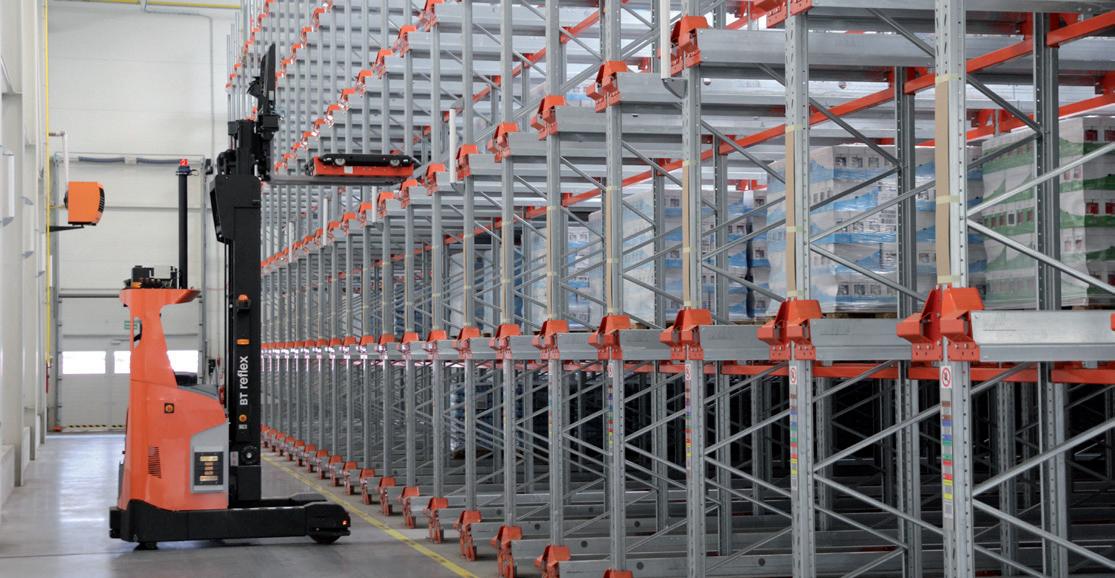
8 minute read
Unikátní řešení automatizace manipulace
Úspěšná kooperace více technologií, včetně systému Radioshuttle
Fáze zaskladnění a vyskladnění palet, při které premiérově kooperují automatický retrak s jednotkami Radioshuttle, je konečnou etapou projektu souvislé automatizace manipulace a skladování hotových výrobků ve společnosti LINEA Nivnice a.s. Proces začíná u 4 dopravníků, které přivážejí palety od 4 výrobních linek a končí přípravou vyskladněných palet u nakládacích ramp v expediční zóně.
Advertisement
Základním předpokladem bylo vyřešení kooperace, propojení toku informací a interakce více technologií od více dodavatelů (WMS, vozíky Toyota Autopilot, systém Radioshuttle, paletizátor, ovinovací stroj, výtahy, dopravníky) a bezchybné svázání jejich činností do logického funkčního sledu. Jde o vyšší úroveň propojení než v jiných aplikacích využívající automatické vozíky a současně o unikátní zapojení poloautomatického systému Radioshuttle.
Celý systém je navržen, dimenzován a odzkoušen v provozu tak, že kapacitně vyhovuje maximální úrovni výroby na všech čtyřech výrobních linkách a zajišťuje plynulý odvoz a následné zaskladnění/vyskladnění všech palet v potřebném čase při zachování bezpečnosti manipulace.
Proč padla volba na Radioshuttle
Sortiment dětské výživy představuje relativně malý počet položek (3 druhy obalů – kapsičky 100 a 200ml, sklo, různé příchutě), ale s většími šaržemi. Jde o naplnění základního předpokladu pro instalaci vysokohustotního bezuličkového regálového systému, ve kterém nejsou jednotlivé palety přístupné, a proto je důležité skladovat v jednom regálovém kanálu jen jeden druh zboží.
Odbourání uliček, vysoké využití objemu skladu (až 85%) a rychlost manipulace (obslužný vozík - zde automatický retrak - odváží paletu, manipulační jednotka Radioshuttle mezitím může manipulovat další objednávku) vytvářejí vysoce efektivní a produktivní řešení simultánní manipulace a skladování a urychlují návratnost investice.
Parametry systému Radioshuttle v Linea Nivnice (režim FIFO) V ČR jde o středně velkou realizaci, která je tvořena:
• regálovým systémem pro 3 360 palet (28 řad/6 úrovní s max. výškou zakládání cca 8 m) • hloubka každého kanálu umožňuje uskladnit až 21 palet • celkem je nasazeno 5 manipul. satelitních jednotek Radioshuttle, 3 na straně zakládání, 2 na straně expedice Počet 5 jednotek se osvědčil a zajišťuje s dostatečnou rezervou potřebnou produktivitu, protože snižuje celkový počet situací, kdy je nutné převážet satelitní jednotky mezi jednotlivými kanály regálového systému.
1. ETAPA
Odebírání palet na konci výrobního procesu
Manipulaci vykonává zakladač Toyota Autopilot SAE160 s li-ionovou baterií. Odebírá palety z každého ze 4 dopravníků od 4 výrobních linek za paletizačním automatem a jeho převoz na dopravník vedoucí k ovinovacímu stroji a k výtahu, který paletu vyveze do 7m výšky na dopravník spojující výrobní provoz a sklad.
Ve chvíli, kdy hotové výrobky vyjedou z výroby, jsou v paletizátoru vyskládány na paletu, zabaleny a opatřeny štítkem, který je odeslán do WMS. Ten vyrobí objednávku pro odeslání do skladu a zaskladnění, a pošle ji do vozíku, do ovinovacího automatu a k automatické etiketovačce.
Na konci dopravníku, který ústí do skladu, je kontrolní kamera, která načte a zkontroluje obsah štítku a potvrdí automatickému retraku, že paleta může být zaskladněna a kam - viz 2. etapa.
2. ETAPA
Odebírání palet z dopravníku ve skladu
Ze spojovacího dopravníku ve výšce 7m paletu odebere retrak Autopilot RAE200. Do zprovoznění propojení se systémem Radioshuttle - viz 3. etapa - odkládal automat palety do předepsaného prostoru ve skladu a zaskladnění/vyskladnění bylo prováděno po přechodnou dobu manuálně řízenými retraky.
3. ZÁVĚREČNÁ ETAPA
(předání do plného provozu 4/2021) - automatické zaskladnění a vyskladnění v regálovém systému Radioshuttle
Princip vysokohustotního skladování Radioshuttle
Je založen na bezuličkovém regálovém systému, který je tvořen skladovými kanály, jeden kanál vždy pro jeden druh výrobků. Každý kanál je přístupný buď z jedné strany (režim FILO), nebo z obou stran (režim FIFO, realizovaný v Linee). Obslužný vozík umístí paletu na kraj kanálu, další manipulaci v celé délce kanálu již zajistí satelitní jednotka Radioshuttle. Regálový systém obvykle obsluhuje více jednotek, které jsou podle potřeby obslužným vozíkem přemisťovány mezi jednotlivými kanály.
1. část - fáze zaskladnění
Zaskladnění palety na první pozici v příslušném regálovém kanálu provede automatický retrak kooperující se satelitními jednotkami Radioshuttle. Satelitní jednotka odveze paletu na volnou pozici v hloubce kanálu. Ve výjimečných případech může být paleta odložena k okamžité expedici, nebo, například v případě nečitelného čárového kódu, uložena na místě určeném pro palety s tímto typem chyby.
2. část fáze vyskladnění

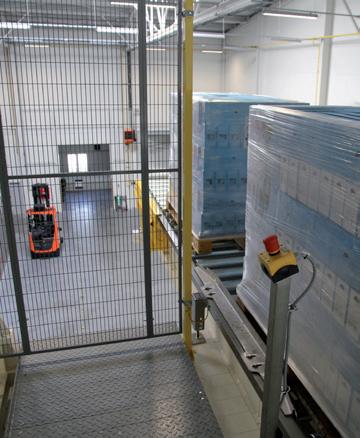
Druhý retrak Autopilot RAE200 na základě objednávek z WMS systému paletu vyskladní z první pozice regálového kanálu na straně expedice a odveze ji na určené místo, odkud je realizována nakládka vozidel.
Během obou částí 2.etapy musí retrak Autopilot on-line komunikovat s manipulační jednotkou Radioshuttle, ověřovat si její polohu a v případě potřeby si ji před zaskladněním/ vyskladněním palety přemístit do příslušného kanálu regálového systému.
Klíčem pro dobré fungování celého řešení je moment vytvoření objednávky na odvoz a zaskladnění palety a předání této informace automatickým vozíkům, a to každému jen tu část, kterou potřebuje znát. Objednávku vytvoří Warehouse Management System (WMS). Stacker dostane informaci, že je paleta z výroby připravena k odebrání, retrak dostane z WMS informaci, jaká paleta přijede na spojovací dopravník a kam ji má v regálovém systému uložit.
WMS řídí logistiku zboží, Autopilot je jen vykonavatel příkazů
Nejnáročnější složkou celého projektu bylo dotažení propojení řídícího systému retraku Autopilot (System Manager, dále jen SM), jednotek Radioshuttle a WMS zákazníka.
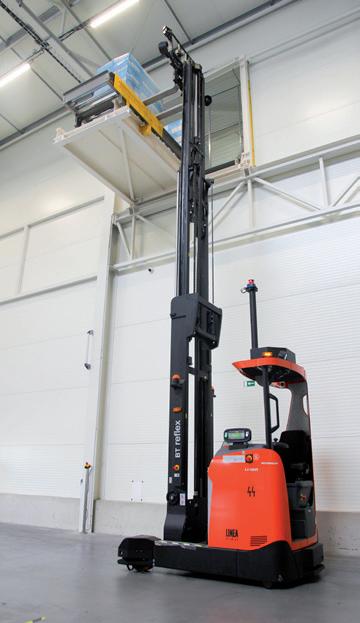

• System Manager (SM) - řídí vozíky
SM řídí provoz vozíků Autopilot, tedy jízdu, orientaci v prostoru, součinnost a bezpečnostní prvky. Vozík stoprocentně vykonává příkazy, které mu SM zadává. Aby byl automat schopen paletu z dopravníku převzít a zaskladnit, musí udělat několik kroků.
Musí se "podívat", kde se právě nachází jednotka RS, jestli je v příslušném regálovém kanálu. Podvozek musí být v kanálu vždy dříve, než je do něho zaskladněna, případně z něho vyskladněna paleta.
• WMS - určuje odkud a kam mají být palety manipulovány
Úlohy se řadí ve WMS a vozíky mají k dispozici vždy právě jen 2 úlohy. Jednu aktuálně řeší, druhá čeká na vyřízení. Jednou úlohou je vždy uskladnění jedné palety.
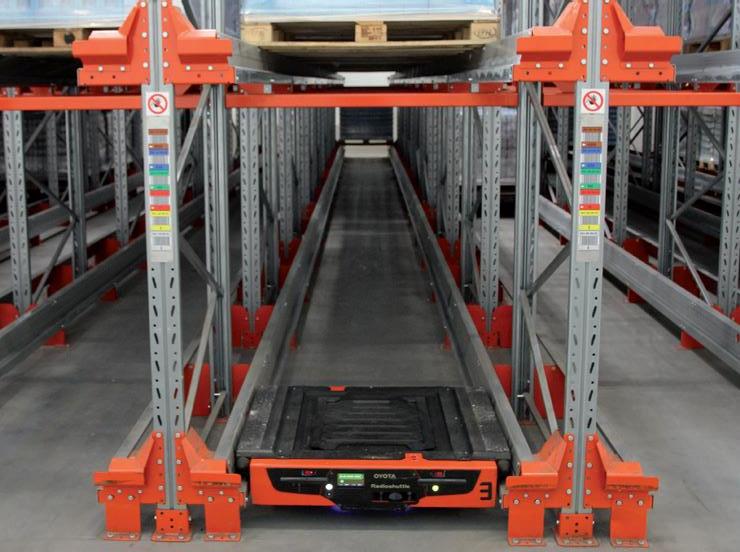
Vaktuálně zveřejněné soutěži Impuls Logistika, pořádané magazínem Logistika vydavatelství Economia, ovládlo toto řešení kategorii Top logistický projekt, ato svelkým náskokem. Porota hodnotila především inovativnost myšlenky, využití nových postupů nebo zařízení vpraxi, kterých lze vprojektu najít celou řadu.
Když vyjede paleta na dopravníku z výroby do skladu, přejede na konci dopravníku kolem čtečky čárového kódu. V tu chvíli dostane retrak Autopilot příkaz z WMS, kam má paletu zaskladnit. Vozíky Toyota dostávají všechny příkazy z WMS systému přes standardizované IT rozhraní.
WMS posílá příkazy a zpětně dostává prostřednictvím SM informace o stavu retraku a všech jednotek Radioshuttle (stojí, jede, je nabíjen, stav baterie, přesun jednotek mezi kanály), o provedení úlohy a aktualizuje si stav skladu a ukládá, registruje a zpracovává všechny získané informace.
Nabíjení
Každý vozík má svou vlastní nabíjecí stanici, kam je v případě potřeby nebo volného časového okna "odvelen" WMS systémem. Pro vozík v expediční zóně je nabíjecí místo současně parkovacím místem, kde vozík vyčkává na doručení další objednávky. Vozík obsluhující dopravník z výroby a zaskladňující palety má parkovací místo na "své" straně regálového systému a k nabíjecí místnosti musí přejet. Má tedy situaci o něco složitější, reálně i v oblasti programování. Je-li jeden ze dvou strojů Autopilot mimo provoz (nabíjení, údržba, preventivní prohlídka, TK apod.), druhý automaticky přebírá dočasně jeho roli a může pracovat v obou sektorech.
Jak Autopilot reaguje na chyby
Je-li určený regálový kanál z jakéhokoli důvodu nepoužitelný, Autopilot příkaz k zaskladnění ignoruje. Takové situace jsou pečlivě monitorovány, protože jsou kriticky důležité pro hladký chod systému, pro dosažení vysoké produktivity a korektního fungování celého manipulačního procesu. Jiným důvodem, proč nemůže být paleta zaskladněna a Autopilot příkaz neprovede, je poškozený nebo chybný čárový kód, jeho zakrytí visící fólií a podobně. Pro takové palety je určeno odkládací místo ve skladu, kam Autopilot "anonymní" paletu umístí. Tento postup je nutný, aby problematická paleta neblokovala dopravník a plynulý chod následujících palet. Informace o nemožnosti paletu uskladnit je odeslána do WMS.
Automat je spolehlivý a přesný
Automaty chtějí mít neustále jasno na 150%. V běžném provozu mohou vznikat nenadále situace, například poškození etikety, výpadek proudu, požární poplach, a vozíky musí vědět, jak se má v každém jednotlivém případě zachovat. Reagují vždy na splnění nějaké definované podmínky. Provádějí soustavně bezpečnostní kontroly a vysílají dotazy, ověřují svoji pozici vůči regálům nebo dopravníkům, načítají svou pozici před každým nabráním nebo uložením palety, ověřují si připravenost jiné části systému. Dotazy probíhají přes WMS. Obdobně si Autopilot monitoruje i pozici pro správné nabírání i ukládání jednotek RS.
Současně si vozík permanentně "hlídá" své okolí. V případě jakékoli překážky na trase, ať již osoby, jiného vozíku nebo jiné palety vozík zastaví a vyšle signál, že nemůže vykonat příkaz/objednávku. Jakmile je překážka odstraněna, pokračuje v práci. Je úkolem uživatele, aby automatu zajistil volné pracovní trasy, aby nedošlo ke snížení produktivity.
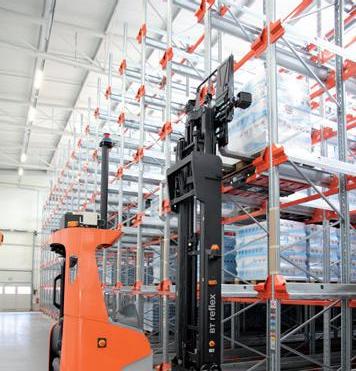
Shrnutí dosažených cílů
• Automatizace vylepšila efektivitu, zjednodušila personální situaci a radikálně zvýšila bezpečnost celého manipulačního procesu ve výrobě i ve skladu.
• Ve třísměnném provozu došlo k úspoře 3 až 3,5 pracovníka na směnu (řidiči vysokozdvižných vozíků, retrakáři, manipulanti u výrobních linek nebo výtahů), k vyřešení nezájmu lidí o víkendové a noční směny. Stabilizovala se výkonnost pracoviště díky nezávislosti na lidském faktoru.
• Odpadlo mnoho neproduktivních činností odpovědných manažerů, uvolnil se prostor pro řešení dalších rozvojových úkolů.
• Posílila se bezpečnost všech provozů, nekříží se žádné trasy vozíků s pracovišti osob.
• Snížily se náklady na škody (způsobené nárazy vozíků řízené lidskou obsluhou do regálů, do zboží).
Stabilizovala se energetická účinnost li-ionových baterií a energetická hospodárnost pracoviště, protože automaty jezdí plynule a úsporně.
FAKTA A ČÍSLA
Společnost: LINEA Nivnice a.s. Lokalita: Nivnice Odvětví: Výroba nápojů a potravin Aplikace: Automatizace manipulace ve výrobě i v regálovém systému Radioshuttle (pro cca 3 360 palet), automatické propojení všech fází toku zboží Řešení: Satelitní jednoty Radioshuttle (5ks), retrak Autopilot RAE200 (2 ks), stacker Autopilot SAE160 (1 ks)