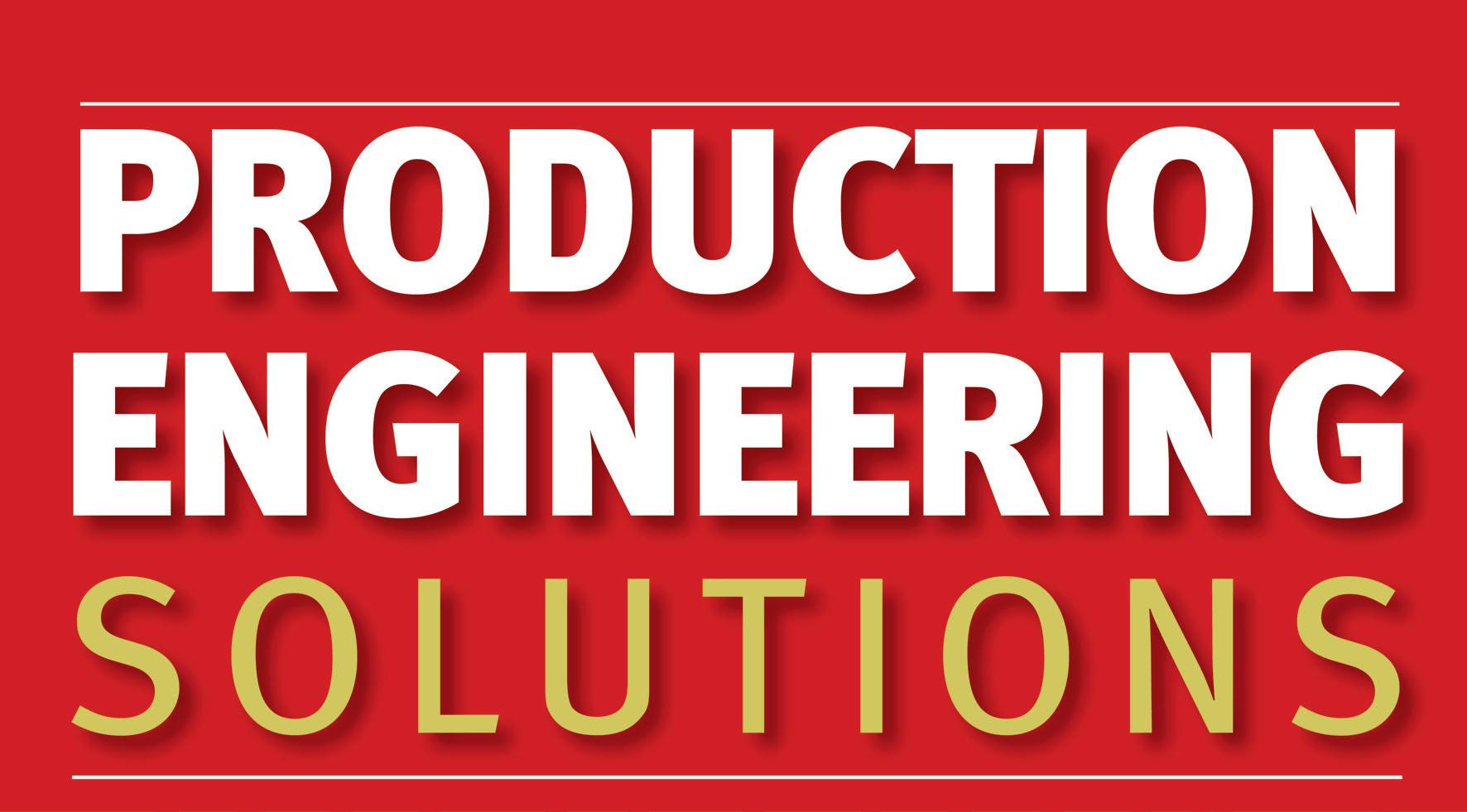
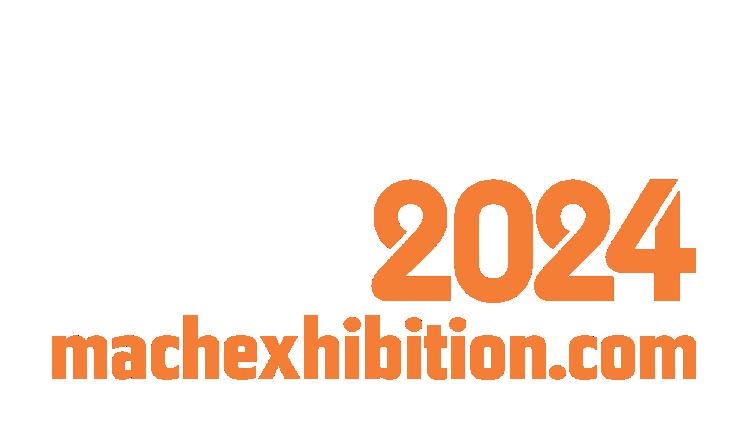
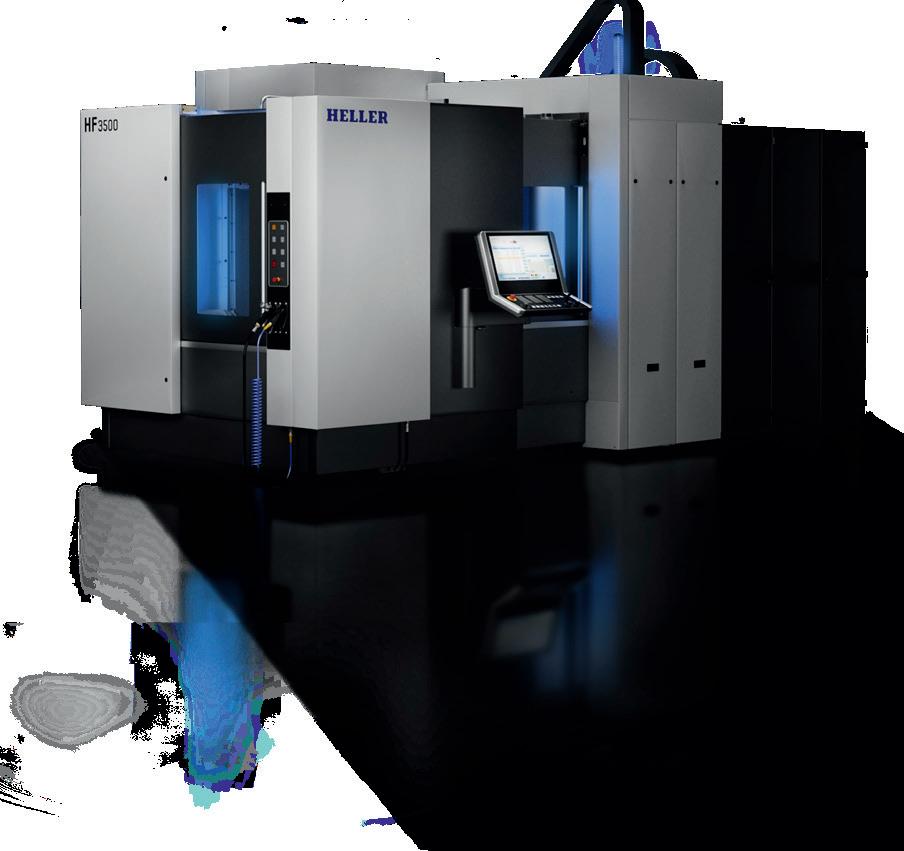
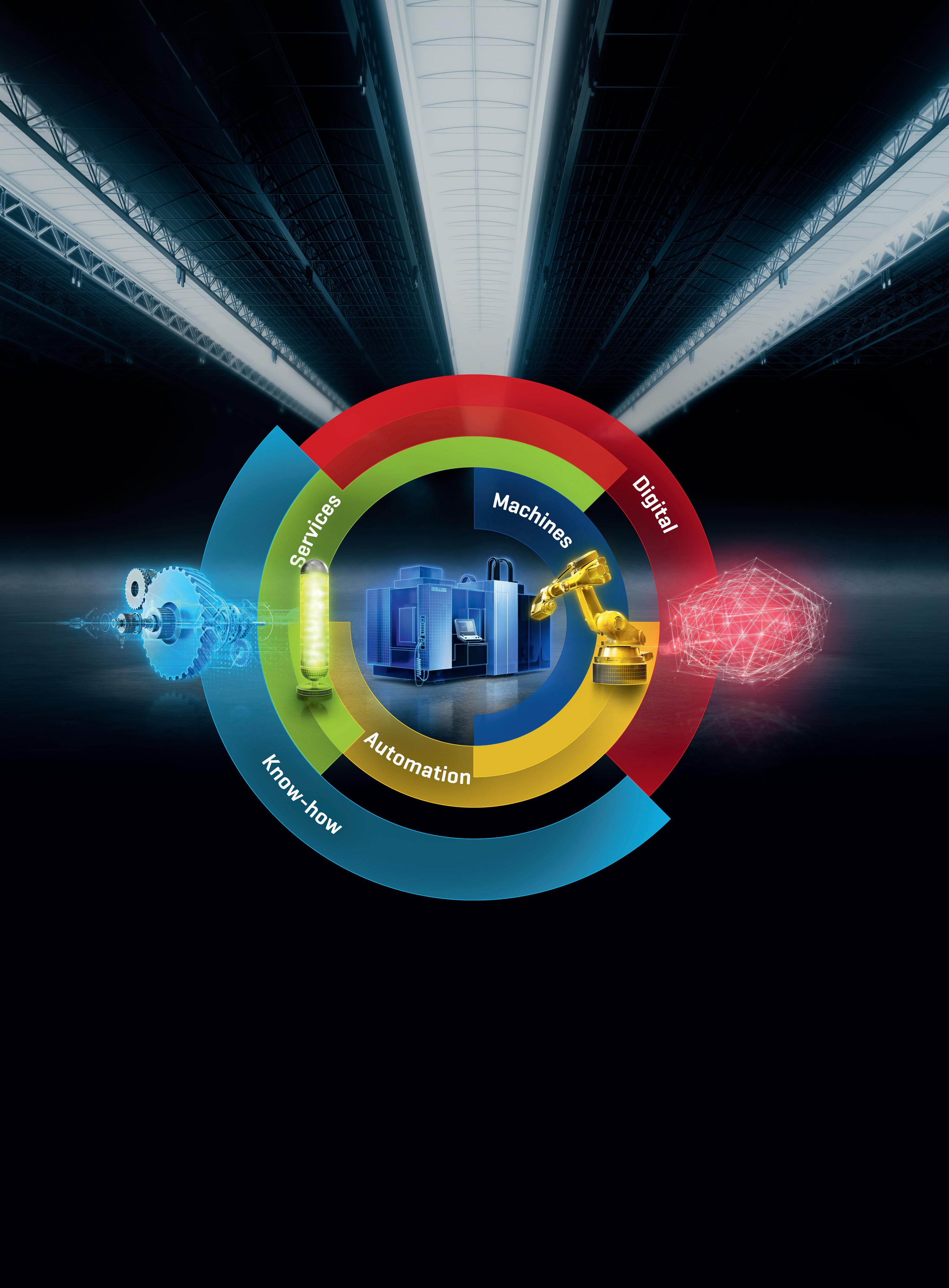
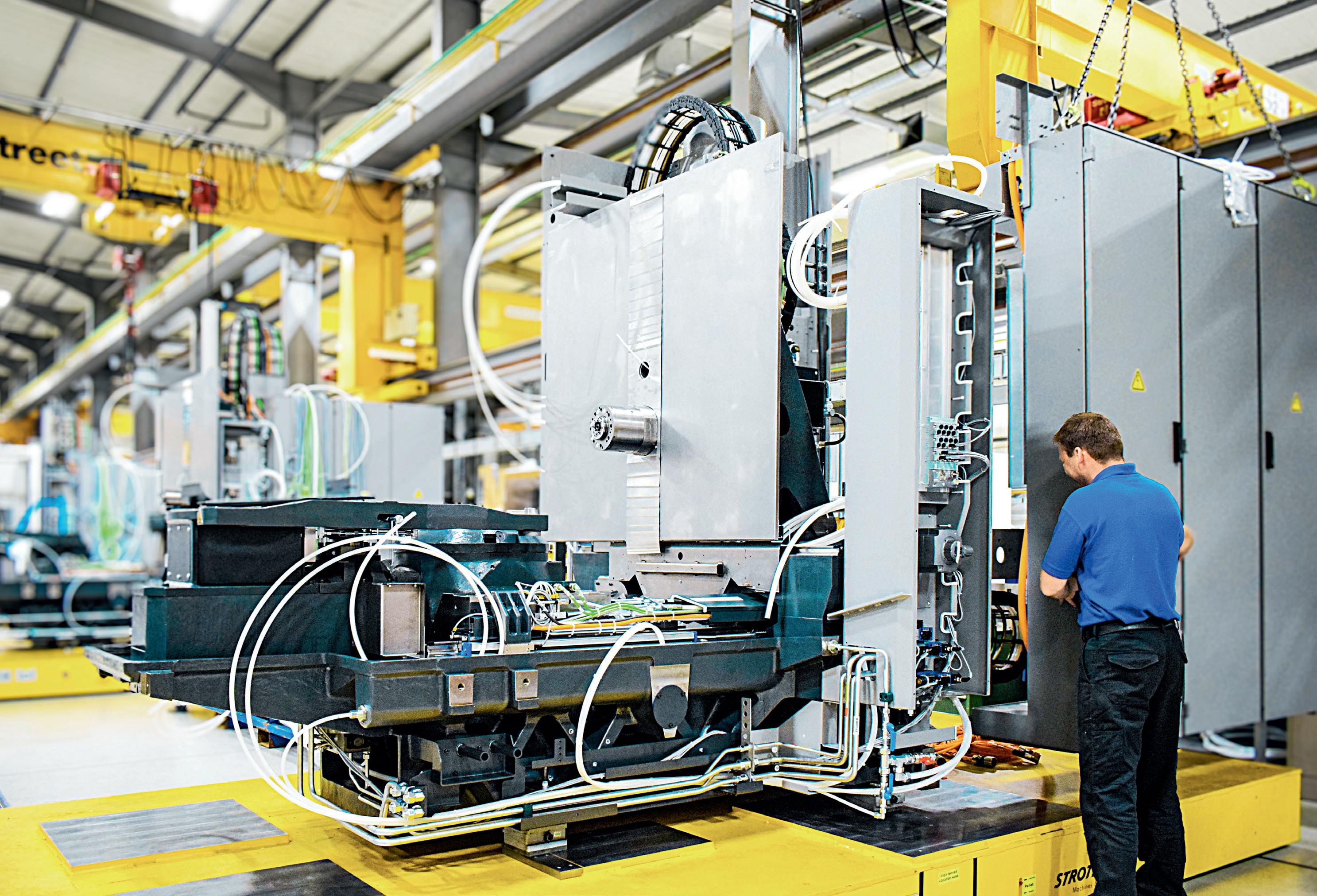
The pre-eminent machine tool manufacturer in the machining sector, Gebr. Heller Maschinenfabrik GmbH based in Nürtingen, Germany, is now 130 years old, while its wholly owned subsidiary in Redditch, Heller Machine Tools, is celebrating its 50th anniversary this year. Machines are also manufactured at the UK site, which is a global competence centre for turnkey projects and innovative manufacturing solutions.
The symbiotic relationship between the parent and daughter companies, both of which have their own manufacturing programmes serving world markets, results in a level of service to customers that is unsurpassed in the industry, especially in the UK.
In 1894, engineer Hermann Heller opened a trading and manufacturing company for patented products and watchmaking tools. He entered the mechanical engineering sector four years later manufacturing sawing, skiving and thread cutting machines, laying the foundations for the long-term success of what is now an international group of companies.
In the UK, both 4-axis and 5-axis HMCs are built using flow line manufacturing principles. There are advanced applications engineering capabilities on-site and a well-equipped demonstration area. Customers are welcome to visit to see the quality of engineering input that is standard across all HELLER factories, including in Sorocaba, Brazil (which is also celebrating its 50th anniversary this year), in Troy, Michigan, US and finally in Changzhou, China.
Join us at MACH 2024 on stand 19-330 and celebrate with us. It will be an opportunity to see an exciting live machine demonstration on a HELLER HF3500 5-axis machining centre. See you there!
HELLER UK Facility Drone Flythrough:
Don't want to hear 8-12 months lead time for a new machine?
How does 8-12 weeks sound?
Throw
It’s easy to think of the UK’s objective to reach carbon neutrality by 2050 as something that’s a long way in the future but as we all know, targets of this magnitude simply don’t happen overnight.
Without using too many cliches, it is a ‘journey’ albeit quite a long one. And the best approach to achieving success with sizeable undertakings such as this is to take a little and often approach. It requires a plan; it requires accountability; and it requires commitment. Progress will be on an incremental basis.
And the wheels of change are definitely moving in the right direction. Leading equipment manufacturers – machine tool producers for example – through their own Net Zero initiatives and pressure from customers and supply chains are taking this very seriously.
Generally, machines are being manufactured much more responsibly today, and with intentioned and deliberate consideration for the environment at every stage of the process. From a customer perspective – the people actually buying the equipment – it’s not just solely about feeds, speeds and specifications anymore (although that’s important of course).
Nowadays, many end users will want to know how much energy a machine uses, if it has any energy saving technology built-in and the overall carbon footprint. It’s an ever-increasing part of the overall purchasing decision and for the equipment seller, it could ultimately be the difference between making a sale and not.
For our cover story this month, I spoke to two guys from the AMRC North West in Lancashire about sustainable manufacturing and factories. The AMRC of course needs no introduction as a world-leading research and innovation network that very successfully bridges the gap between academia and industry. It’s also one of seven centres that make up the High Value Manufacturing (HVM) Catapult.
The North West site, located adjacent to BAE Systems’ facility in Samlesbury, is a little different from the others however. It’s the lead site in the group for additive manufacturing; it’s a pioneer in developing battery and battery cell technology; and its home to the largest 5G testbed in the country.
But it also operates as a Low Carbon Smart Building Demonstrator. A somewhat ambiguous title perhaps, but it’s pretty self-explanatory. The entire building –including infrastructure, equipment and the manufacturing processes and research carried out within – is designed to be a demonstrator of advanced and sustainable technologies.
Check out the article on page 16 for more information, but basically, if you’re a manufacturing company looking for advice on how to start on your Net Zero journey, the AMRC is a great place to start.
Dave Tudor Editorial DirectorSustainability, green credentials, Net Zero –these are all terms that are interwoven into the very fabric of our everyday lives. And we all know this is about as serious as it gets. In the face of escalating climate change impacts, limiting global warming through carbon emission reduction is paramount to ensure a sustainable future. Dave Tudor caught up with Iain Martin and James Valentine of the University of Sheffield Advanced Manufacturing Research Centre (AMRC) North West to find out more about its sustainability endeavours. See pages 16-18
Introducing the latest generation of NEO products and state of the art automation
Industry-leading aftersales service, applications support and training for the lifetime of your machine
Offering secure, digital services through Mazak iCONNECT
Mazak can help your business build for the future by offering a range of new technologies and UK-built machines that provide increased productivity, delivering profitability and competitiveness. Whether it’s 5-axis, entry-level machine, automation or laser cutting, Mazak has the technology and short lead-time availability that can provide an immediate boost to your production.
Visit us in Hall 20 Stand 330 at MACH 2024 and see how we can help you build for your future.
discover.mazakeu.com/MACH
At the start of 2024, Dormer Pramet further strengthened its UK sales team with the appointment of three area sales engineers to cover various parts of the UK.
Puru Gunasekaran, area sales engineer for the West Midlands started his career in India working for a technical distributor selling and technically supporting cutting tools, machine tool probes and calibration solutions, working closely with manufacturers.
Mr Gunasekaran has an MBA (Master of Business Administration) from Loughborough University and holds a Bachelor of Mechanical Engineering degree.
Craig Lampitt, area sales engineer for the East Midlands has excellent knowledge of the territory having spent the past five years building key strategic relationships with some of the largest end users in the area while working collaboratively with key channels.
New area sales engineer for the North West, Paul Elliott has been working in the cutting
GF Machining Solutions, the milling, EDM, laser and additive manufacturing (AM) machine tool specialist and advanced automation and tooling systems supplier, has appointed Gary Purcell as its new country sales manager for Northern and Southern Ireland.
Previously employed as an applications engineering manager at Waterford-based Schivo Medical, an innovative contract manufacturing organisation specialising in the medical device and life sciences sectors, and with considerable sales experience from working in and across Ireland’s and Europe’s medical device and mass spectrometry manufacturing supply chains, Mr Purcell joined GF Machining Solutions in February 2024.
Employing a sales manager with such extensive, firsthand experience of Ireland’s MedTech sector as well as an in-depth knowledge of medical devices and the manufacturing processes involved in making them, is a significant development for GF Machining Solutions offering significant new business and growth opportunities.
Ireland is Europe’s largest per capita employer of medical device professionals and the second largest exporter of medical device products. The country exports MedTech
tool industry since 2014 with a particular speciality in the aerospace sector. From his many years in the industry, he has developed solid relationships with key end users and channels in the region.
UK sales director Richard Wright commented: “We are delighted to have Puru, Craig and Paul onboard as we make fantastic progress in our growth journey.”
n Dormer Pramet
www.dormerpramet.com/uk-ie/en/
Scan here for more Dormer Pramet articles
products worth €12.6 billion to more than 100 countries.
Ireland is also a global leader in the design, manufacture and supply of cardiovascular devices, orthopaedic implants, diagnostic equipment and surgical instruments – and is home to numerous multinational MedTech companies supported by a large, buoyant and strong supply chain.
Mr Purcell commented: “As GF Machining Solutions’ new country sales manager for Northern and Southern Ireland and armed with my knowledge and experience of working in the MedTech sector through my previous employment at Schivo Medical and Takumi Precision in Limerick, I am confident that I can make a telling contribution.
“I am no stranger to GF’s advanced machine tool technologies and automation systems, and how they can help, and are helping, Irish component and mould tool
manufacturers improve their productivity and process efficiencies.
“I aim to use my knowledge and experience to help improve GF Machining Solutions’ sales performance not just in the Irish MedTech supply chain but across the board, with OEMs, tier one companies and precision subcontractors operating in Ireland’s aerospace, pharmaceutical, electronics, materials handling and transport sectors.”
Mr Purcell has numerous qualifications (L7 & L8) in sales and marketing, international selling and pharmaceutical and medical device operations.
n GF Machining Solutions www.gfms.com/uk
Scan here for more GF Machining Solutions articles
Bridgeport Machine Tool Company was recently acquired by InCompass, the platform company of Colchester Machine Tool Solutions.
As an InCompass brand, Bridgeport will continue to evolve its business with the other InCompass manufacturing partners, contributing to the vision of creating manufactured growth solutions. It means Colchester and Bridgeport effectively become stablemates, pooling their respective knowledge and expertise going forward.
The Bridgeport name and legacy live on in the form of various milling machines still in use today, as well as through the influence of its design principles on the machine tool industry.
Bridgeport, a leader in metal machining since 1938, offers CNC and
manual milling solutions. Renowned for advanced metalcutting capabilities, it caters to a diverse range of industries such as aerospace, agricultural, automotive, construction, consumer products, defence, energy, medical, technology, transportation and more.
Bridgeport’s product range supports various applications with precision and reliability, symbolising excellence in the machining world. Its commitment to innovation is evident in its extensive range of CNC vertical machining centres.
Bridgeport’s first revolutionary design was the Series 1 standard milling machine which featured a turret-style head that could be swivelled and tilted, allowing for versatile machining operations.
The Series 1 quickly gained popularity among machinists and manufacturers due to its simplicity, versatility, and reliability. With the increased awareness of the brand, Bridgeport began to build its legacy and over the years, the company introduced various improvements and innovations to its milling machines, such as digital readouts (DROs), CNC capabilities and other modern features, while maintaining its longstanding reputation in the industry.
The latest Series 1 standard knee mill will be present on Colchester Machine Tool Solutions’ stand at the MACH 2024 exhibition taking place at the NEC in April. It will sit alongside Colchester’s range of renowned CNC and manual machine tools, including new Storm vertical milling machines, Tornado CNC turning centres and the Student CNC lathe.
n Bridgeport
https://bridgeportmachinetools.com/
n Colchester Machine Tool Solutions
www.colchester.co.uk
Mr Burley joins the organisation at a pivotal time, collaborating closely with Chris Holehouse who is gradually reducing his hours in alignment with his planned retirement in 2024. This strategic move allows for a seamless transition, ensuring a smooth transfer of knowledge and expertise.
Collaborative efforts from Mr Burley
Mr Holehouse
aim to bring substantial benefits to the team and, most importantly, to valued customers.
The company says the well-planned transition will secure the future of its financial operations, as well as enhance the overall experience for its clients.
Kyocera SGS is a manufacturer of solid round carbide cutting tools and provides machining solutions and services to a variety of industries, including
The next Control international trade fair for quality assurance (QA) held at the Stuttgart Messe exhibition centre will take place from April 23 - 26 this year.
The 36th instalment of the show will feature the latest advances from the fields of vision inspection, image processing, sensor technology, as well as metrology.
Fabian Krüger, Control project manager at P. E. Schall, promoters of the trade fair said: “We’re once again expecting impressive, trailblazing solutions for quality assurance and an expanded range of topics. QA solutions are used in industrial production, in all operational processes, in non-industrial fields of application, in medical technology as well as in defence applications.
“Measurement, testing, inspection, evaluation, documentation and endto-end solutions for these functions is required because more and more data is being captured, analysed, linked and fed back to the respective systems in order to achieve transparency and consistency. This is why software and intelligent evaluation algorithms play an increasingly important role.”
Control attracts QA experts from around the world. An intensive exchange of expertise takes place, which is highly valued by exhibitors and expert visitors alike. Solution suppliers come together directly with quality managers, engineers and production experts involved in routine daily operations.
As part of Control 2024, the Fraunhofer Vision Business Unit will organise a
special show on contactless measuring technology. This show within a show will feature a cross-section of innovative technologies, applications and system components from the field of contactless measuring and test technology across approximately 300m² of exhibition floor space.
Currently QA is being driven by automation, digitalisation, networking and inline inspection. Digital mapping of processes, infrastructure and components in real-time is becoming more and more important because these developments serve as the basis for forecasting and optimisation. Digitalised processes make it possible for manufacturing companies to identify quality problems and their causes more quickly.
Bettina Schall, managing director of P. E. Schall concluded: “Quality inspection and quality assurance affect all industries and Control 2024 will demonstrate just how rapidly technology is developing. “The show’s user-orientated trade fair format, which features the presentation of top technologies, outstanding expertise, direct practical relevance, and high levels of internationalism, offers ideal conditions for the successful and useful implementation of efficient QA measures in production. Efficient production and remaining competitive are key and in this spirit, we’re looking forward to an exciting and vibrant Control 2024.”
aerospace, automotive, medical, power generation, mould and die, casting and foundries, general engineering and firearms. The company maintains a customer commitment to providing ‘Value at the Spindle’, whether a client’s value is measured in cost savings, time savings, or ease of use.
n Kyocera SGS
Precision Tools Europe
www.kyocera-sgstool.com
Trumpf’s Bend TecDay 2024, held at the company’s Luton headquarters in February, proved a resounding success with an impressive number of visitors attending from both existing and potential customers.
The highlight of the event for visitors was to get up close with Trumpf’s new TruBend Series 1000 press brake. Designed as the ideal entry to the company’s bending solutions, the new TruBend 1000 offers simple and reliable operation at high levels of precision and speed.
The new machine set the theme for Bend TecDay 2024, delivering an easy-tounderstand introduction to the Trumpf world of bending and focusing on all the essentials that provide the ideal start to any company’s bending journey.
The TruBend Series 1000 has a sturdy system structure, high-quality components and intuitive programming system, reducing the skill level required for operation.
Bend TecDay 2024 included an overview of Trumpf’s TecZone Bend programming software. Visitors could discover how this advanced software automatically creates a program proposal based on 2D and 3D data in just seconds. TecZone Bend is available at no cost for 12 months.
Through live demonstrations, attendees could learn about machine attributes such as precision bending: the fouraxis back-gauge positions the sheet metal to within 0.05mm and enables users to bend complex parts with high levels of repeatability and speed (up to 400mm/s). Another key feature is automatic, intelligent wedge crowning, with users benefiting from high angle accuracy along the entire bend length and the automatic calculation of angle correction.
Visitors to Bend TecDay 2024 could also see for themselves the machine’s large open height and stroke, its BendGuard optical protection system and the 19” touchscreen user interface fully loaded with Trumpf bending data technology and network connectivity. Notably, the control’s photorealistic 3D visualisation aids both simulation and production, providing operators with step-by-step guidance
from tool set-up to component completion.
Aside from the TruBend Series 1000, those attending Bend TecDay were able to experience the broad spread of
CNC bending machines on show at Trumpf’s Luton showroom. Based on pioneering innovation, the company’s extensive portfolio includes machines for die bending and panel bending,
as well as large-format bending tools and fully automated solutions.
n Trumpf www.trumpf.com
Mayor of West Midlands Andy Street visited Unipart Manufacturing in Coventry to find out more about green economy job creation.
The mayor toured Hyperbat, Unipart’s electric vehicle battery production facility joint venture and a leading UK provider of high-voltage batteries for specialist applications based at the site in Holbrooks.
He also visited the Institute of Advanced Manufacturing and Engineering, Unipart’s collaboration with Coventry University to give the next generation of engineers experience in a live factory environment and provide Unipart with cutting-edge research and development.
The mayor was hosted by Unipart Manufacturing managing director Carol Burke CBE, who as a West Midlands Regional Business Council member is championing business in the region.
Ms Burke is also a non-executive director for the UK Battery Industrialisation Centre and on the UK Battery Strategy Taskforce, which published a report in December on boosting the domestic supply chain for lithium-ion batteries.
She commented: “I’m honoured to be working with the West Midlands
Leading engineering company Applied Automation (UK) has increased its precision engineering capabilities following the recent acquisition of PTG Workholding. Bristol-based PTG Workholding has been trading for over 30 years and supplies both UK and overseas markets with expanding mandrels capable of automatic and manual clamping in component bores. Thanks to their outstanding accuracy, PTG’s mandrels deliver excellent holding power that can resist even the harshest cutting forces often imposed on the workpiece.
Managing director of Applied Automation David Rowe said: “We’ve been looking to increase our existing precision engineering offering and with the purchase of PTG Workholding we will now be able to manufacture custom jigs and fixtures along with specials based around PTG’s standard expanding mandrel range.
“It’s a great fit for our business and we’re firmly committed to continue delivering high quality engineered parts at great prices, which was the bedrock of PTG Workholding’s success for more than three decades, to both existing and new customers.”
Applied Automation (UK) is an
internationally renowned supplier of high-quality automation and control equipment. Based in Plymouth, with satellite offices and warehouses in both Cardiff and Portsmouth, it designs, manufactures and delivers both standard or bespoke automation and control solutions for industrial engineering, the marine sector and smart homes.
The company employs more than 150 designers, engineers, project managers, sales engineers and professional specialists who work in a number of specialist divisions and wholly owned subsidiaries, which enables them to provide high levels of technical support and customer service across a number of industry sectors.
As a responsible business, Applied Automation recognises the need to build a sustainable world and coupled with its commitment to Corporate Social Responsibly (CSR), endeavours to be a company that can be trusted by all its employees, customers and suppliers.
n Applied Automation UK
www.appliedautoamation.co.uk
n PTG Workholding
www.ptgworkholding.co.uk
Regional Business Council. We have a fantastic opportunity to leverage the region’s rich heritage in the automotive industry to embrace alternative forms of propulsion. Through our Hyperbat electric vehicle production facility and the Institute of Advanced Manufacturing and Engineering, our own people and the engineers of tomorrow are building their capability in cutting-edge innovation.
“Unipart’s experience is a fantastic example of how businesses in the region can transition to the green economy. As a supply chain solutions and performance improvement technologies partner, and a tier one supplier to original equipment manufacturers, Unipart is supporting our customers’ shift to sustainable technology in the automotive, rail and construction sectors. This competitive edge is at the heart of our manufacturing partner strategy.”
Andy Street, Mayor of West Midlands, said: “We have an amazing heritage of car making and innovation in the West Midlands and by working together we can be a world leader in the new clean electric vehicle and battery industries.
“Unipart is a wonderful example of what our automotive companies can achieve by embracing change and innovation to put themselves at the cutting edge of the EV industry. They are a key player in the powerful EV cluster around Coventry which includes the likes of JLR and the UK Battery Industrialisation Centre.”
Unipart Manufacturing employs 300 people across its Holbrooks site, and its joint venture Kautex Unipart Limited at Coventry Business Park which recently celebrated its 25th anniversary.
n Unipart Group www.unipart.com
Wallwork’s Hot Isostatic Pressing (HIP) Centre has passed EN/AS9100 certification for its new manufacturing process.
Installed and commissioned by Quintus Technologies in the last quarter of 2023, the HIP Centre is now entering its fourth month of operation. For customers from a range of industries, the aerospace Quality Management System AS9100 certification provides the highest assurance about the systems in place to ensure Wallwork HIP Centre will meet their requirements.
“Preparing for the audit has been a massive effort by all the team,” said Wallwork HIP Centre business manager, David Loughlin. “I extend a personal thank you to all those involved in the process of adding hot isostatic pressing to the extensive scope of Wallwork Bury’s AS9100 approvals. I know they will continue to ensure that the highest quality standards are adhered to on a daily basis.”
He added: “With additive manufactured components playing an increasingly
vital role in aerospace, demand for hot isostatic pressing is rising rapidly. Adding the second HIP, recently announced, means we will be in front of the curve and ready to provide the high service standards expected by aerospace and all other manufacturers.”
The Wallwork HIP Centre is wholly integrated with Wallwork Group’s dedicated national transport systems for speedy pick-up and delivery, assuring aerospace component manufacturers of total end-to-end responsibility for their components.
As an entirely UK-based, ITAR compliant business, Wallwork says it is an ideal partner for defence as well as civil aerospace projects.
n Wallwork
www.wallworkht.co.uk
Hydrafeed, a leading manufacturer of automation equipment and a subcontract supplier to the aerospace industry, has gained real-time visibility into its factory operations through a new partnership.
Machine monitoring technology from FourJaw Manufacturing Analytics has enabled Hydrafeed to meet growing demand with its existing workforce and achieve energy savings worth more than £17,000 a year within a month of implementation.
Based in Milton Keynes, Hydrafeed relies on 50 people and 19 milling and turning machines to produce barfeed and machine tool automation products for CNC machine users and several of the world’s most prestigious OEMs.
Hydrafeed installed FourJaw’s plug-and-play platform on 14 of its machines in September 2023, enabling it to automatically recognise when they were productive, record reasons for downtime, generate a digital work schedule to guide factory operations and improve communication with machine operators.
FourJaw’s platform has provided Hydrafeed with a real-time understanding and visualisation of its factory data, enabling it to establish a production efficiency benchmark
and a detailed account of energy use. This has already improved the dayto-day management of manufacturing operations and provided a clear understanding of where Hydrafeed can achieve productivity and sustainability gains.
During the first five weeks, Hydrafeed
was able to generate the same output in its milling cell with four fewer machines, allowing the reallocation of machine operators to its turning cell, where it has boosted utilisation by 30%.
Hydrafeed identified further opportunities to reduce energy usage through more efficient machine operation
within days of installation. The energy savings already identified will deliver a complete return on its investment in FourJaw.
Paul Gilligan, operations director at Hydrafeed, commented: “We had a strong business before FourJaw but limited visibility of shopfloor operations. We’ve addressed that with FourJaw, and the response from management and machine operators has been positive. Everyone has clarity of what needs achieving and has bought into our plans to improve productivity and profitability.
“FourJaw has been a revelation. We’ve already reduced energy consumption and identified further opportunities for improvement.”
Chris Iveson, FourJaw CEO, commented: “We see manufacturers who are proactively using FourJaw’s technology, can typically achieve productivity gains of anywhere between 10-20% which can increase output capacity by as much as 30%, so we are excited to see what more Hydrafeed will achieve with FourJaw.”
n Hydrafeed www.hydrafeed.co.uk
n FourJaw www.fourjaw.com
Machine tool manufacturer Heller is hosting an open house at its headquarters in Nürtingen, Germany from 23-26 April.
Visitors will have the chance to experience the company’s range of machining solutions up close over the four-day event.
Highlights will include the latest generation F 5000 5-axis machining centre, a new development concept for a rack-type tool magazine and a machining unit with tilting head kinematics.
The open house will feature live demonstrations of 4- and 5-axis machining centres and other Heller solutions focusing on digitisation, automation and services. There will also be factory tours with exclusive insights into production, an exhibition and exchange with partners and companies of the Heller Group.
Founded in 1894, the global group develops and produces machine tools and manufacturing systems for machining operations. As one of the leading machine tool manufacturers in the machining sector, Heller employs 2,600 staff worldwide at five production facilities in Europe, Asia and North and South America.
The Heller product range includes 4 and 5-axis machining centres, milling-turning machining centres, custom machines
and process machines, coating modules, machines for crankshaft and camshaft machining, as well as a comprehensive modular range of services.
With Heller4Industry and Heller4Use, the company offers an extended range of solutions to achieve increased productivity and flexibility in production.
Heller generates tailor-made complete solutions for a diverse range of manufacturing requirements, from the standalone machine to the fully automated turnkey production system. Customers include companies from the automotive industry and their suppliers, from general mechanical engineering, energy technology, fluid technology, aerospace and other sectors. n Heller www.heller.biz
Scan
The history of Bowers Group’s Moore & Wright brand is being brought to life by the Hawley Tool Collection as its new exhibition launches at the Kelham Island Museum in Sheffield.
With a history dating back over 100 years, Moore & Wright is one of the most prominent names in measurement tools and one that is deeply rooted in the history of the steel city. Famous for its range of tools and measuring equipment, this new exhibition tells the story of the brand and its products, as well as some of its former employees.
Bowers Group marketing manager, Ellie Skinner, said: “This new exhibition really demonstrates the impact that Moore & Wright has had throughout its history, and it’s exciting to have our brand being celebrated in its birthplace. Sheffield has such an important legacy in industrial and manufacturing Britain, and it’s a real eye-opener, even to us within the business, of just how much Moore & Wright meant to the people of
The exhibition offers a journey through the brand’s history, showcasing its products and featuring personal stories from former employees. Two years in the making, highlights of the display include a BBC video spotlighting Moore & Wright’s groundbreaking Micro 2000, hailed as the world’s first digital micrometer.
Visitors can re-live the experiences of former apprentices while archived photographs capture the company’s vibrant community spirit. For those who have connections to Moore & Wright, the exhibition presents an opportunity to reconnect and maybe even spot familiar faces among the displayed images.
Founded in 1906 by engineer Frank Moore and businessman Charles Wright, Moore & Wright quickly became a recognised name in the manufacturing industry, establishing itself as a leading producer of precision
measuring instruments and tools. The company’s roots were deeply planted in Sheffield, a city renowned for its industrial heritage. Over the years, Moore & Wright expanded its product range to include a diverse range of high-quality tools and instruments, earning a reputation for accuracy, reliability, and innovation.
Today, as part of the Bowers Group, Moore & Wright remains dedicated to upholding its legacy of craftsmanship and precision while embracing
new technologies to drive continued growth and success in the global market.
The Moore & Wright exhibition is expected to be displayed within the Hawley Gallery, alongside the wider Hawley Collection until the later part of 2024.
n Bowers Group www.bowersgroup.co.uk
Scan here for more Bowers Group articles
David Martin has joined ScotMaz – the sole distributor of Yamazaki Mazak machine tools in Scotland – as sales manager to support the manufacturer’s growing presence north of the border.
Mr Martin, who has 25 years’ experience in the metalworking industry, began his career as a toolmaker before moving into technical sales roles with ABT Machine Tools, Arno UK and most recently Kyocera Unimerco Tooling.
He joins ScotMaz with a remit to promote Mazak’s extensive machine tool portfolio to customers in the oil and gas and general subcontracting industries, while also targeting growth opportunities in the country’s aerospace, food and beverage and renewable energy markets.
The role will see him work closely with ScotMaz directors Scott and Steven Hunter out of ScotMaz’s Technology Centre in Stirling.
Jason Butler, sales director at Yamazaki Mazak, said: “The Scottish market is particularly dynamic and it is not often you find someone of David’s considerable experience in the right place at the right time.
“Both our flagship Integrex range of multi-tasking machines and UK made VTC series of vertical machining centres are already popular choices for Scottish machinists with demanding cutting requirements. I am very confident David’s appointment will bolster what is already a robust presence for Mazak in Scotland.”
Mr Martin added: “Mazak is one of the iconic brands in the metalcutting industry and, through my tooling experience, I know the company is already the machine tool provider of choice for many Scottish engineering firms.
“With more and more customers in need of ancillary support, particularly with offline
programming and integrating automation, Mazak’s offering is perfectly placed to deliver a turnkey solution. I’m looking forward to getting out on the road and connecting with many of my existing contacts while forging new relationships throughout the country.”
n Yamazaki Mazak www.mazakeu.co.uk
Scan here for more Yamazaki Mazak articles
THE LATEST END MILLING TECHNOLOGY FOR TITANIUM, HEAT RESISTANT ALLOYS, STEELS and STAINLESS.
NEW DOUBLE GASH GEOMETRY IDEAL for RAMPING
A typical first gash is combined with an innovative secondary gash to provide high chip evacuation without weakening the structure.
Numachine, a thriving Hereford-based business specialising in CNC machining and subcontract manufacturing, has embraced the advantages of a new Hyundai-Wia LV800RM vertical turning lathe (VTL) supplied by T W Ward CNC Machinery (Ward CNC).
The quality and performance of the machine have impressed Numachine in contributing to the optimisation of its manufacturing processes.
Brandon Davies, managing director of Numachine and a dedicated mechanical engineer by trade expresses his passion for problem-solving and
continuous improvement: “I enjoy solving problems,” he enthuses. “Even if I work 15-16 hours a day, I don’t feel tired because my hobby is my job, and I absolutely thrive on it. I like to come in every day, go around the shop and see how we can improve. I’d say this ethos is something we all share at Numachine; everyone is trying to contribute to our continuous improvement.”
Numachine primarily serves industries such as automotive, medical, aerospace, laboratory/ instrumentation, and renewable energy, all requiring the highest quality standards. Mr Davies
keeps a keen eye on the electric vehicle (EV) segment, given his personal interest as an EV driver and Numachine’s supply of components to prestigious automotive companies for use in EVs.
A key focus for Numachine is cost reduction for customers, achieved through value engineering across the CNC machining process. Mr Davies highlights the company’s diverse capacity. “We have a strong range of CNC machine tools, ranging from various horizontal lathes and mills to 5-axis machining centres, vertical lathes and multi-
tasking machines. This extensive range provides differentiation from the
competition, while our inhouse quality control and measurement capability is
another key factor for many customers.”
He adds “We’re always thinking about how we can expand our service capacities and are now in the process of selecting a metal 3D printer. Additive manufacturing will allow us to produce prototypes much faster for our customers and, with our machining capabilities, we can achieve high-quality finished parts in a very short time period.”
Design for Manufacture (DfM) is another significant service at Numachine, actively reducing the cost of machined components for diverse applications, including planes and trains to breweries and roulette wheels. The company manufactures its fixtures inhouse, supporting optimised clamping mechanisms with quick turnaround times, emphasising its role as a onestop-shop, catering to customer demands for high-quality, rapid services.
Numachine has recently incorporated a Hyundai-Wia LV800RM VTL from Ward CNC into its diverse machinery lineup. Renowned for its robust and heavy-duty cutting platform, the machine features a one-piece, square-type column that delivers excellent stability. This machine is equipped with a stable shaft structure, providing
a high cutting capacity suitable for handling substantial loads.
Noteworthy highlights of the Hyundai-Wia LV800RM include a two-step chuck pressure mechanism designed to minimise workpiece deformation and ensure optimal
chip evacuation. Within the LV series, a dedicated protection device has been integrated to prevent chips and other foreign materials from entering the main spindle, guaranteeing continued high-precision performance.
The Hyundai-Wia LV800RM is characterised by its impressive specification, offering a maximum turning diameter and turning length of 800mm, coupled with a maximum spindle speed of 2,000rpm. This addition to Numachine’s workshop enhances its machining capabilities, reinforcing a commitment to precision and efficiency throughout its manufacturing processes.
Speaking on the experience of working with Ward CNC, Mr Davies comments: “It was a very smooth experience. Ward CNC took care of processes such as specifying the machine based on our application, placing the order, delivery, installation, and operator training.
“We’re pleased with the quality and performance of the
Hyundai-Wia vertical lathe; it’s a good addition to our range of machines. There was only one small issue a few months ago which was solved rapidly by the supplier. We’re completely satisfied with the service.
“Looking ahead, Numachine plans to enter the bespoke motorbike and mountain bike manufacturing segment, combining my passion for offroad biking with the company’s manufacturing capabilities. Ward CNC is likely to play a crucial role in these future projects.”
TW Ward CNC Machinery
www.wardcnc.com
Numachine
https://numachine.co.uk
Sustainability, green credentials, Net Zero – these are all terms that are interwoven into the very fabric of our everyday lives. And we all know this is about as serious as it gets. In the face of escalating climate change impacts, limiting global warming through carbon emission reduction is paramount to ensure a sustainable future. Dave Tudor caught up with Iain Martin and James Valentine of the University of Sheffield Advanced Manufacturing Research Centre (AMRC) North West to find out more about its sustainability endeavours.
as its Low Carbon Smart Building Demonstrator. Clearly visible in the shot are two state-of-the-art solar flowers which are connected to the building and help reduce its carbon footprint
For UK manufacturing companies, transitioning towards Net Zero not only helps address the urgent need to limit global warming but also aligns with national goals to achieve carbon neutrality by 2050.
It’s worthwhile setting the scene a little and taking a brief look at the current AMRC structure in the UK. The University of Sheffield Advanced Manufacturing Research Centre is a world-leading and pioneering research and innovation network. It has sites in Rotherham and Sheffield, but also a footprint in Lancashire with AMRC North West, and Broughton, North Wales with AMRC Cymru – a facility it shares with Airbus. The organisation is part of the University of Sheffield – as is its sister centre the Nuclear AMRC and the AMRC Training Centre used to nurture and train the engineers of tomorrow. From a wider perspective, it’s one of seven centres that make up the High Value Manufacturing (HVM) Catapult, a national network of research and innovation centres.
As a group, the AMRC works very collaboratively and there are many core strategies that are common across all sites but AMRC North West does have some unique skillsets such as our battery and battery cell technology expertise – from design through to manufacturing and assembly
was formed to bridge the gap between academia and industry – turning groundbreaking ideas into reality. It does the research, develops the technology, tests the processes and generally de-risks everything in readiness for manufacturers and businesses to pick up the baton and take things to market.
And it’s keen to emphasise that it works with companies at all levels –from primes and mid-tier businesses through to lower tier and SMEs. It’s a misconception that the AMRC exists just for the big boys – it works with the entire supply chain. Often cost-reduction, efficiency and Net Zero pathways are primary drivers.
To comprehensively list all the work the AMRC is involved with would swell the wordcount of this article unimaginably, but in simplistic terms, essentially it
The AMRC has specialist expertise in many disciplines including digital manufacturing, machine learning and artificial intelligence (AI), composites, automation and robotics, additive manufacturing, testing and training. It also drives forward sustainable
manufacturing technologies for Net Zero, creating the vital step changes needed in the low carbon transition.
The purpose-built facility in the North West however is a little different. Located in Samlesbury, it was officially opened in March 2022 as a Low Carbon Smart Building Demonstrator supported by the Lancashire Enterprise Partnership.
It’s very much a work in progress, but its intention is not only to help develop pioneering manufacturing processes in a similar vein to the other AMRC sites, but also to help create a roadmap for manufacturers – large and small – in their respective journeys towards Net Zero by 2050.
“We’re located in the Samlesbury Enterprise Zone adjacent to BAE Systems – a company we work very closely with – and the site employs 70 members of staff,” explains Iain Martin, senior business engagement manager and senior theme lead for the low carbon smart building demonstrator. “It’s all about extending the AMRC’s reach through regionalised support and in conjunction with our other sites, AMRC North West forms part of a northern arc that covers North Wales, through Lancashire and into Yorkshire.
“As a group, the AMRC works very collaboratively and there are many core strategies that are common across all sites but AMRC North West does have some unique skillsets such as our battery and battery cell technology expertise –from design through to manufacturing and assembly,” he adds.
“Also, although this is a discipline common across all facilities, we’re the lead site in the group for additive manufacturing. And, although we have digital teams across the AMRC network, the focus of the team in the North West is the development, application and rollout of 5G technology in manufacturing and smart factories. We have the largest 5G testbed located here.”
For manufacturers starting their Net Zero journey or perhaps are a way into it, the AMRC is a good place to start because it’s independent. James Valentine, senior technical engagement manager elaborates: “Often, a company will approach us and ask us to evaluate how much a particular manufacturing process costs or how much energy it uses, or even wider issues like are we operating as efficiently as we could be in terms of our carbon footprint?
“The drivers for these initiatives could simply be self-generated or perhaps it’s being imposed by the supply chain that company is in,” he affirms. “We’ll visit the company and install one or two low-level wireless sensors on perhaps a press brake or a machine tool. We’ll then gather data from the machine and the process and feed it back to the customer.
“They’ll get lots of useful information from the analysis on important elements like costs and energy consumption. Often this is only the start of the Net Zero journey – the company will then look at what other cost and energy saving initiatives it can implement. The really good thing about this however is that the principles can be applied across any manufacturing company irrespective of sector or size.
“It’s important to note that we get involved through a number of different routes: companies may contact us directly; it could be through repeat business; or through referrals.”
It’s always good to reference examples when talking about initiatives to improve manufacturing efficiencies and a case in point is HycAero (formerly Hycrome Aerospace), a multi-tier supplier to the
aerospace industry with five NADCAP accreditations for thermal coating, chemical processing, shot peening, NDT and heat treatment. The company has invested heavily in robotics and automation coupled with a commitment to employee training and development.
The investigation carried out by AMRC North West was on a paint booth extraction system at HycAero. Power and State information was gathered and combined with movement data representing the occupancy of the booth to identify process efficiency including changeover times and unproductive power consumption where the extraction
was running but no actual painting was taking place.
The AMRC North West team installed three sensors to measure current, bath overflow and paint booth occupancy, and a fourth (gateway) to store and post the sensor data via mobile network.
The findings from the investigation were extensive and detailed but it was discovered that the running costs of the booth in terms of power consumption could be offset totally by the installation of a 25kW solar panel system. Analysis also revealed that, over the monitored period (just shy of a month), there were 24 hours of time that the booth was
unoccupied for more than 120 seconds, while the extractor fan was running.
Further to the investigation, HycAero is now considering the installation of dashboards that allow it to monitor long downtime periods across historical data which allows for investigation into unscheduled downtime/unproductive work.
Overall, through analysis of the paint booth ecosystem, temperature and occupancy data, the project has derisked the installation of IoT and enabled the business to pursue the installation of further systems. It has essentially opened HycAero’s eyes to the power of
data and what can be achieved.
Stephen Kelly, operations director at HycAero commented: “Working with the AMRC North West has allowed us to install technology across the business to monitor our processes. The outputs are a reduction of wasted energy, improved operational efficiencies and elimination of risk from equipment failures that could have both financial and environmental impact.”
Yes, it’s a somewhat unusual name perhaps but it does what it says on the tin. As James Valentine succinctly puts it: “The whole purpose behind the AMRC North West’s inception was to ‘become’ a demonstrator of advanced and sustainable technologies – it didn’t start off as one. And ultimately, we can’t demonstrate sustainable technologies to others without outwardly being sustainable ourselves.
“So we use our factory ecosystem monitoring, tracking and sustainability systems to assess how much energy we’re using and carbon we’re producing ourselves. This includes not only the efficiency of our lighting, heating and cooling systems, but also all our machinery and equipment on the shopfloor. We’ll make decisions internally based on that data and then, in turn, feed that back into what we actively demonstrate here. This has a very direct bearing on the machines we purchase and the processes we use.
“We also have renewable energy generation systems on site again as part of the demonstrator so we know not only how much energy we’re using, but also how much we’re generating and storing (the AMRC North West can store up to 1MW of energy). This enables us to set carbon emission targets and goals and, importantly, measure our performance against those targets.
“It’s important to understand that this is work in progress,” he states. “We’re learning as we go, but as we do so, we’re able to pass on what we’re learning to our customers and partners in their own Net Zero journeys. That’s the whole ethos behind the AMRC North West being a Low Carbon Smart Building Demonstrator. It’s not just a ‘do as we say’ scenario; it’s ‘do as we do’ or put another way, practising what we preach.
“Of course the benefits are not purely environmental; producing less waste and being more efficient makes a big difference to a business’ bottom line,” he concludes.
n AMRC www.amrc.co.uk
Scan
Ceratizit recently invited West Pharmaceutical Services staff to its Technical Centre on the Advanced Manufacturing Park in Sheffield for one of the cutting tool maker’s technical training days.
These allow customers to receive in-depth cutting tool training and benefit from Ceratizit’s technical expertise.
West Pharmaceutical Services was invited to the technical training day by Iain Tattersall, technical sales engineer at Ceratizit UK & Ireland, who regularly visits the company, along with application sales engineer Vince Witham, to provide technical and tooling support.
The invitation was extended not only as a gesture of appreciation for being longstanding customers, but also so that staff could be brought up to speed on the tooling specialist’s latest innovations, its advancements in tooling and also be shown the latest and most advanced machine techniques and metalcutting skills to take back to the company’s shopfloor in Cornwall.
More importantly, training days, run on a weekly basis, help to fill the knowledge gap that is blighting the engineering industry. Realising the importance of passing on knowhow that has been learned from years of industry experience, younger generations are encouraged to attend training days so that these technical skills are not lost in the future. Furthermore, sharing innovative machining techniques, practices
and skills, means customers get the most from Ceratizit’s tooling.
For West Pharmaceutical Services, the day started off with a morning of indepth theoretical training delivered by Shaun Thornton, technical manager at Ceratizit UK. Covering everything from materials, tools and sustainability, to speeds, feeds and cutting data, this extensive training equips customers with a solid foundation of background knowledge that is useful in maximising the performance and profitability of machines.
Taking time to answer questions and ensure that
everyone has followed everything covered in the theoretical training, Mr Thornton then led the attendees downstairs to the workshop where they could put the theoretical knowledge to the test.
The engineers at the Technical Centre planned an afternoon of practical learning whereby guests could incorporate the morning’s theory with some engineer-led machine demonstrations.
After lunch, the afternoon’s practical training began with an interactive cutting tool demonstration on a Mazak
Integrex I-250H multi-tasking machine. Allowing the attendees to input the cutting data, the guests could see how each operation ran and which values of cutting data worked best for the specified machining conditions.
Immersing guests in handson, interactive training is at the heart of these training days. Furthermore, live video feeds from the machines, played on large screens throughout the workshop, meant that everyone can get a detailed view of how the operations are running and whether the cutting data has been calculated correctly.
After the demonstration on the Mazak, it was time for more practical work on XYZ machines. On the XYZ 800HD vertical machining centre and the XYZ UMC 5X 5-axis machine, the visitors once again were encouraged to work out the cutting data for themselves, before putting this knowledge to the test and running the specified programs.
On the XYZ UMC 5X, guests took part in a machine demonstration where they were shown how aluminium pen pots – given out to customers at training days – were made. This machine demonstration also showcased Ceratizit’s latest cutting tool technology: KOMflex and ToolScope. ToolScope is a process monitoring control system that can be retrofitted to most CNC machines. Monitoring spindle torque and live cutting data, this information can then be used to optimise aspects such as tool wear and
Tooling expert Mapal has carefully examined critical components used in the fluid power technology industry and their requirements for machining.
One example of this is the axial piston machine. Its series production and the machining of its different components pose a variety of challenges both for processes as well as individual cutting tools. However, Mapal specialists say they have developed a solution that reduces machining time for a
cylinder block part alone by 19%.
Types of axial piston machines perform different tasks in closed and open hydraulic circuits, but they all convert hydraulic energy into mechanical energy or vice-versa. They are used in modern agricultural harvesters and tractors, as well as in heavy road, construction and mining machinery.
“Manufacturers of axial piston machines produce them in mid to large sizes,” says Tobias Stolz, component manager for general machining at Mapal. “A high
degree of accuracy is required to machine their individual parts.”
Mapal is an expert in combining high quantity volumes with precision and has been able to improve processes considerably and save costs for clients in the fluid power sector. It also has all the products in its portfolio required to completely machine the individual components.
This made the axial piston machine an obvious choice for Mapal as a component maker to focus on. Its experts developed a model process which was
prevention of tool breakages and collisions.
Pairing this with KOMflex, an actuated closed loop boring and probing system, the engineers demonstrated how these technologies streamline machining processes. They prevent damages which occur thanks to the advanced monitoring with ToolScope, while reducing the risk of scrapping costly components with KOMFlex.
Once everyone had finished their demonstrations and all questions had been answered, customers were given fully documented training booklets containing information on the tooling, machine demonstrations and cutting data that they had used throughout the day.
Following on from the training day, Vince Whitham helped West Pharmaceutical Services to implement changes to its current tooling and cutting data back onsite in Cornwall. These changes, influenced by the training day, had an immediate positive effect on productivity, cycle times and tool life. To benefit from a training day, the company invites interested parties to speak to their Ceratizit technical sales engineer to enquire about availability and booking.
n Ceratizit UK & Ireland www.ceratizit.com
Scan here for more Ceratizit UK & Ireland articles
successfully put into practice (with individual adjustments where required) for clients.
An axial piston machine is made up of a housing, adjustment unit, port plate housing and cylinder block. When machining the housing made from EN-GJL-250 cast iron, which provides protection for the unit, the machining of the oil leak countersink feature is key.
For this, Mapal recommends a modular boring tool which is particularly economical due to the TTD replaceable head
drill and indexable inserts.
Milling cutters from the NeoMill range are used to machine the housing’s various surfaces.
“This a special feature that we can offer Mapal customers,” Mr Stolz says, referring to the combination of specially designed custom and economical standard tools.
Standard tools are used for the most part to machine the adjustment unit made of ENGJS-400-15 graphite iron, the axial piston machine’s control instrument. Mapal recommends
solid carbide drills from its Mega-Step-Drill family for the threaded bores. In addition, FixReam reamers and HPR replaceable head reamers are used for the fine machining of various bores.
The third component, the port plate housing, is the axial piston machine’s connection plate and therefore the pressure and suction connection to other parts in the hydraulic circuit. It is usually made of either EN-GJL-250 or ENGJS-400-15 materials. In this
case interrupted cuts and partially thin-walled component segments pose challenges during machining.
“We machine some of the bearing seats and rotor bores with multi-stage, specially designed boring tools with indexable inserts that ensure high-quality bores even in difficult conditions,” says Mr Stolz. “As for the last component, if there is a challenge when it comes to machining axial piston parts, then it definitely has to be the cylinder block.”
The cylinder block is at the heart of the axial piston machine and is manufactured from either steel (C45 or 42CrMoS4) or spheroidal cast iron (ENGJS-500-7 or EN-GJL-400-15).
Through the movement of the pistons and oil, this component performs the machine’s main function. For it to work, the piston bores have to be machined with pressed-in liners.
“One customer was struggling with high costs manufacturing cylinder blocks,” Mr Stolz explains. “A great deal of effort is required to ensure the defined surfaces are between Rz 27 and 37µm, as well as the liners maintaining tolerances for roundness, straightness and parallel alignment of 3µm. Our experts developed an economical process with the customer where machining time was reduced by 19% per part in total.”
The customer machines the pressure and suction kidney with the OptiMill-Uni-Pocket solid carbide milling cutter as part of this new process which supports the boring process via inclined plunging. The machining
of these inlets and outlets consequently does not require any other tools.
The Tritan-Drill step drill geometry offers similar benefits when pre-machining the piston bores. The spot face that is normally required is dispensed with and thanks to the sharp cutting edges, the bottom of the bore also does not have to be deburred.
The multi-stage Mapal fine boring tool ensures optimal quality before the brass bush is pressed in. It is not only precise during machining but also particularly efficient and economical thanks to
the HX insert’s six cutting edges. These three tools alone reduce machining time by 19% compared to the previous method.
“We offer customers economical processing solutions to their machining challenges –for all functionally relevant parts in the fluid power industry,” Mr Stolz concludes.
n MapalScan here for more Mapal articles
With a combination of specially designed specials and economical standard tools, Mapal can fulfil all requirements for fast and precise machining of components in axial piston machines
There are many wire EDM machines on the market. Some deliver faster processing speeds, while others lean towards accuracy. So, for customers wanting optimal wire EDM machine performance, there has always been a tradeoff between the two.
However, GF Machining Solutions says that its Cut X series of EDM machines solves this conundrum.
Developed and manufactured at the company’s Losone factory in Switzerland, these EDM machines are available in two sizes: the Cut X 350, with a maximum workpiece size of 800mm x 550mm x 250mm, and the Cut X 500, with a maximum workpiece size of 1,050mm x 700mm x 250mm.
The machines are extremely accurate because of a new thermal management system and optimised mechanics, which also help improve surface finish quality.
Consistent thermal conditions are maintained by the machines’ sealed cabinets and doors that ensure that cold air containment within the workspace as well as controlled air flow is achieved. By keeping heat sources away from the machine mechanics, Cut X models perform consistently without the ill-effects of temperature fluctuation outside the machine.
The CNC also collects data from an array of temperature and humidity sensors located inside and outside of the work area to further maintain ambient workspace conditions. The data drives an artificial intelligence
(AI) algorithm that predicts possible thermal deformations and compensates the positioning of the X-, Y-, U-, and V-axes. This AI-driven compensation enables high accuracy results even with the environmental temperature fluctuations that are common during long cutting cycles.
The machines also have the ability to switch between open and closed wire guides, sometimes known as V and round guides, respectively, on the same machine. The wire guides have interchangeable cartridges that can be switched by the operator in less than 15 minutes (five minutes to change the cartridge and 10 minutes to align the wire circuit).
Open guides are suitable for straight or less than 3º taper angle cuts and provide flexibility for varying wire diameters without changing the guide. Closed guides offer high accuracy, speed, and surface finish for taper cuts up to 30º.
New additively manufactured upper and lower heads increase the cutting speeds of the Cut X series. The heads reduce the distance between the guides and the part, creating improved accuracies during the cut, while also increasing the amount of fluid that is pushed through to optimise flushing and cutting speeds.
Additionally, Advanced software accessed by the operator through the Uniqua human-machine interface (HMI) is used to set the necessary power settings to achieve the desired results.
The machines’ intelligent
power generators with direct power supplies (IPG-DPS) dial in the correct power settings with algorithms based on decades of work by GF Machining Solutions to deliver specified surface finishes and accuracies at specific speeds.
When it comes to the control, the machines have a 19-inch vertical touchscreen and a full keyboard and mouse.
The control supports legacy file types from various older Charmilles (ISO-based) and Agie (dynamic-based) EDM programs. The interface also has a graphics tool for programming both offline and at the machine, that’s compatible with major CAD/CAM programs.
In addition to the series’ cartridge-based wire guides, flexibility and continuous production is obtained through the incorporation of automatic wire changer (AWC) technology that includes two identical, symmetrical wire circuits.
With this, operators can use a thicker wire for a fast, aggressive main cut followed by a thinner variant to trim-cut small corner contours. The technology also enables the use of two wires of identical diameter – with and without coating – to optimise speed during the main cut and the surface finish during the trim cut.
To prevent wire breakage, the system uses Spark Track technology and an Intelligent Spark Protection System (ISPS) to constantly monitor and evaluate the position of each discharge between the wire and workpiece in real-time against set parameters. If the discharge concentration exceeds the threshold, ISPS automatically adjusts the spark energy for optimal wire condition and cutting speeds.
The machines also have 90º corner doors that automatically open so the operator can enter the entire work area. The doors also enable robotic loading and unloading.
Further lights-out productivity is possible thanks to the integrated Z-axis touch probe that automatically measures the top surface of the workpiece and aligns the wire perpendicular to this new plane and an automatic slug management system that removes slugs and deposits them in a dedicated bin.
Wire management is also automated for autonomous operation with automatic wire threading, an integrated wire chopper that reduces downtime, and a double-wire spool with AWC technology.
GF Machining Solutions says manufacturers looking for a wire EDM machine without compromise, should take a
look at its new Cut X series of machines.
n GF Machining Solutions www.gfms.com/uk
Midlands-based Master Abrasives has recently been appointed as the Rosa Ermando S.p.A authorised agent in the UK and Ireland, a leading worldwide supplier of grinding machines based in Italy.
For this brand addition to Master’s range, discussions have been handled slightly differently and it has been mutually agreed with Rosa’s current distributor, NL Machine Tool Consulting, that Master Abrasives will work closely together in a gradual handover as NL’s managing director Norman Loughton heads towards retirement.
Following a three-way discussion, it was mutually agreed that Master would represent Rosa from 1st January 2024, working closely with Mr Loughton during the handover. Paul Batson, Master Abrasives’ managing director, stated: “While we are honoured to have reached an agreement to represent Rosa and work with them on potential new business, we also want to show our respect for the work that Norman has put into the brand and customer base over recent years.
“For this reason, it was critical that Norman was on board, and we’re glad he was happy to work with us on the smooth transmission from NL Machines Tools’ distributorship to Master Abrasives.”
Rosa, founded in 1964 by Eng. Ermando Rosa, designs and builds horizontal spindle grinding machines for plane surfaces and profiles, grinding machines with universal heads for slideways and profiles and creep-feed grinding machines. Mr Rosa bought rival Favretto Machine Tool company in recent years so it can also offer the range of Favretto machines, sitting well beside the Rosa range for a comprehensive
machine portfolio.
Giuseppe Bucci, export manager at Rosa stated: “This new partnership with Master Abrasives is a wonderful opportunity to continue serving the manufacturing community in the UK. Our surface and profile grinders are optimally targeted towards many high-end grinding applications offered by British market.
“Master Abrasives’ expertise and knowledge will add value to the quality and reliability supplied with any Rosa surface grinder by providing processrelated support and guidance. I am sure this collaboration will provide the foundation for increasing our market
Tamworth cutting tool manufacturer Industrial Tooling Corporation (ITC)
On Stand 432 in Hall 20,
presence by assisting existing customers and becoming a reference for new prospects.”
Ian Meredith, Master Abrasives applications engineering manager added: “Rosa have a great history and pedigree in the machine tool industry and their range falls very nicely into our machine tool portfolio. We can offer our customer base top quality machine tools but with the support of abrasive products to ensure they get the optimum productivity out of their machining set up.”
The main industrial sectors where Rosa surface
grinders are to be found are mould and die manufacturers, toolmakers, the machine tool industry, aerospace industry guideways and linear guiding systems, and circular and straight knives for the steel, aluminium and paper industries – all of which will be a target markets for the Master team amongst others.
AT MACH 2024, Master Abrasives will be featuring a Rosa machine on its stand.
n Master Abrasives
www.master-abrasives.co.uk
Hall 6, Stand 430
From its portfolio of bore
respectively. The full EWN monoblock family of products ranges from the smallest CK1 to the largest CK7 which now supports fine boring from 20mm to over 200mm diameter. Also new from the Big Kaiser
bore machining stable will be the new MW rough boring bars.
Manufactured from carbide, the new boring bars deliver significantly improved precision levels when compared to steel alternatives by reducing
vibration and chatter.
Typically, cylindrical boring bars are manufactured from steel, and this has the disadvantage of creating considerable deflection and vibration during operation. By
using carbide, which has four times the density of steel, flexing is decreased by a factor of more than 16 which significantly reduces vibration.
The reduction in deflection means that carbide tools are
much more precise and exhibit reduced levels of chatter. The rough boring system will be complemented by the new EWA 68 intelligent fully automatic fine boring tool that received its world premiere at the EMO exhibition last September.
The new EWA 68 is an intelligent fully automatic fine boring tool that performs closed-loop boring operations without human intervention. With the EWA 68, there is no need to stop the machine tool to take measurements and manually adjust the boring tool. This significantly reduces cycle times, increases productivity and reduces failure rates due to human error, reduces costs and improves accuracy.
Precision, concentricity and surface finishes are only as good as the toolholders and this is why Big Kaiser has expanded its range with the arrival of the new PG (perfect grip) Straight Collet system.
The PG Straight Collet system includes a new anti-pullout system that locks the collet and cutter to the toolholder body, a design which eliminates cutter slippage and also the potential for cutter pull out during demanding metal removal
applications. The new system is particularly suited to high dynamic milling and high-speed milling in difficult materials.
Big Kaiser has launched three sizes of collet with the new anti-pullout system – all of which received world premieres at EMO. The three size variations include a 10, 12 and 16mm PG Straight Collet system and, unlike other systems, the PG does not require specially modified and inherently expensive end mills. Instead, it uses existing standard carbide or HSS end mill designations. Standard notches found on typical Weldon-type end mills will readily accept the locking key insert on the new PG system.
At MACH, the PG system will be shown alongside the new Ultra Precision Hydraulic Chuck. The new hydraulic chuck is suitable for all machine shops that require the lowest possible runout for high-precision milling. With runout guaranteed to be less than 1µm at 4xD, this ultralow runout retains this precise level even after intensive use.
ITC will also present a new line of hydraulic chucks for turning machines that provide outstanding repeatability and damping characteristics. The
advantage of the new Big Kaiser chucks is that they enable simple and straightforward assembly using just an Allen key, while the holder remains mounted on the machine. The chucks have been designed to
be compatible with major sliding head automatic turning centre brands such as Citizen, Star, Tsugami and Tornos.
Also newly introduced to Big Kaiser’s HDC (hydraulic chucks) series and available at MACH
will be the Hydraulic Chuck Jet chuck series. Easy, fast and safe to use with no heat shrink clamping machines required, the life of the toolholder is extended indefinitely, saving money and reducing the environmental
impact of holder replacement when compared to shrink-fit holders.
n ITC
www.itc-ltd.co.uk
Hall 20, Stand 432
Sodick Europe and UK distributor Sodi-Tech will exhibit new product innovations focused on the mould tool manufacturing sector on Stand 350 in Hall 20 at MACH 2024.
The company will introduce six machine tools with many of these innovations receiving their MACH exhibition premiere. For the injection mould and toolmaking industry, Sodick Europe and Sodi-Tech UK will unveil their new 30-tonne hydraulic hybrid GL30-LP injection moulding machine.
As a world-leading brand, Sodick will give MACH show premieres to the new VN600Q, the ALC600G iG+E precision wire-cut EDM with new iGroove+ technology and the UX450L linear motor driven machining centre.
Appearing alongside these MACH debutants will be the AD35L die sink EDM and the AL60G EDM die sink machine which will incorporate an Erowa Compact 80 robotic loading system with a Zeiss DuraMax measurement and probing system that will provide live demonstrations at the event.
The groundbreaking innovations will offer technology and productivity enhancements for every machine shop and toolmaking business. Nowhere at MACH will this be more evident than with the show premiere of the new GL30-LP injection moulding machine that is destined to be a crowd-
pleaser for the injection mould segment – especially for manufacturers of small, complex and high-precision components. Perfect for manufacturers in the medical, electronic and precision instrumentation sectors, the GL30-LP is equipped with Sodick’s V-Line technology, direct pressure mould clamping and the new Total Servo Drive system. With so much technology packed into a small-footprint machine, the GL30-LP demonstrates exceptional stability, traceability and usability that combine with a host of advanced injection moulding functions to improve operational accuracy, productivity, performance and energy efficiency.
As with all Sodick injection moulding machines, the new GL30-LP is equipped with Sodick’s V-Line two-stage plunger injection system. This innovation separates the injection and plasticisation processes in one unit, resulting in extremely accurate, rapid and repeatable resin injection.
This suppresses outgassing, reduces fibre fracture and prevents backflow to provide high levels of performance, consistency and quality throughout the manufacturing process. V-Line technology also delivers excellent plasticisation and injection performance with high stability and reliability.
This contributes to accurate and highly repeatable resin
injection while the hydraulic accumulator mechanism enables high-speed injection with dynamic responsiveness.
From a technical specification perspective, the GL30-LP has a compact footprint of just 3,150 x 1,030 x 1,679mm with a maximum clamping force of 294kN (392kN optional).
The machine has a tie bar distance of 310 x 310mm with a minimum and maximum die height of 150 and 360mm respectively.
Capable of accommodating tools up to 200kg, the GL30-LP
is available with three screw diameters of 14, 18 and 22mm. Depending upon the variant selected, manufacturers can achieve a maximum injection specific pressure (MPa) from 260 to 288 with an injection volume from 4.5 to 27cm³ and an injection rate by volume from 57 to 190cm³/second.
Sodick has three core principles for its moulding machines and the GL30LP achieves these with its consistent plasticising heat profile, constant filling volume and constant holding pressure
Leading manufacturer of metal and composite forming machinery, Group Rhodes, will be demonstrating one of its innovative metalforming presses within the MMMA Metal Working Village at MACH 2024.
The Rhodes Interform product on display was designed and manufactured in-house at the company’s Wakefield factory as part of a full turnkey solution to produce a bespoke twin press facility for forging forklift truck components.
The entire project, which consists of two Rhodes
Interform multi-axis presses, a complete robotic handling line and an integrated conveying system, is capable of processing the largest forks at a rate of one part per 70 seconds.
Group Rhodes will also be discussing the global patents it has registered for its Superplastic Forming & Diffusion Bonding Technology (SPF/DB), including the territories of China, India, The United States and Europe. This innovative solution is applied extensively to the lightweighting of components within the
aerospace and automotive industries.
Operations director James Gascoigne, comments: “We are looking forward to attending
– all of which work in perfect harmony to achieve ultraprecise injection moulding results.
In addition, the mould open/ close clamping mechanism adopts both an electronic system to achieve accurate positional control and a hydraulic mould clamping mechanism that ensures a repeatable and highly accurate clamping force.
With a direct pressure mould clamping system utilising the merits of the electro-hydraulic hybrid system, precision and repeatability are assured.
With manufacturers increasingly conscious of energy costs and carbon footprint, the new GL30-LP incorporates Sodick’s Total Servo Drive that provides even greater energy saving performance through electric servo motors for the hydraulic pump drive and the mould open/close and ejection mechanism.
Furthermore, the green efficiency credentials of the machine are enhanced by its quick start to production and improved ratio of crushed and recycled material and moulds.
n Sodi-Tech EDM
www.sodi-tech.co.uk
Hall 20, Stand 350
since we secured international patents for Superplastic Forming & Diffusion Bonding and it will be a great chance for our team to discuss how this technology works and its potential applications globally.
MACH 2024, which will give us the opportunity to demonstrate our latest innovations in metalforming technology.
“This will be our first exhibition
“Given that our 19th century patents were for improvements to the steam hammer, it is amazing to think that our most recent innovations are helping to form components for spacecraft. We are very proud to showcase these innovations – especially in our 200th anniversary year.”
Alongside its SPF/DB technology, Group Rhodes’ highly knowledgeable personnel will also be in attendance to discuss the company’s extensive portfolio of machinery for the hot and cold forming of metals and composites.
The company actively manufactures and markets bespoke machinery from its facilities in Wakefield, West Yorkshire, which it sells to both the UK and global markets.
The four companies that make up the group offer extensive capabilities, including the design, development and manufacture of bespoke equipment to serve the metalforming, composite
forming, heavy ceramics and material handling sectors.
Rhodes is celebrating its 200th anniversary in 2024 and is proud to nurture a dedicated workforce in a traditional yet dynamic manufacturing environment.
The parent company of Rhodes Interform, Group Rhodes’ metalforming history spans two centuries. It has been forming composite materials from as early as the 1930s. The business has won Queen’s Awards for both Innovation and International Trade in recent years.
Group Rhodes www.grouprhodes.co.uk Hall 6, Stand 599
Starrag will be presenting its latest innovations from across the company’s diverse portfolio of high-performance solutiondriven machine tools at this year’s MACH show at the NEC.
From the Bumotec machine range, the company will present its latest turn/mill product lines that can now be viewed in the company’s new virtual showroom: (https:// showroomvud.starrag.com/).
The virtual showroom is a replica of the Starrag facility in Vuadens, Switzerland and it provides manufacturers with
an opportunity to investigate a wide range of solution-based innovations that range from the small and compact s128 simultaneous 5-axis machining solution to the 36-axis s1000/C transfer machine with eight machining stations in a single footprint platform.
The virtual showroom enables manufacturers to view videos of individual machine tools, application demonstrations and machine specifications from the comfort of their connected devices.
As a system integrator of highly productive manufacturing solutions, the Bumotec virtual showroom gives engineers a flavour of what is possible when they invest in leading technology. The virtual showroom has a multitude of machines in the demonstration hall that include the Bumotec s128, Ringma XX, s191V, S191H, the s1000/C, S100multi, the s181, s100mono, the s200, the brand new s191neo as well as the SIP5000 and SIP7000 ultraprecision vertical boring and milling centres.
Lee Scott, director of sales and applications at Starrag says: “Starrag is the go-to machine tool partner for everything from ultra precision micro-machining through to heavy engineering applications. Our reputation
as a solution integrator for clients is unparalleled across diverse industry sectors from the aerospace/turbines industry to the transport/industrial and precision/medtech markets.
“As a solution-based business, our new virtual showroom provides visitors with a sample of just what can be achieved through partnerships that deliver the lowest cost per part possible. We encourage manufacturers to view the virtual showroom and then come and speak to us at MACH 2024 regarding what we can offer.
“Since MACH 2022, we have launched several groundbreaking new machines and we have also completed a company merger with Tornos, a leading manufacturer of Swisstype sliding head and multispindle machining centres. With so much to offer at MACH, the event promises to be a mouthwatering prospect for the Starrag-Tornos Group and visitors to our stand.”
Starrag
www.starrag.com
Hall 18, Stand 320
Scan
As the company celebrates its 50th anniversary, Paul Maxted, director of industrial metrology applications at global engineering technology company, Renishaw, explores the changing role of metrology in manufacturing over the last few decades and predicts how it is set to develop in the future. PES reports.
Metrology has always been vital in precision manufacturing to ensure products meet both quality and design specifications.
As industry demands have increased over the years, we have seen a transformation in measurement technology – advances in metrology and improvements to manufacturing capability typically go hand-inhand.
At Renishaw, we’ve always understood the role of metrology in optimising manufacturing processes. Indeed, the company was founded on exactly that, when Sir David McMurtry developed the first touch-trigger probe to solve a dimensional measurement issue for the Olympus engines which powered Concorde.
The creation of this industrychanging sensor enabled measurement on a coordinate measuring machine (CMM) to be automated for the first time. Since our company was
founded in 1973, there has been a revolution in measurement processes – so let’s take a look back.
Manufacturers are now able to use realtime process and measurement data to improve operations part-by-part, batchby-batch, and drive long-term improvement, with a smart factory approach to analysing process data. Monitoring patterns in process data over time enables engineers to continuously improve and optimise
Processes in a traditional machine shop have always been reliant on skilled individuals – toolmakers, setter/operators and other experts, producing quality machined parts in batches.
In CNC machining operations the setup of a recurring batch of parts requires skilled input and often results in balancing a batch quantity with an excessively long set time. This not only ties up valuable machine time but adds inventory costs to a business.
It was, and is still, common for a manufacturing facility to have a dedicated CMM room and skilled inspection staff. CMM rooms are often remote from the shopfloor where parts can be measured in a temperaturecontrolled environment.
Separating machining and metrology ensures measurement traceability,
however, it creates a disconnect between manufacturing and quality.
CMM measurement is often a bottleneck that delays production, with CNC operators often waiting to get first-off approval before producing parts in volume. However, the alternative of immediately starting production increases the risk of non-conforming parts, waste and quality costs which quickly escalate – so there’s a dilemma.
Implementing on-machine probing and tool setting systems to automate and reduce setup times allow for smaller batch quantities and increased productivity.
Further evolutions in shopfloor measurement and gauging equipment mean that metrology systems empower production people to measure accurately in-line or near-line production.
Ultimately, bringing metrology to the shopfloor enables faster, more frequent part and process measurement and the ability to react more rapidly to process drift and dimensional changes.
Over the years, Renishaw has helped hundreds of global customers integrate metrology and proactively apply controls using our Productive Process Pyramid concept, supporting them through four core steps.
These are:
l The process foundation requires engineers to consider how they set up the entire factory for consistent performance, including CNC machine assessment, control of tooling, fixtures and other
critical sources of variation
l Manufacturers can look at process setting; checking the machine, tooling, material and fixtures before machining – integrating metrology to automate and eliminate manual intervention
l Adding probing within a CNC operation: in-process controls automatically react to any real-time changes, for example temperature variations, tool wear and process drift, again,
sales@njmetrology.com
07831
www.njmetrology.com
avoiding expert intervention and adjustment
l Following machining: measuring at the postprocess stage enables engineers to validate the process step or final part. However, if manufacturers have already taken the previous preventative, predictive and active steps to improve process control, quality confidence should already be high
To derive the full value of metrology, manufacturers require a great deal of process data to be collected, as well as the ability to leverage the measurement results. With the right tools, manufacturers can use this data to gain valuable insights into the entire process chain, finding where they can make changes that will be most impactful to process control, quality and productivity.
Organising manufacturing data to provide valuable insights at each of these stages has traditionally been difficult
Metrology data integration will increasingly help to drive productivity in manufacturing
on the shopfloor. However, the introduction of Renishaw Central a manufacturing data
and machine shop connectivity platform, is a gamechanger.
With this system we can
digitalise all process and metrology data, visualise, and automatically control
all manufacturing and measurement processes. The results can be significant
– Renishaw Central, piloted in our own machine shops allowed us to reduce unplanned automation stoppages and increase machining capacity by 79 hours per week. We were also able to reduce CNC setting times by over 80% when it was applied with our Equator gauging system and IPC (Intelligent process control) software.
Manufacturers are now able to use real-time process and measurement data to improve operations part-bypart, batch-by-batch, and drive long-term improvement, with a smart factory approach to analysing process data. Monitoring patterns in process data over time enables engineers to continuously improve and optimise. This could mean enhanced product performance, more robust process design or making products faster at lower cost.
In our factories today, there are still occasions where we experience minor, frustrating stoppages, process alarms or events that impact productivity. However, as
we gain more visibility of our processes, over time, we can adapt and continuously improve them. As we begin to understand our longer-term manufacturing capability, we can make informed decisions to refine the frequency for measurements and controls.
As manufacturing becomes more autonomous, we see a trend towards metrology being directly integrated into all automated CNC machining systems. With this approach, manufacturers can leave machines running unmanned making good parts, safely, improving productivity, and freeing up engineers for more proactive value-added activities.
Fully automated systems become critical as manufacturing looks to reshore operations. To enable manufacturers to become more globally cost competitive and ensure a resilient, local supply chain, it will be vital to manage these operations using automated metrology systems
that collect real-time data.
There has been a huge shift in measurement technology in the last 50 years, taking metrology from an offline inspection process into a fundamental pillar of high-precision, automated manufacturing.
It has been a privilege to work alongside so many passionate engineers and manufacturing customers over the last few decades. They have helped to drive this change and transformed the performance and quality of products globally including cars, jet engines, mobile phones and anything precision moulded or machined. All these products are influenced by Renishaw technology at some point during their manufacture.
n Renishaw www.renishaw.com
Scan here for more Renishaw articles
In this article, automation leader FANUC, which has subsidiaries across the world, examines the potential reasons behind the UK’s reluctance to automate and asks what we can learn from our continental cousins. PES reports.
Despite punching well above our weight as a manufacturing nation, the UK is in danger of slipping down the international rankings unless we increase our levels of automation.
Now sitting at 25th in the global robotics league table, we are the only G7 nation outside the top 20 and have been eclipsed by most of our European counterparts in terms of numbers of robots per 10,00 workers, including Italy, Belgium, Switzerland and the Czech Republic.
The benefits to UK manufacturing of robotics and
automation technology are greater than ever, helping us to meet Net Zero targets, boost productivity and underpin our key industries. And with an estimated 70,000 vacancies in manufacturing, robots are also alleviating the longstanding labour shortages which have only worsened since Brexit and COVID.
In regard to automation uptake, it is certainly an improving picture. Led by the automotive sector, UK robot installations were up by 3% in 2022, with operational stock growing by 7%.
But at just 98 robots per 10,000
workers we are still well behind European leaders Germany (415).
Among the many potential explanations for this are a focus on short-term payback rather than longer-term total cost of ownership (TCO); a fear of change; outdated perceptions of engineering as a career; a lack of government incentives; our reliance on cheap manual labour; and no long-term national manufacturing strategy.
While some of these are beginning to change – the Government recently announced a £4.5bn package of support for British manufacturing, for example – should we also be looking to our European neighbours for some automation inspiration?
Dr Bob Struijk certainly thinks so. As the vice president of FANUC Europe, he has overseen automation installations across numerous countries, and believes there are a variety of reasons why certain nations are further ahead of the UK on their automation journey.
“Germany is the clear European automation powerhouse and owes a large part of its success to a profound respect for engineering and manufacturing,” he explains.
“The German model emphasises the meticulous craftsmanship of products, fostering a culture that places a premium on precision and innovation. Catapulted by the automotive industry, robotics and automation have been at the forefront of bringing Germany to its position today as a manufacturing leader.”
In addition, bridging the gap between industry and academia has helped to boost German innovation.
“In Germany, collaborative efforts between industry and academia contribute to a continuous cycle of research, development and implementation, creating an ecosystem that thrives on technological advancement,” Dr Struijk notes. “The German apprenticeship system also provides a seamless flow of skilled labour into industry, at low cost. The UK can learn from this by cultivating a similar synergy between its educational institutions and industrial sector to breed a culture of continuous improvement.”
In this regard, FANUC UK is working hard to help develop a pipeline of manufacturing talent through a range of different initiatives. The company’s Training Academy at its Coventry headquarters offers accredited courses that feed into educational programmes, giving students hands-on robotics experience. It recently held its first ever Work Experience Week for young people aged 16-18, and the 2023 FANUC UK open house played host to the finals of the WorldSkills UK Industrial Robotics competition.
However, for a nation built on SMEs, Dr Struijk is also clear that UK Government support is critical to future success: “The penetration of robotics and automation in the UK is
especially low among small and medium sized enterprises. Government tax breaks or accelerated depreciation of robots could certainly help to change this,” he affirms.
At sixth place in the global automation league table, Sweden boasts an impressive 343 robots for every 10,000 workers. Neighbours Denmark have 274, Finland has 168 and Norway has 103 – all sit higher than the UK.
“With their realistic approach towards return on investment (ROI), the Nordic countries have successfully integrated automation into their industries,” outlines Dr Struijk. “By focusing on the long-term benefits, these nations have cultivated a business environment that encourages companies to invest in automation technologies.”
By looking at Total Cost of Ownership (TCO) rather than just ROI – considering indirect cost savings such as reduced energy bills, less waste, higher productivity and increased production capacity – investing in automation could be a far more attractive proposition to UK manufacturers than it is today. But again, the importance
of government support cannot be overlooked.
“While the UK could draw inspiration from the Nordic model by fostering an environment where companies can confidently invest in automation, this must also be backed by supportive government policies and incentives,” Dr Struijk states.
“In the Nordic countries, robust government initiatives have provided financial support and created favourable conditions for the adoption of automated solutions. For example, in the city of Odense, the government has stimulated the set-up of a ‘Robot Valley’ – a cluster of private companies, start-ups and academic institutions – that is helping to drive the Danish robotics market forward.”
Finally, Eastern European countries such as Slovakia, Hungary and the Czech Republic have embraced automation as a means of prioritising worker welfare.
“By automating dull, dirty and dangerous tasks, these nations have not only increased their manufacturing efficiency but have also enhanced the overall wellbeing of their workforce,” states Dr Struijk.
“They have benefitted from their close proximity to the German automotive market and used a combination of skilled labour and investment in robots to take a large share of the Tier 1 market, as well as a host of greenfield investments by major European and Asian automakers.
adopting a similar mindset; using automation to alleviate workers from monotonous and hazardous tasks, thereby improving job satisfaction and increasing overall productivity.”
manufacturing is already one of the UK’s greatest success stories. By investing in automation and robotics, UK manufacturers can help to futureproof their business and ensure we continue to compete on the international stage in the years to come.
Time for a spot of crystal ball gazing. Anders Billesø Beck, vice president of strategy and innovation at Universal Robots, presents his predictions for how automation may develop in the next 12 months.
Looking ahead, 2024 will be a significant turning point for the world of robotics and automation.
The emergence of artificial intelligence (AI) technologies, such as generative AI, has captured global attention and dominated headlines. However, the adoption of generative AI for businesses is still very much in its early stages and questions around how best to harness this technology remain at the forefront of many minds.
Digital transformation is an ongoing process so we can expect to see this year’s breakthrough trends continuing to shape society into the future. But how will these trends impact robotics and automation and what can the manufacturing industry expect to see in the next year?
Firstly, AI will set a new pace of development in robotics and automation. It is transforming the world of software development, making
For example, AI allows robots to have human-like perception, handle variation, move parts precisely, adapt to changing environments, and learn from their own experience. With time, these capabilities will lead to unprecedented flexibility, quality and reliability in manufacturing.
Robotics software is the glue that binds users to their mechanical counterparts –a digital connectivity that transcends physical interaction. Software developments are enabling a new dimension of collaboration, connecting the people that use robots. This year will see software developments leading to new levels of sharing and reusability. Imagine a world where, instead of reinventing the wheel, we leverage existing software assets – components, interfaces, algorithms – across multiple applications. It’s a principle that already underpins our UR+ partner ecosystem,
and machines and thus help manufacturers simplify complex processes and make smarter decisions.
The benefits of this digital evolution are significant. Remote access to manufacturing data enables quick responses to issues and continuous automation improvement. With dynamic systems now essential, trusted cloud technologies offer the latest in security and state-ofthe-art services.
Industrial Internet of Things (IIOT) companies highlight this progression,
promising improved efficiency and reduced downtime through Overall Equipment Effectiveness (OEE) visualisation and predictive maintenance.
Manufacturers stand to gain from these advancements, achieving higher quality, reduced downtime, better predictability, and cost optimisation. This transition is a strategic necessity, supporting the shift towards high-volume, high-mix production, resilient supply chains, competitive data utilisation, and sustainability goals.
Logistics uptake
Earlier this year, Interact
Analysis looked at projected growth rates in robot shipments across industries. The standout projected growth area was logistics, where Interact Analysis put the projected CAGR for collaborative robot (cobot) shipments at 46% for 2023-2027. I’m not surprised as the market for non-industrial applications is growing fast. Like manufacturing, many logistics companies face serious labour shortages while pressure is increasing
as a result of globalisation, e-commerce and complex multichannel supply chains.
More logistics, warehouse and distribution centres will turn to automation next year to provide
Automation systems will become more integrated thanks to data management in the cloud
services faster and with greater accuracy.
To take an example – facing the challenge of surging e-commerce demands, one logistics company we worked with revolutionised its fulfilment centre with collaborative robots, resulting in a 500% surge in efficiency and order accuracy. The automation system, adept at processing thousands of orders daily, particularly excelled during peak periods, like Black Friday, where a robot managed up to 4,400 orders in one day with just a small crew for replenishment.
Robots – and the smart use of data – are poised to revolutionise logistics businesses across the whole value chain from incoming packages to outbound logistics. The pace of development with robotics remains impressive and I look forward with great anticipation to another exciting year of progress.
n Universal Robots www.universal-robots.com
Scan here for more Universal Robots articles
TCI Cutting, a leading company in the manufacture of laser and waterjet cutting machines, industrial automation and
production management software, has launched a new compact automation system onto the market.
The Spanish based manufacturer says the system saves 60% space, compared to other standard automation solutions.
non-ferrous metals, is highly autonomous thanks to its intelligent functions allowing 24/7 productivity.
The new loading system can be paired with the Dynamicline Fiber 1530 laser cutting machine
We
We also have
This system (Automation Systems Compact Load & Unload Storage) brings together the automation of loading, unloading and storage in a compact and user-friendly configuration. This solution has been specially developed for customers with limited space in their production facilities.
The integration of this solution with TCI’s Manager Lite software facilitates data control and allows the optimisation of machine performance in real time.
TCI Cutting’s factory in Valencia, Spain is structured in ten business units and has a showroom where its laser and
waterjet cutting machines and scalable automation systems are on display, along with its production management software to optimise the benefits of the Smart Factory.
www.tcicutting.com
Scan here for more
TCI Cutting articles
The lifting and discharging modules are independent, as the load is executed from the front while the discharge movement is produced from the rear. This two-module system streamlines movements and speeds up the production process.
The automatic storage racks incorporate five trays with a load of up to 3,000kg each, with a sheet thickness of up to 12mm.
The new automation solution can be integrated into the Dynamicline Fiber 1530 laser cutting machine. This machine for flat cuts (2D) of ferrous and
4-axis machining centres
HTailor-made off the peg: Flexibly configurable 4-axis machining centres with unbeatable productivity and unparalleled resilience
5-axis machining centres
F5-axis machining centres
Productivity in 5 axes: 5-axis machining centres with the 5th axis in the workpiece for dynamic and productive machining
The benchmark in 5 axes: 5-axis machining centres with the 5th axis in the tool for high-performance 5-sided and simultaneous 5-axis machining
Flexible,
5-axis milling/turning machining centres
CPowerful complete machining: 5-axis milling/turning machining centres for combined milling and turning on one machine
Flexible manufacturing systems
Highly-productive series production of light duty to heavy duty automotive components
Finally, it is time again for the HELLER Open House 2024. We invite you to share your enthusiasm for innovative manufacturing solutions with us!
Come and visit us at our headquarters in Nürtingen in April and see for yourself how we make the hearts of machine builders beat faster: with powerful machines live in action, innovative solutions and inspiring discussions – four days focused on our passion for production.
Save the date now – we look forward to seeing you!
Highlights
first presentation: the latest generation of the F 5000 5-axis machining centre a new development concept for a rack-type tool magazine & a machining unit with tilting head kinematics
4-axis and 5-axis machining centres demonstrated live in operation wide range of automation solutions to ensure maximum availability innovations in the areas of technologies, applications, services and digitalisation insights into production with fascinating factory tours opportunities for an exchange with partners and companies of the HELLER Group
Save the date: 23 – 26 April 2024 in Nürtingen, Germany
Keep me informed Visit www.heller.biz/en/newsletter, and sign up for the newsletter to receive all updates on registration and the programme.