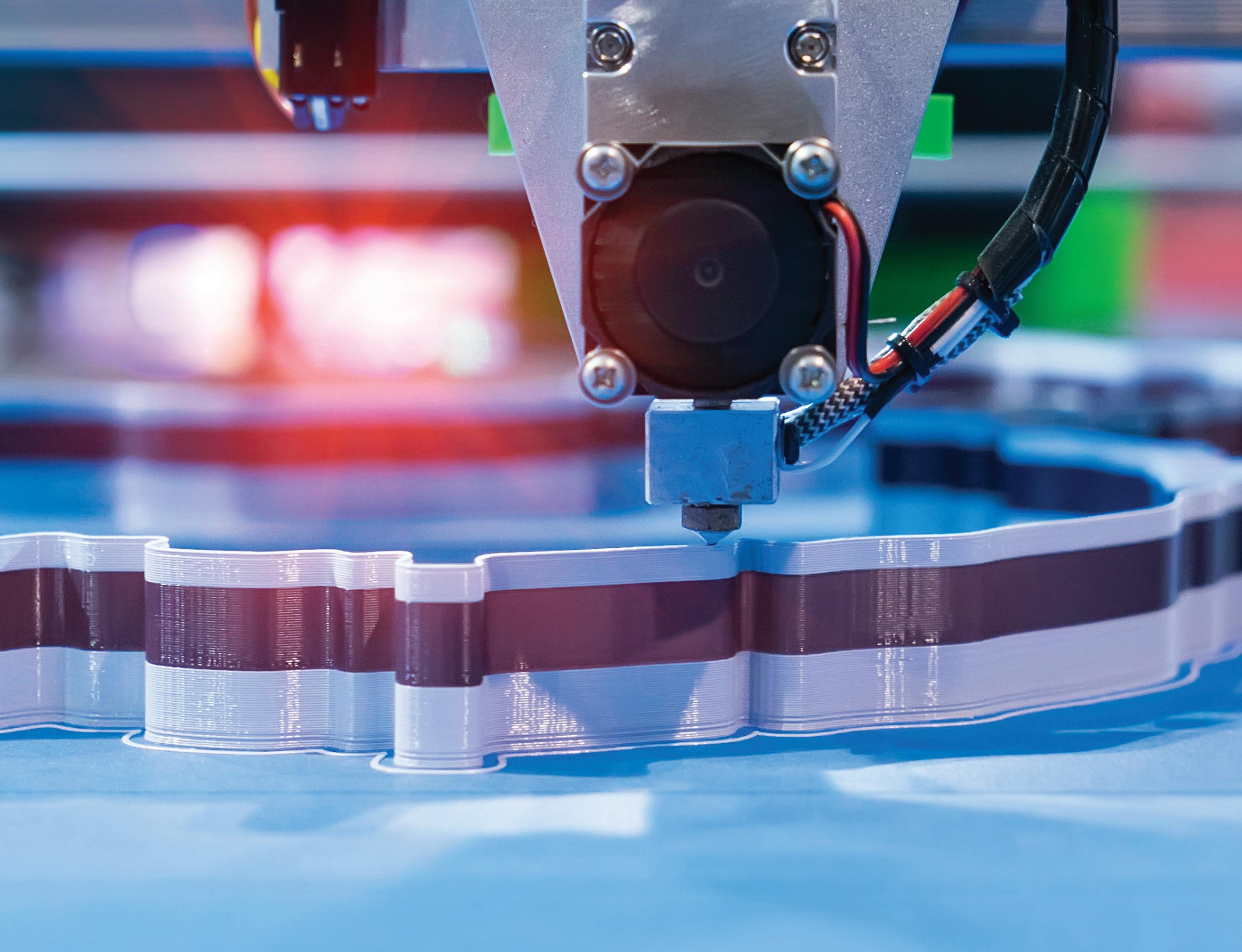
DUCATION WITH ULTIMAKER E
Oliver Johnson speaks to UltiMaker CEO Nadav Goshen about the new MakerBot SKETCH Large
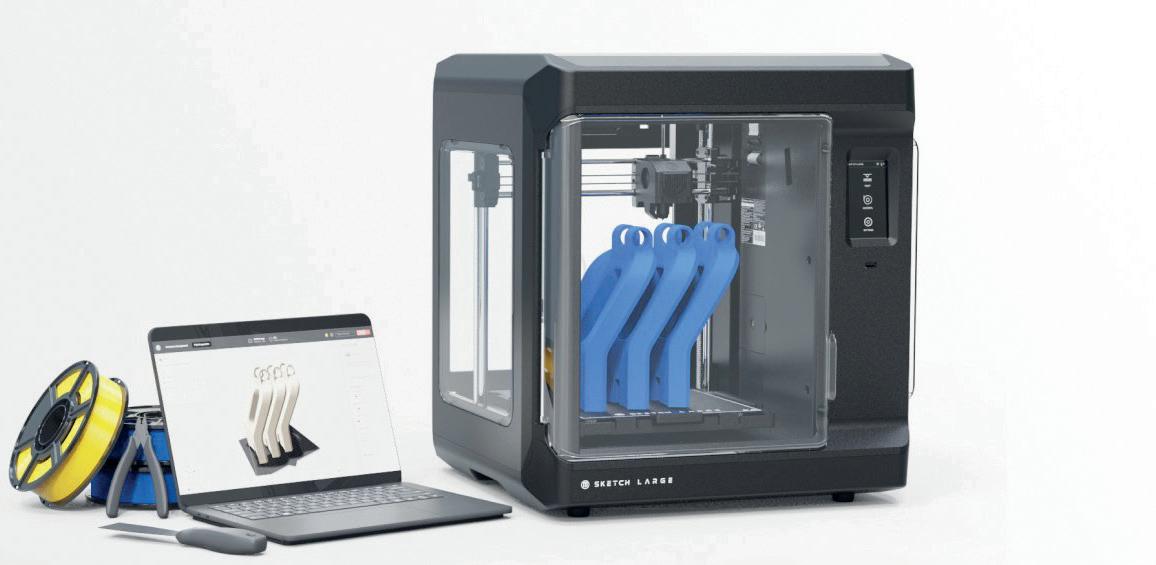
The merger between two leaders in desktop 3D printing, MakerBot and Ultimaker, was completed in September, promising to ‘fuel innovation and expansion into new markets’. Just a month later, the newly formed UltiMaker announced the launch of the MakerBot SKETCH Large, the first system to be released under the new brand.
The latest addition to the MakerBot SKETCH range of education-focused 3D printers is available as a single unit or two-unit classroom package. The machine includes a fully enclosed chamber, particulate filter, a heated and flexible build plate, touchscreen capabilities, onboard camera, materials sensors, and WIFI and USB capabilities. It also features a larger build plate compared to previous editions, hence the name, which can fit up to ten student projects in a single build, according to UltiMaker.
Nadav Goshen, CEO of MakerBot for close to six years, and now CEO of UltiMaker, recently spoke to TCT about the launch of the new printer, the importance of introducing additive manufacturing (AM) to those in education, and the future under the new brand.
Goshen said: “The build volume is significantly bigger, and with that comes the ability to service full classrooms with one printer, I think that’s the main advantage that we are going to bring to the market. That connects to our combined software workflow that we have, and all of our other materials. With the student
submission forums, with our cloud offering, we can really build a package that is serving one classroom. The SKETCH Large is a continuation of our previous generation, the SKETCH, which we launched a few years ago, and since then we have seen a great adoption of this platform in schools.”
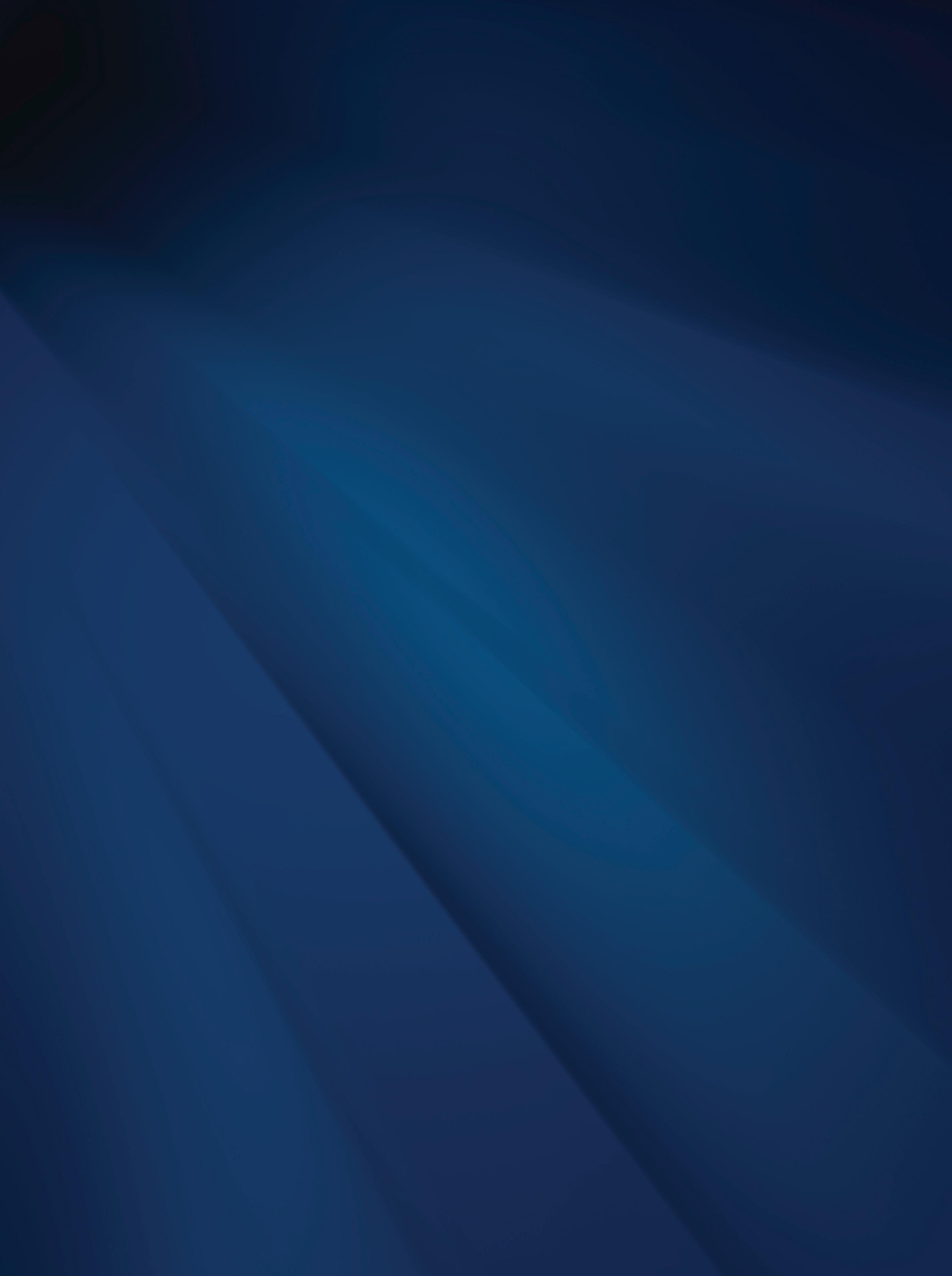
Goshen stated that after receiving feedback from educators about the previous models, it became clear that teachers would prefer to have one large printer that could service a whole classroom, rather than two separate machines.
The new system is compatible with MakerBot TOUGH materials, and arrives with three spools of MakerBot PLA. It also benefits from MakerBot’s 3D printing education ecosystem including its CloudPrint 3D printing software, which can be connected to Google Classroom, and allows users to slice and prepare prints from a browser.
A key aim of UltiMaker is to target STEM education. To make a real impact, Goshen believes the combination of the SKETCH printers, the curriculum and the cloud
workflow is making it easier for teachers to integrate 3D printing.
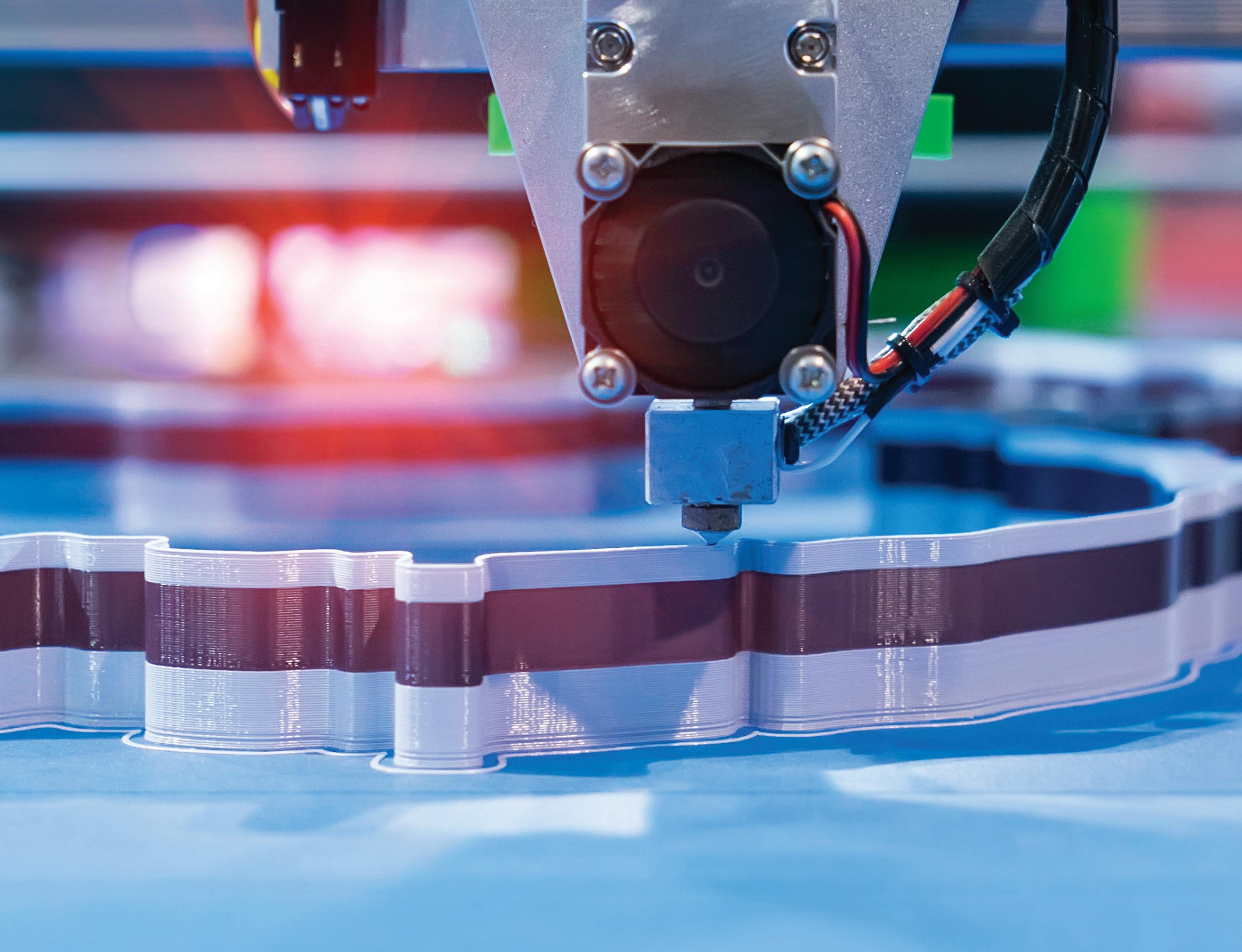
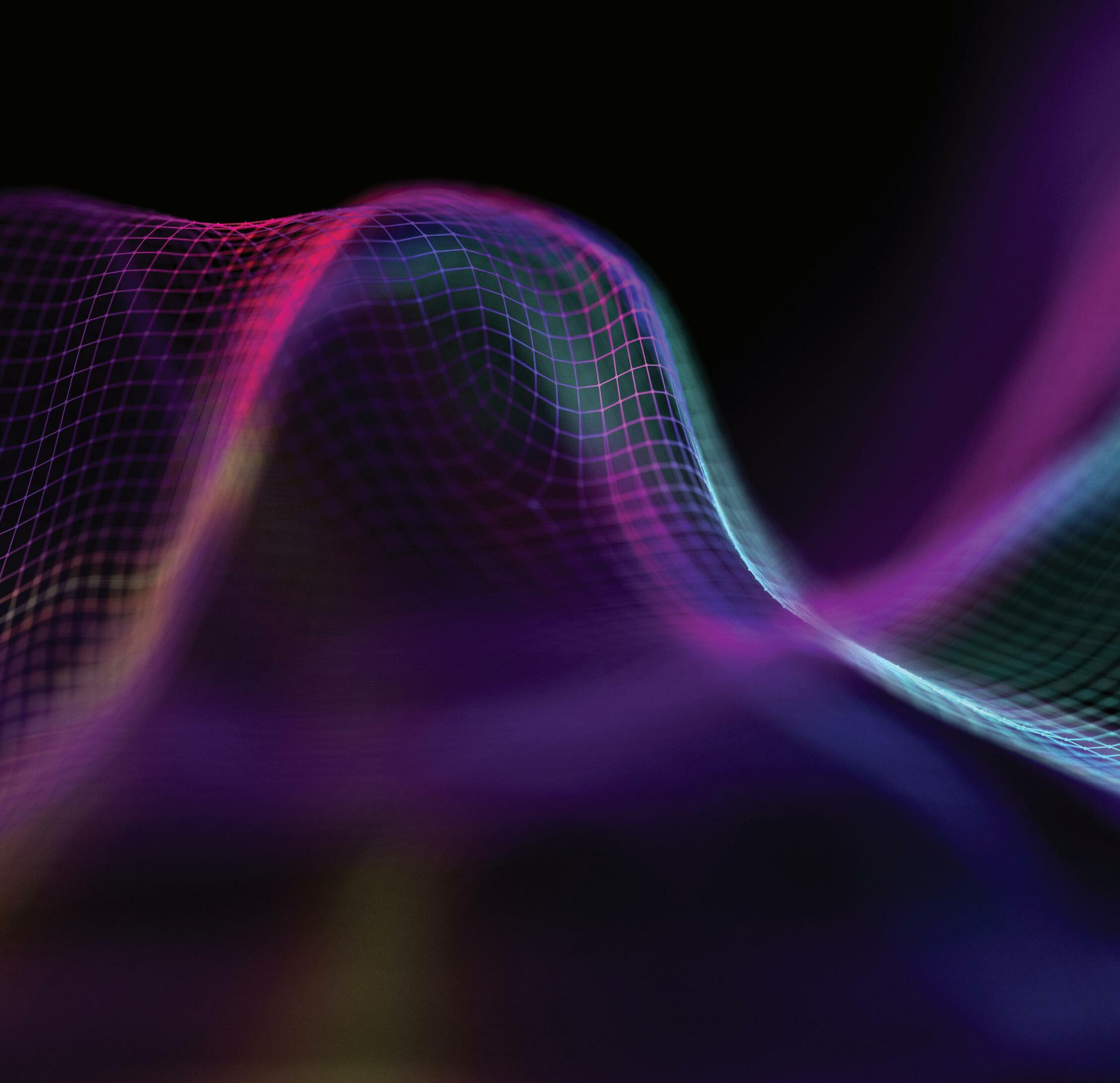
When asked about the importance of introducing young people and students to 3D printing skills, Goshen said: “We are in a technical, digital world, and the sooner you get introduced to technology, the better prepared you become for the future. That goes for elementary school and beyond. When you talk about what 3D printing brings, it’s two things. One is dealing with futuristic technology, you have something that is very exciting, you have it in your mind, you work it out, and then you have the physical object in your hand. That experience for kids is transformational in the way that they think about what technology can do, it’s very inspiring to them to really experience technology and transformation first-hand. The second thing is the problemsolving element of it. The complexity of taking your idea and then materializing it is great, but when you combine some different challenges, and you think, ‘How do I tackle that problem?’ then you iterate on it, and you print and try to solve it and it doesn’t work. The process of iteration and trial and error on the physical level is really important.”
Speaking more broadly about his ambitions for the future under the new brand, Goshen added: “Engineers’ time is very expensive and valuable, and they want access to technology that has to perform to a certain degree. Both companies are introducing products that are really aiming to get to the point where the technology is accessible in many ways, price points, workflow, even physical accessibility to the engineers, but they’re performing to the level of an industrial machine.”
WORK AND
Laura Griffiths takes a tour inside a Mattel innovation engineer’s home toy workshop.
The blending of home and workplace over the last few years has become the norm. Kitchen tables have become desks, spare rooms now double up as offices, and for an inventor, a garage can be a toy workshop.
For Jack Peach, Key Lead Innovation Engineer at leading global toy company Mattel, the latter is where the inkling of early product development for new toys at Fisher-Price, designed to inspire, entertain, and develop children through play, all happens.
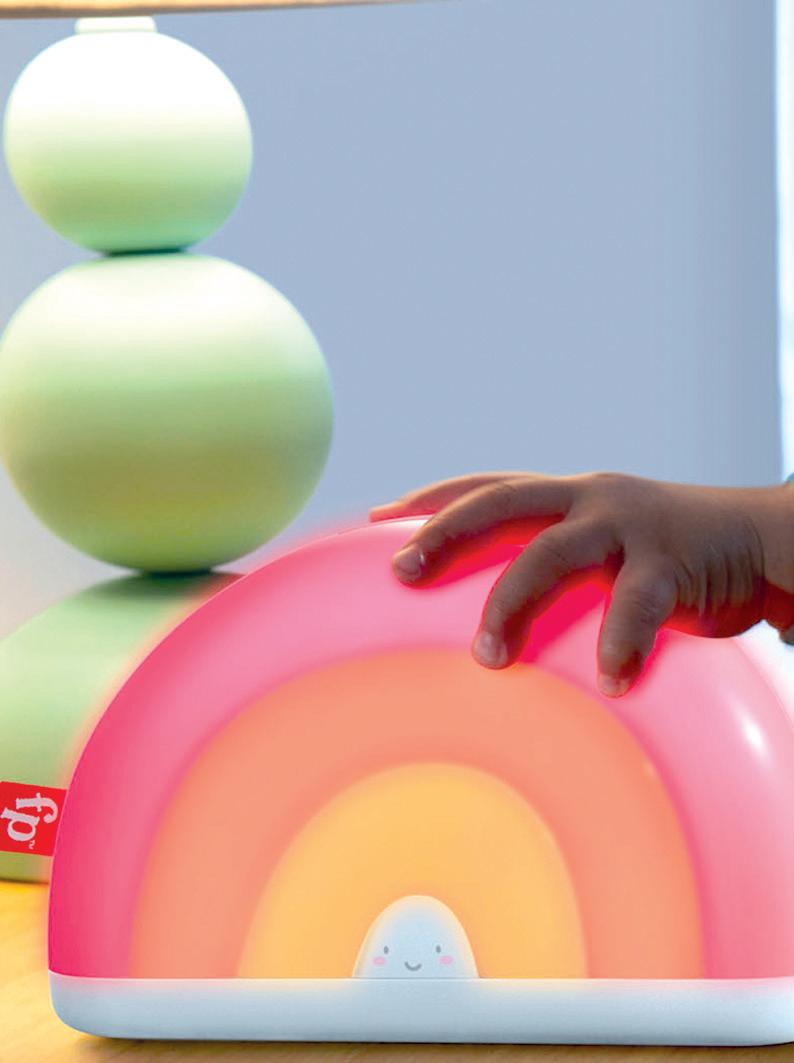
Meeting with TCT over Zoom, surrounded by shop tools and electronics, Peach’s workshop is filled with, not just the stuff of kids’ dreams, but also several toys that would be a dream for many engineers.
And as Peach told TCT: “Fabricating prototype toys in a home office can be challenging without the right tools.”
Two of those tools, and some of the latest additions to Peach’s collection, are a MakerBot METHOD and METHOD X, both professional desktop FDM printers, one designed for concept modelling and prototyping, the other for functional protoypes and tools, from the newly unified UltiMaker.
Amongst the hand tools, grinder and soldering irons, it was the pandemic that led Peach, who has been working in the toy industry for over 15 years and, like many, found himself working from home in early 2020, to finally pull the trigger on installing a 3D printer.
Prior to that, Peach and his team were already employing a range of digital design tools to produce new toy concepts. That workflow typically involved prototyping with a variety of woodworking, metals and polymer shop tools before sharing with Mattel’s cutting edge machine shop to create functional parts that could be demonstrated in a pitch meeting before
sharing with brand partners and testers. Now, with 3D printing capabilities in-house, Peach is able to quickly mock up designs, test mechanical functionality, prove out electronics, and quickly share and evaluate physical working models.
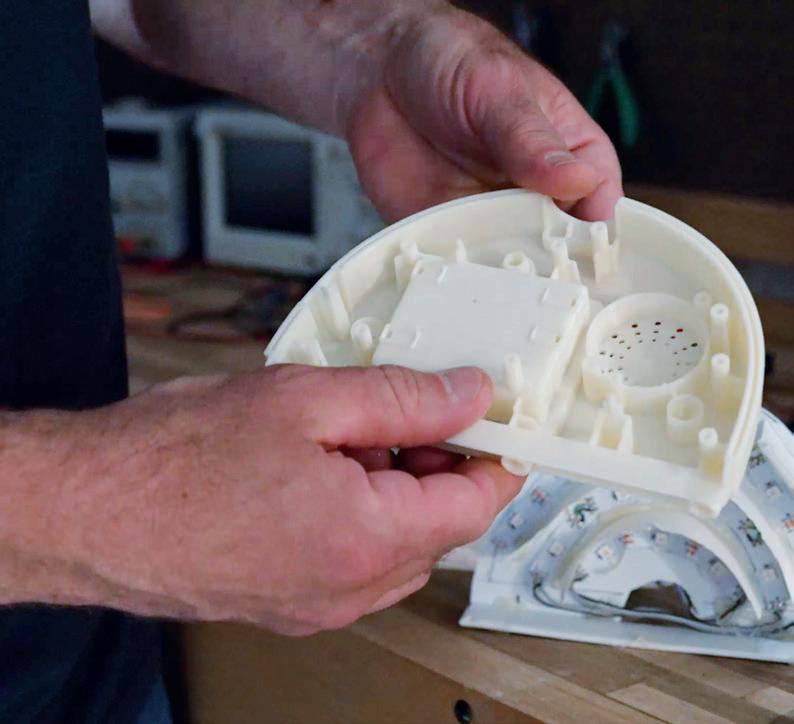
“At home, before the printer, I could do really crude prototypes,” Peach explained, demonstrating with an example of a complex plastic toy model which would be incredibly difficult to prototype using traditional methods. “In this case, I would reach out to our fabulous CNC shop at Fisher-Price. They have industrial sized CNCs, SLA 3D printers – they definitely have all the tools. I would go through that workflow and put in my job and request it to be manufactured.”
Often that workflow meant several days before a part was ready, and even longer if design changes needed to be made and prototyped again. Given the hit and miss ratio in the toy business – Peach suggests if just one out of one hundred ideas makes it to the shelves of a toy store, that’s pretty good going – those time savings are invaluable.
“3D printing allows us to use our time more efficiently and effectively,” Peach said. “We really don’t want to print every single concept that we brainstorm but when the idea is right, 3D printing is definitely a time saver, and allows us to focus on other aspects of the concept. Instead of manually fabricating it or working out toolpaths for the CNC, you can spend that time developing your concept pitch, or maybe working on the electronics, hardware, electronics software, or maybe the audio that’s going to go into that model. So you could be multitasking and then all your parts come off, you can put it together and you’re ready to go to show it to the brand team.”
The flexibility and freedom that comes with having such capabilities on your desk makes it possible to print one
iteration while already working on the next. Peach recalls an example from a recent Saturday morning while getting ready to take his children to soccer practice, when he had a sudden spark of inspiration.
“We had this one off-the-shelf product and I’m thinking, if we add some lights and sounds and add a different mechanism to it, maybe this could be a fun game?” Peach recollected. “My kids
AND PLAY
and I were talking about it and then right before we left, I drew it up real quick and sent over to the printer. Then we left for the game. Hours later, we came back, and it was ready to go. We pulled out the build plate, cleaned it up and then started playing with it.”
Peach says, while 3D printing allows him to try out ideas more rapidly, the technology has also inspired his own family, whether it’s building a solar system for homework or helping to create components for pressured rockets at the local Boy Scouts den. “It’s an amazing tool,” Peach adds, and with three children at home, what better experts could you hope for to get some qualified feedback?
Peach described a recent example of an early-stage toy he had been working on some electronics and

motor controls for: “My youngest son just grabbed it, brought it upstairs, and was playing with it. I ended up taking a quick little video to show the designers he was having a good time and he had a smile on his face. It’s still a rough form but you can see that there’s something there.”
Since its founding in 1945, Mattel has been renowned for creating innovative products and experiences across iconic brands including Barbie®, Hot Wheels®, Fisher-Price®, American Girl®, Thomas & Friends®, UNO®, Masters of the Universe®, Monster High® and MEGA®. The company even launched its own sub-300 USD 3D printer in 2016, a modern spin on its 1960s ThingMaker, which allowed children to think up and print their own creations. While it may have offered its young customers the tools to print their own toys from home, Mattel isn’t currently deploying 3D printing for mass production applications, though Peach does have some interesting thoughts on how that could look.
“I think maybe far into the future,” Peach says, emphasising the ‘far’, “perhaps we’ll have a virtuous cycle where toys can be printed at home and then played with and then the material could be recycled or part of it could be recycled and maybe you could reprint that into a new toy.”
While injection molding may still be the way to go given Mattel’s huge production volumes – its products are available in 150 countries – Peach emphasizes that for new toy development, which typically takes around 18 months depending on emerging trends and complexity, “3D printing has been a game changer.”
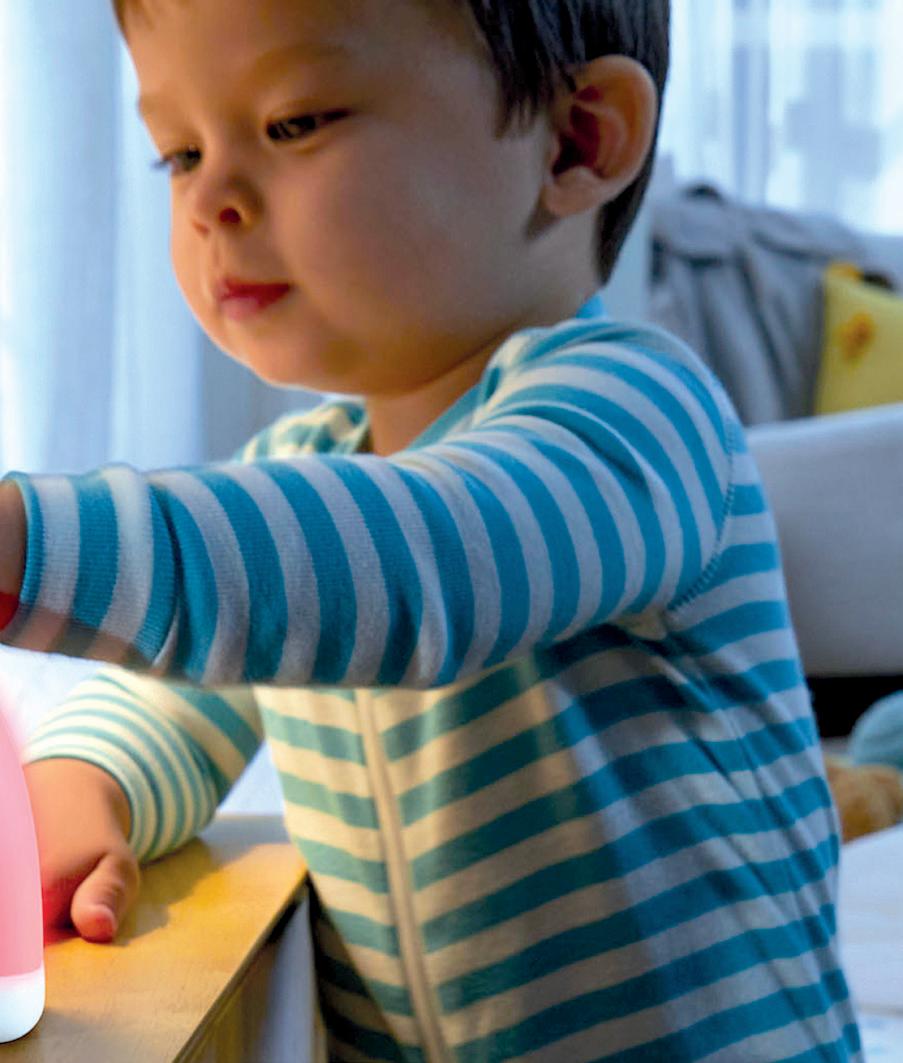
“3D printing allows you to create a lot of parts and assemblies that were very challenging to make otherwise,” Peach concluded. “We’re working on the very front end, the early prototypes, and then it gets sent on to other teams to really develop and make it designed for manufacturing. In my case, you can print these very complex assemblies very quickly and really just try to get to that magic spot. I think that when you’re thinking of a toy that might have some kind of feature or you turn this knob and the transformation, it’s nice to see that virtually or drawn out but until you get your hands on it and you understand how it’s going to work, even if it is going to work, then the magic is not there. Once you get it together, then you can really see that, 'wow, this is a really cool toy,' and the kids are going to have a good time with it.”
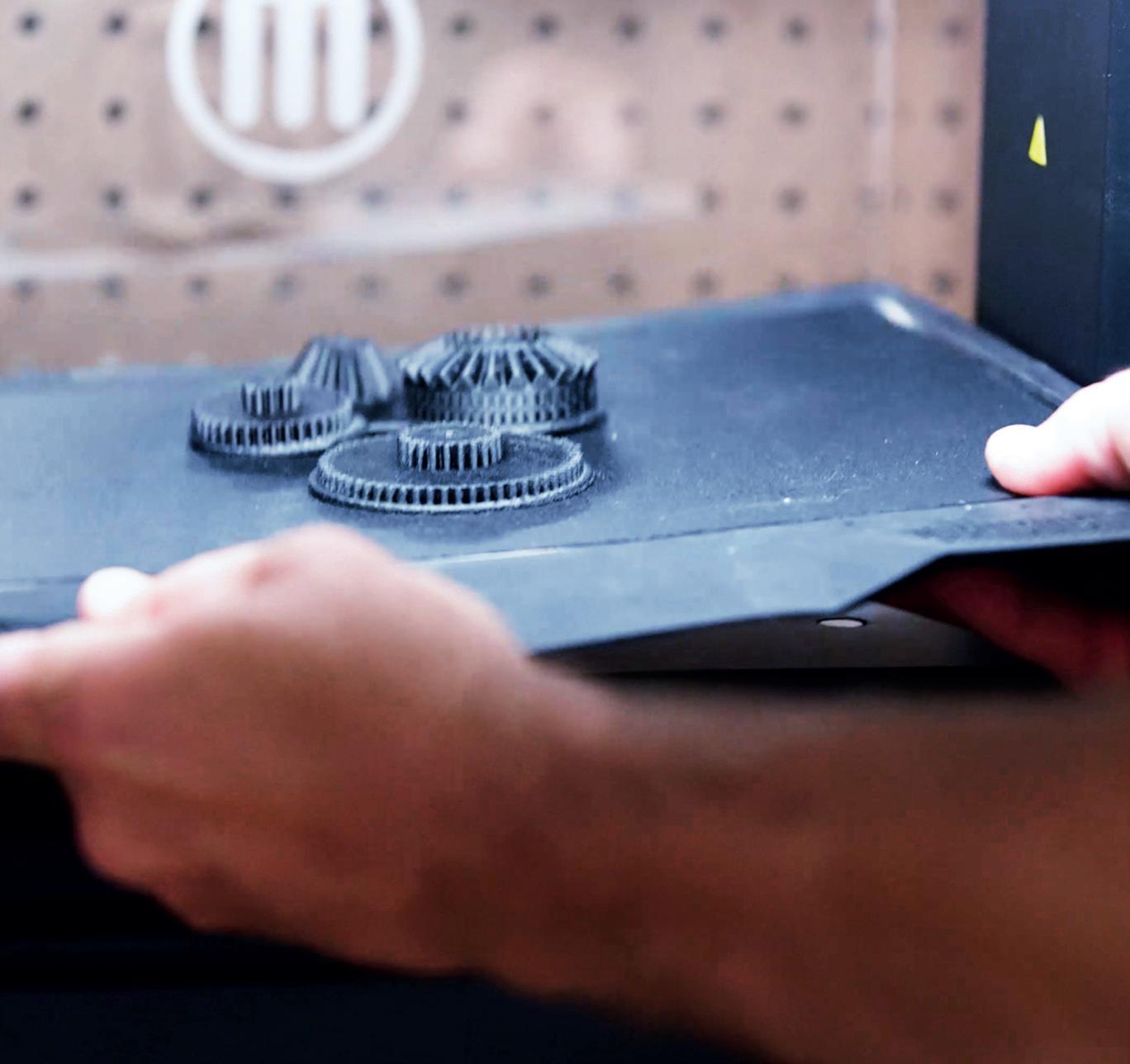
“3D printing allows us to use our time more efficiently and effectively.”
KEEP COOL AND
How 3D printing is providing enhanced comfort on Jack Wolfskin’s 40 liter 3D Aerorise Carry System.
In Northern Italy, the autumn sun beats down, casting a shadow high up against a massive grey cliff face. The view from the country’s largest lake below is just a tiny spec. You have to squint to see it. But as the hands stretch to grip and the lower limbs find whatever foothold they can, you can just about spot some movement.
Magdalen Hamel is two days into her week-long vacation at Lake Garda, where she is living the dream of any climber by scaling the mountains that overlook a body of water some 32 miles long and 10 miles wide. It is a spectacle she is taking in at every belay station on her multistage climb, an ascent in which she is debuting the first Jack Wolfskin product produced with the help of additive manufacturing (AM) technology.
As she recuperates from that climb, Hamel is back at the hotel, with headphones in ears and the 3D Aerorise 40 Carry System by her feet, answering questions for TCT Magazine.
We are nearly two years on from when Jack Wolfskin received the first samples of Carbon’s Digital Light Synthesis technology. The round, latticed pucks would soon evolve into ergonomically shaped pads that support the lumbar and shoulder areas on the back of a carry system that is now available for purchase.
“I think it was end of 2020 [when we started to use 3D printing] and close cooperation [with OECHSLER, a Carbon Production Network partner] started in ’21,” Hamel, Category Manager, Equipment
at Jack Wolfskin, tells TCT. “It was our Innovation Manager that had the contact with Carbon and gave us the first sample. With this first touch, we were addicted, because we can combine so many material properties with only one material, which [translates] into using less
need a lot of different degrees of hardness and more firm or soft foams, EVAs, spacer mesh and the air mesh. And with only one material, we can [now] create an even better performance because it doesn’t collapse.”
Per OECHSLER’s Senior VP of Global Product & Technology Development Matthias Weißkopf, the service manufacturer expects AM to ‘significantly change the design of outdoor equipment and sporting goods in the coming years.’ Jack Wolfskin believes with the 3D Aerorise 40, it's leading the way on the former, while joining several other household names in leveraging 3D printing within the
For the development of the 3D Aerorise 40 Carry System, the outdoor apparel company implemented a body mapping process which considered how the weight of the backpack needed to be distributed. The optimum distribution of weight and pressure, in addition to forming the ideal ergonomic shape, was important to ensure sufficient air circulation to

Printing four parts per build, Jack Wolfskin is putting the latticed pads
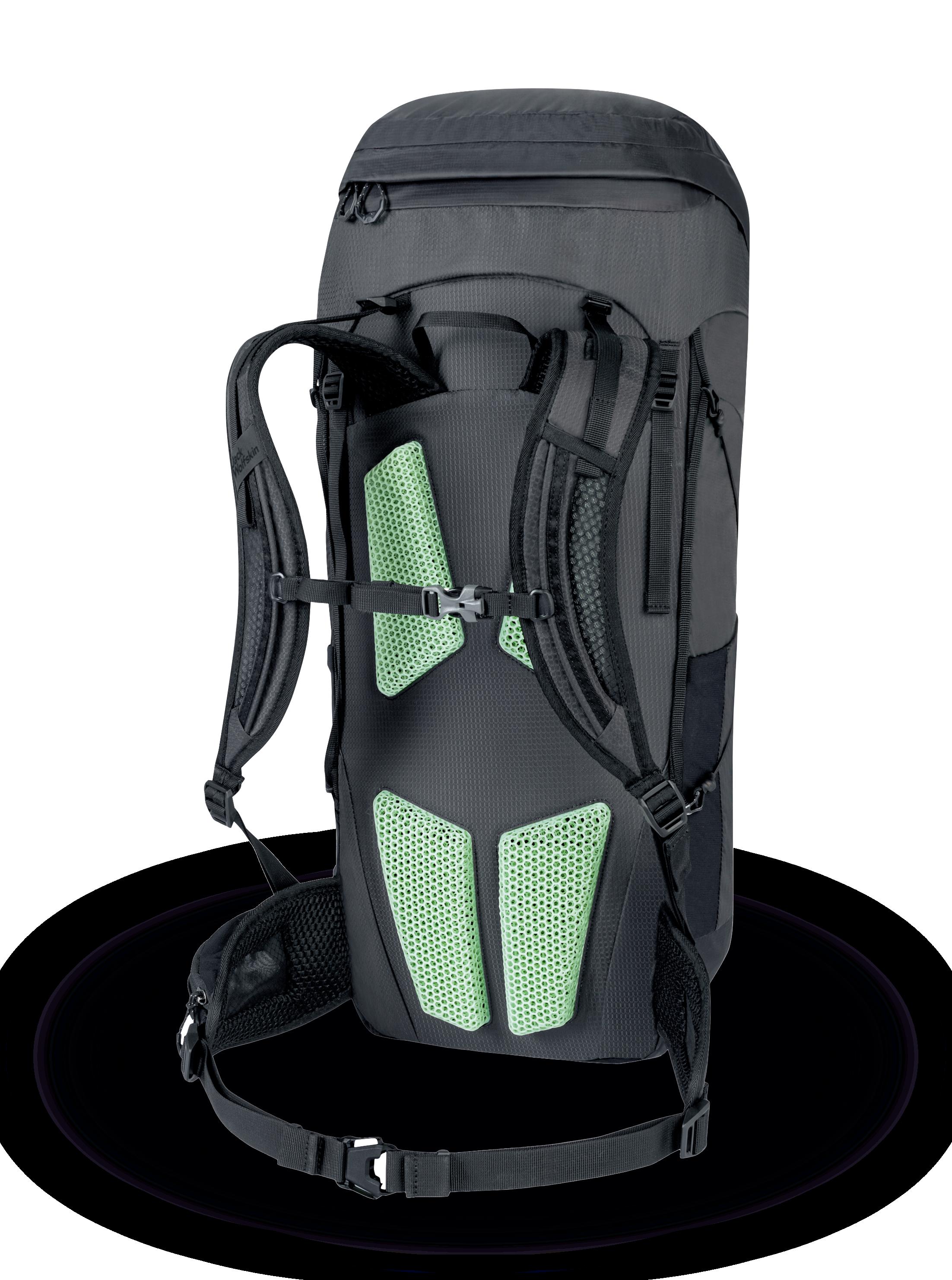
“With this first touch, we were addicted.”SHOWN: JACK WOLFSKIN’S 3D AERORISE 40 CARRY SYSTEM WITH 3D PRINTED LUMBAR AND SHOULDER PADS WORDS: SAM DAVIES
AND CARRY
into series production via OECHSLER, with the 3D Aerorise 40 already available via pre-sale. The four pads have replaced traditional foaming layers that cover the entire back panel and harness an open grid structure lattice that boasts thousands of rod-shaped struts. These struts have different vertical and horizontal strengths, with zonal cushioning offering different degrees of hardness throughout areas of the pads. Pads are firmer the closer they are to the back panel, and softer the closer they are to the skin for enhanced comfort. They're also firmer on the narrower side to support the back, as this is where the weight is concentrated, and softer at the wider ends to add comfort again. To ensure cooling ventilation, the degrees of firmness are infinitely variable.
These pads have been designed with Carbon’s Design Engine and leant on the latticing capabilities that brands like Adidas, Riddell and Rawlings have all benefited from.
“It was a 0 to 100 experience. This is an entirely new field for us,” Hamel says. “We see a lot of potential there so this is why we’ve been attracted so much by the pucks we got from Carbon. We touched, we squeezed it and we directly felt the benefit because the cushioning has so many density zones, it was smooth when we grabbed it and then we squeezed it, it got hard but it didn’t collapse. [Then we said], ‘hey, how can we translate it into benefits for our consumers?’
The consumer need is, for sure, always centre of our [thinking].”
As Hamel stands on the balcony of her hotel
room, she picks up the 3D Aerorise 40 to demonstrate the energy return capabilities of the pads, outline their rhombus shape, and indicate how the formation and stretchiness of the pads facilitates air circulation and reduces the temperature on the user’s back.
After making those gesticulations, Hamel has now placed the bag out of shot and is demonstrating the diagonal movements hikers make on their trails.
“When you are on a hike, you’re always in this diagonal movement,” Hamel says, pushing her right limbs forward and left limbs back, before swapping over to mimic a hiker. “We want to make sure that our customers can carry their load very easily. It is also about load control. This was the main story for us because usually the consumer needs to decide, ‘do I need a ventilated backpack with the usual gap we have at the back, but the load is a little far away from the back, or will we go for a body contact carrier system to have very good load distribution, but I don’t have this great ventilation?’ Here, it comes in both.”
Considering the actions of the consumer in this detail, and supplementing it with body mapping, is how Jack Wolfskin came to best place the pads on the back of their carry system. After the parts are printed by Oechsler and put through the necessary post-processing steps, two symmetrical pads are placed in the shoulder region of the backpack and two symmetrical pads are placed in the lumbar area. They work to support the areas of the body that come under the most pressure from the load the hiker or climber is carrying on their back.
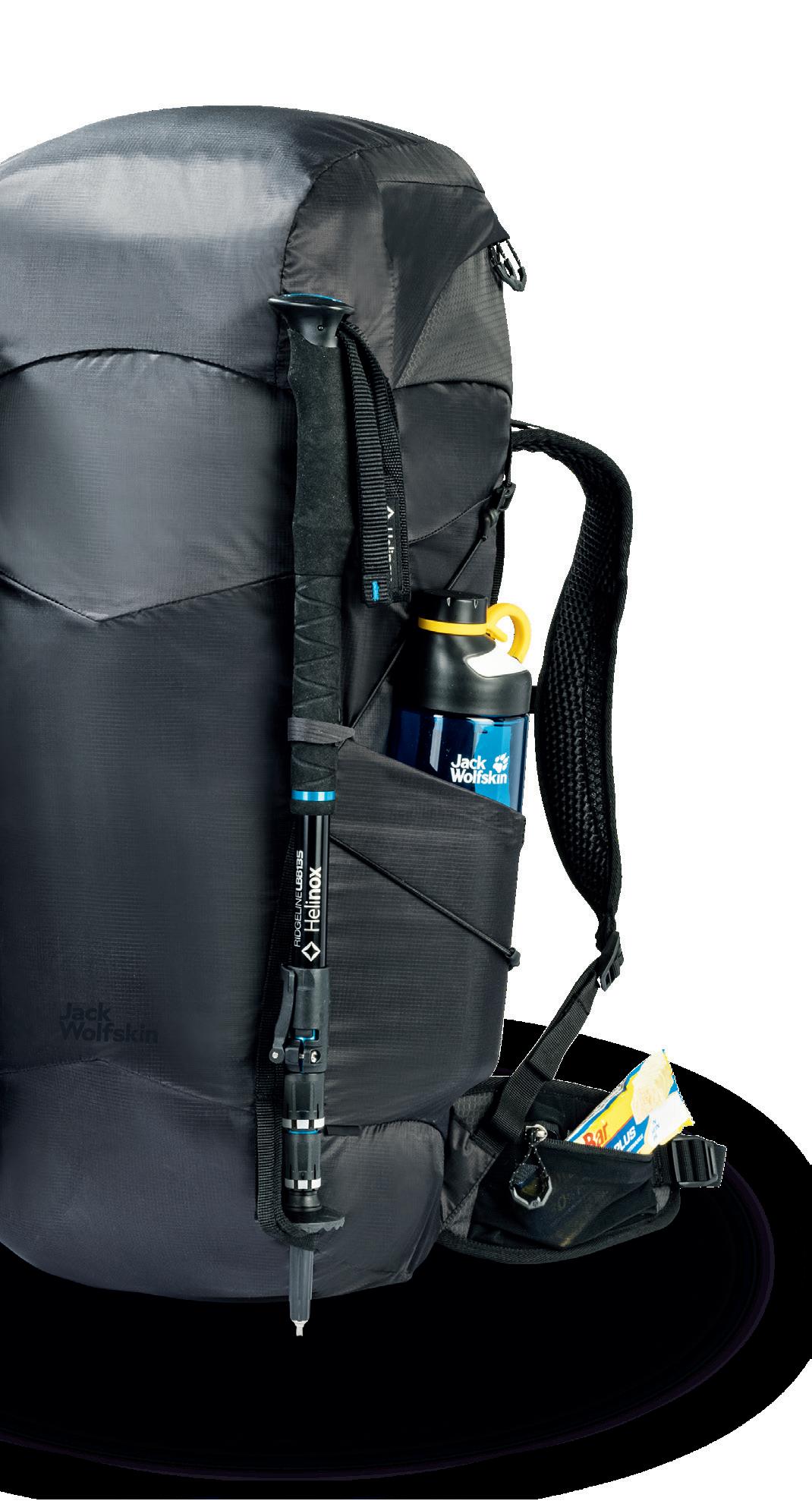
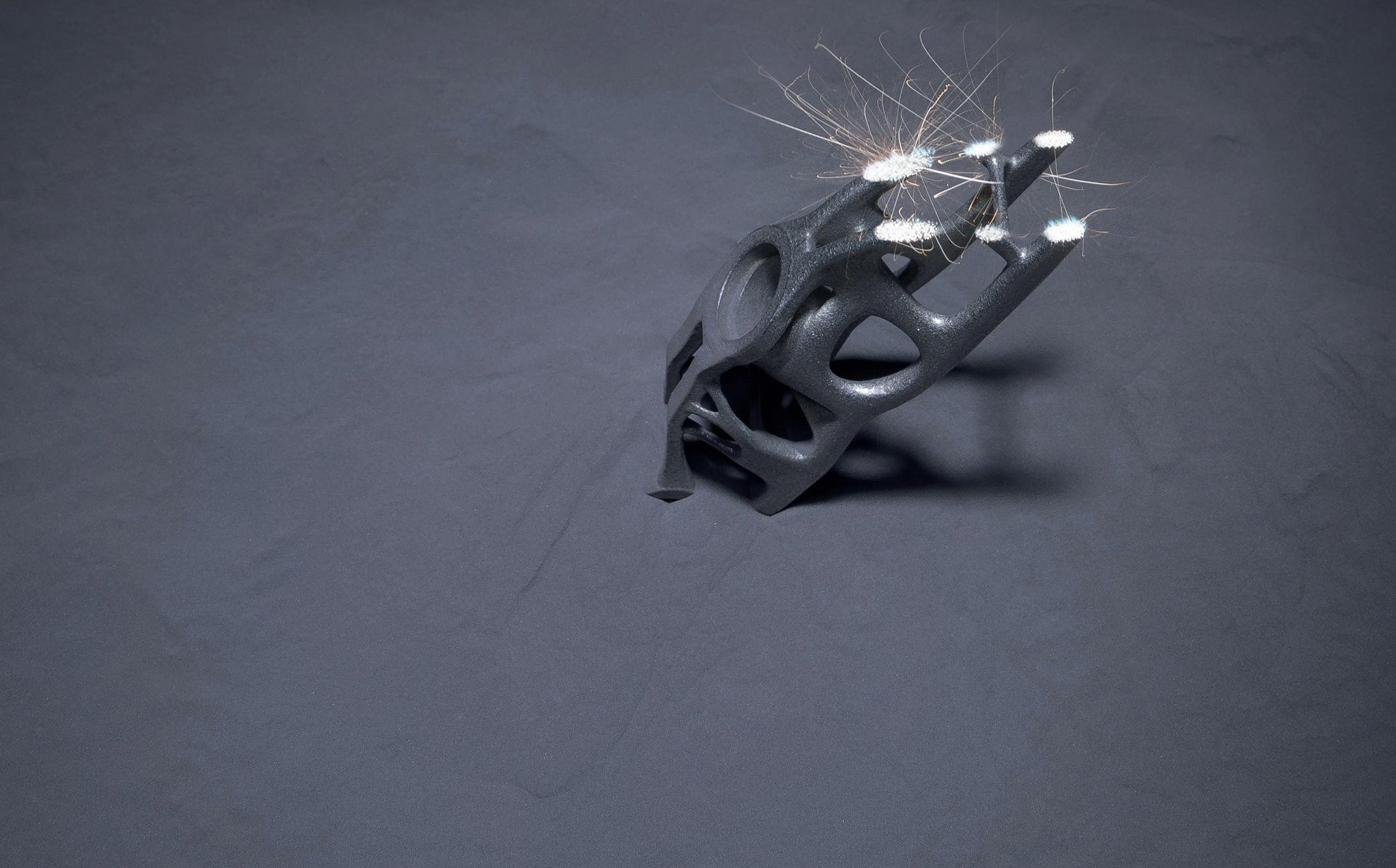
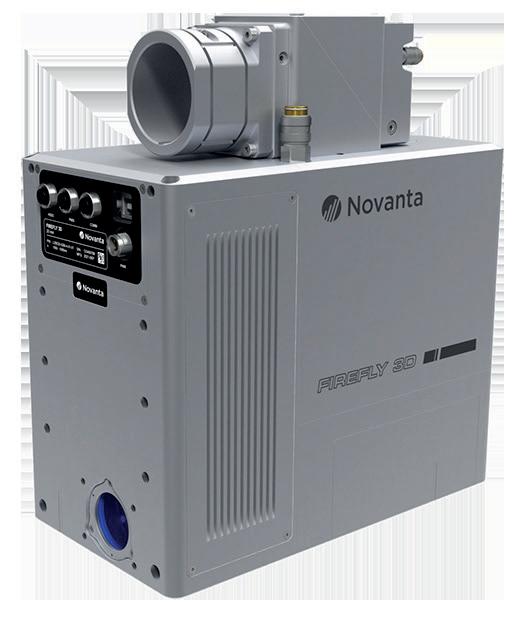
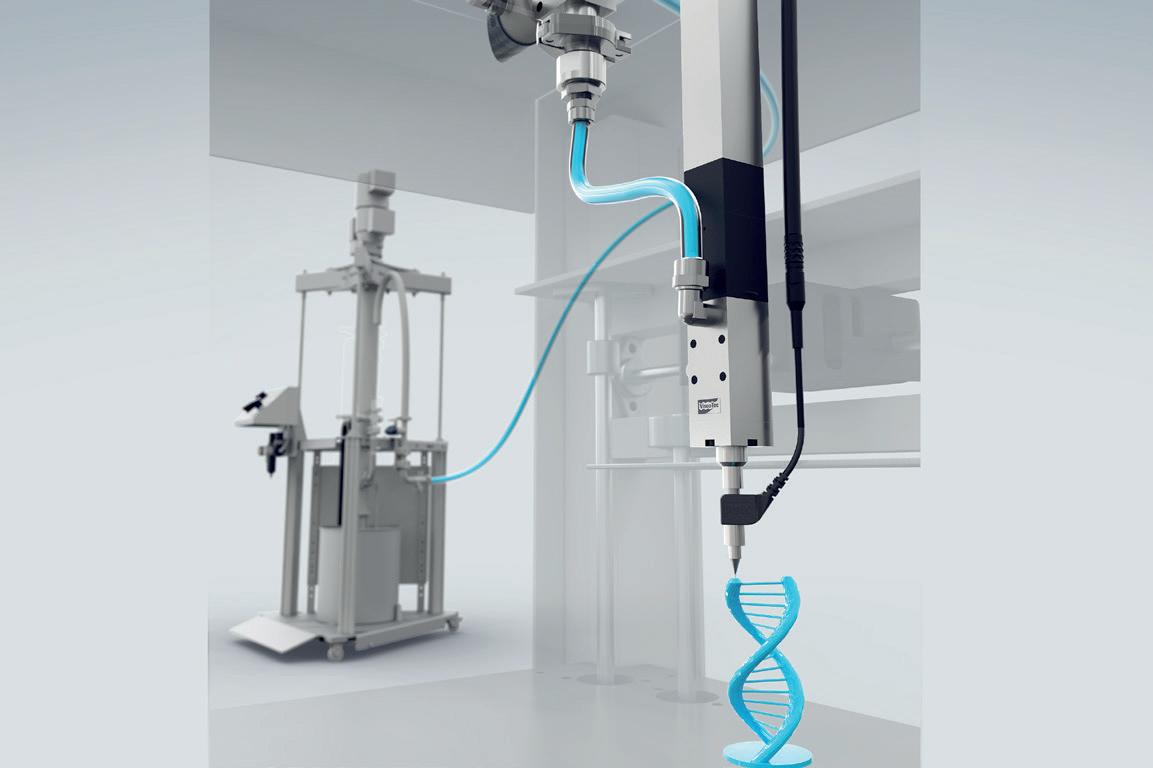
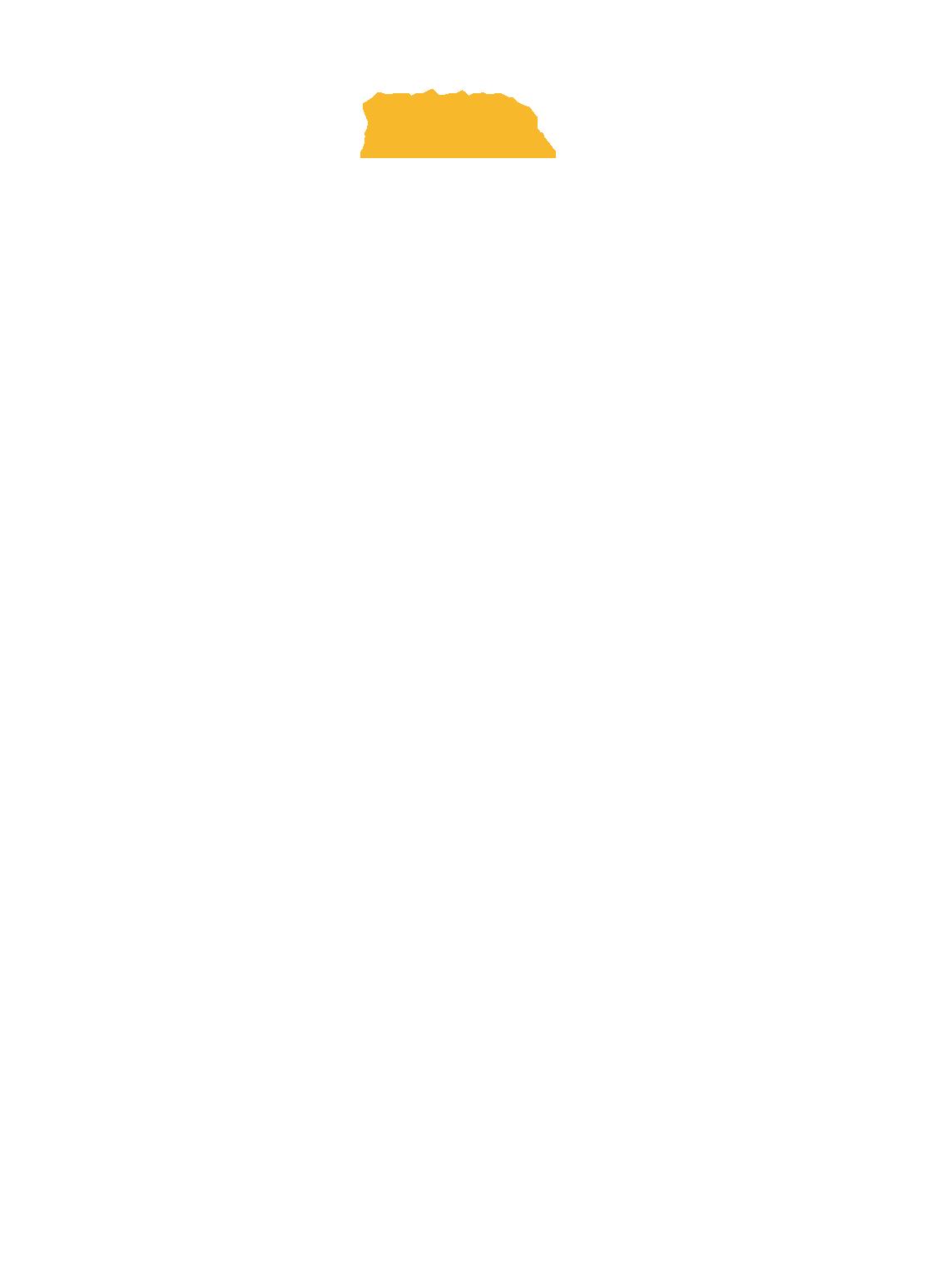
By 3D printing the pads, Jack Wolfskin has been able to reduce the weight of its carry system, improve the ventilation, and provide a temperature reduction brought on by friction in the pressure zones of up to 5°C. In working with OECHSLER, Jack Wolfskin is also reinforcing a commitment to engineering products in Germany with manufacturers located nearby.
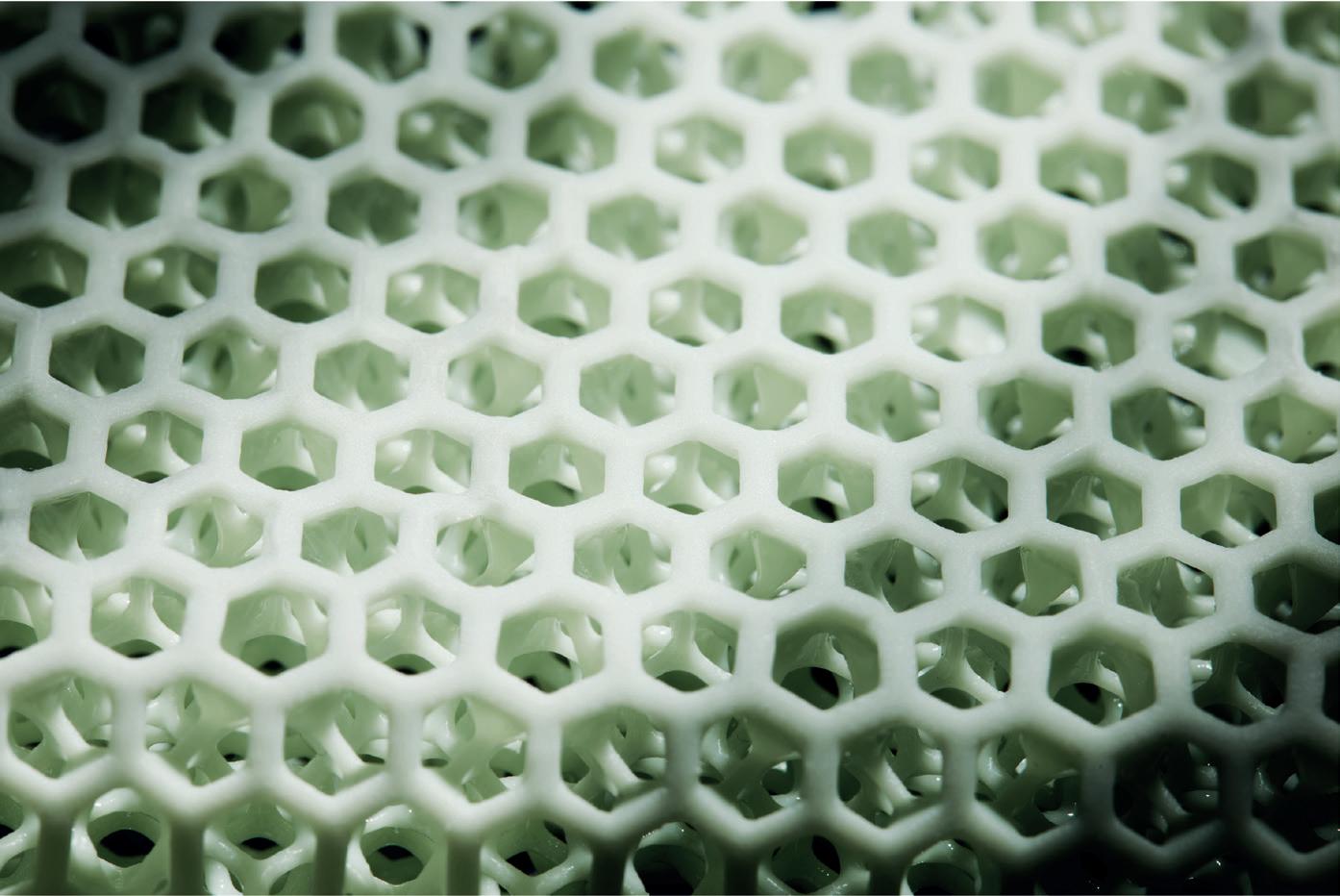
“We are pleased to support Jack Wolfskin in the development of the Aerorise backpack series,” Weißkopf commented. “With our expertise in additive manufacturing, we have been able to significantly improve the product features of the backpack for the benefit of the customer. We see significant growth potential for 3D printing development and series production in these areas.”
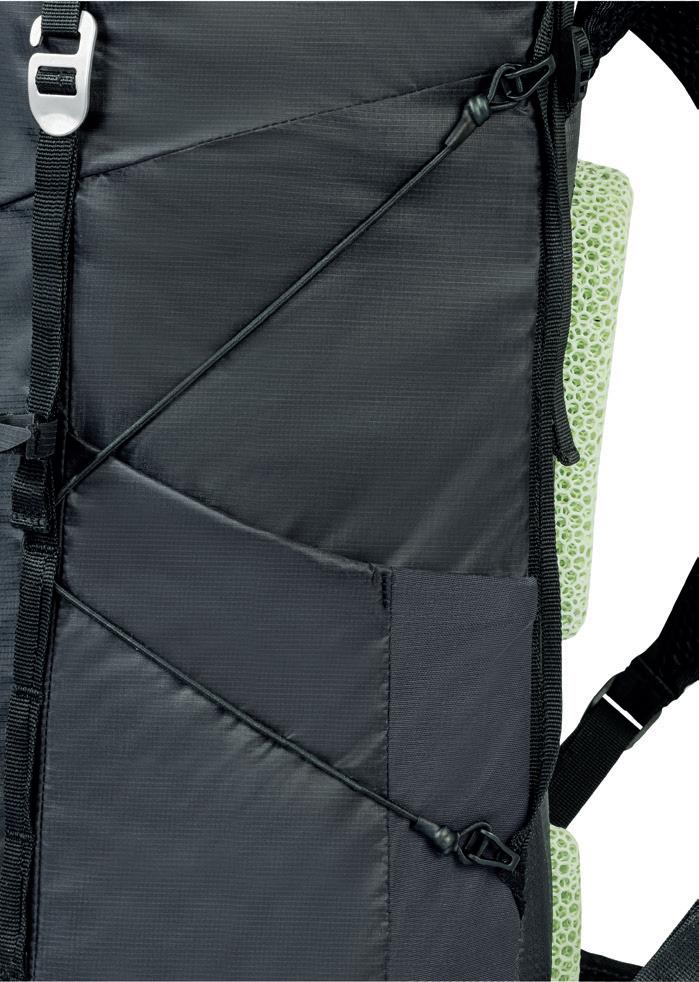
Jack Wolfskin does too. Throughout the product development process, the company went through ‘countless iterations’ with OECHSLER to arrive at the ergonomically shaped final designs. They started with the round pucks, moved towards rectangular shaped pads, and then came to the rhombus-shaped components with a seam allowance attaching them to the back panel.
With close links to OECHSLER, the Aerorise 3D 40 is now in series production and is already getting rave reviews from users. Feedback to Jack Wolfskin has included, ‘I feel cold when I’m wearing it,’ ‘I can’t feel anything at all after a minute,’ and simply, ‘so cool.’
Hamel, who will make her way back up the mountains surrounding Lake Garda tomorrow, is similarly impressed with what her and her team have developed. And, of course, is already looking forward.
“There are so many opportunities,” she finishes. “We would really like to understand [3D printing] much better, much more in the future. This really will be a game changer in our industry. We see that additive manufacturing can give us a lot of benefits in the research and development part, for sure.
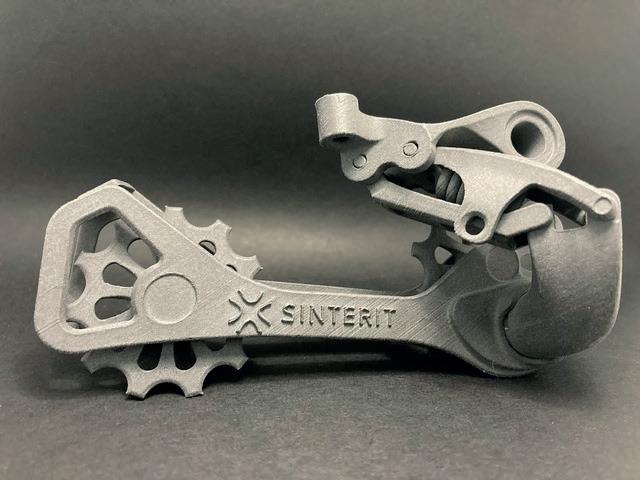
“I think it will take time to get it set on a manufacturing base to make it accessible to a wider range of consumers, but we, as a brand, are absolutely convinced that the consumer is aware of it and will see the benefits. And we’re also proud too that we are one of the first brands that already have taken the first step and we are already live with that product.”
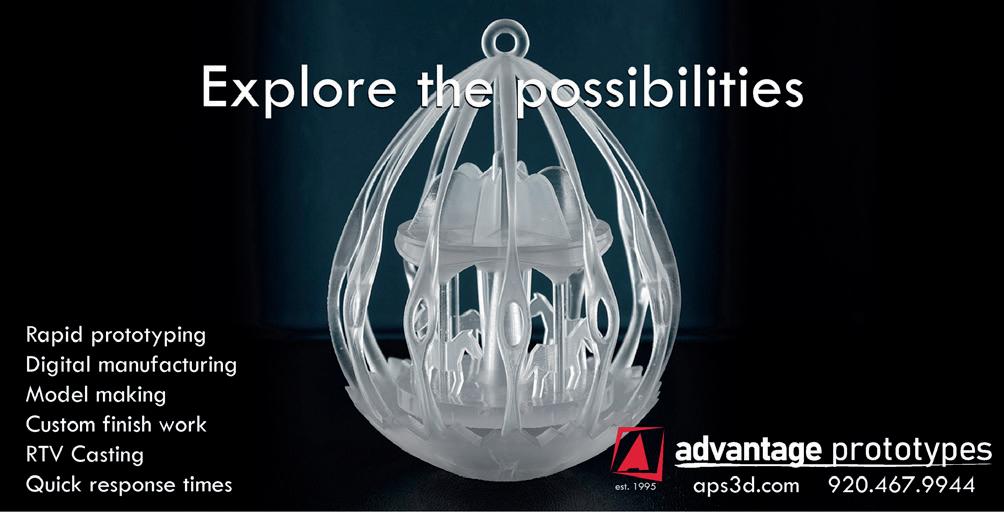
This summer, Hasbro announced the Selfie Series, a new product range which allows customers to have their face 3D printed onto the body of a six-inch action figure; a Stormtrooper, Spider-Man, a Ghostbuster, a Power Ranger, amongst several others.
The production process starts by taking a scan of the customer’s face through the Hasbro Pulse mobile app, where they can also select their preferred action figure and hair color. The information is then sent to the Hasbro print factory and queued up for 3D printing. Multiple customized heads are printed at the same time on a single build plate, using Formlabs stereolithography (SLA) technology. The heads are then assembled with a standard off-the-shelf action figure body, before finally being shipped to the customer.
The IPs that Hasbro works with are some of the most beloved in the world of pop culture. To create a product that would be well-received by fans, selecting the right 3D printing process for this range of action figures was crucial. The toy company has been using 3D printing since 1995, primarily for rapid prototyping, and began using Formlabs printers in 2014. According to Hasbro, as it saw 3D printing cross over from being a prototype-centric technology, it had the dream of developing something with the technology that was truly innovative, hence the idea of mass customization.
Gary Rowe, Global Head of Business Development at Formlabs, told TCT: “Many companies turn to SLA 3D printing for the strength and resolution of the prints, and Hasbro had used Formlabs SLA 3D printers for prototyping in the past. When seeking the right solution for the Selfie Series, Hasbro selected the
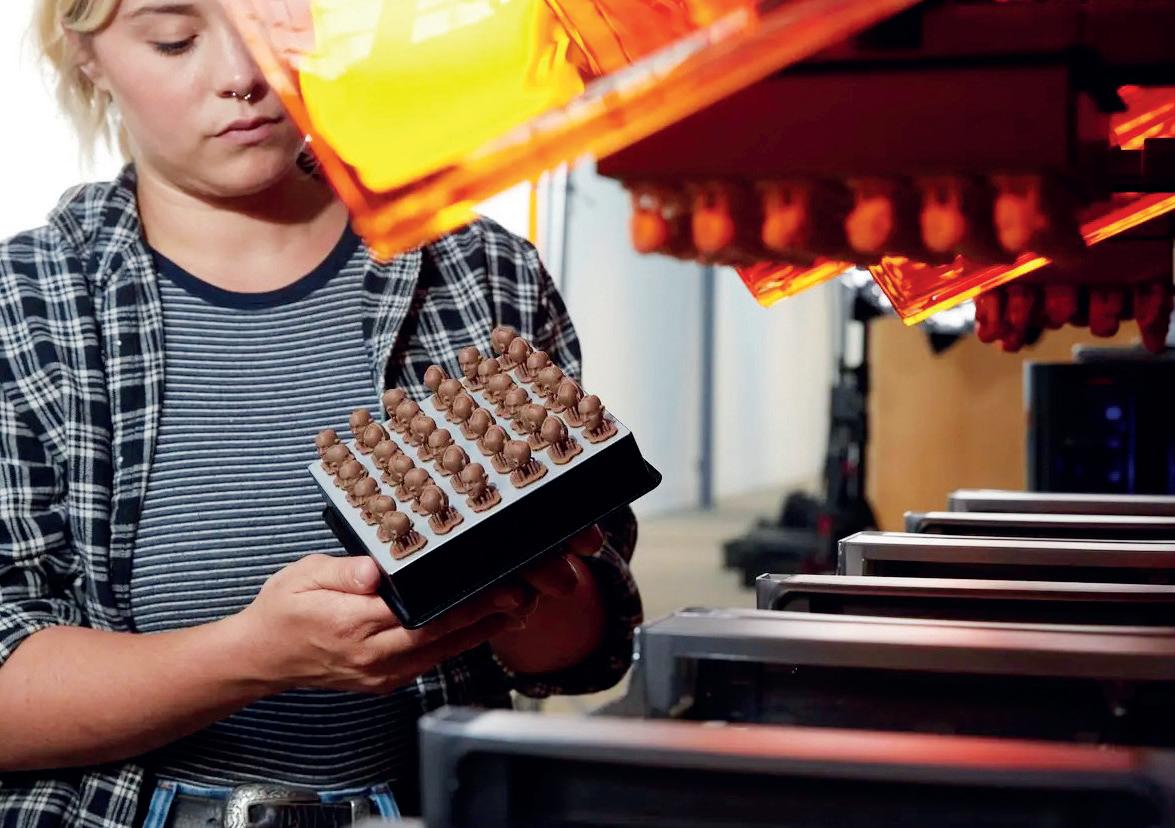
Form 3 SLA 3D printer that would provide the high resolution and accuracy needed to create life-like faces of Hasbro’s fans, with a smooth finish that would also be durable. In addition to the quality of the prints, the Form 3 worked well with the resin created for the manufacturing of these action figures.”
Mass customization enabled by 3D printing allows for the commercialization of products that are unique to the customer. The audiences the Selfie Series are targeted towards - Star Wars fans, Marvel fans, Power Rangers fans and more - often embrace the opportunity to dress up as their favorite characters at fan conventions and premieres, so Hasbro believes the market is there for products that invite fans to put their face onto their favorite characters too.
Patrick Marr, Sr
spoke to TCT about the implementation of mass customization in Hasbro products: “Our fans continue to look for new ways to engage with our brands and see becoming their favorite action figure as the ultimate expression. 3D printing has allowed us to offer that experience at scale in a quality that was never possible before. We see utilizing 3D printing as
Development
Oliver Johnson speaks to Hasbro about its new range of customizable 3D printed action figures, the Selfie Series.Director of Model at Hasbro,
“Selfie Series is an example of how Formlabs 3D printing solutions can deliver mass customization to consumers.”
opening many future opportunities for our fans. Leveraging the technology allows us to deliver products faster, create custom products, and then continue to evolve that platform by offering new features.”
The material that Hasbro chose had to be able to create figures that were highly detailed, to accurately replicate the consumer’s face, but also durable enough for everyday wear and tear. Formlabs assisted in the process of deciding on a material that could be available in a variety of skin tones and hair colors, which ultimately led to the creation of a new resin, based on its Tough 1500 material, specifically for this application. Rowe shared how Formlabs worked closely with Hasbro to meet quality assurance and safety testing standards required for commercial products in the toy industry. While the hair pieces for the figures are currently not personalized, these are also manufactured using the same SLA technology.
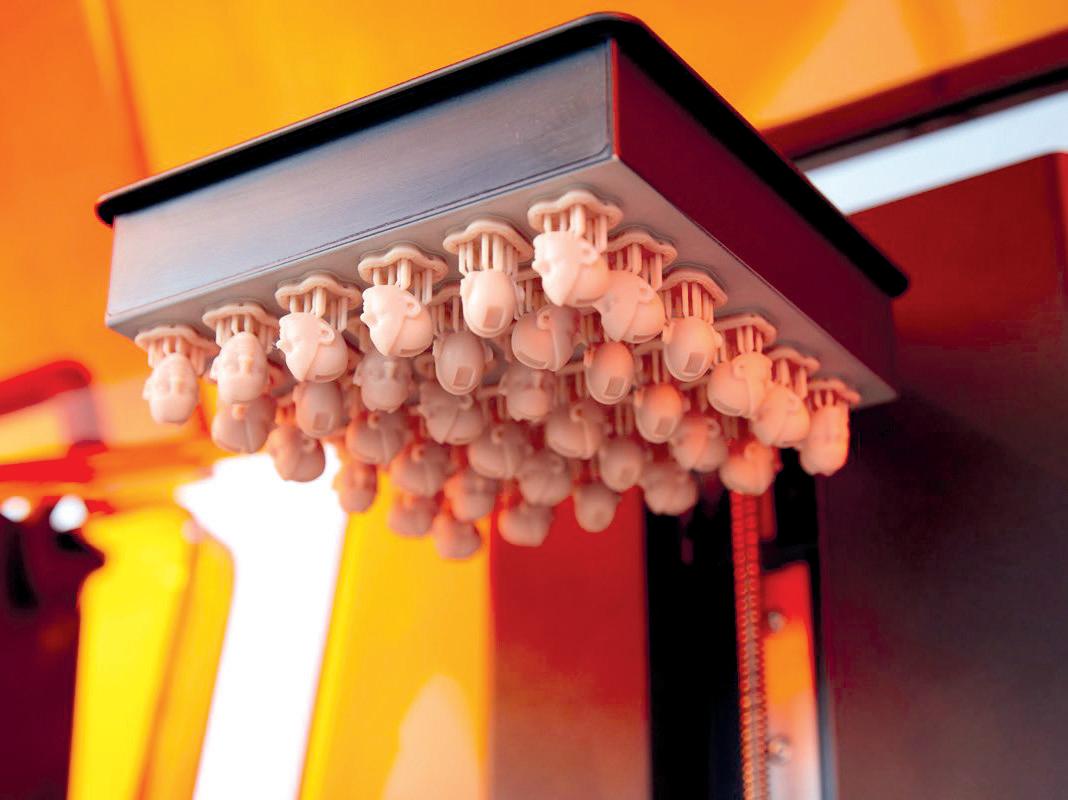
Marr added: “Hasbro Selfie Series is really our first consumer-directed product that utilizes 3D printing in the mass customization space. The product was driven by leveraging our 25-year knowledge in 3D printing to bring an experience and product to market that sets the bar on personalization and quality. We spent about two years developing the scanning, printing, and production process to ensure we could offer an amazing customer experience.”
An important aspect of the production for Hasbro was the ability to match the quality of its collector figure lines. Hasbro action figures have been a staple for collectors for decades, and the company wanted the Selfie Series to match the quality that fans have been used to.
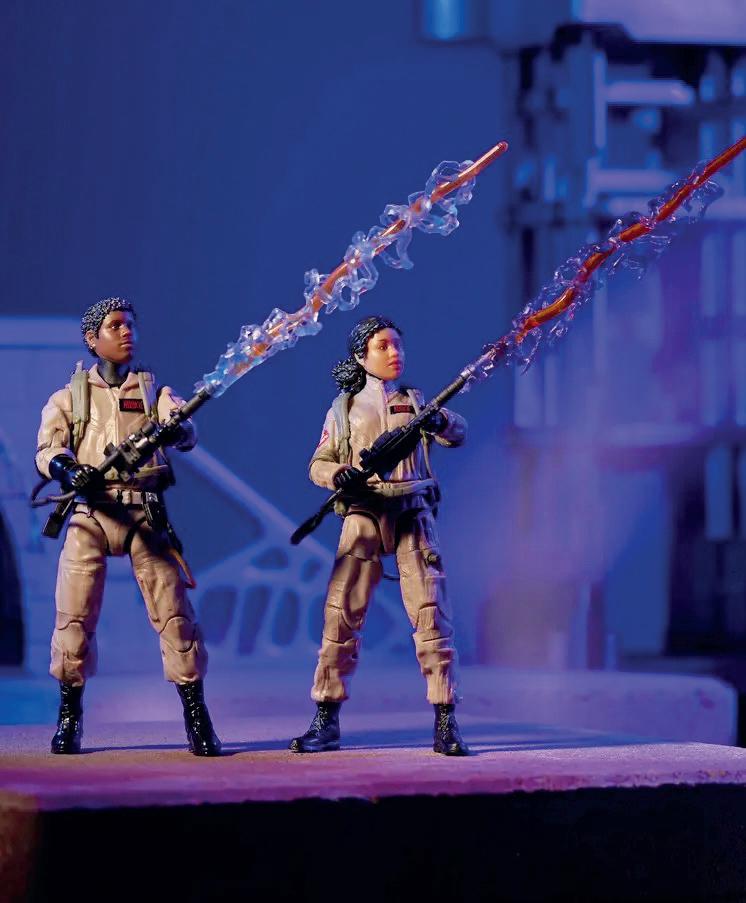
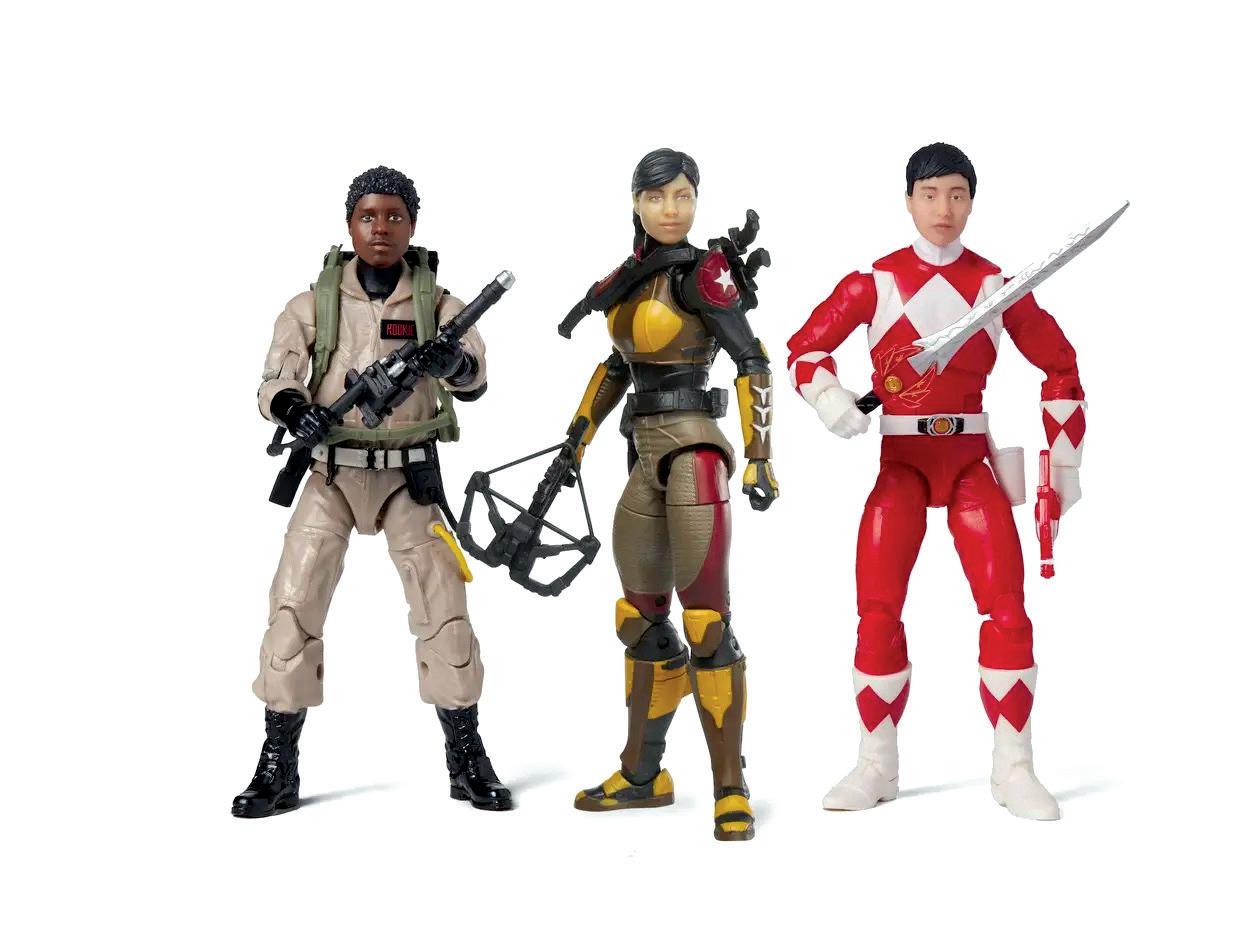
Rowe spoke about the future for Formlabs and Hasbro, and for mass customization, saying: “Selfie Series is an example of how Formlabs 3D printing solutions can deliver mass customization to consumers. Hasbro has understood this potential innovation and created this first application of mass customization to foster engagement with its customers. 3D printing will continue to advance in end-use-parts and mass customized products as complimentary technologies such as scanning technology and material development increase the quality, speed, and applications. Consumer demand for personalized products will also rise
in tandem with this technological development to make 3D printing a more sought-after approach for delivering new products that strengthen brand awareness and loyalty.”
Emphasizing Hasbro's ambitions for future personalized products, Marr added: “We look at Hasbro Selfie Series as just the first expression in this space, and we want to continue developing and expanding our engagement with our fans. Again, it is really the perfect flexible platform that allows us to leverage ideas from some of the company’s amazing talent.”
Celebrating ten years of accelerating the adoption of additive manufacturing
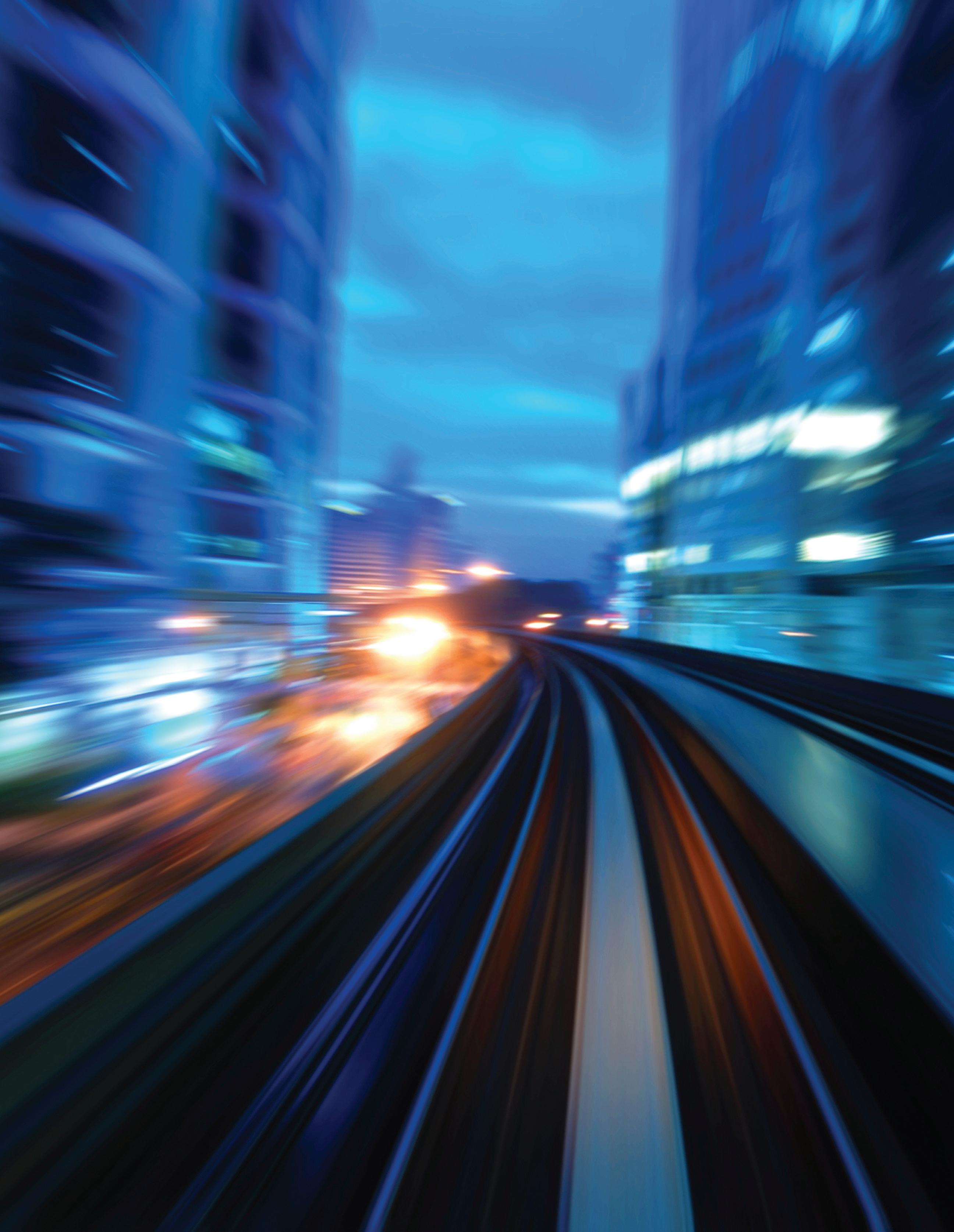
'AMAZON FOR ADDITIVE'
Laura Griffiths speaks to MakerVerse CEO & Managing Director Markus Seibold about AM services, supply chain, and lessons learned from Siemens Energy.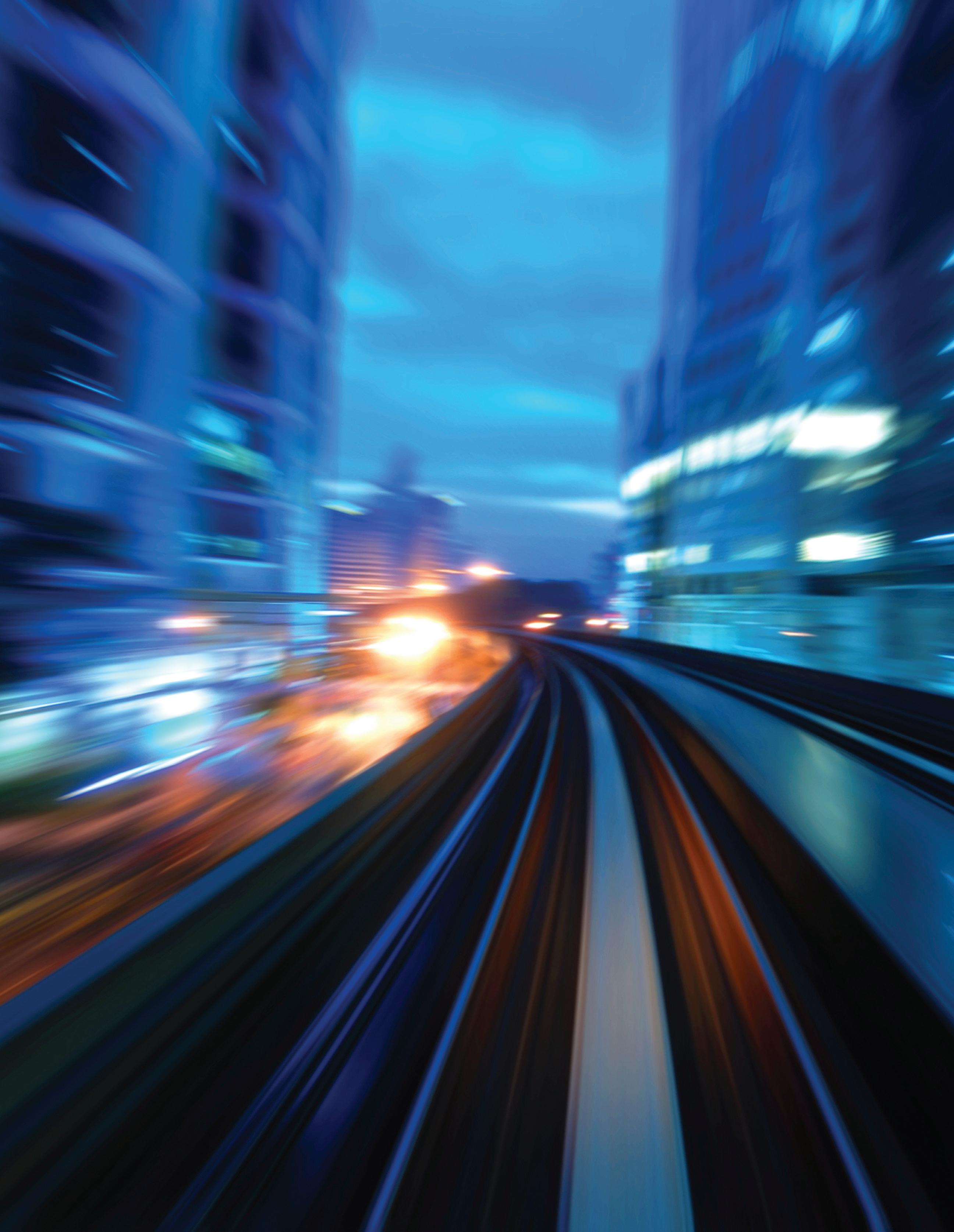
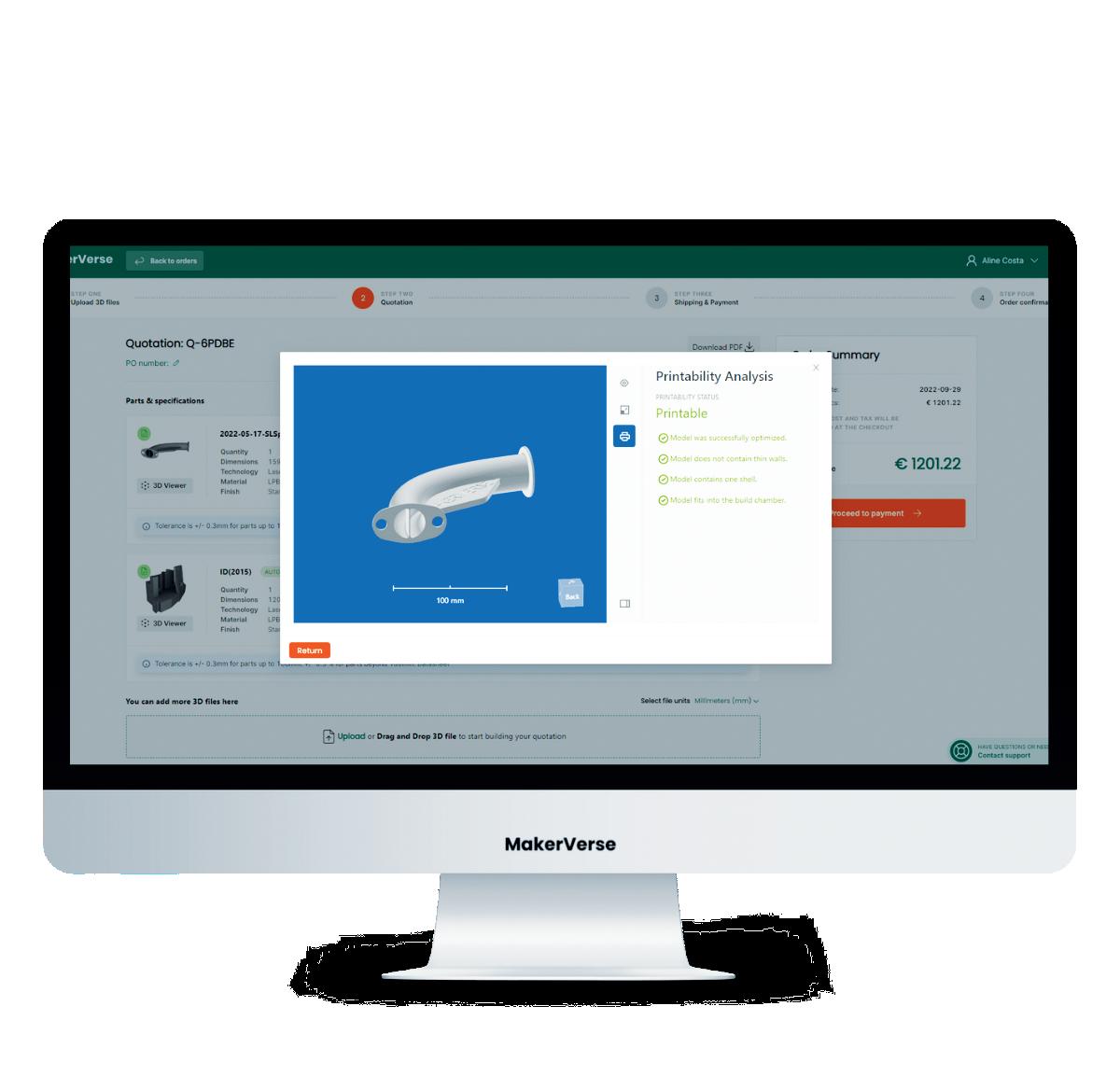
Q: You spent the past seven years as VP Additive at Siemens Energy. Tell us about how MakerVerse came about. Siemens Energy has gotten really deep and really good [at] metal powder bed fusion for high temperature applications for gas turbines. This was the real sweet spot. When I left, early 2022, there were more than 200 people now working on additive and the company overall has more than 50 metal powder bed fusion printers installed in our global Siemens Energy network.
[…] There is the saying ‘when you have a hammer, then everything looks like a nail’ and what happened at Siemens Energy, we looked at every potential component like a metal powder bed fusion, hightemperature AM component. The reason Siemens initially started to think about MakerVerse was that there was a need for a second pillar in the strategy. To fulfil a few requirements, it should give Siemens Energy access to a whole array of different
additive manufacturing technologies and materials that the company didn't have in its own very deep footprint. Number two, it should do that at industrial-grade quality so that Siemens Energy really could take prototypes all the way to a certified spare part. And number three, it should support specifically the on-demand nature of nonplannable prototypes, of unsteady spare parts. And with those three requirements, one-stop shop, industrial grade quality and on-demand manufacturing, the idea was created to turn this into a digital platform model. It's intended to be something like the Amazon for industrial 3D printing.
the metal side, metal powder bed fusion, and on the polymer side, you will find Selective Laser Sintering, HP’s Multi Jet Fusion and FDM technology. Then there's, of course, a different set of materials below each of those four technologies and our operations team is continuously working on expanding the technology and materials portfolio. […] We will broaden our scope step by step. Currently we are an additive manufacturing platform but we believe that this needs to be integrated with conventional technologies like CNC machining, so over the next weeks and months we will also broaden the technology focus beyond additive to also include conventional technologies so MakerVerse is a true one-stop shop for both additive and conventional
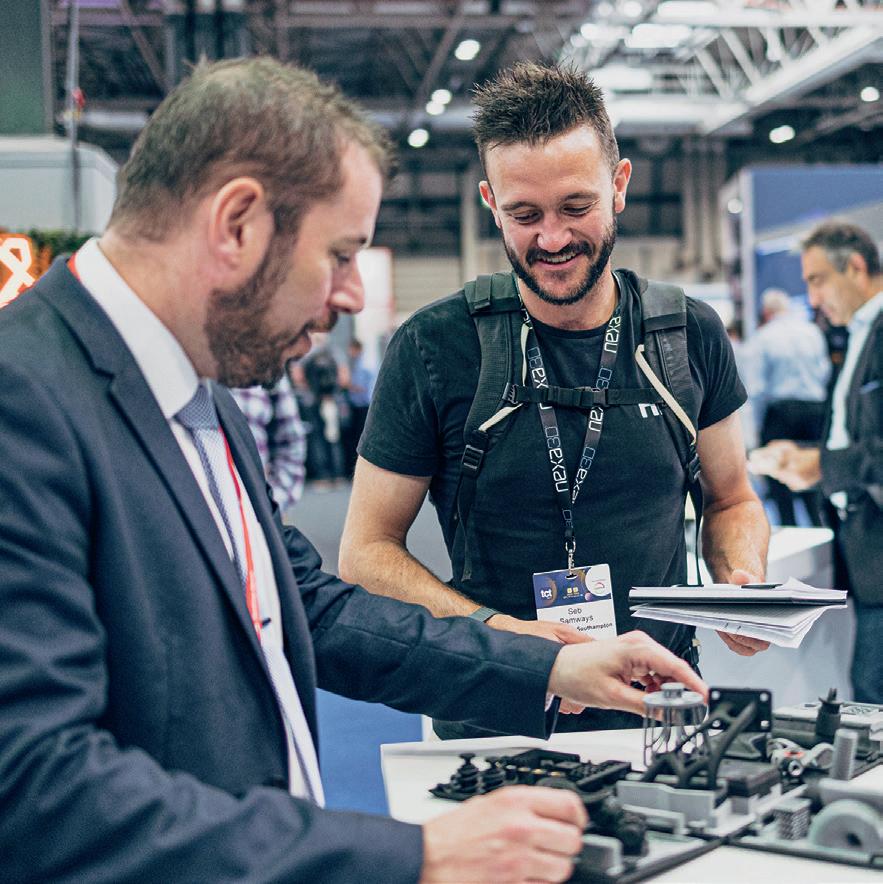
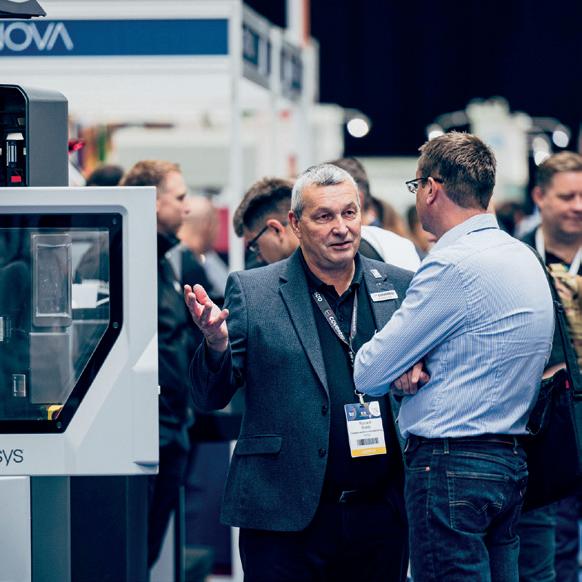
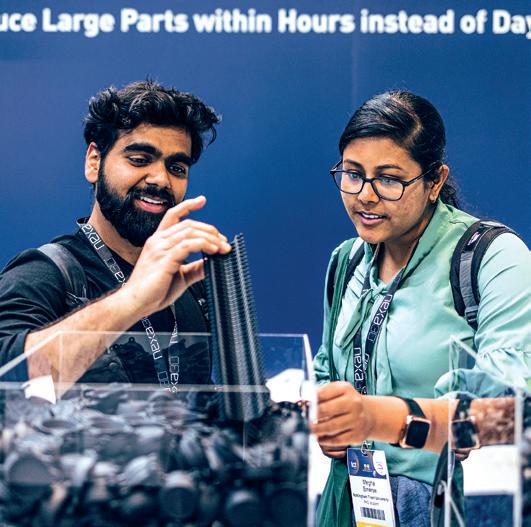



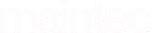
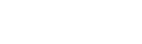
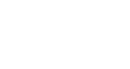
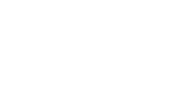
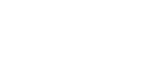
Q: We’re talking a lot in this issue about how AM can bring agility to supply chains. How does MakerVerse fit in? There are two very fundamental different use cases [for AM]. One is, you design a new part, taking into account the design possibilities that additive offers and then you can think about all these topics like performance improvement, weight reduction. So, you start a new project, you design a new component for a new product. Then you can, from the very beginning, design for additive and then you also need to think about industrialization of this part in terms of qualification of the entire process: machines, powders, printing processes, post-processing. The second category is that you have an existing part, you have an existing supply chain, and you want to mitigate your supply chain risks by, for instance, reducing lead times by nearshoring production through additive manufacturing, and then usually your design is an existing design that has been sourced from wherever, and rather than improve the design of the part, you want to mitigate the supply chain situation. The big challenge that I see still for additive here is cost because the original design wasn't designed for additive. So, you usually face higher product costs and you need to trade these higher product costs with the effects you gain on lead times or on not having a part at all, because of supply chain disruptions. And yet, in the second case of supply chain resilience, you still need to make sure that when you convert a conventional part to an additive part, you meet certain properties in terms of material.
What a digital platform like MakerVerse can offer for the first category, the design iterations, it can offer you super-fast access to different technologies and materials, and it can really help you to accelerate development speeds, that's the classical use case. When it comes to the second use case, of on-demand, supply chain needs, […] for every technology/ material we offer on our platform, we have multiple suppliers behind each technology/material combination. So
when you have an on-demand situation, that you need certain parts that run in your supply chains, quickly, on-demand, in unsteady quantities, MakerVerse as a digital platform has the advantage of always having, at any point in time, multiple suppliers qualified for this material/ technology combination so we can react super quickly.
Q: Who is currently using MakerVerse? I can't share names but I can share applications that I think are quite interesting. One category we are currently seeing is development projects. Heat exchangers being one example where companies are currently developing and designing different designs for heat exchangers, trying to see how much they can push the engineering limits in terms of wall thicknesses, cooling hole sizes in the internal structures and they want [quotations] for different designs quickly, they want to know how fast it is until you can really have hardware so that they can test this. […] Another customer category that I see now emerging is potential spare parts on-demand. So, it’s parts that are not necessarily designed for additive from the get go, this is a legacy part and in most of the cases actually, even unsteady demand or potentially even lower volume parts.
[…] We currently see traction from customers that are prospectively interested in converting these legacy spare parts to 3D printed spare parts.
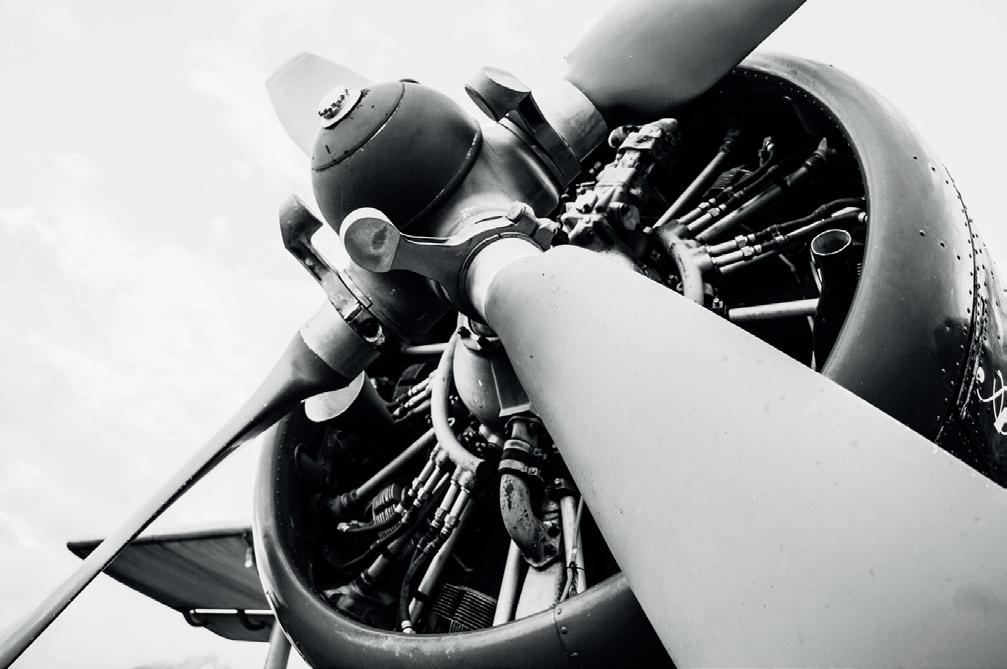
A third category is production aids, grippers for robots and certain toolings or jigs and fixtures.
Q: Siemens is arguably one of the biggest industrial users of AM. What lessons were you able to learn there about adopting the technology?
I spent quite a bit of time in the past years reflecting with the team on what were certain hurdles and what were success factors for Siemens Energy because I believe our global teams have really done a fantastic job of being super effective and focused on driving additive into serial production.
[…] I think an already very commonly accepted success factor is that you need to stop trying to quote the same designs that you optimized for turning, milling, injection molding, and hope that additive can make those parts cheap - it just doesn't work. Usually when you try to copy the same design, and make it by additive, additive is at a cost disadvantage. It's all about design for additive. At Siemens Energy, for instance, you can build internal cooling channels into parts that you could never cast, you could build combustion system components that allow you to better mix air and fuel in a way that you reduce emissions.
In a corporation like Siemens Energy, like any automotive OEM, like any aerospace OEM, additive is a new thing and big companies have a lot of responsibility for the end product. It's very hard to introduce a new method of manufacture and design because you have no long-term proven experience.
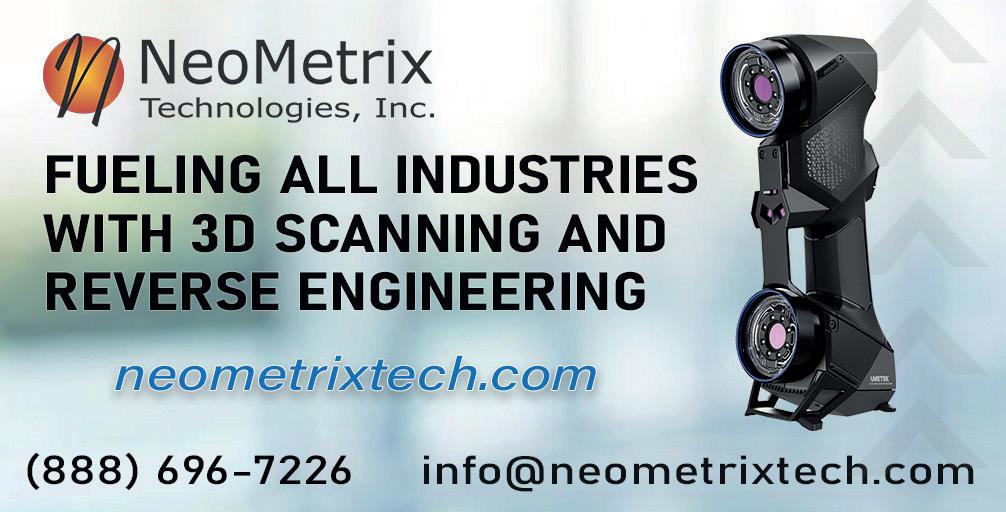
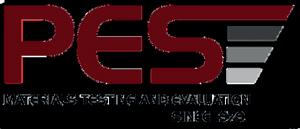
So, it's actually really difficult for an engineering-driven business to say, 'I'll put an additive component on my car, on my plane, on my gas turbine,' because you just don't know how this material or how this part will behave over time. So, you need a certain risk culture. This doesn't mean that you go just completely crazy and put parts you don’t understand on engines, but you need openness on the level of the famous middle management in terms of product owners, component owners, part owners. […] So, you need this risk culture on the mid-level so that you incentivize additive, look at it, and push it against real component applications.
Listen to the interview in full on the Additive Insight podcast: mytct.co/AIPodMakerverse
[Editor: Answers have been edited for brevity and clarity.]
America Makes’ Josh Cramer on how we can build a strong talent stream in AM.
Manufacturing has taken a journey from low-tech high labor to high-tech low labor, which has increased automation, efficiency, and capabilities. Additive manufacturing (AM) is a rapidly growing industry. Many industries utilize AM technologies, including aerospace, medical, automotive, and energy. This is amplified through the investment in technology fueling growth across manufacturing and industry 4.0 technology deployment. Therefore, the development of manufacturing jobs and the need for those jobs will continue to grow further, as well as the diverse skills needed. Manufacturers must have access to qualified talent and, more specifically, talent pipelines, assets, and resources to maintain and grow. The additive manufacturing industry knows this all too well.
America Makes, an organization in which I am privileged to lead the work of education and workforce development, is a dedicated national collaborator and accelerator. The institute’s mission is rooted in the development, maturation, and adoption of additive manufacturing through publicprivate partnerships. One of the most critical threats to that mission – is available human capital. Though a “renewable” resource in almost every community,
manufacturers are lacking the mass of available talent and probably more so the “right” talent. There continues to be a “mismatch” in the industry due to several factors. The factors include new technologies, miscommunications, and myths about their adoption.
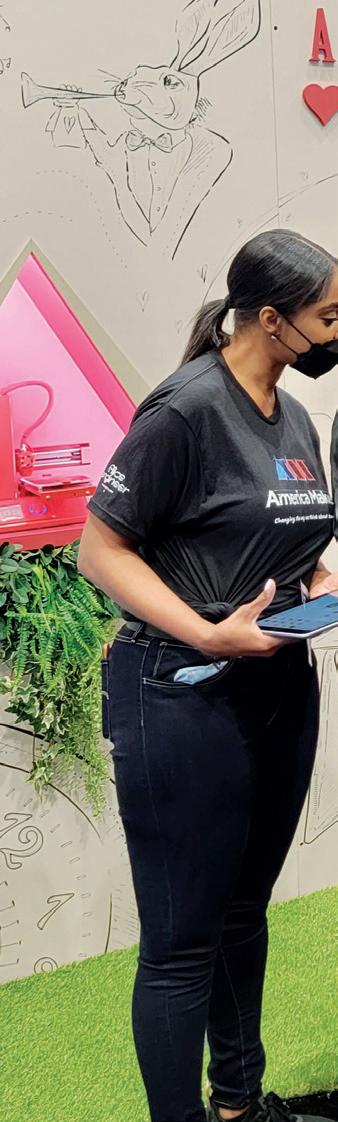
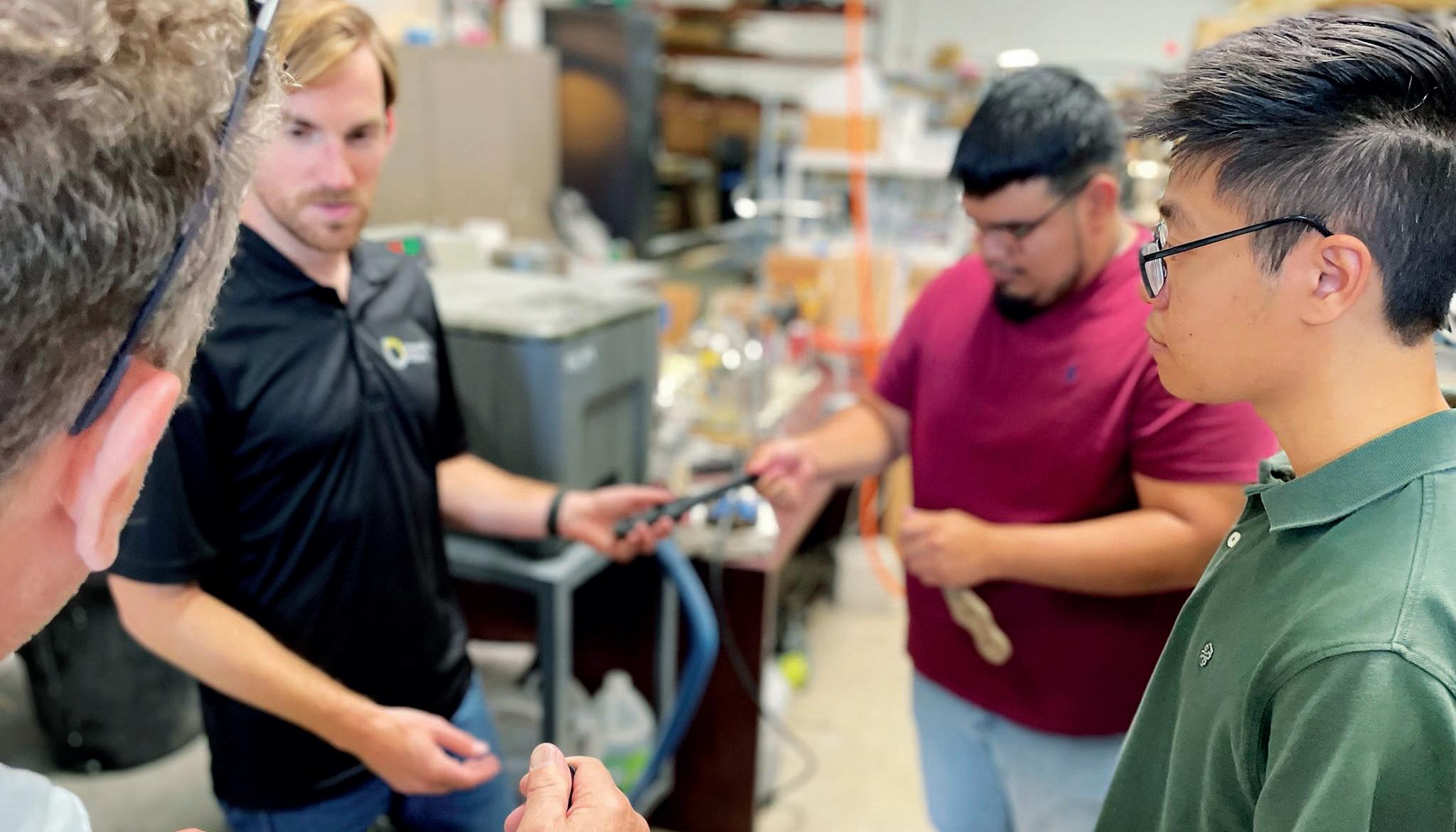
Today’s manufacturing roles are very different than those of the past. One of the most significant critical issues is the awareness vacuum that includes misperceptions of the industry, qualifications, and opportunities these careers possess and provide. I have accepted the challenge of working on navigating and stocking this “K-Grey” talent stream.
Whether you are fishing the talent stream or part of the stream’s vibrant ecosystem, you are not alone. In a true sense, today’s workforce is a
multifaceted common core algebraic equation (for those parents out there). Our talent stream is a reasonably complicated terrain and involves many obstacles and currents. Translation of skills and competencies to include varieties of applicants from all walks of life can be confusing. For example, separating veterans and their competencies and how they translate or relate to civilian sectors. In manufacturing, some of the terminology and rankings are very different. Imagine you were a human resources manager or talent manager and came across someone applying for an open position. On their resume, they listed “Cryptologic Technician.” Would you be able to link their competencies and work experiences from their military time served and specialties? Many may think this must be a new role focused on cryptocurrency or something. This person is an expert in IT systems, coding, communications, and communication systems, can maintain and service equipment, and possibly speaks different languages.
I have always believed that if a tree falls in the forest, it doesn’t make a sound because there is no one there to hear it. Contributing to the awareness vacuum in the manufacturing industry is that many people need to be made aware of the jobs, roles, tasks, and opportunities the industry can offer. Although we still have positions that involve core manufacturing functions, so much of the industry today is different from what it was in the
past. This is especially true when we think about additive manufacturing. Clean, hi-tech spaces with remarkable technologies solving real-world problems for humanity. A little different than Henry Ford’s assembly line. This industry allows an easy ticket through the gate where inspiration and entrepreneurial dreams flourish. Ideas can become a reality at the kitchen table, and problems can be solved in ways never imagined. However, when this tree falls, who gets to hear it? Well, those who can be in the forest. I have witnessed firsthand where some with limited opportunity or with limited experiences cannot see the sign or have access to the forest. I have found potential in many places and walks of life.
Sometimes in a classroom, sometimes in an airport, sometimes in a grocery store, or even out to dinner. Invite those you feel would be great additions to our industry. Share a business card or a piece of your story. Let’s ensure we don’t just make flawed assumptions that their experiences match ours and that their pathways offer the capacities. In many instances, we will find that their journey may have just started without a map or possibly with an outdated map. We must first invite them, ensure they
feel welcomed and wanted, and, most importantly, realize the prospect of what it is and can be. The most vibrant talent streams are the diverse ones.
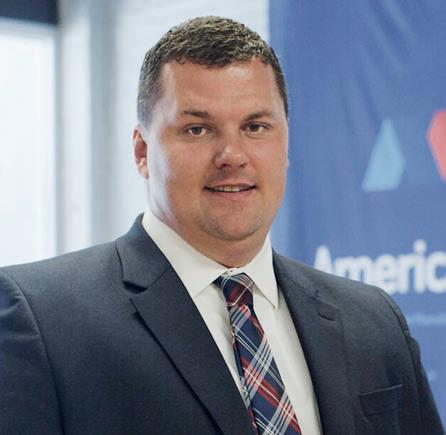
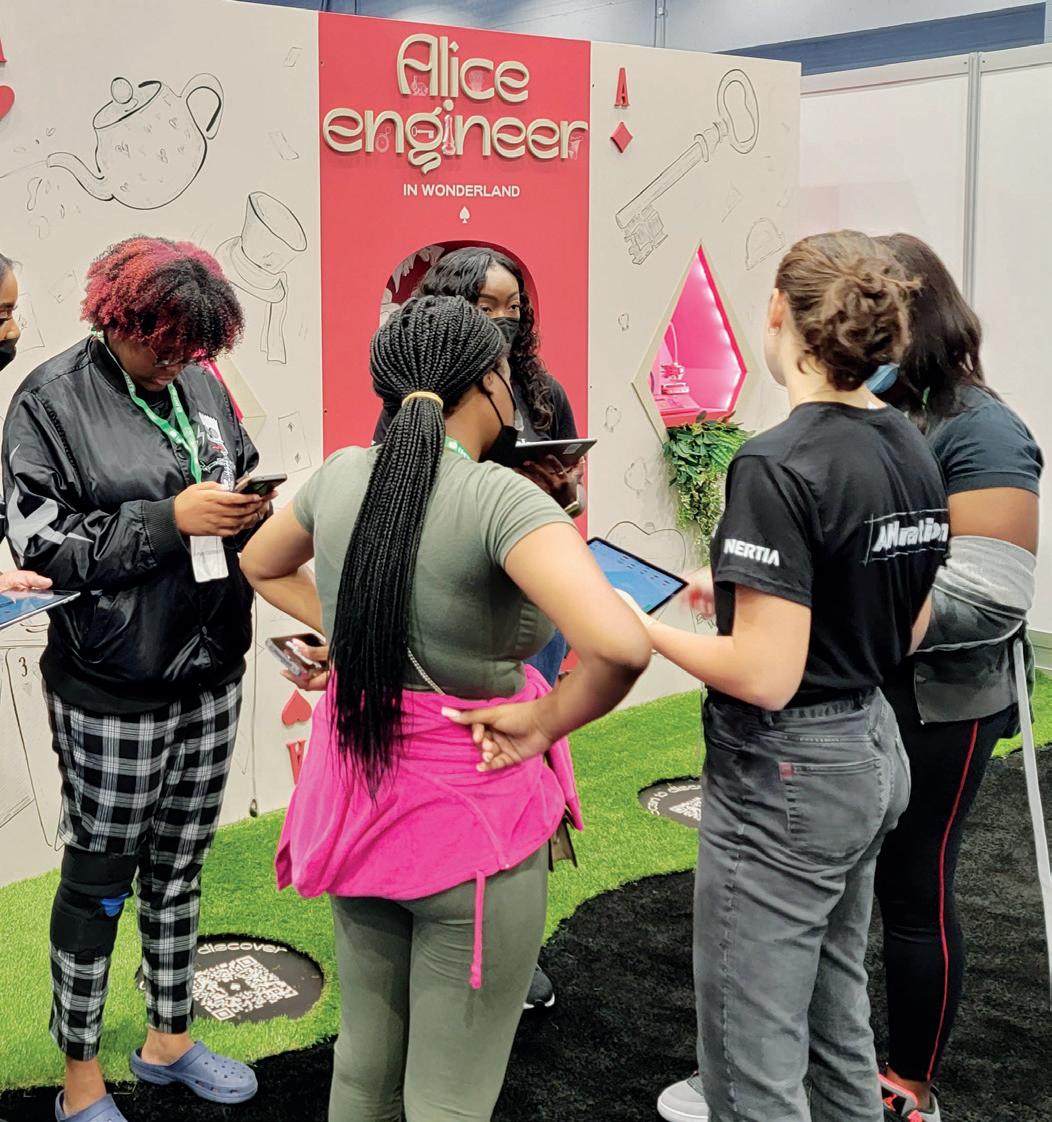
On the first day of the fishing season, anglers pack into the best spots where they know the potential is considerable to catch their limit. Successful companies have employed this same thought in talent. They know the good fishing spots! They have worked with local ecosystems of academia and community-based organizations to recruit and hire adults and inspire youth. It is complicated by diverse generations in the talent stream. We have Gen X, Millennials, or Gen Z, along with Gen Alpha, on the doorstep. Although everyone is different, some of these trends within these generational differences bring some great possibilities to all. Generations in the past may have led with a “live to work” mentality. This mentality was anchored by their lives revolving around their work schedules. In contrast, today’s workforce is more of a “work to live” mentality. In this mentality, they are more focused on using work to do, buy and experience the things they really want in life.
So how do you know the odds of a big catch? Validation is a critical key for the industry to assess strength in the talent stream. One essential tool in the toolbelt is industry-backed programming and credentials. For example, America Makes anchors a body of knowledge built with industry and the defense sectors with a wide range of partners. It maintains the ability to ensure it is accurate and aligned. Third-party objectivity exists when we anchor new learning assets to the body of knowledge, and its alignment is promoted to members, partners, and stakeholders. A key component is third-party validation throughout the process and several working groups from the industry to set standards, bodies of knowledge, frameworks, and even assessments. One critical phase in the process includes both a knowledge and performance-based assessment. Doesn’t it make more sense to go fishing where you know the water is stocked with a trophy catch?
Share your secrets. All of us in the industry had a spark. We all had that moment when that spark of inspiration emerged as a blazing fire that propelled us into the industry. For some, it was a parent or family member. For others, maybe an educator or instructor. The talent gap, whether skills or awareness, can only be solved by us. We need to drive the narratives and the activities. We need to be the voice in local classrooms, sharing our stories.
We need to be the ones who can drive innovation at work and inspire by volunteering, contributing, and sharing.
We need to be the ones who ensure that this message reaches every learner, how they learn, and where they know, regardless of their situation. Talent is something that everyone has inside, but opportunities can be determined by circumstance. The talent stream runs right through the village. Although many stand on the banks fishing, you could be the one with the correct tackle and bait. So, join us.
FORMNEXT LAUNCHES
A selection of key hardware, materials and software announcements
MATERIALISE ADDS NEW COAM TECHNOLOGY PARTNERS
NEW HP JET FUSION MACHINE ANNOUNCED FOR 3D PRINTING WHITE PARTS
HP announced the launch of its HP Jet Fusion 5420W 3D printing system to facilitate the additive manufacture of white parts. A partnership with DyeMansion allows these parts to be dyed.
“There are some applications which required lighter tones, bright colors, this was the demand from the market, especially in healthcare, for example, in surgical guides,” Francois Minec, HP’s Global Head of Strategy, Personalization & 3D Printing told TCT. “So, we're covering this gap. We're going beyond that because our solution has a much better UV resistance and the white that you can see is really a very nice color, whatever the angle.
This machine is said to provide all the benefits of HP's Multi Jet Fusion technology, initially commercialized via the 4200 and 5200 Series, and is geared towards automotive, consumer goods, healthcare, and industrial markets. Early customers using the new system to produce innovative white applications include DI Labs, Prototal Industries, and Weerg.
“The response is huge. We're really happy,” Minec added.
Full story: mytct.co/HP5420W
Materialise announced seven additional technology partners on board its CO-AM platform including Trinckle, Twikit, Additive Marking, SLM Solutions, AMT, DyeMansion, and PostProcess. CO-AM allows users to access a range of software tools from Materialise and third parties, enabling AM operations to be planned, managed and optimized. When CO-AM was first announced, Materialise said the platform will help manufacturers address the ‘untapped potential’ of AM for serial manufacturing and mass personalization.
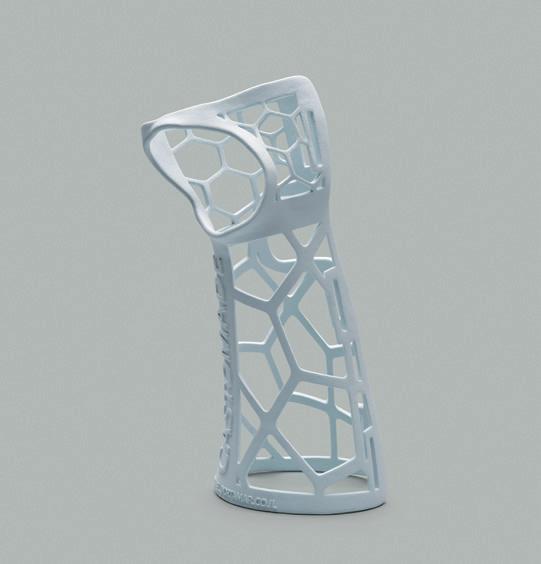
CTO and EVP of Materialise Bart van der Schueren spoke to TCT about what the new partners will bring and how AM companies have a responsibility to learn from each other.
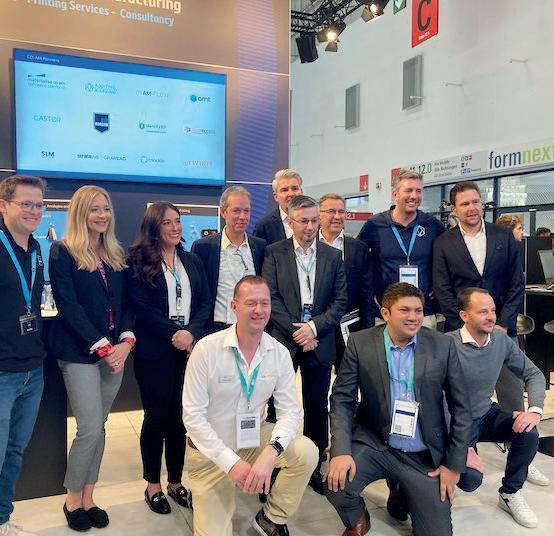
“Materialise is really opening up our ecosystem for third parties,” van der Schueren told TCT.
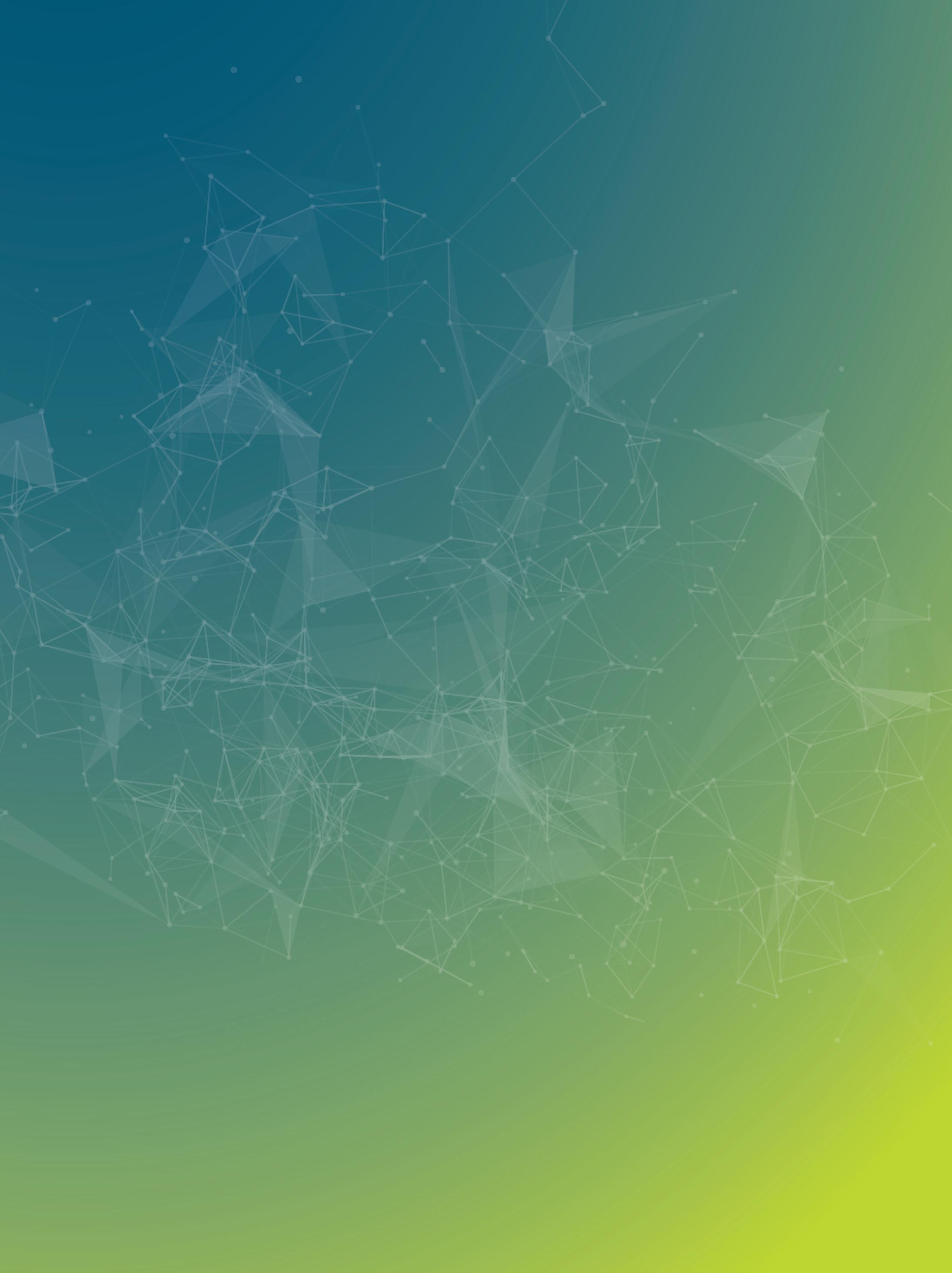
“We recognize that we are able to not develop every single step. If we would be able to do that we would not have the time because this industry is needing solutions today. Not tomorrow, not next year. That’s why we opened up CO-AM by design, so the whole architecture of the system is an open system with API’s and allows us to have partners that log on to the CO-AM platform.”
Full story: mytct.co/co-am
6K ADDITIVE LAUNCHES
ULTRA-LOW OXYGEN TI64
During Formnext, 6K Additive announced the immediate availability of ultra-low oxygen titanium 64 with a parts per million (PPM) rate of 500-700.
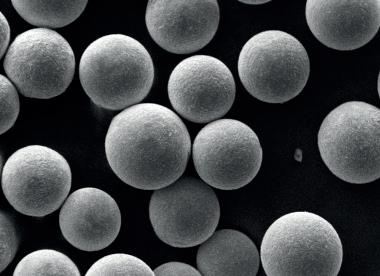
The company says this announcement 'greatly surpasses' what is available with today's AM capabilities, and provides customers with a high-quality material that enables low oxygen levels at production scale, and the ability to
process additional jobs through their 3D printers without sacrificing quality.
“The global supply chain crisis has caused volatility in the market for metals like titanium which leads to uncertainty in costs and availability. Our ability to provide low-oxygen titanium at production volumes enables our customer to stretch their powder use well beyond what’s available today, essentially increasing value and lowering costs for their Ti64 parts,” said Frank Roberts, President of 6K Additive.
Mark Barfoot, Director of AM programs at EWI, added: “When we talk to Ti64 users in the market, quality always is top priority with costs following a close second. Increasing the value of their Ti64 purchase by extending the life of the powder with more uses is a definite win.”
Full story: mytct.co/6KTi64
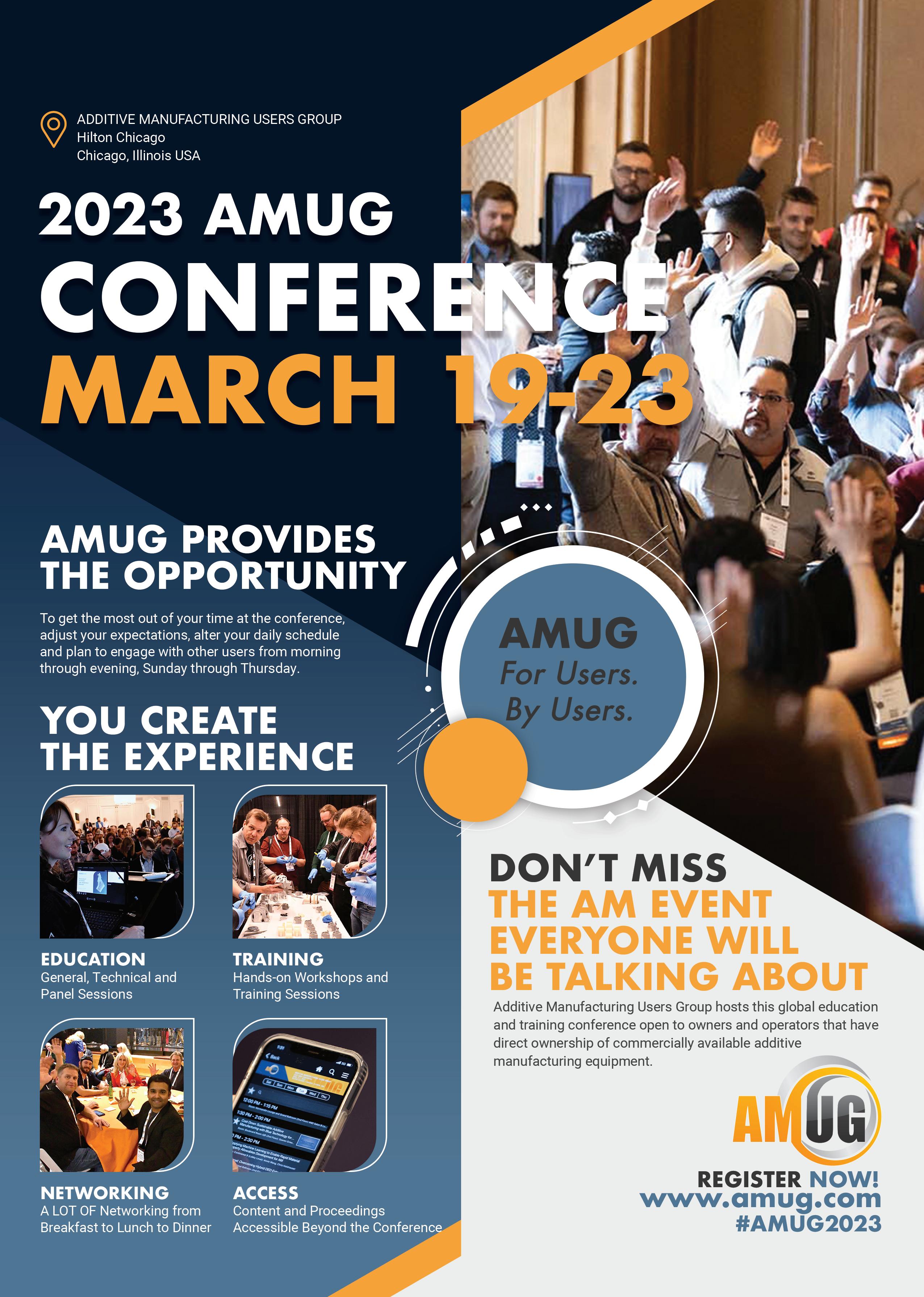
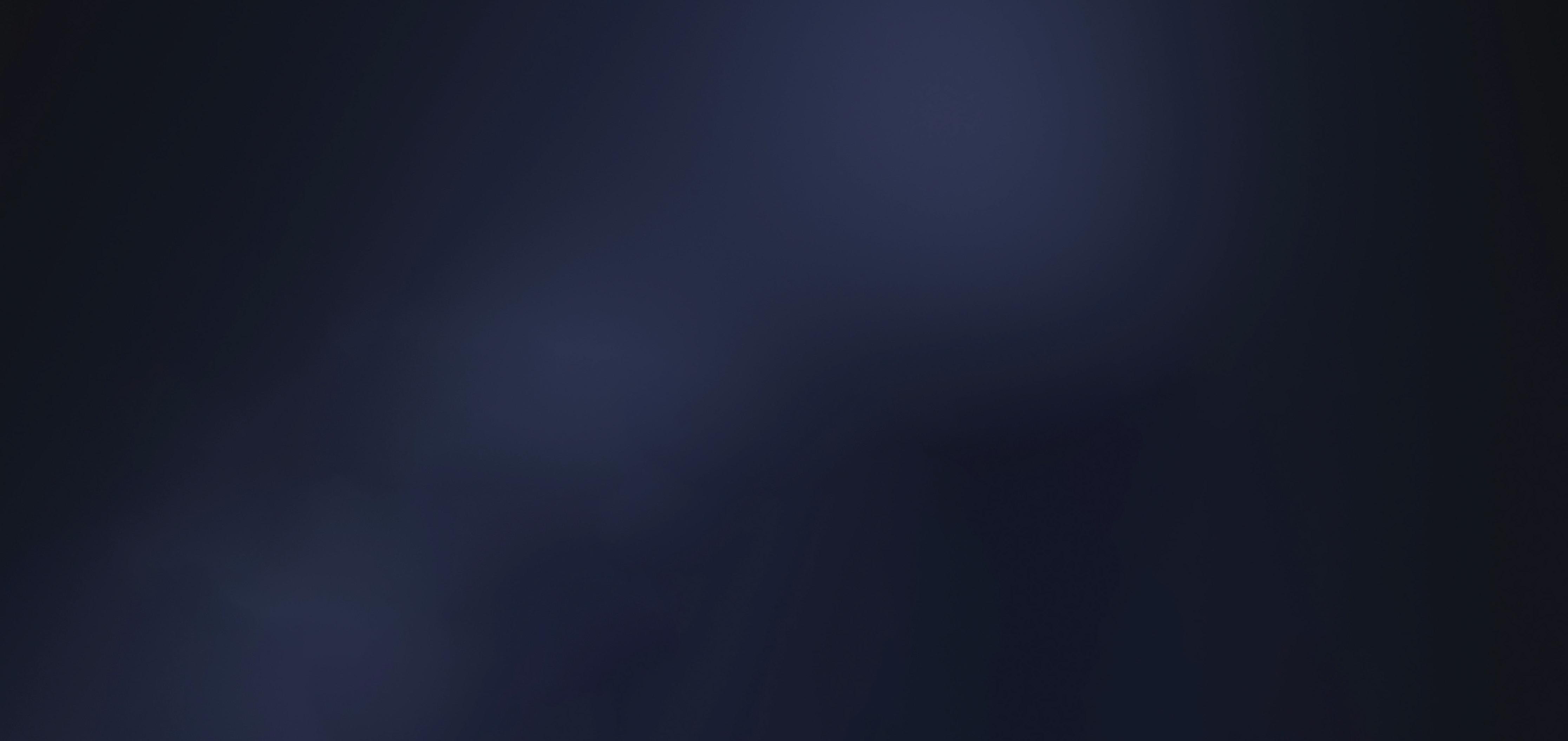