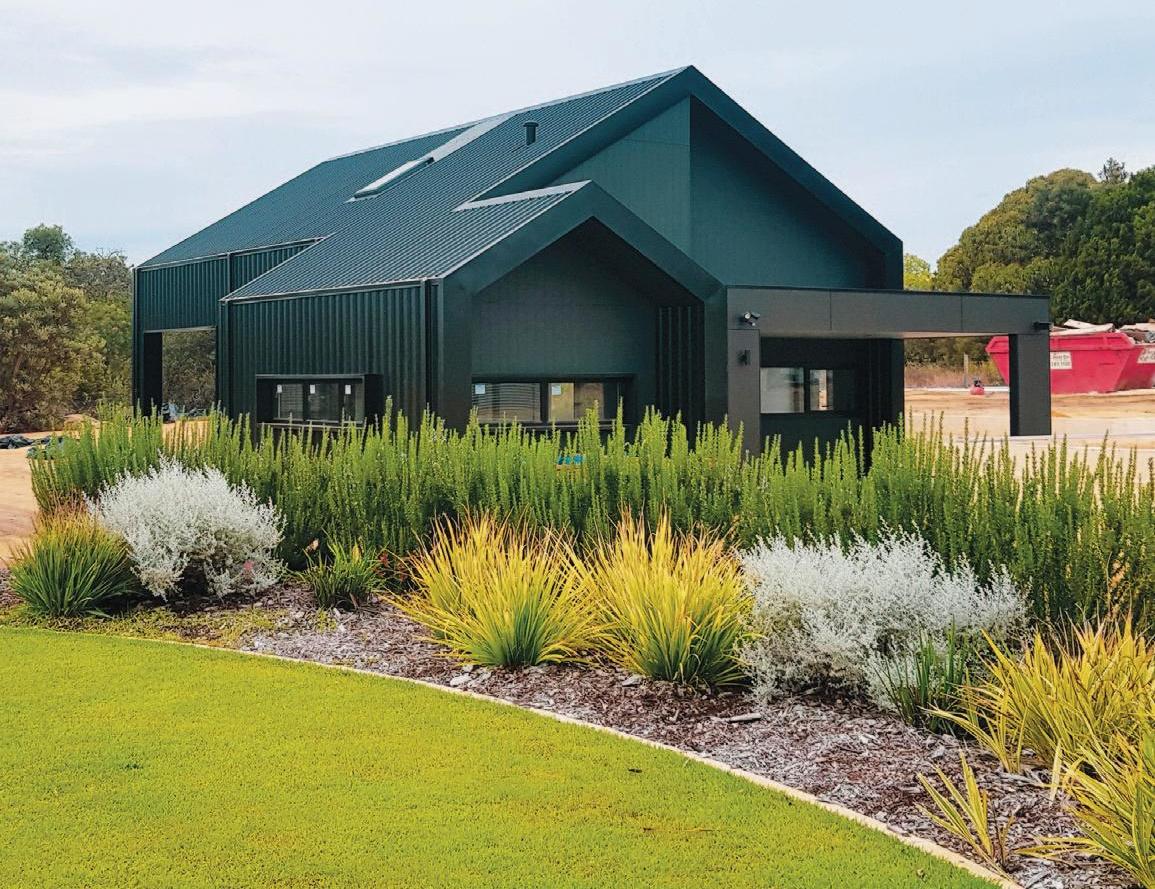
7 minute read
Sid Thoo
Timber and Steel Framing for Tomorrow
PHOTO DARKLIGHT DESIGN & IRONSTONE HOMES
Advertisement
Cavity brick has been the predominant choice for external wall construction in Perth for many decades. There are a variety of reasons for this – an abundance of clay, availability of materials and labour, well-draining sandy soils that can be easily compacted to accommodate heavyweight construction, and a long held belief that houses built from brick are "just better".
However, I think this trend has been slowly changing. While the majority of the project home building industry still build using cavity brick, in my own work I have observed an increasing interest in alternative methods of wall construction. Of the last ten or so projects I have designed, only two have used cavity brick, and then only for the ground floor level.
My first experience of working with wall materials other than brick occurred in 2009. I was designing a home for a young family who had recently returned from living in Melbourne, and who were accustomed to living in a timber-framed house. Their site was in Swanview, and had highly reactive soils – cavity brick wall construction would have required expensive concrete footings and pile foundations. We ended up using a structural insulated panel system (SIPS) that was lightweight and had high levels of insulation, which could be built quickly and cost-effectively in conjunction with a conventional concrete slab on ground. The SIPS system we used was relatively new at the time, but has now become a popular alternative construction method.
There's certainly nothing wrong with building with brick. Civilisations around the world has been using brick for many thousands of years, and it is tried and tested method of construction. However, there are a few of reasons why brick isn't always the best option:
Thermal mass: brick has a high level of thermal mass, which can help keep a building warmer in winter and cooler in summer by regulating the way heat is retained and released. However, too much thermal mass in a building can compromise the thermal comfort in a building, by making it harder to keep warm in winter (by absorbing too much heat from the air), and cause the building to overheat in summer (by retaining too much heat). In my experience, a house with good solar passive orientation and exposed thermal mass on the floor eg. concrete slab on ground is about the right amount of thermal mass.
Insulation: building materials with high levels of thermal mass generally lack insulation, which means they can't resist the flow of heat from one side of the material to the other. To build a wellperforming home using cavity brick will generally mean that insulation needs to be installed in the cavity. A loophole in the energy efficiency performance requirements in the current National Construction Code (NCC) has been exploited by a number of builders in Western Australia, allowing houses to be built without cavity insulation. However, this has now been addressed in the new edition of the NCC which comes into effect in May 2019.
Embodied Energy: refers to the amount of energy that is required to produce a particular product or material, and typically accounts
THE TEAM
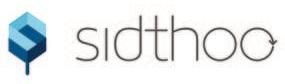
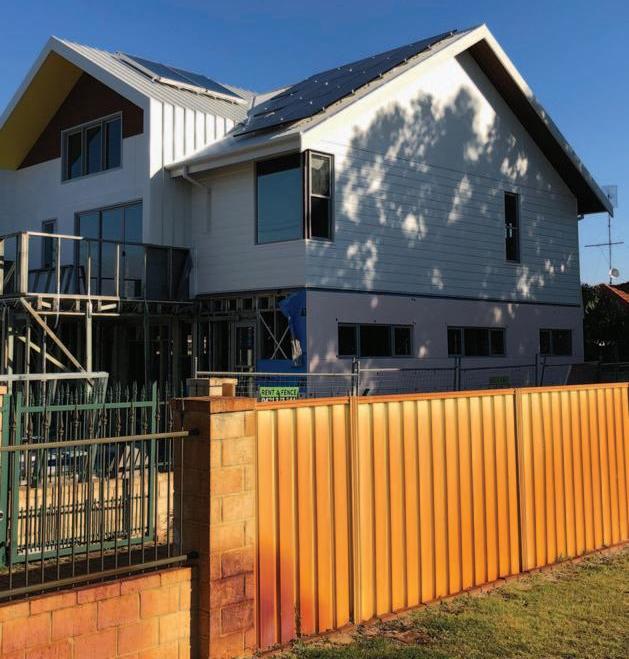
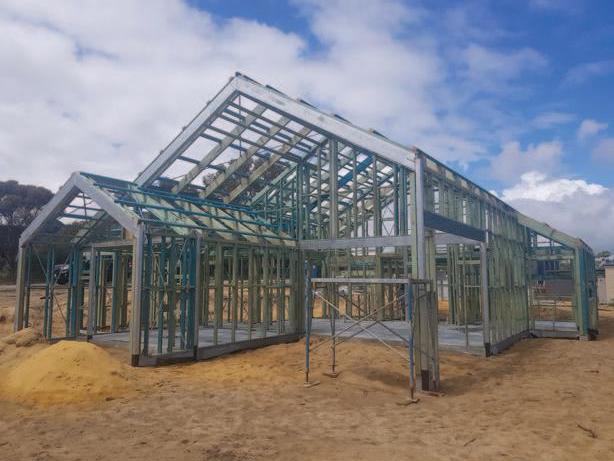
for the extraction, manufacturing, transport and disposal of the material. According to the Australian Government Your Home website*, a cavity brick wall (860MJ/sqm) has between 2-5 times the amount of embodied energy compared to a timber framed wall (169- 377MJ/sqm). While materials with high embodied energy are not necessarily "bad", high embodied energy often means high carbon emissions, and so we will need to think more carefully about the materials used in building construction as we transition to a lower carbon economy.
PHOTO DARKLIGHT DESIGN & IRONSTONE HOMES
These are some of the reasons why the builders I work with and many of the homes I design today tend to use framed construction (mainly timber, but sometimes steel). Some of the advantages to framed construction include:
Speed and convenience: framed walls can be modularised and pre-fabricated, and then assembled quickly once delivered on-site. For the houses where I have still used cavity brick, upper floor walls are built from framed construction, eliminating the need for brick hoists. Services such as plumbing and electrical wiring can be easily installed inside the wall frames – no need for brick chasing.
Flexibility and choice: There are variety of cladding materials and external finishes available that can be used in conjunction with framed construction – this makes it possible to articulate the facade of a building in different materials, which can help to create more interesting designs. Framed construction can also accommodate changes in the building geometry such as projecting or recessed walls, which is helpful since I'm an architect and tend to design more complicated shapes!
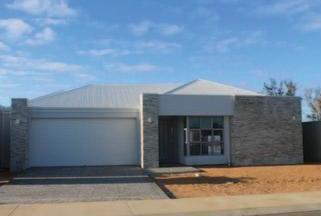
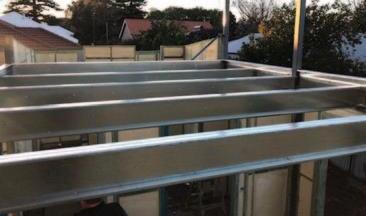
ONE SYSTEM TICKS ALL THE BOXES
Do you want:
✔ Faster build times ✔ Faster stage claims ✔ Higher R Value ✔ No plaster cracking issues ✔ Clients with lower energy costs ✔ To be an industry leader in thermal construction
‘‘Control your living environment temperature with minimal cost’’ MALULITE (R) BEAM
THE MULTIPURPOSE LIGHTWEIGHT WALL, FLOOR & ROOF BEAM
The Patented MALULITE (R) Beam and connectors are prefabricated off site, which creates efficiencies in installation as well as reducing site cleaning costs. If required, modifications can easily be done onsite. Ceilings can be fitted to the underside of the flooring system, facilitating access for sewer, water, power and air-conditioning services. Compared to traditional concrete suspended slabs, the MALULITE (R) Beam flooring system reduces costs and saves time by removing the need for:
■ Formwork/props erection and removal ■ Engineering Inspections ■ Concrete labour ■ Curing Time When used as a flooring system, the lightweight MALULITE (R) Beam allows for a multitude of floor options, including a 75mm concrete slab, timber, Hebel panels and much more. It can be utilised as a single storey stumped floor, multi storey residential.
Polyurethane Panel System
Our patented High Density Polyurethane Panel System (PPS) is a structural light weight high-density and fire resistant panel design that is a unique and an innovative way to complete your project. It has the same design capabilities as conventional materials, but with significant thermal advantages and costs.
For more information contact:
NIGEL 0448 580 854 MAL 0415 177 313 nigel.pollitt@karlayura.com.au admin@panelswa.com.au
McDonalds, Mundaring
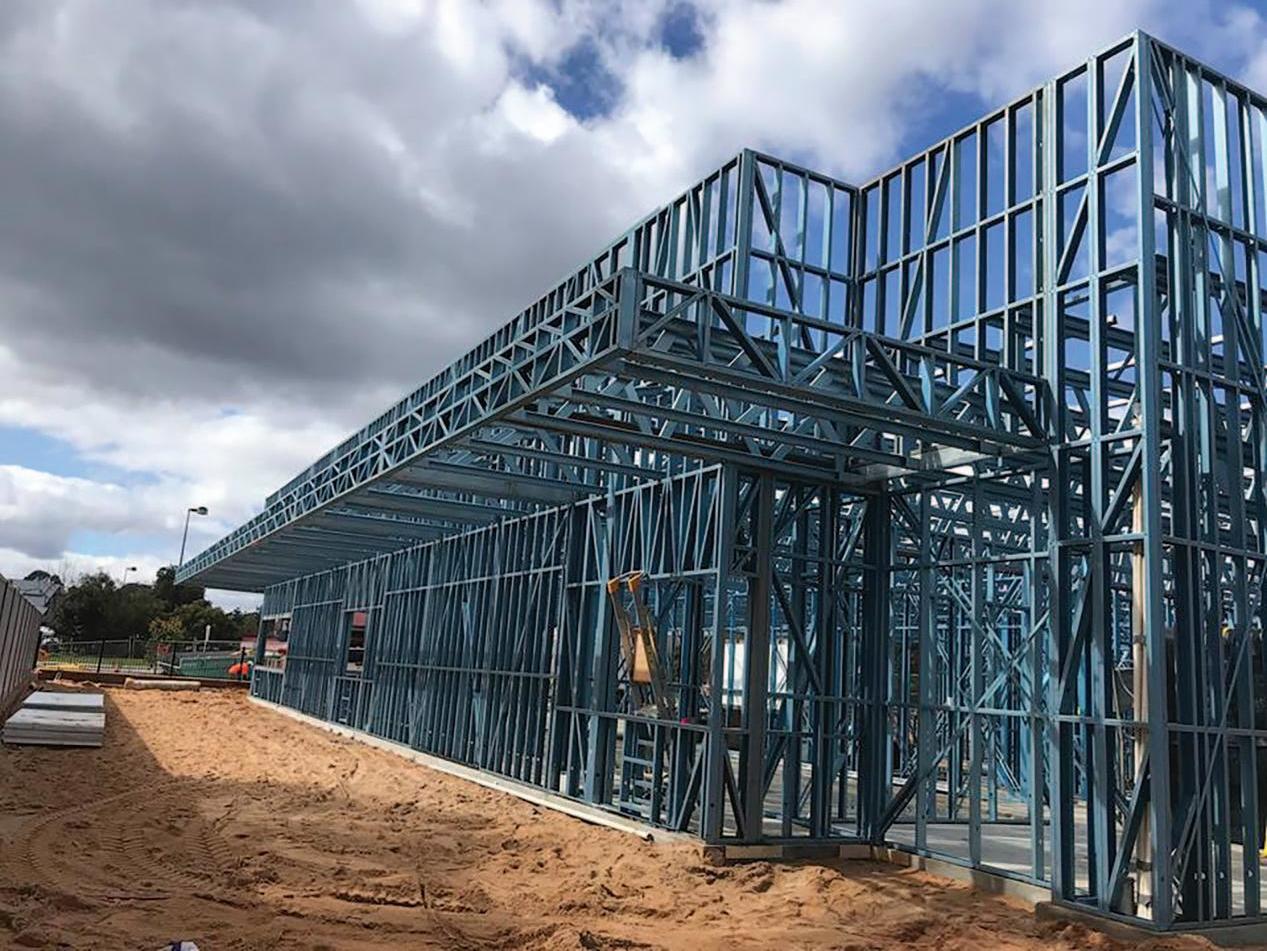
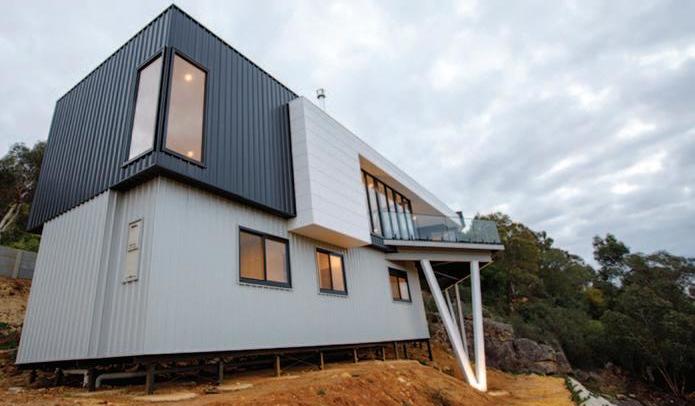
PHOTO DARKLIGHT DESIGN & IRONSTONE HOMES

Performance: With appropriate levels of bulk insulation and sarking correctly installed as part of the external wall, framed construction can provide a high level of thermal performance, while also avoiding moisture and condensation issues. Steel framing requires the addition of a thermal break between the external cladding and the steel studs to minimise thermal bridging, but there are easy to install products available for this purpose. Framed construction can sometimes experience issues with sound transmission compared to masonry construction, but there are a variety of factors that can impact this other than just the wall construction. Incorporating higher density wall insulation or plasterboard, resilient mounts and ensuring gaps are properly sealed can also help to address unwanted sound transmission.
Cost, of course, is probably the most significant, influencing factor in the decision making process: we've found that for the houses I design, framed construction is more cost-effective compared to cavity brick and masonry construction.
As I wrote earlier in this article, there's nothing wrong with brick, and it can still be a cost-effective way to build a well-performing home; new and innovative building materials are not necessarily better. However, we are developing a greater understanding about the impacts of the building and construction industry, and now consider a wider number of factors when deciding how we build. I've found the ubiquitous use of brick isn't always the best option, and saying "but that's the way we've always done it" is becoming a less convincing justification for keeping things unchanged. I believe greater choice – brick, framed and no doubt others – will ultimately result in better quality, higher performing buildings that will benefit homeowners as well as industry. *http://www.yourhome.gov.au/materials/embodied-energy
PHOTO DARKLIGHT DESIGN & IRONSTONE HOMES