
18 minute read
Alessandro Merlino, Luciano Corbetta con Giovanni Mauri
TECNOLOGIE
NEL CUORE DELL’INDUSTRIA
Advertisement
LE CATENE PORTACAVO COME ELEMENTO INDISPENSABILE NELL’INDUSTRIA: L’ESEMPIO DI BREVETTI STANDALTO.
Dopo la tavola rotonda pubblicata sul numero di Sistema Serramento che ha visto protagonisti i referenti di Working Process, il leader tecnologico nel campo degli impianti e delle linee per la produzione di serramenti e i responsabili commerciali di Brevetti Stendalto, il marchio di riferimento nel campo delle catene portacavi, abbiamo pensato che fosse di interesse per i nostri lettori una visita presso le due unità produttive di Monza e di Mesero dell’industria e abbiamo incontrato nella prima delle due Alessandro Merlino e Luciano Corbetta, con Giovanni Mauri, fondatore dell’azienda che ci hanno dedicato cortesemente un po’ del loro tempo. SONIA MARITAN – Come è nata questa realtà? GIOVANNI MAURI – Questa azienda è nata con il nome Brevetti Stendalto, proprio perché originariamente produceva stendibiancheria. Quarantacinque anni fa nel 1976 c’era una piccola azienda che produceva questo tipo di casalingo, dunque tutt’altro dalle catene portacavo. Sono partito dalla cantina, dalla cantina siamo passati al garage, mentre contemporaneamente a 24 anni ero all’ufficio tecnico della San Rocco di Monza, nel tempo libero ho cominciato a disegnare. I primi anni sono stati duri. Allora si cominciava a vedere l’inizio dell’automazione. Alla metà degli anni Settanta, I cavi delle automazioni, sempre più diffuse, andavano sostenuti; esistevano già delle catene in acciaio, io invece ho pensato di realizzarle in nylon. Ho lasciato, visto il successo, la San Rocco di Monza e mi sono organizzato con gli agenti, con i cataloghi, con la produzione, poi sono passato a un capannone di 1250 metri quadrati, oggi siamo passati a 14mila metri quadrati, poi abbiamo i 3500 metri quadrati di Mesero dove si produce il componente base. Abbiamo fatto un salto nell’automazione via via fino ad avere venti linee automatiche che girano 24 ore al giorno per produrre 300 metri al giorno, abbiamo dovuto addirittura costruire stampi doppi per far fronte agli ordini, questo è iniziato una decina di anni fa. Oggi spaziamo a 360 gradi dal mobile d’arredamento alle macchinette del vending,
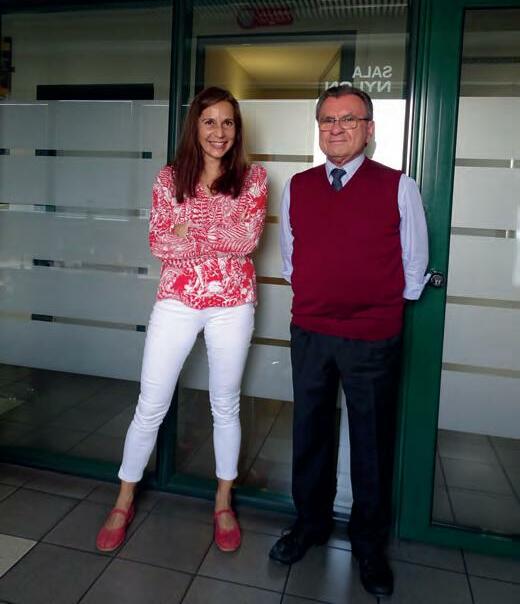
A destra: il top management famigliare della Brevetti Stendalto, Giovanni Mauro con i figli Claudio e Laura.
Noi siamo partiti con “due catenelle” e oggi abbiamo un catalogo di 5500 articoli di base senza pensare alle varianti. I nostri colori, il giallo con il nero, sono diventati il logo dell’azienda. Valorizzando questa integrazione si riescono a progettare composizioni altamente personalizzabili che rispondono a diverse funzioni e necessità.
Diventa quindi cruciale il ruolo del progettista che deve essere bravo a sfruttare al meglio questa libertà di integrazione che rende il nostro prodotto anche complesso.
Da ultimo, ma non meno importante, questa personalizzazione è permessa anche dal fatto che il nostro prodotto lascia personalizzabili anche le lavorazioni sul singolo pannello.
Per questo motivo è diventato necessario impostare la produzione con al centro la personalizzazione e quindi investire su una macchina nesting, abolendo di fatto il magazzino con i pannelli di serie.
PIETRO FERRARI – Le catene metalliche che pro-
blemi presentavano?
GIOVANNI MAURI – Soprattutto il peso, perché l’acciaio, ovviamente era molto pesante. Con tutto ciò produciamo anche noi catene in acciaio però in percentuale minore rispetto al nylon che ha una grande leggerezza e versatilità. Oggi la catena in nylon copre l’85 per cento del mercato, mentre utilizzano catene in acciaio le macchine che svolgono compiti pesanti, per esempio nel settore petrolifero o nelle acciaierie. PIETRO FERRARI – Voi con la varietà di utilizzi che
proponete non siete soggetti a crisi di settore?
GIOVANNI MAURI – No, perché se non è trainante un settore ce n’è un altro che funziona.
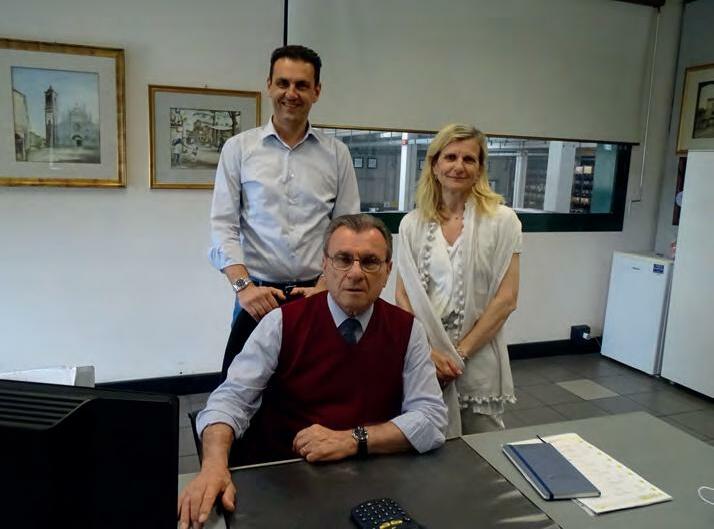
CABLE CHAINS AS AN INDISPENSABLE ELEMENT IN INDUSTRY: THE EXAMPLE OF BREVETTI STANDALTO
■■ After the round table published in the issue of Sistema Serramento which saw as protagonists the representatives of Working Process, the technological leader in the field of systems and lines for the production of doors and windows and the commercial managers of Brevetti Stendalto, the reference brand in the field of chains cable holder, we thought it would be of interest to our readers a visit to the two production units of Monza and Mesero of the industry and we met in the first of the two Alessandro Merlino and Luciano Corbetta, with Giovanni Mauri, founder of the company who they kindly took some of their time SONIA MARITAN – How did this reality come about? GIOVANNI MAURI – This company was born with the name Brevetti Stendalto, precisely because it originally produced clothesline. Forty-five years ago, in 1976, there was a small company that produced this type of household, therefore quite different from cable chains. I started from the cellar, from the cellar we moved on to the garage, while at the same time I was 24 in the technical office of the San Rocco in Monza, in my free time I started drawing. The first few years were tough. Then we began to see the beginning of automation. In the mid-seventies, automation cables, increasingly widespread, needed to be supported; steel chains already existed, but I thought of making them in nylon. I left, seeing the success, the San Rocco in Monza and I organized myself with the agents, with the catalogs, with the production, then I moved on to a shed of 1250 square meters, today we have gone to 14 thousand square meters, then we have the 3500 square meters of Mesero where the basic component is produced. We took a leap in automation gradually until we had twenty automatic lines that run 24 hours a day to produce 300 meters a day, we even had to build double molds to meet orders, this started about ten years ago. Today we range at 360 degrees from furniture to vending machines. We started with "two chains" and today we have a catalog of 5,500 basic items without thinking about the variants. Our colors, yellow with black, have become the company logo.
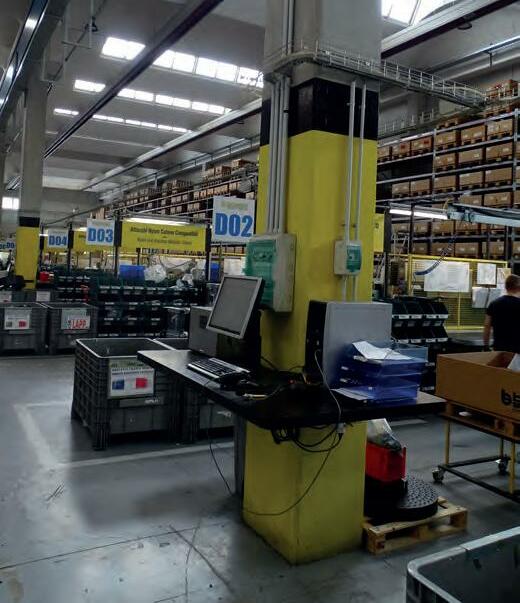
SONIA MARITAN – Voi avete da subito aperto filiali
di rappresentanza in tutt’Italia, e all’estero?
GIOVANNI MAURI – All’estero sono stati i nostri competitor a cercarci, pensiamo alla Cavotec che si occupava della connessione tra macchinario fisso aemacchinario mobile, un’azienda che ha conosciuto una crescita straordinaria con un riflesso sul proprio valore azionario, che ha poi portato a un grande valore quel dieci per cento che avevamo acquisito. Nel frattempo ci siamo consolidati qui a Monza, dove abbiamo assunto un management importante e abbiamo creato sei filiali in tutto il mondo. ALESSANDRO MERLINO – È importante sottolineare che tutto viene prodotto di base a Mesero e da qui a Monza viene assemblato e distribuito un prodotto uguale in tutto il mondo. GIOVANNI MAURI – Elemento fondamentale è lo stampo per il prodotto che deve essere programmato mesi e mesi prima. SONIA MARITAN – Come fate a mantenere riserva-
to il nostro know-how?
GIOVANNI MAURI – Qualcuno ha tentato di copiarci ma oggi per avere il nostro grande parco di stampi servono degli investimenti ormai insostenibili. ALESSANDRO MERLINO – Partire oggi è impossibile. I nostri concorrenti sono tedeschi, per quanto siano grandi non sono in grado di offrire prodotti speciali, come si è visto nel caso Working Process. GIOVANNI MAURI – La mancanza o la speculazione sulla materia prima oggi è un grande problema. Oggi ci stiamo riprendendo dopo la pandemia, con dei ritmi straordinari, grazie anche alla legislazione 4.0. SONIA MARITAN – C’è una seconda generazione? GIOVANNI MAURI – Ci sono due figli, Claudio si occupa delle vendite e dei programmi interni, Laura di contabilità, poi ci sono cinque nipoti, stanno studiando, e sono benvenuti in azienda.
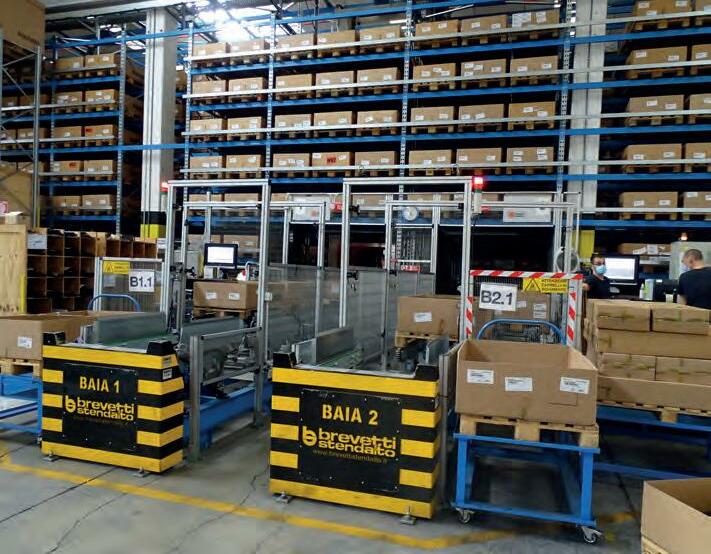
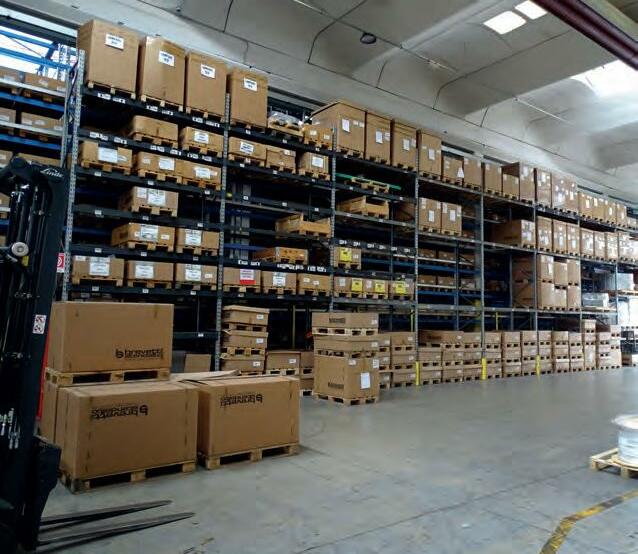
PIETRO FERRARI – What problems did the metal chains
present?
GIOVANNI MAURI – Above all the weight, because the steel was obviously very heavy. With all this we also produce steel chains but in a lower percentage than nylon which has great lightness and versatility. Today the nylon chain covers 85 percent of the market, while the machines that perform heavy tasks, for example in the oil sector or steel mills, use steel chains. PIETRO FERRARI – With the variety of uses you propose,
are you not subject to sector crises?
GIOVANNI MAURI – No, because if one sector is not driving, there is another that works. SONIA MARITAN – Have you immediately opened
representative branches throughout Italy, and abroad?
GIOVANNI MAURI – Our competitors were looking for us abroad, think of Cavotec which dealt with the connection between fixed and mobile machinery, a company that has experienced extraordinary growth with a reflection on its share value, which then led to a great value that ten per cent we had acquired. In the meantime we have consolidated here in Monza, where we have hired an important management and have created six branches all over the world. ALESSANDRO MERLINO – It is important to emphasize that everything is produced based in Mesero and from here in Monza an identical product is assembled and distributed all over the world. GIOVANNI MAURI – A fundamental element is the mold for the product which must be programmed months and months in advance. SONIA MARITAN – How do you keep our know-how
confidential?
GIOVANNI MAURI – Someone tried to copy us but today to have our large fleet of molds we need unsustainable investments.
ALESSANDRO MERLINO – Leaving today is impossible.
Our competitors are German, however large they are they are not able to offer special products, as seen in the Working Process case.
GIOVANNI MAURI – The lack or speculation on the raw material today is a big problem. Today we are recovering after the pandemic, at an extraordinary pace, thanks also to the 4.0 legislation.
SONIA MARITAN – Is there a second generation?
GIOVANNI MAURI – There are two children, Claudio is in charge of sales and internal programs, Laura is in charge of accounting, then there are five grandchildren, they are studying, and they are welcome in the company.
SONIA MARITAN – How would you like this company
in the future?
GIOVANNI MAURI – It is difficult to make a prediction today, it may be that the energy chains will disappear but it will take a long time to no longer need them, especially when the powers involved are high.
LUCIANO CORBETTA – The chain is a protection: on the signal the sensors will make them less necessary, the power or the fluids will always need an energy chain. The whole world of wireless is important, but the cost benefit is still in favor of cabling. We can also make sure that the chain becomes a more active element, with diagnostic signals and predictive functioning, such work we recently did on a

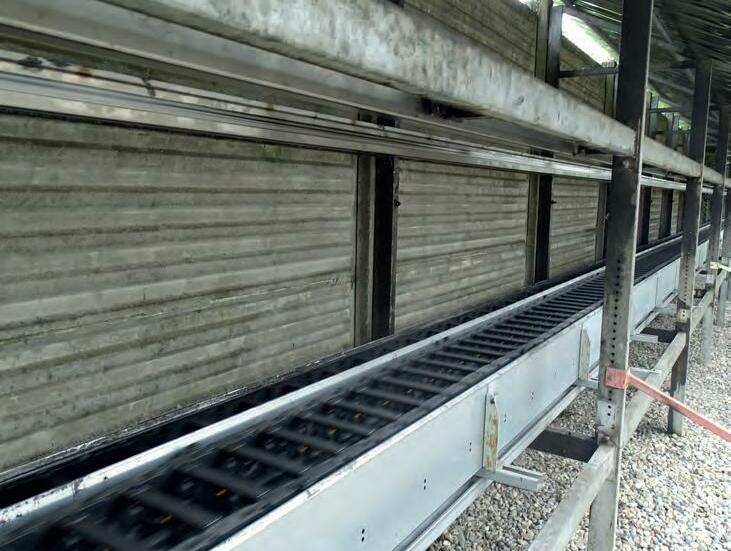
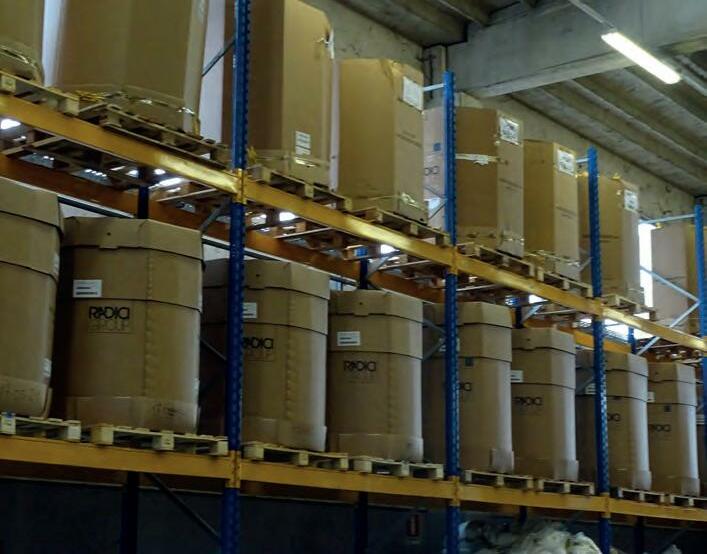
SONIA MARITAN – Lei come la vorrebbe in futuro
quest’azienda?
GIOVANNI MAURI – È difficile fare una previsione oggi, può darsi che le catene portacavi spariscano ma ci vorrà ancora molto tempo per non averne più bisogno, soprattutto quando le potenze in gioco sono alte. LUCIANO CORBETTA – La catena è una protezione: sul segnale la sensoristica le renderà meno necessarie, la potenza o i fluidi avranno sempre bisogno di catena portacavi. Tutto il mondo del wireless è importante, ma il beneficio costi è tutt’ora a favore della cablatura.Noi possiamo anche fare in modo che la catena diventi un elemento più attivo, con segnali di diagnostica e predittività del funzionamento, un lavoro del genere l’abbiamo fatto recentemente su un carro ponte di Fincantieri. Prevenire i fermi macchina e i guasti e proporci al cliente come partner di sistemi e consulenti , come devono essere i nostri venditori, è la chiave del successo in futuro. NEL CUORE DELL’ASSEMBLAGGIO E DELLA LOGISTICA
Nella sede di Monza – che visitiamo – si trovano i reparti in cui si creano i confezionamenti: tutto viene stoccato in magazzino, dai magazzini automatici partono le catene che vanno nelle filiali o presso gli assemblatori anche in Italia o per quei clienti che acquistano gli spezzoni e poi li montano a seconda delle loro esigenze. Oppure si assemblano qui le catene a seconda dell’ordine che vanno poi direttamente al cliente.. Qui c’è il reparto acciaio, il reparto nylon, il reparto Total Chain. «La Total Chain – ci spiega Alessandro Merlino che ci
Nella foto in alto a sinistra: la materia prima stoccata a Mesero. Nella foto in alto a destra: il prezioso patrimonio degli stampi. Nella foto a destra: i reparti di produzione.
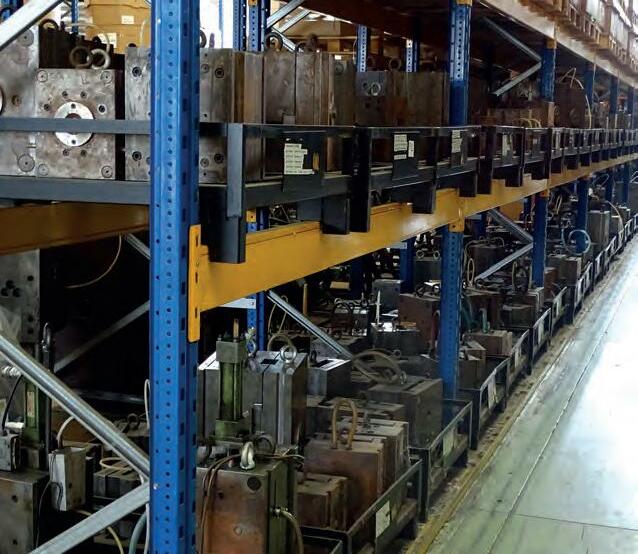
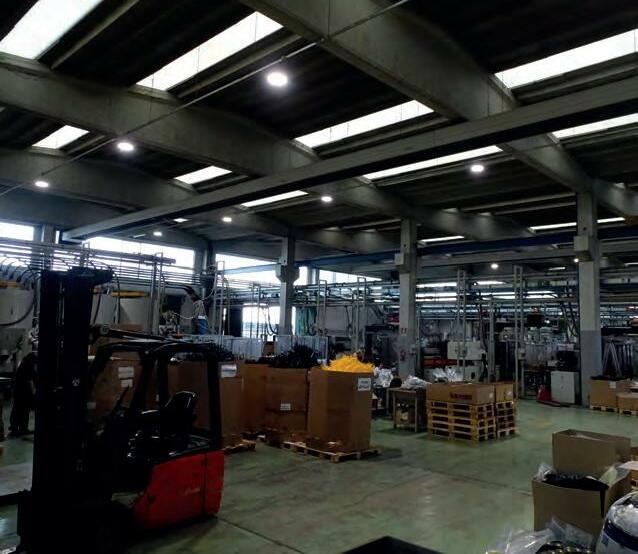
Fincantieri bridge crane. Preventing downtime and breakdowns and proposing ourselves to the customer as a systems partner and consultant, as our salespeople should be, is the key to success in the future. IN THE HEART OF ASSEMBLY AND LOGISTICS
In the Monza headquarters – which we visit – there are the departments where the packaging is created: everything is stored in the warehouse, the chains depart from the automatic warehouses that go to the branches or to the assemblers also in Italy or for those customers who buy the pieces and then they mount them according to their needs.
Or the chains are assembled here according to the order and then go directly to the customer ..
Here is the steel department, the nylon department, the Total Chain department "The Total Chain – explains Alessandro Merlino who accompanies us on the visit – is a turnkey or plug & play system to put it in English, so what arrives is a unique code, an integrated system that reaches the customer today and tomorrow this last can mount it in the car. In this way the customer has a single interlocutor, with a reduction of indirect costs, through a single order with a single code from Brevetti Stendalto and with consequent direct response in the event of problems, without any reimbursement of responsibility. The components are tested and approved in each component before leaving the Stendalto factory, also avoiding the production of waste. A product-system that meets more and more response on the market.
FROM RAW MATERIAL TO SEMI-FINISHED PRODUCT
After the visit to the Monza headquarters, we go to Mesero where the basic production of the components of the energy chains is based, starting from the nylon granulate. Here we are guided, with Alessandro Merlino, Andrea Picciroli, one of the two production managers. SONIA MARITAN – How do you organize the production
layout of these articles?
ANDREA PICCIROLI – We are the production unit of Brevetti Stendalto in the plastic sector but the production specifications come from the Monza technical office on the basis of the commercial specifications requested by customers which are organized by Alberto Bosoni and myself. Once arrived, the information is processed according to these specifications whether it requires the use of a steel mold or a thermoplastic mold. SONIA MARITAN – Does the mold have a fundamental
function?
ANDREA PICCIROLI – Every single mold requires the utmost care to guarantee the physical and mechanical characteristics of the chain, it is a technical product that must have precise specifications to work in dirty and humid environments and is subjected to very strong tensions and accelerations and often must accommodate cables heavy, without absorbing excess water. ALESSANDRO MERLINO – I like to say that inside those caissons there is a raw material consisting of nylon granules, we start from scratch and it is important to emphasize that the mold, which is the fundamental element, we manufacture it directly. There is also a steel part, but in this case, we don't produce the steel, there are specific companies that manufacture the steel links that we are then able to assemble. PIETRO FERRARI – You have a com-
plete cycle also from the maintenance point of view...
ANDREA PICCIROLI – Having an internal tool shop allows us to give an immediate response even to very particular customer requests: we are the boutique of the chain.We have those who know how to print, those who know how to design, who can make the mold and everyone makes a mutual contribution between the various departments. Above all we are able to work or optimize the drawings that are sent to us from Monza.
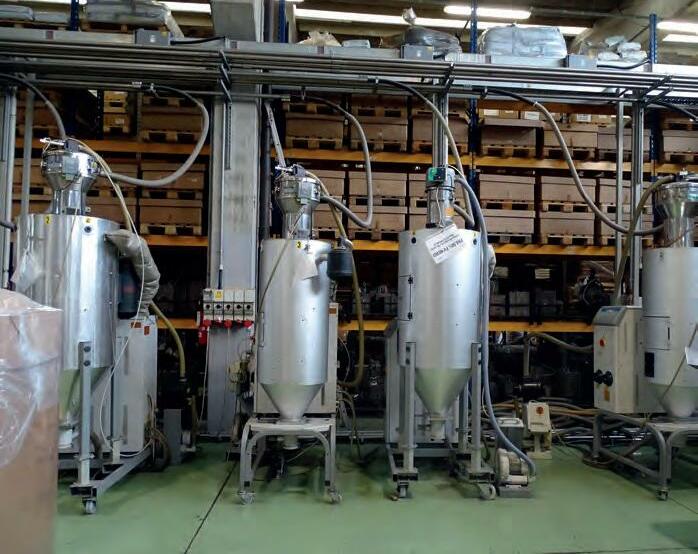
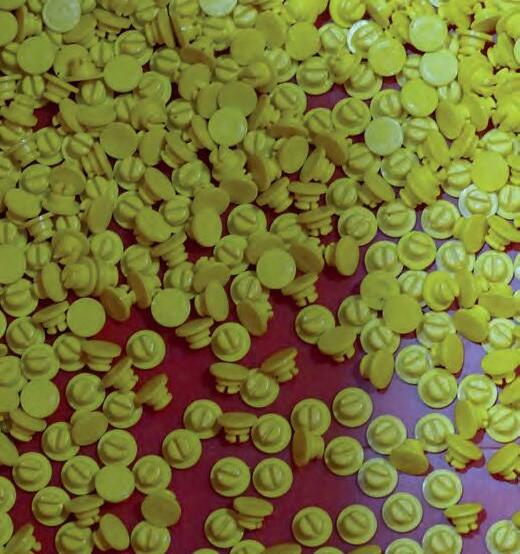
accompagna nella visita – è un sistema chiavi in mano o plug&play per dirla in lingua inglese, per cui quello che arriva è un codice univoco, un sistema integrato che arriva oggi al cliente e domani quest’ultimo può montarlo in macchina. In questo modo il cliente ha un unico interlocutore, con abbattimento dei costi indiretti, attraverso un unico ordine con un unico codice alla Brevetti Stendalto e con conseguente risposta diretta in caso di inconvenienti, senza nessun rimpallo di responsabilità. I componenti sono testati e approvati in ogni componente prima di uscire dallo stabilimento Stendalto, evitando anche la produzione di scarti. Un prodottosistema che incontra sempre più risposta sul mercato».
DALLA MATERIA PRIMA AL SEMILAVORATO
Dopo la visita al quartier generale di Monza, ci portiamo a Mesero dove ha sede la produzione di base dei componenti delle catene portacavi partendo dal granulato di nylon. Qui ci fa da guida, con Alessandro Merlino, Andrea Picciroli, uno dei due responsabili della produzione. SONIA MARITAN – Come si organizza il layout pro-
duttivo di questi articoli?
ANDREA PICCIROLI – Noi siamo l’unità produttiva della Brevetti Stendalto nel settore plastica ma le specifiche produttive arrivano dall’ufficio tecnico di Monza sulla base a loro volta delle specifiche commerciali richieste dalla clientela che vengono organizzate da Alberto Bosoni e da me.
Dettagli di precisione assoluta.
Una volta arrivate, le informazioni vengono elaborate in base a queste specifiche sia che richiedano l’utilizzo di uno stampo di acciaio o di uno stampo termoplastico. SONIA MARITAN – Lo stampo ha una funzione fon-
damentale?
ANDREA PICCIROLI – Ogni singolo stampo richiede la massima cura per garantire le caratteristiche fisiche e meccaniche della catena, è un prodotto tecnico che deve avere specifiche precise per lavorare in ambienti sporchi e umidi ed è sottoposto a tensioni e ad accelerazioni fortissimi e spesso deve ospitare cavi pesanti, senza per di più assorbire acqua in eccesso. ALESSANDRO MERLINO – Mi piace dire che dentro quei cassoni c’è una materia prima costituita da granuli di nylon, si parte da zero ed è importante sottolineare che lo stampo, che è l’elemento fondamentale, lo fabbrichiamo direttamente noi. C’è anche una parte acciaio, ma in questo caso, l’acciaio non lo produciamo noi, ci sono aziende specifiche che fabbricano le maglie d’acciaio che noi siamo in grado poi di assemblare. PIETRO FERRARI – Avete un ciclo completo anche
dal punto di vista manutentivo…
ANDREA PICCIROLI – Disporre di un’attrezzeria interna ci permette di dare una risposta immediata anche su richieste molto particolari del cliente: siamo la boutique della catena.
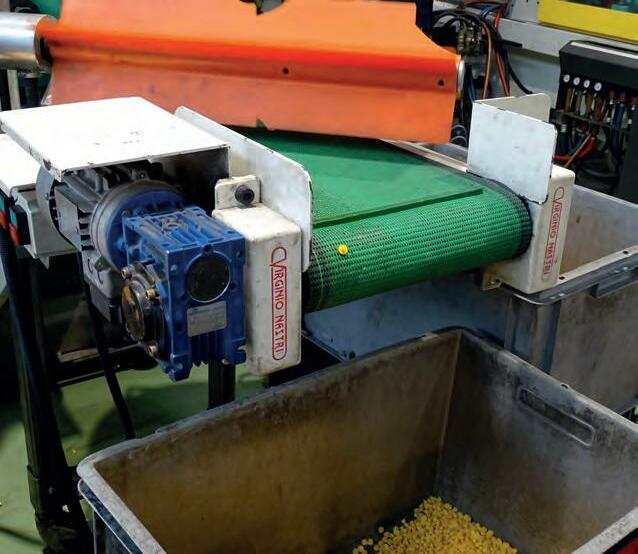
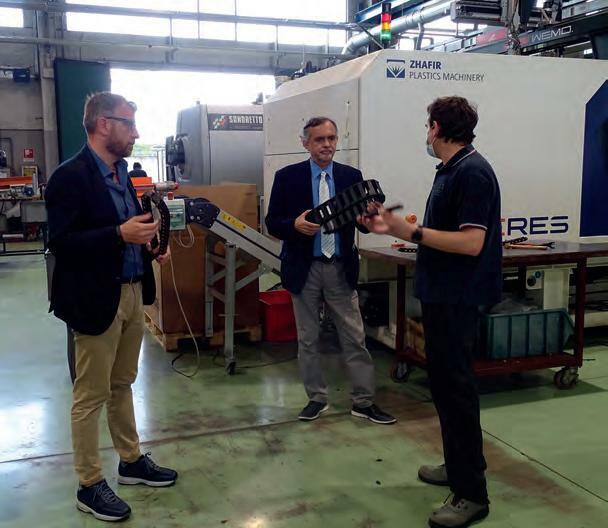
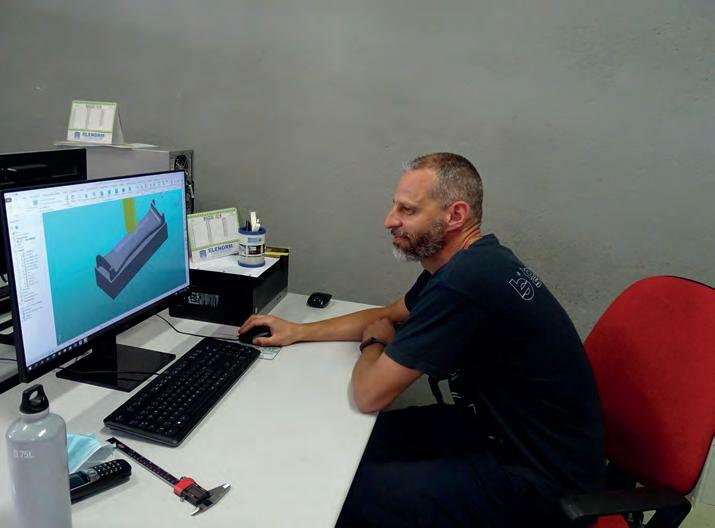
Abbiamo chi sa stampare, chi sa progettare, chi sa fare lo stampo e tutti danno un contributo reciproco tra i vari reparti. Soprattutto siamo in grado di lavorare o ottimizzare i disegni che ci vengono inviati da Monza. SONIA MARITAN – Quali sono le diverse fasi della
lavorazione?
ANDREA PICCIROLI – Partiamo dal granulato di nylon che va praticamente cotto per liberarlo dell’umidità, più propriamente essiccato, lasciando solo l’umidità che serve. Radici o altri fornitori leader ci forniscono un prodotto standard, però possiamo anche richiederlo con delle specifiche particolari, questo in funzione delle dimensioni delle maglie. La bravura sta anche nella selezione della materia prima, perché la plastica è viva, non sta ferma nel tempo, si ritira e cambia la dimensione e forma: noi combattiamo tutti i giorni con questi movimenti per garantire la qualità del prodotto. Le nostre caratteristiche possono cambiare anche in termini di colori, articoli trasparenti e quant’altro vuole il cliente, per questo dobbiamo lavorare quanto più possibile internamente. Possiamo utilizzare anche tipi di nylon diverso: può contenere fibra di vetro al trenta per cento, il che lo rende quasi strutturale, possiamo impiegare anche resina acetalica che viene utilizzata meno per le sue caratteristiche meccaniche che per la sua resistenza ai liquidi e per le sue doti di scorrevolezza. Possono essere realizzate anche catene autoestinguenti con determinate caratteristiche di comportamento ignifugo. Nei reattori il nylon diventa liquido a temperature molto alte in ciclo chiuso prima di passare alle presse a iniezione le cui dimensioni sono in funzione del quantitativo di nylon che devono lavorare. Lavoriamo su tre turni per cinque giorni ininterottamente dal lunedì al venerdì, il procedimento di cambio lavorazione è quanto più possibile veloce e i cicli sono stati ormai da anni completamente automatizzati. Ottimizzare qui ci fa diventare sempre più competitivi, così come lavorare autonomamente gli stampi. Nel reparto attrezzeria, infatti, vengono prodotti tutti gli stampi utilizzati, partendo da un pezzo d’acciaio squadrato dal quale si ricava quanto serve: il portastampo e la figura, il vero e proprio cuore dello stampo dove la materia plastica entra e prende forma. Interviene Stefano Bogioni, responsabile del reparto attrezzeria: «In questo reparto ci sono frese, macchine utensili generiche ed elettroerosori: qui tutto può essere gestito da remoto o da bordo macchina in funzione della complessità delle operazioni. Lo stampo può essere multiplo e produrre ad esempio quattro pezzi assieme in funzione delle diverse esigenze, utilizzando anche parti intercambiabili che modificano le dimensioni e la forma del componente da produrre». «Questa indipendenza produttiva – conclude Andrea Picciroli – ci consente di essere sempre competitivi sul mercato in termini di prezzi e di garantire un servizio completo e tailor-made al cliente».