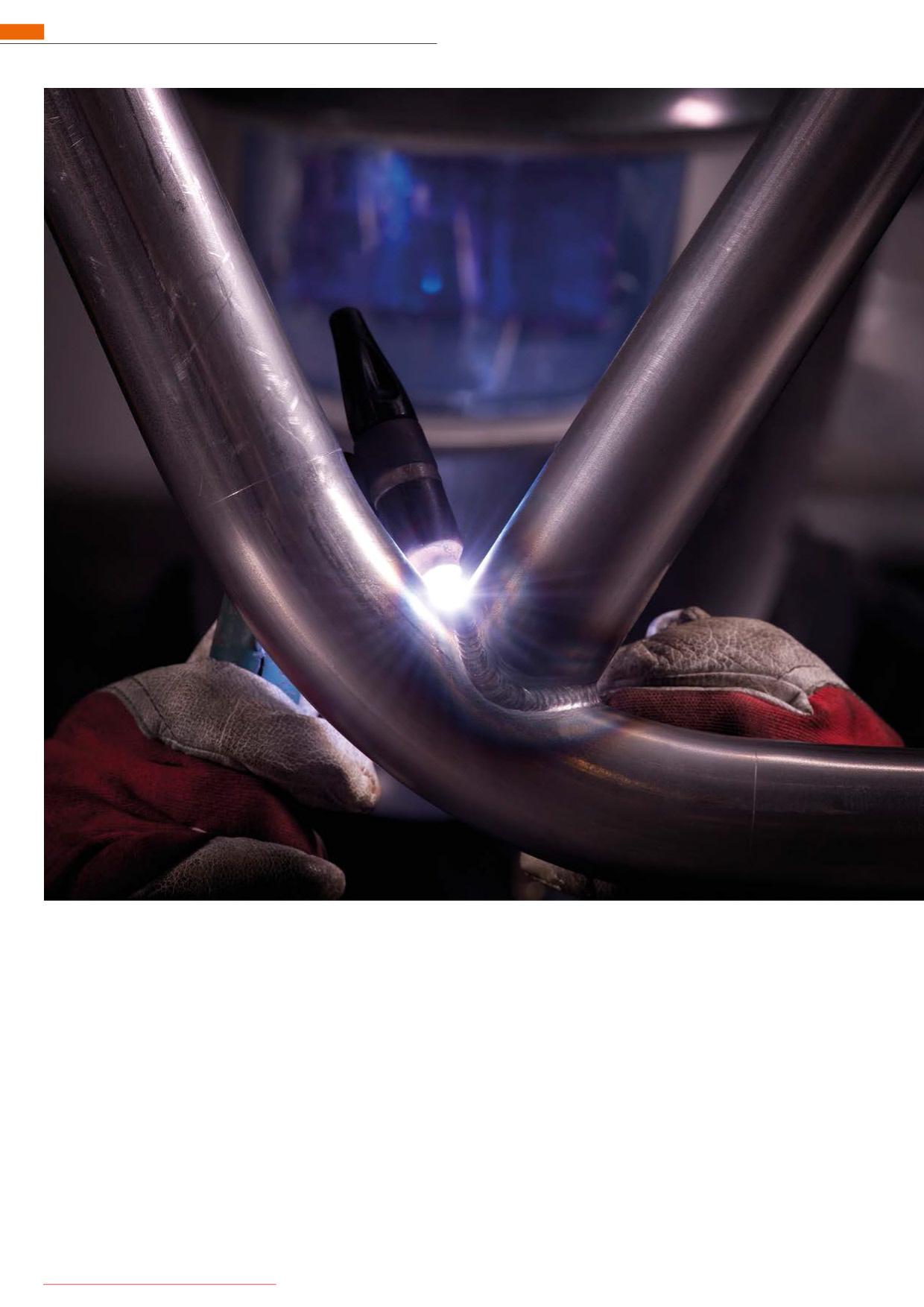
19 minute read
Advanced materials
Metals in motorsport
While plain old steel continues to have its place, developments in manufacturing processes and new material technologies are opening up the materials market in ways we never could have imagined. Racecar investigates
Advertisement
By LAWRENCE BUTCHER
Traditionally, rollcage structures have been made from cold drawn seamless (CDS) steel, which comes in various forms
Materials development has been intrinsic to the advancement of racecar technology since Count Jules-Albert de Dion chugged into Rouen in 1891, to win the world’s first motor race. Materials science has been a key enabler in the realisation of many an engineer’s ideas, which more often than not have outpaced the capabilities of whatever is the ‘current’ state-of-the-art for materials. One only has to look at the the Lotus 88 and McLaren MP4/1 with their carbon chassis, which re-defined the application of fledgling composite technology.
It is, however, easy to give motorsport too much credit, as in the world of industry it is something of a minnow. Aerospace, for example, is responsible for some of the biggest developments thanks to budgets that dwarf even the most lavish spenders in racing. Wars have also played their part; when countries have turned their full might to the development of aircraft, in particular, huge leaps have happened in tiny timeframes.
Sadly, it is the case these days that racing’s ability to harness some of the latest and greatest materials is somewhat curtailed, thanks to never ending cost saving measures by regulators. Formula 1 is a prime example, with an extensive list of materials that are forbidden from use due to their being deemed prohibitively expensive.
Composites may make up the bulk of most modern racecars by volume, but by mass, metals still remain dominant. Obviously in some series, from rallying to drag racing, chassis constructed from metal are still the norm, while in single seaters and sportscars, they tend to be composite, with metal components reserved for the engine, transmission and suspension systems.

In the UK, T45 tube is the first choice, a high tensile, carbon-manganese CDS with excellent bend and weld properties
Steel is real
Starting with steels, these are still used extensively in chassis construction and in this context there have been some interesting developments over the last decade. For rollcage and chassis work, there tends to be regional variations in the materials used, depending on whether one is talking US, British or European standards.
As a general rule, safety-specific parts such as rollcages will be produced from cold drawn seamless (CDS) tubing, with one exception,
which we will cover shortly. CDS is something of a catch-all term that can apply to a variety of tubes. However, in high performance applications, one will be looking at either T45, 4130/ 25CrMo4 or 16CDV6 tubing.
In the US, 4130 CrMo (chromium molybdenum, chromoly for short) has long been the standard for chassis construction, particularly in drag racing classes. Interestingly, though, not in NASCAR, which until Next Gen at least always stuck with mild steel drawn over mandrel (DOM) tubes.
Carbon content
4130 is a low-alloy steel, the properties of which make it ideal for use in welded steel structures. The ‘30’ represents its 0.30 per cent carbon content, which is generally considered to be at the upper level of carbon inclusion that still allows for strong, reliable welds. That’s not to say that higher carbon steels cannot be welded, but the resultant welds are considered more susceptible to cracking, due to the more brittle nature of the material.
Under normal conditions, 4130 has a UTS (ultimate tensile strength) of 90-95ksi, which can be improved with heat treatment. It also has excellent elongation properties, in the region of 28 per cent, before fracturing takes place, and good resistance to crack propagation. To get the best results from 4130, ER70S-2 weld filler rod is often used, which itself has a very low carbon content, nominally 0.06 per cent, and can handle dilution into the relatively high (in terms of weld metal) carbon in the 4130. The resulting diluted weld deposit has a tensile strength of about 85-90ksi, though the actual strength will depend on the amount of dilution with the 4130, weld bead and material thickness.
ER70S-2 also has a higher quantity of alloying elements than the 4130, notably manganese and silicon. In Europe, 4130 is referred to as 25CrMo4.
In the UK, T45 tubing is the go-to choice for rollcages, a composition originally developed for aerospace use between the wars. T45 is a high strength, high tensile, carbon-manganese cold drawn seamless tube with excellent bending and welding properties that, importantly, is weldable without requiring pre or post-heat treatment. Though its chemical composition is different to 4130, its mechanical properties are very similar, with slightly lower tensile strength but greater resistance to cracking under bending.
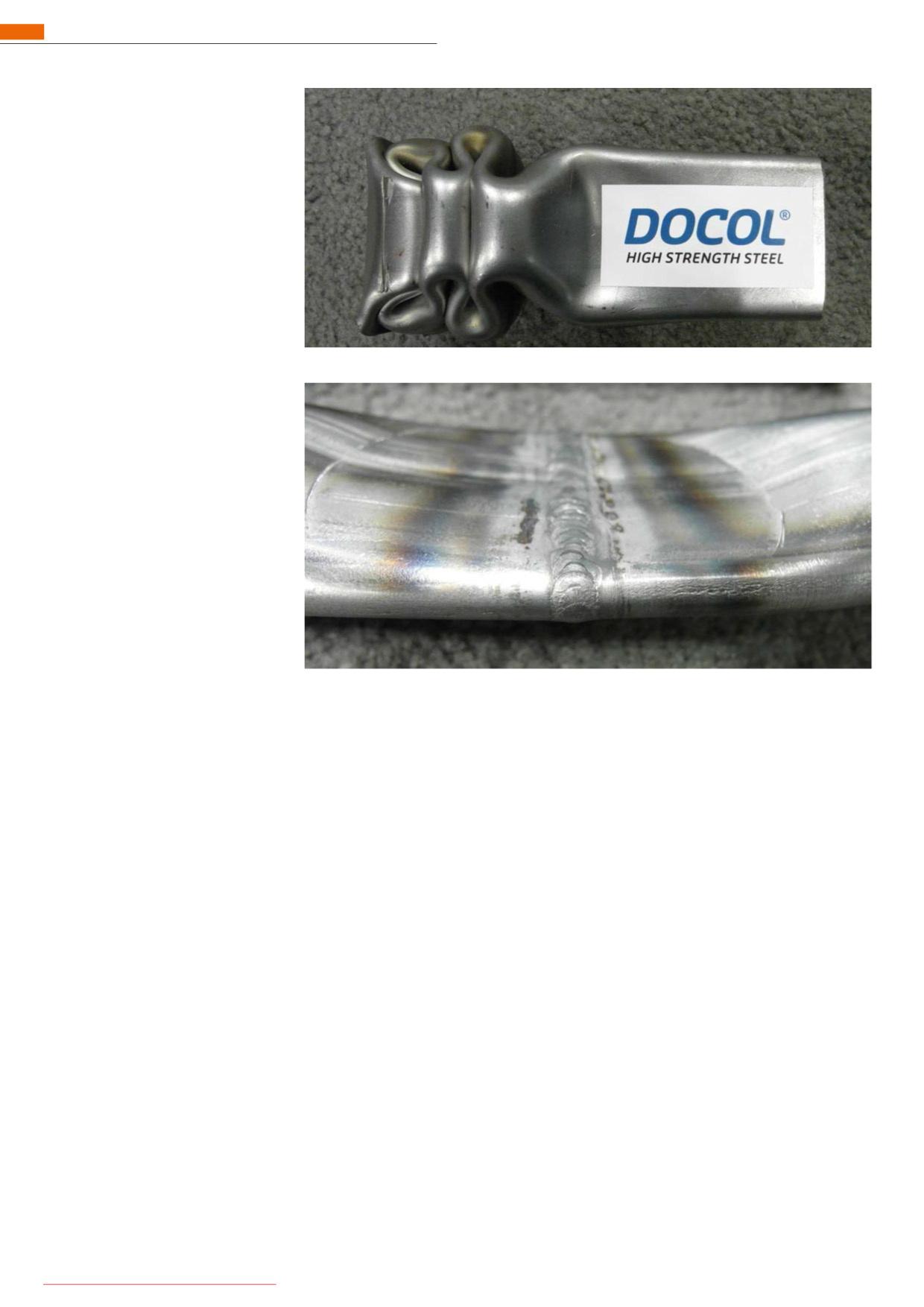
Tensile strength
Another tubing of interest is 16CDV6, which is a micro-structured alloy steel with very high strength and excellent weldability. It has a yield strength of 900Mpa and a tensile strength in excess of 1100Mpa, making it an excellent choice for fabricated suspension components and parts subject to high forces. It is well suited to rollcage construction, though with the FIA stipulating a minimum wall thickness for safety structures of 1.5mm its benefits are somewhat negated, making such as T45 a more cost-effective choice.
A relatively new player on the motorsport market, Swedish-made Docol is a high strength steel with a lower carbon content than CrMo
Docol is a rolled and welded tube with excellent weldability. It comes in two forms, R8 and R10, the latter being higher tensile
Docol rising
For many years, there were no other real options to the aforementioned steels but, over the past decade, Swedish steel manufacturer, SSAB, set out to provide racers with an alternative steel. Branded Docol, it addresses some of the shortcomings of existing steels in motorsport-specific tubing
The use of SSAB’s Docol material in racing stemmed from a collaboration between SSAB and renowned Swedish drag racer, Mats Eriksson. SSAB had been using the material to produce reinforcement panels for OEM suppliers for many years, but found that its properties make it ideal for motorsport use.
Docol R is a high-strength, low-carbon steel available in two variants, R8 and R10, which have slightly different properties. R8 tubing’s strength is very similar to that of 4130 chromoly steel, but with a much lower carbon content (0.12 per cent compared to chromoly’s 0.29 per cent). R10 tubing is a higher tensile version used in areas where lighter weight and high strength are required.
While a higher carbon content increases the hardness and tensile strength of steel, it also reduces its ductility and weldability. So, while 4130 is very effective for use in rollover structures, its relatively high carbon content, and the brittleness this brings under fatigue, can present problems, especially around welded joints and in multiple impact crashes.
The failure mode of a standard 4130 tube is of the brittle type, whereas Docol R8 tube is far more ductile. Despite having less carbon, the tensile strength of R8 is still as high as chromoly, thanks to a higher percentage of manganese – 2.1 per cent over 4130’s 0.56 per cent. Manganese improves the hot-working properties of a steel and increases strength, toughness and hardenability.
Another area where R8 tubing differs from 4130 is that, rather than being mandrel drawn, it is rolled and then welded.
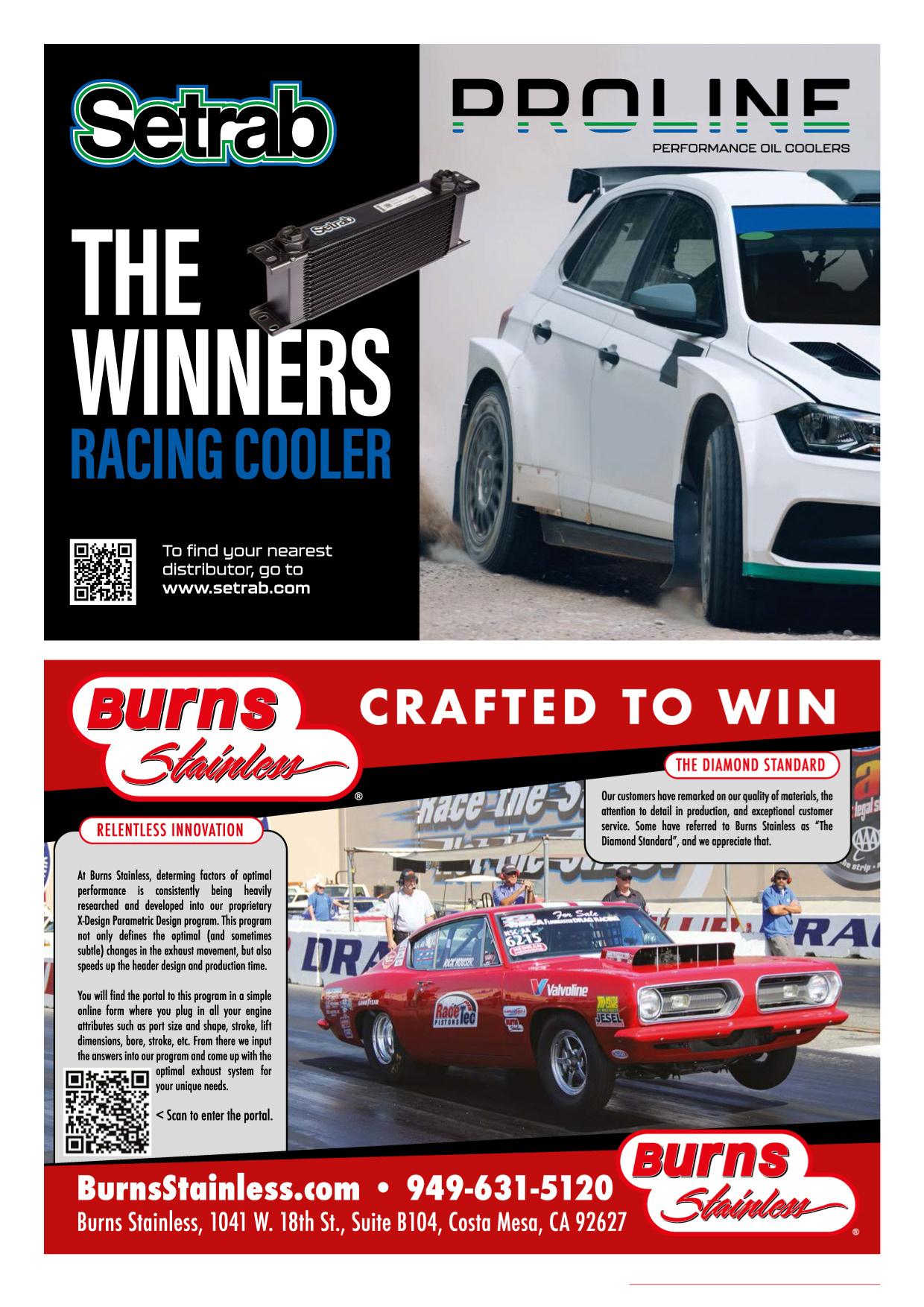
Traditionally, welded tube is seen as inferior to drawn seamless tubing, but SSAB discovered this is not the case with R8, despite initial fears of failure along the longitudinal welds. The lack of issues here is due to the very small area affected by heat during the welding process, a result of the low percentage of the material’s alloying elemens.
In the US, the SFI has granted approval for the use of SSAB’s products in SFI 25.1X-specification drag racing chassis, with the SCCA also allowing it for use in rollover structures. In Europe, it is only FIA approved for drag racing applications, and has yet to make its way into other series due to it being a seamed rather than seamless tube (this, despite the Swedish National Sporting Authority allowing it to be employed).
Mainstream automotive
Advances in mainstream automotive manufacturing technology can also have benefits in racing, particularly where production bodyshells are used. Take the example of Škoda’s Fabia Rally2. Based on the company’s latest road car platform, it is made of high strength and ultra-high strength steel in areas critical for passenger safety. This is beneficial for the new generation Rally2 as well of course. It translates into further improved torsional strength of the floor structure and better strength and durability of the rally car’s bodyshell.
Steels with yield strengths higher than 550MPa are considered advanced high strength steel (AHSS) and, when the tensile levels exceed 780MPa, they are referred to as ultra-high strength steel (UHSS). The key difference between UHSS and AHSS is in their microstructures. AHSS can be engineered to produce unique mechanical properties; some have a higher strain hardening capacity, which gives them a superior strength / ductility balance, while others have higher yield and tensile strengths and demonstrate bake-hardening behaviour.
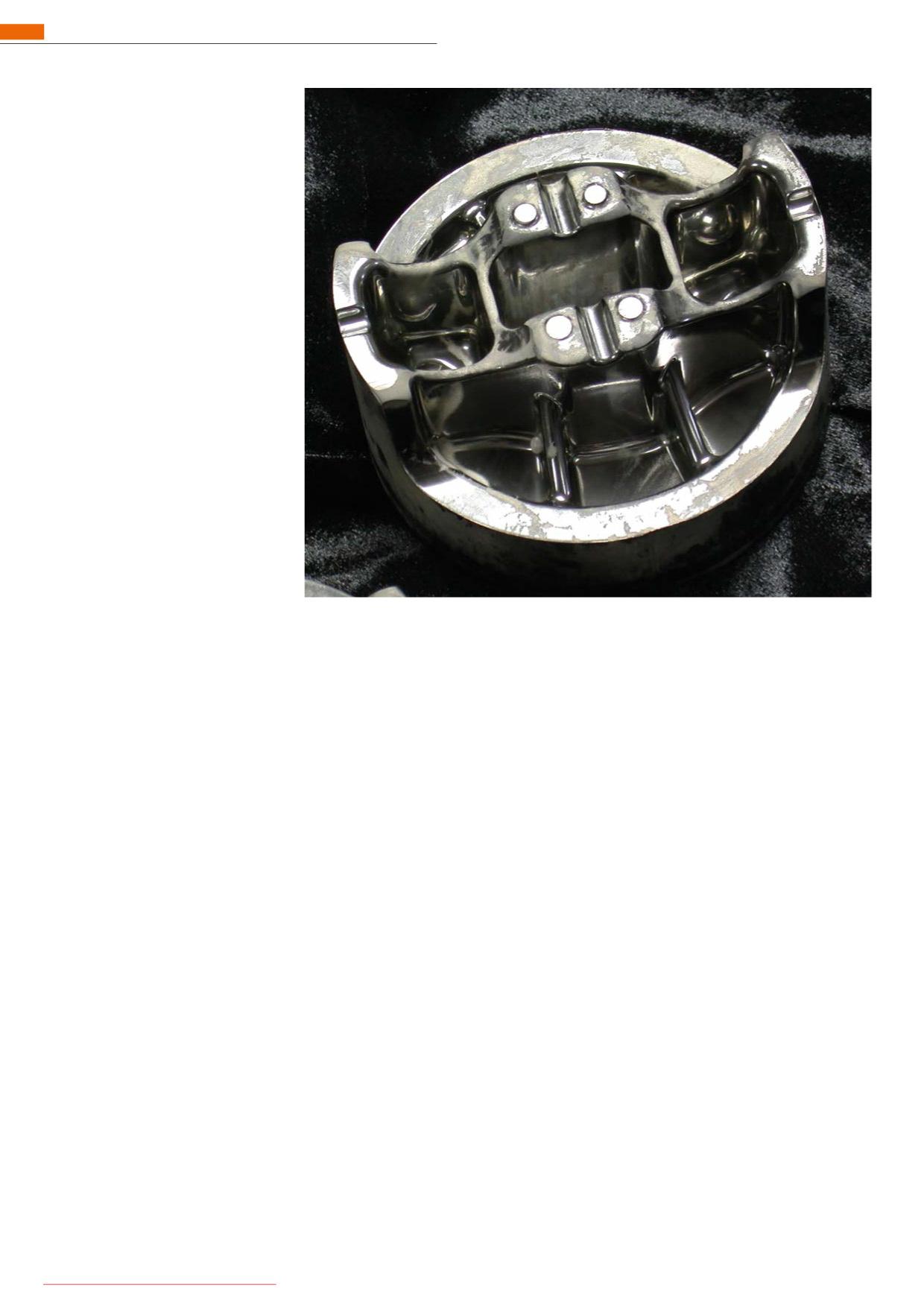
Engine applications
Beyond chassis applications, steels obviously play an important role in racing engines. In many series, regulations mandate a number of the internal components in the engine must be made from iron-based alloys. Aerospace-grade steels are the favoured option here, with the exact material specification depending on the application.
Taking very high-performance crankshafts as an example, materials such as 32CDV13 are used, with products being machined from solid billets. 32CDV13 is a three per cent chromium-molybdenum-vanadium nitriding steel that offers a tensile strength of up to, and sometimes even above, 1300MPa, which develops a hard (around 850HV) wearresistant surface after nitriding.
The alloy is usually produced by a single electric melting and vacuum de-gassing process, but variants are also available as a vacuum arc re-melted version where even greater mechanical properties are required.
It should be noted here that finished cranks are actually often composite items, with dense tungsten counterweights bolted to the steel component. In the past, engine manufacturers have used even denser material, notably depleted uranium, though such materials are obviously now banned.
For camshafts, again most regulations stipulate the use of iron-based alloys. In the past, one of the more popular materials was EN40B nitriding steel. This is a chromiummolybdenum-steel specification usually supplied in the hardened and tempered ‘T’ condition, which offers high wear resistance together with good toughness and ductility. Heat-treated EN40B has a tensile strength of 850-1000N/mm², and is characterised by its suitability for nitriding, which can give a hard, wear-resistant case in the 61-65Rc range.
More recently, engine manufacturers have moved towards through hardening tool steels for camshaft production, a process which creates an extremely stable part that is resistant to surface wear, twist and deflection, with the ability to withstand both high surface loading and shock.
Additive manufacturing has also brought a new dimension to the use of steel parts, and there are an ever-growing number of highperformance variants now available. For example, high hardness tool steels can now be printed, as can various grades of austenitic stainless steel.
Advances are also being made in the processing of Duplex stainless steels (DSSs), which have microstructures of almost equal fractions of δ-ferrite and austenite. This unlocks a wide range of attractive properties such as high strength, good ductility and excellent corrosion resistance. Of particular relevance to electrified motorsport, it is also feasible to use silicon steels for AM, opening up interesting possibilities for the creation of novel motor geometries.
On the subject of electrical steels, it is worth noting the advances made in stamping technology for the laminates that are used to make up the stators in many electric motors. The latest technology allows for laminates
High quality forged components such as this racing piston have been the mainstay of motorsport for years, but times are changing
as thin as 0.025mm to be produced, which can greatly increase the efficiency of motors (though currently in F1, MGU-K laminate thickness is limited to a minimum of 0.05mm).
Though not a steel, additive manufacturing of Inconel 718 is particularly useful for racing, and has been used extensively for the production of complex exhaust components that would be impossible to fabricate using traditional methods.
Aluminium alloys
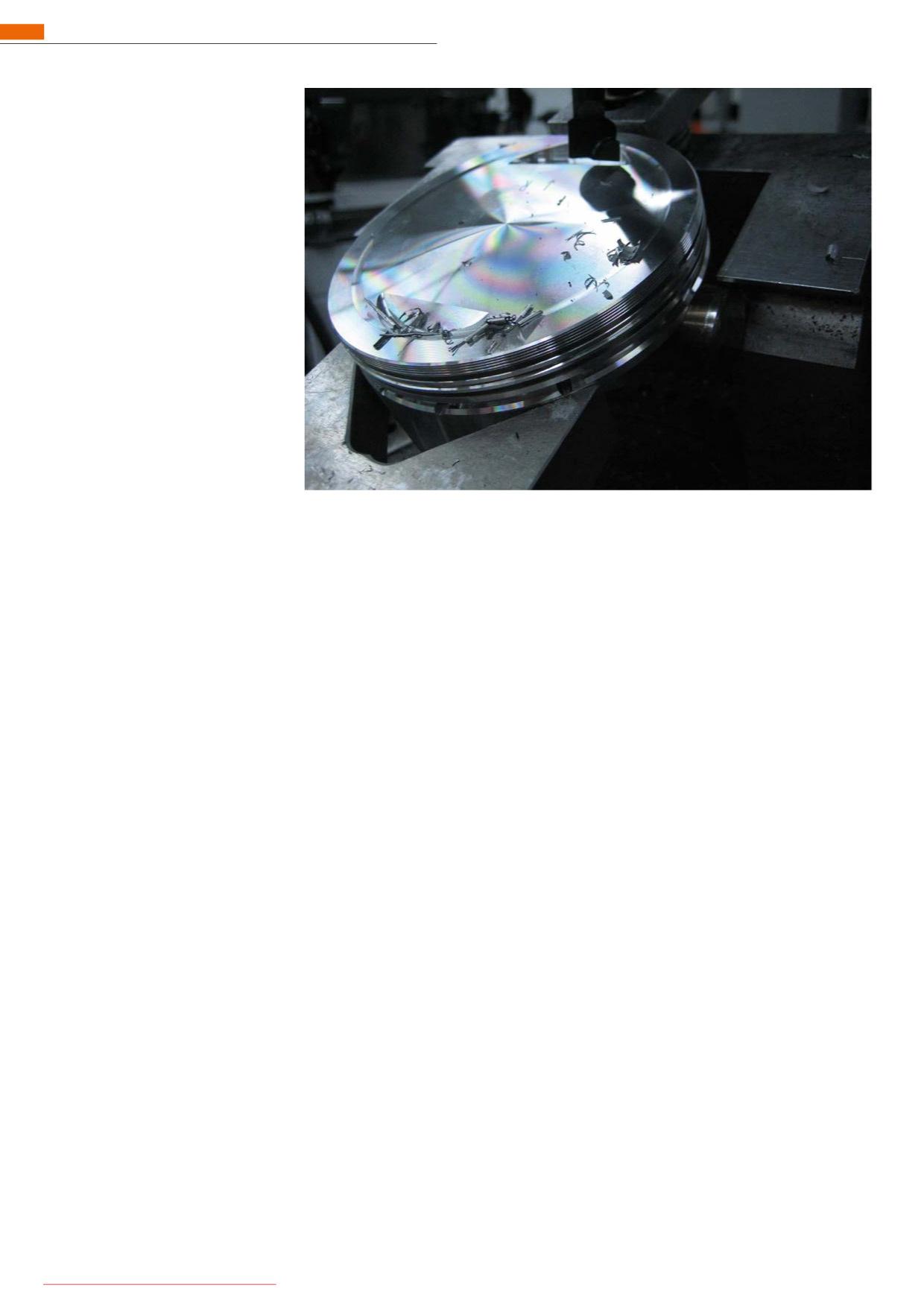
Moving away from steels, one comes to aluminium alloys, deployed everywhere from engine components to suspension uprights. Aluminium is around one third the density of steel, yet some alloys can have the same or greater strength as low-carbon steels. Aluminium alloys are classified by series, from 1-8xxx, with each series having different alloying element (with the exception of 1xxx, which is almost pure aluminium).
The different alloy series each have their own benefits and disadvantages. Some are easy to work with, making them suitable for welded and fabricated parts, while others have excellent strength or fatigue properties. For example, the go-to material for high-performance pistons used to be 2618 aluminium alloy, originally developed by Rolls-Royce for the Merlin engine, though back then it was known as RR58.
Post WW2, when the material became available on the commercial market, RR58 became a firm favourite of high-performance engine builders. 2618 contains both copper (1.9-2.7 per cent) and magnesium (1.3-1.8 per cent) and can be age hardened to give it excellent strength at high temperatures, while still maintaining good machining properties even in a heat-treated state.
More recently, piston manufacturers have turned to aluminium-silicon alloys. High silicone 4032 aluminium, which has a silicon content of 12 per cent, has been extensively used for racing pistons, but for extreme applications 2816 is often favoured thanks to its greater ductility and higher strength.
However, new Al-Si materials have been developed which deliver the benefits of 2618, but with the added advantages of an increased silicon content. These benefits include, but are not limited to, better wear characteristics and lower thermal expansion, an important consideration in an age where race engines are expected to last far longer than in the past. The move towards highly boosted, small capacity engines also has relevance here, with such engines greatly increasing the loads experienced by the piston skirt and ring pack.
Though 2618 and the newer Al-Si alloys have similar surface hardnesses, depending on the level of heat treatment, the silicone particles provide greater wear resistance. If one uses a 2618 alloy for such applications, further treatment of areas like the ring grooves or skirts is needed, for example hard anodising, which may not always be necessary if a silicon alloy was used.
This new breed of Al-Si alloys includes materials such as M142 and M174, which retain a high silicon content, at around 13 per cent, but have a much higher copper content, of between three and five per cent, compared to 4032 which has just one per cent.
For other components such as damper bodies, which require excellent strength and stiffness, 7000-series aluminium alloys are generally used. These provide a good balance between outright strength while not being so stiff that they suffer fatigue under the intensive cyclical loadings they experience. 7000-series materials are alloyed with zinc, and can be precipitation-hardened to the highest strengths of any aluminium alloy (the 7068 alloy for example has a tensile strength of up to 700 MPa). There are also other ultra-high strength aluminium alloys under development, such as A-1500, which has the potential for a UTS in excess of 1000MPa.
High-silicon 4032 aluminum was the material of choice for racing pistons, but new Al-Si alloys offer ever greater wear resistance
Exotic alloys
Looking to more exotic alloys, one enters into the realm of materials deemed too expensive by regulators (particularly in F1), meaning their use is limited. For example, aluminium-lithium has some very attractive properties, notably high stiffness, low density, good temperature stability and resistance to corrosion, particularity when other elements are used to improve its properties further.
One such example is 2099 Al-Cu-Li, developed at the end of the 1990s, which has been used for making brake calipers. In addition to lithium, 2099 contains up to three per cent copper, as well as zinc, magnesium and manganese. The copper forms strengthening precipitates to increase the toughness, the lithium helps reduce density without compromising strength, while the zinc aids corrosion resistance.
Taking 2099-T83 as an example, this material has a modulus of about 78Gpa, placing it just under the 80Gpa elasticity upper limit F1 regulations dictate for brake calipers. However, in addition to a stiffness limit, the rules now also specify that only alloys with less than one per cent lithium can be used, negating 2099-T83 as it has between 1.6 and two per cent of the alloying agent.
Composite metals
Jumping to a higher performance level still, and one that is really only viable in terms of cost for those with very large budgets, one comes to metal-matrix composites (MMC). These combine a metallic base with nonmetallic reinforcement (normally a ceramic), which improves the specific strength and stiffness of the material.
There are three main types of MMC, those that use fibre reinforcement, whisker reinforcement and particulate reinforcement. For the purpose of manufacturing pistons, particulate-reinforced MMCs are the most relevant, as these are isotropic and so can be treated in the same way as unreinforced alloys. So, for example, ingots can be formed using the same powder metallurgy techniques as other aluminium alloys.
In an aluminium MMC, one of the constituents is aluminium alloy, which forms a percolating network and is described as a matrix phase. The other constituent
Alloys for high-performance engine parts that need greater mechanical properties are produced by a vacuum arc re-melting process
is embedded within this alloy matrix and serves as reinforcement. The most common aluminium MMCs use silicon carbine or aluminium oxide.
As with an alloy, the properties of MMCs can be tailored by varying the nature and relative quantities of the constituent parts. The properties of such materials greatly exceed those of traditional alloys and so found favour, when the regulations allowed, as a piston material in Formula 1 (MMC are now banned from used in the powertrain).
In the mid-2000s, Honda developed MMC pistons to replace those made from 2618 aluminium alloy, which it traditionally used in its naturally-aspirated V10s. The results were impressive, and the piston could be made 16 per cent lighter than aluminium components. The extra strength also allowed for a 400rpm increase in engine speed without compromising piston integrity.
A more recent advance in MMC technology has been the development of metal-matrix nano-composites, or MMnCs. As the name suggests, these use smaller reinforcement particles than current MMCs, down to 10nm, allowing for greater distribution amongst the alloy matrix. Much work in this area is still at the research stage, but the results are encouraging, with MMnCs using traditional filler materials such as silicon carbide and aluminium oxide showing improved mechanical properties over MMCs.
Some of the main hurdles to such materials gaining widespread use though are in the processing, for example the difficulty of ensuring an even distribution of the reinforcement throughout the matrix material and consistent bonding between the two.
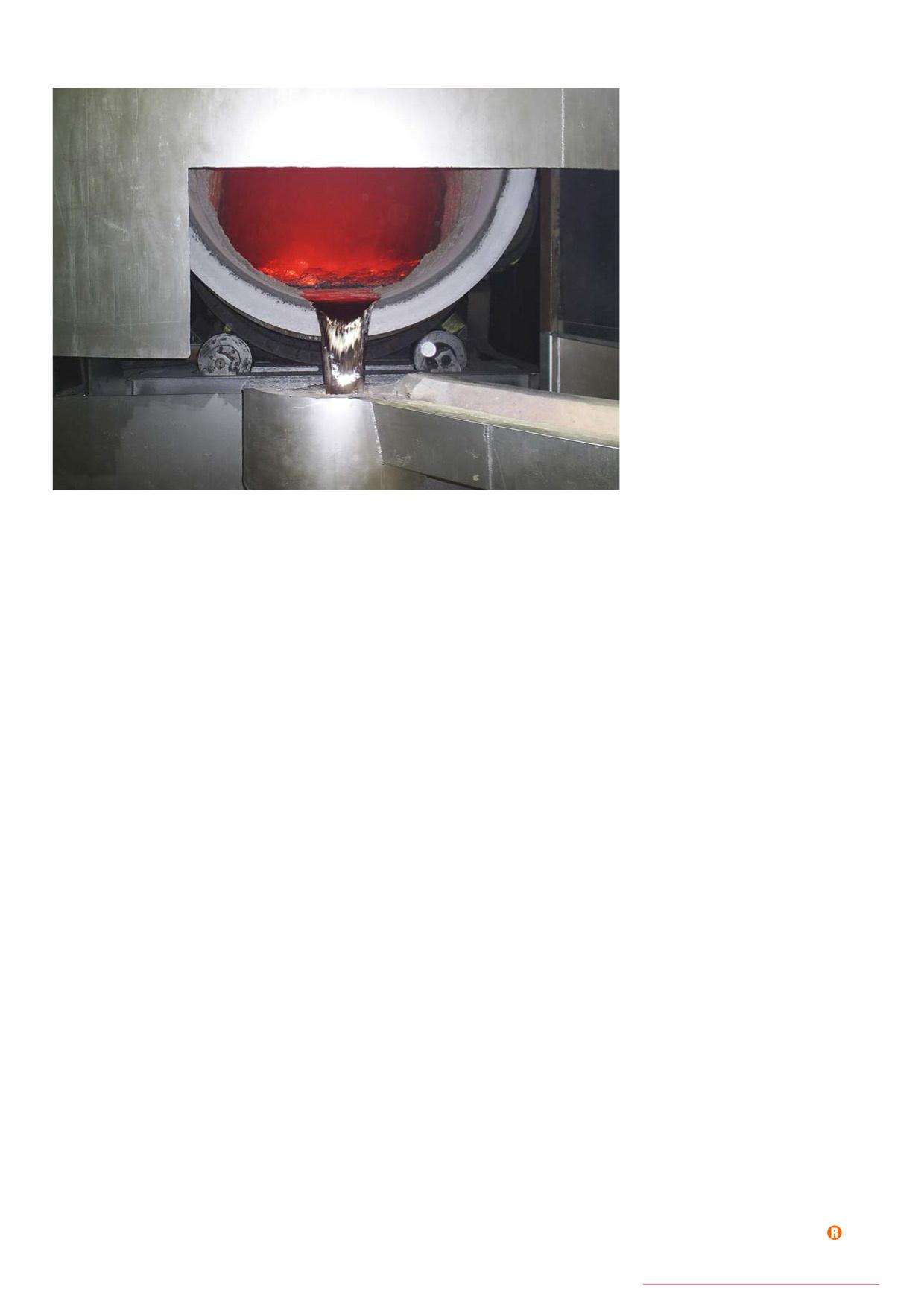
Metal matrix composites
It is an interesting quirk of the F1 rule set that metal matrix composites are specifically prohibited, with the exception of particle reinforced aluminium alloys for additive manufacturing. For example, 6061 RAM 2 is permitted, a proprietary alloy from supplier Elementium, which incorporates two per cent ceramic reinforcement. Claimed to have a 50 per cent faster build time than AlSi10Mg and better surface finish, it has a UTS of 331MPa and a yield strength of 297MPa.
Another interesting aluminium-based AM alloy specifically allowed in F1 is Scalmalloy, developed by specialist AP Works, which sees aluminium alloyed with scandium and magnesium, giving finished properties similar to 7075 wrought alloy. It has an impressive tensile strength of 520MPa (compared with AlSi10Mg at 350MPa), which is about half that of Ti6Al4V, and combines that with a density the same as AlSi10Mg (2.6g/cm3). In addition, its microstructure remains stable up to 250degC.
Finally, titanium is an attractive material for motorsport use, thanks to its relatively low density and good strength, though it is also a difficult material to work with so its application needs to be carefully considered. For example, most titanium alloys that are commercially available have less than ideal behaviour characteristics when placed in sliding contact, and are susceptible to galling.
The most commonly used is Grade 5, or Ti-6Al-4V, a specification that encompasses a number of different sub-grades of the material. This has a chemical composition of six per cent aluminium, four per cent vanadium, 0.25 per cent (maximum) iron, 0.2 per cent (maximum) oxygen, and the rest titanium. It is the workhorse of the titanium world for various reasons, notably that it has the same stiffness and thermal properties as pure titanium, but is far stronger and heat treatable. By varying the alloying elements, it can be modified to improve particular performance aspects. For example, the addition of palladium or ruthenium can increase its corrosion resistance.
There are other grades of titanium, right up to 38, which contains four per cent aluminium, 2.5 per cent vanadium and 1.5 per cent iron. Originally developed for use in armour plating, Grade 38 titanium has similar mechanical properties to Grade 5 but with much better cold workability. Beta C or Ti-3Al-8V-6Cr-4Mo-4Zr has also been used for high-strength fasteners due to its exceptional corrosion resistance and excellent strengthto-weight ratio when heat treated. It is also, however, prone to galling.
Compared to the aerospace and defence industries, motorsport is a very small user of titanium, though the similarities in requirements between the two are many, so racing can benefit from developments there, provided there is enough material available.
As with other materials covered here, there are now also a host of different AM titanium powders available, opening up a world of possibilities for novel designs that circumvent the traditional difficulties of the material to fabricate and machine.
Though some of the largess of the past is no longer practical in motorsport material development and use (think single billets of material worth tens of thousands of dollars being machined away to almost nothing to make a lightweight brake caliper) there is still plenty of innovation and development underway. No doubt the current generation of F1 power units have necessitated some bespoke solutions that we will only ever find out about years down the line.
Even if new materials are not developed specifically within motorsport, racing still provides an attractive crucible within which to test new developments in short time frames and under extreme duress.