SECTOR FOCUS:
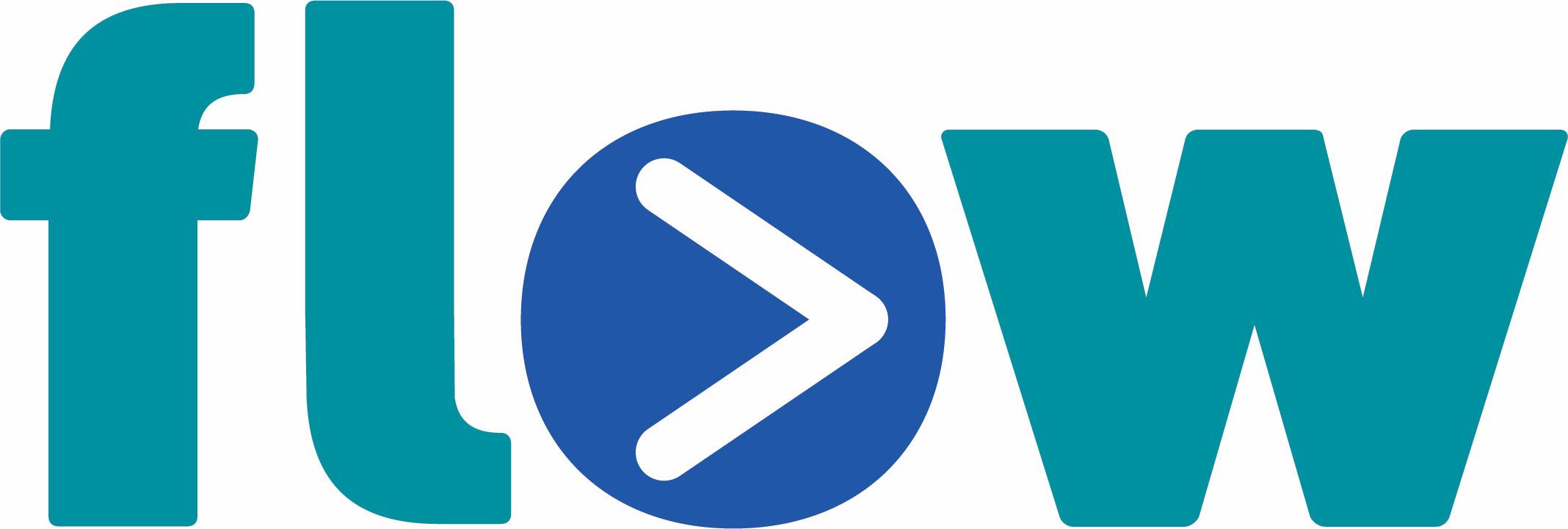
Pump maintenance: can you afford not to?

Pump maintenance: can you afford not to?
In everything we do, we never lose sight of what it‘s all about for you: economical work and easy handling.
Whether chemical substances, oils or media for the food industry, it is important to fill or empty quickly and precisely. Due to the reversible conveying direction, both processes can be carried out with just one pump.
As a result of their compact yet powerful construction, Vogelsang rotary lobe pumps are among the most frequently ordered pumps in many UK industries. They transport highly viscous or aggressive media of all kinds and even pump liquids with rough solids without blocking.
For more information:
sales.uk@vogelsang.info | 01270 216 600
vogelsang.co.uk
Editor Chris Callander chris@flowmag.co.uk
01732 671123
Contributing Editor Suzanne Gill suzanne@flowmag.co.uk
Publisher Andrew Castle andrew@flowmag.co.uk
07785 290034
Accounts
Touchwave Media Ltd accounts@flowmag.co.uk
Production G and C Media Ltd production@flowmag.co.uk
For over three-quarters of a century the British Pump Manufacturers’ Association (BPMA) has been serving the interests of UK and Irish suppliers of liquid pumps and pumping equipment.
In this issue of flow our theme is utilities, water and waste treatment, and we have three in-depth features on this topic.
In England and Wales, the average person used 146 litres of water each day in 2022. Water pipes owned by the water companies totalled more than 347,000km in length in 2021, bringing water to some 25 million homes from more than 1,000 water treatment works. A network of sewage pipes over 571,000km in length then carries away the waste for treatment. And, according to Water UK, this process uses around 3% of the UK’s total energy consumption.
Reducing global energy use is a key focus of efforts to cut carbon emissions, and the high consumption by the water sector offers scope for significant gains. With this in mind, the first feature in our theme looks at how a water utility in Germany has reduced the energy consumption at one of its pumping stations by 15% through an upgrade to the motors and drives running its pumps.
Closer to home, our next feature looks at the high-profile topic of combined sewer overflows. It outlines an innovative approach to catchment management, which, instead of relying on independent pumping stations, focuses on connected sewage pumping stations equipped with intelligent pump control that can maximise overall capacity and minimise the number of overflows.
Our final feature in this section returns to reducing carbon emissions and energy use, sharing how another pumping station providing water to 300,000 residents has reduced its energy consumption by 10%.
This is, of course, just a taste of what the following pages hold, with plenty more news, insights and innovation packed into this issue. I hope you enjoy it.
flow is a controlled circulation journal published quarterly on behalf of the BPMA by Touchwave Media Ltd and G and C Media Ltd. For a copy of the magazine’s terms of control and to request a copy please email circulation@flowmag.co.uk
The content of flow magazine does not necessarily reflect the views of the editor, publishers or the BPMA. The publishers accept no legal responsibility for loss arising from information in this publication and do not endorse any products or processes mentioned within it. No part of this publication may be reproduced or stored in a retrieval system without the publisher’s written consent.
© BPMA. All rights reserved.
THE AES ENGINEERING GROUP HAS made another key acquisition in Australia, providing country-wide coverage as part of the group’s ongoing global growth strategy.
AESSEAL W.A. has been launched following the group’s acquisition of TRISEAL’s operations on the west coast of Australia, making it well placed to serve the important mining and minerals sector and other major industrial customers.
Under the terms of the deal, the AES Engineering Group has acquired all operating assets of the former TRISEAL branches located in Perth and Kalgoorlie, Western Australia. The UK-based group, which owns AESSEAL, the world’s largest homogeneous designer and manufacturer of mechanical seals, will make the entire product and service
portfolio of both AESSEAL and AES Sealing products available to serve the Australian sealing market to the highest global standards.
This move means AESSEAL, also with operations in Queensland and New South Wales, is able to provide a 100% Australia-wide west-to-east and north-to-south product and service support network for all industrial segments in this hugely important marketplace.
David Lauga, former TRISEAL owner and director, said: “This sale allows AESSEAL W.A. to immediately improve its offering to customers for an expanded product range as well as opening up new opportunities in other markets.
Chris Rea, Managing Director of AES
Engineering, said: “This acquisition demonstrates the commitment of the AES Engineering Group to strengthening its already well-established position as a leading sealing technology provider in the global market and builds on its existing business in Australia, reinforcing its position as a recognised leader in the supply of reliability products and services to all customers.”
Armstrong Fluid Technology has relocated its sales office from Mannheim, Germany, to a larger site in Frankfurt, to support the company’s European expansion.
Armstrong has had a dedicated European HQ since 2018, following its acquisition of the circulator pump business unit of German-based HALM Circulators. Having outgrown its current site, the company has now moved to larger offices to make possible the next stage in its European expansion. The new Frankfurt office will provide a base for Armstrong’s European team, with the company’s sales, regional sales enablement centre, customer service and service teams all relocating to the site. Its location, close to Frankfurt am Main airport, also provides good
transport links for customers and international colleague visits.
James Chapman, Commercial Director – UK/ CE for Armstrong Fluid Technology, commented: “Europe is a key growth area for Armstrong Fluid Technology, and the establishment of a dedicated resource in 2018 has enabled us to strengthen our support for customers across the region. In addition to continuing to expand our presence in the domestic circulator, commercial HVAC and fire safety markets, we are experiencing increasing demand for Armstrong products in sectors such as district energy and data centre cooling. We very much look forward to welcoming colleagues and customers to our new offices.”
THE MULTINATIONAL WILO GROUP HAS opened a new plant in India. In Kesurdi in the west of the country, a sustainable and ultra-modern high-tech production complex has been built on a 94,000 square metre site. Here, the technology group manufactures premium pump systems for water management in India, the Middle East, Africa and South-east Asia.
Wilo now has 16 main production sites around the world. “We’re pleased to be able to further expand the global Wilo production network with this opening”, said Oliver Hermes, President & CEO of the Wilo Group. “With the new site, we
meet India’s increasing importance in global trade. The expansion of production capacity in India is thus in line with the group’s global ‘region-for-region’ strategy.” With this strategy, Wilo aims to meet
regional customer needs with products manufactured locally.
“In addition, we’re strengthening our presence in India as an attractive employer”, Hermes continued. Wilo is creating around 1,500 direct and indirect jobs with the opening.
The site combines sustainability and innovation. Wilo only used environmentally friendly prefabricated parts for construction. Complex energy management and water treatment systems significantly minimise the plant’s CO2 emissions.
A NORWEGIAN STARTUP HAS ACHIEVED a patent in Norway for ‘a system and a method for circulation of fluids in nonrestrictive manner to elevated containers’, which the company is calling the ‘zero gravity pump’.
According to the company, 0gcs, the system can circulate water to elevated containers by pushing water through two interchanging ‘siphons’ using only energy to oppose friction in the pipes. As only flow velocity and resistance in the pipes influence the energy usage in the technology, 0gcs’s estimates suggest 90% savings in the energy used can be achieved in some circulation system applications, with 50% reductions when compared to existing systems guaranteed. The energy savings possible through this method are, the company says, greater than the energy recovered from the more traditional approach of utilising turbines powered by water falling under gravity.
The company sees significant benefits from its patented technology in a wide range of applications, including datacentres, fisheries and industrial cooling systems.
The system, which includes a motor
RUHRPUMPEN HAS ANNOUNCED THAT ITS UK fire-water pump manufacturing facility has achieved FM and UL approval as a manufacturer and packager.
For duties up to 3500 USGPM (800m 3/hr), the facility can manufacture, test, and service fire-water packages with diesel engine and electric motor drivers. NFPA compliant, the systems can be supplied with listed controllers, fuel tanks, relief valves, batteries, starters, and waste cones. Much larger capacities and containerised fire-water pumping systems are available from any of RuhrPumpen’s four global manufacturing facilities. EN12845 compliance is also available.
Importantly, the facility is an established manufacturer of mechanical sealed and magnetically-driven sealless chemical pumps in accordance with the industrial and oil & gas standards ISO5199/2858/15783, ANSIB73.1/73.3, and API685/674, ATEX. Other pumps manufactured and supplied from this high-end facility include EN733 end-suction, VTP/ VSP vertical, double-suction horizontal split case, and positive displacement plunger pumps. The company’s water pumps also comply with the ECO-Design directive 2009/125/EC.
With a huge amount of strategic stock held on site, the UK manufacturing facility is equipped to supply the UK, European, and Central Asian industrial process markets with pump systems, bare-shaft replacements, and after-market services.
and a control-system cabinet for the control and monitoring of the pump and valves, is available for pre-order on the company’s website, 0gcs.com, and the company is also interested in talking to potential investors.
2 WEEKS
Established in 1945, the British Pump Manufacturers Association (BPMA), which represents the business interests of UK and Irish suppliers of liquid pumps and pump-related equipment, has enjoyed further membership growth in recent weeks, with four new members joining the Association.
The first of these is Jerseybased Atom Water Pump Solutions (atom.je), a relatively young company that now comprehensively services the needs and requirements of customers throughout the Channel Islands. With a focus on providing cost-effective and reliable solutions for all commercial and domestic applications, its core business is the installation, commissioning, maintenance and sales of booster sets, circulators and pressurisation systems. However, the company also supplies and commissions pumps and pumping equipment across a range of installations, including schools, hospitals, leisure centres, hotels and tourist attractions. It is an authorised agent for many of the leading pump manufacturers, including Lowara, DAB, Calpeda, Caprari, Grundfos, Wilo, ESPA and Stuart Turner. Also recognising the benefits of BPMA membership is Irish pump manufacturer, Tuscan Pumps (www.tucsonpumps. ie). Established in 2005, it has gone from strength to strength and is now one of Ireland’s leading pump brands for domestic
dwelling and light commercial pumping applications. Continuously developing and expanding its product offering, the company strives to provide innovative, affordable, and reliable products for its installer customer base.
Operating from its base in Dublin, the Tucson Pumps range currently consists of energy-efficient circulator pumps, booster pumps, SubPro submersible pumps, Equinox shower pumps, and various pumping accessories.
The third company to recently join the BPMA is the UK arm of Vogelsang (www. vogelsang.info/en-uk), the German manufacturer which uses cutting-edge technology to develop, produce and distribute highly engineered equipment to the agricultural, biogas, industrial, transportation and wastewater sectors. Founded in 1929 as a manufacturer of agricultural machinery, the company has grown to become a specialist in individually configurable machines, plant and equipment, along with their associated systems. As one of the leading producers
of positive displacement pumps, Vogelsang offers customers a variety of application-oriented solutions, including rotary lobe pumps, progressive cavity pumps and centrifugal pumps.
Based in the West Midlands, BIP (Oldbury) Ltd (www.bip.co.uk) completes the quartet of new members. A leading manufacturer of solvent and water-based polyurethane resins, the company’s success derives from its technical expertise, service and eagerness to work to mutually beneficial long-term partnerships. The BIP identity reflects an ongoing commitment to adding value for its customers. The origins of the business date back to 1894, and since that time, it has enjoyed a long and successful history as a chemicals manufacturer with an excellent reputation among its prestigious customer base.
Commenting on these latest additions to the membership, Wayne Rose, BPMA Director and CEO, said: “I am delighted to welcome these four quite diverse companies into the Association and make available to them all that the organisation has to offer. It’s heartening to know, especially during these somewhat challenging economic times, that the commercial benefits associated with BPMA membership are still very much valued by an ever-growing number of pump-related businesses.”
Grundfos Machine Health:
Want to achieve a significant reduction in unforeseen downtime, optimise your maintenance practices and tasks, and avoid significant production losses? With a cloud-based AI-driven machine learning solution for predictive maintenance of your rotating equipment, you can:
• Detect faults and anomalies
• Get real-time perspective outcomes
• Extend asset lifetime
• Improve the efficiency and longevity of rotating assets
• Shift from time-based maintenance to predictive maintenance
Let us show you how Grundfos Machine Health ensures machine reliability in your industrial production or utility, reduces downtime, increases longevity of assets and optimises production across operations.
Get in touch and find out more:
Cathy Mathiesen, +4552327739, cmathiesen@grundfos.com product-selection.grundfos.com/products/grundfos-machine-health
For more information call 01642 379500
6.5 YEARS
PUMP MANUFACTURER, VOGELSANG has launched its new Automatic Supply Unit (ASU), a supply system designed to cut pump operating costs.
The new Automatic Supply Unit has been developed by Vogelsang’s engineering team in Germany to keep mechanical seals in rotary lobe pumps running for longer and increasing the service life by 1.5 times, reducing the frequency of changing the seals by as much as 33%.
Whilst conventional supply systems are essential to keep the lubricant in a mechanical seal at a constant level and maintain the pressure in its buffer chamber, they can consist of a large number of parts that require additional installation space. Vogelsang’s new ASU is much smaller than previous designs, requiring much less installation space.
Jonathan Gutteridge, Managing Director of Vogelsang Ltd, said: “Pumps obviously play a vital role in so many industries, and plant operators will know how frustrating downtime is when pumps need repairs or maintenance work.
“Our team has created this new unit to significantly lower pump operating costs by extending the life of the mechanical seals, reducing the amount of new seals needed and resulting in less stoppage for
maintenance work.”
The patented system, which is a similar size to a drinks can, consists of a reciprocating piston pump that pumps the buffer medium into the chamber with every revolution. In this way, the chamber pressure is kept constant at either 2.0 or 4.3 bar.
vogelsang.info
CONTROLS AND AUTOMATION
specialist, Carlo Gavazzi has launched the RVBS variable frequency drive for speed control applications such as pumps, fans, conveyors, compressors and HVAC systems of up to 0.75kW.
The open board design is available in 0.55kW (2.7 Arms) and 0.75kW (5 Arms) versions, providing a compact solution that especially suits electrical panels where a space-optimised design is essential. Minimal set-up and push-in connectors make for a more simplified, faster and more reliable installation time.
The fanless design increases reliability
in harsh environments and is equipped with optimised features to control the speed of the 3-phase compressors with an induction motor via its two digital inputs and one analogue input; the RVBS
offers a flexible configuration to adapt to varied application needs.
The RVBS can be configured via the configuration software, an optional remote keypad or a PLC, providing increased operational flexibility.
Utilising the built-in Modbus RTU communication port facilitates integration with an automation system and/or PLC, allowing real-time status monitoring and data exchange of motor variables.
www.carlogavazzi.co.uk
PUMP SYSTEMS SPECIALIST, CALPEDA has launched a new line of swimming pool pumps, the I-MPC, which utilise the company’s Mèta technology.
A range of self-priming swimming pool pumps with integrated frequency converters, I-MPC pumps adapt to the demands of the system, giving a calibrated energy consumption that is neither higher nor lower than the needs of the user’s swimming pool.
The optimal balance between energy efficiency and filtering capacity can be reached by adjusting the speed and the
flow rate. Four different speed curves are available, which ensures that the energy consumption is much lower than that of traditional swimming pool pumps. Alternatively, if set with one of the four
pump curves, the pump independently adjusts the speed according to the filtration requirements. In this way, the water quality will always be perfect and performance top-of-the-line, but at a competitive cost.
Adjusting the speed also has a positive effect on the noise generated and, consequently, on the general comfort level of the swimming pool.
www.calpeda.com
THE KSB GROUP HAS LAUNCHED A new generation of pneumatic 90° quarterturn actuators. The double-acting and single-acting pneumatic actuators of the ACTAIR EVO and DYNACTAIR EVO series are designed for actuating all types of part-turn valves, such as butterfly valves, ball valves and plug valves.
Applications covered by the actuators are water treatment, wastewater treatment, power generation, general industry, refinery engineering and shipbuilding.
The double-piston actuators can be operated with compressed air to ISO 8573-1 from 3 to 8 bar. The maximum torque is 8000Nm for the double-acting type series and 4000Nm for the singleacting variant. The maximum ambient temperatures should be between -50 and +150 °C.
With their IP68 enclosure, the actuators are suitable for use in a maritime environment. This means that in the event of flooding they will remain water-
tight for about 169 hours at a depth of up to 30m.
The pneumatic connections comply with NAMUR requirements. For mounting the necessary control units, every actuator is designed with interfaces to the VDI/VDE 3845 standards. Connection to the valve is via an ISO mounting interface to ISO 5211. The scotch yoke mechanism of these pneumatic actuators provides a variable torque, with the peak torque being effective for closing the valve.
As standard, the actuator is fitted with a position indicator and adjustable mechanical stops. The actuators are lubricated with silicone-free grease at the factory;
THE NEW SOLARPLEX solar water pump from Impact Pumps is the culmination of extensive research, engineering expertise, and a commitment to innovation. The pump harnesses the power of solar energy to provide an environmentally friendly and sustainable means of pumping water. By leveraging the abundant energy of the sun, the SolarPlex pump eliminates the need for grid electricity or diesel generators, making it an ideal choice for off-grid and remote locations.
SolarPlex allows farmers and smallholder communities to lift water up to 75m and distribute it at up to 5400l/hr. It meets a need for cost-effective and reliable water for farmers needing to irrigate up to five acres, with sprinklers if required.
The SolarPlex pump can be upgraded in pressure and flow by simply adding more low-cost solar panels, making it the first solar pump to allow users to scale up their daily volume of water to meet significantly increasing demands.
their gear housings are made of anodised aluminium alloy. With their standardised interfaces, the actuators can be connected to higher-level process control systems with solenoid valves, positioners and diverse digital and analogue control units.
£100k ($130,000)
The organisers of the Pump Industry Awards are calling all potential nominees to act early and join those who have already entered the industry’s leading award programme to avoid the last-minute rush when the deadline looms in January 2024.
The BPMA’s annual awards programme has recognised and rewarded the achievements of pump businesses, large and small, for over two decades. Over that time, it has become one of the leading events to serve the industrial and commercial arena.
If you or your company has a pumprelated success to shout about, then this awards programme provides the perfect platform. The closing date for all entries is Friday, January 5, 2024, giving plenty of time to consider, prepare and submit entries. Entering is simple, and putting forward a nomination demonstrates confidence in the quality of an organisation’s work, people, products, and projects.
Maintaining the early Spring timeline and following the success of the 2023 event, the next Gala Dinner and Presentation Ceremony will take place on Thursday, March 14, 2024, at our fantastic new venue – the Hilton at St George’s Park in Burton on Trent.
Situated on the edge of the National Forest, this impressive hotel is part of St. George’s Park – the training ground for all 28 English national football teams – and is recognised the World over as the Home of English Football. Sporting excellence is synonymous with this venue, and early next year, it will once again become the location for heralding engineering excellence across the pump sector.
The online entry forms, which seek submissions for activities and
achievements that took place in the 18 months up to December 2023, will remain on the dedicated awards website – www. pumpindustryawards.com – until the entry deadline of 5.00pm on Friday, January 5, 2024.
The pump sector continues to play a crucial role in ensuring our food production, utilities, manufacturing processes, transportation and other essential services are maintained, and the 2024 awards programme will again give special recognition to those companies and individuals who have gone that extra mile to meet, and more often exceed, the demands and challenges presented by the sectors served.
This recognition and acknowledgement will be represented by eight award categories that collectively honour the full breadth of product and service delivery by the pump industry:
• Product of the Year - Sponsored by DFA Media Group
• Project of the Year - Sponsored by AESSEAL
• Environmental Contribution of the YearSponsored by SPP Pumps
• Manufacturer of the Year - Sponsored by WEG UK
• Distributor of the Year – Sponsorsed by Caprari/Calpeda
• Supplier of the Year - Sponsored by Wilo
• Contribution to Skills & Training –Sponsored by Crest Pumps
Once again, the event has secured the support and backing of a host of leading brands, all of whom recognise the value and importance of promoting excellence across the sector.
In addition to the main category sponsors highlighted above, other sponsorship options also help support specific elements of the 2024 presentation evening.
Several opportunities still exist, so please get in touch if you would like your brand aligned to outstanding engineering achievement.
Wayne Rose, Director and CEO at the British Pump Manufacturers Association, commented: “This year’s awards ceremony – the 22nd such event – was as good as any I can remember. The atmosphere was fantastic, and the competition was intense. Business and professional excellence deserve to be acknowledged and celebrated, and these awards do just that for this most important of sectors. I would therefore encourage all those involved in the pump industry to prepare and submit their entries for the 2024 awards programme.” chevron-circle-right www.pumpindustryawards.com
SPECIALISTS IN DESIGN, MANUFACTURING AND DISTRIBUTION OF SEALS FOR THE GLOBAL MARKETPLACE
High-performance seals for rotary, reciprocating & static applications
All specification, design and manufacture carried out in-house in our 24/7 manufacturing facility
OEM engineered seal design –typically 3-5 days versus 8-10 weeks industry standard
Over £2.5m of semi-finished material and finished sealing products kept in stock
have been pleased by the fast delivery capability of German manufacturer. In early June, Menzel Elektromotoren received two orders for large machines within one week. Due to motor failures, the water supply to 30,000 households was threatened and production in a cement plant was halted. After delivery times of only six and ten days, respectively, both the pump and the cement mill could be restarted in a short time.
Faced with unexpected downtime due to equipment failures, customers often cannot afford to wait for a motor to be manufactured from scratch – standard delivery times in higher output ranges start at six months. Menzel is able to quickly configure motor systems for a wide range of high-output applications from its large, diverse stock of motors, cooling units and ancillary equipment – such as the current two jobs for British customers. The squirrel cage pump motor has a nominal output of
1380kW operating at 3300V. The slipring motor for a cement mill delivers 2000kW at 11kV. Its special features are increased ingress protection rated IP55 and a closed cooling system with a top-mounted air-to-air heat exchanger (cooling type IC 611), ideal for dusty
environments and large temperature fluctuations.
www.menzel-motors.com
Lancashire, a beautiful stone property with stunning views and a brand-new extension to increase the living space; the epitome of domestic bliss for the owners of a home in the hamlet of Grimsagh, which overlooks the Trough of Bowland.
Except for one issue that potentially rendered the extension facilities unusable: With no mains drains servicing the original house, all waste is disposed of via drain pipes to a large drain situated 20m from the property and discharged onwards to a septic tank at the bottom of the garden. However, when it came to the plumbing for the extension, there was simply not enough fall to allow the drainage pipes to reach the existing drain by gravity. With the need to discharge water waste from a new bathroom with shower, two toilets and basins plus a kitchen and washing machine, a solution was needed.
The installer, APG Plumbing and Heating of Leyland, called Saniflo to discuss a possible solution following a meeting at its offices just two months earlier. Recalling the offer of a free site visit for exactly this sort of problem, Howard Chattlee,
owner of APG, met a member of the Saniflo team at the property. A survey was duly conducted, and a solution was proposed; one that wouldn’t be visible to the naked eye but could efficiently pump all waste from the new rooms to the mains drains.
The obvious solution proved to be a Sanifos 110 underground pump, which was subsequently specified by APG and supplied by Andrew Woodruff from a local merchant, Independent Heating and Plumbing, of Bamber Bridge. The unit is an automatic lifting station designed specifically for single dwellings to quietly pump waste away up to 110m horizontally. In this case, the requirement was for a much shorter run of just 20m.
Installed by the APG Plumbing and Heating team in November 2018, the
Sanifos was buried close to the extension and connected to standard 4in waste pipes in the property for incoming waste whilst pumping out of 40mm pipes to the main drain. With 110l capacity, the Sanifos can accept waste from multiple sources in the extension at once and is activated by a float within the unit.
www.saniflo.co.uk
Takes control of guttering rainwater
Gets to grips with grey water from commercial kitchens and bathrooms.
Makes light work of black water from multiple WCs.
You may not see Sanifos at work, but even when drainage is too low for the sewer, this range of powerful lifting stations gets the job done. You can configure Sanifos with a macerator or vortex operation, one pump or two, single-phase or three-phase motors, and choose a capacity from 110 to a huge 3100 litres. So you know that whilst it may be underground, when it comes to waste water, Sanifos is on top of it. See how, at sanifl o.co.uk
PUMP MANUFACTURER AMARINTH has been contracted by John Wood Group to overhaul the three oil containment skid packages managed and operated by Oil Spill Response Limited.
Six years ago, Amarinth supplied ten API 610 OH1 pumps with Plan 53B Seal Support systems to the Subsea Well Response Project for a global containment toolkit that can support subsea well incident response if well shut-in is not immediately possible. The equipment helps contain and quickly remove oil from the sea and offload it into tankers for removal from an incident.
The containment equipment is made available through Oil Spill Response Limited (OSRL) to the international oil and gas industry and is always ready to be deployed anywhere in the world. OSRL is the largest international industry-funded cooperative and exists to respond to oil spills wherever they may occur, providing preparedness, response and intervention services, helping to protect coastlines, wildlife, and communities. OSRL is wholly owned by most of the environmentally responsible oil and gas companies around the globe, and its membership represents the majority of the world’s oil production.
The three skids that form part of the global containment toolkit must always be ready for deployment, which demands a carefully planned overhaul of the skid packages. John Wood Group PLC is tasked with managing this process for OSRL and has contracted Amarinth to undertake the overhaul of the skids based on Amarinth’s ability to deliver reliably and on time against such critical projects.
Amarinth has agreed an overhaul program that will see the three skids, each with three pumps on, come into Amarinth’s facilities in Rendlesham, UK, one by one over a three-month period commencing in June. This ensures that two skid packages are always ready for deployment. Each skid will go through Amarinth’s strip, report and refurbish program. This involves a detailed mechanical and hydraulic assessment of the pumps and the replacement of all important components. Knowledgeable engineers carefully inspect
IN DECEMBER 2005, A MAJOR emergency was announced at one of the UK’s largest oil storage terminals – Buncefield. A faulty high-level alarm had failed, allowing petrol to fill and overflow from a tank; this led to a large explosion and resulting fire that led to nearby evacuations and a five-day firefighting effort.
The Hertfordshire site is currently undergoing a major reconstruction project, building eight tanks for the storage of 65,000m 3 of fuel, with T-T Flow being approached to supply gate valves.
The T-T Flow team supplied five Aquavault DN300 resilient seat gate valves, three with manual handwheel operators and two with bespoke extension spindles to allow for safe remote operation.
Safety is the number one priority
in any project; however, due to the site’s history, sourcing the most dependable equipment was essential. T-T guarantees the reliability of its valves through hydrostatic pressure testing (to EN12266), supported by unique serial numbers that allow for the tracing of each individual valve’s test results.
T-T’s range of resilient seat gate valves are WRAS approved and ideal for effective flow isolation duties within potable, raw and wastewater applications – rated to 16 Bar and with a full clear bore to maximise flow when open.
The Aquavault is designed for guaranteed reliability, with the wedge encapsulated in EPDM rubber to ensure consistent sealing performance and minimise the potential for leaks to occur and a fusion-bonded epoxy
all non-replacement items for wear and to make sure they are within tolerance. The pumps are finally tested at Amarinth’s in-house facility to certify them to the same standards as when they were new, giving peace of mind that they will operate reliably whenever and wherever they are needed until the next planned overhaul.
Online monitoring and intelligent management of the equipment and assset fleet.
The ideal solution for monitoring and increasing the availability of your fleet equipment and assets. Based on cloud computing technology, motors, drives, gearboxes, pumps and compressors can be tracked and monitored at any time and from anywhere in the world. This allows planned and predictive maintenance avoiding costly downtime and ensuring the efficiency and performance of equipment.
Sulzer’s expertise in rotating equipment retrofits and abrasive services has helped a Philippines-based petrochemical plant solve a persistent reliability issue and prepare for a 64% increase in capacity. Critically for the customer, the solution minimised the need for large-scale on-site modifications while extending pump mean-timebetween-failure from less than six weeks to three years.
Located 120km south of the capital, Manila, JG Summit Olefins Corporation’s Batangas Plant is the only naphtha cracker facility in the Philippines. Among other things, it produces ethylene, an essential raw material for the plastics industry. The plant has been in operation since 2014, and rising demand for its products meant that by 2016, the owners were already planning significant capacity upgrades.
However, before those plans could be implemented, the plant’s operators needed to address a critical reliability issue that had emerged during its first years in operation. The Batangas facility uses a proprietary steam cracking technology. In this system, hydrocarbon molecules are broken up at high temperatures in the presence of steam and the resulting product is rapidly cooled to stop the reaction by passing the gas through a heat exchanger and an oil quenching system.
However, this last step was causing concern for the operators. The pumps that moved the quench oil through the system were having issues with the drive end seal barrier pressure dropping and failing frequently, with a mean-time-betweenfailure (MTBF) of less than six weeks. When a pump failed, the whole process had to be shut down, costing the company more than USD 1m a day in lost output.
Looking to address the problem, the company called in pump specialists from Sulzer to examine the failing equipment, which were ‘between bearing single stage’ (BBS) units that featured a single-stage, radially split, between-bearing design. The initial inspection conducted by the Sulzer team revealed damage to several pump components, including the mechanical seals, impeller, and inlet, consistent with operation in a severely abrasive environment.
Further root-cause analysis of the problem by Sulzer’s abrasive services
specialists showed that the culprit was hard carbon coke particles in the oil. Analysis revealed high concentrations of these particles, and many were just large enough (between 75µm and 300µm in diameter) to become trapped between moving and stationary pump components, causing severe wear due to ‘three-body’ abrasion.
Coking is an undesirable but inevitable by-product of the steam cracking process. The build-up of carbon on equipment surfaces leads to a gradual decline in heat transfer efficiency, which in turn accelerates the accumulation of particles. The issue is typically addressed by periodic de-coking of the plant during scheduled shutdowns. The rate of coke accumulation is highly dependent on the characteristics of the hydrocarbon mix being processed; however, in the Batangas plant, this was happening much faster than the designers originally expected.
When Sulzer’s engineers checked the build specifications of the failing quench
oil pumps, they found that they had been designed with the expectation of a less aggressive operating environment. The main hydraulic components were made using S5 steel, a material susceptible to abrasive wear. Based on their experience of demanding process industry applications around the world, the team proposed a targeted package of upgrades designed to dramatically improve the pumps’ durability in the application.
Those changes included the selective replacement of critical pump components with new parts made from high-chromium C6 steel, together with the addition of an abrasion-resistant SUME SA30 coating on the wetted areas, applied using a high-velocity oxygen fuel (HVOF) process. Sulzer’s specialists also made several detailed changes to the pumps’ geometry, including adding large radii on the edges of the wear rings and extended, contoured sleeves to streamline flow in the pump and minimise the turbulence that accelerates wear. Wear ring clearances within the pumps were increased to allow larger coke particles to pass through them. In addition, at the customer’s request, new ports were
also introduced to allow the wear rings to be flushed to remove accumulated particles during pump changeovers.
One benefit of Sulzer’s retrofit proposal was minimal disruption at the plant. The pumps were upgraded and tested at Sulzer’s facilities, ensuring that they could be reinstalled with no major changes to pipework or ancillary equipment. However, to gain even more value from the project, the plant’s management decided to take the opportunity of the retrofit to make other changes designed to pave the way for future capacity increases.
To meet the customer’s request for a 64% capacity increase and 14% pressure increase in the oil quenching system, Sulzer designed new, larger diameter impellers for the existing pumps. Higher-capacity pumps need more power, so the engineering team specified new motors and couplings for the two electrically powered pumps. They also worked with the original equipment manufacturer (OEM) to implement a package of changes to the turbine, which powered a third pump using process steam. The existing motor base plates were retained and adapted to further minimise costs and streamline project speed, with the old mounting points cut off and new ones welded into place. Finally, one additional motordriven pump set was added to the system.
Since the completion of the project, the Batangas plant has been able to put its cracker reliability issues behind it. MTBF for the upgraded pumps is now in line with the three-year specified life. Eliminating excessive wear has improved the system’s operating performance, and the oil quench unit is ready to accommodate planned increases in plant output. chevron-circle-right
www.sulzer.com
Reduce on-site labor time, engineering and installation time and associated costs. Choose a system that arrives on-site in a fully enclosed ready for use pump house. This pre-engineered pumping system saves time and money for our customers.
+353 (0)44 934 7078
company/patterson-pump-ireland-ltd
www.ie.pattersonpumps.com
sales@ie.pattersonpumps.com
Regular pump system maintenance is essential to prevent significant cost and reputational issues. Chris Callander looks at issues that can result from poor pump maintenance, and outlines some of the key steps that can be taken to minimise the chance of them emerging.
Failing to adequately maintain industrial pumps can compromise the safety, efficiency, and longevity of the equipment and the wider systems the pumps are part of. One of the most immediate risks is the failure of the pump itself. Worn-out parts, clogged systems, or misalignments can cause a pump to break down, leading to potentially costly unplanned downtime. In addition, further unnecessary costs can be incurred when a poorly maintained pump consumes more energy to deliver the same output.
Inadequate maintenance can also accelerate the wear and tear of pump components, leading to more frequent parts replacement and higher maintenance costs. And pumps that are not adequately maintained tend to have a shorter operational lifespan, leading to more frequent pump replacements.
Frequent breakdowns, reduced efficiency, and the need for replacement parts can significantly increase operational costs.
Worn-out seals or corroded parts can lead to leakages, resulting in the loss of fluids, environmental contamination, and safety hazards. Without proper lubrication or cooling, pumps can overheat, damaging internal components and reducing their lifespan.
Other issues, such as misalignment or imbalance, can cause excessive vibrations, damaging the pump and its supporting infrastructure. While cavitation, which can be a symptom of poor maintenance, can damage a pump’s impeller and other components as vapour bubbles in the pumped liquid collapse, causing destructive shock waves.
Of course, without regular cleaning, contaminants can enter the pump, affecting the quality of the fluid being pumped and potentially damaging the pump.
Leakages, overheating, and equipment failures can pose safety risks to personnel working around the pumps. This can lead to accidents, injuries, or even fatalities. While leaks or spills due to poor maintenance can also lead to environmental contamination, which
can result in regulatory penalties and damage to a company’s reputation. And for companies that rely on pumps for critical operations, frequent breakdowns or safety incidents can also damage their reputation and customer trust. Indeed, in some industries, ensuring that equipment like pumps are adequately maintained is a regulatory requirement. Failure to comply can lead to financial penalties or legal actions.
Regularly inspecting pumps for signs of wear, damage, or corrosion is essential. This helps identify potential issues before they escalate. Proper lubrication is also vital for the smooth operation of pumps. It is essential to use the correct type of lubricant and to ensure it is applied at the correct intervals.
Regularly checking and replacing worn-out seals is crucial, as is ensuring that cooling systems are working efficiently to prevent overheating.
Vibration can indicate misalignment, imbalance, or other mechanical issues. Regularly monitoring and analysing vibrations can help with the early detection of problems. Ensuring that the pump and its motor are properly aligned is also essential to prevent wear and tear and to ensure efficient operation.
As part of condition monitoring solutions, vibration sensors can now continuously monitor a pumping system to identify vibration-related issues as they emerge, and
other types of sensors can track a pump’s performance and help to identify problems like reduced flow or increased energy consumption. Systems such as these can also monitor the state of bearings to enable them to be replaced as soon as any performance issues are indicated.
Ensuring the maintenance team is well-trained and updated with the latest maintenance practices is crucial. This ensures that they can identify and address issues promptly and are fully up to date with and following necessary safety protocols during maintenance activities to prevent accidents and injuries.
Keeping detailed records of maintenance activities, parts replacements, and performance metrics can help plan future maintenance and identify recurring issues, while having a well-stocked inventory of essential spare parts, which can be informed by historical requirements, can reduce downtime in case of failures. And understanding the expected lifecycle of a pump and planning for eventual replacement or upgrades can help in budgeting and ensuring continuous operations.
Industrial pump maintenance is a comprehensive process that involves a combination of regular checks, timely interventions, and proactive measures to ensure the longevity and efficient operation of the pumps. But it is an essential process to avert the risks that can lead to wideranging consequences which range from increased operational costs to safety hazards and environmental damage. chevron-circle-right
(KUKreg4)
The Kiwa UK Regulation 4 Product Approval Scheme (KUKreg4)a robust method for demonstrating compliance with the Water Supply (Water Fittings) Regulations 1999.
Over 40 years of manufacturing pumps that process harsh and acidic chemicals, Crest Pumps has seen more than its fair share of pumps that have been broken due to mismanagement and misinformation. Here, the company outlines 26 ways to break a pump so you can see if your business is making the same mistakes and take avoiding action.
Relying on reactive maintenance: Too often, pump maintenance is overlooked or forgotten within the maintenance procedures, only carrying out reactive maintenance if the pumps fail, leading to longer process downtime, pump instability and expensive repairs. Instead, schedule biannually or quarterly pump maintenance, including inlet cleaning, corrosion inspection, vibration monitoring and heat maintenance, at the very least to ensure that cavitation or bearing wear is avoided.
Improper bearing fitting: When a bearing is replaced, or the shaft is cleaned, just a tiny fraction of the material on the surface is removed. Over time, a little adds up to a lot and can significantly affect the bearing clearance on the shaft. When this happens, expect the bearings to spin within the housing or on the shaft.
The wrong seals or seal material: Lack of knowledge accounts for the majority of mechanical seal failures. Incorrect mechanical seal installation can lead to seal face damage, heat escalation and ultimately pump failure. Discuss the type of chemicals you are processing and the type of mechanical seal you need with the pump manufacturer.
Hard-starting: A pump should be eased into pumping with a soft start. With a hard start, the pump tries to pump liquid as soon as it powers on. The pressure inside the pump causes the shaft to deflect towards the lowpressure side, causing the shaft to contact the casing. The misalignment will then cause seal failure. Remember to keep the suction valve wide open.
Not detecting vibration: Vibration can signal that the pump is seriously failing in its process. Vibration can damage wear rings, bushings, impellers and the bolts connecting the pump and motor. Vibration leads to the shortening of the pump’s life by over three-quarters, so it is imperative that if excessive vibration occurs, your engineers take the necessary steps to find the root of the problem.
Improper starting: This can lead the motor to trip and the shaft to twist, causing orbital movement directly related to internal parts contact, seal failure and shortening of the bearing life.
Pumping with a bent shaft can cause vibration, leading to the shortening of the pump’s lifespan. A bent shaft can result from either operating away from the best efficiency point (BEP) or pumping solids in a pump that cannot effectively deal with them.
Solids trapped in the seal housing: When the processed liquid
and abrasives get stuck in the seal housing and aren’t properly flushed out, expect a shortened seal life.
Pump imbalance: This can create structural problems, reduced bearing life, increased vibration and reduced machine life. Vibration is the second biggest cause of pump failure and the largest cause of vibration is pump imbalance.
Using the incorrect tools for installation or repair: This includes practices such as using a hammer to install couplings onto shafts or pipe wrenches for anything other than pipes. Pumps are delicate machines that can crack if struck with a hammer.
Plugged vanes or balance holes: These are caused by blockages from solids that have been pulled into the pump that are too large for the pump capacity. Plugged vanes decrease performance, efficiency, priming issues, impeller imbalance and high vibration, resulting in seal damage.
Incorrect wear rings: A wear ring
separates the high-pressure zones of the pump from the low-pressure zones. When clearances open up, the pump experiences increased slippage, and the high-pressure liquid seeps back into the low-pressure areas, causing a loss in efficiency. When clearances are too tight, on the other hand, the wear ring will cause galling and seizing of the pump.
Entrained vapour: This can be caused by a number of factors: A vortex in the tank, insufficient water source, steam injection or incorrect NPSH conditions. Entrained vapour causes performance loss, wear to the impeller and cutwater, and dry running of the seal due to vapour between the faces.
Pipe strain: This is unwanted pressure or movement in the piping system, causing the pipes to put strain on the pump. It can be caused by improper design or installation, thermal or pressure changes, the lack of or improper design and placement of pipe supports, or process changes.
The likelihood is that the discharge piping is incorrectly or inaccurately installed, creating stress on the pump casing that will detrimentally affect the reliable life of the seal and bearing.
Too little lubricant: This can cause premature bearing failure, causing the bearings to seize and fail the pump.
Too much lubricant: This can also cause problems by retaining heat inside the bearing, causing oil leakages and shortening the pump’s life.
Incorrectly adjusting the impeller: This can lead to increased slippage in the pump, creating more turbulence inside the pump, lowering efficiency and increasing pressure inside the stuffing box.
Poor piping connected to a pump: Like pipe strain, this can cause a pump to underperform. Pipework designed with an immediate invert, bend or ‘U’, can cause trapped air in the system. Designs with an immediate 90° bend before the pump can cause turbulence inside the pump. Both result in suction and cavitational problems for the pump.
Using the wrong sized impeller for the pump: This causes the pump to produce too much or too little flow, running away from the BEP. If the
impeller is too big, the pump motor has to work harder to pump the fluid, eventually causing it to burn out and dramatically shortening the pump’s life. If the impeller is too small, it is unlikely to generate enough flow or head. Again, it’s important to talk to the pump engineers or arrange a site visit to get down to the route of the problem and correctly size the impeller to the operation.
Operating too far to the right of the ‘curve’: Pumps are designed to run at their most efficient point, the BEP, which is shown on a pump’s performance curve. This allows for safe pumping at the most energyefficient point of the duty required.
Running outside of the BEP can reduce efficiency and cause a strained operation on the pump. This can quickly lead to excess recirculation, radial loss, vibration, high seal temperature and vastly lower efficiency.
Improper alignment: This is a serious cause of pump failure. Up to 50% of damage to rotating machinery is directly related to pump misalignment. This means increased vibration, premature seal and bearing failures and increased power consumption. Excessive misalignment can even cause breakage of mounts or pump casings.
It is important to check the alignment of the pump before it is fully operational. Two types of misalignment should be checked for: angular and parallel. At Crest Pumps, we deliver pumps mounted on a base plate and pre-aligned at the factory to ensure that the pump stays properly aligned and protected.
Pumping solids or abrasives: In a pump not set to deal with viscous media or solids can clog and break the pump. If the pump is improperly selected for the application, expect to see a shortened life on nearly all components (casing, impeller, stuffing box, etc.). Users should consult with their pump manufacturer, as many pumps can be designed to fit the exact specifications of an application.
The wrong chemicals for a pump: Pumps are designed for specific chemicals using the most efficient, safe and reliable materials for the desired application. If the pump is then used for a chemical that the pump was not built for, the corrosive properties of the new application can erode the insides of the pump, causing immediate pump failure and a potential spillage, disrupting the process, production line and the area around the pump if there is a leakage.
Operation at shut off: When a discharge valve is partially or entirely closed to manually control the flow, it causes 100% of the input energy to be destructive. This leads very quickly to a build up of pressure and pump failure. Consult the pump manufacturer on how to control or get the optimal head, flow or pressure.
Mechanical seal installation error: Improperly installing the mechanical seal will cause damage to the elastomers (O-rings) as well as a wide variety of other issues. Mechanical seals can be very sensitive as the faces are incredibly flat. Even a small amount of dirt or oil (even from fingerprints) can cause the faces to misalign.
Running dry: Both mechanical seal and magnetic drive centrifugal pumps can suffer from running dry if the pump hasn’t been designed to combat it.
Allowing a pump to dry run can lead to catastrophic pump failure in some circumstances. For a mechanical seal pump, running dry could lead to pump cavitation and, therefore, seal damage. The mechanical seal could also experience thermal shock and, under the right conditions, could shatter within 30 seconds.
With a mag-drive pump, the bearings and shaft can rise in temperature due to the absence of liquid lubrication and subsequently melt the plastic casing. chevron-circle-right
Too little lubricant can cause premature bearing failure.
Pump and valve specialist, KSB, explains how its Omega pumps, supported by the company’s Guard monitoring solution, are helping Spanish farmers identify potential energy savings and better plan the maintenance of their irrigation systems.
Irrigating large areas of agriculture involves the use of vast quantities of water, often at times when temperatures rise, and water can be in short supply. To be wholly effective, irrigation needs a controlled and measured programme that ensures equal distribution and conservation. It also requires strategically located pumping stations and pipeline infrastructure that can be relied upon when called into action.
The Zamora region in the northwest of the province of Castilla y Leon, Spain, is one such example of where agricultural irrigation is an essential part of farming life. Close to the border with Portugal, the region is watered by the Elsa, Tormes and Duero rivers. It is cold in winter and hot in summer, making it necessary to water crops during dry periods. Irrigation normally commences in March and continues throughout the growing season.
In 1953, farmers in the region joined forces to form a cooperative to manage the irrigation of their fields more efficiently. Since then, the Páramo Bajo de León y Zamora, through the Comunidad de Regantes del Páramo Bajo, has been responsible for the centrallyoperated irrigation programme. Today, the cooperative employs a workforce of around 80 and is responsible for coordinating irrigation across 17,000 hectares of agricultural land. This involves large volumes of water and many water pumps.
Conscious of its responsibilities to the environment by optimising its water consumption for irrigation and maintaining its many pumps, in 2021, the Comunidad Regantes del Páramo Bajo commenced a pilot project designed to address these issues. The project was headed up by pump manufacturer KSB Spain, with whom the Comunidad had long ties through the supply and operation of over 100 KSB Omega pumps installed in pumping stations across the region. Between eight and 14 KSB Omega pumps
operate at the different pump stations, with the number depending on the size of the surface areas being irrigated.
When selecting sprinkler systems for irrigation, Comunidad del Páramo Bajo has always opted for the modern, sophisticated technologies offered by Omega pumps. KSB’s durable and energysaving Omega water transfer pump is a horizontal, axially-split volute casing double suction pump. The double-entry impeller compensates the axial forces, so the load on the maintenance-free bearings is minimal. The combination of solid bearing brackets, a short and rigid shaft and pre-loaded bearings guarantees low vibration and extended operating life for the bearings, seals and coupling. Corrosion and abrasion resistant materials also contribute to long service life by providing protection to key components.
Being an axially-split case pump
simplifies maintenance procedures, enabling ready access to all parts for thorough cleaning. The axially-split, singlestage volute casing Omega pump features a double entry radial impeller and is ideally suited to the needs of the pumping stations along the irrigation networks as it provides the best duty point and gives operating efficiency levels of above 86%. The interior of the pump has been specifically designed to transport water with the minimum of flow resistance, a factor that also contributes to energy savings and reduced life-cycle costs.
A characteristic of the Omega is its versatility, which is reflected in the large number of hydraulic selection charts, combinations of materials and shaft seal designs, installation options and flange variants. The drive may be positioned on both the left and right of the pump without additional parts or modifications to the casing being necessary.
The latest variable speed pump and tank innovation from Calpeda
Turnkey Solution
Perfect for environments where a conventional cold water booster set and tank are not possible due to size constraints!
Bespoke Options
Single
Options
Ease of Maintenance
Central to the Comunidad Regantes del Páramo Bajo project was the introduction of KSB’s Guard monitoring system as part of a KSBSupremeServ roll-out strategy in the León and Zamora region. First and foremost, the project was aimed at raising awareness of the many benefits that KSB Guard has to offer. The Guard monitoring solution was considered an ideal complement, with the potential to provide a valuable resource for comparing the status of the pumps at the start of the irrigation period in early March, during the season itself, and when it comes to an end.
KSB Guard is a monitoring system that identifies how pump maintenance and service can be improved by using digitalisation. This monitoring device enables bringing existing pumps into the digital world, even when they are already fully operational. The compact device comprises a sensor unit housing a temperature and a vibration sensor. The vibration sensor has an accuracy of 1kHz and measures in all three axes. The sensor unit is fastened to the pump (KSB or any other make) using industrial adhesive. This type of fastening is generally suitable for all dry-installed pumps and can even be fitted during pump operation.
The second hardware component is a transmission and battery unit, which is connected to the sensor unit with a cable and supplies the sensors with power. This does away with the need to install an additional mains power cable to the sensors at the pump. The batteries have a life of up to five years and are easy to replace.
Using a wireless connection, the data recorded is sent to a gateway, which is the third hardware component. The gateway can be used for up to 20 sensor units, and when fitted with a SIM card it provides the required connection to the mobile phone network. This means the entire communication path has been defined and secured by KSB, minimising time and costs for installation and commissioning.
To access the available information about a pump, the pump only needs to be assigned in the KSB Guard app or web portal, and the nameplate data of the pump and motor need to be entered. If it is a KSB pump and its serial number is entered, the data will be called up from KSB databases and entered automatically. Even in all other cases, entering the data takes no longer than a few minutes and is as easy as filling in an entry screen in an online shop. There
is no further requirement for setting any other parameters. The complete installation and commissioning process is so efficient it is easy to make existing pumps in a plant smart and, with that, fit for the future. After commissioning, a multitude of information becomes accessible in the web portal or app. For the Omega pumps, the KSB serial number gives access, via app or web portal, to additional documents, such as the datasheet or a sectional drawing, so searching for pump information has become a thing of the past. Quickly and easily maintaining and calling up a history file for the pump is also an option. Any maintenance and repair work can be recorded with a few clicks and will then be visible to all those responsible.
Particularly valuable are the status data of the installed pump sets. They are not restricted to the current temperature and mean vibration velocity values, but also show trends. Since measurements are conducted once an hour, or more frequently if needed, data can be examined over time, which enables any changes to the pump status to be identified. Alarm and warning limit values have also been defined for this purpose. If the limit values are reached, an alarm or warning message is triggered. These messages can be received by e-mail or as a push message on a mobile phone or tablet – whichever is most convenient. The limit values can be individually adjusted for each pump using the app or web portal.
Apart from information on the temperature and mean vibration velocity, an operating hours counter, the load profile and the load status of the pump can be displayed. The speed can be derived from the measured vibrations. Initially, this
indicates whether the pump is running or at a standstill. For pumps without a variable speed system, the speed and an algorithm patented by KSB provide the facility to further identify the load condition of the pump, overload, optimum, part load or extreme part load. In this way KSB Guard also helps uncover energy-saving potential and optimise plants accordingly.
KSB Guard’s main benefit is certainly that of monitoring the temperature and vibrations and the associated warning and alarm messages, which help identify a change in pump status at an early stage. This allows an early response before any failures or major damage occurs at the pump. The early-warning system has been tried and tested in many applications.
KSBSupremeServ technicians needed just one day to fully install the system on the pumps used in the trial and set up everything on a technical level. By using the Guard monitoring system on five Omega irrigation pumps, KSB’s objective was to ensure more effective pump maintenance planning. This now allows the experts at Comunidad Regantes del Páramo Bajo to make valid decisions for the following season and plan preventive maintenance work very precisely for specific needs.
Following the success of the pilot project, KSB now has plans to roll out its KSB Guard monitoring solution in other regions of Spain. chevron-circle-right
ABB IE5 SynRM and Drives
Lower losses & engineered for ultra-premium IE5 efficiency
Energy saving with our scalable range of compact, variable speed drives
40% 30% 25%
Replacing legacy motors with SynRM and VSD typically reduces energy bills by up to 25%
ABB’s SynRM helps water companies to save energy and reduce costs, while maintaining productivity and process uptime. As well as achieving best-in-class IE5 efficiency, a SynRM motor and drive package runs more smoothly and quietly for reduced maintenance requirements and a longer lifetime, making it one of the most resilient motors on the market.
To find out more, search for “ABB IE5 SynRM”
The safe, smart and sustainable motor solution for across the water cycle.
From New Orleans to the Netherlands, the world is full of places threatened by flood. And the age-old weapon in the fight – the water pump – continues to get more efficient thanks to the use of variable speed motors and the drives that control them, as drive specialist Control Techniques explains.
The World Health Organization estimates that, between 1998 and 2017, floods affected the lives of over two billion people worldwide. Besides the immediate danger to human life, flooding can devastate agricultural land (frequently located in floodplain territory) and wreak havoc on the structural and infrastructural assets of built-up areas.
And with increasingly intense downpours and rising sea levels, both observed consequences of climate change, severe flooding is expected to become more common in at least the short and medium terms.
Floodwater is, by definition, unpredictable. If its arrival – on a potentially overwhelming scale –follows an extended dry period, pumps that have stood for some time at a standstill need to be activated instantly, powerfully and efficiently to start transferring large volumes of water
(the world’s largest pumping station, outside New Orleans, can move 150,000 gallons of floodwater per second) at
continuously fluctuating flow rates. Different strengths of response to a flood event are achieved in the first instance by varying the number of pumps in action.
Multiple pumps are a must in flood defence systems (even in the smallest designs, a duty pump must have a backup). Distributing work over a greater number of smaller pumps rather than fewer larger ones is the first step towards a safer and more controllable system. Plus, the > 28
Pumps that have stood for some time at a standstill need to be activated instantly.
Smart Site is easy to use on any smartphone or tablet device and requires very little training.
Smart Site reduces the waiting time of documents in transit. All job information is visible at the office as it happens.
Smart Site delivers accuracy. The app captures information as it happens, meaning there is less chance that something important is missed or recorded incorrectly.
Smart Site streamlines the administrative process ensuring that contracted and chargeable work can be completed in a timely fashion and invoiced with complete confidence.
Smart Site stores the history of an asset’s repair and service, so your engineer has all of the detail they need to do the job right first time.
smaller the pump, the less vulnerable it is to stress from problems with floating debris, vortices and trapped air.
After this, variable speed motors are a prerequisite if pumps are to engage with the distinctive dynamics of floodwater behaviour with optimum efficiency.
The direct starting (or stopping) of a floodwater pump is likely to cause water hammer following the abrupt change in flow rate through the pipe. These hydraulic shocks shorten the lifespan of equipment and lead to leaks at joints and burst pipes. Using soft starters or variable frequency drives (VFDs) ensures a gentle acceleration of the pump’s rotation up to rated speed, with VFDs offering the added advantage of fully regulated motor speed after that.
Though desirable in principle, effecting an efficient speed regulation of floodwater pump motors can be a complex affair.
For example, while it makes sense from an energy-consumption point of view for a variable speed motor to run no faster than is strictly called for, pumps and pipes that deal with large volumes of floodwater may, depending on the system’s design, be more or less vulnerable to a build-up of sediment. Systems, where this is a problem, may find that by running at a consistently high speed, sediment build-up is kept to a minimum – as, then, is the corresponding mechanical stress on the motors.
It is important, too, that pumps don’t overdo it. For example, in an area like the Fens around the Great Ouse River, water levels have to be managed to allow for navigation. A balancing act needs to be struck between neither underdraining nor overdraining.
The flood defence system designer must, therefore, carefully work out target water levels in the environment to be protected. These are the collection points for the data that the drives will use to determine motor speed: the higher the water rises above a target level, the faster the pump will work, while the lower the
water falls, the more the pump will slow down. Beyond this, the more programmable the system, the more opportunities exist for different kinds of efficiency. Whether through PLC or integrated proportionalintegral-derivative (PID) technology, pre-set values can be made to change with the calendar so that seasonal variations in water level can be taken into account. And, complementing real-time operations, supervisory control and data acquisition systems (SCADA) may be used to supply information about incoming weather developments.
Centrifugal pumps are favoured in flood defence systems because of their power, simplicity and relatively small size. Thus, thanks to the centrifugal pump and fan affinity laws, there are significant energy savings to be made following motor speed reduction (motor speed cut by 25%, equating to energy consumption decreased by nearly 60%, and so on).
This is important when considering the generally high running costs of a pumping station, some of which still favour diesel engines for economic reasons (though such systems must settle for efficiency levels around only the 20-40% mark).
And so, when it comes to building new (or refitting old) floodwater pumping stations, variable speed electrical systems are generally now also favoured. Besides the standout dividends of controllability,
efficiency and economy, they are also comparatively quiet, which is an important design consideration for systems in more populated environments (and hence, some systems prefer liquid cooling over air cooling of the motors and drives).
As the future demands the marrying of more complex automation with increasingly accessible interfaces, the objective must be for ever more efficient systems. In the context of flood defence, this means ever safer environments.
The Pump Drive F600 from Control Techniques brings reliability to water control management and the most efficient use of energy. Offering the same dedicated pump features and capabilities as the standard models, the F600 has been upgraded to enable customers to use both standard and high IP drives for the same project. Mixing and matching vendors or product feature sets is no longer a headache, making project qualification straightforward. chevron-circle-right
Centrifugal pumps are favoured in flood defence systems because of their power, simplicity and relatively small size.
A comprehensive range of fully automatic and standard dynamic balancing machines for pump manufacturers in the UK:
• Superior horizontal and vertical hard-bearing balancing machines for precision balancing.
• Available with milling or grinding correction.
• Intuitive Windows operating system for ease of use.
• Comprehensive installation, service and support services.
• Wide range of genuine parts for swift availability.
We deliver the most comprehensive range of dynamic balancing machines and services in the UK delivered by our locally based team. This combined with considerable application knowledge gained over many years of operation in pump manufacturing means that whatever your balancing requirement we’ve got you covered.
0161 872 3123 or
By installing IE4 motors controlled by variable frequency drives, from power management specialist Eaton, a water utility in Ausberg, Germany, has reduced energy consumption at one of its pumping stations by around 15%. flow found out how this significant saving was achieved.
The Zweckverband StaudenWasserversorgung supplies around 2.4 million cubic metres of naturally pure drinking water annually. The utility’s waterworks are located in Mittelneufnach, in the Augsburg Western Woods Nature Park, an area of outstanding natural beauty. The utility supplies water to approximately 37,000 people across 21 municipalities. Three water towers with a total capacity of 6,500m³ are required to cover the fluctuating demand, with consumption peaks that are at times extremely high. The water is supplied to households via an extensive system of pipes, totalling around 570 kilometres.
Previously, the utility’s pumping station consumed between two million and two and a half million kilowatt hours of energy to supply around 2.4 million cubic metres of clean drinking water each year. This represented an enormous cost factor for the water utility. Most of the electricity was required to drive the three clean-water pumps, which pump the treated water into the mains while also filling up three water towers.
By today’s standards, the energy consumption was considered very high, a result of the outdated drive technology, which was of a type that is still used in many waterworks today. Conventional electric motors, with a capacity of 55kW each, were used to drive the pumps, while the motors were switched using motor starters. The system’s delivery rate was then gradually increased by switching on the three pumps one after the other. To avoid pressure surges during the start-up phase, a
gate valve was used to regulate the flow rate. During start-up, the gate valve, which controlled the flow to the water supply system, initially remained closed. It only opened slowly once the pump reached its full capacity, so the pressure in the water supply system increased gradually. However, this meant that the pump worked against the closed gate valve during start-up, meaning the energy supplied by the motor could not actually be used to pump water.
From a performance point of view, this drive technology was particularly inefficient because the pumps could not operate at their optimum operating point in the most energy-efficient manner. Because the speed of the pumps could not be changed, the pumps either did not run at all or ran at full power. If no water was needed, a non-return valve prevented the water from being
pushed back from the supply system. During shutdown of the pumps, the gate valves were used to reduce the backflow. Nevertheless, each shutdown resulted in increased wear on the non-return-valve.
In 2018, the water utility made the decision to carry out a comprehensive upgrade of the pumping station to reduce the overall life-cycle costs. Improving the energy efficiency of the system was the main priority. The contract was awarded to Aquatech AG, a specialist in electrical, drive and automation technology, with a focus on water supply systems, wastewater disposal and renewable energy, based in Regen, Germany.
As a first step, Aquatech’s experts replaced the conventional electric motors with more energy-efficient IE4
The energy consumption was considered very high, a result of the outdated drive technology.
www.brookcrompton.com
With over 110 years of technical and design expertise, Brook Crompton offers leading edge energy efficient electric motors across global markets. As the original innovator in electric motor development, Brook Crompton are trusted to power limitless industrial processes and its robust motor design drives fans, pumps, compressors, conveyors and more.
Driven by technology and innovation, Brook Crompton has one of the widest available ranges of electric motors for operation in safe areas, hazardous atmospheres and hostile environments.
The extensive range of stock can be quickly modified to suit customers’ needs and with a high level of technical support from our knowledgeable team we ensure the correct selection of motors is provided for your application.
Brook Crompton’s focus on product and service development ensures we continue to move forward to improve efficiency, offer lower cost of ownership throughout their lifecycle and to reduce environmental impact.
motors. Aquatech also implemented a motor-speed control system that ensures smooth start-up and shutdown and prevents the pumps from working against the valves, which would waste a lot of energy. The motor starters were replaced with PowerXL DG1 variable frequency drives from Eaton. Since Aquatech has been working with Eaton for approximately 30 years, it was familiar with all the advantages of the DG1. The PowerXL drives have been designed for motor control up to the highest efficiency class IE4. Thanks to a unique energy optimisation process, driving motors with the DG1 also consumes between 2 and 10% less energy than conventional frequency inverters.
The rugged and easy-to-operate drives come with internal EMC filters (category C2) for connection to the public grid, and while the standard version is suitable for virtually all applications, a version with IP54 protection is also available. This enabled Aquatech to place the drives directly in the pump room without needing any control cabinet. As such, the drives do not require a separate cooling system, which saves additional energy.
“In addition, commissioning the devices was very simple,” emphasised Markus Huber from Aquatech’s project planning team. For many applications, installers can commission the DG1 right out of the box, without the need for any timeconsuming configuration on site. The user-friendly navigation menu on the five-line LCD display, as well as the self-explanatory type codes and the limited number of standard parameters (18), considerably simplify the commissioning process. In addition, the DG1 drives include a number of communication protocols as standard, meaning they can be directly networked without any additional hardware.
“Thanks to the integrated Ethernet IP interface, we have direct access to the individual drives we installed at Staudenwasser,” said Markus. “This makes it easy to implement remote maintenance and thus to increase the system’s availability.” The pumping station is controlled and monitored using a PLC and a process control
system to which the drives connect via Modbus TCP. All drive parameters can also be monitored via the control system.
The combination of DG1 drives with IE4 motors allows for speedcontrolled operation. During start-up, the pumping capacity increases gradually, avoiding the voltage peaks and pressure surges that often plagued the old system. In fact, this has enabled the waterworks to eliminate the gate valves entirely. With the new system, sudden pressure changes in the water mains are also a thing of the past – thanks to the use of variable frequency drives, which gradually reduce the power output of the pumps. As a result, the non-return valves now close much more gently, which translates into less wear.
What contributed most to reducing the overall operating costs was the fact that the new system allows the pumps to run at their optimum operating point of 42 to 53Hz. The process control system calculates the quantity of water required for filling the water towers and uses this information to determine the required number of pumps, taking into account the flow
rate at their optimum operating point – which translates into significant energy savings compared to the old system.
What’s more, the water treatment process is now also more energyefficient. The well water is aerated using two rotary vane compressors –the added oxygen then binds the iron and manganese particles dissolved in the water, causing them to form flakes that can be filtered out.
Aquatech replaced the conventional 5.5kW compressor drives that were previously used for this purpose with IE4 motors, which are controlled using DG1 drives.
With this solution, Aquatech has implemented a system that optimally coordinates the entire delivery process, from the well through treatment all the way to the water towers.
“All in all, combining IE4 motors with DG1 drives enabled us to reduce the water utility’s energy costs by about 15%. At an average of 5,000 operating hours per year for each drive, this translates into major savings,” concluded Markus. chevron-circle-right
“Combining IE4 motors with DG1 drives enabled us to reduce the water utility’s energy costs by about 15%.”
In the heart of England, Anglian Water manages an intricate sewage system that spans 76,000km of pipes. This vast network collects approximately 1 billion litres of wastewater daily, directing it to 1,134 sewage treatment works through 7,165 pumping stations. Instead of separating wastewater from bathrooms, kitchens, and toilets from rainwater, most of the network combines these flows.
Over the next 25 years, the region expects half a million new homes and an influx of one million more residents. Add to this the looming threats of climate change, with its higher temperatures, unpredictable
rainfall patterns, and rising sea levels, and Anglian Water’s system is under undeniable strain. The sewers, at times, become surcharged or overwhelmed. This can lead to two major issues: either the sewage works can’t handle the excess, resulting in pollution events, or the sewage backs up in the pipes, leading to releases through manholes or, in extreme cases, flooding homes.
Storm overflows, known as
Combined Sewer Overflows (CSOs), have been designed to combat this. These CSOs act as an emergency discharge valve, operating once the flow rate exceeds a certain value at vulnerable locations. However, with the increasing strain on the system, these CSOs operate more frequently than intended, leading to detrimental environmental impacts and subsequent fines.
Historically, the management
Over the next 25 years, the region expects half a million new homes and an influx of one million more residents.
of these systems relied on independent sewage pumping stations with basic pump control. This approach was leading to regular issues in the catchment of Strumpshaw, Norwich. Known as a repeat offender for sewer bottlenecks that affected customers, the region needed an intelligent solution. The question was, what would that solution look like?
Enter the era of smart catchment management. Instead of relying on independent stations, the focus shifted to connected sewage pumping stations equipped with intelligent pump control. This new system integrates PLC control, radar level measurement, flow monitoring, pump speed control, mobile communications, storm weather control, inhibit control, rate of change initiation, and tailored control configurations to ensure that all elements of the wider system are working together. This means that the situation at another station in the catchment may inform the operation of an individual pumping station. This enables, for example, underutilised pumping stations to share the workload with others in the catchment, which may be at risk of becoming overloaded – in turn reducing the overall need to discharge to the river network.
At the heart of this intelligent pump control is Schneider Electric’s AquaMetis system. Drawing inspiration from the words ‘water’ and ‘wisdom’, AquaMetis offers a fully configurable solution that reduces energy and operating expenses, wear on assets, and deployment time. Built on reliable, off-the-shelf modular technology, it can be easily integrated into existing systems. AquaMetis offers a series of pump duty modes, with inbuilt burst main and blockage detection and dry run protection. One of its standout features is the ‘Consented Pass Forward Flow’, which allows for configuration, monitoring, and alarming of the
CSO consents, minimising the instances of discharge into rivers and coastal environments.
Setting up and operating the AquaMetis is intuitive. There’s no need for programming for pump station setup. With a simple ‘power and go’ approach, users can easily access station and pump setup, pump status and operating mode, levels, setpoint control, detailed pump data, alarms, and more.
The results?
Since the system went live in Strumpshaw in October 2022 there have been zero system spills and zero environmental impacts.
Customer satisfaction has soared, operational expenses have been reduced, and countless work hours have been returned to Anglian Water, which the utility can use on other priorities.
Looking to the future, Anglian Water has ambitious plans. It aims to expand this system to other, larger, and more complex catchments. The focus will be on flow control, integrating weather data and forecasting, aiding
treatment works compliance, ensuring whole asset base efficacy, predictive maintenance, energy savings, and wider operational expense savings. There’s even talk of a potential £30 million investment to enhance the highest priority catchments.
Anglian Water’s innovative approach to pumping station and catchment optimisation is a testament to the power of technology and forward-thinking. By embracing smart catchment management and the AquaMetis system, the organisation has addressed current challenges and set the stage for a sustainable future. As we look to the future, it’s clear that with such advancements, we’re well on our way to creating sewage systems that are functional, sustainable, and environmentally conscious. chevron-circle-right
This enables underutilised pumping stations to share the workload with others in the catchment.
The city of Bristol, England, receives nearly half of its drinking water from the River Severn, supplied via the Gloucester and Sharpness Canal. flow discovered how new column pumps from Xylem transport an average of 100 million litres of water daily while reducing energy use and CO2 emissions.
The column pumps at Gloucester Docks are vital for managing water levels in the Gloucester and Sharpness Canal and keeping Bristol’s water supply running. The pumps, however, were reaching the end of their working life and maintaining them had become time-consuming and costly as they needed to be lifted out of their positions and manually inspected.
The Canal & Rivers Trust, responsible for the canal, decided to replace the ageing pumps as part of wider activities to reduce energy consumption and CO2 emissions at the site, and to improve water monitoring. Xylem was tasked with replacing the pumps while minimising disruption to the drinking water supply for 300,000 Bristol residents.
Some of the funding for the project was provided via the People’s Postcode Lottery as part of its Postcode Climate Challenge initiative.
Xylem provided end-to-end support on the project, capturing the site’s specific requirements and selecting the most appropriate pumps and control systems to meet The Canal & Rivers Trust’s needs.
The pump replacement project involved the installation of four new, custom-designed Flygt column pumps at the Gloucester Docks site. The pumps were installed over three phases between 2021 and 2023 to minimise disruption.
Flygt column pumps weigh over three metric tons and can fill an
Olympic-size swimming pool every 21 minutes. Because of this, a 40-metric-ton road crane was needed to install each pump.
“The new Flygt pumps are highly efficient, have a higher level of resilience and have been designed to be easier to maintain, helping their sustainability and giving them a life span of around 20 years,” said Ian Bull, Regional Account Manager, Industry and Infrastructure at Xylem. “They are controlled by a monitoring system so the Trust can continuously manage water levels in the canal.”
Xylem also fitted technology to other equipment in the field to allow for remote monitoring and control of the full system.
Xylem provided The Canal & Rivers Trust with end-to-end project management that utilised the breadth and depth of experience across the company. This allowed for the smooth running of the project and subsequent delivery of the customer’s requirements on time and on budget.
The four Flygt column pumps installed by Xylem can take an average of 100 million litres of water per day from the River Severn to feed the Gloucester and Sharpness Canal, ensuring the water levels at the canal remain stable and drinking water makes its way to Bristol residents.
In addition, C02 emissions have been reduced through the use of energy-efficient motors and upgraded propellers, and the pumps have cut the electricity consumption for the pumping station by around 10%. Since the Trust’s
SCADA software can control the pumps, the need for on-site visits and physical inspections has been reduced, helping the Trust to save on maintenance costs.
“Since 1834, water has been pumped from the Severn into the canal, and these new pumps are the latest exciting step in helping us to continue reducing energy consumption and CO2 emissions while supplying hundreds of millions of litres of water each week,” said Nigel Taylor, Senior Maintenance Engineer from the Canal & River Trust.
“Xylem’s work on this project demonstrated its end-to-end customer offering – from the bespoke design of pumping equipment based on the exact needs of our site, through phased installation and commissioning, and ultimately, its invaluable ongoing post-project service.” chevron-circle-right
22
This international event provides a unique opportunity for the European pump industry to come together to discuss and debate the important issues currently impacting this key manufacturing sector. A comprehensive programme of talks and presentations, combined with a wonderful social programme will deliver a highly focussed and productive business experience for all those attending.
For more information, and to take advantage of the ‘early bird’ discount , please visit the website today. With a limit to the number of delegate places available on this first release, please ensure you book your place by 31 st o ctober 2023
THE ABB ABILITY OPTIMAX ENERGY management system has unlocked efficiency potential at the Schwarzenbruck wastewater treatment plant in Germany, controlling and optimising energy flows.
Treating and processing wastewater to make it safe to return to the watercourse takes a lot of energy. Research has shown that wastewater plants consume up to 3% of global energy output. When connected, state-of-the-art facilities can consume 20-45 kWh per population equivalent (PE) a year. Improving the processes through the latest technologies to increase productivity, reduce energy usage, minimise losses and optimise the use of chemicals, is an integral part of achieving the overall sustainability goals.
In September 2022, the German sewerage association, Schwarzachgruppe, put its energy-intelligent wastewater treatment plant in Schwarzenbruck into operation. The new wastewater treatment plant is an environmental innovation showcase project, which automatically balances energy consumption and production so that an external power supply is required only rarely, or when needed.
Thanks to this energy-intelligent concept, it is estimated that the plant can save about 300 tons of CO2 per year.
ABB Ability energy management and optimisation OPTIMAX is at the heart of this project, enabling energy efficiency potentials to be exploited and existing energy generation and storage options to be networked, controlled and optimised.
These include a hydroelectric power plant in the wastewater treatment plant outlet, photovoltaic solar panels, two combined heat and power plants using the sewage gas, electricity storage in batteries, sewage gas storage, heat storage (hot water storage) and the coupling of the various storage units for the continuous provision of energy (thermal or electrical as required).
In addition, the wastewater treatment plant operates in a grid-serving manner. This
means that some assets at the wastewater treatment plant can be controlled via the OPTIMAX energy management system. In the event of an oversupply of electricity, for example, the battery storage system is charged, and vice versa, the battery storage can be discharged during low production. The solution can calculate the optimum usage of the storage options based on load and production forecasts.
A ROTARY LOBE PUMP MADE BY Börger has helped solve a wastewater processing problem at a textile manufacturer.
Taking effluent from the bleaching process into a storage tank, the Börger pump has to contend with significant fibrous material that also contains elements of hydrogen peroxide and
caustic soda.
When the defined fill level of the wastewater has been reached in the collection tank, the Börger rotary lobe pump automatically conveys the liquid in measured amounts from the collecting tank into the sewage system.
Made of Duplex stainless steel and
equipped with a maintenance-free mechanical seal, the compact Börger rotary lobe pump is very easy to service, requiring only basic tools.
www.boerger.com/en_UK
A COMPREHENSIVE AI-BASED approach to maximise solar photovoltaic (PV) system efficiency for water pumping stations has won Riventa a place as a finalist in the £4M Water Discovery Challenge competition, an 18-month event that brings together a blend of financial and non-financial support to help innovative solutions launch and succeed in the water sector. Riventa’s method of offsetting electricity use on pumping stations by installating solar PV systems, is one of just 20 new cutting-edge solutions to be chosen.
Encouraging bold and ingenious innovation that can help solve the biggest challenges facing the water sector, the Discovery challenge aims to facilitate engagement for suppliers with
water companies, backed by a £200M Innovation Fund that has been established by Ofwat, the Water Services Regulation Authority for England and Wales.
The 20 finalists will initially share £1M in funding, and then, up to ten companies will go on to be awarded up to £450,000 each (as well as additional support), to further develop and test their ideas.
Wayne Rose, Director and CEO at the BPMA, welcomes the Government’s potentially permanent step away from implementing a UK-specific product conformity mark but believes it should have happened long ago.
On behalf of the £1.9 billion UK pump sector, the British Pump Manufacturers Association (BPMA), has welcomed the recent Department of Business and Trade announcement regarding the indefinite extension to the use of CE marking for UK businesses.
The CE (Conformité Européenne) mark is used across Europe to certify that a wide range of items – including pumps and related equipment – meet stringent product safety standards. As a member of the European Union, the UK had for decades adopted the use of this safety marking for products being sold both within the UK and throughout the European continent.
However, as part of a wide range of proposed post-Brexit legislative changes, the Government had planned for this safety marking to be replaced by a new UKCA (UK Conformity Assessed) mark for all goods sold in Great Britain from the end of 2024, a deadline which had already endured several postponements and extensions.
UK businesses and their respective trade organisations have for many years been calling on the authorities to extend the use of the long-established CE mark, explaining that forcing them to meet the new UK rules, which simply duplicate EU product standards, would add a significant and unnecessary cost burden to UK industry. With the UKCA mark not being recognised in the EU and only required for goods sold in Great Britain, manufacturers would have needed to adopt both conformity
protocols for products destined for both marketplaces. Notably, this would have also been the case for all overseas manufacturers wishing to sell products into the UK – with the potential risk of a wide range of products becoming unavailable.
At the BPMA, we have been key among this growing voice of objection, having pushed for the retention of the CE Mark from the moment a UK replacement had been suggested. Our pump manufacturing members have always been at the forefront of technology adoption whilst seeking improvement gains for both sustainability and energy efficiency. They have also led the way in developing the current European safety standards, so we welcome this decision by the Department of Business & Trade as a common sense and pragmatic approach to assisting UK Industry.
What is frustrating, though, is that some of our members have already endured the unwelcomed expense and bureaucracy of dual safety mark adoption, to be prepared to continue selling the same products to the same markets when the new mark was mandatory, so although they too will welcome this announcement, a good deal of wasted time, effort and cost has already been expended. I dread to think how much money could have been saved across Government and industry had this frankly inevitable decision been made
some time ago, or had the UKCA mark never been dreamt up. However, despite the political use of the term ‘indefinite extension’ rather than simply the abandonment, I know the BPMA membership, along with many other manufacturers, will be relieved that the cliff-edge deadline of UKCA mark adoption has been removed and that they can now redirect their efforts into product innovation and business growth. chevron-circle-right
“What is frustrating, though, is that some of our members have already endured the unwelcomed expense and bureaucracy of dual safety mark adoption.”
The BPMA’s annual Pump Industry Awards programme has been recognising and rewarding the achievements of pump businesses, large and small for over two decades. Throughout that time it has become one of the leading events to serve the industrial and commercial arena. So, if you or your company have a pump related success to shout about, these awards provide the perfect platform.
The gala presentation dinner caps off the awards programme in style, providing excellent networking opportunities, great food and superb entertainment. It’s your chance to celebrate with colleagues, interact with peers, entertain customers and be part of the pump industry’s biggest and best celebration. Manufacturing and distribution prowess, product development and application, environmental consideration, skills development and customer support will all be acknowledged through this wide reaching awards programme. So why not consider which of your engineering successes are deserving of industry wide recognition, and be sure to join us at our wonderful venue - the home of English football - on Thursday 14th March 2024.
Event Calendar
Nominations Open : 1 st August 2023
Nominations Close : 5 th January 2024
Judging Session : Mid-January 2024
Voting : 12 th -16 th February 2024
Winners Announced : 14 th March 2024
Venue: Hilton at St George’s Park, Burton upon Trent
Date: Thursday 14th March 2024
The 2024 entry forms open on the 1st August, so be sure to visit the Pump Industry Awards website to review the award categories and decide which ones you will be entering!
Dale Croker, BPMA President, says of the Pump Industry Awards, “The pump industry continues to be a hotbed of competitiveness, where the constant search for greater operational performance and improved efficiencies amongst its broad customer base, demands all those operating within this important sector to be at the top of their game. This BPMA backed awards programme allows the pump industry to come together in celebration of that drive for engineering excellence.”
www.pumpindustryawards.com
The NEW Aquaboost iBolt and iMatic range of high flow, high head, cold water pressure and flow boosting solutions. Designed to optimise space and provide a very quiet, simple to install solution for domestic and commercial applications.