
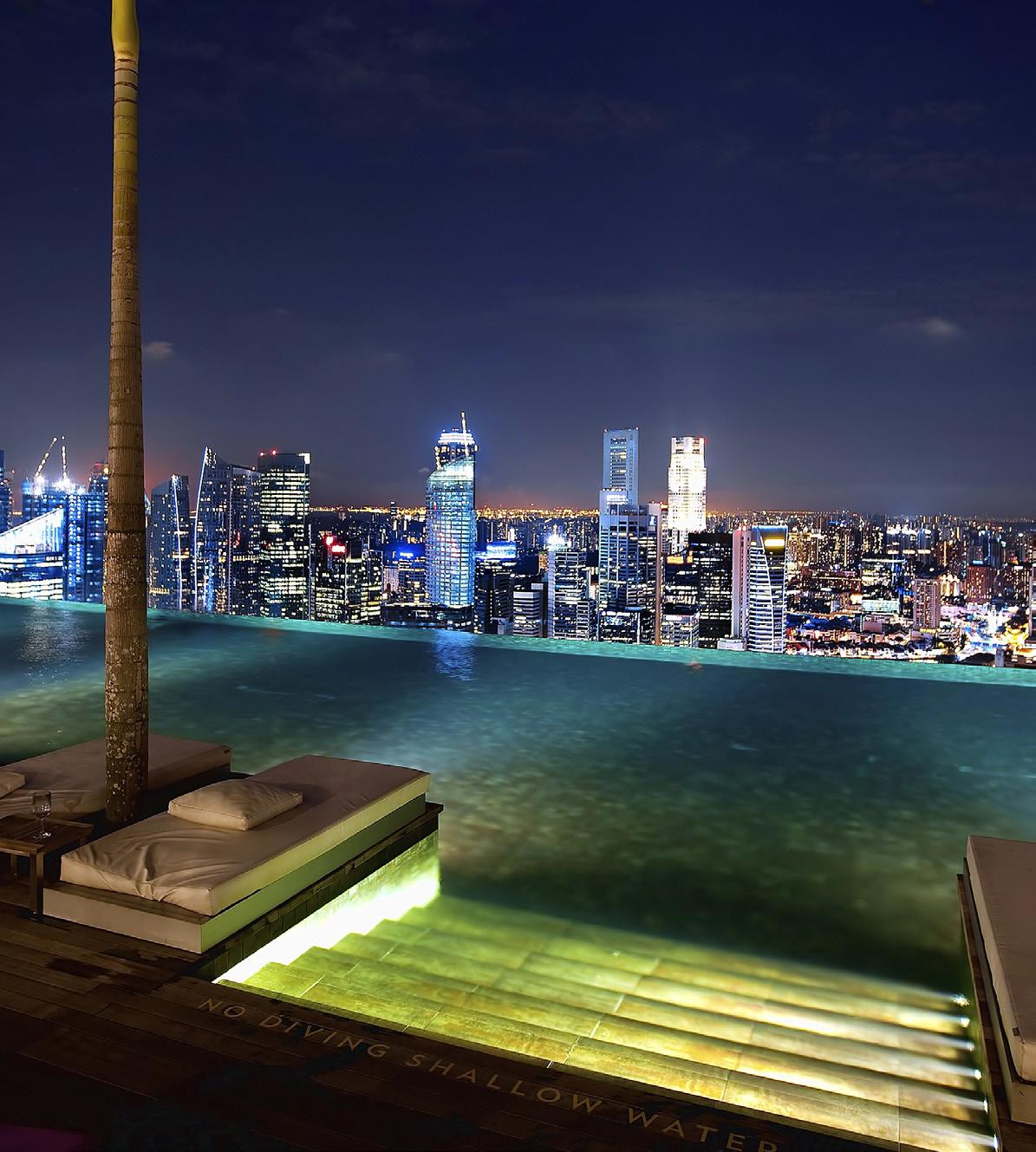
SECTOR FOCUS:
Building Services
The future of data centre cooling
The future of data centre cooling
Smart Site is easy to use on any smartphone or tablet device and requires very little training.
Smart Site reduces the waiting time of documents in transit. All job information is visible at the office as it happens.
Smart Site delivers accuracy. The app captures information as it happens, meaning there is less chance that something important is missed or recorded incorrectly.
Smart Site streamlines the administrative process ensuring that contracted and chargeable work can be completed in a timely fashion and invoiced with complete confidence.
Smart Site stores the history of an asset’s repair and service, so your engineer has all of the detail they need to do the job right first time.
Editor Chris Callander chris@flowmag.co.uk 01732 671123
Contributing Editor Suzanne Gill suzanne@flowmag.co.uk
Publisher Andrew Castle andrew@flowmag.co.uk 07785 290034
Accounts
Touchwave Media Ltd accounts@flowmag.co.uk
Production G and C Media Ltd production@flowmag.co.uk
For over three-quarters of a century the British Pump Manufacturers’ Association (BPMA) has been serving the interests of UK and Irish suppliers of liquid pumps and pumping equipment.
Centre 47 Birmingham Road West Bromwich B70 6PY www.bpma.org.uk
flow is a controlled circulation journal published quarterly on behalf of the BPMA by Touchwave Media Ltd and G and C Media Ltd. For a copy of the magazine’s terms of control and to request a copy please email circulation@flowmag.co.uk
The content of flow magazine does not necessarily reflect the views of the editor, publishers or the BPMA. The publishers accept no legal responsibility for loss arising from information in this publication and do not endorse any products or processes mentioned within it. No part of this publication may be reproduced or stored in a retrieval system without the publisher’s written consent.
Apaper published by Massachusetts Institute of Technology’s Schwarzman College of Computing states that ‘the cloud’ has a greater carbon footprint than the airline industry. The major component of the cloud is, of course, data centres, and the majority of a typical data centre’s footprint comes from its energy use. However, only a tiny percentage of that energy – the report suggests between six and 12 per cent – is consumed by active computational processes. The rest is drawn by multiple layers of redundancy protection, which is often vital but rarely called into full service, and the cooling systems needed to deal with the immense amount of heat generated by the technology in operation.
The demand for processing power is never going to reduce; indeed, its growth is exponential, fuelled by the surging demand for smart devices and, of course, generative AI (apparently, a ChatGPT query uses six times the energy of a Google search). So, it is essential that ways to reduce the energy requirements of data centres are found and implemented quickly.
On page 20 of this issue, we examine the role energy-efficient pumps can play in tackling this challenge as part of a revolutionary cooling method.
Elsewhere in this issue, we look at the parameters that should be considered when sizing a pressure-boosting system; we examine some pump alternatives for severe-duty applications; and we discover how ultrasonic flow measurement can revolutionise sewage systems.
We also cover the latest industry news, reveal a range of new products for pumping applications and share details of a selection of projects demonstrating how often experienced challenges are overcome. I hope you enjoy the issue.
Dale Croker, President, BPMACHEMUK 2024 OPENED ITS DOORS ON 15 and 16 May at the NEC in Birmingham to what the organisers say is a record attendance of 4,641 visitors over the two days, representing an increase of 17% from the 2023 edition. The total twoday attendance combining visitors and exhibitors was 6,677.
CHEMUK show founder Ian Stone summed up the positive response to this year’s event: “Standing in the hall midmorning on the first day was electric. There was so much volume and energy in the hall, with our biggest concentrated audience ever from literally every corner of the sector.
“I think the seniority of attending technical, scientific, supply chain, and business visitors rocketed to a whole new level this year, with one visitor badge after the next from the biggest names across the sector.”
Visitors to the event were invited to an exclusive pre-recorded address by Minister Mak, Minister for Industry and Economic Security at the Department for Business and Trade, and Minister for the Investment Security Unit at the Cabinet Office.
The address was supported by a comprehensive UK Government footprint at the show, with several government departments exhibiting this year, including the Department for Business and Trade,
the Department for Environment, Food and Rural Affairs, the Health and Safety Executive, the Home Office, and the Department for Energy Security and NetZero.
CHEMUK redefined itself this year with the introduction of several subbrands, including the Chemical & Process Engineering Show, the Chemicals Supply Show, the Chemicals Management Show, and the Chemical Laboratory Show.
The organising team was delighted to see an increase in both the number and quality of visitors, which they largely attribute to the introduction of these more focused show
zones.
Ian added: “The introduction of individual sub-branded shows underneath the ‘single destination’ CHEMUK24 brand has been a great success and allowed attendee groups to lock onto their primary focus area, whether as a process engineer, analytical chemist, hazardous transportation manager, and so on, whilst still benefiting from the serendipitous opportunities, intelligence, and connections drawn from the other branded show streams.”
The 2025 edition of CHEMUK will take place at the NEC, Birmingham, on 21 and 22 May.
SIEMENS HAS APPROVED THE SALE OF its electric motors and large drives company Innomotics to KPS Capital Partners, LP (KPS). The deal, reportedly worth €3.5 billion, is expected to be concluded in the first half of fiscal 2025, subject to customary foreign investment and merger control approvals.
“By selling Innomotics to KPS, I am pleased that we have made further significant progress in optimising our portfolio. The search for the best new owner has been successful,” said Ralf P. Thomas, Chief Financial Officer of Siemens AG. “This decision gives customers and those who work at Innomotics clarity and paves the way for extensive opportunities for further successful business development.”
In November 2022, Siemens decided to combine its large drives and electric motors businesses under one roof and set them up independently, outside Siemens AG’s core business, under the Innomotics brand.
The positive responses from customers and the market, as well as the growth of Innomotics during the carve-out, underline
Innomotics’ strong positioning as a leading supplier of large drives and motors capable of addressing its customers’ most demanding technical requirements. Siemens believes that the future setup, with KPS as the new owner, will offer Innomotics the best framework conditions for sustainable and growth-oriented development.
“The partnership with KPS will support Innomotics in further expanding our extensive track record of successful technological innovation and of providing our customers with world-class products, solutions and services,” said Michael Reichle, Chief Executive Officer of Innomotics. “We look forward to working closely together with KPS and our talented people as we continue to deliver significant value for our customers around the world and enhance our strong technological leadership. Innomotics will continue to benefit from strong growth potential driven by the sustainability-oriented demand for highly efficient electrification and energy consumption in industry and society.”
Following a 17-month period of construction, Menzel Elektromotoren has celebrated the opening of its new headquarters near Berlin with a grand inauguration party. In honour of company founder Kurt Menzel, the date was set for his 120th birthday – 14 May 2024. The German manufacturer markets its industrial motors and tailor-made drive systems worldwide, with increasing numbers year on year. This ongoing
growth set the requirement for more space and modern production facilities
designed for efficient processes and larger, heavier machines. In addition to state-of-the-art machinery, efficient paint shops and test fields that can accommodate even the largest motor configurations, the new plant is prepared for further growth. In the coming years, the workforce at this site can be expanded from around 100 to 150, allowing the manufacturer to meet ongoing customer requests.
SKF UK has announced the launch of its Maintenance Partner programme in EMEA and that ERIKS is the first SKF Maintenance Partner in the UK and Ireland, a new status that recognises authorised distributors that can offer industrial customers more than just a traditional transactional relationship.
SKF Maintenance Partners have SKF’s support in implementing best practices, and always use SKF components for repairs. As a highly skilled service supplier, ERIKS uses its industry-specific knowledge to
perform root-cause failure analyses and advanced troubleshooting. It is recognised by SKF as a knowledgeable advisor on maintenance matters, trained by SKF and with access to the very latest SKF technology.
ERIKS UK & Ireland has been appointed by SKF due to its investment in the SKF brand and its strategic alignment
THE AVT RELIABILITY GROUP HAS PASSED A significant milestone: sales for the 12 months to April 2024 exceeded £20 million for the first time.
AVT Reliability Group is a fast-growing part of AES Engineering Ltd, whose main global brand is AESSEAL.
It is a full-service condition monitoring business and has developed and owns world-beating Internet of Things technology and machine sensing software which enable remote monitoring of the health of industrial machinery worldwide.
Tony Gales, the recently promoted Head of AVT International, said: “In 2019, when our group had sales of less than £7 million and an EBITDA of less than £1 million, we set ourselves a goal to create a £50 million conditionbased monitoring business by the end of 2029.
“Exceeding £20 million in sales for 12 months, and the current growth trajectory of the business, means that the £50 million goal is much more of a vision than a dream.”
The AVT Group’s growth has been driven by a combination of product and business development along with acquisitions. Unusually for a company introducing innovative solutions into traditional industrial environments, its combination of reliability expertise and technology means high sales growth and profits.
in adding long term value to customers through engineering capability, innovation and knowledge and meeting the high-level criteria and accreditation process set by SKF. To support this partnership ERIKS is extending the range of SKF products it stocks and will exclusively use SKF products in its UK repair facilities.
2 WEEKS
in the servicing, engineering and remanufacturing of electrical, mechanical, and power management assets, has acquired Houghton International. Newcastle-upon-Tyne-based Houghton is an electromechanical services provider with expertise in the repair and remanufacturing of electric motors, generators, pump systems, and of electric coils for electric motors, generators, and alternators for customers in the rail, power generation, industrial, water/wastewater, and mining industries. The acquisition represents IPS’s entry into new markets in the UK, Europe, and the Middle East and an expansion of its network of operations in the US and Canada. Financial details of the transaction have not been disclosed.
Houghton International was founded in 1984 by Ron and Christine Mitten. Since 2006, Michael Mitten has operated as Houghton’s CEO and has led the company into significant services expansion, resulting in a quadrupling of sales and a tripling of the employee base while expanding served markets into Europe and the Middle East. Houghton has highly integrated operations at the Ronnie Mitten Works service centre, a well-equipped, 124,000-square-foot facility with capabilities from electrical coil
manufacturing to pump repair, motor and generator repair, and testing. This facility’s addition to IPS makes it part of a 51-location service centre network spanning the US, Canada, UK, and Europe.
As a leading aftermarket provider of operating and maintenance services for Renewable Power generation customers in the US and Canada, IPS will now be able to build on and expand Houghton’s wind market asset lifecycle services with IPS technologies in power management, generator repair, pitch, and yaw systems. IPS will now look to bring its repair, distribution, and field service offerings to new customers in the on and offshore markets in the UK and Europe.
original equipment manufacturers and operating companies.
Houghton will also join 11 IPS locations that specialise in services for propulsion systems used in freight rail, people transit, and mining applications. This will build on IPS’s capabilities in undercar transformers, traction motors, alternators, inductors, fans, pumps, and field services supporting
“The acquisition of Houghton International not only brings a wellrespected, customer-focused company into IPS, it also marks a milestone in our company’s growth by expanding beyond the US and Canada into new markets in the UK, Europe and the Middle East,” said John Zuleger, IPS President and CEO. “IPS and Houghton have an incredible opportunity to expand and improve our service offering to new customers and markets. We are committed to delivering an unmatched customer experience and creating a special workplace where employees can grow and develop through our training programs.”
WATT DRIVE ANTRIEBSTECHNIK, AN Austrian manufacturer of geared motors and drive solutions for the industrial sector, which has been part of the WEG Group since 2011, has been renamed as WEG Gear Systems.
The Brazilian group has greatly expanded its product range in recent years to offer integrated solutions for the entire drive train. This has also given Watt Drive a specialist role within the group. Under the new name, the WEG Gear Systems site in Austria will be upgraded to a competence centre for gear technology and will be responsible for the group’s global business for gears and geared motors with immediate effect.
“The new company name expresses the affiliation to our parent company,
WEG, even more clearly and further increases awareness of the WEG brand in Austria as well,” explained Klaus Sirrenberg, Managing Director at WEG Gear Systems. “In this way, we can make even better use of our parent company’s global presence and leading market position to further expand our position as a provider of drive solutions and specialist in gear technology worldwide.”
The company was founded in 1972 as an engineering office for drive technology by engineer Hans Wustinger. This was followed by expansion with its own assembly plant and production machines for small series production. In 1990, the company was given the name Watt Drive Antriebstechnik GmbH and the location in Markt Piesting in southern Lower Austria, including its own production department for gear components and the assembly plant. This was followed by the establishment of branches in Germany and Southeast Asia. The WEG group took over in 2011 and the gradual integration into the group began with major investments in the conversion and renovation of production halls and warehouses.
HELPING TO PROTECT PUMPS FROM running dry and detecting even the tiniest bubbles in flow control applications is a good example of how system engineers can prevent unwanted and expensive downtime due to pump malfunction caused by unwanted gas inclusions.
The PAD20 sensor from Baumer, a finalist in two categories at the recent Pump Industry Awards, is a ‘smart’ sensor that not only protects pumps from running dry but also ensures maximum system performance and optimum resource use.
The PAD20 sensors are an effective, robust solution for detecting air and gas bubbles in any liquid or viscous media, such as fruit preparations and cooling agents (DC>1.5), particularly in harsh ambient conditions. Switching outputs are individually adjustable with IO-Link for definition of switching range, or two-stage alarms (early warning), and
they provide optional multi-colour process visualisation through 360º of switching state.
The sensor can reliably and quickly measure air in all types of liquids, regardless of whether they are pasty or viscous.
The PAD20, initially developed for a German dairy company, proved its worth by solving their decades-old problem of containers not being fully emptied. This sensor is not just about protecting pumps; its reliable detection of gas bubbles also optimises the energy efficiency of cooling and heating systems in various industrial
A UK MANUFACTURER OF water-boosting solutions has expanded its offering with a new, innovative device following a two-year development process.
AquaScan, from Salamander Pumps, is a robust digital water multimeter designed to make water testing easier and more efficient for professional installers, with 4-in-1 measurement capabilities including water flow, pressure, temperature and hardness to deliver precise water insight.
Manufactured in the UK, AquaScan combines cutting-edge technologies to provide the key measurements needed to diagnose a water system. It aids installers with a range of tasks, including specifying combination boilers, servicing unvented cylinders, selecting the right water-boosting product, and troubleshooting water systems.
Gareth Richards, Technical Director at Salamander Pumps, said: “With a focus on quality and accuracy, plumbers are
applications, making it a valuable asset for any flow control setup.
looking forward to having access to, and using, a professional device that will set a new standard of customer service.
“Our new tool is a first here in the UK and takes out the guesswork compared to existing measurement tools, providing trust and empowering our customers to deliver the right solutions confidently. We’ve already had several pre-orders and positive feedback from user trials, and we expect this device to make the installer’s job easier.”
Supplied in a hardwearing and robust case, AquaScan includes a variety of accessories to allow the product to connect to a range of outlet types; the supplied fittings allow connection to pipework, hoses, showers, plus both indoor and outdoor taps.
The rechargeable battery has a life of up to 12 hours and can be charged via the USB C cable included in the kit,
meaning an installer doesn’t need to keep AquaScan plugged in to use it.
AquaScan is available from July, includes a one-year warranty, and is IPX5 rated.
www.baumer.com/gb/en/ www.salamanderpumps.co.uk
KSB GROUP’S NEW 3D-PRINTED CONTAINMENT SHROUD
for mag-drive pumps in the Magnochem type series, named MagnoProtect, offers the same safety as a double-walled containment shroud – without the latter’s disadvantages of heating up strongly and having high eddy current losses.
While providing comparable safety, the overall efficiencies of the new mag-drive designs exceed those of canned motor pumps. Designed with a structure of channels, the new containment shroud offers a second, redundant, static safety barrier preventing leakage of the fluid handled.
A pressure transmitter monitors the vacuum generated, which is present during normal operation in the channels of the containment shroud. If the monitored pressure rises to atmospheric pressure, the outer containment shell is leaking. If the pressure rises above the ambient pressure, the inner containment shell is damaged. The containment shroud design is characterised by high mechanical strength and good wear properties. It has been optimised to minimise heat losses and eddy currents.
Converting a standardised chemical pump with a mechanical seal to a magnetic drive is easier and more cost-efficient than retrofitting it with a canned motor. The geometry and dimensions of the new containment shroud are integrated
THE NEW TR SERIES WOBBLE PLATE PUMPS FROM Lutz Pumpen enable the sensitive pumping of up to 30,000 litres of highly viscous liquids per hour.
A spherical pump housing accommodates a wobble plate that sits at an angle on a shaft. The rotation of the shaft causes the plate to perform a characteristic wobbling movement. This continuously changes the volume of two chambers on both sides of the shaft which creates alternating positive and negative pressure, and draws liquids into the pump and expels them through an outlet opening. An efficient principle that has proven itself with highly viscous liquids such as oils, lubricants, varnish, sealants and silicones.
The new industrial pumps can handle thick or viscous liquids and media containing solids with a viscosity of up to 1,000,000 millipascal seconds and a temperature of up to 205 °C. They are suitable for applications in a range of industries, including paints and coatings, sealants and adhesives, pharmaceuticals, cosmetics, oil and the food processing. www.lutz-jesco.com/en
into the modular system of Magnochem, allowing metallic or ceramic containment shrouds to be replaced easily. This enables operators to upgrade older pump sets that are still in service without difficulty.
www.ksb.com
6.5 YEARS
WEG, A GLOBAL LEADER IN energy solutions, aims to set a new milestone in energy efficiency with the release of WEGSEE+.
Launched in the UK at the recent Europump Annual Meeting, which WEG sponsored, this powerful software tool looks to revolutionise companies’ approach to energy management, offering a comprehensive and innovative solution for the analysis and optimisation of any motor-driven system, whether it involves pumps, compressors, conveyors, or more.
Equipped with advanced simulation and analysis capabilities, WEGSEE+ enables users to input details of the driven system, the current parameters such as motor output, number of poles, voltage, motor age, etc., and make strategic decisions to optimise resources through identifying
energy efficiency opportunities by replacing motors, gearboxes, and inverters, measuring return on investment periods and evaluating the potential to
avoid or reduce GHG emissions.
According to WEG, the platform goes beyond conventional tools, providing valuable insights that drive sustainability and operational efficiency in organisations of all sizes and industries.
WEGSEE+ is said to be not just a tool but a complete solution for companies seeking to maximise energy efficiency, reduce operating costs and achieve sustainability goals. With an intuitive interface and comprehensive features, it simplifies the analysis of energy efficiency projects, providing informed guidance for making strategic decisions.
www.weg.net
BLUELINQ PRO, THE LATEST ADDITION to the Sulzer pump controller lineup, uses an intuitive, quick setup wizard for simplified configuration and uses experience-designed presets to solve complex operating scenarios.
Operators can interact seamlessly via the 7in touchscreen and use the integrated variable frequency drive (VFD) control to maximise pump efficiency and reduce energy costs. The new BlueLinQ Pro offers excellent scalability and is capable of controlling up to six assets, including pumps, mixers and valves, for the most effective operations.
The Sulzer BlueLinQ Pro offers advanced control features and a setup wizard that improves pump availability and reduces energy consumption – all within a small footprint that makes retrofitting easy. Built-in best efficiency point (BEP) and proportional integral derivative (PID) control logic functionality ensure that all pumps in the station operate as close to peak efficiency as possible. This reduces running costs and
minimises stress on the mechanical components.
Smart control functionality provides multiple features that optimise pump operations and minimise the need for interventions from the maintenance team. The ability to calculate in and outflows, measure the speed of level changes and vary pump start and stop points ensures each pumping station operates to its full potential. This includes the addition of mixers and valves, which can also be included in the control logic delivered by the BlueLinQ Pro.
With so many similar pumping stations in each network, the variety of controllers across sites can add unnecessary complexity for operators. The inherent flexibility of the BlueLinQ controller makes it ideal for many locations. Once the first station has been configured, all the settings can be easily transferred to others using the SD memory card facility, minimising commissioning time.
To further enhance the benefits of the
BlueLinQ Pro, modern communications protocols offer excellent connectivity and remote access possibilities to maximise the effectiveness of operators and technicians. Centralised monitoring and programming ensure valuable staff and resources are only dispatched when absolutely necessary.
www.sulzer.com
DELEGATES FROM 19 COUNTRIES came together recently for the Europump (the European Association of Pump Manufacturers) 2024 Annual Meeting and General Assembly. The annual gathering of representatives from 15 National Associations in 12 EU Member States, Switzerland, Turkey, and the UK, was hosted and organised by the British Pump Manufacturers’ Association (BPMA) with the sponsorship and support of motor, drive, and asset management systems technology specialist WEG.
Over 80 delegates from across the European pump industry attended the three-day event in Windsor, benefiting from updates on regulatory and standards-related topics, including the Circular Economy, PFAS (polyfluoroalkyl substances), EPD (Environmental Product Declaration), the Eco-design Directive, the Machinery Regulation, the Carbon Border Adjustment Mechanism (CBAM), GHG Emissions, and more.
The event also featured keynote speeches from industry experts, who shared valuable insights. These included discussions on the introduction of Digital Product Passports, the use of Artificial Intelligence in pumps, and sustainability with motors and drives. In a broader context, delegates were provided with an overview of the political landscape in the
UK, specifically in relation to manufacturing, by Stephen Phipson CBE from Make UK. They also received a detailed presentation on the latest Oxford Economics’ World Pumps Report, ensuring they were equipped with the most up-to-date industry knowledge.
Commenting on the event, Wayne Rose, CEO at the BPMA, said: “We were delighted to host this year’s Europump Annual Meeting on behalf of our European colleagues, and I could not be more pleased with how the entire event has been received. I do not doubt that the three days spent in Windsor have been productive and enjoyable for all concerned.”
Lisa Kretschmann, Secretary General at Europump, echoed these thoughts by saying: “It was wonderful to see the number of attendees to this year’s event return to pre-pandemic levels, which is a testament to the importance of the work delivered by Europump on behalf of our industry. Our thanks go to our hosts for organising such a wonderful event – on
both a business and social level – and to WEG, whose support and sponsorship enabled such a comprehensive programme to be presented and enjoyed.”
Marek Lukaszczyk, European & Middle East Marketing Manager at WEG, added: “The pump sector is a hugely important business area for WEG, and so the opportunity to engage and network with senior personnel from the leading pump manufacturers at this key event is very much appreciated. We were delighted to offer our support and look forward to building on our relationship with the BPMA and Europump going forward.”
The next Europump Annual Meeting and General Assembly will be held in Prague from 21-23 May, 2025.
The new W23 Sync+ Ultra is the most energy efficient industrial motor available on the market.
With 20% lower losses than IE5 energy ratings, this new motor combines permanent magnet and synchronous reluctance technology. Available in frame sizes from 80 up to 450, the W23 Sync+ range promises:
• Lower carbon emissions
• Lower total cost of ownership
• Highest efficiency rating on the market
• Widest range up to 1,250 kW For more information visit www.weg.net
The Pump Industry Awards have been recognising and rewarding the achievements of pump businesses, large and small, for well over two decades and for the 2025 staging of the event, The British Pump Manufacturers Association is once again calling for nominations.
This awards programme provides the perfect platform for any company with pump-related success to gain industry-wide recognition. The closing date for all entries is Friday, 29 November 2024, giving plenty of time to consider, prepare, and submit entries.
Maintaining the early spring timeline and following the success of the 2024 event, the next gala dinner and presentation ceremony will take place on Thursday, 13 March 2025, once again enjoying the facilities at the Hilton at St George’s Park, Burton on Trent.
Situated on the edge of the National Forest, St. George’s Park is the training ground for all 28 English national football teams and is recognised worldwide as the home of English football. Sporting excellence is synonymous with this venue, and early next year, it will once again become the location for heralding engineering excellence across the pump sector.
The online entry forms, which seek submissions for activities and achievements that took place in the 18 months prior to the entry deadline, will remain on the dedicated awards website — www. pumpindustryawards.com — until 5.00pm on Friday, 29 November 2024.
The pump sector plays a crucial role in ensuring our food production, utilities, manufacturing processes, transportation and other essential services are maintained, and the 2025 awards programme will give special recognition to those companies and individuals who have gone that extra mile to meet, and more often exceed, the demands and challenges presented by the sectors served.
This recognition and acknowledgement will be represented by a suite of award categories that collectively honour the full breadth of the pump industry’s product and service delivery. The categories will include recognition of sustainable contributions to a better world.
• Product of the Year – Sponsored by Plant & Works Engineering
• Project of the Year – Sponsored by BPMA
• Environmental Contribution of the Year – Sponsored by SPP Pumps
• Manufacturer of the Year –Sponsored by WEG UK
• Distributor of the Year –Sponsored by Calpeda & Caprari
• Supplier of the Year – Sponsored by Wilo
• Contribution to Skills & Training –Sponsored by Crest Pumps
• Rising Star Award – Sponsored by World Pumps
• Sustainable Contribution for a Better World – sponsored by AESSEAL
Once again, the organisers have secured the support and backing of a host of leading brands, all of whom recognise the value and importance of promoting excellence across the sector. In addition to the main category sponsors highlighted above, there are also other sponsorship options to help support specific elements of the 2025 presentation evening. Some opportunities still
exist, and the event’s organisers encourage anyone who would like their brand aligned with outstanding engineering achievement within the pump industry to get in touch.
Wayne Rose, Director and CEO of the British Pump Manufacturers Association, commented: “This year’s awards ceremony – the 23rd such event – was a superb evening of celebration for our sector and provided a fantastic showcase of innovation, technical endeavour, engineering prowess and professional excellence. Pumps and pumping systems provide the bedrock and essential support for every aspect of our lives. A world without pumps is unthinkable, so it is only right that we have a strong platform to acknowledge, celebrate, and highlight the achievements of this crucial business arena. I would therefore encourage all those involved in the pump industry to prepare and submit their entries for the 2025 awards programme.”
Simply
With sensors that are smarter and more resilient we improve the sustainability in your process automation. Numerous awards and prizes prove us right. You can rely on the Baumer expertise.
Contact us: www.baumer.com/award-winning
AT THREE SINGLETON BIRCH biogas plants in Northern Lincolnshire, four rotary lobe pumps, made by Borger, have completed ten years of uninterrupted service.
Operating at the main Singleton Birch 2MW site in Barnetby, which has three 2800m 3 digesters, two Borger pumps are an important part of a process that, at full power, utilises imported maize (70 ton), sugar beet (40 ton) and chicken litter (10 ton) for its feedstock.
Established in 2014, and then expanded two years later with a third digester, additional silage clamps and two more CHP engines, the principal Singleton Birch facility contributes 86% of the power required for the 2.3 hectares Singleton Birch site, which for over two centuries, has produced high quality lime products.
At two smaller (500kW) AD plants
at Elsham, near Scunthorpe, and Willoughton, near Lincoln, a Borger pump operates at each, transferring liquid feed overflow into a drying system.
“Over the years, we’ve developed a very good partnership with Borger,” said Danny Mason, Renewable Energy Manager at Birch Energy.
“The equipment is very reliable and easy to maintain, and when we need spares or just a bit of advice, Borger’s Richard Marcinkowski is just a phone call away, always ready to help us out. This gives us peace of mind that our AD operation won’t be affected by any downtime.”
He added: “The pump application here means that wear and tear is inevitable, but Borger always keep right on top of the servicing schedule and the flow of spare parts, so that we are never without.”
www.boerger.com
In 2018, the HVAC system at a popular Caribbean holiday resort suffered a series of failures and leaks, resulting in frequent downtime. An initial review determined that the existing pumps were the cause and had to be replaced. The review also noted that the pumps were oversized, which affected system efficiency. With the resort occupancy rates near 95% for most of the year, HVAC performance and reliability are crucial, so managers decided to go ahead with an upgrade.
Because local rates for electricity averaged $0.28 per kilowatt-hour (kWh) at the time, the project represented an opportunity for the resort to reduce its energy costs as well as its carbon footprint. After assessing the HVAC system, Armstrong recommended Design Envelope Vertical In-Line pumps to replace the existing primary and secondary pumps.
The team at the facility was impressed by the space savings created by the Vertical In-Line design and noted that subscribing to the Pump Manager service, which provides alerts, alarms and performance analysis data, made it easier to track equipment status
and performance and support optimal efficiency and occupant comfort.
“Since our hotel is located on an island, we need a system that’s easy to maintain. The performance reports and messages provided by the Pump Manager are very helpful. Plus, the team at Armstrong is always available if we have any questions,” explained the resort’s manager.
The upgrade project provided a simple payback of less than two years and saves over $170,000 annually. The management team at the hotel is very focused on reducing its carbon footprint, so the annual energy savings of 558,000 kWh are an important measure of success.
in Trafford Park recently ran out of water to the top two floors due to ever-decreasing mains pressure, it caused large-scale operational issues on site. They quickly needed to find a permanent solution to boost the water supply to the property.
Working with its customer Equans, which undertook several enabling works, Pressboost was able to locate a room on site that it could use for tanks and a booster set and quickly sourced the equipment needed.
Then, over the course of two days, the incoming mains to feed two new storage tanks was modified and a Lowara GHV20 Hydrovar X Booster Set was installed to boost the supply to the property.
The entire property now has boosted supply and a future-proofed solution for its water distribution.
The two tanks allow for future maintenance without disruption. The new booster set benefits from highly efficient IE5 rated motors, a flow through expansion vessel and valve, and Hydrovar X inverters.
In everything we do, we never lose sight of what it‘s all about for you: economical work and easy handling.
Whether chemical substances, oils or media for the food industry, it is important to fill or empty quickly and precisely. Due to the reversible conveying direction, both processes can be carried out with just one pump.
As a result of their compact yet powerful construction, Vogelsang rotary lobe pumps are among the most frequently ordered pumps in many UK industries. They transport highly viscous or aggressive media of all kinds and even pump liquids with rough solids without blocking.
For more information: sales.uk@vogelsang.info | 01270 216 600 vogelsang.co.uk
CLIMATIC CHANGES FORCE US TO save water. Given that the pollution load has remained the same, the solids content in wastewater has increased, which has been a technical challenge for wastewater treatment plants. Until now, upstream pumping stations have had to implement costly measures to ensure reliable operation. KSB has responded to this problem with a new technical development that eliminates a previously essential step in pumping stations.
Many years of close partnerships with customers have provided KSB with detailed insights into the problems and challenges its products face in daily work. This has enabled KSB to tune its technical solutions precisely to what customers need. KSB’s sales engineers recognised that cutting back on processes in wastewater pumping stations would save considerable costs. In the end, they just had to convince their customers of this solution.
The city council of Oelde, located in the southeast Münsterland region in Germany, operates a public sewer system of about 280km in length for its 30,000 inhabitants. Nineteen pumping stations make the wastewater flow from suburbs such as Stromberg, Sünninghausen and Lette to the wastewater treatment plant, where 8,500 cubic metres are treated mechanically and biologically every day.
In addition to pump technology, wastewater pumping stations are fitted with components such as screens and strainers that mechanically pre-clean the wastewater upstream of the pumps. This prevents clogging or damage to the pumps. Wet wipes from hygienic applications, in particular, make wastewater transport difficult. Having to remove solids and
service the screens incurs extra costs.
KSB has further developed its Amarex KRT and Sewatec pump type series. A new impeller has been designed that can handle wastewater with a high solids content without clogging the pump. This means the pumping station operator can do away with any upstream components for mechanical pre-screening—a distinct advantage.
Once several prototypes were available, KSB started a field test where the pumps had to prove their worth in practice. Oelde’s Obstromberg pumping station was the first to use one of the newly developed pumps for a free trial operation. KSB supplied a Sewatec D-max and had it installed by engineers from the KSB service network. Installation was straightforward as the technically advanced pump was designed with standard dimensions. Only the hydraulic part of the pump has changed, and a larger suction pipe has been fitted.
In the one-month trial operation, Sewatec D-max 100-403 was used with the previously fitted upstream screen.
After running successfully for this period, the pump was then operated without the screen. And it worked: Even without mechanical pre-screening, the pump was able to handle coarse solids together with the wastewater without clogging. Twelve months after the trial operation had started, the Oberstromberg pumping station ordered a second Sewatec D-max. This additional pump has provided trouble-free operation together with the first pump since mid-2022.
The upstream screen, initially planned to be renewed, has since been completely removed from the pumping station, saving the operator a six-digit investment. A useful new technical development has eliminated a process that had been established for decades, including the associated costs for disposal and servicing.
www.ksb.com
XYLEM HAS TEAMED UP WITH partners in Bavaria to launch Reuse Brew, a beer crafted from high-quality treated wastewater. The initiative was created to raise awareness of the opportunities recycled water offers to help communities combat water scarcity in the face of climate change. Reuse Brew is the culmination of a collaboration with the Chair of Brewery and Beverage Technology at Technical University of Munich (TUM), the Chair
of Urban Water Systems Engineering at TUM, the city of Weissenburg in Bavaria and Xylem.
“Reuse Brew exemplifies the vast capabilities of water recycling in combating the pressing issue of water scarcity,” said Roxana Marin-Simen de Redaelli, Vice President of Central Europe and Nordics at Xylem.
Reuse Brew production leverages oxidative processes, ozonation and advanced oxidation with UV irradiation
and hydrogen peroxide, paired with sophisticated filtration and purification processes, including nanofiltration. These technologies effectively remove chemical and microbial contaminants through oxidation and adsorption, ensuring the beer’s quality.
www.xylem.com
With the accelerating demand for data centre capacity, the sector’s energy demands are growing at a colossal pace. The consequence, however, is carbon emissions that have surpassed those generated by the aviation industry, so it is essential that action is taken to reduce the industry’s energy usage. One solution is for data centres to adopt single-phase immersion cooling, which, when powered by high-efficiency pumps, can offer significant energy savings, as pumping specialist Crest Pumps explains.
Adata centre is a facility that houses and manages a large amount of data and the IT infrastructure required to process and store that data. It is the backbone of the digital economy, supporting critical organisations, from hospitals to small businesses, and can vary widely in size, power requirements, redundancy needs, and overall structure. Without data centres, many of our daily digital activities would not be possible.
The data centre market is experiencing significant growth due to the increasing demand for digital technologies and cloud computing. As more businesses and individuals rely on cloudbased services and storage, the need to store and process this data is skyrocketing. The market size stood at $263 billion in 2022 and is expected to advance at an annual growth rate of 10.9% during 2022–2030. This growth is driven by the digitalisation of corporate operations and the increasing use of streaming, internet usage, and, of course, AI.
This substantial growth brings about the challenge of making data centres more energy efficient. Data centres consume an enormous amount of electricity, often 100 to 200 times more than standard office buildings, due to the highpower requirements of the servers and cooling systems. The recent annual electricity report from the International Energy Agency (IEA) says that globally, data centres consumed 460TWh of electricity
in 2022, a figure that could rise to more than 1,000TWh by 2026.
Servers generate a lot of heat, and over the years, data centres have relied upon a variety of cooling methods to maintain the optimal temperature for equipment. In the early days, air conditioning units were the primary cooling method. However, these systems had limitations in terms of energy consumption and scalability, as they struggled to handle the increasing heat loads generated by modern equipment. As technology advanced, raised
Globally, data centres consumed 460TWh of electricity in 2022.
floor cooling systems emerged, with cold air delivered through perforated floor tiles. While this improved energy efficiency, cooling high-density server racks effectively was still challenging. Hot aisle/cold aisle containment is another commonly used practice, segregating hot and cold air streams to minimise mixing and improve cooling efficiency. Liquid cooling systems, such as chilled water or refrigerant-based systems, then became popular. These offered better heat dissipation capabilities but were complex and required additional infrastructure.
MORE THAN 20.000 MOTORS AVAILABLE FROM STOCK!
Motors up to 25 MW and 13.8 kV
• Low voltage slip-ring and squirrel cage motors up to 3,000 kW
• Medium voltage slip-ring and squirrel cage motors up to 15,000 kW
• Direct current motors up to 2,000 kW
• Frequency converter-proof drives
• In-house load test facility up to 13.800 V, 2.300 kVA, 120 Hz
Customized special designs
• Custom designs for special applications and operating conditions
• Optimized motor design for higher efficiency
• Mechanically and electrically interchangeable motors
• Commissioning worldwide
MENZEL Great Britain Ltd. | UK Branch Office
27 Hunt Drive | Melton Mowbray | Leicestershire LE13 1PB
Martin Rooney | Tel.: +44 1664 500 844 | Mobil: +44 7957 618046 martin.rooney@menzelgb.co.uk NEW ELECTRIC MOTOR PLANT FROM JANUARY 2024
MENZEL Elektromotoren GmbH
German Headquarters
Am Alten Walzwerk 2 | 16761 Hennigsdorf | Germany
menzel-motors.com info@menzel-motors.com
24,000 m 2
More recently, rear-door heat exchangers and direct-to-chip liquid cooling have been adopted for high-density computing environments, providing efficient cooling solutions for advanced data centres. However, these methods often require specialised equipment and maintenance, making them less accessible for smaller data centres.
In modern data centres, best cooling practices focus on energy efficiency, temperature control, and humidity management.
Single-phase immersion cooling is a revolutionary method that involves immersing the data centre equipment in a fluorinert non-conductive liquid. This liquid efficiently absorbs and dissipates heat, providing a highly efficient cooling solution.
Single-phase immersion cooling offers superior cooling performance, reduced energy consumption, and improved reliability compared to traditional methods. Servers or IT components are fully submerged in a thermally conductive dielectric coolant. This coolant, which is in its liquid state, is circulated by a cooling distribution unit (CDU) to a heat exchanger outside the tank, where the heat is transferred to a secondary cooling circuit. The coolant is non-electrically conductive, ensuring it does not disrupt the servers’ function.
By eliminating the need for fans and air conditioning units, this cooling method significantly reduces energy consumption. According to industry experts, immersion cooling can achieve energy savings of up to 95% compared to traditional air-cooling systems with Power Usage Effectiveness (PUE) values as low as 1.03, resulting in substantial energy savings.
The benefit of immersion cooling is that it eliminates the need for traditional air-cooling infrastructure,
reducing capital expenditure and operational costs. This cooling method relies on the principle of direct liquid-to-heat contact, providing a more efficient and effective cooling solution for data centres. The main benefits of single-phase immersion cooling include:
Environmental: Immersion cooling uses less energy and can decrease carbon footprints by 40%, real estate footprints by 30%, and water use by an astounding 8 million gallons per megawatt.
Space: Immersion cooling allows for higher server density, saving space in high-density data centres.
Safety: The coolant used in immersion cooling acts as a fire suppressant, reducing the fire risk in the data centre.
Scalability: As data centres grow, so do their cooling requirements. Immersion cooling is easily scalable and can accommodate future growth and changes in cooling needs.
Single-phase immersion cooling enhances the reliability of data centre equipment. By providing precise temperature control, it reduces the risk of equipment overheating and failure. This improved reliability ensures uninterrupted operation and minimises downtime.
Immersion cooling can achieve energy savings of up to 95% compared to traditional air-cooling systems.
fan-less design make it the ideal choice for immersion cooling and the model has already been successfully installed within Ali Baba and Intel systems. By reducing energy consumption, data centres can significantly lower their operating costs and improve profitability. Investing in high-efficiency pumps is a strategic decision that saves money and contributes to a greener and more sustainable data centre industry, which is vital when the sector is under increasing pressure to reduce its environmental impact and comply with energy efficiency regulations.
Immersion cooling systems are designed to minimise energy consumption and maximise uptime, so it is crucial to choose a pump with the same ethos. The AVF-C pump by Assoma (available exclusively in the UK via Crest Pumps) is the first thermoplastic canned motor pump to exceed Europe’s highest MEI >0.7 energy efficiency standard.
The pump’s low power consumption, small footprint and
As data centres continue to play a crucial role in our digital world, implementing effective cooling strategies is paramount. By implementing single-phase immersion cooling and utilising high-efficiency pumps to optimise temperature and humidity control, data centre managers can ensure efficient operations, minimise downtime, and reduce energy consumption. chevron-circle-right
www.crestpumps.co.uk
The latest variable speed pump and tank innovation from Calpeda
Perfect for environments where a conventional cold water booster set and tank are not possible due to size constraints!
Single or Twin MXS Pump Options
Ease of Maintenance
UK
UK
Robbie Graham, Business Development Manager for the Process & Chemical Solutions group at SPP-Rodelta – a strategic partnership between SPP Pumps and Rodelta –looks at the advantages of OH5 pumps, which include smaller physical footprints and lower weight, less downtime at installation, and reduced costs and carbon footprints.
The API 610 standard for centrifugal pumps is a watchword for safe pumping operations in the petroleum, petrochemical and natural gas industries. This stringent standard applies to pumps operating in environments where a spark would be catastrophic and is strictly enforced.
API 610 'overhung' (OH) pumps are used in a wide range of offshore and onshore applications. These include common applications such as crude oil export, process transfer, cooling water, and booster pumps,
as well as more specific onshore applications like flare knockout Drum (KOD) pumps, reflux, and oil recovery pumps.
These pumps are a common feature of the oil and gas fluid handling world, but that is not to say that they cannot be improved on to deliver more than just extremely safe, mission-critical performance. When designing pumps, hydraulic performance and safety are of paramount importance, but manufacturers are increasingly taking into account things like cost and environmental impact. While the OH2 pump is widely specified and used across
many scenarios that call for API 610, it is by no means the only choice.
In specifying and selecting pumps according to API 610 standards, all parties must be able to grasp the intricacies of the various pump designs outlined within the standard. This understanding is crucial for OEMs, EPCs, consultants, and end-users alike. While there may be overlap between designs, certain applications – particularly those where OH2 pumps are commonly specified – can significantly benefit from considering an OH5 design, especially when dealing with low
NPSHa applications, lower temperature fluids (below 250°C) and lower head applications (less than 300m). There are several advantages of opting for an OH5 design in such scenarios: reduced footprint and weight, longer mean time between failures, and ultimately, diminished cost and carbon footprint. Moreover, the vertical, in-line configuration of the OH5 design offers additional benefits, such as simplified maintenance access and enhanced fluid flow efficiency, making it a compelling choice for a diverse range of operational requirements.
This has significant benefits, especially for offshore and prepackaged skid applications, where space is at a premium, and where they could be used to pump anything from boiler feed to oily surface water, crude oil and sour water to hydrocyclone feed and condensate recovery.
The highly versatile OH5 pumps typically weigh around 25% less than a comparable horizontally mounted pump because they lack a large baseplate.
The standardised dimensional features of OH5 designs, compliant with BS4082, facilitate the straightforward design and provision of installation templates, which can be supplied prior to pump delivery. This enables the installation process to proceed concurrently rather than sequentially, with tasks such as grouting of the baseplate and welding of pipework completed ahead of the pump's arrival.
Such an approach offers several advantages to the customer: it allows the absorption of project overruns, streamlines the installation timeline, and provides a reusable method for preventing contaminants from entering the process system. Additionally, the installation dummy serves the dual purpose of keeping the line open for the process if needed, further enhancing operational flexibility and efficiency.
Of increasing importance to manufacturers is adherence to the United Nation's Sustainable Development Goals. This is another area where the OH5 pump has a significant impact. Because it involves less steel in its configuration, there is already a reduction in carbon in its manufacture. Because of its compact nature, its installation requires less supporting concrete and steel and lightens the overall weight, important for LNG ships and offshore rigs. What's more, it costs less to ship and accounts for fewer emissions than larger, heavier OH2 equivalents.
Of course, not every API 610 pumping application can be switched to an OH5. There are many scenarios where OH2 or other OH solutions will be optimal, such as higher-energy applications or applications with higher temperatures. But just because an application has traditionally used OH2, it doesn't mean that it always has to. From a safety, cost, size, weight, and environmental perspective, the OH5 alternative offers some compelling benefits. chevron-circle-right
Patterson Pump Ireland is a complete pump manufacturer, offering our customers some of the most reliable pumping solutions available. Our fire pumps stand over life and property throughout the world.
Reduce on-site labor time, engineering and installation time and associated costs. Choose a system that arrives on-site in a fully enclosed ready for use pump house. This pre-engineered pumping system saves time and money for our customers.
+353 (0)44 934 7078 company/patterson-pump-ireland-ltd www.ie.pattersonpumps.com sales@ie.pattersonpumps.com
With the chronic need to reduce sewage overflows, Emerson explores how its Flexim brand can offer an unintrusive option for measuring flow rates in sewage systems, which can, in turn, enable them to be optimised.
Britain’s water system, a relic of decisions made in 1856, has long struggled with sewage overflows, leading to many environmental and health concerns. The root of the issue lies in the widespread use of combined sewage systems, where rainwater and sewage intermingle, causing spills during heavy rainfall. The current infrastructure, designed by Sir Joseph Bazalgette in response to the 19th-century ‘Great Stink’, has become outdated and unable to handle the challenges of modern urbanisation.
The inherent flaw in combined systems is their vulnerability to overflow events. Although these were originally intended to be infrequent, climate change, population growth, and underinvestment have all exacerbated the problem. The need for a transformative solution is clear, and one promising technology is clamp-on ultrasonic flow measurement.
Combined sewage systems, prevalent in most major British cities, create a significant environmental hazard. These systems, designed to discharge sewage into rivers when it rains heavily, have become increasingly inadequate as the frequency of overflow events has risen. Bazalgette’s design, hailed as a marvel in its time, has struggled to keep pace with the demands of a rapidly growing population and changing climate.
The core issue lies in intermingling rainwater and sewage within the same pipes, leading to overwhelmed systems and frequent spills. As the problems persist, there is a growing realisation that a fundamental shift in sewage
system design is necessary to mitigate environmental impact and protect public health.
Enter clamp-on ultrasonic flow measurement, a technology that offers a revolutionary approach to monitoring and managing sewage systems. Unlike traditional methods that involve intrusive installation of flowmeters inside pipes, clamp-on ultrasonic devices can be externally attached, eliminating the need for system shutdowns or extensive construction.
This non-intrusive solution delivers real-time data on flow rates, allowing for precise monitoring of sewage and rainwater volumes. The technology’s adaptability makes it a cost-effective option for retrofitting existing combined systems, providing a means to optimise performance without requiring extensive renovations.
While the historical decisions that led to the prevalence of combined sewage systems cannot be reversed, the integration of clamp-on ultrasonic flow measurement represents a step towards modernising and optimising existing infrastructure. This technology enables water authorities to gain comprehensive insights into system behaviour, identify areas prone to overflows, and implement targeted solutions.
The transformative potential of clamp-on ultrasonic flow measurement extends beyond the monitoring of combined systems. In new developments, where separate sewage and rainwater pipes are now favoured,
this technology ensures efficient operation and helps maintain the integrity of these modern designs. By preventing overflows and optimising the flow of sewage and rainwater, clamp-on ultrasonic flowmeters contribute to sustainable and resilient urban water management.
Implementing clamp-on ultrasonic flow measurement has its challenges. Overcoming historical underinvestment, regulatory hurdles, and industry-wide resistance to change will require a concerted effort from water authorities, policymakers and technology providers. However, the potential benefits – from reduced environmental impact and improved public health, to enhanced system efficiency – make it a compelling investment for the future. chevron-circle-right
The Kiwa UK Regulation 4 Product Approval Scheme (KUKreg4)a robust method for demonstrating compliance with the Water Supply (Water Fittings) Regulations 1999.
In larger buildings, the pressure supplied by water utilities is usually insufficient to supply the upper levels with enough water. The solution is pressure booster systems. These pump systems respond to fluctuating demand in water supply and adjust their output accordingly, so all consumer points in the building are supplied with the required minimum flow pressure at all times. KSB explores the factors which influence the sizing of such a system.
Usually, water utilities supply drinking water at an average minimum supply pressure of about 2 to 3.5 bar in the piping. This is generally enough to provide the furthest consumer point in a two-storey building with sufficient water. In higher buildings or when pressurereducing water meters, filters or water treatment systems are used in the inlet, the pressure is no longer sufficient – and the water only trickles out of the tap. In such cases, a pressure booster system (PBS) has to be installed to provide the pressure required.
In mathematical terms, according to DIN 1988 Part 500 (a standard for PBSs with frequency inverter; cascade-controlled systems are to be avoided in the future) a pressure booster system is required specifically when the sum of the pressure loss from geodetic height
difference (Δpgeo), the water meter pressure loss (ΔpWZ), the pipe friction and other individual losses [Σ(R · l + Z)], and the apparatus pressure losses (ΔpAp) (e.g. from filters or drinking water posttreatment systems) exceeds the minimum supply pressure pmin, v (or SPLN according to the latest standard) of the local water utility. Summarised in a formula:
SPLN < Δpgeo + ΔpWZ + [Σ(R · l + Z)] + ΔpAp + pmin, FL
The technical challenge is that the PBS has to provide a constant pressure at all times. This especially applies to times of peak demand. Today, new systems or replacements are designed as pressure booster systems with several variable speed pumps arranged in parallel on a baseplate. This means the electronically speed-
controlled pumps start up or stop depending on the demand. These pumps generally work in alternation: The next pump to start up is always the pump with the least operating hours; the next pump to stop is always the pump with the most operating hours. This ensures an even distribution of operating hours and prevents water from stagnating in the pumps.
In buildings with fire-fighting or fire-protection systems, the PBS provides a fast and reliable supply of fire-fighting water. In high-rise buildings it is essential for the wall hydrants on all storeys to be supplied with a suitable flow rate and the required minimum flow pressure. The fire-fighting lines further have to be separated from the drinking water system to protect the drinking water from contamination and other hygienically negative impacts.
We supply a large range of high precision horizontal, vertical and automated hard bearing dynamic balancing machines suitable for all industries.
All machines are supplied with guarding meeting the requirements of Machinery Directive 2006/42/CE.
RANGE OF PRODUCTS AND SERVICES
• Horizontal hard bearing balancing machines
• Vertical axis hard bearing balancing machines
• Semi & fully automated balancing machines
• Portable vibration analysers/balancers (on-site balancing)
• Site service directly from the UK
• Sub-contract balancing service
• Applications engineers support
• Genuine CEMB spare parts
For further information contact us:
T: 0161 872 3122
E: sales@cembhofmann.co.uk
Installing a pressure booster system is linked with stringent legal regulations that cover many different aspects. Here is an overview:
Drinking water hygiene
To continuously prevent microbial contamination of the water and ensure a high drinking water quality, the installation of PBSs is governed by the stringent guidelines of the drinking water regulation as well as by generally applicable regulations such as DIN EN 806, DIN EN 1717 and DIN 1988.
Operating reliability
DIN 1988 recommends an additional stand-by pump that is installed and ready for operation. This is why even small pressure booster systems have to be fitted with a minimum of two pumps. (This regulation does not apply to single-family or two-family houses.)
Installation room
According to DIN 1988-500, pressure booster systems have to be installed in suitable rooms, for example in a control room. The surface they are positioned on has to be level and of sufficient loadcarrying capacity. The room has to be frost-proof, and the temperature in the room must not cause the drinking water temperature to rise to 25°C or above, during stagnation, as stated in VDI 6023.
Further national and regional regulations apply to PBSs regarding the installation, connection types, commissioning, regular servicing, etc.
The precise sizing of a PBS for a larger building is far from trivial; it requires comprehensive understanding and know-how. For calculating the discharge pressure, the following basic formula is generally recommended:
ΔpP = pdischarge - p (in bar)
This means that the required discharge pressure (ΔpP) should
equal the start-up or set pressure at the peak flow rate downstream of the PBS (pdischarge) minus the available minimum supply pressure upstream of the PBS (pinl). So far, so simple. The complicated part is to determine pdischarge and pinl, which are influenced by a number of parameters:
• The minimum supply pressure of the water utility upstream of the PBS (at the water connection point of the house). This is also referred to as SPLN (lowest normal service pressure) in the standard.
• The minimum flow pressure at the hydraulically least favourable consumer point.
• The pressure loss caused by the height difference between the PBS and the highest consumer point (geodetic height difference) downstream and upstream of the PBS.
• The pressure loss of pipe friction and other individual losses downstream and upstream of the PBS.
selecting the right PBS variant and determining the total cost of ownership would go well beyond the scope of this article.
Installing a pressure booster system is linked with stringent legal regulations.
A pressure booster system is required whenever the minimum pressure supplied by the local water provider is insufficient. Pressure booster systems and their ancillary components must be designed and operated in such a way that neither the public water supply nor any other consumer units are interfered with – any degradation in the quality of drinking water must likewise be ruled out.
• The pressure loss of the water meter.
• The pressure losses of any apparatus installed in-between (e.g. filters, dosing equipment, mixing taps, waterfall shower head, etc.) downstream and upstream of the PBS.
For a rough calculation of the peak flow rate the type of building should also be considered: The water-use behaviour in schools is quite different to that in hotels, for example.
Calculating the exact required pressure (head) and flow rate (peak flow rate) downstream of the PBS,
Given the many options for pressure booster systems (cascade control, variable speed control of one or several pumps, direct or indirect connection) it is particularly important to select the right concept as early as possible in the planning phase of a project.
A detailed guide titled ‘Planning Information for Pressure Booster Systems’ is available to download from KSB via the link below. chevron-circle-right
For the transition to high-efficiency, low-carbon buildings, retrofitting outdated heating, cooling and water systems with modern components such as variable speed drives and efficient pumps can offer significant opportunities, as Paul Winnett, Operations Director at Xylem UK, explains.
Retrofitting ageing buildings with high-efficiency pumps and drives offers one of the biggest opportunities to achieve smarter, more efficient buildings. This directly aligns with the International Energy Agency’s (IEA) Net Zero Emissions 2050 roadmap, updated in September 2023, which urges the global energy sector to double existing efforts to improve building efficiency.
Accelerated action will support the UK government’s net zero pathway, given that heating the UK’s 30 million buildings contributes to almost one quarter of all UK emissions. As a result of the Government’s Heat and Building Strategy, businesses across almost every sector are already taking steps to use less energy in response to rising utility bills and to achieve environmental goals.
Across the UK, many buildings, such as office blocks, shopping centres, hospitals, and hotels, were built between 20 and 40 years ago, and many have outdated heating and cooling systems that consume a lot of energy.
Simply replacing ageing equipment like-for-like is not the solution. The Government’s Heat and Building Strategy recognises this, saying: “Decarbonising heat and buildings will require the adoption of new, smarter technologies and practices”.
Widescale programmes to replace old equipment with high-efficiency technology for heating and cooling, as well as water pressure boosting, would accelerate decarbonisation goals and bring older buildings into a net zero world.
One way to significantly reduce the energy consumption of pumped systems is to switch to variable-speed technology. Older pumps typically run at a fixed speed, regardless of demand. Retrofitting with variable-speed drives enables the system to adjust to usage curves.
Due to the advanced technology involved, variable-speed solutions may have higher
upfront capital costs, but these costs will be offset over time by savings on energy bills. In addition, the operational and maintenance costs of variable-speed pumps are generally lower, as they are not running continually and experience less wear and tear.
For large commercial buildings, Xylem’s hydrovar X range of intelligent variablespeed pump drives, with high-efficiency IE5 motors, can cut the power needed to operate a pump by up to 70%. This reduction is achieved by ensuring the pump is only operating at the required speed, linked to the system’s demand variations.
The ability to adjust pump speed will immediately impact the energy consumption of large buildings, such as hotels, where demand for water and heating fluctuates throughout the day.
Take water pressure in a hotel; in a traditional system, the pumps would be on and the pressure constant. With a variable speed drive, the pumps could run at half their speed during periods of low demand, such as lunchtime when fewer people are in their rooms, and increase as guests start checking in and using facilities.
As the evening continues and demand rises, the system will automatically adjust to ensure constant pressure throughout the building. To achieve this, the system takes pressure or flow readings from sensors to adjust the number of pumps running and their speed, ensuring demand is met while maximum operating efficiency is delivered.
Of course, while retrofitting is essential to decarbonise existing buildings, using low-carbon technologies in new builds is a must – the Government’s Future Homes Standard comes into effect in 2025, bringing a set of rules to ensure new homes produce less carbon.
For contractors who are value engineering a project, using cheaper technology may reduce the capital outlay, but if they consider the whole lifecycle of the product, high-end low-carbon technology is likely to be more efficient and deliver the most value because of the significant long-term energy savings. chevron-circle-right
www.xylem.com/en-uk
•
•
•
•
•
•
Full members of the British Pump Manufacturers Association (BPMA) include manufacturers, contractors, distributors, importers, and repairers of industrial pumps, with operations in the UK and Republic of Ireland. Membership is also available to suppliers of pump-specific equipment to pump companies. Associate Membership is available to companies and
ABB Ltd
PHONE 01925 741111 desktop new.abb.com/uk
AESSEAL Plc
PHONE 01709 369 966 desktop www.aesseal.com
Albany Engineering Co. Ltd
PHONE 01594 842275 desktop www.albany-pumps.co.uk
Altecnic Ltd - CALEFFI Group
PHONE 01785 218200 desktop www.altecnic.co.uk
Ambic Equipment Ltd
PHONE 01993 776555 desktop www.ambic.co.uk
Apex Pumps
PHONE 0117 907 7555 desktop www.apexpumps.com
Armstrong Fluid Technology
PHONE 08444 145 145 desktop www.armstrongfluidtechnology. com/en-gb
Atlas Copco Power Technique
PHONE 01442 222 350 desktop www.atlascopco.com/en-uk
Atom Water Pump Solutions Ltd
PHONE 07797 827 044 desktop atom.je
AVT PUMP
PHONE 03303 322101 desktop www.avtpump.com
AxFlow Ltd
PHONE 01753 255600 desktop www.axflow.co.uk
Barnwell Services Ltd
PHONE 0121 429 8011 desktop www.barnwell.co.uk
individuals who work with or supply services to BPMA members, such as industry journals, technology centres, or consultants. BPMA members have agreed to a code of conduct which states that they must demonstrate the highest degree of professionalism, expertise and ethical standards in every aspect of their operations.
Further information about the association’s members can be found on the BPMA website at www.bpma.org.uk/members.
BIP (Oldbury) Ltd
PHONE 0121 544 1555 desktop www.bip.co.uk
BPS Pumps Ltd
PHONE 0121 503 3000 desktop bpspumps.co.uk
British Autogard Ltd (Regal Rexnord)
PHONE 07884 091 307 desktop www.regalrexnord.com/contact
Brook Crompton
PHONE 01484 557200 desktop www.brookcrompton.com
Calpeda
PHONE 01869 241 441 desktop uk.calpeda.com
Campion Pumps
PHONE +353 56 883 4288 desktop www.campion.ie
Caprari Pumps (UK) Ltd
PHONE 01733 371605 desktop www.caprari.com
CELEROS FT - ClydeUnion Pumps
PHONE 0141 637 7141 desktop celerosft.com/clydeunion-pumps
CEMB Hofmann UK Ltd
PHONE 0161 872 3122 desktop www.cembhofmann.co.uk
CHC Group
PHONE 01539 729395 desktop www.chcgroup.co.uk
Chemquip Ltd
PHONE 01663 741753 desktop www.chemquip.co.uk
Combined Pumps Ltd
PHONE 0 1224 724 177 desktop www.combinedpumps.com
DAB Pumps Ltd
PHONE 0333 777 5010 desktop uk.dabpumps.com
Built to last in the UK with lifetime support for every pump
Tel: 01425 627700 Web: www.crestpumps.co.uk
DESMI Ltd
PHONE 01782 566900 desktop www.desmi.com/pumps.aspx
DPS Ltd
PHONE 028 91 818347 desktop dpswater.com
EagleBurgmann Industries UK Ltd PHONE 01926 417600 desktop www.eagleburgmann.com/en
Eastern Seals (UK) Ltd PHONE 01670 840529 desktop www.easternseals.co.uk
EBARA Pumps Europe S.P.A - UK PHONE 01895 439027 desktop www.ebaraeurope.com
ERIKS UK PHONE 0121 508 6000 desktop www.eriks.co.uk
ESPA Pumps (UK) Ltd PHONE 01206 391291 desktop www.espa.com/uk
Euroflo Fluid Handling Ltd PHONE 01892 832144 desktop www.euroflo.com
Exalto Bearings Ltd PHONE 01332 340501 desktop www.exaltouk.com/en
Flowserve PHONE 0161 928 6371 desktop www.flowserve.com
Flowtech Water Solutions Ltd
PHONE 0333 200 1756 desktop www.flowtech.org.uk
Flux Pumps International (UK) Ltd
PHONE 01202 823304 desktop www.flux-pumps.co.uk
G.M.Treble Ltd
PHONE 01902 333 111 desktop trebles.co.uk
GMT Electrical Services Ltd
PHONE 0208 683 0464 desktop www.gmtservices.co.uk
Greene, Tweed & Co Ltd
PHONE 0115 9315 777 desktop www.gtweed.com
Grundfos Pumps Ltd
PHONE 01525 850000 desktop www.grundfos.co.uk
Hayward Tyler PHONE 01582 731144 desktop haywardtyler.com
HMD Kontro Sealless Pumps
PHONE 01323 452000 desktop www.hmdkontro.com
HOSS Engineering
PHONE 0203 601 6075 desktop hossengineering.com
Houghton International Electrical Services Ltd
PHONE 0191 234 3000 desktop www.houghton-international.com
Ingersoll Rand Pumps
PHONE 01159 325 226 desktop www.irco.com/en-gb
ITT Industries UK
PHONE 07585 882916 desktop www.itt.com/home
John Crane
PHONE 0161 872 2484 desktop www.johncrane.com
KGN Pillinger
PHONE 0208 681 0097 desktop kgnpillinger.com
KSB Ltd
PHONE 01509 231 872 desktop www.ksb.co.uk
KTR U.K. Ltd
PHONE 0114 258 7757 desktop www.ktr.com/uk
Lafert Electric Motors Ltd
PHONE 01270 270022 desktop www.lafert.com
LFH Fluid Control Ltd
PHONE 01358 726310 desktop www.lfhfluidcontrol.com
Lincoln Crankshaft & Machine Ltd
PHONE 01522 522 855 desktop www.lcandm.co.uk
M Seals UK Ltd
PHONE 0116 275 4720 desktop www.m-seals.co.uk
March May Ltd.
PHONE 01480 214 444 desktop marchmay.co.uk
Martin Sprocket & Gear UK Ltd
PHONE 01926 962161 desktop www.martinsprocket.com
MDM Pumps Ltd
PHONE 01684 892 678 desktop www.mdmpumps.co.uk
Megator Ltd
PHONE 0191 567 5488 desktop www.megator.com
Metcor Group
PHONE 020 8310 2000 desktop metromech.co.uk
Michael Smith Engineers Ltd
PHONE 01483 771 871 desktop www.michael-smith-engineers.co.uk
MJB Engineering Precision Ltd
PHONE 0161 476 5811 desktop www.mjbengineering.net/
Morgan Advanced Materials
PHONE 01753 837000 desktop www.morganperformancecarbon. com/en-gb
NOV Process & Flow Technologies UK
PHONE 0161 339 9000 desktop www.nov.com/industrial
Patterson Pump Ireland Ltd
PHONE +353 44 9347078 desktop www.ie.pattersonpumps.com
PressBoost Ltd
PHONE 0161 798 5872 desktop www.pressboost.co.uk
Pumps (UK) Ltd
PHONE 01322 292 415 desktop www.pumpsukltd.com
Pumps and Gearboxes Ltd
PHONE 01924 284321 desktop www.pumpsandgearboxes.co.uk
Pumps and Motors UK Ltd
PHONE 0208 507 2288 desktop www.pumpsmotors.co.uk
PumpServ PHONE 020 8337 7249 desktop pumpserv.co.uk
Ram Pumps Ltd
PHONE 01903 206622 desktop www.rampumps.co.uk
Rapid Solutions (International) Ltd
PHONE 01223 841 757 desktop rapid-solutions.net
Rauschert Ltd
PHONE 07984 538 179 desktop rauschert.com/en
Reflex Winkelmann GMBH
PHONE 0161 266 1043 desktop www.reflex.de/en
Roto Pumps Ltd
PHONE 0161 477 5511 desktop www.rotopumps.co.uk
RuhrPumpen
PHONE 01273 956410 desktop www.ruhrpumpen.com
Salamander Pumps
PHONE 0191 516 2002 desktop www.salamanderpumps.co.uk
Seal & Pump Engineering (UK) Ltd
PHONE 01283 512866 desktop www.sealandpump.co.uk
Secure Meters (UK) Ltd
PHONE 01962 840048 desktop www.securemeters.com
Selwood Pump Company Ltd
PHONE 0121 777 5681 desktop selwood-pumps.com
SFA Saniflo UK Ltd
PHONE 020 8842 0033 desktop www.saniflo.co.uk
Siemens DF PD
PHONE 08458 507600 desktop www.siemens.co.uk/drives
SPP Pumps
PHONE 0118 932 3123 desktop www.spppumps.com
SPX Flow Europe Ltd
PHONE 01909 535 054 desktop www.spxflow.com
Stuart Turner Ltd
PHONE 01491 572 655 desktop www.stuart-turner.co.uk
Sulzer Pump Solutions Ireland Ltd
PHONE +353 14 608 888 desktop www.sulzer.com
Super Drain Ltd
PHONE +353 14 097 070 desktop superdrain.ie
TEC Electric Motors Ltd
PHONE 01299 252990 desktop www.tecmotors.co.uk
The Pump Company Ltd
PHONE 01293 533665 desktop www.thepumpco.co.uk
Tomlinson Hall & Co Ltd
PHONE 01642 379500 desktop www.tomlinson-hall.co.uk
TORISHIMA
PHONE 01236 443951 desktop torishima.co.uk
Tsurumi UK Ltd
PHONE 01622 355000 desktop www.tsurumi.co.uk
T-T Pumps Ltd
PHONE 01630 647200 desktop www.ttpumps.com
Tucson Pumps Ltd
PHONE +353 1 842 6255 desktop www.tucsonpumps.ie
Unibloc Hygienic Technologies UK Ltd
PHONE 01444 881 871 desktop unibloctech.com
Viking Pump Hygienic Ltd
PHONE 01323 509 211 desktop www.vikingpump.com
Vogelsang Ltd
PHONE 01270 216 600 desktop www.vogelsang.info/en-uk
Watson-Marlow Fluid Technology
Solutions
PHONE 01326 370 370 desktop www.wmfts.com/en
WEG (UK) Ltd
PHONE 01527 513800 desktop www.weg.net/uk
Weir Minerals Europe Ltd
PHONE 01706 298 476 desktop www.global.weir
Wilo (U.K.) Ltd
PHONE 01283 523000 desktop www.wilo.com/gb/en
Xylem Water Solutions UK Ltd
PHONE 0115 940 0111 desktop www.xylem.com/uk
AEMT (Association of Electrical and Mechanical Trades)
PHONE 01904 674899 desktop www.theaemt.com
BPMA
PHONE 0121 601 6691 desktop www.bpma.org.uk/home
Eurofins E & CML Ltd
PHONE 0151 559 1160 desktop www.cmlex.com
Fluid & Energy Solutions
Consultancy Ltd
PHONE 0207 101 3911 desktop www.fluensys.co.uk
Pump Industry Insight from the BPMA
The only publication exclusively for UK-based users of pumps and pumping systems Sent to 10,220 readers every quarter – in print and online
Advertising: Andrew 07785 290034
Editorial: Chris 01732 358823
Fluid Performance Solutions Ltd
PHONE 07983 744718 desktop www.fluidperformancesolutions. co.uk
HHIC (Heating & Hotwater Industry Council)
PHONE 01926 513777 desktop www.hhic.org.uk
International Data Entry & Access
PHONE 020 7731 7151 desktop www.idea-business-tracker.co.uk
Kiwa Watertec PHONE 01495 308185 desktop www.kiwa.com/gb/en
Rustek PHONE 01582 792709 desktop www.rustek.net
Solutions in IT Ltd
PHONE 0845 009 4588 desktop www.emirsoftware.com
Touchwave Media Ltd
PHONE 07785 290034 desktop www.touchwavemedia.co.uk
World Pumps
PHONE 07967 169154 desktop www.worldpumps.com
YPSEE Ltd
PHONE 07973 833193
For an enhanced entry in the BPMA Member directory, contact Andrew Castle. 07785 290034 andrew@flowmag.co.uk
To make sure you continue to receive your
Choose flow , in print or digital format, and stay up to date with the latest products, technical insights, news and innovations, for the design, specification, installation and management of pumps in:
z Manufacturing
z Construction
z HVAC
z Building services
z Mining
z Utilities
Make UK CEO Stephen Phipson, who recently addressed the Europump annual meeting at the request of the BPMA, explains why his organisation is calling on whoever is in government after the election in July to ensure a modern, long-term industrial policy is announced within the first 100 days.
Manufacturing holds a vital place in the UK economy, contributing £224bn of Gross Value Added in 2023. It’s a major driver of innovation, with 43% of R&D investment stemming from the sector. Notably, it’s a significant contributor to job creation, employing 2.6 million people nationwide. Moreover, manufacturing offers solutions to pressing economic challenges like climate change and the volatility of global supply chains.
This sector is renowned for its high-skill, high-wage nature, boasting average wages 9% higher than the national average. Across the length and breadth of the country, manufacturing businesses of all shapes and sizes are leaving their mark. They’re not just factories churning out goods but are engines of local prosperity, injecting life into communities and driving economies forward. The sector’s heartlands are primarily in rural and regional areas that are often overlooked by the spotlight of London and the Southeast. These companies are the backbone of regions that are eager for growth.
But it’s not just about jobs; it’s about skill-building too. Every year, nearly 50,000 engineering and manufacturing apprenticeships are offered by UK manufacturers, nurturing the next generation of talent and keeping skills alive in communities. They’re not just places of work; they’re the heartbeats of towns, fostering a sense of belonging and opportunity. They attract investment, bring innovation, and shape the identity of the places they call home.
And they’re not stopping there.
Manufacturers have their eyes set on the horizon, aiming to ride the wave of a netzero economy and embrace cutting-edge technologies like AI and digitalisation. Their goal? Nothing short of becoming the most innovative economy on the planet. They’re not content with the status quo; they’re striving for a future where sustainability and prosperity go hand in hand.
The sector has demonstrated resilience and adaptability in recent years, setting the stage for further growth in the future. Ambitious plans aim to boost UK competitiveness by increasing manufacturing’s contribution to GDP from 10% to 15% by the end of the next decade.
Achieving this target would inject an additional £142 billion into the UK economy, fostering longterm domestic and foreign investment.
and that is why Make UK’s manifesto published ahead of the election is calling for a modern, long-term industrial policy to be announced within the first 100 days. The UK is an outlier in not having one, which is the Achilles heel of the UK economy. In particular, this strategy must embrace a skills revolution throughout the education and training system to provide future talent, as well as the upskilling and re-training of the current workforce.
In particular, this strategy must embrace a skills revolution throughout the education and training system.
By 2050, UK manufacturers aim to achieve net-zero emissions, prioritising energy efficiency and industrial innovation every step of the way. We envision a world where every factory operates without a single sheet of paper and where automation fuels productivity and progress. To achieve all of that, we need support that compares to what other countries and governments are giving their manufacturing sectors around funding, regulation and guidance.
As such, we are now at a tipping point,
Such a vision is essential given the huge changes in the policy landscape, the need to shock the UK economy out of its anaemic holding pattern and take advantage of the opportunities provided by rapidly accelerating technologies, investment in infrastructure and the move to a greener economy.
A policy framework for the economy beyond 2030 is also essential to counter the march of the US and China in green technologies in particular, as well as the need to make the UK as attractive a destination as possible for investment, given the rate at which other countries are gearing up.
If the next Government were to commit to delivering such a strategy and make it a cross Government priority then I am confident that the sector can lead the economy into the 2030s and beyond. chevron-circle-right
The BPMA’s annual Pump Industry Awards programme has been recognising and rewarding the achievements of pump businesses, large and small for over two decades. Throughout that time it has become one of the leading events to serve the industrial and commercial arena. So, if you or your company have a pump related success to shout about, these awards provide the perfect platform.
The gala presentation dinner caps off the awards programme in style, providing excellent networking opportunities, great food and superb entertainment. It’s your chance to celebrate with colleagues, interact with peers, entertain customers and be part of the pump industry’s biggest and best celebration. Manufacturing and distribution prowess, product development and application, environmental consideration, skills development and customer support will all be acknowledged through this wide reaching awards programme. So why not consider which of your engineering successes are deserving of industry wide recognition, and be sure to join us at our wonderful venue - the home of English football - on Thursday 13th March 2025.
Dale Croker, BPMA President, says of the Pump Industry Awards, “The pump industry continues to be a hotbed of competitiveness, where the constant search for greater operational performance and improved efficiencies amongst its broad customer base, demands all those operating within this important sector to be at the top of their game. This BPMA backed awards programme allows the pump industry to come together in celebration of that drive for engineering excellence.”
The 2025 entry forms open on the 1st July, so be sure to visit the Pump Industry Awards website to review the award categories and decide which ones you will be entering!
Venue: Hilton at St George’s Park, Burton upon Trent
Date: Thursday 13th March 2025
Nominations Open: 1st July 2024
Nominations Close: 29th November 2024
Judging Session: Mid December 2024
Voting: 13th – 17th January 2025
Winners Announced: 13th March 2025
www.pumpindustryawards.com
www.brookcrompton.com
With over 110 years of technical and design expertise, Brook Crompton offers leading edge energy efficient electric motors across global markets. As the original innovator in electric motor development, Brook Crompton are trusted to power limitless industrial processes and its robust motor design drives fans, pumps, compressors, conveyors and more.
Driven by technology and innovation, Brook Crompton has one of the widest available ranges of electric motors for operation in safe areas, hazardous atmospheres and hostile environments.
The extensive range of stock can be quickly modified to suit customers’ needs and with a high level of technical support from our knowledgeable team we ensure the correct selection of motors is provided for your application.
Brook Crompton’s focus on product and service development ensures we continue to move forward to improve efficiency, offer lower cost of ownership throughout their lifecycle and to reduce environmental impact.