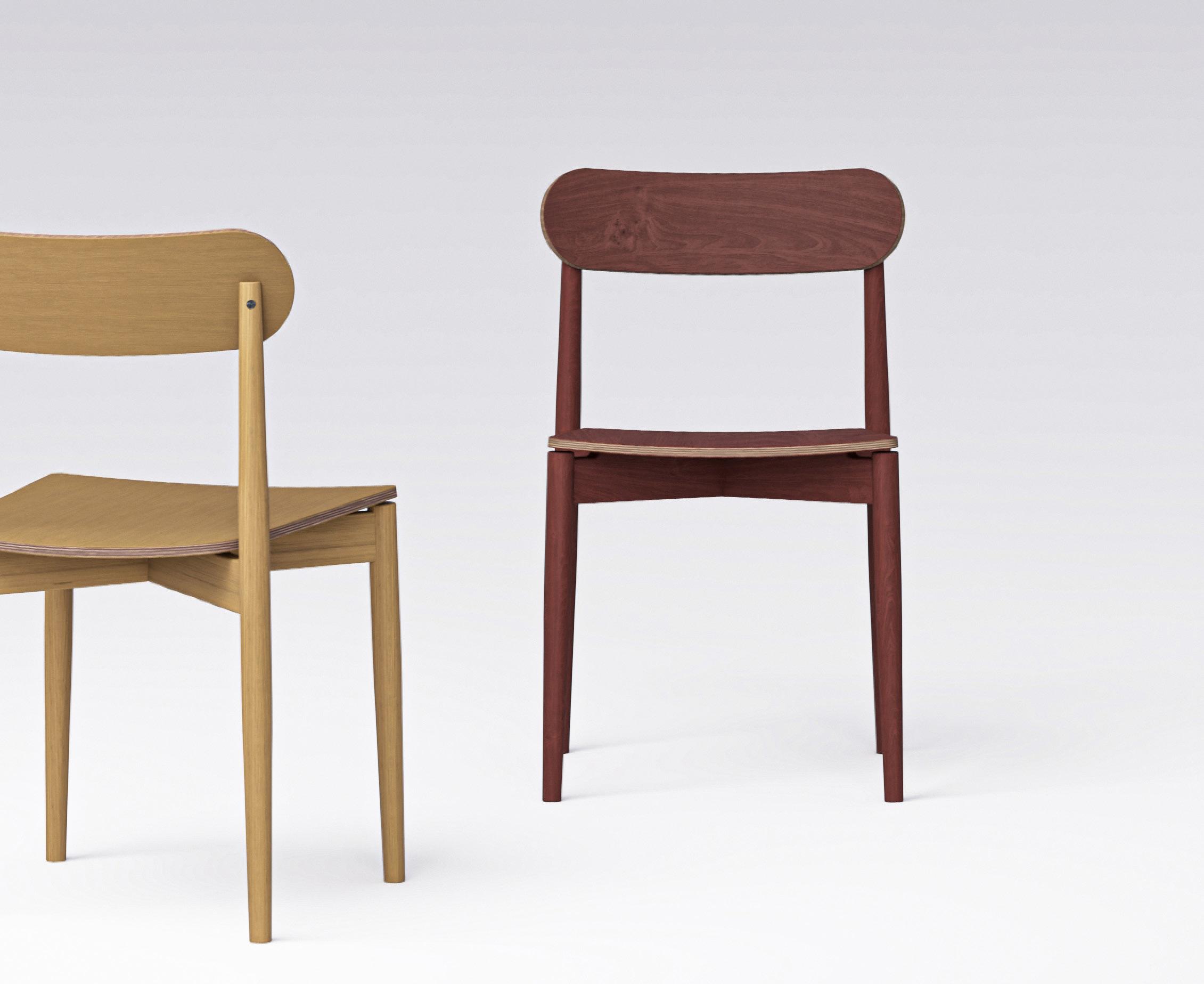
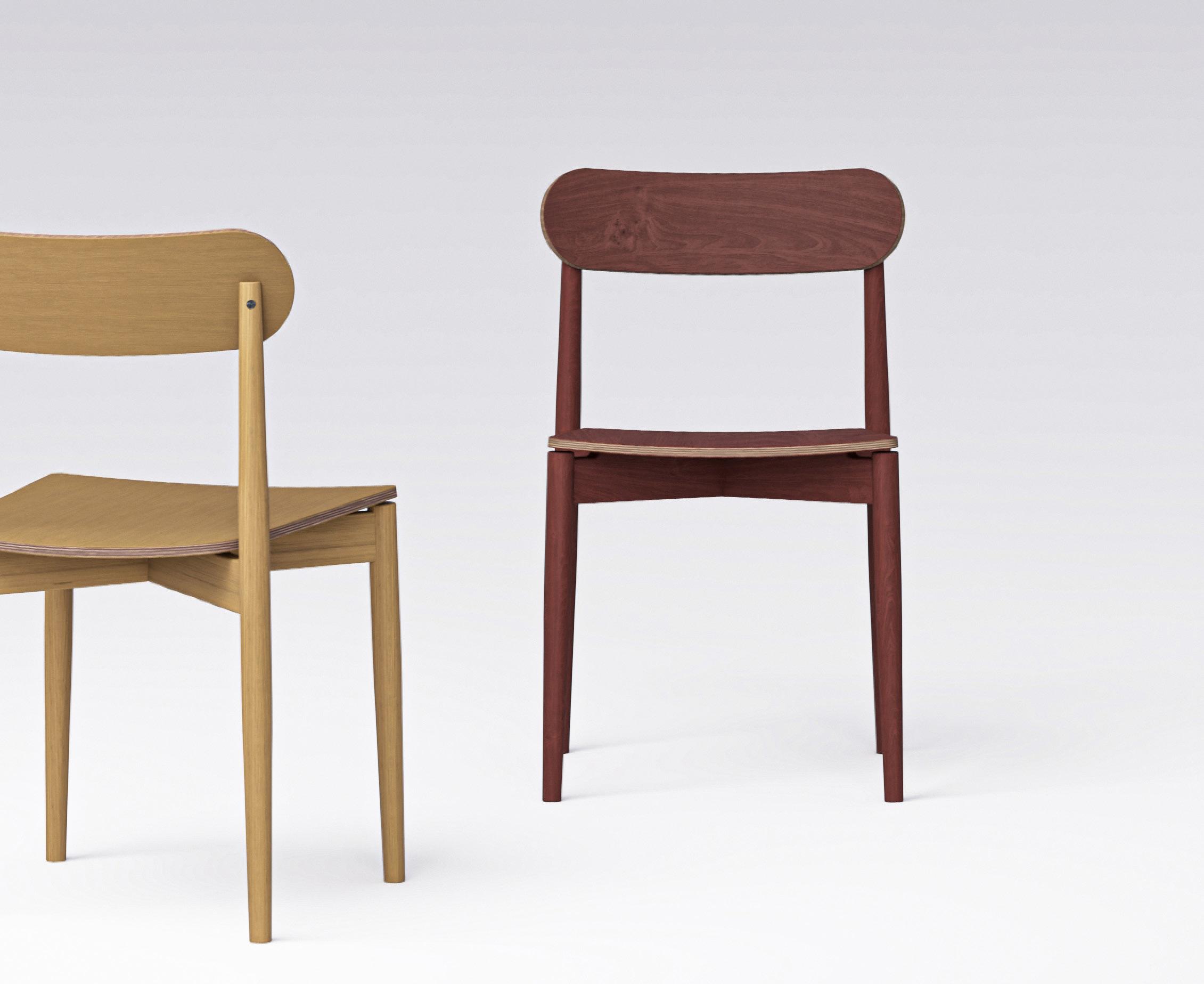
X.01 Chair : from Prototype to Production
UNIT COORDINATOR:
PETER KITELY
GUY EDDINGTON
STUDENT NAME:
EUGENE TIONG
22768315
This unit required the design, full documentation, and prototyping of a complex furniture piece, emphasizing sustainable design and life-cycle analysis. Students engaged with both traditional workshop skills and advanced techniques like rapid prototyping and CAD/CAM machining. Practical considerations for transportation and distribution, such as “knock-down” self-assembly packaging or efficient “nesting” for stacking products, were key to the design process. The result was a commercially viable product that balanced functionality, aesthetics, and efficiency, while addressing sustainability and broader networks of production and consumption.
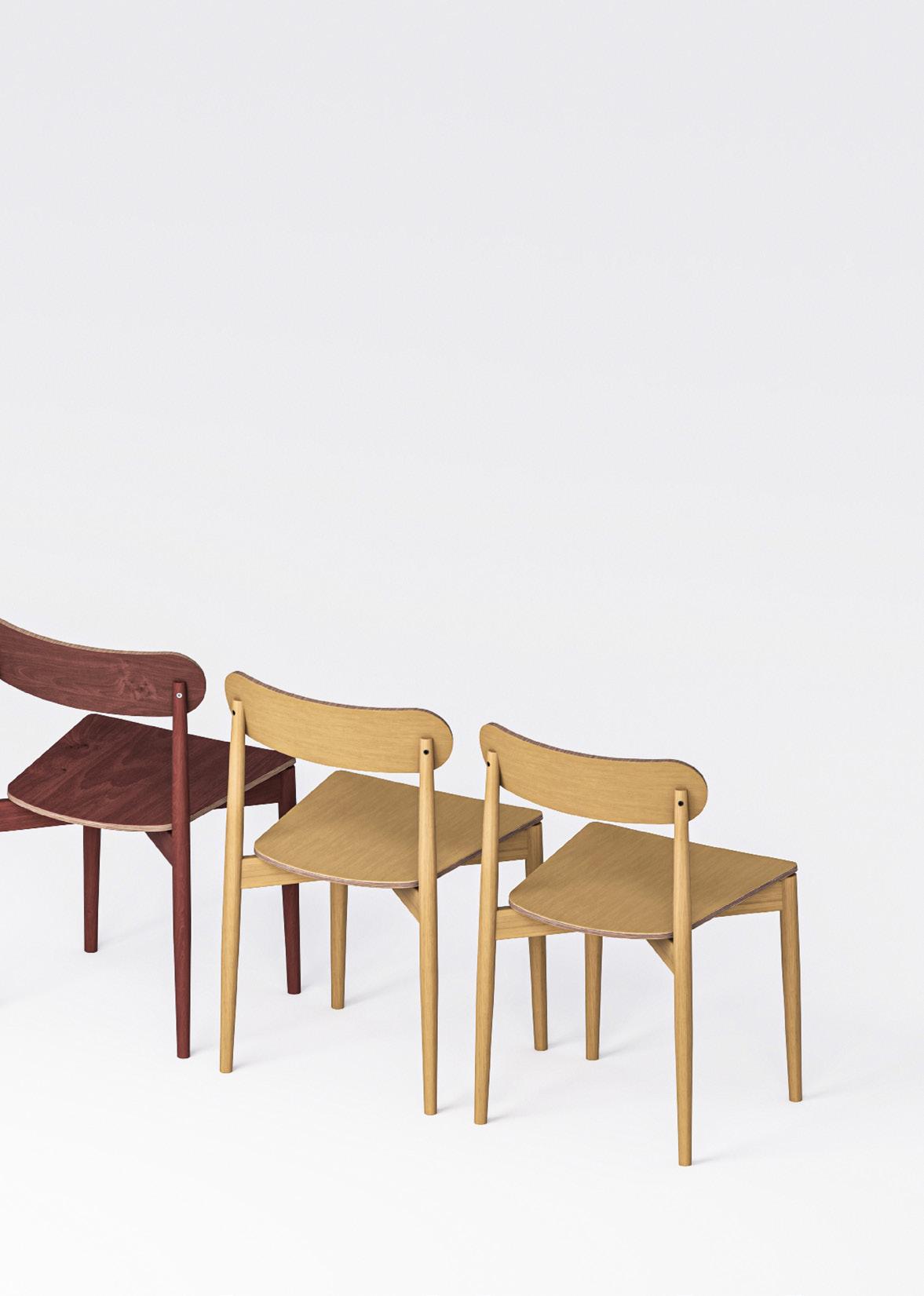

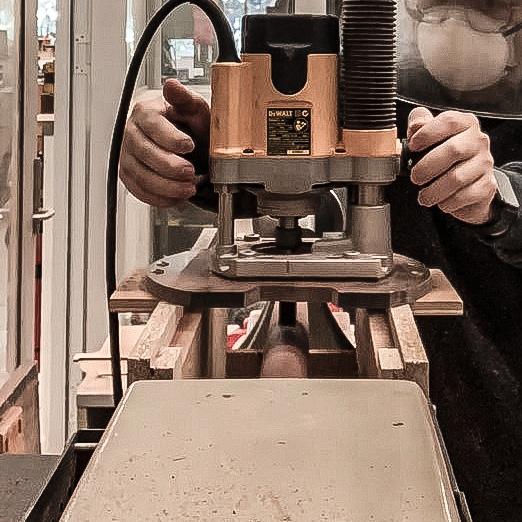
18
X.01 Chair Overview easy-to-assemble stackable flat-pack
Design Process
inspiration research concept development
1:1 prototype mock up
Prototype Construction legs rails backrest seat assembly
Technical Drawings chair packaging
X.01 Chair Overview
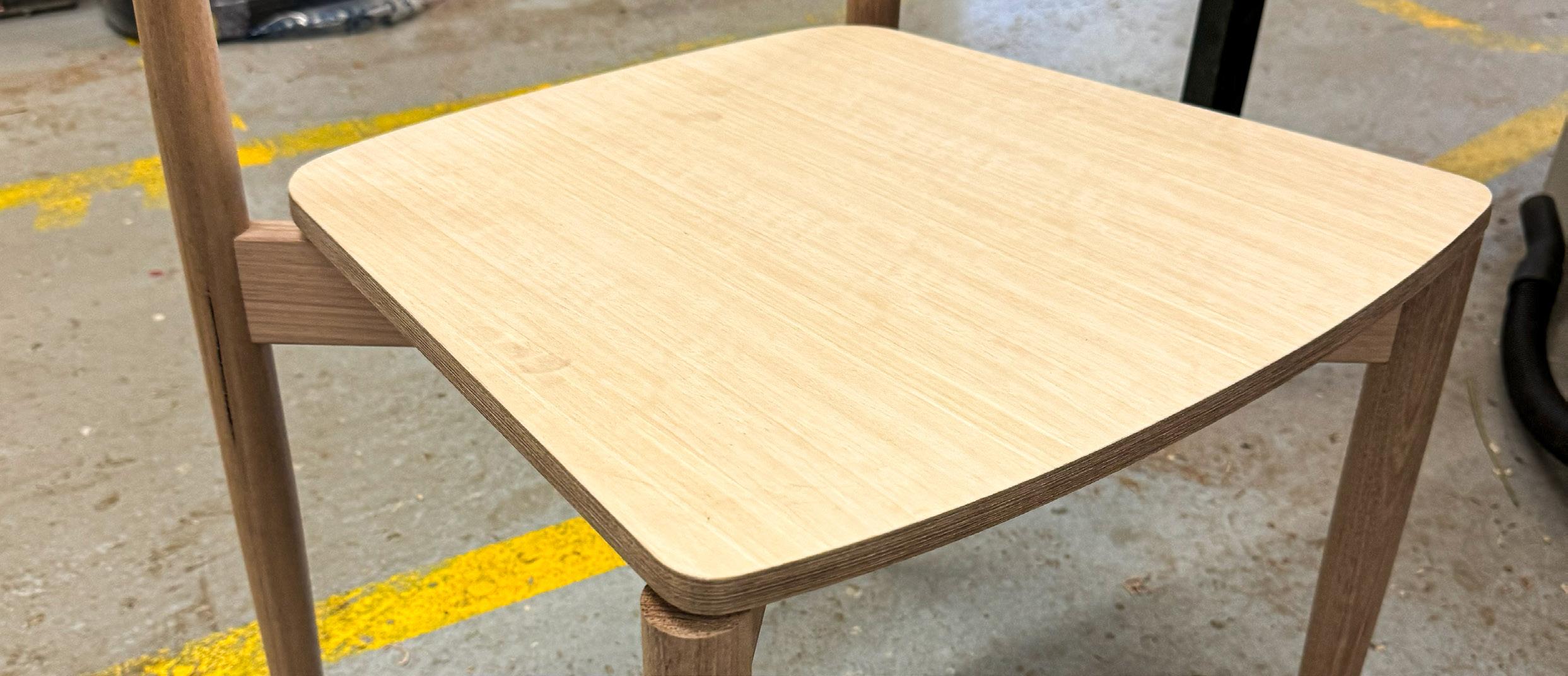
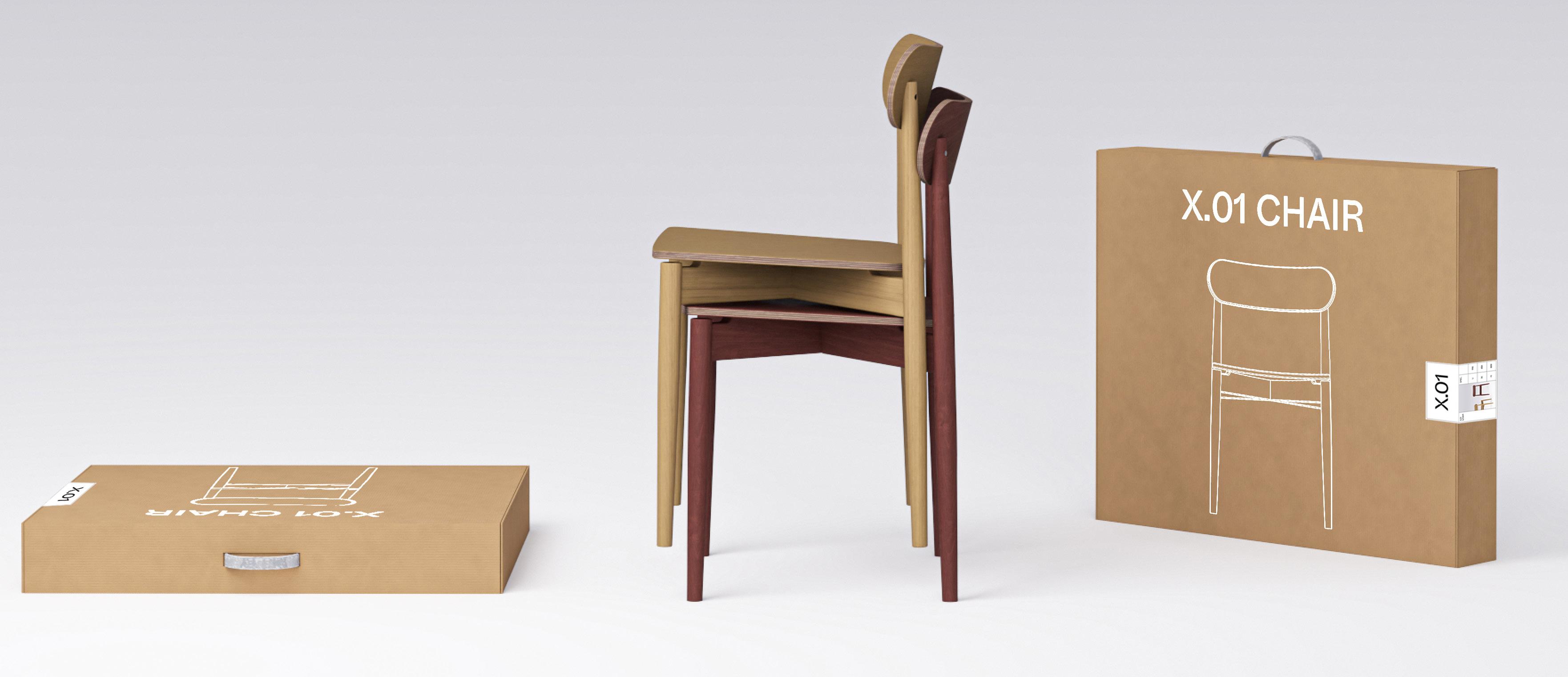
EASY-TO-ASSEMBLE STACKABLE & FLAT PACK
The X.01 Chair is a minimalist, flat-pack dining chair designed by Eugene Tiong, a Master of Architecture student at The University of Western Australia School of Design. Drawing inspiration from the braided channels of Western Australia’s iconic Fitzroy River, the chair features a unique crossing leg structure that mirrors the river’s dynamic flow and convergence.
Expertly crafted from high-quality Australian hardwood, the X.01 Chair combines timeless elegance with refined craftsmanship, making it ideal for residential and commercial settings. Designed
with ergonomic comfort in mind, it also offers practical functionality, including the ability to stack up to five chairs.
Merging aesthetics with environmental responsibility, the chair is engineered for efficient shipping, easy assembly, and ultra-low carbon emissions. Thoughtfully constructed for disassembly, the X.01 Chair allows for material recycling and part replacement, making it as sustainable as it is beautiful— an ideal choice for the modern, conscientious consumer.


PRODUCT: DESIGNED BY:
Material: Jarrah & Vic Ash
H: 800 W: 494 D: 476 Seat H: 462
Weight: 5 kg
DESIGINED IN: DATE:
PRICE: DINING CHAIR EUGENE TIONG WESTERN AUSTRALIA 2024 $ 400
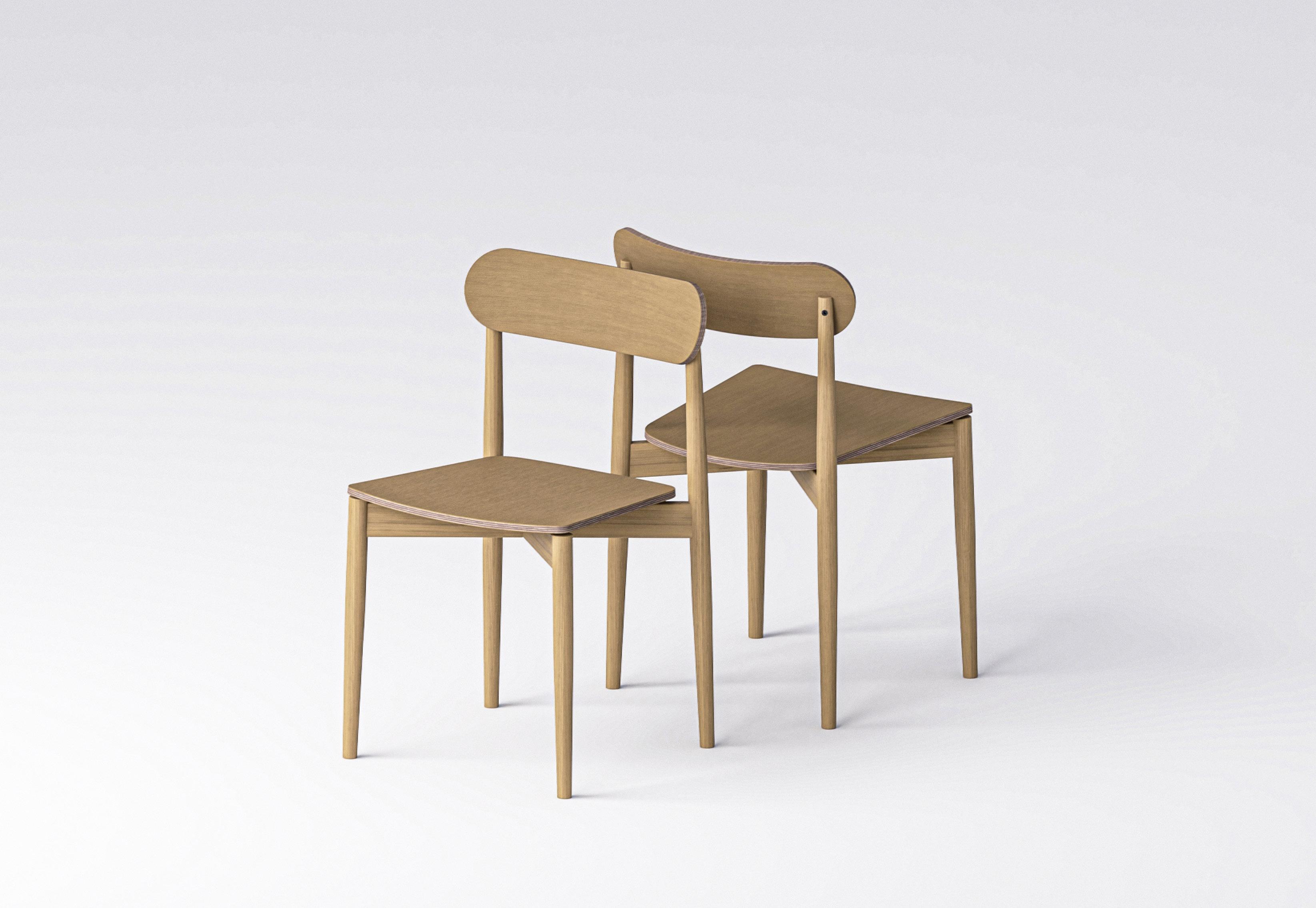
MINIMALIST LUXURY
In today’s world, smaller living spaces demand the efficient use of every square inch, making intentional design essential.
The X.01 Chair meets this need with a minimalist aesthetic that embraces open spaces and reduces visual clutter. Its design is visually lightweight, featuring clean lines, open legs, and floating elements that create a sense of spaciousness.
Engineered for versatility, the chair’s modern form seamlessly integrates into various interior styles, while its stackability—up to five chairs at a time—maximizes space efficiency. This makes it an ideal choice for compact living spaces, optimized storage, and bustling restaurant environments.
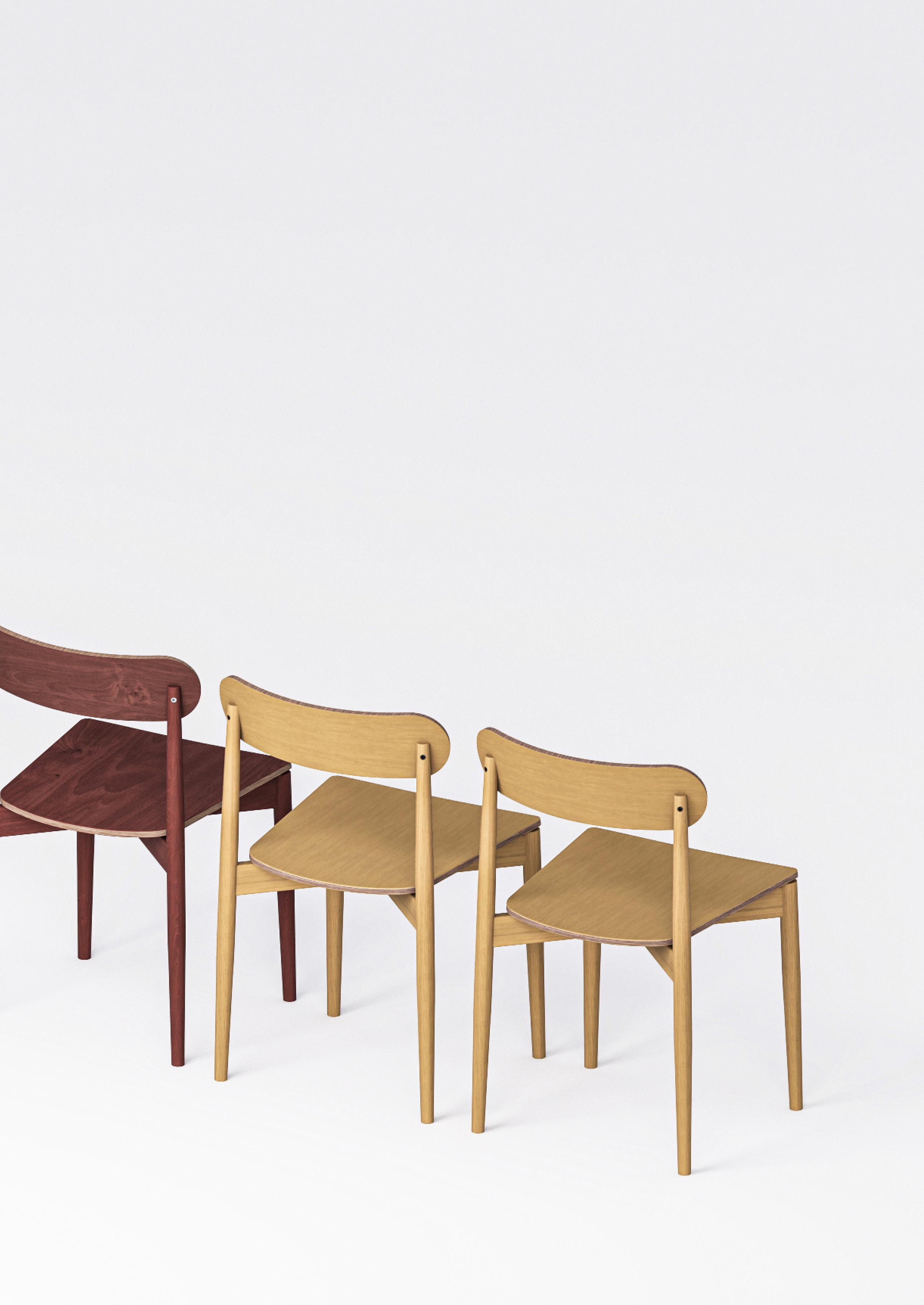
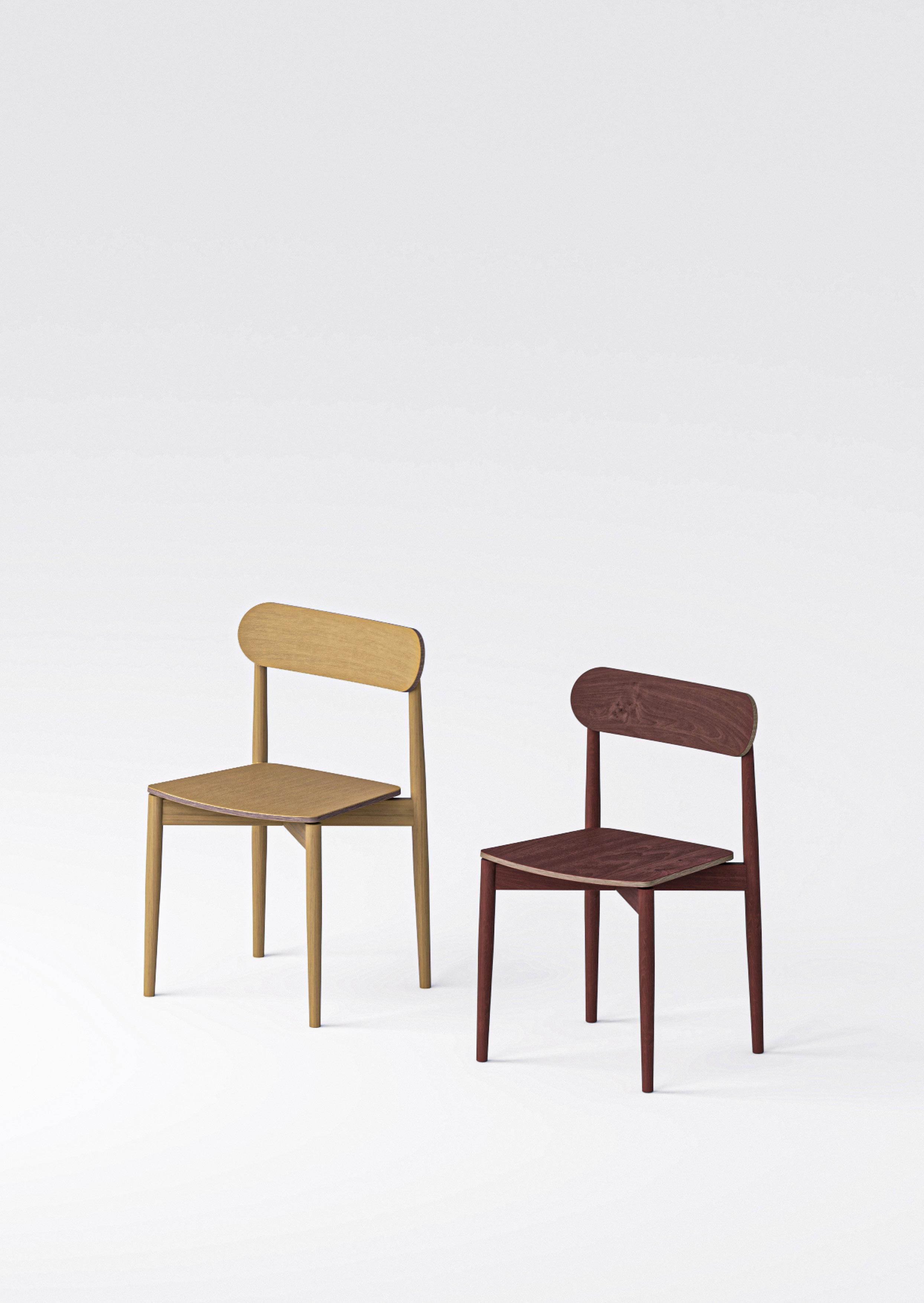
ENVIRONMENTAL SUSTAINABILITY
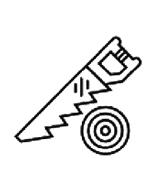

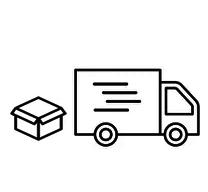

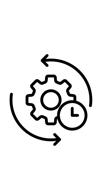
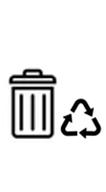
The X.01 Chair is available in two premium wood options: deep red Jarrah and warm pinkish-brown Victorian Ash, each lending a distinct, natural character that complements both minimalist residential and commercial settings. Crafted from 100% eco-certified wood sourced from sustainable forests, this choice supports responsible forestry practices where forests are allowed to regenerate, local wildlife is preserved, and worker conditions are prioritized.
Designed for longevity, the X.01 Chair can be easily disassembled for recycling, with replaceable parts to extend its lifespan, embodying a commitment to both beauty and sustainability.

Raw Material Manufacturing Transportation Use Repair/ Replace Diposal/ Recycle
Life Cycle Diagram of the X.01
Total Climate Emission 0.0 kg CO2eq
FLAT-PACK DESIGN
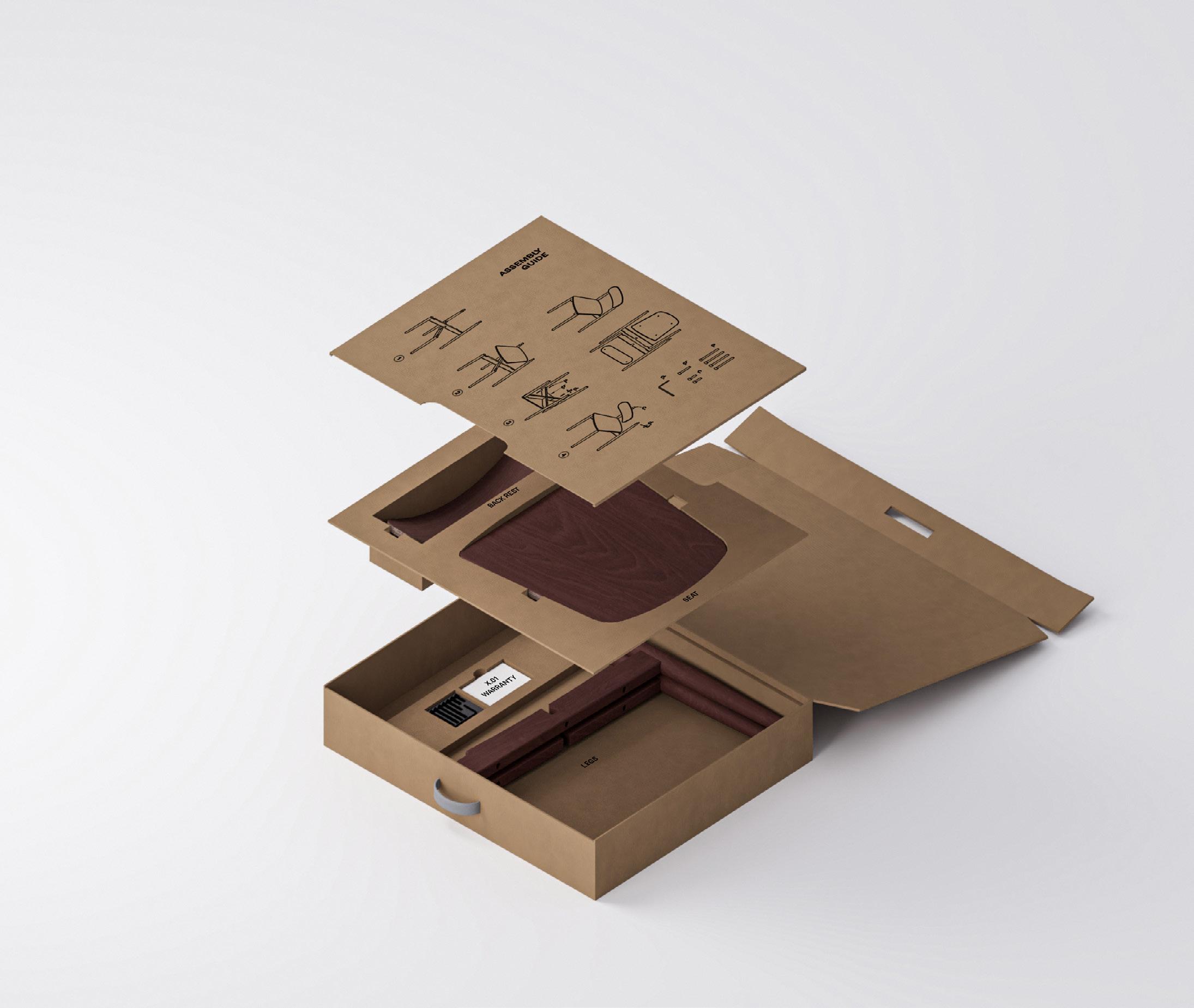
The X.01 Chair is designed with sustainable principles and shipped as a flat-pack, component-based product. Packaged in recyclable materials, it allows 3 to 5 times more units to be transported in the same volume, significantly reducing CO2 emissions during shipping. Weighing only 5.5 kg, it conveniently fits into a standard family vehicle and comes with a 5-year warranty, ensuring both ease of transport and long-lasting quality.
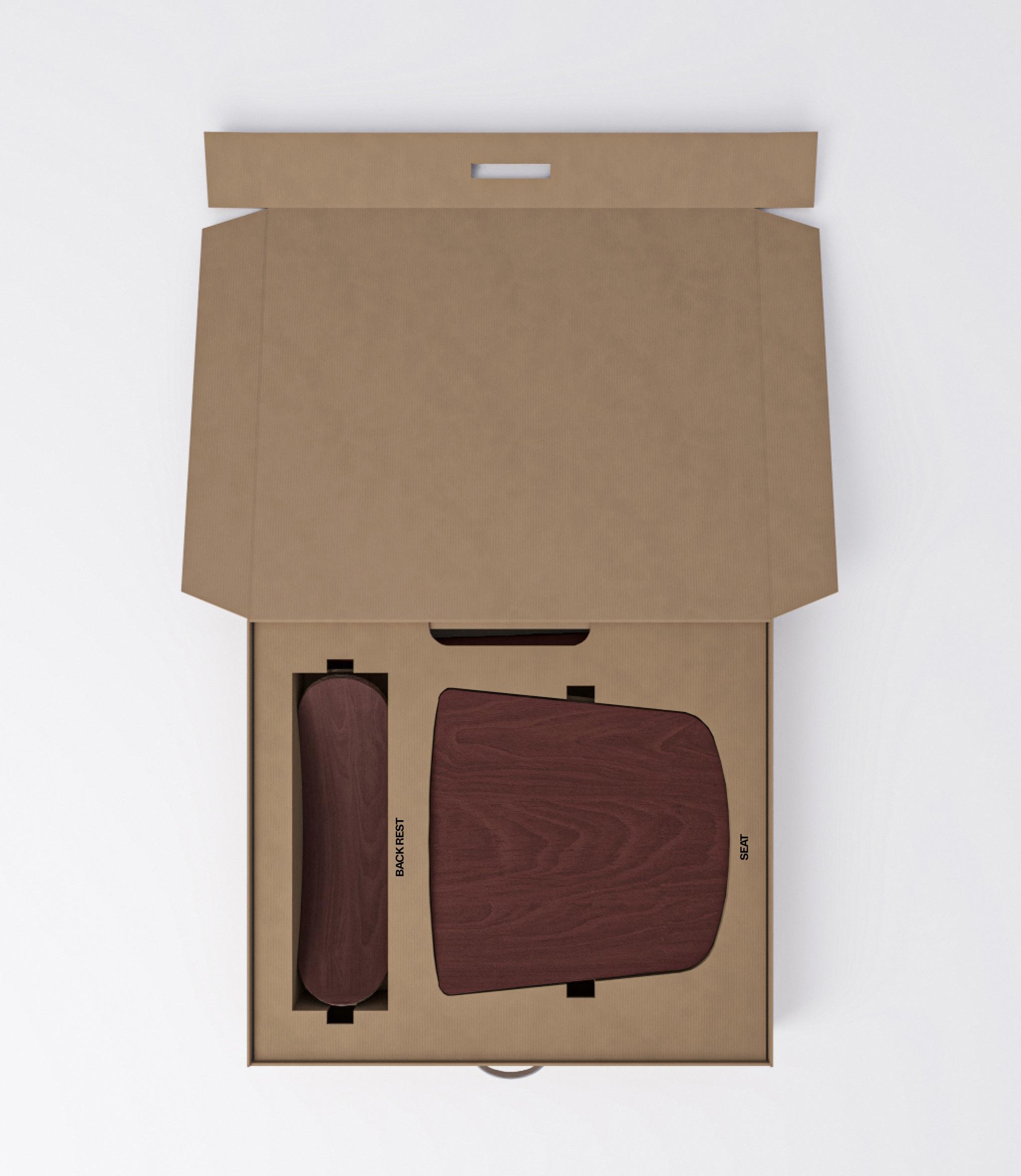
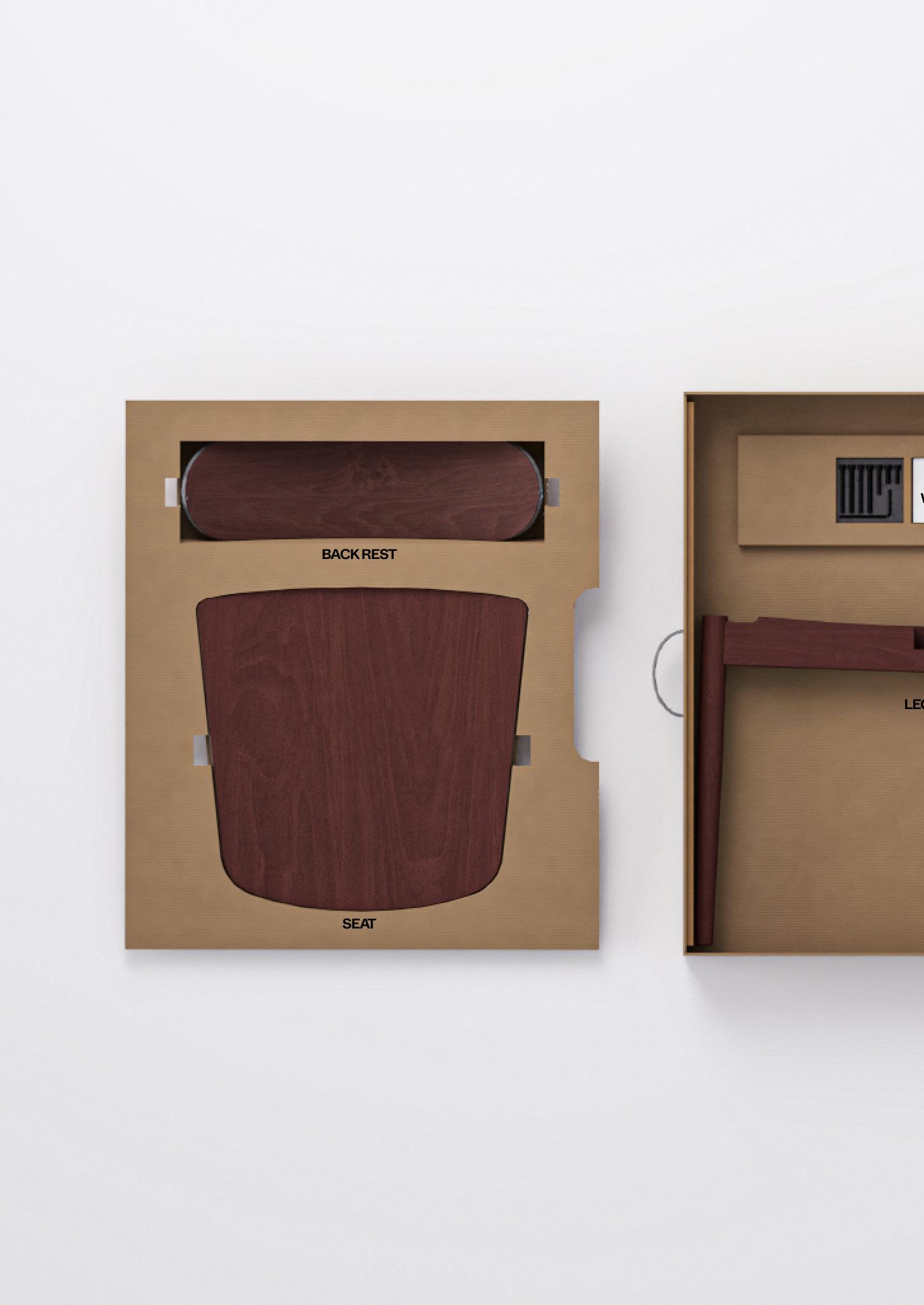
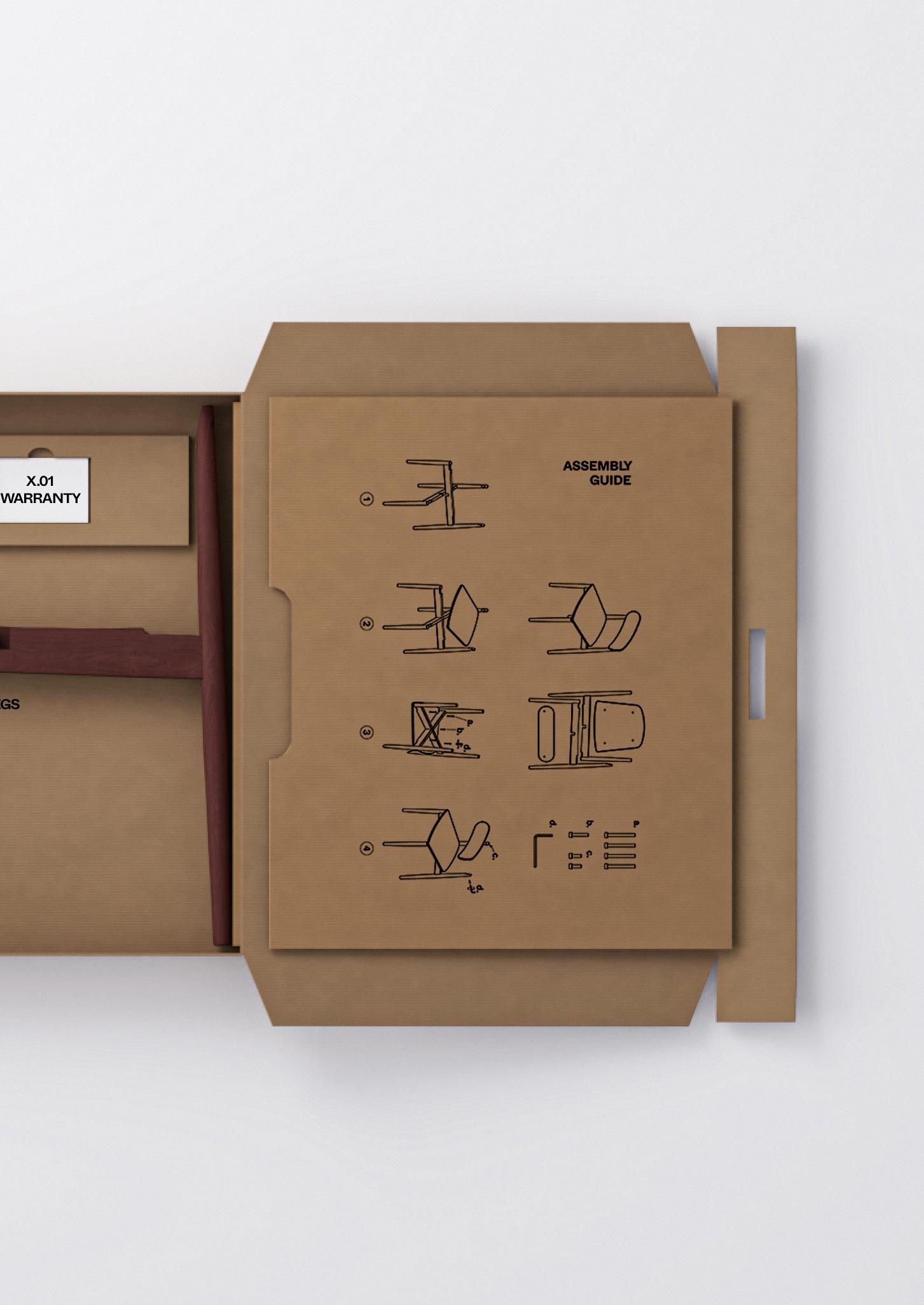
Design Process

INSPIRATION
X.01 Chair is inspired by the Fitzroy River, one of Western Australia’s longest rivers. The design features a crossing leg structure that reflects the intricate and interwoven patterns of the river’s navigation.
Influenced by the river’s dramatic gorges and layered rock formations, the chair also embodies the cultural significance of the Fitzroy River as a living ancestral being, central to Dreaming stories and spiritual heritage. This integration connects the design to the natural and cultural landscapes of Western Australia.
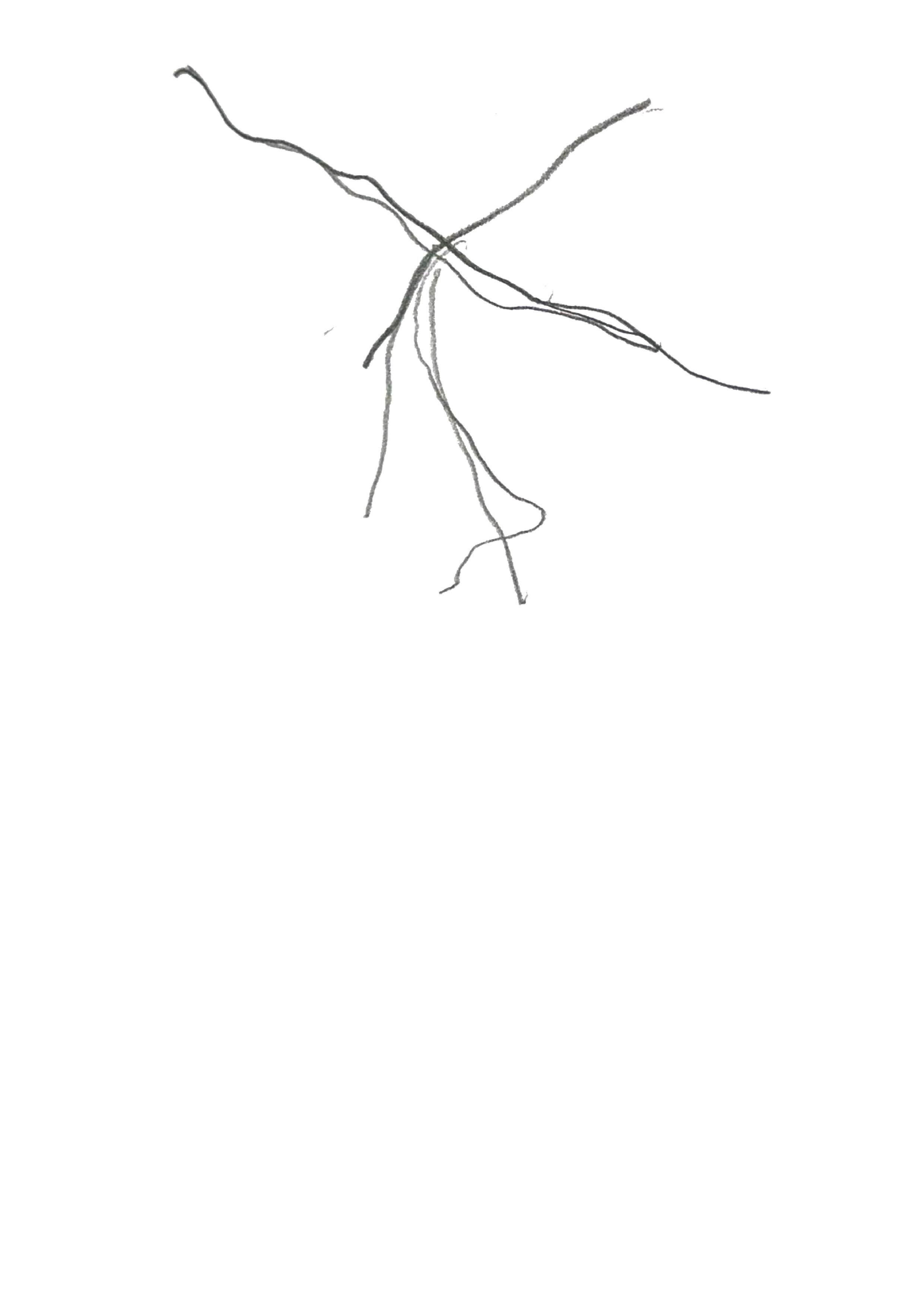
The material choice for the X.01 Chair marks a significant step in its design, thoughtfully selected to echo the essence of the Fitzroy River’s landscape. The use of Jarrah and Victorian Ash, with their deep red and warm pinkish-brown tones, beautifully mirrors the layered rock formations along the riverbanks.
Jarrah, in particular, is native to Western Australia, making it a meaningful representation of the region’s natural heritage and grounding the chair in the unique character of its origins.

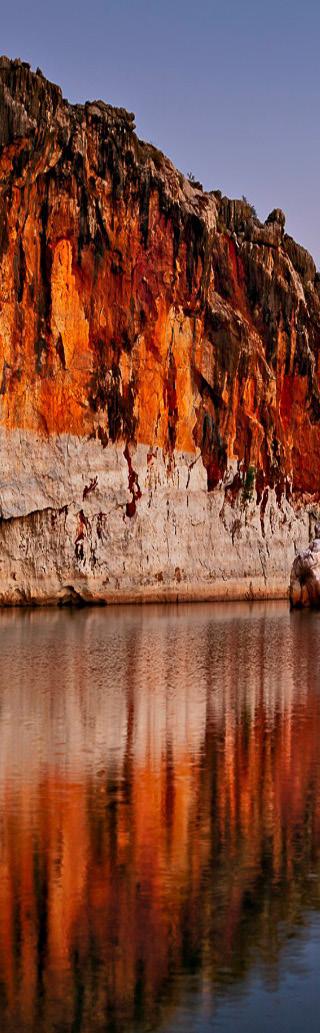
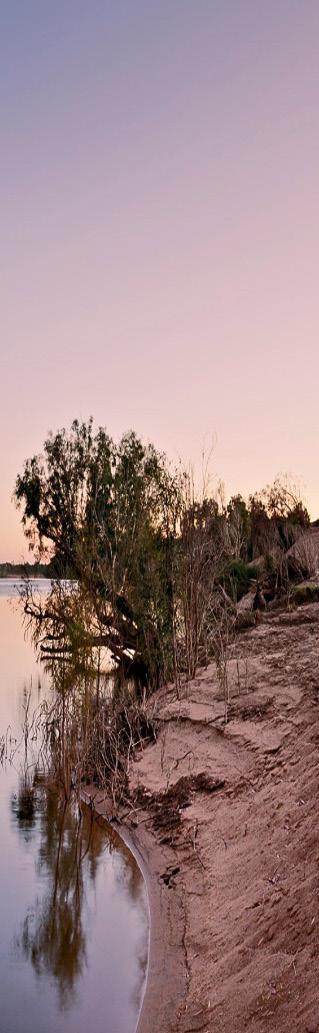
Mood Image & Colour Inspiration
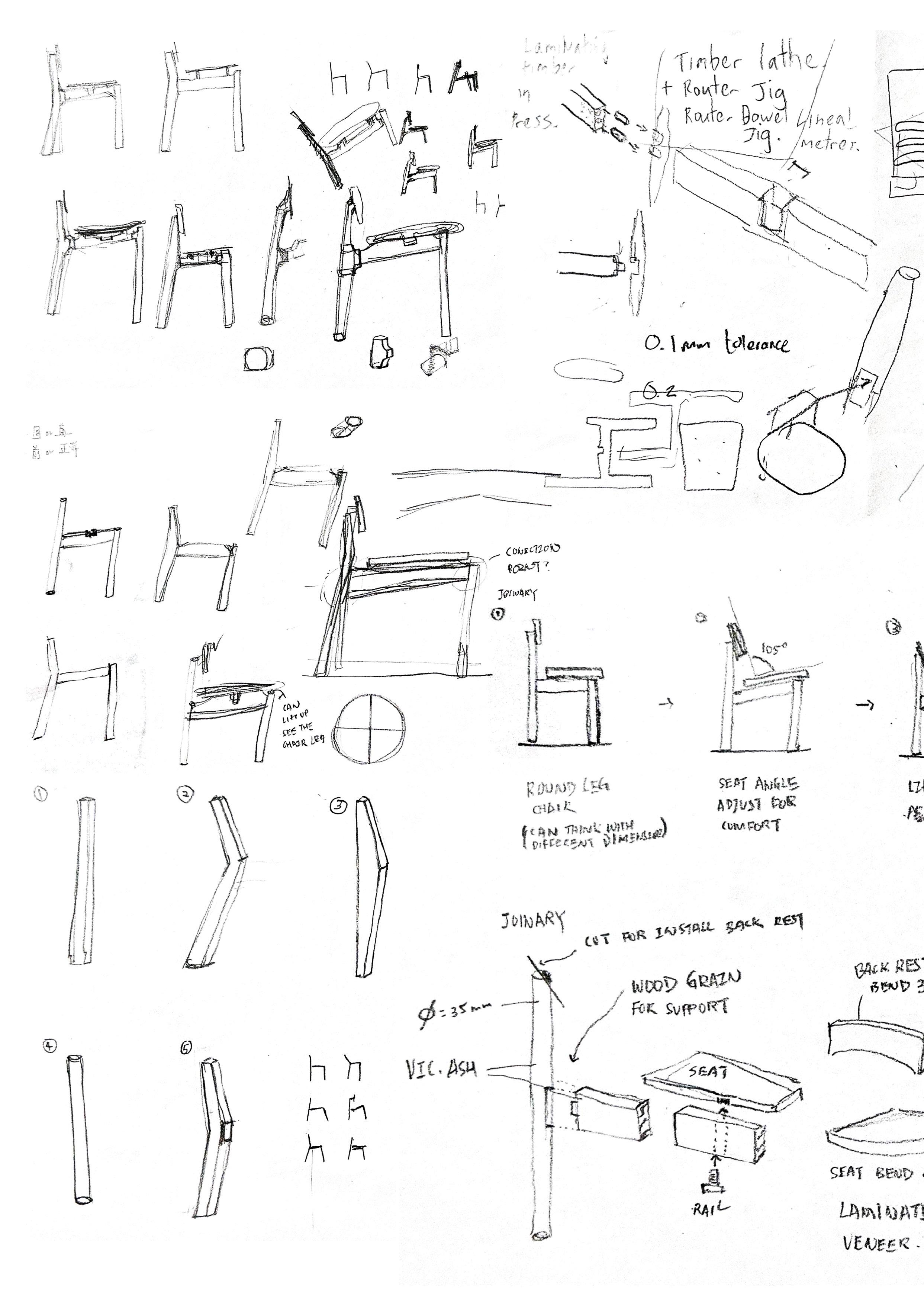
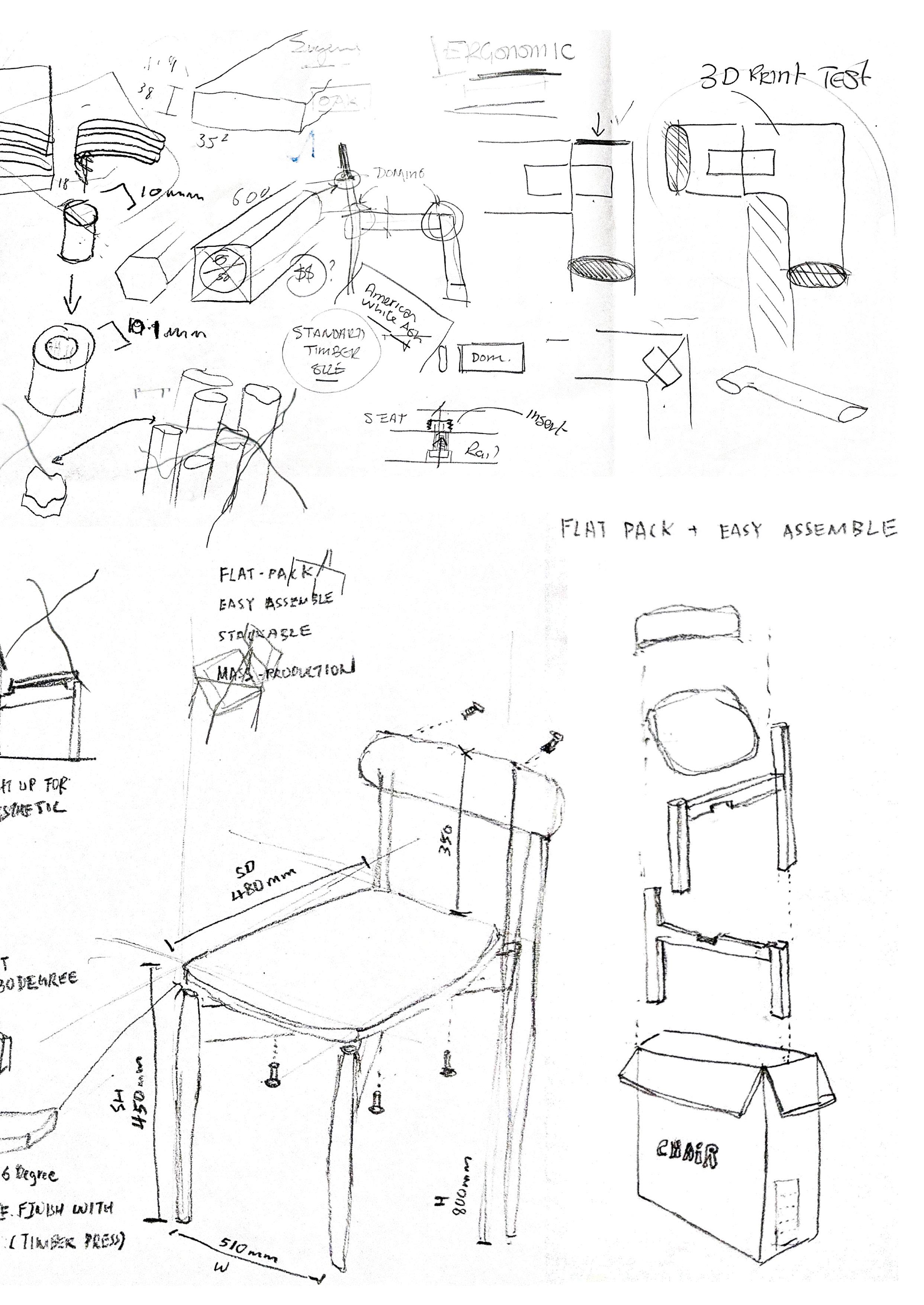
ERGONOMIC DATA & MATERIAL RESEARH
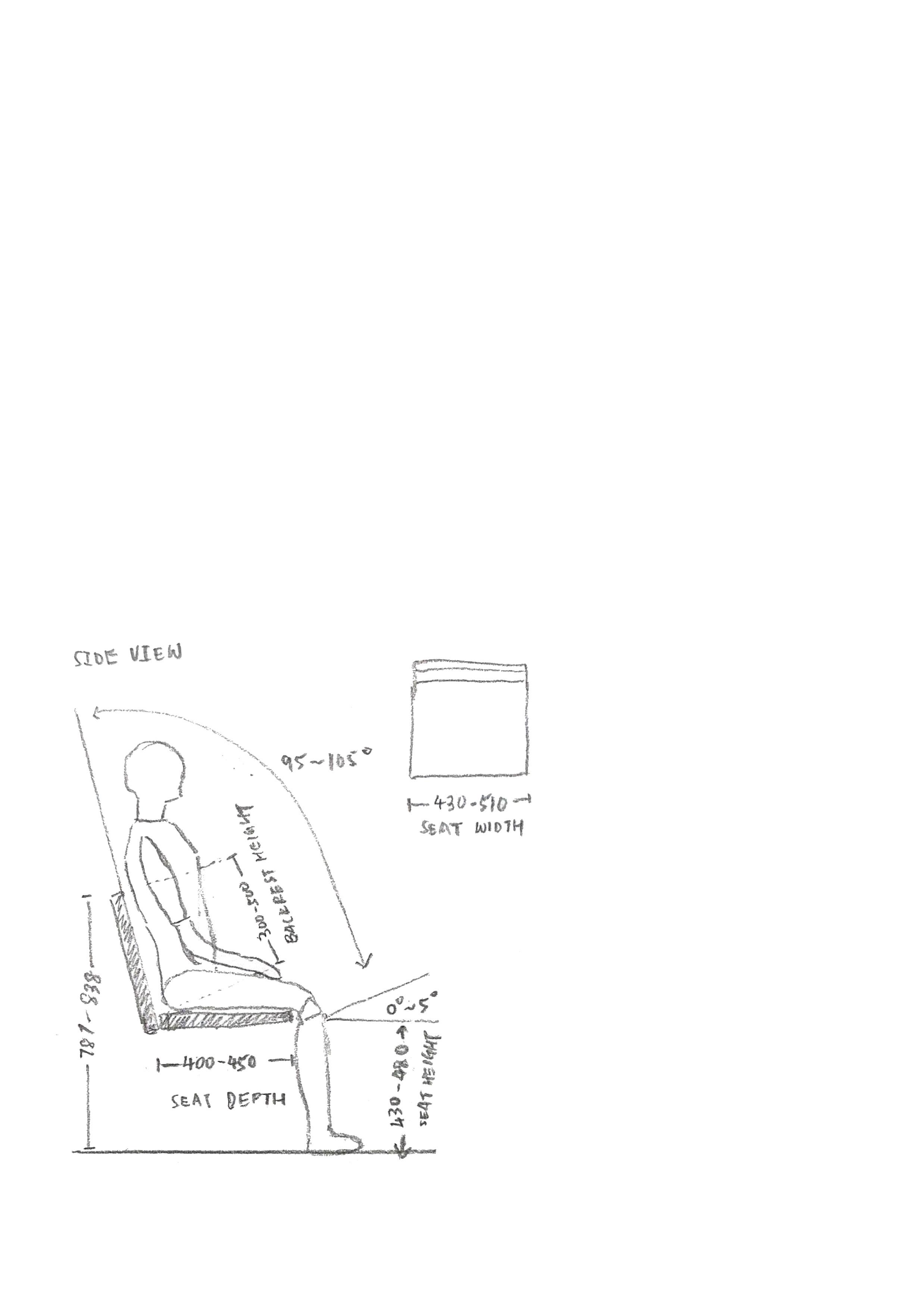
The dining chair is designed for moderate use, recognizing that people often spend extended periods seated for meals, socializing, or working. It offers essential ergonomic support to ensure comfort and ease throughout these longer periods of use.
Data Specifications
Seat Height: 430 - 480 mm
Seat Depth: 400 - 450 mm
Seat Width: 30 - 510 mm
Back Rest Height: 300 - 500 mm (Above the Seat)
Back Rest Angle: 95 - 105 degrees (From the Seat)
Seat Angle: 5 to 10 degrees (Sloped Backward)
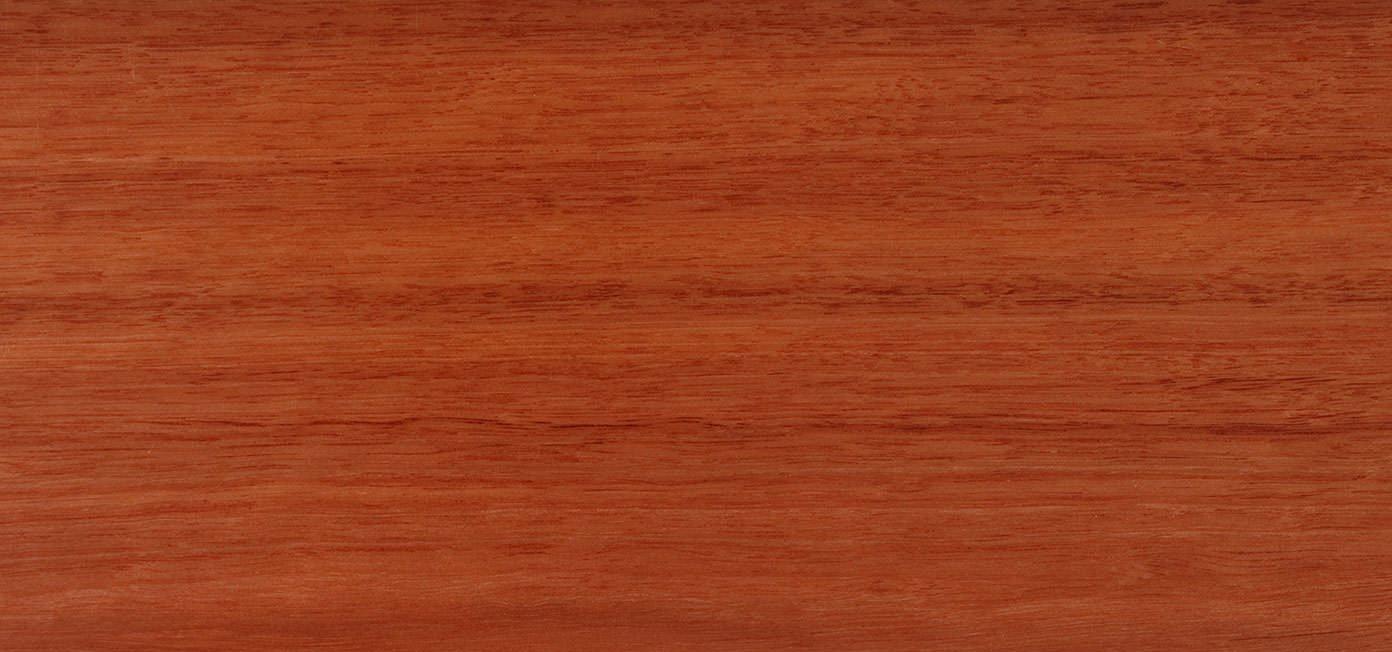

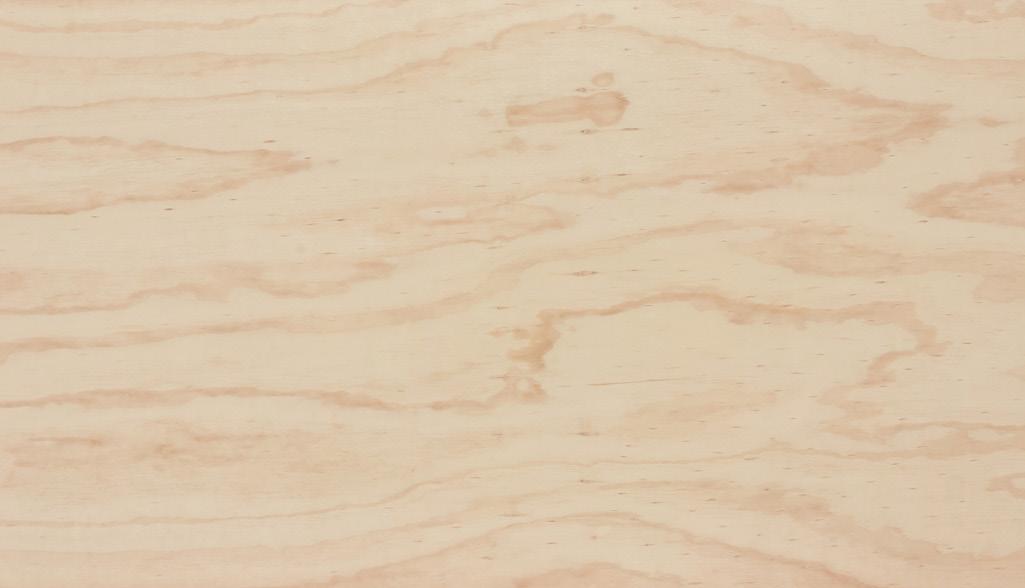
Jarrah, native to Western Australia, is known for its rich red tones and fine, even grain. This exceptionally hard wood is resistant to wear, termites, and rot, making it ideal for durable furniture. Sourced sustainably to support forest regeneration, Jarrah is perfect for high-use indoor and outdoor furniture where longevity and vibrant color are key.
Victorian Ash, sourced from Victorian forests in Australia, has a light pinkish-brown tone with a subtle grain that suits modern designs. This medium-density wood is easy to machine, making it ideal for indoor use. Grown in certified, eco-friendly forests, Victorian Ash offers warmth and versatility, perfect for minimalist and contemporary furniture.
1.5mm Bendy Plywood is a highly flexible, thin plywood designed for applications requiring smooth curves and bends. Additionally, it can be finished with various veneers to achieve the desired look, making it both a practical and aesthetically versatile material for innovative designs.
Once the design is refined, it transitions into a digital format using advanced CAD software. This step allows for precise detailing, adjustments, and the creation of accurate 3D models, enabling a comprehensive view of the chair’s form and functionality. The digital representation facilitates further iterations and optimizations, ensuring that every aspect of the chair is meticulously crafted before moving to the prototyping and manufacturing stages. This seamless integration of traditional sketching and modern digital tools embodies a holistic approach to furniture design, balancing creativity with technical precision.

CONCEPT DEVELOPMENT & CAD/CAM MACHINING
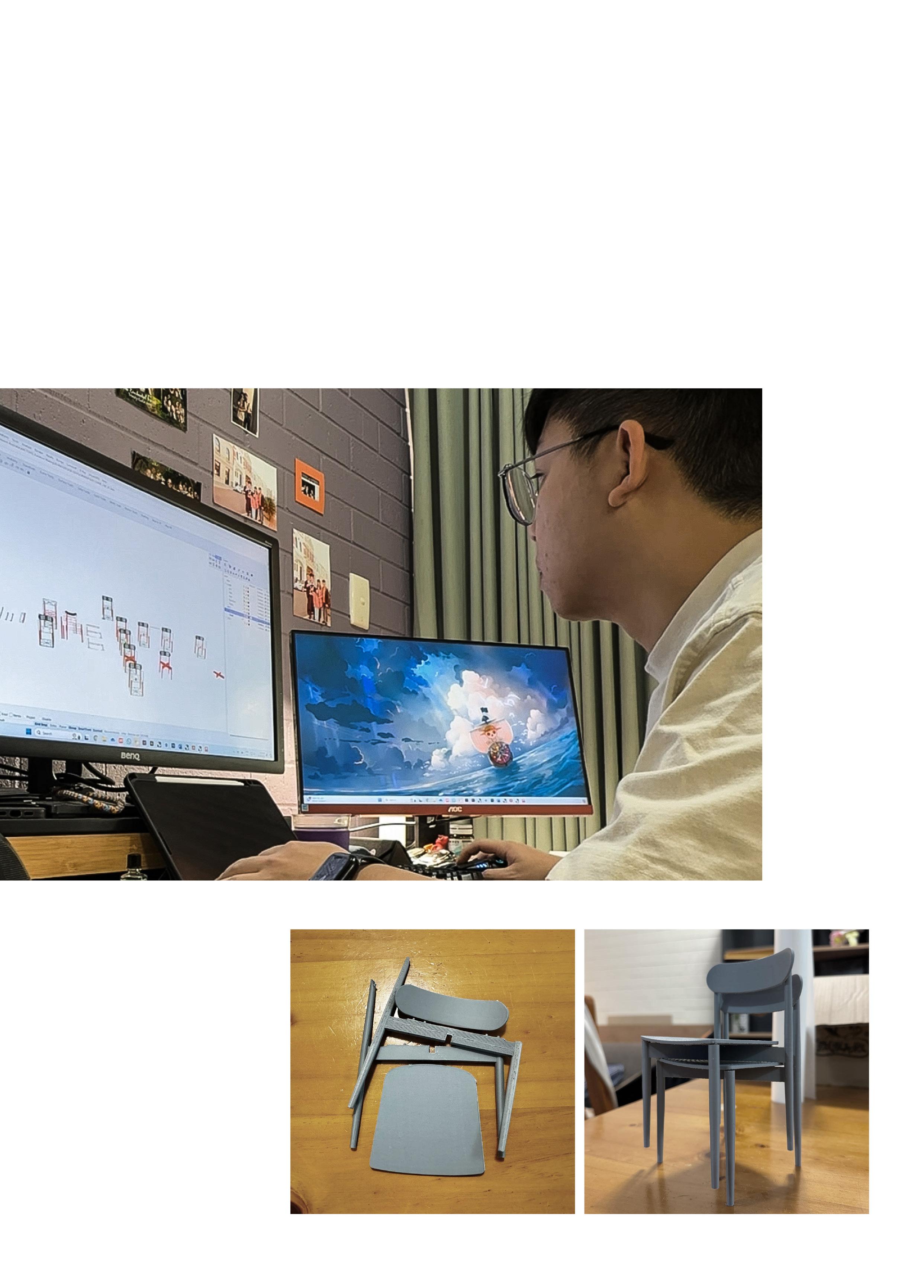
CONTACT SUPPLIER & MATERIAL PURCHASE

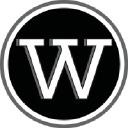
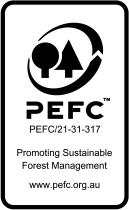
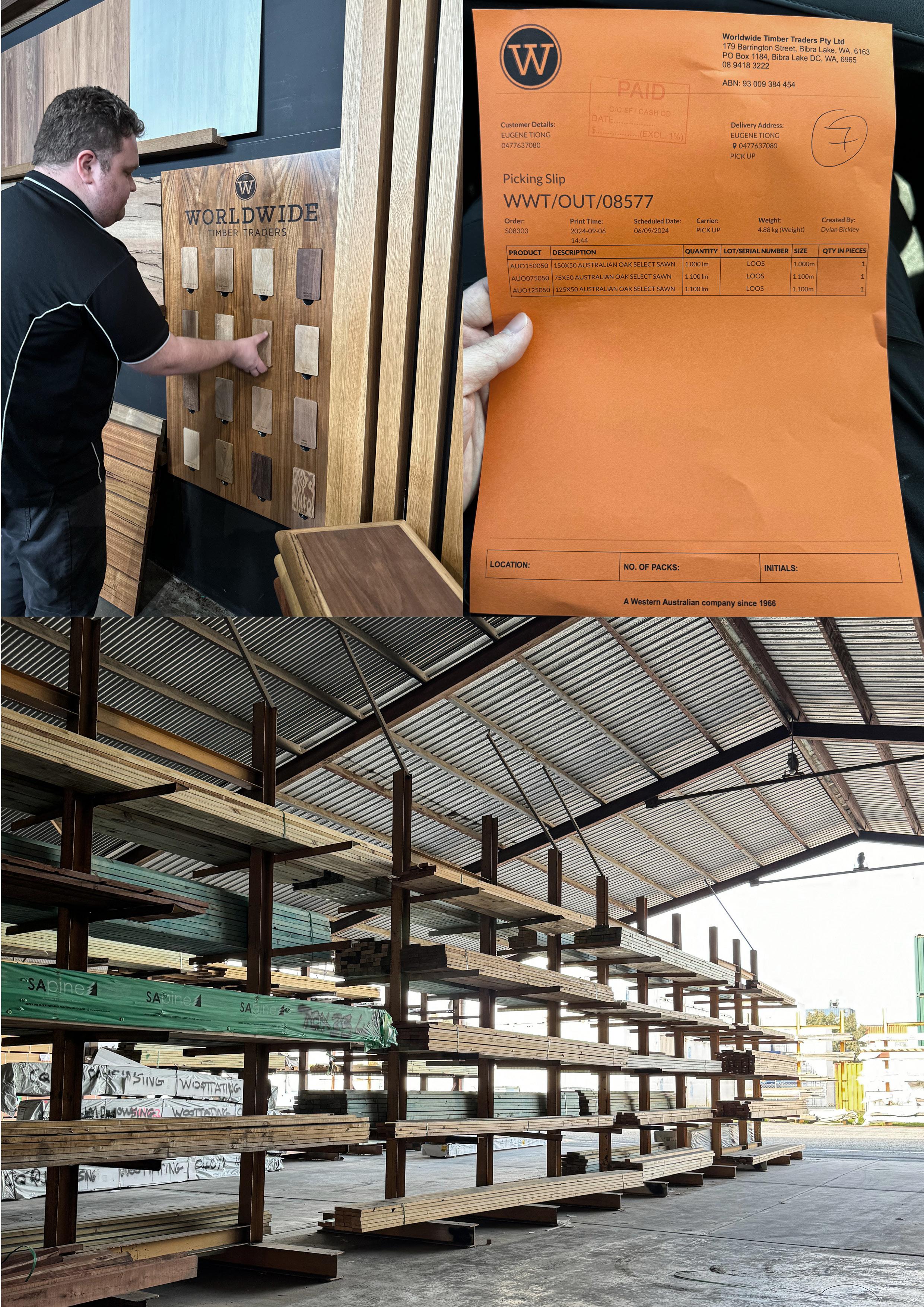
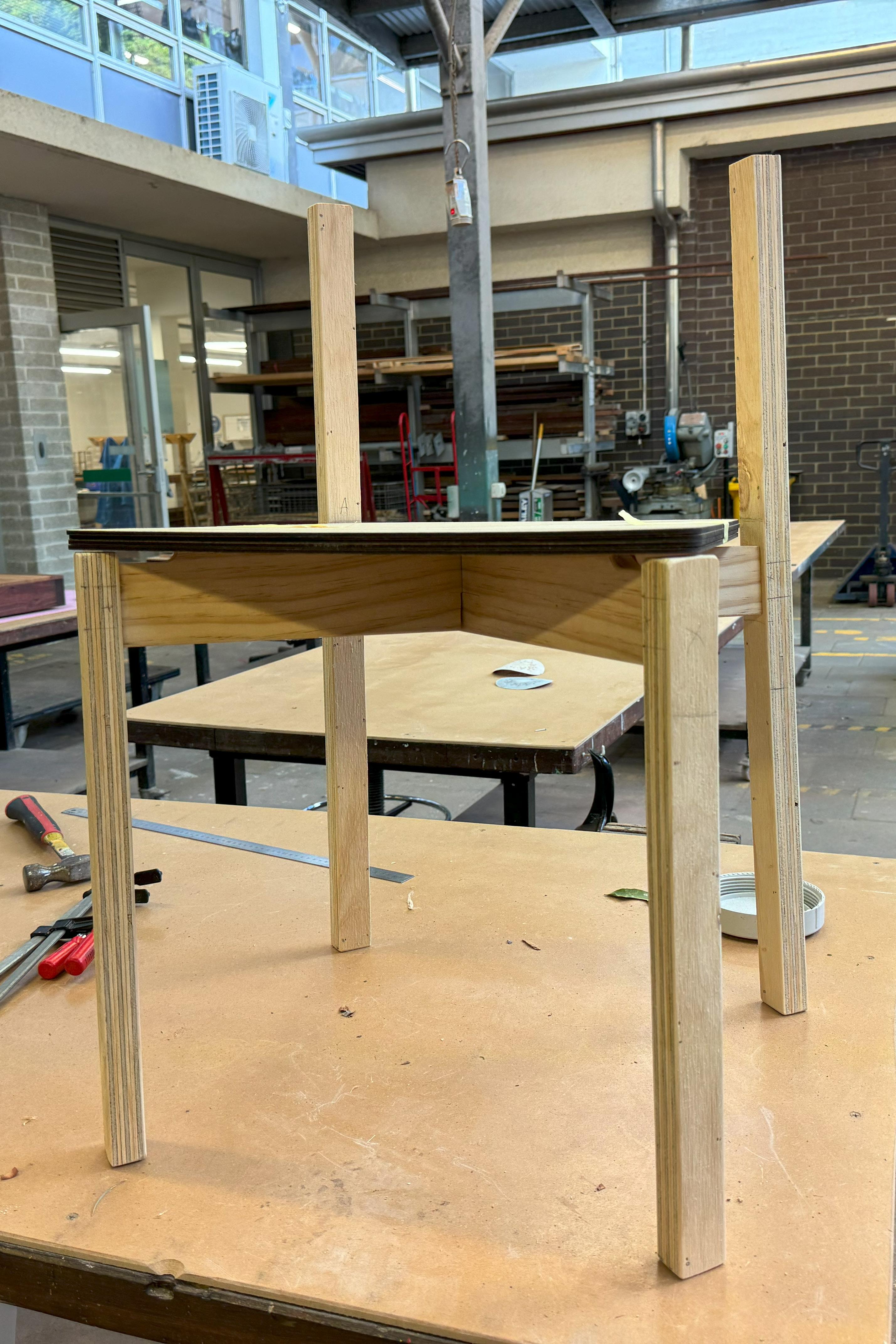
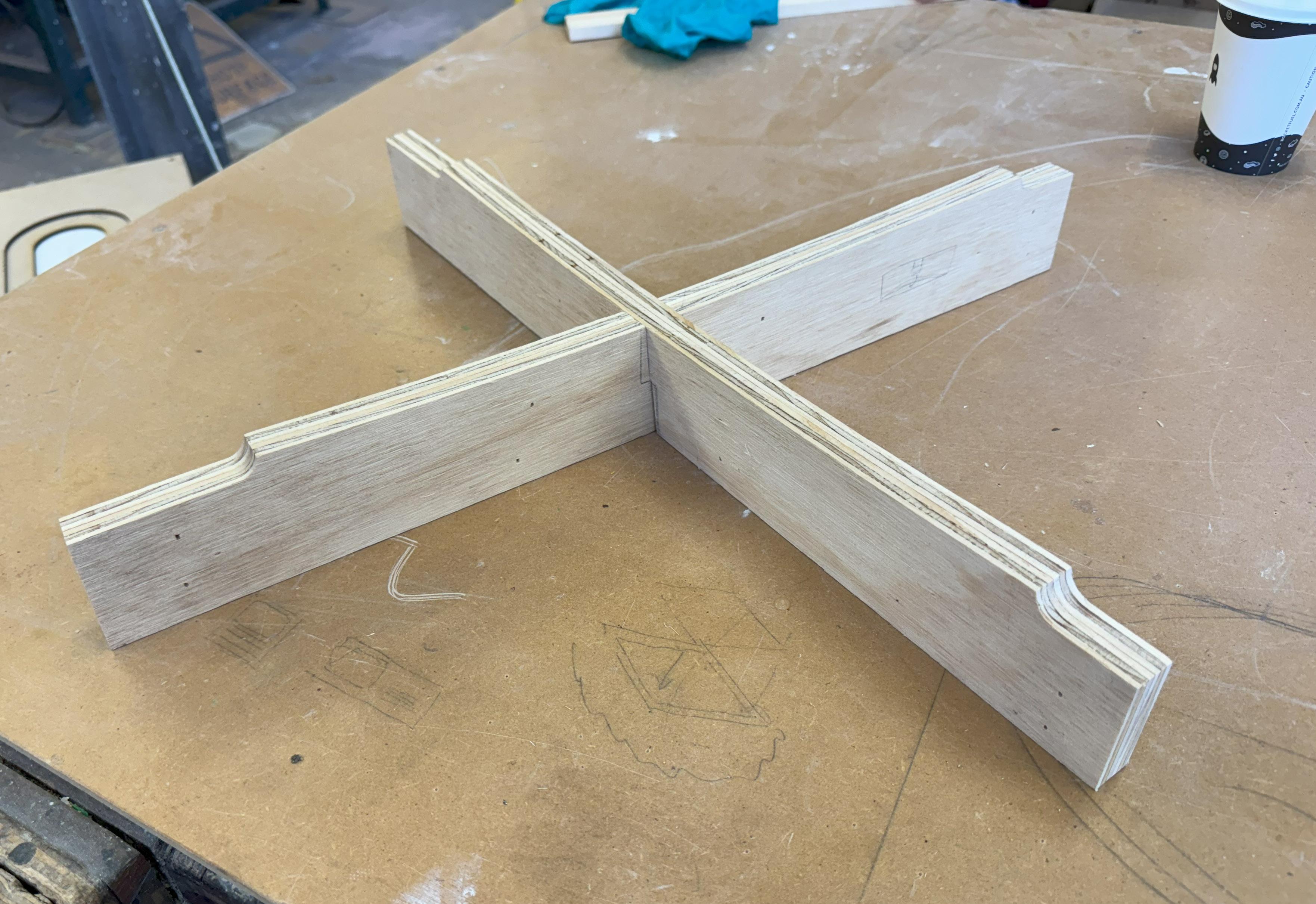
1 :1 PROTOTYPE MOCK-UP
A full-scale 1:1 mock-up is essential to thoroughly test the X.01 Chair’s design integrity, joint strength, and installation process before advancing to the final prototype.
Legs/Rails:
The cross-leg structure is a key element for the X.01 Chair’s structural integrity. Unlike conventional rightangled joints, this joint features a 5-degree offset, allowing the back legs to be slightly wider than the front, enabling stackability. Each rail includes precision-drilled openings with dominos for secure, seamless connection to the legs.

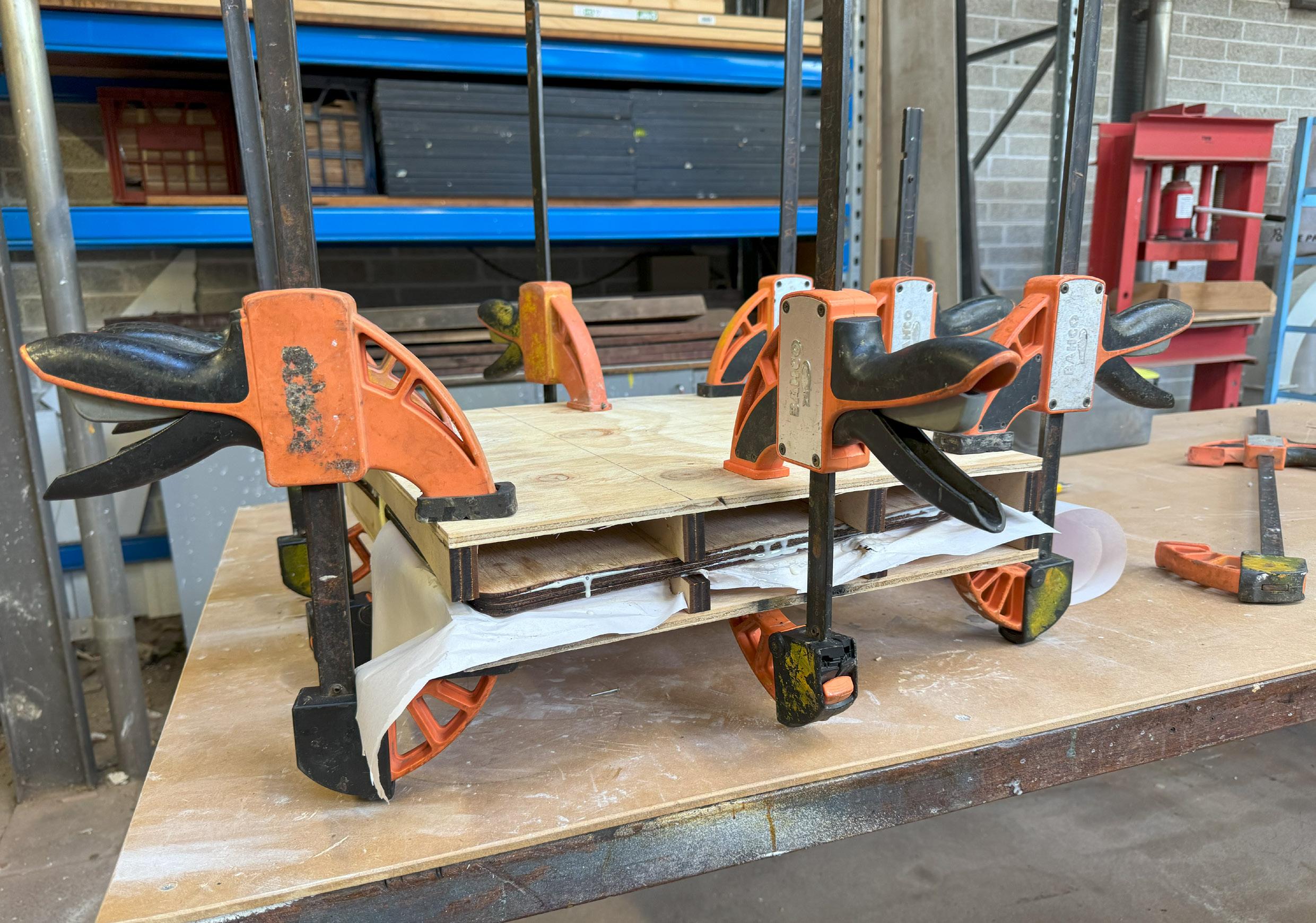
Seat & Back Rest:
To achieve the curved design, the bending process requires both a male and female mold to press and shape the plywood to the desired curve. For this mock-up, 3mm plywood and a simplified mold were used, with PVA glue applied between layers to secure the bend effectively.
Installation:
After pressing for 24 hours, the shape held successfully, allowing for the assembly phase to begin. The next challenge involved determining the precise spots for drilling holes on each component to ensure a smooth, user-friendly installation process for consumers.

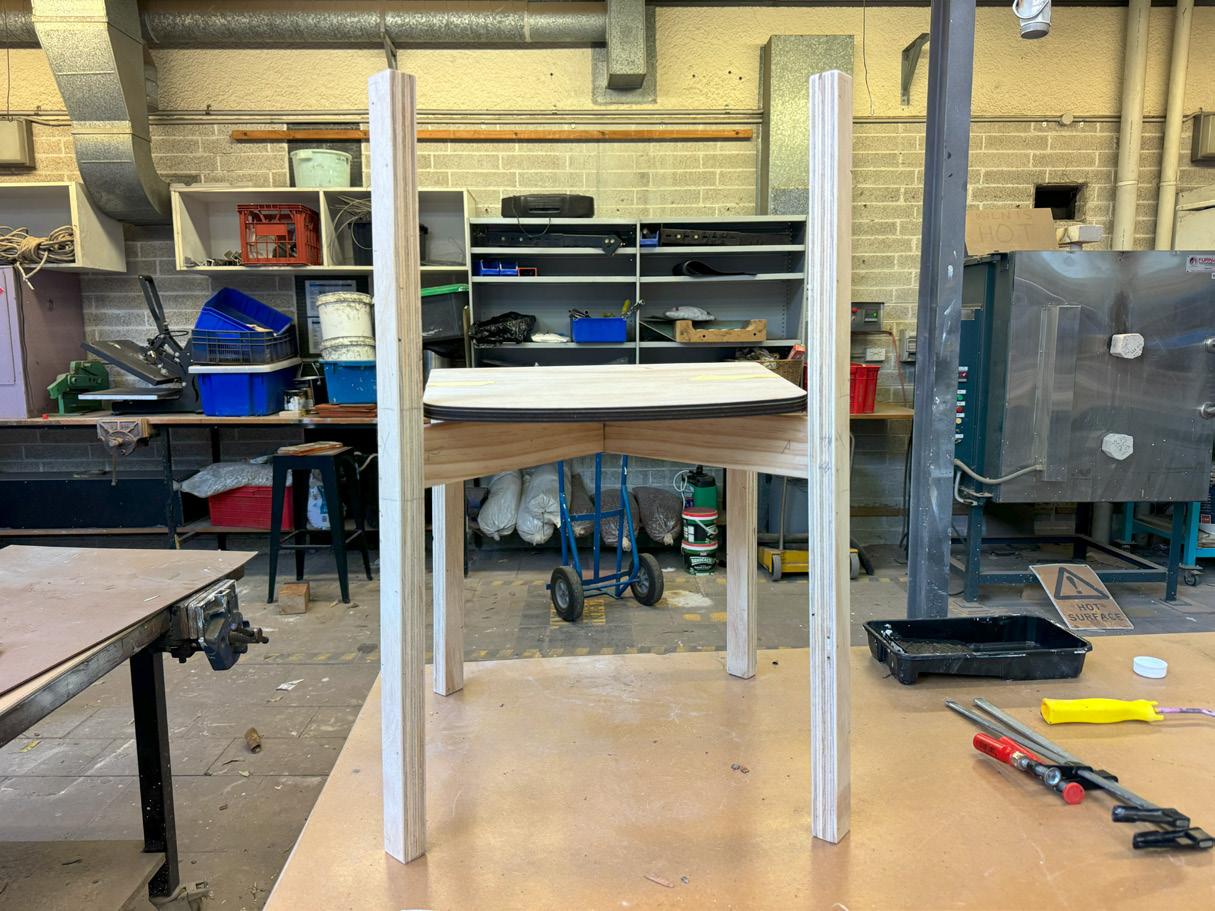
Prototype Construction Process

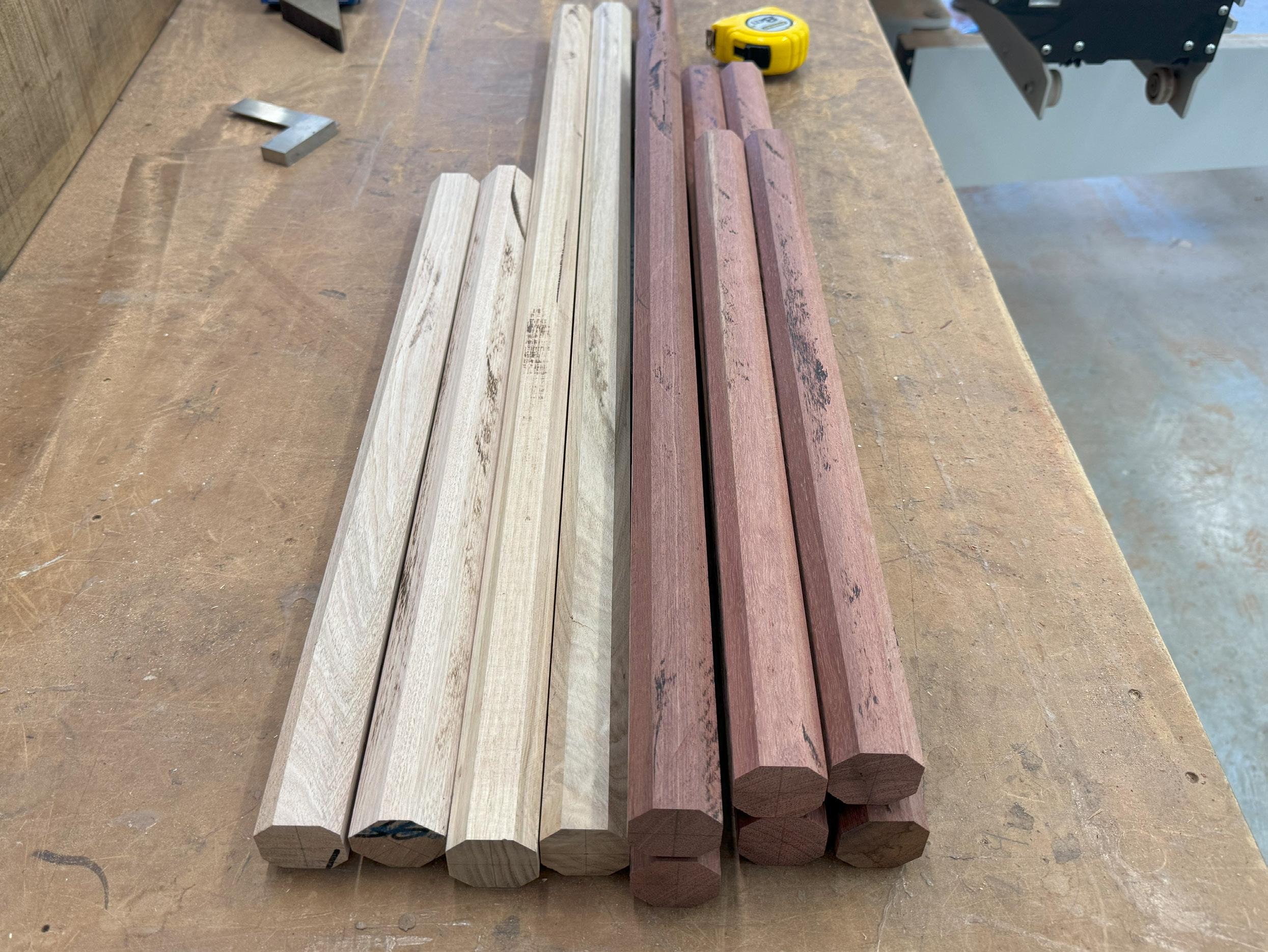
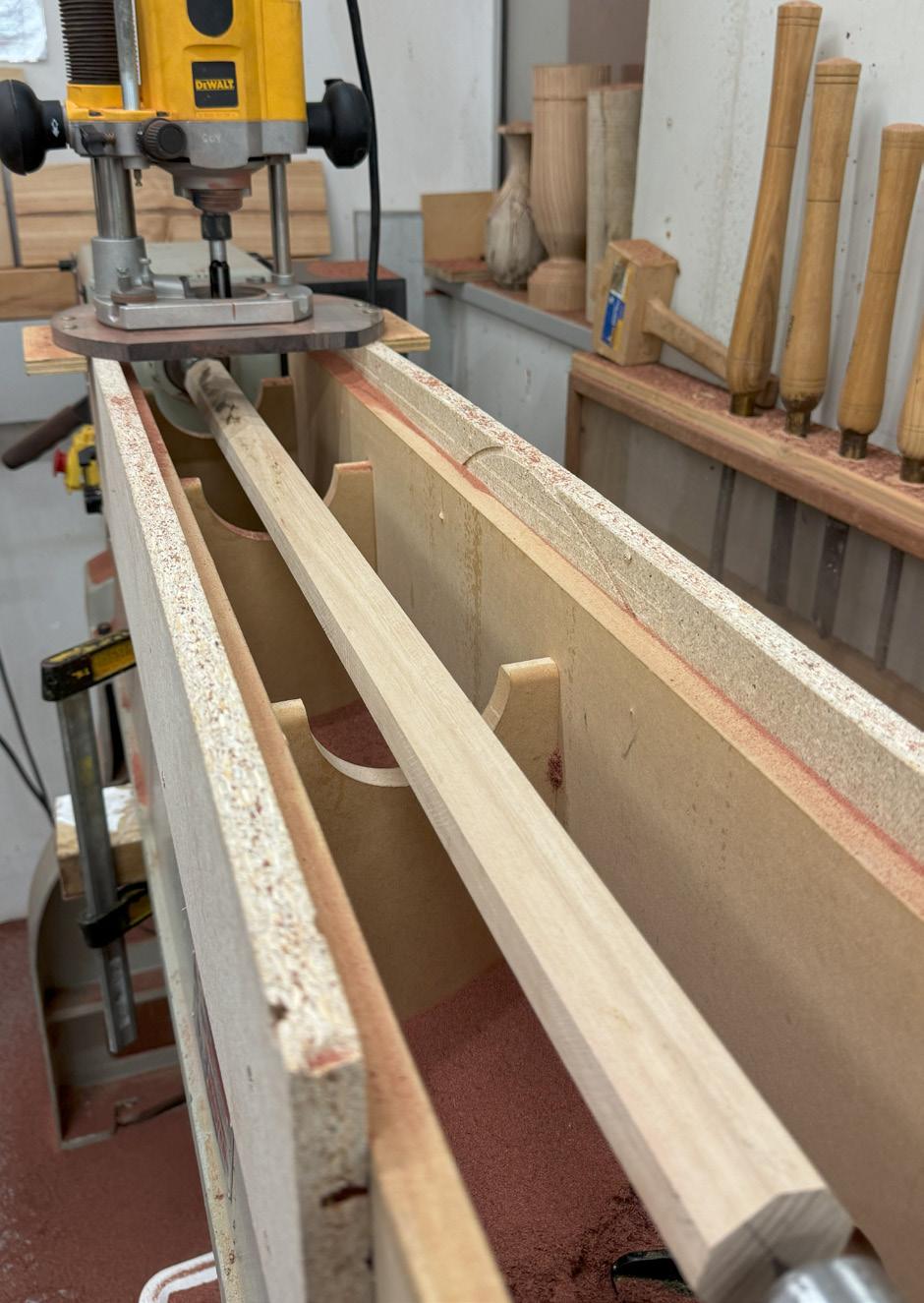

TIMBER SHAPING: CRAFTING ROUNDED LEGS
Cut to Octagon Shape:
Cut the planed timber into an octagonal shape to ease the rounding process.
Mount on Lathe and Set Up Router:
Secure the octagonal timber on the lathe, ensuring stability, and attach the DeWalt router to a lathe-mounted jig for consistent, controlled passes along the timber’s length
Rough Shaping:
Start the lathe at a low speed and guide the router along the length of the timber to gradually round it into a cylinder. Adjust the router depth incrementally to avoid removing too much material at once.
Refine and Finish:
Use the router for precise shaping, followed by sanding on the lathe to achieve a smooth, polished contour, preparing the leg for CNC.
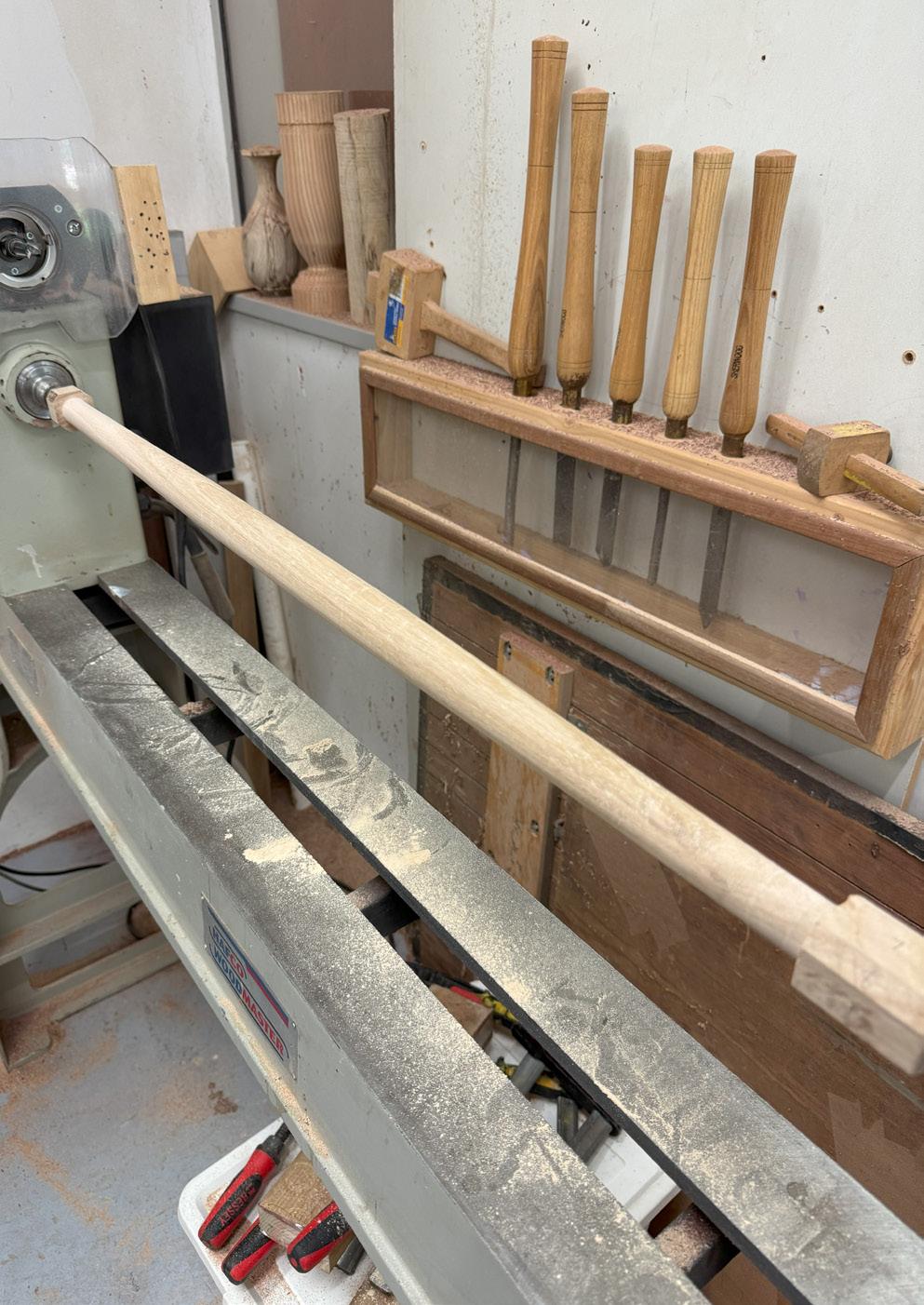
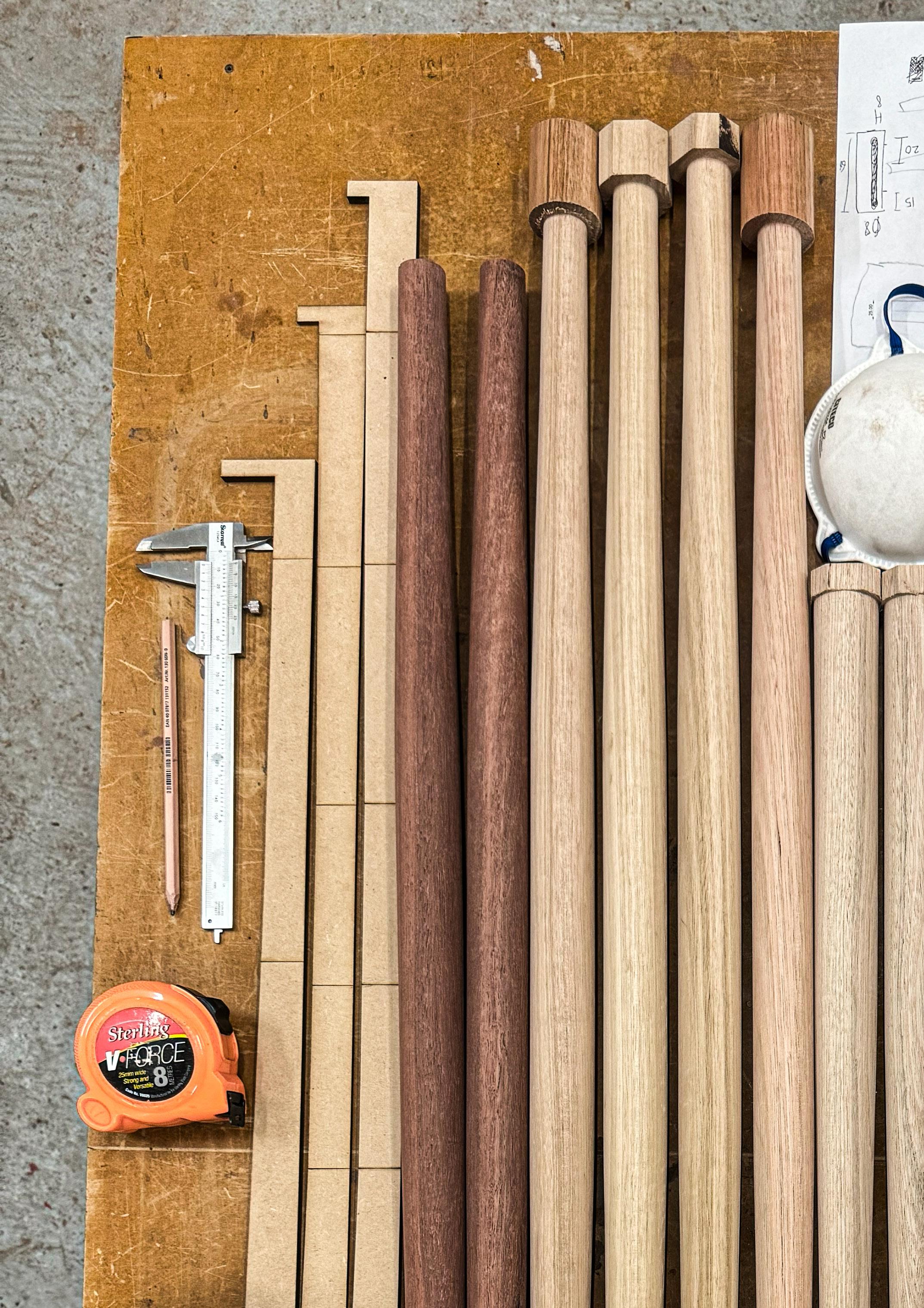
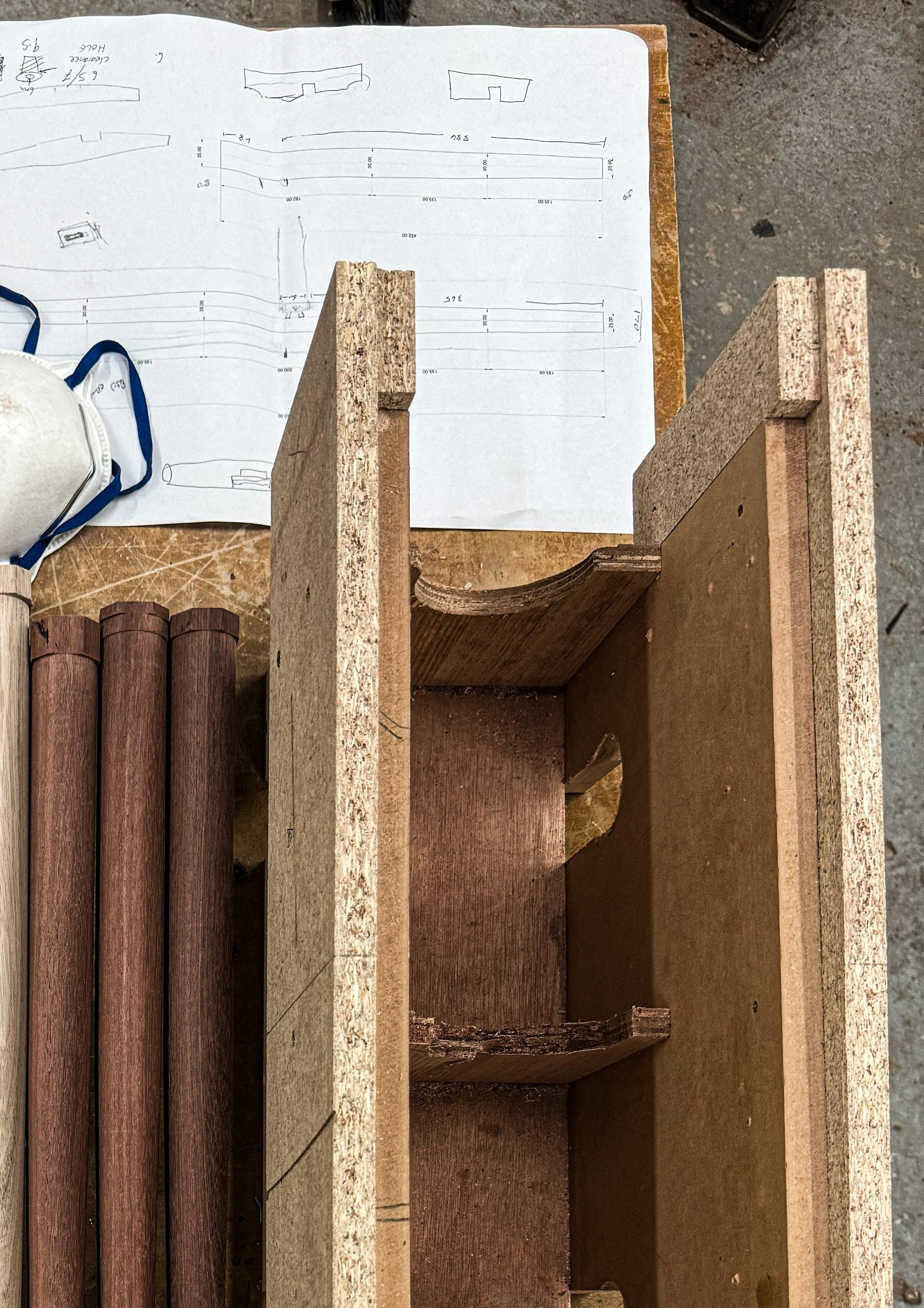

PRECISION SLOTTING & SHAPING WITH CNC
Jig Preparation:
Design a custom jig to position the rounded leg facing upward on the CNC, ensuring stability and the correct cutting angle for the domino slot.
CNC Slotting and Shaping:
With the leg secured in the jig, use the CNC machine to cut slots at the desired angle for the domino joints, providing a strong rail connection between front and back legs. Shape the top of each leg for precise backrest alignment, ensuring easy and accurate assembly.
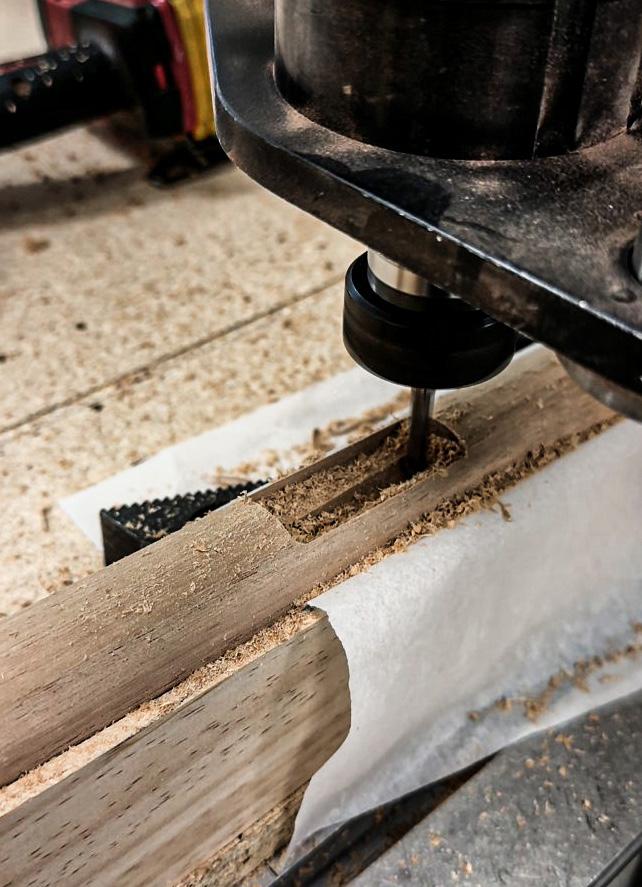

RAIL SHAPING & JOINT PREPARATION
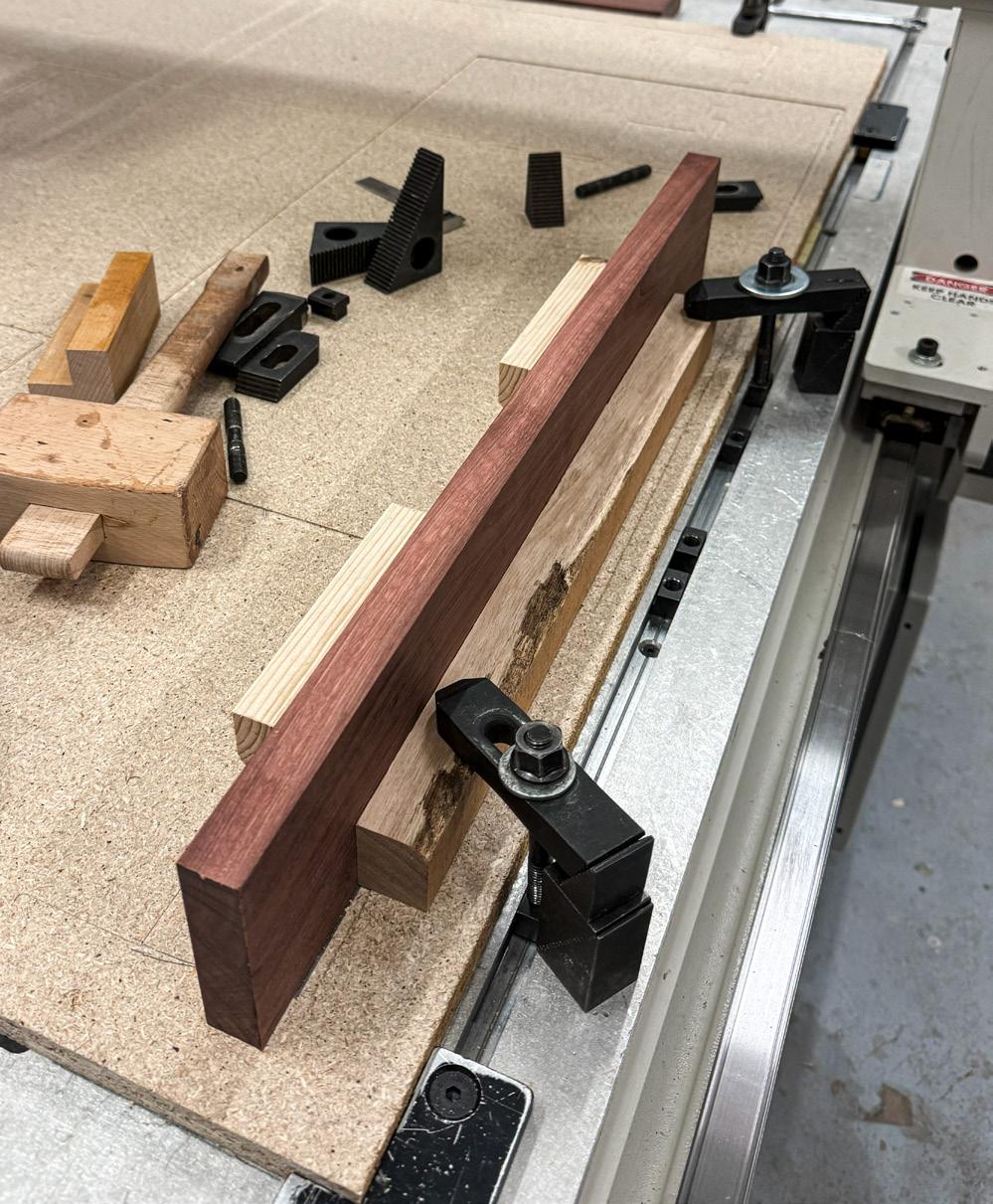
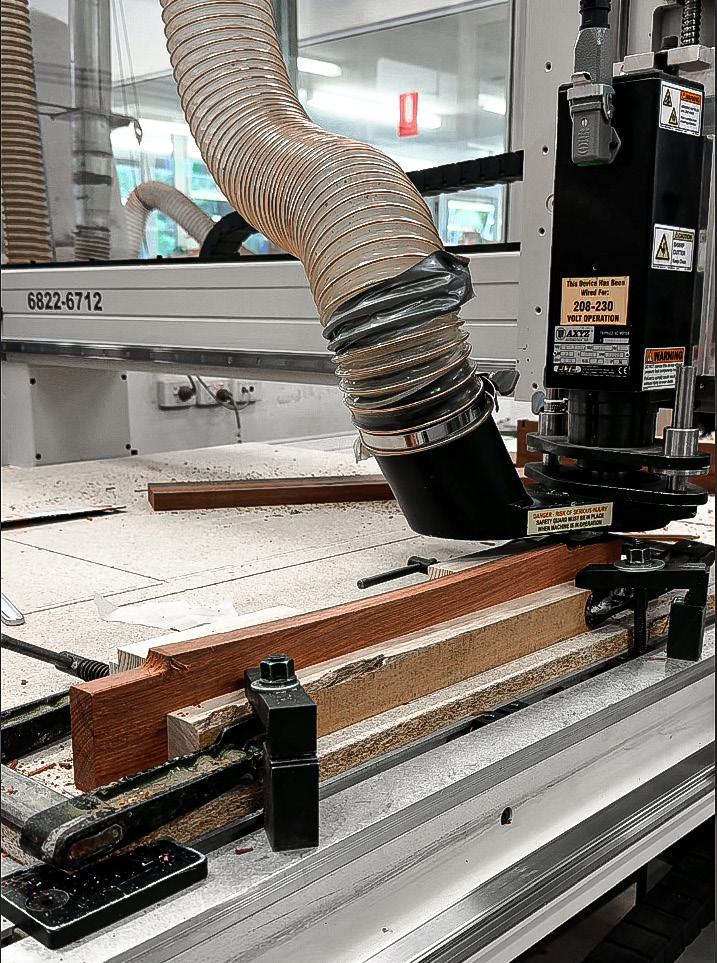
Prepare Timber Blank:
Start by docking the planed timber to precise dimensions of 600mm x 88mm x 22mm.
CNC Shaping:
Secure the timber on the CNC machine and initiate the cutting sequence by carving the unique curve along the rail for a snug seat fit, creating a precise 5° slot to align with the crossing leg joint, and drilling holes for screws to secure the rail to other chair components.
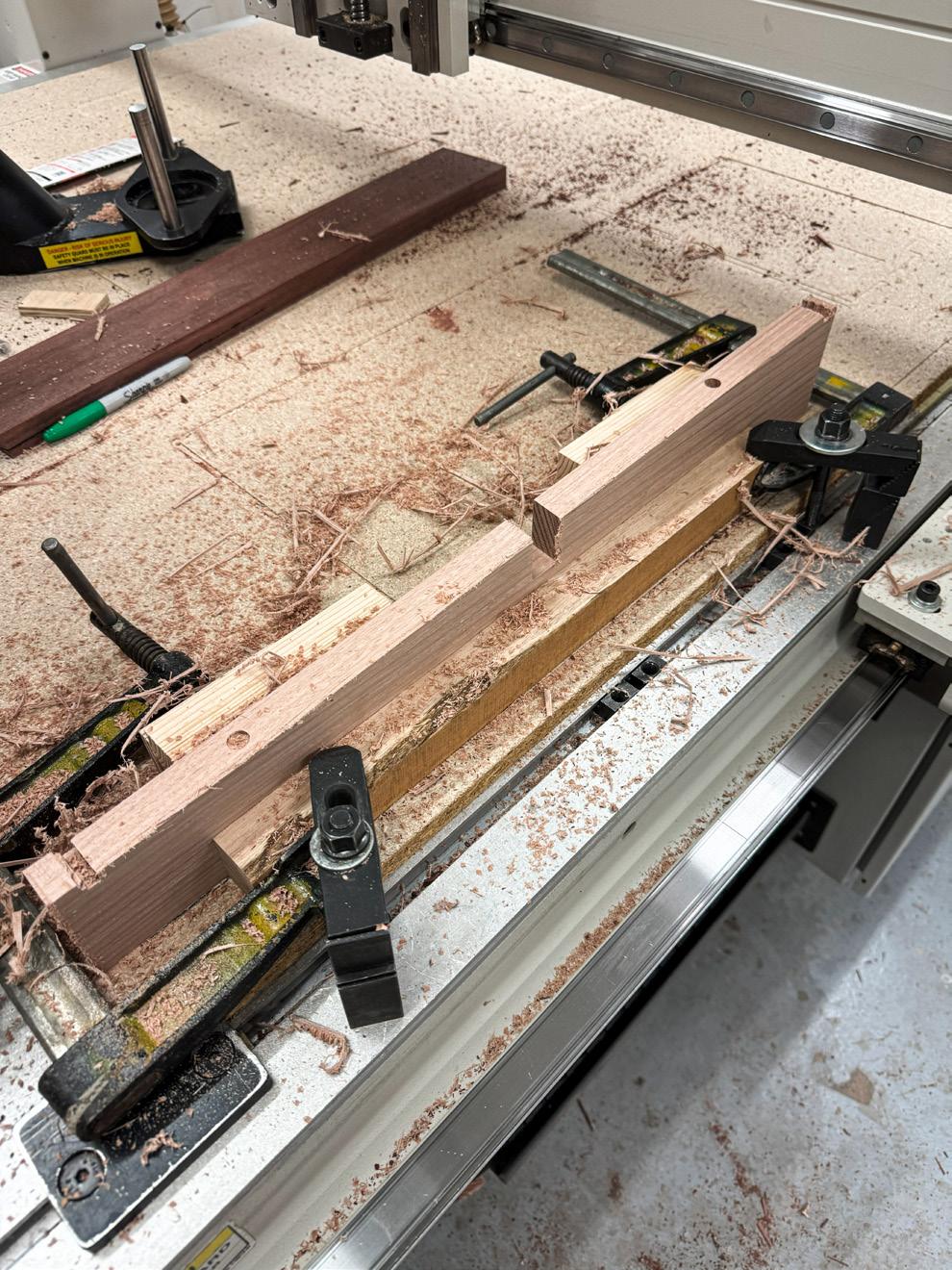
Tenon Placement & Sanding:
Use a domino joiner to create mortises on both ends of the rail. These mortises will house the tenons for a sturdy connection to the front and back legs. Sand the rail to achieve a smooth finish, ensuring all surfaces are prepared for assembly.
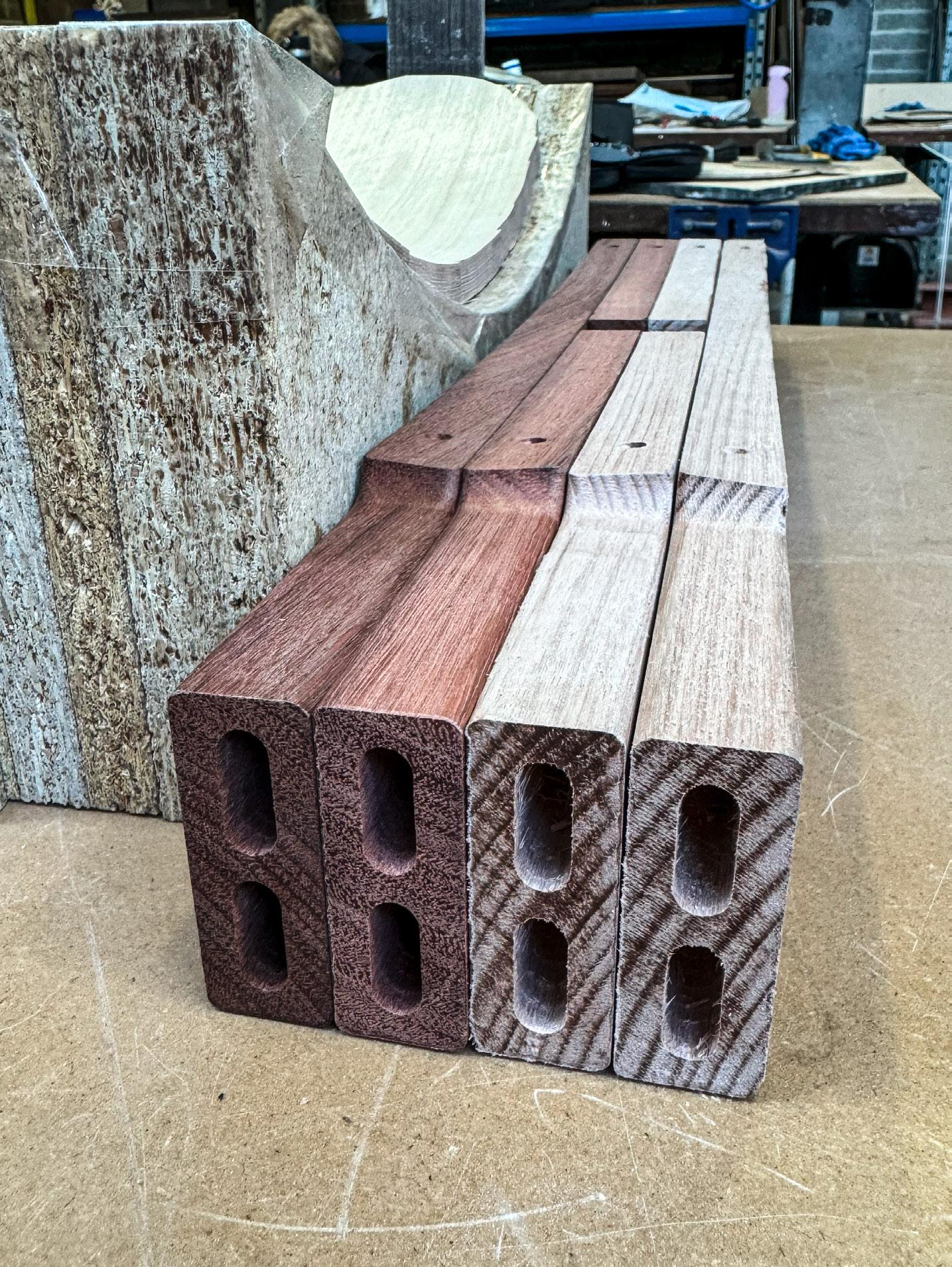
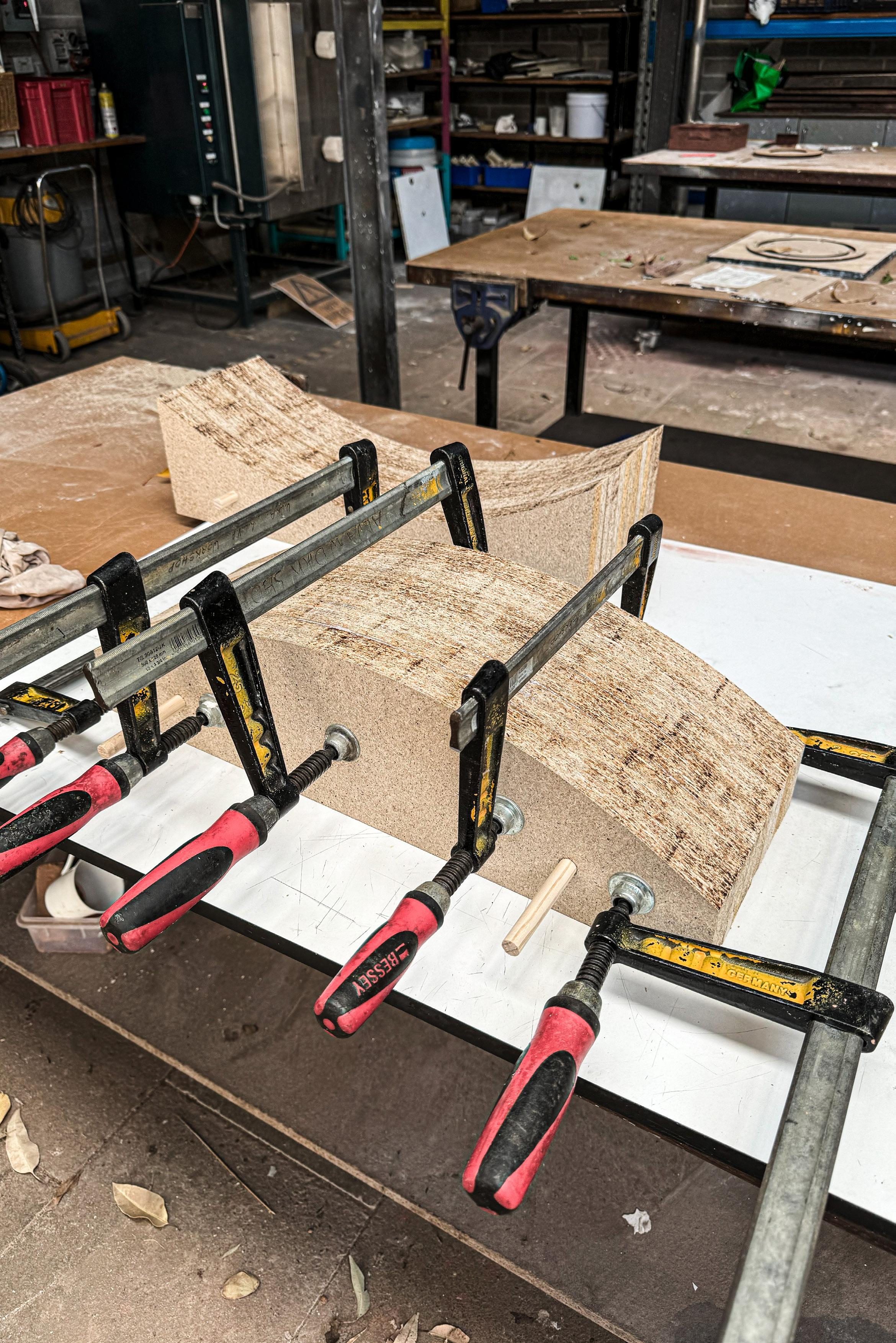
BACK REST & SEAT FABRICATION PROCESS
Mould Creation:
Start by constructing a mould using chipboard. The backrest should be shaped to a 30-degree bend, while the seat is designed with a 6-degree angle
Plywood Preparation:
Cut the bending plywood into a rectangular shape. Glue together nine layers of 1.5mm bending plywood, oriented in a cross grain pattern to enhance structural integrity. Use epoxy and resin for strong adhesion.

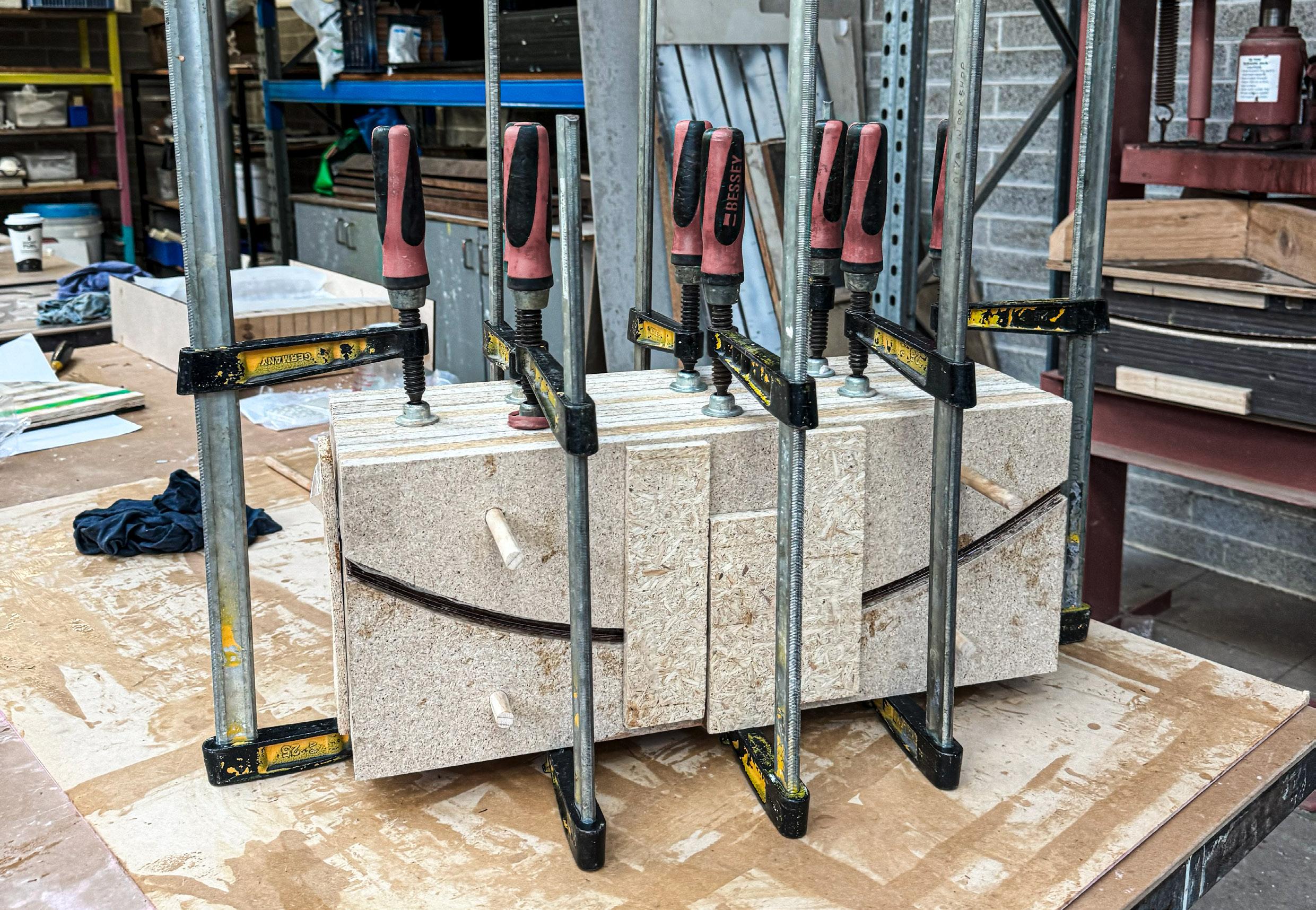
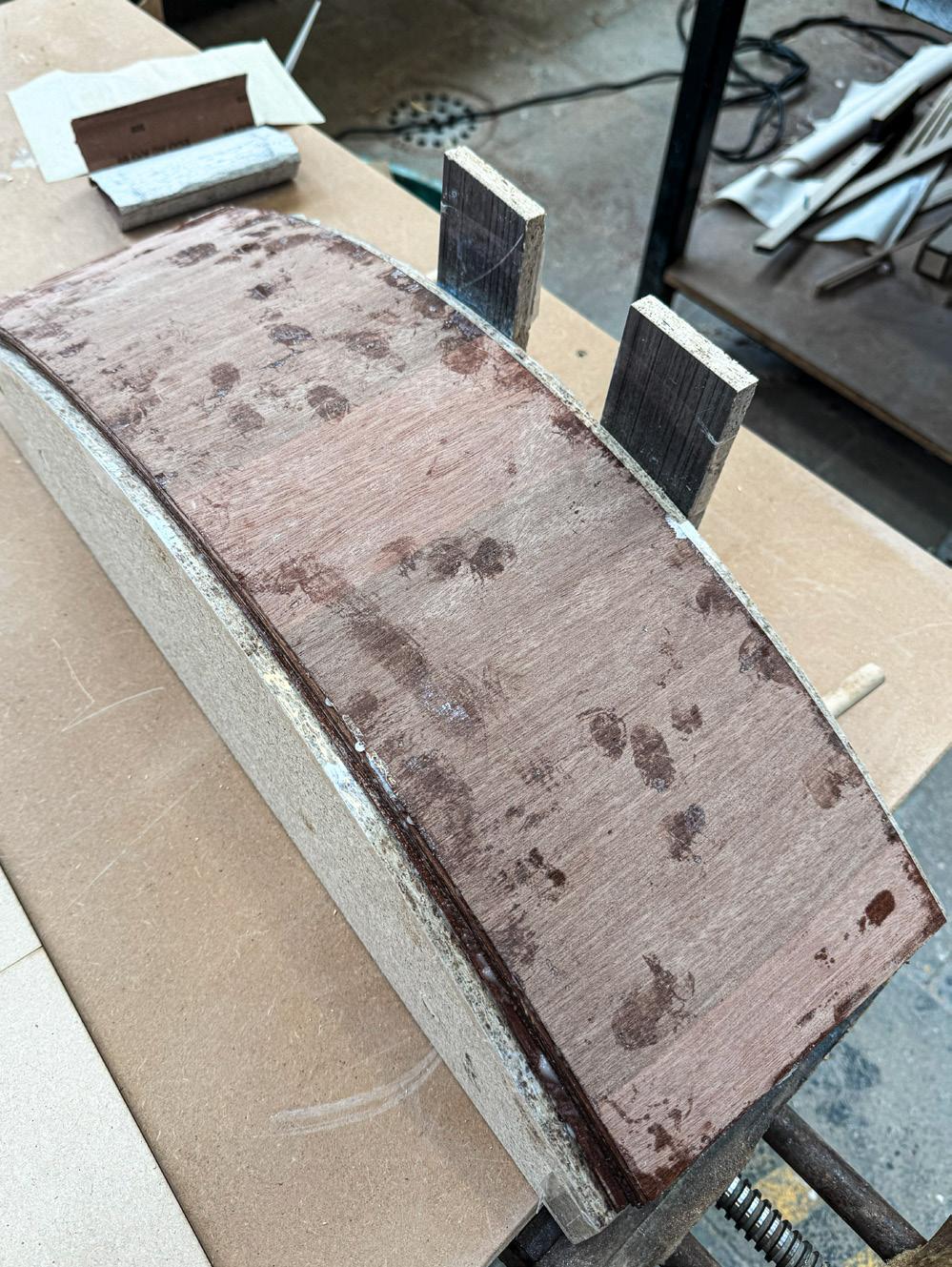
Moulding Process:
Place the glued layers inside the mould. Utilize a hydraulic press and metal F-clamps to apply pressure, ensuring the layers conform to the desired shapes. Allow the assembly to cure for 24 hours to achieve the correct curvature.
Veneer Application:
Once the desired shape is achieved, cut veneer sheets to size and glue them to both sides of the bent plywood using PVA glue. Return the laminated piece to the mould for an additional 12 hours to ensure proper bonding.
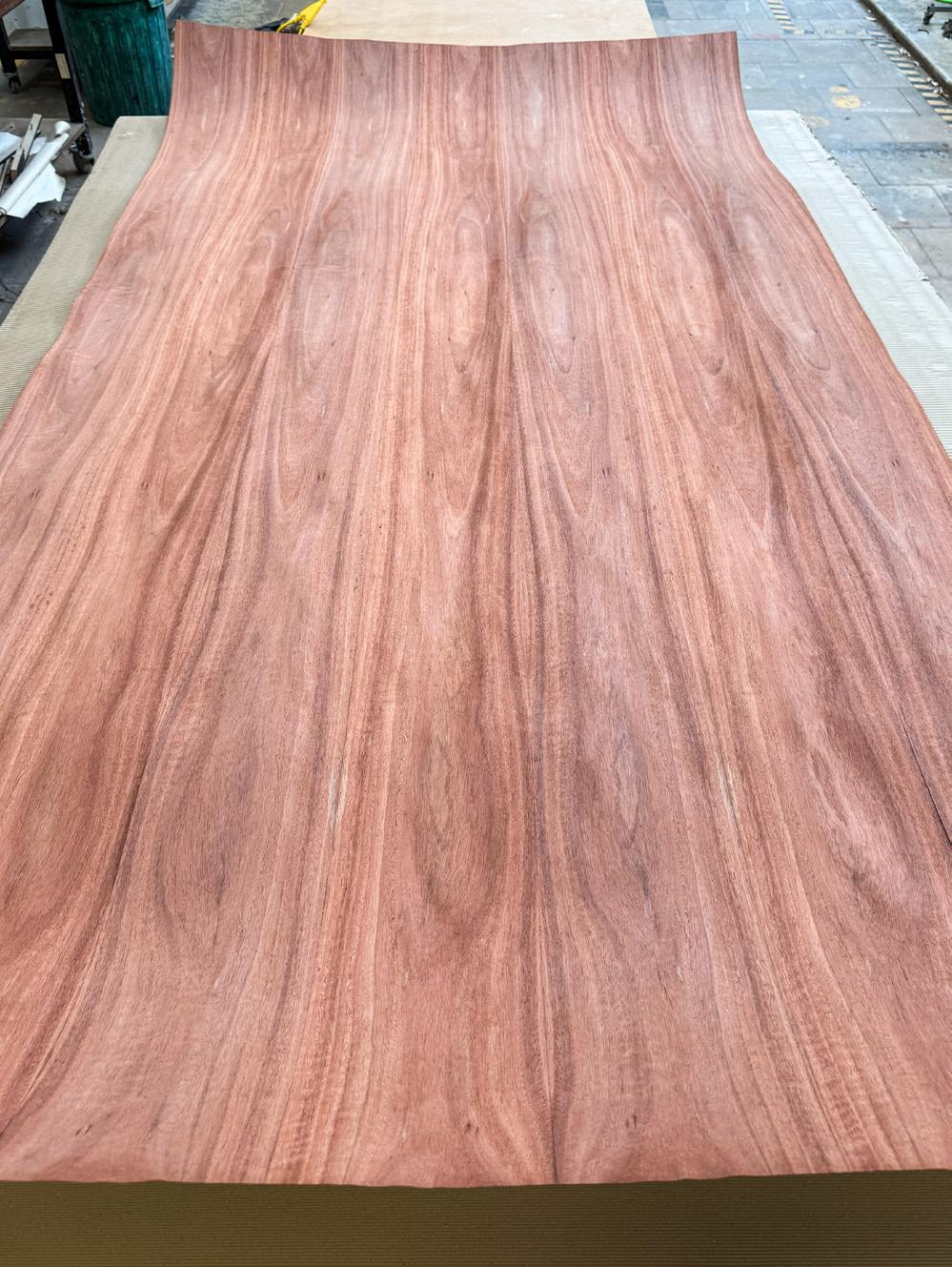
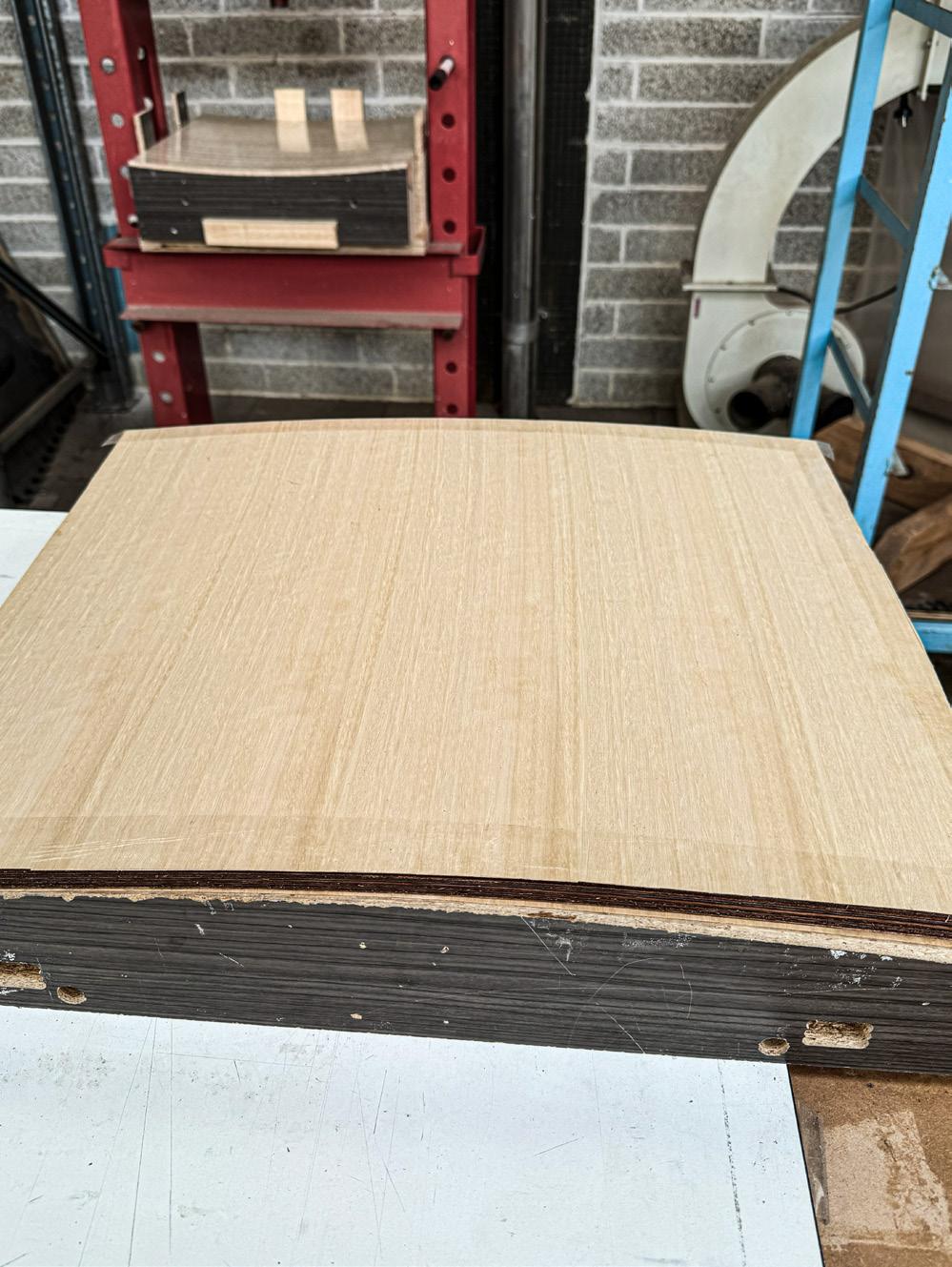
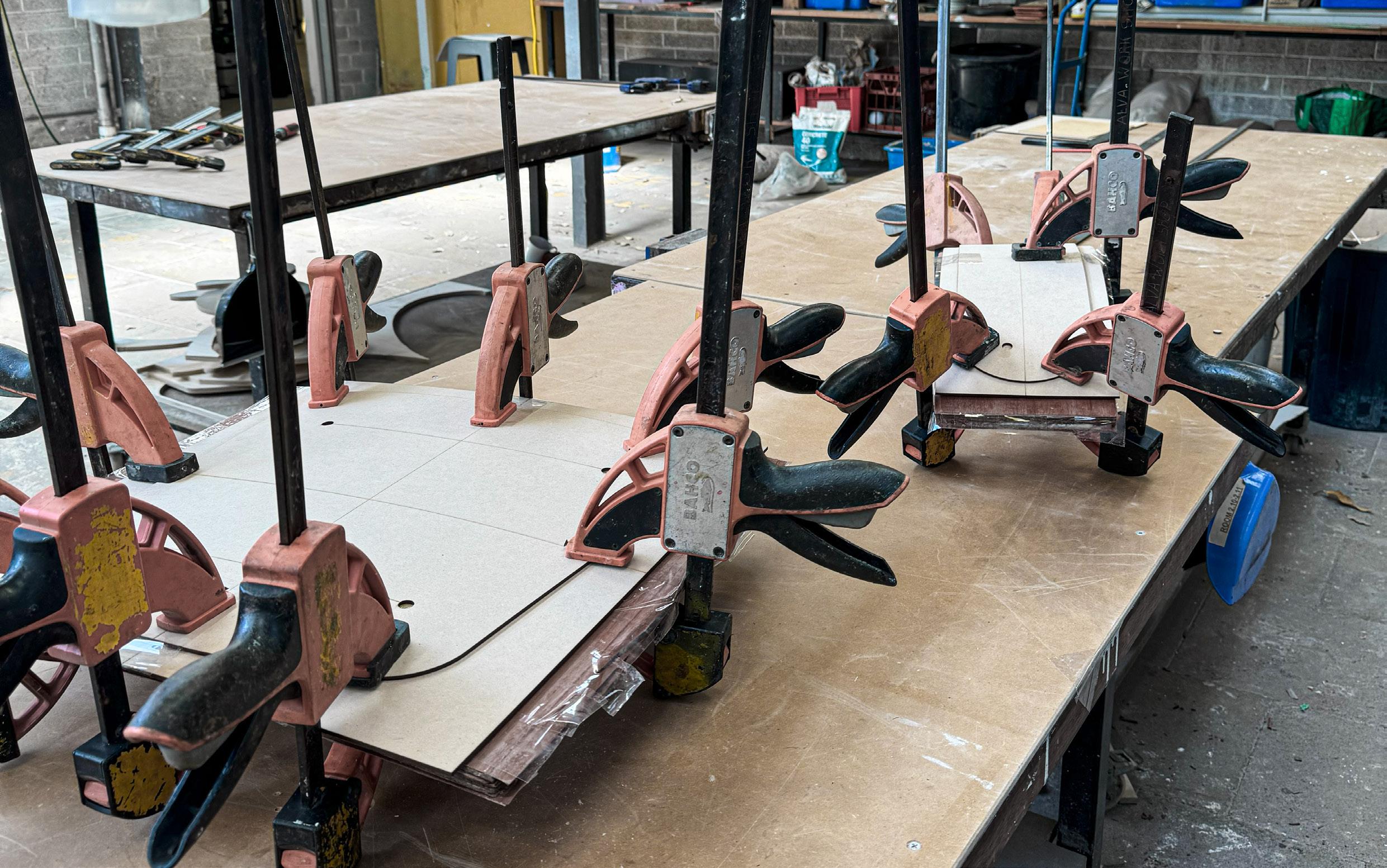
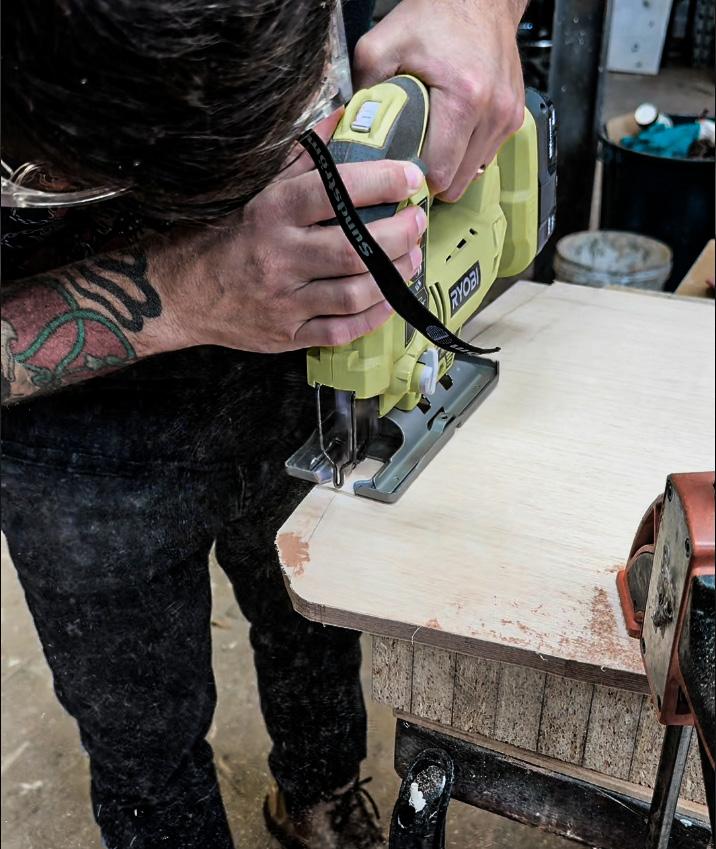
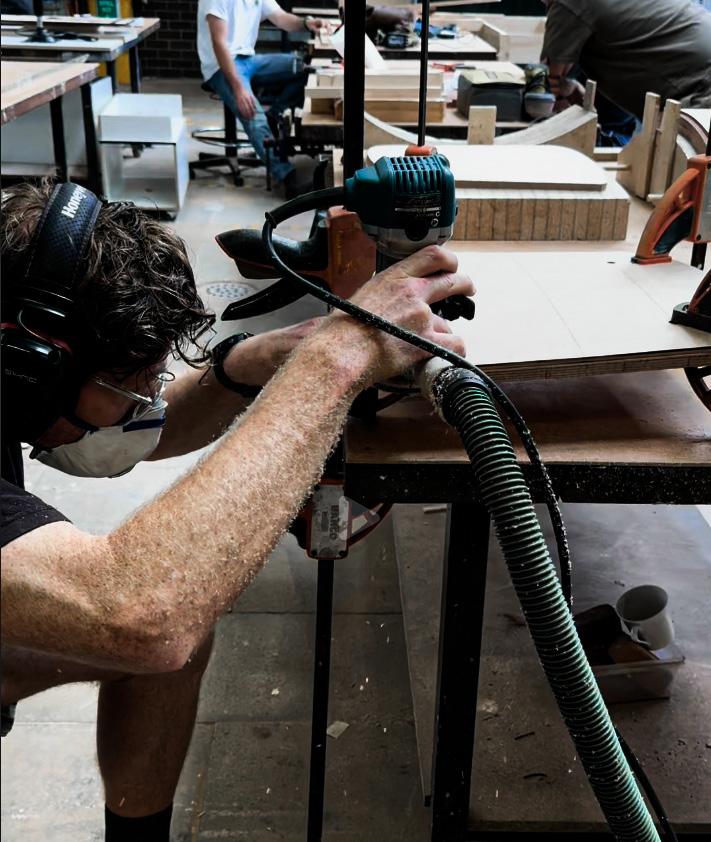
Shaping:
Use prepared templates for the backrest and seat profiles to cut them into rough shapes. Employ a router to trim the edges for a smooth finish.
Drilling:
Utilize the templates to drill holes for threaded inserts, ensuring precise placements for assembly.
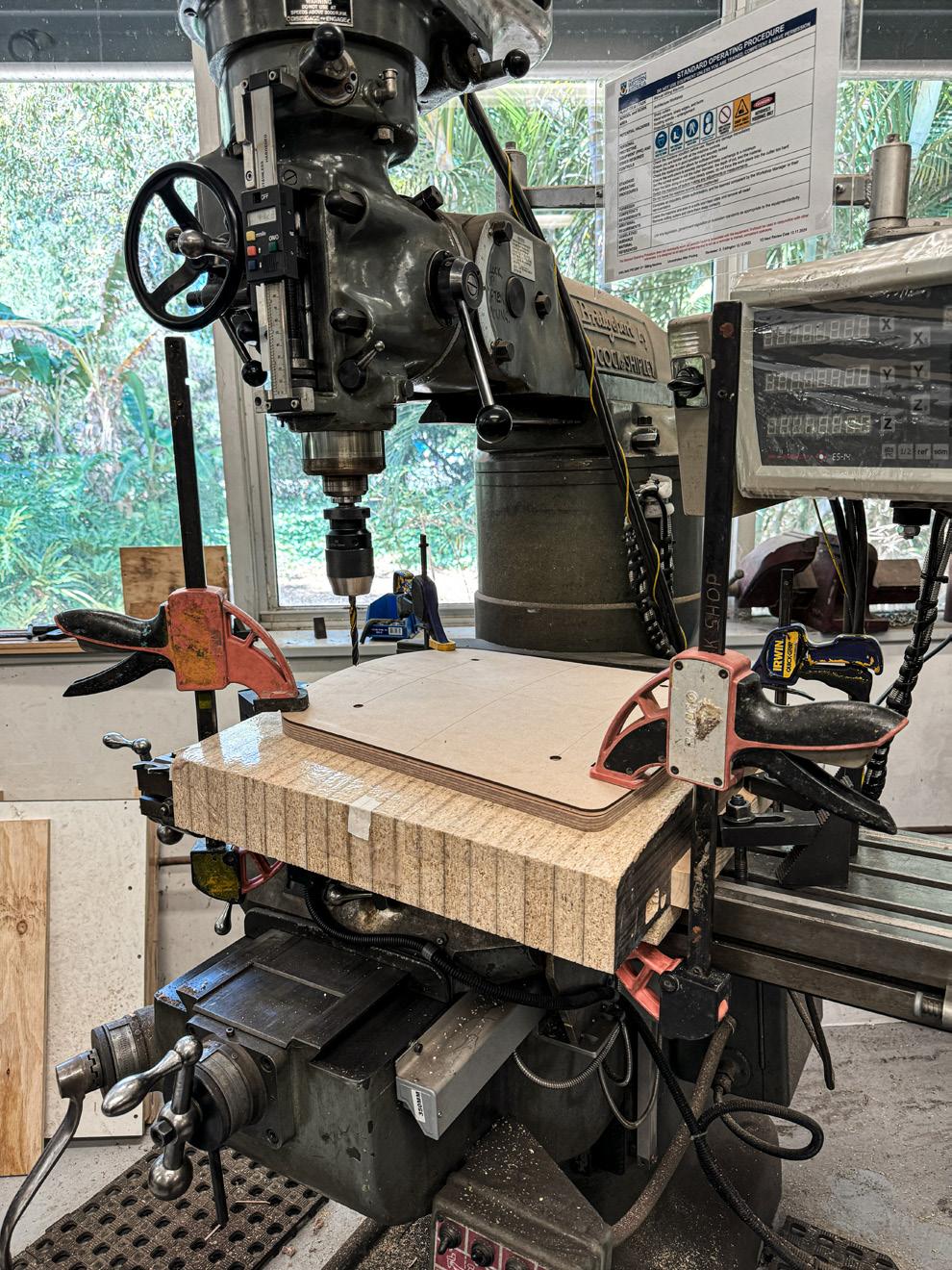
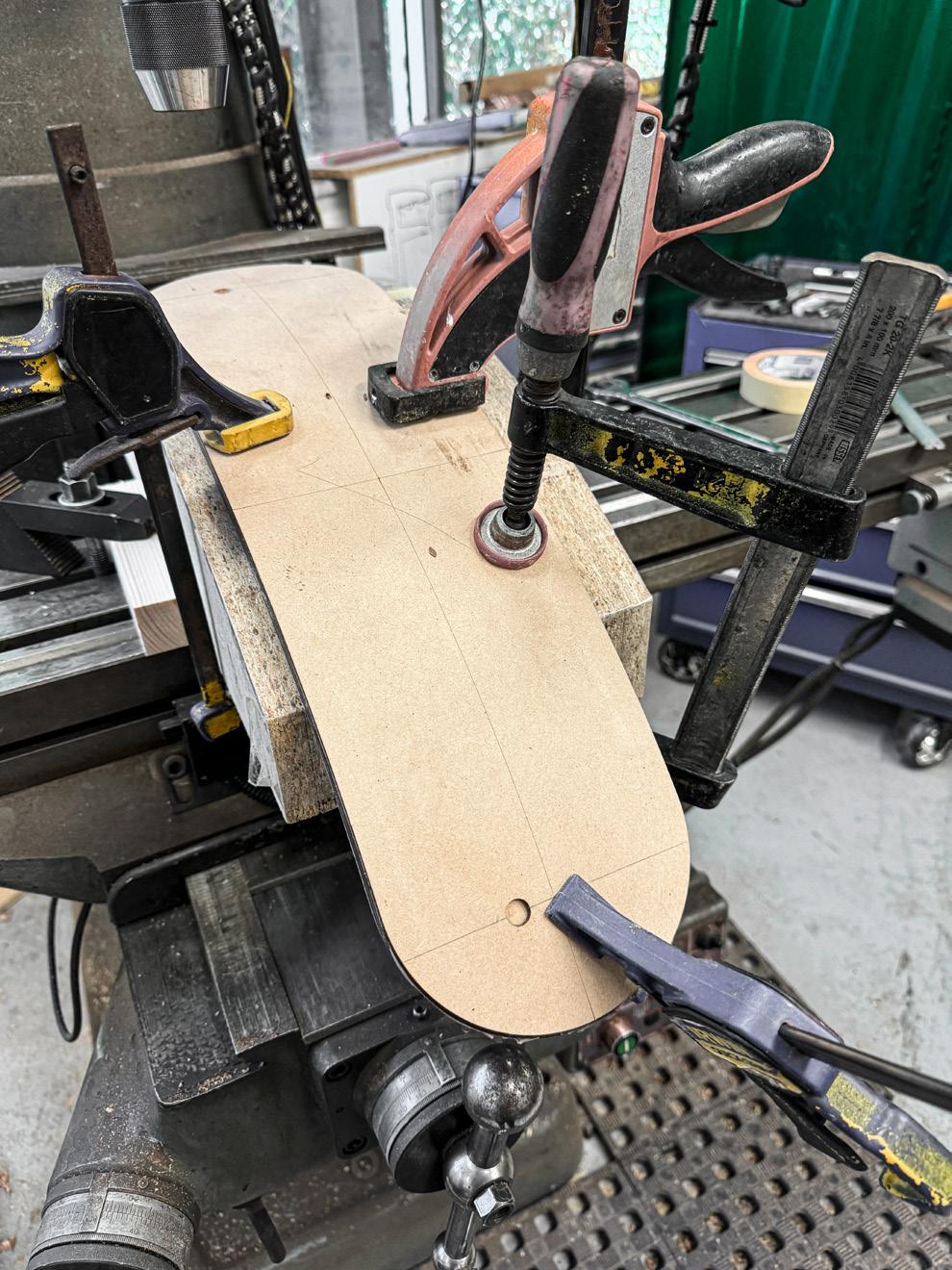
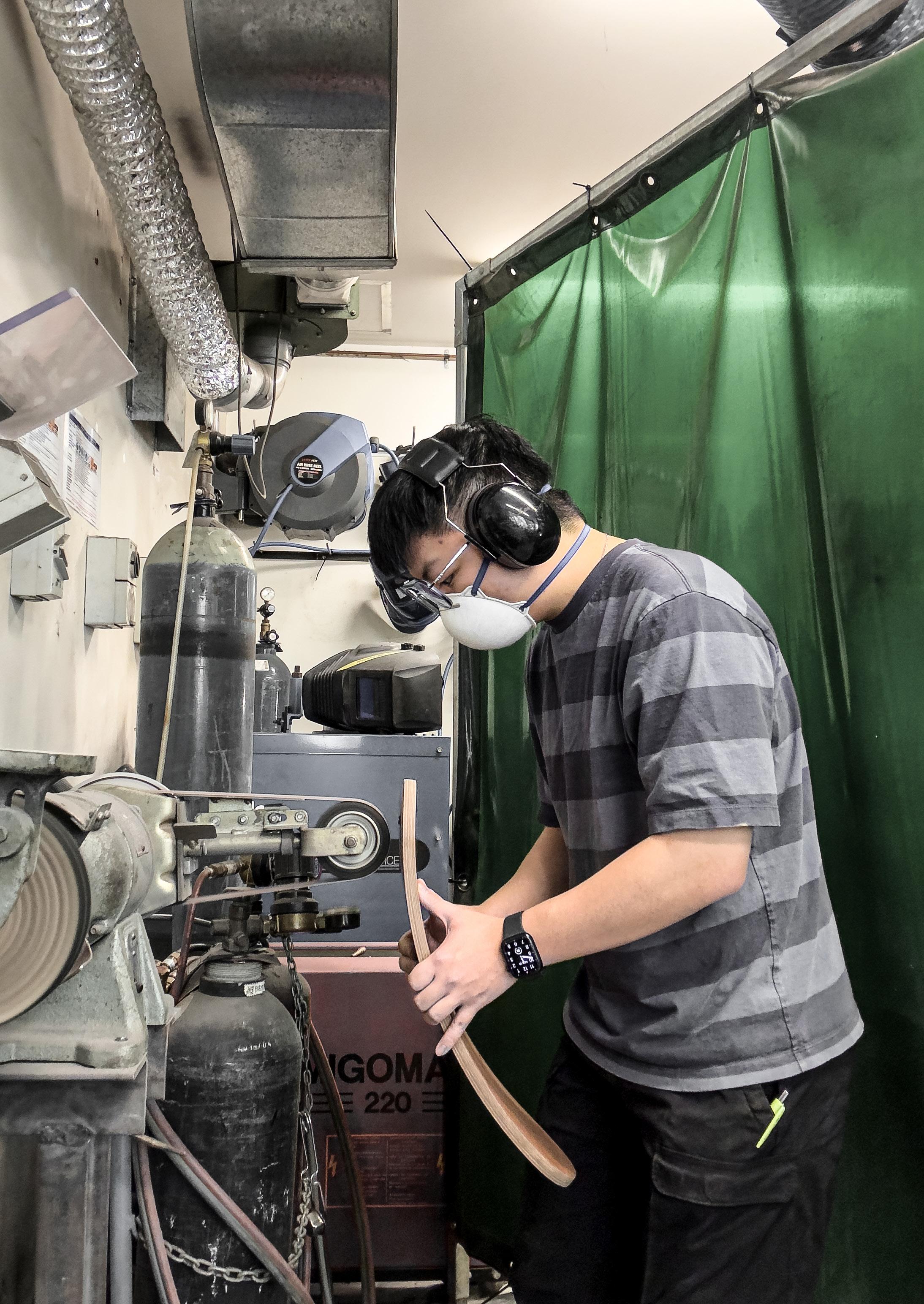
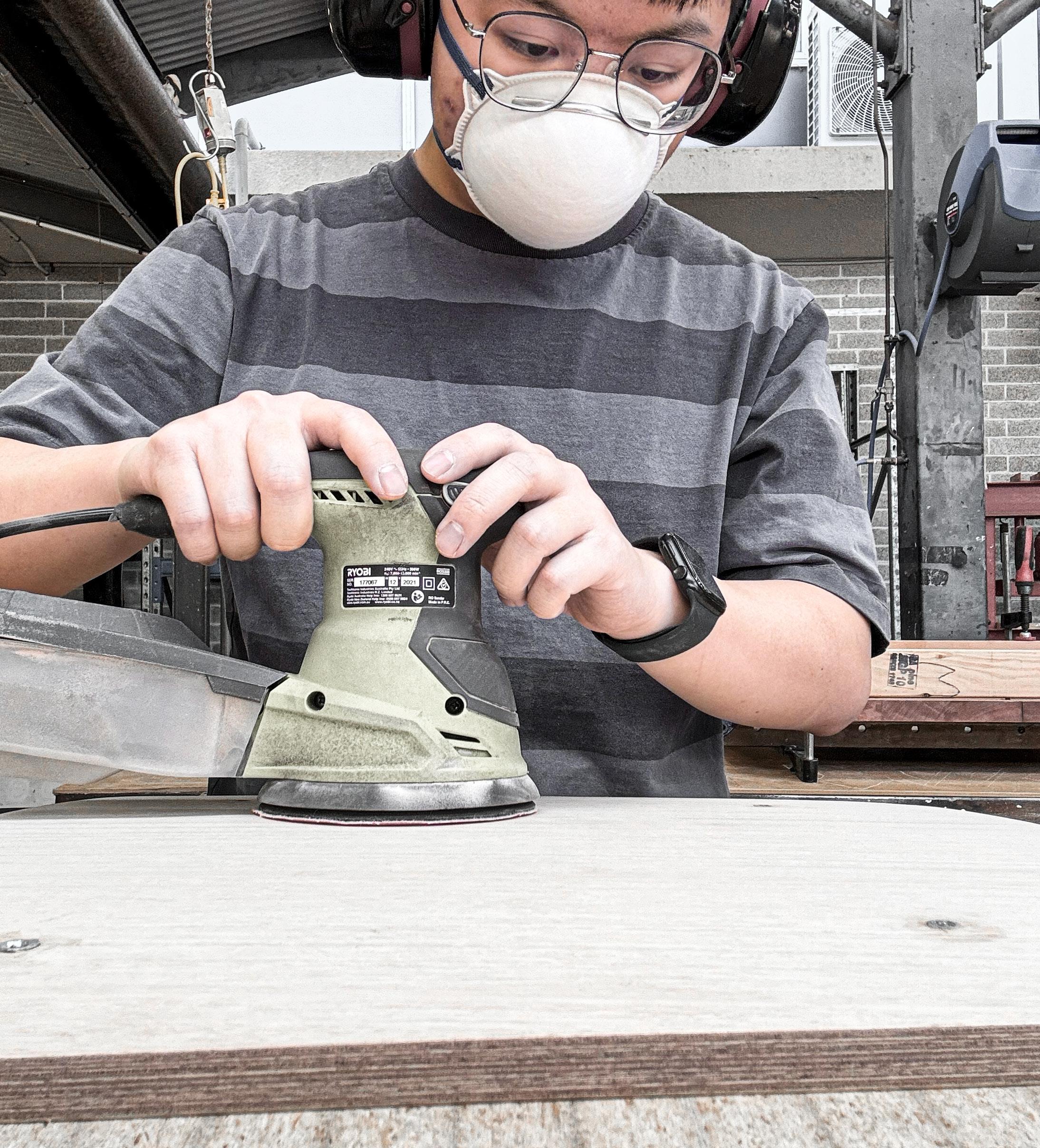
Finishing Touches:
Finally, sand the seat and backrest to achieve a polished surface, preparing them for assembly into the X.01 Chair.
ASSEMBLY PROCESS
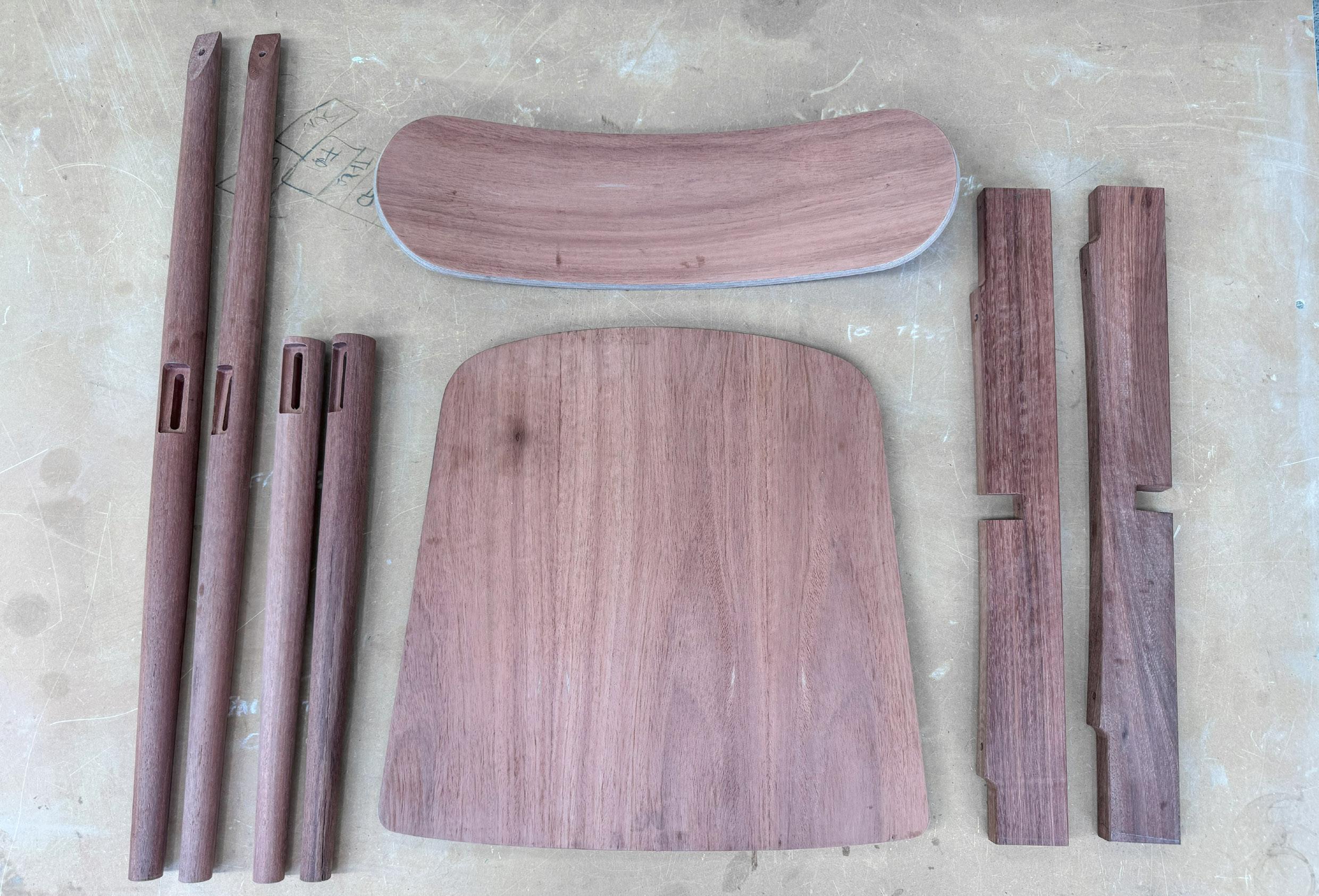
Prepare Components:
Gather the 4 legs, 2 rails, 1 backrest, and 1 seat. Before gluing, do a dry fit by assembling the legs and rails. Use masking tape to mark the rail insertion depth on the legs, ensuring full contact with the cut slots.
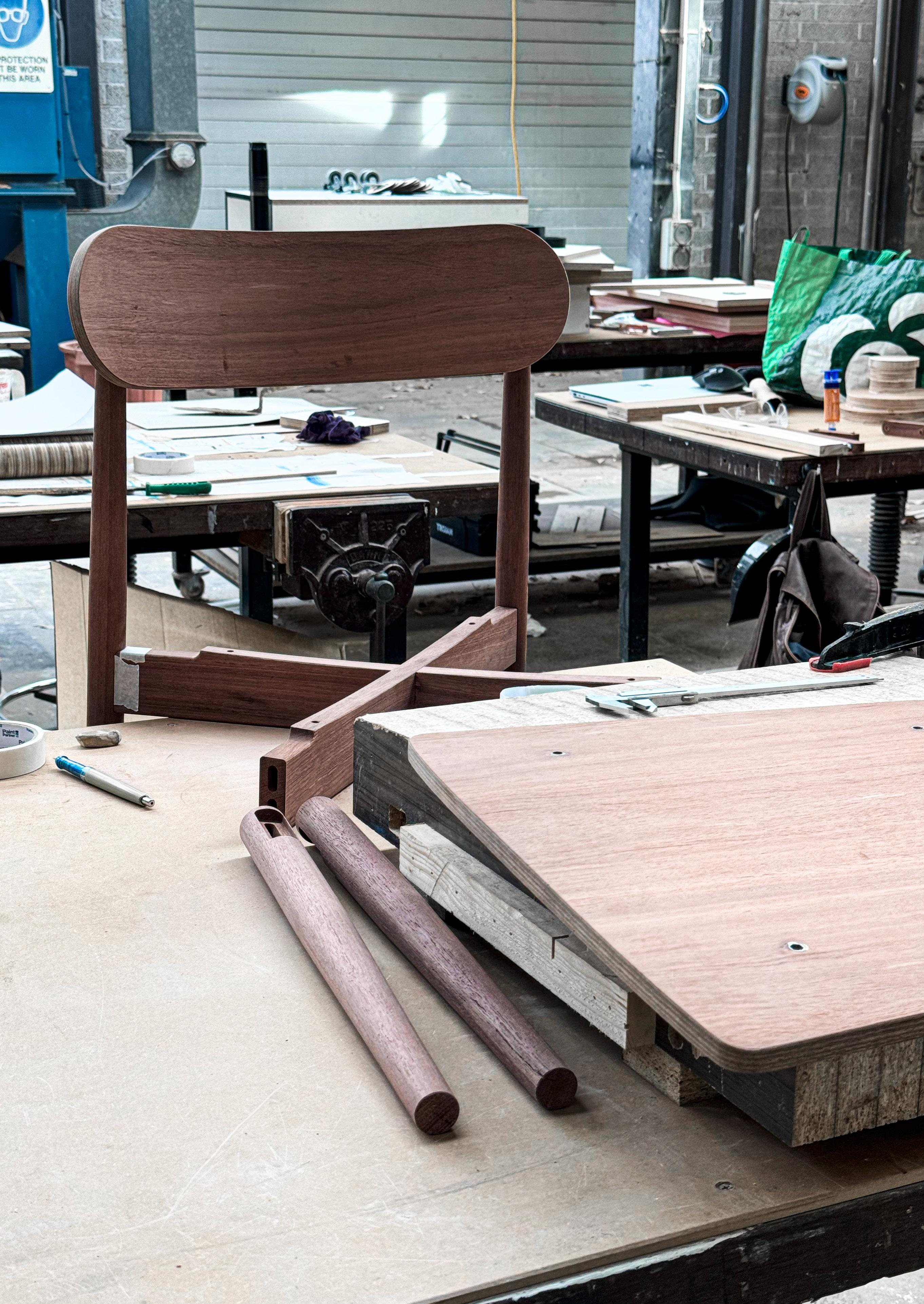

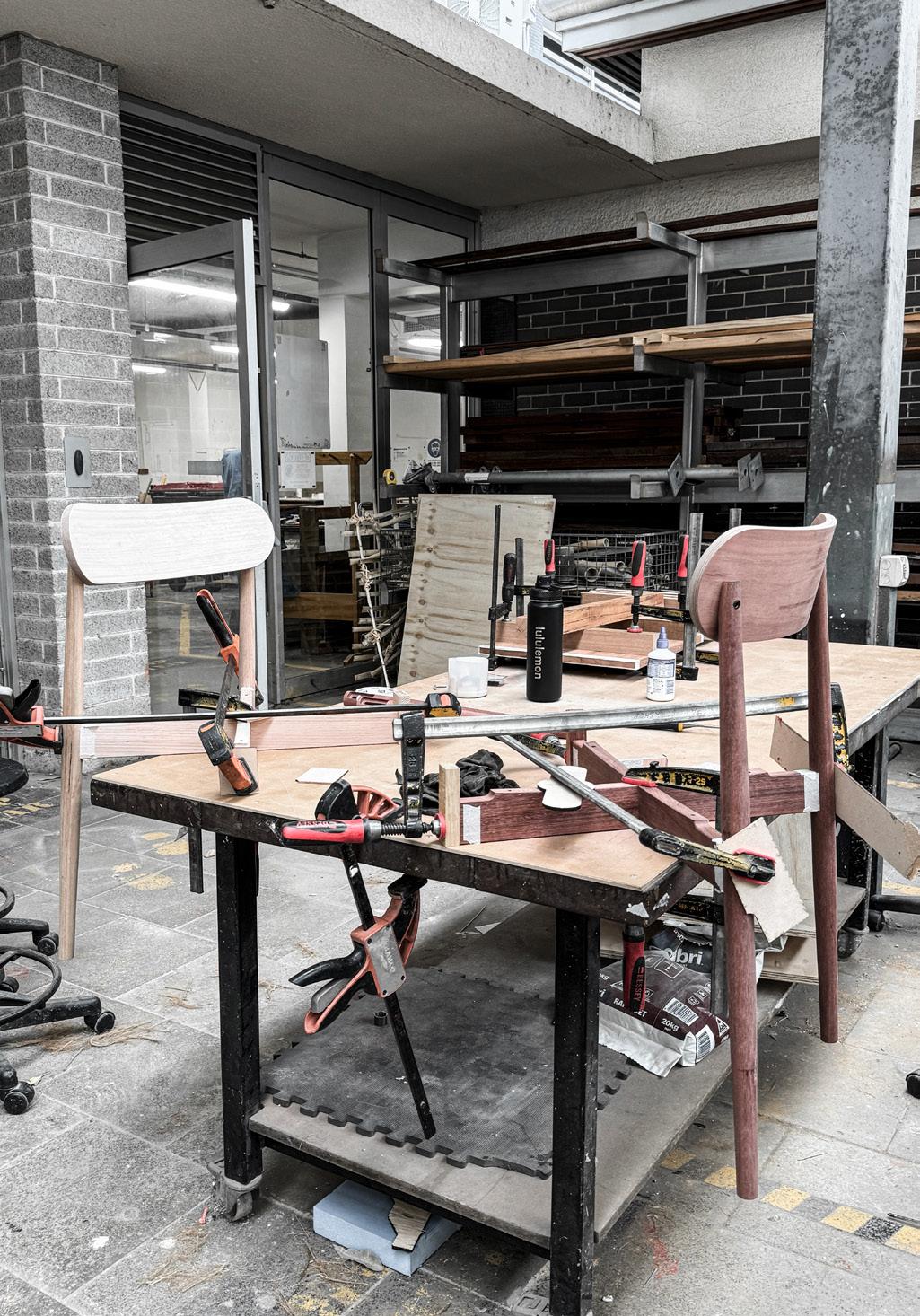
Apply Glue:
Using exterior-grade PVA glue, coat the tenons and the corresponding slots on the legs. Position the rails carefully to align with the marked depths, ensuring a secure fit.
Clamp and Set:
Once the legs and rails are in place, use clamps to hold the assembly securely, applying even pressure to reinforce joint strength. Leave the clamped assembly to dry for 24 hours.
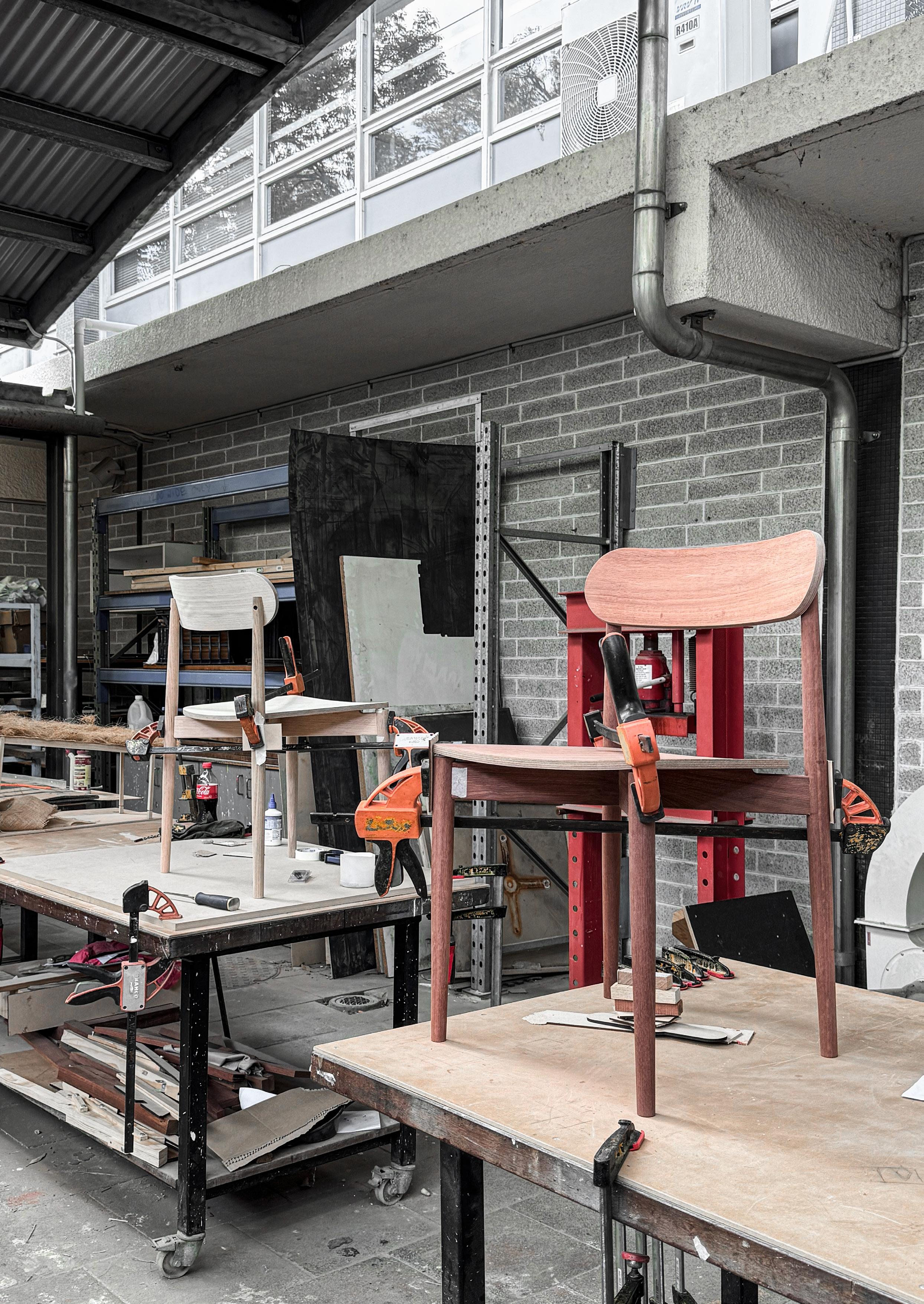
Oiling Process:
After sanding, wipe down the chair to remove dust. Using a cloth, apply Scandinavian oil along the grain, ensuring full coverage. Let it sit for 10–15 minutes, then wipe away any excess. Allow 6–8 hours for drying in a dust-free area. Apply three more coats, wiping excess and allowing full drying time for each. Once fully dried, buff the chair with a soft cloth for a smooth, polished finish.
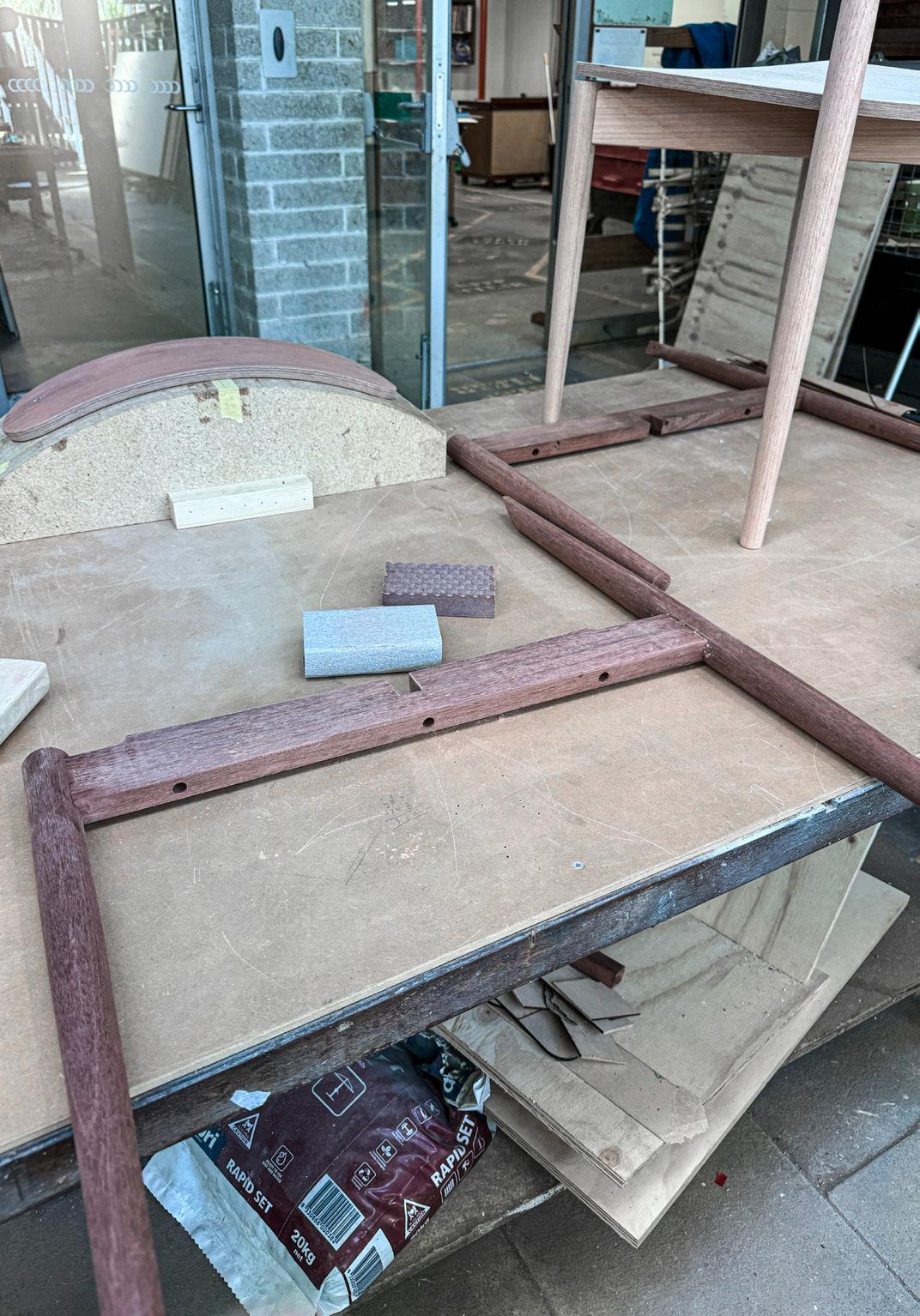
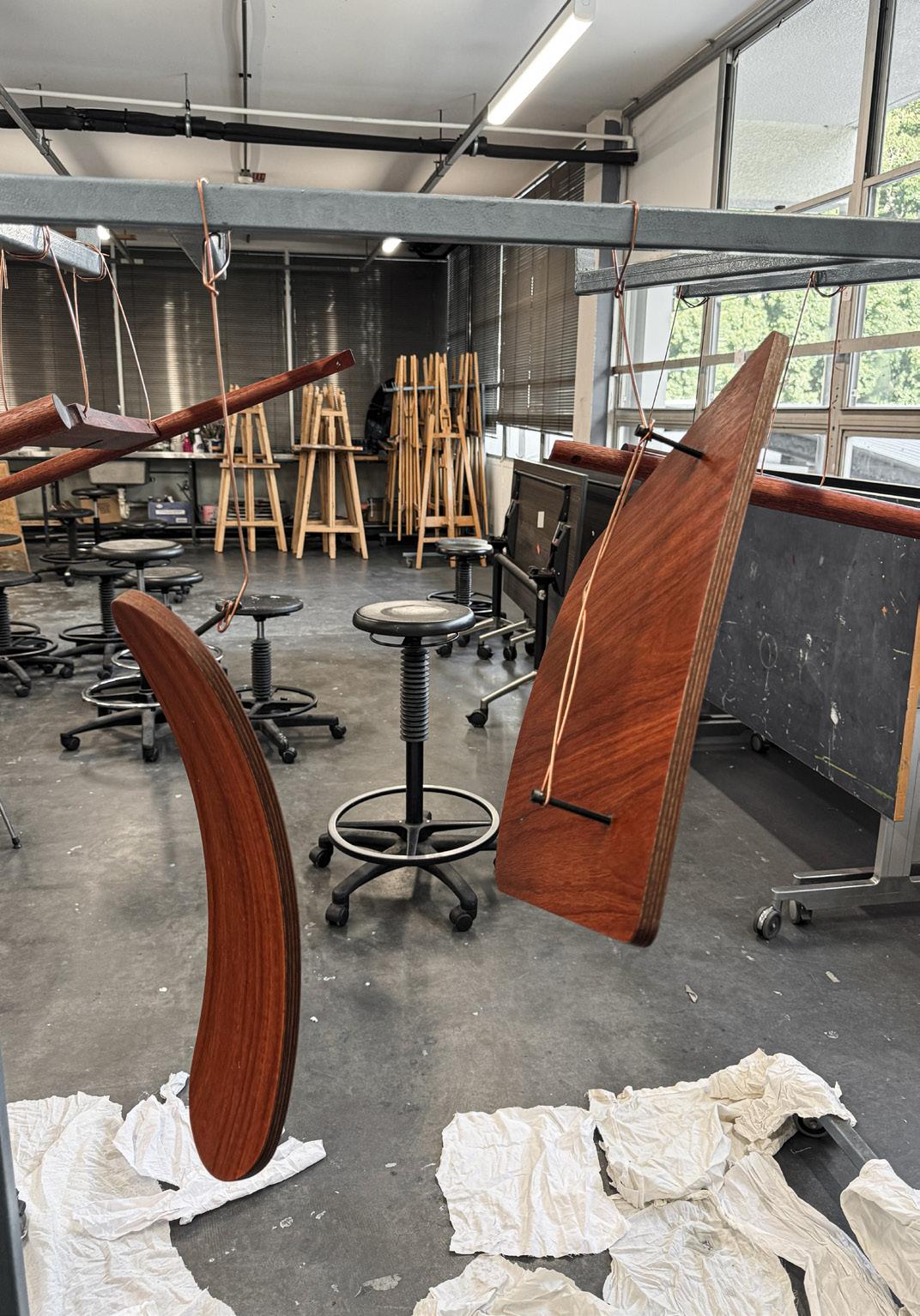

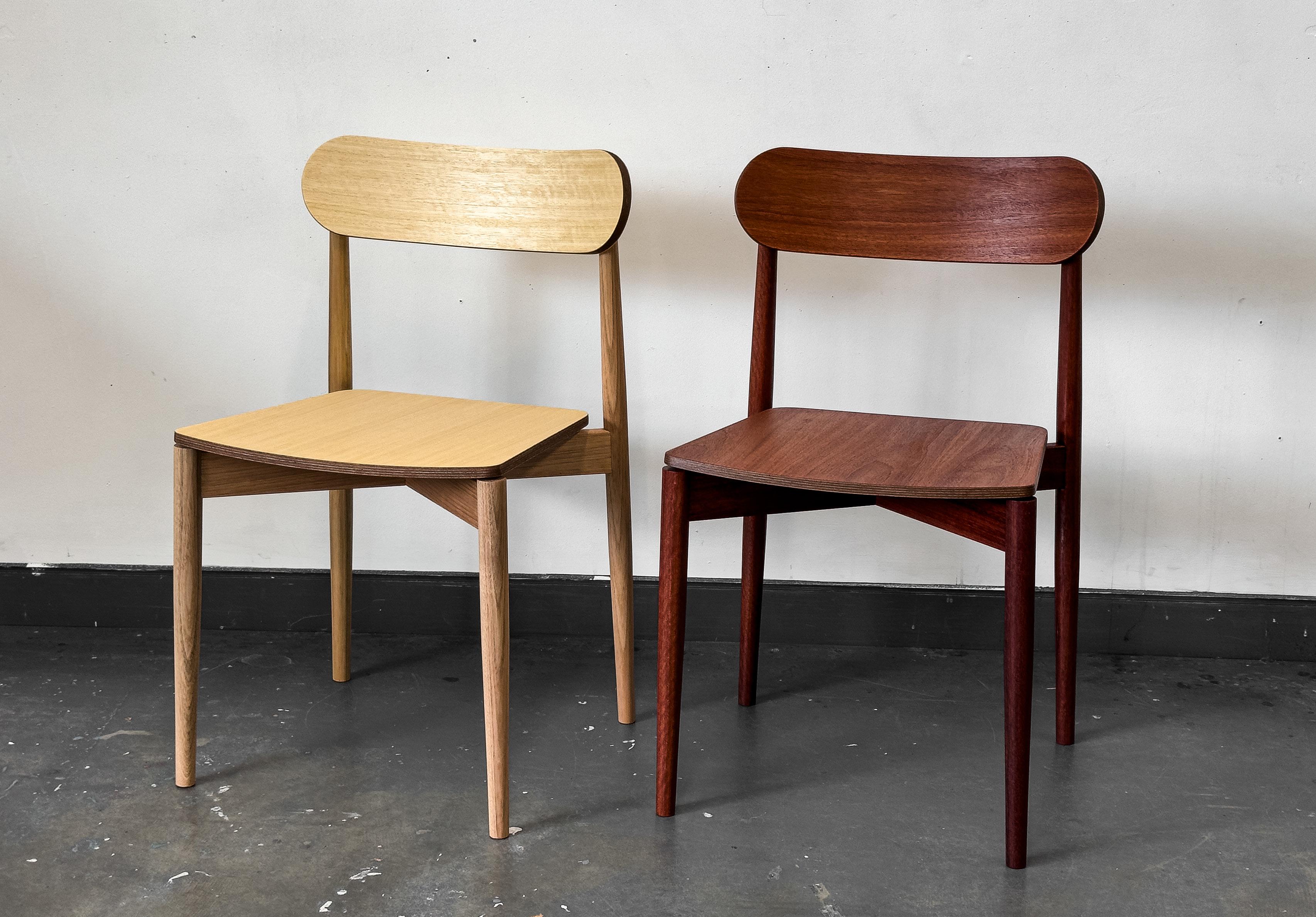
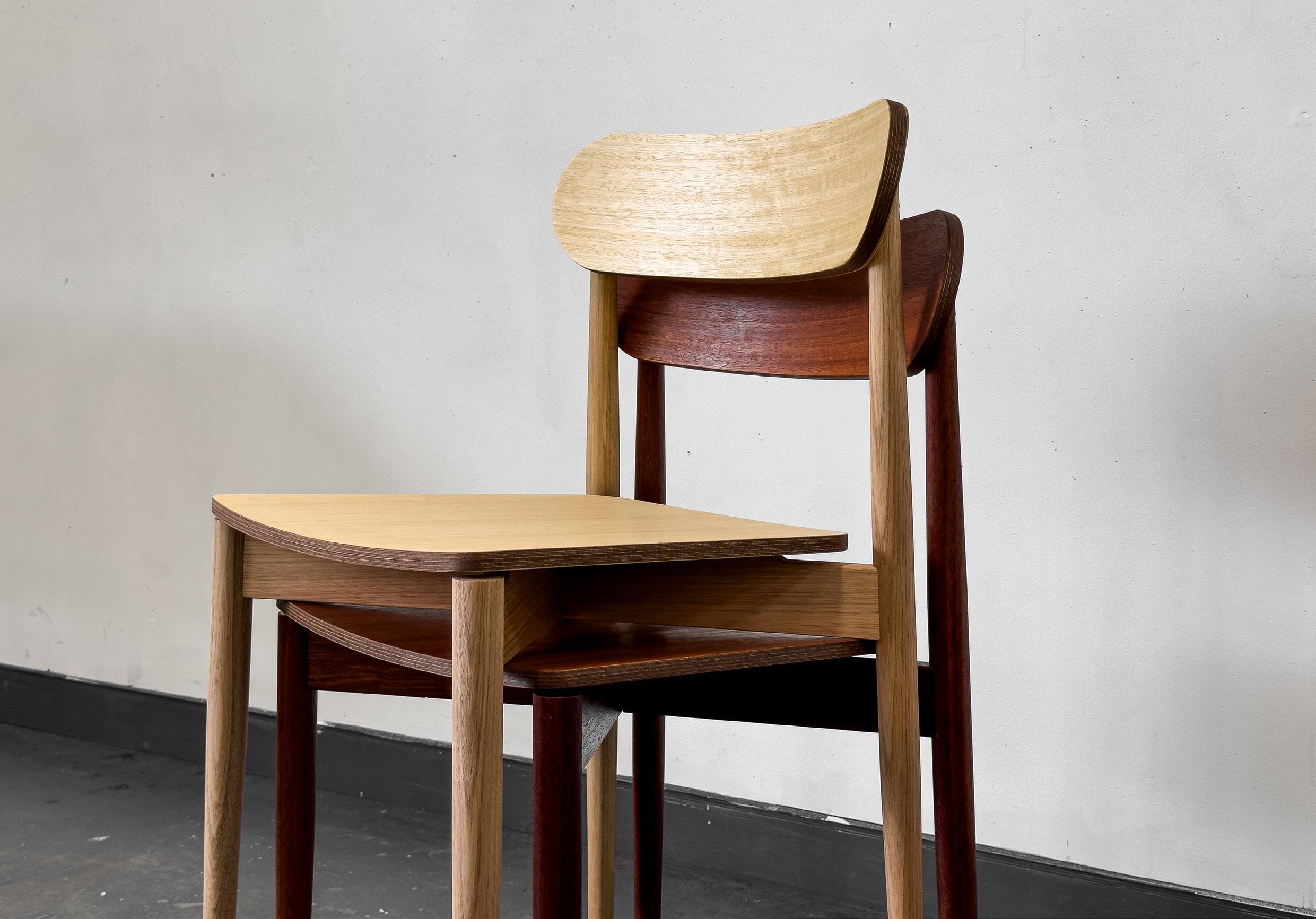
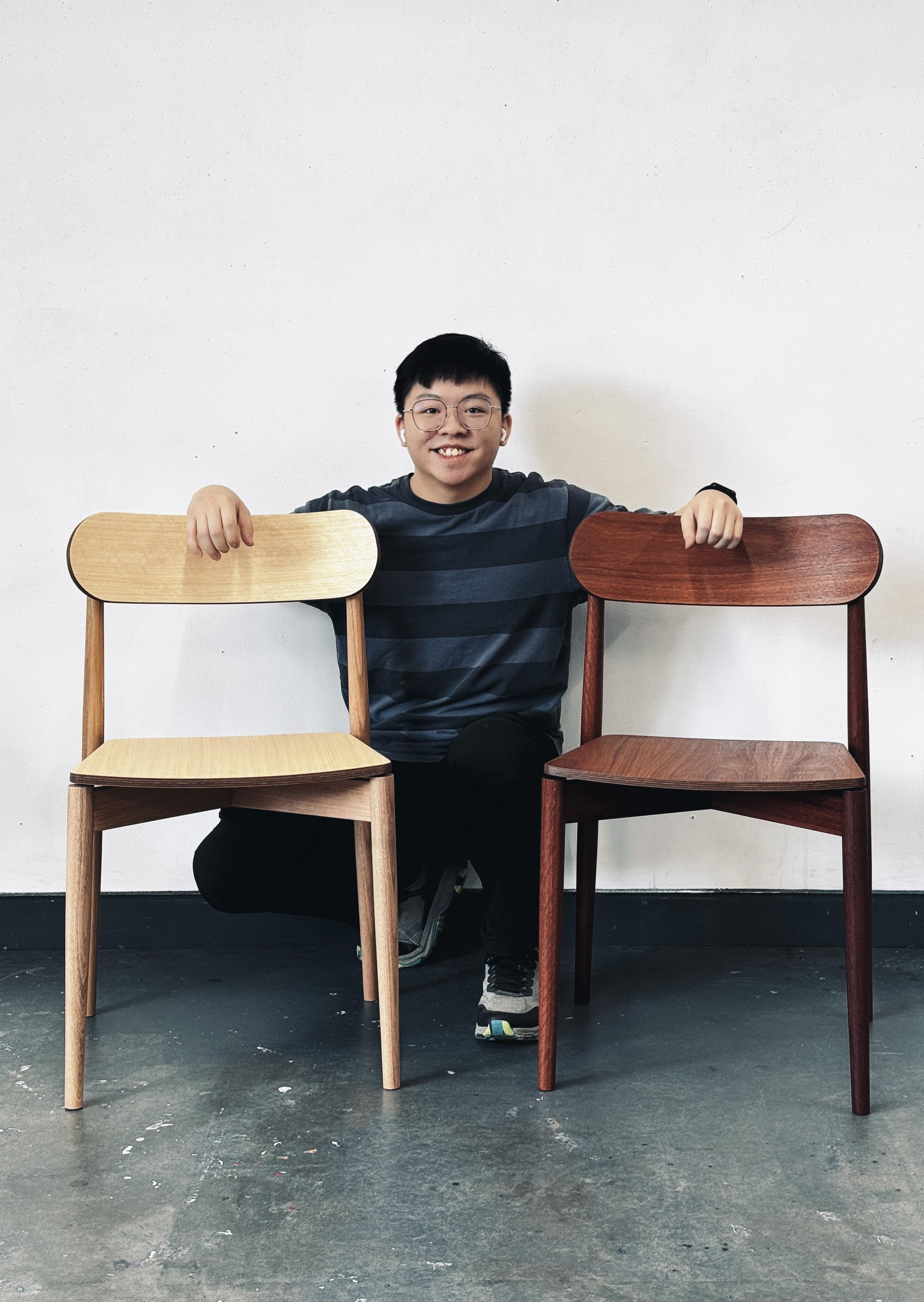
TECHNICAL DRAWINGS
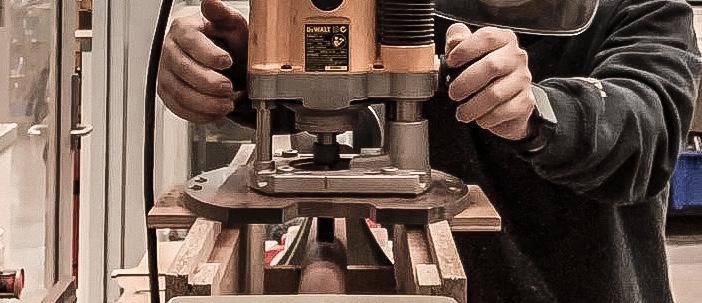
Top View
Scale 1:10
Front View
Scale 1:10
Product Specifications
Dimensions
H 800
D 476
W 494
Seat Height
462
Weight
5kg
Side View
Scale 1:10
Material & Finish
Jarrah
Victorian Ash Year 2024
Left Back Leg - Long Right Back Leg -Long Front Leg - Short
Notes: All timber components are finished with three coats of Scandinavian Oil to enhance their natural beauty and provide durable protection. Code QTY Component
M6 Cap Head Screw
M6 Cap Head Screw
M6 Cap Head Screw Domino Tenons
Hardwood - Jarrah/ Vic Ash
Hardwood - Jarrah/ Vic Ash
Hardwood - Jarrah/ Vic Ash
Hardwood - Jarrah/ Vic Ash
Hardwood - Jarrah/ Vic Ash
Plywood with Veneer Finishes
Plywood with Veneer Finishes
Black Uncoated Alloy Steel
Black Uncoated Alloy Steel
Black Uncoated Alloy Steel
Beech
(Scale 1:6)
(Scale 1:6)
L02 (Scale 1:6)
L01
Side View Side View Front View
L03
Side View Front View
Front View
Scale 1:6
Scale 1:6
Scale 1:6 P02
Scale 1:6
Veneer Grain Direction
Bottom & Side View
The backrest and seat are laminated with 1.5 mm bendy plywood, comprising nine central layers oriented in varying directions, and finished with Jarrah or Vic Ash veneer on both sides.
Veneer Grain Direction
Bottom & Side View
Part B
Leg Assembly
Top View
Part A
Leg Assembly
Part A
Leg Assembly
Part B
L01 + R01 + L03
L02 + R02 + L03
PACKAGING
Material
Box Dimension
H: 660 W: 780 D: 114
4MM KRAFT BROWN (K4M) SHEET
LEGS
ASSEMBLYGUIDE
BACKREST
SEAT
Bottom Level
Top Level
Top Cover Exploded Axonometric
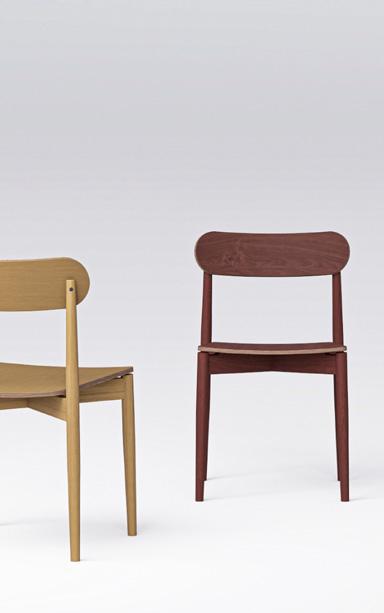
X.01
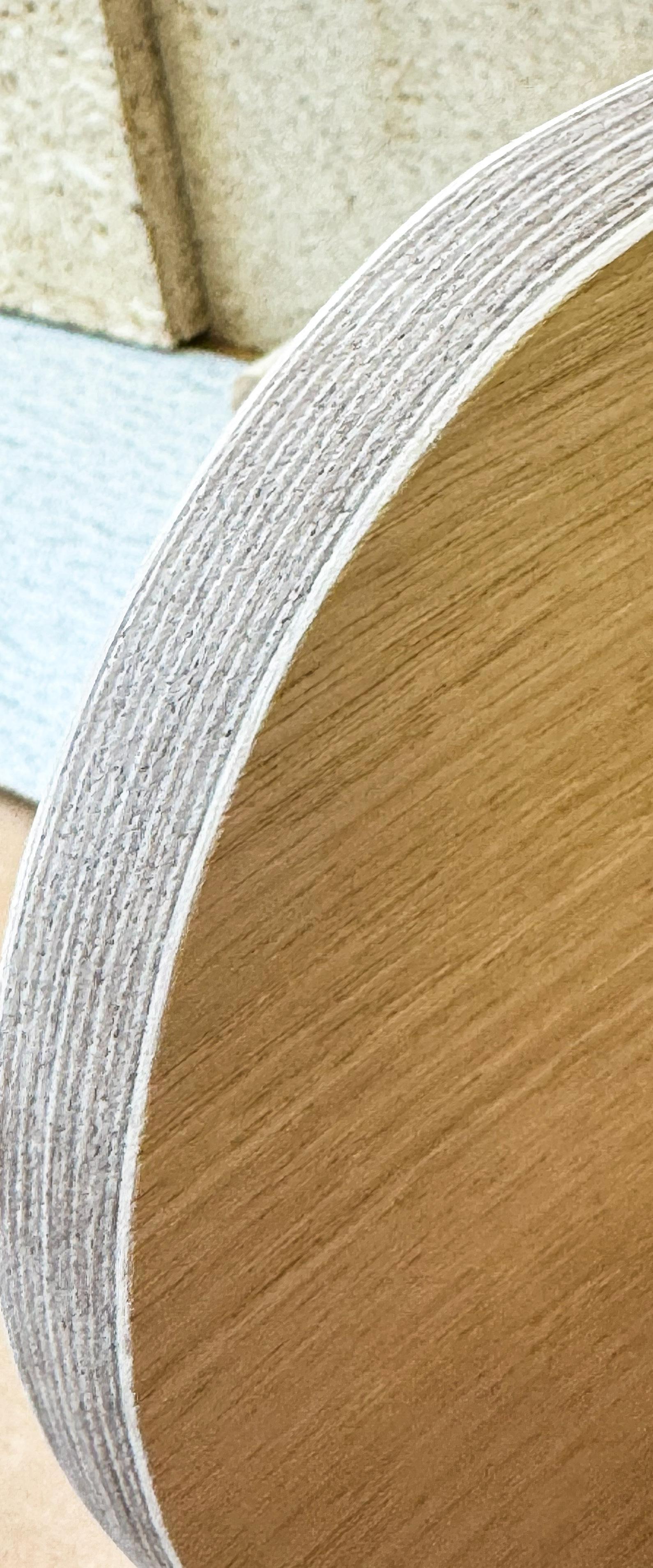
THANK YOU
With heartfelt appreciation to Unit Coordinators Peter Kitely and Guy Eddington, as well as the UWA School of Design Workshop team—Guy Eddington, David Marie, and Khaynan MacCarthy—for their invaluable guidance, support, and expertise throughout this project. Thank you for making this journey possible.
Copyright © 2024 Eugene Tiong. All rights reserved. No part of this publication may be reproduced or transmitted in any form without prior permission from the author.