
8 minute read
Devils Tower Forest Products − classement à l’usine de bois sec pour les produits d’atelier
from Millwide Informateur No. 49
by USNR
Devils Tower Forest Products
Classement à l’usine de bois sec pour les produits d’atelier
Advertisement
Le désir d’automatiser le processus de classement pour améliorer la récupération pour ses produits d’atelier, et la rareté de classeurs qualifiés ont mené Neiman Enterprises à investir dans un système THG (Transverse High Grader) d’USNR pour son exploitation à Devils Tower Forest Products à Hulett, Wyoming. Avec l’expérience que possède USNR dans le classement des produits d’ateliers et de moulage dans l’usine de bois vert, l’entreprise avait confiance que le système THG pouvait faire la même chose pour ses produits d’ateliers dans l’usine de bois sec.
Le système fait un merveilleux travail à l’atelier. La récupération par classement est à la hausse et, sur certaines largeurs, elle est importante.

Le projecteur de classement est monté sur un cadre au-dessus du dispositif de sortie du système THG. Il projette des renseignements sur la surface des planches et suit cette projection avec la planche comme elle passe par un classeur de vérification.
RÉCUPÉRATION AMÉLIORÉE, PRODUCTION ACCRUE
Devils Tower, fondée en 1958, est l’une des quatre opérations de traitement du bois qui appartiennent à Neiman Enterprises. Ses usines sœurs comprennent celles de Rushmore Forest Products à Hill City, SD (ajoutée en 1998), de Spearfish Forest Products et de Spearfish Pellet à Spearfish, SD (2008), et de Montrose Forest Products à Montrose, CO (2012). Neiman Enterprises est une entreprise familiale de quatrième génération qui a commencé avec sa première usine en 1936. De nos jours, l’entreprise est un producteur intérieur important de planches de pin de Black Hills et de bois de modelage. Devils Tower Forest Products exploite une scierie et une usine de rabotage, produisant des produits 5/4 et 6/4 de haute qualité, du bois d’œuvre de 1x4, de 1x8, de 1x10 et de 1x12 et des copeaux qui sont commercialisés principalement sur le marché intérieur. La production annuelle varie dans la plage de 40 millions de pieds-planche et l’installation emploie 85 personnes. Tom Shaffer est directeur général pour Neiman Enterprises. Il explique les motifs justifiant le changement vers un système de classement automatisé à Devils Tower. « Nous ne pouvions amener les gens à s’intéresser à apprendre le métier de classeur. Avec tout ce matériel d’atelier lourd, cela avait des effets négatifs sur nos classeurs vieillissants. Nous pensions que nous pouvions obtenir une plus grande précision de classement et prendre de meilleures décisions d’éboutage avec un système automatisé et que nous pourrions redéployer notre équipe. » L’usine utilisait trois systèmes de classement sur la ligne et avait continuellement besoin de former d’autres classeurs. L’automatisation du procédé de classement semblait être une option logique. Les produits d’atelier représentent une partie importante de la production de l’usine, avec les produits d’atelier désignés représentant environ 40 % et
Projecteur de classement

Projections

Pour les produits d’atelier, les coupes claires sont projetées sous forme de rectangles pleins. Les symboles projetés peuvent être personnalisés de sorte que les clients peuvent créer des symboles auxquels leur installation est habituée.
les produits de planches de 1 po représentant le reste. Le classement pour les produits d’atelier constituait une exigence majeure pour tout système que l’usine choisirait. Tom a dit qu’il avait confiance dans la technologie THG, plus particulièrement avec l’expérience d’USNR dans l’utilisation de cette même technologie sur les produits d’atelier et de moulage dans la scierie. « Vous faites cela dans la partie du bois vert, le refendage et la séparation pour le classement. Nous étions convaincus qu’USNR pourrait mettre en service ce système dans notre usine de rabotage. » Nous avons également observé que l’entreprise utilisait l’équipement d’USNR dans ses quatre usines et qu’elle était familière avec le niveau de service et de soutien auquel s’attendre.
Application unique, nouveaux développements Le système à Devils Tower doit classer de manière différente en raison du mélange de produits, lequel demandait un travail de développement supplémentaire pour satisfaire tous les critères. Avec la technologie Deep Learning d’USNR utilisée, le système reconnaît facilement les défauts, dont les nœuds, la pourriture, la résine, les veines de résine, les poches de résine, l’écorce enfermée, les mouchetures, la moelle et le bleuissement. Un autre aspect important de cette application est l’utilisation d’un second ensemble de courroies pour transporter les planches à travers le châssis de scannage, pour un scannage sans occlusion. Combinées à des capteurs déportés montés sous le flux, les quatre surfaces de la planche sont complètement balayées sans obstruction. Le classement des produits d’atelier est centré sur la recherche de sections de bois sans défauts, de sorte qu’il est essentiel d’obtenir des données complètes de toutes les surfaces. Cette nouvelle configuration de courroies et de scannage permet d’exposer toutes les surfaces inférieures au scannage et à la collecte de données. Juste en aval du scanneur, le projecteur de classement affiche toutes les décisions de classement sur les planches autant pour les produits d’atelier que de planches.
La récupération est à la hausse! Maintenant que le système fonctionne depuis plusieurs mois, la direction de l’usine est satisfaite de son rendement. Ron Bears, superviseur du bois sec, disait « Le système fait un merveilleux travail à l’atelier. La
Capteurs déportés
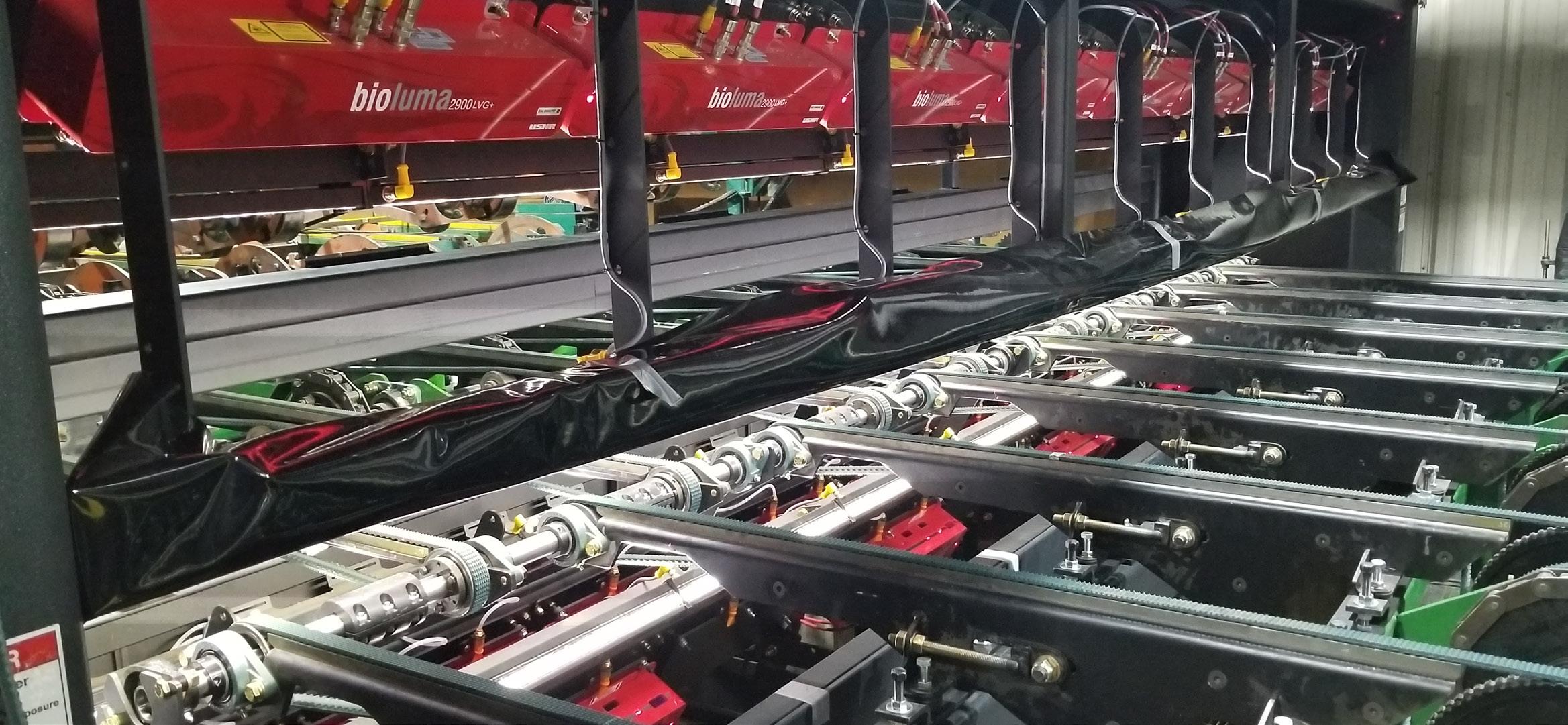
Courroies déportées
Des paires décalées de courroies transportent les planches à l’intérieur du cadre de scannage et, avec des paires déportées de capteurs montés sous le flux, le système balaie les quatre surfaces de chaque planche. Cette nouvelle configuration de transport et de scannage sans occlusion génère toutes les données requises, s’assurant que le système ne manque aucun défaut.
matière première pour les produits de planches de 1 po varie de semaine en semaine, de sorte que l’apparence de nos planches change et que nous voyons des choses que nous pouvions voir auparavant. Cela nécessite certains réglages. Les produits de l’atelier présentent une apparence plus constante, de sorte que nous n’avons plus à isoler diverses caractéristiques sur ces produits. » Ron a décrit leur manière de redéployer les classeurs. « Nous avons déplacé notre classeur principal dans le service de contrôle de la qualité. En tant que classeur certifié, il s’occupe du fonctionnement et de l’entretien du système de classement et règle les paramètres de classement selon les besoins. Il vérifie également les paquets pour s’assurer que le système fonctionne de manière à satisfaire les critères de classement selon les exigences de l’agence. Nous avons ensuite deux nouveaux classeurs qui gèrent le préclassement avant la machine pour repérer certains défauts de la machine comme la vérification des rouleaux. » Quand nous l’avons interrogé au sujet des résultats, Tom a dit : « Je ne connais pas nos chiffres exacts, mais je sais que la récupération par le classement est à la hausse et qu’elle est importante sur certaines largeurs.» Ron a ajouté qu’il pensait que la récupération par le classement était à la hausse de l’ordre de plus de 10 %, selon le produit. En plus de l’amélioration dans la récupération, Ron a ajouté que cela avait permis à la scierie d’augmenter sa production. « Nous épuisions les classeurs aux vitesses de production. Nous pouvons désormais fonctionner plus rapidement. Nous traitons davantage de bois d’œuvre dans le système en moins de temps et avec une plus grande récupération. » Ron a participé au projet sur une base quotidienne et a observé que tout s’est bien déroulé. «
À droite : 6/4 3-Solution d’atelier montrant 2 no 1, coupes de cadres et un montant (scannage du dessus et du dessous sur la même planche). Le chiffre entre parenthèses montre la taille d’échelle du bois d’œuvre.

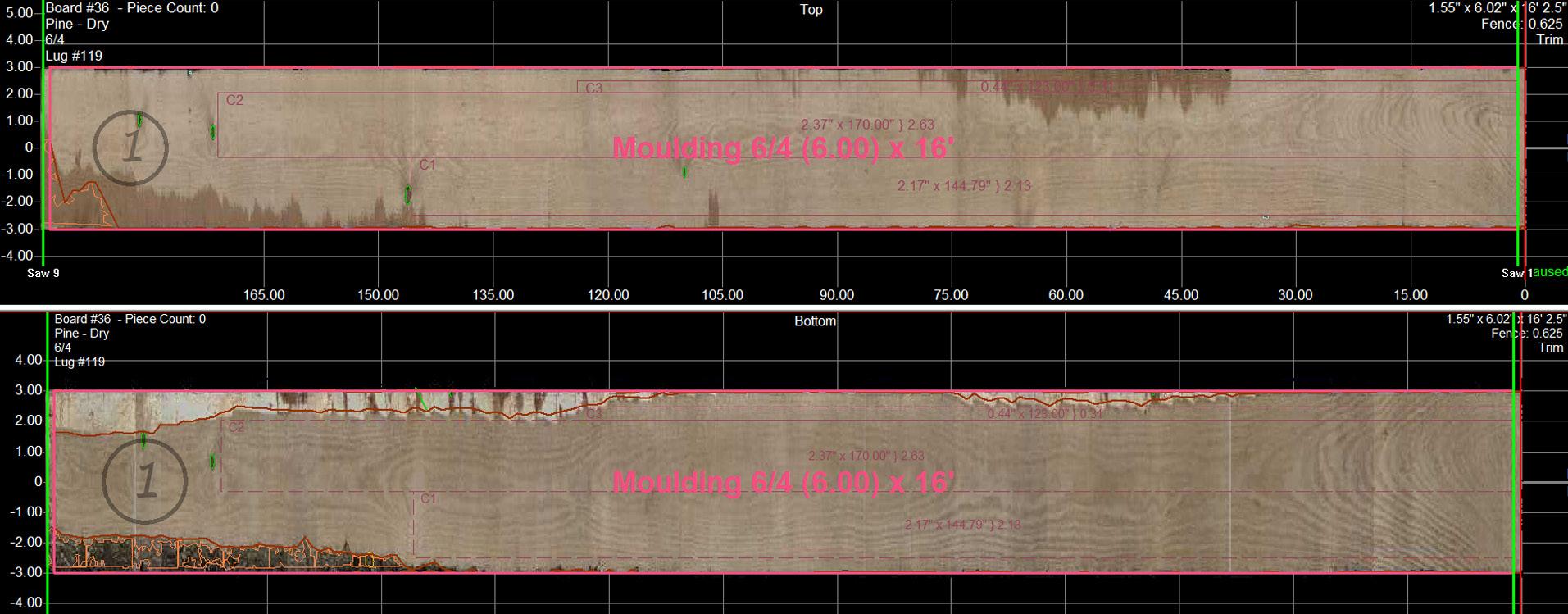
À droite : Solution de moulage 6/4 et écaille de 1 po se soulevant en raison d’une flache excessive (la flache est ombragée sur les surfaces). Le chiffre entre parenthèses montre la taille de l’écaille du bois d’œuvre.
L’installation et le démarrage ont pris environ trois semaines. Le plus gros défi fut la formation pour Mike Bears (le frère de Ron) qui était le classeur principal. Il devait apprendre à faire fonctionner et à entretenir la machine de classement et son groupe d’ordinateurs, et également apprendre à les régler pour classer les produits d’ateliers et de planches. » La formation de Mike Bears et d’autres employés de la scierie a eu lieu au centre de formation d’USNR à Salmon Arm, C.-B., y compris une formation pratique de trois jours. La formation sur place a été donnée une fois le système installé, pour une connaissance approfondie de la configuration du système, du réglage des paramètres pour une gamme de produits, du fonctionnement et de l’entretien quotidiens, de la résolution de problèmes, etc.
Changer la mentalité Passer d’un procédé de classement manuel à un procédé automatisé nécessite un changement de l’ancienne mentalité d’effectuer une tâche difficile, mais familière avec des critères bien connus à laisser une machine effectuer la même fonction à une vitesse bien supérieure. Cela nécessite d’avoir confiance que le système reconnaît chaque petit détail des caractéristiques de chaque planche et qu’il classe cette dernière de manière précise. Les résultats ont calmé tous les doutes antérieurs. Avec ce nouvel investissement qui rapporte de plus d’une façon, Tom affirme : « Nous ne sommes plus limités, nous sommes presque parfaitement équilibrés.» Et avec quatre scieries chapeautées par Neiman, on retrouve toujours de nouveaux défis à relever quelque part.
Deep Learning
augmente la vitesse et la précision de la détection des défauts
réduit de manière importante le temps requis pour le démarrage et la mise en service des systèmes de classement automatiques
permet une détermination précise des défauts uniques aux espèces, à une région ou à un classement, détermination qui serait autrement longue et difficile à réaliser avec des procédés traditionnels
procure une plus grande valeur et une meilleure récupération grâce à une optimisation d’avant-garde