SECTOR FOCUS:

Improving pumping processes for Phenol unloading
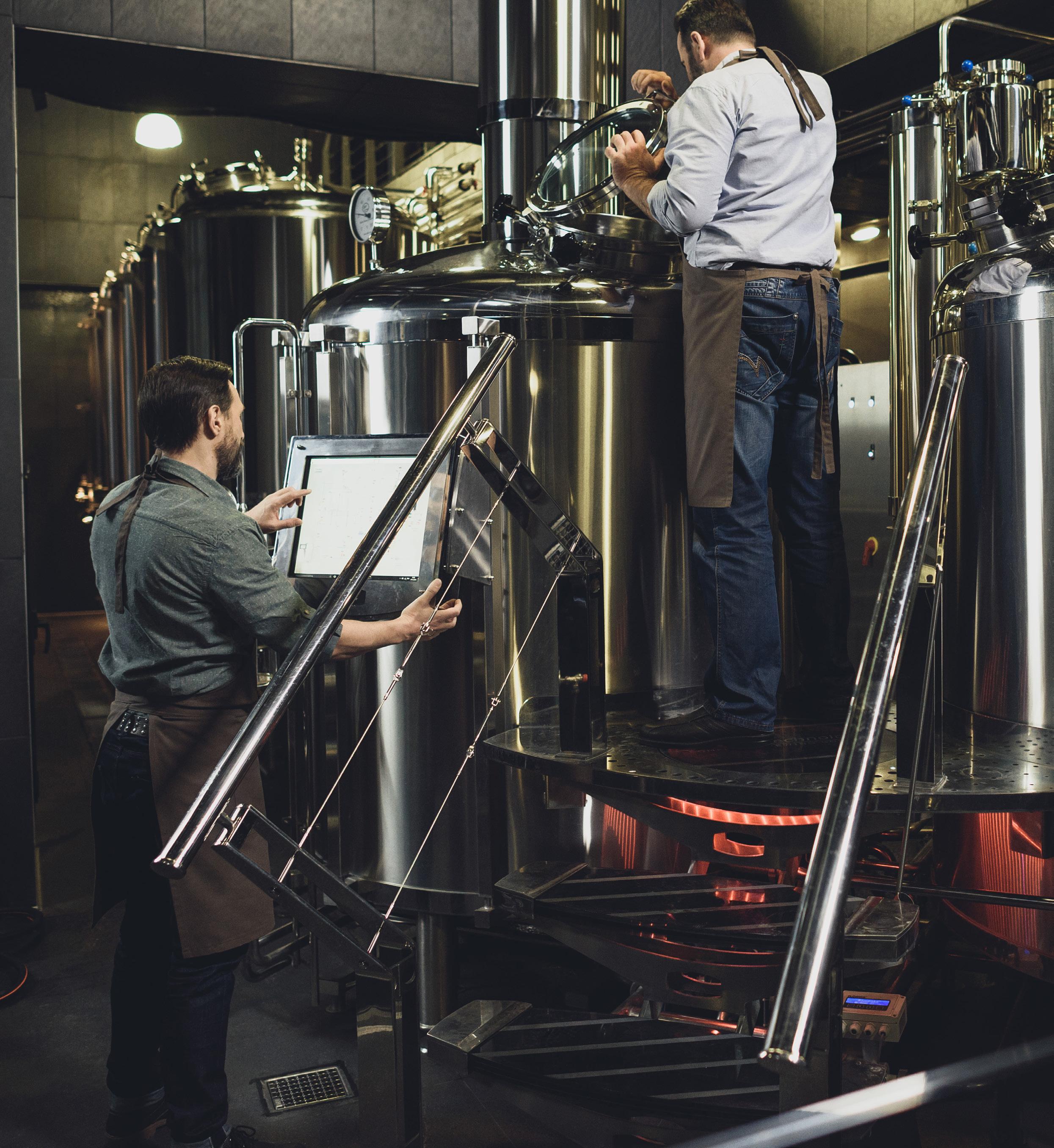
Improving pumping processes for Phenol unloading
Online monitoring and intelligent management of the equipment and assset fleet.
The ideal solution for monitoring and increasing the availability of your fleet equipment and assets. Based on cloud computing technology, motors, drives, gearboxes, pumps and compressors can be tracked and monitored at any time and from anywhere in the world. This allows planned and predictive maintenance avoiding costly downtime and ensuring the efficiency and performance of equipment.
Editor Chris Callander chris@flowmag.co.uk
01732 671123
Contributing Editor Suzanne Gill suzanne@flowmag.co.uk
Publisher Andrew Castle andrew@flowmag.co.uk
07785 290034
Account Manager Fawad Minhas fawad@flowmag.co.uk
Accounts Touchwave Media Ltd accounts@flowmag.co.uk
Production G and C Media Ltd production@flowmag.co.uk
For over three-quarters of a century the British Pump Manufacturers’ Association (BPMA) has been serving the interests of UK and Irish suppliers of liquid pumps and pumping equipment.
As I write this, the 2023 Pump Industry Awards are just over two weeks away. The annual event is always an excellent opportunity for the pump industry to come together and celebrate the amazing work that is going on across the sector.
This year’s event, at the home of English football, St Georges Park Hotel in Burton-on-Trent, and with footballing legend Kevin Keegan taking to the stage, promises to be a fantastic evening. But what I think is the most incredible part is the excellent work represented by the 46 organisations and individuals that have been shortlisted for the eight award categories.
It is often said that there is no innovation in pumps, and the basic principles behind pumping technology have not changed for decades, centuries even. But innovation is not just about new products. It’s about how they are applied, how they are managed, how they are supported, how they are produced, and so much more. And therefore, I do believe there is evidence across our sector of great innovation taking place.
This is particularly the case in how we are dealing with some of the global challenges being faced today. Within those shortlisted this year, you will find examples of how pumping systems are helping to reduce energy costs. You will see projects, products and systems enabling carbon emissions reduction. How suppliers are mitigating supply chain issues is demonstrated. You will discover the work being done to encourage people to join the sector and support them through their careers. And, yes, you will find innovative new products.
This all needs to be celebrated, and I, for one, am proud to be a part of an organisation which does just that.
Dale Croker, President, BPMAflow is a controlled circulation journal published quarterly on behalf of the BPMA by Touchwave Media Ltd and G and C Media Ltd. For a copy of the magazine’s terms of control and to request a copy please email circulation@flowmag.co.uk
The content of flow magazine does not necessarily reflect the views of the editor, publishers or the BPMA. The publishers accept no legal responsibility for loss arising from information in this publication and do not endorse any products or processes mentioned within it. No part of this publication may be reproduced or stored in a retrieval system without the publisher’s written consent.
© BPMA. All rights reserved.
A PREMISES MOVE FOR MARINE AND pump bearing specialist, Exalto Bearings UK Limited, is enabling the company to increase its turnover by more than 20%.
Exalto, which makes bearings for a number of OEM pump manufacturers and repair centres worldwide, moved to a new site in the Autumn of 2022 when it had outgrown its previous facilities.
Exalto’s Global Sales Director, Dennis Rawle, explained: “Before the move, we had been working from three separate buildings. Aside from the practicalities, a growing order book meant we were struggling with limited space.”
The company took four months to find its current location, which is only three miles from its previous sites. Thanks to the close proximity, all staff have been retained, which was important to the company.
The increase in production space has enabled the company to invest in eight new machines worth over £400,000 and
increase its staff count by 20%. “With the space available now, we have been able to purchase two new CNC machines. This has enabled us to bring work in house which we had previously sub-contracted,” continued Dennis. “As well as giving us better control over production, it has reduced lead times for our customers and resulted in a further increase in orders.”
When the new facility was identified, it was initially considered too large. But the extra space has proved to be a real benefit and is supporting further growth potential.
Mike Cosgrove, Operations Director at Exalto, explained: “We now have the space to develop new products with lining materials we couldn’t use before. This will open up the potential for yet more growth, and we will need to recruit more staff to support this.”
Concluding, Dennis said: “The move has brought about a significant benefit. We have a better facility for our staff, we have already shown significant revenue growth, and we have the potential for even more growth. It is underpinning an exciting time for Exalto.”
FEBRUARY 2023 SAW BRITISH PUMP MANUFACTURER
Crest Pumps celebrate its 50th anniversary.
The company was founded by Les Dashwood in 1973 when an opportunity arose to move from subcontract precision engineering to manufacturing a complete product. When a friend told Les he was riding the ‘crest’ of a wave and to maximise the opportunity, it seemed apt that this should become the company’s name.
The next phase of Crest’s journey saw Les’s son, Tony take over the day-to-day management of the business in 1978, before Tony’s son James became the third generation of the Dashwood family to join the business in 2007, taking over the day-to-day running of the business in 2018.
During the last 50 years, central to Crest’s focus has been to be the most trusted company for chemical pumps.
As a British manufacturer of chemical-resistant pumps, the company says it understands how the financial and reputational cost of a plant shutdown is unthinkable. So, when Crest puts its name on a pump, it says it makes a serious commitment to give its customers lifetime support for its products to last in the most corrosive of environments.
Commenting on celebrating 50 years as a British manufacturing business, Managing Director James Dashwood said: “It’s an honour to be the third generation in my family to continue to build Crest Pumps as a proud British manufacturer of chemical resistant pumps.
“The recent difficulties in supply chain issues, along with the increased environmental costs of importing from across the globe, have highlighted the need for businesses to consider local supply chains. Our UK manufacturing flexibility allows us to provide solutions to our customers far quicker than others. Being part of a local supply chain also helps to reduce the carbon
emissions associated with our products.”
As for what the next 50 years hold for Crest Pumps, James is excited: “The UK has a long history of manufacturing excellence and is renowned for its quality and innovation. We are investing in the future through apprenticeships to help young people develop the skills they need. We are also adopting lean production techniques to further enhance our efficiency and speed of delivery for customers.
“This year will also see the launch of our Channel Partner Network to help us reach a wider customer base and better serve our target market in the years to come. We are looking to partner with distributors who share our values and commitment to customer service and integrity.”
THE CHEMUK 2023 EXPO WILL return this May 10 and 11 to the NEC, Birmingham.
CHEMUK 2023 continues to grow, with over 400 exhibitors confirmed for this year’s event showcasing the latest technology and specialist services to UK plant, process, control and engineering professionals from across the chemical and wider process industries.
A number of BPMA members will be exhibiting at the show, including ABB; Apex Pumps; AVT Pump; Crest Pumps; DESMI; Flux Pumps Int; Grundfos; March May, and Siemens.
During the event, ABB will be running two panel sessions. The panel will see representatives from ABB and invited industry experts address Energy Management, looking at how managing your energy correlates to managing your business risk from current/future market forces and global events. The second covers Digital APM, exploring how AI and machine learning improve business
performance when applied to asset management.
In addition to the exhibition floor, visitors can attend any of the 40+ hours of keynotes, feature sessions, and panel discussions running across the show’s five auditoriums, embracing some 150+ contributing speakers.
The speaker programme will address the key challenges and opportunities facing today’s chemical industry covering R&D, innovation, industrial process efficiency, flow chemistry, plant & asset management, HSE, REACH regulation and sustainability.
Speakers already provisionally confirmed to present this May include Richard Haldimann, Chief Technology & Sustainability Officer at Clariant; Chris
FOLLOWING A COMPETITIVE TENDER PROCESS, electro-mechanical engineering specialist, Houghton International has secured a place on the United Utilities Water Limited (UU) Motor Repair Services Framework.
United Utilities Water Limited (UU) provides water and wastewater services to nearly seven million people in the North West of England, supplying 3.2 million households and over 400,000 business premises.
The framework agreement, which commenced in November 2022, is valid for four years, with the option to be extended a further four years if required. It covers the overhaul, repair, rewind and testing of motors and encompasses all United Utilities sites, including 96 water treatment works and 575 wastewater treatment works. Houghton International is one of six companies selected for the framework agreement.
With over 25 years of experience working with the water sector, Houghton International carries out repair, maintenance and life extension services for motors, generators, pumps and all electrical rotating equipment, both in-situ and at their 135,000sq ft Newcastle upon Tyne facility.
Jessica Pooley, Business Development Manager at Houghton International, commented: “We are delighted to have been selected for the framework agreement, and we look forward to working with United Utilities over the coming years.”
Finnegan, Safety & Sustainability Science Leader at Unilever SEAC; Professor David Bogle, President at IChemE; Professor Gill Reid, President, Royal Society of Chemistry; Thomas Birk, Managing Director at BASF UK & Ireland; plus many more. The full speaker schedule will be hosted on the CHEMUK website.
Registration for free entry badges is available at www.chemicalukexpo.com
2 WEEKS
HAVING BEEN WITH THE BRITISH Pump Manufacturers Association for the better part of 25 years, Steve Schofield is retiring from his position as the Association’s CEO in April of this year.
Steve has enjoyed employment at four different pump manufacturers throughout his 47-year career, although for a little under half that time, he has worked with and supported many, many more such companies working for, and latterly leading, the BPMA.
His pump engineering career began in 1975 with a 13-year term at Mather and Platt, where he successfully completed a mechanical engineering and business management course via Tameside College before moving on to become an Area Manager for Durco Europe.
In 1990 he relocated from the NorthWest to the South of England to become Sales Manager for Flowserve, where he spent six years increasing sales and overseeing seven field engineers.
There then followed a move to Hayward Tyler in 1996, where he managed both internal and external sales engineers and where he first gained his love of airports, travelling extensively throughout the Middle East, South Africa, Canada, and America.
But in 1998, after 23 years in the industry, he was encouraged to join the BPMA as its Technical Director, working alongside the then CEO, Brian Huxley. Making that role very much his
own, he became actively involved in European Commission energy efficiency programmes, including the much-valued Pump Life Cycle Costing initiative. Assuming the role of Secretary for a host of European standards-based working groups, Steve has been heavily involved in the creation of various international guides in areas such as variable speed pumps and system efficiency in Rotodynamic pumps.
Over the years, he has worked closely with UK Government departments such as DEFRA, DECC and BEIS, on numerous initiatives, including the development and introduction of the Certified Pump Systems Auditor Scheme (CPSA) as well as becoming Convener for the ISO TC115 Pump System Assessment standard ISO 14414.
His knowledge and expertise, particularly in relation to pump system efficiency, has made him a highly sought-after participant in meetings and conferences the World over, during which he has tirelessly represented the interests of the pump manufacturing sector at national and international levels.
In 2013, he took over the role of CEO at the BPMA, and throughout his tenure has continued to engage both directly and indirectly with other trade bodies and organisations and has maintained a strong and influential involvement with Europump, the Association of European Pump Manufacturers, of which BPMA is a
founding member.
The Association will be left in the safe hands of Wayne Rose, who, having shadowed Steve for the past three months, will officially take over the position of CEO in April, with Steve remaining on-hand for a while longer to help and assist if needed.
Steve’s colleagues at the BPMA, Steve Smith and Gary Wilde, the Association’s Council, wider membership and all those that have worked with him during his career, wish him all the best for a long and happy retirement.
For more information or to book any of the courses listed please visit www.bpma.org.uk/lectures *All
AT THE ISH TRADE FAIR, TO BE HELD in Frankfurt in March, KSB will be launching a new series of fully integrated in-line water pumps. The EtaLine Pro series has been developed to offer extremely low energy consumption and the economical use of materials for intelligent and highly efficient performance.
By using a hydraulic system designed for high speeds, KSB’s designers were able to achieve a compact design. Thanks to a significant increase in output per size, the new pumps require up to 48% less aluminium, 49% less grey cast iron, 68% less magnetic steel sheet and 73% less copper, compared to conventional units.
The classic ferrite magnets used in the motors do not contain any rare earth metals, which are a cause of significant environmental damage during their extraction. Motor rating ranges from 0.8 to 2.6kW. With their wide voltage range of 380 to 480V at 50 or 60Hz, the pump sets can be used worldwide. International product certifications such as CE, UKCA and UR/UL are contributing factors to their suitability for worldwide acceptance.
Suitable for applications including heat transfer, cold water transfer (acclimatisation) and many types of water transportation, the new units offer a high degree of planning reliability,
as they have several pump functions. Examples include dynamic control, sensorless control and multiple pump operation, as well as heat quantity measurement.
These intelligent functions allow adjustments to be made to the operation or operating points, even after the pumps have been installed. The pumps adjust their flow rate and head based on an algorithm, moving the operating point along a programmed control curve. Thanks to various digital interfaces, integration into modern building management systems is possible without any problems.
With just five hydraulic system sizes, the quiet running close-coupled pumps cover a broad selection range. Their maximum flow rate is 63.6 cubic metres per hour, with the maximum discharge head possible being 42.9m. The pumps and the mechanical seals are designed for operating pressures of up to 16 bar.
As standard, the pumps are fitted with mechanical seals selected for a maximum operating temperature of 120°C, depending on the application, and the fluid handled. A cathodic e-coating of the cast pump casings provides all the necessary corrosion protection.
When designing the new series, KSB paid particular attention to ensuring that pump servicing is very easy. Standardised mechanical seals and a reduced variety of components, combined with an extensive global service network, ensure the rapid availability of spare parts when needed.
www.ksb.com
NEW FROM CELEROS FLOW TECHNOLOGY, UNIQ-FLOW is a high-performance range of liquid/liquid coalescers for separating hydrocarbons from water phases. Offering a verified efficiency to <10ppm and outstanding contaminant capture rates, UNIQ-FLOW liquid/liquid coalescers enable a reduction in vessel size and a longer time between filter changes, which results in a lower total cost of ownership (TCO).
UNIQ-FLOW coalescers are designed to help customers improve product quality, reduce or remove unwanted haze and impurities, and recover other valuable products. Typical applications include condensate cooling, MEG removal, amine gas sweetening, removal of water from diesel, kerosine or condensates, recovery of hydrocarbons from water, and glycol applications.
Commenting on their introduction, Chris Nixon, Head of Filtration at Celeros Flow Technology, said: “Market demand for higher quality products and prolonged periods of uptime mean that flow control equipment like coalescers has to
work more accurately and more reliably for longer. We tested our UNIQ-FLOW liquid/liquid coalescers against their nearest rivals to validate their performance, and the results are impressive. Customers can be confident that they will benefit from superior performance, reduced maintenance and lower lifecycle costs.”
The new UNIQ-FLOW liquid/liquid coalescers are equipped with both pleated polymer and glass fibre filtration media in absolute ratings at 10 microns. They are available in standard size ranges or can be custom designed to meet individual process requirements for optimum performance.
Housing constructions are offered in a range of carbon, alloy, stainless steel and duplex stainless steel materials with alloy 625/825 overlayed materials. Each unit is designed specifically to end-user code requirements, including ASME U-1, PED, GB-150 and PD5500, amongst others.
www.celerosft.com
THE EFFICIENCY AND SERVICE LIFE of pumps can be greatly extended by following the manufacturer’s installation recommendation for a straight pipe run entering the pump. When cramped pump houses or restricted pipe runs make this impractical and costly, flow conditioners overcome this challenge by delivering a uniform, swirl-free flow profile to the pump inlet in as little as three pipe diameters.
Upstream flow disturbers, such as elbows, expanders or reducers, and valves, often produce non-uniform, non-repeatable and swirling fluid flow entering the pump that can lead to pump cavitation and other issues causing premature wear. The result is extra maintenance, expensive repairs and/or premature replacement, which can take equipment offline.
The Vortab Company’s product line of process flow conditioners correct flow disturbances to mimic adequate pipe straight runs and produce a highly repeatable, symmetrical flow profile.
Their use also eliminates the extra pipe cost and technician labour for additional lengths of pipe straight run and/or moving equipment around to accommodate new pumps.
Swirl reduction and velocity profile correction occur naturally in long lengths of straight pipe due to diffusion, friction and turbulent mixing. The Vortab flow conditioner’s anti-swirl and inclined vortex generating profile correction tabs, projecting from the inside pipe surface, generate vortices that accelerate these natural pipe effects to create a uniform, non-swirling, symmetrical flow profile in a much shorter section of pipe.
The simple, flexible designs of the Vortab Elbow and the Vortab Insertion
Sleeve configurations provide a costeffective, easy-to-install solution that supports proper pump installation. They can be made from carbon steel, 316L stainless steel or Hastelloy C-276 and in almost any pipe size. A variety of process connections are also available – ANSI flanges, male NPT threads, butt welded preps or retaining wafers.
www.vortab.com
THE QDOS 60 PU PERISTALTIC pump, launched by Watson-Marlow Fluid Technology Solutions, offers precise and repeatable flows for many hard-to-handle fluids, including viscous flows and aliphatic hydrocarbons, at linear flow rates of up to 60 l/hr and pressures of up to 5 bar. The pump provides compatibility for complex polymers such as polyacrylamide (PAM) and other flocculants and coagulants used in wastewater treatment.
The pump is optimised for low-shear, gentle pumping to protect polymer chains and maintain product integrity. As with the Qdos 20 PU, it uses an aliphatic hydrocarbon-resistant tubing material, enhancing chemical compatibility in peristaltic pumps.
Peristaltic pumps have notable advantages over diaphragm pumps in PAM metering applications, including enhanced accuracy and reliability. There is no need for diaphragms, valves, or seals that risk clogging.
The design of Qdos pumps means the only part of the pump that ever requires replacing is the ReNu pumphead. It offers repeatable, accurate flow rates and lasts longer for tough applications in the field, and it takes less than a minute to replace the pumphead.
www.wmfts.com
£100k ($130,000)
PERISTATIC PUMP FOR COMPLEX POLYMERSFollowing yet another exhaustive judging session, which was held virtually on 26th January, the finalists of the 2023 Pump Industry Awards have now been chosen.
From the record number of entries received, and through some incredibly tight scoring, the judges shortlisted 46 finalists across the eight award categories who went through to the public vote. Those that were fortunate enough to be selected are as follows:
Product of the Year
Sponsored by Process Engineering
• ABB: SynRM IE5 Motor & Drive Package
• ARMSTRONG FLUID TECHNOLOGY: DEPM Single Phase Pump
• ARO: EVO Series Electric Diaphragm Pump
• BAKER HUGHES: Water Injection
Centrifugal Pump
• BROOK CROMPTON: EC Motors
• FLUX PUMPS: Viscopower
• JOHN CRANE UK: Global
Standardized Upstream Pumping Support System
• JOHN CRANE UK: MPFAutomated Backflush High-Flow Filter
• SALAMANDER PUMPS: TapBoost
• WILO UK: Wilo-Actun ZETOS-K12 Borehole Pump
Project of the Year
Sponsored by Stuart Turner
• ABB: Glendevon Project
• APEX PUMPS: Hindås
Waterworks Project
• BAKER HUGHES: Northern Lights CO2 Pumping Storage
• SULZER: Retrofit of Five Membrane Feed Pumps for a Desalination Plant
Environmental Contribution of the Year
Sponsored by SPP Pumps
• ABB: Glendevon Reservoir
Hydroelectric Project
• AES ENGINEERING
• HAYLEY 247
• STUART TURNER: Monsoon & Showermate - Digital Installation Manual
• SUNDYNE HMD KONTRO
SEALLESS PUMPS: LMV-801S
Sealless Vertical API 685 Pump
• WATER POWERED
TECHNOLOGIES: The Papa Pump
• WILO UK: Wilo-Actun ZETOS-K12
Borehole Pump
Manufacturer of the Year
Sponsored by WEG UK
• APEX PUMPS
• CREST PUMPS
• SPP PUMPS
• STUART TURNER
• WILO UK
Distributor of the Year
Sponsored by Stuart Turner
• BPS PUMPS
• SEAL & PUMP ENGINEERING
• TOMLINSON HALL & CO.
Supplier of the Year
Sponsored by Wilo
• ABB
• AESSEAL
• EMiR SOFTWARE
• JOHN CRANE UK
• SUTTON CASTINGS
• WEG (UK)
Contribution to Skills & Training
Sponsored by Crest Pumps
• ADC ELECTRICAL: ADC Pump Services Division
• AEMT: Ex Repair Course
• AESSEAL
• CDR PUMPS: Fundamentals of Pump Training
• KIWA WATERTEC: Water Regulation 4 Compliance and Certification
• SULZER: Sulzer Academy for Pumps and Systems
• WILO UK
Rising Star Award
Sponsored by World Pumps
• Sam Kemp, APEX PUMPS
• Josh Bottomley, EMiR SOFTWARE
• Lewis Wilkes, SALAMANDER PUMPS
• Jack Linley, SULZER
Details of all the finalists are
available to view on the dedicated awards website www.pumpindustryawards.com/ finalists
Places are still available at the Gala Awards Dinner on 16th March at the Hilton at St George’s Park Hotel, Burton-on-Trent. Whether it’s taking a table to host customers or booking a few seats for you, your team and partners, don’t miss this fantastic opportunity to enjoy a wonderful evening of great food, fine wine, fantastic entertainment and that all-important networking until the early hours, when our now infamous ‘survivors’ breakfast’ will be served.
To help deliver the 22nd staging of this annual industry awards ceremony, we will be joined by Kevin Keegan, one of the most recognisable faces in British football. An illustrious playing career included time at Liverpool, Hamburg, Southampton and Newcastle, as well as the national side, captaining England for six years until his international
retirement after the 1982 World Cup. As a manager, he held the reins at Newcastle, Fulham, Manchester City and England.
Places can be booked online, and with a record number of tables booked already, it’s looking to be a great event. chevron-circle-right
www.pumpindustryawards.com
A CHEMICAL PROCESSING PLANT HAD been experiencing high vibration and bearing failures on its boiler feed water (BFW) circulation pumps. This application used a sealless pump, due to the high pressure and high temperature water being circulated. This vibration and wear required that the motors be overhauled approximately once per year at a cost of more than $100,000. Investigations after initial commissioning of the units indicated that the vibration frequency being measured, 177 Hz, also matched the first bending mode frequency of the rotor. However, the phenomenon which excited this mode was not conclusively identified.
Hayward Tyler was contracted to perform a thorough review of the existing hydraulic design, specifically focused on the impeller and diffuser blade combination. This design used a mixed flow, six-blade impeller and a radial, sevenblade diffuser. The review identified that
the blade pass frequency was also 177Hz and the corresponding radial load was exciting the bending mode of the shaft resulting in excessive damage.
Hayward Tyler’s engineers evaluated different hydraulic options (impeller blades and diffuser blades) to remove the radial load and settled on a new eight-blade diffuser. Computational Fluid Dynamic analysis of the new combination showed a 92% reduction in load at the problematic 177Hz frequency. Furthermore, this new diffuser was designed to fit in the existing footprint meaning only a new diffuser was needed to solve the problem.
The plant ordered new diffusers manufactured by Hayward Tyler, and confirmed upon installation that the 177Hz vibration had been eliminated from the pump. The total cost of the engineering and new diffusers was less than the cost of one motor overhaul.
haywardtyler.com
WHEN PRESSBOOST ATTENDED A school in the Northwest of England which had suffered a water outage, the company was able to restore the water supply. However, given the obsolescence of the cold-water booster unit which had caused the outage, the client wanted to explore replacement options rather than attempting modifications of the set.
In recent years, the existing cold water booster unit has begun to fail increasingly often. The pumps had been repaired but the set had been superseded by more modern equipment. Furthermore, this set was designed in a master/slave configuration. This was a significant issue for a critical building like a school, as when the master inverter failed, it caused water outages. The set had also been reduced to two pumps some time earlier when a pump was removed and not refitted.
Given the previous control issues the client wanted something with inbuilt reliability. A Stuart Turner MAB booster was selected for the project as the manufacturer is known to engineer out single points of failure wherever possible. The MAB booster set specified in this project comes with multiple pressure transducers, multiple pump accumulator vessels and three master inverter drives. The control panel provides the client with much more usability with a clear controller and hand/ off/auto switches for each pump. Coupled with the build quality of the Stuart Turner booster sets it meant they were the ideal solution. All works were carried out on the first Saturday of a half term to provide minimal disruption to the school.
www.pressboost.co.uk
LANDIA HAS SUPPLIED 17 PUMPS for a new water and wastewater treatment plant in the north east of China. For the new facility in Shandong province, Landia has supplied its axial propeller pumps (AXP), which will provide recirculation of activated sludge. The AXP model can also pump large amounts of water at low back pressure.
Landia has also provided two styles of
chopper pumps. Submersible DG Pumps will handle heavily contaminated liquids, as well as liquids with a high dry matter content. Meanwhile, Landia’s MPTK chopper pump was also specified for its effectiveness in handling dewatered sludge and the total cost of ownership. Both chopper pumps benefit from being equipped with Landia’s external knife system that prevents clogging.
Thorkild Maagaard, Sales Director at Landia, said: “Once again, China has demonstrated its understanding of investing in pumps that will stand the test of time. And although our equipment was transported by train for 15 days, we are proud to have delivered within the project deadline.”
www.landiaworld.com
Do you want to save time, energy, and resources on finding the perfect product for your specific application requirements? Caprari has the solution that meet all your needs!
Our new interactive and intuitive website caprari.com offers a user-friendly browsing experience with filtering options to guide you towards the ideal product.
Whether you need high-efficiency pumps for irrigation, solutions for aqueducts and wastewater management, or advanced water management solutions for special applications and infrastructures, with Caprari you can be sure to find the perfect product for you!
SEVERN TRENT WATER HAS 16 LANDIA chopper pumping assets on its Minworth Bio plant, which are used for recirculating the site’s digesters. The current annual spend on new Landia pump wear parts is in excess of £100k per annum.
Severn Trent Water approached Hayley247 regarding a trial of applying a Belzona coating to the wear components to reduce the amount spent on wear components.
Severn Trent provided Hayley247 with new Landia wear components consisting of a front wear plate, a back wear plate
and a volute casing. The new components were grit blasted to achieve the correct surface profile in line with SA2.5. Belzona 1321 Abrasive Resistant coating was then applied to the parts.
Landia Pumps installed the coated components during a planned service. After three months in service they were inspected and the coating was still in place.
Commenting on the trial, Alan Butcher,
Strategic Maintenance Manager, Bioresources, at Severn Trent Water, said:
“The service and inspection was a success. We have saved the parts in-between servicing and they will last until the next service, doubling their life. We will now put a plan in place to ensure we have an ongoing stock of coated parts.”
www.hayley247.co.uk
A LARGE INDIAN WATER PURIFICATION COMPANY HAS increased the efficiency and reliability of its water purification plant with 20 hours per day running, thanks to Wanner HydraCell pumps.
The plant, which the company was running for a pharmaceutical organisation, previously had to slow or stop operations due to frequent leakages and a lack of reliability in critical pumps. The company quickly spotted the problem and, working with Wanner International, found a solution. The Hydra-Cells (G35s, G12s, and G21s) easily handled a range of corrosive chemicals and liquids with high solids.
In the old system, pumps would have to run at lower speeds. Production would frequently stop, meaning losing a day in downtime was not uncommon. This was caused by solid particles becoming lodged in the packing – which would have to be replaced every couple of days, typically four to five hours – and the plungers, which would only last three to four months.
Wanner’s Hydra-Cell seal-less pump solved these problems with high reliability and little ongoing maintenance achieving low operating expenses. The pumps are saving the company millions of dollars every year.
With the water purification specialist billing its customer per litre of processed fluid, leakage meant the company was effectively pouring money down the drain. Worse still, no
money would be generated if the plant was shut down. The plant now operates 20 hours per day with Wanner’s Hydra-Cell pumps running constantly.
Paul Davis, Managing Director of Wanner International, said: “Working in partnership with this multi-national water purification company, we were able to design and install an efficient and reliable pumping solution, solving these operational problems in one fell swoop.”
Wanner International supplies the company with over 100 pumps a year for reverse osmosis, handling effluent and industrial waste.
www.hydra-cell.co.uk
FLUID SEALING PRODUCTS SPECIALIST
M Barnwell Services, has provided the RRS Sir David Attenborough with hygienic seals for its Science Sea Trial in Antarctica. The RRS Sir David Attenborough is one of the world’s most sophisticated polar research ships. On 17 November 2021 the state of the art vessel departed the UK for its maiden voyage to
Antarctica.
The RRS Sir David Attenborough is currently on its second Antarctic Voyage, which set off from Portsmouth on 22 November 2022. During its time in Antarctica the ship will undergo science tasks such as deploying argo floats. This gathers data for the international programme that organises global
observations of ocean temperature to study climate change. M Barnwell Services’ DIN 11851 seals will assist the ship with its seawater pumps, keeping out contamination. The RRS Sir David Attenborough will return to the UK in May 2023.
www.barnwell.co.uk
farming methods are becoming more prevalent as concern grows for our planet’s wellbeing. When an environmentally conscious farm approached T-T’s Agricultural & Environmental team looking for a solution to its dwindling waste storage facilities, the pump specialist’s experts provided a solution with additional eco-friendly benefits.
The automated dairy farm was running low on waste storage facilities and had noticed a recent decline in the quality of its soil. It was looking for a solution that didn’t involve building more storage space because of the impact that construction would have on the environment as well as the space it would occupy, with larger waste storage meaning a higher risk of environmental contamination.
T-T’s Agricultural & Environmental experts
decided on an SM Range dewatering separator, manufactured by design expert Cri-Man.
T-T team members assessed the site, using its head size and waste output to inform the specific choice of pump for maximum effectivity.
An SM 260 was selected for the job, ideal for use in livestock, biogas and industry applications.
This separator can remove up to 30% of
dry matter from animal waste, drastically reducing the amount of waste material being sent to storage. By reducing the volume of waste, you are also reducing the amount of greenhouse gasses generated in storage. Separating the liquid and solids in the waste means the matter can be utilised more effectively. The nutrientrich solid material is perfect for soil amendment, while the liquid can be used for crop fertilisation – forgoing the need for chemical solutions that could disrupt the local ecosystem.
The customer was elated with this solution, as it solved its storage concerns at the same time as improving the soil quality and organic farming methods. T-T left the automated dairy farm with overall more effective processing, storage and utilisation of waste matter.
www.ttpumps.com
THE TORONTO, ONTARIO, METROPOLITAN AREA HAS SEEN rapid population growth over the last several decades and has also developed a wet weather flow master plan that aims to virtually eliminate combined sewage overflows (CSO) from the sewage collection system.
To support this expansion, Xylem has been selected by the City of Toronto to supply customised equipment for a new integrated pumping station (IPS) – a critical component that ensures reliable and safe transport of wastewater. The project will replace two existing pumping stations, one operating since 1911 and the other since the early 1970s, both adjacent to the Ashbridges Bay Wastewater Treatment Plant.
The plant’s new IPS will include 14 Flygt A-C series dry pit pumps. These pumps, designed for low maintenance and operational costs, will reduce Toronto’s energy consumption rate and ensure reliable station operation.
“As Toronto continues to grow, we are proud to support such a large and complex project,” said Matthew Pine, Chief Operating Officer at Xylem. “Xylem’s highly efficient solutions, expertise and local presence will help ensure safe, reliable and sustainable wastewater treatment for generations to come.”
Once operational, this IPS will move raw sewage from the underground sewer system into the treatment plant. In addition, the IPS will add wet weather flow pumping capability to pump collected CSOs from the new Don River and Central
Waterfront tunnel system, to a new high-rate treatment facility. Xylem’s Pewaukee, Wisconsin facility will design, build and test the customised equipment. Life cycle services will be provided by Xylem’s three Service Centres near Toronto in Etobicoke, Ottawa and Sudbury. Certified and factorytrained technicians will provide the necessary expertise for installation, training, monitoring/diagnostic and maintenance. The project is currently in its design stage; construction is expected to start in 2025 and take ten years to complete.
www.xylem.com
www.brookcrompton.com
With over 110 years of technical and design expertise, Brook Crompton offers leading edge energy efficient electric motors across global markets. As the original innovator in electric motor development, Brook Crompton are trusted to power limitless industrial processes and its robust motor design drives fans, pumps, compressors, conveyors and more.
Driven by technology and innovation, Brook Crompton has one of the widest available ranges of electric motors for operation in safe areas, hazardous atmospheres and hostile environments.
The extensive range of stock can be quickly modified to suit customers’ needs and with a high level of technical support from our knowledgeable team we ensure the correct selection of motors is provided for your application.
Brook Crompton’s focus on product and service development ensures we continue to move forward to improve efficiency, offer lower cost of ownership throughout their lifecycle and to reduce environmental impact.
Steve Schofield, CEO of the British Pump Manufacturers’ Association, considers whether there is, at last, a change in attitude towards energy efficiency amongst the general public. And if so, whether this can have a meaningful impact on decreasing energy consumption across UK industry.
The subject of energy, or rather energy efficiency, has long been a topic of vague disinterest among the majority of households and billpayers. Energy, or rather the complex business sector that produces and delivers it, has historically struggled with engagement. Energy efficiency, in particular, has more often than not been misrepresented as simply a penny-saving exercise involving the change of lightbulbs for modern replacements, and switching lights off when rooms are unoccupied. Boiling the kettle less is another suggestion often heard.
However, with the huge global rise in the cost of energy and its near constant headline coverage by the broadcast media, not to mention the financial pain we are all now enduring, perhaps 2023 has the potential to see a real change in attitude. A change that could positively impact all aspects of energy use.
Of course, greater autonomy in our energy provision is now understood and acknowledged as a stand-out way to protect ourselves from market volatility caused by unstable regimes.
But the drive for improved efficiency across all the avenues of energy use will simply mean that the energy we do produce and secure as a country will go that much further. This will not only allow us to make big savings on our domestic bills and ensure our homes stay warm through the winter months, but it will also have a massive impact on the efficiency and, ultimately, the profitability of our commercial and industrial sectors.
The British Pump Manufacturers Association (BPMA) has been a longstanding advocate of the need for improved energy efficiency across the UK’s vast installed base of pumps and pump systems but also the massive opportunity it presents for significant emissions reductions.
The operation of pumps and their associated systems accounts for around 20% of the world’s entire electrical energy consumption, and in some high-use industrial applications, this can be as much as 25-50% of the total electrical energy usage. Across the European continent pumps are the single largest user of electricity within industry, consuming over 300 TWhpa of electricity, which in turn accounts for over 65 Mton of CO2 emissions.
Unfortunately, the vast majority of pump systems operating today were not originally designed with energy conservation as a major consideration.
It is now well documented that rotodynamic pumps, which account for 80% of the installed base across Europe, are between 20-30% oversized. This is usually due to an in-built ‘safety factor’ allowing for potential future
uprates or any wear in the pump or fouling of the system. But this simply means they are using far too much energy for the required duty. As such, there is huge potential to save massive amounts of energy if these pumps are properly sized, operated and maintained. In fact, if pump systems are initially designed with energy use in mind and the pumps are optimised for efficiency, a saving of up to 50% in electrical energy can be achieved.
In essence, it is important to know as much about the pump system as possible and to create a pressure/flow profile for the system, as the energy required to drive the pump is directly related to the flow and pressure required.
The vast majority of pump systems operating today were not originally designed with energy conservation as a major consideration.
It is also important to carry out regular energy audits to help determine where energy use reduction measures can be employed and, in turn, how operating costs can be lowered. The government has estimated that most companies can reduce their energy consumption by 10-20%, and energy audits carried out in accordance with ISO 14414 have shown that savings of 30-50% are not unusual. By reviewing utility bills, you can get an indication of the savings to be made and the investment that you should be prepared to put into the auditing process.
Across most industrial sites, some two-thirds of the total energy consumption is used to power electric motors, an integral part of any pump system. The overall cost associated with operating these essential pieces of equipment throughout their entire life span can be broken down as follows; 5% accounts for the initial purchase/installation costs, 10% for ongoing maintenance and a massive 85% for the energy used to run them.
Clearly, any reduction in the energy consumed by electric motors is important, and with modern designs, that reduction can be as much as 30%. It is also evident that many pumps and motors are constantly operated at full power, irrespective of process needs, something which can be managed with the addition of variable speed drives. So, across Europe’s installed base there is the potential for significant energy savings, savings which can in turn drop to the bottom line and increase the profitability of any business.
Given the amount of energy consumed by pumps in their normal operation and the potential for energy efficiency gains within pump systems, the BPMA has developed the Certified Pump System Auditor Scheme (CPSA).
Through the CPSA, pump engineers are being trained to correctly assess the efficiency of pump systems and to provide appropriate recommendations in order to improve the efficiency of those systems. The CPSA accreditation is achieved by successfully completing a four-day residential course, followed by the satisfactory completion of a pump system audit.
Within the full ESOS Guidance document, the ISO/14414Pump System Energy Assessment standard is referenced as an auditing methodology that can be accepted by “Lead Assessors” approved by the Environment Agency. Accordingly, it is hoped that CPSA accredited persons (who are trained according to the IS0 14414 standard) will be recommended by Lead Assessors to undertake the pumping system elements of company-wide energy audits.
The next CPSA training course is scheduled for 9th-12th May 2023, details are available at www.bpma-cpsa.co.uk
It is hoped that with the heightened publicity around the cost of energy and society’s growing appreciation of its importance to our very existence, we will begin to see far greater urgency in the adoption of energy reduction measures across our commercial and industrial sectors.
Ultimately it’s a question of choice and whether businesses are prepared to finally address the ‘Capex vs Opex’ argument and begin to enjoy the long-term financial gains available through improved operational efficiency. The offer being; pay for the new equipment now, and recoup the cost through the energy savings made over its operational life.
www.bpma.org.uk
Reduce on-site labor time, engineering and installation time and associated costs. Choose a system that arrives on-site in a fully enclosed ready for use pump house. This pre-engineered pumping system saves time and money for our customers.
+353 (0)44 934 7078
company/patterson-pump-ireland-ltd
www.ie.pattersonpumps.com
sales@ie.pattersonpumps.com
flow found out why Dutch pump manufacturer, Rodelta has introduced drinking water pumps powered by ABB’s SynRM motors.
Synchronous reluctance (SynRM) motors save energy, cut energy bills and reduce emissions in water pumping applications. The pumps feature diffuser technology and are designed with a wide operating range to handle large variations in water demand. SynRM motors have proven to be an excellent fit for the application.
“We supply our LS diffuser pumps for drinking water pumping stations because they offer high efficiency over a wide operating range. ABB SynRM motors are ideally suited for driving the pumps – they are very efficient across the entire range,” said Andre van der Moolen, Sales Engineer, Rodelta.
There are clear reasons why Rodelta focuses on this type of technology in the drinking water pump market. The pumping stations often run 24/7, so efficient equipment can quickly produce big energy savings. In terms of the total cost of ownership, the motor and pump typically account for around 20% of total lifetime costs, with energy consumption making up the remaining 80%.
“SynRM motors offer IE5 ultrapremium efficiency,” said Michel Jansen of ABB in the Netherlands. “Advanced technology and high efficiency mean they cost a little more than regular induction motors, but SynRM motors use much less energy. When energy prices are around their long-term average, the payback time for purchasing an IE5 SynRM rather than an IE3 induction motor is around
18 months. High energy prices mean accelerated payback, and payback times of just a few months are possible. Once payback is achieved, the SynRM keeps on saving energy over its entire lifetime.”
Another advantage of SynRM motors in pumping applications is their lack of slip. In an induction motor, the shaft rotates at a lower speed than the synchronous speed, and this difference is known as slip. When an induction motor drives a pump, slip can be particularly marked during the start-up phase. As a result, a larger – and therefore more expensive – motor tends to be specified. Switching to SynRM, a synchronous technology with zero slip, often means that a motor one frame size smaller can be selected, which produces an immediate saving.
BOOSTING SUSTAINABILITY
Lower energy consumption helps to cut emissions of greenhouse gases, making SynRM motors a more sustainable choice than induction motors. A further sustainability benefit is that SynRM motors do not contain any rare earth materials, unlike permanent magnet motors.
“At Rodelta, we are proud of our efforts to design more efficient pumps that help to save energy and cut emissions, and SynRM motors support us in these efforts,” Andre added.
Rodelta’s first two LS pumps with SynRM motors have been
installed at a pumping station in Leut, Belgium. The motors are rated at 132 and 75kW and drive pumps with capacities of 350 and 240m3/hr. The facility is operated by De Watergroep, the largest drinking water company in Flanders.
De Watergroep had already used a SynRM motor and requested the same type of motor for its new drinking water pumps. In fact, there are signs that SynRM technology could become the preferred choice for driving drinking water pumps, with water supply companies in the Netherlands also showing interest. chevron-circle-right
new.abb.com
Pumping stations often run 24/7, so efficient equipment can quickly produce big energy savings.
From our well-equipped workshop facility in Manchester, our knowledge and expertise of designing and manufacturing dynamic balancing machines is available to the pump industry via our contract balancing service.
Our workshop is equipped with a large range of both horizontal and vertical balancing machines to cover a multitude of applications, including shaft and impeller balancing for pump manufacturers and repair and overhaul companies across the UK.
Our experience covers a range of pumps including Centrifugal, Submersible, Vacuum, Vane, Stirrer Shafts, Vertical, Sumps, Bilge and Multi-stage.
We provide a quick turnaround service, ideal if you need to cover any capacity or capability constraints and offer a palletised UK wide return service if required.
Mike Oxley, National Training Manager at Salamander Pumps, explores the impact of the skills shortage in the pump sector and outlines some ways his company is working to overcome the challenges it presents.
The widespread skills shortage within the UK’s pump sector is rightly causing concern among manufacturers. The demand for highly skilled individuals far outweighs supply, with vacancies remaining unfilled for long periods.
With many experienced professionals nearing retirement and the younger generation lacking the skillset and motivation to learn the craft, future industry innovation and growth are at risk.
The long-term impact of the skills shortage is only being escalated by the pace of change happening in the wider marketplace. Put simply, technological advancements have transformed how many industries operate. And the pump manufacturing sector is no different.
From checking our bank balance to ordering groceries, smartphones are now the easiest and most effective way for customers to interact with businesses. Therefore, it is no surprise that this pattern is repeated in the home and the workplace.
Whether it’s processing customer data, monitoring heating usage and water flow rates, or reducing energy consumption and water wastage, smart technology can be a costeffective solution to monitor the efficiency of appliances.
Spearheaded by the public’s growing interest in becoming more sustainable and Government legislation aiming to reduce carbon emissions by 2025, many manufacturers are exploring smart technology to develop innovative and sustainable alternatives to ensure they remain competitive and stay ahead of any market changes.
To meet these evolving customer demands and enhance their service offering, manufacturers need to ensure that training is a top priority. Success relies upon consistently
upskilling the workforce so they can not only lead on product innovation, but also educate and promote the benefits to the customer.
This is where the main challenge lies for a multitude of reasons.
Firstly, the experienced professionals embarking on retirement are not able to pass on the knowledge they have acquired throughout their careers due to the depleting workforce. With a lack of labour, the younger generation may be spread too thinly and be unable to find the time to acquire the skillset needed to meet the demands of today’s consumer.
The solution will undoubtedly take time and investment, but the long-term impact of failing to act now and provide sufficient training programmes will be significantly damaging.
Here at Salamander Pumps, we offer a free online e-school with a host of helpful training modules, which includes games, interactive
imagery and animated technical videos, for installers, students and
Experienced professionals embarking on retirement are not able to pass on the knowledge they haveMike Oxley, National Training Manager at Salamander Pumps.
effective solutions. This approach provides students with first-hand experience of their future careers and valuable best practices to gain a competitive edge ahead of joining the workforce.
Ultimately, providing students with expert industry insight will help them recognise the potential opportunities they can pursue and, consequently, enhance recruitment and retention rates across the UK.
It is also essential for manufacturers to offer robust training in-house and encourage some of the more experienced professionals to learn alternative solutions, such as Air Source Heat Pumps, as this will also be a major factor in closing the skills gap.
Some of the most effective training resources available can be found online. For those looking to learn and upskill, there are a plethora of webinars and online training courses available within the industry, but open days and training events are equally as practical. However, the full impact of these resources will
only be truly felt if they are promoted and made accessible to the largest possible audience. And that responsibility falls onto us – those already in the industry.
Implementing targeted marketing campaigns is most effective to ensure those in the industry or entering the workforce have visibility of useful webinars and online training courses.
For younger audiences, this may involve collaborating with prominent digital influencers to promote the courses through their social media platforms. In addition, advertising in respected industry publications can also be utilised to ensure seasoned installers and manufacturers are informed about new training opportunities.
Arguably, however, the most effective way to gain invaluable experience and learn on the job is through apprenticeships, and the importance of this cannot be
overlooked.
Apprenticeships can play a critical role in shortening the skills gap by providing on-the-job training, helping trainees develop confidence and maturity quickly, and offering real-life knowledge that cannot always be gained from a textbook or classroom. Having apprentices learn as they earn means they are motivated to be upskilled and remain ahead of any new industry or technological developments.
As the National Training Manager for Salamander Pumps, my passion truly lies in supporting and advising others so our industry can continue to thrive. Whether it’s installing, developing or identifying the correct products, meeting customers’ everchanging demands through training is critical to narrowing the ongoing skills gap. chevron-circle-right
www.salamanderpumps.co.uk
Some of the most effective training resources available can be found online.
Europump, the European Association of Pump Manufacturers, which represents 16 National Associations in 12 EU Member States, Russia, Switzerland, Turkey and the UK, has recently produced a position paper that explains how the European Pump Industry interprets the requirements of the Circular Economy Action Plan and how the associated initiatives will dovetail into its future work and activities.
The European Commission has adopted the Circular Economy Action Plan (CEAP), which was initially introduced in March 2020. It is one of the main building blocks of the European Green Deal, Europe’s agenda for sustainable growth. The transition to a circular economy is expected to support the efficient use of natural resources and create sustainable growth and jobs. It is considered a prerequisite to achieving the EU’s climate neutrality target and halting biodiversity loss.
The new action plan announces initiatives along the entire life cycle of products. It targets how they are designed and encourages sustainable consumption. It aims to ensure that waste is minimised and the resources used are kept in circulation within an optimised ecosystem for as long as possible.
Europump’s position paper addresses a number of areas outlining how its members are currently aligned with the CEAP and how future developments within the sector will further meet the objectives of the action plan.
Pump applications and operational conditions can vary, and therefore the lifetime of a pump varies significantly – a few weeks for a slurry pump up to decades for clean water pumps. The key to a long pump life is the proper selection of the operating point. If the operating point is close to Best Efficiency Point (BEP) or within the recommended range of operation, this will increase the pump’s lifetime.
The correct and regular
maintenance of pumps prolongs their life and reduces the risk of serious failure.
Maintenance and repair of larger industrial pumps is common practice. However, further investigation is required on the smaller and domestic pumps.
The use of recycled materials is already customary practice in the pump industry, e.g. cast iron is a mixture of new iron and scrap metal. However, such processes could be challenged by substance regulations – for example, lead in nonferrous alloys, as specified by REACH regulation.
In some circumstances, industrial-grade plastic parts (non-recycled) can be more ecofriendly. Plastics can enable the reliable pumping of hazardous fluids and can last the lifetime of a pump (on average more than ten years).
In some pumping applications, e.g. chemical types, there is no effective
recycled substitute. Non-recyclable technical plastics are not intended not to end up in the environment but in a controlled waste stream. In some instances, they can be incorporated into construction material, for example concrete. As soon as technical plastics become more readily recyclable, Europump can investigate whether they can be integrated more into new pump products.
In general, all metals used in pumps are already recycled. Pump
> 23
The correct and regular maintenance of pumps prolongs their life.
manufacturers, as well as users, are well aware of the value of scrap material, which ensures that virtually all metal is recycled. Substances listed under the REACH directive may prevent or limit the recycling of materials in the future. Improvements in actual recycling are ongoing thanks to the application of the WEEE directive and the use of recycled plastic is also increasing. Packaging material such as cardboard, plastic foils and strapping are currently recycled. Euro pallets made from timber have a deposit system which exists for circularity.
Pumps are made primarily of metals. Current approximate average composition of water and wastewater pumps is referenced in Table 1:
Pumps in the chemical industry have very different compositions, such as more plastic and elastomers, due to the aggressive properties of the pumped medium. Slurry pumps are another example of different compositions due to the high rate of wear experienced. Recycling plastics and elastomers is more challenging than recycling metals due to the complex chemistry involved.
System components such as motors, VSDs, sensors etc., are covered under the WEEE directive and recycled through the proper channels. The responsibility of this is with the pump manufacturer, but the process varies across Europe.
Packaging materials such as cardboard, plastic foils and strapping are currently recycled and plastics used in packaging have an increasing proportion of recycled content. Ongoing transition in the industry is away from plastic-based packaging and a move towards renewable materials.
Euro pallets, made from timber, have a deposit system that exists for circularity. They are reused and, if damaged, can be repaired and put back into circulation. However, there are different packaging materials for consumer goods than industrial goods. Packaging is used to protect the product during transportation,
with modern sales channels requiring more rugged packaging for shipping.
Some pump companies have experience in reusing parts, usually within their service centres. For example, rotating or wear components might be replaced, but the pump housing and base plate might be reused. Or a new pump head might be fitted to an existing pump housing. Due to legal and safety aspects, this can only be done in agreement with the customer.
Refurbishment services are already well-established within the pump industry. In general, the larger the pump unit, the more actions are taken to increase its lifetime. The assessment of resource efficiency vs energy efficiency influences whether to refurbish or replace a pump unit.
Examples are:
• Repairs to the motor: Based on an assessment of the Total Cost of Ownership (TCO) of a new motor versus that of a rewound motor.
• Refurbishment or replacement of worn parts: Pump housings, impeller, shafts, restoration of internal coatings.
• Refurbishment or replacement of bearings or mechanical seals: This is generally undertaken upon service inspection, during pump dismantling, or after the recommended running hours.
• Efficiency gains: The decision to refurbish or replace may also be influenced by possible increases in the efficiency of the new replacement pump.
Digitalisation will positively affect the circular economy. Europump first understood the importance of digitalisation near the end of the 20th century. Life cycle cost analysis started the digitalisation of products and realised its effect on both the circular economy and sustainability.
Pump monitoring and controls enable customers to run pump units at optimum efficiency and determine possible pump failures ahead of time. Europump supports the idea of a Digital Product Passport. However, this must be limited by Intellectual Property (IP) concerns.
The growth of digitalisation and the acquisition of pump performance data will help to improve life cycle analysis.
Commenting on the publication of this position paper, Jim Wall, Chairman of Europump’s Circular Economy Working Group, said: “This important body of work is a further example of the proactive role Europump continues to adopt in promoting the technical and economic progress of the pump manufacturing sector, whilst ensuring the regulatory landscape in which it operates fully supports its future development.”
He continued: “Having delivered its position statement on the effective adoption of circular economy principals and objectives, the pump sector can continue along its already established and proven path of delivering optimum levels of sustainability and energy efficiency for itself and its end-user customers.” chevron-circle-right europump.net
Refurbishment services are already well-established within the pump industry.Table 1: 28 base cases described in the EcoDesign Pump Review study prepared by VMAS/VHK for the EC, December 2018. Metals include the final recycling components of electronics.
Established in 1987 as a subcontract engineering company, machining parts for companies in various industries such as pumps, printing, packaging and food processing.
Our experience and machining capabilities mean we can work with and machine various grades of material including:
Carbon Steel
Stainless Steel
Duplex
Super Duplex
Inconel
Hastelloy
“With our latest investment of a XYZ RLX 555 Proturn we have increased our CNC turning capacity to 550mm diameter and 1.75m between centres”
If you need a reliable and efficient machining contractor, look no further
: 0161 476 5811
: sales@mjbengineering.net : www.mjbengineering.net
flow learns how motor and drive manufacturer, WEG, partnered with Thames Water and BGEN to upgrade the large pump motors at Ashford Common water treatment works.
Ashford Common water treatment works, located in Surrey, England, is one of Europe’s biggest water treatment works. With a maximum output of approximately 680 megalitres a day, Ashford delivers around one-third of London’s water supply, with the remaining supply being delivered by 20 or so smaller works.
Inaugurated in 1953, Thames Water’s Ashford site underwent an extensive infrastructure upgrade in the early to mid-90s and this was when the pumping station was built. The pumping assets on site were therefore about 25 to 30 years old before the upgrade, and coming to the end of their service life.
This vast plant has five Weir Group axial flow pumps, powered by 7.5 tonne electric motors, each capable of pumping about 180 megalitres of water. The stored water pumping station brings raw, untreated river water from large storage reservoirs onto the site, ready for treatment. When the levels are low, for instance during the period of drought in the summer of 2022, all four out of five pumps are needed. In a situation like this, if two pumps fail, it could be catastrophic.
Losing one of these units represents a 25% loss of output from the site, and because Ashford Common is so big, this loss is equivalent to the complete closure of two of the smaller treatment works. There isn’t the resilience in the network to take such a significant hit. If two pumps failed, low pressures and loss of water would be experienced — something that the industry hasn’t seen in decades. Therefore, these pumps are critical in maintaining the water supply into London.
In 2018, equipment breakdown became a real concern. Two key issues were afflicting the motors, firstly overheating, which caused degradation of the insulation, and although the bearings had been maintained, they were also coming to the end of their life.
Ashford was also experiencing a
number
of faults. The insulation was degrading so much that it resulted in a short circuit between two phases, an issue which could cause a failure of the motor.
When this happens, the motor must be removed and rewound. A rewound motor will lose some of its efficiency unless the work is carried out according to strict guidelines set out by the Association of Electrical & Mechanical Trades (AEMT), and some of these motors have been rewound three to four times. Following refurbishment, Ashford’s engineers expected to get a lifespan of between five and ten years out of the motors. However, they were failing within a couple of years of the work being carried out.
Consequently, Thames Water approached three of its framework suppliers to provide a replacement motor, and WEG was brought on board to combat the high failure rates. According to Ashford’s engineers, one of the key reasons WEG stood out was that it offered a turnkey solution instead of simply acting as a supplier. For Ashford Common’s small team, already covering a big works with loads of assets, it wasn’t an option to project manage the installation internally. Its maintenance team is usually busy with repairs and reactive work, so WEG’s offer to do all the troubleshooting and make sure that all the right equipment and the right people were on site was welcome.
As a commissioning partner, the company chose a business that both WEG and Thames Water had worked with
before – BGEN, previously known as Boulting Group. BGEN provided the onsite installation and project management in collaboration with WEG’s engineers.
WEG came to the site on a number of occasions, looked at the existing motors, reviewed the setup and advised Ashford to opt for a bespoke WEG HGF high-performance line 600kW, 415V, ten pole flange mounted motor due to its reliability and rugged nature. The HGF line is highly energy efficient, with low maintenance costs and highperformance characteristics. This product line is ideal for operating in the toughest environments, such as water applications which require increased strength and durability.
The way that the huge power cables feed the motor required out-of-the-box thinking. There are nine connectors on the power side and about 24 on the control side. The cables are stiff and not easy to manipulate due to their large size, and they are about two metres tall. Instead of having to chop the cables and then re-terminate and gland them – which is messy, difficult and physical work – WEG’s engineers suggested manufacturing a bespoke terminal box so the glanding where the cable goes
through the metal on the junction box could be kept the same. WEG measured everything up and purpose made a connection box so that the existing plate could be married up. This took a lot of accurate measuring because the cables are a set length, and each cable is slightly different.
The motor was replaced in 2019. Due to the reliability results of the first installation, the team at Ashford proactively purchased a second identical motor which was installed in 2021.
“Our Brazilian assembly plant has extensive experience manufacturing motors of this size for water applications,” explained Gustavo Da Silva, WEG Sales and Development Manager for high voltage solutions in Europe and the Middle East. “In fact, WEG has high voltage motors fitted in several key water plants in the UK. With the first motor, our team built the motor with the junction box to suit, and that significantly minimised the time on site.
“When you’re dealing with something
of this size, these small details make the difference. With this second motor, there were a few alterations in terms of physically how the cables were mounted. Additionally, guarding was retrofitted to the first motor on site. The second time around, this was done in the WEG factory instead.”
“Everything is supersize at Ashford,” explained Iggy Pont Lezica, Operations Technical Lead, Ashford Common WTW. “This introduces complexity from an operating and maintenance point of view because you can’t just go and get things off the shelf. Finding suppliers that can fulfil our needs and crucially have the forwardthinking approach and prior experience of working on this scale is a challenge. WEG filled us with confidence from the start.
“The newfound stability of the station has been noticeable. Four years ago, it
was at the highest risk by far, and now it just works away in the background and receives routine maintenance. There are so many other aspects for the maintenance team to look at; we expect the equipment that simply shifts the water from one place to another to work effectively and reliably. Thanks to WEG’s involvement, it does,” Iggy concluded.
Three months before the second motor was delivered, another old motor failed. However, since this failure, Ashford hasn’t experienced any further breakdowns. A significant amount of work was done between 2018 and 2020, including replacing five drives and proactively conducting refurbishments on the pumps. The last pump is currently being refurbished, and two further motors will be replaced in 2023 and 2024. chevron-circle-right
www.weg.net
The way that the huge power cables feed the motor required out-ofthe-box thinking.
Schneider Electric, a specialist in the digital transformation of energy management and automation, has announced significant upgrades to its digital twin tools for water and district energy utilities, EcoStruxure Water Cycle Advisor – District Energy (formerly ‘Termis’) and EcoStruxure Water Cycle Advisor – Water Simulation (formerly ‘Aquis’).
These latest releases announced by Schneider Electric, which have been grouped in version 8.2 of the software, deliver powerful benefits to users seeking to maximise digital capabilities to ensure efficiency, quality and insight across the water and district energy lifecycles.
With advanced data and formula capabilities, alongside a range of usability improvements, District Energy and Water Simulation deliver on Schneider Electric’s promise to ensure companies reach maximum efficiency while supporting decarbonisation, reducing water and heat loss, and ensuring network operation optimisation.
Today’s modernised and digitised water and district energy utilities rely on vast amounts of data to ensure efficiency and quality. To support next-generation digital transformation across the lifecycle, both District Energy and Water Simulation now deliver optimised data management performance.
The new releases harness new asynchronous database data insertion processes, using parallel computing to ensure data is delivered quickly. Similarly, new algorithms, including a topological sorter and step tag processor, significantly speed up data processing and deliver efficient historical data reprocessing.
Not only do the latest upgrades deliver on speed and efficiency in big data management, but the user experience has been optimised to ensure ease of use, no matter the size of the data. For example, importing tens of thousands of real-time tags for online network
optimisation can now be completed in just a few seconds. The same performance improvements are seen across step functions, processing, and reprocessing, reducing computation times from hours to seconds.
Additionally, users can take advantage of improved .csv export functionality. Making the most of the data and calculations made possible through District Energy and Water Simulation, users can now export all information related to any object in the model for a given simulation, or a fraction of it, via .csv files.
Water Simulation and District Energy users now also benefit from a new formula editor, Neptune. Alongside optimising existing programming functions, users are now able to create custom key performance indicators using one of the world’s most powerful and supported programming languages in C#, alongside Roslyn.
Commenting on the latest iteration of these powerful digital tools, Jose María Santos, Product Manager of District Energy and Water Simulation at Schneider Electric, said, “We are dedicated to ensuring that our water utility and
district energy customers have the most powerful digital capabilities at their fingertips to reach ambitious goals across quality, efficiency, and sustainability, which is particularly important in the context of today’s climate and energy crisis.
“The latest release of EcoStruxure Water Cycle Advisor – District Energy and EcoStruxure Water Cycle Advisor – Water Simulation tools will help users to acquire and process external data as well as extend software capabilities by creating custom KPIs more safely and faster. We continue to work closely with our partners across the industry to provide the expertise and digital transformation solutions that deliver sustainability and operational advancements.”
Schneider Electric continues to invest in developing digital twin solutions for water, wastewater and district energy utilities. The next releases of the offers will include AI modules for predictive analytics, improved user experience and performance, integration with thirdparty systems, and a set of new features that will continue to drive customers towards the industries of the future. chevron-circle-right
CDR Pumps explains how updating a solution for unloading hazardous chemicals is saving a performance additives manufacturer over £31,000 per year in reduced energy costs, and cutting carbon emissions by around 180 tonnes.
SI Group is a global specialist in the manufacture of performance additives. The company’s UK manufacturing facility, based in the Midlands, produces Phenol-based products and constantly looks to improve working practices, save energy, and minimise hazards. Moreover, it allocates resources to create and manage sophisticated, accurate and productive facilities that emphasise a no-waste, high-efficiency philosophy.
A review highlighted the process of unloading Phenolic from 26,000l capacity road tankers and moving it to bulk storage tanks for further processing. Phenol, also known as Carbolic Acid, Phenylic acid and Benzophenol, is an organic substance used in the production of many chemical compounds. This material is subject to the highest tier of COMAH (Control of Major Accidents Hazards) regulations and has a number of associated handling precautions due to its tendency to solidify at low temperatures, as well as its hazardous and flammable nature.
When the tanker unloading applications were installed, a selection of canned seal-less pumps had been fitted. These pumps were powered by 11kW ATEX-rated hazardous area electric motors. Since the product solidifies at lower temperatures, it was necessary to keep the pumps running constantly. The product is agitated, heat conductivity is spread throughout the entire feedstock, and the pump is kept warm and ‘moving’ to make sure small lubrication ports are clear. The pump runs constantly for
180 days, totalling 4,320 hours, which consumed 99,360kWh of electricity each year. As there are four pumps, the total energy used annually is 397MWh.
The right unloading pump for this application was a magnetically driven centrifugal pump manufactured in stainless steel. Offering a zero-vapour loss, seal-less design means that the fluids and vapours have been contained and present no hazard to the immediate or wider environment or to the individuals working in that environment. Choosing a UTS-B mag drive pump also meant that the power needed to drive the pump could be significantly reduced, dropping from an 11kW motor to 5.5kW. This reduced the amount of energy being used by the solution whilst not compromising on loading and unloading times or compromising the operational effectiveness and lifespan of the pumps.
The solution also included heating jackets, which had been evaluated for their capacity to work with high pressure. This made it possible to harness the steam that was already accessible at the location and use it to maintain the necessary temperatures.
Reviewing and modifying the original operating procedures on site also meant that the UTS-B pumps could be safely switched
still maintain efficiency thereby lowering energy consumption further still. This not only helped to conserve energy but also spared the components from unnecessary wear and tear. Additionally, it decreased the risks associated with operating process lines with liquids in them.
As a result, the new pumps operate for fewer than five hours a day, resulting in a yearly energy saving of 9,866 kWh per pump. The collective energy savings of installing four pumps is estimated to be 39MWh per year, with an annual financial benefit of over £31,600 at the current 2022/23 costs. As an additional benefit, CO2 emissions were reduced by 90%, amounting to a total of 186 tonnes of carbon reduction. chevron-circle-right
www.cdrpumps.co.uk
CO2 emissions were reduced by 90%, a total of 186 tonnes.
A common misunderstanding over water fittings regulations in the UK is creating confusion over clean water equipment compliance and specification and could be a barrier to innovation, according to Paul Carrington, Managing Director at Aquacheck Engineering
Safeguarding water supplies and helping utilities and other clients protect public health is a top priority for water network fittings and component manufacturers. Regulatory compliance is key to delivering high-quality products that are fit for purpose and minimise risk.
Government regulations set legal requirements for designing, installing, operating, and maintaining water fittings, systems, and appliances. They have been designed to prevent drinking water contamination and prevent misuse, waste, undue consumption, and erroneous measurement of water supplied by a water undertaker.
Innovation is a watchword for the UK water sector as it grapples with multiple challenges, including those on the clean water network. In maintaining some of the highest water quality standards in the world via some of its oldest networks, it is essential that all new equipment meets agreed standards when it enters the UK market, to ensure public health and to create a level playing field for manufacturers and suppliers.
For many years, consultants and other specifiers of water equipment – including architects, developers, and designers of electrical & mechanical systems – have stated that fittings and components must be approved by WRAS – the Water Regulations Approval Scheme. WRAS approval was routinely stated in project specifications and thought to demonstrate compliance of network components with water regulations.
It now needs to be recognised that WRAS is, and has always been, a voluntary scheme, and WRAS approval is not necessary for products to comply. The minimum legal requirement for products and components coming into contact with clean water supplies is compliance with Regulation 4(1) (a) and (b) from the Water Supply (Water Fittings) Regulations 1999.
Regulation 4(1)(a) “requires all water fittings supplied, or to be supplied, with
water by a water undertaker to be of an appropriate quality and standard”, and Regulation 4(1)(b) says equipment must be suitable for the circumstances in which it is used.
In addition, Regulation 4(2) provides companies with options to demonstrate equipment compliance. These are:
• Conforming to a specification approved by the regulator
• Conforming to an appropriate British Standard
• Conforming to some other national specification which provides an equivalent level of protection and performance.
There are currently three approval schemes operating in the UK for Reg 4 compliance in relation to water fittings and components, of which WRAS is only one. The other two are NSFreg4 and the Kiwa UK Regulation 4 Product Approval Scheme (KUKreg4).
Like many manufacturers, Aquacheck Engineering uses KUKreg4, which is a robust process for demonstrating full compliance with the UK Water Supply (Water Fittings) Regulations 1999 England & Wales, 2009 Northern Ireland and 2014 Byelaws Scotland. Water utilities widely accept Kiwa certification, which, in Aquacheck’s experience, has much more visibility and acceptance than WRAS approval.
The tests on Aquacheck Engineering products meet the requirements of Reg 4 and are performed at Kiwa’s testing and calibration laboratories, which are UKAS accredited to ISO17025. Certificates are issued through a system complying with ISO17065, which is also UKAS accredited.
Given the current regulatory requirements, the insistence on WRAS approval for water equipment from some consultants and specifiers is not only out of step, but it also risks their clients missing out on best-in-class products and technologies – from pumps and pipes to valves and tapware. More seriously, specifying one test when others are readily available to the market and meet the same standards is wholly inappropriate.
Aquacheck is already working closely with suppliers of pipeline components to ensure that information regarding Reg 4 is readily available to installers. This is part of our plan to enable distributors as safekeepers of water in the UK building services market.
With water utilities also asking for Regulation 4 compliant products and manufacturers investing in appropriate certification, it is time for all equipment specifiers to catch up. chevron-circle-right
aqua-check.co.uk
The Nkomati mine near Machadodorp is one of the largest nickel reserves in South Africa. Having an estimated 408.6 million tonnes of ore grading 0.33% nickel, large amounts of water must be moved around for ore processing and pit dewatering operations.
These processes rely on water pumps and, crucially, pump monitoring systems. Furthermore, because mines are in difficultto-access, unsafe locations, monitoring pumps isn’t always easy. It’s an expensive task installing control cables through a whole site, so plant managers are increasingly adopting wireless systems – for example, radio telemetry.
Plant managers have used licence band radio frequencies to monitor and control pumps for some time. This system uses controllers and separate radio remote terminal units (RTUs) with a data interfaces. However, maintaining annual radio licences is costly, and much of the equipment becomes obsolete over time. The original equipment manufacturers (OEMs) can no longer support the products because they either went out of business, were sold to other companies, or simply don’t make the products anymore.
With failing and expensive instrumentation, plant managers have no way of monitoring water conditions and switching the pumps on and off. If water can’t be managed or waste can’t be pumped out, the mine’s ability to process concentrate efficiently is put at risk.
By exploring wireless products that blend radio and controllers into a single DIN rail mounted package, it is possible to control pumps remotely over a large distance. Products like these use licence-free band frequencies to avoid unnecessary engineering and administration. Replacement is plug and play, eliminating downtime and optimising spares holding.
A typical solution is a system comprising multiple radio RTUs (outstations), interfaced into a SCADA system using an onboard ethernet port. This simple plug-and-play system has one RTU housed at the local control end, with all the inputs and outputs dedicated to control and feedback status via the ethernet connection, and another located remotely hardwired to the pump electrical control and any instrumentation. The only necessary wiring is for the power supply and any required control circuits.
Unlike traditional systems, simple configuration templates on each unit are edited to share the I/O status between each RTU. For example, if a switch on one side is triggered, it will promote an output on the other side to turn the pump on or off. This makes programming a line of code unnecessary. A simple wireless solution that needs no programming will reduce expenditure by saving time and resources. The system ensures mines can monitor the conditions of their pumps wirelessly over distances of up to 20km. The RTUs are also robust, housed in a weatherproof casing with power supply charger units and backup batteries. What’s more, the low power consumption of the system makes it suitable for solar power outstations at remote reservoirs.
With any remote monitoring system, ease of use is imperative to ensure efficient and productive operations. Therefore, a wireless distributed RTU with data acquisition capability is a no-brainer over cable-based systems. The units can be interfaced with an existing SCADA or DCS system via onboard Ethernet ports. This makes installation quick and simple, and plant managers also save on additional hardware and engineering time.
Once collected, all data can be viewed on fully customisable HMIs. Operators can easily review their pump and view statuses and alarm conditions on an LED touch screen from any connected HMI. Adding Omniflex’s cloud-based Data2Desktop service also allows plant managers to reap the benefits of remotely monitoring their site using a tablet or phone, rather than having to be onsite at a PC.
Mining is a productivity-driven operation, and downtime is lost revenue that can’t be recovered. When plant assets are spread over a large area, wireless remote monitoring technology makes control and management more simple, efficient and cost-effective. chevron-circle-right www.omniflex.com
Ian Loudon, International Sales and Marketing Manager at wireless pump monitoring and control specialists Omniflex, discusses how a South African mine uses wireless pump monitoring to keep production efficient.
A new dawn for single-phase motors is coming. Whilst three-phase motors have been required to meet increasing levels of efficiency over recent years, single-phase motors have escaped similar demands. That will change on July 1, 2023, as Brian Bannister of Lafert Electric Motors explains.
From July 1 this year, most single-phase motors will be required to meet or exceed IE2 efficiency levels to comply with EU EcoDesign regulation EU2019/1781. This new efficiency will be demanded for single-phase motors with rated outputs from 0.12kW upwards.
Variable speed drives intended for use with single-phase motors will also be required to meet new efficiency standards compatible with the new motor requirements.
The new Regulation establishes ‘EcoDesign’ requirements for the placing on the market or the putting into service of single-phase electric motors and variable speed drives, including where they are integrated into other products.
Achieving the new levels of efficiency required to meet IE2 will come at a cost, due to the need for much more active material, low-loss steel laminations and copper. The consequence of these factors could lead to possible changes to either frame size or performance, or maybe even both.
Producing dual voltage (230/15v) motors might not be possible, whilst dual frequency motors (50/60Hz) will present their own issues. Also, 60Hz motors will be challenging and more costly to produce because of the winding losses incurred at higher running speeds.
A number of motor manufacturers have decided that the new legislation is far too complex and demanding and, consequently, have dropped single-phase motors from their ranges. In contrast, Lafert Electric Motors has expanded the powers that can be offered as the required design changes have been made. Furthermore, the company’s flexible
designs can provide many variations of customised shafts and flanges along with very specific electrical designs.
Due to current production lead times across all industries, however, it is vitally important that any OEM or customer using single-phase motors should ensure they either meet compliance or will have assured continuation of supply from their current supplier after the summer of 2023. The concern is that many machine builders are still in the dark regarding this important mandatory legislation, which might significantly impact their production planning.
There are some single-phase motors to which these new efficiency requirements will not apply. Typically, such motors are designed to operate under specific conditions or configured to perform a particular function. Exempt motors might be employed in challenging environments or used for applications that make it impossible for the new efficiencies to be implemented. For guidance regarding these exceptions and the latest regulatory requirements, it is advisable to consult a motor specialist. chevron-circle-right www.lafert.com
From July 1 this year, most single-phase motors will be required to meet or exceed IE2 efficiency levels.
The NEW Aquaboost iBolt and iMatic range of high flow, high head, cold water pressure and flow boosting solutions. Designed to optimise space and provide a very quiet, simple to install solution for domestic and commercial applications.
The time-sensitive, overnight installation and commissioning of an advanced custom turnkey solution with four booster sets has increased production for Britvic, supporting the company’s growth plans. The system upgrade, supplied by Grundfos, also achieved a reduction in wastewater and energy usage, with the reduced carbon footprint supporting the company’s sustainability agenda.
Britvic is an international soft drinks business rich in history and heritage. Founded in England in the 1930s, it has grown into a global organisation with 37 much-loved brands sold in over 100 countries. The company combines its leading brand portfolio, including Fruit Shoot, Robinsons, Tango, J2O, London Essence, Teisseire and MiWadi, with PepsiCo brands such as Pepsi, 7UP and Lipton Ice Tea which Britvic produces and sells in Great Britain and Ireland, under exclusive PepsiCo agreements.
With an increase in demand for soft drinks and high energy consumption for moving the water required for their soft drink production, Britvic turned to Grundfos to look at options to increase production and reduce energy consumption across their plant in Rugby, United Kingdom.
Britvic was looking to support its sustainability agenda, focusing on its ‘Healthier People, Healthier Planet’ strategy, where the company is committed to creating a better tomorrow and delivering timely responses to the health and environmental challenges currently faced on a global level. Britvic has fully integrated the UN Sustainable Development Goals into this strategy and aligned objectives and targets with these goals. It was important to Britvic to select a supplier that supports this ambition and lives and breathes these goals. Grundfos, with its own ambition of contributing to the UN’s Sustainable Development Goals (SDG) #6, Clean Water and Sanitation, and SDG #13, Climate Action, was the perfect match.
“Improving our cooling system
means that the chilled beverage water supplied to production stays cooler, resulting in faster production and higher output,” said Calvin Winch, Engineer, Operations Development GB&I, at Britvic.
“Specifically, we were looking at acquiring a pumping solution that helps us meet our sustainability goals by reducing wastewater and energy usage, resulting in a reduced carbon footprint and improved water efficiency.”
Water is essential to Britvic’s production processes and widely used throughout its value chain. An element of this includes the heating and cooling of water at its factory in Rugby – a process that provides
the opportunity to explore alternative ways to manage Britvic’s water use and protect this vital resource.
“Because we have an excellent working relationship with Britvic, simply spending time on site working with their staff meant we were able to identify possible production improvements. This made it possible for us to advise Britvic and work with them towards an optimised, tailored solution,” said Mark Bennett, National Business Development Manager, End User Industry, at Grundfos. “For a system upgrade, I recommended our advanced digital offering Grundfos iSOLUTIONS, which utilises intelligent pumps, cloud connectivity and digital services. Together they enable real-time monitoring, remote
“Spending time on site meant we were able to identify possible production improvements.”
control, fault prediction and system optimisation to help meet the level of performance needed in a demanding manufacturing site.”
Grundfos performed an ‘Energy Check Advanced’ to measure the actual energy use in the system. This is not simply a ‘nameplate’ check of efficiency; sensors are placed in the system to get the live data from the existing setup, helping operators find potential energy savings in their pumps.
The proven and validated measurements help Britvic support its ‘Healthier People, Healthier Planet’ strategy and the focus on energy and carbon emissions reduction using science-based Scope 1-3 targets to attain a sustainable supply chain.
To help achieve these twin goals, the recommended Grundfos solution was a full turnkey project consisting of four Grundfos Hydro MPC-E booster sets. The booster sets were custom built for Duty/Assist/Standby operation, delivering the optimal amount of chilled water to the facility’s production lines, to allow for the high-speed filling of cans. Each installed booster set incorporated three Grundfos CR pumps with integrated speed control.
Grundfos booster sets are designed to use multiple pumps to maintain a constant delivery flow or pressure at maximum energy efficiency. When demand increases or decreases, you will still experience a constant water supply. This is achieved using the Grundfos CU352 controller, which ensures the pump set operates at its best performance.
This intelligent booster set adapts automatically to a site’s varying demand 24/7. The new generation of inline vertical multistage centrifugal (CR) pumps can be used in a wide range of applications and are designed for world-class efficiency and reliability – with millions of customisable solutions.
Eight weeks were set aside for design and build, including a limited 18-hour overnight installation and commissioning window. The booster sets were connected to the Britvic PLC via the Grundfos Communication cards.
Having a manufacturing site in Sunderland, UK, means that Grundfos can offer a quick response time, offering customers flexibility when it comes to achieving bespoke, custom, offsite build solutions. These come as plug-andplay, helping to achieve minimal disruption when installed at the manufacturing site.
With the new booster sets and improved cooling system, Britvic has achieved the increase in production it wished for, helping meet increased demand and future-proofing the production line. As the beverage water stays cooler and temperature control has improved, faster production with an increased output is now possible, as more cans can be filled.
This project also helps Britvic work towards its sustainability goals with total energy savings of £374,420 per year expected with the four new booster sets (as of September 2022). The existing system consumed over 60kW per set, and this is now reduced to less than 20kW per system, with the future-proof flow included. The return on investment (ROI) is less than twelve months. With complete control over the
system, Britvic now also experiences a reduction in wastewater because the optimal amount of water for cooling is being used.
“We have set ambitious sustainability goals for energy reduction, a lowered carbon footprint and water reduction in our beverage production,” added Calvin.
“Grundfos installed an energy, water and cost-saving solution with no production disruption through time-sensitive overnight installation and commissioning. This solution future-proofs our business, meeting the increased production demand, and shows when you work closely with your supply partners; we are much more effective, efficient and stronger together”.
“We are very happy to have helped Britvic with validated savings from a solution that contributes to its sustainability agenda, and in a way that is very much in line with our own approach,” concluded Mark.
“And this is only possible because of a strong customer relationship, where our ongoing collaboration shows that we understand Britvic’s challenges. I’m sure the savings we have shown here will lead to further projects together.” chevron-circle-right
www.grundfos.com/uk
The return on investment (ROI) is less than twelve months.The four Hydro MPC-E pressure booster sets with Grundfos CR pumps.
To make sure you continue to receive your free copy of flow register online at: flowmag.co.uk
Choose flow , in print or digital format, and stay up to date with the latest products, technical insights, news and innovations, for the design, specification, installation and management of pumps in: z Manufacturing
z Mining
z Utilities
Brewing companies face an ongoing challenge to reduce the amount of water consumed in their processes and must constantly seek new ways of achieving, and surpassing, their environmental impact targets. However, many brewers may be unaware that they could achieve a step-change in their Water Use Ratio simply by rethinking their pump sealing plans, as AESSEAL explains.
The brewing industry has made significant progress in its efforts to move from a takeuse-discharge approach in its production processes, to what Nick Martin, Executive Director of the Beverage Industry Environmental Roundtable (BIER), called ‘water circularity thinking’ when announcing the publication of the industry guide ‘Context-Based Decision Guide for Water Reuse and Recycling’ in January 2020.
In its 2018 Benchmarking Study, Trends & Observation Report, BIER reported that breweries achieved a 9% improvement in their average water use ratio (WUR) between 2013 and 2017.
They reduced their WUR – the metric which measures the ratio between the total litres of water used to produce one litre of end-product – from 3.68l/l in 2013 to 3.35l/l in 2017. This amounts to around 27 billion litres of water saved, or almost 11,000 Olympic swimming pools, over this period.
This is a positive sign that the industry is open to investigating and implementing methods of reducing water consumption at every stage of the brewing process, from milling to carbonation.
However, if brewers focus their sights on their pump systems, particularly how the pump seal support system is configured, they could achieve a sizeable reduction in their WUR.
In brewing processes, dual mechanical seals are commonly used on pumps on hot wort, mash, kettle and adjunct duties, as well as clean-in-place (CIP) pumps.
These dual seals require a secondary fluid which acts as a barrier between the seal faces, keeping them cool and lubricated to prevent overheating, dry-running and eventual seal failure.
This supply of secondary liquid is
supplied to the inner and outer seal faces via an American Petroleum Institute (API) designated piping plan – API Plan 55 – at a rate of 1.5 gallons (6.8 litres) per minute. Often this flush water goes down the drain at the end of the cycle, which is a substantial waste.
Most breweries would assert their commitment to combatting the global water crisis.
Yet what they may not be aware of is that, by replacing the API Plan 55 pump sealing plan with an advanced water management system, they could transform their environmental commitment into a quantifiable reduction in WUR while at the same benefiting from improved pump reliability, better operational efficiency and reduced costs.
These ‘continuous loop’ water management systems employ a modified API Plan 53-A seal support system. This isolates cool, clean water in a vessel and
recirculates it to the seal faces, using an internal flow inducer and/or through thermal convection, in a continuous circuit. Less than a teaspoonful of fluid is lost in the process, mainly in the form of vapour, all but eliminating waste.
For example, based on data averages in the BIER benchmarking study, one brewery producing 221,108kl of beer reduced its water consumption from 740,812kl to 669,268kl by employing a continuous loop water management system on 25 pumps. This corresponded to roughly a 10% reduction in WUR.
A water management system also removes the risk of mechanical seal faces becoming contaminated by abrasive process fluids such as mash and wort.
The inner faces of mechanical seals are precision lapped to one helium light band, with one face rotating against the stationary seal face. The face set is spring-energised, and hydraulic closing
forces create a thin fluid film between the faces. However, this abrasive mix becomes the fluid film if the water buffer is pressurised lower than the process fluid. Inevitably, this eventually crosscontaminates the secondary buffer seal. As a result, mechanical seal efficiency is compromised, and the mean time between failure (MTBF) is reduced.
In a continuous loop system, the pressure of the water buffer is increased to achieve optimum barrier pressure across the seal faces and maintain a regulated supply of clean, cooling, lubricating fluid. Each seal, therefore, operates to its maximum potential, increasing its reliability and lifespan.
By extension, the pump also functions at optimum levels, and the risk of failure and unscheduled downtime is reduced considerably, with inevitable financial benefits from this improved productivity.
The stringent adherence to hygiene and clean-in-place (CIP) requirements demanded by the beverage industry is
an ongoing challenge for even the most meticulously maintained brewery.
The traditional seal support fluid vessel is one of the worst offenders for harbouring dirt and breeding bacteria in its interior, often undetected due to its inherently enclosed design.
However, advanced continuous loop water management systems, such as the AESSEAL SW range, have the option of a simple, low-cost seal support vessel, EasyClean, which enables easy inspection and cleaning.
This self-filling unit incorporates internal filler welds to eliminate bug traps and a detachable lower section with a quickrelease clamp, which allows it to be easily removed. Easy visibility into the interior
A WIDETHROAT EZSTRIP progressive cavity pump, made by Fluid Motion Solutions (part of NOV Inc), is playing a vital role in the processing of olives for a major producer in Andalucia, Spain.
Designed to transfer highly viscous or bulky materials, the EZStrip Widethroat pump’s enlarged rectangular inlet (with a screw conveyor) assists the waste fruit into the pumping element as part of the olive oil production process –moving the material quickly, efficiently and reliably on its way to being recycled.
The positive displacement action
of the pump benefits from not having to rely on any centrifugal force to generate pressure energy. This means that because there are no significant changes in the velocity of the pumped material, a consistent flow is created as agitation and turbulence are greatly minimised.
For this type of highly viscous or bulky material, such as fruit and vegetable waste slurries, Fluid Motion Solutions can modify the inlet with either large diameter augers or integral bridge breakers. The range is based on single, two, four, six and eight-stage
means residue is captured before it can become a breeding ground for bacteria, and cleaning is hassle-free.
WUR is an important metric for the beverage industry, and an opportunity to yield an improvement of 10% on just 25 pump applications should be incentive enough to consider upgrading to an advanced continuous water loop seal support system.
However, with the added value of improved pump reliability, operational efficiency and enhanced CIP procedures, making this decision should be not only a matter of environmental necessity, but of common sense too. chevron-circle-right
bit.ly/SWRange
pumps that can develop pressures up to 48 Bar and capacities up to 215m³/hr.
nov.com/industrial
GLENDULLAN, THE MULTINATIONAL brand Diageo’s second largest distillery in Scotland, is located near Dufftown in the glens of Speyside, Scotland.
When there was a requirement for new air valves at the distillery, a custom solution was required in order to handle the media involved, a waste product from the distilling process that is viscous and reaches temperatures of 100°C – much higher than conventional air valves can handle. As specialists in designing and manufacturing custom valves, T-T Pumps knew it could
design and supply the right solution.
T-T supplied customised air valves manufactured entirely in corrosion-resisting stainless steel (grade SS316/1.4401) – ideal for demanding aggressive environments. The valves were designed together with upgraded elastomers to ensure a reliable seal at high temperatures and low line
pressures.
T-T supplied directly acting air valves that negate internal levers/mechanisms which are prone to failure. The valves also feature a large chamber with sloped walls to ensure solids/fats are encouraged to fall back into the pipeline rather than foul the free movement of the float.
www.ttpumps.com
The pump also functions at optimum levels, and the risk of failure and unscheduled downtime is reduced considerably.
Outdated attitudes to sharing knowledge risks holding back progress on sustainability and resilience in UK industry, according to a new report by Siemens.
The study, The Digital Transformation Imperative, explores how businesses can overcome major challenges with the help of digitalisation – and the barriers organisations face in accelerating their deployment of new technologies.
The report found that more collaboration is needed across sectors like utilities, engineering and manufacturing, as firms look to their peers to understand how they can meet ambitions like net zero with the help of digital tools.
According to the study, the Government, trade bodies and strategic technology partner networks have critical roles to play in enabling collaboration without exposing competitive intelligence.
Brian Holliday, Managing Director at Siemens Digital Industries, said: “Businesses are naturally protective of any competitive advantages they create. But digital transformation represents something much bigger than an opportunity for incremental market gains.
“To accelerate progress, industries need to pool their experiences with digital transformation, and how individual companies have succeeded in protecting themselves against future shocks or working towards major goals like net zero.
“Siemens Xcelerator is designed to increase the accessibility of digital transformation, to inspire and facilitate change within businesses. While public sector bodies and trade associations also have a pivotal role in disseminating success stories and new concepts.”
Skills are also highlighted in the
report as another key barrier to progress. It outlines how a better interface between industry and education is needed to improve skills development for digital transformation, with people remaining a critical factor for its success.
Speaking in the report, Stephen Phipson, CEO at Make UK, said: “The first steps to transformation aren’t about technology, but people. For SMEs, this needs to be driven by leadership and investment in training for staff to be able to cope with the change.”
The Digital Transformation Imperative addresses how technology available today could be deployed more widely by firms to achieve their goals. For example, monitors, sensors, energy use metering and data analytics can be used more widely to digitise physical environments. Meanwhile, digital twin technology could be used more to help firms simulate ideas and concepts.
Carl Ennis, CEO at Siemens UK and Ireland, added: “The significant impact of COVID-19 on our industries, coupled with additional energy and inflationary pressures at the fore, have accelerated rapid transformation in leading organisations at an unprecedented scale.
“The influential role that digital transformation has in enabling sustainable and resilient business is clearly recognised by industry and public sector leaders. Yet our report finds how lack of collaboration, skills and investment represent top barriers in achieving these goals.”
The launch of the report follows Siemens convening more than 2,000 industry, governmental and economic thought leaders at its inaugural Transform event last year.
Industry leaders lending their voice to the report include engineering group Arup, and utilities giant Irish Water.
Contributions from leading public sector figures and trade bodies include Mayor of Greater Manchester Andy Burnham, the CBI’s chief policy director, and the Vice Chair at the Northern Powerhouse Partnership, who also give their views for the report. chevron-circle-right
To read the full report, visit: www.siemens.com/transform-report
The digital transformation imperative
The BPMA’s Pump Industry Awards Dinner has become the highlight of the pump industry’s social calendar, celebrating the industry’s best and brightest with the added bonus of excellent networking opportunities and great entertainment.
This year’s event will take place on Thursday 16th March at the Hilton @ St. George’s Park - the training ground for all 28 English national football teams - which is recognised the World over as the Home of English Football. Sporting excellence is synonymous with this venue, and in March it will also become the location for heralding engineering excellence across the pump sector. Fittingly, the evening will be hosted by Kevin Keegan, one of the most recognisable faces in British football.
Whether it’s taking a table to host customers or booking a few seats for you, your team and partners it’s a fantastic opportunity to enjoy a wonderful evening of great food, fantastic live entertainment and networking until the early hours.
Just visit the website www.pumpindustryawards.com and complete the simple online booking form to secure your places at this must-attend event.
Kevin Keegan
Venue: Hilton at St George’s Park, Burton on Trent
Date: Thursday 16th March 2023
Takes control of guttering rainwater
Gets to grips with grey water from commercial kitchens and bathrooms.
Makes light work of black water from multiple WCs.
You may not see Sanifos at work, but even when drainage is too low for the sewer, this range of powerful lifting stations gets the job done. You can configure Sanifos with a macerator or vortex operation, one pump or two, single-phase or three-phase motors, and choose a capacity from 110 to a huge 3100 litres. So you know that whilst it may be underground, when it comes to waste water, Sanifos is on top of it. See how, at sanifl o.co.uk