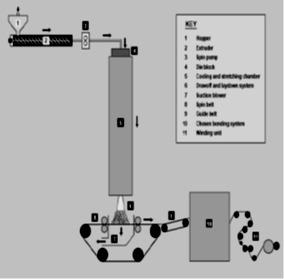
25 minute read
TEXTILE MANAGEMENT
Sandeep Vinod Vishwakarma Guided by: Prof. S.G.Kulkarni
Advertisement
D.K.T.E Society’s Textile & Engineering Institute, Ichalkaranji-416116, Kolhapur
Abstract
Fifty years ago, Karl Ziegler and Natta were awarded by the Nobel Prize for his discovery of catalytic polymerization of ethylene and propylene using the titanium compounds with aluminum-alkyls as co-catalysts. Polyolefins has grown to become one among the most important produced polymers. New metallocene/methylaluminoxane (MAO) catalysts opens the likelihood for synthesize polymers with highly defined microstructure, tacticity and steroregularity, also like longchain branched or blocky copolymers with excellent properties. This paper reviews melt spinning of the fibers of metallocene catalyzed isotactic polypropylene (PP) and standard equivalent of Ziegler-Natta isotactic Polypropylene (PP); the properties of PP and a few thermal and mechanical properties of fiber. Ziegler-Natta catalysts is prepare by reaction which employed Mg (OEt) 2 as a precurosor. The newly developed Metallocene catalyst PP possesses higher isotacticity and crystallinity than the commercial ones, which assures the mechanical properties of the final products.
KEYWORDS: Catalysts, Metallocene, Polypropylene, Polyolefins, ZieglerNatta.
Introduction
Nonwoven fabric became a particularly important segment of the textile industry. Compared to the global market average of 24%, Indian market has a 12% share of technical textiles which are being manufacture by non-woven technology. The Non-woven market is expected to grow from USD 40.5 billion in 2020 to USD 53.5 Billion by 2025. For the manufacturing of nonwoven fabric, different web formation methods are used; Dry Laid nonwoven, Spun laid nonwoven and wet-laid non-woven. These are supported web bonding; Mechanical bonding, Thermal Bonding and Chemical Bonding. The bonding types, the fiber type and therefore the manufacturing parameters determine the characteristic feature of non-woven. In contrast to standard engineering materials, these fabrics have better specific mechanical properties, strength to weight and stiffness to weight ratios [1]. Melt Blown and Spun laid nonwoven are most generally used method for the production of nonwoven fabric. Melt blown nonwovens are made in one continuous process. Fibers are spun, then directly dispersed into a web by deflectors or are often directed with air streams. This results in faster belt speed and cheaper costs. Spun laid also called spun bond, nonwoven fabric are produced by extruding melted polymer fibers through a spin net or die consisting of upto 40 holes per inch to create long thin fibers which are stretched and cooled by passing hot air over the fibers as they fall from die. The approaching web is collected into rolls and subsequently converted to finished products. Spun blown plays a role of imparting strength to the nonwoven fabric and Melt blown is employed for Barrier Properties of nonwoven fabric. Differing types of polymers are utilized in the assembly of nonwoven fabric like Polyester, PET, Polypropylenes; they are either in the form of small chips or in the form of powder. Spun bond Melt blown Spun bond, commonly called SMS could be a tri laminate non-woven fabric. It is made from top layer of spun bond polypropylene, a middle layer of melt blown polypropylene and a bottom layer of spun bond polypropylene. Polypropylene is a downstream petrochemical product derived from the olefin monomer, propylene. The polymer is produced through a process of monomer connection called addition polymerization normally by using the Ziegler-Natta catalyst System. ZieglerNatta is heterogeneous catalyst, the primary efficient and stereospecific catalyt. Catlystic polymerization method was developed by Karl Ziegler and Natta in 1950. Isotactic polypropylene resins had been produced from ZieglerNatta catalysts for over 45 years now. the upper relative molecular mass and broad relative molecular mass distribution were characteristic for resins as produced within the polymerization reactor. The features of metallocene isotactic PP are uniformity in polymer with narrow relative molecular mass which is convenient for fiber spinning [2, 5].
1.1 Heterogeneous catalysts
These are industry-dominating catalysts that are supported titanium compounds (and sometimes vanadium-based) and used for polymerization reactions; usually together with organo-aluminum compounds, like triethylaluminium (TEA=Al (C2H5)3) as co-catalysts [3].
Homogeneous catalysts
These are the second broad class of catalysts and are supported complexes of Ti, Zr, or Hf. They are generally used in combination with a variety of organoaluminum co-catalysts called metallo-
cene/methylaluminoxane (MAO). Traditionally, they include metallocenes but also feature multi-dentate oxygen- and nitrogen-based ligands [5].
2. Manufacturing Process 2.1 Materials
Isotactic polypropylene with metallocene catalyst and Ziegler-Natta catalyst for melt spun fiber and by using melt blown thermal bonding method production of nonwoven fabric are happen. The commercial metallocene PP purchased from Lyondell Basell Industries [4].
2.2 METHOD
For the manufacturing of nonwoven fabric there are mainly two methods used i.e. Melt-Spinning and SpunSpinning method. The melt-extrusion spinning was conducted by using single-screw extruder equipped with metering-pump and eight-hole spinneret, and diameter was about 0.5-0.6 mm. The spun-extrusion spinning was conducted by using single screw extruder with metering pump and six-hole spinneret, and diameter of 0.4 mm. By using Spun blown or Melt blown method production of nonwoven fabric was produced [6].
2.3 Manufacturing Method
The manufacturing method for nonwoven fabric is completed with Spun bonding method or melt blown method and sometime both are combined to make a nonwoven fabric. Spun bond process, first patented in 1940s and with further development has since become more and more popular across the globe. The technique itself includes fibers being spun, then directly being dispersed into a web by deflectors or air streams, Figure 1. They use no chemicals, and are thermo bonded. This method is preferred, because it is cost effective for manufacturers. Over the past 20 years, it has been used to make several household products such baby diapers, adult diapers, medical products, protective apparel and hygiene products. Spun bonds also are flame-retardant or have antistatic properties, and may therefore be used for increased ultraviolet and gamma radiation protection. Many of its features include: low weight, high strength, high air permeability, hydrophilic properties, and excellent wear and tear properties. Furthermore, with the development of the technique, spun bonds are now far more soft and comfy than previous types, and on the average only weigh between 10 to 150 grams per square meter [3,8].
Figure 1. Schematic spun bonding process
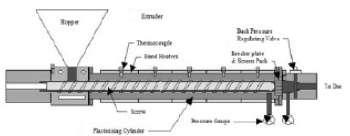
Figure 2. Extruder
Melt-Blown Method
The melt blown process came after spun bond technology and the process whereby ultrafine filament (micro-fibers) nonwovens are often produced at low costs. The technique includes hot air being blown onto molten thermoplastic that is extruded through a linear die containing many small holes, to create a fine fibered self-bonded nonwoven web. Its key feature is that it is a very thin fiber. As a result this material is usually used for filters for air, liquids and particles, or as absorbents in products like wipes, oil absorbents, incontinence products, and feminine
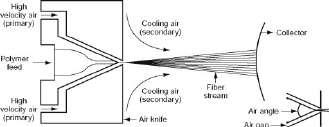
Table 1. Physical properties of Polypropylene (PP) and Polyethylene (PE), preprinted with permission from [6]
hygiene, but also can be utilized in the production of certain electronics, adhesives, and other apparel [7,8].
2.4 Properties of Fiber
The fiber produced from Ziegler-Natta Catalyst PP has long starched on the conveyor belt of the machine through spun bond machine and fiber produced from melt blown are finer than the spun blown it do not require any types of stretching. The properties of the fabric are summarised in Table 1.


2.5 Preparation of Catalysts
TiCl4/MgCl2 catalyst was prepared by recrystallization method reacting MgCl2-ethanol adduct with TiCl4 within the following procedure: 2 g (0.0210 mol) of anhydrous magnesium dichloride was suspended in 100 ml of heptane and 0.1259 mol of ethanol was added drop wise at temperature. After the end of addition, the solution was stirred for two hours. Then 28 mol of aluminum compound was introduced drop wise and heated to 90oC and hold for two hours. Thereafter, 0.0255 mol of titanium tetrachloride was added and the mixture was stirred for two hours. Finally, the catalyst obtained was washed with heptane several times. [9]
Polyethylene and Polypropylene
PE is preferred and widely used polymer so far. The formation of PE occurs by the polymerization of the ethylene monomer in an insertion reaction. Despite the easy structure of PE, its manufacturing route is kind of complex with differing types of synthetic procedures. Because of a number of its peculiarities, it is considered as a novel polymer having high crystallization rate and chain flexibility, which are mostly derived from its perfect chain structure. Therefore, it is not available in an amorphous state and most of its properties are derived by extrapolating
from those of semi-crystalline samples. The properties of various types of PE can vary as a consequence of structural changes resulting from the polymerization technique. Generally, LLDPE and HDPE are conventionally synthesized via the catalytic ethylene polymerization reaction at low temperatures and pressures, as compared to the LDPE manufacturing. Especially, LLDPEs prepared via Ziegler-Natta catalysis have more uneven co-monomer distributions, whereas, a reverse trend is observed for those synthesized by metallocene catalysts. Such differences in co-monomer distributions are mainly attributed to the difference within the available active sites within the two catalysts that manifests itself within the rheological and mechanical properties of the polymers and their melt miscibility. However, polymer density is often controlled by the ethylene/comonomer molar ratio, temperature, and therefore the catalyst type. The power to crystallize the substance suffers from its relative molecular mass, concentration of branches, and their distribution along the backbone of the co-polymer. So as to know the crystallization behavior of the branched molecules, more homogeneous fractions of the co-polymer are required. The processing ability and therefore the properties of the ultimate product depend strongly on the branching of the polymer [10, 11].
3. Result and Discussion
In this study, two different catalyst preparation methods namely reaction and recrystallization were synthesized and compared so as to clarify the correlation between their nature and polymerization behavior. During this paper a review of the changes and current state of PE and PP manufacturing processes has been given, including role and kinds of catalysts and co-catalysts employed over the years. Even though Ziegler-Natta catalysts are used significantly, metallocene catalysts and cocatalyst systems have replaced them in recent times. More laboratory-scale work is usually recommended, to know the complexity of the polymerization process, as greater amount of information is obtained for optimization purposes. [10]
Effect of Temperature
Based on polymerization temperature for catalyst Ziegler-Natta and Metallocene found that metallocene catalyst exhibited higher activities than Ziegler-Natta Catalyst. It was observed that activities increased with increasing the polymerization temperature from 40℃ to 60℃. However, activities decreased with increasing the temperature to 70℃. The dependence of polymerization temperature on isotacticity of PP produced from both catalysts i.e. Ziegler-Natta and Metallocene [11].
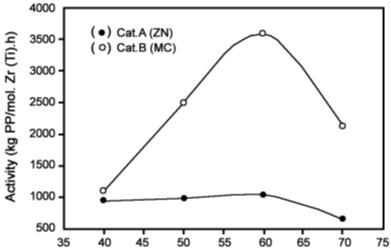
Figure 4. Effect of polymerization temperature on activities for Ziegler-Natta catalyst and Metallocene Catalyst [10].
Effect of Pressure
It was observed from Patinya Pipatpratanporn article that metallocene catalyst were much more? than that of the Ziegler-Natta Catalyst. Activities of metallocene catalyst was found to extend almost linearly with increased propylene pressure. By considering activity of Ziegler-Natta catalyst, it indicated that propylene pressure had weaker effect. The explanation behind the various catalytic responses to propylene should be drawn on the solubility of propylene within the reaction media for both catalytic systems [12].
Microscopic structure of Ziegler-Natta and Metallocene PP
Tm of PP produced from the ZN catalyst was higher indicating higher crystallinity. The catalyst sample was characterized using SEM (Scanning Electron Microscopy). There was no significant change in the morphologies (as shown in Figures 5a and 5b) of PP upon changing the propylene pressures between 40 and 100 psi. It has been known that the temperature and pressure because the polymerization time, may effect on the fragmentation of heterogeneous catalyst. However, it seems that these effects are pronounced only at a particular level. As reported by Fink group [16] for propylene polymerization, the pressure of 80 bars and temperature of 50o C were used for 12 h. The activities of the MC catalyst were much higher compared to the ZN catalysts. However, activities for the MC catalyst essentially decreased when high concentrations of catalyst were used. At high catalyst concentrations, the coupling reaction of active complex can occur leading to the catalyst deactivation [13].
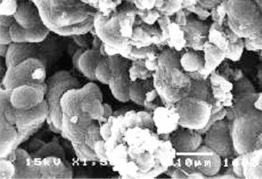
Figure 5 a Ziegler Natta PP
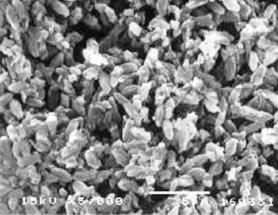
Figure 5b Metallocene PP
Conclusions
In this paper a review of the changes and current state of PE and PP manufacturing processes, including the role and kinds of catalysts and co-catalysts employed over the years has been discussed. Even though Ziegler-Natta catalysts are used significantly since their discovery, metallocene catalysts and co-catalyst systems have replaced them. The yields and mechanisms for the production of both PP and PE have been reported. A perspective on future research directions have also provided. The influence of crystalline properties on the processing ability alongside the mechanical properties of melt spinning fibers are discussed. The low Tm and high isotacticity of Ziegler-Natta catalyst PP are liable for its advantages both within the fabrication conditions
and therefore the properties of the fibers. The newly developed metal locene catalyst PP is confirmed to be a promising candidate for producing high-performance fibers from the melt spinning process.
Reference
1. A. Marcindin, M. Hricov and K.
Marcind,”Fiber Based o metallocene PP”
Fiber Forming Polymer Vlakna textile, 2008.
2. Patinya Pipatpratanpor and Piyasan
Praserthdam, “Impact of process variable on Properties of Polypropylene Derived from theSupported Ziegler-Natta and
Metallocene Catalysts”Iranian Polymer
Journal 2007,Pg.123-131.
3. Renwei Xu,Peng Chen and Zhicheng
Zhang,“Structure and Properties of a
Metallocene Polypropylene Resin with
Low Melting Temperature for Melt Spinning Fiber Application”, polymers journal, 2019, pp11-729.
4. Karin Weiss, Sandra Botzenhardt and Monika Hofmann,“Ziegler-Natta and Metallocene Polymerisation of Olefins with Heterogeneous Catalysts”,Metaloganic Catalysts for Synthesis and Polymeriza5. Ahmad Shamiri, Mohammed
H.Chakarbarti, Purushotaman V. Aravind and Wageeh A. Yehye,“The Influence of Ziegler-Natta and Metallocene Catalysts Polyolefin Structure, Properties and
Processing Ability” Materials 2014.
6. Piyavit Pokasermsong and Piyasan
Praserthdam,”Comparison of Activity of Ziegler-Natta Catalysts”,Engineering
Journal, Vol 13, Jan 2009.
7. Gobi N, Evangelin S, and Kasthuri R,
“Multilayer non woven fabric”, Journal of Textile and Fashion Technology,Vol 5
August-2018.
8. Agnieszka Brochocka, Aleksandra
Nowak, Michal Puchalski and Slawomir
Sztajnowski, “Multifunctional Polymer
Composite Produced by Melt-Blown
Technique to Use in Filtering Respiratory
Protective Devices”, Journal of Materials, pp.13-2020.
9. Nakayama, Y.; Sogo, Y.; Cai, Z.; Shiono, T. “Copolymerization of ethylene with disubstituted olefins catalyzed by ansa(fluorenyl)(cyclododecylamido)dimethyltitanium complexes”, Journal of Polymer. Science. A Polym. Chem. 2013, 51, pp 10. P.J.Cotter and J.E. Model, “Ziegler-Natta alpha-Olefin Polymerization Catalysts” J.
Am. Chem. Soc. 1994, P.116.
11. Kunz K. “How to synthesize a constrained geometry catalyst (CGC)”A Journal of Organomet. Chem. 2007, pp 4411–4423.
12. Unverhau. K., Kehr. R. and Erker G.
“Synthesis of ferrocenophane-bridged
Cp–amido zirconium complexes and ansa-zirconocene complexes and their use in catalytic polymerisation reactions”Dalton
Trans. 2011.
13. Stevens J.C. and Wilson D.R. “Olefin Polymerization Process Using Supported
Constrained Geometry Catalysts” U.S.
Patent 26 April 2005.
14. Wocadlo S., “Synthesis and Characterization of Zirconium Complexes Containing a Linked Amido-Fluorenyl Ligand” Organometallics 1995.
15. Aulbach M., Bachmann B.“Stereospecific metallocene catalysts: Scope and limits of rational catalyst design”, Journals of
Polymer 1995, 89, 237–247.
16. Reddy S.S. and Sivaram S.,“Homogeneous
NEWS
INDIA’S JK AGRI GENETICS WORKING WITH BANGLADESH FOR GM COTTON TRIALS
Hyderabad-based JK Agri Genetics Ltd, an arm of the JK Organisation, is collaborating with the Bangladesh government to hold field trials of genetically-modified (GM) cotton there. The field trials have been completed for the first season and the results are good. Such trials will be held for the second season this year between April and November, according to JK Agri Genetics (JK Seeds) president and director Gyanendra Shukla.
Bangladesh’s Cotton Development Board (CDB) began trials of the genetically-modified Bt cotton with two varieties—JKCH 1947 Bt and JKCH 1950 Bt—which can resist bollworm and fall armyworm. According to the US Department of Agriculture, the CDB obtained the cotton varieties under the material transfer agreement from JK Seeds, an erstwhile division of JK Tyres and Industries Ltd.
“Though the first season trials gave good results, more trials need to be done. Once the Bangladesh government is satisfied with the results, it will begin the deregulation process wherein farmers will be allowed to cultivate the Bt variety,” Shukla told a leading business daily from south India. The CDB completed the greenhouse trial of the cotton varieties successfully on March 4 last year, and it got the permission of Bangladesh’s National Committee on Biosafety Clearance to start confined field trials for the current crop year (August 2020-July 2021), USDA said. Currently, Bangladesh meets about 25 per cent of its raw cotton requirements through imports from India. USDA has pegged Bangladesh’s 2020-21 crop at 1.86 lakh bales (of 170 kg) on 46,000 hectares.
CLOTHING FROM MILKWEED FIBRES
DR N.N.MAHAPATRA
Business Head (Dyes) Shree Pushkar Chemicals and Fertilizers LTD., Mumbai
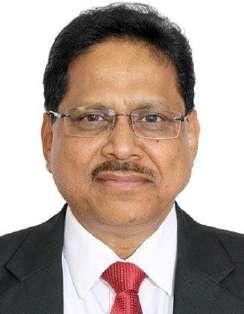
The French tried weaving silky soft fabrics with the clusters in the 1600's. Native Americans swaddled their young and lined their buffalo robes with the warm clusters. The sap from the plant has been used to remove warts and age spots. In 1753, Carl Linnaeus named milkweed Asclepias, after the Greek god of healing. People used milkweed for many home remedies and the uses for milkweed seemed endless.
During World War II, School children collected the milkweed pods and the fluff was used as a filling for Mae West Life Jackets. The motto of the day was, "Two bags save one life." meaning two bags of milkweed would keep a downed serviceman afloat for days. During the energy crisis in the late 1970's, Standard Oil of Ohio used Milkweed biomass to produce synthetic crude oil; unfortunately, the project was not cost effective. Kimberly-Clark Corporation worked with Standard Oil to develop nonwoven products and facial tissues that incorporated Milkweed Clusters. A small niche market in the facial tissue industry would consume about 40 million pounds of clusters annually. At that time, the Milkweed Cluster inventory was about 10,000 pounds and the project was abandoned. Knowing the positive characteristics of Asclepias, (Milkweed), its gardening benefits of attracting butterflies, soil conservation and the success of Ogallala Down, seed was allocated for the development of Asclepias Seed Company. Seed is sold for land reclamation, highway beautification, and butterfly gardens and to butterfly farmers.
Our most recent development and Company is ASCLEPIUS, which sells the pain relieving Milkweed Balm from the oil of the milkweed seed. Milkweed balm is used to relieve pain and restore function. It is the topical application of natural oils. Every part of the plant can be used in a commercial application. The challenges are dovetailing supply with demand and trying to get a "weed" to act like a crop. Natural Fibers Corporation plans to develop markets and uses for Milkweed and turn it into a thriving and profitable agricultural business. Silky, soft milkweed fiber is available for commercial applications ranging from a goose down enhancing agent, to nonwovens, oil absorption products, cosmetics and more. Milkweed seed is used for planting butterfly gardens, squeezed for oil, can be used in cosmetics and nutraceuticals. Pods and stems have their own unique properties and commercial applications. People have used milkweed for fiber, food, and medicine all over the United States and southern Canada. Most people know milkweed simply as food for the monarch butterfly's caterpillar, or as a tenacious, pesky weed of hayfields. If those butterflies were not so beautiful, and if their annual migration to Mexico were not so amazing, few people would care what happened to this herb. But milkweed isn't your average weed. In World War II, schoolchildren across the Midwest collected thousands of pounds of milkweed fluff to stuff life preservers for the armed forces in the Pacific, because kapok, the normal material used for this purpose, came from Japanese-occupied Indonesia and was unavailable. Today, you can buy pillows, jackets, and comforters stuffed with this material, which is wonderfully soft and has a higher insulative value than goose down, from a company called Ogallala Down, in Ogallala, Nebraska. Some people believe that milkweed will become an important fiber crop, as one of its attributes is that it is perennial and therefore does not need to be replanted every year. Milkweed stalks also produce a coarse, sisal-like fiber that can be used for twine, which varies in strength from one plant to the next. This possibility has been little explored commercially, but it was well known to Native Americans.
Production of Milkweed fibres
The milkweed that we are talking about here is the common milkweed Asclepias silica. There are numerous other species of milkweed in North America, but common milkweed is by far the best known. It is abundant in the whole area east of the short grass prairies, north of the Deep South, and south of the boreal forests of Canada. It is a common sight of roadsides, fencerows, meadows, sunny woods, and abandoned fields. Common milkweed produces pairs of large, oblong, thick leaves all along its unbranching stem, which is typically three to six feet tall. Both the
flowers and the okra-like pods are quite distinctive, as is this herb's growth form. When broken, all parts of the plant produce white latex, but there are many other plants with this characteristic. Overall, milkweed is a beautiful and very distinctive plant. I am amazed that, as much attention as milkweed has received as a fiber crop and a butterfly planting, so little has been said about its use as food. Ethnographic records show that common milkweed was eaten as a vegetable by tribes throughout its range. It provides edible shoots (like asparagus), flower bud clusters (like broccoli), and immature pods (like okra). The soft silk inside the immature pods is a unique food, and the flowers are also edible. Milkweed conveniently provides one or more edible parts from late spring until late summer, making it one of the most useful wild greens to learn. Milkweed fiber (Asclepiadaceous) is obtained from the stem of milkweed. The family is represented by several genera such as Asclepias, Caltrops, Ceropigia etc. Milkweed contains an abundance of milk sap in its leaves, stem and pods. Many parts of milkweed are used in medicinal applications. Common milkweed (Asclepias syriaca) is a perennial herb growing from a deep rhizome. The hairy stems are usually solitary from a simple to branched and thickened base, and are 6-20 dm (1.9-6.5 ft) tall. The opposite leaves have broadly ovate to elliptic blades that are 10-20 cm (3.9-7.9 in) long and 5-11 cm (1.9-4.3 in) wide. The leaves are sparsely hairy above and densely hairy below, and the petiole is 0.2-1.4 cm (0.08-0.77 in) long. The inflorescence occurs in the upper leaf axils, and there are 20-130 flowers per inflorescence. The flowers are small, 11-17 mm (0.4-0.7 in), and bloom from May to August. The five petals are green to purpletinged, and are topped by a crown of five erect lobes that are rose to purple, rarely white. The fruits are spindleshaped follicles covered with soft hairs. The small, round, hairy seeds are 6-8 mm (0.2-0.3 in) in diameter. Milkweed stems are collected after the stalks senesce in late fall-early winter. The dried stalks are split open to release the fibers; milkweed fibers are sometimes mixed with fibers of Indian hemp (Apocynum cannabinum). The bark is removed and the fibers released by first rubbing between the hands and then drawing the fibers over a hard surface.
Twisting the fiber opposite each other and twining them together forms the cord. Often this is accomplished by rolling the fibers on the thigh while twisting them together.The young shoots, stems, flower buds, immature fruits, and roots of butterfly milkweed were boiled and eaten as a vegetable by various indigenous groups of eastern and mid-western America. The Meskwaki steam the flower buds as a food source; they are nutritious but not considered very flavorful.
Properties of Milkweed fibres
Milkweed fibres are hollow, with a thin wall and are therefore lightweight. The hollow structure of milkweed fibre has led to its use in items where good insulation or buoyancy properties are needed. Like cotton, it is a single cell fiber, but unlike cotton, it is free from convolutions and has low cellulose content. Due to its very smooth surface, spinning of 100% milkweed fibre is difficult. However, it can be blended with other fibres and spun into a yarn. The fibre is extracted from the stem of the milkweed plant. The distinct properties are better durability, stability and tenacity. These fibers are good moisture absorbency. The project mainly deals with testing of properties and medicinal application. The basic tests of this fibres is length, diameter, strength, etc. similarly the properties of these fibres are also studied and compared with cotton.
Lightweight milkweed fibers, also known as mudar, are thin walled and hollow. The silky needle-like fibers have some unique properties—including high moisture regain and excellent thermal insulation and buoyancy. However, due to the fiber’s very smooth surface, it is difficult to spin into yarn, therefore, the fiber has had limited use as a textile product. Recently, researchers have made exciting headway—successfully producing a milkweed-rich yarn. Milkweed is a perennial plant that can adapt to adverse soil conditions. It is grown in many parts of the world, including Central and South America, India, Thailand, Africa and throughout the U.S. Milkweed is the common name for Asclepias syriaca. The fiber is obtained from the seedpod of the plant.Various parts of the plant have been used throughout history in a wide variety of applications. Named after Asclepius, the god of medicine and healing in ancient Greek mythology, milkweed was used for medicinal purposes because of the cardiac glycosides found in its tissue. The monarch butterfly also uses the cardiac glycosides to its benefit. Milkweed is the host plant for the monarch butterfly and as the larva consumes the milkweed leaves, it absorbs the cardiac glycosides making the monarch toxic to predators.
In Chinese folk medicine, milkweed fibers were used as compresses to stop wound bleeding. The sap from the plant has also been used to remove warts and age spots. The fiber’s textile applications have been sporadic.
Milkweed has been used as a stuffing material for upholstery since the 18th century. The fiber was utilized relatively extensively as a stuffing material during World War II. During the war, kapok fiber, a soft, cotton-like material from the kapok tree, was used to fill life jackets. The fiber was supplied to the U.S. by Japan but imports were cut off during the war. Because milkweed is exceptionally buoyant and lightweight, it was used as a substitute for kapok. During World War II over eleven million kilograms of milkweed fibers were collected—enough fiber to make 1.2 million emergency flotation devices.
Due to their exceptional insulation and buoyancy properties, the fibers are still used as filling for comforters, life vests and winter jackets. However, recent attempts have been made to broaden the fiber’s use by spinning it into yarn. It is well known that the lack of cohesiveness of the milkweed fibers causes extreme challenges in spinning
100% milkweed; however, researchers believed that it might be possible to spin a blended yarn. In 1987, researchers attempted to spin milkweed fibers blended with cotton fibers into a yarn. Cotton fibers are similar in length to milkweed fibers and have similar chemical and dyeing properties. Various blended yarns were produced—including 75% cotton and 25% milkweed; 67% cotton and 33% milkweed. Various processes had to be hand executed, such as the blending stage, making a full fledge commercial launch of the yarn impossible. The desire to spin a milkweed-rich yarn on conventional spinning equipment prompted additional research. Like cotton, milkweed is a single cell fiber, but unlike cotton it does not have convolutions—the natural reversing axial twists. The absence of convolutions makes spinning difficult.
In 2005, researchers treated the milkweed fibers with 5% NaOH in an attempt to create convolutions. It was believed that the presence of convolutions would create friction between the fibers, making processing easier. The NaOH treatment did in fact create convolutions, however, the fibers tended to stick together, therefore some equipment needed to be run at low speeds. A 75% milkweed and 25% cotton blended yarn was successfully spun. This project led researchers to believe that with chemical modification, a 100% milkweed yarn might be possible to spin.
Milkweed fibers are inexpensive and hypoallergenic. The high moisture regain and excellent thermal insulating and buoyancy properties of milkweed suggest that it might be utilized for a variety of high-performance applications. As researchers continue to make headway in spinning milkweed fibers on conventional equipment, the reality of seeing milkweed-rich and even 100% milkweed yarns in the market place might not be far off.
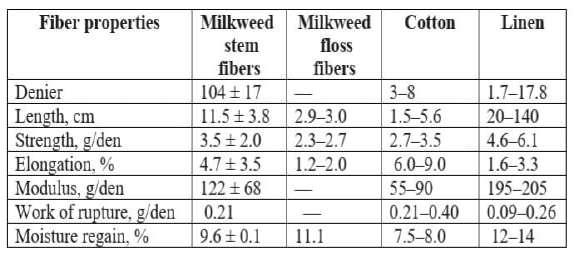
Experimental fabrics have been knitted from high level blends of cotton and common milkweed fibers. The milkweed fiber (Asclepias syriaca), often called "vegetable silk," is a seed floss that is similar to the Rux fiber (Calotropis gigantea) of Southeast Asia. Reactive dyes, vat dyes, sulphur dyes can be used for Milkweed fibers, which are cellulosic in nature and structurally comparable with cotton fibers. As it is seen from Table 1,
Table 1: Physical properties of milkweed and cotton fibers
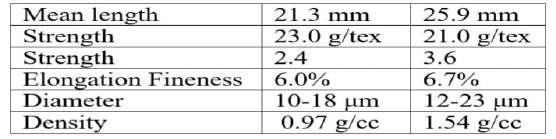
Table 2. : Comparison of the % composition of natural cellulose fibers from milkweed stems with milkweed floss, cotton, and linen
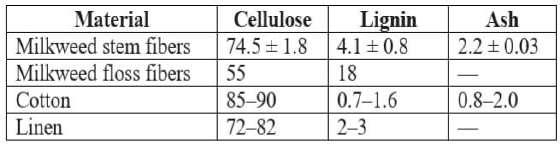
Table 3.: Fineness, length, mechanical properties, and moisture regain of milkweed stem fibers compared with milkweed floss, cotton, and linen
Uses of Milkweed
Milkweeds supply tough fibers for making cords and ropes, and for weaving a coarse cloth. Used for making comforter, or duvet and also mattress, enhancers which conform to your body, so your muscles relax, your circulation improves, you toss and turn less. Used for making comforters, pillows and featherbeds will help you sleep better. Used in pillows that will cradle and support your head. You will fall asleep the minute your head hits the pillow.
• The milkweed plant gets its name because when cut, it gives out a white liquid that looks like milk. • The floss that the seeds give off is used for stuffing soft toys. • The fibers of the plant can be used to make several things like jackets, pillows and ropes. • Most parts of the plant can be used for cooking (after washing it carefully). • The sap that is secreted by the plant is used for treating several conditions like flax, hemp, backaches, bee stings, ringworm and warts.
FACTS
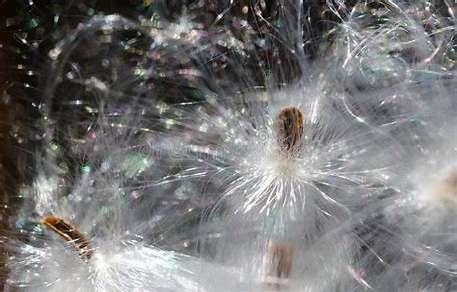