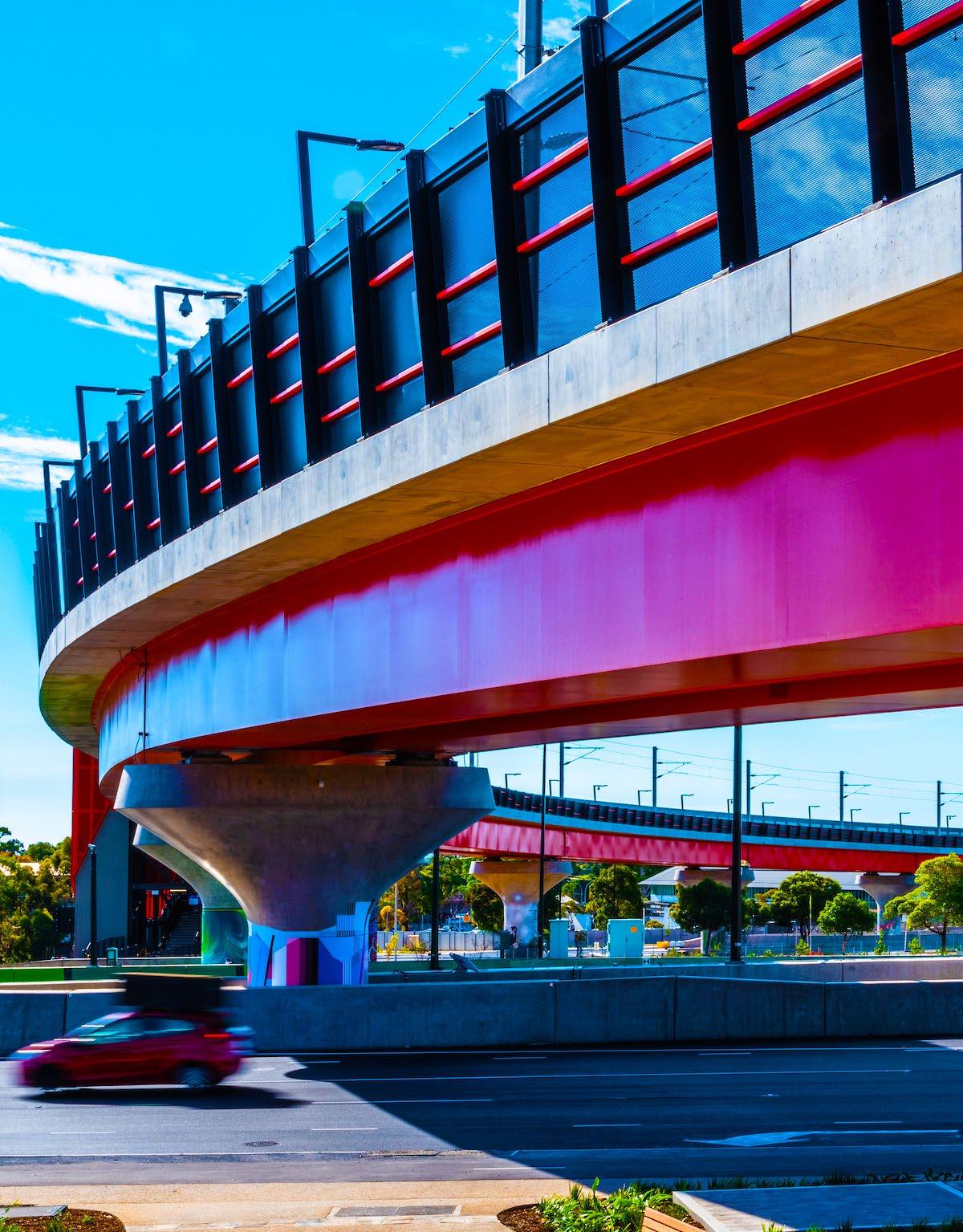
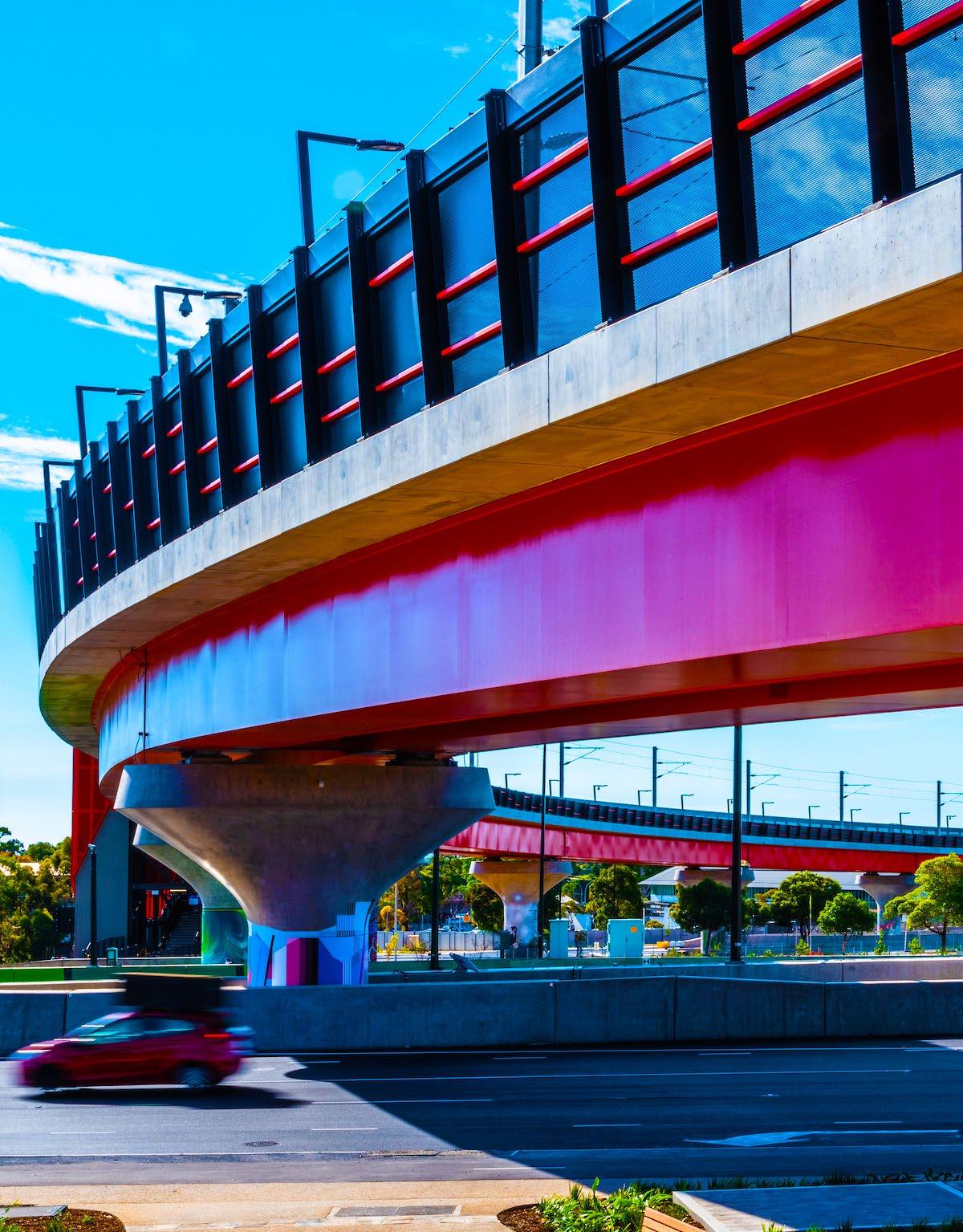
IN THIS ISSUE
12
Results of Weld Australia’s 2023 Member Survey
20
Weld Australia’s 2023 Member Survey results demonstrate that Australia’s welding and fabrication industry is facing a whole raft of challenges—from severe labour shortages, through to rising material and labour costs.
32
IIW Report on the Global Welding Industry
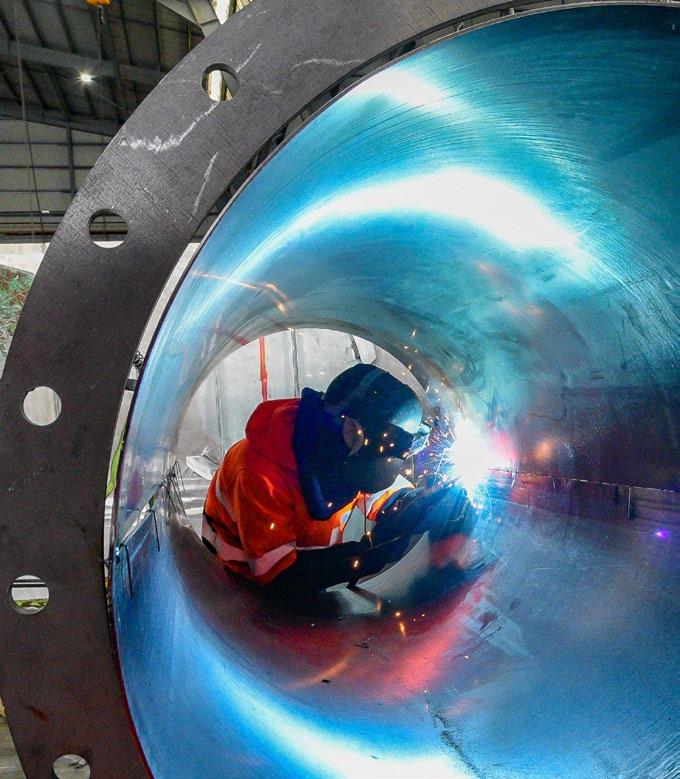
The International Institute of Welding (IIW) recently asked industry representatives about their key priorities in the international welding space. Interviewees were asked to rank the global issues affecting their industry.
24
Q&A with a Weld Australia Member: Arnekin Loftus
Manufacturing the Renewable Energy Revolution International expert, Adam Hersh, will address the opportunities and challenges presented by Australia’s renewable energy revolution at the National Manufacturing Summit in Canberra on 2 and 3 August. 34
Technology-Rich Welder Training
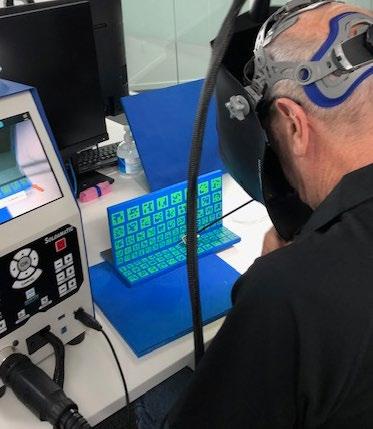
Across the Ditch: How ATNZ is Engineering a Brighter Future
40
Bowhill
Engineering:
Together We Thrive
Arnekin started work straight out of school as a tradesassistant before getting an apprenticeship. He has shown outstanding dedication and commitment to his Certificate III in Engineering, as well as his work at Formula OffRoad. 36
Based in South Australia, Bowhill Engineering is a multigeneration, family-owned and operated business that has been giving Australian businesses the edge since the early 1970s.
Wheelchair-Bound Worker Gains Autonomy
Illawarra companies Evermil and Leussink have come together to ensure wheelchair-bound boilermaker Clay Kelly can work more efficiently and autonomously by utilising a 3D welding table.
28
Nurturing the Future of Shipbuilding: Inside Incat’s masterful fusion of innovation and education
WELD AUSTRALIA CONTACTS
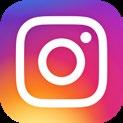
National Office PO Box 197 Macquarie Park BC NSW 1670 02 8748 0100 office@weldaustralia.com.au weladustralia.com.au
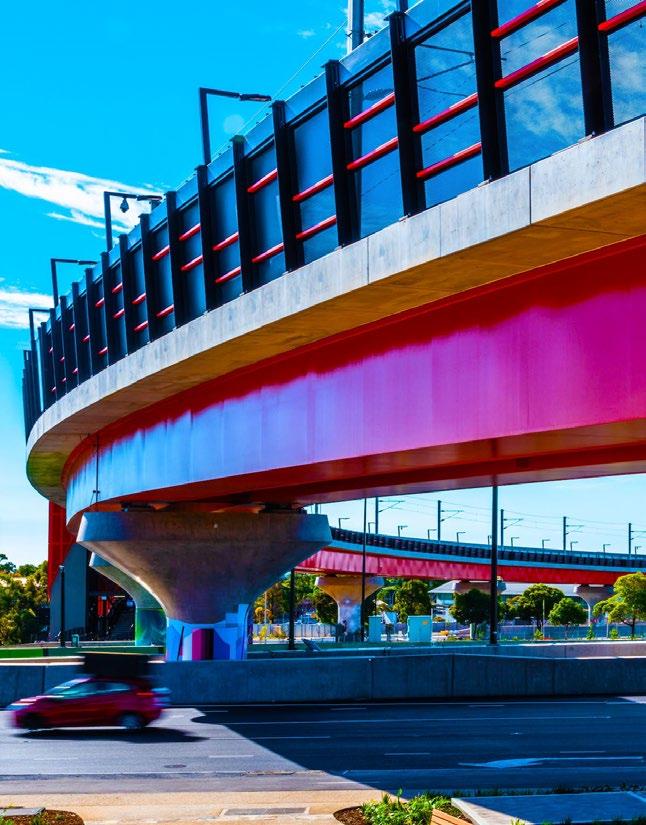
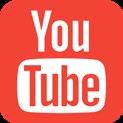
Chief Executive Officer Geoff Crittenden 02 8748 0100 g.crittenden@weldaustralia.com.au
ENGINEERING
Victor Blain, Engineering Team Manager 0409 823 991 v.blain@weldaustralia.com.au

TRAINING
Guy Brooks, Training Manager 0488 743 322 g.brooks@weldaustralia.com.au
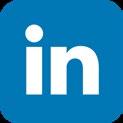
MARKETING
Michelle Bignold, National Manager, Sales & Marketing 0437 106 726 m.bignold@weldaustralia.com.au
MEMBERSHIP
David Choudry, Membership Manager 0417 878 104 d.choudry@weldaustralia.com.au
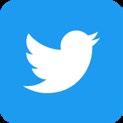
QUALIFICATION & CERTIFICATION Deniz Yalniz, Qualification and Certification Team Manager 0487 487 170 d.yalniz@weldaustralia.com.au
Subscription to Australian Welding is a Weld Australia member benefit included in annual membership fees. All rights reserved. No part of this publication may be reproduced or copied in any form without the written permission of Weld Australia. Weld Australia and its agents are not responsible for statements or opinions expressed by contributors in this publication, which are not necessarily those of Weld Australia. Publication of any advertisement does not constitute endorsement by Weld Australia of any product, nor warrant its suitability.
A MESSAGE FROM WELD AUSTRALIA’S CHAIR
manufacture renewable infrastructure in Australia.
Events
Our calendar of in-person events returned across the country has remained strong. We have facilitated a range of member events, including partnering with TAFE NSW and TAFE Queensland on two highly successful Industry Drinks Nights.
We hosted the very successful and much expanded 2022 Welding Excellence Awards. The Awards proved so popular that we will host them again in October and November this year.
As the 2022-2023 financial year draws to a close, I thought it pertinent to reflect on Weld Australia’s key achievements this year. At all times, the Weld Australia team focused on providing the resources and services that members needed most. Our primary goal is to ensure that the Australian welding industry remains locally and globally competitive, both now and into the future.
I am pleased to report that Weld Australia had a very successful 2022-2023 financial year. The organisation continues to record steady growth and a strong financial position. With re-investing and supporting the broader welding and fabrication industry always top of mind, a range of exciting projects contributed to our success.
Advocacy
Advocating for excellence in the welding industry with Federal and State Governments, other industry groups, major public authorities and private companies is an important aspect of Weld Australia’s operations.
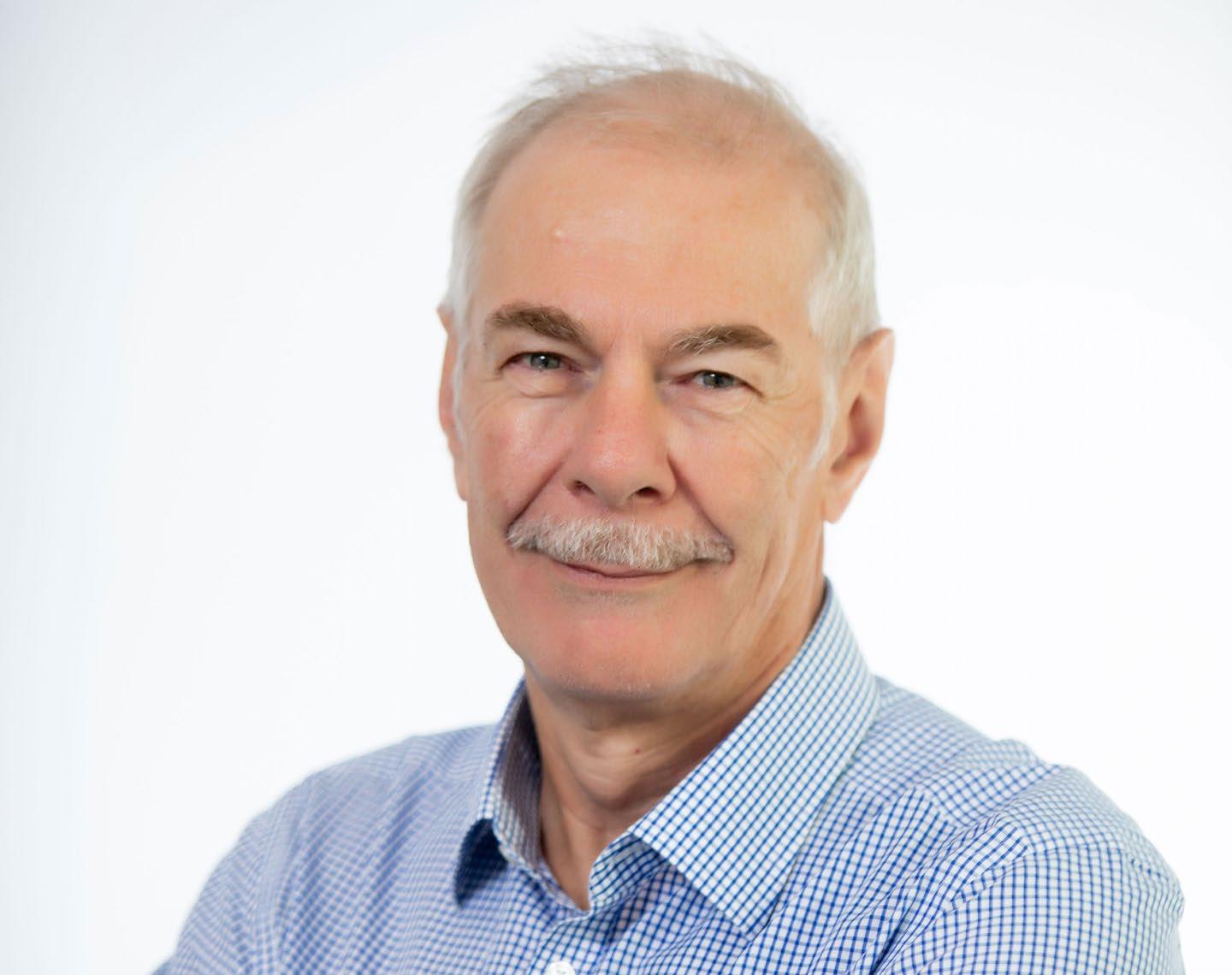
Weld Australia’s advocacy agenda focused on training initiatives for the next generation of welders and fabricators, building a sustainable and productive local industry, and ensuring superior welding quality standards and public safety. We generated significant media coverage and political interest.
There has been a substantial shift in government thinking with a much greater emphasis on local fabrication. Representation at the Job Summit hosted by Minister for Climate Change and Energy, Chris Bowen, revealed a strong intention to
Planning is also well underway for the 2023 National Manufacturing Summit in Canberra on 2 and 3 August. The theme of the Summit is ‘Manufacturing the Energy Revolution: Industrial Opportunities from Renewable Energy’. By uniting industry leaders from both the manufacturing and energy sectors, the Summit aims to leverage the opportunities presented by the renewable energy revolution and translate these into action. The Summit will foster collaboration, drive innovation, and facilitate the exchange of knowledge, empowering sustainable growth and technological advancements in these interconnected industries.
Training and Skills
Our training department went from strength to strength, with hundreds of students completing courses this year, qualifying as International Welding Engineers (IWE), Welding Supervisors, and International Welding Specialists (IWS).
Our program of technical training—facilitated by international experts—featured the ASME Section IX course by Walter Sperko, and Design and Modeling of Welded Structures by Pingsha Dong.
Our work on the MEM2.0 Learning Resources project with the National TAFE Consortium continued, with pilot programs run in Western Australia. The feedback received from students, teachers and the TAFE has been exceptionally positive.
We expanded our Advanced Manufacturing School Outreach Program in New South Wales significantly, with over 80 welding simulators installed in more than 40 schools.
Our VET Centre of Excellence program with Corrections Victoria at HM Prison Langi Kal Kal commenced and is already returning great results. In 2022, Corrections Victoria expanded the VET Centre of Excellence model to deliver Fusion Welding to ISO 9606 certification standard to complement their Metal Fabrication industry at HM Prison Langi Kal Kal. Federation University delivers the training program with the support of Weld Australia and on-site prison industry staff. As part of the program, augmented reality training was introduced to expand the welding skills of the inmate learners to meet international standards.
Qualification and Certification
Our qualification and certification services remained as popular as ever over the last 12 months, with a host of new companies certified to AS/NZS ISO 3834, EN 15085 and DIN 2303 In addition, numerous welders were qualified according to ISO 9606-1.
We are also working towards obtaining Joint Accreditation System-Australia and New Zealand (JAS-ANZ) accreditation for our AS/NZS ISO 3834 company certification program.
Industry Networks
With the appointment of an Industry Networks Manager, our activities in this space continue to grow. In the last 12 months, we launched the new Advanced Manufacturing Industry Network, and reinvigorated the Defence Industry Network. We are also in the process of establishing a Renewable Energy Industry Network.
With a whole host of exciting projects and programs underway, the new financial year is sure to be just as successful as the last. On behalf of the Board, I’d like to thank our CEO, Geoff Crittenden, and the entire Weld Australia team for their hard work and dedication.
by B öhler WeldingDIAMONDSPARK SEAMLESS CORED WIRES
brilliance established in 1967
Your ultimate goal must be diamondspark. A cored wire of highest quality and performance. Designed by the leading pioneers in filler materials, diamondspark wires are tailored to match the highest requirements for demanding applications. diamondspark seamless cored wires –brilliance established in 1967.
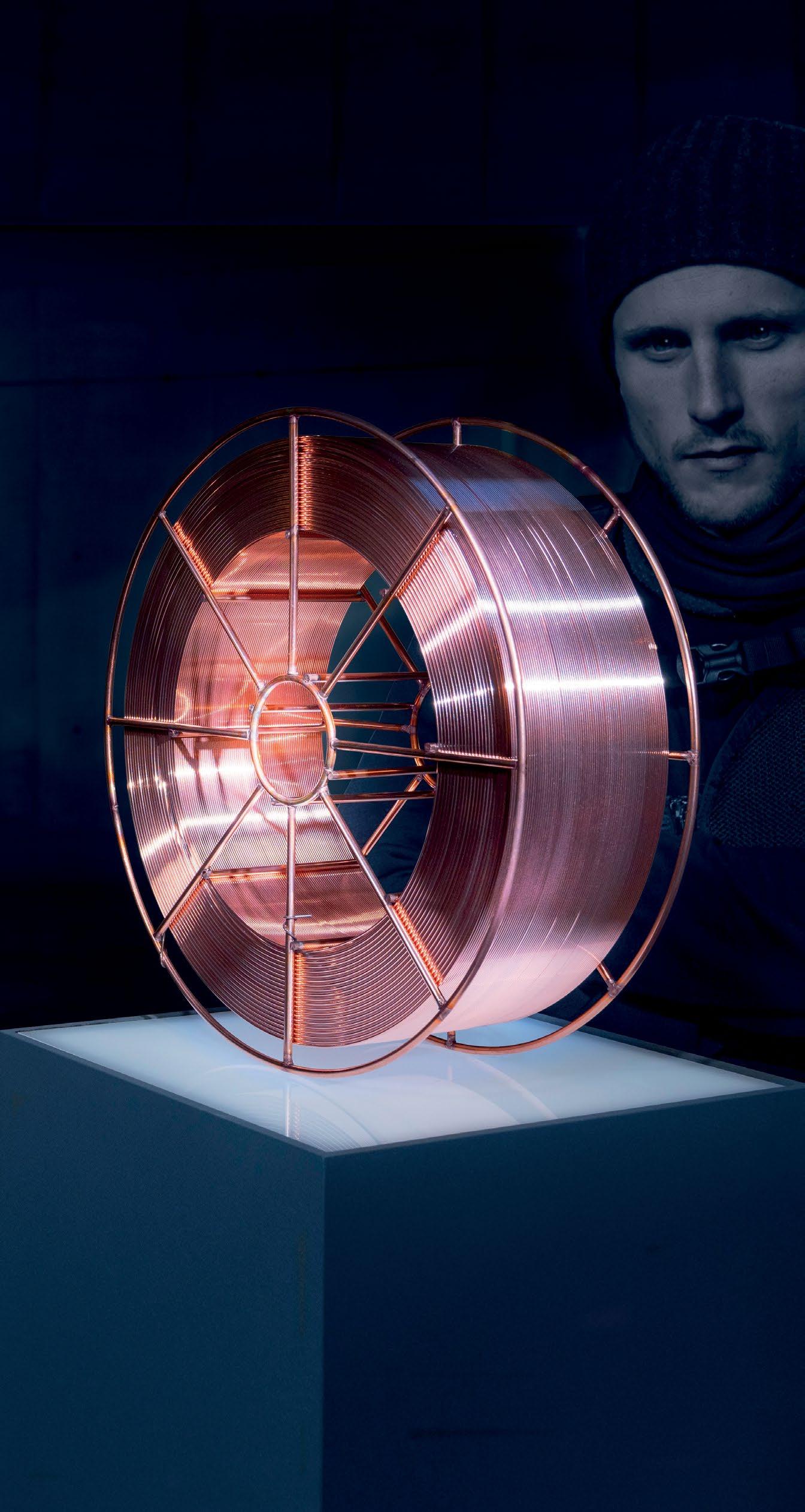
Curious?
See the full video OPERATION: DIAMONDSPARK online on our website!
voestalpine Böhler Welding www.voestalpine.com/weldingINDUSTRY, GOVERNMENT & STATUTORY BODIES WORK TOGETHER TO IMPROVE WELDER SAFETY OUTCOMES NATIONALLY
Industry, government and statutory bodies are working together to ensure that appropriate strategies are in place to reduce welder exposure to fumes and prevent long-term health effects.
Established by Weld Australia in early 2019, the Welding Safety Council provides a forum for industry and legislative safety authorities to discuss issues and work collaboratively to identify solutions.
By drawing together key government stakeholders, statutory bodies and industry into a single independent body focused on eradicating welding related injury, the Australian welding industry continues to take a significant steps forward in protecting both the general public and welders.
Recent media coverage has raised the issue of lowering the limit for exposure to welding fumes. In recent years, the welding industry has become increasingly aware of the hazards posed by metal fume produced during the welding process. This fume, comprising of microscopic particles of hot metal and gases, poses serious risks when inhaled by welders.
In early 2017, the International Agency for Research on Cancer classed welding fumes as ‘Carcinogenic to Humans’. However, when appropriate precautions are adhered to, risk of exposure is greatly minimised.
Welding can and should be considered a safe occupation; when proper precautions are taken, welders have no cause to fear accident or injury. But when safety isn’t taken seriously in the workplace, the risk of a severe incident becomes a real concern.
It is vital that appropriate strategies are in place to reduce welder exposure to fumes and prevent the long-term health effects that can result from exposure. All welders should receive training on methods to mitigate the effects of metal fume, including positioning themselves to reduce exposure and investigating less toxic alternatives where possible.
Education is the key to ensuring a safe and productive working environment for everyone. Employers need to invest in thorough and up-todate training for all their employees to ensure that they understand the risks associated with welding, the
mitigation strategies they can use, and the equipment available to prevent accident and injury.
As the Responsible International Institute of Welding (IIW) representative in Australia, Weld Australia is at the forefront of global welder safety best practice. We regularly participate in international research and development programs designed to improve welding fume safety practices.
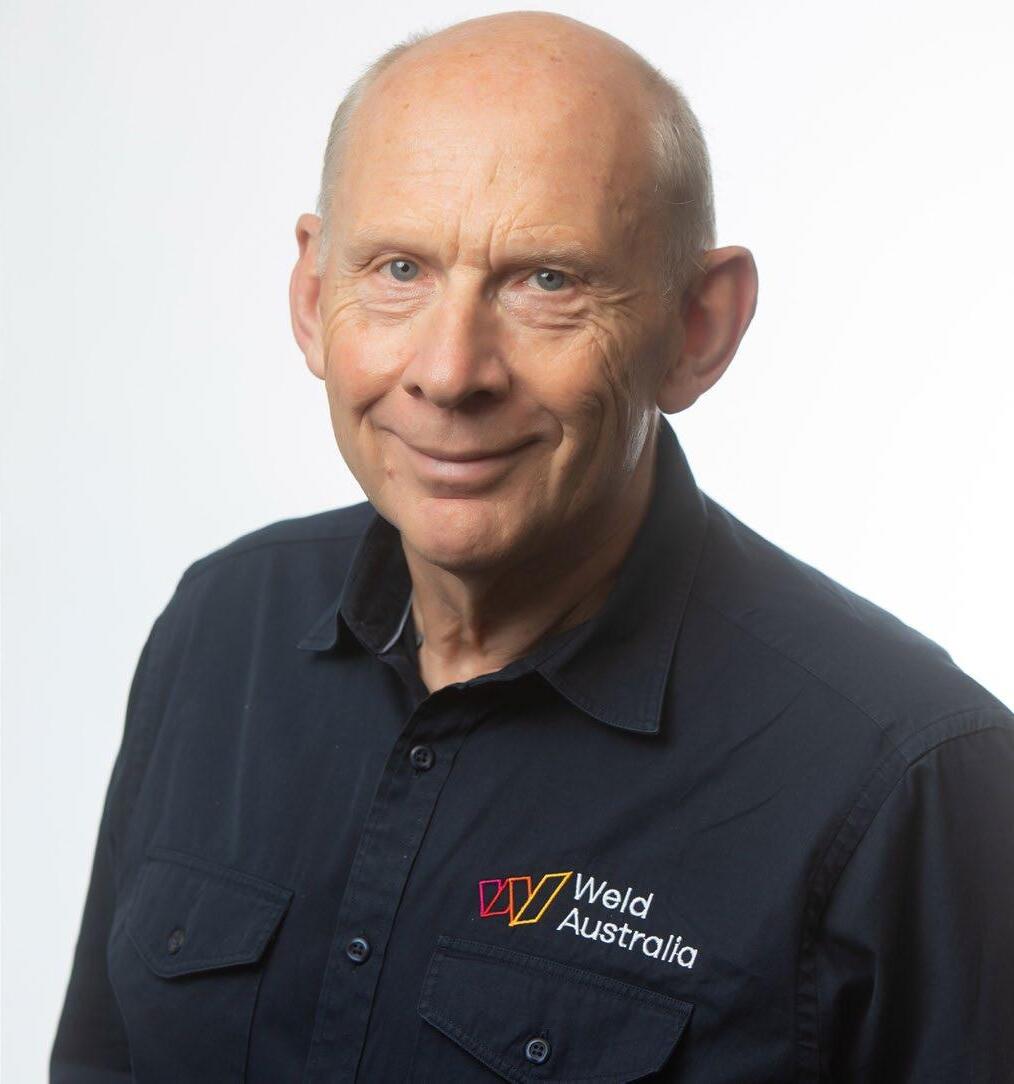
Local Exhaust Ventilation (LEV) systems capture and extract welding fume at the source and are a proven way of reducing exposure. All workplaces should have fit-forpurpose LEV systems installed and regularly maintained. Powered air purifying respirators (PAPR) are also a proven method to minimise the welder’s exposure to welding fume in conformance with WHS regulations.
Initiatives to Improve Welder Safety
In collaboration with industry, Weld Australia has implemented a range of other initiatives to help improve welder safety.
Weld Australia has published a wide
Skilling the fabrication and welding workforce of the future.
An additional 70,000 welders are needed by 2030 to meet industry demand.1 To support this growth, TAFE NSW is now offering fee-free* training to help upskill existing employees and attract more qualified professionals into the industry.
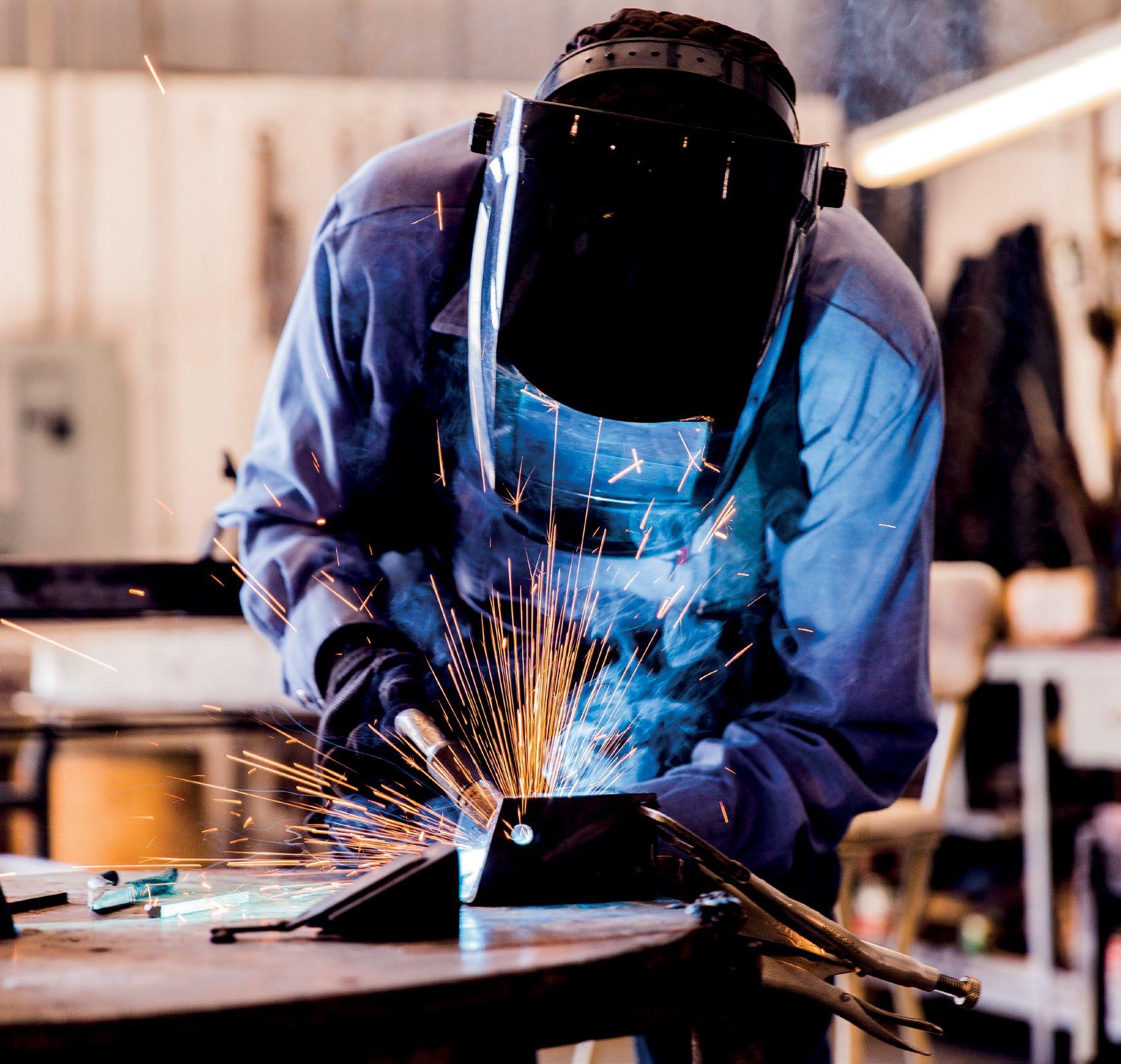
Learn to work with steel and sheet metal, as well as nail traditional blacksmithing techniques, plus the latest electronic automation. Taught by industry-experienced teachers, TAFE NSW’s nationally recognised qualifications provide the practical, hands-on skills required to construct a successful career.
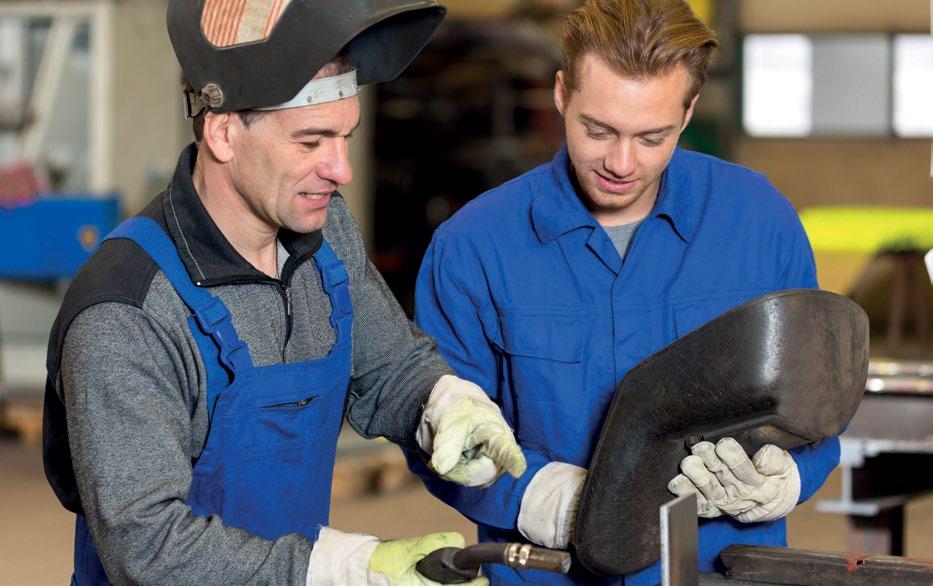
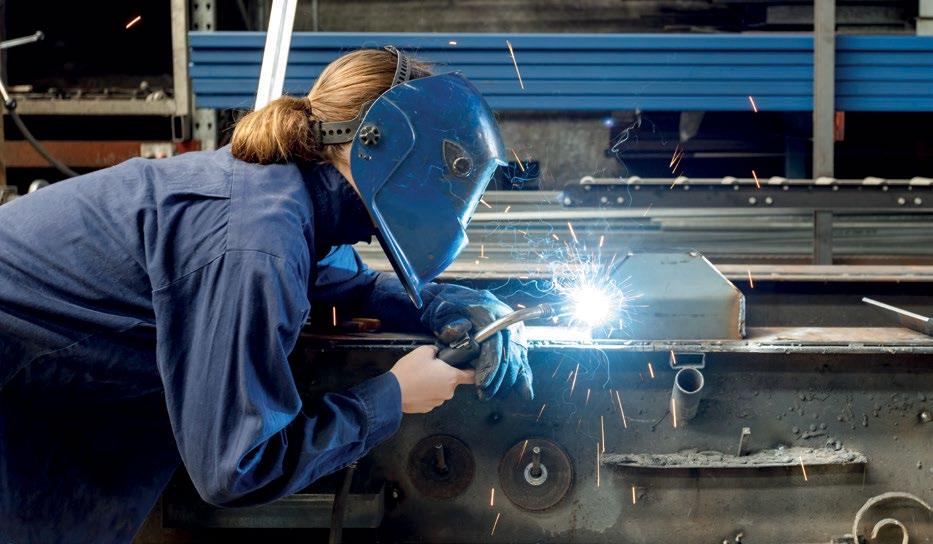
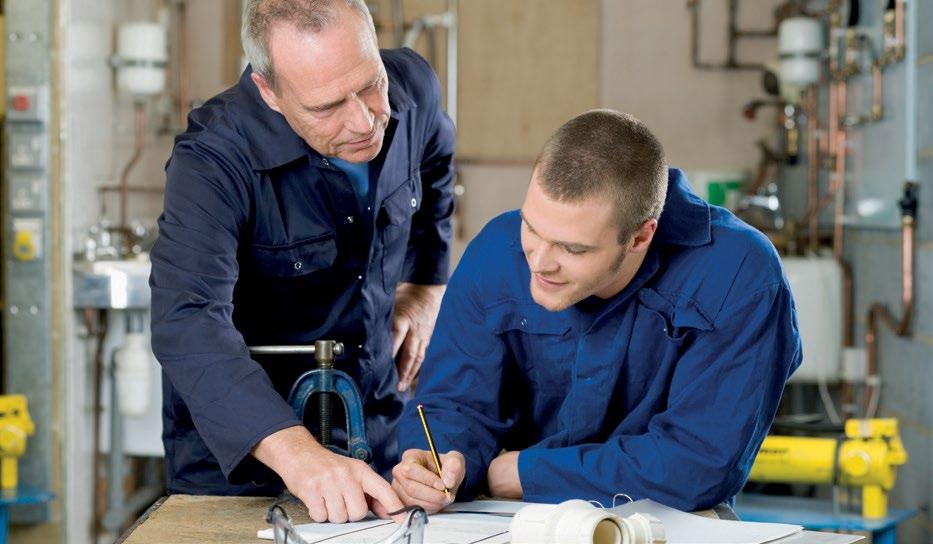
Enrol now for Semester 2, 2023.
+ Certificate II in Engineering MEM20105
+ Certificate III Engineering – Sheetmetal working MEM30319-06 (Apprenticeship)
+ Certificate III Engineering – Boilermaking MEM30319-02 (Apprenticeship)
+ Certificate III Engineering – Boilermaking/welding MEM30319-04 (Apprenticeship)
+ Certificate III Engineering – Blacksmithing MEM30319-05 (Apprenticeship)
range of welding safety resources, which are available to the public completely free of charge.
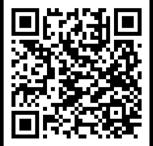
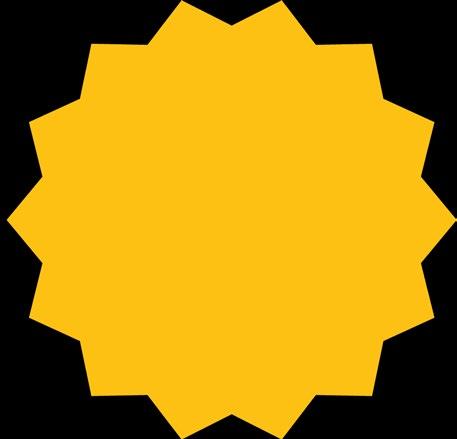
Fume Minimisation Guidelines: Welding, Cutting, Brazing and Soldering
This Guide includes all the information required to help protect workers from the hazards associated with welding fumes.
Technical Note 7: Health and Safety in Welding
This Technical Note gives guidance on health and safety practices in welding, cutting and allied processes such as brazing, soldering, pre- and post- weld material treatments and metal spraying, for the prevention of injury, ill health and discomfort, as well as damage to property, equipment and environment by fire, and explosion.
Various chapters deal with:
• Basic principles of safe working
• The main hazards and safety measures in welding, cutting and allied processes
• Precautions required in particular working situations
Technical Note 22: Welding Electrical Safety
Although electric arc welding can be performed perfectly safely, there are circumstances when there is a substantial risk of electric shock. Precautions against this risk include use of properly maintained equipment, correct protective equipment and sound work practices. With reference to Industry best practice, Technical Note 22 addresses how to safeguard a person against electric shock, reviewing elements such as: equipment, the human body, the workplace Australian Standards.
Weld Australia is currently developing two comprehensive online welder safety training courses. One course is tailored for welders, while the other is aimed at welding engineers and supervisors. These courses cover a raft of activities across a range of welding processes, from electric arc welding and flame cutting, through to topics like welding fume safety, and welding in confined spaces, at heights, or in hot and humid conditions. These courses will be completed towards the end of this
year and made freely available via the Weld Australia website.
The Weld Australia website was recently reconfigured to enable the issue of Safety Alerts. These Alerts will draw attention to welding safety incidents, including the known causes of the incident and what steps can be taken to help prevent a similar incidents occurring.
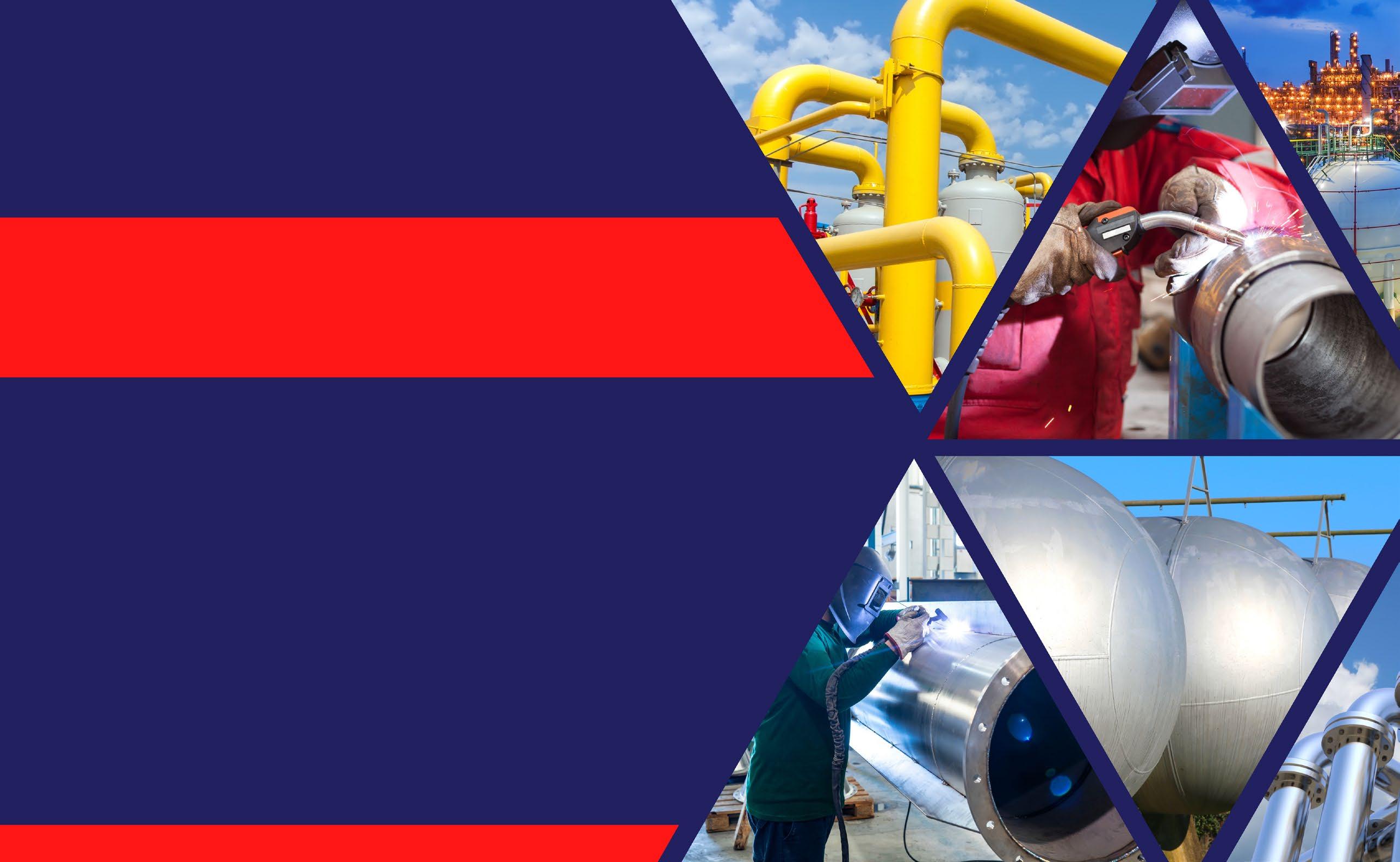
Education is the key to ensuring that anyone who welds is safe. Employers, professional welders and DIY enthusiasts alike must invest in thorough and up-to-date training to ensure an in-depth understanding of the risks associated with welding, the mitigation strategies that can be used, and the equipment available to prevent accident and injury. In 2023, Weld Australia’s goal is to help ensure every welder makes it home safely at the end of every day.
If you know someone who is welding without the proper training or experience, be sure to pass along Weld Australia’s free resources. All of these resources are available via the Resource Centre on our website.
BREAKING NEWS
Downer Wins $4.6 billion Train Manufacturing Contract
Downer has signed a $4.6 billion contract to design, manufacture and deliver new suburban trains, returning train manufacturing to the Maryborough region, under the landmark Queensland Train Manufacturing Program.
The contract will deliver 65 passenger trains, for use on the South East Queensland rail network, and support 800 jobs in construction and manufacturing. The first train set to be delivered in 2026, with all 65 on track for 2032.
The $7.1 billion Queensland Train Manufacturing Program is now in motion with Premier Annastacia Palaszczuk announcing the signing of the contract. Palaszczuk said, “Not only does this $7.1 billion program secure generations of job security, skills and training in Maryborough, but it sets our state up for a strong transport future. Because Queensland trains should be made in Queensland.”
Downer was announced as the preferred supplier for the program earlier this year.
Queensland VET Strategy to Meet Jobs Demand
The Queensland Government is developing a new Queensland Vocational Education and Training (VET) Strategy to drive the government’s annual $1.2 billion investment in skills and training.
The Government has released a discussion paper asking Queenslanders to have their say to ensure its skills and training investment – as part of the Good People. Good Jobs: Queensland Workforce Strategy 2022-2032 – is delivering priority skills for the jobs in demand.
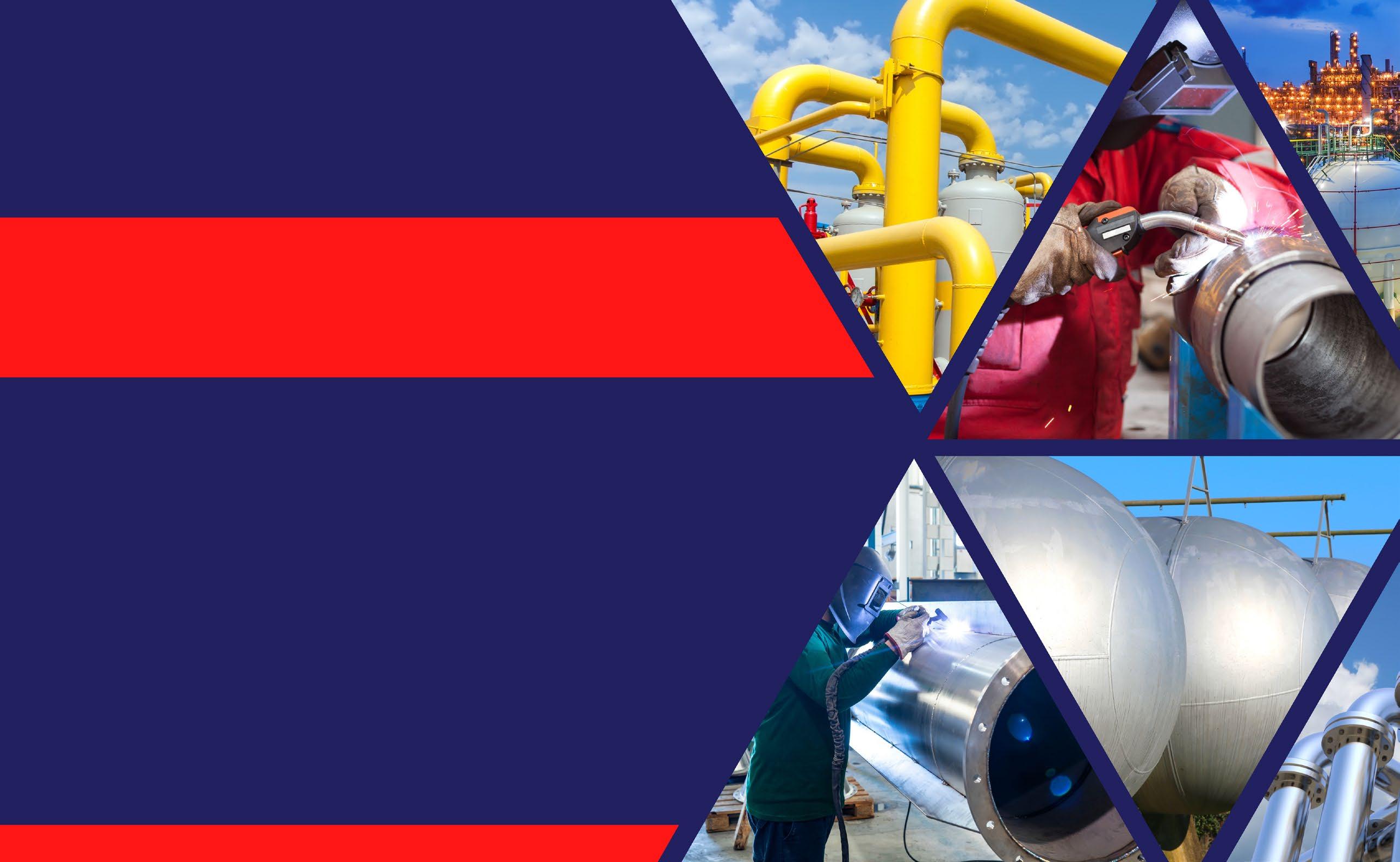
A discussion paper and online survey are now live with forums to be held across the state to gather the views of stakeholders and users of the VET system.
Small businesses, employers, industry groups, training providers, job seekers, students, apprentices and trainees are invited to have their say to ensure government investment is delivering the best outcomes for Queenslanders, employers and communities.
Beacon Expansion Puts the Spotlight on STEM
BAE Systems Australia is expanding its science, technology, engineering and maths (STEM) outreach program with immersive technology company, Lumination, to young people in Victoria. This means more than 600 students in years four to six across Victoria, South Australia, Western Australia and New South Wales will benefit from the Beacon program this year, which involves in-school learning and intensive STEM focused camps.
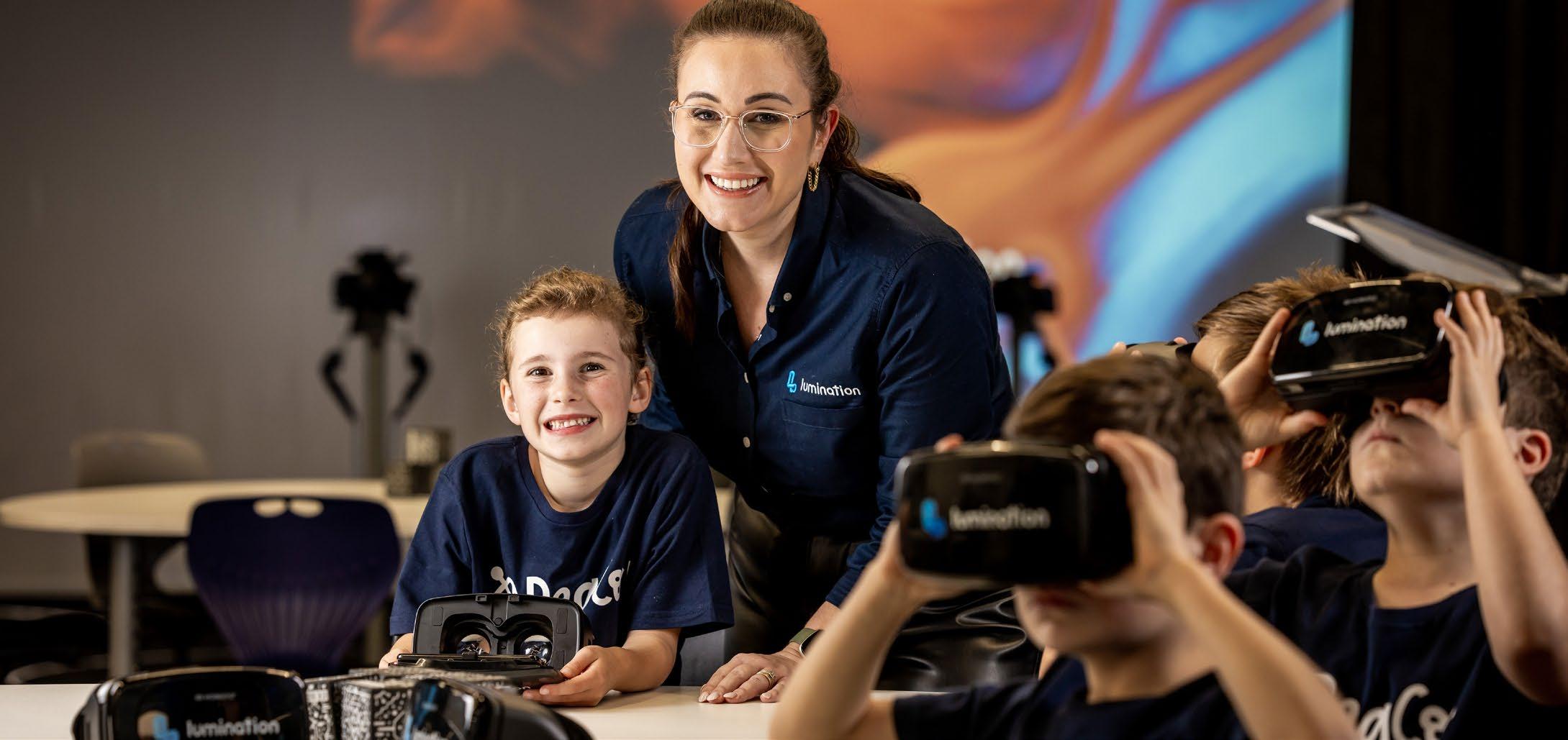
Beacon focuses on young people aged between eight and 11, helping them understand more about technology early in their education and to encourage more children from diverse backgrounds consider STEM subjects.
Last year, almost half of all participating students were female and 6% were Indigenous children. Around 80% of those who took part said they would now choose a future STEM career. BAE Systems Australia invests around $1 million annually in partnerships that support the communities in which it operates.
BREAKING NEWS
Government Seeks Opinion on $392 million Industry Fund
The Federal Government has taken another step towards launching the Industry Growth Program (IGP). A discussion paper was released in late June, asking how the program should be designed and operated. The discussion paper is available here, with consultations closing on 30 July 2023.
The IGP will support small and medium-sized enterprises (SMEs) and start-ups to turn ideas into real products and businesses, particularly through earlier high-risk and highcost phases.
The program will target priority areas under the Government’s landmark $15 billion National Reconstruction Fund including: value-add in agriculture, forestry and fisheries; value-add in resources; transport; medical science; renewables and low emission technologies; defence capability; and enabling capabilities.
The program will help transform industry in Australia by providing expert business advice and matched grant funding to support enterprises to increase revenue, grow their workforce and attract investment.
Austal Australia Delivers Fifth Cape Class Patrol Boat to RAN
Austal Australia has delivered the fifth of eight Evolved Cape Class Patrol Boats to the Royal Australian Navy. The vessel, ADV Cape Woolamai was officially accepted by the Commonwealth of Australia on 22 June 2023.
Austal Chief Executive Officer, Paddy Gregg said the delivery of the fifth Evolved Cape-class Patrol Boat again highlights Austal’s proven shipbuilding capabilities, efficiency and productivity from the Henderson, Western Australia shipyard. “With the delivery of every Evolved Cape-class Patrol Boat, Austal is demonstrating the capacity, capability, and expertise to construct naval vessels for Australia to the highest quality, efficiently.”
“This latest vessel, the ADV Cape Woolamai, is the fifth we have delivered in just 15 months. We’re launching and delivering a new patrol boat every three months, following approximately 12 months construction.”
The 58m aluminium monohull patrol boat is the fifth of eight to be delivered to the Royal Australian Navy since the project commenced in May 2020.
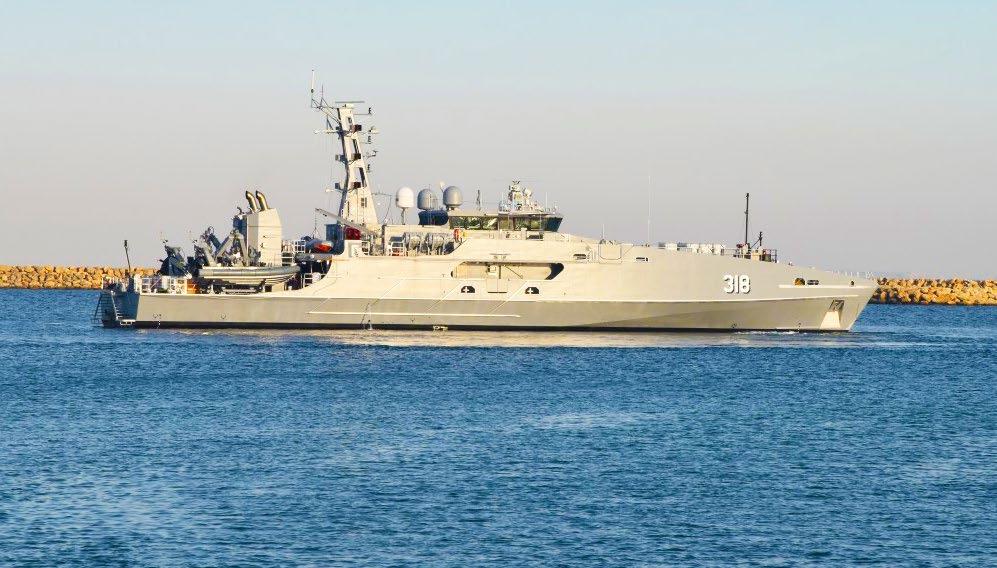
Western Australia Moves Towards Green Steel Production
Western Australia has joined South Australia in ambitions to create a green steel manufacturing capability, with the release of a new report by the Minerals Research Institute of Western Australia (MRIWA).
The Western Australia’s Green Steel Opportunity report maps five ways WA iron ore can be used to reduce emissions from steelmaking:
• Green iron ore mining and export using renewable energy sources
• Green iron pellets production using renewable hydrogen
• Hot Briquetted Iron production using hydrogen to make the pellets and natural gas processes for HBI
• Hot Briquetted Iron production using green hydrogen instead of natural gas
• The domestic production of green steel using fully renewable energy solutions.
However the MRIWA report found that the levelised cost of green steel compared to steel made with fossil fuel was significantly higher.
Minister for Industry
and Science,
Ed Husic, said, “We are laying strong foundations for future economic growth and job creation through our $392 million Industry Growth Program. This is about supporting companies to navigate the difficult aspects of getting ideas to market. We’re particularly keen to help bridge the ‘valley of death’ – where great ideas, often backed by solid research, are hamstrung only by a lack of funding and expertise. This consultation is about creating the right conditions to ensure brilliant Australian entrepreneurs can grow and thrive here at home.”
AIMEX is the destination for the mining sector to collaborate and hear from industry thought leaders. AIMEX provides an unmatched opportunity to connect and do business with some of the best mining suppliers from around the world, while sourcing solutions to boost productivity and meet sustainability goals. New at AIMEX this year are the Transformative Technology Pavilion and the Decarbonisation Zone.
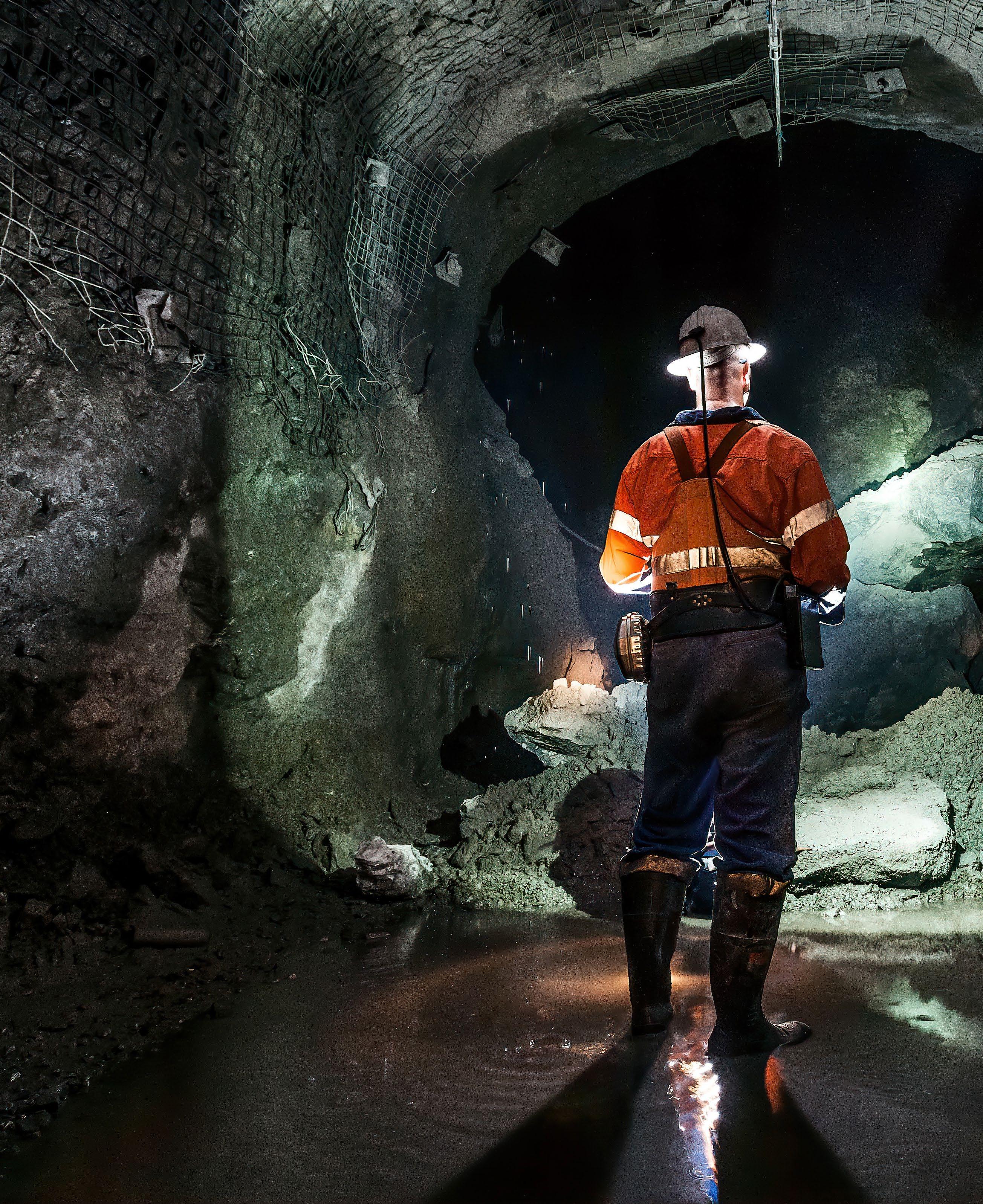
6,000+
industry connections
5-7 SEPTEMBER 2023
SYDNEY SHOWGROUND
local and international suppliers
50+
250+ expert speakers
MANUFACTURING THE RENEWABLE ENERGY REVOLUTION
International expert, Adam Hersh, will address the opportunities and challenges presented by Australia’s renewable energy revolution at the National Manufacturing Summit in Canberra on 2 and 3 August.
Hosted by Weld Australia in conjunction with the Australia Institute’s Centre for Future Work, the theme of the National Manufacturing Summit is ‘Manufacturing the Energy Revolution: Industrial Opportunities from Renewable Energy’.
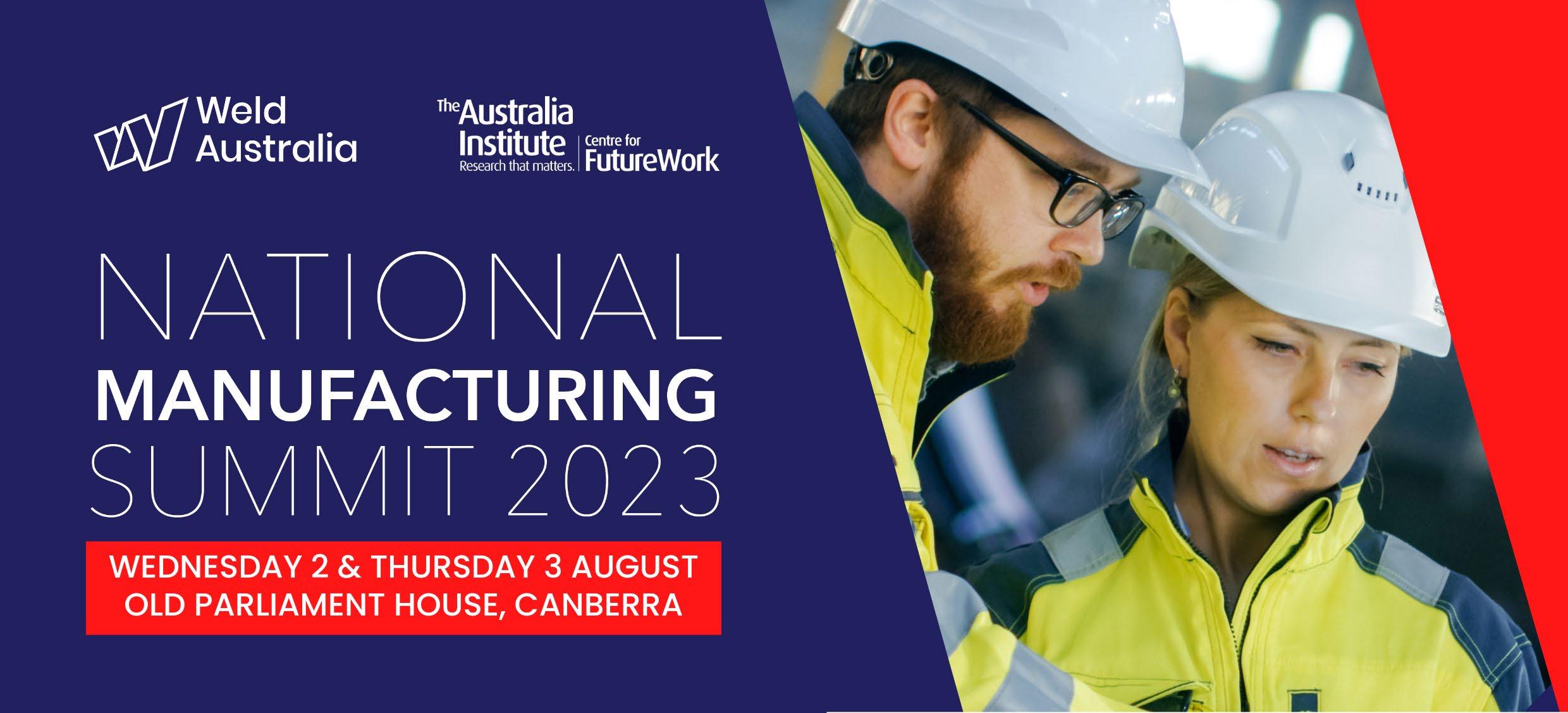
Adam Hersh is Senior Economist at the Economic Policy Institute in Washington, DC, one of Washington’s most influential think tanks. Adam’s work focuses on international trade, industrial, climate, China, and macroeconomic policies. He is currently leading a major research project on the industrial opportunities associated with new green energy policies. Adam will be the keynote speaker at the Summit dinner on 2
August, and a panellist at the Summit on 3 August.
According to Geoff Crittenden (CEO, Weld Australia), “By uniting industry leaders from both the manufacturing and energy sectors, the Summit aims to leverage the opportunities presented by the renewable energy revolution, and translate these into action.”
“The Summit will foster collaboration, drive innovation, and facilitate the exchange of knowledge, empowering sustainable growth and technological advancements in these interconnected industries. Local and international experts will delve into the challenges and opportunities of the renewable energy revolution.”
Renewable Energy Opportunities and Challenges
The Australian Government has legislated emissions reductions targets of 43% (on 2005 levels)
WITH THANKS TO OUR SPONSORS
by 2030 and net zero by 2050. Importantly, these targets will necessitate the construction of new infrastructure on a massive scale. Australia’s existing renewable energy generation of 64GW is forecast to grow to over 218GW by 2050. This will comprise 90GW of wind, 39GW of solar, 18.7GW of water, and 35.9GW of battery storage.
Over 11,000 wind towers will need to be produced, each requiring 500 tonnes of plate steel (for onshore wind towers) or 750 tonnes (for offshore wind towers). The annual production of plate steel in Australia is currently 400kt.
To connect all this new generation to consumers, AEMO estimates that more than 10,000km of new transmission lines and 25,000 transmission towers (at 30 to 60 tonnes of steel per tower) will need to be constructed around the country.
“The renewable energy industry will need a raft of additional resources to deliver on these ambitious projects, including: manufacturing and fabrication capacity, raw materials (particularly steel), and contracting and contractor resources. Plus, new technologies will need to be developed and deployed.”
“All this the renewable energy infrastructure will require a veritable army of skilled workers, including welders. While this represents enormous opportunities for Australia’s manufacturing industry, there are also enormous challenges ahead,” said Crittenden.
“While our governments can wish, and hope, and make public pledges about Australia’s transition to renewable energy, we simply do not have the sovereign manufacturing capability to make this a reality. The Federal Government and state governments can wish their renewable energy policies into existence, but without a massive investment in local manufacturing, it will not be achievable.”
With tickets selling fast, now is the time to register. The Program is also available for download. For further information, simply email: events@weldaustralia.com.au
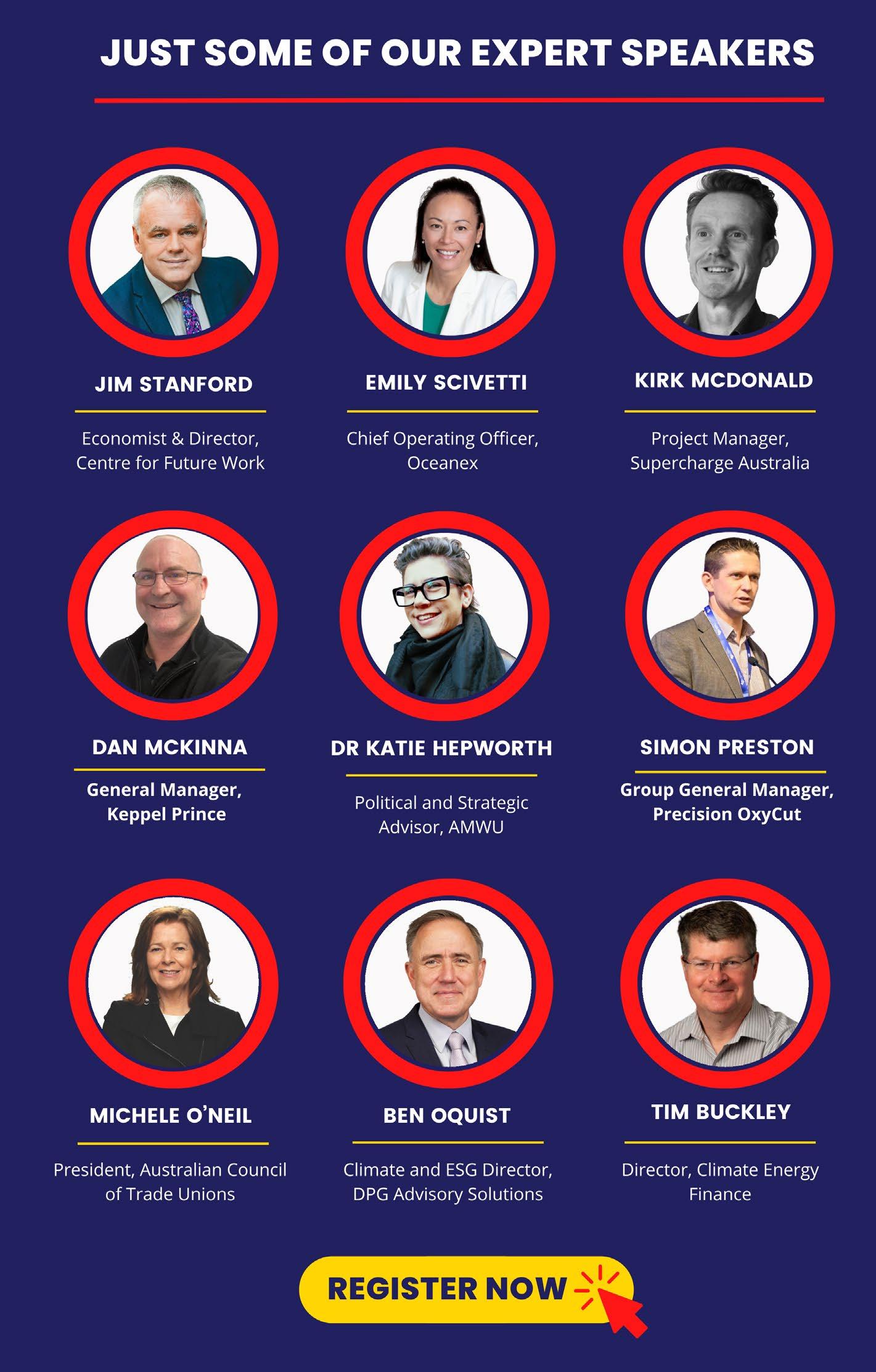
SUMMIT DINNER KEYNOTE SPEAKER: ADAM HERSH
Adam Hersh is Senior Economist at the Economic Policy Institute, in Washington. Adam’s work focuses on international trade and industrial policy, climate, macroeconomics and US-China relations. He is currently leading a research project on the industrial opportunities associated with new green energy policies, including the Inflation Reduction Act and the CHIPS and Science Act. For two years running, Washingtonian magazine named Adam among DC’s 500 most influential people. Adam regularly provides expert Congressional testimony and advises US and international policymakers and civil society leaders. He is a contributing author of Rewriting the Rules of the American Economy (2015) with Nobel Prize-winner Joseph Stiglitz. Prior to joining the Economic Policy Institute, Adam co-directed the Global Initiative for a Shared Future. He was also Chief Economist for Congressional Joint Economic Committee Democrats, and worked at the Franklin and Eleanor Roosevelt Institute, the Center for American Progress, and the Asian Development Bank. Political Economy from the University of Puget Sound.
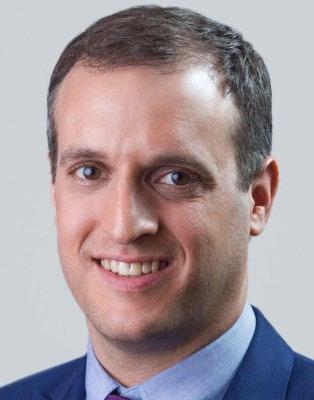
Weld Australia’s Excellence Awards are one of the most prestigious events on the welding industry calendar. The Awards embody and promote the highest standards of craftsmanship, quality and professionalism. The 2023 Welding Excellence Awards are a fantastic opportunity for welders, fabricators and educators across Australia to showcase their people and their operations. Winners will be awarded in each state for each of the award categories below. Award entries close on 15 September 2023.
Company of the Year
The Company of the Year Award recognises superior performance across a comprehensive range of business metrics including: innovation, quality assurance, market success, corporate social responsibility, health and safety, sustainability, and training and development of employees. There are three sub-categories:
• Company of the Year – Fabrication Award Criteria | Enter Now
• Company of the Year – Gas & Gear Award Criteria | Enter Now
• Indigenous Company of the Year Award Criteria | Enter Now
Welding Professional of the Year
This Award recognises professionals who are making a valuable contribution to the Australian welding and fabrication industry. The individual should demonstrate a high level of skill, knowledge or craftsmanship, be dedicated to their profession, and have professional development plans in place. There are three sub-categories:
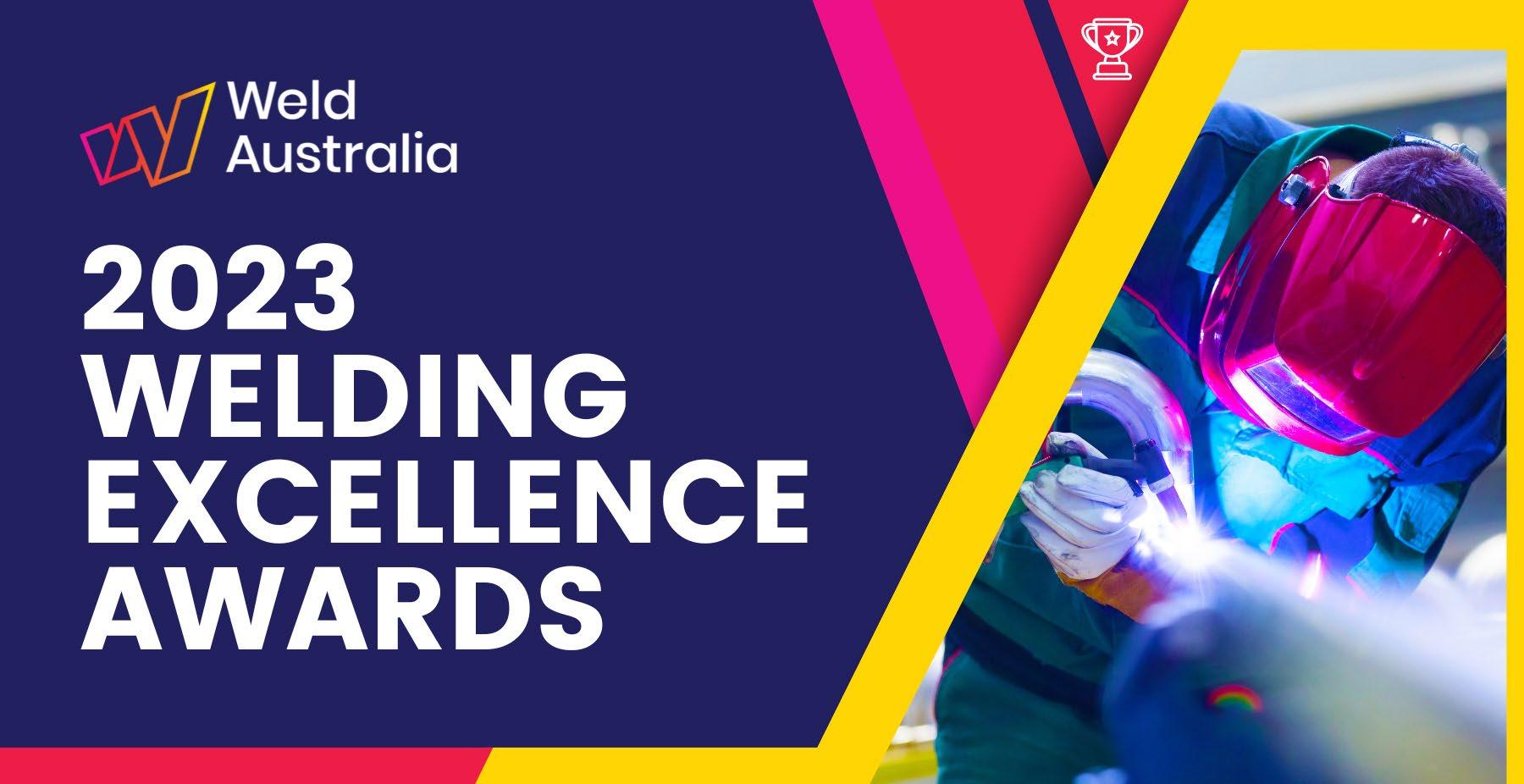
• Welding Professional of the Year – Welding Coordinator
Award Criteria | Enter Now
• Welding Professional of the Year – Welding Supervisor Award Criteria | Enter Now
• Welding Professional of the Year – Welding Inspector Award Criteria | Enter Now
How to Enter the Welding Excellence Awards
Entries must be submitted via the specific online form for each category by 15 September 2023. These forms can be found via the Weld Australia website, by clicking on the relevant red button.
Entry forms can be saved. However, before starting your entry, it is recommended that you download the Award Criteria (also available via the Weld Australia website). You will need the information outlined in the Award Criteria on hand to complete your online entry form.
Project of the Year
Award Criteria | Enter Now
The Project of the Year Award recognises excellence in welding and fabrication projects, with a focus on exceptional craftsmanship, a commitment to Australian and International Standards, environmental sustainability and innovation. Projects must have been completed in the 12 months preceding 1 October 2023.
Health and Safety in Welding
Award Criteria | Enter Now
The Health and Safety in Welding Award recognises organisations that are leading the way in encouraging and promoting health and safety throughout the Australian welding industry, and ensuring the health and safety of their own team. Organisations will be judged on criteria such as design and implementation of innovative programs or initiatives, the outcomes of these programs, and the health and safety of their team.
Trades Person of the Year
This Award recognises tradespeople who are making a valuable contribution to the welding and fabrication industry. The individual should demonstrate a high level of skill, knowledge or craftsmanship, be dedicated to their profession, and have professional development plans in place. There are three sub-categories:
• Young Trades Person of the Year Award Criteria | Enter Now
• Young Indigenous Trades Person of the Year Award Criteria | Enter Now
• Trades Person of the Year Award Criteria | Enter Now
Training and Education Award – Organisation Award Criteria | Enter Now
The Training and Education Award recognises the outstanding achievements of a STEM or VET provider or program. Entrants may include secondary education and tertiary education providers. Criteria include delivery of quality, innovative training programs, involvement with industry, recruitment and retention of students, and corporate social responsibility.
Training and Education Award – Individual Teacher Award Criteria | Enter Now
This Award recognises the outstanding achievements of a STEM or VET teacher. Entrants will be judged on criteria such as delivery of quality, innovative training programs, high level of knowledge or craftsmanship, strong links with students, and dedication.
Attend the Awards
• Perth: Wednesday 18 October at Beaumont on the Point
• Sydney: Wednesday 25 October at Waterview in Bicentennial Park
• Adelaide: Wednesday 1 November at Glenelg Golf Club
• Brisbane: Wednesday15 November at Indooroopilly Golf Club
• Melbourne: Wednesday 29 November at Huntingdale Golf Club
Registrations for the events are now open, and can be booked by clicking on the links above. The 2022 award events sold out in record time, so be sure to register early to avoid disappointment.
Ken Trevena Award – South Australia Only Award Criteria | Enter Now
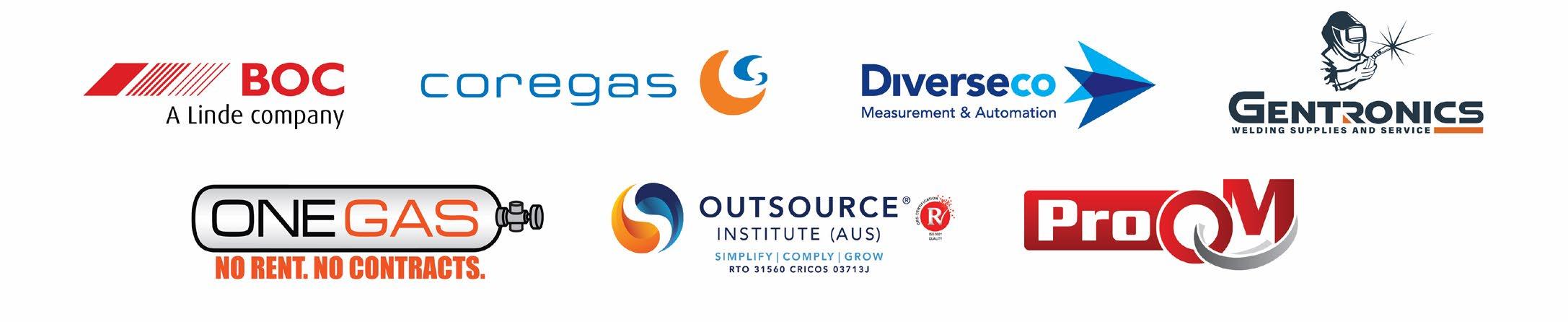
This Award recognises someone who has demonstrated an outstanding welding expertise on a particular project, attained meritorious skill in a Weld Australia Course, made a contribution to the art and science of welding, or developed a welding principle, technique or process.
Further Information
For further information, contact: Michelle Bignold on 0437 106 726 or m.bignold@weldaustralia.com.au
WITH THANKS TO OUR SPONSORS
Why Enter the Welding Excellence Awards?

An industry award win can act as a third party endorsement for your business. A win can give a seal of approval to your activities and is a sign of quality for potential customers.
Business awards can be an overlooked tool in your marketing toolbox. Make sure you maximise PR exposure and update your marketing materials. Winning an industry award can open doors to getting contracts, finding new supply channels and breaking into new markets.
Business awards validate your hiring stature among new recruits. By pitching yourself as the best, you can attract the talent you need to push your business forward.
UNDER PRESSURE: Gas Cylinder Safety in Welding
Gas cylinder safety is paramount in the welding industry to prevent accidents and ensure a safe working environment. Cylinders often contain gases at high pressures, and mishandling can lead to leaks or explosions, causing severe injuries, fatalities, fires and property damage. Adherence to safety protocols and standards for proper use, storage and handling is essential when it comes to mitigating these risks and promoting a culture of safety.
Cylinder safety cannot be compromised when it comes to welding and fabrication. Gas cylinders contain a range of safety hazards and should be treated with ultimate care.
Personnel should use appropriate protective clothing like gloves, boots and safety glasses, and ensure their operations are carried out in the safest way.
Cylinder Valve Safety
When working with cylinders or operating cylinder valves, ensure that you wear appropriate protective clothing. Before operating a cylinder valve ensure that the system you are connecting the cylinder into is suitable for the gas and pressure involved.
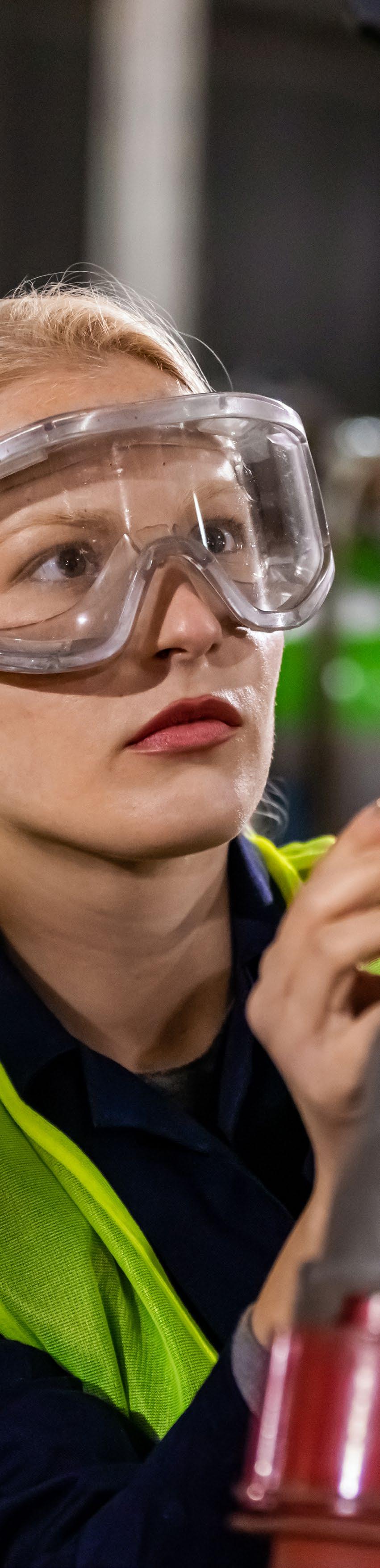
Ensure that any accessories (such as hoses attached to the cylinder valve, or the system being connected to) are securely connected. A hose, for example, can potentially flail around dangerously if it is accidentally pressurised when not restrained at both ends.
Stand to the side of the cylinder so that neither you nor anyone else is in line with the back of the cylinder valve. This is in case a back-plug is loose or a bursting disc vents.
Open the cylinder by turning the valve hand-wheel anti-clockwise. Remember to only use reasonable force. Ensure that no gas is leaking from the cylinder valve connection or the system where the cylinder is connected. Do not use ammonia-
based leak detection fluid, as this can damage the valve.
Once you’ve finished with the cylinder, close the valve by hand by turning the hand-wheel in a clockwise direction.
Storage of Cylinders
All cylinders should be considered and treated as full, regardless of their content. This means:
• Keep cylinders away from heat sources (like flames and heaters)
• Do not store cylinders near combustible materials or flammable liquids
• Keep cylinders in well drained areas away from pools and ponds
• The storage area should be kept well ventilated and clean at all times. Ideally do not store in confined spaces
• Avoid below ground storage, where possible. Where impractical, consider enclosed space risks
• Storage area should be designed to prevent unauthorised entry, to protect untrained people and guard cylinders from theft
• Different types of gases should be stored separately, in accordance with legislation, and AS 4332 The storage and handling of gases in cylinders
• Stores must clearly show signage in accordance with regulations. This includes HAZCHEM, no smoking and naked flame warning signs
• Full and empty cylinders should be stored separately and suitably restrained to prevent a fall
Fire Protection
• Liquefied flammable cylinders must be stored upright on a firm, level floor (ideally concrete)
• Store cylinders away from heavy traffic and emergency exits.
Handling of Cylinders
When handling gas cylinders, and in line with current manual handling regulations, it is advisable that:
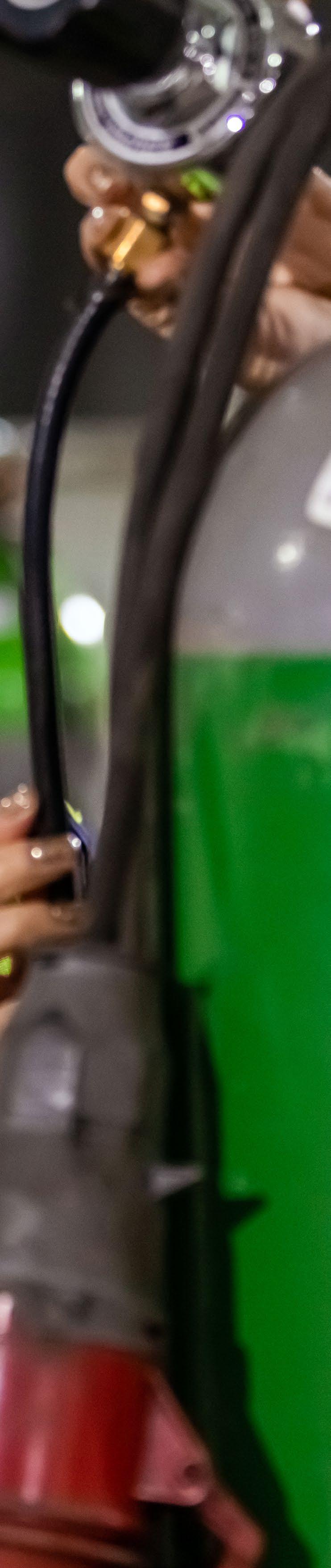
• Larger cylinders are heavy. Manual handling risk assessments and training should be undertaken
• Safety shoes and gloves be worn
• Cylinders should be handled with care and not knocked violently or allowed to fall
• Cylinders should be moved with the appropriate size and type of trolley
• Cylinder valves must be closed and equipment detached
• Never roll cylinders along the ground as this may cause the valve to open accidentally
• Transporting cylinders across a workplace is also crucial—ensure that the valve cannot be accidentally opened in transit.
Operating to Australian Standards
AS 4839 specifies the safe use of portable oxy-fuel gas systems in Australia. This includes advice around the assembly, operation and maintenance of portable and mobile oxy-fuel gas equipment, and cylinder storage and handling. It also offers sound advice around gas equipment specifications, and leak testing and maintenance.
Source: boc.com.au
Ten Steps to Cylinder Safety
1. Always read labels and Material Safety Data Sheet before use.
2. Store upright and use in well ventilated, secure areas away from pedestrian or vehicle thoroughfare.
3. Guard cylinders against being knocked violently or being allowed to fall.
4. Wear safety shoes, glasses and gloves when handling and connecting cylinders.
5. Always move cylinders securely with an appropriate trolley. Take care not to turn the valve on when moving a cylinder.
6. Keep in a cool, wellventilated area, away from heat sources, sources of ignition and combustible materials, especially flammable gases.
7. Keep full and empty cylinders separate.
8. Keep ammonia-based leak detection solutions, oil and grease away from cylinders and valves.
9. Never use force when opening or closing valves.
10. Do not repaint or disguise markings and damage. If damaged, return cylinders to your supplier immediately.
• Do not work near oil and grease containers, flammable vapours or combustible dust
• Move all combustibles at least 10m away from the work site. Otherwise, protect with flame-proofed covers
• Have a fire extinguisher or water and sand available
• After welding or cutting, carefully inspect for sparks and smouldering material before leaving the area.
Gas cylinders in a fire may explode. If cylinders are in a fire, the key actions to take are:
• Evacuate the area (minimum 100m); advise persons between 100m and 300m to take cover
• Call the fire brigade
• If you attempt to fight the fire, do so from a protected position using copious quantities of water
• When the fire brigade arrives, inform them of the location and number of gas cylinders, and the names of the gases that they contain
• Cylinders that are not directly involved in the fire and that have not become heated should be moved as quickly as possible to safe place provided this can be done without undue risk.
FEELING THE HEAT: How to deal with post-COVID burnout
In March 2020, businesses were forced to alter their operations as COVID-19 began to spread. Many organisations implemented physical distancing measures and fiscal conservatism to manage a drier pipeline of projects. Employees were seeking muchneeded job security to support themselves. However, on the flipside of the pandemic, these habits have changed, and a period of COVID fatigue has settled in.
Overnight, the COVID-19 health emergency changed the way businesses operate. The ongoing lockdowns and economic uncertainty led to a major overhaul of the Australian labour market.
This has been particularly felt in the local manufacturing space, which was already stretched prior to the pandemic.
The health emergency cast a variety of challenges—workforce and skills shortages, local supply and demand pressures, and sovereign manufacturing capabilities—into the spotlight even further.
As employers and employees alike weathered the storm, some parts of the world experienced a phenomenon known as the ‘Great Resignation’. In Australia, this has been felt to some extent. Workers who have chosen to stay in their existing jobs are also showing signs of changing attitdues.
Today, one-in-two workers aged between 18 to 54 feel exhausted at work, according to the 2023 State of the Future of Work report from The University of Melbourne. The report found Australian businesses are
at a risk of losing their prime aged workforce because of exhaustion, lack of motivation, and a lack of concentration by younger workers. It recommends workplaces prioritise workplace mental health and provide greater support to address issues like burnout and mental distress.
The World Health Organisation defines burnout as an occupational phenomenon, caused by feelings of exhaustion and depletion, or mental distance from one’s job.
What are the Signs of Burnout?
Australia’s manufacturing sector requires thousands of personnel across a variety of roles and skill levels. In the welding and fabrication sector alone, personnel spend much of the day on their feet and in relatively confined spaces. Welders are exposed to physical and chemical hazards, and safety risks. They operate to high standards of quality, which requires heightened mental focus.
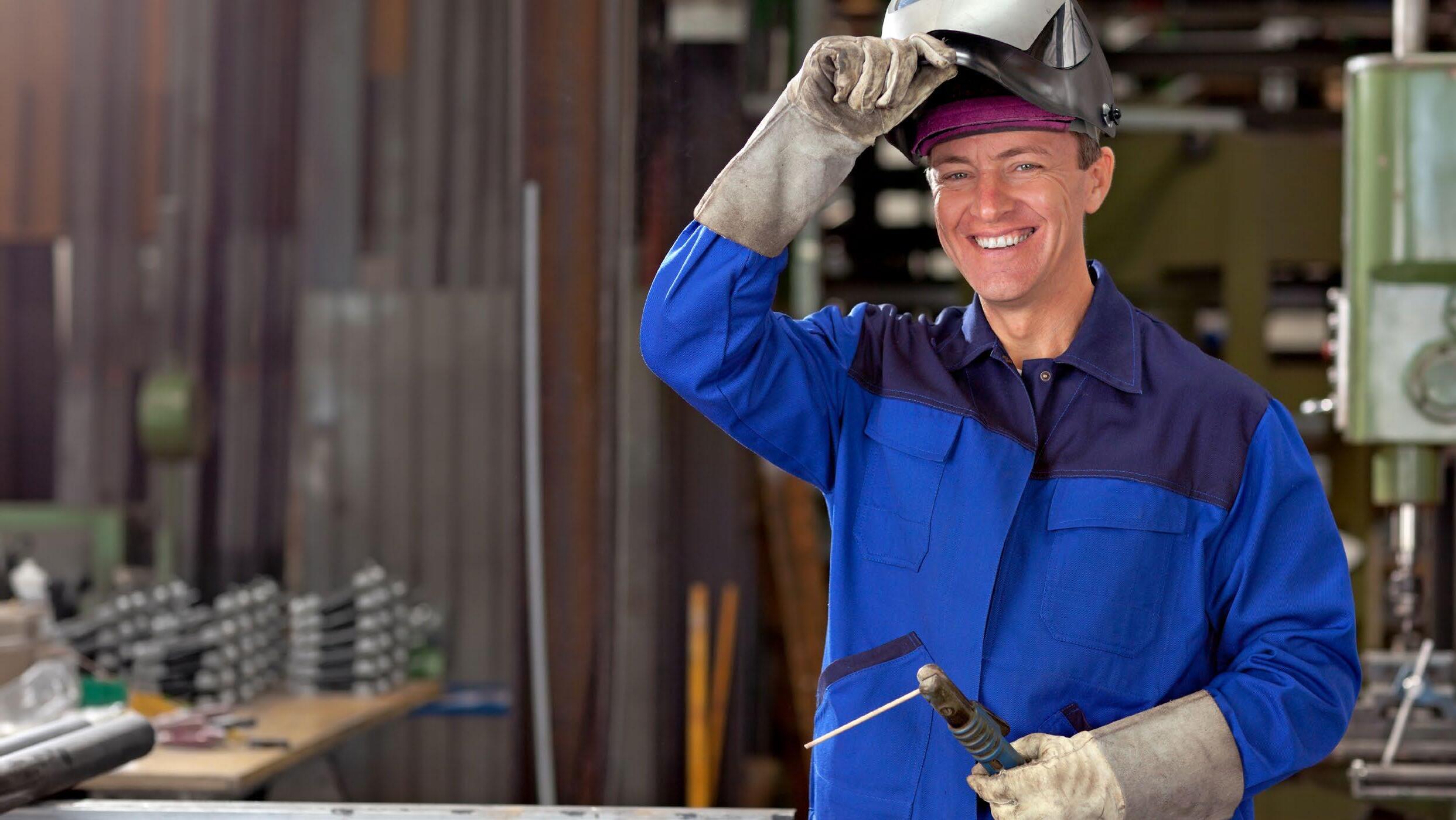
When these experiences are met with a reduced labour force and an ongoing pipeline of new projects, the results can be damaging. At the same time, the pandemic reduced the opportunity to travel and socialise—
two important pillars of a healthy work life balance.
As such, signs of burnout have begun to emerge, including:
• A reduced work life balance
• Long-term stress
• Increased responsibility or working above capacity
• Working towards unrealistic deadlines
• Alack of support
• Unclear direction or professional development
The University of Melbourne’s study focused on the experiences of Australian workers in this context.
Dr Brendan Churchill, who coauthored the report, said workers were in poorer physical and mental health since the pandemic began. “With high rates of fatigue and exhaustion among younger and middle-aged workers, it’s no surprise that over a third of prime aged workers in Australia are considering quitting their jobs.”
As such, managers should be aware of the signs of burnout in their staff and are encouraged to provide a safe and supportive working environment.
How to Know when to Stop
Burnout encompass low energy, increased feelings of isolation or disengagement from work, and lower satisfaction and motivation to perform tasks.
In addition, these feelings can shift into your personal life, and include exhaustion or feeling drained, and physical responses like headaches, struggling to sleep or body pain. Burnout typically occurs when an employee experiences these emotions or feelings collectively.
Personnel should be aware of how long these feelings persist, and the severity of them. For example, it is normal to feel tired after a long day on your feet. However, if you have suffered weeks of poor health and it is impacting your physical response, you may be experiencing burnout.
How to Manage Burnout
Burnout can be an overwhelming feeling. However, it can be managed effectively.
Welding professionals are encouraged to work together to help manage the risks of burnout, and the safe return of colleagues into the sector.
Dr Churchill from the University of Melbourne said organisations should be aware of the signs and work towards a positive work life balance. “Australian workplaces must prioritise workers’ well-being into the recovery to provide greater support in addressing burnout and mental distress.”
There are a variety of tools and techniques to help manage burnout on your work floor:
• Saying ‘no’ to new projects when the team is at capacity of overstretched
• Managing expectations and timelines based on employee output
• Speaking up when personnel begin experiencing burnout
• Ensuring there is a safe and supportive environment for employees
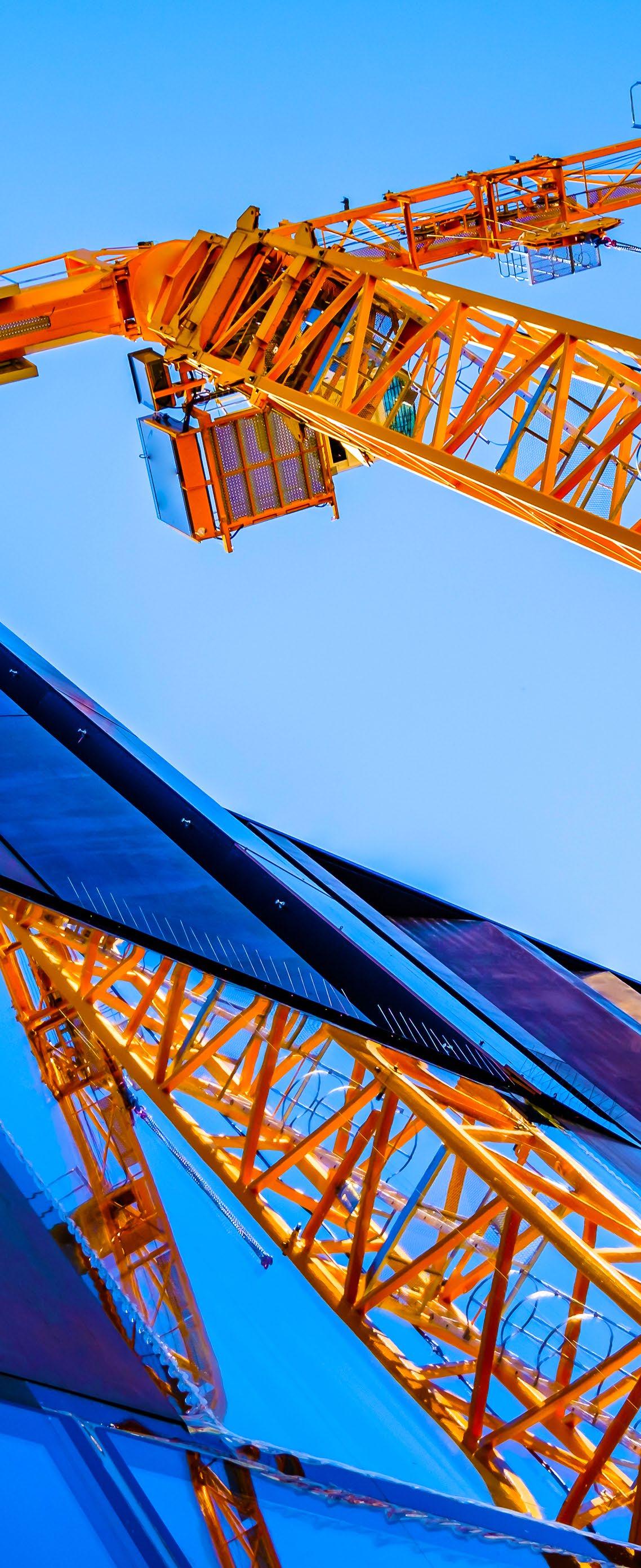
• Encouraging work life balance
Open communication and a supportive work environment are two crucial areas to help employees manage the early onset of stress, fatigue, or exhaustion.
Burnout can be managed when the correct processes are in place at your workplace. Welding Supervisors and management have a key role to play in protecting the physical, emotional and mental wellbeing of their staff.
WELD AUSTRALIA RELEASES THE RESULTS OF ITS 2023 MEMBER SURVEY
Weld Australia has released the results of its 2023 Member Survey. The results demonstrate that Australia’s welding and fabrication industry is facing a whole raft of challenges that will make the delivery of the Federal Government’s plans for a renewable energy revolution almost impossible—from severe labour shortages that are inhibiting the growth of the welding industry, through to rising material and labour costs. The Federal Government must step in and provide real support to industry to make the renewable energy revolution a reality.
According to Geoff Crittenden (CEO, Weld Australia), “Distributed in March 2023 and completed by over 130 companies, our 2023 Member Survey indicates that labour shortages, and the rising cost of materials, energy and labour remain high on the agenda for the welding industry. Without funding and support from governments at all levels, these challenges will make it nearly impossible for industry to deliver the necessary manufacturing capability required for the Federal Government’s ambitious renewable energy revolution.”
When asked to select their top two factors, 60% of survey respondents indicated that labour shortages are most likely to inhibit the growth of their business in 2023. When asked what their main concern is right now, 45% confirmed that labour shortages was on the top of their list. 50% of Australia’s welding workshops are operating at 80% of their capacity or below. When asked why this is, a lack of skilled workers was the overwhelming answer.
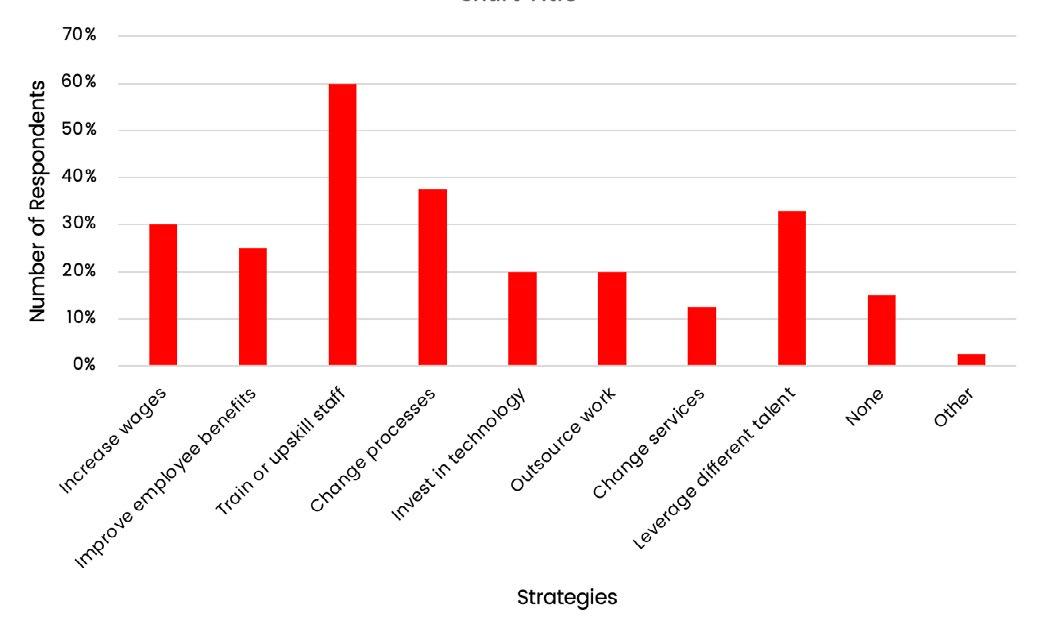
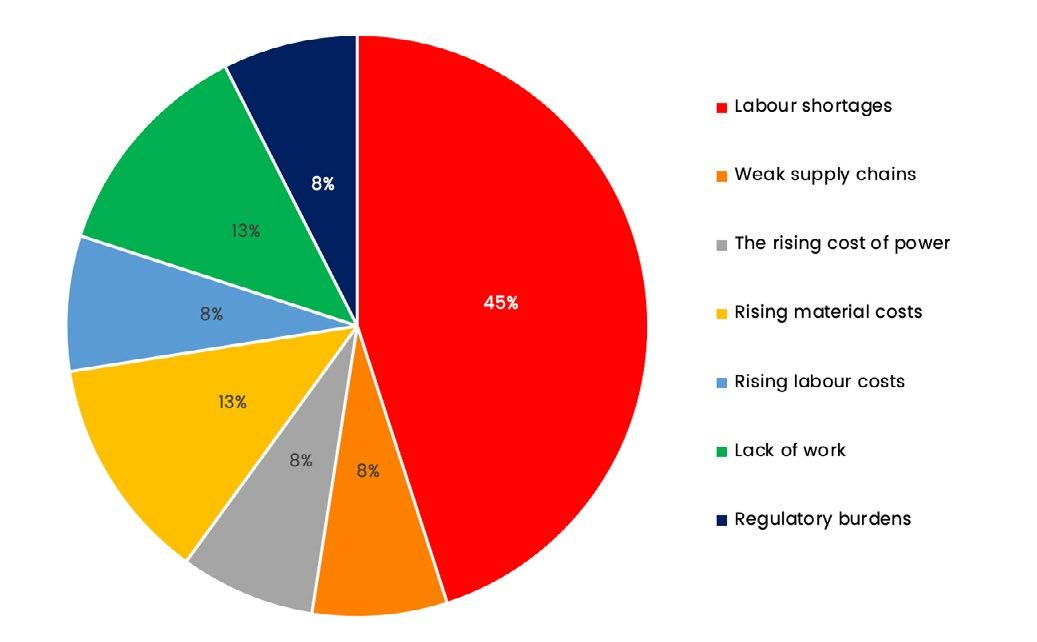
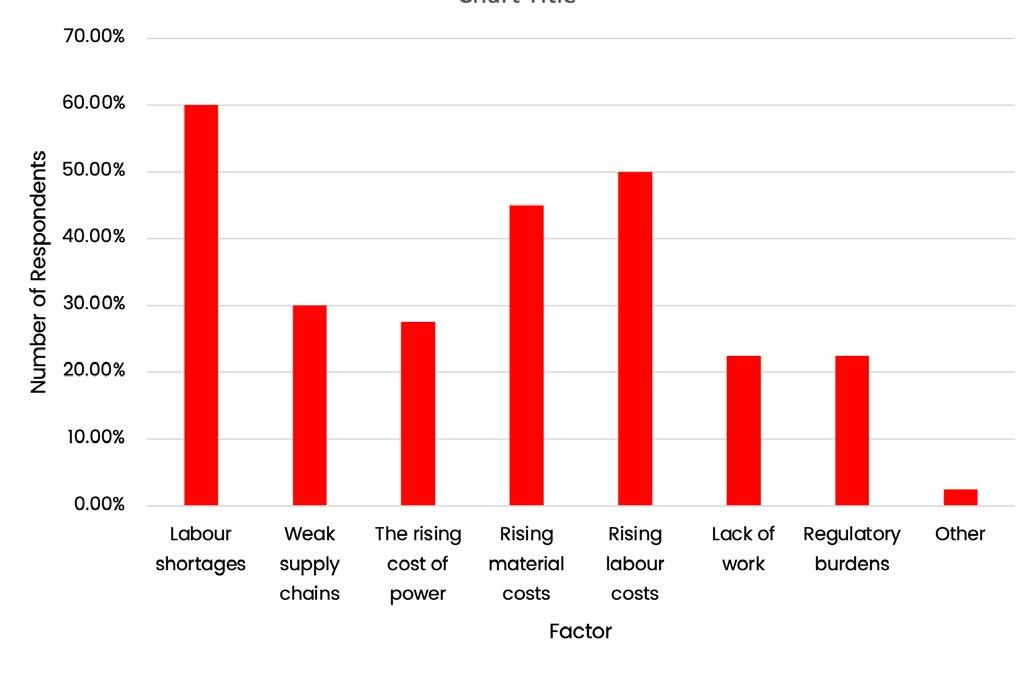
“With a considerable volume of work being onshored and a greater sentiment in the market to ‘buy local’, Australian fabrication companies are so strapped for skilled welders that they are operating well below capacity. They are being forced to turn down jobs because they simply don’t have the manpower to complete the work,” said Crittenden.
“How then, will Australian fabricators cope with the influx of work required to make the Federal Government’s renewable energy revolution reality?”
The Federal Government has legislated emissions reductions targets of 43% (on 2005 levels) by 2030 and net zero by 2050. These targets will necessitate the construction of new infrastructure on a massive scale.
Australia’s existing renewable energy generation of 64GW is forecast to grow to over 218GW by 2050. This will comprise 90GW of wind, 39GW of solar, 18.7GW of water, and 35.9GW of battery storage. It is expected that over 11,000 wind towers will need to be produced, each requiring 500 tonnes of plate steel for onshore towers, or 750 tonnes for offshore wind towers. To connect all this new generation to consumers, AEMO estimates more than 10,000km of new transmission lines and 25,000 transmission towers (at 30 to 60 tonnes of steel per tower) will need to be constructed.
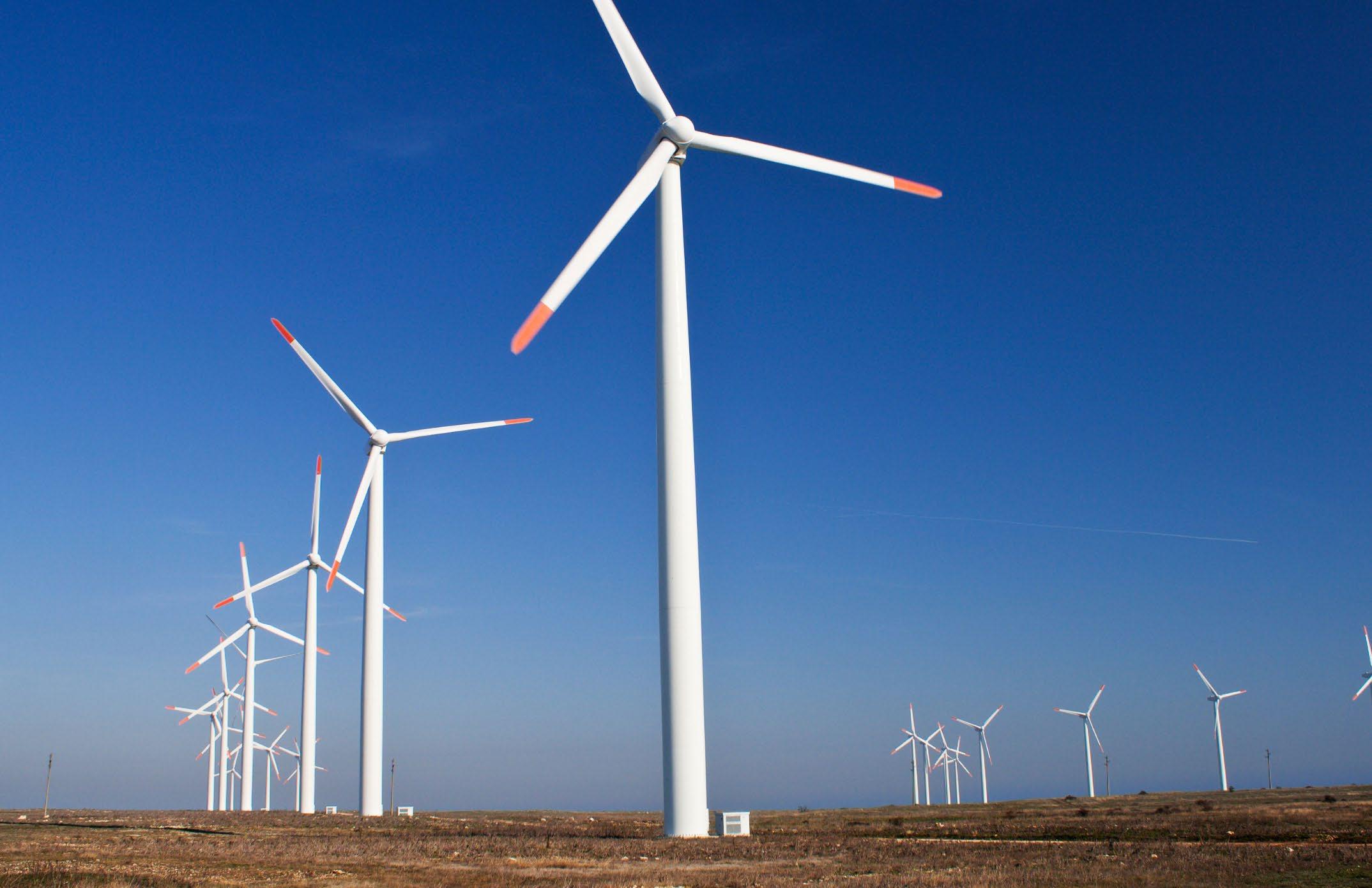
“All this the renewable energy infrastructure will require a veritable army of skilled workers, including welders,” said Crittenden. “Australia will have a shortfall of at least 70,000 welders by 2030.”
And yet, 45% of survey respondents (compared to 47% in 2022) already have a pipeline of work that extends for six months or longer—this protracted pipeline is necessary in the face of ongoing skills shortages. Another 33% of respondents have a pipeline of work that extends between three and six months. This is a marked increase on Weld Australia’s 2020 member survey results; the most common answers were less than one month (at 28%), one month (19%), and two months (16%).
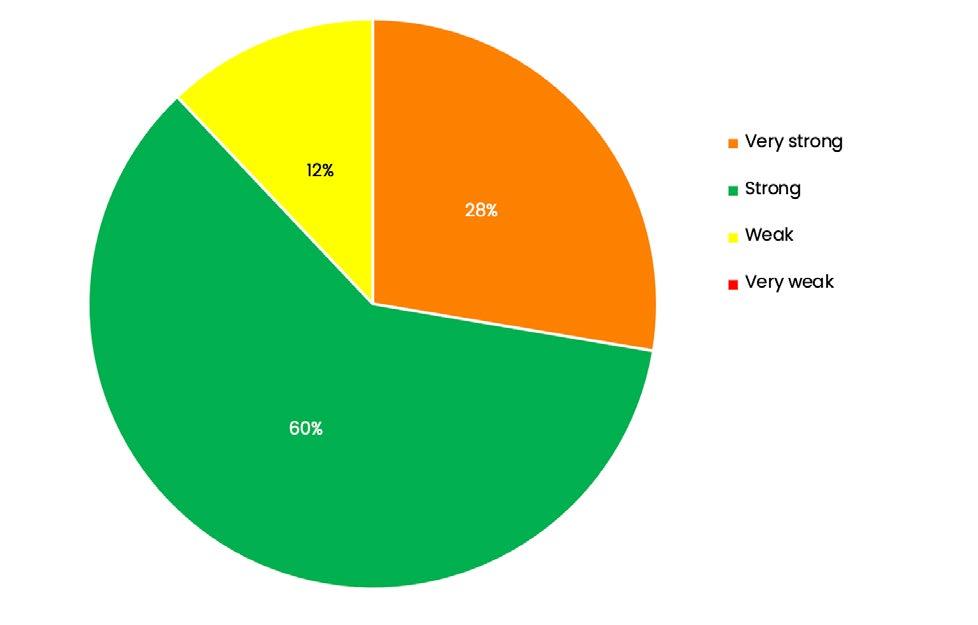
“While our governments can wish, and hope, and make public pledges about Australia’s transition to renewable energy, at the moment, we simply do not have the
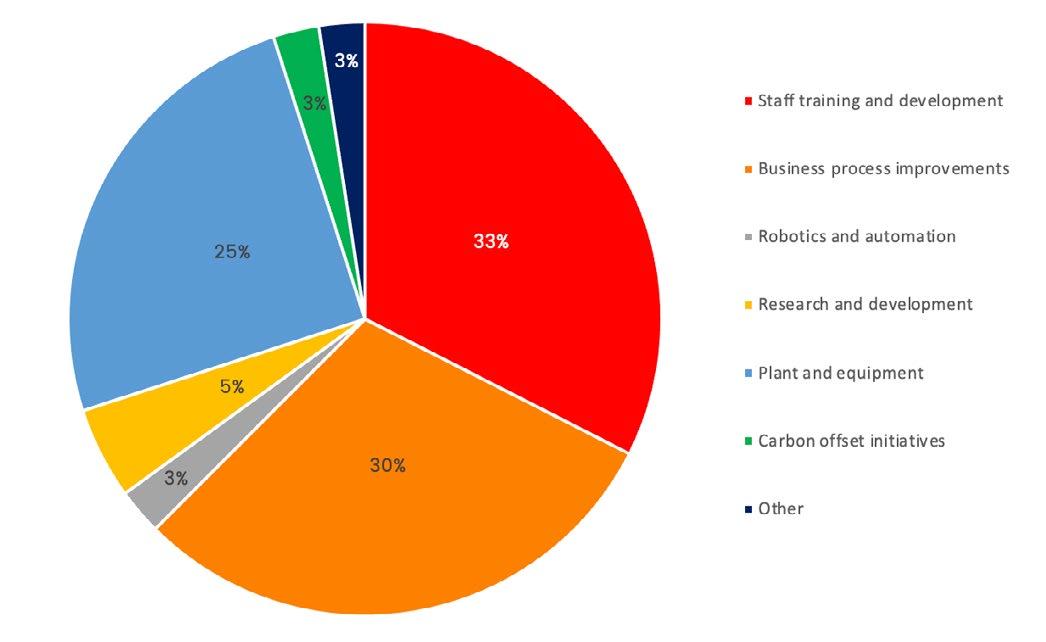
“
Our 2023 Member Survey indicates that labour shortages, and the rising cost of materials, energy and labour remain high on the agenda for the welding industry.”
sovereign manufacturing capability to make this a reality,” said Crittenden.
“According to the results of our survey, at 62%, the majority of the Australian welding industry supports the Government’s carbon emissions reduction targets. However, 75% of the welding and fabrication industry believes that Australia’s governments are not doing anywhere near enough to support industry in achieving these targets. Our governments will need to consider policy and funding opportunities, reduce red tape and regulatory barriers, and support local investment to enable the renewable energy transition.”
“Without a massive investment in fabrication and steelmaking facilities, skills and training in each state, and real, practical support for local industry, Australia’s renewable energy revolution will simply not be a reality,” said Crittenden.

In the meantime, the welding industry is taking steps to try to overcome these labour shortages—without government support. 60% of respondents indicated that they are training or upskilling their existing staff, another 55% are either increasing wages or improving employee benefits, and 32% are leveraging different talent pools, such as apprentices, females and prisoners. Another 57% are either investing in automation and technology, or changing their operational processes.
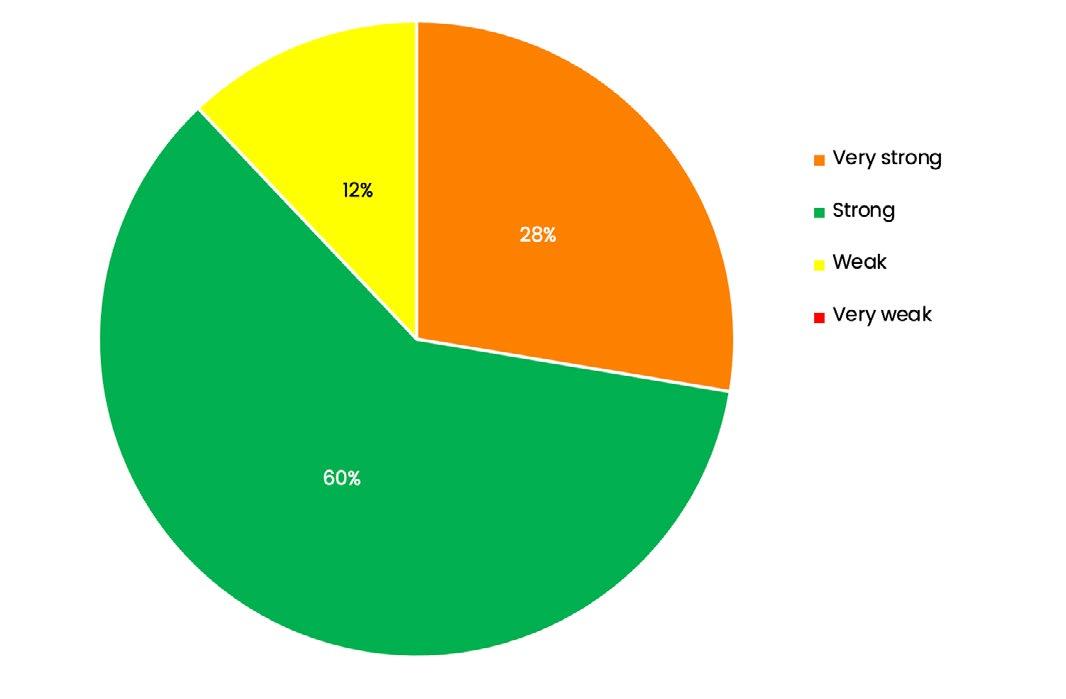
Given these figures, it is little surprise that investment priorities for 2023 include staff training and development
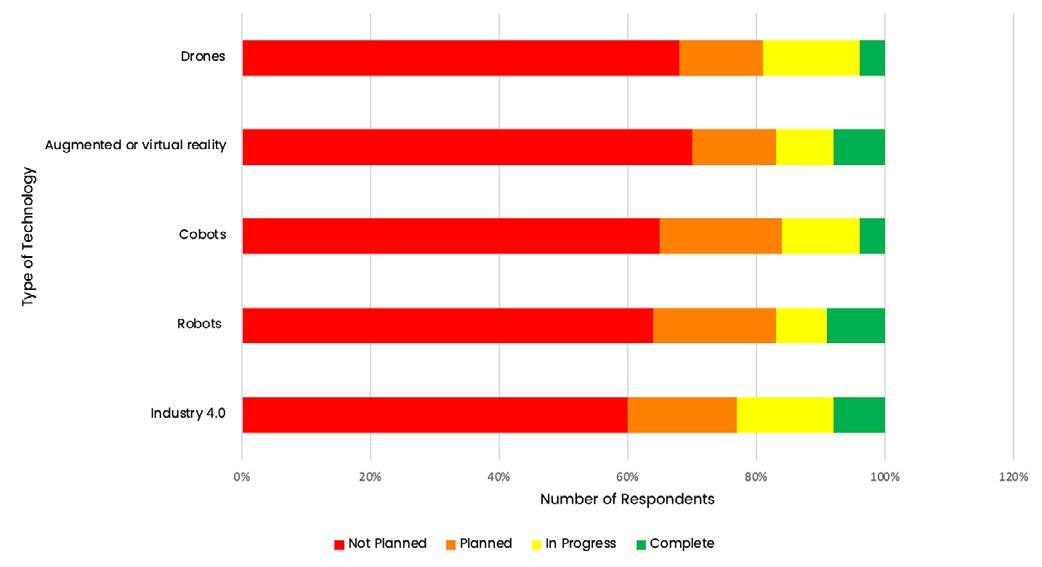
(32%), business process improvements (30%) and plant and equipment (25%). Some companies are also looking to advanced welding technology to help overcome skilled labour shortages. The types of technology that the welding industry has planned, in progress or completed include:
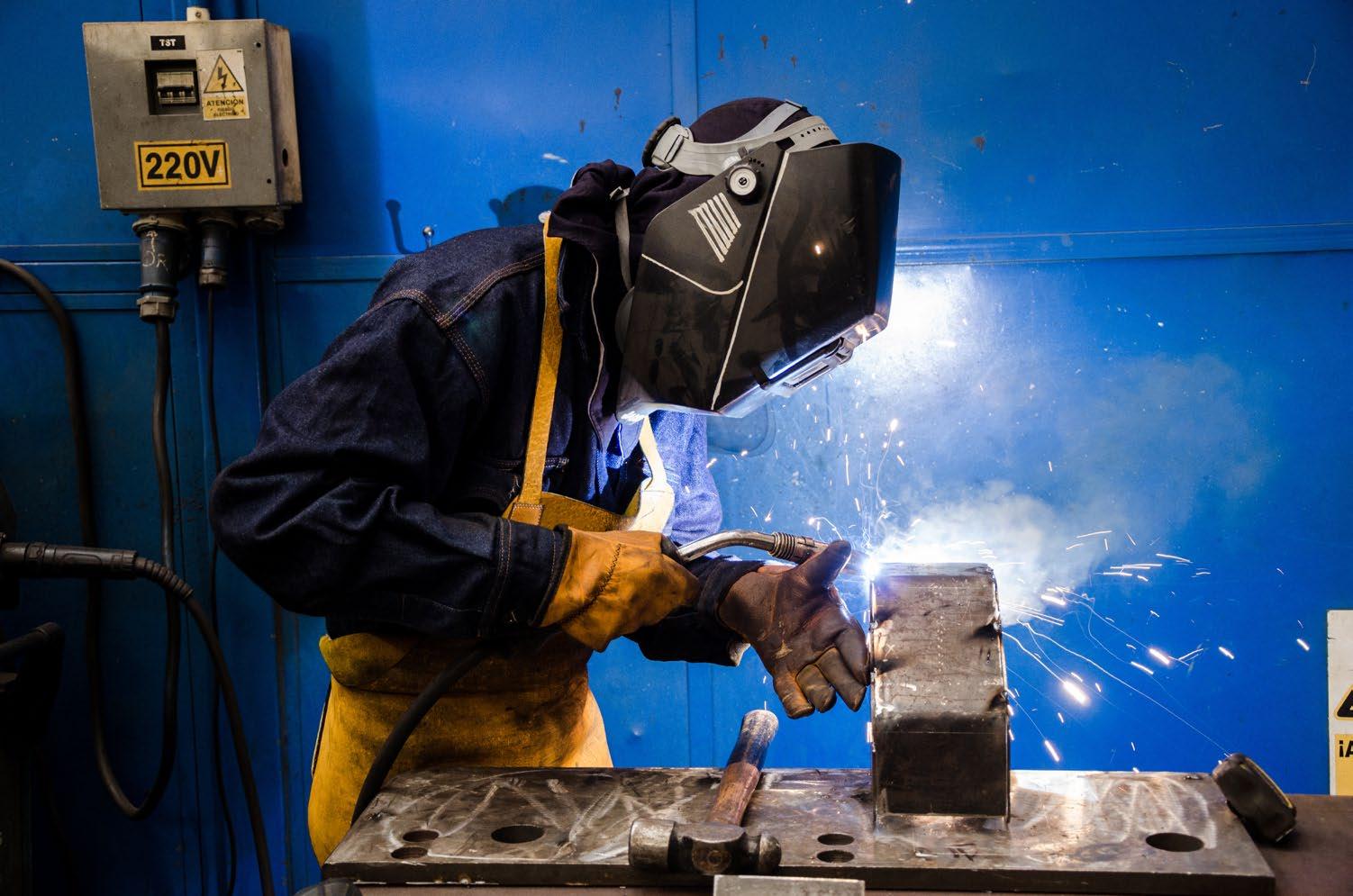
• Industry 4.0 (40%; up from 25% in 2022)
• Robots (36%; up from 28%)
• Cobots (35%; up from 28%)
• Augmented or virtual reality (30%; not reported in 2022)
• Drones (32%; not reported in 2022)
The majority of respondents (at 37%) will not be looking to skilled migrants to help overcome labour shortages, believing that immigration limits for skilled welders should not be increased. While 28% believe that immigration limits should be increased on a temporary basis for short-term contracts.
The welding industry strongly supports investment into TAFE to help combat labour shortages; 21% support free TAFE for apprentices, 14% support increased funding to
upgrade TAFE facilities, and 64% support both options.
The welding industry is also investing in its own sustainability performance and credentials, and has made significant headway in the last 12 months. Some measures include:

• Installing LED or sensor lighting (80%; up from 53% in 2022)
• Waste reduction programs (78%; up from 46% in 2022)
• Recycling, upcycing and repurposing programs (75%; up from 46% in 2022)
• Implementing a net zero carbon plan (50%; up from 13% in 2022).
Australia’s welding industry is also concerned about rising labour costs and rising material costs, with 50% and 45% (respectively) of respondents indicating that they could inhibit their business growth this year. Only 47% of respondents indicated that their gross profit margin had increased over the last 12 months to help cover these rising overheads. Alarmingly, the welding industry expects these overheads to continue to rise this year, with 82% expecting even higher materials prices and 85% expecting even higher energy prices.
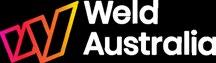
TECHNOLOGY-RICH WELDER TRAINING ACROSS THE DITCH
How ATNZ is engineering a brighter future with the help of augmented reality welding simulators
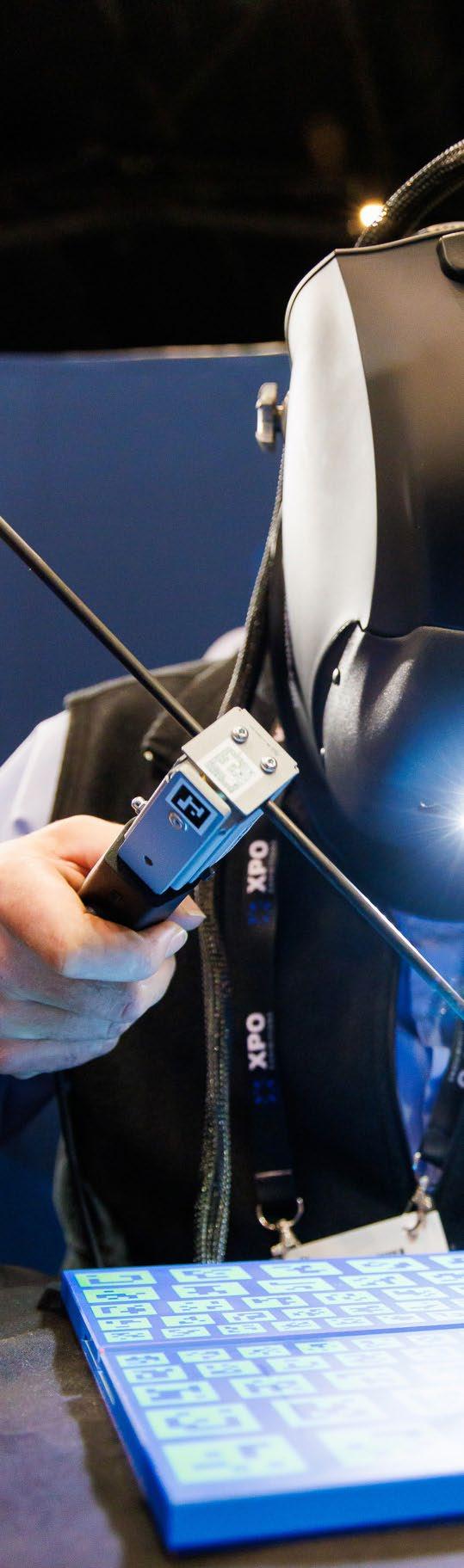
Originally established in Hawkes Bay, New Zealand, ATNZ has grown into a national organisation, employing the largest number of apprentices in mechanical engineering and related fields across the country. With a focus on high-quality apprenticeships and industry-relevant training, ATNZ has made technology an integral part of their learning approach. By incorporating cutting-edge Soldamatic welding simulators, ATNZ is leveraging augmented reality to enhance apprentices’ skills and confidence, all within a safe environment.
ATNZ—short for Apprentice Training
New Zealand—was created as a trust in 1999 to provide dedicated and focused training for apprentices in the engineering and manufacturing industries.
From humble origins in Hawkes Bay, ATNZ expanded quickly to become a national organisation and is now New Zealand’s largest employer of apprentices in mechanical engineering and related industries.
According to Tim Wilson (Chief Executive Officer, ATNZ), “We are New Zealand’s group training scheme for the engineering sector. ATNZ is very similar to the Group Training Organisation model that operates in Australia: we employ the apprentice, and then place them with a workshop for training. We provide support to the apprentice, but their learning is primarily through on-the-job training. We undertake the assessment and award the qualification at the end.”
Today, ATNZ boasts a national footprint, with 410 apprentices placed throughout 170 companies across New Zealand.
The ATNZ team is focused on providing high-quality apprenticeships and industry-relevant training programs to bring a skilled labour force to life. ATNZ provides managed apprenticeships in:
• Engineering fabrication
• Mechanical engineering
• Refrigeration and air conditioning
• Mechanical building services
Technology Enhances Training
Wilson, who has a background in the maritime industry, firmly believes in the benefits of using technology to enhance training.
“When we were creating a longterm strategy for ATNZ, it was really important to the Board and myself that we were technology driven. We
wanted to leverage technology in our learning as much as we could.”
“About two years ago, we undertook an evaluation of what technology was available in engineering. We identified welding as one of the areas in which technology would be really useful for training,” Wilson said.
“We did a quite detailed review of what welding simulators were available in the market and reached the conclusion that the Soldamatic was the best for we wanted to do. We could see that the Soldamatic would work best for both brand new entrants to the welding industry, and for advanced technicians who needed to refine their skills or pick up new skills.”
Soldamatics are cutting-edge welder training simulators that leverage the power of augmented reality. Augmented and virtual reality training systems are student-focused,
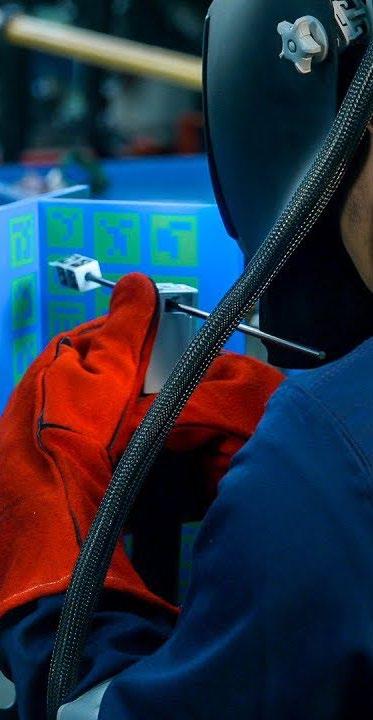
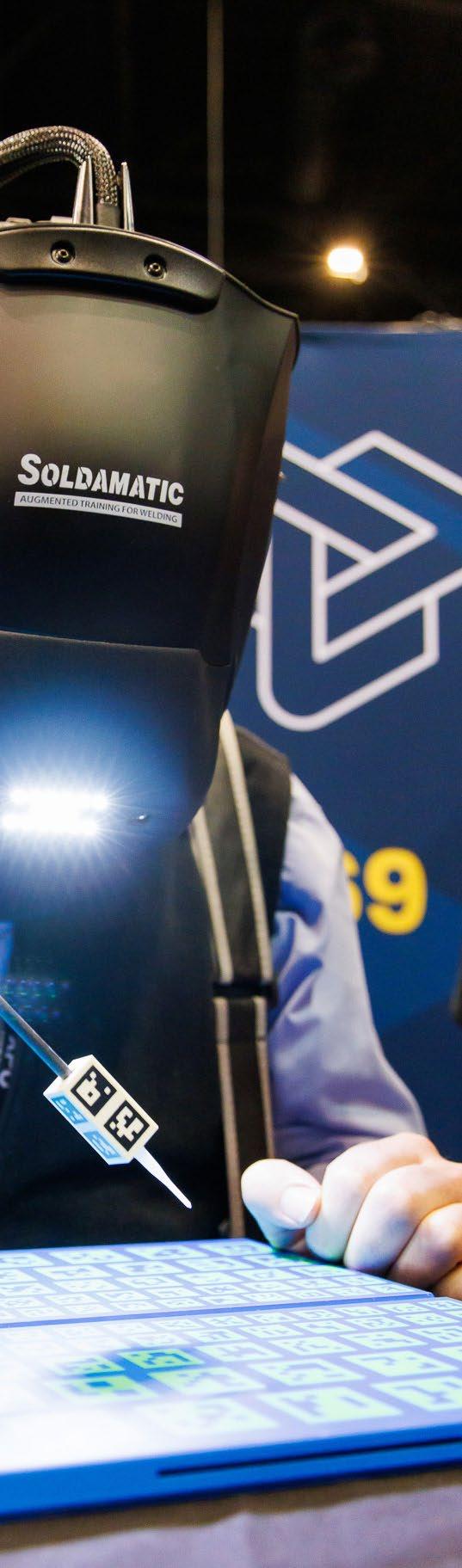
allowing individual students to progress at their own pace. Welding apprentices learn and understand welding procedures and techniques through a more interactive training method, gaining hands-on experience in a controlled, safe environment.
With zero risks involved, apprentices can respond to realistic scenarios without pressure or fear of injury. Augmented and virtual reality training is enabling future welders to acquire the skills and the self-confidence they need before moving into real-world workshops.
The new paradigm in vocational, technical and industrial training, augmented and virtual reality training technologies are proven to be efficient and environmentally sustainable, offering significantly reduced CO2 emissions when compared to traditional welding training and slashing consumable usage. These systems allow training centres and
“
Most critically, we have invested in the Soldamatics to improve the welding skill of our apprentices and ensure they are more confident in some of the techniques they may not get to practice every day in their workplace.”
industry to save costs and time whilst training professional welders.
ATNZ purchased six Soldamatic welding simulators from Weld Australia. The devices are being embedded throughout ATNZ’s operations, helping to equip budding welders with the practical skills necessary to grow their confidence.
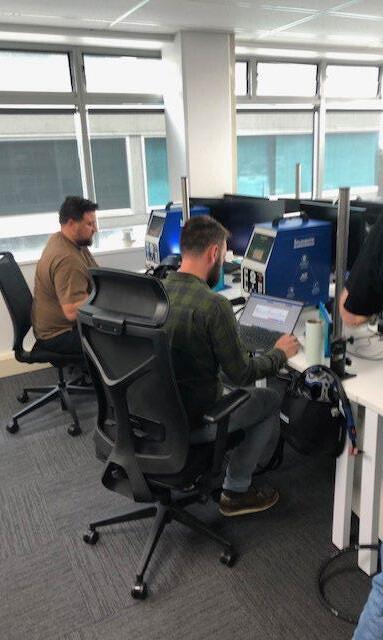
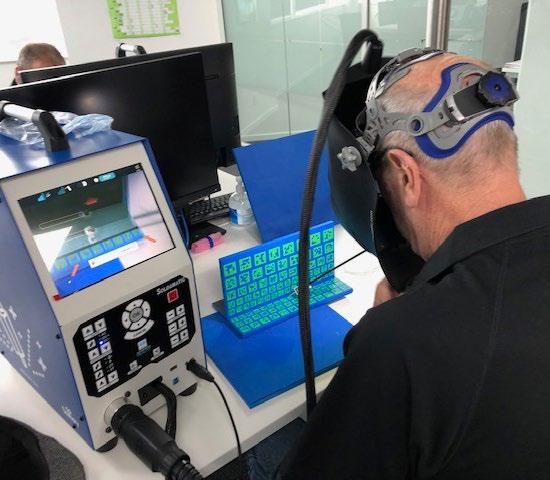
“One of its biggest benefits is that our trainers can load the simulators into a van and transport them anywhere. The mobility of the Soldamatics is a really critical part of why we’ve chosen to invest in them,” Wilson said.
As Wilson explained, ATNZ intends to use the Soldamatic technology for four key purposes. “First, and most critically, we have invested in the Soldamatics to improve the welding skill of our apprentices and ensure they are more confident in some of the techniques they may not get to practice every day in their workplace,” said Wilson.
“Secondly, in New Zealand, a dedicated welding qualification has just been reintroduced. About five to six years ago, New Zealand discontinued welding
qualifications and subsumed them into the engineering apprenticeships. However, we have recognised that there is a need for specialist welders and reintroduced the qualifications. So, the simulators will be used to help welders successfully gain these qualifications.”
“The third thing we plan to use the Soldamatics for is our preemployment programs. Similar to Australia, we have massive skill shortages for welders and fabricators. For a number of reasons, a lot of prospective learners don’t consider welding as a career, or haven’t had exposure to welding. From our experience to date, for people who have never been exposed to welding before, some pre-employment training makes the transition into the noise and heat of a real welding workshop much easier and manageable. It will help with the pipeline into the welding profession.”
“Finally, we plan to use the Soldamatics to promote welding and engineering in schools and at career fairs,” said WIlson.
Teachers and students alike have already begun reporting on the vast benefits of the Soldamatic
technology. “We had some cynics that weren’t sure about the simulators. All our teachers are skilled welders, and were a bit skeptical of technology to begin with. But they all came away from the teacher training seeing the value of the technology, and how it could be used to benefit students,” Wilson said.
Working with Weld Australia to bring the Technology to Life
Weld Australia is working closely with ATNZ to bring this technology to life within their organisations.
Wilson said Weld Australia’s consultative approach allowed ATNZ to implement the technology with ease. “Working with Weld Australia has been really good—it’s been a really positive experience. All of Weld Australia’s team members have been really responsive and great to work with. We’re looking forward to an ongoing strategic relationship with Weld Australia, and working together on other programs and initiatives.”
Further Information
For further information, visit: atnz.org.nz
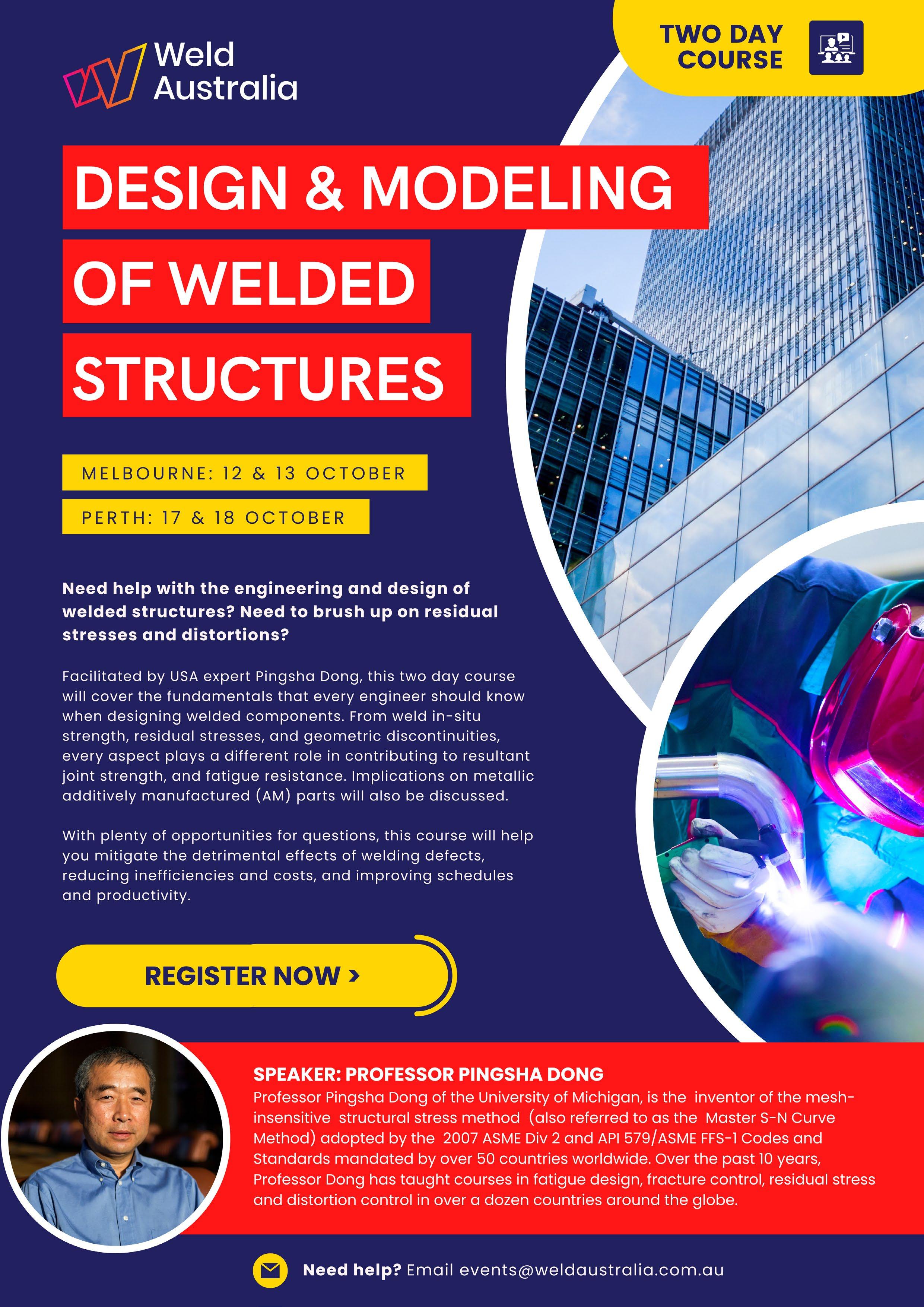
NURTURING THE FUTURE OF SHIPBUILDING
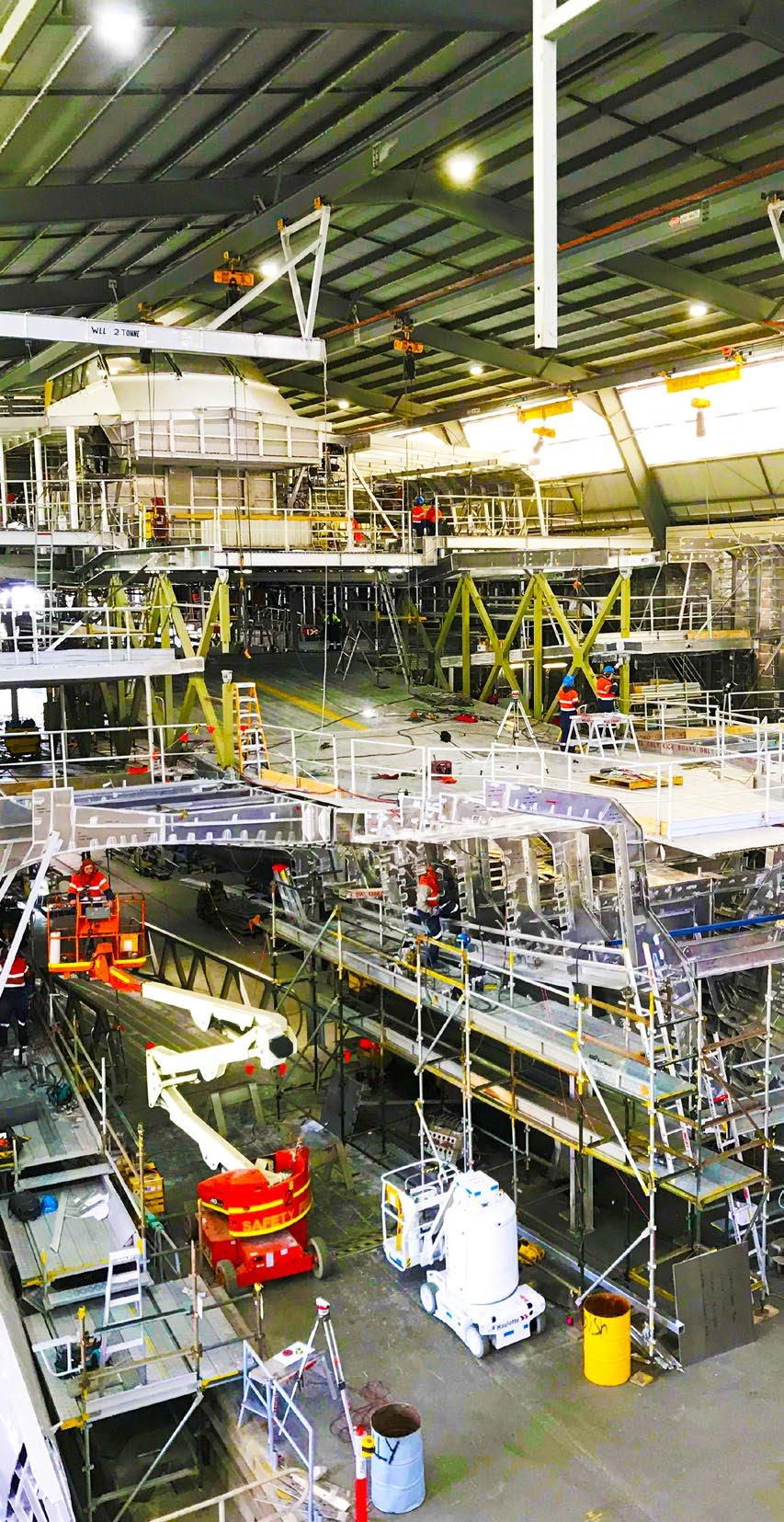
Inside Incat’s Masterful Fusion of Innovation, Education and Dedication
Incat is a leader in the shipbuilding industry with their fuelefficient, eco-conscious, lightweight ferry solutions. What truly sets Incat apart is their dedication to the art of aluminum welding—a challenging feat that demands utmost precision and expertise. Incat prioritises training and education, running an innovative apprenticeship program, investing heavily in their welding workforce, and collaborating with local schools and TAFEs to raise awareness of career opportunities in manufacturing and engineering.
Firmly cemented as experts in cutting edge environmentally friendly vessels, Weld Australia member Incat provides lightweight ship solutions for ferry operators and special service providers. From fast, flexible and efficient vehicle-passenger ferries to crew ships and dynamic platforms, Incat sets the global benchmark in aluminium ship technology.
Continuing the emphasis on ecooperations and fuel efficiency Incat has developed lightweight, environmentally friendly fuel-efficient ships carrying heavier vehicle loads than ever before and at the lowest operational costs. With the focus now firmly on all-electric, zero-emission ferries, Incat is building the world’s largest electric vehicle and passenger ferry. It will have capacity for 2,100 passengers and crew, 225 cars and a massive Duty Free Shop of over 2,000m2 on one level. The battery installation will be four times greater than any other marine vessel in the world.
Incat’s shipyard is on Prince of Wales Bay at Derwent Park near Hobart,
Tasmania, Australia. Their 70,000m2 facility incorporates four building halls, extensive wharf facilities, a slipway and two dry-dock areas. Incat boasts innovative production facilities to construct, launch and deliver small craft through to larger ships of 150m length and of panamax beam.
Incat takes ownership of the customer’s specific needs ensuring on-time delivery of the right ship for the right job. A reputation for quality and excellence in production is supported by an experienced and dedicated workforce.
High Quality, Intricate Aluminium Welding
With Incat specialising in the manufacture of aluminium vessels, their team are experts in welding this lightweight, yet incredibly strong and durable, material. This is no mean feat—learning how to weld aluminium is challenging, requiring care, precision and specialised equipment.
For instance, aluminum has a low melting point, making it more likely to warp, crack, and break during
welding. In addition, when welding aluminum, magnesium oxides can collect at the weld on the base of the material, leading to discoloration.
According to Incat’s CEO, Tim Burnell, “Incat’s welding process are not hugely automated. We have some machines that perform double-sided automated welding, which we actually developed in-house. Our welding and fabrication processes are very labour intensive and this is unlikely to change—the quality and the intricacy of our welding necessitates a very hands-on process,” said Burnell.
“Aluminium welding requires a different skill set compared to carbon steel welding. It requires specialised training, particularly in the maritime industry.”
Like any thriving business, a core of dedicated and loyal staff can be found at the centre of Incat’s success. Many team members’ experience stretches back over two decades across a range of trades.
“We still have people working for us who were apprentices with us 25
years ago—they have honed their welding skills over time and, today, deliver superior quality workmanship on each and every Incat vessel.”
“The expert skills of our team members enable us to deliver a quality product that customers appreciate—it is the reason why so much of our work is repeat business. One of our customers has been with us for over 25 years, and has ordered nine vessels,” said Burnell.
Although Incat builds ships in Tasmania, they operate globally maintaining and delivering vessels, which provides an opportunity for experienced tradespeople to work overseas. Incat welders, fabricators and electronics staff recently travelled to Trinidad and Tobago, Spain and South Korea, working and expanding their skills in a variety of unique environments. The company understands the strength of working overseas in new environments.
Workforce Training Excellence
Incat took out Weld Australia’s 2022 Welding Excellence Award for Training
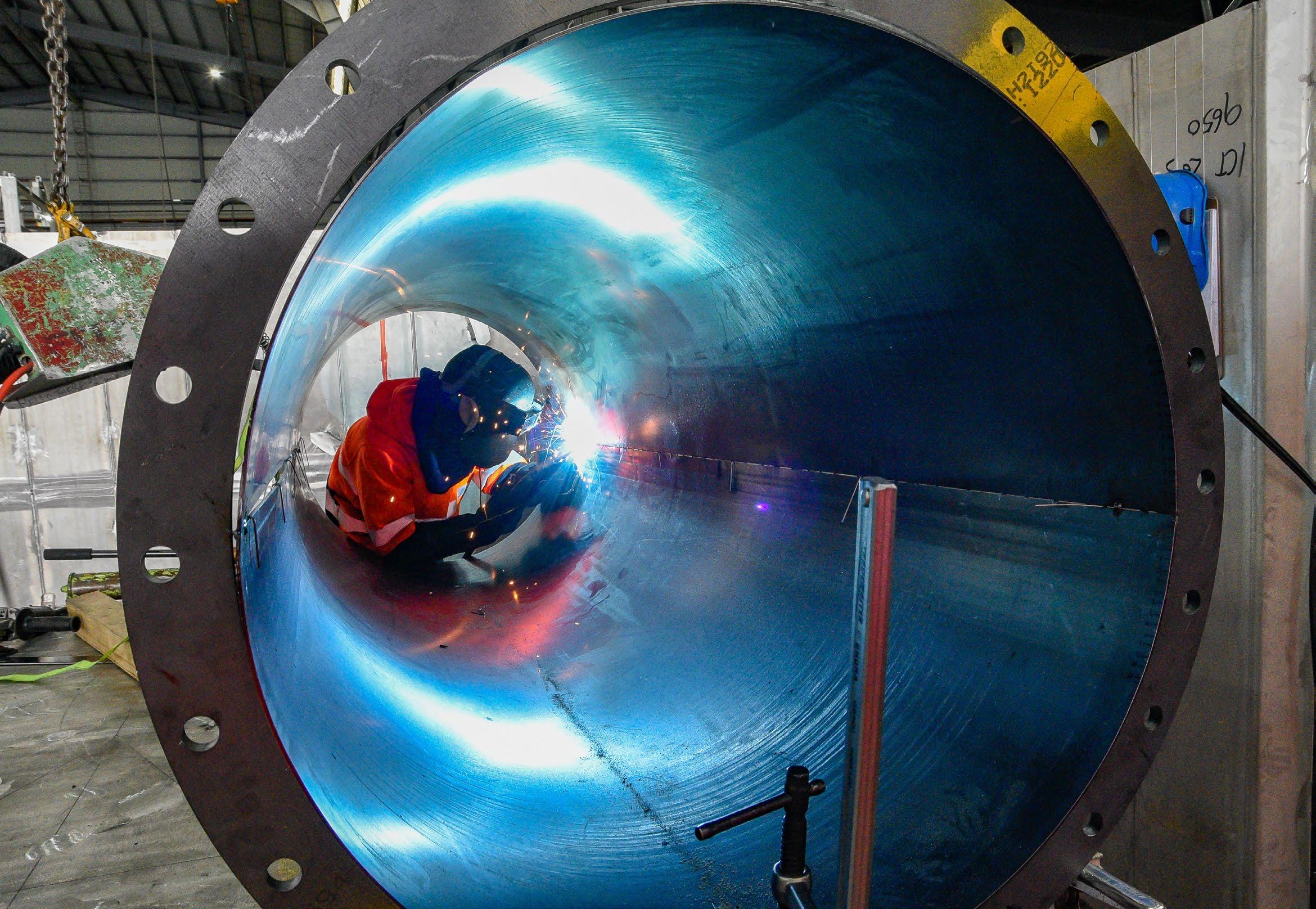
and Education—Organisation. Incat heavily invests in the future of its welding workforce. Training is a core part of Incat’s success. The company has a small, yet highly effective training team whose core focus is providing accredited training.
The key areas of Incat’s training include:
• Apprentice onboarding
• Supporting apprentice on job and off job training
• Developing and delivering post trade training for qualified personnel
• Providing training to enable external certifications
• Ongoing work health and safety
In the 2021-2022 financial year, Incat 900 hours of training per month. A significant percentage of this training was delivered by the Incat’s in-house training team. Their partnerships with training providers and regulators also ensure that the company can provide effective localised, targeted training and assessment in specialist areas with minimal impact to the business.
“
The expert skills of our team members enable us to deliver a quality product that customers appreciate—it is the reason why so much of our work is repeat business. One of our customers has been with us for over 25 years, and has ordered nine vessels.”
An Innovative Apprenticeship Program
Incat’s apprentice program has two intakes of 15 apprentices per annum, with upwards of 70 apprentices in training across four separate trades at any one time. Incat encourages everyone to apply for their apprenticeship program; the current apprentice mix includes two mature apprentices aged over 45 years, two Indigenous and two female apprentices.
Apprentice rotation is managed by a dedicated apprentice supervisor to ensure apprentices receive a broad cross-section of skills. The responsibility for this role entails tracking profiling progression, and linking on the job training requirements to align with off the job training. Incat has mapped sections of the ship building process to specific competencies of each apprenticeship or traineeship.
This forms the baseline for charting each apprentice or trainee’s individual journey through their training, ensuring no element of on-the-job training is missed. Competency is not signed off until the team leader agrees the apprentice has met the required level of competency in the workplace.
Across the company, Incat apprentices collectively spend around 1,000 hours per month attending off the job training opportunities, where they develop important skills relevant to their line of work.
Incat has a strong relationship with TasTAFE. There is a purpose-built TAFE campus adjacent to the shipyard, which offers a unique training advantage for apprentices. It means Australia’s future workforce gets a rare insight into the world’s best practice aluminium shipbuilding operation.
TasTAFE teachers also gain access to a range of industry opportunities to further their development. The two-way communication focus means trainers learn about modifications or changes in welding techniques and technology implemented during the construction phase of Incat vessels in a steadfast manner. Together, this ensures apprentices gain valuable experience and knowledge of various aspects of shipbuilding.
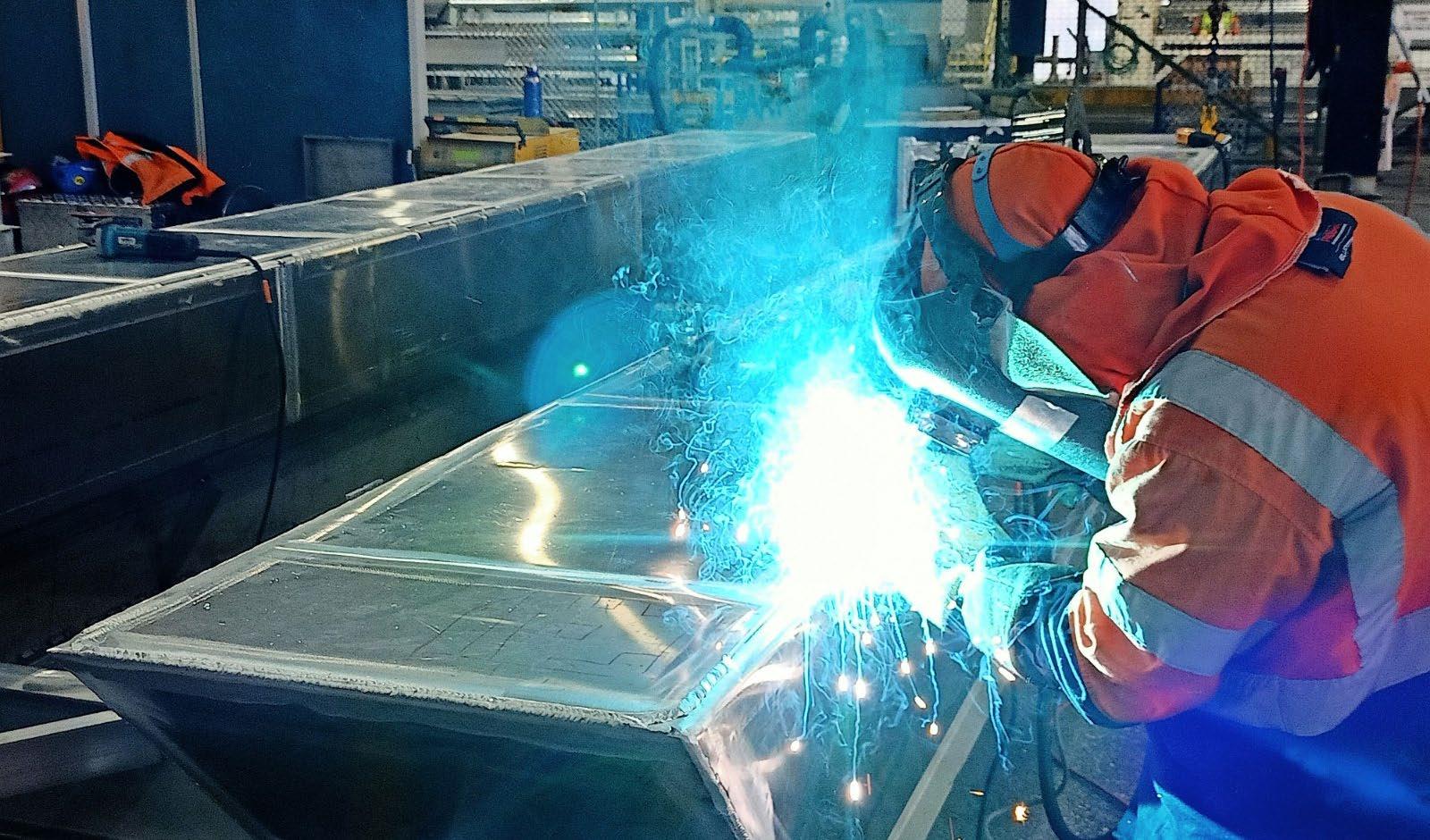
Finally, Incat apprentices graduate into employment, with ongoing training, throughout the shipyard. Importantly, there is an ongoing safety and skills on-the-job training across the workforce, which is crucial for new and longer-term employees to ensure workplace standards are met across the range of skill sets.
Strengthening the School to Employment Transition
Incat is working with schools and colleges in their local region to raise awareness of the career opportunities which can result from undertaking a manufacturing or engineering apprenticeship. The company regularly engages with vocational students and teachers, hosting information sessions and answering any questions.
Incat has worked with the Jordan River Learning Federation, hosting a ‘try a trade’ program for students interested in an engineering career. The program commenced with a tour of the Incat Shipyard and then two classes where Incat’s training team worked with the students in the school facility. Incat has developed a series of exercises that include an introduction to MIG welding in which the students made a set of drink coasters from aluminium.
Incat has also developed a first year apprentice support
network where a fourth year apprentice acts as a big brother or sister. Fourth year apprentices must complete the competency requirements for ‘Assist in the Provision of on-the-Job Training’, which develops their leadership capabilities. Placing new apprentices with more experienced apprentices has resulted in the older apprentices enthusiastically taking ownership and showing the new apprentices the ropes.
Incat has observed that apprentices are settling into the workplace more quickly and are more comfortable raising concerns or issues when they have the support of an older apprentice.
The Welder Non-Trades Program
In 2018, Incat identified job applicants who demonstrated high level vocational skills, or came with overseas welding qualifications, but were missing opportunities to undertake apprenticeships in welding and fabrication. So that they could provide employment and training opportunities to those within this demographic, Incat developed their Welder Non-Trades (NT) Program.
The Welder NT program is comprised of 21 Enterprise Units of Competence which are internally delivered over a five-month period. The program is delivered to small groups of four to six trainees. This ensures that Incat can provide adequate attention and support to each of the trainees. Successful completion of the course results in a DNV certification process.
To date 29, trainees have completed this program. Three of those have transitioned into an apprenticeship and completed MEM30305 Certificate III Engineering –Fabrication Trade.
For further information about Incat and their capabilities, simply visit: incat.com.au
King of the Pack Wins Training and Education Award
Simon King (Technical Training Officer at Incat) took out the 2022 Weld Australia Training And Education—Teacher (Tasmania) Award.
With 26 years in aluminium and steel welding, King holds a Certificate III in Engineering Production, is an International Welding Inspector and a Det Norske Veritas (DNV) Certified Welder, which he has maintained since 2010. King’s DNV certifications make him the perfect candidate to prepare Incat’s qualified welders for their own DNV certification assessments.
King brings a wide variety of experience to his technical training, having worked in a diverse range of settings and roles, including:
• Fly-in fly-out on the BHP Billiton Olympic Dam project as a Shutdown Supervisor and as a welder
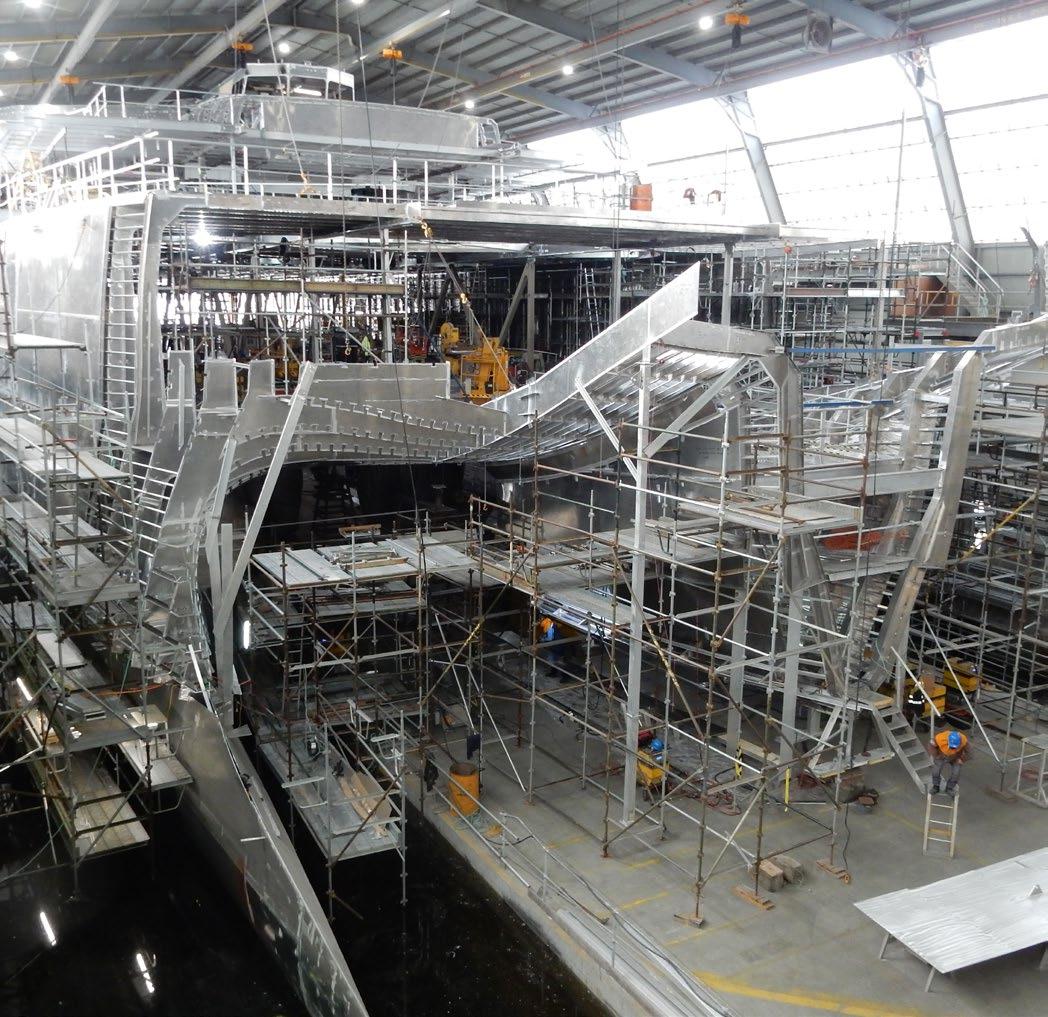
• Fly-in fly-out worker at the Newcrest Mining Cadia Gold Mine
• Caterpillar Elphinstone
• Impact Fertilser
• One Steel Reinforcing
• Richardson Devine Marine and North West Bay Ships involving aluminium and steel welding
According to King, “I absolutely love training and teaching and passing on my knowledge to first year apprentices and trainees and work colleagues.”
King is responsible for teaching Incat’s first year apprentices about the fundamentals of welding aluminium. Initially, he demonstrates the skill being taught and then breaks it down into smaller bite sized learning packages.
Once his apprentices have been assessed for their initial weld, and improvement opportunities have been identified, King provides targeted training.
Incat’s strong emphasis on training and professional growth means the candidate’s knowledge and skills quickly reach the required standard.
Since taking on the role of Technical Training Officer in February 2022, 97% of Incat’s DNV certification candidates have successfully complete their certification on their first attempt. This is testament to King’s skill and ability as a specialist trainer.
What is the International Institute of Welding (IIW)?
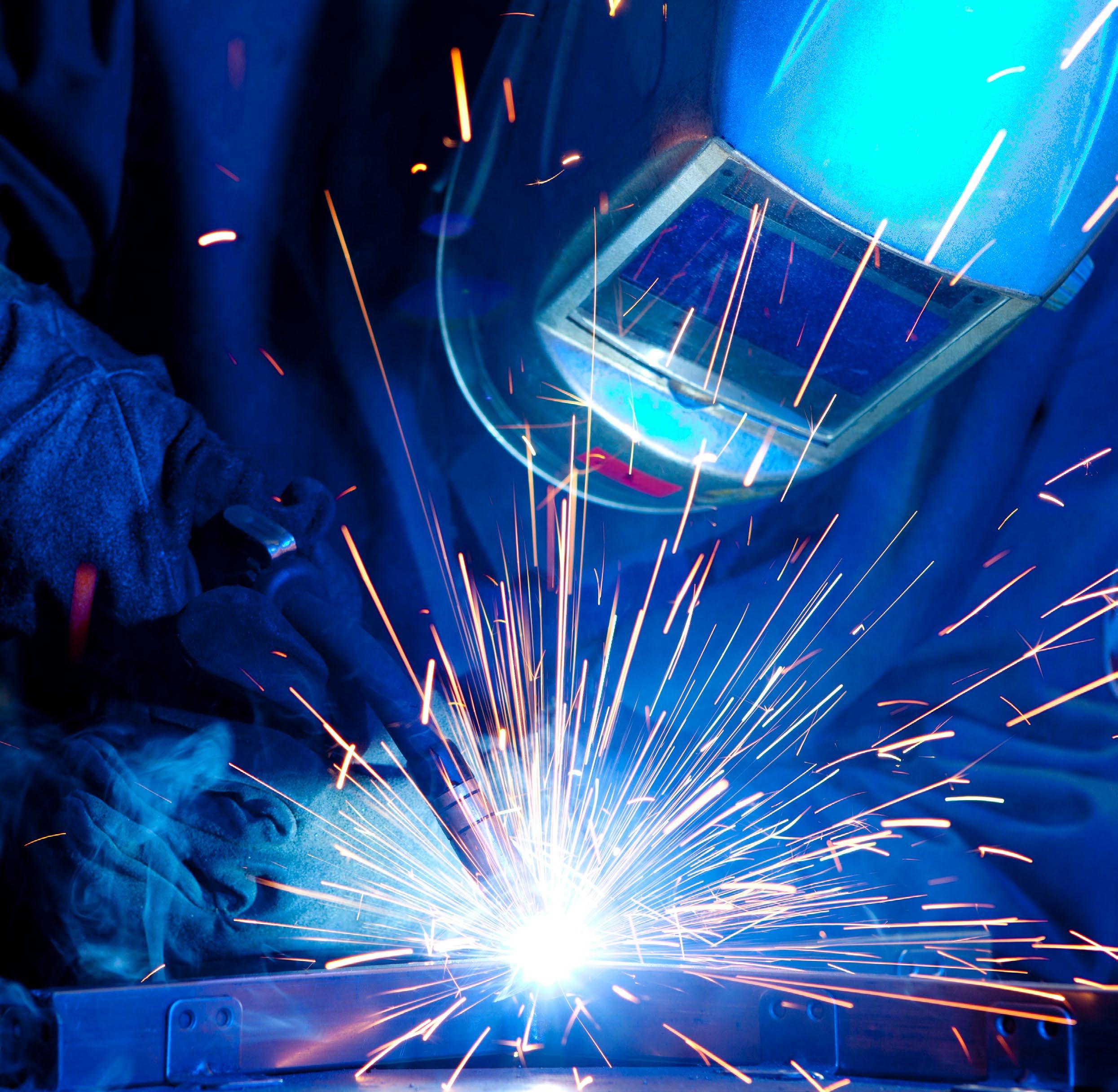

The International Institute of Welding (IIW) was founded in 1948 by the welding institutes or societies of 13 countries that considered it crucial to make more rapid scientific and technical progress possible on a global basis. Today, IIW membership comprises welding associations from 51 countries worldwide, with ever more nations continually indicating interest. IIW is recognised as the largest worldwide network and centre of reference for welding and allied joining technologies. It operates as the global body for the science and application of joining technologies, providing a forum for networking and knowledge exchange among scientists, researchers, industry and educators, and disseminating leading-edge information and best practices. The IIW is a standardising body approved by the International Organisation for Standardisation (ISO) to develop standards in the field of welding and related processes. IIW’s Technical Database constitutes the world’s largest online resource for welding information available today. The most outstanding papers are published in the prestigious journal Welding in the World registered in Thomson Reuters Science Citation Index® since 2009.
Weld Australia is the Australian representative member of the International Institute of Welding (IIW). For more information, visit: iiwelding.org
International Welding News IIW REPORT ON PRIORITIES OF THE GLOBAL WELDING INDUSTRY
The International Institute of Welding (IIW) recently asked industry representatives about their key priorities in the international welding space. IIW members, industry representatives, standard developers, training and research institutions, and global association representatives were involved in the survey. Interviewees were asked to rank the global issues affecting their industry.
Global Issues Affecting Industry
When asked what the most pressing global issues affecting your industry, respondents returned the following answers, ordered by relevance:
1. Lack of welders and welding personnel in general
2. Lack of interest in welding, specifically in young generations
3. Inhomogeneity of welding regulations and requirements, locally and globally
4. Health, safety, and environment
5. Limited support to manufacturing in developing countries.
According to the IIW, these answers underline the importance of developing knowledge of all aspects of welding. This knowledge has to be shared on a global scale and at all levels and to all personnel directly involved in the industry (from welders through to welding engineers), indirectly involved (standardisation and inspection bodies, design and purchasing departments, and so on) and the regulatory institutions.
How IIW Can Help Industry
Those interviewed also identified the areas of study where IIW can help the industry to deal with the technical issues affecting manufacturing:
1. Less conservative fatigue approach (optimised fatigue design to consider a probabilistic approach)
2. Characterisation of failures
3. Automation for production
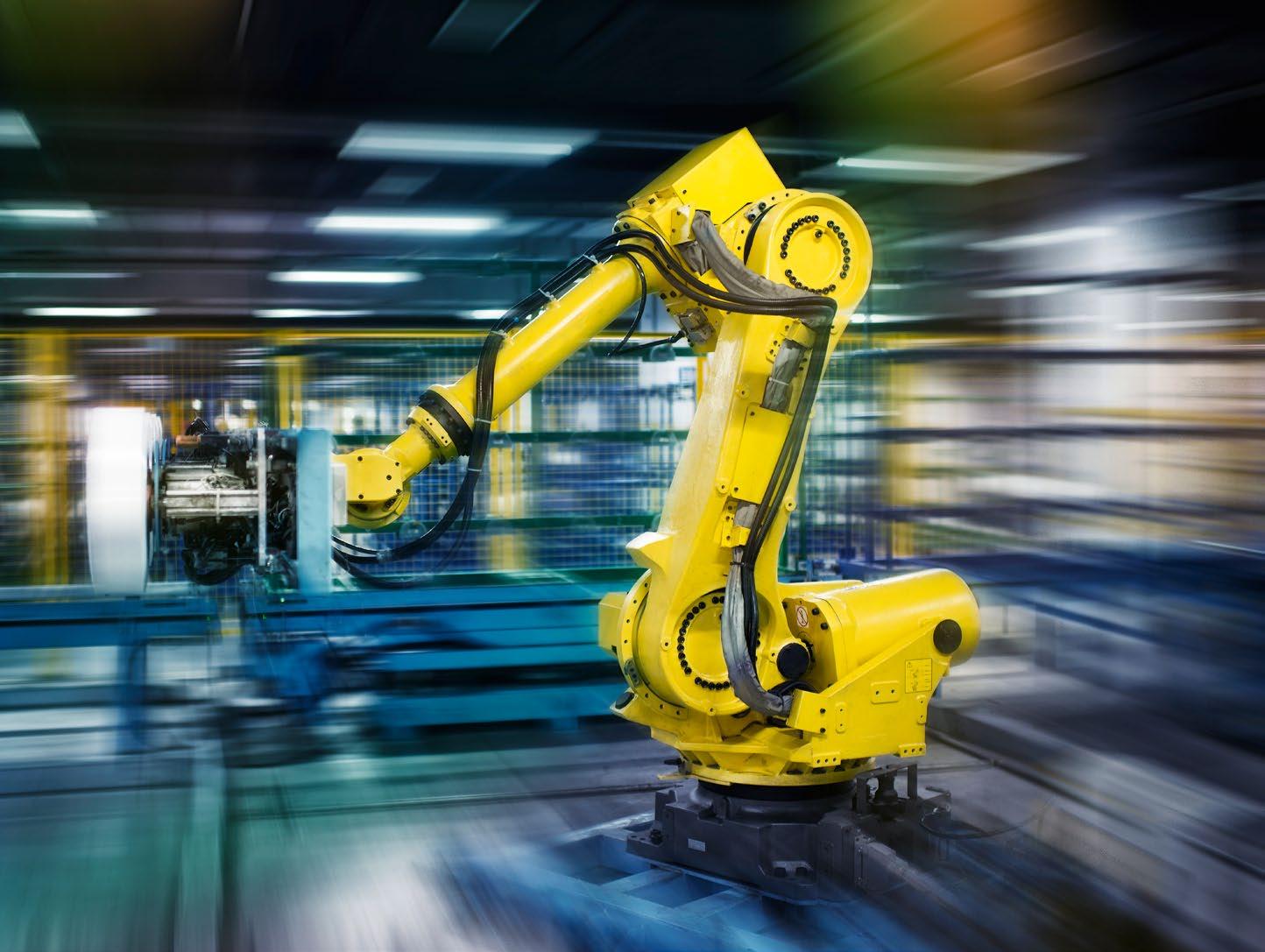
4. Joining of new materials and multi-materials
5. Sustainability (health and safety, cost, and quality assurance)
6. Energy transition industry (battery, lightweight, ITER)
7. Management and prediction of welding distortions
8. The virtual domain, including digitalisation, big data, artificial intelligence and digital twins.
The IIW continues to develop a suite of activities through working groups, focused on the areas of the highest impact and relevance:
• Efficient design of welded structures
• Behaviour of joints with new, high-performance materials
• Development of appropriate consumable materials and joining techniques
• Modern welding technologies, manufacturing processes, digitalisation and big data
• Welding personnel to meet industrial needs in a global market, technical and soft skills
• Healthier and safer welding environments
• Harmonisation of rules and requirements at the global level
• Increased training, qualification, certification and witnessing.
Q&A WITH A WELD AUSTRALIA MEMBER
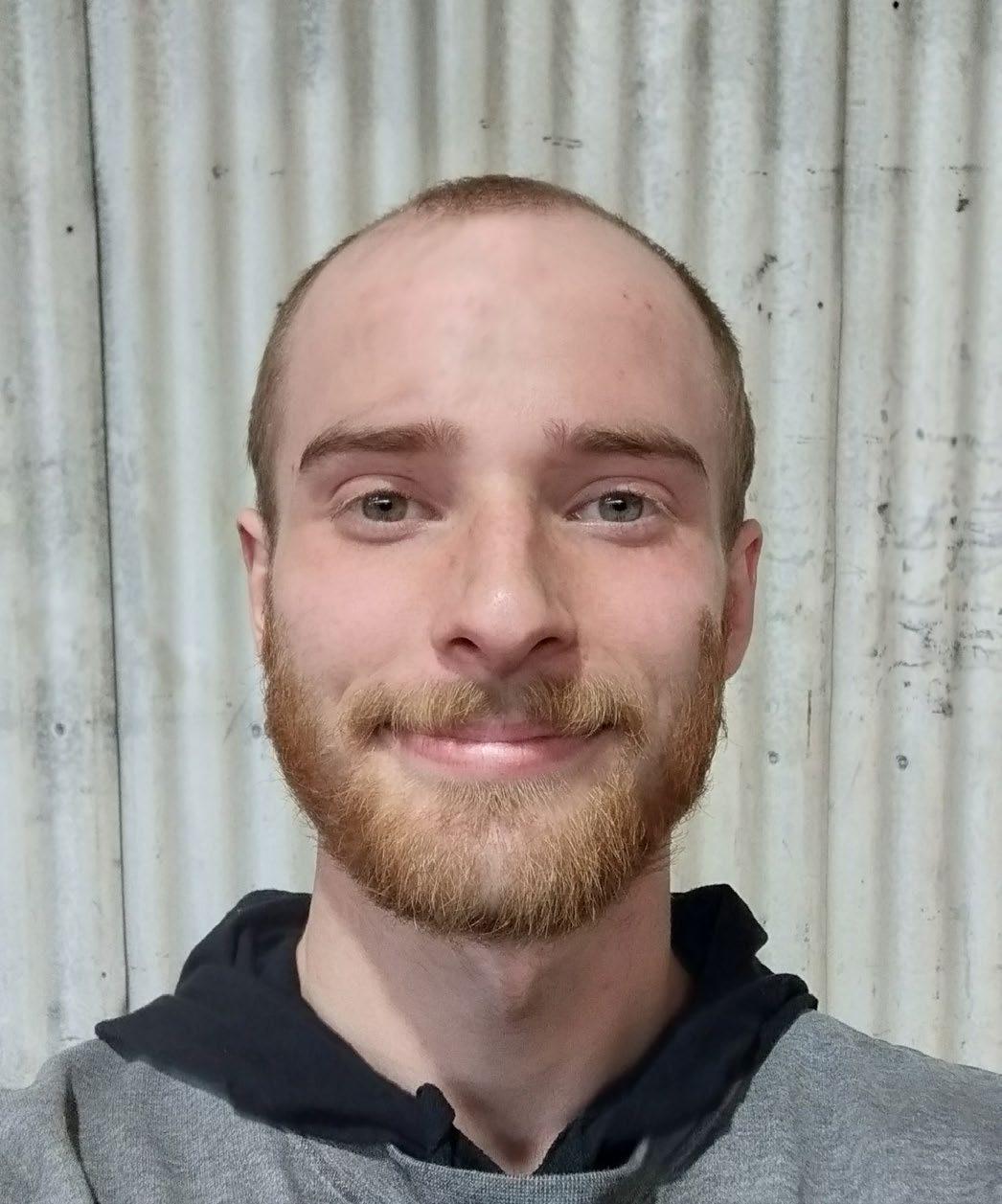
Arnekin Loftus, Formula OffRoad
Arnekin knew he wanted to have a career in the welding and fabrication industry, and even before enrolling into his Certificate III in Engineering-Fabrication trade course, he had achieved his general construction induction card. Arnekin started work straight out of school as a trades-assistant before getting an apprenticeship. His desire to take pride in all his work along with an ability to use his initiative to problem solve has resulted in swift career advancement for him. He has shown outstanding dedication and commitment to his Certificate III in Engineering at TAFE NSW, as well as his work at Formula OffRoad, and he recently won the Gold Medal for the Welding Category at the WorldSkills Regional Competition for Sydney West. Long term goals for Arnekin include working as an underwater welder or in the mining industry.
Can you describe your job?
I work at Formula OffRoad—it’s a small workshop in St Mary’s in New South Wales. We make tow bars, bullbars, nudge bars, rear steps and many other products for vehicles. My job at Formula OffRoad consists of running our plasma cutter, oxy-cutting, mandrel bending, and fabricating and welding of products. I also assist in designing and test fabricating new products.
What inspired you to choose a career in welding?
I’ve always enjoyed working with my hands and being able to create something from nothing. As a kid, I remember eagerly awaiting the chance to get into
the metalwork shop and learn how to work with raw materials to create. When it was time for my first job, my grandfather suggested welding and so I started my apprenticeship.
What do you enjoy most about your job and welding?
I really enjoy the designing and test fabrication of our new products as it gives me the chance to be creative and challenge myself to create something functional strong and stunning.
Why do you think other young people should consider a career in welding?
I believe other young people should consider welding as a career because it’s a valuable skill to learn—being able to create and repair almost anything made of metal is a really valuable skills to have. Plus there are many positions available, in all sorts of industries, as well as specialised work out there that you can to upskill into.
Do you have any advice for young people considering a career in welding?
Welding can be dangerous and hard on the body. So, it’s very important to follow the safety regulations and be switched on while you’re on the job. If you are considering a career in welding have a look around at all the industries available and think about where you’d like to be in 20 to 30 years down the line. Don’t feel locked in to one position—have a look around and find what suites you best.
What is the most interesting project you’ve worked on?
This is a bit of a tough question—I work on a lot of the same projects day-to-day. But, I would say the most interesting project I’ve probably worked on is developing and fabricating new ladder racks for the Ram Dodge. I had to help design them with my manager to have the correct width rise and mounting points for easy installation and removal. They also had to have reinforcing beams that connect the two with the Ram logo. We
tested these to hold around 800kg without any issues.
The other project I really enjoyed was the training I did to prepare myself for the WorldSkills Australia welding competition. I won the gold medal, which means that I will be competing in the national competition in Melbourne later this year.
Who has inspired you professionally?
That honour would have to go to my previous manager and my current one. They have both been extremely supportive and have pushed me to achieve everything I’ve done so far. They have both been extremely good teachers and I don’t think I’d be where I am without them.
What do you believe is the biggest challenge for the welding industry?
I believe the biggest challenge for the welding industry at the moment is the lack of skilled labour in the industry. It’s difficult to find anyone who knows what to do, how to weld properly, and how to be good at welding.
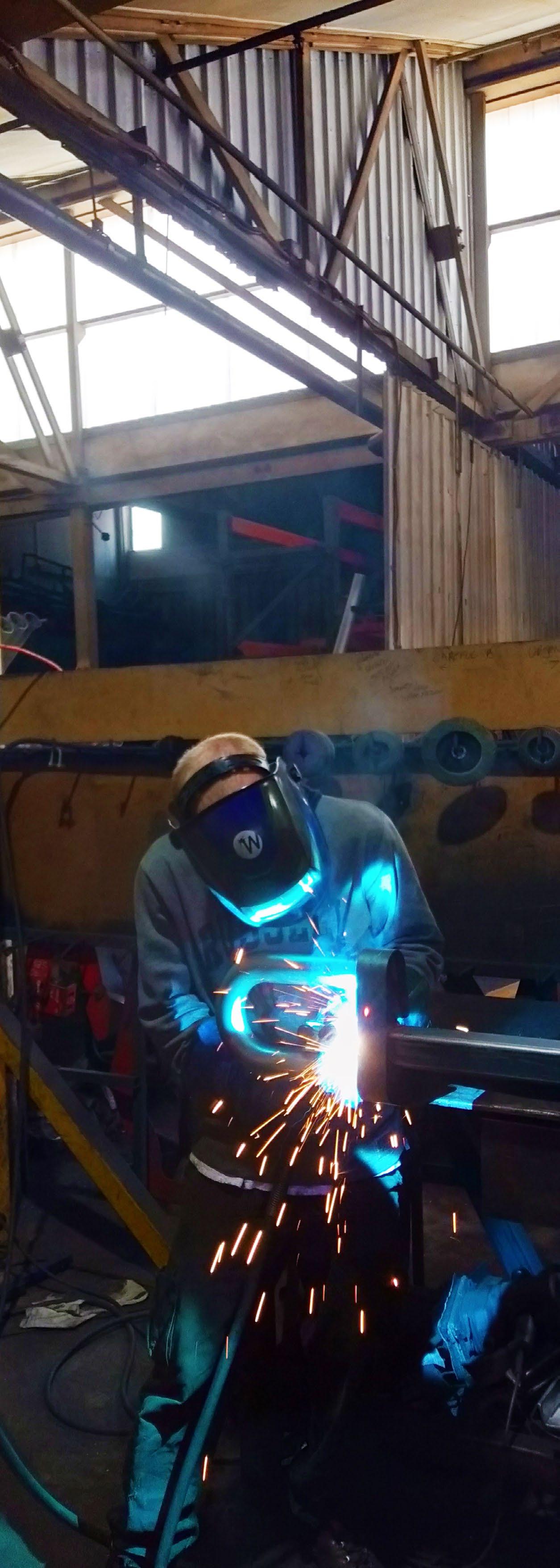
What about the biggest opportunity for the welding industry?
I believe the biggest opportunity in at the moment is that a lot of other downstream industries rely on welding. You need welding to create infrastructure and a whole range of other valuable assets. This creates huge volumes of welding work and plenty of job positions.
RAPID FIRE
What are your top 3 ‘bucket list’ items?
1. Visit every continent
2. Buy a house
3. Become a specialist in my trade.
If you could be famous, what would you want it to be for? My work.
If you could meet anyone, who would it be? I wish I could have met Steve Irwin before he passed; or maybe Neil Degrasse Tyson.
What is your favourite:
• Food: Mangoes
• Song: Move 2 Da Beat by Rooler
• Sport: Footy
What is your top tip for welding excellence?
Practice, practice and more practice.
TOGETHER WE THRIVE
Based in South Australia, Bowhill Engineering is a multigeneration, family-owned and operated business that has been giving Australian businesses the edge since the early 1970s. Specialist fabricators of heavy and complex structural steel, Bowhill Engineering collaboratively builds structures, from design optimisation through to installation, that benefit many Australians.
In the increasingly competitive game of winning, and successfully completing, infrastructure contracts, Bowhill Engineering knows how to deliver good outcomes. The familyowned and operated business has offered Australian clients unbeatable service since the 1970s.
Back then, Bowhill Engineering was a small rural machinery maintenance, repair and modification workshop run by Brendon and Averil Hawkes. The business built its reputation by putting clients first and always finding unique solutions.
Since then, the company has increased its competitive advantage and service offering. Today, Bowhill fabricates even some of the most complex and critical steelwork projects across Australia.
Jodie Hawkes carries on Brendon and Averil’s legacy as a secondgeneration business owner. She is the Chief Finance Officer at Bowhill Engineering, who said it did not take long for the company to grow from its humble beginnings.
“We originally focused on mechanical repairs, and then machining. The business then evolved to structural steel when Jeremy and his brother
Simon wanted to make big cool things in the mid-90s, rather than the traditional mechanical repairs they’d been doing.”
The company has since expanded to over 60 staff, and boasts an annual turnover of $13 million. It has a diverse portfolio across multiple industries like mining, defence, infrastructure and marine.
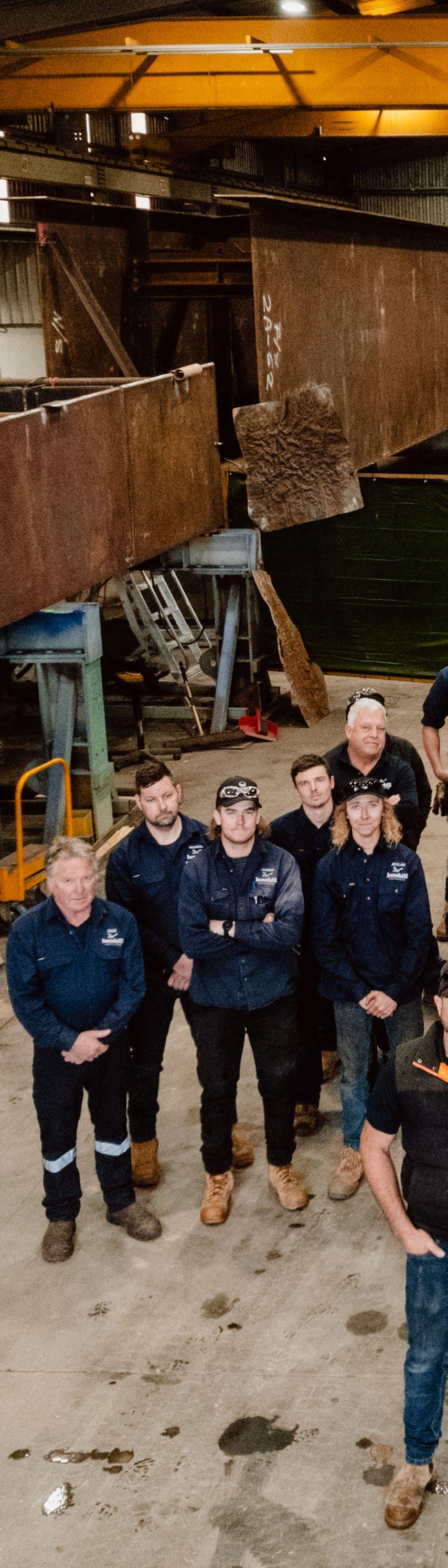
Despite the perils of the pandemic, Hawkes said the company has become a beacon for success. “Most of this growth has occurred in the past five years.”
Bowhill’s reputation has been built on a wide range of areas:
• Specialising in large complex structural steel
• Being easy to do business with
• Offering a collaborative problemsolving approach
• A high capability for developing innovative solutions to complex projects
• A positive track record for delivery on time and with high quality
• Price competitiveness.
There is a wide variety of projects in Bowhill’s workshop at any one time.
“We specialise in heavy and complex
How Bowhill Engineering is transforming communities and their people by optimising and building the structures that matter
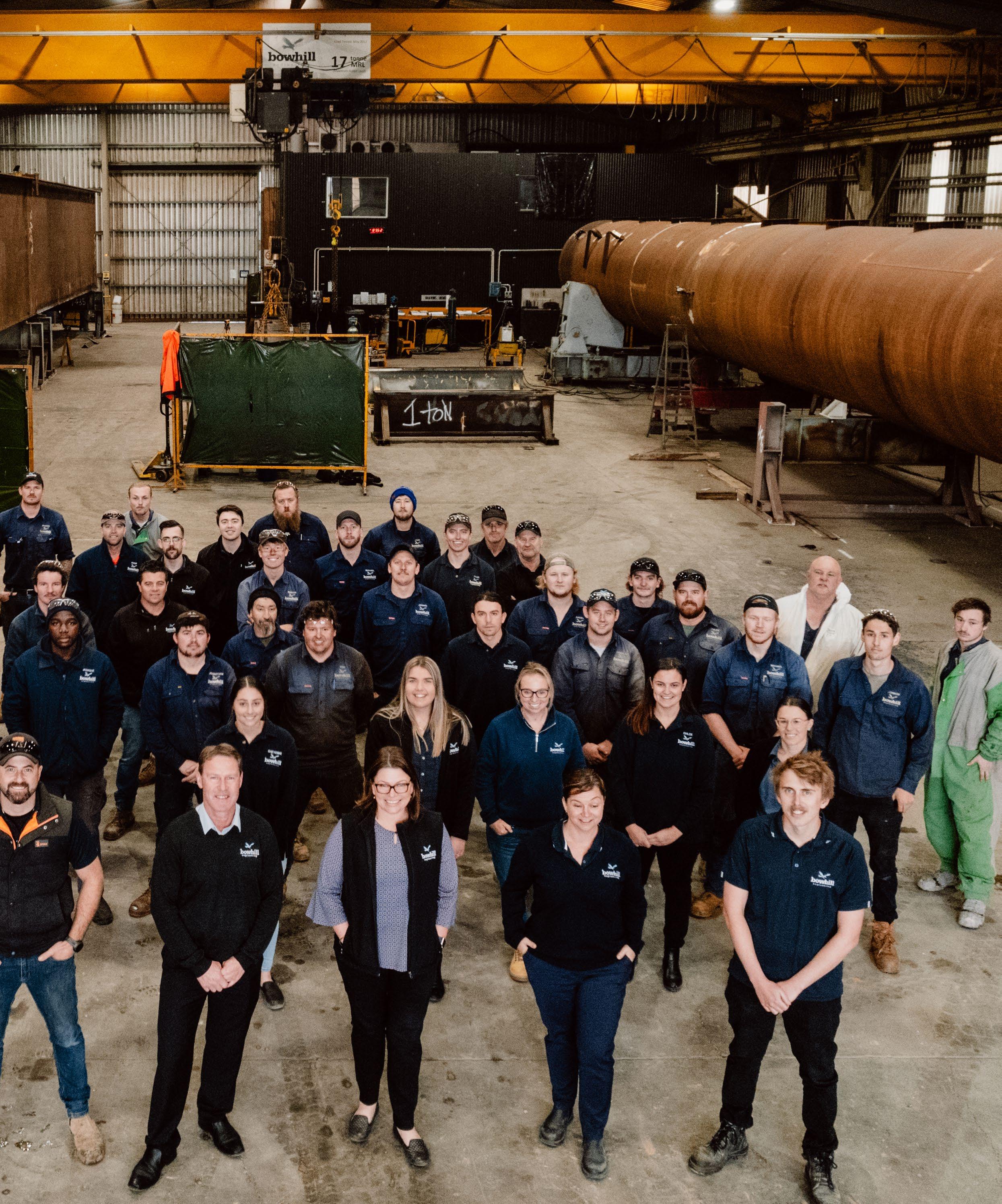
“ We focus on our X Factor, which is our employees. They are our key to sustained growth. We focus heavily on training, and not just for skill.”
structural steel fabrication. Think bridge girders and mining equipment. We service multiple industries including infrastructure, mining, defence and water,” Hawkes said.
However, Bowhill Engineering is best known for building large steel bridge girders. In all, the company has completed over 15 bridges on the North-South Expressway in South Australia, and over 25 bridges in the past 20 years.
Part of this success has been identifying and aligning with key clients, who fit the same culture and values as Bowhill.
Loyal Staff Pave the Way for Success
The company’s values drive its success. Together, Bowhill staff are goal-driven and determined to make a difference in the Australian engineering landscape. Bowhill Engineering is committed to quality and ongoing professional development for staff.
“We focus on our X Factor, which is our employees. They are our key to sustained growth. We focus heavily on training, and not just for skill,” Hawkes said. “Over 50% of our staff are on training contracts,
ranging from leadership, WHSE and project management, through to metal fabricator traineeships. We’ve had a 95% success rate, with over 40 staff completing our trainee and apprenticeship program.”
“We are working hard on developing three levels of leaders to ensure sustainability and succession within our leadership team. On top of training programs, all leadership staff are currently involved in external mentoring and internal coaching programs. This has been extremely successful and we have seen huge growth within our middle management team,” said Hawkes.
The company operates an Emerging Leaders Group, which participates in a range of interactive sessions targeted towards the company’s core values. According to Hawkes, their group of 19 emerging leaders recently participated in a two day strategic planning session to review the company’s purpose, core values and core competencies.
“We have developed our 90 day goals and broken them down into 12 steps to make the goals easier to achieve,” said Hawkes.
“Our strength is with our systems and ‘chocking the wheel’ to ensure we capture the intellectual property
of our people and processes. We hold ourselves accountable. We train to EQ. We train our leaders to make decisions based on our values: do what we say we are going to do; we get things done together; we work smarter; we help our clients win. We are true to our core values and living our purpose: Together we Thrive,” Hawkes said.
Flying the Flag with High-Profile Projects
The Bowhill team has an abundance of skills and experience to bring even the most complicated projects to life.
In the Cable
Stayed
Pedestrian Bridge project in Canberra, innovative technologies were used to achieve a contemporary architectural effect. Personnel conducted post-weld grinding on a welded box section to ensure the bridge had a high aethetic appeal.
In addition, Bowhill worked on the Oaklands Railway Station project—a high profile striking architectural statement in South Australia. The complex structure required 200 tonnes of steelwork and a level of accuracy and diligence that is in the upper echelon of engineering in Australia. The company instigated weekly face to face meetings with the client to help ensure the project came
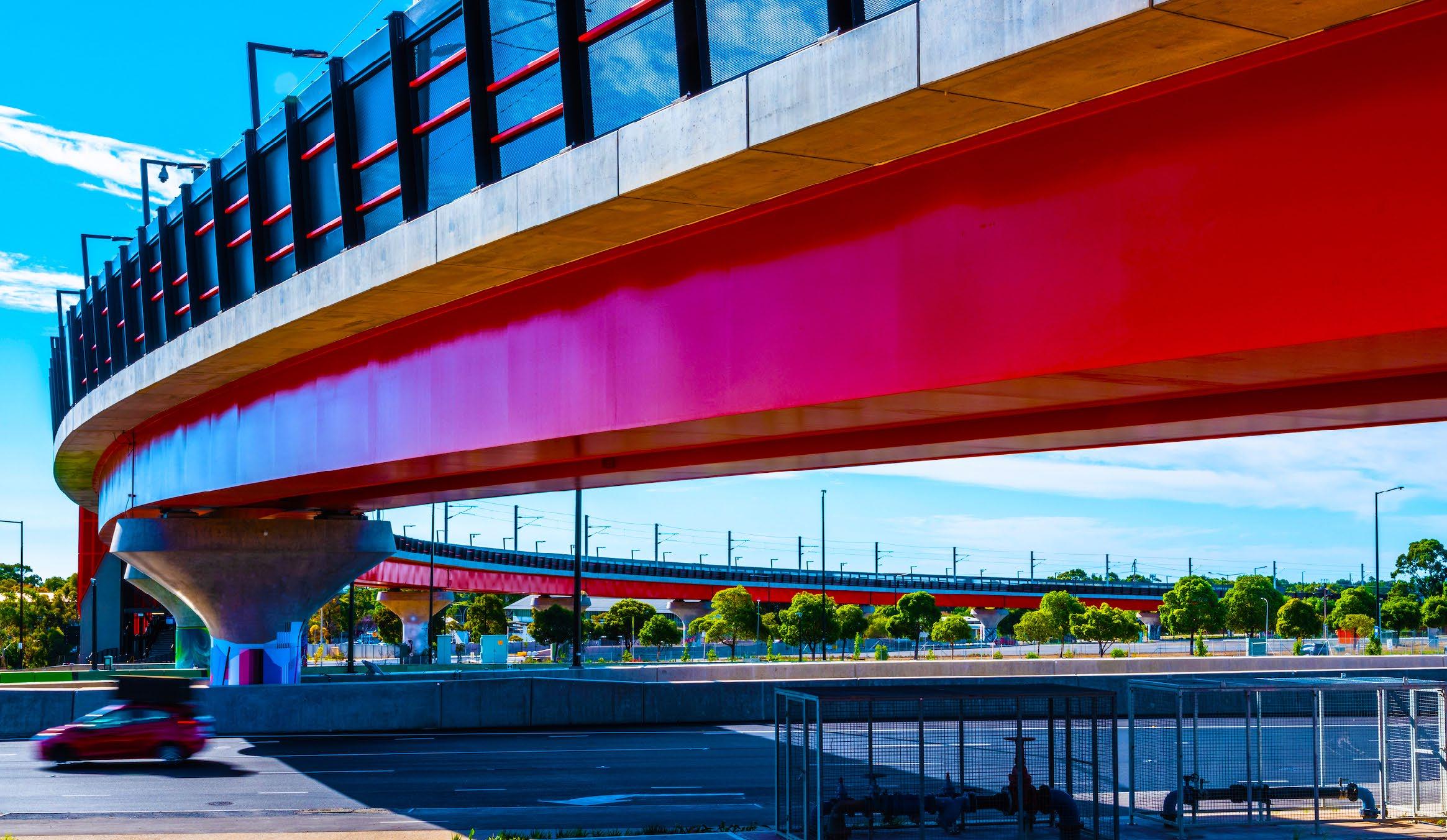
to life, the technical requirements were met and the flow on effects were felt positively throughout the whole project stakeholder team.
Hawkes said Bowhill is working on a range of high-profile projects at the moment. “We are in the final installation stages of a Head Frame for Oz Minerals—a bright blue 60m tall structure with four legs of 2.6m each in diameter—it’s an impressive structure. We have some bridge girder work at Sydney Gateway and Mt Derrimut and some significant Temporary Steelwork in Bridgewater, Tasmania too.”
To achieve these impressive feats of manufacturing, Bowhill operates a 3,500m2 workshop floor area, and five hectares of hardstand.

“We are also at the final planning stages to build a third 22m x 70m workshop, which is being designed to manage our niche of heavy and complex structural steel. It will encompass a 100 tonne crane and building height of 23m.”
“We have also recently invested in point cloud software, to develop our capacity in 3D computer-aided design post fabrication processes. This allows us to understand increasingly complex geometric steel
structures. It’s an internal process allowing us to minimise risk and maximise capacity,” Hawkes said.
To win such an impressive list of contracts, Bowhill understands the importance of certification and innovation. The company has been ISO 9001:2015 certified since 2014, and holds AS/NZS ISO 3834.2 certification, AS/NZS 5131 certification. Bowhill also runs a cloud-based Integrated Management System, which has been consistently reviewed and managed to ensure a high quality of results.
“Our system has been around and reviewed annually for nearly nine years—some of the document revisions are over 1000. We built the system ourselves, never taking a pre-made off the shelf option. So we know it inside out and how it integrates with all functions of our business model,” said Hawkes.
Celebrating Success on the National Stage
In a testament to Bowhill’s strength and position in the Australian manufacturing sector, the company won Weld Australia’s 2022 Excellence Award for Company of the Year— Fabrication (Small) in the South Australia category.
Hawkes said the award strengthens Bowhill as a true leader in the heavy engineering infrastructure space. “We are very honoured and humbled by this award. There are some amazing fabricators out there doing a great job.”
“Our purpose is Together We Thrive, and winning this award is about giving back to our stakeholders (clients, suppliers, employees, community, shareholders) to show them that our hard work and dedication is being recognised,” Hawkes said.
The award showcases Bowhill’s enviable track record for project delivery, quality, safety and environmental excellence. The Weld Australia Awards are the premiere event for welders and fabricators in Australia. The Awards highlight some of the best projects, and shine a light on craftmanship, professionalism and people in the sector.
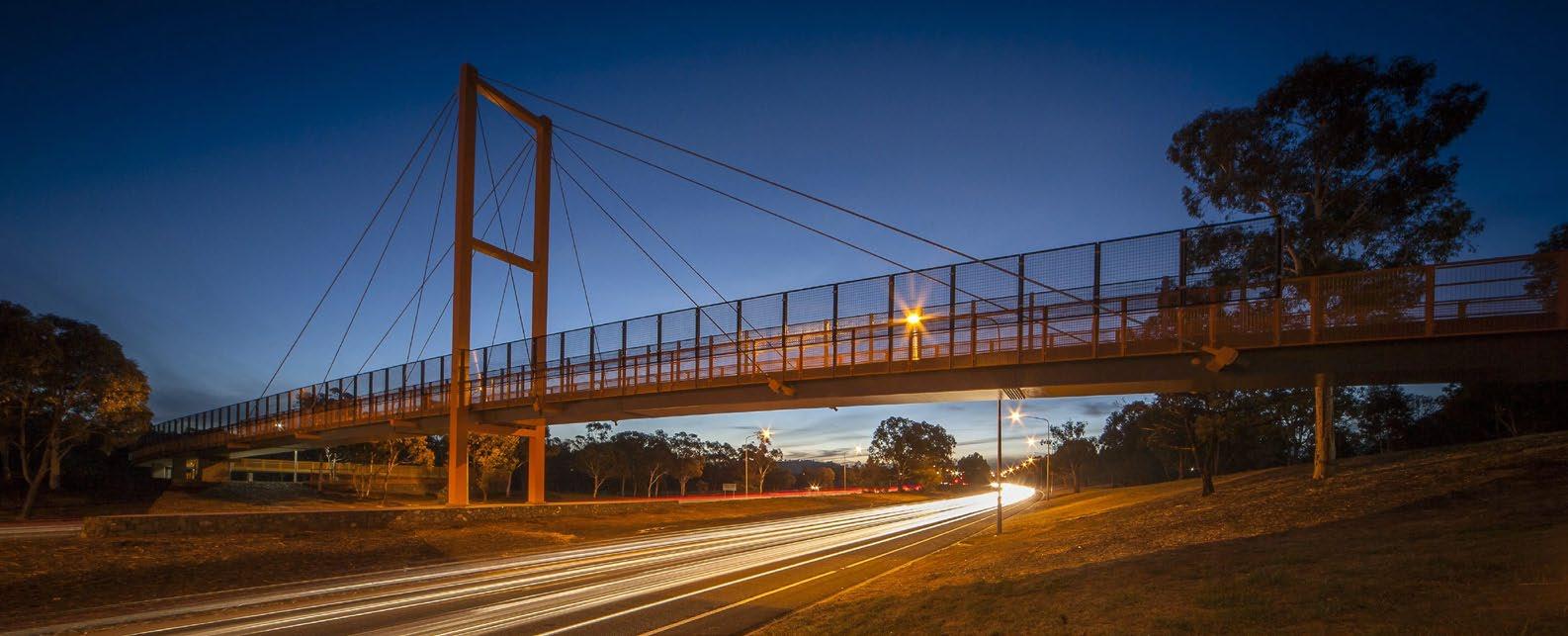
Further Information
For further information about Bowhill Engineering, visit: boweng.com.au
“ We train our leaders to make decisions based on our values: do what we say we are going to do; we get things done together; we work smarter; we help our clients win. We are true to our core values and living our purpose: TogetherweThrive.”Bowhill Engineering’s 3,500m2 workshop, and five hectares of hardstand. Cable Stayed Pedestrian Bridge in Canberra.
WHEELCHAIR-BOUND WORKER GAINS AUTONOMY WITH LEUSSINK’S ASSISTANCE
Illawarra companies Evermil and Leussink have come together to ensure wheelchairbound boilermaker Clay Kelly can work more efficiently and autonomously by utilising a 3D welding table.
Steel fabrication business Evermil employs Clay Kelly as a skilled boilermaker to undertake a variety of work. Clay lives with a physical disability and is a wheelchair user following an accident riding bulls 23 years ago, causing an injury to his spine.
His day-to-day tasks include interpreting blueprints, cutting, moulding, and welding metal and steel to fix faults, welding and bolting structures together, and identifying and solving challenges. As a boilermaker, Clay also needs to lift items of various weights and move
things around the workshop, and at times he needs to ask his colleagues for assistance.
Managing director of Evermil, Chris Beck, was keen to find ways to make Clay’s role more accessible and called on colleague Paul Baxendale to undertake research. Paul found JobAccess and the Employment Assistance Fund, and Evermil applied.
The goal was to allow Clay to work autonomously and independently. Clay also had difficulty undertaking some aspects of fabricating tasks using his existing workbench.
Through JobAccess, a workplace assessment was organised to understand Clay’s challenges and requirements at work. As a result, the assessor recommended equipment to support Clay in working more effectively, safely, and efficiently. The recommendations included a
three-dimensional welding table, a perching stool that Clay can sit on to make him more comfortable when working on a job, and a selfpropelled electronic scissor lift trolley, supporting Clay to lift things onto his trolley and transport them over to the workbench.
The obvious choice for the 3D workbench was the Demmeler table system because it is precise, adaptable and provides consistency.
Leussink’s Russell Brinkworth visited Evermil and spent time with Clay to understand exactly what he needed to achieve and how a table could be accommodated to provide the best solution. As a result, the Demmeler table was mounted on the scissor lift which allows Clay to work autonomously.
On the Demmeler table, Clay can attach various items to it and adjust
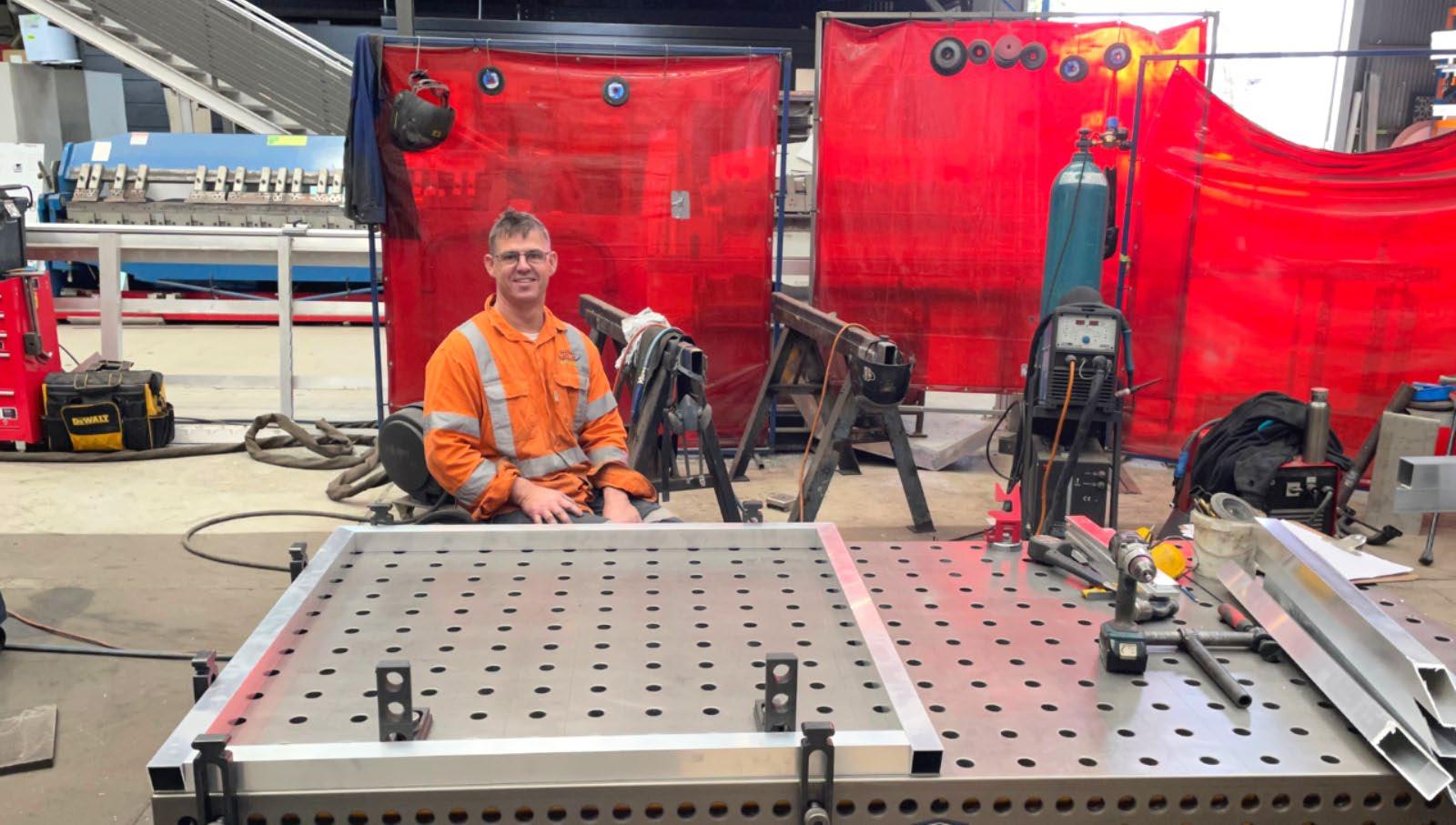
its height depending on the job. He can also move the table to different angles, so he can turn it where he needs it, instead of turning sideways or crawling under it. “Essentially Clay can work with the table on a ‘funny angle’, rather than him being on a ‘funny angle’,” said Evermil’s Paul Baxendale.
Clay is also impressed with the versatility of the Demmeler table, “I can lower it down, making it easier, and I can clamp stuff onto it. It has been amazing, it helps me out a lot.
“Not many people in roles like mine get to use a worktable like this. I’m pretty stoked,” said Clay.
Paul commented that working with JobAccess “opened Evermil’s eyes to what is possible” when hiring a diverse workforce and wanting to create an inclusive workplace.
Clay is now taking on more tasks with the help of his equipment. “Clay is a top guy. He can do more tasks now, it’s great to see and makes his job a lot easier,” said Paul.
Leussink’s Sales and Marketing Manager, Stuart Ward said, “We love
the opportunity to work with people where we need to think outside the box. It’s awesome to see professional tradespeople fully utilising the skills and experience they have gained over the years.”
“The combination of JobAccess funding, Evermil’s commitment to its employees, and the Leussink technology and support have come together to achieve this,” said Ward.
The Demmeler 3D workbench and welding table is a versatile jig and fixturing system for all types of welding and fabrication work.
Illawarra-based steel fabrication business Evermil has been in operation for over 35 years and is proud of its family ownership. Evermil undertakes high-quality metal fabrication work for the residential, commercial, and industrial sectors.
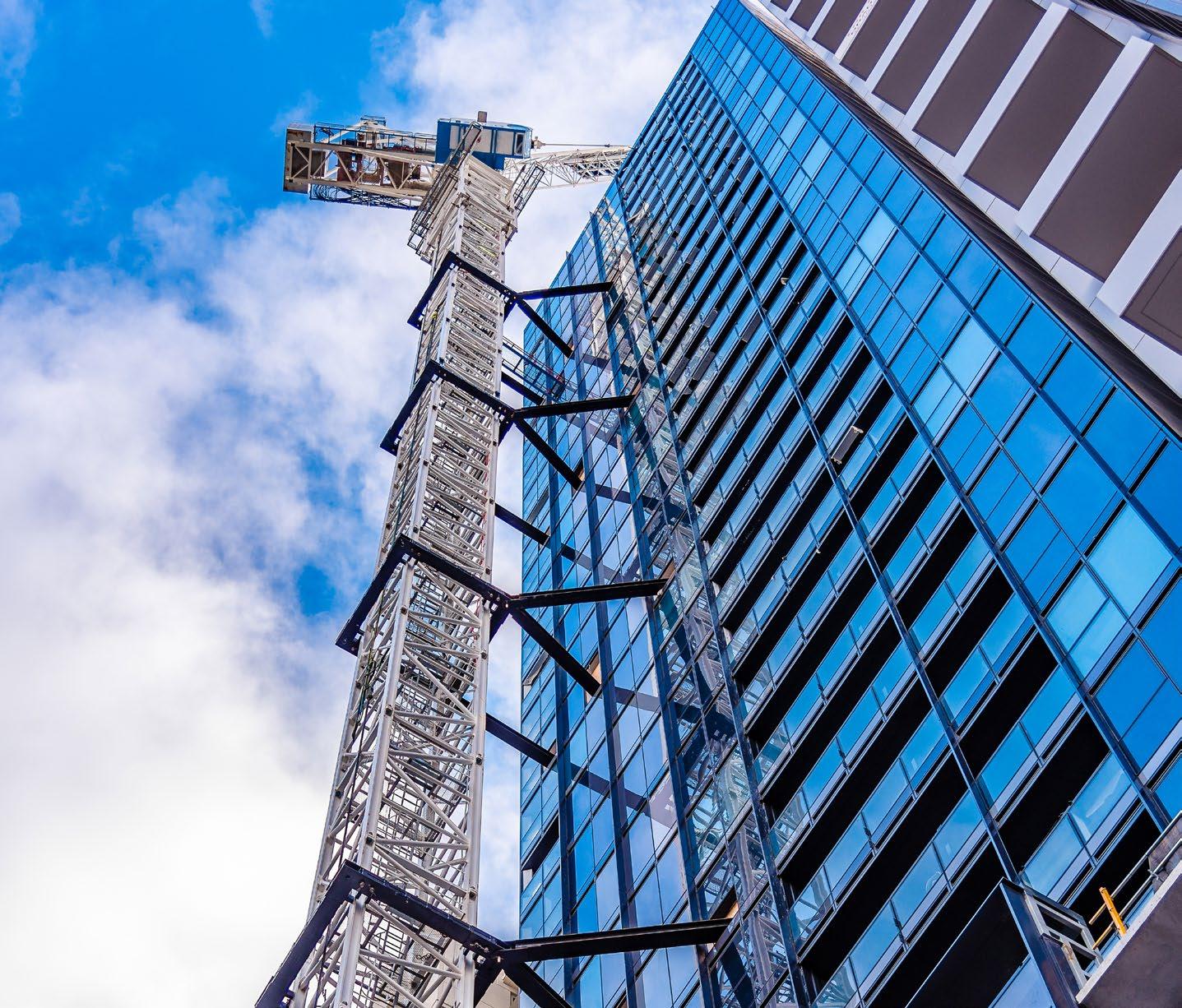
Leussink is an Illawarra-based engineering firm that provides complete design, fabrication, and machining services and solutions for all industry sectors, as well as modular fixturing and metrology solutions that revolutionise workshops around Australia.
GOOD BUSINESS SENSE
Around 1 in 6 (18%) people in Australia – or 4.4 million individuals – are living with a disability. Alarmingly, people with disability make up 37.9% of the population living in poverty (despite only making up 18% of the overall population).
One reason for this is that Australia ranks lowest among OECD countries for the relative income of people with disabilities. Overall employment rates for people with disabilities remain low, with workforce participation at around 54% compared to 83% for people without disabilities. Disappointingly, this labour force participation rate for people with disability has remained largely unchanged over the last 20 years—it was 53% in 2003.
The economic benefits of employing people with disability would add over $50 billion to Australia’s Gross Domestic Product GDP by 2050 – but only if Australia moved up into the top eight OECD countries for employment of people with disability.
There are significant business benefits when employing someone with a disability. According to the International Labour Organization, employees with disability are:
• Reliable: People with disability take fewer days off, less sick leave and have a higher retention rate than others.
• Productive: Once in the right job, people with disability perform equally as well as other employees.
• Affordable: Real cost savings are realised through reduced turnover, recruitment and retraining costs. People with disability have fewer compensation incidents and accidents at work in comparison to others.
• Good for business: People with disability build strong relationships with customers and boost staff morale and loyalty by helping to create a diverse workforce. Teamwork is enhanced.
AN UPDATE FROM OUR HOTLINE
Weld Australia offers a ‘Hotline’ service to all Corporate Members. The purpose of the Hotline is not to provide a solution, but to advise the enquirer on practical next steps. For further advice, Weld Australia’s highly experienced welding consultants can speak to you over the phone or visit your site in person. If you have a Hotline query, complete our online form: weldaustralia.com.au/hotline
A member recently contacted Weld Australia to ascertain the testing requirements when validating the Annex C single bevel butt joint with material backing referenced in Clause 5.4(b) of AS/NZS ISO 9606-1 Qualification testing of welders — Fusion welding

Weld Australia has recommended that the completed joint be tested as per butt joint requirements in the standard. However, some users in the industry claim that two macro tests are also required to validate the fillet joint component of the test, particularly if the butt joint is examined ultrasonically.
We responded by indicating that Weld Australia has always been of the view that the Annex C joint once completed, had to be tested as a butt joint (it is after-all a single bevel butt with material backing), and that an ultrasonic testing (UT) examination of the joint by a competent technician would readily locate the position of the root of the fillet component of the joint.
We arrived at this opinion based on the fact that this test is a standard Canadian weld test and it is tested once completed as a butt joint. Discussion with regular users of UT assessments of this joint also confirmed the suitability and validity of the test method.
Confusing the issue for users though is that the drafting committee ISO TC44/SC11 had issued two interpretations essentially stating that: all testing requirements specified in this part of ISO 9606 shall be fulfilled. This has confused the situation, leading some to interpret the requirements as to include the need to test two macros from the joint to validate the fillet component of the combination test.
When considering the application of rulings, it is important to understand that the ISO drafting committee can only answer with a yes or no to the question(s) asked of it when finalising a ruling for publication. This requires the enquirer to carefully craft the question to ensure that the matter of concern is clarified.
In July 2022, a testing organisation wrote to Standards Australia seeking clarity on this same question. In turn, in accordance with ISO protocols, the Australian mirror committee to
This Hotline update covers a specific query encountered during the last few months. Whilst accuracy in welding is critical, it is impossible to report in detail the full circumstances of the query. As such, Weld Australia recommends that further technical advice is sought in relation to specific, individual circumstances.
ISO T44/SC11 was asked to rule on the issue. The Australian committee ruled that the fillet had to be visually assessed before the completion of the butt component, then the butt joint had to be visually assessed and then tested as per requirements for butt joints, with the additional requirement that complete penetration was required in the root of the fillet when the butt joint was assessed.
The standard permits assessment of the butt joint via UT examination or mechanical testing, or in some situations radiographic testing with supplementary mechanical tests as defined in Table 13. The addition of two macro tests as claimed by some standards users is therefore unnecessary if the butt joint is tested as specified.
Anticipating that this would probably not resolve the issue until the ISO 9606-1 standard was amended, Standards Australia submitted a formal interpretation request to ISO in December 2022. A ruling was provided on 27 February 2023 that confirmed the ruling made by the Standards Australia mirror committee. ISO advised the original enquirer accordingly at the time. Unfortunately, publication of the ISO ruling on their website has been delayed.
Irrespective of the ISO publication delay, the drafting committee revising ISO 9606 and its parts has taken cognisance of the situation and the next edition of ISO 9606, which will combine all five parts, will clarify this situation.
Separate to this enquiry on ISO 96061, another member contacted Weld Australia regarding a possible error in Table 8 of the Australian edition of ISO 9606. Weld Australia contacted Standards Australia and confirmed that an error was present in the table where a mathematical operator had reversed. A similar error was also located in Table 14. Standards Australia has since corrected the two errors in question in the AS/NZS edition of the standard. Users should note that the original ISO text was correct.
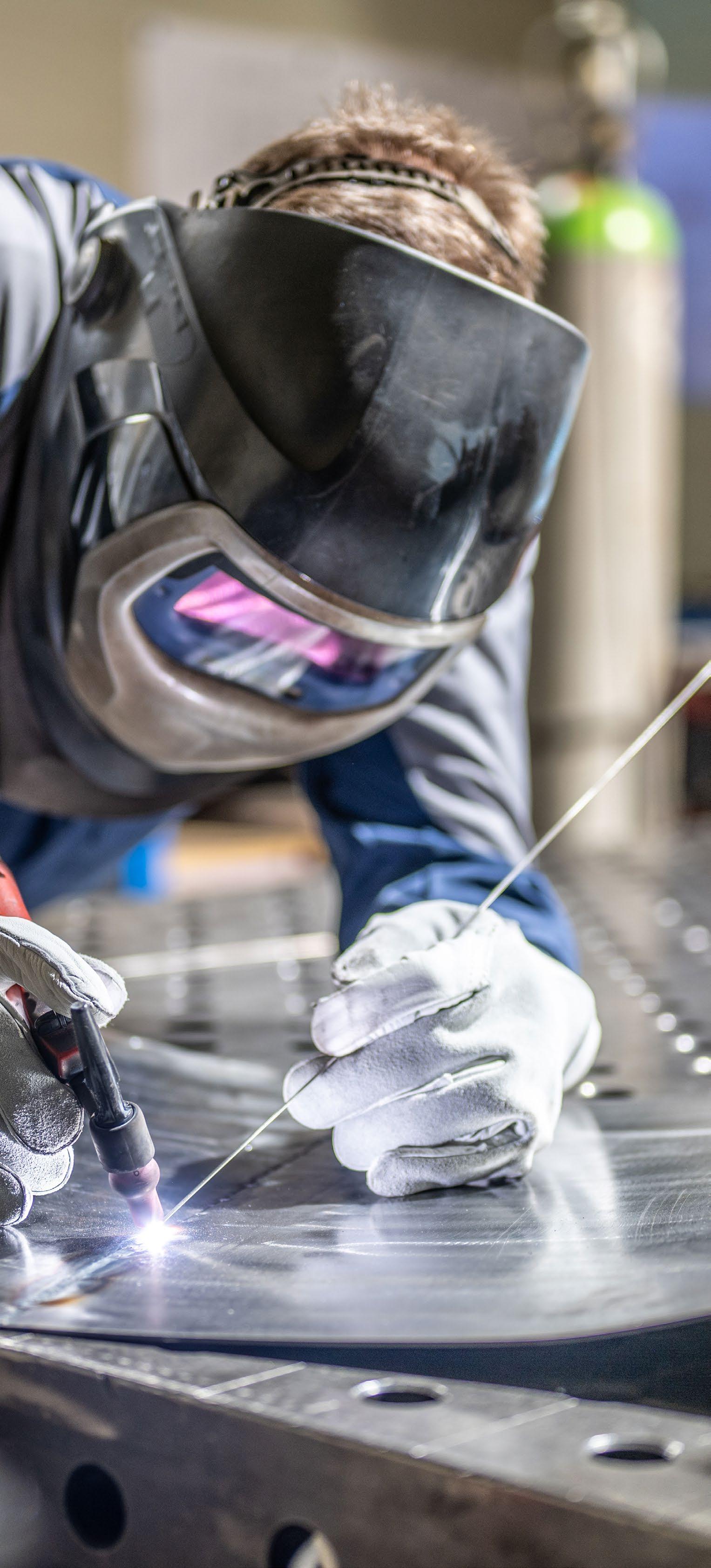
THE CHANGING FACE OF AUSTRALIAN STANDARDS
Australian Standards are living documents. They reflect progresses in science, technology and systems To maintain their relevancy, all Standards are periodically reviewed, with amendments and revised editions published. The last few months have seen several developments, including an urgent review into Standards related to rubber hoses for welding, cutting and allied processes, and ongoing reviews into Standards related to pressure equipment and steel structures.
Pressure Equipment
As previously reported, the revision of AS/NZS 3788 Pressure equipment—In-service inspection is progressing well. Public review of the draft was completed in June and comments received are currently being reviewed by the drafting committee.
Welding Consumables
Following the suite of ISO consumable standards adoption in October 2022, Committee WD-002 reviewed the aged AS/NZS 1167 suite (Welding and Brazing — Filler metals) and a project is now underway to replace these aged standards via the direct text adoption of the relevant ISO consumable standards. Separate
to this review, the Committee has formed a working group to revise AS 2576 Welding consumables for build-up and wear resistance.
Welding Safety
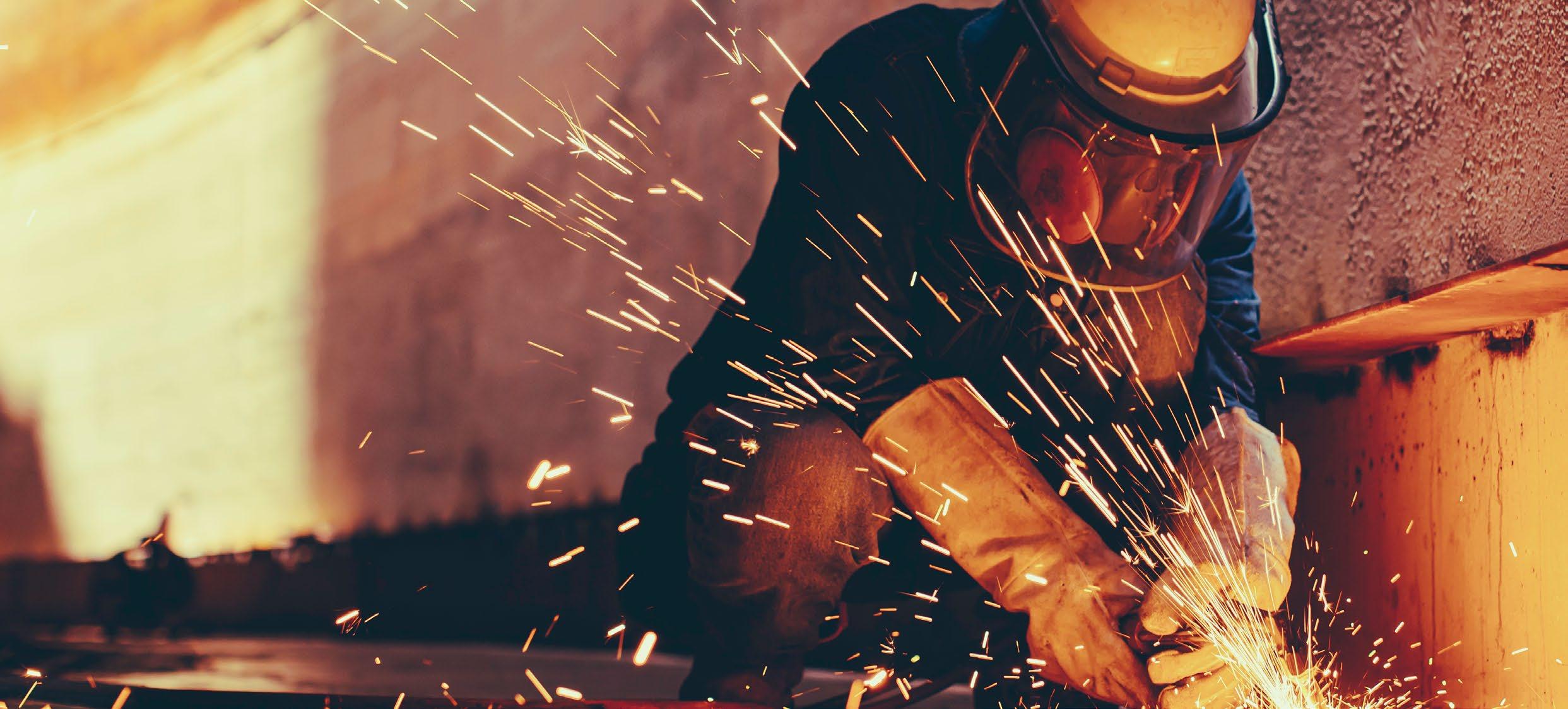
A proposal was submitted and accepted by Standards Australia to revise AS 1674.1 Safety in Welding and allied processes—Part 1 Fire precautions. The standard is used extensively in industry to establish fire preventative measures whilst welding in locations not necessarily designed for hot work. The project kick-off meeting was held by a reconstituted WD-004 in March and the revision is well advanced.
A proposal to revise AS 1674.2 Safety in Welding and allied
processes—Part 2 Electrical has also been received and accepted by Standards Australia and the committee responsible EL-019 is currently being reconstituted. The project kick-off is currently anticipated in August.
Bridges
The revision of AS/NZS 5100.6 Bridge design — Part 6: Steels and composite construction via amendment is well advanced. The revision will align the requirements of the standard with the latest revision of AS 4100 Steel structures, AS/NZS 5131 Structural steelwork —Fabrication and erection and the New Zealand steel structures design standard NZS 3404.1, and resolve known conflicts and anomalies.
Public comment on the proposed amendment closed in June, and resolution of public comment is now underway.
Steel Structures
Standards Australia has accepted a proposal for a major revision of AS 4100 Steel structures. Committee BD-001 will manage the project and a kick-off meeting was held in April.
Committee WD-003 has been working to revise and update AS 2812 Welding, brazing and cutting of metals — Glossary of terms. A draft has been submitted for preparation for public comment.
The Committee has also submitted a project to revise the current edition of AS/NZS 2214 Certification of welding supervisors — Structural steel welding. The revision will align this standard with the latest revision of AS 1796 Certification of welders and welding supervisors including the addition of requirements for a welding inspector. In addition, the standard will be renamed and spilt into parts with the incorporation of a new Part 2 to cover bolting supervisors. Project kick-off is anticipated in August. The longer term intention is to add further parts to what will become
the AS 2214 series in support of the qualification of key personnel relevant to AS/NZS 5131.
Committee WD-003 has also been made aware of errors in two Tables within AS/NZS ISO 9606-1 Qualification testing of welders — Fusion welding. A mathematical operator in Tables 8 and 14 was reversed and Standards Australia has since corrected the error. The original ISO text was correct and remains unchanged.
ISO Update
ISO TC44/SC10 has completed the revision of ISO 3834 Quality requirements for fusion welding of metallic materials series of standards and Parts 1 to 5 inclusive have been published. Standards Australia has accordingly adopted these latest revisions as direct text adoptions. The revision of Part 6 of ISO 3834 is currently at the DIS ballot stage. Consideration for adoption in Australia will commence after finalisation by ISO.
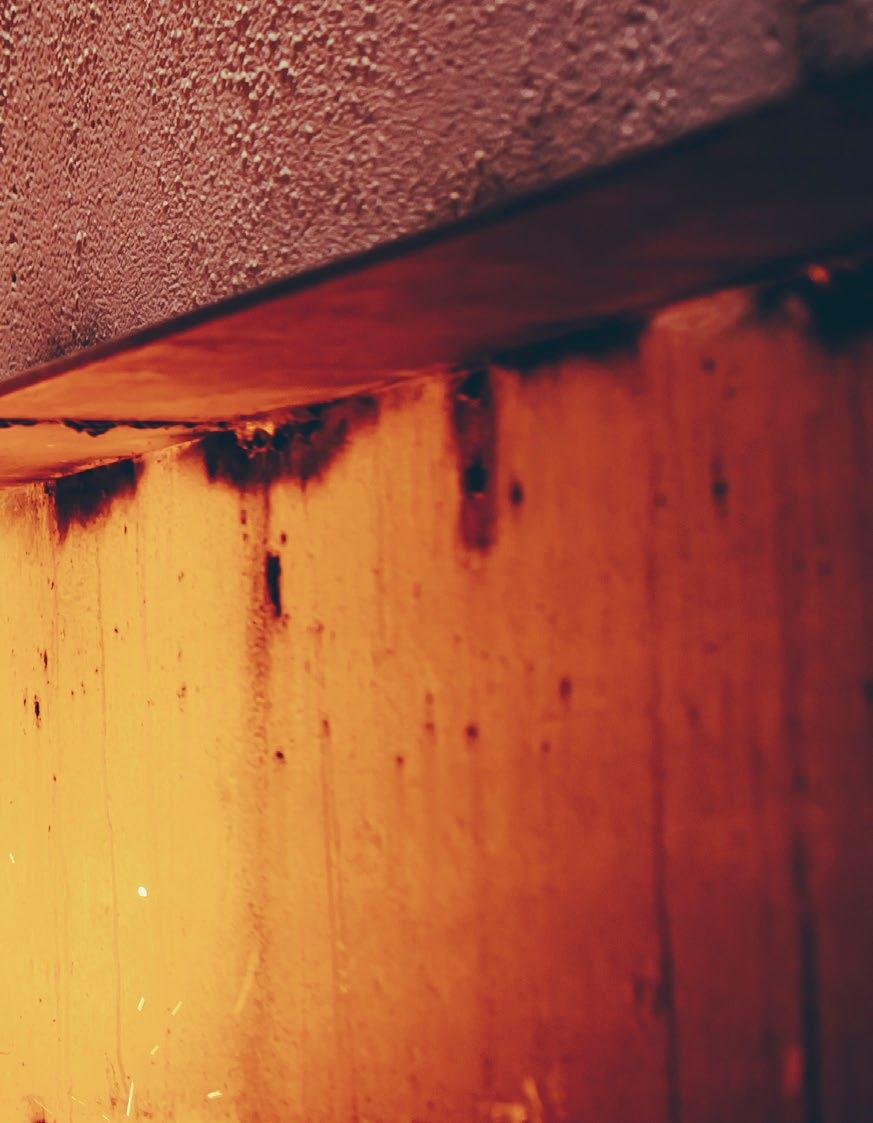
BRUCE CANNON WINS STANDARDS AUSTRALIA AWARD
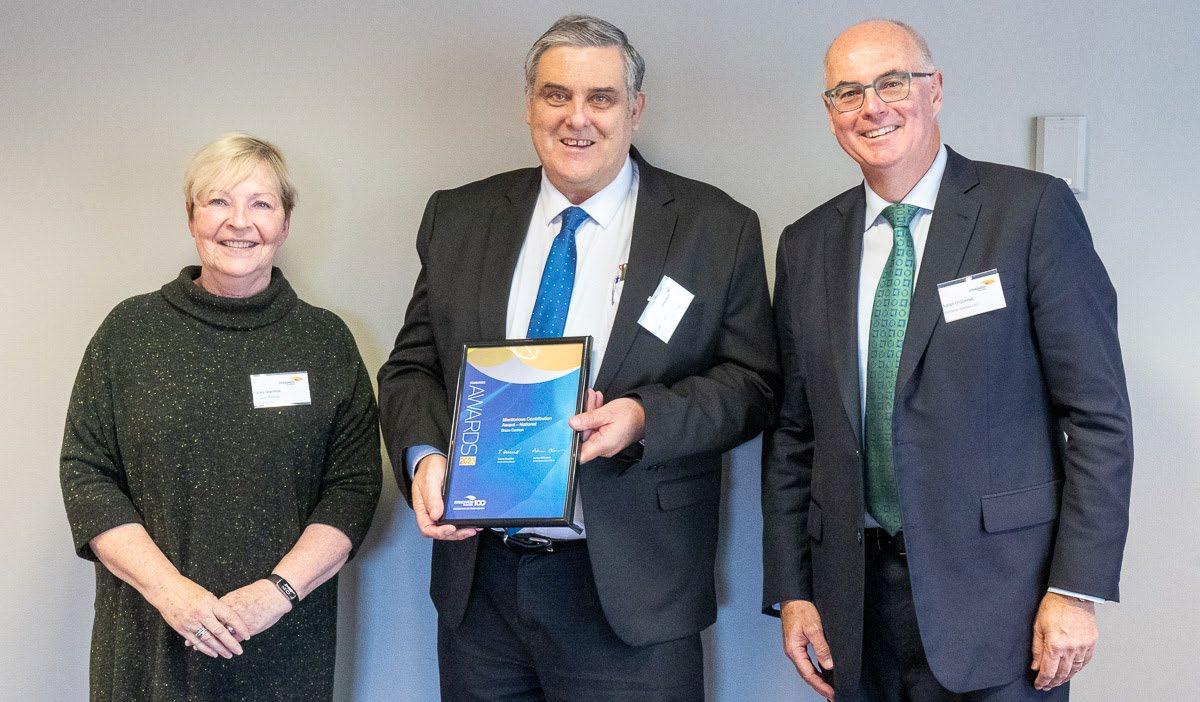
Bruce Cannon (Principal Welding Engineer, Weld Australia) was recently honoured with a Meritorious Contribution Award (National) by Standards Australia. The Standards Australia awards recognise the remarkable achievements of members within the Australian standards development community, especially those who have demonstrated outstanding leadership, technical expertise and contributed positively to the development and enhancement of standards.
TC44/SC10 has also been revising ISO 17660 Welding—Welding of reinforcing steel. This edition is planned to combine the two existing parts into a single document. A DIS ballot has been held and comments are currently under review. Due to the large number of technical changes within, a second DIS review and ballot will need to be held. Work is ongoing. TC44/SC10 are next expected to meet in Genoa (Italy) in November during TC44 week.
Bruce is active in the revision of five standards across a range of committees, including numerous direct text adoptions of ISO standards to update Australia’s aged welding and related standards. His involvement in standards development has given him the opportunity to represent Australia’s interests at ISO in the revision of ISO 9606, and provide feedback to the drafting committee on the Australian experience with this standard. He was also involved in the alignment of the welder qualification standard AS/NZS 2980, with the core requirements of ISO 9606-1, which led to New Zealand co-joining the standard in 2007.
Bruce’s work has gained in importance within the transport and pressure equipment sectors, in addition to its primary use within the steel structures sector. He is an invaluable member of the Weld Australia team, with technical expertise that is second to none.
Similarly, ISO TC44/SC11 has been revising ISO 9606-1 Qualification testing of welders—Fusion welding— Part 1: Steels to combine all 5 parts into the one standard. This will simplify the ongoing maintenance and review requirements for the standards currently published as parts 2 to 5 of ISO 9606-1. The drafting committee is next scheduled to meet in July
AN UPDATE FROM WELD AUSTRALIA’S INDUSTRY GROUPS
Weld Australia’s Industry Groups provide a forum for technology transfer and research and development, linking members with industry and research organisations. Weld Australia works with Technology Network members to ensure they remain diverse and resilient in the ever-changing and increasingly challenging global markets.
WELDING SAFETY COUNCIL
The Welding Safety Council met online in late May, with representatives from Australian Institute of Occupational Hygienists (AIOH), AWS, Industrial Laser Solutions, SafeWork NSW, TAFE Queensland, SafeWork Australia, SafeWork SA, DMIRS WA, WorkSafe ACT, WorkSafe Victoria and Weld Australia in attendance.
The Welding Safety Council is currently addressing several areas of concern, including protective clothing, electric shock, and the dangers of welding fume, as well as hand held laser welders and the lack of standards and regulations around their use.
Bruce Cannon (Principal Welding Engineer, Weld Australia) provided an update on the work of IIW
Commission VIII, as well as an update on various Standards. AS 1674.1 Safety in welding and allied processes is undergoing revision and a public review draft should be available later this year.
ISO 11611 Protective clothing for use in welding and allied processes was also discussed. It is likely that this standard will be considered for adoption in Australia once the ISO revision is complete.
The revision of AS/NZS 3957 Lighttransmitting screens and curtains for welding operations is also under consideration, with the ISO Standard currently being updated.
Several case studies were presented by attendees that demonstrated the risks of electric shocks from welding, as well as incidents in which
the cotton clothing of welders have caught fire causing serious injuries. As such, the use of protective welders’ leathers is recommended. David Chippendale (Director of Marketing and Sales, AWS) gave a presentation on welding fume controls and how various controls compare.
Cameron Jamieson (Director, Industrial Laser Solutions) gave a presentation on handheld lasers that are commonly found in the Australian marketplace. Cameron highlighted that while some lasers have high levels of protection and interlocks to prevent inadvertent use of the laser—others do not. Weld Australia is developing a Safety Alert on hand-held lasers that will be widely distribbuted.
Weld Australia is developing two comprehensive online training courses designed to improve safety outcomes across the country. One course is tailored for welders, while the other is aimed at welding engineers and supervisors.
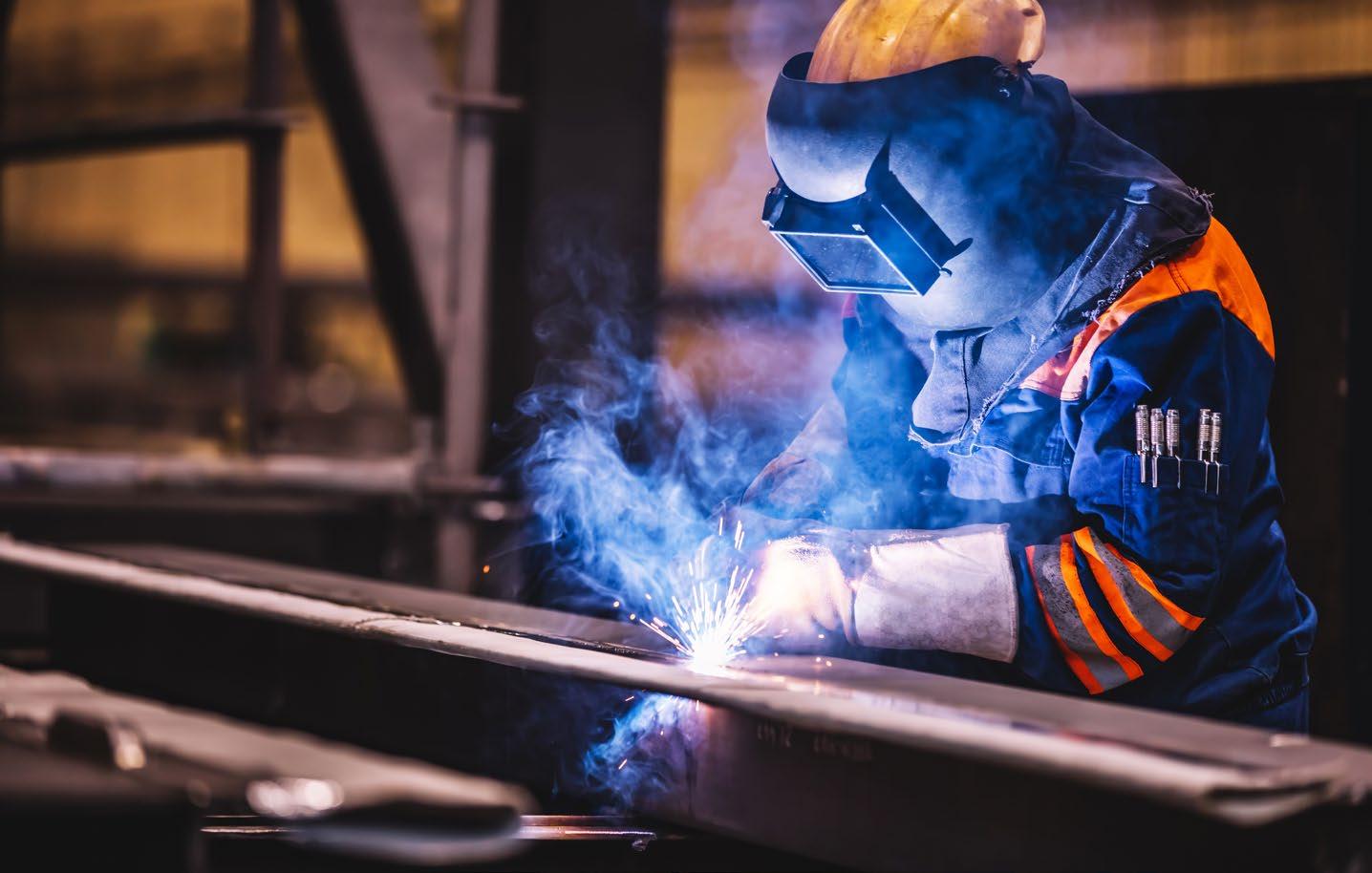
These courses cover a raft of activities across a range of welding processes, from electric arc welding and flame cutting, through to topics like welding in confined spaces, at heights, or in hot and humid conditions. These courses will be completed towards the end of this year and made freely available via the Weld Australia website.
The next Welding Safety Council is due to be held in September 2023.
DEFENCE INDUSTRY NETWORK
Weld Australia hosted the second meeting of its Defence Industry Network in June. The purpose of the Network is to support, grow and sustain the local Australian defence Industry. The meeting was attended by representatives from the Austal, Baker & Provan, Bisalloy, the Department of Defence, DVR Engineering, HRL, Lincoln Electric, Marand, Precision Metal Group, Thales, Uneek and Weld Australia.
The meeting was opened by Chair Jason Elias (Owner, Precision Metal Group), who led a discussion on sovereign industrial capacity priorities in defence. Atttendees shared the challenges and opportunities prevelant in the industry at the moment.
Thomas Lau (Senior Structural Design Engineer, Thales) provided a presentation focused on the manufacture of the Bushmaster combat personnel vehicle and the Hawke Eye.
Lively discussion of several topics followed, including skills and labour shortages and ways to help overcome these shortages; the importance of collaboration within Defence supply chains to mitigate risk, share resources and learnings and create sovereignty; and the importance of a range of different certifications and qualifications.
Interested in Joining?
The Defence Industry Network will focus on companies who are either already operating in the defence supply chain, or have ambitions of joining. Our aim is to ensure that contractual commitments to Australian Industry Content and Indigenous Participation are honoured.
The Network will also focus on:
• Contracting issues and the supply chain issues
• Compliance with Australian Standards, and certification and accreditation to Australian Standards
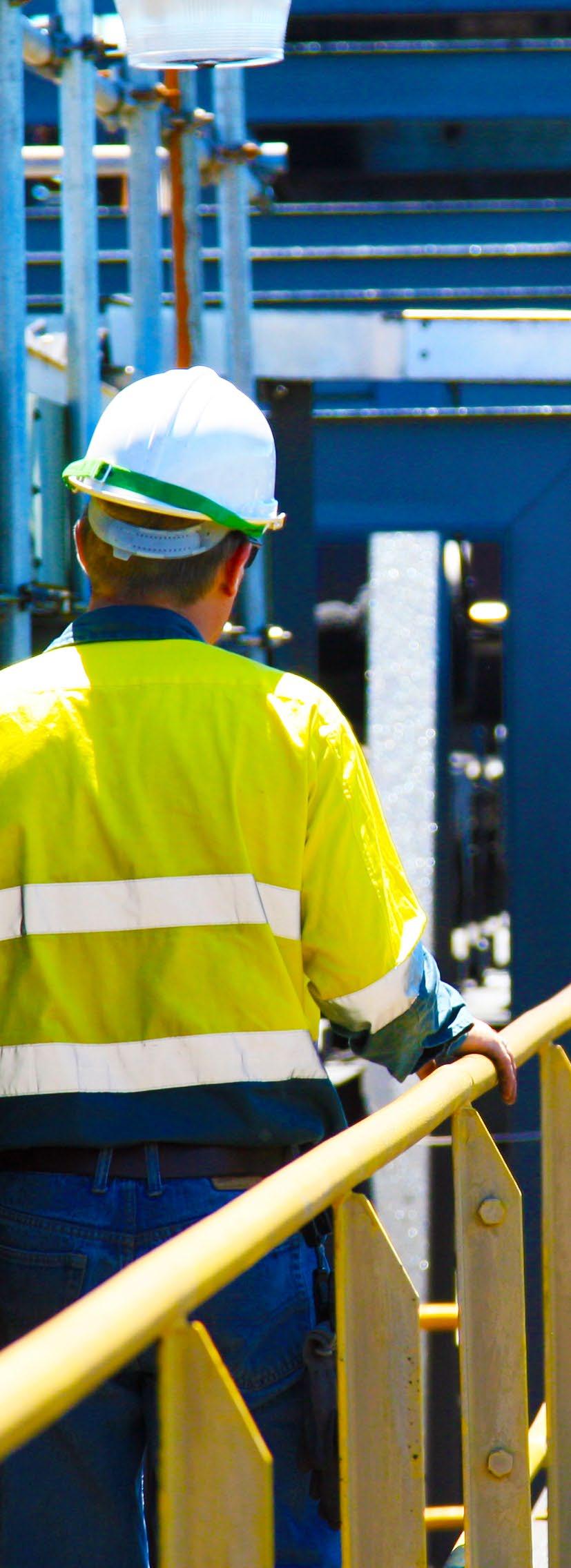
• Australian local manufacture and equal opportunity
• Advocacy to Government
Membership of the Defence Industry Network is free of charge for all Weld Australia Premium Corporate Members. Just some of the benefits include: networking with others in the defence industry, addressing technical and welding issues, discussing supply chain issues and solutions and accessing Weld Australia training, resources and specialist personnel.
To join, contact: Andrew Davies (Manager Technical Industry Networks) on 0438 428 966 or a.davies@ weldaustralia.com.au
POWER GENERATION INDUSTRY GROUP
Boiler Industry Group Meeting
The Boiler Industry Group met in early April, hosted by Synergy in Perth. The meeting was attended by over 30 people representing power generating companies, consultants and industry suppliers.
Geoff Crittenden opened the meeting with an update on Australia’s renewable energy transition, touching on challenges such as the sheer volume of materials and labour that will be required.
Bruce Cannon provided a presentation on updates to Standards and Technical Guidance Notes, including:
• Amendment 1 to AS 3992 was published in February. This fixed some anomalies and issues identified by users following the 2020 revision. It also incorporates some recent changes to welding consumable standards.
• The revision of AS 3788 is progressing well. The draft is currently being prepared for
public comment.
• AS 4458 is being considered for revision, once the revision process to AS 3788 is largely completed.
• Welding safety standards (AS 1674 series) are being revised. Part 1 (Fire) is progressing, Part 2 (Electrical) is being prepared for kick-off and committee reconstitution.
• Consumables standards are being updated.
Tanya Langdon (Oceaneering)—Chair of the subcommittee revising AS/NZS 3788 Pressure Equipment – In Service Inspection—gave a presentation providing a summary of the primary changes to the standard and the reasoning for the changes. A draft of the updated AS/NZS 3788 is currently with editors and will soon to be open for public comment.
Wayne Hill (EnergyAustralia) gave a detailed and informative presentation on a program developed by EnergyAustralia to develop a structured approach for the detection, repair, analysis and
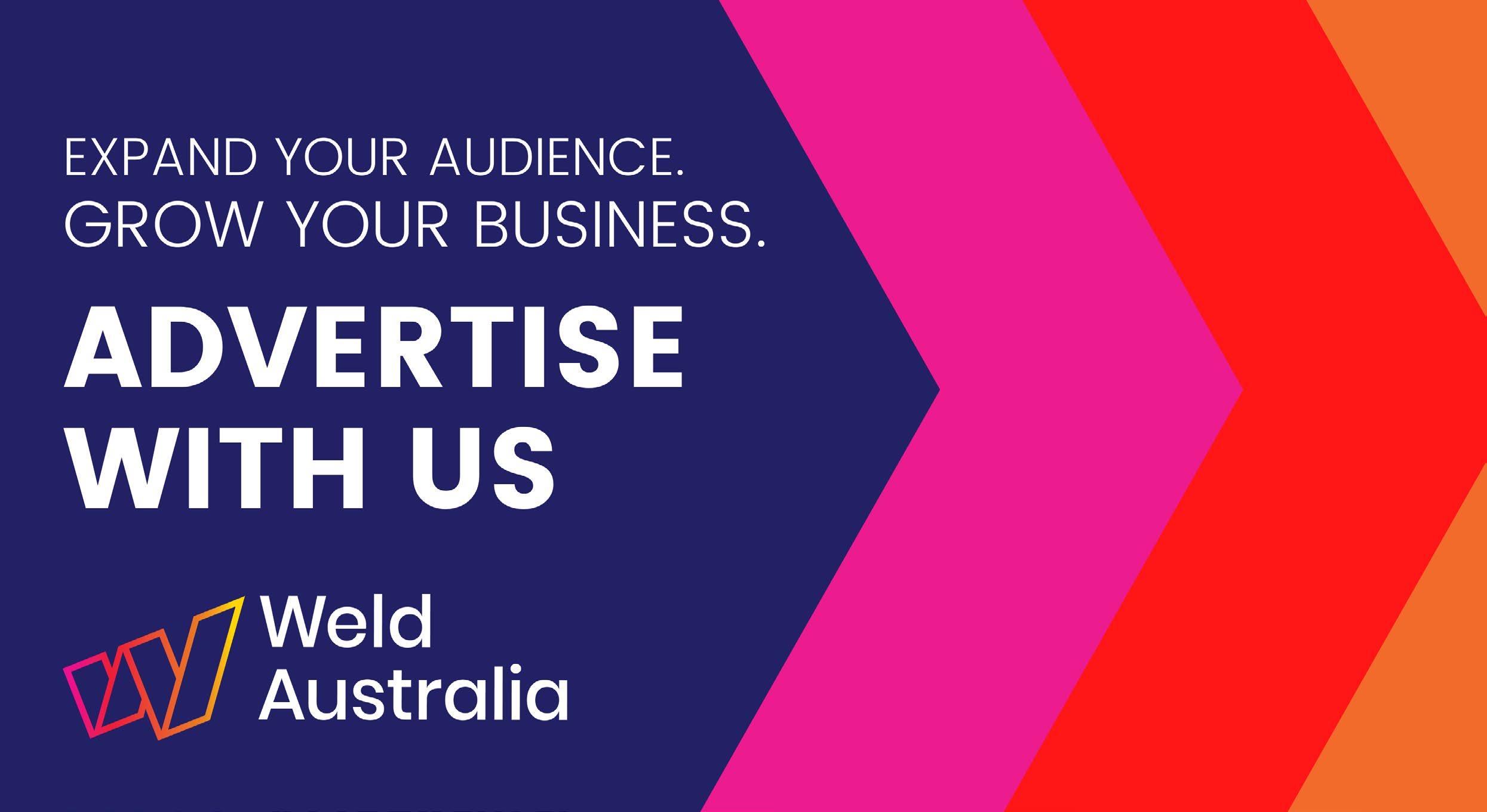
prevention of boiler tube failures.
Joseph Freeland (Delta Electricity) gave a presentation of a waterwall tube failure at Vales Point Power Station. Joseph explained the analysis of the failure to determine the root cause and to understand the risk of other similar failures on the boiler. The cause was determined to be an original weld failure. Joseph also described the process for repair of the failure.
Abi Babu (HRL) gave a presentation of strategies to best preserve units during times of storage and layup. In particular, a strategy for dry storage was discussed involving dehumidification and the control of relative humidity.
Damien Charman (IRIS NDT) gave a presentation on Low Frequency Electromagnetic Testing (LFET) on reheater tube standby pitting at Loy Yang A. The project involved 256 cut outs for repairs. This approach uses specific probes for specific tube IDs. There was also a lively discussion of
recent plant issues, safety incidents and key learnings, skills shortages and renewables.
Process Safety Industry Group
The Process Safety Industry Group meeting was held in early April in Perth, attended by 28 people.
Geoff Crittenden opened the meeting with an update on Australia’s renewable energy transition, touching on challenges such as the sheer volume of materials and labour that will be required.
James Ryan (OXT Group) presented on process safety bow ties for power generation. This presentation focused on the idea of creating value through good asset management and building a highly reliable organisation.
Sam Clayton (HRL) gave a presentation improving the operational performance of the Diamantina Power Station (Mt Isa) in terms of maximising plant output and improving operational flexibility.
Salim Talib (Synergy) described a
process where Synergy is managing projects, bringing projects to completion and handing over completed projects to stakeholders. The process covers all areas of project management and ensures that projects are delivered as per stakeholder requirements, specifications and budget.
Alex Horner and Ninh Nguyen from Synergy gave a presentation on the installation of additional electric heaters for the deaerators at Muja Power Station.
There was also a lively discussion of recent safety incidents and key learnings.
ADVANCED MANUFACTURING INDUSTRY NETWORK
Weld Australia launched its newly created Advanced Manufacturing Industry Network via a webinar in mid-May. The webinar focused on the additive manufacturing (AM) of metals and components with prominent technology providers doing talks on the current state of the technology on the market. There was also a

strong focus on the quality assurance of additive manufacturing with a member of ISO Technical Committee 261 – Additive Manufacturing, doing a talk on the standardisation with regards to the qualification of AM processes, personnel, and 3D printed parts.
Attendees heard from the Chair of the Industry Network, Dr Cornelis Van Niekerk (Business Manager Defence Welding, Weld Australia), and Geoff Crittenden (CEO, Weld Australia).
Brad Coulter (Senior Technical Sales Consultant, AML3D) provided an overview of the capabilities of AML3D; Professor Stephen Pan (University of Wollongong) spoke about wire-arc AM at the Facility of Intelligent Fabrication; Professor Huijun Li (University of Wollongong) gave an update on quality assurance, including the ongoing work of the ISO Technical Committee 261 and Standards Australia around AM. Finally, David Gerrard (Director APAC, Xiris) gave a presentation on the technology that Xiris has available for in-situ quality management of AM.
For details, contact: Andrew Davies (Manager Technical Industry Networks) on 0438 428 966 or a.davies@weldaustralia.com.au
WELD AUSTRALIA TO ESTABLISH NEW RENEWABLE ENERGY INDUSTRY GROUP
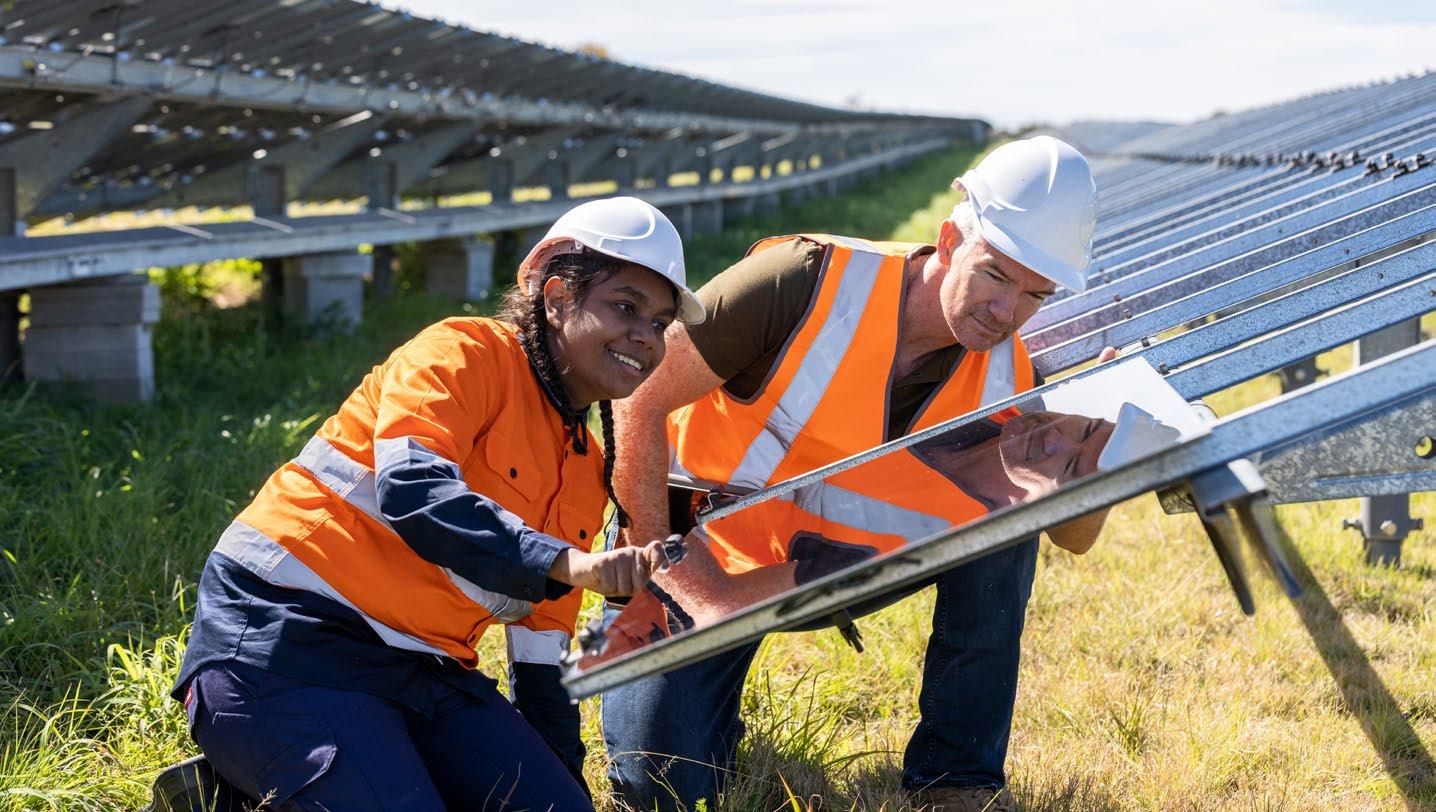
Weld Australia is proposing to establish a Renewable Energy Industry Group to bring together existing generators, new players, manufacturers, suppliers, specialists and consultants.
REGISTER YOUR INTEREST
Interested in joining? To register your interest, please contact Andrew Davies (Manager Technical Industry Networks, Weld Australia) on 0438 428 966 or a.davies@weldaustralia.com.au
The Federal Government has established a policy and targets to reduce carbon emissions by 43% by 2030, and reach net zero by 2050. These targets will play a key role in limiting global temperature increases and ensuring Australia’s transition to a low carbon future consistent with our commitments under the Paris Agreement.
These targets will necessitate the construction of new infrastructure on a massive scale. A veritable army of skilled workers, including welders, will be required. New technologies will also need to be developed.
Australia’s renewable energy industry will need a raft of additional resources to deliver on these ambitious projects, including:
• Manufacturing and fabrication capacity
• Raw materials (such as steel)
• Generation projects
• Energy infrastructure projects
• Skills and labour
• Contracting and contractor resources
All this is within the context of several broader Australian energy market
issues, including:
• Market volatility
• Thermal electricity generation operational limitations
• Energy generation supply and demand gaps
In face of these challenges, Weld Australia’s new Renewable Energy Industry Group will bring together existing generators, new players, manufacturers, suppliers, specialists and consultants to:
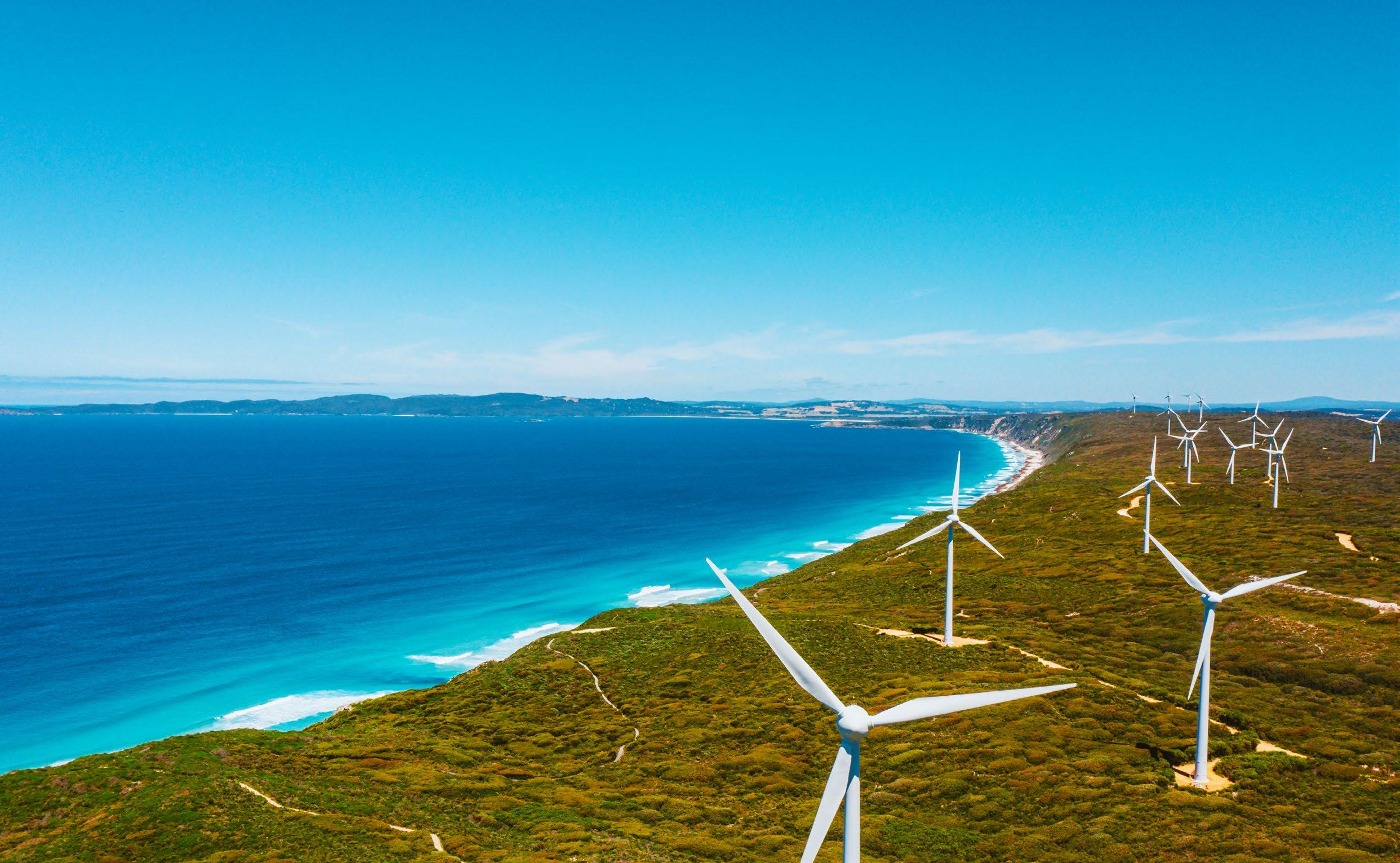
• Share knowledge experience, and learnings
• Discuss and workshop renewable energy issues
• Network and collaborate with likeminded industry colleagues
Weld Australia will facilitate meetings on behalf of members of the Renewable Energy Industry Group. Meetings may be face to face, online or a combination of both. The Group members will determine the frequency and structure of meetings, agenda items, and strategic direction of the Group.
There are two fusion welding courses that adhere to ISO 9606 Qualification testing of welders on Training.gov.au. This is the authoritative source of nationally recognised training and Registered Training Organisations (RTOs). These two courses were developed in Victoria in 2018 and use augmented reality welding simulators as a key component of the training.
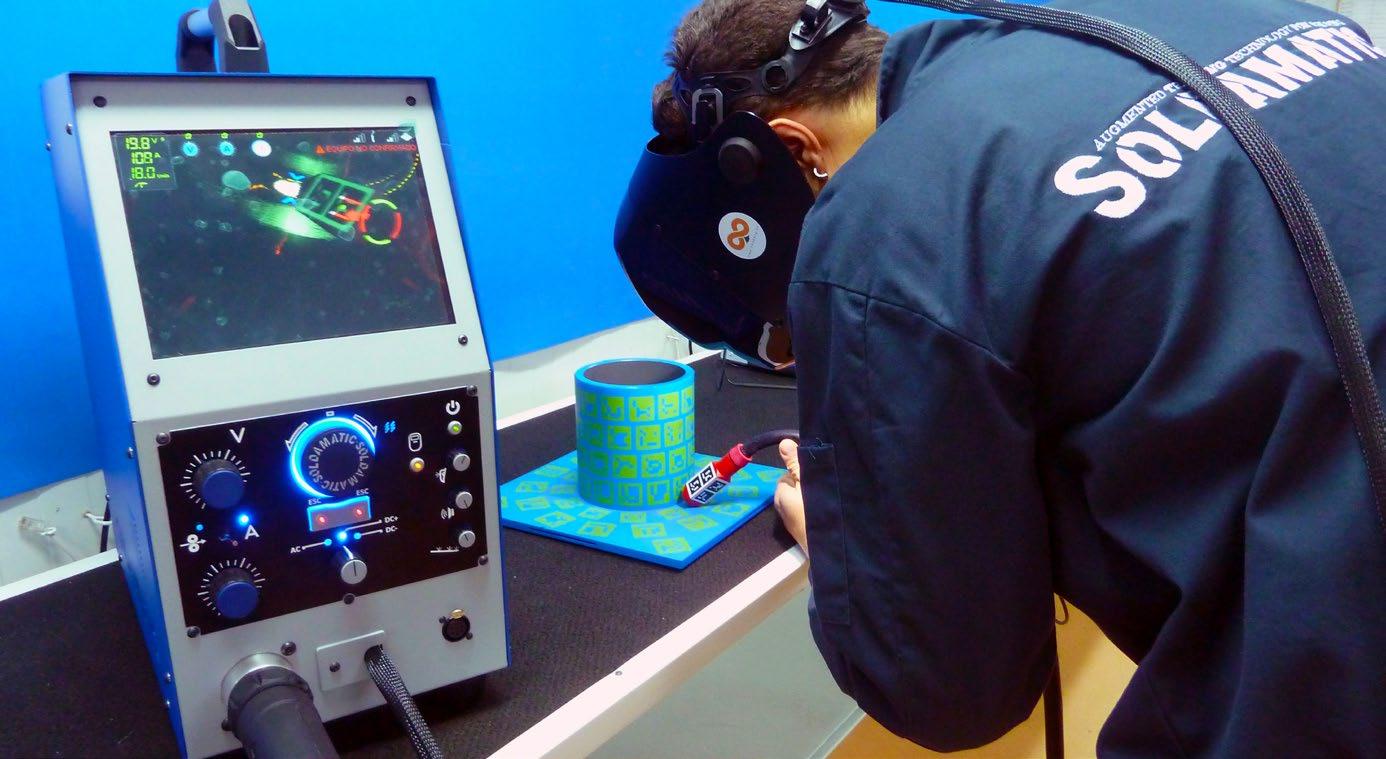
TRANSITION WORKERS
To be awarded a certificate for the Course in Fusion Welding to AS/NZS ISO 9606 for Transition Workers, you must successfully complete seven units of competency (four core and three elective). Core units:
• Simulate fusion welding processes using augmented reality equipment
• Identify welding processes, safe welding practices and use of hand and power tools
• Interpret and apply AS/NZS ISO 9606 for fusion welding processes
• Perform fusion welding procedures to meet the procedures of ISO 9606-1 (Steels – carbon steels)
EXPERIENCED WELDERS
To be awarded a Statement of Attainment for the Course in Fusion Welding to AS/NZS ISO 9606 for Experienced Welders, you must successfully complete three units of competency (one core and two elective). The core unit is: Interpret and apply AS/NZS ISO 9606 for fusion welding processes.
FURTHER INFORMATION
For further information, contact: training@weldaustralia.com.au
ENROL IN A FUSION WELDING COURSE TODAY
Enrol in a fusion welding course through any Advanced Welder Training Centre below.
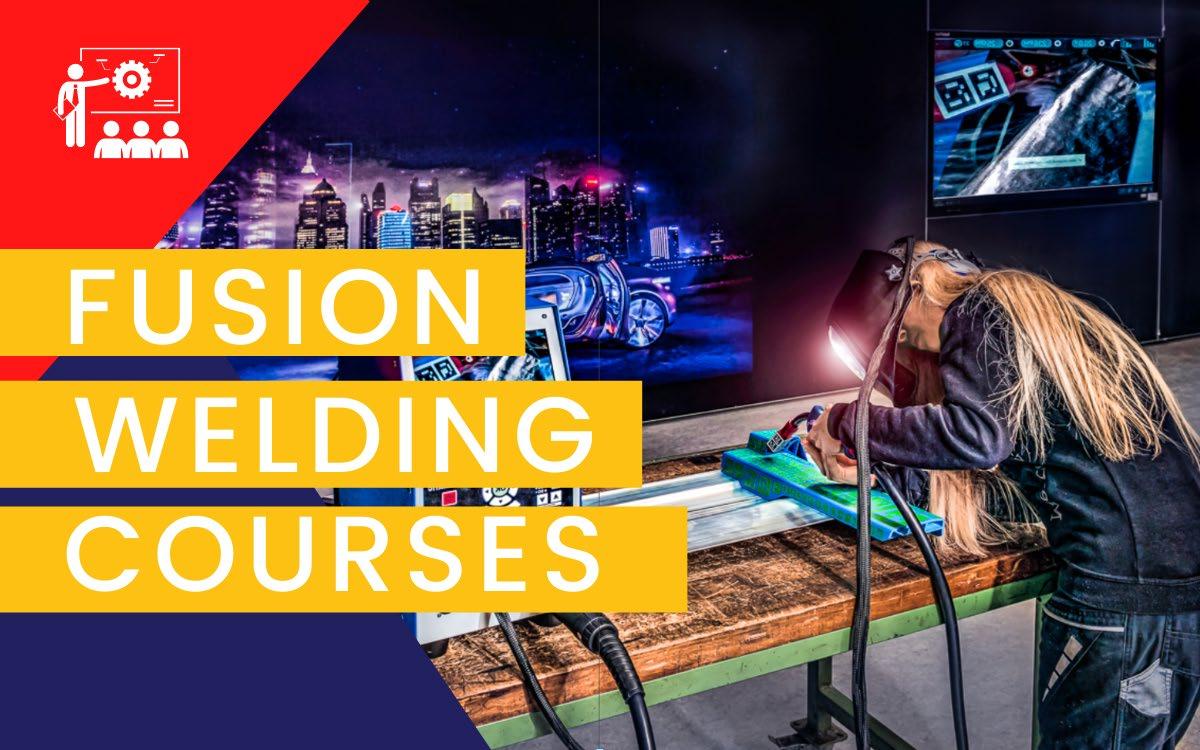
ACT
Canberra Institute of Technology cit.edu.au
81 Mildura Street, Fyshwick
Queensland TAFE Queensland tafeqld.edu.au
• Cairns Campus: Gatton, Newton, Eureka and, Wilkinson Streets, Manunda
• Townsville (Trade Centre Bohle) Campus: 763 Ingham Road, Bohle
• Toowoomba Campus: 100 Bridge Street, Toowoomba City
• Ashmore Campus: Benowa Road & Heeb Street, Ashmore
• Nambour Campus: 91 Windsor Road, Burnside
• Bundaberg Campus: 118 Walker Street, Bundaberg West
Tasmania
Tasmanian Minerals and Energy Council
tasminerals.com.au
13 Wellington Street, Burnie
Victoria
Box Hill Institute boxhill.edu.au
465 Elgar Road, Box Hill
Bendigo TAFE
bendigotafe.edu.au
23 Mundy Street, Bendigo
Federation University federation.edu.au
Lydiard Street South, Ballarat
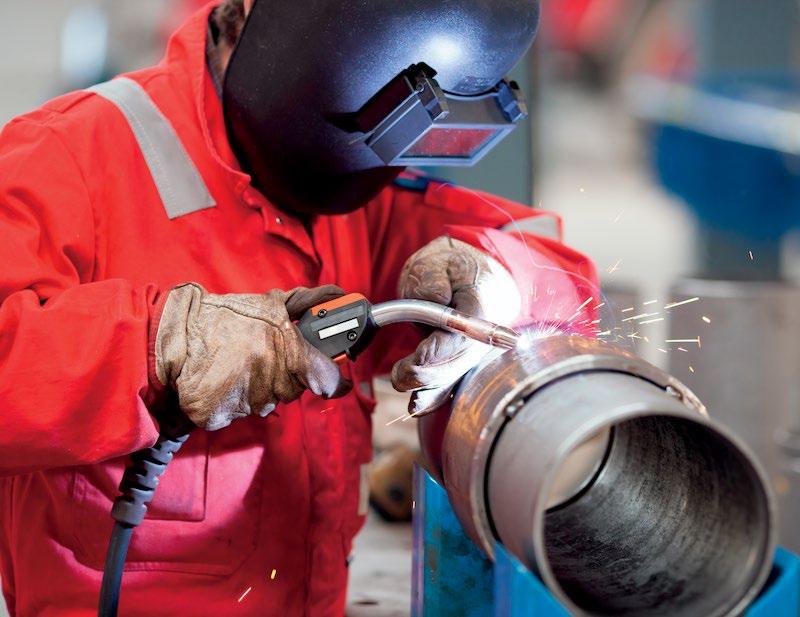
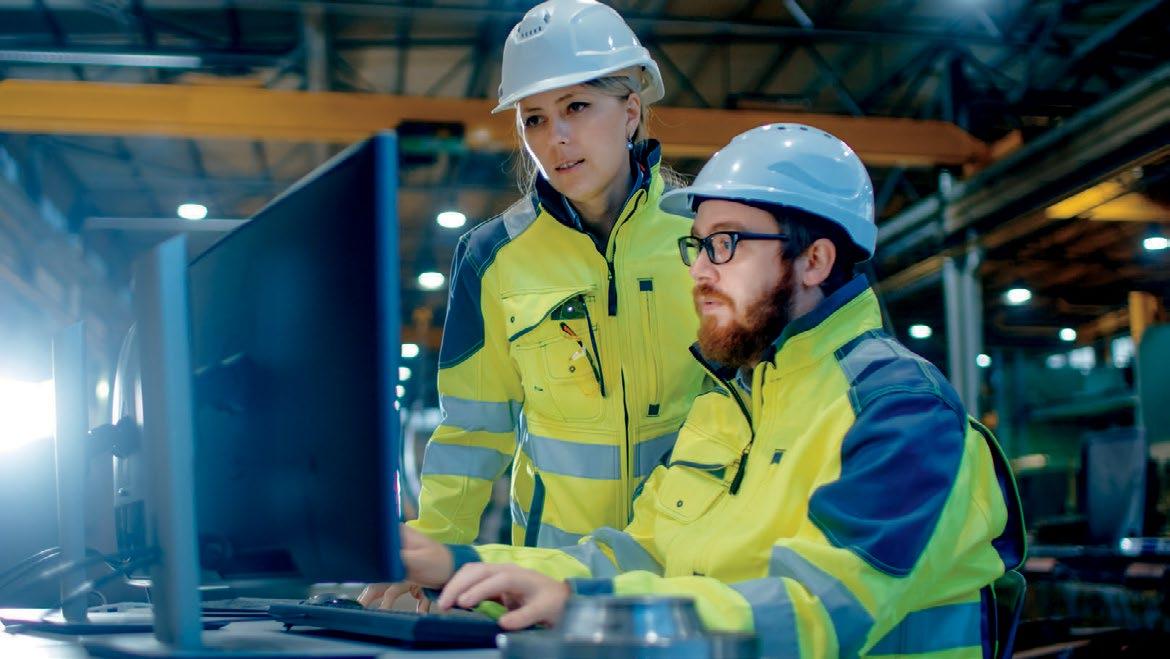
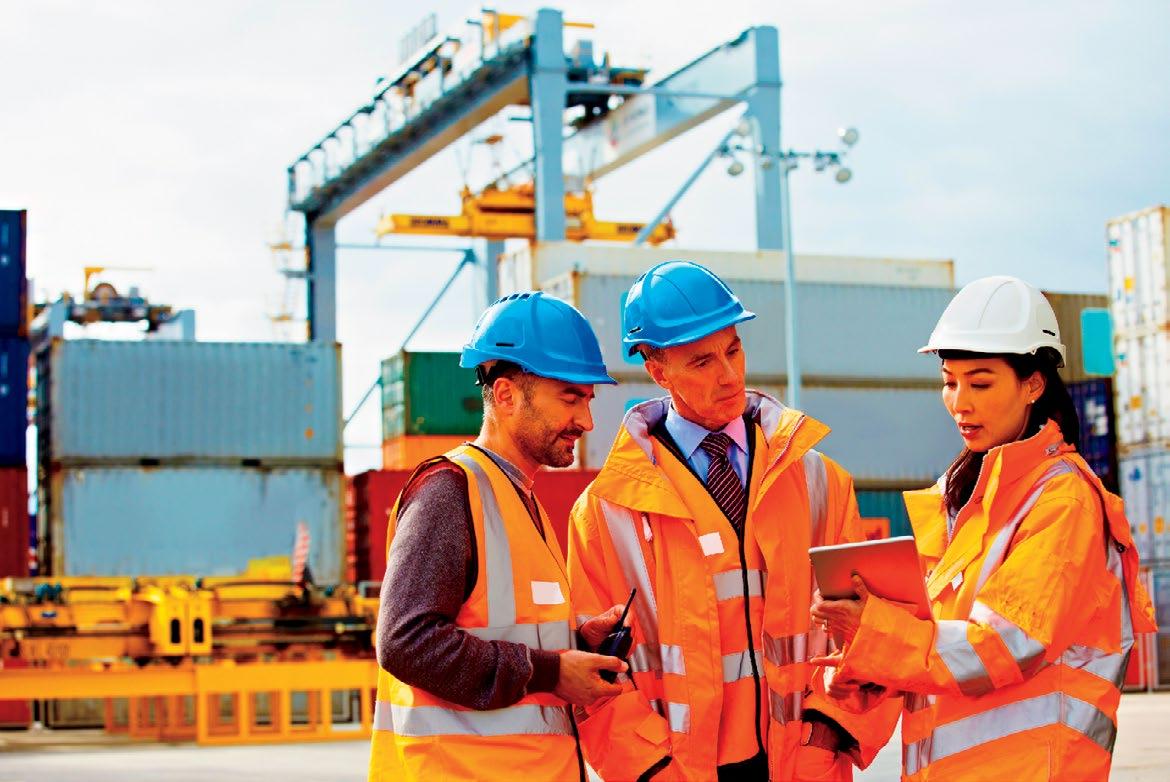
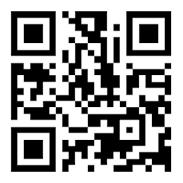