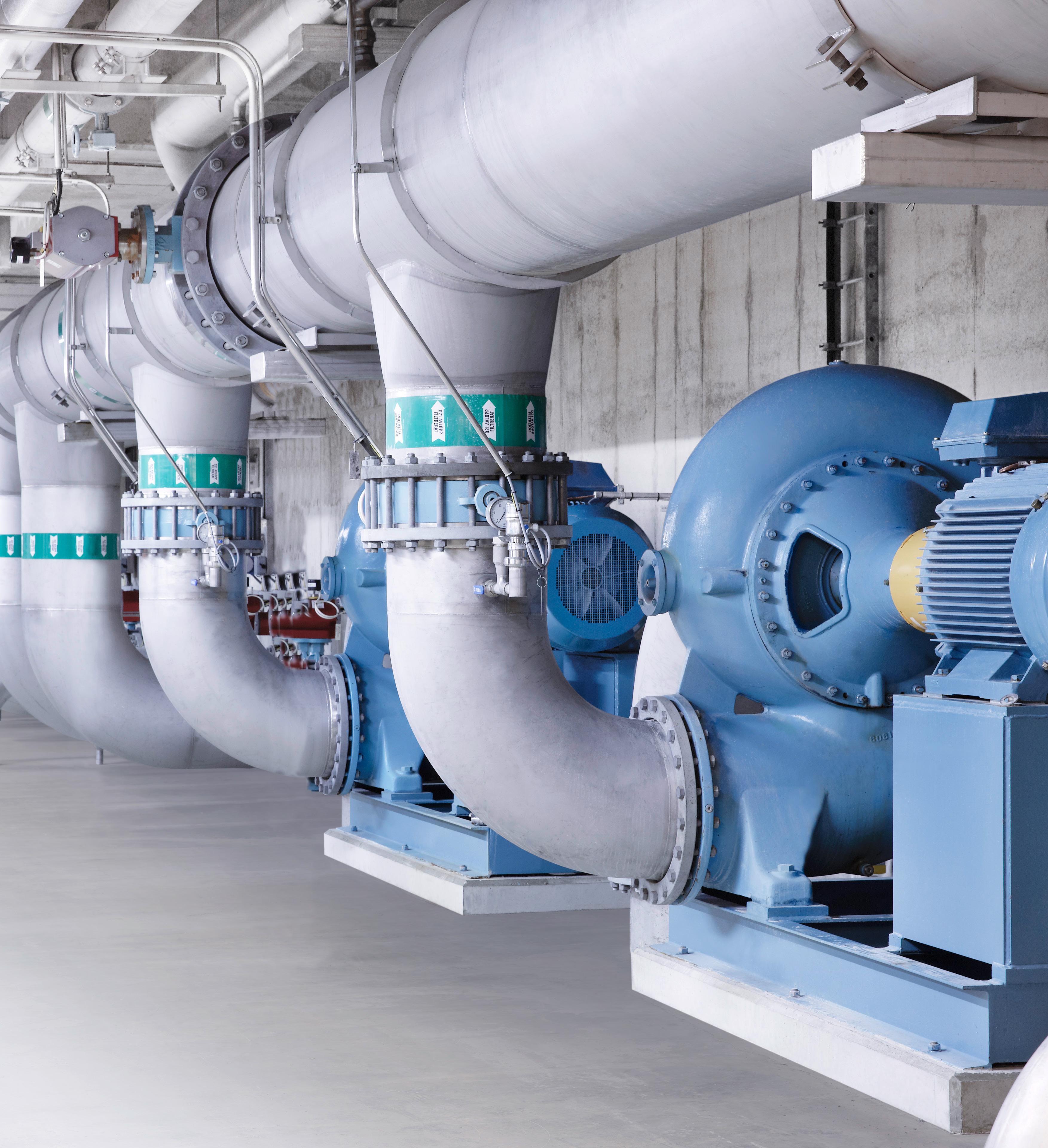
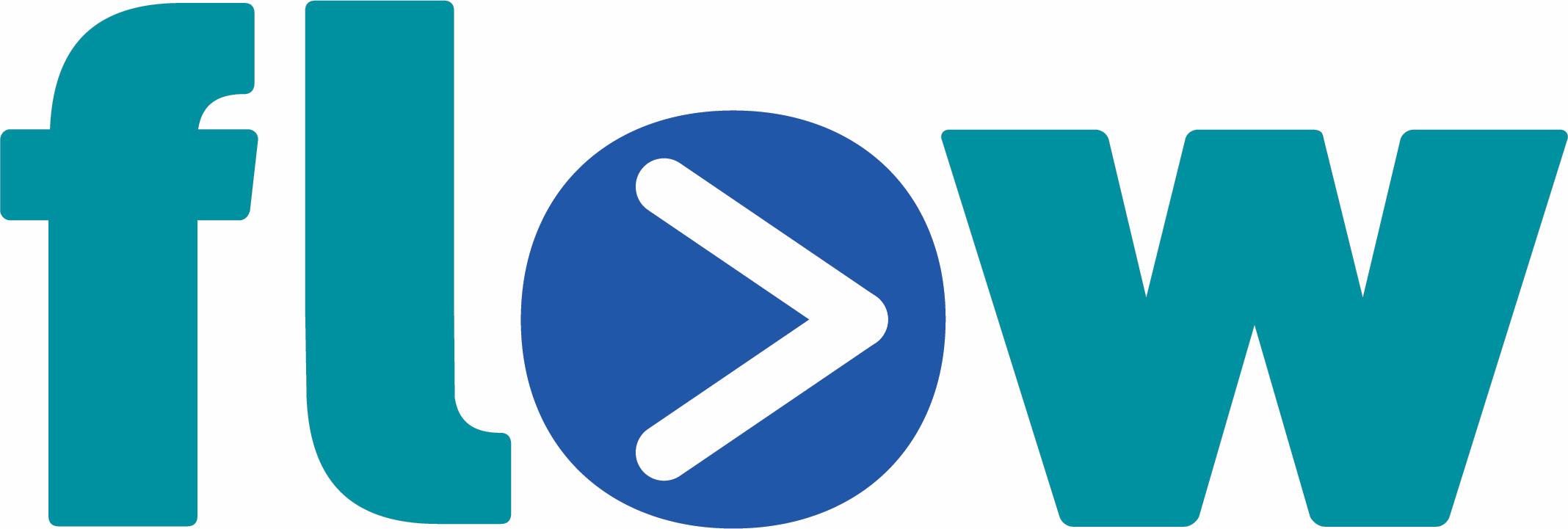
The NEW Aquaboost iBolt and iMatic range of high flow, high head, cold water pressure and flow boosting solutions. Designed to optimise space and provide a very quiet, simple to install solution for domestic and commercial applications.
Editor
Chris Callander
chris@flowmag.co.uk 01732 671123
Contributing Editor
Suzanne Gill suzanne@flowmag.co.uk
Publisher
Andrew Castle andrew@flowmag.co.uk 07785 290034
Accounts
accounts@flowmag.co.uk
I’m delighted to be writing this, my first introduction to Flow magazine as the newly appointed President of the British Pump Manufacturers Association (BPMA).
Being appointed as President of the BPMA is a privilege, and I look forward to working with the BPMA staff and members as we navigate our way through a very strange and challenging time here in the UK. It’s no surprise that ongoing economic and political turmoil continues to present obstacles and uncertainty in the pump market, making the BPMA’s role as a support for its members more relevant than ever.
We have a number of uncertainties affecting the pump sector, from supply-chain issues and ongoing skills shortages to the rising cost of energy, the changing legislative landscape, and the onset of a recession.
Through these times of change, the Association will continue its mission to influence the pump sector business environment in the interests of members’ competitiveness and sustainability and to increase sector awareness by providing technical support and pump technology training to members, operators and purchasers of pumping equipment. All of which will go on to benefit you, our member’s customers.
Having spent the last two years as Vice President of the Association, I have worked closely with outgoing President, Richard Harden. I have seen the dedication and commitment he has given to the role and I am determined to carry on his good work. I am enormously grateful to Richard for all that he has done for the BPMA during his Presidency and am delighted that he will continue to support the Association as a Member of its Council.
This issue of Flow is packed with news and insights, many addressing the challenges I have already outlined. If there are any topics you would like to see in future issues of the magazine, please let us know; you can email the editor at chris@flowmag.co.uk
flow is a controlled circulation journal published quarterly on behalf of the BPMA by Touchwave Media Ltd and G and C Media Ltd. For a copy of the magazine’s terms of control and to request a copy please email circulation@flowmag.co.uk
The content of flow magazine does not necessarily reflect the views of the editor, publishers or the BPMA. The publishers accept no legal responsibility for loss arising from information in this publication and do not endorse any products or processes mentioned within it. No part of this publication may be reproduced or stored in a retrieval system without the publisher’s written consent.
© BPMA. All rights reserved.
BUSINESS SECRETARY, GRANT SHAPPS has announced that businesses will be given an additional two years to apply new product safety marking, giving thousands of businesses the freedom to focus on growth.
The UK Conformity Assessed (UKCA) marking has been introduced as part of the UK’s own robust regulatory framework. It shows that products comply with our product safety regulations which are designed to protect consumers.
However, given the difficult economic conditions created by post-pandemic shifts in demand and supply, alongside Putin’s war in Ukraine and the associated high energy prices, the government says it does not want to burden businesses with the requirement to meet the original (31 December 2022) deadline.
The government will continue to
recognise the CE marking for two years, therefore allowing businesses until 31 December 2024 to prepare for the UKCA marking. Businesses can also use the UKCA marking, giving them flexibility to choose which marking to apply.
Commenting on the announcement, Shapps, said: The government is determined to remove barriers to businesses so they can get on with their top priorities, like providing quality customer service, enabling growth and supporting their staff.
“This move will give businesses the breathing space and flexibility they need at this crucial time and ensure that our future system for product safety marking is fit for purpose, providing the highest standard for consumers without harming businesses.
“To support manufacturers, the
PACKAGED PUMPS SYSTEMS HAS LAUNCHED AN E-Team of engineers who will travel to service call outs on e-bikes.
The team is made up of two engineers who will travel around London’s Zone 1 on their e-bikes, supported by an engineering supervisor in an electric van who will deliver additional parts, but also be on hand to support on certain jobs.
The initiative means that the engineers will be able to undertake approximately 50% more jobs in a day by reducing the amount of time they spend travelling, leading to an even better customer experience.
The introduction of e-cargo bikes will have an immediate impact on reducing carbon emissions, as well as a reduction in congestion and noise.
It’s estimated that the project will save over £15,000 a year in fuel costs per engineer, as the e-cargo bikes replace diesel vans.
That means each E-Team engineer will be using 8,000 fewer litres of fuel per year (160 litres every week) – giving a significant reduction in emissions. The engineers have also completed a course on how to use the bikes safely.
“Feedback
government is also reviewing the wider product safety framework, ensuring we minimise the burdens on business while keeping our system up to date with new innovative methods such as e-labelling.
“As part of this, the government will make it easier than ever for businesses to apply product markings.”
The government says that this package will give thousands of businesses additional time to focus on delivering growth and creating jobs while giving them flexibility in how they meet their legal obligations.
There will be different rules for medical devices, construction products, cableways, transportable pressure equipment, unmanned aircraft systems, rail products, and marine equipment. Government departments responsible for these sectors are making sector-specific arrangements.
and reliability company, AESSEAL has created a new £500,000 AESSEAL Lieutenancy Fund, which will be administered by the South Yorkshire Community Foundation.
The new fund adds to the £1.8 million already committed by AESSEAL plc to support charities in South Yorkshire, bringing the company’s support for the Foundation to £2.3 million.
The company, which has its global headquarters in Rotherham, says that during the pandemic it was able to target support to local charities who were in great need, based upon feedback from the unique network of local Deputy Lieutenants, who assist the region’s Lord-Lieutenant in representing His Majesty the King.
Chris Rea, the Managing Director of AESSEAL plc said: “The purpose of the fund is to reach into the community and support
local organisations that do not have a national voice and many of which are run by a large number of unpaid volunteers. Deputy Lieutenants, who are all also volunteers, often have in-depth knowledge of local needs that would otherwise go unnoticed.”
This is the third charitable fund administered by the South Yorkshire Community Foundation on behalf of AESSEAL plc.
THE LATEST IN A SERIES OF acquisitions for Stuart Turner, a manufacturer of residential and commercial pumps and water-boosting products, sees the company acquire Aquatronic Group Management (AGM), a provider of cold-water boosting installation and maintenance equipment and services in the UK.
Stuart Turner supplies water-boosting products that manage water pressure in residential and commercial/industrial applications. These range from domestic shower pumps, where the company’s Monsoon product is the UK market leader, to bespoke systems that combine coldwater boosting, pressurisation units and circulators to manage hot and cold water supply in commercial buildings and for industrial purposes.
Based in Colchester, AGM designs and manufactures pressurisation and water booster units and installs and maintains
fresh and waste-water pump systems. The company offers a nationwide service from its Manchester, Colchester and Southampton centres.
This complementary acquisition not only expands the overall product range offered by Stuart Turner but also brings a hugely important servicing capability into the business. It supports the strategy to transform the company into the leading provider of water-boosting solutions and services in the UK.
Commenting on this latest purchase, Richard Harden, Stuart Turner’s Chief Executive, said: “AGM is a great fit for our product portfolio and gives us immediate access to the services market, which is seen as a significant area of growth for the company. The team at AGM have established a fantastic reputation for both service and technical capability, and we look forward to welcoming them into the Stuart Turner family.”
BECKER UK HAS ANNOUNCED A PARTNERSHIP WITH Samoa, offering its customers access to a wide range of high-quality, pneumatically driven air-operated double diaphragm pumps (AODD) for fluid handling applications. Samoa’s air-operated pumps offer high levels of air efficiency, wearfree valve technology and ATEX certification alongside a range of additional features. The pumps can also be connected with local PLC/SCADA/U-Pump systems for automatic and real-time pump remote control, monitoring and feedback.
Becker UK has also announced a partnership with NITTO KOHKI, which sees the Japanese manufacturer’s liquid diaphragm pumps added to the Yorkshire-based company’s portfolio, alongside a range of air compressors and vacuum pumps.
Both Samoa and NITTO KOHKI are family-run and owned businesses, as is Becker UK. The three organisations’ shared values make the partnerships an ideal fit.
WILO’S SMART FACTORY AT THE company’s headquarters in Dortmund has been awarded ‘Factory of the Year 2022’.
The award’s organisers, A.T. Kearney and SV Veranstaltungen, recognise specifically used digitalisation solutions that have significantly increased the efficiency of the new production within a very short period of time.
According to the jury, the new factory in Dortmund is setting standards in digitalisation and sustainability. Among other things, the jury also recognised the company’s hydrogen strategy.
NOVEMBER THIS YEAR SAW THE BPMA’s annual AGM take place at Wychwood Park Hotel in Crewe. The event was well attended, with the many delegates at the hotel joined by several who accessed the AGM virtually.
In accordance with the BPMA’s Articles of Association, members of the BPMA Council are elected at the AGM. They hold office for two years but are eligible for re-election for successive periods of two years. Several Council members did indeed offer themselves for re-election, including Richard Harden from Stuart Turner, Ken Hall of Calpeda, Stephen Shaw from AESSEAL, KSB’s Dale Croker, Adam Ferneyhough from DAB Pumps, Glynn Williams of Grundfos, Dan McClusky from NOV, David Noble of SPX Flow, and Jim Wall representing Sulzer Pumps. Two Council members had been co-opted during the year preceding the AGM – Morgan Warren-Ross from Stuart Turner and Muhammad Haroon of Siemens – and both also offered themselves for re-election. In addition, Tony Lawson and Julijana Ristov had retired from Council during the time leading up to the AGM. All those who had been and were serving on the Council were thanked for their continued support of, and service to, the BPMA.
Also at the AGM, the president’s report shared details of 160 meetings which had been held with BPMA representation, six CEN, ISO and API standards that are currently
active and are being monitored by the BPMA, and over 24 European pieces of legislation, be they Directives or Regulations, which are currently active and also being monitored by the Association.
Alongside the formal business of the AGM, those attending were given a presentation on the World Pump Report by Jeremy Leonard from the report’s producer, Oxford Economics. The report is a benefit of membership circulated free of charge each year and covers pump market forecasts across 71 countries, 16 end-use sectors and five pump categories. A post-Brexit update was also presented by Terry Boniface, Assistant Director, Electronics and Machinery, from the Department for Business, Energy & Industrial Strategy (BEIS).
The final piece of business at the AGM was the appointment of the Association’s president. Richard Harden, CEO of Stuart Turner, had completed his tenure as BPMA President and Dale Croker, MD of KSB UK, was proposed as president for the next two years. Mr Harden was duly thanked for his service, which, because of the COVID pandemic, had been four years rather than the normal two-year period.
Three new members have joined the BPMA since the last issue of flow, bringing the total membership to 114. ITT Industries UK is a wholly owned subsidiary of ITT Inc and
part of ITT’s Industrial Process business, one of the largest suppliers of pumping equipment and aftermarket services in the world. Its portfolio includes Goulds Pumps, Rheinhutte, Bornemann, i-Alert, PumpSmart, ProCast and Plant Performance Services. From six regional depots in the North East, new member, the CHC Group, is a specialist supplier of heating equipment, components and spares from a wide range of brands. And the latest member, KGN Pillinger, is a specialist in the design, manufacture and service of bespoke water pumping equipment.
USED THROUGHOUT MINING AND civil engineering schemes, dewatering pumps are vital to keeping projects running to time. For the day-to-day removal of water, Sulzer has completed its lineup of dewatering pumps with the launch of five new models for drainage and sludge applications.
Designated as ‘J’ for drainage and ‘JS’ for sludge, the new J4, J7, JS4, JS7 and JS8 models offer flow rates from 5.5 l/sec with heads up to 16m. Their slim design and low weight of construction make the pumps easy to transport between locations and set up for work.
Drainage applications are always challenging, and for pumps that need to operate round-the-clock, reliability and efficiency are essential. Stainless steel construction ensures long-term reliability against erosion and corrosion.
The pumps are designed for safe and effective operation without supervision.
A float switch provides automatic level control and ensures water levels are maintained reliably while built-in sensors protect the motor from overheating. The natural cooling provided by the double outer casing enables the pumps to run continuously at low levels and even run
dry without damaging the electric motor.
In these applications, the impeller must withstand the harsh pumping environment, and Sulzer’s design includes adjustable wear parts and a nitrile rubber coating for maximum abrasion resistance. The JS models are equipped with an agitator at the base of the pump to ensure the continuous flow of sludge and to prevent airlocks in the pump, minimising the risk of clogging.
Available with hose or threaded connections for ease of installation in either temporary or fixed applications, the pumps are suited to a range of dewatering tasks. Maintenance is easy to manage with inspection ports to assess seal integrity and simple spare part management thanks to the modular design of the pump.
www.sulzer.com
CAPRARI’S RANGE OF FLANGED PUMPS HAS BEEN extended with the addition of new MEC-AG65, MEC-MG65 models.
The new pumps, with modular support, offer installation flexibility and the possibility of pump coupling with diesel motors with SAE3, SAE4 and SAE5 flanges. The version with SAE3 monobloc support, is still available.
The hydraulic performance and the exclusive technical solutions are designed to ensure high energy saving and operational reliability.
The multistage and single-stage centrifugal horizontal shaft pumps are ideal for irrigation and water supply, thanks to their robust structure, they can be used in heavy duty conditions ensuring long term durability.
A new Easy Fit stuffing box is also available for the MEC-MG and MEC-AG pump series, allowing the removal of the stuffing box with the pump in place, giving access to the packing seal for replacement directly in the field. The Easy Fit geometry and materials make the device practical, lightweight and sturdy. At the same time its cataphoresis-treated components provide resistance to oxidation.
www.caprari.com
TIGHTENING REGULATORY requirements on phosphorus removal have resulted in the largest ever order of Qdos ReNu chemical metering pumps for Watson-Marlow Fluid Technology Solutions (WMFTS).
The 240 pumps are required by process specialist Colloide Engineering Systems which has built 115 chemical dosing skids for site upgrades by Severn Trent Water (STW). Colloide says four or five versions of each chemical dosing rig and multiple setups may be required at a single site. In addition, Colloide placed a further order for 40 Watson-Marlow 630 series process pumps for the skid packages.
The skids are being used to deliver the UK utility’s phosphorous removal programme for AMP7, the regulatory asset management period 2020-25.
Phosphorus is a normal part of domestic sewage and new legislation in the European
Water Framework Directive requires water utilities to meet much tighter environmental discharge limits to reduce the amount entering rivers and streams. The minimum total phosphorus consent level has been tightened to 0.25mg/litre, which means introducing a range of processes and techniques, and investing in new equipment.
Chemical dosing is one approach being used by water companies to meet the new phosphorus consent, and equipment needs to be flexible and multi-chemical compatible. This means a range of dosing pumps able to handle different chemicals used in flocculation and coagulation – including ferric, aluminium chloride and polymers – may be required for each skid.
The order from Colloide includes Qdos peristaltic pumps with three different flow
rates – Qdos 30, 60 and 120. These dosing pumps offer repeatable flow up to 120l/hr and a maximum operating pressure of 7 bar, whilst metering accuracy is assured to ±1%.
Unlike traditional diaphragm metering pumps, the flow remains the same whatever the pressure value which provides greater dosing control leading to tangible chemical savings.
www.wmfts.com
ULTRASONIC CLAMP-ON FLOWMETERS CAN OPERATE
wherever contact with the fluid to be measured is not feasible. They are not subject to the same wear and tear and the resulting loss of accuracy of traditional wetted meters, and they can undertake a range of data logging tasks, delivering the baseline and load profile evidence necessary to maximise pump station efficiency and help to reduce energy use.
A leading metropolitan water authority in Sydney, Australia, was pumping water from a wet well into a common manifold, where wastewater was then diverted to various pipelines for further treatment or an ocean outfall sewer. But because no flowmeters monitored the pipelines after the manifold, there was no way to optimise the duty and standby pumps so that they would operate in the most efficient configuration. It’s impossible to manage what isn’t measured, and better management of such an energyintensive process is needed to deliver maximum pump station operation.
High risk and expensive, interrupting the process at a pumping
station that serves such a large population was not an option. The plant’s process engineers needed an alternative way to equip a flow measuring device, so FLEXIM undertook an on-site trial to demonstrate the reliability and stability of ultrasonic clamp-on technology and build confidence in this measuring method.
Despite spiral welded steel pipes presenting a challenge in mounting the transducers, on-site tests showed that readings aligned to expected pump flow curves, but they also detected an unexplained reverse flow. Further investigations by engineers found that a faulty valve in the manifold caused a previously unknown flow diversion.
With confidence in the ultrasonic flowmeter’s capabilities growing, a permanent system was quickly installed, with no shutdown of the pumping station necessary. The duty and cycle pump strategy is now fully optimised, and energy consumption can be reduced.
www.flexim.co.uk
AN ABB ACS880 VARIABLE SPEED drive has been chosen by Torishima to provide precision motor control for the company’s new test bed. A smaller 22kW regenerative drive has also been specified, specifically to allow Torishima to demonstrate its regenerative capabilities.
The state-of-the-art test rig is intended
to support Torishima’s growth in the UK water and utilities markets, and will be used for factory acceptance testing of new products at its facility in Glasgow. The rig will also be used to provide enhanced support to service customers, by allowing Torishima to optimise the energy efficiency of refurbished and up-graded equipment, reflecting an increasing
desire from the company to improve the sustainability of its products and operations.
The project, which commenced in August with assistance from ABB Value Provider EDC Scotland, is expected to be completed by the end of 2022.
new.abb.com
If you or your company have a pump related success to shout about, this awards programme provides the perfect platform. But you had better be quick, as the closing date for all entries is Friday, January 6, 2023.
Entering is simple, and by putting forward a nomination you are demonstrating confidence in the quality of your work, people, products and projects.
Maintaining the early Spring timeline, the next Gala Dinner and Presentation Ceremony will take place on Thursday, March 16, at a fantastic new venue – the Hilton at St George’s Park in Burton on Trent.
Situated on the edge of the National Forest, this impressive hotel is part of St. George’s Park – the training ground for all 28 English national football teams - and is recognised the World over as the Home of English football. Sporting excellence is synonymous with this venue, and early next year it will also become the location for heralding engineering excellence across the pump sector.
The online entry forms, which seek submissions for activities and achievements that took place in the 18 months up to December 2022, will remain on the dedicated awards website – www. pumpindustryawards.com – until the entry deadline of 5.00pm on Friday, January 6, 2023. Please note this important date, and begin considering which key developments, initiatives, staff, and successes you will be putting forward for industrywide recognition.
The recognition of those companies and individuals that have gone that extra mile to meet, and more often exceed, the demands
and challenges presented by the sectors served by the pump sector will be represented by eight award categories:
• Product of the Year - Sponsored by Process Engineering
• Project of the Year - Sponsored by Stuart Turner
• Environmental Contribution of the Year - Sponsored by SPP Pumps
• Manufacturer of the YearSponsored by WEG UK
• Distributor of the Year –Sponsored by Stuart Turner
• Supplier of the Year - Sponsored by Wilo
• Contribution to Skills & Training –Crest Pumps
• Rising Star Award - Sponsored by World Pumps
Once again, we have secured support and backing from a host of leading brands, all of whom recognise the value and importance of promoting excellence across the
sector. In addition to our main category sponsors, there are also other sponsorship options to help support specific elements of the 2023 presentation evening. Several opportunities still exist, so please get in touch if you would like your brand aligned with outstanding engineering achievement.
Steve Schofield, Director and CEO at the British Pump Manufacturers Association, commented: “This year’s awards ceremony – the 21st such event – was as good as any I can remember. The atmosphere was fantastic, and the competition intense. The quality of entries was extremely high, which echoes the creativity and engineering skill that exists within this key sector.
For further information and to submit your entry(s), please visit the event’s website. chevron-circle-right
www.pumpindustryawards.com
The Pump Industry Awards has recognised and rewarded pump businesses’ achievements, large and small, for over two decades. And once again, with the deadline fast approaching, the BPMA’s annual awards programme is calling for your nominations.
“The quality of entries was extremely high, which echoes the creativity and engineering skill that exists within this key sector.”
Discover the new Calio Pro glandless pump - the simple and smart circulator for heating large buildings. One pump for all three pressure classes, PN6/PN10/PN16. Now featuring Dynamic Control as standard: smart controlling that saves you about 40% in energy. Makes installation easy and savings fast!
EURIS, an organisation with 12 UK trade association members, including the British Pump Manufacturers Association, represents industrial product suppliers with a combined turnover of over £148 billion. Recognising that skills shortages across the advanced manufacturing sector are a growing issue for its members, the organisation initiated a membership survey to gather data about skills gaps and vacancies. The survey received 171 responses, with 133 from SMEs and 38 from large companies, and highlighted key actions that need to be taken.
The research carried out by EURIS sought to ascertain how widespread skills shortages are and where the impact is most acute. It is clear from the results that a lack of suitable candidates with skill and experience is reducing the output and potential of UK technology industries. Too many vacancies remain open for too long, and the problem is getting worse.
The results showed that 40% of respondents have vacancies of 5-10% of their workforce, while 20% of respondents said these vacancies take, on average, five to six months to fill. Some 75% of respondents have witnessed an increase in vacancies in the last three years, with over 55% having vacancies for R&D staff, engineers and scientists. Over 60% of those completing the survey reported that vacancies are causing issues with day-to-day operations, and over 40% said that vacancies had reduced business capacity and turnover.
Over 80% believe skills shortages are due to a lack of local labour – not enough suitable candidates are available. Responders reported that a requirement for skilled engineers with degrees that take years of training and a lack of in-house training resources across many SMEs meant that many of the 3-5 million currently unemployed and underemployed people in the UK could not be trained to fill the vacancies. This was also reflected in almost 60% reporting lengthy training periods for new staff – between 6 and 24 months – due to the highly technical and industryspecific requirements.
Overall, these statistics give a worrying picture of the breadth and depth of skills shortages across the advanced manufacturing sector – shortages are significantly impacting the day-to-day operations of businesses across the UK.
As part of regular meetings with ministers from the Department for Business, Energy
& Industrial Strategy (BEIS), EURIS wants to work with the government to address skills shortages in the advanced manufacturing sector and used the survey to try and understand how best to tackle the issue.
EURIS members believe that the government has a role to play in seeking solutions to the issues of skills shortages, and EURIS would like to work in partnership with the government to address skills shortages. This would benefit the whole UK economy and the organisation believes success can only be achieved by industry and government working hand-in-hand on this important issue.
EURIS, therefore, believes It is clear from the survey that the following initiatives would help to resolve the current skills shortages that exist in the UK in the advanced manufacturing sector.
Apprenticeships – The government needs to work with industry to make apprenticeships easier to manage and to incentivise SMEs to set up apprenticeships and recruit trainees. The introduction of apprenticeships for mature workers would also allow for retraining.
Higher education – There should be the creation of more work placement opportunities within Higher education degrees. While the government needs to work with industry and colleges to ensure the introduction of more T Level courses focused on engineering – including work placements – and to raise awareness of these courses to encourage take up.
Training resources – Additional training resources for small companies, including grants and incentives, need to be provided, and training providers should be
encouraged to work with sectors with acute skills shortages to attract more recruits through apprenticeships and T Levels.
Overseas labour – The government should consider short-term skilled visas for Commonwealth countries and minimise obstacles for skilled workers from Europe to work in the UK.
Education and career choices –Training and education programmes should be created to raise awareness of apprenticeship options for school leavers. Closer links between industry and schools and colleges should be made to provide a route straight into industry for those who don’t wish to go to university. Engineering should be included in the school curriculum so, from an early age, it becomes a career young people are aware of and can aspire to. The government and industry need to work together to ensure careers advisers at schools and colleges are fully briefed on the opportunities of working in the manufacturing sector and the opportunities available through apprenticeships and T Levels. And the government should introduce more STEM initiatives to target women who are still hugely under represented in engineering. chevron-circle-right www.euristaskforce.org
The WEG Motion Fleet Management allows operators to check the status of low and medium voltage motors and drives (VSDs and soft-starters), gearboxes, gearmotors, pumps, compressors and other assets installed in any type of industry or facility. Through periodic data collection and advanced data processing, both on the edge and in the cloud, valuable insights are obtained. Thus, it is possible to establish predictive maintenance plans taking into account the operating condition of the fleet (condition-based maintenance) whether on site or working from a remote location. The result is increased uptime and a reduction of the drive fleet TCO (total cost of ownership).
In this issue of flow, Matthew Taylor, National Internal Sales & Marketing Manager at KSB, answers a selection of reader questions.
Question: What information do I need to give to a pump supplier/ manufacturer to get an accurate a quote?
Matthew Taylor: Typically, a pump manufacturer will need the flow required along with the units of measure, and the head needed, again with the units of measure.
To get an accurate selection, as much of the information below as possible must be supplied.
What medium is being pumped and at what temperature? If it is not water being pumped, then as much information about the medium as possible should be sent, such as specific gravity and viscosity.
Any pipework details are also useful (suction and discharge).
The supplier will need details of the application (boiler feed, circulation, submersible waste water, central heating, pressurisation, pressure booster etc.).
The power supply available is an important consideration. Is 415V available? A 3-phase supply? And what is the frequency; 50Hz?
The supplier will also need to know if the pump needs to be in a specific material or requires any special coatings, plus what certification is needed.
How you want to control the key parameters of the pumps (on/off, pressure, flow) is also important to understand alongside whether you want the pumps to be fixed speed or variable speed.
The minimum information required though is flow rate, head, the medium being pumped and its temperature.
Question: Is there a limit on how many times you can stop and start a pump?
Matthew Taylor: Yes. All manufacturers will detail the maximum stop/starts per hour in their documentation. Remember, if you have more than one pump
operating on duty/ standby, you can increase the stop/starts by that amount, so long as you have an auto changeover system.
Question: Should you maximise or minimise the number of stops/starts?
Matthew Taylor: This depends on the application. On pressure boosting clean water, you would look to minimise the number of stop/starts by fitting an accumulator to the system or booster. On wastewater, you do not want the solids within the medium settling at the base of the tank, therefore the idea is to pump it away from the chamber as quickly as possible. Here you would maximise the stop/starts.
Question: On start-up I noticed a leak from the mechanical seal on one of our pumps. Is this normal?
Matthew Taylor: It is normal for a mechanical seal to allow some leakage. The way the mechanical seal works is to allow some of the pumped medium to get between the faces to lubricate the seal and prevent heat build-up. On start-up, there can be some leakage while the seal faces bed in, but this should stop after a short period. Again, there will always be some leakage, but if selected correctly the leakage would normally not be seen as it would vaporise into atmosphere.
Question: Can you run a centrifugal pump with no liquid in it?
Matthew Taylor: One of the most common forms of failure is the mechanical seal where the pump has been run without any medium being pumped. This is called dry-running. The mechanical seal needs the pumped medium to lubricate the seal faces and keep them cool. If the pump
is operated with no medium, the heat will build up causing the seal to fail. In addition, if this is over a prolonged period, it can result in the shaft getting hot and causing bearings to fail. It is generally acceptable to do a quick direction of rotation test, but the pump should not be operated without being primed or vented where appropriate.
Question: Can a submersible pump be operated un-submerged?
Matthew Taylor: This depends on the design. Typically, submersible pumps rely on the medium surrounding the pump to cool the motor, as these motors cannot have fans fitted to them due to the fact that they are submerged. All manufacturers will specify the minimum submergence level needed to allow the pump to cool. In applications where you need the pump to operate unsubmerged, manufacturers have solutions such as jacketed pumps, or dry well pumps that can be installed in a separate chamber. Speaking to the pump’s manufacturer for advice is always advisable.
www.ksb.com
If you have questions you’d like to put to a pumping systems expert, email them to flow's editor at chris@flowmag.co.uk
Issues with seals can cause costly downtime and expensive repairs. When problems caused by failing seals were identified at Nestlé Purina’s plant in Poland, AESSEAL was able to offer a solution, as Arkadiusz Jurzak, the company’s Strategic Project Manager, explains.
The installation of DMSC seals and MagTecta bearing protectors at its European plants has led to significant savings for the pet food manufacturer Nestlé Purina. The company asked AESSEAL to provide a solution to two persistent problems. One problem was at a meat processing plant and was caused by a leaking and unreliable seal on a mixing machine. The water-based barrier fluid system could not cope with pressure fluctuations inside the mixer, so when the pressure in the mixer exceeded that of the barrier system, product began to penetrate the gland packing. This resulted in shaft wear and contamination of the barrier fluid system, resulting in mixer downtime and high maintenance costs.
The solution suggested by AESSEAL was to replace the gland packing with a DMSC dual mechanical seal, which is resistant to temperature and pressure fluctuations.
Just ten months after its installation, the DMSC seal was working continuously, maintenancefree, and had saved the company more than £182,000, with payback achieved in just three months. The company also estimated that it would save an additional £200,000 per line per year as a result of increased mixer uptime.
These savings, resulting from the performance and reliability of the AESSEAL DMSC seal, led to the decision by Nestlé Purina to install them in its plants across Europe.
The second problem that AESSEAL was asked to solve was how to remedy the persistent leakage from the lip seals on the rotary valves in the
product packaging line at Nestlé Purina’s plant in Poland. This was causing damage to the valve housing and shaft sleeve, resulting in the seals needing to be replaced every four weeks. This process took around 33 hours, with the parts alone costing £68,000 a year per line.
AESSEAL recommended replacing the lip seals with MagTecta bearing protectors, which use mechanical seal technology to prevent leakage. The product’s noncontacting design also prevents wear on the shaft or housing. The result was an immediate improvement in the meantime between failure (MTBF) to three months. Subsequent upgrades to the bearings and housing sleeves have increased this to six months. The success of the MagTecta at its facility in Poland led Nestlé Purina to implement similar upgrades at its plants in Hungary, Russia, France, and the UK.
Arkadiusz Jurzak, Strategic Project Manager at AESSEAL Poland, explained how the relationship with Nestlé Purina came about: “The story started in 2015 when Nestlé Purina set up its plant in Poland. Until then, the company knew nothing about AESSEAL. My first contact in Nestlé Purina, Poland, was a reliability engineer who had transferred from
Cargill, Poland. We had worked together for many years and had already co-operated on several important projects at the Cargill plant.”
The crucial factor which finally convinced Nestlé Purina to install the AESSEAL products was their long life. The first 85mm DMSC mechanical seal installed on the Siefer Trigonal Mixer in 2015 was tested for more than a year before being adopted as standard in the rest of Nestlé Purina plants.
Arkadiusz continues to have regular contact with Nestlé Purina Poland and visits the plant at least once every two weeks. As a result, AESSEAL now has the status of ‘Strategic Mechanical Seal Supplier’ for the entire Nestlé Purina group. Any new equipment supplied to Nestlé Purina should have an AESSEAL mechanical seal or bearing protection installed. chevron-circle-right www.aesseal.com
Philip Aude Skeldrup, Sales Manager, North Europe Region, at Danfoss, explains the role pumping systems play in ensuring a growing global demand for farmed salmon can be met.
As the global population grows in number and wealth, we continue to add more animal protein to our diets. In fact, the global per capita supply of animal protein has more than doubled since 1960. Seafood leads the trend: fish is the fastestgrowing animal-based food group, and we’re eating more than ever.
Increasingly, however, the fish we eat is farmed, not wild. The supply of wild-caught fish is stagnating while that of farmed fish continues to grow. In 2020, the world harvested 86 million tons of fish for direct human consumption and caught 76 million tons of wild fish.
The global salmon market was estimated at 3.3 million tons in 2021 and is expected to grow to 4.2 tons by 2027.
Aquaculture plays an important role in explaining salmon’s worldwide availability and popularity. Today, people around the world eat five times more farmed salmon than wild. The Atlantic salmon is the most farmed salmonid, but steelhead trout, cohos, and chinooks are also raised. Because salmon farms depend on cold water for productivity and profitability, most are found in countries such as Norway, Scotland, Canada, and Chile.
Farmed salmon are usually raised in opennet pens in coastal areas. The free flow of seawater through the nets ensures a constantly replenished natural environment for the fish but allows parasites to enter the cages. One of these parasites is particularly harmful to farm-raised salmon.
Lepeophtheirus salmonis is a parasitic sea louse whose larvae feed on salmon skin, mucus, and blood. Less than one millimetre long, the tiny larvae do find hosts in the wild, but salmon farms provide high fish densities that are far more susceptible to infestation.
Sea lice are highly problematic for salmon farmers. Infected salmon cannot be sold; their health deteriorates, and severe infestations can lead to mass mortality. In addition, the high concentrations of sea lice
made possible by thousands of salmon in open pens put wild fish populations near farms at a higher risk. Delousing infected salmon is thus an ongoing challenge for farmers.
Farmed salmon is a big business – and so is salmon delousing. In Norway alone, where salmon exports totalled more than €7 billion in 2019, salmon farmers spent an estimated €500 million fighting lice in 2018.
Worldwide, chemical treatments that kill sea lice have been the main way farmers delouse penned salmon for years. Hydrogen peroxide, cypermethrin, deltamethrin, and azamethiphos have all been deployed. Hydrogen peroxide and azamethiphos are now the most commonly used chemicals.
While effective in delousing farmed fish, chemical treatments result in other problems. For one thing, chemically treated salmon cannot be eaten or sold for weeks after treatment. Even more critically, the chemicals kill organisms other than sea lice: unintended toxicity to non-target
species is a major environmental concern. Finally, there is a real risk that sea lice will genetically adapt to the chemicals. Farmers have thus had good reason to experiment with a variety of non-chemical delousing methods.
Trials with everything from lasers to cleaner fish have narrowed the search for more sustainable lice treatment to three mechanical methods. One of these, thermal treatment, kills lice by briefly transferring salmon to tanks with seawater heated to 28-34°C. While effective against lice, thermal treatments are associated with fish injury and mortality.
Another mechanical delousing technology is flushing salmon with low-pressure water jets; again, this is effective against lice but can result in scale loss, gill bleeding, and other wounds to the fish.
The third mechanical delousing technique is freshwater treatment. To remove lice, salmon from open net pens are temporarily pumped into wellboats filled with fresh water. Sea lice are sensitive to seawater
Salmon farmers spent an estimated €500 million fighting lice in 2018.
salinity and cannot survive in fresh water. By comparison, infected wild salmon typically shed any lice when they return to streams to spawn. Freshwater treatment has no harmful impact on either salmon or non-target species. However, freshwater treatments must be carefully controlled and monitored to ensure that the lice do not genetically adapt.
This innovative method is effective and efficient but requires large volumes of fresh water, which may not be readily available near open-net pens at sea. To avoid hours-long trips to coastal sources of fresh water in sufficient volumes, some salmon farmers have recently begun to utilise purpose-built wellboats equipped with tanks and seawater reverse osmosis (SWRO) plants. The number of wellboats equipped for SWRO freshwater treatment is so far limited, but we can expect to see more of them in the future.
Engineers designing marine SWRO plants face several challenges when selecting components such as pumps, variable frequency drives (VFDs) and energy recovery devices (ERDs).
Of course, energy efficiency is a priority for any SWRO plant. However, in a marine application such as a wellboat, where all electricity is generated by diesel fuel, it is even more important to specify a design and components that enable the lowest possible specific energy consumption.
Similarly, reliability and ease of maintenance are always important. But when a vessel is at sea for much of the year, the greater the dependability and the longer the service intervals, the better.
Finally, space onboard a vessel is at a premium. Therefore, compact SWRO plants with optimal footprint-output ratios are preferred.
With a tank capacity of 7,500 m3, the Gåsø Høvding is the world’s largest wellboat. Designed specifically for salmon aquaculture, the high-capacity vessel began operations in Norway at the end of 2021. The SWRO plant’s designer, Quantum Water, selected Danfoss APP high-pressure pumps, iSave ERDs, and VFDs for the SWRO plant to save space, energy, and maintenance.
“Of course, energy efficiency was one of the key criteria,” explained Nicolás Alberte, General Manager of nb. “However, even though this is the world’s largest wellboat, space onboard a vessel is always at a premium. Therefore, maximising capacity and ensuring easy access to key components while minimising plant footprint was essential. Finally, operational reliability is critical: salmon welfare and aquaculture productivity depend directly on these treatments to mitigate the risks of sea lice infestation and amoebic gill disease, so reliable performance and long service intervals are vital.”
To meet these demands, Quantum Water designed a tailormade SWRO plant that would produce the required water; 5,000 m3/day.
Four APP 65/1000 high-pressure pumps and four iSave 70 ERDs make up the core of the plant, each connected to a Danfoss VLT AQUA Drive FC 202 for optimal control and efficiency.
“The combination of Danfoss APP pumps and iSave ERDs played a significant role in achieving the goals set by our client for the desalination plant,” Alberte said. “Not only does it provide a reliable low-energy solution with low maintenance needs, but it also delivers high production capacity in a compact package.”
“That Danfoss APP pumps use only the pumped medium for lubrication, thus presenting zero contamination risk, is also a plus,” concluded Alberte. chevron-circle-right
Reduce on-site labor time, engineering and installation time and associated costs. Choose a system that arrives on-site in a fully enclosed ready for use pump house. This pre-engineered pumping system saves time and money for our customers.
+353 (0)44 934 7078 company/patterson-pump-ireland-ltd www.ie.pattersonpumps.com sales@ie.pattersonpumps.com
Pushing older equipment to meet an increased duty requirement can sometimes create reliability issues down the line. However, achieving this by sourcing newer replacements can be costly and prohibitively time consuming. To avoid either outcome, one of the largest oil refineries on the island of Java, Indonesia, relied on the specialist knowledge of Sulzer to refurbish and modernise eight diesel pumps.
Recently, the refinery in Java has undergone a long-term, facilitywide upgrade project designed to maximise production capacity and meet the future energy demands of Indonesia. The targeted overhaul program helped the equipment attain a new operating point, providing a 50% cost saving compared to purchasing new units and a five-month reduction in the overall lead time.
As part of this initiative, the equipment identified for modernisation included eight diesel pumps used to transfer fuel from the refinery. The pumps used six diesel drives and two steam turbines for power. One of the assets dated from 1975, and no documentation was available on site for any of the units.
As a result, operators were unsure how to improve the performance of the pumps to meet the increased fuel demand while safeguarding reliability. Consequently, the engineering contractor approached a number of pump specialists to see how a new duty point could be effectively achieved.
Finding a service provider who can work effectively with older equipment is often challenging. However, after a rigorous tender process, the contractor selected Sulzer.
Sulzer’s local service centre in Indonesia provided access to engineering services and the company’s wider global network. This worldwide support proved crucial in collating all the necessary information and expertise to deliver this project effectively.
To overcome the lack of documentation, the Indonesian team contacted Sulzer Pumps UK. The UK team was able to source all the documentation and data for the diesel pumps installed at the refinery.
With this information, the team in
Indonesia then collaborated with the Sulzer Pumps engineering team in the USA. Building upon this, the USA team also delivered additional training to the customer’s team.
Throughout the project, the Singapore service centre acted as a central hub for all the teams to organise their findings and recommendations. After the close international collaboration, it was clear that the new duty point could be met without any modifications to the pumps.
Rather than modifying the pumps, new gearboxes would be used to increase the speed of the pumps to reach the new process requirements, which could be achieved well within the performance envelope of the units.
Armed with this information and a plan of action, Sulzer Indonesia carried out detailed inspections of the units. The team then conducted a full refurbishment of the eight pumps, bringing them back to asnew standard. New skid frames were fitted with efficient electric motors connected to gearboxes to deliver the desired speed increase, replacing the old diesel drives and steam turbines. To ensure a complete drivetrain package, Sulzer also installed new couplings and lube oil systems. The rebuilt skids were a plug-and-play solution, allowing simple reconnection with existing refinery pipework, unlocking a quick installation and minimising time on site.
This approach not only ensured a
reduced lead time on the project, but also meant the retrofit could be carried out at 50% of the cost of sourcing new pumps. Furthermore, the retrofit offered a time saving of five months compared to delivering replacement units. No modifications to the pumps themselves also allowed easy plug-and-play reintegration into the surrounding process equipment back at the refinery once work was complete. What had initially been a complex problem was solved with a straightforward solution that saved time and costs.
Updating the drive technology for the pumps ensured that the new duty point was also met with increased efficiency. By using the operational data for the pumps, the complex new performance requirements could be met with speedincreasing gearboxes, with future system reliability assured.
Ultimately, a cost-effective and efficient solution was provided to the refinery, ensuring that it could deliver increased fuel supply while safeguarding availability. chevron-circle-right www.sulzer.com
www.brookcrompton.com
With over 110 years of technical and design expertise, Brook Crompton offers leading edge energy efficient electric motors across global markets. As the original innovator in electric motor development, Brook Crompton are trusted to power limitless industrial processes and its robust motor design drives fans, pumps, compressors, conveyors and more.
Driven by technology and innovation, Brook Crompton has one of the widest available ranges of electric motors for operation in safe areas, hazardous atmospheres and hostile environments.
The extensive range of stock can be quickly modified to suit customers’ needs and with a high level of technical support from our knowledgeable team we ensure the correct selection of motors is provided for your application.
Brook Crompton’s focus on product and service development ensures we continue to move forward to improve efficiency, offer lower cost of ownership throughout their lifecycle and to reduce environmental impact.
Contact us at: T: +44 (0)1484 557200
E: sales@brookcrompton.com
For half a century, residents and commerce across eight municipalities of the greater London Area of south western Ontario have received their potable water supply from the Lake Huron Water Treatment Plant near Grand Bend. In 2017 the Lake Huron Primary Water Supply System announced an energy audit and pump optimisation study that identified a significant opportunity for energy savings and the optimisation of pump operations for the pumping station. flow found out how the savings were realised, with a solution from KSB
The outcome of the study commissioned by the Lake Huron Primary Water Supply System (LHPWSS) has been the modification of the original five-pump configuration in the pump station and its replacement with a six-pump configuration. This has involved removing three of the original 50-year-old 3000hp (2237kW) pumps and replacing them with four high-lift pumps from KSB. With the new pumps running on their operational curve, substantial energy savings can be made. As an electrical transmission-connected entity, the LHPWSS was eligible under the Independent Electricity Systems Operator’s (IESO) Industrial Accelerator Program (IAP) for financial incentives for eligible energy efficiency projects.
Four international pump manufacturers submitted bids, but KSB Canada’s submission stood out. Despite being the highest capital expenditure cost by a significant amount, KSB’s submission actually offered the lowest overall anticipated lifecycle cost over 25 years. This was possible due to KSB’s energy efficiency and creative solution offering a single type for all four pumps (large and small). This reduced the spares requirement, in turn reducing the lifecycle cost and providing flexibility to easily increase pump capacity in the future as demand continues to increase. The contract was awarded to KSB Canada, which commenced design and consultation work in 2019.
The LHPWSS plant has a current treatment capacity of 340 million litres per day and serves the city’s population of approximately 420,000 people in the eight municipalities, including 80% of the city of London.
The pumping station was originally designed for a single pipeline, but later,
in 1996 and 2014, The Regional Water Supply Division of the City of London (RWS) partially twinned the 47km main transmission pipeline to a terminal reservoir resulting in the pumps no longer running on their curve.
The overriding issues the pump suppliers faced were delivering energy savings and ensuring that pumps could be accommodated in the limited amount of space in the pump hall and that the floor could withstand the weight of the pumps. In addition, the supplier needed to guarantee a wide operating range with low available NPSH, covering multiple duty conditions with pumps operating at full speed.
KSB’s proposal, using just a single type for all four pumps, meant only the impellers and motors were different, in accordance
with the size of the pump. The base plates for each pump were the same size.
A significant benefit of the proposal was that with the smaller pumps using the same size casings and base plates as the two larger pumps, they had engineered the opportunity to increase the pump size by fitting larger impellers and motors at a future date. This can be done on site without any civil works needing to be carried out. Thus, if demand grows for the water supply to be increased, it can be accommodated with the minimum cost and disruption to the plant.
Following a 25-year Life Cycle Cost analysis, taking into account the capital cost, energy consumption and maintenance costs made by AECOM Canada, consultants for LHPWSS, the contract was awarded to KSB.
“The eventual scope of the project involved the supply of four bottom
suction horizontal split case pumps, vibration monitoring system and flow straighteners (suction conditioning spools) for potable water distribution (water supply),” explained Marcus Henderson, KSB National Operations Manager. “Also, part of the contract was to supply two TECO make 1494kW/2000hp @ 1200rpm, 4160V / 3Ph/60Hz and two TECO make 2611Kw/3500hp @ 1200rpm, 4160V / 3Ph/60Hz electric motors.”
The plant’s pumps are rated for 1,158 l/sec, and each of the pumps’ discharge piping is equipped with a 500mm diameter tilting disk check valve, along with a 500mm diameter metal seated ball valve equipped with a motorised electric actuator. The water treatment plant has two hydropneumatic tanks, each with a capacity of 580m³, for transient protection of the 47km partially twinned 1200mm diameter water main distribution system.
The pumps specified were 2 x RDLO 500-835 B SC G O BS with a design flow capacity of 900 l/sec and a design flow pump head of 125m TDH, along with 2 x RDLO 500-835 A SC G O BS with a design flow capacity of 1,300 l/sec and a design flow pump head of 150m TDH.
Proven in many water applications worldwide, the RDLO pumps were identified as more than capable of meeting the customer’s specific demands. KSB’s RDLO axially split, singlestage volute pumps have been developed specifically for handling raw water, clean water, service water and transport fluids with minimal flow resistance. As a result, they lower the energy and life cycle costs of the systems in which they are installed. They also meet the twin demands of reliability and high availability. Reliability results from the casing halves being sealed by solid casing split flanges at the upper and lower casing part, and high availability is attributable to the use of generously dimensioned bearings and high-quality shaft seals. Smooth running is ensured at all times thanks to the flow-optimised, vortex-free intake elbow and rigid shaft with a short bearing span. Because the shaft is completely sealed without steps/threads in the wetted area, the RDLO offers reliable power transmission.
The combination of solid bearing brackets, a short and rigid shaft and preloaded bearings guarantees low vibration and extended operating life for the bearings,
seals and coupling. Being axially split case pumps simplifies maintenance procedures, enabling ready access to all parts for thorough inspection. The drive may be positioned on both the left and right of the pump without additional parts or modifications to the casing being necessary.
“Two of the pumps are connected to 3500 hp motors, and the other two to 2500 hp motors. These are the main pumps supplying drinking water to the entire LHPWSS, with many customers over 50km away, so they consume a significant amount of energy. It is marginal improvements such as these that can improve efficiency by one or two per cent, but they work out to big dollars when you consider the plant’s overall size,” added Marcus.
“Because the pumps were being retrofitted into the original premises, it was necessary to run the plant at half capacity on one transmission side during installation,” explained Billy. “As there was a spare bay already in the plant it was possible to utilise this for the installation of the first pump. The procedure then involved running pumps one, two and three while pumps five and six were being installed before switching to running pumps four, five and six while pumps one, two and three were installed.”
The introduction of the new pumps also provided the opportunity to retrofit isolation valves. Historically the lack of isolation valves on the existing pumps required the complete isolation of half of the discharge header board (three pumps) to facilitate the repair to one pump, effectively limiting the pump capacity of the plant to half of its rated capacity. The selection of a combined control/check valve to replace two valves on each pump discharge meant that each pump would have a dedicated isolation valve for each pump discharge. Isolation valves on each pump discharge will enable the complete isolation of the
A significant element of the project was the issue of the pumps delivering energy savings, which involved factory acceptance testing at KSB’s Halle facility in Germany. Marcus explained: “Factory testing involved shipping one motor of each size to our factory and coupling them up to the pumps for string testing and recording the overall pump performance. The motors also underwent type testing under full load in accordance with the IEEE Standard so that they could determine motor efficiency.
“There were strict penalties on performance guarantees on this project, so if we failed to meet the efficiency guarantees given, KSB would be required to pay LHPWSS the difference in energy costs delivered and those which were guaranteed over the performance lifetime.
“It is worth noting that when the pump tests were carried out, they had to be on bare internals. The coatings were only applied after testing, so it was a true test of the raw efficiency of the pumps. Given that coating can improve efficiency by one to two per cent, we faced some tough conditions.” chevron-circle-right www.ksb.com
The VEBK500/TFM/TFO is our brand-new machine designed for the dynamic balancing of pump impellers for high volume production environments.
Supplied with either milling correction or industrial belt sanders depending on the material, the correction units follow the profile of the impeller.
Please contact us for a full technical specification.
We deliver the most comprehensive range of dynamic balancing services in the UK, and all delivered by our locally based team of experts. This combined with considerable application knowledge gained over many years of operation and experience in pump manufacturing means that whatever your balancing requirement we’ve got you covered.
Electric motors account for a significant proportion of the water industry’s energy consumption. Many motors are run without any kind of speed control, while some use mechanical means such as valves and dampers to modulate flow and pressure. This is inherently inefficient, as the motor is still running at full speed, regardless of demand. A variable speed drive (VSD) instead controls the motor electronically, to always match motor output with actual demand. As such, the motor only uses the minimum amount of energy that it needs, which can save both energy and money.
Pumps, fans and compressors, are centrifugal applications, and as such obey the cube law. This means that a small decrease in speed results in a proportionally higher decrease in energy use. In practice, running a motor at 80% speed requires 50% of the energy required to run at full speed.
In most cases, installing a VSD will lead to improved energy efficiency almost overnight simply by reducing the motor’s speed. However, VSDs are highly complex, with modern devices boasting huge amounts of functionality, and so the real savings come when you start exploring what else a VSD can do for you.
For instance, energy tariffs are generally higher during peak demand and lower at night (depending on your supplier). A VSD provides the flexibility to operate intensive or noncritical processes at the right point in time to achieve the lowest cost. Reservoir controls, for example, can pump water into a reservoir overnight when tariffs are lower. And the more you get into this level of detail, the
more you can gain control over processes to uncover other efficiency savings.
Pumping slower for longer can also make a big difference. Consider the example of using a pump to empty a tank. Pumping slower may take more time, but even a small change in pump speed can lead to a disproportionately higher energy saving.
At a basic level, a VSD will save energy on pumping applications. But it also provides the flexibility to rethink control philosophies for applications driven by motors in the water industry and helps to optimise processes so that they reflect varying changes in costs upstream and demand downstream. Modern VSDs are also packed with sophisticated application-specific features such as multi-pump control, which can make a big difference to the resilience of operations.
Reducing leakage and bursts will be crucial in working towards the industry’s Net Zero goals. Prevention clearly is better than cure when it comes to leakage; however, many leaks are only detected when roads start flooding with water. As well as wasting water and potentially causing damage to the surroundings, digging up roads to repair pipes uses enormous amounts of carbon. VSDs incorporate internal PID loops, which, in this context, can ensure that pressure is maintained at certain levels regardless of any other variables in play, as the VSD is able to constantly adjust motor speed depending on the circumstances. The VSD can also provide an early warning system for any potential leaks, as issues can be inferred from the behaviour of the motor
and pump. For instance, if a booster pump is running with VSD control and is operating at full speed for more than, for example, one minute, then this usually suggests that there is an issue that needs resolving somewhere, and the VSD can flag this up. Running motors at lower speeds generally will also reduce strain on pipes and valves.
When people think about how to save energy, often the first suggestions are to turn lights off and reduce the heating. However, the difference this makes can be negligible when compared to reducing the energy usage of, for instance, a pump at a pumping station by up to 50%.
Moreover, turning off lights and reducing temperatures can end up compromising comfort. A VSD, on the other hand, allows required output to be maintained, at a much higher efficiency, and with no compromise on productivity and effectiveness. When looking for cost-effective ways to save energy, the VSD could be the key to unlocking significant progress on the water industry’s road to Net Zero. chevron-circle-right
bit.ly/ABBwawacost-effective way for the water industry to progress rapidlyto Net Zero.
Beginning production of a new formulation batch or liquid product can often bring difficulties. We found out how North Ridge Pumps recently helped an innovator within the supplement industry to scale production and perform trials on a new product.
Knowing which pump technology to use to ensure a safe, efficient process and provide flexibility for small-scale batches, whilst undertaking refinements before commercialisation, can prove challenging.
Not only are you trying to ensure accurate, repeatable, traceable results and avoid transferring fluids manually, but you also need to ensure any technology selected will stand the test of time and ensure crosscontamination does not skew results.
The client was looking to transfer one of several highly viscous blends of chemicals that would not flow under gravity, and they wanted to consistently batch set amounts.
High-viscosity liquids often cause difficulty in transfer applications. They do not flow under gravity and require a specialist pump technology which, if used, can also pose issues if run without fluid and can be easily damaged.
Such fluids are sometimes so thick that when delivered in barrels or containers, if the incorrect pump technology is chosen, the fluid is not pumped – holes are made with the pump within the fluid container rather than it being completely emptied, with large amounts of product remaining.
Not only is the product within the centre of containers a cause for concern, but also fluids which may remain stuck to the side of the container. With more expensive fluids, this can generate costly waste, or cause problems with fluids which must be disposed of via waste collection. So, what factors should be considered when looking at scale production or conducting trials?
Sensitivity to shear: Some fluids may be shear sensitive, meaning they must
be handled gently to avoid adversely affecting them during transfer.
Solid handling: When solids are transferred, careful consideration needs to be given to how they are handled. They can be transferred with technologies preserving their shape and consistency, or with designs which can assist with the next stage of production, with solids broken down or partially blended.
Volatile and corrosive liquids: Volatile and corrosive liquid handling is another consideration, such as whether an ATEX-approved design is required or a sealless pump is needed to ensure the full containment of fluids. Other options include the swaging of hose fittings for the safety and security of leak-free connections, nozzles for ease of fluid dispensing and speed control to alter dispensing rates and prevent splashing.
Accuracy and repeatability: The ability
to repeatedly batch pre-set amounts with ease, or record the amounts dispensed with high accuracy, is crucial to ensuring consistency.
Accreditation: Material choice can be puzzling. This can include whether to adopt an accredited hygienic design, or a stainlesssteel design which can be easily disassembled and cleaned –providing peace of mind during testing – or to simply what is chemically resistant.
For the supplement project, North Ridge was tasked with assisting a client in dispensing a product being developed which had the consistency of molten fat.
When cold, the product would solidify, making it unpumpable and nearly impossible to remove from the container.
The equipment needed to be hygienic, easily cleanable and able to handle a wide temperature range, yet consistently transfer differing volumes of liquid as accurately as possible.
North Ridge supplied, commissioned, and installed a complete automatic batching system to dispense the liquid accurately and repeatedly.
The unit was supplied complete with a heat-traced hose to ensure the liquid did not solidify in the hose, with the barrel also heat-traced to ensure the contents remained liquid and pumpable. As the fluid was heated, it became easily pumpable, enabling the client to trial new processes, test small-scale batches and trial packing methods.
Their results are accurate, repeatable and fully traceable, enabling them to accelerate production and scaling. chevron-circle-right www.northridgepumps.com
—
Turn the hidden potential in your motor applications into real energy savings with ABB’s free, no obligation Energy Snapshot. The service uses data gathered from your facility to identify the motor-driven assets that offer the greatest opportunities to cut energy costs in the shortest possible time. A comprehensive report is then provided to you, containing all the information you need to build a compelling case for investment in energy efficient technologies.
campaign.abb.com/EnergySnapshot2022
Let’s write the future. Together.
Daryl Williams, the Commercial Specialist at Pumps UK, outlines the differences between fixed- and variable-speed booster solutions, explaining the applications where each approach is most appropriate.
One of the solutions to avoiding supply interruptions (and unhappy clients) is to opt for cold water booster solutions that are designed with built-in ‘redundancy’, often extra pumps that can take over during maintenance cycles or failures.
Some systems rely on a common controller and run at a fixed speed. Others are fitted with inverters that can vary the speed of the pumps. Both have advantages for certain applications.
A general definition of a water pump inverter is a device that maintains constant and stable pressure in a water system by varying the speed of the pump motor to deliver the pre-set pressure at the outlet regardless of how many outlets or appliances are in use, up to the maximum capability of the pump. In recent times, booster sets fitted with inverters have become increasingly popular.
Naturally, these hi-tech innovations come at a price. The addition of inverters to a water-pressure booster set is not an insignificant cost. That said, opting for less expensive fixedspeed sets can, potentially, be more expensive in the long term for some applications.
Booster sets, such as the PUK VARI COM range, designed with Nastec inverters, allow individual pumps to be isolated and the system to continue the supply even if a pump is removed or is offline. These smart inverters allow for precision control via the Nastec Now application and Bluetooth technology.
There are further advantages in booster sets designed with inverters, as they can be programmed to vary the performance of the set based upon demand, so less power
is consumed compared with a similar fixed-speed set. The wider the operating range of the pumps, the greater the potential for energy saving.
While inverters do not directly save energy, the programmed operational parameters of the set can offer substantial energy-use reductions to the end-user. With some sources suggesting that reductions between 10% and 40% of the energy consumed by the industrial and service sectors in some countries are possible, the potential for savings and energy consumption reduction is a hot topic.
According to the Harvard Business Review, Dec 2021, nearly all the world’s largest companies have annual sustainability reporting and a sizeable number pledging to be net zero by 2050. With rising energy costs, due diligence dictates weighing higher initial outlay against energy consumption, maintenance costs and reliability.
One of the great things about packaged variable speed booster sets, PUK VARI COM, for example, is the flexibility in configuration.
In a three-pump set, one pump can be assigned as the ‘duty’ pump, supplying the required flow rate most of the time, with a second pump designated ‘assist’ to help cope with higher demand cycles. The third pump is used as a standby to replace the duty pump if it is offline, increasing the overall reliability of the set. Similarly, twin-pump configurations can have a second pump as standby to mitigate against interruptions during maintenance or in the event of a failure.
In addition to the reliability of booster sets with in-built redundancy, Nastec inverters can perform another rather clever trick, courtesy of their networking connectivity capability (via Bluetooth), creating a ‘combined operation’. In practice, one of the inverters can reassign its pump as the ‘master’ or duty pump in the event of the duty pump going offline, thus maintaining the operational program.
Fixed-speed sets still have a place and offer advantages in certain scenarios, such as operations requiring a constant flow rate, like an irrigation system or a factory with machines that use a steady flow during production. But for water supplies that have variable demand, variable speed booster sets offer some significant advantages in energy saving, water saving, noise reduction and reliability. chevron-circle-right www.pumpsukltd.com
The potential for savings and energy consumption reduction is a hot topic.
To choose the right floating pump station for a dewatering project, it is important to understand the factors which affect its environment, deployment, operation and maintenance. Dewatering specialist, Weir, outlines seven things which need to be considered when choosing a dewatering barge.
Three elements will determine the type of barge suitable for any given application: the hydraulic requirements of dewatering, the physical conditions on site and the bathymetry of the water the barge will be deployed on.
While some mines enjoy reasonable weather year-round and are readily accessible by heavy transport, it’s not uncommon for the climate to significantly affect the installation and operation of waterborne dewatering equipment.
Unsurprisingly, the most common issues come from areas where temperatures regularly fall below 0°C for sustained periods. Not only can the resulting ice interfere with the dewatering itself, but surface ice can cause substantial damage over time to barges and pontoons, necessitating a de-icing solution to keep an area around the barge fluid.
Weir Minerals’ Multiflo barges employ deicing systems to manage temperatures as low as -50°C, which have been tested in the trying conditions of the Canadian tundra, and other arctic-like environments. They allow for worry-free, year-round operation when combined with heat tracing, self-draining pipes, and other freeze-prevention systems.
Areas prone to seasonal flooding or extended rainfall experience drastic changes in water level, which have to be accounted for in the mooring or anchoring system used, access to the barge, and bottomout protection (filled foam used to protect against hull breach) for the pump.
For many remote sites, a seasonal or permanent lack of readily accessible roads designed for heavy-load traffic will affect which barges can be deployed. Weir Minerals’ engineered-to-order dewatering pump systems have been deployed in a number of hard-to-access regions around the world and can accommodate sites requiring airlift or traffic over ice roads.
Many other site conditions have to be accounted for when designing a barge system; wind, snow, and seismic loading all affect the buoyancy and stability of the barge.
A pond bathymetry survey should be conducted to map the body of water’s geotechnical data. This hydro-acoustic survey produces maps showing the water depths based on location. This information is crucial to analyse wave formation, which is used in the marine analysis to simulate wave loading on the barge structure, pipeline, and access walkways.
These factors will determine where the barge should ideally be placed and how much mooring or anchoring it will require to stay in place. This requirement can be substantial, with some projects requiring hundreds of tonnes of anchoring to prevent high winds from forcing the barge to break free and collide with land or other equipment, or even capsizing.
coatings or anti-corrosion systems such as cathodic protection.
A number of secondary factors, such as the provisioning of input power, pump maintenance strategies and barge access, are key to the ongoing efficiency of the dewatering operation.
In most cases, a floating walkway is a preferred method of accessing a barge – combining economic efficiency with constant personnel access to the platform. It also simplifies power distribution, as cable trays can carry electrical and control cables.
For platforms which require direct vehicle access, a suspension bridge or gangway between the barge and the shore is the most elegant solution, although they typically aren’t economically practical over long distances, particularly in areas prone to snowfall.
For areas where neither of these are practical, marine access involving boats or hovercraft is generally used to access the barge.
The ideal maintenance strategy generally depends on the type of dewatering being performed – while all pumps require regular maintenance, those deployed in clear-water applications generally have more flexibility in their planning than tailings and slurry dewatering, where maintenance is always a core part of the conversation.
Larger, monolithic or pumphouse style barges with space for a monorail or crane within the pumphouse allow pumps to be refurbished and repaired on the barge itself, while other barges need to be pulled to shore for the pumps to be extracted.
The provisioning of power is another key factor in designing a dewatering solution, particularly for sites which are too remote for standard electrical access.
For most applications, a shore-based electrical genset is the ideal solution, as it simplifies management and operates more efficiently than a diesel engine.
The last key decision point is how portable the barge needs to be. Will one barge be dewatering in multiple locations over its lifespan or deployed in a particularly remote location?
If it’s being reused in multiple locations, does it need to be draggable between ponds?
For larger installations, it’s important to consider if the operation is likely to be scaled up or down further on, which could require modular barges or leaving extra space for additional pumps to be added down the track. chevron-circle-right
www.global.weir
The last key decision point is how portable the barge needs to be.
Pump systems account for 20% of the world's electrical energy demand and between 25% - 50% of the electrical energy usage in certain applications. Pumps are the single largest user of electricity within industry across the European Union, consuming over 300 TWhpa of electricity, which in turn accounts for over 65 Mton of CO2 emissions.
It is also well documented that rotodynamic pumps, which account for 80% of the installed base, are typically between 20-30% oversized. There is, therefore, a major potential to save energy if rotodynamic pumps are properly sized and operated.
To identify if a pumping system is sized correctly and assess the potential for savings, make the following checks:
• Are you wasting liquid flow?
• Are you creating additional pressure?
• What is the monitoring & controls philosophy?
• Are there any oversized pumps installed for your required duty?
• Are there any significantly old pumps employed in the system?
• Is there excessive noise in the system?
• Are there any throttling valves installed in the system?
• Have you the correct size of pipework?
• Inadequate maintenance lowers pump system efficiency, so what maintenance procedures are in place?
• Are you adopting a proactive equipment replacement programme to current EU legislation
The vast majority of existing pump systems operating today were not originally designed with energy conservation as a major consideration. If pump systems are initially designed on an energy-efficient basis and are correctly applied and sized, the energy savings will
often exceed 50%.
To design an energy-efficient pump system, all the following criteria should be considered:
• Basic plant layout
• Pipe size, configuration and restrictions to limited pipework losses
• Information on the liquid (viscosity, density, aggressiveness, temperature)
• System characteristics and pump selection
• Pump/system control
• Correct sizing of the pump units
• Selecting the most energy-efficient pumps at the best efficient point
• Selecting the most energy-efficient motors
• Fitting variable speed drives to match the system design and demand
Low energy costs are a direct result of knowing the minimum flow and pressure that the system requires to operate successfully (system demand) and then selecting the correct sized pump and matching it to the system.
When selecting a pump, it is important to determine the required flow and pressure to be generated by the pump. The flow may be determined by a process requirement, the heating or cooling required in the system, or the peak water demand for utilities. The pressure required may be to elevate the liquid within the system or to overcome the pressure losses created as the liquid passes through it.
It is important to know as much about the pump system as possible and to create a pressure/flow profile for the system. The energy required to drive the pump is directly related to the flow and pressure required. To generate high pressures generally leads to designs which may be inefficient, and therefore neither the flow nor the pressure must be over specified.
When specifying a new pump, ask for a high-efficiency motor to be fitted. If
you are replacing or rewinding a motor, then evaluate the cost of fitting a highefficiency motor remembering to factor in the running savings, which will pay back any increase in cost. The overall cost associated with operating these essential pieces of equipment throughout their entire life span can be broken down as 5% for the initial purchase/installation costs, 10% for ongoing maintenance and 85% for the energy used to run them. Clearly, any reduction in the energy consumed by electric motors is important, and with modern designs, that reduction can be as much as 30%.
It is also evident that many pumps and motors are constantly operated at full power, irrespective of process needs, so across Europe's installed base, there is the potential for significant energy savings. These savings can, in turn, drop to the bottom line and increase the profitability of any business. Using an electrical variable speed drive is the simplest and most economical way of controlling the pump and matching it to the pump system. chevron-circle-right
europump.net
The BPMA’s annual Pump Industry Awards programme has been recognising and rewarding the achievements of pump businesses, large and small for over two decades. Throughout that time it has become one of the leading events to serve the industrial and commercial arena. So, if you or your company have a pump related success to shout about, these awards provide the perfect platform.
The gala presentation dinner caps off the awards programme in style, providing excellent networking opportunities, great food and superb entertainment. It’s your chance to celebrate with colleagues, interact with peers, entertain customers and be part of the pump industry’s biggest and best celebration. Manufacturing and distribution prowess, product development and application, environmental consideration, skills development and customer support will all be acknowledged through this wide reaching awards programme. So why not consider which of your engineering successes are deserving of industry wide recognition, and be sure to join us at our wonderful new venue - the home of English football - on Thursday 16th March 2023.
The 2023 Call for Nominations is now open, so be sure to visit the Pump Industry Awards website to review the award categories and decide which ones you will be entering!
Richard Harden, BPMA President, says of the Pump Industry Awards, “The pump industry continues to be a hotbed of competitiveness, where the constant search for greater operational performance and improved efficiencies amongst its broad customer base, demands all those operating within this important sector to be at the top of their game. This BPMA backed awards programme allows the pump industry to come together in celebration of that drive for engineering excellence.”
Organised by on behalf of
A single IoT platform to design, deploy and iterate. With 100,000+ devices live, gathering billions of data points, Particle helps connect you to your machinery in the field.