FOOD AND DRINK NETWORK
The Smarter Choice: Selling Food and Beverage Machines at Online Auction
Want to buy or sell your company assets? Turn to page 04
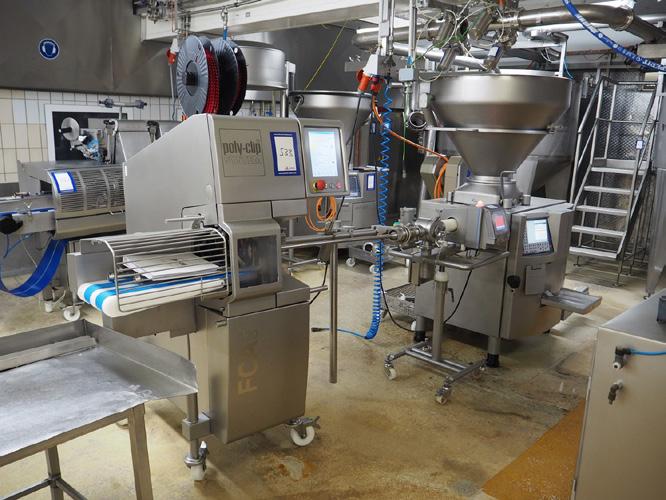
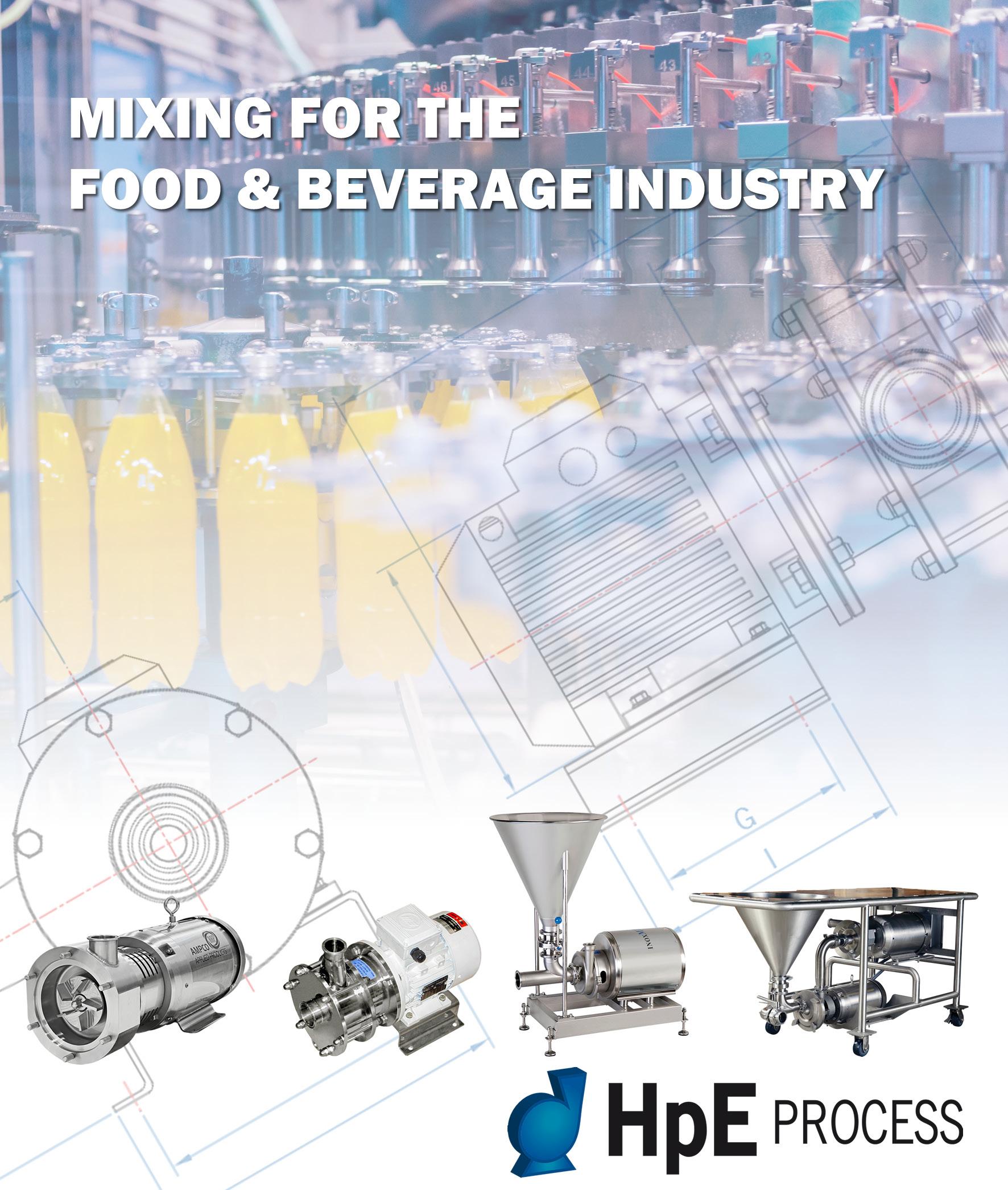
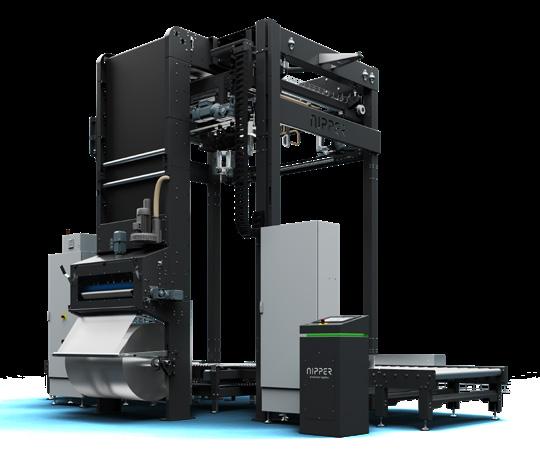
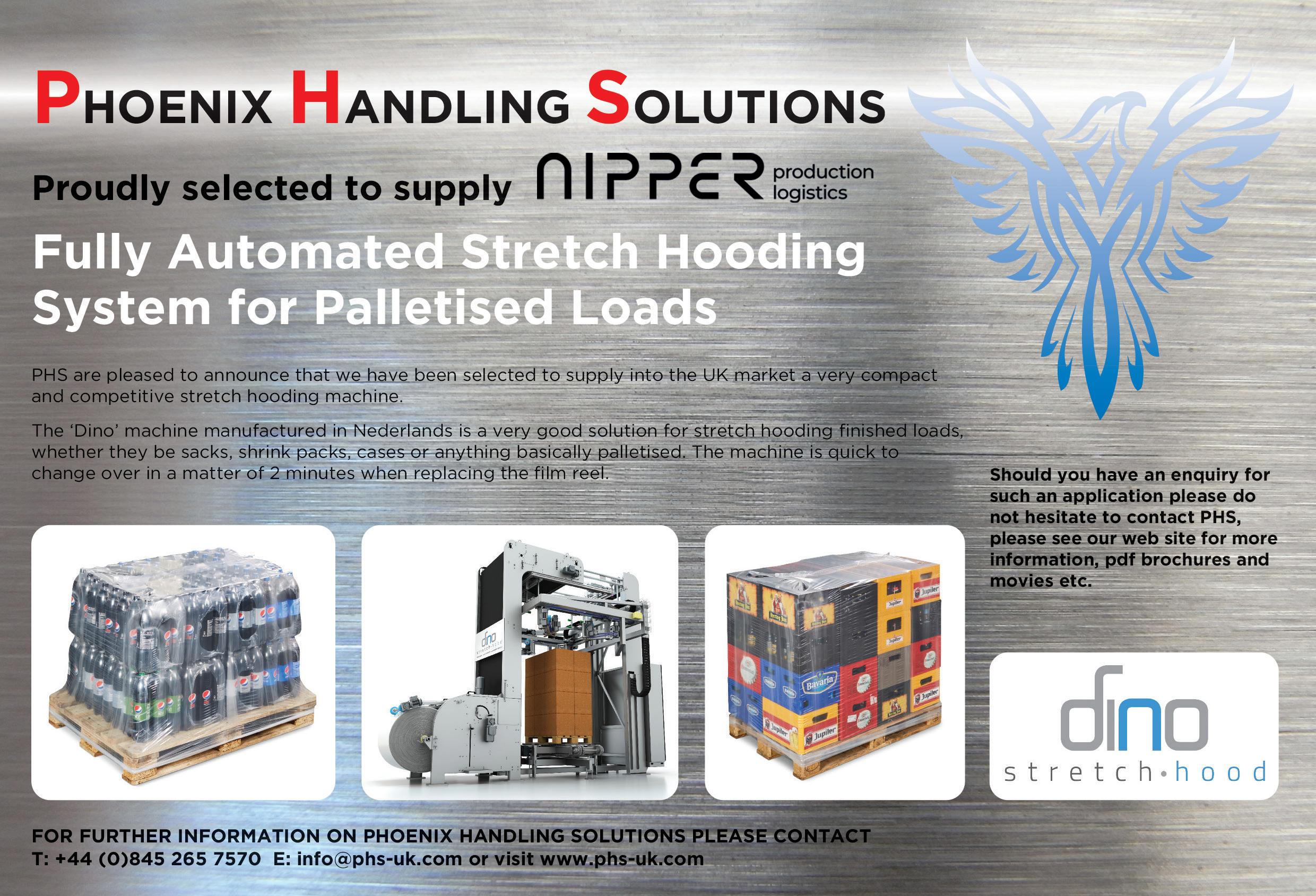
The Smarter Choice: Selling Food and Beverage Machines at Online Auction
Want to buy or sell your company assets? Turn to page 04
EDITORIAL:
Braubeviale Easyfairs
First Light Group
Fortem International Ltd
Harford Control
Golden Frog Marketing Peppersmith PLMR
PHD Vetroplas Packaging
ADVERTISEMENT SALES:
KIMBERLEY READ (Advertisement Sales Manager) JOANNE MURPHY
AMANDA WALMSLEY EVELYN WOOLSTON
RACHEL RILEY - Designer
WALTONS PUBLICATIONS LTD
46 HENEAGE ROAD, GRIMSBY N.E. LINCOLNSHIRE DN32 9ES
Kimberley Read at: kimberley@ foodanddrinknetwork-uk.co.uk or Joanne Murphy at: joanne@foodanddrinknetwork-uk.co.uk
foodanddrinknetwork.co.uk
& TAKEAWAY INNOVATION EXPO 2024 Europe’s Premier Event for Restaurant Growth and Innovation Returns to ExCeL London
& FILLING TECHNOLOGY
Samson Pallet Stability (part of the Samuel Grant Group) is proud to announce new additions to the awardwinning Samson Nano range.
By adding the rotating arm machine and fully automated pallet wrapping lines to the offering, the team are now able to offer even more solutions, especially to companies who need to wrap high volumes of pallets 24/7.
The rotating arm machine was added in response to popular demand. The film wraps around the pallet, allowing the machine to wrap more unwieldy or unstable pallets that would be challenging to wrap on a revolving turntable. The rotating arm machine can be used with manual, EPT or FLT loading at floor level, or in line with conveyors.
The Samson Nano fully automated pallet wrapping line in-feeds multiple pallets on the conveyor. Pallets are wrapped to EUMOS standard in seconds with machines capable of 40rpm. This option provides the fastest wrapping solution for any business needing to wrap pallets consistently and efficiently.
As Day of the Dead approaches (1-2 November), it’s time to stock up on the quintessential liquid to celebrate this Mexican feast that is now a worldwide phenomenon. One of the most admired ultra-premium, no additives tequila available in the UK is SUAVE, notable for the quality of its spirits and the elegance of its bottles.
Tequila is a category that is growing rapidly and which has expanded in volume in recent years. According to IWSR the category is expected to grow at a volume CAGR of 7% globally between 2021-2026. The tequila category has been flooded with premium brands that are piled high in supermarkets. But in the ultra-premium category something more interesting is happening. Slow, careful production by companies that have a proven track record in environmental sustainability and a commitment to no additives in their liquids is leading to new interest.
Underlining its sustainable credentials, SUAVE is one of only three tequilas in the world to have been granted a Butterfly Mark – the coveted accreditation of Positive Luxury which rewards and recognises brands in fashion, beauty, jewellery, lifestyle & wellness, and hospitality.
There are a number of things that make SUAVE stand out. One is price. With retail prices ranging from just under £100 for Blanco to £2000 for SUAVE Ultra Añejo, this is unashamedly one of the most expensive tequilas available.
Another is craftsmanship. One reason for the relatively high prices of these liquids compared with many on the market is the fact that the company uses solely the very heart of the agave pina. All the green outer surface is stripped away so that only the pure white core of the pinas makes it into production. These strict quality standards are designed to minimise the amount of green leaf stalk that is left. This results in a purer alcohol, creating a glorious product that avoids the tequila hangover. All this time and skill adds to the cost of an ultra-premium liquid.
SUAVE stands out from the crowd amongst tequila aficionados because of what it does not have. There are no additives whatsoever. Under current rules, up to 1% of a tequila can be made up of four styles of additive: oak extract, caramel colouring, sugar syrup and glycerine. SUAVE does things differently: flavours and colour are entirely natural emanating from the agave and from the barrels used for ageing the tequila. It’s also Kosher certified.
With a choice of conveyor lengths, height and bespoke infeed and outfeed options available, the Samson Nano Autoline is proving to be a very popular yet cost effective solution, with less labour resource required to achieve the highest throughput possible.
The rotating arm and Autoline have an inbuilt roping and sealing device as standard, so no loose tails of film are left hanging from the pallet after wrapping.
Both types of machine are available on the Samson Nano’s unique fixedprice-per-wrapped-pallet offering. This means there is no capex for their installation, with stretchfilm, servicing, maintenance, parts and guarding for auto lines, and 24/7 login portal all included in the fixed pallet price.
Peppersmith, one of the UK’s leading providers of premium, naturallysourced mints, is thrilled to announce its new partnership with Starbucks. Starting this month, Peppersmith mints will be available at Starbucks stores throughout the United Kingdom, bringing a new impulse option to customers nationwide.
This exciting partnership aligns two brands committed to delivering high-quality products that prioritise both taste and responsible sourcing. Peppersmith’s range of mints and chewing gum have been endorsed by the Oral Health Foundation as they are made with 100% xylitol, a plant-based sweetener derived from gluten-free oats.
The peppermint and spearmint used in Peppersmith products are sourced from a small farm in Hampshire, building on Starbucks’ previous work supporting exceptional British brands.
“Partnering with Starbucks marks a significant milestone in Peppersmith’s journey,” said Kevin Grant, CEO of Peppersmith. “We’re delighted that Starbucks shares our vision. We look forward to enhancing the Starbucks experience.”
The partnership will see Peppersmith’s best-selling Peppermint Mints available at Starbucks locations across the UK. This launch allows Peppersmith to reach a broader audience, continuing their mission to promote healthier, tasty alternatives in the confectionery market.
For more information, please contact: Peppersmith Ltd Phone: 020 8788 2080 | Email: Hello@peppersmith.co.uk
The move is part of the company’s mission to produce sustainable products and packaging. A BCorp certified company Sapling has demonstrated its commitment to outstanding sustainable performance and transparency about its practices.
Sapling Spirits, the London based spirits company, have recently launched a range of vodkas available in eyecatching aluminium bottles supplied by Vetroplas in conjunction with its Spanish manufacturing partner Envases. cap. The distinctive decoration was achieved by offset printing the artwork over a white base coat and sealed with a matt lacquer.
Aluminium is 100 per cent recyclable and resonates with a strong consumer trend for environmentally friendly packaging. Additionally, as aluminium is lighter than glass, fuel usage is reduced when transporting the finished packs. Aluminium recycling uses, on average, 90% less energy than glass bottles. Sapling also chose to use 100 per cent recycled aluminium (PCR), further increasing the packaging’s green credentials.
The 5cl aluminium bottles supplied by Vetroplas – which feature a ROPP neck thread and a BPA NI PE liner – are finished with an aluminium screw
The Glenlivet redefines tradition with the release of its oldest
The 55 year-old expression – the highest age statement ever to be released by The Glenlivet – is unveiled as it marks a 200-year legacy
Commenting, Ned Neville-Rolfe, Head of Operations said: ‘We have a distinctive range of vodkas, and this new packaging format provides both further low carbon credentials and really strong stand out on shelf. The ease with which aluminium bottles can be recycled, as well as them offering 100% PCR aluminium, were also major factors in our choice of Vetroplas’ bottles. We know this element is appreciated by customers and forms part of our philosophy of reducing carbon footprint where possible.”
The Glenlivet, the iconic Speyside single malt Scotch whisky, has unveiled a masterpiece that celebrates its excellence in whisky craftsmanship and design, embodying the originality that has defined it since its inception in 1824: The Glenlivet Eternal Collection, First Edition, 55 Year Old, in collaboration with computational architect, Michael Hansmeyer.
A true rarity, The Glenlivet’s oldest and most ambitious expression to date comprises just 100 beautifully crafted bottles, while every aspect of the new release has been considered with meticulous attention to detail. Crafted from a seasoned sherry cask and carefully matured over more than five decades, this precious single malt offers a complex flavour profile and astonishingly long finish.
In partnership with pioneering artist, Michael Hansmeyer, the 55 Year Old single malt whisky sits within a strikingly beautiful sculpture that takes inspiration from the home of The Glenlivet. Mirroring the eternal essence and flow of the River Livet, which is located deep in the Spey Valley where The Glenlivet was born, Hansmeyer brought his unique expertise in computational architecture to create this highly original art piece.
With hand-sculpted jesmonite and rose-gold plating, the sculpture perfectly houses the spherical decanter of the 55 Year Old. In a stunning display of contemporary modelling through computer programming, this art piece brings subtle intricacies that are testament to the craftsmanship at the heart of every creation from The Glenlivet.
This exceptional 55 Year Old single malt is the First Edition of The Glenlivet Eternal Collection – a new range of highly collectable precious whiskies, released annually. All future releases, each taken from a single, extraordinary cask, will be aged for one additional year and will be accompanied by an original artform crafted by a new visionary artist. Together, this will create a collection to cherish.
The First Edition of The Glenlivet Eternal Collection, will be released in September 2024. The masterpiece was first unveiled during an exclusive 200 year anniversary celebration hosted at The Glenlivet’s iconic distillery in Speyside, Scotland. The Glenlivet Distillery is open for guests to explore the full portfolio from The Glenlivet and enjoy interactive visitor experiences.
The Glenlivet Eternal Collection, First Edition: 55-Year-Old in collaboration with Michael Hansmeyer, will be available exclusively at The Whisky Exchange for RRP €50,000. For more information, visit theglenlivet.com or follow @theglenlivet.
Pip & Nut strengthens its board with appointment of Mindful Chef CEO as non-executive director
Pip & Nut, the allnatural nut butter and snack brand, has announced the appointment of Mindful Chef CEO Tim Lee to its board as a non-executive director.
Tim joins at a key moment for Pip & Nut as it looks to capitalise on its position as the UK’s fastest growing nut butter brand, while expanding its offer with their launch into Cereal Bars category earlier this year.
Tim brings a wealth of experience in scaling purpose-driven brands, having held senior leadership roles at both Tesco and M&S, alongside his current roles as Chair & CEO of Mindful Chef, and the CEO of Simply Cook. His appointment aligns with Pip & Nut’s ambitions to drive further expansion and tap into growing consumer demand for nut butter and snacks that are better-for-you and better for the planet.
The move to expand the Pip & Nut board follows the decision to appoint Giles Brook, the lead investor of Pip & Nut and advisor to several food and drink start-ups including Bio & Me and Freja, as Chairman. Giles will continue to support to the senior leadership team throughout the brand’s growth.
“His hire is just the latest in a series of decisions that we are making to strengthen our expertise, deepen our engagement with customers and consumers, and continue to deliver products that taste great, and are good for people and the planet”.
Tim Lee, non-executive director of Pip & Nut, said :
“I am delighted to be joining the Pip & Nut team at such an important time for the growth of the company. I’ve watched as Pip has led this brand from a challenger start-up to the fastest growing nut butter brand in the UK and am excited to get stuck in to help her and the team take it even further.
“From leading my own purpose-led brands I know how important it is to stay true to Pip & Nut’s commitment to ethical and sustainable sourcing, while also scaling their offer to reach new and larger audiences. I hope my experience will support them on this journey and we can bring healthier, delicious, products to even more people across the UK”.
In today’s rapidly evolving manufacturing landscape, businesses often face the need to reassess their equipment to stay competitive. Whether it’s due to the closure of a production site, to create space for new machinery, or changing production demands, selling your food and beverage machines can be a strategic move. Unused or depreciating equipment represents untapped capital that could be reinvested into new production opportunities.
By auctioning your surplus equipment, whether just a few machines or an entire production site or line, you not only maximize your returns but also contribute to a more sustainable industry by reusing machinery. You can maintain your focus on optimizing production and meeting your business goals, while the auction platform handles every aspect of the sales process. From listing and marketing to finalizing the sale, the auctioneer ensures a smooth and efficient transaction, allowing you to unlock the value of your unused equipment without diverting attention from your core operations.
Auctioning by Industrial Auctions offers several advantages. “The shortage of qualified personnel in the food industry presents significant challenges for food producers and traders. We aim to alleviate this burden by taking the entire sales process off their hands. Additionally, we have a large international database, which allows us to reach a wide network of professionals within the industry, effectively connecting supply and demand”, explains the CEO of Industrial Auctions.
“We are always committed to making each auction a success. The hard work pays off when we see the satisfaction on everyone’s faces at the end. Working closely with a committed team not only makes the process more enjoyable but also drives us to achieve even greater results.”
Want to buy or sell your company assets? Visit the website now by scanning the QR code: https://www.Industrial-Auctions.com/ sell-your-food-beverage-assets/
An article By Roy Green, Harford Control Ltd. September 2024
Many people will remember the ‘Horsegate’ scandal, where horse meat entered the supply chain as beef, leading to the withdrawal of millions of products across Europe and costing businesses millions of pounds. It has now been a decade since one of the biggest food fraud cases, yet consumers remain vulnerable to food safety issues as instances of food fraud continue to rise. According to Professor Chris Elliott, a food safety expert, the UK food safety system faces “absolute chaos.”
The EU reported a record number of potential olive oil fraud cases in the first quarter of this year. The cost of olive oil has more than doubled since 2018 due to production being affected by extreme weather. As prices spiked, so did instances of potential fraud and safety concerns related to olive oil. In July, authorities in southern Italy broke up a racket selling fake olive oil, seizing 42 tonnes of the ‘extra virgin’ variety worth almost $1 million.
Meanwhile, an FSA report found that lead dyes, chalk dust, and brick dust were being used to adulterate chilli powder and paprika. The lucrative black market within the spice industry emerged as some businesses sought cheap substitutes to cut costs and boost profits.
There is no doubt that cost pressures and the need to remain compliant, have posed significant challenges to the food industry. Systemic corporate greed, gross negligence, and appalling dishonesty have heightened risks to food safety in the pursuit of cost reduction. What happens when profits are prioritised over everything we know to be right?
There is a growing catalogue of incidents, and mislabelling is one of the key challenges within the food sector. From misleading health claims and false origin statements to non-compliant labelling, the industry is grappling with a string of labelling issues.
With increasing awareness of healthy eating, people are seeking better alternatives amongst their food choices. However, many consumers are misled about the true nutritional values and the high fat, salt, and sugar (HFSS) content of the products they are purchasing.
Some companies substitute fats with modified starches like maltodextrins to make ‘low calorie’ claims and use non-nutritive sweeteners as sugar replacements. This practice misleads consumers into believing they are choosing ‘healthier’ options. This can be especially problematic for individuals with metabolic conditions such as obesity, Type 2 Diabetes Mellitus, hypercholesterolemia, and fatty liver, as they cannot accurately calculate the true glycaemic effects by reading the food label alone.
While misleading health claims can deceive consumers about the nutritional value of their food, false origin labels are another common tactic used to manipulate purchasing decisions by creating the illusion of local or premium sourcing.
Which? found that some product labels contained ‘fairly meaningless’ information, such as a pack of gammon joints at one major supermarket where the pork was labelled as “EU and non-EU origin”, in other words ‘anywhere in the world’.
In fact, 64% of consumers said they are more likely to buy a product labelled ‘British’ than one without this origin. Some businesses exploit this by labelling food products as originating from a specific country or region to attract customers, even when the actual source is elsewhere. This practice can erode consumer trust and damage the reputation of genuine local producers.
Whilst misleading origin claims can undermine consumer confidence in product sourcing, inaccurate allergen labelling poses an even greater risk, directly impacting the health and safety of millions of people with food allergies.
A major study by the Food Standards Agency (FSA) revealed that around 2.4 million people in the UK live with a clinically confirmed food allergy. Although Natasha’s Law came into effect in 2021, there have still been fatal allergen incidents due to incorrectly labelled products.
Celia Marsh, a 42-year-old with a severe dairy allergy, died in 2017 after eating a ‘super-veg rainbow flatbread’ wrap from Pret a Manger in Bath. The wrap was contaminated with milk protein, which was not listed on the food label. A product marked as dairy-free should be totally free from dairy.
Since Mrs. Marsh’s death, the Food Standards Agency (FSA) announced that it had updated its food allergen business guidance. The new recommendation states that a precautionary allergen label, also known as a ‘may contain’ statement, can be applied to vegan products if there is a risk of cross-contamination with allergens of animal origin, such as fish, shellfish, milk or eggs.
From food fraud to food mislabelling, the food sector is under immense pressure to improve clarity and transparency across the entire supply chain. For manufacturers, it’s crucial to have technology that ensures sufficient laboratory testing and accurate labelling to detect mistakes and prevent genuine human errors.
As an end-to-end MIS/MES provider, Harford Control offers Laboratory Information Management System (LIMS) and Autocoding Solutions to support quality control and labelling accuracy. Whilst laboratory testing helps to detect fraud and raw material mistakes, automated set up of date coders and barcode scanners, especially on frequent
product changeovers, helps prevent mistakes, often due to complacency. Genuine mistakes and complacency are often the biggest threats to manufacturing operations.
Risks of complacency are easy to understand, simply because, as is often stated, ‘the longer a company manufactures without a coding or labelling error, the greater the risk of them having one’.
Harford LIMS helps manufacturers track and trace approved materials and monitor noncompliant products while our Autocoding Solutions ensure that HFSS, origin and allergen information on each package and outer case is accurately labelled. Harford LIMS and Autocoding Solutions can be integrated seamlessly. Any batches from the shop floor will automatically initiate certain actions based on predefined triggers to the laboratory.
If your factory is looking to tackle food fraud issues and minimise inaccurate labelling challenges, please reach out to us at info@harfordcontrol.com or give us a call on +44 (0)1225 764461.
Foodservice professionals across the country are eagerly awaiting the return of Restaurant & Takeaway Innovation Expo. Known as Europe’s leading event dedicated to the growth and success of restaurants and takeaways, this trade show and industry conference will return to ExCeL London on the 15th & 16th of October
This year promises to be the event’s most dynamic yet. The expo is set to be attended by thousands of restaurant and takeaway owners, ready to gather and explore a vast array of innovative products, groundbreaking ideas, delivery solutions, essential services, and more. The Expo is designed to help businesses grow, boost profits, and attract and retain loyal customers. It’s an exceptional opportunity to discover emerging trends, cutting-edge products, and network with professionals shaping the future of the food service industry.
THE RESTAURANT & TAKEAWAY INNOVATION EXPO 2024 WILL FEATURE:
500 INNOVATIVE EXHIBITORS: The show will feature a wide range of exhibitors at the forefront of the industry, showcasing products and services to give businesses a competitive edge. From the latest in kitchen technology to advanced delivery solutions, visitors can expect to find everything needed to elevate operations and improve customer satisfaction.
200 INSPIRING SPEAKERS: Attendees can expect to glean insights and inspiration from the brightest minds in the industry. The lineup of speakers will share expertise on a range of topics, including business growth strategies, marketing tactics, customer engagement techniques, and more. It’s a
great opportunity to learn from the challenges and successes of representatives of the sector’s biggest institutions.
THOUGHT-PROVOKING PANEL DEBATES: The seminar stages are also set to feature lively discussions on the most pressing issues facing the industry today. These panel debates and discussions offer a platform for thought leaders to discuss and dissect key topics, providing attendees with a deeper, more well-rounded understanding of the trends and challenges that could impact your business.
INNOVATION AWARDS: Time is set aside at the show to celebrate the most groundbreaking products and services of the year in an Innovation Awards ceremony. Recognising excellence and creativity, these awards highlight industry game-changers, offering a glimpse into the future of restaurant and takeaway innovation.
NETWORKING OPPORTUNITIES: The event offers attendees the opportunity to connect with like-minded professionals, industry experts, and potential partners. The Expo provides countless chances to build relationships, collaborations, partnerships, and business opportunities, with a diverse yet relevant clientele.
Additionally, the Expo runs alongside six other industry-leading events under The Hospitality B2B Portfolio umbrella, the largest B2B event for the hospitality industry’s growth. This convergence offers attendees a comprehensive view of the industry, allowing them to explore diverse opportunities and insights under one roof.
Restaurant & Takeaway Innovation Expo is known as being more than just an event; it’s seen by many as a hub for innovation, education, and collaboration. For both seasoned industry veterans and newcomers looking to make a mark, the Expo provides the tools and connections needed to succeed in a competitive marketplace.
Mark your calendars for the 15th & 16th of October at the ExCeL London. Secure your FREE ticket today to take advantage of the countless opportunities on offer to help your restaurant thrive. Register now and prepare to be inspired, informed, and connected at the Restaurant & Takeaway Innovation Expo 2024!
FOR MORE INFORMATION AND TO SECURE YOUR FREE TICKET, VISIT https://tinyurl.com/286h9sa9
We’ll be in attendance, so join us in London this October and be part of Europe’s most influential event for the restaurant and takeaway industry. We look forward to seeing you there!
Discover state-of-the-art solutions for the production of beer, wine, spirits and more at BrauBeviale in Nuremberg. Expand your network and discuss current topics. Be there when industry leaders set the course for tomorrow!
• Impulses from the BrauBeviale 2024 supporting programme
• Comprehensive presentation programme for the wine sector
BrauBeviale 2024, scheduled from 26 to 28 November in Nuremberg, is set to offer a comprehensive package for attendees, including a diverse exhibitor portfolio covering brewery, beverage, and wine sector technology. Complementing this, the conference programme promises to provide extensive insights and inspiration for industry professionals.
The forums in Halls 1 and 9 will serve as key platforms where experts from research and industry will discuss critical topics related to raw materials, marketing, technology, and packaging. In addition, special areas dedicated to Start-ups & Young Talents, Logistics, and Wine & Spirits will be available for visitors. A highlight of the event will be the Craft Drinks Area, a must-visit for craft brewers, and Hall 6 will once again host home and hobby brewers. Updated programme details, including confirmed topics and speakers, will be accessible from late August at www.braubeviale.com.
Hall 1 will focus on raw materials and marketing, aligning with the exhibitor offerings in this space. The forum here will tackle essential questions regarding raw materials, including discussions on climate-resilient barley varieties, the challenges of malt production amid climate change, and the potential of new hop varieties. Environmental protection and economic efficiency in hop cultivation, as well as future scenarios for yeast cultivation, will also be covered. These discussions will take place on 26 and 28 November 2024.
The marketing segment in Hall 1 will explore what it takes for a beer to succeed in the market, balancing the fine adjustments between marketing and technology. Topics will include innovative thinking for revitalising beer, the success factors behind beverage innovation, and lessons from successful brands and newcomers. This marketingfocused content will be presented on 27 November 2024.
In Hall 9, the focus will be on technology and packaging, under the guidance of the Verband Private Brauereien Bayern e.V., the conceptual sponsor of the exhibition. On 26 November, the programme will delve into “Energy efficiency for SMEs,” discussing sustainability in new building projects, energy management systems, and the use of heat pumps. Integrated energy concepts for SMEs will also be highlighted.
On 28 November, the forum will explore “Non-alcoholic beers,” focusing on the role of yeast in production, product development, and best practices from European Beer Star winners. Attendees will have the opportunity to engage with experts about the processes used in this segment.
Packaging will take centre stage on 27 November, with discussions on the preferences of young consumers regarding glass, metal, and composites. The implementation of the PPWR in various markets will also be addressed, providing an assessment of implications and solutions for beverage packaging in Europe. Marketing specialists are encouraged to attend on this day to gain insights into key areas of marketing and packaging.
Special Areas and Initiatives
Wine@BrauBeviale, located in Hall 4A, will provide a platform for winegrowers, featuring a varied programme focused on cellar technology, sustainability, quality assurance, wine marketing, distribution, operations management, and digital developments. The programme is supported by key players in the wine sector, including the German Winegrowers’ Association, LWG, Geisenheim University of Applied Sciences, and HBLA Klosterneuburg, Austria. The next generation of winemakers will also be a focal point, with an innovations-forge dedicated to young talent.
Following its successful debut in 2023, the LOGISTICS LOUNGE returns, doubling in size and emphasising “The efficiency of reusable logistics.” The lounge, now centrally located, will feature a wide range of digital solutions, particularly for the digitalisation of logistics processes. The participation of diverse partners from logistics and digitalisation sectors will enrich the offering.
The Craft Drinks Area will once again be a vibrant space for professional tastings, discussions, and the presentation of the winning beer from the Maisel & Friends hobby brewing competition. Additionally, the recruitment of young talent remains a pressing issue, which is why the Start-up Area and Young Talents Camp have been integrated into Hall 6, providing a dedicated forum for these groups to connect and explore opportunities within the beverage production and machine manufacturing industries.
Free entry to BrauBeviale 2024 voucher code BB24UK
Explore the future of packaging with top industry brands and groundbreaking innovations at Packaging Innovations & Empack 2025 – register now for a free visitor pass.
Packaging Innovations & Empack 2025 is the premier event where the entire packaging supply chain converges to connect, collaborate, and innovate. Taking place on 12 & 13 February 2025 at NEC Birmingham, this highly anticipated gathering is a must-attend for industry professionals seeking to stay at the forefront of the trends and technologies shaping the future of packaging.
With over 460 exhibitors and more than 7,000 visitors expected, Packaging Innovations & Empack 2025 offers an unparalleled platform to showcase cutting-edge solutions in packaging design, materials, machinery, and technology. From sustainability to smart packaging and food service innovations, the event serves as a hub for the industry’s biggest players to exchange ideas and drive progress.
“As 2025 approaches, the need for businesses to stay ahead of the latest trends in packaging has never been more crucial,” said Naomi Stewart, Marketing Manager at Easyfairs UK. “Many businesses set ambitious sustainability targets for 2025, and whether they hit those targets or not, they have to keep moving forward as 2030 is on the horizon – and with it comes another raft of sustainability goals, including the UN’s Sustainable Development agenda.
“Between the increasing emphasis on sustainability and new regulations, the challenges are plentiful — but so are the opportunities. By attending Packaging Innovations & Empack, businesses will be well-placed to take these opportunities.”
A Meeting Place for the Industry’s Best Packaging Innovations & Empack 2025 presents a unique opportunity to connect, learn, and get inspired. It is the ideal
space where suppliers, buyers, designers, and specifiers gather to exchange knowledge, discover trends, and explore emerging technologies. Whether it’s smart packaging, sustainable materials, or advancements in labelling and printing, the event covers all facets of the packaging industry.
“There are very few opportunities where you can gather almost the entire sector in one place, and Packaging Innovations is truly that opportunity for anyone interested in packaging,” said Margaret Bates, Head of the UK pEPR Scheme administrator. “This is the place to catch up with people, learn about the latest innovations, discover current trends, and even learn about future plans. You can see not only what’s currently on the shelves but also what will be on the shelves and what influences those behaviours.”
For exhibitors, the event provides access to thousands of targeted visitors, including CEOs, R&D leaders, procurement managers, and marketing professionals. On average, exhibitors generate over 86 leads per stand, benefiting from networking opportunities and VIP programs designed to foster connections with decision-makers across the FMCG and packaging sectors. A wide range of marketing tools allows exhibitors to raise their company profile and attract traffic to their stands.
The 2025 event will once again feature three dedicated zones, each spotlighting key growth areas in the packaging sector:
Food Service: Engage with the UK’s top food retailers and foodto-go outlets. Whether focusing on shelf life, sustainability, or recyclability, this zone is the gateway to opportunities in the fast-
growing food service sector.
Label & Print: Explore the machinery, software, and processes that drive packaging success. Ideal for suppliers of labels, corrugated, and flexible packaging, this zone connects exhibitors with brands seeking to invest in new technologies.
Smart Packaging: Showcase intelligent packaging innovations like NFC chips, RFID tags, and AR technologies, which offer interactive, futuristic experiences for customers and brands.
The Contract Pack & Fulfilment zone, powered by BCMPA, is the UK’s only dedicated event for outsourced packaging services. This area allows brand owners and retailers to discover trusted partners in co-packing, gift packing, and e-commerce fulfilment.
Emma Verkaik, CEO of the BCMPA, praised the Contract Pack & Fulfilment Zone, highlighting the success of previous shows: “BCMPA enjoys its relationship with Easyfairs in Contract Pack & Fulfilment. It is always a busy event, and our members continue to respond positively.”
The Future Trailblazer Awards return to honour the industry’s brightest visionaries driving creativity, Innovation, and sustainability in packaging.
The programme spotlights and rewards the industry’s most innovative and forward-thinking professionals who are reshaping its future. These include technologists, designers, print technicians, engineers and production operatives, sustainability managers and specialists, project managers, artwork coordinators, and production leaders, and those excelling in operational roles such as buyers, supply chain managers, logistics experts, and quality assurance professionals.
Organisers Easyfairs have announced that entry submissions for the 2025 awards are now open, free of charge, and will close on Sunday, November 10th, 2024, at 5 pm. The winners will be announced as part of the event’s stellar conference programme.
Building on the success of the inaugural Packaging Start-Up Awards, the 2025 edition, sponsored by Ocado, will spotlight groundbreaking start-ups in the packaging sector. Last year’s winners were Konvoy Group, Releaf Paper, and The Good Cup, demonstrating how fresh ideas can lead to significant industry advancements.
Additionally, the Innovation Gallery offers visitors a firsthand look at the future of packaging, from advanced materials to automated solutions.
“The reason I attend this show is to find new opportunities and see the latest innovations happening around the world,” said Muhammad Usman Zafar, Senior Procurement Manager – Global Packaging at PZ Cussons. “I always try to attend these exhibitions—I was at the one in London as well—because they provide a great way to understand where the world is heading, where suppliers focus, and whether it aligns with customer needs. Being in the FMCG industry, we are closely connected with consumers, but it’s also important to ensure that the upper or secondary industries think along the same lines.”
The 50+ speaker conference program at Packaging Innovations & Empack 2025 offers attendees expert insights into the latest trends, challenges, and innovations shaping the industry. Featuring thoughtprovoking presentations, case studies, and interactive discussions, the program covers key topics such as sustainability, smart packaging, and cutting-edge technologies. Best of all, access to this comprehensive educational content is free, providing a valuable opportunity for professionals to gain new perspectives and stay ahead in a rapidly evolving industry.
Don’t miss the chance to experience Packaging Innovations & Empack 2025 firsthand. Register for your free visitor pass to gain exclusive access to groundbreaking packaging innovations, industryleading brands, and the 50+ speaker conference program. This event offers an opportunity to connect with top decision-makers, explore the latest trends, and be inspired by the future of packaging.
Exhibiting at Packaging Innovations & Empack 2025 is about more than showcasing products—it’s about capturing qualified leads, connecting with industry leaders, and expanding market reach. With VIP programs and networking initiatives, exhibitors gain unparalleled access to decision-makers.
At Packaging Innovations & Empack 2025, exhibitors can engage with major brands like Aldi, Asda, Britvic, Boots, Cadbury, and Unilever. These industry leaders, representing sectors from food and beverage to personal care and e-commerce, underscore the event’s significance as a hub for networking, Innovation, and growth in the packaging industry.
Secure a stand today and be part of an event where the brightest minds in packaging come together to innovate, collaborate, and drive the future of packaging forward.
Food & Drink Network prides itself in providing the very latest industry news from the Food & Drink Industry, selected from 13 sector headings including Exhibitions, Packaging & Labelling, Beverages, Machinery, Food Science, Processing, Warehousing, Tranport and Logistics & more...
You can filter news from 13 sector headings including Exhibitions, Packaging & Labelling, Machinery, Ingredients & Product Development, Beverages, Food Science, Processing, Food Safety & Hygiene Warehousing, Tranport and Logistics & more...
When selecting from this box or the ‘Our Magazines’ tab at the top of the website you can read the latest magazine online for free via our e-book hosted by Issuu. You can also access the back catalogue of the ‘Food & Drink Network’ and ‘Industry Insight’ magazines
Visit our featured suppliers and customers via these interactive logos. Click the logos to visit their website and support them as industry experts within their field and to the Food & Drink Industry.
HpE Process supply industrial emulsifiers and blenders. These are key in material processing across a wide range of industries, including food, cosmetics, pharmaceuticals, and chemicals.
These devices are essential for processes that require the homogeneous mixing of two or more immiscible substances, achieving a uniform and stable emulsion.
It is important to highlight that they stand out for their innovative design and robust construction. They are equipped with sealing systems specific to each application, ensuring efficient and safe operation. The use of materials such as AISI 316L stainless steel in parts in contact with the product ensures high corrosion resistance and easy cleaning.
In the food industry, they are used to emulsify mayonnaises, sauces, and dressings. In the cosmetic and pharmaceutical industries, they are essential for the creation of creams, lotions, and medicinal emulsions.
Additionally, in the chemical industry, they facilitate the production of paints, varnishes, and other compounds.
Ampco’s Applied Products POWDER-max reduces processing time and provides optimal product consistency with no batch size limitations. An innovative design allows PM Powder Mixers to quickly blend wet and dry ingredients in a single, fully portable unit.
The POWDER-max combines Ampco’s SP Series liquid ring pump and the SBH Shear Blender in-line to facilitate limitless production runs.
The even flow of liquid created by the self-priming SP liquid ring pump, ensures product is mixed consistently from batch to batch. The SBH Shear Blender, runs at high speeds to continuously mix the fluid and powder providing a superior product.
The POWDER-max is CIP-able and is designed, assembled with cleanability being at the forefront.
The EML and EMLT models are innovative in-line emulsifiers designed to deliver exceptional performance in continuous mixing processes. These units are particularly well-suited for applications that require a constant and homogeneous integration of ingredients, which is essential in industries such as food and beverages.
Their efficiency lies in their ability to maintain a uniform and consistent mixture throughout the entire production process. This ensures that the quality and characteristics of the final product are uniform, a crucial factor in the production of food and beverages where consistency in taste, texture, and appearance is fundamental.
Furthermore, these in-line emulsifiers are distinguished by their flexibility and adaptability. They can handle a wide range of viscosities and types of ingredients, making them ideal for a variety of formulations, from juices and beverages to complex sauces and dressings. For further information visit hpeprocess.com
At Cross+Morse we aim to fulfil all industry demands, from the simplest to the highest level of precision required. Our objective is to offer a complete solution - not just products - to your power transmission challenges.
Cross+Morse are known in the industry as pioneers in quality standards, which is why we take our quality control processes very seriously. Quality assurance is central to our organisation with controls encompassing all aspects of design, manufacture, logistics and customer service. We are ISO 9001:2015 accredited and have been for over 30 years.
freewheels, roller ramp clutches, combined sprag and bearing units and many more.
At Cross+Morse we have continuously invested in top of the range measuring equipment: Co-ordinate Measuring Machine (CMM), digital tri-bore gauges and micrometers which are constantly calibrated to comply with ISO standards. Our stringent inspection process guarantees that when manufacturing each operation is thoroughly inspected by either a highly trained shop-floor staff supervisor or an inspector, ensuring that manufacturing is only allowed to continue when each phase has been approved. Our hardening treatment is checked using either our Rockwell or Vickers hardness testing machines.
We review our quality procedures continuously to provide up-to-date mechanisms for ensuring conformity to the quality system; different audits are carried out on all activities in the company throughout each year.
Cross+Morse is the largest authorised distributor and stockist for American transmission products manufactured by RegalRexnord (formerly EPT) in the United Kingdom. The range includes Sealmaster®, Browning®, Jaure®, Kop-Flex®, McGill® and Morse®.
Inverted tooth chain: including the standard SC type from 3/16” to 2” pitch and HV type from 3/8” to 2” pitch; as well as conveyor chains up to 12” width in centre or outside guide construction. We manufacture standard and special sprockets in-house for a complete drive solution.
We pride ourselves in offering a complete range of overload protection devices ranging from the simplest to the most accurate and precise overload clutch: Sheargard range of overload clutches, wedge pin type, available as a chain coupling and the option of low inertia rubber elastic couplings for higher speed drives. The Crossgard range, ball detent type, comes in 3 versions and also available with roller chain and low inertia rubber coupling option. The Safegard CS series, ball/roller detent type, comes in 2 two basic types (standard or mini) and also available as shaft couplings. Series CZ and CN zero backlash Safegard clutches for responsive overload protection, available in both basic and shaft coupling types.
We offer a wide stock range of flexible shaft couplings to accommodate different types of misalignment: Jaw couplings, elastomeric couplings, roller and Delrin® chain couplings, gear couplings GFA & GFAS, polymer gear couplings, Morflex elastomeric disc couplings and Crossflex disc couplings.
Our Crossbore® rework service includes reboring, keywaying and setscrewing of standard sprockets, pulleys and gears in a dedicated production area with specialised CNC machines for a rapid response. Induction hardening of teeth is also offered in-house.
Shaft clamping elements for precision transmission of torque with no backlash: a complete range from stock. Three ranges of locking devices available in corrosion resistant stainless steel.
Our range of Freewheel clutches for overrunning, indexing and backstopping applications; including sprag clutches, industrial ratchet
For further information contact:
Telephone: +44 (0) 121 360 0155
Email: sales@crossmorse.com or visit www.crossmorse.com
Fulton’s class-leading fuel-fired and electrically-powered steam boilers and portfolio of aftercare solutions can help with your decarbonisation strategy and put your company on the Road to Net Zero. As a complete solutions provider, Fulton can provide you with:
· fuel-fired and electric steam boilers
· off-grid and point-of-use solutions
· ancillary plant / engineered systems
· steam surveys
· project management
· water treatment contracts
· accredited / certified training
· installation / commissioning / upgrades
· repair / service / maintenance programmes
Want to know more? Scan the QR code, click www.fulton.co.uk, email sales@fulton.co.uk or call +44 (0)117 972 3322.
Fulton has introduced new, re-designed VSRTs (VSRT-100 and VSRT-125) with outputs of 1565 and 1956 kg/h. But what are the benefits of these two larger output models for end users?
As Fulton’s Carl Knight explains, these models are groundbreaking for their output range: models, there are no truly efficient tubeless vertical steam boilers in the marketplace with similar output ranges, the VSRT is the only tubeless boiler available with the capability of efficiently producing nearly two tonnes per hour of steam. In short, what we are delivering with these new models is much higher output versions without compromising efficiency!”
The new VSRT models maintain exceptionally high operating efficiencies (up to 86% gross thermal efficiency compared to approximately 80% from typical boiler designs), which results in lower operating and lifecycle costs and improved return on investment. In fact, using the lower-output VSRTs as an example, many of Fulton’s customers are achieving fuel savings of between 20% and 30%.
And Fulton fully expects the VSRT-100 and VSRT-125 to achieve the same savings because, like lower output models, the latest VSRTs boast the same impressively high 10:1 turndown capability and continue to achieve ultra-low NOX emissions of less than 20ppm or 40mg/Nm3 at 3% O2, which falls well below MCPD’s requirement of <100mg/Nm3. The VSRT also therefore complies with the stringent City of London Air Quality Strategy requirements.
These advanced, energy-saving and environmentally beneficial features are standard across the now expanded VSRT range. Compared to other steam boilers, the VSRT is also a more durable and, in many cases, compact boiler that is energyefficient, produces an increased output of higher quality steam and is easy to maintain.
So how do the new VSRTs compare to other steam raising solutions with similar outputs?
The new VSRTs are the only tubeless boilers available with the capability of efficiently producing nearly two tonnes per hour of steam. To achieve similar outputs, end users would have to consider horizontal shell and tube boilers or steam generators.
The water volume of the VSRT is equivalent to or greater than these alternatives yet, combined with an impressive steam chest volume, can
Introducing our new stainless steel barriers and bollards engineered for safety and durability in high-demand hygienic facilities.
Our range of barriers can be used to nudge staff through the changing room flow, reducing the chance of important steps being missed and preventing congestion.
These barriers and bollards can be stationed around expensive equipment and buildings to give added protection from costly mishaps.
Head to our website for great deals across our range of bollards and barriers so that you always get the best for your budget.
Order today for free delivery! Call now on +44 (0)1603 788 833, visit teknomek.co.uk or email mail@teknomek.co.uk
We have utilised over 30 years experience in the industrial cleaning sector to design and manufacture high performing cleaning equipment. Combine this with ease of use and British manufacturing and our cleaning apparatus is among the best available.
We believe in building products that find solutions to existing cleaning problems, improve ease of use and longevity of product life. Our commitment to quality has lead us to create the CHESS range of equipment which is fully interchangeable and is designed with you in mind. Parts can be integrated together to create a solution that is unique to your requirements.
• Established for over 30 years
• Our expert engineers design all products in-house and fully test them before adding our seal of approval for sale.
• The highest quality British manufacturing means your products have a much longer life than inferior imported equivalents.
• We continually evaluate, add, and develop our products so you can be totally satisfied that by using Central Hygiene, you are buying the best on the market.
From user-friendly analytical tools and intelligent operator prompting right through to AI-based concepts: Our digital services help you keep on top of complex processes and optimise both costs and output while also saving valuable resources.
krones.com
• On 1 July 2024, Krones Recycling GmbH, under the management of Dr Michael Gotsche, commenced business operations with headquarters in Flensburg.
From user-friendly analytical tools and intelligent operator right through to AI-based concepts: Our digital services on top of complex processes and optimise both costs
• The newly founded company takes over all activities relating to plastics recycling, but continues to utilise Krones’ global production, sales and service network.
• The Krones Recycling plays in achieving Krones’ sustainability goals.
The demand for recycled plastics is increasing rapidly worldwide: consumer awareness is growing, companies are setting themselves ever more ambitious sustainability targets and recycling requirements from international governments are also increasing. As a company with almost 30 years of experience in plastics processing and almost 25 years in the field of recycling, Krones has now taken the pioneering decision to pool its recycling expertise in the independent subsidiary Krones Re-cycling GmbH from July 2024.
A logical step, as Krones CEO Christoph Klenk explains:
“The spin-off will enable Krones Recycling to develop faster and in line with market requirements. Because in line with our claim Solutions beyond tomorrow, this division makes a decisive contribution to protecting the environment by returning plastic waste to the value-added cycle.”
In addition, thanks to leaner processes and structures, the new company will be able to respond more quickly to changes in the constantly changing recycling market, says Michael Gotsche, Managing Director of Krones Recycling GmbH:
“The newly founded company offers us the necessary flexibility and scope for action to be able to implement decisions in a customer-oriented, fast and optimised manner.”
For all its independence, however, the name Krones Recycling not only symbolises the focus on plant engineering in the field of recycling, it also reflects the close connection to the Krones Group.
“We know that our clients appreciate Krones’ overall line expertise, which means they get everything from a single source. They can continue to rely on this in the future. The worldwide sales and service network is also available to us without restriction,” Gotsche continues.
A large number of plastics such as PET, PE, PP and PS are already being processed on Krones Recycling’s lines worldwide.
“Our vision is to make a daily contribution to a global circular economy for all plastics by offering our customers sustainable and profitable recycling solutions,” says Michael Gotsche, describing the overarching business objective.
There is also a clear marker in relation to Krones’ sustainability targets: at least 30 per cent of the plastics processed on Krones lines are to be returned to the cycle as a recycled resource.
Consequently, Krones Recycling will continue to conduct intensive research into new innovations at its in-house Recycling Technology Centre. There, tests on the recyclability of various plastics, including adhesives and colours, can also be carried out under real conditions on behalf of customers.
For more information visit krones.com
• Materials & machinery for the complete solution
• Transit & display packaging
• Fully-recyclable, sustainable, anti-fog, barrier, MAP packaging and more...
• High-speed equipment for demanding environments
• Supported by expert engineers, across the UK & Ireland
DISCOVER THE RIGHT INGREDIENTS FOR FOOD PACKAGING SUCCESS.
Welcome to National Flexible’s New Technical Training Workshops, where innovation meets expertise!
If you’re ready to transform your packaging capabilities and lead with cutting-edge solutions, our workshop is for you. Designed to provide the latest knowledge and hands-on experience, our insights will help you excel in the fast-paced world of flexible packaging.
With constant changes in the industry, we’ve updated our workshops to ensure you receive the most relevant and up-to-date information. Join us to master the art and science of flexible packaging and stay ahead in this dynamic field.
Originally created for our team, our workshops have evolved to address an ever-changing industry where sustainability, efficiency, and consumer preferences lead the way.
Discover the latest advancements in packaging technologies and materials, and learn how to use these innovations to stay ahead and differentiate your products in a competitive market.
Engage in interactive sessions led by our experts, who will share their extensive knowledge and help solve your most pressing packaging challenges.
Our workshops cover a wide range of topics, including the latest in material science, packaging design, sustainability practices, and technological innovations.
Our workshops are perfect for anyone who is wanting to enhance their technical skills and stay updated on the latest industry trends. We help you to discover new materials and techniques to elevate your product designs.
If you are ready to transform your packaging knowledge and skills, don’t miss this opportunity to learn, grow, and lead with confidence. Book your spot in our Technical Training Workshops today and step into the future of packaging excellence. For more details or to book your place, reach out to us at 01274 685566 or marketing@nationalflexible.net
Here at National Flexible, we believe in empowering our people, clients and partners through knowledge and innovation. That’s why we are proud to introduce The New Academy!
An interactive presentation designed to elevate your understanding of packaging solutions and industry trends. Through a holistic view of the future of flexible packaging, we use our expertise to provide you with the tools and knowledge needed to protect and preserve products without causing harm to the environment.
Deep Dive into Packaging: Stay ahead of the curve by exploring ‘where we are now’ when it comes to packaging. From sustainable materials to looking at the future of packaging, our Academy covers it all, giving you the insights needed to make informed decisions.
Sustainability Focus: With a growing emphasis on ecofriendly solutions, our Academy provides in-depth knowledge on sustainable packaging practices. Learn how to implement environmentally responsible packaging that meets your business goals and aligns with global sustainability trends.
Interactive Experience: Engage in practical, interactive sessions and be in with the chance of winning prizes through our fun and informative quiz.
Networking Opportunities: Connect with like-minded professionals, industry leaders, and potential collaborators. The National Flexible Academy offers a platform to exchange ideas, build relationships, and foster collaboration within the packaging industry.
It’s FREE: Yes, that’s right, there is no charge for this service! We even throw in some refreshments & treats : )
So, why would we provide this for free?
Choosing the right packaging and avoiding greenwashing is essential for creating genuine environmental impact, maintaining regulatory compliance, building consumer trust and achieving sustainable business growth. Sharing our knowledge gives us the opportunity to answer any questions you may have to accomplish this.
It’s about us helping you to make a real difference rather than just appearing to do so. By prioritizing authentic sustainable practices, you enhance your brand’s credibility, operational efficiency and market competitiveness.
‘Caring, Sharing, Being Different’ are the values which shape our culture and by providing services, such as our Academy, we are able to share our expertise with you and your team, helping you to make informed decisions when it comes to selecting the best packaging for you and the planet.
“Really informative presentation, especially on the impact of plastic” - Amelia Lewis, Melton Foods.
“One of the most thought-provoking presentations I’ve been to” - Emma Heath, Nairns.
“Great presentation with good engaging content” - Elliot Morgan, Premier Foods.
“Very engaging. I particularly liked the ‘myths’ quiz” - Fran Holmes, Sleaford.
Contact us today to learn more about our upcoming sessions and secure your spot! 01274 685566 marketing@nationalflexible.net www.nationalflexible.co.uk
Food packaging and labelling is evolving rapidly, driven by the need for solutions that prioritise sustainability, efficiency, and consumer engagement. As awareness of environmental issues increases, so too does the demand for packaging that balances functionality with eco-friendliness. This shift is prompting manufacturers to explore innovative materials and technologies, ensuring that their products meet the expectations of today’s conscientious consumers.
Introducing Datamark’s latest machine, the Proflex 250 manufactured by Focus from Nottingham. This cutting-edge machine offers unparalleled capabilities, featuring up to 6-colour UV flexo printing, cold-foil blocking, over-laminating, reverse printing, and sheeting. For Datamark, renowned for its expertise in plain label converting, this investment marks a transformative leap in print quality, surpassing their previous 4-colour capabilities.
Among the most significant advancements in this arena is the rise of flexible packaging. This versatile option offers a lightweight and efficient alternative to traditional rigid packaging, often crafted from durable composite materials. By reducing waste and minimising transportation costs through its decreased weight, flexible packaging not only optimises production but also aligns with broader goals to lower the environmental impact of the packaging industry.
The emphasis on sustainability is becoming increasingly critical. Many companies are now turning to eco-friendly materials, such as biodegradable plastics and recycled content, as they strive to create packaging solutions that fit seamlessly into a circular economy. This approach not only reduces landfill waste but also appeals to consumers who are more environmentally conscious than ever. Additionally, sustainability extends to labelling practices, with brands increasingly opting for eco-friendly inks and adhesives. This ensures that every aspect of their packaging reflects a commitment to environmental stewardship.
Consumer safety and hygiene are also paramount considerations in food packaging. With an increasing number of hygiene-conscious shoppers, manufacturers are adopting advanced technologies such as Modified Atmosphere Packaging (MAP) and Vacuum Packaging (VAP). These methods create environments that significantly slow down spoilage and help maintain product freshness, directly addressing consumer demands for quality and safety.
Labelling is another integral component of this transformation. Modern labels serve not only to identify products but also as vital communication tools. As consumers grow more health-conscious, the need for clear, informative labelling becomes essential. Brands are embracing transparency by detailing ingredient sources, nutritional information, and sustainability credentials, which fosters trust and encourages informed purchasing decisions. Moreover, the incorporation of interactive features such as QR codes enables consumers to engage with brands more deeply, providing insights into production practices and sustainability efforts.
With the growing preference for convenience, ready-to-eat meals and meal kits have surged in popularity. Packaging solutions for these products must ensure freshness while also facilitating ease of use. This highlights the importance of innovation in meeting evolving consumer needs. By integrating attractive designs, informative labelling, and user-friendly formats, brands enhance the appeal and marketability of their products.
With over £500,000 invested in the past year, including a new mezzanine floor, modern offices, and expanded factory space, Datamark is poised for even greater advancements in label technology. Embrace excellence with Datamark and redefine your label expectations today.
As the food packaging and labelling industry continues to adapt, the commitment to environmentally friendly practices and consumercentric design is crucial. Flexible packaging emerges as a key player in this transformation, offering a sustainable alternative to traditional methods. The future of packaging lies in its ability to balance these priorities, ensuring that it meets both current and emerging needs in an increasingly dynamic marketplace.
The food and drink industry, a cornerstone of the global economy, is increasingly prioritising sustainable practices to minimise environmental impact while enhancing operational efficiency.
A notable advancement in this pursuit is the integration of Ecofill technology with benchtop autoclaves, particularly exemplified by the AMB benchtop autoclave equipped with Ecofill. This development signifies a substantial leap towards eco-friendly and cost-effective sterilisation processes within the sector.
At the core of this innovation is the Ecofill system, a sophisticated solution designed to capture and reuse both water and heat energy. Traditional autoclaves often consume significant amounts of water and energy during sterilisation, leading to elevated operational costs and added strain on the environment. By implementing the Ecofill system, these challenges are effectively
addressed, allowing for the recycling of water and heat, which drastically reduces waste and energy consumption.
When combined with the AMB benchtop autoclave, the Ecofill system creates a formidable combination of efficiency and sustainability. The design of this autoclave minimises the frequency of refilling due to the Ecofill’s water recycling capabilities. This not only conserves water but also reduces the labour and downtime typically associated with the refilling process, enhancing overall productivity.
The heat recovery feature of Ecofill further underscores its importance in promoting energy efficiency. By capturing and reusing heat generated during sterilisation cycles, the AMB benchtop autoclave with Ecofill can operate at lower electrical energy levels. This results in reduced energy bills and a smaller carbon footprint, aligning seamlessly with the food and drink industry’s growing commitment to environmental stewardship.
The economic advantages of employing the AMB benchtop autoclave with Ecofill are substantial. Lower water and electricity usage directly translate into reduced operational costs, enabling businesses to experience noticeable decreases in utility bills. This aspect is particularly beneficial in a competitive market, as improved profitability can be a decisive factor for many enterprises.
From an environmental standpoint, the diminished consumption of vital resources signifies a significant reduction in the industry’s ecological footprint. By adopting this innovative technology, businesses in the food and drink sector not only enhance their operational efficiency but also actively participate in global initiatives aimed at combatting climate change and promoting sustainable resource management.
The integration of Ecofill technology with autoclaves such as the AMB benchtop model represents more than just an advancement in sterilisation; it showcases the potential for the food and drink industry to lead in sustainable practices. As businesses increasingly seek out environmentally friendly and cost-effective solutions, technologies like Ecofill are poised to play a crucial role in shaping a more sustainable future.
The adoption of the AMB benchtop autoclave with Ecofill signifies a meaningful step forward in the food and drink industry’s commitment to sustainability. By capturing and reusing water and heat energy, this innovative technology not only improves operational efficiency but also reflects the sector’s dedication to environmental responsibility and economic viability. As its implementation expands, it sets a valuable precedent for other industries, signalling a new era of eco-conscious industrial practices.
Recent discussions at the 22nd IUFoST World Congress in Rimini, Italy have shed new light on the often-complex relationship between dietary fats, human health, and sustainability. Amid widespread concerns about the link between saturated fats and heart disease, experts are challenging oversimplified narratives.
Prof. Francesco Visioli from the University of Padova presented a sophisticated view on saturated fats, emphasising that their health impacts are not uniform. While foods such as palm oil, coconut oil, butter (dairy) and animal fats are frequently criticised for raising cholesterol and increasing cardiovascular disease (CVD) risk, Prof. Visioli highlighted that the effects of these fats vary based on their source—be it meat, dairy, or plants. A meta-analysis incorporating data from the Global Burden of Disease Study reveals that the influence of saturated fats differs across various populations and regions.
The overall impact on cardiovascular health is influenced by multiple factors, including overall lifestyles, dietary habits, other nutrients, and fat processing methods. The presentation underscored that trans fats, rather than saturated fats, are a more significant contributor to poor heart health. Prof. Visioli advocates for precision nutrition— tailoring dietary advice to individual responses to fats to optimise health outcomes—calling for a shift away from generalised warnings against saturated fats.
In a related discussion, Dr. Roger Clemens from the University of Southern California, Dr. Peter Pressman from the University of Maine and Dr. Walles Hayes from the University of South Florida addressed concerns about palmitic acid, a fatty acid prevalent in both the human body and vegetable oils, including palm oil. They challenged claims linking palm oil’s high palmitic acid content to cancer, arguing that there is no credible evidence supporting such conclusions.
Palmitic acid constitutes 20-30% of the fatty acids in the human body and is a major component of human milk and infant fat
stores. Although palm oil contains the highest concentration of palmitic acid at 44%, the presenters clarified that dietary palmitic acid does not significantly influence its production in the body, nor is it a central factor in cancer development. They critiqued studies linking palm oil to cancer for their reliance on unrealistic levels of palmitic acid and failure to account for cancer’s complexity. The experts called for more rigorous, human-centred research to better understand palmitic acid’s role in cancer.
Dr. David Ross Appleton from SD Guthrie Berhad, one of Malaysia’s leading palm oil producers, highlighted the critical role of palm oil in food security. He cautioned that shifting to less efficient oil sources could worsen environmental damage by necessitating more land, potentially leading to deforestation and biodiversity loss. He stressed the importance of sustainability certification scheme, such as the Malaysian Sustainable Palm Oil certification (MSPO) developed by Malaysia, to ensure responsible palm oil production.
Sustainable palm oil, as highlighted by Dr. Appleton, is produced without deforestation or peat exploitation and includes a strong commitment to community development and transparency. SD Guthrie aims to achieve net-zero greenhouse gas emissions by 2050 and implement circular economy practices to address waste. He also emphasised the need for improved worker conditions, including better living standards, ethical recruitment, and transparent wage practices. Strategies for enhancing food safety and quality through optimised harvesting, minimised handling, and advanced processing techniques were also discussed.
The insights from the 22nd IUFoST 2024 World Congress highlight the need for a nuanced and whole food approach to dietary fats, as well as a commitment to sustainable practices in palm oil production, ensuring a healthier and more sustainable future.
PHS are a market leading provider of end of line automation, which includes the following technologies from our Italian and Dutch suppliers:
• Cobot palletisers, Industrial robots or layer palletising / de palletising
• Pallet stretch wrapping machines
• Pallet strapping machines
• Case packers
• Shrink packers
• Automated warehouse solutions
• AGV / LGV automatic guided vehicles
• Case and pallet conveying systems
Our strength has been gained over a 35 year period providing complete ‘Turnkey’ solutions to the food and beverage industries in particular. We have many UK references within major ‘Blue Chip’ producers, many of which can be viewed if required. Having such a large data base of customers, means that we have a robust and efficient after sales support service. Over the years we have developed new technologies with our partners to keep ahead of ever changing market requirements, meaning that we are often top of our game in terms of having the latest technology at our finger tips.
Some of our latest developments include, a Fanuc Cobot capable of handling up to 25kg, this is the only Cobot on the market with a 7 year warranty, its predecessors being industrial robots of which we have supplied many. They are incredibly reliable with immense accuracy and repeatability. The base of the unit is made from stainless steel, so ideal for the food sector, often it includes for a fork type gripper to be able to handle any type of pack, whether it be open trays, full cases, or SRP delicate products. There is an option for a layer sheet placer also.
Another development by our Italian supplier Tosa S.P.A. is ‘Smart Wrap’ technology which utilises the minimum film usage by adjusting its pre stretch anywhere on the load. This is a great feature for delicate products, ensuring that the tension and pre stretch does not compromise load stability or create damage to the goods. Also these days most of our 300+ machines in the UK are using 30% re cycled film, meaning that they are saving the planet to some extent and saving customers having to pay government waste taxation.
To find our more about PHS and our large range of products, then please go to our web site as follows, we are looking forward to being of service to your business.
Given the escalating cost of land, it is essential for companies to maximize their existing warehouse space when considering expanding their business. Maximising the use of the current warehouse space is especially important for cold storage. In addition to the extremely high costs of constructing a new facility, refrigerating a larger area results in further energy expenses.
Thermo King’s commitment to innovation and decarbonising the cold chain is unwavering. Increasing investment in research and development has enabled the company to provide fully qualified electric solutions across all transport segments, positioning Thermo King, a brand of Trane Technologies –(NYSE:TT), a global climate innovator - as an industry leader.
“It is clear that electrification is no longer a future concept; it is our present reality,” said Claudio Zanframundo, president Thermo King EMEA Truck, Trailer, Bus and Global Marine, Rail and Air. “Our investments in electrification, hybridisation and digitalisation propel the transformation of the cold chain, setting new benchmarks for efficiency and sustainability. We are leading the change with solutions that meet the dual demands of environmental responsibility and operational excellence. This vision fuels our innovation delivering exceptional value to our customers and the planet.”
At the IAA Transportation 2024 exhibition held in Germany in September, Thermo King unveiled a new lineup of electric refrigeration solutions designed to accelerate the industry’s shift towards electrification while supporting businesses in their transition to low-carbon operations.
The reveal included new models in the E-Series electric transport refrigeration unit portfolio for vans and small to large trucks, as well as the electric Advancer-e Spectrum multi-temperature trailer refrigeration unit. Thermo King also showcased digital and power management solutions designed to enhance performance, including the Thermo King AxlePower energy recovery and management system, Energ-e and E-COOLPAC battery solutions.
Thermo King’s electric Advancer A-500e powered by AxlePower was recognized with the prestigious International Trailer Award 2025 in the Environment category. Additionally, Thermo King won the ETM Awards Best Brand category with its Transport Management Systems with ThermoKare 24/7 Fleet Monitoring and received second place in the same category for its Trailer Refrigeration with A-500 Spectrum.
Alongside its latest electric and hybrid-electric innovations, Thermo King showcased advancements in its existing solutions. These innovations reflect Thermo King’s commitment to offer a strong business case for customers at any stage of their sustainability journey, with efficient, reliable, connected and environmentally friendly products also compatible with alternative fuel options like HVO and B100.
The new lineup is the latest examples of Thermo King’s long-standing commitment to develop innovative transport refrigeration solutions that reduce carbon emissions and waste of food and pharmaceutical products in the cold chain. Solutions like these are helping Trane Technologies make significant progress toward its bold 2030 Sustainability Commitments, including the Gigaton Challenge, and its 2050 net-zero carbon emissions target. The company is first in its industry with near and long-term emissions reduction targets externally validated by the Science Based Targets initiative (SBTi)
In a new packaging development partnership, SN Maschinenbau and Südpack have developed an overall concept for the in-house production of stand-up pouches with spouts, which is designed for the packaging of paste and liquid products. The concept is aimed at food manufacturers and bottlers who previously use premade spout bags and will be presented at Anuga FoodTec 2024.
makes handling much easier and allows staff to process a larger number of pouches more efficiently, for example because there is no need for timeconsuming separation of the rails. The low-maintenance machine works highly efficiently and, thanks to its compact design, can also be used in production environments with limited available floorspace. This means it can be set up flexibly either directly on the filling machine
For more information contact