
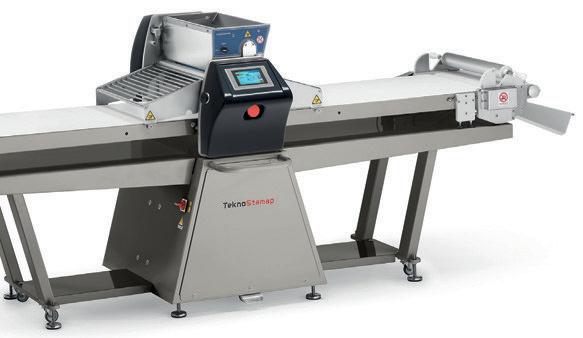

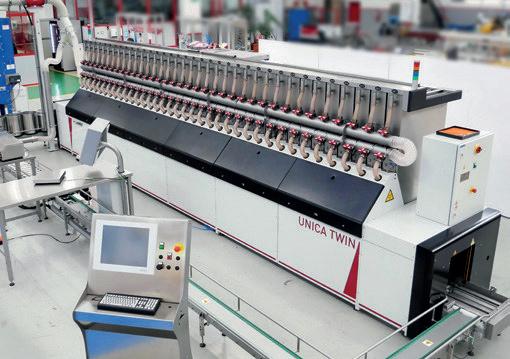
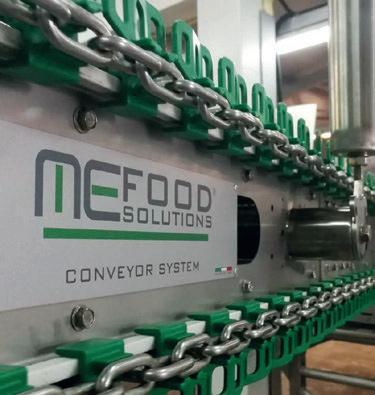
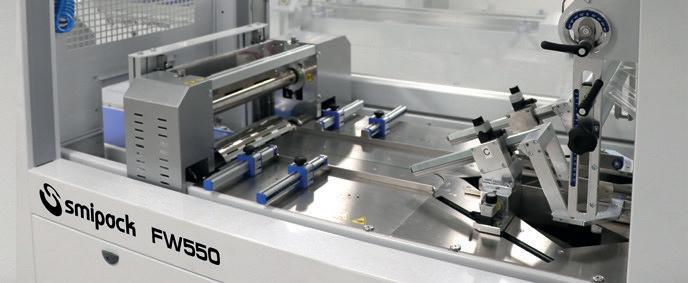
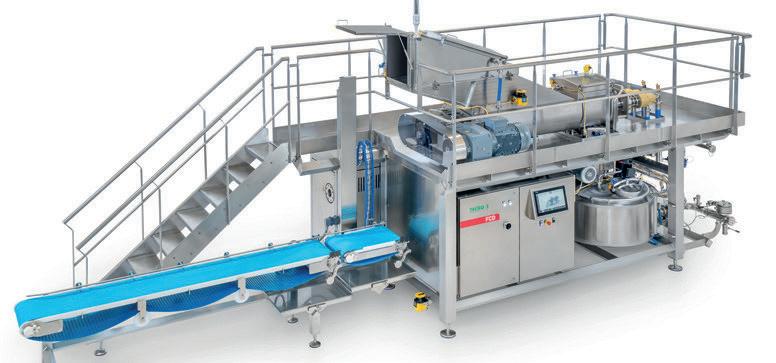
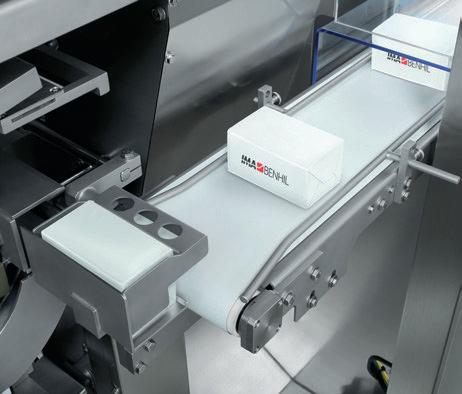
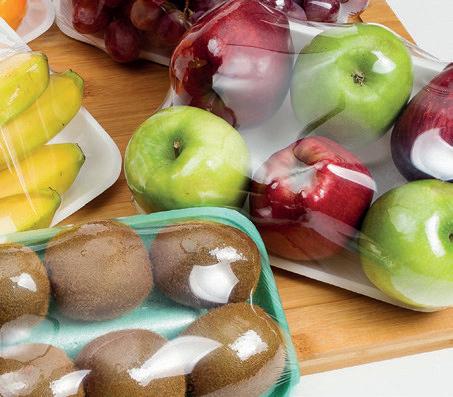

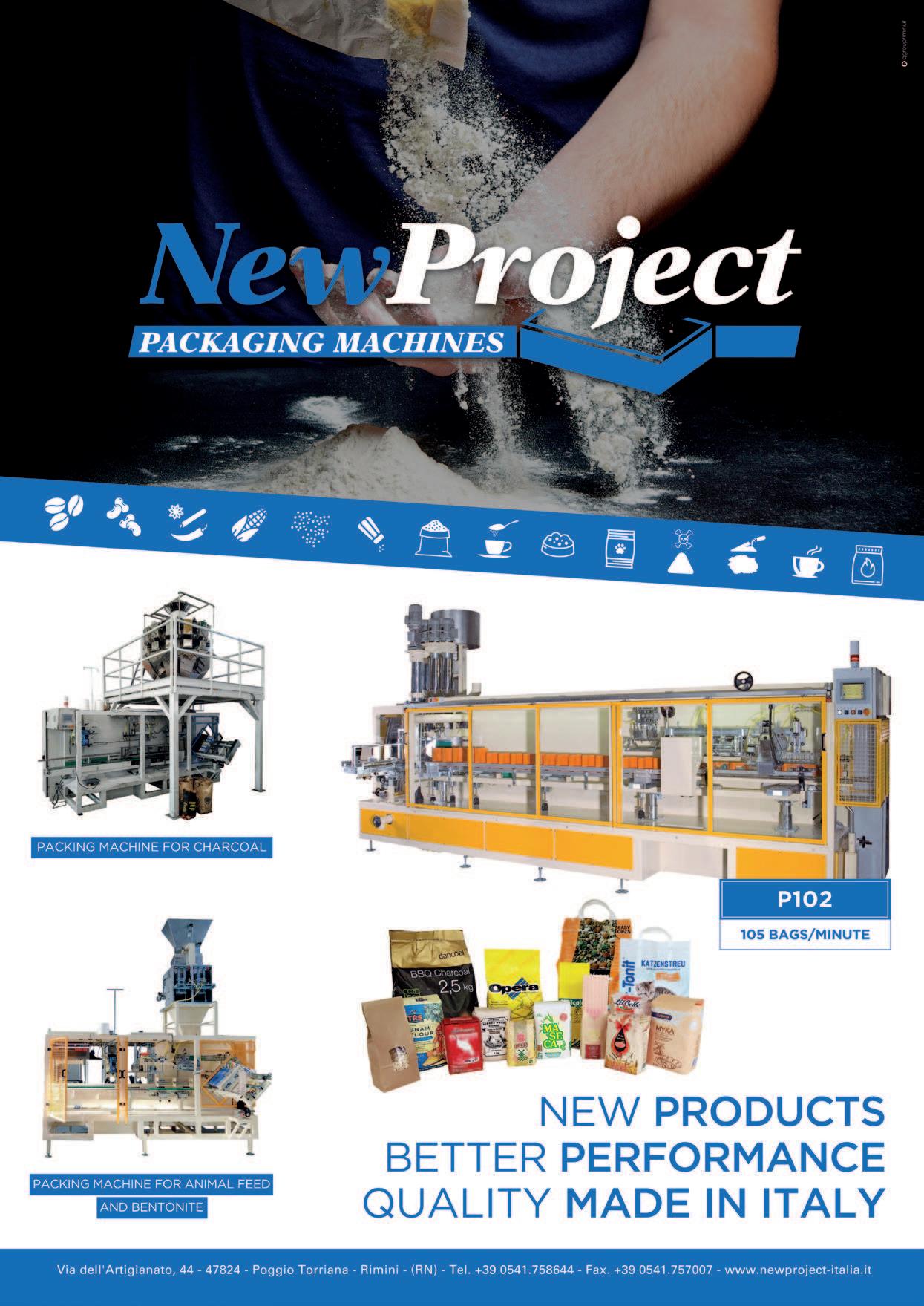
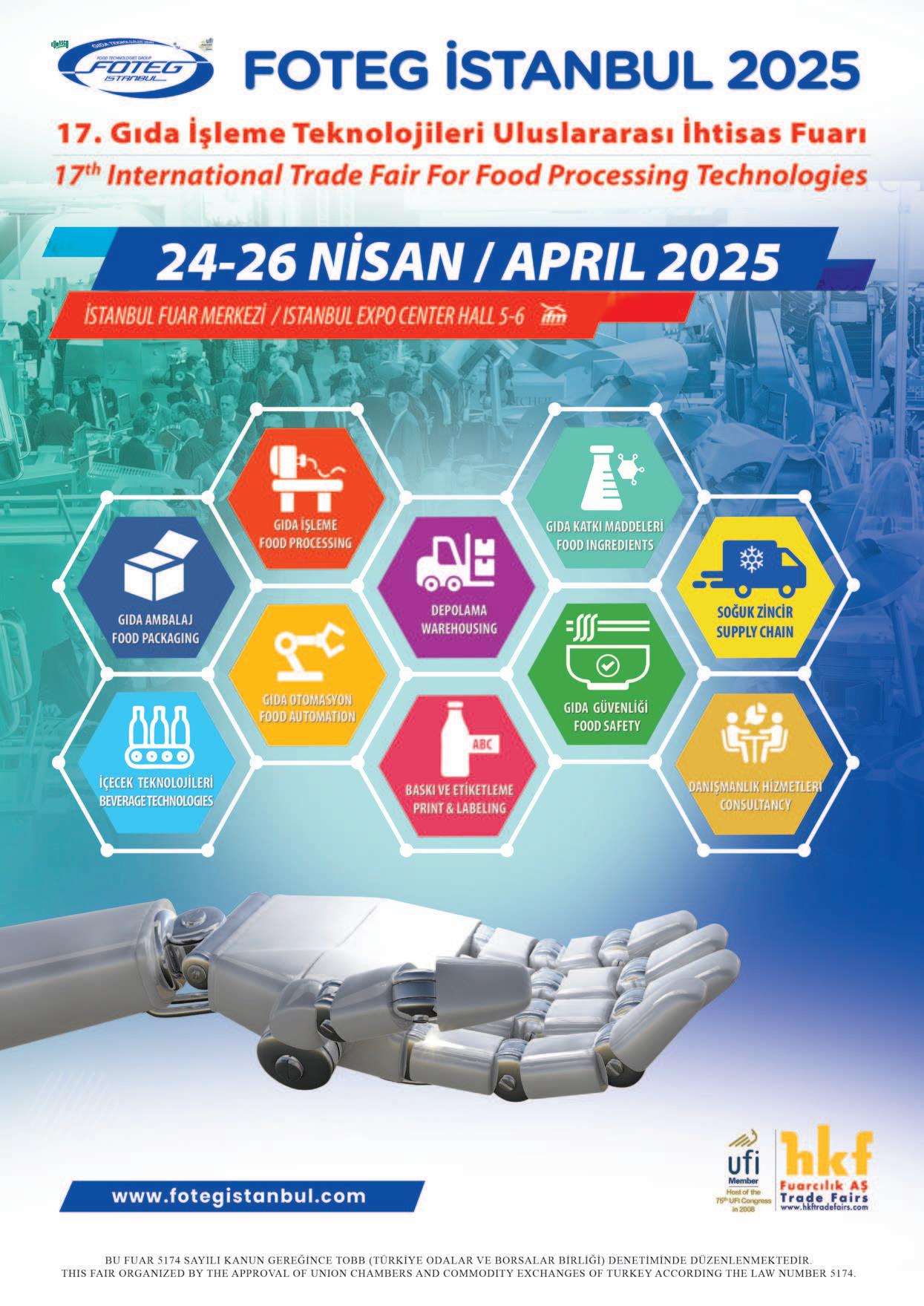
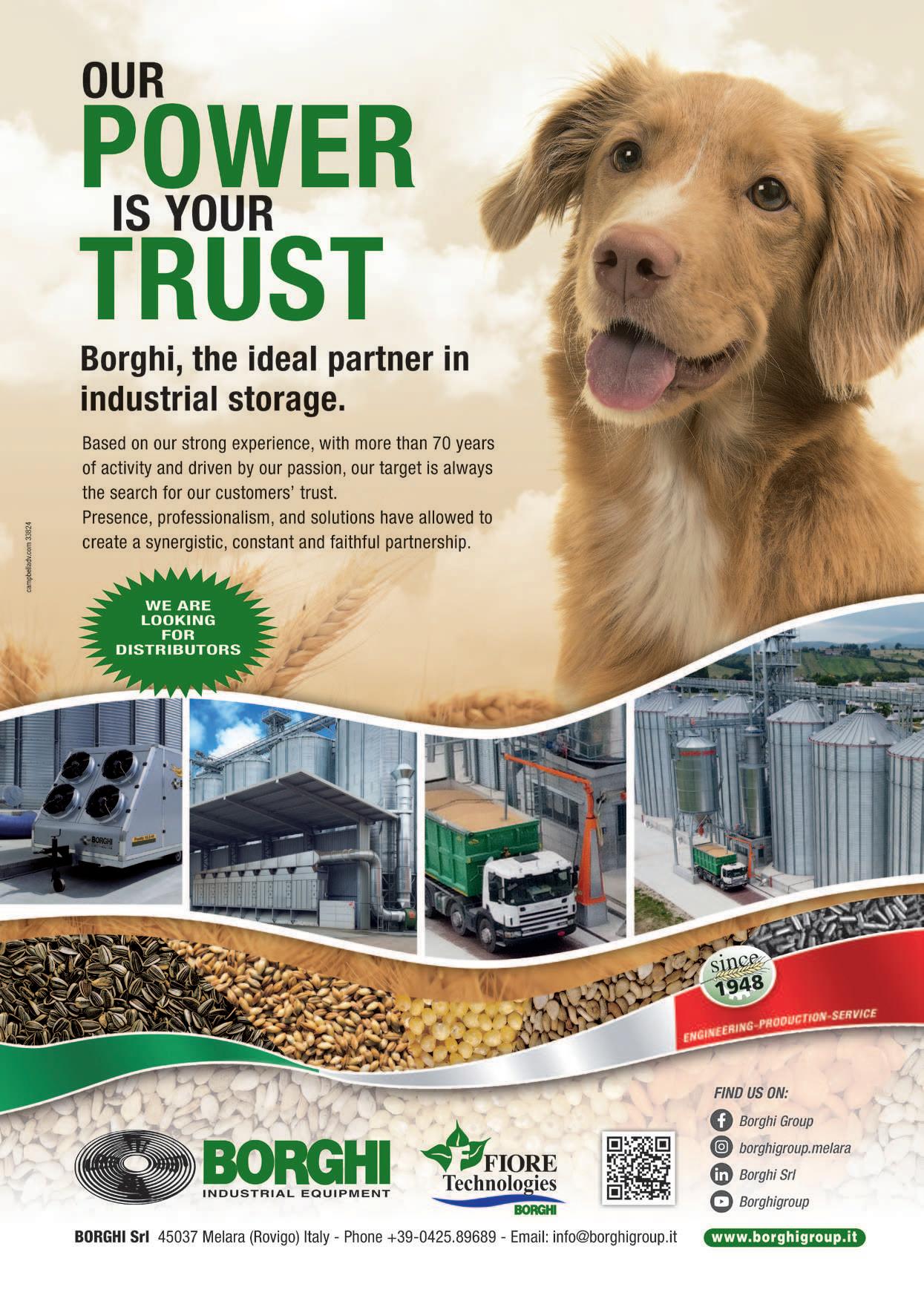

Via Mantova, 65 - 43122 Parma, Italy
Tel. +39 0521 490211 - Fax +39 0521 243701
info@zacmi.it - www.zacmi.com
ZACMI: Advanced solutions for the food and beverage industry
ZACMI is an Italian industrial company based in Parma specialized in the design and production of filling and seaming machinery for the food industry. The Company, founded in 1954, has a solid history of success in its field.
ZACMI’s mission is to offer innovative and technologically advanced solutions to satisfy the customers’ needs and improve production efficiency.
The strength of ZACMI’s highly skilled team lies in its vision into the future, engaged on a daily basis to provide the highest-level service for its customers.
Machinery and solutions
ZACMI has developed top quality solutions in terms of applied technology, as a result of constant long-term research and testing with the help of a highly specialized R&D department.
Due to its expertise in manufacturing filling and seaming machinery, ZACMI also has the competence to design and produce entire processing lines.
Filling
ZACMI offers a vast range of ultramodern filling machinery.
ZACMI Piston Fillers are designed to accurately dose liquid or semi-liquid ingredients, guaranteeing the uniform distribution of the product with an extremely high filling precision and the total absence of dripping, using a patented product dosage method.
ZACMI Vacuum Fillers ensure an airtight filling, thus preserving the products’ freshness and quality. This filler offers the perfect solution in topping up containers that have been pre-filled with solid product or for the total filling of thick products into the containers.
ZACMI Telescopic Fillers are ideal for a rapid and accurate filling of bottles, cans and other containers, reducingwastetoaminimumwiththemaximumefficiency.
The special design and the choice of specific instruments make this Telescopic Filler reach the highest standards in filling accuracy to satisfy all customers’ needs.
ZACMI Monoblocks perfectly integrate the rinsing, filling and closing phases into a single compact solution, to guarantee a higher production yield, whilst optimizing space.
Seamers
ZACMI also distinguishes itself for its innovative seaming solutions. The specific design facilitates cleaning and maintenance, reducing handling costs, with a completely washable Wash-In-Place system, the ZACMI Clean Design Seamer satisfies the strictest hygiene standards set by the food industry.
On the other hand, ZACMI Vacuum Seamer exploits a new technology that preserves the integrity of the filled product, eliminating the risk of contamination and extending its shelf life.
Furthermore, ZACMI seaming machines offer a wide flexibility of configuration, adapting to the specific needs of the customer, guaranteeing a high-quality productivity. Processes
Apart from filling and seaming machinery, ZACMI also supplies complete solutions for crucial food industry processes, such as pasteurization.
The machines are designed to provide an accurate thermal disinfection, eliminating harmful bacteria and micro-organisms, without jeopardizing the organoleptic characteristics of the product.
ZACMI’s avant-garde technology application, ensures the maximum energy efficiency and conformity to the strictest food safety standards.
ZACMI offers high quality machinery, but also engages in providing a full and reliable service to its customers.
The ZACMI team of experts, supplies technical support, personalized consultancy and a complete range of after sales service assistance, including preventive maintenance and spare parts supply.
This strongly customer-oriented approach, assures that ZACMI customers obtain a continuous and reliable support, saving time and workforce.
ZACMI has continued for decades to satisfy the requirements of the sectorial companies worldwide, with its innovative solutions, competence of its work team and constant commitment to customers with its after sales service,improvingproductionefficiencyandinternationally establishing its place as a trustworthy point of reference.
For further details please visit the website:www.zacmi.com
Via dell’Artigianato IV^ Strada, 6 - 35020 Candiana (Padova) Italy Tel. +39 049 95 99 935
info@zmatik.com - www.zmatik.com
Z.matik, cutting-edge technology for bakery and pastry shops
Z.matik has forty years of experience in the production of machines for bakeries and pastry shops, in particular of manual dough sheeters, croissant groups, work tables, planetary machines and cutting rollers in Aisi 304 steel.
From this year the company began a real revolution, but always maintaining tradition. It starts with the manual table top and floor standing sheeters that are much more compact and ergonomic.
The modern style and cutting-edge materials are captivating even the most demanding customers.
The mechanics maintains some key points, but is also renewed, allowing the customer less maintenance and greater resistance. The goal is to
make this range even solider and more intuitive, thus facilitating the operator especially in routine cleaning.
The new dough sheeter is good for multiple applications: from pastry shops to hotels, catering, etc. The existing options have been made even more advanced, for example the thickness detector, which allows you to calibrate the lowering of the calibrating cylinders to exactly check the thickness of the dough. Now this accessory counts a lot of digital display larger, in color and very accurate in reading.
Z.matik is certified according to the TÜV SÜD - ISO 9001 quality system and complies with all standards for food contact. Finally, each product is sanitized before packaging, in order to guarantee the customer greater safety of use.
Piazzetta Osvaldo
de
Bortoli,
Vimco, your unique partner for the secondary packaging
The company know-how and the ability to provide custom-made solutions, let Vimco be a turnkey partner for complete lines. Vimco, born in 1980, is a vibrant, dynamic and flexible company whose core business focuses on the engineering and manufacturing of complete lines in the secondary packaging, end of line equipment and robotic solutions for the food and non-food industries.
All machines’ components are manufactured and assembled in-house in order to allow an efficient, well-controlled, internal work-in process flow aimed to supply reliable and durable solutions to customers worldwide.
The company’s know-how and ability to customize tailor-made solutions and turn-key systems represent a “unique” asset customers can take advantage of, making Vimco a reliable, qualified packaging partner.
An experienced technically skilled team leads Vimco to be an eclectic, versatile company, capable to offer customers a good variety of top-class solutions across all food market segments with an after-sales service up to the tasks and customers’ expectations. Vimco mainly operates in food sector,especially bakery,confectionery,dairy,ready meals, grocery,snacks,petfoodandcoffeebusinesscategories.Themachines’portfolioincludes forming, closing, lidding, cartoning, sleeving, robotic loading systems, monoblock units, end of line and complete solutions.
The company is riding sustainable business practices and represents a good venue to help customers to pursue automation in an eco-friendly environment.
Why Vimco?
• Wide range of standard and customized machines for cardboard packaging.
• Innovative systems.
1 - 22073 Fino Mornasco (Como) - Italy Tel. +39 031 92 95 39 vimco@vimco.it - www.vimco.it
• High flexibility in designing and project management.
• Machines studied and developed in relation with the features of the product/packaging.
• Customer-focused and service-focused orientation.
• Immediate after-sales service.
• Preventive maintenance service of the machines to guarantee the proper operation in their entire lifespan.
• High-quality products and performances thanks to the use of high-tech components.
• Highly skilled and specialized R&D department.
Via Vivare, 425/B - 47842 San Giovanni in Marignano (Rimini) Italy
Tel. +39 0541 955276
info@universalpack.it - www.universalpack.it
Advancing sustainable solutions for singledose packaging
Universal Pack, a leading manufacturer of packaging machines and automated lines for single-dose solutions, promotes environmentally conscious practices in the food industry. Their scientific approach ensures packaging technologies are compatible with compostable and recyclable laminates, maintaining efficiency and reliability.
Fortheplanet:Compostableandrecyclablepackaging
Universal Pack’s relentless research has led to optimized machinery design for packaging with compostable, recyclable, and recycled laminates. Using Life Cycle Assessment (LCA) to measure environmental impact, our holistic approach includes every step of the packaging machinery production process. Collaborating with global film suppliers and major multinational companies, Universal Pack provides turnkey solutions for the production of sustainable packages.
Global partnerships
To achieve the best results in sustainable packaging, Universal Pack has been working hand in glove with international film suppliers, multinational customer corporations and University research centers. This tightknit collaboration allows each stakeholder to contribute their expertise and benefit from the know-how of others to achieve the desired outcome. For example, the customer brings their initial requirements, the film supplier develops a compostable or recyclable laminate, Universal Pack
tests it on its machines in order to optimize the packaging process, and the University contributes their know-how at every stage of this process.
Universal Lab
Each project begins with a careful personalized analysis of customers’ products and laminates, in order to optimize the design, efficiency and reliability of the machinery. For over 30 years, Universal Pack Laboratory has been lying at the core of project management and design review, as the whole engineering process is always backed up by science principles used to meticulously analyze various aspects. As a result of many years of experience, Universal Pack is not only
packaging experts at your service, but also a team of experienced packaging scientists.
The company
Universal Pack, with over 50 years of experience and 8,000 systems in 150 countries, is a leader in designing VFFS machines and automated lines for single-dose packaging, such as stick-packs, 4-side-seal sachet and cartons.Currently,the company is focusing on packaging with compostable, recyclable, and recycled materials, and integrating systems into Industry 4.0 environments.
Via Vivare, 425/B - 47842 San Giovanni in Marignano (Rimini) Italy Tel. +39 0541 955276 info@universalpack.it - www.universalpack.it
Tekno Stamap designs, develops and manufactures dough-processing systems and machinery for bakery and pastry industries.
Founded in 1982 by Antonio Baldovin and Remigio Dante, Tekno Stamap straightaway stood out in the market of mechanical equipment for the food industry; over the years, it has enriched its offer with dough sheeters (manual or automatic) and planetary mixers, still today constituting the core of the company’s production. More recently, Tekno Stamap’s range of products has been further integrated with croissant machines and make-up lines for bread, pizza and pastries. This is what allows Tekno Stamap to provide its final clients (mainly resellers and producers from large restaurant services) with the dough-processing equipment required by their activities.
Tekno Stamap manufactures internally almost all machine components, thereby actually establishing an autonomous production line: the design, development and assembling phases are entirely carried out within the company’s plants with significant advantages, among which the possibility of maintaining a highly competitive quality-cost ratio. Innovative design, state-of-the-art technology and top-notch
quality are the factors completing the offer of a by now global brand
For more than 3 decades now, Tekno Stamap has been writing its own history of success, both at a national and international level. Born as a Vicenza-based firm, it has nowadays become an affirmed global reality, with branches in Europe, Japan, South Africa, Asia and North and Latin America. The client can find in Tekno Stamap a dynamic, autonomous, reliable, flexible, and technologically advanced commercial partner and a thriving business as well.
Tekno Stamap has gained a significant share of global market thanks to its expertise, state-of-the-art technology and attention to the client’s needs. The company’s mission statement is to constantly improve the offer of appliances, all the while maintaining high quality and technological standards and investing in research and development of the production process. Tekno Stamap aims at becoming an international benchmark in the sector of professional doughprocessing machinery for the bakery and pastry industry.
Tecno Pack means technology, experience, service in flow and pillow-pack packaging, primary and secondary.
Market leader Tecno Pack provides all the technology your company needs: from small electronic packaging machines with manual loading, right to complete plants.
Skilled trade team, experienced technical department, in-house production of mechanic parts, accurate material selection, excellent production team and after-sales assistance for the world over, enable Tecno Pack to propose machines and plants that are thought as “tailored suit” and broadly recognized as cutting-edge technology by Gruppo Barilla, Nestlé, Pavesi, Kraft, Baxter, Chipita, PepciCo, to name some but a few.
Speed, flexibility, modified atmosphere, shelf life, integration of the packaging into the corporate system, are the issues that Tecno Pack deals with enthusiastically every day and that gives it new evolution leaf of live.
IFP Packaging is a sound benchmark in heat-shrink film wrapping technology. At the end of 2011, it became part of Tecno Pack SpA group, thus beginning a new course of greater technological, commercial and industrial development.
Electronic continuous wrapping machines built on fully cantilever structures, and high performance, high reliability, sanitization, versatility and customization are just some assets of IFP Packaging’s offer.
Automatic loading systems, bundling machines of any size, complete end of line systems are fully customized by the company’s skillful and versatile technical department. Adjusting the state-ofthe-art technology upon customer’s peculiar requirements is IFP Packaging’s main goal. Moreover, the company also proposes the market its sturdy and versatile wrapping machines, standard built, for a quite interesting quality-price ratio.
General System Pack continues evolving and implementing its range of machines and automation flow-pack dedicated. 30 years of continuous development have turned this company into a world leader able to study, produce and install machines from horizontal single flow-pack packaging to fully electronic machines and complete packaging lines for any kind of product.
General System Pack introduces its GSP 50 EVO model to package a broad range of products thanks to full control of brushless motors and reduce time for change of format down to the minimum.
High speed, controlled atmosphere, full automation of the entire primary, secondary and end-of-line cycles are carried out ordinarily by applying the highest state-of-the-art mechanical and electronic technology.
Via Lago di Albano, 76 - 36015 Schio (Vicenza) Italy
Tel: +39 0445 57 56 61 - Fax: +39 0445 57 56 72 comm@tecnopackspa.it - www.tecnopackspa.it
Via Lago di Albano, 70 - 36015 Schio (Vicenza) Italy
Tel: +39 0445 60 57 72 - Fax: +39 0445 58 03 44 sales@ifppackaging.it - www.ifppackaging.it
Via Lago di Albano, 82 - 36015 Schio (Vicenza) Italy
Tel: +39 0445 57 62 85 - Fax: +39 0445 57 62 86 info@gsp.it - www.gsp.it
Via Mastri Cestai, 2 - 12040 Corneliano D’Alba (Cuneo) Italy
Tel. +39 0173 61 05 64 - Fax +39 0173 61 94 94
tecno3@tecno-3.it - www.tecno-3.it - www.beantobarmachine.com
For two generations, TECNO3 has been technical partner of the best confectionery companies
• Production of fat creams (from dosing and mixing to the finished product)
• Continuous dosing and mixing (for the characterisation of chocolate, compounds, fat creams and pastes)
TECNO3 is an Italian entrepreneurial reality, a reference point for technological innovation in the confectionery industry to provide complete industrial solutions for:
• Cocoabeanprocessing (fromcleaningtoalkalinisation)
• Nut processing (from cleaning to dried fruit paste)
• Chocolate production (from dosing and mixing to conching)
• Melting of loaves of fat, anhydrous and hydrated butter, chocolate and cocoa mass
TECNO3’s competitive strength is research and development, based on a deep understanding of production processes to continuously increase the value of its plants, focusing on the needs of the food industry to design, engineer and deliver turnkey plants based on new technological knowledge.
Headquarters: Tecno3 S.r.l. – Corneliano d’Alba – Italy
TECNO3 optimises business performance for long-term value creation and more efficient process management:
• Reorganisation of the production layout in a Lean Transformation path to significantly reduce delivery times
• Strengthening the Tecno3 team to ensure a high rating thanks to industrial know-how and the ISO 9001 certified quality system.
• Integration of Lean Thinking principles to continue to raise the level of products and services offered, maximise plant performance and achieve excellent results
• Use of SAP software, a technology that fits seamlessly into business process management to achieve a significant increase in production efficiency
TECNO3 is committed to improving processes and enhancing the characteristics of the final product:
- Ensuring plant reliability
- Significantly reducing the amount of product required for recipe changes
- By streamlining processes thanks to continuous processing
- Facilitating the disassembly and sanitisation of equipment
- Optimising space with company-wide solutions
- Reducing consumption and promoting energy savings
- By providing a test area where the production cycle can be reproduced
- By respecting the nutritional and organoleptic properties of raw materials through to the final product
- Favouring increased and optimised productivity
Every day TECNO3 works to create innovative, inspiring and enjoyable technologies for everyday life around the world; it operates and exports to 5 continents and 30 countries.
Tecno3 Switzerland
Tecno3 USA INC
Via Mastri Cestai, 2 - 12040 Corneliano D’Alba (Cuneo) Italy
Tel. +39 0173 61 05 64 - Fax +39 0173 61 94 94
tecno3@tecno-3.it - www.tecno-3.it - www.beantobarmachine.com
Via Piazzalunga, 30 - 24015 San Giovanni Bianco (Bergamo) Italy
Tel. +39 0345 40 400 info.smipack@smigroup.net - www.smipack.it
Continuous innovation to meet a changing market Food and non-food companies, influenced by a strong trend towards product diversification, need very flexible and efficient packaging machines to reach high levels of competitiveness.
Present on the market since 1997, SMIPACK (a company part of the SMI Group) is one of the main producers of packaging machines worldwide.
SMIPACK designs and manufactures a wide range of manual, semi-automatic and automatic packers that provide thousands of customers all over the world with smart solutions capable of meeting their requirements in terms of competitiveness, production efficiency, operational flexibility, energy saving and ease of use.
Tradition and innovation: the basis of a solid business reality
Year after year, the story of SMIPACK features a sequence of projects and initiatives combining passion,commitment, research, customer support and above all continuous innovation, factors that have allowed the company to grow
In the modern and functional SMIPACK headquarters in San Giovanni Bianco (Bergamo), all design, assembly, sales and after-sales activities are performed
in terms of sales turnover, product range, international presence and surfaces occupied.
Today SMIPACK proudly looks back at the year 1997, when it started its activity with the production of L-sealing machines from the S range, that in only two years reached stunning results.
Research and development of new packaging machines still characterize the activity of SMIPACK, which invests significant resources every year to develop new technologies and launch on the market increasingly
innovative and competitive products, designed for easy use by the operator and for the optimization of the packaging operations.
FW series for flow pack packaging
An example of SMIPACK continuous evolution is represented by the flow pack packers from the FW series; an extremely versatile, flexible and cost-saving solution, suitable for any type of food and non-food products. SMIPACK offers a wide range of flow pack machines, including several models, even for the entry-level sector.
Main advantages of flow pack packers by SMIPACK:
• high efficiency and production speed: depending on the model chosen, the FW packers meet production requirements up to 200 products/minute
• versatility: products are packed in packs made of simple or coupled flexible material
• high customization possibilities: the FW range is equipped with several standard devices which make it the ideal solution for any packaging need, ensuring a great quality/ price ratio
• compact structure: machines suitable for any packaging line
• accessibility and ergonomics: all models adopt solutions that optimize the manmachine interaction, guaranteeing easy access to any part of the machine and improving performance in terms of ergonomics
• subsequent easy maintenance
• advanced technology: the FW range adopts cutting-edge solutions that ensure high performance and high safety standards
• wide operational flexibility: packers suitable for a wide range of products, even with irregular shapes and small sizes, which arrive at the machine loose (single pack) or grouped (multipack)
• easy management even for less expert operators, thanks to the innovative FLXMOD® control system, equipped with an operator interface with PC panel and color touchscreen display
• advanced control system inspired by Industry 4.0 principles
Customer-oriented company
Thanks to the trust of an even higher number of customers and the collaboration with an extensive network of partners, SMIPACK is nowadays well known in the world for the quality of its machines, for the development of innovative packaging technologies and for the constant attention to customers’ satisfaction.
Today the installed packers in the world are 87,000. Thanks to an annual production of about 4,000 units, designed and produced in Italy, the company is among the world leaders in its sector and throughout the years has become a reference point for a growing number of companies operating in the food and non-food industries.
Via Piazzalunga, 30 - 24015 San Giovanni Bianco (Bergamo) Italy
Tel. +39 0345 40 400 info.smipack@smigroup.net - www.smipack.it
In an increasingly competitive and demanding market, SMIPACK plays a key role in ensuring its direct presence on the main international markets, in order to offer a highprofile, well-organized sales and technical assistance.
A wide range of products to meet the 4.0 Factory
Innovation and advanced technology have always been distinctive elements of the packers produced by SMIPACK, to such an extent to significantly contribute to their huge success on the market thanks to key aspects including process automation, ease of use, operation flexibility and reduced maintenance.
SMIPACK machines are designed to offer all the advantages of IoT (Internet of Things) solutions for data and information exchange through 4.0 Factory supervision and control systems.
Via Piazzalunga, 30 - 24015 San Giovanni Bianco (Bergamo) Italy Tel. +39 0345 40 400 info.smipack@smigroup.net - www.smipack.it
Via A. Tomba, 15 - 36078 Valdagno (Vicenza) Italy
Tel. +39 0445 43 15 76 - Fax +39 0445 43 95 88 info@sitecsrl.it - www.sitecsrl.it
144 Blue OLED
For over 25 years, Sitec has been synonymous with excellence and reliability in the field of professional timers and temperature controllers for the baking and pastry sector. We are pleased to introduce the new 144 Blue OLED electronic timer, a technological evolution that retains the appreciated features of the original 72X144 timer while enhancing it with a modern design and innovative functionalities.
Main features
This new model has been designed to meet the modern needs of the baking world by improving user interaction and simplifying use. The new setup includes a single dial supported by a high-resolution 2.42-inch Blue OLED
display, which allows for more detailed visualization of the various functions thanks to its high contrast.
Optimal control with physical buttons, not simple touch
The timer is specifically designed for dough mixers with two or three working times. The dial, equipped with 11 LEDs, allows precise and intuitive adjustment of the desired time. Four additional LEDs indicate the movement of the bowl and spiral, while an alarm signal LED ensures immediate control over the work cycle.
Exclusive features of the new model, standard for all mixers, whether equipped with inverter motors or not
• Improved design and user interface
The display is accompanied by three ergonomic buttons that facilitate the setting of times and various timer functions, even when wearing gloves
• TR backward time management for perfect dough optimization
This function now allows managing the reverse rotation time (TR) during T1 time. The bowl, which normally rotates forward, can now rotate backward for the TR time before resuming forward rotation to complete the remaining T1 time and then proceed to T2 time.
• Up to 10 stored and editable recipes
It is possible to set and automate the working times for frequently used doughs, with the ability to store up to 10 customized recipes, ensuring significant time savings and quality assurance.
New features available for mixers with inverter motors, thanks to an additional card
• Ability to control motor speeds, ensuring greater flexibility and customization of recipes
The optional card features two 0-10V outputs for controlling the bowl and spiral inverters and two inputs for managing any alarm signals (FAULT), allowing the machine to be paused and the alarm reset if necessary.
• Dough temperature display
The timer is setting to control dough temperature via a 4/20mA current loop input, to which the probe (not included) can be connected.
• RS422/485 interface for future expansions
The expansion possibility with the RS422/485 interface paves the way for further developments and future integrations, ensuring that your investment remains at the forefront of technology.
Conclusion
The new timer 144 Blue OLED from Sitec is the ideal choice for professionals in the baking and pastry sector who are looking for a cutting-edge product that is easy to use and capable of significantly improving work quality. Thanks to its innovative functionalities and intuitive design, the timer 144 Blue OLED offers superior performance and precise control, making each processing step more efficient and reliable. Choose excellence and innovation. Choose Sitec.
Via G. Fabbri, 9 - 47034 Forlimpopoli (Forlì Cesena) - Italy Tel. + 39 389 6145402 info@silosrevolution.com - estero@silosrevolution.com www.silosrevolution.com
Silos Revolution is a company specializing in the design, development and customization of Raw Material Storage, Conveying and dosing systems for the food, chemical and pharmaceutical industries. Silos Revolution puts the customer’s needs at the first level and then tailors on them what will be the customer’s tailor-made system.
Dealing with particular and unique systems, there can be no copy and paste. Each system is different because the requests of the individual customer are different, only the gained experience on how to deal with certain particular ingredients that can be a game-changer.
This technical conception of work combined with the availability and flexibility of the company’s engineers and technicians has initiated important collaborations with large Italian and foreign groups.
On the company website you can find all storage solutions for powders, granules and liquids suitable for all needs, from the most economical fabric silos to monolithic stainless-steel outdoor silos to thermo-conditioned tanks. Bag emptying systems for bags up to 1 ton or bag emptying systems of 25-50 kg conclude the range of products dedicated to powder storage.
Indicate the precision in the dosages of individual ingredients you would like to have, and Silos Revolution will build the appropriate system to guarantee those accuracies. Silos Revolution micro-dosing systems guarantee accuracy of +/- 5 grams per individual ingredient.
Special production processes such as:
- Flour disinfestation
- Flour cooling
- Powder mixing stations
- Powdered sugar
- Inverted sugar are designed and sized ad-hoc so that they can be integrated into classic storage facilities.
Each system is managed by industrial PLC, and if the customer wishes, we can supplement the supply with management supervisors open to dialogue with existing systems and remote assistance.
Ifyoualreadyownarawmaterialstoragetransportanddosing system, but you are not satisfied with its performance, Silos Revolution can safely solve your problems and guarantee you the production you set out to achieve.
Choose to be free is Silos Revolution’s slogan, come and find out how!
Via Artigianato, 85 - 25030 Torbole Casaglia (Brescia) Italy Tel. +39 030 2650488 - Fax +39 030 2650143 info@sigmasrl.com - www.sigmasrl.com
Sigma started its activity in 1974 as one of the most important European manufacturers of mixers. Sigma production consists of:
Pastry machines
Planetary Mixers. Different lines characterize the production of planetary mixers for craft and catering:
• Best Mix, a line with mechanical speed variator from 10lt to 80lt
• Chef line with electronic speed variator (inverter) from 7,5lt to 60lt
• Powermix planetary mixers for industrial use from 60 up to 160lt, with motorized bowl lift and descent, total tool disengagement and programmable control panel
• Aeromix with a worldwide patented system. With their outstanding speed ratio,they offer the best results in terms of quality when used for making emulsions, mixtures and dough for pastry-making and food preparations. What makes them truly unique is the combined use of three special tools in the production of the mixtures. The range of machines for pastry also includes:
• Sheeters
• Electric cookers
• RF300 grinding machine
• Twin-arm mixers
Pizza machines
Worth of special mention the “Sprizza” cold spreading system, a machine that reproduces the manual skills of a pizzaiolo as closely as possible by imitating his unrivalled delicateness with a cold working process, and the rounding cutter Dr 1411 to cut and round 800/1000 portions of dough per hour, from 150 to 650 gr with 2 different cutting groups.
The portfolio is completed with:
• Spiral mixers Silver Line with removable bowl in the following models: 80,120,160,200,250, 300 kg of dough capacity.
• Spiral mixers Super Premium with removable bowl
• Spiral mixer bench model Tauro from 12 to 40 kg dough
• Screw rounder Sfera for dough ball from 30 to 1000gr
• Vertical sheeter T50
Bakery machines
The production of spiral mixers is composed of different lines, such as:
• Benchtop spiral mixers Tauro for kneading from 12 to 40k g of pizza dough. Available with fixed or removable bowl
• Red Line spiral mixers with fixed bowl of capacity from 60 to 280 kg of dough
• Green Line with fixed bowl, able to save around 20%25% energy compared to the traditional mixers
• Self-emptying spiral mixers available in models of 80120 - 160 - 200 - 280 kg of dough, able to automatically empty the dough onto a table or into a divider
Other kinds of machines to complete the range:
• Bowl lifters
• Feeding hoppers
• Hexagonal dividers
• Squared dividers
• Bun dividers
• Conical rounders
• Moulders for wrapped bread and baguette
All the Sigma manufactured equipment complies with EU safety and hygiene directives. Today, Sigma is present in over 100 countries in the world through its 500 regular dealers. The attention paid to its customers and constant commitment to innovation have always distinguished the Sigma’s philosophy.
Since 1982
Satinox has been manufacturing perfectly welded stainless steel bowls for more than 30 years. They are made by hands to fit the machines used to knead and mix dough for the bakery and pastry sector as well as for the chemical and pharmaceutical sector.
The company was founded in 1982 and since then it has been a strong believer in the value of manual metalwork fabrication.
All bowls are made by expert and specialized workers, able to manufacture robust, versatile and long-lasting tailor-made products.
Satinox can count on a team that works together with passion and professional expertise, uses high quality materials and is continuously fine-tuning its metal fabrication and welding techniques.
In fact technical expertise and knowledge go hand in hand with the quality of the materials and the ability to turn traditional artisan metalwork fabrication into expert joining technique.
From project development to product manufacturing careful examination of any special production needs is definitely essential to find the ideal solution to optimize bowl performance, and consequently machine performance.
Strict compliance with the drawings, the painstaking attention to tolerances along with machining precision guarantee tailor-made products of any shape and size.
Diameter: from 240 mm up to 2000 mm
Customized height
Thickness: from 2 mm up to 8 mm
Bottoms available in high thickness
Upper ring: plate or round bar
Customized flange
Discharging bolt, auto discharging system
Diameter: from 400 mm up to 1400 mm
Customized height
Thickness: from 2 mm up to 5 mm
Upper ring: plate or round bar
Customized flange
Diameter: from400 mm up to 1400 mm
Customized height
Thickness: from 2 mm up to 4 mm
Upper ring: plate or round bar
Customized flange
BOWL FOR PLANETARY MIXER
Capacity:
Electrically
Optionals: product discharge valve, washing discharge valve, brackets
Diameter: from 900 mm up to 2000 mm
Customized height
Thickness: from 4 mm up to 6 mm
Upper ring: plate or round bar
Customized flange and bolt
Diameter: from 700 mm up to 1500 mm
Customized height
Thickness: from 2 mm up to 4 mm
Upper ring: plate or round bar
Optionals on demand
Diameter: from 220 mm up to 1700 mm
Customized height
Thickness: from 1,5 mm up to 2 mm
Truncate Conical, Truncated pyramid
Upper ring: plate or round bar
Customized flange
BOWLS FOR PRALIN CANDY MACHINE, CHOCOLATE MELTER, CREAM COOKER
Diameter: from 250 mm up to 1500 mm
Customized height
Thickness: from 2 mm up to 3 mm
Entering round ring
Optionals on demand
Via Sempione, 82 - 28053 – Castelletto S. Ticino (Novara) Italy
Tel. +39 0331 92 20 86 sales@robox.it - www.robox.it
ROBOX, since 1975, has been developing and producing axis controls, programming languages and development environments ideal for robotics and for “motion control” in general.
The multiplicity of programming languages (structured text, ladder, object blocks) and the wealth of libraries make learning the Robox systems easy for any willing child with the right foundations in electronics and IT provided by Italian higher education.
Robox controls can manage any application, thanks to the variety of fieldbuses on which they communicate, including Ethercat, CANopen, profibus and modbus.
The current flagship product of Robox S.p.A. it is the RP-2 controller, a Robox branded brain with ARM A9 processor that can manage up to 32 interpolated axes. RP2 has gained an important place in robotics and industrial automation in the most varied types of machines, such as flowpackers, fillers, cappers and case packers.
In recent years, the demands for safety in systems and the appearance on the market of many Safety devices have pushed Robox towards the integration and interfacing of these elements and protocols. After the fruitful use of Phoenix safe I/O, Robox has entered into a collaboration with BBH, a German company that has been dealing with security for more than 30 years.
The combination of Robox motion controllers and BBH safety PLCs offers OEMs operating in every sector the possibility of achieving functional safety requirements (SLS, SLP, ...) also for TCP.
The Robox / BBH combination has also found an important application in the AGV sector, where Robox has been operating successfully for decades and has gained experience in all the most used guidance systems: guide wire, laser guidance, inertial guidance, magnetic guidance and natural driving (SLAM).
The integration between control systems and drives has also significantly increased. On the hardware development front, we mention the RID20-E drive which replaced the RID20 drive. We remind you that RID20 is a drive designed to be installed directly on the motor; 14 years after its birth, a
redesign was carried out - the RID20-E - to take advantage of the technical developments during these years. RID20-E is available in a version suitable for direct installation on the engine (shuttle configuration) and in a version suitable for being placed in the immediate vicinity of the engine (nearby configuration). Thanks to the integration with the motor,RID20-E is suitable for use in all multi-axis applications that require drastic reductions in size and wiring, such as applications in the beverage, food and packaging sectors. www.robox.it
The breakthrough innovation in processing systems
Roboqbo is on the market since more than 40 years and is one of the leading companies worldwide for food processing system manufacturing. Roboqbo manufactures Qbo, a versatile processing system capable to cook, cool down, concentrate, refine and vacuum-process any food product. Qbo is a complete, compact and patented transformation system that integrates different machines into a single process.
Via Mazzini, 1 - 40010 Bentivoglio (Bologna) Italy
Tel. +39 051 892483 - Fax +39 051 893 162 www.roboqbo.it - info@roboqbo.com
It’s an all-in-one system that lets you introduce all of the ingredients in one step. This is a radical break with old methods,bringing down the number of stages to one single uninterrupted cycle. It’s a one-for-all system because it meets the needs and demands of whoever uses it, and because it can be adapted to multiple fields of application. Qbo can replace traditional equipment such as dough kneaders, stand mixers, stoves, cookers, ball mills, cylinder mills, pasteurisers, concentrators, candying machines, emulsifers, turboemulsifer mixers, tilting frying pans, mills, granulators.
The revolutionary technology and the wide range of models from a capacity of 5 to 860 liters, make Qbo an essential ally for those operating in the food industry, as it meets all production needs.
Thanks to its extreme versatility, Qbo is ideal for sectors such as pastry, confectionery industry, chocolate, ice cream, gastronomy,catering, food processing, ready meals and dairy
It is a technological tool available in its 4th generation with a large 10.1” touchscreen display as well as an easyto-use interface with advanced control functions of the production process and automatic cleaning.
Made of Inox Aisi 316L., Qbo comes with a microserrated blade knife, bowl scraper, speed control, PLC and software, pressure cooking and cooling system, automatic steamjet cleaning program to clean concealed parts and the lid, pneumatic extrusion to deliver the product and automated ejection system for fluid and semi-fluid products, ingredient loading hopper from the lid, inspection window
with glass wipers, lighting inside the bowl for direct control of the process, complete vacuum system, automatic bowl tilting movements, opening and closure of the lid, steam generation, compressor, USB port for updates and technical support.
Qbo is perfect for all professionals and for anyone who is constantly looking for the highest quality without compromising on creativity,full efficiency and technological innovation.
Popping machine RP-EVO: Re Pietro’s innovation for the production of cereal cakes and no-fried snacks
Popping machine RP-EVO is the press of the latest generation manufactured by Re Pietro Srl to produce both cereal cakes and no-fried snacks, products that following a worldwide trend are having a constantly increase in demand. With this new press, the highly innovative attitude of Re Pietro Srl is setting new standards in cereal cakes and snacks production, by offering one solution that will revolutionise and simplify the manufacturing of these products. In fact, once the mould has been chosen and installed, the popping machine RP-EVO transforms the cereals and/or the micro-pellets into fragrant cakes or crunchy snacks. Its efficiency and flexibility allow to have a wider range of products, using one press only. Nowadays these products not only are appreciated as healthy alternatives to conventional bread, but they are also valued for their versatility by professionals and consumers: they are perfect as carbs supply during meals, as crunchy snacks for a quick bite or as fancy decorations to dishes and desserts.
You may wonder how many moulds and which shapes can allow you to produce both cakes and snacks with the new press. Round big and small, round with ridges, triangular or square, hexagonal and rectangular just to name a few. But Re Pietro can also produce customised moulds based on the customers’ requests.
Popping machine RP-EVO – focus on
Structure in nickel coated steel, certified food contact material, electric panel in stainless-steel with a side rotating and swivelling touch screen control panel set at eye’s level for easier use.
Equipped with a hydraulic system that produces the high pressure needed for the expansion of the cereals or micropellets turning them into fragrant cakes or crispy snacks. The volumetric dosing is carried out by a pneumatically operated feeding plate. The moulds which shape the popped cakes and snacks are made by hardened steel coated with titanium nitride, to guarantee solidity and a long-lasting life, and to prevent
Via G. Galilei, 55 - 20083 Gaggiano (Milano) Italy Tel. +39 02 90 85 025 info@repietro.com - www.repietro.com
the sticking of the products on the moulds. The moulds, as well as all the parts that get in touch with the products, comply with the MOCA specification for food processing machines as per Reg.No.1935/2004 CE (MOCA compliance).The upper and lower moulds are heated by cartridge heaters separately controlled by thermoregulators. Each press has got its own PLC (Siemens S7-1200) and 7” control panel. From the HMI it is possible to set up each production phase, to save the recipes and check any malfunctioning thanks to its efficient diagnostic system. Popping machine RP-EVO is another milestone in the production of Re Pietro Srl, where the manufacturing of food processing machines and plants has always been approached with an eye to innovation and development, relying on 90 years of solid experience. In fact, the company, surrounded by paddy fields in the southern outskirts of Milan, celebrates this year the 90th anniversary of the great intuition of its founder Mr. Carlo Re, who saw the potential of rice and its processing. Without forgetting the incredible added value of the Made in Italy quality.
PND: A new system for processing pineapples in Taiwan
The pineapple offers an increasingly segmental product, which lends itself to both fresh consumption and other types of processing.
PND, a leading manufacturer of fruit-processing machinery, is working tirelessly to install a dedicated pineapple processing plant in Taiwan by June.This system, which can process up to two and a half tonnes per hour, employing a
Via Brancaccio, 11 - 84018 Scafati (Salerno) Italy
Tel. +39 081 850 93 68 info@pndsrl.it - www.pndsrl.it
total of only 9 operators, is composed of two machines: the PL4D peeling-coring machine and the SS8 cutting machine. The intuitive, user-friendly, manual-feed, semi-automatic PL4D peeling-coring machine has a productive capacity of 24/28 fruits per hour. The double-adjustment product and blade rotation enable all fruits to be peeled, even if they are uneven and irregular, achieving a 55% yield, without affecting their nutritional and organoleptic integrity. The machine is equipped with two conveyor belts; one for the peeled product and one for the rejects, with inspection and product certification counters, and a reject chute. Its foodgrade stainless steel structure also guarantees maximum durability and hygiene in the processing area.
Aligning perfectly with the PL4D, the SS8 universal segmenting and cutting machine guarantees the production of 40 fruits per minute.This is a semi-automatic machine, which enables quality cutting, in various shapes (slices,wedges,cubes,depending on production demands) and sizes, made possible by the option to replace cutters and plungers. The operator only has to load the fruit, as the automatic mechanism pushes it through the cutters, producing the desired form, which is then collected on the appropriate output belt for packaging.
While one of the first systems in Taiwan, this is not an innovation, as the pineapple production lines have already been tried and tested by several customers around the world (Australia, Europe, America, India, Asia and Africa);
in fact, PND boasts more than 170 of them for peeling pineapples and melons.
With impressive versatility, ease of use and integration into production processes, effective and fast maintenance and customer care, it not only reduces costs, but also improves results. Thus PND, with its tailor-made processing lines, has succeeded in winning the trust of industry technicians and customers alike, who appreciate its machines as irreplaceable business partners.
You can visit the websitewww.pndsrl.it to consult the machinery catalogue and view the equipment lines available, as well as the international trade fairs in which the company will take part.
For further information: info@pndsrl.it
Omag, your partner for primary and secondary packaging for over 50 years
Since 1973, Omag has been designing and manufacturing customized packaging machines for the packaging of powdery, granular, liquid and solid products in sachets and single-dose stick-pack dedicated to the food, cosmetic, chemical and pharmaceutical sectors. The product range is very wide: starting from limited size packaging machines useful for laboratory tests or new product launches to complete packaging lines for high productivity.
Dedicated technologies for the food sector
Omag’s offer for the food sector consists of a wide range of packaging machines - horizontal or vertical, continuous or intermittent motion - according to the customer’s specific production needs. In fact, packaging machines can be equipped with different dosing systems for powdery, granular, liquid and pasty products, combined with robotic counting systems, cartoning machines and a wide range of optionals such as markers, smart cameras, sensors, etc. At the technological level, issues concerning technology and augmented reality remain focal points to which much of the R&D investment is devoted.
In addition, Omag is testing and implementing predictive maintenance processes on packaging machines: thanks to IoT technologies, remote control and machine interconnection, in the very near future it will be possible
Via Santi, 42/A - 61012 Gradara (Pesaro e Urbino) Italy Tel. +39 0541 950854 commerciale@omag-pack.com - www.omag-pack.com
to constantly monitor the performance and status of packaging machines, receive specific information on individual machine components so as to intervene more effectively at the customer’s premises and zero in on the risks of downtime.
Customer at the center: Omag as a reliable allaround partner
An important novelty concerns secondary packaging:Omag used to supply complete lines by working with partners, while now,thanks to continuous investment in research and development and favorable tests on different prototypes, Omag is finally able to offer a complete 360° solution, from primary to secondary packaging
Omag wants to be a reliable partner for the customer, able to offer a complete,easy-to-use and intelligent solution that allows monitoring all parameters and intervening - even
remotely - to solve any anomalies. In this way, production is continuous, downtime is minimized, and losses are minimized.
My-O: new Omag’s dedicated customer portal
With the aim of offering the best customer experience, the brand new My-O portal was launched in recent months. This is an online reserved area and accessible to Omag customers that allows them to consult the documents of their machines and lines, from certificates to machine manual, from electric and pneumatic schemes to spare part list, organized by contents and by machine models.
In addition, customers can view the 3D of the machine making easy the spare parts offer, in a secure way and with the 24-hours support of the Service Omag.
Visit www.omag-pack.com to be always update with the latest news and events.
Via del Santuario, 41 - 12045 Fossano (Cuneo) Italy
Tel. +39 0172 69 25 79 - Fax +39 0172 69 25 78 info@vdlolocco.com - www.olocco.eu
Olocco Srl has been manufacturing valves and components for pneumatic conveying and metering since 1950. Its valves are used in the feeding, unloading and pneumatic conveying of any kind of product in grain or powder, in the food, chemical or plastic industry, with low, average, high-pressure lines. Olocco’s commitment has always been characterized by constant research from design to production of valves and accessories, ensuring the manufacturing of products at the top technical specifications, quality and safety. In recent years, the production department has undergone a profound renovation with the commissioning of new machining centres equipped with the most modern, flexible production systems, with high levels of automation for the handling of pieces, pallets, tools. New milling, boring and turning
centres have produced a great increase of internal manufacturing capacity and brought our quality standards to ever-higher levels. During the last years, despite the difficult situation caused by the pandemic, Olocco has been able to complete the construction of the new office building and assembly department. All this demonstrates the will to grow and bet on the future.
In 1997,Olocco Srl obtained the quality certification UNI EN ISO9001:2015 and afterwards certified most of its products according to ATEX Directive 2014/34/EU. In 2007, it so started manufacturing rotary valves in accordance with EN15089:2009, the European Standard that describes the general requirements for explosion isolation systems. Olocco Srl is also able to guarantee the food compatibility of the materials used in the manufacturing of any valve, in compliance with the provisions of EC Regulation No.1935/2004 concerning materials and objects in contact with food products (MOCA), and the EC Regulation No.2023/2006 on good manufacturing practices.
Due to the increase in demand for stainless steel components, the manufacturing of a new range of rotary valves, “UPH”, entirely built in AISI316 stainless steel, with unified round flanges according to UNI PN10 / DIN2576 standards, in the sizes from DN150 to 300 and flow rates from 3 to 37 litres/rev, is at an advanced stage. These valves will be also available in the quick disassembly version with extraction bars, “SMD”, typically to ensure the safety of the operators, to facilitate cleaning and general maintenance, inspection tasks or where rapid cleaning times are requested. A fully disassemblable rotor gives the possibility to clean it separately and remove any deposit. In advance inner surfaces can be completely polished and blended to meet the strictest hygienic standards in food, chemical and pharmaceutical industries.
Via Massarotti, 76 - 26100 Cremona - Italy
Tel. +39 0372 40 11 - Fax +39 0372 41 26 92 info@ocrim.com - www.ocrim.com
The company OCRIM, headquartered in Cremona, is globally renowned as a reliable partner for the construction and supply of milling, feed, and cereal processing plants, as well as end-of-line plants. Its commitment in research, customer care, training and communication has always been an incentive for innovative and productive teamwork.
In Cremona, Ocrim boasts two large sites, due to the ever-increasing insourcing of processing: The original headquarters in Via Massarotti, which houses offices and parts of its production factories, and the premises at the industrial area of the city for some important production and logistics departments, and not far, there is also the Milling Hub created jointly with Bonifiche Ferraresi, is meant to strengthen Italian agro-food supply chain by offering food industries without milling plant the chance of using a customized plant, as well as the technical and technological knowledge of OCRIM team.
Turnkey projects are one of OCRIM’s strong points, supplied in tailor-made solutions, increasingly welcomed by international customers who decide to rely on a single partner who can guarantee a high professional level and respect programmed time. OCRIM is an irreplaceable partner also for the supply of machines only, and in milling plant upgrade/modernization.
The FBC department designs and manufactures end-ofline plants for palletization and packaging of bags and other packing, supplied turnkey and personalized upon customer’s requirements. Today, it is fully integrated in OCRIM and further piece to complete the industrial chain, which means internalizing all processes, thus
guaranteeing a traced, controlled, and certified Italian Made product.
OCRIM’s versatility and seriousness have been further highlighted at the beginning of 2024, thanks to the acquisition of the company SIMA of Treviso, specializing in storage system design and construction for more than thirty-five years. All that grounds on shared values, such as honesty, reliability, team feeling and availability, and above all, attention to Human Capital.
OCRIM has always been an attentive and well-prepared supplier of storage plants,and this partnership adds further and crucial element not only to“The ItalianAgri-Food Chain Choice”, of which OCRIM is one of the main players, but also to the increasingly complete production chain.
OCRIM’s reliability is also evidenced by an important agreement reached with Italian company Molitecnica Srl, to build nixtamalized flour plants for tortilla, snacks and chips production.These products are mainly part of Central and Southern America’s food culture, but also highly appreciated and consumed all over the world. OCRIM will supply its process machines for these plants, thus guaranteeing high performance in line with the targets set. With the goal of supplying long-lasting milling plants and efficient high-quality services, OCRIM proposes increasingly innovative solutions in terms of sanitation, reduction of energy consumption, maximization of technological results of the plants, and reduction of operating and maintenance costs down to the minimum.
In fact, as for strategies and management related to maintenance and improvement of technological results, OCRIM has introduced the Modular Mill Concept, an innovative technology that enables stopping some parts of the grinding section, for any reason (ordinary and extraordinary maintenance, or else), while letting another run, thus granting uninterrupted specific production. This solution is chosen and highly appreciated by many customers thanks to the benefits it generates.
As far as automation is concerned, OCRIM plays the role of direct reference, thus avoiding external bodies for the study and implementation of plant management systems. The general automation package @mill, which includes many application packets, the innovative @rollermills, which enables controlling the mills remotely via tablet, and the Immersive Reality are futuristic solutions created to improve and simplify the work activities of those in the milling sector.
Inaddition,OCRIMalsooffersitscustomerscomprehensive support with its innovative Service, and its customers can be granted specialised after-sales technical support in real time, and can easily and quickly require their own. This state-of-the-art approach to customer service sets this company apart in the milling industry, offering timely and customised solutions for every need.
OCRIM also excels in terms of training and higher education, in fact,thanks to the extensive training experience of OCRIM International School of Milling Technology, active since
1965, and in line with the Milling Hub initiative, the Milling Hub Masterclass training hub has been established. This hub enriches the training with an innovative perspective. Access to the Masterclass is reserved to previously trained technicians only, with proven expertise, as to guarantee a high-degree training. 360° advanced training focusing on the knowledge of seeds, through cereal and pulses processing, to finished product sales.
On account of this corporate positive development, OCRIM’s R&D department is committed to experimenting new strategies and state-of-the-art projects can be broadly acknowledged as unique in the milling sector and in full harmony with the innovation the company has been experiencing. The partnership between OCRIM and some prestigious Italian universities is further strengthened, broadly contributing to get valuable results for the milling sector in general.
OCRIM’s communication instruments mean to finetune the corporate language to the new trends.
The company boasts considerable visibility through both national and international sector publications, via its LinkedIn and Instagram profiles, and three Internet websites: the corporate website www.ocrim.com, one dedicated to the company’s museum www.ocrimcore. com, one dedicated to the blog www.ai-lati.com, strongly wanted by OCRIM as a real information provider for the entire The Italian Agri-Food Chain Choice chain, and therefore for its member companies.
In 2020, the company’s media department was greatly and successfully developed with the start of highly technical-scientifical Webinars into the milling world. Yet, the real novelty arrived at the end of 2022 with the new format O-News Live, a TV news hosted by three OCRIM employees, whose stage is the new O-Theatre, a space that OCRIM strongly wanted for events like this, as well as for meetings with customers. In addition to this, OCRIM also continues offering its customers tailored solutions featuring customized machines, participates in events such as “Wheat, flour, and …”, and welcome its guests at O|HOUSE, a historic residence in the center of Cremona, and at O|FARMHOUSE,a farmstead typical of the Cremona area, renovated and inaugurated on occasion of the company’s event “Wheat, flour and …” 2022). Those are the events and projects created to provide a close-up view of a company that is continuously and constantly evolving.
Via Massarotti, 76 - 26100 Cremona - Italy
Tel. +39 0372 40 11 - Fax +39 0372 41 26 92 info@ocrim.com - www.ocrim.com
Superior – the compact mill by OCRIM
Superior is a compact mill representing a strategic and smart investment that offers safe and versatile productive solutions for an excellent final product.Pre-assembled at OCRIM warehouse, Superior reduces the costs of a dedicated multi-level building and bureaucracy expense for urbanization works, and offers high energy performance for reduced production and management costs.
Meant for customers with different entrepreneurial courses,Superior is suitable for people approaching the milling world for the first time as well as for those who want a compact plant to extend or diversify their offer, without revolutionizing their industrial production.
Create in the 1950s, Superior is a state-of-the-art engineering icon that has highly contributed to OCRIM’s industrial development internationally.
The mill offers the possibility to personalize its technical, technological, and design equipment, with four different solutions available: Passion, Natural, Gold, and Style. Back to OCRIM home in a futuristic shape, from the technological and design points of view, Superior has generated great interest and significant demand, as to persuade OCRIM to create dedicated Internet website (www.ocrimsuperior.com) and e-mail address (info@ ocrimsuperior.com) for information and request, accompanied by a as well as a brochure that fully conveys the elegance of this compact mill.
OPARTS: Ocrim’s world is just a click away OCRIM launched the innovative platform www.oparts-shop.com, an e-commerce portal with interactive catalogues where spare parts for milling plants can be bought.
The entire website has been designed with the customer in mind.The aim is to ensure the best user experience in terms of ease of navigation, speed, and intuitiveness. The is available worldwide and allows customers to directly purchase milling products 24 hours a day via certified international payment circuits.
The portal is structured in two parts: a B2B e-commerce platform for the immediate and direct purchase of milling plant articles, and a customised section for loyal customers with interactive catalogues. In the latter area, the user’s machine catalogues are uploaded for browsing, with the minimising the chance of error when searching for a specific component.
Thanks to this portal, with just a few clicks, the user can choose and order the spare parts he needs for his machine, by selecting them directly from the table and order, and also find dedicated promos in the “My Area” and keep track of requests and orders at all times.
For more information visit www.oparts-shop.com or e-mail to info@ocrim. com for more details and to receive a brochure about this service.
Founded in 1926, Novacart is the biggest company operating the full-cycle production of paper and cardboard products for confectionery and food sectors, with production of millions of moulds and boasting branches all over the world.
Novacart has always stood out for the quality,sustainability, and versatility of its products, registering more than 100 patents out of the will to develop solutions able to fully meet market’s requirements, from craft confectionery to industrial.
Novacart’s experience in the food and confectionery industry enables offering tailored solutions and an allround service, to meet specific requirements and particular needs; The R&D laboratory is at the customer’s disposal to select the best material and design ad-hoc products, from mould creation to the supply of automatic spraying lines.
Some Novacart products for the industry, and don’t call them packaging!
NTS baking trays are the Novacart’s international patent ideal for automatic spraying lines: A system of trays with cups in paper or cardboard suitable for oven high temperatures, freezing and food fats. They do not need to be buttered before use and require shorter baking temperature and times. In addition, the trays also feature hatches for easier cutting of the portions for packaging. Tulip Cups and cases are made in paper resistant to high temperatures in ovens up to 220°C, freezing down to -40°C, and they do not need to be buttered. Cases and Tulip Cups can be used in industrial environments: Inserted in classic metal pans, in reusable cardboard supports, and in automatic spraying machines.
Baking methods and PM moulds are in corrugated microwave paper resistant to baking temperature to more than 220°C.The design of Novacart baking moulds is wellfinished and elegant, studied to enhance the product, and makes any additional presentation element superfluous.
Zona Industriale - 73043 Copertino (Lecce) Italy
Tel +39 0832 931184 / 935458
info@newplast.eu - www.newplast.eu
Founded in 1984, New Plast is a national and international leader in the production of innovative, sustainable and eco-friendly packaging for:
• Food Industry and non
• Packaging resellers
• Hypermarkets and cash & carry.
Manufacturers of high-quality vacuum pouches, New Plast bags are ideal for professional and domestic use and are suitable for storing fresh and processed foods such as meat, cheese, fish and vegetables.
New Plast vacuum pouches are made from up to 11 layers in PA/PE that provide a high barrier, extend shelf life and ensure food preservation and hygiene.
The wide range, available from stock in over 150 sizes and different thicknesses, ranges from smooth and embossed to cooking vacuum pouches.
In addition, the company is able to satisfy any customer requirement, including the possibility of private label production.
New Plast boast also the production of BOPP and PP bags, square bottom bags and compostable bags.
Moreover, it converts multi-purpose baking paper for professional market, silicone-coated on both sides, fully recyclable and biodegradable.
The high quality of production, customers satisfaction, workplace safety, energy efficiency, environmental
protection, the compliance with the Good Manufacturing Practice (GMP) are the core values of New Plast business. In compliance with the requirements of BRC Global Standard, New Plast scrupulous traceability system tracks every raw material in all the phases of the production process, ensuring the quality and the integrity of its products from manufacturing to customer satisfaction. Indeed, its production department is staffed by trained and competent personnel who ensure the quality and the integrity of the products.
New Plast exhibits at the most important international trade fairs, such as Pack Expo Chicago, Pack Expo Guadalajara, Iba, Innovation Packaging Birmingham, Gulfood, IFFA, ProPack Africa, Fachpack, Scanpack and Qazpack in order to keep up with the market, learn about new consumer trends and retain new customers. Understanding, meeting and solving customer needs is New Plast philosophy.
For New Plast, every milestone represents a new starting point!
Zona Industriale - 73043 Copertino (Lecce) Italy Tel +39 0832 931184 / 935458 info@newplast.eu - www.newplast.eu
Via Virginio, 252 - 50025 Montespertoli (Firenze ) Italy
Tel. +39 0571 671661 - Fax +39 0571 671636
info@moelsrl.com - www.moelsrl.com
Moel® is an Italian company located nearby Florence, specialized in the production of PVC based plastic films
Located in the Tuscan countryside in an area of 15,000 sqm and with yearly capacity of 7,000 tons of stretch, cling and shrink film, Moel srl is leader in the production of flexible packaging films for food and non-food wrapping. Decades of experience in flexible packaging film production allow this company to offer a large range of high-quality films.
All films manufactured by Moel Srl are extremely performing, very easy to use and are the result of long experience and technical knowledge gained in the sector of flexible packaging.
Moel Srl production is guaranteed through extremely accurate checks during the several steps, from the early arrival of raw material to the final delivery of the goods to the customer. Moel R&D department follows and checks day by day the outcoming production, certifying the highquality standard of the rolls.
Almost half Moel’s capacity goes to export market, that’s why this company is well-trained in export procedures. It delivers the goods all over the world, such as in Europe, Asia,Africa, DROM-COM countries, etc.
Stretch and cling films manufactured by Moel Srl are destinated to the food sector packaging: Fresh meat, poultry, fish, fruit and vegetables, ready meals and more. The high stretchability, self-adhesion, memory effect and antifog properties are the main features.
AllMoelfoodcontactfilmsarerecyclableandmanufactured in compliance with EU REG. 10/2011.
Shrink films PVC based and polyolefin based manufactured by Moel are destinated to non-food and food packaging sectors. The unbeatable shrink speed at low temperatures permits a higher productivity with energy saving. Transparency and brightness typical of these films assure an excellent product presentation.
Last February 2023, Moel Srl also got ISO 9001:2015 certification.
If you are looking for a long-term reliable partner, Moel is at your complete disposal!
Via Virginio, 252 - 50025 Montespertoli (Firenze ) Italy Tel. +39 0571 671661 - Fax +39 0571 671636 info@moelsrl.com - www.moelsrl.com
Via Martin Luther King, 12 - 35010 - Curtarolo (Padova) Italy
Tel. +39 049 96 24 258 - Fax +39 049 96 23 823 info@me-foodsolutions.com - www.me-foodsolutions.com
Millennium Engineering redefines the food industry
These years have brought the company recognition for its expertise in stainless steel processing, primarily focusing on AISI 304 steel. The company’s exceptional precision in metal sheet and tube laser cutting, punching, welding, and bending has been pivotal in forging significant partnerships for the manufacturing of food machinery. Their cutting-edge systems cater to various stages of food processing, including deep-freezing, cooling, leavening, pasteurizing, and conveying. With over 25 years of extensive research and development, ME Food Solutions has proven itself to be an innovative and dependable company. Additionally, its global distribution network, adept at facilitating the parent company’s ventures in the international market, attests to the company’s esteemed reputation.
ME is glad to offer customers the most suitable solutions for the entire factory line, starting from components preparation and finishing with packing and storage. A wide range of solutions for freezing, cooling, leavening, pasteurizing, and conveying are available. All systems are designed with the aim to provide customers with the best solution improving their business in terms of quality, safety, and hygiene. Every system is designed considering mechanical and thermodynamical aspect and considering the special features of the processed food.
Bread and bakery products have always held a special place in our lives. They are not just food items, but symbols of tradition, comfort, and nourishment. From the crispy crust of a freshly baked baguette to the soft texture of a warm croissant, bakery products have the power to evoke memories and bring people together.
In the bustling world of bakery production, precision and efficiency are key. ME Food Solutions understands the importance of quality bakery products in our daily lives. That’s why it is dedicated to providing the best services in the food industry market to help its customers produce the finest bread and bakery items.
When you choose ME Food Solutions,you can be confident that you are receiving the best equipment designed and
manufactured by its team of experts. Engineer Luca Priore leads the design process, working closely with the Technical and Development Departments to ensure that each installation meets the client’s specifications. Within a few months, the equipment is ready to be tested and put into operation, allowing customers to create the best bread and bakery products possible.
So, if you want to take your bakery production to the next level, choose ME Food Solutions. With its high-quality equipment and dedicated team, you can be sure that your customers will enjoy the finest bakery products every time. Let ME Food Solutions help you make delicious bread and bakery items that will leave a lasting impression on everyone who tastes them.
From the initial design phase to the installation and operation of the equipment, ME Food Solutions will be by your side to ensure that everything runs smoothly and efficiently. Its experienced team is always ready to provide support and assistance, making sure that your production process is optimized for success.
Once the work is completed and the equipment is up and running, ME Food Solutions offers a convenient service that allows its clients to remotely control and monitor the entire production process. Through innovative technology clients can access real-time data and insights from anywhere, allowing them to manage their bakery operations efficiently. Consequently,this feature gives you the flexibility to manage your production line from anywhere,providing you with realtime data and insights to make informed decisions.
With ME Food Solutions, you can trust that top-quality equipment is provided and advanced solutions offered to enhance the efficiency and productivity of your bakery production. Let ME Food Solutions help you take your bakery business to new heights and achieve success in the food industry market.
Millennium Engineering, a leading manufacturer of spiral conveyors for the food industry, delivers cutting-edge solutions built on a deep understanding of technological processes and customer needs.
Complete control, uncompromising quality: Unlike most competitors, Millennium Engineering designs and
manufactures its own conveyor belts.This not only ensures exceptional quality at every stage but also provides comprehensive knowledge of material properties and characteristics, unattainable for those relying on third-party components.
Unmatched flexibility and adaptability: Utilizing an external drive instead of a traditional drum mechanism unlocks unprecedented possibilities. Millennium Engineering constructs spiral conveyors in a variety of shapes and configurations, perfectly tailored to each customer’s unique requirements and production specifics. Strength and reliability redefined: At the heart of Millennium Engineering’s conveyor belts lies the Genoa chain, boasting 25% greater strength compared to counterparts used by competitors. This guarantees uninterrupted equipment operation under heavy loads and extends the lifespan of the conveyor system.
Three-in-oneefficiency: EngineersatMEFoodSolutions,a division of Millennium Engineering, have developed a unique spiral conveyor configuration featuring three independent belts moving within a single housing.This unlocks previously unimaginable possibilities for food manufacturers to optimize and accelerate their technological processes.
Millennium Engineering represents:
• Cutting-edge technology: In-house belt production, innovative design solutions.
• Personalized approach: Flexible conveyor configurations tailored to individual customer needs.
• Unsurpassed reliability: High-strength materials, extended service life.
• Maximum efficiency: Unique solutions for production optimization.
Choose Millennium Engineering, choose the future of food production!
MIllennium is already conducting large projects in Arab countries. One of the major projects is a collaboration with Salalah Mills Co.
High efficiency in a packaging line is the primary objective of any project manager, when he begins the design phase. In the present days packaging machines have reached performance levels that were unthinkable just a few years back, but as much as a single machine can be efficient, the overall result when you put all the pieces together can be extremely different.
The first result of a Google search with the keywords “Buffering System” is a Wikipedia page on the pH balancing system of the blood that is needed by the human body to maintain the proper functioning of the metabolism.
A packaging line behaves in a very similar way, the different machines need to be connected to each other by an efficient circulatory system and that is able to balance the operating differences that may exist between them. Conveyors represent this circulatory system and are too
Via G. di Vittorio, 3 - 20826 Misinto (Monza Brianza) Italy Tel.+39 02 96720176 - Fax: +39 02 96720215 info@mhmaterialhandling.com - www.mhmaterialhandling.com
often underestimated in the design phase with dramatic results on the final efficiency of the line.
Buffering systems,ensure that the packaging line operates smoothly and efficiently. They are able to compensate for any variations in the speed or performance of individual machines, preventing bottlenecks and ensuring that the entire line operates at maximum capacity. Some kind of buffering systems should always be present in the packaging line, as they can have a significant impact on the final throughput of the line. Providing consultancy in the identification of the correct solution and subsequently supplying the machines to the customer is exactly the core business of M.H. Material Handling Spa, an Italian company that has been operating in this market for almost forty years now, being founded in 1986.
There are a number of different buffering solutions available tocoveranypossiblerequirements,farfrombeingacomplete list we can point out the LIFO spiral systems Heliflex, that finds its sweet spot for long buffering requirements of thin products and the BAT-Buffer, a modular system that allow great flexibility to fit any kind of product. For naked products handling M.H. has a FIFO solution for the confectionery industry: the 5L multilayer belt, specifically designed for placement upstream rank distribution lines. Even if buffering systems are the easiest way to increase line efficiency, they are not the only important node: mergers, dividers, elevators and products manipulation systems are also part of the mix that allow to walk the path towards maximum productivity. M.H. has expertise in each of these devices, as well as the engineering capabilities to put them together in a layout that is fit every time to the customer’s needs. These last devices cover many needs in the line design: some are mandatory features because there’s the need to connect different numbers of machines along the process, others are useful to optimize the use of floor space available in the plant. Often the focus on efficiency is so high
that brings to neglecting other aspects,like the ergonomics of the line,accessibility of machines for the operators,passages and storage areas for packaging materials and other utilities. Balancing productivity, line ergonomics and return on investment is M.H. Material Handling’s mission.
M.H. operates in the Middle East with the support of Novadim Food Technologies, for further contact you can reach the company directly through the website www.mhmaterialhandling.com or ask for the responsible for your country on Novadim’s website: https://novadimft.com/.
Via Isaac Newton, 12 - 41015 Nonantola (Modena) Italy Tel. +39 059 74 71 235 info@marottaevolution.it - www.marottaevolution.it
Marotta Evolution Group was founded thanks to the passion of Carmine Marotta and has a long experience in the design and production of industrial plants.
It operates in the field of machinery production and in the Research and Development of automated solutions for industry. It specialises in the creation and production of burrata machines: the only company in the world, to date, capable of creating and marketing automatic machines for the production of burrata, a typical Italian dairy product with a strong artisanal connotation.
With the aim to innovate an industry that relied solely on pneumatic volumetricians and experienced cheesemakers, who were increasingly difficult to find and hire and on the strength of its decades of experience in the industrial automation sector, Marotta Evolution Group was able to successfully design and manufacture an automatic burrata machine in 2019, achieving a result never before achieved by any other company in the world, thus giving entrepreneurs in the sector the opportunity to enjoy a major increase in the production capacity of their factory.
Making a machine that produces burrata is the solution that automates the production process, as well as significantly reducing the risk of contamination, as the product is not touched and handled by the operator and, as a result, the shelf-life of the finished product
is increased, helping companies to guarantee a fresh product for longer, without sacrificing quality and the Made in ltaly tradition.
Furthermore, the Marotta Evolution machine is capable of making the product while respecting the Italian character of the dairy product, ensuring that on every table in the world there is the same product, good and of quality, exactly as the consumer requires. A further peculiarity of Marotta Evolution machine is that it can
make burratas of different sizes: from the very smallest 30 g, tiny gems of milk, up to 500 g burratas. Another important plus is that the same machine, with a simple click, can make the “figliata”, a burrata filled with mozzarella chunks.
Marotta Evolution is socially aware by supporting the less fortunate, which is why it chose to support the Core’ a core’ association, which distributes basic necessities to families in need,homeless people and children’s hospitals.
Via Canvelli, 21 - 43015 Noceto (Parma) Italy
Tel. +39 0521 25 87 23/4 - Fax +39 0521 25 87 17 info@lcz.it - www.lcz.it
Welcome to LCZ, dedicated since 1971 to design, manufacturing, installation, service and maintenance of industrial boilers for standard and special applications: plug in solutions, package solutions, site erected plants.
LCZ over the years has been able to adapt the proposal to market evolutions, thanks to constant and continuous improvement, regarding the product as well as the fabrication processes, without forgetting the hallmark: careful analysis of customer’s requirements by its technical department aimed at drawing up the most focused, customized and detailed answer.
It’s source of pride for LCZ to affirm how its products are fully realized in its manufacture plants emphasizing an Italian identity and a “Made in Italy” have always stood for high quality.
A manufacturing system, organized in two manufacture plants both in Italy and one of this with a covered area of more than 40.000 sqm, is well-characterized by automated welding processes, non-destructive tests (X-rays-L.P.), an home production of the furnaces FOX (corrugated) all supported by management using software as SAP ERP. These are some evidences of a capacity and a productive
process that allow LCZ to be one of the best worldwide manufacturers of boiler. Its internal technical department provides process and mechanical design in compliance to PED, machinery and ATEX directives, GOST-R, TS-TR and ISO 9001 certifications; according to European standards. In addition to historical products as Firetube steam boiler (up to 30Ton/h) and thermal fluid generator (up to 9MW), LCZ propose Firetube boiler for hot and superheated water, Watertube steam generator, Waste gas heat recovery boilers downstreamcogenerationandindustrialplants.Therelentless pursuit of the satisfaction of customer’s requirements has led LCZ to introduce the prefabricated thermal plants for the production of hot and superheated water, steam and thermal oil. They allow to have a turnkey thermal plant ready to use, for outdoor installation and removable.
Current commitments: energy saving, energy efficiency’s improvement efficiency during the plant lifetime and emission reduction. For this aim, LCZ boilers can be configured with an efficiency up to 95,5% (in specific application up to 105%) and for operating without continuous supervision up to 72 hours and/or with a global control system of the plant or the whole boiler room by a PLC or a multichannel electronic control device.
Via Amendola 12/14 - 13836 Cossato (Biella) Italy Tel. +39 015 98 99 511 - Fax +39 015 98 42 211 sales@lawer.com - www.lawer.com
Automaticmicro-ingredientsweighingsystems
The ideal partner for food manufacturers
The weighing process of micro-ingredients that form part of the recipes for food products of all kinds, must guarantees precision, quality, repeatability and, above all, traceability of the operations carried out, as well as perfect hygiene and safety in handling Lawer supports food manufacturers with automatic weighing systems of powder micro-ingredients, which guarantee:
• Highest quality of the finished product
• Highest weighing precision
• Replicability of the recipes
• Right balance of raw materials
• Production management, efficiency and cost reduction
• Complete confidentiality of know-how
• Optimisation of production, less production time Lawer can supply different models of automatic weighing systems, with mono – double or multi scales technology, with different levels of accuracy (1 g –0.1 g or 0.01 g) and different capacity of powders’ storage (from 50 l up to 1800 l capacity each hopper). With the control software we guarantee effective crosschecks and traceability on all the operations carried out by the system, generating at the same time reports, and allowing integration with external systems For medium-large productions Lawer proposes the SUPERSINCRO weighing system. For small-medium productions, the solution is UNICA
SUPERSINCRO is totally customizable according to the different products used, which can be stored in fixed and interchangeable silos, hoppers, and big bags. The system includes a station for the automatic generation of bags of variable size (from 9 to 36 l).
UNICA TWIN consists of a number of independent storage silos in stainless steel, to store different ingredients. Each silo is equipped with dosing screw (Lawer patented) which allows fast and accurate dosing; an efficient suction-filtering device guarantees maximum safety and a clean working area
UNICA HD is equipped with stainless steel silos with a capacity of 50 l, and it can be configured with 8-16 or 24 silos. The products are dosed through stainless steel screws into buckets placed on the weighing trolley, which has an electronic scale, with 30 kg capacity and a resolution of 1 g
Founded in 1970, Lawer is an Italian company specialized in industrial weighing systems. It has developed advanced technologies and know-how in the automatic weighing of powder and liquid products, with single- or multi-weighing systems. Its products, solutions and services supply the food industry to increase reliability, safety, and efficiency. www.lawer.com
Via Landucci, 1 - 51100 Pistoia, Italy
Tel. +39 0573 53 25 46 - Fax +39 0573 53 30 67 landucci@landucci.it - www.landucci.it
Landucci has always been the perfect combination of tradition and high technology, a brand with almost a century of experience that constantly embraces innovation.
Landucci catalogue offers a wide range of solutions for pasta industry: Dies and inserts for each shape, cutting equipment for the production of short pasta, machines for “Bologna” past shapes, machines and inserts for the production of snacks, diewashers and stickwashers; moreover, Landucci also offers all the accessories necessary for the perfect functioning of a pasta factory, supporting its customers in every stage of production.
This company’s history is marked by almost a century of tradition,values and commitment, and today it is proud to have reached the fourth generation of the family to lead the company towards an ever-brighter future.
Being a family-run company makes them particularly involved in everything they do, in fact in every product that leaves this company, you can find its passion, its attention and pride in providing something exceptional,innovative,something that can really make a difference for customers and consumers. It is this dedication to excellence that has allowed this company to earn the trust of pasta factories around the world, becoming a reliable partner and a reference for the pasta industry; The customers know they can count on Landucci to obtain performance and reliability corresponding to their production needs.
Landucci’s gaze is aimed at a future that offers infinite challenges and possibilities, the constant global change pushes to look towards wider horizons and engage in far-reaching initiatives, for this reason its commitment focuses on the constant optimization of resources, saving water and energy and the pursuit of sustainable innovation; at Landucci they are proud to have patented die cleaning systems that use only half the water and energy resources compared to traditional standards, achieving exceptional results. This technology not only allows Landucci to bring concrete benefits to the pasta factory, but also to actively contribute to environmental sustainability.
Landucci means vision and passion:in Landucci you will always find the same determination that has distinguished it since its foundation, together you will continue shaping excellence.
Strada Solarolo, 20/B-C-D - 46044 Solarolo di Goito (Mantova) Italy
Tel. +39 0376 60 82 82 - Fax. +39 0376 60 81 80 info@inoxmeccanica.it - www.inoxmeccanica.com
PIC 99 BCE: evolving technology since 1987
Inox Meccanica has been providing complete services in innovative technology for automatic industrial meat processing machines for 40 years.The product portfolio is very broad and ranges from machines for pressing, forming and automatic bagging of product in nets and casings to a whole series of machines designed for industrial washing.
One of the spearheads of Inox Meccanica’s range is certainly the PIC 99 BCE, the automatic machine for forming, pressing, stuffing, tensioning and clipping anatomical products, such as bacon,pork neck,bresaola,hams,loins,roasts and muscles in general.With PIC 99 BCE, it is possible to fill into cellulosic,collagen,plastic and elastic casings and the product can be packed in casing and net at the same time bringing considerable time savings. Currently, PIC is the best solution on the market for the production of product bars to increase slicing yield. Over the years, Inox Meccanica R&D department together with the team of designers and programmers have made significant updates and technical improvements to this machine. Improvements that Inox Meccanica is constantly updating, adapting the machine to each of its customers’ production requirements.
The PIC 99 BCE is equipped with both manual loading, which has been made safer and more ergonomic, and automatic loading by means of a belt that allows automatic
positioning of the product to be bagged inside the mould, considerably speeding up the bagging cycle and leaving the operator with the sole task of positioning the product on the belt.
Another factor is the automatic tubes change system thanks to which the operator no longer has to constantly monitor the level of casing and net consumption, which once finished activates the tube changing system so that there is no downtime, and the operator can load the new casing and net onto the tube while the machine continues its cycle.
Inox Meccanica automatic bagging machine is versatile and available with moulds from ø800mm up to ø1100mm. The versatility is given not only by the multitude of products that can be filled, but also by the brand-new electric pusher with which it is possible to adjust the filling speed and, above all, the force with which the product is pushed into the filling tube, a decisive factor especially when using very delicate casings.
Inox Meccanica’s innovation in process technology does not end here, because with a view to offering ever more punctual services and complete solutions, the company has also added to its PIC a state-of-the-art Stick Loader (basting machine) that allows sausage products to be placed on sticks for hanging to be cured.
The entire Inox Meccanica line is super-tested and constantly evolving because the real result that is cared about is customer’s satisfaction.
Innovation and efficiency: Engines of industrial competitiveness
The coffee roasting industry is constantly evolving, with a growing demand for comprehensive and technologically advanced solutions to ensure efficiency and consistency in every production cycle. In this competitive scenario, IMF, a company founded on innovation and a commitment to quality, has distinguished itself for its ability to dynamically adapt to the changing market demands. The IMF team offers tailor-made solutions to meet the specific requirements of customers, while ensuring optimal operational efficiency of its machinery and consistent productivity throughout the roasting process.
The custom-designed plant solutions include:
• Reception, selection, and cleaning of green coffee,
• Green coffee storage,
• Roasting and cleaning of roasted coffee,
• Roasted coffee storage and blending,
• Grinding,
• Ground coffee storage,
• Final product packaging lines.
Via delle Scienze, 6 - 45030 Occhiobello (Rovigo) Italy Tel. +39 0425 76 01 09 - Fax +39 0425 76 11 26 info@imf-srl.com - www.imf-srl.com
Whether in large-scale plants or smaller solutions dedicated to the specialty coffee and micro-roastery sector, IMF’s innovative technology is at the heart of the entire production process, ensuring precision, quality, consistency, and above all, repeatability in every roasting cycle.
The specificity of the technology lies in the hot air roasting method, supported by the integrated emission abatement system that ensures low emission levels, in line with global reference limits. IMF roasters use a single combustion chamber, positioned separately from the machine, serving two functions: heating the roasting air to be sent to the drum and simultaneously treating emissions to the atmosphere, ensuring significant energy savings. To enhance control capabilities and ensure greater accuracy and precision not only during the coffee roasting phase but throughout the processing flow, a dedicated software update has been implemented. This crucial step in Research and Development contributes to optimizing various intermediate steps and internal processes, enabling more efficient resource management and quicker response to market demands.
By following the IMF Roasters profile on social channels, you can stay updated on the latest news, productions, IMF installations worldwide, and successful case studies. Staying connected and being part of the IMF online community is a way to stay abreast of industry trends and to gain inspiration for your business.
Via Emilia, 428-442 - 40064 Ozzano Emilia (Bologna) Italy
Tel. +39 051 65 14 111 sales.coffee@ima.it - ima.it/coffee
Able to ensure market-leading competences, industry experience and application-specific know-how encompassing all stages of coffee handling, processing and packaging, through its brands
IMA Coffee Petroncini, IMA Coffee Packaging and IMA BFB, IMA has created the hub in an aim to leverage expertise at every step of coffee processing or packaging and be the one-stop answer to large and small coffee producers worldwide.
The coffee you want
IMA Coffee Hub reaches every corner of the coffee handling, processing and packaging universe and can now address any issue facing coffee producers, offering competence and expertise with regard to coffee production.
The process you need
With exactly 100 years in the industry, IMA Coffee Petroncini supplies complete coffee roasting plants for any capacity needs, starting from the green coffee
handling and processing, up to roasters for all capacity requirements and next-generation degassing systems. When it comes to roasting, IMA Coffee Petroncini enables customers to envisage roasters featuring different systems to manage unlimited roasting profiles. The range includes traditional roasters handling batches from 5 to 400 kg as well as modular solutions with external heat generation units roasting up to 720 kg per cycle. Next comes grinding and along with a host of flexible degassing systems for large or small production volumes, ensuring consistently reproducible quality of ground coffee.
The packaging you desired
Once your coffee is ready for the next major step, there is no need to look further than IMA Coffee Packaging. Capsules, pods, cartoning, form-fill-seal, end-of-line packaging. Single serve capsule fillers are also at the core of IMA Coffee Packaging, with a full range of equipment, providing high, medium and low-speed solutions to
answer 100% of market demands. Coffee capsules will benefit from cutting-edge secondary packaging solutions, for product integrity and top-rate protection right through to delivery. Machines for soft and hard pods are part of the line-up. IMA Coffee Packaging has a full array of machines handling dosed filling of flexible, sealed packages in all shapes and sizes. End-of-line packaging, to which IMA’s BFB Division has dedicated its efforts for many years is literally the end of the line-up.
The service you wish for
The advantages of speaking to one single supplier are numerous. Synergies come into play, timing issues are easier to coordinate, everyone you speak to is focused on your key objectives, and consistent quality and shared knowledge are guaranteed. IMA Coffee Hub is the ideal starting point from where you will reach your destination. This is precisely the benefit the coffee industry obtains from IMA: just one supplier, already coordinated from within.
Via Emilia 428-442 - 40064 Ozzano dell’Emilia (Bologna) Italy
Tel. +39 051 6514 111 dairyfood@ima.it - www.ima.it/foodanddairy
IMA packaging technologies for the dairy market
Within the IMA FOOD sector, IMA Group gathers a considerable number of companies offering technologies for the food industry. As far as the dairy market is concerned, IMA has proven experience and know-how thanks to the following brands:
IMA Benhil, IMA Corazza, IMA Erca, IMA Fillshape, IMA Gasti, IMA Hassia, IMA Ilapak, IMA Intecma.
The above IMA FOOD companies offer dedicated and cutting-edge solutions to respond to the packaging needs of the following products.
Butter
Machines for dosing and wrapping of butter and margarine bricks and sticks, from singleserve up to 500g portions, from low to high-speed production output.
Filling and sealing machines designed to fill pasty products with high hygiene requirements into preformed containers in different sizes, and shapes.
Forming, filling and sealing machines (FFS) for a huge variety of portion cup designs and materials. They offer maximum accuracy, precise product cut-off and gentle product handling.
Cheese
Complete lines for dosing and wrapping of processed and spreadable cheese in triangular, rectangular, and square portions of different weights, including mini portions. State-of-theart technology to preserve cheese properties and package integrity.
IMA’s range for processed and spreadable cheese also includes fill and seal machines (FS) for pre-formed containers and FFS machines for cups, and portion packs.
IMA provides horizontal FFS flow wrapping machines to pack portioned, blocks and prewrapped sliced cheese and vertical FFS baggers and weighing solutions suitable for shredded, grated, and diced cheese.
Creme fraîche, sour cream, white cheese, yoghurt, dessert, UHT milk and coffee creamer
The FS as well as FFS solutions are known for their outstanding filling accuracy. Covering a wide range of filling styles, countless customized and tailor-made design possibilities for cups are available to satisfy any customer demand. Fillers benefit from automatic, fully controlled SIP/CIP systems for maximum hygiene, and are supplied in full compliance with European regulations.
Filling systems for flexible stand-up pouches - with and without spout - complete our machine portfolio, guaranteeing top hygiene design with ultra-clean and aseptic solutions. Turnkey solutions for sustainable production
Taking advantage of synergies and integrations within the IMA Group, the IMA FOOD companies are able to supply complete turnkey packaging solutions:from primary packaging up to any secondary and end of line equipment tailored specifically for dairy products.
IMA Group companies stand out not only for their manufacturing capabilities but also for the competence in supporting customers in the research and development of new sustainable packaging styles and materials as well as Smart Manufacturing products and services.
Via per Sassuolo, 1933 - 41058 Vignola (Modena) Italy
Tel. +39 059 768 411 - Fax +39 059 762 864
info@gruppofabbri.com - www.gruppofabbri.com
Over 70 years of active market experience make Fabbri Group a renowned leader in the manufacture and sale of machines and films for fresh and ultrafresh food packaging (typically red meat, poultry, fish, cheese, fruit, vegetables, sauces, ready meals, sweets…). Thanks to over 35,000 machines installed globally and thousands of tons of film produced per year, Fabbri Group advises and supports more than 2,500+ companies worldwide, and preserves the freshness of billions of packs commercialized every year on the total market.
Fabbri Group’s winning strategy comes from a combined supply of machines and films, completed by an extensive network of experienced, qualified, multilingual technical teams
Fabbri’s wide offer includes automatic stretch wrappers, tray-sealers, traditional, biobased and compostable stretch or “lid” films, which can be neutral and/or printed according to the different applications.
All Fabbri solutions can be used as stand-alone in combination with all most popular packaging equipment on the market, or as a whole composite packaging system
Fabbri Group caters for everyone (retail, industry, brandowners, and big to small food processors), covering with care all food markets: main objective for Fabbri’s R&D Dept. is offering safe and effective solutions at improved sustainability and performance, as proven by the more than 130 active patent registrations related to machines and films projects.
Environment, we care!
Fabbri Group’s attention has always revolved around the concept of sustainability: since the beginning, its mission has always been to “preserve without waste”. It focuses on preserving food products and extending their shelflife thanks to the most appropriate and environmentally sustainable packaging solutions. Related to films in particular,Fabbri Group recognises and protects the value of resources by developing different food packaging solutions in all the most required materials by the different markets worldwide, all of them in their most sustainable form.
Fabbri Group offers printed film both on the basis of the customer’s design and by developing specific and customized projects for every need
Performance products for every need
• Elixa: this range of stretchwrappers is ideal for retail and small packaging centres (productivity from 14 to 35 ppm).
• Automac: these high-speed stretch wrappers answer all most stringent needs from the food industry (productivity from 40 to 90 ppm).
• The Elixa and Automac equipment can be both optimally integrated with all major weigh-pack-label solutions available on the market.
• Stretch and lid films in different formulations, layouts (plain or printed) and materials (traditional, biobased, compostable) according to the various applications.
• Automatic tray-sealers for the food industry and retail. These machines can be adapted into complete customised lines for packaging solid, liquid and semiliquid products, such as pasta, ready meals, hamburgers, fruit and vegetables, dairy products, olives, pickled vegetables, sauces, pizzas, desserts, candies...
Some popular features of Fabbri’s offer
• Fabbri Hybrid: The stretch wrapping machines are able to handle any kind of materials (traditional, biobased, compostable), ideal for multiple productions or for a gradual transition to sustainable packaging.
• Nature Fresh: The innovative and multi-awarded cling film with domestic and industrial/commercial compostability certification according to EN 13432 and ASTM 6400 Standards. In its “cutterbox” version for manual packaging, Nature Fresh is highly appreciated and perfect for the Ho.Re.Ca. sector.
• Nature Lid: The certified compostable “lid” film according to Standard EN 13432.
TopLidplus traysealer: compact, easy, fast, with a smooth format change, "hybrid" as using traditional & compostable materials. Available in "sealing only" or "sealing + gas flushing" configuration
Voluntary Certifications: Quality,Environment,Health & Safety
Companies within Fabbri Group also boast the following certifications:
• ISO 9001:2015 - Quality Management System (Gruppo Fabbri Vignola S.p.A., Gruppo Fabbri Svizzera S.A., Fabbri Group France S.A.S.)
• ISO 14001:2015 - Environmental Management System (Gruppo Fabbri Vignola S.p.A., Gruppo Fabbri Svizzera S.A.)
• EMAS Regulation EU no. 2018/2026 (Gruppo Fabbri Vignola S.p.A.)
• ISO 45001:2018 - Occupational Health and Safety Management System (Gruppo Fabbri Vignola S.p.A.)
For more information and offers: Info: www.gruppofabbri.com
Offers: sales@gruppofabbri.com
LinkedIn: https://it.linkedin.com/company/fabbrigroup YouTube: https://www.youtube.com/@Fabbri-Group
European-based Italian excellence requested worldwide
• Head office located in Vignola (Modena, Italy)
• Production plants in Italy and Switzerland)
• Different seats for commercial and technical assistance in Italy, Switzerland, France, Germany, UK, Russia
• Active in around 90 countries worldwide
• A hundred dealer companies and authorised service centres
The Fabbri films are produced in the most innovative formulations to be as environmentally friendly as possible according to the chosen application
smartest solution for compostable packaging in the Ho.Re.Ca.
Via per Sassuolo, 1933 - 41058 Vignola (Modena) Italy Tel. +39 059 768 411 - Fax +39 059 762 864 info@gruppofabbri.com - www.gruppofabbri.com
Automac Ultra is a “hybrid” packaging machine, as it can handle trays, films, and labels in any material available on the market (traditional, biobased, compostable)
Via Piemonte, 1 - 29122 Piacenza (Italy) Tel. +39 0523 554012 - Fax +39 0523 554004 info@gampackgroup.com - www.gampackgroup.com
Gampack Group: Excellence and innovation at the service of industrial packaging
In the competitive scenario of industrial packaging, Gampack Group stands out as a leading player. The Italian company excels in designing and manufacturing secondary packaging and end-of-line systems, offering advanced and customized technological solutions, which have bolstered its growth in a particularly demanding and ever-evolving market.
The core of Gampack Group’s offerings lies, on one hand, in the design of automatic machines to pack various rigid products, from beverage cartons to cans and glass jars, intended for liquid and semi-liquid products such as fruit juices, jams, milk, and pet food. On the other hand, the company’s drive for innovation is also reflected in its robotics division, enhancing its portfolio with classic packaging machines, integrated with highly customizable robotic systems and specific for the packaging of both the
aforementioned rigid items and flexible products, such as doypacks, flowpacks, and pouches.
In an era where sustainability is imperative, Gampack Group meets regulatory and environmental challenges with cutting-edge green solutions. The introduction of the “plastic tax” has prompted the company to revamp its production processes with an eco-friendly approach, developing sustainable packaging like innovative clusters, Mini-trays,Eco-labels,and I-Layers,made from renewable, biodegradable, compostable, and recyclable materials. This sustainable approach has been well-received by clients, demonstrating market sensitivity to these issues and proving that environmental impact reduction can indeed go hand in hand with production efficiency. Flexibility is another cornerstone for Gampack Group. The company’s machines are designed to quickly adapt to different sizes and production parameters, ensuring high versatility. With over 1,500 installations worldwide,
Gampack Group guarantees solutions tailored to customer’s needs, backed by excellent After-Sales service that includes timely spare parts supply and technical interventions on production lines, within the next 24 hours from the costumer’s request.
As far as its R&D activities are concerned, Gampack Group keeps a keen eye on the future, starting to implement Artificial Intelligence in its systems, used, for instance, to analyze production statistical data and optimize processes. The quality of the software algorithms developed in-house leads to increased production efficiency, fault prevention, and waste reduction, ensuring optimal operational continuity and improving working conditions for operators. With a steadfast commitment to innovation and sustainability, Gampack Group confirms its leadership in the packaging industry, offering trailblazing solutions that meet the new challenges of the global market.
Via Trivulzia, 54 - 23020 Mese (Sondrio) Italy
Tel. +39 0343 410 51
fic@fic.com - www.fic.com
Conclusion
Ice water systems by FIC SpA offer a compelling alternative for industrial chilled water production. These innovative solutions provide efficient, sustainable cooling with options for precise temperature control, continuous production, and space-saving designs. As industries strive for environmental responsibility, Ice water systems position FIC SpA at the forefront of the “cool revolution”.
Via Trivulzia, 54 - 23020 Mese (Sondrio) Italy
Tel. +39 0343 410 51
fic@fic.com - www.fic.com
Precise chilled water production with ice accumulation
Everest ICE BANK excels at providing precisely chilled water (+1°C) through controlled ice accumulation.This system is ideal for applications with fluctuating chilled water demands, including those with limited daily usage or requiring short bursts of heavy use.
Continuous chilled water production
For applications demanding constant chilled water production exceeding 10-12 hours daily, the RED System is the answer. This insulated tank features a pillow plate heat exchanger for efficient heat transfer, ensuring continuous chilled water production.
Precision cooling with flexibility: Falling film chillers
Falling Film Chillers provide a unique approach to water cooling,achieving temperatures as low as +0.5/+1°C. These open systems are easy to clean and offer low refrigerant content, minimizing environmental impact. Their compact design makes them ideal for space-constrained applications.
Advantages of ice water systems
• Energy cost savings: Ice water systems can leverage off-peak energy rates for ice accumulation, reducing overall energy costs.
• Scalability: Falling Film Chillers and RED systems can be customized to meet specific cooling capacities by adding modules.
• Sustainability: All three systems are compatible with various refrigerants, including environmentally friendly options like R717 (ammonia) and R744 (CO2).
Investigating the advantages of ice water for industrial cooling
This article explores the benefits of ice water systems,a revolutionary technology in industrial chilled water production. FIC SpA, a leader in the field, offers three innovative solutions: Everest ICE BANK, RED system, and falling film chillers.
Via del Lavoro, 53 - 36034 Malo (Vicenza) Italy
Tel. +39 0445 63 74 44 - Fax +39 0445 63 74 55 europa@europa-zone.com - www.europa-zone.com
For more than 30 years, EUROPA has been selling professional ovens to a large number of bakeries, pastry and pizza shops, hotels and supermarket chains, exporting to more than 70 Countries worldwide. Established in 1990, the brand EUROPA has become synonymous with reliability and innovation, specializing in the production of commercial ovens and equipment for bread, pastry and pizza baking. The company grew and expanded in a very short time, leading the business over the main international markets.This could happen thanks to a dynamic team, characterized by a professional and fresh approach. The management group has always
been supported by a qualified and experienced technical staff, ready to understand market’s requirements and to meet customers’ needs. Experimentation and research, in fact, have always represented the primary purpose of this company. Over the years, EUROPA has consolidated world-wide its own position, thanks to a constant renewal of its range with increasingly more advanced products. It continues to grow year by year,consolidating its presence both in Italy and abroad, relying on a strong mark, which means quality and modernity.
The wide range of products offered by EUROPA includes both rotary ovens and deck ovens, with models of various
types and sizes, to meet the needs of all bakers and pastry chefs in the world,from small artisanal productions to large industrial productions. In particular, EUROPA is proud to announce two new models that become part of our range: Giotto: Convection oven with revolving trolley, designed to guarantee excellent performances even for the most delicate products, suitable for the artisan who seeks the highest cooking quality, for large-scale distribution for reliability and for industry for “heavy” use at loop. Giotto is available in both the electric and gas versions, and is built in such a way as to give maximum attention to energy efficiency starting from the door seal up to the heat exchanger, and is also equipped with door glass with lowemissivity treatment. The cooking air flows from bottom to top constitute a “ground” cooking effect, and they are controlled by 4 rows of dampers, guaranteeing excellent homogeneity and excellent cooking quality. Giotto is available in the “F” version (with heat exchanger left side to the oven with burner / heating elements access from the front), and “R” version (with heat exchanger rear to the oven with burner / heating elements access from the rear). Palladio is the next-generation electric deck oven designed to be robust and high-performance, with advanced technology. Equipped with totally independent cooking chambers and steamers, a simple and intuitive color Touch Screen interface, and latest generation electronics for power management with 3 modes. In addition to the reduced dimensions on the floor, and ease of installation and transport, Palladio guarantees perfect uniformity and consistency in cooking.
Discover EUROPA and its range of ovens on the site:www. europaovens.com
EUROPA:Your baking specialist!
Via del Lavoro, 53 - 36034 Malo (Vicenza) Italy
Tel. +39 0445 63 74 44 - Fax +39 0445 63 74 55 europa@europa-zone.com - www.europa-zone.com
Corso Genova, 28 - 27029 Vigevano (Pavia) Italy
Tel. + 39 0381 19 71 359
info@esg-italy.com - esg-italy.com
ESG - Innovation for the snack industry: The service
ESG, whose slogan is “Innovation for the Snack Industry,” is a general contractor company specializing in the design and construction of production plants for salty snacks. Founded by a team of highly experienced professionals who have worked for multinationals and possess exceptional expertise in the field, ESG stands out for offering innovative and high-quality solutions for the entire snack production cycle.
What is a “general contractor”?
A general contractor engineering company like ESG takes on the role of project manager, coordinating all phases from start to finish. This includes planning, designing, procurement and/or construction, and the implementation of every aspect of a production plant. The goal is to provide clients with a comprehensive and integrated service that allows them to focus on their core activities while we handle their project.
ESG unique approach
ESG’s approach is unique in the industry. To complete a medium-sized project, a snack manufacturer typically needs to engage, both technologically and contractually, with at least a dozen top manufacturing players, plus another 20-25 minor producers. From the project’s conception to its completion and the start of production, various managers, often with operational duties, must dedicate significant energy and time to ensure the project is completed.
The ESG team takes care of everything, freeing up company resources and allowing them to focus on operational activities. Additionally, ESG brings years of experience from numerous projects across the snack industry, leveraging knowledge of multiple technologies and market innovations, strong relationships with key stakeholders, and significant work volumes to offer clients the best available technologies. This enables the client to complete their project with final investments equal to or sometimes less than what would be required if they used only their internal resources
ESG is distinguished in the industrial landscape by its dedicated and personalized services designed to optimize and exceed customer expectations in the snack sector. With a clear focus on quality and efficiency, ESG is committed to providing tailored solutions that specifically address each client’s unique needs and goals. Its personalized design offering is the core of its commitment. Every operation is unique, so ESG strives to design layouts and workflows that not only optimize efficiency but are also ergonomically planned to increase productivity, reduce operational costs, and minimize environmental impact. With its extensive experience, ESG guarantees projects that meet and exceed expectations in terms of functionality and performance.
Selection
The selection of partners is another fundamental pillar of ESG services. Through an established and in-depth network of trusted partners and suppliers, the company carefully select each component of the plant, ensuring that every machine and material meets the highest standards of quality and reliability. This approach not only ensures continuous and uninterrupted production but also optimizes costs, providing cost-effective solutions without compromising on quality.
Comprehensive support
ESG commitment goes beyond design and supplier selection. It encompasses full support throughout all project phases.From initial consultation and design to final delivery and installation of equipment, ESG is alongside its clients to ensure a smooth process. Its goal is to provide not just a solution, but a long-term partnership based on trust and customer satisfaction.
ESG is constantly committed to staying at the forefront of the latest technologies and trends in the snack sector. This allows the company to continuously offer innovations that improve the efficiency, quality, and sustainability of its clients’ operations. ESG dedication to innovation distinguishes it as industry leaders, ready to anticipate and meet emerging market needs.
Conclusion
In summary, ESG is not just a supplier of industrial solutions but a strategic partner offering expertise, commitment, and tailored solutions to drive the success of its clients in the competitive snack market.ESG is ready to guide you toward a future of success and innovation.
The future of ESG
ESG future goal is to actively contribute to the growth and development of its clients, enabling them to establish and maintain their leadership in the sector, expanding its partner network, and staying at the forefront of technological innovations. The company aims to be recognized as the go-to partner for all companies looking to start or improve their snack production plants.
ESG is committed to supporting the growth and success of its clients, positively contributing to the snack industry with sustainable and innovative solutions. It is ready to face future challenges and continues to provide exceptional service that meets and exceeds our clients’ expectations.
In conclusion, ESG - Innovation for snacks is more than an engineering company. It is a dedicated partner working alongside its clients to bring their visions to life, offering expertise, quality, and innovation in every project.
Corso Genova, 28 - 27029 Vigevano (Pavia) Italy Tel. + 39 0381 19 71 359 info@esg-italy.com - esg-italy.com
Via Copernico, 62 - 36034 Malo (Vicenza) Italy Tel. +39 0445 57 66 92 - Fax +39 0445 57 72 80 mail@eschermixers.com - www.eschermixers.com
Escher Mixers specializes in the production of mixing machinery for the bread and pastry-making sectors. Over the years, Escher Mixers has gained specialized knowledge that has allowed this company to develop machines and solutions to meet the needs of a variety of clients and different types of markets.
Escher Mixers machines are renowned for their sturdiness, durability, accurate finishes, and for the quality of the dough they produce.
Bakery equipment
Escher Mixers proposes Spiral and Wendel mixing concepts. Both solutions can be with removable bowl through a patented® bowl locking and motion system MR-MW Line or bottom discharge system MD-MDW Line with conveyors belts or bowl lifters which can be matched with automatic solutions with linear system and storage of the resting bowls in vertical or linear storages, rotating automatic systems-carousel, scraps recovery systems, transverse hopper systems and star-cutting/ guillotine/roller with guillotine and other customized solutions.
Pastry equipment
The range of planetary mixers with double tool for the pastry industry is characterized by the lack of oil
lubrication systems, improving hygiene and reducing machine maintenance. A wide range of interchangeable tools is available for different uses and doughs.
For industrial productions, Escher Mixers has developed the PM-D Line with independent tool movement, with individual speed regulation and the possibility to reverse
the motion. While the PM-DB Line with the bridge structure allows automatic insertion of the ingredients, air insufflation to reduce mixing times and increase volume, dough processing with negative/positive pressure and cleaning through CIP washing system. Various bowl discharge options are available.
Dini Argeo has specialized in the production of weighing systems since 1846. We offer solutions ranging from mobile weighing systems to scales for commercial and industrial use, including a wide range of components, electronic solutions, and software for industrial automation and system integration.
In 2016, Dini Argeo joined Rice Lake Weighing Systems, an international group with divisions in America, Europe, Asia and Oceania.
Via Archimede, 27/33 - 70024 Gravina in Puglia (Bari) Italy
Tel. +39 080 326 61 96 - Fax +39 080 326 58 54 info@defino-giancaspro.com - www.defino-giancaspro.com
Defino & Giancaspro “has its roots in the time of mills made by wood”. The company was founded in 1965 in Gravina in Puglia (Bari-Italy) thanks to some craftsmen, whose main occupation was the assembling of milling plants and whose only capital was the work of their hands and their commitment to the world of wheat and cereals.
The master-fitter Vito Antonio Giancaspro, the father of the current General Manager, had many skills in various fields
such as carpentry, mechanics, plants and food technology. This“artisan”disposition,after more than 50 years,remains the cornerstone of the company philosophy and is one of its strengths. The company continues nowadays to provide its customers with all the experience and expertise of over one hundred employees with the same passion and enthusiasm. The goal of the Defino &Giancaspro is not to simply offer a machine or a plant, but to supply all the technologies and means to adapt them to the customer’s requirements.
Just like a high-quality tailored dress, the product meets the customers’ needs but always respect the company style with the unmistakable Made in Italy quality. Engineering, prototyping, research and continuous development ensure always the best solution to the customer. In Defino & Giancaspro design is meant with the overall conception of work planning, with the aim to turn ideas into product specification through the precious and constant sharing of information between young engineers and expert workers.
The company is a specialist in realization of carbon and stainless steel spouting and accessories, has a pool consisting of more than fifty types of machines in various sizes and operates construction and assembly of structures and silos. Its success lies in the precision and accuracy of working, always realized within their own workshop, and in the use of forefront machinery and certified welding techniques, which offer an excellent finishing and quality.
The service does not end at the delivery of the supply, the relationship with the customer continues through the optimization and the implementation of the new product, ensuring support, maintenance and constant assistance, namely a complete turnkey product.
Plants and machines manufactured and assembled by Defino & Giancaspro are requested and appreciated all over the world. Almost daily and constant are collaborations not only in Italy and Europe, but also with Russia, the United States, Mexico and North Africa.
Proud of their work, everywhere, from the offices to the workshop, all the departments work daily to improve and expand the range of products and services to satisfy both historical and new customers.”
Strada Paniate n°1 - 15040 Occimiano (Alessandria) Italy
Tel: +39 0142 40 06 11 - Fax: +39 0142 80 94 56 info@coldcar.it - www.coldcar.it
https://www.facebook.com/ColdCarSpa
https://www.linkedin.com/company/coldcarspa/mycompany
https://youtu.be/iMsgaUdu7Ws?si=vHUhyhRXsS9yuIm8 .https://www.youtube.com/watch?v=6c0mYhmCy9I
Cold Car thanks to its competence and long experience started in 1968, is a worldwide market leader in manufacturing eutectic refrigerated truck bodies and delivery vans for logistic cold chain last mile delivery.
These “bodies” are ideal for the ice cream and frozen food distribution in every market and with every ambient conditions and specifically developed to maximize the number of customers daily deliveries.
Cold Car is also specialized in manufacturing multi-temperature truck bodies with eutectic refrigeration unit, for various market segments as retail, horeca catering, gastronomies and fast food
The “refrigerated bodies” are always tailored according to the specific customer’s need and designed for direct sales/van selling, or for the pre-sales distribution and, using inner fixed or movable bulkheads, can be developed sections to deliver different temperatures food products as: ice-cream/frozen food at -33°C, fresh products (dairy, meat/fish, groceries, etc..) at +4°C, chocolate at +16°C, and dry products at ambient temperature. The refrigeration unit is only electrically powered and operates only during the overnight stops. Therefore this refrigeration system has got very cheap running costs and allows to have: zero noise during the daily delivery, zero fuel consumption for operation of the refrigeration unit and is ready for alternative and fuel electric vehicles.
Thanks to the huge above experience, Cold Car manufactures reliable and long life durable refrigerated bodies with high thermodynamic efficiency.
For further information, please visit the website www.coldcar.it. Facebook: https://www.facebook.com/ColdCarSpa/ LinkedIn: https://www.linkedin.com/company/coldcarspa/mycompany/ To watch the company’s videos, please check on You tube: https://youtu.be/iMsgaUdu7Ws?si=vHUhyhRXsS9yuIm8 https://www.youtube.com/watch?v=6c0mYhmCy9I.
Via Giuseppe Verdi, 13 - 23847 Molteno (Lecco) Italy
Tel. +39 031 87 98 11 - Fax +39 031 85 63 73 sales@camagroup.com - www.camagroup.com
Multiple lines in the Middle East’s biggest confectionary plant end with packaging perfection thanks to Cama technology
The Zar Group is one of the Middle East’s biggest diversified food companies. Serving the region for over 30 years, it not only owns and operates the region’s largest pasta production site, but recent investment following a portfolio enlargement has led to the design and build of the region’s largest confectionary plant too.
Construction of the new plant for the newly formed Zarkam brand began in 2018 and Cama delivered its first machine in 2019, but work was subsequently stalled and put on hold for 18 months, due to the Covid pandemic. However, it started back up again in 2021 and is already producing products from two complete lines and one partially completed line.
“Interestingly, unlike many other plants around the world that specialise in single product types, this plant produces a huge variety of confectionery from a single site, including cakes, wafers, sandwich biscuits and crackers. This product variety means that the plant has to deploy a wide range of technology solutions for every element of the individual processing and packaging steps. But Cama is the only company handling secondary
packaging across all the lines, no other machine supplier has this depth of technology in the plant.”
“Cama’s BTG Series has design and operational features that are setting the standard in secondary packaging. Their modular, scalable and hygienically designed frameworks house contemporary automation solutions – including advanced rotary and linear servo technology – which can be tightly coupled to in-house-developed robotics, to deliver the all-important flexibility and adaptability required by modern packaging operations. The machine range is also based on a digital platform that supports full Industry 4.0 capabilities, including AR, VR and virtual testing, training and operation.”
“For such a prestigious project, we deployed a dedicated Iranian support team for the Zar Group for installation and commissioning. Zar Group can call up on three full-time local Cama engineers, without worrying about language barriers, visas and travel times, something for which they are very appreciative. We also acted as a consultant in the early stages, as they did not have deep knowledge of the confectionery industry. We helped them with packaging design, material selection, machine locations and product launches, based on our in-depth knowledge from other industries and applications around the world. We always explain to our customers that we are not just a supplier, we are a partner that is happy to share skills and knowledge to ensure success.”
Mr. Mohsen Amini CEO at Zarkham explains:“To be the best in the world, you have to use the best in the world, so it was essential that we chose technology partners that could help us achieve our aims. Cama’s machines are used by many of the world’s leading confectionery brands, so we know there is an established pedigree behind the name. Their digital infrastructure makes integration easier, and the user interface is the same across all the Cama machines, so there is less to learn for the operators. The support before, during and after installation and commissioning has been excellent.” www.camagroup.com
Via Giuseppe Verdi, 13 - 23847 Molteno (Lecco) Italy Tel. +39 031 87 98 11 - Fax +39 031 85 63 73 sales@camagroup.com - www.camagroup.com
WE ARE LOOKING FOR DISTRIBUTORS
Via M.Buonarroti, 3 - Z.I. Sipro - 44020 San Giovanni di Ostellato (Ferrara) Italy Tel. +39 0533 31 11 63
commerciale@bebsilos.com - commerciale1@bebsilos.com- www.bebsilos.com
B&B Silo Systems, solutions for high standards
B&B Silo Systems was established as a design and construction company for the storage, transport, dosing and automation systems of raw materials.
With a dynamic and successful management group, offering engineering solutions associated with a vast know-how in technological processes, it successfully established itself on the national and international scene, addressing the food, chemical, cosmetic and pharmaceutical sectors.
This company is constantly engaged in the research of technicalandsystemsolutionsabletomaketheproduction process more efficient and qualified, guaranteeing high standards:
• Qualitative (authenticity specific-physical characteristics of the products)
•Economic(savingonthepurchasepriceofrawmaterials)
• Logistics (warehouse space recovery)
• Hygienic (elimination of containers and equipment that can favour bacterial contamination).
This is why B&B Silo Systems considers itself as supplier of the entire system, creating custom-made systems for each individual customer, according to their specific production needs.
Each system adapts to its context, providing the storage of raw materials in internal and/or external silos, that can be loaded through sack or big-bag unloading systems, or directly from the supplier’s truck. Subsequently, raw materials are conveyed to the dosing point, through appropriate mechanical or pneumatic transport systems. Finally,the powder and/or liquid ingredients are dosed and mixed in the hoppers placed near the mixers. For microingredients B&B Silo Systems has, instead, designed micro-dosers with manual or automatic loading.
B&B Silo Systems also provides accessories or special components: dust extraction systems, sieve shakers, mixers, mills for sugar grinding, fermenters, flour cooling systems.
Moreover, B&B Silo Systems designs software for PLC, HMI and microprocessors to manage and control systems of weighing, dosing in weight addition or subtraction,
volumetric dosage, liquid dosage, multi-line and multiscale dosage, continuous raw material supply, mixing.
B&B Silo Systems develops software for the production management, monitoring and remote control of the system and synoptic software for the supervisor of the entire system.
It also takes care of the control and the management of production, warehouses and shipments, by barcode or QR Code, ensuring a perfect integration of the solutions and reliability of the interface, with the consequent saving of resources.
Via M.Buonarroti, 3 - Z.I. Sipro - 44020 San Giovanni di Ostellato (Ferrara) Italy Tel. +39 0533 31 11 63 commerciale@bebsilos.com - commerciale1@bebsilos.com- www.bebsilos.com
At ATS FAAR we have the right solution for small production units that process vegetable products, produce juices, jams, marinated and candied products. If you are in the milk sector ATS FAAR Industries is your ideal partner! Contact us!
Fruit processing lines for high-quality jam production, with capacity of about 150 Kg/h of finished products in glass jars with twist off capsules.
Via Leonardo da Vinci, 11/B - 20051 Cassina de’ Pecchi (Milano) Italy Tel. +39 02 36636340 atsfaar@atsfaar-ind.eu - www.atsfaar.it
ATS FAAR Industries is an Italian company specializing in the design and supply of turnkey control laboratories.
Thanks to its extensive experience, ATS FAAR Industries can grant a qualified technical support during the entire design stage of your laboratory, from advice right to supply, and start-up and, in many sectors: Chemical, petrochemical, plastics, natural gas, water treatment, cosmetic industries, school and university, and of course the agro-food sector, as well.
This business reality was established to meet customers’ request for a unique partner for any issue to be analysed during the design of a laboratory. In addition to space designing, ATS FAAR Industrial has also its own line of technical furniture, fume hoods, special tables, storage cabinets for chemical products, electrical and hydraulic systems, pure gas distribution that serve instrumentation, as well as installation and start-up for a truly turnkey service.
Historical partnership with the major producers of laboratory instruments gives ATS FAAR Industries the possibility of offering customers products at competitive prices.
The after-sales service includes instrument installation, machinery and, upon request, also training courses for laboratory operators.
For the agro-food sector, as well as product control laboratory, ATS FAAR Industries also specializes in pilot plant creation for fruit processing.
ATS FAAR Industries operates both in Italy and abroad and has already created laboratories in more than 20 countries across the globe, carrying forward its values of transparency, cooperation and professionalism with the goal of building trustful relationship and long-lasting mutual respect with its customers.
Do contact ATS FAAR Industries and do not be concerned, they will take care of your laboratory!
Horizontal mixer
Via Bradolini, 21 – 31020 Castello Roganzuolo di San Fior (Treviso) Italy
Tel. +39 0438 40 18 22 - Fax: +39 0438 40 19 67
apinox@apinox.it - www.apinox.it
Apinox’ mixer type “RM” is a high speed and high output batch mixer particularly suitable for hard biscuits (tp. Marie – Petit Beurre), soft biscuits, crackers, snacks and/ or soft and delicate dough.
Vertical mixer This mixer has been specifically designed for the production of soda cracker, cream cracker, two phases fermented dough and delicate dough. Excellent qualitative products can be obtained with this mixer with high hour production capacity.
Industrial mixer with double sigma-shaped mixing arm For the production of chewing gum and bubble gum.
ALaboratory mixers
Universal mixers dedicated to the mixing of tests and samplings.
Laboratory mixers with sigma shaped arm, available with capacity from 1 to 10 litres. They are designed to process medium and high viscosity dough.
pinox offers a long experience in the design and production of mixers. Apinox was founded in 1981 by a small group of people who shared a great desire to work hard and a huge wealth of experience, which was the result of studies but above all of hard work. Over the years Apinox has grown continuously and constantly, not forgetting to invest, year after year, in new technologies that allowed the company to obtain a flexible staff. To date, Apinox has a staff of 50 people divided between Production Dept.,Warehouse,Technical and Design Dept., Quality Control, Administration and Commercial Dept. Apinox is one of the most important manufacturers worldwide of mixers for the bakery, confectionery, chemical and pharmaceutical industries.The company supplies a wide range of mixers for biscuits, crackers,
snacks, chewing gum, bubble gum, gum base, toffee, broth cubes, pharmaceutical products, butyl sealants, mastics, putties, glues, colours and pigments, special lubricants.
Apinox mixers are the result of years of experience both in the mixing techniques and in the level of technology used. The mixing arm, without a central shaft,has been designed to perform a rapid dispersion of all the ingredients and a controlled processing of the dough. The unloading of the dough can take place in wheeled tubs or on a conveyor belt/hopper. Apinox mixers are equipped with safety systems that guarantee the safety of the operators and comply with the regulations in force. All Apinox mixers are EC certified and upon request also ATEX, UL, CSA and HAZLOC certified.
Via Fossano, 33 - Bene Vagienna (Cuneo) Italy
Tel. +39 01 72 654755 - Fax + 39 01 72 65481 1 anselmo@anselmoitalia.com - www.anselmoitalia.com
The Anselmo Group today is a landmark for food manufacturers interested in high quality equipment, 100% made in Italy, with great reliability and productivity. The increasingly range of new products proposed,highlight the ability of theAnselmo Group to remain at the forefront of the latest trends and consumer needs. Innovativeandsustainablesolutionsconfirmthecompany’s commitment to the best quality and the environment. The Group is always attentive to seize new opportunities and overcome challenges, maintaining its mission of offering high-quality products and advanced solutions that meet the needs of a constantly evolving world market, and all this is thank to the union of the solid competences and synergies between the various companies of the Group. In 2017, ANSELMO Impianti started a new growth way with the incorporation of other three companies:
FEN Impianti, LTA and Omar Impianti, giving life to actual Anselmo Group.
The range of products offered by Anselmo Group, entirely made in Italy, has now considerably expanded, fully responding to all the needs of the food industry worldwide, boasting today over 45 years of experience in the production of industrial plants for both long and short dry pasta.
It is important to underline that in 2004, Anselmo Impianti strengthened its position of leadership in the sector with the acquisition of Braibanti business branch.
FEN Impianti, leader in the world for the manufacture of industrial plants for snacks, breakfast cereals, functional flours and gluten-free pasta, offers customized and flexible solutions based on its thirty-year experience in the industry.ThecompanyboastsanadvancedR&Dcenterthat has been enlarged and improved with several upgrades over the years. Actually, the R&D center is equipped with pilot plants for the development of new products, allowing excellent collaborations with customers for staff training and product characterization. Furthermore, the addition of two new extruders is enriching the center, expanding the range of developable products, and strengthening collaborations with important companies in the field. LTA, specialized in the manufacture of automatic and semi-automatic machinery for the production of special shapes, such as nests, lasagna, and cannelloni, which perfectly combine and complete the range of shapes offered by Anselmo Impianti.
With over 70 years of experience, OMAR Impianti stands as a leader among major Italian manufacturers in the design and construction of plants to produce stuffed and laminated pasta. Over the years, OMAR Impianti has provided and continues to provide its services to many prestigious pasta factories worldwide. One distinctive feature of OMAR Impianti is the customization of all its machines and plants to meet every specific market requirement. In a constantly changing scenario, Anselmo Group confirms its position as a reference point for innovation and excellence in the industrial equipment field for the food industry, looking with determination to a future of success and satisfaction for its prestigious customers.
Via Ruca, 400 (Z.I) - 25065 Lumezzane (Brescia) Italy Tel. +39 030 892 59 53 info@4gghidini.it - www.4gghidini.it
G® GHIDINI Srl is specialized in producing stainless steel ball valves and fittings. Founded in 1978, with over 40 years of experience, 4G® GHIDINI has always set the product and service quality as its main objective. Product quality is ensured by using raw materials exclusively sourced in the European Union and by processing them entirely in the production site located in Lumezzane, Brescia. Service quality relies on prompt stock availability of all the proposed items, added value in terms of offer and timely deliveries.
All the products are designed, manufactured and 100% tested before being marketed, following a correct certified construction practice and with the aid of highly advanced machinery to guarantee end-users a high-level product.
The company is UNI EN ISO 9001:2015 certified. Product traceability is guaranteed throughout the entire production process, from the entry of raw materials to subsequent processing,up to the finished product.4G® GHIDINI product is 100% Made in Italy, no import particulars are used. 4G® GHIDINI products are used in the most varied industrial applications, including pharmaceutical, biotechnological and cosmetic industry; food and beverage; chemistry, process, water treatment and energy production. Pharmaceutical industry needs the best technologies to meet the needs of its productions in sterile and aseptic environments.4G® GHIDINI valves with integral seals without dead points eliminate the deposits of fluid inside them; high performances and certifications make them the ideal
product for clean applications. The valves, easily removable, guarantee ease of cleaning and quick maintenance. Food industry requires components such as ball valves and fittings that together with performance and reliability guarantee suitability for contact with foods through certificationssuchas “MOCA” 1935/2004/CE and FDA.For this sector 4G® GHIDINI provides specific solutions, such as predispositions for washing with CIP system, for sterilization by steam and for PIG product recovery systems. All 4G® GHIDINI valve models are available also in the version with heating jacket,ideal for the use in chocolate production.
For the chemical industry, the valves and fittings made entirelyinAisi316Lfrombarensuremaximumcompatibility with the most aggressive fluids and the most critical conditions of use; the possibility to configure them ad hoc allows to obtain the maximum yield.
The valves can be installed in hazardous areas given the ATEX II 2 G-D T4 certification. Products also comply with the technical regulation EAC TR CU 010/2011 and EAC TR CU 032/2013
The different types of connections allow 4G® GHIDINI to customize ball valves according to customer’s needs, making them suitable for installation on any system.
Strengthened of the past and present challenges, 4G® GHIDINI is ready for the future ones.
FoodIndustry www.vimco.it
FoodIndustry
TecnAlimentaria supplement N°8/9 August/September 2024 - Year XXIX
Publisher Fabiana Da Cortà Fumei
Editorial Staff & Design redazione@tecnalimentaria.it
Sabrina Fattoretto
Claudia Bosco
Elena Abbondanza
Cinzia Beraldo
Vanessa Tarantino
Marketing and Advertising
Anita Pozzi
anita.pozzi@edftrend.com
Franco Giordano franco.giordano@edftrend.com
www.zacmi.com
Management, Editorial Office
Editrice EDF Trend srl
Corso del Popolo, 42 31100 Treviso – Italy
Tel. +39 0422 549305
Fax +39 0422 591736 www.tecnalimentaria.it www.edftrend.com
Translation into Arabic
Ann Nasr
Printing L’Artegra ca Srl
TecnAlimentaria is
Autorizzazione Tribunale di Forlì n. 5 del 19.01.1996 N° iscrizione ROC (Registro degli Operatori di Comunicazione): 22054
In questo numero la pubblicità non supera il 45% Sped. in abbonamento postale 45%Art. 2 Comma 20/B Legge 662/1996 DCI-TV All right reserved.
Reproduction in whole or in part without written permission is prohibited.
The Publisher is not responsible for any materials, nor for writers’ nor contributors’ expressed or implied opinions. Informativa ex D.lgs 196/03
Ai sensi dell’art.2 comma 2° del Codice Deontologico dei giornalisti si rende nota l’esistenza di una banca dati di uso redazionale presso la sede di Corso del Popolo, 42 - Treviso. Responsabile del trattamento dati è il direttore responsabile a cui ci si può rivolgere presso la sede di Treviso - Corso del Popolo, 42 per i diritti previsti dalla legge 675/1996.
Member of:
FoodIndustry www.4gghidini.it 10-11 4GGHIDINISRL
Food&BeverageIndustry www.aeraque.com 13 AERAQUESRL
FoodIndustry www.anselmoitalia.com 14-15 ANSELMOIMPIANTISRL
FoodIndustry www.apinox.it 16-17 APINOXSRL
FoodIndustry www.atsfaar.it 18-19 ATSFAARSRL
FoodIndustry www.bebsilos.com 20-21 B&BSILOSYSTEMSSRL
FoodIndustry www.borghigroup.it 23,129 BORGHISRL
FoodIndustry www.camagroup.com 25-27 CAMAGROUP
FoodIndustry www.coldcar.it 28-29 COLDCARSPA
FoodIndustry www.cuomoind.it 30-31 CUOMOF.LLI
FoodIndustry www.defino-giancaspro.com 32-33 DEFINO&GIANCASPROSRL
FoodIndustry www.diniargeo.com 34-35 DINIARGEOSRL
FoodIndustry www.eschermixers.com 2,36-37 ESCHERMIXERSSRL
FoodIndustry www.esg-italy.com 1,39-41 ESGSRL
FoodIndustry www.europa-zone.com 42-43 EUROPASRL
FoodIndustry www.fic.com 44-45 FICSPA
FoodIndustry www.gampackgroup.com 46-47 GAMPACKGROUP
FoodIndustry www.gsp.it 112-113 GENERALSYSTEMPACKSRL
FoodIndustry www.gruppofabbri.com 49-51 GRUPPOFABBRIVIGNOLASPA
FoodIndustry www.ifppackaging.it 112-113 IFPPACKAGINGSRL
FoodIndustry www.ima.it 2^Cover,52-53 IMAGROUP
FoodIndustry www.ima.it/coffee 3,54-55 IMACOFFEE
FoodIndustry www.imf-srl.com 56-57 IMFSRL
FoodIndustry www.inoxmeccanica.it 58-59 INOXMECCANICASPA
FoodIndustry www.landucci.it 60-61 LANDUCCISRL
FoodIndustry www.lawer.com 62-63 LAWERSPA
Food&BeverageIndustry www.lcz.it 64-65 LCZSRL
FoodIndustry www.mhmaterialhandling.com68-69
FoodIndustry www.marottaevolution.com 66-67
FoodIndustry www.marvil.it 22
FoodIndustry www.me-foodsolutions.com 70-71
M.H.MATERIALHANDLINGSPA
MAROTTAEVOLUTIONGROUP
MARVILENGINEERINGSRL
MILLENNIUMENGINEERINGSRL
Food&BeverageIndustry www.minimotor.com 24 MINIMOTORSPA
FoodIndustry www.moelsrl.com 72-73 MOELSRL
FoodIndustry www.newplast.eu 74-75
NEWPLASTSRL
FoodIndustry www.newproject-italia.it 131 NEWPROJECTSRL
www.newteclabelling.it 12
30 up to 200 kg