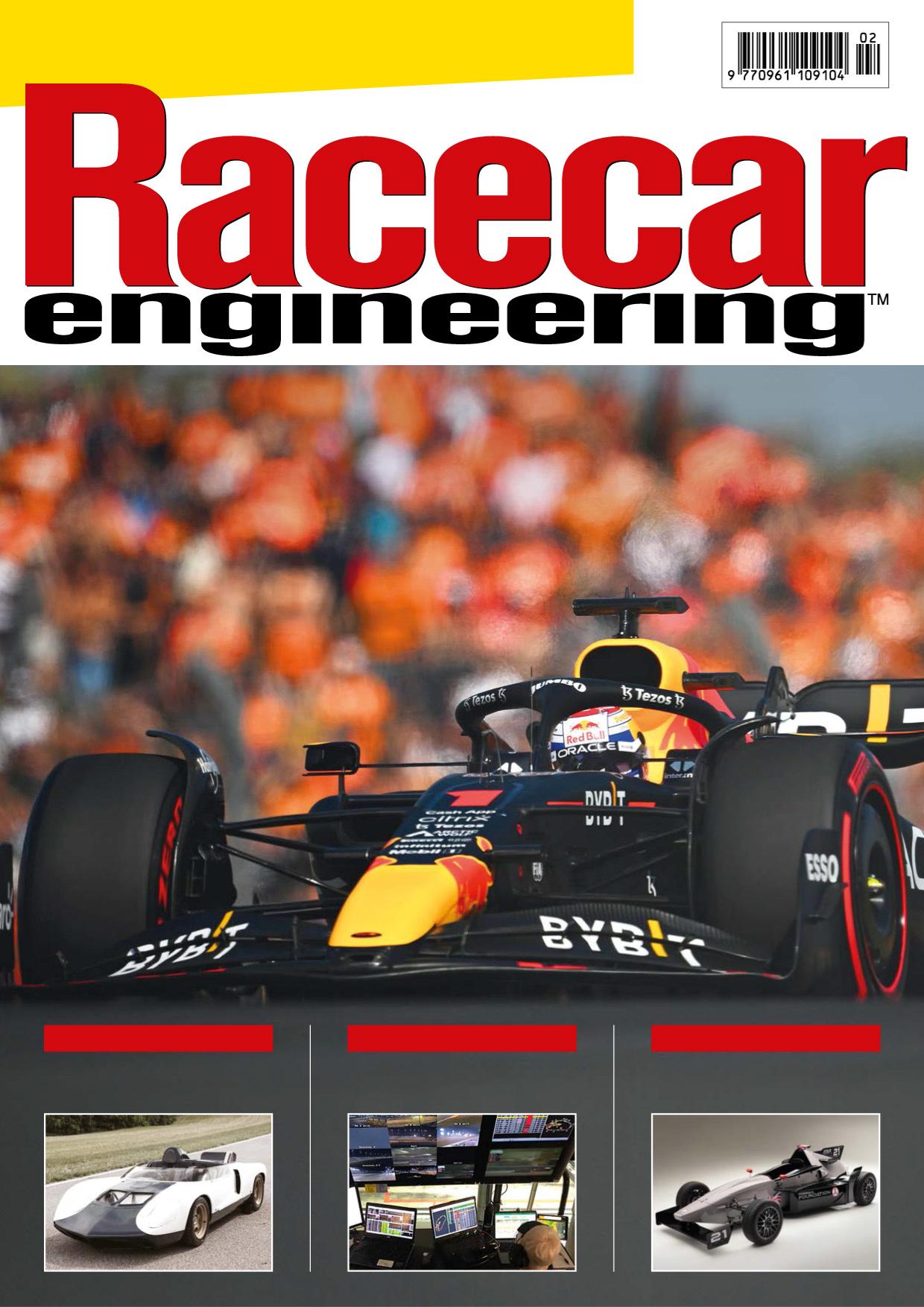
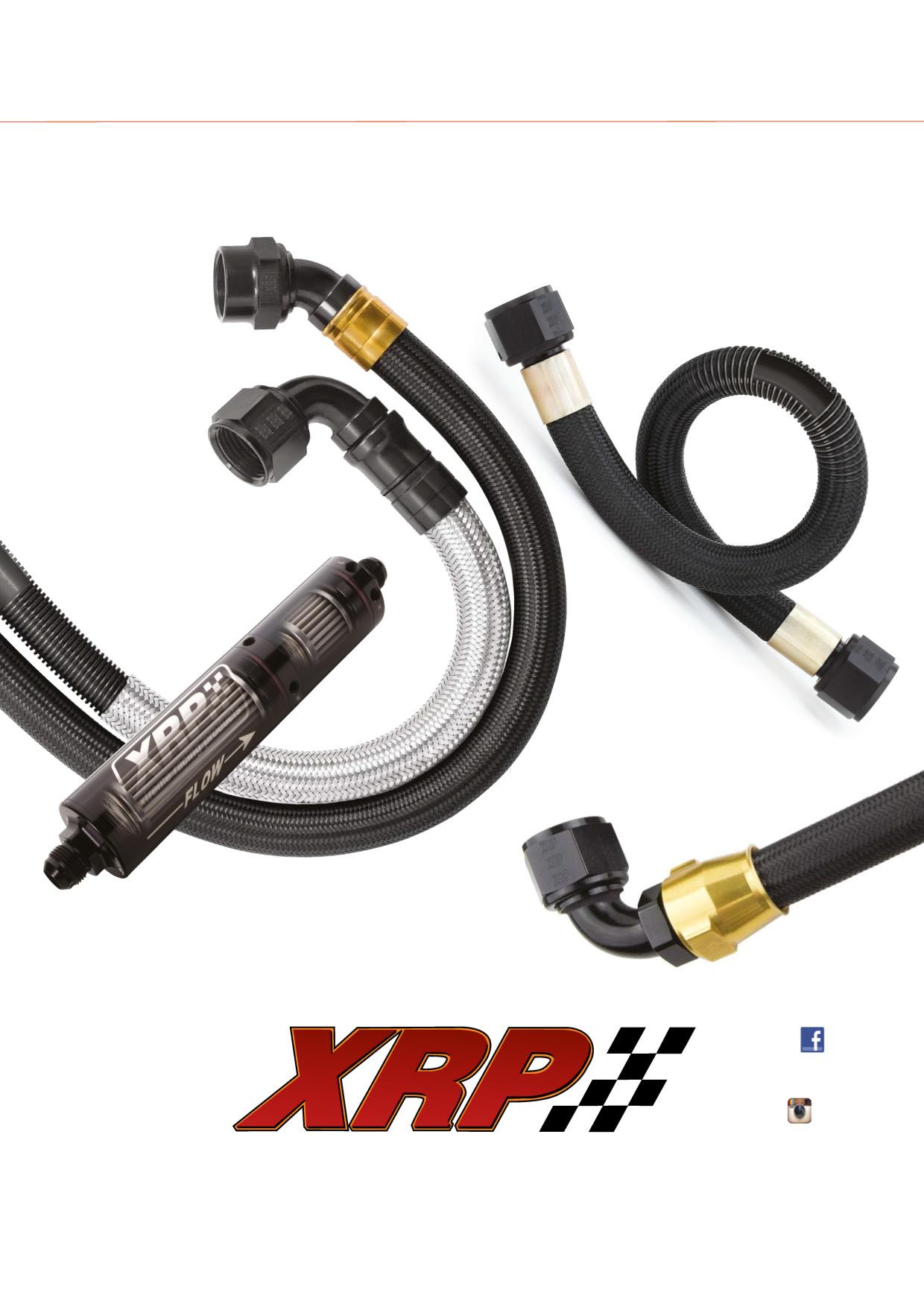
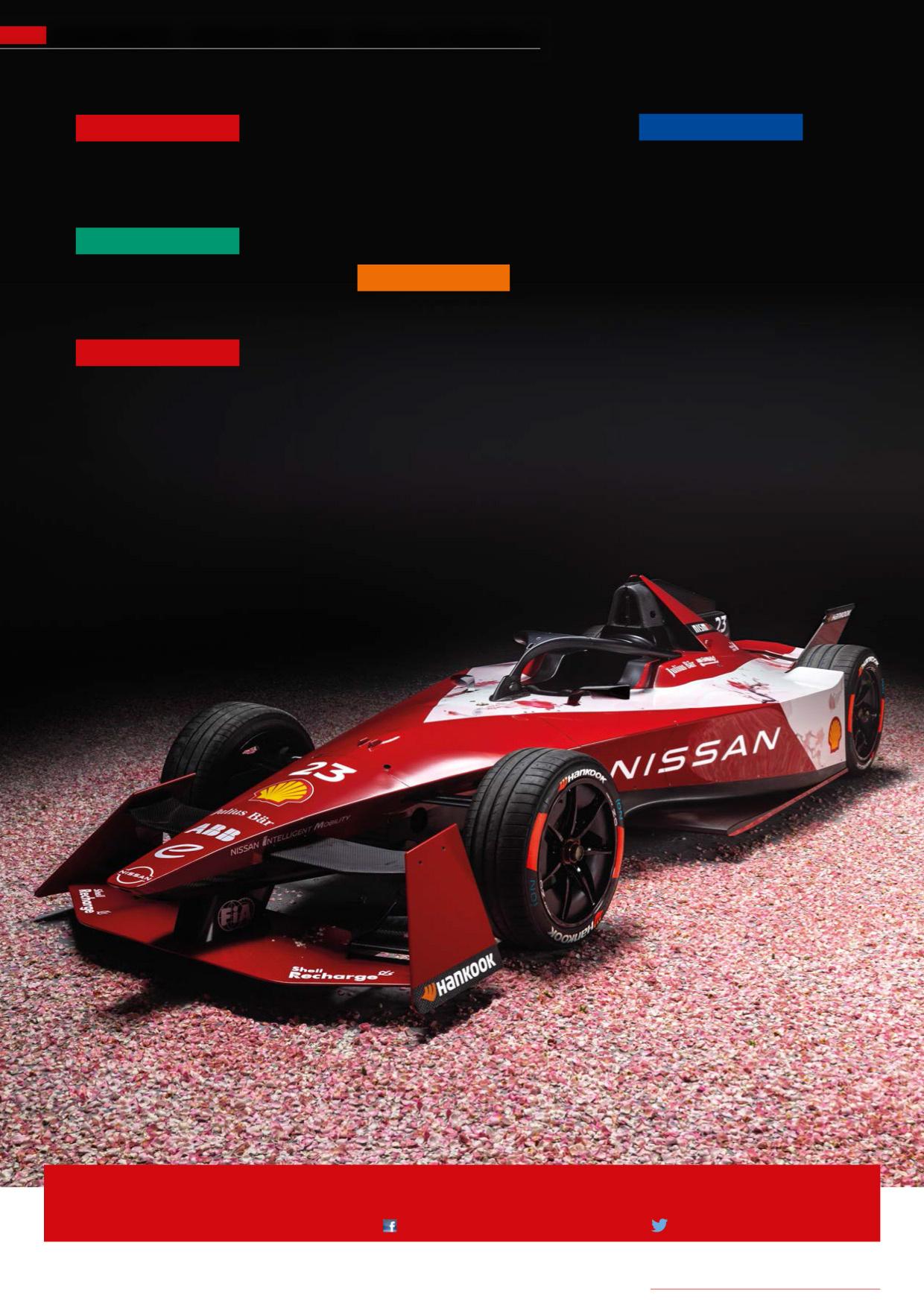
Intercomp’s RFX® HubScale360™ Wireless Scale System is the Industry’s first vehicle alignment system with selfcontained wireless scales. Bluetooth® Technology is included with all RFX® Wireless Scale Systems and securely displays live weight data from the indicator to the user’s Bluetooth ®-enabled mobile device with the Intercomp iRaceWeigh™ app installed.
Mercedes is currently a continuing and dominant force in Formula 1, but its record at Le Mans is rather more sketchy. The horrific accident in 1955 saw the Silver Arrows stay away from motorsport for decades. Then, in 1985, a Sauber Mercedes driven by John Nielsen performed a back flip over the Mulsanne hump (a feat emulated by flight officer Mark Webber and others again in 1999).
In 1988, the team was providing stiff competition to the Jaguars in Group C races but, again at Le Mans, its aero calcs were not so clever. The maximum speed on most circuits was around 200mph, but on the Mulsanne 250mph was possible. That’s a 25 per cent increase in speed, but almost a 65 per cent increase in downforce. The cars were obviously not trimmed out enough for the constant high speed and the tyres promptly exploded, causing the cars to be withdrawn from the race.
Towards the end of 1985, I took up a new post as chief engineer at TWR Jaguar on the Group C team. It was not an easy gig as one of Jaguar’s stipulations was that we use the road car V12 engine. The motor weighed over 250kg, with a high c of g and was almost as long as a Cadillac!
But Tom’s team boasted some well chosen and very talented people. Tony Southgate’s elegant and superbly aerodynamic design added to the cutting-edge engine development by Kiwi, Alan Scott, gave us a fighting chance.
By the end of 1986, we had a quick and reliable car and, come the end of 1988, the TWR Jaguar Team had delivered two world championships and wins at both the Daytona and Le Mans 24 hours.
However, after three seasons with the big V12, Tom persuaded Jaguar that a new engine was required if we were to continue winning in Group C and IMSA. A smaller, lighter, 3.5-litre, twin-turbo engine was therefore developed in house from the engine that had powered the Metro 6R4 Rally Car for the 1989 season.
The initial shakedown at Donington in February showed great promise, the turbo car instantly a second a lap quicker than the XJR9 V12 car. But two weeks, five engines and only 30 laps of the Jerez circuit later, it was clear we had a great deal to learn about turbo engines.
So the V12 cars were pressed back into service for the start of the ’89 season, and the plan had always been to run these cars at Le Mans. Over the course of the 24-hour race, the cars do a similar mileage as a whole season of F1, at a higher average speed, and (hopefully) without service.
New, smaller diameter primary pipes were dyno tested on the V12 engine and run successfully at the Daytona race early in ’89 on the 6.0-litre IMSA cars. The smooth, low-down torque was a hit with drivers and the stopwatch alike, but they would prove to be our undoing at Le Mans.
After Jan Lammers won the 1988 Le Mans race with only fourth gear, it was clear we would also be developing the gearbox prior to the 1989 race.
It consequently underwent a number of internal upgrades to reduce the operating temperature and (hopefully) prolong its life. Our partners at Castrol had their chemists working on a trick new oil that would replace the ‘go to’ American Neo gearbox oil used by most of motorsport in the ’80s.
In testing, the new oil reduced the bulk temperature of the gearbox by up to 15degC, so we felt in reasonably good shape heading for Le Mans.
I was pulling triple duty in the lead up to the race as development engineer for the new turbo car, chief engineer and race engineer for the Lammers, Tambay, Gilbert-Scott car. It was a busy time.
We had expected the turbo cars to dominate practice, with the ability to turn up the wick to gain a grid slot, so we concentrated primarily on race preparation, and it all looked quite promising.
The real race contenders were the multitude of droning Porsches, the pair of rumbling Mercedes and the howling Jaguars.
After one hour of racing, we had a car in the lead, with the rest of the pack in close company. Two of the Jags had made first lap pit stops with high tyre temperatures, indicating perhaps a puncture, but they were soon back out with a higher warning threshold on the infrared ‘heatspy’ units.
In the fourth hour, my car lost almost two laps when it came in with a broken exhaust, and one of the other cars was having gearbox issues – not unheard of at Le Mans.
By midnight, though, my car was back in the lead and was a lap ahead by 6am. Then it all started to unravel. By 06.30, my car was having its gearbox changed in the pit road (no garages at LM until the following year) and lost over 40 minutes.
Three of the four Jags suffered similar issues, and one a blown engine probably before the other problems arose.
My car eventually did a Moses (it came fourth), while the Mercedes rumbled its way to victory.
The new exhausts that had been so successful at Daytona on the 6.0-litre engine did not like the sustained high-speed running Le Mans demands on the 7.0-litre version. The heat signature and vibration nodes were obviously different, and they all cracked like eggshells on the day.
With the benefit of a long investigation and 20:20 hindsight, we discovered the new gearbox oil made a wonderful foaming agent after prolonged usage, and that after about six hours the whole gearbox casing was full of foam, leaving very little liquid oil to be collected by the scavenge pump in the gearbox sump. I’m sure you can guess what happens next.
I had carefully considered the ‘upgrades’ made to the cars that year, but unintended consequences had come into play and confirmed my mantra for Le Mans of ‘if it’s new, it will give a problem.’
It was a hard lesson learnt that day in France, but one we all learned from, and hats off to Mercedes for being there to pick up the pieces.
Unintended consequences had come into play and confirmed my mantra for Le Mans of ‘if it’s new, it will give a problem’I’m major Tom’s left-hand man… and just about to have a bit of
adisaster. This is where the term ‘the pits’ comes from
The familiar sight to spectators of F1 in 2022, a Red Bull Racing RB18 taking the chequered flag
‘We looked at the results from our initial CFD tests and made a judgement on how best to operate a ground-effect car at all the circuits’
Paul Monaghan, chief engineer of the RB18By STEWART MITCHELL AND DIETER RENCKEN
The Red Bull RB18, Red Bull Racing’s response to a set of radically new technical regulations for 2022, proved insuperable in the first season of F1’s new era. The team sealed the 2022 Formula 1 Constructors’ Championship as Max Verstappen won the United States Grand Prix in Austin, the 19th round of the 24-round season.
The Constructors’ title, paired with Verstappen’s second successive Drivers’ Championship, is Red Bull’s first since 2013 and ends an eight-year streak of domination by German manufacturer, Mercedes.
The RB18 finished the 2022 season as one of the most successful cars to date in F1, taking the chequered flag at 17 races in total – 15 for Verstappen and two for Sergio Perez.
The RB18’s concept stood out from the outset at Barcelona testing in February 2022, featuring some unique design elements, including the extended lower lip of the sidepod intake openings and the swept back rear leg on the front suspension. However, it was the car’s well-behaved driving manner that caused the most interest when it seemed to suffer significantly less from so-called porpoising than many of its rivals. This smooth introduction to F1’s new era saw it at the sharp end of the grid from there on out.
Despite Red Bull’s 2022 success, the realisation of the RB18 could certainly have been smoother sailing for the Milton Keynes, UK-based outfit. The team was forced to pull resources from the 2022 project in the latter stages of 2021 as the season came down to a shootout with Mercedes in the later races. Therefore, the personnel, wind tunnel, CFD and design resources that would have otherwise been directed toward the 2022 car remained on the 2021 RB16B, right up until the very last lap of that season.
‘The 2021 campaign dramatically affected our 2022 car development,’ Paul Monaghan, chief engineer of the RB18, freely admits. ‘With much of our capacity staying on the RB16B for longer than we had readily planned, the severe regulation changes for 2022 and finite resources we had remaining, we were worried we had damaged the development of the 2022 car going into the start of the season.
‘That said, the RB18 proved to be the ‘least-worst’ car on the 2022 grid, the result of hard work, research, design, manufacturing, and realisation of our business with our available resources. We were at least as efficient as anybody else, and we had a great car from the outset.’
As for the RB18’s overall concept, Monaghan explains: ‘During our development of the 2022 car, we looked at the results from our initial CFD tests and made a judgement on how best to operate a ground-effect car at all the circuits. We took our design route early in the development process and stuck with it to exploit the potential of the road we chose.
‘The main thing was getting our heads around the car’s aerodynamic demands. In terms of how you operate it relative to the ground, it is quite different to the 2021 and preceding cars. We knew we would run lower rear ride heights compared to the last regulation set, so the travel at the rear axle
compared to the front would be significantly less. But that reduced rear travel has compliance benefits.
‘As such, in the 2022 regime, if you’re making high aerodynamic loads on the straight, the heave stiffness must be higher than it would otherwise have been for a 2021 car. This forces your hand in some elements and forces you to carefully design for the desired compliance.’
One of the few people in F1 with significant experience with ground-effect aerodynamics is Red Bull Racing’s chief technical officer, Adrian Newey. In fact, Newey wrote his university thesis on just that subject, and his first job was chief aerodynamicist at Fittipaldi Automotive, working on the 1980 F8, itself a ground-effect car.
He would go on to design the March 82G GTP, which featured a significant hole between the front fenders that fed air to massive underbody tunnels to generate ground effect. The March 82G won two IMSA GTP titles and saw two further evolutions, namely 83G and 84G trim. This experience with ground-effect cars from early on in his career made him aware of some of the possible hazards lying in wait with F1 2022’s car with its ground-effect underbody.
Despite Newey’s extensive experience in the field, he only fed into the Red Bull technical group that created the RB18, and his design input was limited to the suspension. Nevertheless, the suspension is a critical part of the car’s platform control, and arguably the most significant contributor to a groundeffect car’s performance.
Monaghan explains: ‘Suspension proved to be the most sensitive area of the 2022 car, given that the FIA had simplified its technology with the introduction of the latest regulations and ride height control.
Of the 2022 F1 contenders, Red Bull Racing appeared to have the best overall package. Racecar talks to the team about the RB18’s development, and the effect of its recent budget cap penalty
‘We were worried we had damaged the development of the 2022 car going into the start of the season’
Paul Monaghan
This coincides with developing the suspension stiffnesses, which is paramount in this new regime.’
To put that statement into context, for 2022 the FIA changed the suspension system regulations, banning any inerters, mass dampers or acceleration-sensitive valves in the dampers, thereby prohibiting any systems or configurations that change the response of the suspension elements to body accelerations and / or angular acceleration of the rockers.
‘If you want to run the car lower to the ground, you must raise the suspension stiffnesses, which can have severe compliance side effects,’ Monaghan continues. ‘Ride height was the element of the set-up that received the most attention in 2022, but it does not come in isolation. As such, one part of the ride height vs suspension stiffness set-up wasn’t dominant over another. These cars are sensitive, so you cannot change one aspect without manipulating another.
‘The aerodynamic operation is the most critical to the fastest lap time. Still, if you get the complementary functions wrong, you will be punished by things like porpoising and driveability issues.’
The RB18 features a pull rod front suspension which allows for a lower installation for the suspension mechanisms, aiding a more dynamic, lower c of g, frontend capability. It also allows the rearwardmoving flow field path to the ground effect venturi throat to be kept cleaner, free of any disturbance that might induce unwanted turbulent flow into the floor’s venturi.
‘Ride height was the element of the set-up that received the most attention in 2022, but it does not come in isolation’
Paul Monaghan
Moreover, because the pull rod concept is a second-class lever system, its characteristics are softer than the pushrod’s first-class lever system, aiding compliance between the unsprung and sprung masses when there is a significant displacement between them.
However, when the front lowers at speed, the characteristics of the second-class lever system stiffen as it is a rising spring rate, which supports the platform as aerodynamic loads are introduced to the car’s inputs. This design is likely part of why Red Bull has suffered significantly less from porpoising
than its rivals throughout the 2022 season. The multi-link arrangement of the front suspension sees the trailing wishbone swept back and intersecting with the chassis significantly further down than the front one. This design was implemented as an anti-dive measure. Anti-dive geometry diverts the forces transmitted under high aerodynamic and braking loads away from the springs and dampers and through the suspension links to minimise disruption to ride height, limiting the rear ride height increase and the downforce loss it entails during braking.
This multi-link system sees the mechanical elements of the suspension needing to be made stiffer, and therefore heavier, than a more conventional wishbone suspension design. As proven, the benefit of platform control and compliance outweighed the weight deficit.
At the rear, the pushrod arrangement was perceived to provide stiffer and lighter mechanical installation to preserve the platform control needed to support the ground-effect aerodynamic regime. Additionally, the pushrod concept allowed tighter packaging of the suspension, keeping it free from encroaching on the diffuser exit, which aids the efficiency of the ground-effect floor and the rear beam wing interaction.
The RB18’s long rear suspension travel accommodates a variety of ride heights, allowing it to ride low at high speed, reducing drag. Despite it having a greater static ride height than much of the grid, the long rear travel, combined with a relatively soft spring rate, meant the car could settle low in such a way as to enable high straight-line speed compared to the competition.
Red Bull Racing took a different approach to the design of the RB18’s floor. Most of the cars on the 2022 grid feature a teardropshaped central section between the tunnels, providing a smooth, continuous surface on
the inside of each tunnel from the intake to the diffuser exit. This coincides with a consistent throat and diffuser ceiling angle into and out of the venturi point, respectively.
In contrast, the centre section of the RB18’s floor features a number of stepped elements on its outer wall (inside wall of the tunnels) and the roof of the tunnels also appear deeper, narrower and more sculpted in some sections along its length. The step changes of the central section, along with the varying profile to the height of the tunnels, is likely an effort to keep the tunnel volume consistent along its length to provide a steady mass flow from intake to diffuser.
‘There are multiple aspects of the floor that are weighted differently, depending on how you want to extract performance,’ explains Pierre Waché, technical director of Red Bull Racing. ‘You can be aggressive with the floor design, but you then narrow the window within which it works most effectively. Where you put the main load on the floor, which is around the centre of pressure of the venturi section, affects the overall concept of the car in terms of load distribution and aero balance.
‘The main aspect of this year’s car was the development of this, and the rest of the components were associated with that.’
The RB18’s floor design seemingly provides higher resistance to stalling the underfloor flow, compared to a floor with a consistent throat and diffuser ceiling angle into and out of the venturi point. In theory, Red Bull’s design should enable softer
suspension to work to maintain grip and compliance between the tyre and the track, with the ability to engineering the set-up to manage weight transfer where necessary.
With a stable underfloor aerodynamic regime, Red Bull could potentially decouple some of the influence of the floor on the suspension, combining the wheel travel frequency, damping ratio and weight transfer for the best spring and damper set-up for the track, which can then be optimised for the conditions more readily than its competitors.
Red Bull went on to use a variety of inlet vane and floor edge arrangements to tune the car to individual circuits throughout the season. Changing these elements alters the aerodynamic centre of pressure acting upon the front and rear axles, adjusting the aerodynamic balance of the car. This suggests the team had a very high-fidelity control of its underfloor airflow.
The result was the RB18 struggling far less with porpoising than many others in the field, and the combination of floor and suspension design is likely the largest contributing factor.
Perhaps the most significant development of the RB18, though, has been its ongoing weight reduction programme. The car began the year 20kg over the minimum weight limit of 798kg, and a number of significant elements contributed to that.
‘The cost cap influenced everything on the RB18, but it was most influential when it came to the weight,’ notes Waché. ‘Compared
to what we used in the past, plenty of parts are compromised compared to what you might do if there was no financial constraint. The resulting component is not necessarily compromised in terms of performance, but questioned in much more detail than they were before the cost cap was implemented.
‘With the cost cap in place, you must extend the life of parts, which typically sees them designed to be more robust and heavier, to make it economically effective and last longer. Sometimes we choose a material that is cheaper, which is typically heavier as well. Sometimes you don’t do development because the performance gain is not there at the cost it requires, and this balance is a big part of Formula 1 now.’
The aerodynamic loads generated by the powerful floors mean they must be stiffer, and consequently heavier, than the previous generation of cars to remain rigid. The newfor-2022 18in tyres and bigger brakes are also much heavier than the previous generation.
The RB18 struggled far less with porpoising than many others in the field, and the combination of floor and suspension design is likely the largest contributing factor
Unlike the previous generation of cars that relied primarily on the outer surfaces of the car for aerodynamic gains, the floor is now the primary aerodynamic load generating part. As such, the tight Coke bottle shapes of the previous generation cars is less prominent now
A lot of the car’s excess weight was originally toward the front, which gave the early version more understeer and made it prone to front brake locking. The weight came off via a series of upgrades throughout the season, including a new floor at Imola, re-designed brakes and the hollowing out of some components that had originally been manufactured as solid because of time constraints in the design phase. Gradually, the weight distribution moved towards the rear. This coincided with an accompanying rearward shift in the aero balance, giving greater rear stability on corner entry without affecting the initial direction change.
‘In terms of making the weight savings, there are only so many areas of the car that can be addressed to bring the weight down to the level that would make us competitive,’ Waché notes. ‘There were some ancillary components that were designed conservatively and heavier and they were easy to work on to save weight. However, this was not the goal for the start of the season.
‘Our strategy was to replace parts for mileage and put lighter ones on when we could. This was the best way to control the costs. There are some parts of the car, especially the floor, that we deliberately made heavier for reliability reasons. We knew it needed to be robust to prevent destroying it on the kerbs and so on.
‘When we saw the car in operation for the first time, it gave us the data we needed to start developing a new, lighter version. That was an easy opportunity to reduce weight.’
It is not all roses in the Red Bull Racing camp, though, as it has been found to have breached the cost cap regulations for the 2021 season, the first year of its implementation. Over the 2022 Mexican GP weekend, Formula 1 finally confirmed the team’s penalty, hitting it with a $7 million fine and a 10 per cent reduction of its aerodynamic testing allowance for the next 12 months. The FIA adjusted the strength of the penalty after its initial £1.8m overspend was amended to just over £400,000 after a tax credit had been correctly applied.
Despite this, many of its competitors are of the opinion that Red Bull has got away lightly, and the integrity of Formula 1’s budget cap has been in jeopardy throughout this process. There are many critics of the result of Red Bull’s breaching the cost cap regulations, especially as a $7 million fine is small beer for a company of Red Bull’s size. Moreover, it does not come out of its present or future cost cap, it must be settled separately.
Reducing Red Bull’s budget cap in the future somehow wasn’t an option available to the FIA under the terms of an accepted breach agreement.
The more significant damage to the team is the reduced aerodynamic testing element of the penalty, which impacts its CFD and wind tunnel programmes. This penalty is the equivalent of 1.5 finishing positions in the Constructors’ Championship, associated with the diminishing testing scale as a function of the team’s place in the championship when wind tunnel allocations are determined.
Formula 1’s new handicap system means successful teams already have less aero testing allowance than those finishing lower down. The team finishing last is given a 115 per cent baseline allowance, dropping by five per cent for each position until the winning constructor is given 70 per cent of the nominal amount within its aerodynamic testing period, of which there are six per year, each lasting around eight weeks.
Because Red Bull won the 2022 Constructors’ Championship, the development allowance would see it entitled to 70 per cent of the baseline limit for 2023. This amounts to 224 wind tunnel runs and 1400 CFD items per period. That is 16 fewer wind tunnel runs than the next highestplaced team, and 32 fewer than the third.
In CFD terms, it represents 100 fewer components than the second-place team, and 200 fewer than the third. However, because Red Bull’s penalty for breaking the budget reduces this by a further 10 per cent, it now has a reduction of 22 wind tunnel runs and 140 CFD items per period, equating to 38 fewer wind tunnel runs, and 240 fewer CFD runs during each period compared to the second-place team.
Red Bull’s testing limitation lasts for 12 months from the execution of the accepted breach agreement, October 26 2022. The penalty will impact whatever development work the team completes in the final part of 2022 and 2023 car development until the
same date in October next year, which will affect both the in-season development of the 2023 car, and the 2024 one that follows.
Red Bull indicates the effect of the penalties could be worth anywhere between 0.25 and 0.5 seconds of lap time.
‘With the limited testing allocation that we must work to from the penalty, we don’t want to burn resources on the wrong things,’ says Monaghan. ‘The car for next year will be similar because the regulations are similar, but we are using the resources we have now to develop the car in the most efficient way.
‘The wind tunnel and CFD testing deficit are connected. These are our main tools of development. The rules are set up to somewhat balance the performance of the teams across the grid as a function of the handicap associated with aerodynamic development. This system is very effective and will have a significant impact on us for next year, and the grid over the years.
‘It is very difficult to offset this handicap. We have some of the best F1 engineers in the world, but the other teams also have very effective members of their teams. We can work harder, but the others will be, too.
‘What is true is we will have to be more efficient with the resources if we are going to make up for the deficit.’
‘Our strategy was to replace parts for mileage and put lighter ones on when we could. This was the best way to control the costs’
Pierre Waché, technical director at Red Bull Racing
180 mph without moving an inch
Take cutting-edge wind tunnel technology. Add a 180 mph rolling road. And build in the best in precision data acquisition capabilities. When we created the world’s first and finest commercially available full-scale testing environment of its kind, we did much more than create a new wind tunnel. We created a new standard in aerodynamics.
The LMDh cars were on track at Daytona in December in final preparation for the opening round of the WeatherTech series. Racecar was there to see how they got on
By ANDREW COTTONThe LMDh category has been a long time in gestation but it’s finally here, and ready for competition debut at the 24 Hours of Daytona at the end of January. The cars had a final group test at Daytona early in December and, although each of the manufacturers that were present, including Cadillac, Acura, Porsche and BMW, had car-stopping problems, the teams set about fixing them in test conditions, rather than a race weekend and go into the first race with some optimism after a challenging year.
This test was the first time teams had sight of the new tyres from Michelin that will be used next year, and was supposed to be a performance test to help organisers with the Balance of Performance for the 24-hour race. However, failures of the motor generator unit (MGH) and other electrical issues, along with dramas at customs shipping new parts in, prevented much meaningful running. Following the test, teams were more concerned with making their cars run cleanly than worrying about the obvious lack of grip on cold tyres fresh out of the pits, or even what their rivals were doing.
Official times were not available from the testing, but from data available to teams it appears the Acura was fastest, at 1m35.75s, Cadillac narrowly behind at 1m35.80, Porsche 1m35.90 and BMW 1m36.35s. The cars were at similar pace over long runs, too.
Just to re-cap, the cars are based on chassis provided from a choice of four manufacturers: Dallara provides the base car for BMW and Cadillac, the Italian firm continuing its relationship with the latter that started in the DPi era of prototype racing. ORECA supplies the chassis for the Acura, again a long-standing relationship that has won big races and titles. Porsche opted for Multimatic, which was supposed to produce cars for the other VAG manufacturers, Audi and Bentley. Audi confirmed its participation but then backed out shortly before switching its allegiance to Formula 1 for 2026, while Bentley’s bid to take over the Audis was rejected by Bentley’s board in October 2022.
As none of the chassis builders are allowed to exclusively supply one manufacturer, their products are all commercially available. Lamborghini will come in 2024 with a Ligier chassis, Alpine with ORECA, while McLaren is scheduled to arrive in 2025 and is expected to choose either Dallara or Multimatic.
The manufacturers provide the engines and aero kits. This means the cars are all very different looking, with brand styling cues readily apparent in each one. They are powered by a variety of engines and only Acura has produced a brand new power unit.
Honda Performance Development, based in California, produced its 2.4-litre, twin-turbo V6 from scratch, and the company says it has very little in common with the proposed IndyCar engine that first ran in 2021, but which was dramatically dropped by IndyCar in the same week the Daytona test took place.
BMW opted for its old 4.0-litre, naturallyaspirated V8 taken from the DTM and which first raced in 2011, while Porsche went even older on its design, taking the 3.4-litre naturally-aspirated V8 from its RS Spyder that first ran in 2005, and was later used in the 918 Spyder road car.
The last power unit is that of Cadillac, which has taken over the design of its 5.5-litre V8 in house, where previously it had been prepared by ECR Engines in North Carolina.
The cars run with a spec hybrid system comprising the MGU from Bosch, battery from Williams Advanced Engineering and gearbox from Xtrac. This is designed to supplement the power from the engines, replacing the demand on the ICE with that of the electronic unit instead.
Power is limited to 500kW from either the ICE or the combination of ICE and hybrid, with deployment strategies open for the teams to choose how they want to use it.
Electronics are all supplied by Bosch, including telemetry, scrutineering harnesses and the safety systems, unlike in the DPi era when the choice of provider was open.
Teams are free to write their own software, as the ECU is not regulated, and it is up to the manufacturers to ensure the ECU is integrated into the operation of the hybrid system. This has not been easy – much of the testing and the subsequent failures have involved the demands made by the ECU on the hybrid system, which has been blamed for many days of lost track time.
The LMDh cars are performance balanced and, to help the organisers achieve parity, the cars must hit a point on the lift / drag graph in all conditions, including different ride heights and wing angles. Weight and power are also strictly regulated. Power is no longer measured by output from the engine, instead torque sensors have been introduced to monitor power at the wheels, which will make the balancing more accurate.
Minimum weights have been mandated for overall car (1030kg), as well as such items as the engine (180kg). Similarly, the location of the engine is closely monitored, which helps the chassis manufacturers design their cars to accept different engines, including in the future the new LMP2 power unit.
Tyres come from Michelin, who will provide the same rubber as in the FIA World Endurance Championship. At the Daytona race, due to the cold overnight temperatures,
a choice of two compounds will be available to teams, although IMSA has yet to determine whether the softer compound will be available for the whole race or just a 12-hour window overnight.
For the remainder of the season, Michelin will bring only one spec of tyre to each race, and it will be up to the tyre manufacturer to decide which will be available to teams on any given weekend. In contrast, in the FIA WEC Michelin will provide the choice of rubber for every race and teams will be free to use each compound as they choose.
A further change for next year is the way the sanctioning body, IMSA, deals with the energy used by each of the cars per stint. Reminiscent of the old Equivalence of Technology rule set, the body is considering limiting the energy per stint available for each car. The idea is to reduce the impact of the different choices of engine, and to retain the element of strategy. Teams will still benefit from fuel saving as they look towards the end of the race and that crucial final pit stop. This is a marked change from looking purely at fuel consumption and balancing that using different size tanks and fuel hoses.
Testing has proven to be challenging and, although each of the manufacturers claim to have racked up high mileage, all have experienced problems of one sort or another. Early testing has been hampered by a shortage of materials, and therefore components, from core suppliers as demand on such items as electronics and carbon are high due to the war in Ukraine.
According to reports from the teams, each session has been punctuated with red flags as an LMDh car has been towed back to the pits after a mechanical breakdown. The Daytona test was no different.
Teams, and crucially the suppliers, are now under huge pressure to get everything right for the biggest test of them all – a 24-hour race to kick the season off in cold overnight temperatures, followed by a 12-hour race at Sebring in March.
Early testing saw the teams use the old 29/34 tyres from the 2022 Hypercars, but the Daytona test provided a first glimpse of the all-new 2023 tyre from Michelin that has a higher bio-content than the previous generation rubber.
The shape, construction and compound will be the same across the LMDh cars in both IMSA and the FIA WEC, as well as the Ferrari and Toyota Hypercars, while for the Peugeot, which is allowed to run the same size tyre all round, the fronts will be stretched and the backs squashed to fit the needs of
predominantly front-biased car.
the
A choice of two [Michelin] compounds will be available to teams, although IMSA has yet to determine whether the softer compound will be available for the whole race or just a 12-hour window overnightAn official 3D scans the Porsche to confirm it fits within the expected parameters ahead of on-track testing The Porsche 963 suffered with a gearchange issue early on but managed to fix that and put in some longer runs on day two Bosch, Williams and Xtrac engineers were all on site for the Daytona test
Although the teams’ pre-test run plans focused on performance testing, much of the session times were used fixing niggling issues that prevented cars from extended running. None were able to complete a full stint length on track, for example, let alone a double stint. BMW and Cadillac both brought brand new chassis for their roll out, but both spent the first day in the garage waiting for their Bosch scrutineering harnesses to clear customs. They were denied permission to run without the system by the sanctioning body.
Porsche suffered a gearchange issue on the first day, having installed new components into the system, but managed to start its longer runs on the second day.
Acura has developed a complex antilag and traction control system for its turbocharged engine that sounded like a mechanical bag of nails as the car negotiated slow-speed corners. The teams confirmed codes were being re-written to help, but it took nearly two days before any meaningful running was achieved, meaning any performance testing only occurred on the afternoon of the second day.
Michael Shank’s Acura broke an MGU on the second day of testing and was unable to complete any significant running. The team was so concerned with its lack of track time that it has scheduled another test early in January, while the Wayne Taylor Racing car suffered a split header tank, though this was quickly rectified. Taylor’s team will not take part in the early January test, preferring to work towards the 24-hour race.
Throughout the Daytona test, the teams were reporting how complicated these cars are to work on. One driver commented that the controls were not integrated with each other and that, if one change was made, others have to be made in sequence to complete the process.
‘It is the most mentally draining car I have ever had to drive,’ said BMW driver, Augusto Farfus, while manufacturers confirmed it will take some time and running before customer drivers will be able to operate these cars.
For other professionals, though, the complications were not a drama. ‘The car is a completely different animal to the LMP2 cars
Throughout the Daytona test, the teams were reporting how complicated these cars are to work on
To underline the fuel efficiency with which modern racecars can be run, the 2022 BTCC required a hybrid power unit. Mated to Xtrac’s groundbreaking transmission, made available in front and rear wheel drive configurations, the system has helped provide close and exciting racing throughout the season.
I drove last year. It’s far more complicated, but to me it’s logical,’ said WTR driver, Louis Delétraz. ‘Yes, one thing leads to another, but I am comfortable doing that.’
However comfortable some drivers may be, having the systems operating separately means the teams have to hire technologically-literate professional drivers until new programmes can be written to make controlling these complex cars a more straightforward process.
The test was supposed to be one of performance running, with many teams believing they had got on top of the reliability issues that have plagued these cars from the start, but the electronics appear to be an issue, specifically getting the different elements of the system to talk to each other.
Another consequence of the lack of meaningful fast running was IMSA did not have the opportunity to accurately correlate its simulation data on track, something it
needs for the performance balancing to take place. The technical team at IMSA was confident it will get the process right as its simulation is so advanced, and says it has a good handle on what the cars are capable of, but this was the first time the cars ran on the new tyres, and the last time they will run on the Daytona track before the race week.
The BoP tables will therefore be largely based on simulation, and IMSA and the FIA and ACO are working closely together to align their approach.
In the past, the FIA’s BoP has affected the GTE-Pro class and changes have been applied retrospectively. For example, an FIA performance balancing change would rely on a prescribed number of green flag laps of the previous two races before being applied to the next race. However, that does not account for the nature of the circuit on which the change will be applied.
IMSA’s approach has been different, and more proactive. The body started to predict the Balance of Performance for its cars on the
next circuit based on experience of DPi cars. However, without that option available, it has turned to simulation experts for help.
The cars will run at Daytona at the pre-race test, the so-called Roar before the 24, one weekend before the start of the 24-hour race . That’s normally considered a fine-tuning test, and it will be too late then to make any major changes. But with teams still busy making their cars run reliably, and worrying about how their new tyres will work on a low-grip surface, it could be different this year.
Certainly standing at the International Horseshoe, it was clear that even in moderate ambient temperatures the first laps out of the pits on new tyres (unheated in IMSA for many years) are going to be difficult for the drivers. Even the front end seems to be hunting, while the option of running a lower ride height would appear to be out, judging by the sparks coming from under the Cadillacs as they passed the pits on the second afternoon while the drivers waited for pressures to rise.
Last word goes to Connor de Phillippi, driver of the BMW Hybrid V8: ‘Especially this year with where everybody is in development, I think just focusing on your own [programme] and not getting sucked into the competitive aspect, especially early in the race. It’s going to be about keeping it all together and performing at the end when it actually matters.’
The lack of meaningful fast running… [means] the BoP tables will therefore be largely based on simulation, and IMSA and the FIA and ACO are working closely together to align their approach
When Honda decided to continue its endurance racing programme in the US, it pulled a clean sheet of paper from the drawer on which to work. ORECA was designing an all-new prototype for the regulations and Honda Performance Development (HPD) wanted to continue its relationship with the French manufacturer.
There were options for the Californiabased company to re-use certain key elements, such as the 3.5-litre, twin-turbo engine it already had, which would undoubtedly have saved money, but with the president of the company also being the technical director, and with a reputation for innovation in racing that is enjoyed by Honda, the company embarked on an all-new, 2.4-litre, twin-turbo engine instead.
Although it shares its capacity with the IndyCar engine that was due in 2024, there was little crossover between the two, not least because the LMDdh engine had a minimum weight of 180kg by regulation, the IndyCar requirement nearly 70kg less.
Racecar sat down with HPD’s president and technical director, David Salters, at the Daytona LMDh test to discuss development of the engine for the prototype, and the decision to drop the 2.4-litre IndyCar engine.
RE: Are you satis ed with what you have seen so far at this test?
DS: You have good days and bad days. We are doing okay, but we have so much to do.
With Covid, we finished up a bit later [in our preparation] than we would like, so we are still in catch up mode. There is no point in getting too excited about it, though, you just have to get on and do your work.
RE: Hybrid integration seems to have been underestimated by many of the teams.
DS: Not by me. I have done this twice already. I worked for Ferrari [in Formula 1] for nine years [as head of engine development] to 2015, so I was fully embroiled with the KERS, and then with the hybrid V6, and it is not easy.
My admiration of IMSA has grown a lot. They have done a good job. You have to stretch yourself and, if they weren’t trying to make a big step, that would worry me
Like all the other cars at Daytona, Honda’s test wasn’t without incident, but the team is confident development of the ARX-061, and its cleansheet-of-paper engine will soon bear fruit
To fit in a racecar it needs to be too small, not cooled enough and then it is shaken to death. It is how I expected it to be. No one is doing anything wrong, it’s just a difficult thing to do.
RE: In F1 you have a large budget to develop hybrid, but here it’s a different animal as it’s private teams supported by manufacturers. DS: We have helped Bosch and Xtrac and Williams. We have tried to test everything for them on our test cell. Is it perfect? No. Could the car stop? Yes, but you have to work through it. That is what you should be trying to do.
We ran DPis for five years, so that was good, but if that carried on for another four years we would be bored. That’s not why we go racing. The fact that this is a big challenge is pretty cool. We have a hybrid, try to integrate it and we write our software in house. We had a guy yesterday who re-wrote some of the code and we put it on the car today, and that’s what racing is about. That’s why you get up in the morning. Is it going well? No, but we are not trying to cure cancer here. We are trying to make a car go around in circles, so let’s not get too excited. I might live to regret some of this, but right now my boys and girls are loving it because it is a challenge, and that is how racing should be.
The good thing about this is that while it is a lot of money, the costs are not stupid. When you look at these cars you can see the designs of the future. The cars have all this
integration, we can write our own software, and this is one of the very few series with open software architecture; maybe the only one outside F1. F1 is a bit constrained, but that’s good company to be in, isn’t it?
RE: The price of the cars has risen dramatically from what was originally intended. Reports say the Porsche is now more than $2.5 million. DS: That’s still not bad, is it? We go for quality not quantity. Yes, it is more expensive, but it is not outrageous. LMH is about a 40-million dollar car, so this is the bargain of the century when you look at it like that.
Yes, the teams must have sponsors, but I have a queue of teams wanting my car. I have no problem selling the cars. I can’t support that, though, we have our hands full doing what we are doing. There is no shortage of people who can raise the funds to run them, but do they have the skill to do that?
RE: There are rumours IndyCar programmes are paying higher wages than IMSA teams can afford. Have you come across this?
DS: We have similar problems with retention. We are based in California, which is not a motor racing hub, and we are competing against Apple, Google and SpaceX. I have lost half a dozen people to SpaceX, but I have also had people come from Formula 1 and they want to be involved in this. There is big demand at the moment.
Under Covid, the salaries went stupid. We have big challenges, but it is exciting. What I really like is that we have great engineers.
We are trying to bring on the next generation of engineers who are enthused by this, and it is down to the hybrid.
RE: Has there been frustration with the spec suppliers not coming up with some of what they are supposed to?
DS: You have to be careful with that. It is really hard to do what we are trying to do. I’ve been there. We have to work together. I wouldn’t like to be critical because this is a hard job, but I have yet to see anyone do anything complex and get it perfect.
So no, I am not frustrated. I would be if we dropped out of a race, that’s for sure, but right now it is just all working together to make it work. Pointing fingers is not the best way to motivate everyone.
My admiration of IMSA has grown a lot. They have done a good job. You have to stretch yourself and, if they weren’t trying to make a big step, that would worry me. The proof of the pudding is Porsche, Acura, BMW and Cadillac. Lamborghini is coming and we
I might live to regret some of this, but right now my boys and girls are loving it because it is a challenge, and that is how racing should be
the workin house as part of its expansion as a company
2.4-litre,
have to see about Alpine. I applaud them for taking the risk as it’s easy not to.
We have to help, because it will benefit us all. We had a component failure [in testing] –the MGU – so let’s fix it. Let’s find out why first, and then figure out what we will do.
I like the fact they committed to it, and now we all want to see it work.
RE: One of the big challenges is writing software, and many have struggled to integrate everything. Are you?
DS: We are trying to understand that stuff, and that’s cool. We have TAG 320 sat in our cars, an F1 ECU, so it’s go big or go home. We also have one of our own boxes on the car that is very fast at processing. We do that all in house, and we do our own software, so we do the powertrain control, hybrid control, energy management and vehicle control, brake-by-wire system and we have an in-house group that sorts all that out.
We also have a vehicle dynamics group, so we have our own Driver-In-the-Loop simulator, so it goes through DIL, then HIL, then here, we write code in the truck. That is the lovely bit about working for Honda, we are encouraged to do that. I get given money to do that, so I find the right people to do that, and they have Honda badges and Honda pensions.
RE: You are the only ones to have built a new engine, and it has attracted a lot of praise.
DS: Again, I may regret it, but I am president and technical director, so you want to do your best engineering job. I’ll admit I have had a few sleepless nights over it.
We already had a nice DPi engine, and so the easy choice would have been to use that, except it’s heavier and bigger, and we thought we could do better.
When you start something like this, you ask how do you make the best racecar that you can? I worked for Ferrari for nine years, Ilmor for seven years, and for McLaren. You make the lightest, most compact racecar you can. And you start with the basics – make it light and close to the ground. There’s still a lot to be said for that.
How do we make the best car we can? We have a good group of engineers. I am an engineer and have some self-respect. I’m also the president, so we decided to do the best job we could, and be proud of it.
RE: What made you decide to go with the twin-turbo V6 format?
DS: We have some brilliant vehicle dynamicists, and we did a lot of simulations to understand what we needed. We read the rule book a lot to work out what was required to make the best car. The point of making the decision on the engine came over Christmas. It’s only a 2.4-litre, and the question was can we make the power while also making it live?
One of our simulation guys went away and simulated how to make the power with the combustion loads low, so he worked all Christmas and came back on the second of January with a 100-page report. We sent all the groups off to figure out what was their best thing, and then we sat down, had a three-hour meeting and decided we would use this engine.
RE: So you didn’t sit there and think we can do this, and it will also service IndyCar?
DS: No. We knew we would have elements of the new IndyCar engine that we liked. But we also worked with our F1 guys, and we looked at the history of sportscar racing to know what the best engine was. We could use some of the bones of the IndyCar engine, but it
was an amalgamation of everything that HPD has done over the last 30 years.
We put it together and a lot of smart people did the evaluation. So, we had the core concept, that used a lot of our stuff. We then set the guys off to do the best packaging, in the most compact way we can.
Sure, there are some risks, some areas we have really gone out on a limb, but time will tell if we are right. We are always just trying to make the best engineering decisions we can.
RE: Do you use the full 10,000rpm rev range?
DS: The way the IMSA power curve is, you choose your peak, but we use pretty much the full 10,000rpm. We just tried to look at everything and make the best racecar we can. ORECA did something similar, and made a lovely racecar, and we made a lovely powertrain. We helped them with the DIL simulator, did lap time simulation and we tried to find out what we thought the best racecar was. That involved some investment, some new stuff and learning.
RE: Will you take this car to Le Mans?
DS: The teams are not the only ones who want to do it! We are here to look after racing in North America and we will focus on doing that first. After that, it’s global interest, but
There are some risks, some areas we have really gone out on a limb, but… we are always just trying to make the best engineering decisions we canThe decision to go with the twin-turbo V6 came about after a detailed simulation programme concluded the format would make the power and longevity required
that is outside our jurisdiction so it would be a decision from Honda. We will crawl, walk and then run. Let’s make sure we do a good job here, represent our brand and ourselves well, and then we will see where we are.
Would I like to go to Le Mans? Hell yes. But I am under no illusions about the challenge we face.
RE: Why was the decision taken to abandon the 2.4-litre IndyCar engine?
DS: I can only speak from a Honda perspective. IndyCar racing is great, the Indy 500 is one of the greatest races on the planet. That’s brilliant, but there needs to be electrification at some stage. That is moving along, which is good, and now it needs to move to the next step.
It is one thing making prototype stuff, another to make it race ready. There is a big IndyCar field, and trying to productionise it, it became obvious we had to work with IndyCar, Ilmor and GM, but we can’t do it all.
We are going to concentrate on the hybrid moving forward. There is only so many people and so much budget, so you have to make decisions. The priority from our point of view was to make the hybrid work, rather than the engine. It’s a difficult decision, but it is the right one.
Having some electrification and sustainability is more like the future. Just sticking with engine is not what we should be doing. Next year we have 100 per cent renewable fuel, which has 60 per cent less CO₂, so we are already on the right path. If you do some research, you will find the lowest CO₂ cycle for a road car that exists is a low-carbon fuel on a hybrid car, for road car. It costs quite a lot of CO₂ to make a battery, so at this moment a low-carbon fuel on a hybrid is the ticket.
Medium-term hybrids are great, and my company thinks the same. There needs to be an element of electrification, but you have to make some priorities and that is to move electrification and sustainability forwards. That’s the decision. We tested the engine on the track last year, it won’t be wasted.
There is a lot of open software here [in IMSA racing], but in IndyCar we want to give it more to the drivers. That is a different way of doing it. If you can improve the racing with the hybrid, that would be cool, and then that will promote itself.
Right now, the hybrid is hidden and we need to make it more visible as an energy to help you race. The first thing we have to do is create close racing. This year we set the fastest ever pole speed, so we are not doing too badly with the old 2.2-litre, but we have done a great deal of development to get it there.
This year we went two seconds a lap quicker at Long Beach, but no one talked about it. Let’s use the technology there to help the racing.
IndyCar racing is great, the Indy 500 is one of the greatest races on the planet… but there needs to be electrification at some stage. That is moving along… but it needs to move to the next stepThe decision as to whether the ARX-061 will go to Le Mans has yet
to be taken, and will come from Honda in Japanwhen it does Future development will concentrate on the hybrid, rather than the engine, as HPD believes that combination, along with a 100 per cent renewable fuel, is the way forward
Ford plans to discontinue production of its iconic Fiesta in mid-2023. This A-segment model not only won over entry-level drivers and two-car families alike, but also numerous World Rally Championship rounds. Shortly after it ends production of the Fiesta, the Blue Oval will also cease to market the Fiesta’s high(er) riding IC-engined sister, the Puma, which also enjoys WRC successes, as it switches to a battery electric range.
Given the direction the motor industry has been forced into by emission legislation, such developments are no surprise and likely to be emulated by most, if not all, manufacturers of A-segment models. As batteries add enormously to the basic weight and cost of
vehicles, sales are expected to plunge. An equivalent electric vehicle is expected to price 60 percent higher than fossil-fuelled equivalents that already provide slim margins of profit, adding pressure to manufacturers.
The bottom line for followers of the FIA World Rally Championship and its feeder series is that A-segment derivatives currently provide the core models for the WRC’s staircase, from Rally5 to Rally1. With the likelihood of model cut-backs in this sector, the very existence of the WRC is threatened unless the championship reinvents itself in something of a hurry.
Three manufacturers, including Toyota, Hyundai and Ford, are contractually committed to global motorsport’s governing
Current World Rally Championship models are being discontinued as electric mobility takes over the A-segment market. What does that mean for the WRC?
body, the FIA, throughout the current 202224 formula, but what happens after that, particularly given the accelerating changes in the automotive landscapes?
In addition to the issue facing the top class, Citroen, Opel, Peugeot, Renault, Skoda, VW are represented in lower categories, and all are also on the fast track to electrification.
Should they take the decision to also withdraw from competition such models as the VW Polo, Skoda Fabia, Peugeot 206 and Renault Clio, the impact upon the WRC’s feeder series will be significant. This in turn will affect the top category given that fewer crews will come through the lower cost ranks. In addition, manufacturer support is likely to decrease commensurately.
Clearly a rapid rethink is required. The championship’s major players, including the FIA, commercial rights holder WRC Promoter GmbH, the current three teams and some prospective entrants are, of course, totally aware of the situation. Indeed, they confirmed to Racecar Engineering during Rally Belgium in August that they are collectively investigating various solutions.
Fortunately, the current spaceframe concept whereby a percentile ‘top hat’ is fitted over the chassis in whatever shape or form a manufacturer elects provides a solid base, so the real conundrum lies in choosing the best power unit for the category.
This, though, is the hard part. For starters they face the now-standard choice of two power unit options, namely ICE or BEV. Thereafter it gets more complex. Within
these two categories there are a raft of further options such as range extenders, ICEs powered by e-fuels or hydrogen, potentially complemented by battery hybrid elements, or the powering up of batteries via standard electric sources or hydrogen fuel cells.
Compounding the issue is the point that virtually every prospective manufacturer has a different take on the energy solution of the future. Even where the stars align they are at different stages of development. Ask Ford about the future and the answer is likely electric; ask Toyota the same question and they are likely to point to the Prius hybrid or the H2 ICE-powered Yaris GR that ran selected demonstration stages in Belgium.
Hyundai would likely go with fuel cells, as would Honda were it to enter WRC, while if Audi (or another VW Group brand) joins the WRC Rally1 fray they will probably push for a range-extender solution as per the Four Rings’ Dakar entry. Then there are myriad Chinese electric-only brands who will surely one day be attracted into WRC at some level if the FIA chooses an appropriate powertrain.
There is another consideration that causes additional headaches for the decision makers. Rallies are usually staged through remote areas where the chances of finding sufficient high voltage chargers or hydrogen tanks are slim. Indeed, between their demonstration runs Toyota discreetly trucked the H2 Yaris to Brussels for gas recharging. Now consider a 20-50-strong field racing for three days solid through the wilds of Kenya, snow of Sweden or mountains around Monte Carlo.
Should they take the decision to also withdraw from competition such models as the VW Polo, Skoda Fabia, Peugeot 206 and Renault Clio, the impact upon the WRC’s feeder series will be significant
‘So far we’ve had a city car (Yaris), fivedoor hatchback (Hyundai i10) and a crossover (Puma) win this year,’ says Robert Reid, FIA Deputy President for Sport and world champion co-driver in 2001. ‘There is no reason why [the spaceframe concept] can’t be extended to other manufacturers, so I think we’ve got the basis of something [for the future].
‘By the end of this year, the target that I’ve given to the WRC people is to work out what [we need] for 2025.’ That might be an interim solution for 2025/6 followed by battery technology in 2027. Then, though, he adds another layer to the challenge: ‘There are also some manufacturers who are interested in coming now with something electric.’
The man tasked with the WRC overhaul by the FIA is the governing body’s Rally Director, Andrew Wheatley. Formerly Business Development Manager for Malcolm Wilson’s M-Sport operation which operates Ford’s WRC programme, the Briton is perfectly qualified to expand on the championship’s future plans from commercial, regulatory and manufacturer perspectives.
In an exclusive interview with Racecar Engineering, Wheatley says: ‘When you look back to 10 years ago, the talk was “Do we make it a two-litre, 1600cc; two-wheel drive or four-wheel drive?”
‘Now the opportunities are so wide you need to be some sort of mind reader to see what’s going on [in the automotive sector] and we have this huge opportunity at the FIA to be able to identify which products work best in which environment.
‘Electric was perfect for Rallycross as the events are run in heats. If you look at cross country, you have range extender, you have petrol, you have diesel, you have synthetic fuels, you have two-wheel drive, and fourwheel drive and they’re all competing in the same event. You’ve got vehicles derived from production vehicles and things derived from people’s imagination.’
The issue is, though, that cross-country marathons last for up to two weeks, whereas rally stages are short and sharp, with two cars finishing within a tenth of a second on the same stage. This year each of the three manufacturers has taken home top honours and any equivalence formula is unlikely to deliver the same level of intense competition. Thus, whatever is decided upon needs to tick all boxes, or WRC risk losing popularity.
‘If we want to try and keep that level of competition, we need to pick a technology and focus towards it,’ believes Wheatley. ‘That doesn’t mean to say that there couldn’t be different classes that could do different technologies, but at the pointy end of the competition there needs to be probably one technology. At the moment we are talking with the manufacturers that are both
the current stakeholders in rallying, and potentially future stakeholders to understand what their thoughts are.’
Wilson, who has been in the rally business as both a successful WRC driver and team owner for over 40 years, admits to genuinely not knowing the solution, pointing to the fact that ‘[Fewer] manufacturers are now producing a 1.6 IC engine that you can run in [feeder] categories. The clearest [solution] for me at the moment is probably Rally1, with what we’ve got now with this chassis, this safety cage structure.’
That implies rolling over the current regulations for another year or two, but that simply kicks the can down the road. The other issue is costs. Wilson is adamant that any WRC formula needs to reduce costs. Current Rally1 cars come in at more than 700 000 Euros, in line with the Toyota Hilux Dakar featured in the January edition of Racecar Engineering, but any new-fangled power unit technologies are unlikely to decrease costs.
That said, to delay the decision might lead to a wider the choice of powertrains available, and lower costs are likely given the present rate of change for alternate energies. Equally, WRC has to look at least five years
Racecar
‘You have to compare it to a standard GR Yaris, [and] the engine is different, there is more torque and maybe a little bit more power,’ he explained. ‘I was changing gears all of the time and it was going to rev limiter straight away, the response is good from the engine, surprisingly good.’
There was, though, a diesel-like ‘knocking’ after startup, which decreased as the four-cylinder warmed up.
Indeed, he admitted to being pleasantly surprised by throttle response, saying; ‘I thought it would be less [responsive] and lazy but it is quicker than the standard car, and there is no difference in engine braking because it is still [like] the petrol engine.’
Asked about the potential adoption of H2 in rallying and the wider industry, Akio Toyoda admitted that a lack of infrastructure was likely to be the main impediment. ‘Hydrogen or electricity, we kind of need some infrastructure,’ he said. ‘We have a hydrogen station in the only city of Belgium (Brussels), so we need some kind of infrastructure. However, if we move to this kind of power unit, if we continue with it and all the people feel the same [opinions], then we can make a future together.’
Kankunnen, though, believes firmly that hydrogen ICE is WRC’s future. ‘Rallies are too long for full electric cars plus they are very heavy and they have no noise, but if you have clean fuel like hydrogen, I think it will be the future for rallying,’ he said.
‘At the pointy end of the competition there needs to be probably one technology’
Andrew Wheatley, FIA Rally Director
is theEngineering quizzed four-time WRC champion Juha Kankunnen and Toyota President Akio Toyoda, who co-drove the car and raced one in Japan, about driving the Toyota Yaris H2 after they completed a set of stages in Belgium. The WRC has introduced hybrid technology this year, but it’s an interim solution and a more permanent solution must come soon
Mezzo Technologies is hiring a Business Development Manager with an engineering background.
Mezzo Technologies designs bespoke high-performance microtube heat exchangers for automotive, motorsports, aerospace, defence, and power generation sectors. The company is searching for a Business Development Manager with an engineering background to prepare proposal packages for a wide variety of projects and related business development activities. The successful candidate should be proficient in commercial and technical factors applied to the business of heat exchangers and will report to the Chief Operations Officer and Director of Engineering.
The role is in-house at the company's Baton Rouge, LA, USA HQ and requires travel to clients and prospects worldwide. The salary and compensation package are competitive and dependent on experience and performance. If you are interested in learning more about this career opportunity or applying directly to the role, contact us using the details below. From everyone in the Mezzo Technologies team, we look forward to hearing from you!
Kevin W. Kelly | President
Mezzo Technologies
10246 Mammoth Avenue, Baton Rouge, LA 70814
Email: kevin.kelly@mezzotech.com
Phone: (+1) 225 442 6965
ahead, yet cannot afford to be left behind through the wrong choices. But who knows, a miracle solid state 100kW battery weighing 200 kilogrammes may be on the horizon, as could be a sudden breakthrough on the e-fuel front.
Speaking to Racecar Engineering during the recent FIA Gala Awards evening JariMatti Latvala, team boss of the (double) championship-winning Toyota Gazoo WRC team, made no secret of the fact that his company’s future rally car would preferably be hydrogen-powered via an ICE engine as demonstrated in Belgium and raced in Japanese endurance events.
‘During Rally Belgium, we tested this H2 hydrogen car with Juha Kankunnen and [company boss] Akio Toyoda,’ said the Finn, himself a former 18-time WRC winner. ‘Whenever we think about sustainability, for sure we have [taken] great steps in motorsport with these hybrids and with e-fuels, but if we think about the future, and we need to think about it, I believe that hydrogen could be one option.
‘But is it ready in three four to years’ time? I’m not sure about that and I can’t give you an answer about how many years it could take, but it certainly has potential because I was myself driving on the Fuji race circuit this season with the H2 Corolla.
‘When you have an internal combustion engine which is like in a [current] rally car but it is working with hydrogen I think this is a great way to continue with a motorsport [category] which has the sounds and you have the same [sensation], with a proper engine but zero emissions.’
extending the current formula for another year. ‘There are several options for 2025,’ he admits. ‘First of all, we [could] extend the current regulations with a combustion engine and wait for a few more years to maybe give us some more time for a bigger step with new technology.’
The Frenchman believes that a ‘more efficient or more powerful hybrid system than is currently available could provide a better balance between a combustion engine and electric, like [future] Formula 1 it could be 50/50.’ But he admits some current and potential entrants would prefer to go down the full electric route sooner rather than later.
‘I guess most of the manufacturers would have interest is that right now, but we [WRC] are not ready for that in 2025. Maybe in the future or longer term, but not right now,’ he says, adding that the teams need to work with the FIA to develop even better sustainable fuels as a matter of priority.
Asked about hydrogen, Moncet references fuel cells. ‘It is an area we have an interest,’ he says. ‘Our brand is investing a lot and is quite active with hydrogen fuel cell technology, but we have as well the hydrogen combustion engine technology.’
Although the parties currently have divergent thoughts about the future of WRC, they do agree that they need more than three manufacturers. However, where does the optimum level of ‘works’ entrants lie? ‘I’ve worked for 25 years in WRC, and I’ve seen where we’ve had two and I’ve seen where we’ve had seven,’ says Wheatley. ‘For me, the
best was when we had four; five is great, because it’s an insurance.’ Crucially, he adds that when there were seven entrants, three failed to score a podium. It is vital that all teams are in with a chance. ‘Otherwise, if you haven’t got a podium finish, it’s incredibly difficult to go back and justify to your board of directors why the company is doing this.’
Therein lies the crux. Any new powertrain formula needs to attract more manufacturers and create a larger fan base, particularly among emerging audiences, via a better spectacle delivered by relevant technologies. These targets are a massive ask, but the biggest challenges facing the WRC are to achieve these targets while simultaneously reducing costs of entry and operating budgets in the face of new technology.
According to regulations a final decision needs to be taken within the next three months. The chances are therefore that the current rules are extended for another year whilst the optimum solution is sought.
Our brand is investigating a lot and is quite active with hydrogen fuel cell technology, but we have as well the hydrogen cumbustion technology
Hyundai WRC Team’s Deputy Team Principal Julien Moncet
How and why a proposed budget single-seater formula has morphed into one of the world’s first club level electric racing seriesThe Formula Foundation FF-E1 made its public track debut at Brands Hatch during the Formula Ford Festival in the autumn of 2022
The pit garages on the Saturday of the Formula Ford Festival weekend at Brands Hatch in late October were occupied by cars from the Modified Ford Series, a wonderful collection of bewinged and fat ’arched Escorts and other Blue Oval favourites, all supporting the main event. Except for one garage, that is, within which sat a racecar that could not be further from a flame-spitting Sierra Cosworth in looks, concept and certainly sound. That car was the Formula Foundation FF-E1 electric racer, which was to complete a few demonstration laps in the lunchbreak.
Regular readers will be familiar with Formula Foundation, because Racecar featured its proposed entry-level racer, the RSR 001, in the V32N6 issue. For those that missed it, this was a car designed to be cheap and easy to run, the sort of thing – to use a term favoured by its builder, RSR Technology – a dad and lad could campaign successfully throughout a season of racing.
The car featured a standard, transverselymounted, 1.6-litre Ford Sigma SE engine and gearbox, which could be picked up very cheaply, even from a scrapyard, and simple, cost-effective outboard suspension. Many of the other components could be sourced at a reasonable price from local motor factors. The wheels and brake discs, for example, were from a Mini, while the single radiator was Vauxhall Corsa in origin.
The only really hi-tech element was the spaceframe, designed on CAD and constructed from T45 and ROPT CDS aerospace-spec steel, incorporating Diolen side-impact panels for extra protection.
Interest in the RSR 001 was initially very high, yet it proved difficult to sell the car in the UK. This led to a bit of an epiphany at RSR, a recognition that perhaps the days of parent/ child running a car might be over.
‘We realised that things have changed, and people don’t seem to want to buy cars and run them themselves any more,’ says Richard Huddart, who is a partner in RSR with former Formula Ford builder, Steve Wills. ‘There are plenty of kids who want to race the petrol car, but they don’t want to buy it. These days they just want to turn up and drive.’
Building a fleet of Formula Foundation cars to run a series centrally was beyond the capacity and means of RSR, and it looked unlikely teams would buy the cars without a championship to race them in. Yet it also seemed there was simply not room for another junior single-seater series on the British race calendar.
‘It’s just the commercial marketplace,’ says Greg Graham, head of formulae development at the BRSCC. ‘As a club, we understand the marketplace and what opportunities are out there, what might work and what might not. We were approached with a view to try and introduce the petrol car as a junior formula for 14 to 16-year olds.
‘But understanding how the junior market works, and how it’s governed as far as licences being issued by Motorsport UK [the British governing body], we knew that was a bit of a non-starter. So we advised Steve and Richard from RSR that this was the case.
‘However, that didn’t deflect from the fact that the car is absolutely stunning, the chassis had been built to a proper top standard and a lot of engineering expertise had gone into it.’
There was, however, another potential way, which was briefly explored in a box out in Racecar’s original feature.
‘There were a number of conversations, and somebody mentioned the electric word, and it sparked our imaginations,’ says Graham.
From there, the electric project came together remarkably quickly, helped by the fact that work had already begun on the concept – which originally was seen as just another version of the RSR 001 and perhaps an avenue to explore further in the future.
So, in autumn this year, the electric version of the car was unveiled at Croft, with the BRSCC announcing that it hoped to run demonstration races in 2023 and a full championship in 2024 – the first electric single-seater series at this level.
Since then, there has been plenty of interest ‘from credible people that want to race EVs,’ says Graham enthusiastically. ‘We wouldn’t have asked the guys to invest time, effort and energy, and also our own resources, if we didn’t think there was a marketplace.
‘And after the launch, we are hugely confident there is, and not from people that race other things, other formulae, these are people that simply want to race EV.’
This is perhaps the most interesting thing to come out of the whole project so far.
With the compact electric motor and battery box on board, weight distribution is said to be close to that of the original ICE version, although overall car weight has increased by around 50kg. To compensate, power output has increased by approximately 40bhp
We are hugely confident there is [a market], and not from people who race other formulae, these are people who want to race EV
‘It seems that there is a community of motorsport enthusiasts that have no interest in racing petrol cars,’ Graham continues. ‘So they’ve got nowhere to race. Some of them have been involved in electric karting because they chose electric karts over petrol karts, and the next step is Formula E, almost, as far as competitive EV racing is concerned.
‘That community, that marketplace, these youngsters, in general, have been getting in touch and they’re desperate to know what the next steps are, desperate to know how to become involved.
‘It’s people that want to drive an electric car, but they wouldn’t dream of driving an F4 or a GB4 or a Formula Ford,’ Graham adds. ‘They don’t want that. It seems the marketplace is going to come from people who have grown up with electric cars. Their mum and dad have an electric car, they’ve never owned a petrol car. That’s possibly a mindset thing, but it doesn’t stop them being motorsport enthusiasts.’
The car this new breed of racer will drive does differ from the original Formula Foundation offering, and not just in terms of the power source, for while safety was always a priority, things have stepped up a notch.
So, along with the existing front and rear crash structures, which go beyond FIA requirements, eight tonne-rated wheel tethers have been fitted on all four hubs and, most noticeably, a Halo has been attached – a first for a tube-frame single seater.
‘That’s one of the things we’ve instigated through Motorsport UK and the FIA, because there has never been a Halo fitted to a steel spaceframe chassis before,’ explains Graham. ‘So there isn’t a regulation, currently, that states how you test it, what the loading should be, what it should do. Motorsport UK are assisting us and we’re in constant dialogue. They are assisting us to re-define, or re-write, the rulebook. And that’s a work in progress.’
The wide nature of the original spaceframe chassis facilitated the mounting of the Halo, which is made from T45 steel, and also helped when it came to fitting the various components of the electric powertrain. ‘Fortunately, because we had a transverse engine and gearbox in the petrol car, which made the rear quite broad, all the electric stuff fits in,’ says Huddart. ‘We were very lucky in that sense.’
The electric package has been developed by Nick Mason of ECOClassics, a company that converts classic cars to electric. Amongst its work is a Lotus 11 (Mason’s own car), Jaguar E-Types, Mustangs and Land Rovers. Mason also led the development of Ford’s E-Transit electric van, so he knows his stuff.
At the heart of the new drivetrain package is a 120kW motor and inverter from China,
of which ECOClassics is the sole importer, marketing it here in the UK as a Torq-X.
‘It’s a production car part that we use in a lot of our conversions,’ confirms Mason. ‘It’s coupled up to an inverter, so you take the DC out of the battery and invert it into AC. It’s a three-phase AC magnet motor, and it gives about 160bhp.’
That power is transferred through a clever yet simple transmission system. ‘It’s direct drive,’ says Steve Wills. ‘It goes through one reduction gear, and then another reduction into the final drive, so it’s twin-stage reduction, about 6:1 ratio. The motor runs at 12,000rpm, whereas the wheel speed is around 800.’
The car is said to be capable of reaching 60mph in three seconds, with no pause for gearshifts, of course. ‘It’s just one single speed,’ confirms Mason. ‘We can reach a top speed of about 135mph, just on the one ratio. And we get about 1800Nm [of torque] at the driveshaft.’
Which has meant uprated driveshafts, but otherwise there wasn’t that much, beyond the entire powertrain of course, that needed to be changed to make the RSR 001 into the FF-E1. In fact, even fitting the battery pack proved to be less problematic than expected, though this has also contributed to a weight gain from just under 500kg to 550kg.
‘The modules weigh about 11.5 kg each,’ explains Mason, ‘and there are nine of them. So, with the battery box itself, that’s probably 125-130kg of the overall weight.’
The 18kWh, 350V, DC, Li-ion battery pack is steel encased and designed to meet ECE R100 requirements. Because the pack fits just behind the driver’s seat, the balance of the car has not been affected much, especially as it all sits low down in the chassis. ‘The batteries are right behind the driver’s bum,’ notes Wills.
‘They are arranged in rows of four, then there’s three, and then there’s two. That’s how we’ve kept the weight as low down and as forward in the car as we can.’
Indeed, we’re told that when you lift the car at the roll hoop, it still dips at the front.
‘We did a lot of mass calculations about where the central mass moves, and it’s not that different [from the petrol car],’ confirms Mason. ‘If anything, it’s a little bit further forward, because you have got quite a bit of weight in that battery pack, which is mounted closer to the front.
‘The engine was obviously quite a long way back, and that weighs a lot more than the motor, which is only about 40kg. So you’ve got rid of all that engine weight there.’
As for the batteries themselves: ‘We use pretty standard production car parts, again, in terms of the battery modules,’ says Mason. ‘We arrange it so we get 450V peak, so it basically runs between 350 and 450V. Most cars run a little bit less than that, maybe 420V, but we managed to push it up a little bit. We get more power that way.’
Those words will be music – albeit very quiet music – to many drivers’ ears, as will the possibility of playing with regen’ during a race, which could offer a multitude of strategy and race craft options.
‘The regen’ comes back though the gearbox,’ explains Mason. ‘As you lift off, the wheels are driven by the momentum of the car, and that goes back through the gearbox into the motor, and then the motor becomes a generator, rather than a motor.
‘But we can control that level of regen’, so we can demand a certain amount of torque out of the motor. You can generate more electricity, but then you start to slow down.
Chassis:
aerospace-grade
10mm
Diolen
Bodywork: GRP body,
Power: Torq-X 120kW motor and inverter. ECE R00-compliant 350V (450V peak) DC Li-ion battery pack with 18kWh useable capacity
Transmission: Bespoke power transfer unit and differential Suspension: Double wishbone front and rear; two-way adjustable Protec 600 Series coilover dampers fitted outboard; eight-tonne rated Technora wheel retaining tethers on all four hubs; collapsible steering column; lightweight aluminium steering rack
Aerodynamics: Single-plane, partially adjustable front wing; rear wing with space for extra elements; possibility that rear diffuser will be developed
Wheels and tyres: 15in Mini wheels; Hankook treaded tyres
Brakes: 290mm discs; Wilwood aluminium four-pot front and two-pot rear calipers; bespoke stainless steel pedal box
Dimensions: Front track: 1727mm; rear track: 1720mm; wheelbase: 2412mm Weight: approx. 550kg
The idea is we want to give the driver some level of control over that. In effect, it becomes an electronic brake balance.
‘If we were to put full torque reverse in you would lock the rear wheels on regen’. So it’s getting that balance. If the competitor uses that regen’ well, they will get an advantage, because they will have more battery voltage. And power is proportional to battery voltage.’
Because of the extra torque and power –up 40bhp from the 120 on the ICE car – there is a strong chance more aerodynamic devices will be added as the FF-E1 is developed. At time of writing, the electric car featured the same adjustable, single-plane front wing as the original version, though it appears to now have larger end plates, plus the same small, fixed rear winglets, but there’s also a proper rear wing on the car now, with plenty of room to add more elements as required.
‘We can go mad on aero if we want to,’ says Wills. ‘I’m thinking of putting a diffuser on the back, as we could tweak the chassis rails to fit one. It’s got a little rear wing on the back now too, and we can certainly enhance the aero there if we want to. And we may have to.’
While bolting on aero is good old fashioned racecar engineering, running a Formula Foundation E is sure to be a very different proposition to running an ICE car over a race weekend. The main diference is these cars will need recharging between qualifying sessions and races, and between races if there are two a day, which is quite common at UK club events.
‘It takes about two to two and a half hours to charge it because it’s only got a 7kW onboard charger,’ says Mason. ‘We did talk about doing fast charge – we could charge in 15 minutes [using a CCS DC system] – but then you need an array of fast chargers and the capacity on site to actually charge them. If you have 20 cars, that’s a lot of power you need over 15 minutes. With cars charging over two hours, the call on the electrical infrastructure of the circuit is significantly less.’
The car can be charged via 240V 32A outlets, so it’s like plugging in your laptop.
One complication here is that while there’s usually at least two hours between sessions, the safety regulations for electric racecars state you cannot work on the car while it’s charging. So, if you have picked up damage in race one, or if you want to make a set-up change after qualifying, you will have to factor the charging time into your schedule.
Handling the cars on track also requires a bit more thought, with the safety of marshals and recovery crews of particular importance. Fortunately, the UK’s governing body, and its technical commissioner, Roger Ratley – a man who has worked closely with RSR and the BRSCC in recent months – are on top of this.
‘Motorsport UK and the marshalling community have put together training programmes and info packs in preparation for electric car racing,’ says Graham. ‘Now that’s in its infancy, and we’ve kind of pushed that process ahead a little bit by what we’ve introduced. So while there are potential gaps in the people that have been trained so far, we’ve opened a dialogue with Motorsport UK to assist them and us in understanding what else needs to be in place. The main thing is there are no massive hurdles to get over because it’s all been pre-planned. But until now nobody’s actually said, right, we need to utilise these services now.
‘For example, at Brands Hatch [for the demo run], we had to make sure all the marshals were briefed on the car ahead of the weekend,’ Graham adds. ‘We needed to make sure the recovery crews had the
front wing is the same as on the original ICE car, but there’s now also one at the rear, while there are plans to add a diffuser, too
right equipment, which means specialist equipment for dealing with high voltage cars. It’s quite a complex process, but it all exists.’
It seems, then, that Formula Foundation E has covered all the bases. But there is a rather large elephant in the room, and that’s the price. While the earlier ICE car was offered for £40,000, this version is close to £80,000. There are sound reasons for this, which go beyond the considerable expense of going electric.
‘The car is not an unsophisticated piece of kit, even without the electric drivetrain,’ says Graham. ‘It’s a properly built steel spaceframe chassis, and it isn’t cheap to build. It will be put through FIA crash testing next year, and it will pass FIA crash testing, because it’s been designed to do so.
‘Even with the petrol engine, it was going to be a £40,000 car. Now that raw materials have increased in price substantially, you can add another 10 to 15 per cent without even speaking about the electric system.’
But even if the initial outlay is large, teams will be able to make big savings with the low running costs, with no fuel or engine and gearbox rebuilds to worry about, for a start. On top of that, the car will come with a twoyear battery and motor warranty.
‘Those batteries will go on for years,’ says Wills. ‘So, where we’ve got a high initial purchase price, the running costs, other than your damage and your motorhome or whatever, should be extremely cheap. We’ve also kept a lot of the ethos from the petrol car and carried it over to the electric car. I think that’s what excited the BRSCC. They can see we have tried hard to not make it expensive. You can buy discs from Halfords, for instance.’
There is another cost-related element to this, though, and that’s how attractive a green
head of formulae development at the BRSCCracecar might be to prospective sponsors. ‘Because it’s an EV, people are confident they can go and get sponsorship that might not be able to support them with petrol cars,’ says Graham. ‘Different types of sponsorship, too. That’s another thing that’s coming through, that interested parties seem to think it’s an easier route to try and gain sponsorship and support because it’s an EV.’
It is still early days, but it’s hoped that six cars will be delivered to customers by the spring and, as mentioned earlier, RSR and the BRSCC say there has been plenty of interest
‘We have a nice project that we think the market needs and the market is going to demand,’ says Graham. ‘And so far the feedback is that there is a demand. Because there’s nothing globally that allows people to come and race at this level in an electric car.’
But maybe the best indicator is the reaction of people you might assume would not be interested in a car like this: those fast Ford-driving, fire-in-iron denizens of the other garages on pit row at Brands, for instance.
Suffice to say, Racecar heard a ‘wow’ or two when they set eyes on the Foundation FF-E1. Unscientific feedback? Perhaps. But possibly still a positive sign that the UK club scene is ready for electric racing.
‘It will be put through FIA crash testing next year, and it will pass FIA crash testing, because it’s been designed to do so’
Greg Graham,
Much has been made of the way in which cars of the future are powered due to the focus on emissions from the tail pipe, but there is so much more to having an enviromentally sustainable car. In this special issue we highlight the full range of advances that have been made by racing companies through their motorsport activities. We look at the major advances in efficient motors, battery storage, using natural fibres instead of carbon fibre, and also at how the tyre companies involved in the FIA World Endurance Championship have focused their attention on producing less enviromentally impactful products.
In doing so, Racecar Engineering has highlighted the effect that racing can have on a wider community. Racing is about prototypes, experimental machines that can be used to test new technologies and this is where the organising bodies have headed. Now in most major FIA World Championships there is some form of electrification, be it hybrid or full electric. Yet in others, notably in the US, series have yet to take on this technology and are looking in other areas to maintain the relevance of racing. On the track, particularly in Europe, companies are working hard to bring evolving technologies to a level that they can be proven to work or discarded as unworkable.
There is so much more to the impact a car can have on the planet than what is put in the fuel tank, or how far a battery can take the car. We do look at the options that are available for powering our cars, including hydrogen and synthetic fuels, but we also take a look at weight saving ideas, as weight is the biggest penalty that can be caried by a vehicle. While we worry about the fuel and emissions, we are also as a society buying heavier and bigger cars.
Evolution of a Racecar is not an exhaustive product, but it is intended to highlight the impact of the whole car, and get our readership discussing the full range of options that are available, and what has to be done to maintain our transport needs.
Order online at www.chelseamagazines.com/evolution-of-a-racecar, priced at £9.99 including postage and packing (UK only), $19.99 including postage and packaging (US).
When Ford broke with the AMA agreement and went racing, Chevrolet lost no time preparing its counterattack. In the vanguard was Zora Arkus-Duntov with the radical CERV II
This amazing, four-wheel drive automobile was conceived in the autumn of 1963 as a contender for victory in the great international long-distance races. Styling staff marked the official beginning of project XP-817, as it was known, as 27 September 1963.
A year earlier Ford had unveiled its midengined Mustang at Watkins Glen. It was an early stage of Ford’s Total Performance initiative, openly promoted as the forerunner of a future Ford sports racer designed to compete on the world’s great racetracks.
Ford’s negotiations to buy Ferrari for this purpose hit the buffers in February 1963. And so, on 1 July that year, the company hired the exclusive services of British racecar manufacturer, Lola, to help build a car that could wave the Ford flag higher than Ferrari’s at Le Mans in its world famous 24-hour race.
For Chevrolet, this was a step too far. Chevy boss, Semon ‘Bunkie’ Knudsen immediately approved the plans of his
Corvette head honcho, Zora Arkus-Duntov, to show the Bow Tie could fly the flag higher still.
CERV II, as this car became known, wasn’t the first Chevrolet Engineering Research Vehicle II. The same name was given to a rearwheel drive spaceframe roadster conceived in 1962 to compete in long-distance racing as a 4.0-litre prototype. It never progressed to the metal, though, the lightweight Sting Ray Grand Sport being built instead.
Chevy’s plan for the XP-817 called for the building of one prototype, plus five racecars. These were to be ‘purchased’ by well-established teams to take to the races, where they would enter them at arm’s length from Chevrolet to evade GM’s management policy of non-racing, in a similar way to how such teams were also entering race-prepared Chevrolets into NASCAR races.
At that time, the World Sports-Car Championship posed no limit on engine size.
This meant Duntov, his designer, Walt Zetye, and technicians Bob Kethmann and Ernie Lumus could think big with the engine. Their choice was one of the most exotic V8s in Dr. Duntov’s capacious cabinet of power.
The very special aluminum engine had a single overhead cam on each bank, driven by a train of gears in pure race engine style. The cams operated two valves per cylinder through rocker arms, feeding hemispherical combustion chambers.
Displacing 377ci, or 6.2-litres, this V8 was developed to produce more than 500bhp by Duntov’s engine team of Cal Wade, Fred Frincke and Denny Davis. While it was being tested in parallel, the engine actually used in the CERV II was a different all-aluminum, 377ci unit with pushrod valve gear like the ones used in the 1963 Grand Sport Corvettes. In fact, the engines, and other components in those GS cars, were being evaluated in the December races at Nassau to determine their suitability for the CERV II project.
The power unit installed in the CERV II prototype was fed fuel by Hilborn constantflow injection instead of the multiple Weber carburettors used in the Bahamas. This allowed methanol to be used so the output of the overhead cam V8 could be simulated during development of the new car’s chassis.
Putting this prodigious power on the pavement was the next requirement. Thanks to Duntov’s close relationship with Firestone, the CERV II was able to use the most advanced racing tyres then available. Duntov was the first engineer outside Firestone to test the new, wider, low-profile tyres it was developing late in 1963 for the 1964 Indy race. He found them highly adhesive and gratifyingly forgiving of driver error.
Duntov chose the 9.50 x 15 size for all four wheels, on 8.5in rims cast of magnesium by Kelsey-Hayes. Knock-off hubs were fitted with the long-distance races in view.
All four wheels and tyres were identical because Duntov had decided to equip the CERV II with four-wheel drive. The Belgianborn, Berlin-educated Duntov had been thinking about various ways of driving all four wheels since he saw the 4WD Bugatti Type 53 win a standing-start sprint event in 1935. However, as the Bugatti was so strong on the straights but so poor in the corners, Duntov reasoned that there must be some way to combine good handling with the fine road grip given by four-wheel drive.
Consequently, in 1937, he presented some of his thoughts in a technical paper on four-wheel-driven racecars.
By 1963, though, the first great wave of enthusiasm for 4WD racecars was still half a dozen years in the future. Duntov elected to use it because his calculations showed it could provide a higher cornering speed, as well as much-improved acceleration with a very powerful engine, more than offsetting the 125lb weight handicap.
Compact and purposeful, the CERV II was packed with innovations that could have made it a formidable competitor in long-distance races for which it was designed
Early in the 1960s, Chevrolet’s Research & Development department had been doing experimental work with torqueconverter transmissions in racecars that led directly to the Chevy-built unit used in the Chaparrals from 1964 onward. Duntov had planned an automatic transmission for his 1962 CERV II study all along, but it was a pure mechanical, power-shifted gearbox. Considering the torque converter approach less efficient, though admittedly far simpler, Duntov saw he could use it for his new car, which would be generously powered for its 1900lb design weight.
Duntov took a further big step with his concept, deciding to drive the back wheels through one torque converter and the front wheels from the front of the engine through another one. It was a completely new principle on which Duntov lodged a US patent on 23 June 1966.
Duntov elected to use [4WD] because his calculations showed it could provide a higher cornering speed, as well as much-improved acceleration with a very powerful engine
Not pretending to be a torque converter specialist, Duntov presented the parameters of his proposed driveline to the experts on GM’s engineering staff. As planned, the CERV II (or GS-3, as it was by then known, and later GS-10) had a static front / rear weight distribution of 46.5 / 53.5 per cent. With a c of g 14in high, the proportion of weight on the front wheels would drop to only 32 per cent when the car was accelerating at 1g, which was well within its capability.
‘What I want,’ Duntov told the transmission experts, ‘are torque converters that will deliver 35 per cent of the engine torque to the front wheels at low car speeds and up to 40 per cent at higher speeds.’
Excepting schemes that use separate engines to drive the front and rear wheel pairs, this was the first time anyone had tried to achieve a variation in the front / rear torque distribution of a four-wheel-drive car while it was in motion. Engineer, Raymond P Michnay, took on the job and handled it to perfection.
At the back of the engine, driving the rear wheels, Michnay specified an 11in Powerglide torque converter, modified so it didn’t approach a locked-up, or nearly 1:1, drive condition until 4500rpm. Then for the front wheels he provided a 10in converter from a Corvair Powerglide, placed ahead of the front-wheel centreline just as it was ahead of the Corvair’s rear wheels. It was rotated in the same sense by the universal-jointed shaft running forward from the front end of the crankshaft. The front converter approached lockup at 4100rpm.
Performance calculations showed that with a low final drive ratio, the CERV II would accelerate from zero to 60mph in 2.8 seconds, and reach a top speed of 115mph. With a higher ratio, maximum speed would go up to 183mph, though the time to reach 60 would be much longer, about four seconds.
Deciding to have the best of both worlds, Duntov equipped both axles of CERV II with compact two-speed gearboxes like those used in the Chaparrals through 1965.
Controlled by a single cockpit lever, the gearboxes gave a direct drive and a 1.5:1 reduction. With a 3.55:1 axle ratio, this gave speeds of 107mph in low and 160 in high, at 6500rpm, taking into account three per cent slippage in the converters above 6000rpm.
The gearbox at the front had to be specially made with concentric shafts that allowed the torque converter to be overhung at the front of the chassis.
Though a limited slip differential was made for the rear-wheel drive, it was never used. Open differentials were kept at both front and rear. Open driveshafts to the wheels had Hooke-type universal joints outboard at the rear, CV joints at the outer front ends.
Inboard ends of all four driveshafts had conventional pot-type universal joints that allowed plunging movement of the shafts as the suspension flexed.
Unlike many 4WD cars, no attempt was made to mount the brakes inboard. Instead, Girling wheel cylinders were adapted to wider caliper bridges to accommodate ventilated brake discs at the wheel hubs.
The suspension design for CERV II was disarming in its simplicity.
‘The front roll centre height is about 3.5in,’ said Duntov, speaking at the time of its parallel wishbone layout. ‘That’s a standard number with me. At the rear, it’s about three inches above the ground.’
Trailing radius rods locating the rear hub carriers and reversed wishbones were angled to give a mild anti-squat effect.
On a four-wheel-drive car there’s a tendency for the front to lift under the direct influence of drive forces. To counteract this, Walt Zetye built an anti-lift effect into the front suspension design by inclining the axis of the lower wishbone pivots upward toward the rear at an angle of eight degrees.
Unusual on a car intended for racing were rubber bushings for the inboard wishbone pivots. Duntov felt they should be used for their simplicity and shock absorption capability where the design didn’t demand a hard-surfaced bushing.
CERV II’s rear hub carriers were machined steel and those at the front made of cast nodular iron with forged steel steering arms. Outer balljoint locations at the front were angled to give a steering axis that intersected with the ground three inches inboard of the centre of the tyre patch.
Concentric coil springs and adjustable Armstrong dampers were fitted at all four wheels. Their placement at the front provided
‘What I want are torque converters that will deliver 35 per cent of the engine torque to the front wheels at low car speeds and up to 40 per cent at higher speeds’
Zora Arkus-DuntovA single overhead camshaft on each cylinder bank operated the inclined overhead valves of the 377ci, all-aluminium V8 designed and built to power CERV II. Sadly, this too never had a chance to strut its stuff on the racetrack Gear trains from the crankshaft drove the overhead cams of the 6.2-litre V8 intended to power the CERV-II in endurance racing. A patented feature, the paired gears on each side allowed their running clearances to be fine tuned A section view of CERV II showed the sliding inboard universal joint and lower wishbone angle that helped lift its roll axis height
an abject lesson in the packaging of a lot of machinery into a very confined space.
Ahead of the front suspension was rack and pinion steering gear, built by GM’s Saginaw division to Duntov’s requirements. It required only 1.8 full turns of the steering wheel from lock to lock.
Fabricated steel arches carrying the front suspension components were welded to the monocoque tub, adopted instead of the tubular spaceframe used for the 1962 design study. Like that of Ford’s GT40, the CERV II’s tub was fabricated from sheet steel, 0.025in thick instead of the 0.024 and 0.028in thicknesses used by Ford. The tub began at the footwell, extended back around the fuel cells at the sides, where it was stiffened by glued-on aluminum braces, and ended at the transverse firewall behind the seats.
From the firewall to the rear, the big V8 was the major frame member, a design technique that later became commonplace but was then rare and adventurous. The engine was attached to the firewall at the front and to a 2.5in transverse tube at the back, above the rear torque converter, this being further braced by two 1.0in tubes at each side of the engine.
Initial tests in torsion showed the complete frame structure was well below par with a stiffness of 2000lb.ft per degree. With the curve of frame deflection in torsion showing a sharp break through the engine area, measurements of the engine’s cylinder bores showed they were being distorted significantly by the application of torsion to the frame. The addition of a four-legged tubular brace above the engine raised stiffness to the more satisfactory level of 5000lb.ft per degree, though even this was less than half the 12,500lb.ft figure quoted by engineers at Ford for its GT40.
From the firewall to the rear, the big V8 was the major frame member, a design technique that later became commonplace but was then rare and adventurous
At the time CERV II was created, driving positions were sinking lower and lower to reduce the frontal areas of the power poor, 1.5-litre Formula 1 cars. Duntov decided not to cater to this trend because his car was designed to do its job at relatively low speeds, through better acceleration and cornering, and would have a plethora of peak power with which to generate any required maximum speed.
Using a more upright seating position allowed Duntov to keep his car short, with just a 90in wheelbase and 157in overall length. Front and rear tracks were set at 53.5in and overall width at 66in.
Around CERV II’s upward-ducted front radiator – a Duntov feature dating from the Corvette SS – and built-in rollover bar, Larry Shinoda and Tony Lapine in Styling’s underground studio came up with a bold body shape. For the German-born Lapine, this was one of his last major projects before he returned to Europe, to Opel, later becoming director of styling for Porsche.
Their roadster shape executed in glass fibre had a low, peaked nose and indentations at the rear, with ports for the twin tuned exhaust pipes part of the original plan. Quarter-scale models were tested in a California wind tunnel to refine the shape before the full-size contours were confirmed.
Initial tests showed the body worked well. Only a slight curve in the front windscreen was needed to deflect air completely clear of the driver. However, after high-speed trials showed instability, a spoiler – called a ‘cow’s tongue’ by Duntov – was fitted at the rear, protruding from the transverse slot in the engine cover in such a way that it could be deployed when needed. This made CERV II
entirely stable at the 214mph it reached on the Milford five-mile track with a high final drive ratio and the 377ci pushrod engine.
The designers also modelled a coupé version of the CERV II. This had its water radiators mounted in its rear quarters, requiring substantial scoops along the sides of the cockpit. This alternative design allowed the nose to be lower and sharper.
CERV II first rolled on its four driven wheels in March 1964. In early tests at Jim Hall’s private and well-instrumented Rattlesnake Raceway at Midland, Texas, in comparison with the rear-wheel drive GS-2 (forerunner of the Chaparral 2C) built by the Chevy R&D department, it didn’t show to its best advantage for several reasons. The special two-speed gearbox for the drive to the front wheels hadn’t been completed, so it could muster only a single ratio. Its brake discs were also at the time an experimental – and, as it turned out, unsatisfactory – forged aluminium protected by sprayed-on facings.
During the tests at Midland, the CERV II was tried by Jim Hall and Roger Penske. Both found its traction and handling very impressive. Penske, in particular, liked its driving position and said he was unable to detect any sensation that the engine was powering the front wheels as well as the back ones. At the limit in a turn, the CERV II did require an unorthodox technique because releasing the throttle tended to cause a fast flat spin. Up to that point, however, its tyres and drive system made this the only road racer of its era that could make full use of a very large engine and horsepower well in excess of the 500 level.
In the on / off cycle of attitudes toward racing that prevailed during the Bunkie Knudsen regime at Chevrolet, the stop light facing CERV II turned from green to red late in the summer of 1964. Chevy decided it didn’t want to pose an open challenge to Ford at Le Mans (though later it did offer opposition, indirectly, with the 2D Chaparral in 1966
Fed by a specially developed, constant flow fuel injection, the chain-drive version of the 377ci V8 developed 545bhp at 6000rpm and 512ft.lb of torque at 4800rpm
and the 2F in 1967) and another promising Duntov idea came to a ‘screeching halt.’
Several years later, for tyre tests conducted by Corvette development driver / engineer Bob Clift, CERV II was fitted with an allaluminum ZL-1 engine of 427ci displacement. It carried a single four-barrel carburettor and individual exhaust stacks, both fitted for maximum operating ease rather than ultimate performance. External piping from the rocker covers drained oil to its wide wet sump with a swinging oil pick-up. Wider rims allowed 10.50-15 tyres to be fitted.
With this powerplant, CERV II went back to Rattlesnake Raceway to take part in tests when Chevy’s R&D Department was assessing new design approaches for the Can-Am series, then in full flow. Weighing several hundred pounds more than R&D’s version of a Chaparral, though, it was significantly outperformed. Duntov, who hadn’t been able to attend the tests, never got over the feeling that his brainchild had deliberately been disadvantaged in some manner.
Although the prototype’s ability to make full use of a big engine, thanks to its four-wheel drive, was well in advance of its time when it was conceived, it had been impossible to foresee that the Goodyear / Firestone tyre wars would soon produce rear tyres so wide that all-wheel drive wouldn’t
give an advantage for road racing. The CERV II’s design didn’t allow it to run the latest wide rims at the rear, so it was denied this chance to exploit its attributes.
Nevertheless, the CERV II’s torqueconverter propulsion was shrewdly thought out and striking in its logic and effectiveness. Considering its primary mission was longdistance racing, in which weather conditions often influence the outcome, such a system might have been useful. Not least because it would have allowed the use of narrower tyres that were less likely to suffer from aquaplaning on a wet track.
In the form you see here, with its blue and white livery, CERV II was first revealed to the world by this author in the November 1970 issue of Motor Trend. Though it never took part in a race, CERV II was spurred into being by the pressure of competition. As such, it made a valuable contribution to the evolution of the Corvette, and Duntov would take full advantage of what he’d learned with CERV II in his future Corvette designs.
The CERV II’s torque-converter propulsion was shrewdly thought out and striking in its logic and effectivenessAfter high-speed testing showed instability, the CERV II was equipped with what Duntov referred to as a ‘cow’s tongue’ rear spoiler during its development to give it the stability required Another version of the 6.2-litre V8 had a wider vee angle for its inclined overhead valves and chain drive to its single overhead cams
While plain old steel continues to have its place, developments in manufacturing processes and new material technologies are opening up the materials market in ways we never could have imagined.
Materials development has been intrinsic to the advancement of racecar technology since Count Jules-Albert de Dion chugged into Rouen in 1891, to win the world’s first motor race. Materials science has been a key enabler in the realisation of many an engineer’s ideas, which more often than not have outpaced the capabilities of whatever is the ‘current’ state-of-the-art for materials. One only has to look at the the Lotus 88 and McLaren MP4/1 with their carbon chassis, which re-defined the application of fledgling composite technology.
It is, however, easy to give motorsport too much credit, as in the world of industry it is something of a minnow. Aerospace, for example, is responsible for some of the
biggest developments thanks to budgets that dwarf even the most lavish spenders in racing. Wars have also played their part; when countries have turned their full might to the development of aircraft, in particular, huge leaps have happened in tiny timeframes.
Sadly, it is the case these days that racing’s ability to harness some of the latest and greatest materials is somewhat curtailed, thanks to never ending cost saving measures by regulators. Formula 1 is a prime example, with an extensive list of materials that are forbidden from use due to their being deemed prohibitively expensive.
Composites may make up the bulk of most modern racecars by volume, but by mass, metals still remain dominant. Obviously in some series, from rallying to
drag racing, chassis constructed from metal are still the norm, while in single seaters and sportscars, they tend to be composite, with metal components reserved for the engine, transmission and suspension systems.
Starting with steels, these are still used extensively in chassis construction and in this context there have been some interesting developments over the last decade. For rollcage and chassis work, there tends to be regional variations in the materials used, depending on whether one is talking US, British or European standards.
As a general rule, safety-specific parts such as rollcages will be produced from cold drawn seamless (CDS) tubing, with one exception,
For rollcage and chassis work, there tends to be regional variations in the materials used, depending whether one is talking US, British or European standards
which we will cover shortly. CDS is something of a catch-all term that can apply to a variety of tubes. However, in high performance applications, one will be looking at either T45, 4130/ 25CrMo4 or 16CDV6 tubing.
In the US, 4130 CrMo (chromium molybdenum, chromoly for short) has long been the standard for chassis construction, particularly in drag racing classes. Interestingly, though, not in NASCAR, which until Next Gen at least always stuck with mild steel drawn over mandrel (DOM) tubes.
4130 is a low-alloy steel, the properties of which make it ideal for use in welded steel structures. The ‘30’ represents its 0.30 per cent carbon content, which is generally considered to be at the upper level of carbon inclusion that still allows for strong, reliable welds. That’s not to say that higher carbon steels cannot be welded, but the resultant welds are considered more susceptible to cracking, due to the more brittle nature of the material.
Under normal conditions, 4130 has a UTS (ultimate tensile strength) of 90-95ksi, which can be improved with heat treatment. It also has excellent elongation properties, in the region of 28 per cent, before fracturing takes place, and good resistance to crack propagation. To get the best results from 4130, ER70S-2 weld filler rod is often used, which itself has a very low carbon content, nominally 0.06 per cent, and can handle dilution into the relatively high (in terms of weld metal) carbon in the 4130. The resulting diluted weld deposit has a tensile strength of about 85-90ksi, though the actual strength will depend on the amount of dilution with the 4130, weld bead and material thickness.
ER70S-2 also has a higher quantity of alloying elements than the 4130, notably manganese and silicon. In Europe, 4130 is referred to as 25CrMo4.
In the UK, T45 tubing is the go-to choice for rollcages, a composition originally developed for aerospace use between the wars. T45 is a high strength, high tensile, carbon-manganese cold drawn seamless tube with excellent bending and welding properties that, importantly, is weldable without requiring pre or post-heat treatment. Though its chemical composition is different to 4130, its mechanical properties are very similar, with slightly lower tensile strength but greater resistance to cracking under bending.
Another tubing of interest is 16CDV6, which is a micro-structured alloy steel with very high strength and excellent weldability. It has a yield strength of 900Mpa and a tensile strength in excess of 1100Mpa, making it an excellent choice for fabricated suspension components and parts subject to high forces.
It is well suited to rollcage construction, though with the FIA stipulating a minimum wall thickness for safety structures of 1.5mm its benefits are somewhat negated, making such as T45 a more cost-effective choice.
For many years, there were no other real options to the aforementioned steels but, over the past decade, Swedish steel manufacturer, SSAB, set out to provide racers with an alternative steel. Branded Docol, it addresses some of the shortcomings of existing steels in motorsport-specific tubing
The use of SSAB’s Docol material in racing stemmed from a collaboration between SSAB and renowned Swedish drag racer, Mats Eriksson. SSAB had been using the material to produce reinforcement panels for OEM suppliers for many years, but found that its properties make it ideal for motorsport use.
Docol R is a high-strength, low-carbon steel available in two variants, R8 and R10, which have slightly different properties. R8 tubing’s strength is very similar to that of 4130 chromoly steel, but with a much lower carbon content (0.12 per cent compared to chromoly’s 0.29 per cent). R10 tubing is a higher tensile version used in areas where lighter weight and high strength are required.
While a higher carbon content increases the hardness and tensile strength of steel, it also reduces its ductility and weldability. So, while 4130 is very effective for use in rollover structures, its relatively high carbon content, and the brittleness this brings under fatigue, can present problems, especially around welded joints and in multiple impact crashes.
The failure mode of a standard 4130 tube is of the brittle type, whereas Docol R8 tube is far more ductile. Despite having less carbon, the tensile strength of R8 is still as high as chromoly, thanks to a higher percentage of manganese – 2.1 per cent over 4130’s 0.56 per cent. Manganese improves the hot-working properties of a steel and increases strength, toughness and hardenability.
Another area where R8 tubing differs from 4130 is that, rather than being mandrel drawn, it is rolled and then welded.
Docol addresses some of the shortcomings of existing steels in motorsportspecific tubing
Traditionally, welded tube is seen as inferior to drawn seamless tubing, but SSAB discovered this is not the case with R8, despite initial fears of failure along the longitudinal welds. The lack of issues here is due to the very small area affected by heat during the welding process, a result of the low percentage of the material’s alloying elemens.
In the US, the SFI has granted approval for the use of SSAB’s products in SFI 25.1X-specification drag racing chassis, with the SCCA also allowing it for use in rollover structures. In Europe, it is only FIA approved for drag racing applications, and has yet to make its way into other series due to it being a seamed rather than seamless tube (this, despite the Swedish National Sporting Authority allowing it to be employed).
Advances in mainstream automotive manufacturing technology can also have benefits in racing, particularly where production bodyshells are used. Take the example of Škoda’s Fabia Rally2. Based on the company’s latest road car platform, it is made of high strength and ultra-high strength steel in areas critical for passenger safety. This is beneficial for the new generation Rally2 as well of course. It translates into further improved torsional strength of the floor structure and better strength and durability of the rally car’s bodyshell.
Steels with yield strengths higher than 550MPa are considered advanced high strength steel (AHSS) and, when the tensile levels exceed 780MPa, they are referred to as ultra-high strength steel (UHSS). The key difference between UHSS and AHSS is in their microstructures. AHSS can be engineered to produce unique mechanical properties; some have a higher strain hardening capacity, which gives them a superior strength / ductility balance, while others have higher yield and tensile strengths and demonstrate bake-hardening behaviour.
Beyond chassis applications, steels obviously play an important role in racing engines. In many series, regulations mandate a number of the internal components in the engine must be made from iron-based alloys. Aerospace-grade steels are the favoured option here, with the exact material specification depending on the application.
Taking very high-performance crankshafts as an example, materials such as 32CDV13 are used, with products being machined from solid billets. 32CDV13 is a three per cent chromium-molybdenum-vanadium nitriding steel that offers a tensile strength of up to, and sometimes even above, 1300MPa, which develops a hard (around 850HV) wearresistant surface after nitriding.
The alloy is usually produced by a single electric melting and vacuum de-gassing process, but variants are also available as a vacuum arc re-melted version where even greater mechanical properties are required.
It should be noted here that finished cranks are actually often composite items, with dense tungsten counterweights bolted to the steel component. In the past, engine manufacturers have used even denser material, notably depleted uranium, though such materials are obviously now banned.
For camshafts, again most regulations stipulate the use of iron-based alloys. In the past, one of the more popular materials was EN40B nitriding steel. This is a chromiummolybdenum-steel specification usually supplied in the hardened and tempered ‘T’ condition, which offers high wear resistance together with good toughness and ductility. Heat-treated EN40B has a tensile strength of 850-1000N/mm², and is characterised by its suitability for nitriding, which can give a hard, wear-resistant case in the 61-65Rc range.
More recently, engine manufacturers have moved towards through hardening tool steels for camshaft production, a process which creates an extremely stable part that is resistant to surface wear, twist and deflection, with the ability to withstand both high surface loading and shock.
Additive manufacturing has also brought a new dimension to the use of steel parts, and there are an ever-growing number of high-
performance variants now available. For example, high hardness tool steels can now be printed, as can various grades of austenitic stainless steel.
Advances are also being made in the processing of Duplex stainless steels (DSSs), which have microstructures of almost equal fractions of δ-ferrite and austenite. This unlocks a wide range of attractive properties such as high strength, good ductility and excellent corrosion resistance. Of particular relevance to electrified motorsport, it is also feasible to use silicon steels for AM, opening up interesting possibilities for the creation of novel motor geometries.
On the subject of electrical steels, it is worth noting the advances made in stamping technology for the laminates that are used to make up the stators in many electric motors. The latest technology allows for laminates
Additive maufacturing has also brought a new dimension to the use of steel parts, and there are an ever-growing number of high-performance variants now available
as thin as 0.025mm to be produced, which can greatly increase the efficiency of motors (though currently in F1, MGU-K laminate thickness is limited to a minimum of 0.05mm).
Though not a steel, additive manufacturing of Inconel 718 is particularly useful for racing, and has been used extensively for the production of complex exhaust components that would be impossible to fabricate using traditional methods.
Moving away from steels, one comes to aluminium alloys, deployed everywhere from engine components to suspension uprights. Aluminium is around one third the density of steel, yet some alloys can have the same or greater strength as low-carbon steels. Aluminium alloys are classified by series, from 1-8xxx, with each series having different alloying element (with the exception of 1xxx, which is almost pure aluminium).
The different alloy series each have their own benefits and disadvantages. Some are easy to work with, making them suitable for welded and fabricated parts, while others have excellent strength or fatigue properties. For example, the go-to material for high-performance pistons used to be 2618 aluminium alloy, originally developed by Rolls-Royce for the Merlin engine, though back then it was known as RR58.
Post WW2, when the material became available on the commercial market, RR58 became a firm favourite of high-performance engine builders. 2618 contains both copper (1.9-2.7 per cent) and magnesium (1.3-1.8 per cent) and can be age hardened to give it excellent strength at high temperatures, while still maintaining good machining properties even in a heat-treated state.
More recently, piston manufacturers have turned to aluminium-silicon alloys. High silicone 4032 aluminium, which has a silicon content of 12 per cent, has been extensively used for racing pistons, but for extreme applications 2816 is often favoured thanks to its greater ductility and higher strength.
However, new Al-Si materials have been developed which deliver the benefits of 2618, but with the added advantages of an increased silicon content. These benefits include, but are not limited to, better wear characteristics and lower thermal expansion, an important consideration in an age where race engines are expected to last far longer than in the past. The move towards highly boosted, small capacity engines also has relevance here, with such engines greatly increasing the loads experienced by the piston skirt and ring pack.
Though 2618 and the newer Al-Si alloys have similar surface hardnesses, depending on the level of heat treatment, the silicone particles provide greater wear resistance.
If one uses a 2618 alloy for such applications, further treatment of areas like the ring grooves or skirts is needed, for example hard anodising, which may not always be necessary if a silicon alloy was used.
This new breed of Al-Si alloys includes materials such as M142 and M174, which retain a high silicon content, at around 13 per cent, but have a much higher copper content, of between three and five per cent, compared to 4032 which has just one per cent.
For other components such as damper bodies, which require excellent strength and stiffness, 7000-series aluminium alloys are generally used. These provide a good balance between outright strength while not being so stiff that they suffer fatigue under the intensive cyclical loadings they experience.
7000-series materials are alloyed with zinc, and can be precipitation-hardened to the highest strengths of any aluminium alloy (the 7068 alloy for example has a tensile strength of up to 700 MPa). There are also other ultra-high strength aluminium alloys under development, such as A-1500, which has the potential for a UTS in excess of 1000MPa.
Looking to more exotic alloys, one enters into the realm of materials deemed too expensive by regulators (particularly in F1), meaning their use is limited. For example, aluminium-lithium has some very attractive properties, notably high stiffness, low density, good temperature stability and resistance to corrosion, particularity when other elements are used to improve its properties further.
One such example is 2099 Al-Cu-Li, developed at the end of the 1990s, which has been used for making brake calipers. In
addition to lithium, 2099 contains up to three per cent copper, as well as zinc, magnesium and manganese. The copper forms strengthening precipitates to increase the toughness, the lithium helps reduce density without compromising strength, while the zinc aids corrosion resistance.
Taking 2099-T83 as an example, this material has a modulus of about 78Gpa, placing it just under the 80Gpa elasticity upper limit F1 regulations dictate for brake calipers. However, in addition to a stiffness limit, the rules now also specify that only alloys with less than one per cent lithium can be used, negating 2099-T83 as it has between 1.6 and two per cent of the alloying agent.
Jumping to a higher performance level still, and one that is really only viable in terms of cost for those with very large budgets, one comes to metal-matrix composites (MMC). These combine a metallic base with nonmetallic reinforcement (normally a ceramic), which improves the specific strength and stiffness of the material.
There are three main types of MMC, those that use fibre reinforcement, whisker reinforcement and particulate reinforcement. For the purpose of manufacturing pistons, particulate-reinforced MMCs are the most relevant, as these are isotropic and so can be treated in the same way as unreinforced alloys. So, for example, ingots can be formed using the same powder metallurgy techniques as other aluminium alloys.
In an aluminium MMC, one of the constituents is aluminium alloy, which forms a percolating network and is described as a matrix phase. The other constituent
is embedded within this alloy matrix and serves as reinforcement. The most common aluminium MMCs use silicon carbine or aluminium oxide.
As with an alloy, the properties of MMCs can be tailored by varying the nature and relative quantities of the constituent parts. The properties of such materials greatly exceed those of traditional alloys and so found favour, when the regulations allowed, as a piston material in Formula 1 (MMC are now banned from used in the powertrain).
In the mid-2000s, Honda developed MMC pistons to replace those made from 2618 aluminium alloy, which it traditionally used in its naturally-aspirated V10s. The results were impressive, and the piston could be made 16 per cent lighter than aluminium components. The extra strength also allowed for a 400rpm increase in engine speed without compromising piston integrity.
A more recent advance in MMC technology has been the development of metal-matrix nano-composites, or MMnCs.
As the name suggests, these use smaller reinforcement particles than current MMCs, down to 10nm, allowing for greater distribution amongst the alloy matrix. Much work in this area is still at the research stage, but the results are encouraging, with MMnCs using traditional filler materials such as silicon carbide and aluminium oxide showing improved mechanical properties over MMCs.
Some of the main hurdles to such materials gaining widespread use though are in the processing, for example the difficulty of ensuring an even distribution of the reinforcement throughout the matrix material and consistent bonding between the two.
It is an interesting quirk of the F1 rule set that metal matrix composites are specifically prohibited, with the exception of particle reinforced aluminium alloys for additive manufacturing. For example, 6061 RAM 2 is permitted, a proprietary alloy from supplier Elementium, which incorporates two per cent ceramic reinforcement. Claimed to have a 50 per cent faster build time than AlSi10Mg and better surface finish, it has a UTS of 331MPa and a yield strength of 297MPa.
Another interesting aluminium-based AM alloy specifically allowed in F1 is Scalmalloy, developed by specialist AP Works, which sees aluminium alloyed with scandium and magnesium, giving finished properties similar to 7075 wrought alloy. It has an impressive tensile strength of 520MPa (compared with AlSi10Mg at 350MPa), which is about half that of Ti6Al4V, and combines that with a density the same as AlSi10Mg (2.6g/cm3). In addition, its microstructure remains stable up to 250degC.
Finally, titanium is an attractive material for motorsport use, thanks to its relatively low density and good strength, though it is also a difficult material to work with so its application needs to be carefully considered. For example, most titanium alloys that are commercially available have less than ideal behaviour characteristics when placed in sliding contact, and are susceptible to galling.
The most commonly used is Grade 5, or Ti-6Al-4V, a specification that encompasses a number of different sub-grades of the material. This has a chemical composition of six per cent aluminium, four per cent vanadium, 0.25 per cent (maximum) iron, 0.2 per cent (maximum) oxygen, and the rest titanium. It is the workhorse of the titanium world for various reasons, notably that it has the same stiffness and thermal properties as pure titanium, but is far stronger and heat treatable. By varying the alloying elements, it can be modified to improve particular performance aspects. For example, the addition of palladium or ruthenium can increase its corrosion resistance.
There are other grades of titanium, right up to 38, which contains four per cent aluminium, 2.5 per cent vanadium and 1.5 per cent iron. Originally developed for use in armour plating, Grade 38 titanium has similar mechanical properties to Grade 5 but with much better cold workability. Beta C or Ti-3Al-8V-6Cr-4Mo-4Zr has also been used for high-strength fasteners due to its exceptional corrosion resistance and excellent strengthto-weight ratio when heat treated. It is also, however, prone to galling.
Compared to the aerospace and defence industries, motorsport is a very small user of titanium, though the similarities in requirements between the two are many, so racing can benefit from developments there, provided there is enough material available.
As with other materials covered here, there are now also a host of different AM titanium powders available, opening up a world of possibilities for novel designs that circumvent the traditional difficulties of the material to fabricate and machine.
Though some of the largess of the past is no longer practical in motorsport material development and use (think single billets of material worth tens of thousands of dollars being machined away to almost nothing to make a lightweight brake caliper) there is still plenty of innovation and development underway. No doubt the current generation of F1 power units have necessitated some bespoke solutions that we will only ever find out about years down the line.
Even if new materials are not developed specifically within motorsport, racing still provides an attractive crucible within which to test new developments in short time frames and under extreme duress.
It is an interesting quirk of the F1 rule set that metal matric composites are specifically prohibited, with the exception of particlereinforced aluminium alloys for additive manufacturing
Race engineer and strategist, Jeff Braun, explains how teams in IMSA have to play the strategy game to be in with a chance of victory
By ANDREA QUINTARELLITop motorsport classes are often associated with an environment where the quest for pure performance is the heart of every decision, both on track and out of the circuit. Indeed, the main goal of a racecar is to perform better than its competition.
Winning races is not ‘just’ this though. In the past, with less advanced tools at engineers’ disposal, reliability was a crucial factor, and the really good drivers knew they had to be kind to their hardware during a race to avoid a retirement.
Nowadays, retirements because of reliability issues are much less frequent than they once were, but there are still important aspects that transcend pure performance and can make a big difference on race and championship results. Among the most important ones is how a team handles race preparation and strategy.
Data analysts are a critical part of any modern race team, but the real skill comes in knowing what to do with the masses of data collected, and making the right decisions at the right time
Something unexpected can always happen, but this can even become an opportunity, if teams are flexible enough to react quickly
If a team’s pre-race preparation is good then a car should behave over the course of a race event, so that’s when strategy comes into play, particularly in endurance racing. It can differ greatly depending on the series so the very first step is to understand the regulations for the class in which you are competing
Being prepared for a race is important in every class, and every team that is serious about winning invests time and resources into pre-event work. This can be trying to anticipate how a weekend could evolve and analysing possible scenarios, in order to have all the required information once at the track. The aim is to reduce the risk of having to work in emergency mode, while facing something unexpected, and needing to diverge resources to solve problems that could have been analysed at the factory. Of course, something unexpected can always happen, but this can even become an opportunity, if teams are flexible enough to react quickly.
Race strategy is also crucial, especially in longer competitions where teams need to perform pit stops. Besides Formula 1, where tyre management is probably the most important factor, endurance racing is the environment where strategic decisions can influence the final results the most.
In most endurance racing championships, pit stops are performed under rules that limit the number of team members that can work simultaneously on the car, but different approaches are still required, depending on the regulations. The best example is comparing the World Endurance Championship and the European Le Mans
‘Over the years I developed tools to help me manage driver rotations… but I am still more worried about breaking the fourin-six rule than anything else during a race’Richard Dole
Series with the IMSA Weather Tech Sportscar Championship. These series employ some common classes, albeit with slightly different technical regulations, but the sporting side of the racing is accounted for in completely different ways.
Racecar Engineering had a chance to talk to Jeff Braun, a highly experienced race engineer who has successfully run a diverse range of cars, from GT to IndyCar, and won every major race in North America during his career.
In recent years, Braun was mostly active in the IMSA Weather Tech Championship. In 2018 and 2019 he led CORE Autosport’s campaign in the top class, first with an LMP2
car and then with a Nissan DPi. In 2021, he again supported CORE Autosport on the strategy side in its assault on the LMP3 class.
‘The first thing you have to do is understand the rules, because they can be so diverse,’ notes Braun. ‘Take, for example, WEC and IMSA: the regulations are way different and, as a consequence, your strategy needs to work in a dissimilar way.’
One main difference between endurance racing on the two sides of the Atlantic is the way yellow flags and safety car situations are handled. While in WEC and ELMS, virtual safety cars have been implemented in the last few years, this is not the case in IMSA, where
real safety cars are still employed to handle dangerous situations on track. With a virtual safety car, the gaps between cars remain mostly unchanged, while cars leading by a big margin can abruptly find competitors hot on their heels under a real safety car event.
‘We saw it often with teams coming into IMSA from the ELMS or WEC,’ continues Braun. ‘They often kept their non-professional driver for the last stints, which makes sense with virtual safety cars because if you build up a good lead during the race, you put your slower driver in a position to win, even in the event of a neutralisation. Such a situation can even help you, because the other cars have less time to catch you.
‘But this is not the case in IMSA. If a safety car comes on track during the last phases of the race, you are in a very bad position if your amateur driver is at the wheel. Your lead is gone, and you have a slower driver needing to handle a very stressful situation against a pro driver after a restart. That’s why in IMSA we always plan to have our fastest driver in for the closing stints.
‘This is just an example to demonstrate the importance of knowing the regulations.’
Another critical aspect in any endurance championship are the rules related to driving time. This is tightly regulated and IMSA makes no difference with this respect, at least in longer races like the 24 hours of Daytona, the 12 hours of Sebring and Petit Le Mans.
‘In IMSA, we have what we call the ‘four-in-six rule’, which means that no driver can drive more than four hours in any six hours period… to prevent fatigue,’ explains Braun. ‘A violation of this rule leads to a huge penalty – cars have lost podium positions in the past because of not respecting it. It seems something easy to manage, but it is not.
‘Everyone wants to run their fastest driver at the end of the race but, if the same driver was in the car before, you have to be careful that the previous six-hour block of time and the current one do not overlap in a way that leads the sum of the driving times to be bigger than four hours. ‘Sometimes, to avoid a violation, you would need to have your fast driver out of the car for a few minutes before getting back in to finish the race.’
‘And, as the race engineer or strategist, you’re often having to work this out when you’re already very tired yourself, for example at the end of a 24-hour race.
‘Over the years I developed tools to help me manage driver rotations and the time they spend in the car, but I am still more worried about breaking the four-in-six rule than anything else during a race.’
In shorter races, this is not a factor, as the rules simply stipulate every driver must be in the car for at least 45 minutes.
The aim is to reduce the risk of having to work in emergency mode, while facing something unexpected
Another important difference between the Weather Tech Championship and the WEC or ELMS is that in IMSA it is possible to regain a lap during a neutralisation.
‘Especially in a class with both professional and non-professional drivers in the car, having chances to get a lap back is important, and your strategy to achieve this is crucial. The longer the race, the more opportunities you may have.
‘Assuming your car is a lap down, you have to put yourself in a position to get that lap back, perhaps by offsetting your fuel strategy. If a yellow flag comes out and you manage to pit before the safety cars goes on track, you
do not need to tank during the neutralisation, while your competitors may need, or want to. This way, your crew would unlap and find themselves in front of the leader, between them and the safety car. Before the race goes to green again, IMSA allows all the cars ahead of their class leaders to overtake the safety car and get behind the last car. So now your car is not a lap down any more and is right behind the cars in front. You will still need to tank before them, because you got off sequence, but at least you are in the same lap now.’
In the event of another safety car event close after, a team could even eliminate the disadvantage of being off sequence with their fuel strategy as most teams would choose to pit anyway in such a situation.
Gone are the days of standing in a windy pit lane with a stopwatch and a clipboard. Now it’s all about screen time
Similarly, in a scenario where a safety car needs to suddenly be sent on track, if a crew find themselves between the race leader and the safety car, they can still profit from what Braun describes and queue up behind the group, even before the pit lane is opened, gaining significant time.
‘The reason they do that is that in multiclass racing it would be unfair to block a car between the overall leader and the safety car. If you had just one class racing, the safety car would simply come out in front of the race leader. The goal is to recreate a situation where each class would have the safety car coming out exactly in front of their race leader. They call this the ‘pass around.’ After this, they do the pit stop sequencing and, before the race gets green again, there is a final ‘wave by’, where everybody ahead of their race leader can come around again. This is a kind of a free lap, and the reason they do that is mainly to make the racing more entertaining, as well as placing the leading cars at the front of the line for the re-start.’
A further interesting element of IMSA regulations is that each team can listen to other teams’ radio communications between car and pit wall. This adds another strategical element to the picture because teams develop ‘codes’ to communicate with their drivers without showing their cards.
And if you’re thinking teams could just use scrambled radios, they are not allowed as IMSA wants the spectator to be able to listen to what the teams are saying as well.
Braun stresses how race strategy has to pivot around one, crucial point for a good result: the car must be on the lead lap at the last pit stop, even though IMSA regulations offer means to achieve this, even if you are one or more laps down.
‘This is the most important element during a race, and affects the strategy even more in the longer races. It’s what we work towards from the very start of the race. The fastest driver, who normally is in the car for the last part of the race, must be on the lead lap to have any chance to fight for victory.’
On the other hand, tyres are not normally a particular issue in IMSA, while they can be a decisive strategy element in WEC or ELMS.
‘IMSA give a tyre allocation for the whole weekend, from the first free practice to the end of the race, and we are free to use them the way we want,’ explains Braun. ‘Also, most of the classes only have one compound –sometimes even the same compound for the whole year – which takes away any strategic considerations with respect to tyre choice during the race.
‘The number of tyres we are allowed to use for a race is normally enough not to need to double stint any, with the exception of the longer races, where we usually had to double stint a couple of sets.
‘In those races, you can decide when you want to do that. For example, it could help to leave the car with worn, but warm tyres when a new driver jumps in, especially if it’s the non-professional driver and they haven’t driven for some hours. Being already warm, the tyres would have grip from the moment the car leaves the pit, which would give the driver confidence and help bring them up to their peak performance in a shorter space of time.’
The advantage any such choice might bring is difficult to quantify, but it’s still a strategic decision that has to be made.
‘[In IMSA], the fastest driver, who normally is in the car for the last part of the race, must be on the lead lap to have any chance to fight for victory’Using pit strategy can reap huge rewards for a team that has lost time early on. Getting ahead is useful, but with yellows in IMSA racing, it’s usually all about the final pit stop and final stint Michael L Levitt
As the Weather Tech championship also has some pretty short races in its calendar, there are other situations where a team might decide not to change tyres at all during a race, or only change two of them.
‘I reckon in Detroit, where you normally do only one pit stop [in an hour and 40-minute race], some GTD teams stayed with the same set of tyres for the whole race, or only change the left ones, because the majority of corners are right handers. This surely compromised their performance, but made their pit stop significantly shorter and so put them out in front on a circuit where it is notoriously hard to overtake, even with the grip advantage of fresh tyres.’
Despite the effort teams put into preparing for races and trying to manage them the best possible way on track, they will still face issues that cannot be foreseen.
Braun remembers how CORE Autosport was frustrated in its attempt to secure LMP3 class victory during the 2021 Daytona 24 hours by a problem more connected to car design than to the team’s race preparation.
‘We had brakes issues during the whole race,’ he recalls. ‘The drivers complained that the car did not slow down effectively, and we could not understand why. The only thing we were left with was to stop the car
and put on new brakes. This improved the situation for some time but, after about six hours, the problem presented again.
‘Of course, this ruined our race, but it wasn’t until the car returned to the workshop that we were able to figure out what the issue was. We were using the pedal box in its most forward mounting position and, when the pads became worn, the brake pedal was hitting the steering column, effectively preventing the drivers from braking.
‘In a normal situation, we would change the brakes on an LMP3 car only once during the 24 hours. IMSA even mandates one single eight-minute stop during the race, and this is when most teams take the opportunity to change the brakes, but in that particular race we found we had to change them every six hours!’
As annoying a that was, this is a good example of how sometimes teams have to decide whether to try and keep going or bring the car in for assessment and repair.
‘I always have a sheet that helps me make such decisions quickly, and it’s based on my whole endurance racing experience. I call it my stay out or fix sheet. In there, I have the time I think it would take to fix certain problems. I also consider the remaining race time, with intervals of 40 minutes. Based on all this information, I can look at the lap times to estimate how much
a certain issue is costing us. This can be then put into a chart, taking into account how long the race still has to run and how much we would lose each lap. I can then compare it to see if the repair time could be recovered after a stop, thanks to a better pace, or not.
‘It is pretty simple, but it’s another example of how helpful it can be having something that tells you in a second in which direction to go, without the need for any complicated analysis in the heat of a race. It is not exactly a strategy item, but being prepared will always help.’
Next month, Jeff Braun shares further insight into specific pre-event work that helps handle the invariably stressful situations that occur during an endurance race.
‘I always have a sheet that helps me make such decisions quickly, and it’s based on my whole endurance racing experience. I call it my stay out or fix sheet’Strategy can lead to some incredible results. Here Jon Bennett celebrates a race win with his co-driver Colin Braun, son of Jeff who called the races from the pitwall for the Core Autosport team Richard Dole
One of the most revered topics in motorsport engineering is racecar design. If you mention to anyone that you are designing a racecar, and are serious about it, you tend to be treated with something akin to super natural deity status. Very sadly, this is a reflection of the fact that, due to the modern motorsport environment, this doesn’t tend to happen that much anymore.
Consequently, most vehicle dynamics simulation these days is focused more on race engineering than racecar design.
ChassisSim is no exception to this rule, and this is a sad reflection of the times we live in. That being said, over the last couple of years ChassisSim has found itself being used in the racecar design process on a number of different projects. What these projects are I’ve been sworn to secrecy on, but that doesn’t mean I can’t tell you in rough terms what the process has been. Some of it was reflected in a previous article I wrote on this subject about 10 years ago but, as some other new stuff has been learnt along the way, I thought it worth re-visiting.
The first step in racecar design is to understand that nothing happens in a vacuum, and without a shadow of a doubt your start point should be a well-sorted vehicle model that most closely resembles your car. This is something I was remiss to leave out of that earlier article.
However, since ChassisSim has gone on to be used in so many race categories we now have a broad library of well-sorted models to draw upon. The car in Fig 1, for example, an LP560 GT3 car, is the progenitor of every GT3 car model we have out there.
The first step in racecar design is to understand that nothing happens in a vacuum, and... your start point should be a well-sorted vehicle modelFig 1: Consolidated Chemical Co LP560 GT3
basexnewx
baseynewy
base tm new tm II baseznewz
basewb new wb II
Consequently, we would be crazy not to take advantage of this situation.
Before we go any further, though, one thing I will say as about this process is to treat any data you get from a tyre test rig with great caution. Particularly if this is a high-performance tyre. The reason I say this is because most tyre test rigs don’t correctly duplicate the load and temperature conditions you see on track. There are some that come close, the SOVA motion rig in Alton Virginia in the US is a good case in point, but typically what tends to happen is they give you overly optimistic peak loads, which can quickly lead you up the wrong path if you are not careful.
While these rigs are great at comparing compounds to compounds, they are not a copy and paste solution to an accurate vehicle model. This underscores the importance of using a well-sorted and validated vehicle model to start with.
2 basewbbase tm newwbnew tm II
÷ ÷ ø ö ç ç è æ =
2
2 2
÷ ø ö ç ç è æ = 2 2
One thing that is worth revisiting from my earlier article is what happens to the inertias as you start changing tracks and wheelbase. What I summarised in equation 1 is a good rule of thumb to work to in this regards. (1) ÷ ÷ ø ö ç ç è æ + + =
Ix_new = new moment of inertia about the x axis (kgm) Iy_new = new moment of inertia about the y axis (kgm) Iz_new = new moment of inertia about the z axis (kgm) Ix_base = current moment of inertia about the x axis (kgm) Iy_base = current moment of inertia about the y axis (kgm) Iz_base = current moment of inertia about the z axis (kgm) tm_base = current mean track (m) wb_base = current wheelbase (m) tm_new = current mean track (m) wb_new = current wheelbase (m)
I realise equation 1 isn’t going to win any prizes for elegance or subtlety, but it will ensure you don’t go down any blind traps as you start changing wheelbases and tracks. This will allow you to adjust your inertias to suit, which will add a degree of sanity to the sim’ results you’ll get back.
Once you have a good base model, the next step is to determine your aero and tyre targets. What this will determine is the spring rates you are going to have to run on track.
Now, in terms of aero, more often than not it will be coming from CFD. Here is another place where you have to be a little careful. Typically, CFD results will over predict downforce and under predict drag. There are some exceptions to that rule, TotalSim / TotalSim USA being a good case in point, and the work done by Andrew Brilliant, Scott Beeton and Kyle Forster is all first rate. Still, keep that warning in the back of you mind at all times and you won’t go far wrong.
Also, remember the tyre compound you run will dictate the spring rate you have to run. Your best bet there is to look at historical data and see where the wheel rates fall. There are no brownie points to be had here for showing how intellectually pure and righteous you are, you are doing it for results.
Once you have this sorted, your next step is to do some very basic ground clearance and spring simulation work. For that, lap time simulation is about to become your very best friend, and figure 2 is an example of some bump rubber / spring work I did for a Time Attack customer.
At this stage of the game, I couldn’t give two hoots about lap time. What I am much more interested in is taking the basic CFD data and making sure I didn’t have any bottoming issues and that I was sizing the bump rubbers appropriately.
Once the springing is squared away, you can move on to suspension geometry. There are a number of excellent tools you can use for this, but SusProg and OptimumK
are the more commonly used ones, while ChassisSim also has basic geometry viewers. Both figures 3a and 3b are where I spend the bulk of my time when I’m considering suspension geometries.
Neither will win any beauty awards, but they don’t need to. They are brutally simple and effective. Figure 3a gives me a very good read of where the instant centres are, which in turn gives me a good insight into what I’m shooting for. Then I use figure 3b to see what the roll centre migration and camber variation is. Here you are going to have to prioritise what counts. For example, if you are running really high bar rates, or dealing with low-grip situations, the pitch variation takes precedence. Conversely, if you are dealing with a low downforce, softly sprung car, the roll modes takes precedence.
The other thing to keep in mind during this process is where the lateral load transfer lands. To that end, the spreadsheet shown in figure 4, which you can find on the ChassisSim website by searching for ChassisSim tyre modelling from nothing, is a really good tool to make sure you keep things under control.
What you are looking for here is to make sure the lateral load transfer distribution stays in the order of 45-55 per cent. This is a rough rule of thumb, and it will vary between car types, but it’s a good start. The really great thing about this sheet is it will also tell you the stability index plots. Again this is a useful tool to make sure things stay in check.
Once you have a handle on the springs and the geometry, you can then move on to the damping. There are two tools available here that will save your bacon – and I speak from personal experience here. The first of these is the ChassisSim damper workbook. As a quick summary, the damping guide shown in figure 5 is a great place to start.
Once you have a base in place, you move on to the ChassisSim shaker rig toolbox. This will help you nail down the damper spec.
Once all this is settled, the next step in the process is the lap time simulation. Here is where you are looking at bringing all this knowledge together, and you are race engineering the car, albeit in virtual form. Anyone familiar with my writings on this matter will quickly work out that the same rules in race engineering also apply here. As a quick summary they are as follows:
• Focus on small deliberate changes.
• Stay within +/-20 per cent of known spring and bar rates.
• Keep roll centre migration +/-30 per cent from a good known base set-up.
• Remember you can be a bit adventurous on camber changes.
• Don’t go over a damping ratio of 1.5 and don’t go below 0.3.
These are all good rules of thumb, and the more experienced you are, the more adventurous you can be. That said, you need to know what the rules are before you can start to break them.
One thing to watch like a hawk during this process is your driveability channels. In ChassisSim this is measured by the stability index, and you want to be watching for situations like that shown in figure 6 Pay particular attention to the last plot here, which is stability index. The coloured
line was an aerodynamic configuration that was borderline stable, the black was when the aerodynamic balance was shifted back five per cent. Watch areas like this In the car design phase very carefully indeed.
The last step in this process is Driver in the Loop simulation. To briefly re-cap, what we have done is specify a base set-up / configuration and then use the lap time simulation and other tools to sort out the options. The Driver in the Loop simulation will see if the nut behind the wheel can actually hang onto what you have created on track. While this is the full stop at the end of the process, it is nonetheless an important one. As all grammar should be. It can also very quickly diagnose if you have gone off piste somewhere along the line. This has saved my neck on more occasions then I care to remember.
Only when all these steps have been completed can the fun stuff really start. It might seem long winded, but we needed to reach this stage in very deliberate steps so you had a firm basis in place. As you then try different ideas, you’ll be using all the tools we have discussed interchangeably.
For example, you might have a call to increase front lateral load transfer distribution.
While this might sacrifice overall pace on the lap time simulation, when you try it out on Driver in the Loop it gives you a bit more understeer / stability. That then gives the aerodynamics team a bit of wiggle room so they can move the balance further forward.
One of the great things about ChassisSim here is because the numerical engine is identical for all of its tools, it greatly aids this process. You can then continue going back and forth until you land upon something you are satisfied with.
In closing, using simulation in racecar design can greatly aid the design process itself, in particular giving you a firm idea of what targets to shoot for. While what has been discussed here should not be treated as gospel, it nonetheless should give you a firm basis and framework to start with. The key is to start from a known, validated template, and then define your aero and tyre targets. Once you know that, everything will flow downstream from there, and even more so if you are bringing tools like the ChassisSim shaker rig, lap time simulation and Driver in the Loop.
Key to remember is that these tools are calculators, not magic wands. Treat them so and the results will speak for themselves.
The Driver in the Loop simulation will see if the nut behind the wheel can actually hang onto what you have created on track
Our specialism is in the detail of race engineering – the hard to source simple things that can make or break a deadline.
Check online, call us or call in.
The one-stop shop for parts and components
Supplying the parts that others cannot reach
IndyCar has confirmed it will not run the new 2.4-litre V6 engine in 2024 as originally planned, retaining the 2.2 litre twin turbo V6 engine instead. IndyCar’s two manufacturers pushed for the decision in order to focus on the introduction of a hybrid system.
The American single-seat category had planned a new chassis for 2023, but elected to continue with the Dallara IR18 as it remains fit for purpose. The series had also planned
to introduce the new 2.4-litre, twin-turbo engine and hybrid one year later but that, too, is shelved.
With its partner manufacturers, GM and Acura, placing emphasis on the introduction of hybrid and a sustainable fuel, the decision has been taken to continue with the current 2.2-litre engine rather than introduce a new and expensive replacement.
GM and Acura have both tested their 2.4-litre engines on
track, but it is understood that the financial pressure of scaling up to fill the grid with only the two engine manufacturers was a factor in the decision.
IndyCar has for a long time searched for a third manufacturer to join and help supply the grid, particularly at the Indy 500, but has failed to do so since Lotus ran engines in the 2012 race as re-branded Judd power units. The failure to land this third
manufacturer, despite extensive research with suppliers from Europe and Japan, means GM and Acura will have to supply a grid of 27 cars for next season, and may have to go even further in 2024.
The introduction of heavily subsidised engines would be too costly for the two manufacturers, coupled with their investment in testing and development of the hybrid system that has proven to be challenging.
The Japanese Super GT series is set to introduce carbon-neutral fuel for the 2023 season and has completed a test day with it following the final round of the series in November.
The GTA has announced its Super GT Green Project 2030, an environmental road map for cutting total CO2 emissions resulting from the entire Super GT series in half by 2030 as part of efforts to make the entire series carbon neutral.
The fuel is part of that strategy, and is derived from non-fossil fuel-based biomass, produced by Germany’s Haltermann Carless. During the test, the new fuel was compared to the existing fuel and drivers were quick to comment on the different smell, and engine characteristics.
‘The GT500 car has what you could call an ‘aggressively designed engine’
with a lot of advanced technologies applied in it,’ said Nissan driver Ronnie Quintarelli. ‘So, I thought that changing the fuel used would result in some changes, but in fact the changes were so small that I wouldn’t have noticed them if I hadn’t been told about the fuel change.’
‘Of course, there were careful adaptations made to the mapping, but I didn’t have any uncomfortable feelings about the acceleration response we drivers want. I thought that was rather incredible.
‘NISMO has already done some bench testing, and we had used carbon-neutral fuel in this year’s Super Taikyu competition, so I believe we were able to put to use data gained from those experiences.’
Ryuichiro Tomita’s comments were slightly less favourable: ‘There were no big problems that I felt,
but I did feel there was a little less power and some negative effects in the feeling of the drive. I felt something lacking in the depth of power in the high rpm range.
‘Also, since it is a turbo engine, there is backfiring each time you up shift, and I feel the size of that was
somewhat larger, and there was also some gap in our lap times with those we would get with the usual fuel.
‘However, the differences were only on the level of a feeling that today’s engine condition is a little off. If I hadn’t known it was a new fuel, I probably would have thought that.’
The FIA has confirmed a change to the roll hoop testing procedure in light of Guanyang Zhou’s accident at Silverstone in July 2022. Test loads will now be applied horizontally so improved fixing of the roll hoop to the chassis will be required.
At its World Motorsport Council meeting in December the FIA confirmed further changes to the naming of the World Rally Championship feeder series. The FIA WRC2 Open and FIA WRC3 Open will be known as the FIA WRC2 and FIA WRC3 respectively. Meanwhile, the FIA WRC2 Junior Championship is re-named the FIA WRC2 Challenger and the FIA WRC3 Junior class is now the FIA Junior WRC Championship. The FIA WRC2 Masters Cup is now the FIA Masters Cup
The FIA WEC will feature only two choices of tyre specification for each race other than Le Mans, where three will be available. As predicted, tyre heating will be banned in the series for 2023, following the long-term plan of the FIA.
GT3 cars will replace the GTE category in the FIA WEC from 2024 and the class will be called LMGT3. The cars will run with torque sensors on the driveshafts to help with performance balancing. The bodykits for Le Mans, which are limited in cost and inert in terms of aero effect, are now permitted but are not mandatory.
The FIA World Rally-Raid Championship has acquiesced to its manufacturers and introduced an equivalence of technology for its T1.U and T1+ classes. This will allow organisers to adjust, if necessary, the level of longitudinal acceleration between marathon rallies such as the Dakar. The system is intended to allow more sporting fairness between cars of different engineering designs and limit cost escalation.
The Goodyear FIA ETRC Sporting and Technical Regulations allowing allelectric and hybrid powertrains to compete alongside ICE engines have been approved for next season, which will kick off in Italy in May.
The Goodyear Tire and Rubber Company has been confirmed to continue its supply of NASCAR’s top three national series in a new multi-year agreement. This continues Goodyear’s designation as the ‘Official Tyre of NASCAR’, as well as the title sponsor of the Goodyear 400 held at Darlington.
‘From our manufacturing plants to offices around the world, racing is ingrained in our culture, and the importance of our relationship with NASCAR is reflected in the quality, performance and engineering we put into every Goodyear Eagle race tyre,’ said Richard J. Kramer, chairman, chief executive officer and president at Goodyear.
‘Our performance on the racetrack plays an active role in the success of the sport and inspires the development of our consumer tyres, fuelling our commitment to take performance and innovation to the next level.’
For nearly 70 years, NASCAR has served as a proving ground for generations of Goodyear racing tyre engineers, innovating, preparing and supplying tyres that meet the most gruelling and demanding conditions at the tracks the series visits. The technology required to perform under race conditions also informs development and differentiates Goodyear’s consumer tyres.
‘Goodyear has been a trusted partner to the NASCAR industry since 1954, playing a critical role in our shared pursuit to deliver the best racing in the world,’ said Steve Phelps, president of NASCAR. ‘For more than 25 years, Goodyear Eagle tyres have been the only component that connects the Stock Car to the racetrack. Our continued partnership will allow us to push boundaries and innovate our racing product for generations to come.’
Goodyear and NASCAR’s nearly seven-decade relationship is built on shared values of competition and innovation. As the sport has evolved, so have Goodyear’s Eagle race
Ford has introduced the final, and most extreme
only 67 of the track day-only
powertrain
as well as a
longer wheelbase for improved handling on track. Deliveries of the hand-built, S1.7m
tyres, leading to the introduction of new tyre technology, such as the racing slick in 1972, the radial tyre in 1989, the multi-zone tread design in 2013 and the 18in tyre used on NASCAR’s Next Gen racer.
Fittingly, Darlington Raceway –one of the Cup Series’ oldest active tracks – is also home to the Goodyear 400, and many of Goodyear’s milestones, including the brand’s first official NASCAR tyre test in 1954.
Goodyear produces more than 100,000 tyres for NASCAR’s top three series every year, and each one is hand built by Goodyear associates in Akron, Ohio, Goodyear’s global headquarters.
As we enter a new year, the future for the business of motorsport is bright, covid is well behind us and revenues have grown every year since. The 2023 season looks set to deliver more growth but needs hard work to overcome supply and recruitment problems.
This positive picture became obvious at the MIA’s new CTS22 Motorsport Trade Show, in the Silverstone Wing, a sell-out which demonstrated the health of the industry. Highcalibre technology-based business leaders were amongst the large audience. MIA CTS23 in October this year at Silverstone again has already sold 70% of space, so more space will be made available. Don’t miss the chance to exhibit and capture a share of this growth.
Major race series are prime influencers which bring large audiences and sponsors to our sport. Their popularity resonates across all levels of motorsport which is where the real volume of new business lies. Just as the World Cup encourages people to play football, Formula One does the same in motorsport increasing demand across the entire sector.
This popularity also helps businesses who constantly need new engineering talent. Seeing motorsport on TV and social media triggers interest in engineering generally and encourages young people to enrol for motorsport engineering degrees. MIA’s popular School of Race Engineering has seen a rise in interest from females who look positively on the clean, high-tech working environment and exciting competition.
Almost every engineering sector is resolving supply issues which will be with us for quite a while. However, engineers in motorsport know how to overcome problems of design, performance, and materials fast. Companies are using these problem-solving skills to resolve supply issues. Having seen that pressurising and criticising a supplier fails to secure supply, most changed course. They now personally visit, meet
or speak with each supplier to better understand the problems. The supplier, being keen to keep the business, appreciates this collaborative approach as they need help and good ideas.
Jointly, they uncover various solutionsfor example, accepting different packaging, altering delivery methods, accepting smaller, more regular quantities. It can also identify a supplier who will never have the capacity to deliver the volumes needed so a new supplier can be sourced. This new relationship between customer and supplier is creating a stronger and more responsive supply chain than before.
For the last three years, demand for all motorsport products has remained high which will be true for the rest of this decade. The change in ownership of Formula One has, at long last, brought mass entertainment into the mix alongside competitive, on-track highperformance engineering battles. This has opened up a new world of sponsorship for Formula One
The MIA’s ever popular EEMs Conference and Showcase event on 21 March at Gaydon this year, will have ‘Tomorrow’s World of Motorsport’ as its theme. Leading technologists will discuss the many business opportunities that a future of sustainable motorsport will create. This period will be a real bonanza for innovative, creative engineering businesses, who can learn more of these opportunities for growth at this MIA ‘must-attend’ conference.
Outstanding technology and world-class engineering talent is the internationally recognised hallmark of companies in Motorsport Valley UK. This unrivalled business cluster is home to over 3,000 specialist companies in competitive engineering. Their customer base is world-wide – every car in Formula One, Le Mans, NASCAR and IndyCar and many others, rely on supplies from this specialist community, as do most road and rally series around the world.
Constant improvement in manufacture, design, material and delivery has driven this business community to success as has an outstanding R&D spend. Some 30 percent of revenues is spent on R&D, ten times that of automotive, and double that of pharmaceutical. The Government’s commitment to a sustainable future for transport will further increase R&D activities. The variety of solutions will give an exciting boost to challenges in motorsport competition.
teams where brands from many sectors now fight for attention from the increasing millions of ‘eyeballs’ - the vital measure of most sponsorship.
The whole commercial side of motorsport will increasingly benefit – touring cars, single seaters and even heritage. Just look at the audience numbers – 420,000 at the British GP, 200,000 for Goodwood Festival of Speed and the BTCC has already secured full grids for 2023.
The current financial downturn may mean teams require four main sponsors instead of three, but even this is good for the future as the sponsorship pool will grow.
This is the start of an exciting period in motorsport engineering which offers a unique opportunity for growth. You will need to update and add to your network of contacts to maximise your success. It’s the right time for you to look into becoming a member of the MIA and gain access to our proven and substantial business networks. As a member the cost of attending the events mentioned is reduced and we pro-actively help you meet business leaders. The MIA exists to help members in whatever way we can, so to find out more please email me at info@the-mia.com. I wish you a happy and prosperous New Year, and good luck.
Almost every engineering sector is resolving supply issues which will be with us for quite a while
The increased popularity of F1 recently has filtered through to engineering courses, which have seen a large uptick in interest particularly from female engineers
@RacecarEngineer
The Formula 1 team principal merry-go-round hit new levels of activity in December, once it became clear Ferrari would release its leader, Mattia Binotto. The Italian had hit every target set by the management, but it was not enough. The team had a car capable of challenging for the title, and two drivers who were also up to the task, and it was this opportunity that was not fulfilled. One therefore assumes the targets for the future were more acute but, having failed to mount more of a challenge this year, Binotto is out.
Email jodie.green@chelseamagazines.com
I find it a shame that teams play that blame game so readily. There were some graphic strategic errors throughout the year and the pit wall sometimes looked like it was manned by residents of the circus. Simply put, the strategy calls cost them points and dropped the pressure on Red Bull, which was in a position to take full advantage. However, to think that getting the strategy right is an easy thing would be to sorely underestimate how complicated such things are.
Computer programmes need to be written, need to be accurate and need to be read correctly, and when the weather changes, or the safety car comes out without warning, you can take all the data in the world and still get it wrong through no fault of your own.
Admittedly, Ferrari made something of a habit of it mid-season and, as is the way these days, social media was quick to jump in, but to say that was the only reason Ferrari didn’t win would be unfair to Red Bull. It got more calls right because it did its homework better, and had a talented team of engineers able to use the information better. That is as much of a skill required to win a world championship these days as being able to drive the car well, or to set it up optimally.
Sadly, though, it is one of the skills that is only really noticed when things go wrong.
According to McLaren boss, Zak Brown, the announcement that Audi will enter Formula 1 in 2026 was the green light for his team principal, Andreas Seidl, to indicate he wanted to lead that team. The German has his family in Germany, and so a switch to Switzerland makes sense for commuting. To return to the VW Group also makes sense for him. With Porsche, he won Le Mans three times in succession, and the FIA World Endurance Championship Teams’ title in 2015, ’16 and ’17. That said, he still left scorch marks in the Weissach tarmac as he left to take what he described as his ‘dream job’ at McLaren.
He was in line to be the motorsport director of the group at the time, yet knew his heart did not lie in electric or customer racing, which at the time was all Porsche had to offer. The LMDh programme was not announced until later. There is a small part of my mind that wonders whether he simply wanted to stick it to Porsche by taking the Audi gig, but he wouldn’t admit that, even if it were true.
Since he joined the team at McLaren, he has got the big calls right. The team moved from the back of the grid to the leading pack, and there is little doubt it would have stayed there and started to compete for wins. It is easy now to forget how bad things had become before he arrived.
It was heartening to read the story of what happened within McLaren. It would be easy to point to a broken promise to deliver a new wind tunnel as the catalyst for his departure, but actually it was more straightforward. Seidl wanted to leave to go to Audi at the end of the 2025 season, Frédéric Vasseur wanted to go to Ferrari to replace Binotto, and Brown already had Seidl’s replacement lined up. Rather than play gardening leave games, they reached agreement without recriminations or back stabbing, and will get straight on with their jobs. It is as business should be.
For Williams to lose Jost Capito to retirement also seems relatively good natured, although Capito headed for retirement doesn’t quite square with the loss of FX Demaison from the team at the same time. He is not retiring, but was out of the door within two years of joining the team. The answer to that one could lay in the departure of David Wheater, the aerodynamic director who was with Williams for nine years. The car simply did not perform and its drivers, Alex Albon, Nicholas Latifi and Nyck de Vries finished only above Nico Hülkenburg in the drivers’ standings, the German having competed just twice this year for Aston Martin.
Williams also finished 10th and last in the Teams’ title standings with just eight points, so it’s hardly surprising management wanted a head or two to roll. Quite why the car didn’t perform is not yet clear, but I am sure the stories will come out soon enough. Williams is rumoured to be in discussion with Porsche, who still apparently wants into F1, having lost the Red Bull gig during the season. However, German media say even that deal is unlikely to go ahead.
Let’s wait and see what the new year brings.
ANDREW COTTON EditorIf one is great, dual is better.