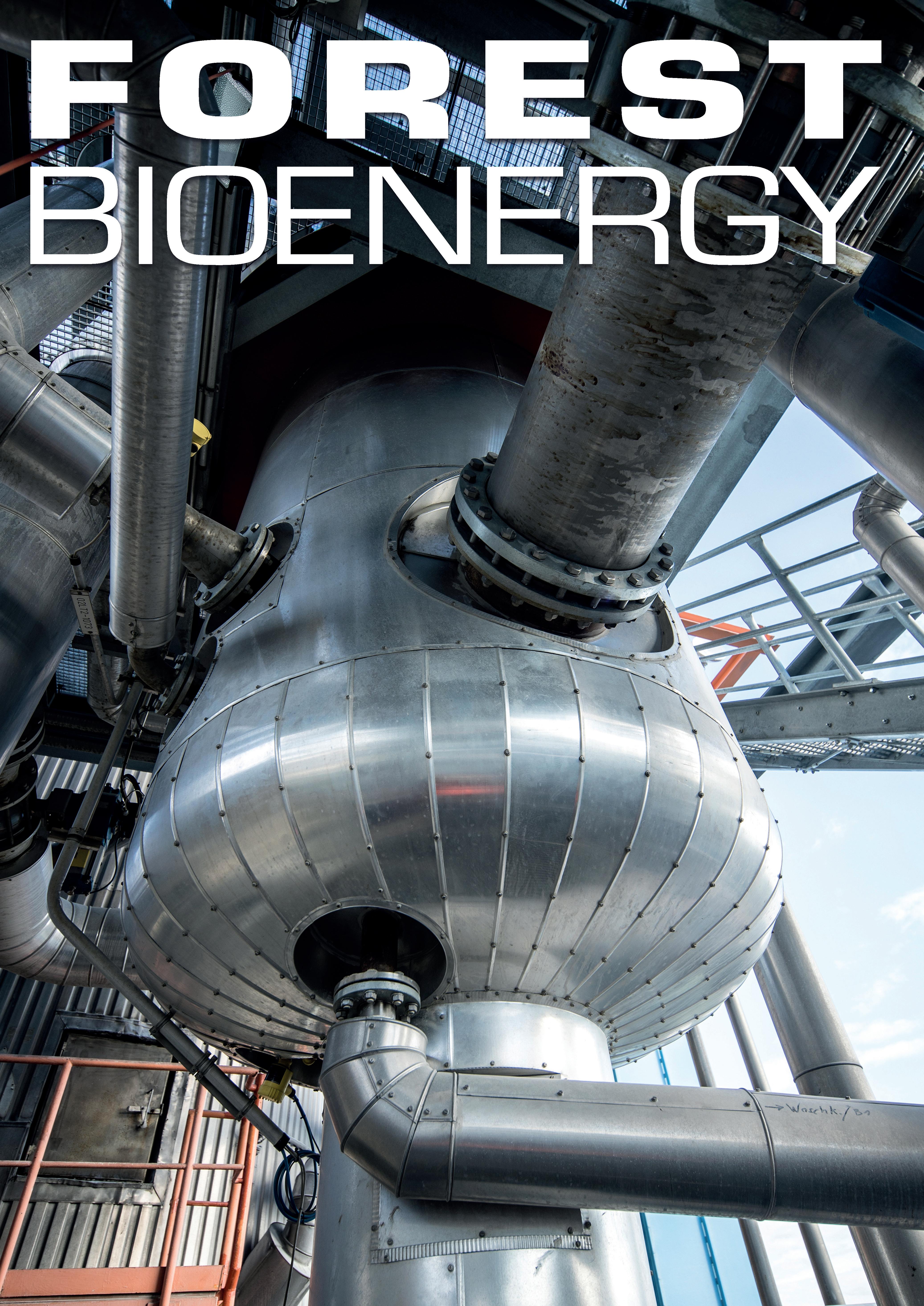
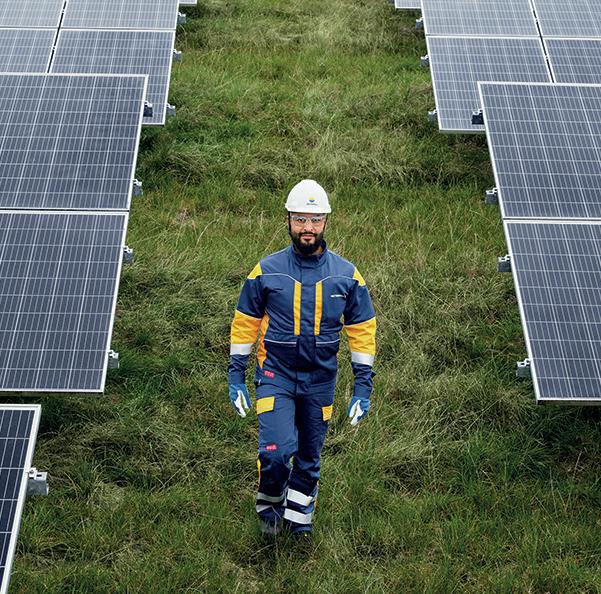

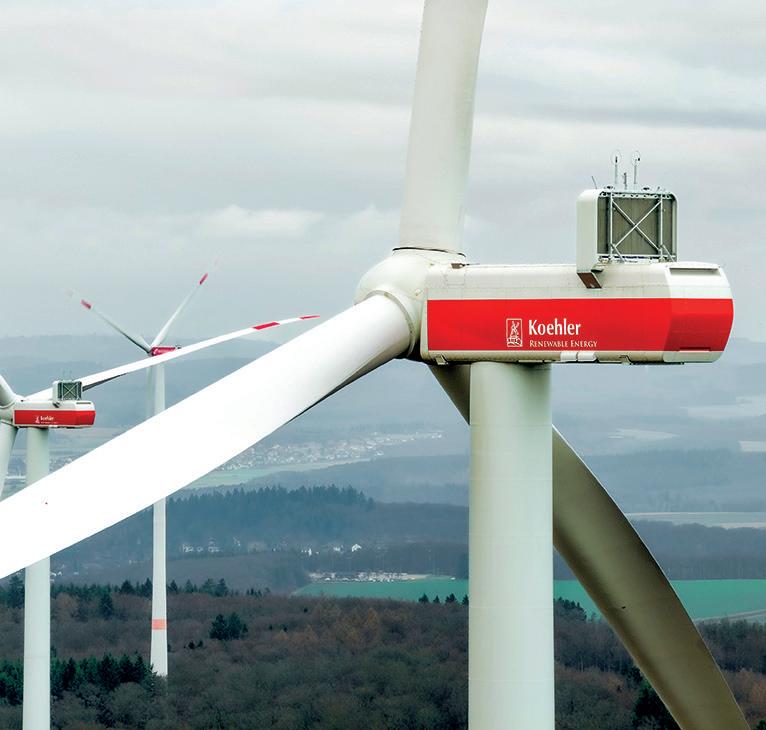
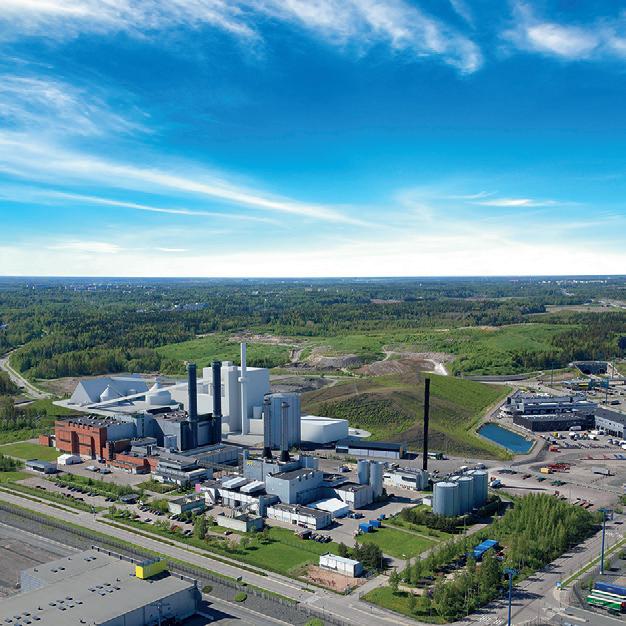
Valmet DNAe is a next-generation distributed control system. As a fully web-based platform, it delivers an industry-leading user experience and cybersecurity by design.
The system brings the process know-how of the world’s leading experts directly to your control applications and improves efficiency. It provides unique data collection and utilization capabilities, enabling informed decision-making.
Valmet DNAe is a catalyst for sustainable practices, and it sets the stage for autonomous operations and a digitalized future. Empower people to perform at their best, reach and exceed your targets, enable path to autonomous operations and evolve throughout the lifecycle with the new DCS. Are you ready to evolve?
For more information, visit valmet.com/dnae
Welcome to the Summer issue of Forest Bioenergy Review incorporating PIM Renewable Energy. As the global power generation industry adjusts to the growing need –increasingly enforced by legislation – to produce greener and more sustainable options, it will be those companies who supply power generation equipment and technology that will ultimately offer solutions for the future.
While solar, wind, hydro and bioenergy already have well-established bases, it is in the areas of energy storage and hydrogen power that some great leaps forward are being witnessed in terms of R&D spend and technological advancements.
Energy storage can be seen as an integral part of the loop when producing both solar and wind energy. Because both rely on natural resources, the development of means for storing their energy for later use when there is a downturn in production is essential. Such storage techniques provide both a back-up and make renewables a more obvious choice of power.
Looking ahead to the Autumn issue, we will be focussing on topics of growing interest, including: Multi-fuel energy production; Automation in energy production; Carbon capture and storage; and Biogas. The deadline for contributions is 15 August and should be sent to: pulppaperlogistics@ virginmedia.com
Vince Maynard, Publisher
Volume 12, Number 61 – Summer 2024 Contact information
PUBLISHER & EDITORIAL DIRECTOR
Vince Maynard
KVJ Enterprises, Tralee, Hillcrest Road, Edenbridge, Kent, TN8 6JS, UK
Tel: +44 (0) 1732 505724
Mobile: +44 (0) 7747 002286
E: pulppaperlogistics@virginmedia.com
CONSULTANT EDITOR
David Young
Tel: +44 (0) 1737 551687
Mobile: +44 (0) 7785 796826
E: youngeditorial1@btinternet.com
ISSN 2045-8514
PRODUCTION
Anthony Wiffen
ASTAC Business Publishing
Tel: +44 (0) 1460 261011
Mobile: +44 (0) 7851 612799
E: anton_print_1@mac.com
PRINTING
KNOCK OUT PRINT
+44 (0) 1892 823540
Unit 2 The Coppice, Petteridge Lane, Matfield, Kent TN12 7LP info@knockoutprint.co.uk www.knockoutprint.co.uk
2 7
Aleading global renewables manager specialising in the solar+ infrastructure sector, NextEnergy Capital (NEC), has announced that its third fund, NextPower III ESG (NPIII ESG), has energised two further utility-scale solar assets for a total of 260 MW across Spain and Portugal. This takes its Iberian exposure to 356 MW in operation with an additional 110 MW under construction. NPIII ESG successfully completed its investment period last year and has committed all of its raised capital.
The newly energised assets consist of a 210 MW solar project located in Santarém, Portugal, known as Santarém, and a 50 MW solar asset located in Cadiz, Spain, known as Agenor. The combined assets will produce an estimated annual production of 445 GWh, the equivalent of powering an estimated 126,700 homes’ annual electricity consumption needs.
Both Santarém and Agenor benefit from long-term contracted revenues through Power Purchase Agreements (PPAs) with Statkraft, a high-quality corporate off-taker in Europe’s energy market. The
PPA covering Santarém is notable, being the largest PPA in the history of Portugal to date, showing the continued demand for high-quality corporate PPAs across the European market.
NPIII ESG is a private fund exclusively focused on the international solar infrastructure sector, principally targeting projects in carefully selected OECD countries, including the US, Portugal, Spain, Poland, Greece and Italy. NPIII ESG has 173 solar and storage assets, totalling 1.8 GW. NPIII ESG completed its fund raise in 2022, with a total of $896 million, including an SMA. The target of the fund was $750 million.
More information: www.nextenergycapital.com
In the presence of representatives from politics and the media, the shareholders of Hy2B Wasserstoff GmbH and the project partners, the go-ahead was given for the commissioning of the first grid-connected 5 MW hydrogen production plant in Bavaria at the site of the future hydrogen centre in Pfeffenhausen.
Kraftanlagen Energies & Services SE has been appointed as general contractor for the construction and commissioning of the plant. Commercial operation of the
electrolyser is scheduled to start in the second half of the year.
Once operational, the electrolysis plant will be able to produce an average of 1,200 KG of green hydrogen per day. This will then be compressed to 450 bar and filled into transport trailers at a filling station. The trailers will then distribute the hydrogen to bus and truck refuelling stations in the Munich and Ebersberg districts, supplying Munich’s regional bus services with green fuel for a total of ten hydrogen fuel cell buses. In
the coming years, an increasing proportion of the green hydrogen will be produced using solar energy from photovoltaic systems in the immediate vicinity of the plant and, in the future, with additional wind power.
Alfons Weber, CEO of Kraftanlagen, explained how the plant works: “With the help of the alkaline electrolyser from the company Nel – the key component of the plant – hydrogen and oxygen are produced from electricity, or more precisely from direct current,
by electrolysis. This process takes place in a virtually pressureless system and therefore ensures very safe and hazard-free operation of the plant”.
One day after the official inauguration of the electrolyser, local residents had the opportunity to take a closer look at the plant and learn more about the production and use of the green hydrogen produced in Pfeffenhausen.
More information: www.kraftanlagen.com
At a recent networking seminar hosted by Vattenfall IDNO UK, developers representing PV and BESS projects flagged grid issues as the primary obstacle to achieving the UK’s fast-approaching net zero deadline.
Hitting net zero emissions by 2050 is a formidable goal, but for many developers in the energy sector, one challenge looms larger than most: the UK’s archaic power grid. This key insight emerged from Vattenfall IDNO’s recent networking seminar in London, where 95% of the 20 developers highlighted grid-related issues as their primary obstacle.
The Electricity Grids and Secure Energy Transitions report by the International Energy Agency (IEA) underscores that globally, grids are struggling to keep pace with the rapid progress in renewable energy development. This revelation highlights the urgent need for modernisation of grid systems, many of which haven’t been updated since the 1960s and are unable to adequately manage the fluctuations in supply from renewable energy generation.
“When it comes to working on a new project, the grid is definitely the
biggest hurdle to overcome,” stated Ian Chisholm, Head of Greenfield Development at Vantage RE. “Starting from timeframes for a connection and finishing with a lack of flexibility on the Dependent Network Operator (DNO) side when it comes to decisions over cable routes, design decisions or selection of equipment.”
Capacity constraints are another major obstacle, with many renewable energy developers being told by their local DNOs that they must wait in a 15-year backlog of applications before being considered for a connection to the grid. Hamzah Ahmed, Network Infrastructure Lead at Amberside Energy, points out: “The grid often lacks the capacity to handle the influx of renewable energy. This results in bottlenecks that delay projects and increase costs.”
For everyone in the energy sector, this is not breaking news, but a frustrating, daily reality. The more important question is how renewable energy developers can thrive given the circumstances. According to McKinsey & Company, achieving net zero will require extensive investments from both governmental and private funding. This includes scaling up
renewable energy capacity, such as offshore wind and solar installations. Earlier this year, Ofgem and the UK government set out a plan for reforming grid connections and regulatory policy. While promising, these are long-term projects and businesses can’t afford to wait. So, what is the solution?
Historically, developers had to gain grid connections through the local DNO in the regions where they develop projects. Now, however, to introduce competition and reduce costs, Ofgem allows Independent Distribution Network Operators (IDNOs) to develop, operate and maintain local electricity distribution networks across the UK.
Vattenfall IDNO, with over 100 years of specialist grid infrastructure knowledge, has energised more than 50 commercial grid connections, significantly benefiting renewable energy developers through competitive asset adoption values and other techniques that free up Capital Expenditure (CAPEX) and expedite project connections. Their Grid Connections Consultancy helps developers obtain grid connections faster while reducing costs. Services include reserving grid capacity,
assessing design requirements, negotiating with landowners and conducting compliance audits. In addition, Vattenfall IDNO offers asset adoption payments for adopting new grid connections, freeing up funds for developers to reinvest.
“At Vattenfall IDNO, we recognise the urgency of achieving net-zero goals and that many businesses find it challenging to manage the intricate process of securing grid connections,” said Stewart Dawson, Managing Director of Vattenfall IDNO. “Understanding how we deliver value engineering and alternative solutions, which make difficult projects feasible is pivotal for renewable energy developers looking to drive business growth and sustainability, and especially important for the UK’s net zero targets.”
When it comes to tackling the grid hurdle, the importance of innovation and partnerships between developers and energy experts cannot be overstated. The journey to net-zero is demanding but, with the right strategies, the UK can achieve its ambitious goals.
More information: www.idno.vattenfall.co.uk
According to the latest statistics released on 7 May by Ocean Energy Europe, the marine energy sector made significant progress towards commercialisation in 2023.
Responding, Claire Mack, Chief Executive of Scottish Renewables, said: “Our world-leading marine energy industry will provide a predictable, low-carbon energy source and will play a key role in delivering clean power to our future energy system.
“The latest statistics released by Ocean Energy Europe show clearly that the UK’s marine energy industry has a bright future and it is encouraging to see the projects we have in development making such substantial progress towards commercial deployment. We have high hopes that a significant number of these projects will be successful in Contracts for Difference Allocation
Round 6, the results of which will be announced later this year.
“Scotland will welcome the Ocean Energy Europe conference later this year and I look forward to working closely with all the key players in the industry on how we can create a thriving marine energy economy with multiple projects deployed at scale around the UK coastline.”
Sumitomo SHI FW (SFW) has signed an agreement with Capwatt to provide Front-End Engineering Design (FEED) services for a state-of-theart syngas production plant, integral to the ground-breaking Mangualde Renewable Methanol project in Portugal.
This initiative aims to build a cutting-edge biorefinery capable of producing 80,000 tons of renewable methanol annually, utilising locallysourced biomass residues and renewable electricity from a nearby photovoltaic (PV) solar park.
The core of the plant will feature an advanced SFW gasification unit, designed to transform the carbon in biogenic residues into syngas. This syngas will then be combined with green hydrogen from electrolysis in the methanol synthesis process.
Renewable methanol, a versatile platform chemical, is set to become a cornerstone of future carbon
For a future-proof energy supply, batteries already in use from electric cars are given a new lease on life in commercial buildings. This is made possible by a new partnership between Voltfang of Aachen, Europe’s leading developer and manufacturer of high-performance green energy storage systems for industry and commerce, and the owner-managed construction and service company Goldbeck, with headquarters in Bielefeld and more than 100 locations in Europe.
Voltfang combines multiple batteries from electric vehicles to create energy storage systems that ensure innovative and green electricity management in commercial buildings. A pilot project featuring a
200 kWh large-scale energy storage system from Voltfang, including energy management systems and a powerful inverter, marks the start of the partnership between Voltfang and Goldbeck. The fully integrated solution is compatible with solar PV systems, as well as heat pumps.
Goldbeck is building a 9,000 sq m logistics hall and offices for the sporting goods manufacturer Teveo in the Nuremberg metropolitan area. Voltfang is equipping the facility with a sustainable energy concept, including a 749 kWp photovoltaic system and 16 charging points for electric cars. The aim is to determine the optimum storage system size for various buildings in Goldbeck’s portfolio. Future projects with
commercial storage systems will be effectively scaled on this basis. This first project includes the possibility to increase the battery storage system’s capacity to a maximum of 700 kWh.
“When my father founded Goldbeck, he was already considering systematising construction and doing things differently. We are characterised by a pioneering spirit and a desire to innovate; we plan, construct and operate forwardlooking buildings. That is why we focus on smart solutions such as an energy-optimised building envelope, efficient building technology and renewable energies. Together with Voltfang, we want to make the energy management of buildings even more efficient and less dependent on
management solutions for both the transport and chemical industries. Its applications are vast, from serving as sustainable shipping fuel to being converted into sustainable aviation fuel, plastics and other essential chemicals.
As global Net Zero targets drive the demand for renewable methanol, production needs to surge from zero today to an estimated 400 million tons per year by 2050.
SFW’s comprehensive scope includes the oxy-steam fluidised bed gasifier, syngas cooler, hot gas filter, tar reformer and final syngas scrubber. The FEED is expected to be completed in 2024, with the project set to start in Q2/2025. The plant is anticipated to begin renewable methanol production by the end of 2026, marking a significant leap forward in the quest for sustainable transportation fuels. More information: www.capwatt.com
electricity suppliers. Customers have the ability to control the consumption of green electricity in their properties more precisely with their own battery storage systems,” emphasised JanHendrik Goldbeck, Managing Partner at Goldbeck.
“The co-operation with Goldbeck is good news for Voltfang and an important step for the future of circular building operation. We are looking forward to integrating our storage solution into Goldbeck buildings. It is an exciting project that will further define the future of the energy supply,” agreed Roman Alberti, founder and Managing Director of Voltfang.
More information: www.voltfang.de
On 14 March, UPM Biochemicals announced another important milestone in the development of the world’s first biorefinery in Leuna, Germany. In partnership with DB Cargo, the first deliveries of wood have now been made to Leuna by rail, establishing and testing the direct rail link to the Leuna operations’ woodyard.
This will enable UPM to transport wood sustainably and to strengthen local supply chains, increasing the security of supply with critical raw materials. DB Cargo, a specialist in the sustainable and climate-friendlier transport of goods, is a long-standing partner for timber transportation in the rail sector and has been handling UPM’s paper and pulp freight for several years.
“We are excited to welcome the first rail-based wood transports at our newly established woodyard in Leuna,” said Andreas Meggendorfer, Director Supply Chain & Sourcing at UPM Biochemicals. “We will offer fully sustainable renewable chemicals with a significantly better CO2 footprint compared to fossil alternatives. It is paramount that we work on strategies to continuously optimise the environmental performance of our products further. Using rail as a transport mode does exactly that and by partnering with DB Cargo, we can now rely on a well-known and capable rail logistics partner, and have built a resilient and sustainable wood
logistics set-up for our biorefinery in Leuna.”
Thorsten Wartenpfuhl, SVP Sales Consumer Goods, Pulp & Paper, Timber at DB Cargo, agreed:
“UPM and DB Cargo have been linked by a successful partnership for rail-based inbound logistics of timber for many years. We are therefore very pleased to now be an important supply chain partner for UPM at the new biorefinery in Leuna”.
It is worth mentioning that wood handling and processing activities have begun as part of the commissioning and start-up work for the biorefinery. The first wood
chips made of wood from sustainably managed regional forests have been produced, confirming the overall
Nexergy Holdings PLC, an industry leader committed to enhancing sustainable energy solutions, has announced a strategic collaboration with Lorentz, a visionary company pioneering the production of green hydrogen. This partnership marks a significant step towards advancing the sustainable energy landscape and addressing the increasing demand for environmentally-friendly fuel sources.
Production of green hydrogen is expected to start in 2024, with the potential to reshape the future of energy and transportation.
Commenting on the collaboration, Jason Turner, Managing Director of Nexergy, said: “Green hydrogen serves as a highly-efficient and eco-friendly form of fuel, utilising water and solar energy to power vehicles and industries. This collaboration aims to leverage Lorentz’s ground-breaking technology to commercialise green hydrogen, positioning it as a viable alternative to traditional fuel sources”. Furthermore, the partnership is set to provide seamless integration into
existing infrastructure, facilitating widespread access to this innovative energy solution.
The potential applications of green hydrogen span multiple industries, with endorsements from key players such as Airbus, BMW and JCB. Representatives from
Airbus have expressed confidence in hydrogen as a crucial technology for achieving low-carbon commercial aviation by 2035, highlighting its significance for the aerospace industry.
In addition, BMW’s Chairman of the Board of Management, Oliver Zipse, emphasised the pivotal role of
The new H series of harvesters and forwarders from John Deere offers more productivity, fuel efficiency, stability and comfort of use. By investing in product development, innovation and technology that strengthens customers’ business now and in the future, John Deere is setting a new standard in wood harvesting.
The large size harvesters 1270H and 1470H and the loader tractors 2010H and 2510H were launched at an event in Järvenpää, Finland, on 24 April. The load tractor size class is completely new, with the load capacity of the 2010H truck at 20 tons and the 2510H truck at 25 tons.
The high-performance engine of the new H series harvesters has 10% more power and torque. The new hydraulics, which includes three separate pumps, produces
hydrogen in enabling emission-free mobility on a global scale.
Lorentz’s patented technology, with an initial project site planned in Spain, is poised to revolutionise sustainable hydrogen production, paving the way for decarbonisation in the energy sector and beyond. Through harnessing renewable sources like wind and solar, the process employed by Lorentz promises to significantly reduce carbon emissions, offering a compelling solution for a greener energy transition.
Showcasing the significant cost savings and environmental benefits through utilising Lorentz’s technology, the comparative profile of a 1,100mile journey, (Rome to London) would cost a mere fraction of diesel, petrol or electric power. Using Lorentz technology, at a production cost of €17, there would be no CO2 emissions, just 157 kg of pure water. This highlights the potential of green hydrogen as a game-changing solution for sustainable and cost-effective transportation.
More information: www.nexergyholding.com
more power and a higher working pressure for the feed. The optimised system ensures good fuel economy. The new active frame lock offers better stability to the machine when working both on steep slopes and on flat terrain. This makes it easier to work when the boom is on the side of the machine, giving the driver a larger working area. Compared to the G series, the H series harvesters increase
productivity significantly. At the same time, fuel consumption per cubic metre produced is lower than before.
More information: www.johndeere.fi.
In March, Agrar GmbH Reichenbach commissioned its Kumac digestate processing system from WELTEC BIOPOWER. This is the first Kumac plant to go live in Germany, in addition to the 16 that have been built worldwide to date. The agricultural company based in the Vogtland region of Saxony, Germany, specialises in dairy farming and the cultivation of feed crops. In addition to the dairy farm with 1,400 cows and breeding cattle, the farmers have been operating a biogas plant with an electrical output of 845 kW since 2006. The facilities generate up to 72,000 t of liquid manure and digestate a year.
Every day, the biogas plant feeds 12,000 kWh of electricity into the public grid. In addition, the plant supplies up to 500 kW of heat to small consumers and to the site of the former Paracelsus Clinic in Reichenbach via a heating network.
The plant’s main business consists of the delivery of biogas via a 3.2-km raw biogas pipeline to the heating plant of Stadtwerke Reichenbach for the base load supply of flats and social facilities. The amount of electricity generated each year corresponds to the annual consumption of around 6,000 private households.
“In Reichenbach, the output of the Kumac process consists of
around 25 percent solid and 20 percent liquid farm manure and 55 percent dischargeable water. The resulting solid matter and the nutrient concentrate are applied as organic, high-quality fertiliser to our own crops. In this way, long transport routes are avoided,” explains Lars Bittermann, Managing Director of Agrar Reichenbach GmbH. “This closes an efficient material flow
cycle, and the individual areas of our portfolio interlock perfectly. From the cultivation of feed crops to dairy farming to the utilisation of the liquid manure in the biogas plant and the processing of digestate into fertiliser and water, all components have their place.”
The scalable modular system can be used from an amount of 70,000 t of liquid manure or digestate a year. Should the processing needs increase, several Kumac lines can easily be combined. “The processing here is almost fully automated, which also minimises the amount of personnel required”, says Managing Director Lars Bittermann. “By the way: Operators who decide to set up a system can receive funding from the European Agricultural Fund for Rural Development”, adds Nico Sudbrink, process engineer at Weltec Biopower. More information: www.weltec-biopower.de
As a manufacturer of specialty paper, Koehler Group is involved in an energy-intensive industry and is keenly aware of its responsibility towards the environment and the climate. With this in mind, the company has been investing in renewable energy generation for over 20 years, setting up a second division of
the business, Koehler Renewable Energy, over a decade ago to focus on this area. With the ‘2030 Koehler Promise’, Koehler Group set itself the goal of generating more energy from renewable sources with its own facilities than it consumes producing paper by 2030 at the latest.
In its current sustainability report, Koehler Group provides detailed information for the first time about
its sustainability strategy and the many areas in which it is taking action. “As a family business, our focus is not on quarterly results, but rather on the long-term and the generations to come. This means that we do not view sustainability as a trend, but rather as a necessity for our society’s long-term survival,” said Kai Furler, Koehler Group CEO Kai, who realised early on that investing in renewable energy was a
key issue for the future. In 2022, the Koehler Group was already able to generate 69.9% of the energy required for its paper production from renewable sources on a balance sheet basis. With a view to increasing this share, Koehler has made building its own power generation facilities part of its sustainability strategy. Several wind farms are currently being constructed, which will
also be operated by Koehler after commissioning. After over ten years of planning and assessing projects, the company’s first two wind turbines in Germany, with a combined output of 8.4 MW, were completed in February, 2024, at the Wetzlar-Blasbach wind farm in Middle Hesse.
In order to use these two wind turbines directly for paper production, the Koehler Group decided to sign a Power Purchase Agreement. PPAs are becoming increasingly important in Germany as a tool for expanding the use of renewable energy, e.g. for funding wind turbines and supplying
industrial clients with green energy in the long-term. “Energy is one of the most important tools for business success these days,” underlined Cornelius Schulthess, Corporate Director Energy Supply Management at Koehler Renewable Energy and energy industry expert. He went on to explain: “Companies have various options for improving their carbon footprint, starting from energy efficiency projects through to generating their own renewable energy and associated PPAs. This enables us as a company to gain further independence from the prices on the energy market”. For Koehler, practically speaking, this
means that the energy produced in the Wetzlar wind farm is fed into the grid via a service provider and can be directly purchased by the Koehler Group’s German production sites. At the start of 2023, after almost five years of planning, approval was granted for a wind farm with
five turbines North of Waldeck in North Hesse. The wind farm is due to be commissioned in 2025 and is expected to generate around 70,000 MWh of electricity per year. The same applies for another wind farm with two turbines in Lich in Middle Hesse that is expected to generate around 28,000 MWh of electricity per year. There is also a pipeline of projects with over 100 MW of installed capacity. Above all, Koehler Group would also like to invest in wind turbines in the immediate vicinity of its sites in Baden-Württemberg.
More information: www.koehler.com
At Helen’s Vuosaari bioenergy heating plant, Valmet’s solution combines flue gas condensation and combustion air humidification with heat pump technology, driving the overall plant efficiency beyond 120% and the stack temperature to 11°C.
In an era when environmental sustainability and energy efficiency are paramount concerns, industries and residential sectors are increasingly seeking innovative ways to maximise their energy efficiency and reduce their carbon footprint. Helen Ltd., one of the largest energy companies in Finland, is doing this, too. It is phasing out coal and aiming for carbon-neutral energy production by 2030. Its Hanasaari coal-fired power plant was closed in April, 2023, and its Salmisaari coal-fired power plant will be closed in 2025. Heat production at these power plants will be replaced by recycling excess heat with heat pumps, as well as by using biomass and heat storage.
In late 2022, Valmet started up a flue gas condensing plant and condensate treatment equipment, including a boiler make-up water
production system, at Helen’s Vuosaari bioenergy heating plant.
By combining its heat recovery process with condensate treatment, Helen can reduce freshwater consumption, promote the circular economy and gain water bill savings. In turn, combustion air humidification has a profound impact on the plant’s combustion process. It increases the temperature at which water vapour in the flue gas condenses, improving the entire system’s efficiency. This allows a more substantial recovery of latent and sensible heat, which, when coupled with the benefits of heat pumps, results in a cascading energy recovery effect.
To maximise Helen’s overall plant efficiency and heat recovery
“Flue gas condensation and heat recovery combined with combustion air humidification and a heat pump are cutting-edge technologies that harness the potential of waste heat from combustion processes,” said Lari-Matti Kuvaja, Director, Environmental Systems.
for its district heating network, Valmet developed a novel solution, which combines traditional flue gas condensation and combustion air humidification with absorption heat pumps.
Description automatically generated
Heat pumps extract heat from a low-temperature source and transfer
it to a higher-temperature destination. Typically, a heat pump increases efficiency by cooling an incoming district heating waterflow and transferring the heat to a waterflow after the condenser heat recovery. However, while decreasing the incoming flow allows a higher temperature difference for condenser heat recovery, it reduces the heat and humidity available for the combustion air humidifier.
fuel’s effective
“Flue gas condensation and heat recovery combined with combustion air humidification and a heat pump are cutting-edge technologies that harness the potential of waste heat from combustion processes, contributing to energy savings and reduced emissions,” said Lari-Matti Kuvaja, Director, Environmental Systems at Valmet.
“While traditional heat recovery with condensation can reach stack
temperatures of close to 50-60 °C, our optimised process can push the temperature significantly below 20 °C. Recent concept calculations at our customers’ plants have approached single-digit temperature readings.”
Helen’s Vuosaari bioenergy heating plant now features very high energy
efficiency. The heat recovered from flue gases increases district heat production by 69 megawatts.
Energy efficiency has been taken to the highest level, and the minimum temperature of the flue gas it produces is about 11 °C when it leaves the stack. The heat recovery from flue gases after the boiler is maximised, and almost all the water vapour the gases contain is condensed with the
Helen’s Vuosaari C bioenergy heating plant in Helsinki, Finland, has been running a Valmet flue gas condensing plant, condensate treatment equipment and heat pumps since late 2022 with excellent efficiency.
aid of a separate heat recovery plant. Valmet’s patented technology makes the Vuosaari bioenergy heating plant the most energyefficient heat recovery plant in Finland. Water vapour accounts for less than 1% of the flue gas mass leaving the stack, and the utilisation of the entire plant calculated according to the method used in the EU is a whopping 122%.
“Valmet’s solution of using absorption heat pumps at this scale to utilise all the available heat has helped Helen maximise the overall efficiency of the entire Vuosaari bioenergy heating plant. The heat recovery solution also increases the condensate production, from which Helen produces make-up water for the Vuosaari plants and the district heating network, thus reducing Helen’s city water consumption,” explained Timo Kuitunen, Project Manager at Helen.
In June, 2023, Helen and Valmet signed a service agreement to support the smooth operation of the flue gas condensing plant at Helen’s bioenergy heating plant in Vuosaari, Helsinki. Under the service
agreement, Valmet delivers expert services to support the customer in attaining optimal equipment performance.
“Valmet is this plant’s original supplier and as it’s the first of its kind for Helen, we want to ensure a successful commissioning by working with Valmet for at least the first couple of years. We expect to receive expert service during the agreement period and to learn how to operate and maintain the plant in the best possible way ourselves. I’m very confident that our partnership with Valmet will go smoothly,” added Kaj Luukko, Asset Manager at Helen.
With Valmet’s support, Helen can concentrate on its core business of operating the plant and delivering heat to the Helsinki area’s residents. More information: www.valmet.com
European Pellet Conference 2024: As a CO2-neutral fuel, sustainable bioenergy is a key component in the energy transition. Over 400 experts discussed this and more on 6 March 2024 in Wels/Austria at the meeting place for the global pellet community.
The last few years have been challenging for the pellets industry: the sustainability discussions at European level and in some Member States, market fluctuations and supply chain issues were some of the topics.
The European Pellet Conference 2024 showed how we can increase the acceptance of pellets as an important element in the clean energy transition and the positive contribution of pellets to the circular economy. It highlighted latest trends in markets, policies, technologies and innovations, helping the participants stay on top of developments in the pellet and bioenergy world. Cuttingedge developments and R&D results in the pellet and bioenergy sectors were showcased. Also, international experts offered updates and outlooks on pellet markets around the globe.
The European Pellet Conference offers a compact and comprehensive package including the Young Biomass Researchers Conference, a poster presentation, valuable networking opportunities and a major tradeshow on energy efficiency with a strong focus on pellet-related exhibitors (the "Energiesparmesse").
The event is part of the World Sustainable Energy Days (WSED) – an international conference on the energy transition and global climate neutrality with over 650 experts from more than 60 countries each year. The WSED is organised by the OÖ Energiesparverband, the energy agency of the Region of Upper Austria.
The next edition of the event will be held on 5 March 2025 in Wels/Austria. The deadline for the Call for Papers & Speakers (also for the Young Biomass Researchers Conference) is 10 October 2024. For more information: www.wsed.at
Recovering and reusing secondary heat across pulp mill islands
When looking at circularity and sustainability at a pulp mill, it’s easy to just focus on individual process islands, for example, cooking, evaporation or drying in order to improve environmental performance. However, when zooming out and looking at the whole picture, there are huge opportunities for linking islands and recovering and reusing secondary heat.
ANDRITZ is firmly committed to helping customers reach their sustainability goals as they seek ways to reduce carbon footprint and minimise raw material use. The fibreline and drying islands at pulp mills have enormous potential to reuse each other’s secondary heat by installing technology to capture and transport the excess
heat and use it in other process areas, thus lowering the carbon footprint, as well as making major savings in energy and raw water usage.
“When dealing with secondary heat utilisation in pulp mills, the focus up until now has been very much on the individual islands, for instance,
Vapour Reboiler converts clean condensate to fresh steam.
“This has been quite difficult to explain to customers in the past as they tend to be focused on one area in particular,” added Paavo Tolonen, ANDRITZ Vice-President, Global Product Group Manager, Cooking. “So, it’s when we zoom out and take a wider look at the mill, a bigger picture emerges of where secondary heat opportunities can be identified across the process islands.”
Basically, the idea is that relatively small-sized equipment is installed around the mill’s ‘receiving’ process islands that can convert secondary heat to generate clean steam for the process without having to use valuable boiler generated steam. This heat is pumped to the process island from the heat exhaust of the ‘supplying’ process island – the one generating secondary heat. Several benefits are obtained from this heat recovery, including savings in energy, recovery of clean condensates, optimised water and secondary condensate utilisation. Secondary heat can also be recovered from effluent and other sources.
As well as environmental benefits, there are also financial rewards.
“The cost benefits come when we return the primary condensate to the boiler house and we don’t need to create boiler water from raw boiler water from raw water,” explained Aki Muhli, ANDRITZ Technology Manager, Cooking. “In this way we save energy, raw water and demineralisation costs, which can add up to substantial amounts of retained revenue.
“Furthermore, the maximum utilisation of raw water is becoming increasingly important as we have seen with record high temperatures and drought being experienced across Europe and other parts of the globe recently.”
cooking, evaporation or drying,” said Jussi Piira, ANDRITZ Director, Sustainable Solutions. “However, at ANDRITZ we have been stepping back and taking a more holistic view and working on solutions that cross the borders of the process islands and identifying any secondary heat that can be utilised in another process on another island.”
Environment and safety
ANDRITZ has developed several solutions to utilise secondary heat across fibrelines at pulp mills by closing loops across the following processes:
Direct Steam Replacer. The direct steam replacer enables reduced boiler and raw water usage. In this case,
clean low-pressure steam is generated from condensate. The heat resource is low pressure steam from the boiler.
Benefits of a Direct Steam Replacer: reduced boiler water consumption, less boiler water to be heated, increased clean condensate recovery and less condensate to wastewater handling.
Highlights are:
l Clean condensate from fresh steam is returned to the boiler water.
l Secondary condensates or other suitable clean water streams are used as a steam source for direct steam applications. Patented Direct Steam Replacer (DSR) process produces steam from mill condensate.
Vapour Reboiler. Clean condensate is converted to fresh steam using the flash stream as a heat source.
Benefits of a Vapour Reboiler in continuous cooking: Improved health and safety, decreased evaporation load and high turpentine recovery.
Benefits of a Vapour Reboiler in batch cooking: Reduced consumption due to secondary heat recovery, improved yield, reduced shive amount due to steaming and higher turpentine yield.
Highlights are:
l Health and safety is one of the major benefits with the utilisation of the Vapour Reboiler as it reduces or eliminates sulphuric compounds, turpentine and tall oil process based risk when collecting gases from the chip bin.
l Flash steam condenses inside the tubes.
l Falling film of condensate keeps heat transfer surfaces clean from fibres.
l Clean steam generated from secondary condensate is removed through a central pipe upwards. Vapour reboiler converts clean condensate to fresh steam. The heat resource is flash steam.
Digester Evaporator. Steam to the digester is generated from black liquor using MP steam as a heat source. Benefits of a Digester Evaporator in continuous cooking: Higher black liquor dry solids content to
evaporation, smaller heating surface and steam consumption in the evaporation plant, and increased return rate for primary condensate. Benefits of a Digester Evaporator in batch cooking: Energy savings from reduced steam consumption, increased dry solid content in the black liquor and decreased evaporation load.
Highlights are:
l Evaporation of water from weak black liquor from digester upper extraction to be used in digester top for heating.
l Medium pressure secondary vapour from DEvap to digester top replaces direct steam injection to the digester top.
l High dry solids liquor from DEvap increases overall dry solids and decreases black liquor to evaporation.
Maximising secondary heat usage at pulp mills is now well within reach of all pulp mills and ANDRITZ customers are already seeing rewards with the various technologies being installed around the world. Whether a greenfield development, or an existing mill, the utilisation of secondary heat at pulp mills represents an excellent opportunity to further circularise production across the mill, at the same time as make major financial savings.
Piira concluded, “As environmental regulations get tighter and pulp producers focus on their sustainability goals, it
makes perfect sense to utilise every possible area around the mill where reuse of resources is possible.
“Secondary heat utilisation is an excellent solution for our customers to assist them as they aim to reach their sustainably goals at the same time as making major financial savings on energy, water and raw material usage.”
There is a lot of R&D development going on at ANDRITZ as it seeks to reuse secondary heat from mill processes also in the drying line at pulp mills – and excellent results are
already being obtained.
Ola Larsson, Director, Technology and R&D, Drying, ANDRITZ, stated: “This is an area where we have a lot of development going on right now, looking at all possibilities of where secondary, low value heat can be reused. We already have an impressive example at a mill in Sweden where we are saving up to 30% of fresh steam in the drying process by using secondary heat obtained from the boiler stack”.
The ANDRITZ Steam Saving System in this case is taking energy from the stack, producing hot water and releasing the pressure of the water as low-pressure steam, which is then fed to the dryer. The recovered energy is supplying some 20-30% of a pulp dryers need.
“This is a classic case of circularity at pulp mills as we recover energy, and in a long run, save fresh water,” continued Larsson. “Both resources are under the spotlight as mills try to reduce costs and improve on raw material and energy usage.”
ANDRITZ is also working on recovering energy from the drying process, which will again be utilised elsewhere in pulp mill processes.
More information: www.andritz.com
Targeting emissions zero
WE ENABLE OUR CUSTOMERS TO REDUCE CO 2 EMISSIONS