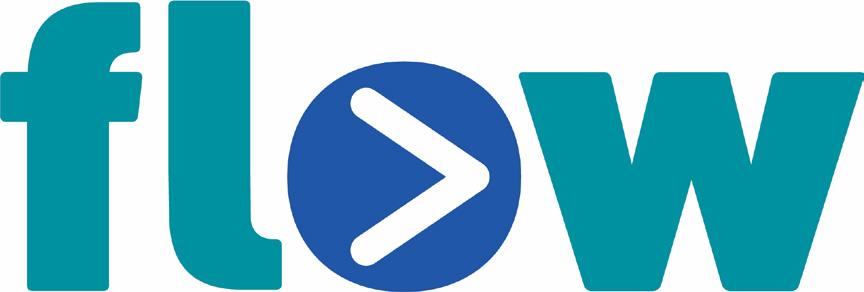
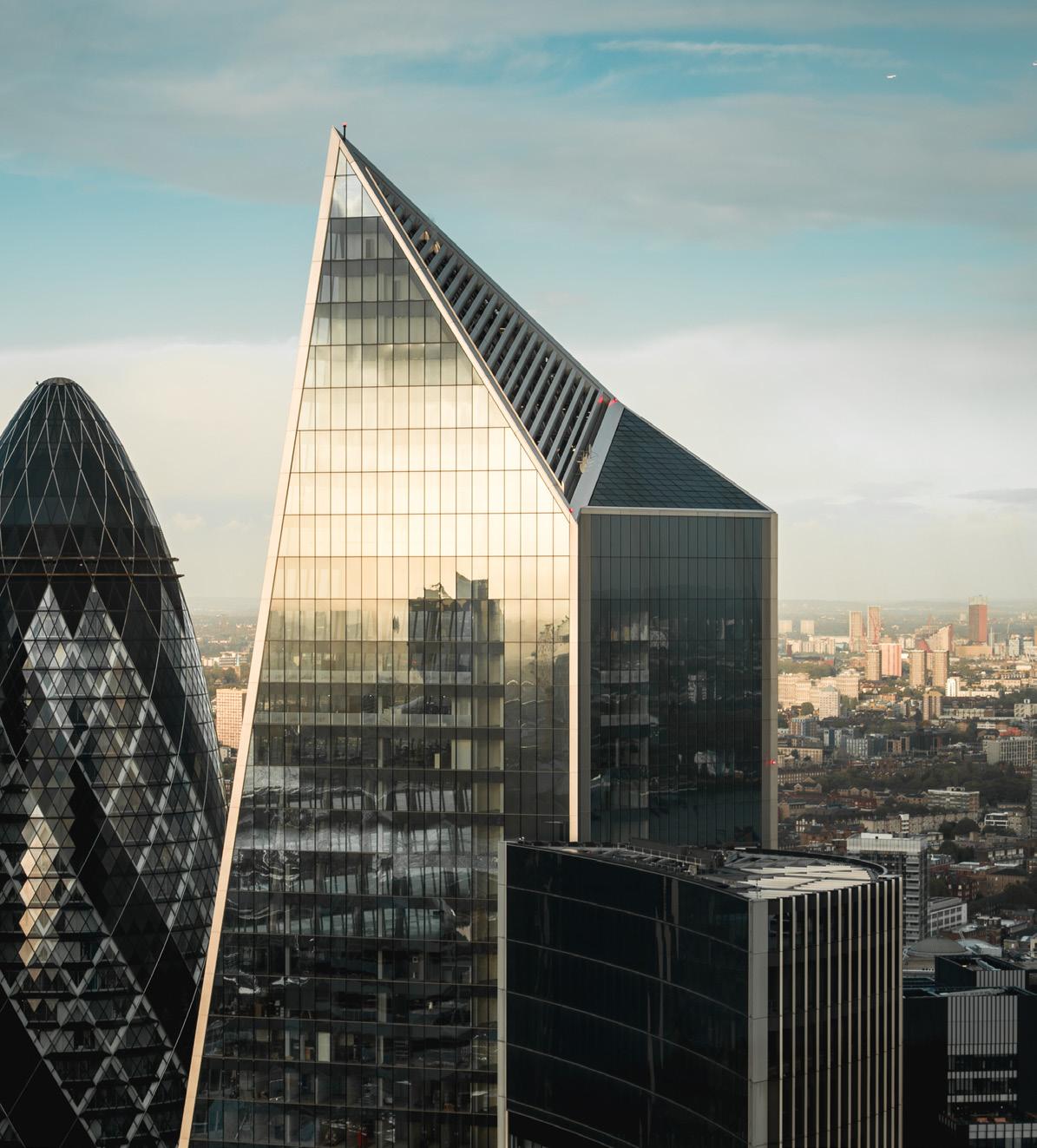
The critical role of energy audits
Low Voltage Motors in asynchronous, reluctance, and permanent magnet technology. Highest quality and efficiency offering.
High Voltage Motors outperforming global standards in industrial applications and supporting megatrends in key vertical applications.
Medium Voltage Drives are first choice for a better, more sustainable future in primary and process industry and in all applications, incl. power-to-power.
Our state-of-the-art electrification, automation, and digitalization solutions for the minerals industry deliver a sustainable advantage for the mine of the future.
Customer Services provides industry-leading services and digitalization to ensure the productivity, availability, and reliability of our customers’ assets.
With a trusted legacy of more than 150 years of engineering expertise, we are and have always been the backbone of reliable motion for industries and infrastructure worldwide.
We are now about to take this to the next level. Our mission is to support you, our customers in the mining and minerals sector, on the road to the future - sustainable, digital, reliable. Redefining reliable motion for a better tomorrow.
Editor Chris Callander chris@flowmag.co.uk 01732 671123
Contributing Editor Suzanne Gill suzanne@flowmag.co.uk
Publisher Andrew Castle andrew@flowmag.co.uk 07785 290034
Accounts
Touchwave Media Ltd accounts@flowmag.co.uk
Production
G and C Media Ltd production@flowmag.co.uk
For over three-quarters of a century the British Pump Manufacturers’ Association (BPMA) has been serving the interests of UK and Irish suppliers of liquid pumps and pumping equipment.
Centre 47 Birmingham Road West Bromwich B70 6PY www.bpma.org.uk
flow is a controlled circulation journal published quarterly on behalf of the BPMA by Touchwave Media Ltd and G and C Media Ltd. For a copy of the magazine’s terms of control and to request a copy please email circulation@flowmag.co.uk
The content of flow magazine does not necessarily reflect the views of the editor, publishers or the BPMA. The publishers accept no legal responsibility for loss arising from information in this publication and do not endorse any products or processes mentioned within it. No part of this publication may be reproduced or stored in a retrieval system without the publisher’s written consent.
© BPMA. All rights reserved.
Welcome to the final edition of flow for 2024, and my first since taking over the role of President of the British Pump Manufacturers Association (BPMA).
As I embark on my two-year tenure, I am excited to work with the Association team, the wider membership, and all those involved in the vital work to support and champion such an important sector.
Pumps touch almost every aspect of daily life. Without them, many people would have no heat, power or water in their homes. We wouldn’t be driving to work. There would be no internet. And our food choices would be much more limited than they are today. Those are just some of the obvious examples; for each of them, there are hundreds more that go unnoticed.
The BPMA membership is at the heart of ensuring these applications work effectively, efficiently and reliably, and I am proud to play my part.
The industry landscape is changing and as a collective, we’re moving the dial on important issues such as water scarcity, energy shortages and climate change. We are driving sustainability across our supply chains and we’re sharing best practice among our members and these are all areas I will have in focus during my time as president
I would like to thank my predecessor, Dale Croker, for his dedication to the President’s role over the past two years. Working alongside Dale during that period, I experienced the energy and commitment he gave to the position first-hand, and I am grateful for the strong and healthy position the Association is in as he passes the baton on to me.
Finally, in exciting news, flow magazine’s website, www.flowmag.co.uk, has been completely redesigned and now brings you more great pumping systems-related content to enable you to get your fix between issues. You can find out more about this fantastic development on page 14, and I heartily encourage you to take a look.
Lee Tebbatt, President, BPMA
A NORTH EAST PUMP ENGINEER finally hung up his tools when he retired after 50 years of service.
Chris Lumsden joined pump distributor and manufacturer, Tomlinson Hall, as a 16-year-old apprentice in 1974 and has worked for the Billingham-based company ever since.
Chris, who held the role of mechanical pump engineer when he retired, started as a mechanical fitter in the company’s original premises in Stockton-on-Tees.
Chris worked his way up the company, and over the last five decades he has used his experience to train new apprentices, brought his expertise to some of the company’s largest pump installation projects, and been an integral part of the workshop team.
Among his first duties were chopping
wood for the workshop’s fire and filling the workshop’s coke bins every morning.
Commenting on his 50 years with Tomlinson Hall, Chris said: “I feel very fortunate to have been employed all of my life, and I have really enjoyed my time with Tomlinson Hall.”
Colin Simpson, Business Development Director at Tomlinson Hall, added: “Chris is a typical ‘grafter’. He loved to work handson with equipment and get his head down, and he inspired the younger members of our team, who really looked up to him. He has passed down his knowledge to the next generation, which is absolutely invaluable.
“There’s no doubt that he has made a huge contribution to getting the company to where it is today. We wish him all the very best for his retirement and thank him for 50 years of impeccable service.”
Pump manufacturer, Grundfos recently held a summit with some of the industry’s top sustainability experts and leading energy users to help them understand and overcome the challenges and pitfalls and to help develop robust plans to meet interim and final targets as quickly and efficiently as possible.
The event brought together leading contractors, consultants and senior engineers with sustainability directors, research managers and representatives of CIBSE, experts who, every day, face decisions on energy and sustainability in an open and inclusive environment where everyone was encouraged to contribute.
Against the backdrop of one of London’s finest five-star luxury hotels, the Rosewood in Holborn, Grundfos’ UK Managing Director, Glynn Williams, welcomed a guest list of 120.
At the event, Ross Crighton, Senior Regional Sales Manager, CBS Aftermarket at Grundfos, explained the crucial role that existing commercial buildings must play in meeting Net Zero targets. Existing buildings in the UK currently use between 20 and 50% more energy than they should, he explained, so this should be the first place to look when staring along the path.
Many of these buildings are ten years old or more, and the technology available when they were built was nowhere near as efficient as today’s digitised E pumps – smart pumps that can judge for themselves when the system is not operating efficiently
and make the necessary adjustments to maintain optimisation.
Grundfos Climate Director Thomas Schrøder was next to speak as he introduced the company’s overriding desire to make life better for people throughout the world, moving from ambition to action by bringing clean water to millions, setting up charitable businesses to support the underprivileged and those isolated communities in some of the world’s toughest environments or developing new and innovative systems to protect precious water supplies and use water more efficiently and sustainably.
Thomas was followed by Mace’s Head of Building Services Construction, Paul Connolly, who outlined the company’s sustainable development, from becoming a carbon-neutral business in 2020, to its pledge to cut its own emissions by 10% every year. He also introduced a new platform the company is developing that will save clients 10 million tonnes of CO2 by 2026.
Next up was Skanska’s Head of Sustainability, Sharon Maynard, who discussed the carbon evaluation and tools to support the company’s plans to achieve a 50% reduction in carbon emissions by the end of this decade, and reach Net Zero by 2045, five years ahead of the Government’s target. As well as to reduce carbon intensity by 130 tonnes per £million pounds of revenue by 2030.
CELEROS FLOW TECHNOLOGY
(Celeros FT) and Carbon Clean have entered into a partnership agreement that aims to accelerate the deployment of carbon capture technology in hard-to-abate industries.
The new partnership will see Celeros FT combining its application knowledge and technical engineering pedigree with Carbon Clean’s specialist expertise in carbon capture solutions. This represents further progress towards Celeros FT’s ambition to become a full chain supplier to the Carbon Capture and Storage (CCS) sector and adds industrial carbon capture technology to its portfolio of specialist CO2 transportation pumps and injection pumps for storage.
refineries, energy from waste, and maritime/shipping. It has more than 15 years of experience in designing, building, financing, and operating industrial carbon capture systems, and its solutions have cumulatively captured more than 2.4 million tonnes of CO2.
Commenting on the new deal, Jose Larios, CEO & President at Celeros FT, said: “Celeros Flow Technology recognises the challenges that the energy transition raises
for customers. This partnership further underlines our commitment to developing fully customised lifecycle solutions that respond to the diverse process challenges of transitioning from fossil fuels to renewable resources. We are excited by the prospect of working collaboratively with Carbon Clean to deliver modular, compact, and scalable solutions for carbon capture across our chosen markets.”
Carbon Clean specialises in carbon capture technology solutions for hard-toabate industries such as cement, steel,
Europump (the European Pump Association) has announced that online registration for its 2025 annual meeting and general assembly is now open. Hosted by the Czech Pump Manufacturers Association (CPMA), this three-day event will be held from 21 to 23 May 2025 at the Hilton Hotel in the historic city of Prague.
The 28th edition of the Europump annual meeting promises an engaging program combining technical insights, regulatory updates, and invaluable networking opportunities. This year, participants will enjoy an enhanced lineup of events and discussions addressing key topics shaping the future of the pump industry.
The program kicks off on 21 May with a meeting of ISO/TC 115, focusing on pumps and their evolving international standards. Attendees will also gain insights into the US market landscape and hear about the impact of recent US elections on global trade and industry operations from the Hydraulic Institute. There will also be updates on regulatory and standardisation developments, including digitalisation, Environmental Product Declarations (EPDs), eco-design, and PFAS specifications for pumps. Plus Oxford Economics will outline the findings in its 2025 World Pumps Report and there will be a special contribution from WEG, this year’s Gold Sponsor.
Full details of the event, and the online booking system can be found at www.europump2025.com.
The new partnership centres around Carbon Clean’s patented CycloneCC technology, which is columnless, compact and modular, delivering high performance while significantly reducing the cost of carbon capture compared to conventional solutions.
Under the partnership agreement, both companies will collaborate to develop industrial-scale carbon capture solutions. Celeros FT provides engineering and fabrication services based on more than 140 years of experience and will leverage its extensive sales and aftermarket support network to support the decarbonisation goals of existing and new customers.
2 WEEKS
Visitor registration is now live for the Process & Chemical Engineering Show, running as part of the CHEMUK 2025 group of events, taking place on 21 & 22 May at the NEC in Birmingham.
The Process & Chemical Engineering Show will showcase the latest technology and specialist services to attending process, plant, and control engineering and safety professionals across the chemical, food & beverage, pharma, oil & gas, water & waste, and energy sectors.
The BPMA team will be exhibiting on stand F66 at the show, and there will be another strong representation of BPMA members exhibiting, including ABB,
Apex Pumps, Crest Pumps, Grundfos, Innomotics, KSB, M-Seals, UK Flowtechnik and Vogelsang.
Attendees can register for their free visitor pass through the website at www.chemicalukexpo.com.
Pump manufacturer Wilo has been accredited with an EcoVadis Platinum rating for the third year running, underscoring its commitment to driving sustainable practices.
The sustainability rating agency’s assessment of Wilo highlighted the business’s “concrete and ambitious” environmental goals.
The company’s goals include reducing group-wide Scope 1, 2, and 3 emissions, driving decarbonisation by minimising annual energy consumption, and providing further transparency around the environmental footprint of its products.
BRISTOL-BASED PUMP manufacturer, Apex Pumps, has recently installed a 150kW solar panel system on its factory roof. The installation was made possible by a £150,000 asset finance package from Lloyds Bank, which was supported in part by the Clean Growth Financing Initiative (CGFI) –which offers fee-free lending for clear, specific, sustainable projects and purchases – and a grant from the West of England Mayoral Combined Authority.
The manufacturer was also included in the outstanding category this year, which fewer than 1% of the 130,000 companies assessed annually by EcoVadis is awarded. The rating is based on criteria such as environmental awareness, labour conditions, ethics, and sustainable sourcing.
Lee Tebbatt, Managing Director at Wilo UK, said: “To receive the platinum award from EcoVadis for the third year running is a testament to the steps that we have taken towards integrating sustainability management across every aspect of the organisation.”
Wilo conducts regular audits of its suppliers, in addition to helping them set
their own environmental precedent through training exercises. This has contributed towards the manufacturer achieving an excellent rating in the labour and human rights category.
Oliver Hermes, President and CEO at Wilo Group, said: “The ratings by EcoVadis show that Wilo has long been one of the frontrunners in terms of sustainability.
“We take responsibility and, as a family business, concentrate on the long-term impact of our actions. The excellent rating from EcoVadis shows once again that we are truly making a difference.”
Earlier this year, Wilo was named among Europe’s Climate Leaders, an initiative led by the Financial Times and Statista that looks to identify companies that are making significant headway towards combatting climate change.
The investment in Apex Pumps’ facility supports the company’s target to become 50% self-sufficient in its energy use through renewables.
Commenting on the installation, Andrew Simpson, Managing Director at Apex Pumps, said: “Overhauling our manufacturing methods and becoming more self-sufficient when it comes to energy usage, boosts our sustainability and competitiveness in global export markets.
“The support we are receiving from Lloyds Bank has been integral to realising these changes, and with solar panels that are projected to pay for themselves in just four years, the benefits to our business and beyond are profound.”
Qualityproducts andexcellentservice We’vegotthelot!
Weprovide flowmetersandinstrumentation foralmostall applications,liquidorgas,highorlowpressure,highorlowflow rates.Westockflowmeterstosuitallrequirementsandbudgets.
• Over50yearsofcollectiveexperienceinflowmetersupply
• CentrallyUKbasedoffices
• Dedicatedtechnicalspecialists
• Manufacturerssupport
• ServiceFocused
• Calibrationandrepairservice
• Supplysupportinginstrumentationeither fittedorremotetotheequipment
£100k ($130,000)
UK FLOWTECHNIK HAS BECOME THE premier distributor of Fluidwell products in the UK, introducing the new robust and user-friendly C581 Flow and Energy Computer.
The Netherlands-based Fluidwell develops and manufactures high-end industrial electronic displays and has over 25 years experience with indicators, totalisers and flow computers.
The company has designed the C581, which was developed for a customer that had a specific application in hydrogen fuel delivery, to be more robust and more user-friendly than what was already on the market, and it marks the first product in what is set to become the C5-series.
The C581 Flow and Energy Computer measures water, superheated and saturated steam at heat exchangers, boilers, condensers and coolers in industrial settings.
It measures the actual flow, temperature and pressure and uses the IAPWS determinations to calculate the energy, mass and volumetric flow. The linearisation enhances accuracy in any flow range, while the large logging register contains all measured and calculated values.
A cornerstone in the design of the
Fluidwell C581 is the high usability of the product, without sacrificing userfriendliness thanks in part, to six buttons and free configuration software. The C581 is designed to withstand extreme weather and industrial conditions, including rain, snow, sandy deserts, salty atmospheres and temperatures between -40 and +70°C.
The device features a main screen with a custom selectable order of measured and calculated variables, a bright backlight for good readability during day and night and multi-language support. It can process various flow inputs, including pulse (pending), (stacked) differential pressure or other 4-20mA signals, Pt100 and Pt500 for temperature input and two status inputs. And there are 11 linearisation points per input for all inputs. There are also two analogue outputs, two digital outputs, and two relay outputs, plus three communication ports – RS485, RS232 and
mini-USB. While it can be powered by 100230V AC or 16-27V DC.
According to UK Flowtechnik, the 11 linearisation points per input, alongside a large datalog memory for all the measured units and calculated units and its large ambient temperature range, makes the C581 Flow and Energy Computer unique in the market.
www.ukflowtechnik.com
VIBRALERT HAS INTRODUCED what it is presenting as a cost-effective pump vibration sensor designed for users prioritising asset reliability without complexity. According to the company, this tool, which has been designed to be user-friendly, offers a straightforward alternative to expensive, intricate vibration analysis products.
In an industry where reliability is paramount, Vibralert’s maker says its new device stands out by offering a straightforward setup thanks to the fact that it needs no power, data cabling, special tools, or knowledge to attach the sensor to a pump. Unlike systems that require extensive training and data analysis, Vibralert aims to allow operators to focus
on maintaining pump performance rather than deciphering data. With a simple-to-understand traffic light type indication, the sensor has been designed to be a straightforward tool for predictive maintenance, helping operators identify potential issues before they lead to costly downtime. Plus, with the sensors offered
at a lower price point compared to high-end monitoring solutions, the company aims to make Vibralert an effective vibration monitoring solution accessible to a wider range of users.
Vibralert’s development has been bolstered by a partnership with the University of Hertfordshire through the Knowledge for Business (K4Bi) scheme. This initiative fosters collaboration between academia and industry, which the company says ensures that the product is rooted in rigorous research while remaining practical for everyday use.
vibralert.io
SEAWATER REVERSE OSMOSIS (SWRO) plants are playing an important role in supplying freshwater to communities that are struggling to find sufficient supplies. Sulzer is supporting these vital facilities with purposebuilt pumps that are designed to optimise efficiency and reliability in this challenging application. The new ZF-RO is designed to match the technical requirements of energy recovery device (ERD) booster pump service. It combines the design used in the ZF range which has extensive references for excellent efficiency both in the hydrocarbon and desalination industries.
Freshwater is a vital resource that is diminishing in many areas of the world. Reverse osmosis is being used to treat seawater and create a cost-effective water supply for local communities. The cost to the consumers for water is directly related to the running costs of the desalination plant. Consequently, optimising efficiency and keeping maintenance costs to a minimum means that plant operators can ensure an affordable water supply.
The launch of the ZF-RO pump complements Sulzer’s range of pumps that are specifically designed for operation in the desalination industry. The latest addition is tailored to deliver seawater or similar liquids across a wide performance range. For flexible operations, ZF-RO pumps are designed to operate with
Biotech Fluidics has introduced the DEGASi life science degassing chamber that provides efficient degasification of aqueous liquids at flow rates up to 20ml/min.
Toxic poly- and perfluoroalkyl substances (PFAS) are known to be highly persistent in the environment and linked to health problems in humans, including higher cholesterol, lower birth weights, and kidney cancer.
Traditionally, most degassing systems have used fluorinated polymer membranes to ensure wide chemical compatibility. However, reflecting the growing demand from environmental, food and healthcare labs to avoid PFAS, the new life science degassing chamber has been designed with a fluid path lined by a silicone membrane, thereby eliminating the chance of contamination by these toxic substances.
The DEGASi life science degassing chamber is designed to improve analytical instrument precision and assay quality by removing dissolved gases from aqueous fluids before they outgas and form bubbles that impact precision dispensing or interfering with detection.
variable speed drives, enabling them to meet the process specifications as the booster pump for energy recovery devices.
Based on the ZF range that has delivered decades of service in the hydrocarbon industry, the ZF-RO pumps are fully configured designs that can ensure minimal delivery times and extended service life. Improved efficiency has been achieved through state-of-the-art hydraulic and mechanical design, making a direct contribution to lowering the cost of fresh water for the local population.
Manufactured from Super Duplex stainless steel, which offers excellent protection against erosion and corrosion, these pumps feature excellent reliability. The minimal footprint of the pumps makes for a compact installation, maximising the available space within a processing plant.
The new ZF-RO range is just part of a Sulzer’s portfolio of pumps that have been specifically designed for seawater reverse osmosis.
6.5 YEARS
Lee Tebbatt, Managing Director of Wilo UK, has been announced as the new President of the British Pump Manufacturers Association (BPMA), following a two-year tenure as Vice President.
The position was officially passed on during the BPMA’s Annual General Meeting and follows the two-year term in office by the previous President, Dale Croker, Managing Director of KSB UK. As his successor, Lee has had the benefit of shadowing Dale since November 2022, and so is now well prepared and fully conversant with all that is required of him as BPMA President.
Wayne Rose, Director and Chief Executive of the BPMA, commented: “This is a great accolade and one that reflects the continuing efforts that Lee makes to raise the industry’s profile in general and tackle the tough issues that it continues to face. The BPMA has enjoyed the support and engagement of some incredibly talented people at its helm over the years, including its immediate past President Dale, and we are delighted to now have Lee join that impressive line-up. I look forward to collaborating with him as we continue to drive the Association forward.”
He continued:” I am enormously grateful to Dale for all that he has done for the BPMA during his presidency and am delighted that he will continue to support the Association as a member of its council.”
The new tenure coincides with a number of uncertainties affecting the pump sector, from supply-chain issues and the ongoing skills shortages to the ever-present concerns over the cost of energy and, of course, the changing political landscape, both here in the UK and throughout the World.
Commenting on his new role, Lee Tebbatt said: “Assuming the role of President of the BPMA is a huge honour, and I look forward to working with the BPMA staff and members as we navigate our way through the challenging times we continue to face here in the UK. It is no surprise that ongoing social, economic, and political developments continue to present obstacles and uncertainty in the
pump market, making the supportive role that the BPMA delivers for its members even more relevant than ever.”
He continued:” Through these times of change, the Association will continue its vision to influence the pump sector business environment in the interests of members’ competitiveness and sustainability and to increase sector awareness by providing promotional channels, technical support and pumpbased training to members, operators and purchasers of pumping equipment.”
In handing over the baton, Dale Croker said: “It has been a real privilege to undertake the role of BPMA President and to help the Association in all its endeavours. I have thoroughly enjoyed working with the BPMA secretariat and fellow council members and would like to thank them for their support and encouragement. I now look forward to offering that same level of support and backing to Lee as he takes over the presidency.”
The BPMA also has the pleasure of
welcoming Andrew Simpson, Managing Director at Apex Pumps, into the vital role of Vice President, taking over the position vacated by Lee Tebbatt. Andrew has been a member of the BPMA Council for several years, and so not only brings a wealth of industry knowledge but also an inherent understanding of the Association and its operational endeavours.
Speaking of his election to Vice President, Andrew Simpson stated: “The BPMA has provided an important support structure to the pump manufacturing and distribution sector here in the UK for over eight decades, and I feel immensely proud to join the roster of pump industry professionals who have helped to steer this great organisation to its many successes over that period. I look forward to assisting Lee and, indeed, the BPMA council in its next phase of development. chevron-circle-right
www.bpma.org.uk
British Pump Manufacturers Association (BPMA) CEO, Wayne Rose, is calling on businesses across the UK’s industrial sector to prioritise energy audits as a key strategy for improving operational efficiency, cutting costs, and reducing environmental impact. With energy prices continuing to fluctuate and sustainability becoming increasingly central to business operations, understanding how and where energy is consumed has never been more important.
Energy audits are an essential first step in identifying areas of energy waste and inefficiency. They provide businesses with a comprehensive assessment of their energy use, highlighting opportunities for improvement and offering actionable recommendations. For industries reliant on energy-intensive processes, such as manufacturing and production, these audits can lead to significant savings in energy consumption and cost while contributing to broader environmental goals. Most existing pump systems were not originally designed with energy conservation as a major consideration. If pump systems are initially designed on an energy-efficient basis and pumps are correctly sized and applied, the energy savings will often be more than 50%.
Central to this process is the BPMA’s Certified Pump System Auditor (CPSA) scheme, which offers a critical foundation of knowledge for conducting energy audits in systems involving pumps. Pump systems are often one of the largest consumers of energy in industrial operations, yet they are also an area where efficiency gains can be most easily realised.
Through the CPSA scheme, professionals are equipped with the expertise to thoroughly assess pump systems, identify inefficiencies, and provide solutions to optimise performance.
By undergoing a CPSA-accredited audit, businesses can ensure they are receiving expert advice tailored to the specific challenges of pump systems. The knowledge provided by a certified auditor goes beyond identifying simple inefficiencies – it provides a strategic understanding of how to enhance overall system performance. This results in direct energy savings and leads to improved
reliability and reduced maintenance costs, driving long-term operational resilience.
Candidates carry out the Pump System Audit in accordance with ISO/ASME 14414:2019, the standard which outlines the requirements for conducting and reporting the results of a comprehensive pumping system energy assessment. This assessment evaluates the entire pumping system, from energy inputs to the work performed, to determine the current energy consumption and identify opportunities to improve system efficiency.
The value of an energy audit cannot be overstated. Pump systems are fundamental to the functioning of many industrial operations, but they also represent a significant opportunity for energy savings. The CPSA scheme is designed to provide the industry with highly qualified professionals who can deliver real, measurable improvements in energy efficiency. We urge all businesses to take advantage of this and make energy audits a priority.
As the UK strives to meet its energy reduction targets, the role of energy audits in industrial settings will become even more pivotal. The BPMA is committed to supporting businesses in their journey towards greater energy efficiency, offering the tools and expertise needed to make a tangible impact.
Through the CPSA scheme, pump engineers are being trained to correctly assess the efficiency of pump systems and to provide appropriate recommendations to improve that efficiency.
By adopting energy audits as standard practice and leveraging the deep expertise provided through the CPSA scheme, UK industries can unlock significant improvements in energy efficiency, reduce operational costs, and contribute to a more sustainable future. chevron-circle-right
www.bpma-cpsa.co.uk
Simply
With sensors that are smarter and more resilient we improve the sustainability in your process automation. Numerous awards and prizes prove us right. You can rely on the Baumer expertise.
Contact us: www.baumer.com/award-winning
Amajor update has seen a range of new content and features added to the BPMA’s Flow magazine website at www. flowmag.co.uk.
As well as being able to access copies of the quarterly flow magazine going back to the very first issue published five years ago, the totally revamped website is now updated with the latest news for users of pumps and pumping systems across the wide range of sectors covered by the magazine. The site also features in-depth technical insights to enable visitors to stay ahead of the new trends and innovations affecting the sector, along with insights and tips for getting the most out of pumps and pumping systems, whatever the application. In addition, visitors can read thought-provoking opinion pieces from leading industry experts.
As the only website exclusively dedicated to sharing the latest news and insights essential to users of fluid pumps and pumping systems in Great Britain and Ireland, the all-new site at www.flowmag. co.uk will feature all the great content from each issue of Flow magazine plus much more that can’t be squeezed into each quarterly issue.
Commenting on the site’s relaunch, its Editor, Chris Callander, said: “We are all bombarded with so much information across a wide range of on and off-line channels each and every day. But spotting the truly valuable information within a vast sea of noise can be increasingly difficult. The new Flow magazine website will make that easier for users of pumps and pumping systems as we find the information that matters and bring it together in one place.
In addition to the wealth of content designed to add value to pump and
pumping system users, visitors to the new website will find a complete list of BPMA members and key suppliers, a regularly updated diary of important dates for anyone working with pumps and pumping systems, and, of course, the opportunity to sign up to receive a free copy of flow magazine – in print or digital format – as soon as each issue is published.
www.flowmag.co.uk
NOMINATIONS HAVE NOW CLOSED for the 2025 Pump Industry Awards as the event prepares to celebrate 25 years of rewarding pump excellence.
Maintaining its early Spring timeline, the next the gala dinner and presentation ceremony will take place on Thursday 13 March 2025 at the Hilton at St George’s Park in Burton on Trent, with finalists due to be announced early in the new year.
Situated on the edge of the National Forest, St. George’s Park is the training ground for all 28 English national football teams and is recognised worldwide as the home of English football.
The pump sector plays a crucial role in ensuring our food production, utilities, manufacturing processes, transportation
and other essential services are maintained and the 2025 awards programme, will once again give special recognition to those companies and individuals who have gone that extra mile to meet, and more often than not exceed, the demands and challenges presented by the sectors served.
This recognition and acknowledgement will again be represented by a suite of award categories, that collectively honour the full breadth of product and service delivery by the pump industry, and will this year include recognition of sustainable contribution, for a better world. Another change to previous years is the introduction of a turnover split within the Distributor of the Year category. This will allow smaller businesses – those with an annual turnover of less than £3M
– to be suitably differentiated from larger businesses.
Wayne Rose, Director and CEO of the British Pump Manufacturers Association, commented: “This year’s awards ceremony provided a fantastic showcase of innovation, technical endeavour, engineering prowess and professional excellence. I look forward to another opportunity to recognise the amazing achievements in this important sector again next March, as the event celebrates its 25th year.
www.pumpindustryawards.com
•
•
•
•
•
•
•
•
MOTOR, DRIVE AND GEARBOX
manufacturer, WEG, will play a key role in a major water transmission project in the Middle East, set to be one of the largest of its kind in the region. WEG will supply a package of motors, variable frequency drives (VFDs) and transformers to support the new project, which aims to deliver water between two of the largest cities in the region.
The new water infrastructure will be a major undertaking as it will be one of the largest water transmission systems in the region. The customer required a holistic package of transformers, watercooled VFDs, and motors with powers up to 9.1MW, which were able to withstand the region’s extreme temperatures and environmental conditions and power pumps in the new system.
The MVW01 VFDs with water cooling, which was a specific requirement for this project, feature an electric panel with a new thermal dissipation design, allowing for a greater range of power output. The MVW01 also features a user-friendly 10in touchscreen HMI that simplifies the programming and monitoring of key parameters. The VFD allows for efficient process speed control, reducing energy consumption, operation and maintenance costs and the total cost of ownership (TCO). The phase-shifting transformers selected as part of this package offer complete isolation to mitigate common-mode voltage
stress on the motor and naturally reduce harmonics on the power supply. Oil-type transformers for outdoor installation were chosen to meet the project requirements. The transformers’ steplap-type magnetic core optimises noise levels and low exciting current while the optimised natural anchoring of the set withstands short circuit stresses. In addition, the external coatings protect the transformers against the harshest environments.
WEG also supplied water-cooled W60 MV motors offering excellent performance across severe and aggressive operating conditions, including extreme ambient temperatures. These modern motors are designed to meet the requirements of industrial applications, including compressors, pumps and fans, and are efficient and modular, allowing for different cooling configurations.
“Water transmission systems are a crucial part of critical infrastructure and require specialised equipment that is both robust and reliable to ensure that they run effectively and safely. This can be a particular challenge in harsh outdoor
environments,” said Alaa Aldrras, HVS Development Sales Manager for HVS Motors & Drives. “We’ve drawn on our experience of developing solutions for the water industry globally to offer a holistic package to meet the customer’s needs, and thanks to our facilities in Brazil, we are able to deliver this well within the project schedule.”
www.weg.net
IN NORTHERN Lincolnshire, a chopper pump made by Landia has completed five years of continuous service at the main 2MW biogas plant run by Singleton Birch, which for over 200 years has produced high-quality lime products.
Working underground as part of an automated system for dirty run-off water, the Landia pump chops up maize and other particles that end up in the drainage, sending the recirculated liquid
to the site’s lagoon or back to the digesters as and when required.
“The Landia chopper pump does an excellent job,” said Danny Mason, Renewable Energy Supervisor at Singleton Birch, where the AD plant’s three 2800m3 digesters use a feedstock of maize, chicken litter and sugar beet.
He added: “The pump is very easy to maintain and has really helped us with drainage on site, chopping up solids that would block up lesser quality pumps.
Landia takes care of the full servicing and always ensures that there isn’t any downtime.”
Invented by Landia in 1950, the chopper pump is designed with an external knife system that continuously reduces solids.
In addition to the unit at Singleton Birch, Landia has numerous chopper pumps installed at biogas plants as part of its digester mixing system. These include Scottish Water, Eco Verde Energy, and Republic Services in California.
www.landiaworld.com
MENZEL ELEKTROMOTOREN, A FAMILY-RUN
motor manufacturer based in Hennigsdorf near Berlin, has manufactured two pump drives with extra-long piping for water supply in Angola. The pumps draw water from the Kwanza River and transport it over a distance of 17km, climbing 135m to a water treatment plant just outside the capital, Luanda. The existing pumps are installed inside the pipework and cannot be removed. The operator, therefore, ordered complete pump systems, including drive and connection pipework.
Menzel had previously assisted this customer by supplying replacement motors at short notice. However, in this case, the motor manufacturer also had to tailor-make pump systems that could easily replace the existing structures.
Production of the units took place at Pawils Elektromaschinenbau. The Menzel subsidiary procured pumps of the right performance class, adapted the mechanical interfaces to the installation on site and fitted them with pipes and motors, which were also designed specifically for the application. Each unit is about 12m long. The pump systems have a flow rate of 900m³/min each. The motors have a nominal power of 500kW, an operating voltage of 6000V and a speed of 1475rpm. Initially, two out of three identical pump systems were
replaced, while the third ensured the continued operation of the water supply. After successful commissioning, Menzel also expects an order for the third system.
www.menzel-motors.com
The Kiwa UK Regulation 4 Product Approval Scheme (KUKreg4)a robust method for demonstrating compliance with the Water Supply (Water Fittings) Regulations 1999.
FOLLOWING THE SUCCESS OF its inaugural year, ERIKS’ 2024 apprenticeship programme has grown 70% with the induction of 22 new apprentices. Of these, 18 are undertaking engineering apprenticeships, and four are taking on the newly introduced sales and service apprenticeships.
Lori Broadhurst, Talent Development Partner at ERIKS, explained: “We’ve seen tremendous success from our first-year apprentice engineers, with many already contributing to real-world projects. This new intake brings even more potential, and we’re excited to continue fostering the next generation.”
As with the first year’s cohort, the engineering apprentices will split their time between hands-on work at ERIKS service centres across the UK and formal training at SMB College in Leicester, where they will pursue Level 3 Engineering qualifications for the next four years, gaining an invaluable grounding from both practical and academic experiences.
For the first time, the 2024 programme
has seen ERIKS offer apprenticeships in sales and service. Those on the sales and service apprenticeships will spend their time completing two courses simultaneously, which will result in both Customer Service Specialist Level 2 and Sales Executive Level 4 qualifications upon completion of the 3-year programme.
Demonstrating the versatility of apprenticeship schemes and in line with ERIKS’ commitment to nurture new talent, regardless of demographic, the age range of the 2024 intake spans 17 to 34.
“We’ve had applicants straight out of school and some who have spent years in other career fields prior to application”, added Lori. “All applicants went through the exact same process, and the best were chosen. We have taken on a 34-year-old
who wanted a career change, and one of our staff, who had been a temp but then became a permanent hire in a workshop, is expanding their career horizons and has become an engineering apprentice. Apprenticeships are for everyone, not just 18–21-year-olds.”
eriks.co.uk
ABB HAS UNVEILED AN analytical training facility, part of its service training centre in Stonehouse, UK, to equip engineers with expertise in its latest water quality measurement technologies.
The Skills Hub features the technologies used in ABB’s continuous water analysis solutions. Used in power generation and water treatment applications around the world, the systems provide complete water quality monitoring, combining high performance, reliability and service.
engineers to develop their skills in a realistic environment that mirrors the solutions we provide to our customers.”
panel design that can be reconfigured to suit different training requirements, enabling engineers to practice commissioning, operating and servicing the ABB products used in typical analytical measurement applications. Parameters include pH/ ORP, conductivity, dissolved oxygen, turbidity, silica, sodium, and chlorine, with the ability for more to be added or swapped out as needed.
“Accurate water quality measurement is key for both the safety of potable water and the effective treatment of water for industrial and power utility processes to boost efficiency and minimise pollution,” said Dr Jonathan Farrington, Technical Manager for ABB Measurement & Analytics’ service business. “The addition of the skills hub to our service training centre enables
The new skills hub features a fully functioning system that is split into two sections: one focusing on ABB’s full range of analysers for key parameters within the power industry and the other showcasing the portfolio of water quality measurement analysers for the water and wastewater treatment industry.
Both sections utilise an adaptable
By familiarising customers’ engineers with ABB’s full range of analytical solutions and the types of problems that can occur in a typical application, the skills hub will help ABB to ensure that their devices deliver optimum performance at all times.
new.abb.com
We offer a wide range of solutions to improve performance, efficiency and reliability for your pump applications.
• WEG Sync+ Ultra, with an IE6 efficiency rating, this is the most efficient industrial motor on the market.
• Pump Genius, a customisable feature of WEG drives that enables your standard VSD to become dedicated for pumping systems ensuring accurate pressure / flow control throughout the process
• Motion Fleet Management, scans and monitors the performance of assets using cloud based technology for preventative and predictive maintenance.
• WEG SEE +, new efficiency calculator enables you to calculate energy savings, return on investment and ultimately reduce GHG emissions.
Learn more at www.weg.net
When aged machinery in a system fails, spare parts are often no longer available. Buying a new machine is costly and can lead to cost-intensive renovations of further components as well as downtime of the entire system. KSB has developed a procedure in which spare parts are reproduced by 3D printing. This is particularly helpful in the case of old pumps from different manufacturers, providing plant operators with fast availability and significant savings.
It is very common today for power stations to operate vertical centrifugal pumps, which have long exceeded their service life, to transport turbine condensate. Regional energy partner EAM Natur Energie GmbH has been using such a centrifugal pump – made in 1967 – in the HKW Göttingen (combined heat and power station) south of Hannover. Even just by looking at this pump set it was apparent that it had long exceeded its useful life when it finally stopped working. After more than 50 years, it was hardly surprising that procuring spare parts was unsuccessful. In this case, KSB SupremeServ took on the task and was able to repair this third-party product.
Oxidised iron had been depositing on the pump for decades. This resulted in magnetite swelling up the surface of the entire pump to such an extent that efficient operation was no longer possible.
The original manufacturer, Halberg, no longer had any spare parts for this pump in its programme, and reproducing the impeller the classic way would have cost nearly as much as buying a new pump.
In addition, if the pump had to be replaced by a new model, costly changes to the entire system, such as piping, valves and condensate tanks, would have been unavoidable.
In conformity with DIN ISO 9001, KSB SupremeServ created a detailed damage report and developed an action plan for an economically viable pump repair. Apart from freeing the casing from magnetite using a special mechanical procedure, repairing the centrifugal pump mainly meant replacing its highly complex impellers.
KSB has been involved in the field
of additive manufacturing, also commonly known as 3D printing, for over a decade. The largest benefits of additive manufacturing are the high speed at which components can be manufactured and its cost efficiency.
Another advantage is the ability to process an immense diversity of materials and shapes, including complex components. Without wanting to outcompete series production by casting, 3D printing is especially suitable for producing single individual components, such as spare parts. It was, therefore, an ideal option for reproducing the two impellers that were no longer available.
At its Pegnitz site, KSB installed the largest 3D printer worldwide to create workpieces from metal powder using a laser beam. KSB was the first ever manufacturer to receive TÜV certification for using this method to manufacture components subject to the European Pressure Equipment Directive.
As soon as the CAD data is available, 3D printing is unbeatable in price and enables a procurement time of only a few days. This means KSB can 3D print components that are no longer produced by other pump manufacturers – or that would be very expensive and take months to produce. In this particular case, 3D printing saved threequarters of the costs.
Using fragments of the old Halberg
impellers, a new virtual 3D model was created. In CAD, engineers precisely redesigned the impeller geometry, including the vane curvature, number of vanes, and outlet width. Based on the operating data on the nameplate, the original hydraulic performance data was also reproduced exactly.
In addition to avoiding expensive and time-consuming re-planning of the system, piping, condensate collector and corresponding valves, the new impellers have also enhanced the hydraulic efficiency of all the pumps, resulting in higher energy efficiency, increased system availability, and therefore clear savings regarding the life cycle costs.
Reproducing the new parts has given the pump a second life. With sustainability in mind the KSB SupremeServ has long focussed on repairing old pumps – no matter what their type and make – instead of replacing them with new pumps, which is cost- and labour-intensive. chevron-circle-right
In everything we do, we never lose sight of what it‘s all about for you: economical work and easy handling.
Whether chemical substances, oils or media for the food industry, it is important to fill or empty quickly and precisely. Due to the reversible conveying direction, both processes can be carried out with just one pump.
As a result of their compact yet powerful construction, Vogelsang rotary lobe pumps are among the most frequently ordered pumps in many UK industries. They transport highly viscous or aggressive media of all kinds and even pump liquids with rough solids without blocking.
For more information: sales.uk@vogelsang.info | 01270 216 600 vogelsang.co.uk
Luboš Michlík, the President of Europump, the European Association of Pump Manufacturers, which represents 15 national associations in 12 EU member states, Switzerland, Turkey, and the UK, highlights the vital role of pumps in powering the drive for a sustainable future.
As the global push for improved energy efficiency and sustainability intensifies across manufacturing, commerce, transportation, housing, and public services, pumps remain the unsung heroes at the heart of these transformations. Europump shines a spotlight on the critical yet often overlooked role that pumps play in shaping a more sustainable, energyefficient world.
Pumps are essential in nearly every aspect of our daily lives, from powering industrial processes and climate control in buildings to enabling clean water and sanitation systems. In this era of climate change and environmental responsibility, their significance in achieving Europe’s sustainability goals cannot be overstated.
Pumps are quietly driving progress in the manufacturing sector, where energy efficiency is a growing imperative. They facilitate vital processes such as cooling, heating, fluid transport, and circulation, all while consuming a sizeable quantitiy of energy. Yet, innovations in pump technology are helping industries cut down energy usage, reduce operational costs, and minimise their carbon footprint.
Industrial pumps represent a key opportunity for energy savings, given that they account for up to 20% of global electricity consumption. By embracing more efficient pump systems, manufacturers can drastically
reduce energy consumption, making a major contribution to global sustainability efforts.
In the built environment, pumps are integral to efficient heating, ventilation, and air conditioning (HVAC) systems, water distribution, fire safety, and waste management. As smart cities and green buildings become the blueprint for future urban development, pumps are pivotal in enabling the technologies that make modern infrastructure energy-efficient and sustainable. Smart, energy-efficient pump systems are not just improving performance in individual buildings but are transforming how we manage water, heating, and cooling across entire cities. They are key enablers in the transition to sustainable urban living.
Pumps are critical in the transportation sector, particularly in electric vehicles (EVs) and public transit systems. They support battery and motor cooling in EVs, enable more efficient fuel use in conventional transport, and ensure safe operation in air, rail, and marine travel. In public services such as water treatment and power generation, pumps keep essential services running efficiently and sustainably. From electric vehicles to wastewater management, pumps ensure that transportation and public services meet modern efficiency and environmental
standards. Their role in enabling cleaner mobility and smarter services is vital to achieving Europe’s sustainability targets.
Pumps are also key players in the renewable energy revolution. Whether through circulating fluids in geothermal systems, powering hydraulic mechanisms in wind turbines, or managing cooling in solar power plants, pumps are crucial to the smooth operation and efficiency of renewable energy technologies.
The future of clean energy depends on the efficiency of every component, and pumps are no exception. They are essential to scaling up renewable energy solutions and achieving net-zero carbon targets.
Beyond industry and public services, pumps impact our daily lives in more personal ways. Every time we turn on the tap for fresh water, adjust the thermostat, or rely on modern appliances, pumps are working behind the scenes to make these conveniences possible. In residential homes, pumps ensure efficient water delivery, heating, and cooling – keeping households comfortable, safe, and sustainable.
Pumps are an often unseen yet essential part of daily life, from individual homes to massive industrial plants. They are indispensable to modern living and key to the sustainable, energyefficient world we are working to build.
Europump and its members are at the forefront of promoting highefficiency pump technologies and advocating for policies
that support sustainability and innovation. Through collaboration with industries, regulators, and other stakeholders, Europump is committed to driving the adoption of innovative solutions that reduce energy consumption and environmental impact.
Ecopump is our flagship project, embodying the organisation’s commitment to energy reduction. In 2004, the Europump Council endorsed the Ecopump initiative as the cornerstone of the energy and environmental policy of the European pump sector. The Europump website now has a dashboard that provides a realtime illustration of the energy savings being made. Since 2016, these endeavours have resulted in the saving of 233 million MWh of electricity
and a reduction of 163 million tons of CO2 emissions.
Additionally, the incorporation of the Extended Product Approach into the upcoming revision of EU Regulation 547/2012 for water pumps could unlock a further 35TWh in energy savings.
“The future of clean energy depends on the efficiency of every component, and pumps are no exception.”
In a world increasingly focused on sustainability, pumps – often the unseen workhorses – must be recognised for their potential to deliver significant energy savings and environmental benefits.
Together, we can ensure that pumps continue to be a driving force behind the green transition in every sector. chevron-circle-right
www.europump.net
When pumps fail, the consequences can be severe, from flooding and water damage to complete operational shutdowns. One way to prevent this – or to foresee potential failures before they happen – is by conducting regular mechanical and electrical checks. Deckpro Pumps looks at what these checks should include, how often they should be performed, and whether there is an ideal time to conduct them.
Mechanical and electrical (M&E) checks enable us to monitor performance, detect deterioration, and flag any issues early to proactively manage risk. The frequency of these checks can vary depending on the specific equipment and its application.
In some cases, routine M&E checks align with a site’s maintenance schedule or a company’s processes. For instance, in wastewater applications, the buildup of solids or fats may dictate the frequency of checks – annually, bi-annually, or quarterly.
Industry standards can also guide check frequency. For example, SFG20, the industry standard for building maintenance specification, recommends performing M&E checks on water booster pumps every three months.
Consulting with pump maintenance experts can often provide invaluable insights into the necessary frequency of checks. Working alongside the customer, these specialist companies can tailor maintenance plans according to the specific pump model, equipment requirements, and environmental conditions.
When planning M&E checks, it’s essential to consider the bigger picture and the demands on each pump. Some pumps experience heavy usage during specific periods and may require checks after certain cycles or events. For instance, a production line pump may need inspecting after a set number of cycles, starts, or operating hours.
External factors also play a role. Major weather events, for example, can
impact storm and greywater systems, making additional checks valuable after heavy rainfall or flooding, when chambers may accumulate solids.
In larger buildings, heating systems often remain inactive during the summer. When turning winter primary and secondary pumps back on, it’s advisable to carry out M&E checks to ensure safe and efficient operation before reinstating the system.
M&E checks vary by pump type, with manufacturers’ guidelines, industry standards, and site requirements often determining a specific maintenance plan. However, there are certain elements that broadly apply to pump inspections. In most instances, mechanical checks will broadly apply across most pump systems. These include the inspection of pumps for any signs of excessive wear, alignment and coupling checks, checking the condition of the pump mounts, fixings and pipework, and looking for signs of overheating. The pump and motor should be checked for physical damage, paying special attention to rotating parts such as impellers and shafts, bearings,
and seals and glands. Any strainer or valve elements should be examined, while gauges, instruments, ventilation slots, and purging points, should also be checked. Finally, performance checks should be made alongside verifying the correct operation of any safety equipment and functions.
In addition to mechanical checks, electrical checks provide insights into a pump’s condition that aren’t always visible, helping to identify issues early and track motor wear over time. These checks should include insulation resistance, running current and voltage checks. The continuity of windings should be assessed, as should the condition of earth bonding and earth loop impedance. Visual checks should be made on the electrical system for any signs of overheating, loose connections, or bad termination. Control checks should be made, including the function of relays,
contactors and any remote systems, as should electrical checks of overload equipment such as RCDs. The integration of inverters or local controls should be tested, as should safety equipment and alarm systems.
It’s important to note that all mechanical and electrical checks should be carried out by a trained and competent person.
Joe Smith, Operations Manager at Deckpro Pumps, commented: “In my 12 years at Deckpro, I have seen the importance of M&E checks first-hand. We are able to help customers manage the risk of downtime to their systems, and it’s often the case that our recommended maintenance plans have resulted in preventable failure, saving considerable inconvenience and cost. We’ve had clients approach us following failed pumps, and based on our engineers’ reports, we have been able to give more economical solutions such as overhaul or repair.”
When it comes to pump maintenance,
thorough inspections are essential. For example, submersible pumps must be removed from their chambers to be inspected properly. Or, a booster pump that’s making unusual noise should be isolated and stripped down to determine the cause and ensure it’s safe to continue operating.
Joe emphasised the importance of avoiding complacency: “I’ve found that preventable failures often stem from subpar routine servicing. I’ve attended sites where submersible pumps have been ‘serviced’ for years by a pump company. Yet, when I’ve lifted the pumps out of the pit to carry out the necessary mechanical checks, the client is surprised because the other engineers never did that.”
A reliable pump partner will ensure all engineers and technicians are fully trained and certified, with any necessary specialist lifting or safety equipment maintained to industry standards and LOLER regulations. Proper calibration and category selection for electrical test equipment is also essential to ensure accurate, compliant results.
When choosing a pump partner, some criteria are non-negotiable. A trustworthy partner will prioritise minimising client risk, recognising that inadequate maintenance can lead to significant disruption and expense. This partner will plan inspections carefully, conduct checks thoroughly, and offer guidance based on their findings.
A key quality to look for is a partner who provides a detailed maintenance report following each visit. This report should outline all checks completed, identify passes, failures, and advisories, and suggest any necessary remedial actions. A good partner collaborates with clients to establish effective maintenance plans and respond proactively to any issues that arise.
Ultimately, the report should meet your standards and provide actionable insights to help you maintain efficient, reliable pump systems chevron-circle-right
www.deckpro.uk.com
With the use of condition monitoring solutions as part of building management systems on the rise, Renew looked at how facilities management company, CBRE is using a system from Fletcher Moorland, powered by technology from Turck Banner, to ensure the efficient and effective running of a range of pumping systems used in the Scalpel building in the City of London.
Completed in 2018, the London-based commercial skyscraper, the Scalpel, is 190m high and comprises 38 floors. Naturally, for CBRE, the facilities management (FM) company looking after the building, it is imperative to ensure tenants are comfortable, and that building services are delivered without interruption, and within a strict budget. A complex HVAC system manages the interior environment, and this must remain operational 100% of the time, with all efforts made to avoid system failures or breakdowns.
Often, in buildings of the Scalpel’s scale, there will be a planned maintenance programme designed to ensure system parts and components are checked to a schedule and, where necessary, repaired or replaced before there is any chance of failure. But this is not ideal, as before they are discovered, emerging issues may be allowed to develop to a point where replacement is the only option. This is something the CBRE team recognised, and they sought out a condition-based monitoring solution that would be more effective – not only from a cost perspective but also from the quality of the building’s environment.
of vibration analysis is required to use them properly. We intentionally designed Meerkat to be very simple from a user’s point of view. We took a demo system to the site and left it online for a few weeks so the facilities company could get a feel for it. They loved it, and it was indeed its simplicity that won us the contract.”
The FM company chose the Meerkat solution from Fletcher Moorland for its building, as the company’s Managing Director, Matt Fletcher, explained: “With the project out to tender, we were approached by the building’s facilities team, who had heard about Meerkat and were keen to find out about the system.
“Many condition monitoring systems are highly complex, and a deep understanding
The Meerkat solution is a complete condition monitoring system that can be as simple as fit and forget or integrated into wider building management systems with a wide range of parameters defined by the user. It can be fitted and fully managed by the Fletcher Moorland team or set up and monitored by the on-site team at the site being monitored. A typical system will comprise sensors, or points – sensing parameters such as vibration, temperature, and, where needed, speed output from the inverter drives. Each point is connected to a network node powered by a battery that lasts, on average, two years. All the nodes are then meshed together over a wireless
network, which sends data to a central gateway in the building. Much of the sensing and wireless technology employed in the Scalpel’s solution, and many other Meerkat installations, is supplied by automation equipment specialist, Turck Banner.
The fact that the Meerkat system can operate over a wireless network is a big advantage at the Scalpel. The building has a plant room in the basement and one on the top floor. This would require vast amounts of cable – challenging to route through the building and adding to the project cost.
Indeed, the system installed at the Scalpel has over 150 sensors, or points. Some assets have more than one sensor attached; for example, a large pump may need two sensors on the pump itself and two on the motor. How this is set up is where the expertise of the installation team comes into play. Fletcher Moorland’s installation team is vibration analysis certified and uses a combination of experience and the parameters set out in ISO 10816 to establish how best to monitor each asset.
The Meerkat software takes the data, and after a baseline is established, thresholds are set. Ongoing data is then monitored, and an alarm can be triggered if any thresholds are breached.
The main benefit of condition monitoring systems is typically avoiding unplanned downtime. In the Scalpel’s case, this means ensuring the best possible service is delivered to its landlord and tenants; in some FM examples, there can even be significant financial penalties for unplanned system downtime. In industrial settings, unplanned downtime can have
The latest variable speed pump and tank innovation from Calpeda
Perfect for environments where a conventional cold water booster set and tank are not possible due to size constraints!
Single or Twin MXS Pump Options
Ease of Maintenance
UK
UK
huge financial implications, with lost production, wasted materials, etc. And in some circumstances, there can be critical safety issues. But for the CBRE team at the Scalpel, there are other benefits to taking a condition-based monitoring approach.
One of the benefits CBRE is experiencing in the Scalpel relates to the replacement of assets, as John Dennis, Account Manager at CBRE Global Workplace Solutions, explained: “We would typically have a budgeted replacement cost for a pump based on the manufacturer’s expected lifespan. However, when monitoring the actual condition of the asset, we might find that the pump’s condition remains well within tolerance for longer than expected, allowing the replacement period to be elongated and the associated cost to be delayed.”
There are further potential financial benefits of employing a condition-based monitoring system, which can be gained from reducing energy usage. John continued: “The Meerkat solution will indicate if a pump has to work harder than anticipated to deliver the same results. If it is, it will be using more energy, which can soon add up when you have as many pumps as we have here.”
The ability to optimise energy usage has financial and environmental benefits, which are very important to the CBRE team. Another environmental benefit comes from being able to repair rather than replace an asset; as Matt explained: “By refurbishing a pump, the energy inputted is a lot less than having to bring in a new pump. Assuming the efficiency of a replacement pump is the same as the original, being able to extend its operational life can have significant benefits in terms of carbon reduction.”
Having a condition monitoring system in play is enabling other changes to the maintenance practices employed by the CBRE team. Under a more traditional planned maintenance approach, the greasing of assets would be carried out on a time-based schedule. Working on a condition-based monitoring basis has improved this regular task, as John explained: “We have put a greasing schedule into Meerkat. Rather than greasing a pump or its motor on, say, a six-month schedule, we have a link to the system’s inverter and can see exactly how many operational hours it has run for. When the system gets to within 100 hours of greasing being due, we will be automatically notified and can grease exactly as needed.”
According to the CBRE team, the ease of use ultimately led to the Meerkat system being chosen. As well as the installation benefits already mentioned, the fact that it is an open system means it is more accessible than some alternatives, and this has made integration much easier, as Tony Coghlan, Managing Director at Turck Banner, added: “There are companies that see the hardware as a commodity and place the value in the software. This can mean expensive subscriptions and the data being locked into the system. It was important to us at Turck Banner and the Fletcher Moorland team that this was an open protocol. For CBRE, this makes it is much easier to bring the data being collected into their building management system and be innovative in how the system is adapted and developed to their needs, such as with the greasing schedule.”
The Scalpel’s chiller room is on the 37th floor. It houses six chillers, which provide chilled water to air handling units and fancool units across the entire building. If the chiller system goes down, cooling for areas including the transformer rooms, lift motor rooms, and, of course, the tenants is lost. When one of the condense pumps started to fail, the Meerkat system was able to give the CBRE team an early warning. John tells the story: “A bearing on the pump system had started to fail prematurely, much earlier than expected. The fact that the Meerkat system was able to indicate an anomaly early gave us much more time to work with the manufacturer, who came in, surveyed the pump and ordered the correct seals, bearings and lifting equipment. As a result, we were able to swap the bearing before it actually failed.
“Now we also keep bearing and seal kits for these on site as part of our critical spares inventory. If another potential failure is indicated, we can replace them much more quickly.”
It’s clear from the example at the Scalpel that having a condition-based monitoring solution as part of the building management system brings a wide range of financial and environmental benefits. The ease of use and flexibility of this open solution certainly enables those benefits to grow as the system in place is developed. chevron-circle-right
www.turckbanner.co.uk
www.brookcrompton.com
With over 110 years of technical and design expertise, Brook Crompton offers leading edge energy efficient electric motors across global markets. As the original innovator in electric motor development, Brook Crompton are trusted to power limitless industrial processes and its robust motor design drives fans, pumps, compressors, conveyors and more.
Driven by technology and innovation, Brook Crompton has one of the widest available ranges of electric motors for operation in safe areas, hazardous atmospheres and hostile environments.
The extensive range of stock can be quickly modified to suit customers’ needs and with a high level of technical support from our knowledgeable team we ensure the correct selection of motors is provided for your application.
Brook Crompton’s focus on product and service development ensures we continue to move forward to improve efficiency, offer lower cost of ownership throughout their lifecycle and to reduce environmental impact.
Electrical equipment specialist, WEG has introduced its new high-efficiency, high-voltage (HV) flameproof motor, the W51Xdb. Tailored for applications in explosive environments, such as petrochemical, oil and gas and energy transition sectors, the W51Xdb motor represents a significant leap in power density, efficiency and sustainability.
Building on the established W22Xdb series, the W51Xdb retains its predecessor’s flexibility while delivering several crucial innovations. At its core, the W51Xdb offers the highest power density in its class, making it possible to generate more power in a smaller, lighter machine. This advancement helps address the growing need for compact, space-efficient equipment in industries where space is a premium.
“We designed the W51Xdb to meet our customers’ current and future needs,” said João Cardante, Sales And Marketing Director at WEG Portugal. “With its high density and energy efficiency, the motor is tailored to support global energy transition goals by offering a product that is ready today but designed for tomorrow.”
Offering the highest power density on the market, the W51Xdb features a compact design that delivers up to 800kW in a frame smaller than the market standard, allowing for more efficient use of space in applications such as pumps, compressors and fans. It is also up to 20% lighter than previous models, providing additional flexibility for installations.
Offered as standard with IE4 – the highest efficiency level defined by the global standard for classifying the energy efficiency of high-voltage induction motors, IEC/EN 60034-30-3 – the W51Xdb exceeds current regulatory requirements and is future-ready for upcoming legislation. While this standard does not mandate customers to specify motors with a particular efficiency level, as regional regulations govern this, it is anticipated that the EU will soon introduce minimum efficiency requirements for HV motors.
“At WEG, we are deeply committed to helping customers maximise energy efficiency in their motors,” said João.
“Although flameproof motors are currently excluded from this new standard, the W51Xdb line has been engineered to meet or exceed its highest efficiency levels.”
The W51Xdb supports the industry’s drive towards a net-zero future by reducing energy consumption and helping companies meet their carbon reduction goals faster. Because the motor is built for explosive atmospheres and is compatible with environments such as Zone 1 and Zone 2, this makes the unit ideal for petrochemical, chemical, oil and gas and hydrogen applications.
In addition, the W51Xdb series is designed with manufacturing efficiency in mind, reducing lead times by up to four weeks compared to previous models.
The motor is currently available in frame sizes of 355 and 400, with a maximum output of 800kW. WEG plans to gradually expand the range of frame sizes available.
With over 90 units in high-voltage format already sold, even before its official release, the W51Xdb has been adopted by key industries, particularly in the Middle East. The initial applications focus on high-demand projects involving pumps, compressors and other highpower machinery. The official global launch took place at ADIPEC 2024 in Abu Dhabi, one of the world’s largest and most influential energy exhibitions, and at SPS, a leading international event for industrial automation held in Nuremberg, Germany.
“The W51Xdb is a testament to WEG’s commitment to continuous improvement and innovation in motor technology,” added João. “Its launch has set a new industry benchmark for efficiency, sustainability and performance.” chevron-circle-right
flow magazine discovered how seal specialist, John Crane, Helped a Chilean mine cut water use by 95% while improving equipment reliability and reducing maintenance requirements.
One of the world's leading copper producers operates a large open pit mine located in northern Chile. The mine produces 324,000 tons of copper concentrate each year and approximately 9,800 tons of molybdenum. Rainfall in this region of Chile is increasingly scarce – compounding the already demanding operating conditions, especially in the mine's critical concentrator grinding and transportation processes. After an internal review, mine management grew concerned about the site's significant water consumption, caused partly by ageing pump packing systems, amounting to approximately 280l/min per pump. Wanting to significantly lower water usage and waste, as well as improve pump maintenance, reliability and emissions to the atmosphere, mine management worked with John Crane to identify a solution.
The two-year project initially focused on seven grinding and transportation process pumps from three different brands, each with a history of high water consumption. The pumps' packing system required frequent adjustments and needed to be changed out every second month, which included bearing repairs due to the packing systems' excessive leakage.
The challenges for John Crane included ensuring the reliability of the pumps and other equipment while reducing water consumption and maintenance. After reviewing the situation and goals, John Crane experts suggested the mine consider a technically superior sealing system upgrade. The upgrade included redesigned mechanical seals with easily changed elements, providing
adaptive pump parts – all with safety and efficiency as priorities.
A 10in mechanical seal was designed that does not require disassembly when technicians maintain the wet parts of the pump and is fixed directly to the bearing box for low vibration. The double concentric mechanical seal design incorporates both seal support Plan 54 and Plan 32, allowing the mechanical seal faces to be constantly lubricated and free of solids. The new seal functions on the same operating principles as a conventional mechanical seal but is modified to adapt to the axial spaces of the pumps. Adaptive parts were also introduced during the project, including a stuffing box, sleeves and union elements.
Soon after the project began, the new seal, the Type 5902TS, was put to the test. Even though surrounding water pipes froze during a cold snap, the new seal continued to operate
thanks to a mixture of water and glycol included in the Plan 54 seal support system.
The three pumps currently in service have reliably operated for two years without interruption – a significant improvement over the two-month repair/maintenance precedent set prior to the update. Water usage has been reduced by approximately 95%, from 280l/min minute to about 20l/min, on each pump upgraded with a John Crane mechanical seal, and process fluid/slurry no longer leaks to the atmosphere.
The upgrade eliminates the timeconsuming operational adjustments previously required, will not damage the shaft or other pump components, and has increased bearing life. chevron-circle-right
z Manufacturing
z Construction
z HVAC
z
z Mining
John Hall, Pump Consultant at Viking Pump, a brand distributed in the UK by Michael Smith Engineers, explains the features and benefits of internal gear pumps, exploring the applications to which they are suited and the key considerations that should be made as part of their selection.
Internal gear pumps are a fascinating invention that has stood the test of time. Created by Viking Pump over a century ago, they remain one of the company’s most recognised products.
Internal gear pumps are a type of rotary positive displacement pump, which means they move fluid by utilising the rotary motion of their components.
The operation of an internal gear pump is based on a simple yet effective principle. Liquid enters through the suction port, which is positioned between the teeth of the rotor gear (the larger external gear) and the idler gear (the smaller internal gear).
The interaction between these intermeshing gears creates locked cavities that hold the liquid, ensuring precise volume control. As the gears turn, they
create low-pressure zones at the suction port. This low pressure pulls liquid into the pump, where it continues to travel between the teeth of the gears.
A key component in this process is the crescent located at the head of the pump. This crescent acts as a seal, preventing the liquid from returning to the suction side. When the gear teeth mesh completely, the liquid is forced out of the pump through the discharge port.
are some of the critical aspects:
• Rotary Motion: The rotary movement of the gears enables the pump to draw in and discharge liquid efficiently.
• Volume Control: The intermeshing gears create locked cavities that ensure consistent volume control of the liquid being pumped.
“This design allows internal gear pumps to handle a wide range of viscosities.”
This design allows internal gear pumps to handle a wide range of viscosities, making them ideal for various applications.
Understanding the features of internal gear pumps helps highlight their advantages. Here
• Low Pressure Zones: As the gears turn and come out of mesh, they create low-pressure areas that pull liquid into the pump.
• Crescent Seal: The crescent effectively seals off the suction side from the discharge side, preventing backflow.
• Versatility: The internal gear design allows these pumps to manage a variety of liquid viscosities, from thin solvents to thick oils.
Internal gear pumps offer several advantages that make them a preferred choice in many industries. Here are some key benefits:
• High efficiency: The design of internal gear pumps ensures a consistent flow rate, regardless of changes in pressure, which translates to minimal energy wastage.
• Self-priming: These pumps can seamlessly evacuate air or gas from the suction line, ensuring uninterrupted operation.
• Robust construction: Built with quality in mind, internal gear pumps are designed for longevity and reliability, even in challenging environments.
• Wide viscosity range: They can handle thin liquids like solvents as well as thick substances like molasses, making them versatile for different applications.
• Quiet operation: The gear design allows for smooth and silent operation, creating a more comfortable working environment.
• Precise flow control: Operators can easily adjust the flow rate by changing the rotational speed, which is crucial for accurate dosing and product quality.
• Low maintenance: With fewer moving parts, the likelihood of breakdowns is reduced, leading to lower maintenance costs.
Due to their unique features and advantages, internal gear pumps are widely used across various industries. In chemical processing, they are ideal for handling chemicals, including corrosive and viscous materials. In the food and beverage sector, internal gear pumps can handle thick and viscous liquids. The precision and reliability of these pumps also make them suitable for the pharmaceutical industry, where accuracy is crucial. Internal gear pumps are often utilised in oil and gas applications for moving crude oil and other viscous fluids, and they can efficiently handle the thick slurries found in pulp and paper production.
Selecting the right internal gear pump for your application involves considering several factors. First, it is important that the pump can handle the specific viscosity of the liquid in which it is intended to move. The flow rate required for the process should be determined, and a pump that meets this demand should be selected. The temperature range of the fluid should be assessed so a pump designed to operate within that range can be chosen. Consideration should also be given to the materials used in the pump construction to ensure they are compatible with the fluids being pumped. And it is advisable to look for a pump that offers ease of maintenance to minimise downtime.
Internal gear pumps provide efficient and reliable fluid transfer solutions across a range of industries. Their unique design allows them to handle a broad spectrum of viscosities while maintaining consistent performance. By understanding how these pumps work and their advantages, businesses can make informed decisions when selecting the right pumping solution for their needs. chevron-circle-right
www.vikingpump.com www.michael-smith-engineers.co.uk
Patterson Pump Ireland is a complete pump manufacturer, offering our customers some of the most reliable pumping solutions available. Our fire pumps stand over life and property throughout the world.
Reduce on-site labor time, engineering and installation time and associated costs. Choose a system that arrives on-site in a fully enclosed ready for use pump house. This pre-engineered pumping system saves time and money for our customers.
+353 (0)44 934 7078 company/patterson-pump-ireland-ltd www.ie.pattersonpumps.com sales@ie.pattersonpumps.com
Ever since its discovery in the 1500s, chocolate has arguably been the World’s favourite vice. It has become the core ingredient in a multitude of confectionary products and the cornerstone of numerous business empires. Richard Charlton of AxFlow explains the philosophy behind the company’s approach to pumping liquid chocolate.
The first thing to recognise is that pumping chocolate isn’t straightforward due to several factors related to its very peculiar mixture of properties. Chocolate is extremely sensitive to temperature; too hot and it will degenerate or even burn, too cold and it solidifies. Chocolate’s structure is delicate as the cocoa butter and cocoa solids can easily separate if subjected to high degrees of shear. Chocolate can be abrasive, and it will coat the internal surfaces and sealing areas of a pump. In addition, not all chocolate products are the same; they can have different viscosities and structures and may contain additional ingredients such as nuts, fruit and dairy products. And many chocolate processes require hygienic certified designs.
At AxFlow, we can provide a range of pump types to ensure solutions are available for all applications required. There are three main pump types – vane, eccentric disc, and external circumferential piston pump.
Vane pumps are normally our starting point as they usually represent the lowest-cost solution. Of course, we are not talking about any vane pump, but only those with very particular features that are not found in all designs. Designed to handle difficult liquids, this pump has been adapted to meet the specific requirements of cocoa and chocolate processing and can be found in many plants around the world.
The key feature is that the pumps do not rely on centrifugal forces to expel the vanes outwards from the rotor. This is because the pump needs to be able to run slowly in order to reduce shear as much as possible. Heating and cooling
jackets must be available to keep the product in the correct state, and FDA materials must be an option. Fortunately, due to chocolate’s preponderance to coat the internal surfaces of a pump, cast iron is an option for those less demanding applications, which goes a long way to reducing costs.
The vane pump contains a number of vanes that are free to slide into and out of slots in the pump rotor. When the drive mechanism starts the rotor, centrifugal force, push rods and/or pressurised fluid causes the vanes to move outward in their slots and bear against the inner bore of the pump casing forming pumping chambers. As the rotor revolves, fluid flows into the areas between the vanes when they pass the suction port. This fluid is transported around the pump casing until it reaches the discharge port.
An influential factor in specifying pumps for chocolate processing is the
requirement for constant performance, including priming and draining, over extended periods. The vane pump provides automatic adjustment of key performance characteristics, with flow rates being maintained without the need for any increase in pump rotation speeds. However, the vanes will wear over time, they struggle with pressures of more than 12 bar, they have a limited choice of seal and they cannot be considered truly hygienic. So, AxFlow, has two other product types in its portfolio: external circumferential piston (ECP) pumps and eccentric disc pumps.
Although ECP and eccentric disc pump technologies comply with the requirements of 3A and EHEDG and offer lower shear pumping actions than vane pumps, they display several different characteristics so that between them AxFlow can cover the full range of chocolate transfer applications.
The ECP pump, also known as the rotary piston pump, is well-established within many sectors of food processing. The operating principle employs arc-shaped rotary pistons or rotor wings that travel in annular-shaped cylinders machined in the pump body. Because the rotors produce a scooping action, they do not squeeze nor compact the medium being pumped. The ECP’s long sealing path reduces slippage and produces a smooth product flow without destructive pulses or pressure peaks and without the need for valves or complex parts. ECP pumps have the lowest NPSH requirement and work well with auger feeders should the need arise.
For products that are sensitive to shear, ECP pumps cater for most requirements as they can run at speeds as low as 50rpm. However, when it comes to products with additional ingredients, such as fruit, then the peristaltic action of eccentric disc pumps offer the gentlest option. This intrinsically
gentler action also enables, in some circumstances, eccentric disc pumps to run at speeds faster than ECP pumps, to satisfy higher flow requirements.
The eccentric disc pump uses an oscillating eccentric piston that produces the pumping performance of a rotary positive displacement pump. However, its action is far more sensitive, making it ideally suited to applications where shear and potential leakage are major issues, as it does not agitate the pumped liquid. The eccentric movement pump consists of a cylinder and a pumping element mounted on an eccentric shaft. As the shaft rotates, the pumping element creates chambers with the cylinder, effectively increasing the size of the intake port and drawing fluid into the pumping chamber. The fluid is transported to the discharge port, where the size of the pumping chamber decreases, moving the fluid out into the discharge pipework. The pump does not require either mechanical seals or magnets, whilst providing leak-free performance.
Both types of pump are good at high pressure, but above 15 bar, it is the
ECP pump that comes out on top as it possesses the ability to reach pressures of 35 bar. ECP pumps are also better at transferring viscous fluids because eccentric disc pumps are limited to about 10,000cP while ECP pumps can cope with viscosities of up to 200,000cP. When it comes to sealing, ECP pumps are normally fitted with a special double O ring seal that utilises a food-grade lubricant between the two O rings. This seal arrangement is far superior to a mechanical seal as it doesn’t seize should hardened deposits form, nor will it burn the chocolate because it is well lubricated. Eccentric disc pumps avoid the whole sealing dilemma altogether as they are considered seal-less pumps. And if low maintenance is a particular concern, eccentric disc pumps have the fewest number of moving parts and, therefore, have the lowest maintenance requirements. chevron-circle-right
www.axflow.com
Full members of the British Pump Manufacturers Association (BPMA) include manufacturers, contractors, distributors, importers, and repairers of industrial pumps, with operations in the UK and Republic of Ireland. Membership is also available to suppliers of pump-specific equipment to pump companies. Associate Membership is available to companies and individuals who work with or supply services to BPMA members,
ABB Ltd
PHONE 01925 741111 desktop new.abb.com/uk
AESSEAL Plc
PHONE 01709 369 966 desktop www.aesseal.com
Albany Engineering Co. Ltd
PHONE 01594 842275 desktop
BPS Pumps Ltd
PHONE 0121 503 3000 desktop bpspumps.co.uk
such as industry journals, technology centres, or consultants. BPMA members have agreed to a code of conduct which states that they must demonstrate the highest degree of professionalism, expertise and ethical standards in every aspect of their operations.
Further information about the association’s members can be found on the BPMA website at www.bpma.org.uk/members.
British Autogard Ltd (Regal Rexnord) PHONE 07884 091 307 desktop www.regalrexnord.com/contact
Bruynseels Ltd PHONE 07526071108 desktop bruynseels.co.uk
Brook Crompton
PHONE 01484 557200 desktop www.brookcrompton.com
Chemquip Ltd
PHONE 01663 741753 desktop www.chemquip.co.uk
Combined Pumps Ltd
PHONE 0 1224 724 177 desktop www.combinedpumps.com
HIGH QUALITY CHEMICAL PUMPS
Altecnic Ltd - CALEFFI Group
PHONE 01785 218200 desktop www.altecnic.co.uk
Centrifugal pumps for a wide range of industrial applications
Ambic Equipment Ltd
PHONE 01993 776555 desktop www.ambic.co.uk
Tel: +44 (0)117 907 7555
Email: sales@apexpumps.com Website: www.apexpumps.com
Armstrong Fluid Technology
PHONE 08444 145 145 desktop www.armstrongfluidtechnology. com/en-gb
Atlas Copco Power Technique
PHONE 01442 222 350 desktop www.atlascopco.com/en-uk
Atom Water Pump Solutions Ltd
PHONE 07797 827 044 desktop atom.je
AVT PUMP
PHONE 03303 322101 desktop www.avtpump.com
AxFlow Ltd
PHONE 01753 255600 desktop www.axflow.co.uk
Barnwell Services Ltd
PHONE 0121 429 8011 desktop www.barnwell.co.uk
Calpeda PHONE 01869 241 441 desktop uk.calpeda.com
Campion Pumps
PHONE +353 56 883 4288 desktop www.campion.ie
Caprari Pumps (UK) Ltd
PHONE 01733 371605 desktop www.caprari.com
CELEROS FT - ClydeUnion Pumps PHONE 0141 637 7141 desktop celerosft.com/clydeunion-pumps
Tel: 01618 872 3122
Contact: sales@cembhofmann.co.uk Web: www.cembhofmann.co.uk
CHC Group
PHONE 01539 729395 desktop www.chcgroup.co.uk
Built to last in the UK with lifetime support for every pump
Tel: 01425 627700 Web: www.crestpumps.co.uk
DAB Pumps Ltd
PHONE 0333 777 5010 desktop uk.dabpumps.com
DPS Ltd
PHONE 028 91 818347 desktop dpswater.com
Eastern Seals (UK) Ltd PHONE 01670 840529 desktop www.easternseals.co.uk
EBARA Pumps Europe S.P.A - UK PHONE 01895 439027 desktop www.ebaraeurope.com
Elmec Energy PHONE 0208 0500851 desktop www.elmecenergy.com
ERIKS UK
PHONE 0121 508 6000 desktop www.eriks.co.uk
ESPA Pumps (UK) Ltd PHONE 01206 391291 desktop www.espa.com/uk
Euroflo Fluid Handling Ltd
PHONE 01892 832144 desktop www.euroflo.com
Exalto Bearings Ltd
PHONE 01332 340501 desktop www.exaltouk.com/en
Flowserve
PHONE 0161 928 6371 desktop www.flowserve.com
Flowtech Water Solutions Ltd
PHONE 0333 200 1756 desktop www.flowtech.org.uk
G.M.Treble Ltd
PHONE 01902 333 111 desktop trebles.co.uk
GMT Electrical Services Ltd
PHONE 0208 683 0464 desktop www.gmtservices.co.uk
Greene, Tweed & Co Ltd
PHONE 0115 9315 777 desktop www.gtweed.com
Grundfos Pumps Ltd
PHONE 01525 850000 desktop www.grundfos.co.uk
H20 Pumping Solutions
PHONE 0800 059 0100 desktop www.h20pumpingsolutions.co.uk
Hayward Tyler
PHONE 01582 731144 desktop haywardtyler.com
HMD Kontro Sealless Pumps PHONE 01323 452000 desktop www.hmdkontro.com
HOSS Engineering
PHONE 0203 601 6075 desktop hossengineering.com
Houghton International Electrical Services Ltd
PHONE 0191 234 3000 desktop www.houghton-international.com
Ingersoll Rand Pumps
PHONE 01159 325 226 desktop www.irco.com/en-gb
Innomotics
PHONE 0161 446 6893 desktop www.innomotics.com
ITT Industries UK
PHONE 07585 882916 desktop www.itt.com/home
John Crane
PHONE 0161 872 2484 desktop www.johncrane.com
KGN Pillinger
PHONE 0208 681 0097 desktop kgnpillinger.com
KSB Ltd
PHONE 01509 231 872 desktop www.ksb.co.uk
KTR U.K. Ltd
PHONE 0114 258 7757 desktop www.ktr.com/uk
Lafert Electric Motors Ltd
PHONE 01270 270022 desktop www.lafert.com
LFH Fluid Control Ltd
PHONE 01358 726310 desktop www.lfhfluidcontrol.com
M Seals UK Ltd
PHONE 0116 275 4720 desktop www.m-seals.co.uk
Leaders in centrifugal & sealless magnetic drive pumps since 1971
MARCH MAY
Tel No: 01480 214444 Email: sales@marchmay.co.uk Web: www.marchmay.co.uk
Martin Sprocket & Gear UK Ltd
PHONE 01926 962161 desktop www.martinsprocket.com
MDM Pumps Ltd
PHONE 01684 892 678 desktop www.mdmpumps.co.uk
Megator Ltd
PHONE 0191 567 5488 desktop www.megator.com
SUPPLIER OF LARGE MOTORS FOR ALL UK APPLICATIONS
More than 20,000 motors available from stock!
MENZEL GREAT BRITAIN
01664 500844 www.menzel-motors.com
Metcor Group
PHONE 020 8310 2000 desktop metromech.co.uk
Michael Smith Engineers Ltd
PHONE 01483 771 871 desktop www.michael-smith-engineers.co.uk
MJB Engineering Precision Ltd
PHONE 0161 476 5811 desktop www.mjbengineering.net/
Morgan Advanced Materials PHONE 01753 837000 desktop www.morganperformancecarbon. com/en-gb
FIRE PUMPS ENGINEERED FOR RELIABLE OPERATION ON DEMAND
PHONE +353 44 934 7078 desktop www.ie.pattersonpumps.com
PressBoost Ltd
PHONE 0161 798 5872 desktop www.pressboost.co.uk
Presspart Manufacturing
PHONE 01254 582233 desktop www.htindustrial.com
Pumps (UK) Ltd
PHONE 01322 292 415 desktop www.pumpsukltd.com
Pumps and Motors UK Ltd
PHONE 0208 507 2288 desktop www.pumpsmotors.co.uk
PumpServ
PHONE 020 8337 7249 desktop pumpserv.co.uk
Rapid Solutions (International) Ltd
PHONE 01223 841 757 desktop rapid-solutions.net
Reflex Winkelmann GMBH
PHONE 0161 266 1043 desktop www.reflex.de/en
Roto Pumps Ltd
PHONE 0161 477 5511 desktop www.rotopumps.co.uk
Highly-engineered and standard pumping solutions for Chemicals, Pharma, Fertilizers, Water & Waste-Water, Oil & Gas and Power
IndustrialPumps@RuhrPumpen.com www.RuhrPumpen.com +44(0)1273 956 410
Salamander Pumps
PHONE 0191 516 2002 desktop www.salamanderpumps.co.uk
Seal & Pump Engineering (UK) Ltd
PHONE 01283 512866 desktop www.sealandpump.co.uk
Selwood Pump Company Ltd
PHONE 0121 777 5681 desktop selwood-pumps.com
SFA Saniflo UK Ltd
PHONE 020 8842 0033 desktop www.saniflo.co.uk
SPP Pumps
PHONE 0118 932 3123 desktop www.spppumps.com
SPX Flow Europe Ltd
PHONE 0161 249 1170 desktop www.spxflow.com
Stuart Turner Ltd
PHONE 01491 572 655 desktop www.stuart-turner.co.uk
Sulzer Pump Solutions Ireland Ltd
PHONE +353 14 608 888 desktop www.sulzer.com
Super Drain Ltd
PHONE +353 14 097 070 desktop superdrain.ie
TEC Electric Motors Ltd
PHONE 01299 252990 desktop www.tecmotors.co.uk
The Pump Company Ltd
PHONE 01293 533665 desktop www.thepumpco.co.uk
Tsurumi UK Ltd
PHONE 01622 355000 desktop www.tsurumi.co.uk
T-T Pumps Ltd
PHONE 01630 647200 desktop www.ttpumps.com
Eurofins E & CML Ltd
PHONE 0151 559 1160 desktop www.cmlex.com
Fluid & Energy Solutions Consultancy Ltd
PHONE 0207 101 3911 desktop www.fluensys.co.uk
Fluid Performance Solutions Ltd PHONE 07983 744718 desktop www.fluidperformancesolutions.co.uk
HHIC (Heating & Hotwater Industry Council) PHONE 01926 513777 desktop www.hhic.org.uk
International Data Entry & Access PHONE 020 7731 7151 desktop www.idea-business-tracker.co.uk
Kiwa Watertec
PHONE 01495 308185 desktop www.kiwa.com/gb/en
Solutions in IT Ltd PHONE 0845 009 4588 desktop www.emirsoftware.com
Touchwave Media Ltd
PHONE 07785 290034 desktop www.touchwavemedia.co.uk
World Pumps PHONE 07967 169154 desktop www.worldpumps.com
YPSEE Ltd PHONE 07973 833193
For an enhanced entry in the BPMA Member directory, sent to over 10,000 pump systems users based in GB & Ireland, contact Andrew Castle.
The only publication exclusively for UK-based users of pumps and pumping systems Sent to 10,220 readers every quarter – in print and online
Advertising: Andrew 07785 290034
Editorial: Chris 01732 358823
07785 290034 andrew@flowmag.co.uk
Following his presentation at UKWIR’s annual conference in October, Marcus Rink, Chief Inspector of the Drinking Water Inspectorate (DWI), shares his thoughts on the role of research, innovation and collaboration in driving the sector forward in the face of increasing challenges.
Water is a fundamental resource essential for life and wellbeing. Its availability, safety, and proper management are crucial for public health, economic development and poverty reduction.
My role is to ensure that the public, industry and future generations have access to a safe, secure and continuous supply of drinking water. This involves overseeing the implementation of water supply and quality regulations and the security management direction under the Water Industry Act.
The good news is England and Wales boast exceptionally high drinking water quality. Compliance rates have consistently exceeded 99.97% in recent years, with over 4 million analyses conducted across 52 parameters. While there have been instances of non-compliance, many of these can be attributed to issues within domestic plumbing systems.
Internationally, England and Wales stand out for their commitment to water quality. The UK has consistently scored 100 on Yale’s global Environmental Performance Index, which ranks water quality on a scale of 0-100, meaning England and Wales have the highest possible score. This achievement is particularly noteworthy considering the global water crisis, where billions of people lack access to clean drinking water.
Despite our nation’s impressive record, addressing the issues that pose significant threats to our water supply is crucial.
From source to tap, we are very dependent on our environment. Abstracting good quality water is directly affected by the changes in our climate, which, to an extent, alters the characteristics of our source water. This can be due to heavy rain causing an increase in turbidity, movement of diffuse pollution from farmland, such as pesticides,
or where there are overspills of industrial water which may contain metals.
However, we are also seeing longer dry periods, where concentrations of some of those parameters that cause problems for treatment works arise. Again, these might be pesticides, metals, or microbiological contaminants.
We need to prepare ourselves for the future, protecting future generations by having the appropriate technologies to treat those substances, and the methodologies to identify those hazards.
As a sector, we can improve the natural environment by improving catchments, and therefore catchment management, and ensuring that microbiological and chemical hazards are identified, along with changes in weather patterns.
The changing characteristics of rivers and society also need to be considered. For example, greater and rising use of pharmaceuticals, hormones, antidepressants and analgesics.
We need to be mindful of how this impacts our source water and ensure the infrastructure can deal with these evolving challenges, both anthropogenic and environmental, and how they impact each other.
It is necessary to adopt a proactive approach. This includes investing in innovative technologies, improving catchment management, and ensuring that water infrastructure is resilient and fit for purpose. Additionally, collaboration between researchers, regulators, and water companies needs to be encouraged, to identify and address emerging risks.
A better understanding of treatment works is needed so that higher levels of turbidity and concentrations of metals, micropollutants and forever chemicals, such
as PFAS, can be tackled. Those chemicals are incredibly useful for industry and our domestic lives, but they are causing some pollution within our environment.
Research & development and innovation are essential for protecting and improving drinking water quality. It plays a vital role in scoping the horizon; for example, as a sector, we know there is an increase in microplastics entering our environment – so we work with researchers to explore what impact that has on drinking water and the ability of water treatment to remove microplastics.
Investing in research allows us to have a deeper understanding of emerging contaminants, develop more effective monitoring methods, and identify innovative solutions to address challenges.
The DWI works closely with leading research institutions, such as UKWIR, to ensure that the latest scientific evidence informs our policies and regulations. UKWIR speaks the same language and has the same specialisms and the same mission as DWI – to ensure clean, secure, and wholesome drinking water.
Across the sector, collaboration is vital. The better the collaboration, the better the understanding of the issue, and the better the decisions will be. Through collaboration, the expertise of researchers can be leveraged to develop innovative solutions that safeguard drinking water supply for generations to come. chevron-circle-right
The BPMA’s Pump Industry Awards Dinner has become the highlight of the pump industry’s social calendar, celebrating the industry’s best and brightest with the added bonus of excellent networking opportunities and great entertainment.
This year’s event will take place on Thursday 13th March at the Hilton at St. George’s Parkthe training ground for all 28 English national football teams - which is recognised the World over as the Home of English Football. Sporting excellence is synonymous with this venue, and in March it will once again become the location for heralding engineering excellence across the pump sector.
And in keeping with the sporting theme of recent years, the evening will be hosted by Perry McCarthy, ex Formula One driver, bestselling author and the original secret racing driver from BBC’s Top Gear - ‘The Stig’.
Whether it’s taking a table to host customers or booking a few seats for you, your team and partners it’s a fantastic opportunity to enjoy a wonderful evening of great food, fantastic live entertainment and networking until the early hours.
Just visit the website www.pumpindustryawards.com and complete the simple online booking form to secure your places at this must-attend event.
at St George’s Park, Burton upon Trent
Date: Thursday 13th March 2025
MORE THAN 20.000 MOTORS AVAILABLE FROM STOCK!
Motors up to 25 MW and 13.8 kV
• Low voltage slip-ring and squirrel cage motors up to 3,000 kW
• Medium voltage slip-ring and squirrel cage motors up to 15,000 kW
• Direct current motors up to 2,000 kW
• Frequency converter-proof drives
• In-house load test facility up to 13.800 V, 2.300 kVA, 120 Hz
Customized special designs
• Custom designs for special applications and operating conditions
• Optimized motor design for higher efficiency
• Mechanically and electrically interchangeable motors
• Commissioning worldwide
MENZEL Great Britain Ltd. | UK Branch Office
27 Hunt Drive | Melton Mowbray | Leicestershire LE13 1PB
Martin Rooney | Tel.: +44 1664 500 844 | Mobil: +44 7957 618046 martin.rooney@menzelgb.co.uk NEW ELECTRIC MOTOR PLANT FROM JANUARY 2024
MENZEL Elektromotoren GmbH
German Headquarters
Am Alten Walzwerk 2 | 16761 Hennigsdorf | Germany
menzel-motors.com info@menzel-motors.com
24,000 m 2