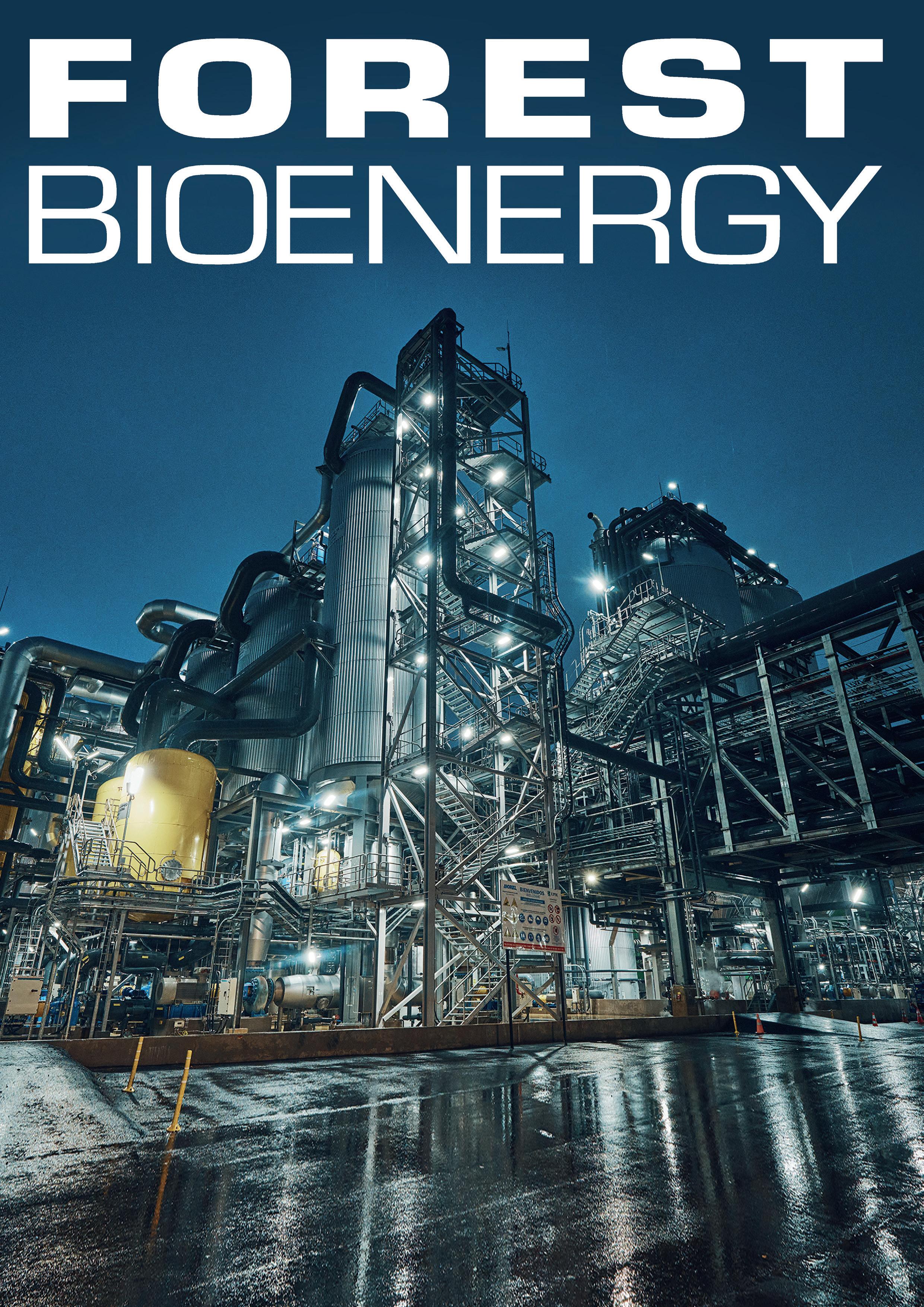
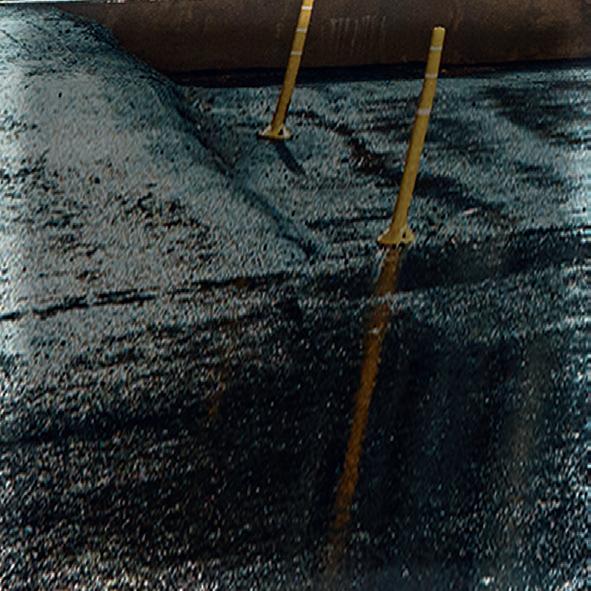


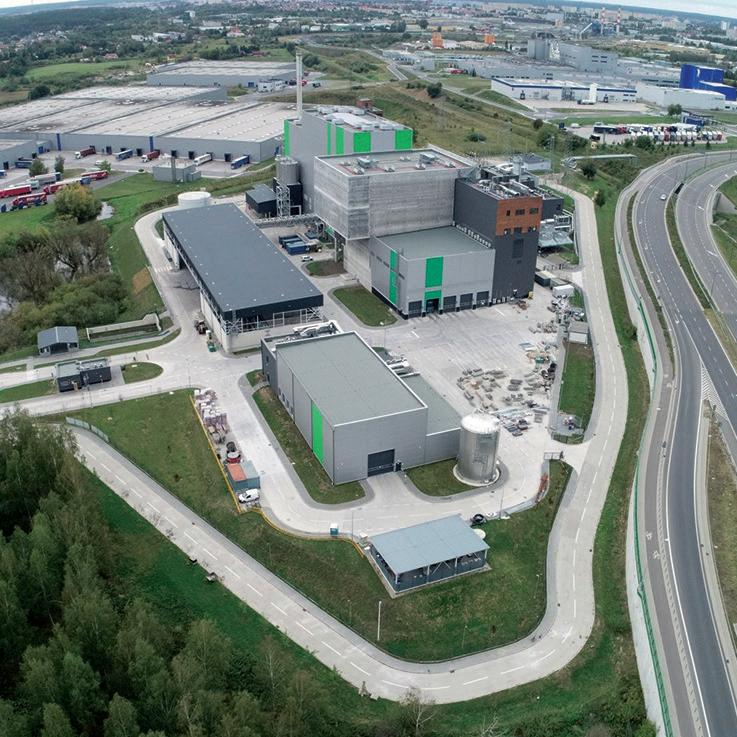
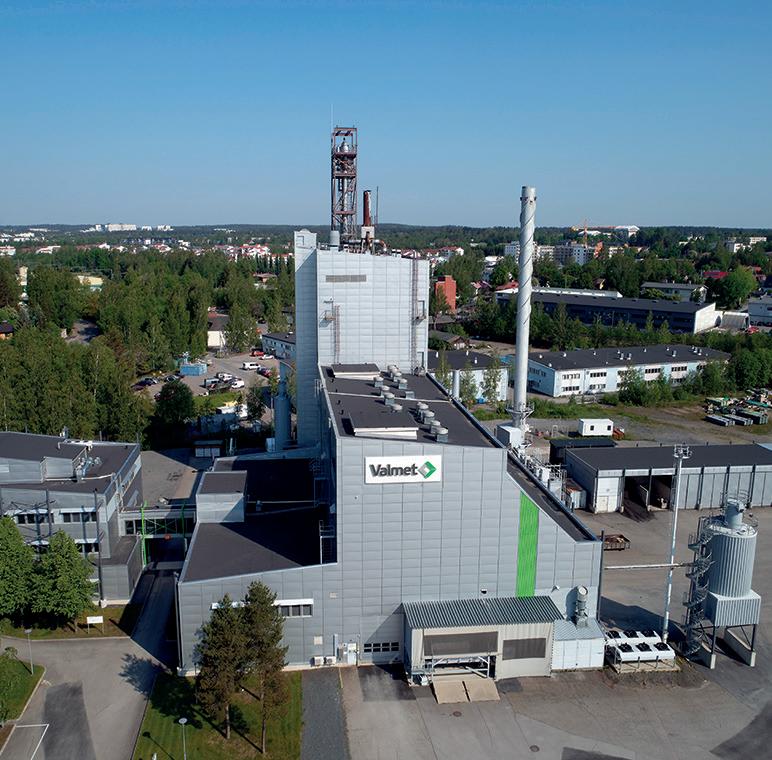
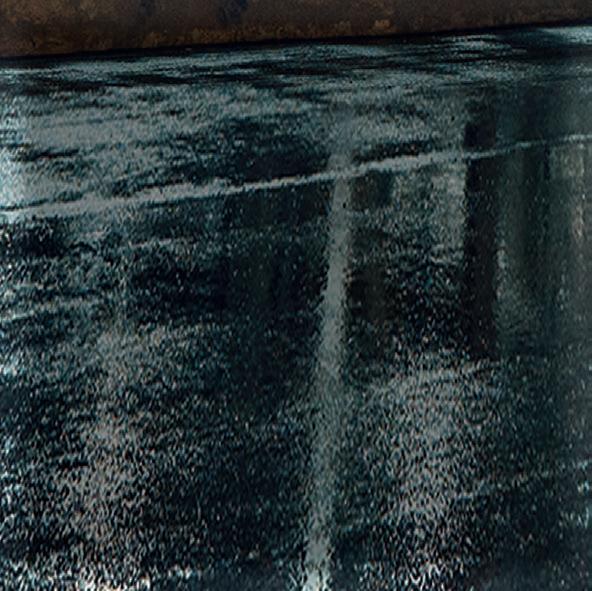
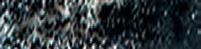
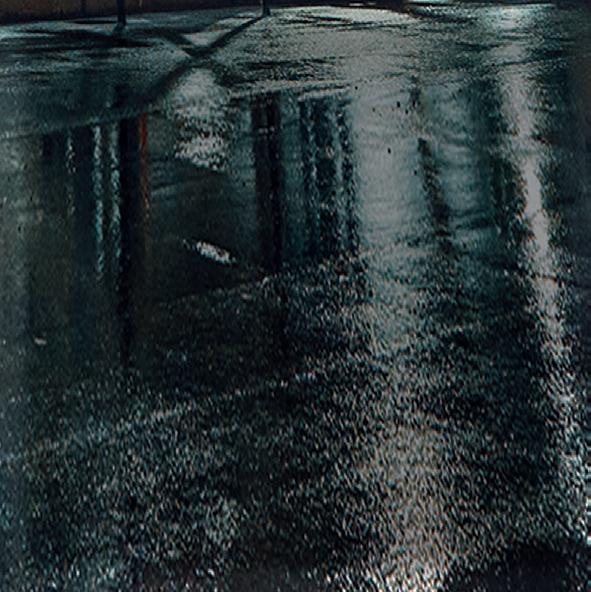
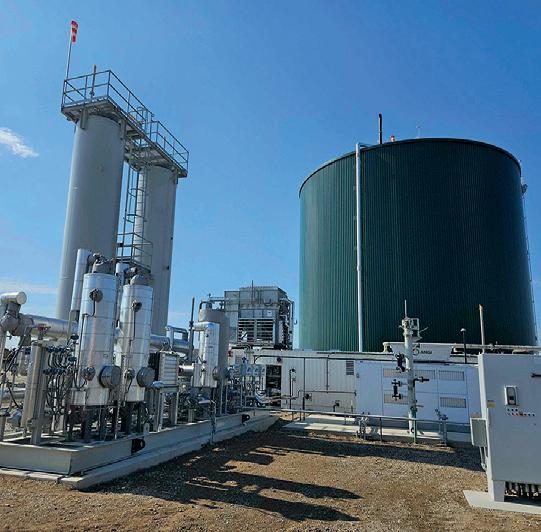
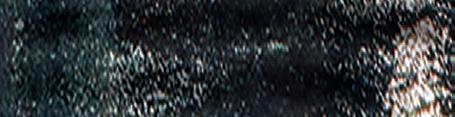
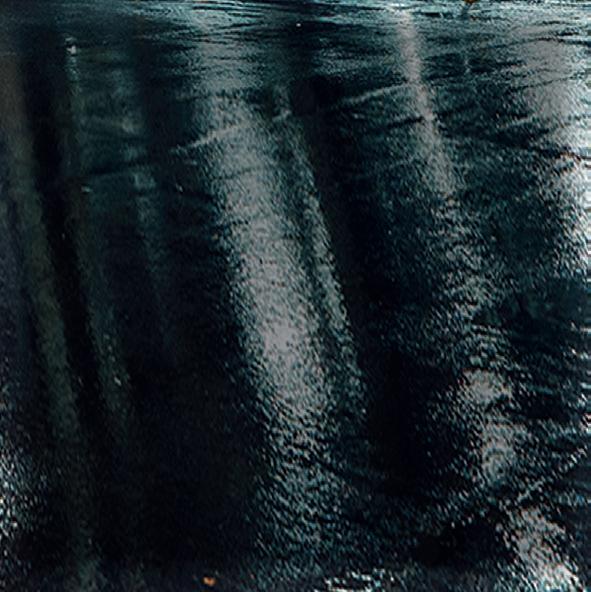
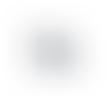
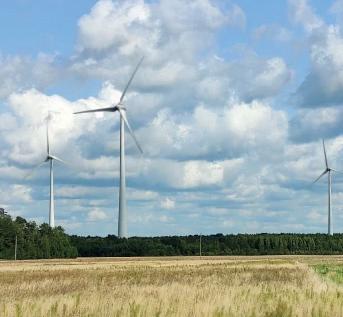


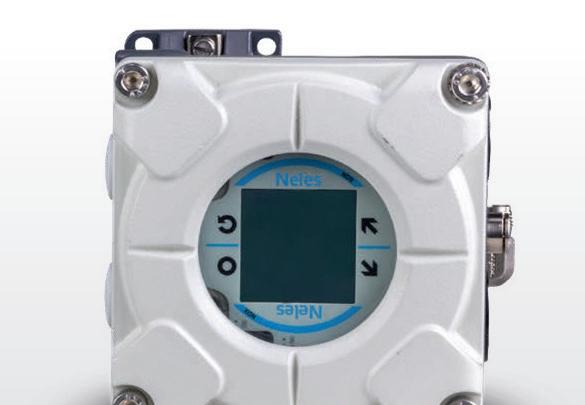
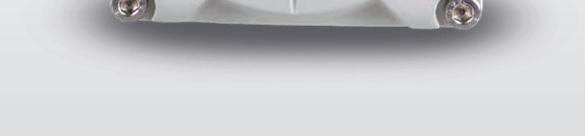

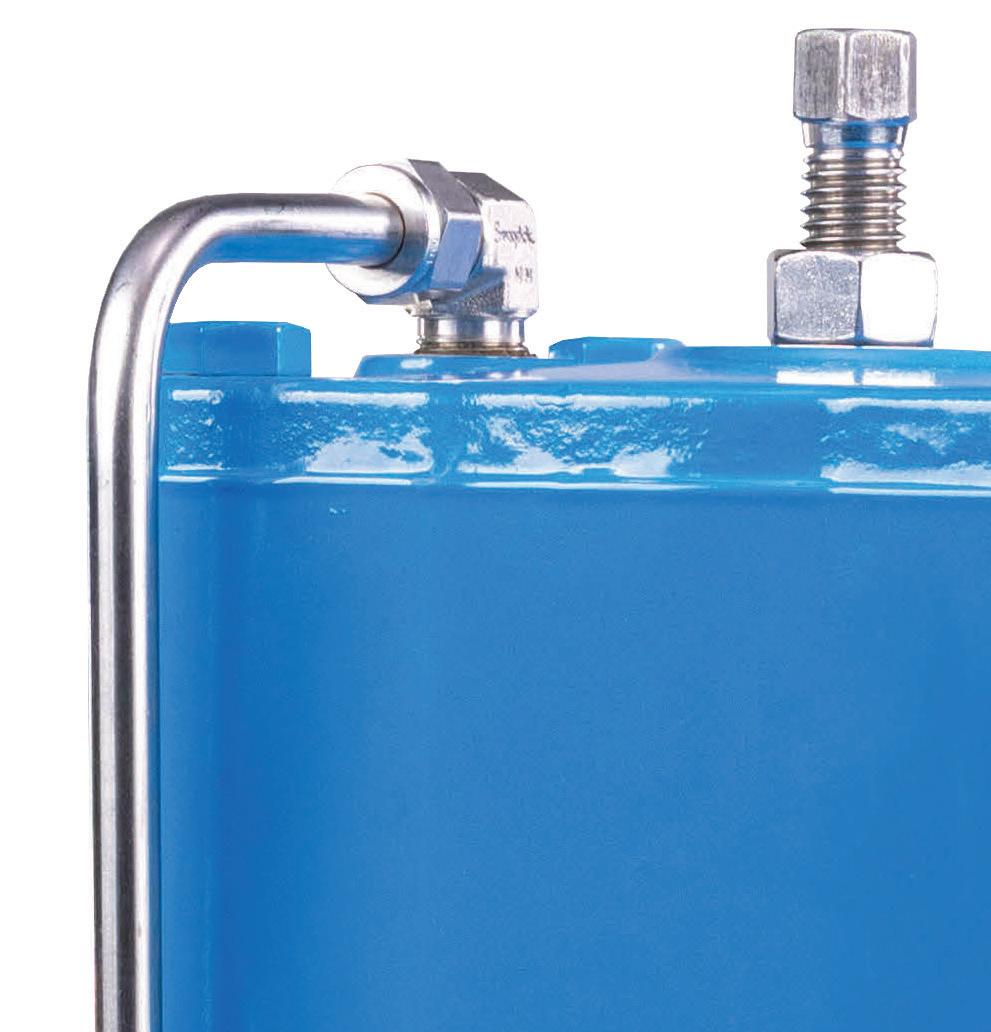


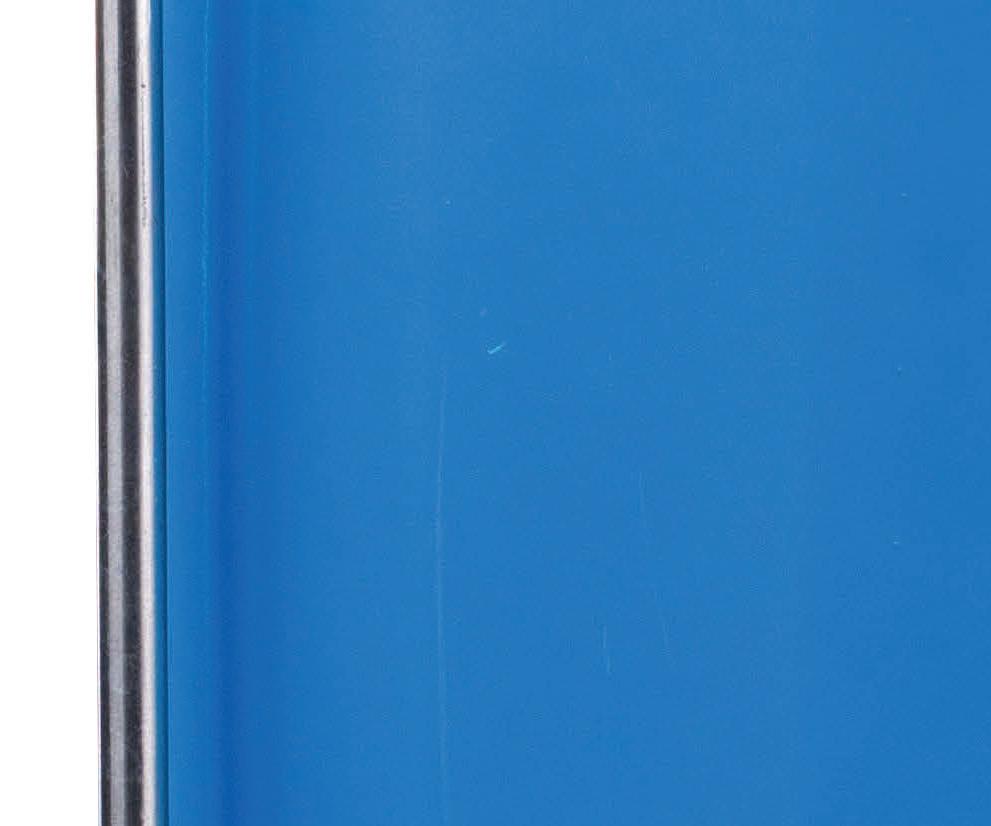
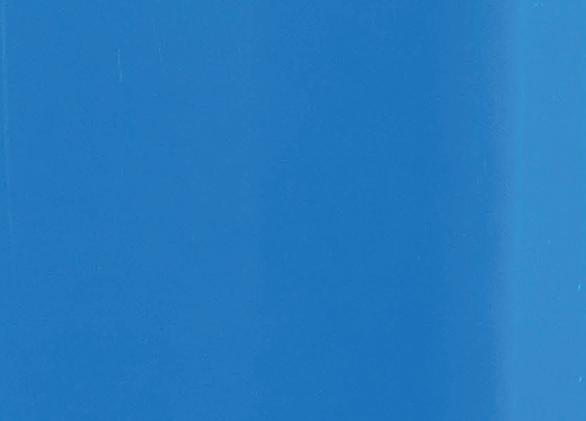
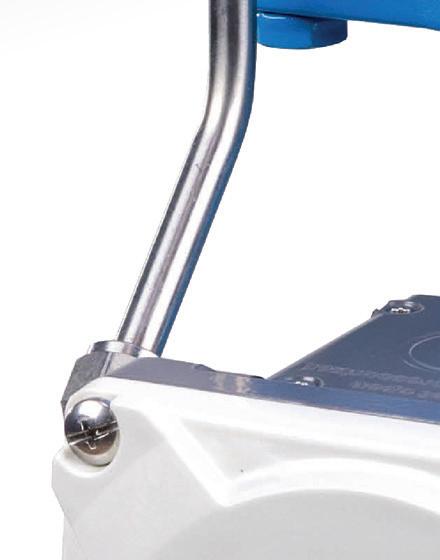
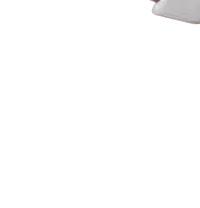

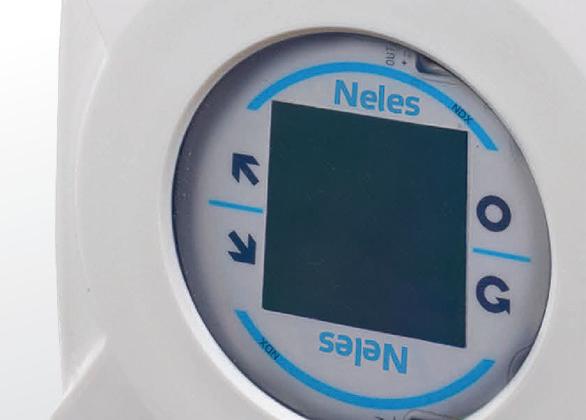
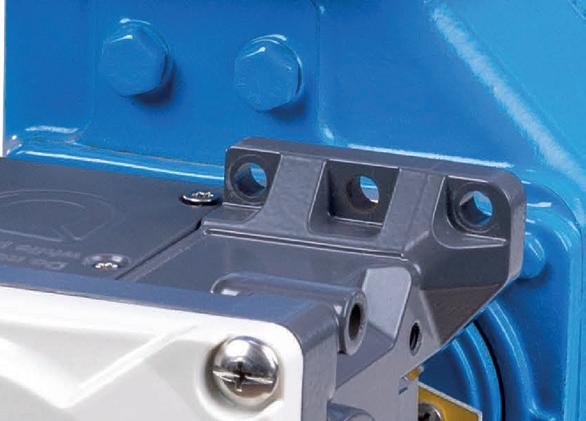

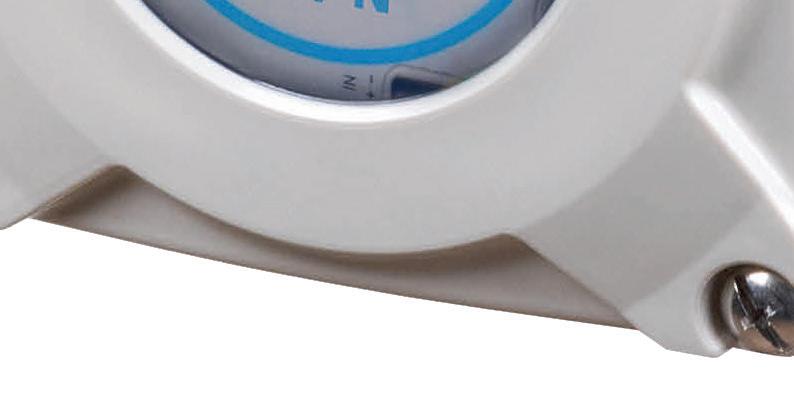
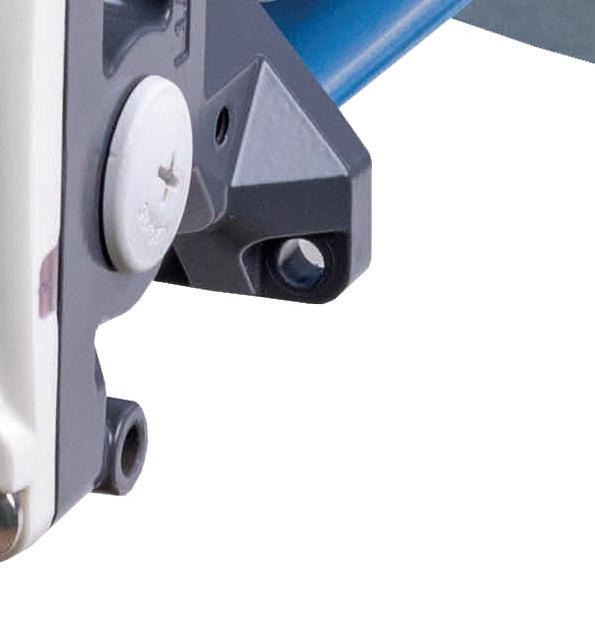

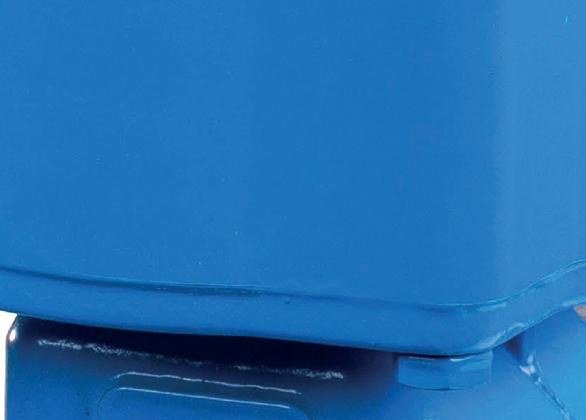
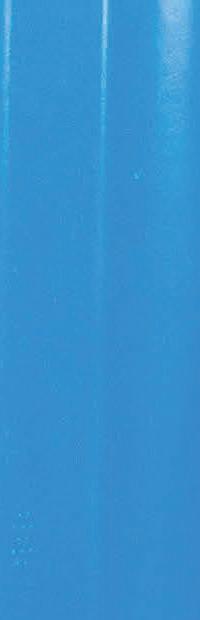


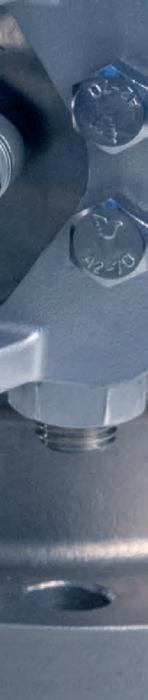
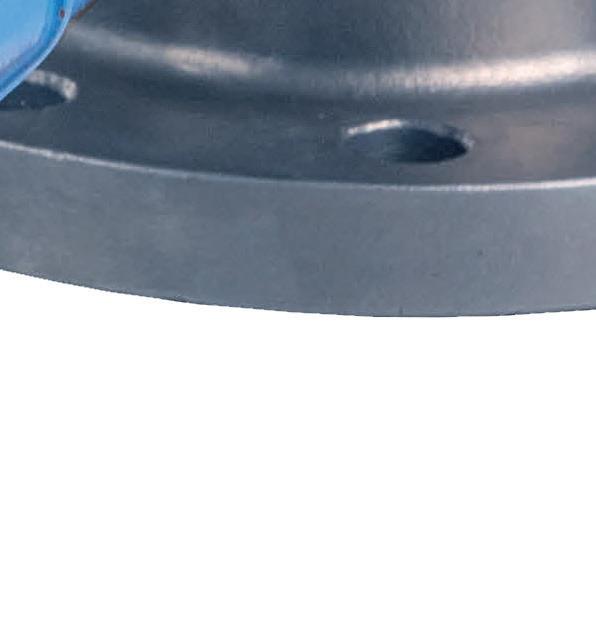
Welcome to the Spring issue of Forest Bioenergy Review incorporating PIM renewable Energy. As we start another year of publication, it is interesting to see just how things have changed in terms of renewables in the energy sector.
Today, renewable energy is at the forefront of those who produce energy and how a mix of forest biomass, solar, wind and hydroelectric can be utilised to meet constantly-changing environmental regulations.
As has been shown by the damage caused during the ongoing conflict in Ukraine, energy infrastructure provides a soft target for bombs and missiles, and the ramifications can have serious consequences on thousands of individuals. Energy security and diversity of supply stock is now playing a more important role when new facilities are being planned whether national or regional.
Looking forward to issue 65 this Summer, we will be looking at the following topics: annual biomass shipping, handling and logistics; wasteto-energy technology and carbon capture; and emissions reduction. The deadline for submissions is 20th May and should be e-mailed to: pulppaperlogistics@virginmedia.com
Vince Maynard, Publisher
PUBLISHER & EDITORIAL DIRECTOR
Vince Maynard
KVJ Enterprises, Tralee, Hillcrest Road,
Edenbridge, Kent, TN8 6JS, UK
Tel: +44 (0) 1732 505724
Mobile: +44 (0) 7747 002286
E: pulppaperlogistics@virginmedia.com
CONSULTANT EDITOR
David Young
Tel: +44 (0) 1737 551687
Mobile: +44 (0) 7785 796826
E: youngeditorial1@btinternet.com
ISSN 2045-8514
Anthony Wiffen
ASTAC Business Publishing
Tel: +44 (0) 1460 261011
Mobile: +44 (0) 7851 612799
E: anton_print_1@mac.com
PRINTING
KNOCK OUT PRINT
+44 (0) 1892 823540
Unit 2 The Coppice, Petteridge Lane, Matfield, Kent TN12 7LP info@knockoutprint.co.uk www.knockoutprint.co.uk
Following a successfully completed trial run, the waste-to-energy (WtE) plant in Olsztyn, Poland, which was supplied by Doosan Lentjes, together with Doosan Enerbility, on a turnkey basis, was officially handed over to the customer on 10 December, 2024. The delivery also included civil works and two gas/oil-fired peak load boilers, which ensure a supplementary district heating supply. The state-of-the-art plant, which makes an important contribution to sustainable energy supply and the circular economy in the region, is now in regular operation.
The project was conceived as a PPP scheme between the local energy supplier Miejskie PrzedsiṦbiorstwo Energetyki Cieplnej (MPEC) and the project company Dobra Energia dla Olsztyna. MPEC is a municipal company owned by the city of Olsztyn and operates the municipal heating plant and the district heating network with a total length of approximately 155 km. Dobra Energia is a joint venture between Meridiam and Urbaser, whereby the latter will also be responsible for operating the plant for 25 years.
With a capacity of 110,000 tonnes of refuse-derived fuel (RDF)
per year, the Olsztyn WtE plant makes a significant contribution to strengthening the local waste management sector and relieving the pressure on landfill sites. The thermal treatment of the waste generates steam, which supplies more than 11 MWe of electricity by means of a turbine. The steam is also used for the city's district heating network, which means that around 30% of the local heating requirements are covered without the use of fossil fuels.
The tried-and-tested, watercooled reciprocating grate and the complex systems for generating electricity and district heating ensure maximum energy efficiency.
The Circoclean® flue gas cleaning system, including downstream SCR technology for nitrogen oxide reduction, is being used for the first time in Poland. Compliance with the strict European BAT emission standards emphasises the environmental friendliness of the plant.
During the trial operation, which lasted several weeks, all contractually agreed performance and availability criteria were met and the high reliability and stability of the system was demonstrated across the entire output range.
More information: www.doosanlentjes.com
On 28 January, Lhyfe announced it is continuing to expand, with its first site in Northern France. The new production site under construction by the company is at Croixrault in the Somme region of Hauts-de-France. Thanks to its strategic location and Lhyfe’s logistical capabilities, this site will provide the many manufacturers in Hauts-de-France and mobility players in the area with green and renewable hydrogen to decarbonise their operations.
The project is part of a wider ambition initiative of the Communauté de Communes Somme Sud-Ouest that aims to boost local employment and provide a favourable economic environment for companies wishing to set up in the dynamic region.
Lhyfe is one of the pioneers of the green and renewable hydrogen sector in Europe. Founded in 2019,
the company inaugurated its first site in 2021 and today already has four installed sites and several other sites under construction across Europe. Lhyfe produces its hydrogen locally through the electrolysis of water using renewable electricity.
When Croixrault is commissioned in
2026, Lhyfe will have the capacity to produce and deliver up to two tonnes of green hydrogen every day, thanks to an electrolysis capacity of 5 MW. Two tonnes of green hydrogen is equivalent to the amount a hydrogen truck needs to travel around 25,000 km, without emitting a single gram of CO2.
This site will complete Lhyfe’s coverage of France – it is already present in the West (Pays de la Loire and Brittany), South-West (Occitanie) and East (site under construction in Auvergne Rhône-Alpes) of the country. More information: www.lhyfe.com
MDF component manufacturer Boardtek has transformed its waste management operations, with the installation of an UNTHA LR1400 wood shredder – significantly reducing downtime and generating cost savings in the process. Founded in 2011, Pontefract-based Boardtek is a manufacturer of MDF-based products for the furniture and DIY markets. Operating from its modern facility, the firm produces over 16,000 cu m of high-quality MDF items each month.
The company struggled to maintain consistent operations with its previous shredder, which suffered from frequent breakdowns,
jamming issues and rapid wear of nylon guides. These persistent problems led to costly downtime, unreliable throughput, and increased maintenance expenses. Seeking a solution that would ensure reliable performance and reduce operational disruptions, Boardtek joined forces with IMA Schelling, UNTHA Austria’s sales partner, to invest in an UNTHA LR1400 shredder.
“Having been repeatedly let down by our previous machinery, the UNTHA shredder has completely changed the game for us,” said Paul Thompson, Director of Works at Boardtek. “We’ve reduced our maintenance costs by £12,000 per year and achieved £30,000 in
savings by not sending waste to landfill. The payback period on the entire project was just 18 months, so the decision was a no-brainer.”
Boardtek’s waste management overhaul has not only reduced costs, but also improved energy efficiency. By using the shredded material in its on-site biomass boiler, which provides heat to the factory, paint line and central heating system, the company has lowered its reliance on external waste disposal, significantly cutting energy costs and improving the sustainability of its operations.
The LR1400 handles approximately six tonnes of input materials per day, including 2.525.0 mm HDF, MDF, chipboard and
pallets, which are all by-products of Boardtek’s production process. Achieving a throughput of around 750kg per hour, with much higher handling capabilities if required, the machine reduces materials down to a homogenous 20 mm particle size.
Commenting on the partnership with Boardtek, Julie Cassidy, UNTHA UK’s parts and maintenance executive, said: “The service plan has been a perfect fit for the team at Boardtek. We’ve developed a great working relationship, ensuring the LR1400 shredder runs smoothly and reliably, without the costly downtime the company experienced with is previous machine”.
More information:
www.untha.co.uk
A new report from the University of Edinburgh has highlighted the potential for tidal stream and wave energy projects to be worth more than £8 billion to the Scottish economy by 2050 and to support more than 15,000 jobs.
Responding, Maggie Olson-Jow, Policy Manager – Offshore and New Technologies at Scottish Renewables, said: “The energy contained in Scotland’s seas is a vast and relatively untapped resource.
“The University of Edinburgh’s
report highlighting the potential economic opportunity of wave and tidal energy should come as a shot in the arm to the marine energy sector and show investors the scale of the prize that is ready to be grasped.
“Scottish Renewables will continue
to work with both the Scottish and UK governments to build support and secure funding for these technologies, which deserve to take their place in the UK’s clean energy toolbox.”
More information:
www.scottishrenewables.com
The European Patent Office (EPO) has granted a European patent for the gravity-based base solution for an offshore wind power plant developed by Enersense. What is special about the base solution is its method of transportation. This is by floating it to the installation site.
Installation on the bottom is done by ballasting and by de-ballasting, so the base can be lifted up and reused in a new location or delivered for recycling at the end of the product's life cycle. When using ballast, the use of large floating crane vessels is avoided when installing the stand.
The development of the
concept began in 2017 and the official patent application was published on 13 March, 2020.
The European patent (Number 3879035) was officially published on 11 September, 2024.
“We are very proud of this new patent, which represents a significant step forward for the offshore wind industry. This patent
A project for powering the Koehler Paper site in Oberkirch, Germany, with self-produced green energy is taking shape. After a detailed analysis, the area on the Schwend ridge between Oberkirch and Kappelrodeck was identified as an ideal site for wind turbines that will be used to power the plant directly. Moreover, a public meeting held by the town council of Oberkirch recently culminated in the decision to allow Koehler Renewable Energy to use the area to set up wind
turbines, with the plan being to erect two of them.
The project will make an important contribution to achieving the Koehler Group’s goal of significantly reducing CO 2 emissions from its paper production operations while simultaneously ensuring that power comes from a reliable, cost-effective and regional source. This is where the area on the ridge close to the plant in Oberkirch comes in, as it was designated as a priority area for
wind power in the corresponding regional plans. In fact, the general suitability of the site was confirmed in the corresponding preliminary survey with the latter’s incorporation into these plans.
In addition, by powering the Koehler Paper plant through wind turbines, the company will be making a vital contribution to decarbonising its production operations while simultaneously providing the region with a valuable asset.
strengthens our position as an innovation leader and gives us even better opportunities to meet our customers' needs and develop new, top-quality solutions,” explained Niko Suomela, VicePresident, Enersense Offshore Business.
More information: www.enersense.com
Given the sharp rise of energy costs in Germany in the past few years, having a reliable source of renewable energy is a key challenge for energy-intensive companies like the Koehler Group. The company needs large amounts of green electricity both to meet its own climate goals and to comply with the requirements set forth by the German government and the state of Baden-Wuerttemberg.
More information: www.koehler.com
Demonstrating its commitment to delivering top-tier forestry equipment, John Deere now offers extended transmission coverage, at no additional cost, through its skidder transmission assurance program. This new program provides coverage up to six years
or 12,000 hours on all eligible skidder models and helps to maximize the machine lifespan with warrantable transmission repairs and replacements. The assurance program applies to all qualified skidders and is transferrable to subsequent purchasers.
“We're giving our customers
added peace-of-mind knowing that their new machines are backed by a robust transmission assurance program,” said Mike Fulton, Service Marketing Manager, John Deere Construction & Forestry. “This is another way we're helping our customers excel in the woods and in their businesses, no matter the
challenge at hand.”
Eligible machines include qualified skidder models 640L-II, 648L-II, 748L-II, 768L-II, 848L-II and 948L-II built on or after 1 January, 2020, and purchased prior to 31 December, 2026.
More information: www.johndeere.com
On 6 February, Johnson Matthey (JM), which specialises in sustainable technologies, and Bosch, a leading supplier to the automotive industry, agreed terms to accelerate future projects together. The agreement confirms both parties’ intentions to develop and produce catalyst-coated membranes (CCM) for use in fuel cell stacks.
Transforming and decarbonising the automotive industry requires
a mix of powertrain systems and solutions across different vehicle classes. Hydrogen fuel cells are electro-chemical devices that combine hydrogen and oxygen to generate electricity. As pure water is the only by-product, fuel cell electric vehicles are a clean, zero-emission option.
JM’s high performance CCMs will be used in Bosch’s integrated, compact and scalable fuel cell
power module for commercial vehicles, which have been designed for longer distances.
JM Hydrogen Technologies Chief Executive, Anish Taneja, and Bosch Mobility’s Executive Vice President of Engineering Power Solutions, Beate Grota, marked the agreement at Bosch’s fuel cell centre in Stuttgart-Feuerbach, Germany.
Anish Taneja commented, “JM is thrilled to be joining forces,
exploring and developing future possibilities to accelerate cleaner mobility and energy generation”.
Beate Grota added: “The fuel cell technology for mobile applications is technologically ready for widespread use. Our partnership aims to further increase the performance and efficiency of the fuel cell stacks”.
More information: www.matthey.com.
By Marjaana
A pioneering BFB concept for 100% agrofuel and catalytic pyrolysis are examples of how Valmet is driving energy technology development forward. Key to these and other advances are the organisation’s continuous innovation efforts and unique pre-industrial scale test facility for energy technologies.
The target of converting renewable resources into sustainable results keeps people at Valmet innovating. One of the facilities where this innovation takes place is Valmet’s Energy R&D Centre in Tampere, Finland. Since 1990, this
has carried out more than 11,000 hours of pilot operations. It offers complete fluidized bed combustion and pyrolysis pilots on a megawatt scale for customer pilot trials, including comprehensive analysis services and access to Valmet’s network of deeply knowledgeable
and experienced experts. In addition to serving customers from around the world, the facility plays a key role in Valmet’s own R&D work.
“This unique pre-industrial scale test facility has enabled us to develop our fluidized bed combustion and
pyrolysis technologies. In combustion, fuel trends over the decades have changed from fossil fuels to more sustainable, but at the same time more challenging biomasses and waste fractions. The driving force for development of pyrolysis technology has been to maximize the value
of resources,” pointed out Katriina Jalkanen, R&D Project Manager.
BFB concept for 100% agrofuels
One of Valmet’s long-term development projects is the Valmet BFB Boiler for agrofuels. This can run
on high-alkaline fuels like wheat straw, sunflower husks, empty fruit bunches and rice straw – fuels that typically are agro-residues and previously were unsuitable for BFB combustion. The concept has been piloted on 30 kW and 2 MW scales at Valmet’s Energy R&D Centre.
“The main issue in fluidized bed technology that use high-alkaline fuels is bed agglomeration. This can now be prevented with Valmet’s advanced combustion principles,” said Jukka Leppälä, Project Engineer. “Another risk for bed sintering with agrofuels is heavy furnace fouling. We have a patented solution for a furnace arrangement using two-zone combustion to keep the bed fluid without disruption.”
Compared to grate combustion, BFB combustion is significantly more efficient and features better emission control.
“After years of development work, the concept is now ready and we’re looking for a customer to build a 30–80 MW demo plant. This could be a new BFB boiler or a boiler rebuild. The latter option is possible, as we can use a lot of an existing plant’s technology and just change the furnace structure,” continued Leppälä.
In accordance with its vision, Valmet is looking for ways to maximise the value of resources. For example, goodquality biomass should be used to produce more valuable products than heat and electricity, such as chemicals or transportation fuels.
Pyrolysis is the thermal decomposition of feedstock without air. In an ongoing R&D project, Valmet is further developing its fast pyrolysis technology with catalytic treatment. With catalytic pyrolysis, the target is to produce renewable feedstock – biocrude – for refineries and the petrochemical industry for the production of transportation fuel from sustainable biomass sources.
“Right now, we use wood biomass and forest residues as fuels and later, we’ll also use agrofuels,” stated Joakim Autio, Solution Development Manager. “In the Spring of 2023, our project entered the test phase in a 400 kg/h pilot plant at Valmet’s Energy R&D Centre. We’ll follow successful piloting with demo-scale development.”
More information: www.valmet.com
By Sanna Semi, Vice-President of Evaporation Plants, ANDRITZ
Pulp mill processes need to be continuous, as well as cost and energy-efficient. The evaporation process plays a critical role here. How do ANDRITZ evaporation solutions truly address these needs?
Over the decades, ANDRITZ has proven the success of its evaporation technology and is now the market leader in the supply of evaporation systems to pulp mills. With around 60% of total market share and with over 500 references worldwide, systems have recently been installed at some of the largest pulp projects around the world, including Suzano’s Ribas do Rio Pardo mill in Brazil, UPM’s Paso de los Toros mill in Uruguay and Liansheng Pulp & Paper in China.
Unique insight
ANDRITZ’s mission has always been to put customers’ needs first, to boost mill performance and maximise uptime. Since its first deliveries of tailor-made evaporation systems in the 1980s, the decades of experience at both greenfield and brownfield sites have enabled the company to gain a unique insight into mill operations, allowing for flexibility to adapt to all customer requests, including capacity increases on existing systems.
This experience, process knowledge and equipment, plus plant engineering expertise, also ensures ease of operation and maximum safety. Furthermore, ANDRITZ partners with mill operational teams in the daily operation during
the whole life cycle of the mill, guaranteeing availability by utilising the latest digital products with continuous support from experienced process experts.
The advanced technology applied to ANDRITZ evaporation systems also enables optimised process concepts, 100% emission-free and with maximised energy efficiency ensuring continuous energy generation. Moreover, the latest technology allows for full utilisation of any side products that can be reused and optimised in other process areas of the pulp mill.
One of the specialties of ANDRITZ when it comes to evaporation plants is its ability to create complete tailor-made solutions that perform exactly to customer requirements no matter what the capacities or applications. This includes a wide range of services to guarantee the highest possible availability in the long run.
Sanna Semi, Vice President of Evaporation Plants at ANDRITZ, said, “Whether it’s for a brand-new greenfield pulp mill or an existing brownfield site, whatever the size, we have a real passion for evaporation plants at ANDRITZ. In fact, we have a high team spirit across our team of dedicated people”.
Greenfield and brownfield customers have also benefitted from ANDRITZ guarantees of production results, which always reach agreed targets and often go beyond.
Technical know-how and passion for pulp mill performance have made ANDRITZ the world’s leading
evaporation plant supplier.
“We deliver what is guaranteed and more. Our passion starts at the sales phase where we endeavour to find the very best in tailor-made solutions for our customers, utilising our 40 years’ experience in the manufacture and supply of evaporation plants.
We believe our team spirit shines through in the quality of our products, partnerships in the daily safe operation of our plants and the life cycle services we provide for lamella evaporation plants,” concluded Semi. More information: www.andritz.com/lamella-evap
The successful commissioning of two innovative biogas upgrading plants in the US states of Wisconsin and Michigan has been announced by Unconventional Gas Solutions (UGS). The two plants, which together feed 800 Nm3/h of biomethane into the local gas grid, are the first UGS systems of their kind. The projects were particularly challenging due to the change in operating procedures and the high grid requirements. The first commissioning, the Three Petals RNG plant in Berlin, Wisconsin, was followed by the second, the Red Leaf RNG plant at the Maple Row Dairy Farm in Saranac, Michigan.
In co-operation with the project developer, Novilla RNG, UGS played
a decisive role in the development, commissioning and optimisation of the systems. The company is thus setting a new benchmark in the treatment of biogas because when high H2S concentrations occur, operators normally have to pre-treat the biogas with costly additives or install an expensive external desulphurisation system for the entire biogas volume. This reduces the H2S load to levels that can be handled by an activated carbon filter. However, this approach is often accompanied by a decisive disadvantage – the need for such systems to increase oxygen addition, which can also affect the quality of the gas produced. At the sites in Berlin and Saranac, however, those
responsible decided to bypass this complex process.
Both plants process H2S concentrations of more than 4,000 ppm, which are sent directly into the compressor of the gas treatment plant and then directly through the first membrane stage. Instead of focusing on protecting the membrane treatment system, Novilla and UGS opted for an unconventional approach. The system uses a multistage, membrane-based treatment process that tolerates very high H2S concentrations of up to 30,000 ppm.
In the first membrane stage, H2S and CO2 are separated simultaneously and fed into the exhaust gas. This means that no costly upstream process is required to reduce the H2S load. For optimum methane yield, the permeate from the subsequent stage is fed back into the process.
The result is almost pure
biomethane in natural gas quality, with only a residual H2S content. The low concentration in the reduced volume flow on the product gas side is then separated in a fine desulphurisation process using an iron sponge reaction bed. Similar to the known activated carbon filters, these vessels are arranged in a leadlag configuration. This allows the loaded material to be renewed during operation. Another positive side effect of this H2S-binding reaction is the consumption of residual oxygen. The by-product of the reaction is water, which must be removed using a TSA dryer system developed by UGS. Ultimately, this process reduces the volume of gas to be cleaned of H2S and avoids the accumulation of O2 or N2, as would be necessary with upstream H2S treatment.
Another argument in favour of the selected system in the Red Leaf RNG plant was the strict grid requirements in Michigan, where an O2 content of
five ppm must not be exceeded. In order to guarantee these extreme limit values in every situation, the catalytic deoxidation system (DeOxo) developed by UGS was installed after the fine desulphurisation of the product gas. “Remarkably, the desulphurisation via the membrane unit itself, followed by the fine desulphurisation on the product gas side, means that the grid specifications can sometimes even be met without using the De-Oxo system. However, the DeOxo system offers absolute safety for all our sites”, emphasised Mark Hill, Co-CEO of Novilla RNG. This is because the oxygen remaining in the product gas is consumed in the reaction beds of the fine desulphurisation system during the reaction of H2S to Fe2S3, so that the limit value of five ppm can be met even without the DeOxo unit installed.
For UGS, these projects represent a milestone because they combine several technical advances developed in recent years with proven results. This is particularly true in light of the fact that the biogas market is not only developing rapidly in the USA, but also in Europe. The German biogas market provides a good example. While the population of biogas plants in Europe has risen
significantly in recent years to over 19,000 plants, 60% are in Germany alone. There, the considerable subsidies provided from 2004-11 initially favoured the production of biogas from energy crops for use in combined heat and power generation.
The new pricing systems that valorise biomethane produced from manure and waste have contributed to the reduction of CO2 emissions and have significantly changed the qualities of biogas.
Today, biogas upgrading plants must be able to cope with significant fluctuations in gas composition, large amounts of pollutants such as H2S above 5,000 ppm and changing O2 and N2 concentrations. These developments are forcing the industry to develop new solutions. Due to its high level of expertise in unconventional gas purification, UGS is in a position to technologically overcome these complex challenges.
“We have innovative solutions that can fill critical niches in this market. UGS offers systems manufactured both in the USA and in Europe, ensuring innovative solutions for the upcoming market requirements,” stated Ben Bikson, CTO of UGS. Ben is one of the founders of
An Article 9 fund advised by EB – Sustainable Investment Management GmbH (EB-SIM) is investing in an onshore wind farm project in Lithuania for the first time. The fund is buying 100% of Vèju Spektras UAB’s shares from Quaero European Infrastructure Fund, a fund managed by Quaero Capital, as part of a share deal. The project has been in operation in the municipality of Silutè since 2012. It has an installed capacity of 21.5 MW and is approximately 30 km from the Baltic coast.
The wind farm supplies 85,000 households with electricity and saves 7,300 tonnes of CO2 per year. With this new investment, EB-SIM is further expanding its Europe-wide expertise in renewable energies. It now manages investments in approximately 50 projects with a total capacity of about three gigawatts in Germany and seven other European countries.
“This project shows that we are continuing to grow internationally. Our aim is to achieve a double return for investors – a positive ecological and a positive economic return,” said Dr Bernhard Graeber, Managing Director and Head of Alternative Assets at
EB-SIM. “In addition, with this first investment in a Lithuania project, we are further diversifying our portfolio.”
EB-SIM acts as advisor to the article 9 fund making the investment and will be in charge of actively managing the Lithuanian investment through its experienced asset management team. To this end, it will work closely with the local workforce.
"We are very pleased to hand over the wind farm in Silutè to such a competent partner as EB-SIM," says Sébastien Bourget, Managing Partner at Quaero Capital. "EB-SIM has convincingly demonstrated that it is well-versed in new markets. It understands the regulatory conditions, as well as the local market dynamics. EB-SIM can also expertly structure
such deals, improve financial returns and thus fulfil the expectations of all stake-holders."
The turbines are maintained by Enercon, which also provided the technology: nine Enercon E82 and one E53 wind turbines are in operation in Ṧilutè.
More information: www.quaerocapital.com
The permits for two Energiequelle wind farms in Germany were granted in December. At Lüben in Lower Saxony and Minden in North Rhine-Westphalia, preparations are now beginning for the tendering and construction of the eight turbines. The wind farms have a total capacity of 38.4 MW and will contribute to a sustainable energy supply in the regions in future.
At Minden, in the North-East of North Rhine-Westphalia, Energiequelle is planning to dismantle two Enercon and three NEG Micon turbines as part of a repowering project. Three Nordex N149 turbines with a total height of 200 metres will then be installed. The new wind turbines each have an output of 5.7 MW and will increase the efficiency of
the wind farm by more than
compared to the old farm
of Wittingen, Lower Saxony, was submitted in March, 2023. Five Enercon E-138 turbines with a hub height of 160 metres and an output of 4.26 MW each are to be erected here. Lüben is Energiequelle's second wind farm in the municipality of Wittingen within a year.
All necessary steps and registrations for both parks were to be completed by February in order to participate in the next tender. Construction work is scheduled to begin this year, with commissioning planned for 2026.
In total, Energiequelle received approvals for 15 projects with a nominal capacity of 290 MW (wind) and 74 MWp (PV) in 2024.
More information: www.energiequelle.de
European Pellet Conference 2024: As a CO2-neutral fuel, sustainable bioenergy is a key component in the energy transition. Over 400 experts discussed this and more on 6 March 2024 in Wels/Austria at the meeting place for the global pellet community.
The last few years have been challenging for the pellets industry: the sustainability discussions at European level and in some Member States, market fluctuations and supply chain issues were some of the topics.
The European Pellet Conference 2024 showed how we can increase the acceptance of pellets as an important element in the clean energy transition and the positive contribution of pellets to the circular economy. It highlighted latest trends in markets, policies, technologies and innovations, helping the participants stay on top of developments in the pellet and bioenergy world. Cuttingedge developments and R&D results in the pellet and bioenergy sectors were showcased. Also, international experts offered updates and outlooks on pellet markets around the globe.
The European Pellet Conference offers a compact and comprehensive package including the Young Biomass Researchers Conference, a poster presentation, valuable networking opportunities and a major tradeshow on energy efficiency with a strong focus on pellet-related exhibitors (the "Energiesparmesse").
The event is part of the World Sustainable Energy Days (WSED) – an international conference on the energy transition and global climate neutrality with over 650 experts from more than 60 countries each year. The WSED is organised by the OÖ Energiesparverband, the energy agency of the Region of Upper Austria.
The next edition of the event will be held on 5 March 2025 in Wels/Austria. The deadline for the Call for Papers & Speakers (also for the Young Biomass Researchers Conference) is 10 October 2024. For more information: www.wsed.at
Cleanability, the ability to maximize condensate reuse, and resistance to plugging are only some of the reasons why ANDRITZ lamella evaporation technology is preferred by pulp producers across the globe. With our lamella evaporation, pulp mills not only achieve higher operational efficiency, they also meet stringent environmental regulations and achieve
lower production costs. These features combined give a remarkable boost to mill uptime.
Our passion for evaporation solutions drives us to find the best outcomes for our customers. We partner with mill teams throughout the mill‘s lifecycle, guaranteeing availability and expert support.
Learn the benefits of lamella evaporation.