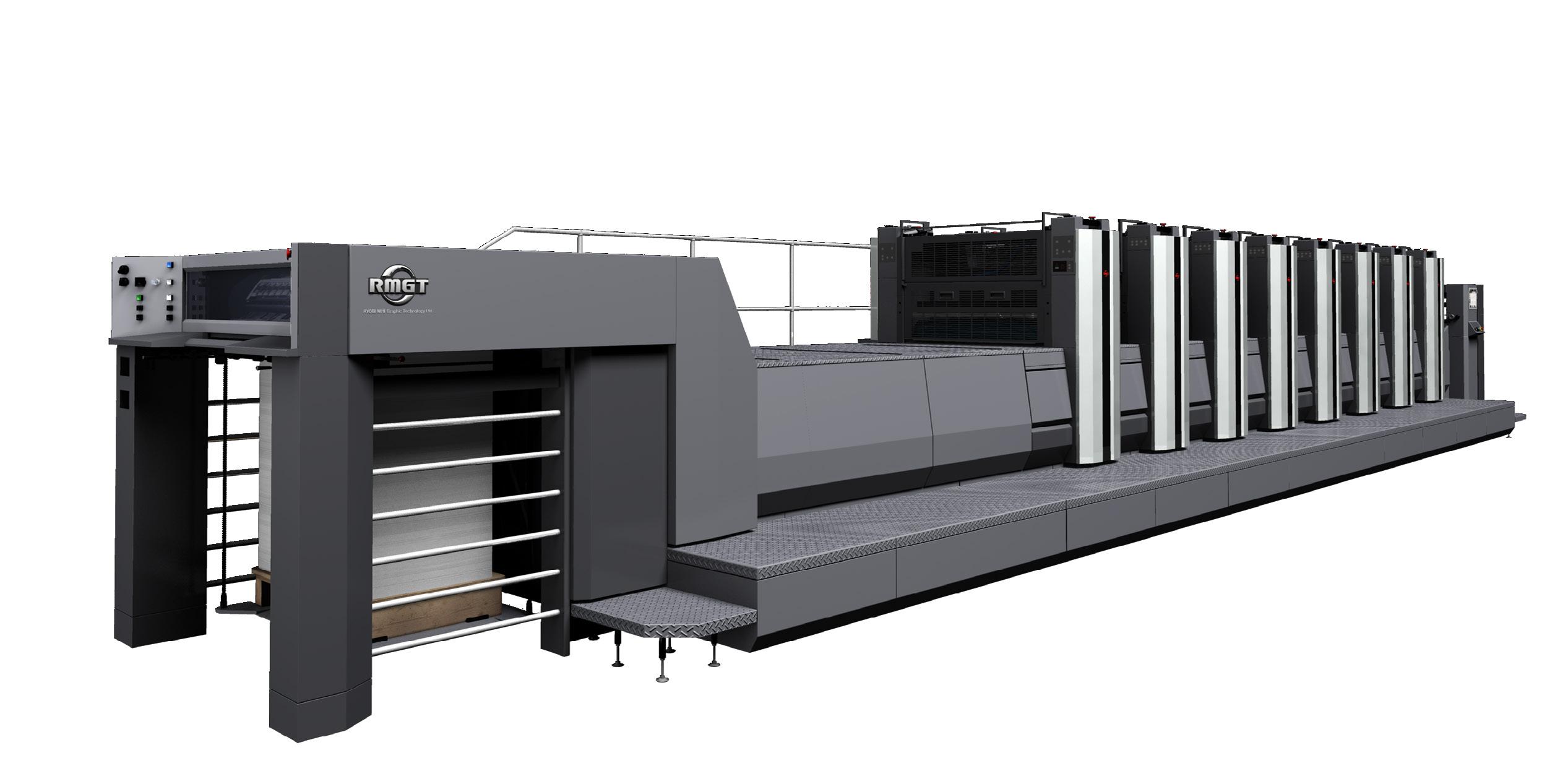
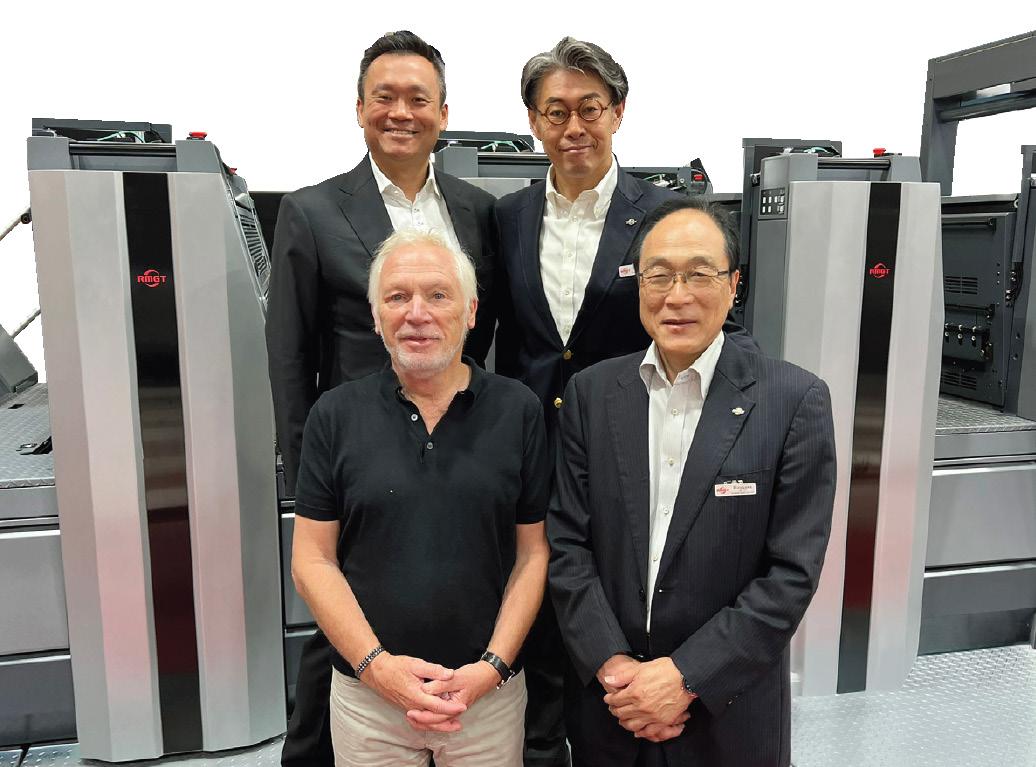
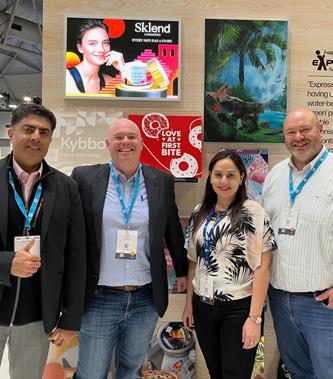
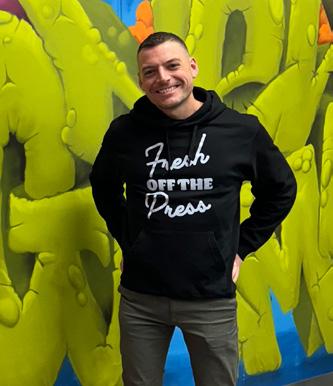
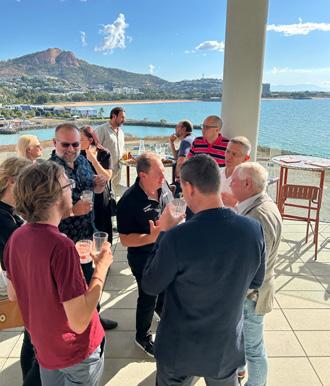
6-15 Update
A news round-up from the world of print
20 Comment: Charles Watson
What you need to know about post-employee restraints
21 Comment: Mick Rowan Silos no more: Unleashing collaborative innovation
22 Women in Print Charters Paper’s Elli Zlatanovski celebrates 30 years of service
24 Cover Story
Cyber has installed a new Ryobi RMGT 970 7 colour offset press at CCS Packaging in Sydney
28 Visual Impact Round Up: Ideas, innovations and industry faces from Brisbane
32 Women in Print announce new partnership with HP
33 Open House Australia’s first Digitech demonstration draws a crowd at Celmac and SS Signs’ joint open house
36 Star Business Leon Wilson, owner of Revolution Print presents the Futurecutter
39 Case Study Canon’s Colorado M5W Series at Evan Evans
40 Case Study SMARTECH installs first Agfa JETI Tauro H3300 for Dashing Group in New South Wales
42 ProPrint Diary
Keep up to date with the latest industry events
If there is one message that drupa and Visual Impact made loud and clear, it’s that print businesses need to stay ahead of the curve when it comes to exceedingly fast technology advancements.
A strong theme that dominates this edition of ProPrint is what the future of the print industry looks like.
More businesses are forced to evaluate output to meet the needs of a faster world and increasingly high customer expectations.
The value of the trade show is the collegiate exchange of
knowledge and information to benefit the industry, and 2024 has delivered on that front with the huge successes of drupa and Visual Impact.
In this edition, we cover the whole gamut of news stories from Visual Impact in Brisbane, which broke attendance records compared to six years ago.
We also talk to print futurist Leon Wilson at Revolution Print in Ballarat about his Australian first technology he accurately dubs the Futurecutter.
Our case studies feature Evan Evans’ Sonya Cameron and her new Canon Colorado M Series plus SMARTECH’s first installation of the Agfa Jeti Tauro H3300 at Dashing Group.
The ProPrint editorial team hope you gain valuable insight from this edition’s indepth reporting on the new technologies available and how they can benefit your business.
Editor Claire Hibbit, chibbit@intermedia.com.au
Design and Production Manager Sarah Vella, svella@intermedia.com.au
Managing Director James Wells, james@intermedia.com.au
Subscriptions (02) 9660 2113, subscriptions@intermedia.com.au
Printed by Hero Print Alexandria, NSW, 2015
Mailed by D&D Mailing Services Wetherill Park, NSW, 2164
Durst CEO Christoph Gamper has confirmed the Australian subsidiary will be expanding to new premises up to four times larger by the end of 2024.
In an interview with Gamper at drupa, he told ProPrint about the expansion plans.
“As you know I love Australia and we are looking for a little bit more space as we are growing, which is a good thing. The ‘little big company’ is becoming a little bit bigger,” he said.
Gamper visited Australia recently to celebrate the company’s fifth anniversary and 100th installation in the local market, and to discuss the future expansion of the business.
Durst Oceania has been located at the same Tullamarine premises in Melbourne since the subsidiary was established five
Westman Printing confirmed its fifth FUJIFILM purchase at drupa increasing digital capacity as offset volumes gradually decline.
Sydney-based Westman Printing purchased a Revoria Press PC1120 which is a single-pass printer with capacity of 120 A4 horizontal pages per minute. It can handle thicknesses from 52gsm to 400gsm and lengths between 98mm x 148mm to longer papers at 330mm x 1200mm.
Owner of Westman Printing, Vik Gulati, told ProPrint this machine replaces the FUJIFILM Versant 2100 that was retired six months ago and complements the FUJIFILM Acuity Prime 20 that is also within the business.
“We have had a long association with FUJIFILM and the company has been an important digital backbone to our business,” Gulati said.
“This is the fifth machine we have purchased from FUJIFILM, and this will now become the main press for our business within our digital workflow. When we purchased this machine, we looked at the GX Revoria Flow RIP front end as well that adds to the automation
years ago. Durst Oceania managing director Matt Ashman said he is excited about the expansion plans and the new premises for the local subsidiary.
“Durst Oceania has now been established for five years and has grown exponentially in this time. It is important for the continued expansion that we have a good presence in Australia, and we are looking for a new building up to four times the space of our current location at Tullamarine. This will provide
our organisation with the ability to store equipment, undertake refurbishments, provide demonstrations to customers as well as host open house events. The new premises will feature a number of sustainable technologies in line with the company’s global ethos,” Ashman said.
Scan the QR code to watch more from Christoph Gamper at drupa:
that we can put into our pre-flight and job preparation process.
“We have found there are now more and more volumes coming off the offset press and shifting to ultra-short runs. We have even started working with a client for a print-on-demand model for a quantity of one. Everything is now last-minute and of course it is our fault that the client is late, and the customer is always right – so we are moving more and more to a ‘just in time’ business model.
“We would like to thank Harry Singh and his team. Harry has helped us out of many tricky situations. Machines sometimes break down, but it is important what happens after a machine breaks down that is important. We have had experience with FUJIFILM and other digital providers, but Harry has always stood out, which is why
we always come back to them,” Gulati said.
According to FUJIFILM Business Innovation Asia Pacific general manager, Scott Mackie, this continues the relationship the company has had with Westman Printing.
“FUJIFILM have been long term partners with Westman Printing for over 14 years and the new PC1120 six colour press is the next part of our journey together. This machine features pink inks which is great for halftones and point of sale. We developed the pink for Manga cartoon production which is a huge industry in Japan. The by-product of that is that pink is the most recognisable fluorescent and when you add it to point of sale or retail products it really gives it a ‘pop’ – and that has been a key factor for the investment in pink with this machine.”
The Acuity Ultra R2 is a modular system with scalable architecture, meaning it can grow and change as your business evolves.
Multi-roll capability maximises productivity for smaller jobs
Auto media thickness and position measurement
Our Acuity Range is known for its excellent high quality, productivity and reliability on a massive industrial scale. Engineered with the operator in mind, LED configurations work in harmony with specialist inks to support the printing of exceptional near-photographic interior graphics and the high speed printing of banners and PVC signage.
With a throughput of over 600 m² per hour, the machine has the potential to produce huge volumes of work when printing on three rolls simultaneously, as well as printing superwide format graphics up to five metres in width.
The Acuity Ultra R2 is equipped with a media detector mounted on the carriage. This is used to determine the position and thickness of the media.
To discover more, scan below:
In an exclusive interview, Benny Landa, has confirmed his local launch plans after numerous Australian printers have offered to invest in the latest nanography technology.
Benny Landa spoke with ProPrint at drupa and was asked directly whether he will be distributing the new products he has recently launched in Australia. Unfortunately, Landa has not made a commitment to the exact timing of when he will commence distribution of the new S11 and S11P products in Australia – as he is focusing on the northern hemisphere and the markets in Europe, America and China.
Ricoh announces 100 sales from drupa 2024 worth $225m
Ricoh’s head of sales has confirmed 100 orders worth $A225 million at drupa including the first confirmed sales of its Pro Z75 B2 sheetfed aqueous inkjet press and Pro VC80000 high speed web fed press.
Ricoh has confirmed the sales represent orders of $US150 million ($A225 million) over five years across all inkjet, toner, software, and industrial printheads technologies.
The two major product releases on the Ricoh stand included the Ricoh Pro VC80000 high speed web fed press – also known as the Harpy Eagle and the Ricoh Pro Z75 B2 sheetfed aqueous inkjet press – also known as the Dragon. Also complementing these machines were its toner-based machines – the Jaguars – Pro C9500, Pro7500 and Pro C5300.
Ricoh has confirmed sales at drupa of the Ricoh Pro VC80000 to Cimpress and the Pro Z75 to Saudi Arabian dealer Samir Group.
Visiting Australia in June to meet with printers following drupa, Gavin JordanSmith, senior vice president and general manager, global sales strategy division and North America sales for Ricoh Graphic Communications discussed the importance of the ‘Henkaku’ theme at drupa which is the Japanese word for ‘transformational innovation’.
Jordan-Smith said the ‘Henkakuverse experience’ at drupa was designed to “create a sense of community that connects our team members with those of customers walking through the booth”.
“I love Australia and I love Australians and we are definitely going to be there,” he told ProPrint exclusively at drupa 2024.
“But we don’t want to come to any country until we have a decent foundation and infrastructure where we can support the customers. We will get there, but it won’t be in 2024,” Landa said.
“Be patient, we promise we will be there – big time – drupa has been phenomenal and amazing for us – digital printing is here,” he said.
A number of Australia’s largest printers made one-on-one approaches to Benny Landa to purchase his printing equipment at drupa – with one printer offering to buy two products – but even this was not enough to convince Landa to start servicing the local market earlier than scheduled.
At drupa 2024, Benny Landa unveiled the S11 and the S11P machines, which are the successors to his S10 and S10P machines.
The Henkakuverse concept was created to deliver a virtual production environment where customers could engage with Ricoh’s technology for the benefit of their individual print needs and requirements. Asia-Pacific was the second largest group to tour the Ricoh stand behind Europe.
In an exclusive interview with ProPrint, Jordan-Smith – who is the global head of sales for Ricoh Graphic Communications – shared key insights into the revenue and return on investment driven by drupa.
“Two years ago, when we set up our [drupa] target, I said if we are going to spend millions of dollars to be at an event, I want ROI driven out of every region. ROI is not top line revenue it is a relationship with that customer we close and transact at the show. People are not going to the show to kick the tyres – these sales cycles were already happening a year ago. When we get to the show they are looking at other equipment and we get them to make the decision by saying ‘you have seen everyone else – so do you want to buy from us?’.
“We had a couple of people that bought $2 million machines that we did not have in the pipeline, but the bottom line is we set very high targets. So, if we spend
$4 million – I want a net profit target over 24 months because an event [like drupa] is an event in time and other touchpoints. We exceeded [those targets] just in top line revenue – so that top line revenue will be more than enough to cover what we already spent on the event. The contract value for that is around $150 million over the next five years – so it pays for us to be at an event like this. These are orders – I didn’t want to sell future – I wanted to show things that customers could buy straight away,” Jordan-Smith said.
According to Ricoh Graphic Communications president, Koji Miyao, “it was a great drupa”.
“We enjoyed a huge amount of success, and it was very exciting and rewarding to see so many orders signed for our groundbreaking inkjet, toner-based, software and industrial printhead technologies. We look forward to supporting those new and existing clients in making a great return on their Ricoh investments. It was also a wonderful honour and privilege to connect with so many valued clients and partners throughout the show with whom we shared our powerful sustainability and co-innovation stories,” Miyao said.
Friday 25 October 2024
Scan to purchase your ticket
Spicers has announced it is the exclusive distributor of the Hahnemühle Digital Fine Art range in Australia.
Ken Booth, general manager – product and marketing, Spicers, said the significant partnership is a testament to Spicers’ unwavering commitment to providing the highest quality products to customers and elevating its offerings to the next level.
“We are particularly excited to bring the Hahnemühle sustainable range to the Australian market, which includes the innovative Hahnemühle Sustainable Photo Satin and the exceptional Hahnemühle Photo Silk Baryta X,” said Booth.
“The Sustainable Photo Satin is a ground-breaking alternative to traditional PE-based inkjet photo papers, featuring a new bio inkjet coating that is free of plastic composites and 100 per cent recyclable through the wastepaper cycle. Its bright white, velvety smooth surface is ideal for sustainable photo and poster printing.
“The Photo Silk Baryta X, with its cellulose base and optimised inkjet
Durst has confirmed the appointment of a sales manager to its team responsible for the Australian market.
Dan Mantel has been promoted from business development manager to the position of sales manager for Durst Oceania.
“Dan will be looking after wide format and textiles as well as continuing in his technical role in the labels and flexible space,” said Durst Oceania managing director, Matt Ashman.
“Dan will continue to oversee the implementation of the Vanguard rollout in Australia as well in his role as technical lead.
“Dan is a true asset to the business and has proved himself to have strong knowledge of all printing systems within the Durst portfolio and I can see him going far within our company.”
coating, offers a traditional silver halide photo paper feel. This smooth, creamy white paper with a silky gloss finish ensures outstanding print quality for both photo and poster prints, making it perfect for daily use,” said Booth.
“The introduction of these new products is yet another reason why our partnership with Hahnemühle is perfect. Spicers is dedicated to sourcing
products from manufacturers and suppliers who are committed to smart and greener practices.
“We are delighted to be the Australian distributor for Hahnemühle and to deepen our commitment to this esteemed partnership. Together, we will continue to set new standards in the world of digital fine art and sustainable printing solutions.”
The Australian Sign & Graphics Association (ASGA) has announced long-time association office bearer Michael Punch will retire from his active roles with the association, handing over his duties to Damian Nielsen.
Mick Harrold, ASGA president, said Punch’s retirement marks the “end of an era” for the association, with the former general manager and current membership and events manager playing a “pivotal role” across many years.
“Virtually every one of our members will know Michael by name and have positive memories of the many conversations and interactions they’ve had with him over the years,” Harrold said.
“In many ways, he has been the face of the ASGA, and the things we have achieved over the past few years are in no small part due to his dedication.
“There will be more to say in the near future about Michael and his contribution
The Truepress JET 560HDX was the most important product for Screen at drupa, according to Screen GP managing director, Peter Scott.
Speaking with ProPrint at drupa, Scott said the newly-designed high speed inkjet press solution represents the flagship of the company’s range with a 560mm web width offering an increase in productivity of up to 25 per cent.
“This machine prints at 150 metres per minute at 1200 x 600 dpi or 100 metres a minute at 1200 x 1200 dpi which is phenomenal,” Scott said.
“It’s a significant improvement in productivity from what we had before. And the new Screen SC2 Truepress inks offer a dramatic increase in vibrancy, density and colour gamut. These inks will print on uncoated and standard offset coated stocks without the need for a primer.
“This newly developed, high-optical density inkset allows printing directly onto offset-coated papers without any pre-treatment. The SC2 inkset’s special properties produce high vibrancy colours
to ASGA, but suffice to say there are few people, in any industry association, who have demonstrated the kind of commitment to members and to this industry that Michael has done, and we are fortunate to have had his contribution for such a long time.”
that ‘pop’ and have deeply saturated hues, as well as dense and neutral blacks for clearer printing of the very finest text and line work,” Scott said.
“This press is targeted at commercial print, publishing and direct marketing applications and we have already sold one unit with a commitment for three more in the US.
Punch’s current role as membership and events manager will be taken up by Damian Nielsen, the creative director of his Queensland consulting company, INbrandigo.
Nielsen has held the vice presidency of the ASGA for the past five years, is the association’s Queensland chair, and sits on its education committee.
Nielsen has more than 30 years’ experience in the signage industry, starting with work experience which was followed by an apprenticeship where he learned everything from brushwork through to fabrication and installation. Having recently stepped aside from his role as general manager of CV Media, Nielsen says he is now planning to balance his consulting work through INbrandigo with opportunities to ‘give back’ to the industry .
“There’s no question I have very big shoes to fill, but it’s exciting to be taking on these responsibilities at such an exciting time for the association,” Nielsen said.
“I am delighted to be stepping into this new role and very much looking forward to connecting with all our members over the coming months as we continue to roll out a busy program of webinars, events, and other initiatives to support their businesses and the wider industry.”
“In addition, a new high-efficiency, intelligent drying system enables substrates with high ink loadings to be dried efficiently, thereby supporting superior quality and wide-gamut printing on a wide range of papers. The Truepress JET 560HDX is also equipped with a new, fast-start operating system that inherits and further improves on the Truepress series’ market-proven technologies. This system ensures flawless integration of all internal hardware and software as well as with both pre- and postfinishing equipment.
“Screen anticipates that the Truepress JET 560HDX will become a benchmark contributor to the next generation of smart factories, where it is expected to introduce new economic efficiency, high-availability productivity, and print quality to satisfy the most demanding customer needs.
This was Scott’s fourth drupa and he was overwhelmed by the event.
“This was the best drupa I have attended – the overall vibrancy and enthusiasm from exhibitors and visitors was tremendous. There were some amazing stands and I was also impressed with the number of customers from Australia and New Zealand who attended and the number of meetings we had.
To hear more from Screen GP managing director Peter Scott scan the QR Code
The Visual Media Association (VMA) worked with Tasmanian industry leaders across ‘in session’ meetings in Launceston and Hobart working through the key needs of the industry.
Mercury Walch, Foot & Playsted, Flying Colours, Think Big Printing, Mark Media, Spicers, and others attended providing insights across the need to retain all government print to be produced in Tasmania, improve the quality of training for the state, build HR/IR Health check services and arm printers with skills to sell print based on effectiveness and environmental credentials that are meaningful to customers.
Kellie Northwood, VMA CEO, and VMA Tasmanian board representative, Tony Bertrand, attended both sessions across the state – a lunch and learn session in Launceston and a breakfast boardroom meeting in Hobart. Bertrand committed to being present and bringing the voice of Tasmanian printers to the board.
“It was a great two days, meeting and
FESPA’s awards programme returns in preparation to recognise industry leaders at the co-located FESPA Global Print Expo, European Sign Expo, and Personalisation Experience in Berlin, taking place in May 2025.
The competition is open for submissions from speciality print providers and sign-makers to showcase their most outstanding projects.
FESPA’s head of association and technical lead and one of the 2025 judges, Graeme Richardson-Locke, said: “Speaking on behalf of the judges, we all hope to be surprised by new levels of technical excellence and clear evidence that the entry has been created with the greatest care, reflecting the professional standards that we’ve seen over many years. For entries this year, we’re interested in seeing the use of appropriate and sustainable materials, reflecting the wider industry’s goal of reducing its environmental impact.”
The FESPA Awards will welcome entries to the following categories:
• Display and POP on Paper and Board
• Packaging on Paper and Board
• Display and POP on Plastic
talking with members to hear about how the association can deliver on local issues for our industry. I thank all who attended in both Launceston and Hobart and commit to bringing your voices to the national board,” said Bertrand, who is also the head of marketing, Ball & Doggett.
Specifically, the industry has outlined its concern of government grants and funding for printed books and material being offshored to China when funding is issued through third party sourcing models. Not an area being experienced by Tasmania alone, as the VMA has long been lobbying government across the some $140 million offshored government print
work nationwide.
“There is simply zero justification for local, state or federal government monies across print procurement going to brokerage arrangements where the broker has print facilities or is offshoring through China or other countries for production,” said Northwood.
“It is on the VMA’s radar, and we will action these concerns both state by state but also federally. Government print work should be procured locally and ethically.
Skills and training was a further key focus with the Tasmanian leadership outlining concerns to the quality of training across the state arguing it is at a very low level which is difficult, after working very hard to attract new talent, the training is considered so poor it is creating challenges for printers to retain new talent.
The expense of environmental and compliance certifications was outlined as an obstacle which printers, despite wanting to build strong environmental certification and policies, is often struggling to fund and resource.
“The two days in Tasmania was terrific, it was wonderful to work face to face with the industry, present solutions from when we met earlier this year and work through more challenges we can resolve,” said Northwood.
• Packaging on Plastics
• Posters
• Serigraphies and Fine Art
• Decals and Printed Labels
• Wrapping
• Creative Special Effects – Paper Board and Plastics
• Special Effects on T-shirts, Garments and Other Textiles
• Printed Garments
• Roll-to-Roll Printed Textiles
• Glass, Ceramic, Metal and Wood Products
• Direct Printing on Three Dimensional Products
• Non-Printed Signage
• Functional Printing – Fascias, Dials, Name plates Printeriors
The Young Star Award, is open to individuals aged 16-25 who are vocational trainees or students in digital or screen printing and design.
“We are always thrilled to review the entries for the Young Star category and impressed by the standard of work submitted,” said Richardson-Locke. To enter, applicants can submit their work in any print related category. The People’s Choice Award will be open to voting from 6 January 2025, with the FESPA online community casting their votes across all categories. The Best in Show Award and the Judges’ Award for Innovation are chosen by the panel of judges from FESPA.
Printers and sign-makers have until Wednesday 12 December 2024 to submit their entries for the 2025 FESPA Awards. The shortlisted entries will be announced on 23 February 2025 and showcased from 6-9 May 2025 at Messe Berlin, Germany. For more information on the FESPA Awards 2025 and how to participate visit: www.fespaawards.com
CMYKhub is entering the soft-signage market after purchasing three EFI machines with EFI’s ANZ channel partner Currie Group.
The order, which includes the new EFI VUTEk Q3h XP and EFI VUTEk Q3h X hybrid printers and the EFI VUTEk FabriVU dyesublimation printer, is the largest sale of EFI machines in Currie Group’s history. CMYKhub is also the first in the world to confirm an order for the EFI VUTEk Q3h XP and EFI VUTEk Q3h X hybrid printers.
The dye-sublimation printer will not only increase the capacity of CMYKhub’s rapidly growing wide-format trade printing service, but also add a new, soft-signage service to the company’s growing offering.
Paul Whitehead said the sale expands on Currie Group’s longstanding relationship CMYKhub.
“These are groundbreaking machines that will take productivity in wide format to a whole new level,” said Whitehead.
The first of the machines to be delivered will be the VUTEk FabriVU 340i+, which is set to arrive in Melbourne within the next few months, quickly followed by the VUTEk Q3h XP which is also expected before Christmas. The VUTEk Q3h X will join its stablemates at CMYKhub’s Sydney premises next year.
CMYKhub national communications manager, Glen Francis, said the new dye-
sublimation printer will complement CMYKhub’s existing wide format offering.
“Dye sub is going to be a great new arm for us,” said Francis.
“It complements our wide format products already so soft signage is what we’re going to enter. We were looking at [dye-sub] in 2018 and then Covid happened. So, we’re now keen to hit the ground running and launch it quick – as soon as the machine arrives.
“Walking around Europe, soft signage is massive here and it’s growing in Australia, so it complements the existing signage mix that we already produce. There’s a lot of other things that we have been looking at to potentially utilise this machine in other sectors as well.”
Alan Nankervis, national wide format manager, CMYKhub, said the company is currently reinvesting in its machinery across the country in response to demand.
“A few years ago, we got back into wide format, reinvesting to prove a point to ourselves that if we grow our capacity, our customers will grow with us and we proved it quickly adding the H5 two years ago, which has really grown our capacity.
“We’ve got more work than we have ever had. So, that proved to us that we needed to reinvest in the whole country, so we have started shuffling our machines around.
“We recently reinvested in Perth adding
in the Fuji. We’re going to move our VUTEk h5+ to Brisbane eventually, drop a VUTEk Q3h X into Sydney, and the VUTEk Q3h XP into Melbourne to give us a massive amount of sheets nationally to service our customers.
“Wide format is just growing and growing and growing – it’s always been growing but we never kept up with it, but we realised that we needed to keep up with it so this has been the investment that we have made in order to keep up with this growing demand.
“The VUTEk Q3h XP should be arriving around August/September in Melbourne, and at the same time we will have the dyesub coming so we’re also going to dip our toes in the water there and hopefully get soft signage up and running.
“We also have a VUTEk Q3h X coming early second quarter next year, that will come into Sydney and at the point the VUTEk h5+ will move will move to Brisbane and the swissQprint machine that we now run in Brisbane will move to Cairns.”
The company’s new two-storey, 6500sqm headquarters in Melbourne is also scheduled for completion around April next year.
“Being on one large site is going to make things a lot easier for us and is that’s really going to change the way we get work to the customer on time, every time.”
Industry professionals gathered in Sydney and Melbourne for a review of the trends and directions set at this year’s drupa exhibition in Düsseldorf.
Visual Connections in partnership with the Visual Media Association, the LIA, and the FPLMA, and sponsored by Currie Group and HP, recently hosted drupa review evenings in Sydney and Melbourne.
of the LIA NSW Graduate of the Year Award, which was presented to lithographic printer Robert Neale from WestRock.
Nankervis from Southern Impact and Andrew Crump from Peacock Bros.
In Sydney, more than 60 industry professionals came together at The Bavarian in World Square. The event featured reflections on the world’s largest print exhibition from Sarah Moore, general manager at Visual Connections, Benn Murphy from Clarke Murphy Print, and Pranil Chandra from Next Printing. The review was followed by the presentation
■Truepressロゴ(型式・シリーズ名)【ポジ版】
In Melbourne, the event was hosted at the Munich Brauhaus at South Wharf. Robyn Frampton, marketing and communications manager at Visual Connections gave an overview of the show, which included the ‘coming of age’ of digitisation, greater emphasis on automation and robotics, the influence of AI, a trend towards vendor partnerships and collaborations, and the ongoing drive for greater sustainability. More in-depth reflections were then shared by Heath
Lindsay Banks from LIA Victoria and Darren Brookes from Heidelberg then presented certificates to 2024 Finalists Imran Yunus from Multi Color Corporation, Emily McEwan from Jamesprint, Michael Bui from Fildes Food Safety, Jason Zhang from Richdale Plastics, and Nicholas Smith from Park Douglas Printing. Yunus was the overall Winner this year earning a grant of $3000 to be put towards his professional development, with McEwan awarded Regional Winner with a grant of $2000.
RELIABILITY
•Dependable performance
•Trusted platform
•Easy maintenance
PRODUCTIVITY
•High machine uptime
•High volume label printing
•Consistently high print speed
AUTOMATION
•Seamless integration
• Streamline production
• Maximum efficiency
Townsville turned on the sunshine and Far North Queensland’s printing trade tuned in to hear from the experts at the second Lamont Print & Signs VIBE Conference.
The Lamont Print & Signs VIBE Conference was opened by the Honourable Philip Thomson OAM MP and big-name industry presenters included Vincent Nair CEO of SMARTECH Business Systems, Keith Ferrell, owner of Cactus Imaging and Easy Signs’ Adam Parnell. Discussion on the state of the industry was encouraged by a Q&A session that lifted the lid on the future challenges for the industry including the fast pace of technology and how to manage it.
Other speakers included director and founder of Explore Property Townsville - Andrew Acton, business coach - James Hooper and directors and co-founders of Queensland Signage Solutions - Wal and Luke
Organiser and founder, Stephen Lamont, was particularly thrilled with the registration numbers and the speaker line
up. Forty percent of Lamont’s entire client base attended this year and delegation numbers increased by 40 per cent on the attendance for the inaugural conference in 2023.
“We had the most interesting and knowledgeable people in attendance and our clients received excellent business training from industry leaders. They all said they’re definitely coming back next year,” said Lamont.
“Many of the North Queensland sign businesses don’t get to some of the big sign events around Australia and they definitely don’t get to rub shoulders with the likes of Keith Ferrell and Adam Parnell,” added Lamont.
“They never get to talk to those guys, and they were able to, and they absolutely loved that.”
Topics that were discussed included the future of print and how technology has changed business.
“The processes of creating a sign have advanced so much that now companies are not only making their own signs, but they’re engaging some of the largest companies in Australia to leverage that technology to help them in business. And that is where most of our clients are at,” Lamont said.
Lamont is confident his VIBE Conference will continue to gain momentum as a key industry event in Far North Queenland.
“The conference is attracting some of the big names in the country who are more than happy to share their time and experience with attendees. It was a conference that reached levels we’d never seen here before and I can’t wait for next year,” Lamont concludes.
Charles Watson of the PVCA offers strategies to safeguard your business against the potentially damaging actions of former employees that could affect your business’s future success.
It has been a challenging year but what does 2023 hold?
It would be great if every termination of employment ended on good terms with a cake and card. However, some employees leave and seek to profit with their next employer using their previous employer’s most valuable assets. This can include working for competitors, soliciting previous clients, soliciting previous co-workers, using confidential information, and or capitalising on their previous employer’s intellectual property.
To overcome such conduct, employers often have post-employment restraint clauses within their employment contracts to protect themselves. However, the general principle is that restraint clauses are likely unenforceable unless an employer can satisfy two essential tests. First, the business has legitimate commercial interests it needs to protect, and second, the restraints are reasonable to protect those interests.
What are legitimate commercial interests?
Generally, the categories of protectable interests refer to an employer’s valuable interests in client and trade connections, trade secrets, properly confidential information, and/or the retention of current employees. Related restraints lessen the benefit an ex-employee and potentially their new employer may obtain from such information until such time as confidential information becomes less impactful or made public or where client
relationships are cemented with the original employer and less open to solicitation by the ex-employer.
In determining whether related restraints are reasonable, the Courts will consider a range of factors, including:
• the employee’s position, duties and whether they were the ‘face of the business’;
• what access and possession of confidential information the employee had;
• the length and geographical area in which the restraint is to apply;
• how much the employee was paid (a large salary may set off any loss of ability to work during the restraint period); and
• the size and nature of the industry where the business and the employees operate.
Often, the first best step is to remind a departing employee of their postemployment restraints and their continuing application after the cessation of their employment. It is recommended that this be done at an in-person meeting and confirmed in writing. However, it is not recommended that an employer behave towards the employee in a way that may be seen as repudiating the
contract of employment. This can potentially result in the entire contract being void, whereby the restraints are unenforceable, although confidentialityrelated obligations are still likely to apply.
If it appears an ex-employee is or is likely to breach those terms, an employer may seek to obtain an interim injunction against the ex-employee to enforce the restraints. The employer will need to establish its case on the basis of the tests discussed above, but the Court will consider other relevant factors, including the employee’s right to be able to use their skills and experience to earn a living. The employer may also seek to injure the new employer if there is evidence of accessorial liability in supporting the employee’s breaches. A full hearing may take place later, which could result in greater enforcement including awarding damages if the employer can establish it has suffered financial detriment due to the ex-employees conduct.
Although a controversial area of employment law, post-employment contractual restraint clauses have a legitimate role in balancing and protecting an employer’s legitimate business interests against the rights and freedoms of employees. However, employers must consider:
• A necessitous person will sign anything, but depending upon the circumstances, a Court may not enforce a restraint that is too harsh. Courts can and do ‘read down’ or sever unreasonable restraints.
• If an employment contract does not contain post-employment restraints there is little chance of having an ex-employee’s conduct restrained.
• To ensure a greater likelihood of a restraint being upheld, and for the reasons discussed, they must be appropriately drafted for the particular circumstances. They should not be too wide and go beyond what is reasonably necessary to protect the employer’s legitimate interest.
This article is of a general nature and guidance only and does not constitute legal advice.
Charles Watson GM – IR, Policy and Governance PVCA
IThe time has come to tap into the power of collaboration.
n the dynamic landscape of modern business, small and medium-sized business owners often find themselves in a delicate balancing act, where the demand for innovation is high, but resources and expertise are limited. Here’s where cross-functional collaboration emerges as a potent force, serving as the great accelerator of a company’s innovation engine.
Traditionally, businesses have organised themselves into functional departments, each with tasks, goals, and priorities. However, this siloed approach can act as a barrier to innovation, hindering the free flow of ideas and information across the organisation. By fostering a culture of cross-functional collaboration, business owners can effectively break down these barriers, tapping into the collective intelligence and expertise of diverse teams.
Small and medium-sized enterprises (SMEs) are well positioned to embrace cross-functional collaboration. With smaller teams, greater opportunities exist to create connections between different functions, leading to quicker decisionmaking and a more agile response to market changes.
Cross-functional collaboration has driven transformative change in businesses across various sectors. For instance, software start-ups have found success by integrating their customer service and development teams. By doing so, they can swiftly identify customer pain points and develop solutions at an unprecedented speed. This virtual closeness allows developers to gain a deeper understanding of the real-world applications of their work, leading to products that better meet consumer needs and expectations.
Another compelling example is a manufacturing plant that brought together its production and sustainability teams. This collaboration led to the development of a recycling program for the plant’s waste materials, thereby reducing environmental impact and saving costs on waste management. The innovative solution stemmed from integrating expertise from
In virtual workplaces, businesses can use collaboration tools and platforms to emulate an interactive environment
various functions, showcasing how collaboration can yield impressive results that benefit both the business and the wider community.
Integrating teams from different backgrounds and disciplines broadens the scope of problem-solving. Each function brings a distinctive perspective, skill set, and approach to the table, which can lead to out-of-the-box thinking and breakthrough innovations. By encouraging employees to work across silos, businesses foster an environment where creativity and innovation thrive.
One effective way to promote crossfunctional collaboration is by breaking down physical barriers within the workplace. For companies operating from physical offices, this could involve creating shared spaces where teams can meet for collaborative discussions and brainstorming sessions. In virtual workplaces, collaboration tools and platforms can be utilised to emulate the same interactive environment, fostering spontaneous interactions and ideasharing among team members.
While the benefits of cross-functional collaboration are clear, integrating teams from different departments can come with challenges. Differences in work processes, communication styles, and priorities can create friction and hinder collaboration efforts. Business owners must proactively address these hurdles by setting clear goals, establishing protocols for communication and decision-making, and fostering a culture of openness and mutual respect.
Leadership also plays a crucial role in cultivating a collaborative culture within an organisation. Managers must lead by example, connecting with colleagues across functions. Leaders must champion collaborative projects and provide the necessary resources and support.
Cross-functional collaboration is an investment in a business’s future success and sustainability. As companies scale their collaborative efforts, they can consider implementing cross-training programmes and team-building activities to familiarise employees with different functions and foster greater understanding and empathy among team members.
Additionally, establishing cross-functional project teams to work on innovation initiatives provides a structured framework for collaboration and ensures that diverse perspectives are represented throughout the process.
Measuring the impact of cross-functional collaboration on key performance indicators and business outcomes is crucial. By tracking metrics such as project success rates, time-to-market for new products or services, and employee satisfaction levels, businesses can gauge the effectiveness of their collaboration initiatives and identify improvement areas.
For small and medium-sized businesses, a strategic emphasis on cross-functional collaboration has the potential to ignite innovation and enhance competitive advantage. By dismantling departmental silos, embracing diverse perspectives, and surmounting challenges through adept leadership and open communication, businesses can cultivate an environment where creativity thrives, and the collective wisdom of their teams is fully realised.
Now is the time to seize the moment and tap into the power of collaboration, propelling your business towards a trajectory of perpetual innovation and lasting triumph.
Mick has spent the past decade building printIQ into one of the most recognised software brands in the printing industry, and with over four decades of experience, Mick truly has ink in his veins.
Charters Paper proudly celebrates a significant milestone in the career of one of its most dedicated and cherished team members, Elli Zlatanovski, who was also one of the winners of the 2022 Printer 50 ProPrint Awards. With 30 years of service, Elli has become integral to the company’s history and success.
Elli’s journey with Charters Paper began when she decided to re-enter the workforce after five years of raising her two boys at home.
“I applied for a part-time telemarketing position at a company called Luv-A-Duck. During the interview, they suggested a different role next door at Charters Paper, which I eagerly accepted. And here I am,” she fondly recalls.
Starting in accounts, Elli quickly demonstrated her potential. “Paul saw I was a talker and asked if I wanted to try selling. He taught me everything I needed to know. Sales became my passion. I love selling and caring for my customers,” she says enthusiastically.
Over the past three decades, Elli has witnessed and contributed to the evolution of Charters Paper. “One of
the most significant changes was in 2005 when we purchased our semi-automated slitter-rewinder Lemu1 machine. Relocating to our own factory in Brooklyn was another milestone. Despite the push towards digitisation, we’re busier now than ever. In 2023, we ventured into packaging, which I believe is the future.”
Elli cherishes many memories from her time at Charters Paper. “Securing my first order over $100K was a thrilling achievement. On a personal note, I treasure the special memories of Paul’s parents, Papou and Baba, who were always caring and supportive.”
“The Charters ‘family’ culture is what I love and has kept me here for so long,” Elli emphasises. She believes this supportive environment is key to the company’s success and her long tenure.
Elli offers valuable advice for newcomers: “You’re lucky to secure a job at Charters
Paper. If you’re a team player, you’ll never want to leave.”
Describing her journey in one sentence, Elli says, “It’s been a roller coaster, where I never want to get off.” Looking ahead, Elli is confident in the company’s resilience. “We have long been the leader in thermal paper rolls in Australia, and as we expand into paper packaging products, we will continue to thrive.”
Michael Sfetkidis, CEO of Charters Paper, said, “As we celebrate Elli’s milestone at Charters Paper, I express my deepest gratitude for her incredible dedication and hard work. Elli’s unwavering commitment and exceptional contributions have been a cornerstone of our success. Her expertise, reliability, and positive attitude have significantly impacted our workplace. Elli’s loyalty and passion are commendable, and we are fortunate to have her as part of our team. Thank you, Elli, for your outstanding service and for being a cherished member of our organisation, a great friend, and an industry icon.”
Paul Sfetkidis, director and owner, said, “In sports, champions leave an everlasting presence. Business is no different. At Charters Paper, we are blessed to have one of these champions – Elli Zlatanovski. Joining us 30 years ago, Elli has become an essential Charters and the Sfetkidis family member. Treated like a daughter by Mum and Dad, she cared for them deeply. Elli was interviewed and employed by my wife Theresa on 6 June 1994. From day one, her dedication, intelligence, and loyalty have driven Charters Paper to success, making us a leader in our field. Her contributions have been vital as we continually improve and embark on new ventures, such as paper food packaging. From all of us at Charters Paper – we love you, Elli.”
With the purchase of the new Ryobi RMGT 970 7 colour offset press with coater and Skeleton Transfer System, Sydney-based CCS Packaging has installed one of only two machines available in the world.
Waiting two decades for a sale requires patience and persistence, but this is precisely what Bernard Cheong from Cyber had to do to confirm his sale of a Ryobi RMGT 970 7 colour offset press with coater to CCS Packaging.
“I first visited Kevin from CCS Packaging over 20 years ago,” Cheong remembers.
“I was joined two decades ago for the first meeting at CCS Packaging with my colleague George Williams who unfortunately didn’t live to see the final sale.
“We were unsuccessful on that occasion and since then Kevin has bought six offset presses from another company, so we feel very fortunate to have confirmed lucky number seven.
“We welcome CCS Packaging to the Cyber family and they join over 200 other RMGT 970 presses sold globally and the second RMGT 970 in Australia,” Cheong said.
Kevin Wilson from CCS Packaging purchased the machine almost a year before it was delivered and installed within his factory located at Silverwater in Western Sydney.
“As our business evolved we told ourselves that we needed a packaging press that was customised for use in the packaging industry. Previously we were using a commercial press for packaging production. Now that we have a customised machine, this is a serious packaging press that is built for purpose. We now have the ammunition to make a serious investment
into the packaging category – whereas before we were merely just assessing the segments in the packaging landscape. We expect this will provide substantial benefits and really open up opportunities for our business,” Wilson said.
The Ryobi RMGT 970 machine purchased by CCS Packaging has been customised with a Skeleton Transfer System and this is the second press in the world with this system – the only other machine is in Korea.
“This does an equally good job as a RMGT 10 Series, and will integrate perfectly into their workflow,” Cheong said.
“For packaging printers, versatility is key. The 7 color Ryobi 970 configuration with
the skeletal transfer system will provide the versatility required to allow CCS packaging to take the company to the next level.
CCS Packaging CEO Gerry van Happen says the business has historically serviced the music and media industries, but is now diversifying into other categories.
“CCS built its reputation over 37 years in the very exciting media business producing packaging for vinyl, CD, DVD, Blu-ray and games categories. These industry segments have declined in the last seven years, but they are still a vital contribution to the business with CCS being the market leader for media packaging in Australia. Interestingly, over the last five years vinyl has been rediscovered and is now worth more than CDs in dollar terms. Vinyl is now a luxury product with high
specifications representing both international and local artists.
“Our largest packaging segment is now represented by the cosmetic, personal health and loyalty card businesses. Our experience in producing high quality products on short lead times has allowed us to grow this area. With in-house coating, rigid box, hard cover and finishing equipment we able to produce the vast majority of products without any outside operations. Further investments this year have also enhanced our position and we are always looking at ways we can offer our customers value options.
“CCS built its business on fast turn arounds and high quality. We have translated this knowhow into the packaging segment. The new Ryobi with its larger sheet size, will sit very nicely against our current eight colour with coater press. We have great fire power,
superb finishing and complimentary equipment to offer to our customers,” van Happen said.
CCS Packaging works closely with its current and potential customers to encourage them to consider the benefits of onshoring their packaging work.
“Even before the recent epidemic we were asking our potential customers ‘what is the real cost of producing offshore?’. We found that by equating the cost of tying up capital in large order quantities we could offer faster deliveries more often. There is more to the real cost than just a cheaper off shore quote,” van Happen said.
CCS Packaging Operations Manager, Simon Studdert, is also very passionate about the benefits of keeping work in Australia and explaining the numerous
benefits this presents for customers and plans to compete directly with overseas printers rather than local businesses.
“We have had success changing the views of several customers who can see the benefits by looking at the entire job as well as the advantages of printing onshore –and not just the unit price. We have taken our hard earned media knowledge to challenge the mindsets of potential customers regarding offshore print and packaging procurement. Are customers really getting a better price offshore compared to onshore? Sure, the unit price may be better, but what about shipping cost and warehousing.
“With higher minimum quantities required for overseas printing, we have seen a number of customers run into problems after a large run when there is a change that needs to be made – particularly with ingredients for food packaging or out of date content for pharmaceutical packaging. All of that stock that has been brought in from overseas that is no longer usable needs to be destroyed. By offering a local solution with a faster turnaround time – customers also don’t need to order as many which can also be very beneficial to cashflow as well as the costs associated with storing a large amount of packaging. Real estate is also very expensive when used to store out of date packaging.”
As part of the extensive research leading up to the purchase of the machine, a trip to Japan was organised by Cyber NSW Account Manager Giorgio Rossi to test the Ryobi RMGT 970.
“Before we purchased the machine, we had a great experience travelling with Giorgio to Ryobi in Japan and we were very well looked after,” Studdert said.
“The professionalism of the team at Ryobi was brilliant and they couldn’t be any more accommodating. We went through the entire assembly plant as well as some of the other parts of the business including the die-casting facilities for the automotive industry.
“To test the machine, we trialled several technically difficult print jobs within the demonstration centre. We tried to push the machine past its limits with work printers have nightmares about. However, the Ryobi RMGT 970 passed with flying colours. We tested thin stock with very heavy ink coverage and fine reverse out type, followed by maximum thickness board at high speed with full solids. The press delivered mark free print with very clean screens. Metallics and fluoros with fine reverse out text remained open with no evidence of roller, gear marks or emulsification.
“During the testing, Ryobi RMGT 970 were very accommodating with their press time and access to the finer mechanical details of the machine. From the research I did, I was quietly confident that the machine would pass the tests, but I expected it to have some trouble with setting up – but that wasn’t the case – it went from one substrate to another with ease.
“Giorgio from Cyber was very helpful with providing us with specifications, configurations and information on all the machine’s systems answering any questions I had about the machine during the research process.”
This press features the Skeleton Transfer System which allows the wet side of the sheet to travel the length of the press without any contact. This also eliminates the need for regular IPC film cleaning and replacement. The new Ryobi RMGT 970
with a sheet size of 970mm x 650mm complements the existing B2 eight colour press within CCS Packaging.
“This is the first installation in the southern hemisphere for this particular machine which is a 0.8mm spec machine that allows the printing of stock up to 800 micrometre boxboard.
“The Skeleton Transfer System means there is no IPC film that always needs to be cleaned by the operator. There is no build-up and then after a certain amount of impressions the cylinder on that film goes blind, so you have to replace it as it is a consumable. All of these issues are eliminated with this set-up – there is no marking and most importantly it creates better quality results. The side-lay on this machine is a new design – it is not just a pull side-lay, it also has a push from the opposite side that gives a more positive registration,” Rossi said.
“Purchasing this machine brings us into a different space in the market. It is also ready for us to embark on using the seven colours to produce the many special colour variants required in packaging. There will also be further technical opportunities that the Ryobi will be asked to achieve for our business and our customers.”
The installation of the Ryobi RMGT 970 was conducted by Cyber demonstrator John McCallum.
“John is based in Sydney and has worked with Cyber’s Ryobi machines for over 20 years. He has full factory training and is always on site when machines are installed,” Rossi said.
“Our installer and demonstrator John McCallum has been fantastic to work with,” said Studdert.
“His knowledge and experience was very thorough. John would stay back for hours each day to ensure the machine was 100 per cent and our operators had the support during the training stage. His enthusiasm and passion for what he does, shows in his work.”
Studdert said the graphical user interface (GUI) on the Ryobi RMGT 970 has been one of the key elements that has helped staff make the transition to the new machine during the training and installation process.
“Having mainly operated German presses, we found the iconology and operating system of the Ryobi to be very intuitive. This was also important, as it makes the transition from one press manufacturer to another a lot easier for our staff.”
Visual Impact Brisbane 2024 proved to be a soaring success, with record attendance figures and strong sales reported by exhibitors.
Visual Impact Brisbane has been hailed an outstanding success by the event’s organisers, with the three-day event exceeding expectations and garnering plenty of praise from exhibitors.
According to the event’s organiser, Visual Connections, initial indications are that almost 2500 people visited the show over the three days, up 20 per cent compared with 2018.
“We are delighted with the way the industry – both exhibitors and visitors – embraced the opportunities provided at Visual Impact in Brisbane,” said Charly Blades, events manager for Visual Connections.
Held at the Brisbane Convention & Exhibition Centre, Visual Impact is the industry’s leading show for sign, display, print and graphics showcased solutions for signage and displays, wide-format, textile and garment printing, LED and illumination, fabrication, routing, engraving and laser cutting, software and workflows.
Most who attended were, as expected, from around Brisbane and across Queensland, however, there were also solid numbers reported from New South Wales and the NT. Visitors also attended from Perth, Melbourne, and New Zealand.
The sold-out show addressed some of the most important market trends and key challenges being faced by industry businesses. With the shortage of skilled staff, a challenge for many attendees, interest was high in any systems which allowed for the removal of touchpoints in production, allowing businesses to ‘do more with less’ and grow despite industrywide staff shortages.
Sustainability was also focus for many exhibitors, with new media releases and features such as improved energy efficiency and reduced waste on show, and new opportunities were also featured, with businesses able to explore a diverse range of technologies to create valuable new revenue streams.
These themes also came through strongly in the seminar program which ran throughout the show in the new Connections Centre presentation lounge. With a variety of topics and speakers, the sessions were well attended, with the more intimate, conversation-focused approach welcomed by visitors.
Interest in the Sign & Print Career Connections stand, and adjacent Try-ATrade area was also steady, with a particular focus was given to promoting the resources which are available to
businesses to support the employment, and retention, of apprentices – a vital component to ensure industry opportunities match the high level of interest from potential trainees.
In line with this year’s theme, ‘connect with success’ Visual Impact was an opportunity for many to reconnect with the Queensland market after more than six years, with the event providing attendees three days of live demonstrations, education sessions, and networking events.
“Visual Impact has been a great opportunity for us to demonstrate all our brands and reacquaint ourselves with the local market,” Tony Bertrand, head of marketing at Ball & Doggett told ProPrint
“The diversification that we have in our business is huge now, so it’s been great to expose our brands to our customers, particularly those in the Queensland market.”
With a focus on sustainability at this year’s event, Ball & Doggett announced its exclusive partnership with GALE Pacific to bring Ecobanner to the Australian market. Ecobanner by GALE Pacific is the only Australian-made, PVC-free flexible banner fabric capable of offering a 100 per
cent closed-loop recycling solution. It is also understood to be the first of its kind to be manufactured in Australia with closed-loop recycling capability.
“We are thrilled to partner with Ball & Doggett to bring Ecobanner to the Australian market,” said Troy Mortleman, GALE Pacific general manager, ANZ.
“Sustainability across technical fabrics has never been more important and we are driven to provide meaningful innovation to our clients to assist them in reducing their environmental footprint. Ecobanner has been developed in partnership with the print industry and sets a new benchmark for sustainability.”
According to Peter Townsend, Graphic Art Mart’s business development manager – equipment for New South Wales and Queensland, Visual Impact was a chance for Graphic Art Mart to connect with the market since its consolidation with the Amari Visual Solutions business earlier this year.
“We now have a total solution for the market and for our customers,” Townsend said of the recent merger.
It was also the first time SMARTECH exhibited together in Australia with Agfa and Canon since their distribution partnerships were announced in February and March this year.
“We had a fantastic experience at Visual Impact in Brisbane,” SMARTECH’s head of marketing and communications for Asia Pacific, Ximena Guzman, told ProPrint
“The show provided an excellent platform for us to showcase SMARTECH’s latest innovations and new portfolio. We experienced good traffic, which allowed us to engage with a diverse range of attendees.
“The event was particularly significant for SMARTECH as it marked our first show showcasing Agfa/Canon. These partnerships are opening doors to several promising opportunities. The positive reception to our combined offerings has been encouraging, and we are excited about the potential for further collaborations and business growth.
“Additionally, our continued partnership with HP was a highlight at the event. As the largest reseller of HP’s mid-range
printers, we were pleased to showcase our comprehensive solutions and strengthen our position in the market. The strong interest and positive feedback we received underscore the value of our ongoing relationship with HP and our commitment to delivering top-tier products and services.”
Industry leading manufacturers and distributors showcased new and innovative equipment and technologies, providing a firsthand look into the future of the industry.
Currie Group showcased a range of innovative applications on its stand, which was produced by Brisbane-based Spyder Displays on an EFI VUTEk FabriVU 340i+, with the group showcasing the latest equipment from partner brands including Canon and EFI, as well as its most recent partner, Elitron.
“Elitron is an important piece of the puzzle in terms of bringing our printing to a complete finished product,” Paul Whitehead, business unit manager sign and display, told ProPrint
The hero product on display for Currie Group was the Canon Colorado M-series with FLXture. The printer was wrapped in a vibrant magnetic media that was also printed on the Colorado M-series.
Currie Group also announced a new partnership with Italian finishing manufacturer Neolt Factory for the supply of a range of loading, unloading and finishing systems for the Canon Colorado M-series printer range.
Currie Group will be the exclusive agent in the ANZ region for the Neolt Wallpaper Factory solutions. These include ‘jumbo roll in – jumbo roll out’ systems which increase the capacity for long run lengths of products like wallpaper without need for operator intervention, and jumbo roll-to-cut solutions which allow rolls to be converted automatically straight off the printer.
Whitehead said Neolt Wallpaper Factory will deliver huge advantages, particularly for businesses doing large runs of wallpapers or similar products, or multiple smaller runs of wallpapers or trimmings that require post-production finishing.
“The Neolt systems will allow Canon Colorado M-series users to lift their productivity with no additional labour requirement, by fully utilising the automated features of the printers and enabling longer, unattended production runs as well as in-line converting.
Taking creativity to a new level, Epson Australia’s paid homage to its local surroundings with its Great Barrier Reef-inspired stand, which was also awarded the Best Custom Stand.
“Our theme this year is ‘beauty in every dimension’,” Priscilla Dickason, Epson Australia marketing manager, told ProPrint
“It’s the perfect way to show the beautiful and vibrant colours of the Great Barrier Reef using our own printing solutions.”
In a world first, Epson Australia unveiled the company’s new SureColor F9560 dye sublimation printer. The new model replaces the previous SC-F9460 and SC-F9460H with a more compact package that offers significant speed improvements, extended colour support, and more convenient consumables management.
Other Australian firsts on display included the new SureColor F1060 compact desktop DTG and DTFilm printer purposebuilt for in store and in-house fabric customisation, the SureColor V1060 compact desktop UV printer purpose
built for customising consumer goods, merchandise and making small signs, and the SureColor P20560 64” aqueous printer that combines an enhanced gamut with a new bulk ink system to enable cost-effective production of fine art and large format interior POS.
Spicers showcased its house of brands including the latest addition to its portfolio, Neschen. Other brands on show included Roland, Mimaki, General Formulations and 3M, which Spicers recently celebrated its 10-year anniversary with.
“The show has been a great opportunity for us to meet and collaborate with new and existing customers,” Spicers’ Wayne Hood said.
Pozitive Sign & Graphic Supplies focused its presence on Summa, debuting the latest Summa S3 for the first time at an Australian trade event.
“Visual Impact has been a great show for us, and visitors have been really interested in the Summa product range,” said Pozitive’s national sales manager, Alfred David.
HP Australia debuted the HP Latex 630W printer, however, it was HP’s Live Production Printer Remote Control software that also garnered significant interested from attendees, according to Craig Hardman, ANZ country manager large format printing at HP.
“It’s been a refreshing change from a very tough market to see people so interested and excited to look at new technologies,” said Hardman.
“It’s been busy across the HP stand but the HP Latex L630W has had a lot of interest from smaller sign shops that have visited the show.
“We’ve also been doing a lot of work on workflow, ecommerce, and design software. We’ve been taking our customers through our new workflow solution on the stand and that’s proved to be really popular. For many printers now, they have less time and more and more jobs come at the last minute so the ability to be able to view and control their business and have a wider understanding of where things are at from a workflow perspective is something they’re looking at.”
The Visual Connections’ Charly Blades said the team is now planning the next Visual Impact Expo, which will co-locate with PacPrint 2025 and the Label & Packaging Expo at the Sydney Showground in May next year.
“Visual Impact 2025 will feature even more information, ideas, and inspiration.”
Mimaki Australia recognises top-selling distributors
Mimaki Australia celebrated its top-selling distributors at an exclusive event held during Visual Impact in Brisbane.
Held at the River Room in the Southbank Beer Garden, the awards were presented by newly appointed Mimaki Australia’s managing director Kohei Kobayashi and national sales manager, Jason Hay.
Kobayashi welcomed attendees and provided an update on Mimaki Australia’s operations and expansion since his appointment earlier this year in April, including new service engineer appointments in Queensland and New South Wales.
Hay spoke of the company’s growth plans and thanked the company’s distributor network for their ongoing support.
“Tonight’s event represents how important our distributors are to our business and to our brand,” Hay said.
“We’re really focused on our partnerships with our dealers
and that focus has been reflected in some of the changes that we have already made in the past three months, and there’s more changes coming in regard to where Mimaki is going in the future.”
Chris Dutkowski, national marketing specialist at Mimaki Australia, said Visual Impact had been a successful event for the team, and that the awards received an overwhelmingly positive response from distributors.
“It’s the first time that we have held these awards in Australia and we’re really happy with the response that they have had,” Dutkowski said.
“Around the world Mimaki is very much a relationship-based brand and we want to continue to build on the relationships that we have in Australia. Our dealers work hard so it is important to recognise that.”
Award winners on the night included Pozitive Sign & Graphic Supplies, Spicers Australia, Velflex, Graphic Art Mart, Spandex Asia Pacific, and Sign Essentials.
Women in Print announced a new partnership with HP at Visual Impact in Brisbane, with the collaboration the first of many planned initiatives by the organisation to support the career development of women across the print, sign and graphics industry.
Women in Print Australia announced a new partnership with HP at Visual Impact, which will see the global supplier sponsor an industry operator to attend the APJ Dscoop event in the Philippines in August.
As part of the partnership, which was officially announced at a networking drinks function hosted by Women in Print at Visual Impact, HP will pay all travel and accommodation, plus seminar entrance costs, for one female operator who is actively employed on an HP Indigo Digital Press within Australia or New Zealand to attend the APJ Dscoop event, which will be held in the beautiful city of Cebu from 29-31 August.
Stephanie Gaddin, chair of Women in Print, said the opportunity is the first of a number of initiatives planned for the organisation, which brings together
women and allies across the print, signage, graphics and related industries.
“We are excited to be working with HP to bring this opportunity to our membership, and thank them for stepping up to help us support the career growth and development of women across the industry,” Gaddin said.
“This is a wonderful opportunity for one of our Women in Print members to expand their knowledge, make important new connections with like-minded professionals within our region, and gain a better understanding of the sector which will help them as they continue to build their career here in the ANZ region.”
Craig Walmsley, ANZ country manager for HP Industrial Print, said the company was delighted to partner with Women in Print and provide this opportunity.
“While our industry has come a long way in achieving more gender balance and inclusivity, there is still a lot of work to be done to ensure that we are developing our people across the entire talent pool and we are excited to be working with Women in Print to help address the imbalance and promote women’s careers,” he said.
“This opportunity to attend the APJ Dscoop event in Cebu will allow a female operator from the local industry to network with industry leaders, experts and professionals to explore how creativity can revolutionise every aspect of print by exploring creative opportunities that will help businesses differentiate, connect with customers and leverage new and emerging technologies.”
For more information, or to apply, visit: https://womeninprint.com.au/dscoopapj-2024/
SS Signs and Celmac Australia hosted a joint open house at SS Signs’ new state-of-the-art signage facility in Brisbane, offering both inspiration and insights to the printing industry.
Celmac Australia partnered with SS Signs and FESPA Australia to host an open house during Visual Impact to celebrate the release of the first Digitech printer in Australia.
The open house at SS Signs’ new state-ofthe-art signage facility in Cleveland, Brisbane, featured the Digitech TruFire LTX2 printer paired with an Aristo 6m long cutter.
Designed and built in the United States, the flatbed UV printer, with its focus on innovative design, high precision and print quality, is a welcome addition to the Australian print market.
It demonstrated its printing and cutting capabilities of more than 60, 8’x4′ sheets per hour with one operator.
SS Signs owner Steve Lambourne said the open house went better than expected, with many people attending to experience the Digitech TruFire.
“I appreciated everyone taking the time to visit and tour our factory. The feedback was so positive. One guest said our facility is world-class,” said Lambourne.
Lambourne understands the interest in Digitech because the machine has
transformed his business. He says the dedicated flatbed is just what his business needs.
“It’s fast. It’s easy to maintain. The machine was installed and running in one day. It has been running for four months, and we have not had one issue.
“The biggest part is the automation. With the added conveyor belt paired with an Aristo 6m long cutter, it requires one operator,” Lambourne explained.
The Digitech recently delivered 2,500 corflute signs with one operator in one eight-hour shift. One key feature of the Digitech that amazes Lambourne is its lack of electronics.
“Compared to opening up competitive machines where there are electronics everywhere, you open up the Digitech, and there is a pump. It baffles me how they can get it to run so well with such little electronics.
“It’s delivering far beyond what we expected. We’re second-guessing how much work we’ve got because all our flatbed work is finished by 10 or 11am.
“We designed our new building specifically for workflow efficiency, and we’re making
higher figures now than ever. We want to open our capacity now. The time is right; I couldn’t be happier with the Digitech. It’s a game changer for us.”
Jonny Rumney NSW state manager for Celmac Australia, said it was an excellent educational experience for the industry to get together and experience the SS Signs facility and the Digitech TruFire firsthand. It was also refreshing to hold an open house in Brisbane.
“SS Signs have a very impressive state-ofthe-art facility that Steve built from the ground up,” Rumney said.
“The Digitech was printing and cutting a board in 40 seconds with one operator. We watched the board go onto the printer, leave the printer, feed into the conveyor and then into the cutter. It was good to see that in action,” he said.
Celmac’s Queensland state manager, Matt Hall, said, “The SS Signs open house event held during Visual Impact in Brisbane received a great turnout and response. Whilst for many, the intrigue was SS Signs’ newly built custom sign manufacturing facility and recently commissioned automated Digitech and Aristo flatbed print cut solution, the open house provided a welcoming platform for industry members to get to know one another, network, and share ideas for the general betterment of our industry.
“It was interesting to hear from Steve Lambourne on how SS Signs fosters employee growth through an extensive apprenticeship program, and Rob Sharp, SS Signs’ GM site tour covered all things from concept, design, manufacture, QA testing, and installation. Both were extremely insightful and inspired all of us to admire and aim for.
“Hats off to Steve, Rob, Luke, and the SS Signs team for hosting an incredible event and opening their doors to share with our industry peers.”
CMYKhub was presented with its Sustainable Green Print (SGP) L1 certificates for Queensland and Western Australia at the company’s networking event in Brisbane.
CMYKhub hosted an exclusive networking event at the Pig ‘N’ Whistle West End Garden Bar in South Brisbane following the first day of Visual Impact in Brisbane.
During the event CMYKhub was presented with its Sustainable Green Print (SGP) L1 certificates for Queensland and Western Australia by Visual Media Association (VMA) CEO Kellie Northwood. The certifications round out the company’s accreditation for SGP following audits conducted earlier this year for Victoria and New South Wales.
Glen Francis, CMYKhub national communications manager, said the certifications align with CMYKhub’s
customers who have been increasingly requesting environmental accreditations.
“When our partners became certified with SGP it made complete sense for us to as well so that chain of custody isn’t broken when they outsource a job to us. We want our customers to know that sending an order to CMYKhub can be done so in good conscience,” said Francis.
“While it’s probably very hard to measure a return on investment in terms of sales, you have to consider what it could cost by not being part of SGP. With increased government, social, and corporate scrutiny we need to consider lost opportunities for not having sustainable practices in place.
“Something Michael [Ellis, CMYKhub’s HSEQ manager] has successfully measured return on from the auditing process is our landfill expenditure. In fact, we have been able to halve our landfill invoices nationwide,” said Francis.
“I would like to thank Kellie Northwood for her support in getting us started on this journey, as well as London Mills who made this SGP project very easy for us, and Michael for making this a priority in our business.
“I would encourage printers of all sizes to look into SGP. Our industry will be stronger if we provide a united front and demonstrate that print is the solution sustainable choice for marketing, branding, and communications.”
When Leon Wilson acquired Revolution Print, he set about future-proofing the business by backing it with knowledge and experience and taking calculated risks on emerging technology. He tells ProPrint about his business decisions, making a global mark in downtown regional Ballarat, and why every printer needs to trust their gut and invest in the future of print.
Business in regional Victoria was tricky during the pandemic. Leon did a lot of soulsearching and questioning his life’s purpose. After diving deep, he branded himself a passionate print geek who prints people’s dreams. The Print Geek appears on Leon’s business card and the Revo website. “I geek out about print. We’re not scared of new technologies. Our whole mission is to share what we discover and create the future of print. We print dreams.”
He is also a self-professed tech nerd and a Mr Fix It. He is brazenly enthusiastic about understanding how things work. “I learn how equipment works and how to fix things, which is super important in the print game,” says Leon.
When Leon Wilson finished school, he didn’t know what he wanted to do, so he started working as a copy shop trainee technician.
He progressed from the copy shop to a brief spell as a salesman to working in tech, systems software, and data. He says his journey has led him to where he is today and why he loves experimenting with new printing technologies.
“Getting into the software space led me into what I’m doing in print. My technical ability, problem-solving skills, and ability to take chances on emerging new technologies gave me a greater understanding. I’m not scared to get my hands dirty and fix stuff,” Leon explains.
After a few hard knocks early in his career, including a stint of glandular fever that led to a prolonged three-year period of debilitating chronic fatigue, Leon found himself at the local family-run printer in his hometown of Ballarat, building its online system and successfully digitising the business. Ten years ago Leon started buying into the business. Previously family-run, it had operated since 1902 and served the local community’s printing needs for over a century.
Leon acquired ownership three and a half years ago from then-owner John Schreenan. John decided to hang up his printing boots during the pandemic and retire. He stayed until December last year to see Leon through the difficult COVID years. John is the godfather of Leon’s kids. Leon says they are incredibly close. “He’s taught me so much, and I have taught him too, being from a younger generation with a different attitude. We’ve had differences of opinion, but our relationship has been beautiful throughout the process,” says Leon. “In the end, we could just be completely truthful and know where we’re going and what each other’s thinking without even saying it.”
Chronic fatigue combined with the COVID experience shaped Leon into a strong advocate for mental health in the workplace. He is not afraid to share his own experiences with mental health and wants to help others feel comfortable talking about it. He says nurturing his people and creating belonging is the company’s soul. Revo’s strategic mission is to take responsibility for the individual, ‘to win, grow and learn as a team’. During the pandemic, Leon built a group fitness studio at the facility. “I care so much about our team, and the big thing that keeps me going is fitness and exercise.”
Eight years ago, Leon and John went to drupa with a plan to learn and explore when Leon discovered the KM-1 at the Konica Minolta stand. A couple of years later, they bought the machine in Japan. It was the second installation in Australia after Simon Crabtree at Jossimo Print.
“It’s downstairs, and it’s Serial Number 30, the 30th in the world, and it is in regional Victoria,” says Leon. “Australia is a small island compared to the rest of the world, and we’re doing some crazy things here. But Ballarat? A population of 100,000 at the time, investing heavily in emerging technology?” It was a big deal.
The purchase was a huge investment for the business, and Leon knew if they could afford the machine, they needed to run it 24 hours a day. Leon became best buddies with the technicians and underwent some in-depth training. “I think I am the only one in the Southern Hemisphere allowed to change the very expensive printheads myself, of course, with permission.”
To the horror of the visiting Japanese KM representatives, Leon drilled holes in the machine and installed webcams to monitor the printer remotely. He commissioned his artist friend to graffiti the wall adjacent to the machine with ‘New Game’ because that was Revo’s new approach. We then went ahead and completely wrapped the KM-1 in Revo branding and colours. It’s a whole new attitude, and we are doing things differently,” says Leon.
Six months later, Revo invested in digital embellishing equipment (The MGI 3DS + ifoil), which became hugely successful and, shortly after that, underwent a complete overhaul of its finishing equipment and purchased more cuttingedge machines, including the latest 4 clamp PUR perfect binder, and the A4 landscape saddle stitcher from Horizon and the Currie Group. Shortly after, Revo closed their offset altogether. “We didn’t need to,” Leon says, “but if we’re going to commit to the B2 digital space, we can’t focus on both.”
While geeking out over print technology online, Leon stumbled upon a compact digital high-speed laser system that cuts, kiss-cuts, engraves, and perforates sheetfed substrates for short-run personalised applications built specifically for the print industry. It was commissioned
and developed by a German direct mail and packaging company when it couldn’t find a suitable cutter for its business needs. It can be used with paper or carton board for various applications requiring intricate, short-run, dieless cutting while the Namecut feature in the included software can personalise every sheet.
To Leon, it epitomised the future of print, and he wanted one. Konica Minolta International distributed it. As an owner of every piece of industrial equipment Konica sells, he thought the process would be easy, but KM said it was a ‘no-go’ because they couldn’t service it in Australia. Refusing to accept the answer, Leon travelled to Germany to meet its inventor, who taught Leon how to service the device for himself.
Leon is now the proud owner of The Futurecutter, the only machine of its kind in the Southern Hemisphere. The machine’s creator travelled to Australia to be at Revolution Print when his Futurecutter arrived. Leon says 12 hours on the Futurecutter is the same output as two staff running a flatbed digital die cutter and rotary cutter for an entire week each.“Our Futurecutter has been running for six months, but we still haven’t officially launched it yet; word is already getting out, and I prefer the personal approach of one-on-one education sessions (demos); organic growth is really important to us,” says Leon.
Leon’s Futurecutter is transforming his business by improving automation, better servicing existing clients, and creating an entirely new market. He says it is simply the most exciting investment the business has ever made, and it sits proudly on the Revolution print room floor. Leon believes
it will cement Revo’s mission to create the future of print in Australia. ProPrint received an impressive demonstration of its capabilities, which must be experienced to appreciate its futuristic attributes.
The Futurecutter has also allowed the business to decommission and sell multiple devices, freeing up much-needed space.
“We have a don’t-give-up attitude. Revo is in the top 20 printers of the ProPrint Awards every year and we are doing some world-class groundbreaking stuff. The next six months are going to be crazy for us. We’ll be very close to reaching our goal of full capacity.”
Leon admits he has heard of his growing reputation in the industry for taking risks, and he’s pretty happy about that. He is also keen to share his speculative bets and experiences for the future progression of print in Australia, including motivating people and leaders and educating them in software, automation and investment.
Check out Revo’s Futurecutter in action
Is this the best value printer in the market? Sonya Cameron at Evan Evans says she would consider a second purchase two weeks after operating her first. ProPrint asks why this is Canon’s machine of the moment.
“Honestly, I don’t know why you’d buy anything else,” exclaims Sonya Cameron as we enter the Evan Evans print room to check out her two-week-old Canon Colorado M5W Series.
“We did a project yesterday that would have taken us 24 hours to do, and we printed it in two hours on the Canon,” beams Sonya of her new purchase. “It’s been smashing out the small jobs and has already completed three major projects.”
She says the company is better off regarding production capacity and power
usage – a bonus considering the recent increase in energy prices.
The Canon M-series saves Evan Evans around 10 production hours per day. It pulls less energy from the grid during drying and, according to Sonya, uses the same energy as ‘a kettle’.
The Canon’s productivity and ease of use has also positively impacted her staff.
“I did a well-being check on Dale Greedy (the Canon operator) yesterday, and he said the current job was already complete
and out the door – the client only signed off on it the night before,” she says.
“The productivity increase it can deliver from a long-term perspective is amazing,” Sonya says. “For us, it’s been the best move.”
Based on her experience, would Evan Evans consider investing in another one?
“Absolutely. Look at the footprint of it. You can buy a larger machine for six times the price that does the same thing, but this is reliable, better and more efficient,” says Sonya.
Dale says the Canon is easy to use and fast, and he trusts it enough to print and walk away.
“Loading is really easy; everything’s simple. It has automation and has self-correction, so there is no need to stop it,” says Dale. “There is no skill in the set-up. It’s so easy to operate, and I needed less than an hour of training. It’s pretty impressive.”
Dale demonstrates loading the roller. Blink, and you’d miss it. Fortunately, we caught that moment on video for playback. See for yourself here (QR). The machine is also connected to Canon if there are any major problems and includes maintenance software.
Evan Evans’ new Colorado M Series has increased the business’s product range.
“We would never have produced a vinyl banner in-house because we couldn’t have efficiently and effectively printed on it. Now we are in the space where we can compete with others printing on vinyl,” explains Sonya.
As the reseller for Canon Production Printing Australia, Currie Group’s Business Unit Manager for Sign & Display, Paul Whitehead, said Evan Evans has been an important customer since purchasing an EFI in 2021. When Sonya contacted Paul for roll-to-roll solutions, Canon was the obvious recommendation.
“We suggested the Canon Colorado M5W, so Evan Evans proceeded with a
demonstration and loved the output,” said Paul.
“The versatility of output you can produce on the Canon Colorado for the footprint is unparalleled.”
Some Canon Colorado technology originated in the office environment and was made for people who are not printing experts, hence why it is so easy to operate.
“That ease of use has now translated into the graphics market,” explains Paul.
One of the unique attributes of the Canon Colorado MSeries is the patented UVgel ink. Back in 2016, Whitehead was part of the original R&D project to develop the technology at Canon. He launched it globally as Canon’s global marketing manager and knows the technology better than most.
The Colorado represents the fourth generation of UVgel ink technology, and according to Whitehead, the industry is feeling more confident about the technology. He says businesses are experiencing an increased acceptance rate as awareness of the benefits spreads.
UVgel has the consistency of hair gel. Because it doesn’t disperse the way liquid ink does, it’s extremely accurate and delivers punchier colour using less ink than alternative technologies.
“From a technology standpoint, the UVgel is not only extremely productive, but the colour consistency is strong, and the versatility is wide,” says Paul.
“The cost to run the system in terms of per page is lower than other technologies because it uses far less ink. It would probably use less than half the ink of Evan Evans’ previous system, which was a latex system,” says Paul.
Word is getting out about Canon’s ease of use, remarkably small footprint, UVgel technology, speed, quality and value for money. CMYKhub is also an advocate for the Canon Colorado M5W.
“The aim is to have that quality and speed technology available in every state,” says CMYKhub’s Alan Nankervis.
“We’re a trade printer. We print for everyone else. That’s what we do. We take several small orders and print a gang of them together. We make lots of stock changes, and that can be time-consuming. On these Canons, the roll change is seconds.”
“Printers love this machine. Anyone who has one loves it. Nobody is negative about it. You’ve sold me,” says Sonya.
Retail in-store and experiential specialist Dashing has purchased the first Agfa
JETI Tauro H3300 in New South Wales recently installed by SMARTECH.
Dashing has purchased the first Agfa JETI Tauro H3300 in NSW recently installed by SMARTECH at its premises in Lane Cove.
Dashing CEO Russell Kavnat received a call earlier this year from Agfa’s Phillip Burns that clinched the sale. Dashing was looking to upgrade its equipment that coincidentally Burns had previously sold them nine years ago while he was working for another organisation.
“Phillip happened to call us at the right time,” said Kavnat. “Dashing has been around for 34 years and I have been in the business for 18.
“At that stage, Agfa were not on our radar, and we hadn’t looked at the range before that and did not know a lot about the products. We had been exploring the market for about 18 months and the other brands we had on the floor didn’t have anything in their product portfolio that suited our future needs.
“Our production manager Matt Boyden and our head of operations Shan Vandiveloo then ran a comprehensive analysis and looked seriously at two or three key options in terms of print quality, speed and efficiency as well as ink utilisation and based on this matrix – the Agfa machine was a clear winner,” Kavnat said.
According to Boyden, there were additional endorsements from local and overseas printers that were also important influencers for the final decision.
“Our visit to see the Agfa JETI Tauro 3300 at Melbourne-based Ancyn Screenprinters really helped get it across the line from our perspective – they were very welcoming and provided us with a great demonstration on the machine. We also spoke to a couple of overseas customers as well including production managers at Bernard Group in the United States that gave us very positive feedback,” Boyden said.
Kavnat said there was a very small window of opportunity available to install the machine due in between retail campaign seasons.
“We could see that we needed to make an installation mid-year in June during our calmer months, but we had to bring it forward as in May we had an issue with our existing equipment, and we were going to have to put a large amount of money in to keep it running. The team at SMARTECH were great as we went ahead with the installation earlier than expected as the machine was already in the country and ready to go. We worked around it and the guys from SMARTECH did a good job of getting it in,” Kavnat said.
According to Boyden, while the Agfa JETI Tauro can perform roll-to-roll work, this was not a key reason for purchase as there is roll-to-roll capability within existing machines already in the business.
“This machine will largely do sheet fed work – and largely synthetic jobs – such as Corflutes, PVCs, screenboards and paperbased media. In terms of criteria for
purchasing, we wanted something that would fit and have scalable architecture in terms of automation and industry-leading quality at high speed and the ink consumption was a benefit as well.
“With the previous configuration, they would use a lot of ink through purging and it has been proven by Agfa that the Tauro has the lowest ink consumption on the market for similar presses – so we wanted to go from wasting a lot of ink in the bin to having something that was very economical but also for sustainability,” Boyden said.
“There is always a teething period when a new machine is installed, but the service we had both remotely and onsite from the Agfa-trained engineers employed by SMARTECH has been great. The machine is now up and running and we have seen immediate quality improvements as well as more throughput and we are looking forward to greater capacity in the future with lower operating costs and that is the reason why we have made this capital investment for the long term. It is hard not to replace a machine that has been running for almost 10 years and not see quality improvements, but we are qualityobsessed – just like our customers – and we needed to get a machine that was going to deliver us with a much higher level of print quality.”
SMARTECH business development manager, Tim Hawes, was pleased to continue the long association with the Dashing business.
“The SMARTECH business relationship with Dashing dates back to the 1990s when the business was GBC, Neopost and then Quadient. There is a lot of equipment on these premises that SMARTECH have looked after and will continue to look after and support. We are excited to have the Agfa JETI Tauro 3300 now installed and we can continue working with innovators in the industry like Dashing and support them with the equipment and services they need,” Hawes said.
Dscoop APJ Philippines Summit 2024
LabelExpo Americas 2024
Printing United 2024
ProPrint Awards 2024
2024 FESPA Australia Conference
Hosting an event? Send an email to the editor Claire Hibbit chibbit@intermedia.com.au with the details
• Near total coverage of roller requirements for the graphic arts sector
• Wide range of rollers for printing and packaging, laminating, gluing, transport and nip
• Specialised services for non-standard applications
• In-house expertise to help you achieve your production goals
Imagination Graphics is your trusted partner in digital printing, graphic and web design solutions. Our team of skilled professionals are ready to assist you with all your design and printing requirements, regardless of size or complexity. Let us transform your ideas into reality and help your business thrive.
Our comprehensive range of trade services include:
• CTP – Computer to Plate
• Graphic Design
• Business Cards
• Brochures
• Posters
• Forms Printing
• Annual Reports
• Books and Magazines
• Signage of all varieties Partner with Imagination Graphics to take your printing business to new heights.
US T O M LAB E L SP E CI A LIST S 24- 4 8 HO U R P RO D U CTIO N
G E T Y O U R R E SE LL E R S A M P L E P A C K T O D AY
JTS Engineering servicing the industry for all machinery and engineering requirements, has partnered with Longer Machine Industrial Co Ltd to supply a specialised range of paper guillotines systems featuring high speed, precision and safety.
Contact us anytime for all service and guillotine requirements
JTS Engineering Services Pty Ltd
Jim Strounis, Owner
Mobile: 0433 100 243 Email: jim@jtsengineering com.au
Scott Mohammed, Service & Account Manager
Mobile: 0431 887 501 Email: scottm@jtsengineering com.au
Unit 5, 80-82 Seville Street, Fairfield, NSW, 2165 Web: jtsengineering.com.au
• Product Labels
• Bumper Stickers
• Outdoor Durable Stickers
• Large Format Sickers
• Vinyl Cut Decals (transfer stickers)
• Transparent Stickers (white ink)
• Specialty Stickers and more for vehicles, shop windows, products, promotion for anything
Volunteer or Sponsor help us grow!
Come and see the extensive expansion and renovations. Need a venue for a function? Talk to us we can help. Visit
Revolutionise Your Bookbinding with Our State-of-the-Art Hard Case Solutions.
Print Logistics is proud to offer cutting-edge, hard case binding technology that delivers a new level of durability and sophistication. Our innovative process involves expert casing of the hardcover, resulting in a final product that exceeds the competition in both robustness and elegance.
Elevate your publications, specialty books, and projects to new heights with our superior hard case binding solutions, perfect for customers who refuse to compromise on quality.
• Fast turnaround times
• Competitive trade-only pricing
• Privileged communication
• Family owned and run
• Variety of customisation options to meet your specific needs
“We’ve relied on Print Logistics for years and couldn’t be happier with their service. Their professionalism, precision, and dedication to confidentiality make them invaluable partners. We highly recommend Print Logistics for exceptional printing and binding services.” Principle Design
Print is perception and we treat it accordingly.
Contact Us Today
Phone: 1300 659 029
Email: contactus@printlogistics.com.au
Visit: www.printlogistics.com.au