PIM METALS NEWS ALLUMINIUM WELDING BEARINGS 4 11 12 16 INCORPORATING IMT VOLUME 1 c ISSUE 4 c AUGUST/SEPTEMBER 2022
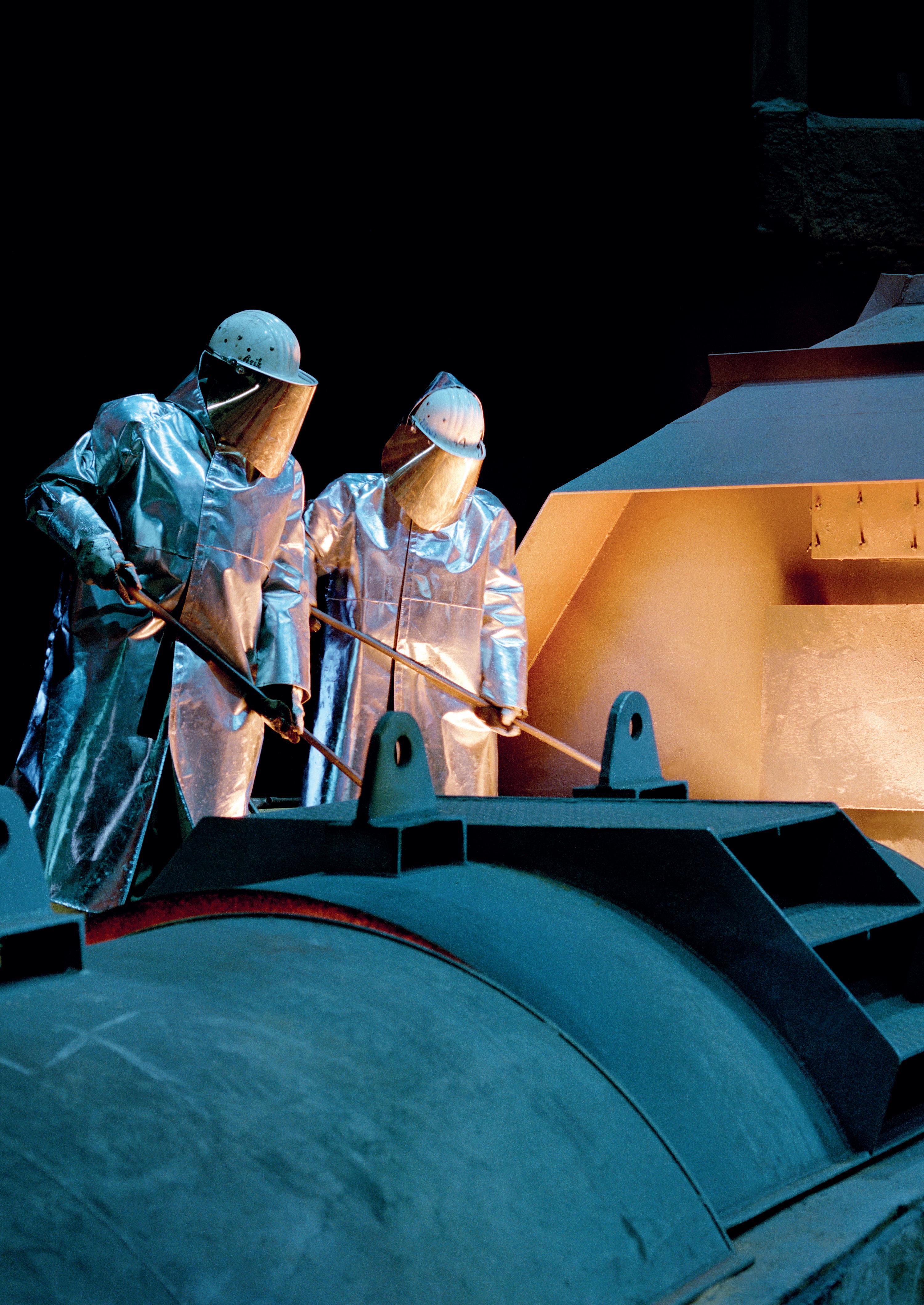

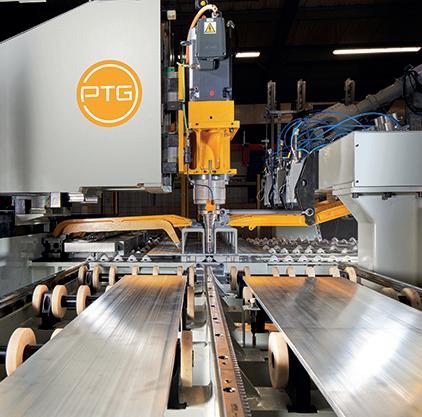
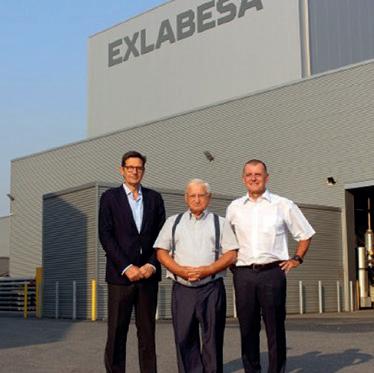
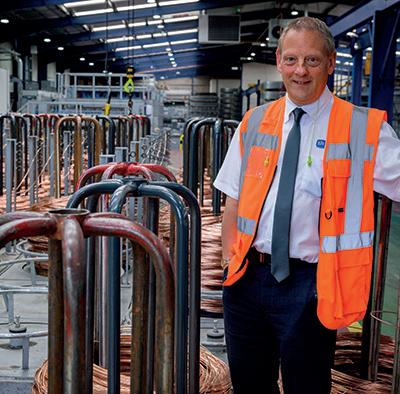
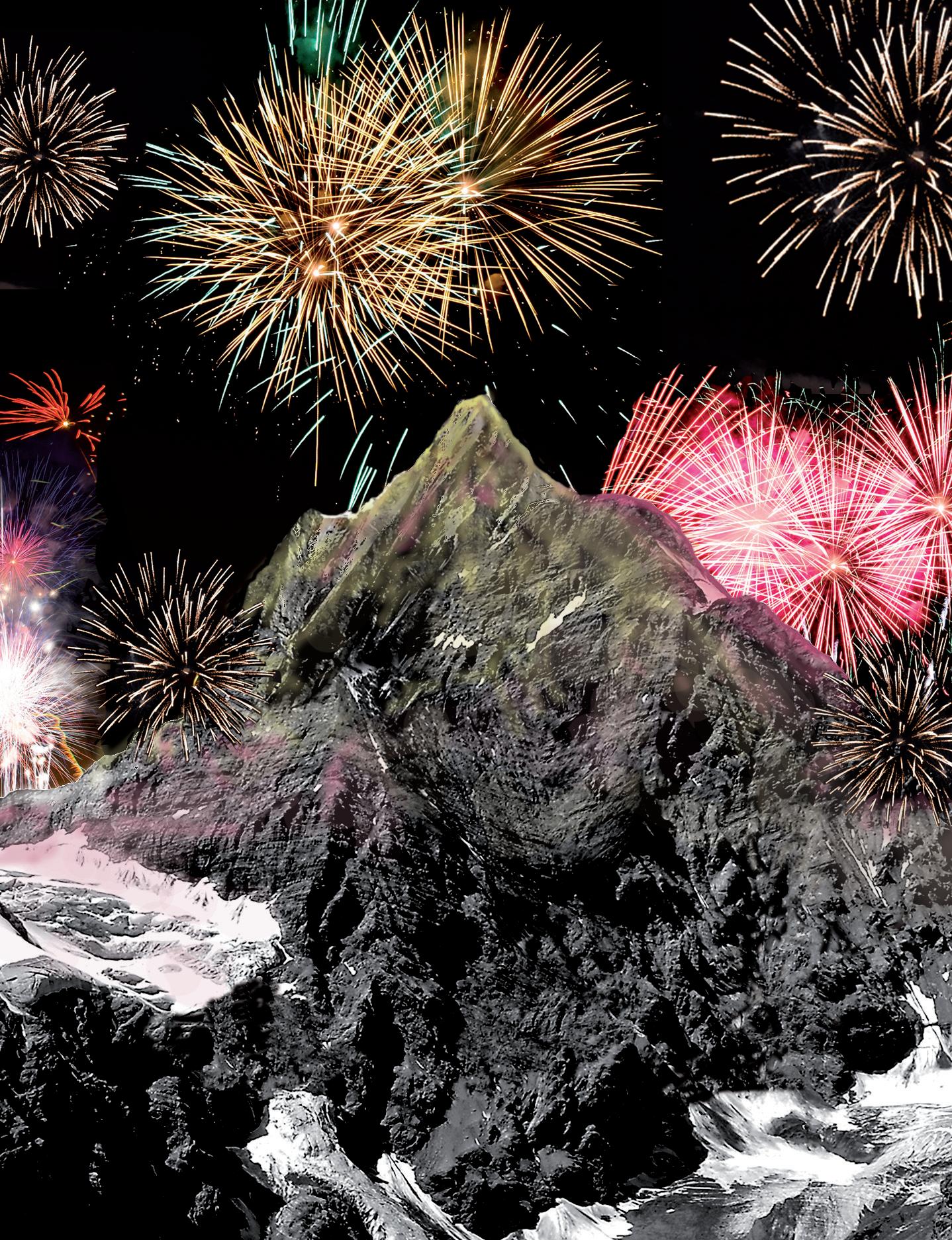
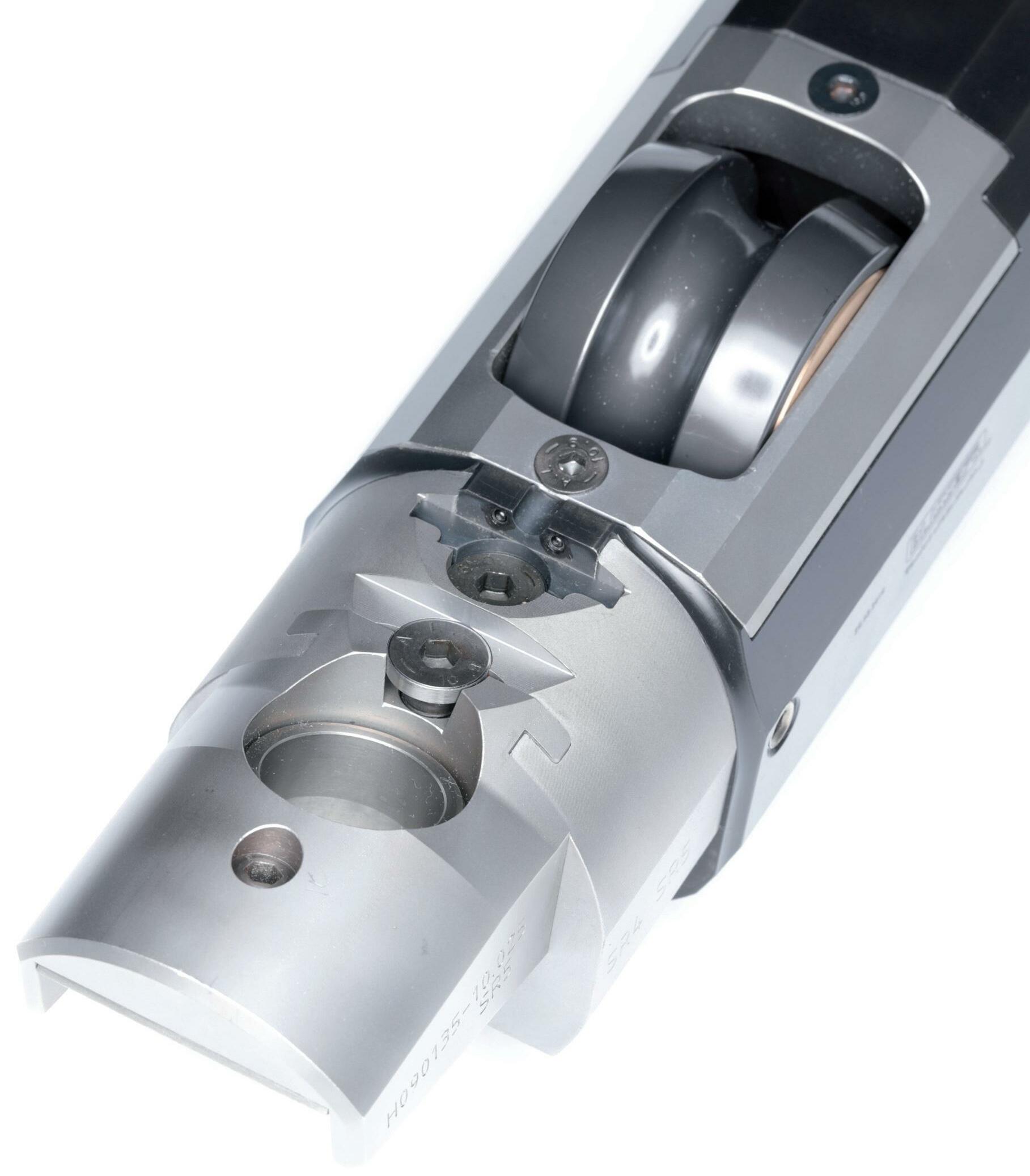
NEWS 1PIMM Metals August/September 2022 IN THIS ISSUECOMMENT PRODUCTSALLUMINIUMNEWSNEW 18 EVENTS WELDINGGAS 16 BEARINGS Metal industries look forward with excitement to regional satellites in Thailand and India When bearing relubrication is not a DIY job ~ The technological secrets of relubrication facilities 14 12 11 8 2 Boiler tube replacementpanelsystem PTG to present Powerstir dual weld-head friction stir welding at Aluminium 2022 SMS group to supply Exlabesa with one of the of Europe’s largest aluminumenergy-efficientextrusionpresses LNG as a new bearer of hope Lesjöfors expands in the US by acquiring John Evans’ Sons Tel:TN2TunbridgeBrownPRINTINGEmail:Mobile:Tel:ASTACAnthonyPRODUCTIONWiffenBusinessPublishing+44(0)146026101107851612799anton_print_1@mac.comKnightandTruscottWells,Kent,3BW,UK+44(0)1892511678PUBLISHER & EDITORIAL DIRECTOR Vince Maynard KVJ Enterprises, Tralee, Hillcrest Email:Mobile:Tel:TN8Edenbridge,Road,Kent,6JS,UK+44(0)1732505724+44(0)7747002286processindustrymatch@virginmedia.comVOLUME1,NUMBER4– AUGUST/SEPTEMBER 2022 Contact information ©2022 KVJ Enterprises Cover picture: NEWS - bp/thyssenkrupp - page 5 COMMENT/IN THIS Welcome to the August issue of PIM Metals. As the metals industry continues to rebound from the COVID slow down, many are looking the recyclability of metals and how to maximise its use in ways to remove certain plastics from industry sectors. The versatility of metal for example in the food and beverage sector has seen huge growth, this has also driven growth in equipment for coil and strip handling and associated welding technology. With PIM Metals covering all aspects of metal production and processing, we have the ability to bridge the gaps between specific industry sector media and join up the entire production and processing chain. Last month the PIM website had over 239,000 unique viewers and is also seeing growth in the number of actual reads for news items. Reads are only recorded after a visitor spends a minimum of 3 minutes on an item making the figures accurate on a daily basis.Our next issue is October 2022 and we welcome editorials/news on Sheet metal processing, Heat & surface treatment plus Bending & end forming, this news should be with us no later than October 10th with supporting print ready image/s to imtmagazine@virginmedia.com . Have a great summer Vince PublisherMaynardandEditorial Director
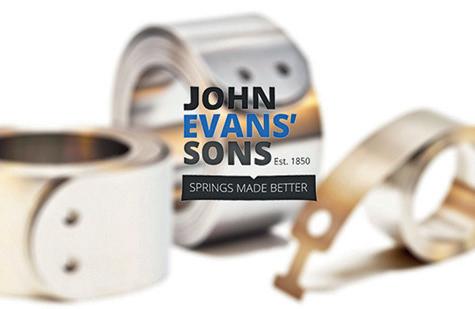
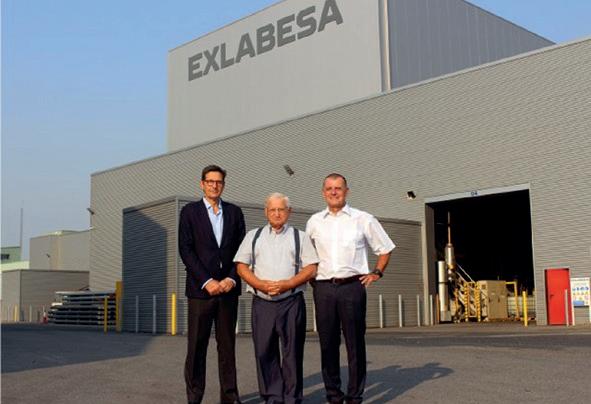


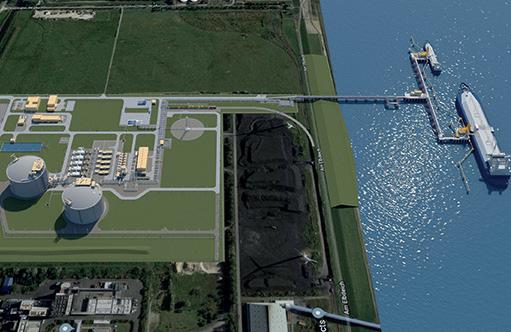
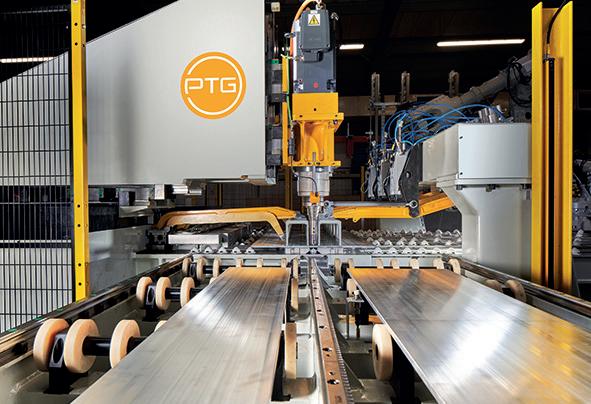

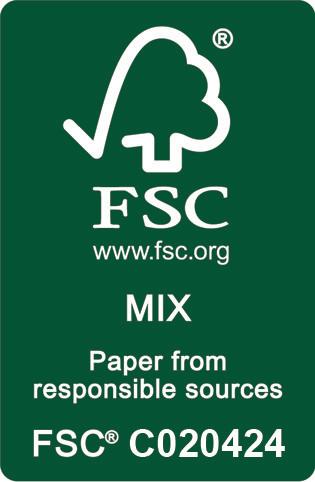
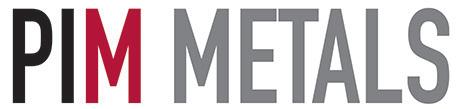
Tata returns to Wire &
NEWS 2 PIMM Metals August/September 2022
L
Steel
Tube 2022
esjöfors, part of the Beijer Alma group, has today signed an agreement to acquire the assets and operations of John Evans’ Sons INC, a leading US spring manufacturer. With the acquisition, Lesjöfors strengthens its US presence and significantly increases its sales to the medical industry, in line with its ambition to build the leading spring, wire and flat strip component group.John Evans’ Sons is the oldest spring maker in the US, founded in 1850, and has a leading position on the US market. The company has a diversified customer base with long customer relationships, attributable to its expertise and ability to support customers early on in their product development projects. Revenue mainly stems from customers within the medical industry but also from customers within the industrial, construction, aerospace and transportation industries. The production facility is located in Lansdale, Pennsylvania, and the company has 72 employees. Similar to Lesjöfors, John Evans’ Sons has close customer relationships, high technical expertise and strong emphasis on tailored solutions. Through the acquisition, Lesjöfors strengthens its position within the medical segment and builds further scale in the US. The acquisition also enables other opportunities for profitable growth, such as purchasing coordination, cross-selling, resource/ knowledge sharing with Lesjöfors’ other US companies.BeijerAlma’s CEO, Henrik Perbeck, comments on the acquisition: “I am excited about this acquisition, which following the acquisition of Plymouth in December 2021, underlines Lesjöfors’ potential and ambition to increase scale in the US and build the leading spring, wire and flat strip component group. I am convinced that John Evans’ Sons will thrive under Lesjöfors’ decentralized governance model and a great fit with Beijer Alma’s model for value-adding acquisitions.” Lesjöfors’ President, Ola Tengroth, comments on the acquisition: “Through this acquisition, we increase our market share in the US significantly by more than doubling revenue in the region. John Evans’ Sons has a long, successful, history and we are excited about what we can achieve together. In addition to a well-matched corporate culture, John Evans’ Sons will strengthen Lesjöfors in the US and enables multiple value creating avenues for Lesjöfors at the same time as John Evan’s Sons can benefit from Lesjöfors’ expertise and footprint. Thus, we are convinced that the companies will strengthen each other goingSamforward.”Daveyand Pate
Lesjöfors expands in the US by acquiring John Evans’ Sons
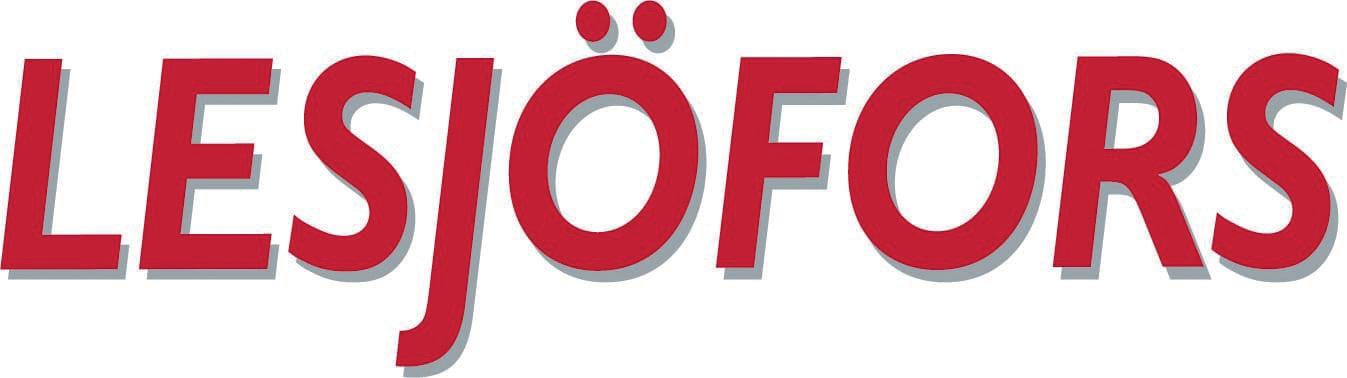
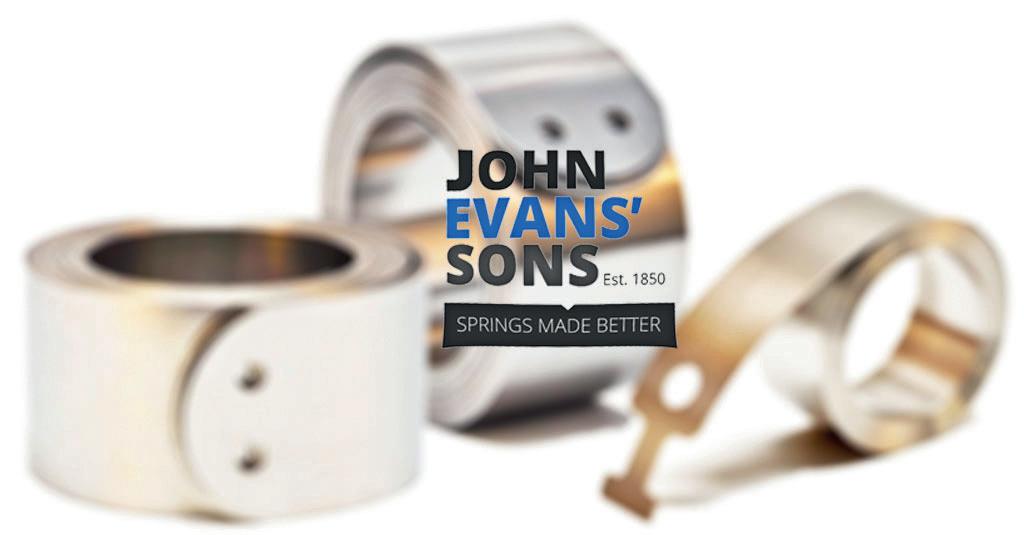
T
The Commerce Department will evaluate the association’s allegation in the coming weeks to determine whether to initiate an inquiry into the alleged behavior. The Aluminum Association has advocated for increased enforcement of global trade laws in the aluminum sector for a number of years – securing several successful AD/CVD decisions; encouraging the creation of the first-ever U.S. aluminum import monitoring system; and working with partners on multilateral solutions to address massive state subsidies in aluminum market, especially in China. To learn more, visit aluminum.org/trade.www.
aluminum sheet from China. “The U.S. aluminum industry has made a commitment to rigorously monitor and enforce unfair trade laws to ensure a level playing field for domestic producers,” said Charles Johnson, president & CEO of the Aluminum Association. “We are confident that the Commerce Department will promptly review our petition and take appropriate action to ensure that unscrupulous exporters are not circumventing U.S. law.” Since AD/CVD orders were imposed, imports of 3003 and 3105 aluminum sheet from China have declined dramatically. Recently, however, Chinese exporters and producers have been marketing and selling increasing volumes of 4017 aluminum sheet as substitutes for 3003 and 3105 alloy aluminum sheet. The heavily overlapping chemistries of alloys 4017 and 3003/3105 indicate that Chinese exporters and producers are simply seeking a “work-around” of the unfair trade orders.
Banmiller, John Evans’ Sons’ current owners and copresidents will remain in their operational roles to continue to develop the business. In line with Lesjöfors’ decentralized organisation, the company will continue to operate under its own brand and management.
John Evans’ Son’s copresidents, Sam Davey and Pate Banmiller, adds:“We are extremely thankful to our two prior family generations who successfully ran America’s Oldest Spring Maker before us, starting in 1967. Since joining the business in the late 1990’s, we have cultivated relationships with our world-class customers and been the recipients of exceptional raw materials and services from our vendors. Far and away, the biggest contribution to the company’s success has come from our talented workforce and their ongoing pursuit of technical and manufacturing excellence. Since purchasing the company in 2016, revenue has more than doubled and profits have increased exponentially. Our growth strategy has been to offer unparalleled product development support in high technology areas, especially the medical industry, while continuing to provide outstanding quality, service, delivery and price to existing customers. We are excited about our new relationship with Beijer Alma and convinced that by joining forces with Lesjöfors, there will be even more opportunities for significant growth.”
he TradeAluminumCommonAssociation’sAluminumAlloySheetEnforcement
Aluminum Association Continues to Push Enforcement of Unfair Trade Orders Group Identifies Possible of Common Alloy Sheet
NEWS 3PIMM Metals August/September 2022
Working Group and its individual members alleged in a recent filingwith the Commerce Department that Chinese exporters and producers are circumventing the unfair trade orders on CAAS from China by selling 4017 alloy aluminum sheet for applications typically reserved for 3003 and 3105 aluminum sheet. The association called on the Department to initiate a “minor alterations” inquiry to address importsorderscountervailingofantidumpingcircumventionandduty(AD/CVD)publishedin2019onofcommonalloy
Trade Enforcement Working
Circumvention

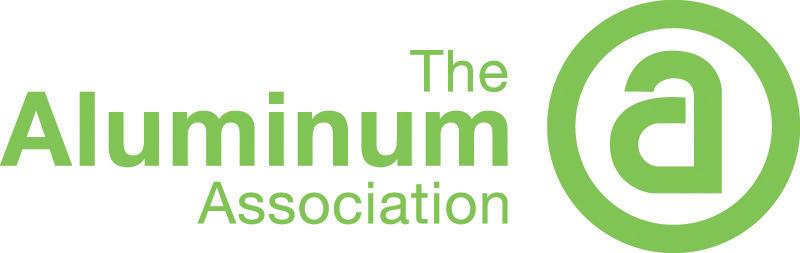
Visit us: Hall 05 / Booth J12 InlinePrecisionProfile Measurement • Full profile measurement • Surface fault detection • 3D image analysis Family owned since 1957, Zumbach is a global leader in the industry. Driven by innovation and experience. We are here for you and ready to build the future together. www.zumbach.com • sales@zumbach.ch
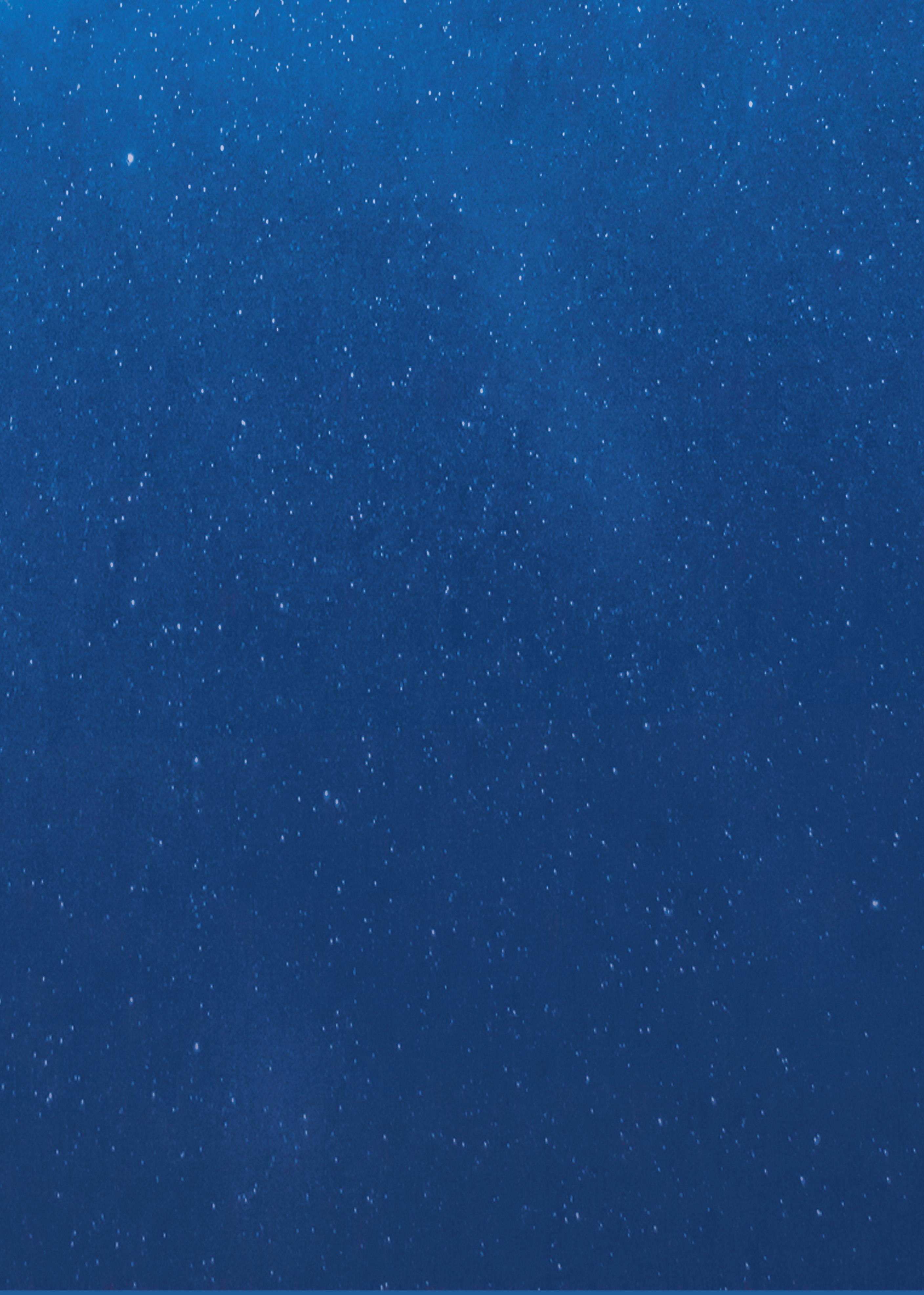

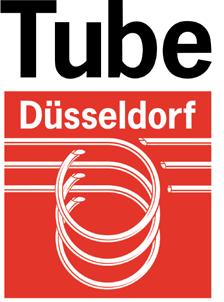
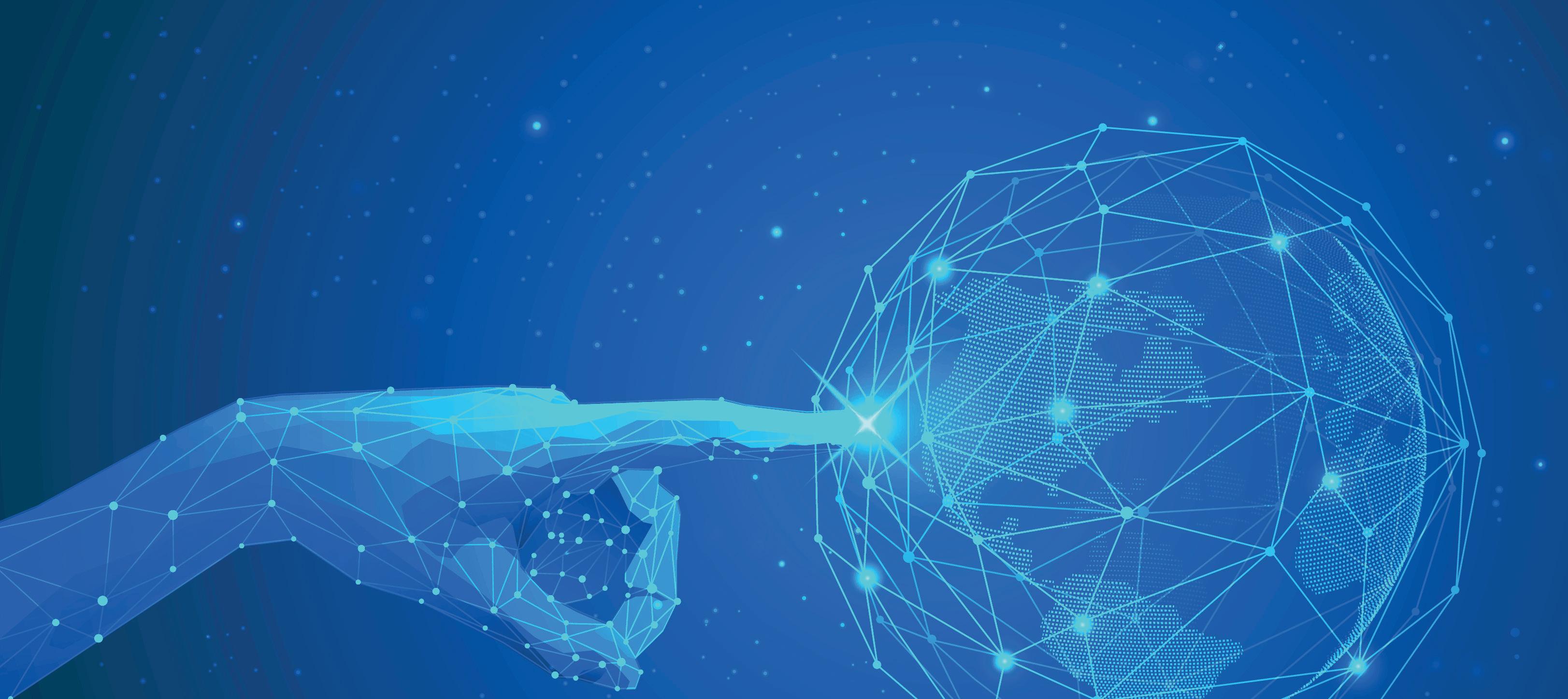
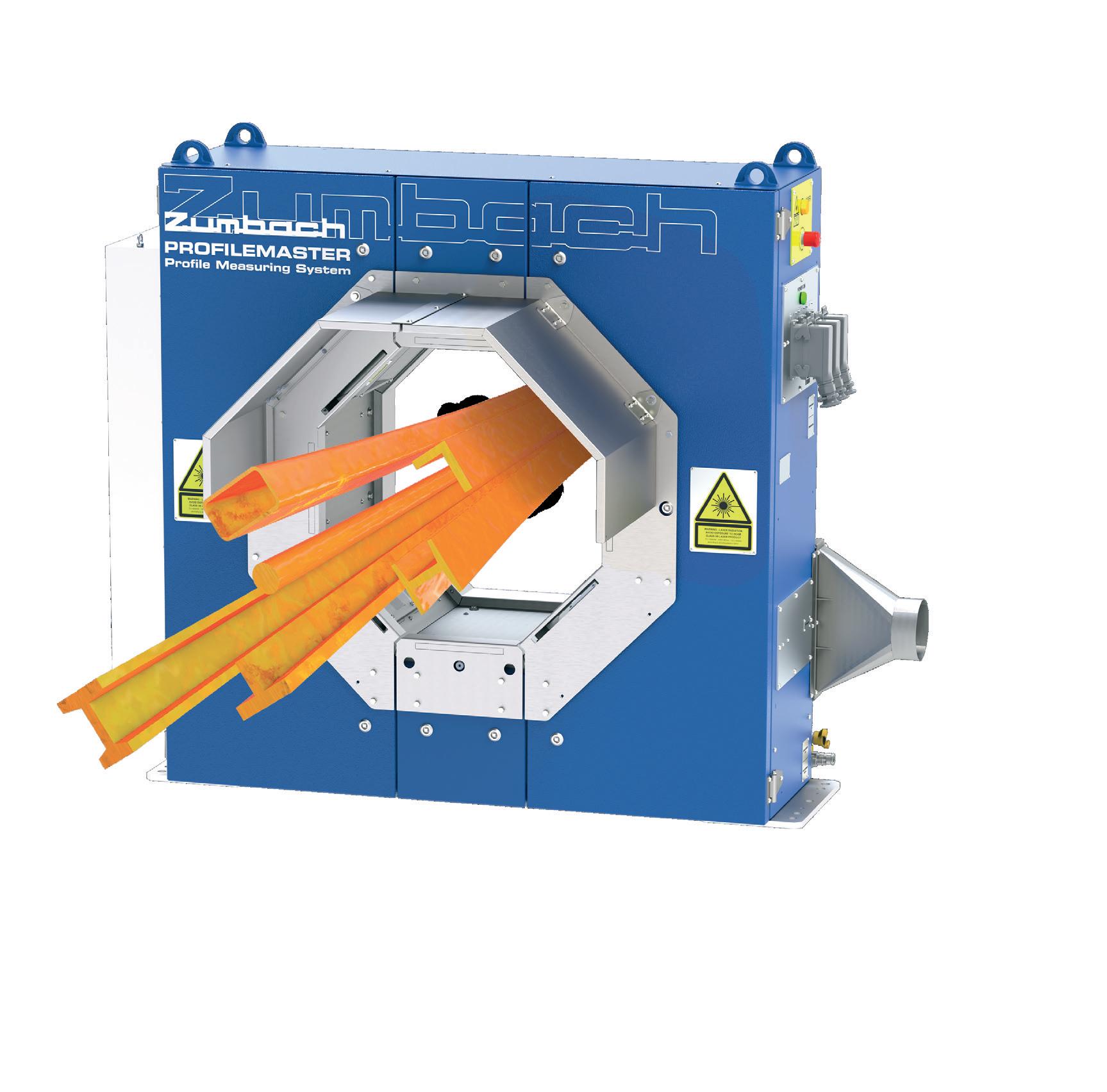
Dr. Arnd Köfler, Chief Technology Officer at thyssenkrupp Steel, added: “The decarbonisation of the steel industry will require enormous quantities of low-carbon and in the long term green hydrogen. This will increasingly require the use of electricity from renewable sources. All this can only be achieved through a well-developed hydrogen infrastructure with a supraregional pipeline network. The MoU is an important milestone for us to set the course with bp for a reliable supply of energy in theSteelfuture.”accounts for 8 to 11% of global CO2 emissions. It is essential for the automotive and construction industries and for the manufacturing of industrial machinery. It also forms the foundation for a string of powerturbines,technologies,decarbonisationincludingwindgeneratorsandsmartgrids.Thecompaniesalsointendto
NEWS 5PIMM Metals August/September 2022 b p and thyssenkrupp Steel today announced they have signed a memorandum of understanding (MoU) focused on the development of long-term supply of low carbon hydrogen and renewable power in steel production, helping accelerate the steel industry’s wider energy transition.thyssenkrupp Steel accounts for 2.5 percent of CO2 emissions in Germany, mainly at the Duisburg site where the main emitters, the blast furnaces, are operated. By replacing the coal-fired blast furnaces with direct reduction plants where iron ore is reduced with lowcarbon hydrogen, thyssenkrupp Steel intends to make steel production climate-neutral in the long term. The companies will explore supply options for both blue and green hydrogen, as well as power from wind and solar generation through the use of power purchase agreements.
William Lin, bp’s executive vice president regions, cities and solutions said: “The steel and energy industries have of course long been closely linked. We provide fuel and feedstock for steel production while our platforms, pipelines, and turbine towers are made from steel. “thyssenkrupp Steel has the ambition to make its steel production climate-neutral by 2045 and low carbon power and hydrogen will play a critical role in achieving that. As part of our strategy to provide a range of decarbonisation solutions to corporates, bp is already investing in and working to develop a portfolio of industrialscale hydrogen projects in Germany, the Netherlands, Spain, the UK and Australia. With our aligned ambitions and complementary investments, thyssenkrupp Steel and bp can together help this hard-to-abate sector decarbonise faster.”
bp and thyssenkrupp Steel work together to advance the decarbonisation of steel production
jointly advocate for policies that will support the development of low carbon hydrogen and the growth of green steel in Europe. thyssenkrupp Steel currently produces 11 million tonnes of crude steel per year and is targeting the production of 400,000 tonnes of CO2-reduced steel by 2025. bp is working to pursue green hydrogen production at its refineries in Lingen in Germany, Rotterdam in the Netherlands, and Castellon in Spain. It is developing both blue and green hydrogen production projects around the world, including in the UK and Australia.
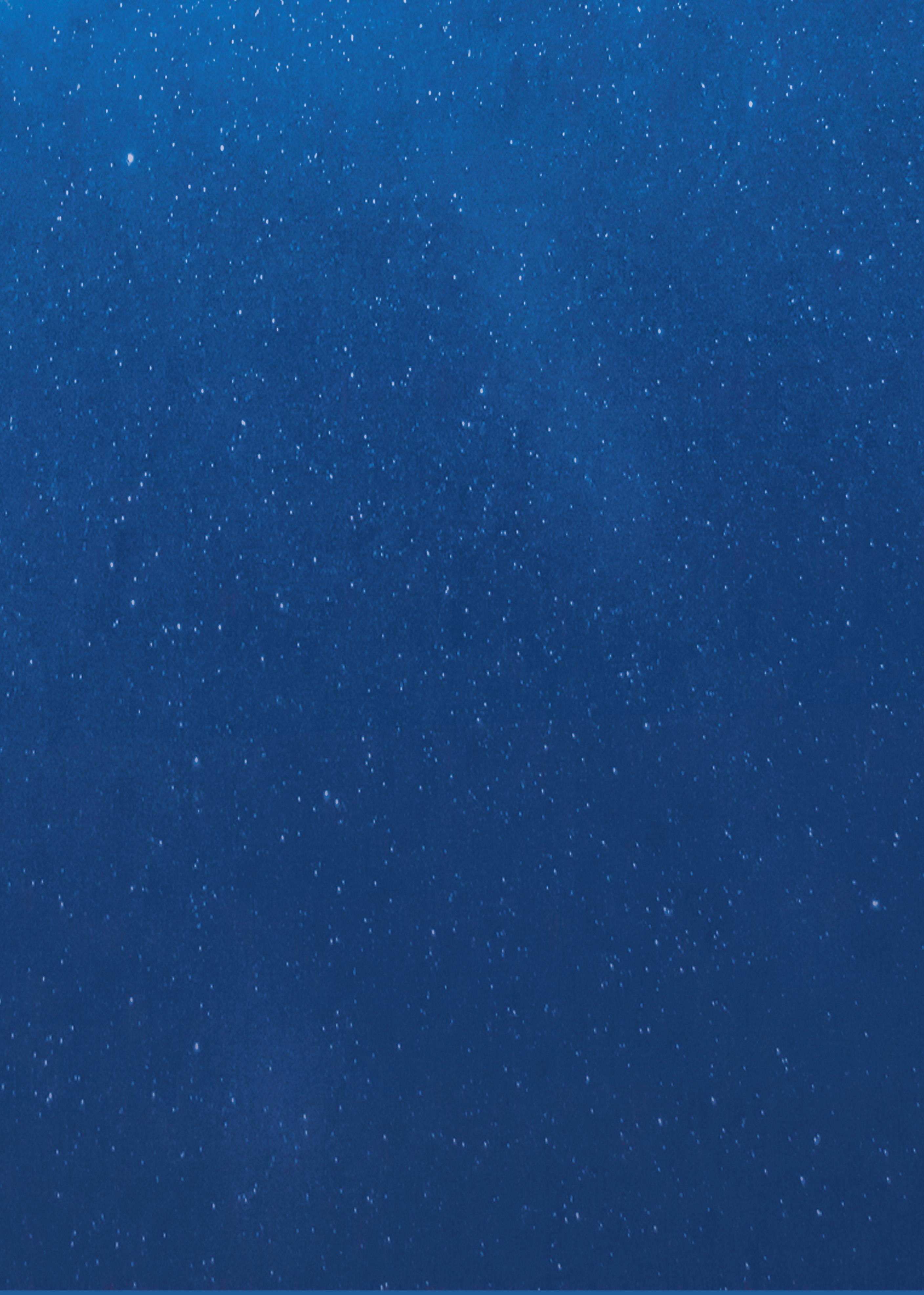


For the year ending March 2022, the company recorded a step change in operating efficiency, whilst scrap reduced by over 7% which helped to drive pre-tax profits to £4.6m, despite its operations and raw material supply chain being adversely impacted by Covidrelated staff absences and HGV driverThurleyshortages.continues:
Siddall and Hilton Products achieves ‘Best Companies’ accolade along with another year of solid growth
“It’s fantastic to see the business going from strength to strength and, since the 2019 MBO, we have been committed to ensuring that we share the company’s success with our loyal team. 2021/22 has been no different with every employee receiving a significant profitrelated bonus. We felt that this was not only well-deserved, but was also important to help with the cost-of-living crisis faced by our “Westaff.are as proud of the cultural change we have driven as we are of Siddall and Hilton’s performance improvement –the company is unrecognisable from the one I joined as a temporary finance manager back in 2012. Not only do we regularly receive positive feedback from our team, we’re also seeing colleagues coming together as one focused team with a common objective. They are determined to do better tomorrow than they did today, there’s a new appetite for learning and development and a palpable, excited buzz around the place as we begin to share and deliver our strategic plans for the business in the form of major investment in site refurbishment and redevelopment, robotics and machinery, along with training and developing our people to become the best that they can be.”Thurley concludes: “The company is about to embark on a hugely ambitious strategic programme to grow and diversify the business, with the aim of creating a high-performing, sustainable business that is set to provide secure and rewarding employment for many generations to come.” Processing over 22,000 miles of wire a month, Siddall and Hilton Products is the UK’s largest manufacturer of industrial welded steel mesh for high-security fencing, general fencing and industrial mesh panels. With a heritage stretching back 127 years, the company is continuing to grow its workforce with the recruitment and training of new mesh operators as well as a range of development programmes to upskill its team. For further press information, please contact: Susan Reid on (01423) 56 99 99 or susan@appealpr.com
NEWS 6 PIMM Metals August/September 2022 S iddall and Hilton Products, goodasprestigiousbeenexecutivejourney,”alongensuringempoweringculturalimprovements,inwithundergoneyearsoutstandingtopersonalaswhichCompaniesitengagementinitiativeforisCompanies’recognisedtooktopreviouslythetheYorkshirethe10wasofclassaccreditationtooftime,manufacturer,meshweldedBrighouse-basedthesteelproductshas,forthefirstbeenrecognisedasonetheUK’s‘BestCompanies’work,achievingonestarforthe‘world-employeeengagement’its60-strongworkforce.Itrankedamongstthetopmanufacturingcompanies,top50companiesinthe&Humberregionandtop75smallcompaniesinUK.Thecompany,whichhadbeengivena‘onewatch’rating,onceagainpartinthenationallyandrespected‘BestschemewhichastandardofexcellenceUKbusinesses.TheassessesworkplaceandmeasuresagainsttherigorousBestIndexscore,coversfactorssuchleadership,wellbeingandgrowth,inordercelebrateandshowcaseemployers.“SincetheMBOthreeago,thebusinesshasatransformationsignificantinvestmentequipmentandprocessalongwithchangeaimedatourteamandthattheycomewithusonourgrowthexplainschiefIanThurley.“Tohaverecognisedbysuchanationalschemeacompanywhichis‘verytoworkfor’isareal achievement, showing that we have been able to create a highly engaged and committed team.”After putting in a resilient performance amid the pandemic disruption of 2020/21, Siddall and Hilton Products also returned a strong financial performance for the year ending 31 March 2022, achieving a turnover of £25.3m, although this was, in part, a reflection of the sharp increase in global steel prices following the pandemic and then accelerated by the war in Ukraine.Having made its largest investment in more than 12 years with the addition of a fifth specialist welding machine as well as recruiting a number of new mesh operators, the company saw overall operating efficiency drop slightly in the first half of the year as operators were trained on the new machine and early teething problems were ironed out, but this showed significant improvement over the final six months.
Chief executive of Siddall and Hilton Products Ian Thurley
More success at Siddall
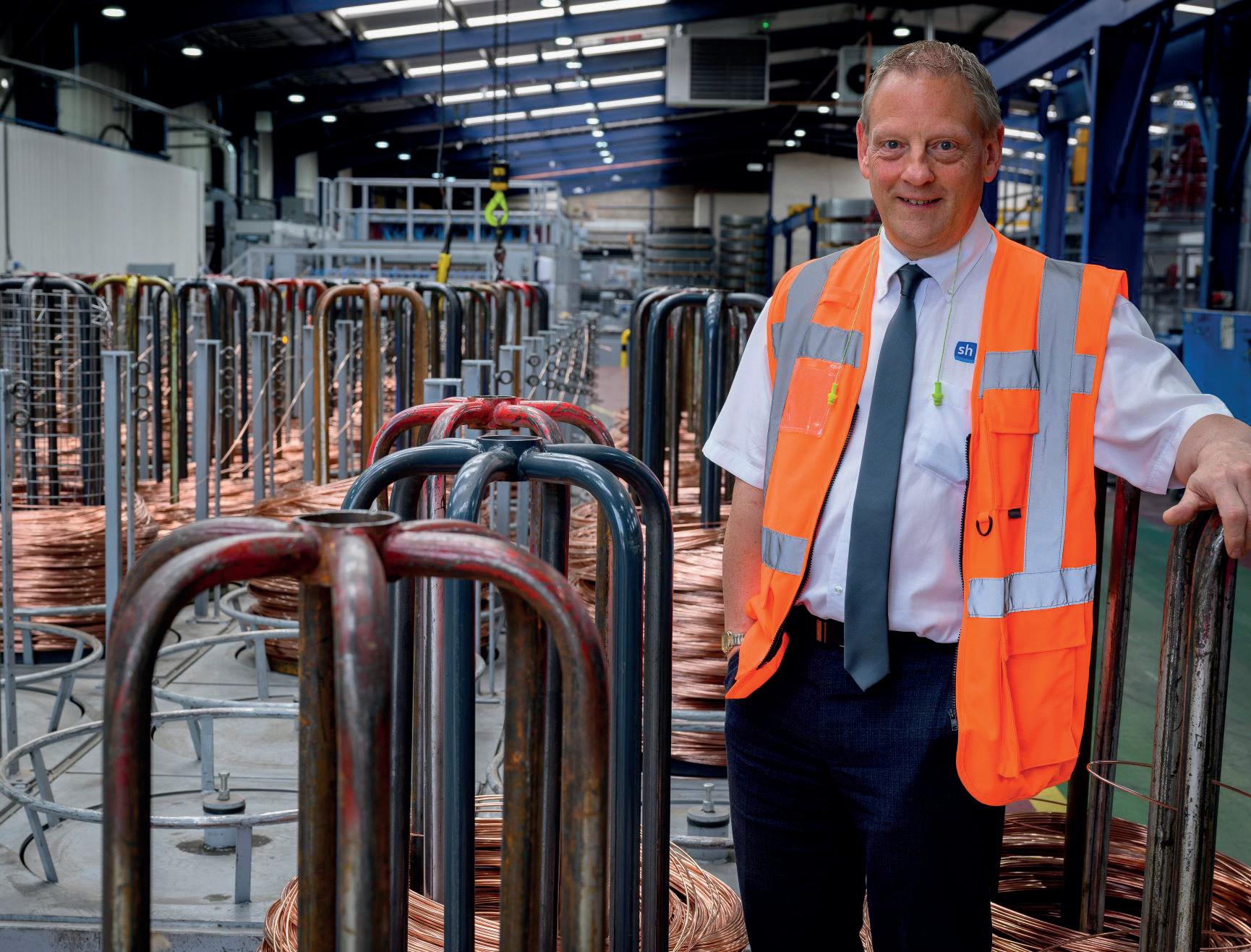
SMS group to supply environmentally-friendly technology for the production of steel bars to Megasider Zaragoza in Spain
includes a walking beam furnace equipped with the latest reheating technology for ecofriendly operation. Specifically, the furnace, based on a capacity of 120 tons per hour, will include SMS Prometheus® Level 2 control – ensuring uniform temperature distribution and low oxidation and carbon enrichment of the steel – as well as the SMS DigiMod combustion management system and SMS ZeroFlame HY2 burners. These extra-low-NOx flameless burners are capable of operating with both natural gas and a blend of natural gas and hydrogen in any ratio, making this furnace hydrogen-ready. The combination of the SMS ZeroFlame HY2 burners, the DigiMod combustion management system, and SMS Prometheus® control will lower NOx emissions to 45 ppm, reduce scale formation to 0.4 percent, and cut fuel consumption to 27 Nm3 per ton.
M
The scope of supply also includes a multi-strand straightening machine with automatic bar positioning and feeding device featuring automatic roll changing system, a cold saw to be used with either abrasive or metallic disks, and a RAM (rotatingarms automatic) magnetic stacker with four independently operating four-meter sections. The high-precision profile gauge with surface defect detection capability, supplied by TBK, a company of SMS group, will allow Megasider to perform contactless precision measurements for optimal bar production processes. The whole plant will be controlled by the X-Pact® automation system, SMS group’s level 1 and level 2 solution. This holistic approach aims to integrate the company’s many years of experience in automation into the rolling process, with the goal of maximising the plant’s performance. At the same time, it also enables the immediate implementation of digital solutions based on harmonized data“Weprocessing.areproud that Megasider is relying on the future-oriented technology of SMS and will obtain a plant that sets standards in the BarLuigiproductionenvironmentally-friendlyofsteelbars,”saysBarbante,VicePresident&WireRodMills,SMSgroup.
NEWS 7PIMM Metals August/September 2022
Megasider Zaragoza - 3D view of the hydrogen-ready ZeroFlame HY2 burner from SMS group
GmbHgroupSMS GmbHgroupSMS
egasider Zaragoza S.A.U., part of the 2016,GroupMegasasincehasplaced an order with SMS group for a merchant bar mill equipped with environmentally-friendly heating technology. The new plant will replace the existing rolling mill, which was delivered by SMS in 2005 and is strategically located in the northeast of the Iberian Peninsula near Zaragoza, Spain, with excellent connections to major industrial areas in Spain and France. The facility will be designed to produce a wide range of merchant bar products to complement and expand the existing product portfolio. SMS supports Megasider in its goal of achieving natural gasfree production and digitalizing the plant. As a systems supplier, SMS will provide an overall concept for operating the flexible burners with a digital control system. This will enable the plant to be operated in a environmentally-friendlyparticularlyway.SMS’scopeofsupply
Megasider Zaragoza - Reference picture of a similar rolling mill from SMS group
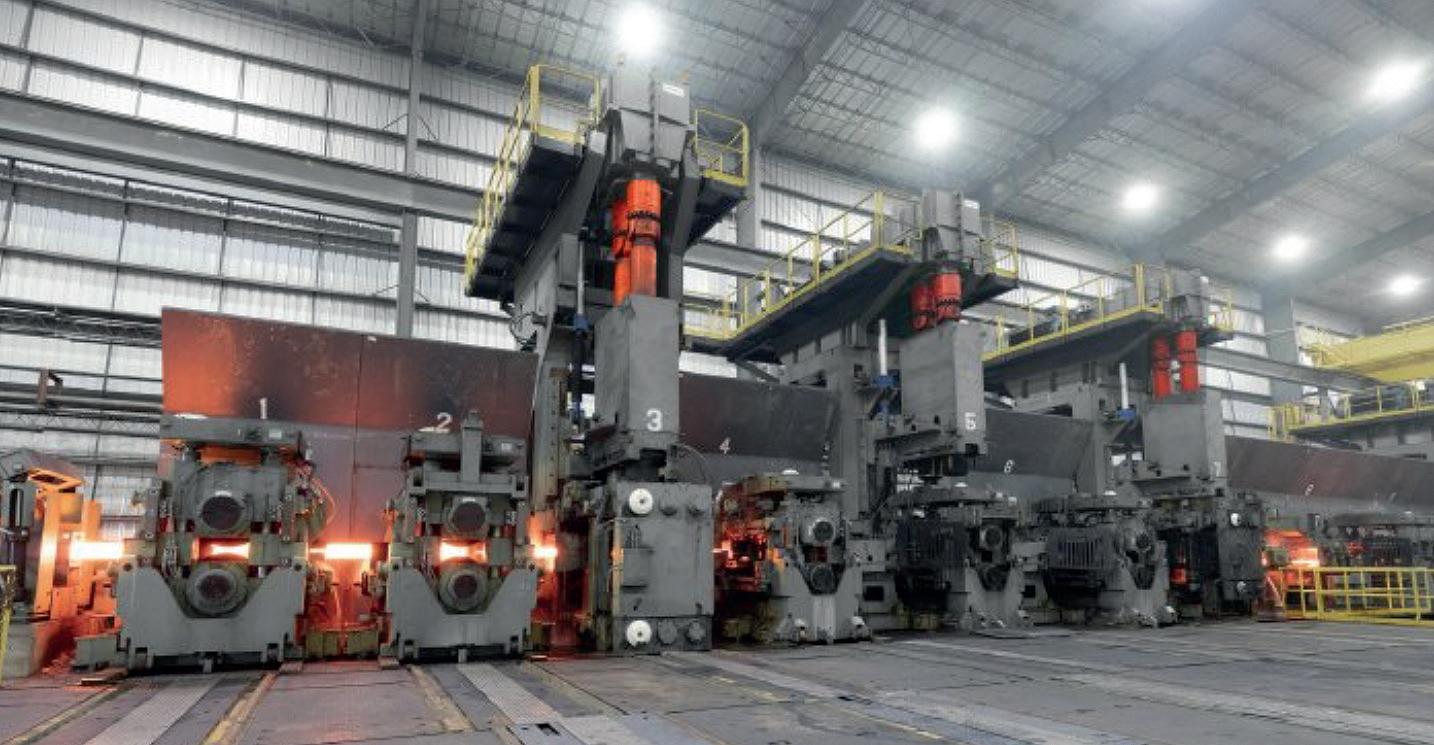
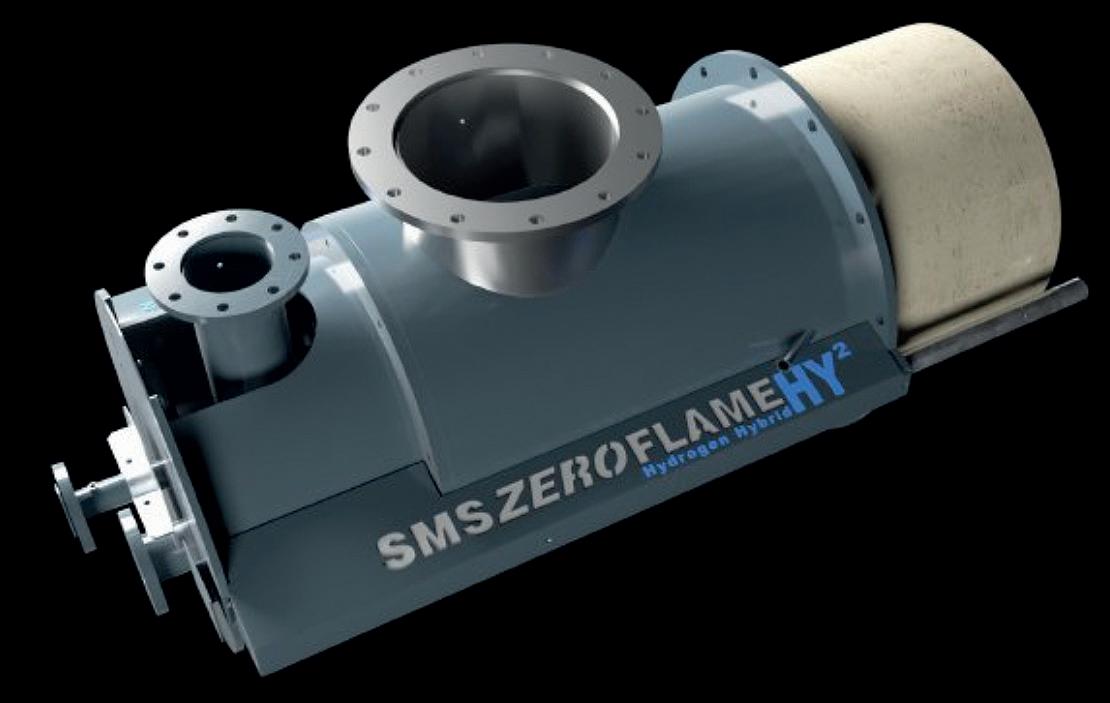
New LNG records are foreseeable According to ICIS LNG edge, Global LNG Hub, European imports of liquefied natural gas reached a record monthly level of at least 8.1 million tonnes as early as January 2022. There are a total of 37 LNG terminals in Europe, 26 of which are in the EU. Throughout Europe, there is a regasification capacity of around 243.6 billion cubic metres per year. After the war in Ukraine started, another 20 LNG projects are now being pushed forward – new records in LNG imports are foreseeable. Two import terminals for liquefied natural gas are planned for Germany, for instance. According to the Federal Ministry for Economic Affairs and Climate Protection, they could cover up to 20 percent of the annual gas consumption in Germany. The terminals and corresponding production facilities shall to contribute to security of supply – but require high investments, which also flow into crucial components such as fittings and drives. High requirements for fittings Herose, for example, has long focused on the emerging LNG sector – and, according to the company’s findings, it is gaining in importance. However, liquefied petroleum gas fittings must meet stringent requirements
LNG has been delivering gas for years and is currently experiencing a strong boom, since the conflict with Russia leads to a greater diversification of energy in the western industrialised countries. Liquefied petroleum gas will play a key role as a new bearer of hope – and fittings will play a leading role.
GAS
BEARINGS 8 PIMM Metals August/September 2022
LNG as a new bearer of hope
onunprovoked2022.February“Russia’sattackUkraineisabove
Anew era began in all a humanitarian disaster, but it has also triggered a major energy supply and security crisis,” said Keisuke Sadamori, Director for Energy Markets and Security at the International Energy Agency (IEA). The fear of a gas shortage is spreading in the industrialized countries, and LNG is supposed to alleviate it.
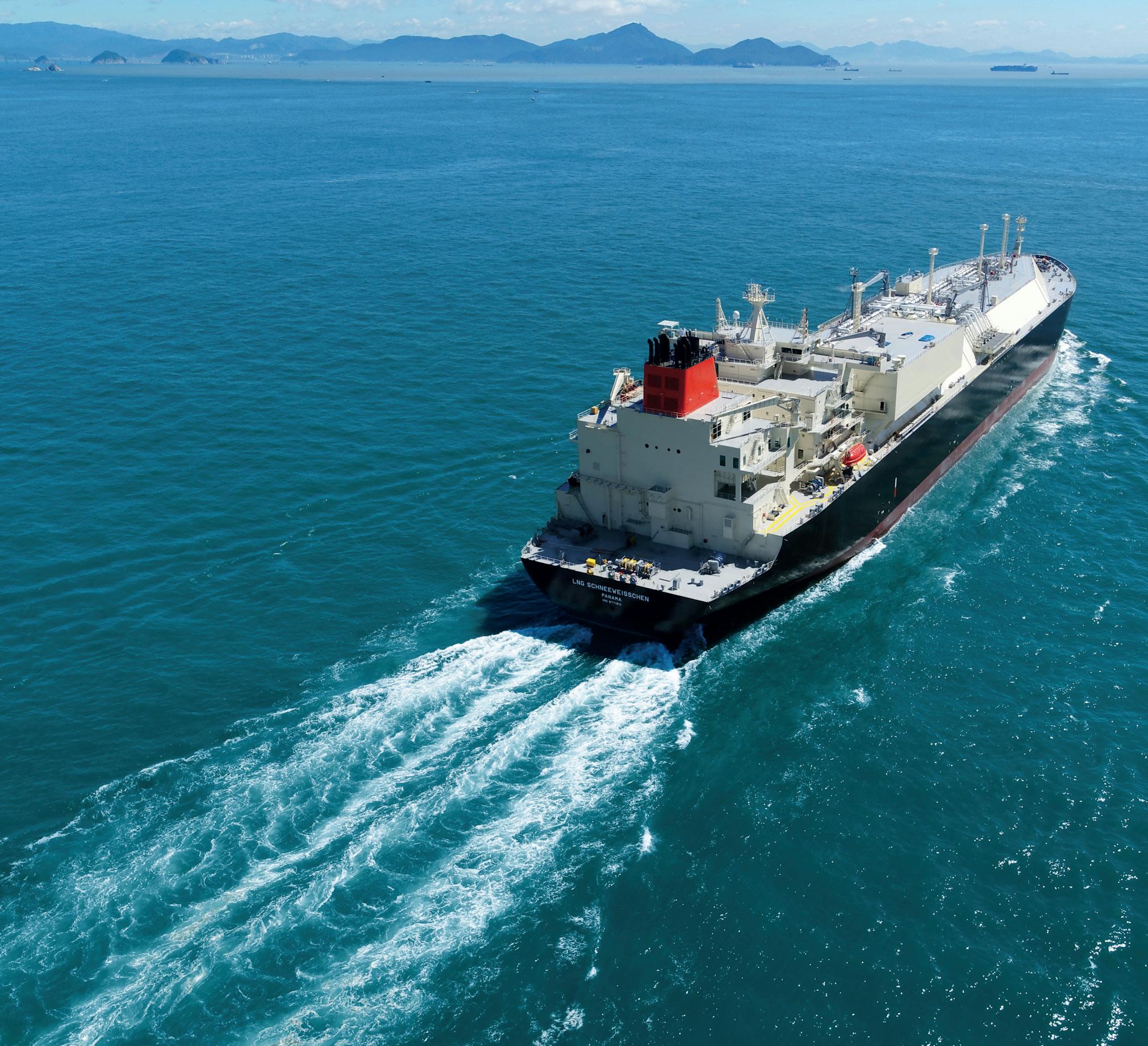
“Our valves meet the explosion protection guidelines and are ATEX certified,” the company explains.LNGwould also be more readily available as an alternative fuel for shipping, lorries and rail. Ultimately, this pathway is “a transitional technology, but also an enabler, for example, for the application of synthetic LNG,” says Herose. This is because a terminal can also be used as a transfer point or storage location for synthetic natural gas, such as power-to-gas.
The conditions at LNG are challenging. This is because the natural gas becomes liquid at a temperature of approx. -162°C. In addition, high safety requirements are imposed – when the LNG evaporates, an explosive gas is produced.
Source: Uniper SE GAS
offensiveInvestmentpays off Essential for LNG systems are safety valves, which, for example, are produced by LESER. The company emphasizes the crucial importance of these valves since with LNG, natural gas is cooled to -162 degrees Celsius and liquefied. However, overpressures arise due to heating and need safeguarding. “Across the entire supply chain, there are different requirements for overpressure safeguarding, which must be covered by suitable safety valve designs – for example, compact
BEARINGS 9PIMM Metals August/September 2022 in order for companies to be successful. “Transport vehicles for cryogenic liquefied natural gas are exposed to the greatest loads due to frequent filling, transport and unloading at the destination,” explains Herose. In addition, service life and work performance as well as safety and reliability are central to the LNG storage. Powerful fittings would also be required for refuelling with LNG. Emerson also has an eye on the LNG market. The company provides automation and control solutions for gas production, liquefaction plants, transport, regasification terminals and pipelines and wants to “contribute to more energy efficiency, reduced emissions, a higher production and use of renewable energies and cleaner fuels”, emphasizes Emerson Automation Solutions. The company develops automated valves for cryogenic use. From a technical point of view, production and transport operations generally require precise controls of pressure and temperature, high system reliability, and systems that minimize process variability and losses. “Emerson is helping LNG producers achieve more efficient operations through the application of digitalization, advanced process control strategies, and plant performance solutions,” the company explains. Explosion protection and certification The fittings of the müller co-ax ag are used, for example, in ship propulsion and in the reliquefaction on LNG tankers.
The planned terminal in Brunsbüttel (Germany) will be built for the import and redistribution of LNG. It will have two LNG tanks with a capacity of 165,000 m³ each and an LNG regasification plant. Under today’s conditions, it is realistic to expect completion in 2026.
“The existing infrastructure could store and distribute significant amounts of wind energy via the natural gas detour. A fossil energy source becomes climate-neutral”, the company says. Carbon in methane would be extracted from the environment during the synthesis of hydrogen. “No more CO is released into the atmosphere from fossil reservoirs. Natural gas lines and storage tanks are already there, no new high-voltage lines are necessary.”
Photo: German LNG Terminal GmbH 3 ‘Snow White’ LNG vessel chartered by Uniper. The LNG business is one of Uniper's strategic growth areas. Uniper is now building Germany's first LNG terminal – the aim is to diversify natural gas sources.
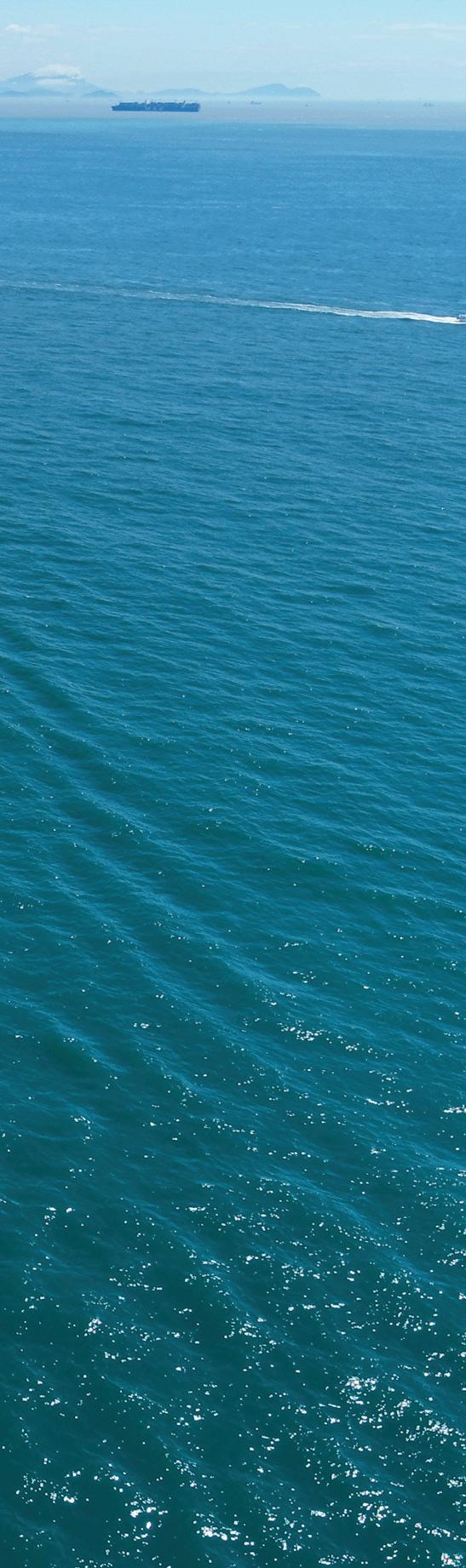

10 PIMM Metals August/September 2022 threaded valves or technologically challenging pilot-controlled safety valves,” explains LESER. It is necessary to address the needs and requirements of the individual process steps of the LNG industry and, if necessary, to further develop products. Safety, control and shut-off valves in the valve industry are therefore urgently needed for the booming LNG. The European market is broadly based here –far from any dependency. And with its quality products, it is ready for the massive investment offensive in the energy sector and in particular in LNG plants. A development that will pay off for the valve companies. From 29 November to 1 December 2022, the key players of the industrial valves sector will present themselves at VALVE WORLD EXPO with an accompanying conference in Düsseldorf. Experts from all over the world will use the Düsseldorf Fairgrounds as an international fittings summit to present their innovations and discuss current research and production processes. Press contact: VALVE WORLD EXPO 2022: Petra Hartmann Bresgen MA Ulrike Osahon Tel.: +49 (0)211/4560-541/-992 Fax: +49 (0)211/4560-87 541 E-Mail: duesseldorf.deHartmannP@messeNauticor in Brunsbüttel refuelling the Scheldt River with LNG ships – the experts from Nauticor, an LNG provider for ships, use a process that has already been successfully used several times during refuelling. In this process a ship is refuelled in parallel from two LNG tankers and the refuelling process is thus considerably accelerated. © Brunsbüttel Ports GmbH
GAS
BEARINGS
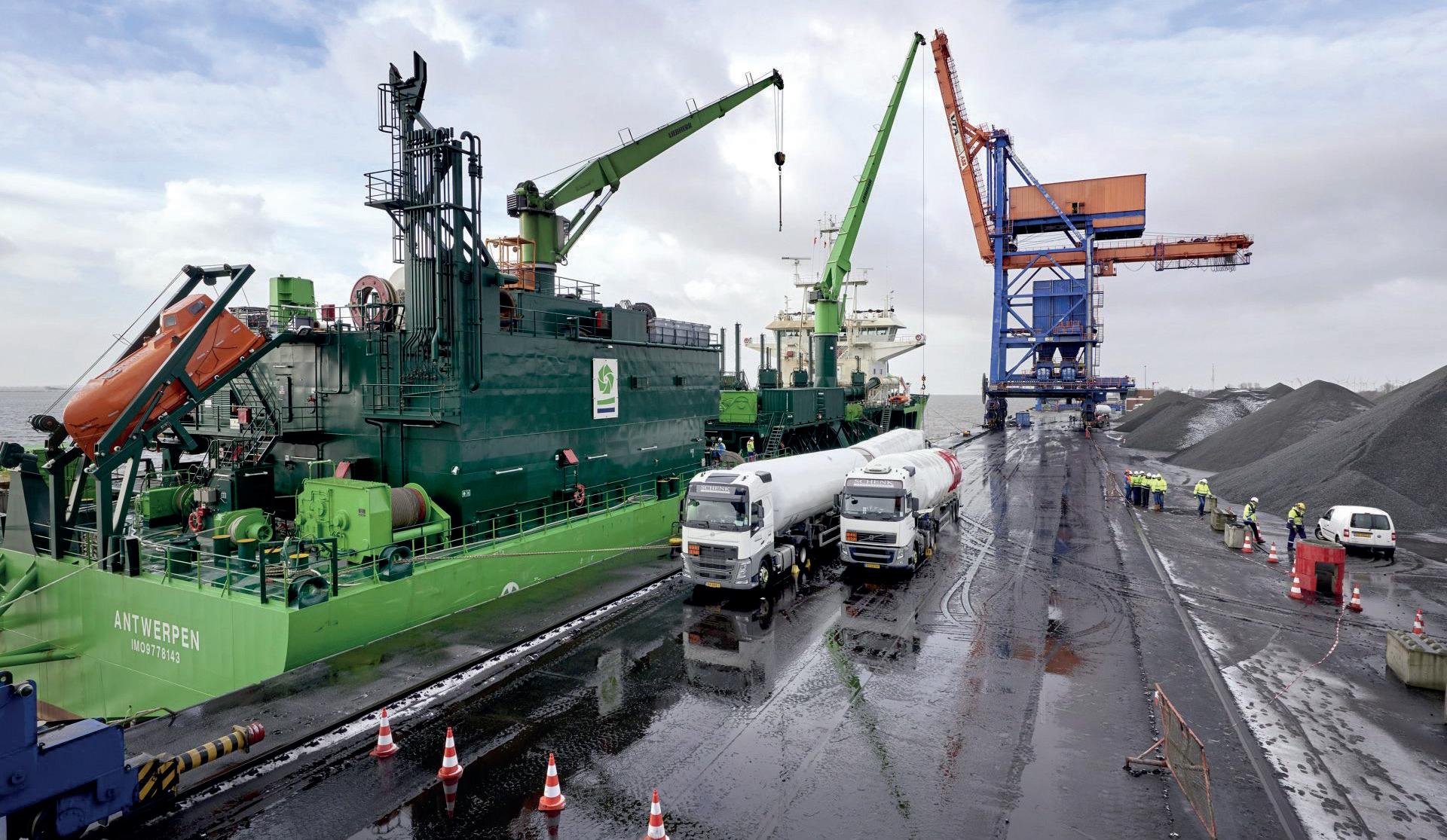
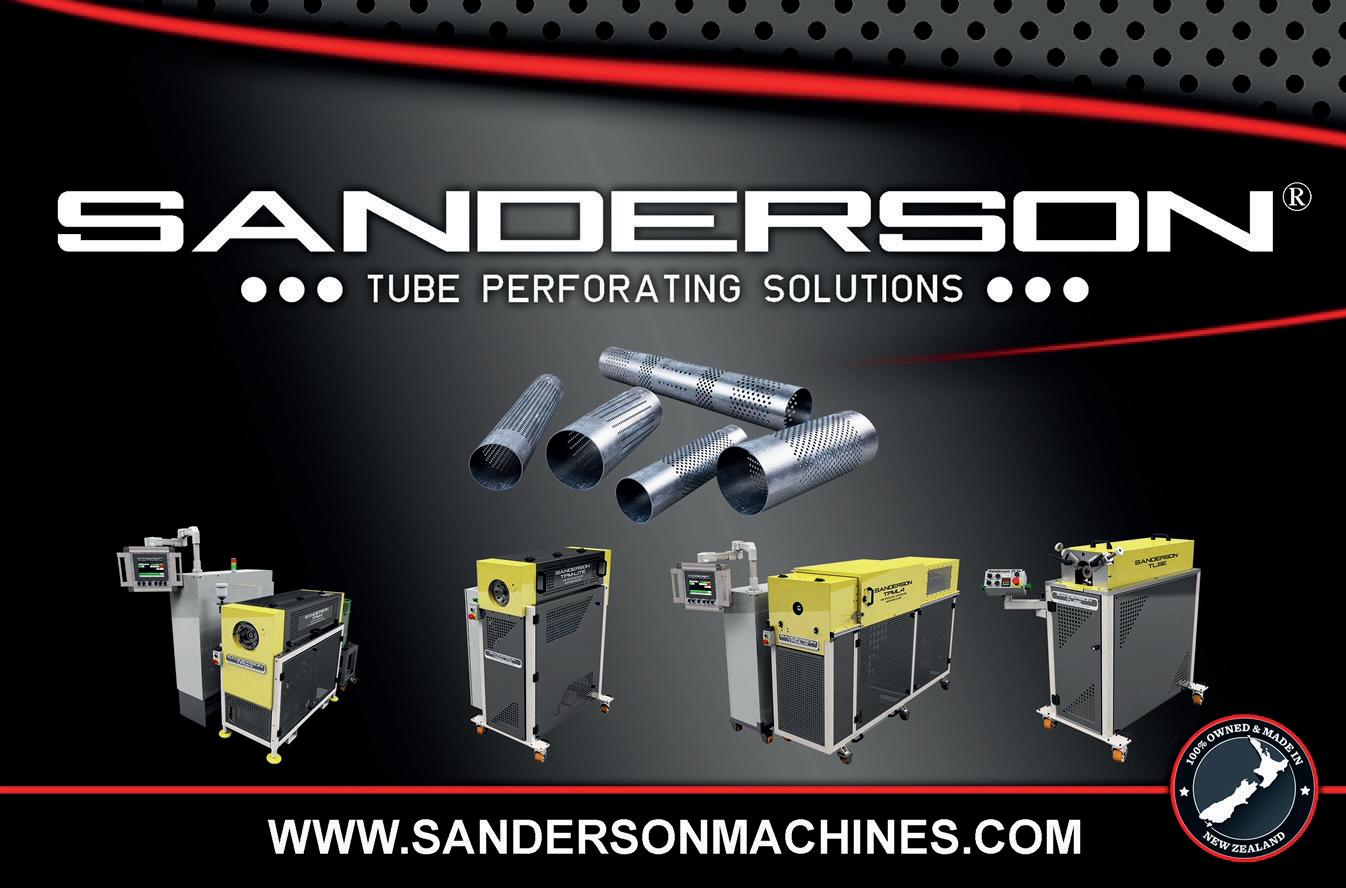
SMS group to supply Exlabesa with one of the largest energy-efficient aluminum extrusion presses in Europe
xlabesa, extrudedincompanymultinationalaspecializingtheproductionofaluminum profiles, has awarded a contract to SMS group for the supply of a 71 MN short-stroke extrusion press of front loader design. With this new acquisition, Exlabesa plans to operate 27 extrusion lines including five state-of-theart SMS extrusion presses at its nine production facilities. The new press will be installed at the company’s Padron site in Spain and will be the largest press in the Iberian Peninsula. The plant is scheduled to go on stream at the beginning of 2024.
“Lighter and, at the same time, safe structural designs, low fuel consumption, and reduced emissions for sustainable mobility are today’s drivers for using high-strength aluminum profiles. With our new, large extrusion press, we intend to double our production output for large profiles and secure the availability of the plant. Furthermore, we will be able to offer new profile cross-sections and widths that were not possible before and strengthen our position as market leader in the European aluminum industry,” says Francisco Quintá, founder of Exlabesa. The new extrusion press will be used mainly for the production of profiles for the growing electromobility market. What’s more, the company also plans to produce extruded profiles, up to 620 millimeters wide, for truck superstructures as well as profiles intended for railway carriage manufacturing. Not only that, the new investment will allow Exlabesa Building Systems division to produce unique architectural solutions, enabling them to target the most demanding bespoke façade projects. Billets with a diameter of 16 inches (406 millimeters) and a maximum length of 1,800 millimeters that are manufactured in-house will also be utilized. Exlabesa produces the aluminum billets required for this in its own recycling plant, using equipment supplied by Hertwich Engineering, an SMS groupThecompany.front-loader press will be built based on the latest SMS group design. The control concept for the new extrusion press is identical to that implemented in equipment already supplied. Thanks to the EcoDraulic concept, a reduction in energy consumption of up to ten percent can be achieved.
Exlabesa plans to manufacture wide aluminum profiles on its new 71 MN extrusion press, to be supplied by SMS group, at the Padron site in Spain from the beginning of 2024. From left to right: Jose Boogen, SMS group representative in Spain, Francisco Quintá, founder of Exlabesa Group, Hans-Uwe Rode, Sales Extrusion Presses, SMS group
The system, with its intelligent, demand-oriented start/stop control function, switches off all hydraulic pumps that are not required during the extrusion process.“Weare proud to support Exlabesa on their expansion course. Through the consistent use of optimized plant technology and the expansion of its portfolio to include Spain’s largest extrusion press, Exlabesa is growing into one of Europe’s leading extrusion press plants,” says Hans-Uwe Rode, Sales Extrusion Presses, SMS group, enthusiastically. Visit SMS group at ALUMINIUM 2022 in Düsseldorf from September 27 to 29 in hall 5, booth A34.
E
ALLUMINIUM
Larger aluminum profiles for tomorrow’s mobility
NEWS 11PIMM Metals August/September 2022

WELDING 12 PIMM Metals August/September 2022
Visitors to Stand 5L07 will be able to discover firsthand how, since their launch a little over two years ago, PTG’s dual weld-head FSW machines have become a favoured choice among electric vehicle OEMs. Designed specifically for use in the volume production of automotive battery tray floor assemblies from extruded aluminium panels, the company’s dual weld-head process is aimed directly at manufacturers of skateboard chassis structures and ensures that a tight weldflatness tolerance is achieved during battery tray floor construction.PTGhasbeen a leading name in the manufacture of friction stir welding machine tools for transport applications for more than 20 years – ever since its first Powerstir FSW machine was launched in 1998 and subsequently won the 2000 Metalworking Production ‘Outright Winner’ and ‘Grand Prix’ awards. More recently, however, PTG has used its considerable knowledge of the FSW process to assist automotive OEMs in producing lightweight, robust and aesthetic components for both battery electric vehicles (BEV) and plug-in hybrid electric vehicles“Since(PHEV).ourPowerstir dual weld-head FSW machines were introduced in 2020, they have achieved double-digit sales –quite an accomplishment during such a challenging trading period for manufacturing industry, and testimony to the quality of the technology,” comments PTG sales director, Mark Curran. “At Aluminium 2022, we look forward to showing the advantages of our dual weldhead approach to OEMs looking to benefit from advanced FSW processes.”
PTG to present Powerstir dual weld-head friction stir welding at Aluminium 2022 UK-based Precision Technologies Group (PTG) will be showcasing its range of Powerstir dual weld-head friction stir welding (FSW) machines at Aluminium 2022.

WELDING 13PIMM Metals August/September 2022
Ensuring a tight weldflatness tolerance A tight weld-flatness tolerance, as provided by PTG Powerstir dual weld-head machines, is essential to ensure that each EV battery cell sits perfectly level within its housing. The PTG dual weld-head method achieves an even and stable welding process – something that is made possible thanks to PTG’s unique ‘matched’ dual-force control systems and balanced upper and lower head welding parameters. The result is exceptionally stable friction stir welding by both the upper and lower weld heads, producing matched weld seams with balanced heat input. This, in turn, minimises post-weld distortion and equips each welded assembly with a significantly improved flatness tolerance when compared to existing conventional single-side FSW
PTG is widely considered to be a leader in the development of FSW technologies for transport Organisationsapplications.involved in the manufacture of aerospace components and the production of aluminium carriage panels for high-speed trains were among the first to recognise the benefits of Powerstir friction stir welding. Working with 5000 and 6000 Series aluminium alloys, and magnesium alloys from 3 mm to 6 mm in thickness, PTG is currently developing new FSW processes for several automotive OEMs. Through the use of industry standard CNC systems, equipped with PTG Powerstirsoftware, data-logging and interpolation technologies, 2D welding - guided by laser tracking - can be carried out on precise tool paths, with force control ensuring consistent welded seams. QR codes are used to identify each extrusion before welding commences. Each completed panel is then DMC coded to identify the panel, for complete and ongoing traceability throughout the manufacturing cycle. Coolant units and body panels In addition to building Powerstir machines specifically for the production of battery tray floor assemblies, PTG is also creating FSW techniques for the production of coolant units, control box panels and car body panels, as well as body panels and components for commercial vehicles. Through its recently opened friction stir welding research centre, the company is also assisting a number of organisations in developing FSW processes for specific manufacturing challenges.
“Ourmethods.dualweld-head FSW techniques, whereby both sides of an extrusion are welded simultaneously, not only remove the time-consuming process of lifting and turning extrusions between welds, but also allow for equal heat dispersion which results in minimal distortion,” comments Mark Curran. “In the PTG Powerstir dual weldhead FSW process, typically four to 12 individual child-part extrusions are brought together for assembly. Following gantry loading, each extrusion is automatically positioned and clamped ready for friction stir welding, after which the partially completed vehicle component is automatically repositioned, ready for the next panel to be welded in place.”
Gain edge.cuttingthe•2D,3Dandtubefibrelasercutting machines from Europe • Accessible high power and high performance – up to 20kW • American-made nLIGHT fibre lasers, with adaptive beam optimisation • Advanced Lantek CAD/CAM nesting software • Only from Ingenium Integration in the UK and Ireland Contact us now to discuss your needs: +44 (0) 1723 582 868 I sales@ingeniumintegration.com ingeniumintegration.com

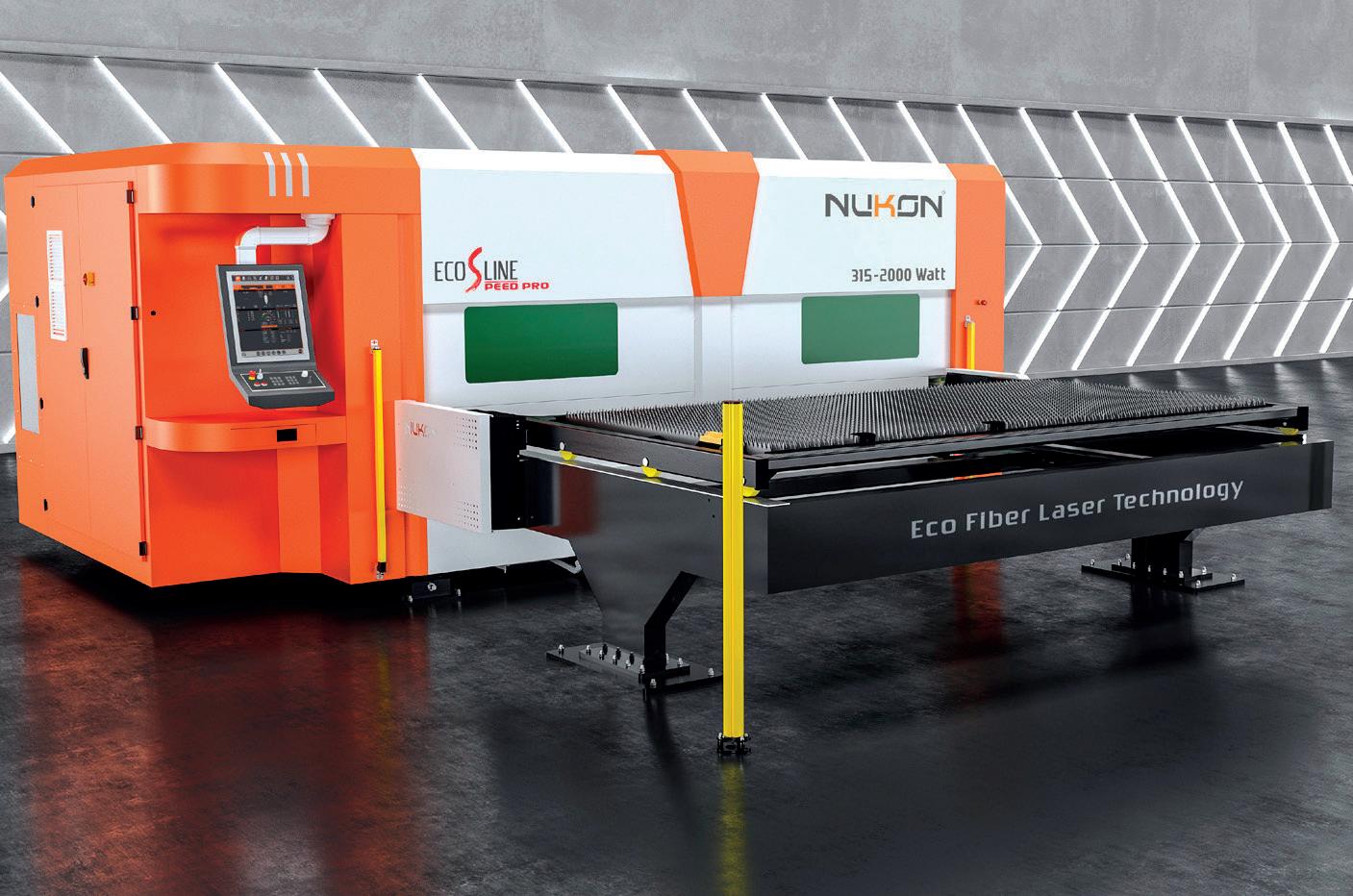
Kennametal has introduced its latest ceramic turning grade, KYHK15B™, designed to deliver increased productivity and lower cost per edge in hard turning operations. The new grade provides greater depth of cut capabilities than PcBN inserts when machining hardened steel, high- temperature alloys, and cast iron, as well as maximum tool life and wear resistance for the most demanding turning applications.“KYHK15B provides excellent edge stability, high chipping resistance, and a PVD gold coating makes wear progression identification very easy. From smooth and varying depths of cut to heavy depths of cut, KYHK15B can be an economic alternative to PcBN inserts,” says Robert Keilmann, Product Manager,KYHK15BKennametal.buildson an existing line of high-performance ceramic turning grades, providing manufacturers a productive solution for hard turning applications even in varying or heavy depths of cut.
Higher wear resistance and longer tool life in hard turning applications up to 58 HRC with Kennametal’s KYHK15B™ grade. New ceramic grade delivers highest productivity when machining hardened steels, hightemperature alloys, and cast irons.
Offers fast, accurate cutting and membrane removal
Higher wear resistance and longer tool life
NEW PRODUCTS 14 PIMM Metals August/September 2022
Boiler tube panel replacement system
Asaw and track system that rapidly cuts through water wall boiler tube up to 102 mm O.D. to produce highly accurate and straight cuts with no HAZ (heat affect zone) has been introduced by Esco Tool of Holliston, MA, USA. The MILLHOG® Boiler Tube Panel Replacement System features the APS-438 Saw and the EscoTrackTM System that easily attaches to a panel using weld tabs. Capable of cutting 102 mm O.D. tubes horizontally perfectly straight with 1.5 mm accuracy and no HAZ, the saw can then be fit with a vertical track attachment for equally fast and accurate boiler tube membraneEquippedremoval.witha2237 Watt
pneumatic motor that runs on 6.2 Bar air and only 80 cfm, the APS-438 Saw uses proprietary reinforced fiberglass abrasive saw blades for quick cutting and long life. Fully supported by the steel track, the saw glides smoothly and the MILLHOG® Boiler Tube Panel Replacement System eliminates the need for tube rework and grinding before beveling.TheMILLHOG® Boiler Tube Panel Replacement System is priced from (USD) $6,295.00 and is available for rent. Pricing is available upon request. For more information contact: ESCO Tool, a Unit of Esco Technologies, Inc. Matthew Brennan E: escotool.commatt@escotool.comwww.
A broad range of styles, sizes, and edge preparations are available. Depending on the surface requirement and the type of cut, the ceramic grade KYHK15B can be an economic alternative to PcBN inserts when machining hard materials >48 HRC

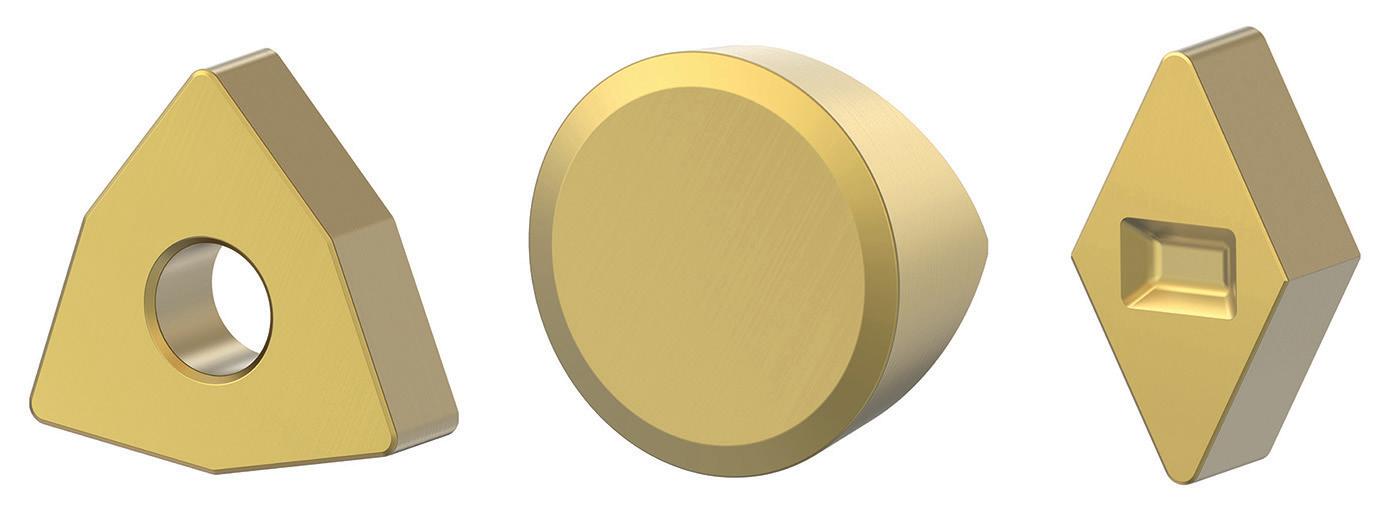
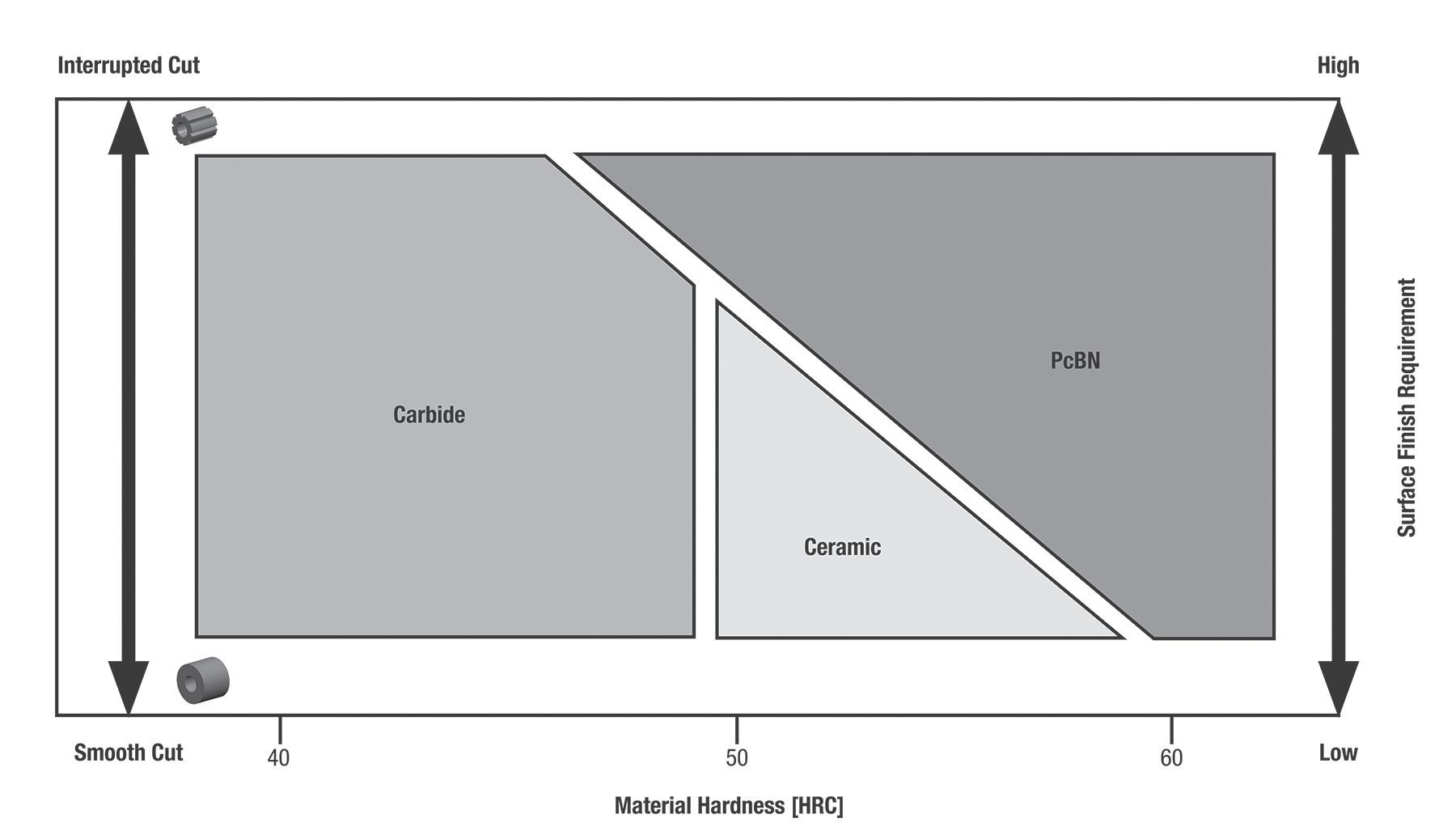
The new range offers a lift capacity of 10 to 18 tonnes with a variety of lift masts and attachments and can operate at speeds of up to 25kph, making them suitable for most heavy applications.Theyhave become an even more attractive option for UK users since the government’s decision to roll back the longstanding rebate on red diesel for all but a few sectors from April 2022. The estimated cost increase is around 47p per litre. For businesses who have come to rely on this historic subsidy, this poses a difficult question. Do they continue to use their existing fleet and take the hit of the increased cost of diesel – or pay a premium to switch over to EVs? Until recently, EVs have not been suited to some heavier applications. Many vehicles are also needed for longer shifts where there is not always time for ‘opportunity charging’ of their lithium-ion batteries.
New electric range from Linde
Manu Patel, heavy trucks specialist at Linde Materials Handling, says: “The new Linde range addresses a lot of historic concerns around EV for heavy applications.“Userswill also benefit from lower levels of noise and no exhaust emissions. For businesses who have been used to diesel vehicles, going electric can have the bonus of dramatically improving the working environment.”
Leading ofunveiledproviderhandlingmaterialssolutionsLindehasanewrangeelectricheavytrucks in response to the rising cost of diesel fuel and new restrictions on the use of red diesel in the UK.
Linde Materials Handling launches new electric 10 to 18-tonne forklift range as the answer to higher diesel costs
Linde’s new E100 – E180 electric heavy forklift trucks are available with lithium-ion or lead acid batteries. That extra flexibility means that customers pay only for the technology they need, reducing the cost of moving to an electric fleet.
NEW PRODUCTS 15PIMM Metals August/September 2022
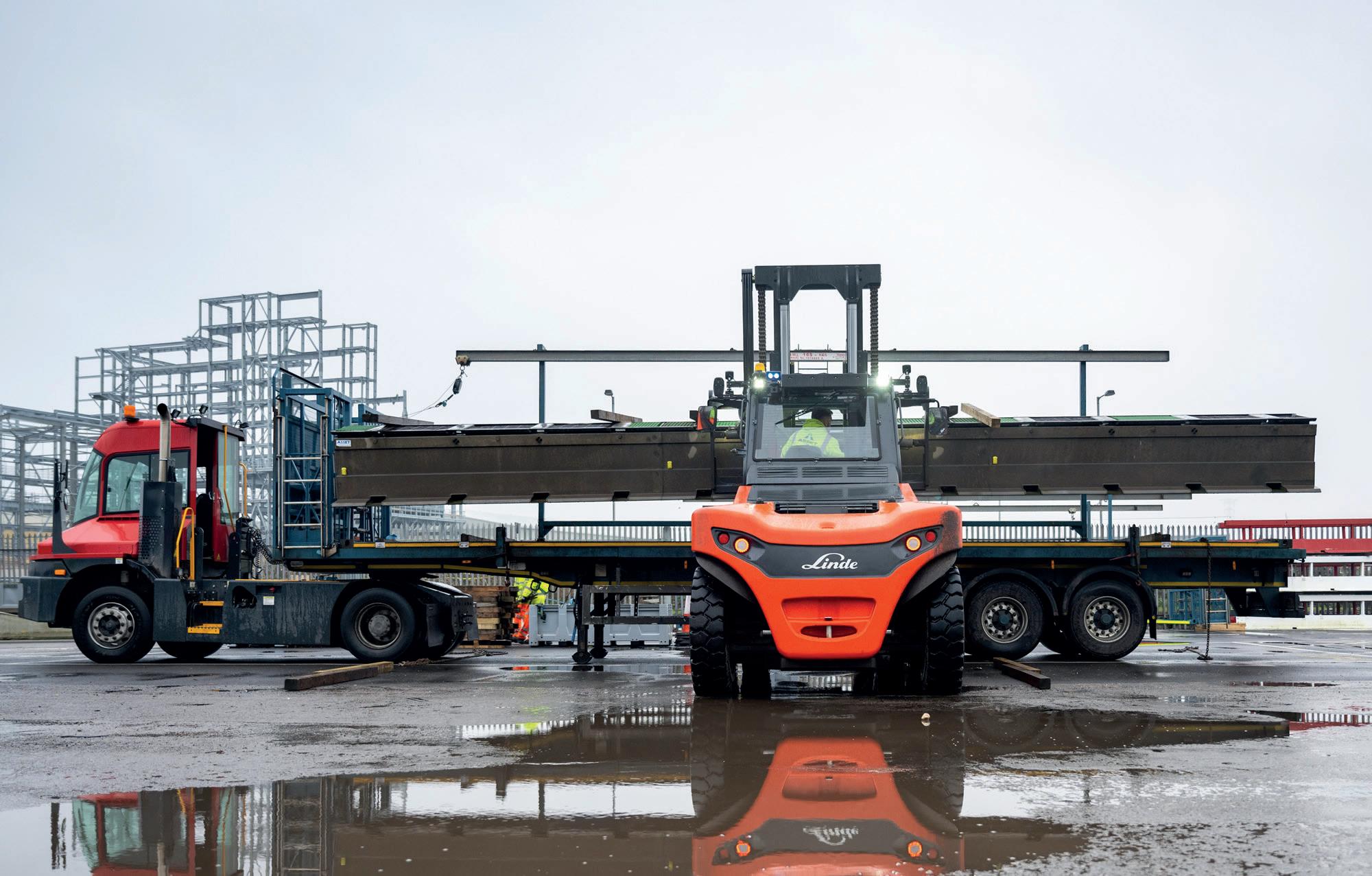

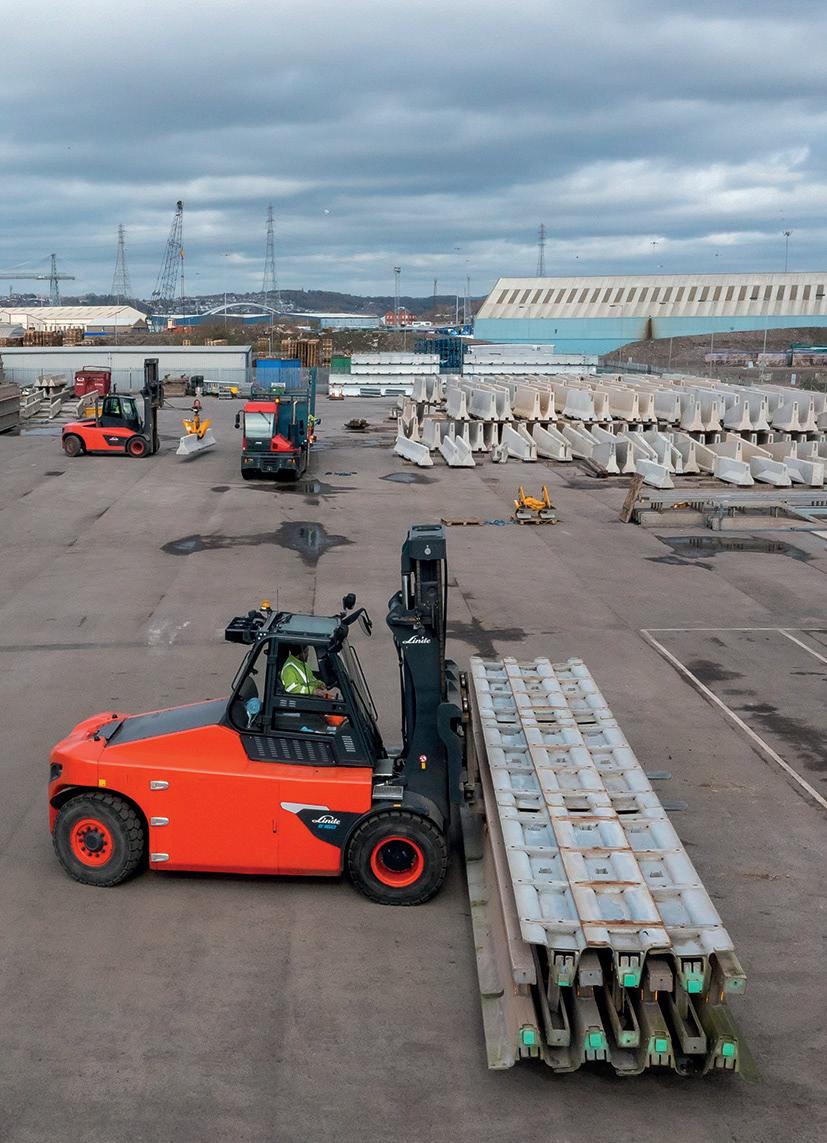
Some relubrication facility equipment is so sophisticated that full details of its operation cannot be disclosed. For example, we have proprietary technology that allows us to relubricate bearings without removing the shields.
Cleanroom environments For precision applications, process of relubrication must take place in a contaminationfree environment. Particles far smaller than the naked eye can see could easily compromise a bearing if they enter and contaminate the lubricant. A good relubrication facility requires filtered air. Although most applications don’t require a certifiedcleanroom, many customers should expect a facility that can offer a highly controlled environment, free from sources of contamination and akin to a cleanroom environment.
Ultrasensitive scales In some applications, the quantity of grease is just as important as the type of grease. For example, while a standard fill might be 30 per cent, for certain low torque applications this would be too stiff, and a ten percent fill would be more suitable. When dealing with miniature bearings and quantities on this scale, precision is key. A job like this requires specialised, ultrasensitive scales capable of providing the necessary level of precision.
Ultraviolet inspection Standard greases can become combustible in high oxygen environments. This highlights the importance of degreasing properly, with the right chemicals and equipment, to avoid potentially explosive consequences. Bearings used in oxygen systems should not have any hydrocarbonbased oil in the lubricant, due to the risk of spontaneous combustion. Making sure the bearing is properly cleaned out is therefore essential. Having cleaned a bearing, a specialist can use ultraviolet light to ensure no traces of potentially combustible material remains, as hydrocarbons will fluoresce under this light. Dry lubricants
Ultrasonic cleaning equipment Degreasing bearings is just as important as adding in fresh lubricant. If degreasing is not done in the right way, traces of the old grease can remain and cause problems. In addition to special solvents and chemicals, relubrication specialists might use ultrasonic cleaning technology. Ultrasonic waves cause cavitation, releasing tiny bubbles that provide a gentle scrubbing effect on the surfaces.
BEARINGS 16 PIMM Metals August/September 2022
- The technological secrets of relubrication facilities
As a specialist bearing supplier, we used to receive requests for bearings non-standardwith lubricants, or for relubrication. Over the years, our expertise in this area and our collection of specialist equipment has grown.
When bearing relubrication is not a DIY job
Often, a problem could be easily resolved with the correct lubrication. One interesting area here is dry lubricants. The inner surfaces of a bearing can be coated in dry coatings, such as molybdenum disulphide, which will help prevent microwelding between steel surfaces in vacuum environments. If you need dry lubricants to be burnished or sputtered on to the balls or raceways of a bearing, this is something that requires specialist expertise, particularly in precision applications such as vacuum environments. Top secret
If you are changing the bearings on a skateboard, you can do it in your garage with a pair of tweezers. For many applications though, the process of relubrication requires precision, expertise and sophisticated technology. Here, Chris Johnson, director of bearing relubricationspecialist SMB Bearings, examines some of the specialist equipment you might find in a bearing relubrication facility.
Relubrication specialists are often called for because of the need for a specialist lubricant.
Customers who need a specialist service like this can inspect the facility to see the equipment in action, but they must sign non-disclosure agreements to make sure the secrets stay with the experts. From ultrasonic cleaning devices to secretive technology that can degrease a bearing without removing the shields, a modern relubrication facility has an impressive array of equipment. If you don’t have the expertise or access to the right equipment, stay clear of botched DIY jobs and rely on the experts.
If you want to know more about bearing relubrication, here are five key elements, plus one that is so secret I can’t really tell you too much about it!

The optimised grease forms a thick oil film between the bearing raceway surface and the rollers to prevent metal-to-metal contact
BEARINGS 17PIMM Metals August/September 2022 Due to equipmentsteelmakingconditions,environmentalharshrequires highly reliable, long-life bearings that resist premature damage. NSK has therefore developed a new high-value-added bearing for the steelmaking industry that improves productivity through stable equipment operation and reduces maintenance costs with its innovative sealing and lubrication technologies. As part of the manufacturing process from crude iron to finished product, steelmaking relies on several different types of equipment, including: equipment that melts raw pig iron to make molten steel; equipment that adjusts the composition of molten steel and hardens it; and rolling equipment that forms hardened steel into plates or bars. Among these processes, bearings for rolling mills have to withstand particularly harsh operating conditions. In addition to accommodating extreme loads and speeds, bearings for the work rolls of rolling mills must also resist infiltration by oxide scale and cooling water. Premature damage to poorly specified bearings will result from the flaking or rusting of raceway surfaces, largely because of poor lubrication. However, over-lubricating is not the answer due to cost and environmental concerns. With these thoughts in mind, NSK set about developing a solution which utilises sealing technology optimised for rolling mill bearings, alongside grease technology that minimises the effects of water intrusion. The outcome is a long-life, fourrow tapered roller bearing that is more water-resistant than conventional bearings and delivers optimal performance in steelmaking equipment applications.Notably,the oil seal on the new bearing is extremely compact, while a new processing method for the cage has increased roller length and diameter, and increased the number of rollers, resulting in a high load capacity design. Optimising the internal design of the new bearing increases the basic dynamic load rating by up to 25% compared with NSK´s conventional product. Furthermore, tight sealing not only suppresses the ingress of particulates and water to extend service life, it also reduces the need for grease replenishment during maintenance periods. By optimising the grease composition it is possible to form and maintain a thick oil film between the bearing raceway surface and the rollers to avoid metal-to-metal contact. Moreover, the use of a special additive prevents water from contacting the raceway surface, inhibiting subsequent corrosion. NSK tests in a water-infiltrated environment confirmed that the new grease has a service life more than twice that of conventional lubricating grease, helping to avert premature damage.Available in sizes from 345 to 615.95 mm outer diameter, NSK´s new sealed-clean, fourrow tapered roller bearings with water-resistant grease are suitable for work rolls in hot/cold rolling mills and other steelmaking equipment. Moving forward, the company will continue its development programme in support of steelmakers, creating products that contribute to both process advancement and environmental preservation.
New NSK bearings deliver long service life for steelmakers
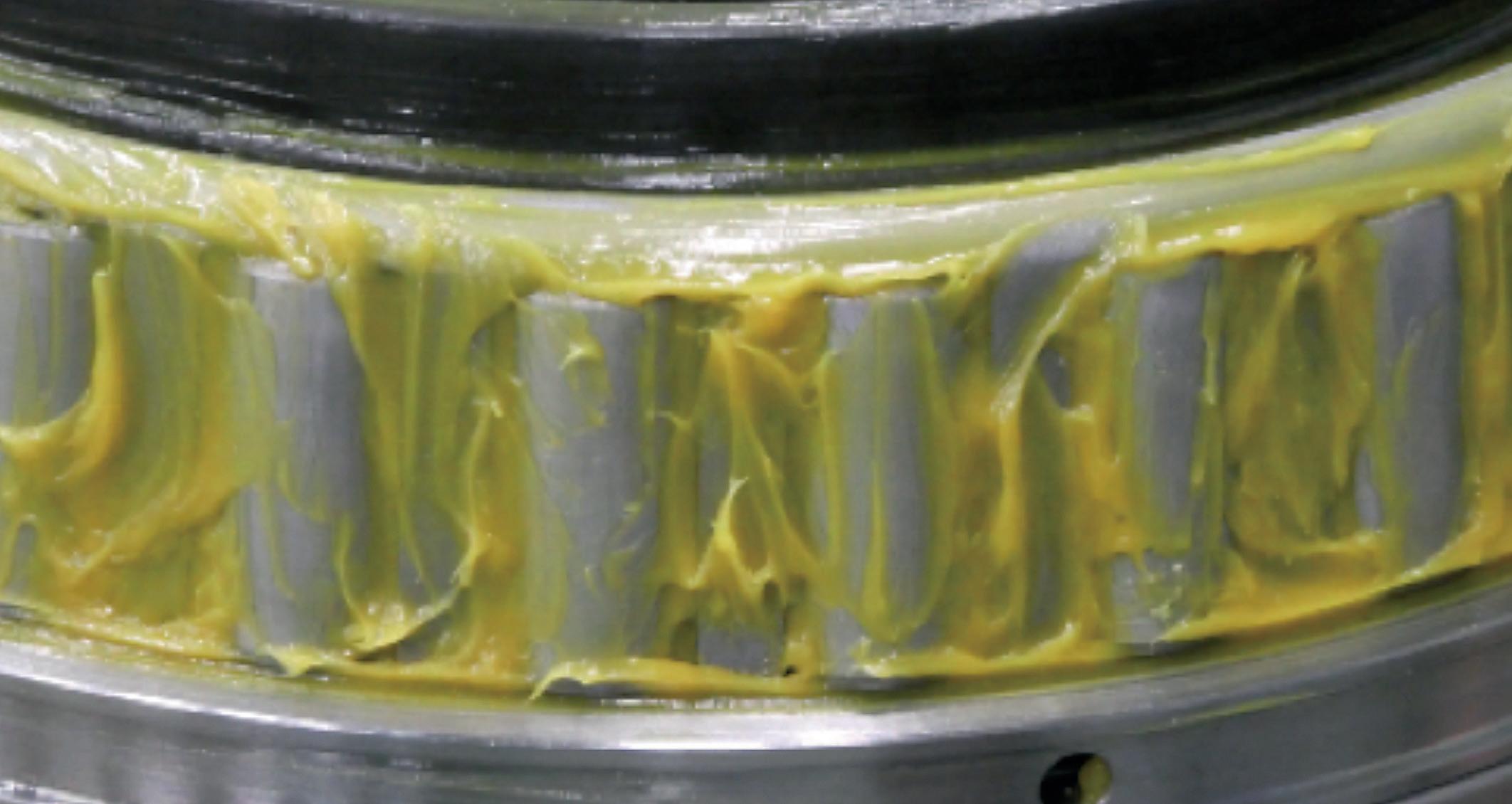
Metal industries look forward with excitement to regional satellites in Thailand and India
EVENTS 18PIMM Metals June/July 2022
18 PIMM Metals August/September 2022
From 5 to 7 October 2022, leadingThailand’sregional trade fairs for wire, cable, tubes and pipes, wire Southeast Asia and Tube Southeast Asia, will be held at the Bangkok International Trade & Exhibition Centre (BITEC). The exhibiting companies come primarily from Southeast Asia. Thailand has been considered the economic hub of the ASEAN countries and a springboard for local and international companies for years. The country is investing heavily in its trade and growing infrastructure. Especially the rethinking within the automotive industry towards more eMobility as well as investments in the fields of electronics, robotics and food industry make Thailand interesting for international investors who want to establish themselves on the Asian market. From Europe, exhibitors from Germany, Great Britain, Italy and Austria will come to Bangkok to present the latest machinery, equipment, technologies and services. In addition, country pavilions will present concentrated technology power. Further information on both trade fairs can be found on the Internet portals at: www.wiresoutheastasia.com and tube-southeastasia.com.www.
Four metallurgy trade fairs in parallel in India
From 23 to 25 November 2022, the four regional Indian metal trade fairs wire India, Tube India, METEC India and India Essen Cutting & Welding will open their doors at the Bombay Exhibition Centre in Mumbai.wire, cable, tube and pipe products are indispensable for investments in India’s growing infrastructure as well as house, road, bridge and canal construction. Also in the oil, gas, water and wastewater sectors - no industry functions without the technologies and products of these industries. This is why the trade fair quartet will once again present itself in 2022 as the leading regional communication and trade platform for meeting new customers and expanding existing business contacts. Due to the international appeal of the trade fairs, a high level of Turkey,fromregistered,frominparticipationinternationalisalsoexpected2022.Sofar,350companies15countrieshaveincludingexhibitorstheUSA,Singapore,Italy,Germany,Chinaand Vietnam. The Indian industry key players will again present themselves united at their leading trade fairs in 2022. The Indian unit of the ITA is also planning an accompanying conference programme. 12 German exhibitors will exhibit on a joint area of 204 square metres as part of a federal participation, and Italian and Swiss companies are also planning their own country pavilions for 2022. The Federal Ministry for Economic Affairs and Energy has significantly reduced the participation prices for the international satellites of wire and Tube in India for 2022 and optimised hygiene protection at the German Pavilions. Further information can be found in the internet portals of the events at: www.wire-india. com, www.tube-india.com, www. metec-india.com and www.iewc. Yourin. press contact in Germany: Petra Hartmann-Bresgen MA Ulrike duesseldorf.deE-mail:Fax:Phone:Osahon+49(0)211/4560-541/992+49(0)211/4560-87541HartmannP@messe-

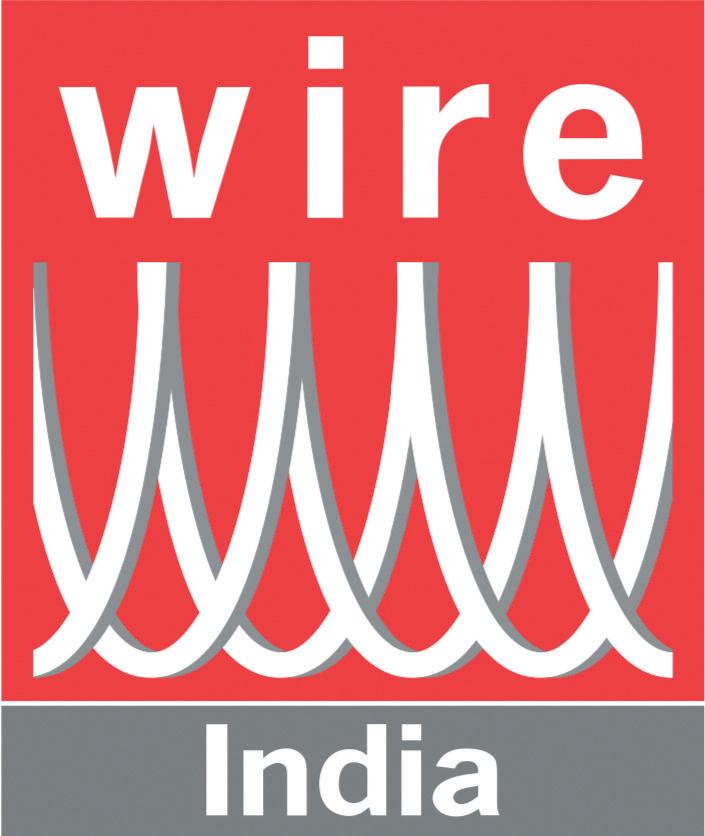

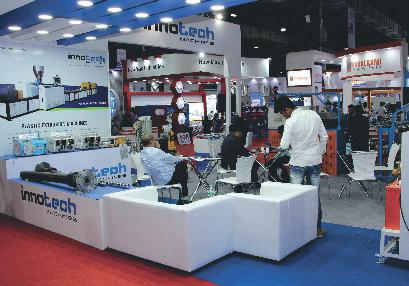
EVENTS 19 PIMM Metals Spring 2022
Jörg Mosser, CEO / Managing Director Europe of Messer Cutting Systems GmbH: “For our industry, SCHWEISSEN & SCHNEIDEN continues to be the leading international trade fair. Innovations and trends in the industry, especially in the context of digitisation, are in special focus, as is, of course, Germany as alocation.productionDue to the long dry spell with regard to trade fairs, the expectations for SCHWEISSEN & SCHNEIDEN are particularly high this time. Of course, we will also set the necessary accents to meet the high demands of our customers as well as our own and are looking forward to the event!”
N o fewer than three new members are supporting SCHNEIDENSCHWEISSENthe&trade fair advisory board. Now, Jörg Mosser from Messer Cutting, Johannes Ried from MicroStep and Dr. Alexander Knitsch from TRUMPF belong to the expert panel. Together with their other colleagues on the advisory board, they will provide important impetus for the world’s leading trade fair, which will be held at Messe Essen from September 11 to 15, 2023. Oliver P. Kuhrt, CEO of Messe Essen: “Whether it’s valuable industry expertise or very concrete support in designing the trade fair - we can count on our Trade Fair Advisory Board! This top- c lass reinforcement once again impressively underlines the importance of SCHWEISSEN & SCHNEIDEN for the industry.” As a new member of the advisory board, Dr. Alexander Knitsch, Head of Sales Laser Division Germany at TRUMPF Laser- und Systemtechnik GmbH, would like to “contribute important impulses on laser welding – from entry into laser welding to market trends and new laser welding applications. TRUMPF’s internationality can also help to attract even more visitors from abroad.
New members strengthen SCHWEISSEN & SCHNEIDEN advisory board. Experts appreciate new focal points of the 2023 event
19PIMM Metals August/September 2022
At their last meeting, the advisory board members once again emphasized the importance of SCHWEISSEN & SCHNEIDEN. Many companies develop their innovations specifically for the trade show in order to present them to the international trade audience there. “Whether for exhibiting companies or visitors, SCHWEISSEN & SCHNEIDEN is justifiably the leading international trade fair for our industry,” said Johannes Ried, Managing Director of MicroStep Europa GmbH. “That’s why we decided to significantly expand our presence and show a variety of cutting technologies in action at the largest booth in our company’s history. Here we will demonstrate what we have to offer in the fields of plasma, laser, oxyfuel and waterjet, as well as in the areas of automation and digitization. In addition, we have some absolute novelties on board!”Formore information, www.schweissen-schneiden.comvisit:
TRUMPF is planning a joint trade show appearance of both business divisions - machine tools and laser technology - to demonstrate the full product range for welding, e.g. with robots or 5-axis machines.
World’s leading trade fair for joining, cutting and surfacing
The appearance will be supplemented by a toolbar with parts advice on laser-compatible design.” Positive feedback on new focus topics at the show In total, the SCHWEISSEN & SCHNEIDEN trade show advisory board now has 26 members. At their last committee meeting, they complimented the new focal points of the trade show, which envisage a much stronger dovetailing of the main exhibition areas and their related topics such as equipment, filler materials or even digitisation.
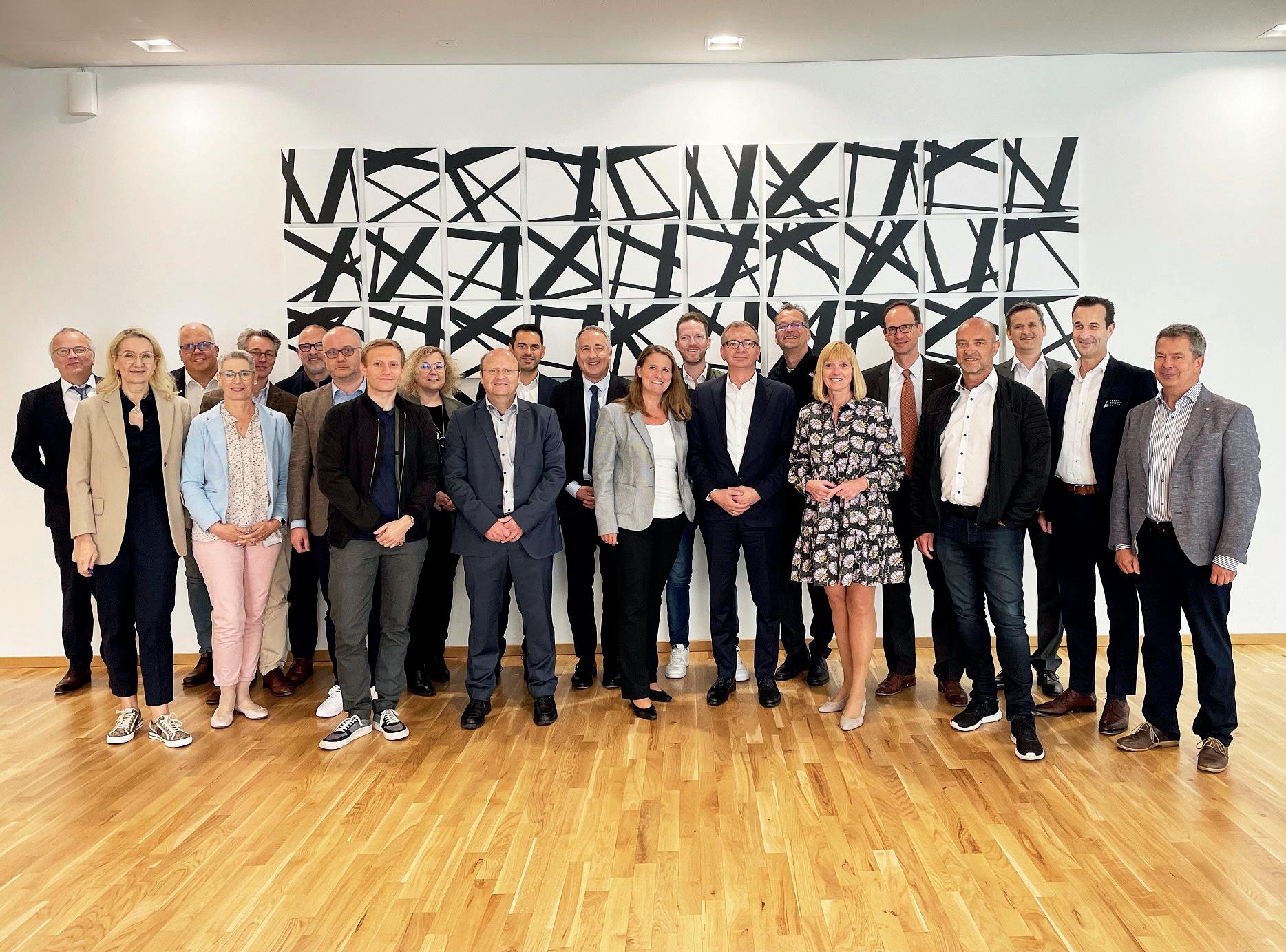
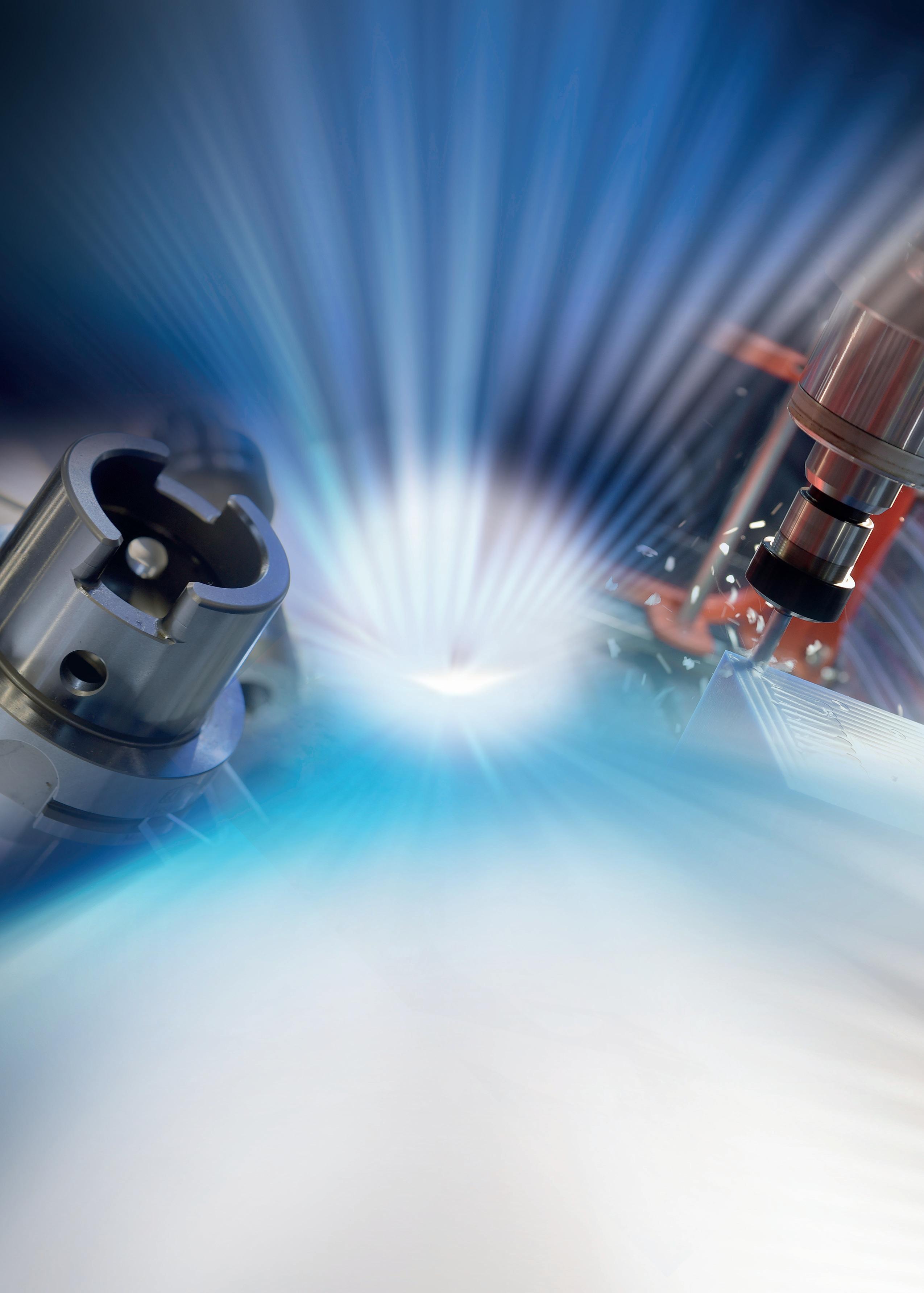
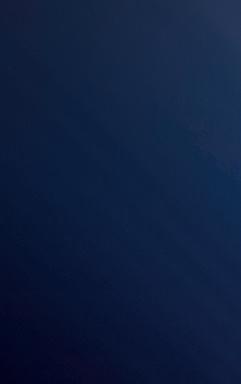
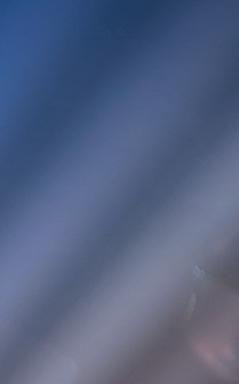
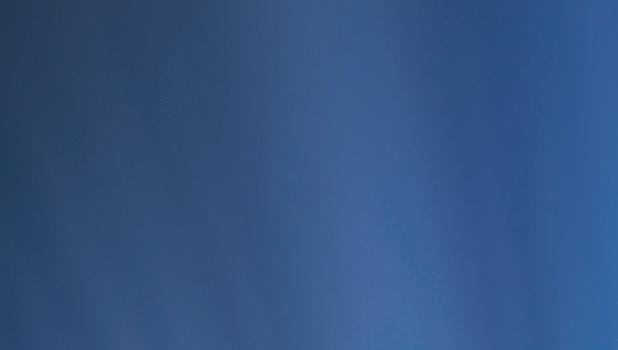
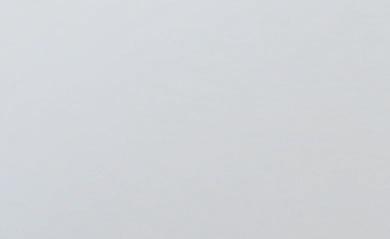