

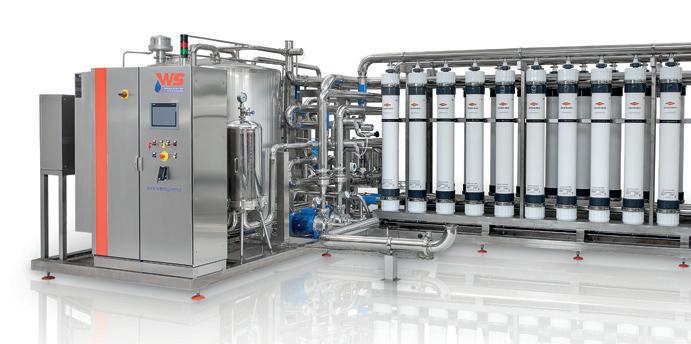
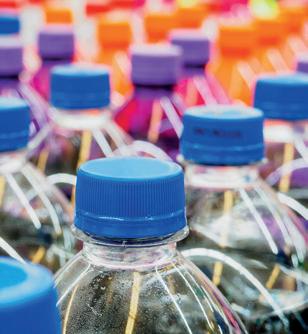
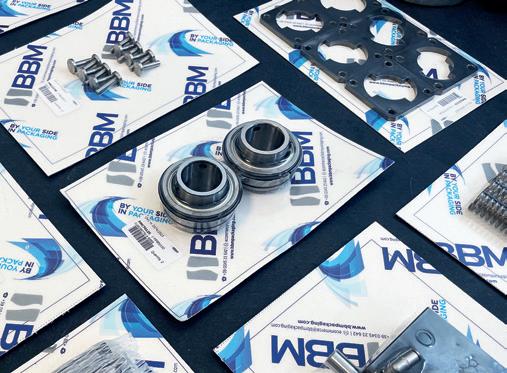
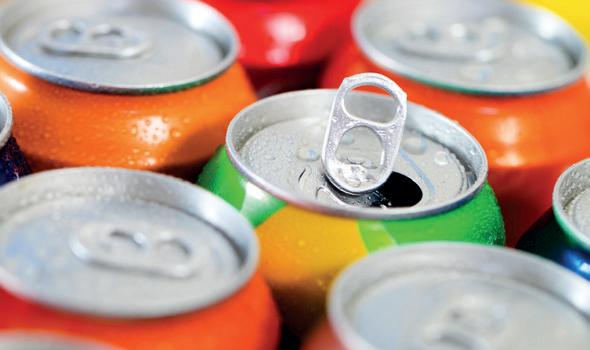
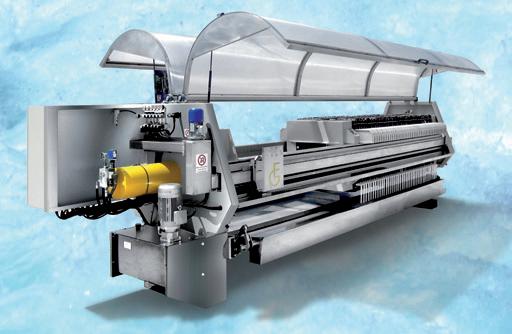
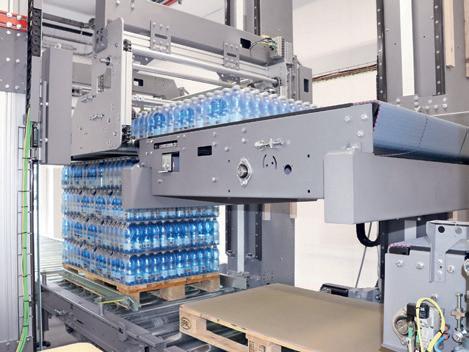
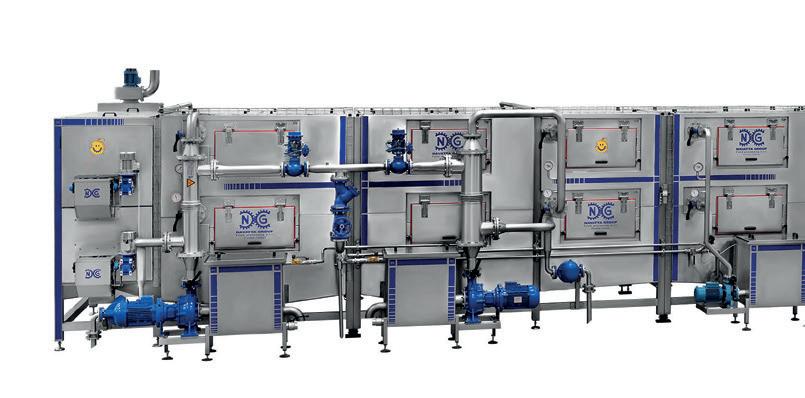

Via Roma, 123 - 46033 Castel d’Ario (Mantova) Italy
Tel. +39 0376 57 001 - Fax +39 0376 66 05 56 export@unical-ag.com - www.unical.eu
Unical power.
Industrial boilers made in Italy
A range aimed at large Industrial sector, a complete range of boilers manufactured in Italy by highly skilled personnel, with unique technological details, some covered by Unical Patent, like the special smoke pipes which significantly increase the boiler efficiency and control panels developed to ensure operator-free control, in total safety, up to 72 hours and with possible remote control.
The design of each boiler allows Unical to build special appliances, fulfilling any customer need.
Unical, an Italian company born in the 1972 to design and produce professional and industrial thermal groups for heating, has, subsequently, expanded its operating field, including air conditioning systems, thermal solar systems, integrated and hybrid systems, heat pumps, radiant panels, etc., coming to have one of the most complete catalogs in the entire sector.
Made in Italy is the focus of Unical.
5 the locations distributed on the national territory, between production and logistics, strategically connected and highly advanced for automation and robotization of the construction phases.
In the Borgocarbonara’s plant are manufactured industrial and steel boilers for jet burners (up to 15,000 kW), known for high-efficiency special boilers by virtue of special patented heat exchange pipes.
The range includes hot / superheated water boilers, up to 22,000 kW and boilers up to 25,000 kg/h of steam
In the Caorso’s plant are built wall and floor-standing boilers, both traditional and condensing (up to 1,500 kW).
The Unical Steamer department is the innovation of Unical power:
- Reverse flame steam boilers at low or high pressure, genuine three pass steam boiler at high pressure,
instantaneous electric steam boilers and all the necessary equipment for a medium or large system (industrial sector: food, canning for storage purposes, petrochemical, chemical, etc.).
- Hot water boilers and Superheated water boilers, with high and very high power, for production cycles and/or large systems (hospitals. pasta factory, district heating).
- Turnkey thermal power stations.
In addition to the CE certification, Unical boilers have obtained numerous certifications that allow them to be exported all over the world.
Unical, in addition to the 5 Italian offices, has 4 foreign branches (France, Germany, Poland and China) and boasts prestigious presences in Australia - New Zealand - Russia - U.K. - U.S.A. and Latin America as well as the Middle East.
www.unical.eu
Via Carlo Ceresa, 10 - 24015 San Giovanni Bianco (Bergamo) Italy
Tel. +39 0345 401 11 - Fax +39 0345 402 09
info@smigroup.it - www.smigroup.it
The food and beverage industry is influenced by the trend of strong product diversification. Food & Beverage industry therefore need very flexible and efficient bottling and packaging plants in order to reach high levels of competitiveness and optimization of production lines. Furthermore, in an economic environment that is increasingly oriented towards eco-friendly solutions in the use of plastic packaging, a growing number of companies have chosen to use rPET (100 % recyclable PET) bottles and cutting-edge technical solutions, like those supplied by SMI, in order to save energy and reduce the production environmental impact
SMI is specialized in the design, manufacturing and installation of complete bottling lines and packaging systems for flat and carbonated beverages and liquid products in PET, rPET and PP containers from 0.10 to 10 L, with output capacity up to 50,000 bottles/hour
SMI manufactures bottling plants and packaging machines providing to its customers, located all over the world, with smart solutions, able to meet their requirements in terms of competitiveness, production efficiency, operational flexibility, energy saving, easy management and monitoring of the whole production process. Furthermore, an advanced automation and control system compliant with Industry 4.0 technology and sophisticated sensors distribuited all along the bottling line (IoT architecture) enable to achieve high machine yields in all of the steps of the manufacturing process.
SMI solution for the primary packaging.
The EBS ERGON series of stretch-blow moulding, available both in “stand alone” version and in “combi” version, integrated with filling and capping systems (ECOBLOC® ERGON series), ensure high performances in the stretch blow-moulding of rPET, and PET bottles of different shapes and capacities from 0.10 L up to 10L mainly used for the food, beverage and detergent industries, able to meet production requirements.
Main advantages of EBS ERGON series
• stretch-blow moulding system based on a high efficiency rotary technology, equipped with motorized stretch rods for a precise management of the stretch rod cycle and a significant energy saving;
• ultra-compact plant: the preform heating section is integrated with the stretch-blow moulding section in a single module;
• reduced energy consumption, thanks to the preform heating module equipped with
high efficiency IR lamps and to the stretch-blow moulding module equipped with a double stage HP air recovery system;
• ergonomic structure that ensures an easy maintenance and a high safety level;
• high performance low dead volume valves, that reduce pre-blowing and blowing times, therefore improving efficiency and quality of the bottles;
• easy and fast format changeover, thanks to MotorNet System® automation and control system that ensures constant maintenance of the optimum processing parameters and the direct modification of the machine settings.
• thanks to an advanced CAD center for 3D design, SMI supports companies in the design and graphic realization of a wide range of 100% recyclable PET containers, featuring high quality and lightweight in order to save energy and material.
The advantages of the ECOBLOC® ERGON integrated solutions of blowing-filling-capping.
• The integration of stretch-blow moulding, filling and capping functions into a single machine allows to considerably reduce costs, as well as
the space occupied by the solution, since the rinser and conveyors between the stretch-blow moulder and the filler are not needed. This also leads to reduce contamination risks and to reach a higher hygiene level.
• High-efficiency rotary stretch-blow moulding system equipped with motorized stretch rods, whose functioning, controlled electronically, does not need mechanical cams. This allows a precise management of the rod path and an accurate control of its position, as well as a significant energy saving.
• The carousel blowing process has been reduced, thus making the stretch-blow moulder more efficient by 17 %.
• The filling process is extremely precise, thanks to the use of the flow meter, an electronic device installed near each valve that detects the flow of the product that fills each bottle by counting the pulses and sends the filling valve the closure sign, once the value of the format in use is reached.
• A wide range of products can be filled thanks to the valve terminal that is changed according to the type of product.
• Solutions for producing containers with tethered caps, that stay attached to the bottle after having been opened, in compliance with directive 2019/904
Green solutions for packaging
All machines produced by SMI are inspired by Industry 4.0 and Internet of Things (IoT) concepts and ensure cost reduction, energy saving, environmental sustainability and increase in competitiveness.
Within secondary packaging, SMI offers a wide range of automatic machines for packing in an efficient and eco-sustainable way several types of containers with an output up to 450 packs per minute (in triple lane) and applications that ensure energy saving. Depending on the type of product to be packed and on the reference market, it is possible to choose the most appropriate packer among a wide range of automatic
Via Carlo Ceresa, 10 - 24015 San Giovanni Bianco (Bergamo) Italy Tel. +39 0345 401 11 - Fax +39 0345 402 09
info@smigroup.it - www.smigroup.it
shrink wrappers for secondary packaging in stretch or recyclable film or among packers that use corrugated, kraft or Arcwise® cardboard
Within tertiary packaging, SMI palletizing systems enable to streamline the end-of-line operations of countless industrial sectors: beverage, food, chemical, pharmaceutical, detergent, glass, paper and many more and meet production needs until 140 packs/minute.
Flexible market-driven organization
In a global market where competition is getting fiercer and fiercer, the possibility to guarantee a “next door” service is for SMI a key factor to effectively and successfully support customers wherever they are.
Via Carlo Ceresa, 10 - 24015 San Giovanni Bianco (Bergamo) Italy Tel. +39 0345 401 11 - Fax +39 0345 402 09 info@smigroup.it - www.smigroup.it
QVision-Tech Srl was founded in 2015, with the desire to take advantage of more than 25 years of experience in the field of artificial vision by creating a company highly specialized and focused on the development of technologies for the automation of the quality control in industrial production.
With a specialized staff operating for years in the field, QVision offers:
• Experience gained over 25 years in the field
• Reliability, ensuring maximum availability and maximum personal commitment at all stages of cooperation, from the initial feasibility study to the realization of the product, its installation, training to the personnel working on the machines, the after-sales, and the possible update of the product over the years, also according to the changing needs of the customer.
• Attention to the specific needs of the customer, in the belief of the fundamental importance of a personal direct relationship, intended to transform the simple suppliercustomer duality in a constructive and proactive cooperation, aimed at achieving a common goal.
Via San Morese, 9 - 50019 Sesto Fiorentino (Firenze) Italy Tel. +39 055 4216422 info@qvisiontech.com - www.qvisiontech.com
• Willingness to growth and innovation in the search for ever higher quality standards, putting in first place the study and the development of increasingly advanced projects, using the most modern technologies in the field of acquisition and image processing. The main field of activity of the company is the design and production of Artificial Vision Systems for the quality control in the packaging industry, mainly for the food and beverage sector. Basic products are the systems dedicated to the control of closures (plastic and aluminium) and the systems for the inspection of vials and bottles. These systems, using digital cameras and image processing systems, allow the automatic quality control at the end of the production line, with the ejection of defective parts, on the basis of the control tolerances set by the line supervisor / operator.
In addition to the standard products, QVision also offers the possibility to supply “custom” systems, designed according to customers’ specifications, to allow performing special requests of inspection. Thanks to the know-how acquired in years of activity in the sector of industrial applications of machine vision, the use of the latest technology and a proprietary software completely developed in house, QVision is able to analyse specific issues and offer “turnkey” solutions, innovative and reliable.
Via I. Giordani, 10 - Z.I. Postumia, 46044 - Goito (Mantova) Italy Tel. +39 0376 689 707 - Fax +39 0376 68 96 44 info@newteclabelling.it - www.newteclabelling.it
To take advantage of the opportunities offered by an ever-changing market, you need machines that can evolve and adapt readily to every challenge. For 40 years, Newtec Labelling has been building label application machines with an eye on tomorrow, and is at the customer’s side at all times to help them achieve their goals.
The machines are used in the beverage, wine, spirits, detergents, cosmetics, milk and oil sectors, where they enable the packaging of products in line with customer requirements.
The new-generation modular construction guarantees flexibility for future requirements. Advanced technology and ease of use allow labels to be applied to any type of surface in a uniform and professional manner. Newtec Labelling models can handle a wide range of product formats and label sizes, guaranteeing maximum precision and speed in the labelling process.
Newtec Labelling offers linear and rotary type machines. These can be equipped with multiple applicator units: wet glue, for self-adhesive labels, for hot melt pre-cut labels, for OPP roll feed labels.
Over the past few years, the machines have been enriched with new technological features. Thanks to advanced software studies, it is now possible to apply labels in a centred position with respect to logos, screen prints, glass mould sealing, just by turning the container in front of a camera. Likewise, it is possible to check that the labels are applied in the exact position and are of the correct type. At all times the machine communicates with the line’s central computer system, and is remotely accessible in case it needs assistance from Newtec Labelling specialist technicians. Hourly production rates vary, depending on the model, from 1,000 to 70,000 bph.
The machines are equipped with all standards of operator safety, which is guaranteed even at maximum productivity.
Newtec Labelling is present worldwide through an extensive network of agents.
Contact Newtec Labelling today to discover all its customized solutions and find the perfect automatic labelling machine for your needs. Newtec Labelling is ready to help you take your production to the next level.
Via Sandro Pertini, 7 - 43013 Pilastro (Parma) Italy
Tel. +39 0521 63 03 22 - Fax +39 0521 63 90 93 info@navattagroup.com - www.navattagroup.com
The company Navatta, founded by Mr. Giuseppe Navatta in 1983, produces and installs fruit and vegetable processing lines and boasts references across the globe.
Navatta, the global supplier of integrated fruit & vegetables processing equipment and lines, providing well proven and innovative solutions for a full range of plants also thanks to the numerous companies’ acquisitions over the years, such as Dall’ Argine e Ghiretti in 2001, a 40–year-old company world famous for rotary can pasteurizers and tomato pulping lines; Mova, in 2010, with extensive experience in bins handling, bins and drums emptying, palletizers and de-palletizers, washing systems; Metro International, in 2012, leader in fruit and vegetables processing, boasting international patents for juice and puree extraction, concentration plants and thermal treatment; Ghizzoni Ettore, in 2012, specialized in special batch plants for ketchup, sauces and jams.
Manufacturing range
Navatta Group manufactures and commissions Processing Lines, Systems, Equipment for Fruit, Tomato, Vegetables for:
• peeled / diced / crushed tomatoes, tomato sauces and purees, tomato paste, all filled into any kind of package or in aseptic;
• diced, puree, juices (single strength or concentrated) from Mediterranean / tropical fruit, all filled into any kind of package or in aseptic;
• Fruit crushing lines from IQF, frozen blocks and frozen drums
• high yield patented fruit puree cold extraction, fruit purees / juices equalized in aseptic.
• Wide range of evaporators to produce tomato paste Mediterranean and tropical fruit concentrate.
• Aseptic sterilizers
• Aseptic fillers for spout bags/ spout-less Bag-in-Box
3 – 20 liters, Bag-in-Drum 220 liters, Bin-in-Box / IBCs
1.000 – 1.500 liters;
• Piston Fillers
• “all-in-one” pasteurizer / cooler spirals
• formulated products productions (jam, ketchup, sauces, drinks) starting from components unloading to dosing, mixing, mechanical / thermal stabilizing, to filling into any kind of package or into aseptic;
• processing pilot plants;
• vegetable processing as receiving, rehydration, cooking, grilling
Navatta Group’s headquarter and the two production units are located in Pilastro di Langhirano, Parma, with a total production area of 10,000 square meters. A new area of 10,000 square meters has recently been purchased and is ready for the third processing unit to be built.
Vision: Passion is the factor that drives us to higher targets, in terms of technology, products and services. Mission: To constantly increase Customers’ satisfaction and fidelity.
Cutter to process high viscosity products: Grinding, cooking, mixing under vacuum or at atmospheric temperature
Via Sandro Pertini, 7 - 43013 Pilastro (Parma) Italy Tel. +39 0521 63 03 22 - Fax +39 0521 63 90 93 info@navattagroup.com - www.navattagroup.com
M.G.M. Motori Elettrici S.p.A. is the leading Italian brake motors technology with a history spanning 75 years in Europe and around the world. The company operates in Italy, primarily at its main production facility in Serravalle Pistoiese (PT) and a warehouse with commercial offices in Assago (MI). Additionally it has facilities in Montreal (Canada), Detroit (USA), Chennai (India), and Izmir (Turkey).
The production of brake motors is concentrated at the Serravalle Pistoiese facility. Global presence is further ensured through a network of distributors for sales and support in over 75 countries.
M.G.M. motors are used in industrial plants and machinery across a wide range of sectors, including packaging plants, the food industry, lifting and handling equipment, the automotive sector, theatrical movements, and wind turbine generators.
Most of the components we find in today’s M.G.M. brake motors with AC brakes originated in the laboratories of M.G.M. Motori Elettrici. Since 2008, the average energy consumption of M.G.M. Motori Elettrici products has consistently decreased. All single-speed motors are available with energy efficiency levels compliant with the new European regulation. The electromagnetic brakes, both AC in the BA series and DC in the BM series, are undergoing improvements aimed at reducing energy consumption and enhancing performance.
100% of M.G.M. brake motors are produced in the Serravalle Pistoiese plant. The components for M.G.M. standard motors without brake are processed and then shipped to foreign branches for final assembly. M.G.M. plants worldwide are equipped with warehouses containing a wide range of brake motors manufactured in Serravalle Pistoiese, as well as assembly centers where standard motors are assembled and tested using components from Italy to meet the demands of local customers. This ensures the flexibility needed to meet customer requirements around the world.
For M.G.M. Motori Elettrici sustainable development and environmental respect are essential goals. The company is committed to reducing energy waste and preserving resources for future generations. The climate control system is supported by a geothermal system, and plastic consumption has been minimized. Furthermore, by rethinking and
redesigning materials and the production process, the company has also reduced the consumption of drinking water and the energy required for manufacturing brake motors, resulting in a reduction of greenhouse gas emissions.
In keeping with this spirit, the existing photovoltaic system has recently been expanded. Previously, it already covered 100% of the energy needs for both the factory and offices. This expansion will accommodate the increased demand of energy, also arising from the transition of the company’s vehicle fleet from combustion engines to electric ones.
Sustainability is not just about internal activities; In fact, M.G.M. Motori Elettrici believes it is important to raise awareness among its suppliers about the importance of energy conservation and to promote sustainable practices on a global scale because it is only by working together that we can make a difference for a greener and more sustainable future.
Via E. Fermi, 5 - 42011 Bagnolo in Piano (Reggio Emilia) Italy Tel. +39 0522 95 18 89 info@minimotor.com - www.minimotor.com
Mini Motor: over 50 years of made-in-Italy innovation and excellence around the world
Founded in 1965 in Bagnolo in Piano, in the heart of the Motor Valley, Mini Motor was born from a combination of passion for mechanics and innovation. Since 1974, the company has specialised in the production of electric motors for the industrial sector, becoming a leading player of Industry 4.0 then and a pioneer of Industry 5.0 today, with a strong focus on advanced connectivity and the integration of electronics and IT.
Mini Motor stands out thanks to the Human Centricity concept, developing technologically advanced products that improve daily work management through remote control and predictive maintenance. Customisation is key: each engine is designed and manufactured in-house, using high-quality, locally sourced materials.
The company values the land and people, promoting sustainability and training. With strong roots in the Emilian tradition, Mini Motor has exported its products
to 55 countries, several subsidiaries and an international distributor network.
Since 1965, Mini Motor has pursued innovation, constant improvement, manufacturing excellence, and cooperation with customers with passion and dedication. The product range includes geared motors, brushless servomotors and frequency converters, characterised by high quality and connectivity. Production follows the lean manufacturing philosophy, integrating human resources and robots to increase the efficiency and flexibility of the production process.
Mini Motor’s electric motors are designed to be compact, durable and suitable for working in extreme conditions thanks to the use of stainless steel, emblems of Industry 5.0, with connection capability supported by the main industrial communication protocols.
Mini Motor’s future commitment is on smart manufacturing, innovative materials and design, maintaining the high standard of its motors, making them ever more efficient and integrated, thus responding to market demands with constant renewal.
Mini Motor has been taking on the challenge of responding to market needs with cutting-edge solutions since 1965, consolidating its leading role in the industry. www.minimotor.com
Via Giancarlo Puecher, 24 - 20842 Besana in Brianza (Monza Brianza) - Italy
Tel. +39 039 23 01 096 - Fax +39 039 23 01 017 customercare@magicmp.it - www.magicmp.it
Industrial machines, the future is now!
Magic has presented during the Open House in November the revolutionary fully electric accumulating machine with patented head and clamping.
Even the field of industrial machines have been revolutionized, the innovative ideas of Magic will give its clients enormous benefits in terms of profit and process.
Principal benefits:
• Reduction of consumption equal to -53%,
• Maximum precision of the movements. Consequent efficiency equal to 99% with a perfect repeatability of the working cycles, potential reduction of the working cycle and potential reduction of the weight of the articles to be produced,
• Reduction of the maintenance costs equal to -52%,
• Machine completely oil free,
• Very silent machine since it is free of hydraulic pumps.
Magic MP S.p.A. is an Italian company founded in 1959, specialized in the conception and construction of extrusion blow moulding machines (EBM) and injection, stretch e blow moulding machines (ISBM) of plastic materials.
Thanks to its constant orientation to innovation Magic has become an excellence of the Made in Italy and a worldwide reference point for all the operators of this field.
MAGIC has been the first company in the world to conceive fully electric machines, revolutionizing the field of plastic and tracing a new technological greener and more sustainable road.
The clients recognize in the MAGIC machines patented technological benefits, which turn into real process improvements and consequent profit increases. Investments and efforts to give to their actual and future clients a unique and solid contact point in the production of bottles: machines, moulds and packaging solutions. Everything is internally developped and produced and commercialized with the best value for money on the market. These investments confirm the continuity of principles, values and skills that has been distinguishing Magic Group for more than 60 years.
With his words reported below the President of the Magic Group, Mr. Ferruccio Giacobbe, devotes the moon’s landing of his company on the planet of industrial machines and he does it always in an innovative and futuristic way.
“Innovation is and always will be the engine that fuel growth and development of Magic. Up to date no one in the world has ever built a completely electrified accumulator head of big size, Magic, which always looks ahead and, driven by this philosophy, has understood that even in the field of industrial machines the complete electrification will become a determining and indispensable factor. We did it in the past with the continuous extrusion technology for machine up to 60 Tons for the production, per example, in 6+6 cavities for 5 litres containers; we do it today also with the industrial machines for containers up to 280 litres. Soon we will do in fact a second Open Day to show the world the new transfer machine with all electric technology of 80-100 Tons for containers up to 280 litres. This machine will have an incredible saving for our clients in terms of energy consumption equal to almost 180.000 Euro per year. We are led to think that electrification is all about the necessity of the energetic economy. But this is one of the aspects, even though very important. The electric motor means also more precision and repeatability in the execution of the movements, that impacts on the efficiency of the machine, in lighter articles and shortest working cycles and with less wastes. It will be easy for our clients to understand how advantageous and innovative is to produce with a machine which consume 50-60% less, that thanks to its stability allows shortest working cycles and allows to produce lighter articles and even more with reduced maintenance costs of 50%.”
We are sure that orientation to ’Green”, to be effectively implemented, must bring to our clients even advantages in terms of profit. In fact, in 25 years and 1800 electric machines sold as well as having “saved” almost 3 billions of Kg in CO2, our clients have saved more than 500 million euro in electric energy. To these many various millions must be added for the economy in maintenance costs.
We want our clients, with our patented technology, win the complex challenge of the market; we aspire to become their partner, grow with them and become their reference point in the field.”
Via Giancarlo Puecher, 24 - 20842 Besana in Brianza (Monza Brianza) - Italy Tel. +39 039 23 01 096 - Fax +39 039 23 01 017 customercare@magicmp.it - www.magicmp.it
Via Canvelli, 21 - 43015 Noceto (Parma) Italy
Tel. +39 0521 25 87 23/4 - Fax +39 0521 25 87 17 info@lcz.it - www.lcz.it
Welcome to LCZ, dedicated since 1971 to design, manufacturing, installation, service and maintenance of industrial boilers for standard and special applications: plug in solutions, package solutions, site erected plants.
LCZ over the years has been able to adapt the proposal to market evolutions, thanks to constant and continuous improvement, regarding the product as well as the fabrication processes, without forgetting the hallmark: careful analysis of customer’s requirements by its technical department aimed at drawing up the most focused, customized and detailed answer.
It’s source of pride for LCZ to affirm how its products are fully realized in its manufacture plants emphasizing an Italian identity and a “Made in Italy” have always stood for high quality.
A manufacturing system, organized in two manufacture plants both in Italy and one of this with a covered area of more than 40.000 sqm, is well-characterized by automated welding processes, non-destructive tests (X-rays-L.P.), an home production of the furnaces FOX (corrugated) all supported by management using software as SAP ERP. These are some evidences of a capacity and a productive
process that allow LCZ to be one of the best worldwide manufacturers of boiler. Its internal technical department provides process and mechanical design in compliance to PED, machinery and ATEX directives, GOST-R, TS-TR and ISO 9001 certifications; according to European standards.
In addition to historical products as Firetube steam boiler (up to 30Ton/h) and thermal fluid generator (up to 9MW), LCZ propose Firetube boiler for hot and superheated water, Watertube steam generator, Waste gas heat recovery boilers downstream cogeneration and industrial plants. The relentless pursuit of the satisfaction of customer’s requirements has led LCZ to introduce the prefabricated thermal plants for the production of hot and superheated water, steam and thermal oil. They allow to have a turnkey thermal plant ready to use, for outdoor installation and removable.
Current commitments: energy saving, energy efficiency’s improvement efficiency during the plant lifetime and emission reduction. For this aim, LCZ boilers can be configured with an efficiency up to 95,5% (in specific application up to 105%) and for operating without continuous supervision up to 72 hours and/or with a global control system of the plant or the whole boiler room by a PLC or a multichannel electronic control device.
Strada Provinciale Colligiana, 50 - 53035 Monteriggioni (Siena) Italy Tel. +39 0577 30 50 04 info@galiganifiltri.com - www.galiganifiltri.com
Galigani Filtri is a leader in the design and construction of filter presses and relevant filtration systems. Since 1958, the company has boasted over 3,000 installations in 5 continents, created with skill and professionalism, in order to offer a high-quality product and a support service for users, installers, and designers.
The company is based in Italy, located in a modern facility in the heart of Tuscany, where it makes use of the most modern systems of research, study, and design so as to best solve the problems of each individual application, as well as provide adequate pre- and post-sales assistance through its qualified technicians.
Furthermore, the company is also equipped with a laboratory for filtration testing on samples supplied by clients to determine all the necessary parameters required for sizing the filter press that is most suitable for their needs. Production includes filter presses and pumping units that feed the filter presses.
The wide range of filter presses varies from manual discharge machines to fully automatic machines run by modern PLCs.
Galigani Filtri manufactures filter presses for all types of applications: food, chemical, pharmaceutical, explosive atmospheres (ATEX), purifying waste water, acid filtration, aggregates, mining, galvanic industries, recycling industries, and so on. All machines are equipped with the most advanced safety devices.
The press filters and filtration systems that are manufactured by Galigani Filtri carry out “mechanical” filtrations, and therefore the liquid does not undergo chemical changes.
Filtration can occur on the synthetic filter cloth, which retains solid particles up to 1 micron, or on cardboard for particles that measure less than or equal to 1 micron. When it comes to the most technologically advanced systems that Galigani Filtri can provide for filtration and clarification before bottling, the Diatom and the Clearness systems are in the forefront.
The Diatom system is comprised of a filter cloth for the filter press and is equipped with all the necessary parts (tanks, pumps, valves ...) that are required for filtration processes using various aids (fossil shell flour or cellulose flour, perlite...).
The Clearness system is a filter press with an Aisi304 or Aisi316 structure, which uses cardboard filters and a plate pack that is entirely sealed and protected from contact with the external environment.
Via Gallarata, 46 - 20019 Settimo Milanese (Milano) Italy
Tel. +39 02 89 77 55 24 info@finpacsleeve.com - www.finpacsleeve.com
Finpac Sleeve: The queen of low- and high-speed labellers
“Labels? Forget the labels! If anything, we are talking about fine dresses since we cooperate with the most renowned world brands in the bottling sector. I’ll tell you more, the image we are coining for this type of material is of a dressmaker about to design – thanks to the use of sleeve – tailored dresses.”
Finpac Sleeve General Manager, Erik Granzon has a clear view. Frankly speaking, this image he describes of a dressmaker suggests a label-container combination, like tailoring. All that thanks to sleeve labelling of both low- and high-speed machines.
Erik Granzon is optimistic (as any manager should be), a visionary man as we will discover soon, and just like the great monarchs of the past who were also the Defenders of Faith, he as a contemporary man is also a Defender of the Environment because he strongly believes in and is committed to sustainability. He immediately tells us his definition of Finpac Sleeve products “We dress these wonderful products with a multifunctional material that, at the same time, gives an important sense of lightness.”
That is the history and goals of Erik Granzon, General Manger, and Ilaria Zilio, CEO of Finpac Sleeve, told by themselves through simple albeit important questions.
Let’s start from the beginning with Ilaria Zilio. Once upon a time...
Once upon a time there was Finpac, and still there is. Established 35 years ago by two members, now old people, who passed over me the honour of running this wonderful business reality, high-speed labelling machines. The brands that use this system have always aroused my attention and fascinated, too. I wanted to be a diplomat or a psychologist, but I dared not tell my father and then thought “why now, let’s try”. Sooner, I fell for these machines and was thrilled to create and develop my own projects.”
Woman, and charismatic. All easy since the beginning?
On the contrary. The beginning was very demanding, as it is today, in a sector that is mainly for men. I was young and unexpert. There were judgements and prejudices about
me, and I had to instantly prove my capacity more than others. In the company, I had to grow not only professionally but also personally, as to arrive where I am now.
Basing on your experience, would you prefer to work with men or women?
I believe that the best work environment needs a balance of women and men. Every person is different, and therefore generalizing is a mistake. I believe that male and female peculiarities can team and improve analytical skills, for a higher attention to details, with the goal of increasing corporate performance.
Is there some advice you would have liked to follow and that you didn’t?
Looking back to my path today may generate different decisions, but I am sure that my entire path, especially the most negative and difficult aspects of it, have contributed to making me the woman and the professional I am today, and ready for future challenges.
Erik Granzon has been appointed as General Manager of Finpac Sleeve by dr. Zilio to broaden the presence and success in the packaging market. How should a figure like yours be to establish a relationship with collaborators?
As far as I am concerned, I have always accepted different challenges and that has led me, not without efforts and commitment, to that level of professionalism that characterizes me. Allow me some advice, I think that we need to be real and coherent to lead as per our values. It is crucial to create commitment and planning ability to generate a new version, to generate enthusiasm and passion necessary so that every collaborator is part of the project with the right trust and freedom.
Always looking for new ideas. What’s your secret?
As it often happens in life, when your goal is your professional growth, some inspirations are generated even when you stop for a while, not only when you analyse your sector but also when you look at other markets. My own experience gained in events thanks to the precious support of international staff has driven me to accept this new challenge in the world of packaging, even though we are talking about two totally different worlds, in terms of technology and innovation.
Then I thought that in life we need some madness. Don’t you agree?
The world of packaging opens endless new frontiers
Today, Finpac Sleeve is present in 130 countries across the globe, and therefore its present goal is entering different distribution channels by creating personalized and exclusive solutions through our machinery. That’s why we have thought of launching a low-speed machine that combines technological know-how and nobility of the sleeve with designer’s creativity. The idea is entering the world of low outputs (i.e. wine, beer) because we know that the demand of fine products is high.
One of our goals is bringing wellness and beauty to the world of packaging. You started with high-speed machine and have been highly innovating. Who has envisaged this path?
I think that one of the most appealing aspects that made me love Finpac Sleeve may be the possibility of creating innovative designs that – combining with our product –generate elegant containers while keeping the technical features unaltered.
In our history there has always been great attention to sustainability. Now, it is a trend
Attaching sustainability to ephemeral fads has always made me smile. You can’t think about sustainable economy without acting for the environment.
In conclusion… constantly growing. Which are your next projects and events in the world of packaging?
I thought you would ask this question and I hope you wouldn’t mind my looking back at our projects and answer that we are working on it. As regards our events in the world of packaging, we want to keep up and continue our development. To this regard, I can also say that we are completing customer-focused projects to meet beverage requirements.
Open House Beverage Division
Finpac Sleeve opens its doors to show the world its latest process and packaging technologies, from small to high speeds. Finpac Sleeve premises will house a wide selection of machinery and machines developed to meet the requirements of the beverage industry: From big multinationals to small-size workshops, and suppliers who will be able to see firsthand the technology purposely designed to satisfy the entire production cycle of a product.
Via Gallarata, 46 - 20019 Settimo Milanese (Milano) Italy Tel. +39 02 89 77 55 24 info@finpacsleeve.com - www.finpacsleeve.com
Via Newton, 4 - 20016 Pero (Milano) Italy
Tel. +39 02 339 271 - Fax +39 02 339 0713
info@bea-italy.com - www.bea-italy.com
ince 1961, BEA Technologies has been a leader in the development, production, and distribution of advanced filtration systems, with a particular emphasis on the food and beverage sector. The company has continually innovated in filtration and purification technologies to ensure the delivery of high-purity fluids, crucial for beverage production. Among their notable offerings is the MAGNEXFLO system, a state-of-the-art filtration solution designed to enhance the clarification and filtration of various beverages, such as water, juices, sparkling drinks, and bottled tea. This system stands out for its technological advancements, operational efficiency, and to provide possibility for a full automation of filtration, thus solving all handling problems of traditional filtration methods.
BEA Technologies has achieved a high level of excellence with its BEAPURE membrane range, which includes “animal-free” and Halal-certified filters. These products are entirely free from animal-derived additives and are made from food-safe materials such as polypropylene,
filters facilitates the exportation of beverages to markets where this requirement is essential.
In the modern beverage industry, it is crucial to use highly efficient filtration systems to stabilize products while preserving their essential characteristics and properties. These systems are designed to remove suspensions, colloidal particles, and microorganisms that could affect product quality and shelf life. The BIOKLARIS sterilizing membrane filters, featuring high-surface PES membranes, are particularly effective in eliminating bacteria and other microorganisms, ensuring the safety and purity of the beverages.
The MAGNEXFLO system, in particular, represents BEA Technologies’ commitment to providing high-performance automated filtration solutions for a wide range of flow rates and applications. BEA Technologies has always been a pioneer in the use of cleanrooms for the assembly of filter elements intended for food use, ensuring maximum cleanliness and quality. Looking forward, the company’s
President, Roberto Bea, has announced significant progresses in the investment to expand the cleanroom production area, reinforcing the company’s dedication to maintaining commitment on delivery times in the production of filtration systems for the beverage industry.
BBM serves as a reliable independent alternative for spare parts supplies, boasting a large inventory of mechanical, pneumatic, and electronic components compatible with leading industry brands.
All parts are tested by BBM in a certified laboratory; indeed, BBM has always invested in research and development to provide customers with high-quality, cost-effective materials, priced 10-20% lower than the market average. Upon request, BBM offers special discounts for its regular customers and creates stock of essential spare parts for routine maintenance.
BBM specializes in supplying revision kits for specific machine groups, enabling customers to save on individual-piece purchases for overhauls. BBM also offers the option to mark spare parts for traceability or easier identification.
BBM has developed a proven and updated minimum stock program to ensure spare part availability and rapid delivery to its customers.
BBM team of experts is always available to ensure prompt delivery, providing telephone and on-site support. Additionally, BBM’s extensive network of foreign agents facilitates commercial and logistical operations for spare parts supply all over the world.
In September 2024, BBM will launch a new e-commerce platform dedicated entirely to the sale of compatible spare parts. Its goal is to streamline and expedite the purchasing process for customers. Customers will be able to independently input their lists of spare parts and receive a quote or proceed directly with the purchase.
Explore the list of machinery and brands compatible with BBM spare parts.
Technical Support and Engineering
With over two decades of experience and a team of over 50 qualified technicians, BBM offers a comprehensive range of services to support its customers: dismantling and relocation of production plants, format changeovers, scheduled maintenance, and training. BBM also provides a hotline remote assistance service with advantageous package options to swiftly address customer needs and resume production in record time. What else?
BBM leverages its expertise in highly specialized engineering interventions. BBM portfolio includes machinery upgrades aimed at maximizing machine potential and achieving energy and cost savings. In particular, BBM specializes in upgrades for blow molding machines from all major manufacturers; with a few simple installations, energy consumption can be reduced by up to 35%.
Contact BBM Service for a free quote at info@bbmpackaging.com.
Success story: supply and installation of used bottling line in record time
At 650 meters above sea level lies the Pradis plateau, in the heart of the Carnic Pre-Alps in Friuli-Venezia Giulia (Italy). This is where the springs of Acqua Pradis gushes out, bottled ‘only 100 steps’ away from the spring, to keep its organoleptic features intact.
The Clauzetto (PN) bottling plant, which had been closed for almost three years, is now back in operation thanks to major investments aimed at renovating its structure and production line. To achieve 30 million PET bottles – 100,000 per day, Acqua Pradis turned to BBM Service.
Acqua Pradis asked BBM’s expertise to carry out the installation of a new PET bottling line. A challenge was posed by the delivery time: the customer needed to start production within a few weeks.
BBM offered the customer a complete 12,000-bottle-per-hour PET line, which it already had in house and ready for. The unique CE-certified PET bottle line was the compact and ideal solution for bottling still and sparkling water in three different sizes: 500, 1000 and 1500 ml. BBM Service’s technical department redesigned the layout of the line to fit the plant area – 800 square metres. In just three months, BBM Service’s skilled technicians relocated, installed and started up the complete line, from blowing to palletizing.
Via Pregalleno, 24 - 24016 San Pellegrino Terme (Bergamo) Italy
Tel. +39 0345 23 642 - Fax +39 0345 41 755 info@bbmpackaging.com - www.bbmpackaging.com
On display: complete 21,000 BPH PET line
Efficient, cost-effective, sustainable, and available immediately
When it comes to the ideal bottling line, there are three qualities that plant managers search for: flexibility, costeffectiveness, and sustainability. BBM Service’s 21,000 bottles per hour bottling line meets all these criteria!
Available in only 90-120 days
The plant is customized to your needs and installed in just a few weeks.
Turnkey service
Layout study, line assembly and start-up, on-site operator training, and scheduled maintenance: BBM handles all these steps
Want to replace a machine? No problem
Choose from over 200 BBM machines and follow the overhaul process from a distance What about the decommissioned line?
Is the 21,000 BPH PET line going to replace an existing line? Through a thorough audit, BBM will assess which components of the “old” line can be recovered and which can be scrapped. BBM will estimate the value of the used equipment and possibly purchase it, ensuring a secure return on investment.
Interested in the 21,000 BPH PET line? Watch the video of the line in operation.
SIDEL SBO16 S2
Food & beverage packaging plants
Second-hand, reconditioned solutions with BBM SERVICE
BBM Service is a partner capable of offering 360° support and a personalized, tailored service Italian excellence
BBM Service is an Italian company with long and renowned experience in the beverage sector, specializing in the turnkey supply of water and beverage bottling plants.
For over 20 years, BBM has been a technical partner of some of the most renowned brands in the sector, such as Nestlé Waters, Coca Cola HBC, Refresco Group, Heineken, and many others.
A single partner, from audit to start-up
Via Pregalleno, 24 - 24016 San Pellegrino Terme (Bergamo) Italy Tel. +39 0345 23 642 - Fax +39 0345 41 755 info@bbmpackaging.com - www.bbmpackaging.com
BBM Service is a single point of contact for market and budget analysis, line layout study, machine supply and installation, safety protocol management, and logistics.
What are BBM Service’s turnkey services?
1. Excellence in used bottling machinery
BBM has an impressive selection of more than 200 second-hand bottling and packaging machines, fully overhauled and upgraded. BBM offers the best of the used market, including blow molders, fillers, labelers, shrink wrappers, cartoners, tray formers, palletizers, and much more!
A highly selected range among the leading brands in the sector: SIDEL, KRONES, ACMI, Procomac, COMAG, OCME, etc.
Clients can view the machines and follow the overhaul and start-up process remotely, or visit the BBM showroom in Lenna (Bergamo, Italy).
2. Available in only 120-150 days
BBM stocks everything needed for a turnkey supply. After the machine customization phase, BBM specialized technicians are ready to carry out transport, assembly, and start-up at the client’s site.
3. Quality assurance
All machines undergo complete tests to ascertain their actual condition. For even greater security, BBM provides a 6-month full warranty on all its overhauled machines.
Go green, go second-hand
The growing problem of industrial material disposal makes it necessary to adopt a new philosophy, where old machinery is not demolished but withdrawn by suppliers like BBM. Purchasing overhauled used equipment means making a conscious, cost-effective, and environmentally friendly choice.
Different sale options
• Seen and liked (AS IT IS): For an even more cost-effective investment, purchasing the machines as-is.
• Ready to use with compatible spare parts kit: Fully operational machines, supplied with a complete kit of compatible spare parts, allowing for autonomous maintenance.
• Overhauled and guaranteed: For those seeking a high level of customization and security.
Discover BBM’s bottling lines and machinery
On the website www.bbmpackaging.com, you can view the complete catalog of BBM’s used machines and accessories.
The information sheets are complete with layouts, technical details, and videos of the machines in action.
Contact info@bbmpackaging.com to receive a free quote.
.info@bbmpackaging.com
Frazione Diolo, 15/D - 43019 Soragna (Parma) Italy Tel. +39 0524 59 90 97 - Fax +39 0524 59 90 12 info@akomag.com - www.akomag.com
SIRA, the washing, rinsing, filling and capping monoblock
The monobloc washer for gallon bottles SIRA has been designed by AKOMAG for washing and sterilizing PET or PC gallon bottles or other bottles of various sizes,
to be filled with still water. The washing cycle adapts to the various production needs of the end customer and is very effective. For this machine AKOMAG has designed and produced a special spraying and brushing device for gallon bottles that ensures total cleanliness. Through the
use of special mobile nozzles furniture (penetrating and rotating), the machine washes the bottle internally at high pressure (5 bar). While the outside is brushed by means of nylon brushes. The machine can be quickly adapted to the different bottle formats by simply setting the type of container to be handled on the control keyboard. The stainless steel control board installed next to the monobloc is easily accessible for the operator. The panel is equipped with a touchscreen for the complete management of all line functions, and the display of operating parameters and alarms. The monobloc features an automatic decapper in stainless steel: A pneumatic system grips the bottle neck while ejecting the cap. The system is safe, but it can be equipped with a system for the selection and ejection of gallon bottles that have not been properly decapped. The bottles are then filled by means of special inverter- controlled pumps.
A valve designed by AKOMAG guarantees a laminar flow and no contact between the valve and the bottle. The filling is carried out by means of a special metering device that ensures extreme filling accuracy. The capper consists of soundproof vibrating hopper, a descent channel, and a tear-off pick-up head.
The closure of the bottle is guaranteed by an inclined pressure belt characterized with adjustable pressure. All adjustments are automatic and managed from the control panel.
Località Piana, 55/D - 12060 Verduno (Cuneo) Italy
Tel. +39 0172 47 02 35 - Fax +39 0173 61 56 33 info@watersystems.it - www.watersystems.it
WS is a company, founded in 2005, working as process equipment supplier for the beverage industry. During these years, WS has achieved a very good reputation in the beverage industry field, managing to cooperate with the major global players, such as Coca Cola, Pepsi Cola, Nestlé Waters and OranginaSchweppes, and with private investors installing new production facilities, quite often green fields, in emerging Countries.
WS has met new standards for product quality, energy saving and maximum plant output while complying with the strictest criteria for hygiene and safety
All the devices are entirely conceived and designed to guarantee the best requirements in terms of microbiological, physical-chemical and organoleptic properties; the entire production process and software development are managed internally, as well as installations and commissionings which are carried out with WS’s own resources. WS’ products for beverage industry are:
• water purification plants (mechanical filtration, microfiltration, reverse osmosis, UV disinfection, sterilisation) designed according to the customer’s exigencies and the chemical analysis;
• sugar dissolving systems (single batch, double batch and continuous up to 35.000 l/h);
• semiautomatic and automatic syrup rooms;
• premix units;
• flash pasteurising units;
• ozone generators;
• carbonating equipment (water, wine, beer, soft drinks);
Località Piana, 55/D - 12060 Verduno (Cuneo) Italy
• in line syrup blending systems and ingredients mixing systems;
• steam sterilisable microfiltering systems (juices, beer, wine);
Tel. +39 0172 47 02 35 - Fax +39 0173 61 56 33 info@watersystems.it - www.watersystems.it
• mineralising equipment;
• equipment for preparation of non-chemical bottles rinsing and disinfecting solutions (such as ozone) and chemical solutions preparing devices (peracetic acid, hydrogen peroxide, chlorine, etc.);
• equipment for the preparation of sterile water;
• manual and automatic CIP systems
Thanks to its skill and process expertise, today WS is widely present worldwide even with turnkey solutions including ancillary equipment (cooling equipment, boilers, etc.).
WS’ philosophy is to manufacture high-quality and reliable equipment, equipped only with top brand components: ALFA LAVAL, ENDRESS+HAUSER, PALL, ANTON PAAR, SIEMENS, FESTO, SPIRAX SARCO are the typical components our Customers will find on Their plants.
The choice of providing only state-of-the-art solutions has brought us to be appointed as officially authorized integrator by ALFA LAVAL
Between main technical references, WS can list the supply of two fruit juice tubular flash pasteurizers for aseptic filling to ORANGINA-SCHWEPPES in France; furthermore, it’s significant to point out that WS is included in NESTLÉ WATERS’ authorized suppliers list for water purification systems: recently an important contract for the supply of a toptechnology water treatment plant in the far East has been finalized. Amongst last supplies (early 2016), WS also boasts a complete line for soft drinks production in Las Vegas – USA (Coca Cola co-packer): from water treatment to hot fill pasteurizer, through sugar syrup preparation and ingredients mixing, also including CIP equipment. WS considers Customer Service one of the greatest keys to success: entire business, marketing, sales and profits depend on customers’ satisfaction so the after sales team is constantly trained to perform the simplest solution in the shortest possible time to support the customer’s business.
The growing market’s confidence gained by process plants manufactured by WS, allowed a continuous development of blending technology for carbonated soft drinks (CSD)
Località Piana, 55/D - 12060 Verduno (Cuneo) Italy
Tel. +39 0172 47 02 35 - Fax +39 0173 61 56 33
info@watersystems.it - www.watersystems.it
production to such an extent that We reached a very high level of specialisation in manufacturing mass controlled blending systems, named BLENDSYSTEM M. BLENDSYSTEM M is a piece of equipment for preparing beverages, completely preassembled on a skid for an easy and quick shipment and installation, conceived mostly for the production of carbonated soft drinks (CSD), but also carbonated mineral water (CMW) and still water (charged with nitrogen in order to increase the mechanical resistance of the bottle). The required quantity of ingredients (water, syrup, and CO2) is carefully measured and dosed in an electronically controlled continuous process.
The whole system, realized to guarantee the highest qualitative standards and a qualitatively constant production, also running in conditions of considerable format change, is completely preassembled on stainless steel circular-section skid for an easy and efficacious cleaning. It usually includes the following subsystems:
• inlet water deaeration: a vacuum pump removes incondensable gases; the pump is conceived to maintain the dissolved oxygen level below 1 ppm values;
• carbon dioxide dosing (or nitrogen in case of still mineral water production): a modulating valve and a mass flow rate transmitter inject carbon dioxide in quantity that is proportional to water quantity loaded to the deaeration tank; the water flow rate is usually measured by a magnetic flow rate transmitter, which may be replaced with a mass flow rate transmitter in case water presents a very low electrical conductivity level. A special gas injecting and mixing systemspecifically developed by WS - performs a careful mixing with the water to be treated and, hence, best results in terms of product perlage; the carbon dioxide contents is maintained constant in the product
receiving tank by a supervising software, which checks possible fluctuations in feeding water temperature and product buffer temperature; the effective dissolved carbon dioxide contents in the product is checked using a carbometric unit, installed in by-pass on the filling machine feeding line;
• syrup dosing and mixing: at first syrup is stored in a small buffer tank, whose atmosphere is modified and enriched with carbon dioxide in order to avoid oxidation occurrence. Syrup injection is made by a sanitary design modulating valve and a mass flow rate transmitter in a quantity which is proportional to the water amount fed from the deaeration tank; furthermore, using the mass flow rate transmitter, it is possible to check constantly the effective density of the inlet syrup and therefore to compensate immediately for the dosing and to stabilize the sugary concentration in the end-product within established bounds (usually ±0,05 °Bx). A specific refractometer installed in bypass on the filling machine feeding line, allows the constant check of the product and, if necessary, its adjustment; similarly, the instruments minimize waste of both syrup and product during transitory phases of production, such as start and stop.
Furthermore, customized solutions for product cooling are also available, depending on the environmental conditions of the system installation.
The supervising software loaded on the mass premix unit - BLENDSYSTEM M - is conceived to guarantee the best results in terms of dosing, offering at the same time an easy control by a friendly user interface; this software enables on one hand to set the main production parameters and visualize their state graphically and on the other hand to set the statistics parameters (ca, cp e cpk) connected to that kind of production.
Using a more advanced version of this software, associated with specific instruments, it is also possible to control automatically saccharose inversion, so that the need of intervention by laboratory technicians is reduced.
The equipment is equipped with field buses (MPI, Profibus or Ethernet) for a complete integration in the bottling line and the control of production, cleaning and sanitizing processes.
TecnAlimentaria supplement N°8/9 August/September 2024 - Year XXIX
Publisher Fabiana Da Cortà Fumei
Editorial Staff & Design redazione@tecnalimentaria.it
Sabrina Fattoretto
Claudia Bosco
Elena Abbondanza
Cinzia Beraldo
Vanessa Tarantino
Marketing and Advertising
Anita Pozzi anita.pozzi@edftrend.com
Franco Giordano franco.giordano@edftrend.com
Management, Editorial Office
Editrice EDF Trend srl
Corso del Popolo, 42 31100 Treviso – Italy
Tel. +39 0422 549305 Fax +39 0422 591736 www.tecnalimentaria.it www.edftrend.com
Translation into Arabic
Ann Nasr
Printing L’Artegrafica Srl
Autorizzazione Tribunale di Forlì n. 5 del 19.01.1996 N° iscrizione ROC (Registro degli Operatori di Comunicazione): 22054
In questo numero la pubblicità non supera il 45%
Sped. in abbonamento postale 45%Art. 2 Comma 20/B Legge 662/1996 DCI-TV All right reserved.
Reproduction in whole or in part without written permission is prohibited.
The Publisher is not responsible for any materials, nor for writers’ nor contributors’ expressed or implied opinions. Informativa ex D.lgs 196/03
Ai sensi dell’art.2 comma 2° del Codice Deontologico dei giornalisti si rende nota l’esistenza di una banca dati di uso redazionale presso la sede di Corso del Popolo, 42 - Treviso. Responsabile del trattamento dati è il direttore responsabile a cui ci si può rivolgere presso la sede di Treviso - Corso del Popolo, 42 per i diritti previsti dalla legge 675/1996.
Member of: